Outline Control structure design plantwide control A procedure
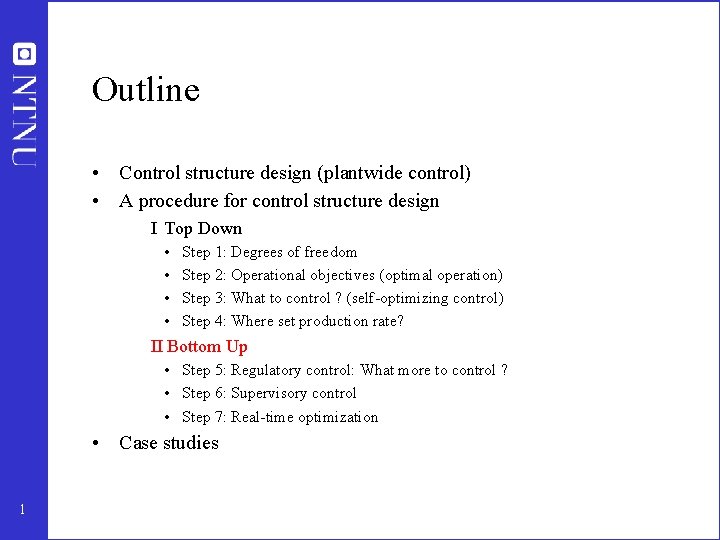
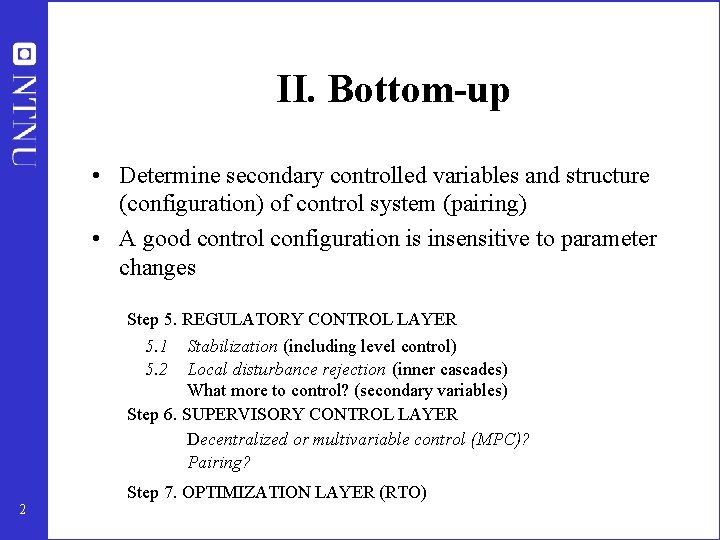
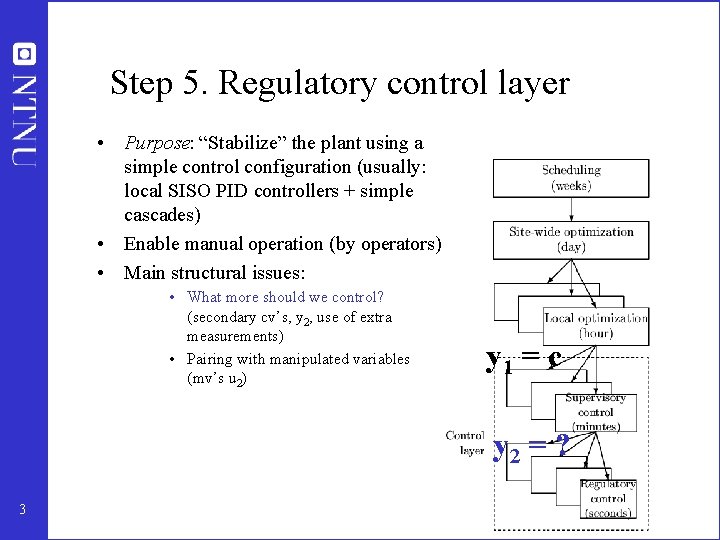
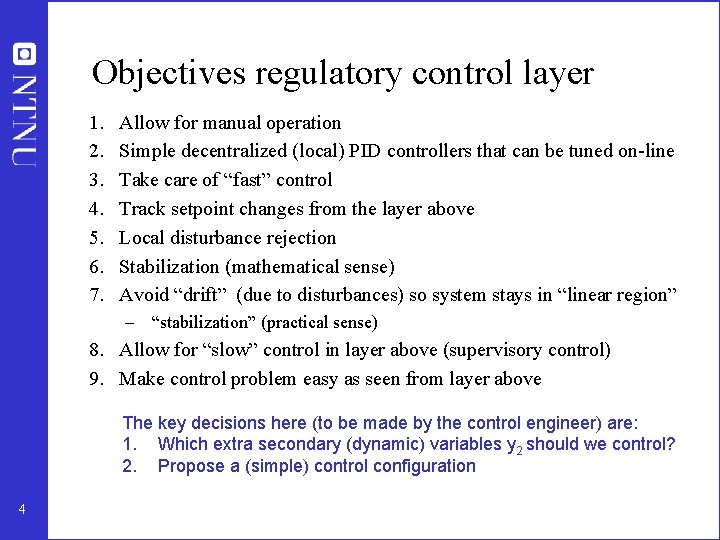
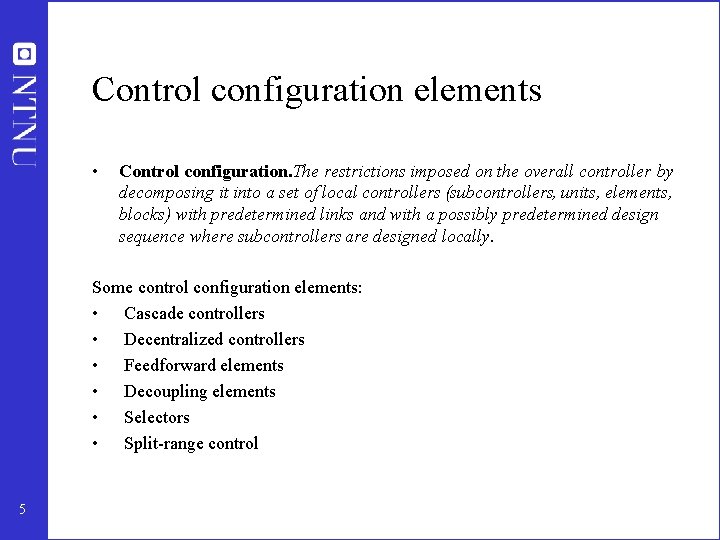
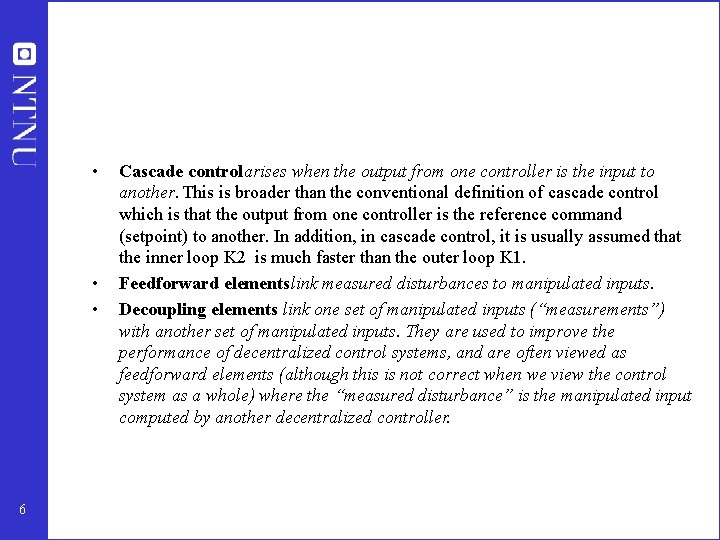
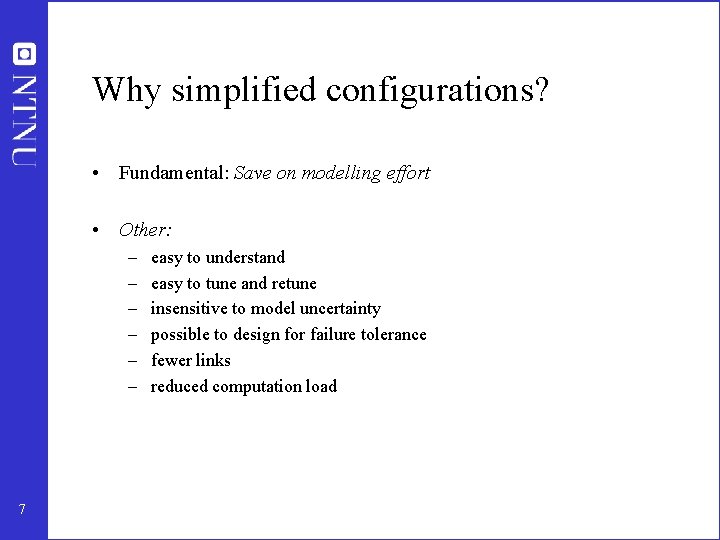
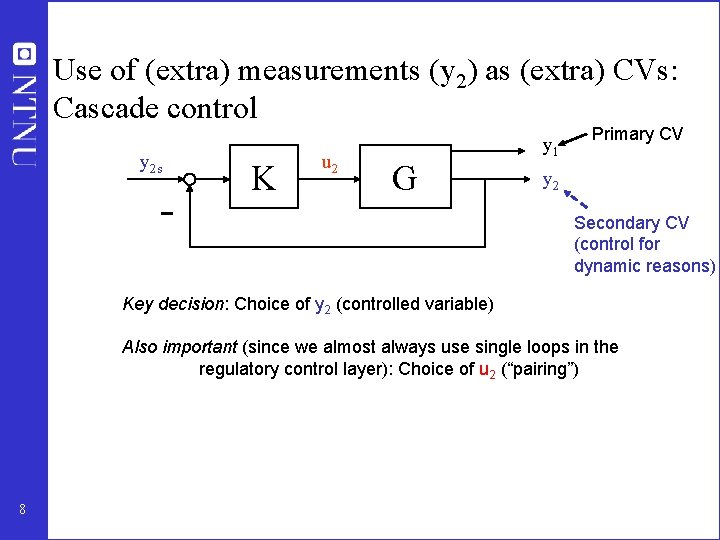
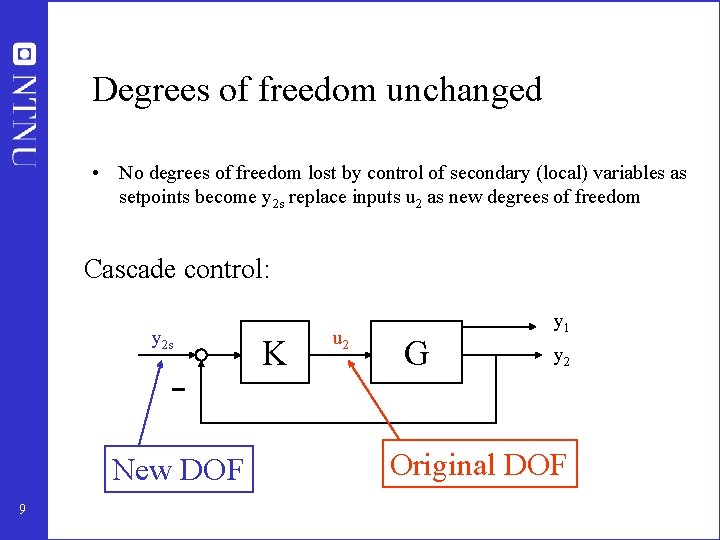
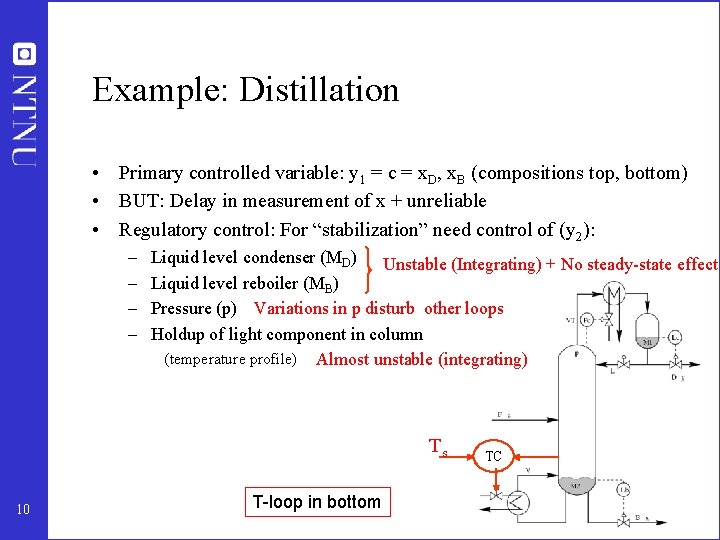
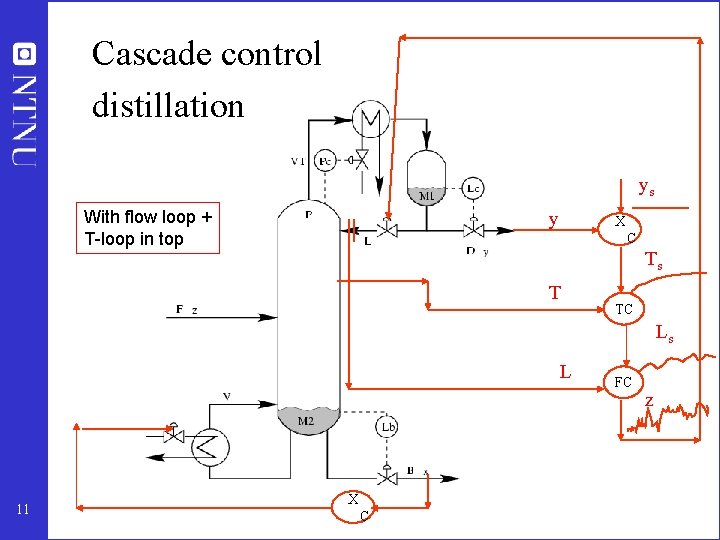
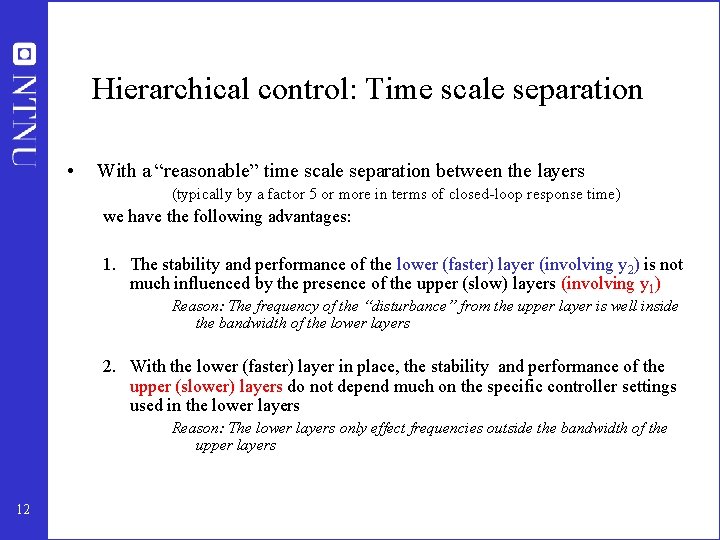
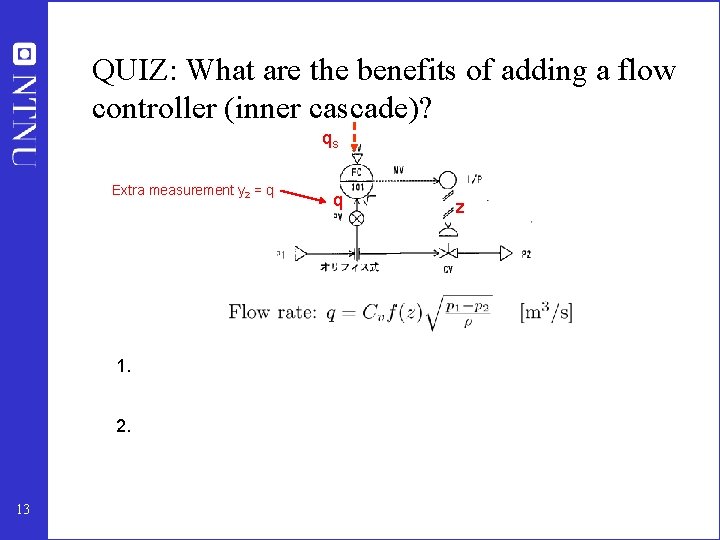
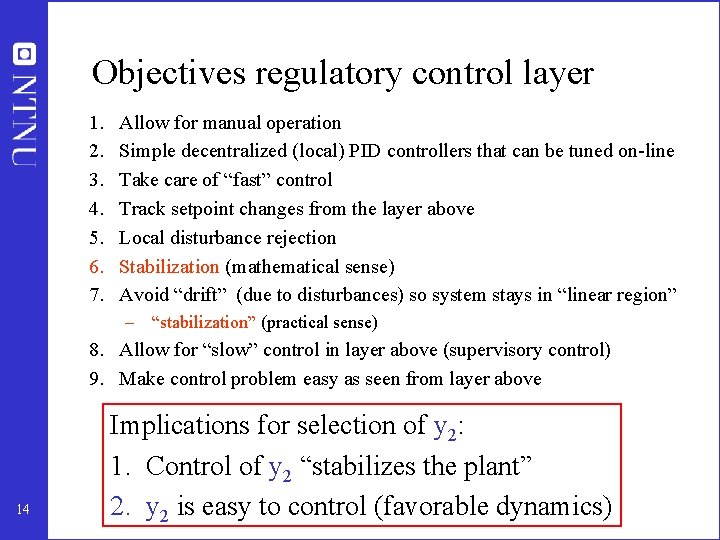
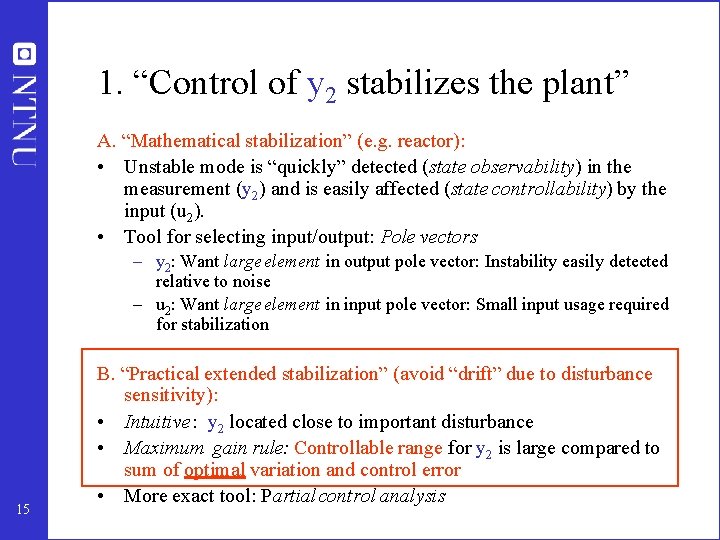
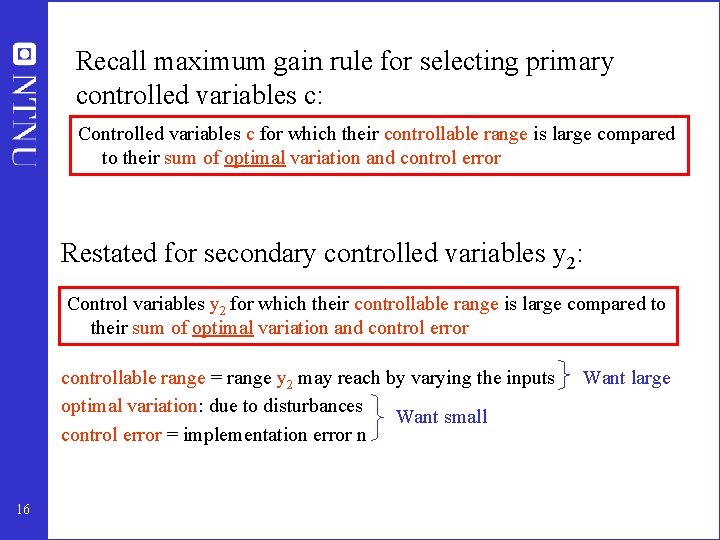
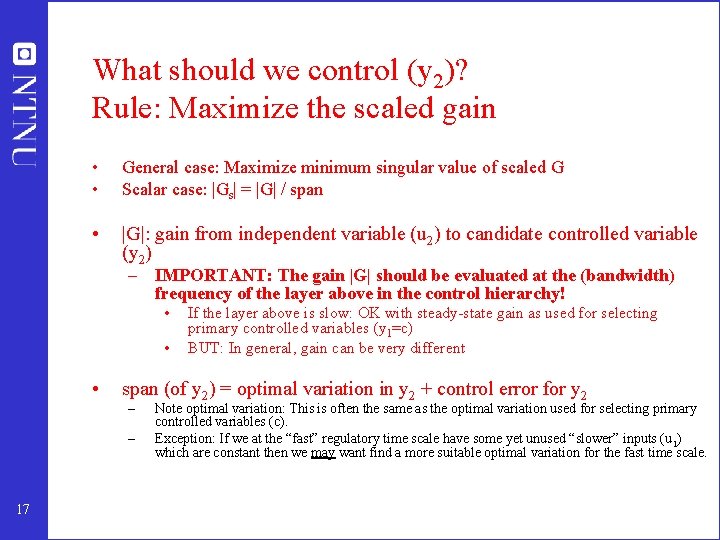
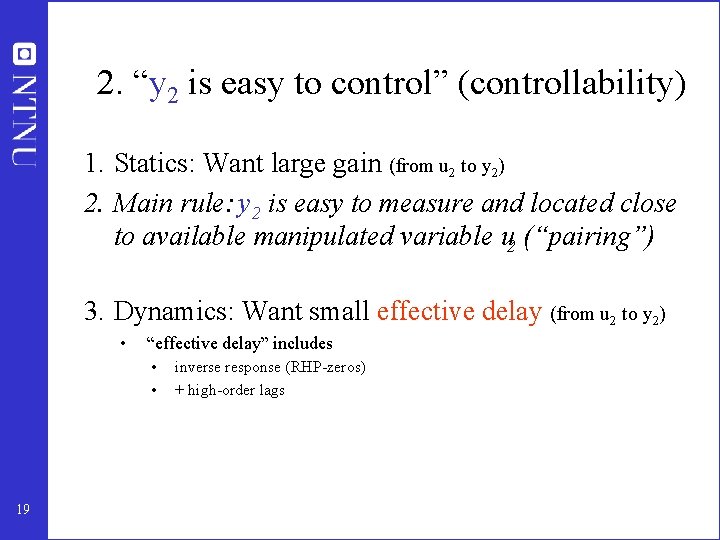
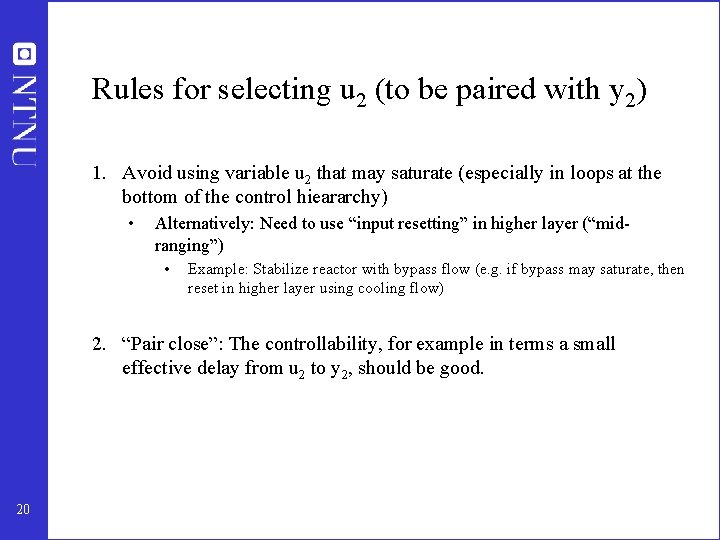
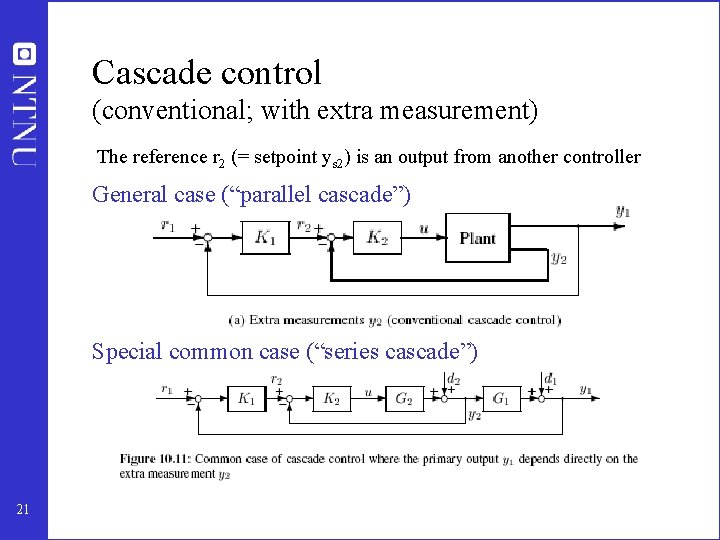
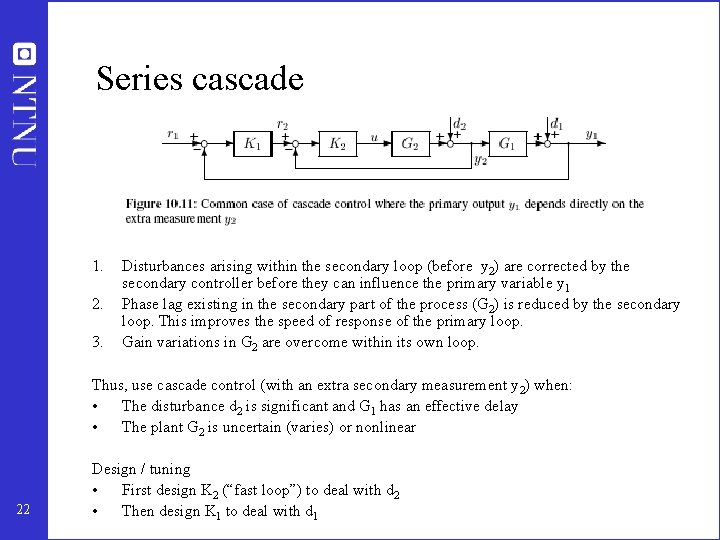
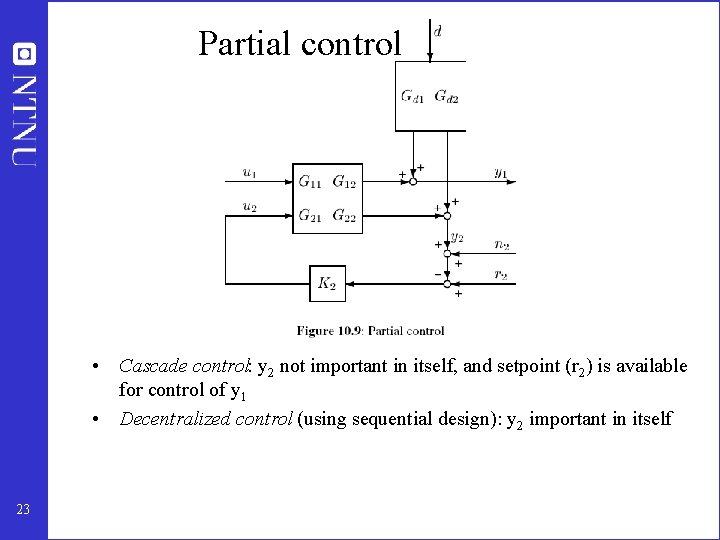
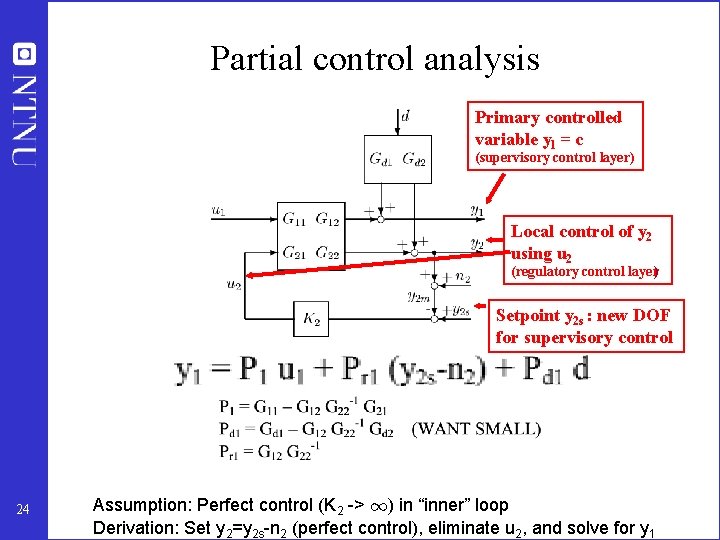
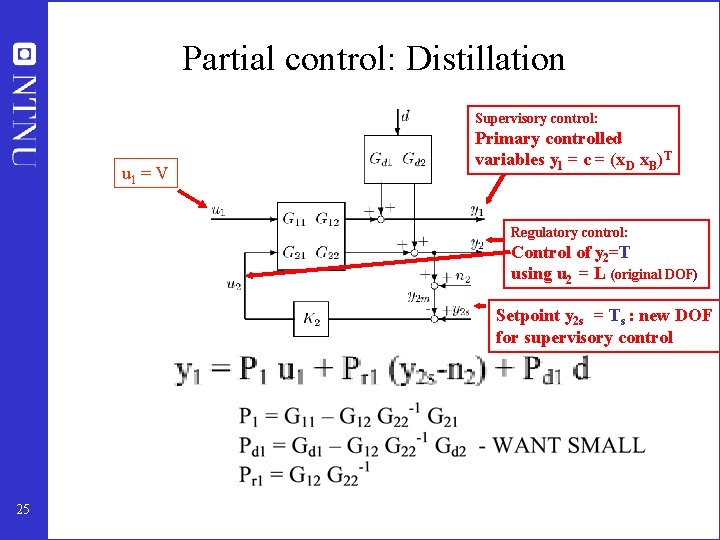
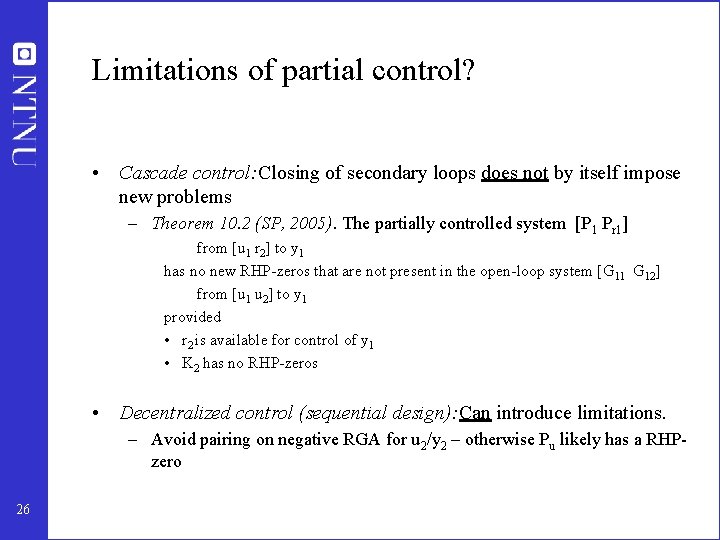
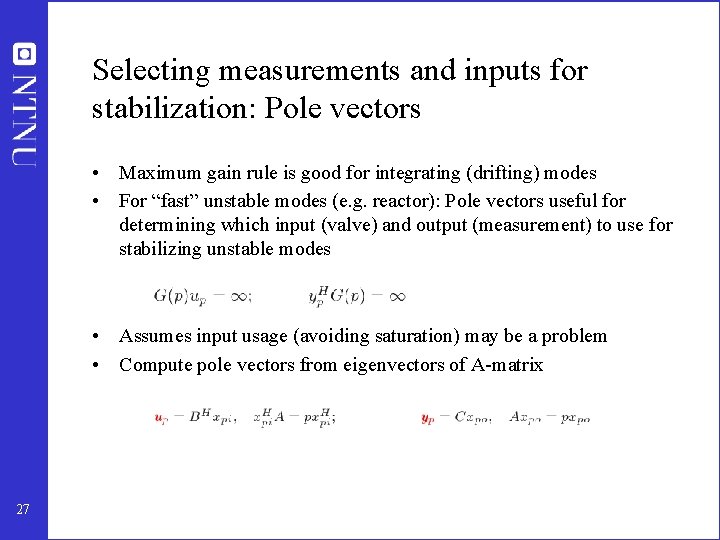
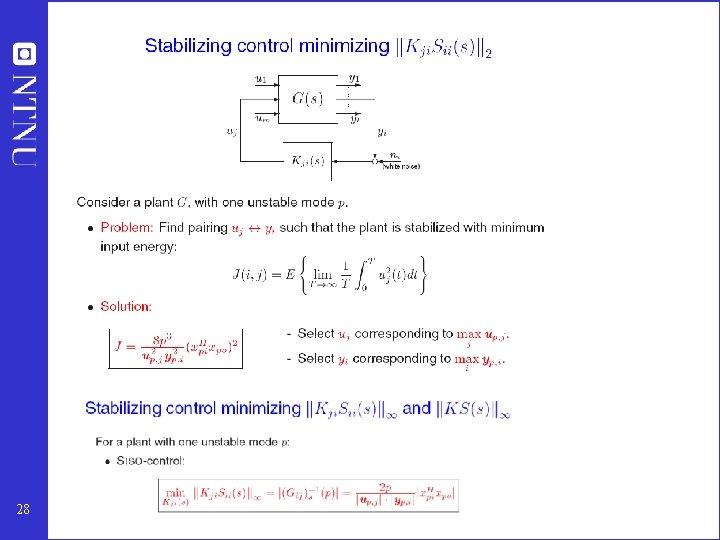
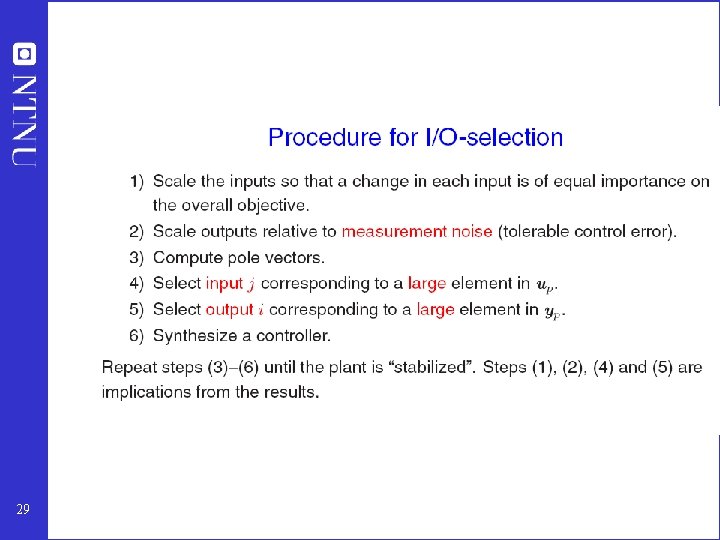
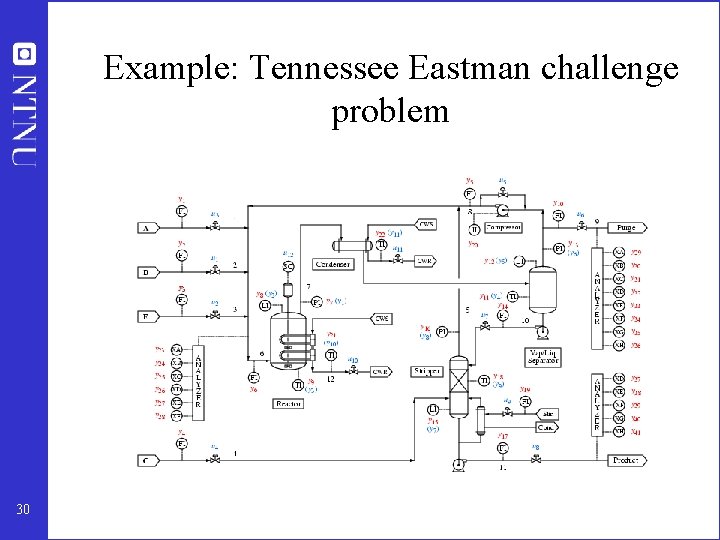
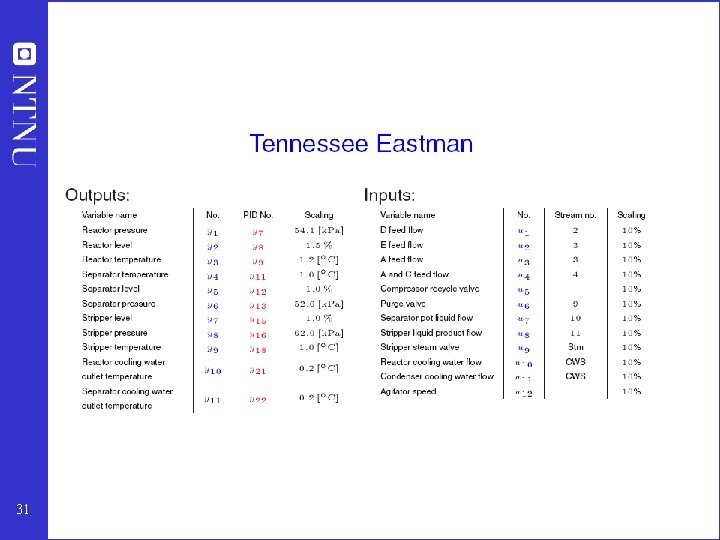
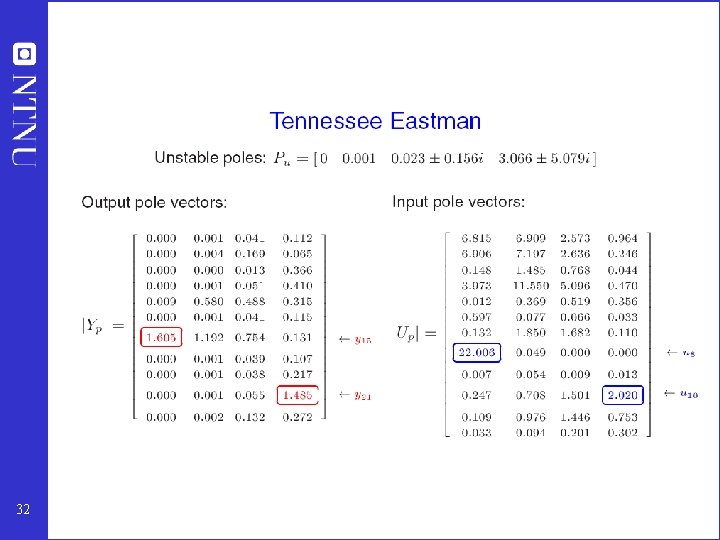
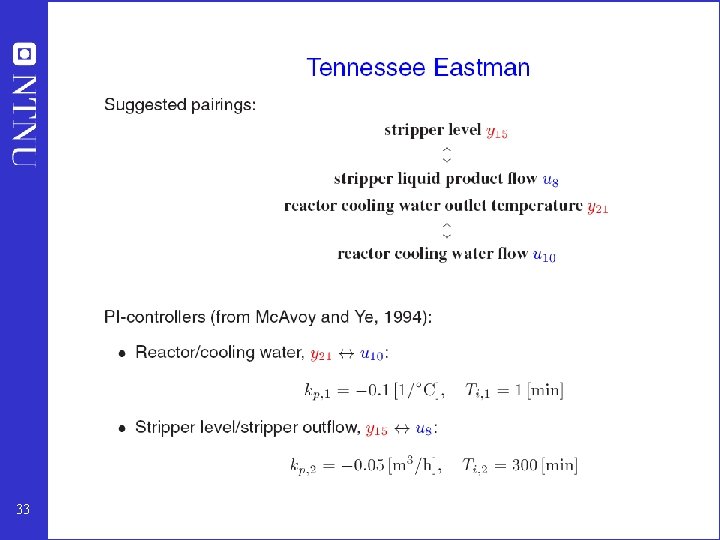
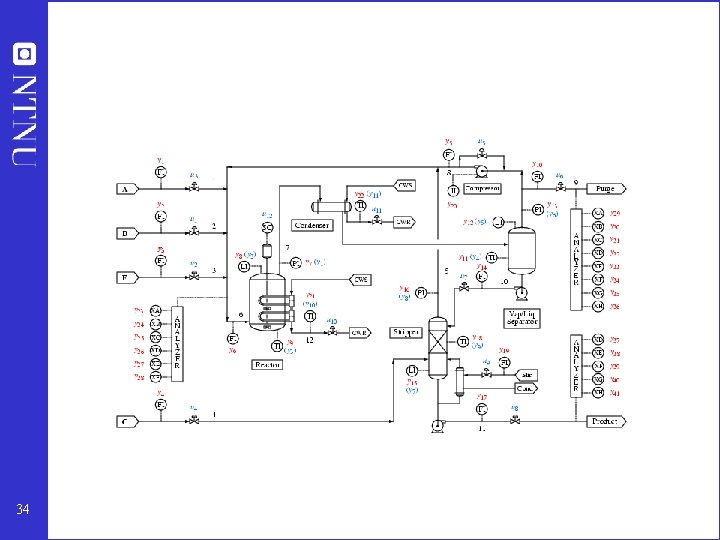
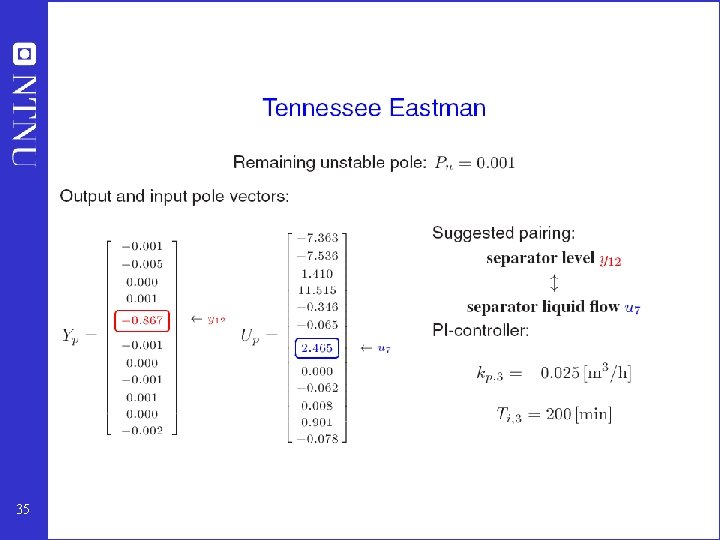
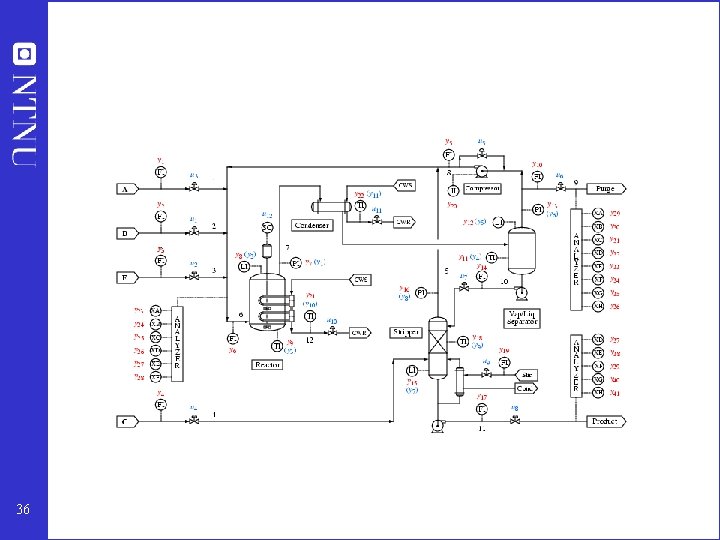
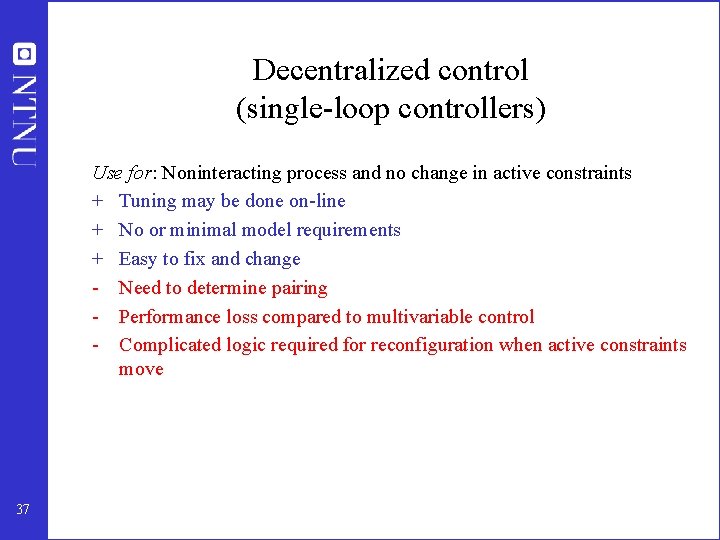
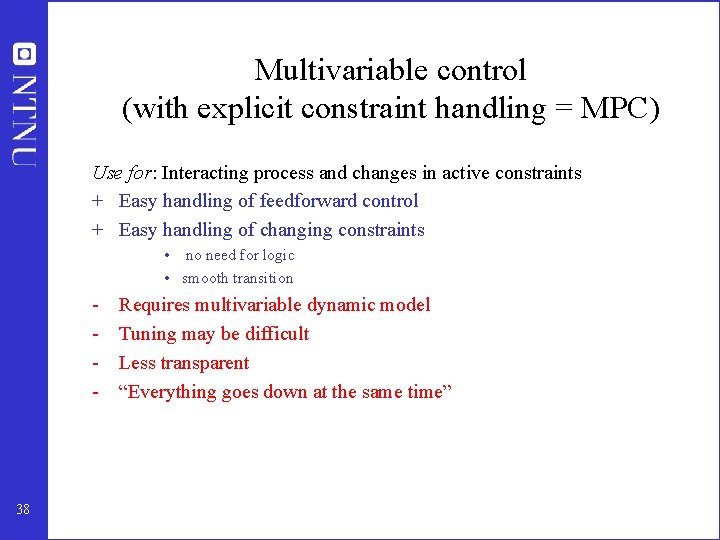
- Slides: 37
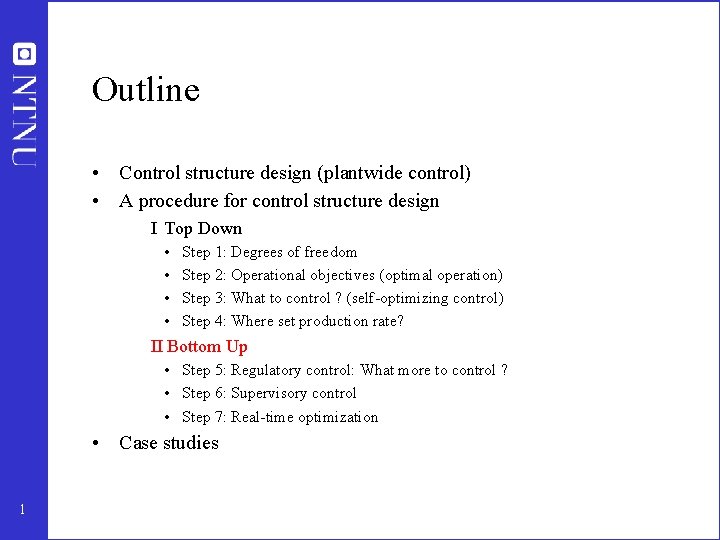
