Methodology to Estimate Dynamic Characteristics of An Airfoil
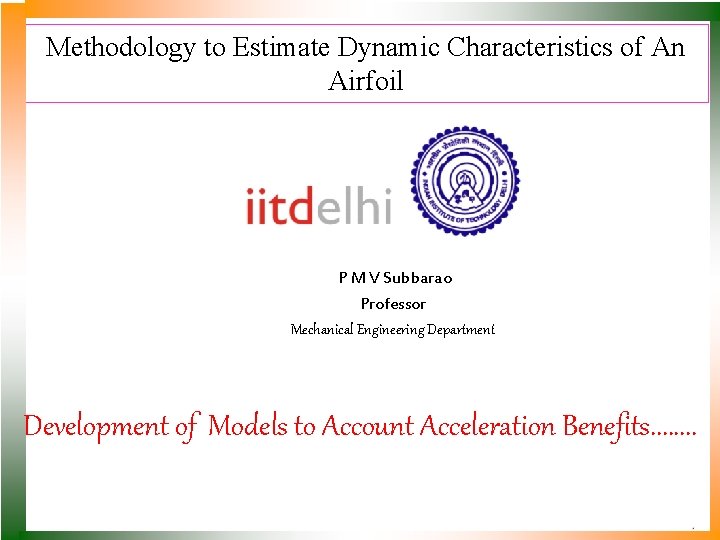
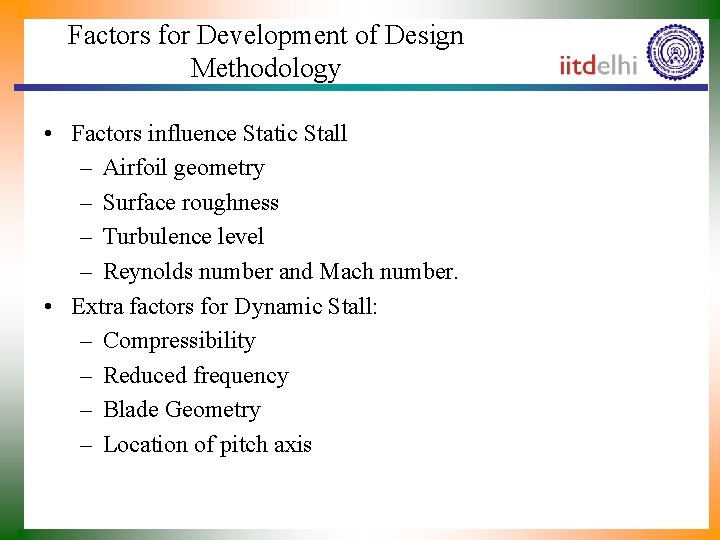
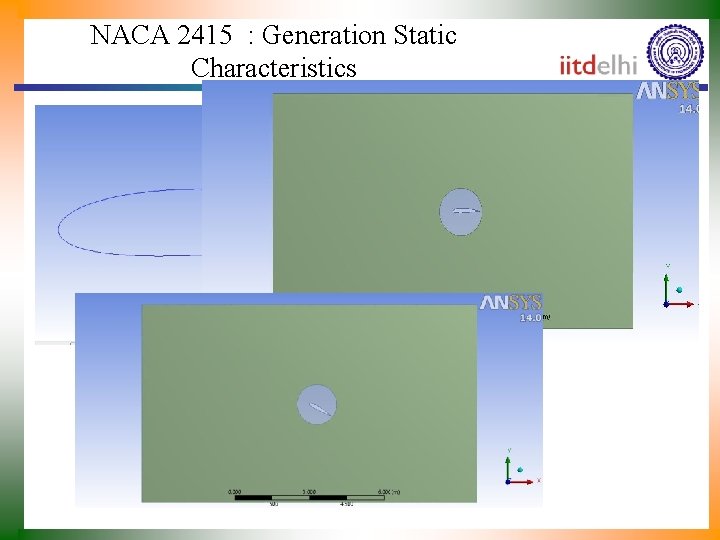
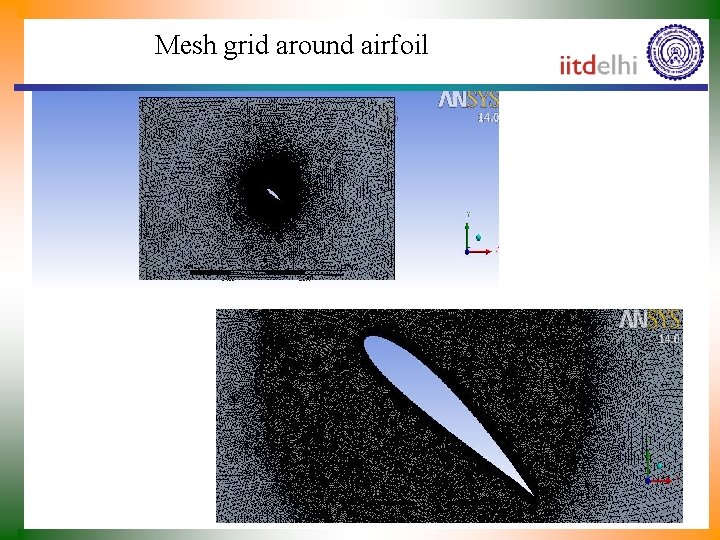
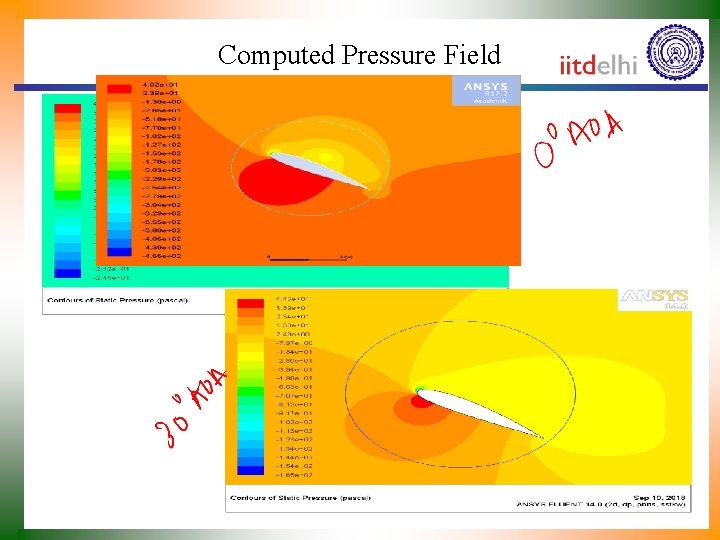
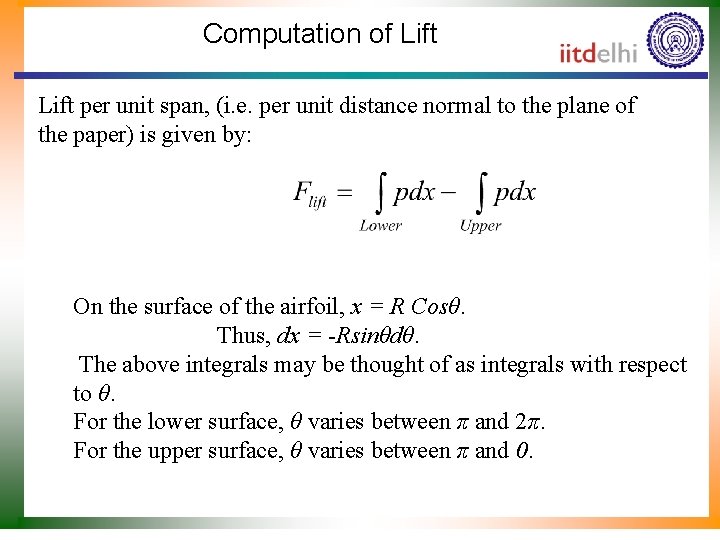
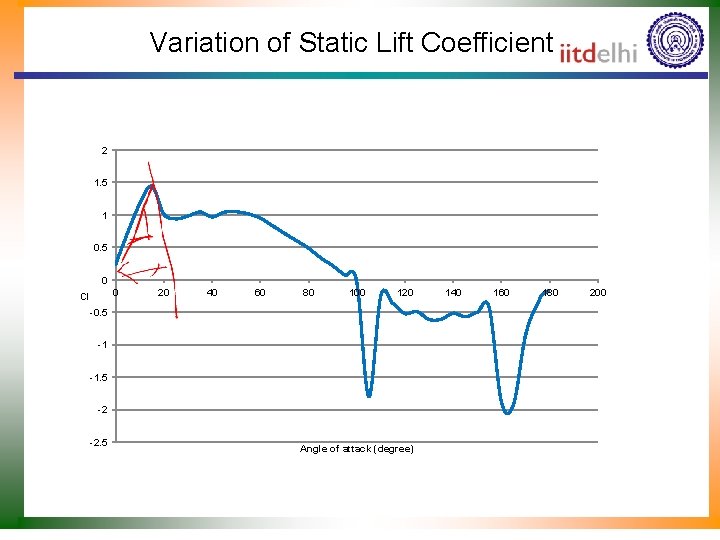
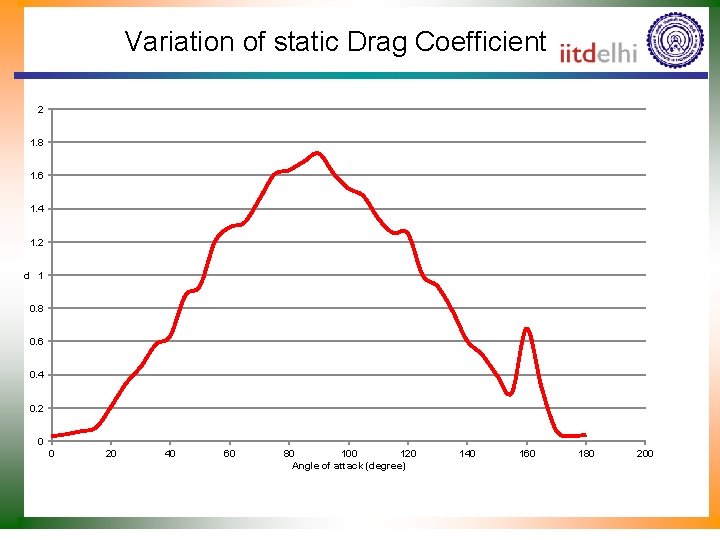
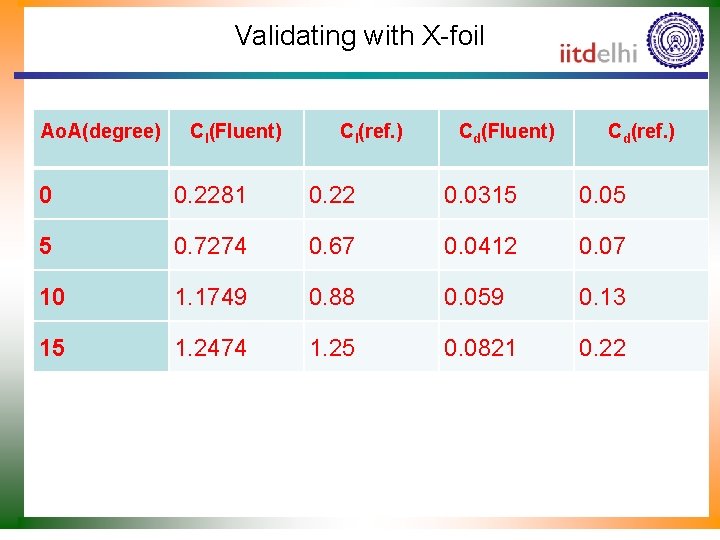
