Lecture 8 0 Silicon Crystal Growth Silicon Mfg
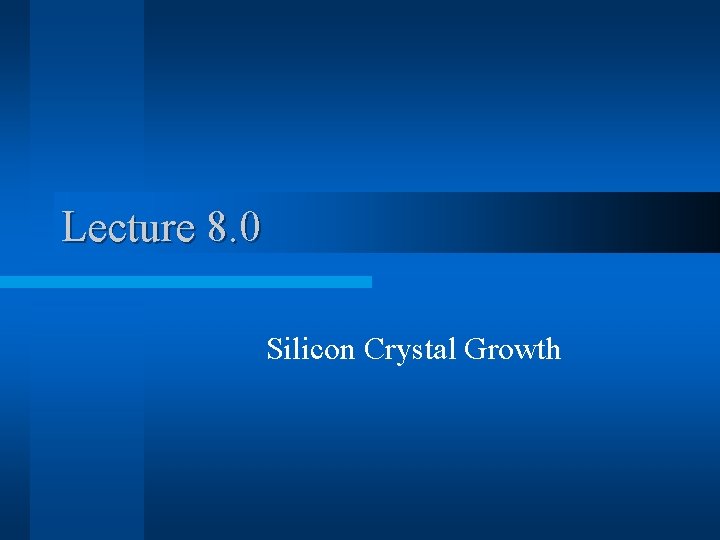
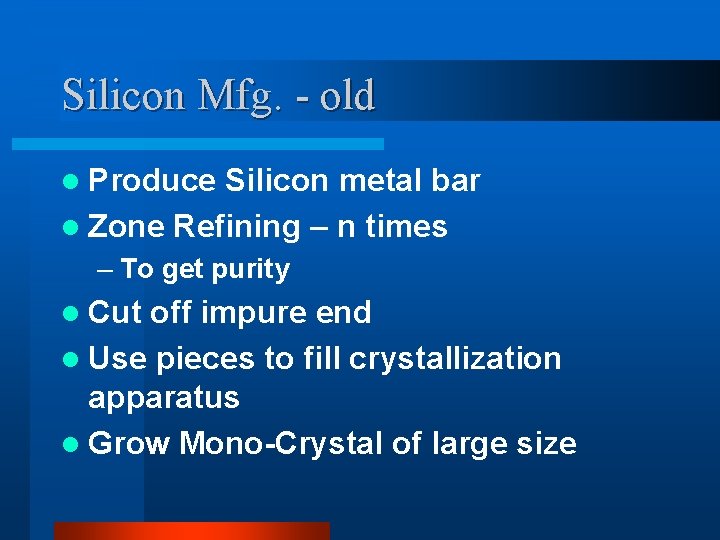
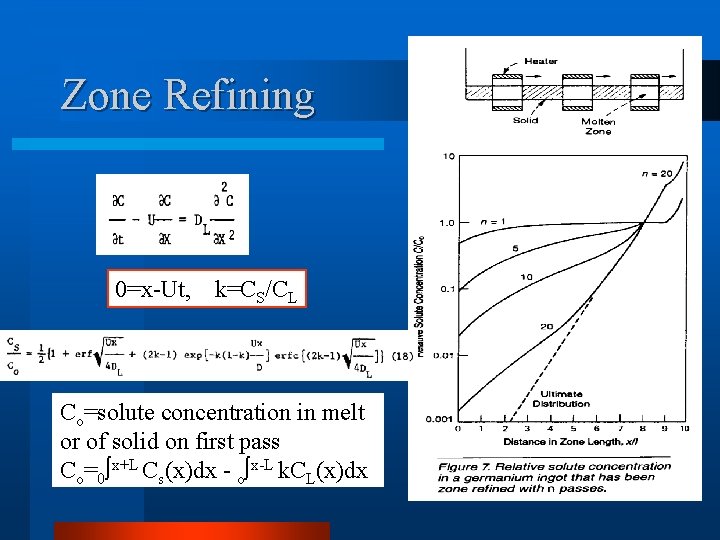
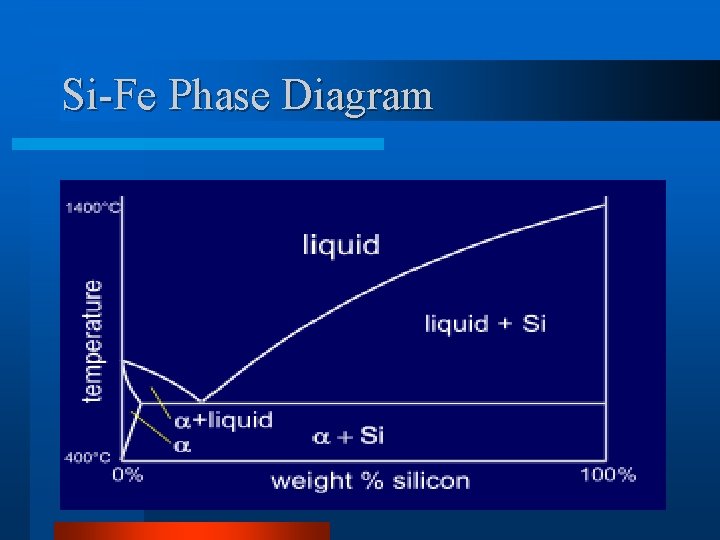
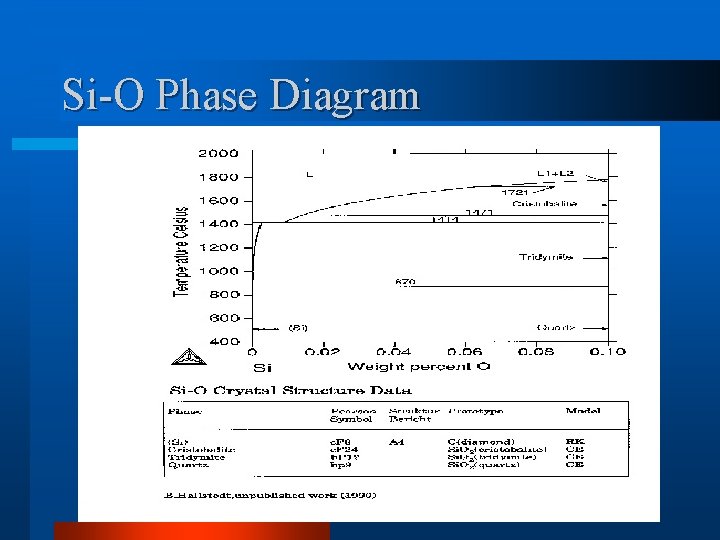
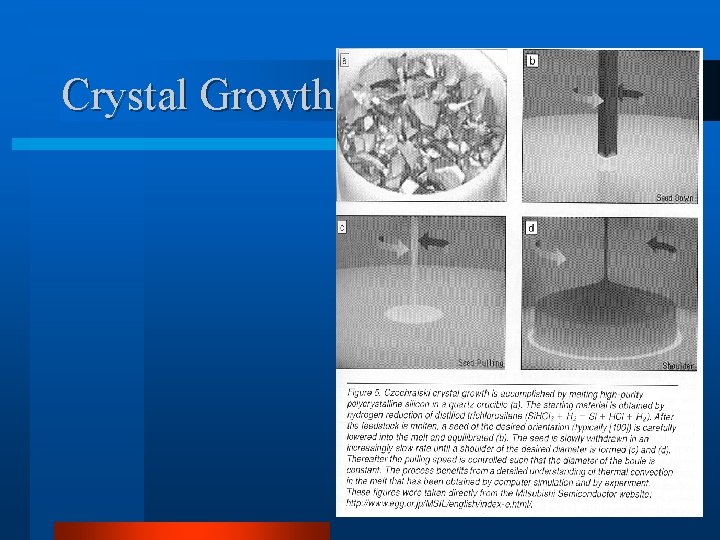
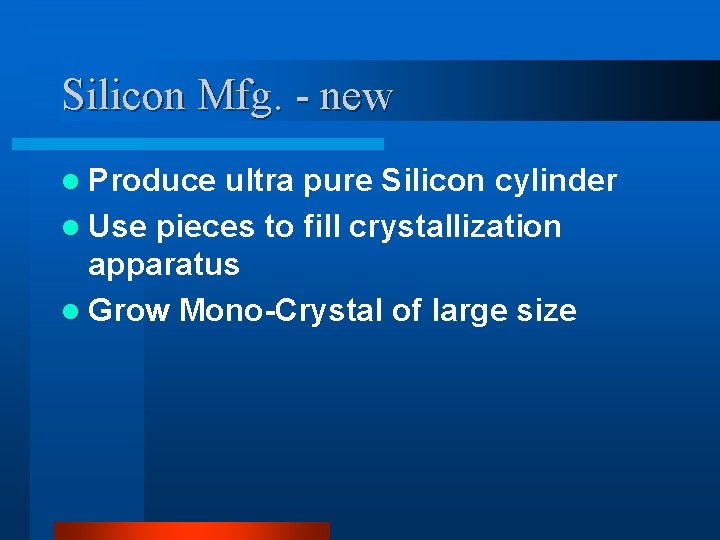
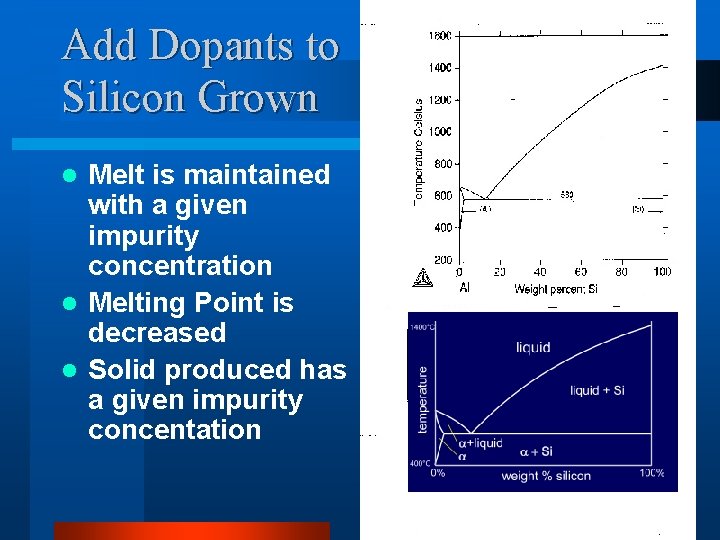
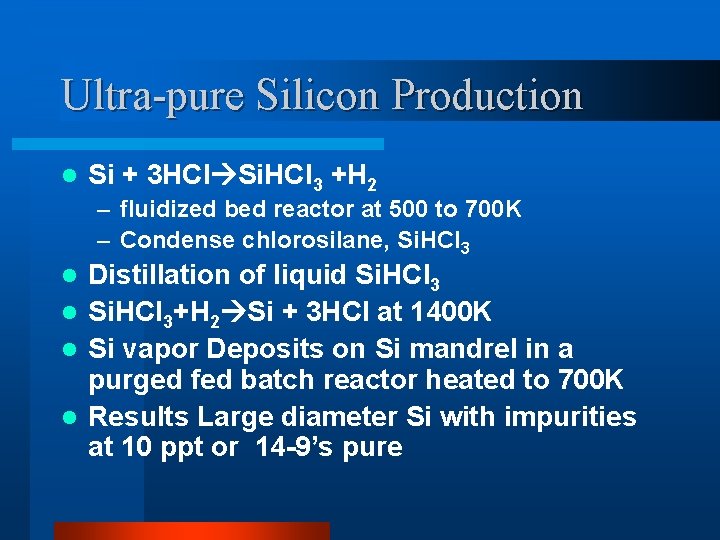
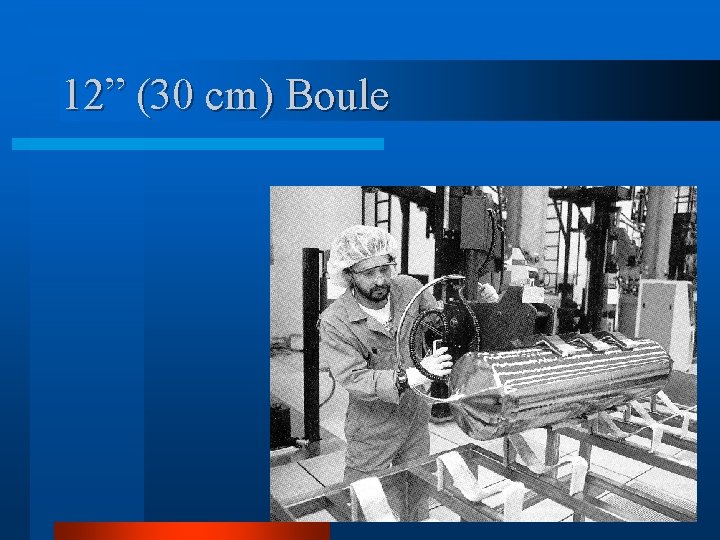
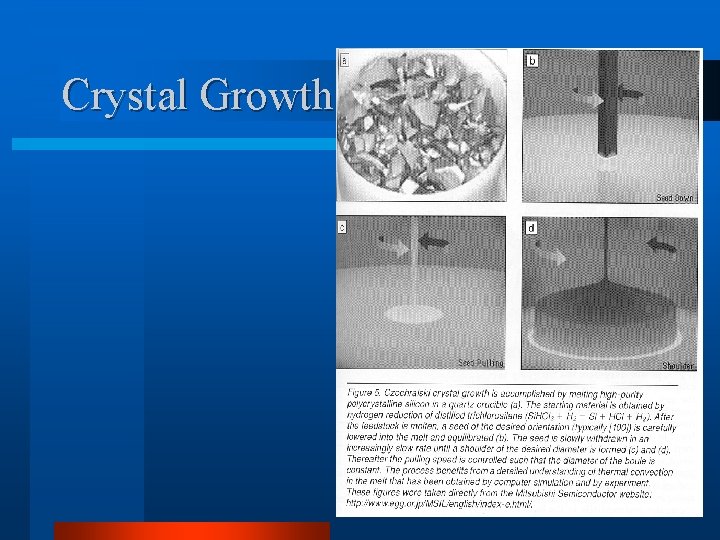
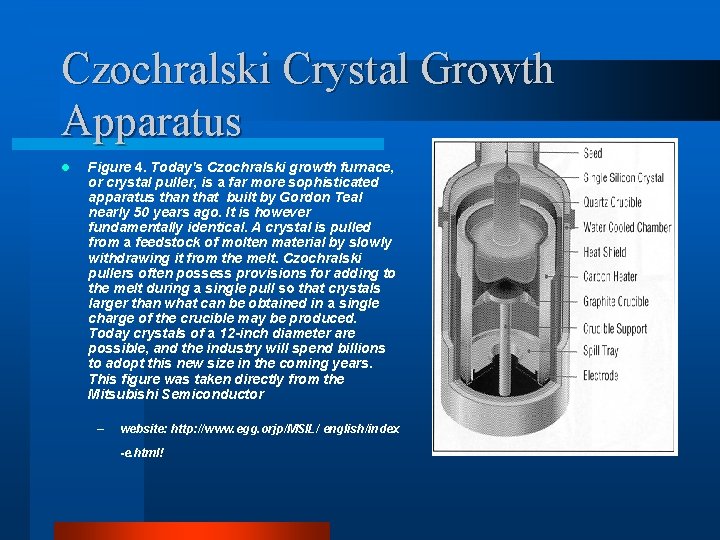
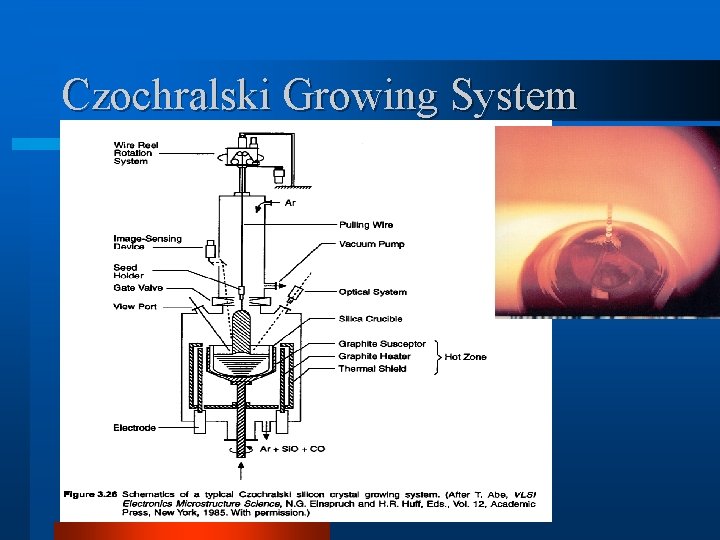
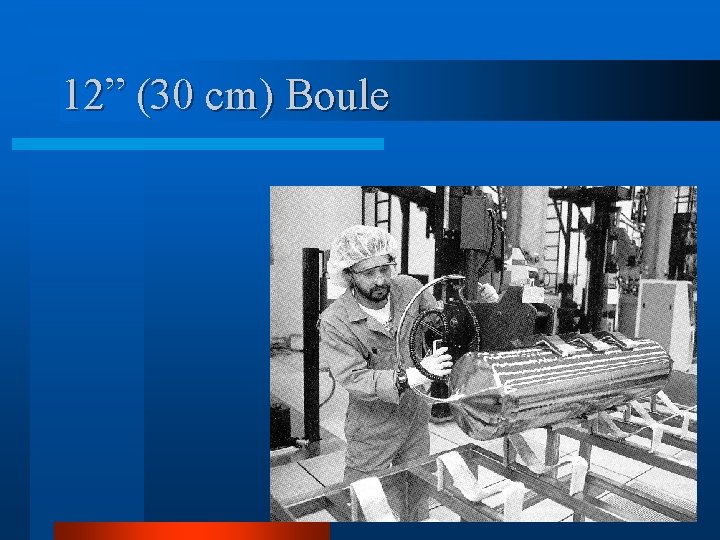
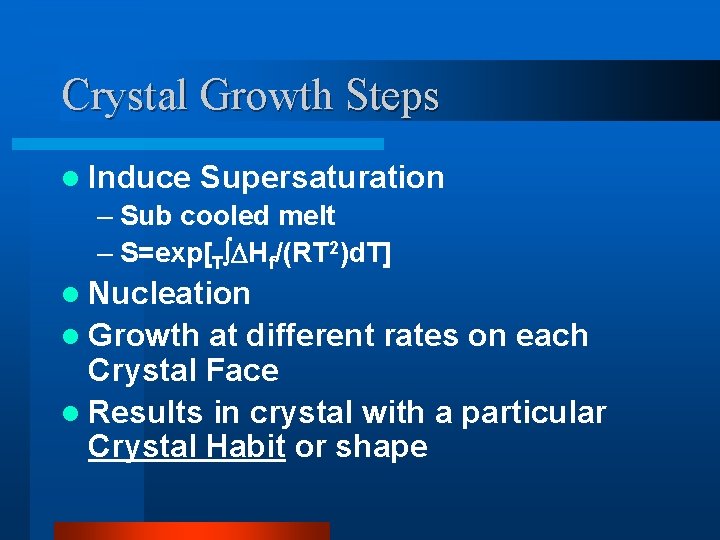
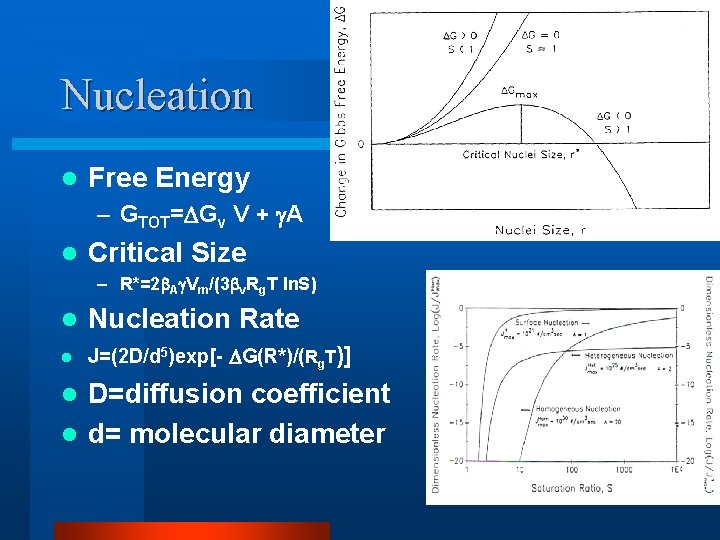
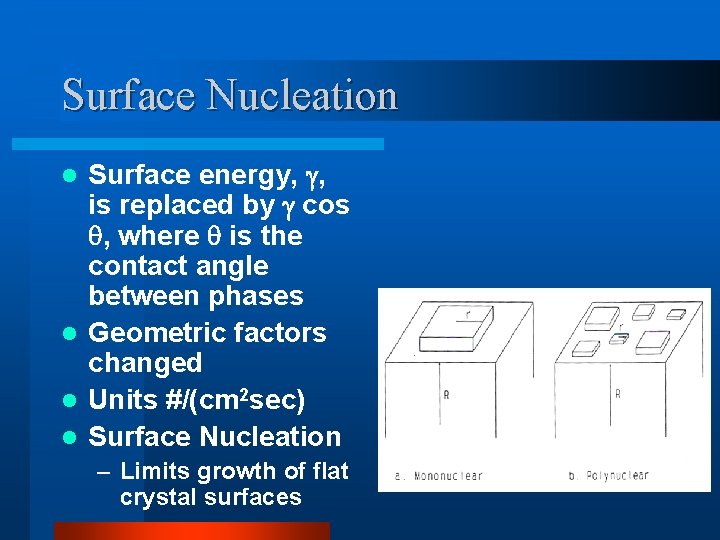
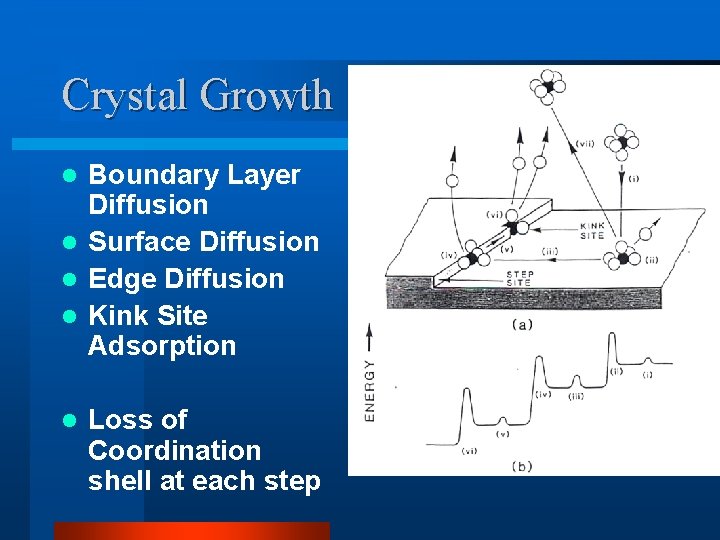
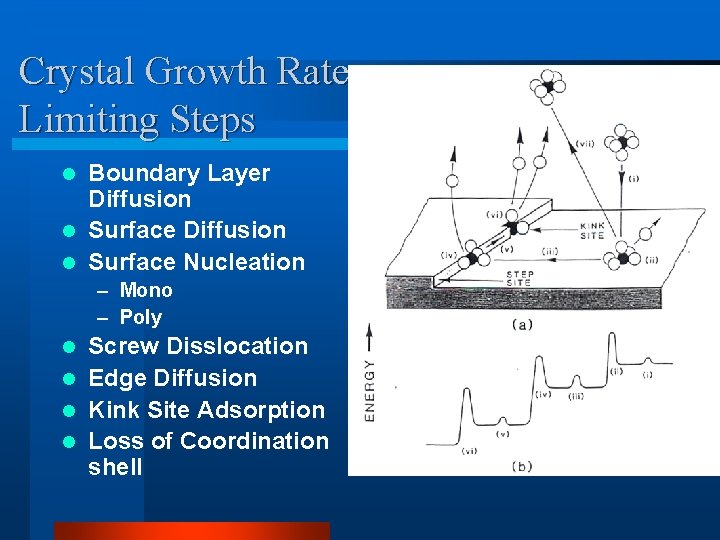
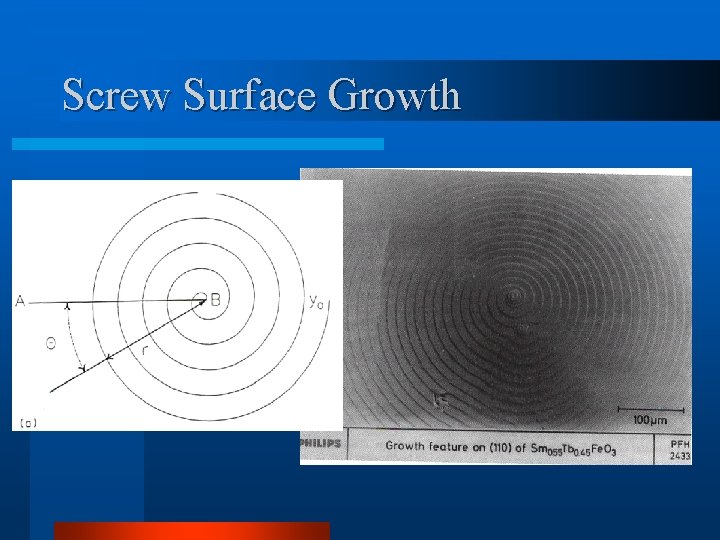
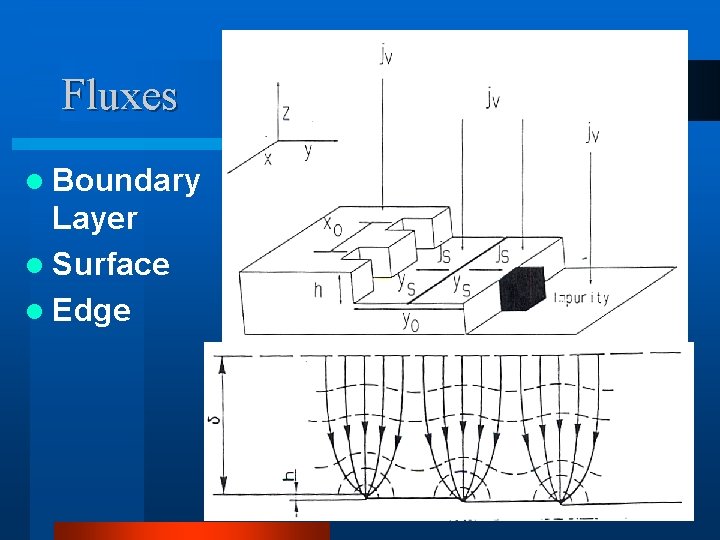
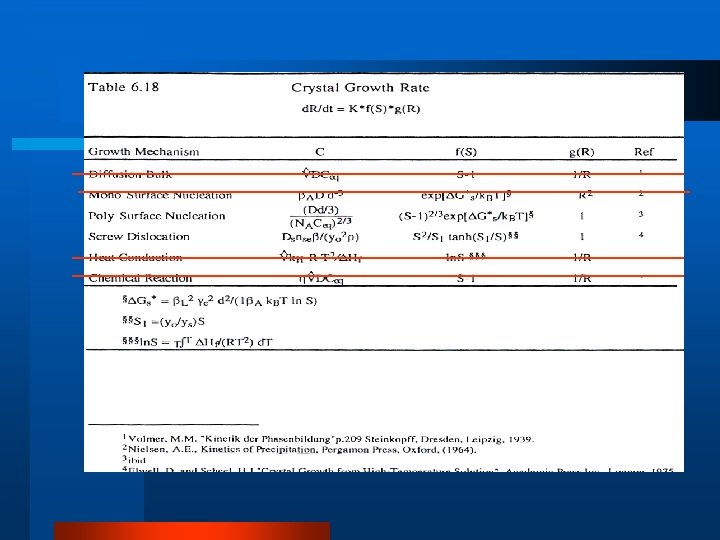