Outline • Control structure design (plantwide control) • A procedure for control structure design I Top Down • • Step 1: Degrees of freedom Step 2: Operational objectives (optimal operation) Step 3: What to control ? (self-optimizing control) Step 4: Where set production rate? II Bottom Up • Step 5: Regulatory control: What more to control ? • Step 6: Supervisory control • Step 7: Real-time optimization • Case studies 1
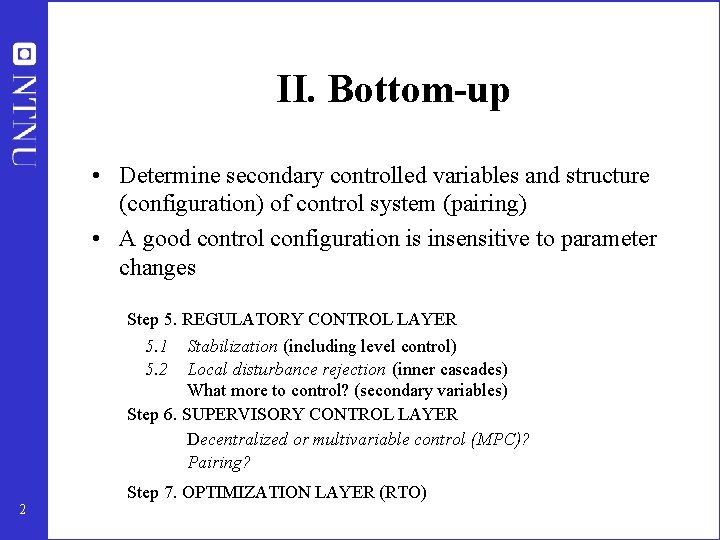
II. Bottom-up • Determine secondary controlled variables and structure (configuration) of control system (pairing) • A good control configuration is insensitive to parameter changes Step 5. REGULATORY CONTROL LAYER 5. 1 Stabilization (including level control) 5. 2 Local disturbance rejection (inner cascades) What more to control? (secondary variables) Step 6. SUPERVISORY CONTROL LAYER Decentralized or multivariable control (MPC)? Pairing? Step 7. OPTIMIZATION LAYER (RTO) 2
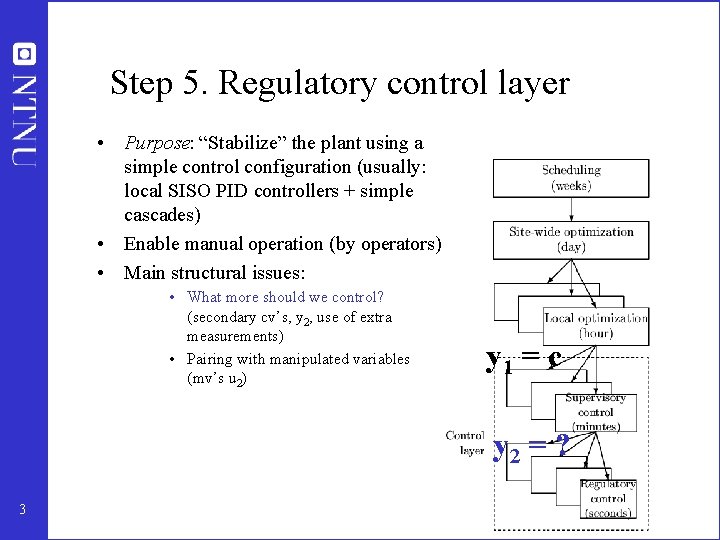
Step 5. Regulatory control layer • Purpose: “Stabilize” the plant using a simple control configuration (usually: local SISO PID controllers + simple cascades) • Enable manual operation (by operators) • Main structural issues: • What more should we control? (secondary cv’s, y 2, use of extra measurements) • Pairing with manipulated variables (mv’s u 2) y 1 = c y 2 = ? 3
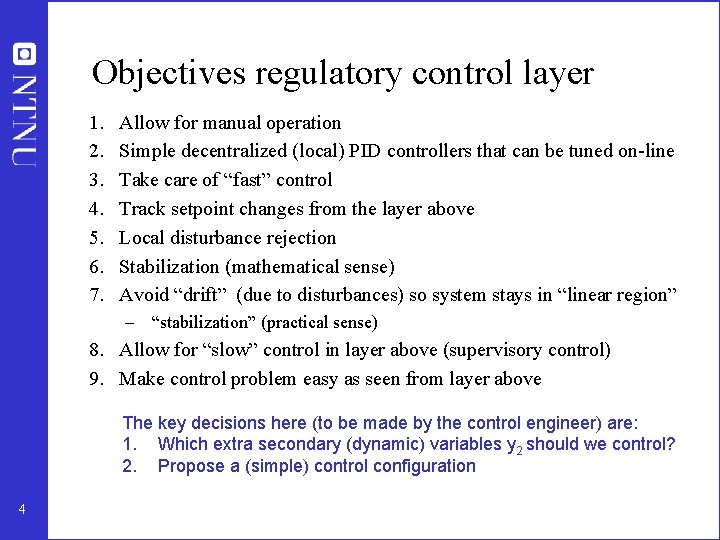
Objectives regulatory control layer 1. 2. 3. 4. 5. 6. 7. Allow for manual operation Simple decentralized (local) PID controllers that can be tuned on-line Take care of “fast” control Track setpoint changes from the layer above Local disturbance rejection Stabilization (mathematical sense) Avoid “drift” (due to disturbances) so system stays in “linear region” – “stabilization” (practical sense) 8. Allow for “slow” control in layer above (supervisory control) 9. Make control problem easy as seen from layer above The key decisions here (to be made by the control engineer) are: 1. Which extra secondary (dynamic) variables y 2 should we control? 2. Propose a (simple) control configuration 4
