Lec 26 Frictionless flow with work pipe flow
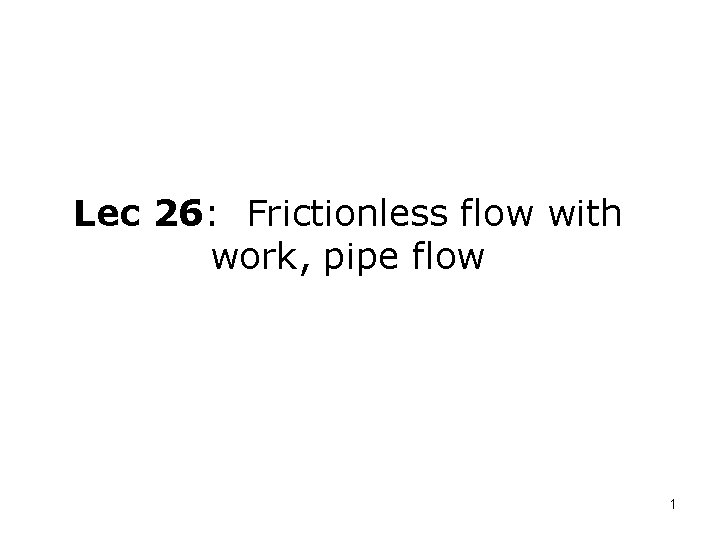
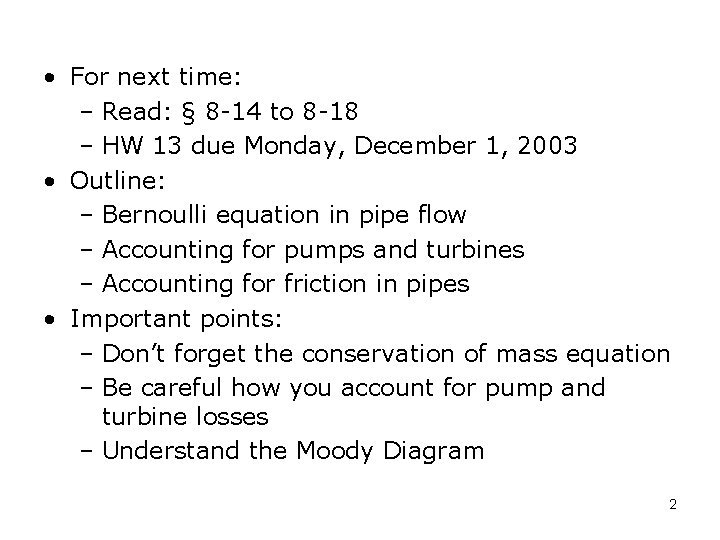
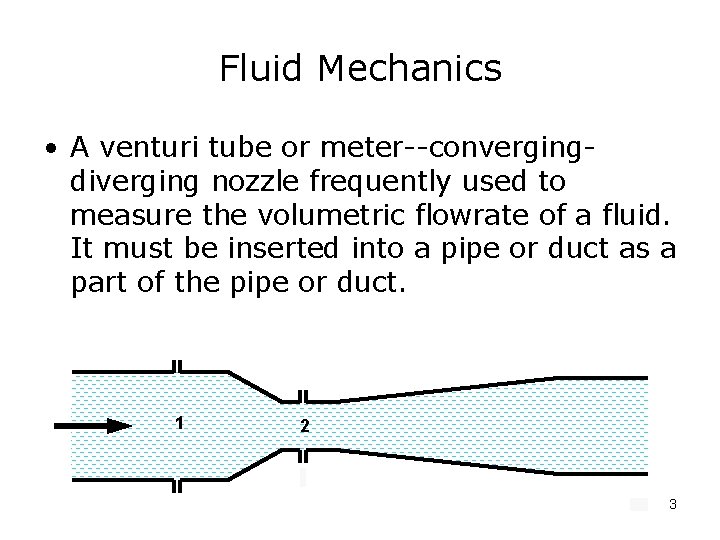

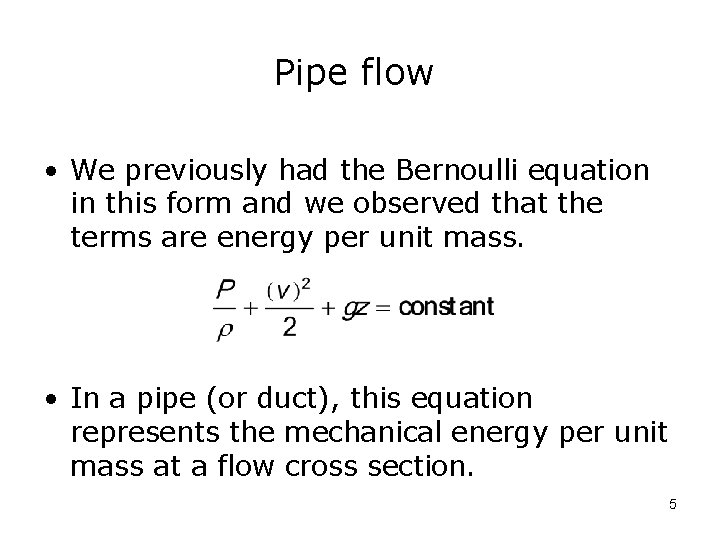
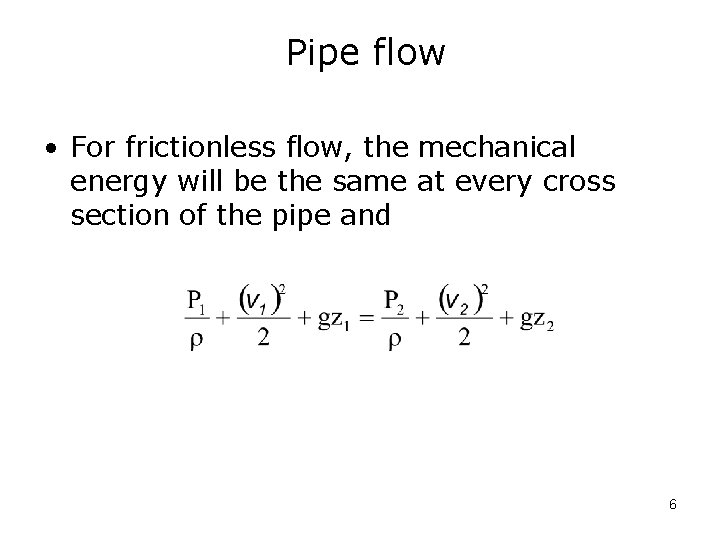
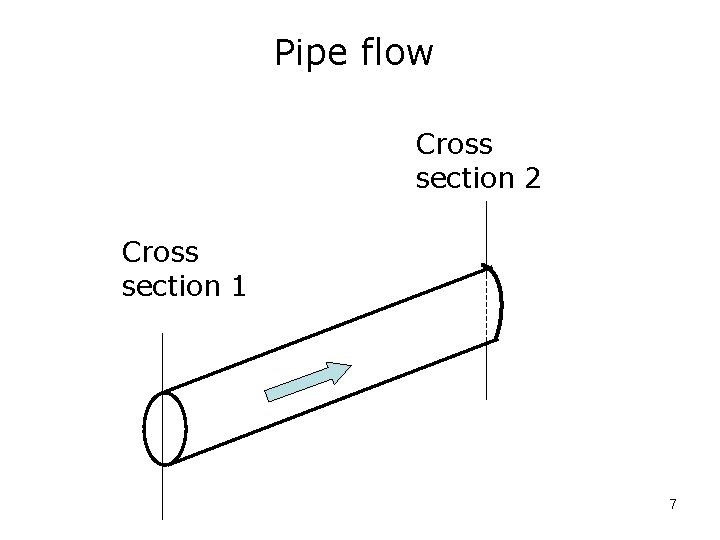
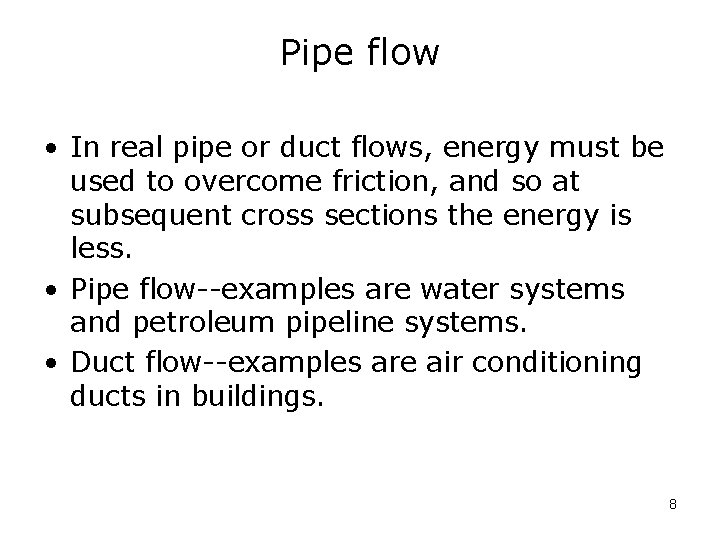
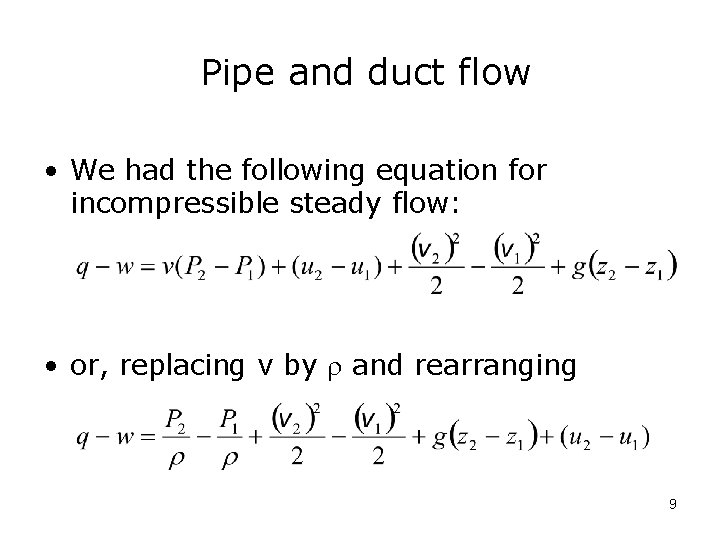
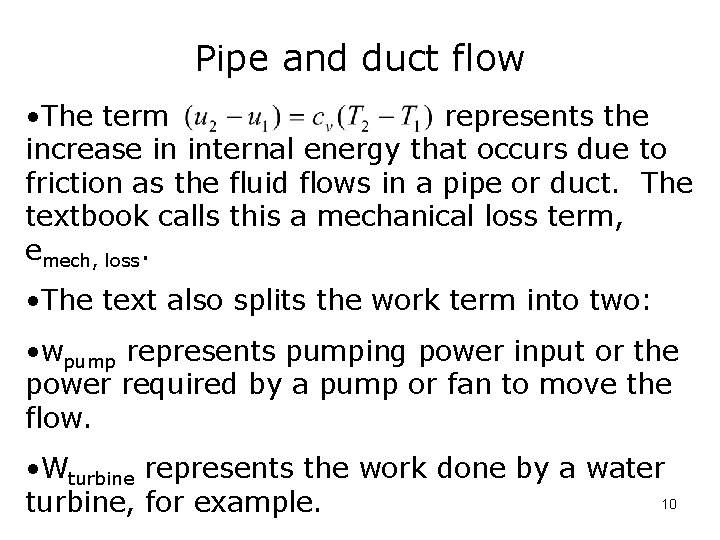
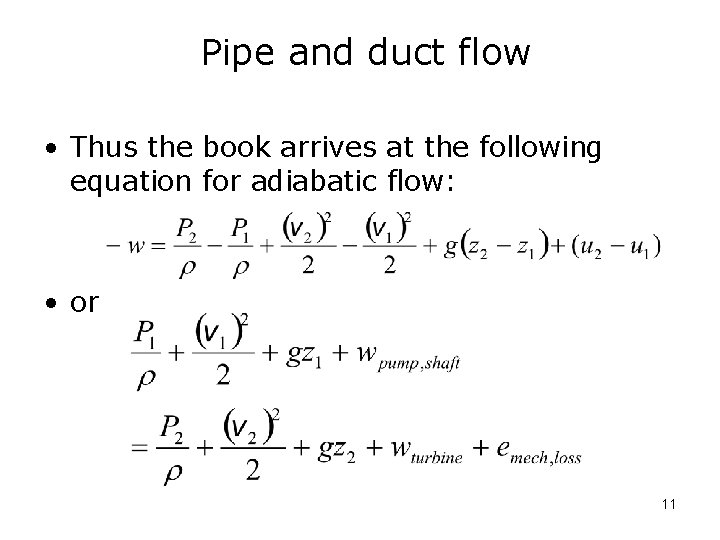
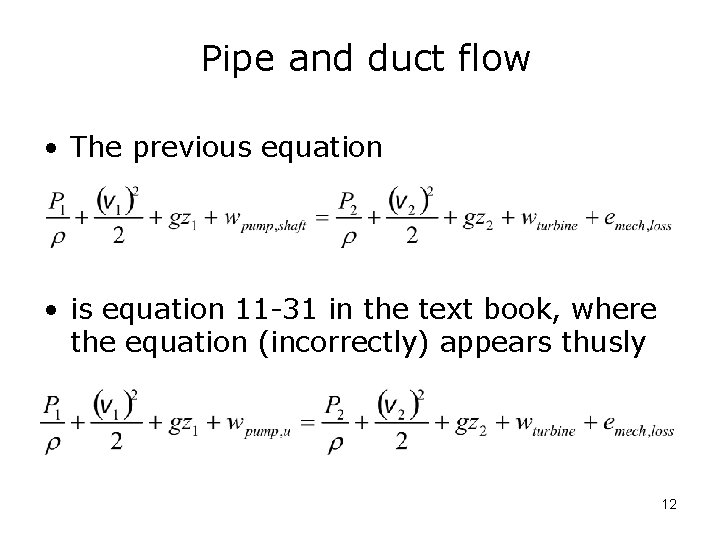
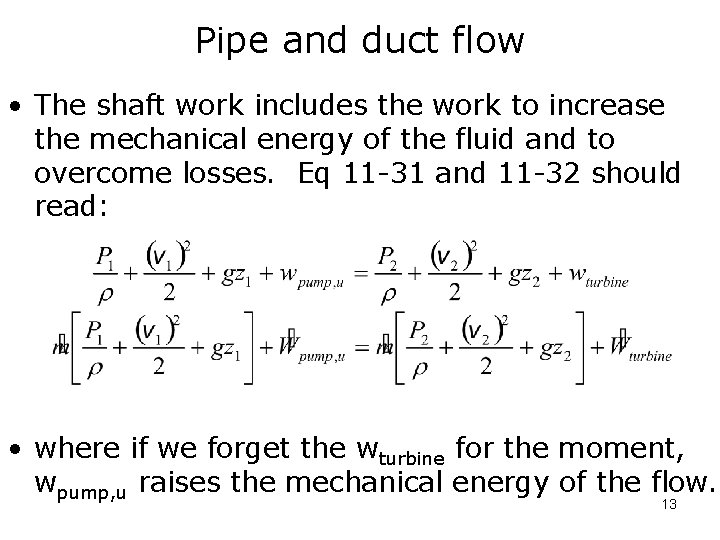
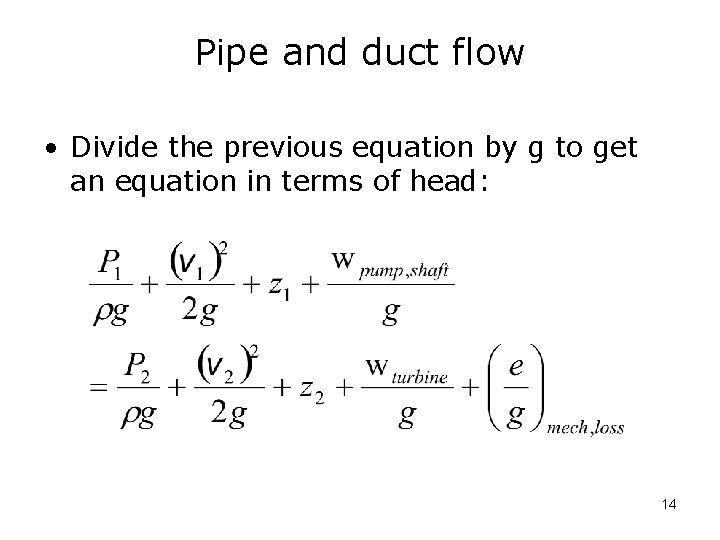
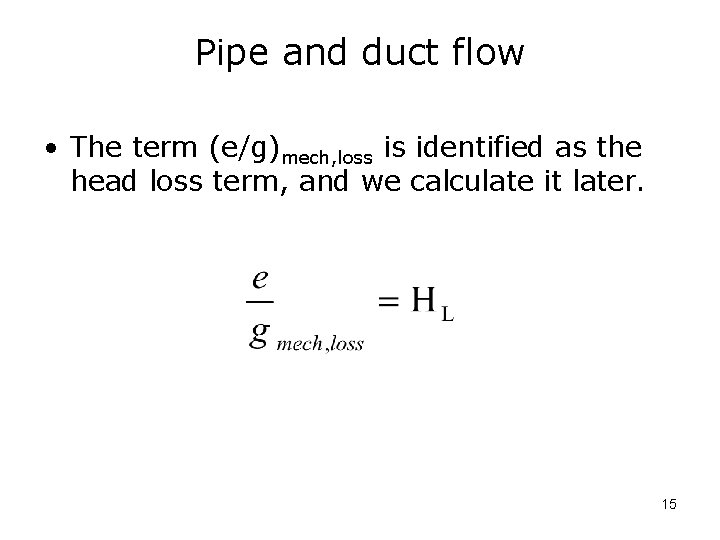
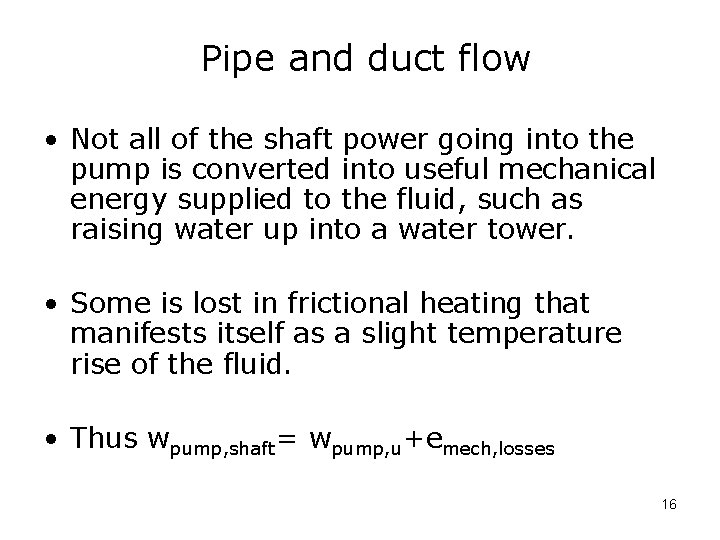
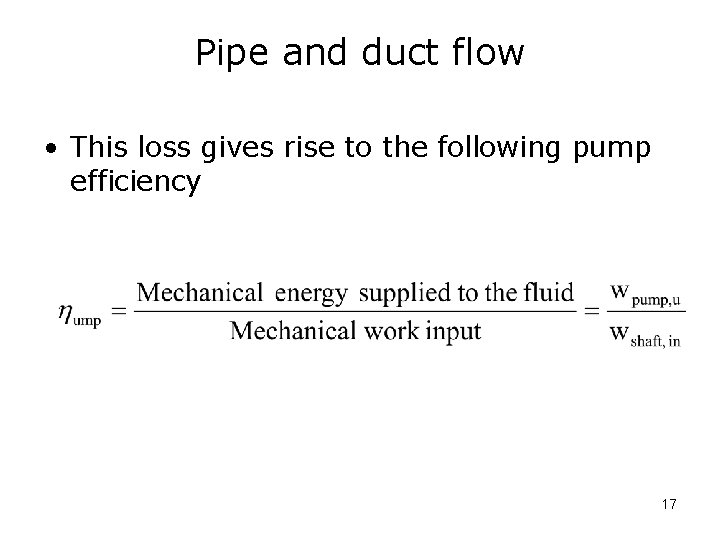
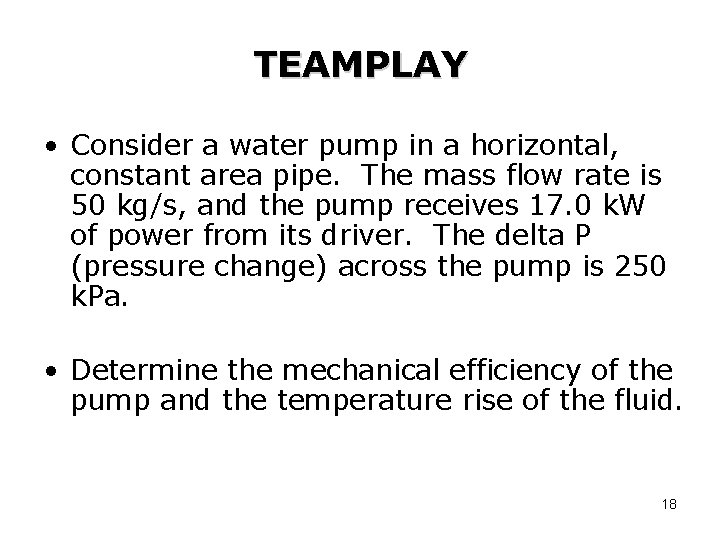
