PROPUESTA PARA REDUCIR LOS TIEMPOS DE INTERVENCIN EN
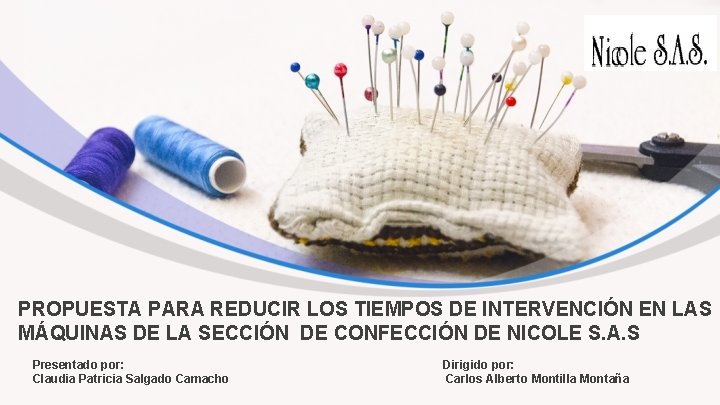
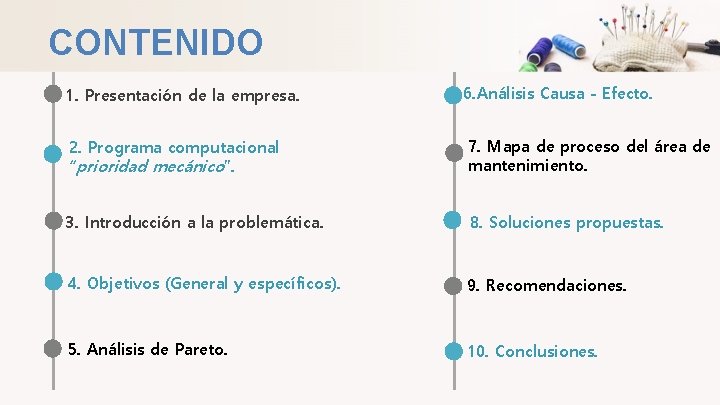
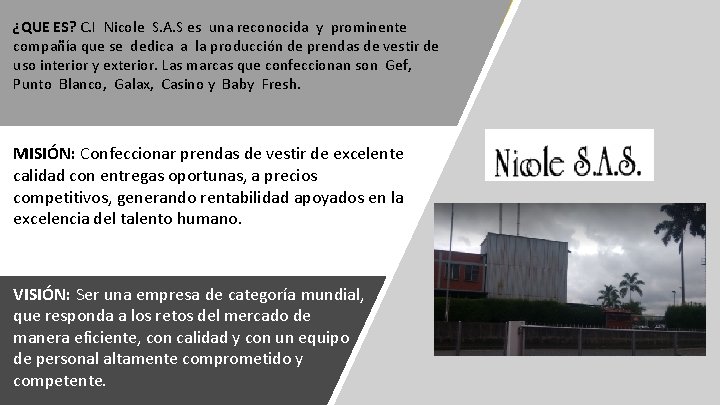
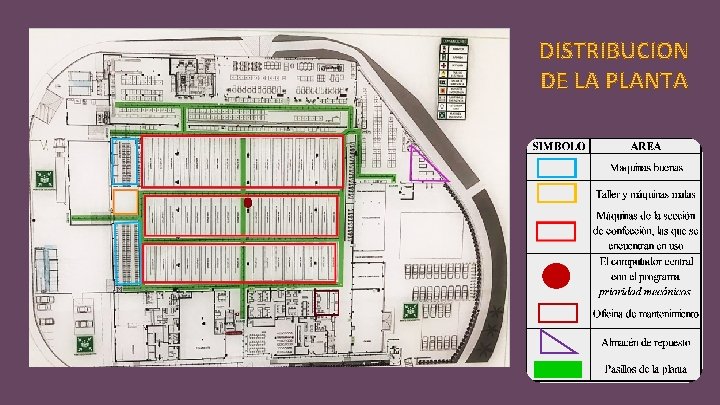
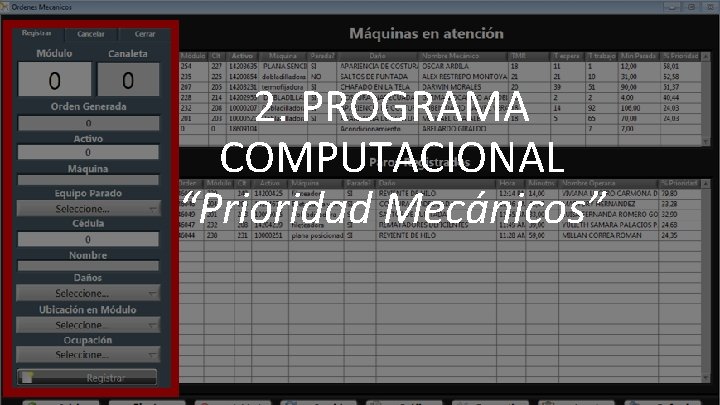
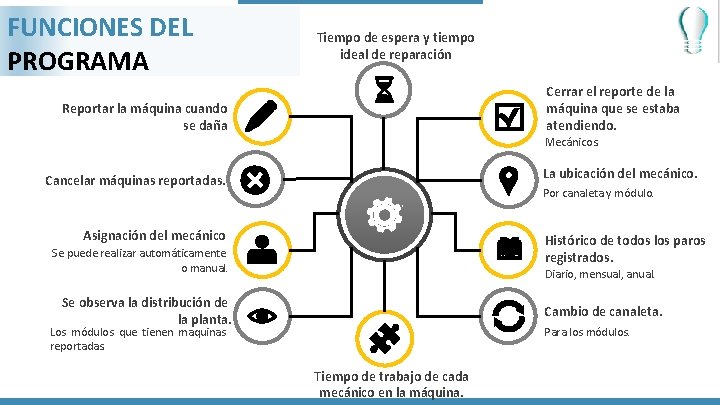
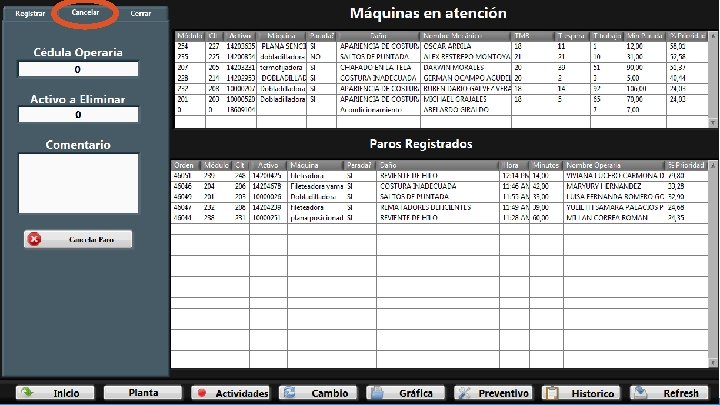
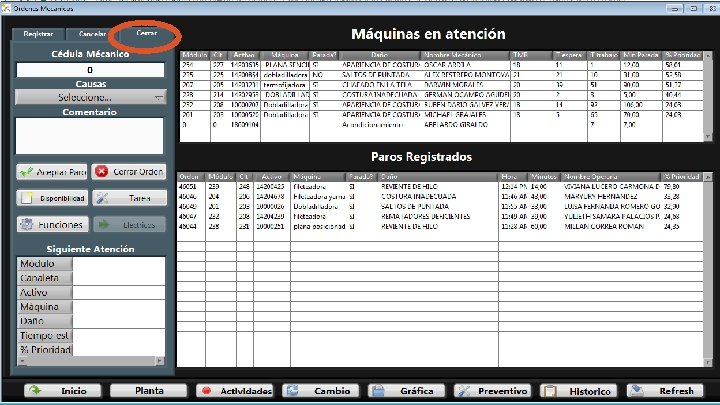
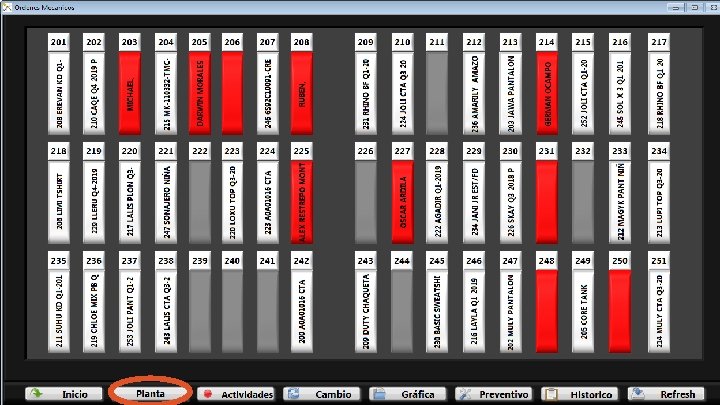
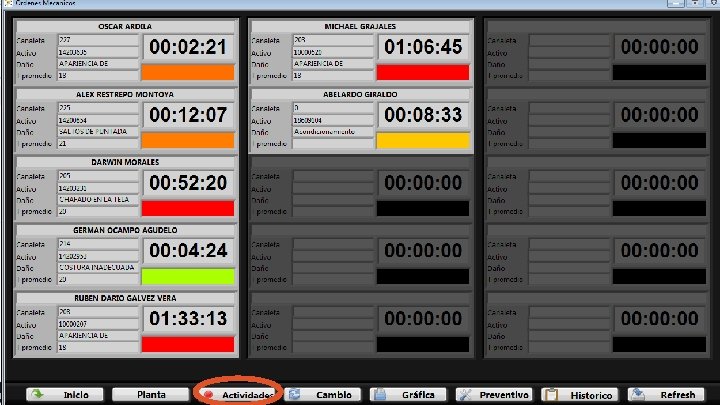
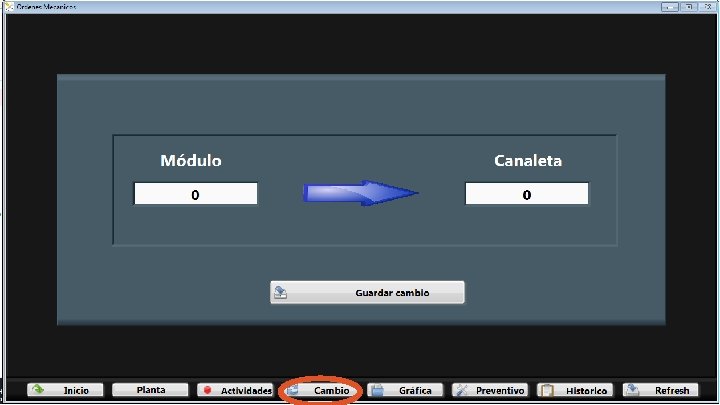
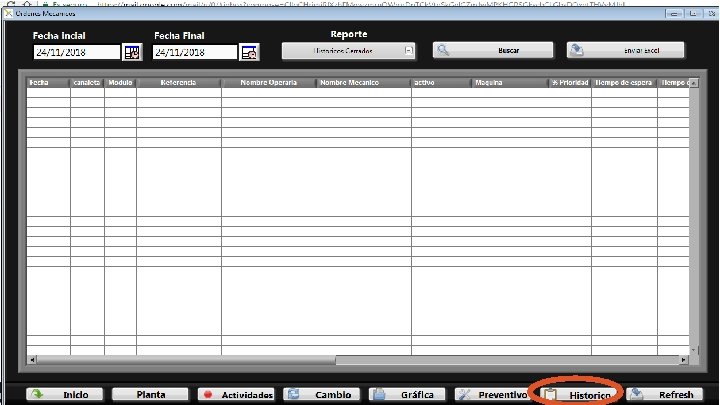
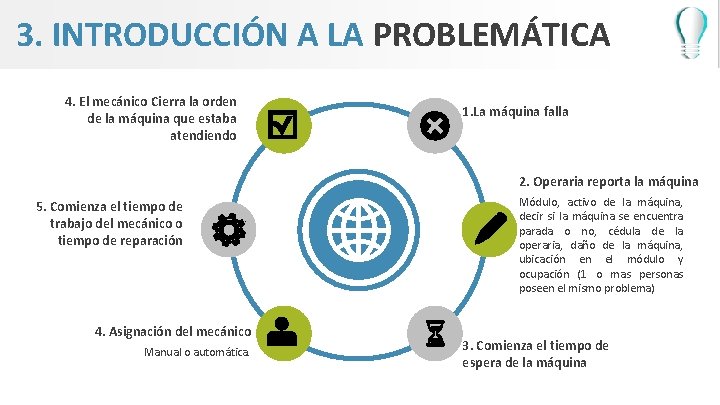
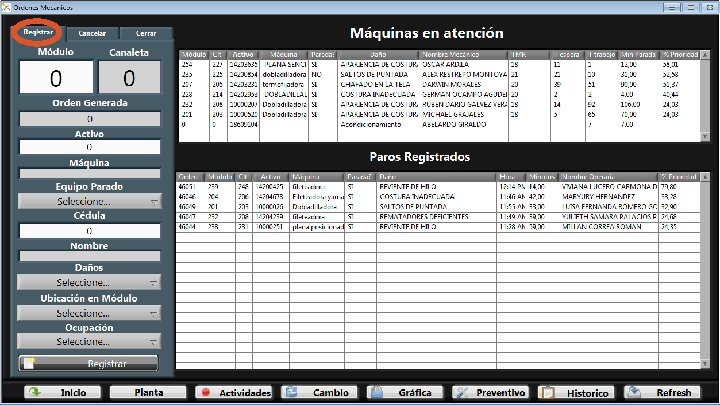

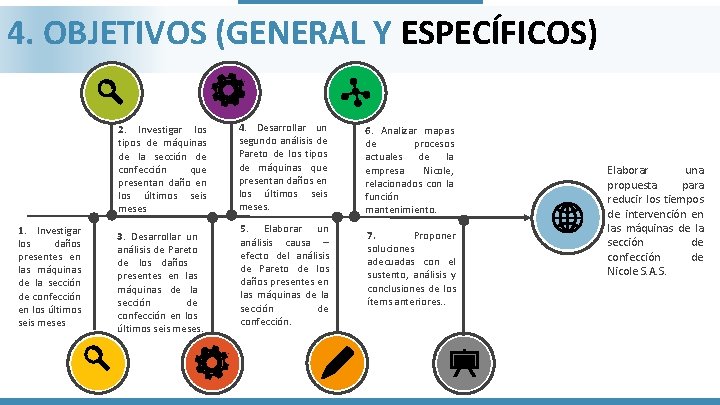
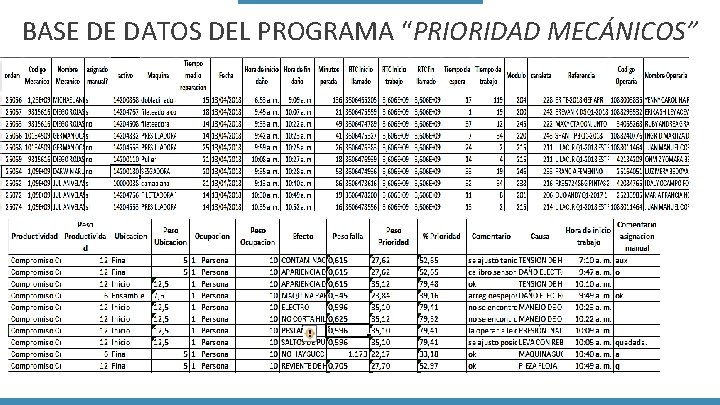
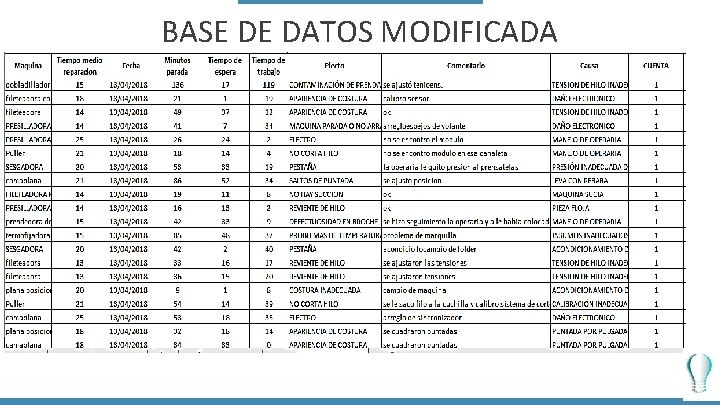
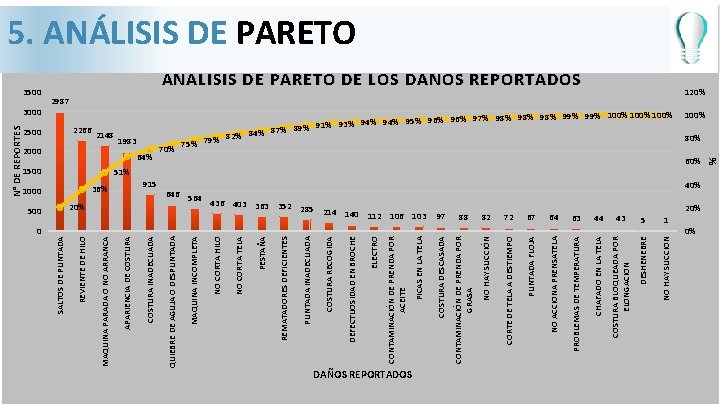
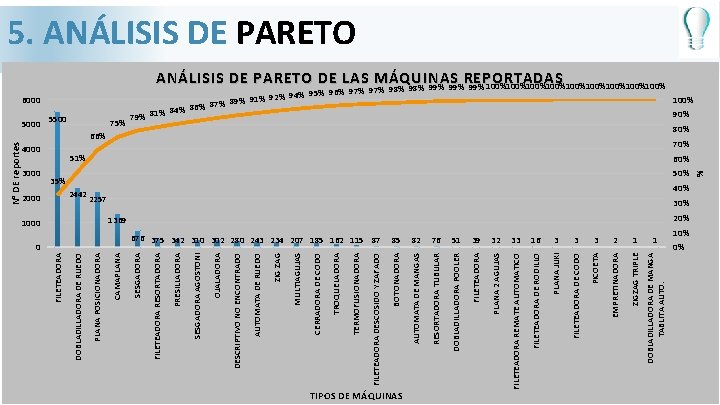
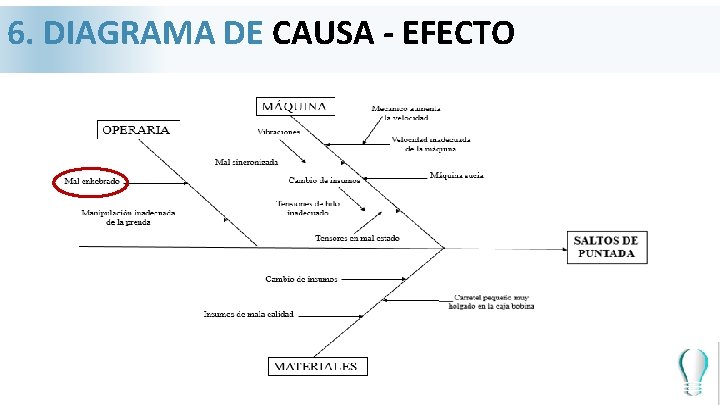
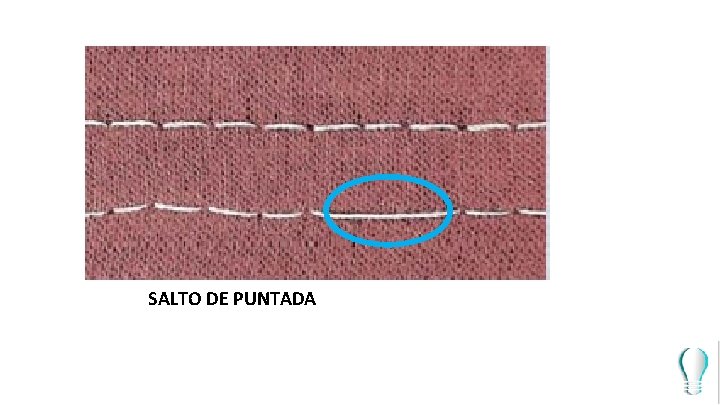
