Hazardous Location Protection Techniques and Wiring Methods Presented
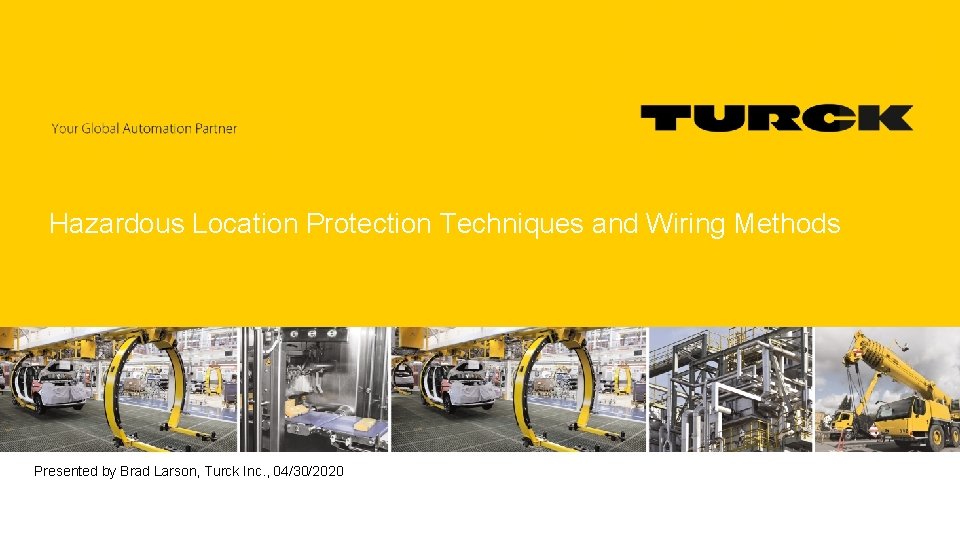
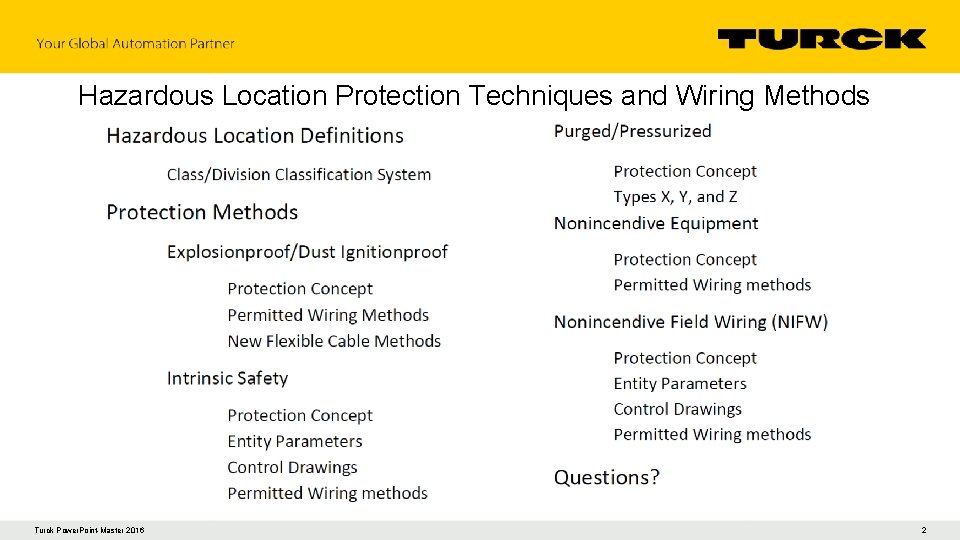
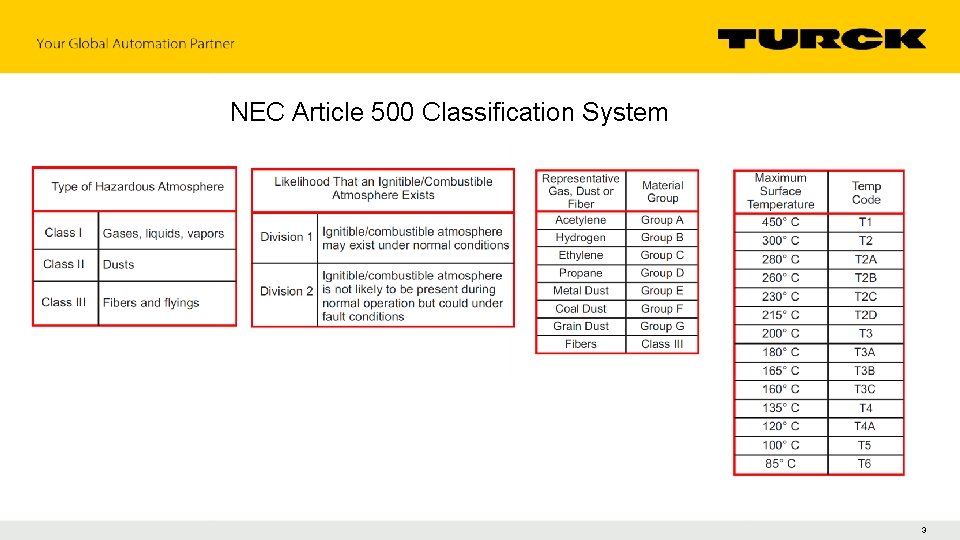
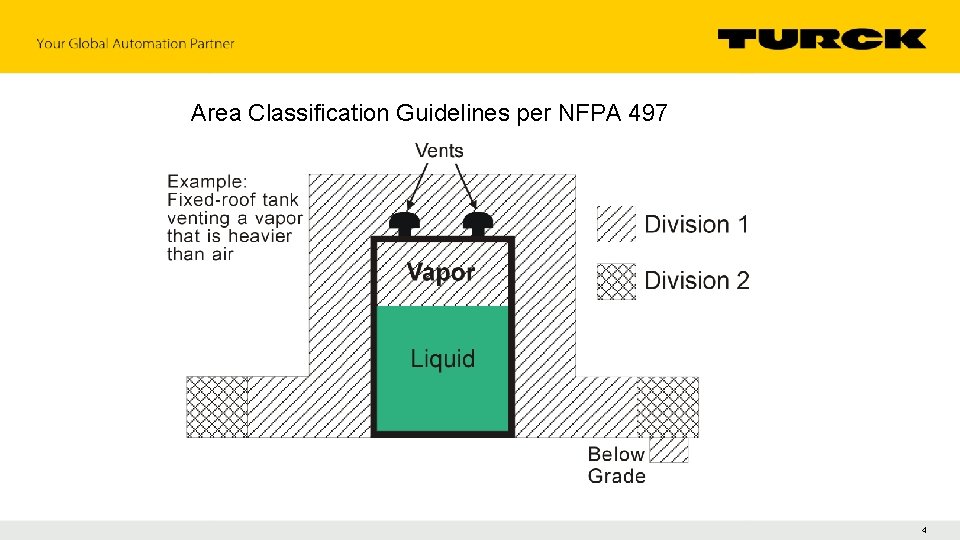
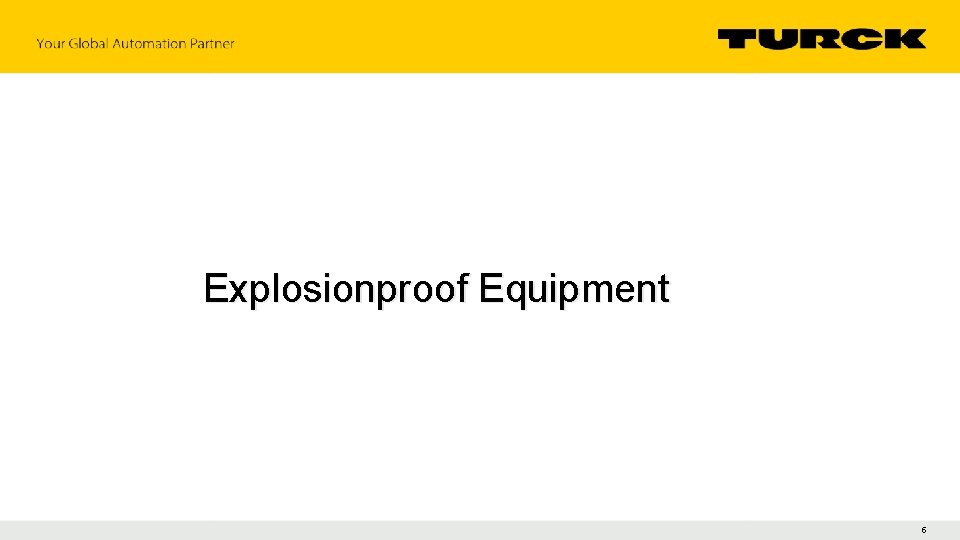
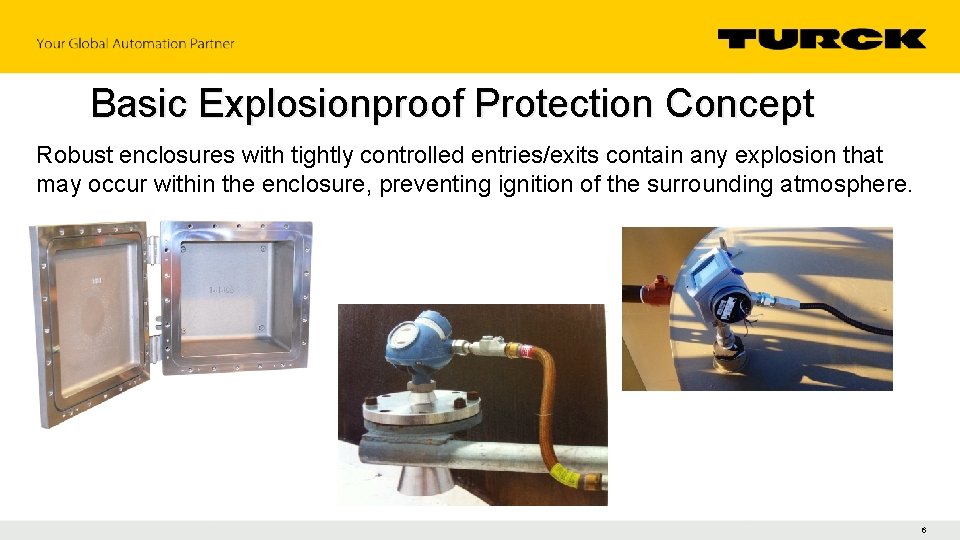
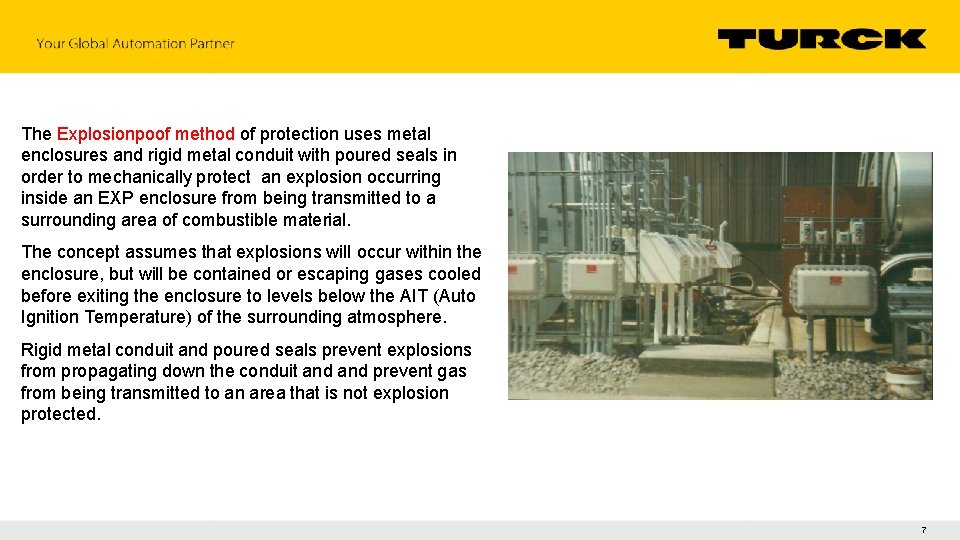
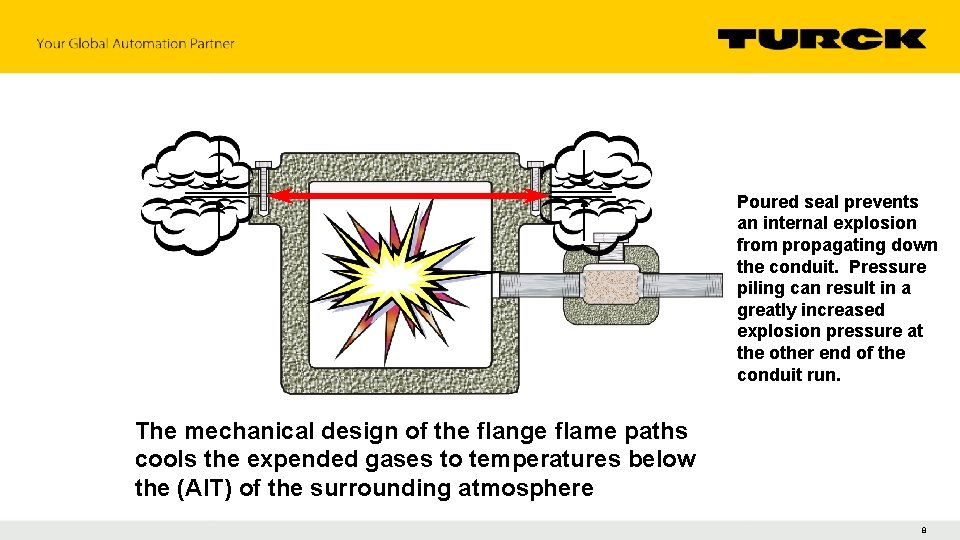
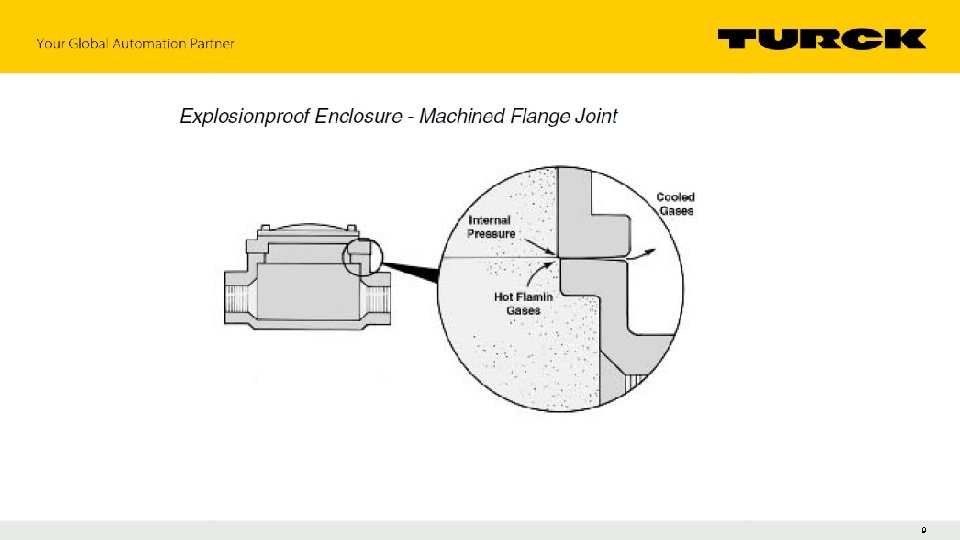
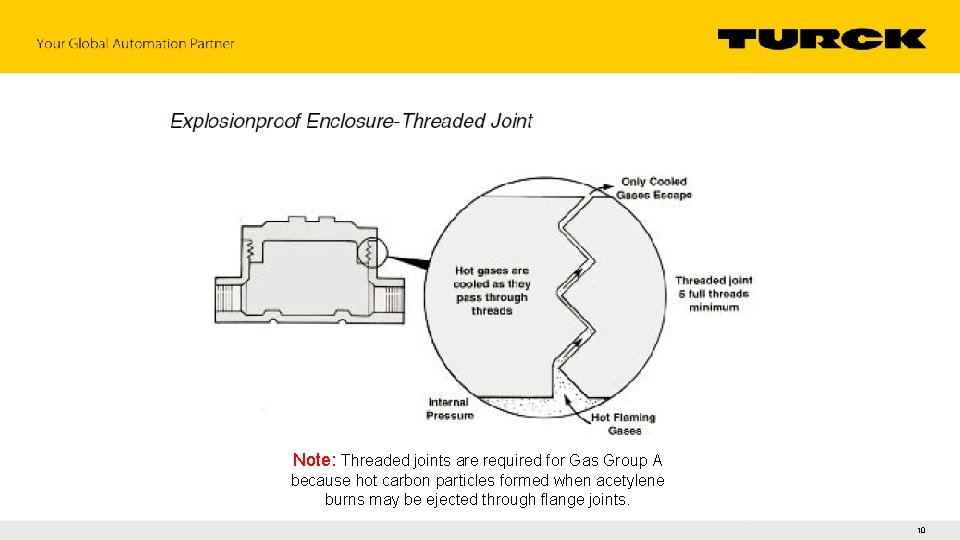
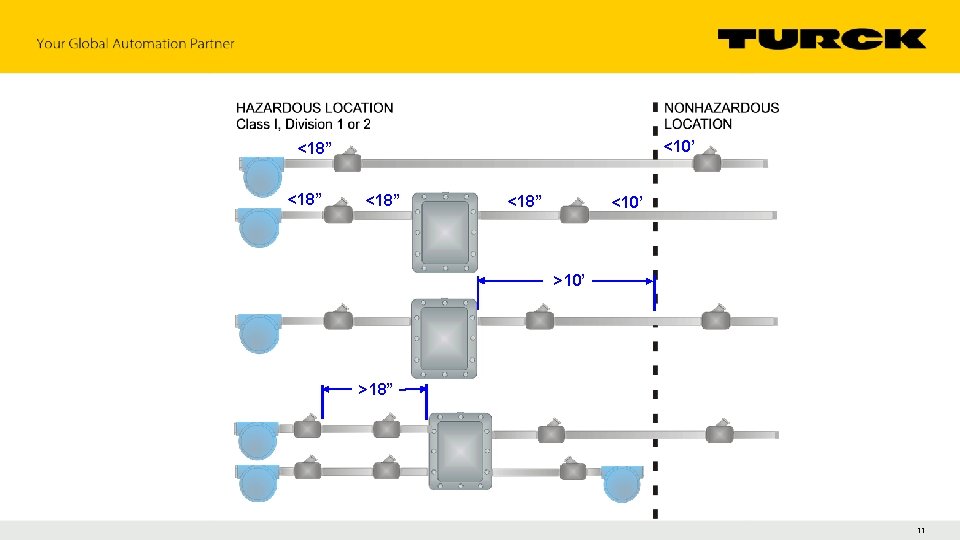
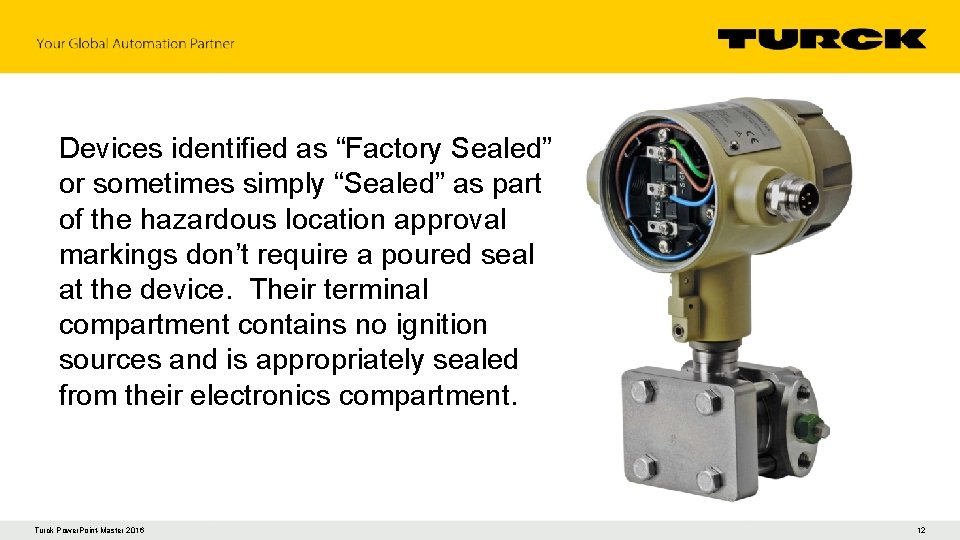
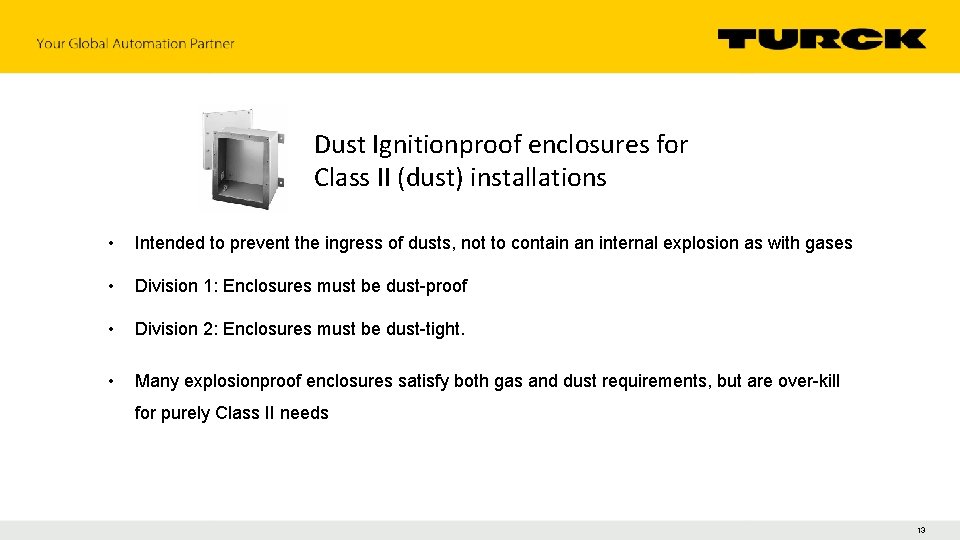
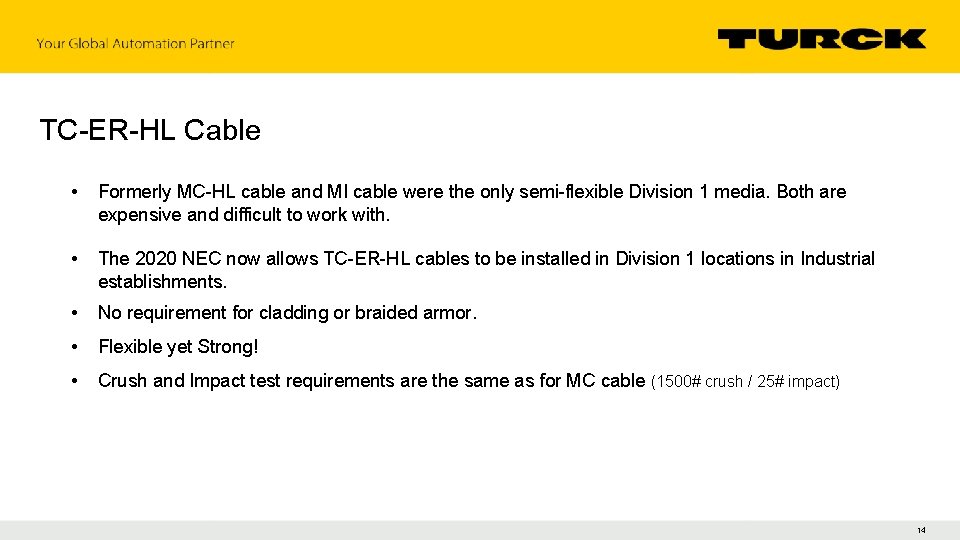
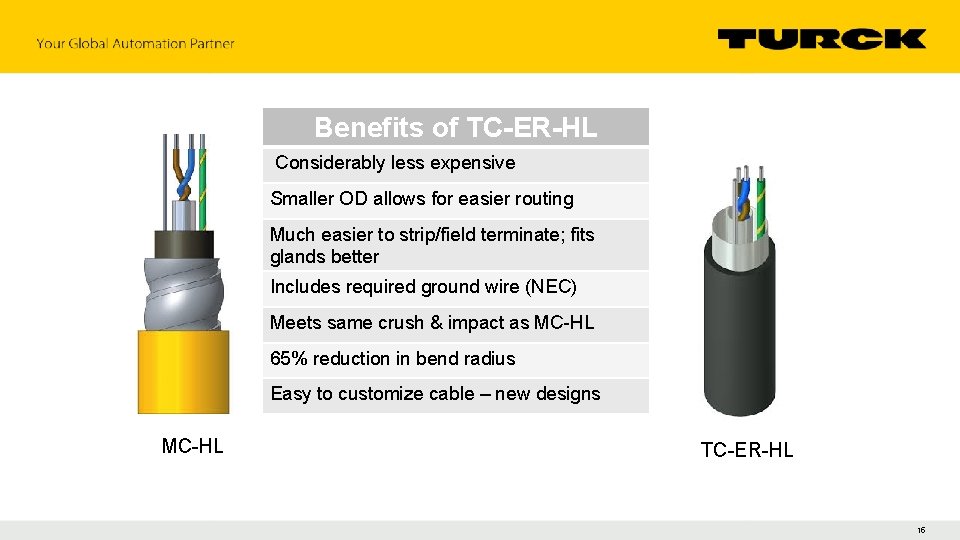
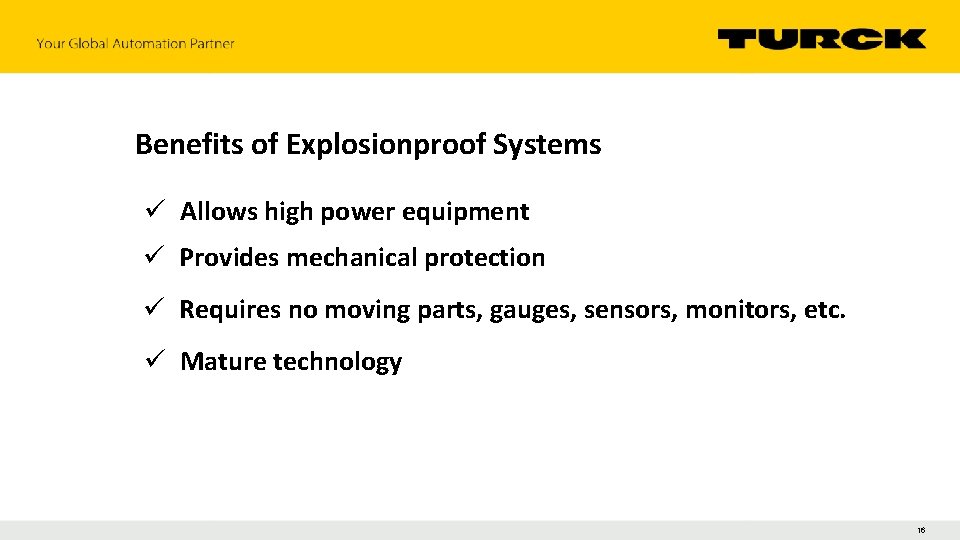
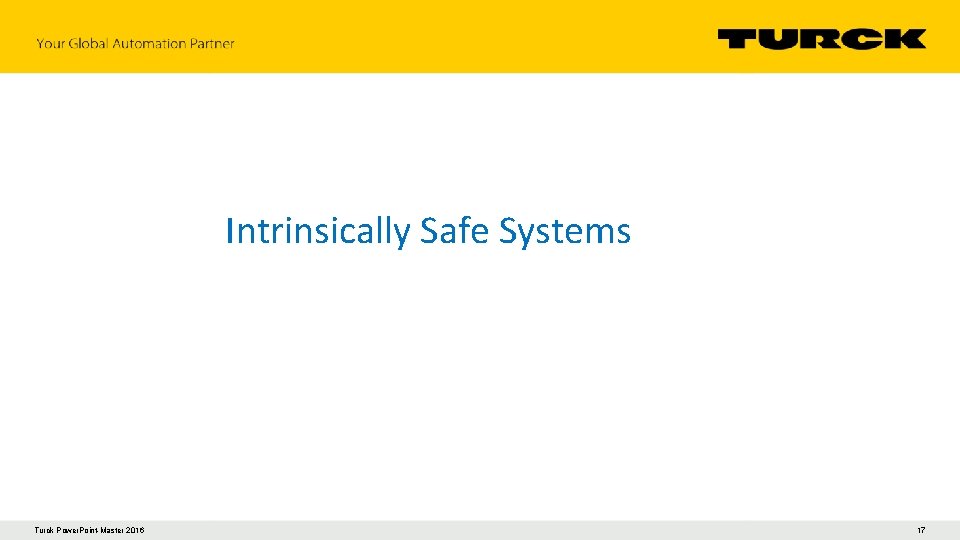
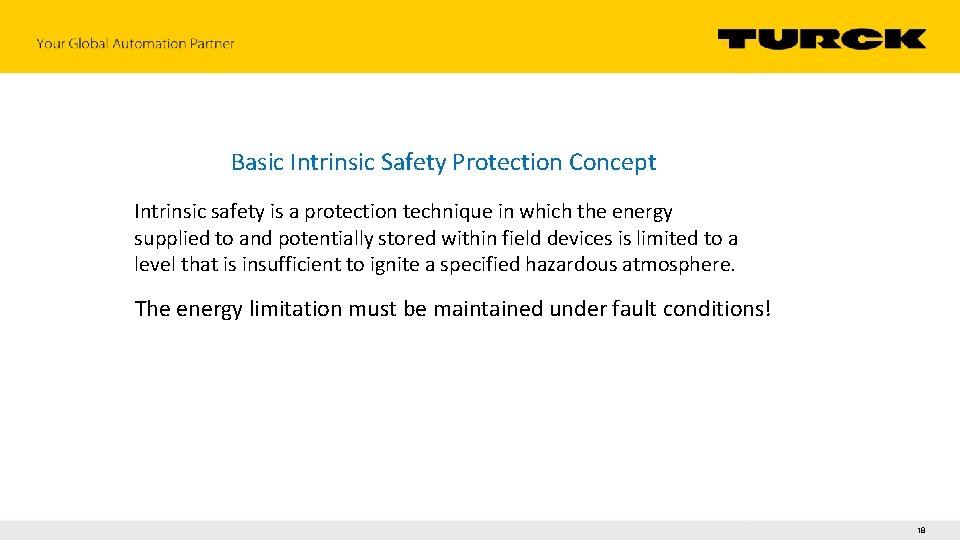
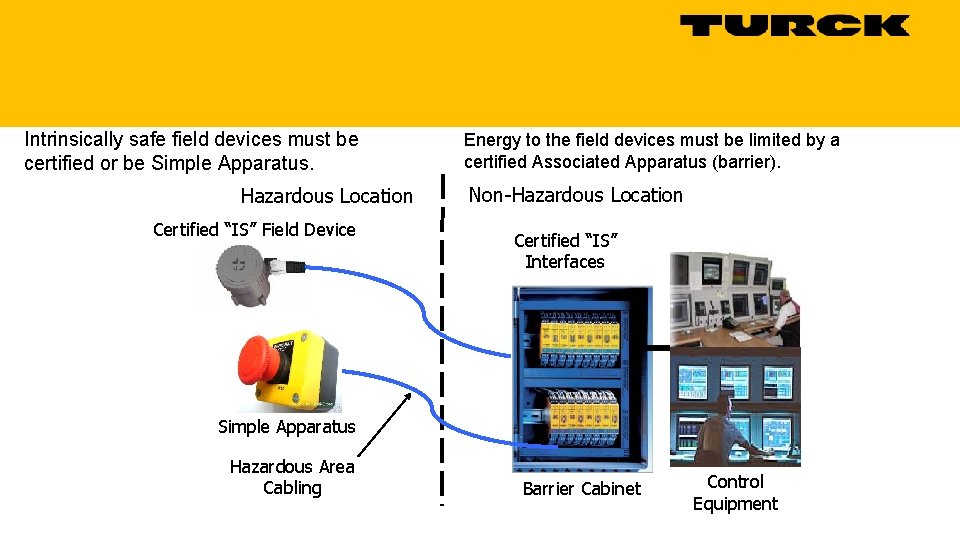
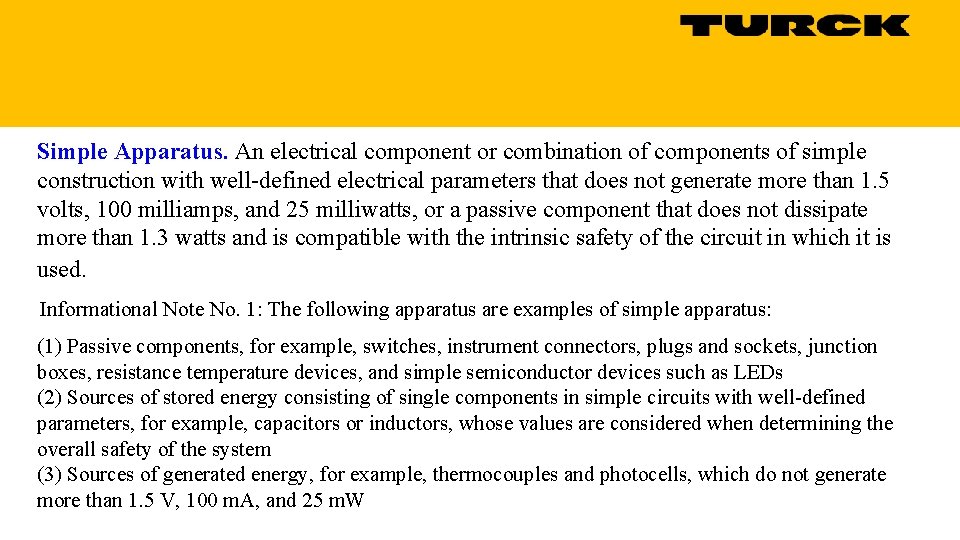
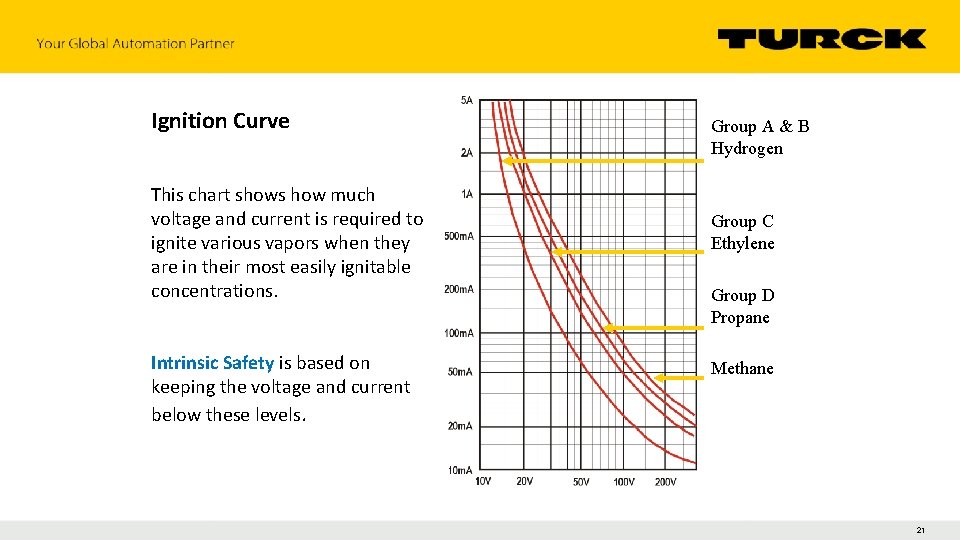
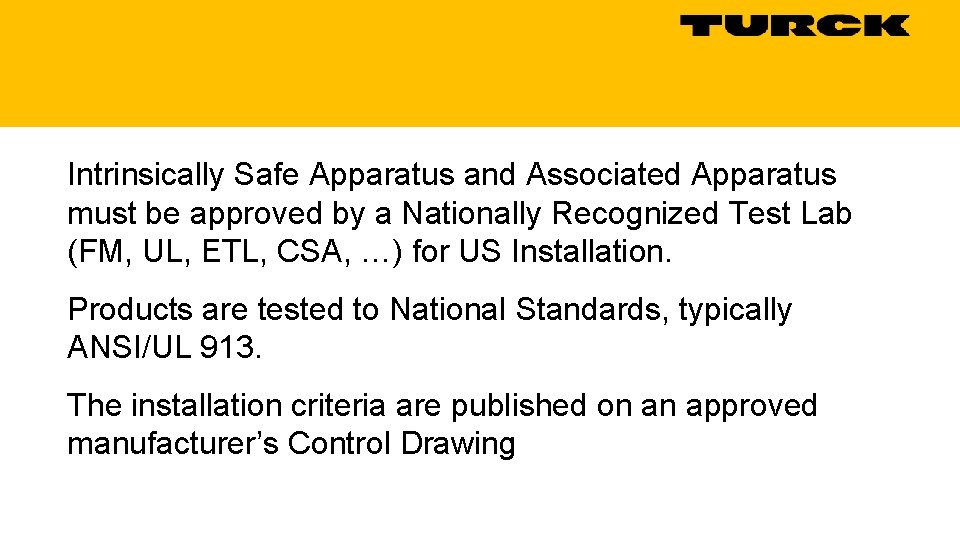
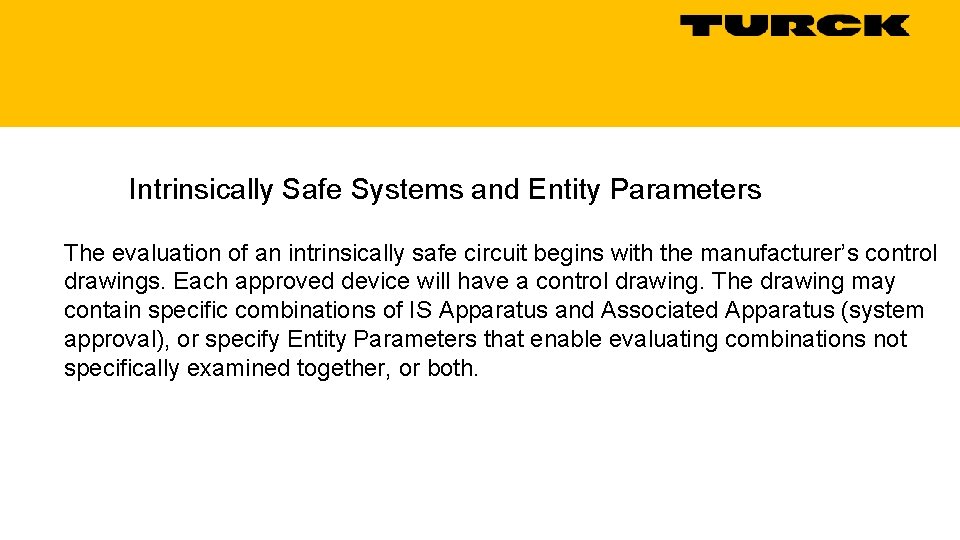
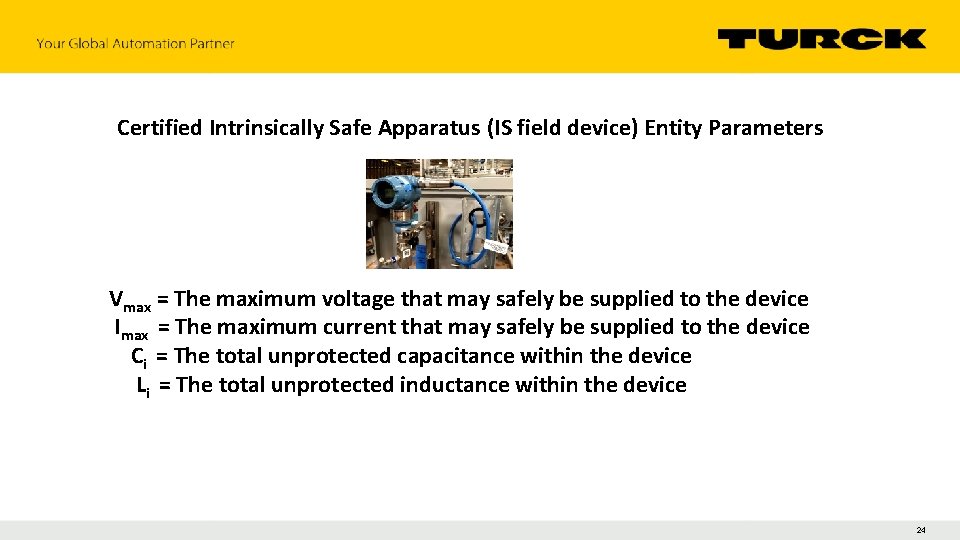
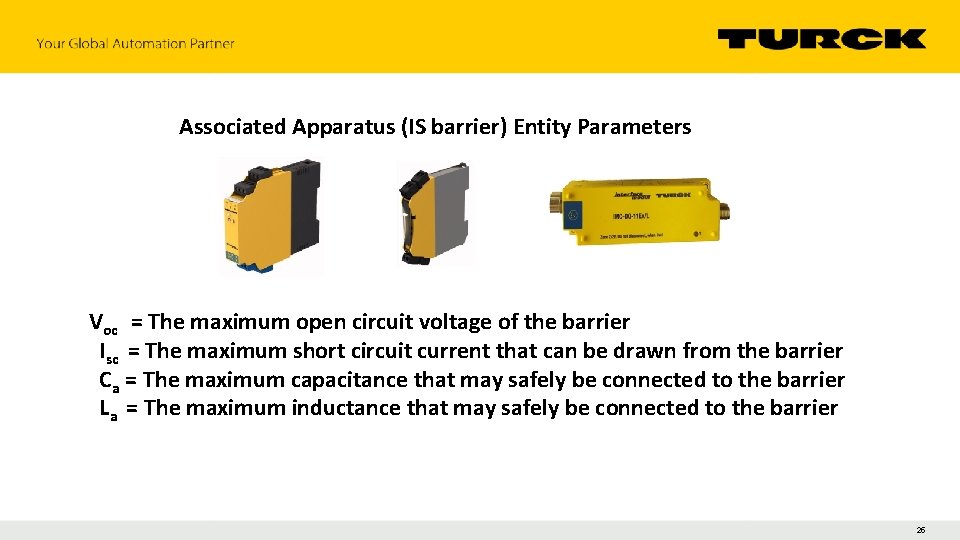
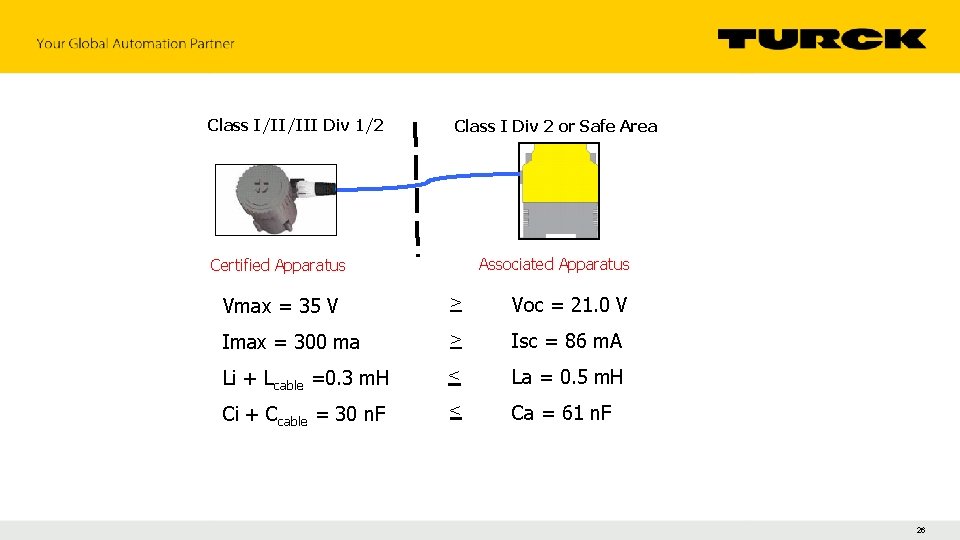
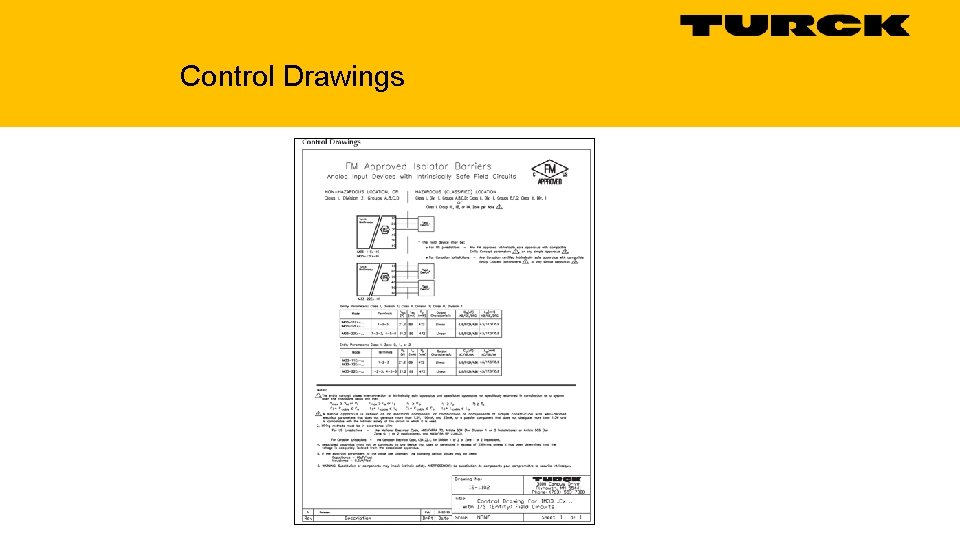
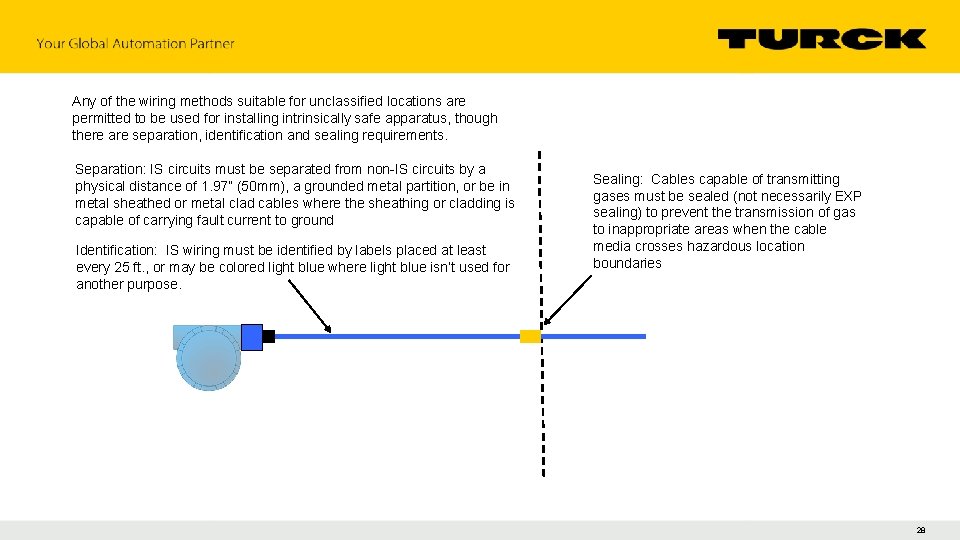
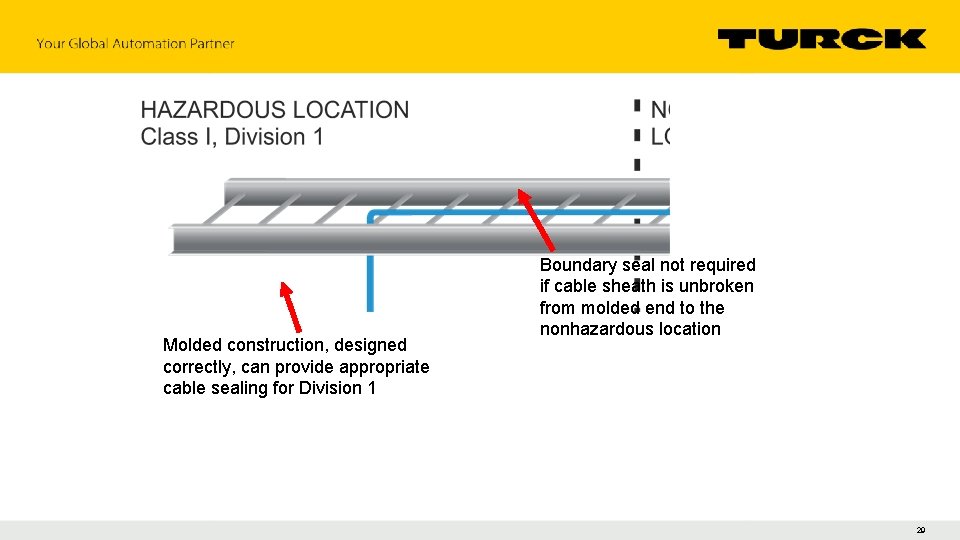
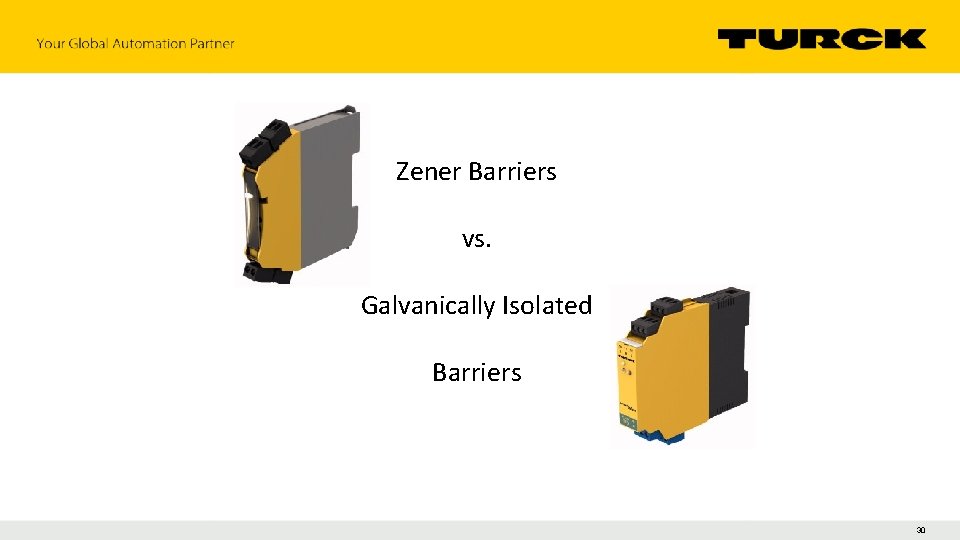
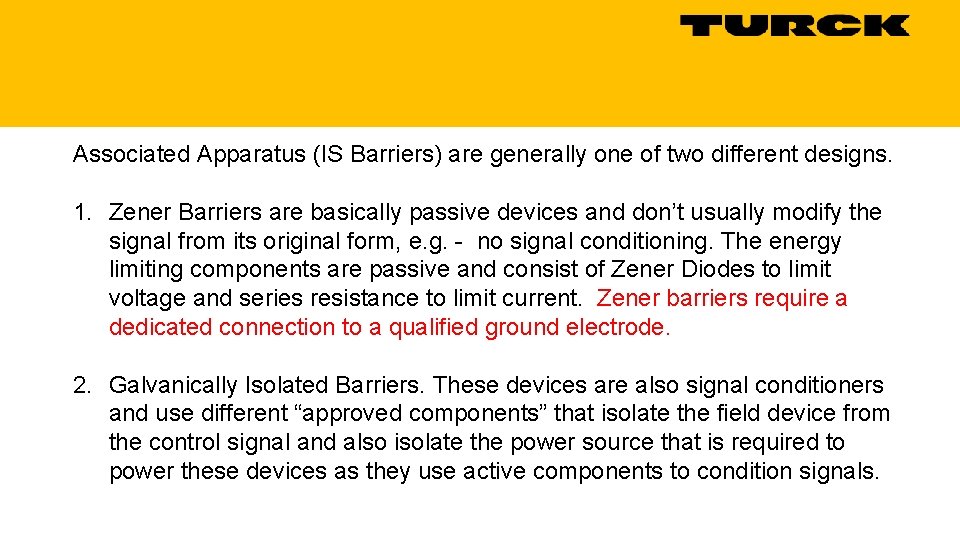