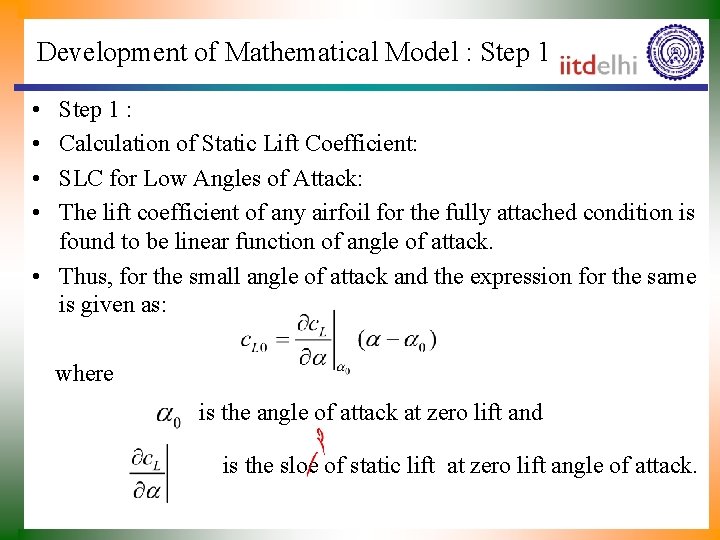
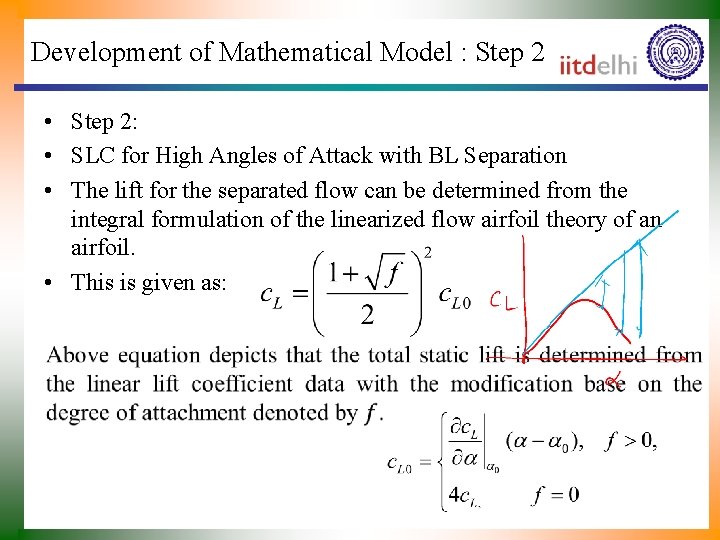
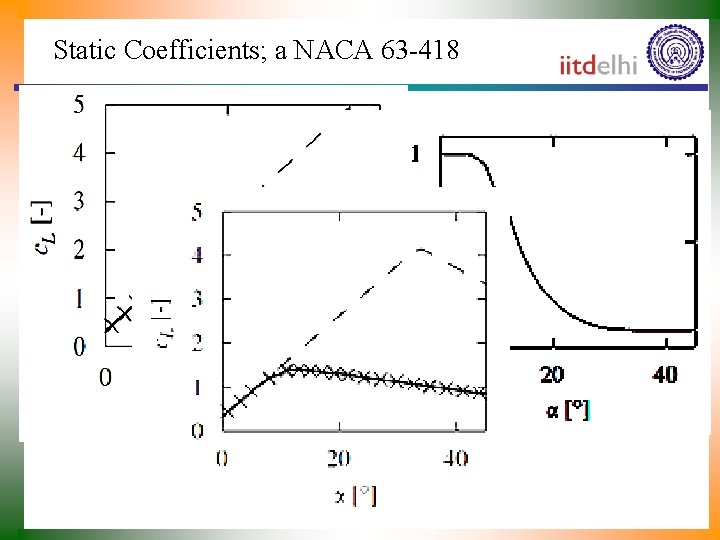
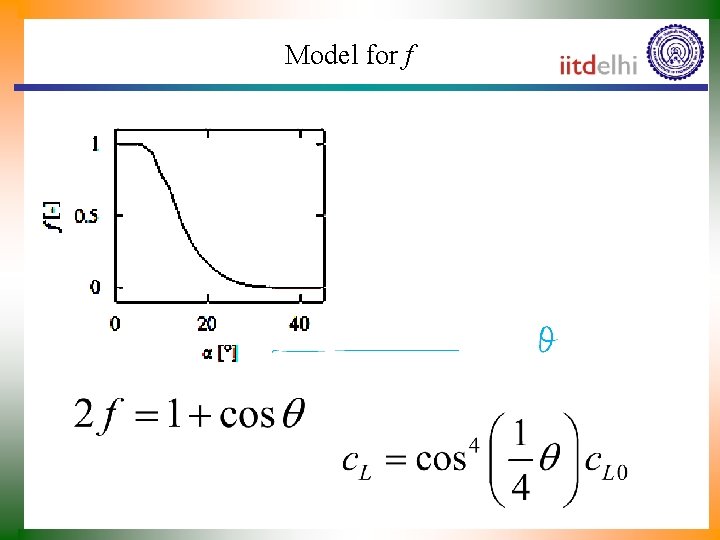
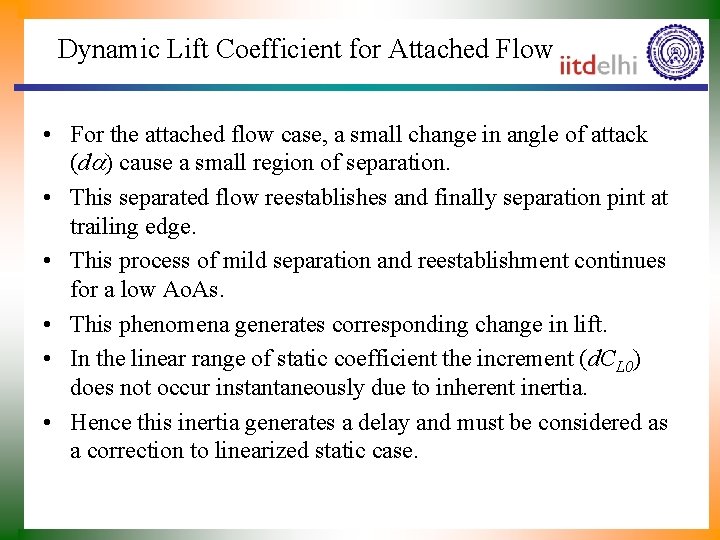
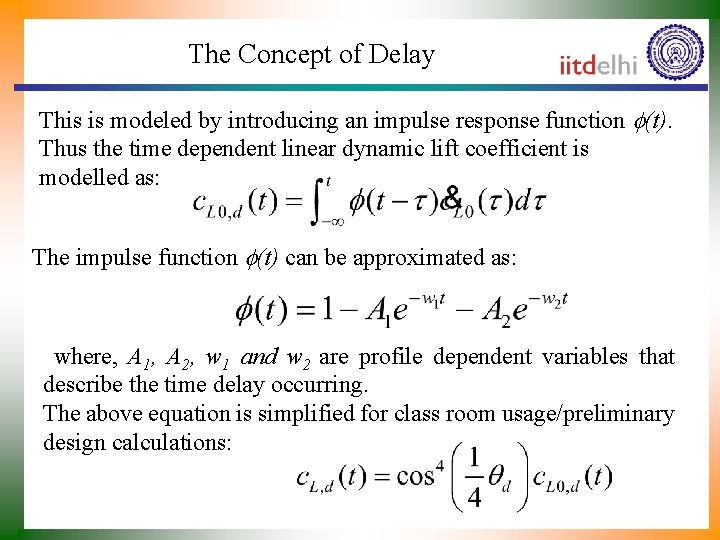
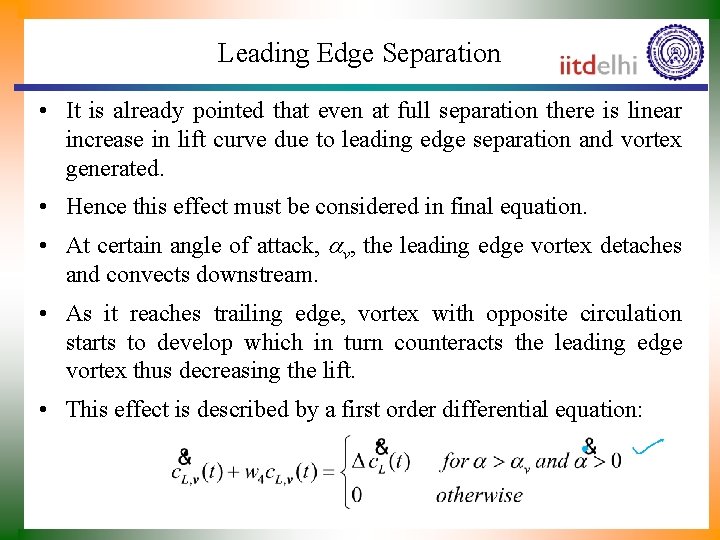
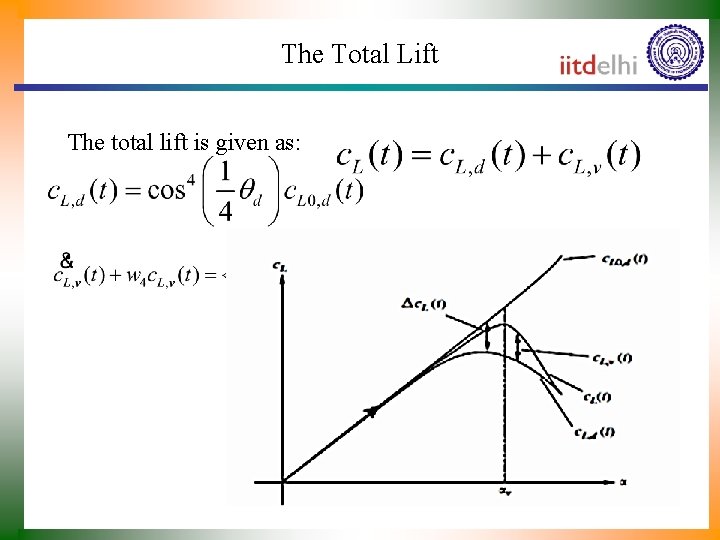
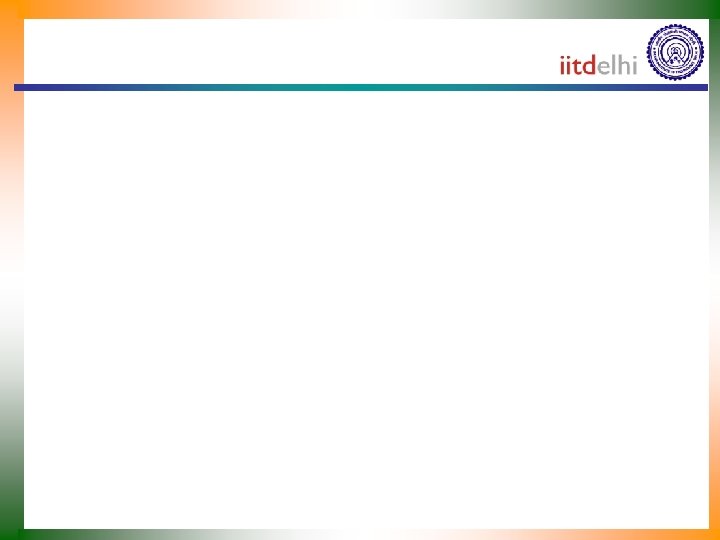
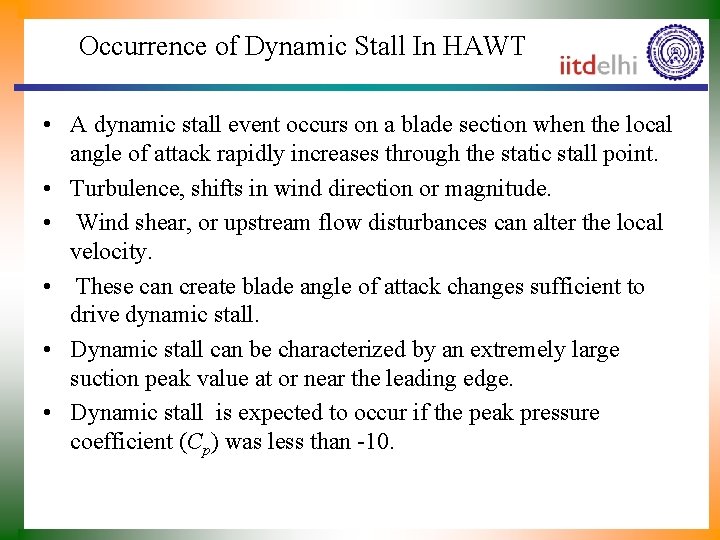
