Process management Dr Kithsiri Edirisinghe MD Process Management
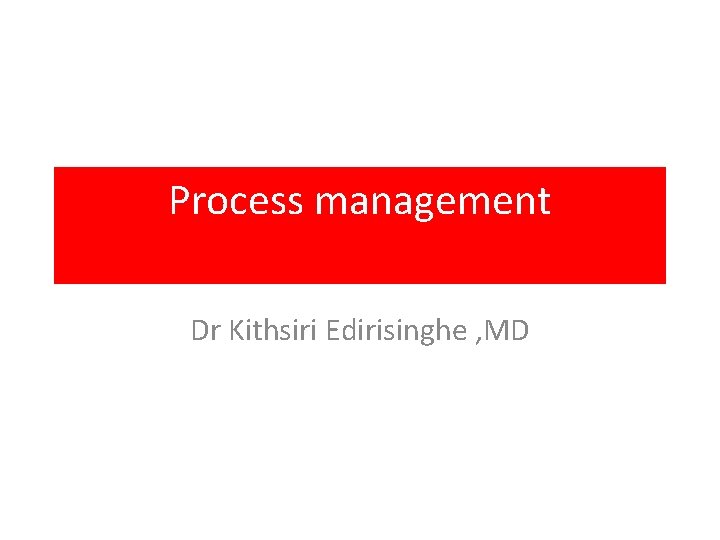
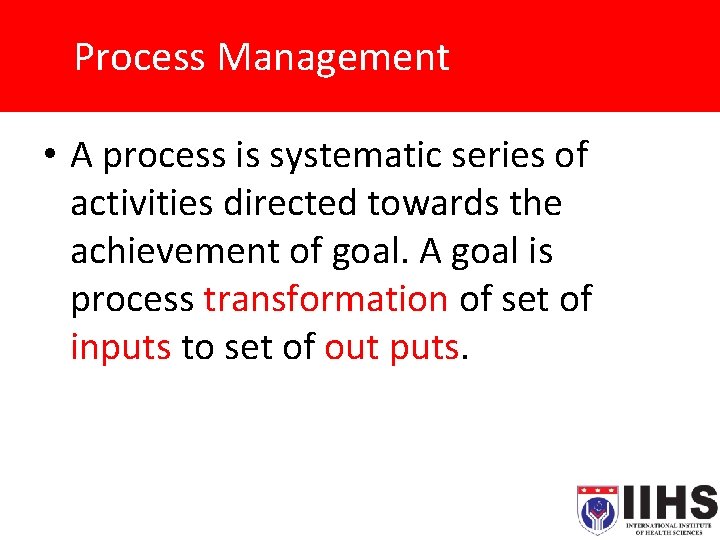
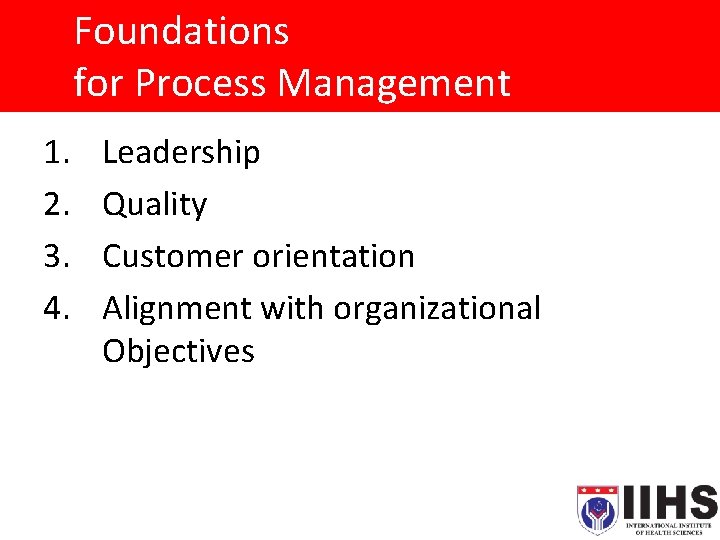
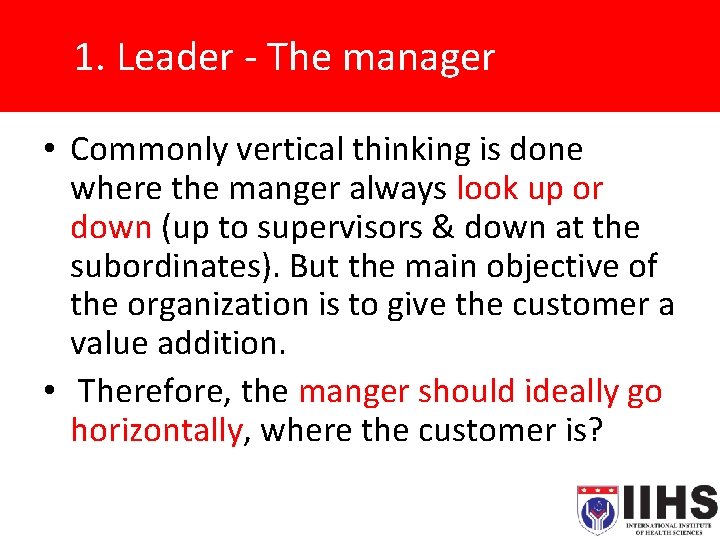
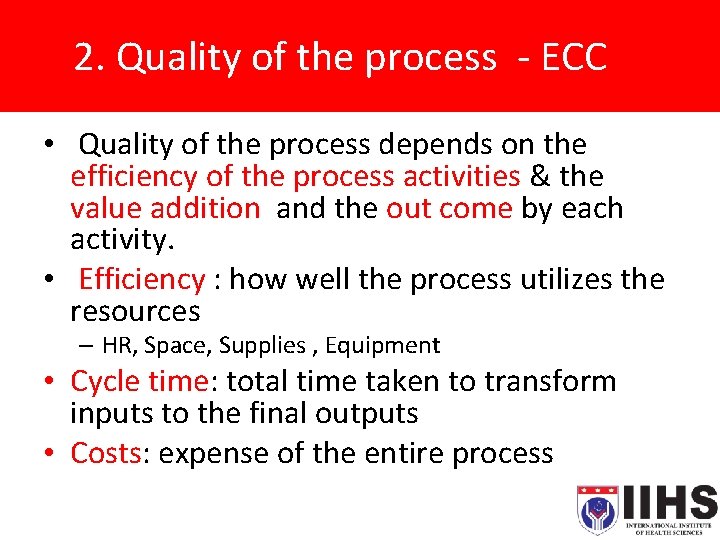
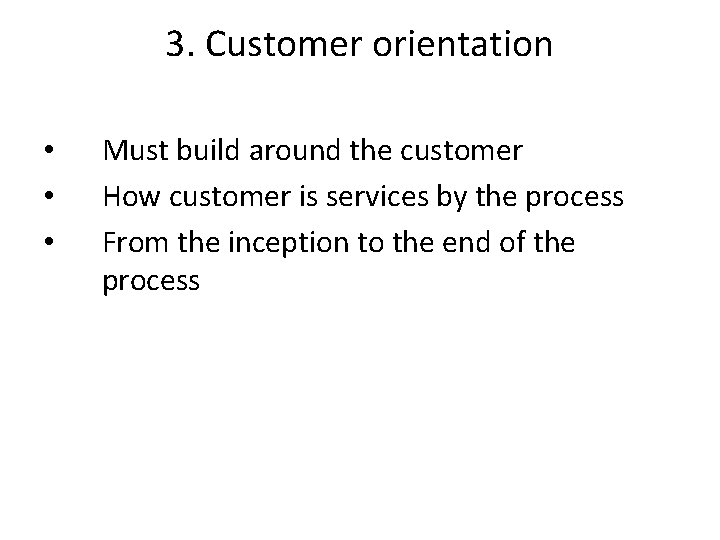
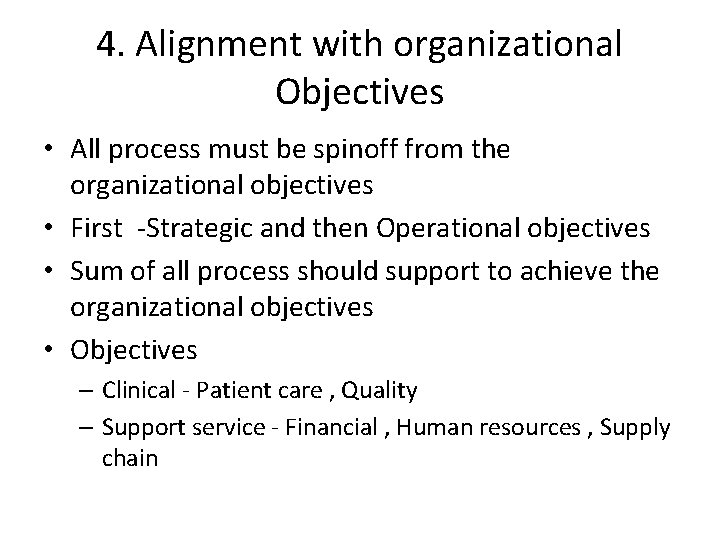
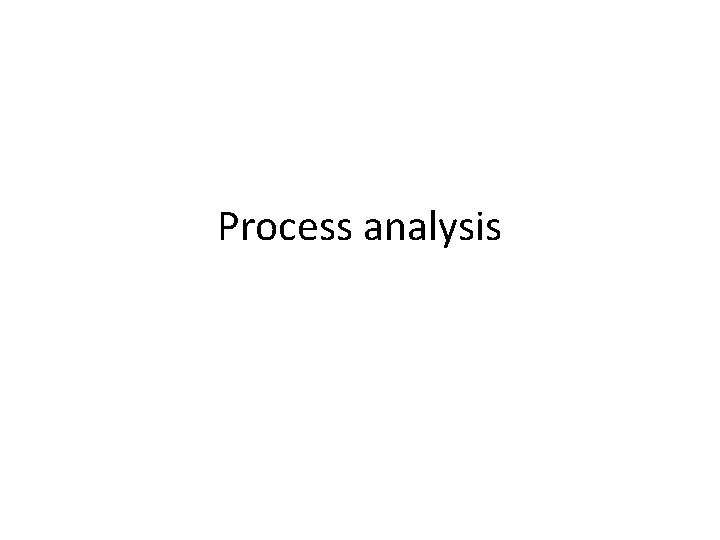
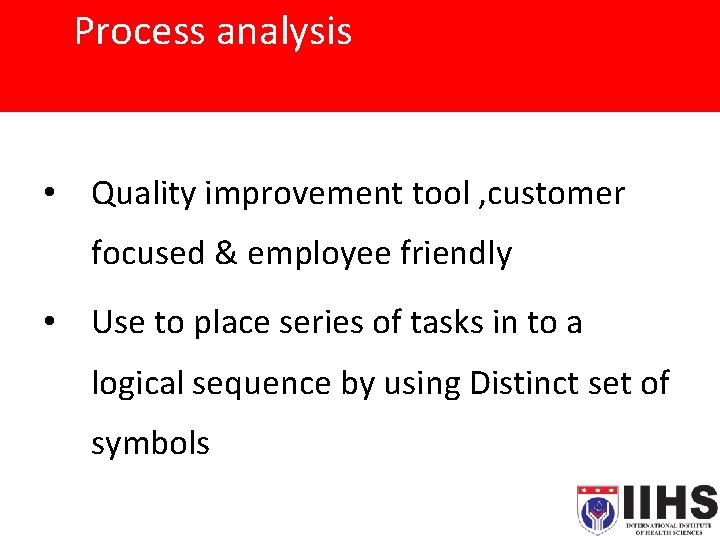
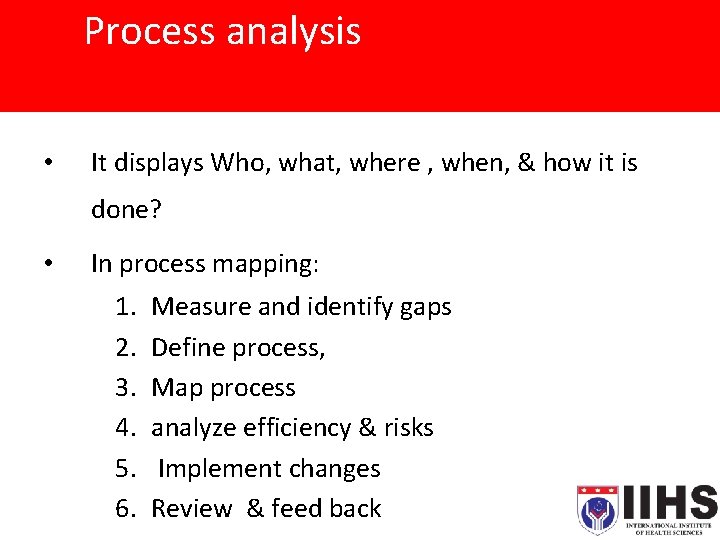
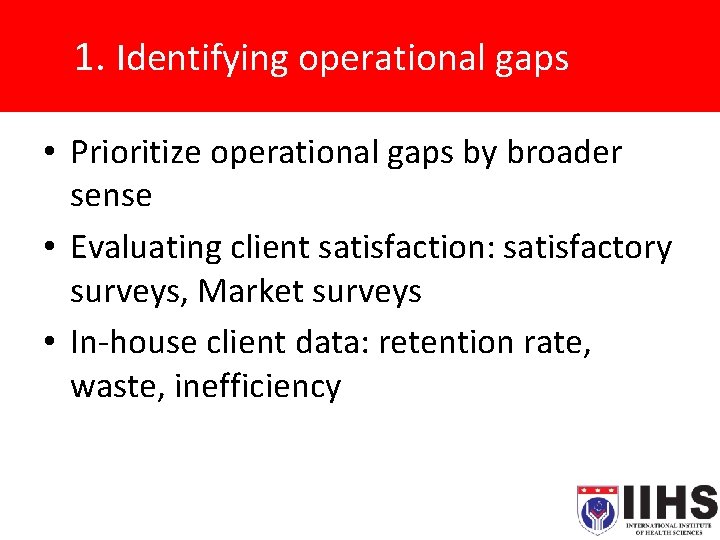
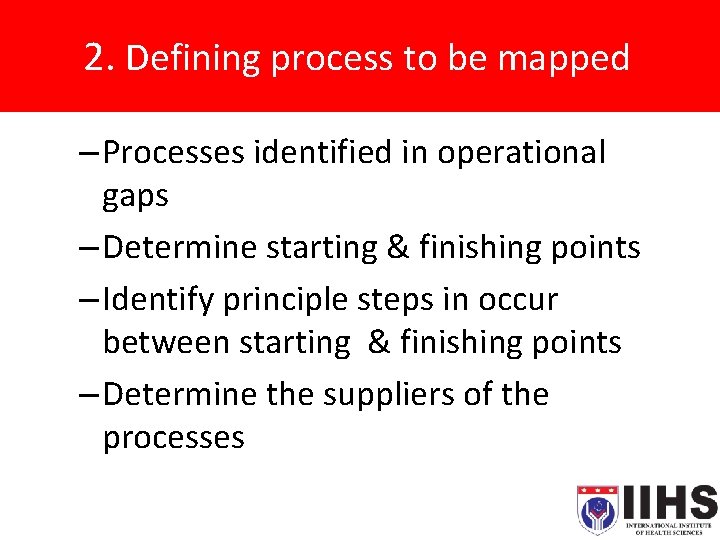
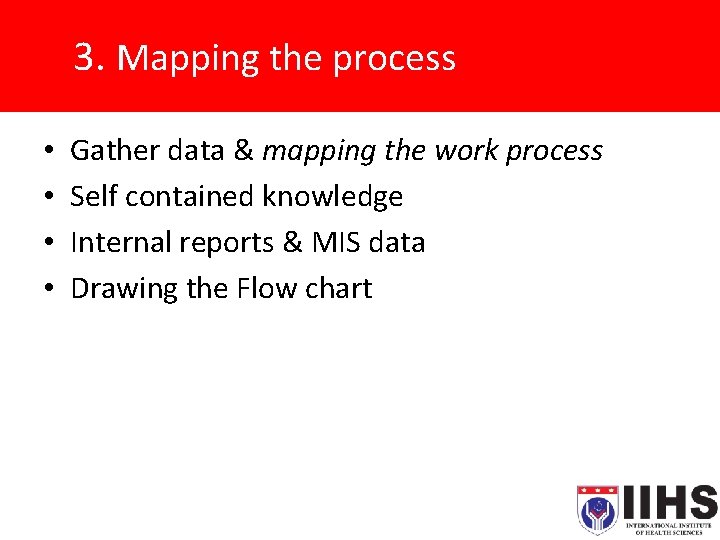
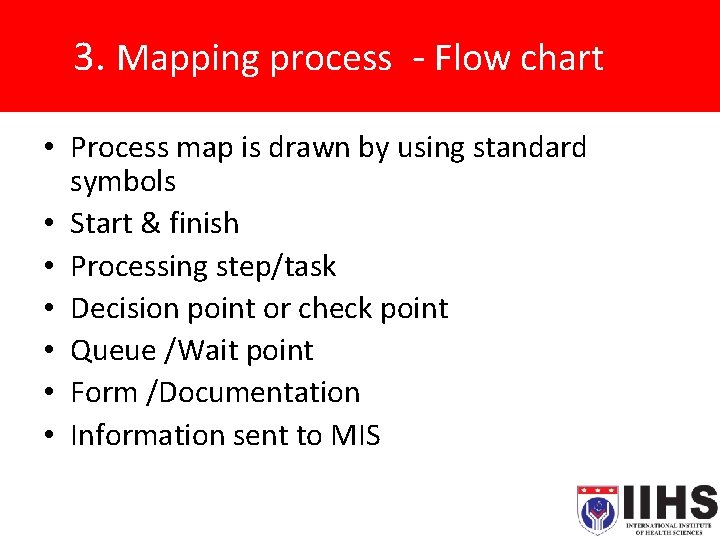
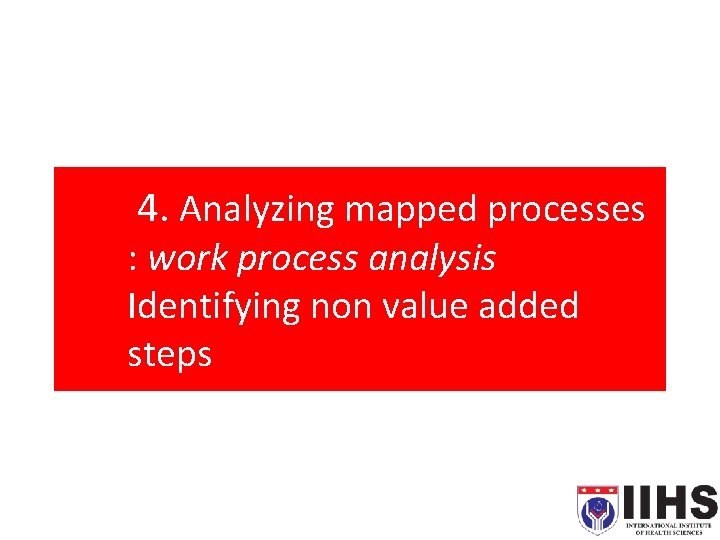
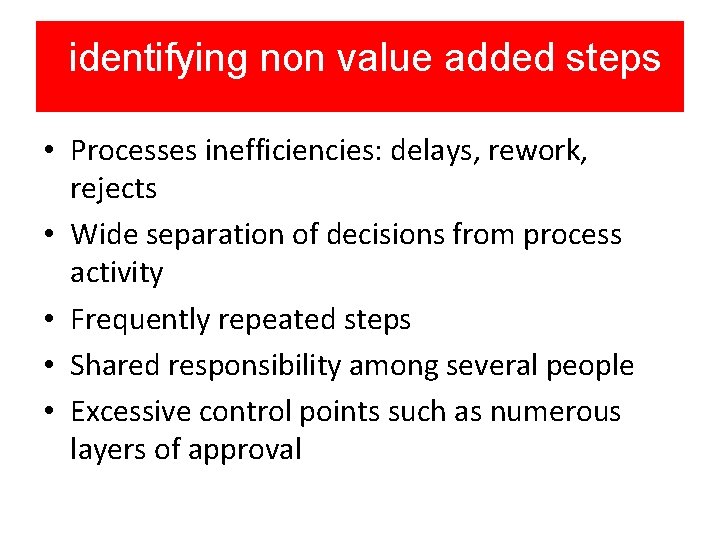
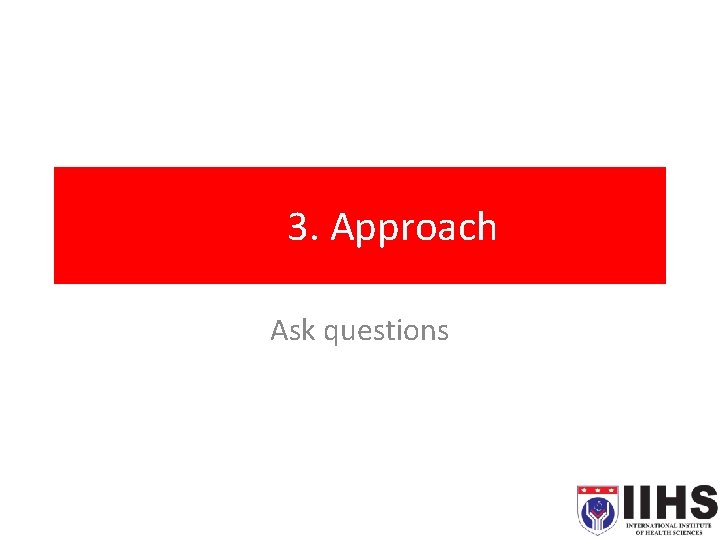
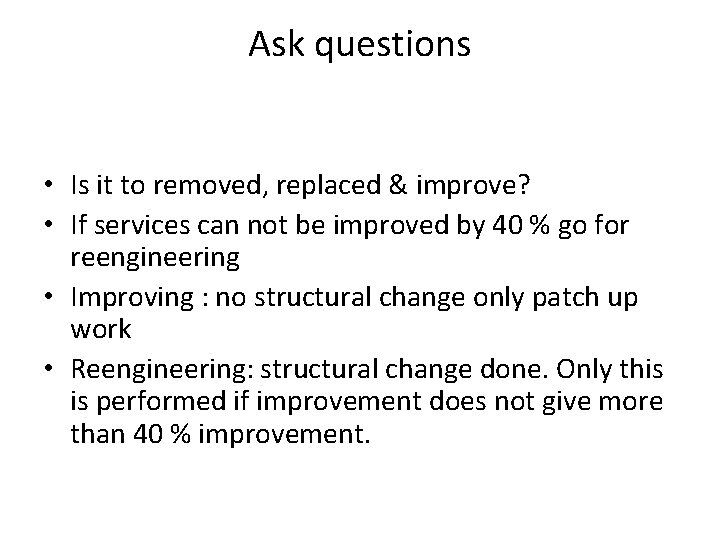
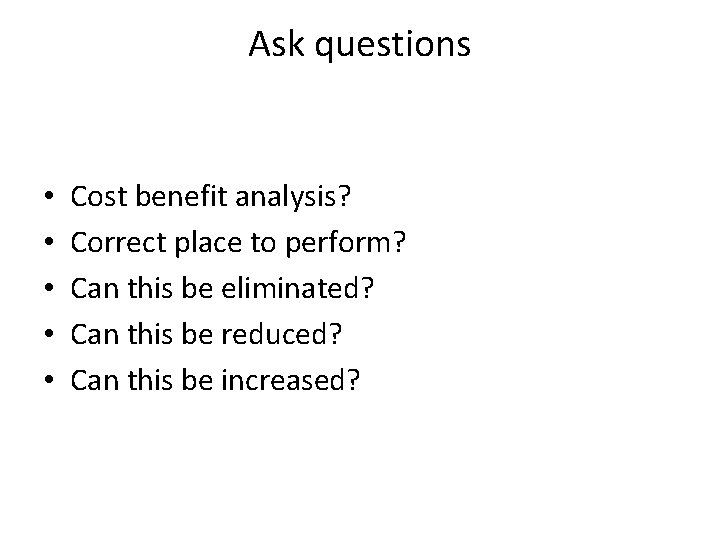