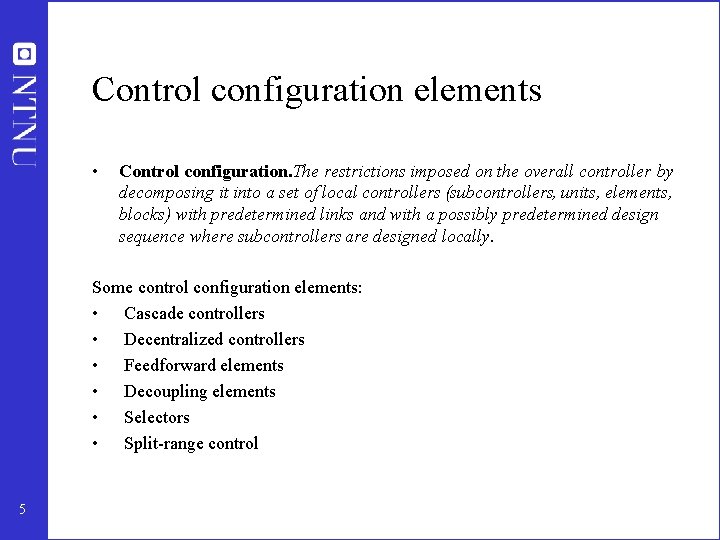
Control configuration elements • Control configuration. The restrictions imposed on the overall controller by decomposing it into a set of local controllers (subcontrollers, units, elements, blocks) with predetermined links and with a possibly predetermined design sequence where subcontrollers are designed locally. Some control configuration elements: • Cascade controllers • Decentralized controllers • Feedforward elements • Decoupling elements • Selectors • Split-range control 5
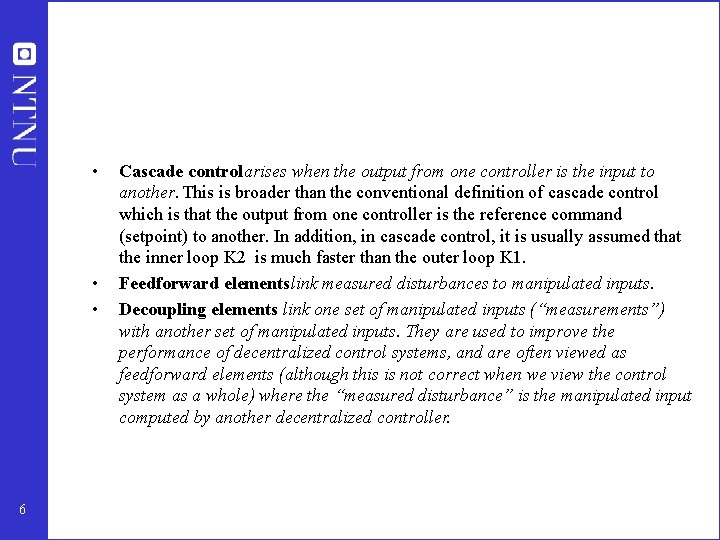
• • • 6 Cascade control arises when the output from one controller is the input to another. This is broader than the conventional definition of cascade control which is that the output from one controller is the reference command (setpoint) to another. In addition, in cascade control, it is usually assumed that the inner loop K 2 is much faster than the outer loop K 1. Feedforward elementslink measured disturbances to manipulated inputs. Decoupling elements link one set of manipulated inputs (“measurements”) with another set of manipulated inputs. They are used to improve the performance of decentralized control systems, and are often viewed as feedforward elements (although this is not correct when we view the control system as a whole) where the “measured disturbance” is the manipulated input computed by another decentralized controller.
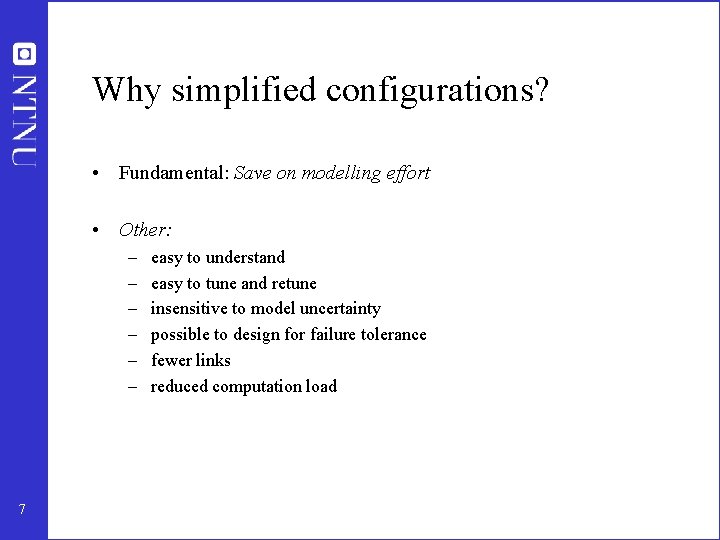
Why simplified configurations? • Fundamental: Save on modelling effort • Other: – – – 7 easy to understand easy to tune and retune insensitive to model uncertainty possible to design for failure tolerance fewer links reduced computation load