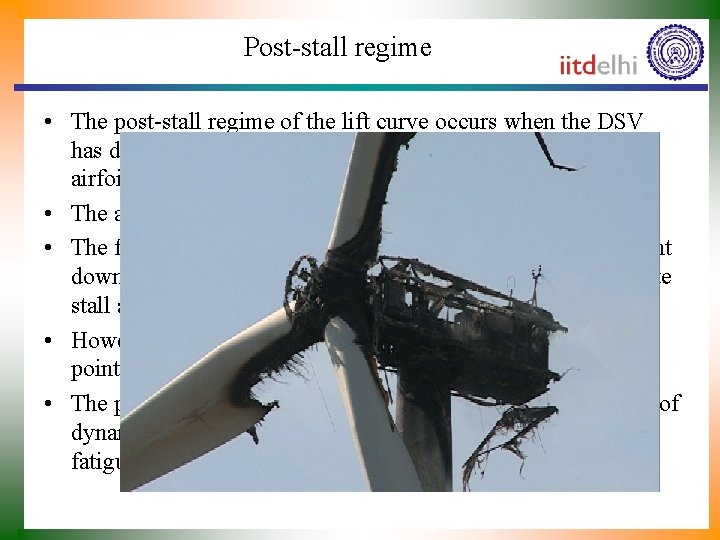
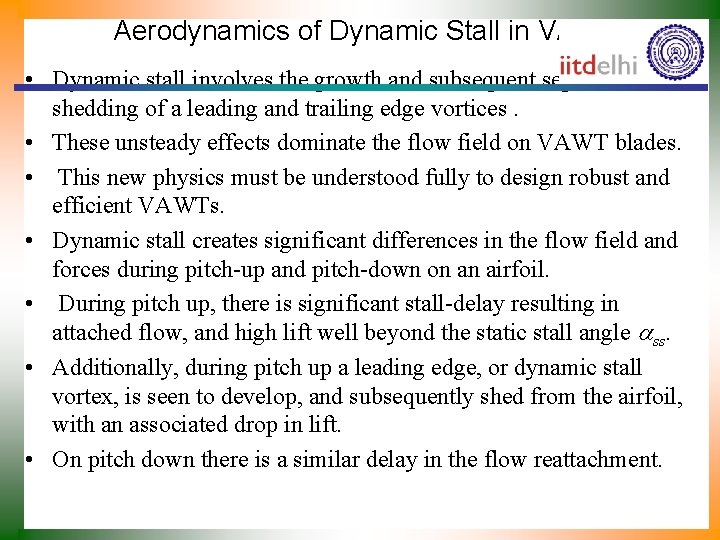
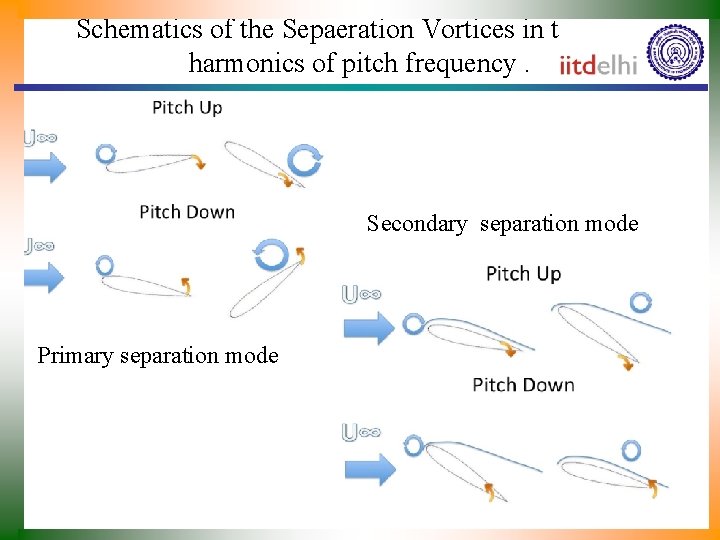
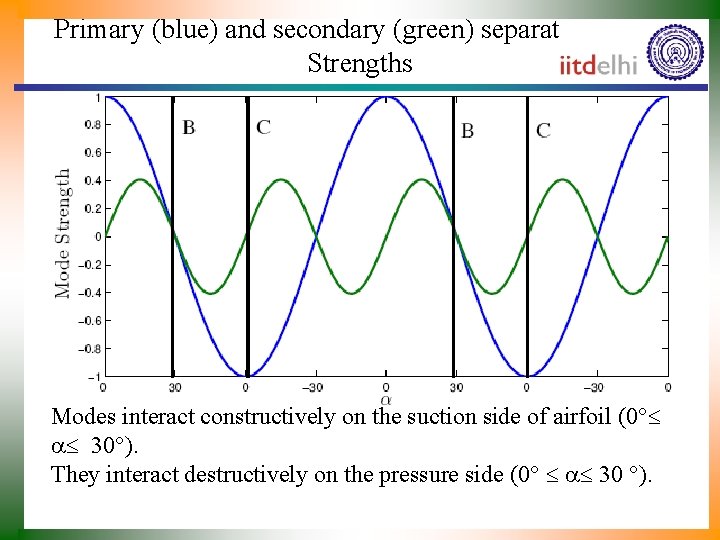
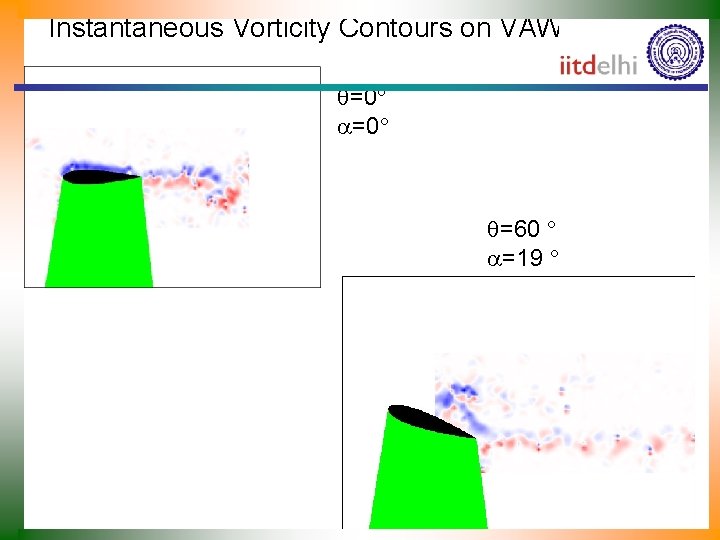
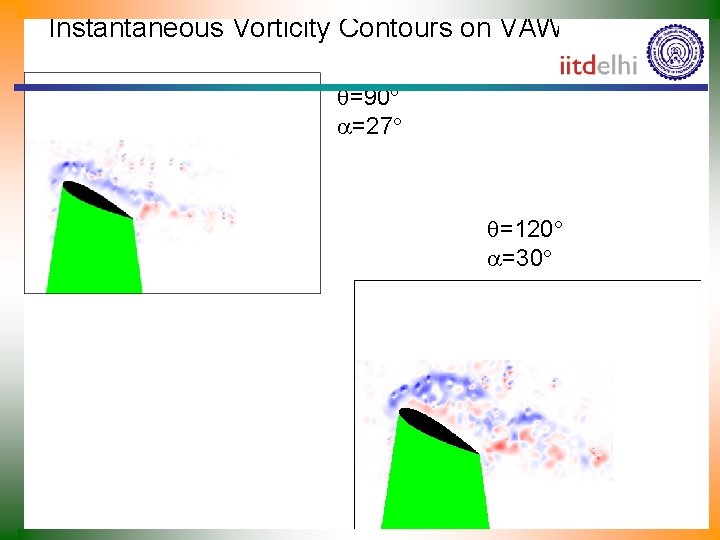
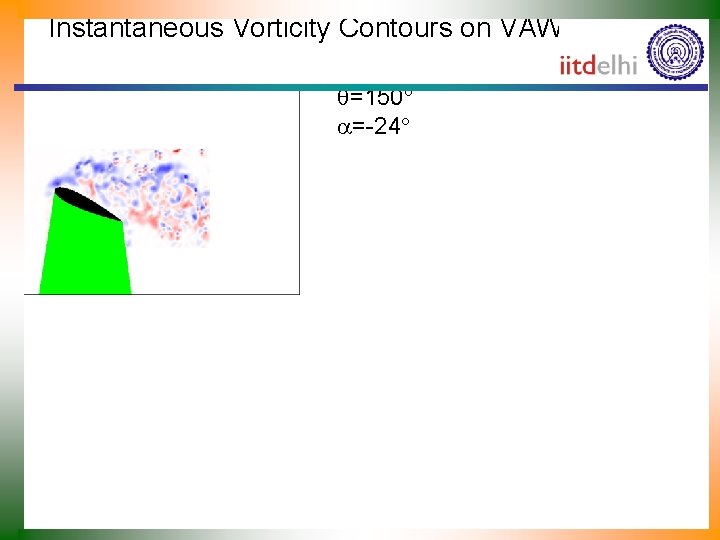
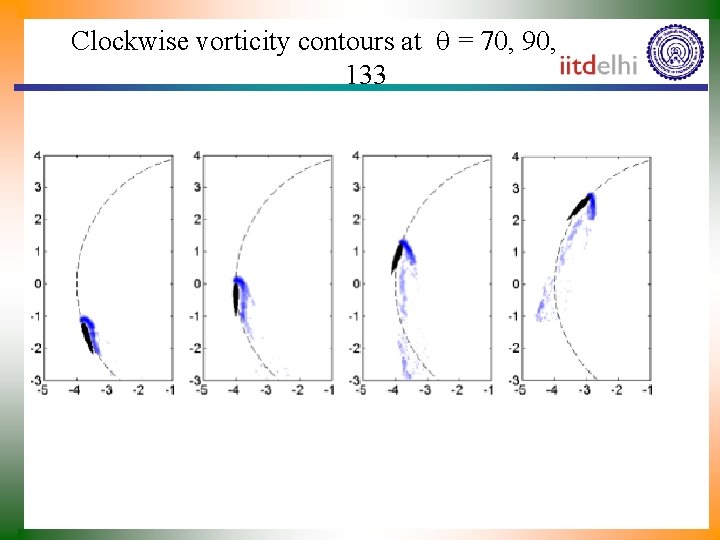
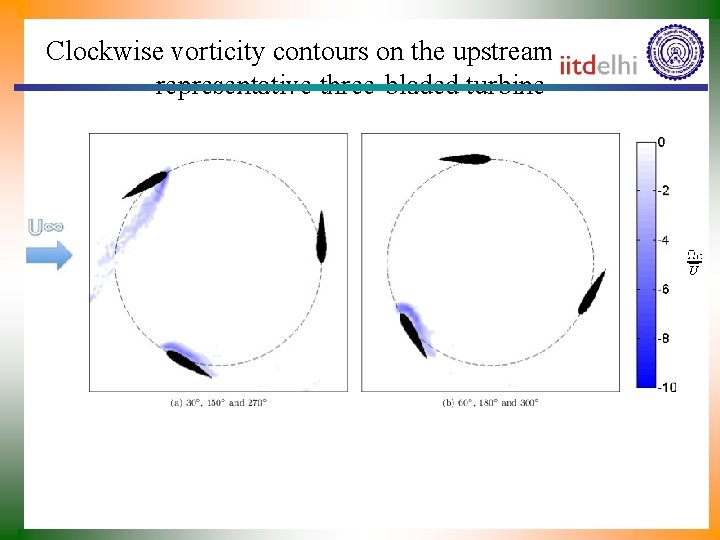
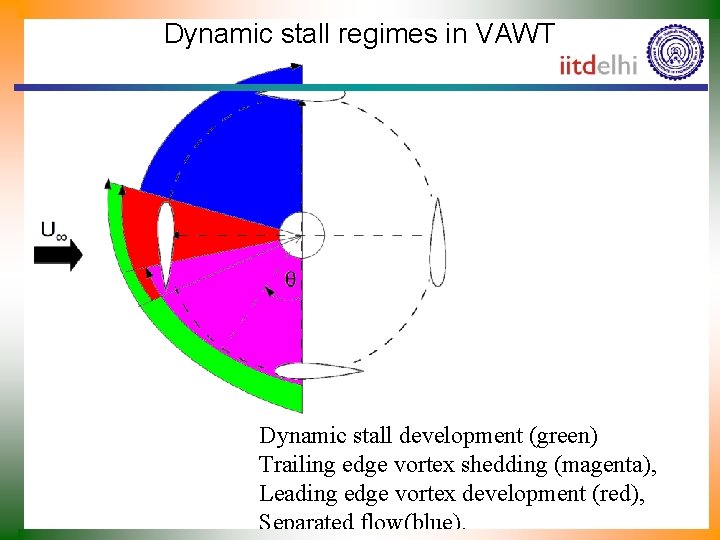
