SPECIFICATION SHEET A garment specification sheet or spec
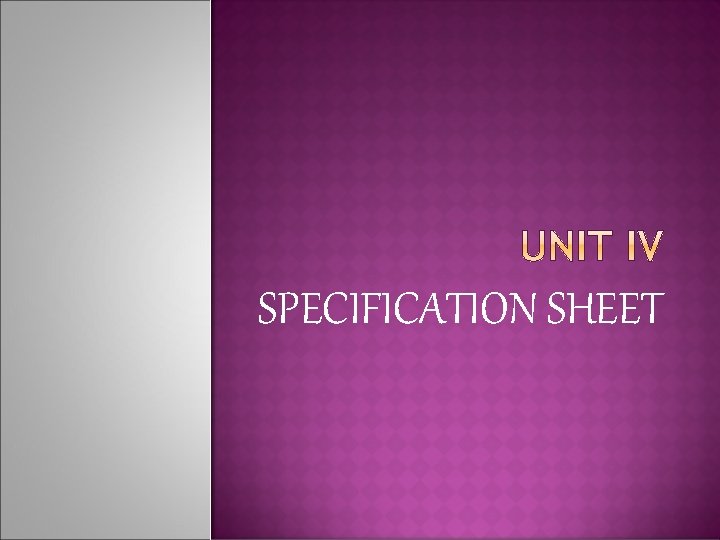
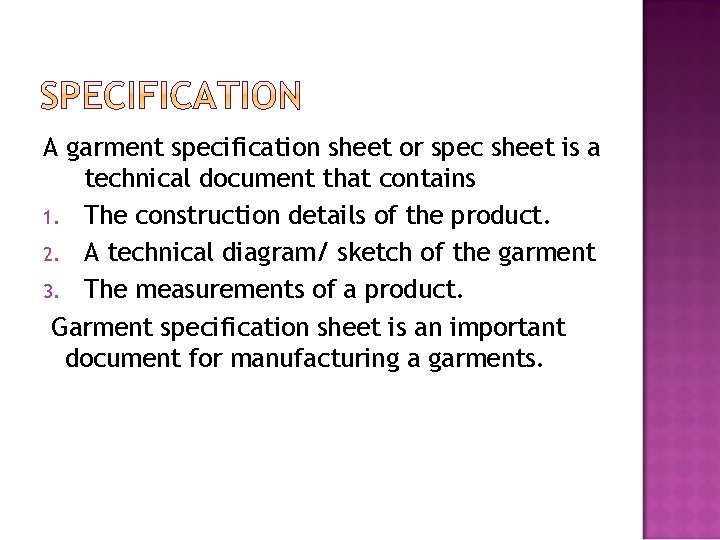
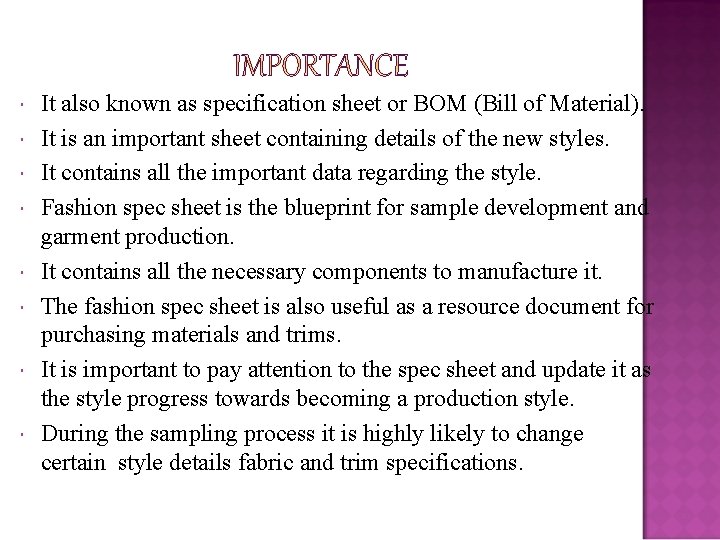
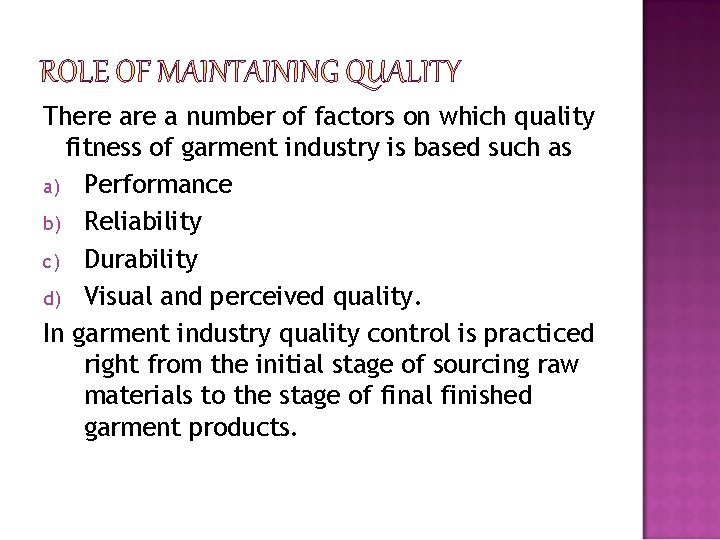
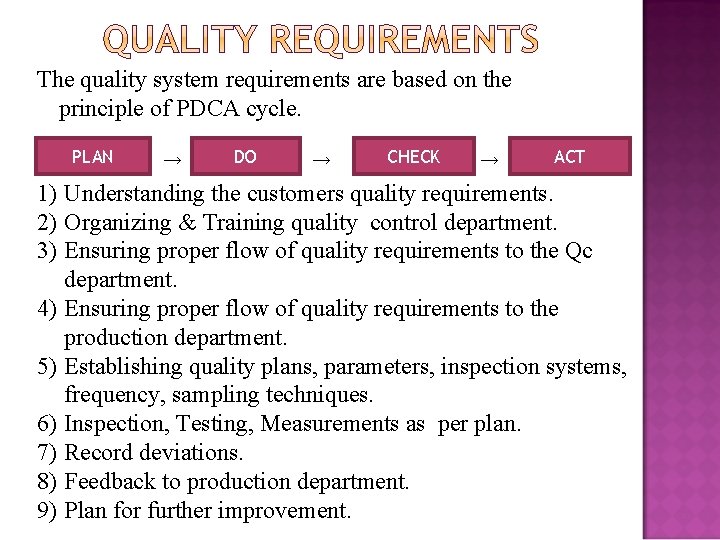
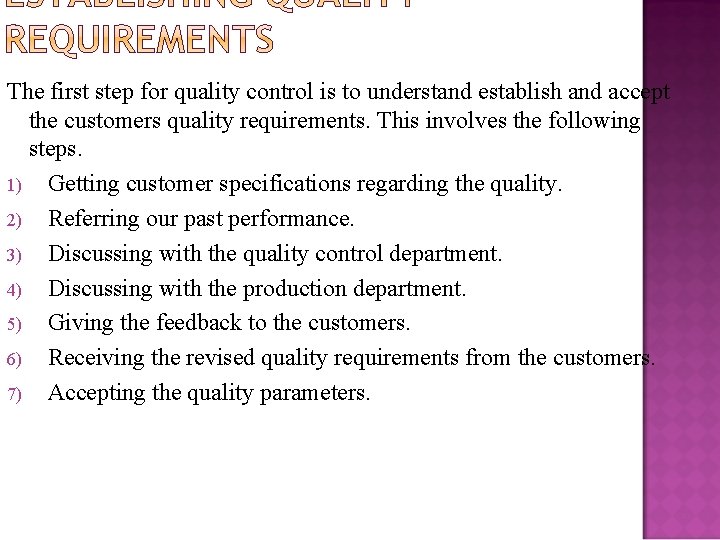