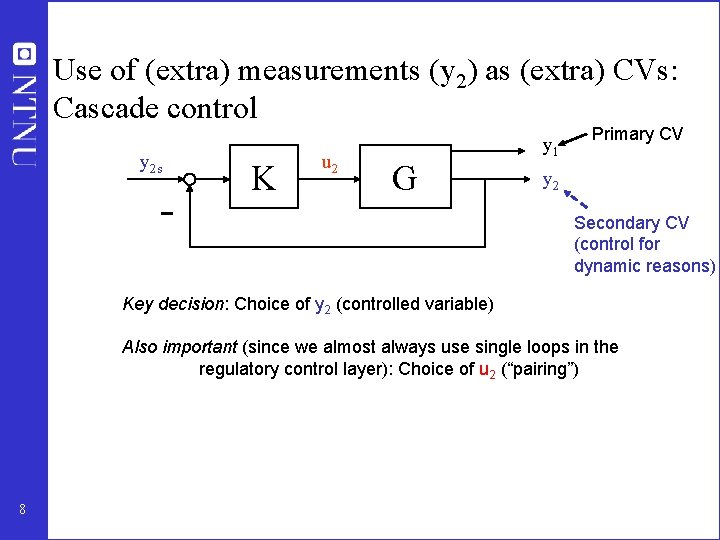
Use of (extra) measurements (y 2) as (extra) CVs: Cascade control y 2 s K u 2 G y 1 Primary CV y 2 Secondary CV (control for dynamic reasons) Key decision: Choice of y 2 (controlled variable) Also important (since we almost always use single loops in the regulatory control layer): Choice of u 2 (“pairing”) 8
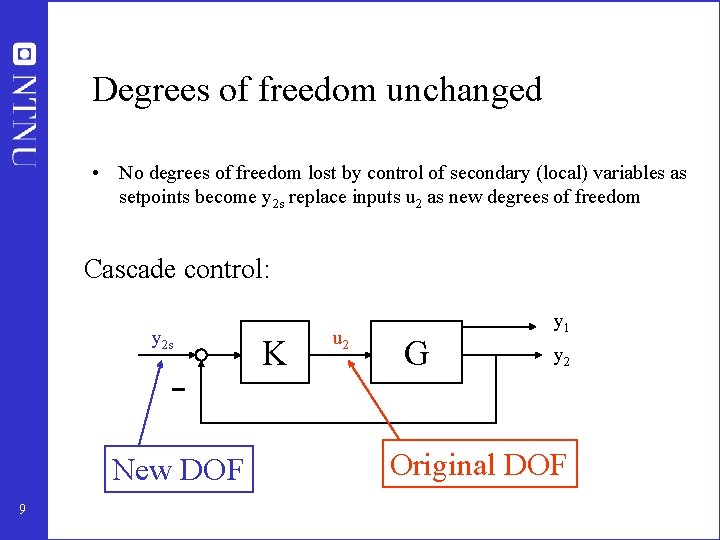
Degrees of freedom unchanged • No degrees of freedom lost by control of secondary (local) variables as setpoints become y 2 s replace inputs u 2 as new degrees of freedom Cascade control: y 2 s New DOF 9 K u 2 G y 1 y 2 Original DOF
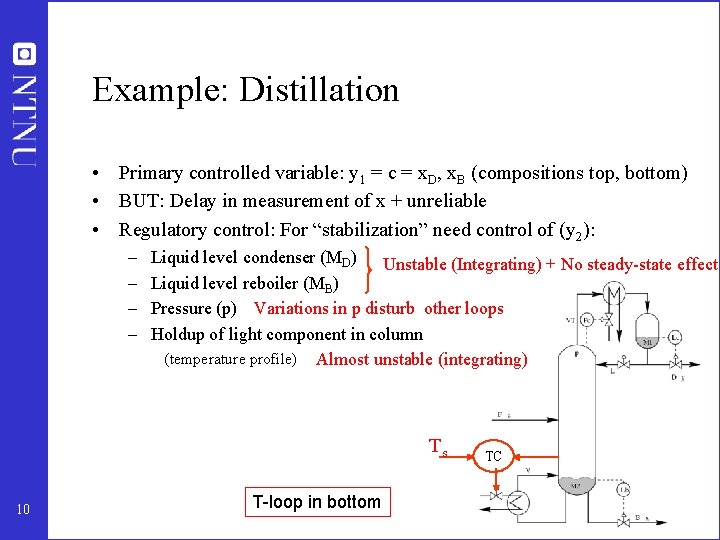
Example: Distillation • Primary controlled variable: y 1 = c = x. D, x. B (compositions top, bottom) • BUT: Delay in measurement of x + unreliable • Regulatory control: For “stabilization” need control of (y 2): – – Liquid level condenser (MD) Unstable (Integrating) + No steady-state effect Liquid level reboiler (MB) Pressure (p) Variations in p disturb other loops Holdup of light component in column (temperature profile) Almost unstable (integrating) Ts 10 T-loop in bottom TC
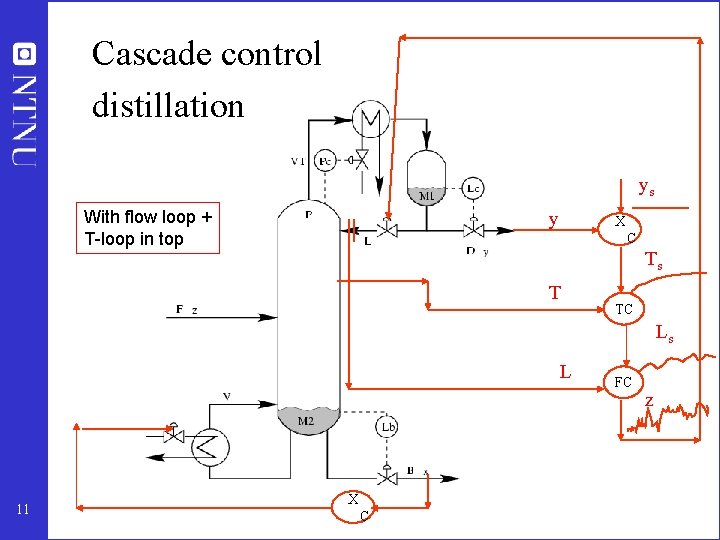
Cascade control distillation ys With flow loop + T-loop in top y X C Ts T TC Ls L 11 X C FC z
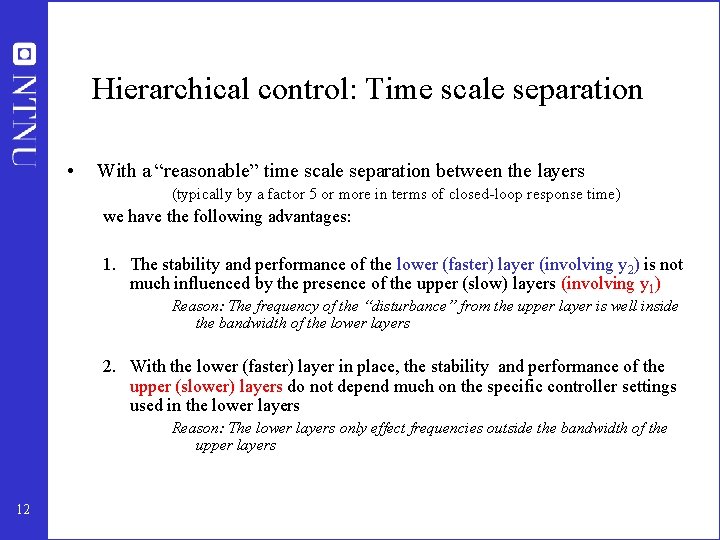
Hierarchical control: Time scale separation • With a “reasonable” time scale separation between the layers (typically by a factor 5 or more in terms of closed-loop response time) we have the following advantages: 1. The stability and performance of the lower (faster) layer (involving y 2) is not much influenced by the presence of the upper (slow) layers (involving y 1) Reason: The frequency of the “disturbance” from the upper layer is well inside the bandwidth of the lower