Introduction Danfoss hydraulic motors convert hydraulic energy pressure
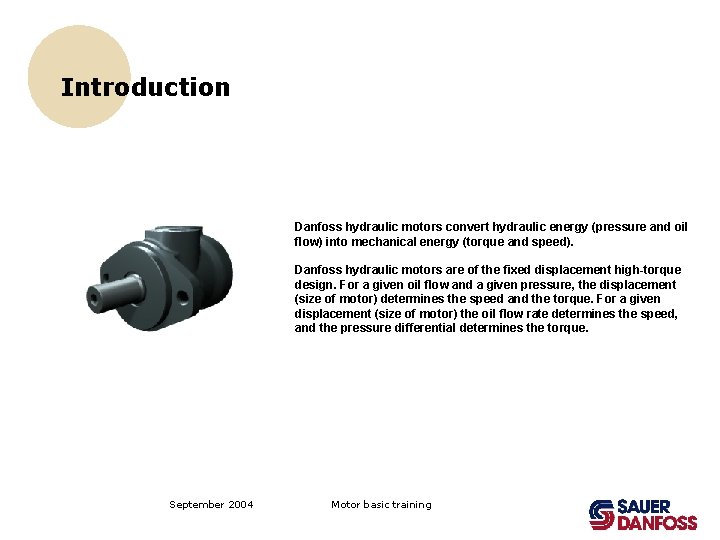
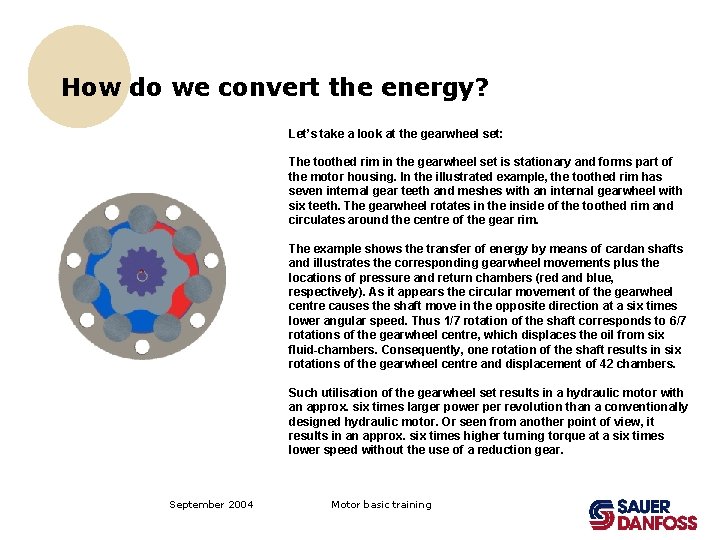
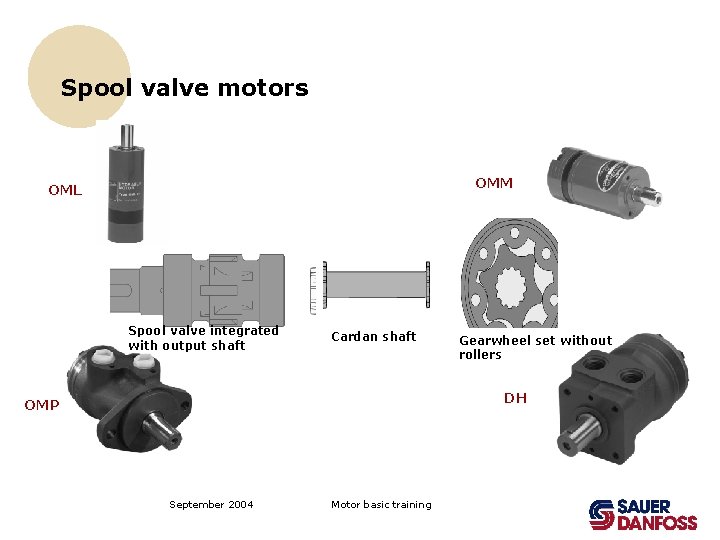
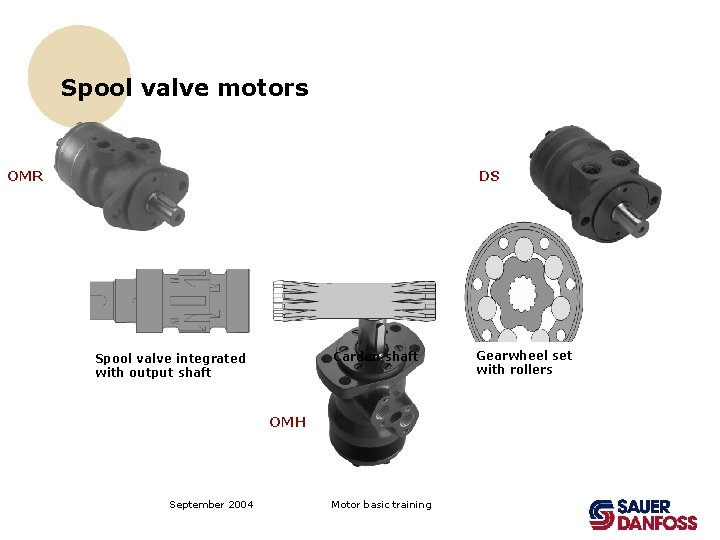
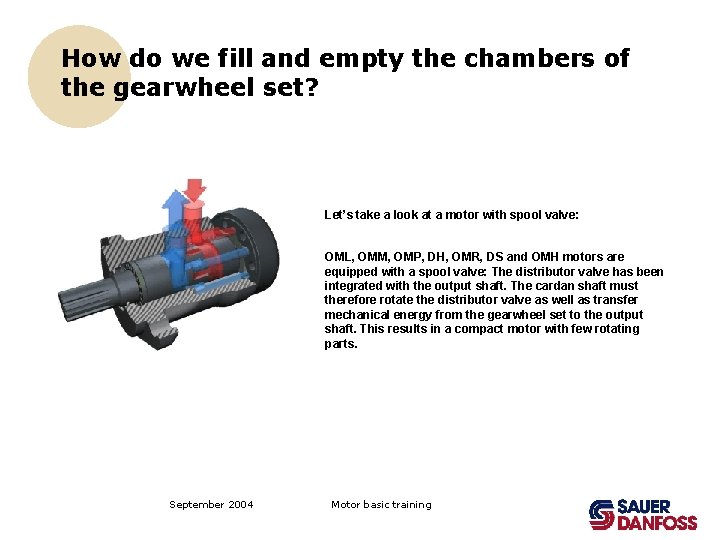
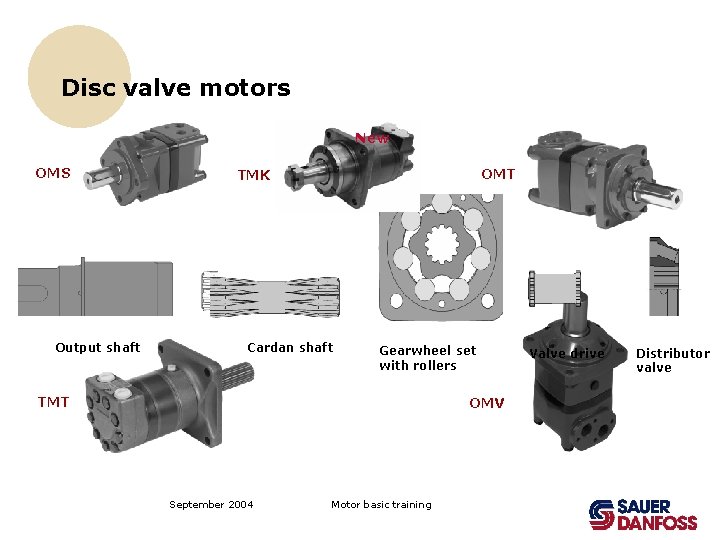
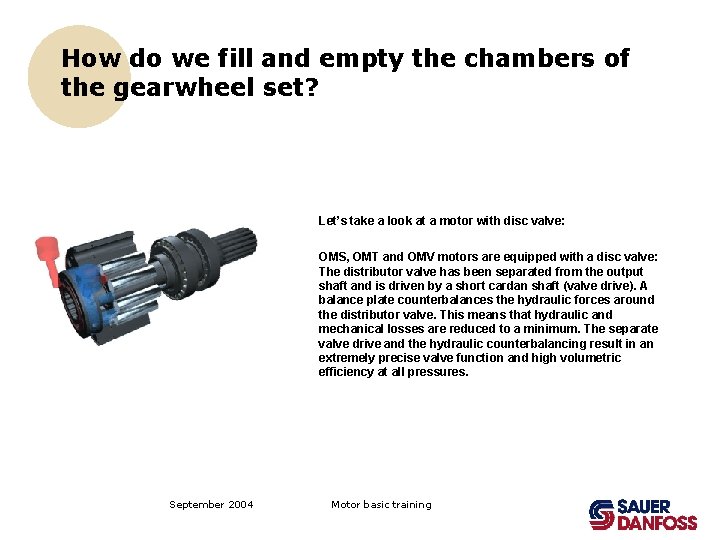
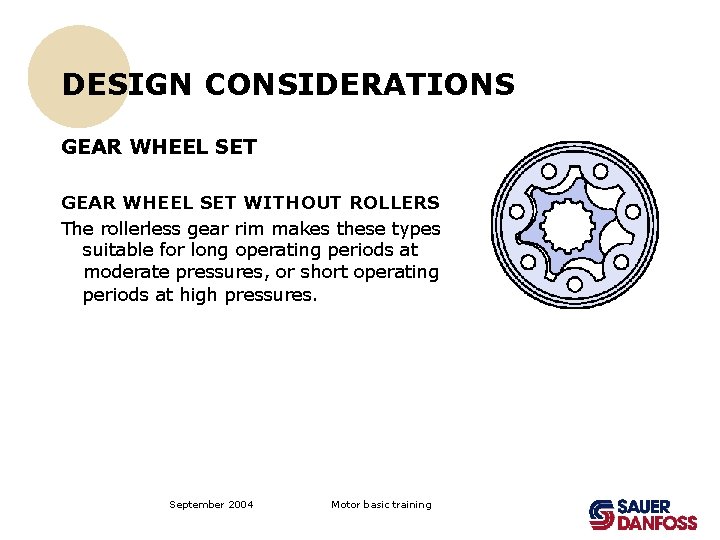

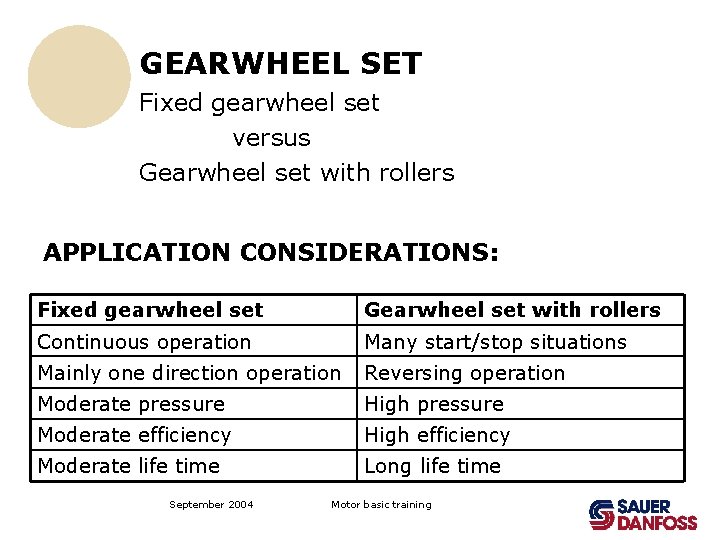
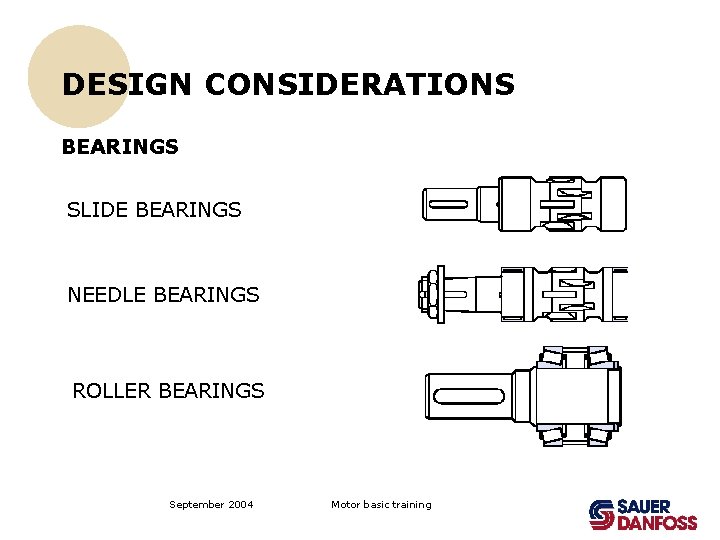
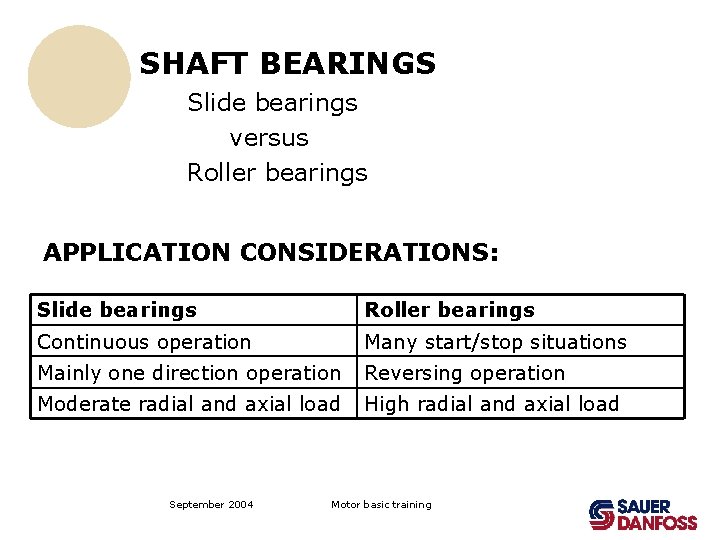
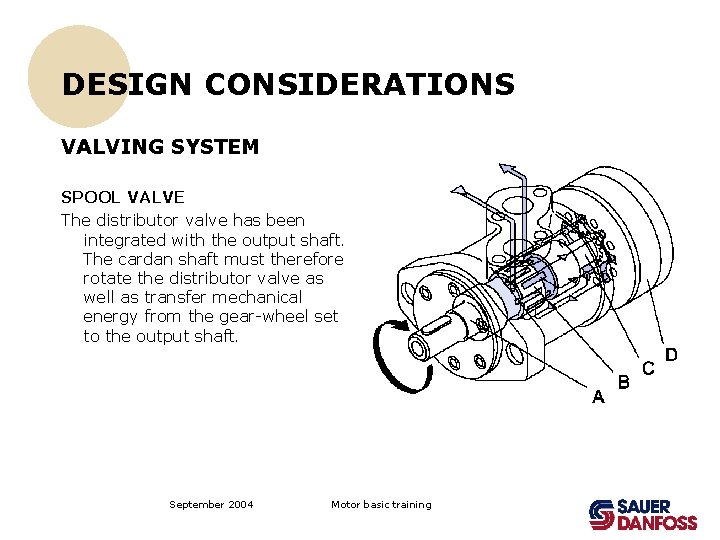
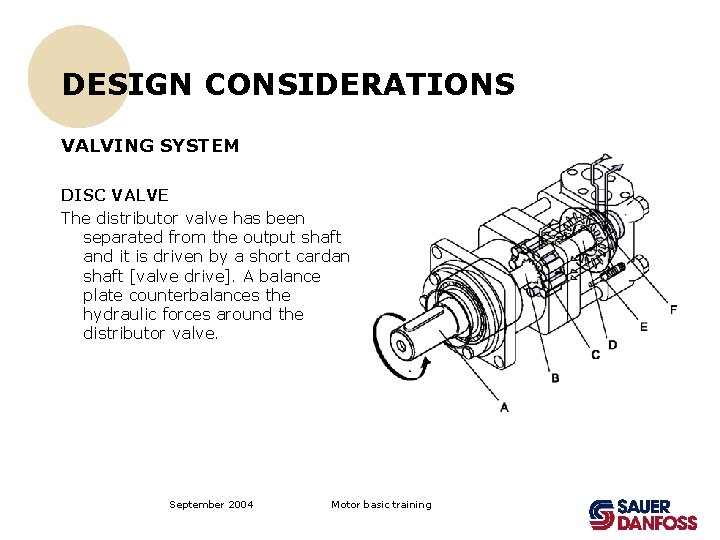
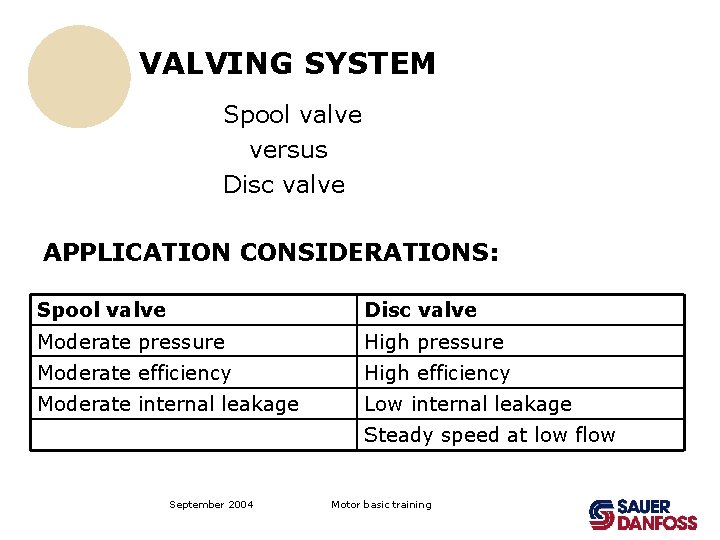
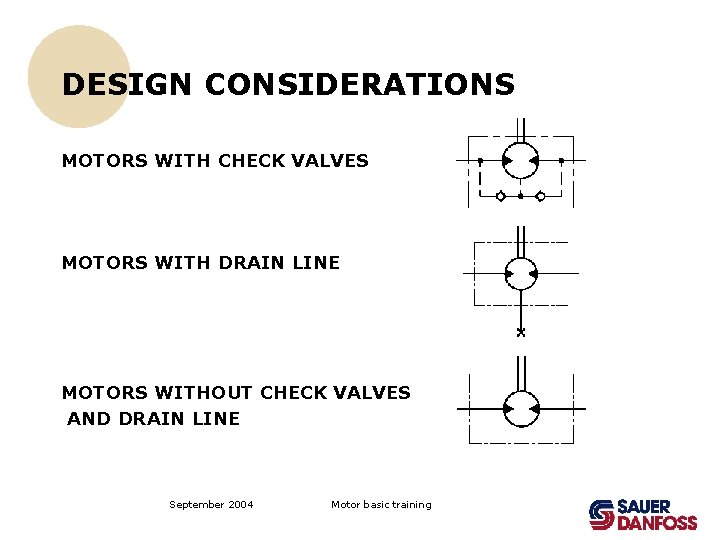
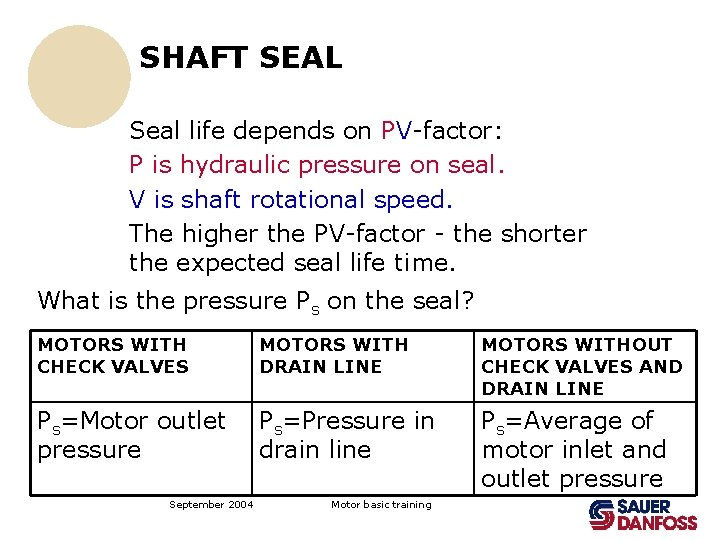
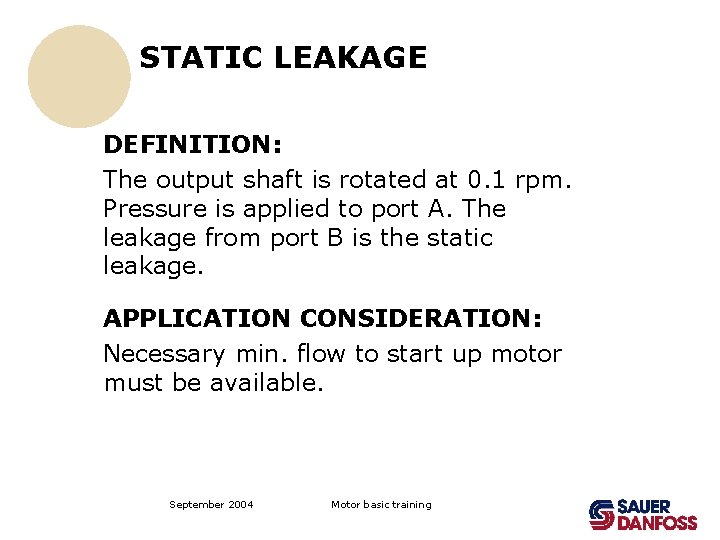
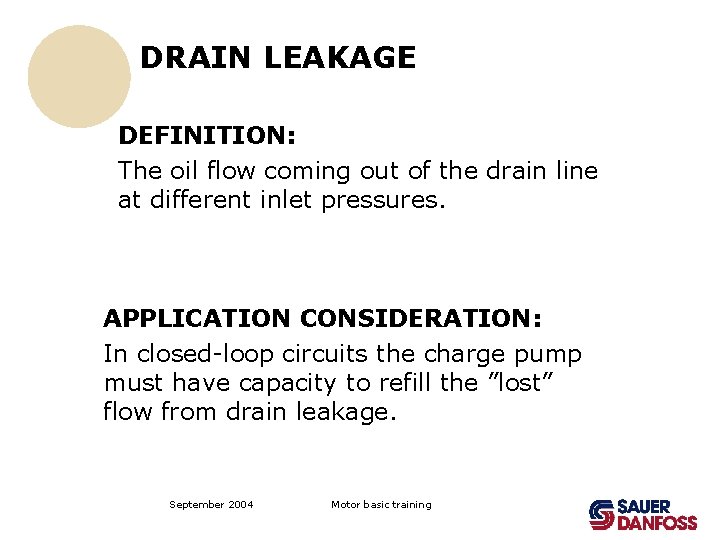
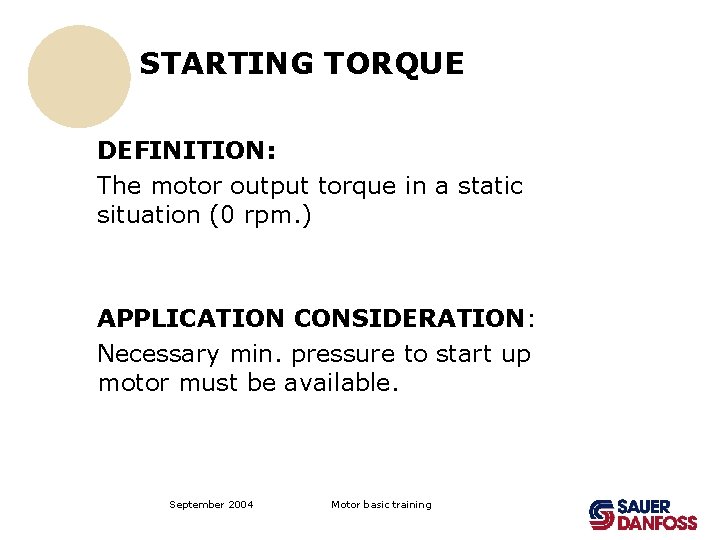
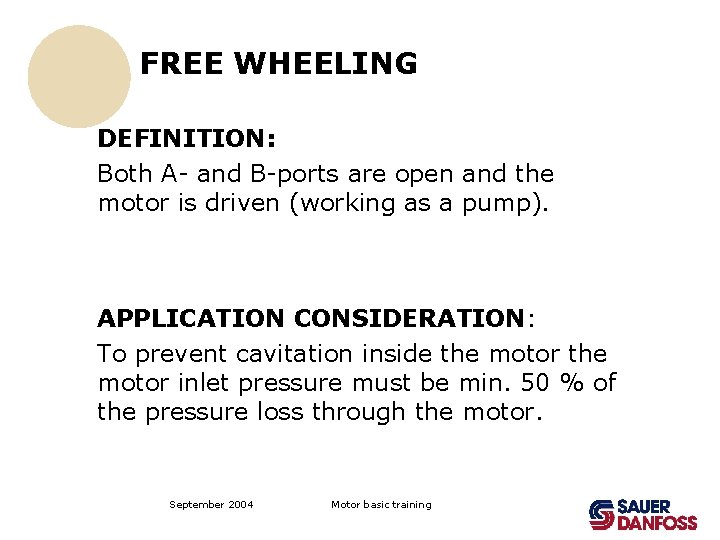
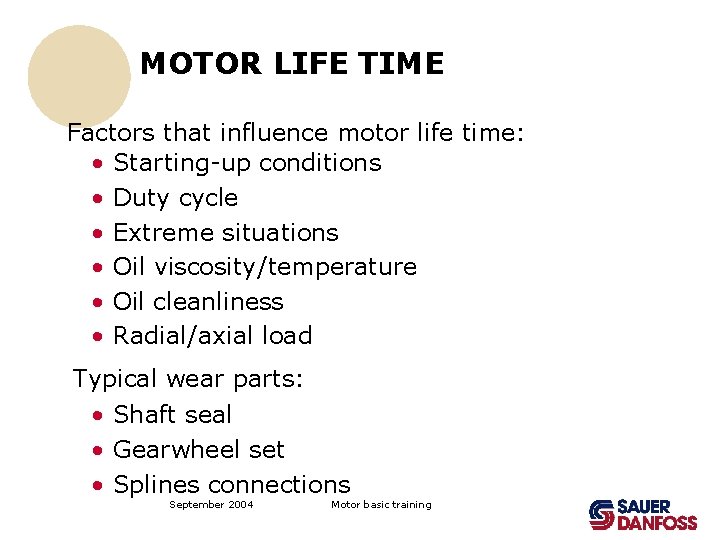
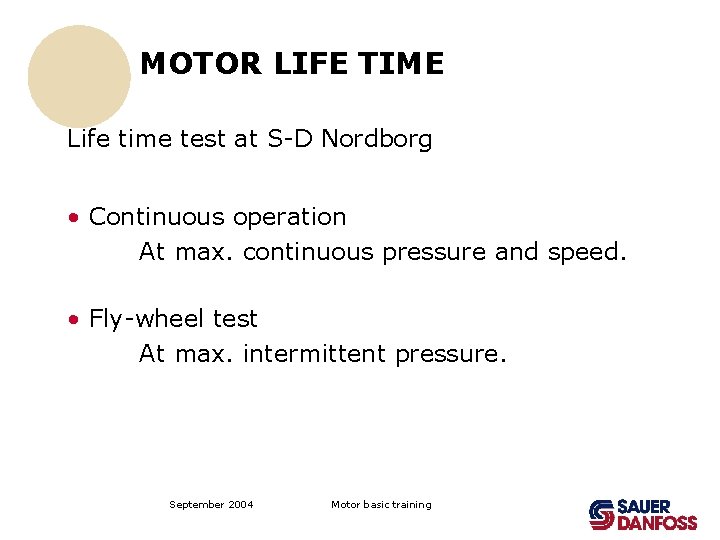
- Slides: 23
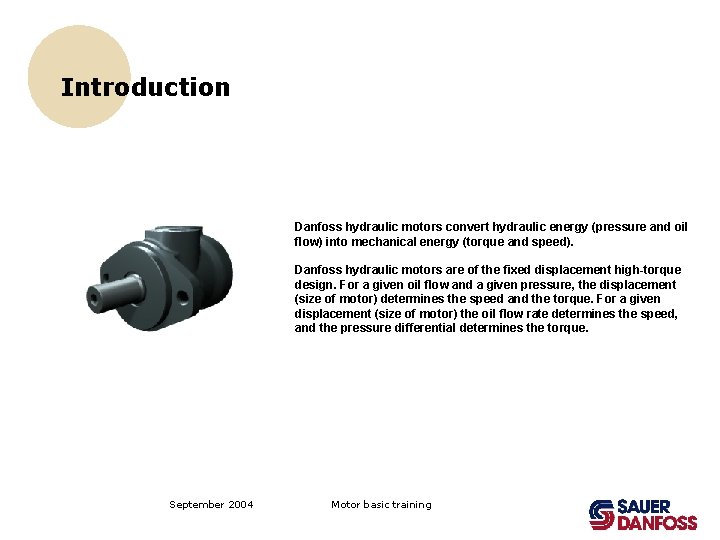
Introduction Danfoss hydraulic motors convert hydraulic energy (pressure and oil flow) into mechanical energy (torque and speed). Danfoss hydraulic motors are of the fixed displacement high-torque design. For a given oil flow and a given pressure, the displacement (size of