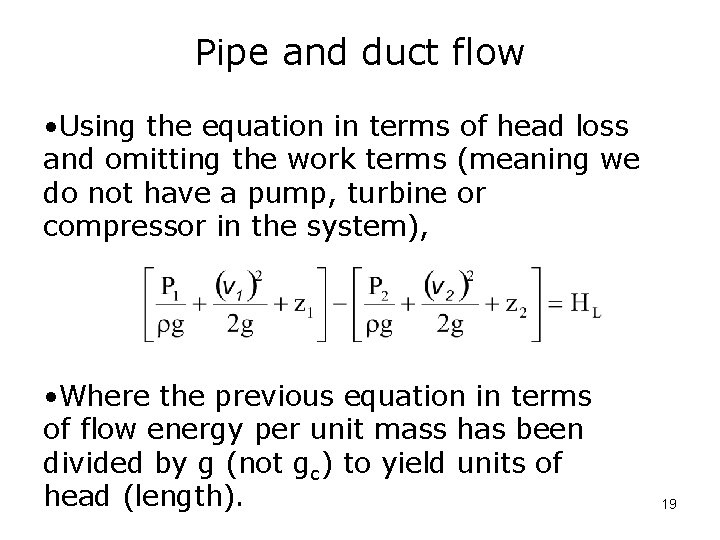
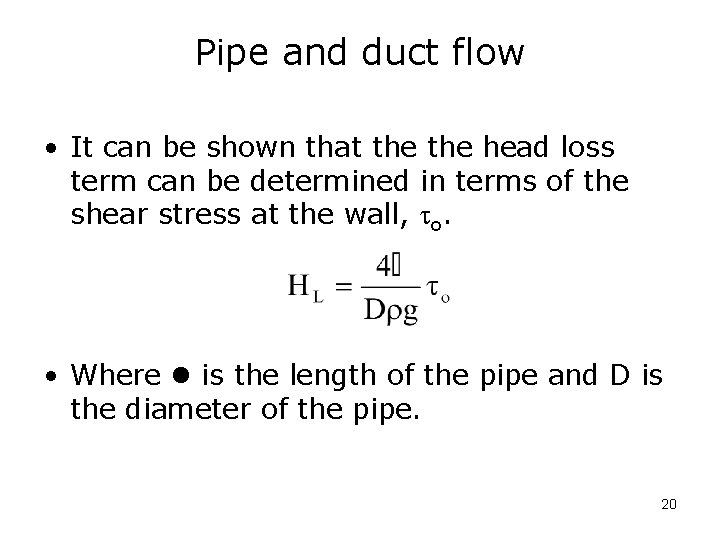
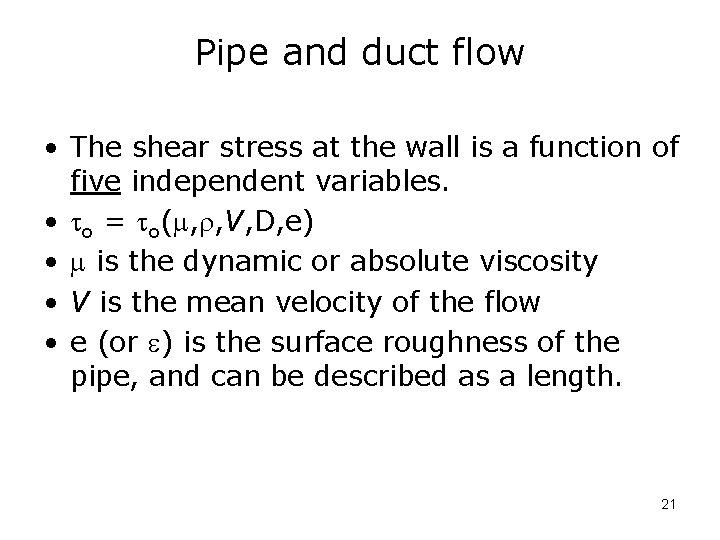
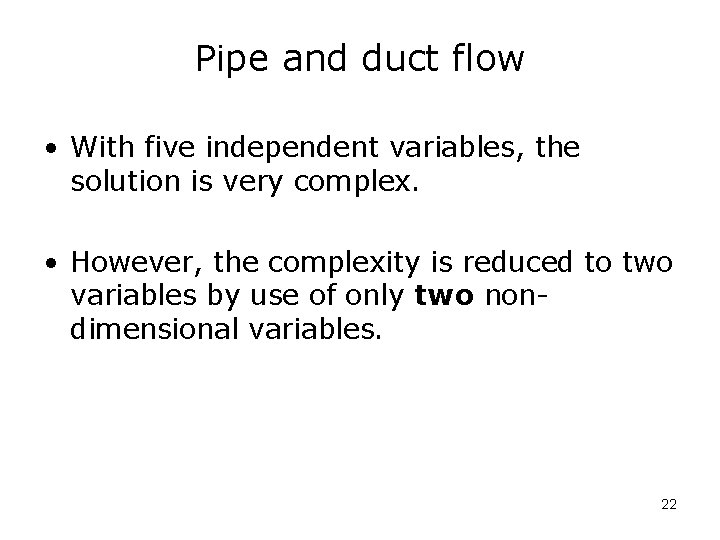
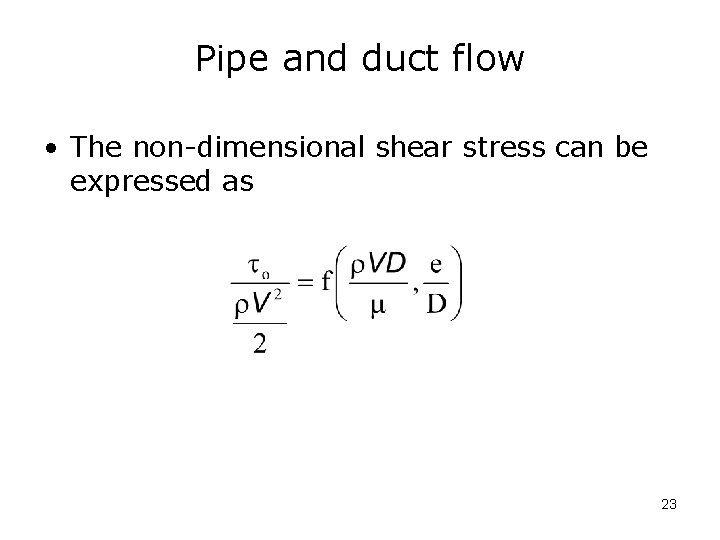
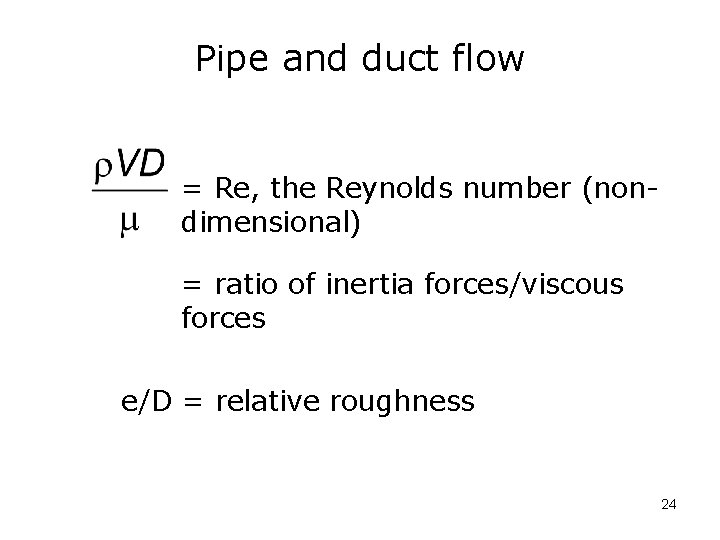
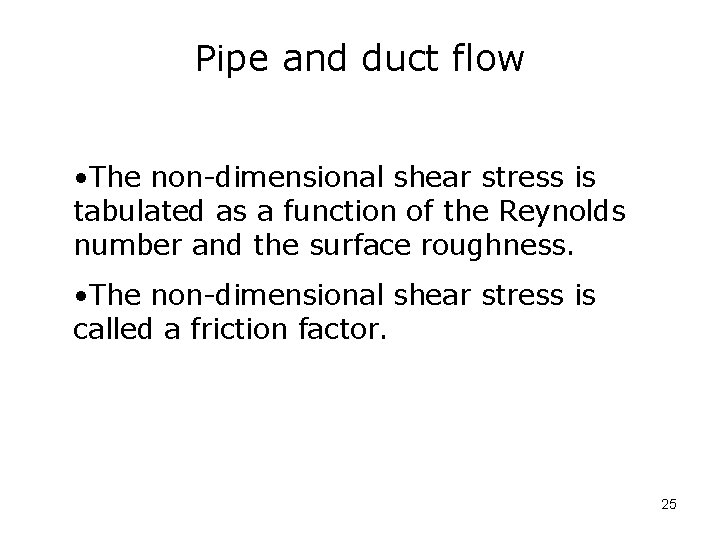
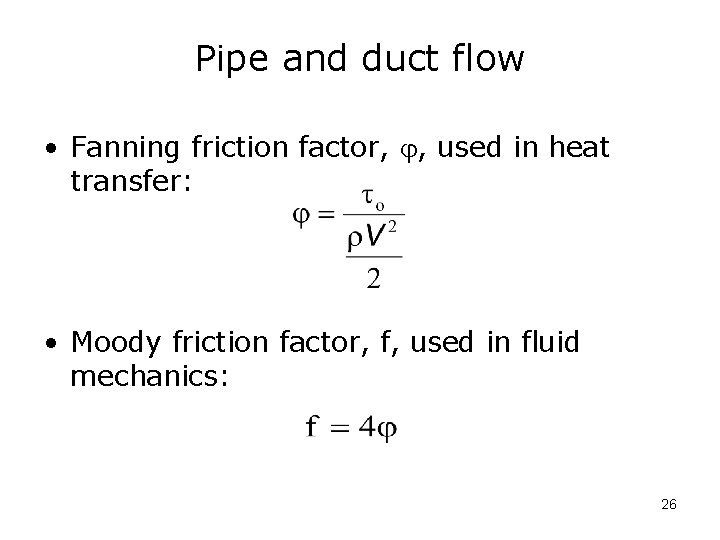
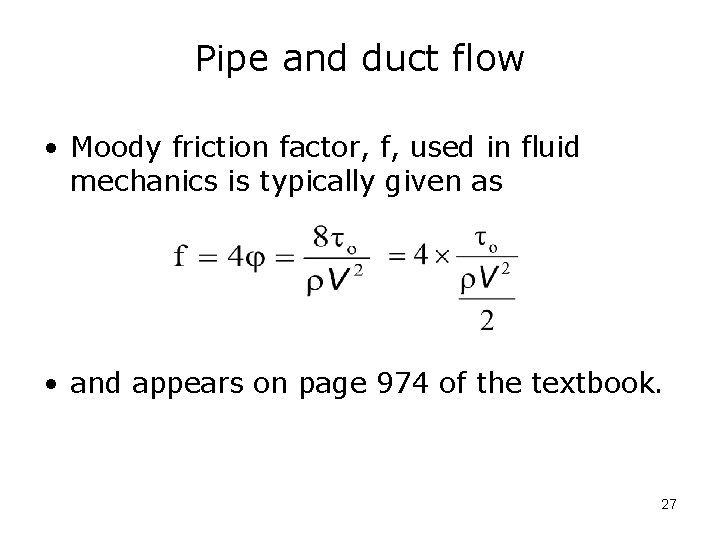
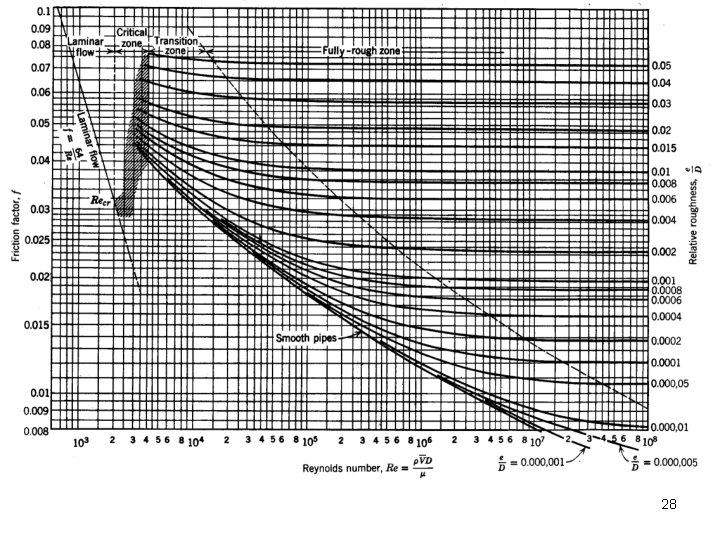
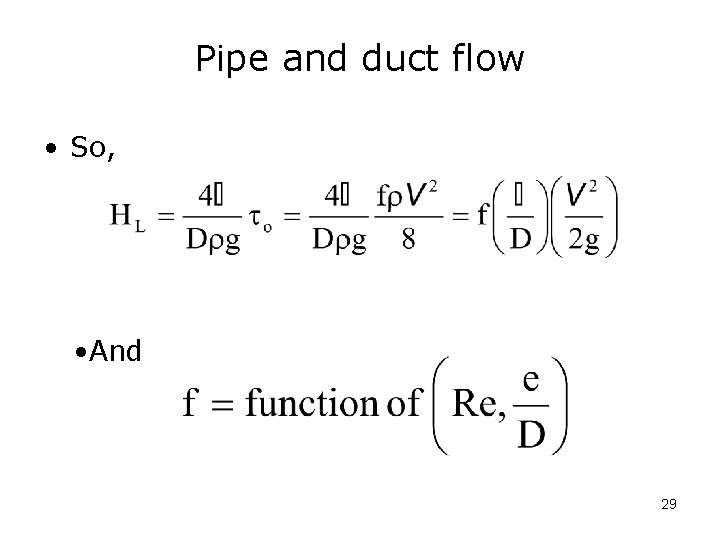
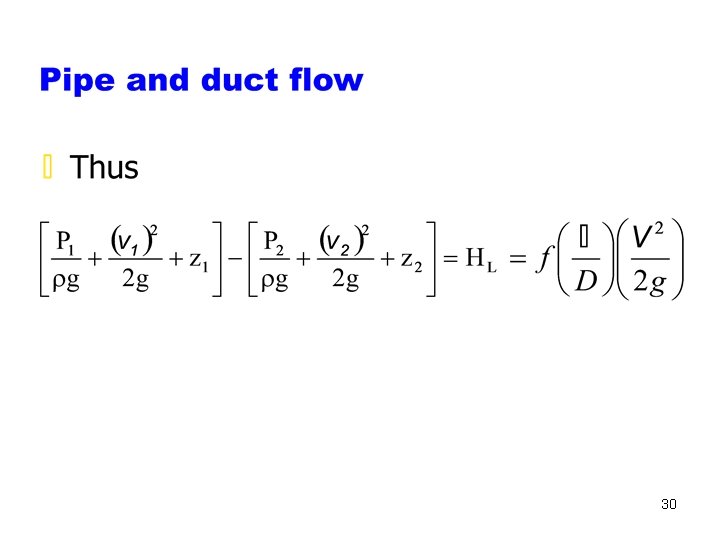
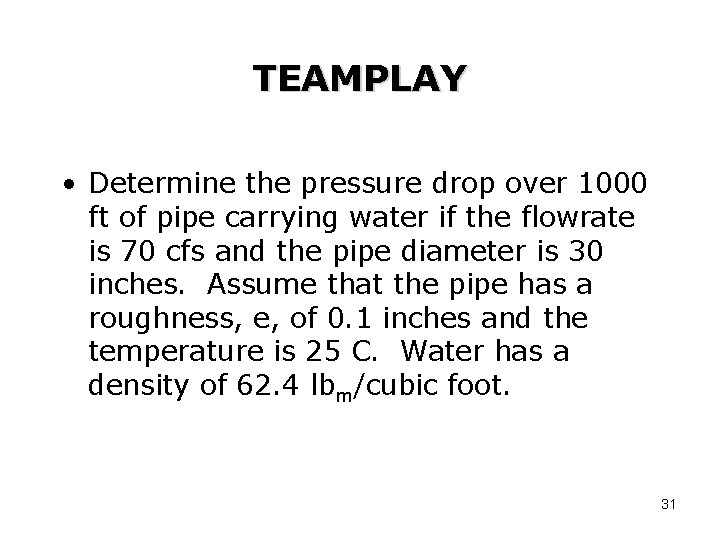
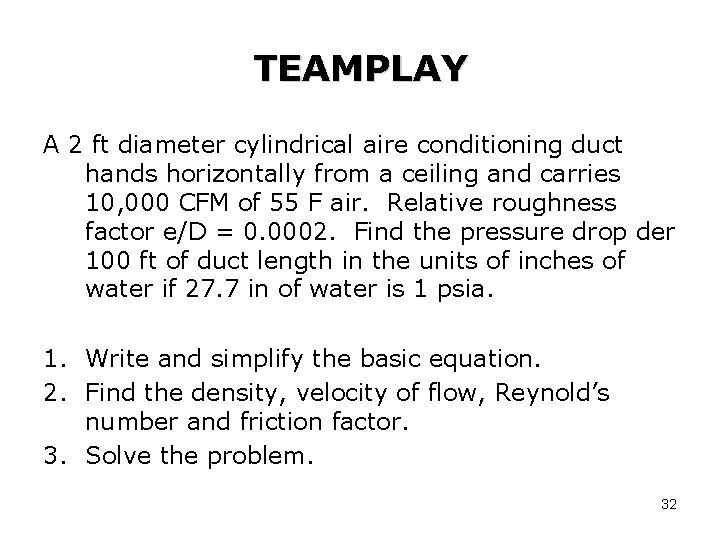
- Slides: 32
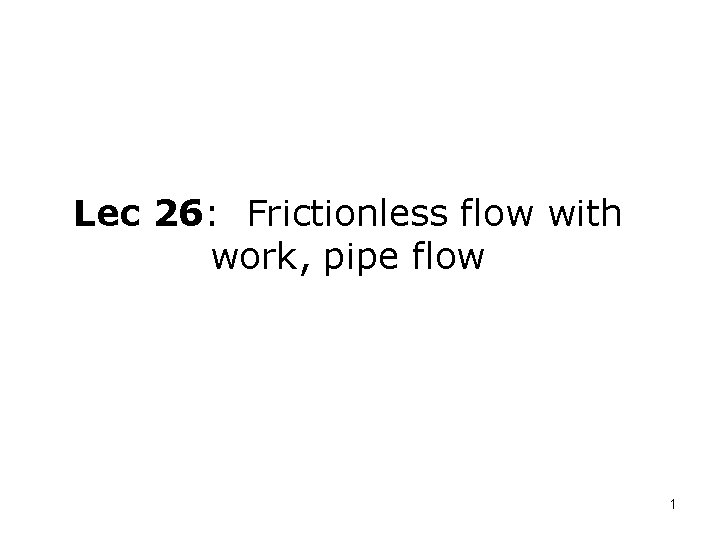
Lec 26: Frictionless flow with work, pipe flow 1
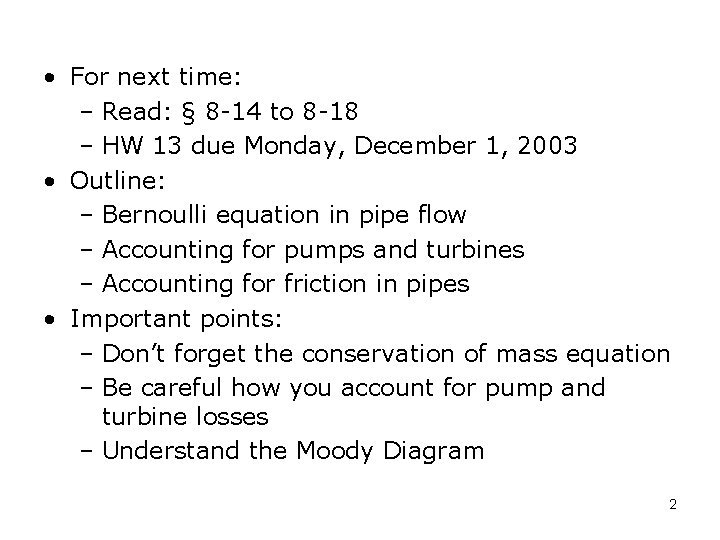
