PTT 444 TEHNOLOGIST IN SOCIETY Knowledge Sincerity Excellence
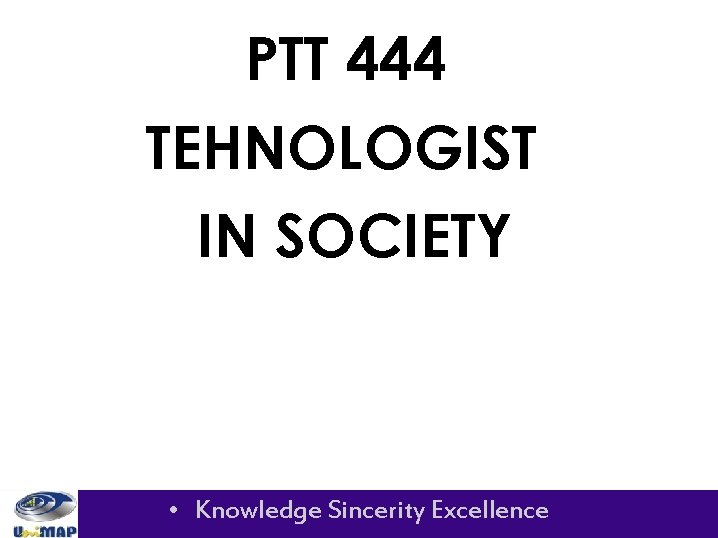
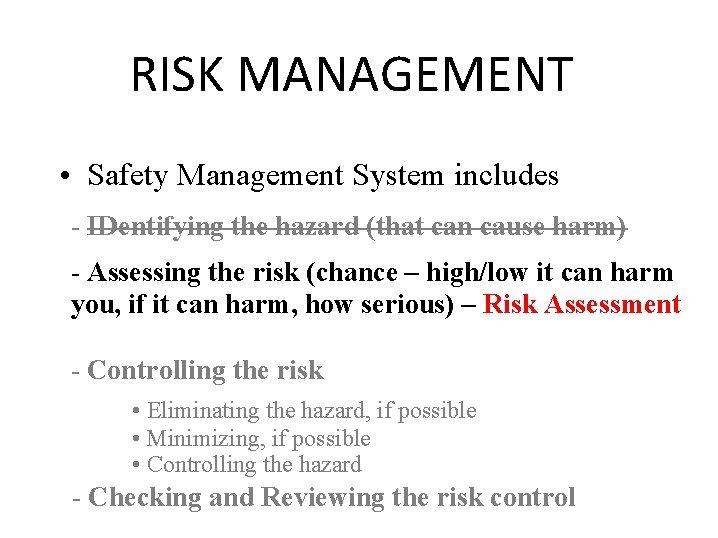
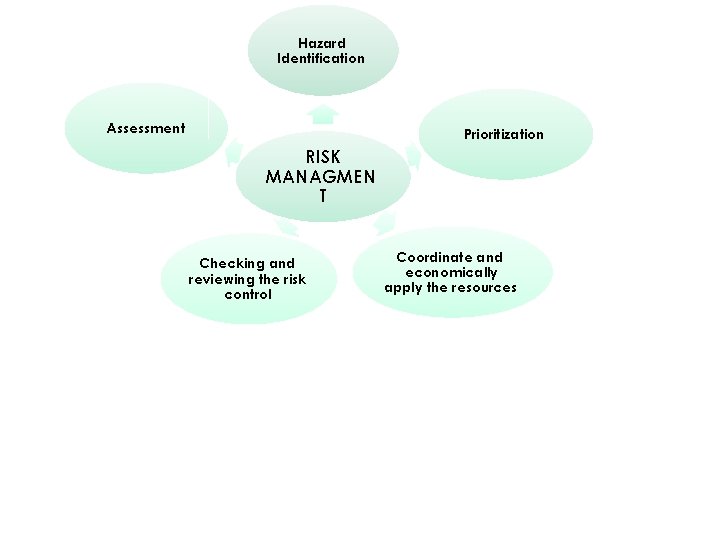
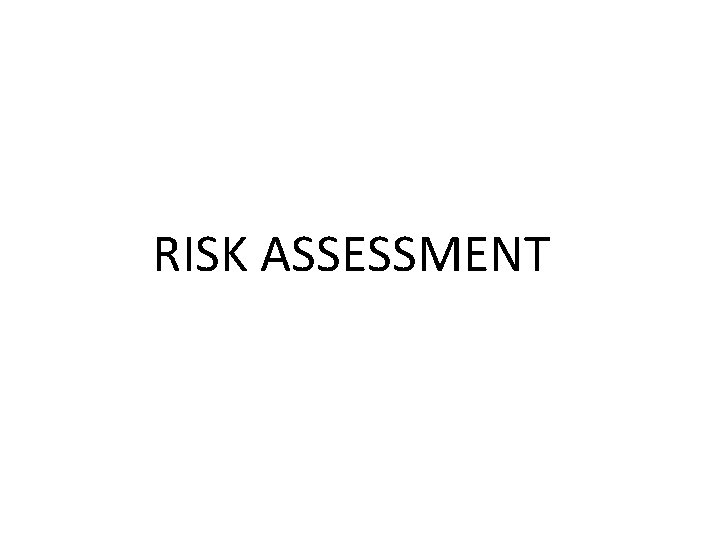
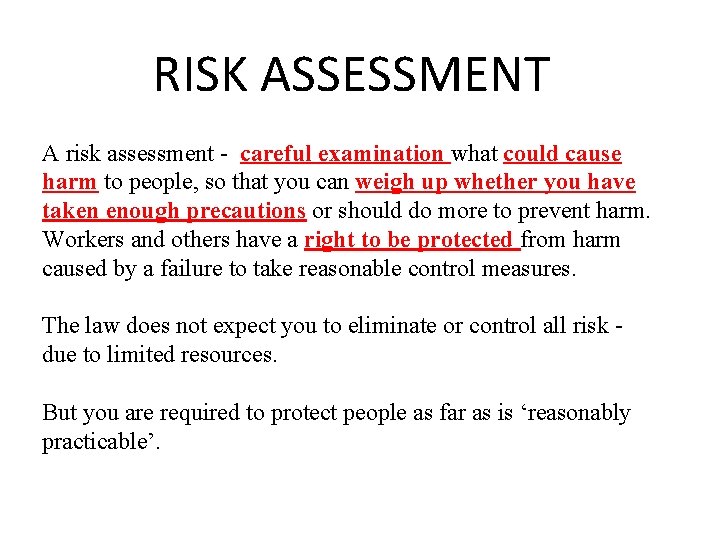
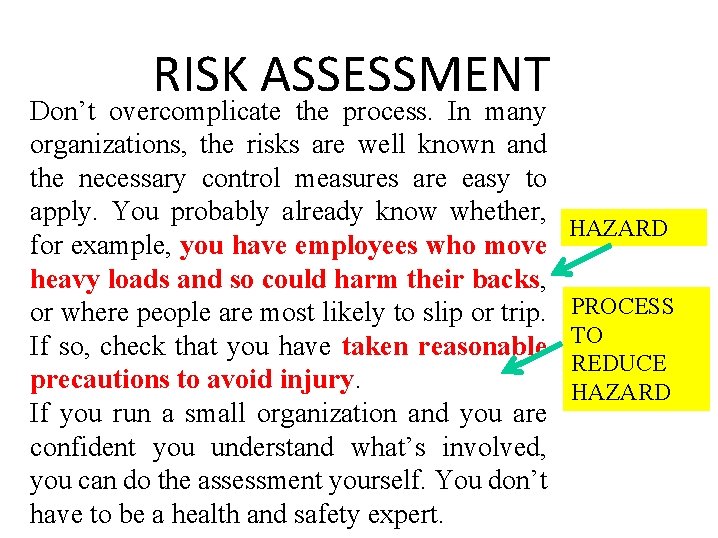
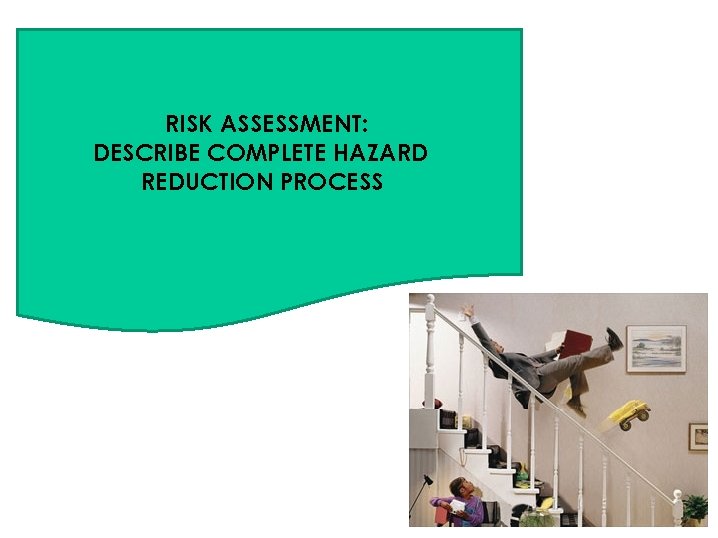
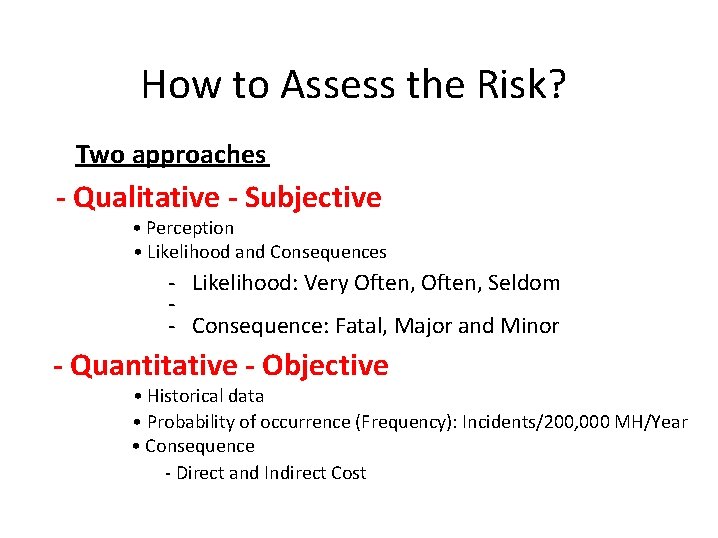

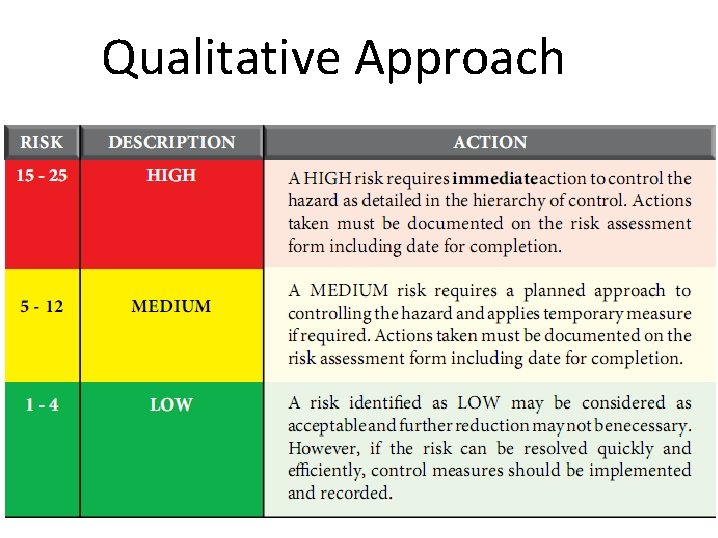
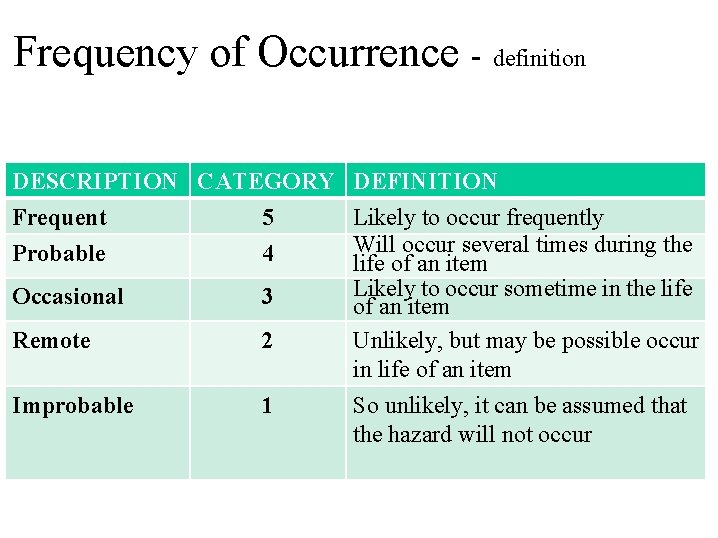
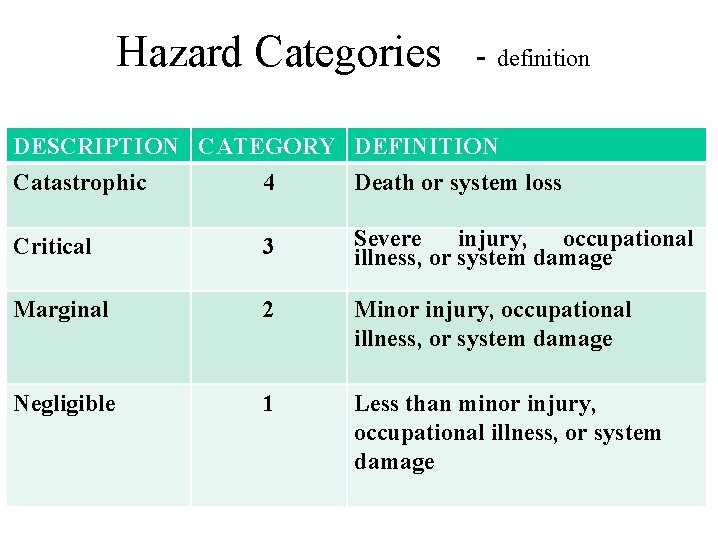
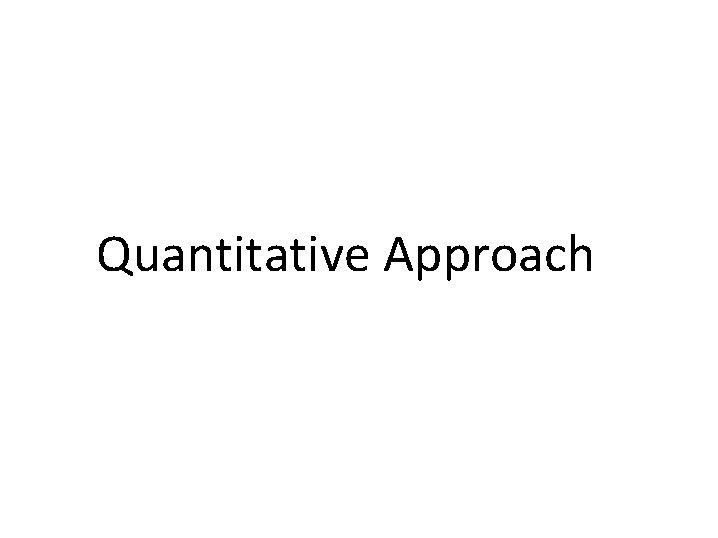
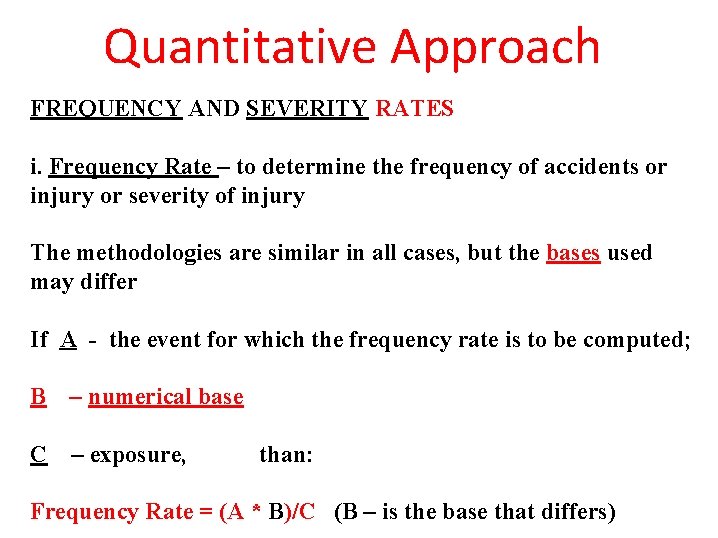
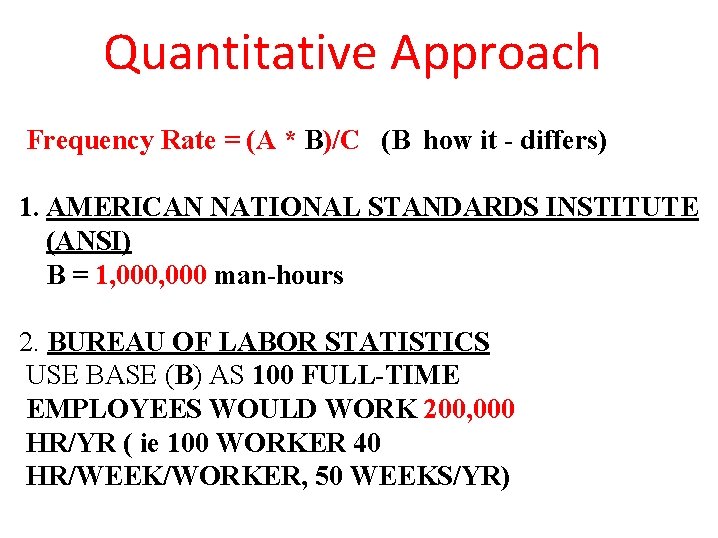
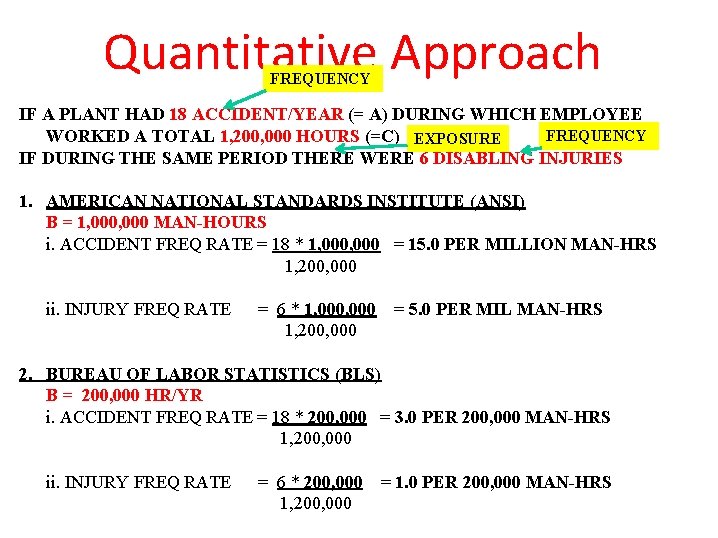
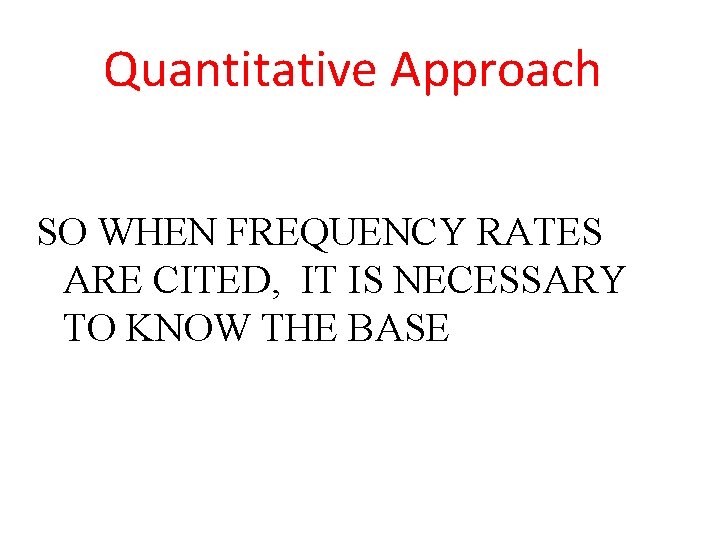
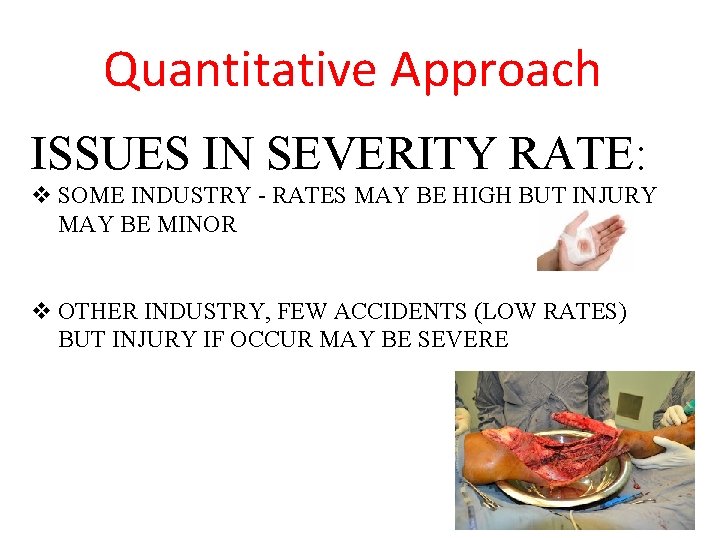
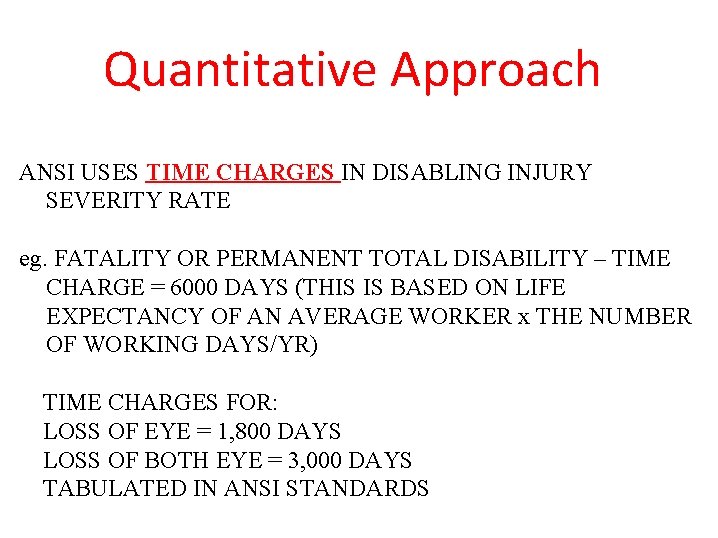
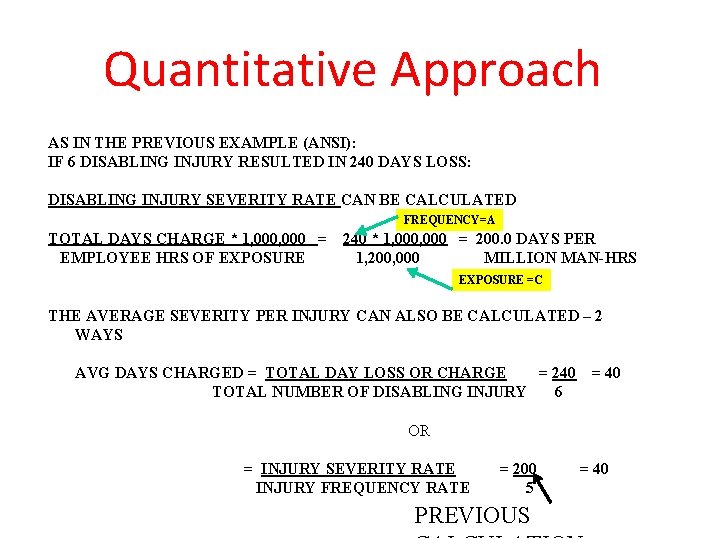
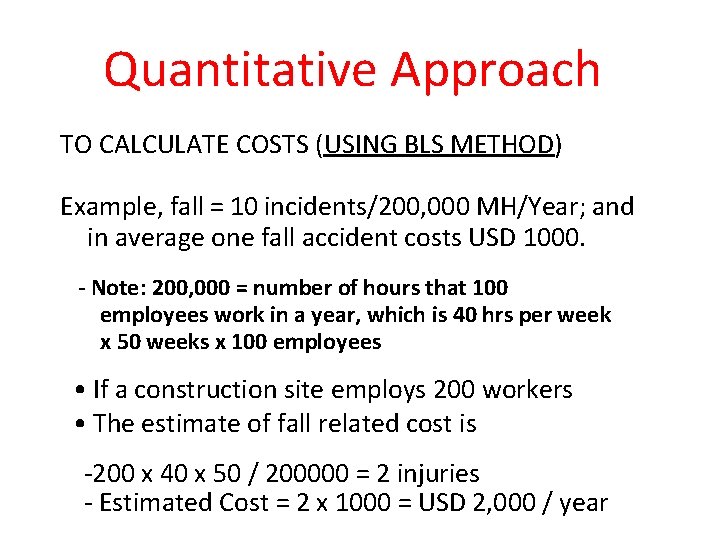
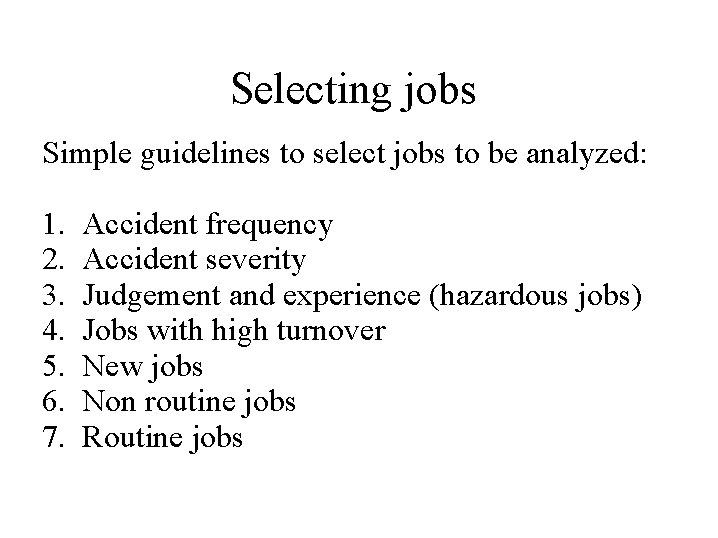