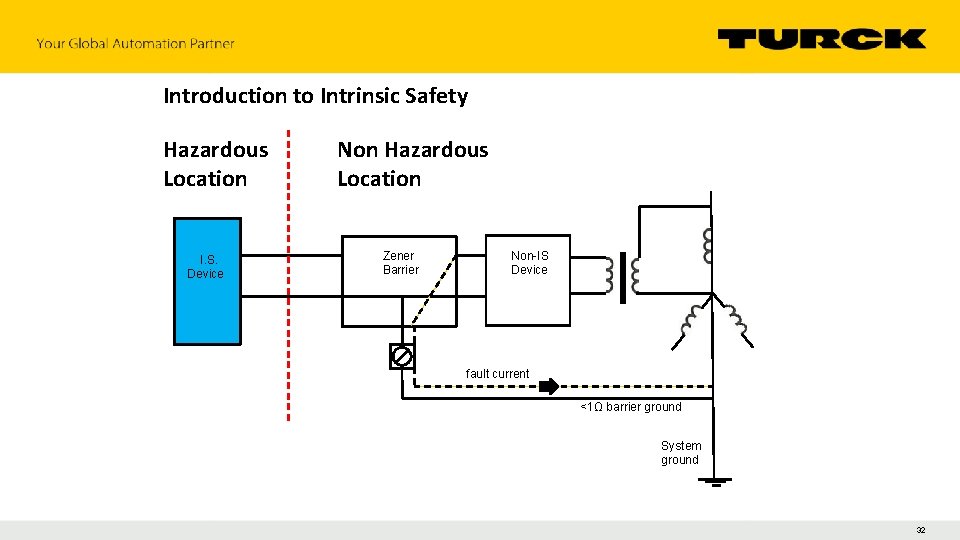
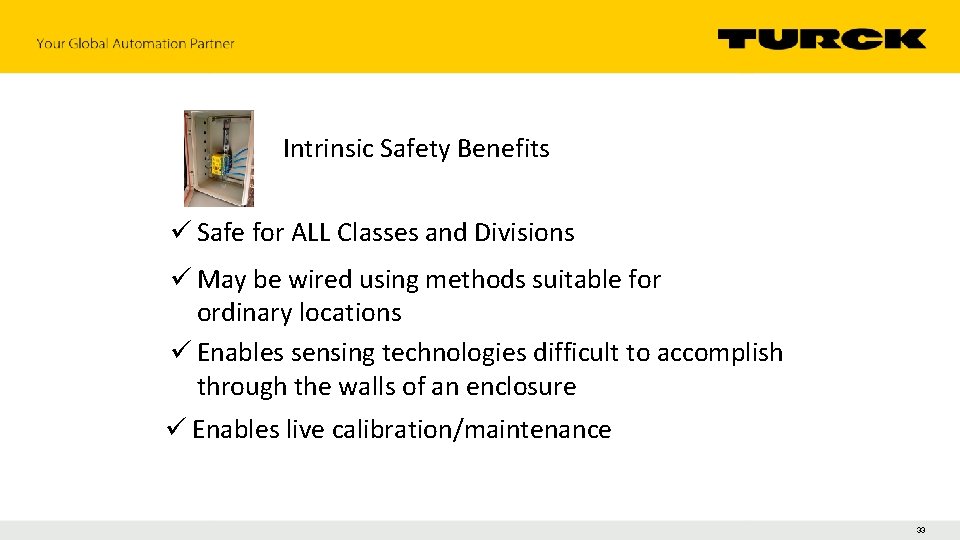
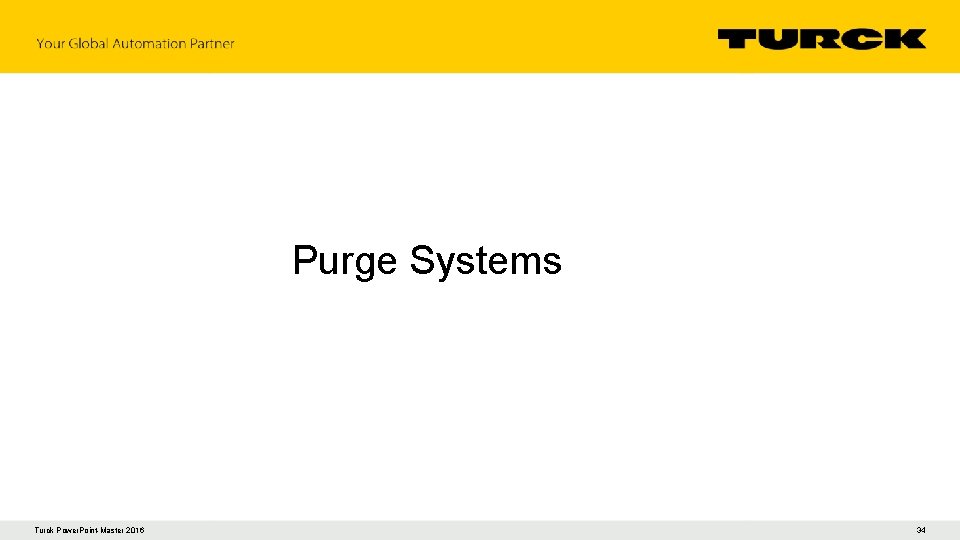
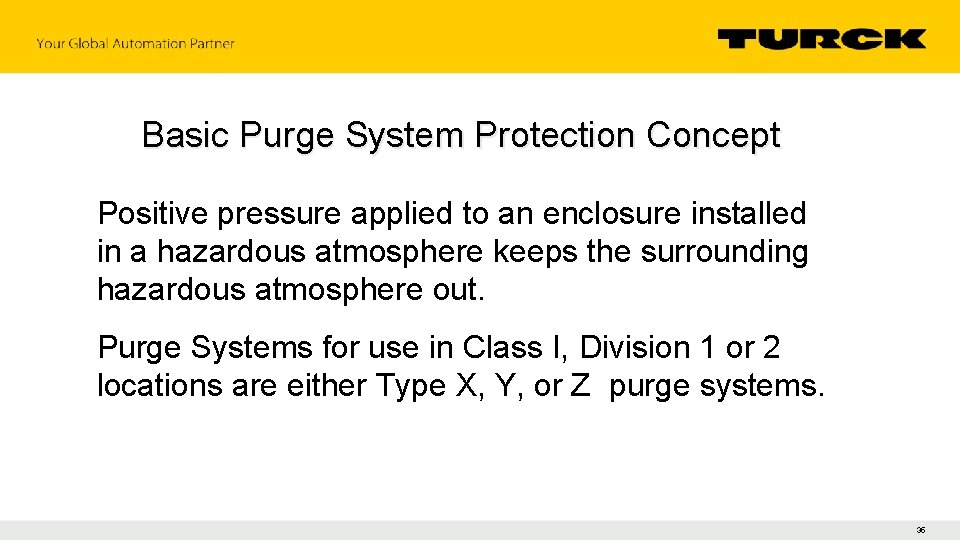
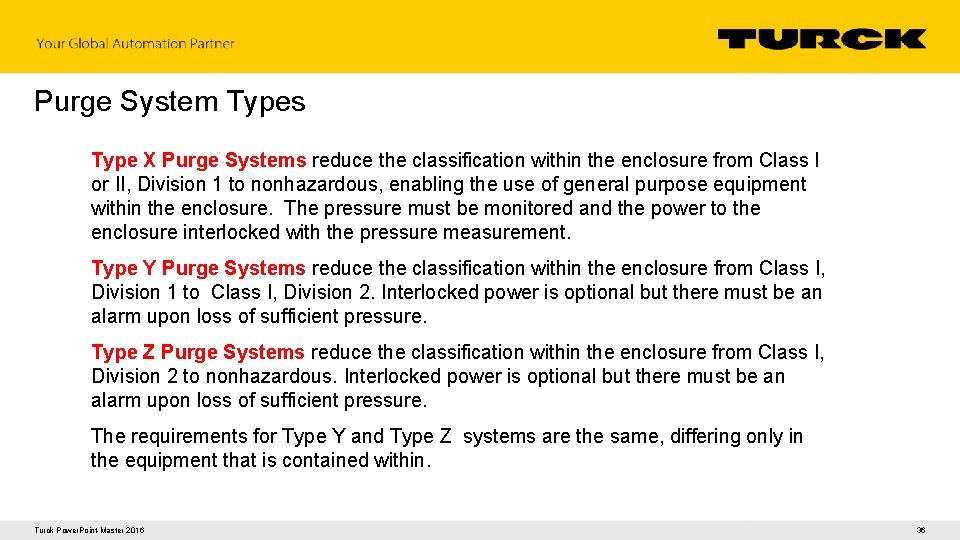
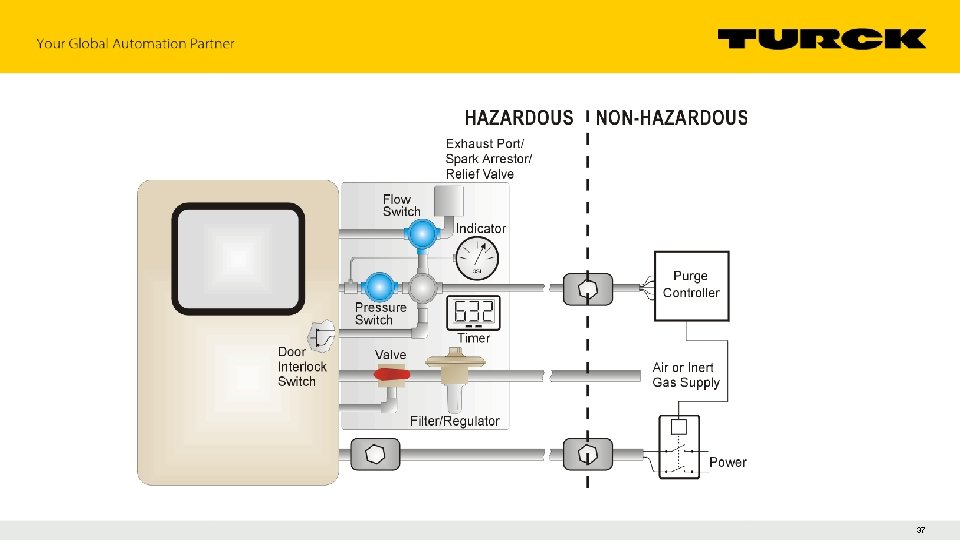
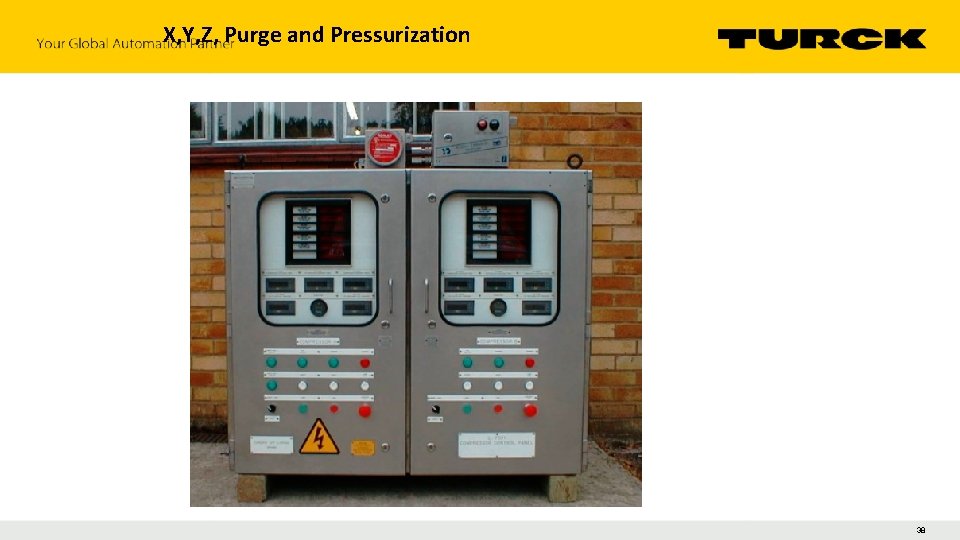
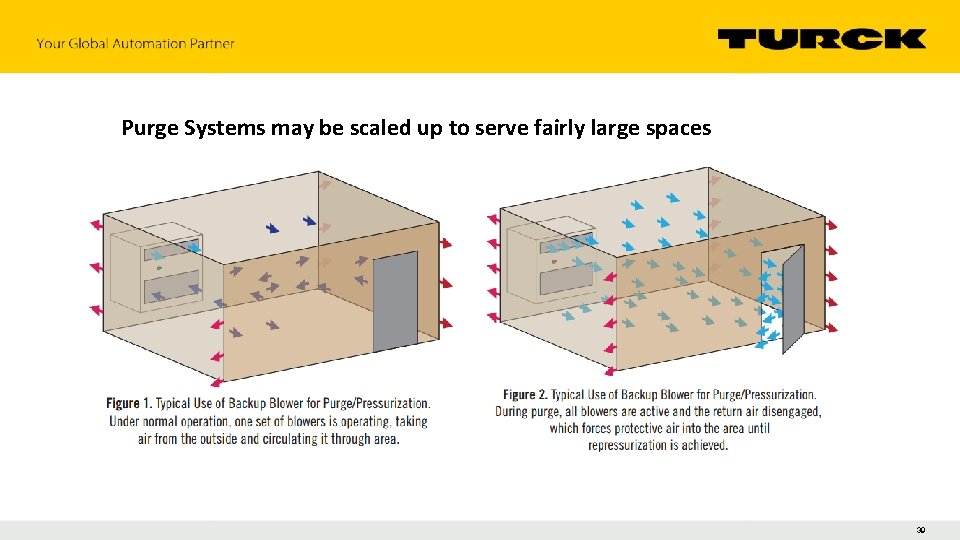
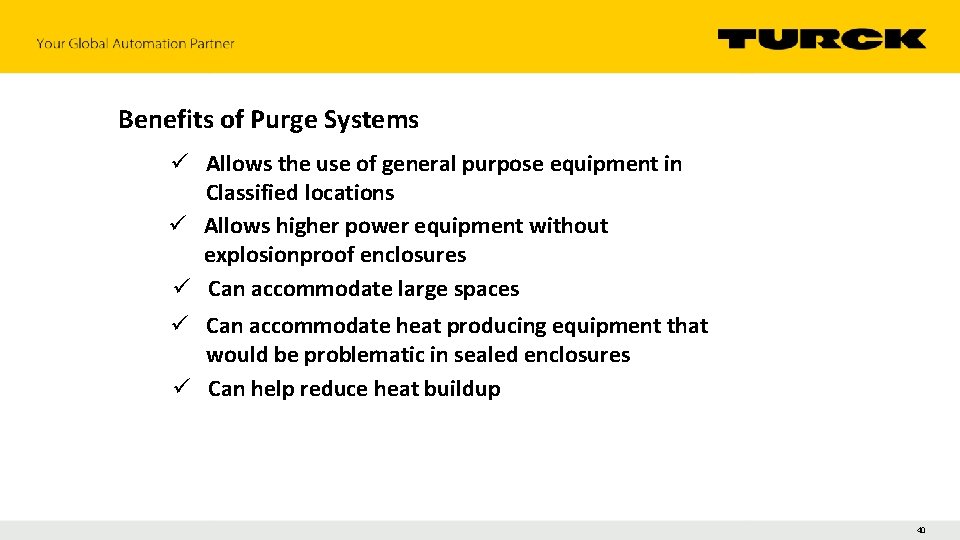
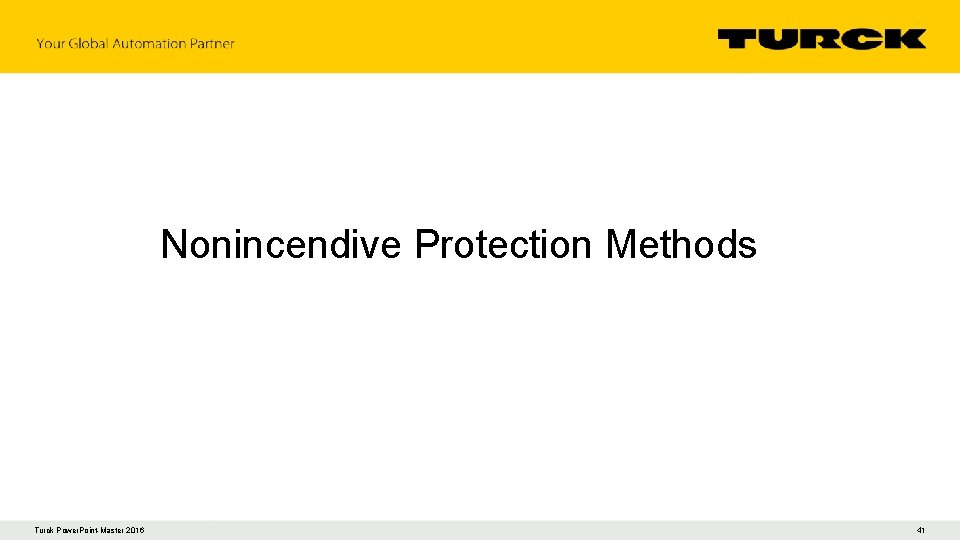
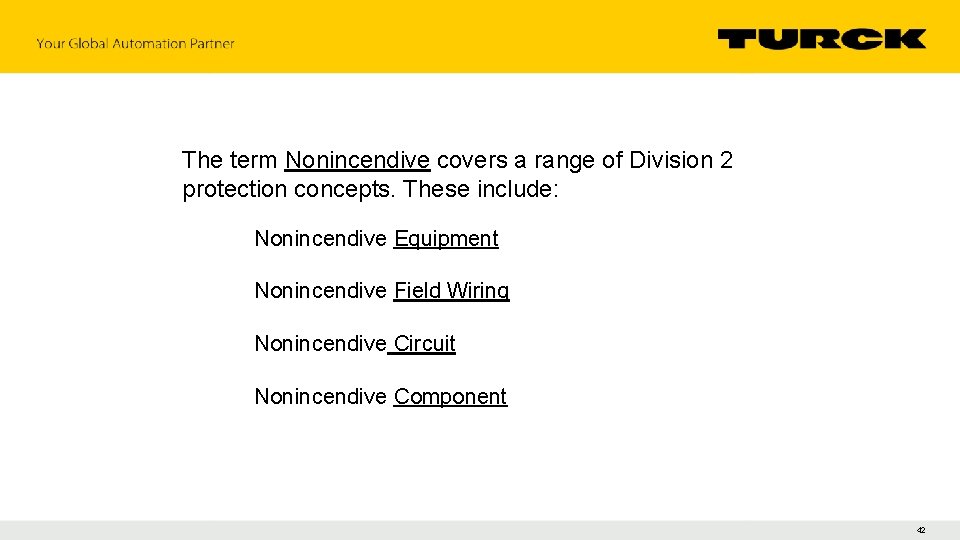
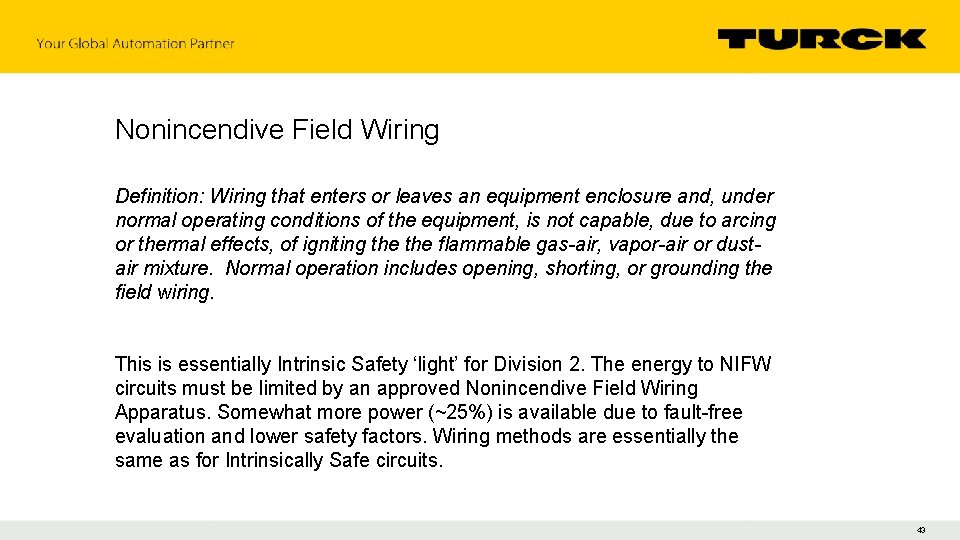
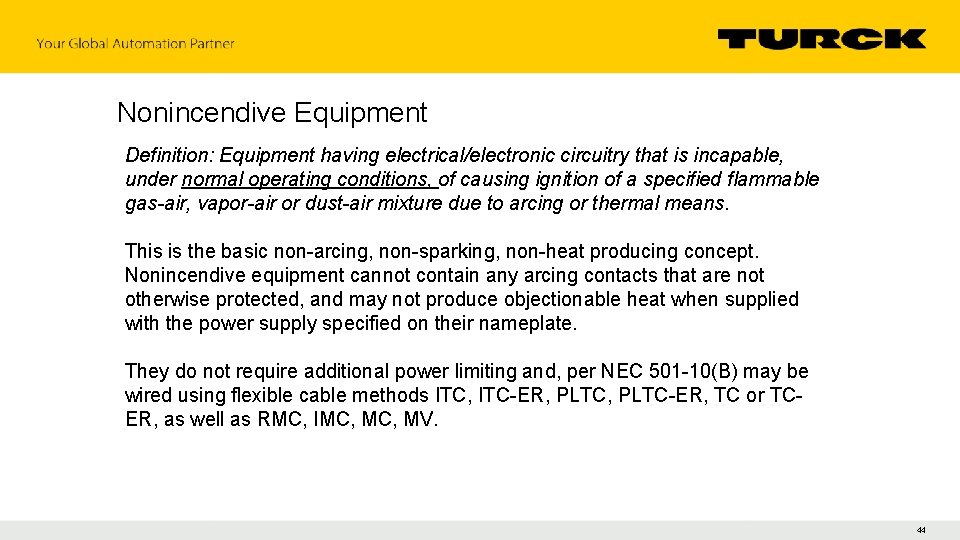
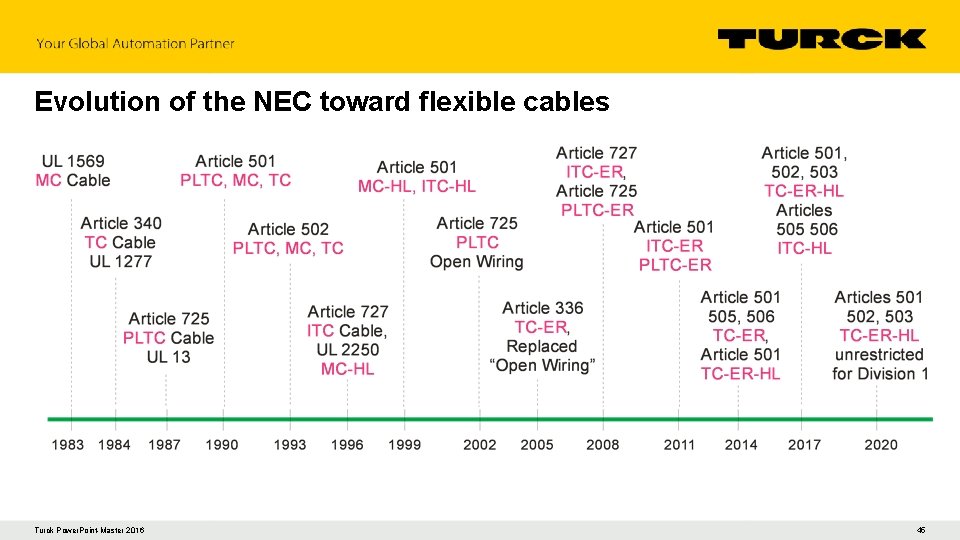
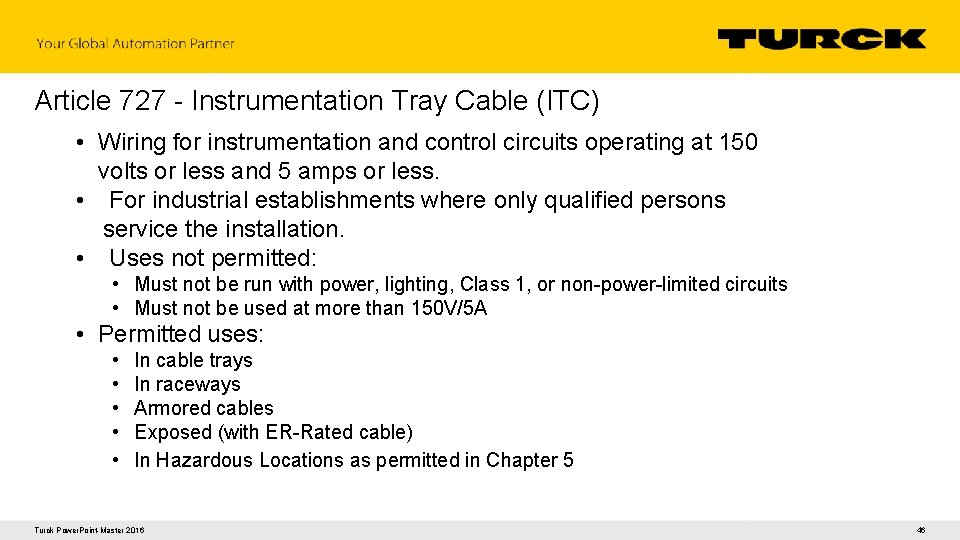
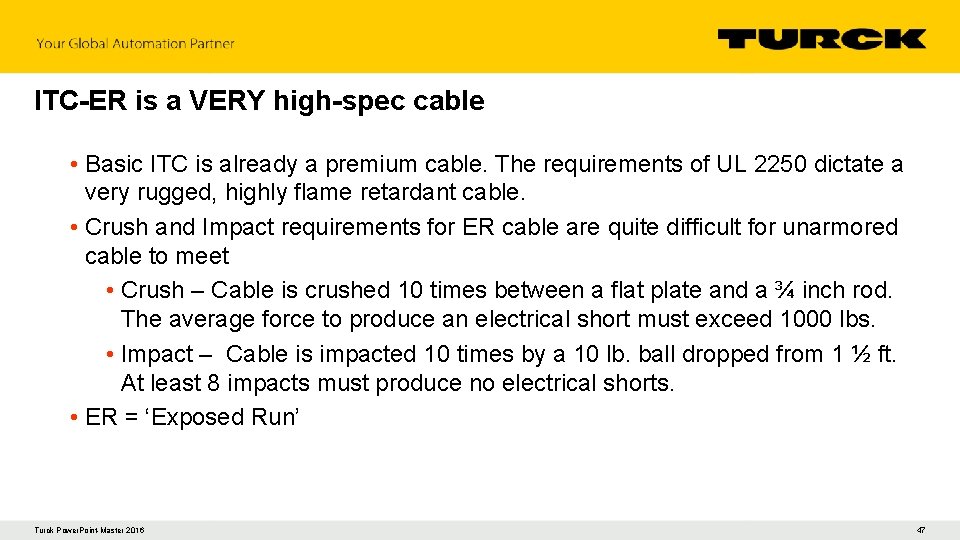
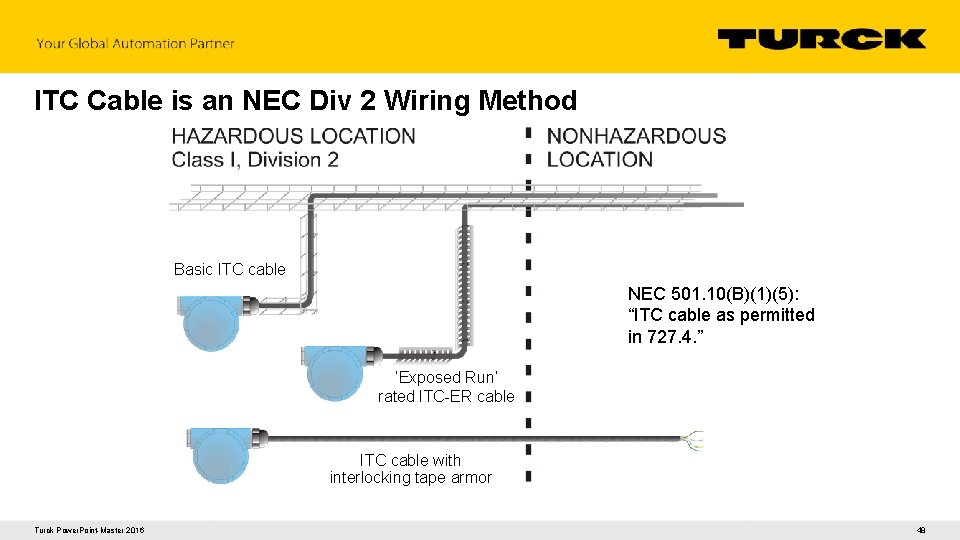
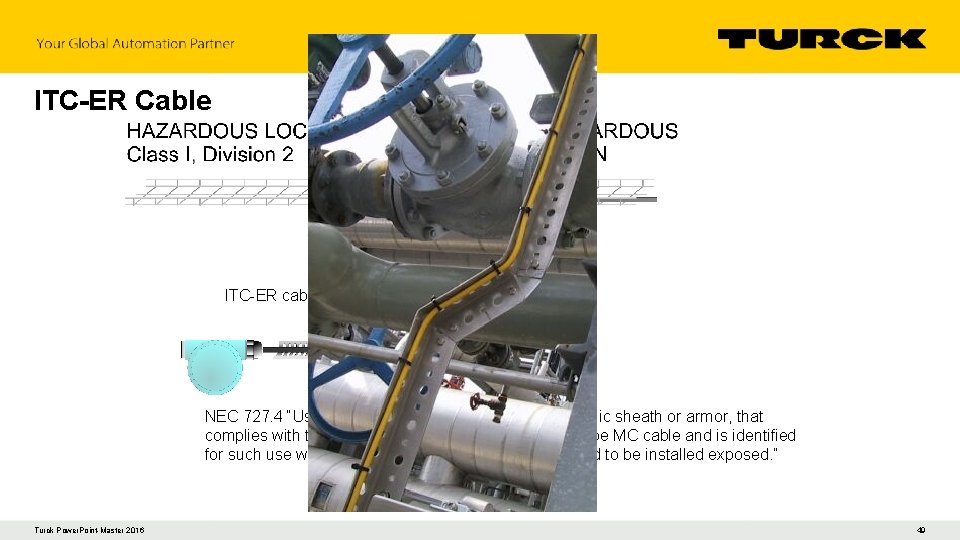
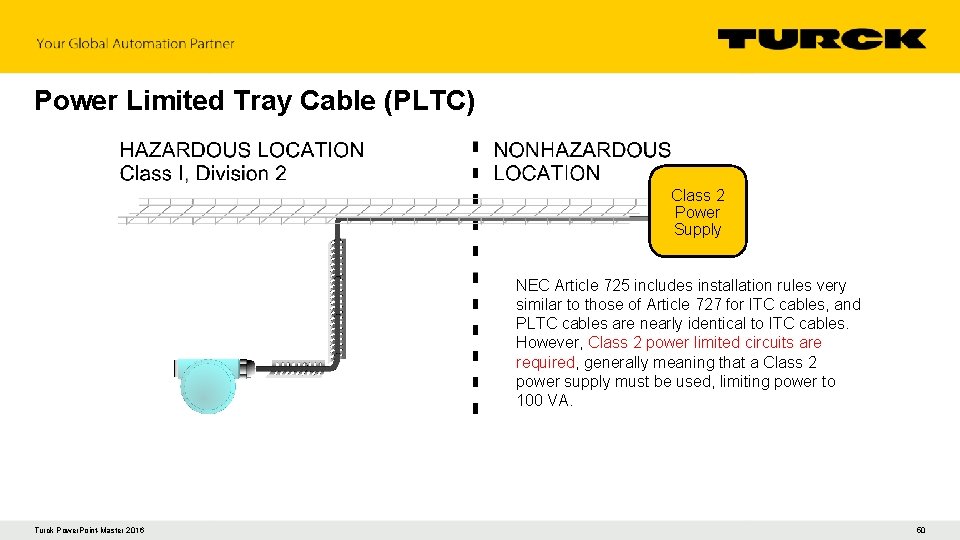
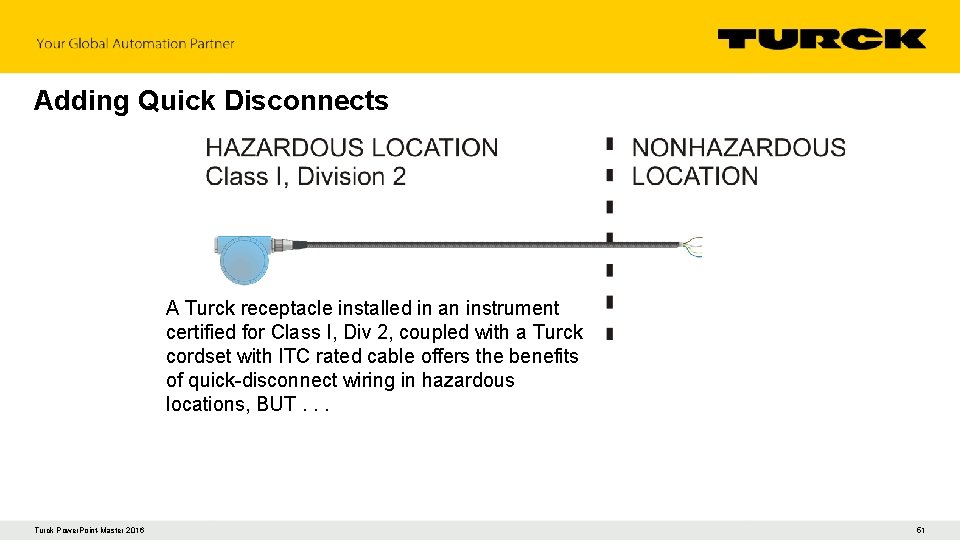
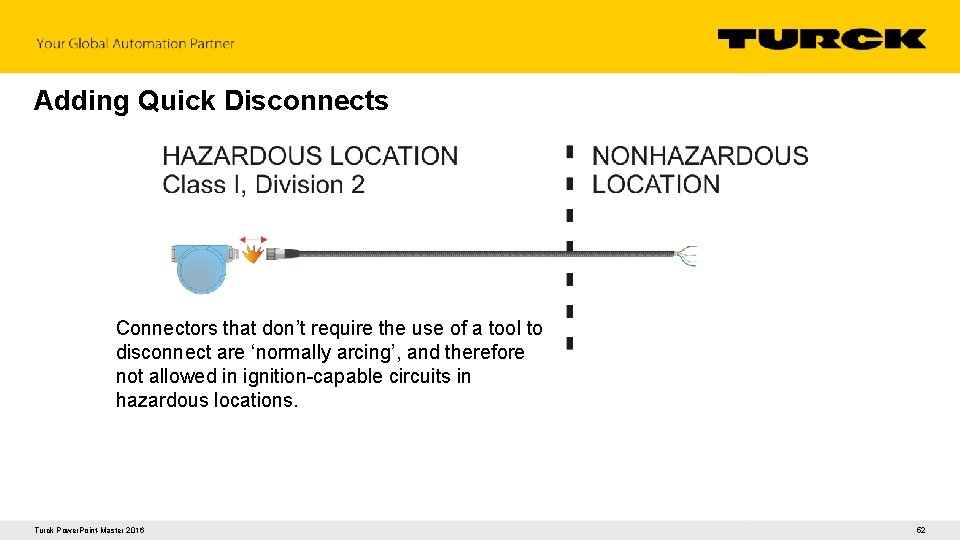
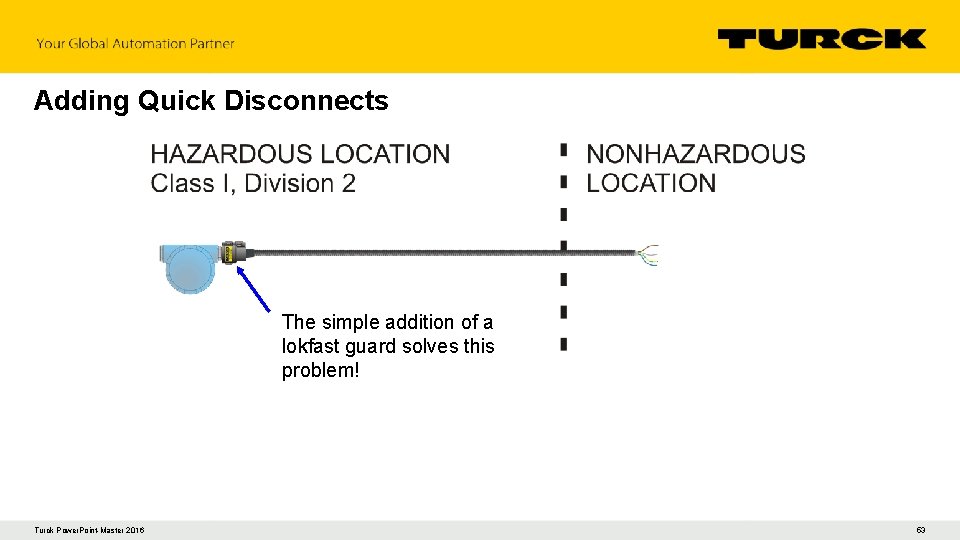
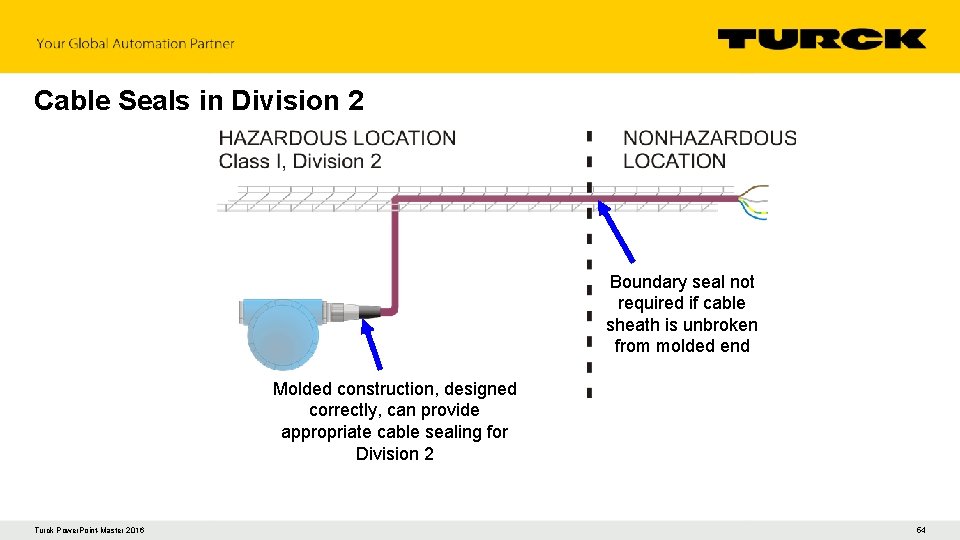
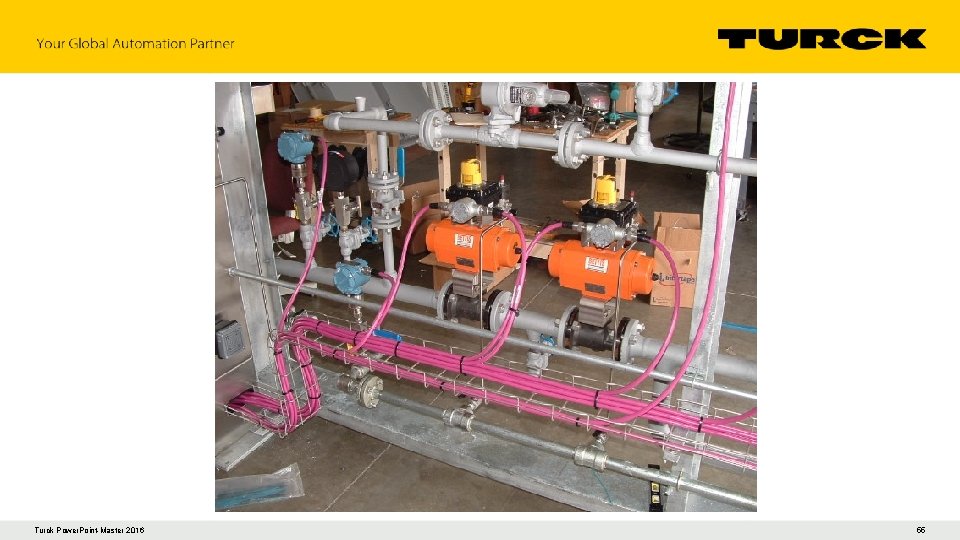

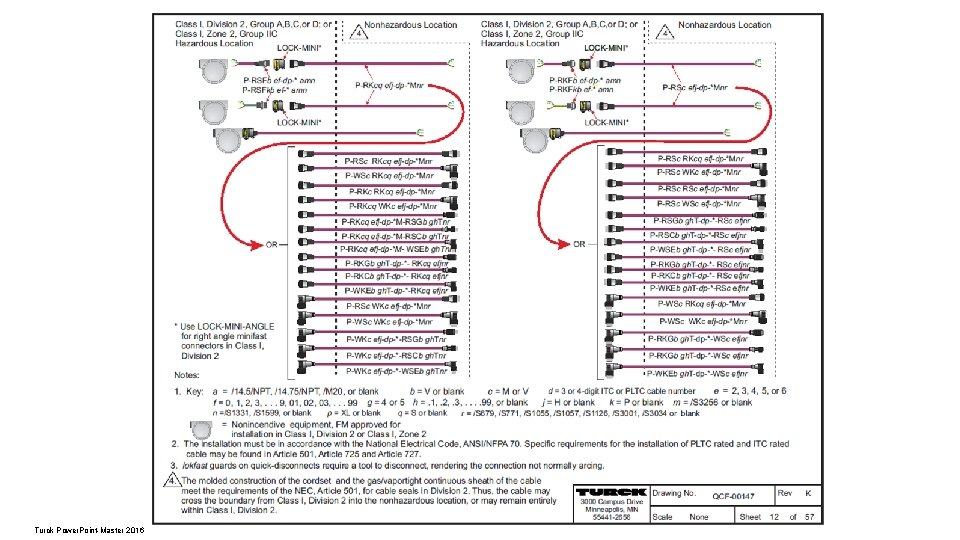
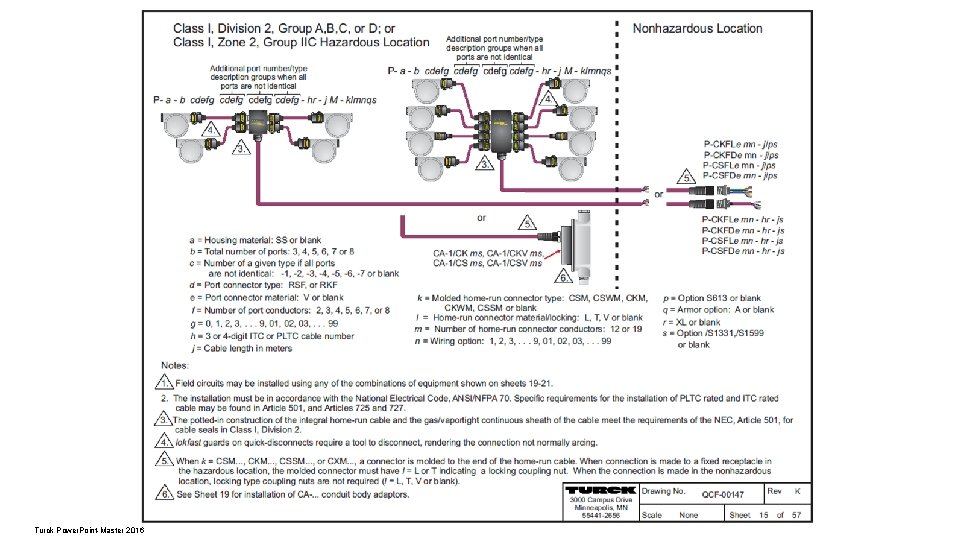
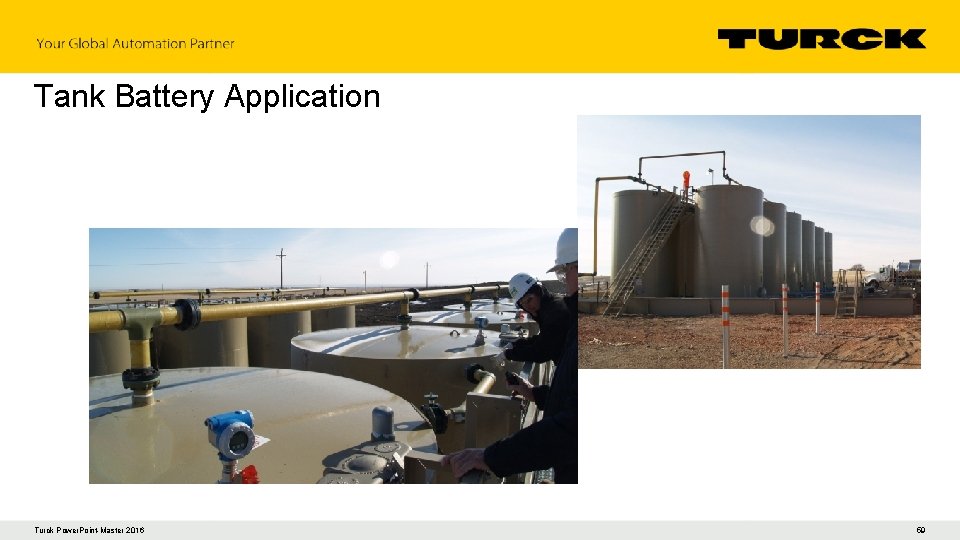
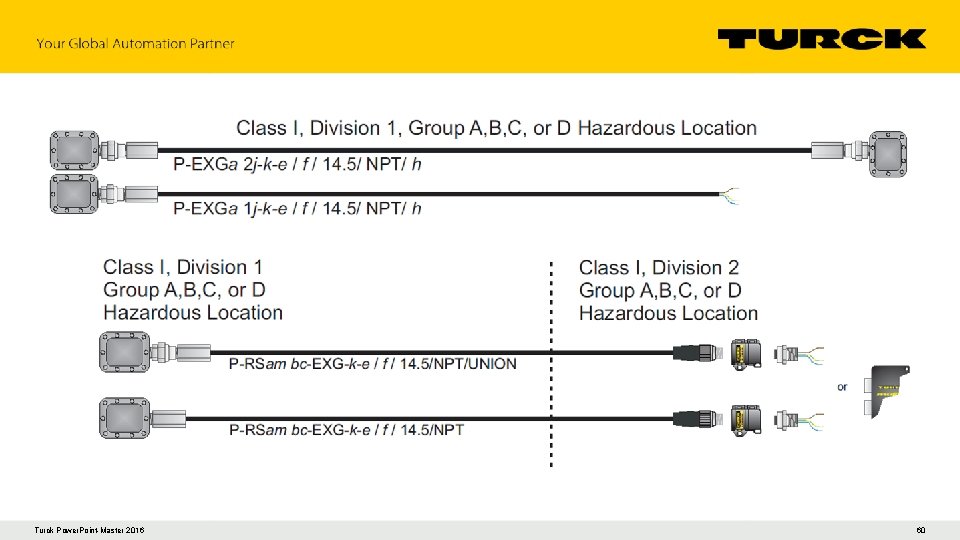
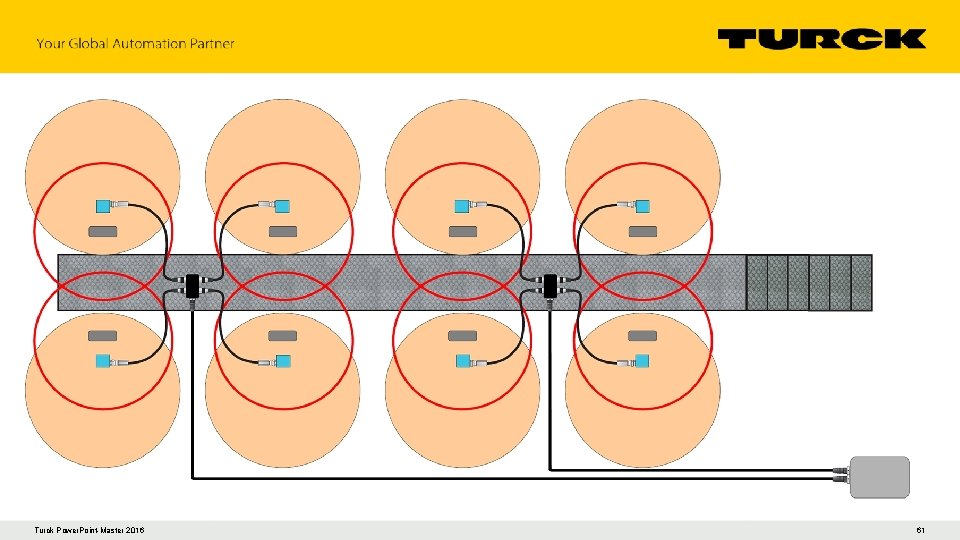
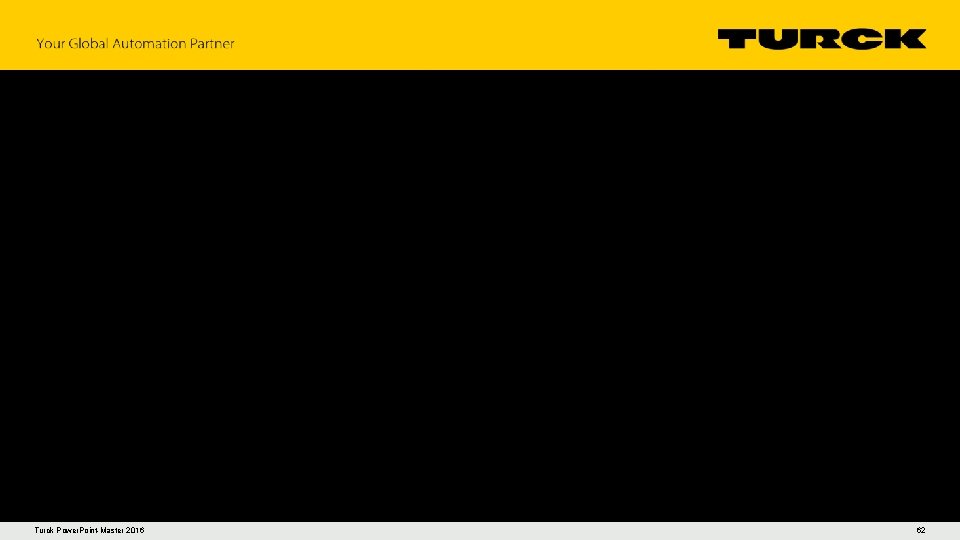
- Slides: 62
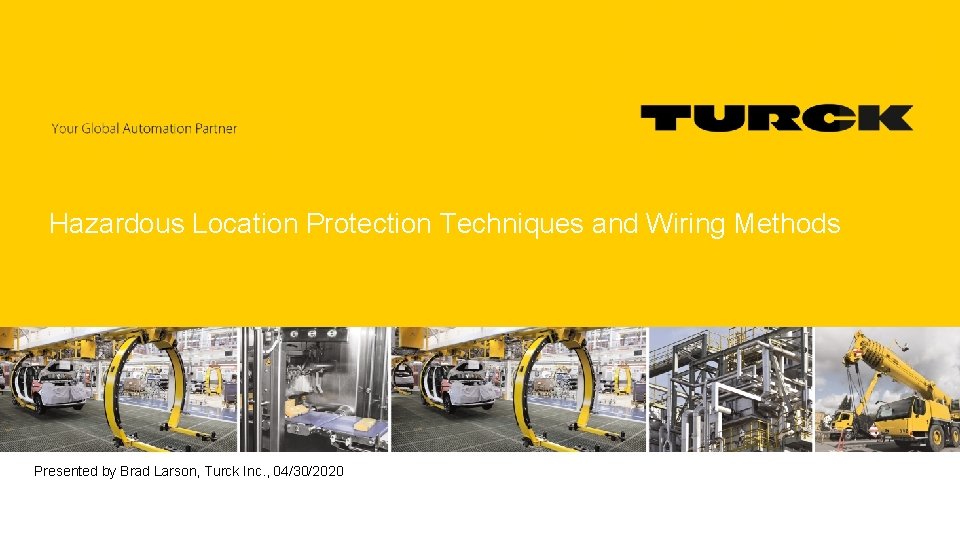
Hazardous Location Protection Techniques and Wiring Methods Presented by Brad Larson, Turck Inc. , 04/30/2020
