INTRODUCTION OF HIGH SPEED TRACK IN INDIAN RAILWAYS
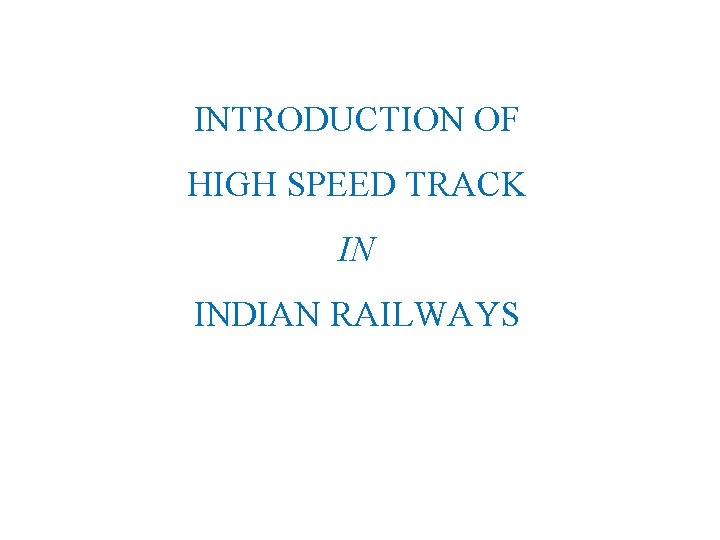
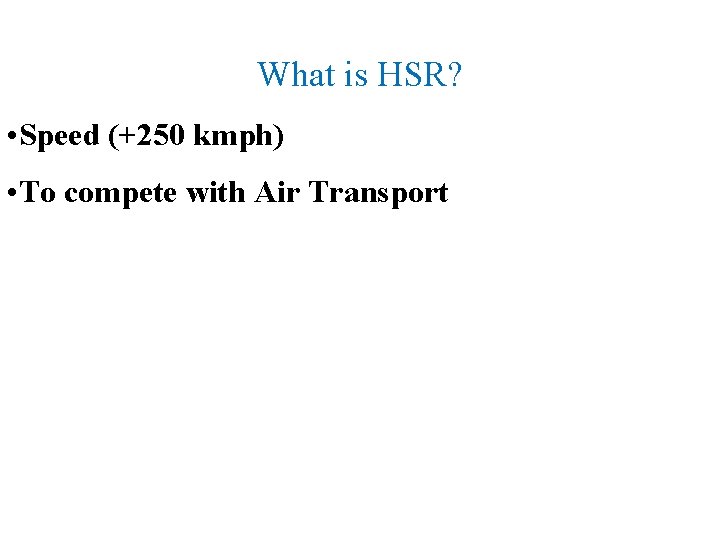
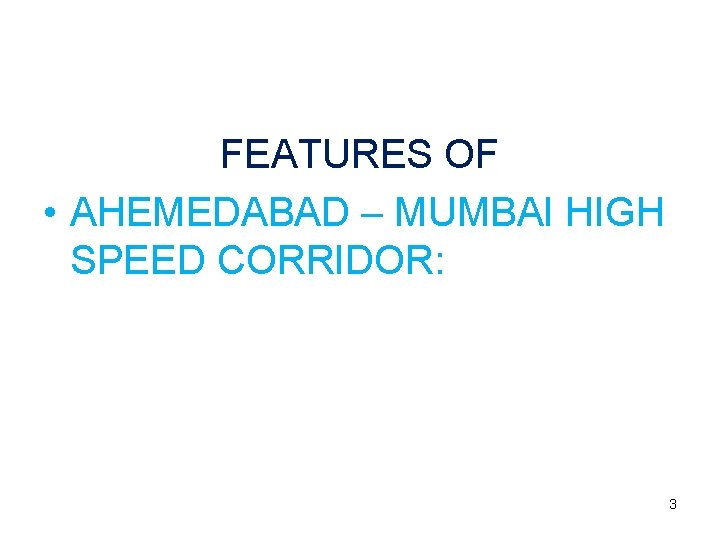
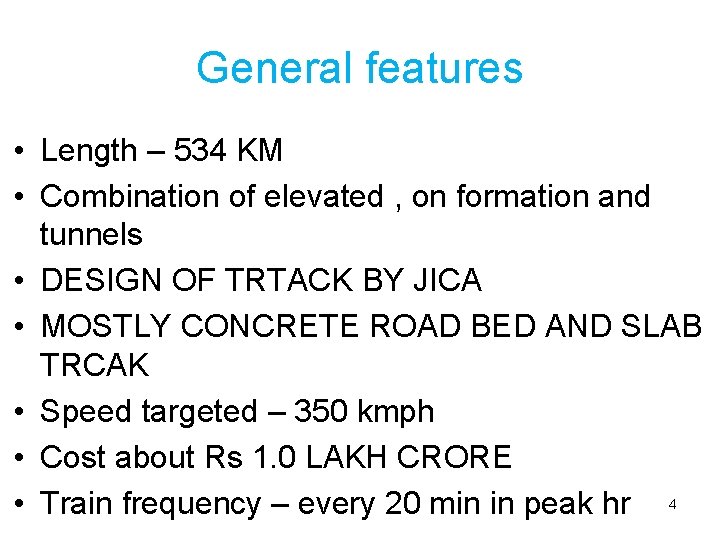
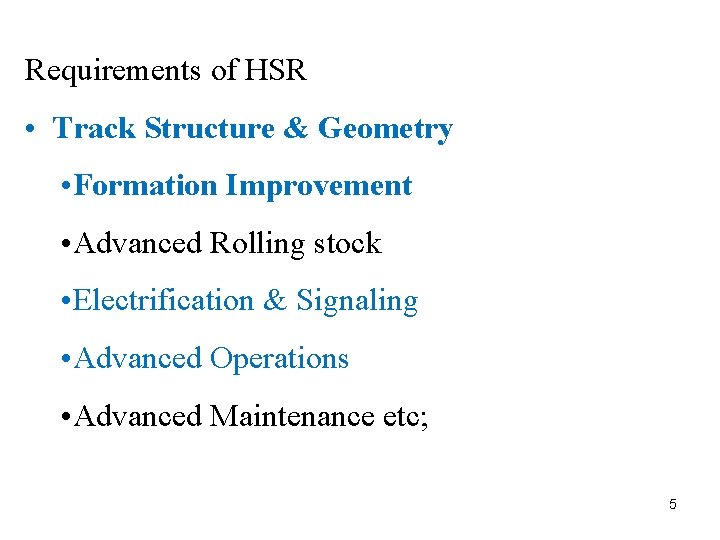
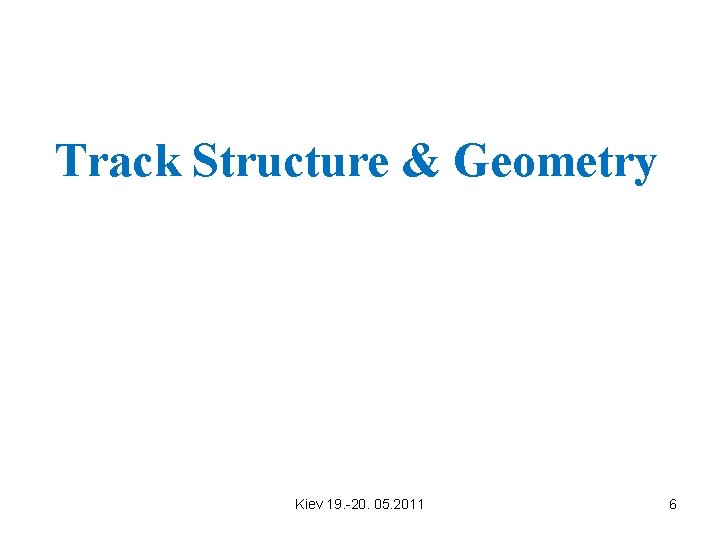
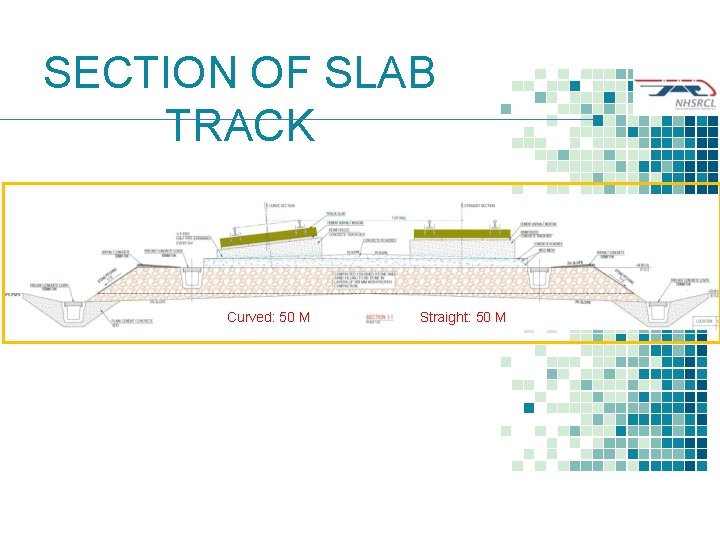
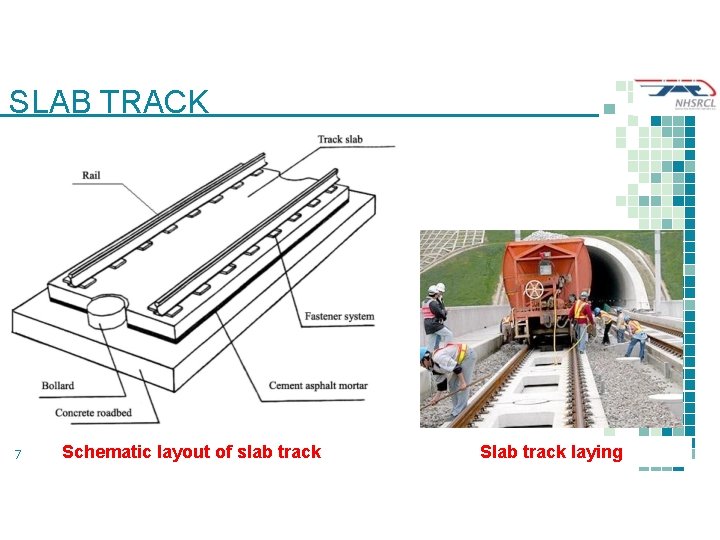
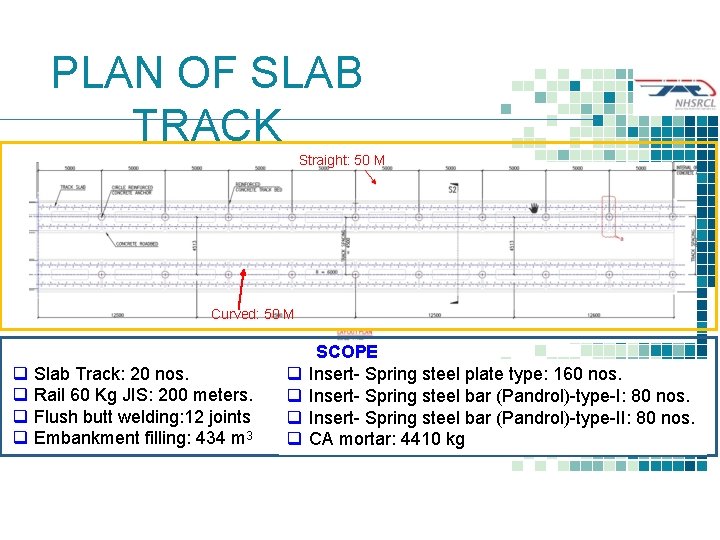

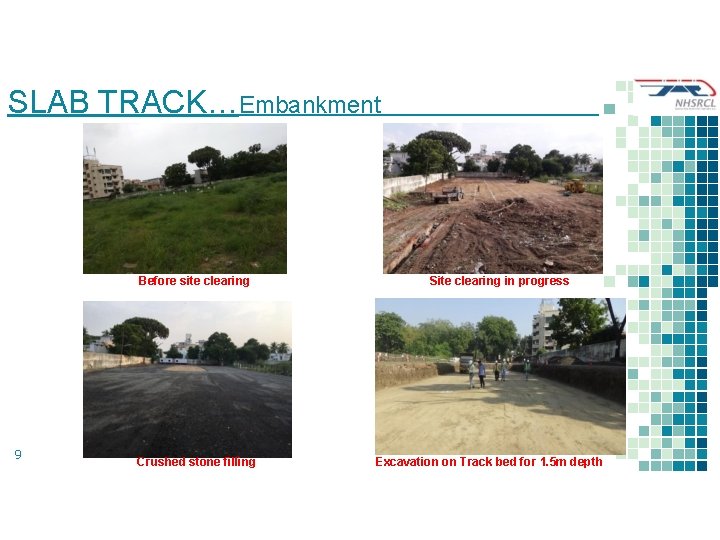
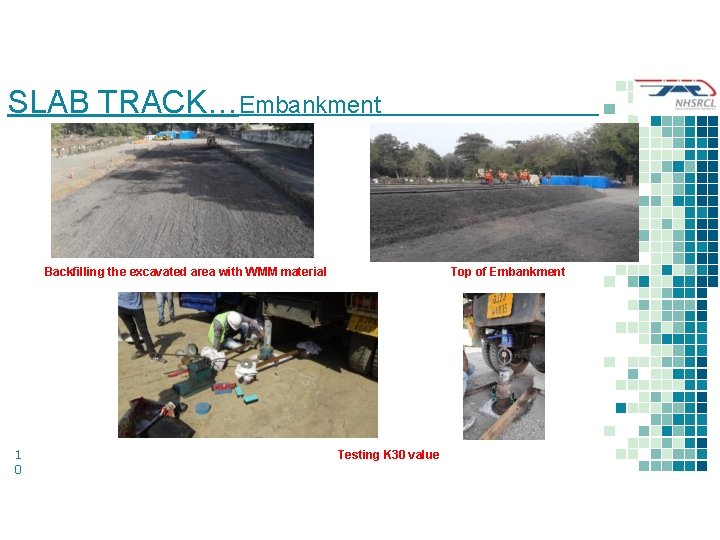
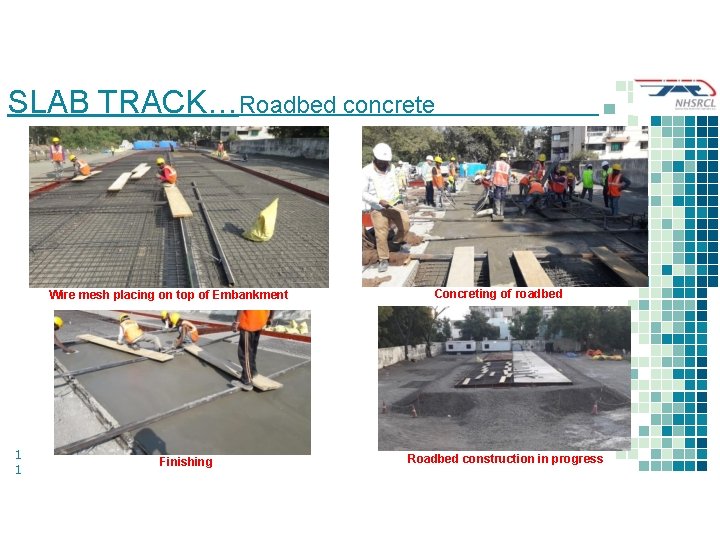
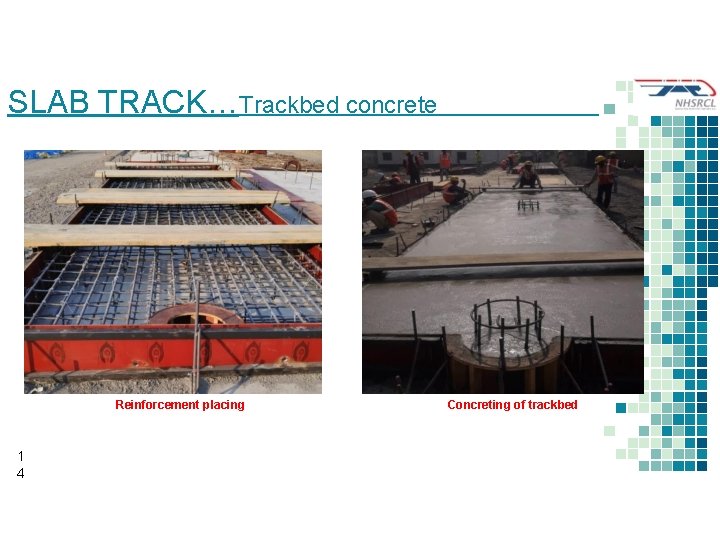
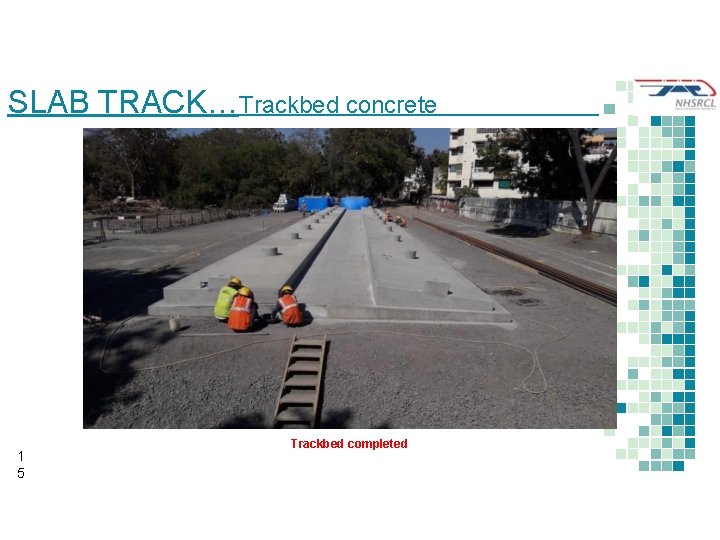
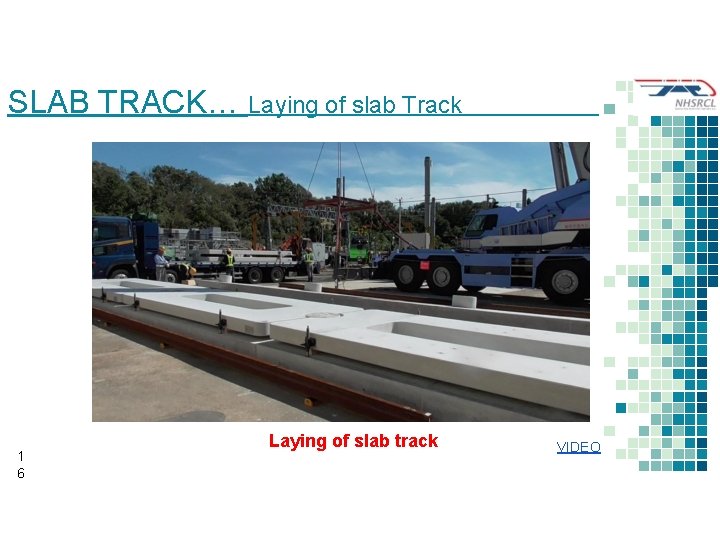
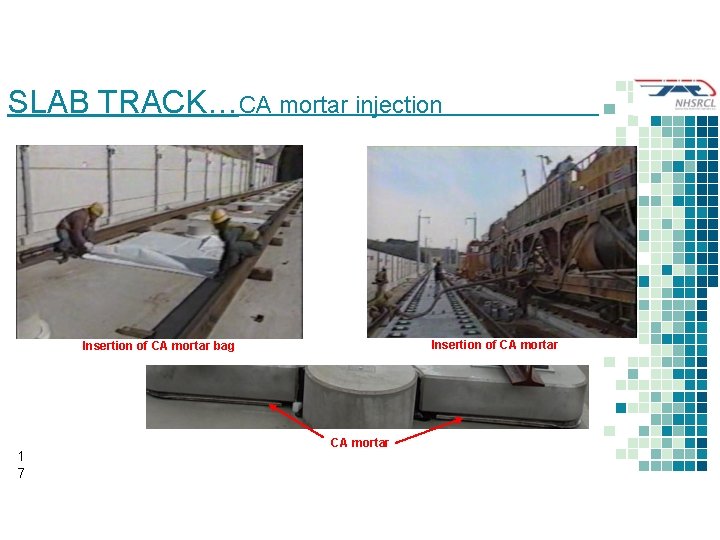
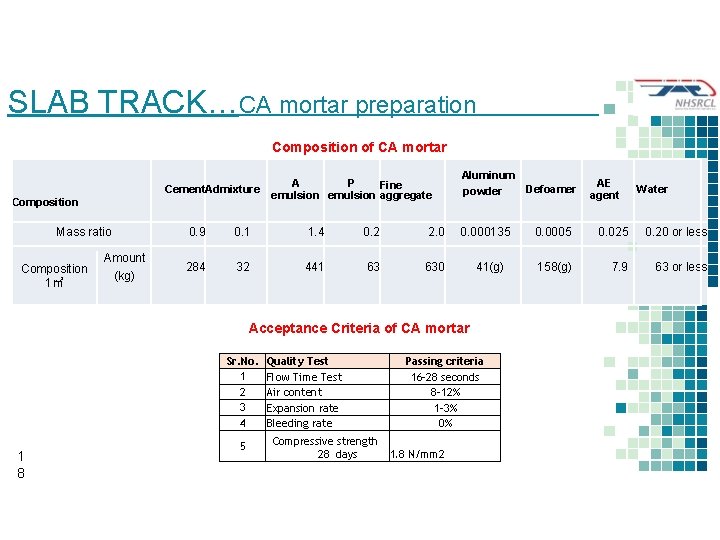
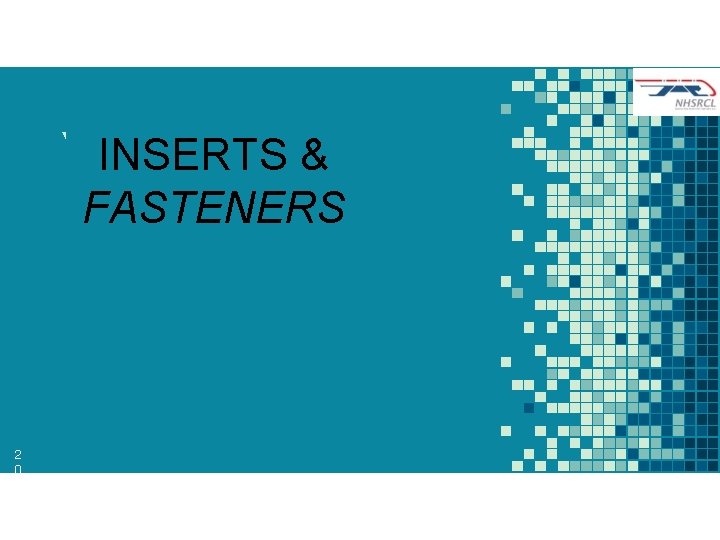

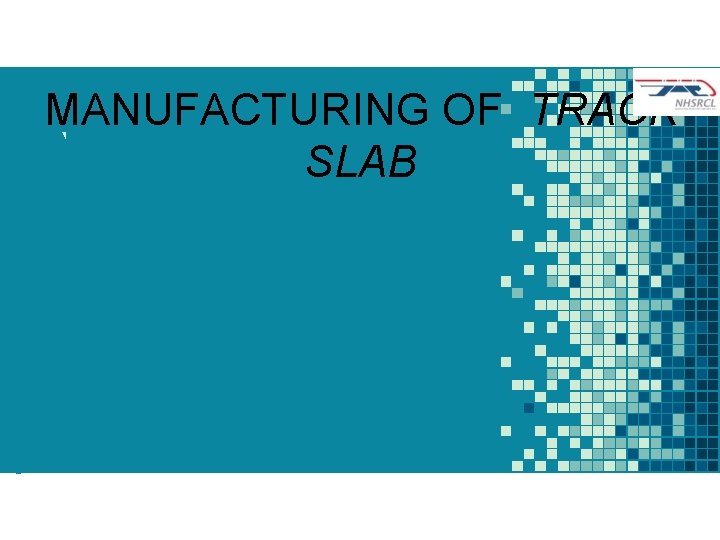
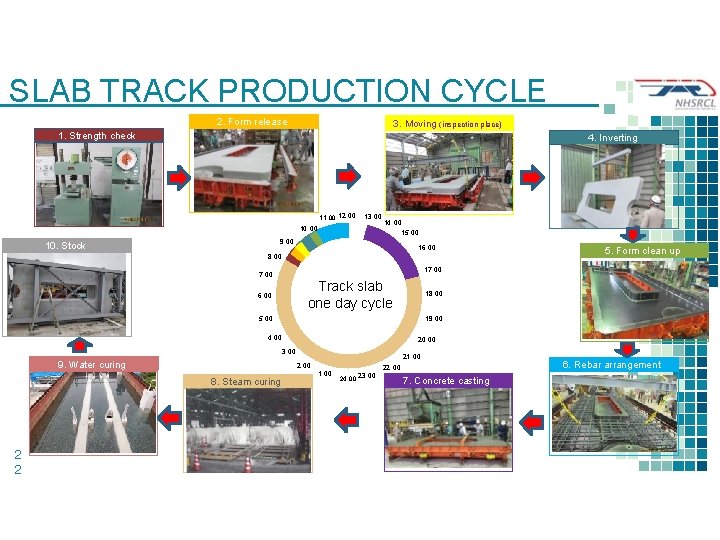
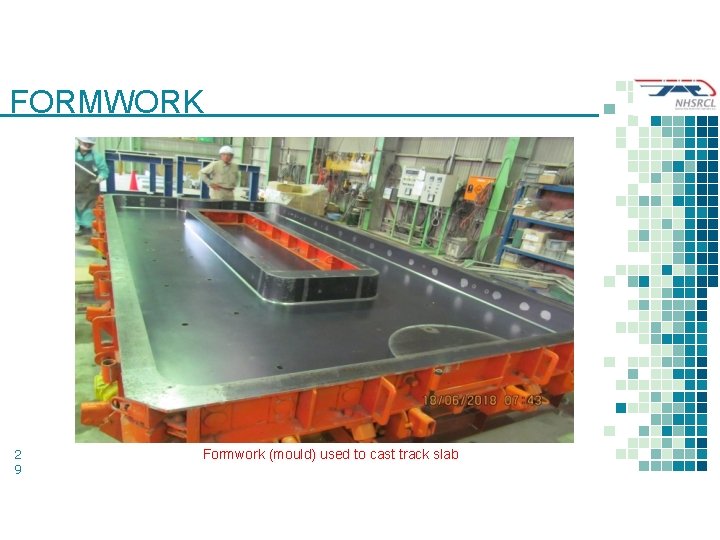
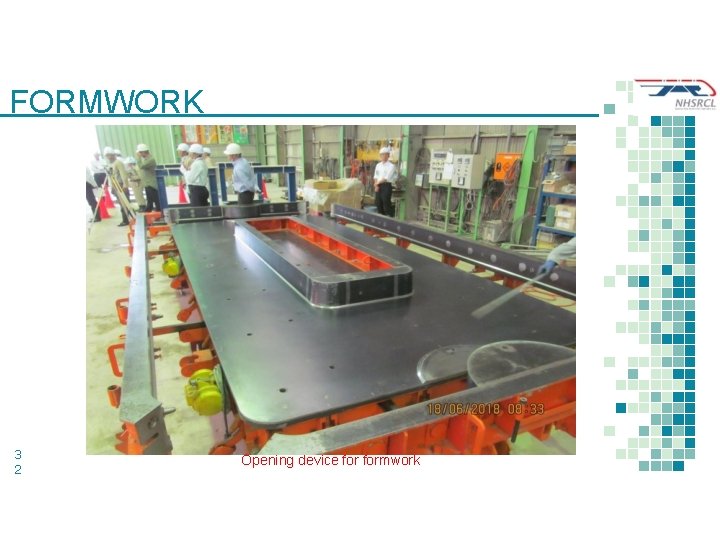
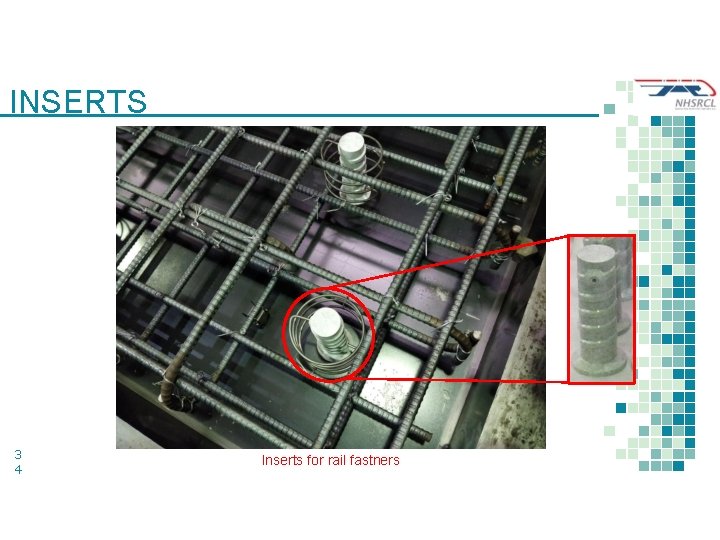
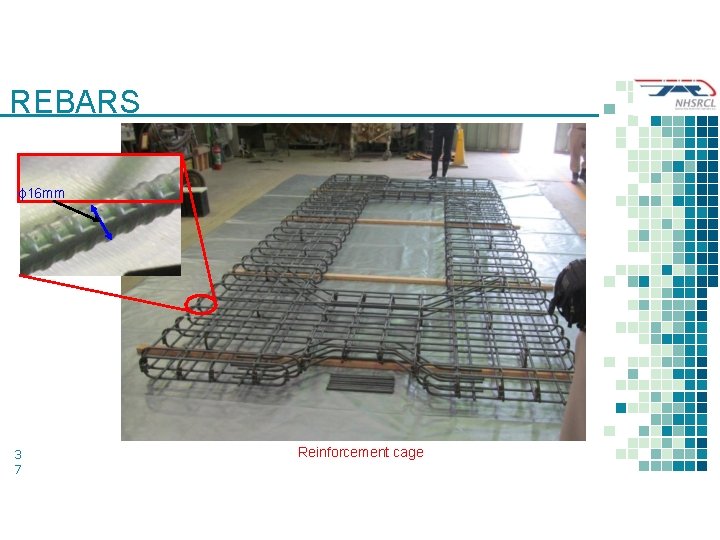
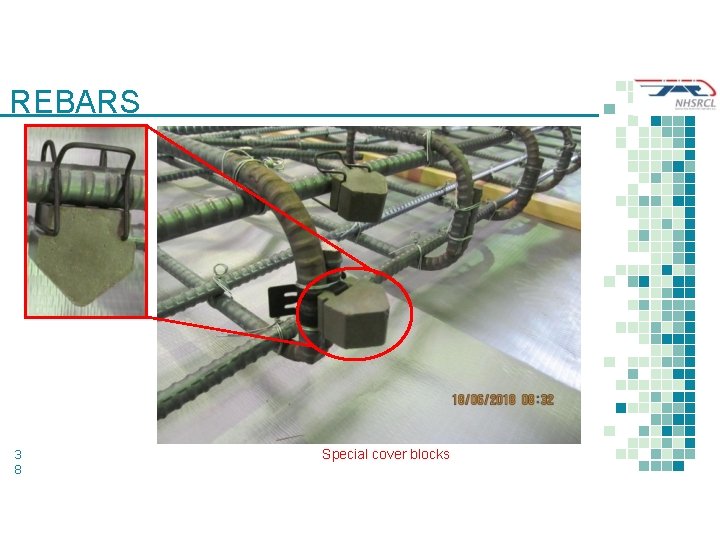
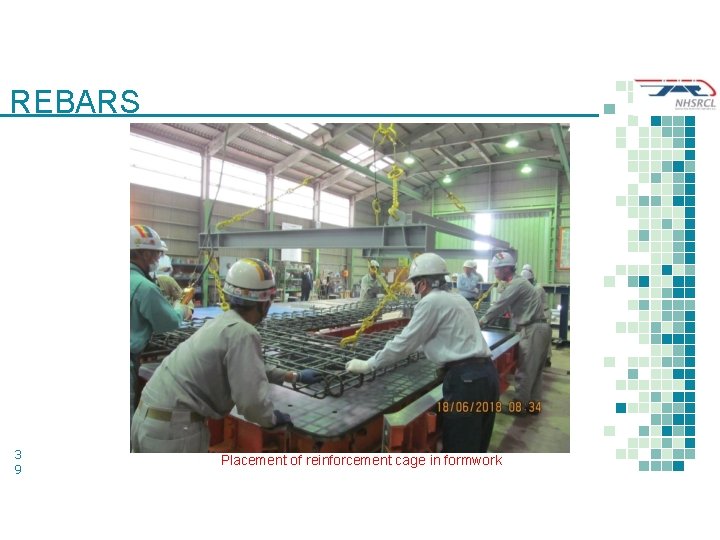

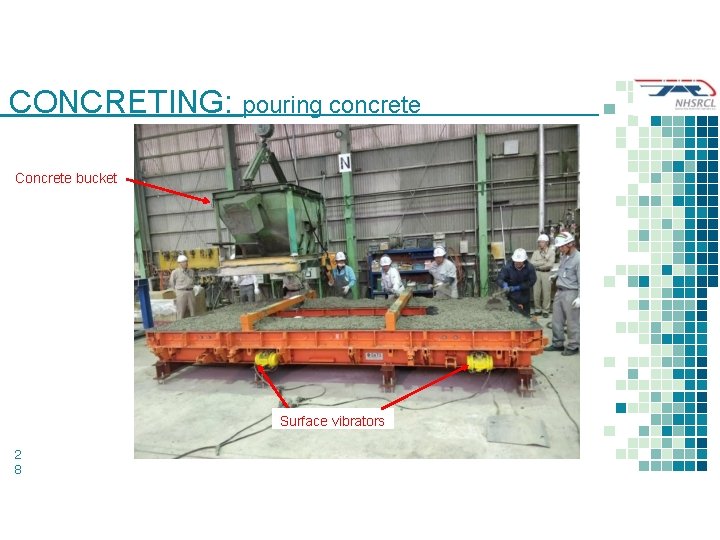
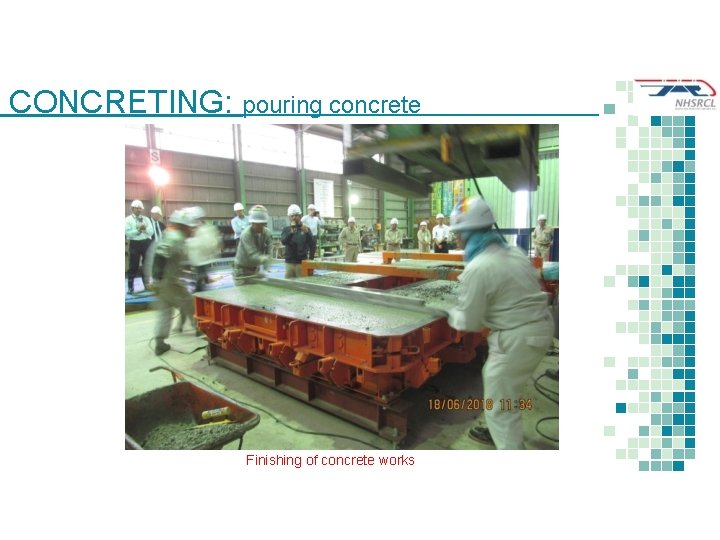
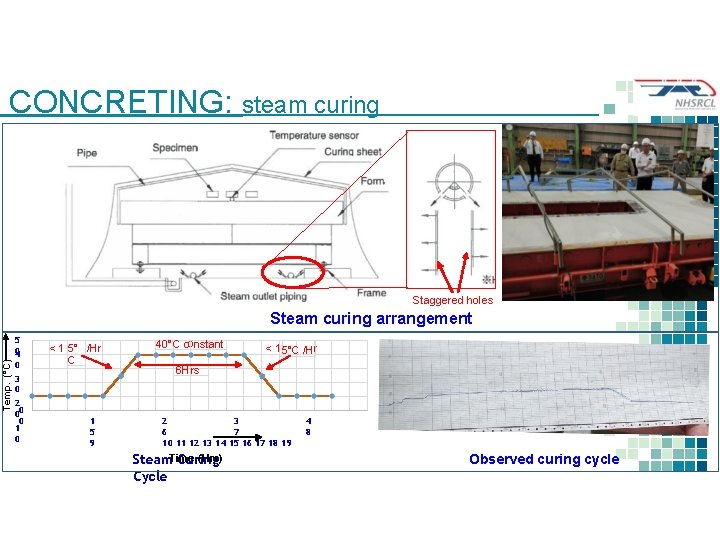
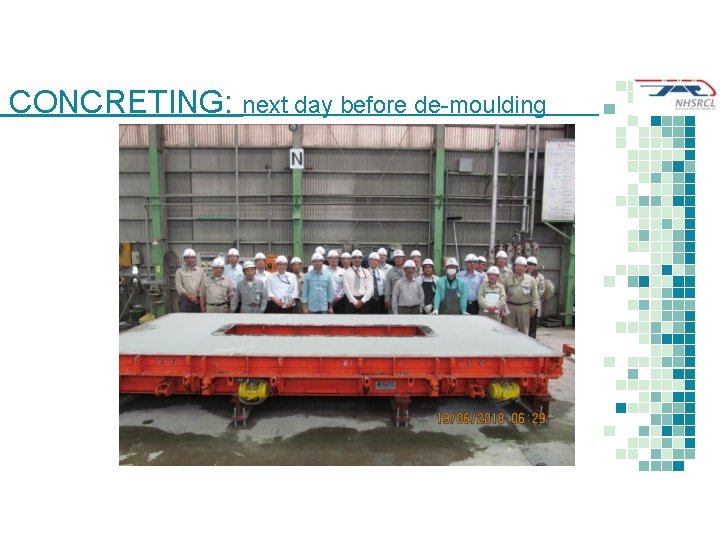
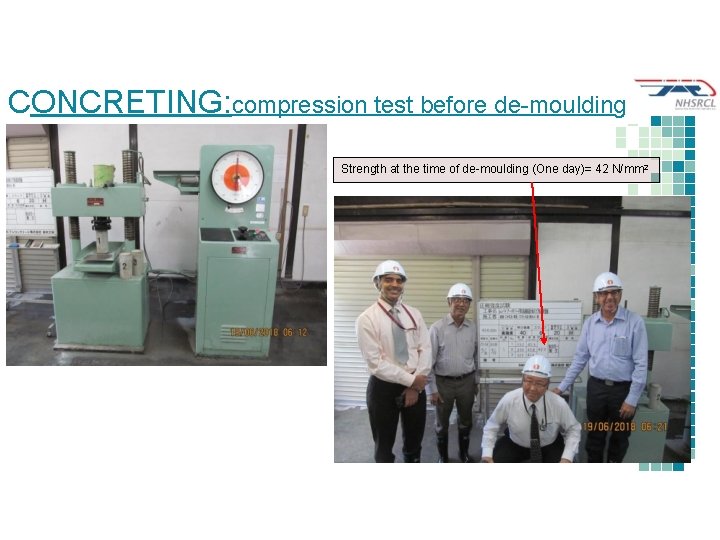
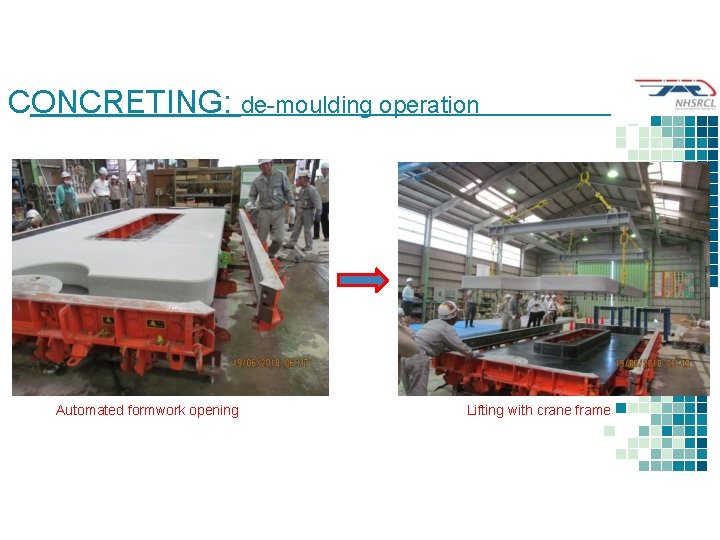
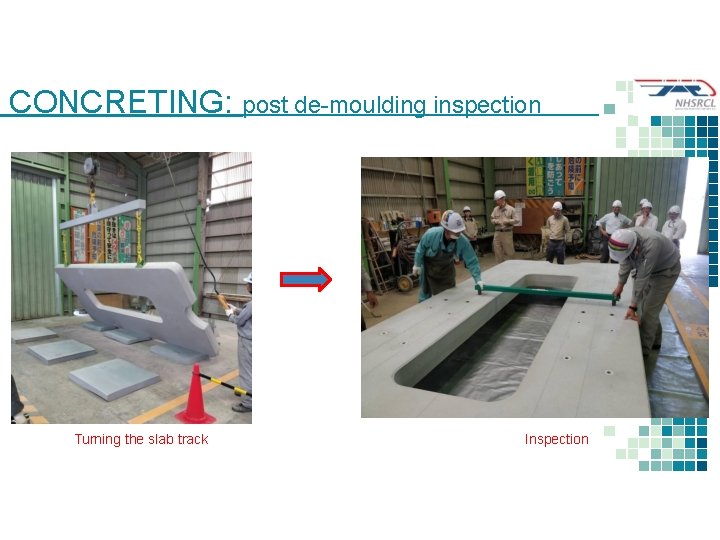