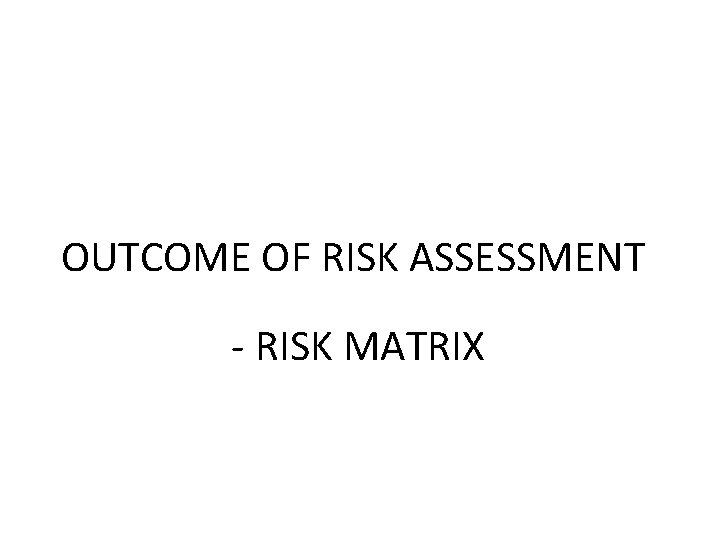
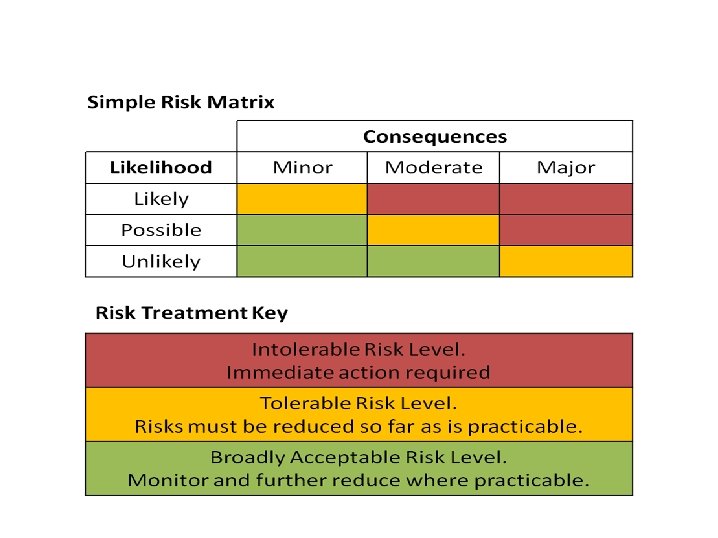
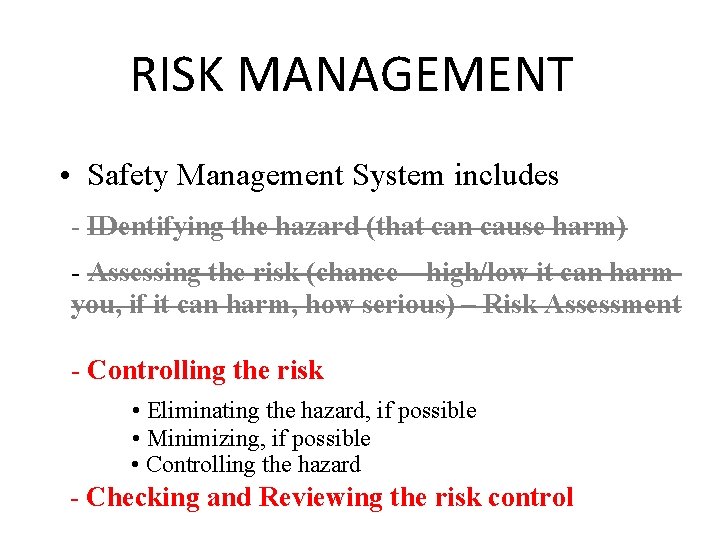
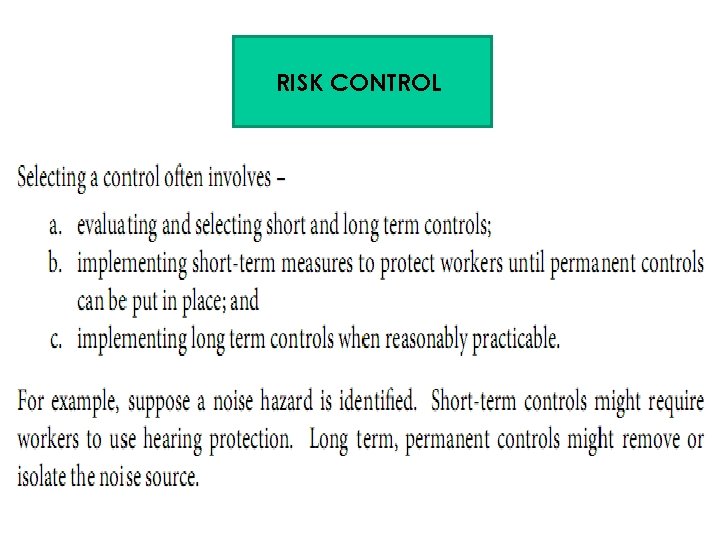
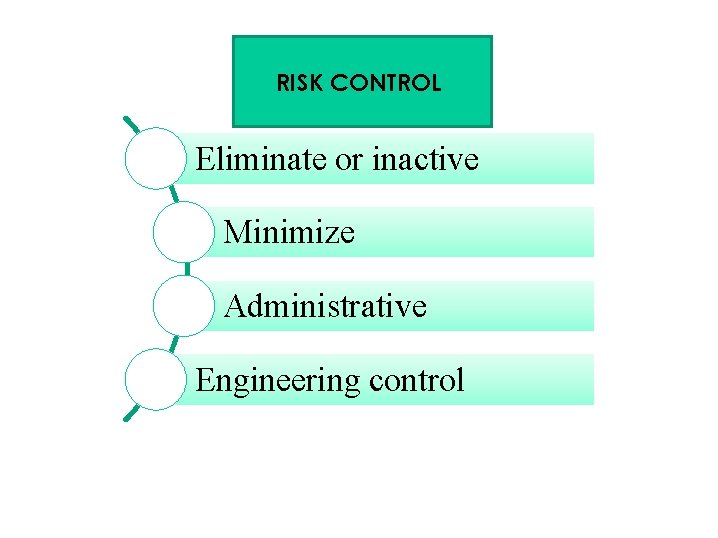
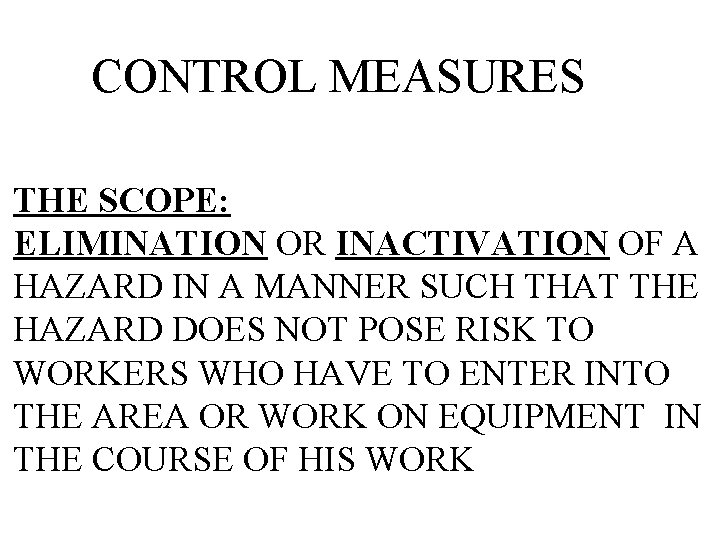

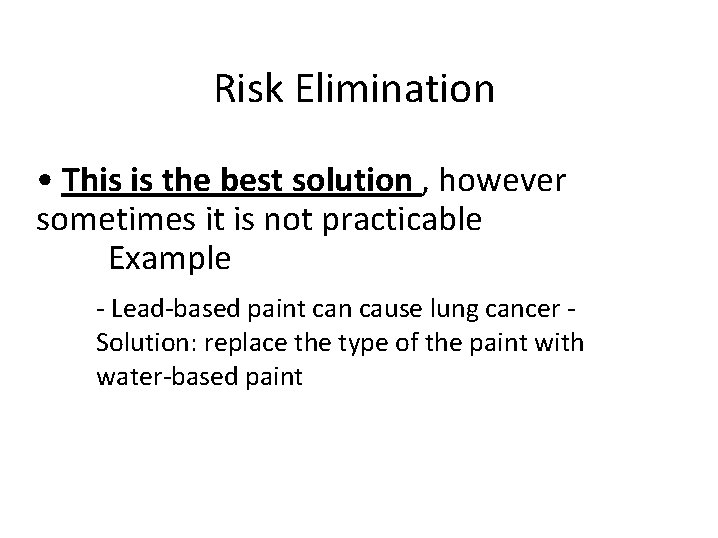
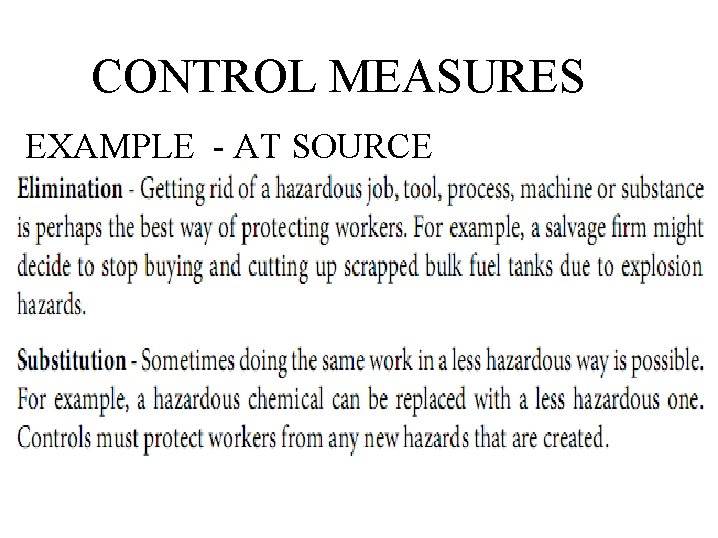
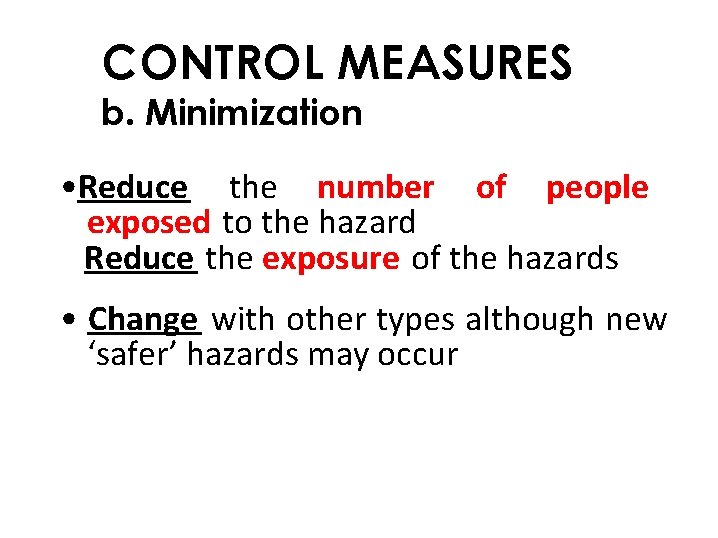
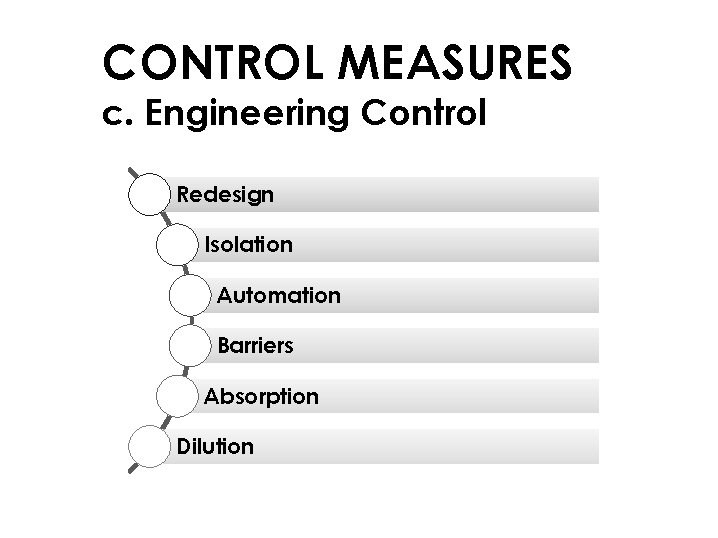
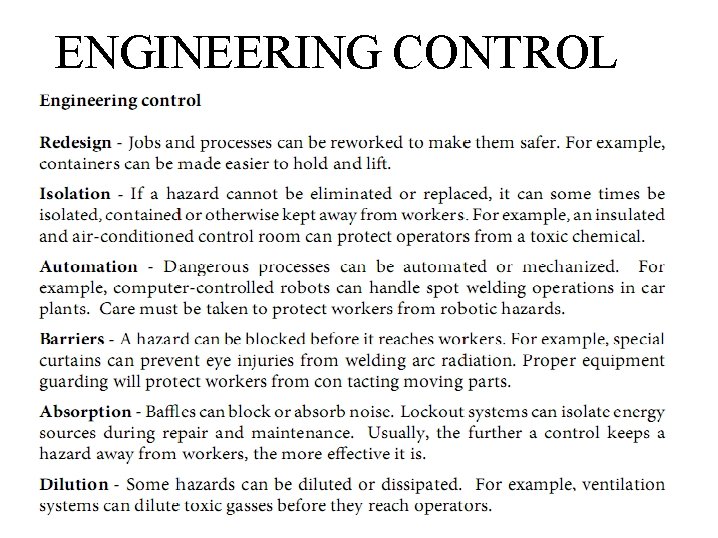
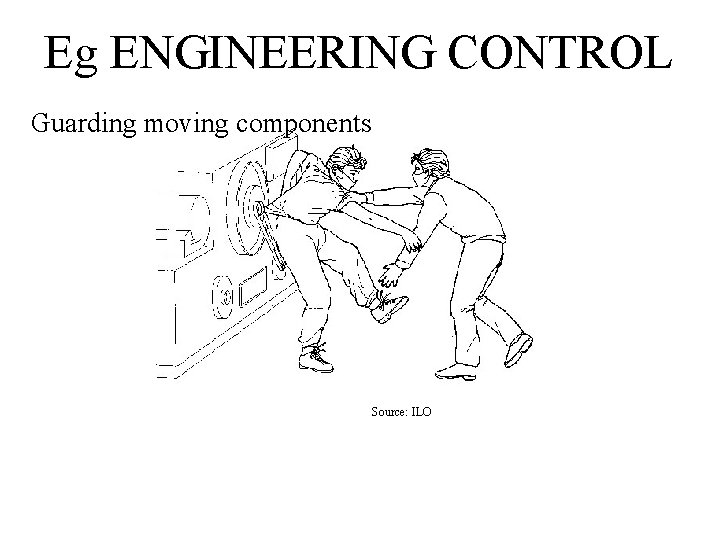
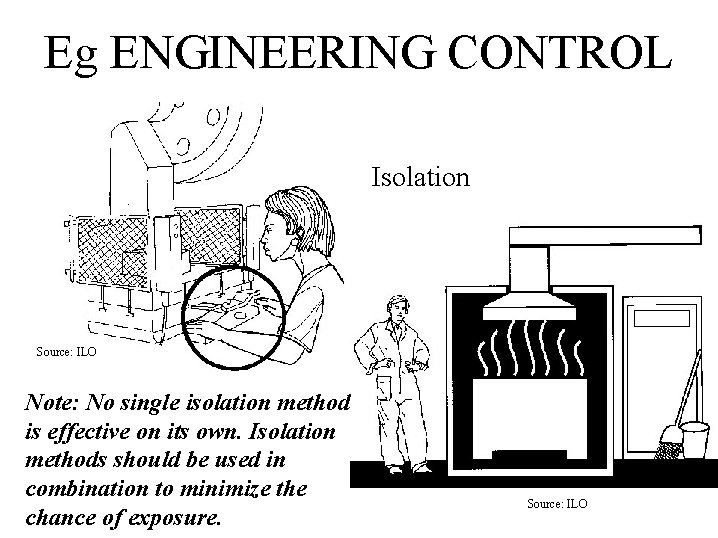
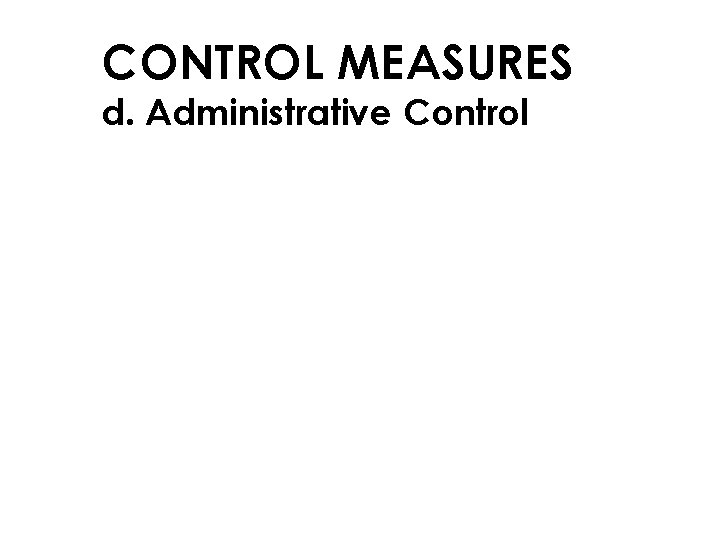

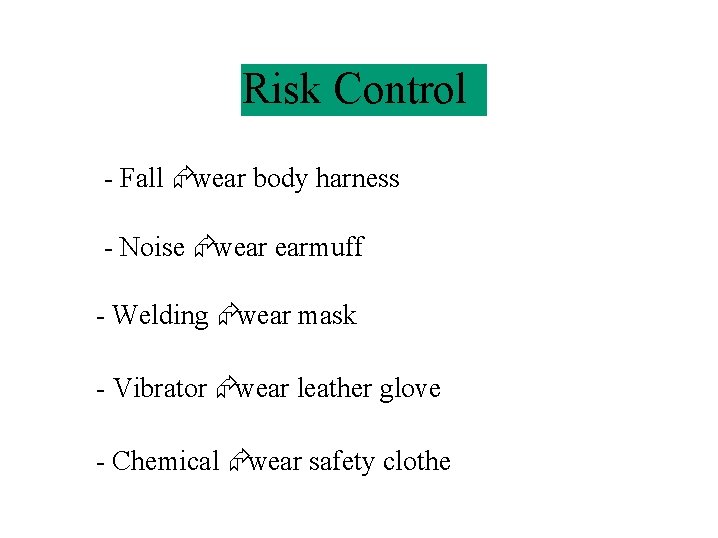
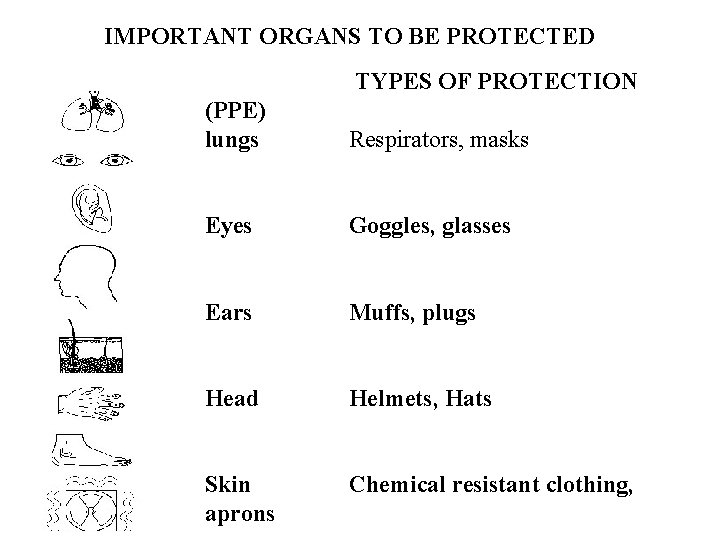
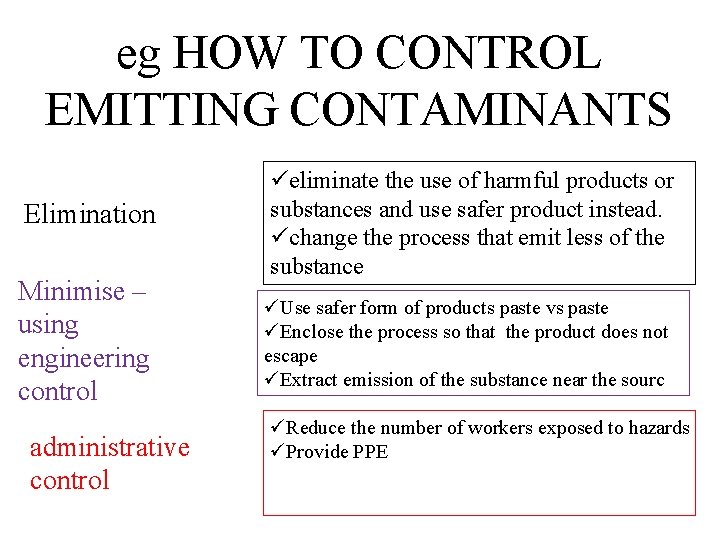
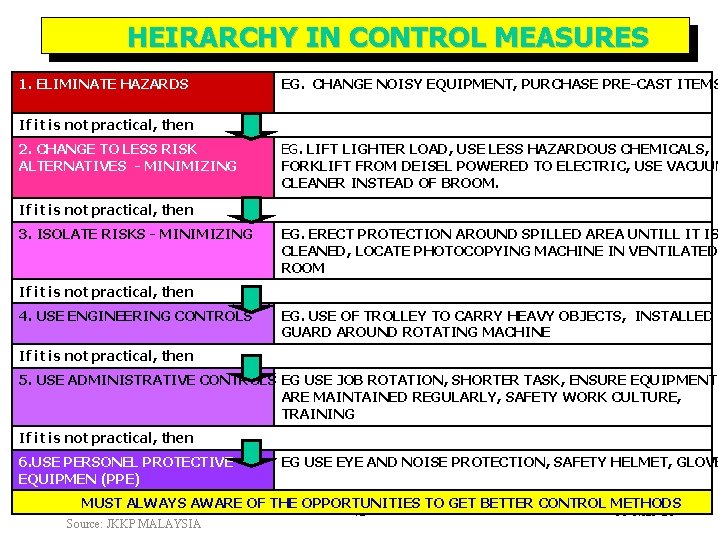
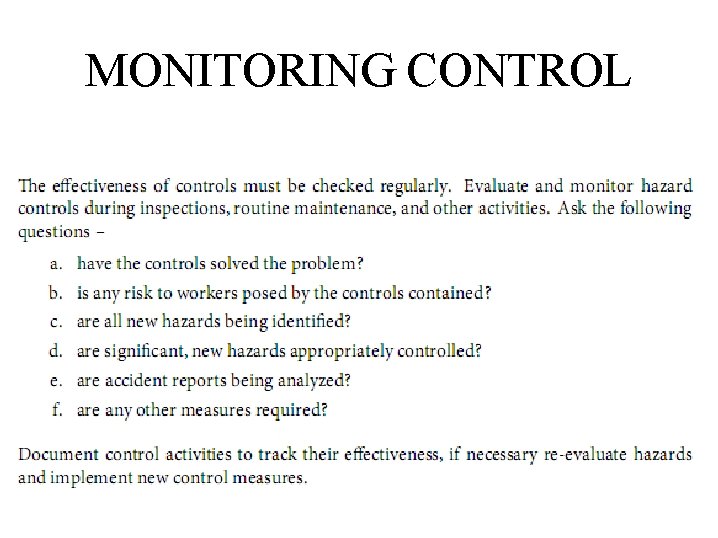
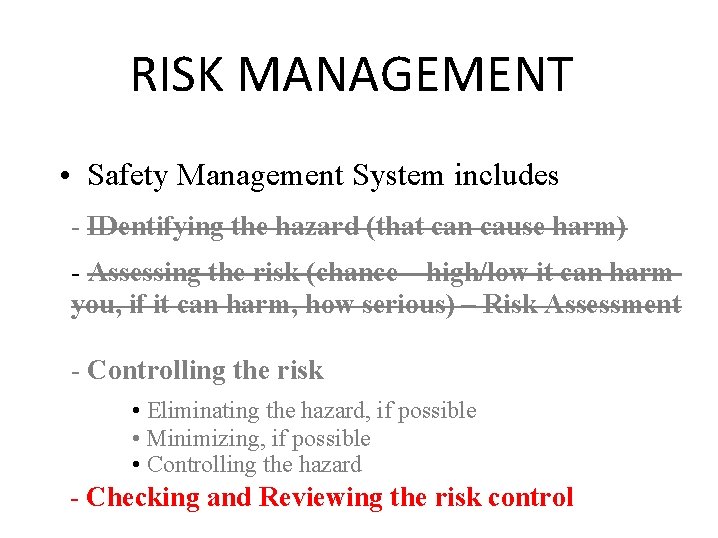
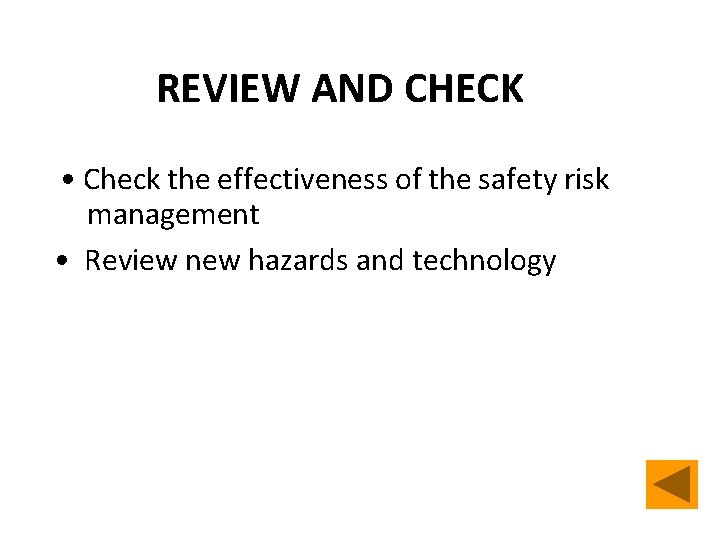
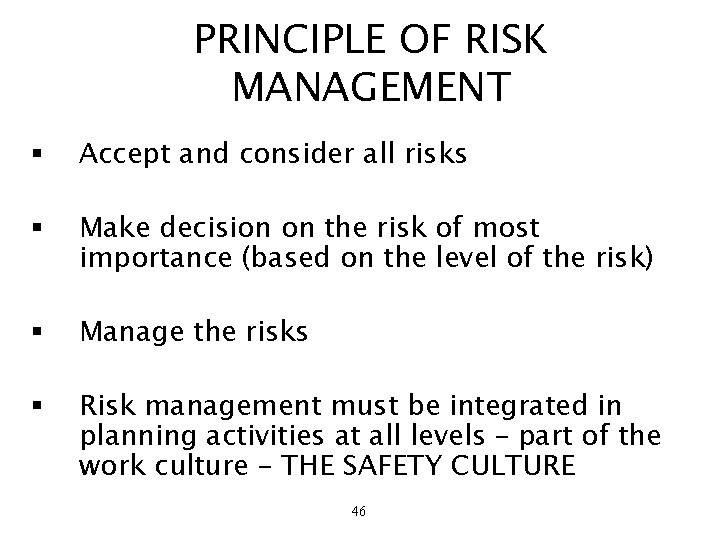
