Integration of Air and Gas Flow Paths P
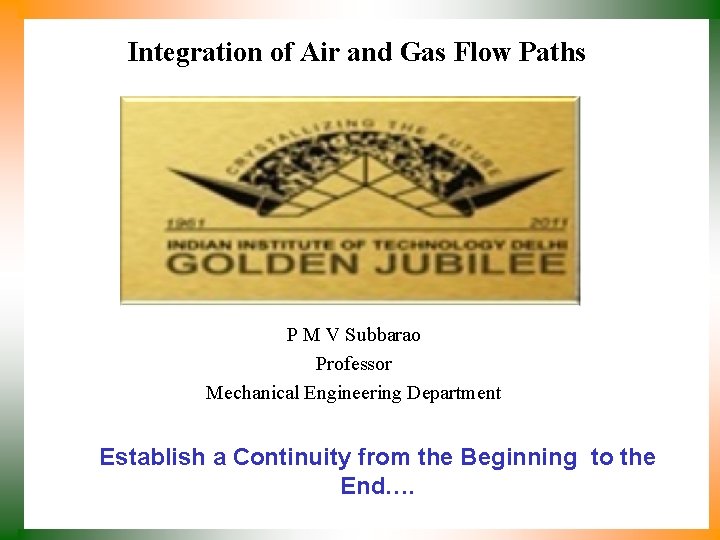
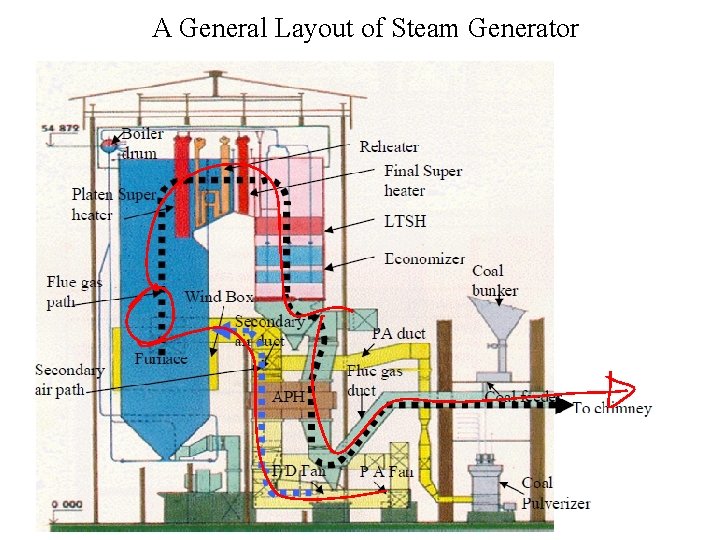
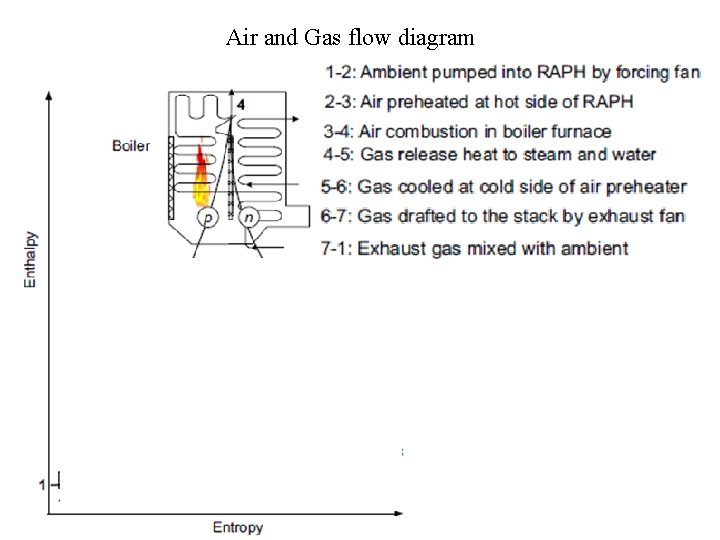
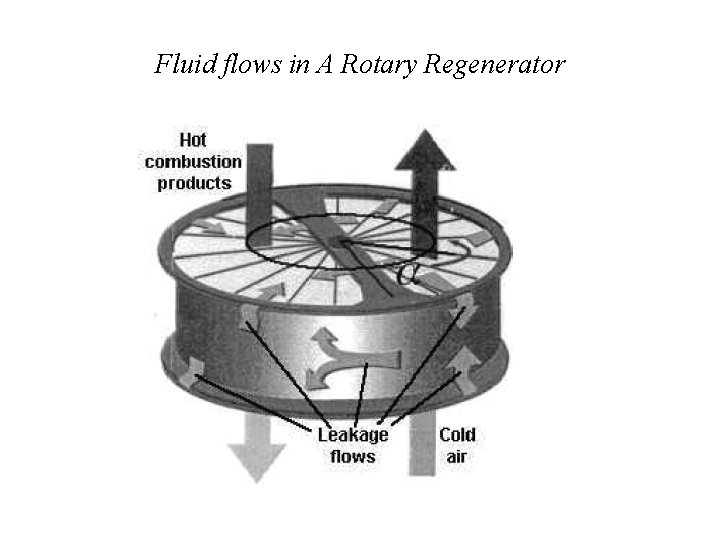
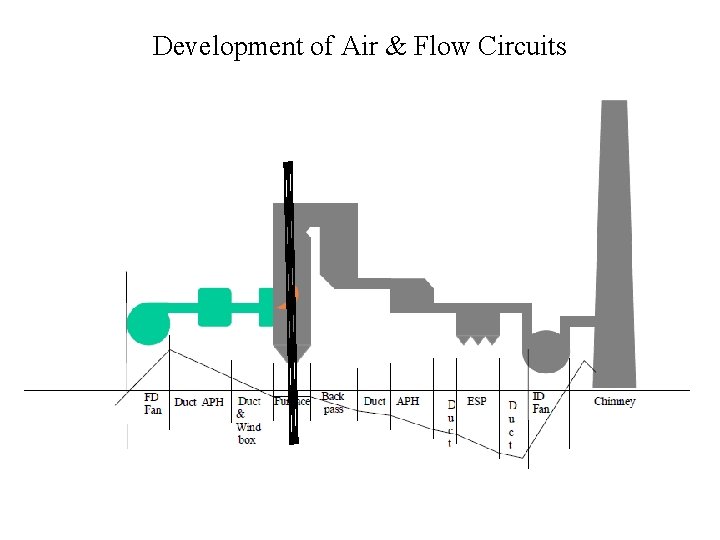
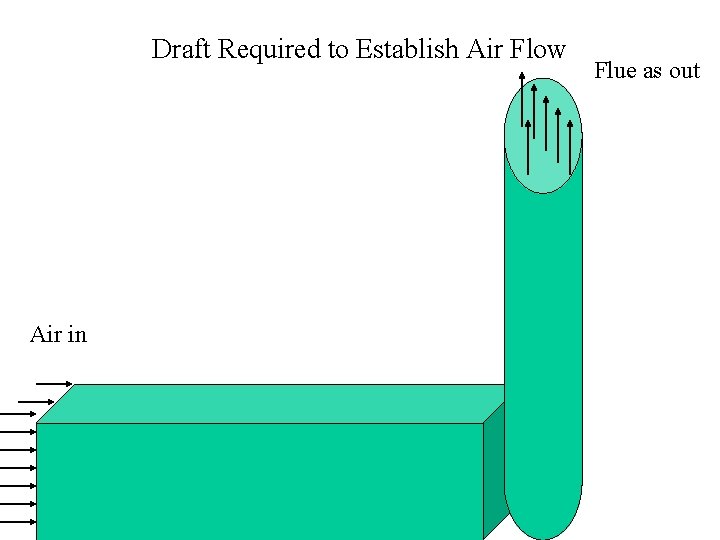
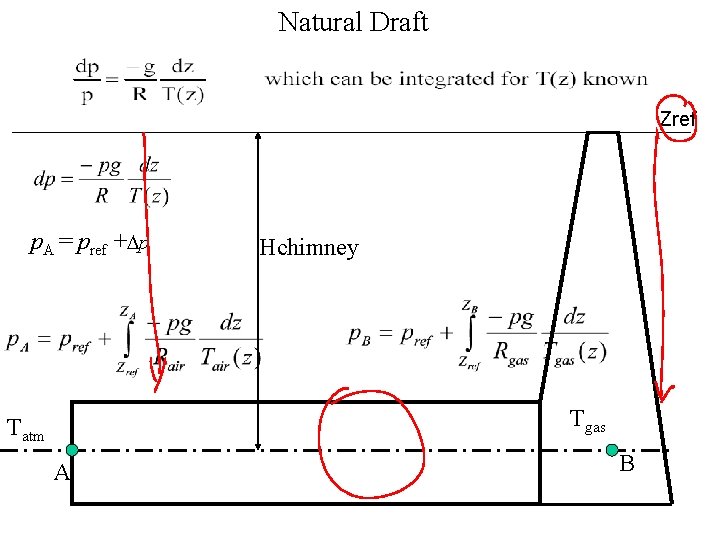