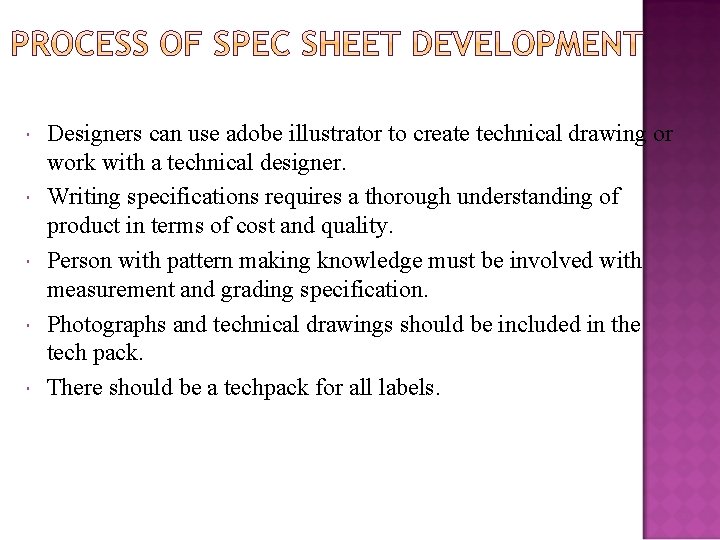
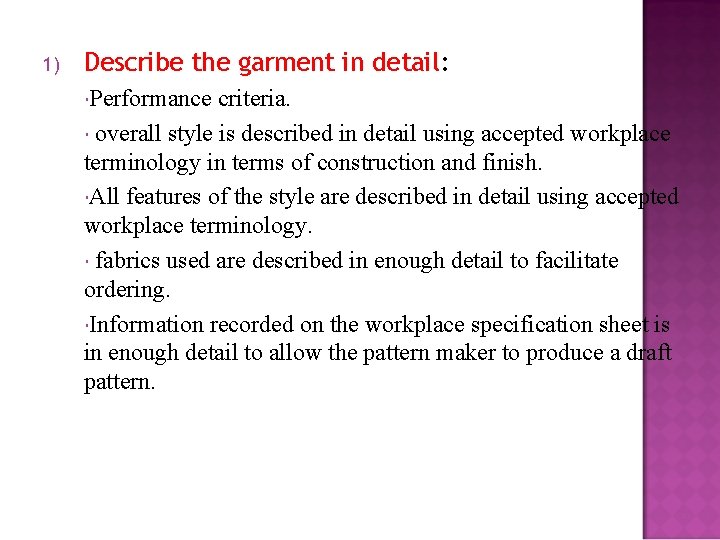
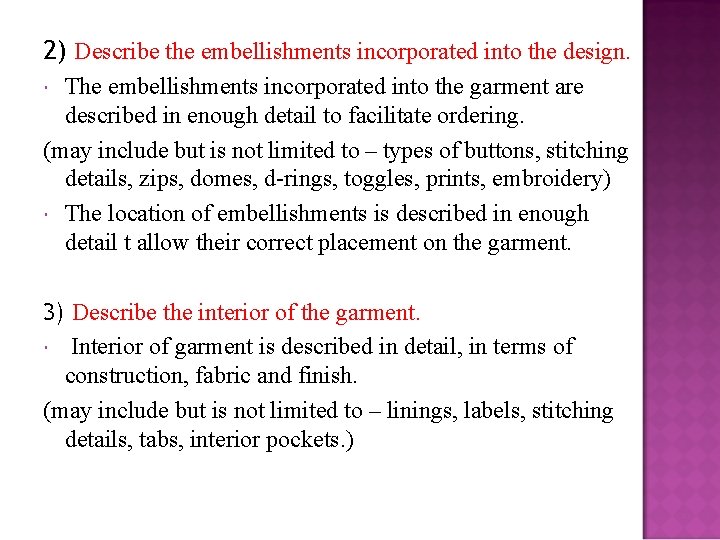
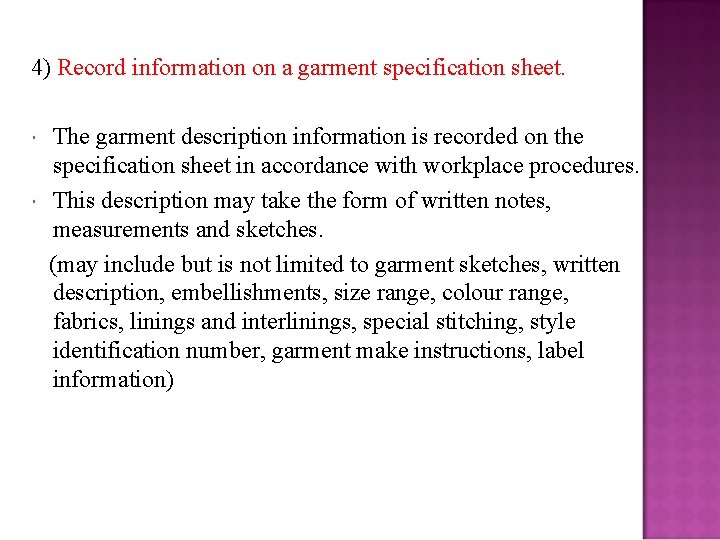
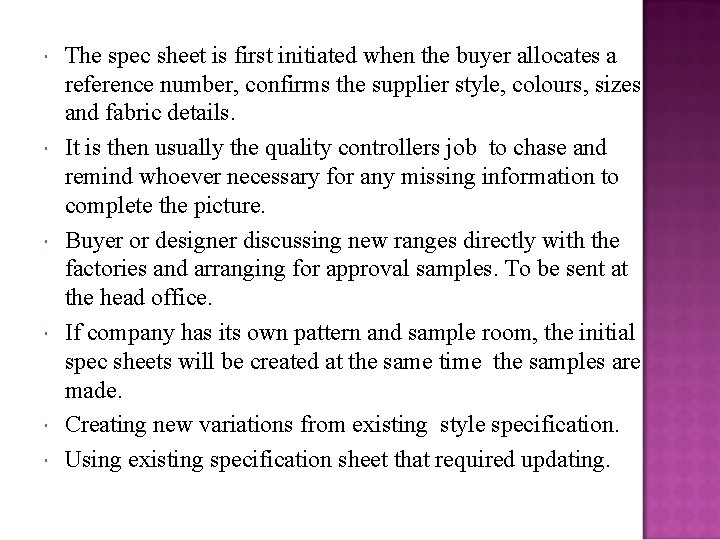
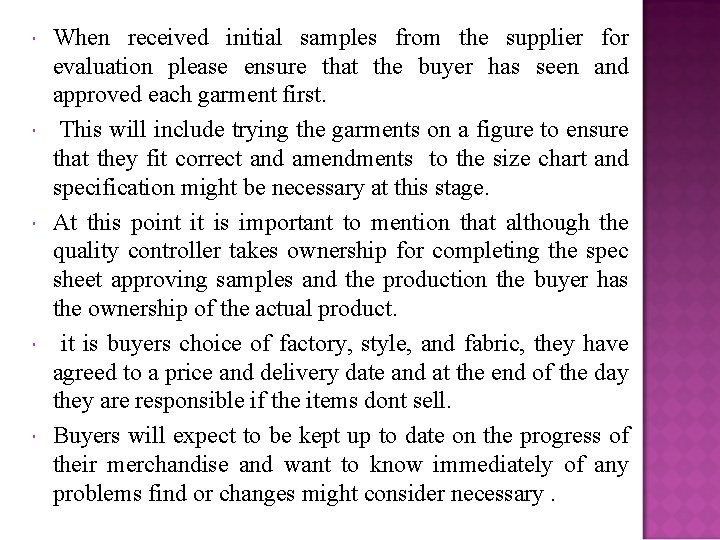
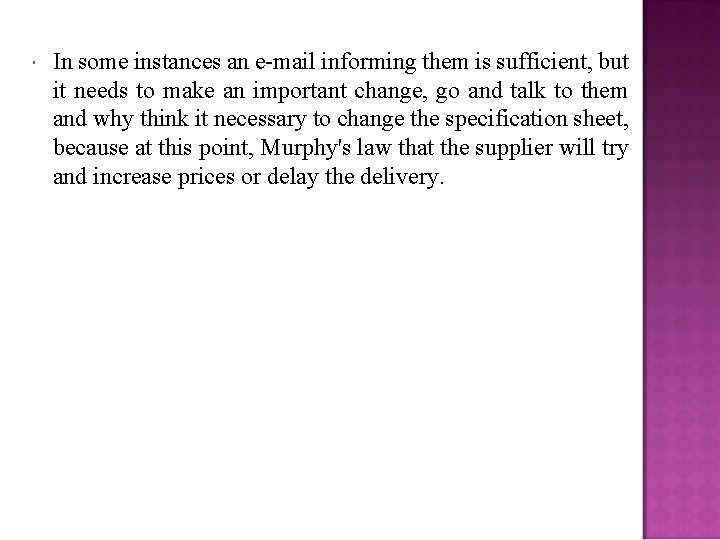
