Protective Chemical Vapor Deposition Coatings for Stainless Steel
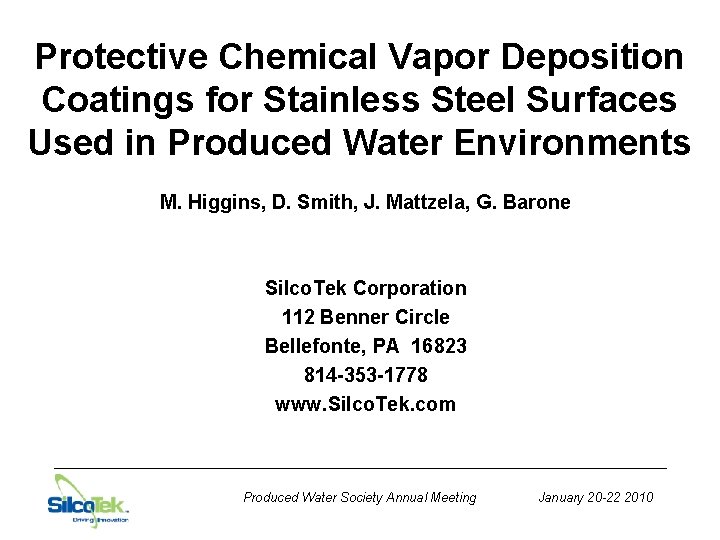
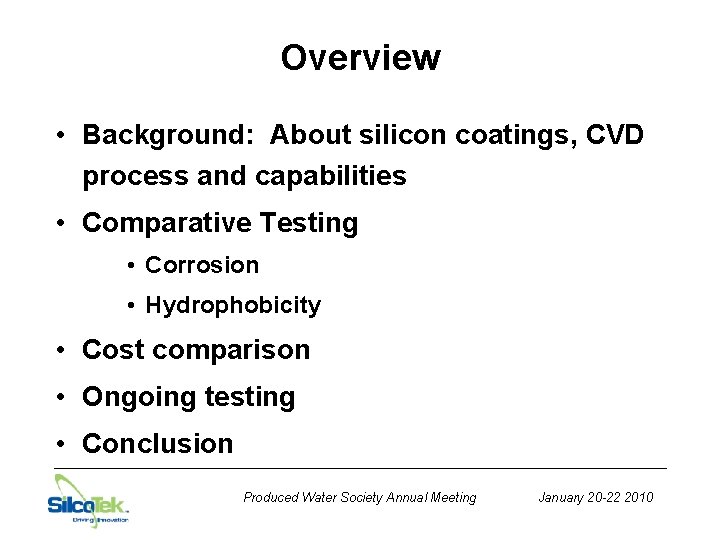
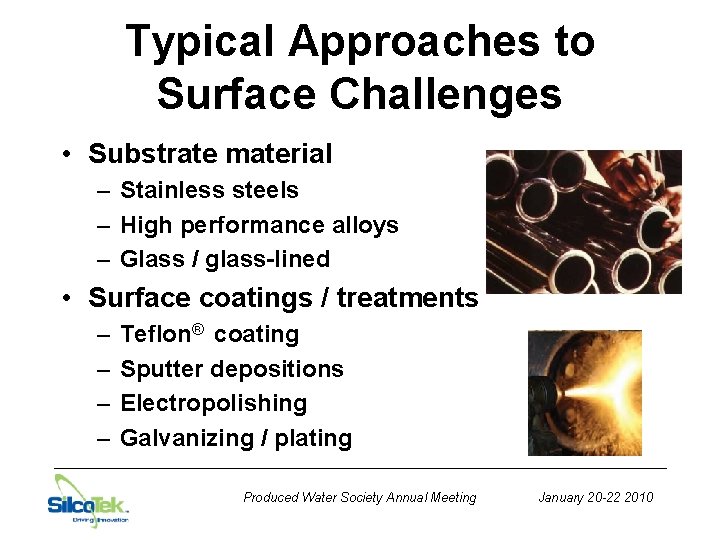
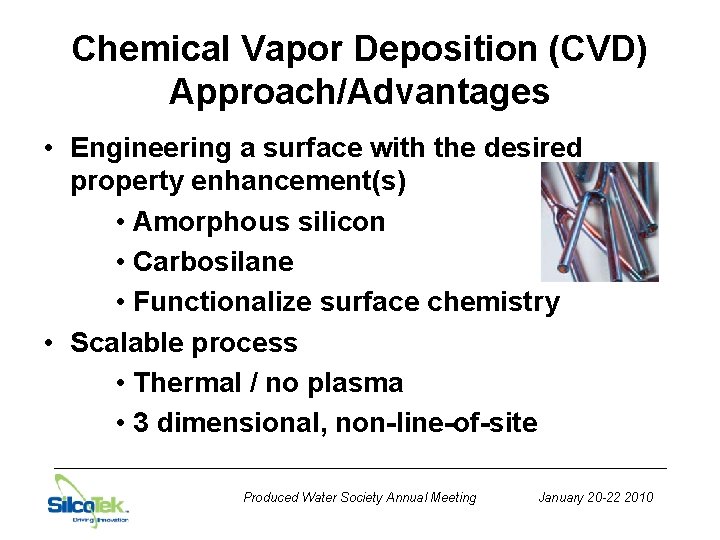
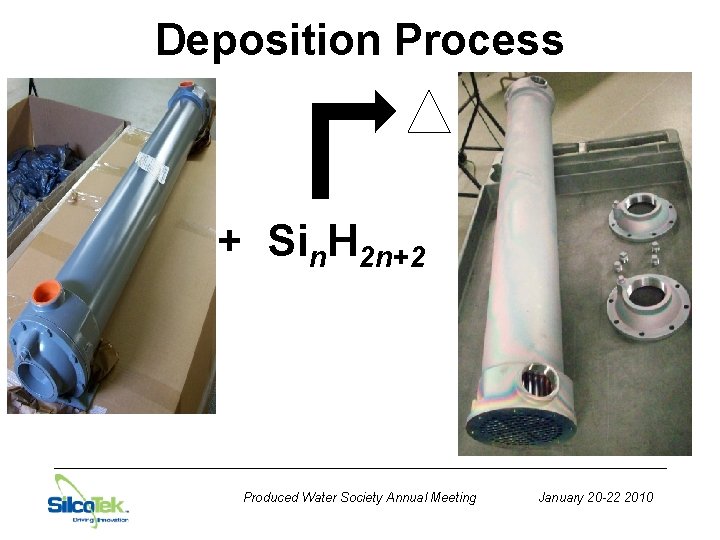
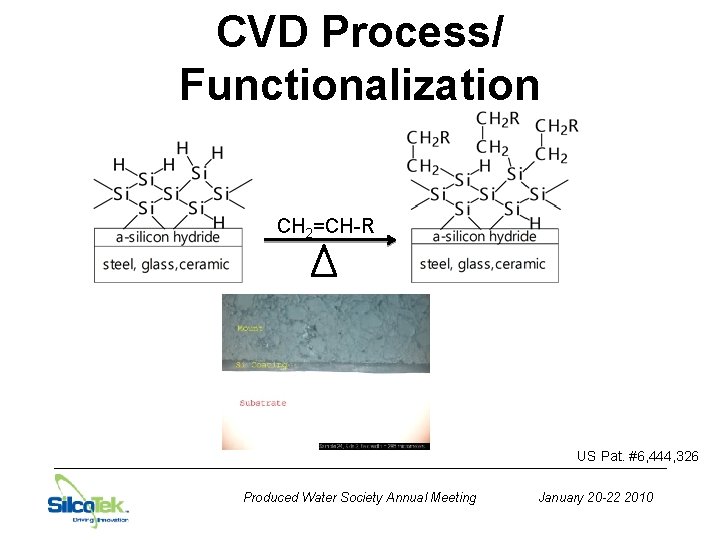
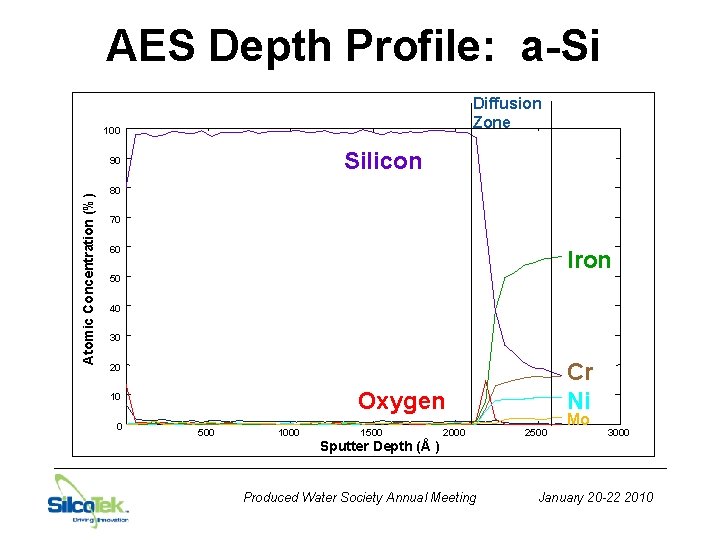
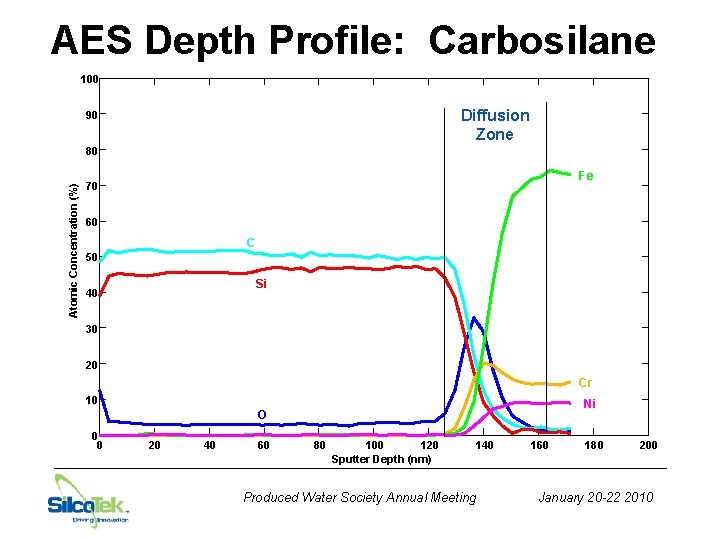
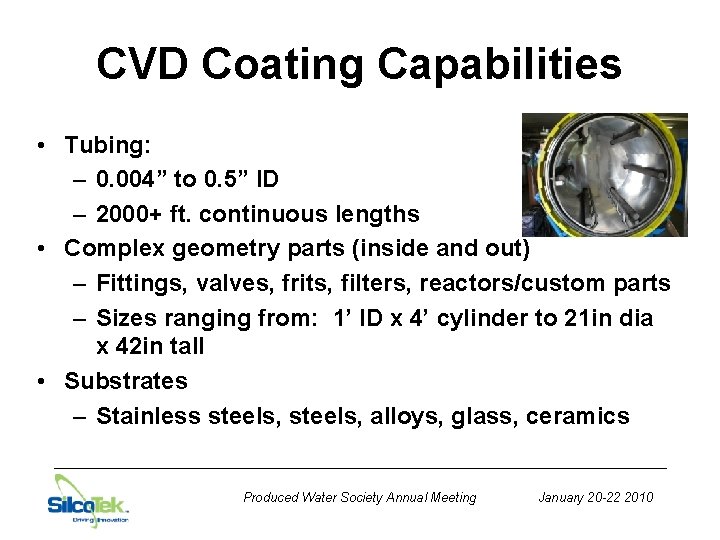
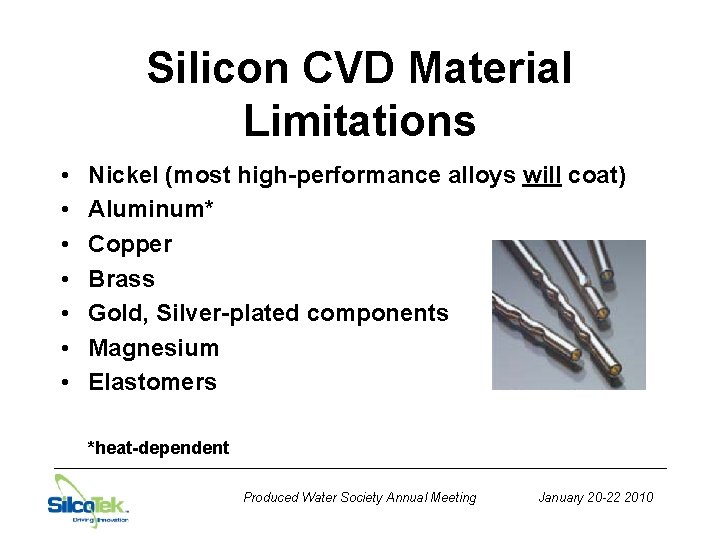
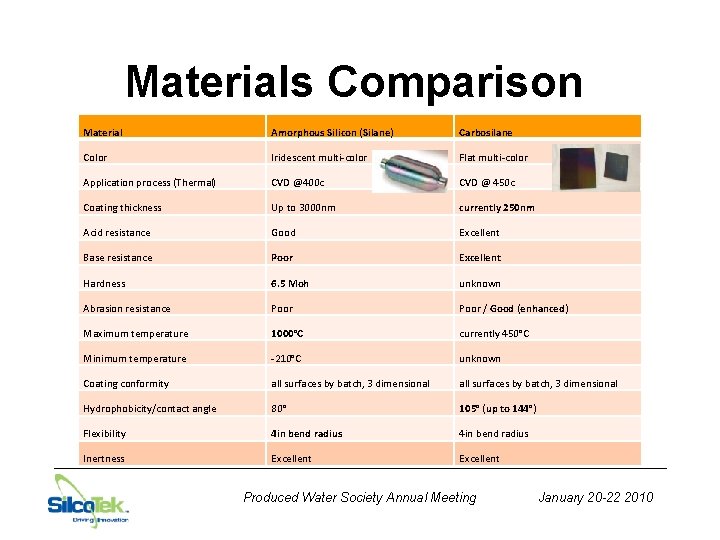
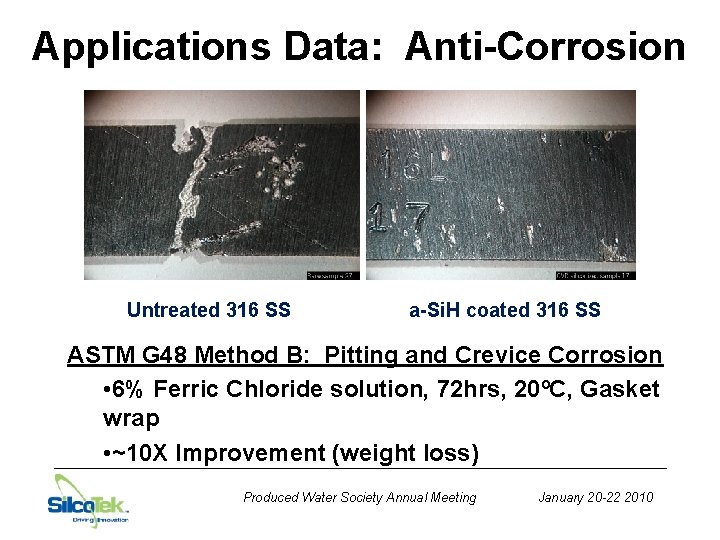
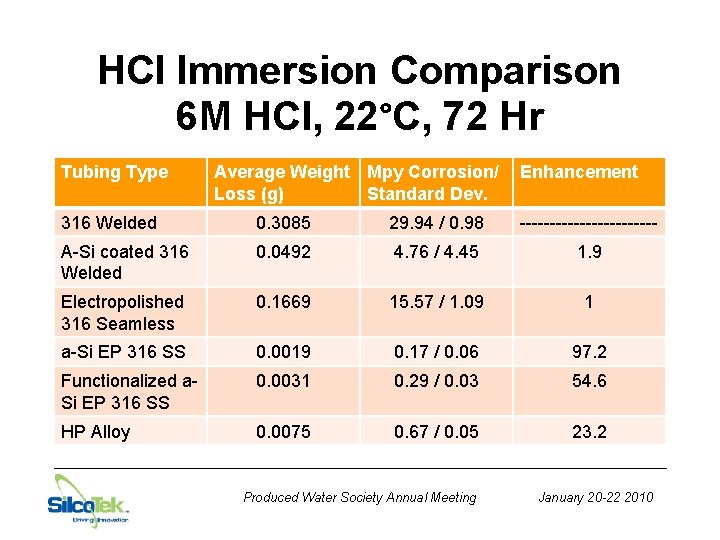
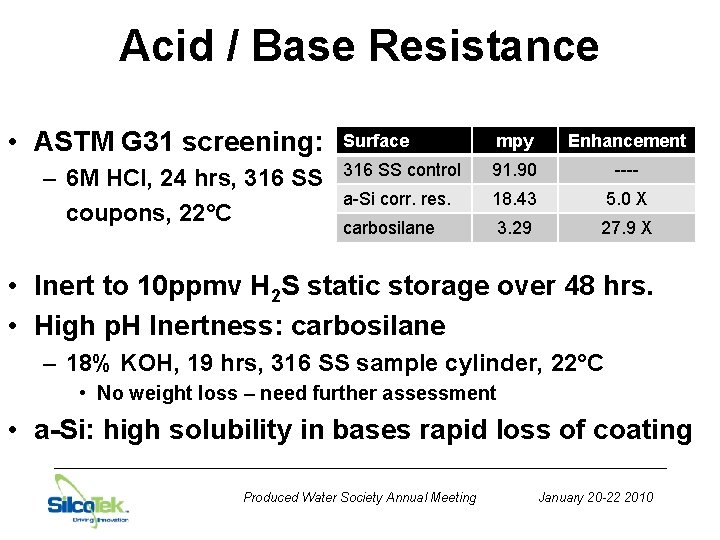
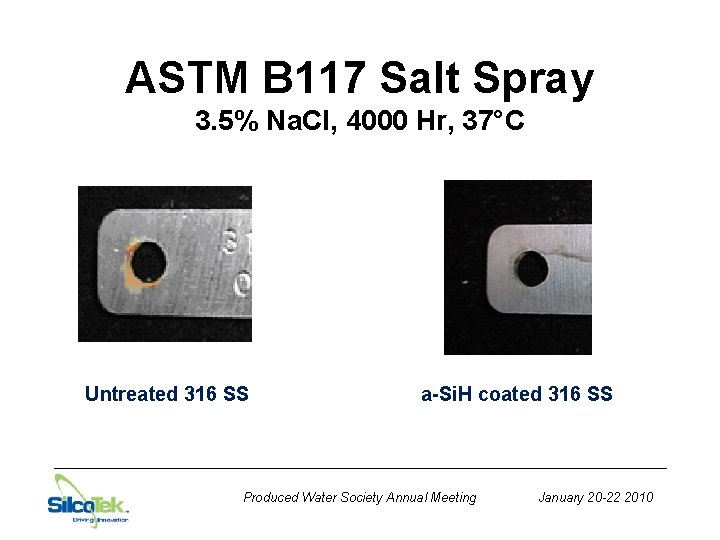


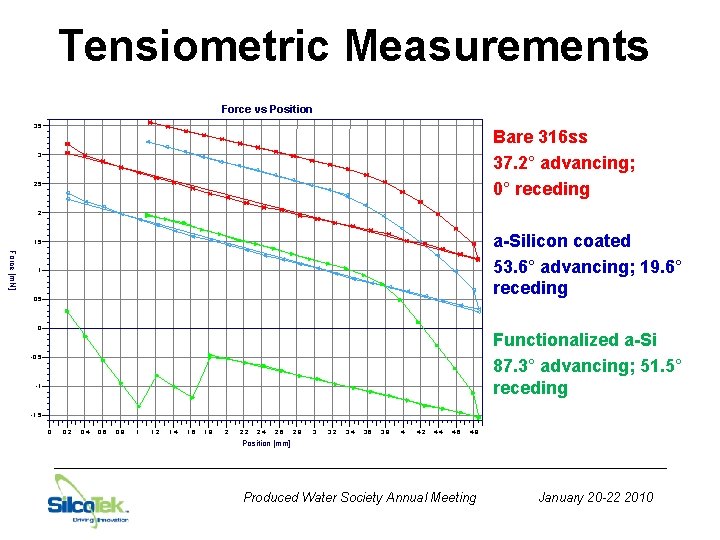
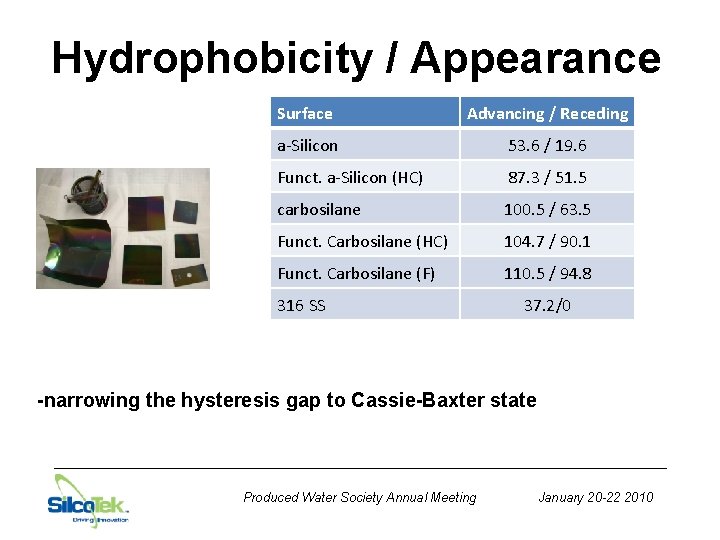
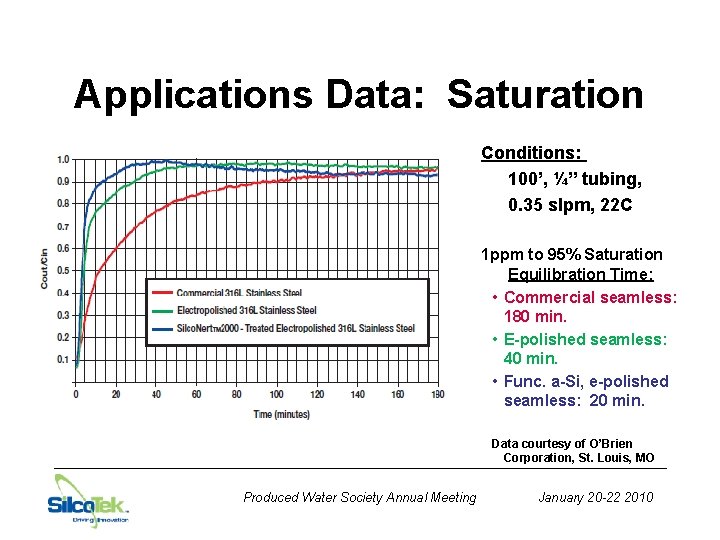
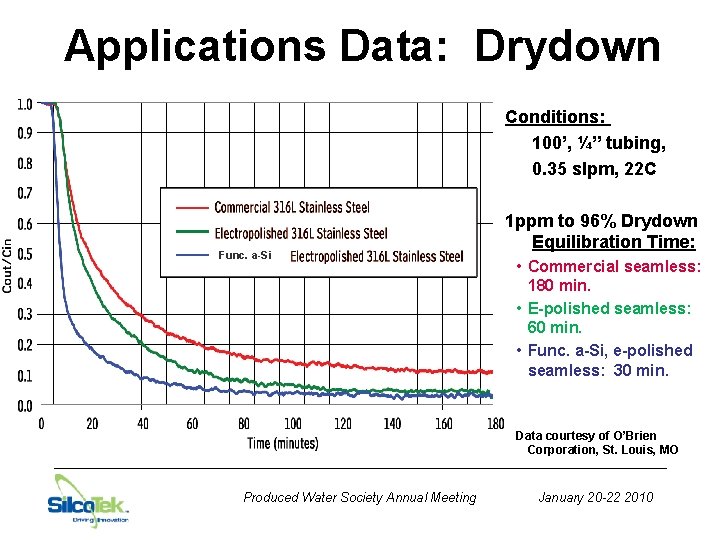
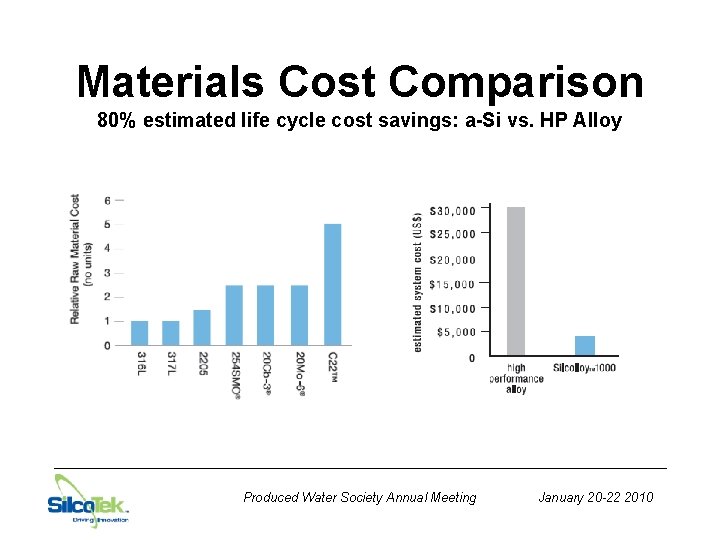
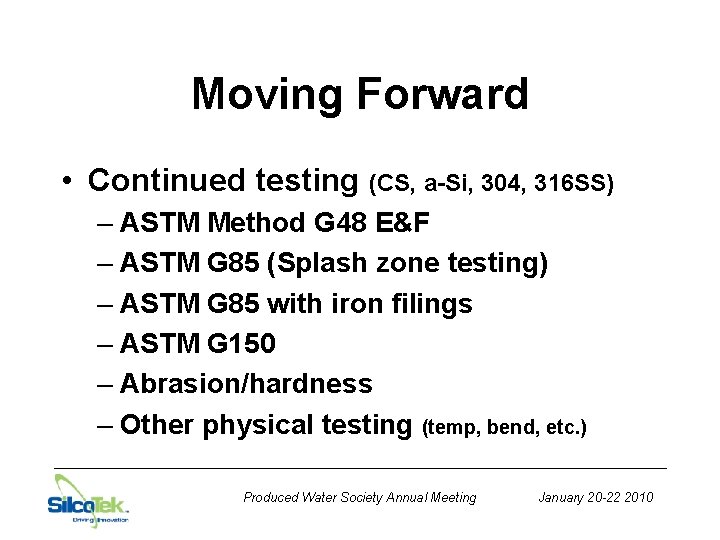
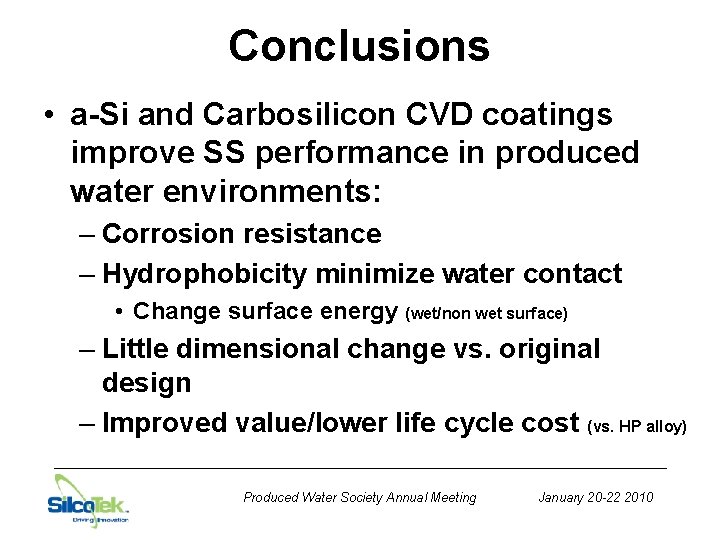
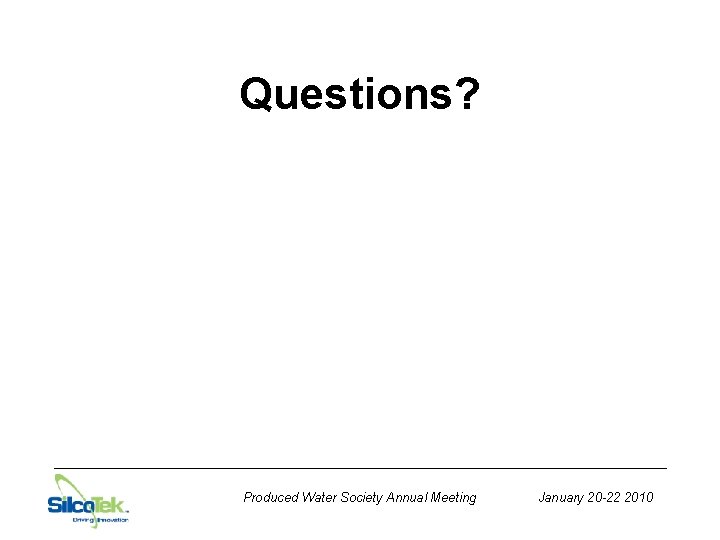
- Slides: 25
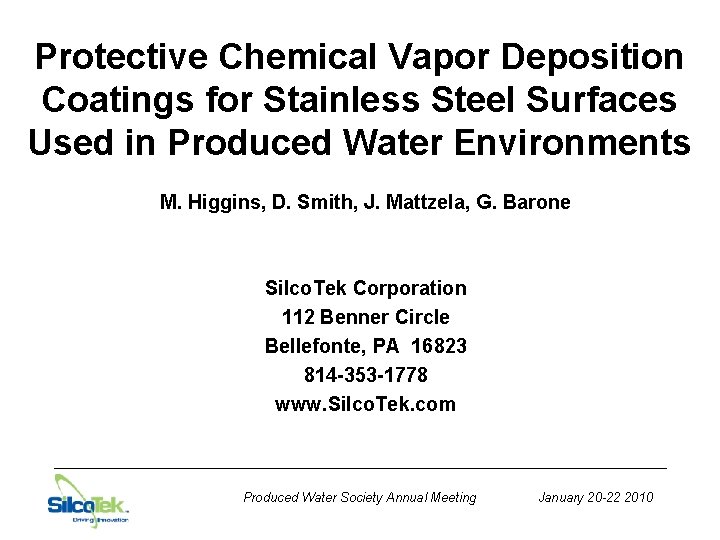
Protective Chemical Vapor Deposition Coatings for Stainless Steel Surfaces Used in Produced Water Environments M. Higgins, D. Smith, J. Mattzela, G. Barone Silco. Tek Corporation 112 Benner Circle Bellefonte, PA 16823 814 -353 -1778 www. Silco. Tek. com Produced Water Society Annual Meeting January 20 -22 2010