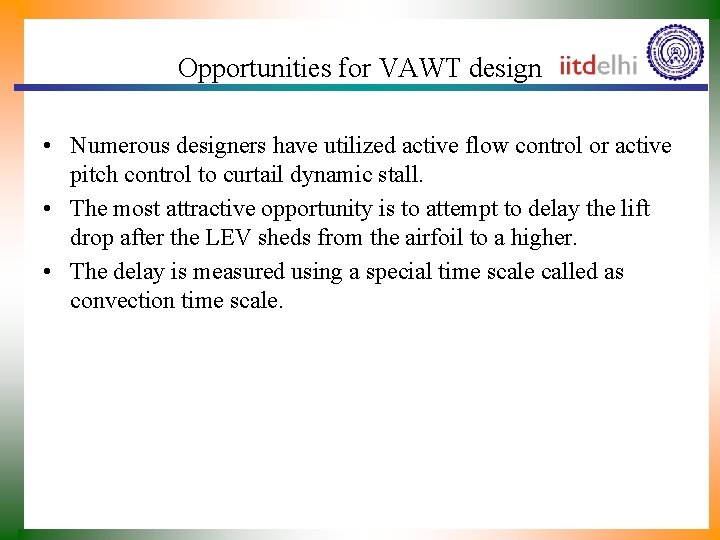
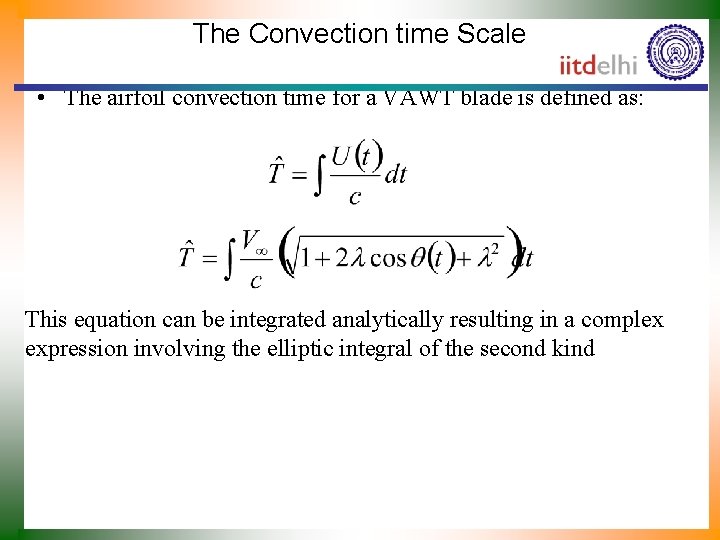
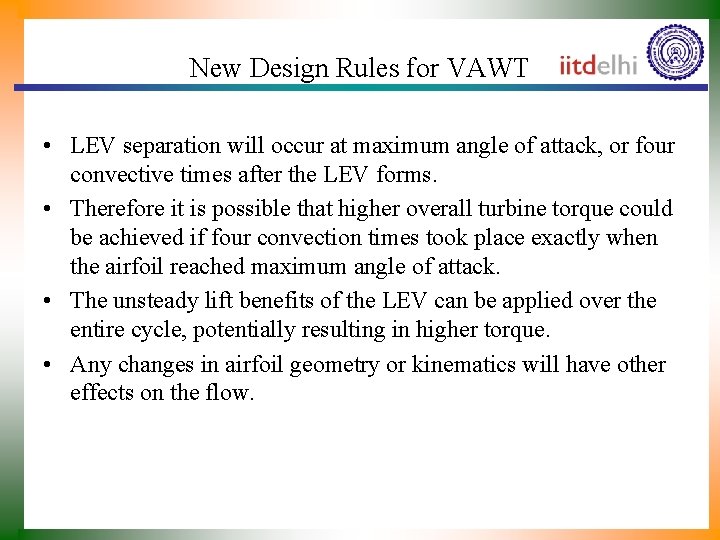
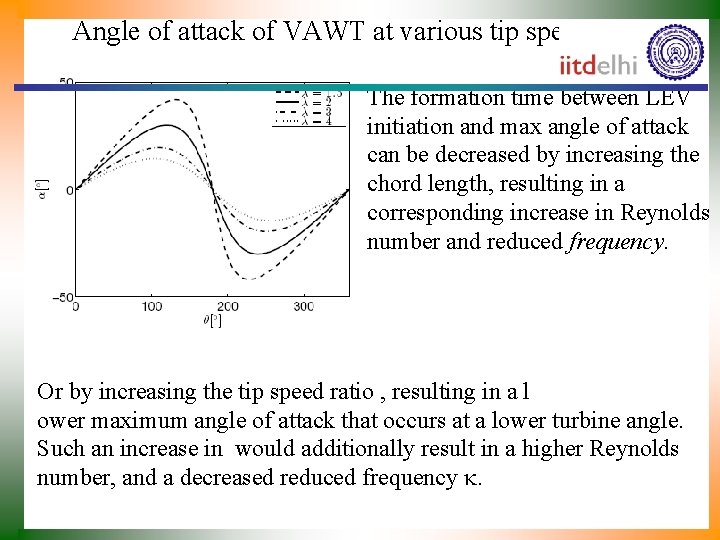
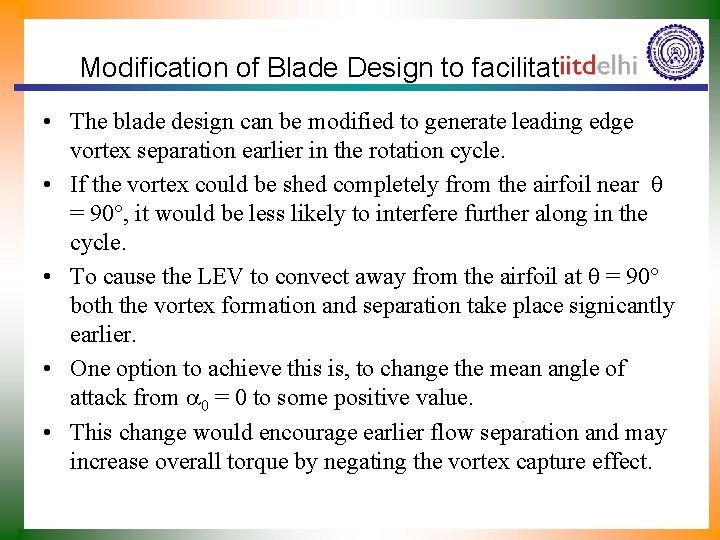
- Slides: 34
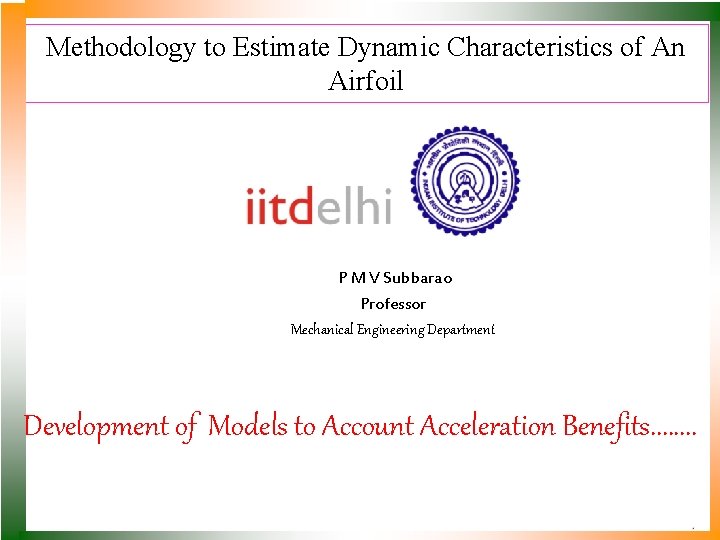
Methodology to Estimate Dynamic Characteristics of An Airfoil P M V Subbarao Professor Mechanical Engineering Department Development of Models to Account Acceleration Benefits. . . .