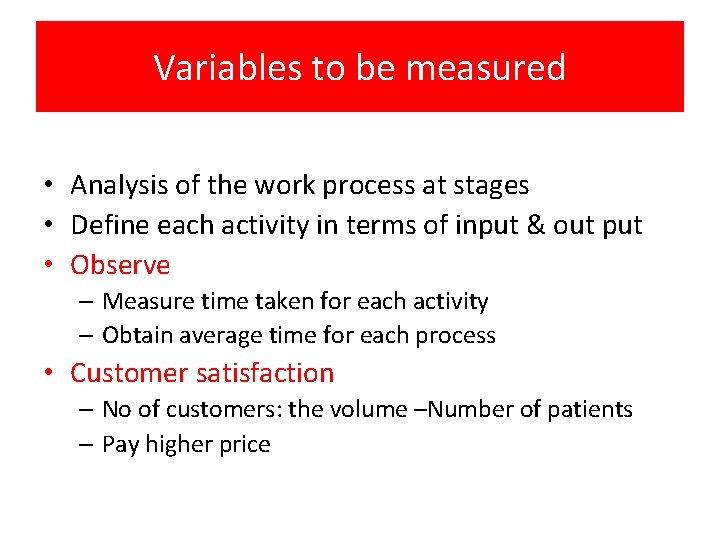
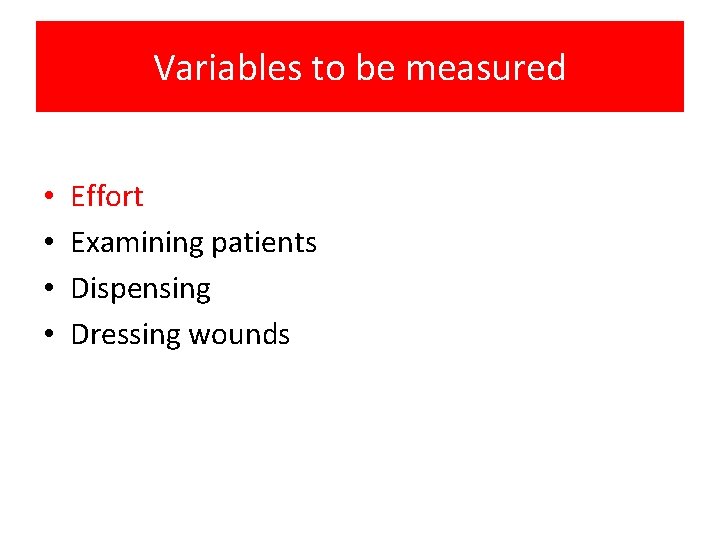
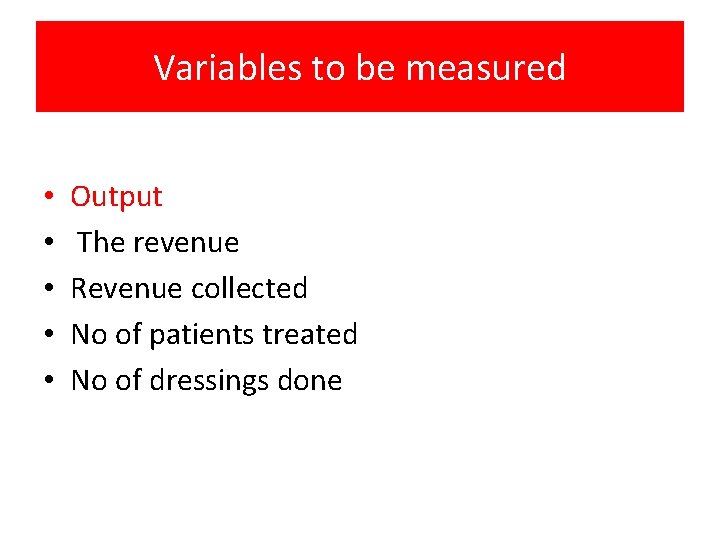
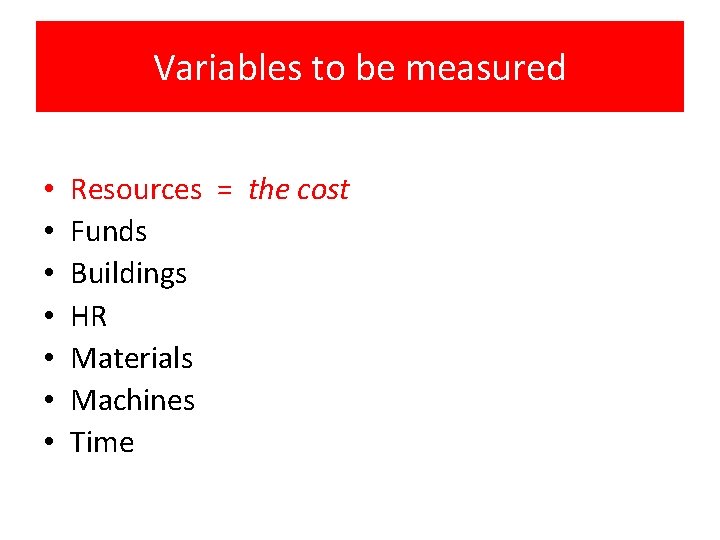
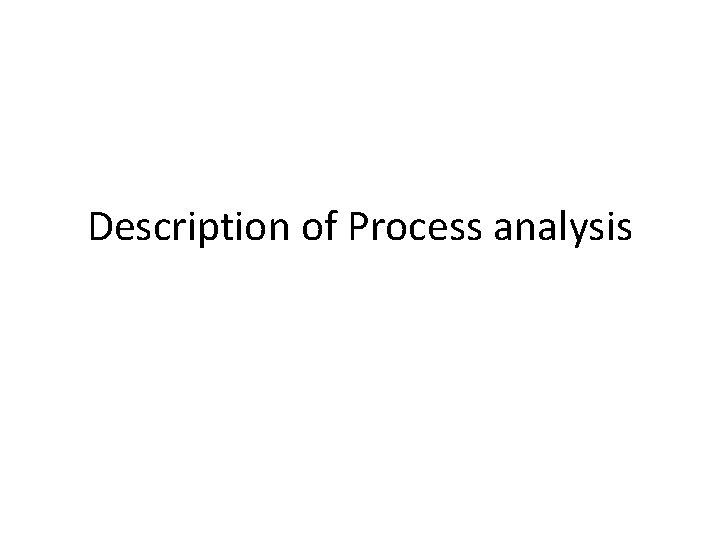
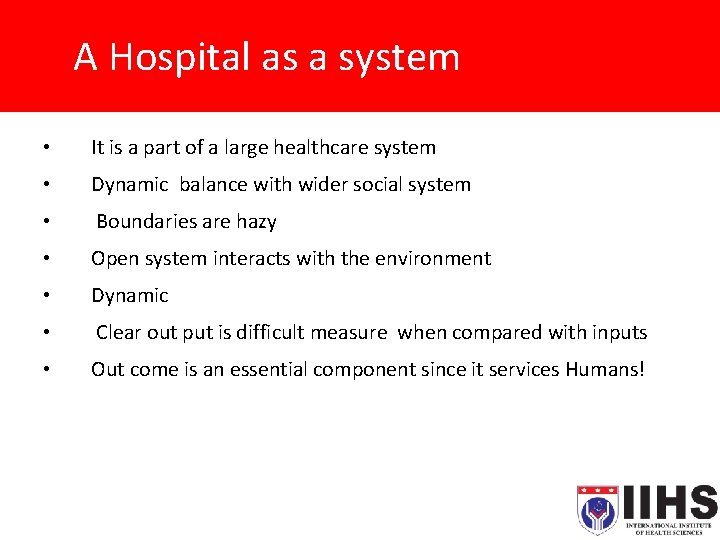
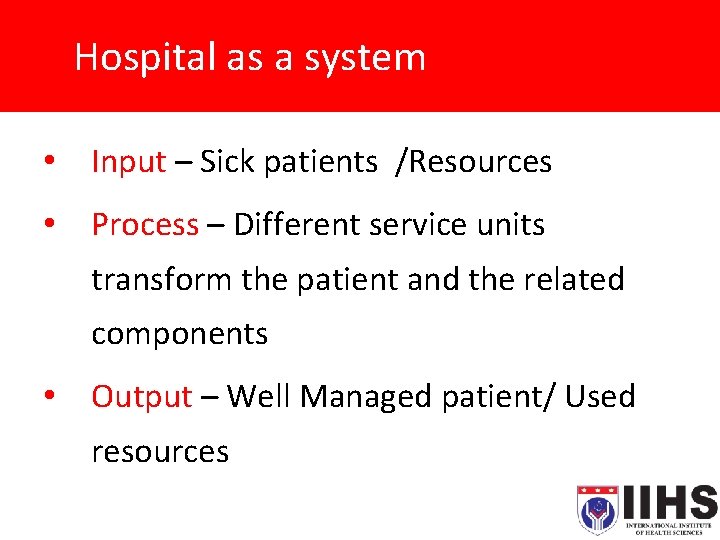
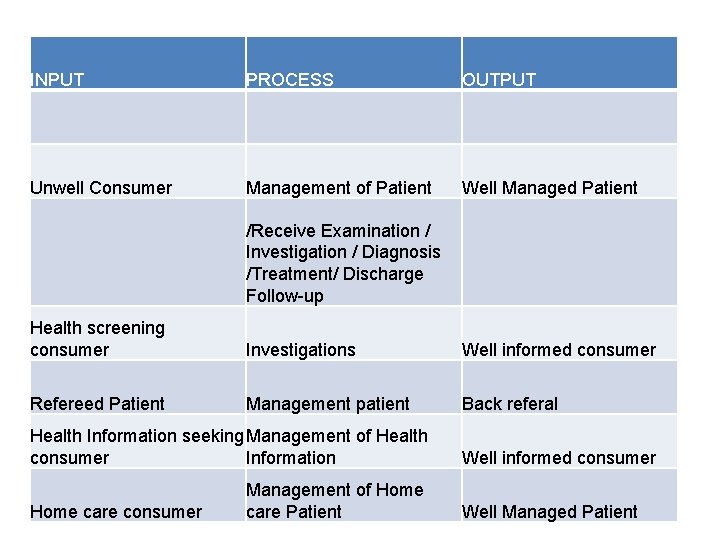
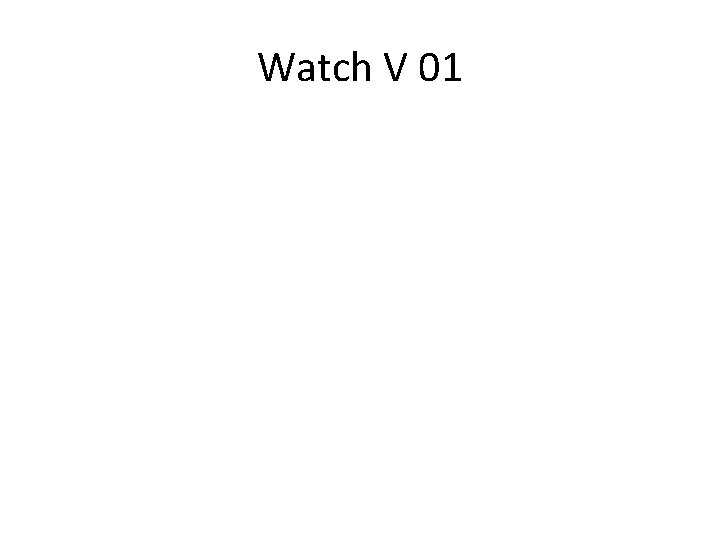
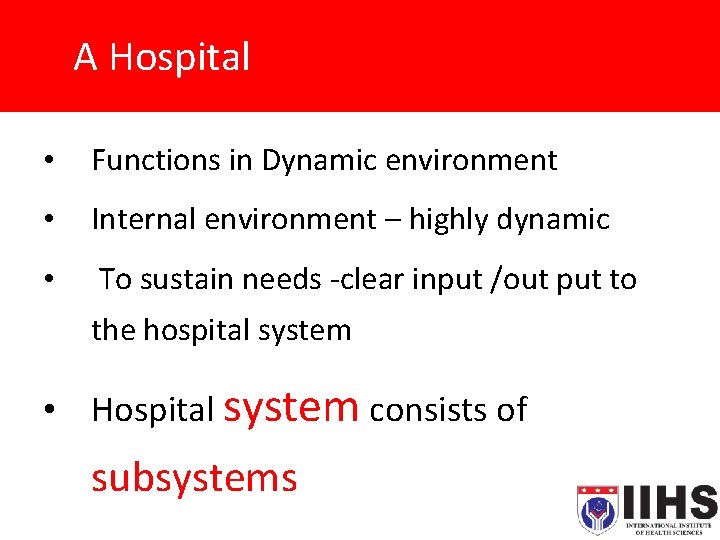
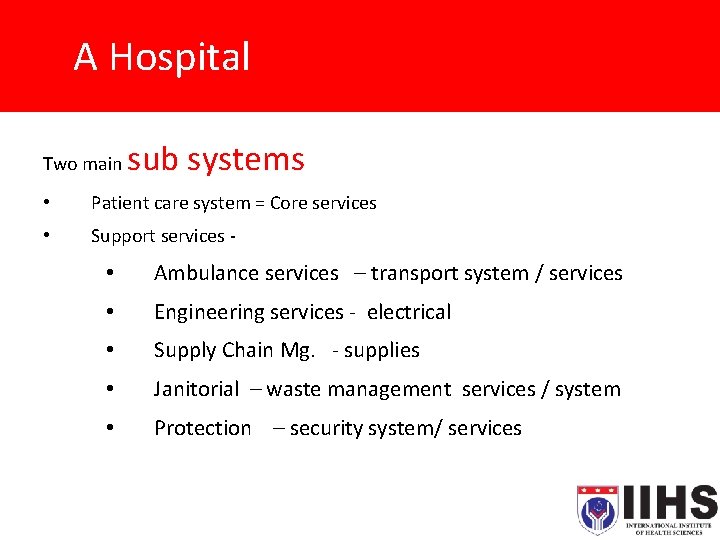
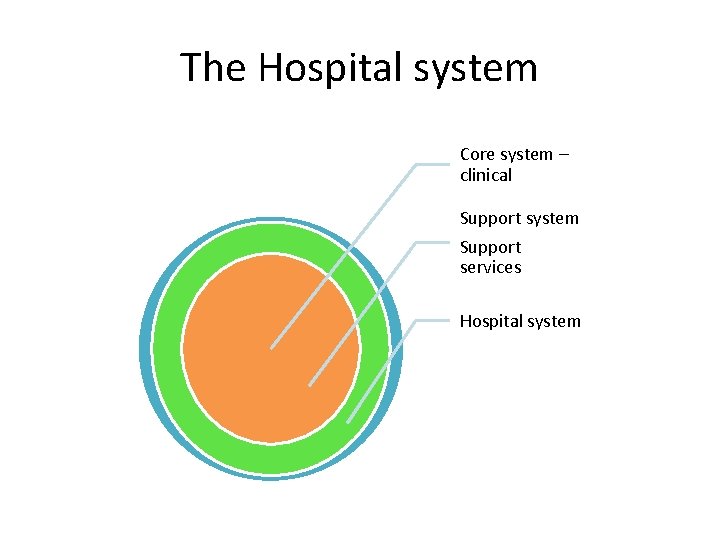
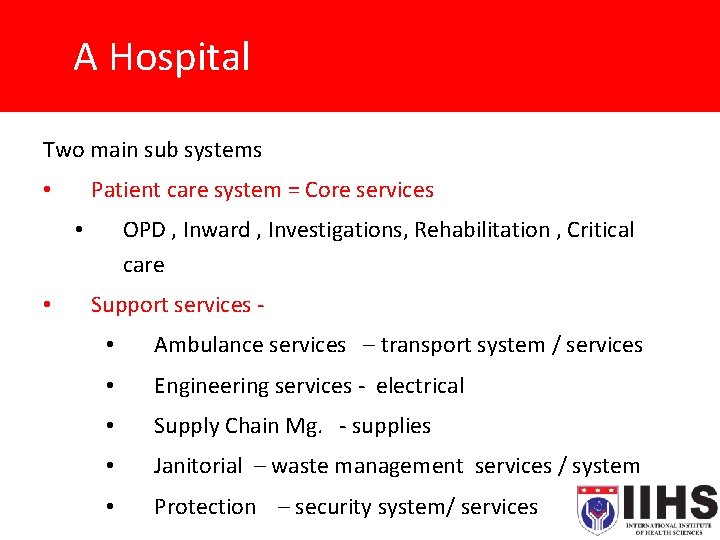
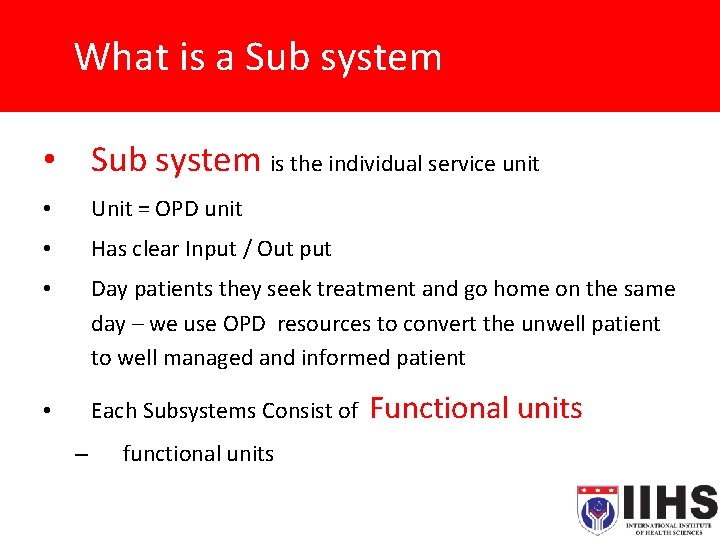
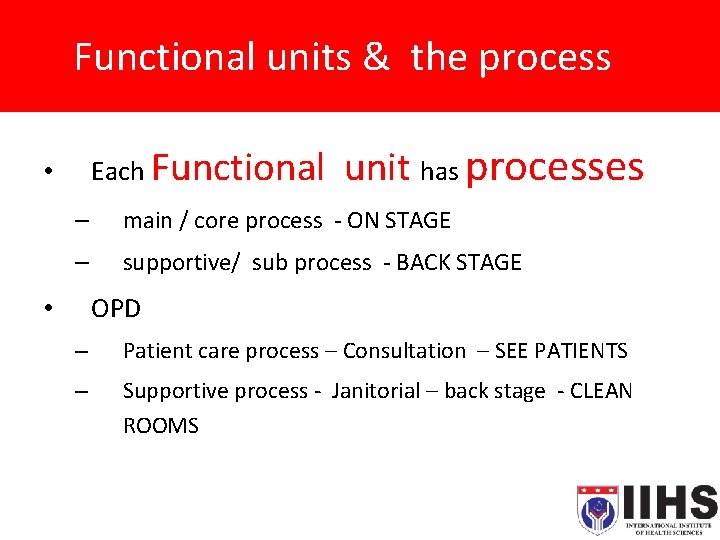
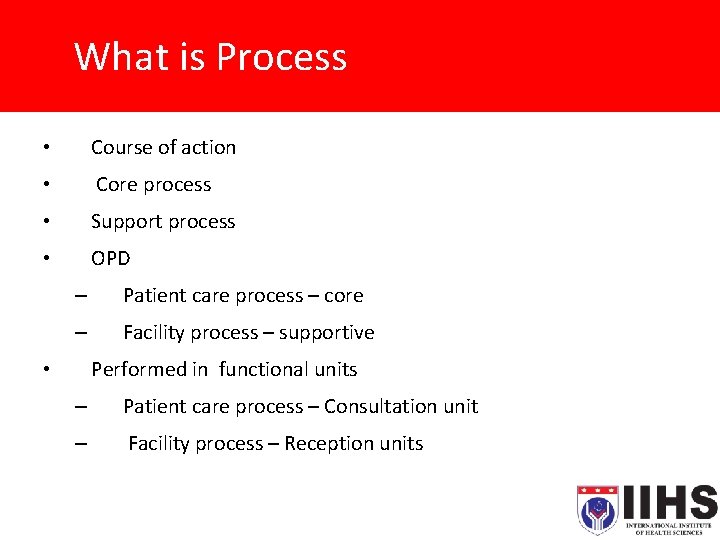
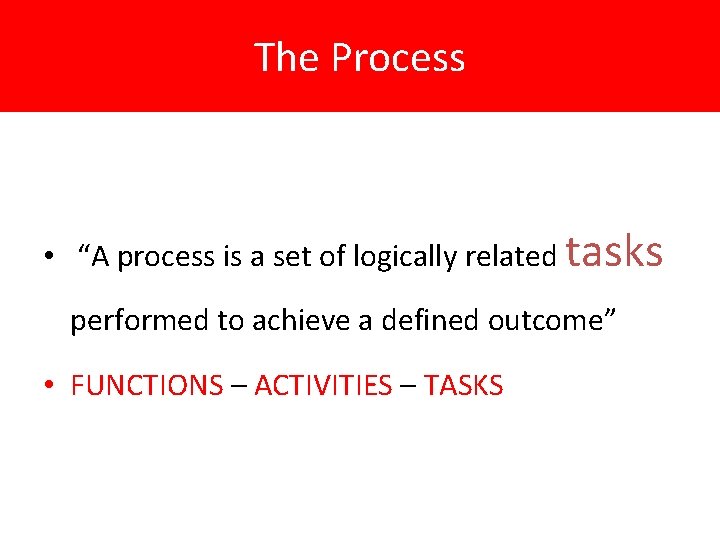
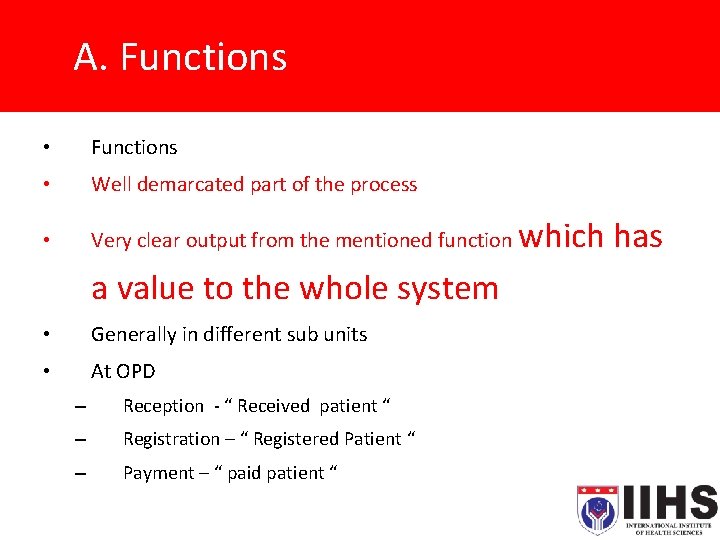
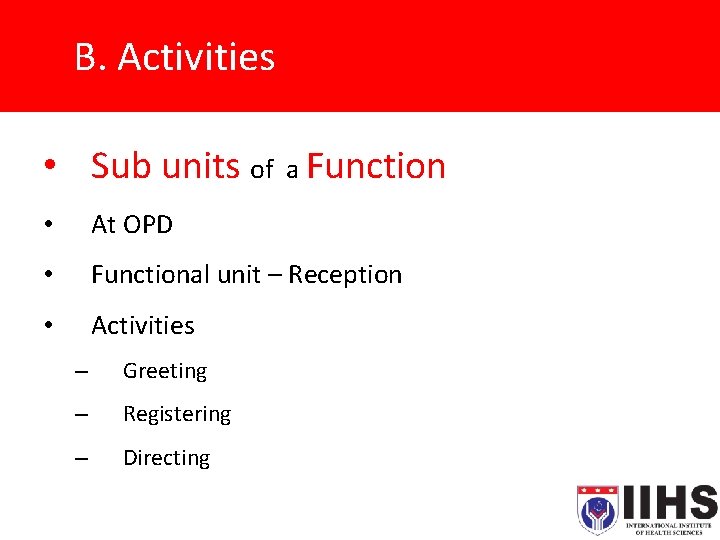
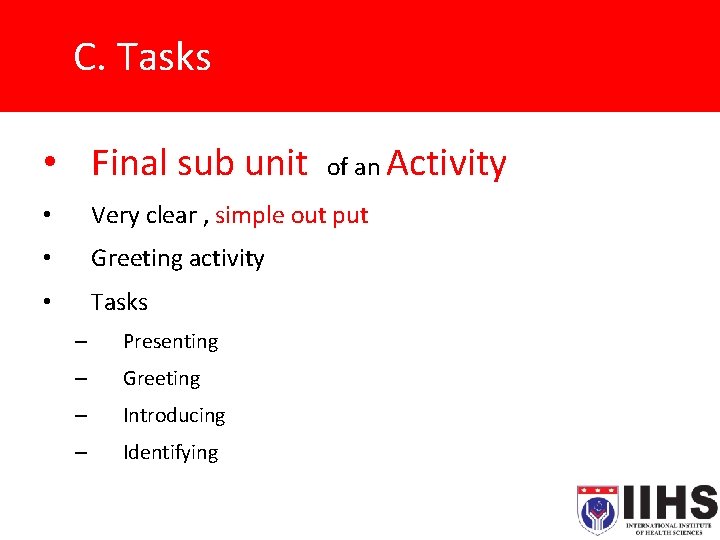
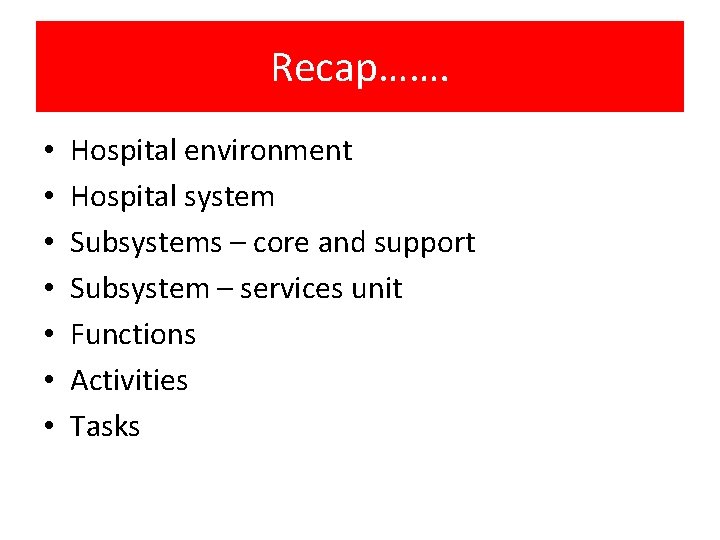