![Mass Transfer to Rotating Crystal l Local BL-MT Flux J[mole/(cm 2 s)] = 0. Mass Transfer to Rotating Crystal l Local BL-MT Flux J[mole/(cm 2 s)] = 0.](https://slidetodoc.com/presentation_image_h2/bf60bc24ceb8c41739e970bec5330a59/image-23.jpg)
![Heat Transfer to Rotating Crystal l Local BL-HT Flux J[mole/(cm 2 s)] = h(Teq-T)/ Heat Transfer to Rotating Crystal l Local BL-HT Flux J[mole/(cm 2 s)] = h(Teq-T)/](https://slidetodoc.com/presentation_image_h2/bf60bc24ceb8c41739e970bec5330a59/image-24.jpg)
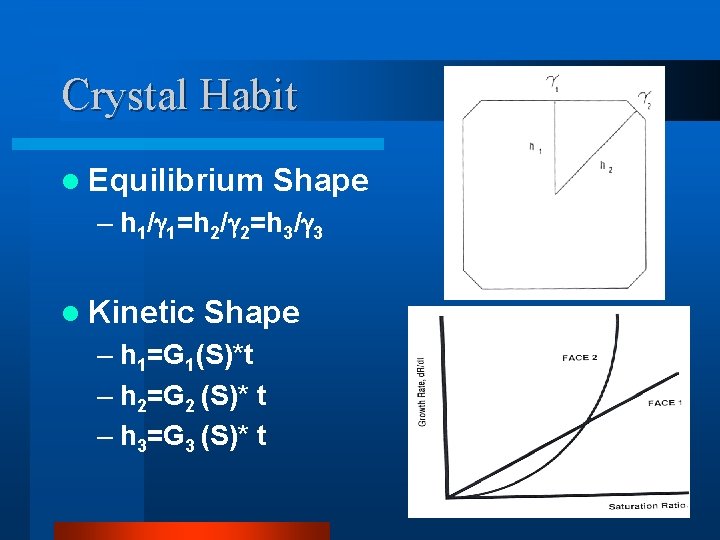
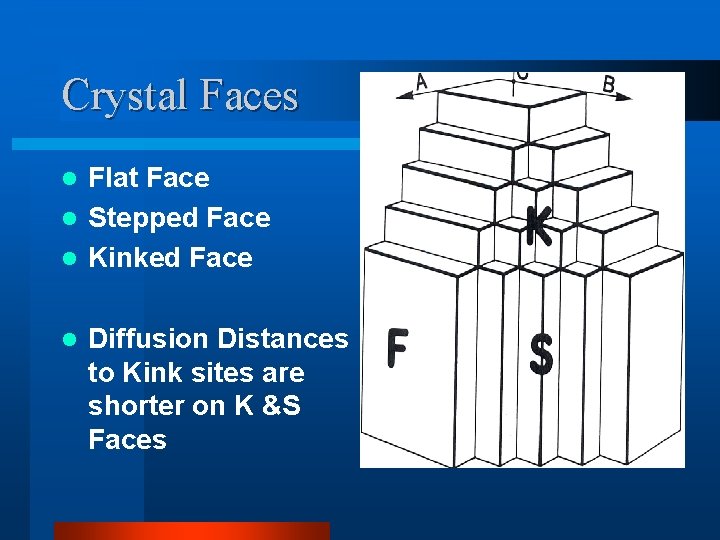
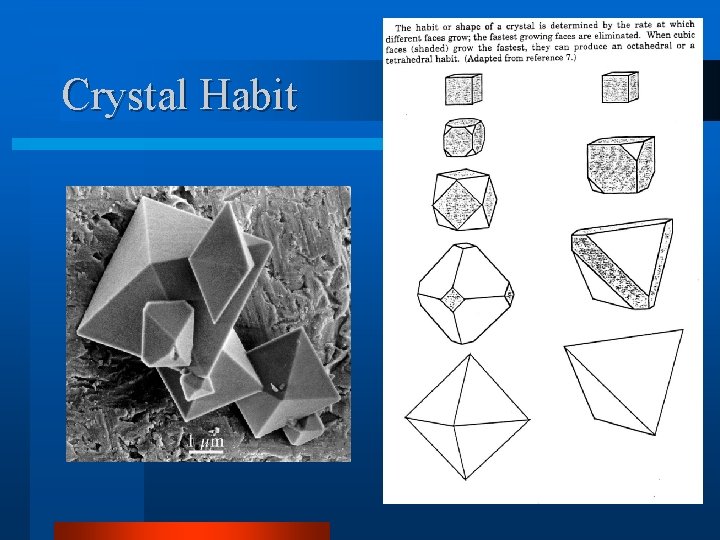
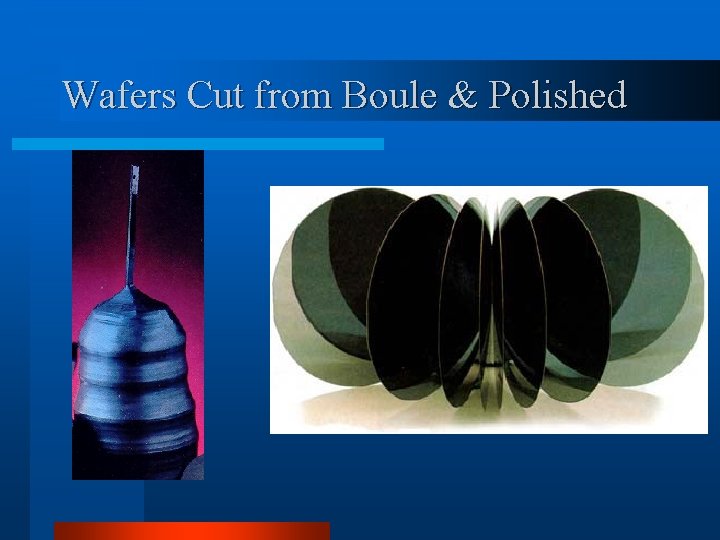
- Slides: 28
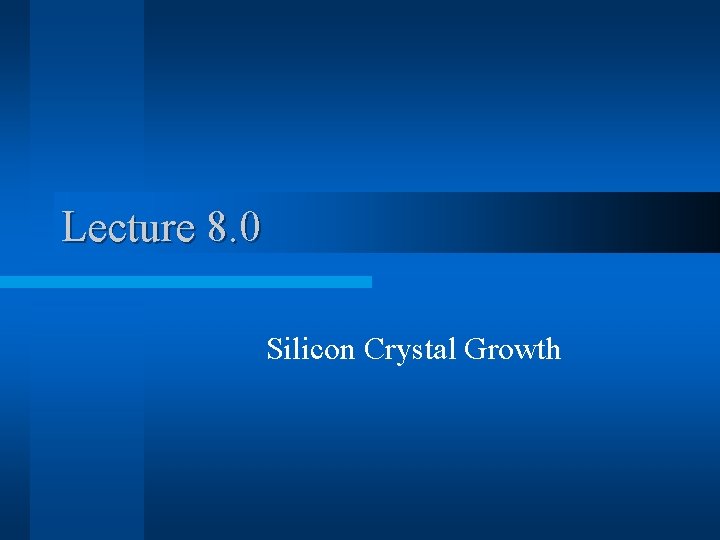
Lecture 8. 0 Silicon Crystal Growth
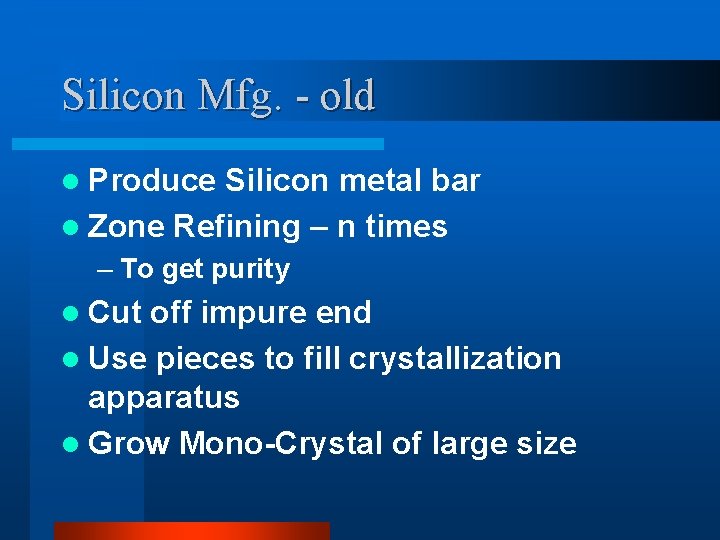
Silicon Mfg. - old l Produce Silicon metal bar l Zone Refining – n times – To get purity l Cut off impure end l Use pieces to fill crystallization apparatus l Grow Mono-Crystal of large size
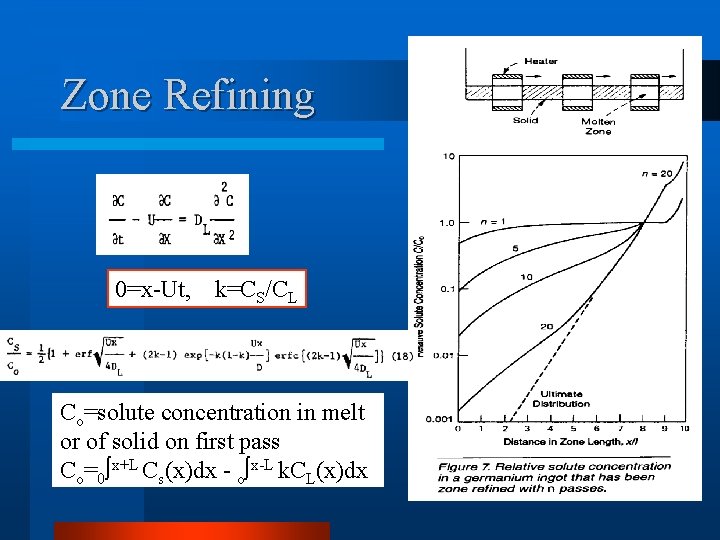