• For next time: – Read: § 8 -14 to 8 -18 – HW 13 due Monday, December 1, 2003 • Outline: – Bernoulli equation in pipe flow – Accounting for pumps and turbines – Accounting for friction in pipes • Important points: – Don’t forget the conservation of mass equation – Be careful how you account for pump and turbine losses – Understand the Moody Diagram 2
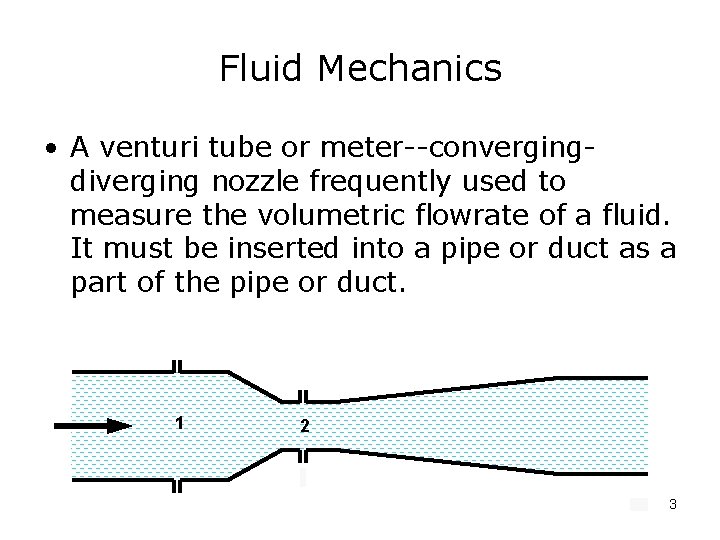
Fluid Mechanics • A venturi tube or meter--convergingdiverging nozzle frequently used to measure the volumetric flowrate of a fluid. It must be inserted into a pipe or duct as a part of the pipe or duct. 1 2 3

TEAMPLAY • For a venturi such as that shown before, the following data apply: dia 1 = 6. 0 in, dia 2 = 4. 0 in. The pressure difference P 1 – P 2 = 3 psi. Water with a density of 62. 4 lbm/ft 3 is flowing. Find the rate of flow in ft 3/min. • Hint: use flowrate Qv = A 1 V 1 = A 2 V 2 4