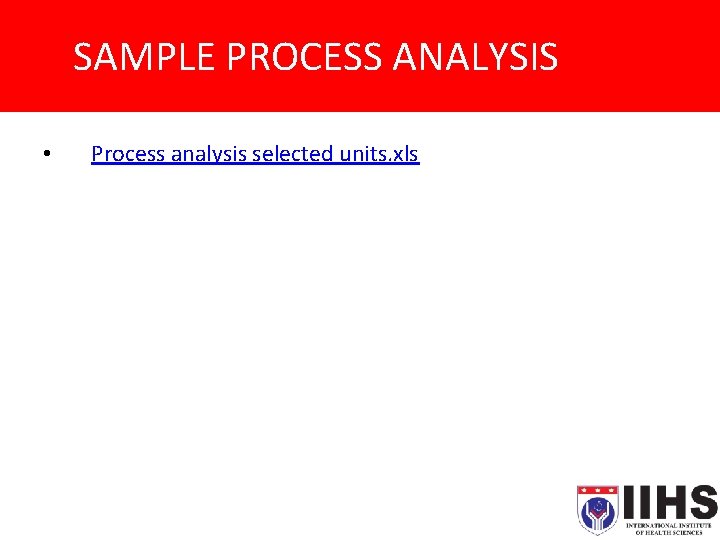
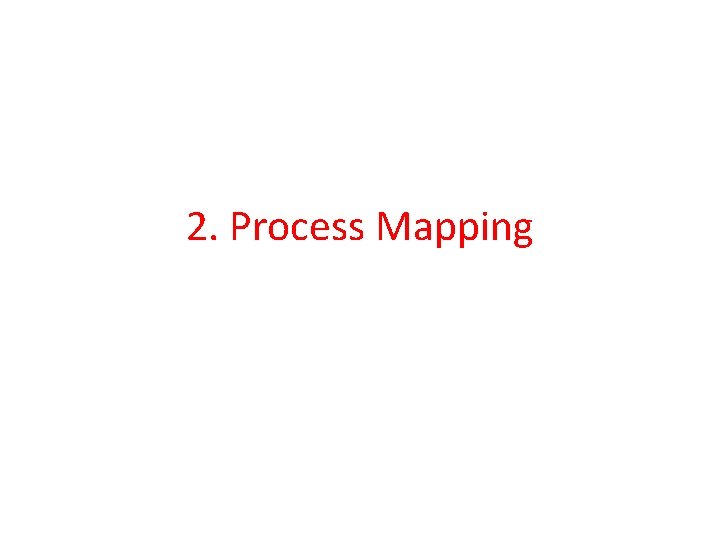
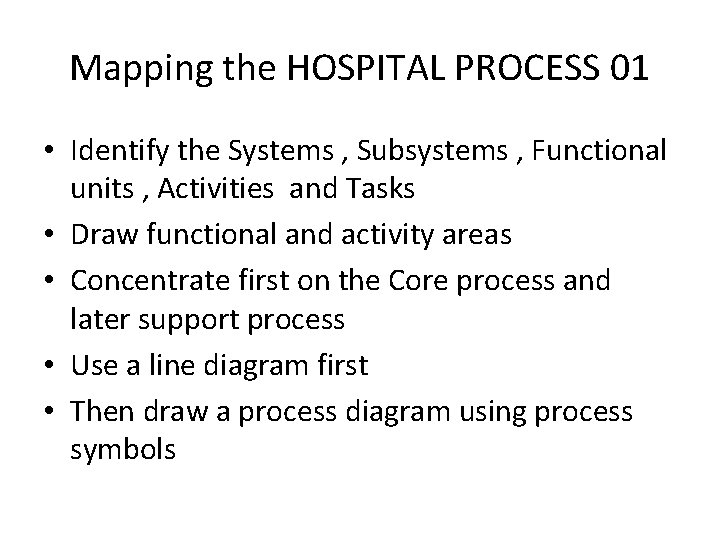
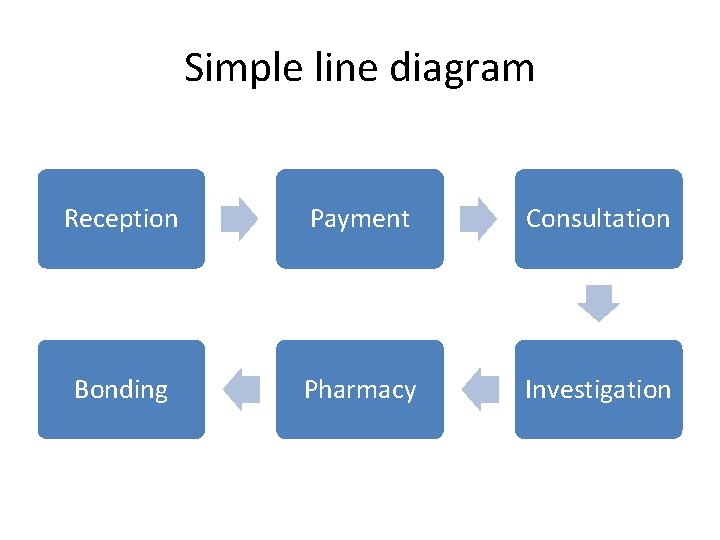
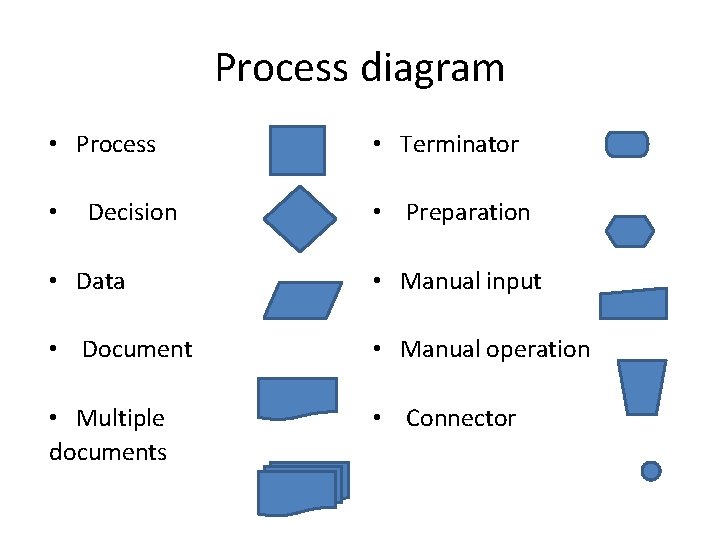
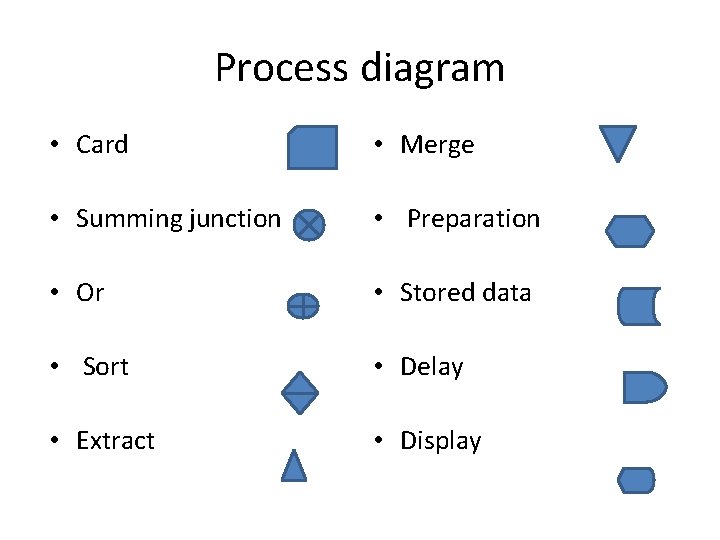
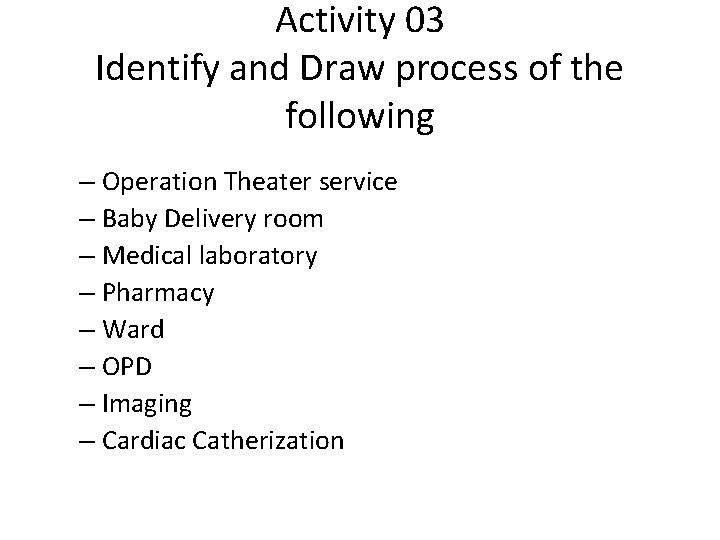
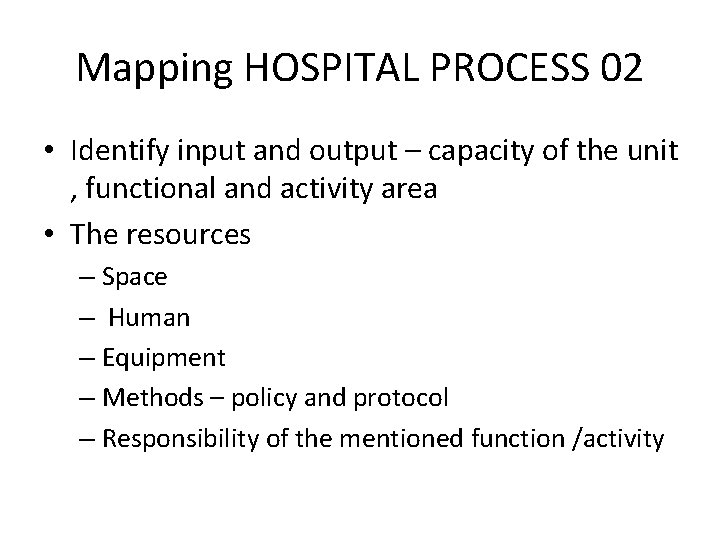
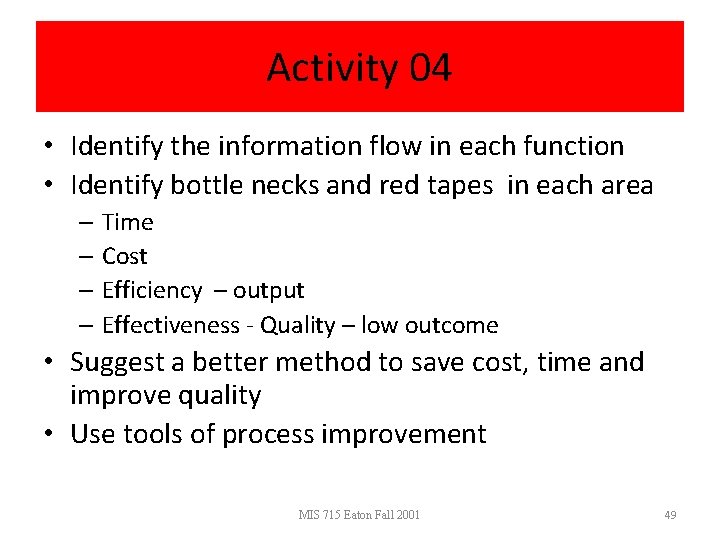
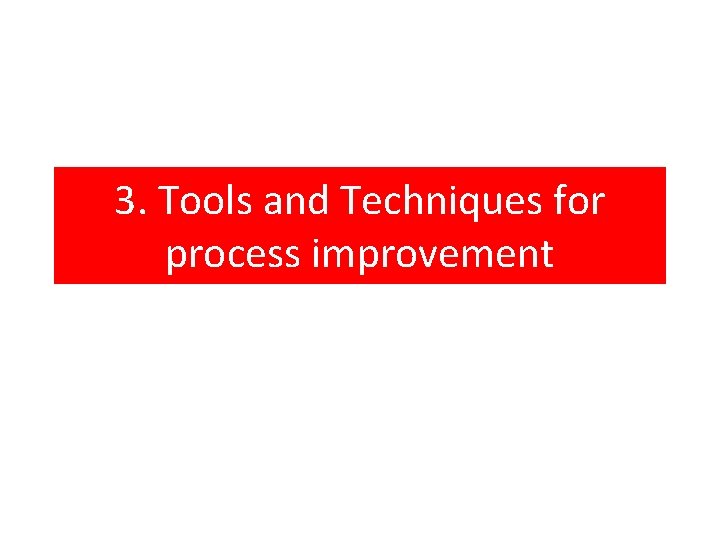
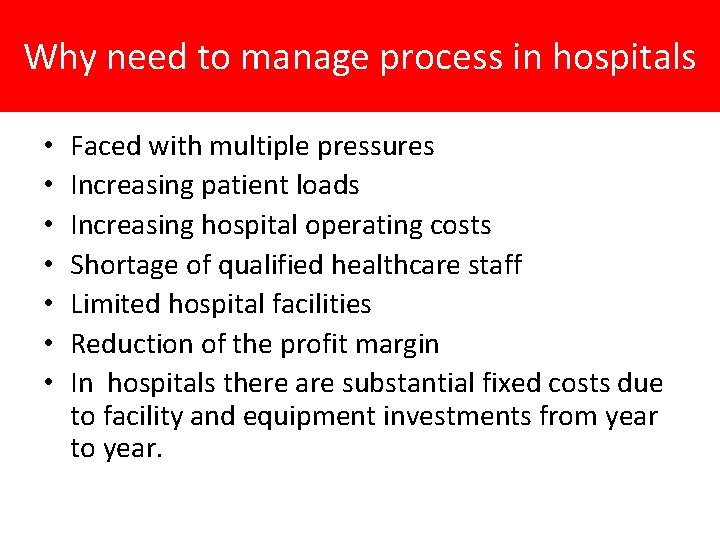
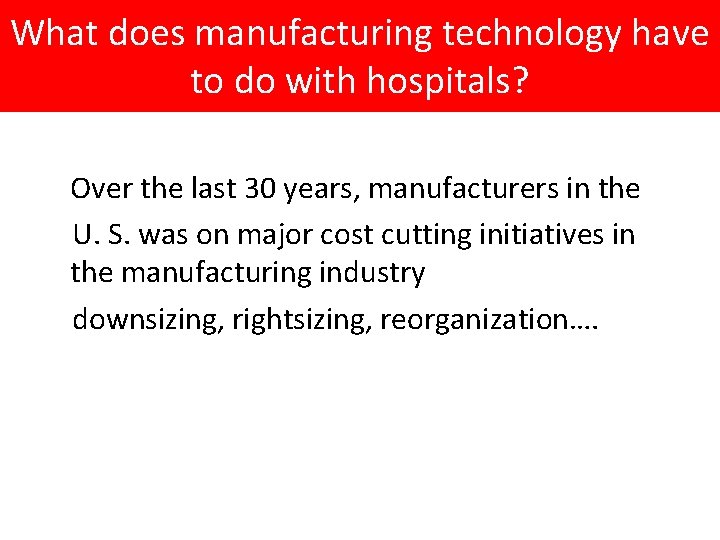
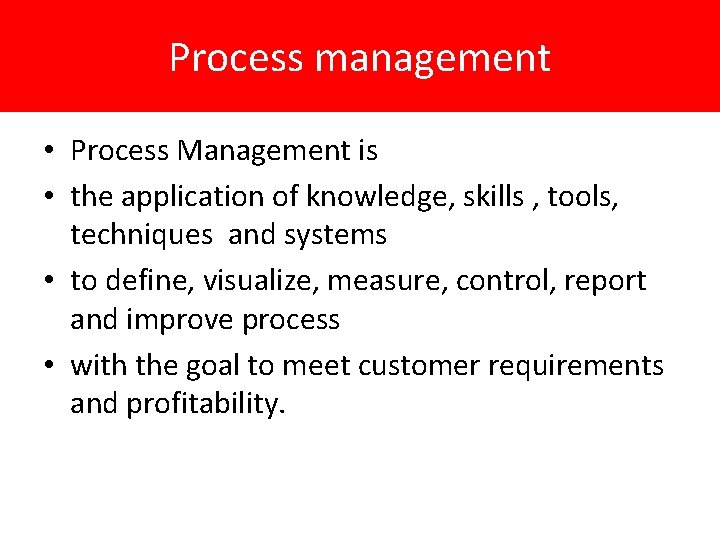
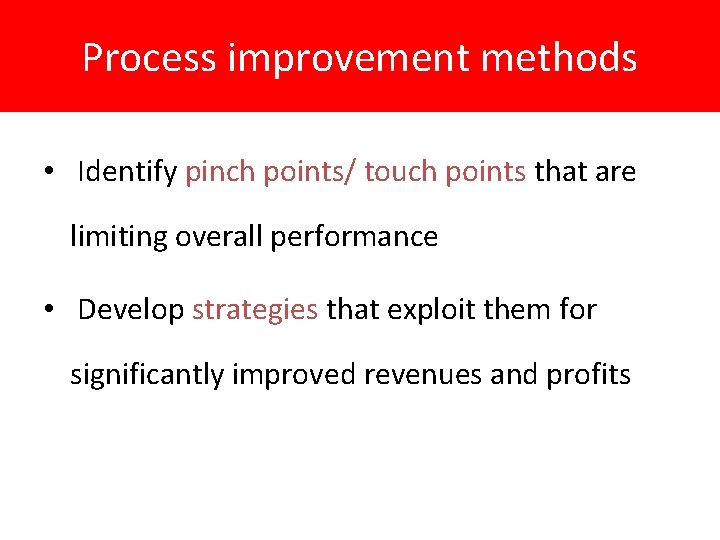
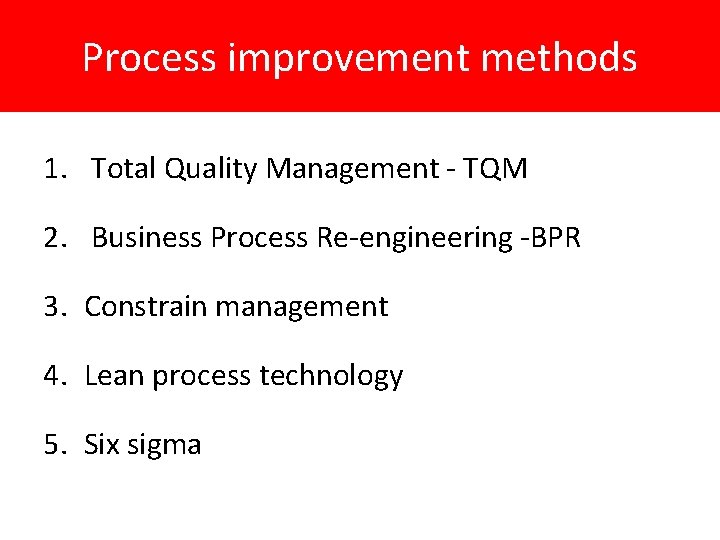
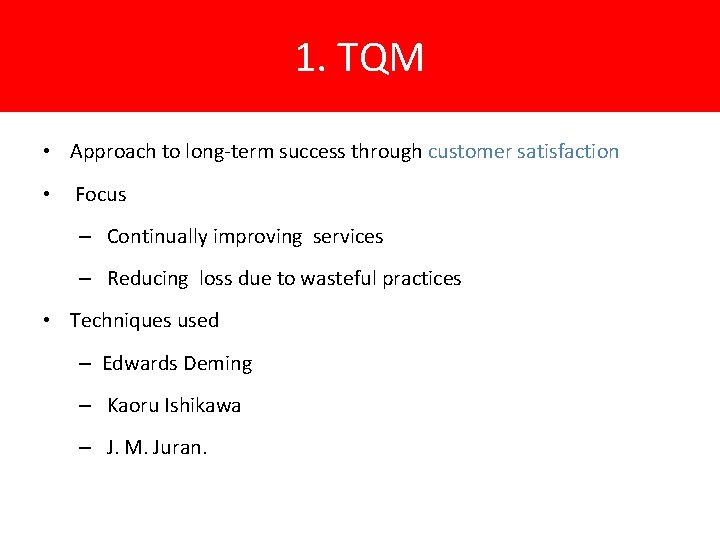
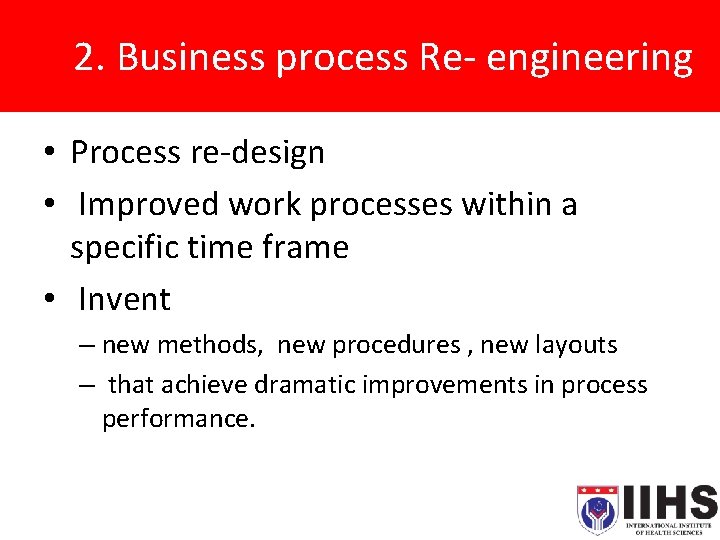
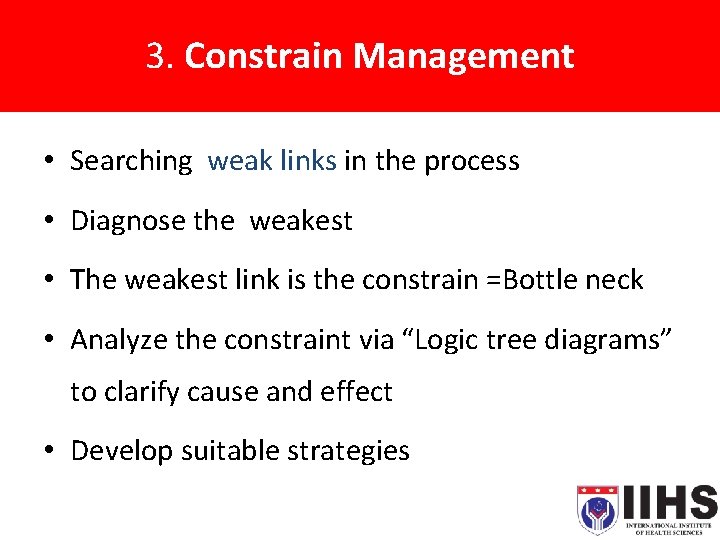
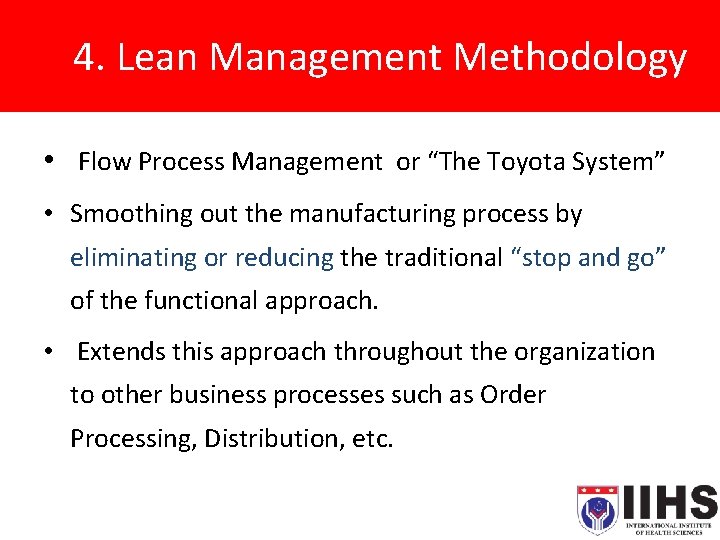
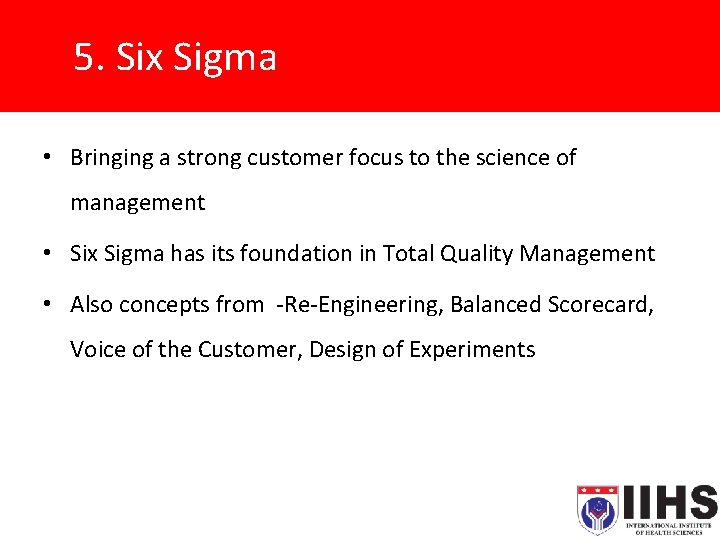
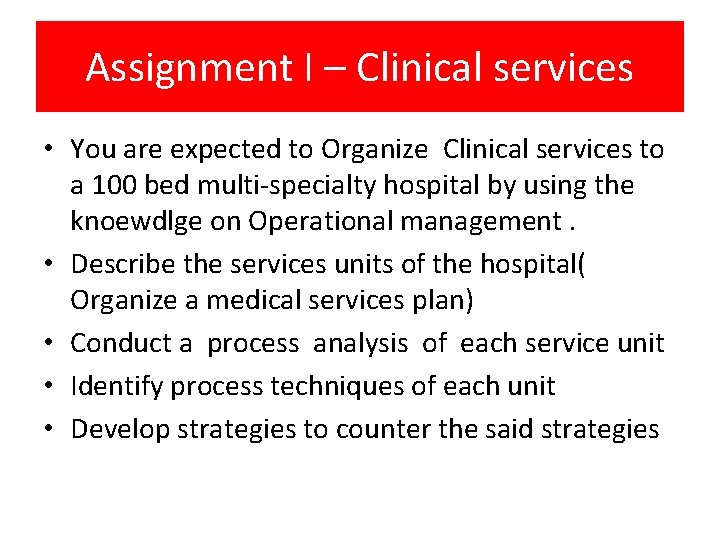
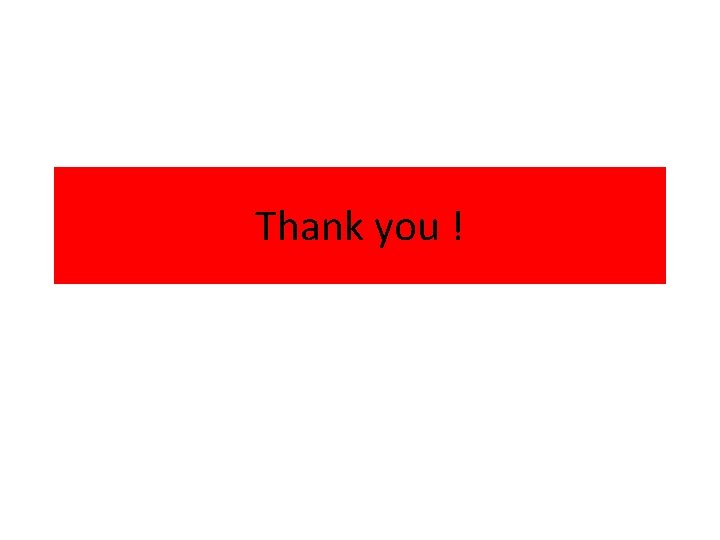