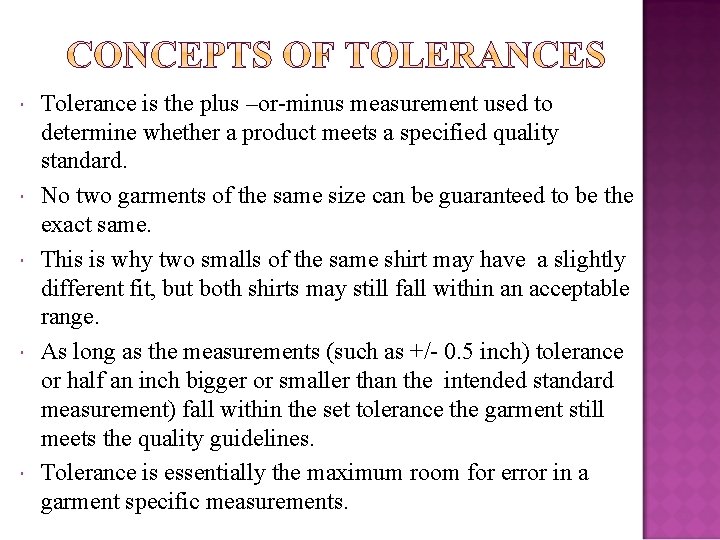
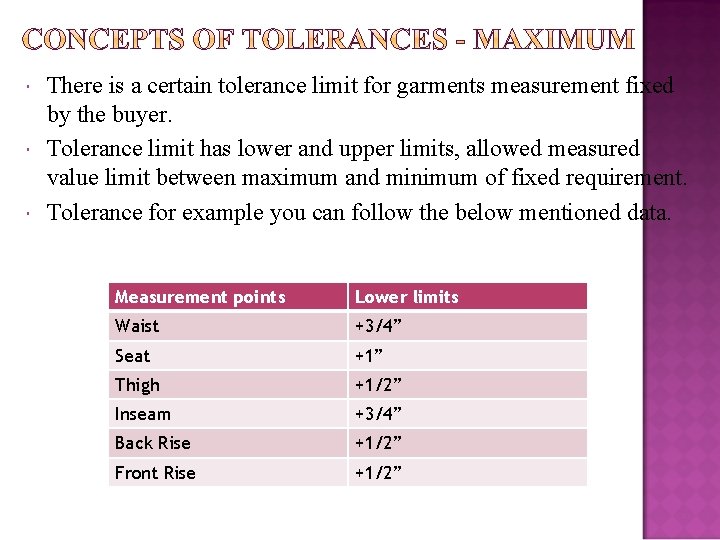
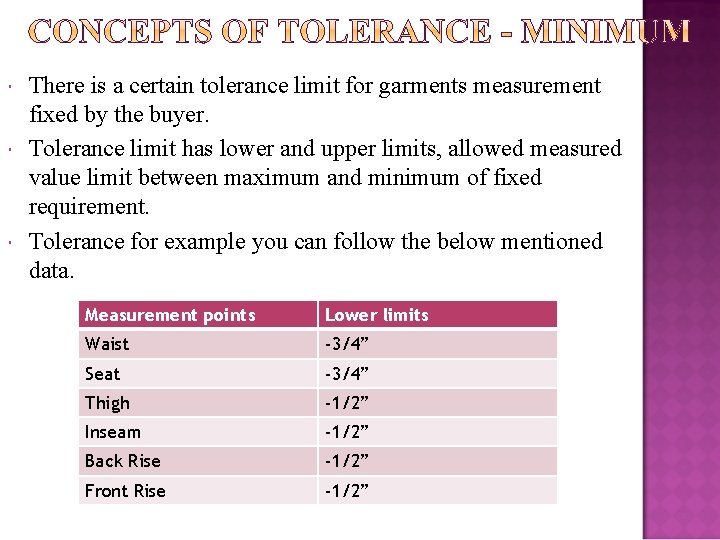
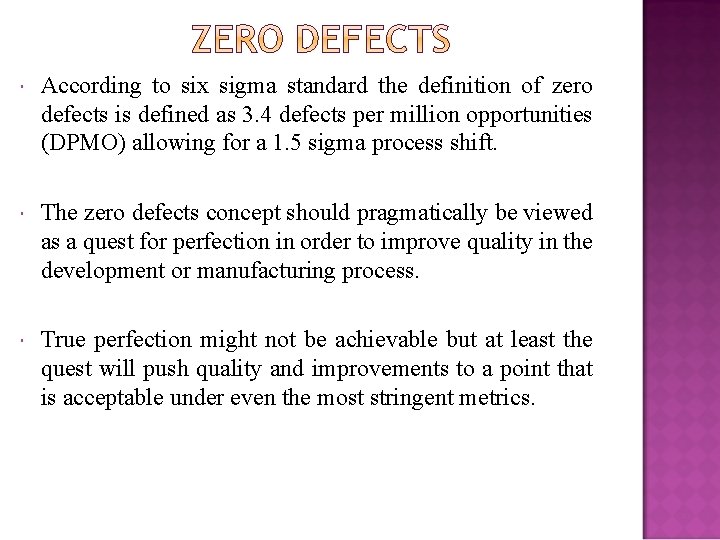
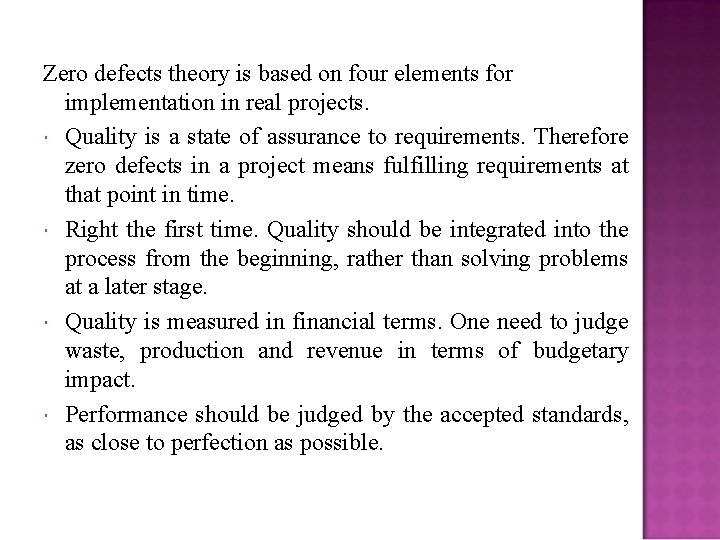
- Slides: 19
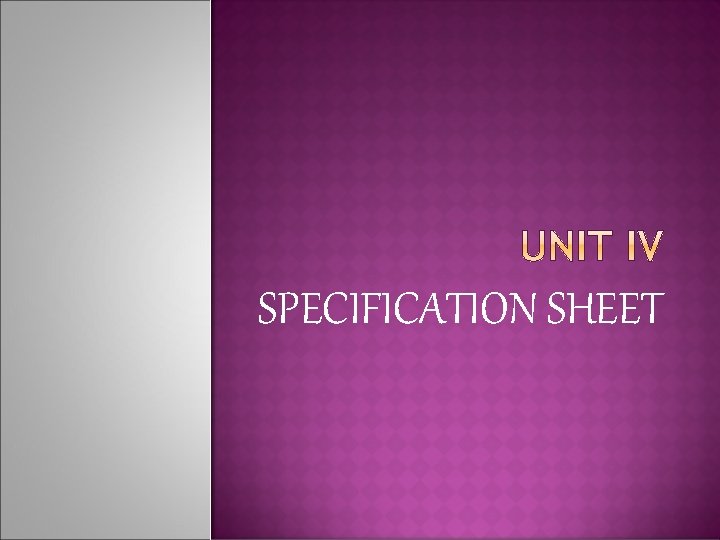
SPECIFICATION SHEET
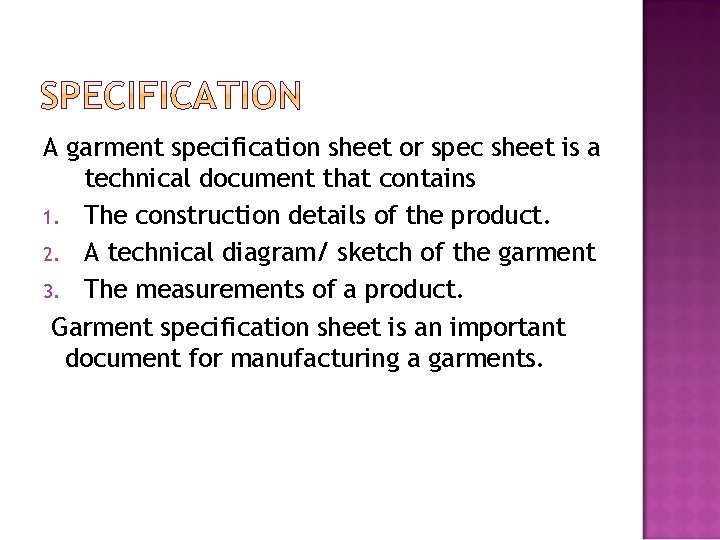
A garment specification sheet or spec sheet is a technical document that contains 1. The construction details of the product. 2. A technical diagram/ sketch of the garment 3. The measurements of a product. Garment specification sheet is an important document for manufacturing a garments.
