Ne SSI Generation II The Elements Power of
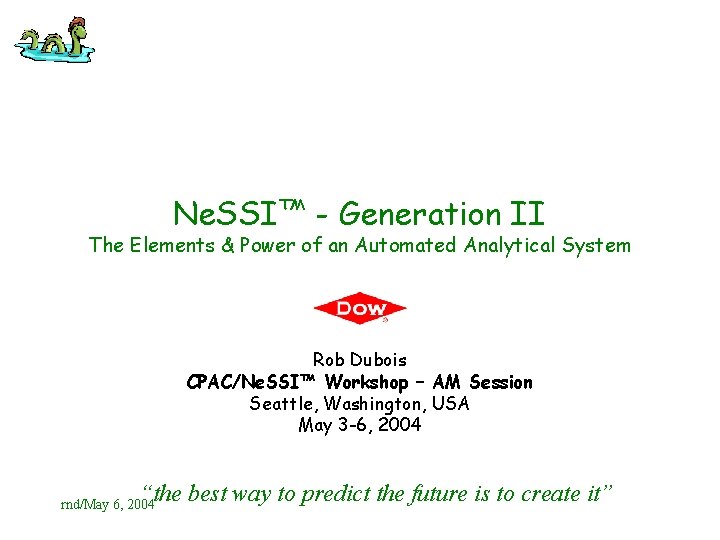
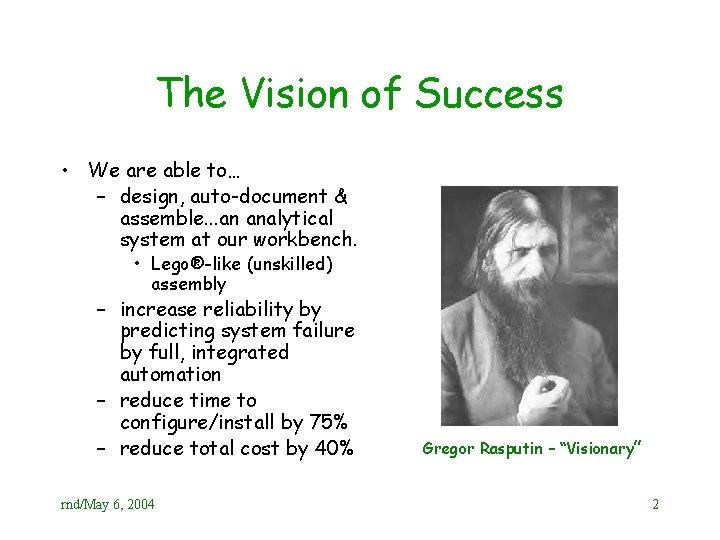
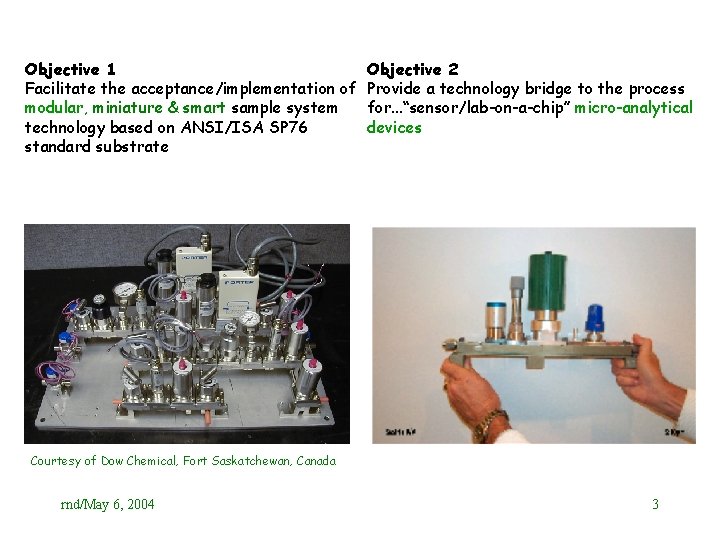
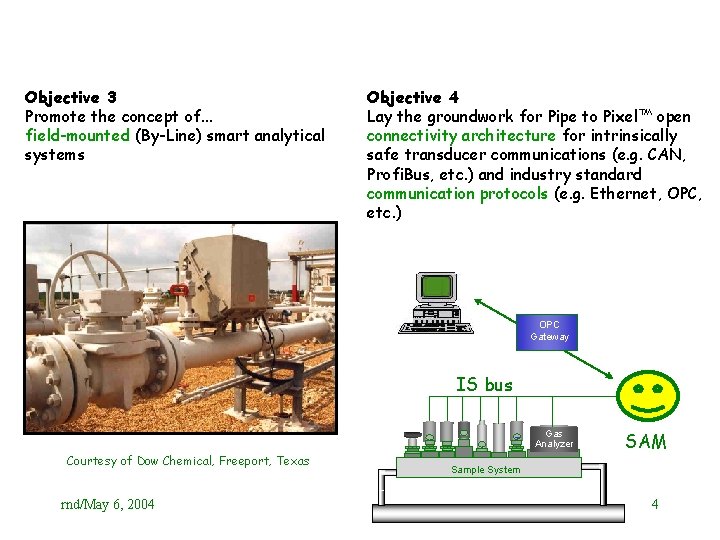
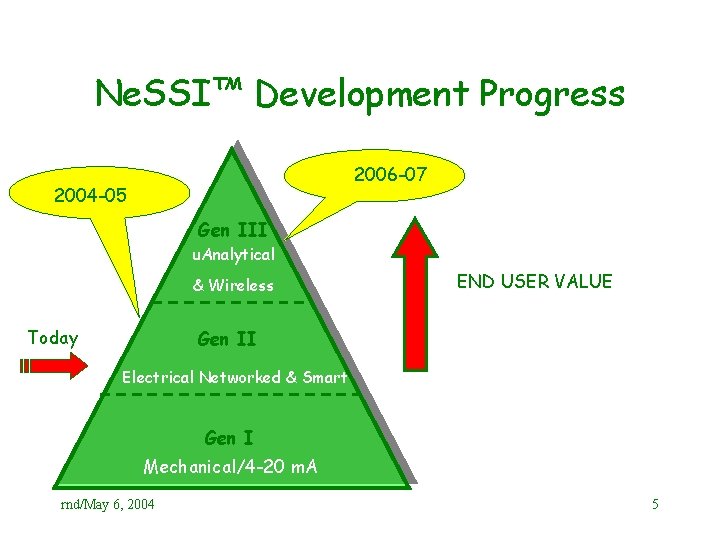
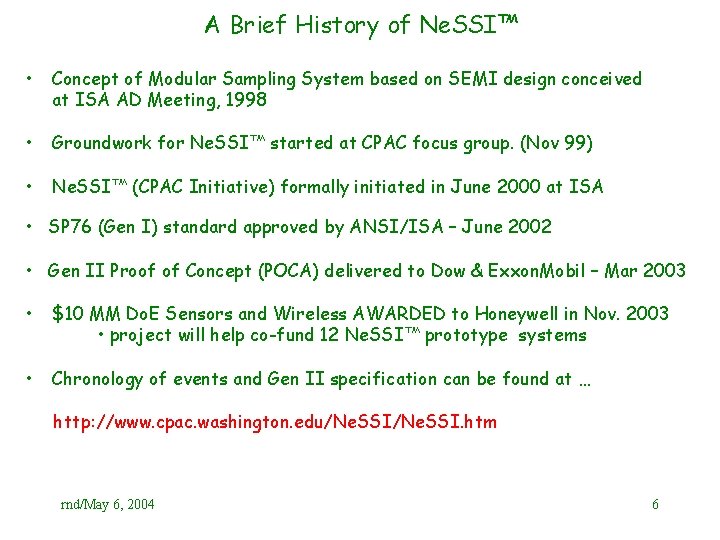
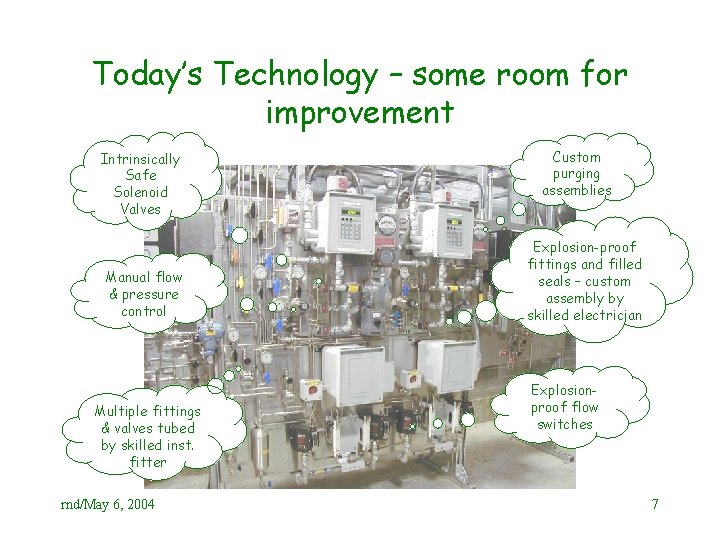
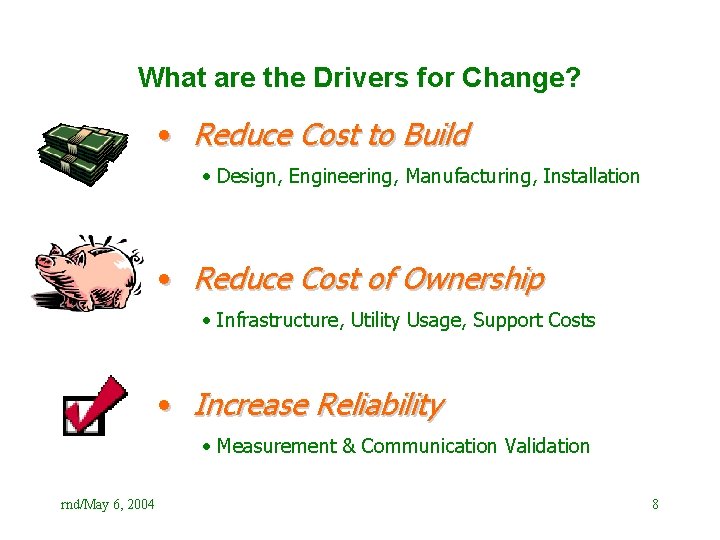

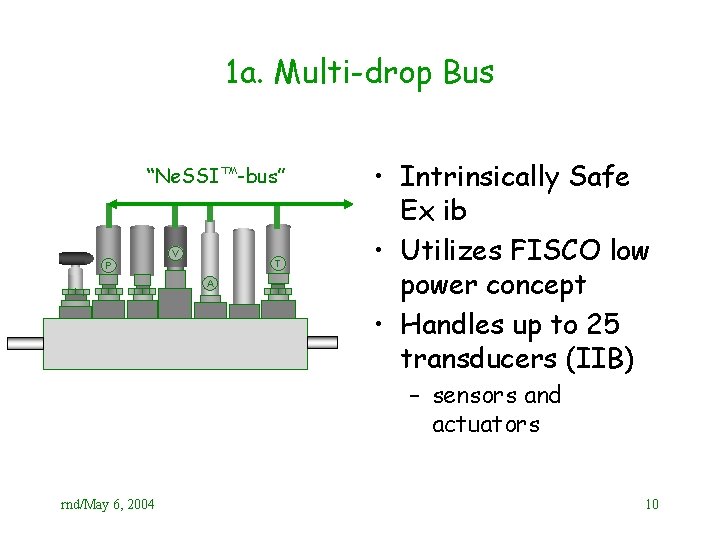
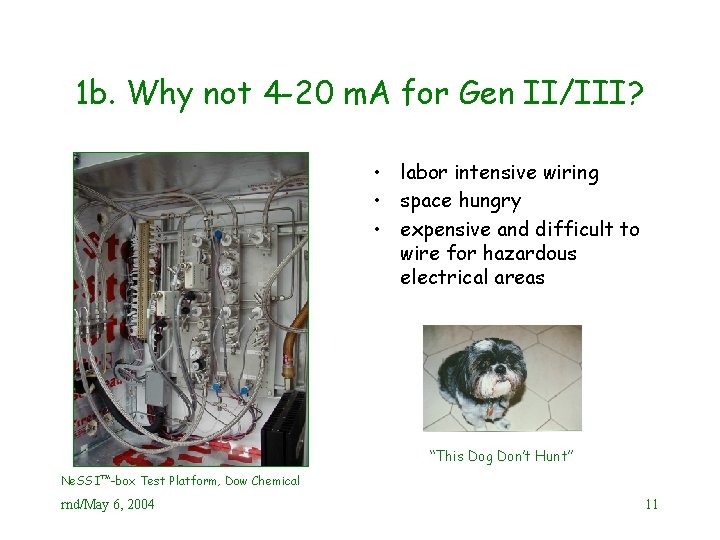
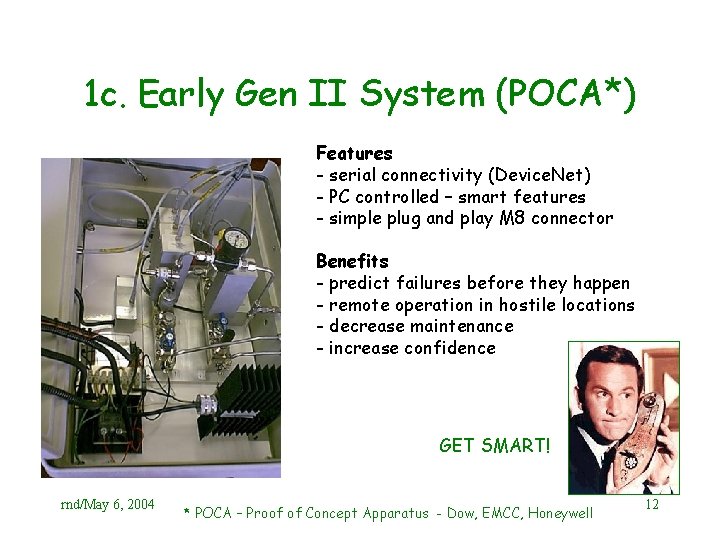
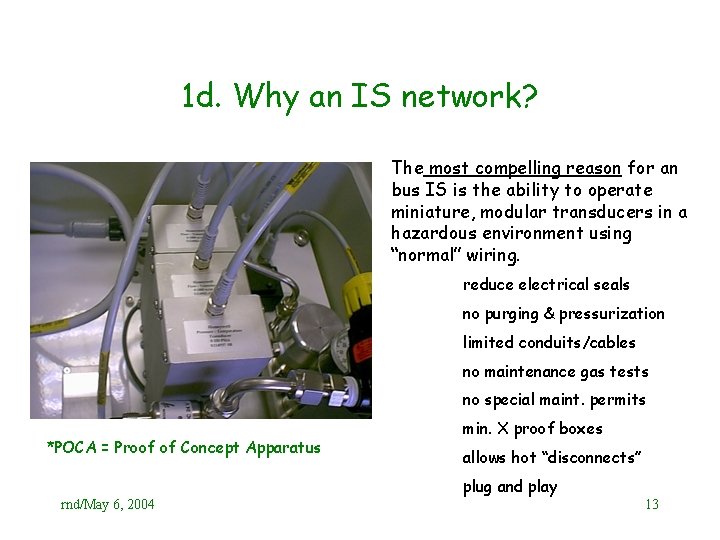
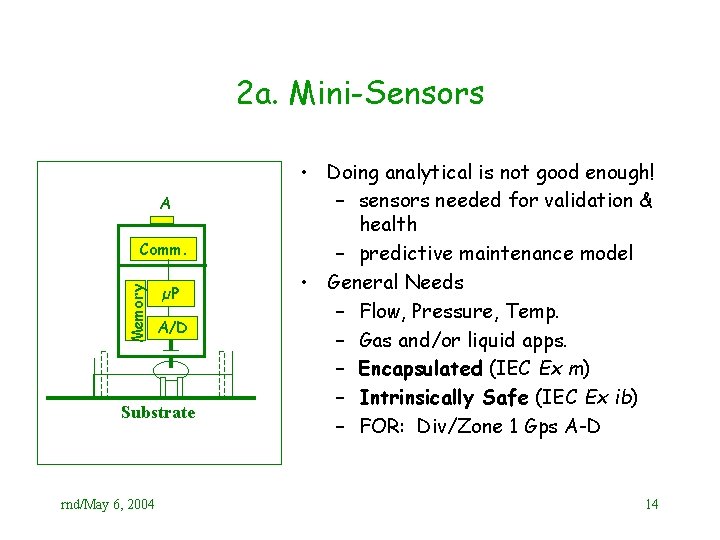
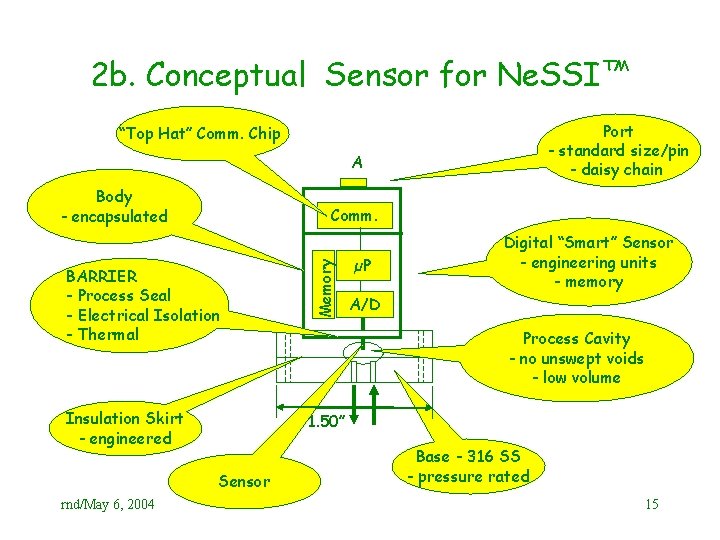
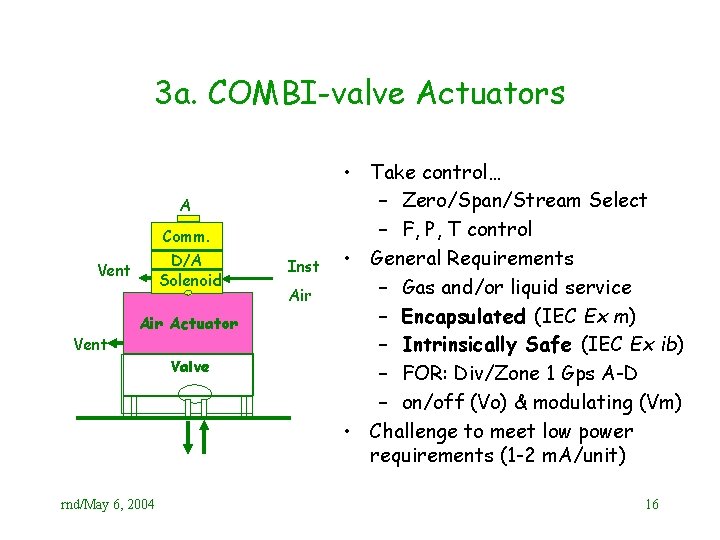
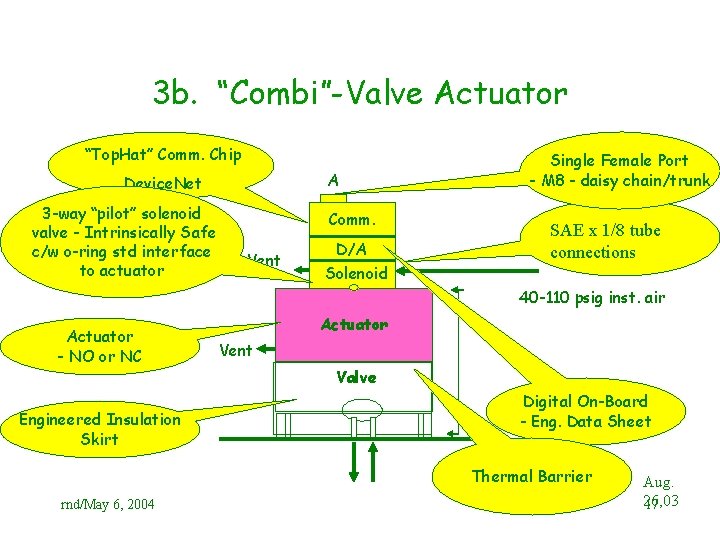
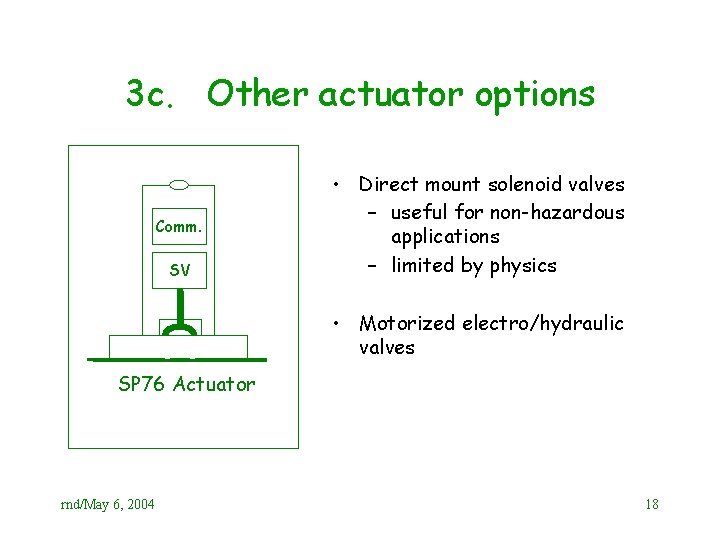
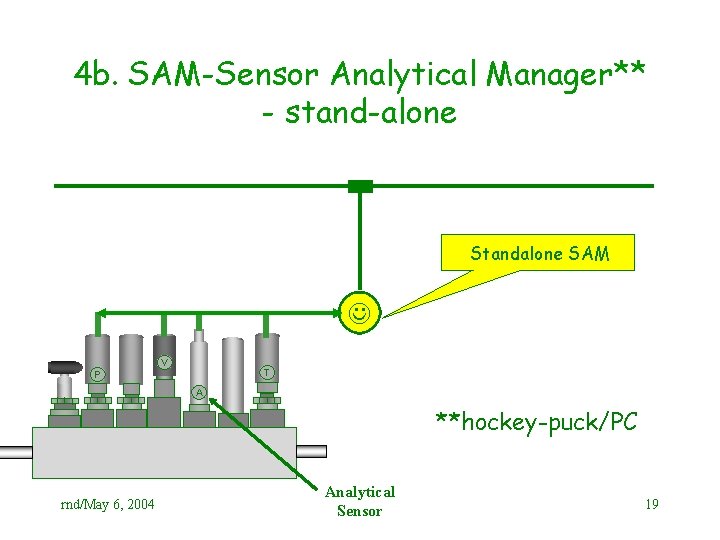
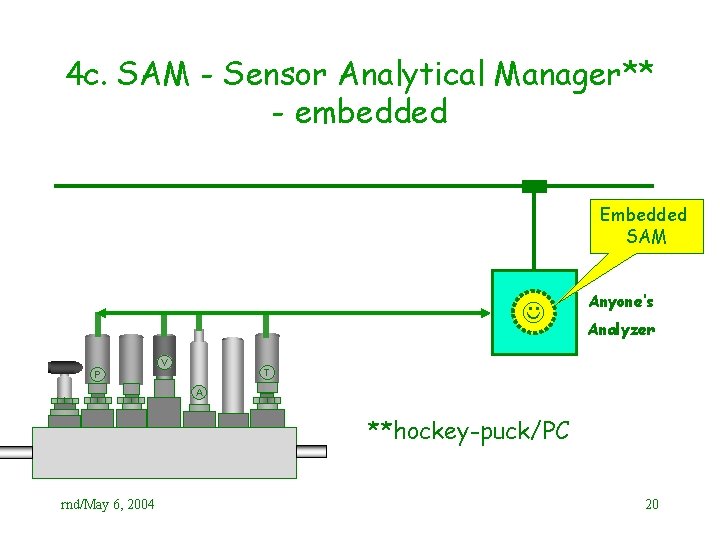
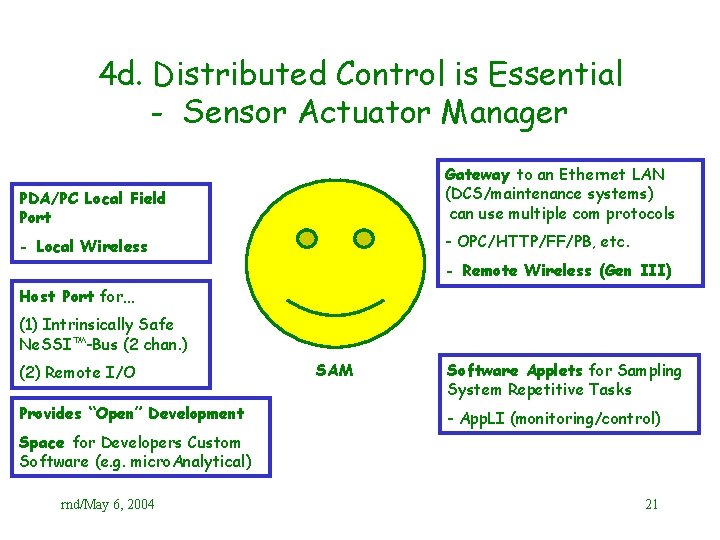
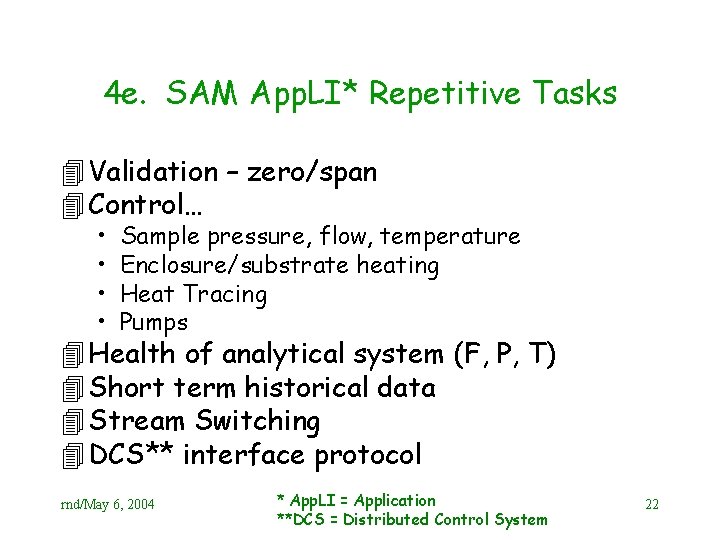
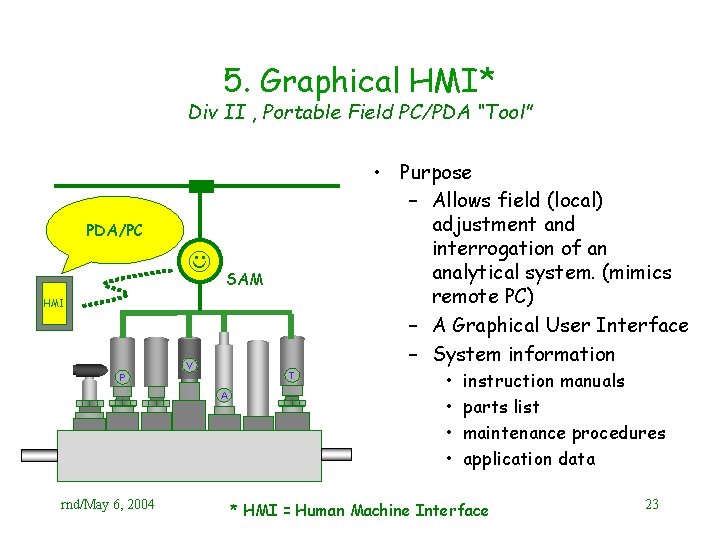
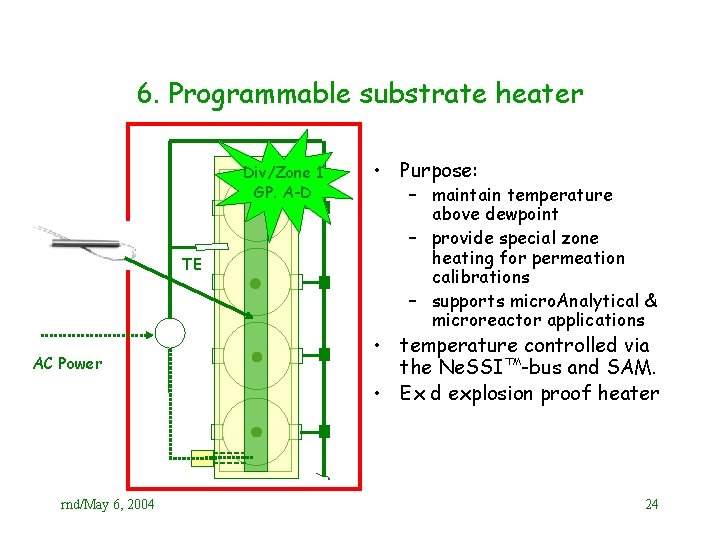
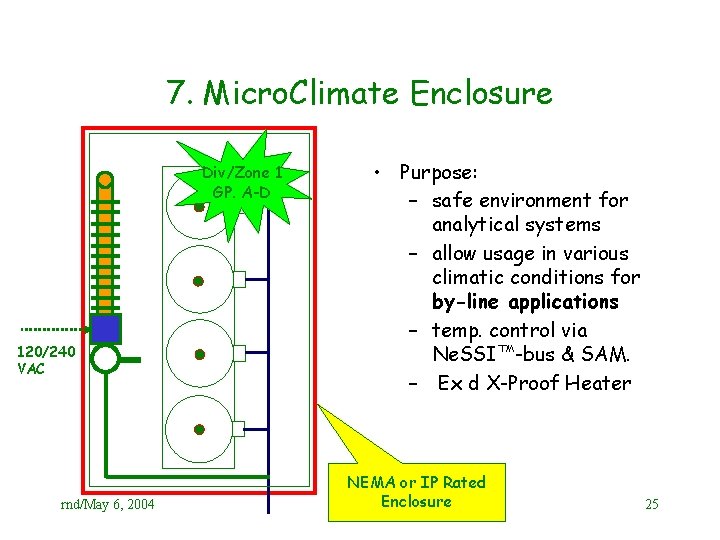
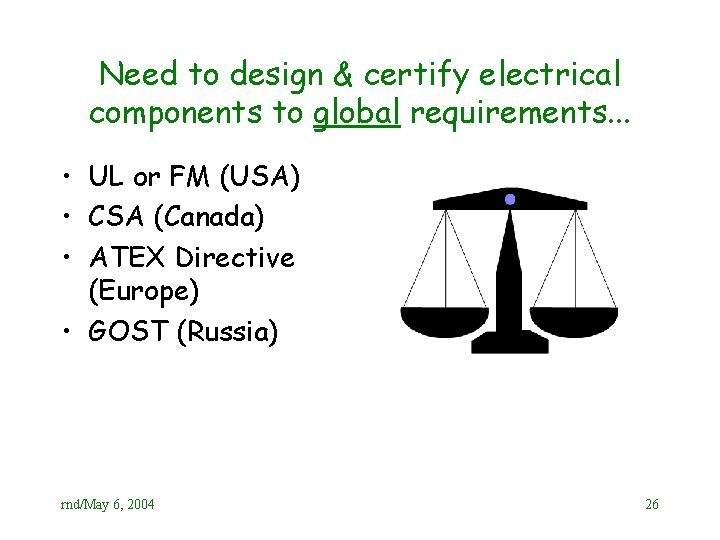
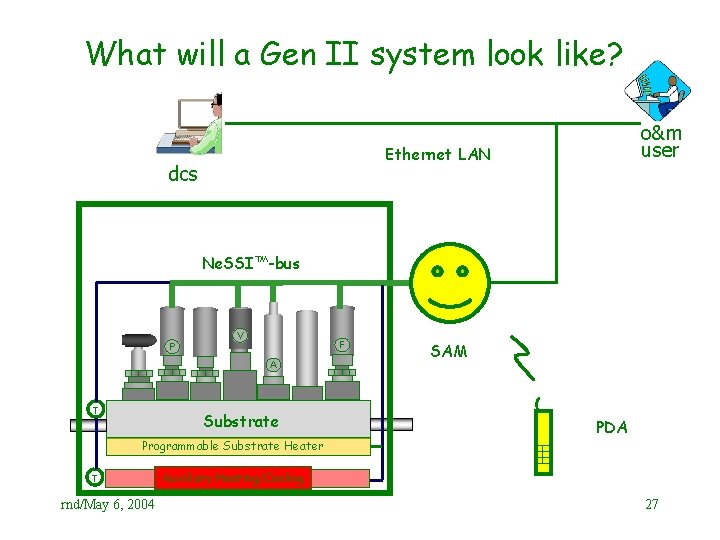
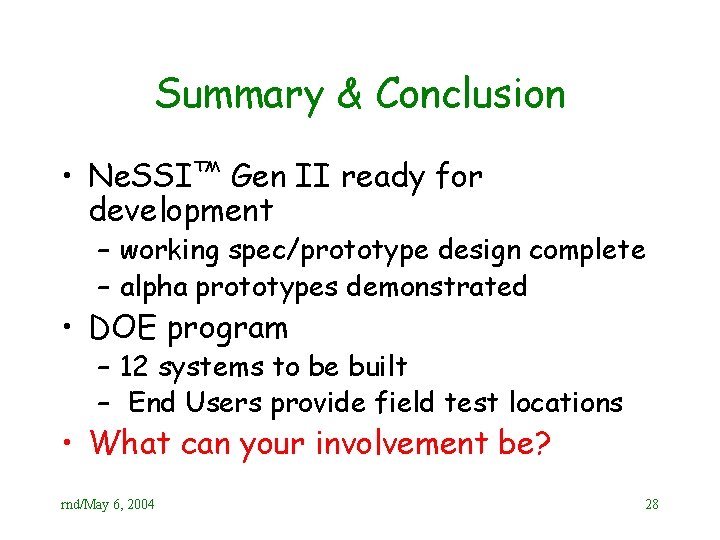
- Slides: 28
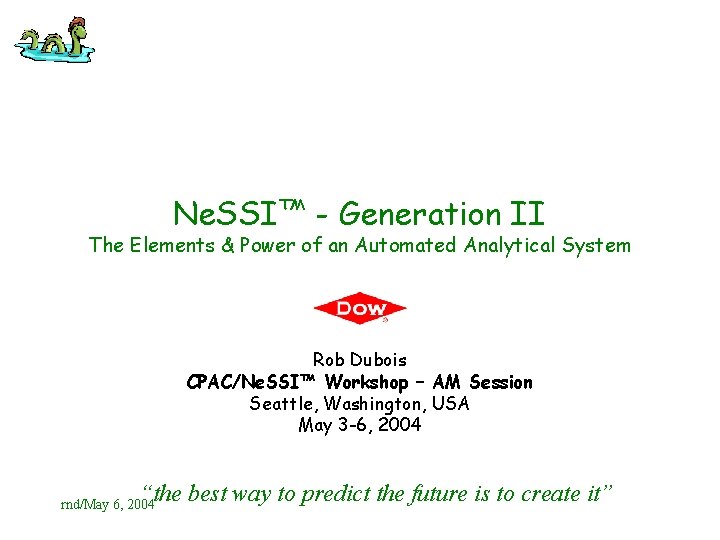
Ne. SSI™ - Generation II The Elements & Power of an Automated Analytical System Rob Dubois CPAC/Ne. SSI™ Workshop – AM Session Seattle, Washington, USA May 3 -6, 2004 “the best way to predict the future is to create it” rnd/May 6, 2004