- Slides: 62
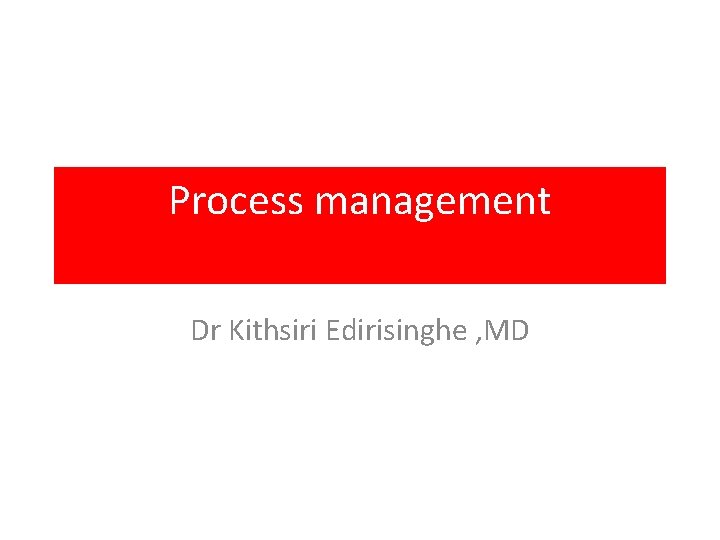
Process management Dr Kithsiri Edirisinghe , MD
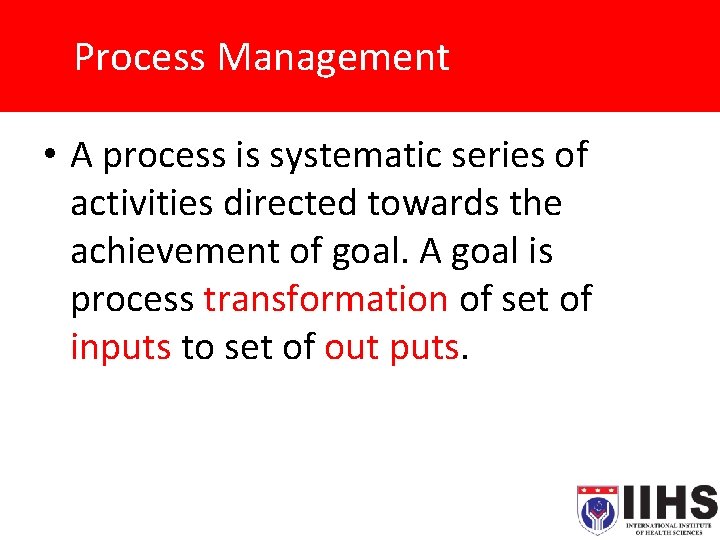
Process Management • A process is systematic series of activities directed towards the achievement of goal. A goal is process transformation of set of inputs to set of out puts.
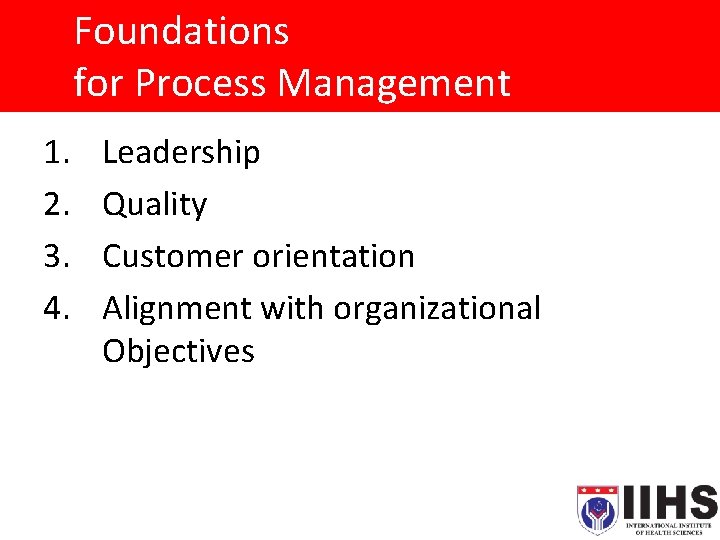
Foundations for Process Management 1. 2. 3. 4. Leadership Quality Customer orientation Alignment with organizational Objectives
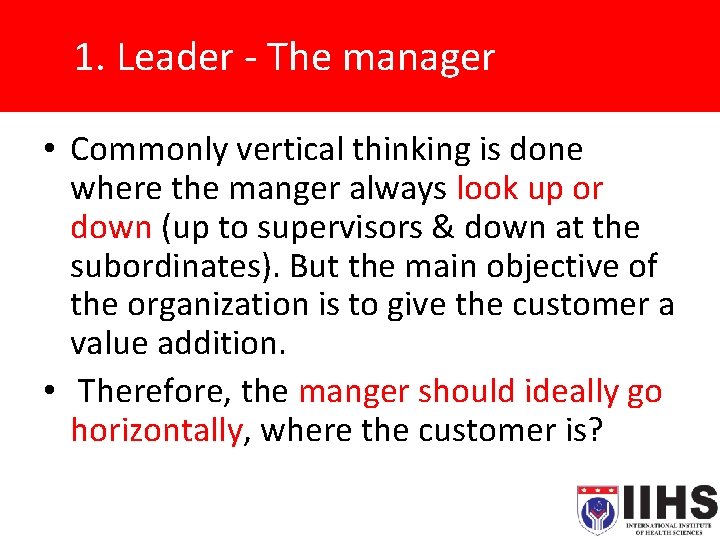
1. Leader - The manager • Commonly vertical thinking is done where the manger always look up or down (up to supervisors & down at the subordinates). But the main objective of the organization is to give the customer a value addition. • Therefore, the manger should ideally go horizontally, where the customer is?