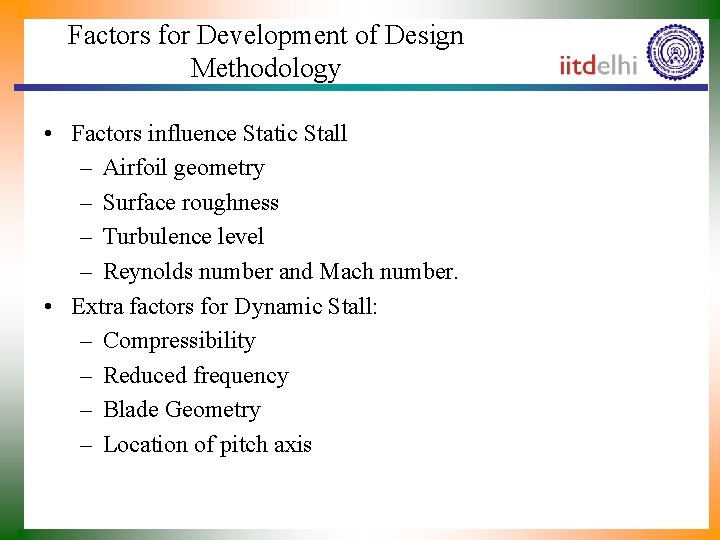
Factors for Development of Design Methodology • Factors influence Static Stall – Airfoil geometry – Surface roughness – Turbulence level – Reynolds number and Mach number. • Extra factors for Dynamic Stall: – Compressibility – Reduced frequency – Blade Geometry – Location of pitch axis
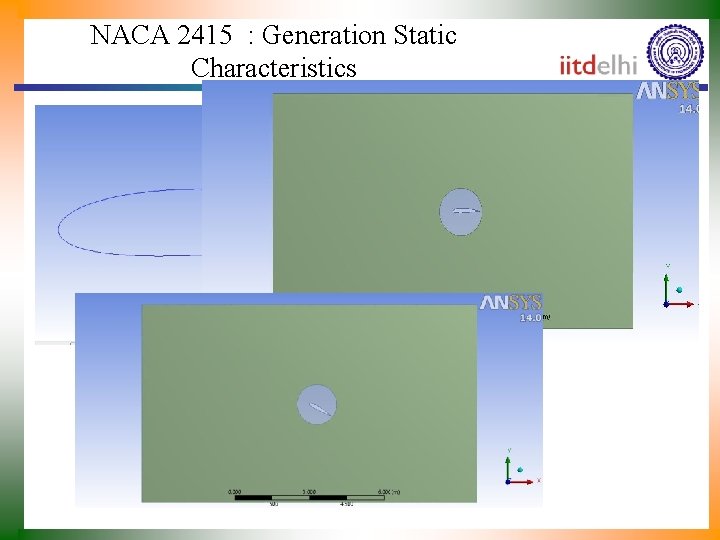
NACA 2415 : Generation Static Characteristics
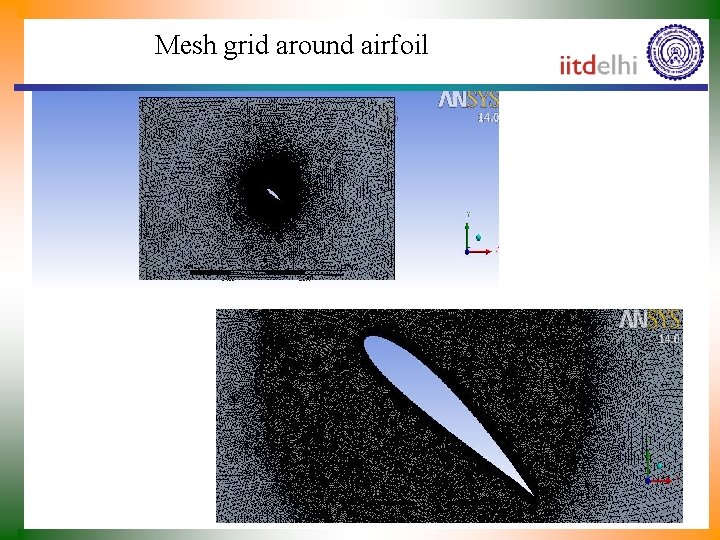
Mesh grid around airfoil
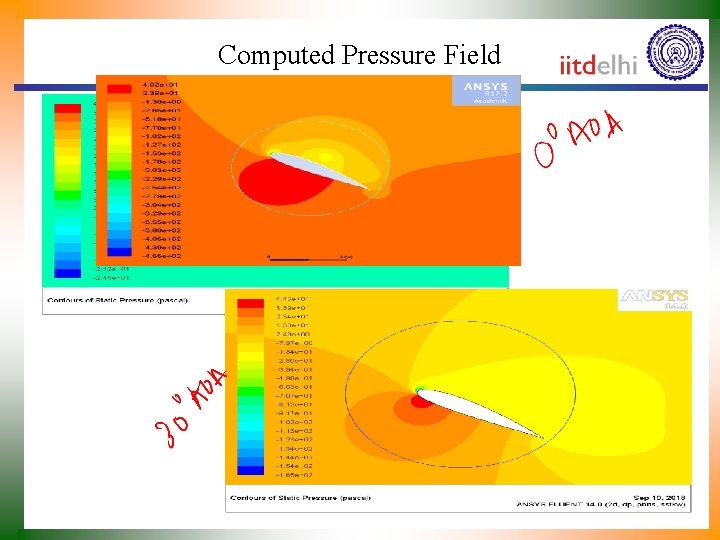
Computed Pressure Field
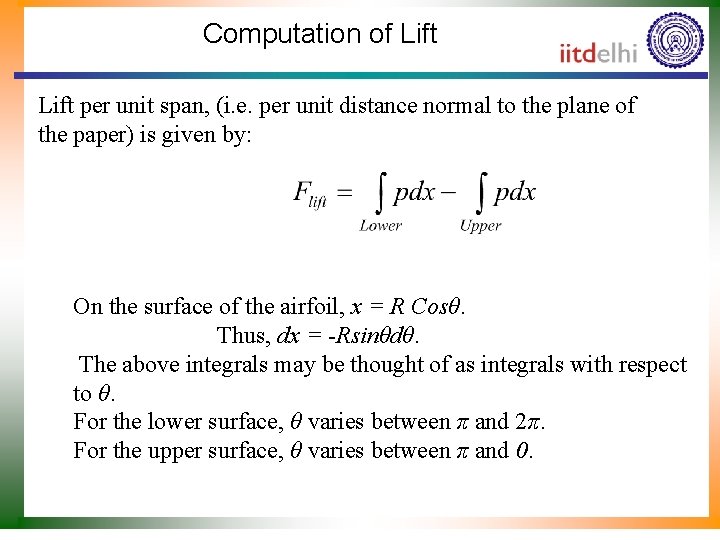
Computation of Lift per unit span, (i. e. per unit distance normal to the plane of the paper) is given by: On the surface of the airfoil, x = R Cosθ. Thus, dx = -Rsinθdθ. The above integrals may be thought of as integrals with respect to θ. For the lower surface, θ varies between π and 2π. For the upper surface, θ varies between π and 0.
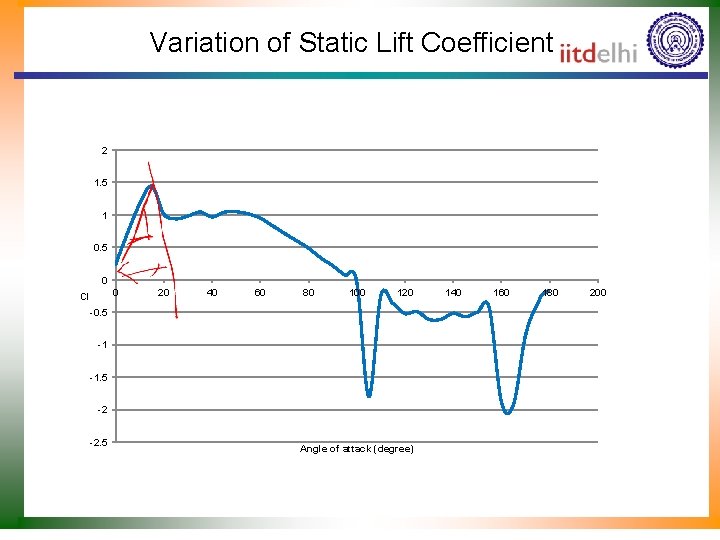
Variation of Static Lift Coefficient 2 1. 5 1 0. 5 0 0 Cl 20 40 60 80 100 120 -0. 5 -1 -1. 5 -2 -2. 5 Angle of attack (degree) 140 160 180 200
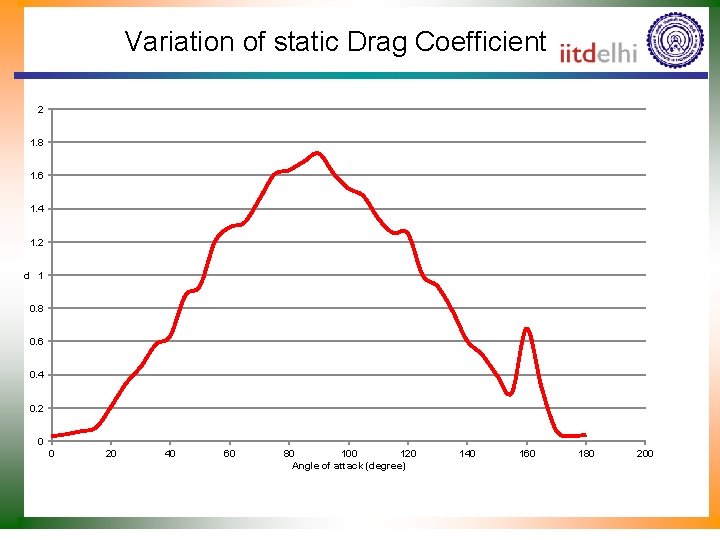
Variation of static Drag Coefficient 2 1. 8 1. 6 1. 4 1. 2 Cd 1 0. 8 0. 6 0. 4 0. 2 0 0 20 40 60 80 100 120 Angle of attack (degree) 140 160 180 200
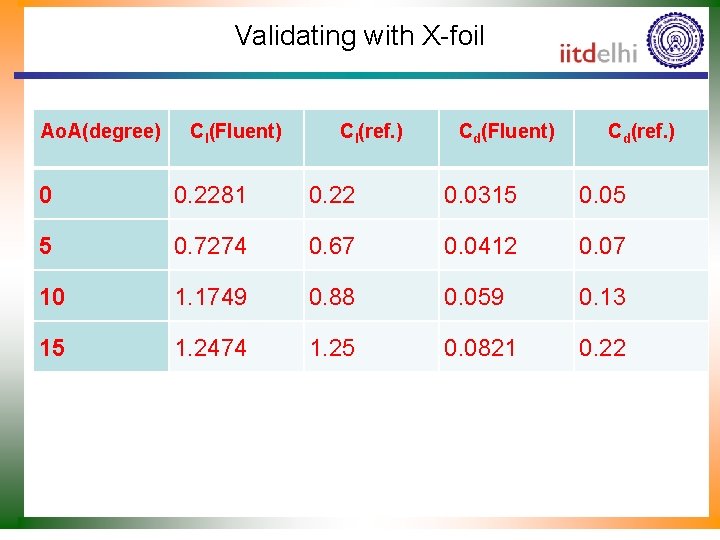
Validating with X-foil Ao. A(degree) Cl(Fluent) Cl(ref. ) Cd(Fluent) Cd(ref. ) 0 0. 2281 0. 22 0. 0315 0. 05 5 0. 7274 0. 67 0. 0412 0. 07 10 1. 1749 0. 88 0. 059 0. 13 15 1. 2474 1. 25 0. 0821 0. 22
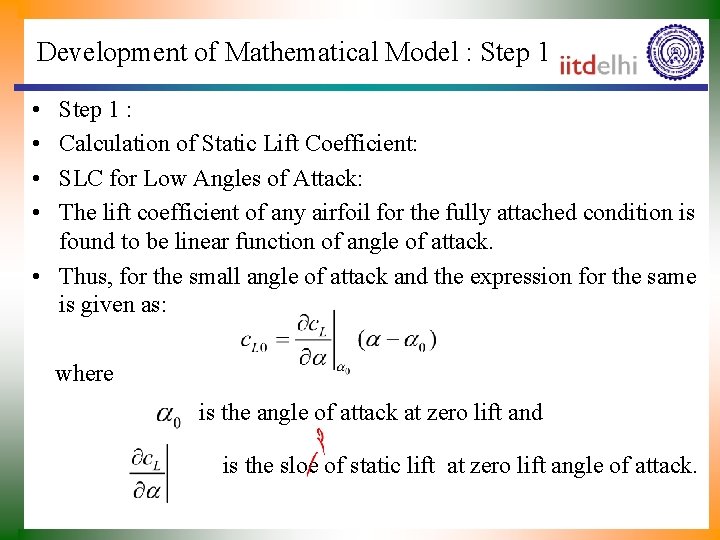
Development of Mathematical Model : Step 1 • • Step 1 : Calculation of Static Lift Coefficient: SLC for Low Angles of Attack: The lift coefficient of any airfoil for the fully attached condition is found to be linear function of angle of attack. • Thus, for the small angle of attack and the expression for the same is given as: where is the angle of attack at zero lift and is the sloe of static lift at zero lift angle of attack.