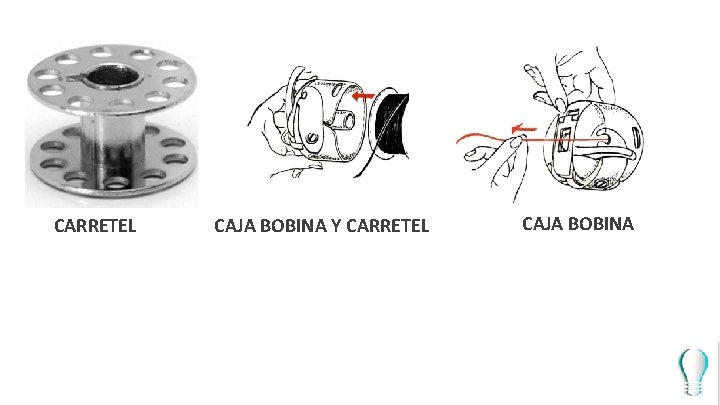
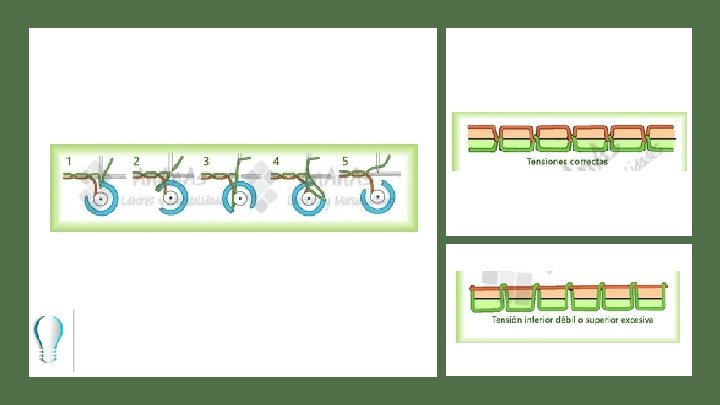
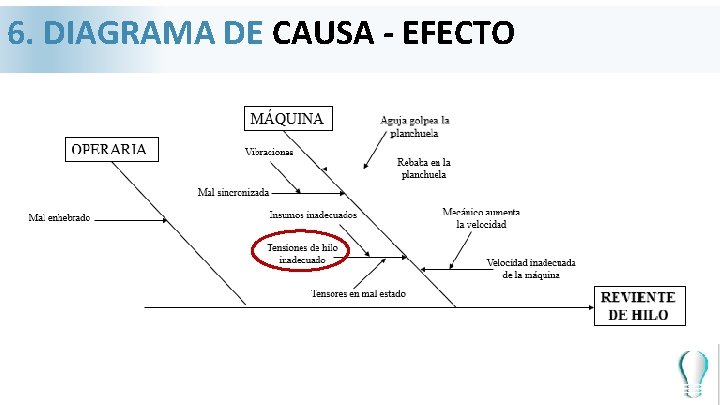
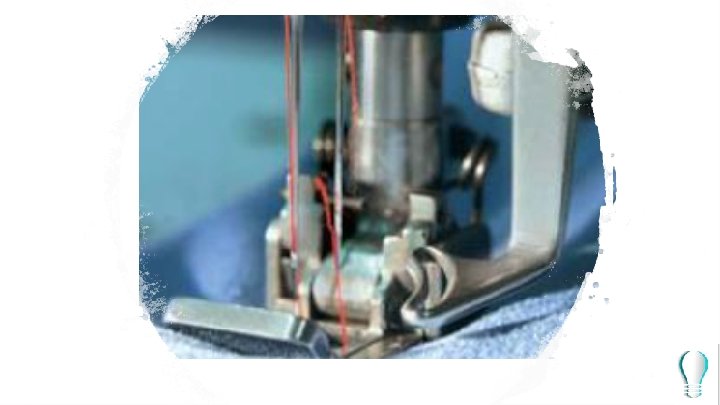
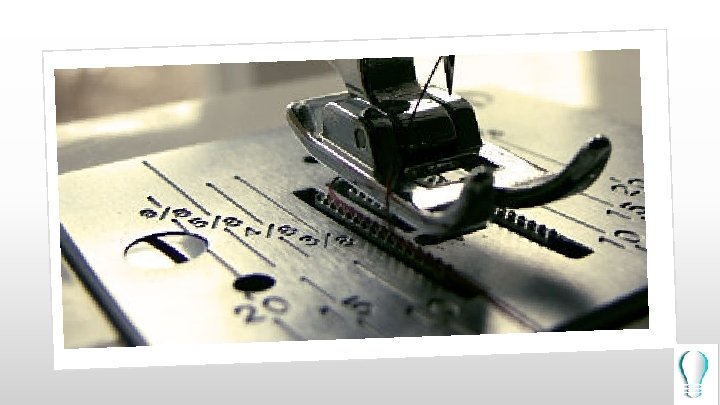
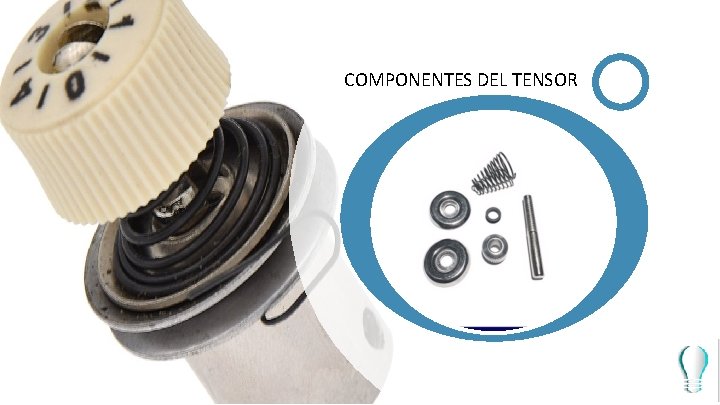
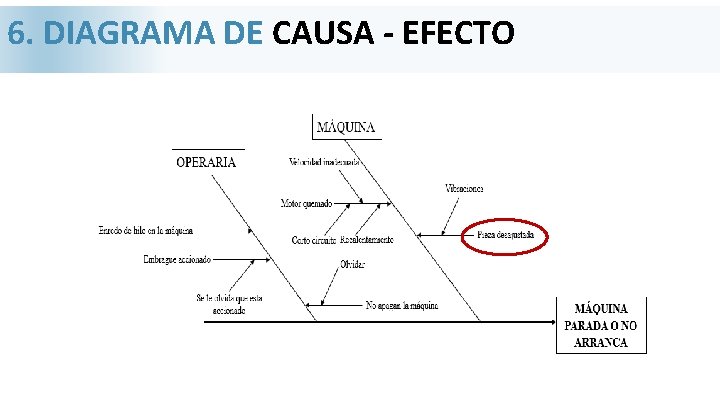
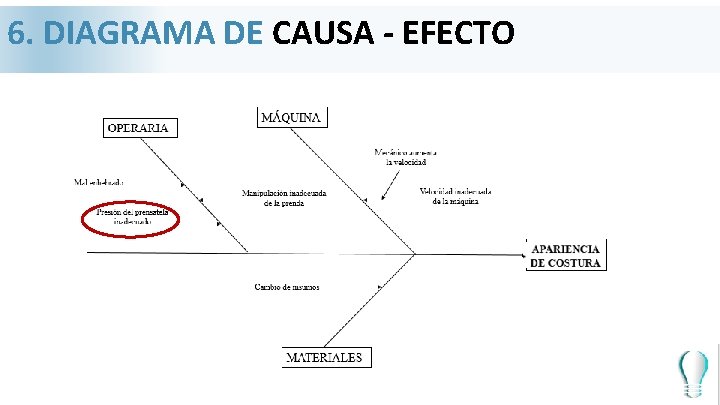
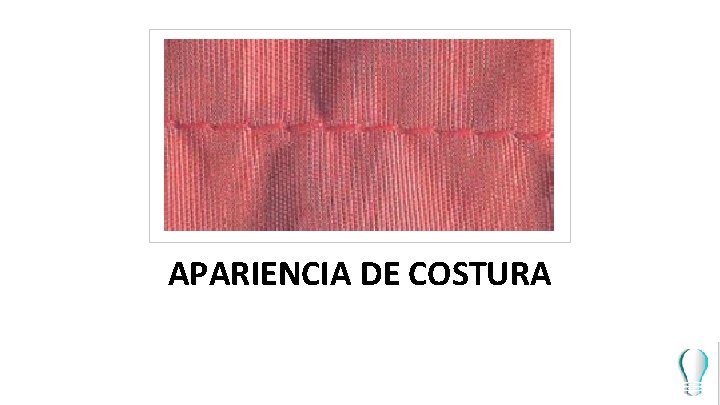
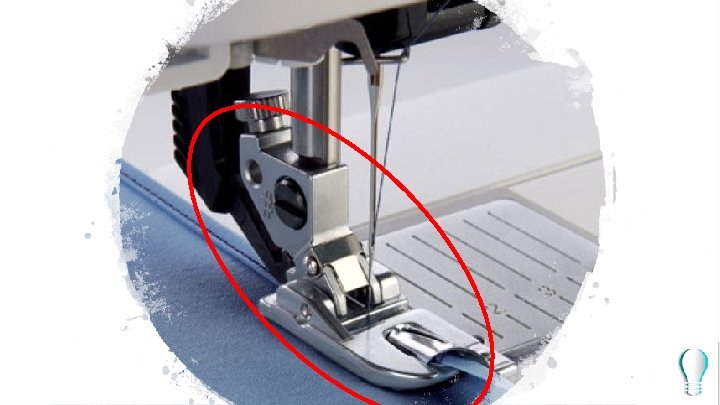

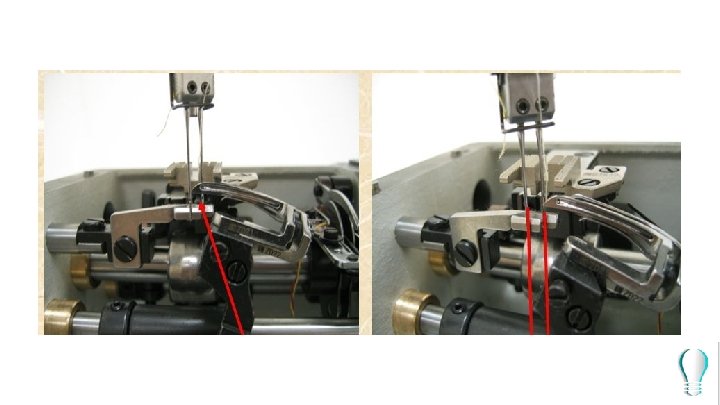
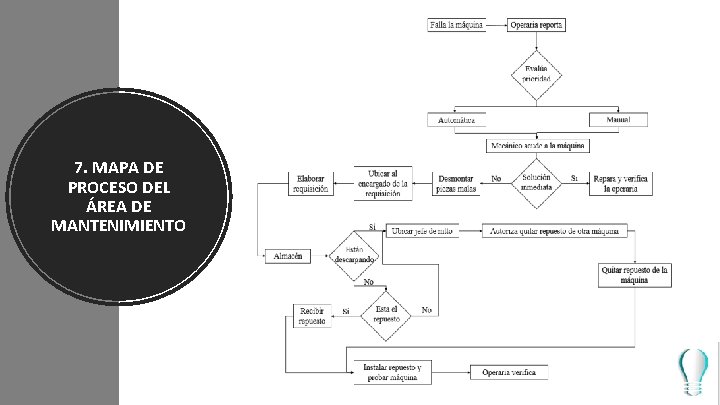
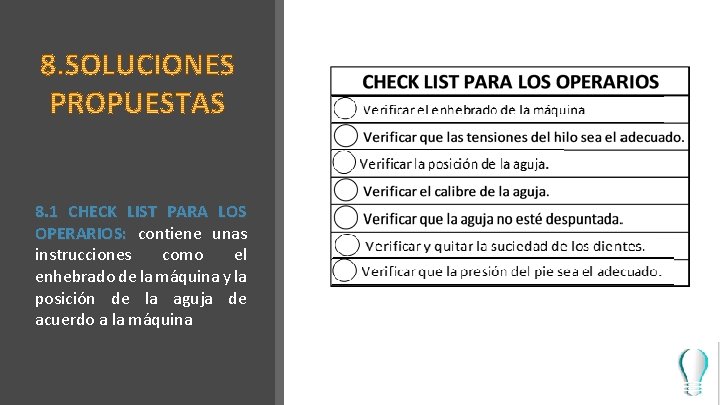
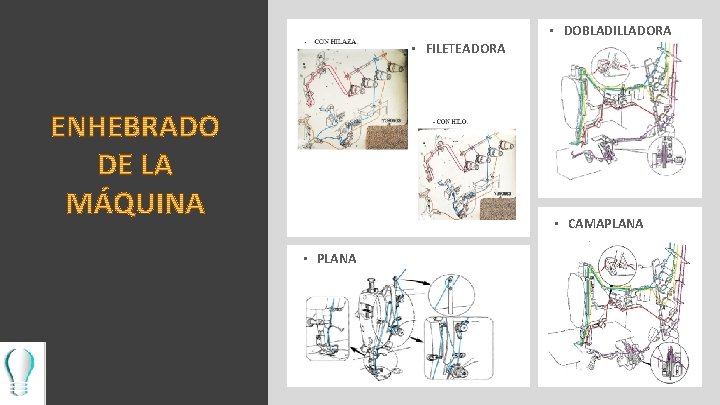
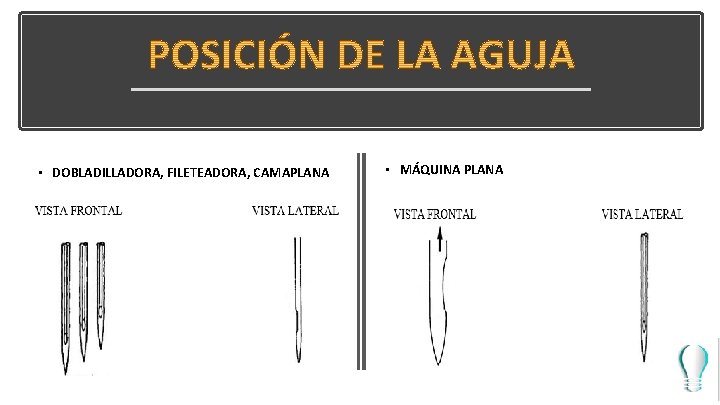
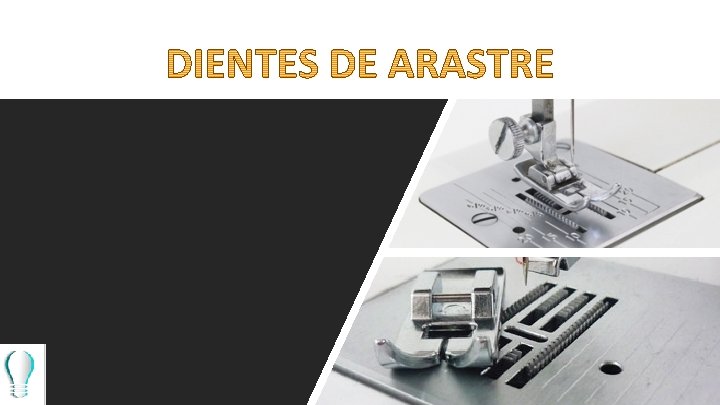
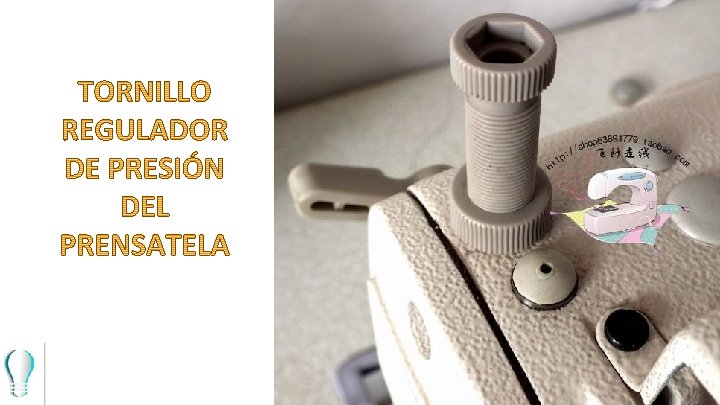
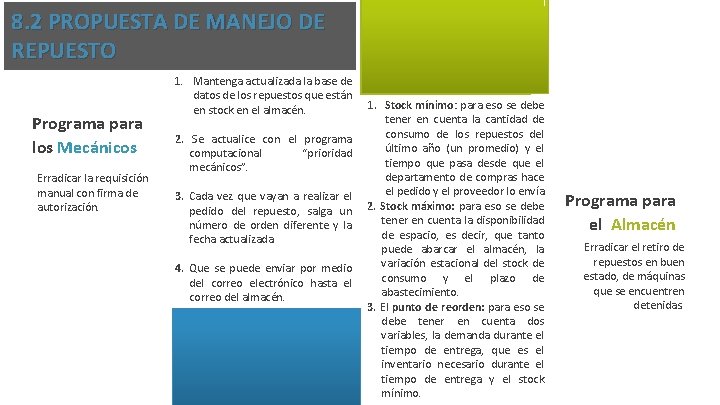
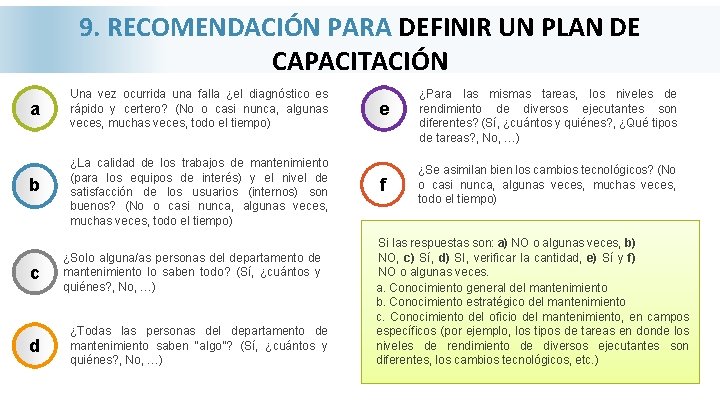
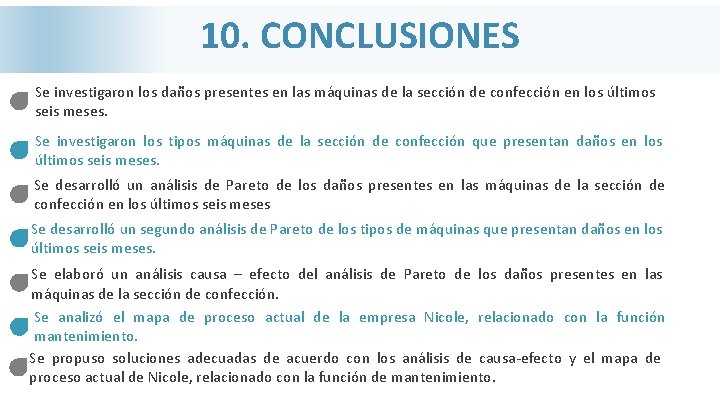
- Slides: 43
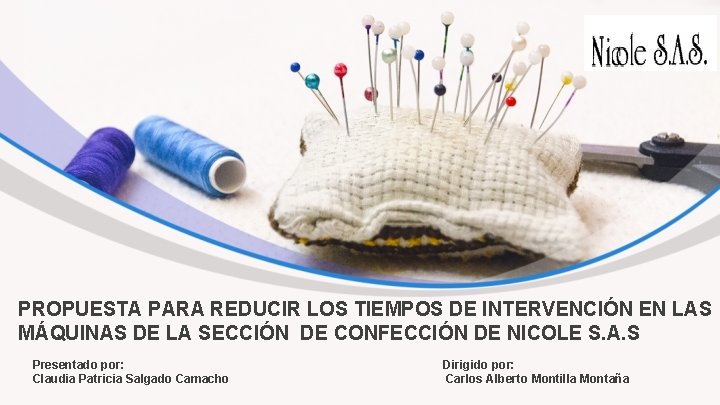