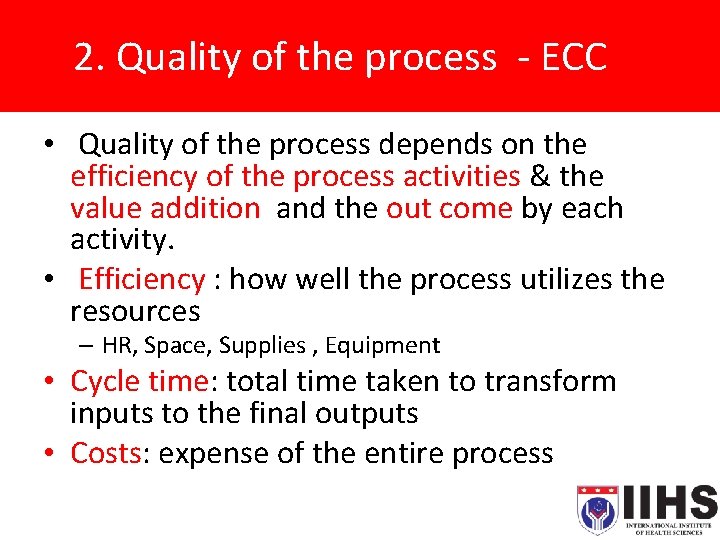
2. Quality of the process - ECC • Quality of the process depends on the efficiency of the process activities & the value addition and the out come by each activity. • Efficiency : how well the process utilizes the resources – HR, Space, Supplies , Equipment • Cycle time: total time taken to transform inputs to the final outputs • Costs: expense of the entire process
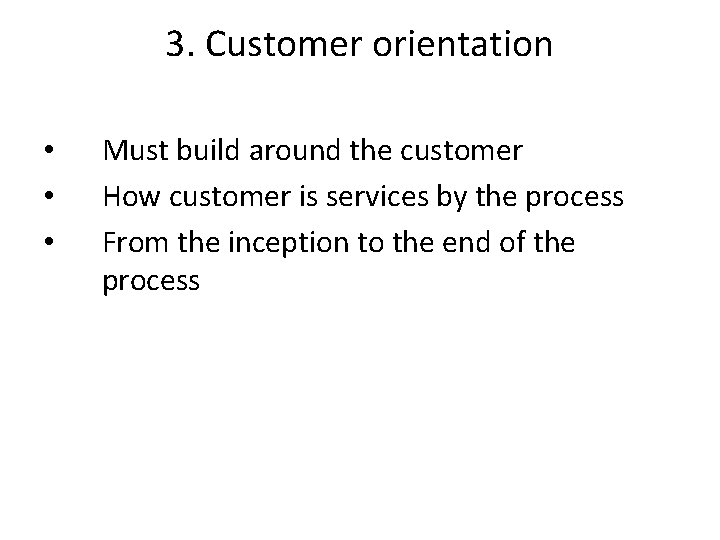
3. Customer orientation • • • Must build around the customer How customer is services by the process From the inception to the end of the process
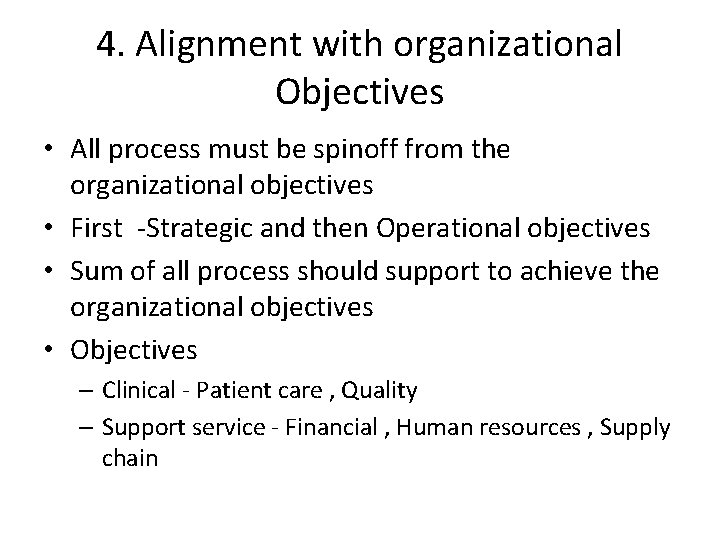
4. Alignment with organizational Objectives • All process must be spinoff from the organizational objectives • First -Strategic and then Operational objectives • Sum of all process should support to achieve the organizational objectives • Objectives – Clinical - Patient care , Quality – Support service - Financial , Human resources , Supply chain
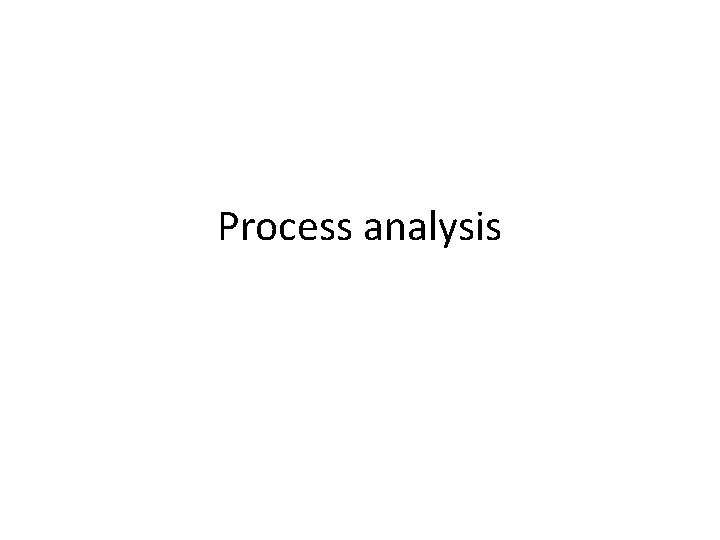
Process analysis
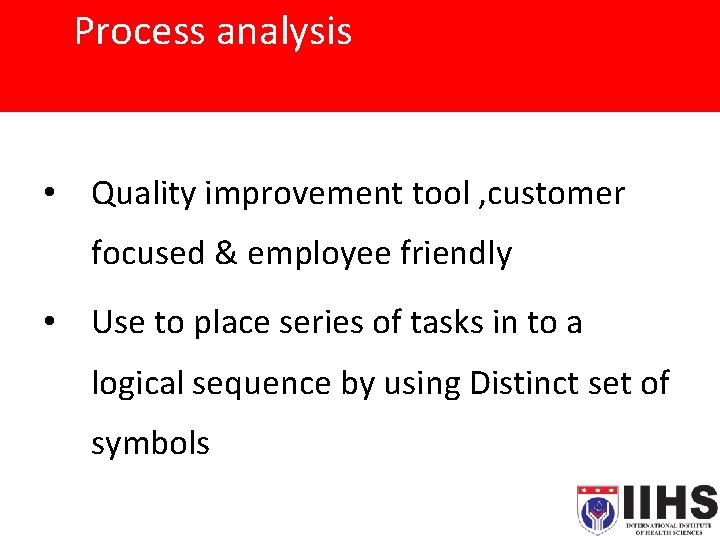
Process analysis • Quality improvement tool , customer focused & employee friendly • Use to place series of tasks in to a logical sequence by using Distinct set of symbols
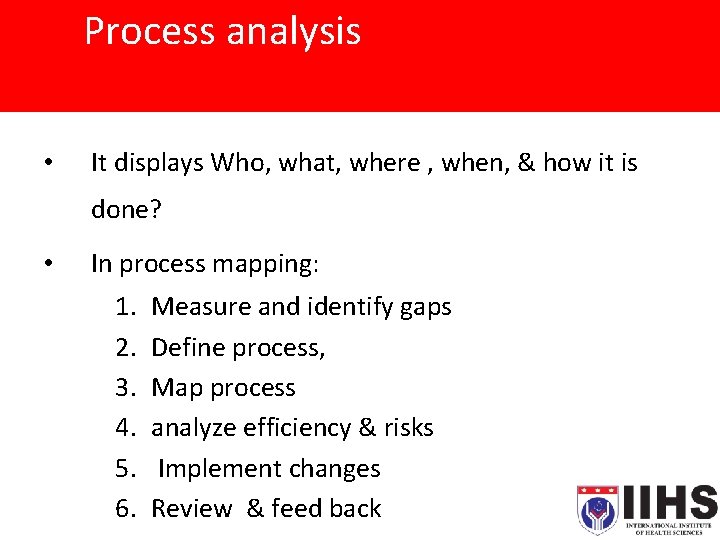
Process analysis • It displays Who, what, where , when, & how it is done? • In process mapping: 1. 2. 3. 4. 5. 6. Measure and identify gaps Define process, Map process analyze efficiency & risks Implement changes Review & feed back
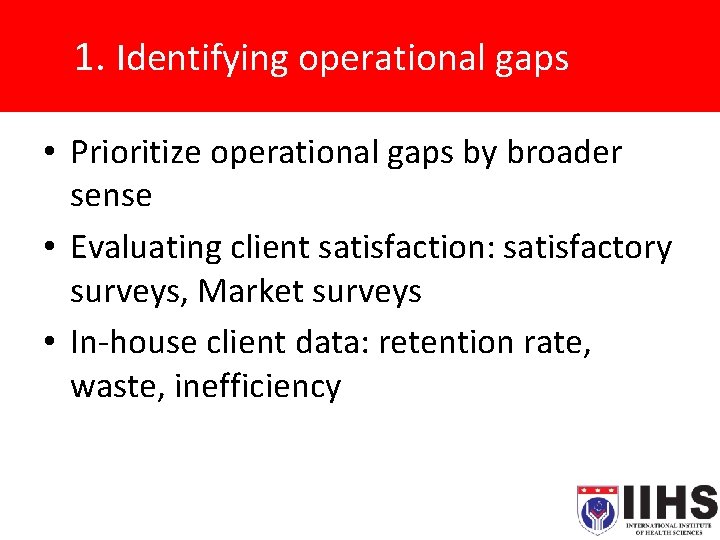
1. Identifying operational gaps • Prioritize operational gaps by broader sense • Evaluating client satisfaction: satisfactory surveys, Market surveys • In-house client data: retention rate, waste, inefficiency
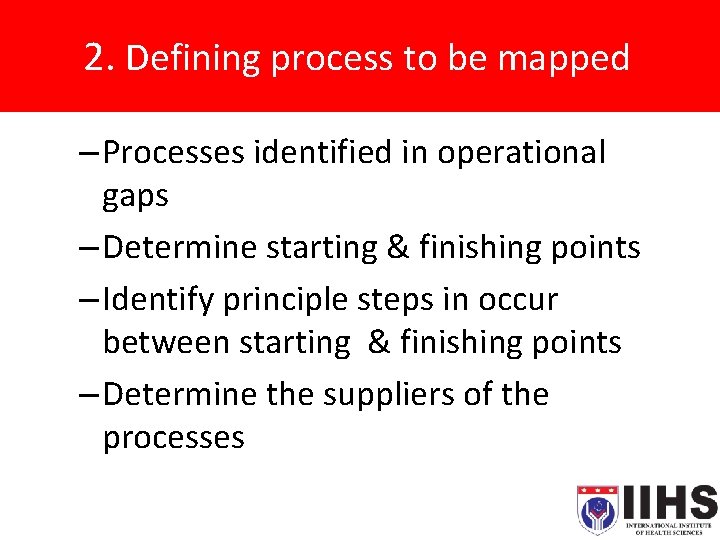
2. Defining process to be mapped – Processes identified in operational gaps – Determine starting & finishing points – Identify principle steps in occur between starting & finishing points – Determine the suppliers of the processes
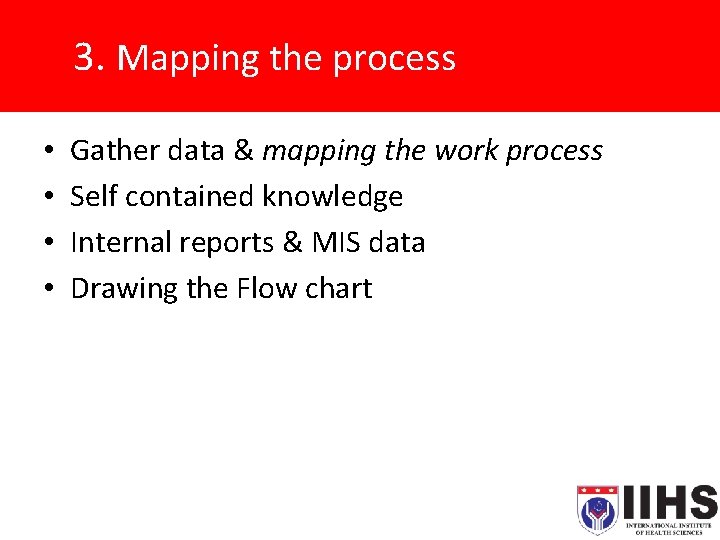
3. Mapping the process • • Gather data & mapping the work process Self contained knowledge Internal reports & MIS data Drawing the Flow chart
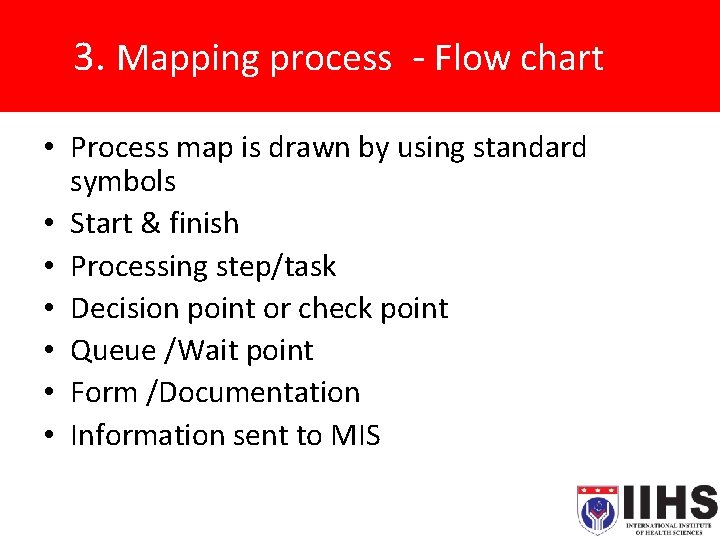
3. Mapping process - Flow chart • Process map is drawn by using standard symbols • Start & finish • Processing step/task • Decision point or check point • Queue /Wait point • Form /Documentation • Information sent to MIS
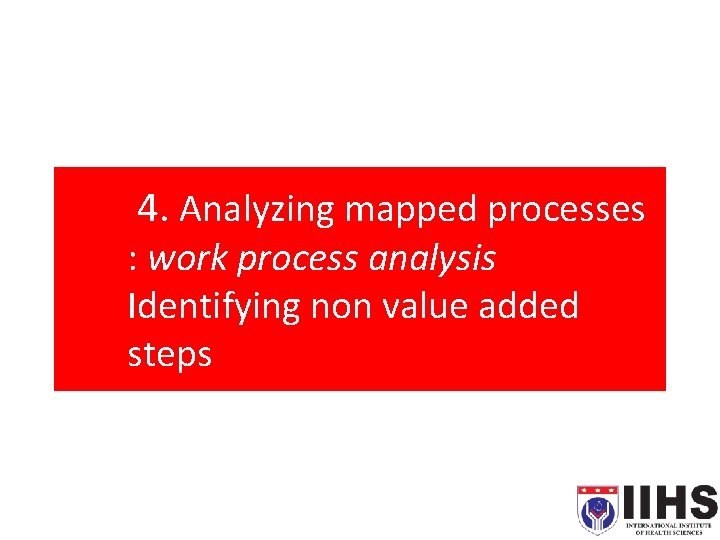
4. Analyzing mapped processes : work process analysis Identifying non value added steps
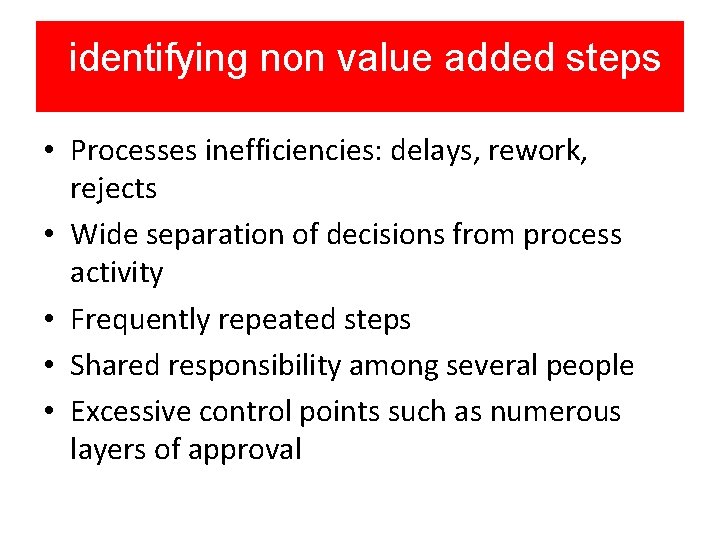
identifying non value added steps • Processes inefficiencies: delays, rework, rejects • Wide separation of decisions from process activity • Frequently repeated steps • Shared responsibility among several people • Excessive control points such as numerous layers of approval
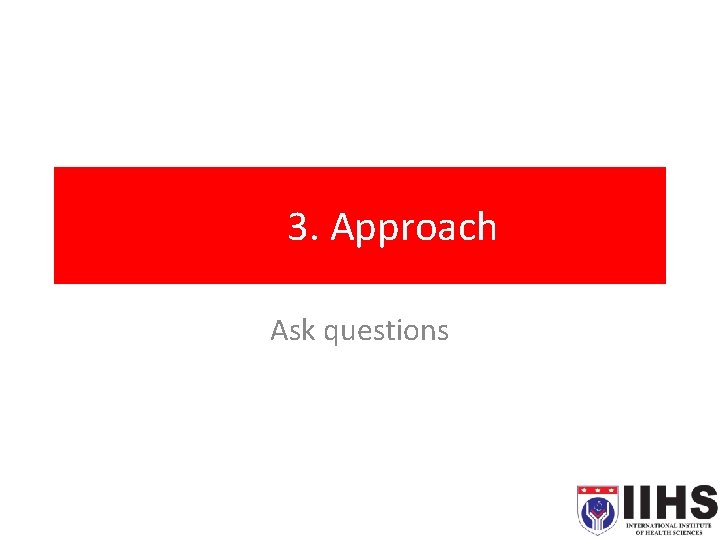
3. Approach Ask questions
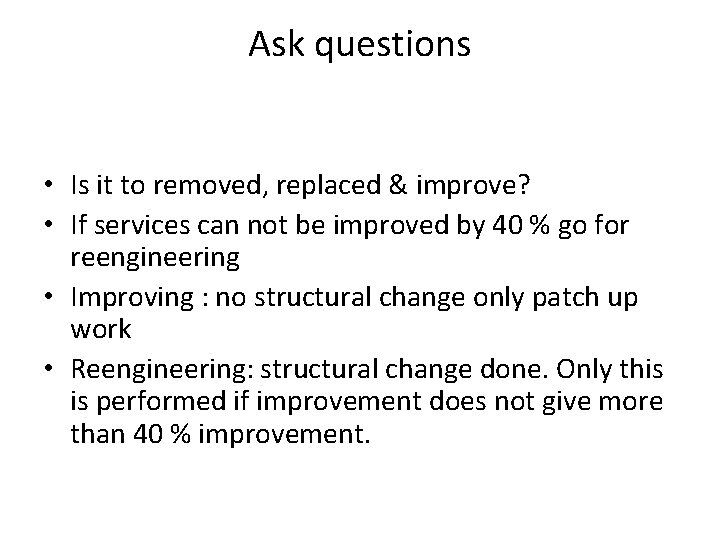
Ask questions • Is it to removed, replaced & improve? • If services can not be improved by 40 % go for reengineering • Improving : no structural change only patch up work • Reengineering: structural change done. Only this is performed if improvement does not give more than 40 % improvement.
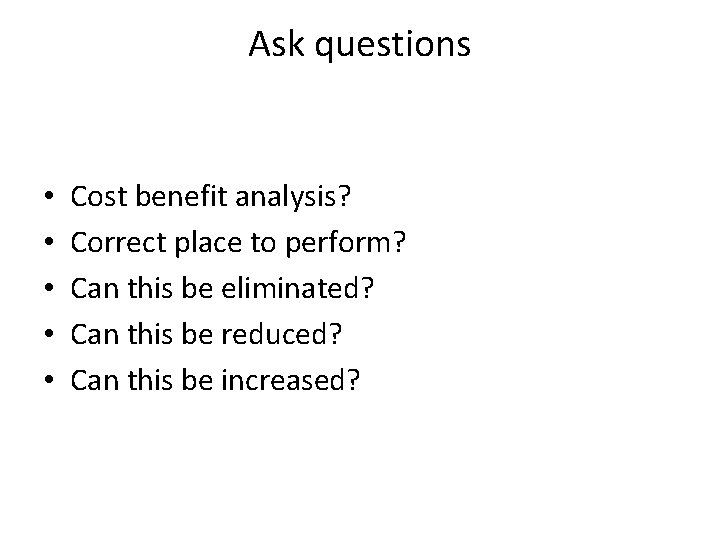
Ask questions • • • Cost benefit analysis? Correct place to perform? Can this be eliminated? Can this be reduced? Can this be increased?