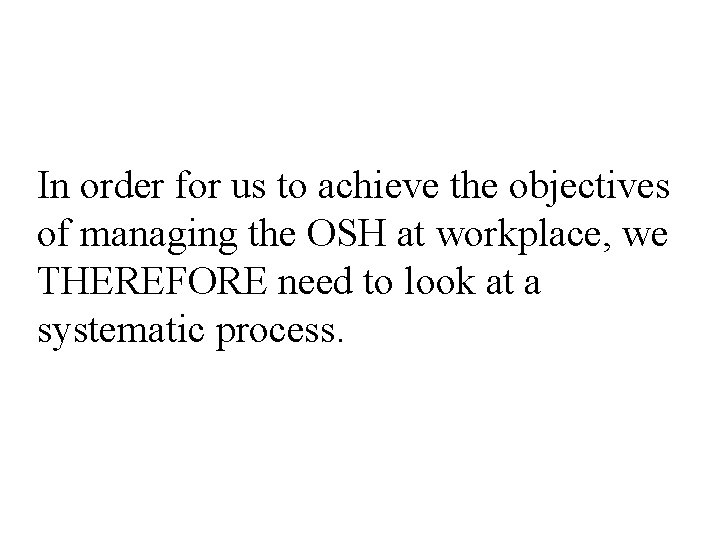
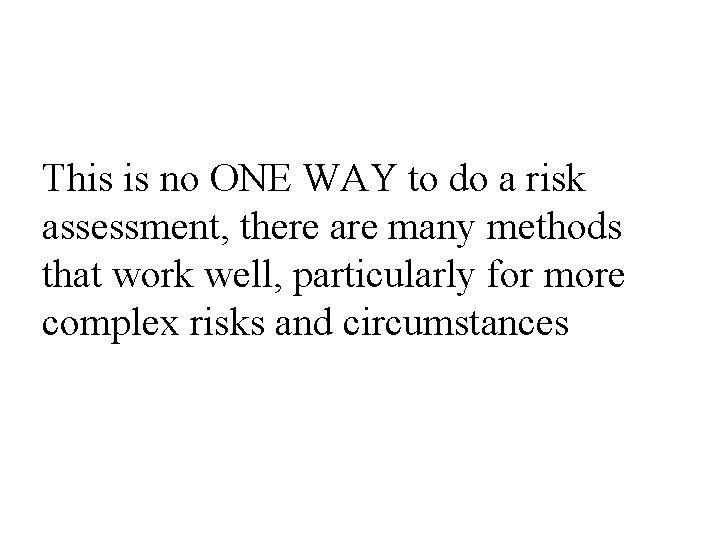
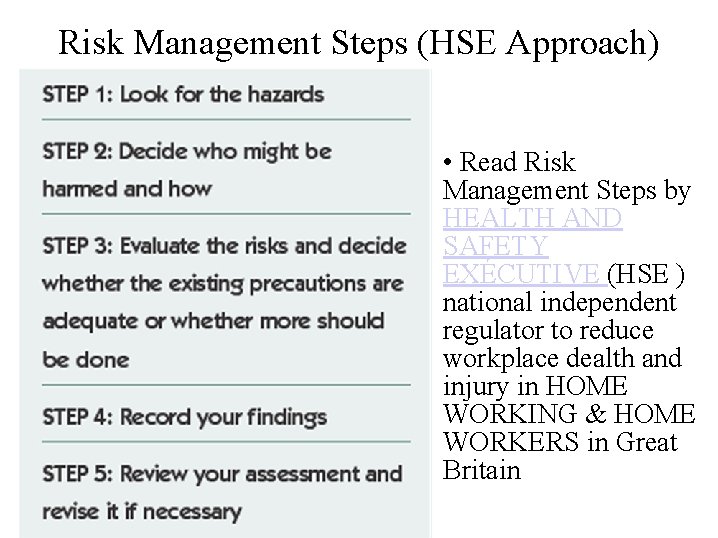
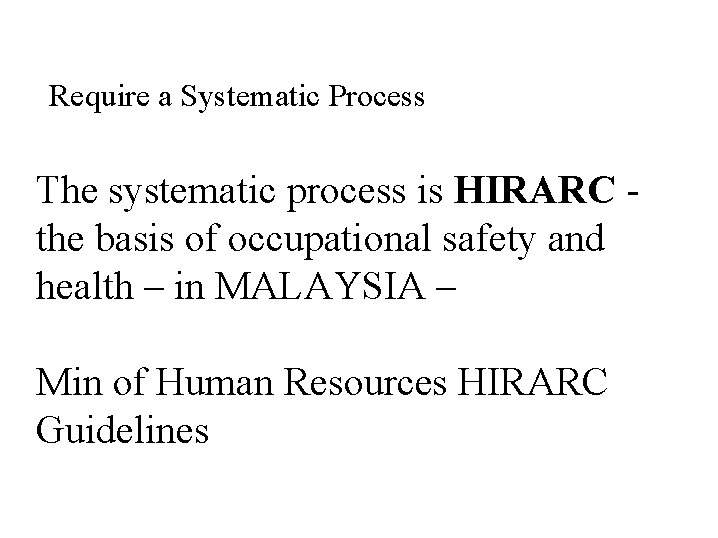
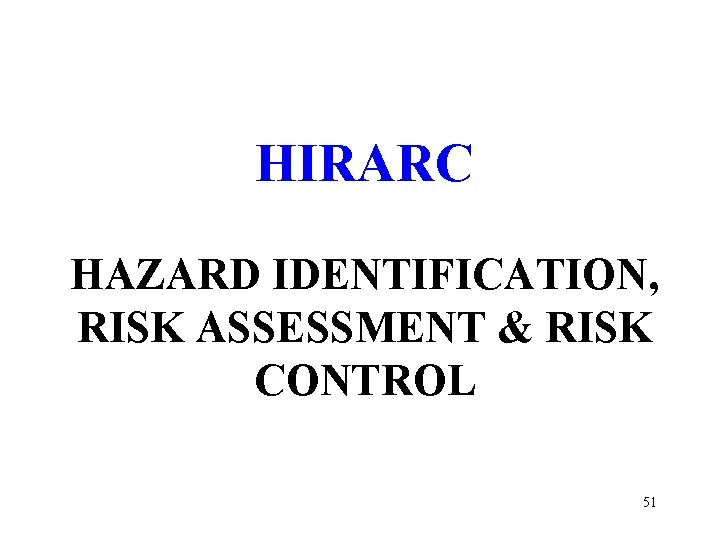
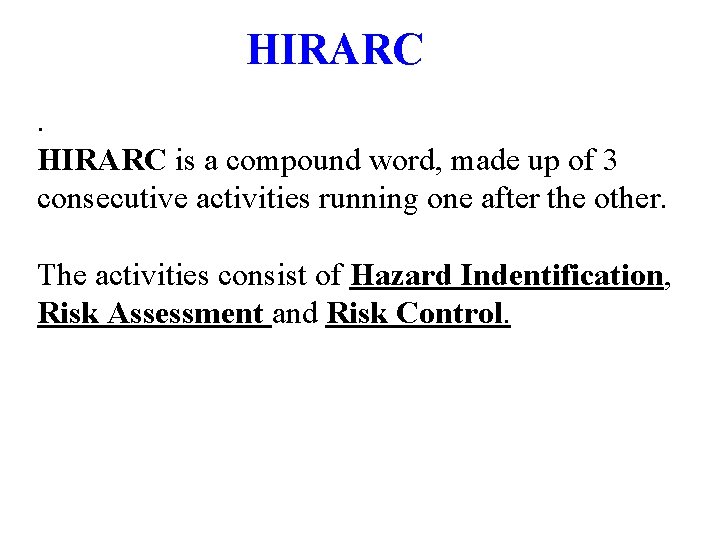
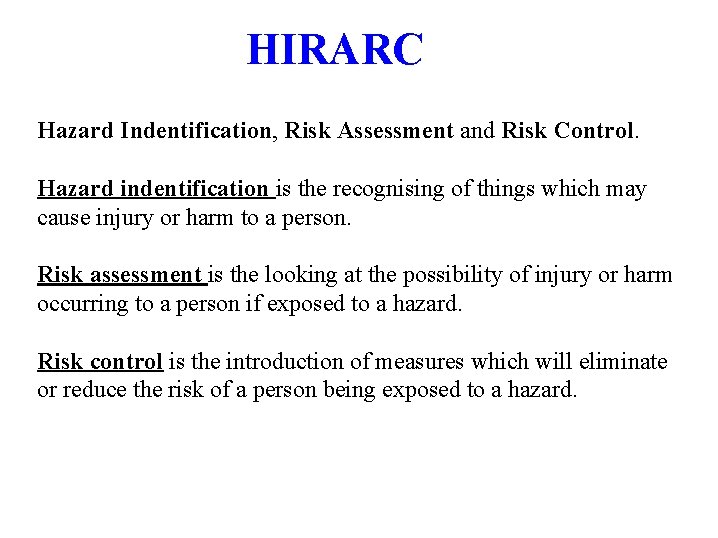
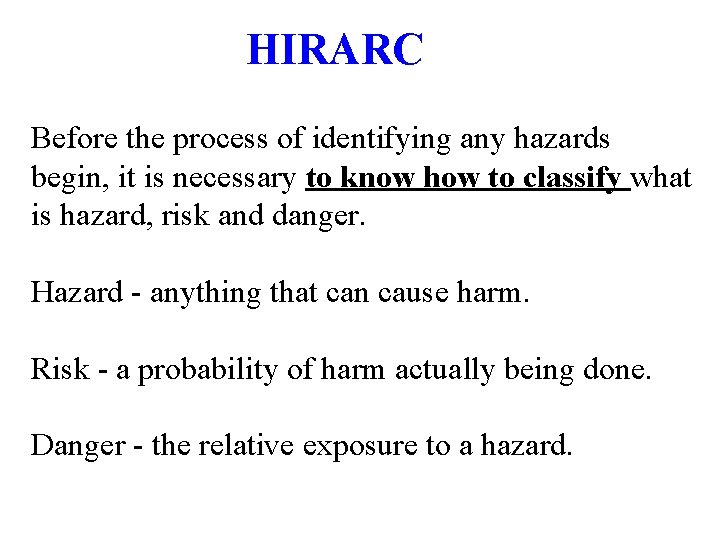
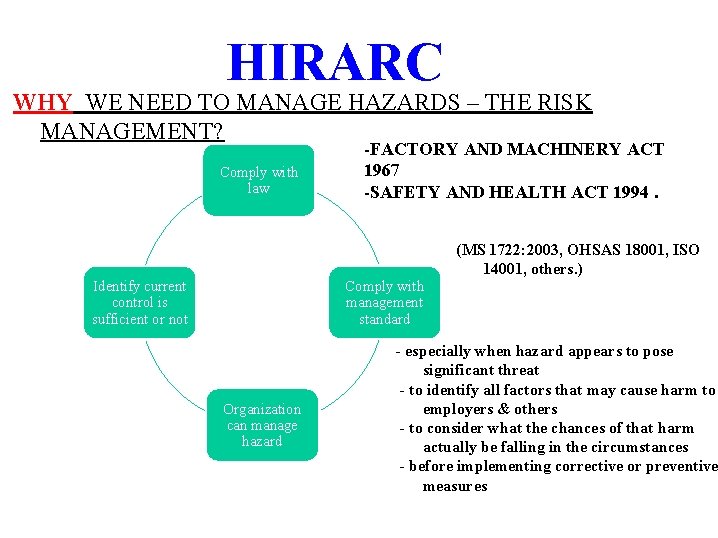
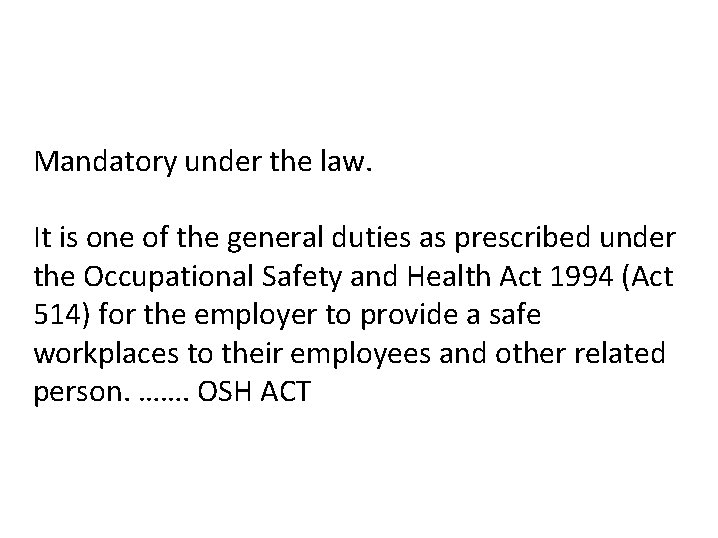
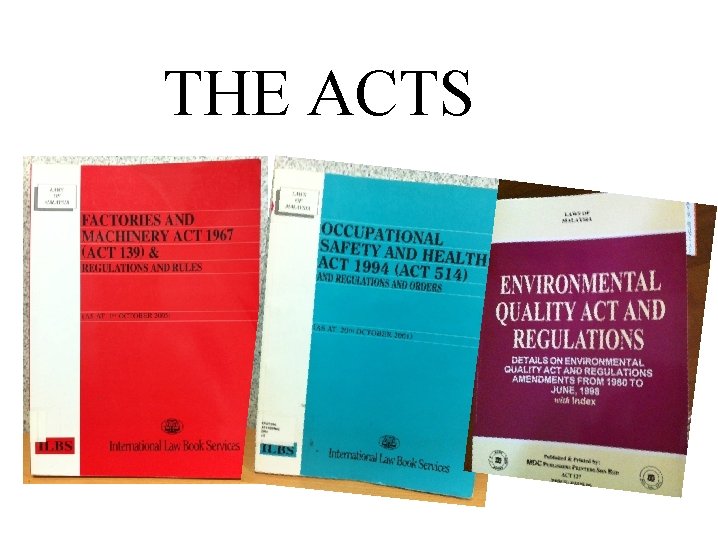
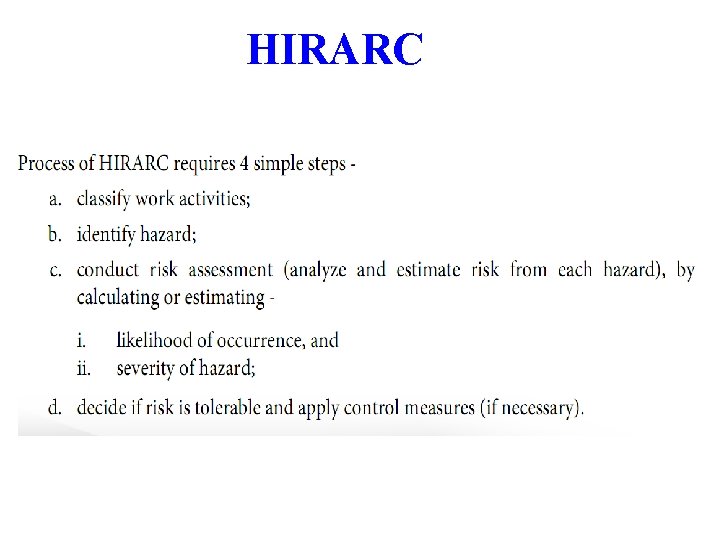
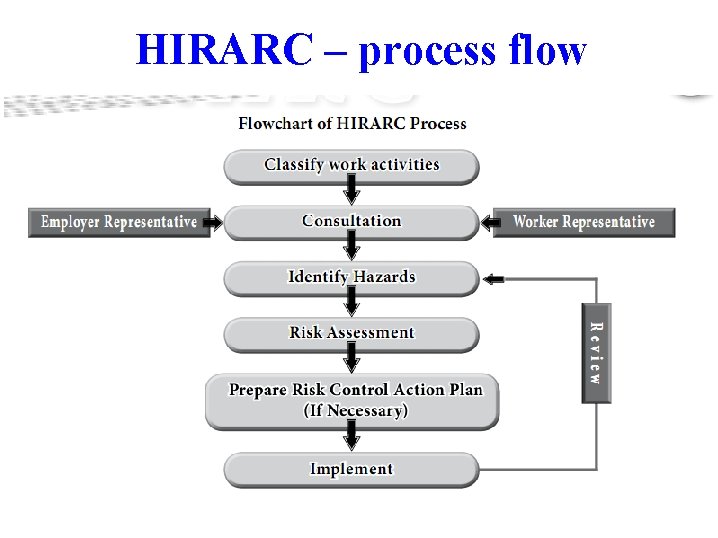
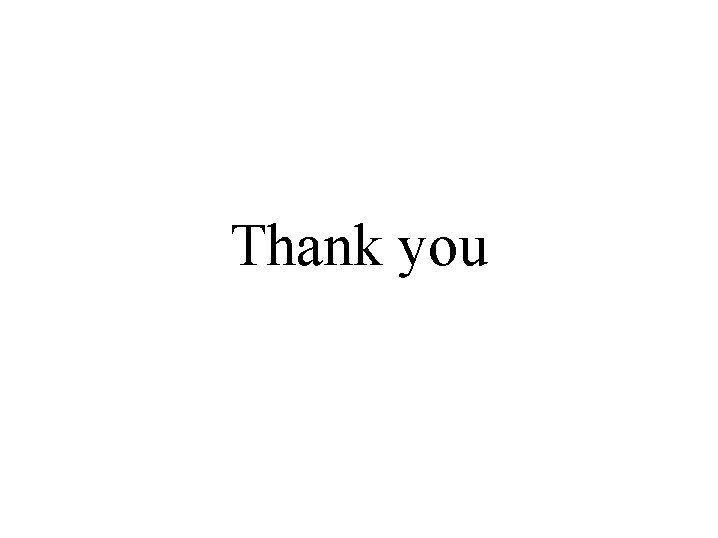
- Slides: 60
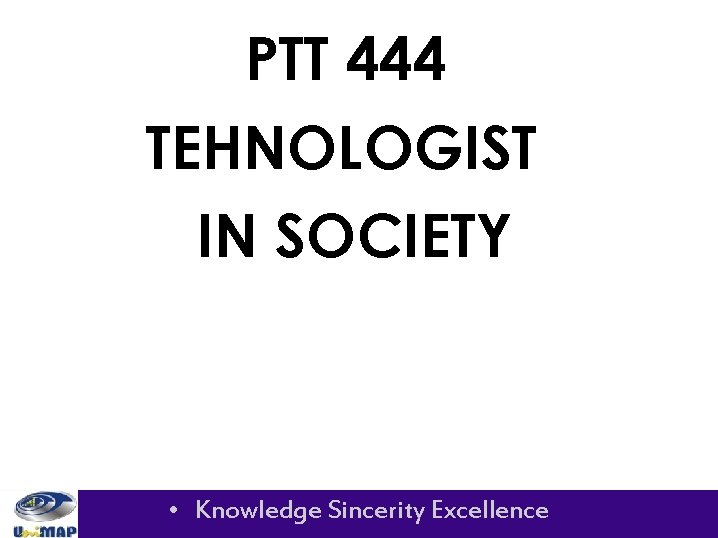
PTT 444 TEHNOLOGIST IN SOCIETY • Knowledge Sincerity Excellence
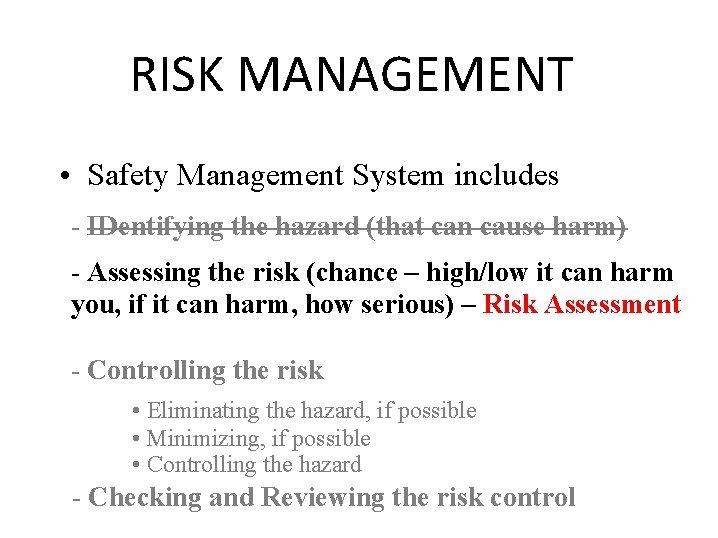
RISK MANAGEMENT • Safety Management System includes - IDentifying the hazard (that can cause harm) - Assessing the risk (chance – high/low it can harm you, if it can harm, how serious) – Risk Assessment - Controlling the risk • Eliminating the hazard, if possible • Minimizing, if possible • Controlling the hazard - Checking and Reviewing the risk control
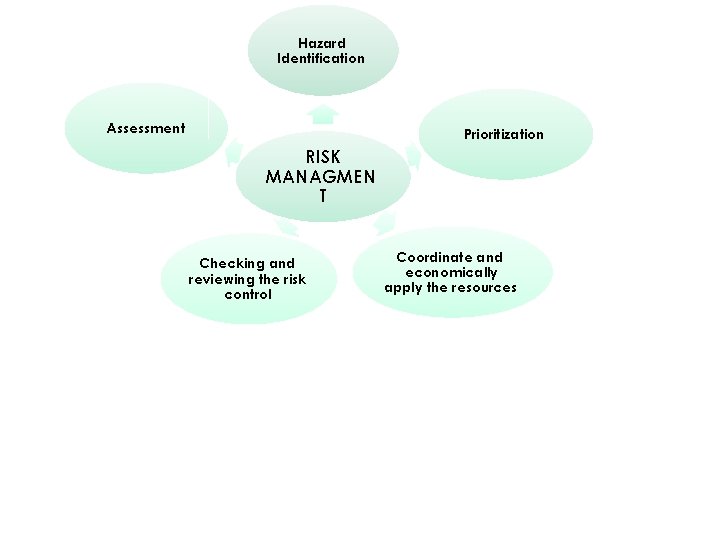
Hazard Identification Assessment Prioritization RISK MANAGMEN T Checking and reviewing the risk control Coordinate and economically apply the resources
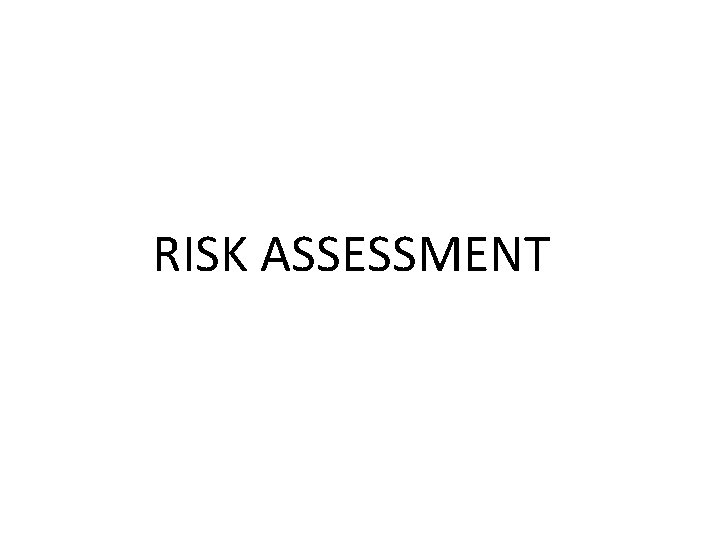
RISK ASSESSMENT
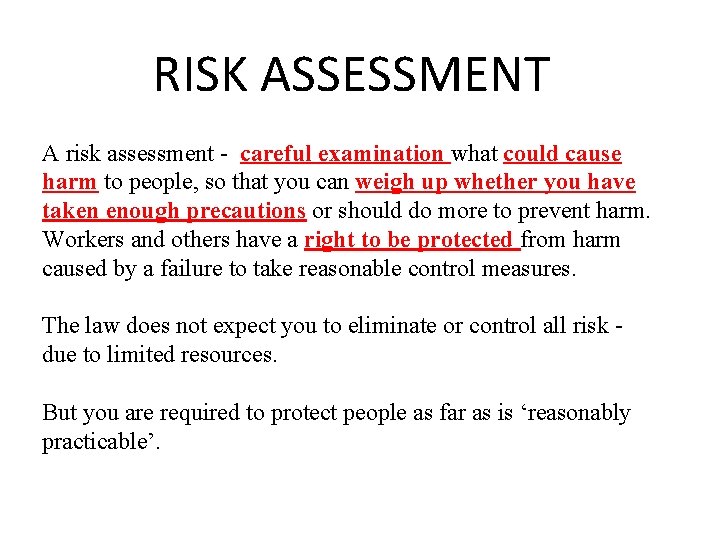
RISK ASSESSMENT A risk assessment - careful examination what could cause harm to people, so that you can weigh up whether you have taken enough precautions or should do more to prevent harm. Workers and others have a right to be protected from harm caused by a failure to take reasonable control measures. The law does not expect you to eliminate or control all risk - due to limited resources. But you are required to protect people as far as is ‘reasonably practicable’.