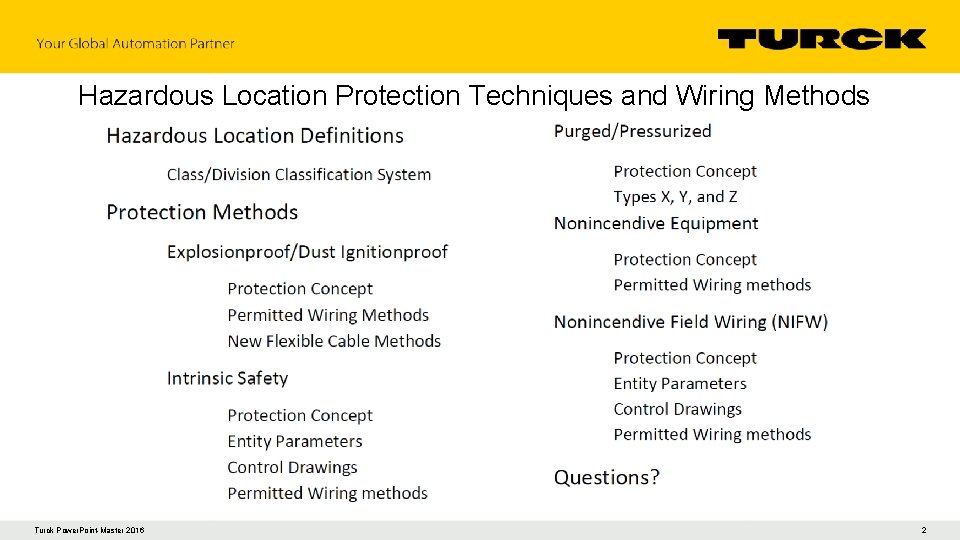
Hazardous Location Protection Techniques and Wiring Methods Turck Power. Point-Master 2016 2
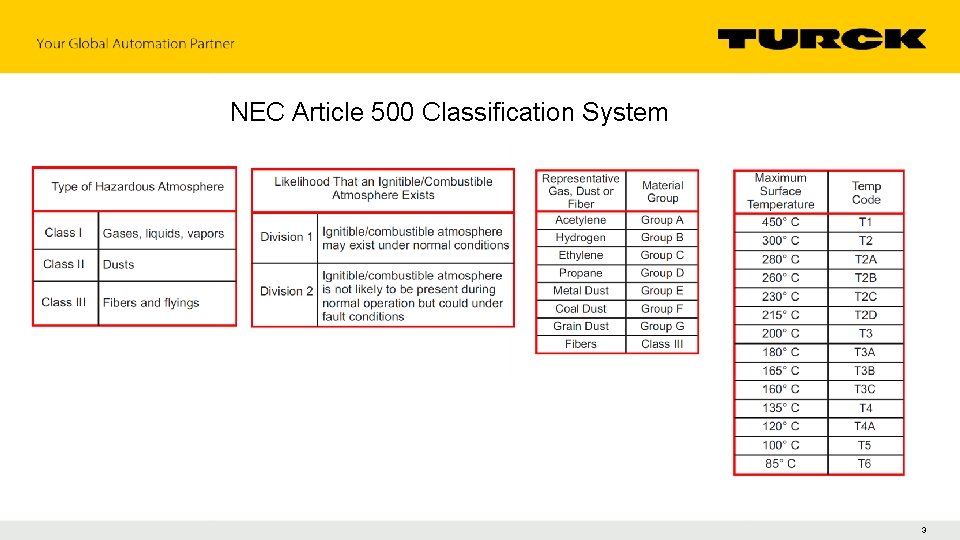
NEC Article 500 Classification System 3
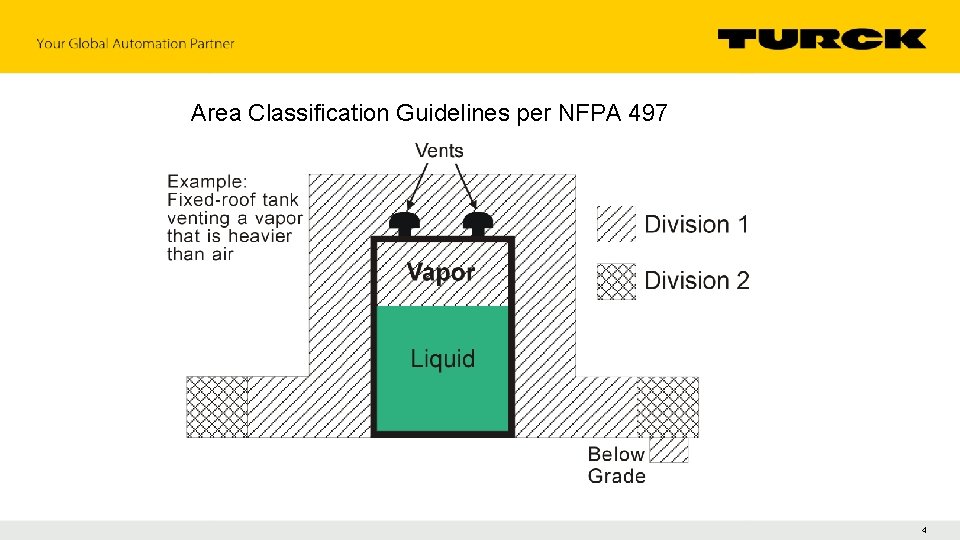
Area Classification Guidelines per NFPA 497 4
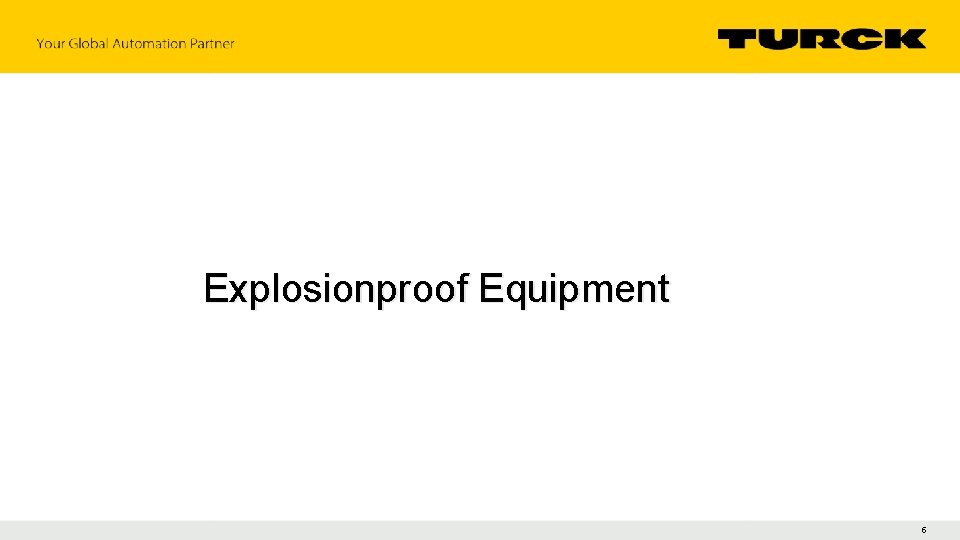
Explosionproof Equipment 5
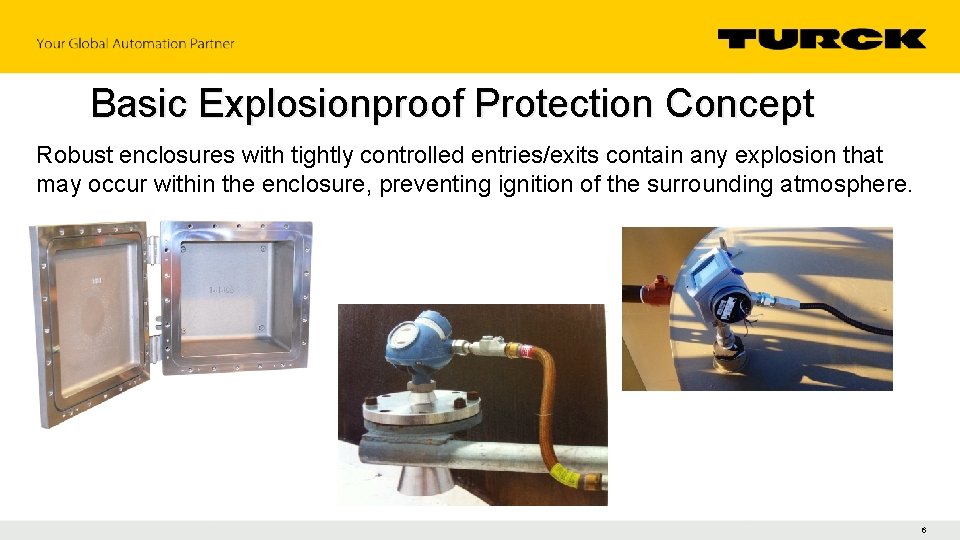
Basic Explosionproof Protection Concept Robust enclosures with tightly controlled entries/exits contain any explosion that may occur within the enclosure, preventing ignition of the surrounding atmosphere. 6
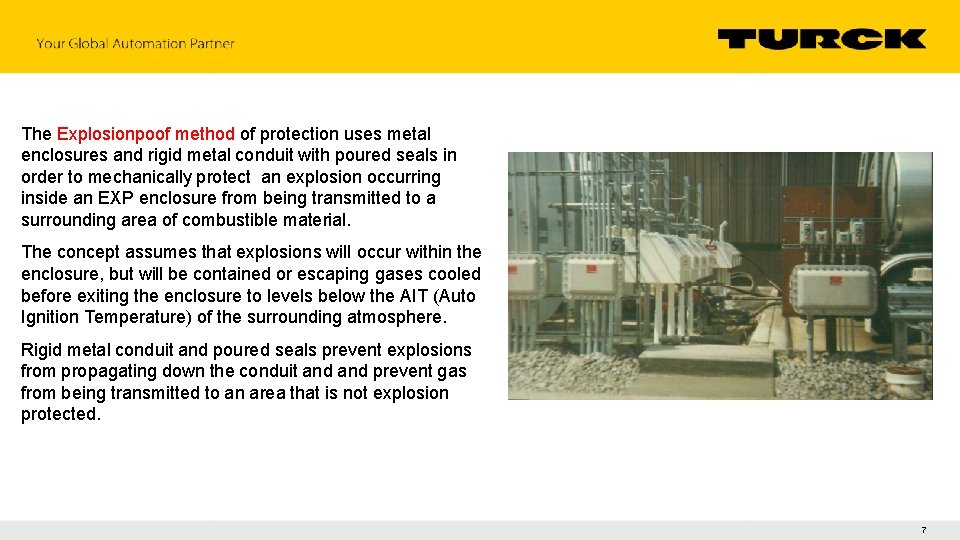
The Explosionpoof method of protection uses metal enclosures and rigid metal conduit with poured seals in order to mechanically protect an explosion occurring inside an EXP enclosure from being transmitted to a surrounding area of combustible material. The concept assumes that explosions will occur within the enclosure, but will be contained or escaping gases cooled before exiting the enclosure to levels below the AIT (Auto Ignition Temperature) of the surrounding atmosphere. Rigid metal conduit and poured seals prevent explosions from propagating down the conduit and prevent gas from being transmitted to an area that is not explosion protected. 7
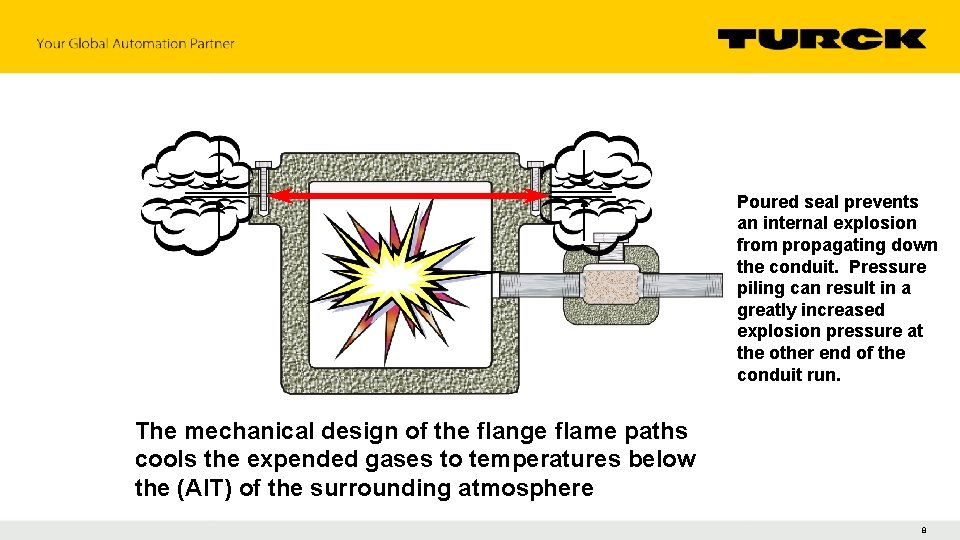