PROPUESTA PARA REDUCIR LOS TIEMPOS DE INTERVENCIÓN EN LAS MÁQUINAS DE LA SECCIÓN DE CONFECCIÓN DE NICOLE S. A. S Presentado por: Claudia Patricia Salgado Camacho Dirigido por: Carlos Alberto Montilla Montaña
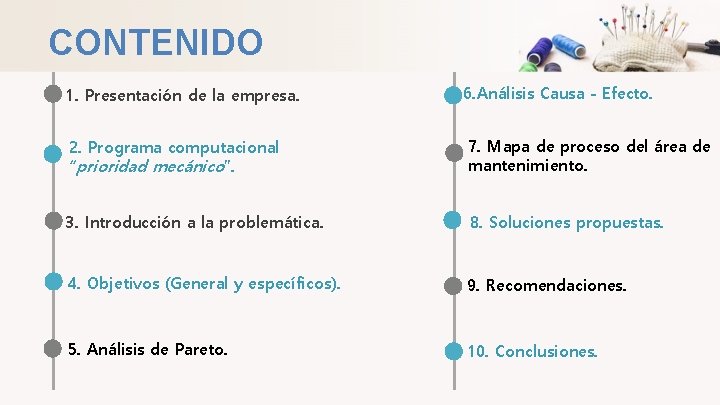
CONTENIDO 1. Presentación de la empresa. 6. Análisis Causa - Efecto. 2. Programa computacional “prioridad mecánico”. 7. Mapa de proceso del área de mantenimiento. 3. Introducción a la problemática. 8. Soluciones propuestas. 4. Objetivos (General y específicos). 9. Recomendaciones. 5. Análisis de Pareto. 10. Conclusiones.
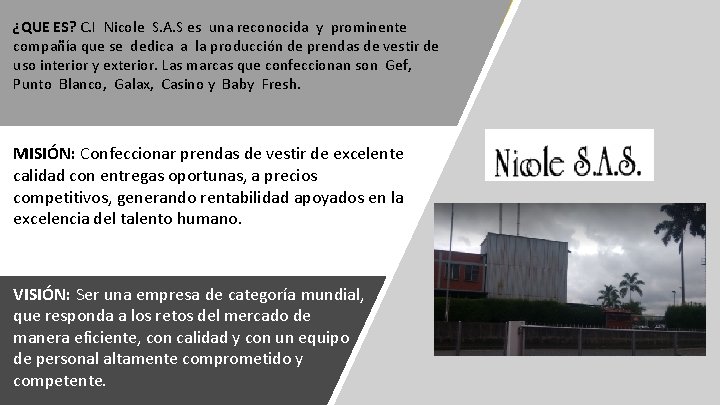
¿QUE ES? C. I Nicole S. A. S es una reconocida y prominente compañía que se dedica a la producción de prendas de vestir de uso interior y exterior. Las marcas que confeccionan son Gef, Punto Blanco, Galax, Casino y Baby Fresh. MISIÓN: Confeccionar prendas de vestir de excelente calidad con entregas oportunas, a precios competitivos, generando rentabilidad apoyados en la excelencia del