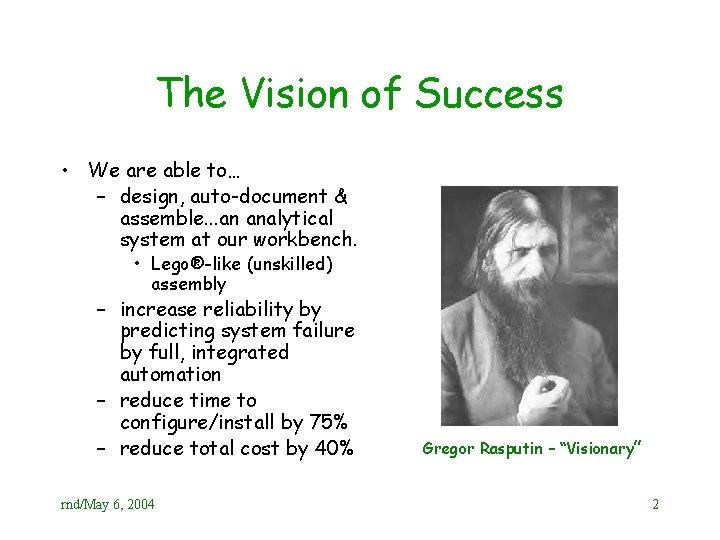
The Vision of Success • We are able to… – design, auto-document & assemble. . . an analytical system at our workbench. • Lego®-like (unskilled) assembly – increase reliability by predicting system failure by full, integrated automation – reduce time to configure/install by 75% – reduce total cost by 40% rnd/May 6, 2004 Gregor Rasputin – “Visionary” 2
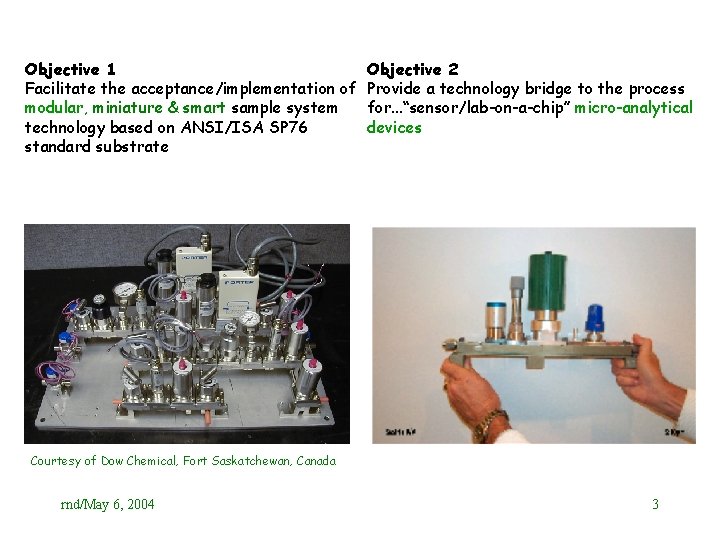
Objective 1 Facilitate the acceptance/implementation of modular, miniature & smart sample system technology based on ANSI/ISA SP 76 standard substrate Objective 2 Provide a technology bridge to the process for. . . “sensor/lab-on-a-chip” micro-analytical devices Courtesy of Dow Chemical, Fort Saskatchewan, Canada rnd/May 6, 2004 3
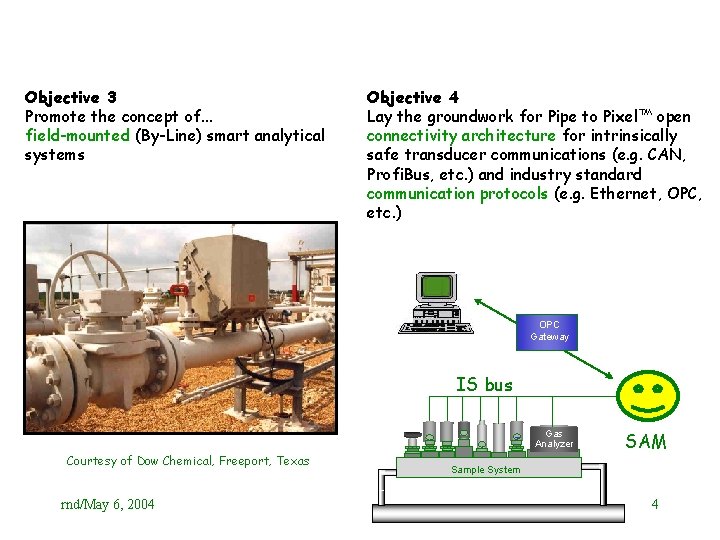
Objective 3 Promote the concept of. . . field-mounted (By-Line) smart analytical systems Objective 4 Lay the groundwork for Pipe to Pixel™ open connectivity architecture for intrinsically safe transducer communications (e. g. CAN, Profi. Bus, etc. ) and industry standard communication protocols (e. g. Ethernet, OPC, etc. ) OPC Gateway IS bus T Courtesy of Dow Chemical, Freeport, Texas rnd/May 6, 2004 Gas Analyzer SAM Sample System 4
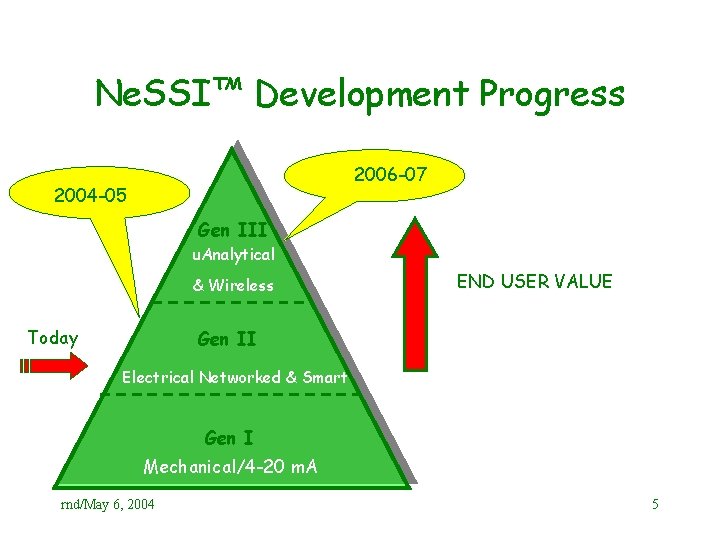
Ne. SSI™ Development Progress 2006 -07 2004 -05 Gen III u. Analytical & Wireless Today END USER VALUE Gen II Electrical Networked & Smart Gen I Mechanical/4 -20 m. A rnd/May 6, 2004 5