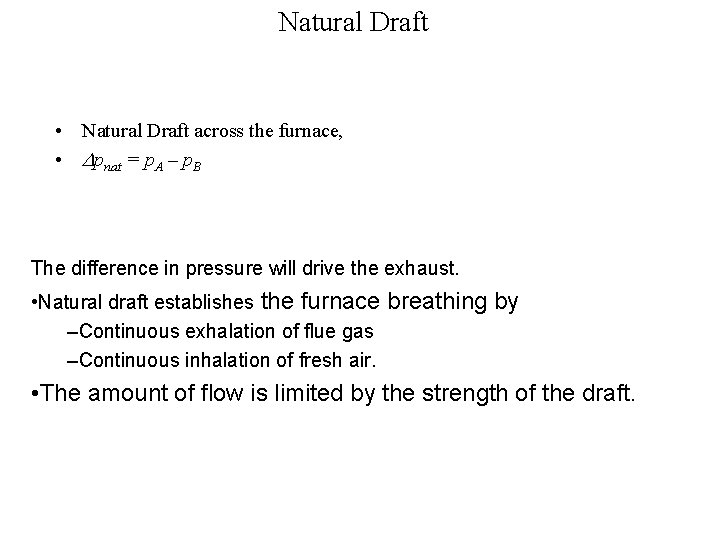
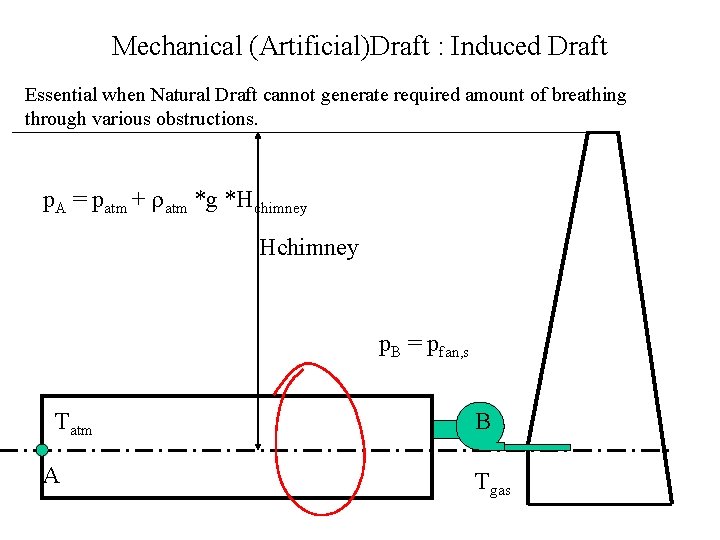
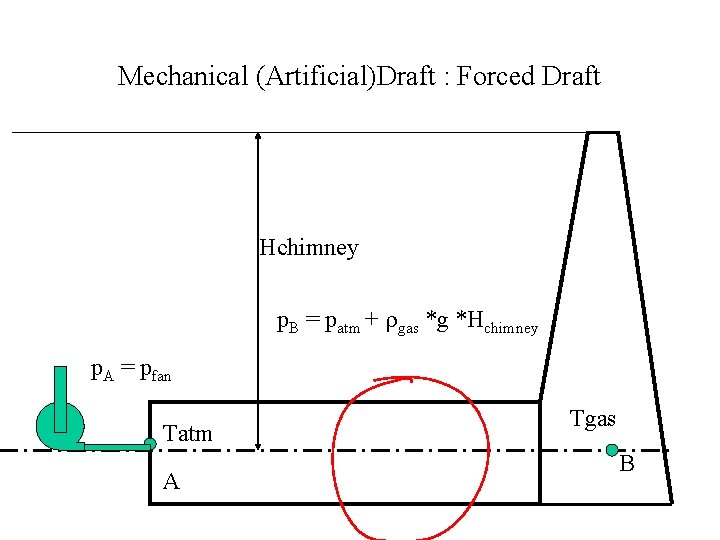
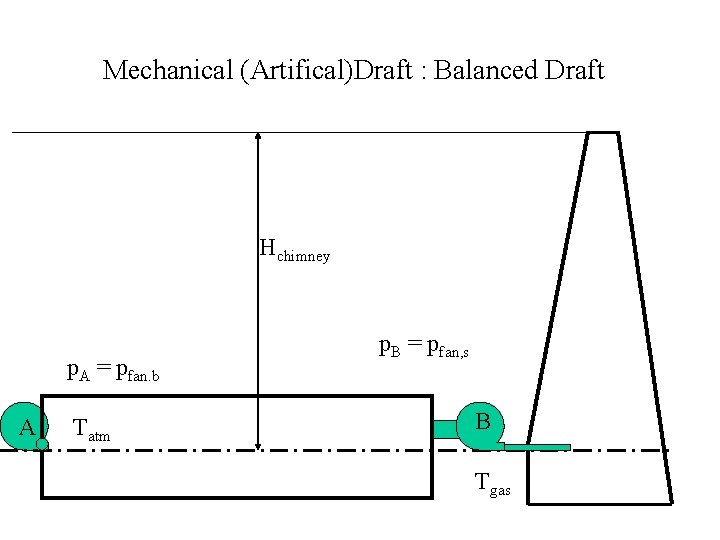
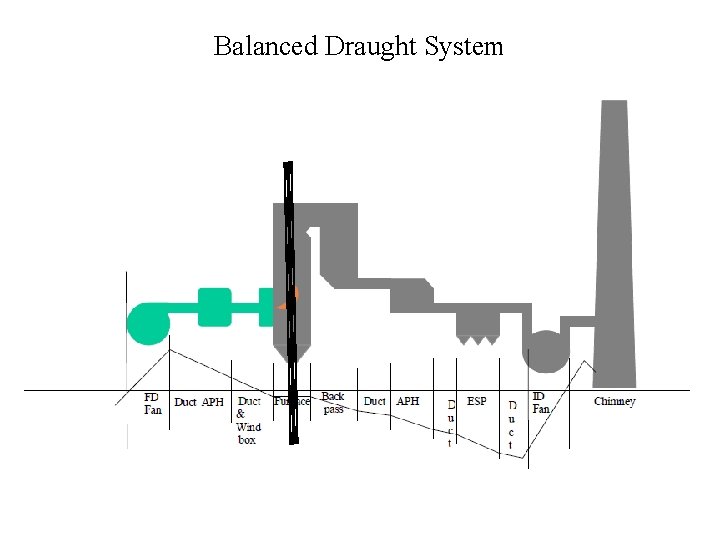
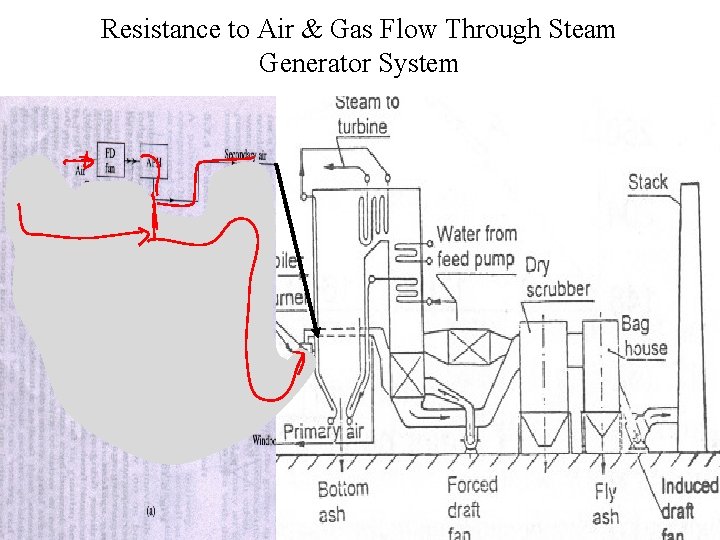
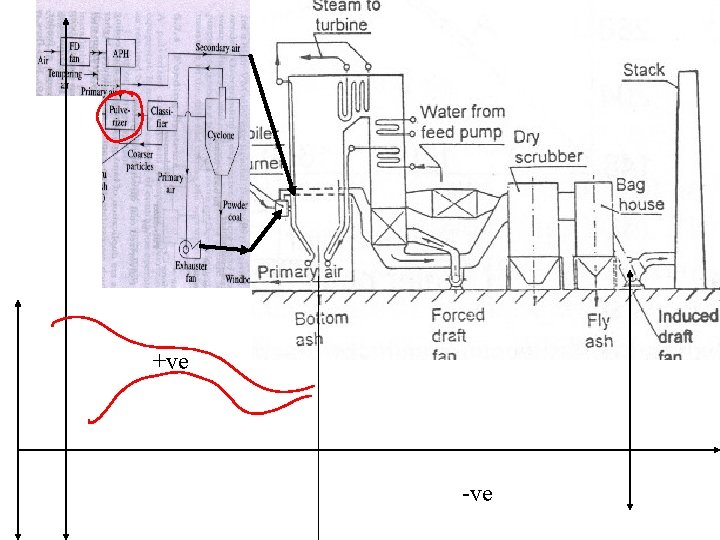