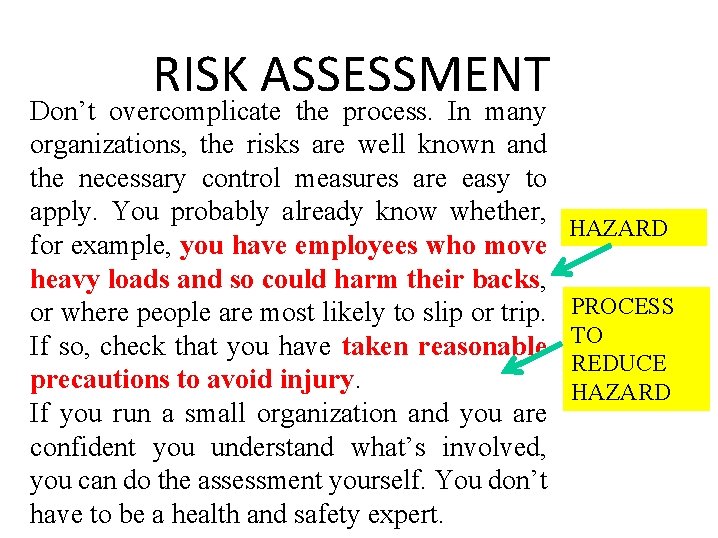
RISK ASSESSMENT Don’t overcomplicate the process. In many organizations, the risks are well known and the necessary control measures are easy to apply. You probably already know whether, for example, you have employees who move heavy loads and so could harm their backs, or where people are most likely to slip or trip. If so, check that you have taken reasonable precautions to avoid injury. If you run a small organization and you are confident you understand what’s involved, you can do the assessment yourself. You don’t have to be a health and safety expert. HAZARD PROCESS TO REDUCE HAZARD
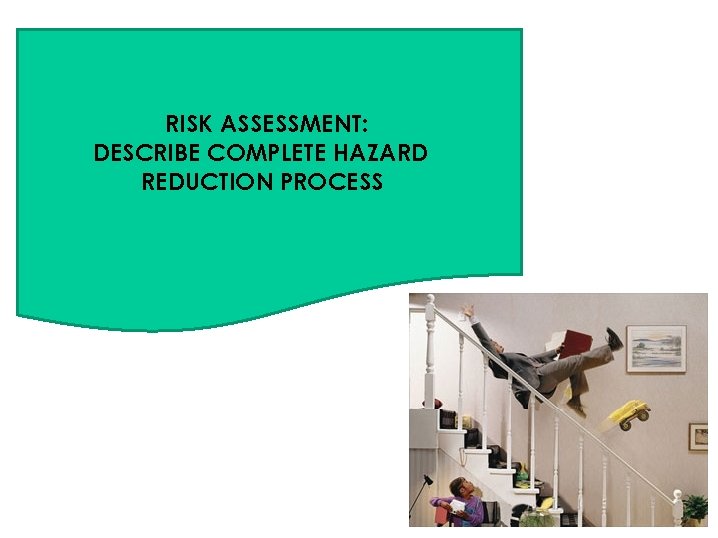
RISK ASSESSMENT: DESCRIBE COMPLETE HAZARD REDUCTION PROCESS
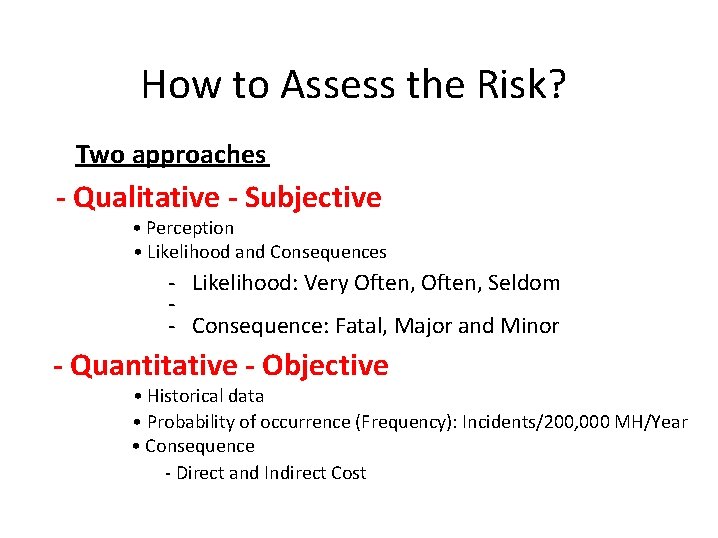
How to Assess the Risk? Two approaches - Qualitative - Subjective • Perception • Likelihood and Consequences - Likelihood: Very Often, Seldom - Consequence: Fatal, Major and Minor - Quantitative - Objective • Historical data • Probability of occurrence (Frequency): Incidents/200, 000 MH/Year • Consequence - Direct and Indirect Cost

eg. Qualitative – risk martix Risk Assessment Matrix Frequency of Occurrence (5) Frequent (4) Probable (3) Occasional (2) Remote (1) Improbable Hazard Categories 4 Catastrophic 20 16 12 8 4 3 Critical 15 12 9 6 3 2 Marginal 10 8 6 4 2 1 Negligible 5 4 3 2 1 Hazard Risk Index Risk Classification – WEIGH FACTOR: From 10 to 20 From 6 to 9 From 3 to 5 From 1 to 2 Risk Criteria: Unacceptable Undesirable Acceptable with review Acceptable without review
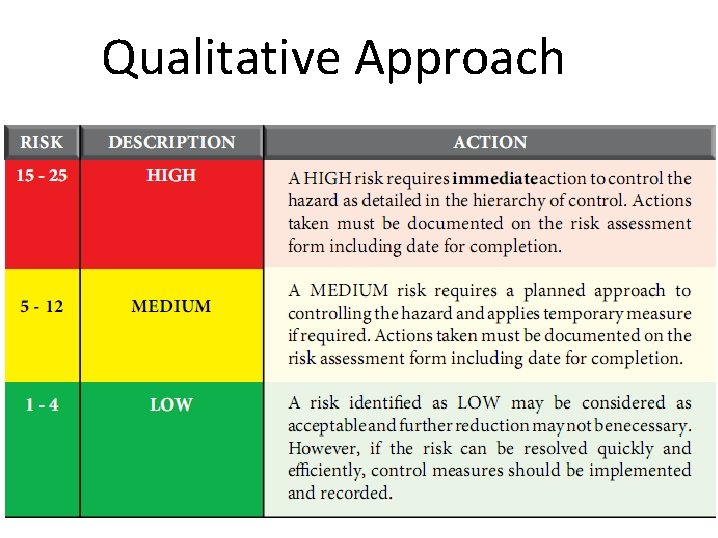
Qualitative Approach
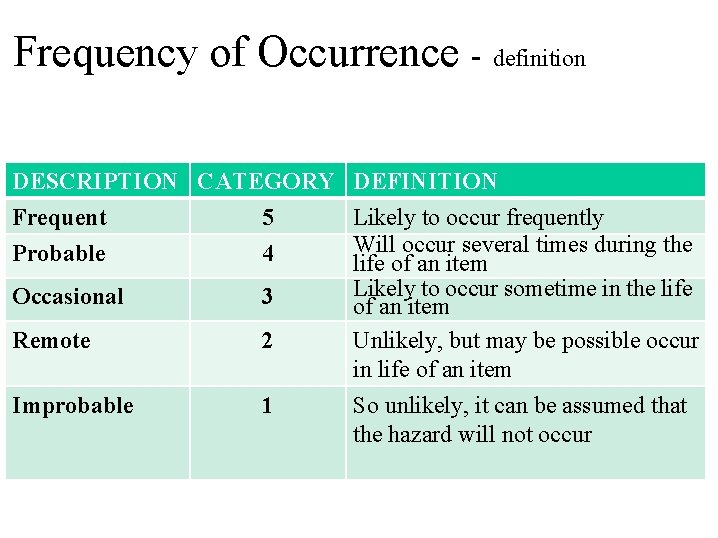
Frequency of Occurrence - definition DESCRIPTION CATEGORY DEFINITION Frequent Probable 5 4 Occasional 3 Remote 2 Improbable 1 Likely to occur frequently Will occur several times during the life of an item Likely to occur sometime in the life of an item Unlikely, but may be possible occur in life of an item So unlikely, it can be assumed that the hazard will not occur
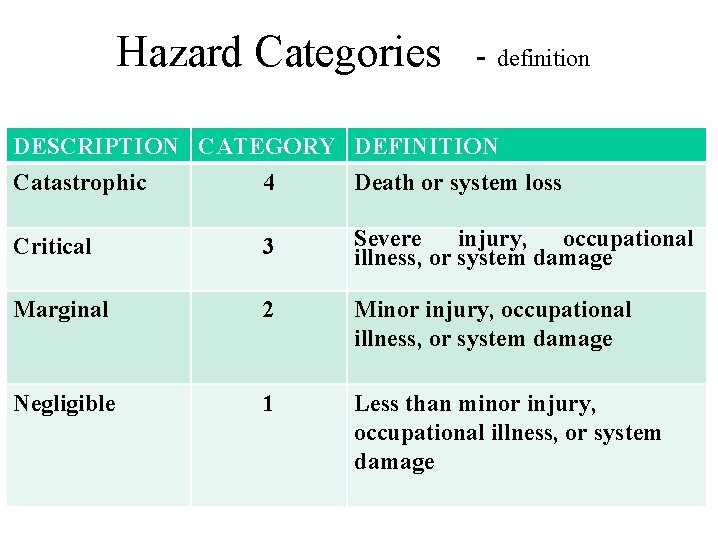
Hazard Categories - definition DESCRIPTION CATEGORY DEFINITION Catastrophic 4 Death or system loss Critical 3 Severe injury, occupational illness, or system damage Marginal 2 Minor injury, occupational illness, or system damage Negligible 1 Less than minor injury, occupational illness, or system damage
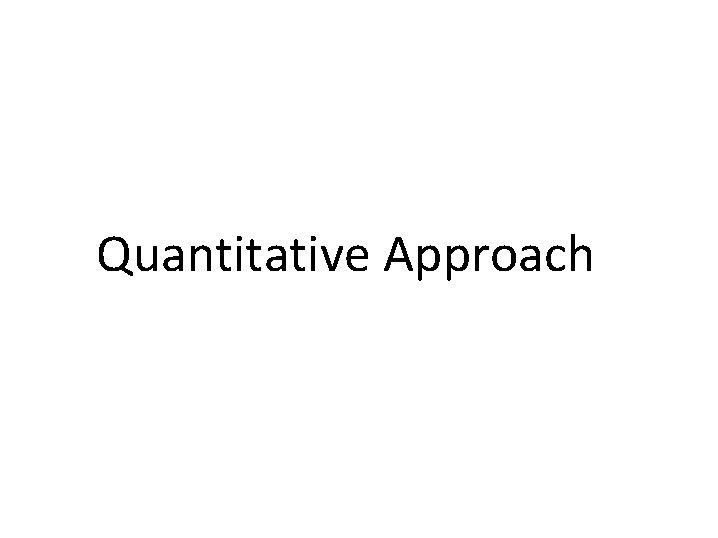
Quantitative Approach
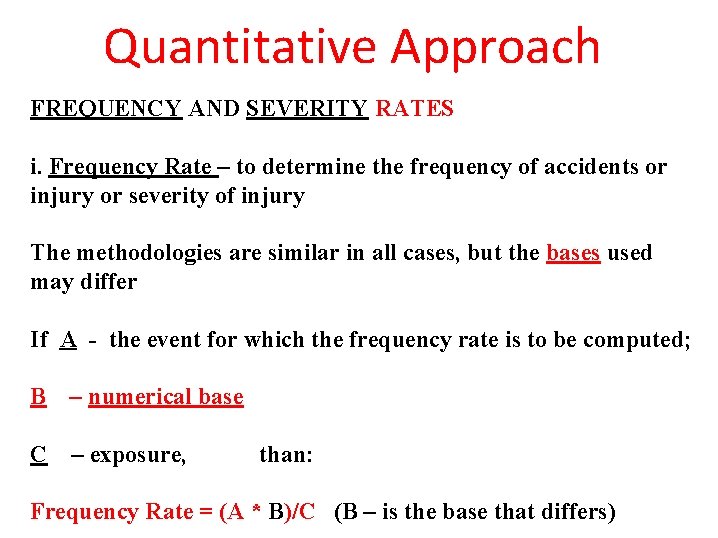
Quantitative Approach FREQUENCY AND SEVERITY RATES i. Frequency Rate – to determine the frequency of accidents or injury or severity of injury The methodologies are similar in all cases, but the bases used may differ If A - the event for which the frequency rate is to be computed; B – numerical base C – exposure, than: Frequency Rate = (A * B)/C (B – is the base that differs)
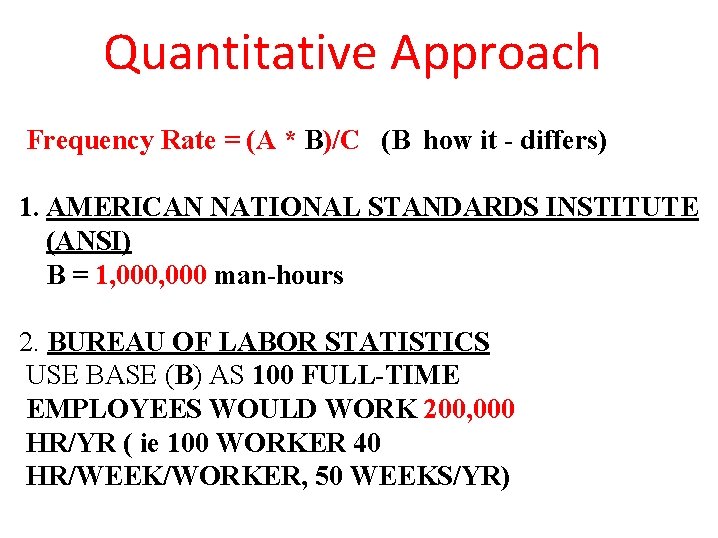
Quantitative Approach Frequency Rate = (A * B)/C (B how it - differs) 1. AMERICAN NATIONAL STANDARDS INSTITUTE (ANSI) B = 1, 000 man-hours 2. BUREAU OF LABOR STATISTICS USE BASE (B) AS 100 FULL-TIME EMPLOYEES WOULD WORK 200, 000 HR/YR ( ie 100 WORKER 40 HR/WEEK/WORKER, 50 WEEKS/YR)
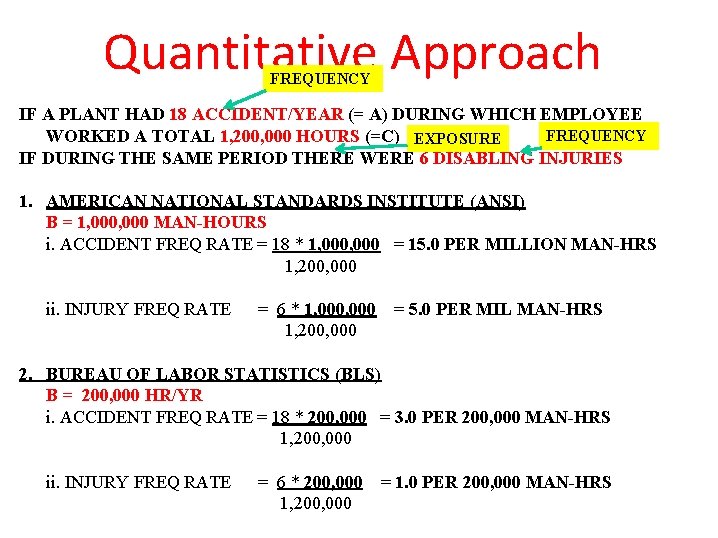
Quantitative Approach FREQUENCY IF A PLANT HAD 18 ACCIDENT/YEAR (= A) DURING WHICH EMPLOYEE FREQUENCY WORKED A TOTAL 1, 200, 000 HOURS (=C) EXPOSURE IF DURING THE SAME PERIOD THERE WERE 6 DISABLING INJURIES 1. AMERICAN NATIONAL STANDARDS INSTITUTE (ANSI) B = 1, 000 MAN-HOURS i. ACCIDENT FREQ RATE = 18 * 1, 000 = 15. 0 PER MILLION MAN-HRS 1, 200, 000 ii. INJURY FREQ RATE = 6 * 1, 000 = 5. 0 PER MIL MAN-HRS 1, 200, 000 2. BUREAU OF LABOR STATISTICS (BLS) B = 200, 000 HR/YR i. ACCIDENT FREQ RATE = 18 * 200, 000 = 3. 0 PER 200, 000 MAN-HRS 1, 200, 000 ii. INJURY FREQ RATE = 6 * 200, 000 = 1. 0 PER 200, 000 MAN-HRS 1, 200, 000