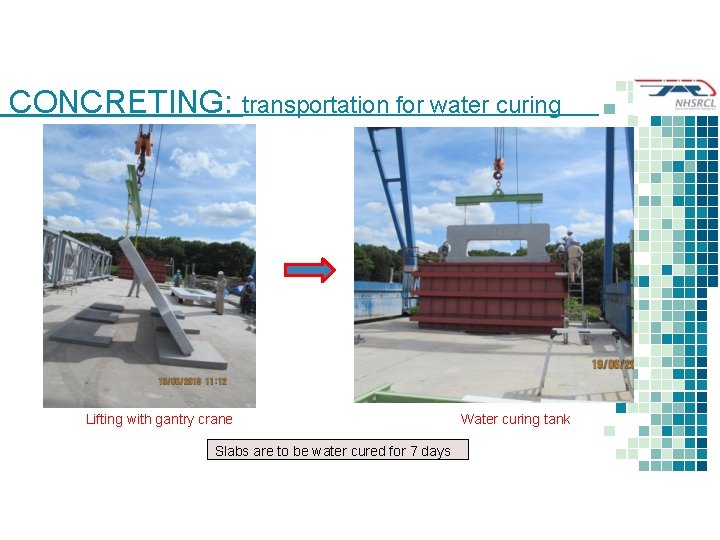
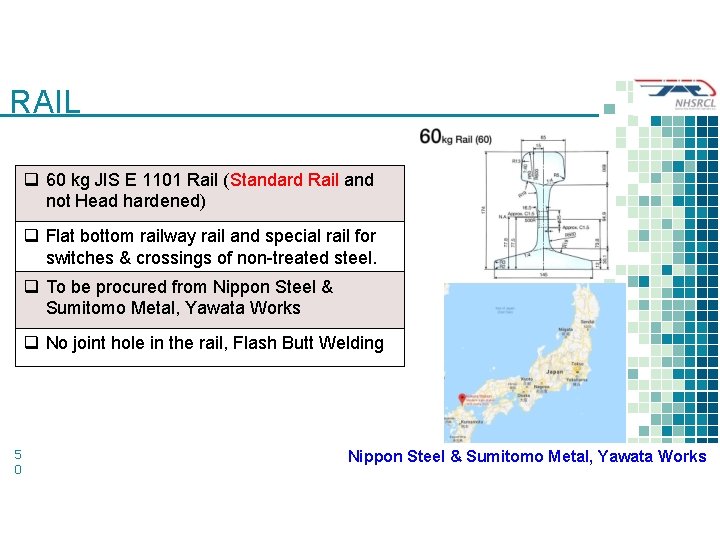
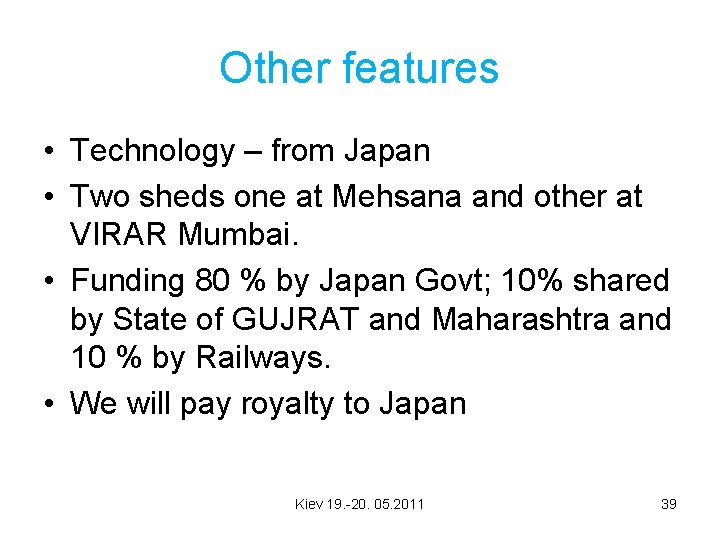
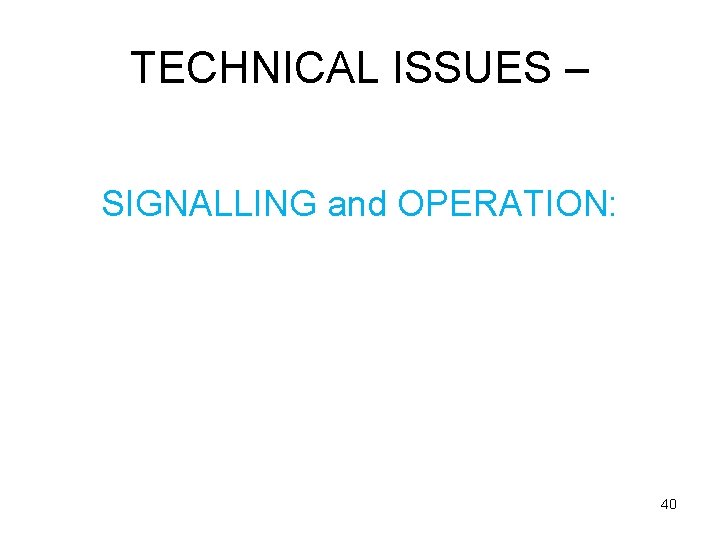
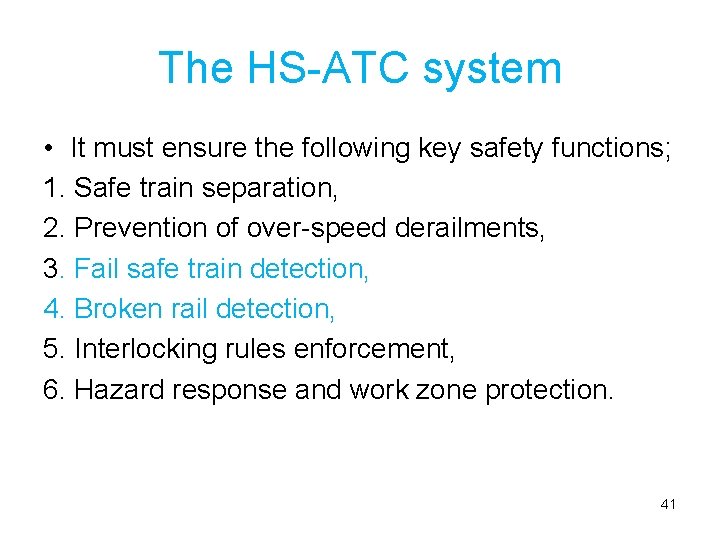
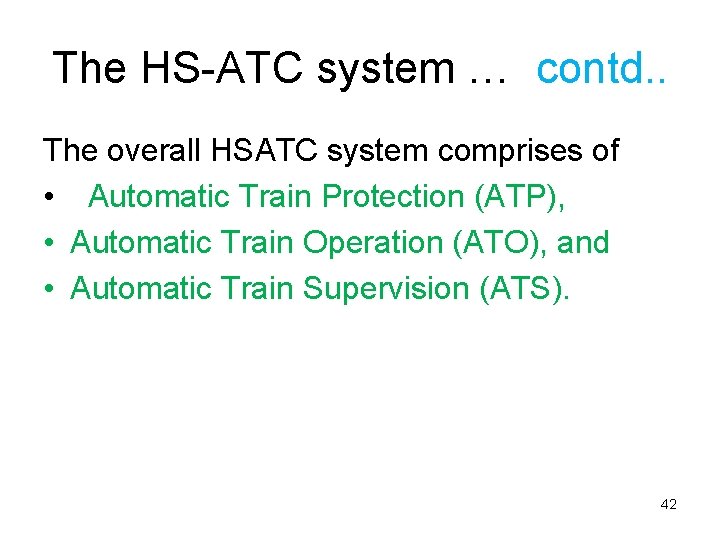
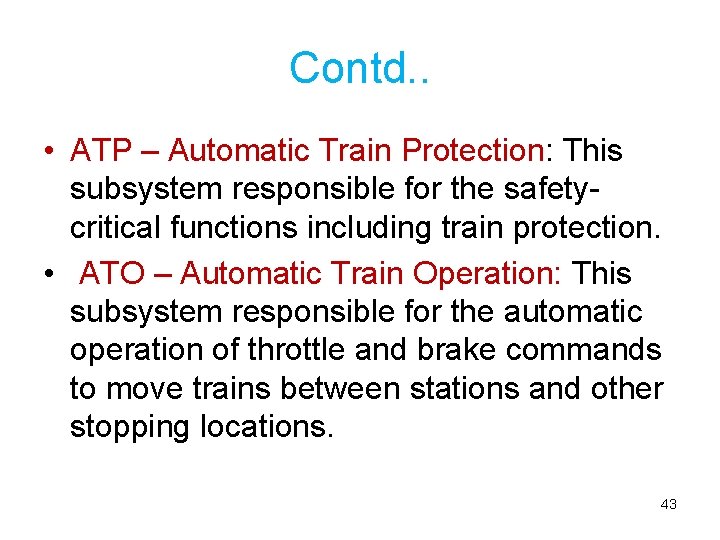
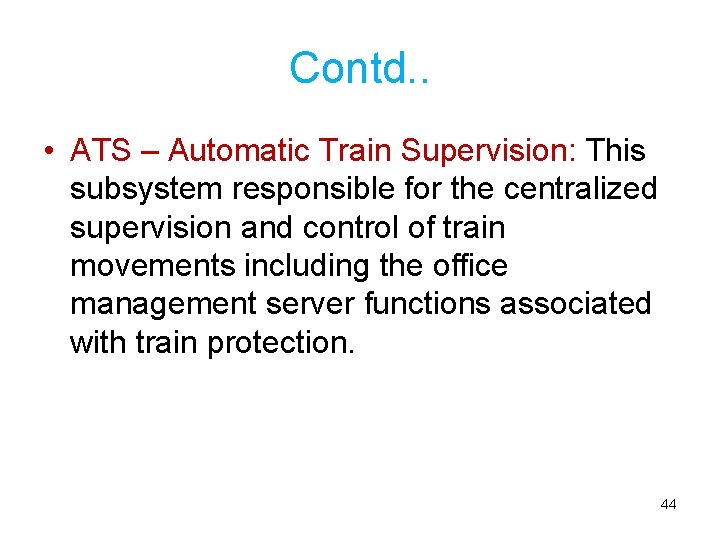
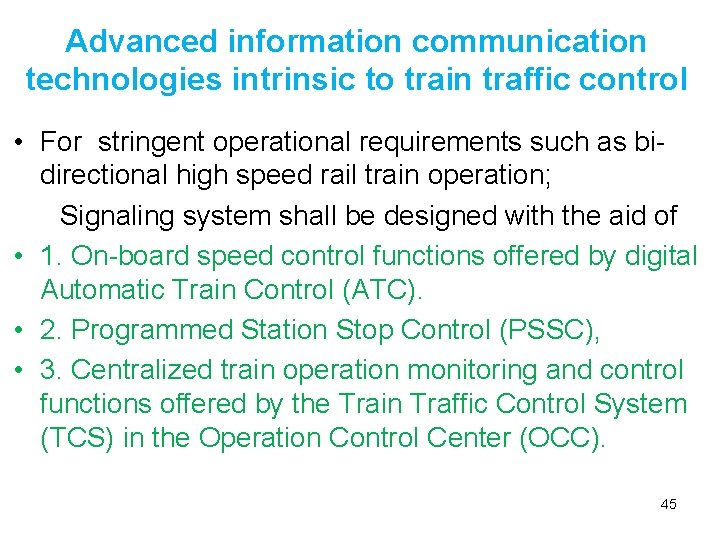
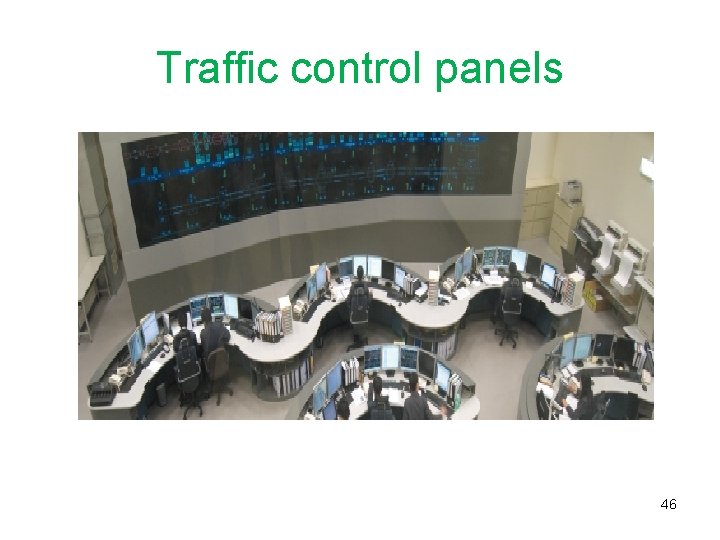
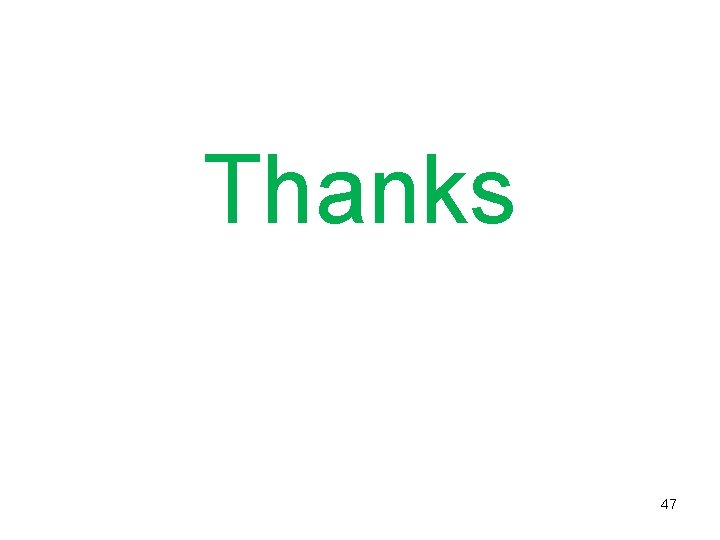
- Slides: 47
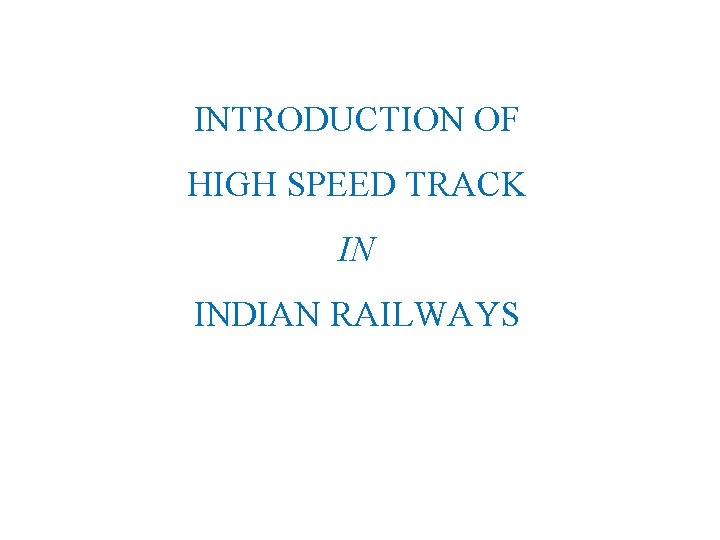
INTRODUCTION OF HIGH SPEED TRACK IN INDIAN RAILWAYS
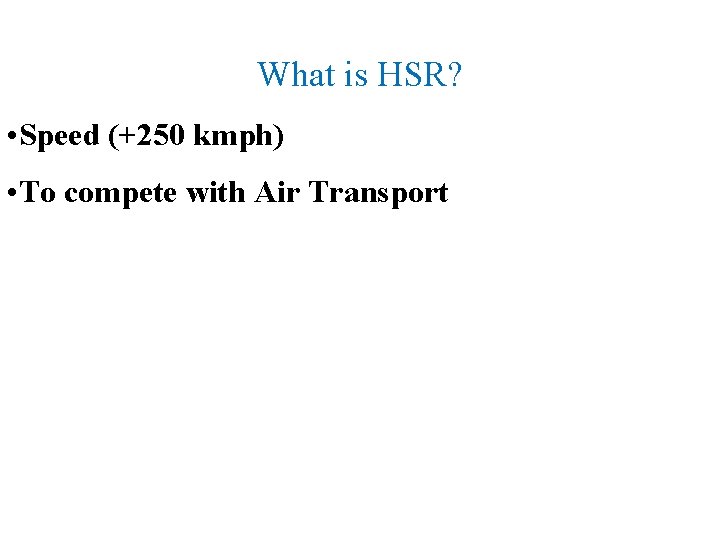
What is HSR? • Speed (+250 kmph) • To compete with Air Transport
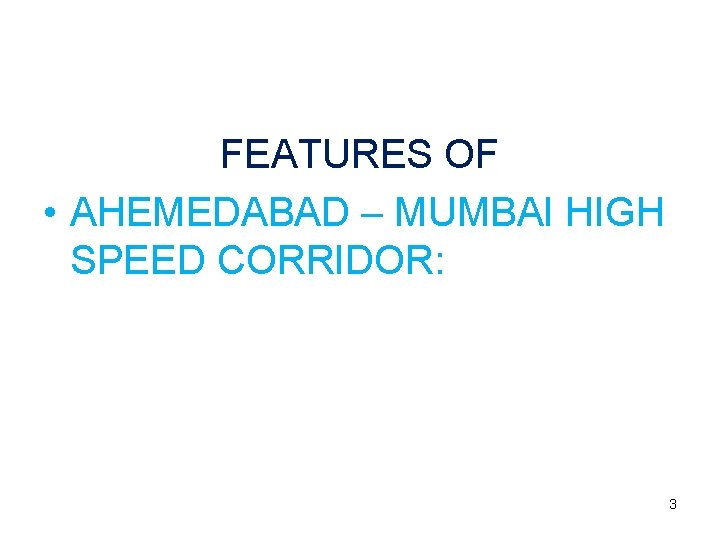
FEATURES OF • AHEMEDABAD – MUMBAI HIGH SPEED CORRIDOR: 3
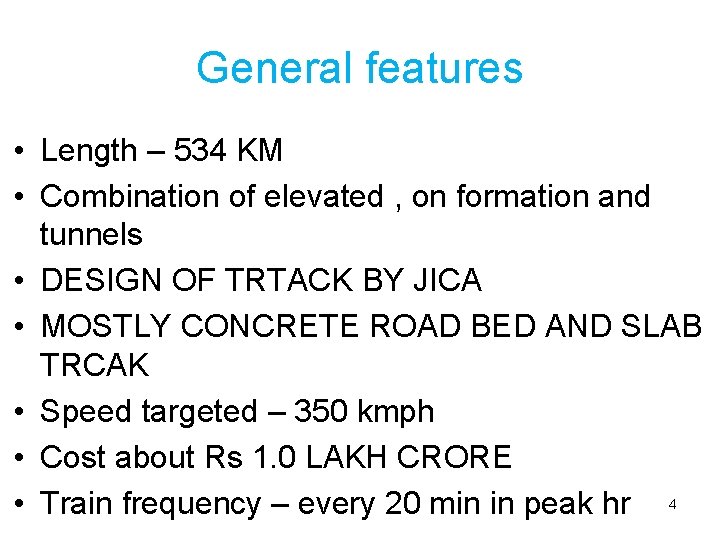
General features • Length – 534 KM • Combination of elevated , on formation and tunnels • DESIGN OF TRTACK BY JICA • MOSTLY CONCRETE ROAD BED AND SLAB TRCAK • Speed targeted – 350 kmph • Cost about Rs 1. 0 LAKH CRORE • Train frequency – every 20 min in peak hr 4
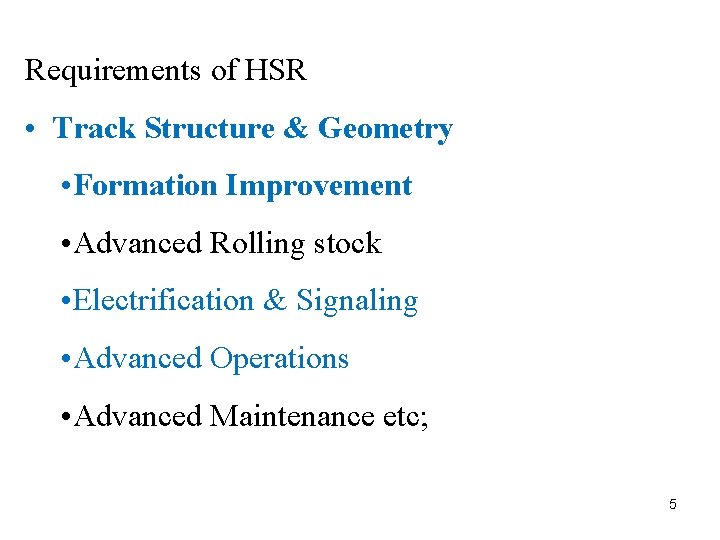
Requirements of HSR • Track Structure & Geometry • Formation Improvement • Advanced Rolling stock • Electrification & Signaling • Advanced Operations • Advanced Maintenance etc; 5
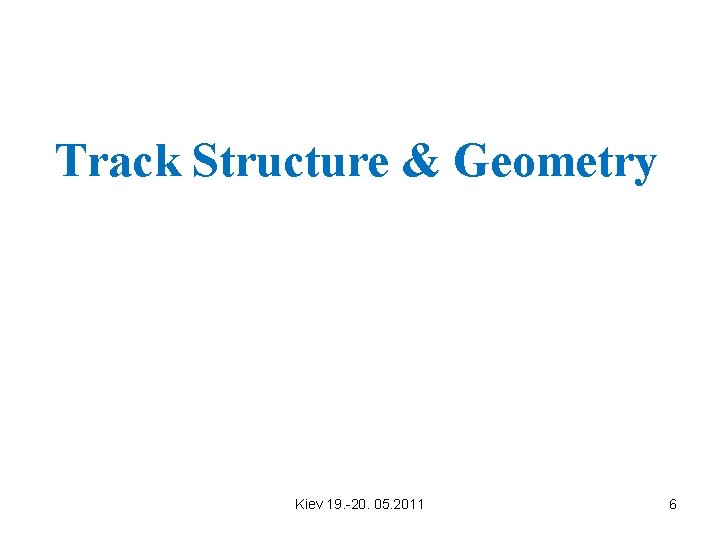
Track Structure & Geometry Kiev 19. -20. 05. 2011 6
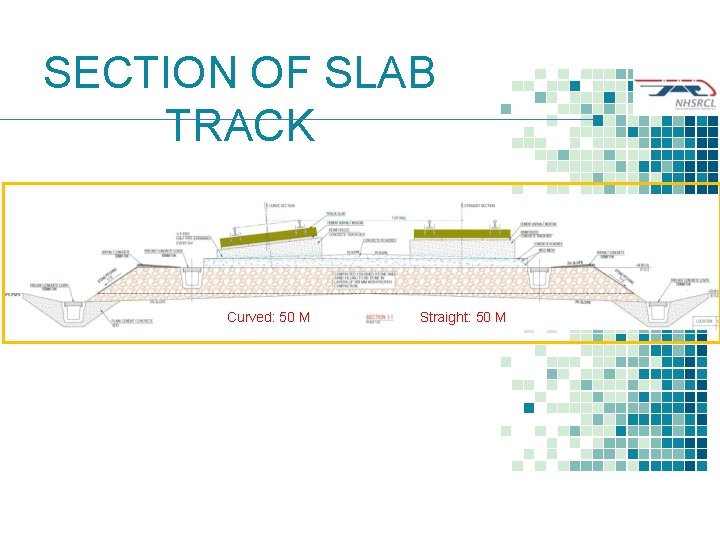