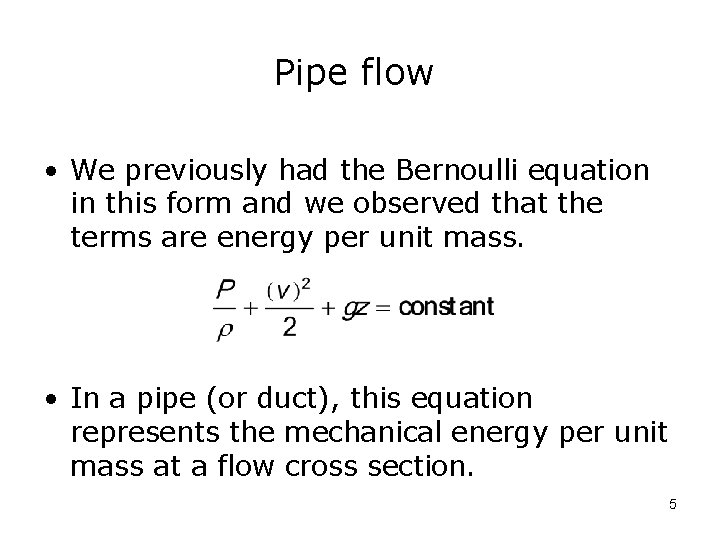
Pipe flow • We previously had the Bernoulli equation in this form and we observed that the terms are energy per unit mass. • In a pipe (or duct), this equation represents the mechanical energy per unit mass at a flow cross section. 5
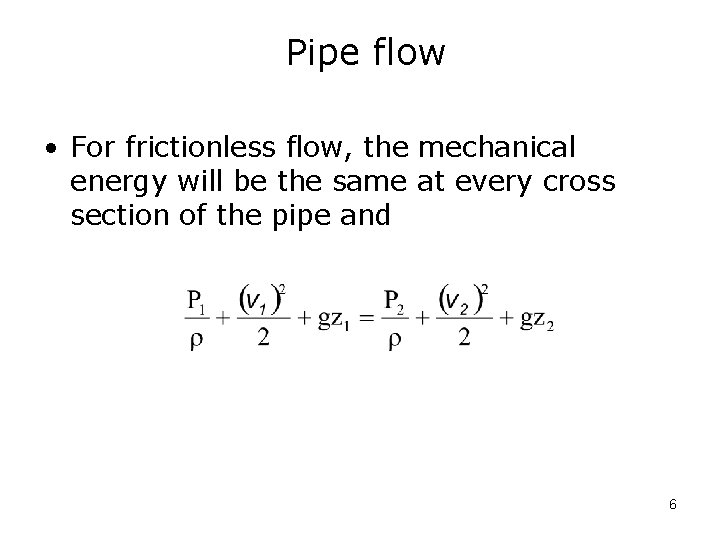
Pipe flow • For frictionless flow, the mechanical energy will be the same at every cross section of the pipe and 6
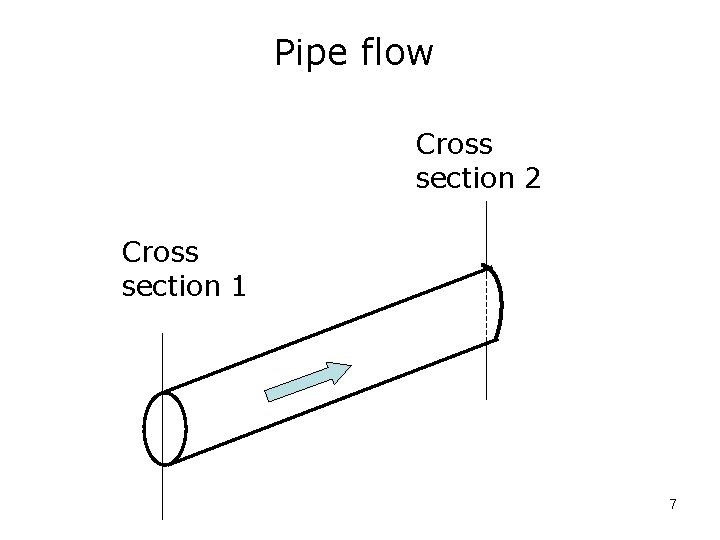
Pipe flow Cross section 2 Cross section 1 7
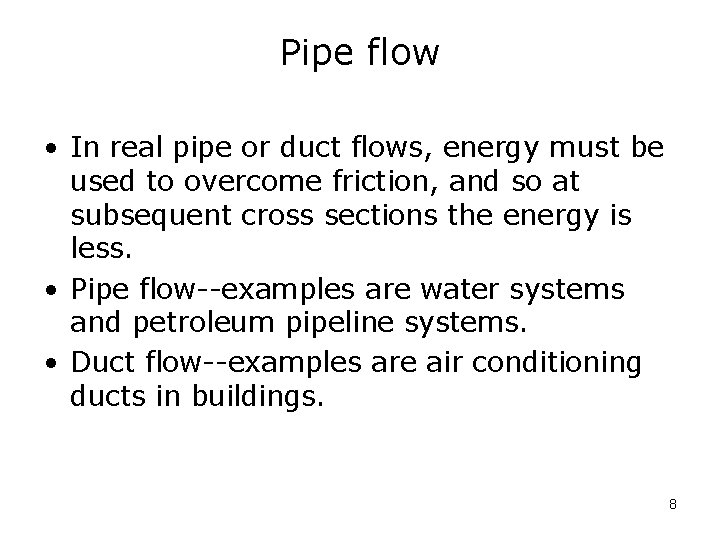
Pipe flow • In real pipe or duct flows, energy must be used to overcome friction, and so at subsequent cross sections the energy is