talento humano. VISIÓN: Ser una empresa de categoría mundial, que responda a los retos del mercado de manera eficiente, con calidad y con un equipo de personal altamente comprometido y competente.
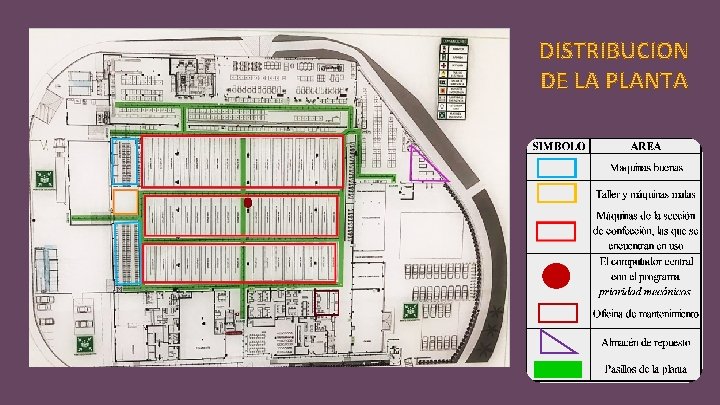
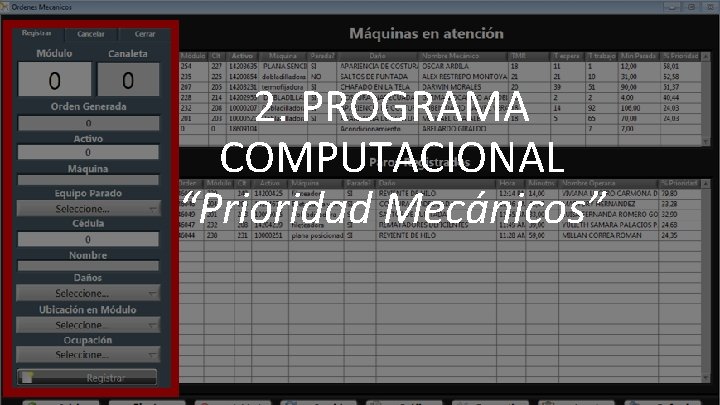
2. PROGRAMA COMPUTACIONAL “Prioridad Mecánicos”
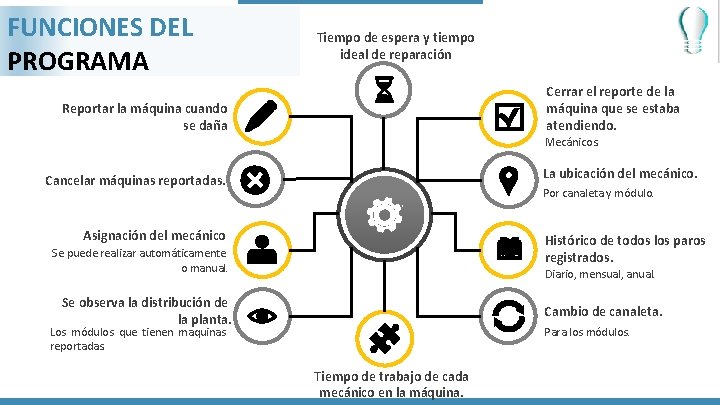
FUNCIONES DEL PROGRAMA Tiempo de espera y tiempo ideal de reparación Cerrar el reporte de la máquina que se estaba atendiendo. Reportar la máquina cuando se daña Mecánicos. La ubicación del mecánico. Cancelar máquinas reportadas. Por canaleta y módulo. Asignación del mecánico Histórico de todos los paros registrados. Se puede realizar automáticamente o manual. Diario, mensual, anual. Se observa la distribución de la planta. Cambio de canaleta. Para los módulos. Los módulos que tienen maquinas reportadas. Tiempo de trabajo de cada mecánico en la máquina.