motor) determines the speed and the torque. For a given displacement (size of motor) the oil flow rate determines the speed, and the pressure differential determines the torque. September 2004 Motor basic training
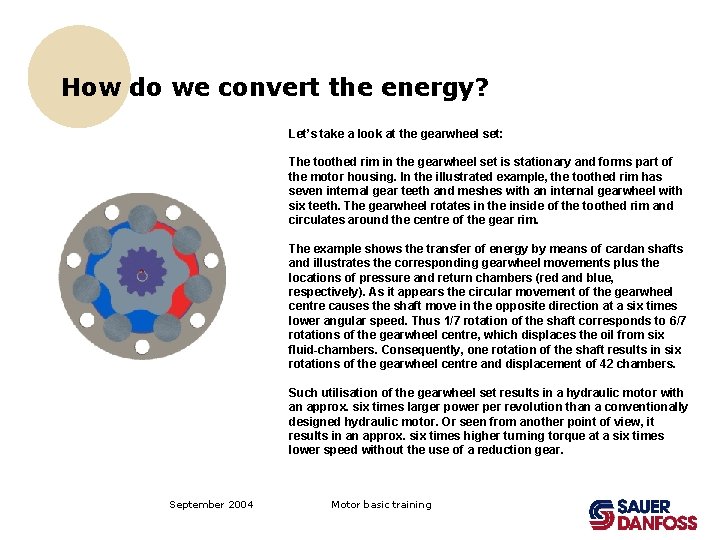
How do we convert the energy? Let’s take a look at the gearwheel set: The toothed rim in the gearwheel set is stationary and forms part of the motor housing. In the illustrated example, the toothed rim has seven internal gear teeth and meshes with an internal gearwheel with six teeth. The gearwheel rotates in the inside of the toothed rim and circulates around the centre of the gear rim. The example shows the transfer of energy by means of cardan shafts and illustrates the corresponding gearwheel movements plus the locations of pressure and return chambers (red and blue, respectively). As it appears the circular movement of the gearwheel centre causes the shaft move in the opposite direction at a six times lower angular speed. Thus 1/7 rotation of the shaft corresponds to 6/7 rotations of the gearwheel centre, which displaces the oil from six fluid-chambers. Consequently, one rotation of the shaft results in six rotations of the gearwheel centre and displacement of 42 chambers. Such utilisation of the gearwheel set results in a hydraulic