SECTION OF SLAB TRACK Curved: 50 M Straight: 50 M
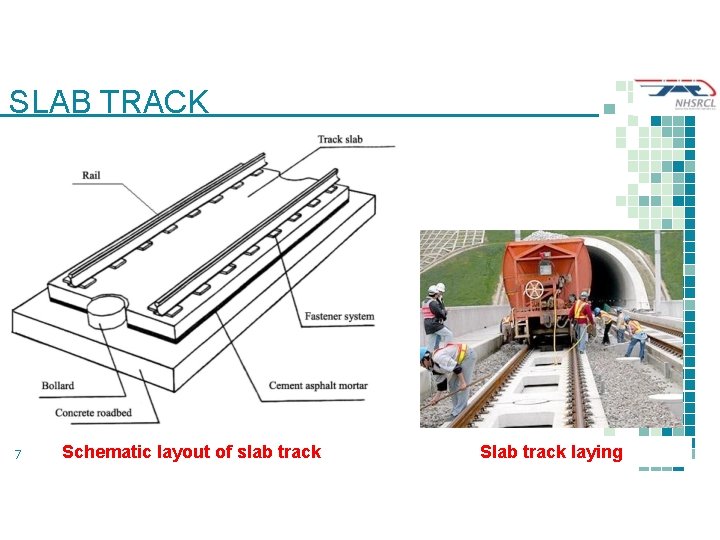
SLAB TRACK 7 Schematic layout of slab track Slab track laying
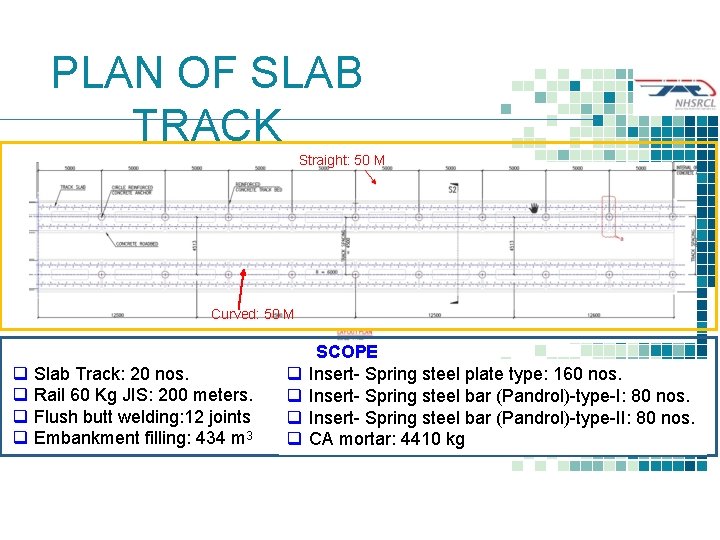
PLAN OF SLAB TRACK Straight: 50 M Curved: 50 M Slab Track: 20 nos. Rail 60 Kg JIS: 200 meters. Flush butt welding: 12 joints Embankment filling: 434 m 3 SCOPE Insert- Spring steel plate type: 160 nos. Insert- Spring steel bar (Pandrol)-type-I: 80 nos. Insert- Spring steel bar (Pandrol)-type-II: 80 nos. CA mortar: 4410 kg

SLAB TRACK 4900 mm 2220 mm ϕ 600 mm 8 2860 mm Key dimensions of slab track
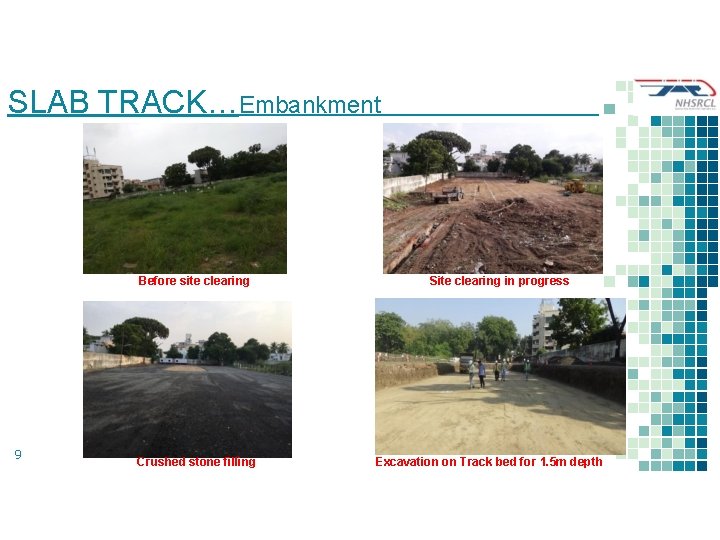
SLAB TRACK…Embankment Before site clearing 9 Crushed stone filling Site clearing in progress Excavation on Track bed for 1. 5 m depth
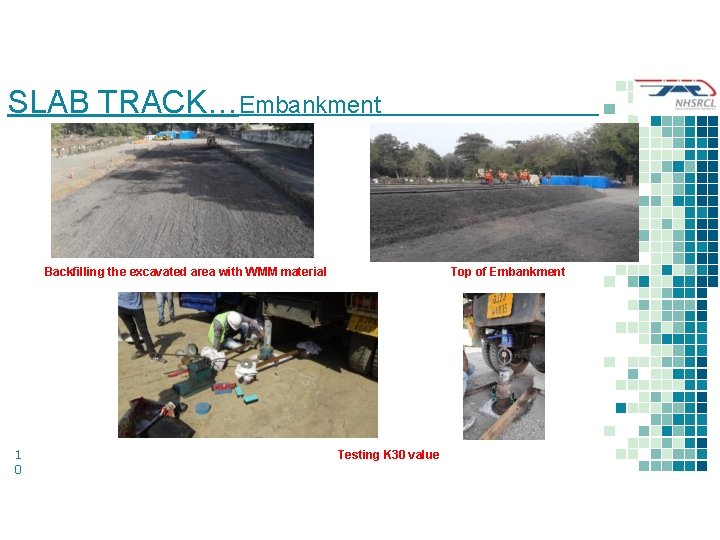
SLAB TRACK…Embankment Backfilling the excavated area with WMM material 1 0 Top of Embankment Testing K 30 value
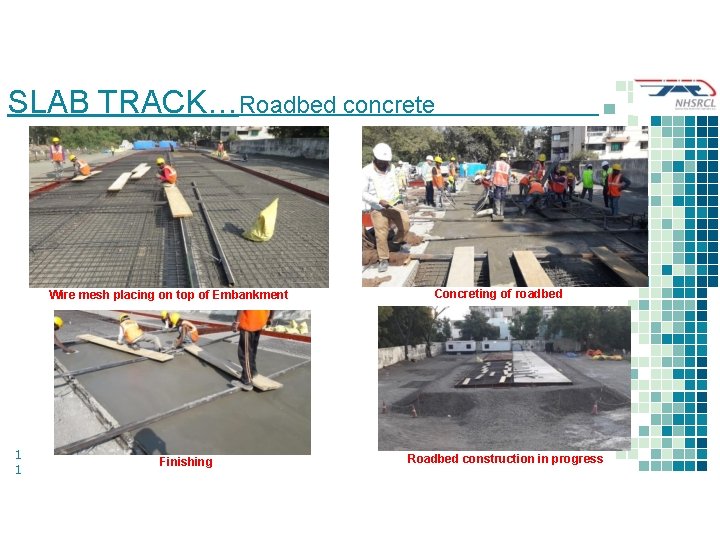
SLAB TRACK…Roadbed concrete Wire mesh placing on top of Embankment 1 1 Finishing Concreting of roadbed Roadbed construction in progress
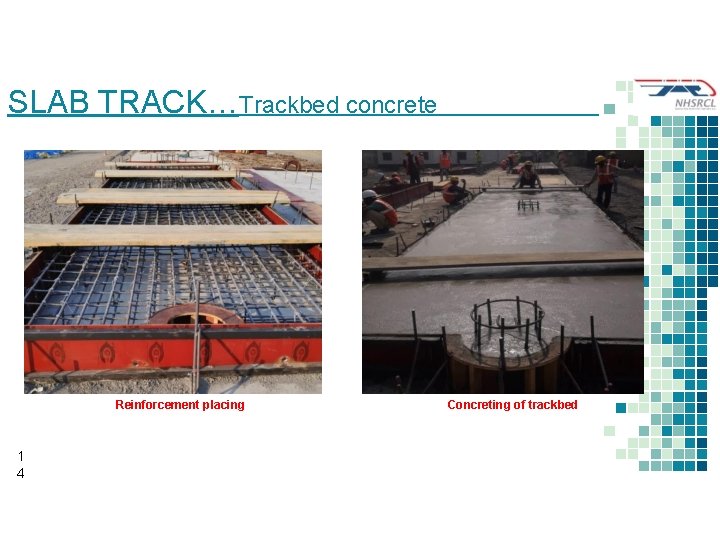
SLAB TRACK…Trackbed concrete Reinforcement placing 1 4 Concreting of trackbed
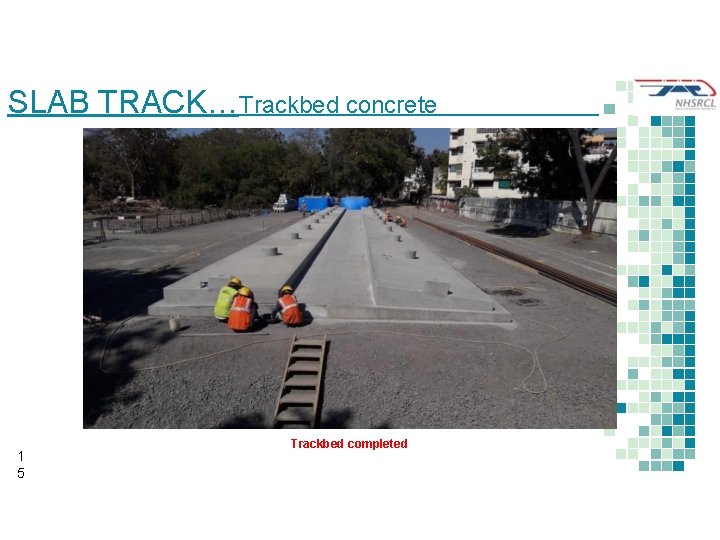
SLAB TRACK…Trackbed concrete 1 5 Trackbed completed
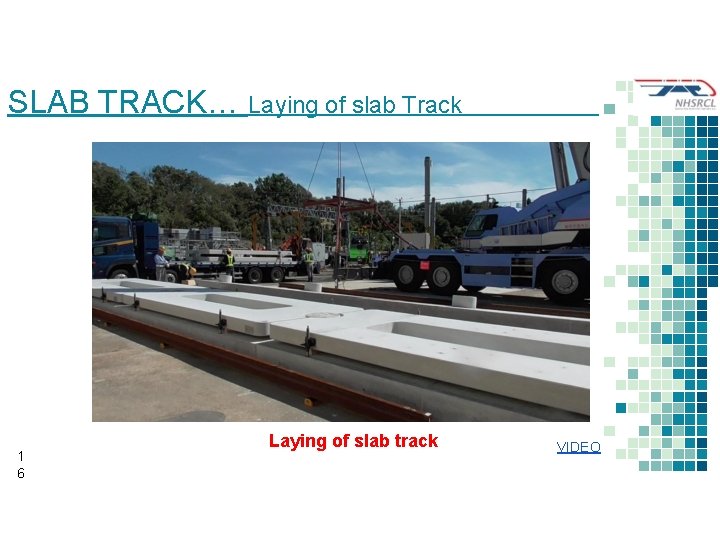
SLAB TRACK… Laying of slab Track 1 6 Laying of slab track VIDEO