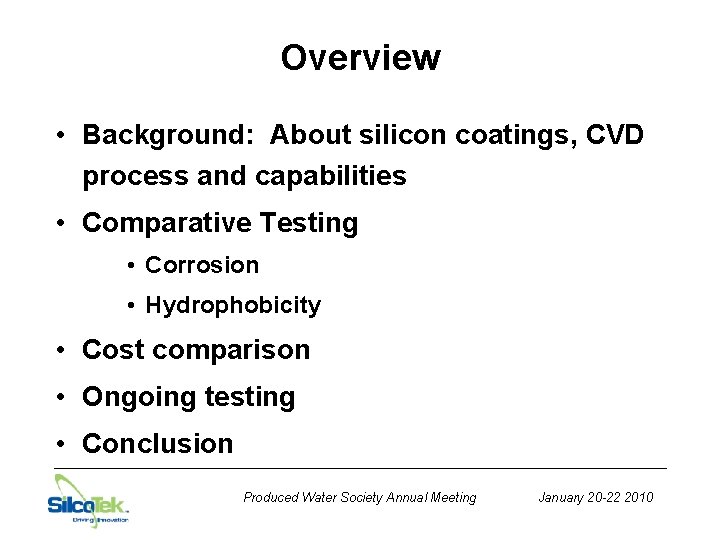
Overview • Background: About silicon coatings, CVD process and capabilities • Comparative Testing • Corrosion • Hydrophobicity • Cost comparison • Ongoing testing • Conclusion Produced Water Society Annual Meeting January 20 -22 2010
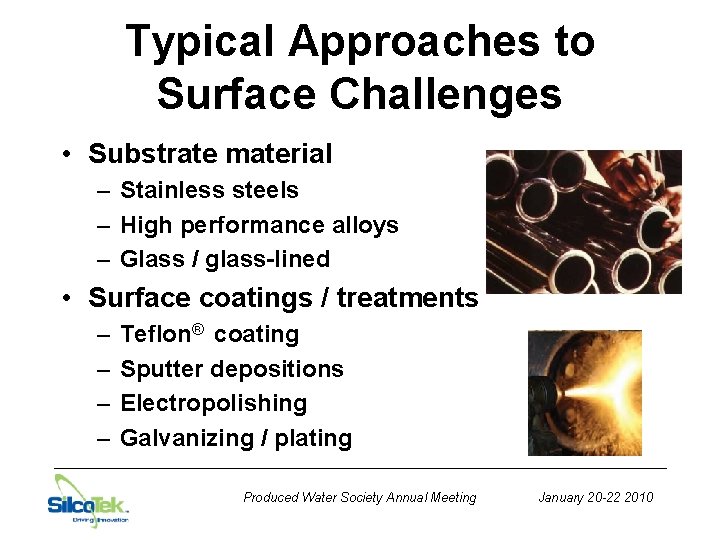
Typical Approaches to Surface Challenges • Substrate material – Stainless steels – High performance alloys – Glass / glass-lined • Surface coatings / treatments – – Teflon® coating Sputter depositions Electropolishing Galvanizing / plating Produced Water Society Annual Meeting January 20 -22 2010
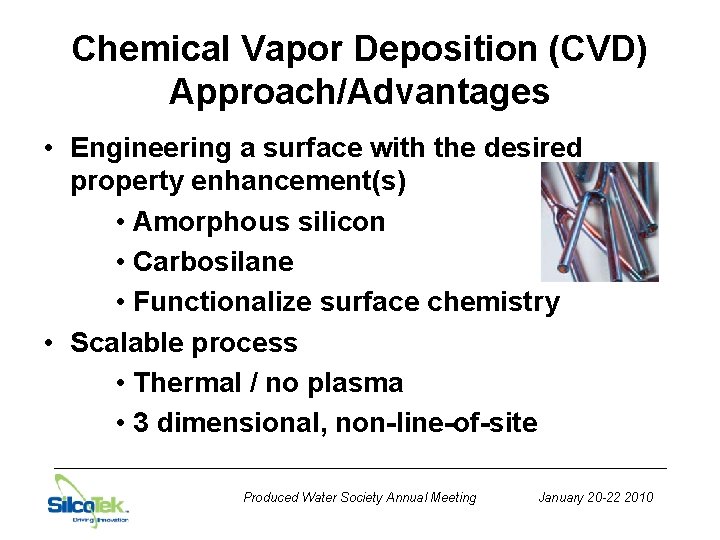
Chemical Vapor Deposition (CVD) Approach/Advantages • Engineering a surface with the desired property enhancement(s) • Amorphous silicon • Carbosilane • Functionalize surface chemistry • Scalable process • Thermal / no plasma • 3 dimensional, non-line-of-site Produced Water Society Annual Meeting January 20 -22 2010
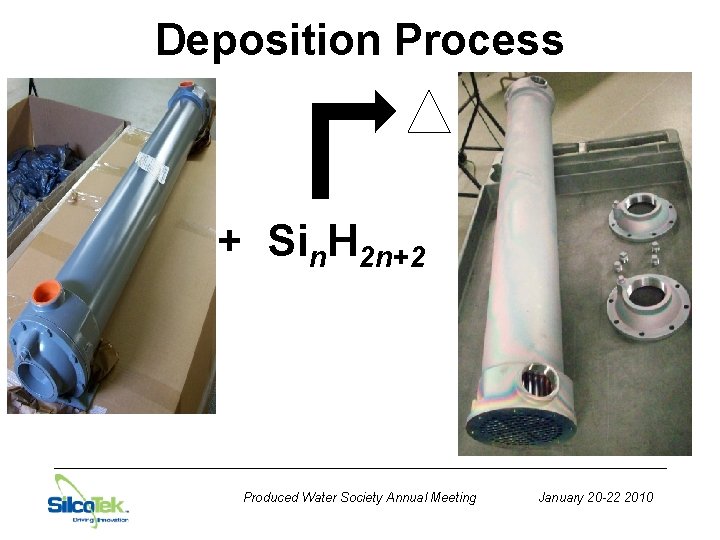
Deposition Process + Sin. H 2 n+2 Produced Water Society Annual Meeting January 20 -22 2010
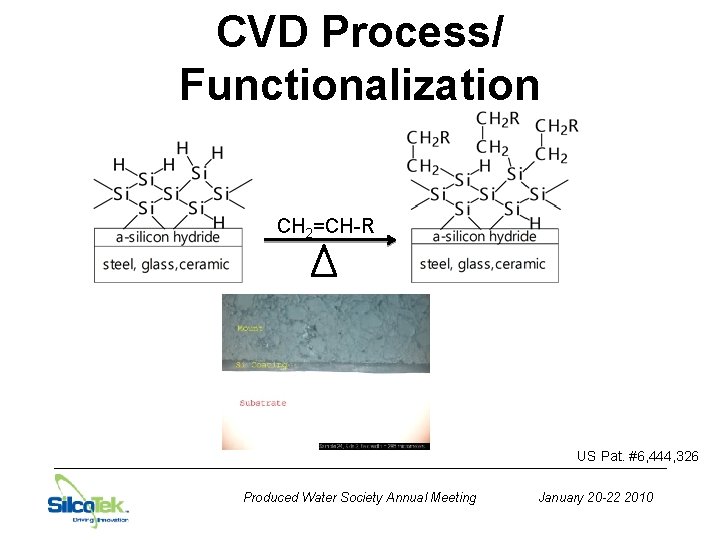