Poured seal prevents an internal explosion from propagating down the conduit. Pressure piling can result in a greatly increased explosion pressure at the other end of the conduit run. The mechanical design of the flange flame paths cools the expended gases to temperatures below the (AIT) of the surrounding atmosphere 8
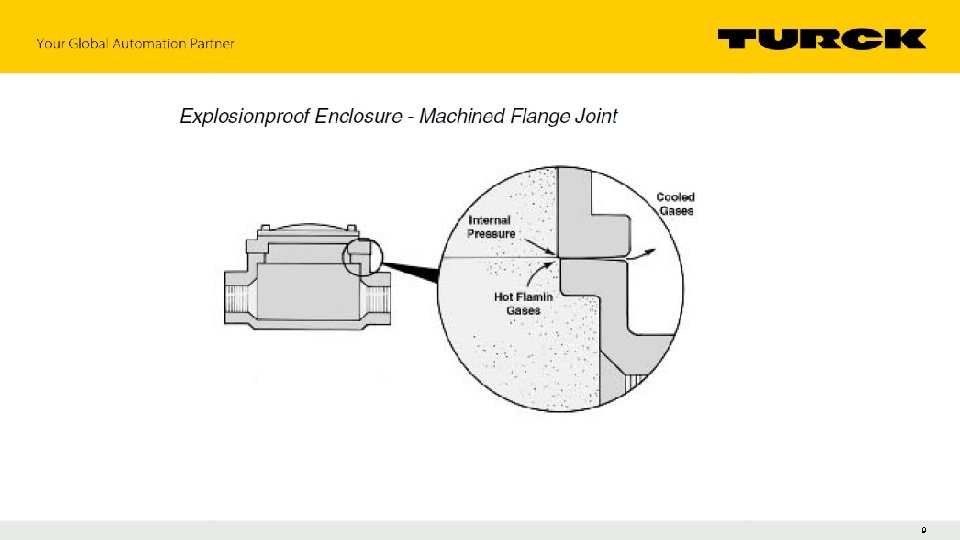
9
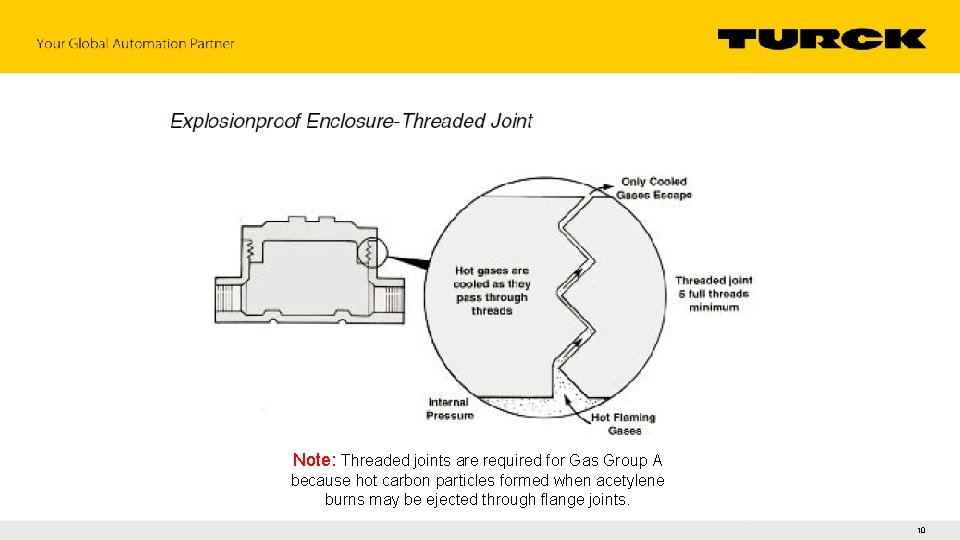
Note: Threaded joints are required for Gas Group A because hot carbon particles formed when acetylene burns may be ejected through flange joints. 10
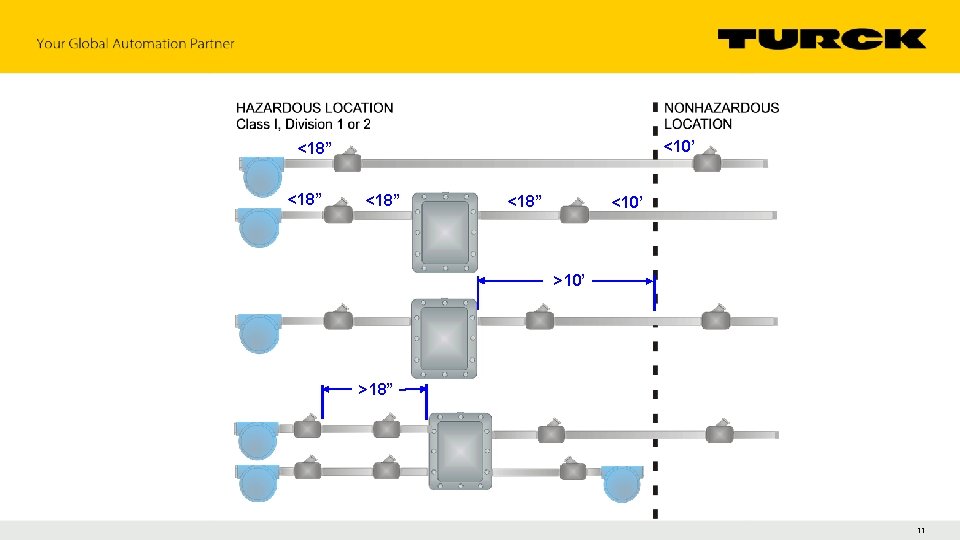
<10’ <18” <10’ >18” 11
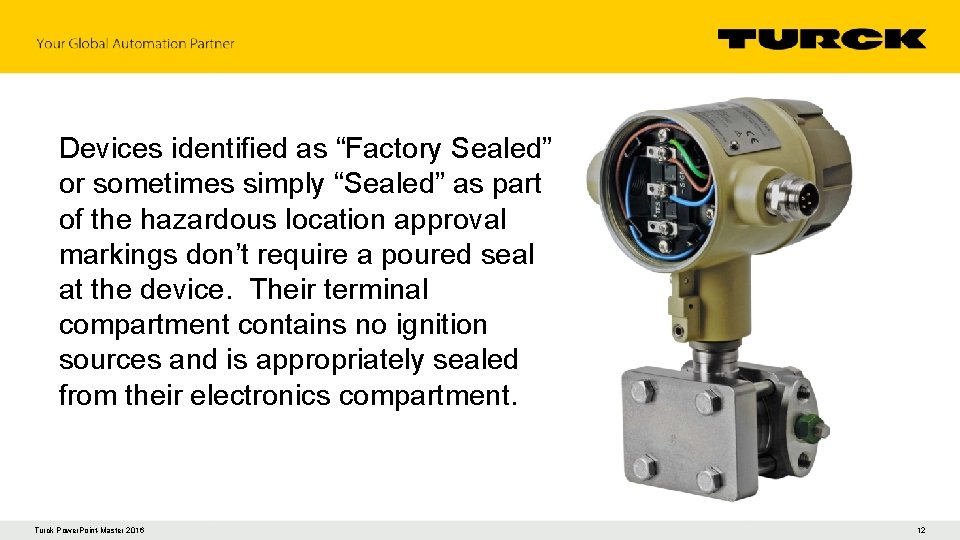
Devices identified as “Factory Sealed” or sometimes simply “Sealed” as part of the hazardous location approval markings don’t require a poured seal at the device. Their terminal compartment contains no ignition sources and is appropriately sealed from their electronics compartment. Turck Power. Point-Master 2016 12
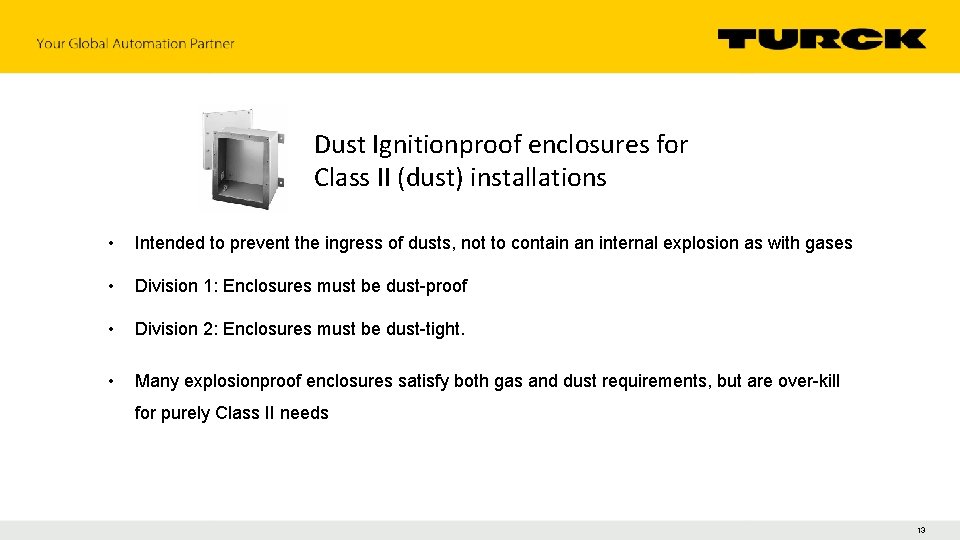
Dust Ignitionproof enclosures for Class II (dust) installations • Intended to prevent the ingress of dusts, not to contain an internal explosion as with gases • Division 1: Enclosures must be dust-proof • Division 2: Enclosures must be dust-tight. • Many explosionproof enclosures satisfy both gas and dust requirements, but are over-kill for purely Class II needs 13