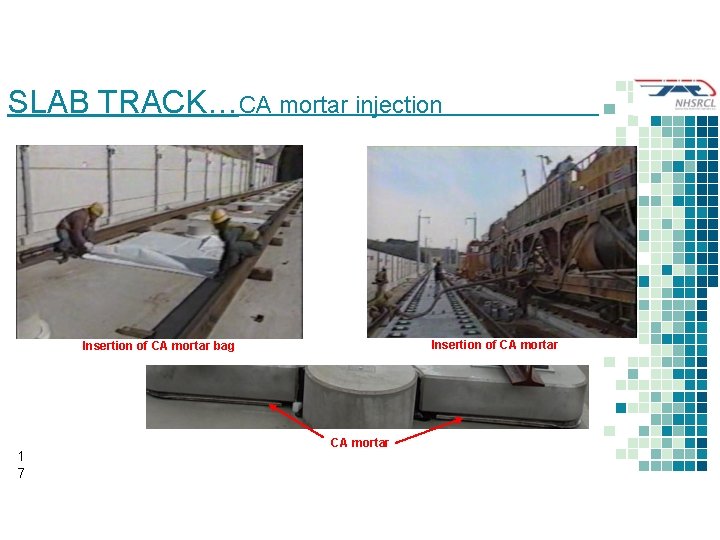
SLAB TRACK…CA mortar injection Insertion of CA mortar bag 1 7 CA mortar
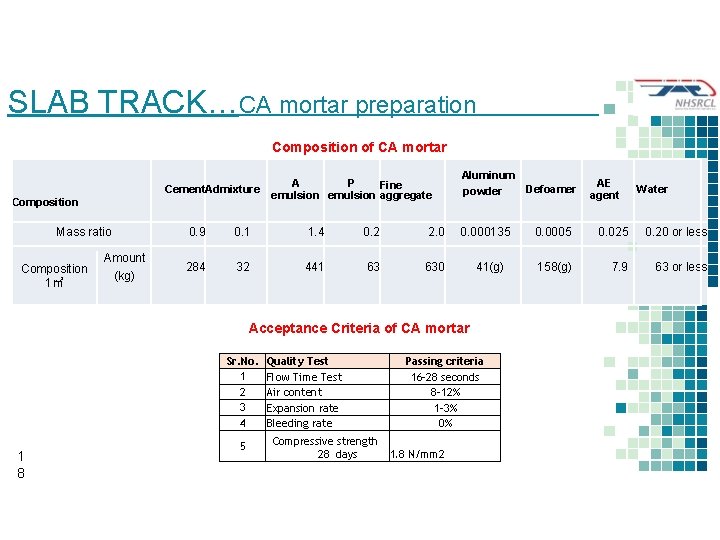
SLAB TRACK…CA mortar preparation Composition of CA mortar Cement. Admixture Composition Mass ratio Composition 1㎥ Amount (kg) A P Fine emulsion aggregate 0. 9 0. 1 1. 4 0. 2 2. 0 284 32 441 63 630 Aluminum Defoamer powder 0. 000135 41(g) Acceptance Criteria of CA mortar Sr. No. 1 2 3 4 1 8 5 Quality Test Flow Time Test Air content Expansion rate Bleeding rate Compressive strength 28 days Passing criteria 16 -28 seconds 8 -12% 1 -3% 0% 1. 8 N/mm 2 AE agent Water 0. 0005 0. 025 0. 20 or less 158(g) 7. 9 63 or less
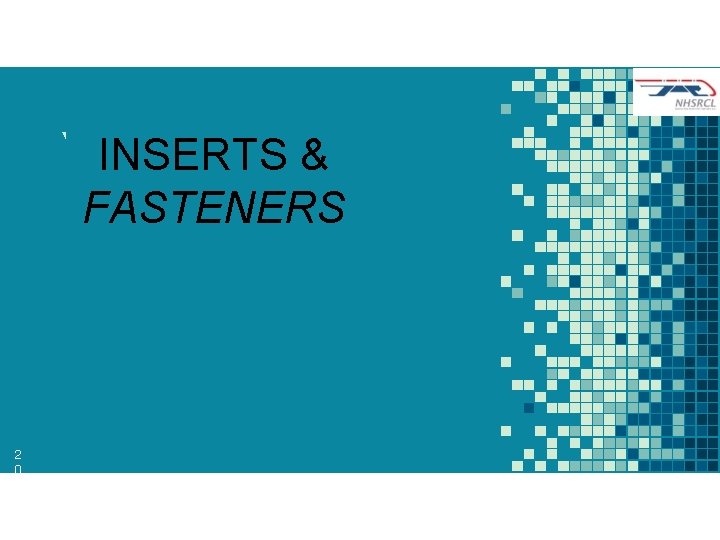
“ INSERTS & FASTENERS 2 0

RAIL FASTENING SYSTEM T-headed Nut & Bolt Rubber pad Adjustable pad Spring steel Hexagonal bolt Embedded plug Tie Plate 21 Insulation plate Spring steel plate type ( Mostly used by Japanese Railways) Spiral reinforcement
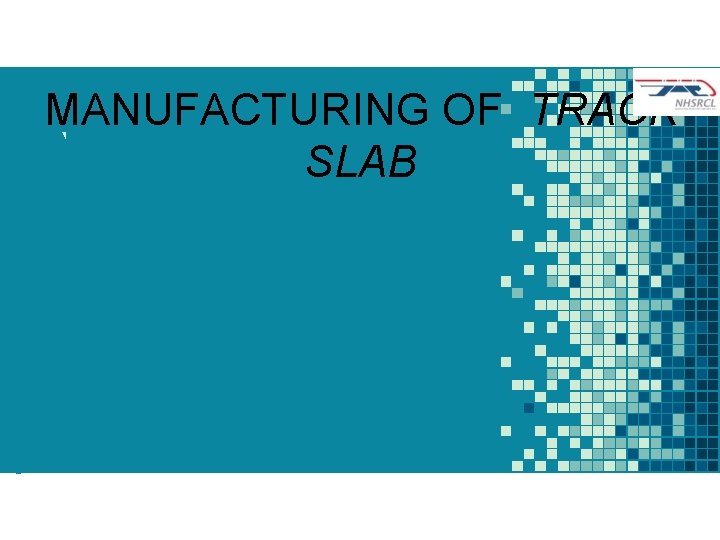
MANUFACTURING OF TRACK SLAB “ 2 1
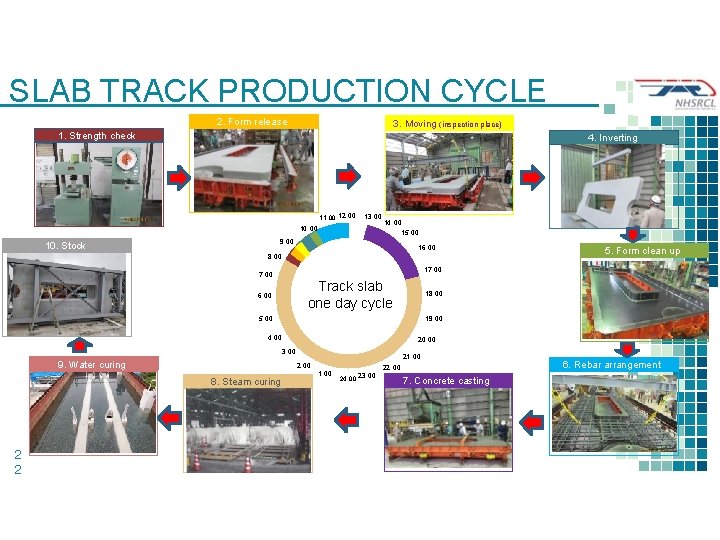
SLAB TRACK PRODUCTION CYCLE 2. Form release 3. Moving (inspection place) 1. Strength check 4. Inverting 11: 00 12: 00 13: 00 10: 00 14: 00 15: 00 9: 00 10. Stock 16: 00 8: 00 17: 00 Track slab one day cycle 6: 00 18: 00 5: 00 19: 00 4: 00 20: 00 3: 00 9. Water curing 2 2 21: 00 2: 00 8. Steam curing 5. Form clean up 1: 00 24: 00 23: 00 22: 00 7. Concrete casting 6. Rebar arrangement