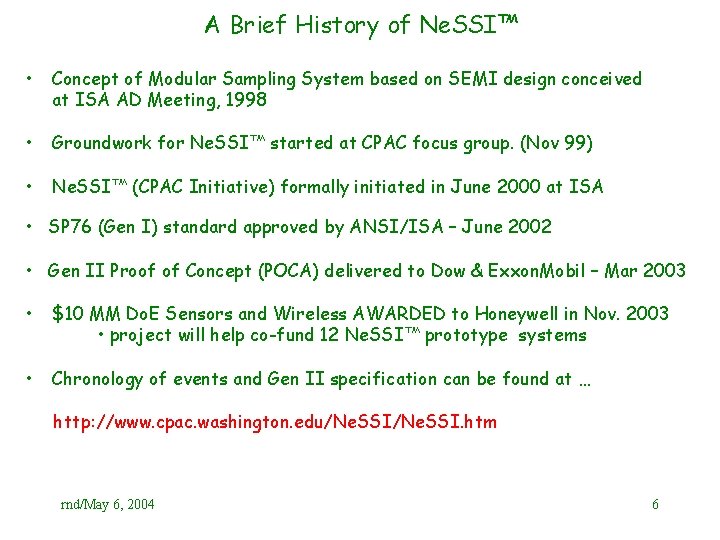
A Brief History of Ne. SSI™ • Concept of Modular Sampling System based on SEMI design conceived at ISA AD Meeting, 1998 • Groundwork for Ne. SSI™ started at CPAC focus group. (Nov 99) • Ne. SSI™ (CPAC Initiative) formally initiated in June 2000 at ISA • SP 76 (Gen I) standard approved by ANSI/ISA – June 2002 • Gen II Proof of Concept (POCA) delivered to Dow & Exxon. Mobil – Mar 2003 • $10 MM Do. E Sensors and Wireless AWARDED to Honeywell in Nov. 2003 • project will help co-fund 12 Ne. SSI™ prototype systems • Chronology of events and Gen II specification can be found at … http: //www. cpac. washington. edu/Ne. SSI. htm rnd/May 6, 2004 6
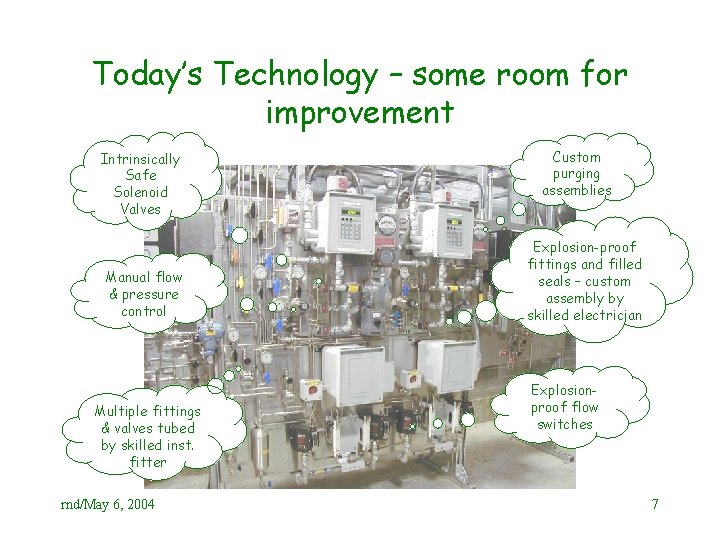
Today’s Technology – some room for improvement Intrinsically Safe Solenoid Valves Manual flow & pressure control Multiple fittings & valves tubed by skilled inst. fitter rnd/May 6, 2004 Custom purging assemblies Explosion-proof fittings and filled seals – custom assembly by skilled electrician Explosionproof flow switches 7
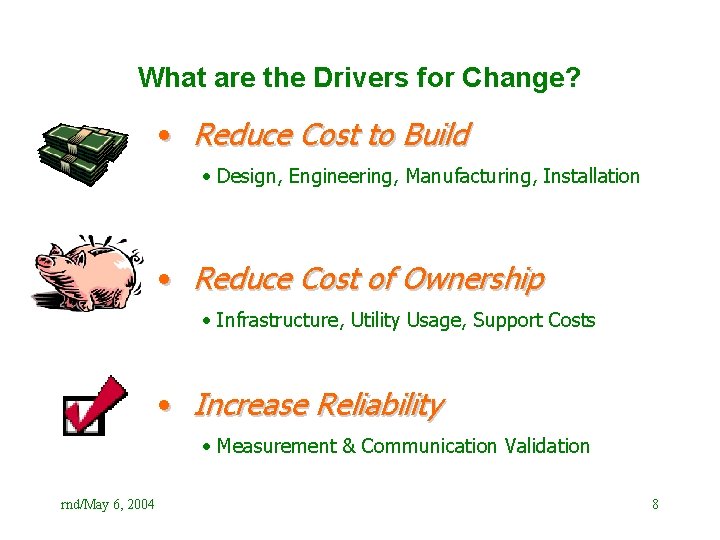
What are the Drivers for Change? • Reduce Cost to Build • Design, Engineering, Manufacturing, Installation • Reduce Cost of Ownership • Infrastructure, Utility Usage, Support Costs • Increase Reliability • Measurement & Communication Validation rnd/May 6, 2004 8