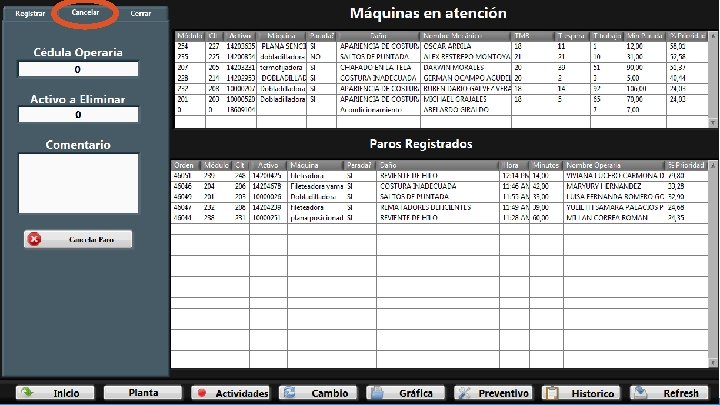
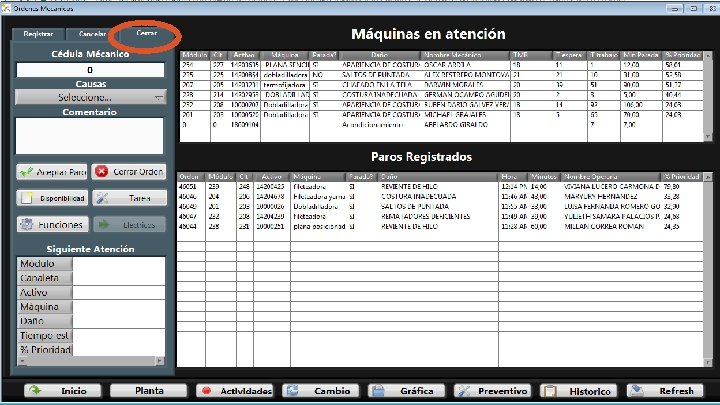
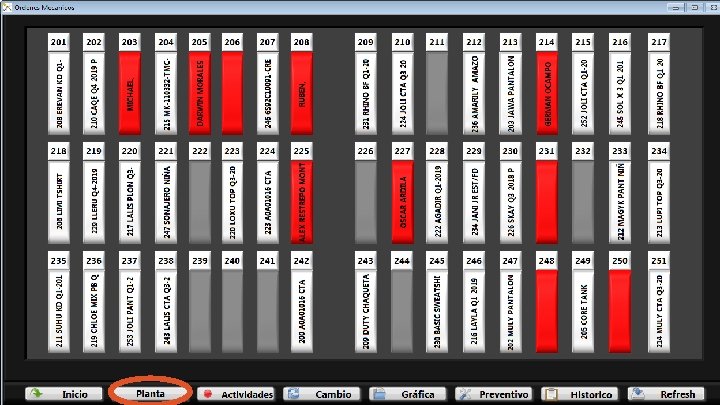
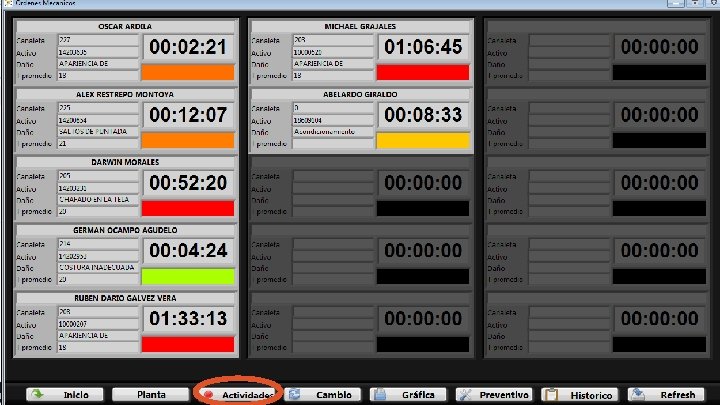
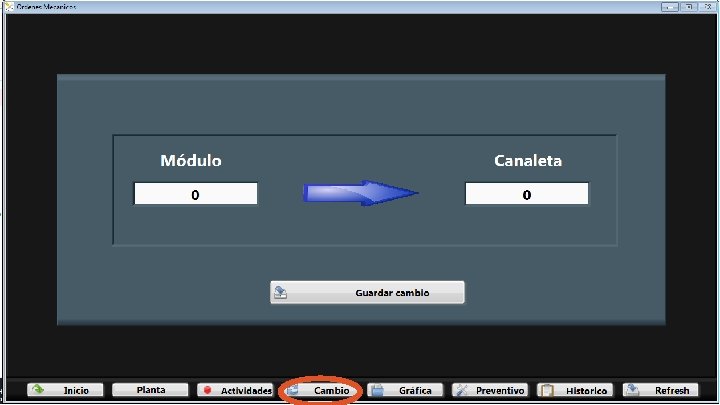
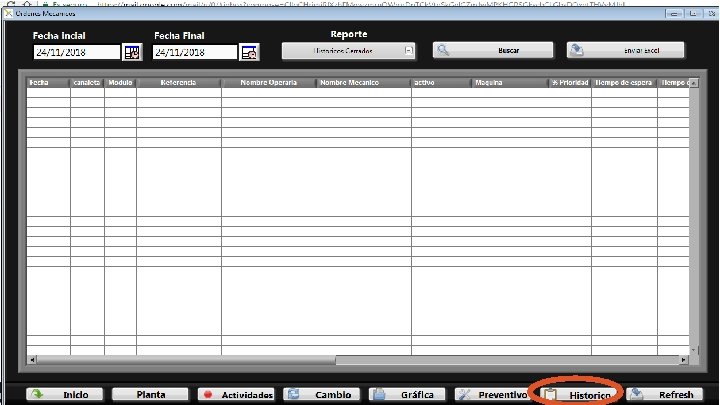
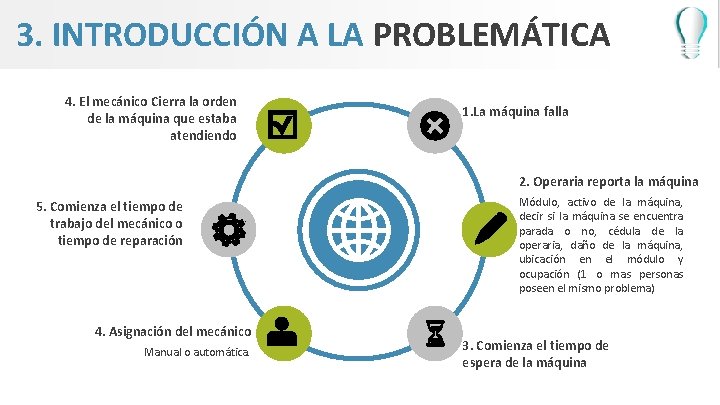
3. INTRODUCCIÓN A LA PROBLEMÁTICA 4. El mecánico Cierra la orden de la máquina que estaba atendiendo 1. La máquina falla 2. Operaria reporta la máquina 5. Comienza el tiempo de trabajo del mecánico o tiempo de reparación 4. Asignación del mecánico Manual o automática. Módulo, activo de la máquina, decir si la máquina se encuentra parada o no, cédula de la operaria, daño de la máquina, ubicación en el módulo y ocupación (1 o mas personas poseen el mismo problema) 3. Comienza el tiempo de espera de la máquina
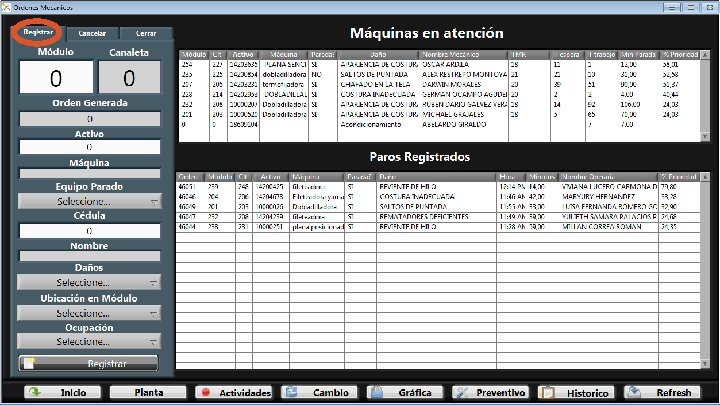

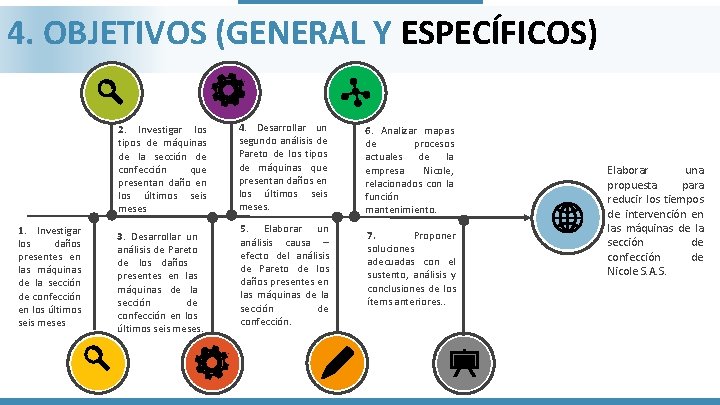
4. OBJETIVOS (GENERAL Y ESPECÍFICOS) 2. Investigar los tipos de máquinas de la sección de confección que presentan daño en los últimos seis meses 1. Investigar los daños presentes en las máquinas de la sección de confección en los últimos seis meses 3. Desarrollar un análisis de Pareto de los daños presentes en las máquinas de la sección de confección en los últimos seis meses. 4. Desarrollar un segundo análisis de Pareto de los tipos de máquinas que presentan daños en los últimos seis meses. 5. Elaborar un análisis causa – efecto del análisis de Pareto de los daños presentes en las máquinas de la sección de confección. 6. Analizar mapas de procesos actuales de la empresa Nicole, relacionados con la función mantenimiento. 7. Proponer soluciones adecuadas con el sustento, análisis y conclusiones de los ítems anteriores. . Elaborar una propuesta para reducir los tiempos de intervención en las máquinas de la sección de confección de Nicole S. A. S.