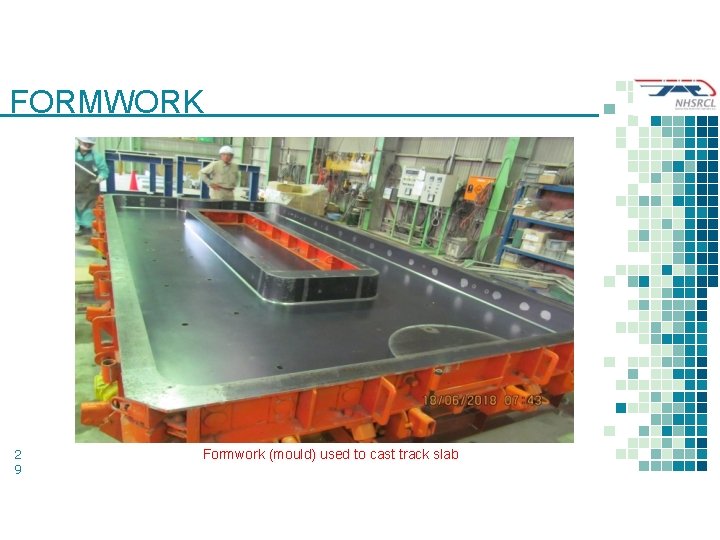
FORMWORK 2 9 Formwork (mould) used to cast track slab
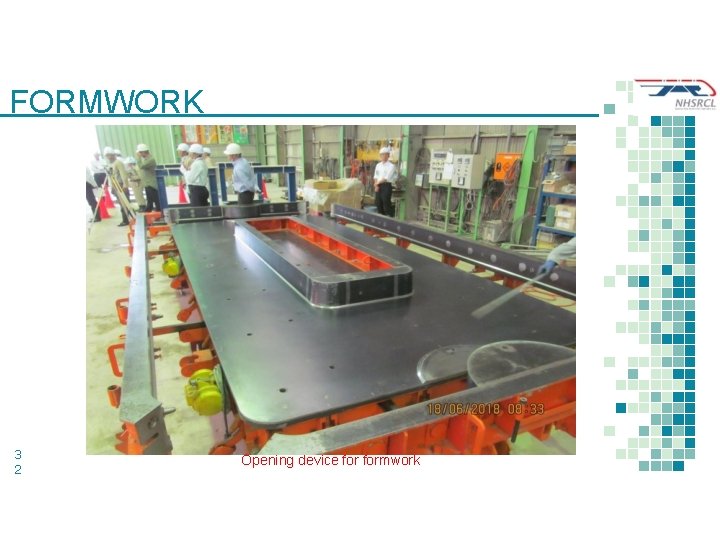
FORMWORK 3 2 Opening device formwork
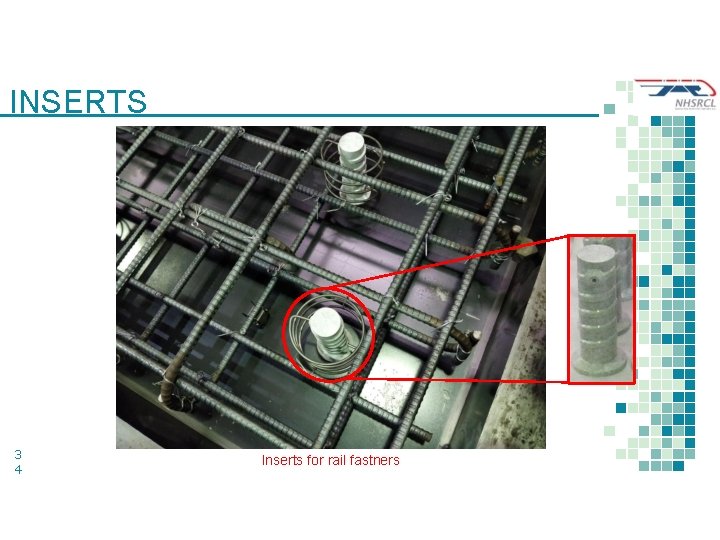
INSERTS 3 4 Inserts for rail fastners
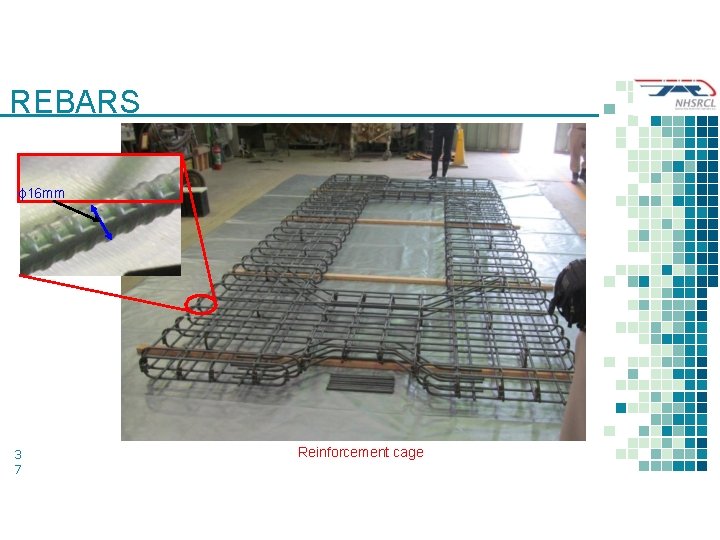
REBARS ϕ 16 mm 3 7 Reinforcement cage
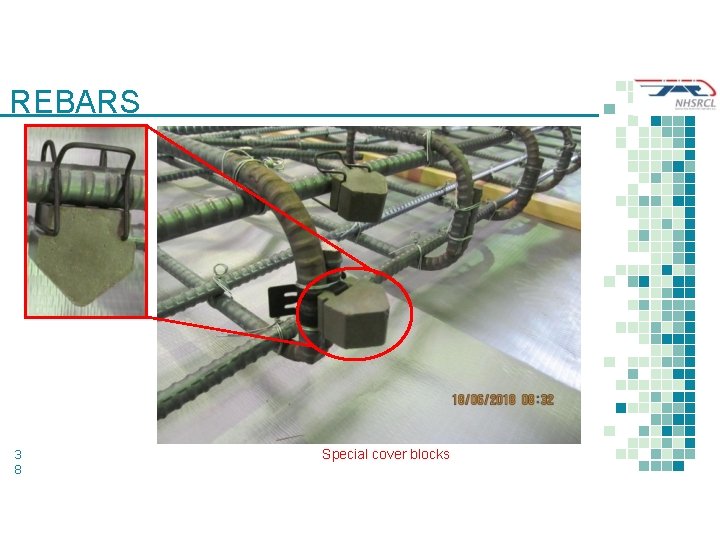
REBARS 3 8 Special cover blocks
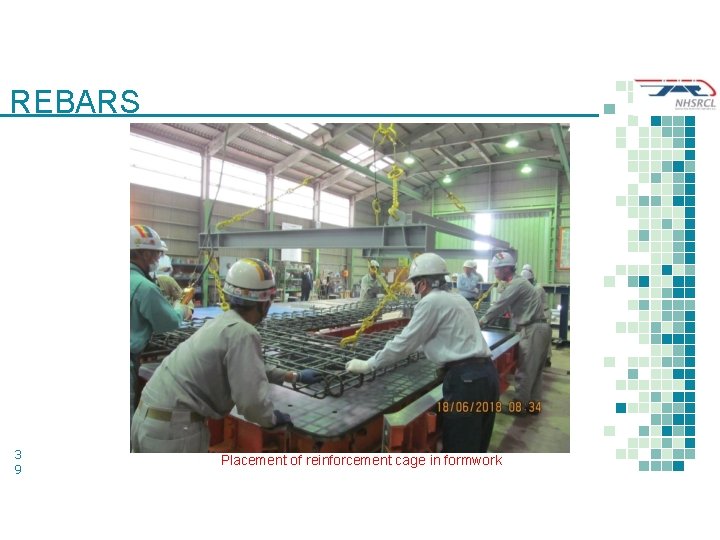
REBARS 3 9 Placement of reinforcement cage in formwork

REBARS 4 0 Checking reinforcement cage in formwork
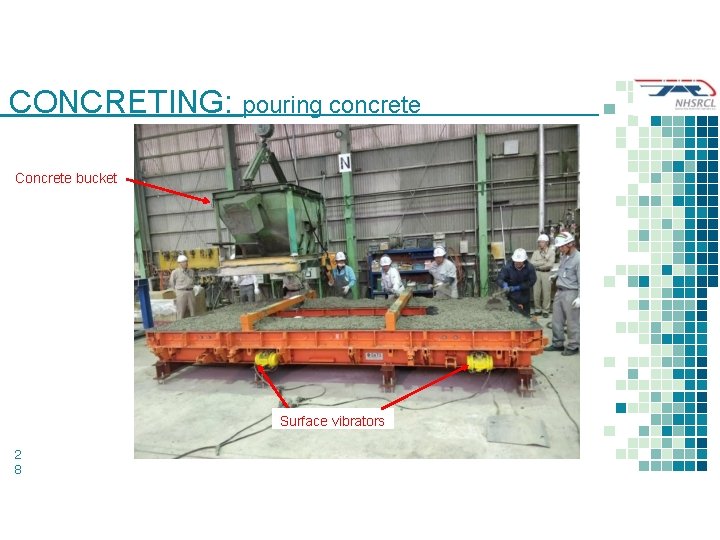
CONCRETING: pouring concrete Concrete bucket Surface vibrators 2 8
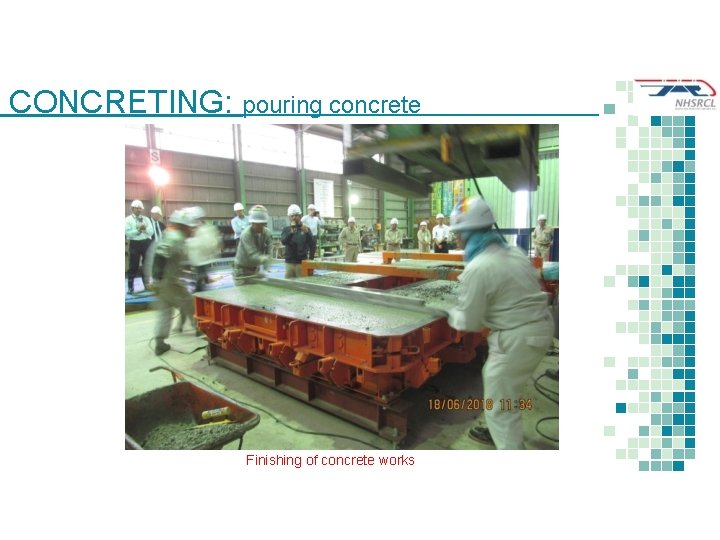
CONCRETING: pouring concrete Finishing of concrete works
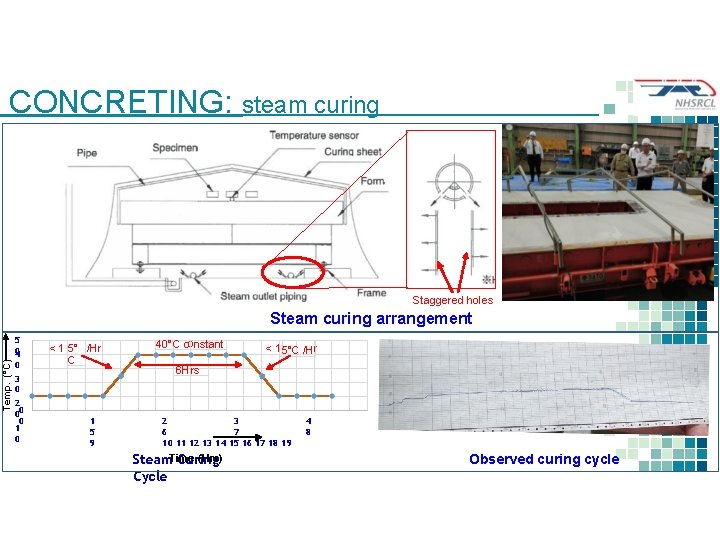
CONCRETING: steam curing Staggered holes Steam curing arrangement Temp. (°C) 5 0 4 0 < 1 5° /Hr C 3 0 2 00 0 1 5 9 40°C constant < 15°C /Hr 6 Hrs 2 3 6 7 10 11 12 13 14 15 16 17 18 19 (Hrs) Steam. Time Curing Cycle 4 8 Observed curing cycle
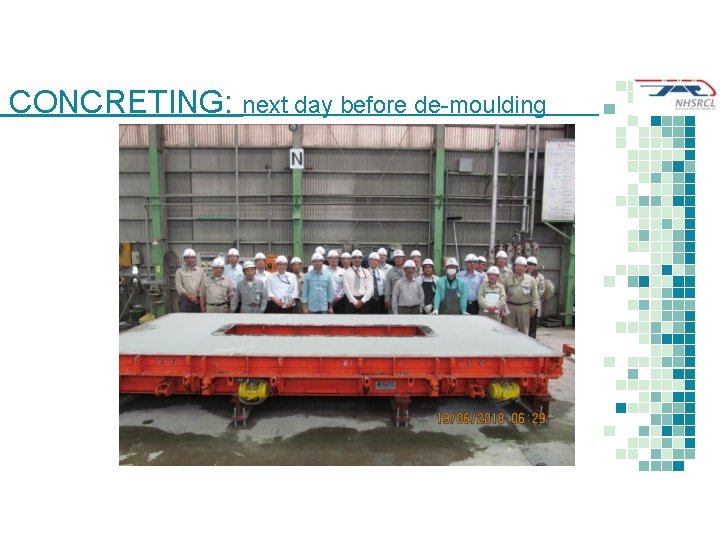
CONCRETING: next day before de-moulding
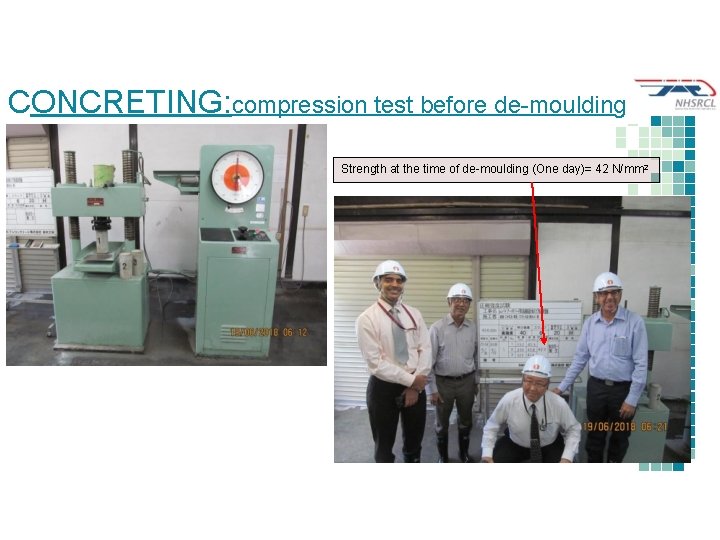
CONCRETING: compression test before de-moulding Strength at the time of de-moulding (One day)= 42 N/mm 2
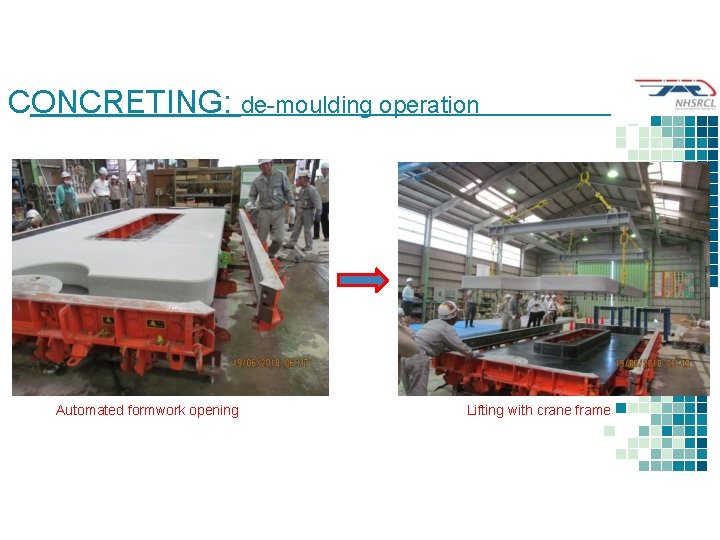