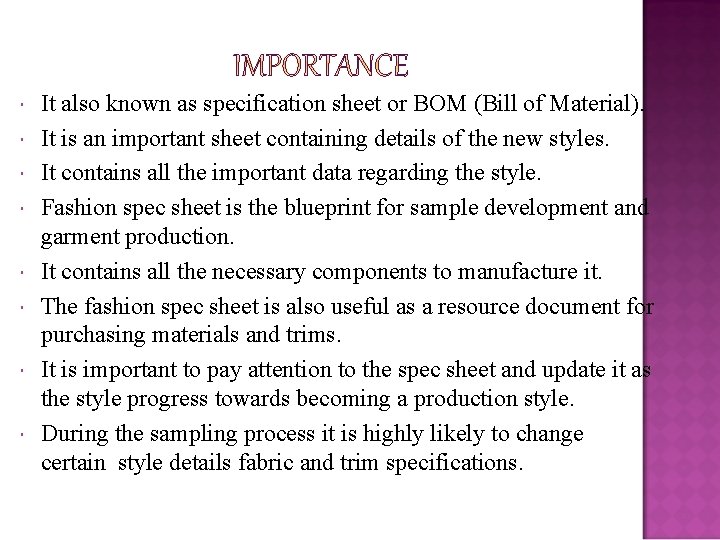
It also known as specification sheet or BOM (Bill of Material). It is an important sheet containing details of the new styles. It contains all the important data regarding the style. Fashion spec sheet is the blueprint for sample development and garment production. It contains all the necessary components to manufacture it. The fashion spec sheet is also useful as a resource document for purchasing materials and trims. It is important to pay attention to the spec sheet and update it as the style progress towards becoming a production style. During the sampling process it is highly likely to change certain style details fabric and trim specifications.
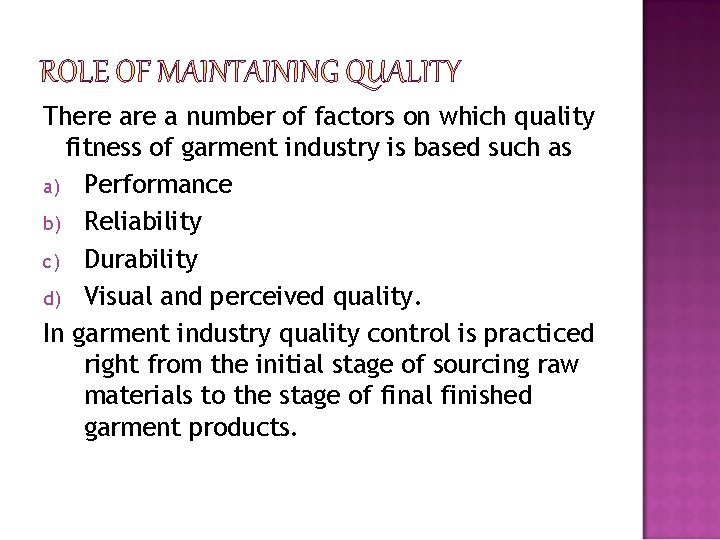
There a number of factors on which quality fitness of garment industry is based such as a) Performance b) Reliability c) Durability d) Visual and perceived quality. In garment industry quality control is practiced right from the initial stage of sourcing raw materials to the stage of final finished garment products.
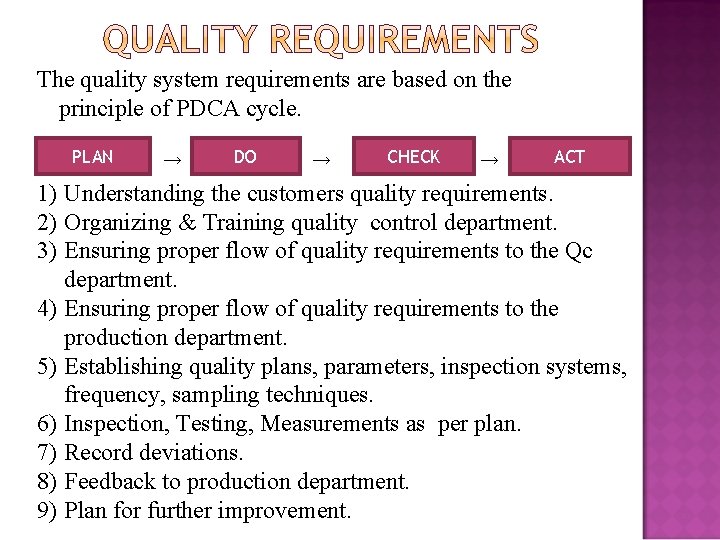
The quality system requirements are based on the principle of PDCA cycle. PLAN → DO → CHECK → ACT 1) Understanding the customers quality requirements. 2) Organizing & Training quality control department. 3) Ensuring proper flow of quality requirements to the Qc department. 4) Ensuring proper flow of quality requirements to the production department. 5) Establishing quality plans, parameters, inspection systems, frequency, sampling techniques. 6) Inspection, Testing, Measurements as per plan. 7) Record deviations. 8) Feedback to production department. 9) Plan for further improvement.
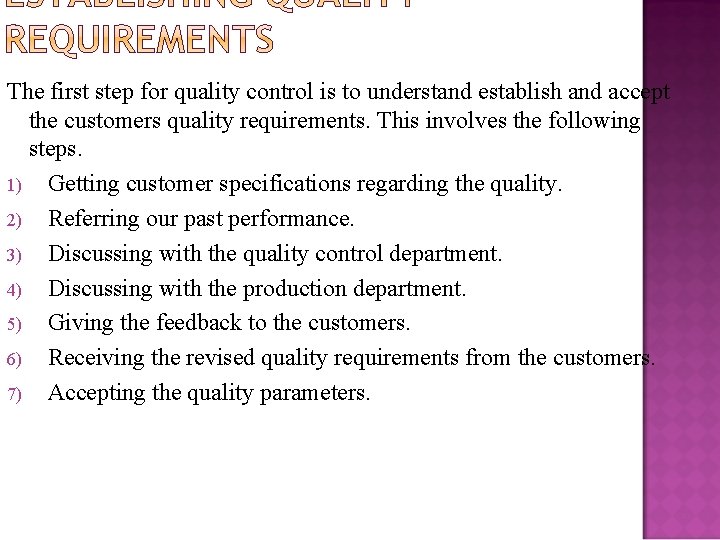
The first step for quality control is to understand establish and accept the customers quality requirements. This involves the following steps. 1) Getting customer specifications regarding the quality. 2) Referring our past performance. 3) Discussing with the quality control department. 4) Discussing with the production department. 5) Giving the feedback to the customers. 6) Receiving the revised quality requirements from the customers. 7) Accepting the quality parameters.