motor with an approx. six times larger power per revolution than a conventionally designed hydraulic motor. Or seen from another point of view, it results in an approx. six times higher turning torque at a six times lower speed without the use of a reduction gear. September 2004 Motor basic training
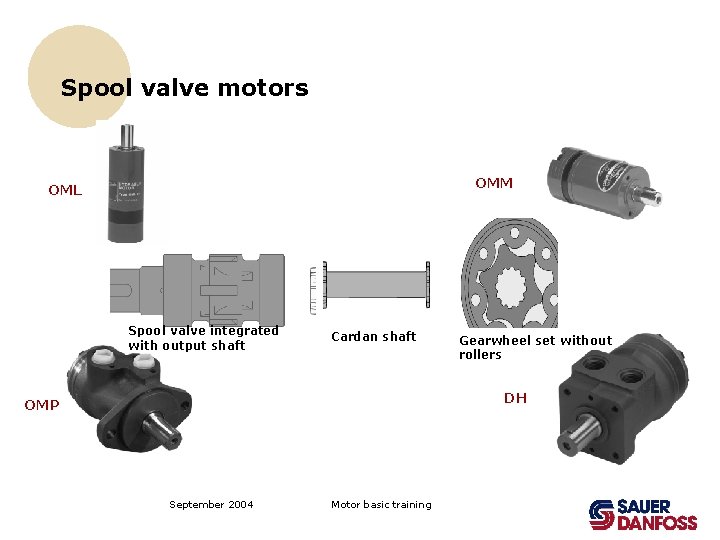
Spool valve motors OMM OML Spool valve integrated with output shaft Cardan shaft Gearwheel set without rollers DH OMP September 2004 Motor basic training
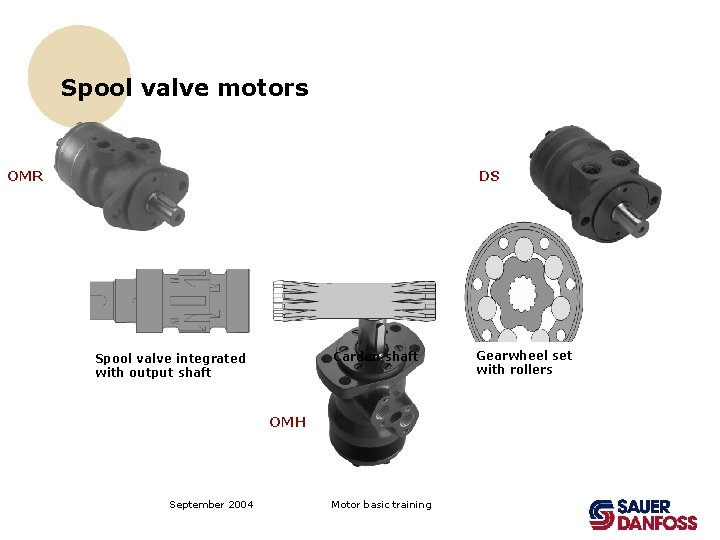
Spool valve motors OMR DS Cardan shaft Spool valve integrated with output shaft OMH September 2004 Motor basic training Gearwheel set with rollers
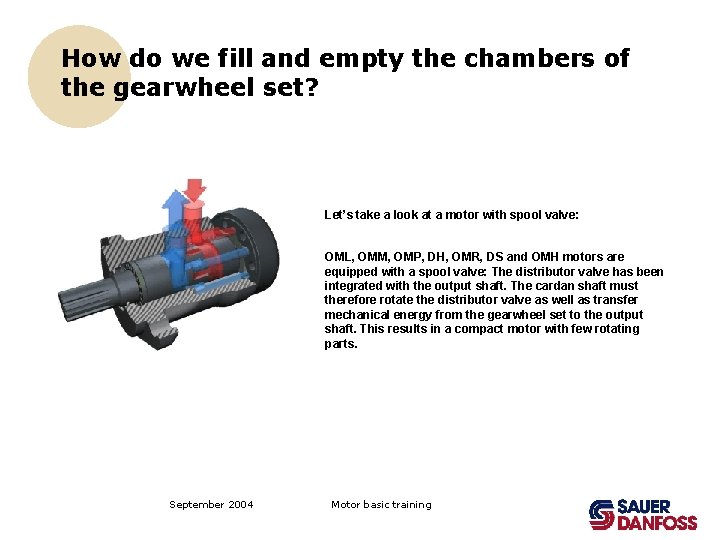
How do we fill and empty the chambers of the gearwheel set? Let’s take a look at a motor with spool valve: OML, OMM, OMP, DH, OMR, DS and OMH motors are equipped with a spool valve: The distributor valve has been integrated with the output shaft. The cardan shaft must therefore rotate the distributor valve as well as transfer mechanical energy from the gearwheel set to the output shaft. This results in a compact motor with few rotating parts. September 2004 Motor basic training
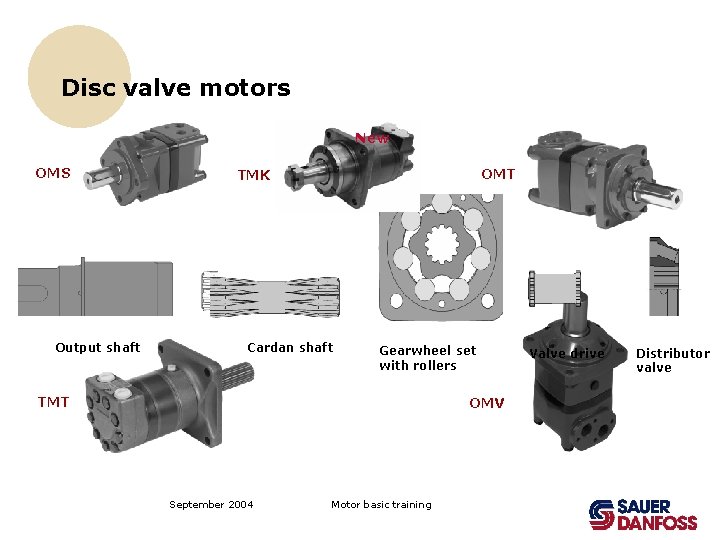