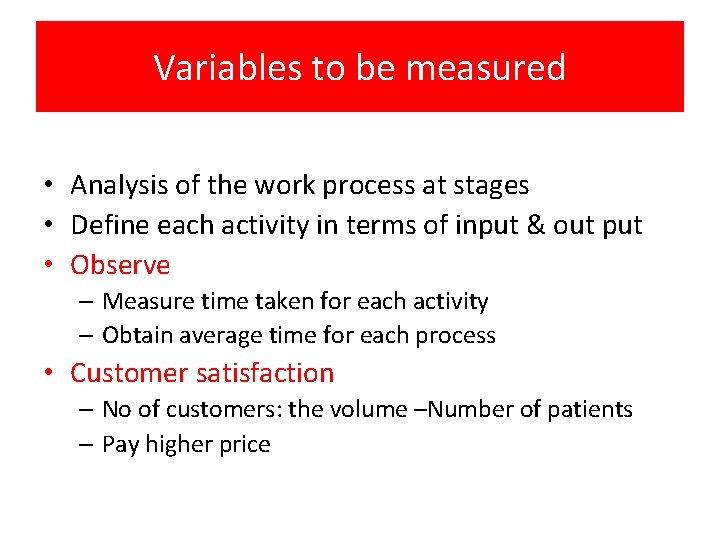
Variables to be measured • Analysis of the work process at stages • Define each activity in terms of input & out put • Observe – Measure time taken for each activity – Obtain average time for each process • Customer satisfaction – No of customers: the volume –Number of patients – Pay higher price
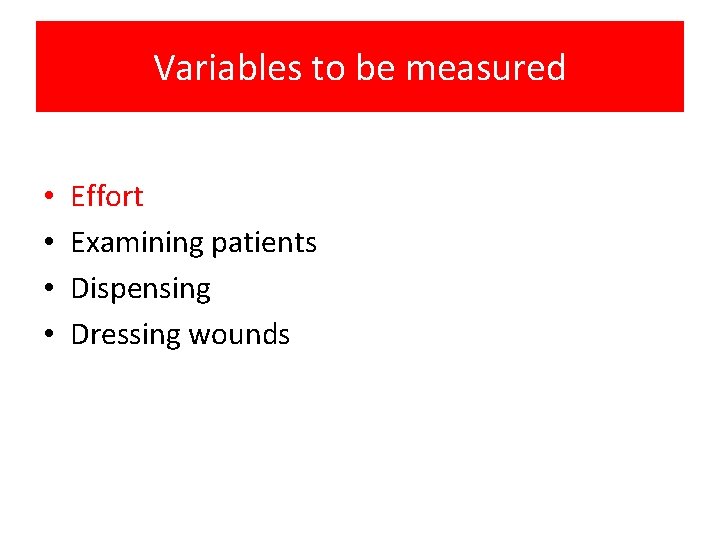
Variables to be measured • • Effort Examining patients Dispensing Dressing wounds
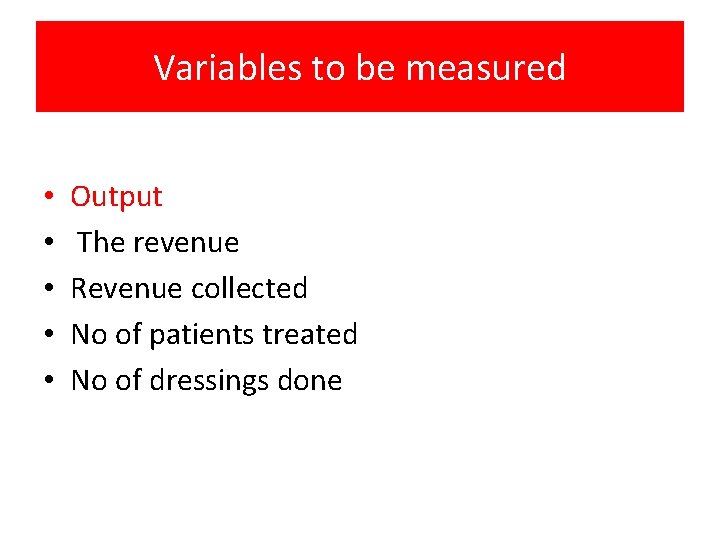
Variables to be measured • • • Output The revenue Revenue collected No of patients treated No of dressings done
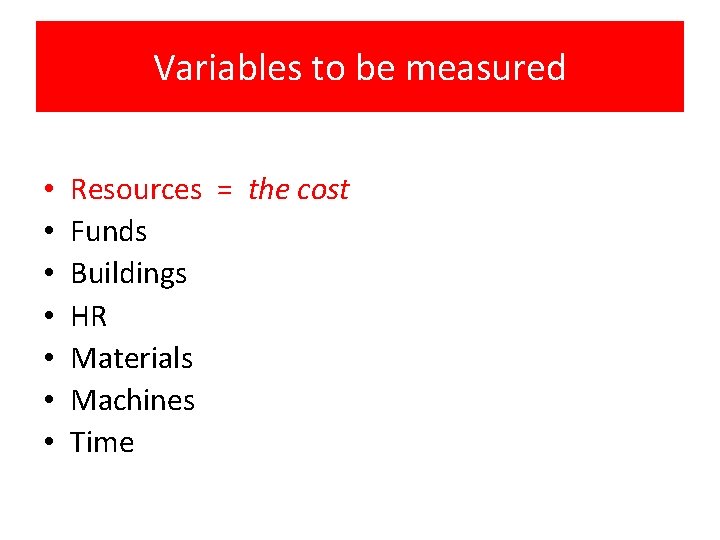
Variables to be measured • • Resources = the cost Funds Buildings HR Materials Machines Time
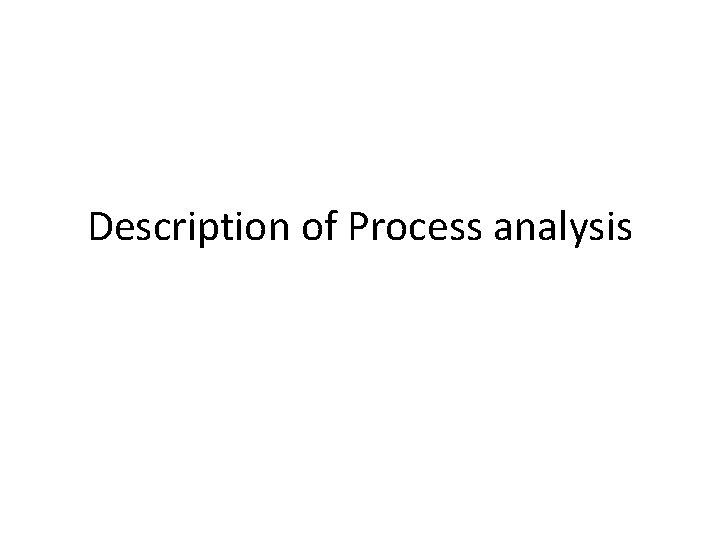
Description of Process analysis
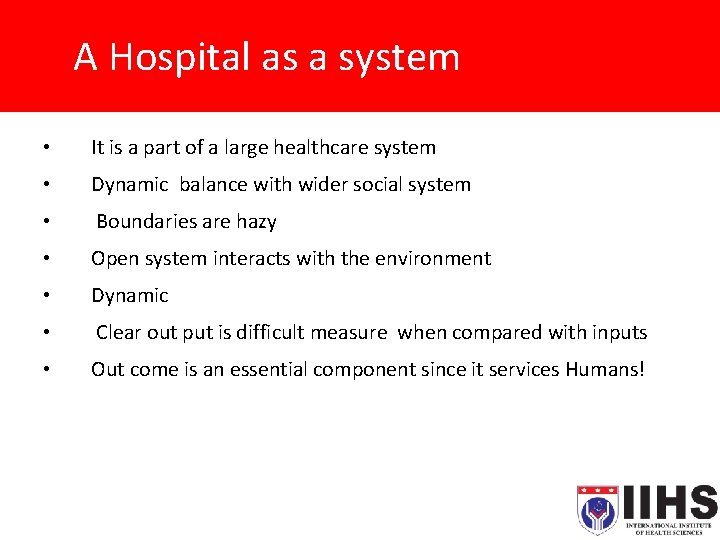
A Hospital as a system • It is a part of a large healthcare system • Dynamic balance with wider social system • Boundaries are hazy • Open system interacts with the environment • Dynamic • Clear out put is difficult measure when compared with inputs • Out come is an essential component since it services Humans!
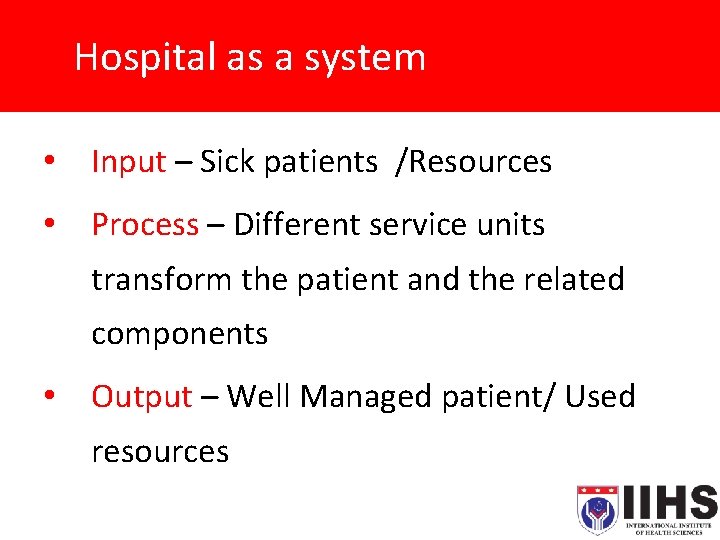
Hospital as a system • Input – Sick patients /Resources • Process – Different service units transform the patient and the related components • Output – Well Managed patient/ Used resources
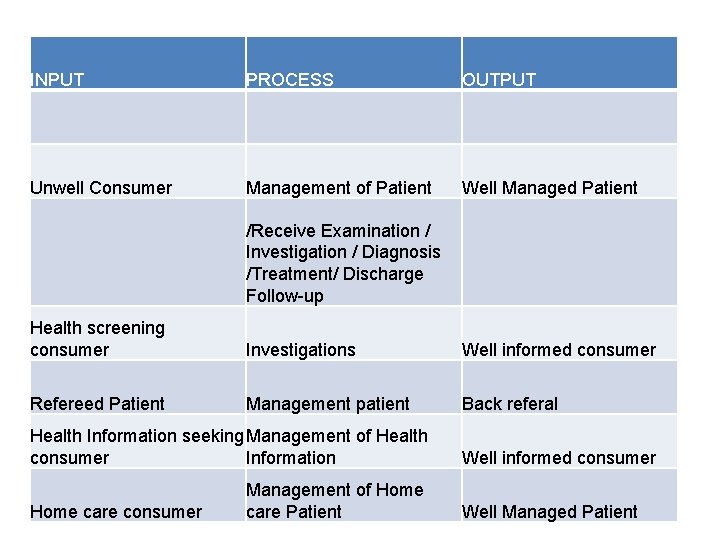
INPUT PROCESS OUTPUT Unwell Consumer Management of Patient Well Managed Patient /Receive Examination / Investigation / Diagnosis /Treatment/ Discharge Follow-up Health screening consumer Investigations Well informed consumer Refereed Patient Management patient Back referal Health Information seeking Management of Health consumer Information Home care consumer Management of Home care Patient Well informed consumer Well Managed Patient
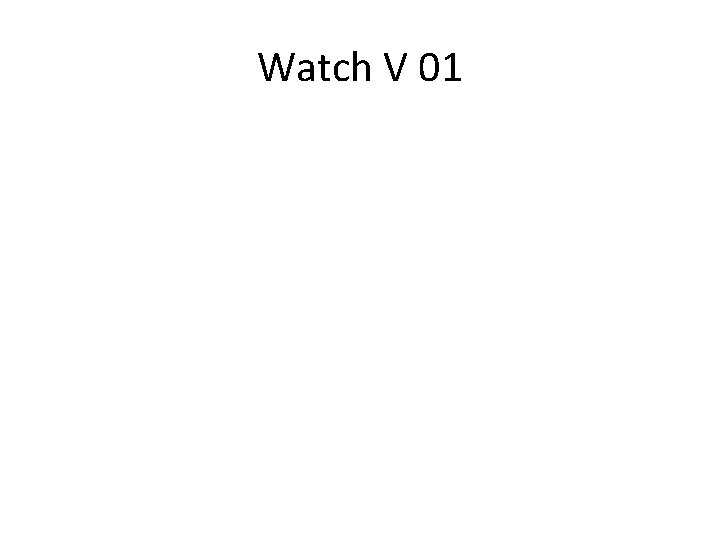
Watch V 01
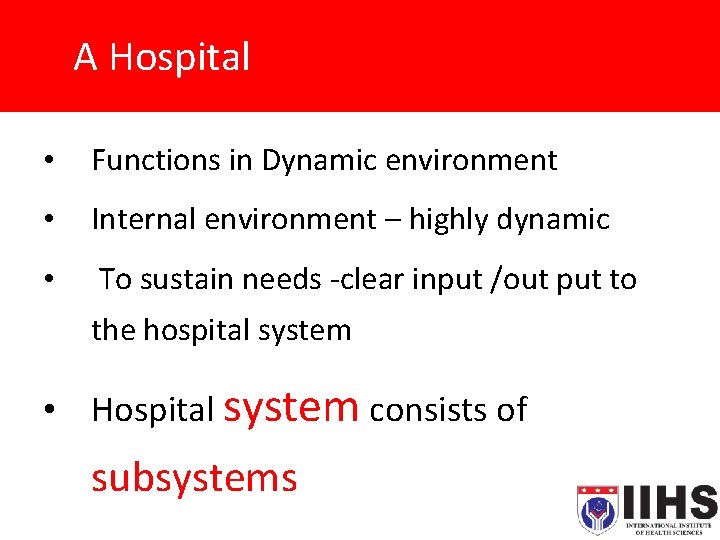
A Hospital • Functions in Dynamic environment • Internal environment – highly dynamic • To sustain needs -clear input /out put to the hospital system • Hospital system consists of subsystems
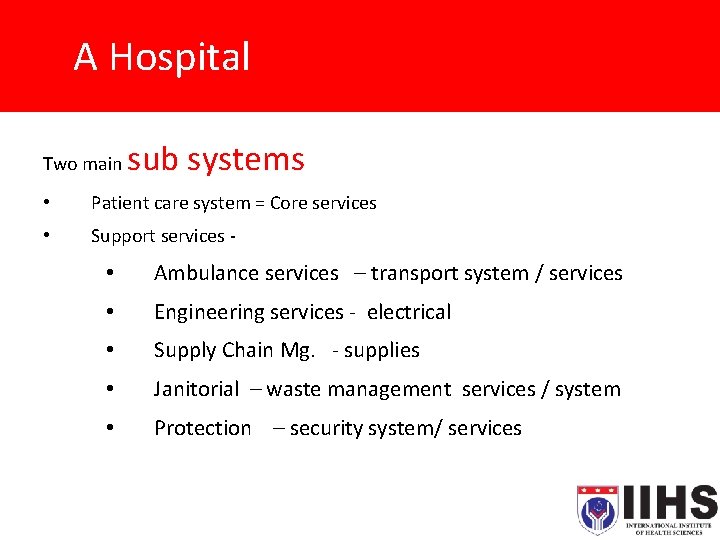
A Hospital Two main sub systems • Patient care system = Core services • Support services - • Ambulance services – transport system / services • Engineering services - electrical • Supply Chain Mg. - supplies • Janitorial – waste management services / system • Protection – security system/ services
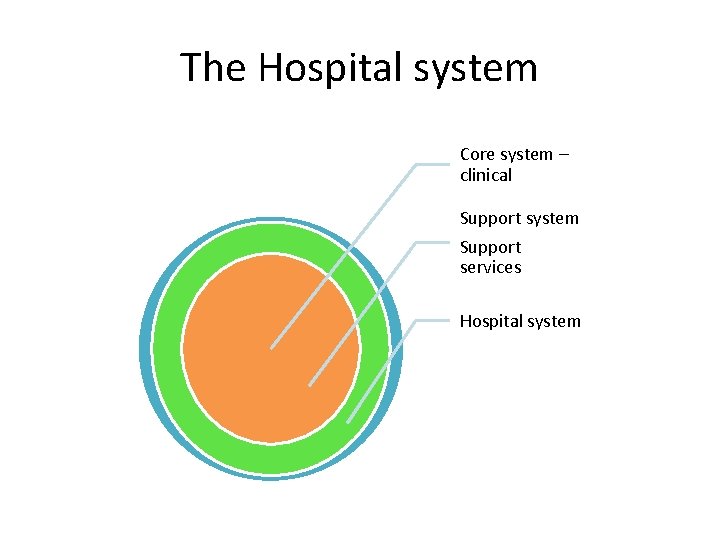
The Hospital system Core system – clinical Support system Support services Hospital system
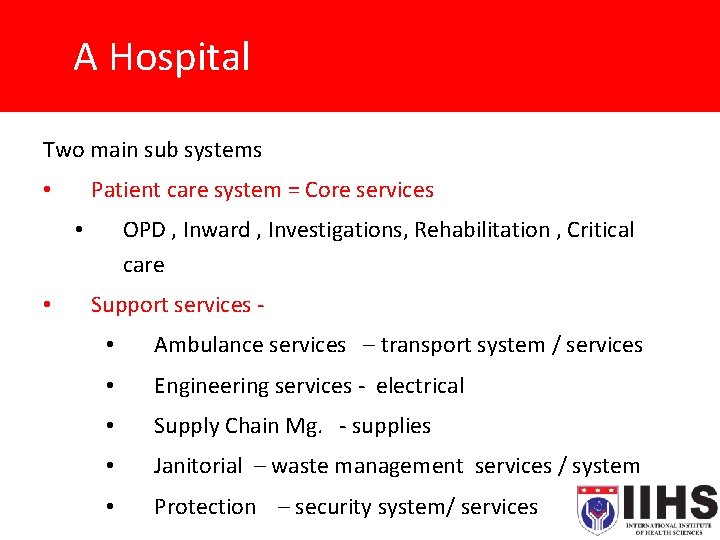
A Hospital Two main sub systems Patient care system = Core services • OPD , Inward , Investigations, Rehabilitation , Critical care • • Support services - • Ambulance services – transport system / services • Engineering services - electrical • Supply Chain Mg. - supplies • Janitorial – waste management services / system • Protection – security system/ services
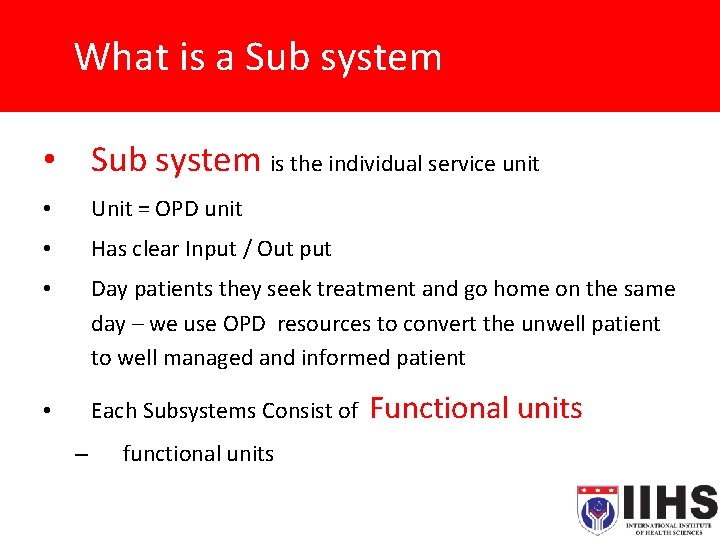
What is a Sub system • Sub system is the individual service unit • Unit = OPD unit • Has clear Input / Out put • Day patients they seek treatment and go home on the same day – we use OPD resources to convert the unwell patient to well managed and informed patient • Each Subsystems Consist of – functional units Functional units
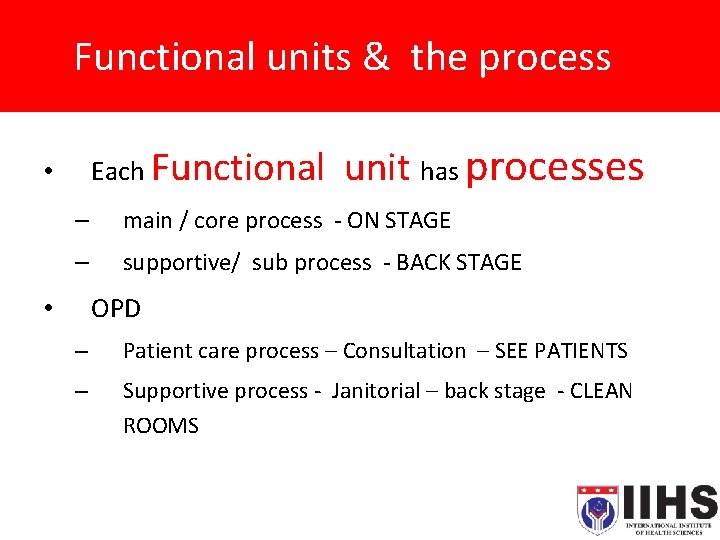
Functional units & the process Each Functional • unit has processes – main / core process - ON STAGE – supportive/ sub process - BACK STAGE OPD • – Patient care process – Consultation – SEE PATIENTS – Supportive process - Janitorial – back stage - CLEAN ROOMS