7 Elements of Generation II 1. Multi-Drop Intrinsically Safe Bus 2. mini-Sensors 3. “Combi”-Valve Actuators 4. SAM* – Sensor Actuator Manager 5. PC/PDA with HMI** [Local Wireless] 6. Programmable Substrate Heater 7. micro. Climate Enclosure * SAM = Sensor Actuator Manager; **HMI = Human Machine Interface rnd/May 6, 2004 9
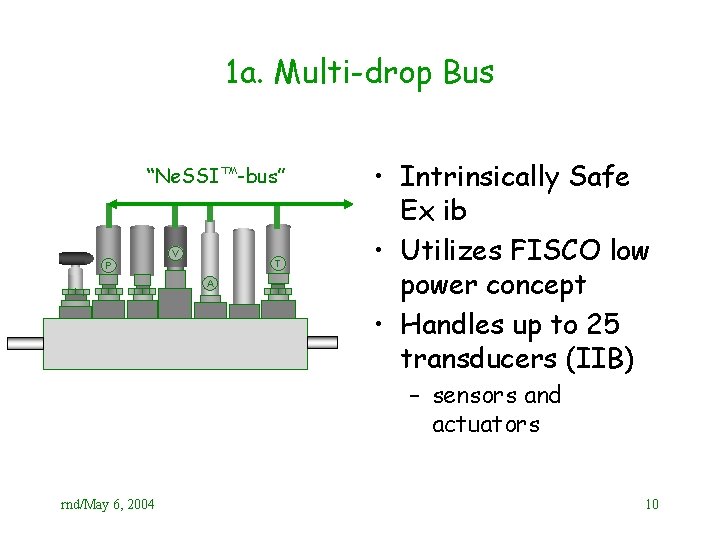
1 a. Multi-drop Bus “Ne. SSI™-bus” V T P A • Intrinsically Safe Ex ib • Utilizes FISCO low power concept • Handles up to 25 transducers (IIB) – sensors and actuators rnd/May 6, 2004 10
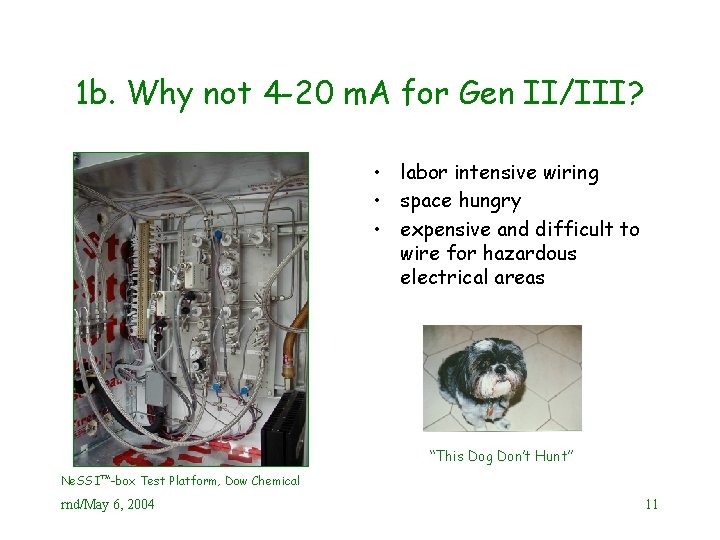
1 b. Why not 4 -20 m. A for Gen II/III? • labor intensive wiring • space hungry • expensive and difficult to wire for hazardous electrical areas “This Dog Don’t Hunt” Ne. SSI™-box Test Platform, Dow Chemical rnd/May 6, 2004 11
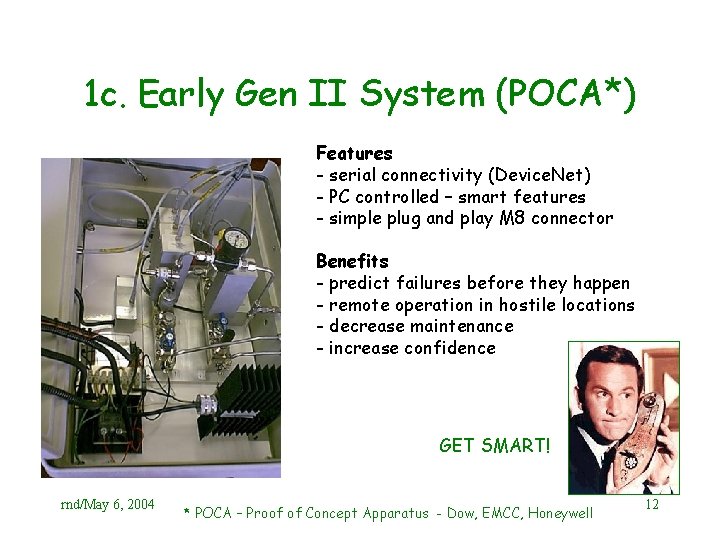
1 c. Early Gen II System (POCA*) Features - serial connectivity (Device. Net) - PC controlled – smart features - simple plug and play M 8 connector Benefits - predict failures before they happen - remote operation in hostile locations - decrease maintenance - increase confidence GET SMART! rnd/May 6, 2004 * POCA – Proof of Concept Apparatus - Dow, EMCC, Honeywell 12
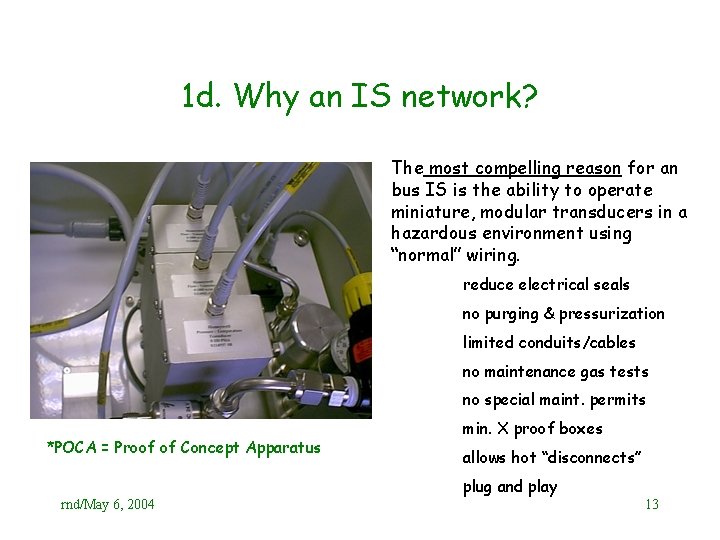
1 d. Why an IS network? The most compelling reason for an bus IS is the ability to operate miniature, modular transducers in a hazardous environment using “normal” wiring. reduce electrical seals no purging & pressurization limited conduits/cables no maintenance gas tests no special maint. permits *POCA = Proof of Concept Apparatus min. X proof boxes allows hot “disconnects” plug and play rnd/May 6, 2004 13