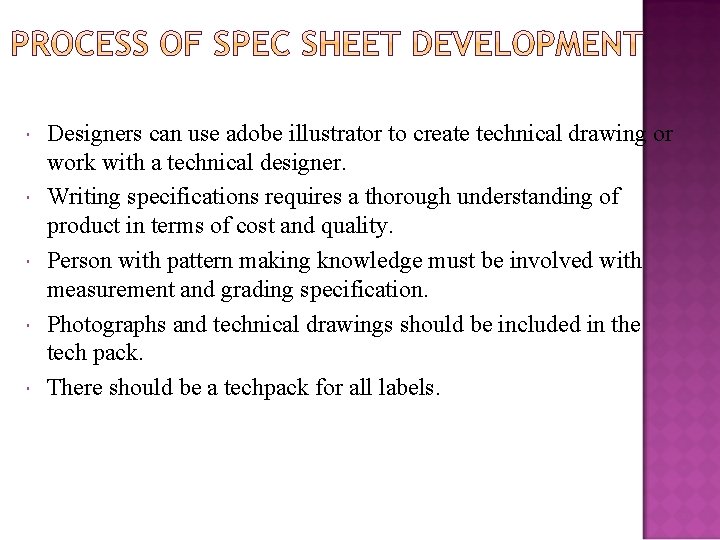
Designers can use adobe illustrator to create technical drawing or work with a technical designer. Writing specifications requires a thorough understanding of product in terms of cost and quality. Person with pattern making knowledge must be involved with measurement and grading specification. Photographs and technical drawings should be included in the tech pack. There should be a techpack for all labels.
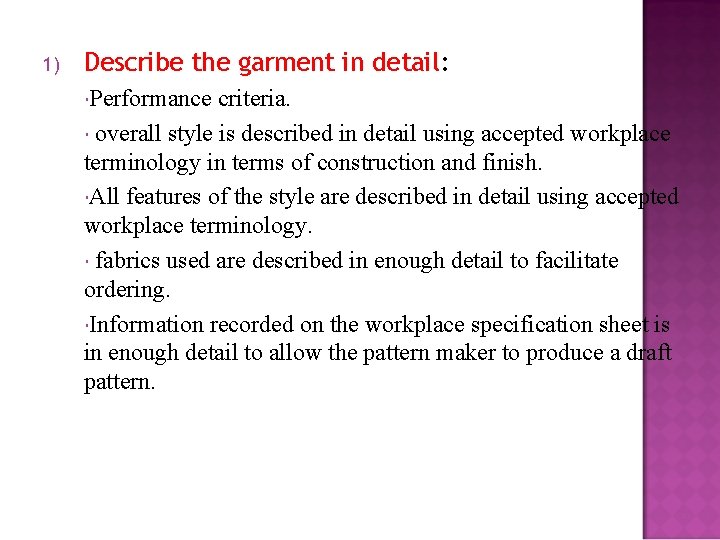
1) Describe the garment in detail: Performance criteria. overall style is described in detail using accepted workplace terminology in terms of construction and finish. All features of the style are described in detail using accepted workplace terminology. fabrics used are described in enough detail to facilitate ordering. Information recorded on the workplace specification sheet is in enough detail to allow the pattern maker to produce a draft pattern.
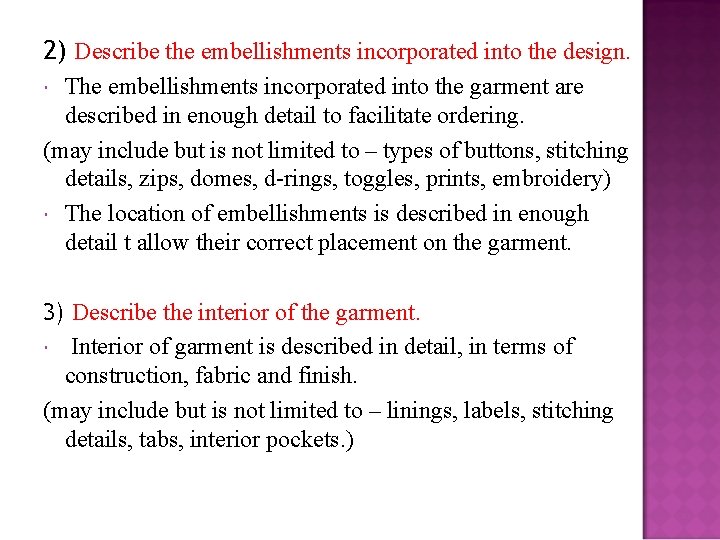
2) Describe the embellishments incorporated into the design. The embellishments incorporated into the garment are described in enough detail to facilitate ordering. (may include but is not limited to – types of buttons, stitching details, zips, domes, d-rings, toggles, prints, embroidery) The location of embellishments is described in enough detail t allow their correct placement on the garment. 3) Describe the interior of the garment. Interior of garment is described in detail, in terms of construction, fabric and finish. (may include but is not limited to – linings, labels, stitching details, tabs, interior pockets. )
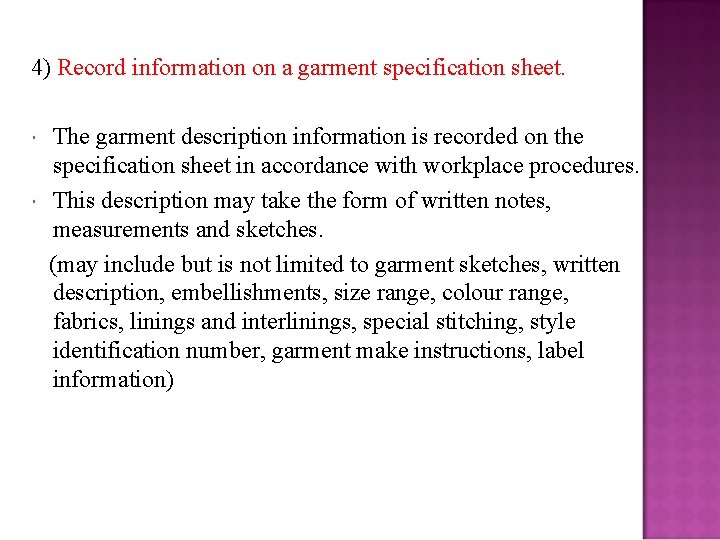
4) Record information on a garment specification sheet. The garment description information is recorded on the specification sheet in accordance with workplace procedures. This description may take the form of written notes, measurements and sketches. (may include but is not limited to garment sketches, written description, embellishments, size range, colour range, fabrics, linings and interlinings, special stitching, style identification number, garment make instructions, label information)
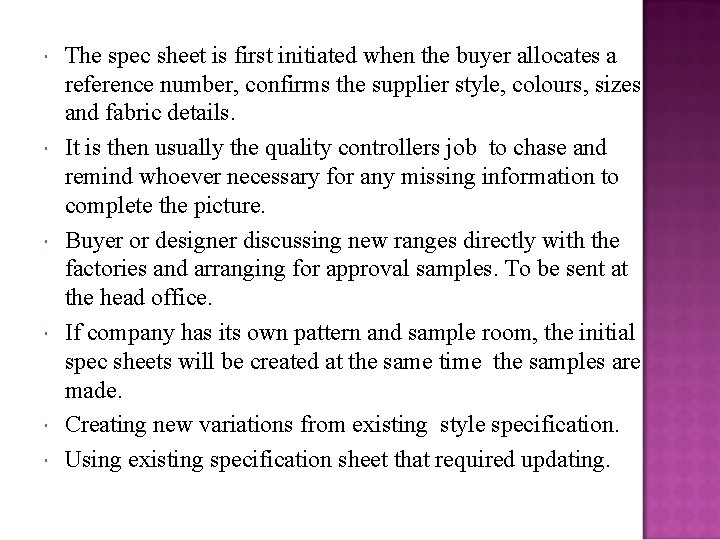
The spec sheet is first initiated when the buyer allocates a reference number, confirms the supplier style, colours, sizes and fabric details. It is then usually the quality controllers job to chase and remind whoever necessary for any missing information to complete the picture. Buyer or designer discussing new ranges directly with the factories and arranging for approval samples. To be sent at the head office. If company has its own pattern and sample room, the initial spec sheets will be created at the same time the samples are made. Creating new variations from existing style specification. Using existing specification sheet that required updating.