Disc valve motors New OMS Output shaft OMT TMK Cardan shaft Gearwheel set with rollers TMT OMV September 2004 Motor basic training Valve drive Distributor valve
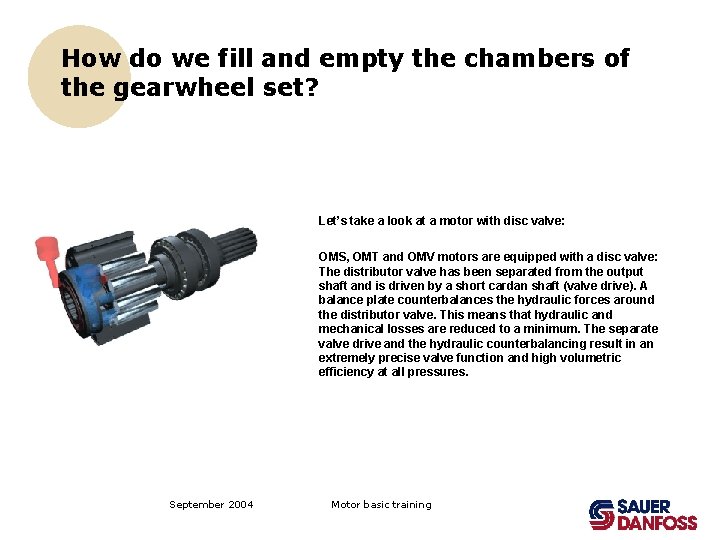
How do we fill and empty the chambers of the gearwheel set? Let’s take a look at a motor with disc valve: OMS, OMT and OMV motors are equipped with a disc valve: The distributor valve has been separated from the output shaft and is driven by a short cardan shaft (valve drive). A balance plate counterbalances the hydraulic forces around the distributor valve. This means that hydraulic and mechanical losses are reduced to a minimum. The separate valve drive and the hydraulic counterbalancing result in an extremely precise valve function and high volumetric efficiency at all pressures. September 2004 Motor basic training
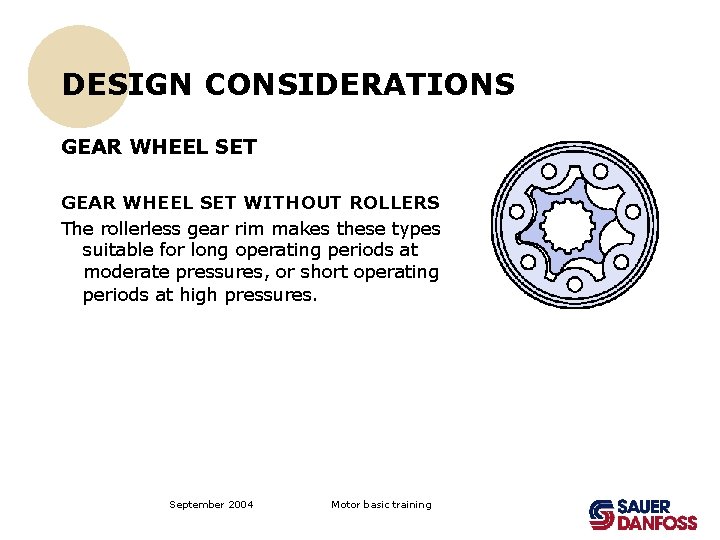
DESIGN CONSIDERATIONS GEAR WHEEL SET WITHOUT ROLLERS The rollerless gear rim makes these types suitable for long operating periods at moderate pressures, or short operating periods at high pressures. September 2004 Motor basic training

DESIGN CONSIDERATIONS GEAR WHEEL SET WITH ROLLERS The rollers in the gear rim reduce local stress, spread the tooth load over their projected area and reduce the tangential reaction forces on the inner gear reducing friction to a minimum. This gives long operating