CVD Process/ Functionalization CH 2=CH-R US Pat. #6, 444, 326 Produced Water Society Annual Meeting January 20 -22 2010
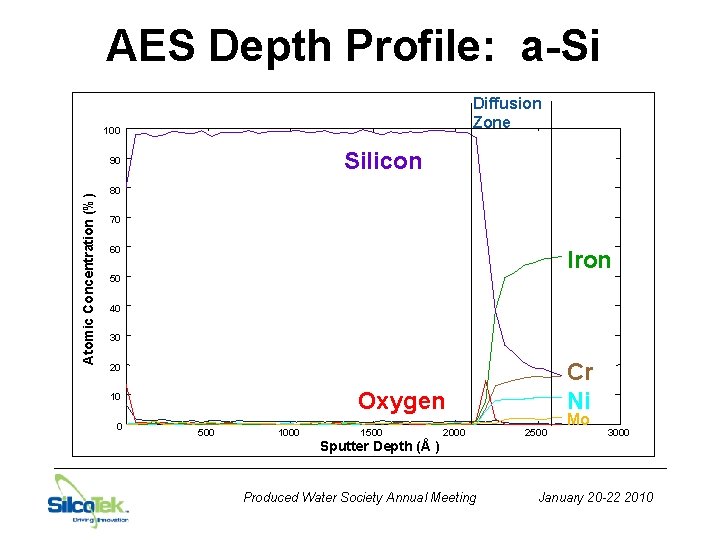
AES Depth Profile: a-Si Diffusion Zone 100 Silicon Atomic Concentration (%) 90 80 70 60 Iron 50 40 30 Cr Ni 20 Oxygen 10 0 500 1000 1500 Sputter Depth (Å ) 2000 Produced Water Society Annual Meeting 2500 Mo 3000 January 20 -22 2010
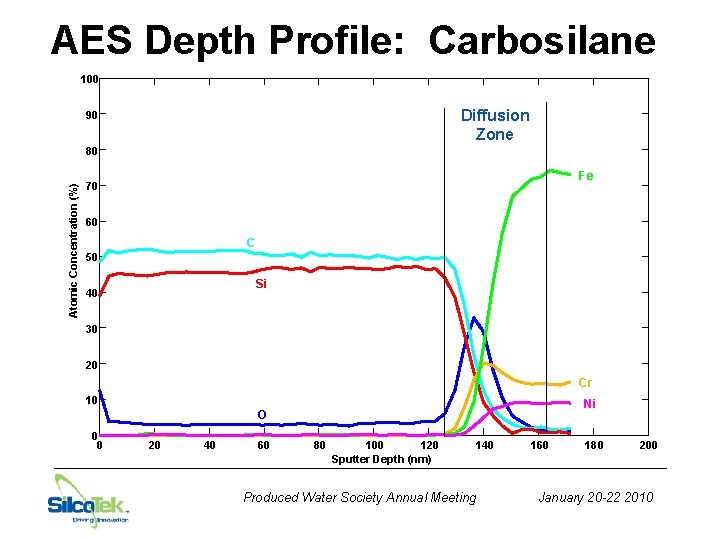
AES Depth Profile: Carbosilane 100 Diffusion Zone 90 Atomic Concentration (%) 80 Fe 70 60 C 50 Si 40 30 20 Cr 10 Ni O 0 0 20 40 60 80 100 120 Sputter Depth (nm) 140 Produced Water Society Annual Meeting 160 180 200 January 20 -22 2010
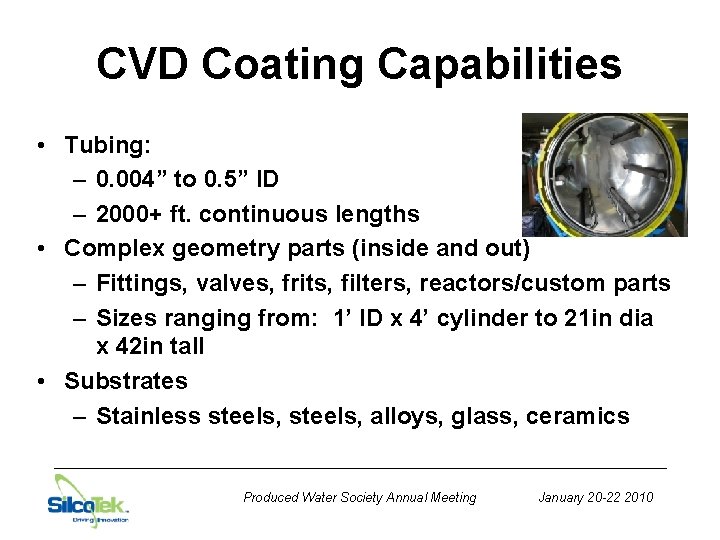
CVD Coating Capabilities • Tubing: – 0. 004” to 0. 5” ID – 2000+ ft. continuous lengths • Complex geometry parts (inside and out) – Fittings, valves, frits, filters, reactors/custom parts – Sizes ranging from: 1’ ID x 4’ cylinder to 21 in dia x 42 in tall • Substrates – Stainless steels, alloys, glass, ceramics Produced Water Society Annual Meeting January 20 -22 2010
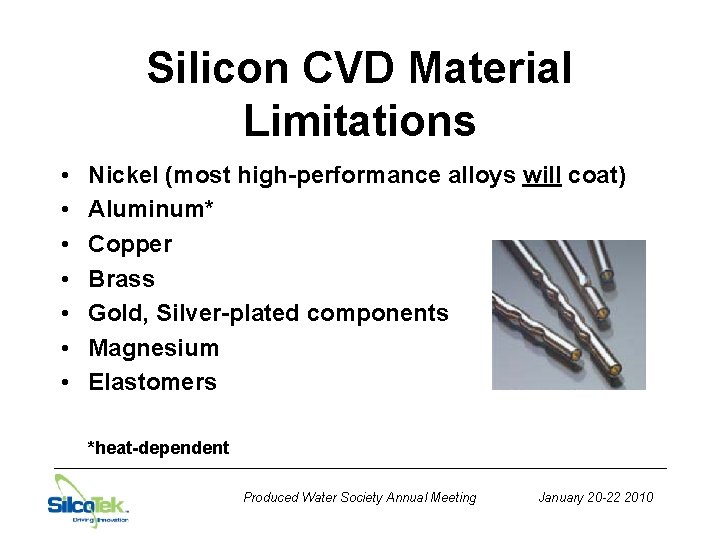
Silicon CVD Material Limitations • • Nickel (most high-performance alloys will coat) Aluminum* Copper Brass Gold, Silver-plated components Magnesium Elastomers *heat-dependent Produced Water Society Annual Meeting January 20 -22 2010