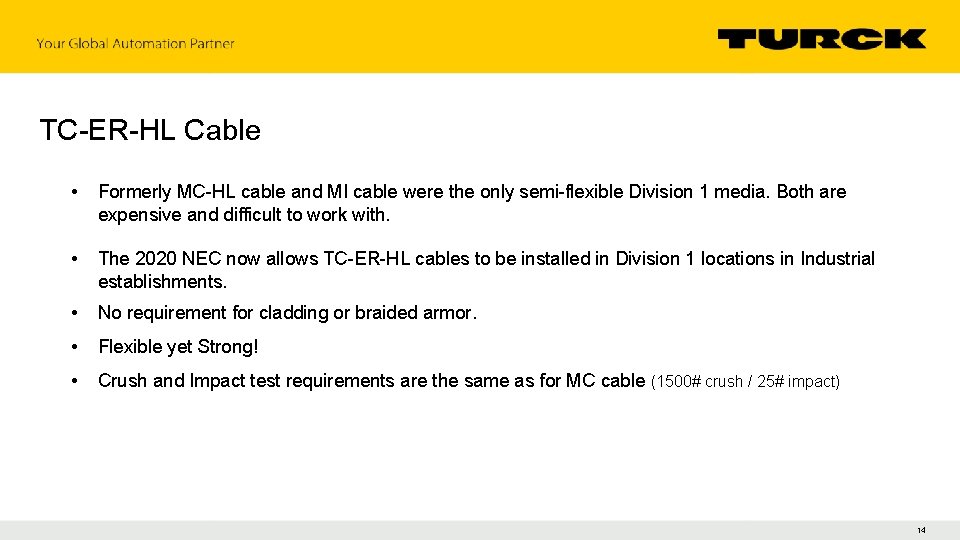
TC-ER-HL Cable • Formerly MC-HL cable and MI cable were the only semi-flexible Division 1 media. Both are expensive and difficult to work with. • The 2020 NEC now allows TC-ER-HL cables to be installed in Division 1 locations in Industrial establishments. • No requirement for cladding or braided armor. • Flexible yet Strong! • Crush and Impact test requirements are the same as for MC cable (1500# crush / 25# impact) 14
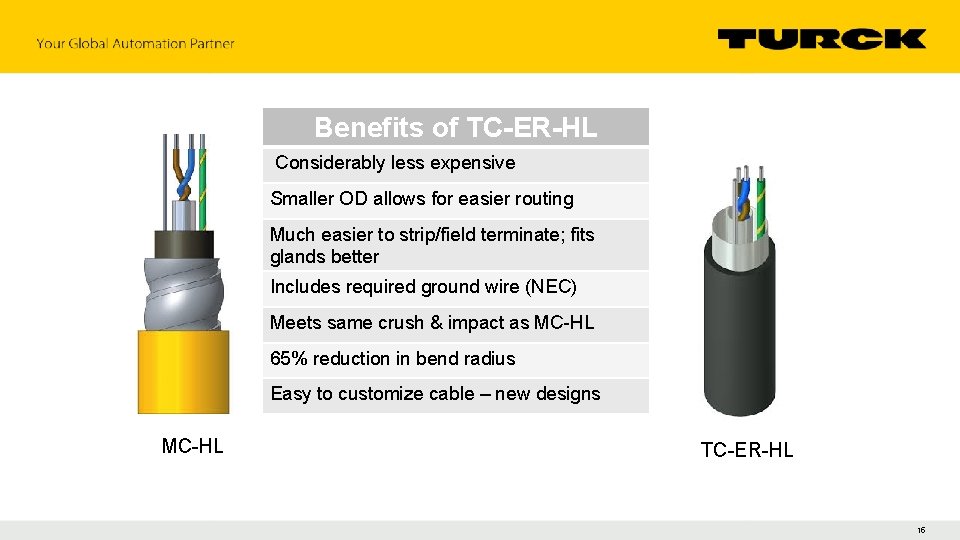
Benefits of TC-ER-HL Considerably less expensive Smaller OD allows for easier routing Much easier to strip/field terminate; fits glands better Includes required ground wire (NEC) Meets same crush & impact as MC-HL 65% reduction in bend radius Easy to customize cable – new designs MC-HL TC-ER-HL 15
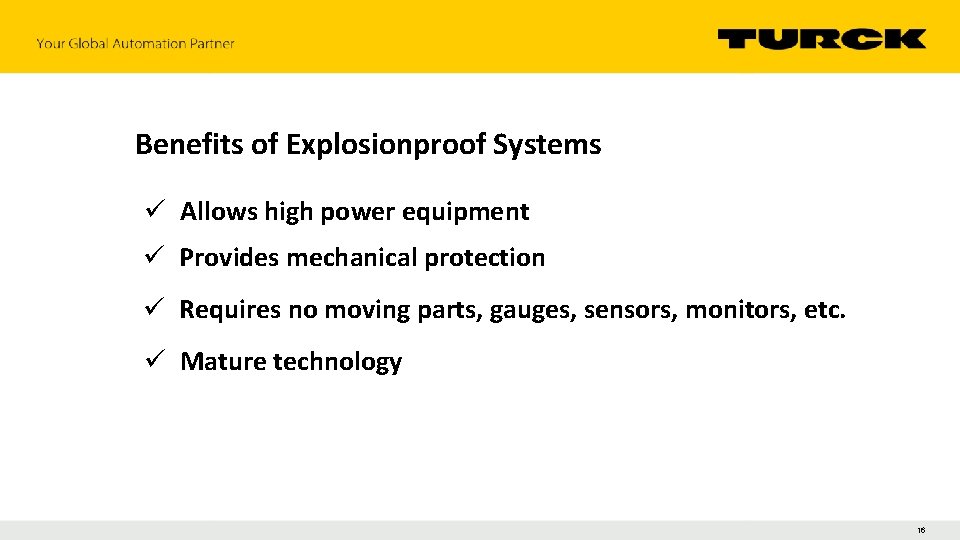
Benefits of Explosionproof Systems ü Allows high power equipment ü Provides mechanical protection ü Requires no moving parts, gauges, sensors, monitors, etc. ü Mature technology 16
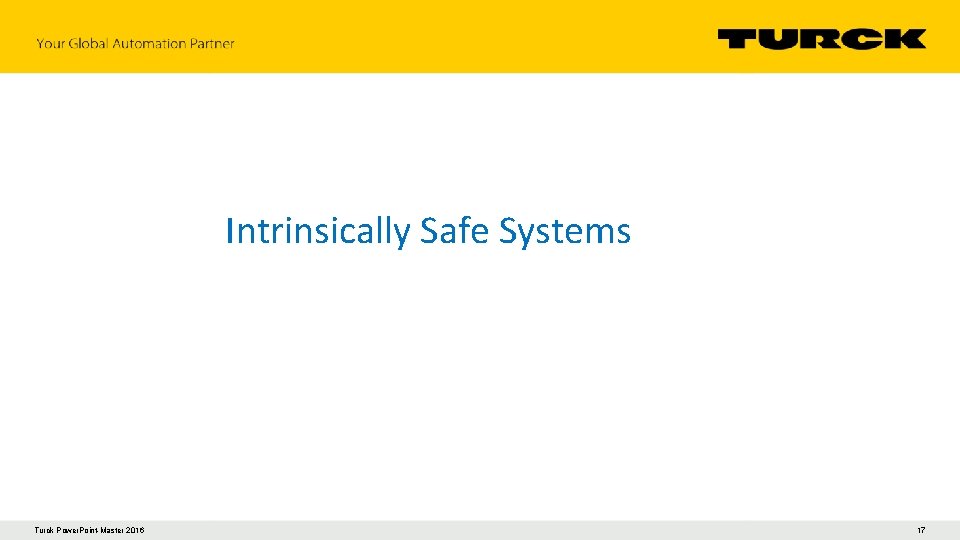
Intrinsically Safe Systems Turck Power. Point-Master 2016 17
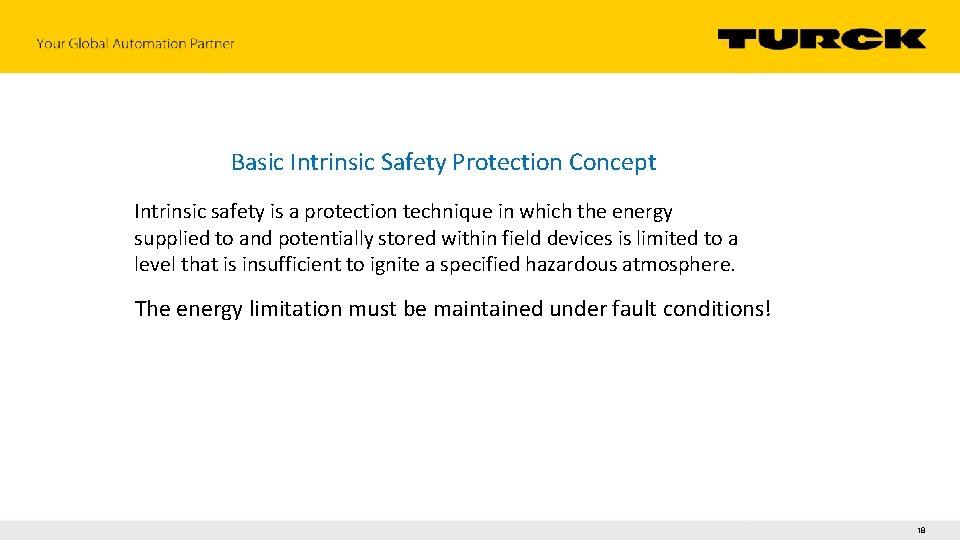