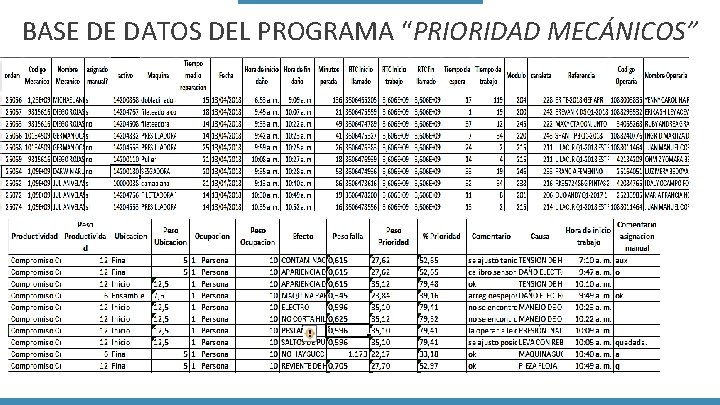
BASE DE DATOS DEL PROGRAMA “PRIORIDAD MECÁNICOS”
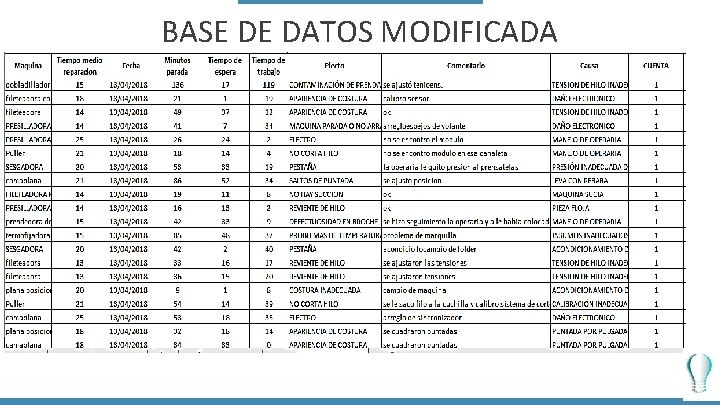
BASE DE DATOS MODIFICADA
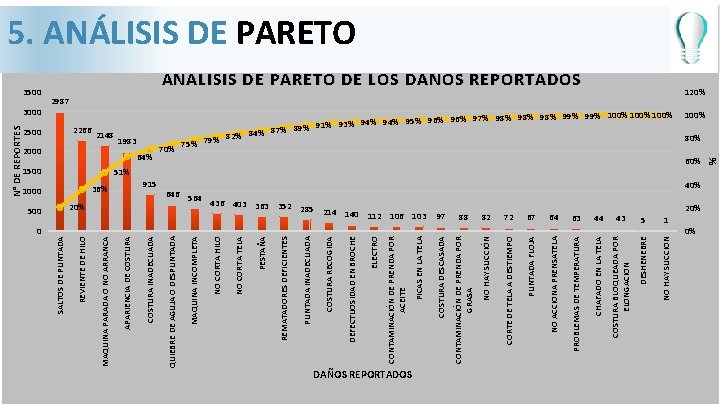
0 ANÁLISIS DE PARETO DAÑOS REPORTADOS 5 NO HAY SUCCION 43 DESHENEBRE 44 COSTURA BLOQUEADA POR ELONGACION 63 CHAFADO EN LA TELA 64 PROBLEMAS DE TEMPERATURA 67 NO ACCIONA PRENSATELA 72 PUNTADA FLOJA 82 CORTE DE TELA A DESTIEMPO 88 NO HAY SUCCIÓN 97 CONTAMINACIÓN DE PRENDA POR GRASA 436 403 363 352 285 214 140 112 106 103 COSTURA DESCASADA PICAS EN LA TELA CONTAMINACIÓN DE PRENDA POR ACEITE ELECTRO DEFECTUOSIDAD EN BROCHE COSTURA RECOGIDA PUNTADA INADECUADA 20% 646 564 REMATADORES DEFICIENTES 500 915 PESTAÑA 36% NO CORTA TELA 64% ANÁLISIS DE PARETO DE LOS DAÑOS REPORTADOS 2987 99% 100% 95% 96% 97% 98% 98% 91% 93% 94% 89% 87% 82% 84% 75% 79% 51% 60% 40% 1 20% 0% % 70% NO CORTA HILO 1500 1983 MAQUINA INCOMPLETA 2000 QUIEBRE DE AGUJA O DESPUNTADA 1000 2148 COSTURA INADECUADA 2266 APARIENCIA DE COSTURA 2500 MAQUINA PARADA O NO ARRANCA 3000 REVIENTE DE HILO 3500 SALTOS DE PUNTADA N° DE REPORTES 5. ANÁLISIS DE PARETO 120% 100% 80%
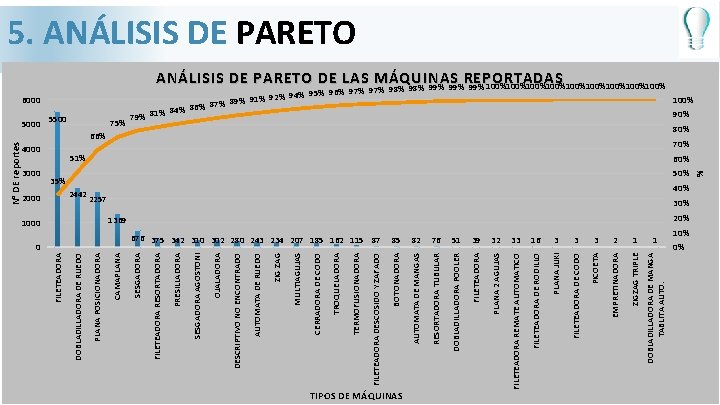
0 ANÁLISIS DE PARETO 82 76 51 39 32 33 16 3 3 3 2 1 1 RESORTADORA TUBULAR DOBLADILLADORA POOLER FILETEADORA PLANA 2 AGUJAS FILETEADORA REMATE AUTOMATICO FILETEADORA DE RODILLO PLANA JUKI FILETEADORA DE CODO PICOETA EMPRETINADORA ZIGZAG TRIPLE DOBLADILLADORA DE MANGA TABLITA AUTO. TIPOS DE MÁQUINAS 85 AUTOMATA DE MANGAS 676 375 342 310 302 280 243 234 207 185 162 115 87 BOTONADORA FILETEADORA DESCOSIDO Y ZAFADO TERMOFUSIONADORA TROQUELADORA CERRADORA DE CODO MULTIAGUJAS ZIG ZAG AUTOMATA DE RUEDO DESCRIPTIVO NO ENCONTRADO OJALADORA 1000 SESGADORA AGOSTONI 2442 PRESILLADORA 2000 ANÁLISIS DE PARETO DE LAS MÁQUINAS REPORTADAS 98% 99% 99% 100%100%100%100%100% 96% 97% 98% 92% 94% 95% 91% 87% 89% 84% 86% 79% 81% 66% 51% 35% 50% 2257 40% 30% 1369 20% 10% 0% % 75% FILETEADORA RESORTADORA 6000 SESGADORA 5500 CAMAPLANA 3000 PLANA POSICIONADORA 4000 DOBLADILLADORA DE RUEDO 5000 FILETEADORA N° DE reportes 5. ANÁLISIS DE PARETO 100% 90% 80% 70% 60%
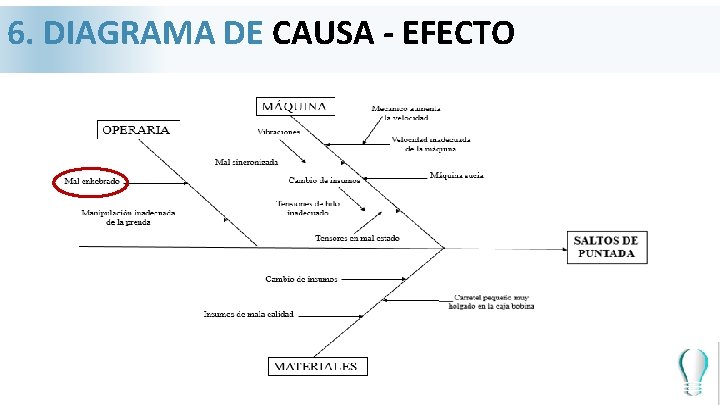
6. DIAGRAMA DE CAUSA - EFECTO ANÁLISIS DE PARETO
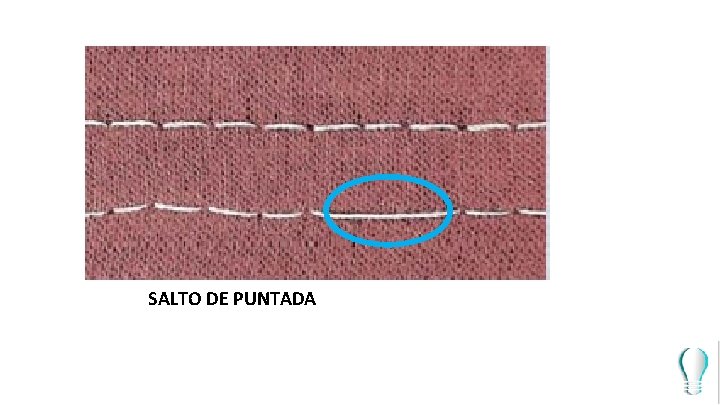
SALTO DE PUNTADA
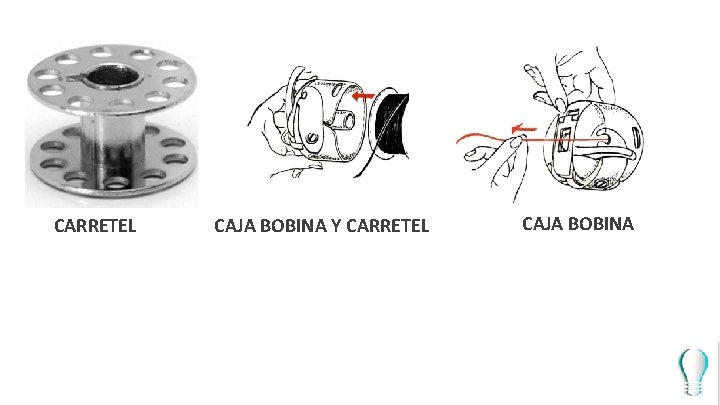
CARRETEL CAJA BOBINA Y CARRETEL CAJA BOBINA
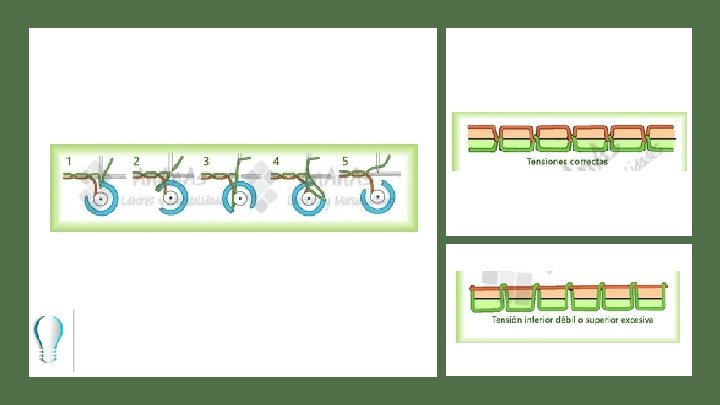
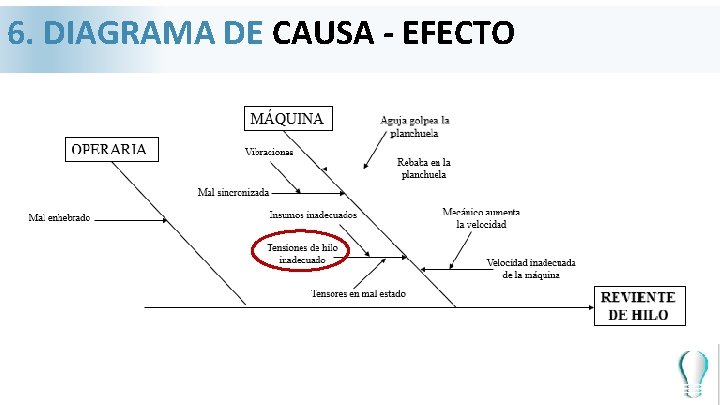
6. DIAGRAMA DE CAUSA - EFECTO ANÁLISIS DE PARETO
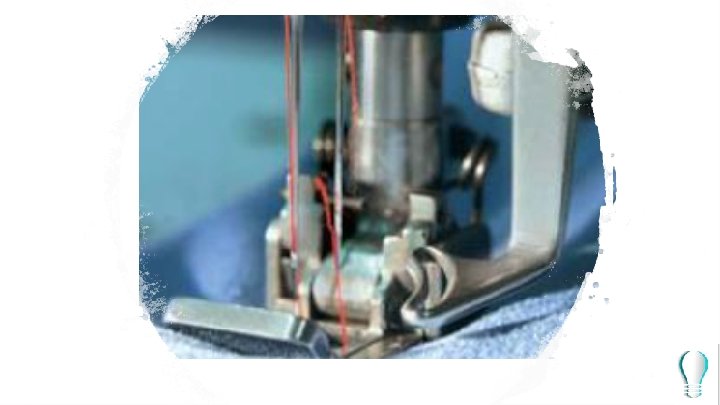
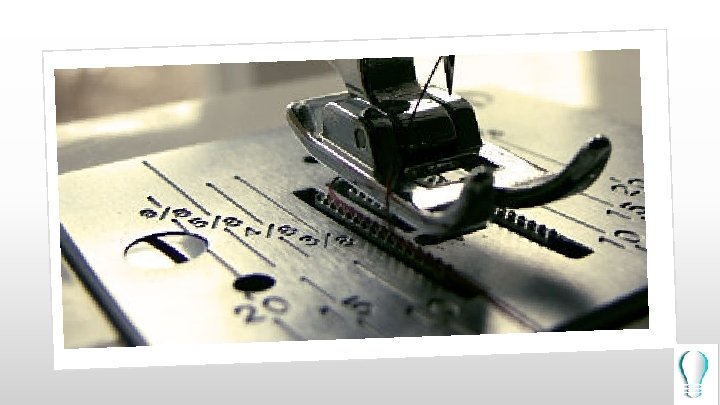
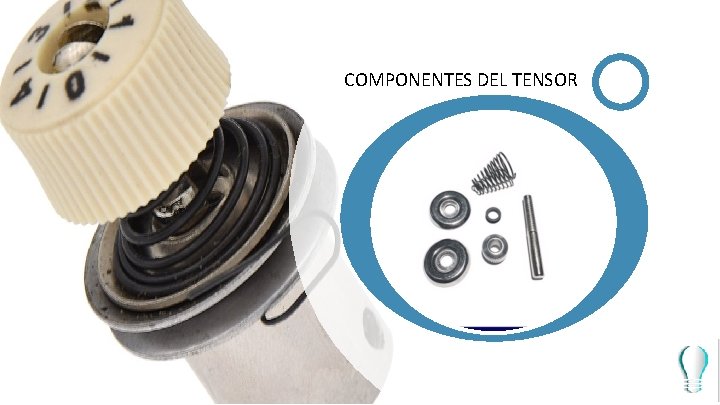
COMPONENTES DEL TENSOR
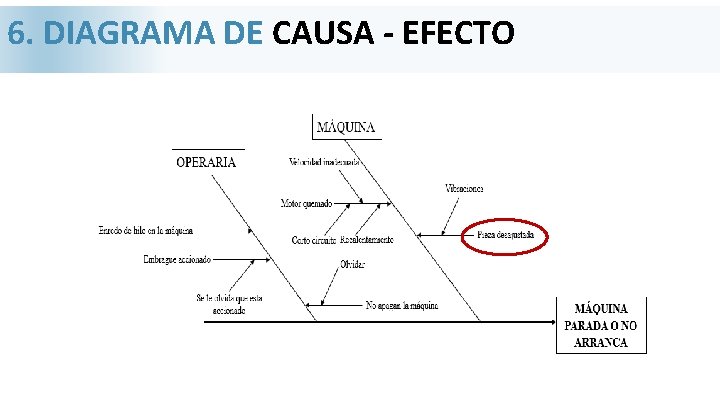
6. DIAGRAMA DE CAUSA - EFECTO ANÁLISIS DE PARETO
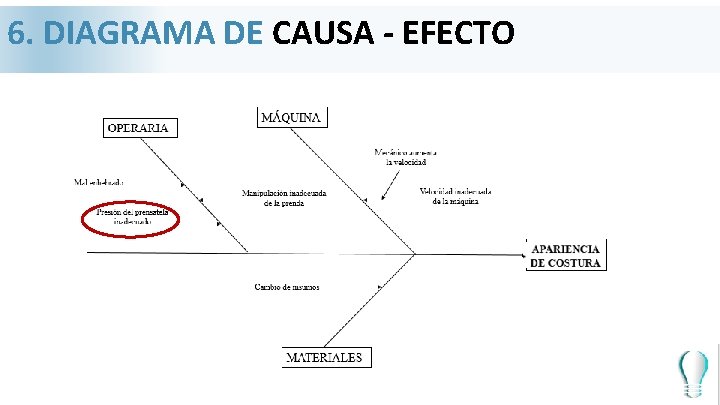