Zone Refining 0=x-Ut, k=CS/CL Co=solute concentration in melt or of solid on first pass Co=0 x+L Cs(x)dx - o x-L k. CL(x)dx
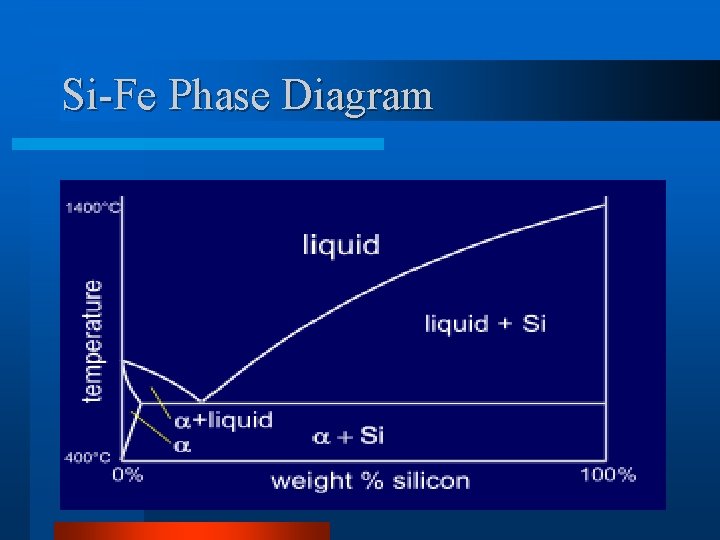
Si-Fe Phase Diagram
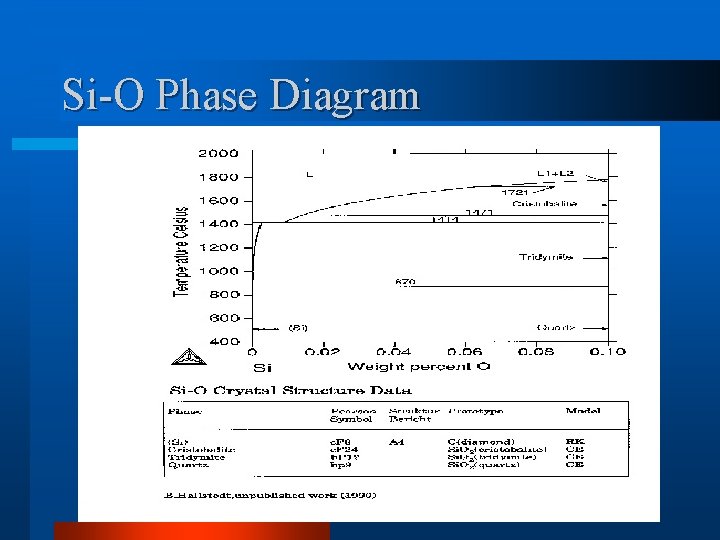
Si-O Phase Diagram
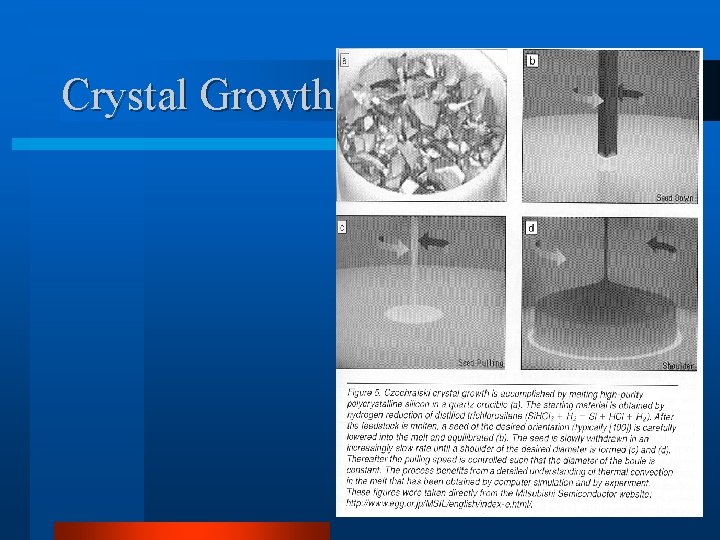
Crystal Growth
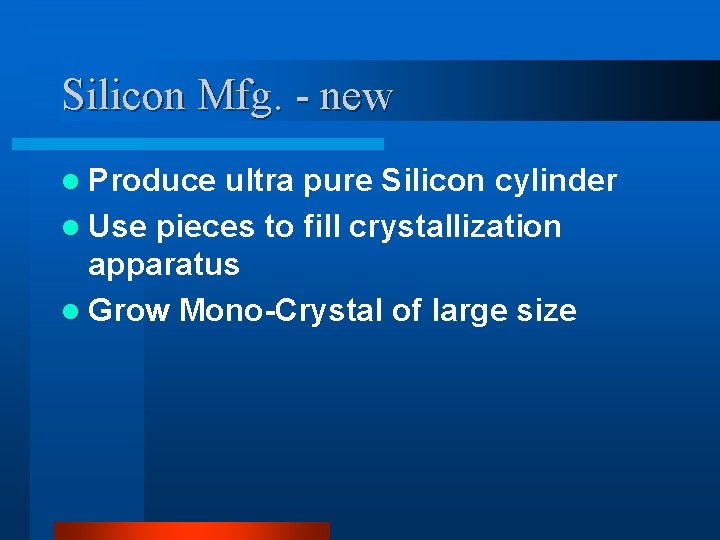
Silicon Mfg. - new l Produce ultra pure Silicon cylinder l Use pieces to fill crystallization apparatus l Grow Mono-Crystal of large size
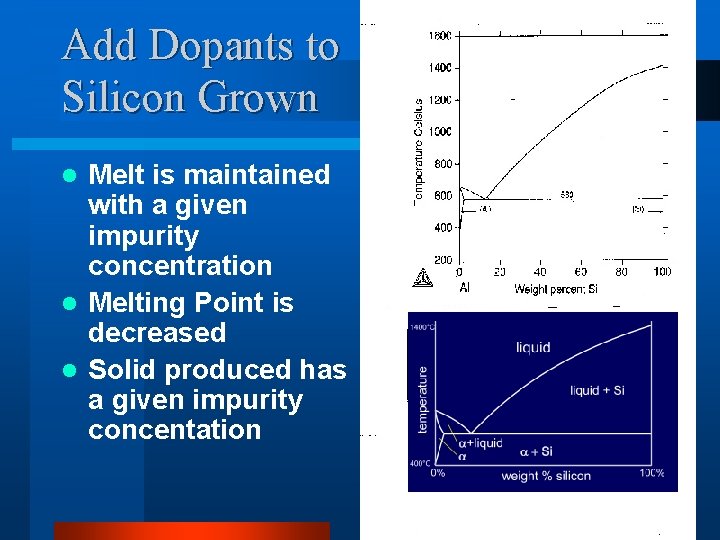
Add Dopants to Silicon Grown Melt is maintained with a given impurity concentration l Melting Point is decreased l Solid produced has a given impurity concentation l
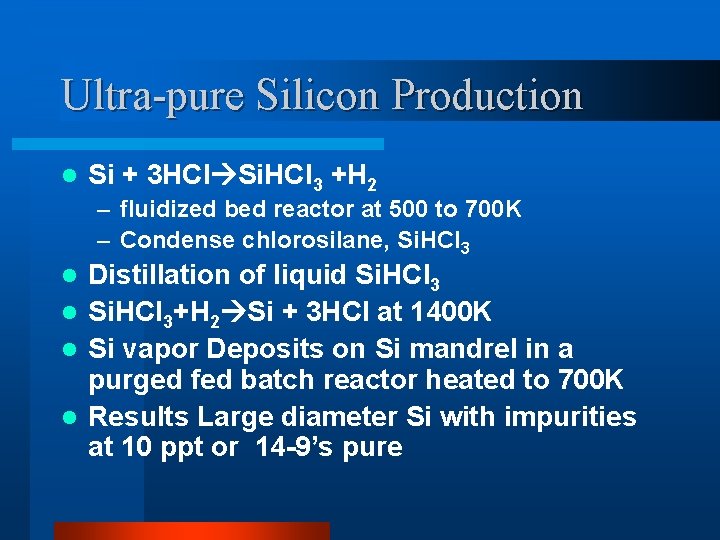
Ultra-pure Silicon Production l Si + 3 HCl Si. HCl 3 +H 2 – fluidized bed reactor at 500 to 700 K – Condense chlorosilane, Si. HCl 3 Distillation of liquid Si. HCl 3 l Si. HCl 3+H 2 Si + 3 HCl at 1400 K l Si vapor Deposits on Si mandrel in a purged fed batch reactor heated to 700 K l Results Large diameter Si with impurities at 10 ppt or 14 -9’s pure l