less. • Pipe flow--examples are water systems and petroleum pipeline systems. • Duct flow--examples are air conditioning ducts in buildings. 8
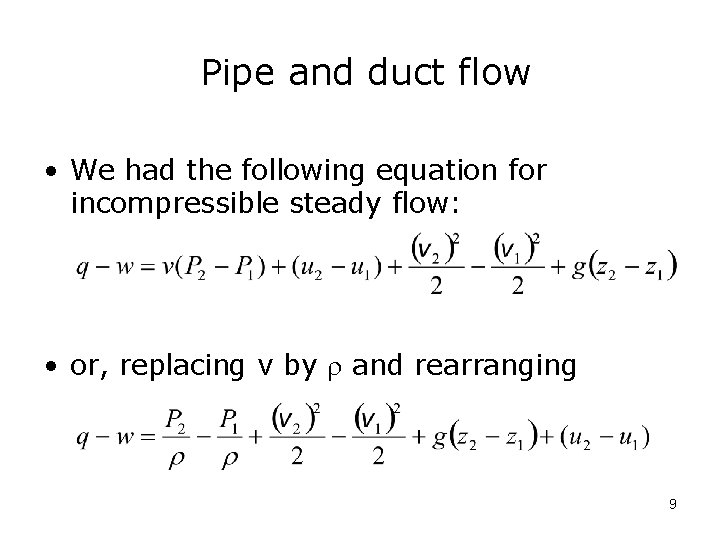
Pipe and duct flow • We had the following equation for incompressible steady flow: • or, replacing v by and rearranging 9
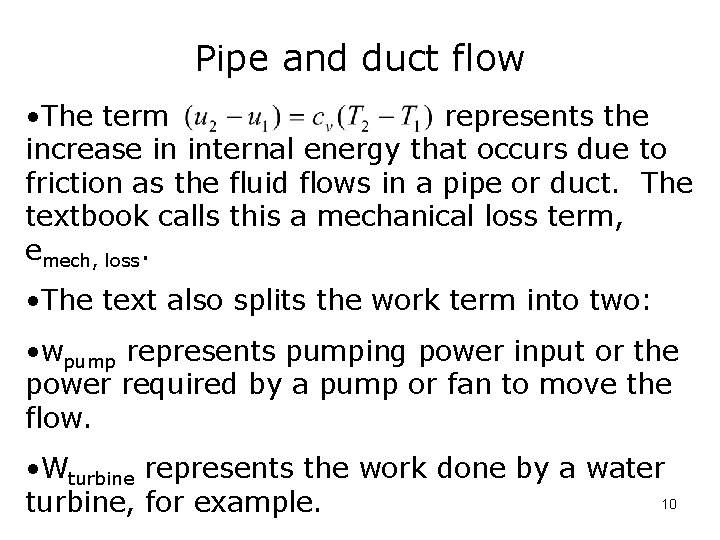
Pipe and duct flow • The term represents the increase in internal energy that occurs due to friction as the fluid flows in a pipe or duct. The textbook calls this a mechanical loss term, emech, loss. • The text also splits the work term into two: • wpump represents pumping power input or the power required by a pump or fan to move the flow. • Wturbine represents the work done by a water 10 turbine, for example.
