IPS 15 19 2015 International Perforating Symposium The
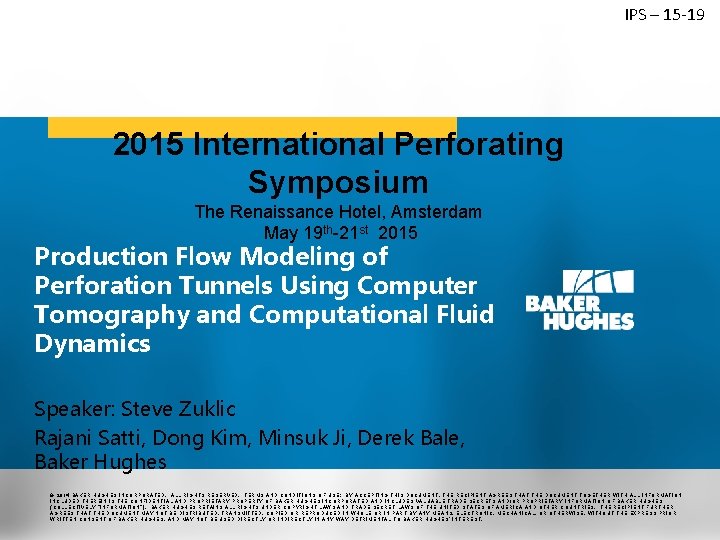
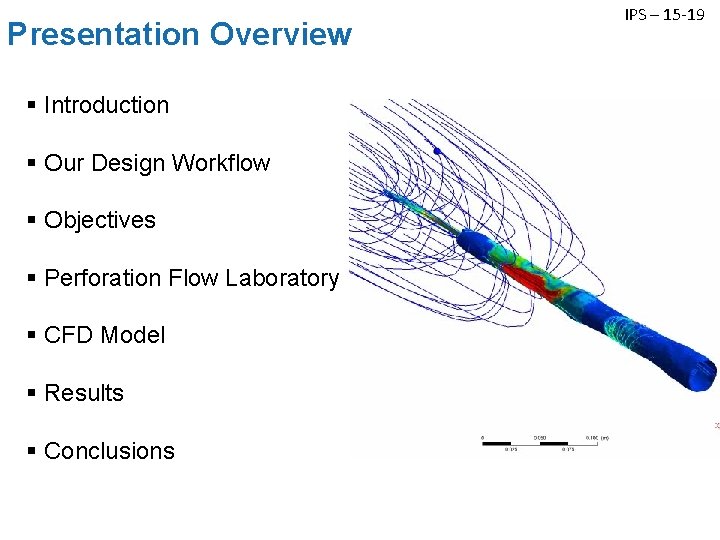
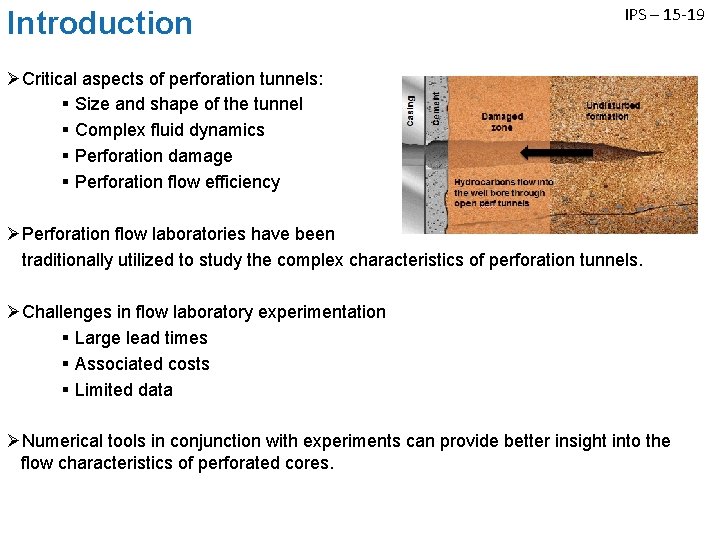
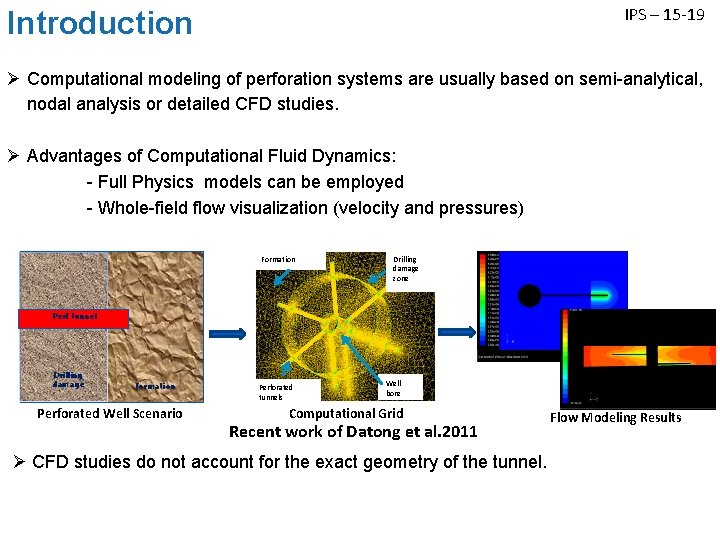
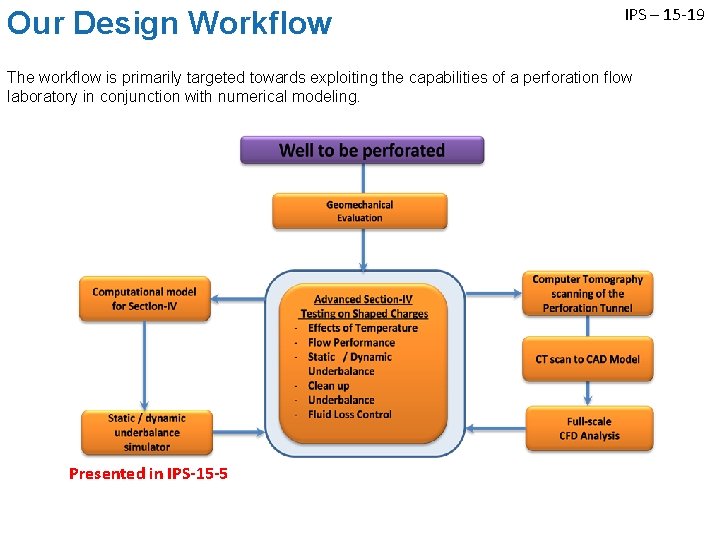
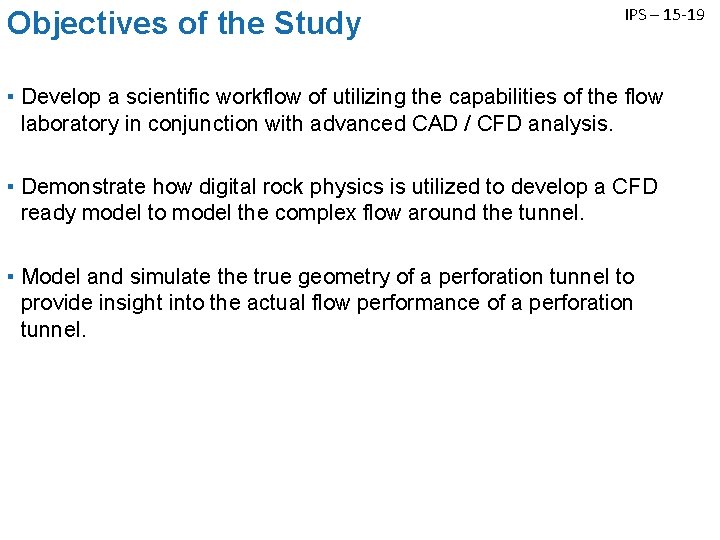
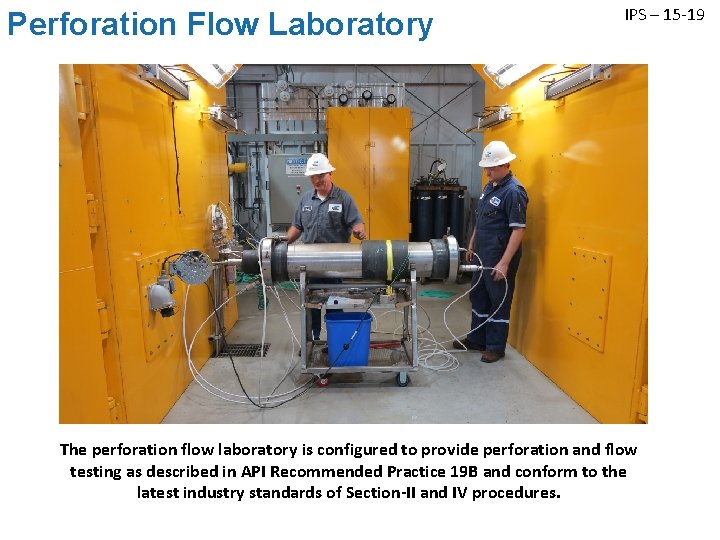
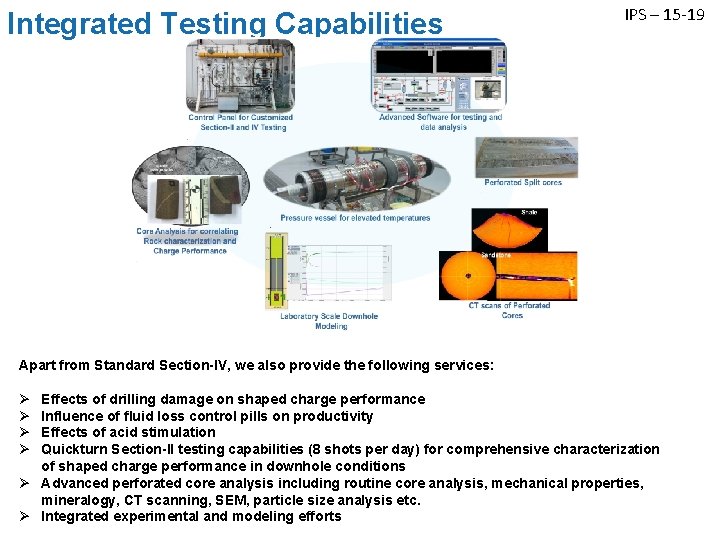
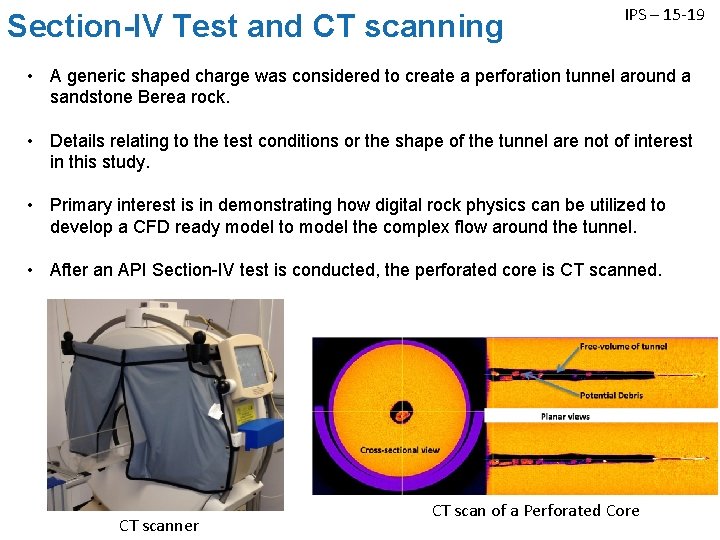
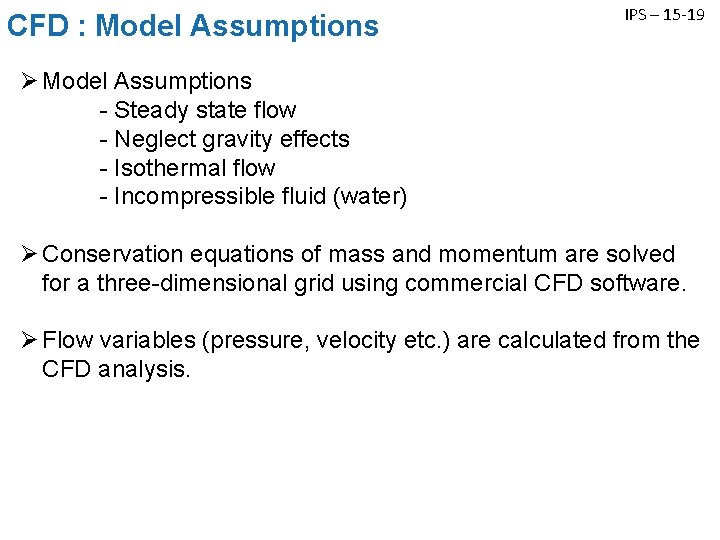
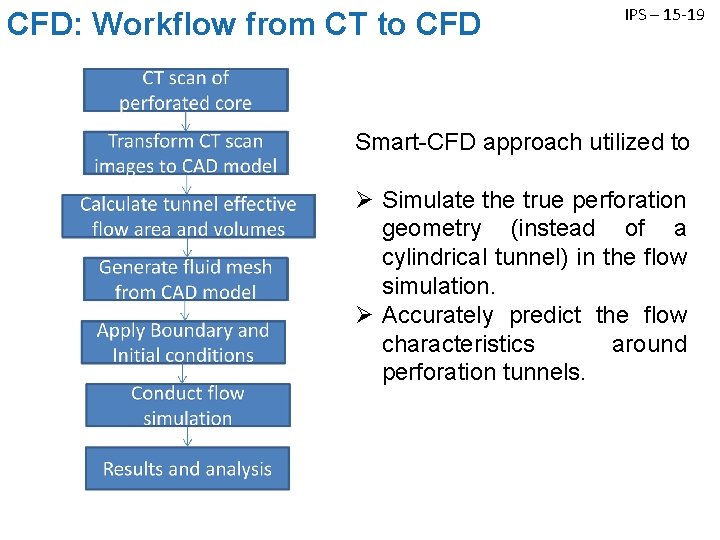
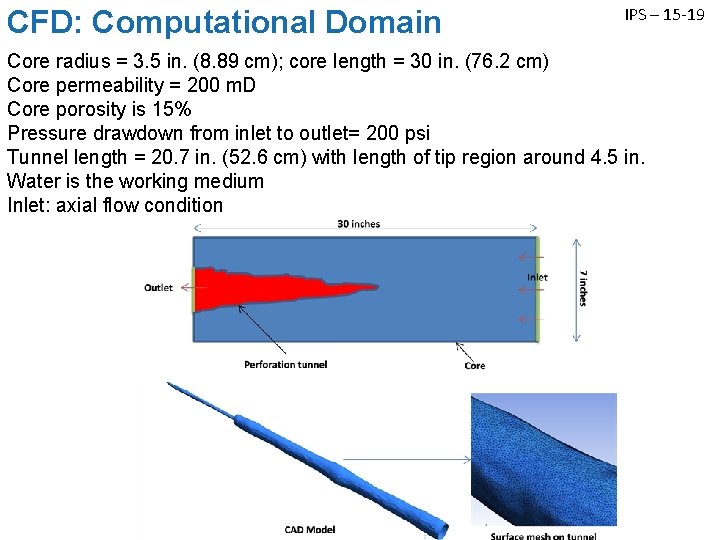