layers 2. With the lower (faster) layer in place, the stability and performance of the upper (slower) layers do not depend much on the specific controller settings used in the lower layers Reason: The lower layers only effect frequencies outside the bandwidth of the upper layers 12
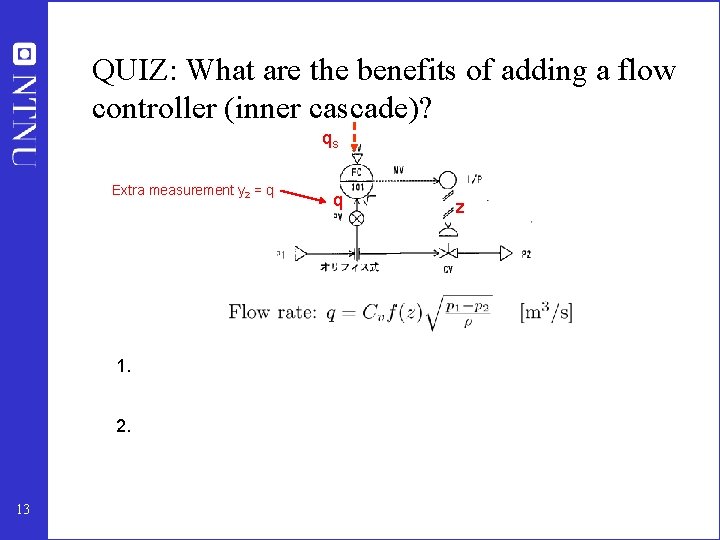
QUIZ: What are the benefits of adding a flow controller (inner cascade)? qs Extra measurement y 2 = q 1. 13 z Counteracts nonlinearity in valve, f(z) • 2. q With fast flow control we can assume q = qs Eliminates effect of disturbances in p 1 and p 2
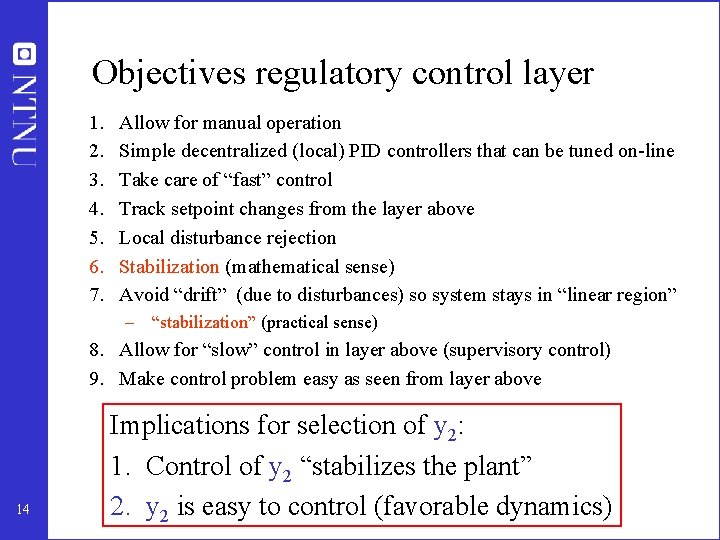
Objectives regulatory control layer 1. 2. 3. 4. 5. 6. 7. Allow for manual operation Simple decentralized (local) PID controllers that can be tuned on-line Take care of “fast” control Track setpoint changes from the layer above Local disturbance rejection Stabilization (mathematical sense) Avoid “drift” (due to disturbances) so system stays in “linear region” – “stabilization” (practical sense) 8. Allow for “slow” control in layer above (supervisory control) 9. Make control problem easy as seen from layer above 14 Implications for selection of y 2: 1. Control of y 2 “stabilizes the plant” 2. y 2 is easy to control (favorable dynamics)
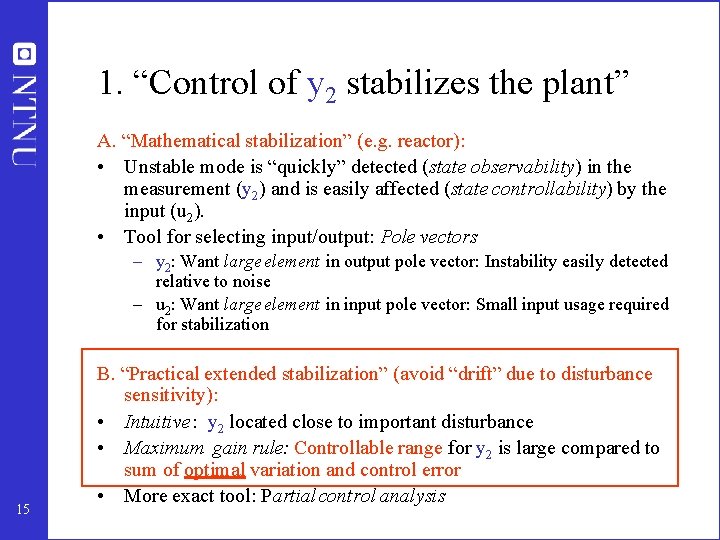
1. “Control of y 2 stabilizes the plant” A. “Mathematical stabilization” (e. g. reactor): • Unstable mode is “quickly” detected (state observability) in the measurement (y 2) and is easily affected (state controllability) by the input (u 2). • Tool for selecting input/output: Pole vectors – y 2: Want large element in output pole vector: Instability easily detected relative to noise – u 2: Want large element in input pole vector: Small input usage required for stabilization 15 B. “Practical extended