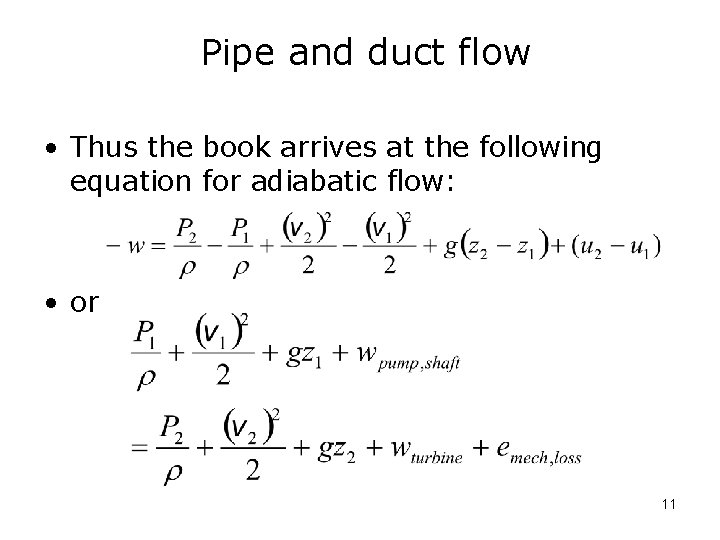
Pipe and duct flow • Thus the book arrives at the following equation for adiabatic flow: • or 11
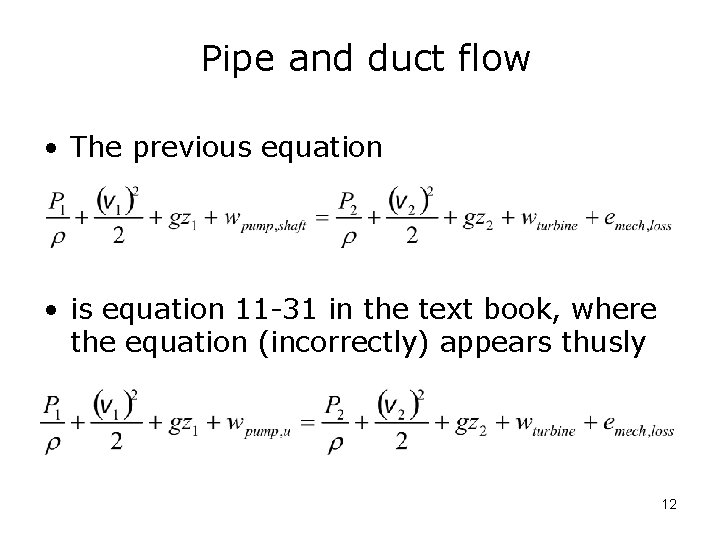
Pipe and duct flow • The previous equation • is equation 11 -31 in the text book, where the equation (incorrectly) appears thusly 12
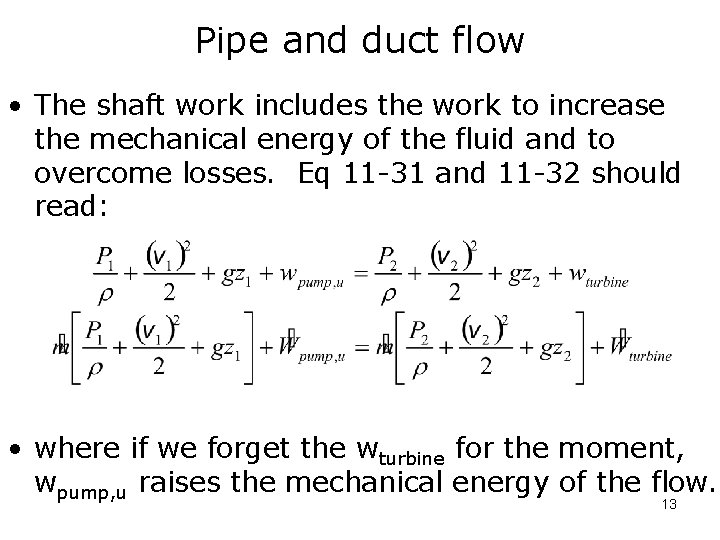
Pipe and duct flow • The shaft work includes the work to increase the mechanical energy of the fluid and to overcome losses. Eq 11 -31 and 11 -32 should read: • where if we forget the wturbine for the moment, wpump, u raises the mechanical energy of the flow. 13
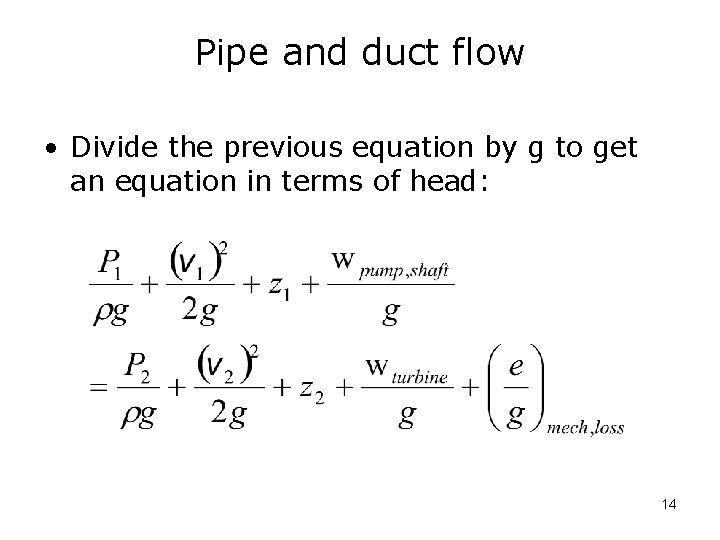
Pipe and duct flow • Divide the previous equation by g to get an equation in terms of head: 14
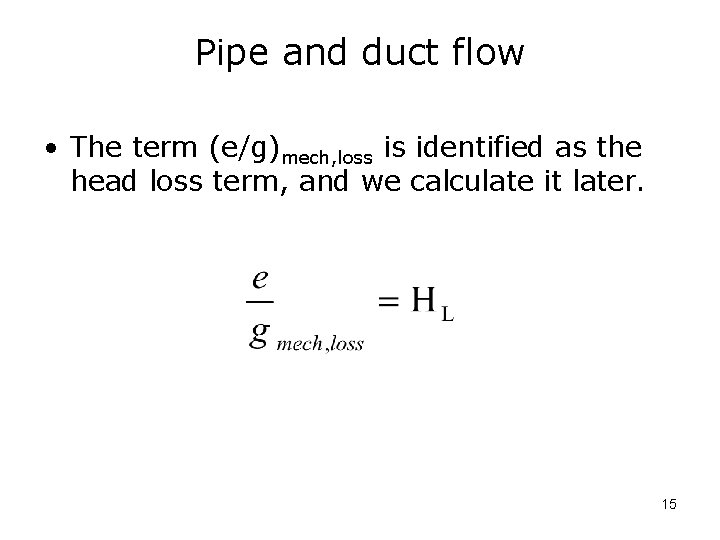
Pipe and duct flow • The term (e/g)mech, loss is identified as the head loss term, and we calculate it later. 15
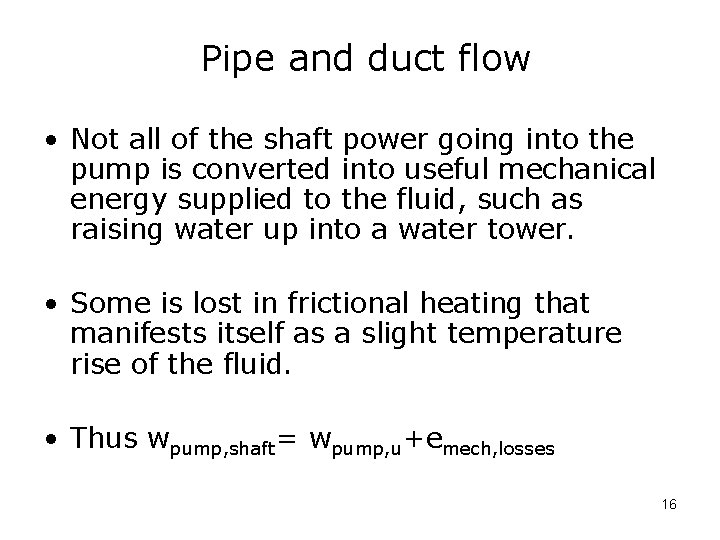
Pipe and duct flow • Not all of the shaft power going into the pump is converted into useful mechanical energy supplied to the fluid, such as raising water up into a water tower. • Some is lost in frictional heating that manifests itself as a slight temperature rise of the fluid. • Thus wpump, shaft= wpump, u+emech, losses 16
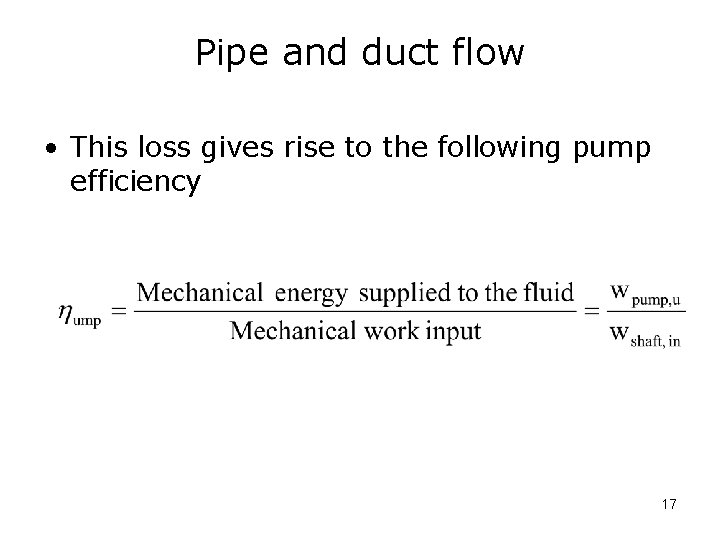
Pipe and duct flow • This loss gives rise to the following pump efficiency 17
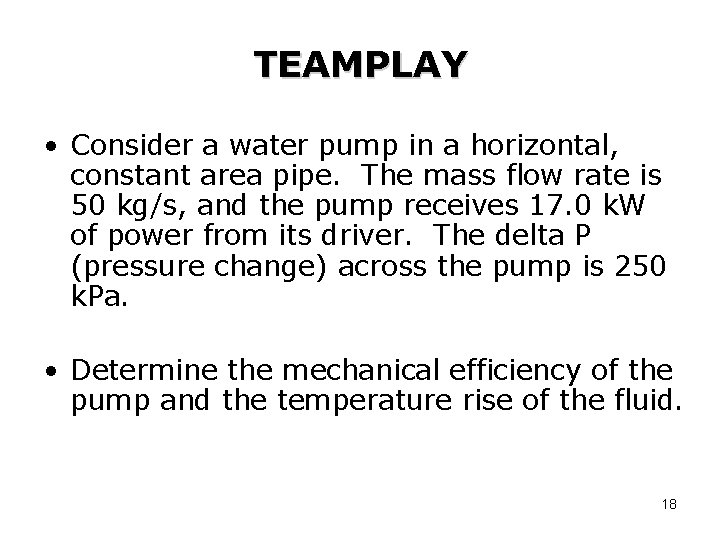
TEAMPLAY • Consider a water pump in a horizontal, constant area pipe. The mass flow rate is 50 kg/s, and the pump receives 17. 0 k. W of power from its driver. The delta P (pressure change) across the pump is 250 k. Pa. • Determine the mechanical efficiency of the pump and the temperature rise of the fluid. 18