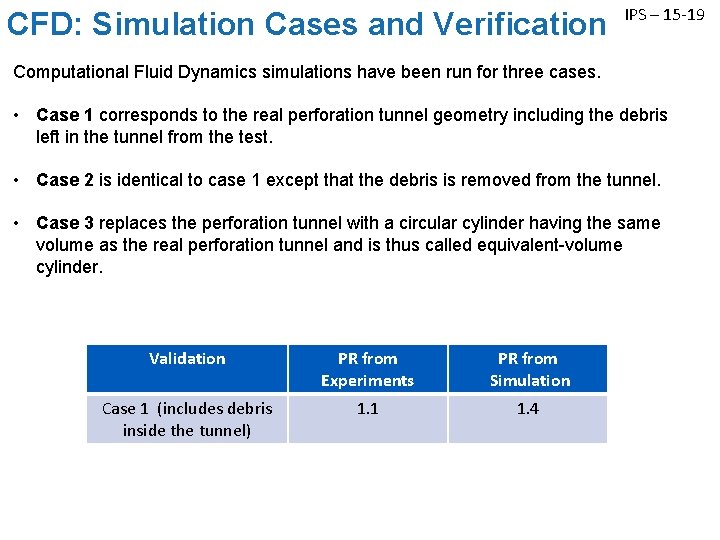
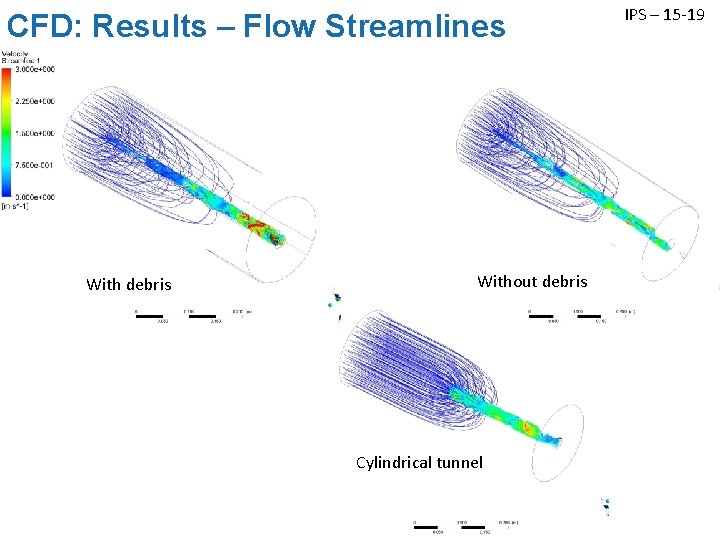
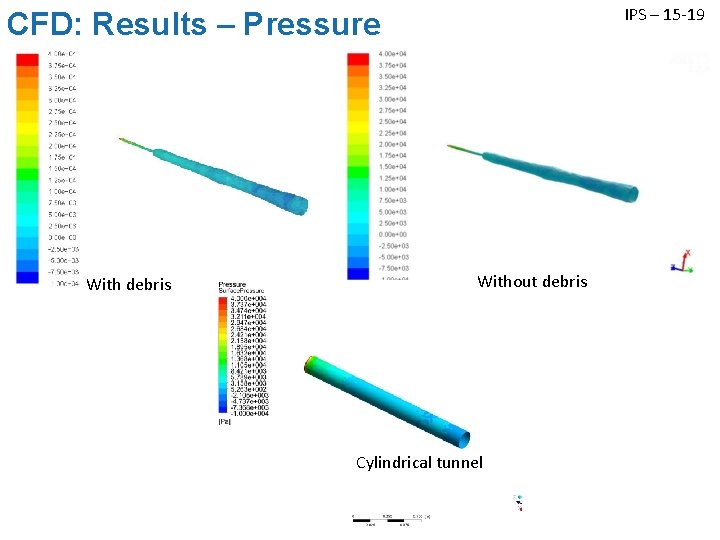
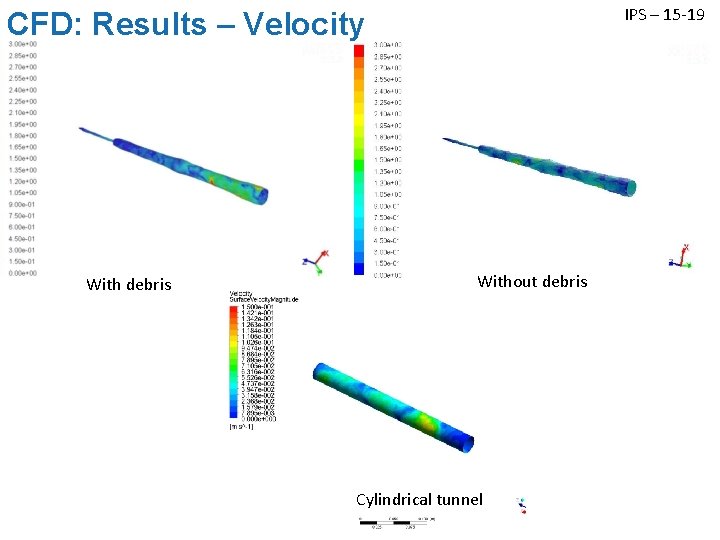
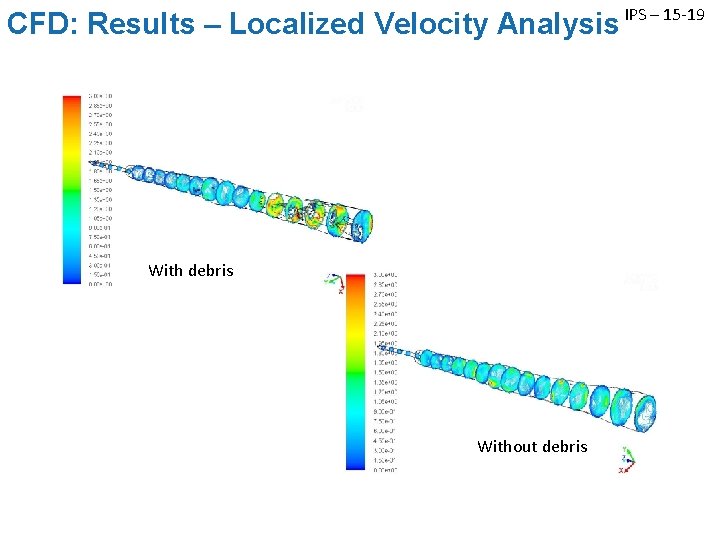
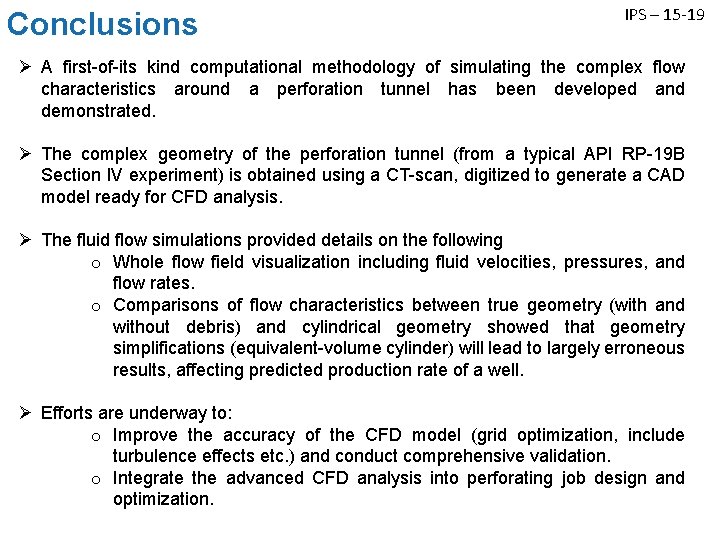
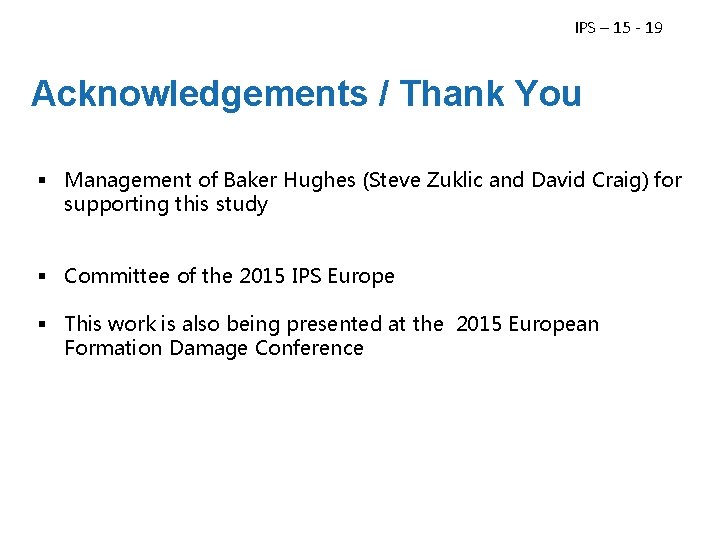
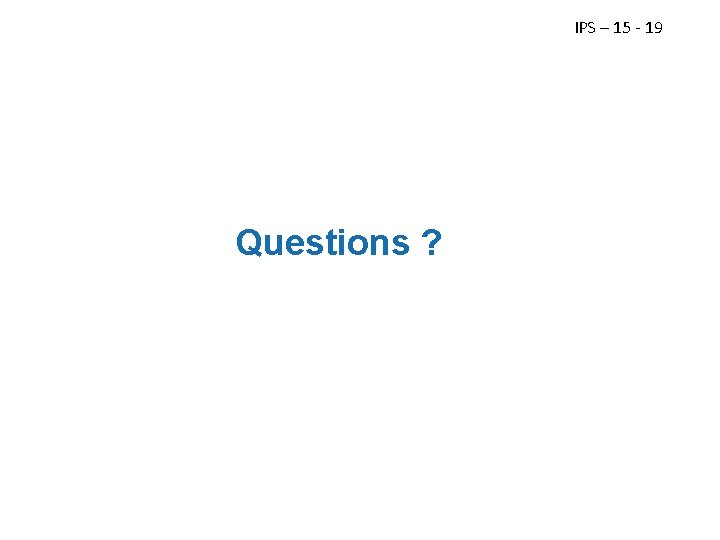
- Slides: 20
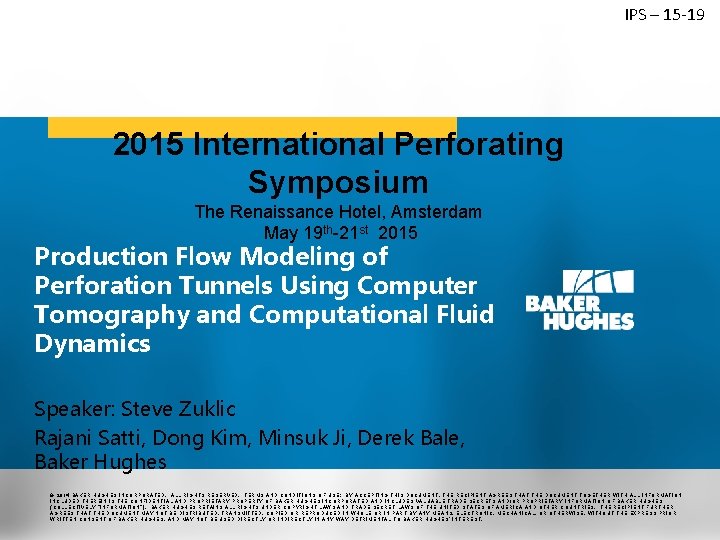
IPS – 15 -19 2015 International Perforating Symposium The Renaissance Hotel, Amsterdam May 19 th-21 st 2015 © 2014 Baker Hughes Incorporated. All