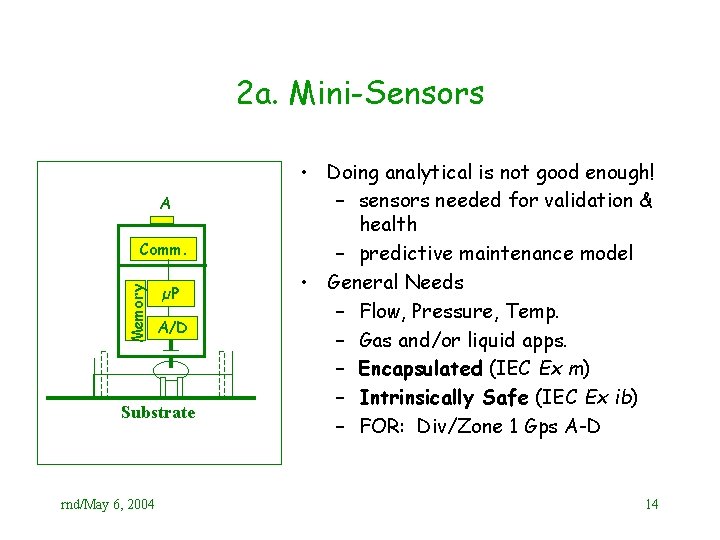
2 a. Mini-Sensors A Memory Comm. µP A/D Substrate rnd/May 6, 2004 • Doing analytical is not good enough! – sensors needed for validation & health – predictive maintenance model • General Needs – Flow, Pressure, Temp. – Gas and/or liquid apps. – Encapsulated (IEC Ex m) – Intrinsically Safe (IEC Ex ib) – FOR: Div/Zone 1 Gps A-D 14
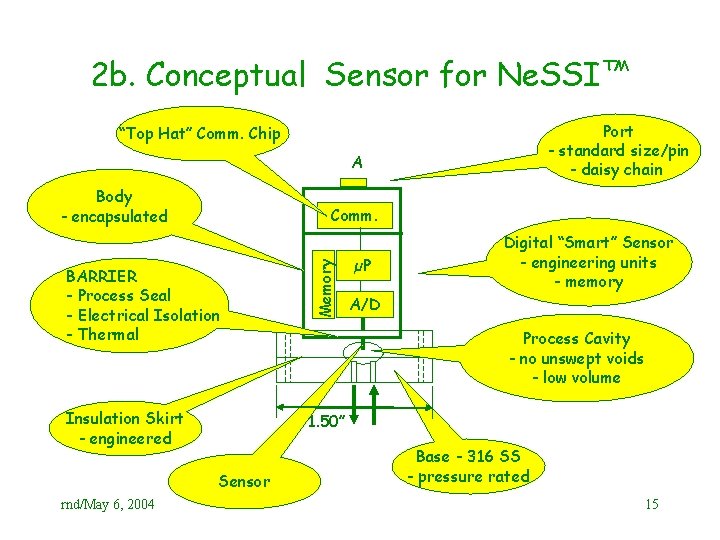
2 b. Conceptual Sensor for Ne. SSI™ Port - standard size/pin - daisy chain “Top Hat” Comm. Chip A Body - encapsulated BARRIER - Process Seal - Electrical Isolation - Thermal Memory Comm. Insulation Skirt - engineered 1. 50” Sensor rnd/May 6, 2004 µP Digital “Smart” Sensor - engineering units - memory A/D Process Cavity - no unswept voids - low volume Base - 316 SS - pressure rated 15
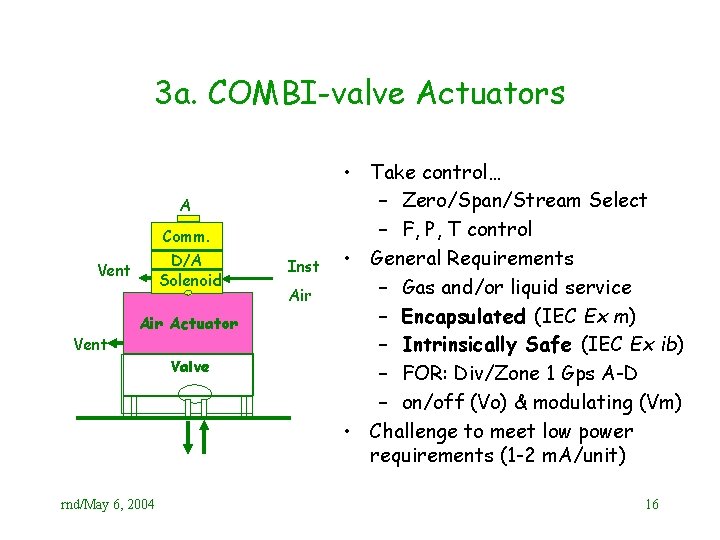
3 a. COMBI-valve Actuators A Comm. D/A Solenoid Vent Air Actuator Valve rnd/May 6, 2004 Inst Air • Take control… – Zero/Span/Stream Select – F, P, T control • General Requirements – Gas and/or liquid service – Encapsulated (IEC Ex m) – Intrinsically Safe (IEC Ex ib) – FOR: Div/Zone 1 Gps A-D – on/off (Vo) & modulating (Vm) • Challenge to meet low power requirements (1 -2 m. A/unit) 16
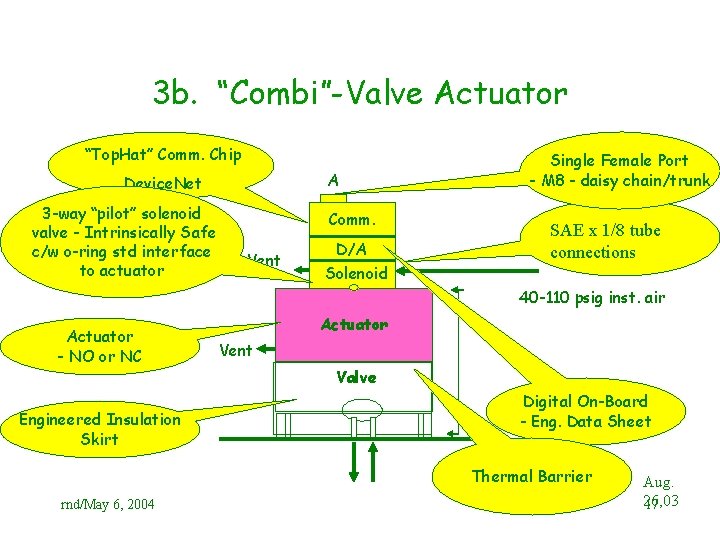