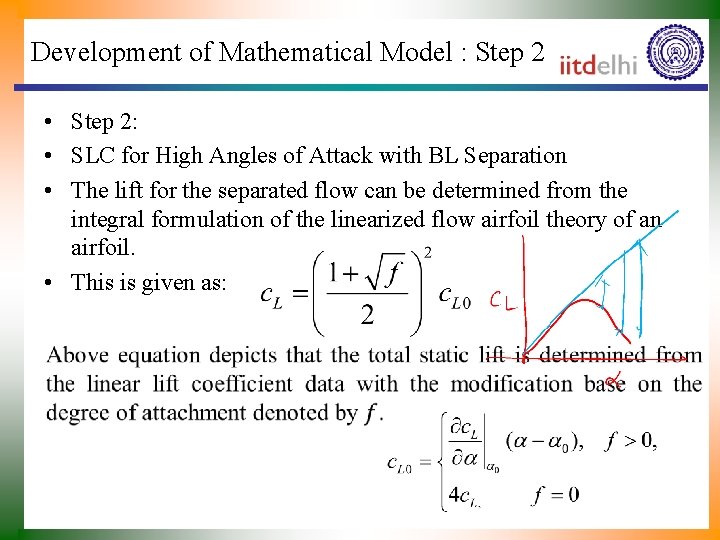
Development of Mathematical Model : Step 2 • Step 2: • SLC for High Angles of Attack with BL Separation • The lift for the separated flow can be determined from the integral formulation of the linearized flow airfoil theory of an airfoil. • This is given as:
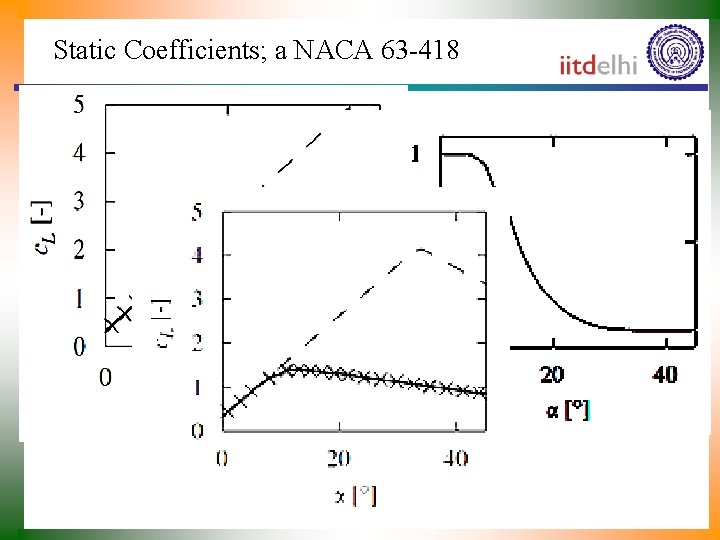
Static Coefficients; a NACA 63 -418
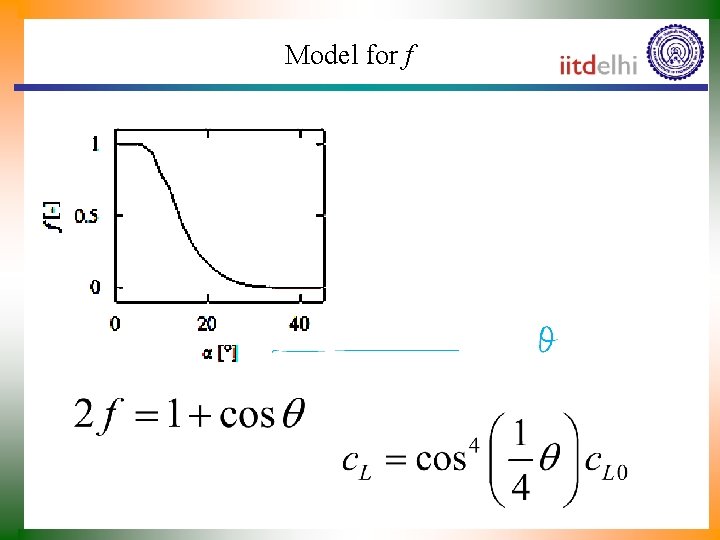
Model for f
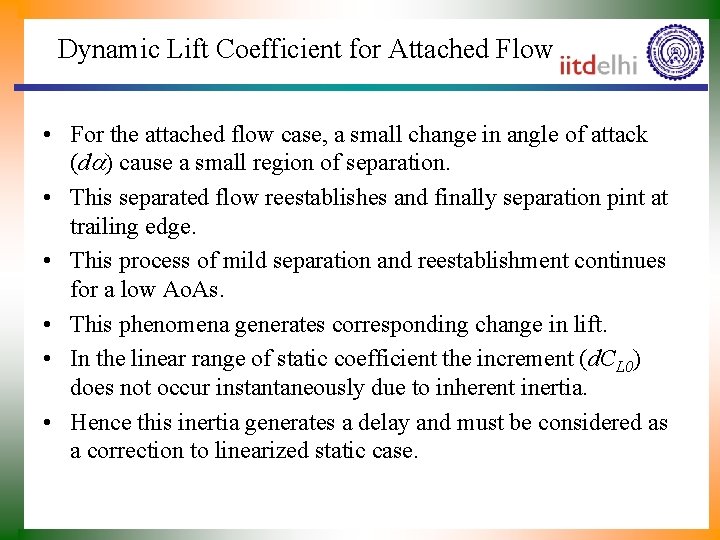
Dynamic Lift Coefficient for Attached Flow • For the attached flow case, a small change in angle of attack (d ) cause a small region of separation. • This separated flow reestablishes and finally separation pint at trailing edge. • This process of mild separation and reestablishment continues for a low Ao. As. • This phenomena generates corresponding change in lift. • In the linear range of static coefficient the increment (d. CL 0) does not occur instantaneously due to inherent inertia. • Hence this inertia generates a delay and must be considered as a correction to linearized static case.
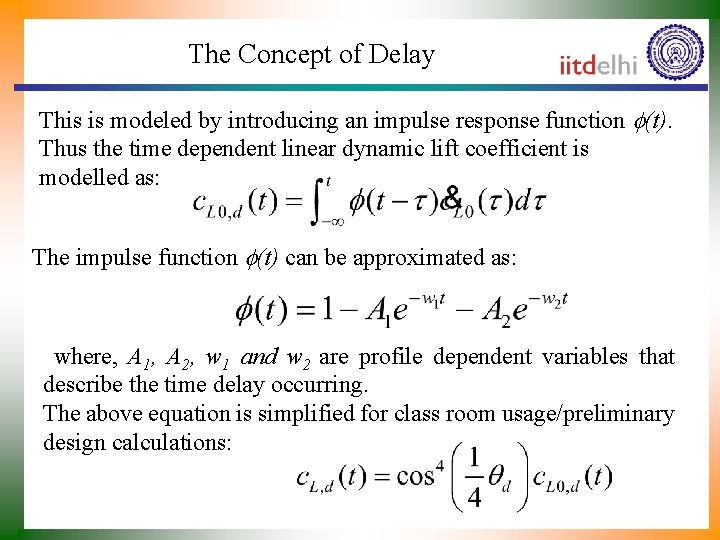
The Concept of Delay This is modeled by introducing an impulse response function (t). Thus the time dependent linear dynamic lift coefficient is modelled as: The impulse function (t) can be approximated as: where, A 1, A 2, w 1 and w 2 are profile dependent variables that describe the time delay occurring. The above equation is simplified for class room usage/preliminary design calculations:
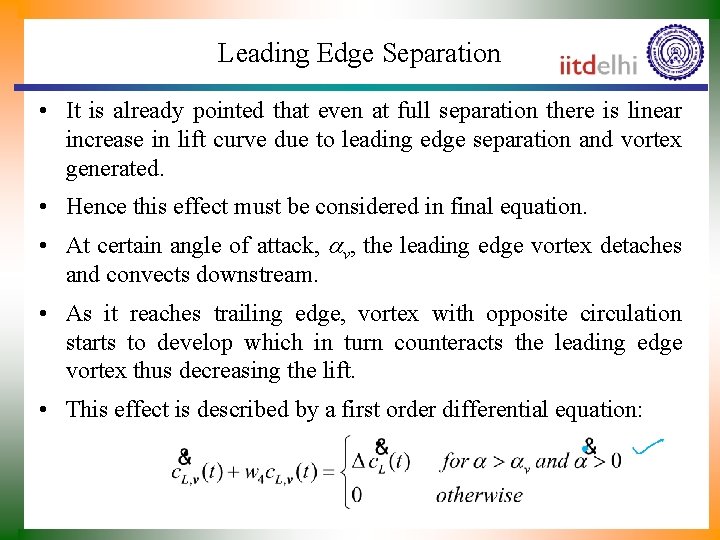
Leading Edge Separation • It is already pointed that even at full separation there is linear increase in lift curve due to leading edge separation and vortex generated. • Hence this effect must be considered in final equation. • At certain angle of attack, v, the leading edge vortex detaches and convects downstream. • As it reaches trailing edge, vortex with opposite circulation starts to develop which in turn counteracts the leading edge vortex thus decreasing the lift. • This effect is described by a first order differential equation:
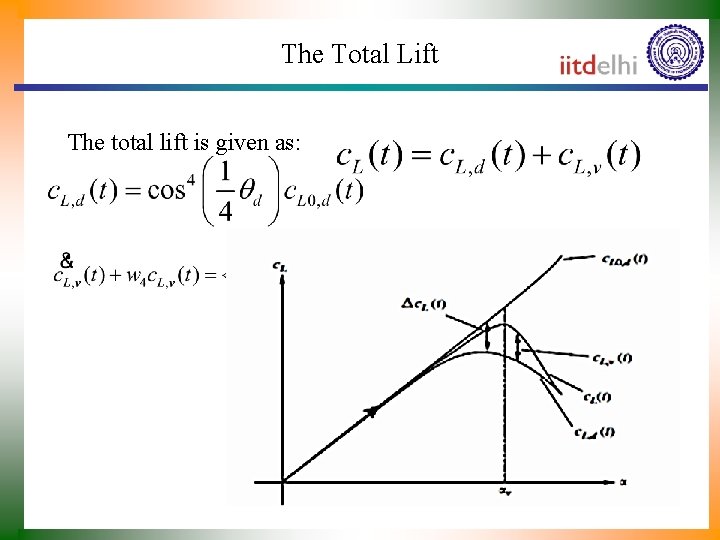
The Total Lift The total lift is given as:
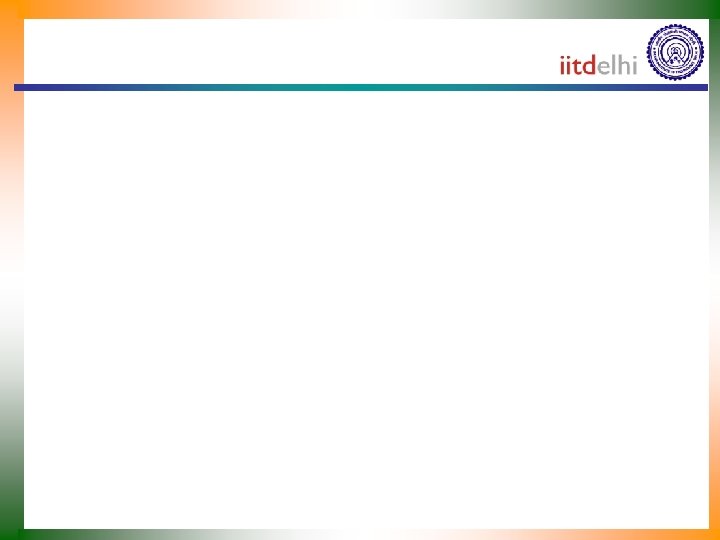
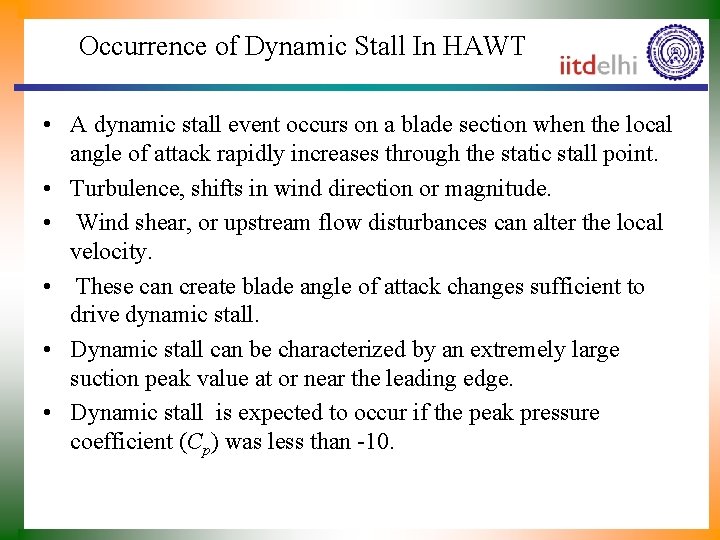
Occurrence of Dynamic Stall In HAWT • A dynamic stall event occurs on a blade section when the local angle of attack rapidly increases through the static stall point. • Turbulence, shifts in wind direction or magnitude. • Wind shear, or upstream flow disturbances can alter the local velocity. • These can create blade angle of attack changes sufficient to drive dynamic stall. • Dynamic stall can be characterized by an extremely large suction peak value at or near the leading edge. • Dynamic stall is expected to occur if the peak pressure coefficient (Cp) was less than -10.