Rights Reserved. Production Flow Modeling of Perforation Tunnels Using Computer Tomography and Computational Fluid Dynamics Speaker: Steve Zuklic Rajani Satti, Dong Kim, Minsuk Ji, Derek Bale, Baker Hughes 1 © 201 4 B AK ER HUGH ES I NCORPO RATED. ALL RIGHTS RESERVED. TERMS AND CONDITIONS OF USE: BY ACCEPTING THIS DOCUMENT, THE RECIPIENT AGREES T HAT THE DOCUMENT TOGETHER WITH ALL INFORMATION INCLUDED THEREIN IS T HE CONFI DENTIAL AND PROPRIETARY PROPERTY OF B AK ER HUGHES INCORPORATED AND INCLUDES VALUABLE TRADE SECRETS AND/OR PROPRIETARY INFORMATION OF BAKER HUGHES (CO LLECTIVELY "INF OR MA TI ON"). BAKER H UGHES RETAINS ALL RIGHTS UNDER COPY RIGHT LAWS AND TRADE SECRET LAWS OF THE UNITED STATES OF AMERICA AND OT HER COUNTRIES. THE RECIPIENT FURTHER AGRE ES T HA T THE D OC UM ENT MAY NO T BE DISTRIBUTED, TRANSMITTED, COPIE D OR REPRODUCED IN WHOLE OR IN PART BY ANY MEANS, ELECTRONIC, MECHANICAL, OR OT HERWISE, WITHOUT THE EXPRESS PRIOR WRI TTEN C ONSENT OF B AKER HUG HES, AND MAY NOT BE USED DIRECTLY OR INDIRECTLY IN ANY WAY DETRIMENTAL TO BAKER HUGHES’ INTEREST.