stabilization” (avoid “drift” due to disturbance sensitivity): • Intuitive: y 2 located close to important disturbance • Maximum gain rule: Controllable range for y 2 is large compared to sum of optimal variation and control error • More exact tool: Partial control analysis
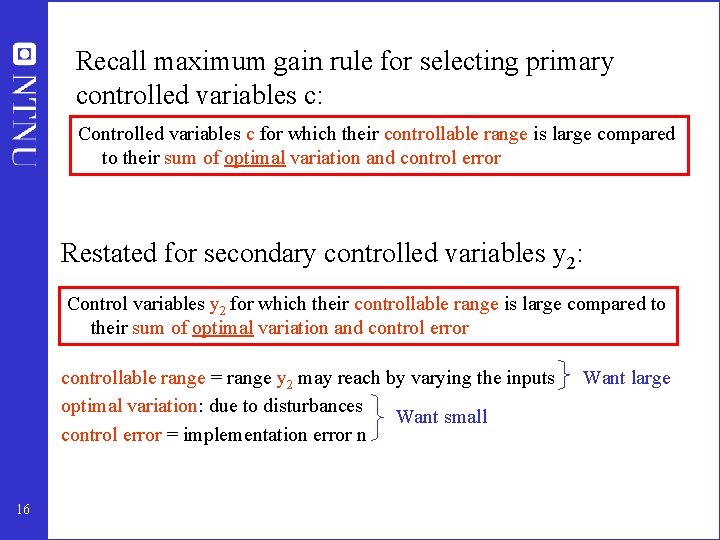
Recall maximum gain rule for selecting primary controlled variables c: Controlled variables c for which their controllable range is large compared to their sum of optimal variation and control error Restated for secondary controlled variables y 2: Control variables y 2 for which their controllable range is large compared to their sum of optimal variation and control error controllable range = range y 2 may reach by varying the inputs optimal variation: due to disturbances Want small control error = implementation error n 16 Want large
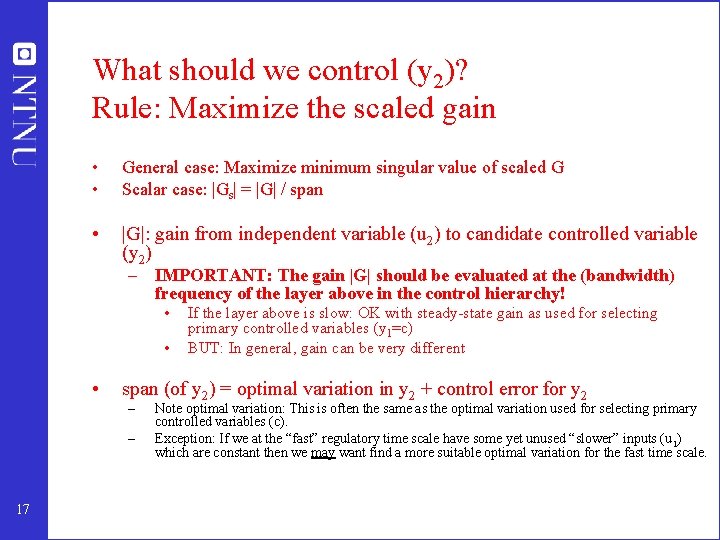
What should we control (y 2)? Rule: Maximize the scaled gain • • General case: Maximize minimum singular value of scaled G Scalar case: |Gs| = |G| / span • |G|: gain from independent variable (u 2) to candidate controlled variable (y 2) – IMPORTANT: The gain |G| should be evaluated at the (bandwidth) frequency of the layer above in the control hierarchy! • • • span (of y 2) = optimal variation in y 2 + control error for y 2 – – 17 If the layer above is slow: OK with steady-state gain as used for selecting primary controlled variables (y 1=c) BUT: In general, gain can be very different Note optimal variation: This is often the same as the optimal variation used for selecting primary controlled variables (c). Exception: If we at the “fast” regulatory time scale have some yet unused “slower” inputs (u 1) which are constant then we may want find a more suitable optimal variation for the fast time scale.