3 b. “Combi”-Valve Actuator “Top. Hat” Comm. Chip A Device. Net 3 -way “pilot” solenoid valve - Intrinsically Safe c/w o-ring std interface to actuator Comm. Vent D/A Solenoid Single Female Port - M 8 - daisy chain/trunk SAE x 1/8 tube connections 40 -110 psig inst. air Actuator - NO or NC Engineered Insulation Skirt Actuator Vent Valve Digital On-Board - Eng. Data Sheet Thermal Barrier rnd/May 6, 2004 Aug. 26, 03 17
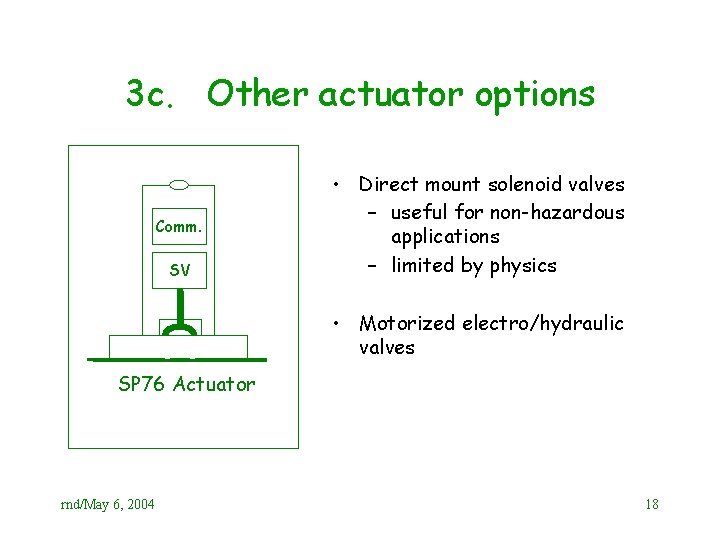
3 c. Other actuator options Comm. SV • Direct mount solenoid valves – useful for non-hazardous applications – limited by physics • Motorized electro/hydraulic valves SP 76 Actuator rnd/May 6, 2004 18
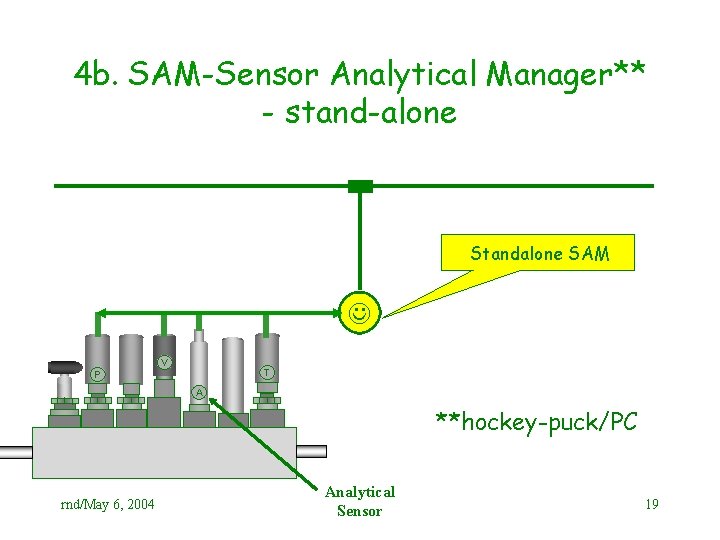
4 b. SAM-Sensor Analytical Manager** - stand-alone Standalone SAM V T P A **hockey-puck/PC rnd/May 6, 2004 Analytical Sensor 19
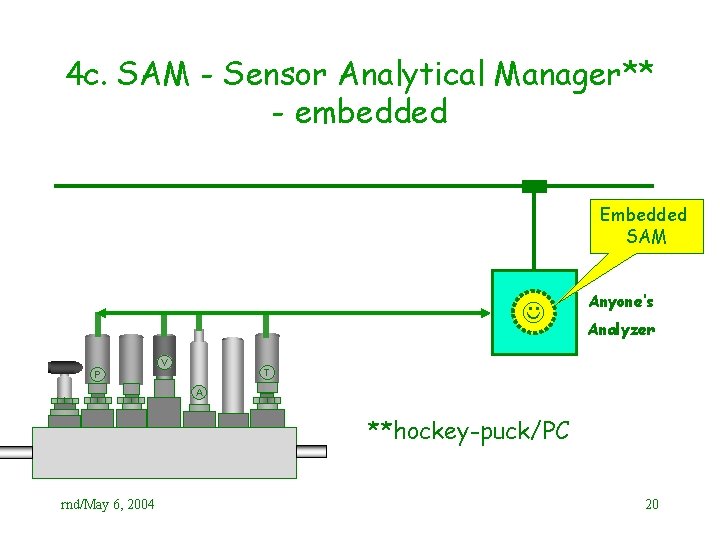
4 c. SAM - Sensor Analytical Manager** - embedded Embedded SAM V Anyone’s Analyzer T P A **hockey-puck/PC rnd/May 6, 2004 20
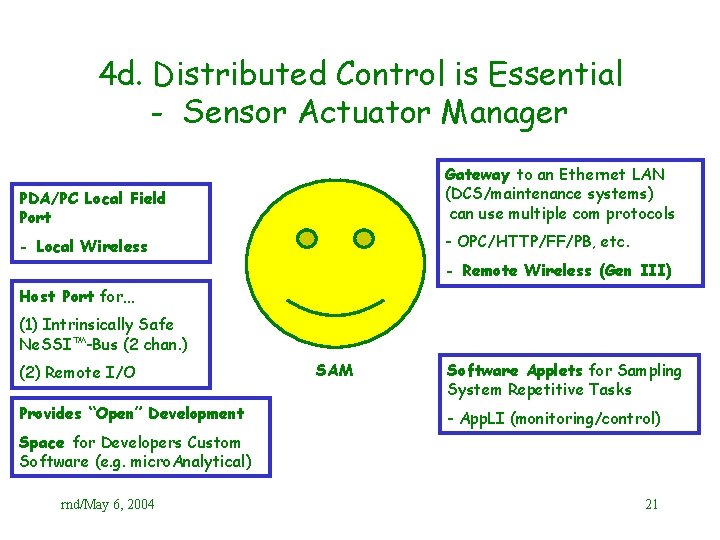
4 d. Distributed Control is Essential - Sensor Actuator Manager PDA/PC Local Field Port Gateway to an Ethernet LAN (DCS/maintenance systems) can use multiple com protocols - Local Wireless - OPC/HTTP/FF/PB, etc. - Remote Wireless (Gen III) Host Port for… (1) Intrinsically Safe Ne. SSI™-Bus (2 chan. ) (2) Remote I/O Provides “Open” Development SAM Software Applets for Sampling System Repetitive Tasks - App. LI (monitoring/control) Space for Developers Custom Software (e. g. micro. Analytical) rnd/May 6, 2004 21