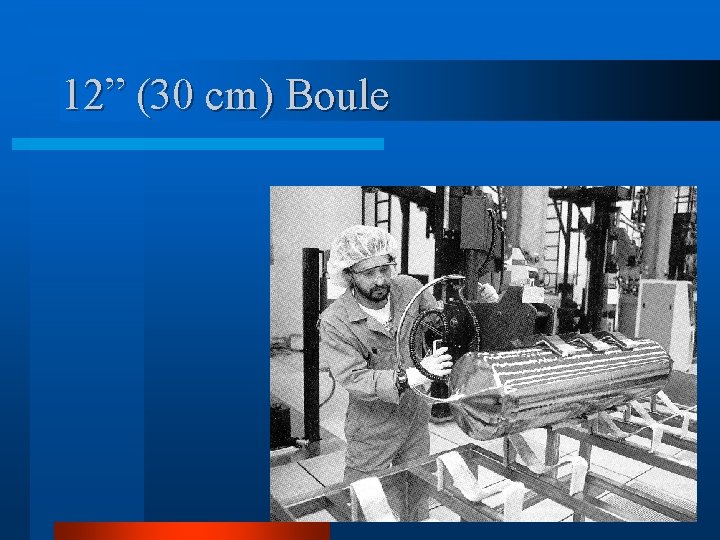
12” (30 cm) Boule
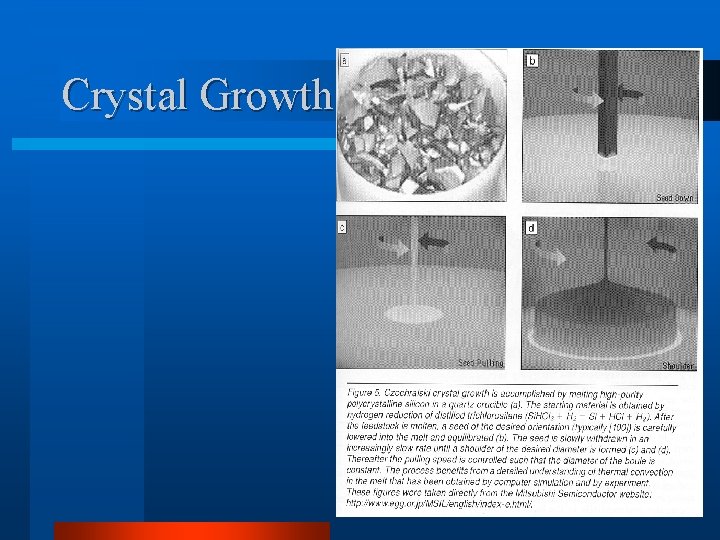
Crystal Growth
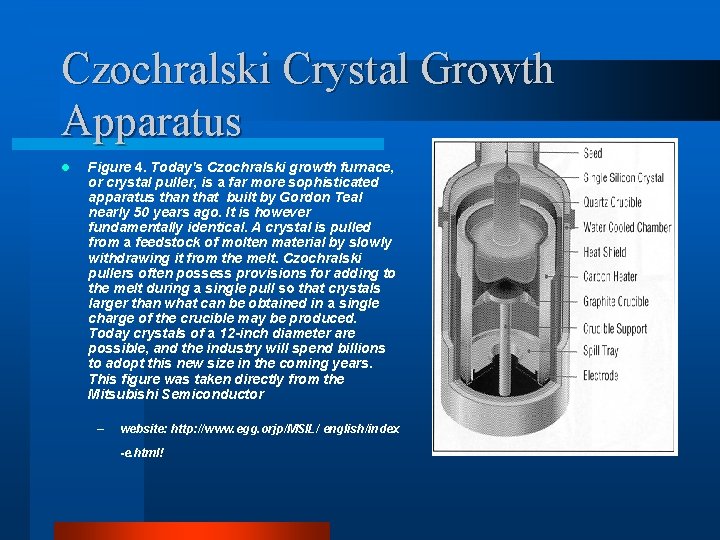
Czochralski Crystal Growth Apparatus l Figure 4. Today's Czochralski growth furnace, or crystal puller, is a far more sophisticated apparatus than that built by Gordon Teal nearly 50 years ago. It is however fundamentally identical. A crystal is pulled from a feedstock of molten material by slowly withdrawing it from the melt. Czochralski pullers often possess provisions for adding to the melt during a single pull so that crystals larger than what can be obtained in a single charge of the crucible may be produced. Today crystals of a 12 -inch diameter are possible, and the industry will spend billions to adopt this new size in the coming years. This figure was taken directly from the Mitsubishi Semiconductor – website: http: //www. egg. orjp/MSIL/ english/index -e. html!