Basic Intrinsic Safety Protection Concept Intrinsic safety is a protection technique in which the energy supplied to and potentially stored within field devices is limited to a level that is insufficient to ignite a specified hazardous atmosphere. The energy limitation must be maintained under fault conditions! 18
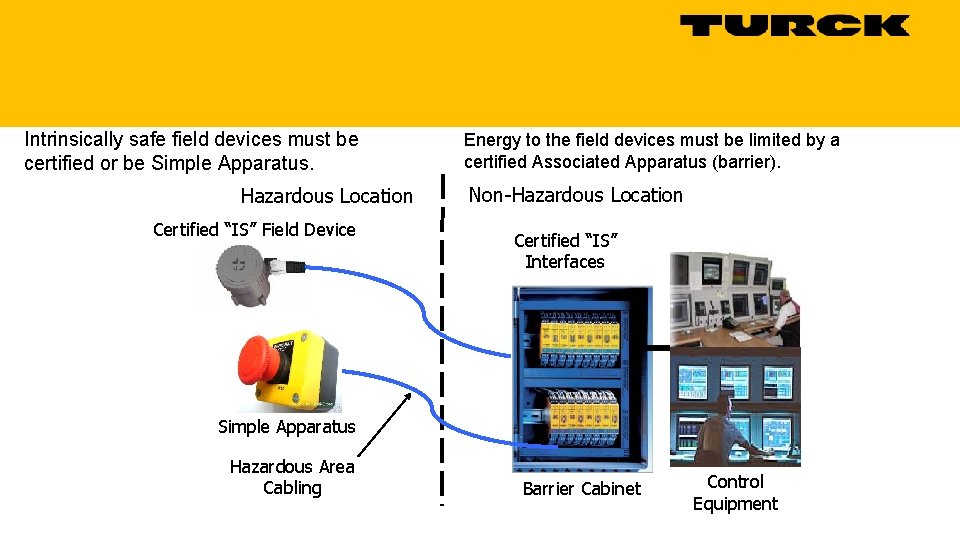
Intrinsically safe field devices must be certified or be Simple Apparatus. Hazardous Location Certified “IS” Field Device Energy to the field devices must be limited by a certified Associated Apparatus (barrier). Non-Hazardous Location Certified “IS” Interfaces Simple Apparatus Hazardous Area Cabling Barrier Cabinet Control Equipment
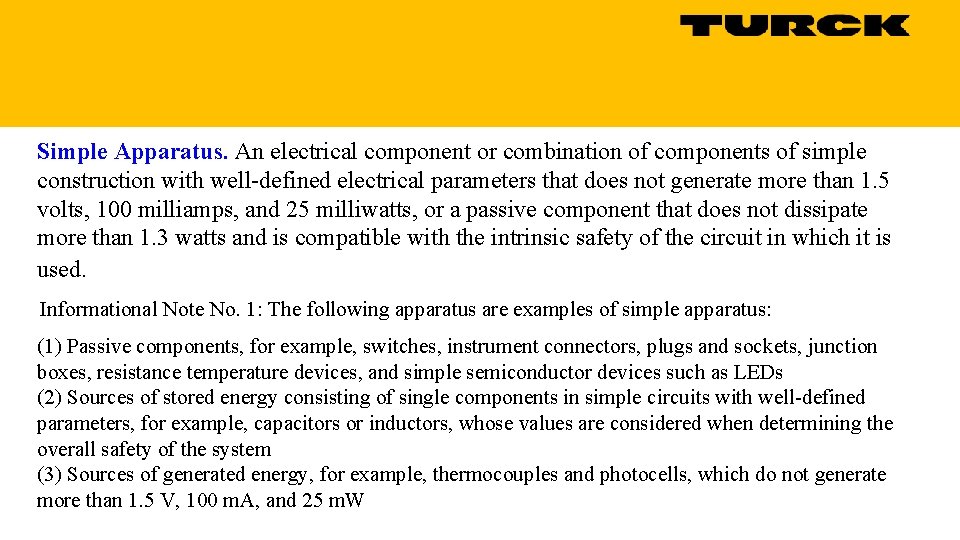
Simple Apparatus. An electrical component or combination of components of simple construction with well-defined electrical parameters that does not generate more than 1. 5 volts, 100 milliamps, and 25 milliwatts, or a passive component that does not dissipate more than 1. 3 watts and is compatible with the intrinsic safety of the circuit in which it is used. Informational Note No. 1: The following apparatus are examples of simple apparatus: (1) Passive components, for example, switches, instrument connectors, plugs and sockets, junction boxes, resistance temperature devices, and simple semiconductor devices such as LEDs (2) Sources of stored energy consisting of single components in simple circuits with well-defined parameters, for example, capacitors or inductors, whose values are considered when determining the overall safety of the system (3) Sources of generated energy, for example, thermocouples and photocells, which do not generate more than 1. 