CONCRETING: de-moulding operation Automated formwork opening Lifting with crane frame
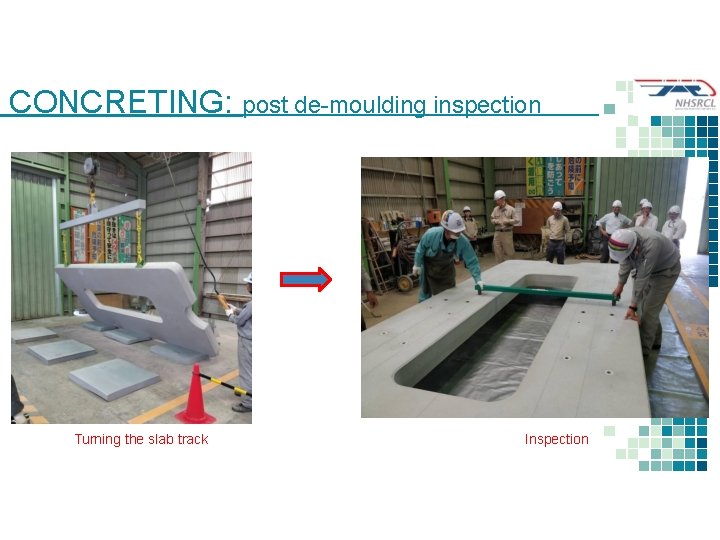
CONCRETING: post de-moulding inspection Turning the slab track Inspection
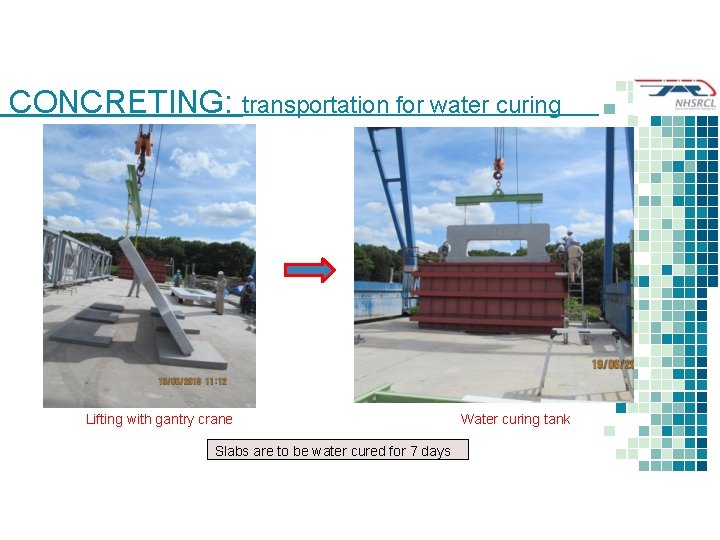
CONCRETING: transportation for water curing Lifting with gantry crane Slabs are to be water cured for 7 days Water curing tank
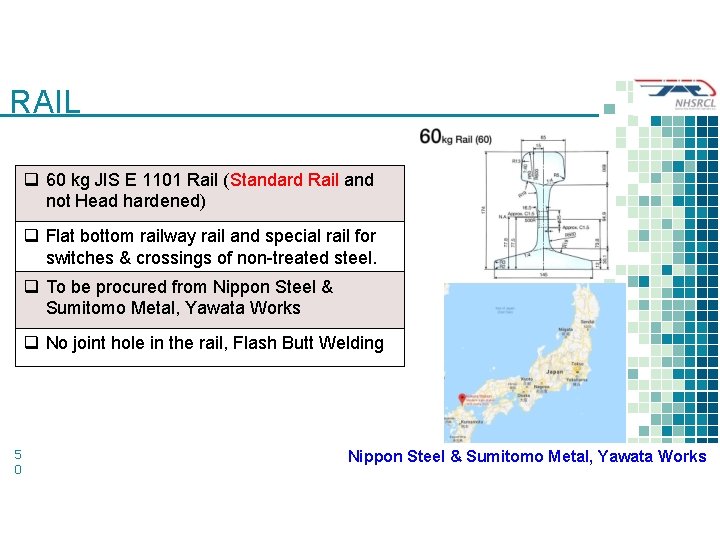
RAIL 60 kg JIS E 1101 Rail (Standard Rail and not Head hardened) Flat bottom railway rail and special rail for switches & crossings of non-treated steel. To be procured from Nippon Steel & Sumitomo Metal, Yawata Works No joint hole in the rail, Flash Butt Welding 5 0 Nippon Steel & Sumitomo Metal, Yawata Works
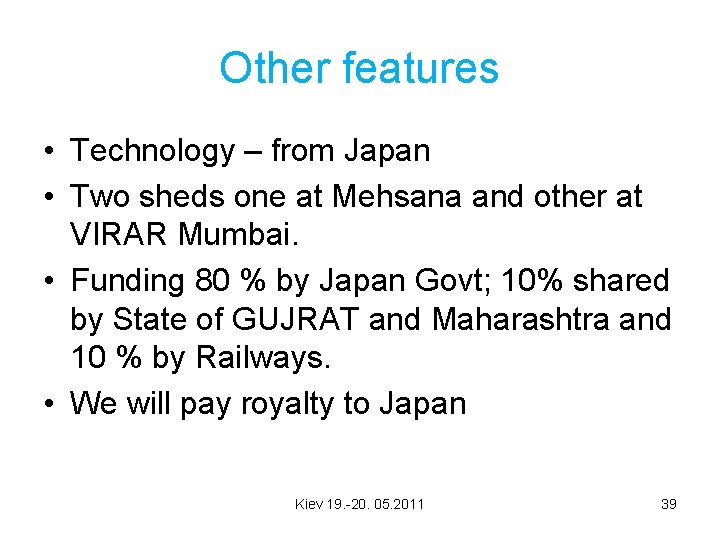
Other features • Technology – from Japan • Two sheds one at Mehsana and other at VIRAR Mumbai. • Funding 80 % by Japan Govt; 10% shared by State of GUJRAT and Maharashtra and 10 % by Railways. • We will pay royalty to Japan Kiev 19. -20. 05. 2011 39
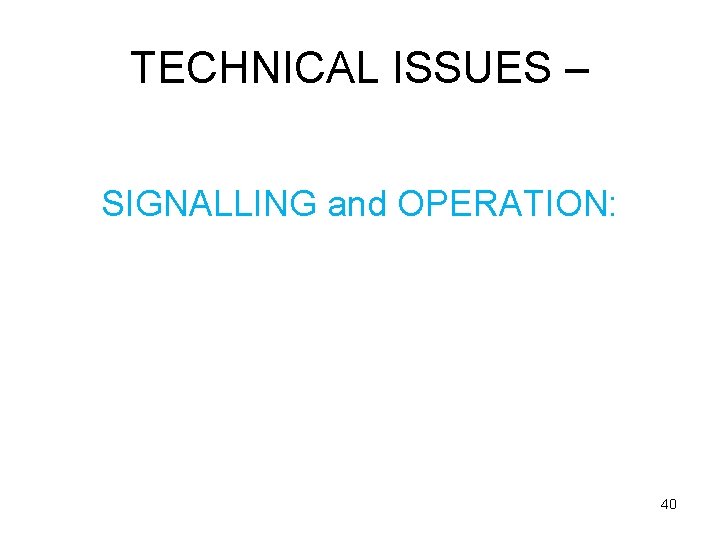
TECHNICAL ISSUES – SIGNALLING and OPERATION: 40
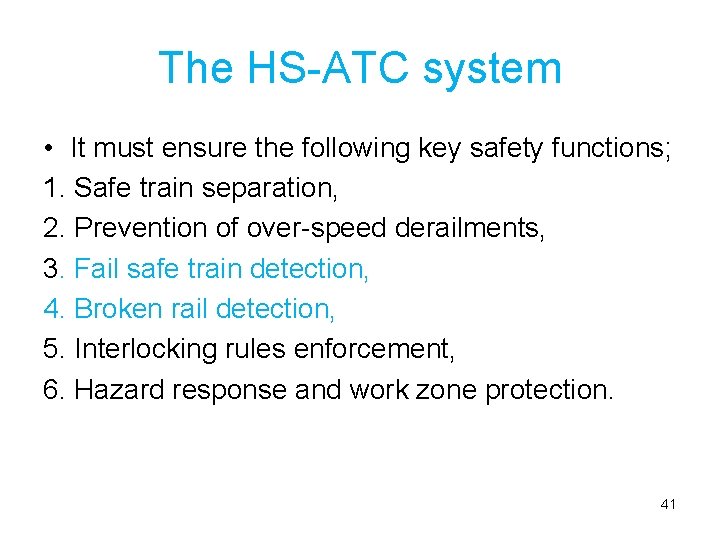
The HS-ATC system • It must ensure the following key safety functions; 1. Safe train separation, 2. Prevention of over-speed derailments, 3. Fail safe train detection, 4. Broken rail detection, 5. Interlocking rules enforcement, 6. Hazard response and work zone protection. 41