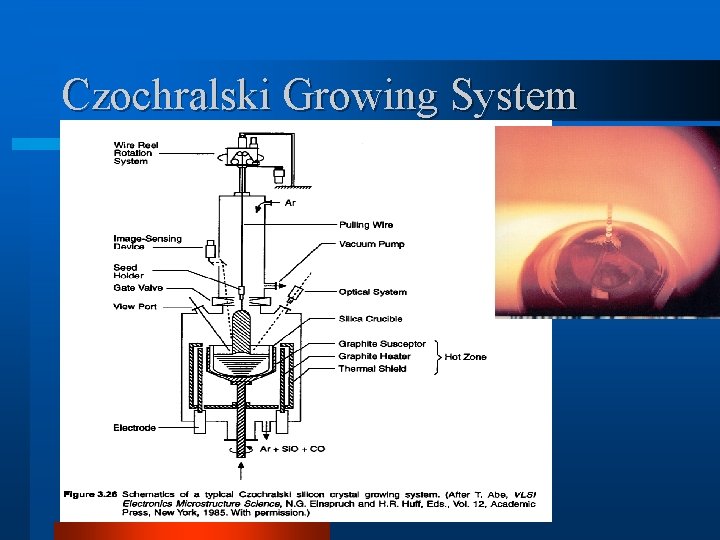
Czochralski Growing System
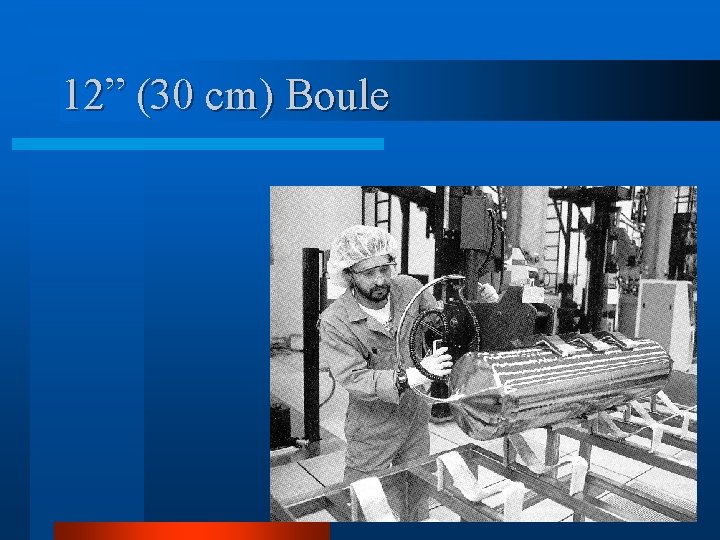
12” (30 cm) Boule
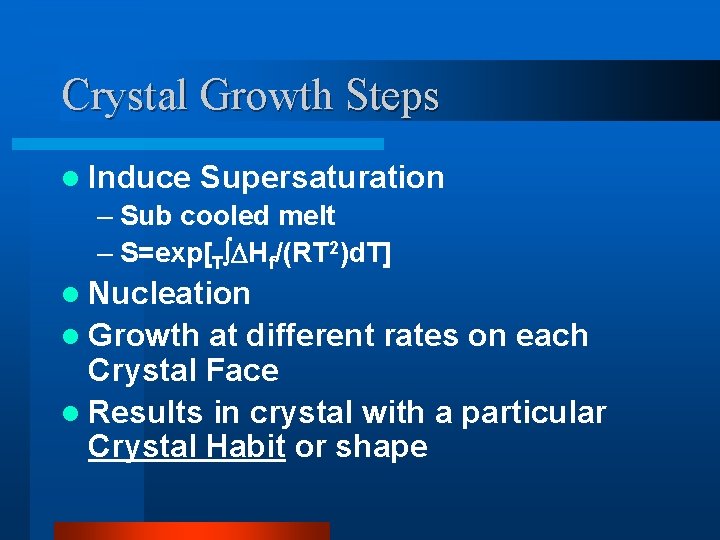
Crystal Growth Steps l Induce Supersaturation – Sub cooled melt – S=exp[T Hf/(RT 2)d. T] l Nucleation l Growth at different rates on each Crystal Face l Results in crystal with a particular Crystal Habit or shape
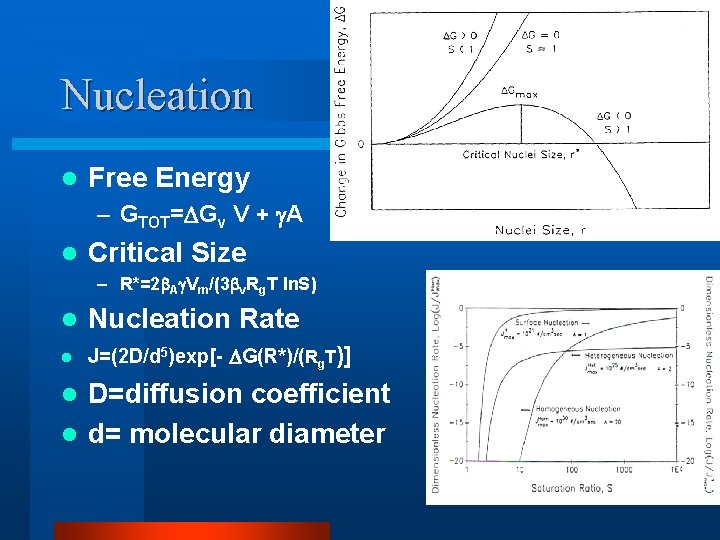
Nucleation l Free Energy – GTOT= Gv V + A l Critical Size – R*=2 A Vm/(3 v. Rg. T ln. S) l Nucleation Rate l J=(2 D/d 5)exp[- G(R*)/(Rg. T)] D=diffusion coefficient l d= molecular diameter l
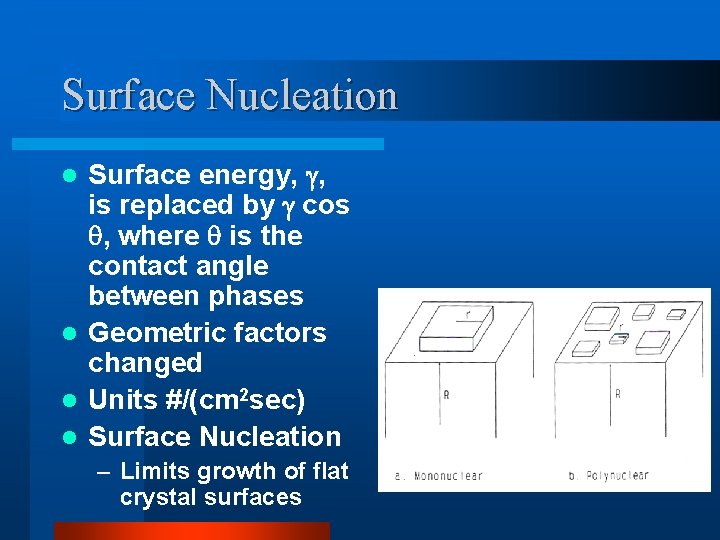
Surface Nucleation Surface energy, , is replaced by cos , where is the contact angle between phases l Geometric factors changed l Units #/(cm 2 sec) l Surface Nucleation l – Limits growth of flat crystal surfaces
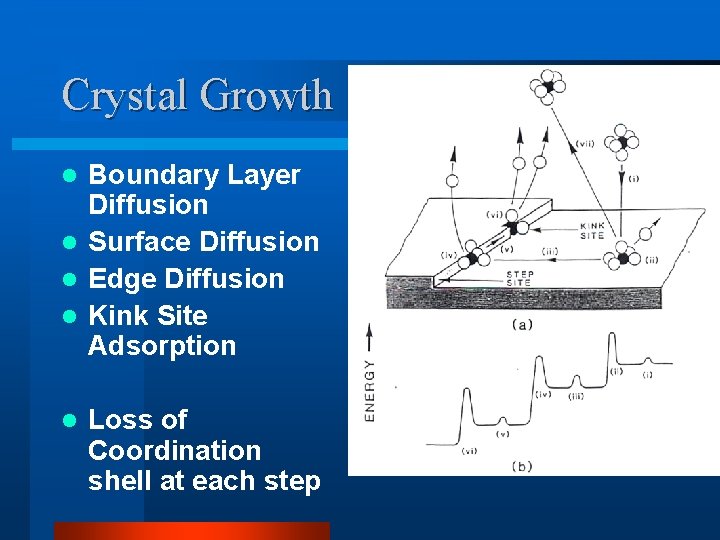