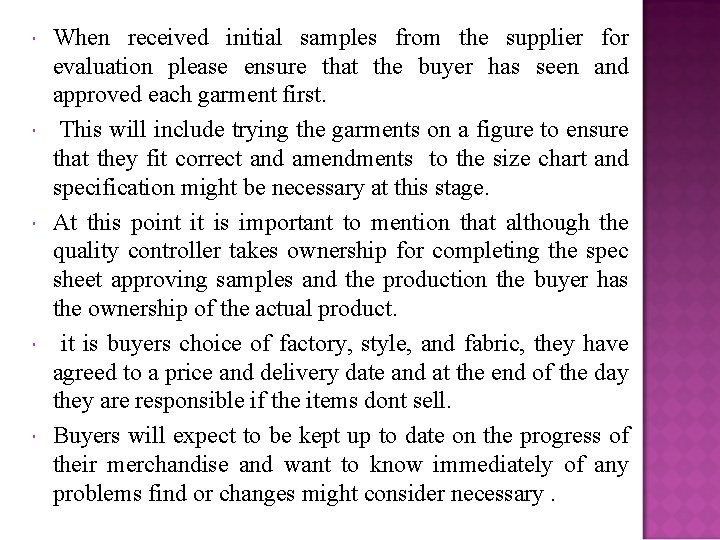
When received initial samples from the supplier for evaluation please ensure that the buyer has seen and approved each garment first. This will include trying the garments on a figure to ensure that they fit correct and amendments to the size chart and specification might be necessary at this stage. At this point it is important to mention that although the quality controller takes ownership for completing the spec sheet approving samples and the production the buyer has the ownership of the actual product. it is buyers choice of factory, style, and fabric, they have agreed to a price and delivery date and at the end of the day they are responsible if the items dont sell. Buyers will expect to be kept up to date on the progress of their merchandise and want to know immediately of any problems find or changes might consider necessary.
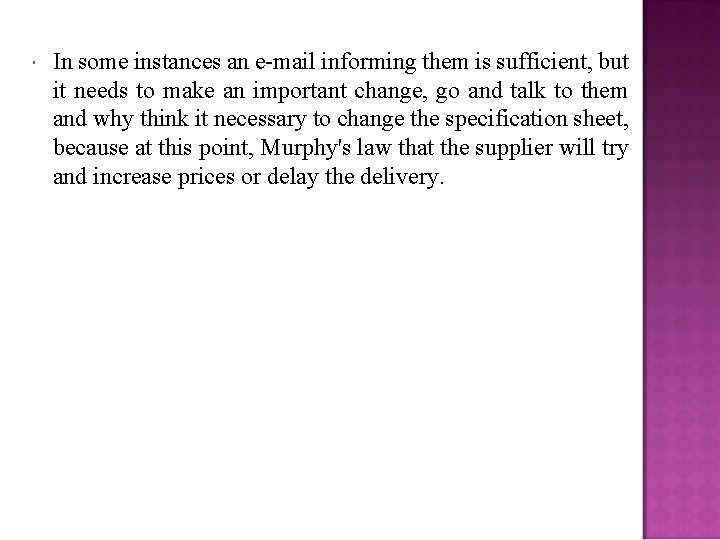
In some instances an e-mail informing them is sufficient, but it needs to make an important change, go and talk to them and why think it necessary to change the specification sheet, because at this point, Murphy's law that the supplier will try and increase prices or delay the delivery.
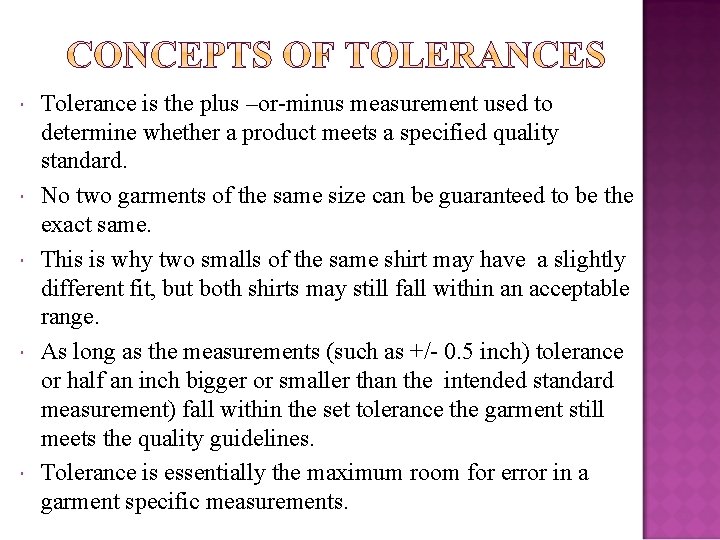
Tolerance is the plus –or-minus measurement used to determine whether a product meets a specified quality standard. No two garments of the same size can be guaranteed to be the exact same. This is why two smalls of the same shirt may have a slightly different fit, but both shirts may still fall within an acceptable range. As long as the measurements (such as +/- 0. 5 inch) tolerance or half an inch bigger or smaller than the intended standard measurement) fall within the set tolerance the garment still meets the quality guidelines. Tolerance is essentially the maximum room for error in a garment specific measurements.