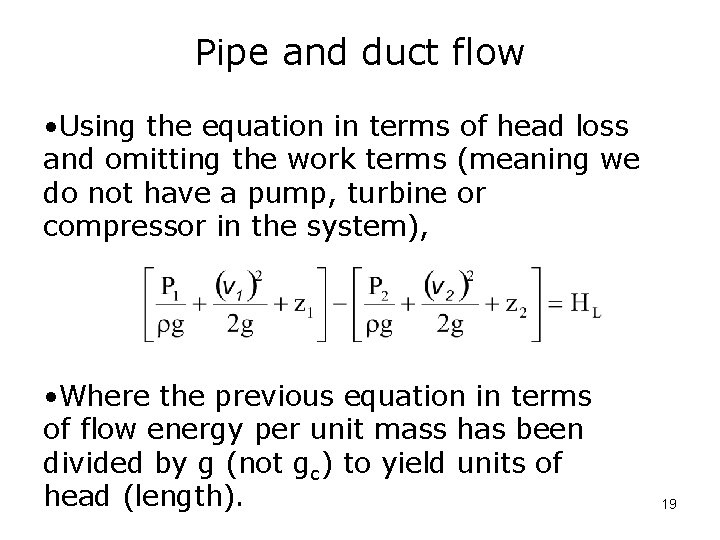
Pipe and duct flow • Using the equation in terms of head loss and omitting the work terms (meaning we do not have a pump, turbine or compressor in the system), • Where the previous equation in terms of flow energy per unit mass has been divided by g (not gc) to yield units of head (length). 19
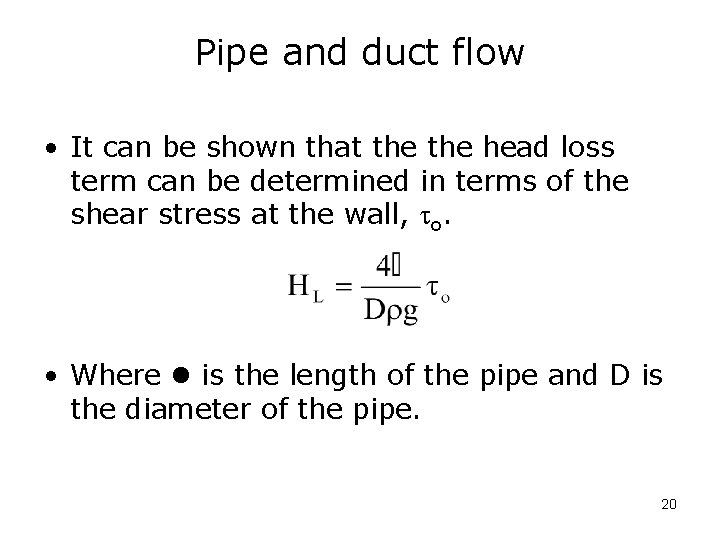
Pipe and duct flow • It can be shown that the head loss term can be determined in terms of the shear stress at the wall, o. • Where is the length of the pipe and D is the diameter of the pipe. 20
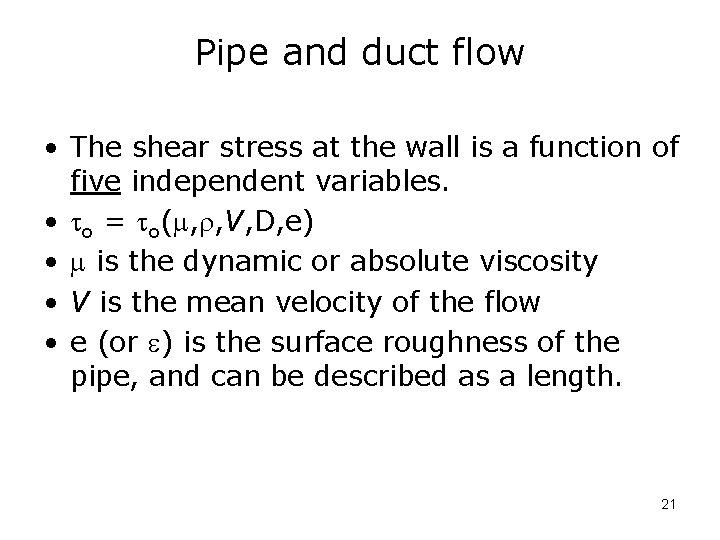
Pipe and duct flow • The shear stress at the wall is a function of five independent variables. • o = o( , , V, D, e) • is the dynamic or absolute viscosity • V is the mean velocity of the flow • e (or ) is the surface roughness of the pipe, and can be described as a length. 21
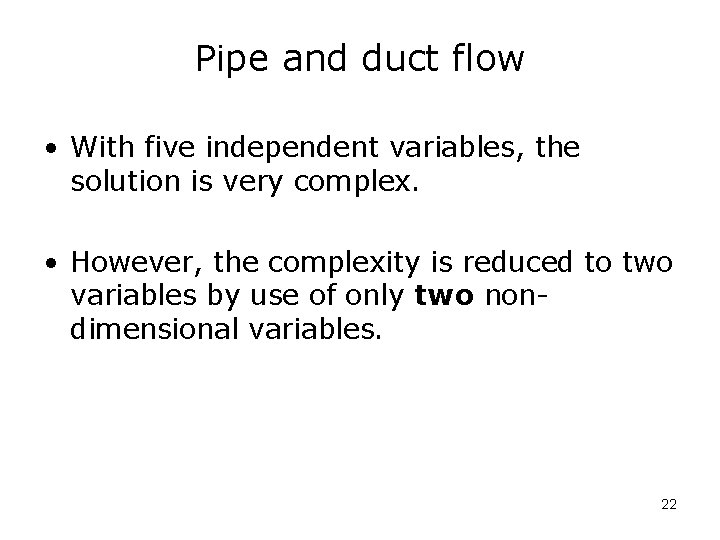
Pipe and duct flow • With five independent variables, the solution is very complex. • However, the complexity is reduced to two variables by use of only two nondimensional variables. 22
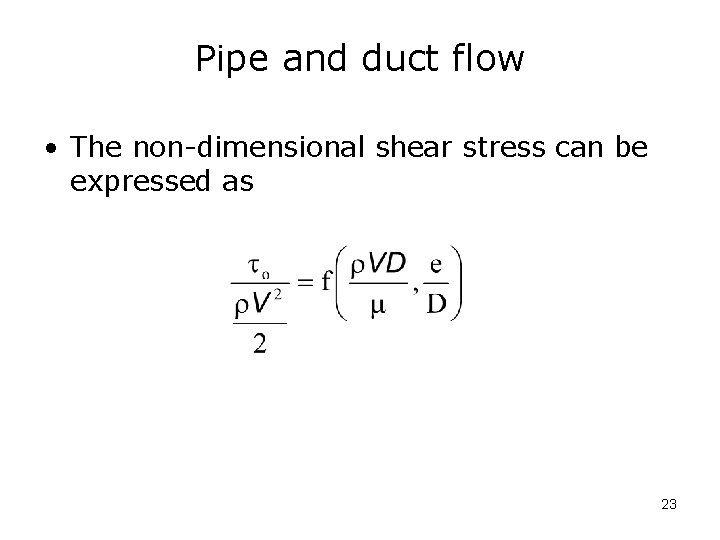
Pipe and duct flow • The non-dimensional shear stress can be expressed as 23
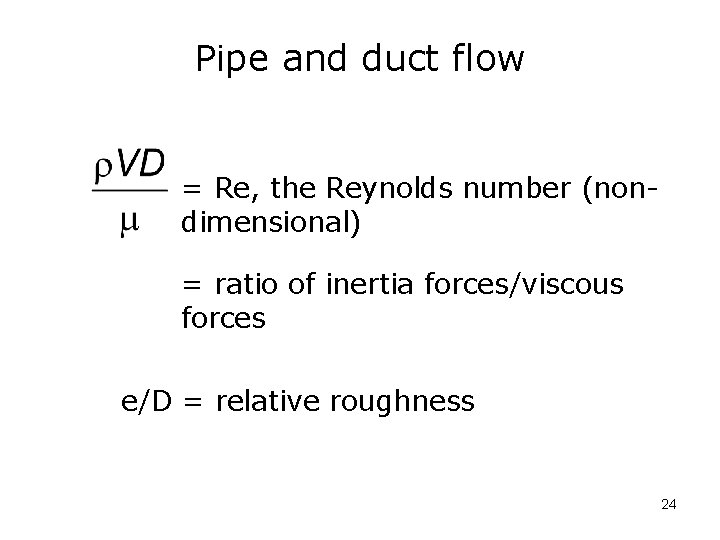
Pipe and duct flow = Re, the Reynolds number (nondimensional) = ratio of inertia forces/viscous forces e/D = relative roughness 24
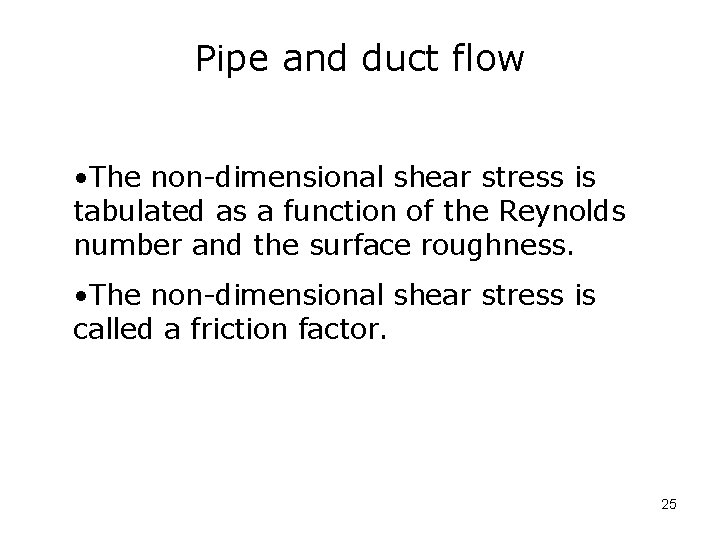
Pipe and duct flow • The non-dimensional shear stress is tabulated as a function of the Reynolds number and the surface roughness. • The non-dimensional shear stress is called a friction factor. 25
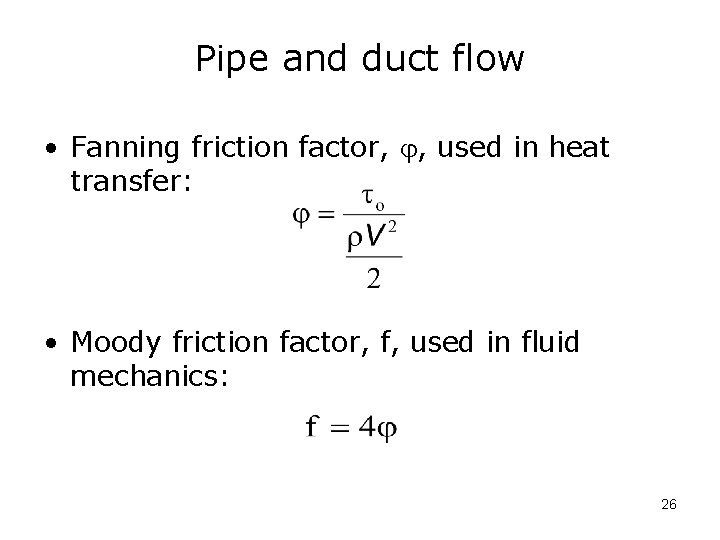
Pipe and duct flow • Fanning friction factor, , used in heat transfer: • Moody friction factor, f, used in fluid mechanics: 26