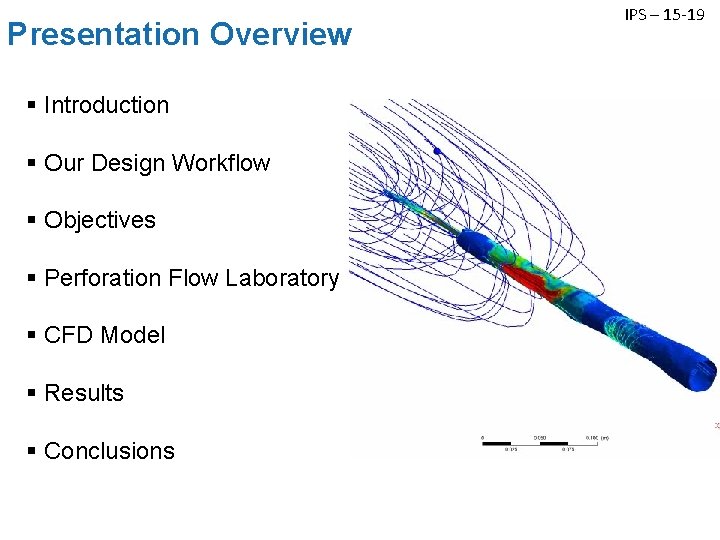
Presentation Overview § Introduction § Our Design Workflow § Objectives § Perforation Flow Laboratory § CFD Model § Results § Conclusions IPS – 15 -19
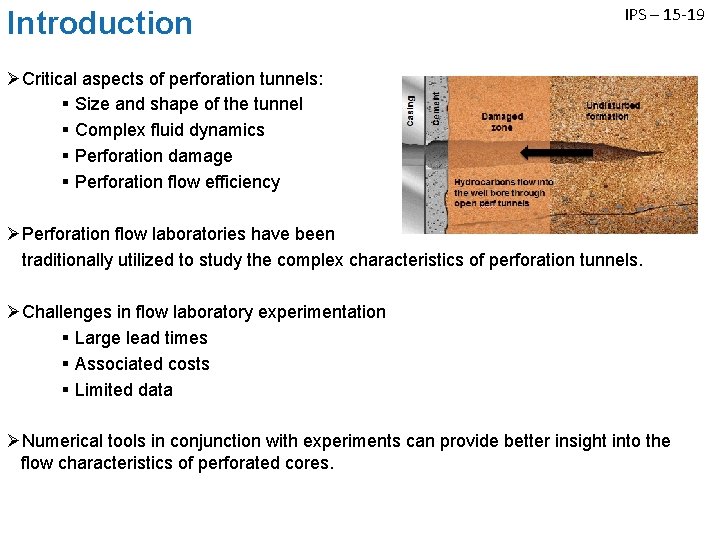
Introduction IPS – 15 -19 ØCritical aspects of perforation tunnels: § Size and shape of the tunnel § Complex fluid dynamics § Perforation damage § Perforation flow efficiency ØPerforation flow laboratories have been traditionally utilized to study the complex characteristics of perforation tunnels. ØChallenges in flow laboratory experimentation § Large lead times § Associated costs § Limited data ØNumerical tools in conjunction with experiments can provide better insight into the flow characteristics of perforated cores.
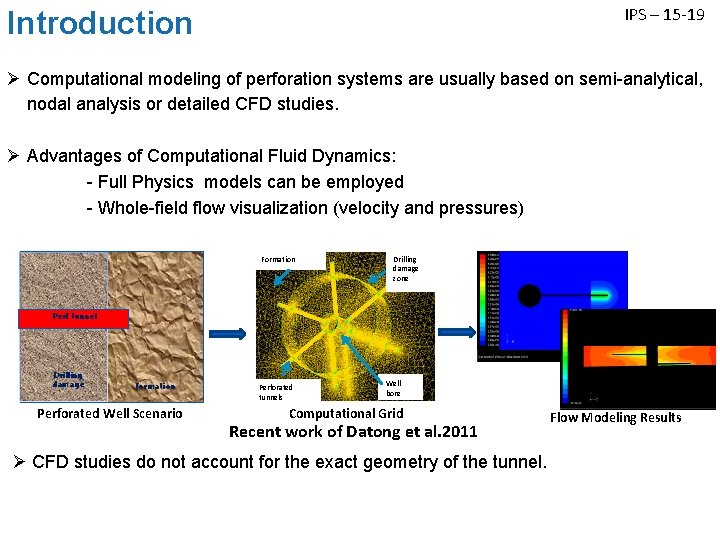
IPS – 15 -19 Introduction Ø Computational modeling of perforation systems are usually based on semi-analytical, nodal analysis or detailed CFD studies. Ø Advantages of Computational Fluid Dynamics: - Full Physics models can be employed - Whole-field flow visualization (velocity and pressures) Formation Drilling damage zone Perf tunnel Drilling damage formation Perforated Well Scenario Perforated tunnels Well bore Computational Grid Recent work of Datong et al. 2011 Ø CFD studies do not account for the exact geometry of the tunnel. Flow Modeling Results
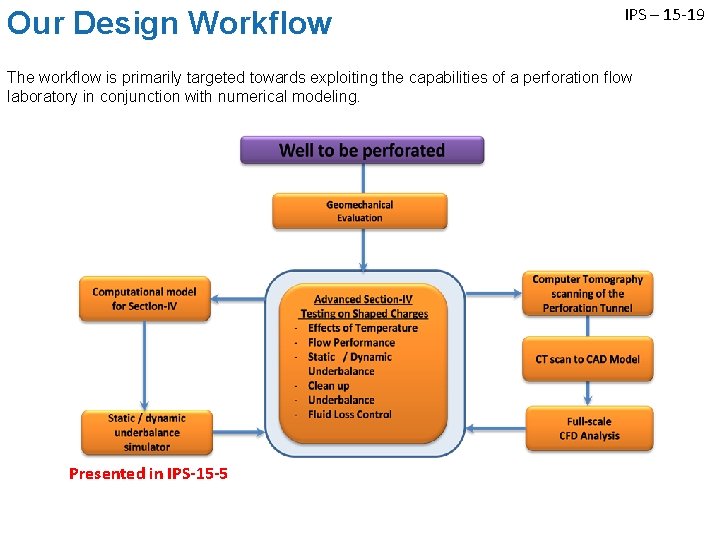
Our Design Workflow IPS – 15 -19 The workflow is primarily targeted towards exploiting the capabilities of a perforation flow laboratory in conjunction with numerical modeling. Presented in IPS-15 -5
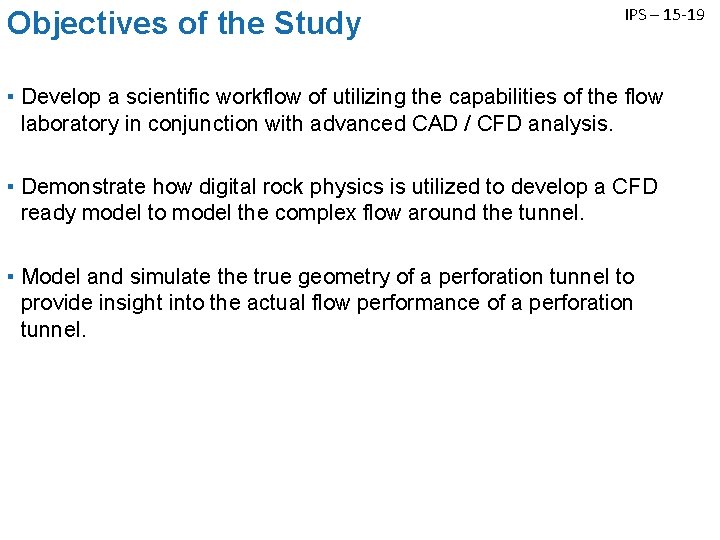
Objectives of the Study IPS – 15 -19 ▪ Develop a scientific workflow of utilizing the capabilities of the flow laboratory in conjunction with advanced CAD / CFD analysis. ▪ Demonstrate how digital rock physics is utilized to develop a CFD ready model to model the complex flow around the tunnel. ▪ Model and simulate the true geometry of a perforation tunnel to provide insight into the actual flow performance of a perforation tunnel.