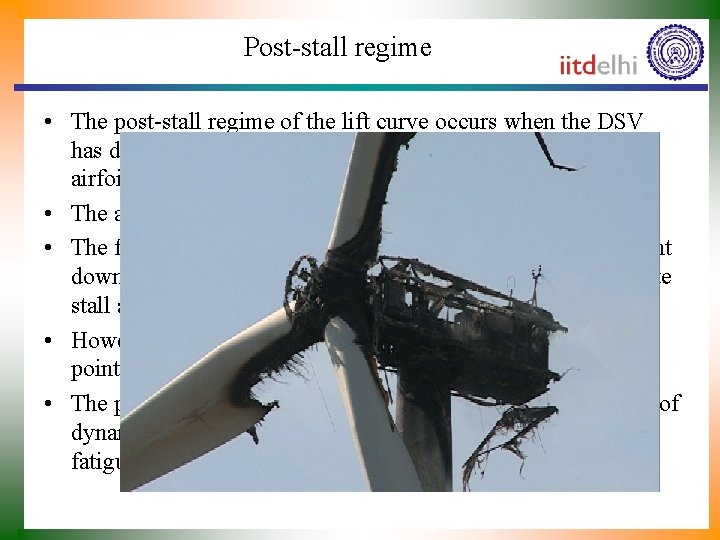
Post-stall regime • The post-stall regime of the lift curve occurs when the DSV has departed and the flow is completely separated from the airfoil. • The airfoil goes into a state of deep stall. • The flow is only recovered when the angle of attack is brought down to sufficiently lower values compared to the steady-state stall angle of attack. • However, if the airfoil is still allowed to rotate beyond the point of flow separation, a secondary peak in lift is observed. • The post stall regime is one of the most investigated features of dynamic stall, primarily due to its large influence on the fatigue life of wind turbine blades.
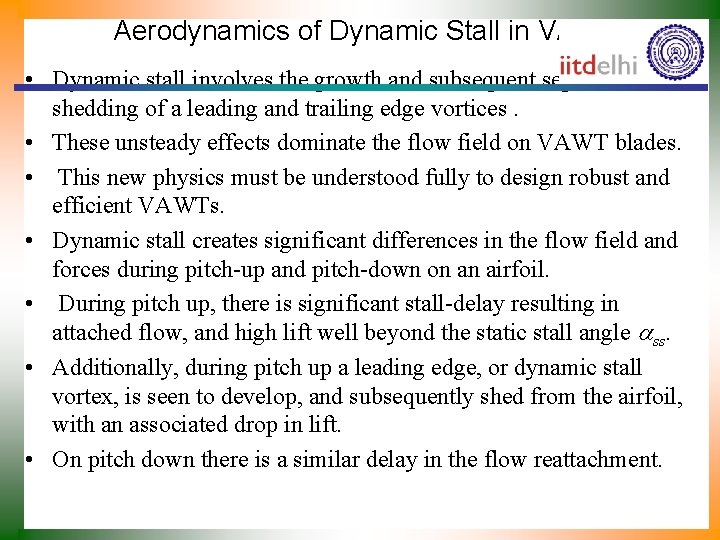
Aerodynamics of Dynamic Stall in VAWT • Dynamic stall involves the growth and subsequent separation and shedding of a leading and trailing edge vortices. • These unsteady effects dominate the flow field on VAWT blades. • This new physics must be understood fully to design robust and efficient VAWTs. • Dynamic stall creates significant differences in the flow field and forces during pitch-up and pitch-down on an airfoil. • During pitch up, there is significant stall-delay resulting in attached flow, and high lift well beyond the static stall angle ss. • Additionally, during pitch up a leading edge, or dynamic stall vortex, is seen to develop, and subsequently shed from the airfoil, with an associated drop in lift. • On pitch down there is a similar delay in the flow reattachment.
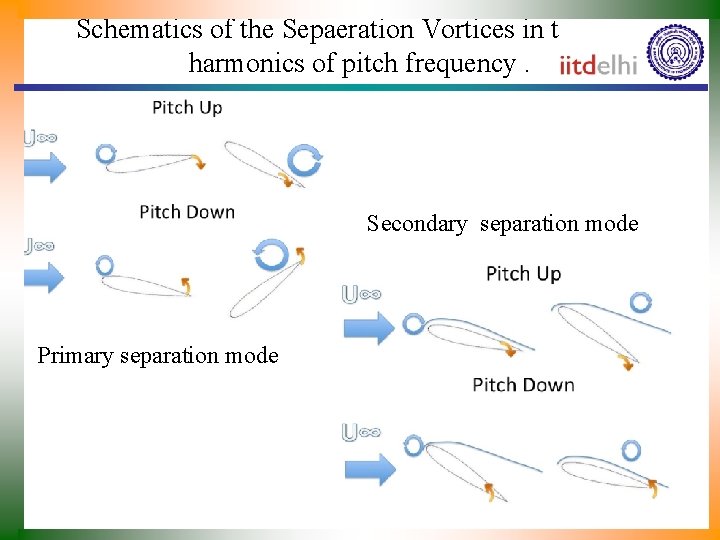
Schematics of the Sepaeration Vortices in terms as harmonics of pitch frequency. Secondary separation mode Primary separation mode
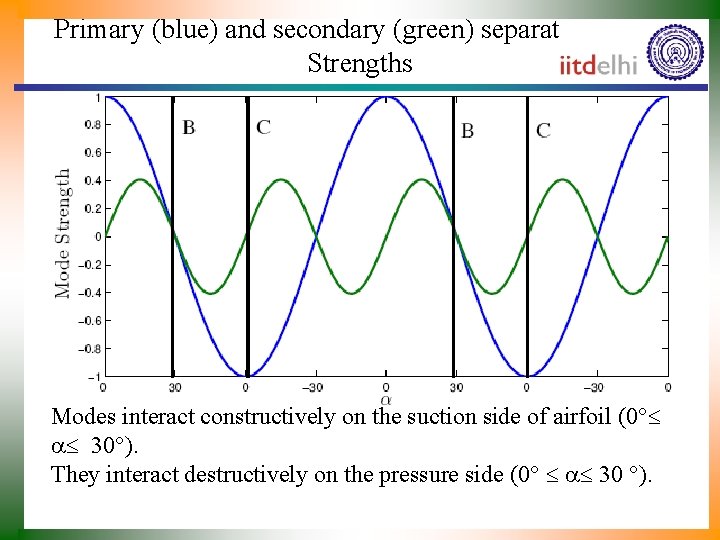
Primary (blue) and secondary (green) separation mode Strengths Modes interact constructively on the suction side of airfoil (0 30 ). They interact destructively on the pressure side (0 30 ).
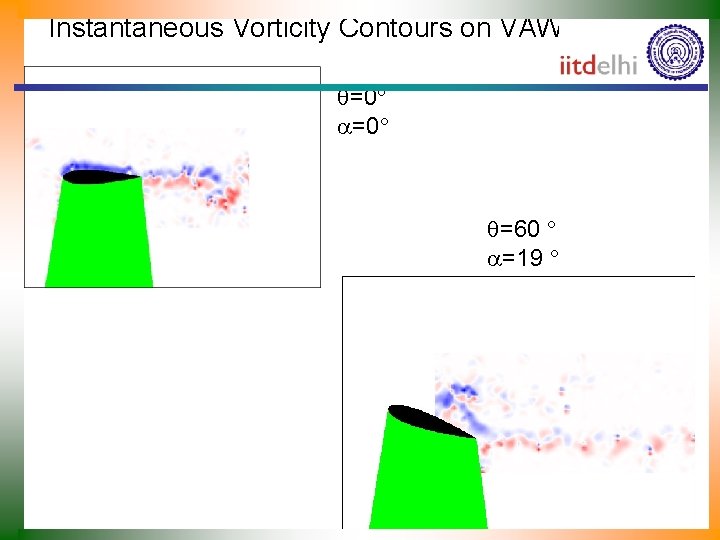
Instantaneous Vorticity Contours on VAWT Blade =0 =60 =19
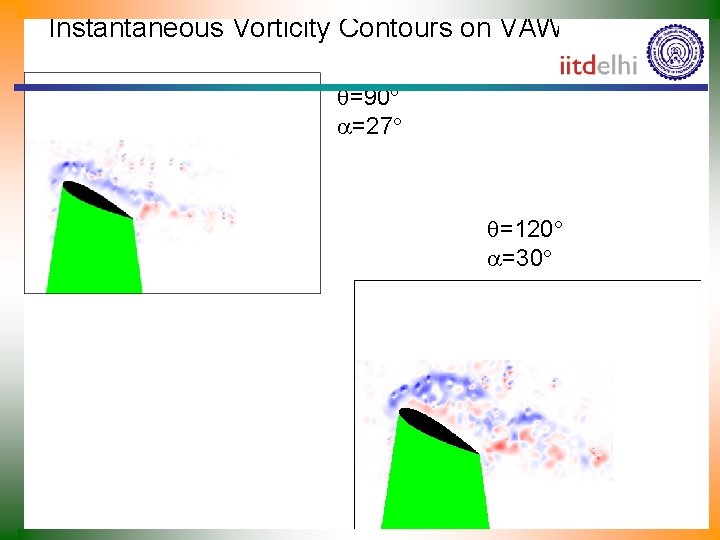
Instantaneous Vorticity Contours on VAWT Blade =90 =27 =120 =30
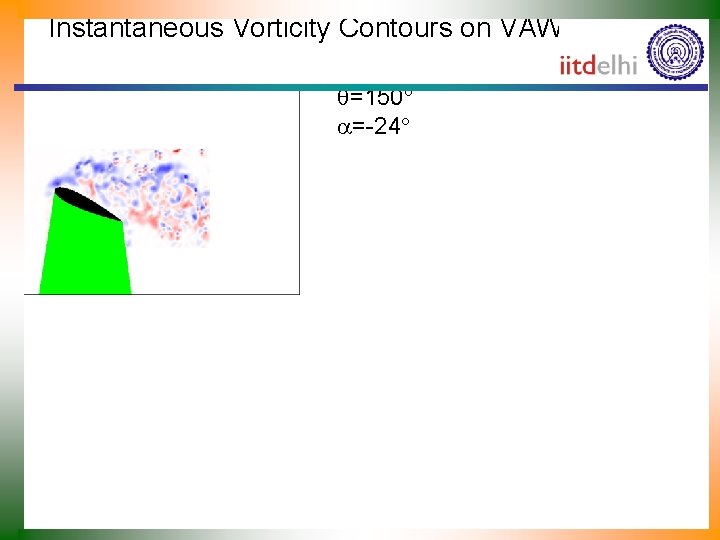
Instantaneous Vorticity Contours on VAWT Blade =150 =-24
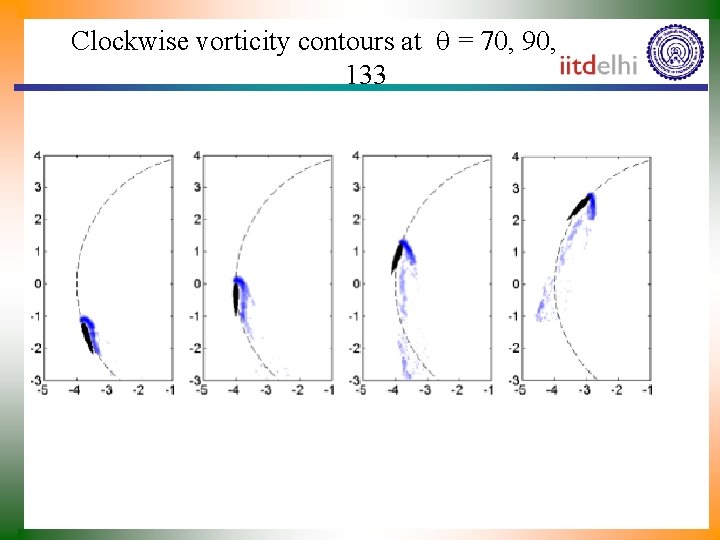
Clockwise vorticity contours at = 70, 90, 108, and 133
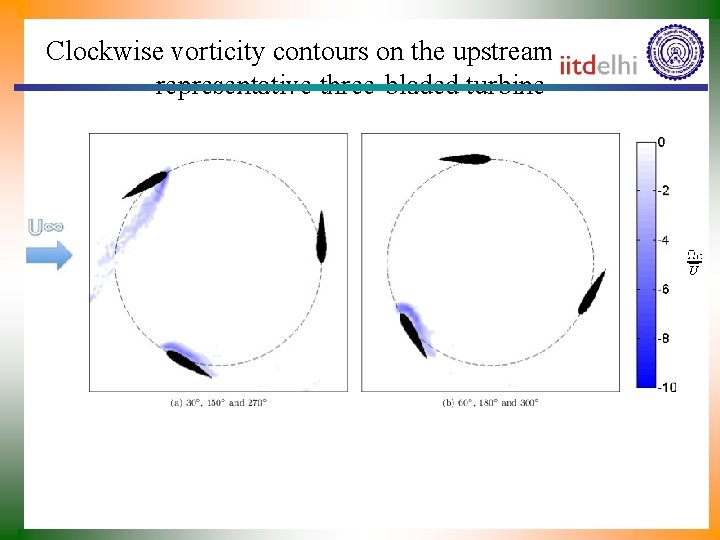
Clockwise vorticity contours on the upstream half of a representative three-bladed turbine
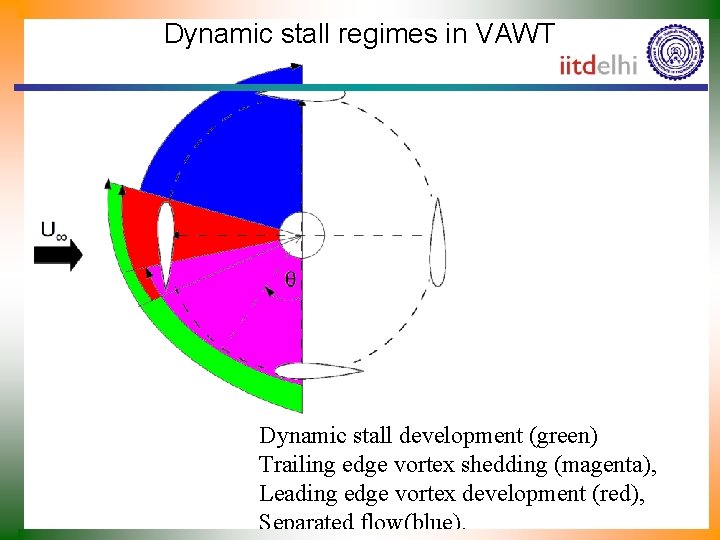
Dynamic stall regimes in VAWT Dynamic stall development (green) Trailing edge vortex shedding (magenta), Leading edge vortex development (red), Separated flow(blue).