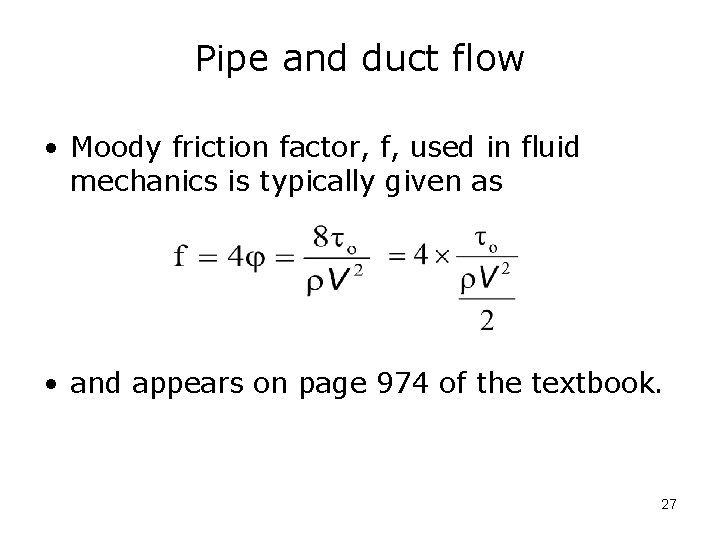
Pipe and duct flow • Moody friction factor, f, used in fluid mechanics is typically given as • and appears on page 974 of the textbook. 27
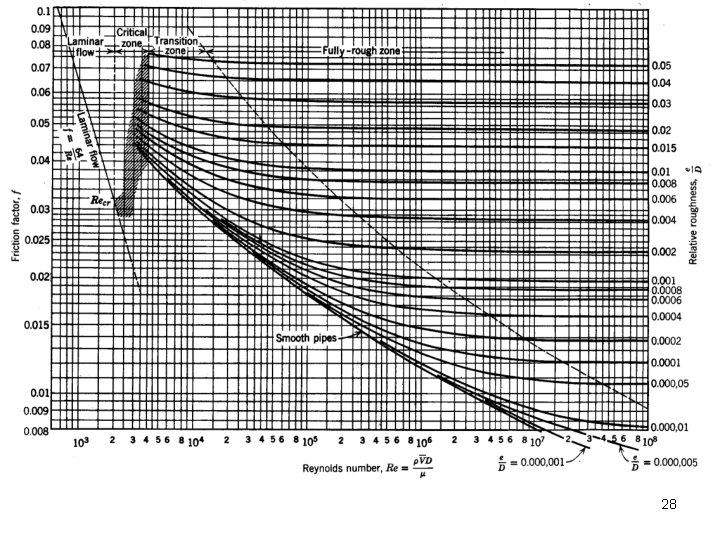
28
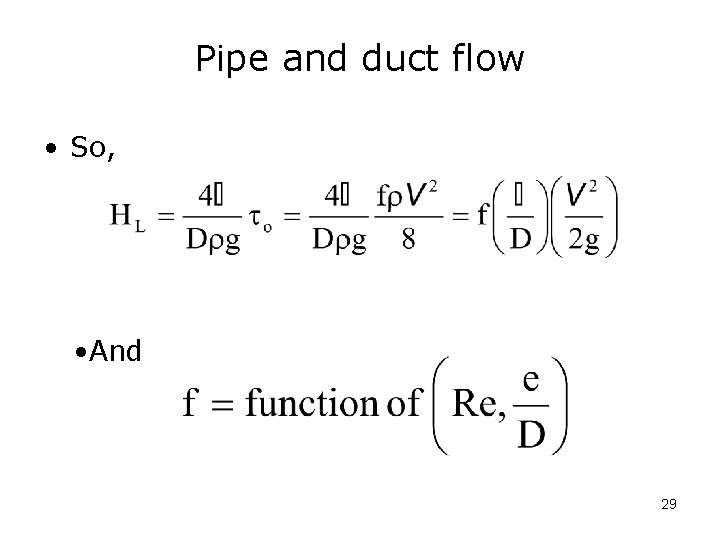
Pipe and duct flow • So, • And 29
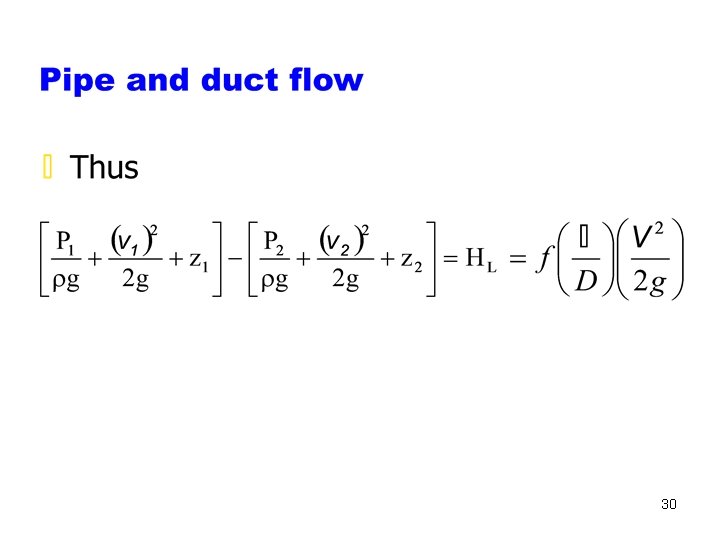
30
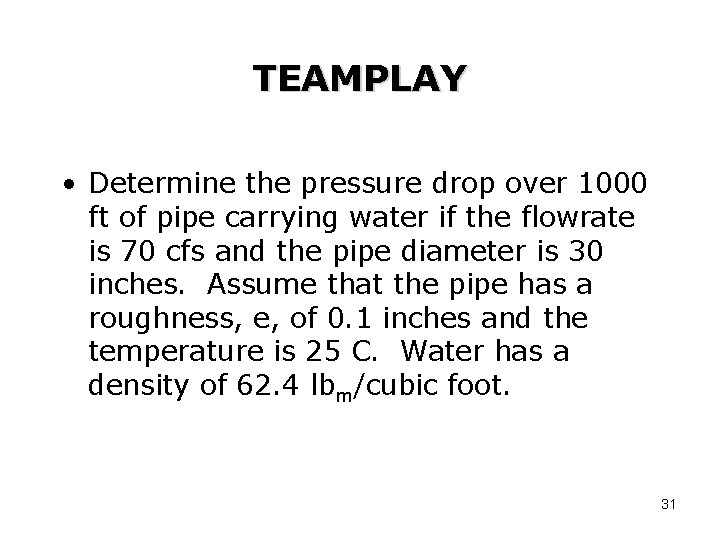
TEAMPLAY • Determine the pressure drop over 1000 ft of pipe carrying water if the flowrate is 70 cfs and the pipe diameter is 30 inches. Assume that the pipe has a roughness, e, of 0. 1 inches and the temperature is 25 C. Water has a density of 62. 4 lbm/cubic foot. 31
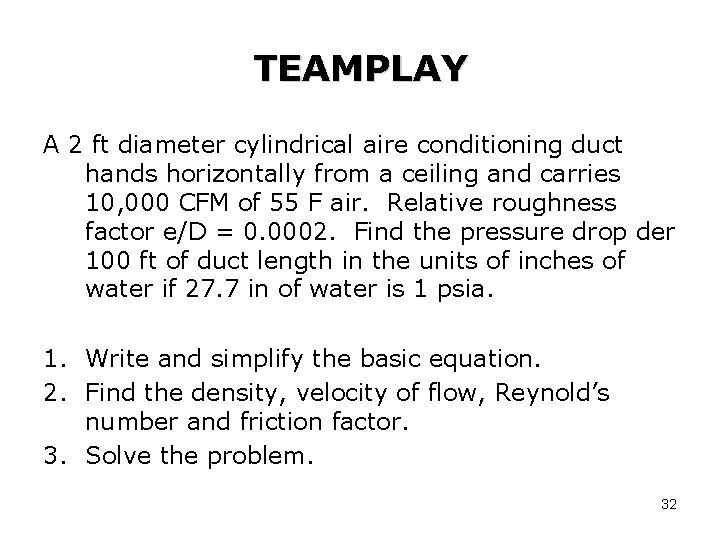
TEAMPLAY A 2 ft diameter cylindrical aire conditioning duct hands horizontally from a ceiling and carries 10, 000 CFM of 55 F air. Relative roughness factor e/D = 0. 0002. Find the pressure drop der 100 ft of duct length in the units of inches of water if 27. 7 in of water is 1 psia. 1. Write and simplify the basic equation. 2. Find the density, velocity of flow, Reynold’s number and friction factor. 3. Solve the problem. 32
Double pipe heat exchanger formula
Single stack partially ventilated system
Frictionless flow
Frictionless flow
Open channel definition
Lec scoreboard
11th chemistry thermodynamics lec 13
Lec ditto
Lec scoreboard
Componentes del lec
11th chemistry thermodynamics lec 10
Biochemistry
August lec 250
Underground pipeline irrigation system
Lec 1
Apelacin
Lec
132000 lec
Lec@b@ret
Tipos de lec
Sekisui s-lec america llc
416 lec
Lec
Brayton
Lec promotion
Lec anatomia
History of software development life cycle
Fenemates
Lec barbate
Lec hardver
Lec renal
252 lec
A sled moves on essentially frictionless ice