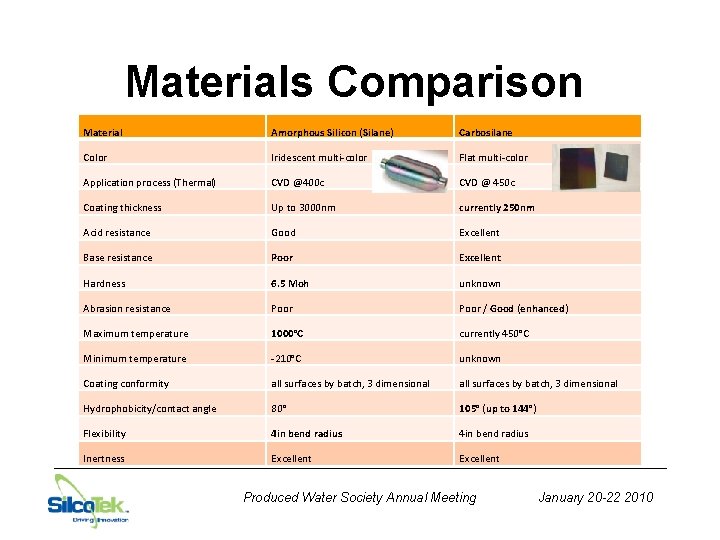
Materials Comparison Material Amorphous Silicon (Silane) Carbosilane Color Iridescent multi-color Flat multi-color Application process (Thermal) CVD @400 c CVD @ 450 c Coating thickness Up to 3000 nm currently 250 nm Acid resistance Good Excellent Base resistance Poor Excellent Hardness 6. 5 Moh unknown Abrasion resistance Poor / Good (enhanced) Maximum temperature 1000°C currently 450°C Minimum temperature -210°C unknown Coating conformity all surfaces by batch, 3 dimensional Hydrophobicity/contact angle 80° 105° (up to 144°) Flexibility 4 in bend radius Inertness Excellent Produced Water Society Annual Meeting January 20 -22 2010
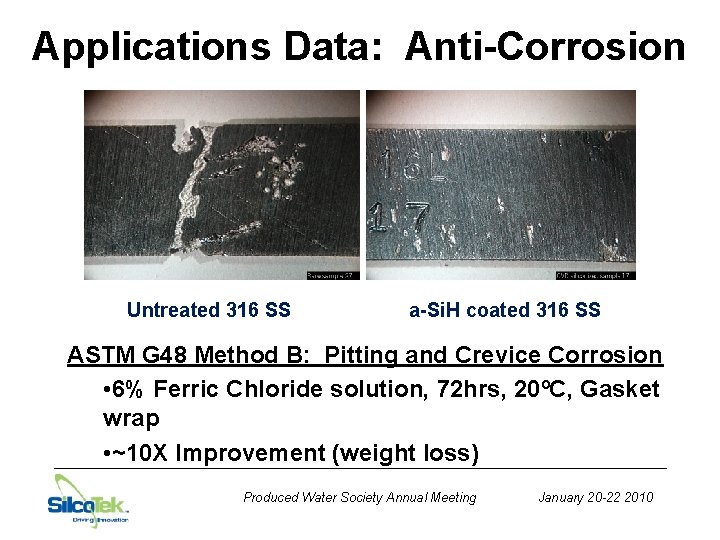
Applications Data: Anti-Corrosion Untreated 316 SS a-Si. H coated 316 SS ASTM G 48 Method B: Pitting and Crevice Corrosion • 6% Ferric Chloride solution, 72 hrs, 20ºC, Gasket wrap • ~10 X Improvement (weight loss) Produced Water Society Annual Meeting January 20 -22 2010
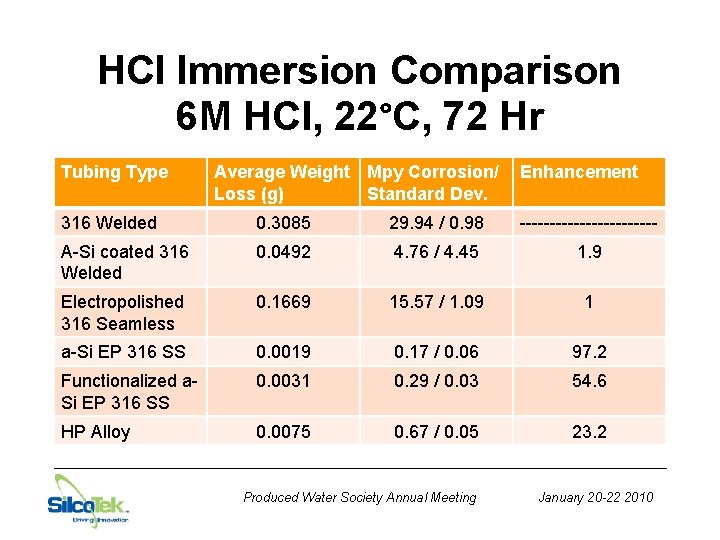