6. DIAGRAMA DE CAUSA - EFECTO
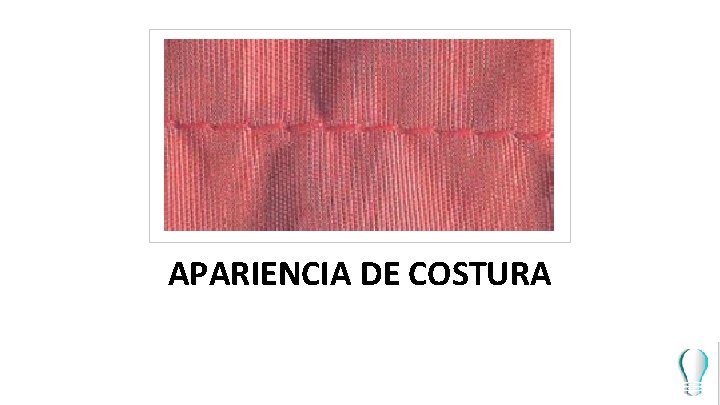
APARIENCIA DE COSTURA
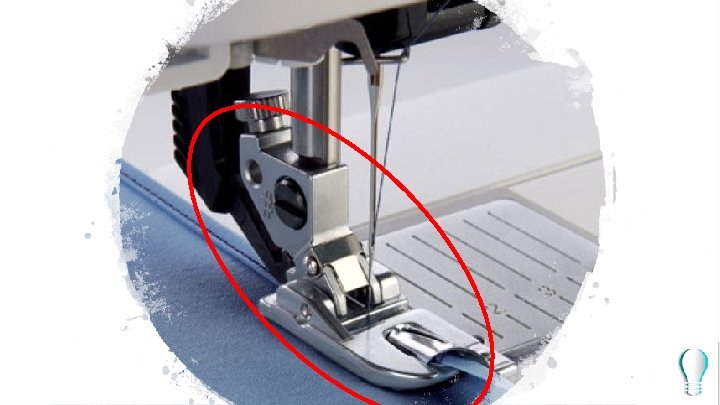

6. DIAGRAMA DE CAUSA - EFECTO ANÁLISIS DE PARETO
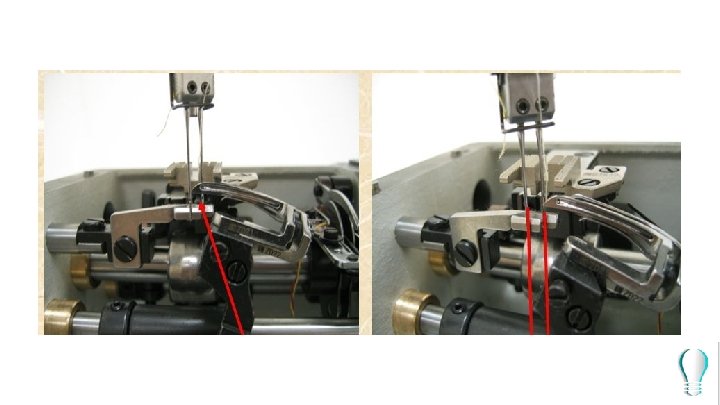
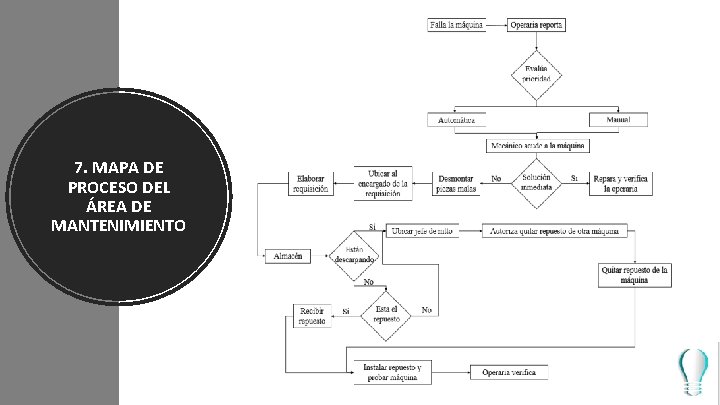
7. MAPA DE PROCESO DEL ÁREA DE MANTENIMIENTO
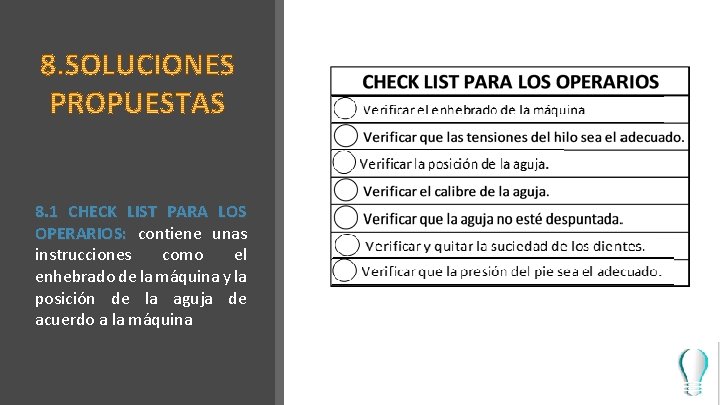
8. 1 CHECK LIST PARA LOS OPERARIOS: contiene unas instrucciones como el enhebrado de la máquina y la posición de la aguja de acuerdo a la máquina
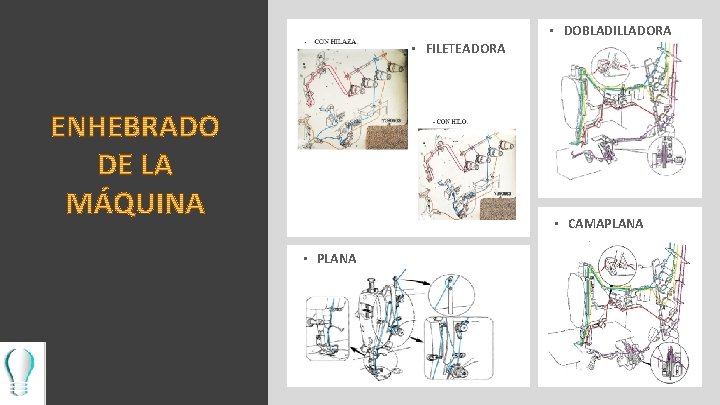
• DOBLADILLADORA • FILETEADORA • CAMAPLANA • PLANA
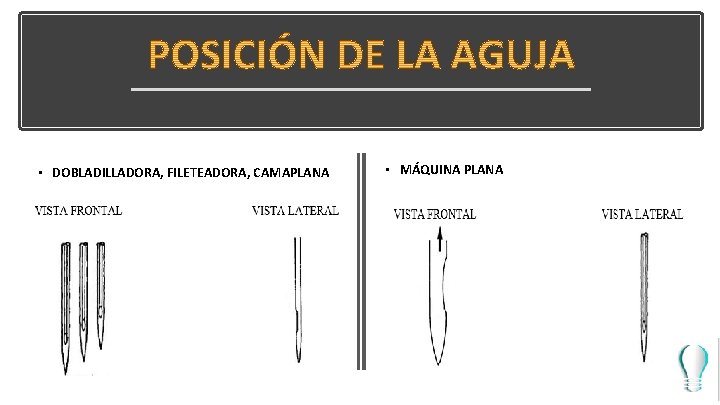
• DOBLADILLADORA, FILETEADORA, CAMAPLANA • MÁQUINA PLANA
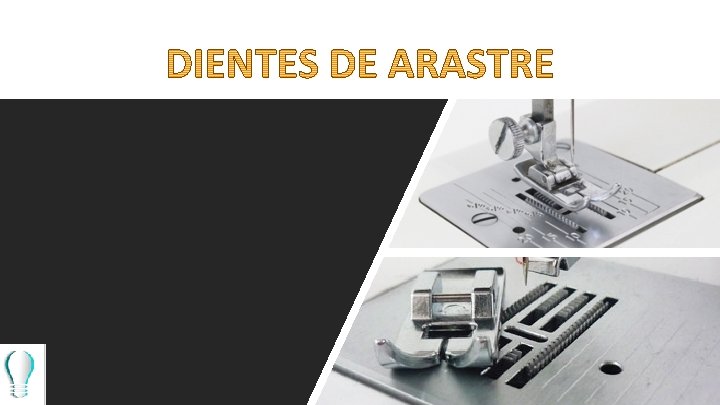
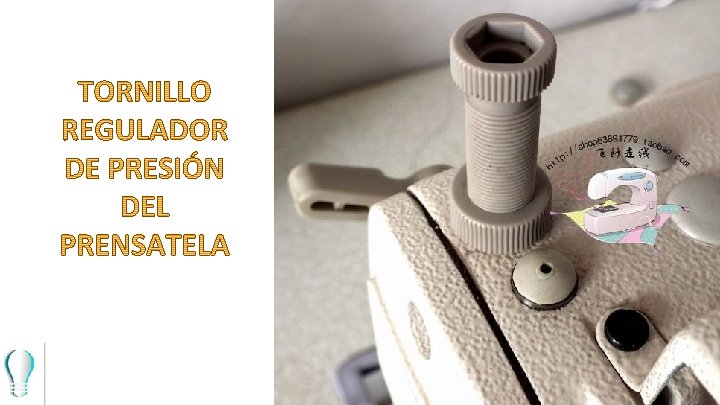
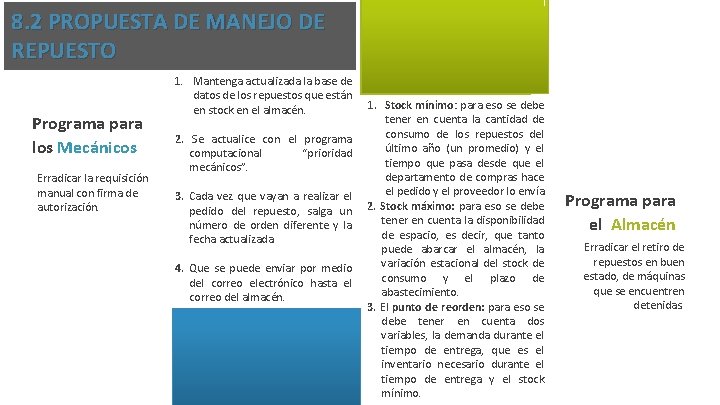
8. 2 PROPUESTA DE MANEJO DE REPUESTO Programa para los Mecánicos Erradicar la requisición manual con firma de autorización. 1. Mantenga actualizada la base de datos de los repuestos que están en stock en el almacén. 2. Se actualice con el programa computacional “prioridad mecánicos”. 3. Cada vez que vayan a realizar el pedido del repuesto, salga un número de orden diferente y la fecha actualizada. 4. Que se puede enviar por medio del correo electrónico hasta el correo del almacén. 1. Stock mínimo: para eso se debe tener en cuenta la cantidad de consumo de los repuestos del último año (un promedio) y el tiempo que pasa desde que el departamento de compras hace el pedido y el proveedor lo envía. 2. Stock máximo: para eso se debe tener en cuenta la disponibilidad de espacio, es decir, que tanto puede abarcar el almacén, la variación estacional del stock de consumo y el plazo de abastecimiento. 3. El punto de reorden: para eso se debe tener en cuenta dos variables, la demanda durante el tiempo de entrega, que es el inventario necesario durante el tiempo de entrega y el stock mínimo. Programa para el Almacén Erradicar el retiro de repuestos en buen estado, de máquinas que se encuentren detenidas.
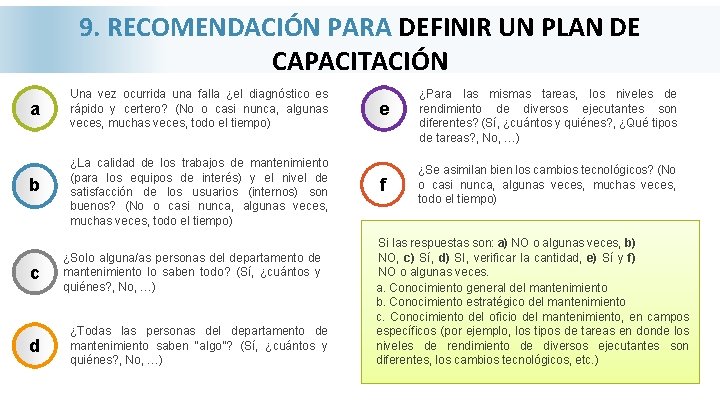
9. RECOMENDACIÓN PARA DEFINIR UN PLAN DE CAPACITACIÓN a b c d Una vez ocurrida una falla ¿el diagnóstico es rápido y certero? (No o casi nunca, algunas veces, muchas veces, todo el tiempo) ¿La calidad de los trabajos de mantenimiento (para los equipos de interés) y el nivel de satisfacción de los usuarios (internos) son buenos? (No o casi nunca, algunas veces, muchas veces, todo el tiempo) ¿Solo alguna/as personas del departamento de mantenimiento lo saben todo? (Sí, ¿cuántos y quiénes? , No, …) ¿Todas las personas del departamento de mantenimiento saben “algo”? (Sí, ¿cuántos y quiénes? , No, …) e f ¿Para las mismas tareas, los niveles de rendimiento de diversos