Crystal Growth Boundary Layer Diffusion l Surface Diffusion l Edge Diffusion l Kink Site Adsorption l l Loss of Coordination shell at each step
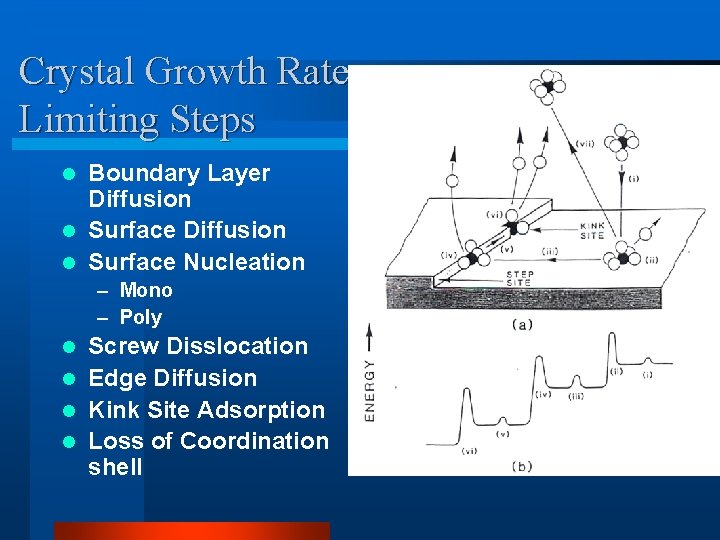
Crystal Growth Rate Limiting Steps Boundary Layer Diffusion l Surface Nucleation l – Mono – Poly Screw Disslocation l Edge Diffusion l Kink Site Adsorption l Loss of Coordination shell l
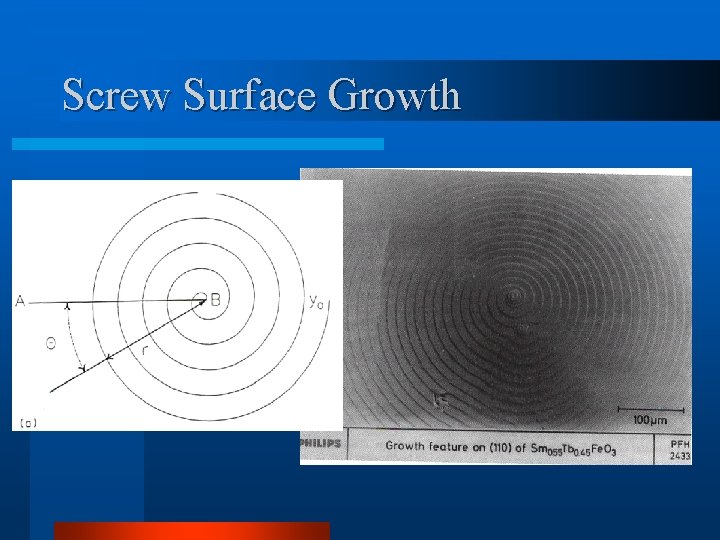
Screw Surface Growth
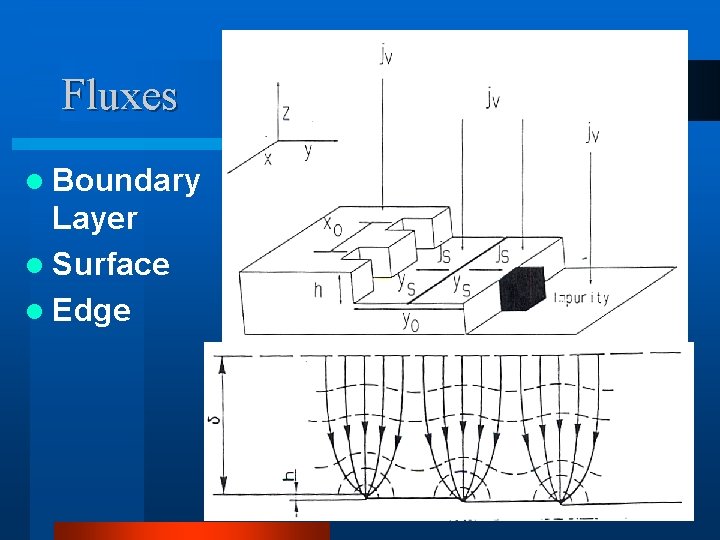
Fluxes l Boundary Layer l Surface l Edge
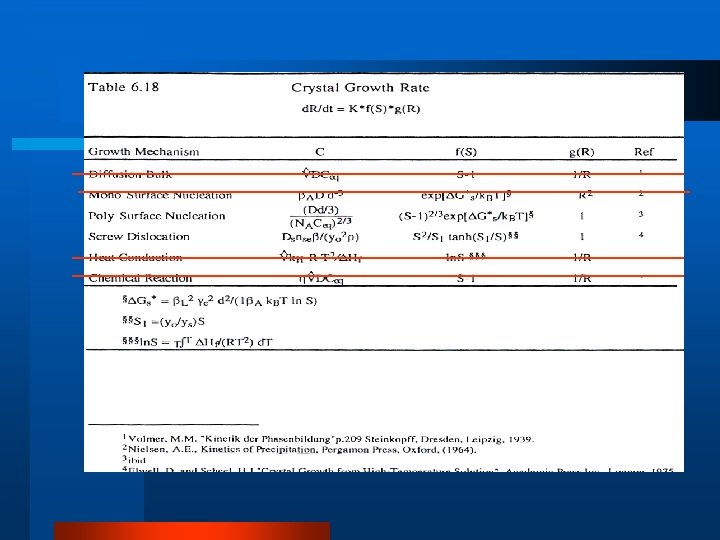
![Mass Transfer to Rotating Crystal l Local BLMT Flux Jmolecm 2 s 0 Mass Transfer to Rotating Crystal l Local BL-MT Flux J[mole/(cm 2 s)] = 0.](https://slidetodoc.com/presentation_image_h2/bf60bc24ceb8c41739e970bec5330a59/image-23.jpg)
Mass Transfer to Rotating Crystal l Local BL-MT Flux J[mole/(cm 2 s)] = 0. 62 D 2/3(Co-Ceq) n-1/6 w 1/2 l J[mole/(cm 2 s)] = 0. 