HCl Immersion Comparison 6 M HCl, 22°C, 72 Hr Tubing Type Average Weight Mpy Corrosion/ Loss (g) Standard Dev. Enhancement 316 Welded 0. 3085 29. 94 / 0. 98 ------------ A-Si coated 316 Welded 0. 0492 4. 76 / 4. 45 1. 9 Electropolished 316 Seamless 0. 1669 15. 57 / 1. 09 1 a-Si EP 316 SS 0. 0019 0. 17 / 0. 06 97. 2 Functionalized a. Si EP 316 SS 0. 0031 0. 29 / 0. 03 54. 6 HP Alloy 0. 0075 0. 67 / 0. 05 23. 2 Produced Water Society Annual Meeting January 20 -22 2010
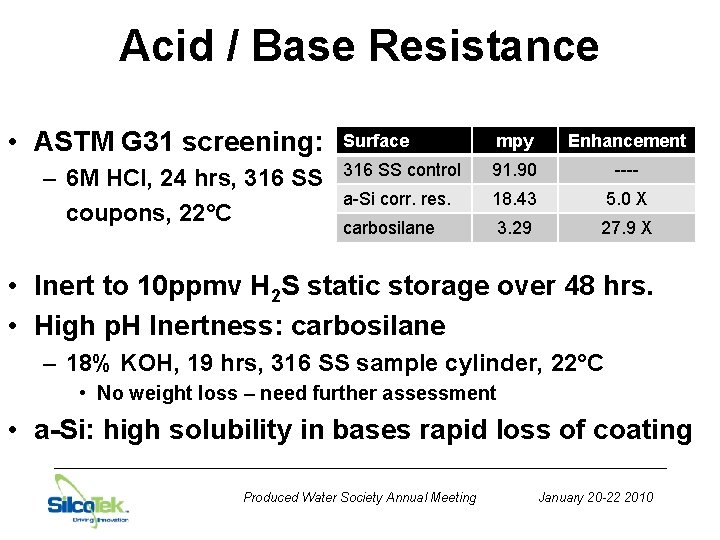
Acid / Base Resistance • ASTM G 31 screening: – 6 M HCl, 24 hrs, 316 SS coupons, 22°C Surface mpy Enhancement 316 SS control 91. 90 ---- a-Si corr. res. 18. 43 5. 0 X carbosilane 3. 29 27. 9 X • Inert to 10 ppmv H 2 S static storage over 48 hrs. • High p. H Inertness: carbosilane – 18% KOH, 19 hrs, 316 SS sample cylinder, 22°C • No weight loss – need further assessment • a-Si: high solubility in bases rapid loss of coating Produced Water Society Annual Meeting January 20 -22 2010
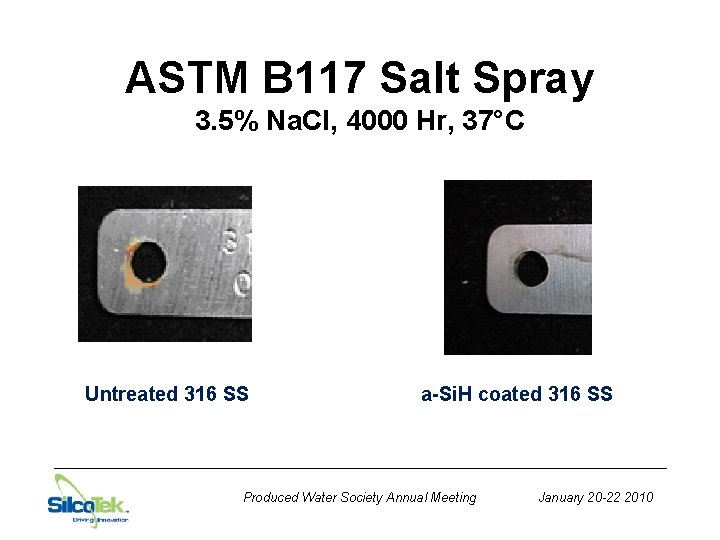
ASTM B 117 Salt Spray 3. 5% Na. Cl, 4000 Hr, 37°C Untreated 316 SS a-Si. H coated 316 SS Produced Water Society Annual Meeting January 20 -22 2010