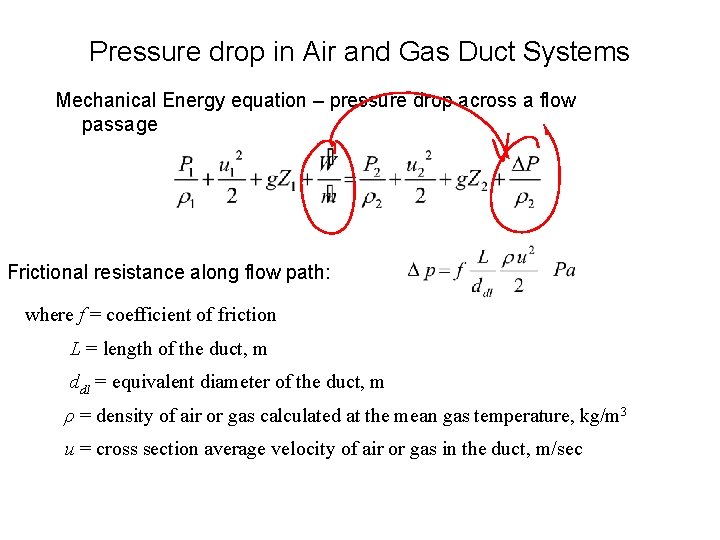
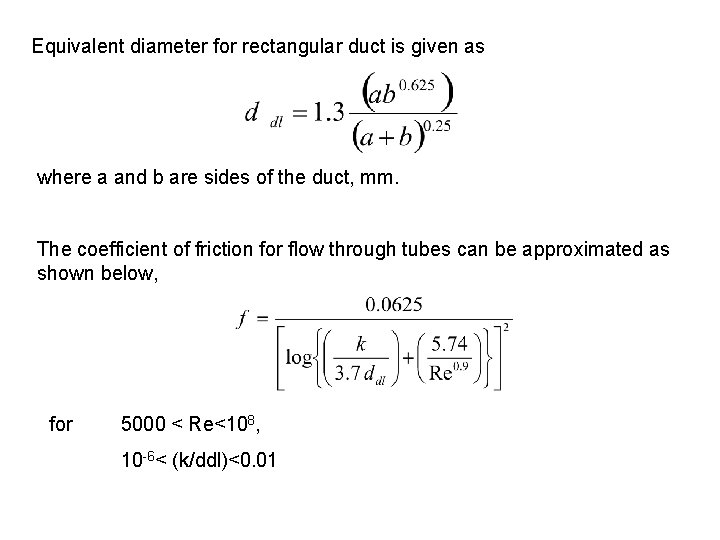
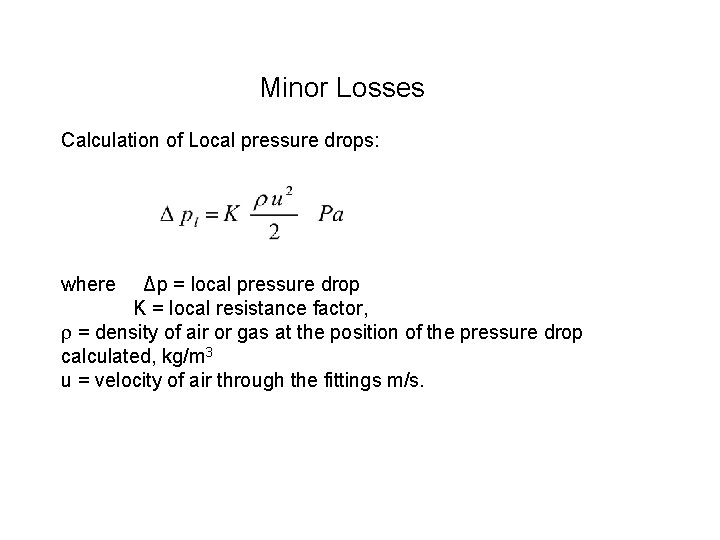
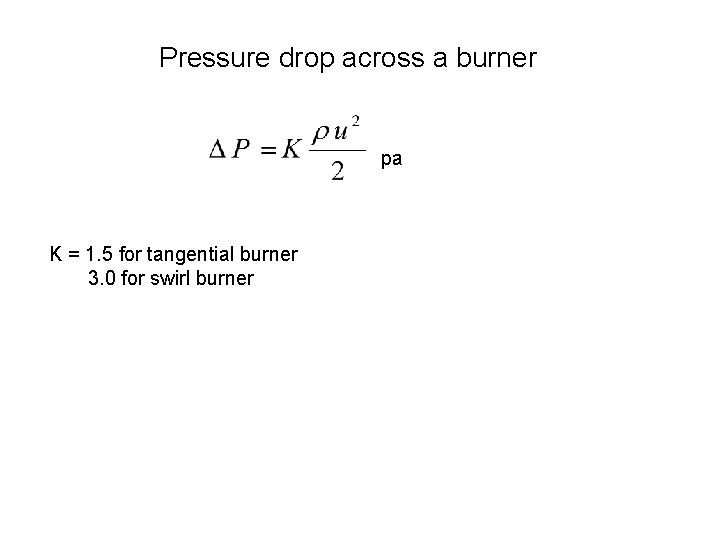
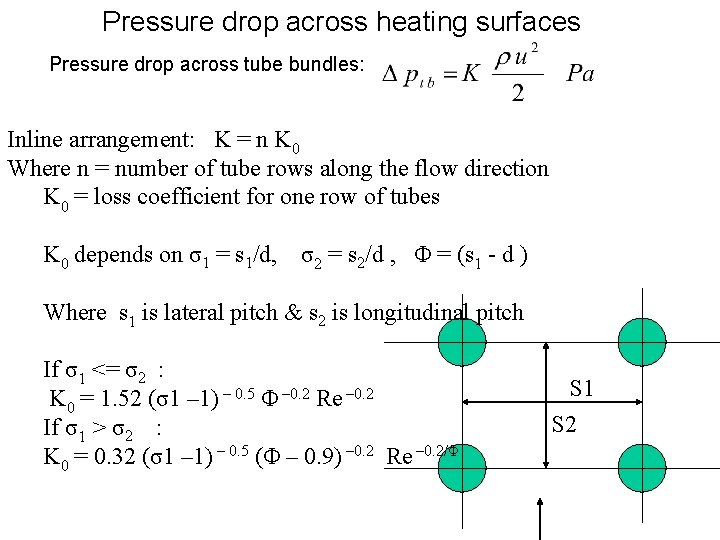
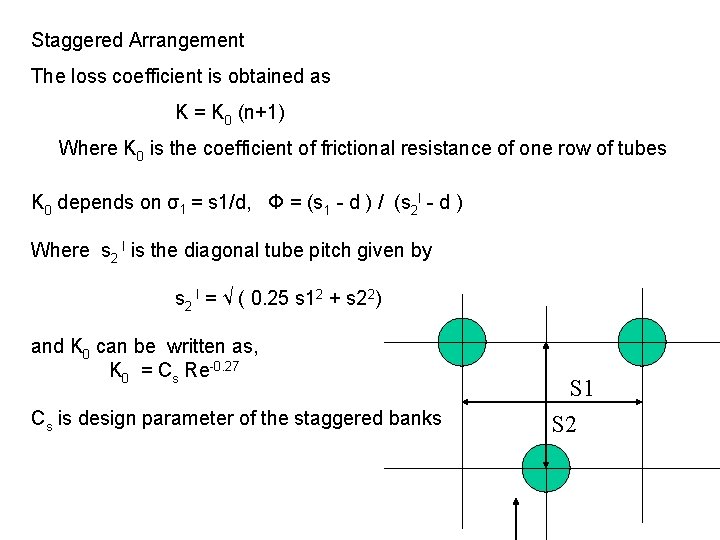
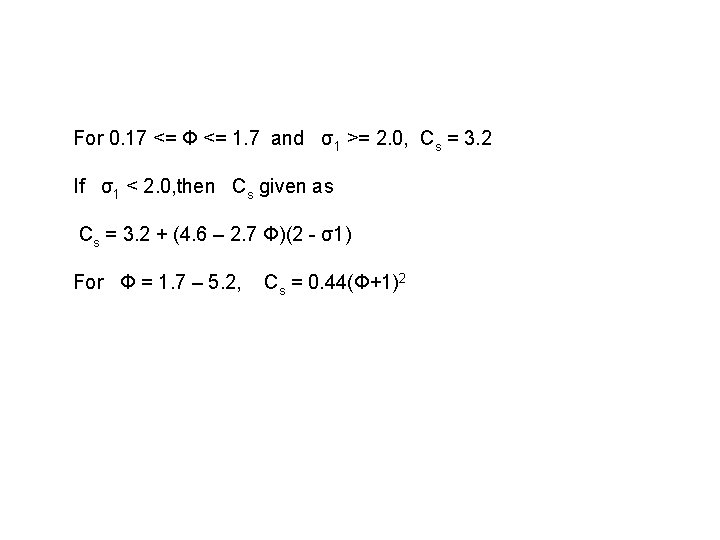
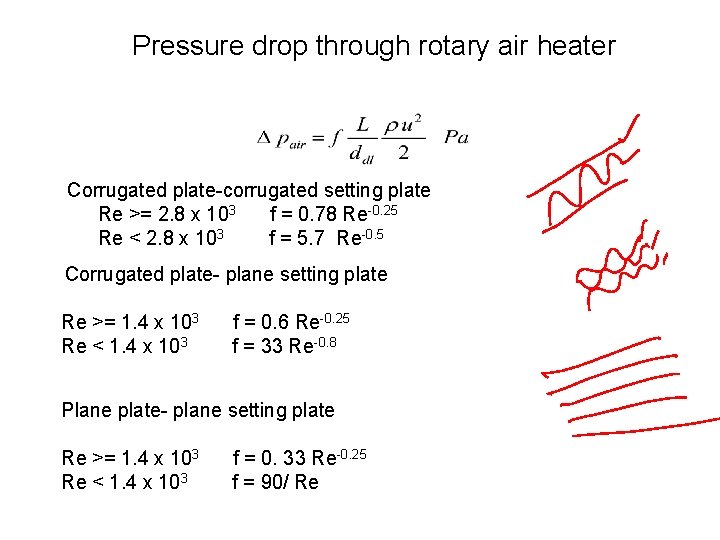