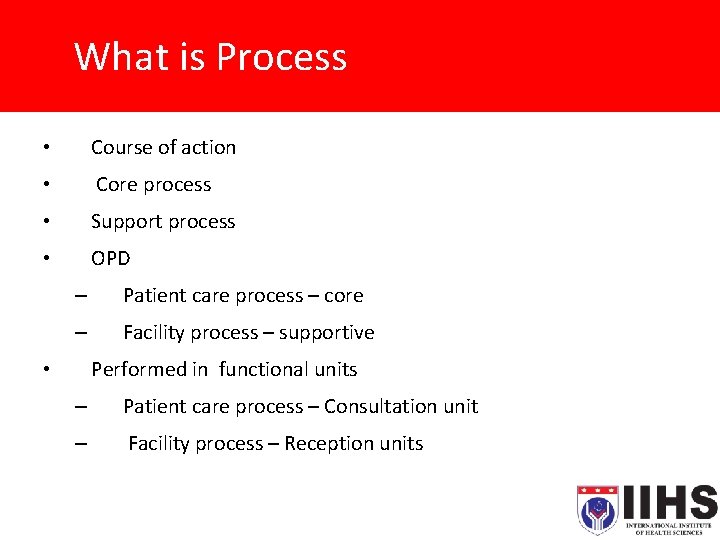
What is Process • Course of action • Core process • Support process • OPD – Patient care process – core – Facility process – supportive Performed in functional units • – Patient care process – Consultation unit – Facility process – Reception units
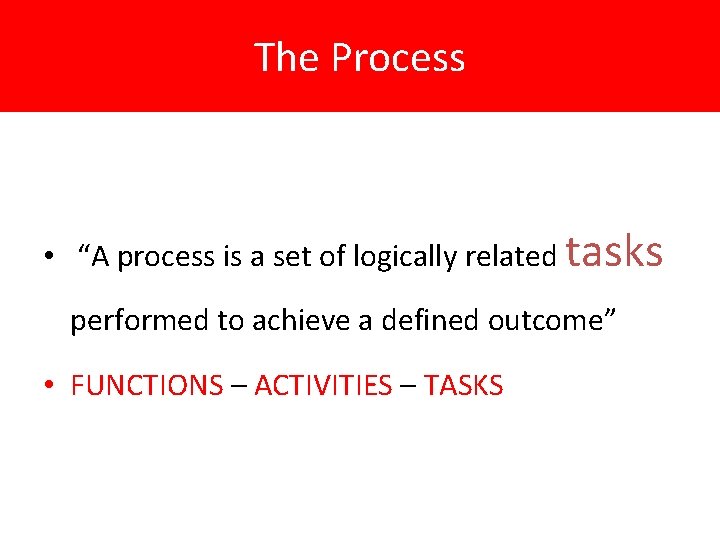
The Process • “A process is a set of logically related tasks performed to achieve a defined outcome” • FUNCTIONS – ACTIVITIES – TASKS
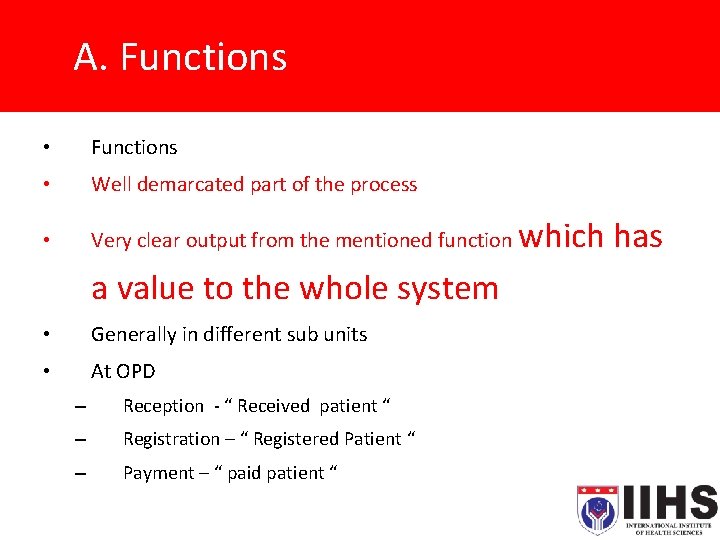
A. Functions • Functions • Well demarcated part of the process • Very clear output from the mentioned function a value to the whole system • Generally in different sub units • At OPD – Reception - “ Received patient “ – Registration – “ Registered Patient “ – Payment – “ paid patient “ which has
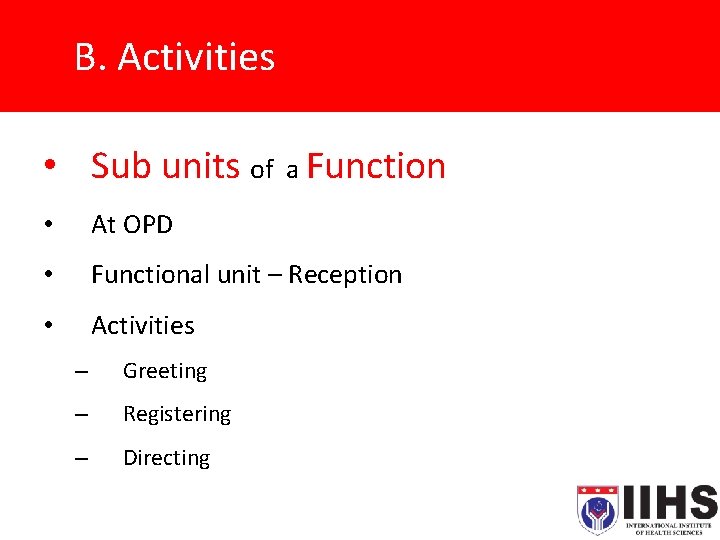
B. Activities • Sub units of a Function • At OPD • Functional unit – Reception • Activities – Greeting – Registering – Directing
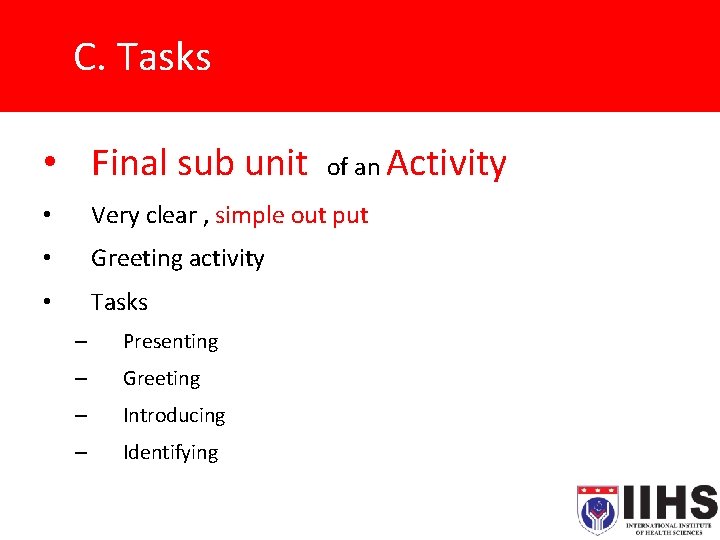
C. Tasks • Final sub unit of an Activity • Very clear , simple out put • Greeting activity • Tasks – Presenting – Greeting – Introducing – Identifying
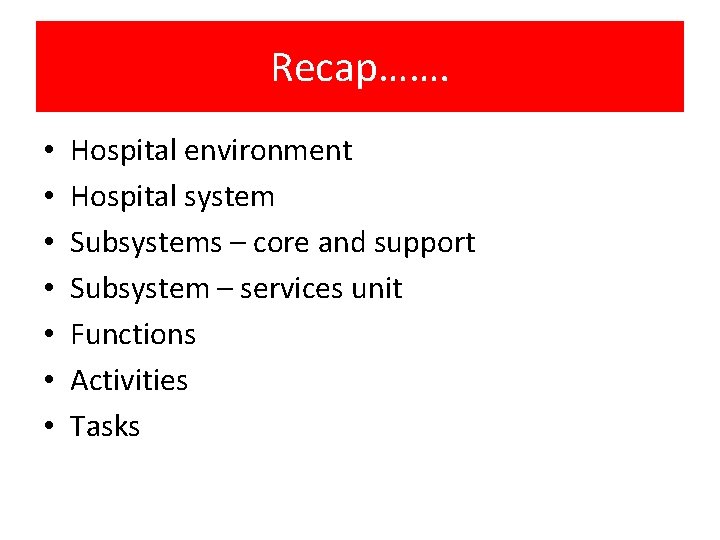
Recap……. • • Hospital environment Hospital system Subsystems – core and support Subsystem – services unit Functions Activities Tasks
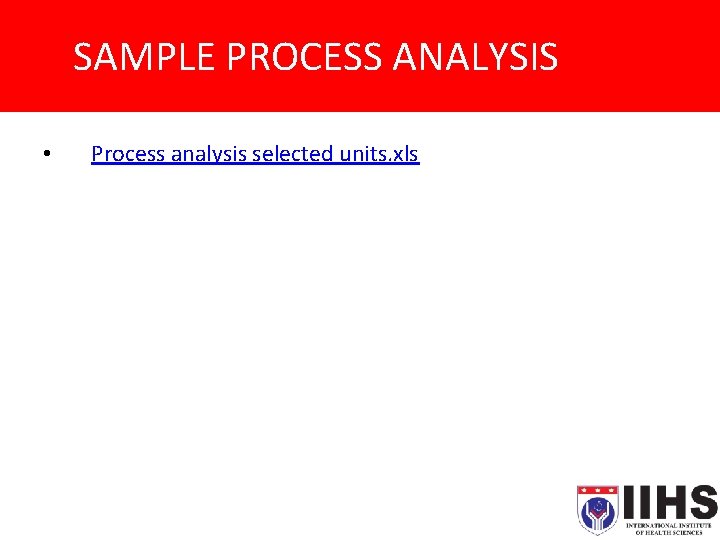
SAMPLE PROCESS ANALYSIS • Process analysis selected units. xls
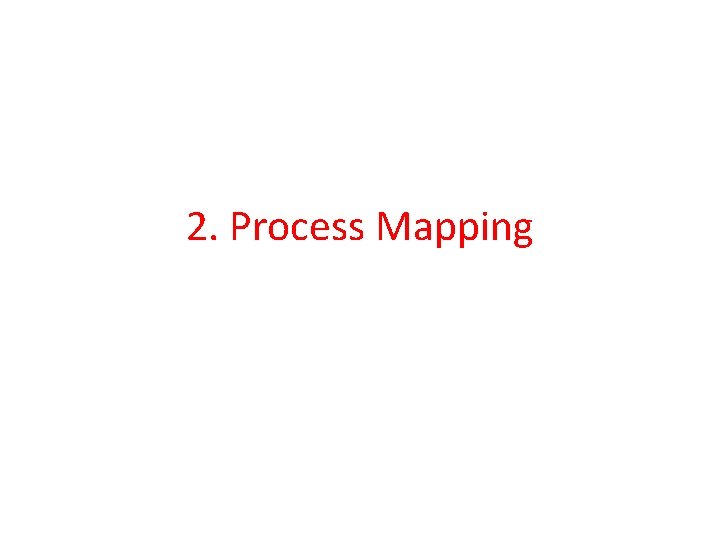
2. Process Mapping
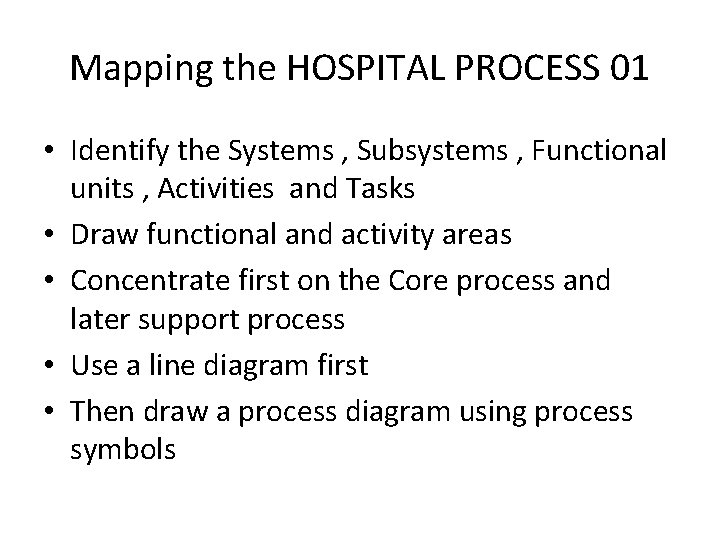
Mapping the HOSPITAL PROCESS 01 • Identify the Systems , Subsystems , Functional units , Activities and Tasks • Draw functional and activity areas • Concentrate first on the Core process and later support process • Use a line diagram first • Then draw a process diagram using process symbols
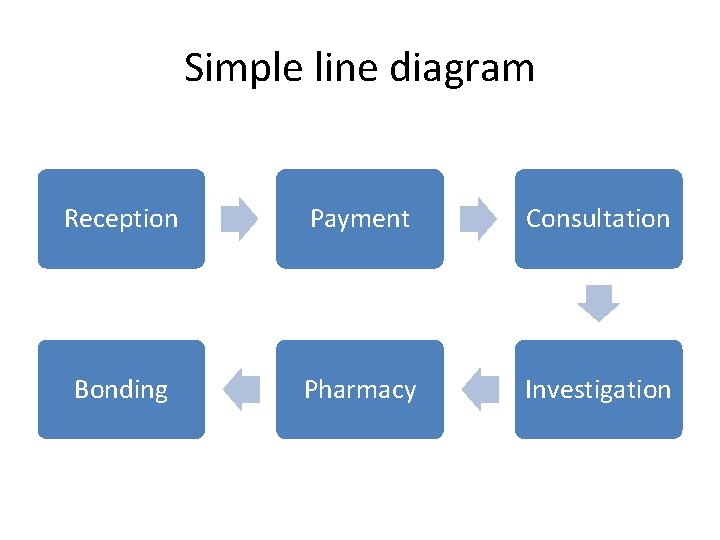
Simple line diagram Reception Payment Consultation Bonding Pharmacy Investigation
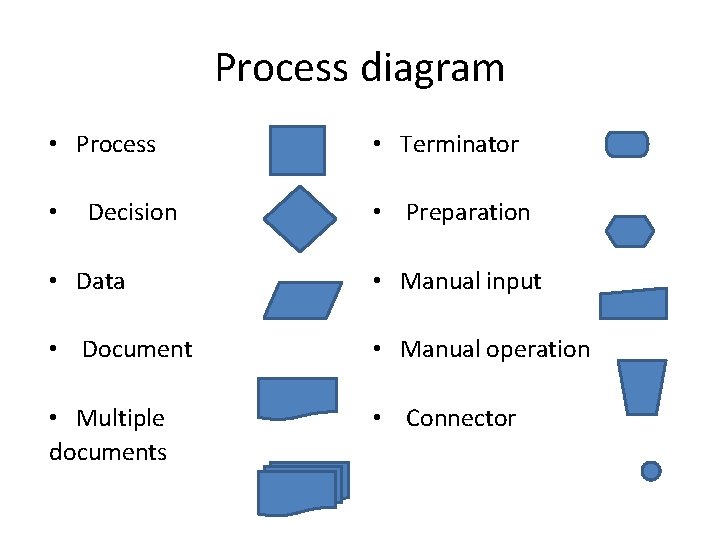
Process diagram • Process • Decision • Terminator • Preparation • Data • Manual input • Document • Manual operation • Multiple documents • Connector
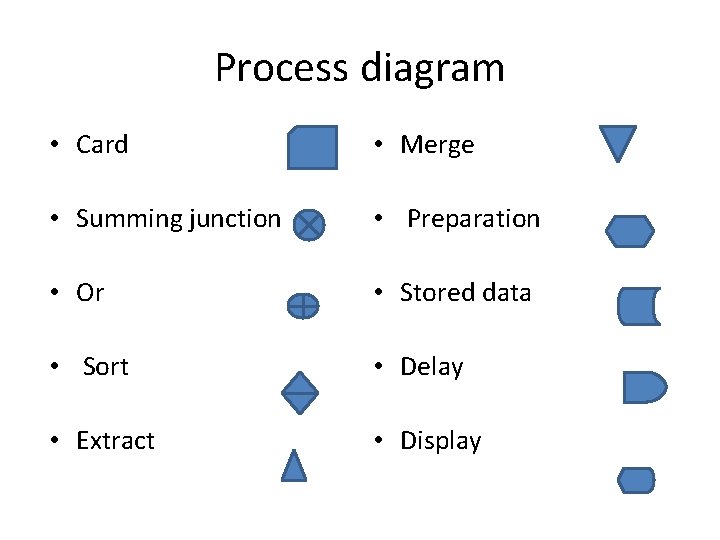
Process diagram • Card • Merge • Summing junction • Preparation • Or • Stored data • Sort • Delay • Extract • Display
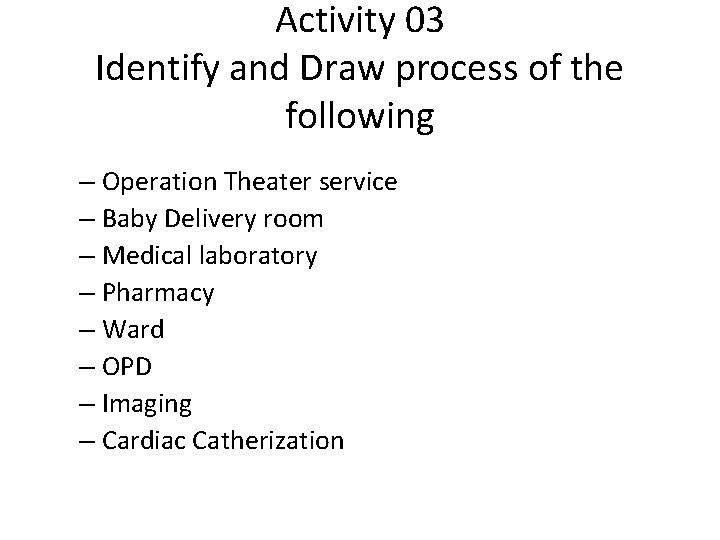
Activity 03 Identify and Draw process of the following – Operation Theater service – Baby Delivery room – Medical laboratory – Pharmacy – Ward – OPD – Imaging – Cardiac Catherization
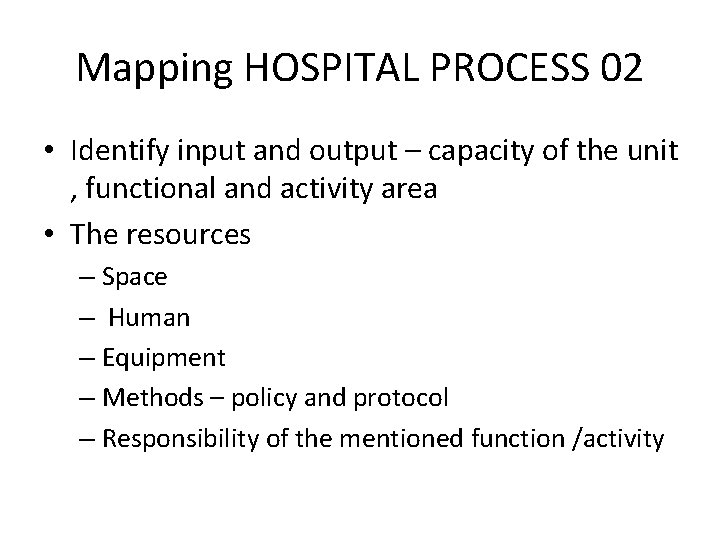
Mapping HOSPITAL PROCESS 02 • Identify input and output – capacity of the unit , functional and activity area • The resources – Space – Human – Equipment – Methods – policy and protocol – Responsibility of the mentioned function /activity
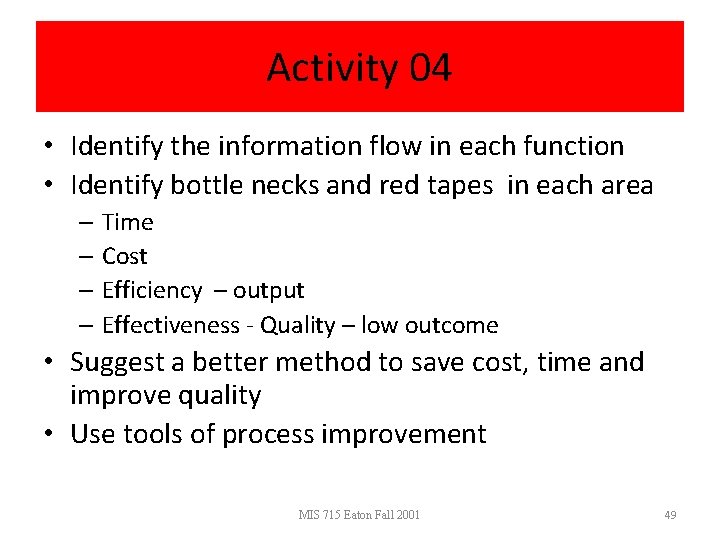
Activity 04 • Identify the information flow in each function • Identify bottle necks and red tapes in each area – Time – Cost – Efficiency – output – Effectiveness - Quality – low outcome • Suggest a better method to save cost, time and improve quality • Use tools of process improvement MIS 715 Eaton Fall 2001 49
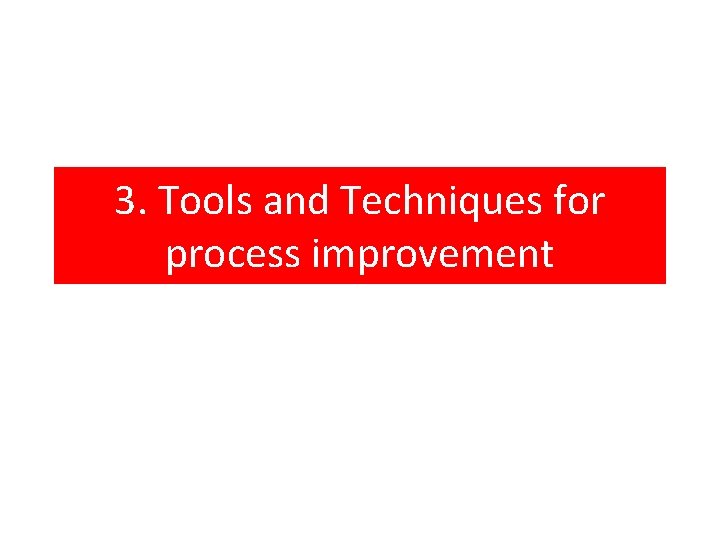
3. Tools and Techniques for process improvement
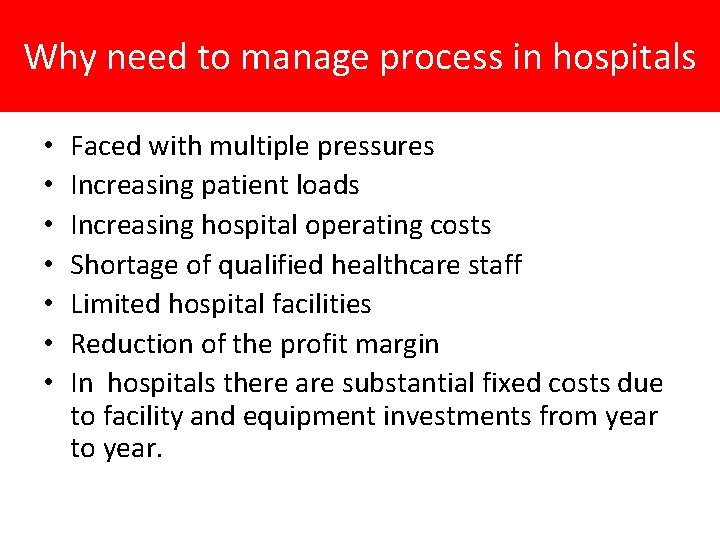
Why need to manage process in hospitals • • Faced with multiple pressures Increasing patient loads Increasing hospital operating costs Shortage of qualified healthcare staff Limited hospital facilities Reduction of the profit margin In hospitals there are substantial fixed costs due to facility and equipment investments from year to year.