62 D 2/3 Ceq(S-1) n-1/6 w 1/2 l – Franklin, T. C. Nodimele, R. , Adenniyi, W. K. and Hunt, D. , J. Electrochemical Soc. 135, 1944 -47(1988). – Uniform, not a function of radius!! l Crystal Growth Rate due to BL-MT as Rate Determining Step
![Heat Transfer to Rotating Crystal l Local BLHT Flux Jmolecm 2 s hTeqT Heat Transfer to Rotating Crystal l Local BL-HT Flux J[mole/(cm 2 s)] = h(Teq-T)/](https://slidetodoc.com/presentation_image_h2/bf60bc24ceb8c41739e970bec5330a59/image-24.jpg)
Heat Transfer to Rotating Crystal l Local BL-HT Flux J[mole/(cm 2 s)] = h(Teq-T)/ Hf l J[mole/(cm 2 s)] • = 0. 62 k -1/3 n-1/6 w 1/2 (Teq-T)/ Hf l – Franklin, T. C. Nodimele, R. , Adenniyi, W. K. and Hunt, D. , J. Electrochemical Soc. 135, 1944 -47(1988). – Uniform, not a function of radius!! l Crystal Growth Rate due to BL-HT as Rate Determining Step
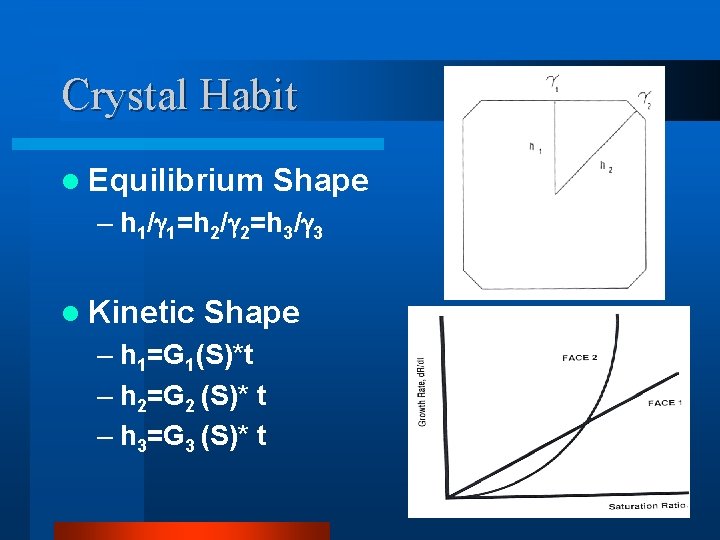
Crystal Habit l Equilibrium Shape – h 1/ 1=h 2/ 2=h 3/ 3 l Kinetic Shape – h 1=G 1(S)*t – h 2=G 2 (S)* t – h 3=G 3 (S)* t
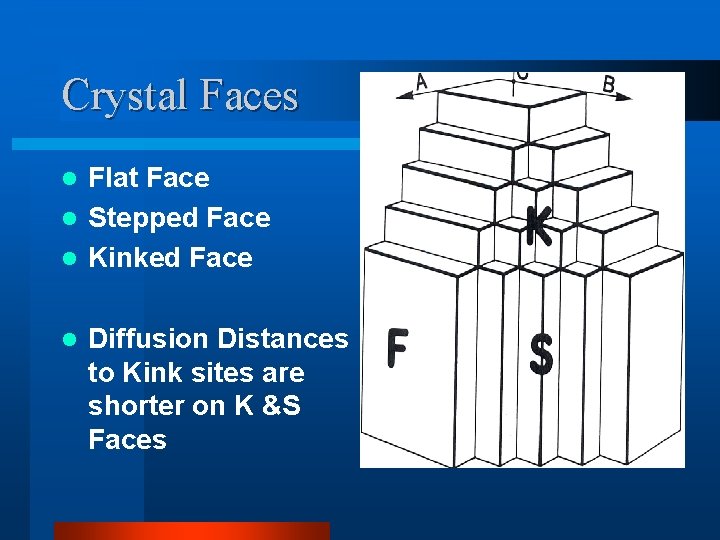