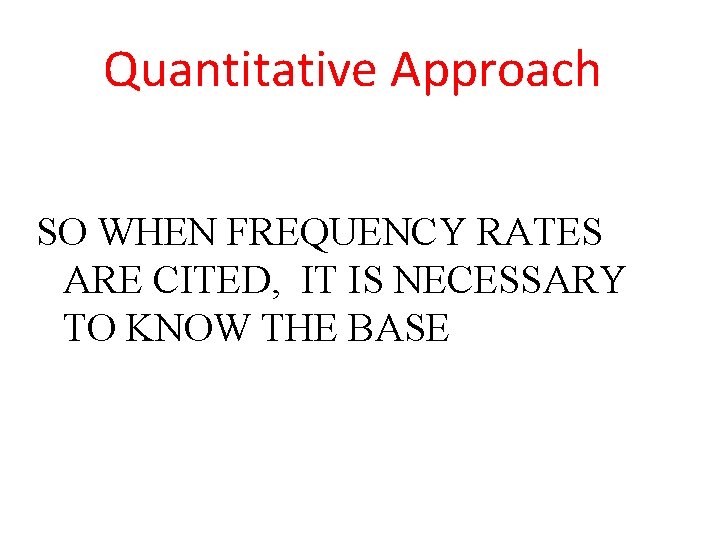
Quantitative Approach SO WHEN FREQUENCY RATES ARE CITED, IT IS NECESSARY TO KNOW THE BASE
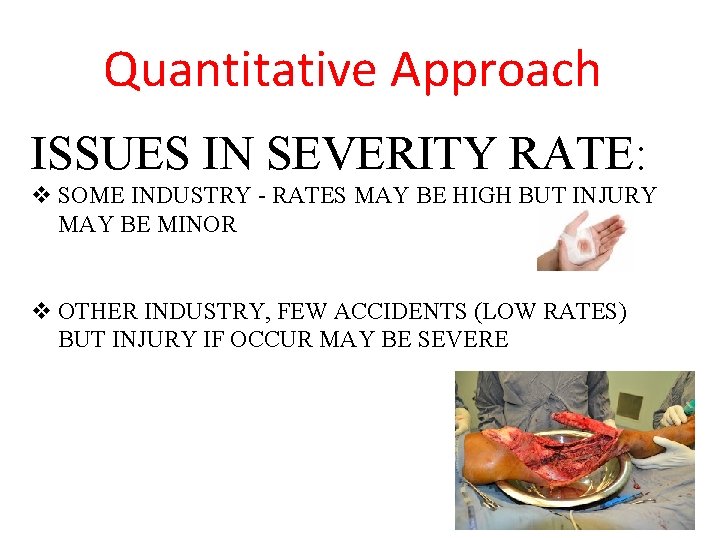
Quantitative Approach ISSUES IN SEVERITY RATE: v SOME INDUSTRY - RATES MAY BE HIGH BUT INJURY MAY BE MINOR v OTHER INDUSTRY, FEW ACCIDENTS (LOW RATES) BUT INJURY IF OCCUR MAY BE SEVERE
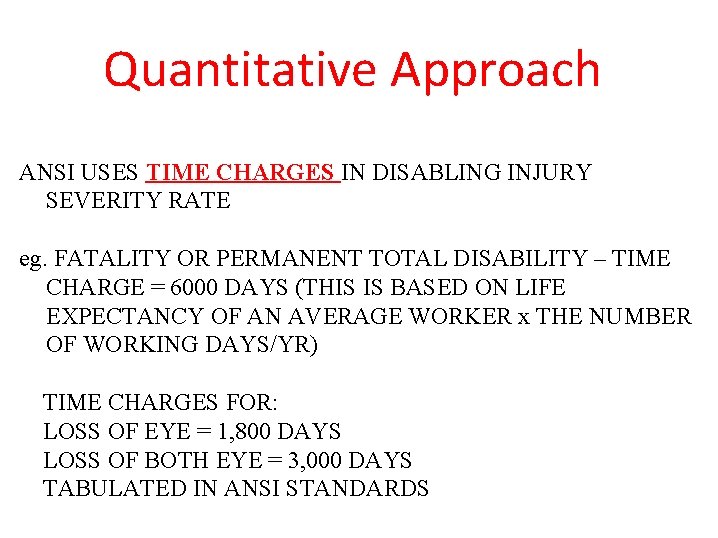
Quantitative Approach ANSI USES TIME CHARGES IN DISABLING INJURY SEVERITY RATE eg. FATALITY OR PERMANENT TOTAL DISABILITY – TIME CHARGE = 6000 DAYS (THIS IS BASED ON LIFE EXPECTANCY OF AN AVERAGE WORKER x THE NUMBER OF WORKING DAYS/YR) TIME CHARGES FOR: LOSS OF EYE = 1, 800 DAYS LOSS OF BOTH EYE = 3, 000 DAYS TABULATED IN ANSI STANDARDS
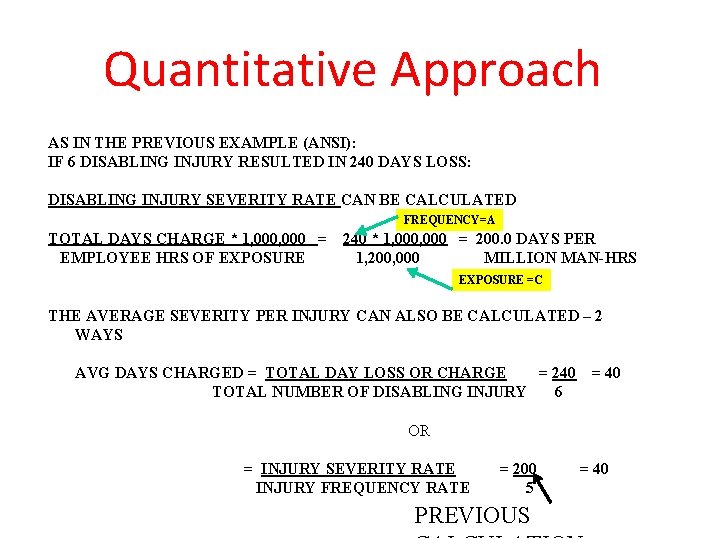
Quantitative Approach AS IN THE PREVIOUS EXAMPLE (ANSI): IF 6 DISABLING INJURY RESULTED IN 240 DAYS LOSS: DISABLING INJURY SEVERITY RATE CAN BE CALCULATED FREQUENCY=A TOTAL DAYS CHARGE * 1, 000 = 240 * 1, 000 = 200. 0 DAYS PER EMPLOYEE HRS OF EXPOSURE 1, 200, 000 MILLION MAN-HRS EXPOSURE =C THE AVERAGE SEVERITY PER INJURY CAN ALSO BE CALCULATED – 2 WAYS AVG DAYS CHARGED = TOTAL DAY LOSS OR CHARGE = 240 = 40 TOTAL NUMBER OF DISABLING INJURY 6 OR = INJURY SEVERITY RATE INJURY FREQUENCY RATE = 200 5 PREVIOUS = 40
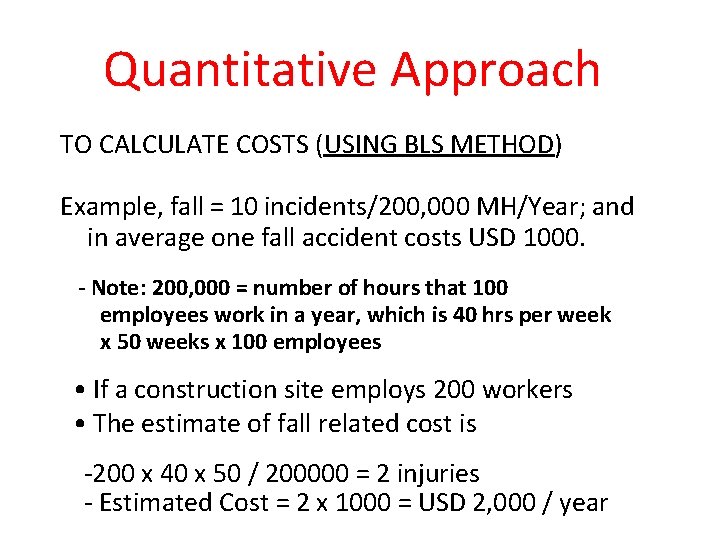
Quantitative Approach TO CALCULATE COSTS (USING BLS METHOD) Example, fall = 10 incidents/200, 000 MH/Year; and in average one fall accident costs USD 1000. - Note: 200, 000 = number of hours that 100 employees work in a year, which is 40 hrs per week x 50 weeks x 100 employees • If a construction site employs 200 workers • The estimate of fall related cost is -200 x 40 x 50 / 200000 = 2 injuries - Estimated Cost = 2 x 1000 = USD 2, 000 / year
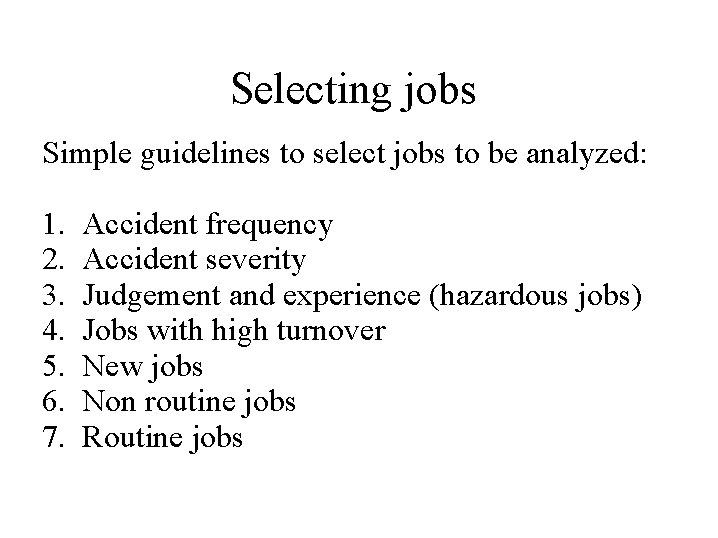
Selecting jobs Simple guidelines to select jobs to be analyzed: 1. 2. 3. 4. 5. 6. 7. Accident frequency Accident severity Judgement and experience (hazardous jobs) Jobs with high turnover New jobs Non routine jobs Routine jobs
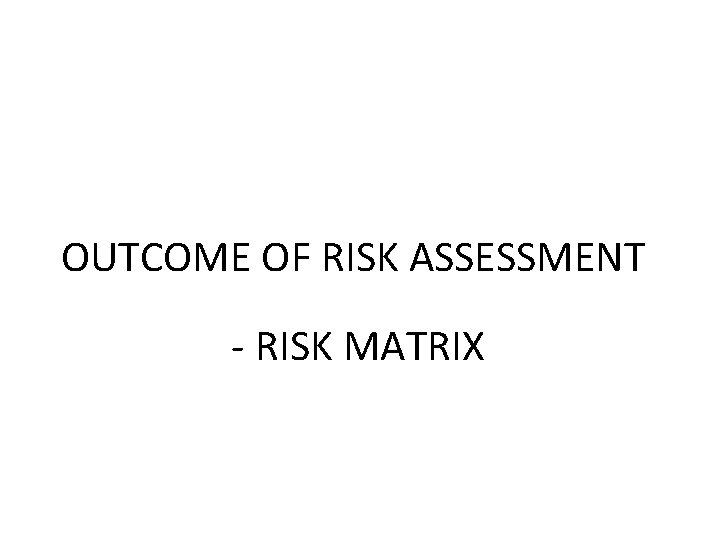
OUTCOME OF RISK ASSESSMENT - RISK MATRIX
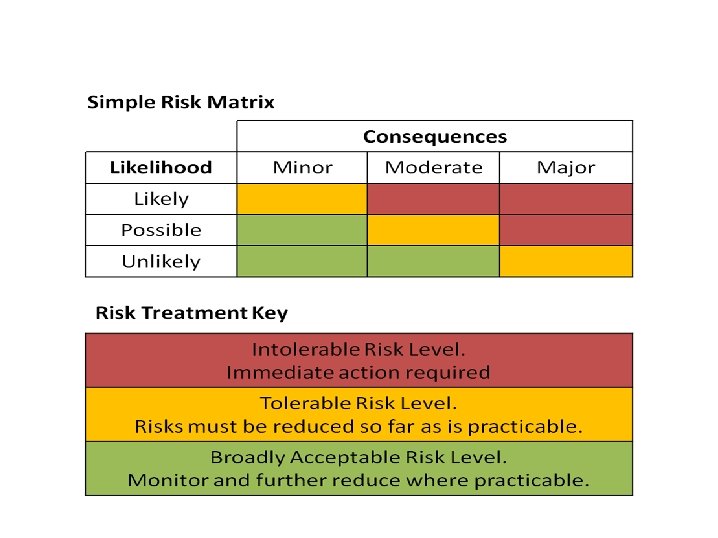
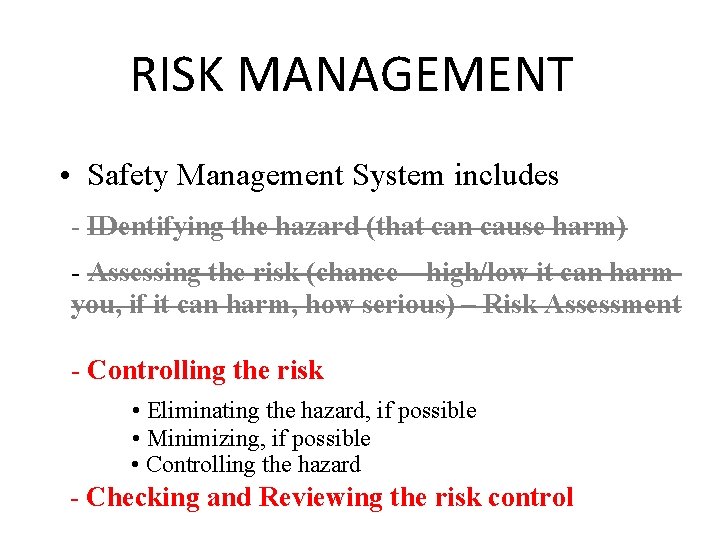
RISK MANAGEMENT • Safety Management System includes - IDentifying the hazard (that can cause harm) - Assessing the risk (chance – high/low it can harm you, if it can harm, how serious) – Risk Assessment - Controlling the risk • Eliminating the hazard, if possible • Minimizing, if possible • Controlling the hazard - Checking and Reviewing the risk control
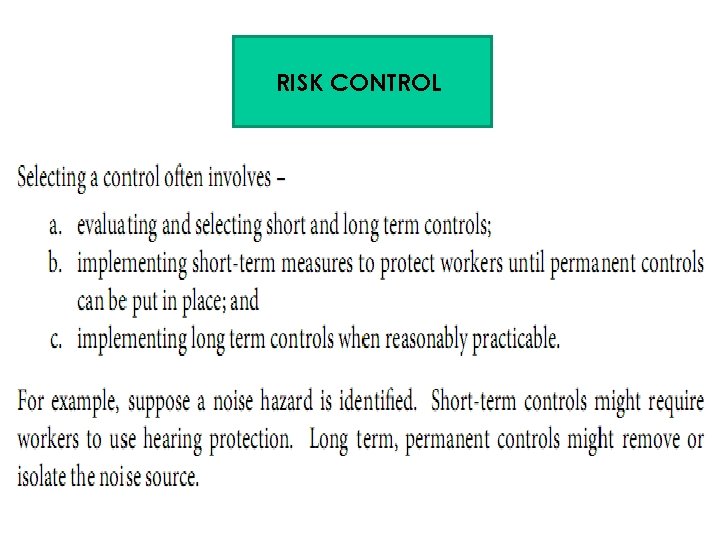
RISK CONTROL
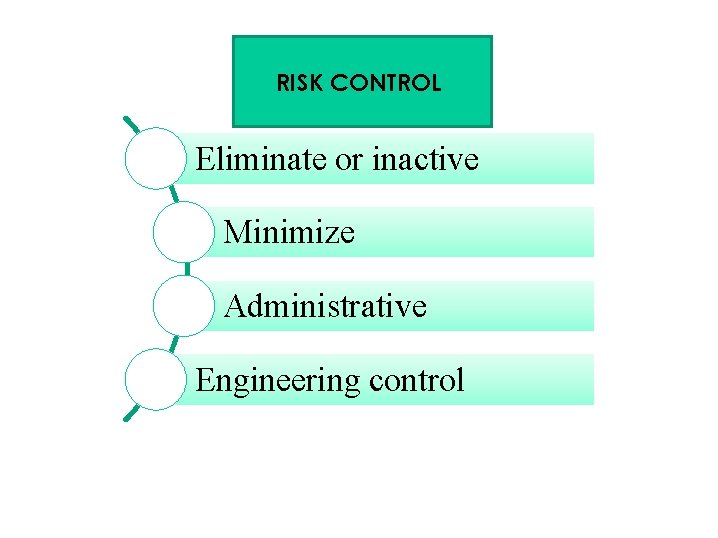
RISK CONTROL Eliminate or inactive Minimize Administrative Engineering control
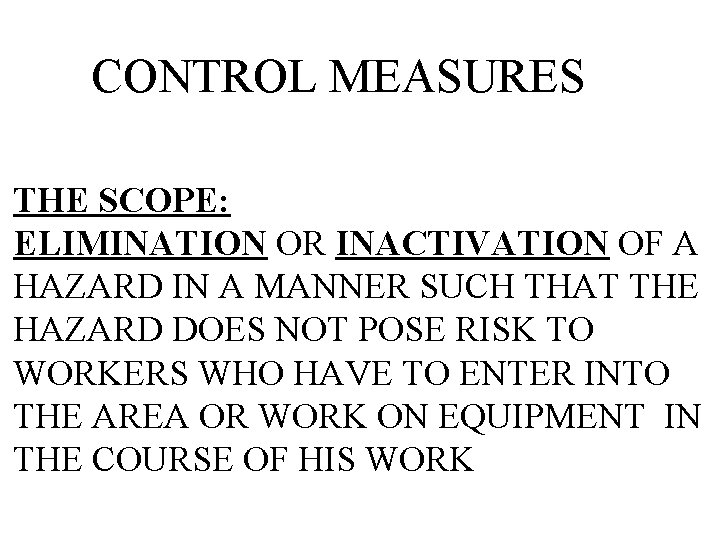
CONTROL MEASURES THE SCOPE: ELIMINATION OR INACTIVATION OF A HAZARD IN A MANNER SUCH THAT THE HAZARD DOES NOT POSE RISK TO WORKERS WHO HAVE TO ENTER INTO THE AREA OR WORK ON EQUIPMENT IN THE COURSE OF HIS WORK

CONTROL MEASURES a. Elimination or inactivation can be carried out: THE CLOSER THE BETTER, APPLYING ENGINEERING CONTROLS At source At the path of the work At the level of the worker APPLICATION LIKE PPE , BUT LEAST DESIRABLE BETWEEN SOURCE AND WORKER CALLED ADMINISTRATIVE CONTROL
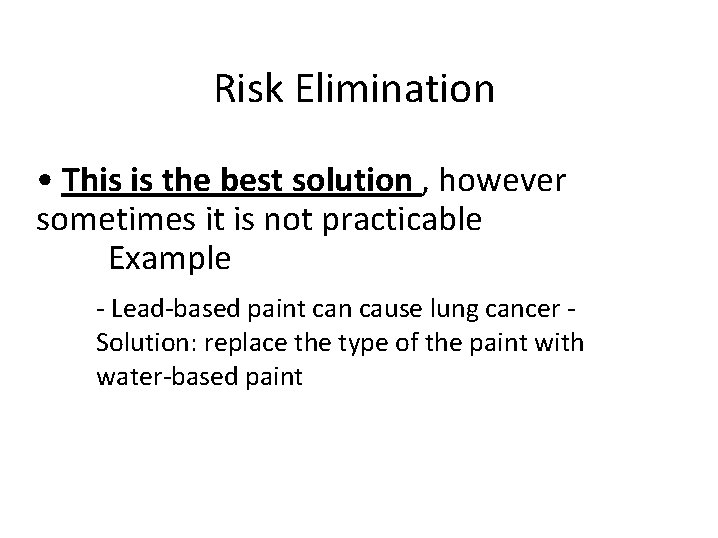
Risk Elimination • This is the best solution , however sometimes it is not practicable Example - Lead-based paint can cause lung cancer Solution: replace the type of the paint with water-based paint
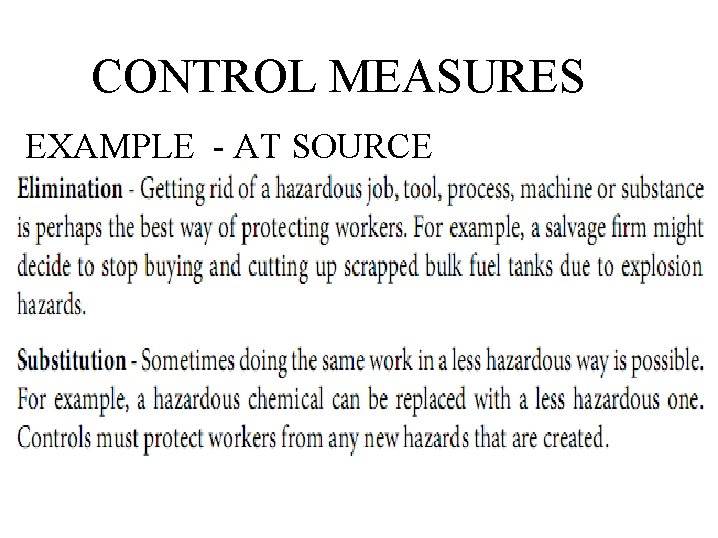
CONTROL MEASURES EXAMPLE - AT SOURCE
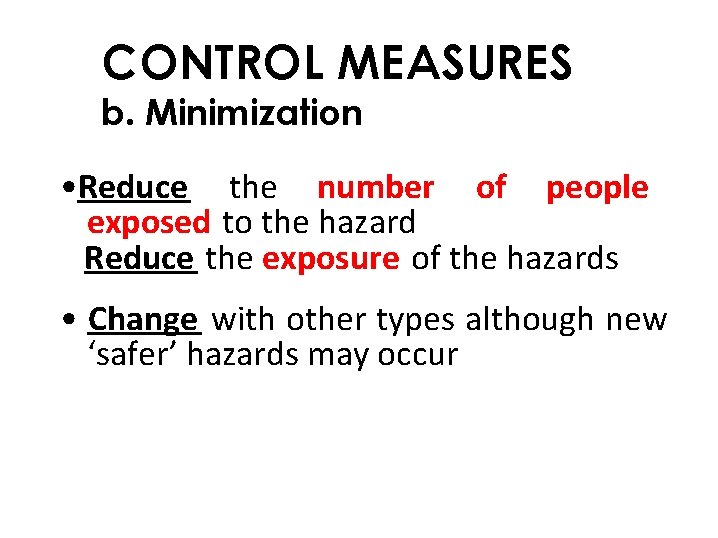
CONTROL MEASURES b. Minimization • Reduce the number of people exposed to the hazard Reduce the exposure of the hazards • Change with other types although new ‘safer’ hazards may occur