life and better efficiency even at continuous high pressures. Gearwheel sets with rollers are recommended for operation with thin oil and for applications having continually reversing loads. September 2004 Motor basic training
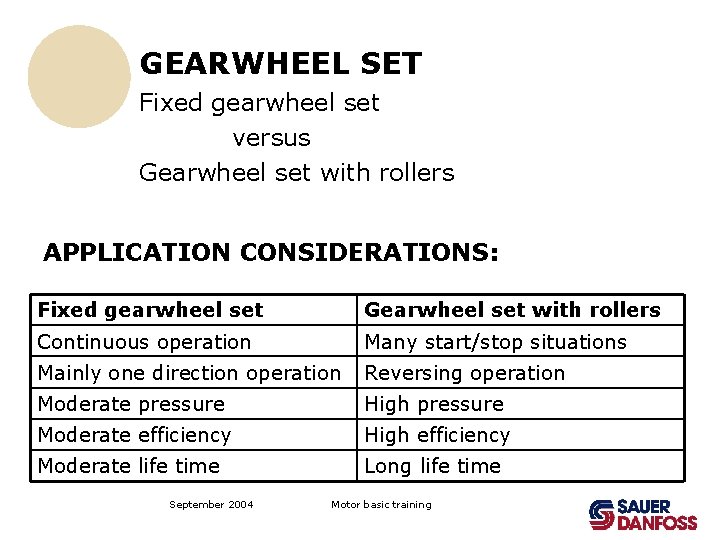
GEARWHEEL SET Fixed gearwheel set versus Gearwheel set with rollers APPLICATION CONSIDERATIONS: Fixed gearwheel set Gearwheel set with rollers Continuous operation Many start/stop situations Mainly one direction operation Reversing operation Moderate pressure High pressure Moderate efficiency High efficiency Moderate life time Long life time September 2004 Motor basic training
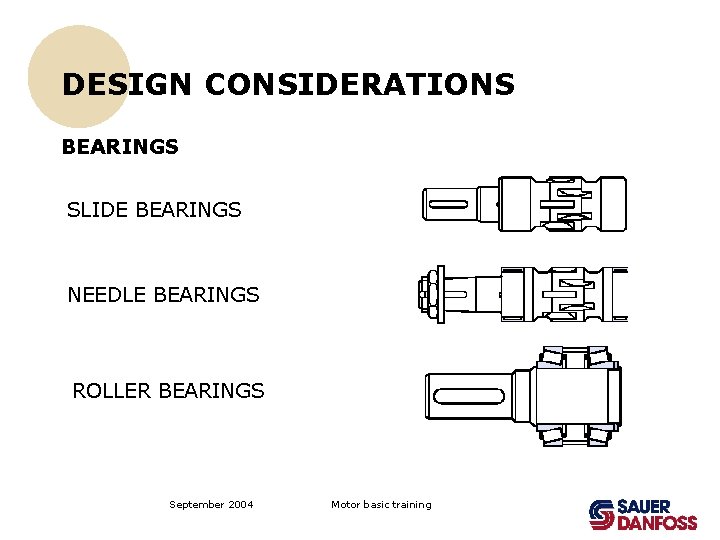
DESIGN CONSIDERATIONS BEARINGS SLIDE BEARINGS NEEDLE BEARINGS ROLLER BEARINGS September 2004 Motor basic training
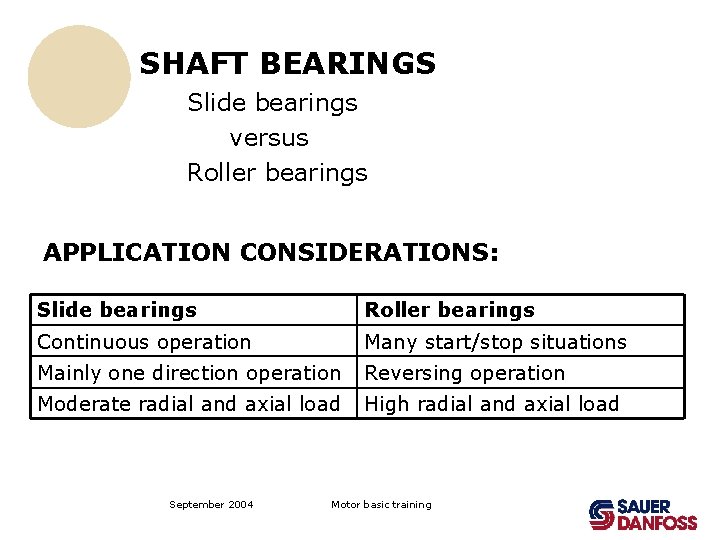
SHAFT BEARINGS Slide bearings versus Roller bearings APPLICATION CONSIDERATIONS: Slide bearings Roller bearings Continuous operation Many start/stop situations Mainly one direction operation Reversing operation Moderate radial and axial load High radial and axial load September 2004 Motor basic training
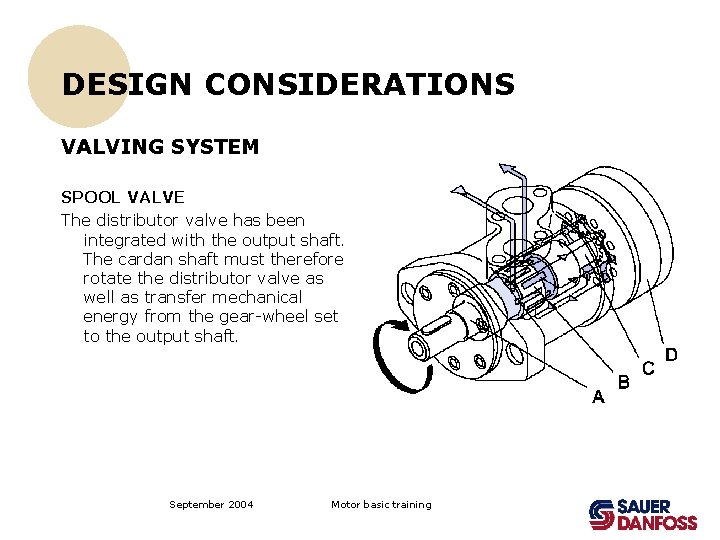