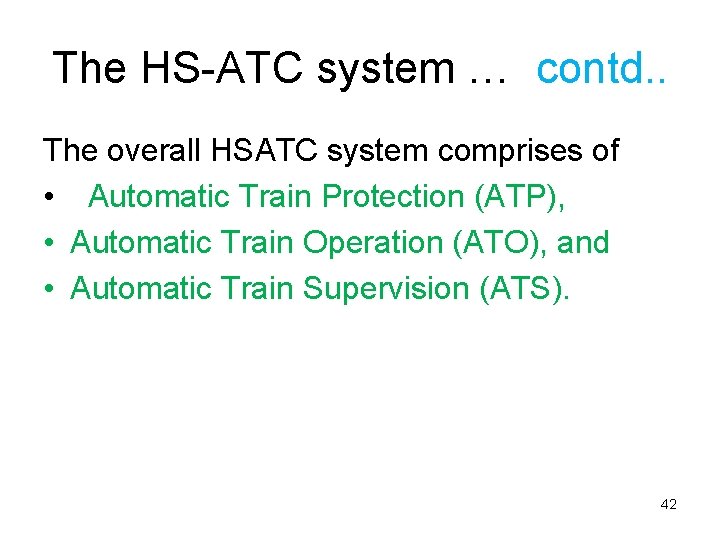
The HS-ATC system … contd. . The overall HSATC system comprises of • Automatic Train Protection (ATP), • Automatic Train Operation (ATO), and • Automatic Train Supervision (ATS). 42
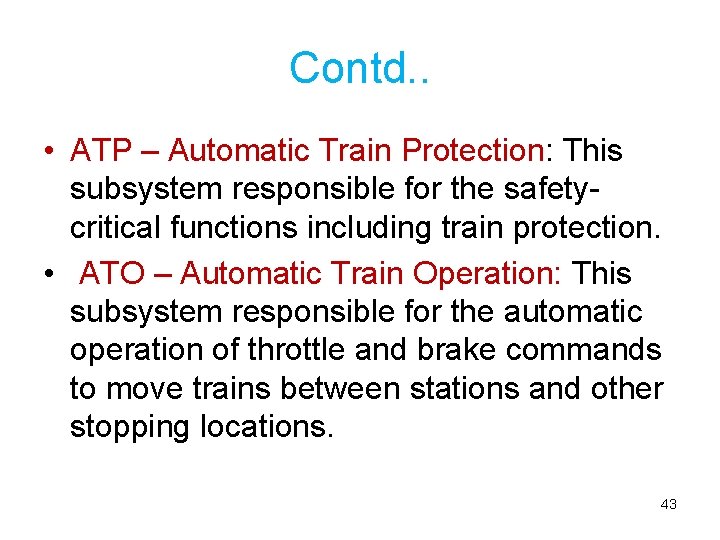
Contd. . • ATP – Automatic Train Protection: This subsystem responsible for the safetycritical functions including train protection. • ATO – Automatic Train Operation: This subsystem responsible for the automatic operation of throttle and brake commands to move trains between stations and other stopping locations. 43
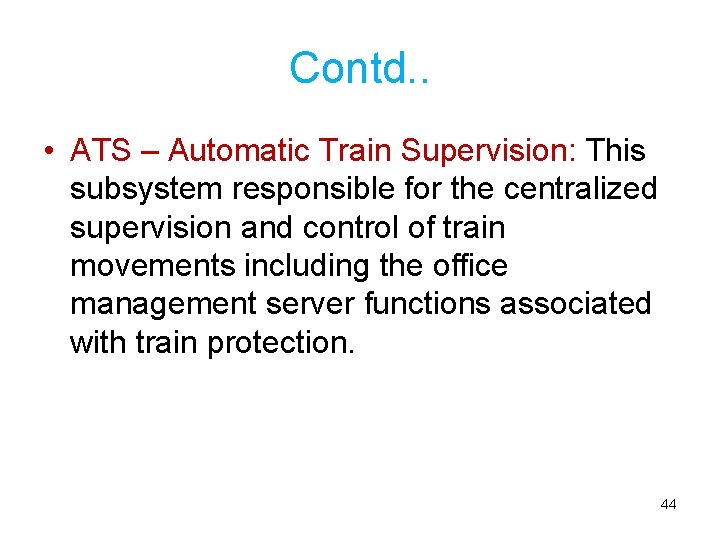
Contd. . • ATS – Automatic Train Supervision: This subsystem responsible for the centralized supervision and control of train movements including the office management server functions associated with train protection. 44
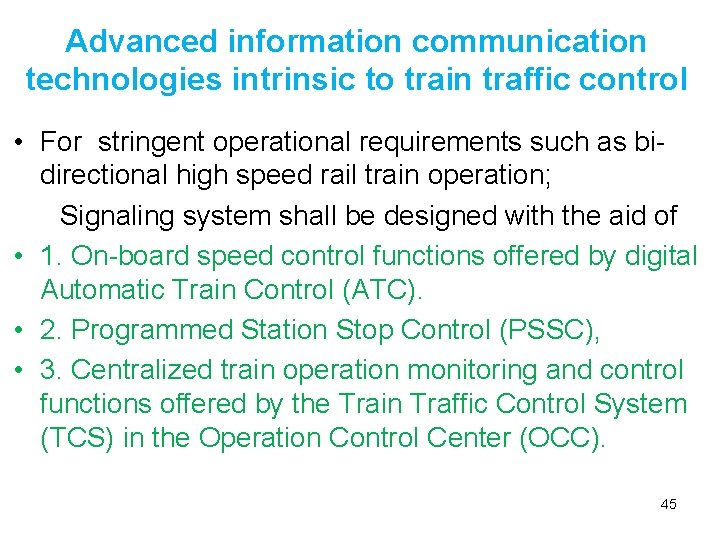
Advanced information communication technologies intrinsic to train traffic control • For stringent operational requirements such as bidirectional high speed rail train operation; Signaling system shall be designed with the aid of • 1. On-board speed control functions offered by digital Automatic Train Control (ATC). • 2. Programmed Station Stop Control (PSSC), • 3. Centralized train operation monitoring and control functions offered by the Train Traffic Control System (TCS) in the Operation Control Center (OCC). 45