Hydrophobicity: Powerful Potential • Silver texture on copper with heptadecafluoro -1 decanethiol coating • Air layer between water and metal coupon • Critical viewing angle = 48. 6° (same as water/air reflection boundary); <1% water in contact with surface (CA = 173°) Larmour, I. A. ; Bell, S. E. J; Saunders, G. C. Angew. Chem. Int. Ed. 2007, 46, 1710 -1712. Produced Water Society Annual Meeting January 20 -22 2010

Contact Angle Illustration Close to Release… • DI water CA: 127° • On 304 stainless corrosion coupon; no topography modification Untreated 316 SS Carbosilane coated 316 SS Produced Water Society Annual Meeting January 20 -22 2010
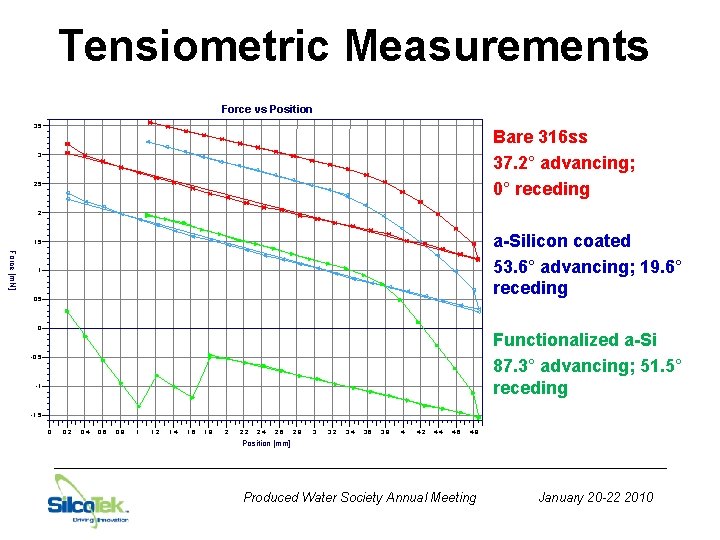
Tensiometric Measurements Force vs Position 3. 5 Bare 316 ss 37. 2° advancing; 0° receding 3 2. 5 2 a-Silicon coated 53. 6° advancing; 19. 6° receding 1. 5 Force [m. N] 1 0. 5 0 Functionalized a-Si 87. 3° advancing; 51. 5° receding -0. 5 -1 -1. 5 0 0. 2 0. 4 0. 6 0. 8 1 1. 2 1. 4 1. 6 1. 8 2 2. 4 2. 6 2. 8 3 3. 2 3. 4 3. 6 3. 8 4 4. 2 4. 4 4. 6 4. 8 Position [mm] Produced Water Society Annual Meeting January 20 -22 2010
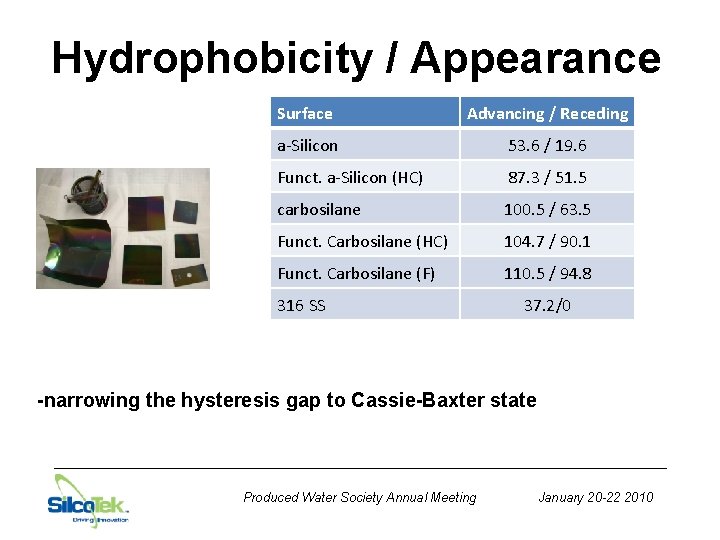
Hydrophobicity / Appearance Surface Advancing / Receding a-Silicon 53. 6 / 19. 6 Funct. a-Silicon (HC) 87. 3 / 51. 5 carbosilane 100. 5 / 63. 5 Funct. Carbosilane (HC) 104. 7 / 90. 1 Funct. Carbosilane (F) 110. 5 / 94. 8 316 SS 37. 2/0 -narrowing the hysteresis gap to Cassie-Baxter state Produced Water Society Annual Meeting January 20 -22 2010