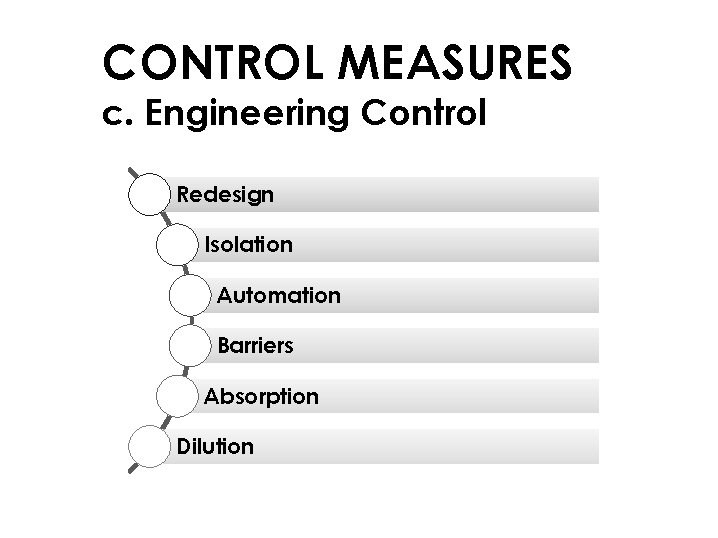
CONTROL MEASURES c. Engineering Control Redesign Isolation Automation Barriers Absorption Dilution
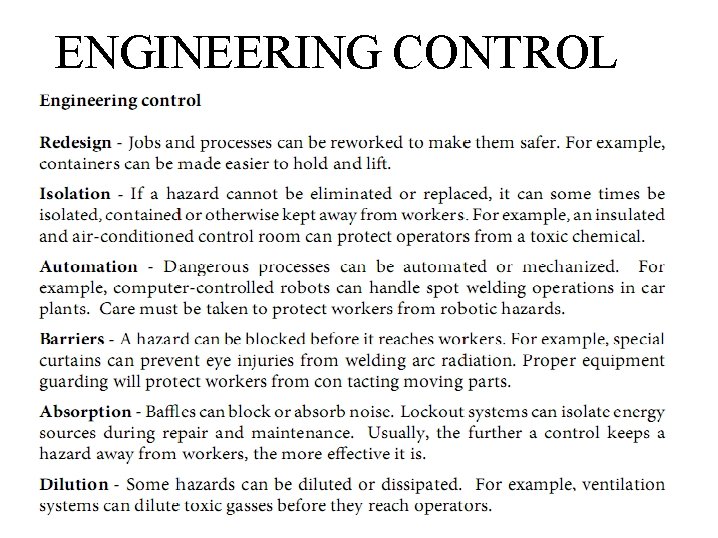
ENGINEERING CONTROL
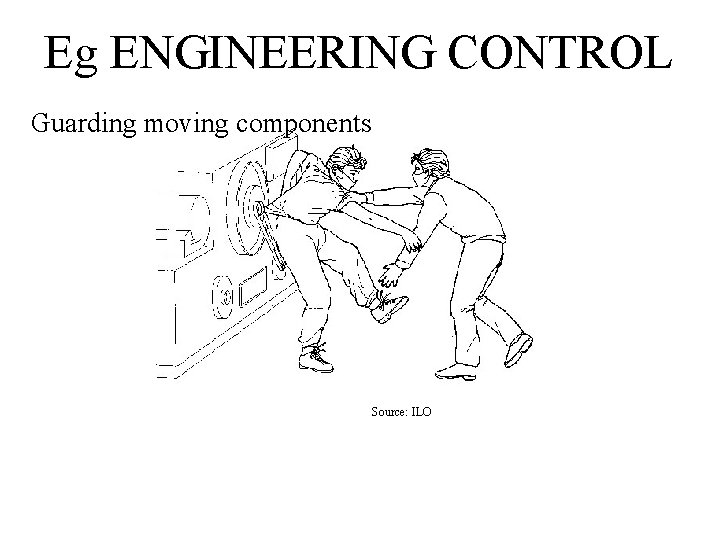
Eg ENGINEERING CONTROL Guarding moving components Source: ILO
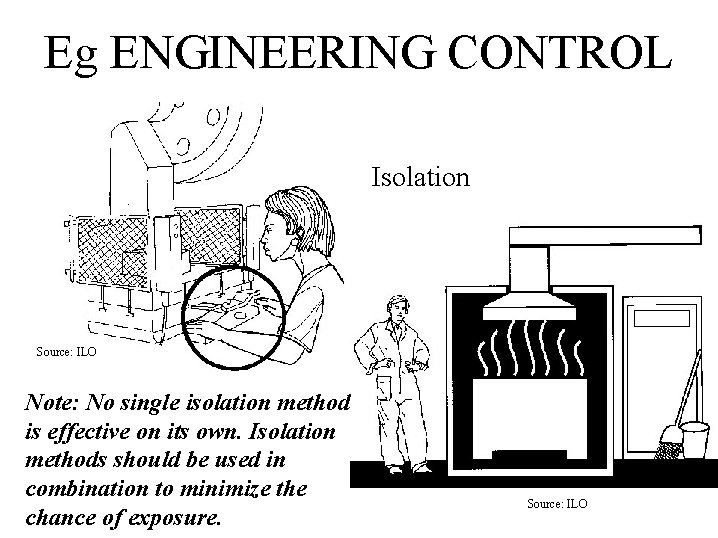
Eg ENGINEERING CONTROL Isolation Source: ILO Note: No single isolation method is effective on its own. Isolation methods should be used in combination to minimize the chance of exposure. Source: ILO
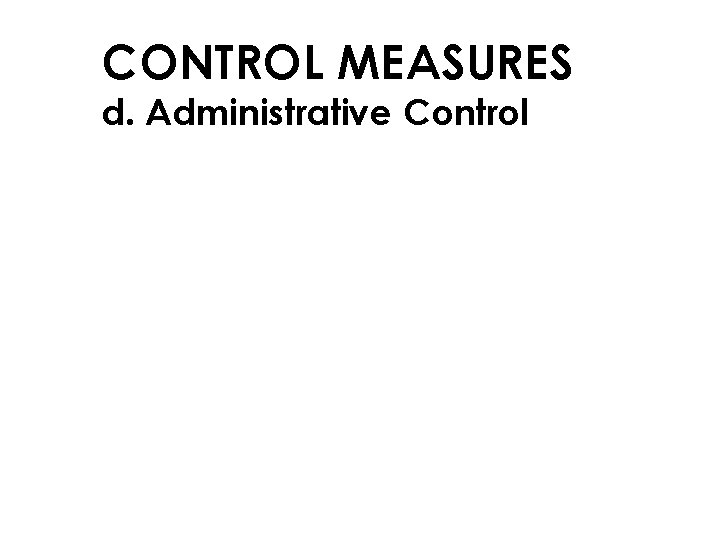
CONTROL MEASURES d. Administrative Control

ADMINISTRATIVE CONTROL
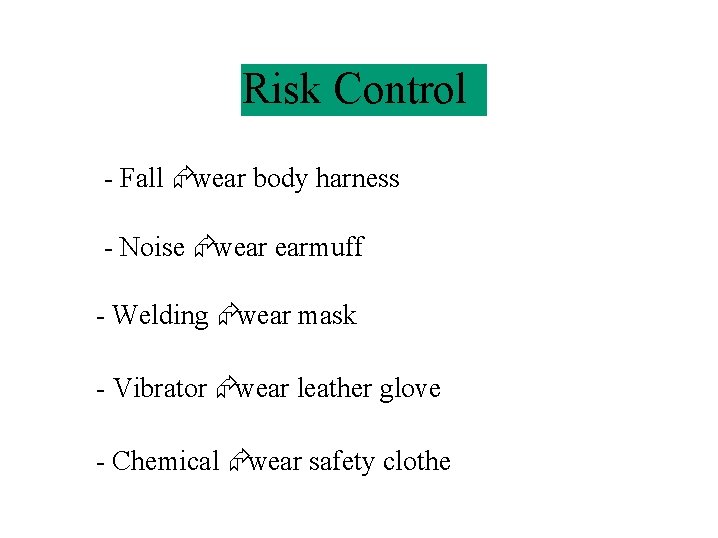
Risk Control - Fall Æ wear body harness - Noise Æ wear earmuff - Welding Æ wear mask - Vibrator Æ wear leather glove - Chemical Æ wear safety clothe
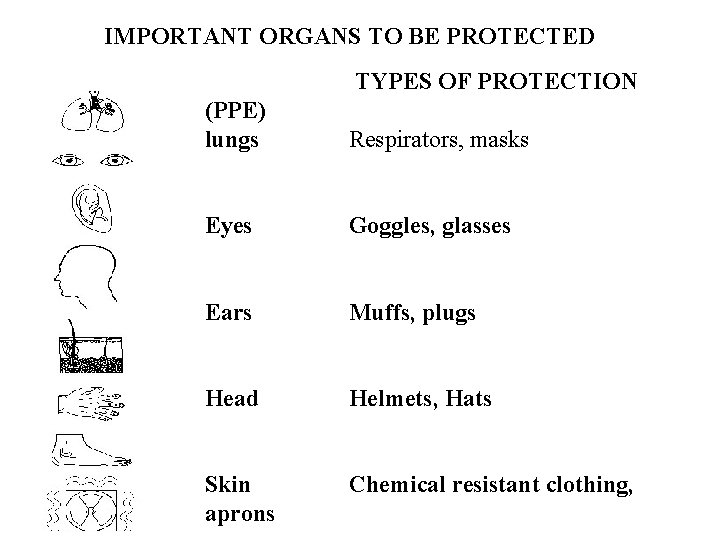
IMPORTANT ORGANS TO BE PROTECTED TYPES OF PROTECTION (PPE) lungs Respirators, masks Eyes Goggles, glasses Ears Muffs, plugs Head Helmets, Hats Skin aprons Chemical resistant clothing,
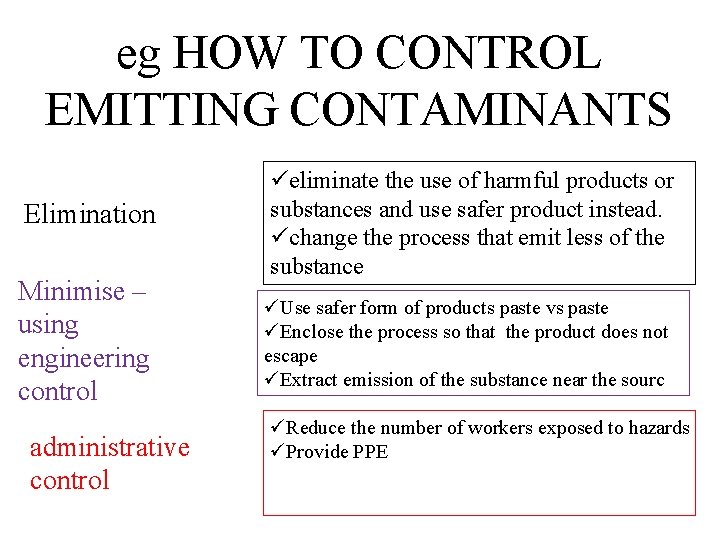
eg HOW TO CONTROL EMITTING CONTAMINANTS Elimination Minimise – using engineering control administrative control üeliminate the use of harmful products or substances and use safer product instead. üchange the process that emit less of the substance üUse safer form of products paste vs paste üEnclose the process so that the product does not escape üExtract emission of the substance near the sourc üReduce the number of workers exposed to hazards üProvide PPE
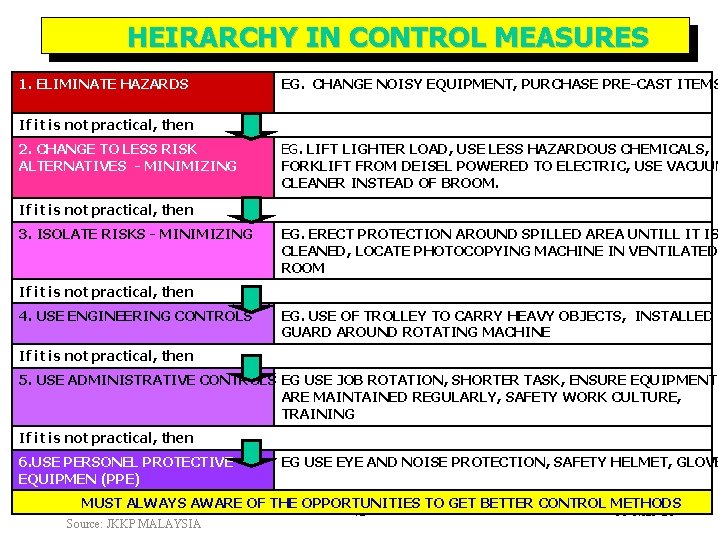
HEIRARCHY IN CONTROL MEASURES 1. ELIMINATE HAZARDS EG. CHANGE NOISY EQUIPMENT, PURCHASE PRE-CAST ITEMS If it is not practical, then 2. CHANGE TO LESS RISK ALTERNATIVES - MINIMIZING EG. LIFT LIGHTER LOAD, USE LESS HAZARDOUS CHEMICALS, FORKLIFT FROM DEISEL POWERED TO ELECTRIC, USE VACUUM CLEANER INSTEAD OF BROOM. If it is not practical, then 3. ISOLATE RISKS - MINIMIZING EG. ERECT PROTECTION AROUND SPILLED AREA UNTILL IT IS CLEANED, LOCATE PHOTOCOPYING MACHINE IN VENTILATED ROOM If it is not practical, then 4. USE ENGINEERING CONTROLS EG. USE OF TROLLEY TO CARRY HEAVY OBJECTS, INSTALLED GUARD AROUND ROTATING MACHINE If it is not practical, then 5. USE ADMINISTRATIVE CONTROLS EG USE JOB ROTATION, SHORTER TASK, ENSURE EQUIPMENT ARE MAINTAINED REGULARLY, SAFETY WORK CULTURE, TRAINING If it is not practical, then 6. USE PERSONEL PROTECTIVE EQUIPMEN (PPE) EG USE EYE AND NOISE PROTECTION, SAFETY HELMET, GLOVE MUST ALWAYS AWARE OF THE OPPORTUNITIES TO GET BETTER CONTROL METHODS 42 08 -Mar-21 Source: JKKP MALAYSIA
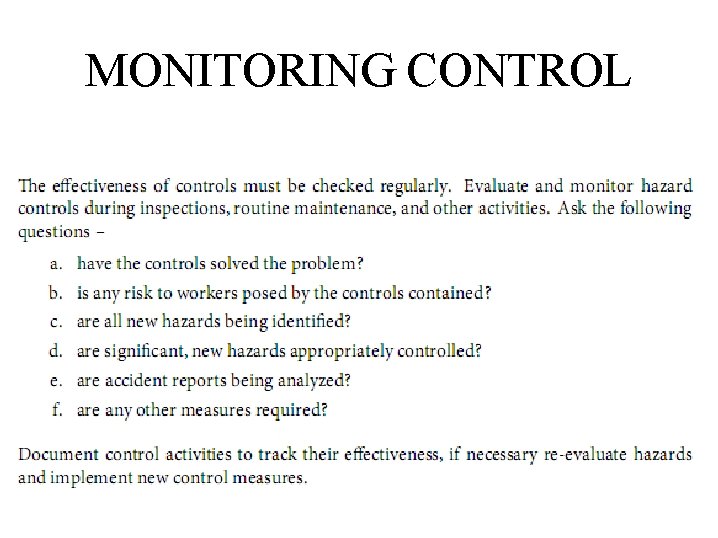
MONITORING CONTROL
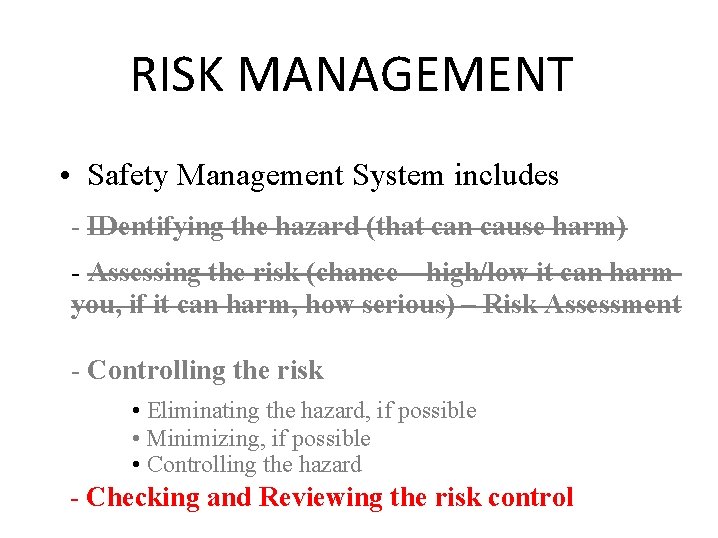
RISK MANAGEMENT • Safety Management System includes - IDentifying the hazard (that can cause harm) - Assessing the risk (chance – high/low it can harm you, if it can harm, how serious) – Risk Assessment - Controlling the risk • Eliminating the hazard, if possible • Minimizing, if possible • Controlling the hazard - Checking and Reviewing the risk control
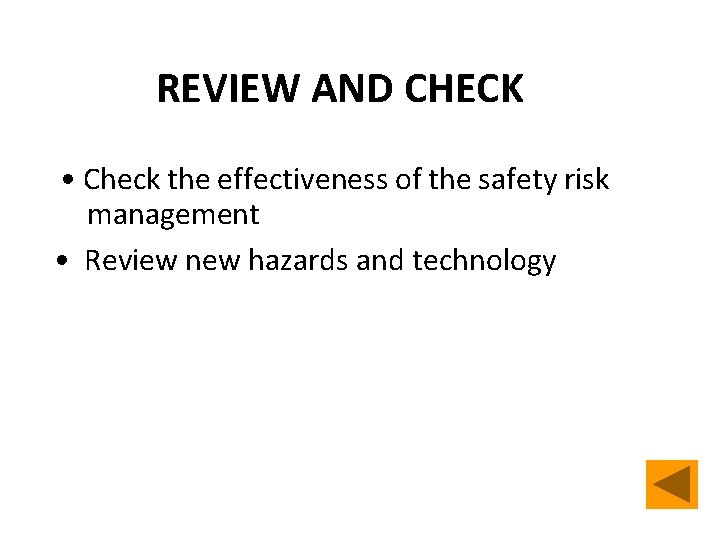
REVIEW AND CHECK • Check the effectiveness of the safety risk management • Review new hazards and technology
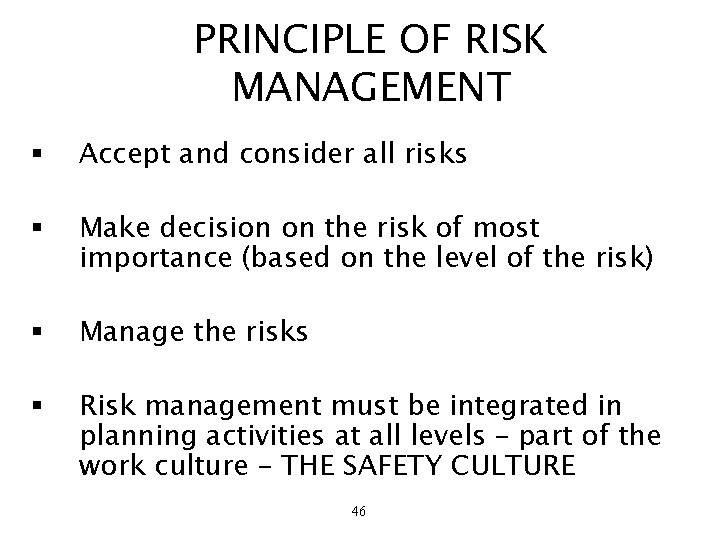
PRINCIPLE OF RISK MANAGEMENT § Accept and consider all risks § Make decision on the risk of most importance (based on the level of the risk) § Manage the risks § Risk management must be integrated in planning activities at all levels – part of the work culture – THE SAFETY CULTURE 46
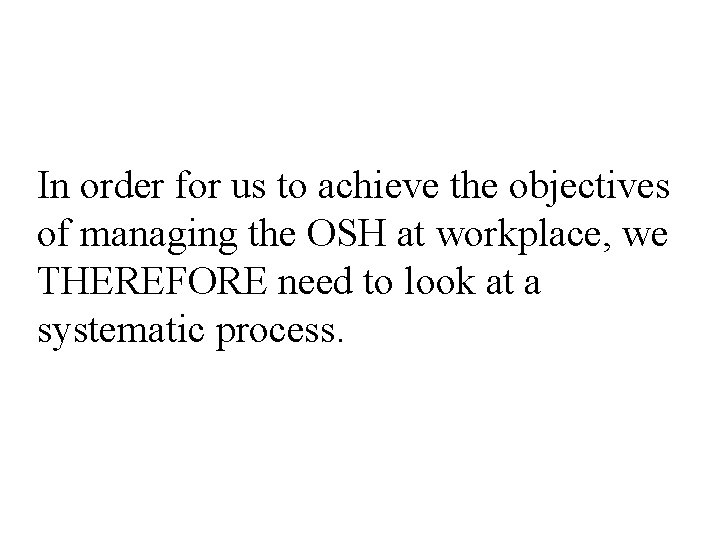
In order for us to achieve the objectives of managing the OSH at workplace, we THEREFORE need to look at a systematic process.