Crystal Faces Flat Face l Stepped Face l Kinked Face l l Diffusion Distances to Kink sites are shorter on K &S Faces
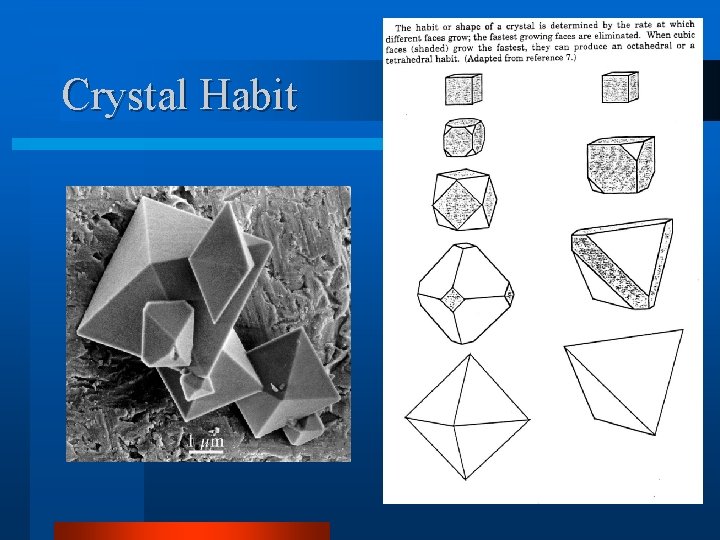
Crystal Habit
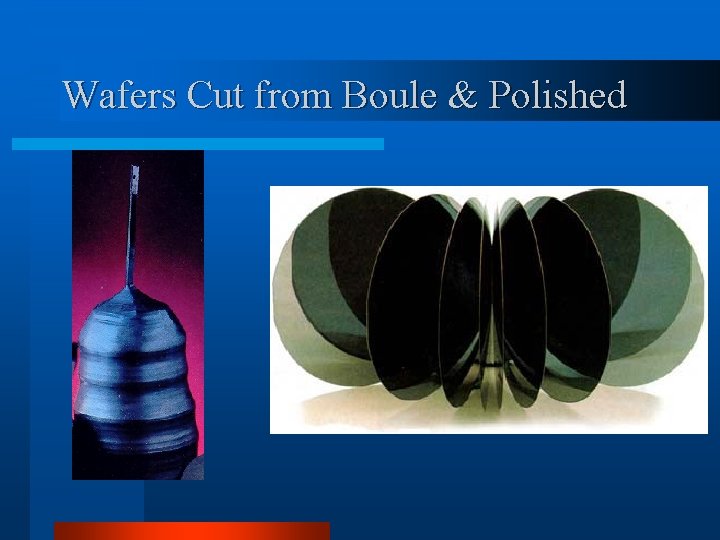
Wafers Cut from Boule & Polished
Silicon crystal lattice
Proutil truncate bi
Discrete mfg
Iem industrial electric mfg
Mfg exp
Mfg systems
Mfg processes
Superior flux & mfg. co
Scranton mfg
Segment reporting and decentralization
Superior flux & mfg. co.
01:640:244 lecture notes - lecture 15: plat, idah, farad
Plant growth analysis
Geometric exponential growth
Root hair structure
Neoclassical growth theory vs. endogenous growth theory
Primary growth and secondary growth in plants
Growthchain
Organic vs inorganic growth
Chapter 35 plant structure growth and development
Hhg
Crystal structure of ceramics
Assumption of cft
Ruby crystal
7 crystal system table
How igneous rocks are formed
Quartz crystal technology
Crystal clear management
Transistor paraset