5 V, 100 m. A, and 25 m. W
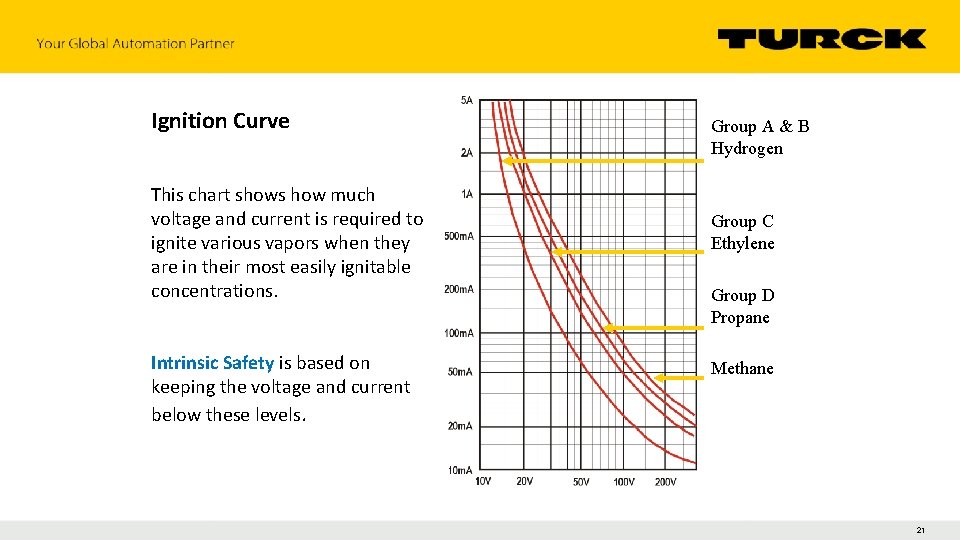
Ignition Curve This chart shows how much voltage and current is required to ignite various vapors when they are in their most easily ignitable concentrations. Intrinsic Safety is based on keeping the voltage and current below these levels. Group A & B Hydrogen Group C Ethylene Group D Propane Methane 21
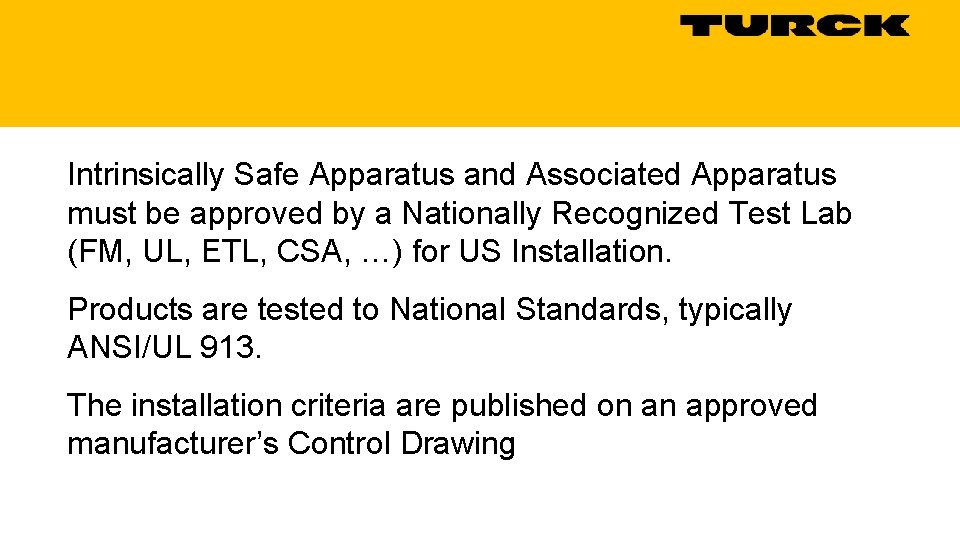
Intrinsically Safe Apparatus and Associated Apparatus must be approved by a Nationally Recognized Test Lab (FM, UL, ETL, CSA, …) for US Installation. Products are tested to National Standards, typically ANSI/UL 913. The installation criteria are published on an approved manufacturer’s Control Drawing
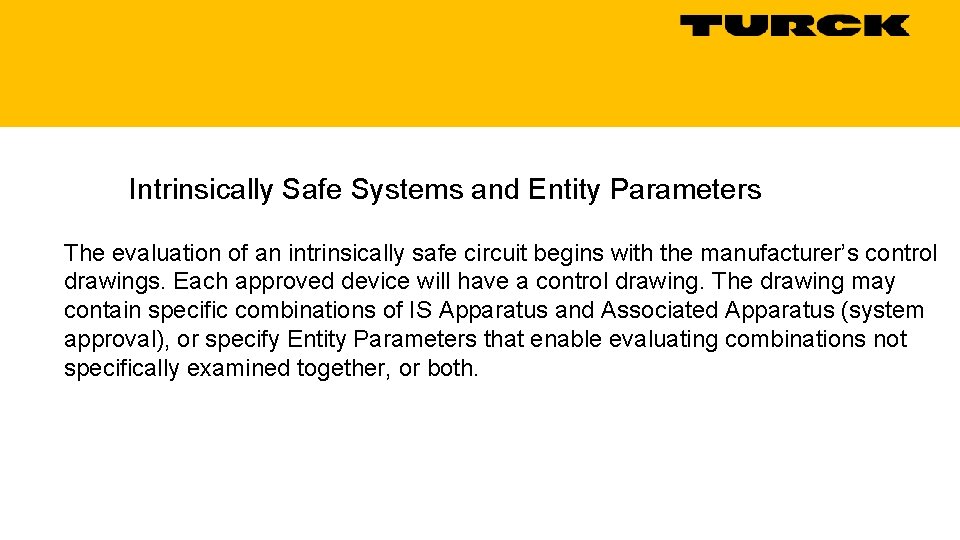
Intrinsically Safe Systems and Entity Parameters The evaluation of an intrinsically safe circuit begins with the manufacturer’s control drawings. Each approved device will have a control drawing. The drawing may contain specific combinations of IS Apparatus and Associated Apparatus (system approval), or specify Entity Parameters that enable evaluating combinations not specifically examined together, or both.