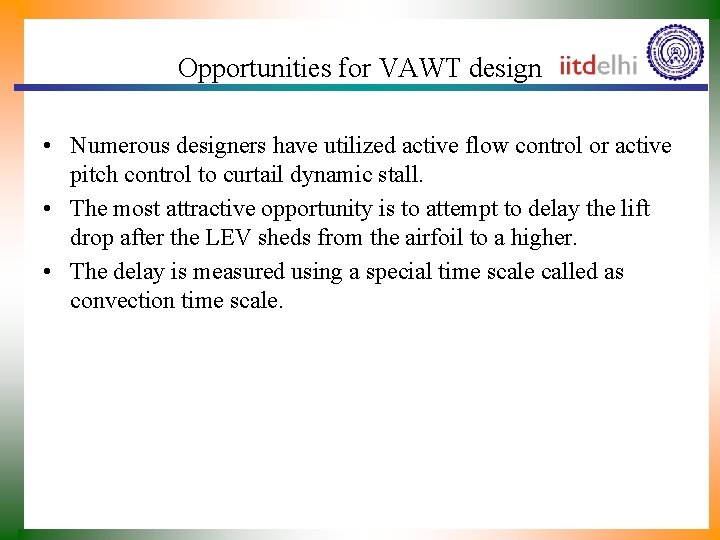
Opportunities for VAWT design • Numerous designers have utilized active flow control or active pitch control to curtail dynamic stall. • The most attractive opportunity is to attempt to delay the lift drop after the LEV sheds from the airfoil to a higher. • The delay is measured using a special time scale called as convection time scale.
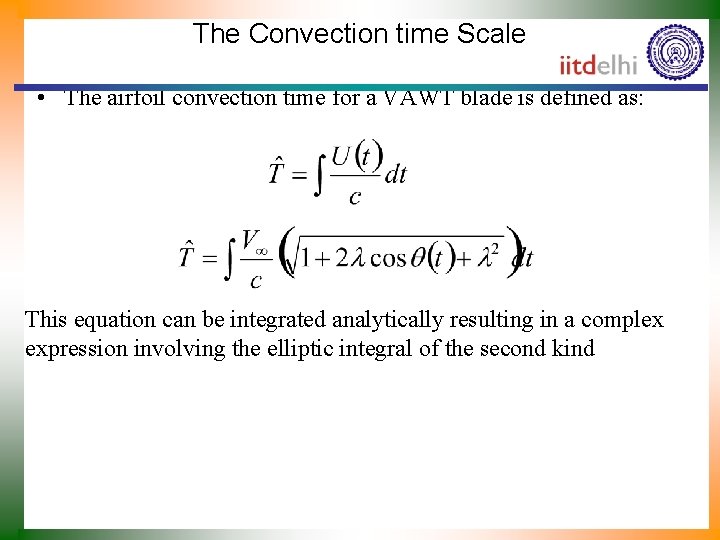
The Convection time Scale • The airfoil convection time for a VAWT blade is defined as: This equation can be integrated analytically resulting in a complex expression involving the elliptic integral of the second kind
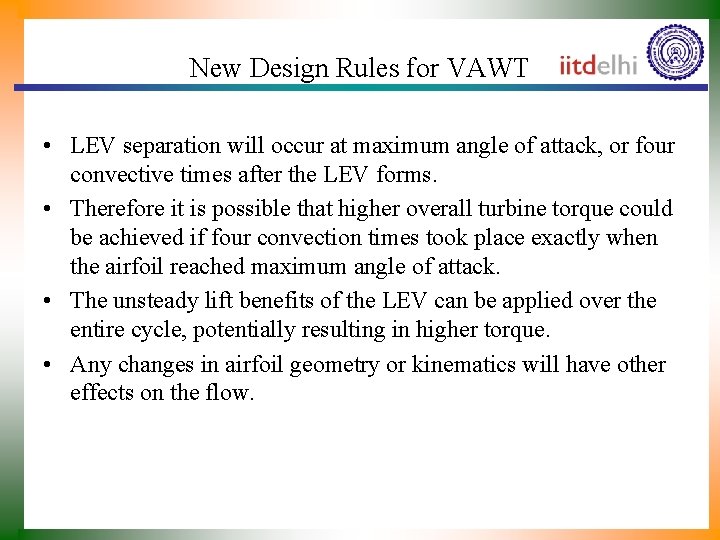
New Design Rules for VAWT • LEV separation will occur at maximum angle of attack, or four convective times after the LEV forms. • Therefore it is possible that higher overall turbine torque could be achieved if four convection times took place exactly when the airfoil reached maximum angle of attack. • The unsteady lift benefits of the LEV can be applied over the entire cycle, potentially resulting in higher torque. • Any changes in airfoil geometry or kinematics will have other effects on the flow.
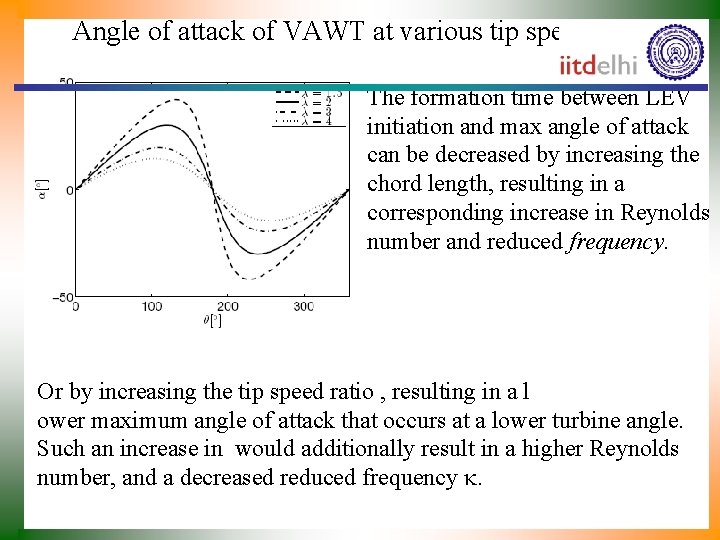
Angle of attack of VAWT at various tip speed ratios The formation time between LEV initiation and max angle of attack can be decreased by increasing the chord length, resulting in a corresponding increase in Reynolds number and reduced frequency. Or by increasing the tip speed ratio , resulting in a l ower maximum angle of attack that occurs at a lower turbine angle. Such an increase in would additionally result in a higher Reynolds number, and a decreased reduced frequency .
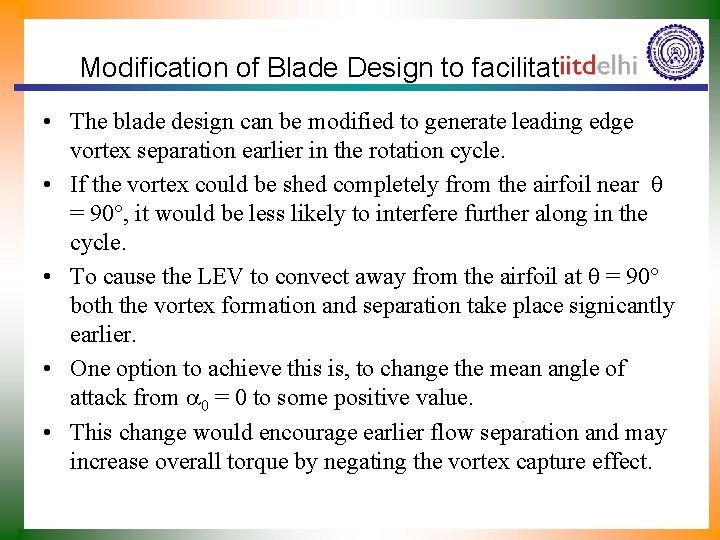
Modification of Blade Design to facilitate DSV • The blade design can be modified to generate leading edge vortex separation earlier in the rotation cycle. • If the vortex could be shed completely from the airfoil near = 90 , it would be less likely to interfere further along in the cycle. • To cause the LEV to convect away from the airfoil at = 90 both the vortex formation and separation take place signicantly earlier. • One option to achieve this is, to change the mean angle of attack from 0 = 0 to some positive value. • This change would encourage earlier flow separation and may increase overall torque by negating the vortex capture effect.
Wing lift coefficient
Kamm tail vs airfoil
Aerodynamic shapes
Airfoil pressure distribution
Cargo plane airfoil
State and prove bernoulli's principle
Parsec airfoil
Airfoil naca 0012
Airfoil terminology
Thin airfoil stall
Maximum lift coefficient formula
Airfoil construction
Transferered
Qualitative and quantitative data analysis
Zero order instrument
Characteristics of dynamic programming
Wecan95
Pooled variance
Inference point
Es ef ls lf calculator
Section
How to find point estimate
Cost management pmp
Contoh project cost management
How to find point estimate
Contoh cost baseline
Contoh cost estimate
Clive wants to estimate the number of bees in a beehive
Upholstery estimate chart
Cal
How to estimate nails for formworks
Estimate the average drawdown over an area where 25 million
What is 239 rounded to the nearest hundred
Fermi problem piano tuner
Estimate and rounding