ejecutantes son diferentes? (Sí, ¿cuántos y quiénes? , ¿Qué tipos de tareas? , No, …) ¿Se asimilan bien los cambios tecnológicos? (No o casi nunca, algunas veces, muchas veces, todo el tiempo) Si las respuestas son: a) NO o algunas veces, b) NO, c) Sí, d) SI, verificar la cantidad, e) Sí y f) NO o algunas veces. a. Conocimiento general del mantenimiento b. Conocimiento estratégico del mantenimiento c. Conocimiento del oficio del mantenimiento, en campos específicos (por ejemplo, los tipos de tareas en donde los niveles de rendimiento de diversos ejecutantes son diferentes, los cambios tecnológicos, etc. )
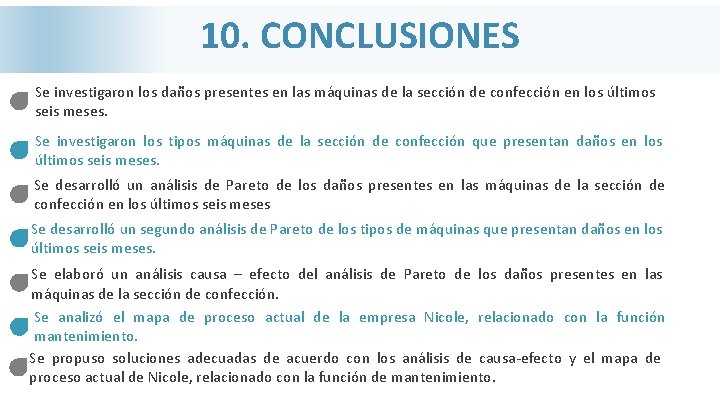
10. CONCLUSIONES Se investigaron los daños presentes en las máquinas de la sección de confección en los últimos seis meses. Se investigaron los tipos máquinas de la sección de confección que presentan daños en los últimos seis meses. Se desarrolló un análisis de Pareto de los daños presentes en las máquinas de la sección de confección en los últimos seis meses Se desarrolló un segundo análisis de Pareto de los tipos de máquinas que presentan daños en los últimos seis meses. Se elaboró un análisis causa – efecto del análisis de Pareto de los daños presentes en las máquinas de la sección de confección. Se analizó el mapa de proceso actual de la empresa Nicole, relacionado con la función mantenimiento. Se propuso soluciones adecuadas de acuerdo con los análisis de causa-efecto y el mapa de proceso actual de Nicole, relacionado con la función de mantenimiento.
Una imagen de reducir
Aun a los escogidos
Plantilla propuesta redes sociales
Propuesta manejo redes sociales
Expresiones algebraicas fraccionarias
Que significa reducir reutilizar y reciclar
Reducir
Agrupar polinomios
Polinomio de forma decreciente
Ur de los caldeos en tiempos de abraham
Los tres tiempos de la biblia
Tiempos verbales español
Verbos progresivos
Cronos tiempos
El imperfecto del subjuntivo
Ur de los caldeos en tiempos de abraham
Forma verbal
Morfemas verbos
Que tiempo estamos viviendo como iglesia
Cumbia de todos los tiempos
Los últimos tiempos serán peligrosos
Conociendo los tiempos
Mis amigos y yo
Frases de los tiempos de dios son perfectos
Principio de los tiempos
Los tiempos perfectos
Fuentes del curriculo
Diferencia entre juego centralizador y juego trabajo
Propuesta general
Eduplan educando
Creador del kindergarten
Modelo curricular de hilda taba
Escribe en palabras cada ecuación propuesta
Elaboramos nuestra propuesta
Aliados estrategicos
Actores sociales características
Propuesta de plan de trabajo
Triada ecológica propuesta por leavell y clark en 1965
Primers degenerados
Como redactar una propuesta de trabajo
Propuesta de revisoria fiscal
Propuesta sindical
La propuesta actores
Pared caliente