DESIGN CONSIDERATIONS VALVING SYSTEM SPOOL VALVE The distributor valve has been integrated with the output shaft. The cardan shaft must therefore rotate the distributor valve as well as transfer mechanical energy from the gear-wheel set to the output shaft. September 2004 Motor basic training
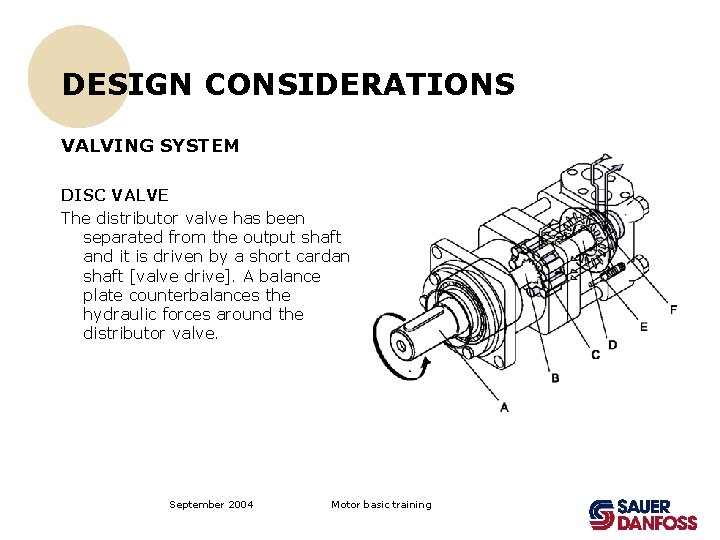
DESIGN CONSIDERATIONS VALVING SYSTEM DISC VALVE The distributor valve has been separated from the output shaft and it is driven by a short cardan shaft [valve drive]. A balance plate counterbalances the hydraulic forces around the distributor valve. September 2004 Motor basic training
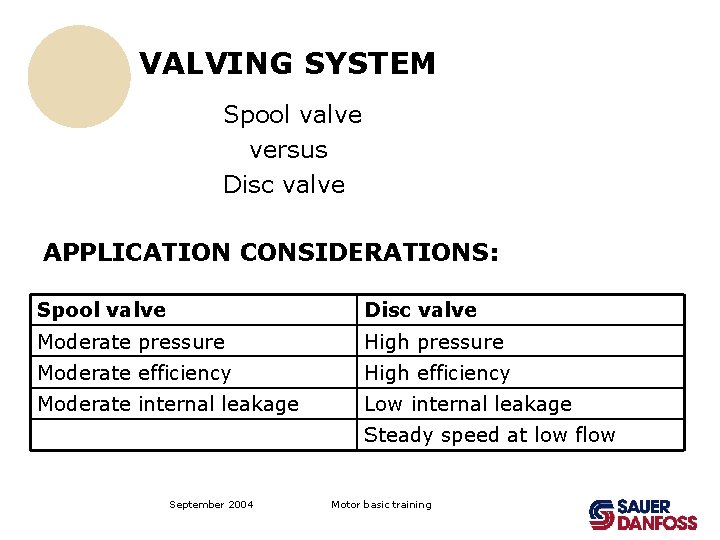
VALVING SYSTEM Spool valve versus Disc valve APPLICATION CONSIDERATIONS: Spool valve Disc valve Moderate pressure High pressure Moderate efficiency High efficiency Moderate internal leakage Low internal leakage Steady speed at low flow September 2004 Motor basic training
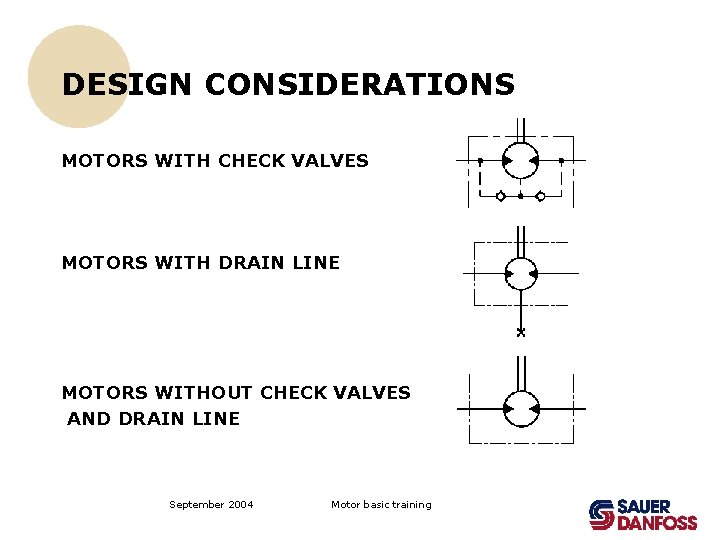
DESIGN CONSIDERATIONS MOTORS WITH CHECK VALVES MOTORS WITH DRAIN LINE MOTORS WITHOUT CHECK VALVES AND DRAIN LINE September 2004 Motor basic training
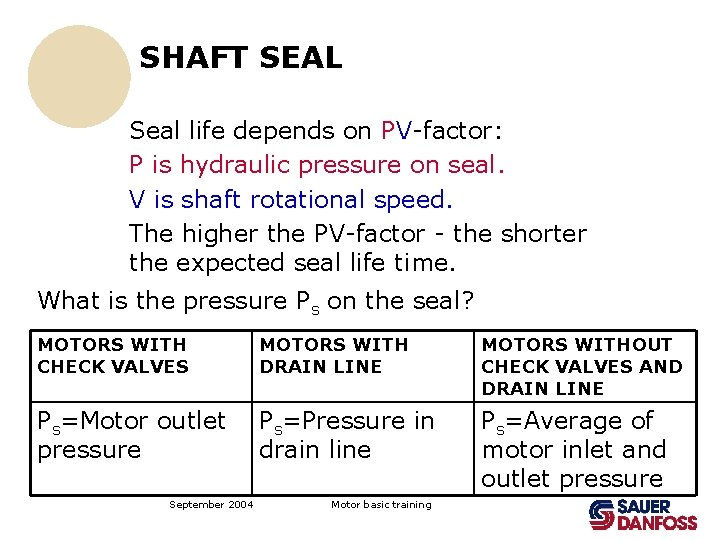
SHAFT SEAL Seal life depends on PV-factor: P is hydraulic pressure on seal. V is shaft rotational speed. The higher the PV-factor - the shorter the expected seal life time. What is the pressure Ps on the seal? MOTORS WITH CHECK VALVES MOTORS WITH DRAIN LINE MOTORS WITHOUT CHECK VALVES AND DRAIN LINE Ps=Motor outlet pressure Ps=Pressure in drain line Ps=Average of motor inlet and outlet pressure September 2004 Motor basic training