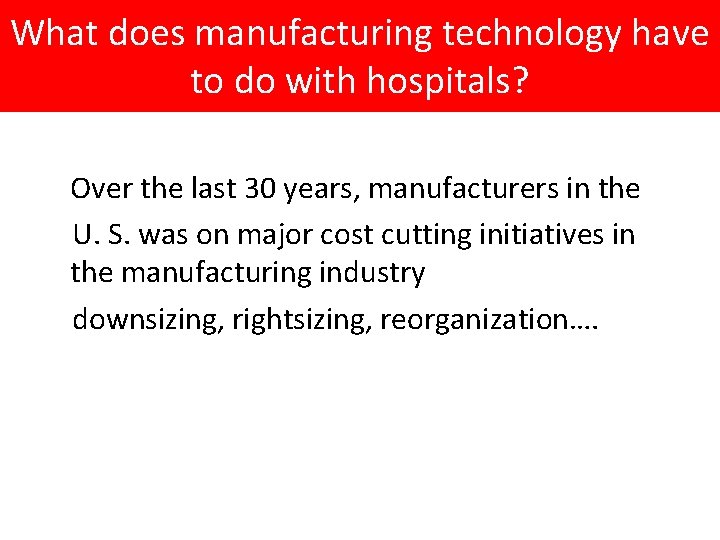
What does manufacturing technology have to do with hospitals? Over the last 30 years, manufacturers in the U. S. was on major cost cutting initiatives in the manufacturing industry downsizing, rightsizing, reorganization….
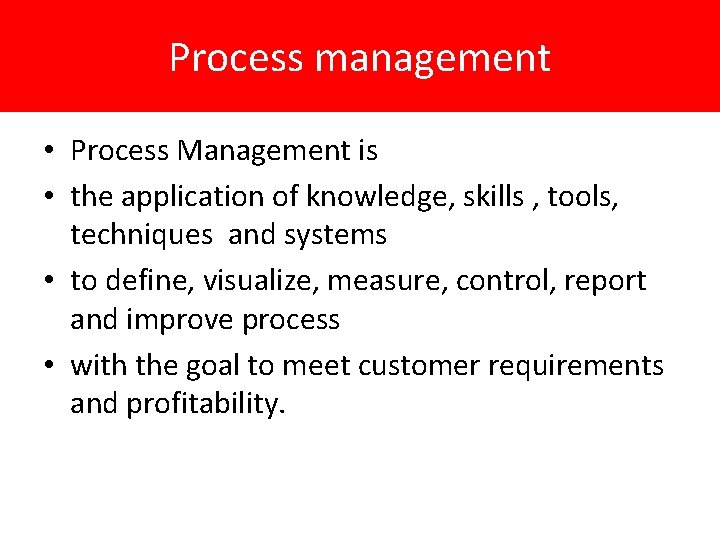
Process management • Process Management is • the application of knowledge, skills , tools, techniques and systems • to define, visualize, measure, control, report and improve process • with the goal to meet customer requirements and profitability.
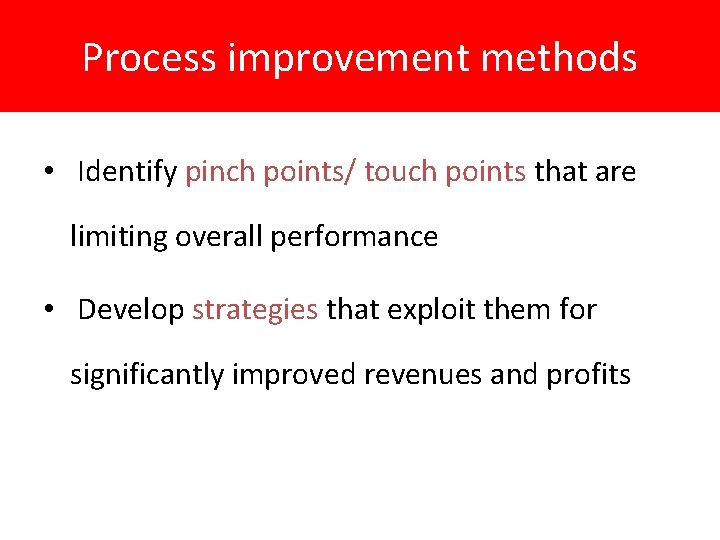
Process improvement methods • Identify pinch points/ touch points that are limiting overall performance • Develop strategies that exploit them for significantly improved revenues and profits
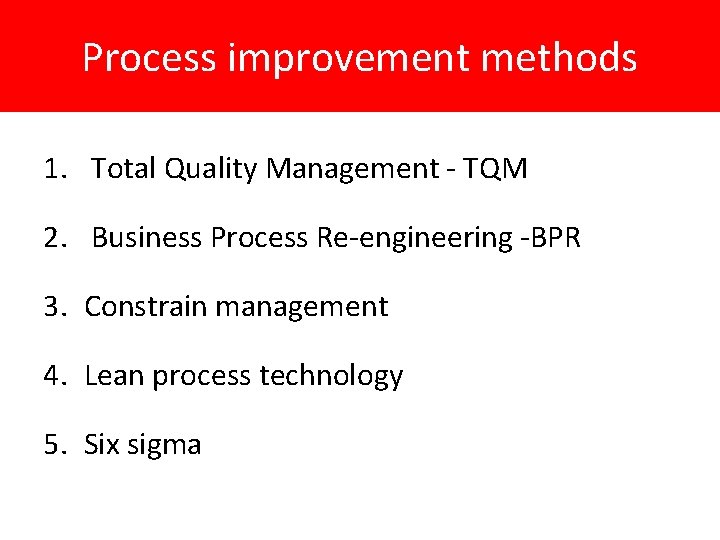
Process improvement methods 1. Total Quality Management - TQM 2. Business Process Re-engineering -BPR 3. Constrain management 4. Lean process technology 5. Six sigma
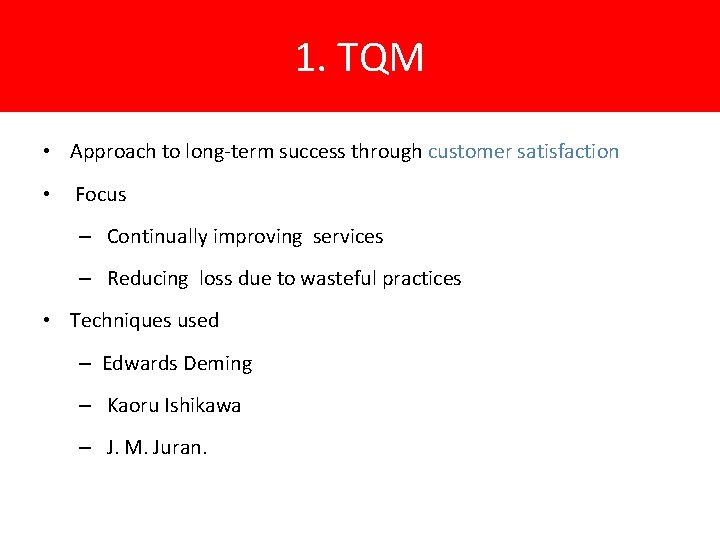
1. TQM • Approach to long-term success through customer satisfaction • Focus – Continually improving services – Reducing loss due to wasteful practices • Techniques used – Edwards Deming – Kaoru Ishikawa – J. M. Juran.
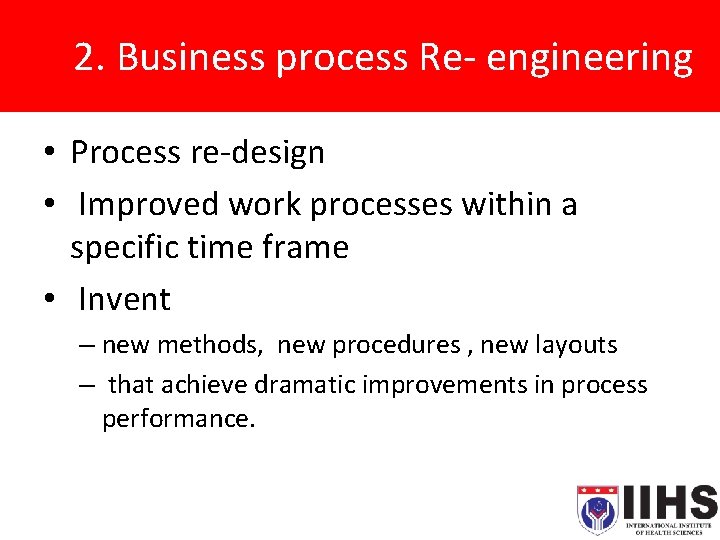
2. Business process Re- engineering. • Process re-design • Improved work processes within a specific time frame • Invent – new methods, new procedures , new layouts – that achieve dramatic improvements in process performance.
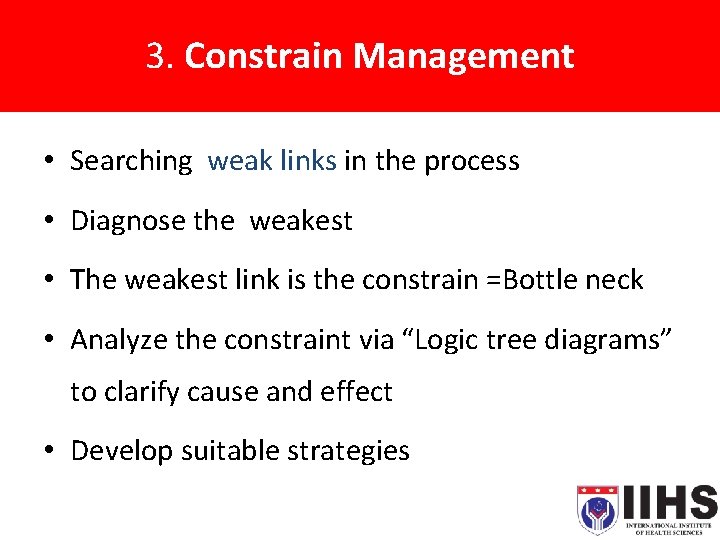
3. Constrain Management • Searching weak links in the process • Diagnose the weakest • The weakest link is the constrain =Bottle neck • Analyze the constraint via “Logic tree diagrams” to clarify cause and effect • Develop suitable strategies
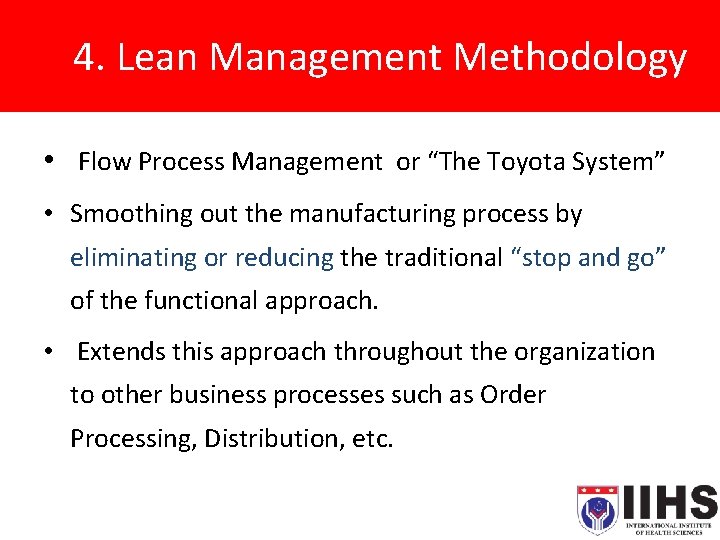
4. Lean Management Methodology • Flow Process Management or “The Toyota System” • Smoothing out the manufacturing process by eliminating or reducing the traditional “stop and go” of the functional approach. • Extends this approach throughout the organization to other business processes such as Order Processing, Distribution, etc.
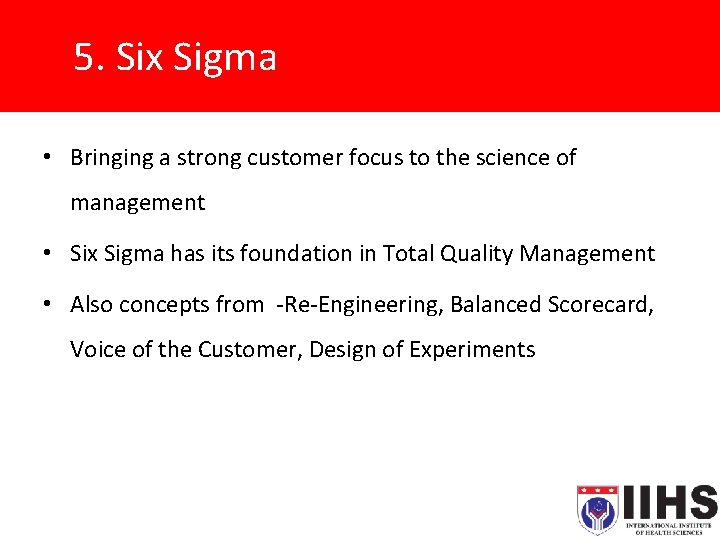
5. Six Sigma • Bringing a strong customer focus to the science of management • Six Sigma has its foundation in Total Quality Management • Also concepts from -Re-Engineering, Balanced Scorecard, Voice of the Customer, Design of Experiments
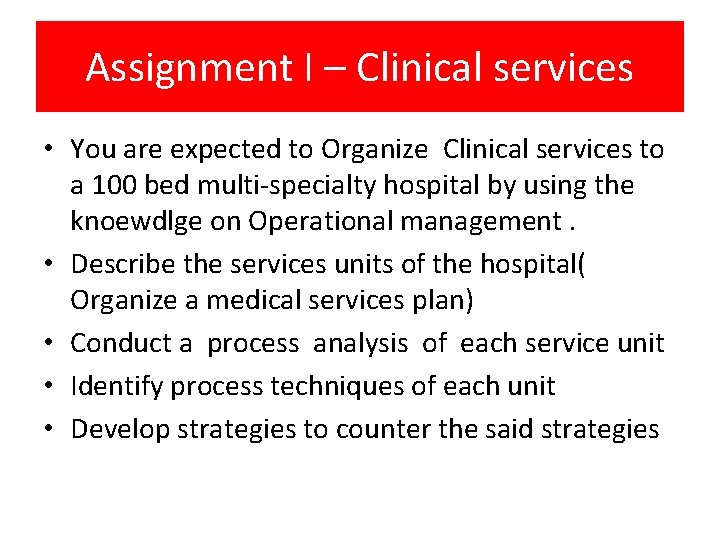
Assignment I – Clinical services • You are expected to Organize Clinical services to a 100 bed multi-specialty hospital by using the knoewdlge on Operational management. • Describe the services units of the hospital( Organize a medical services plan) • Conduct a process analysis of each service unit • Identify process techniques of each unit • Develop strategies to counter the said strategies
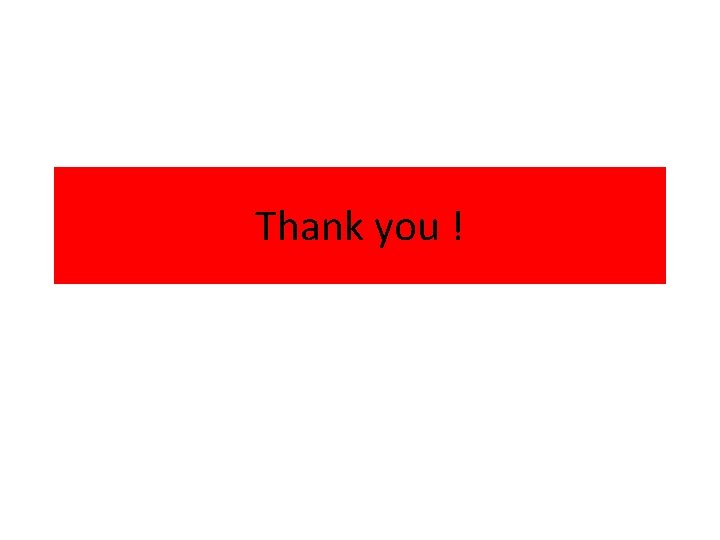
Thank you !
Process hierarchy in process management
Top management middle management first line management
Top management middle management first line management
Middle level management
Bones practical exam
Liberty chapter 20
Ergodicty
What is process to process delivery
Condylar process and coronoid process
Stable process has to be a capable process
Process-to-process delivery
Sweet process review
Process street vs sweet process
Gap analysis of incident management process
5 generation of computer
Process management framework
Supporting facility
Pipeline in supply chain
Strategic brand management process steps
Risk management process
Process discriminants in software project management
Sap sales order management process
Demand management process in sap
Sap solution manager process management
Project procurement management definition
Project procurement management process
Process instrumentation in software project management
Steps involved in portfolio management
Time management process
Procurement management pmi
Oracle trade management process
Process focus strategy example
The objective of layout strategy is to
Process strategy in operations management
Forms of transformation process in operation management
Process management in operating system
Process management in operating system
Nafems pse
Interface management process
Maximo business process management
Chapter 4 job analysis and the talent management process
Performance management process 5 steps
Query management process
Regulatory change management process
Ipssap
Energy institute process safety management framework
Process management in distributed system
Contract risk management process
Jit and tqm
Chapter 6 understanding the management process
Understanding the management process
Process technology in operations management
How will you make the selection of product design
Types of process selection in operations management
Process management in operating system
Personal selling process in sales management
Staple merchandise
Retail human resource management
Human resources today
Operations management transformation process
Bpm phases
Merchandise management process
Brand management process.