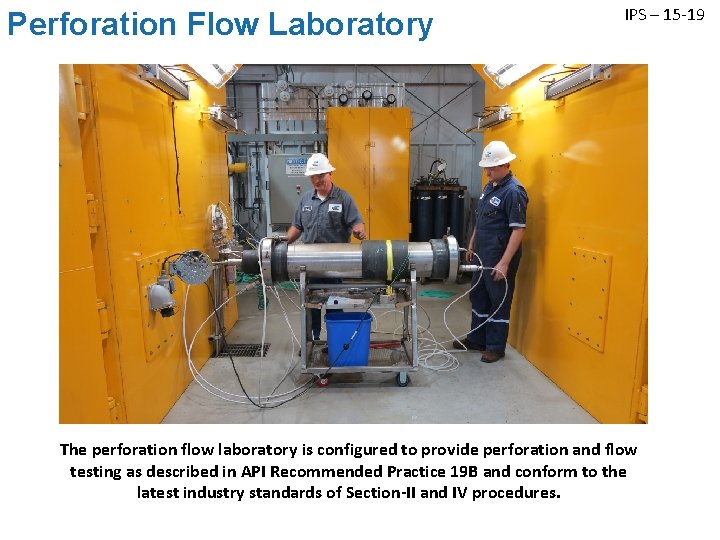
Perforation Flow Laboratory IPS – 15 -19 The perforation flow laboratory is configured to provide perforation and flow testing as described in API Recommended Practice 19 B and conform to the latest industry standards of Section-II and IV procedures.
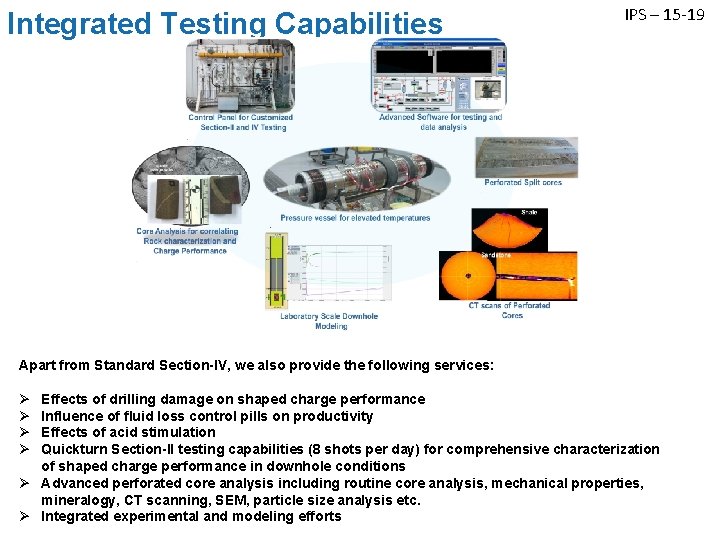
Integrated Testing Capabilities IPS – 15 -19 Apart from Standard Section-IV, we also provide the following services: Ø Ø Effects of drilling damage on shaped charge performance Influence of fluid loss control pills on productivity Effects of acid stimulation Quickturn Section-II testing capabilities (8 shots per day) for comprehensive characterization of shaped charge performance in downhole conditions Ø Advanced perforated core analysis including routine core analysis, mechanical properties, mineralogy, CT scanning, SEM, particle size analysis etc. Ø Integrated experimental and modeling efforts
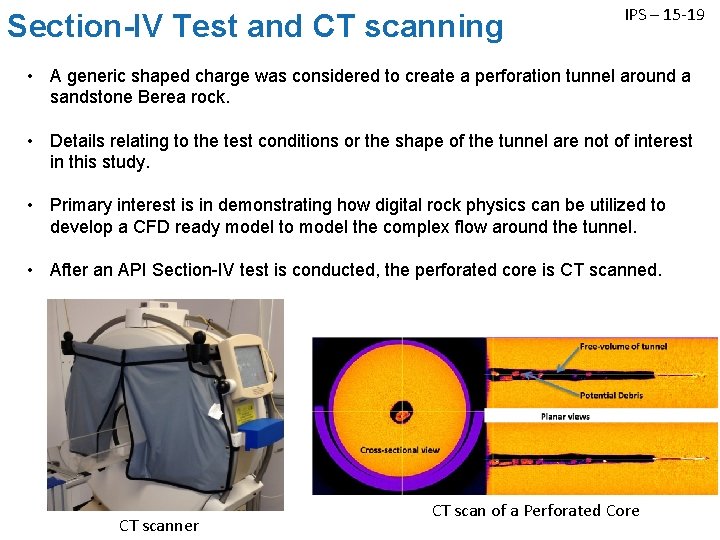
Section-IV Test and CT scanning IPS – 15 -19 • A generic shaped charge was considered to create a perforation tunnel around a sandstone Berea rock. • Details relating to the test conditions or the shape of the tunnel are not of interest in this study. • Primary interest is in demonstrating how digital rock physics can be utilized to develop a CFD ready model to model the complex flow around the tunnel. • After an API Section-IV test is conducted, the perforated core is CT scanned. CT scanner CT scan of a Perforated Core
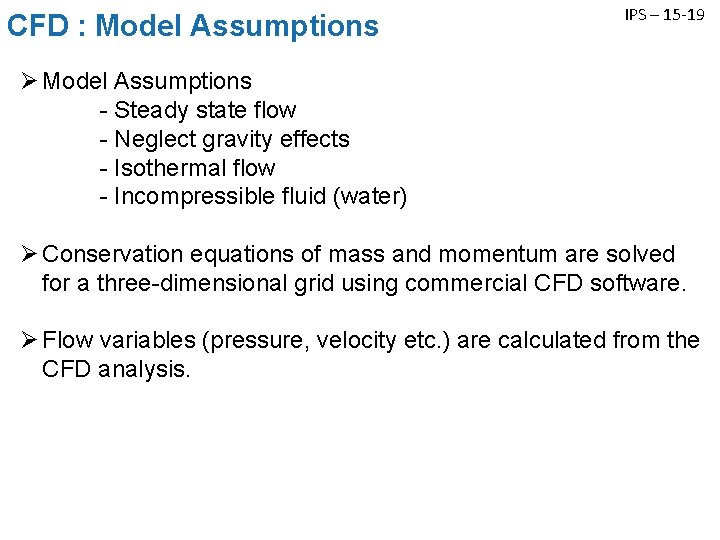
CFD : Model Assumptions IPS – 15 -19 Ø Model Assumptions - Steady state flow - Neglect gravity effects - Isothermal flow - Incompressible fluid (water) Ø Conservation equations of mass and momentum are solved for a three-dimensional grid using commercial CFD software. Ø Flow variables (pressure, velocity etc. ) are calculated from the CFD analysis.
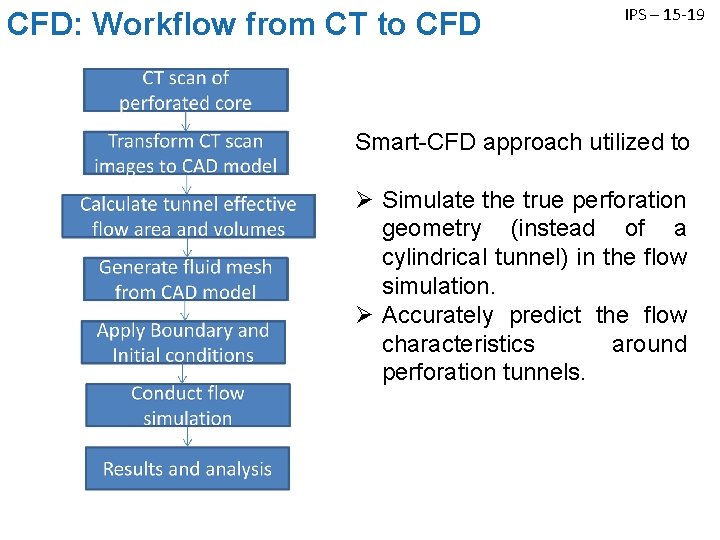
CFD: Workflow from CT to CFD IPS – 15 -19 Smart-CFD approach utilized to Ø Simulate the true perforation geometry (instead of a cylindrical tunnel) in the flow simulation. Ø Accurately predict the flow characteristics around perforation tunnels.