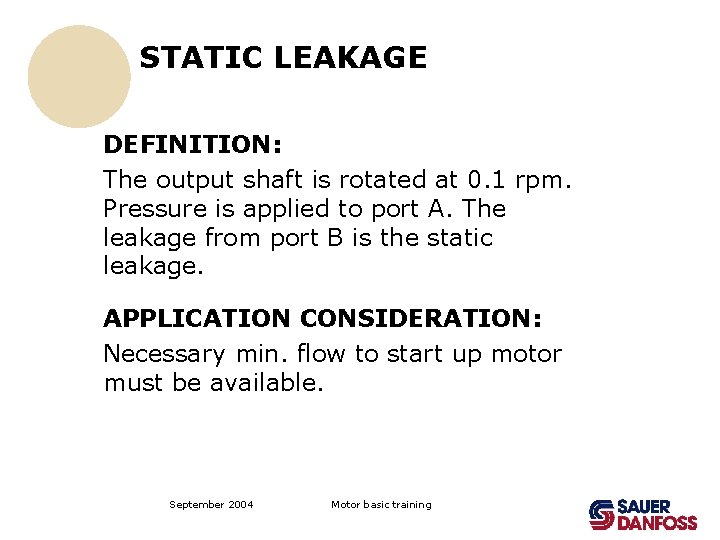
STATIC LEAKAGE DEFINITION: The output shaft is rotated at 0. 1 rpm. Pressure is applied to port A. The leakage from port B is the static leakage. APPLICATION CONSIDERATION: Necessary min. flow to start up motor must be available. September 2004 Motor basic training
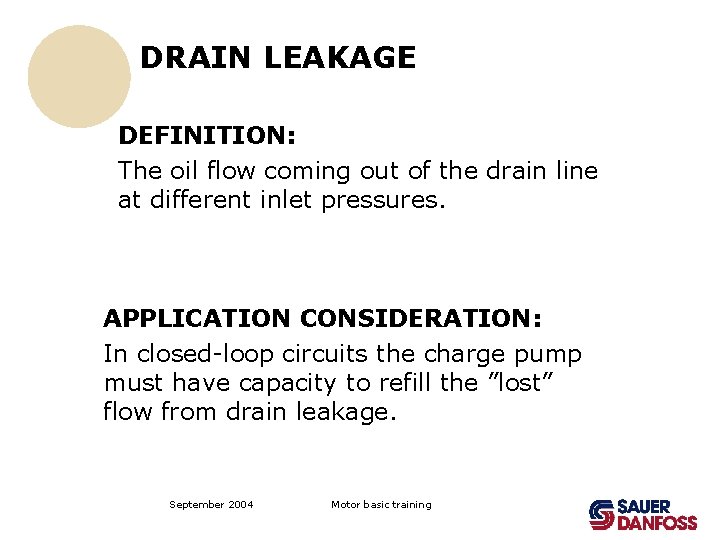
DRAIN LEAKAGE DEFINITION: The oil flow coming out of the drain line at different inlet pressures. APPLICATION CONSIDERATION: In closed-loop circuits the charge pump must have capacity to refill the ”lost” flow from drain leakage. September 2004 Motor basic training
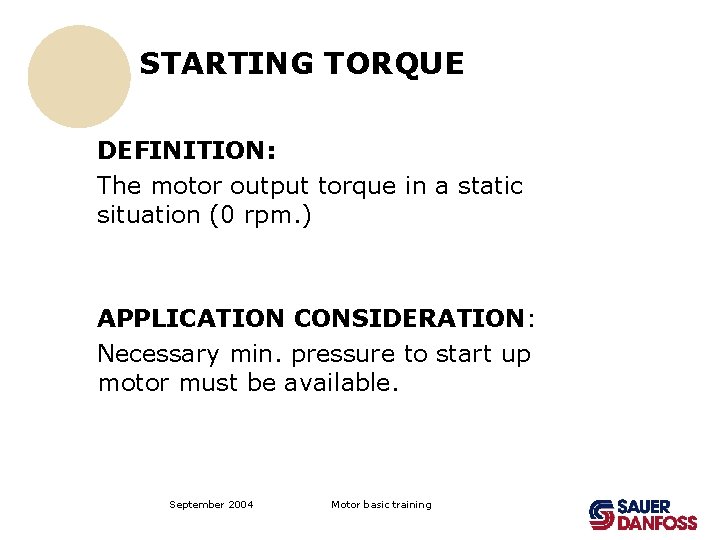
STARTING TORQUE DEFINITION: The motor output torque in a static situation (0 rpm. ) APPLICATION CONSIDERATION: Necessary min. pressure to start up motor must be available. September 2004 Motor basic training
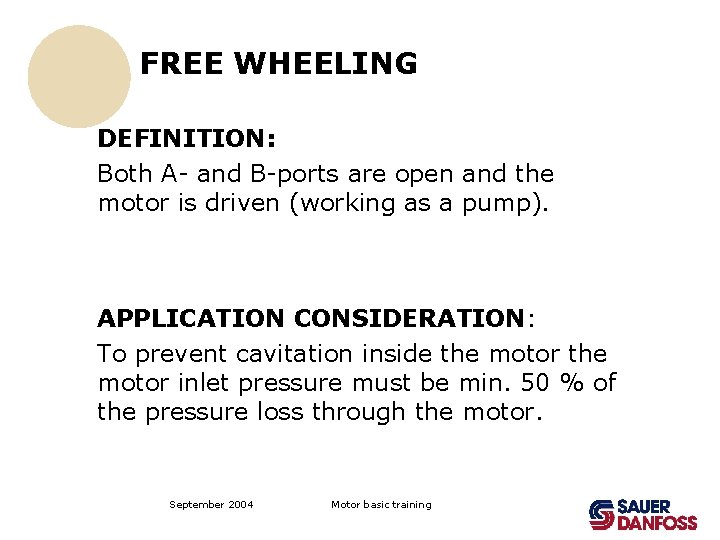
FREE WHEELING DEFINITION: Both A- and B-ports are open and the motor is driven (working as a pump). APPLICATION CONSIDERATION: To prevent cavitation inside the motor inlet pressure must be min. 50 % of the pressure loss through the motor. September 2004 Motor basic training