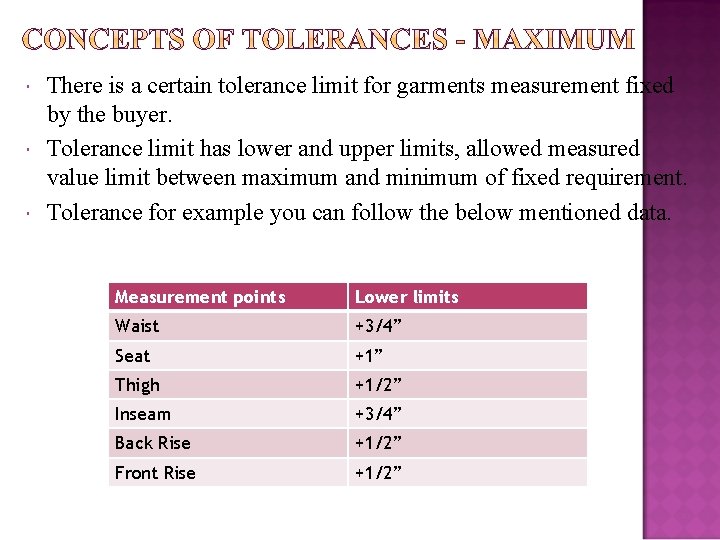
There is a certain tolerance limit for garments measurement fixed by the buyer. Tolerance limit has lower and upper limits, allowed measured value limit between maximum and minimum of fixed requirement. Tolerance for example you can follow the below mentioned data. Measurement points Lower limits Waist +3/4” Seat +1” Thigh +1/2” Inseam +3/4” Back Rise +1/2” Front Rise +1/2”
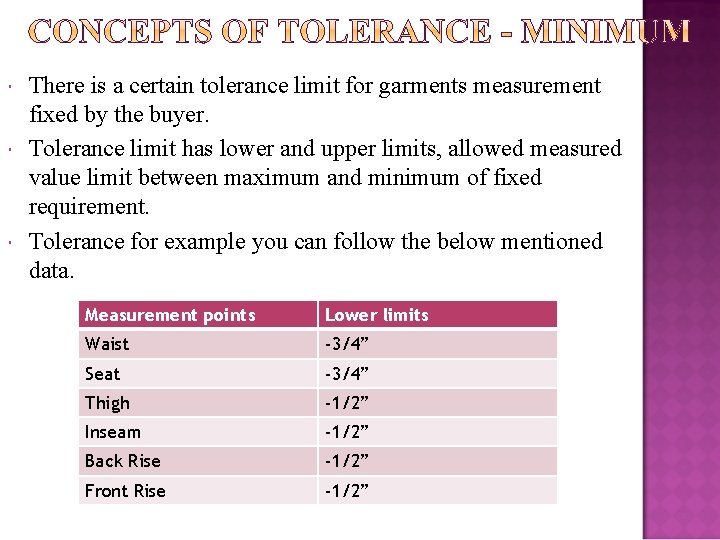
There is a certain tolerance limit for garments measurement fixed by the buyer. Tolerance limit has lower and upper limits, allowed measured value limit between maximum and minimum of fixed requirement. Tolerance for example you can follow the below mentioned data. Measurement points Lower limits Waist -3/4” Seat -3/4” Thigh -1/2” Inseam -1/2” Back Rise -1/2” Front Rise -1/2”
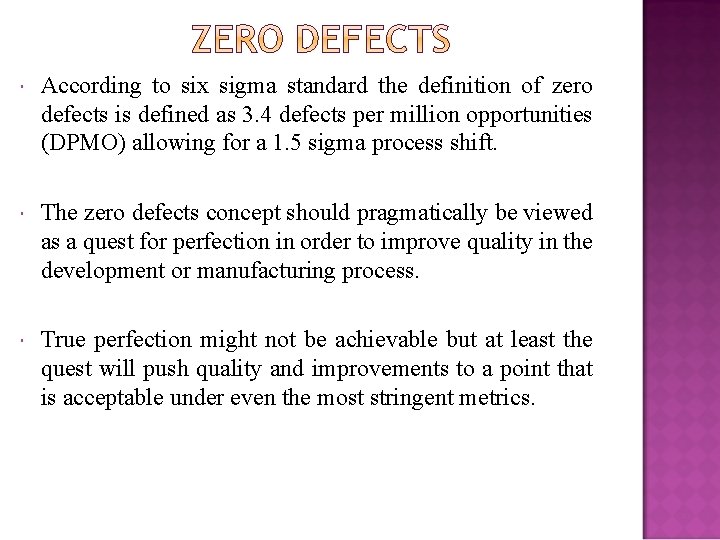
According to six sigma standard the definition of zero defects is defined as 3. 4 defects per million opportunities (DPMO) allowing for a 1. 5 sigma process shift. The zero defects concept should pragmatically be viewed as a quest for perfection in order to improve quality in the development or manufacturing process. True perfection might not be achievable but at least the quest will push quality and improvements to a point that is acceptable under even the most stringent metrics.
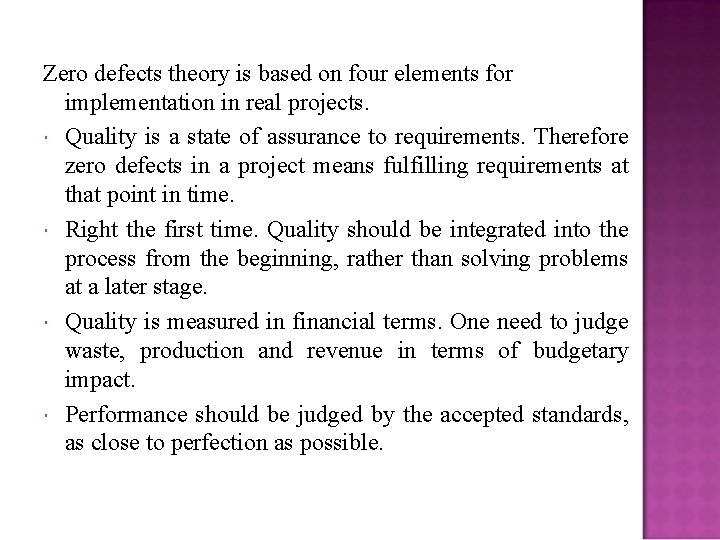
Zero defects theory is based on four elements for implementation in real projects. Quality is a state of assurance to requirements. Therefore zero defects in a project means fulfilling requirements at that point in time. Right the first time. Quality should be integrated into the process from the beginning, rather than solving problems at a later stage. Quality is measured in financial terms. One need to judge waste, production and revenue in terms of budgetary impact. Performance should be judged by the accepted standards, as close to perfection as possible.
Specialist math formula sheet
Rohacell 71 wf
Cost sheet fashion design
Limites de control
Upper specification limit and lower specification limit
Bluetooth core specification
Law of continuity psychology attachment
Människans hörselområde
Pride ebi
Spec innovations
Msfc-spec-522
Crop spec
Specsizer
Jesd204b subclass 1
Aitvaras spec pajegos
Txdot spec book
Epq spec
Sram tester
Gc organic chemistry
Pes and mass spec sample items