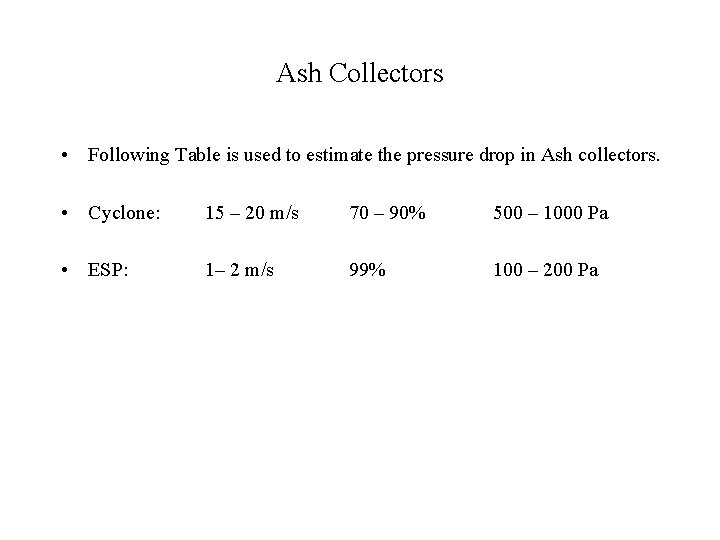
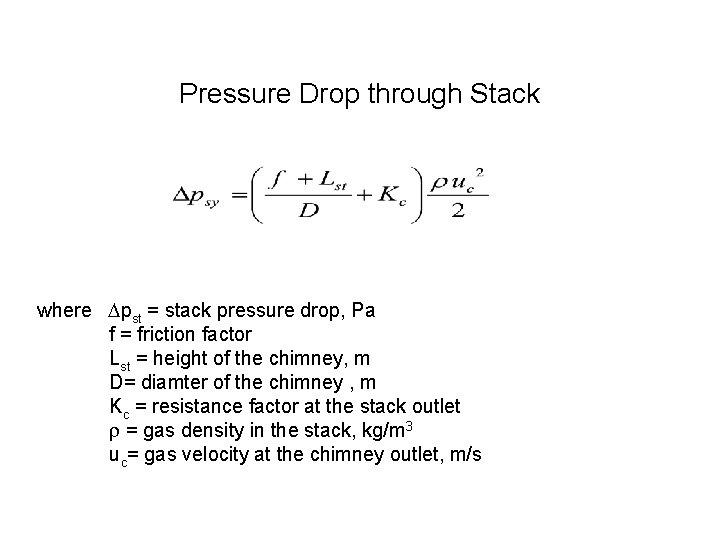
- Slides: 25
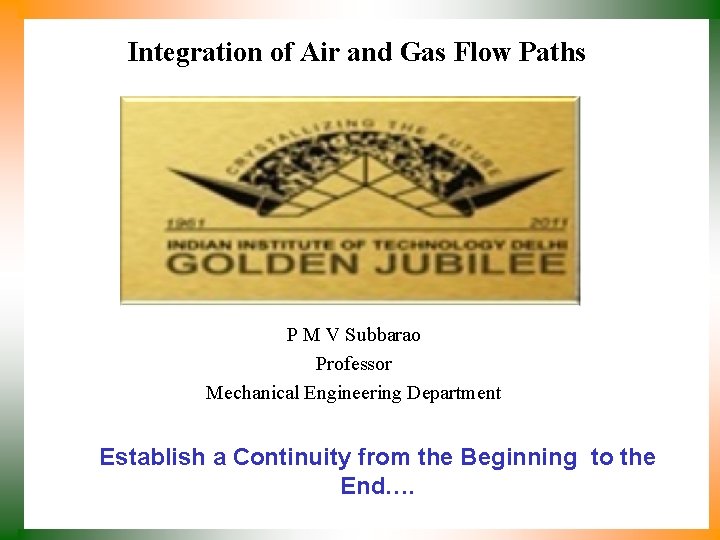
Integration of Air and Gas Flow Paths P M V Subbarao Professor Mechanical Engineering Department Establish a Continuity from the Beginning to the End….