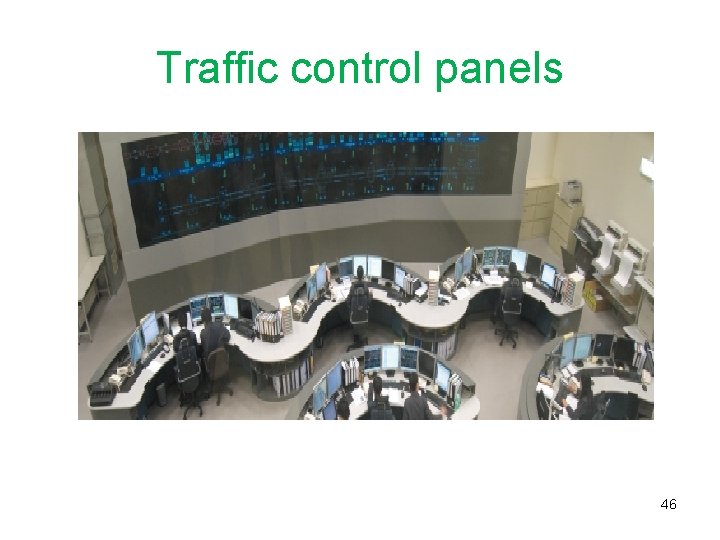
Traffic control panels 46
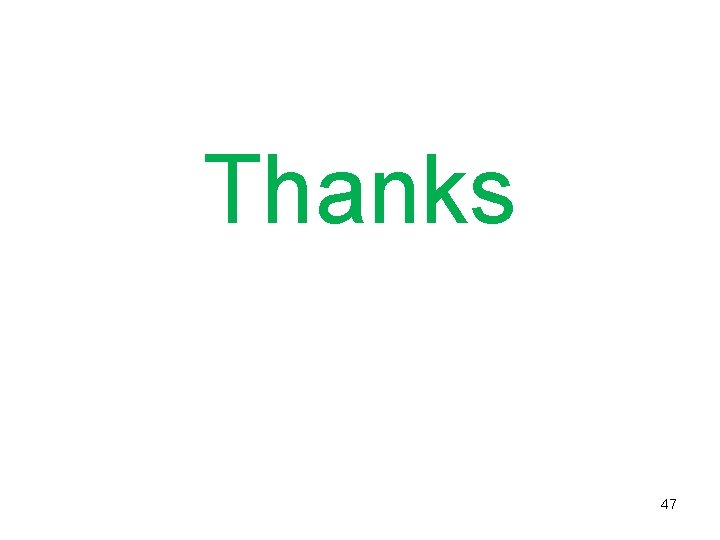
Thanks 47
Track machine manual in hindi
Ballast profile in indian railways
Indian railways monopoly
Modified sej gap
Irwcm
Double gap sej
What is fringe vision
Electronic toe load measuring device
What is dynamic pricing in railways
Thank you for listening any questions
How to find average speed with distance and speed
Speed detection of moving vehicle using speed cameras
Florida high school track
Middleton track and field
Indian valley high school lewistown pa
Vhsic
High speed combers
Nergeco doors
High speed lans
Global wind patterns
Ti high speed adc
High speed fpga design
High speed traffic management
Acn internet canada
Explain interleaved and associative memory
High speed machining titanium
Ch 35 dental handpieces and accessories
Implement carry arbitration encoding in arm9tdmi
Acn internet pei
Midwest high speed rail association
Pcb
High speed wireless lan
City-region
Pcb material selection
Oslo to stockholm high speed train
High speed networks
Semi high speed
High pumping speed large ion pump
Pcb high speed
High speed chapter 7
High speed machining definition
Salishan conference on high speed computing
Global winds and local winds
Acn compensation plan
High precision vs high recall
High precision vs high recall
Directive behavior and supportive behavior
High expectations high support