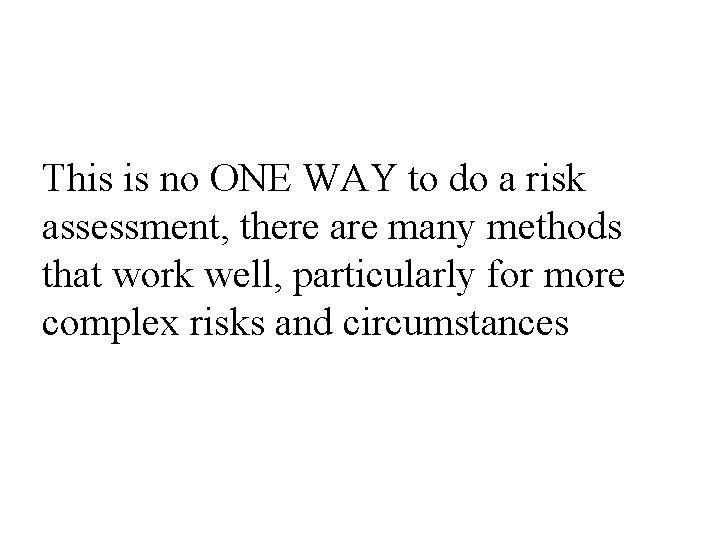
This is no ONE WAY to do a risk assessment, there are many methods that work well, particularly for more complex risks and circumstances
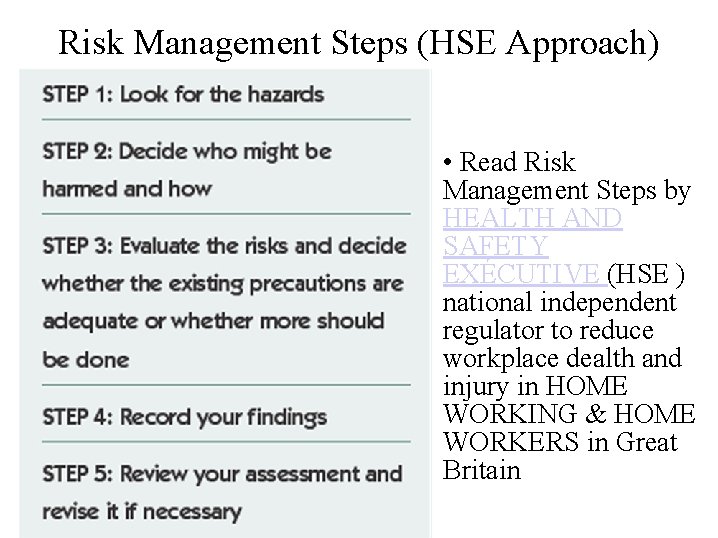
Risk Management Steps (HSE Approach) • Read Risk Management Steps by HEALTH AND SAFETY EXÉCUTIVE (HSE ) national independent regulator to reduce workplace dealth and injury in HOME WORKING & HOME WORKERS in Great Britain
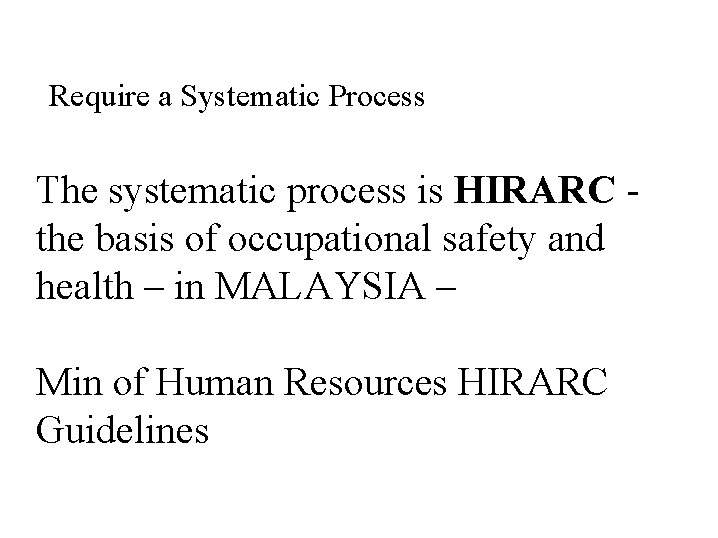
Require a Systematic Process The systematic process is HIRARC - the basis of occupational safety and health – in MALAYSIA – Min of Human Resources HIRARC Guidelines
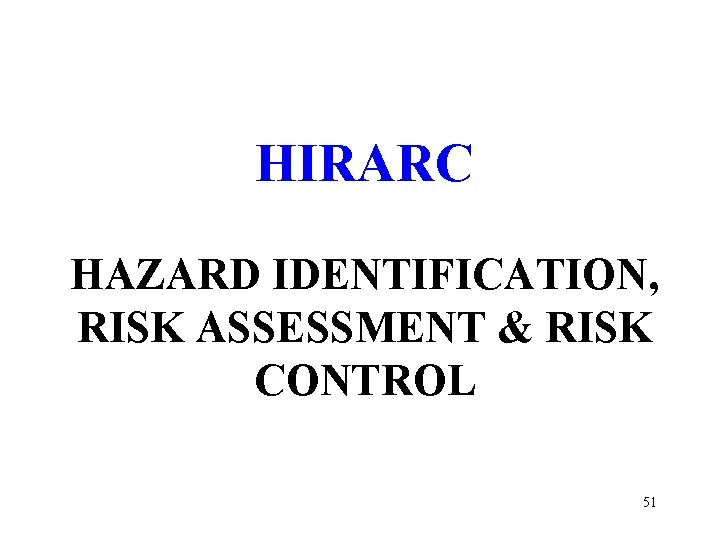
HIRARC HAZARD IDENTIFICATION, RISK ASSESSMENT & RISK CONTROL 51
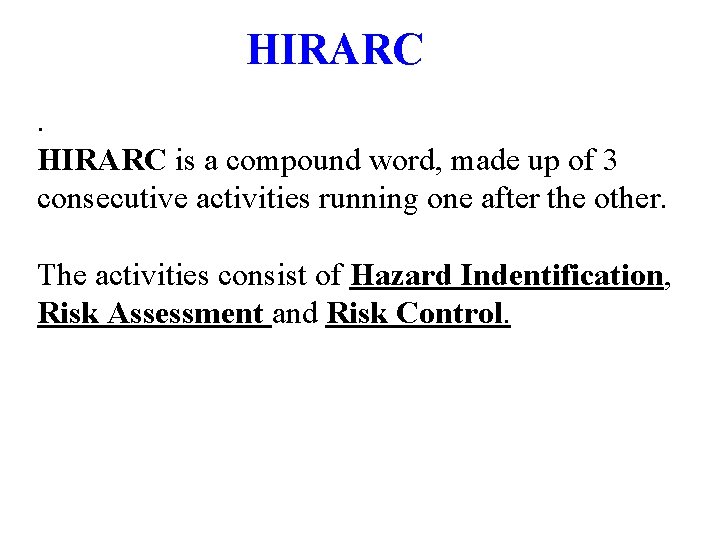
HIRARC. HIRARC is a compound word, made up of 3 consecutive activities running one after the other. The activities consist of Hazard Indentification, Risk Assessment and Risk Control.
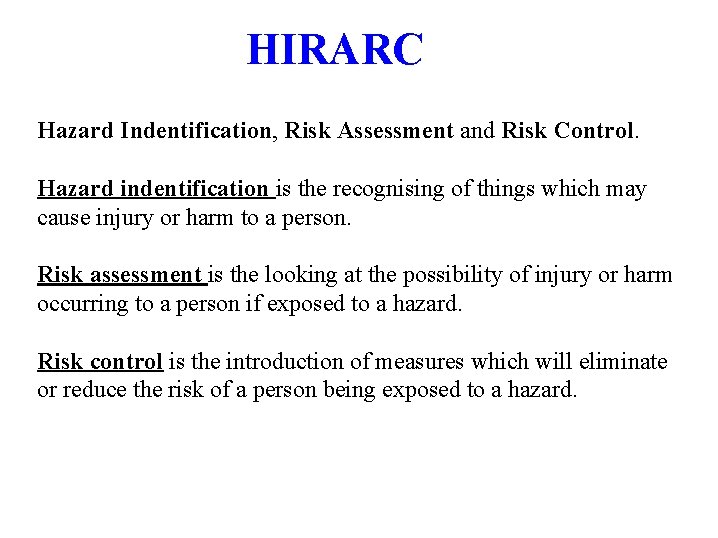
HIRARC Hazard Indentification, Risk Assessment and Risk Control. Hazard indentification is the recognising of things which may cause injury or harm to a person. Risk assessment is the looking at the possibility of injury or harm occurring to a person if exposed to a hazard. Risk control is the introduction of measures which will eliminate or reduce the risk of a person being exposed to a hazard.
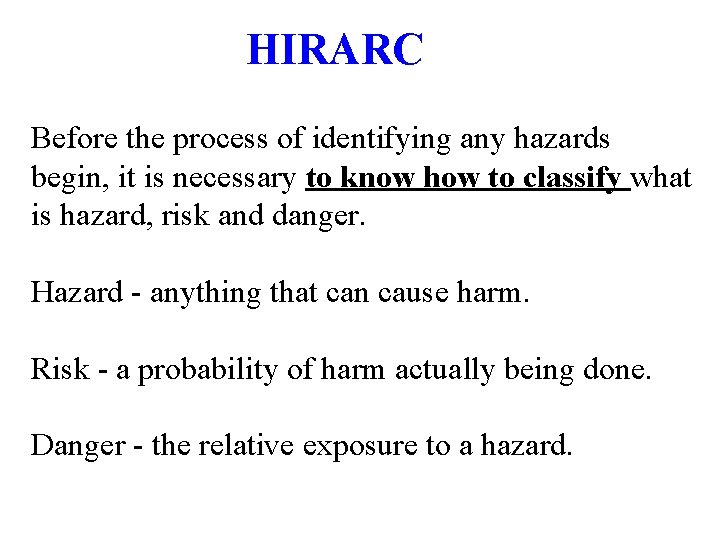
HIRARC Before the process of identifying any hazards begin, it is necessary to know how to classify what is hazard, risk and danger. Hazard - anything that can cause harm. Risk - a probability of harm actually being done. Danger - the relative exposure to a hazard.
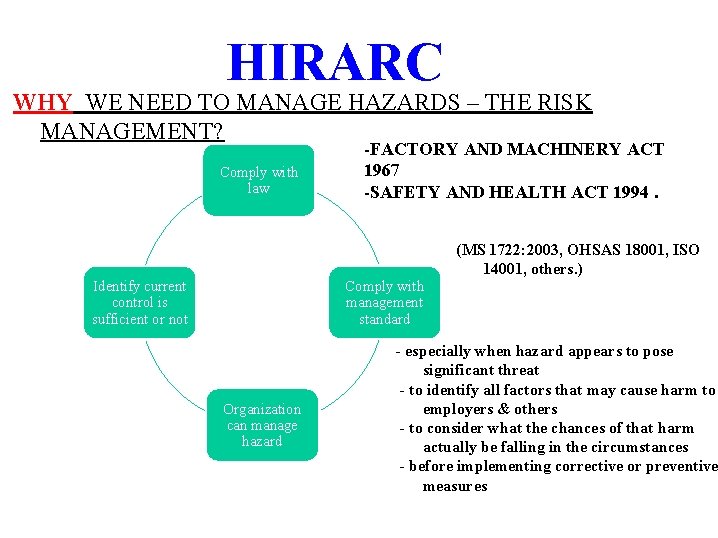
HIRARC WHY WE NEED TO MANAGE HAZARDS – THE RISK MANAGEMENT? Comply with law -FACTORY AND MACHINERY ACT 1967 -SAFETY AND HEALTH ACT 1994. (MS 1722: 2003, OHSAS 18001, ISO 14001, others. ) Identify current control is sufficient or not Comply with management standard Organization can manage hazard - especially when hazard appears to pose significant threat - to identify all factors that may cause harm to employers & others - to consider what the chances of that harm actually be falling in the circumstances - before implementing corrective or preventive measures
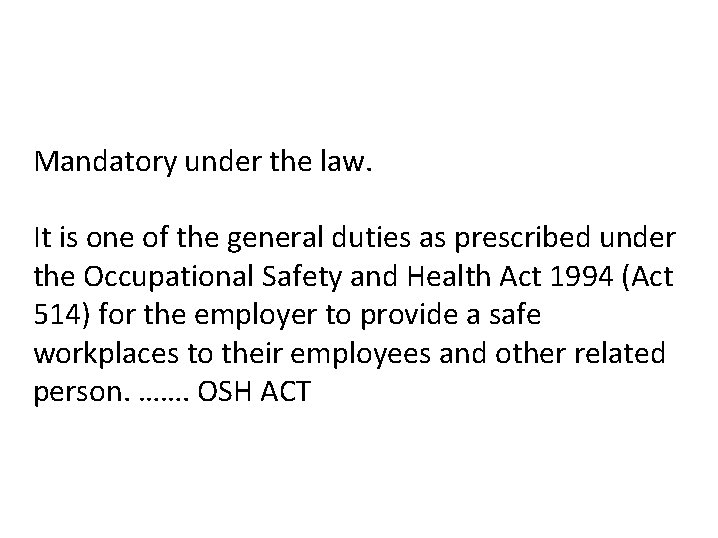
Mandatory under the law. It is one of the general duties as prescribed under the Occupational Safety and Health Act 1994 (Act 514) for the employer to provide a safe workplaces to their employees and other related person. ……. OSH ACT
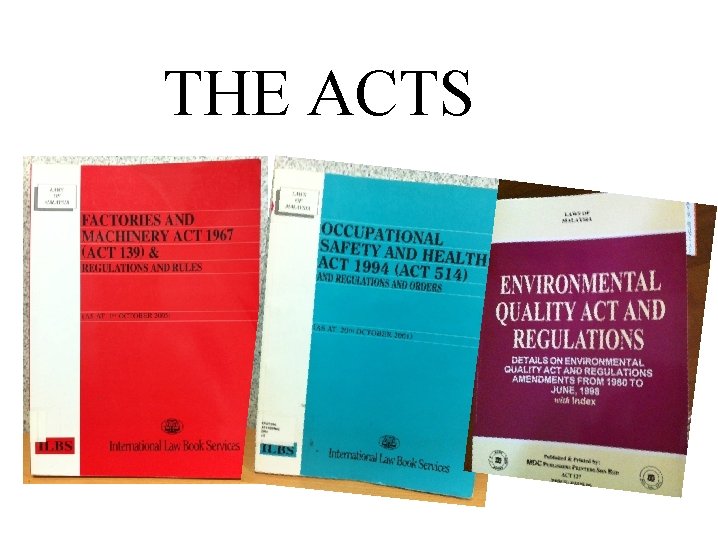
THE ACTS
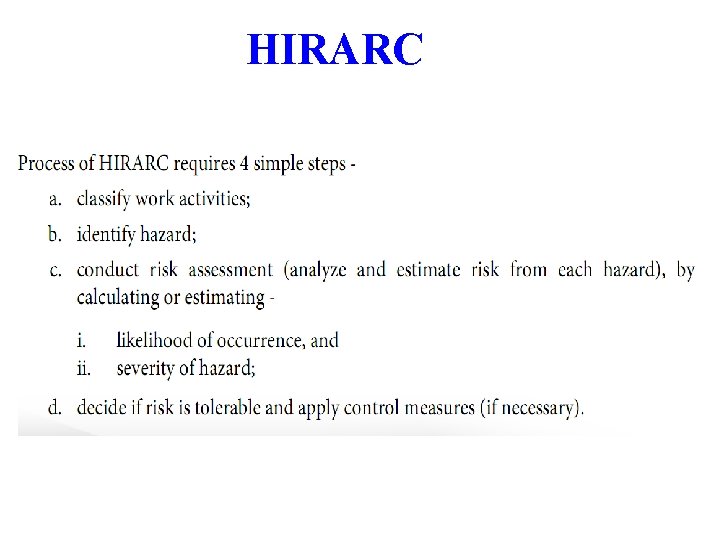
HIRARC
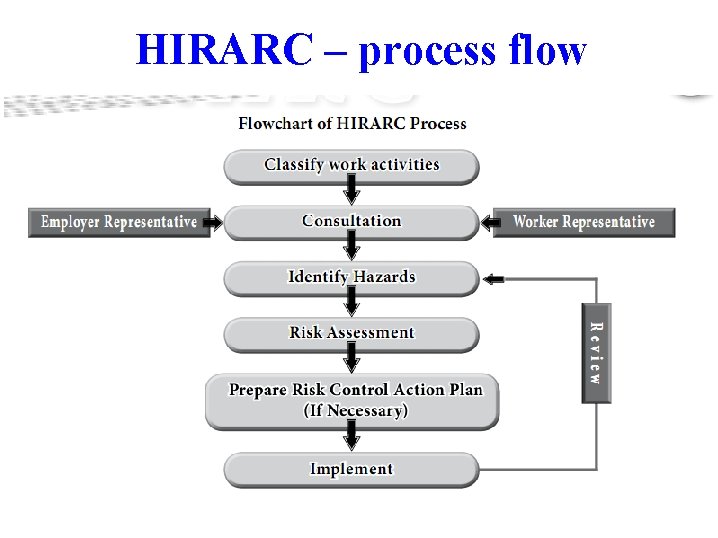
HIRARC – process flow
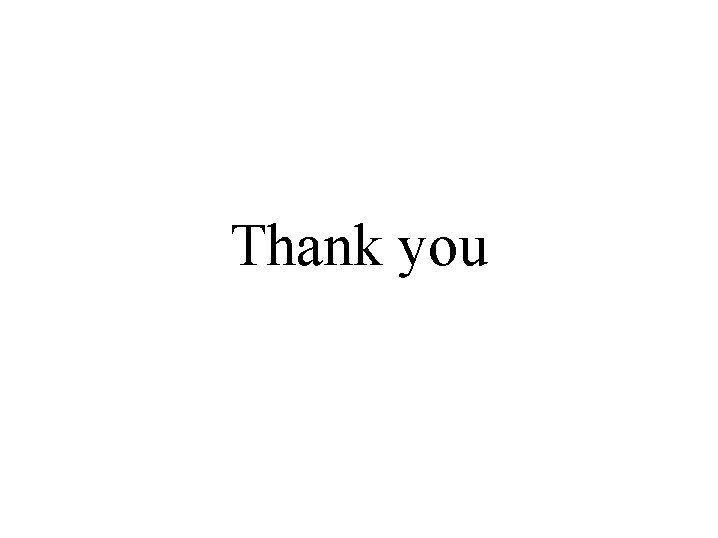
Thank you
Common law
444 ptt
Ptt 444
Contract capacity
Gertler econ
Treat everyone with sincerity
Treat with sincerity
What are social letters
550-444
Mcmxlv число
N 444
444 555 666 888 33 88 artinya
Triumphal entry luke
Isometric riser diagram
Ciferny sucet cisla 444
Mapi/emsmdb
444 outline
444
Cs 444 oregon state
Artaxerxes decree 445
Pneumatic piping system design
Lied 444
Karyay
Https://bit.ly/3fvyjws
Cs 444
Da form 444
Me 444
444 5 lecke
Nfpa 13 sprinkler pipe sizing chart
Pipe design
Knowledge society
Knowledge society
Drucker
Knowledge society perth
Pt vs ptt
Ptt taiwan drama
Ptt
Kavo killer 2020
Open kettle evaporator
Heparin warfarin
Mesh wifi ptt
Ptt-350
Partial thromboplastin time
Ancient biotechnology
Vwf deficiency labs
Johnny talk ptt
Ptt
Thurs ptt
Twitter
Steam ptt
Smart ptt radio
Imzager nedir
Elisez ptt
Prolonged ptt workup
Ptt 304
Ptt normal range
Gerinung
Dic labs
Iridium ptt command center
Biotech ptt
Dilbert