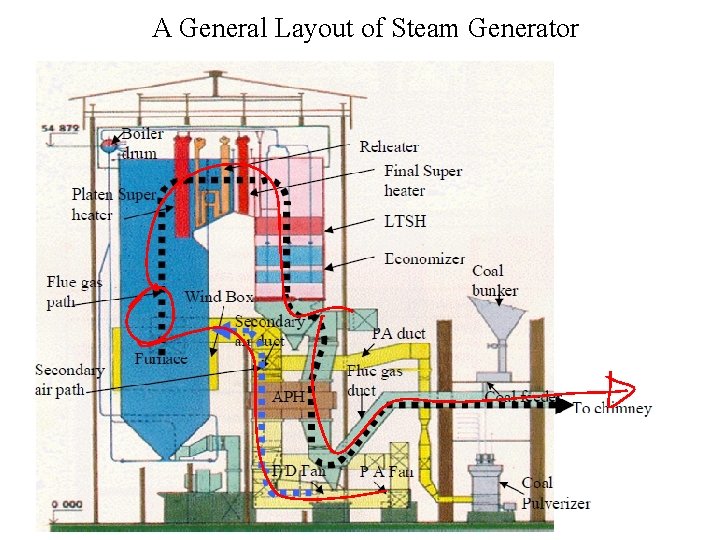
A General Layout of Steam Generator
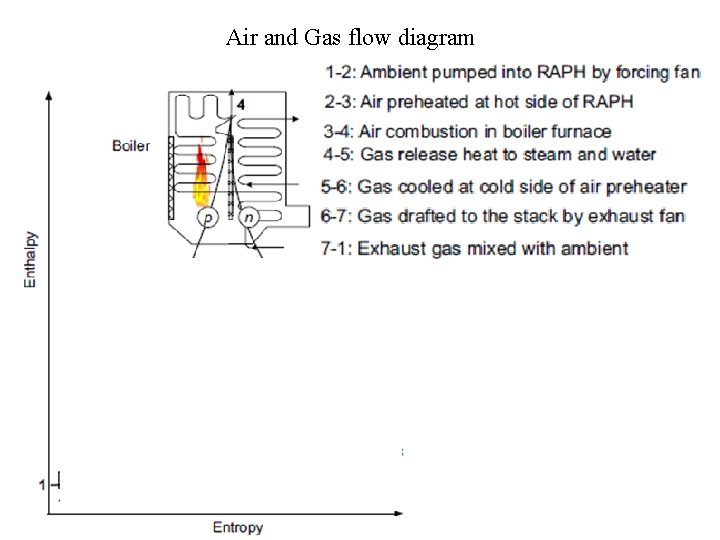
Air and Gas flow diagram
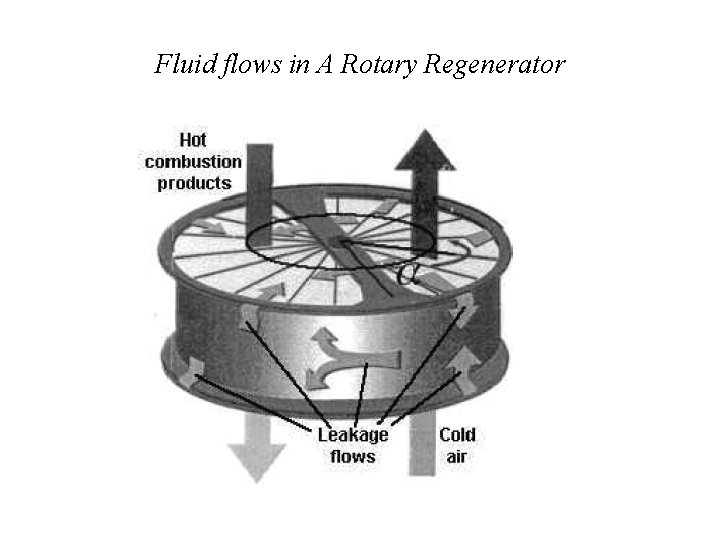
Fluid flows in A Rotary Regenerator
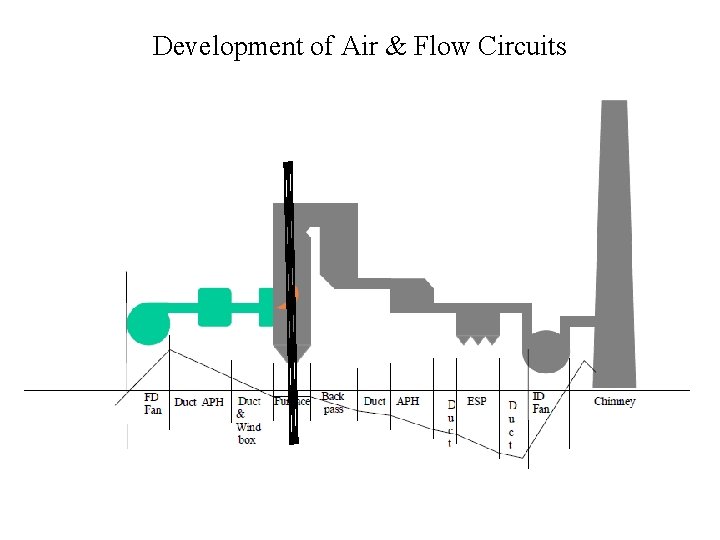
Development of Air & Flow Circuits
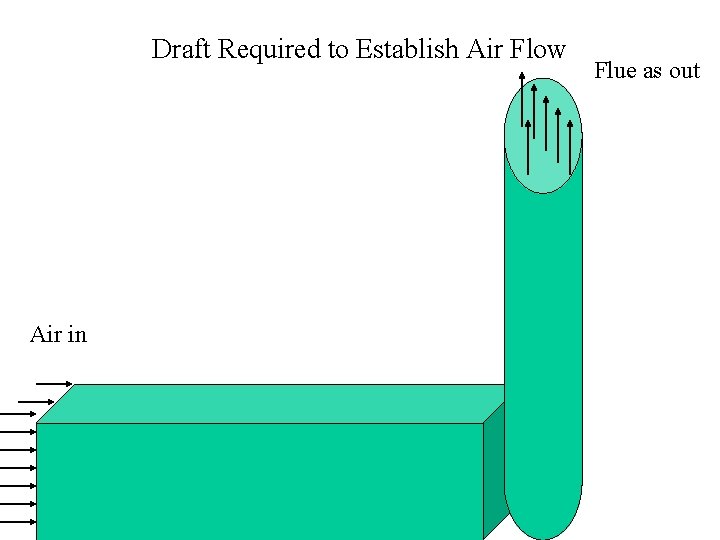
Draft Required to Establish Air Flow Air in Flue as out
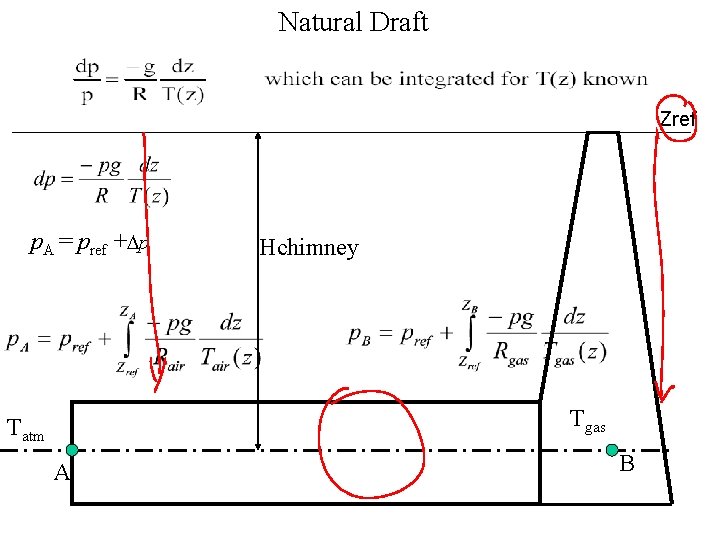
Natural Draft Zref p. A = pref + p Hchimney Tgas Tatm A B
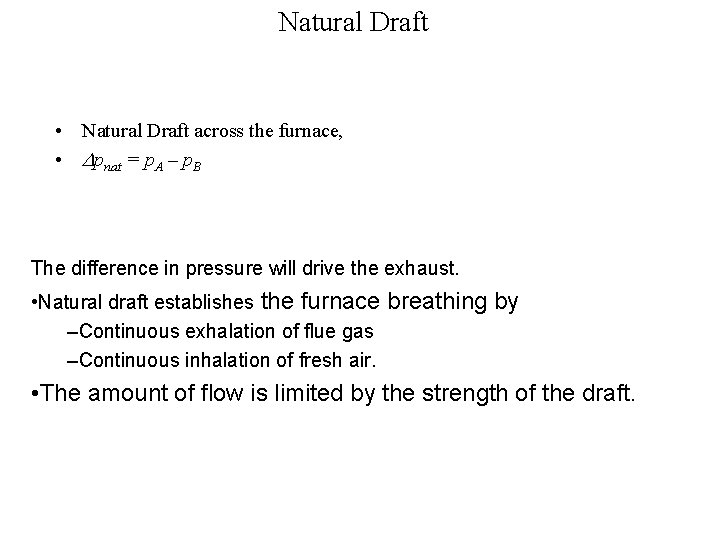
Natural Draft • Natural Draft across the furnace, • Dpnat = p. A – p. B The difference in pressure will drive the exhaust. • Natural draft establishes the furnace breathing by –Continuous exhalation of flue gas –Continuous inhalation of fresh air. • The amount of flow is limited by the strength of the draft.