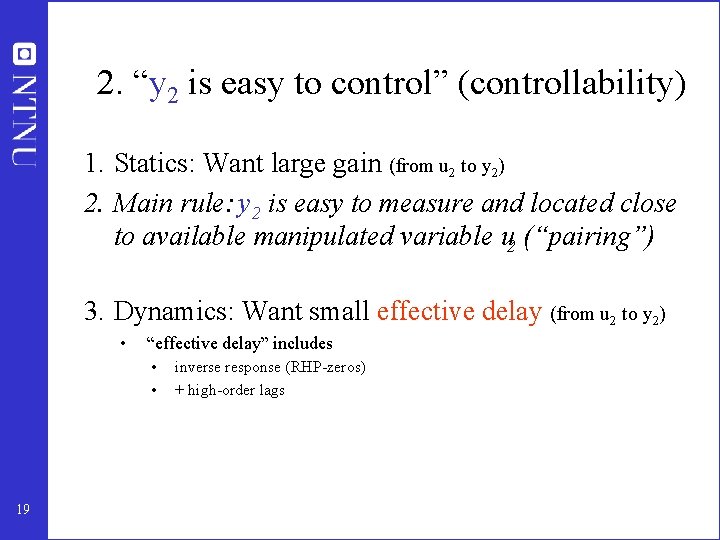
2. “y 2 is easy to control” (controllability) 1. Statics: Want large gain (from u 2 to y 2) 2. Main rule: y 2 is easy to measure and located close to available manipulated variable u 2 (“pairing”) 3. Dynamics: Want small effective delay (from u 2 to y 2) • “effective delay” includes • • 19 inverse response (RHP-zeros) + high-order lags
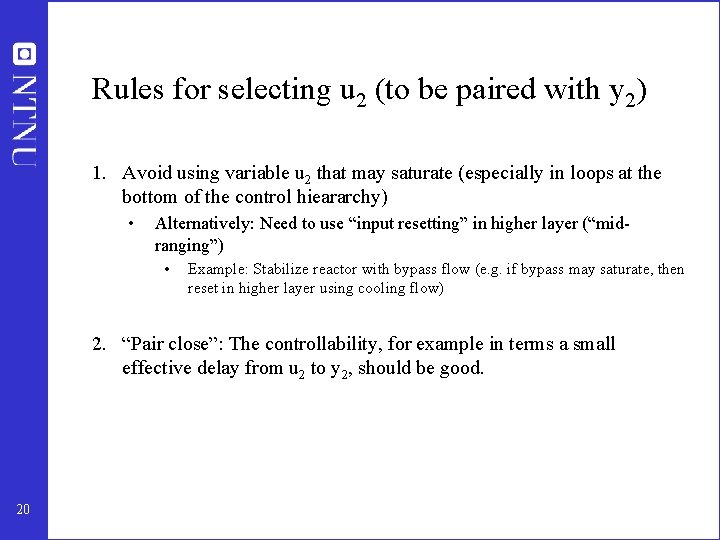
Rules for selecting u 2 (to be paired with y 2) 1. Avoid using variable u 2 that may saturate (especially in loops at the bottom of the control hieararchy) • Alternatively: Need to use “input resetting” in higher layer (“midranging”) • Example: Stabilize reactor with bypass flow (e. g. if bypass may saturate, then reset in higher layer using cooling flow) 2. “Pair close”: The controllability, for example in terms a small effective delay from u 2 to y 2, should be good. 20
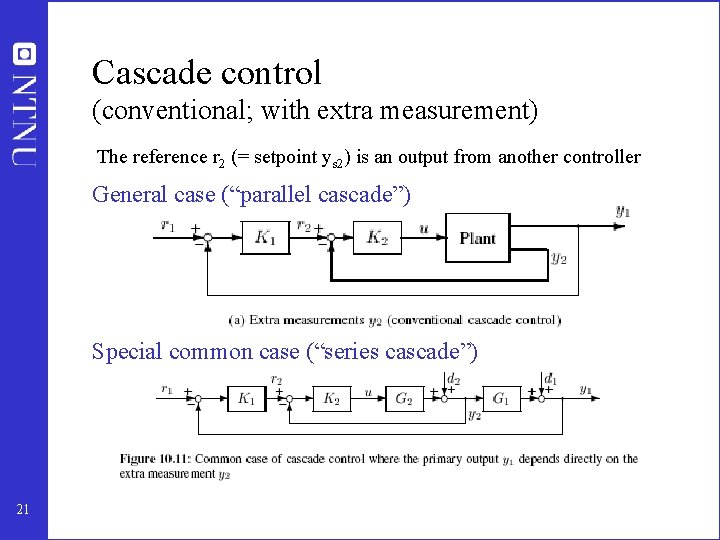
Cascade control (conventional; with extra measurement) The reference r 2 (= setpoint ys 2) is an output from another controller General case (“parallel cascade”) Special common case (“series cascade”) 21
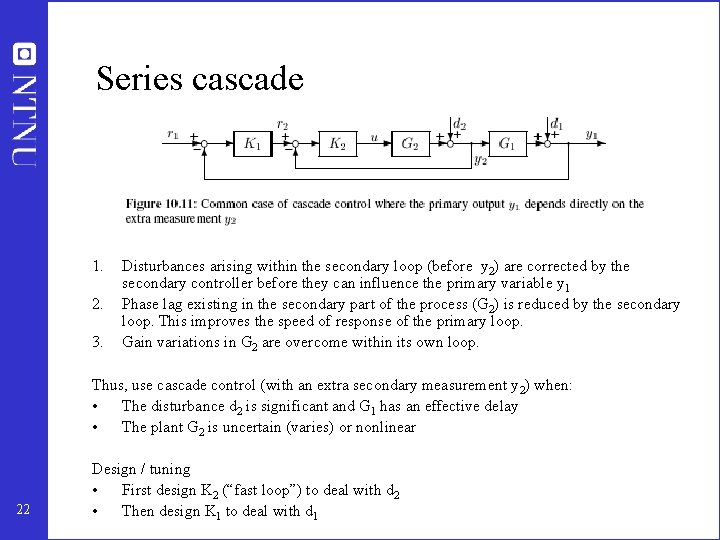
Series cascade 1. 2. 3. Disturbances arising within the secondary loop (before y 2) are corrected by the secondary controller before they can influence the primary variable y 1 Phase lag existing in the secondary part of the process (G 2) is reduced by the secondary loop. This improves the speed of response of the primary loop. Gain variations in G 2 are overcome within its own loop. Thus, use cascade control (with an extra secondary measurement y 2) when: • The disturbance d 2 is significant and G 1 has an effective delay • The plant G 2 is uncertain (varies) or nonlinear 22 Design / tuning • First design K 2 (“fast loop”) to deal with d 2 • Then design K 1 to deal with d 1
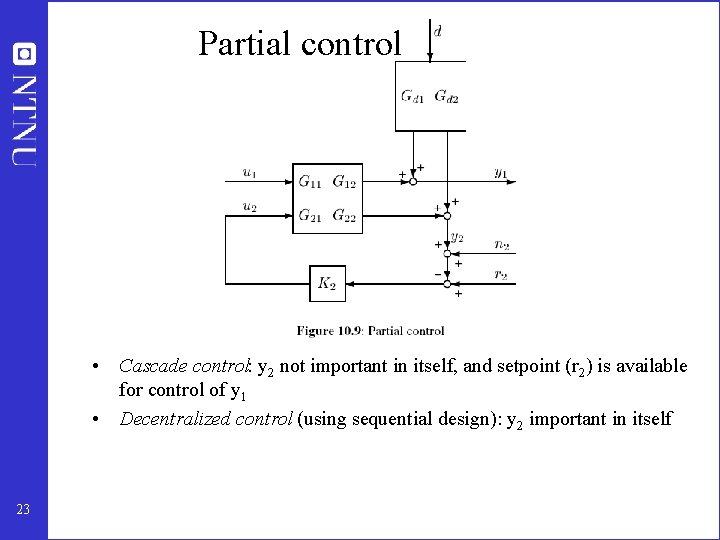
Partial control • Cascade control: y 2 not important in itself, and setpoint (r 2) is available for control of y 1 • Decentralized control (using sequential design): y 2 important in itself 23
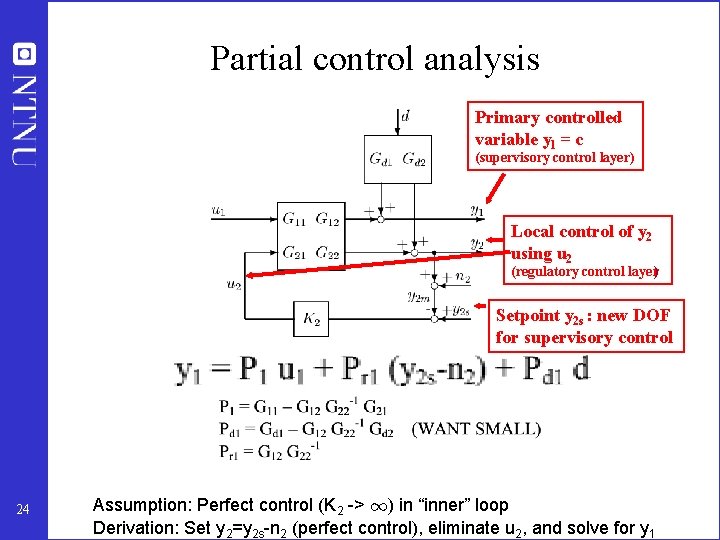
Partial control analysis Primary controlled variable y 1 = c (supervisory control layer) Local control of y 2 using u 2 (regulatory control layer) Setpoint y 2 s : new DOF for supervisory control 24 Assumption: Perfect control (K 2 -> 1) in “inner” loop Derivation: Set y 2=y 2 s-n 2 (perfect control), eliminate u 2, and solve for y 1
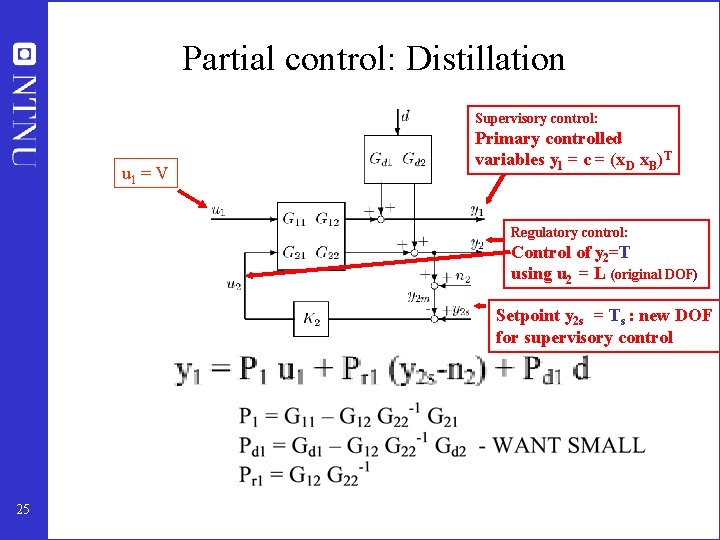
Partial control: Distillation Supervisory control: u 1 = V Primary controlled variables y 1 = c = (x D x. B)T Regulatory control: Control of y 2=T using u 2 = L (original DOF) Setpoint y 2 s = Ts : new DOF for supervisory control 25
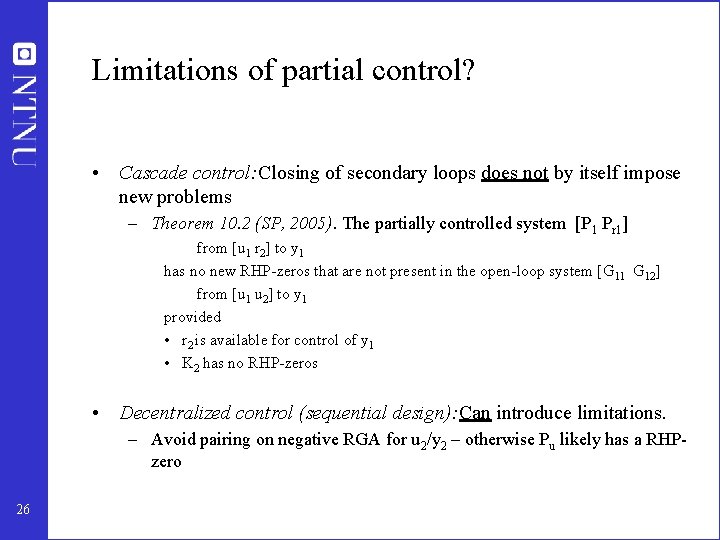
Limitations of partial control? • Cascade control: Closing of secondary loops does not by itself impose new problems – Theorem 10. 2 (SP, 2005). The partially controlled system [P 1 Pr 1] from [u 1 r 2] to y 1 has no new RHP-zeros that are not present in the open-loop system [G 11 G 12] from [u 1 u 2] to y 1 provided • r 2 is available for control of y 1 • K 2 has no RHP-zeros • Decentralized control (sequential design): Can introduce limitations. – Avoid pairing on negative RGA for u 2/y 2 – otherwise Pu likely has a RHPzero 26