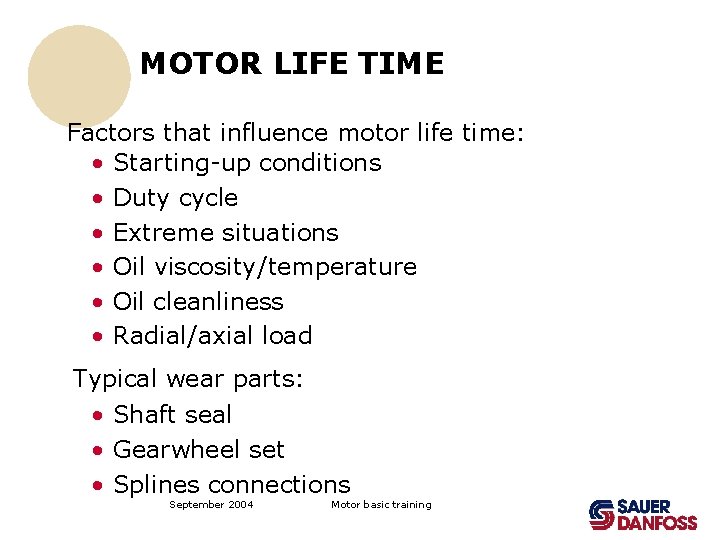
MOTOR LIFE TIME Factors that influence motor life time: • Starting-up conditions • Duty cycle • Extreme situations • Oil viscosity/temperature • Oil cleanliness • Radial/axial load Typical wear parts: • Shaft seal • Gearwheel set • Splines connections September 2004 Motor basic training
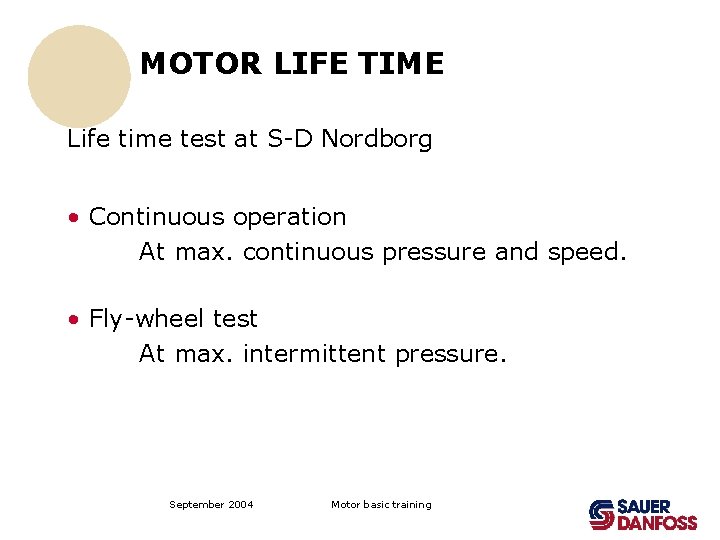
MOTOR LIFE TIME Life time test at S-D Nordborg • Continuous operation At max. continuous pressure and speed. • Fly-wheel test At max. intermittent pressure. September 2004 Motor basic training
Hydraulic pump symbol
How to convert mechanical energy to electrical energy
Correspondance gicleur fioul
Danfoss proportional valve wiring diagram
Danfoss link home assistant
Akpc 551 manual
Magnetische entkalkung
Mcd3000
Danfoss pvg 100
Danfoss kft
Danfoss polypower
Hydraulic schematic symbols chart
What is the pressure in the hydraulic fluid?
What is the pressure in the hydraulic fluid?
Strengths of tata motors
Introduction to electric motors
Energy energy transfer and general energy analysis
Energy energy transfer and general energy analysis
Vmo advancement cpt
Pressure support vs pressure control
Pressure mapping for pressure ulcers
Intrapulmonary pressure
Starling
Partial pressure