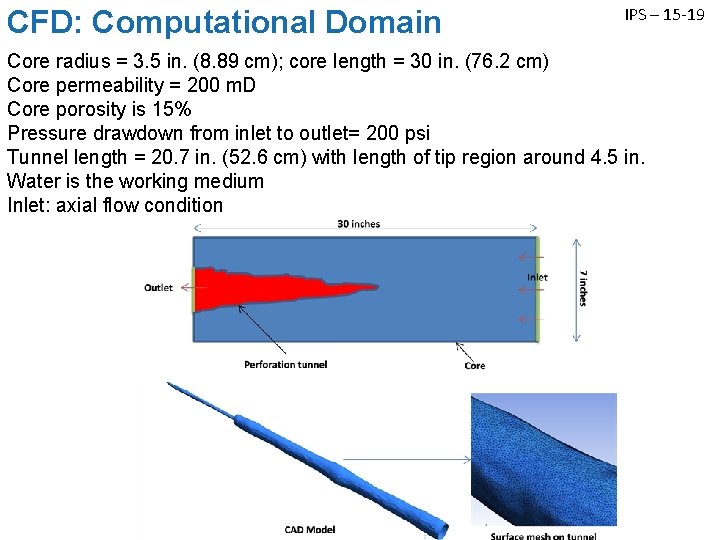
CFD: Computational Domain IPS – 15 -19 Core radius = 3. 5 in. (8. 89 cm); core length = 30 in. (76. 2 cm) Core permeability = 200 m. D Core porosity is 15% Pressure drawdown from inlet to outlet= 200 psi Tunnel length = 20. 7 in. (52. 6 cm) with length of tip region around 4. 5 in. Water is the working medium Inlet: axial flow condition
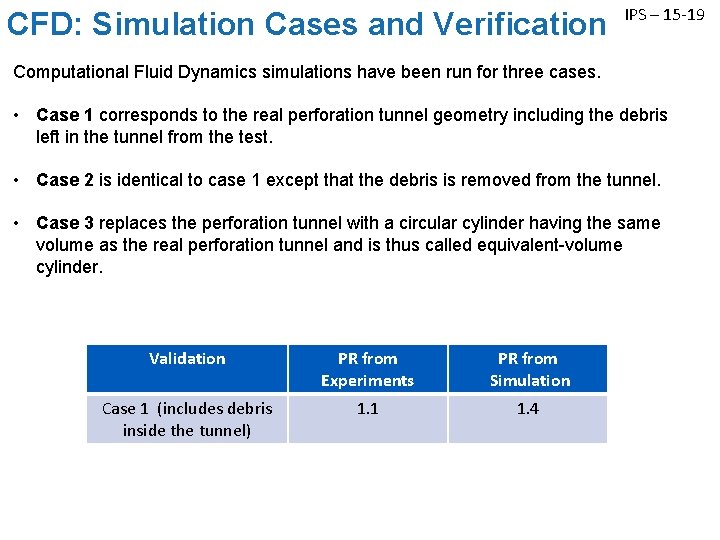
CFD: Simulation Cases and Verification IPS – 15 -19 Computational Fluid Dynamics simulations have been run for three cases. • Case 1 corresponds to the real perforation tunnel geometry including the debris left in the tunnel from the test. • Case 2 is identical to case 1 except that the debris is removed from the tunnel. • Case 3 replaces the perforation tunnel with a circular cylinder having the same volume as the real perforation tunnel and is thus called equivalent-volume cylinder. Validation PR from Experiments PR from Simulation Case 1 (includes debris inside the tunnel) 1. 1 1. 4
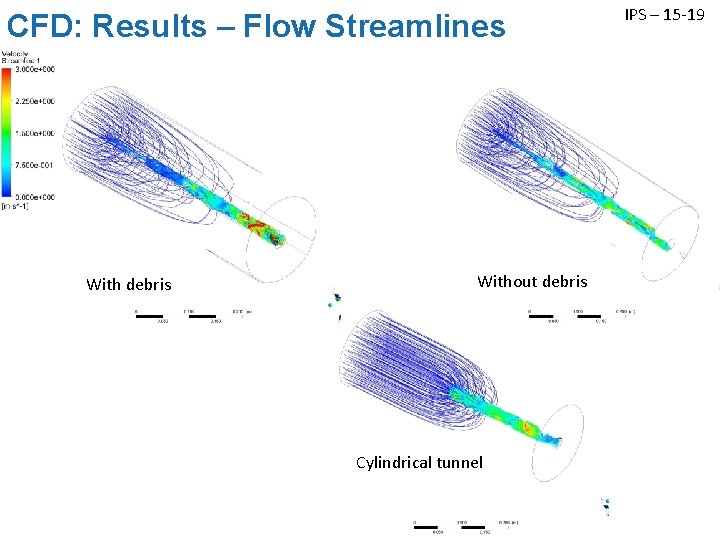
CFD: Results – Flow Streamlines With debris Without debris Cylindrical tunnel IPS – 15 -19
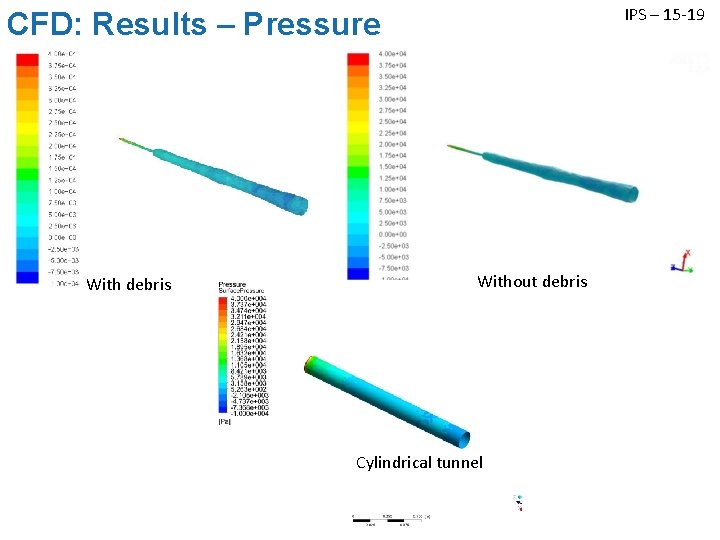
IPS – 15 -19 CFD: Results – Pressure With debris Without debris Cylindrical tunnel
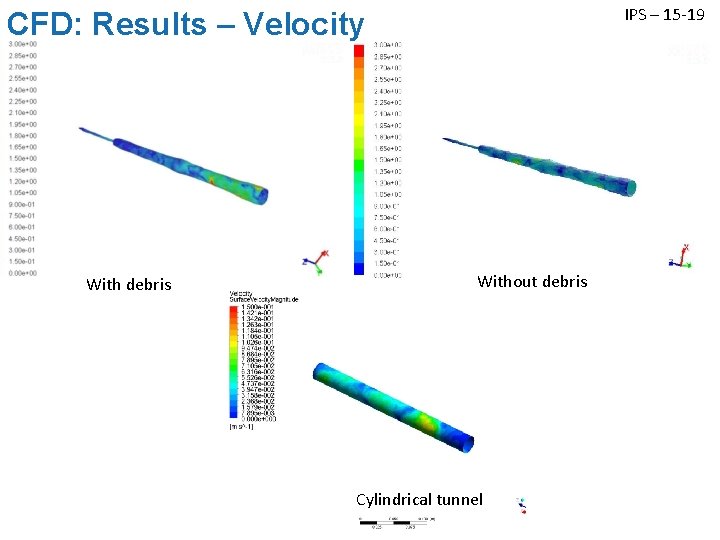
IPS – 15 -19 CFD: Results – Velocity With debris Without debris Cylindrical tunnel
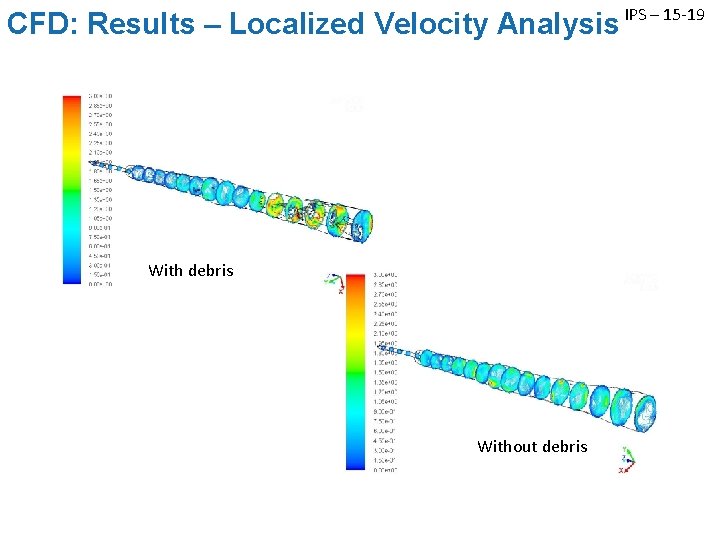
CFD: Results – Localized Velocity Analysis IPS – 15 -19 With debris Without debris
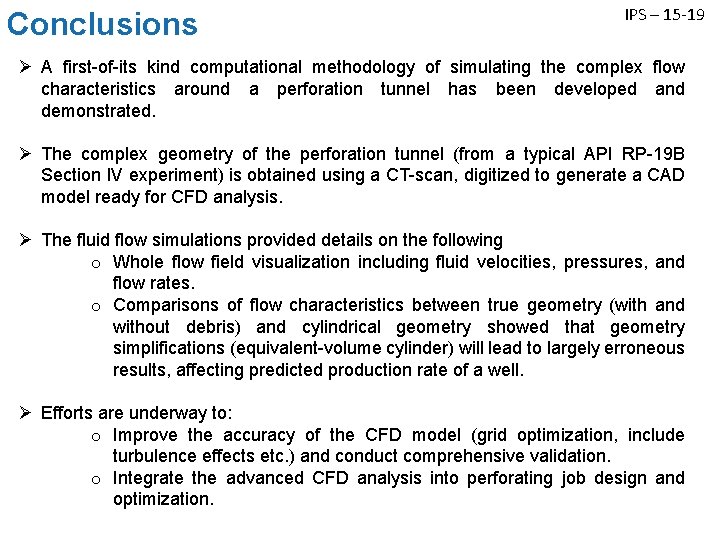