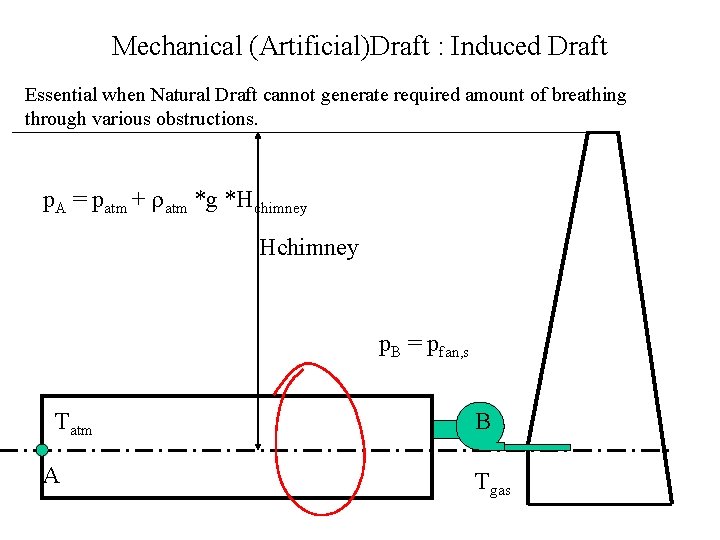
Mechanical (Artificial)Draft : Induced Draft Essential when Natural Draft cannot generate required amount of breathing through various obstructions. p. A = patm + atm *g *Hchimney p. B = pfan, s Tatm A B B Tgas
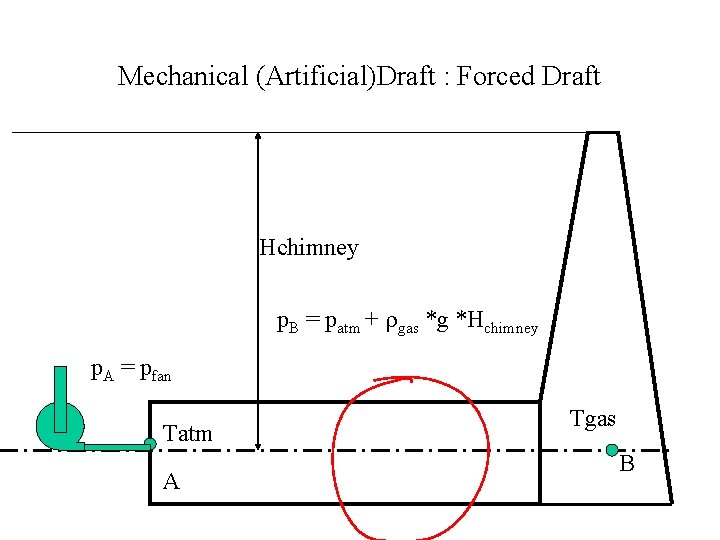
Mechanical (Artificial)Draft : Forced Draft Hchimney p. B = patm + gas *g *Hchimney p. A = pfan Tatm A Tgas B
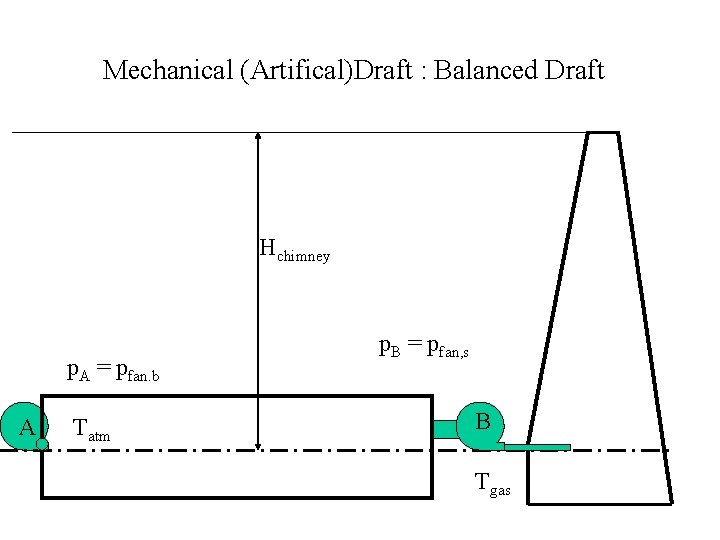
Mechanical (Artifical)Draft : Balanced Draft Hchimney p. A = pfan. b A Tatm p. B = pfan, s B B Tgas
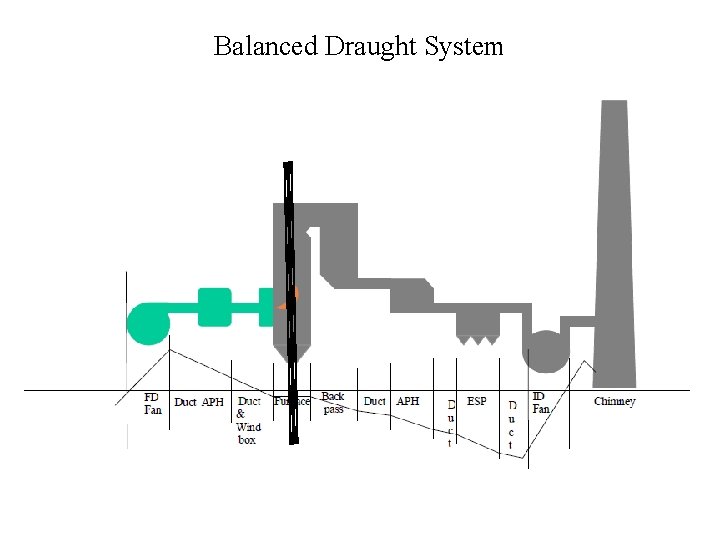
Balanced Draught System
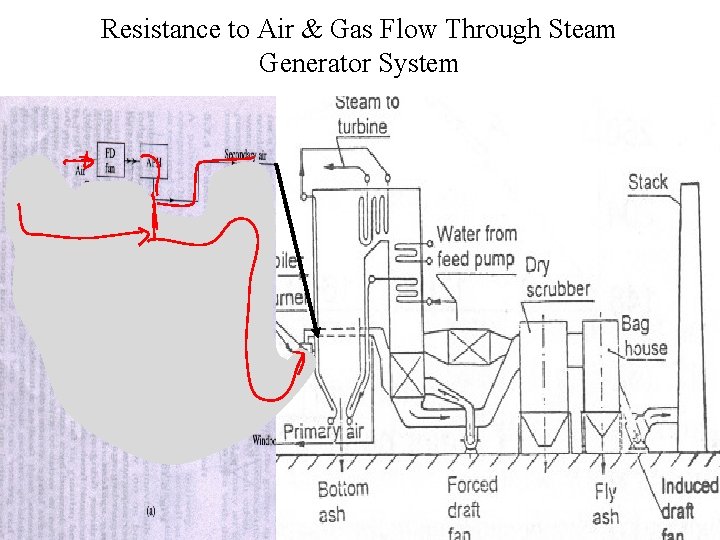
Resistance to Air & Gas Flow Through Steam Generator System
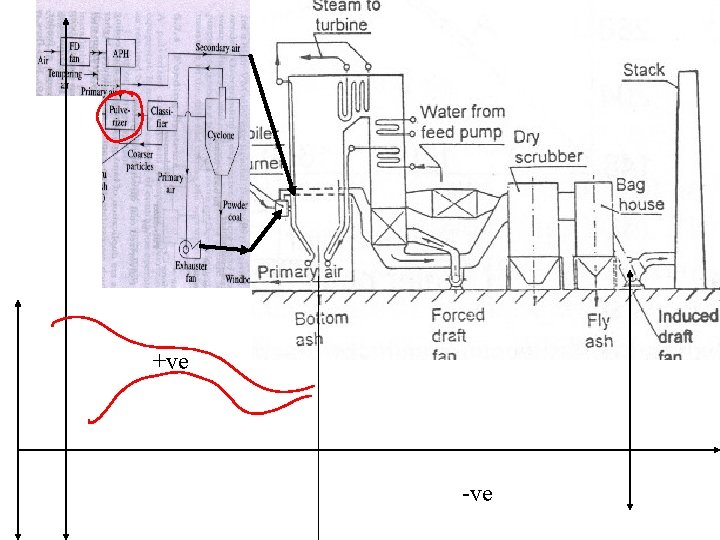
+ve -ve

210 MW POWER PLANT SG Boiler drum Reheater Final Super heater Platen Super heater LTSH Economizer Coal bunker Wind Box Secondary air duct Furnace PA duct APH Flue gas duct F D Fan P A Fan Coal feeder Coal Pulverizer
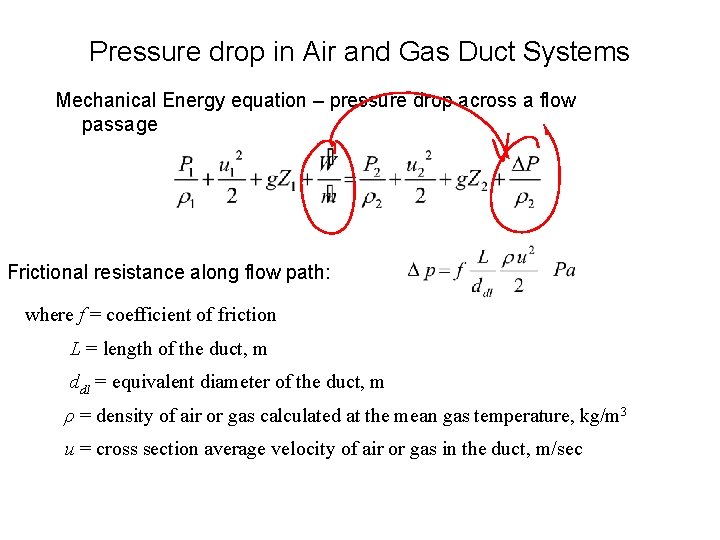
Pressure drop in Air and Gas Duct Systems Mechanical Energy equation – pressure drop across a flow passage Frictional resistance along flow path: where f = coefficient of friction L = length of the duct, m ddl = equivalent diameter of the duct, m ρ = density of air or gas calculated at the mean gas temperature, kg/m 3 u = cross section average velocity of air or gas in the duct, m/sec
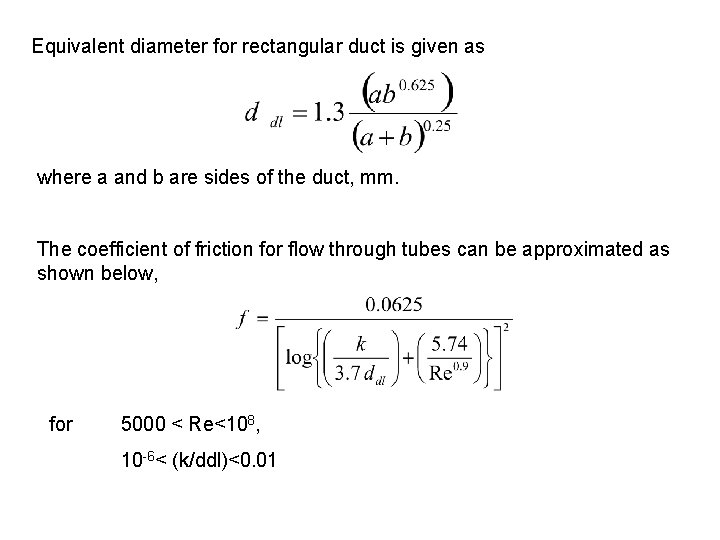
Equivalent diameter for rectangular duct is given as where a and b are sides of the duct, mm. The coefficient of friction for flow through tubes can be approximated as shown below, for 5000 < Re<108, 10 -6< (k/ddl)<0. 01