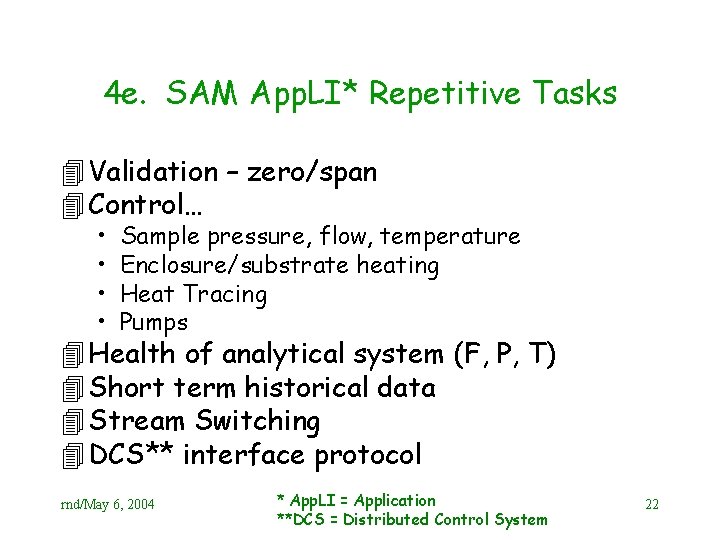
4 e. SAM App. LI* Repetitive Tasks 4 Validation – zero/span 4 Control… • • Sample pressure, flow, temperature Enclosure/substrate heating Heat Tracing Pumps 4 Health of analytical system (F, P, T) 4 Short term historical data 4 Stream Switching 4 DCS** interface protocol rnd/May 6, 2004 * App. LI = Application **DCS = Distributed Control System 22
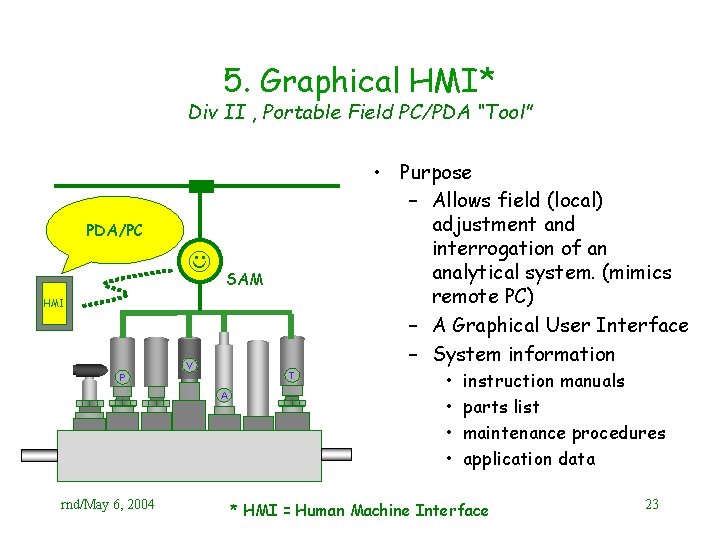
5. Graphical HMI* Div II , Portable Field PC/PDA “Tool” • Purpose – Allows field (local) adjustment and interrogation of an analytical system. (mimics remote PC) – A Graphical User Interface – System information PDA/PC SAM HMI V T P A rnd/May 6, 2004 • • instruction manuals parts list maintenance procedures application data * HMI = Human Machine Interface 23
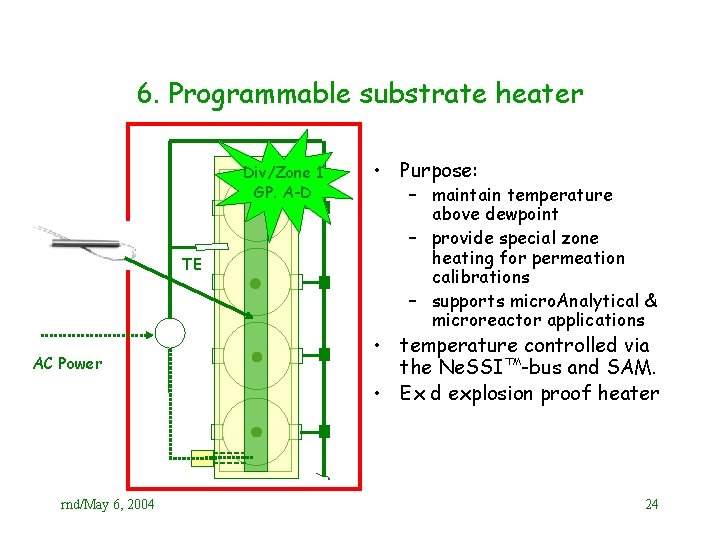
6. Programmable substrate heater Div/Zone 1 GP. A-D TE AC Power rnd/May 6, 2004 • Purpose: – maintain temperature above dewpoint – provide special zone heating for permeation calibrations – supports micro. Analytical & microreactor applications • temperature controlled via the Ne. SSI™-bus and SAM. • Ex d explosion proof heater 24
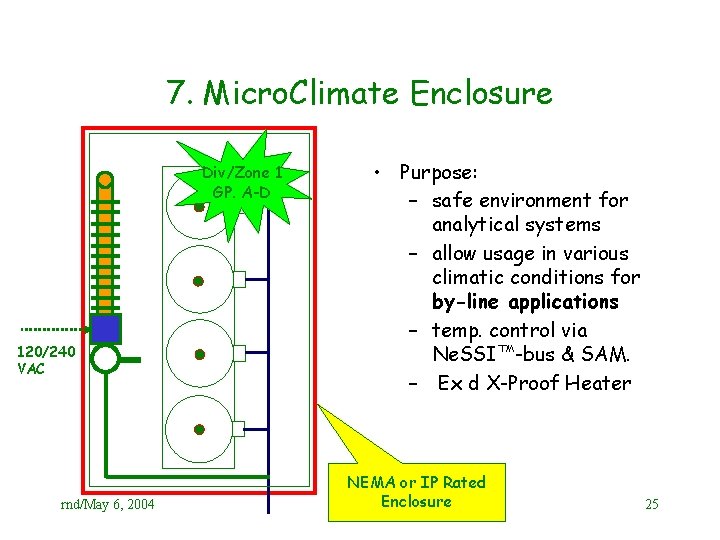