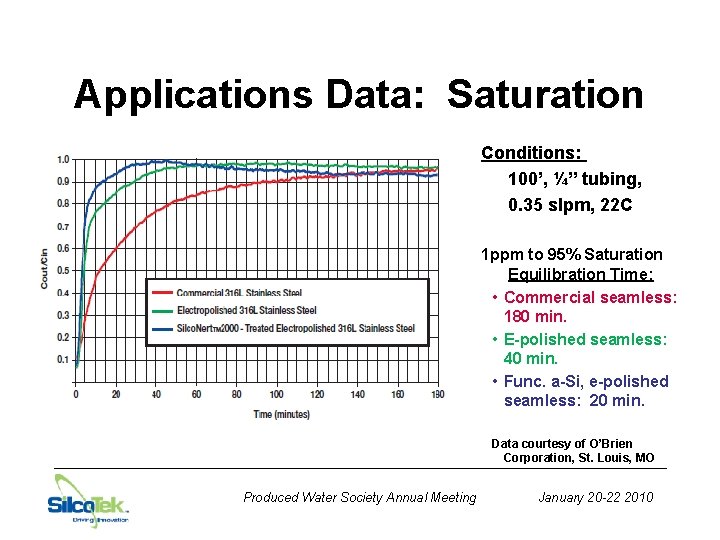
Applications Data: Saturation Conditions: 100’, ¼” tubing, 0. 35 slpm, 22 C 1 ppm to 95% Saturation Equilibration Time: • Commercial seamless: 180 min. • E-polished seamless: 40 min. • Func. a-Si, e-polished seamless: 20 min. Data courtesy of O’Brien Corporation, St. Louis, MO Produced Water Society Annual Meeting January 20 -22 2010
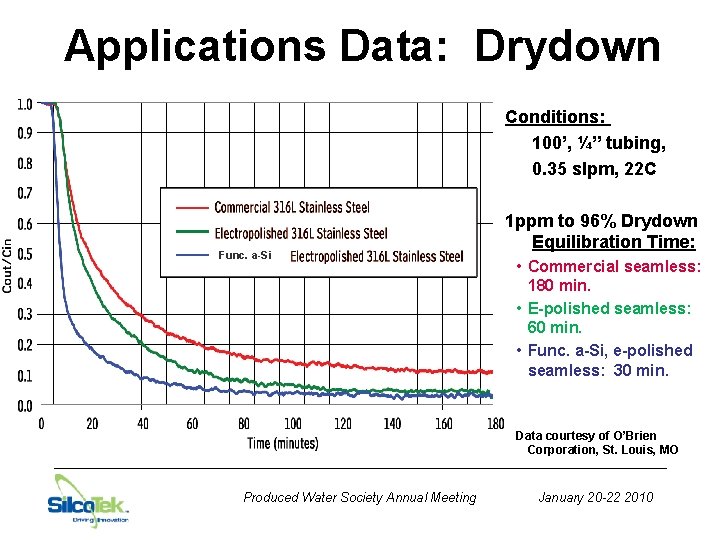
Applications Data: Drydown Conditions: 100’, ¼” tubing, 0. 35 slpm, 22 C Func. a-Si 1 ppm to 96% Drydown Equilibration Time: • Commercial seamless: 180 min. • E-polished seamless: 60 min. • Func. a-Si, e-polished seamless: 30 min. Data courtesy of O’Brien Corporation, St. Louis, MO Produced Water Society Annual Meeting January 20 -22 2010
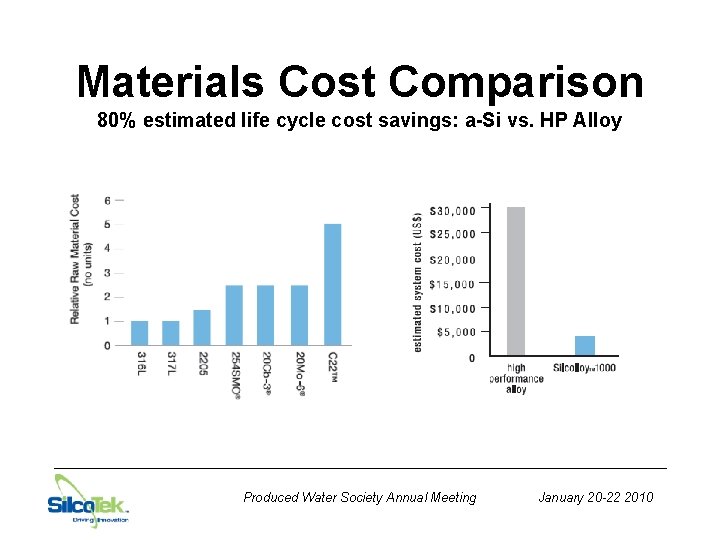
Materials Cost Comparison 80% estimated life cycle cost savings: a-Si vs. HP Alloy Produced Water Society Annual Meeting January 20 -22 2010
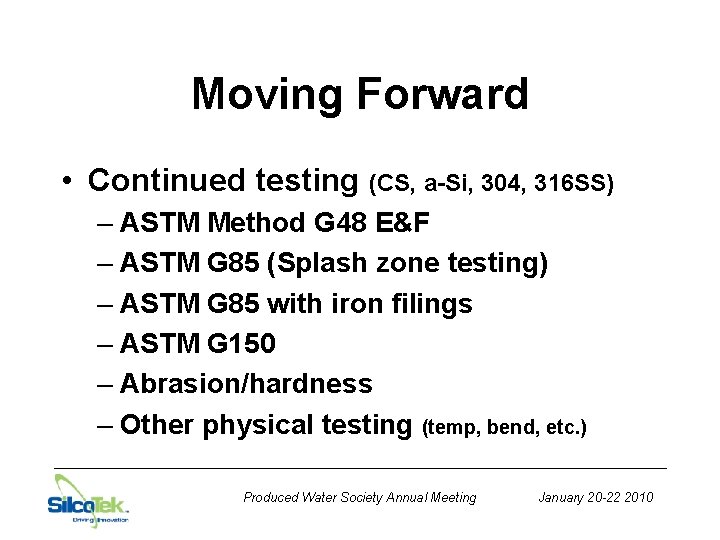
Moving Forward • Continued testing (CS, a-Si, 304, 316 SS) – ASTM Method G 48 E&F – ASTM G 85 (Splash zone testing) – ASTM G 85 with iron filings – ASTM G 150 – Abrasion/hardness – Other physical testing (temp, bend, etc. ) Produced Water Society Annual Meeting January 20 -22 2010