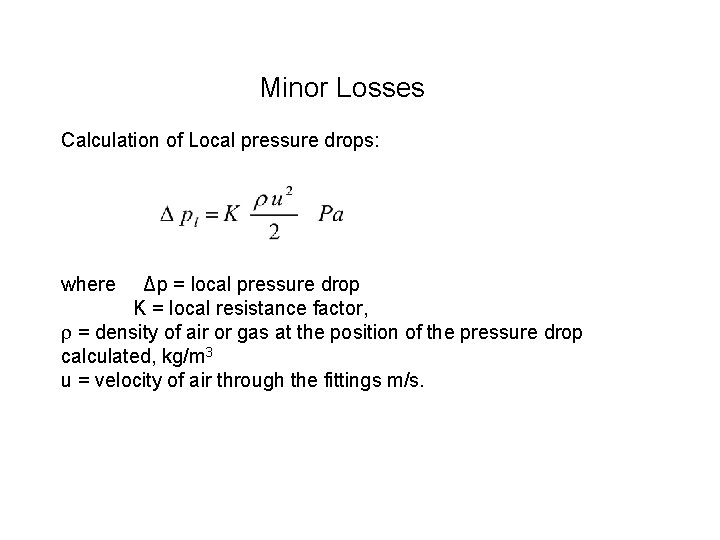
Minor Losses Calculation of Local pressure drops: where Δp = local pressure drop K = local resistance factor, = density of air or gas at the position of the pressure drop calculated, kg/m 3 u = velocity of air through the fittings m/s.
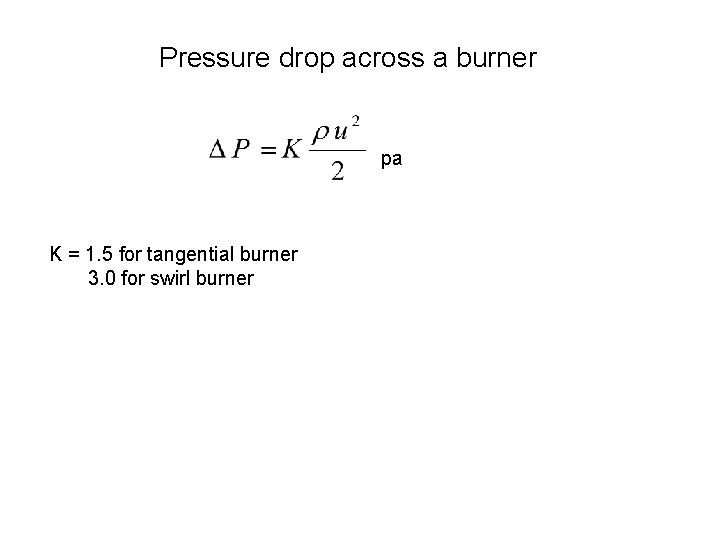
Pressure drop across a burner pa K = 1. 5 for tangential burner 3. 0 for swirl burner
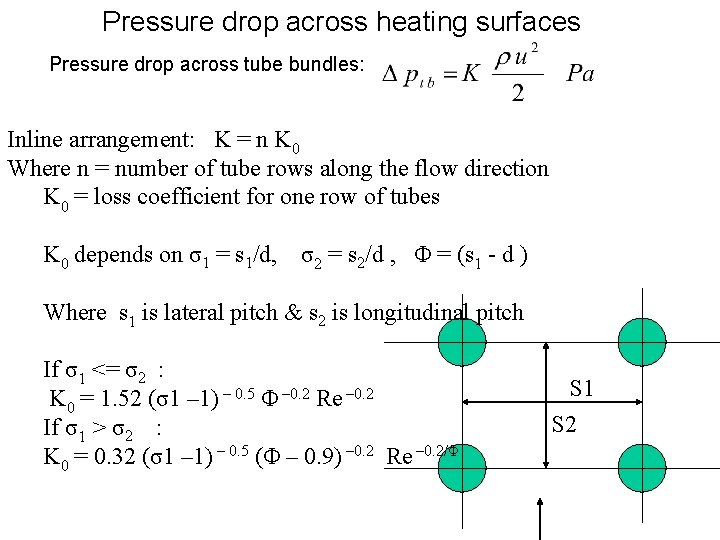
Pressure drop across heating surfaces Pressure drop across tube bundles: Inline arrangement: K = n K 0 Where n = number of tube rows along the flow direction K 0 = loss coefficient for one row of tubes K 0 depends on σ1 = s 1/d, σ2 = s 2/d , Φ = (s 1 - d ) Where s 1 is lateral pitch & s 2 is longitudinal pitch If σ1 <= σ2 : S 1 K 0 = 1. 52 (σ1 – 1) – 0. 5 Φ – 0. 2 Re – 0. 2 S 2 If σ1 > σ2 : K 0 = 0. 32 (σ1 – 1) – 0. 5 (Φ – 0. 9) – 0. 2 Re – 0. 2/Φ
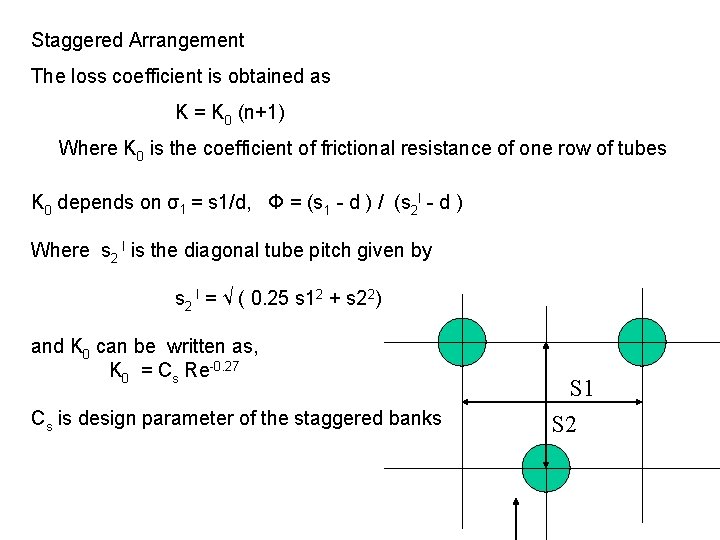
Staggered Arrangement The loss coefficient is obtained as K = K 0 (n+1) Where K 0 is the coefficient of frictional resistance of one row of tubes K 0 depends on σ1 = s 1/d, Φ = (s 1 - d ) / (s 2 l - d ) Where s 2 l is the diagonal tube pitch given by s 2 l = √ ( 0. 25 s 12 + s 22) and K 0 can be written as, K 0 = Cs Re-0. 27 Cs is design parameter of the staggered banks S 1 S 2
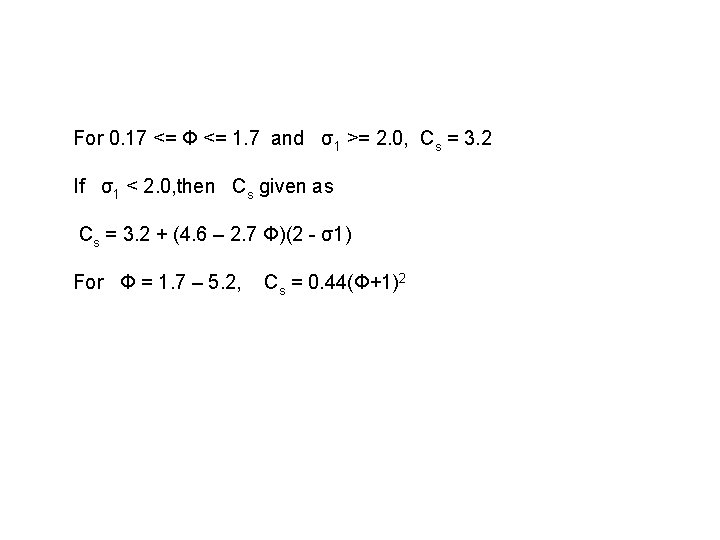
For 0. 17 <= Φ <= 1. 7 and σ1 >= 2. 0, Cs = 3. 2 If σ1 < 2. 0, then Cs given as Cs = 3. 2 + (4. 6 – 2. 7 Φ)(2 - σ1) For Φ = 1. 7 – 5. 2, Cs = 0. 44(Φ+1)2
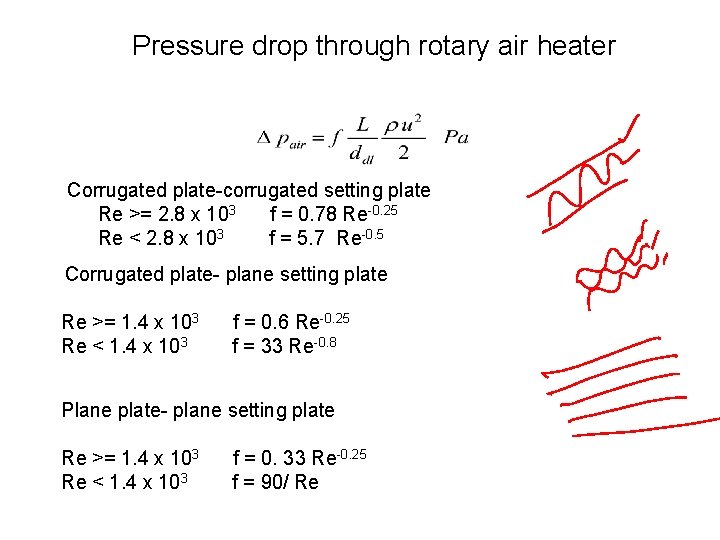