7. Micro. Climate Enclosure Div/Zone 1 GP. A-D 120/240 VAC rnd/May 6, 2004 • Purpose: – safe environment for analytical systems – allow usage in various climatic conditions for by-line applications – temp. control via Ne. SSI™-bus & SAM. – Ex d X-Proof Heater NEMA or IP Rated Enclosure 25
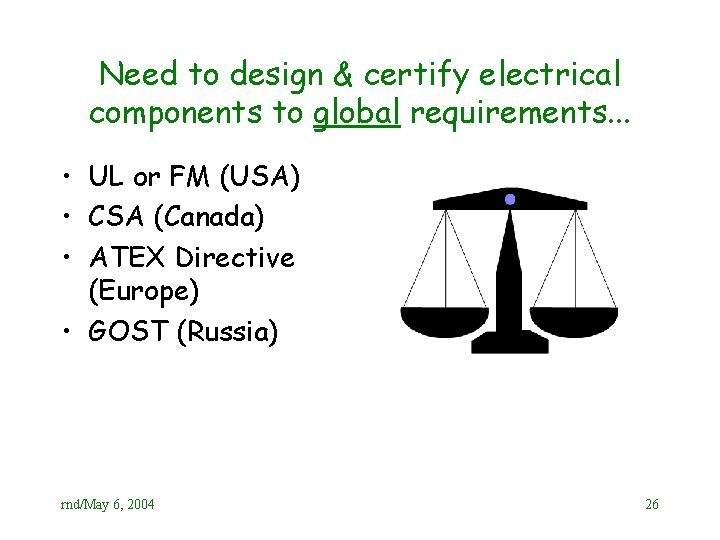
Need to design & certify electrical components to global requirements. . . • UL or FM (USA) • CSA (Canada) • ATEX Directive (Europe) • GOST (Russia) rnd/May 6, 2004 26
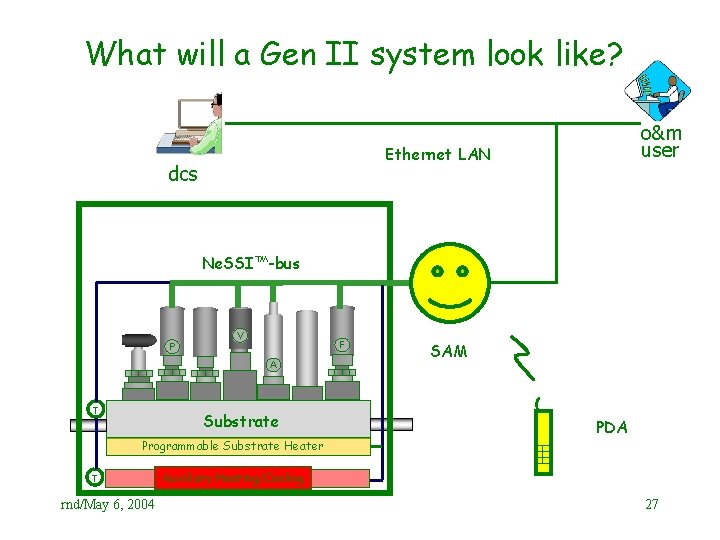
What will a Gen II system look like? o&m user Ethernet LAN dcs Ne. SSI™-bus V F P A T Substrate Programmable Substrate Heater T rnd/May 6, 2004 SAM PDA Auxiliary Heating/Cooling 27
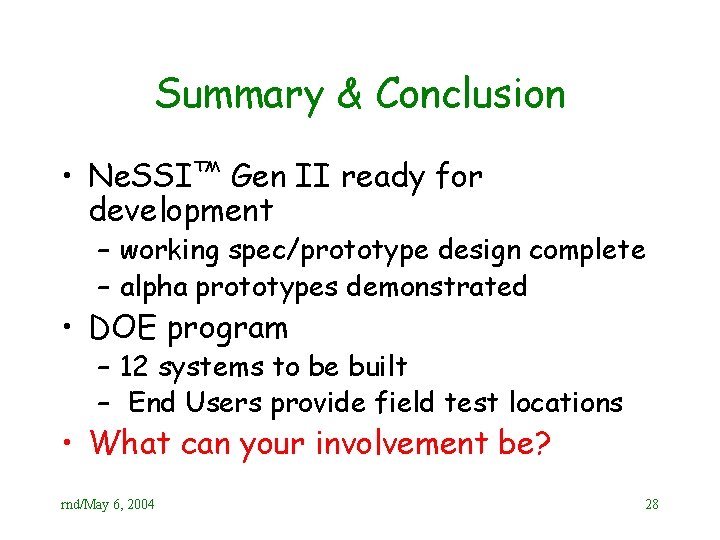
Summary & Conclusion • Ne. SSI™ Gen II ready for development – working spec/prototype design complete – alpha prototypes demonstrated • DOE program – 12 systems to be built – End Users provide field test locations • What can your involvement be? rnd/May 6, 2004 28
First gen antipsychotics
You are good and your mercy endureth forever
Draw power triangle
Disadvantages of foot step power generation
Power generation forging
Mhd power generation ppt
Ssi definition
What is ssi
Ssi bundle
Ssdi vs ssi
Small scale integration (ssi)
Ssi classification
Marcel riedel
Ex collaboratori ssi
Msi circuit
61932
Ssi vs ssdi
What is ssi
Edx720
Ssdi vs ssi
Transducer techniques ssi
Ihss provider login
Rime en ssi
Diagram ssi
Inep no mantis
Cablage ssi
Bac ssi
Ssi cluster
Decoder minterm generator