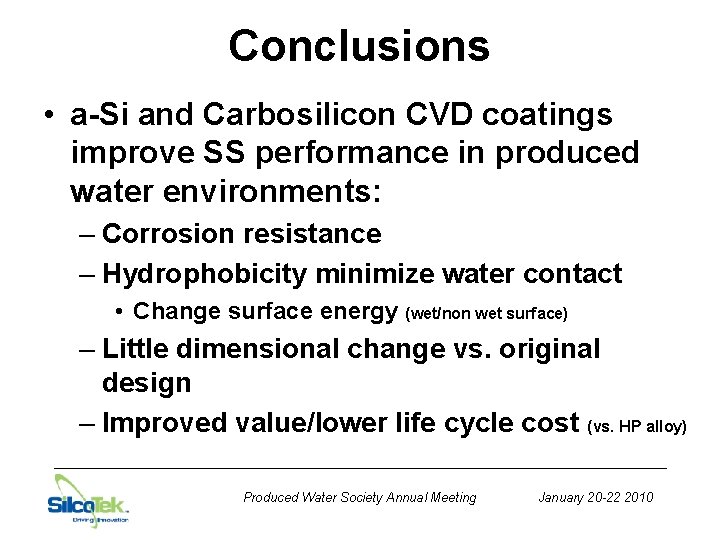
Conclusions • a-Si and Carbosilicon CVD coatings improve SS performance in produced water environments: – Corrosion resistance – Hydrophobicity minimize water contact • Change surface energy (wet/non wet surface) – Little dimensional change vs. original design – Improved value/lower life cycle cost (vs. HP alloy) Produced Water Society Annual Meeting January 20 -22 2010
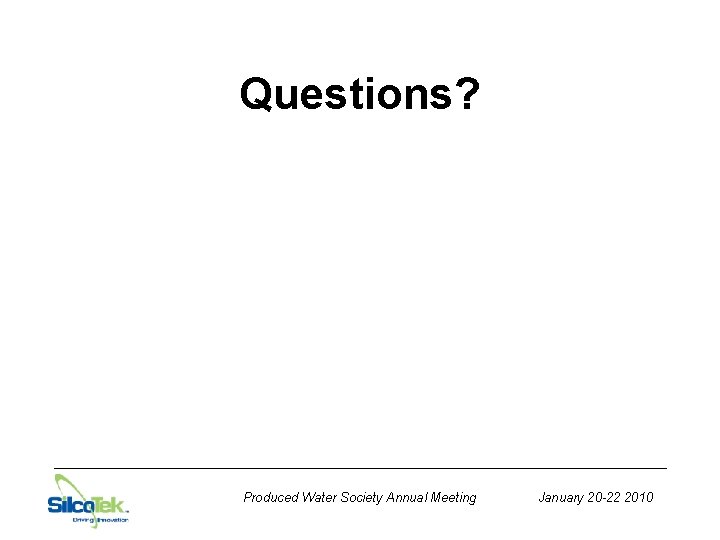
Questions? Produced Water Society Annual Meeting January 20 -22 2010
Scullery sink definition
End closures without tie-bar
Drug basket method
Kettle reboiler design procedure
What is machinability?
Yusco stainless steel
Orthotic knee joint stainless steel ring drop lock
Issf
Stainless steel code number
Stainless steel sheetplat gold 04
Atomy stainless steel scrubber
304lp stainless steel
Stainless steel clothes dyeing machine
316 stainless steel tables
Kitchen exhaust cleaning philadelphia
Dental charting made easy
Lath
Stainless steel heat exchanger tube
Nr-13
Sherwin williams chemical coatings store
Phosphorus equation
Chemical vapour deposition process
Hts coatings
St powder coatings
Epoxy phenalkamine coatings
Alocit