Conclusions IPS – 15 -19 Ø A first-of-its kind computational methodology of simulating the complex flow characteristics around a perforation tunnel has been developed and demonstrated. Ø The complex geometry of the perforation tunnel (from a typical API RP-19 B Section IV experiment) is obtained using a CT-scan, digitized to generate a CAD model ready for CFD analysis. Ø The fluid flow simulations provided details on the following o Whole flow field visualization including fluid velocities, pressures, and flow rates. o Comparisons of flow characteristics between true geometry (with and without debris) and cylindrical geometry showed that geometry simplifications (equivalent-volume cylinder) will lead to largely erroneous results, affecting predicted production rate of a well. Ø Efforts are underway to: o Improve the accuracy of the CFD model (grid optimization, include turbulence effects etc. ) and conduct comprehensive validation. o Integrate the advanced CFD analysis into perforating job design and optimization.
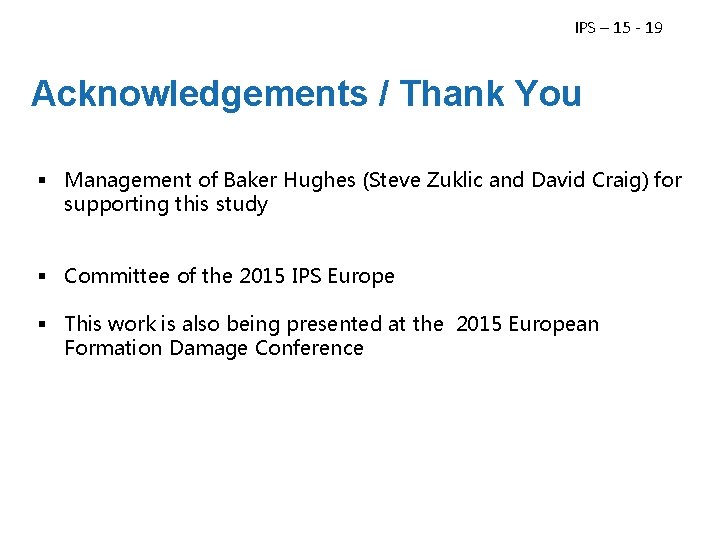
IPS – 15 - 19 Slide 19 Acknowledgements / Thank You § Management of Baker Hughes (Steve Zuklic and David Craig) for supporting this study § Committee of the 2015 IPS Europe § This work is also being presented at the 2015 European Formation Damage Conference
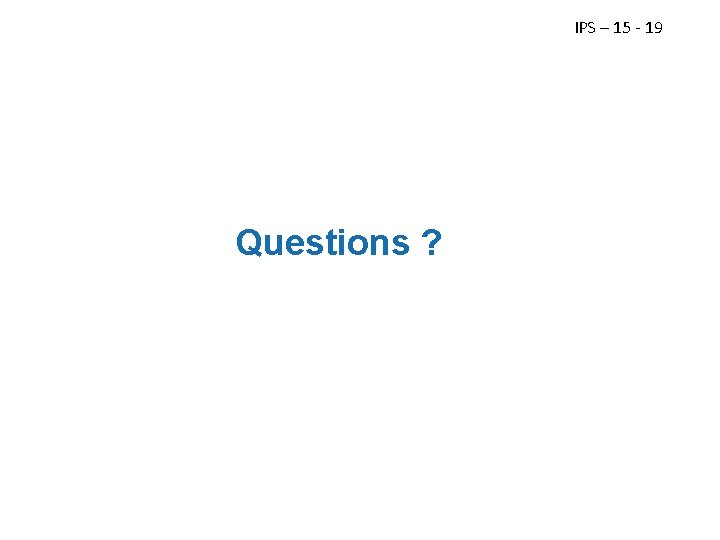
IPS – 15 - 19 Questions ? Slide 20
International perforating symposium
International perforating symposium
International perforating symposium
International perforating symposium
Ips perforating
Ips perforating
International police executive symposium
International symposium on molecular spectroscopy
Great saphenous vein course
Termination of femoral artery
Well integrity
Underbalanced perforating
Trời xanh đây là của chúng ta thể thơ
Voi kéo gỗ như thế nào
So nguyen to
Thiếu nhi thế giới liên hoan
Fecboak
Một số thể thơ truyền thống
Các châu lục và đại dương trên thế giới
Thế nào là hệ số cao nhất
Hệ hô hấp