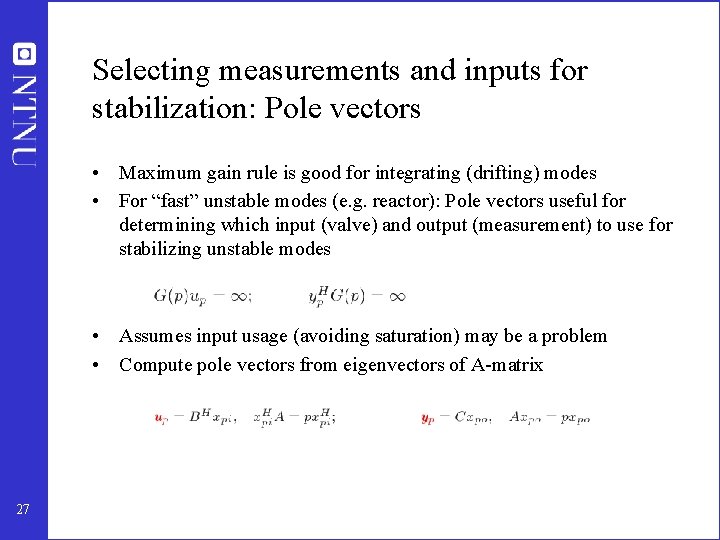
Selecting measurements and inputs for stabilization: Pole vectors • Maximum gain rule is good for integrating (drifting) modes • For “fast” unstable modes (e. g. reactor): Pole vectors useful for determining which input (valve) and output (measurement) to use for stabilizing unstable modes • Assumes input usage (avoiding saturation) may be a problem • Compute pole vectors from eigenvectors of A-matrix 27
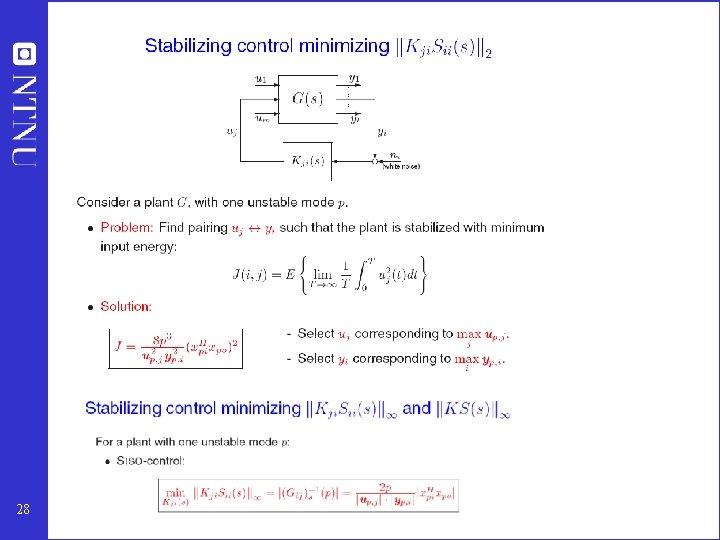
28
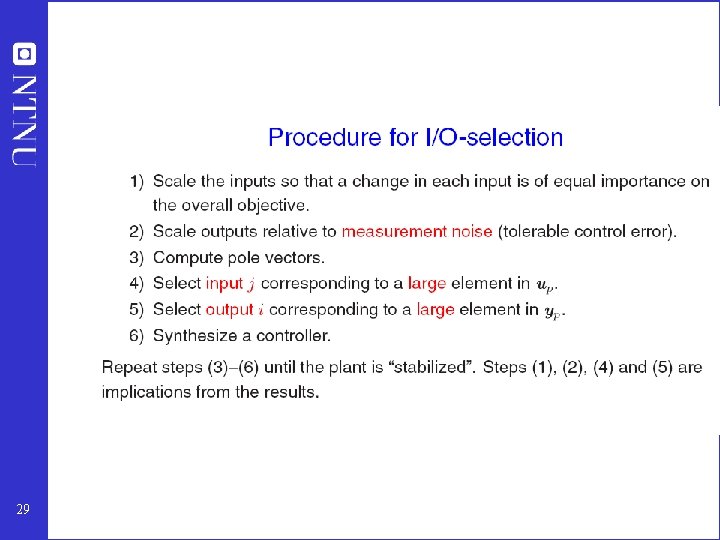
29
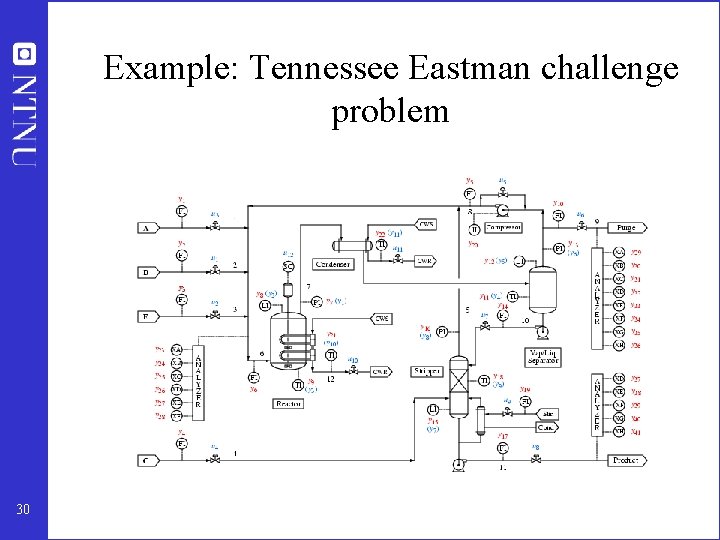
Example: Tennessee Eastman challenge problem 30
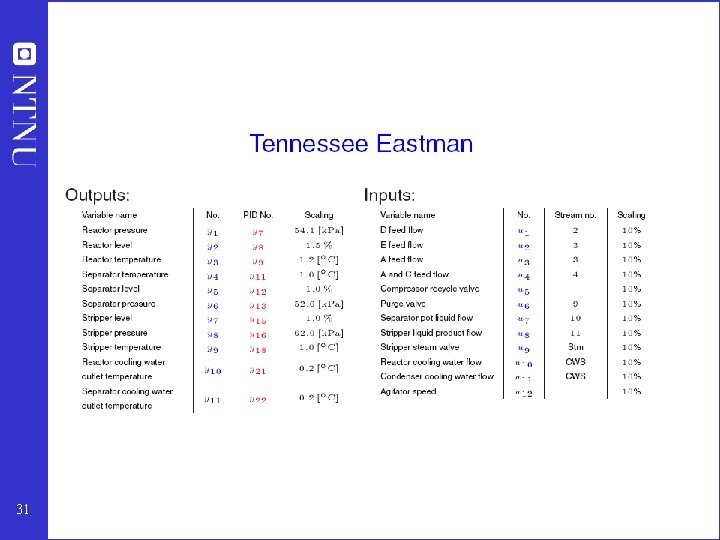
31
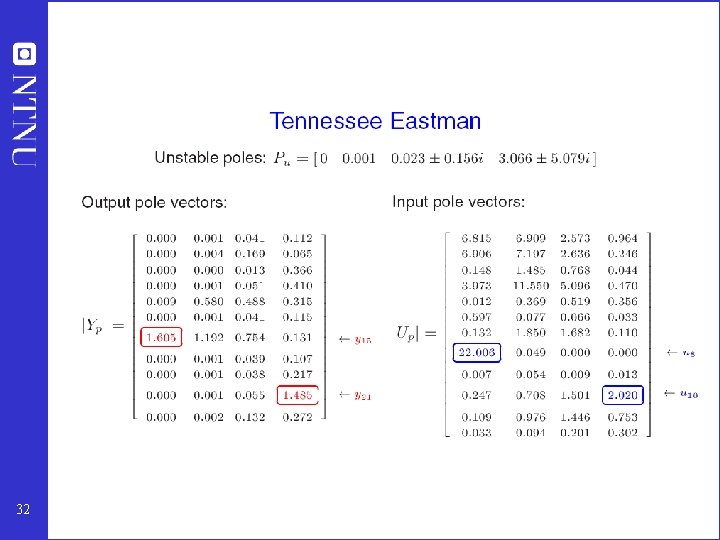
32
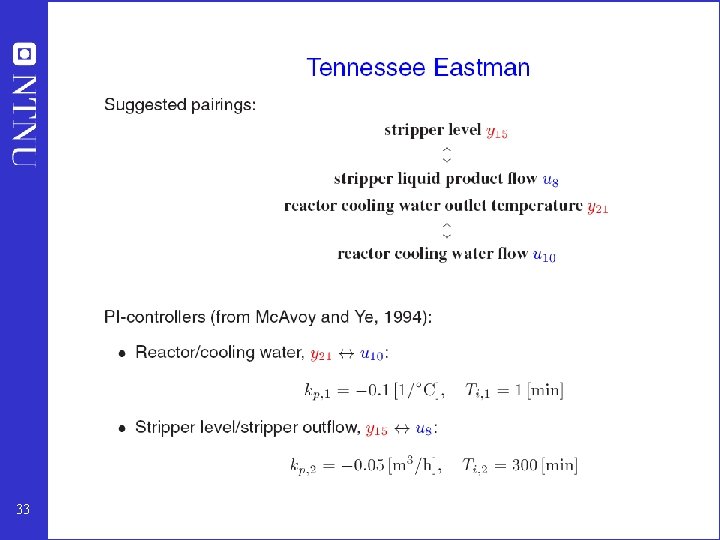
33
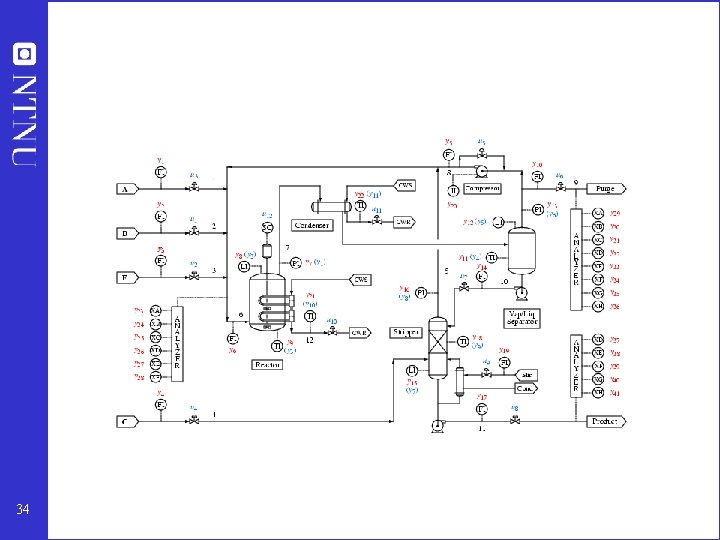
34
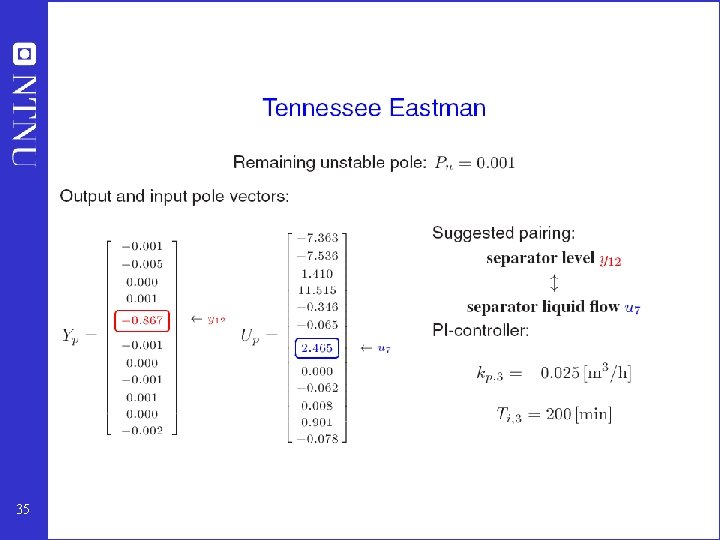
35
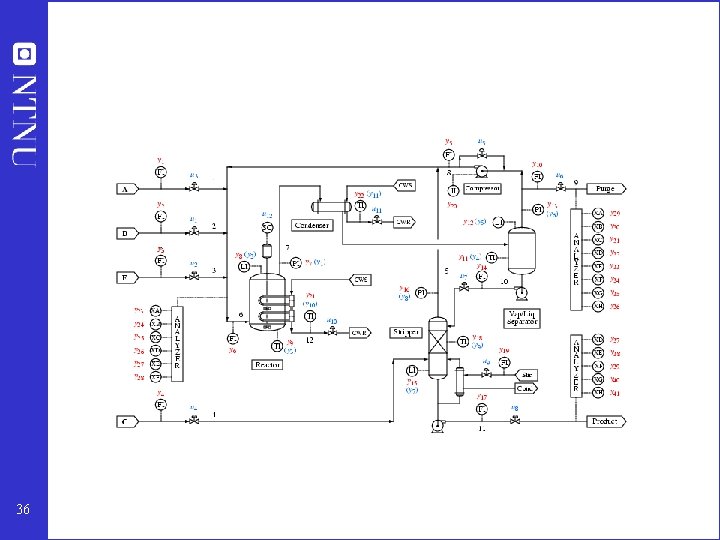
36
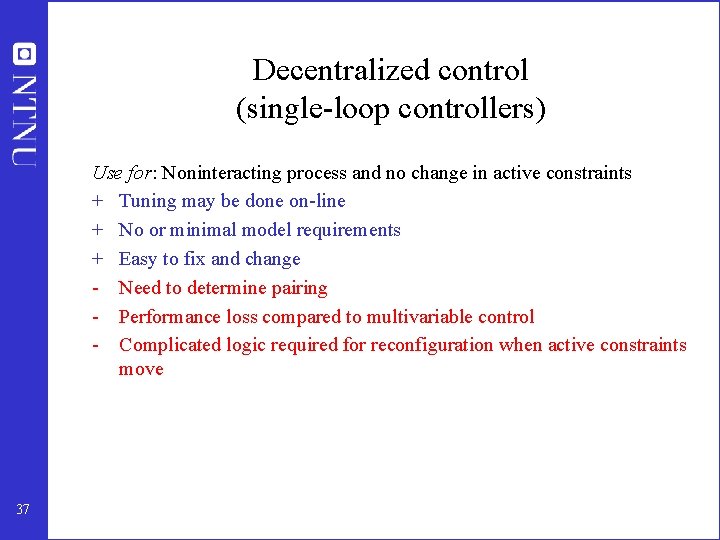
Decentralized control (single-loop controllers) Use for: Noninteracting process and no change in active constraints + Tuning may be done on-line + No or minimal model requirements + Easy to fix and change - Need to determine pairing - Performance loss compared to multivariable control - Complicated logic required for reconfiguration when active constraints move 37
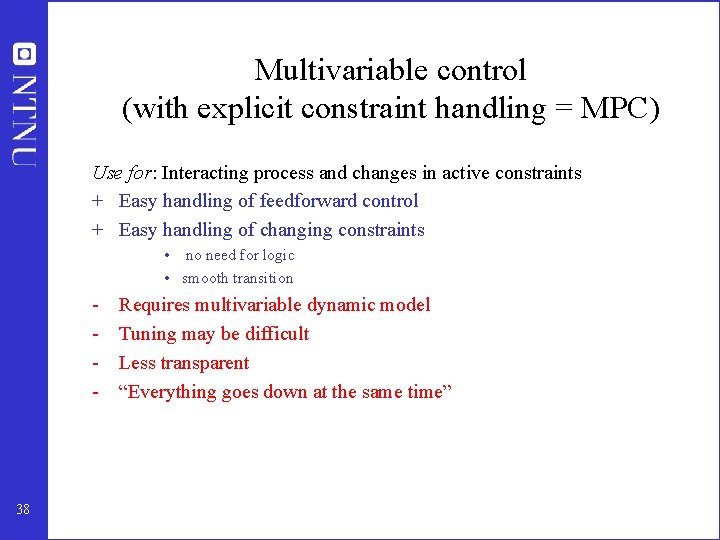
Multivariable control (with explicit constraint handling = MPC) Use for: Interacting process and changes in active constraints + Easy handling of feedforward control + Easy handling of changing constraints • no need for logic • smooth transition - 38 Requires multivariable dynamic model Tuning may be difficult Less transparent “Everything goes down at the same time”
How to find plantwide overhead rate
Plantwide overhead rate method
Lesson outline structure movement and control
Parliamentary procedure outline
It in a sentence
Organizational design: structure, culture, and control
Split range
How is the text presented
Quality assurance of raw materials
Istat training
Internal control structure
Machine design
Process of textbook development
Design and analysis of connecting rod ppt
Tpr technique?
Design issues of rpc
Single knuckle joint
Instrument flight procedure design
Salt water pool heat exchanger
Body paragraph format
Social growth outline structure
Unorganized points and outline structure
Support control and movement lesson outline
World wide web introduction
Types of research
Design process outline
Exploratory research example
Topical outline of quantitative research design
Giant molecular structure vs simple molecular structure
N++++
Giant molecular structure vs simple molecular structure
Surface and deep structure
Deep surface structure
S s' 's grammar
Zinc oxide + nitric acid → zinc nitrate + water
Static and dynamic queue in data structure
Contoh record adalah
Surface structure