Pressure drop through rotary air heater Corrugated plate-corrugated setting plate Re >= 2. 8 x 103 f = 0. 78 Re-0. 25 Re < 2. 8 x 103 f = 5. 7 Re-0. 5 Corrugated plate- plane setting plate Re >= 1. 4 x 103 f = 0. 6 Re-0. 25 Re < 1. 4 x 103 f = 33 Re-0. 8 Plane plate- plane setting plate Re >= 1. 4 x 103 f = 0. 33 Re-0. 25 Re < 1. 4 x 103 f = 90/ Re
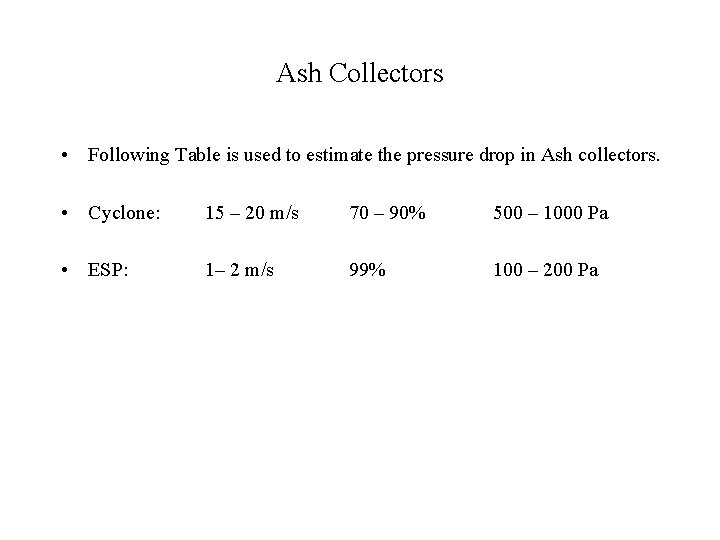
Ash Collectors • Following Table is used to estimate the pressure drop in Ash collectors. • Cyclone: 15 – 20 m/s 70 – 90% 500 – 1000 Pa • ESP: 1– 2 m/s 99% 100 – 200 Pa
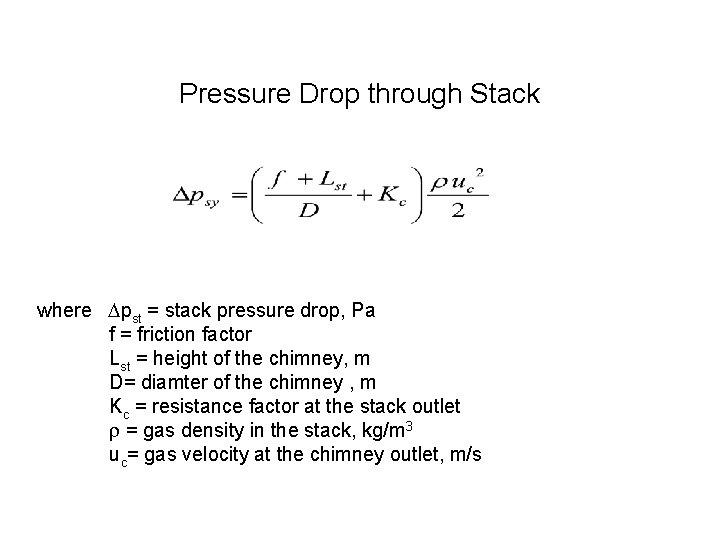
Pressure Drop through Stack where pst = stack pressure drop, Pa f = friction factor Lst = height of the chimney, m D= diamter of the chimney , m Kc = resistance factor at the stack outlet = gas density in the stack, kg/m 3 uc= gas velocity at the chimney outlet, m/s
Linearly independent paths
Flor control doz
Flow time analysis
Air higroskopis air kapiler dan air gravitasi
Forward integration and backward integration
Vertical integration
What is simultaneous integration
Networks and graphs: circuits, paths, and graph structures
Euler path vs circuit
Differences between ideal gas and real gas
Difference between ideal gas and real gas
Shortest paths and transitive closure in data structure
Paths, trees, and flowers
Shortest path problem linear programming
Difference constraints and shortest paths
American idol
Paths start and stop at
Derive ideal gas equation
An ideal gas is an imaginary gas
Ideal gas vs perfect gas
Reason for bhopal gas tragedy
Gas leaked in bhopal gas tragedy
Volume molare
Flue gas desulfurisation gas filter
Poisonous gas leaked in bhopal gas tragedy
Reaksi pembentukan gas no2f dari gas no2 dan f2