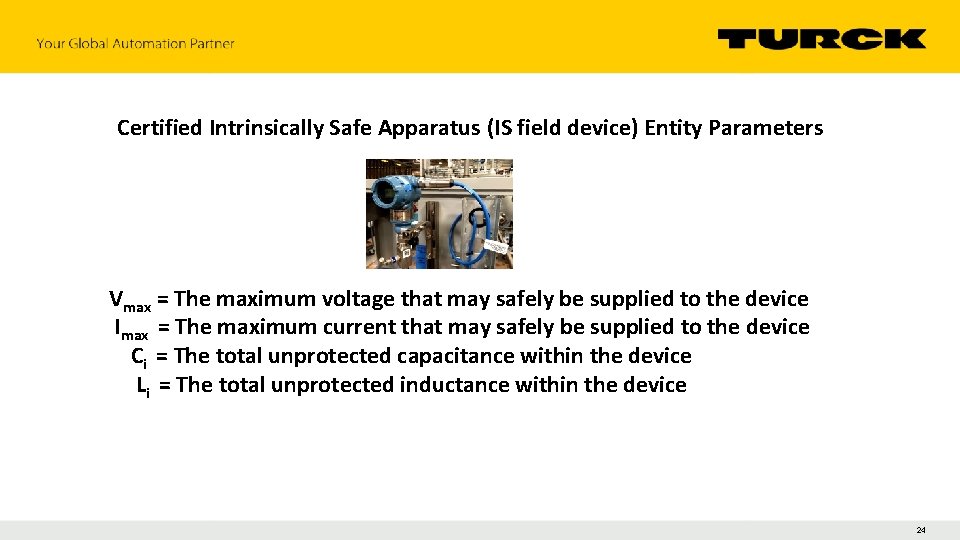
Certified Intrinsically Safe Apparatus (IS field device) Entity Parameters Vmax = The maximum voltage that may safely be supplied to the device Imax = The maximum current that may safely be supplied to the device Ci = The total unprotected capacitance within the device Li = The total unprotected inductance within the device 24
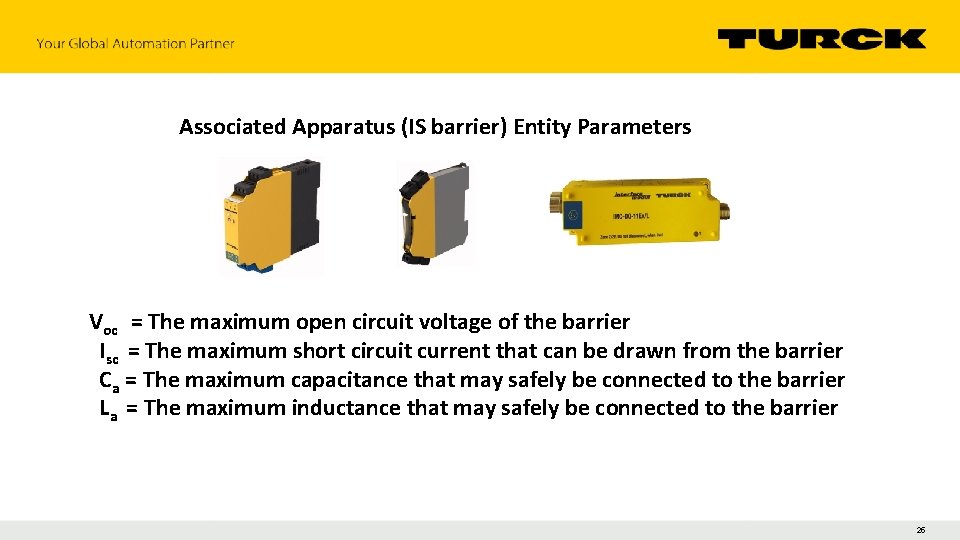
Associated Apparatus (IS barrier) Entity Parameters Voc = The maximum open circuit voltage of the barrier Isc = The maximum short circuit current that can be drawn from the barrier Ca = The maximum capacitance that may safely be connected to the barrier La = The maximum inductance that may safely be connected to the barrier 25
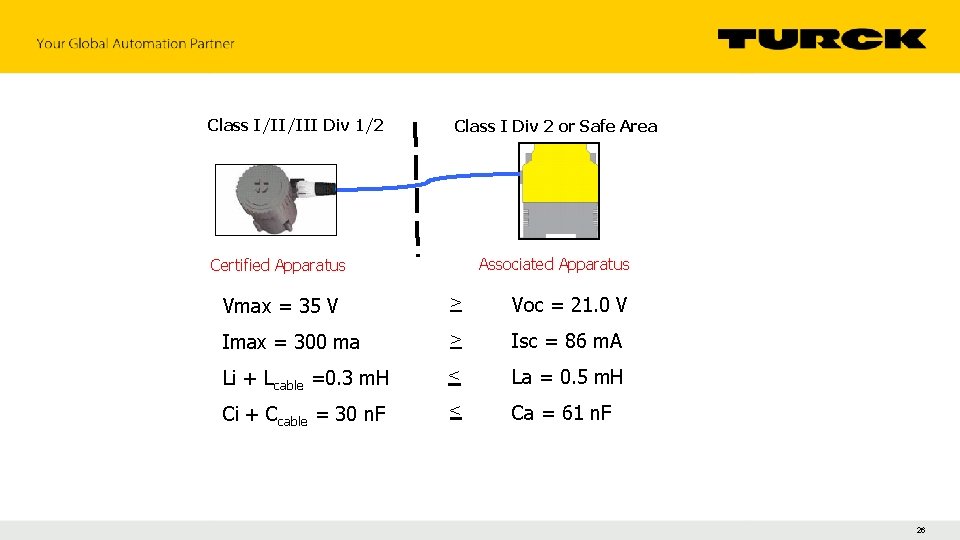
Class I/II/III Div 1/2 Class I Div 2 or Safe Area Associated Apparatus Certified Apparatus Vmax = 35 V > Voc = 21. 0 V Imax = 300 ma > Isc = 86 m. A Li + Lcable =0. 3 m. H < La = 0. 5 m. H Ci + Ccable = 30 n. F < Ca = 61 n. F 26
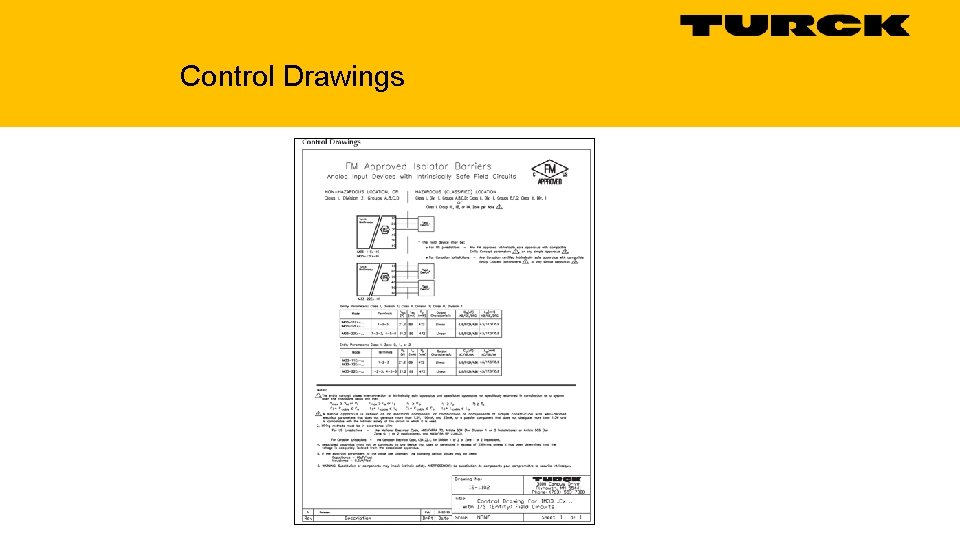
Control Drawings
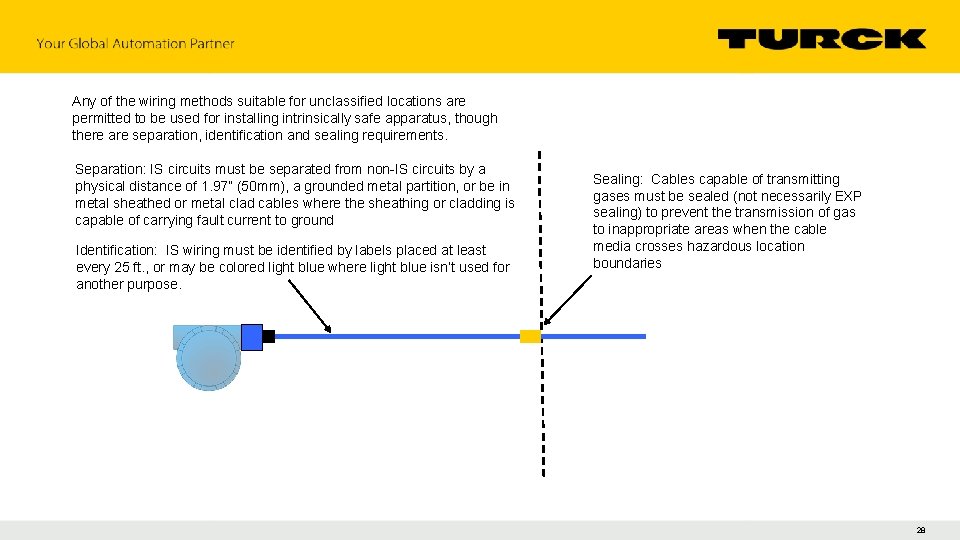
Any of the wiring methods suitable for unclassified locations are permitted to be used for installing intrinsically safe apparatus, though there are separation, identification and sealing requirements. Separation: IS circuits must be separated from non-IS circuits by a physical distance of 1. 97” (50 mm), a grounded metal partition, or be in metal sheathed or metal clad cables where the sheathing or cladding is capable of carrying fault current to ground Identification: IS wiring must be identified by labels placed at least every 25 ft. , or may be colored light blue where light blue isn’t used for another purpose. Sealing: Cables capable of transmitting gases must be sealed (not necessarily EXP sealing) to prevent the transmission of gas to inappropriate areas when the cable media crosses hazardous location boundaries 28
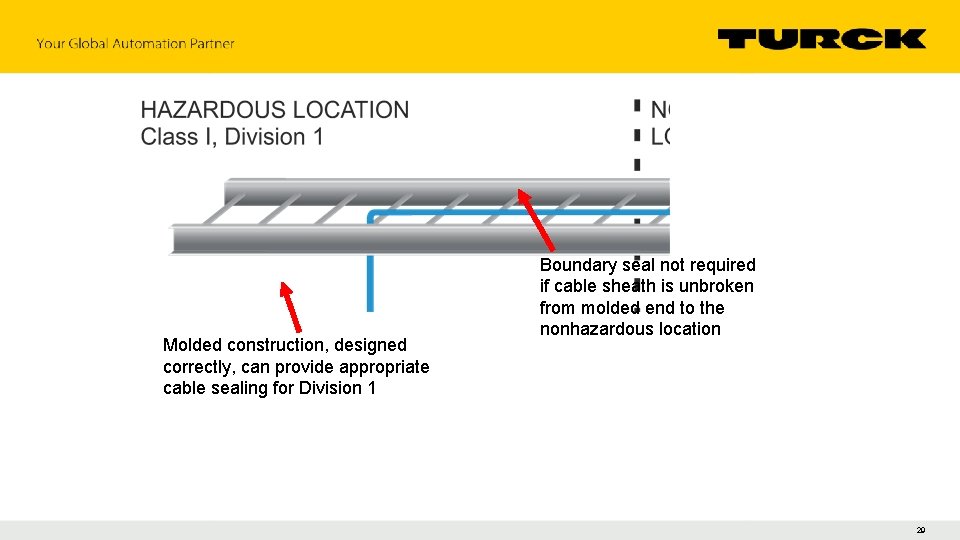
Molded construction, designed correctly, can provide appropriate cable sealing for Division 1 Boundary seal not required if cable sheath is unbroken from molded end to the nonhazardous location 29
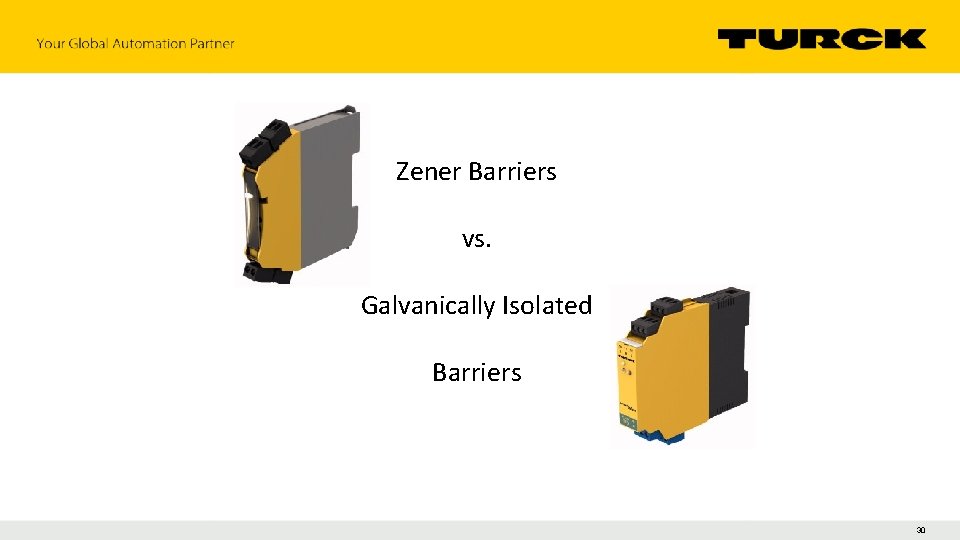
Zener Barriers vs. Galvanically Isolated Barriers 30
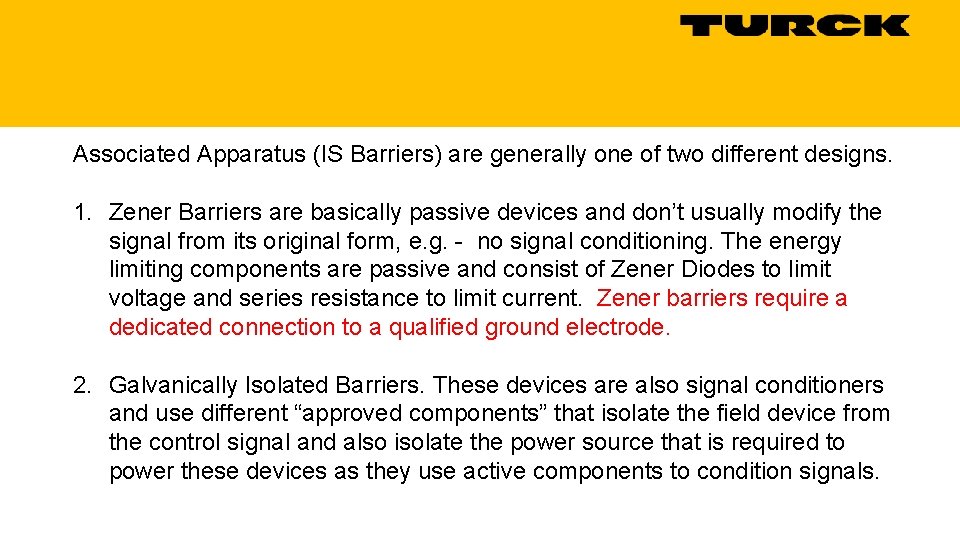
Associated Apparatus (IS Barriers) are generally one of two different designs. 1. Zener Barriers are basically passive devices and don’t usually modify the signal from its original form, e. g. - no signal conditioning. The energy limiting components are passive and consist of Zener Diodes to limit voltage and series resistance to limit current. Zener barriers require a dedicated connection to a qualified ground electrode. 2. Galvanically Isolated Barriers. These devices are also signal conditioners and use different “approved components” that isolate the field device from the control signal and also isolate the power source that is required to power these devices as they use active components to condition signals.
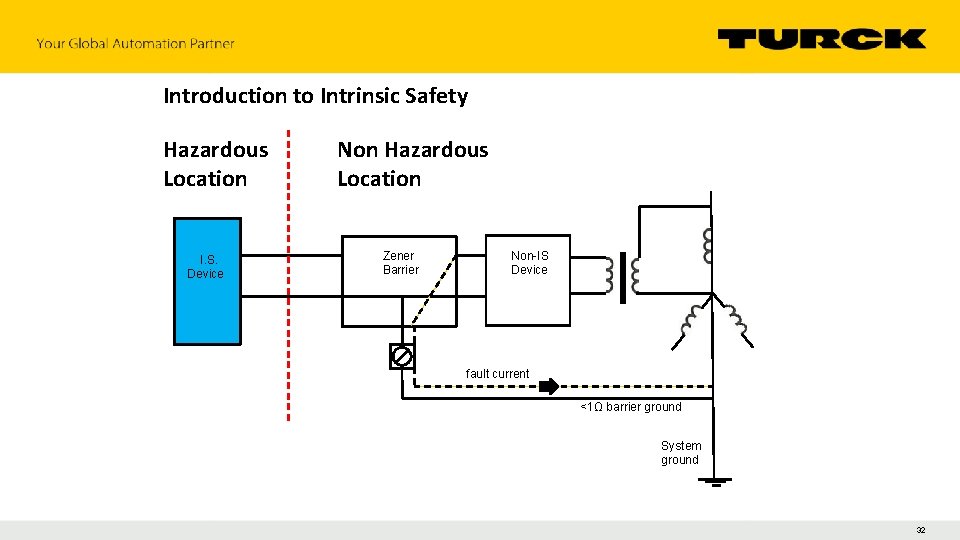
Introduction to Intrinsic Safety Hazardous Location I. S. Device Non Hazardous Location Zener Barrier Non-IS Device fault current <1Ω barrier ground System ground 32
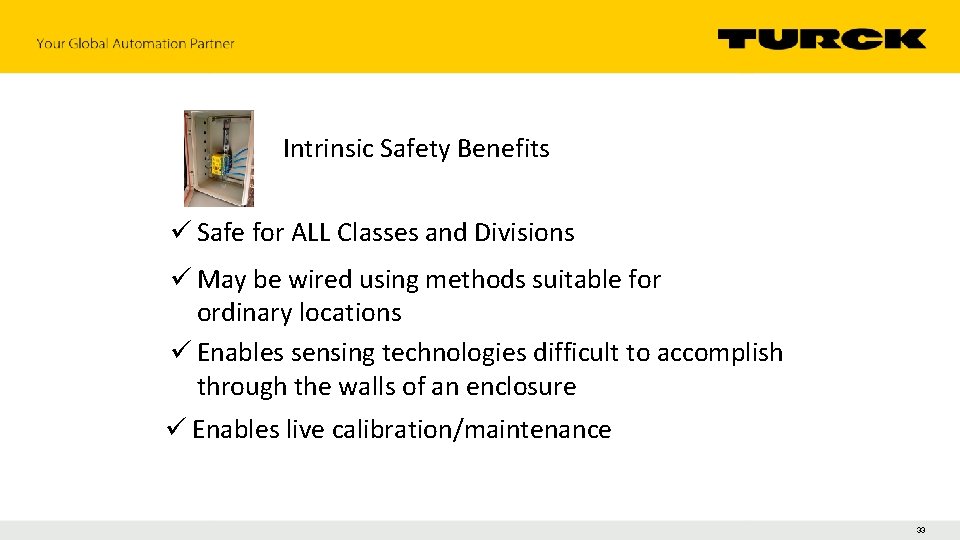
Intrinsic Safety Benefits ü Safe for ALL Classes and Divisions ü May be wired using methods suitable for ordinary locations ü Enables sensing technologies difficult to accomplish through the walls of an enclosure ü Enables live calibration/maintenance 33
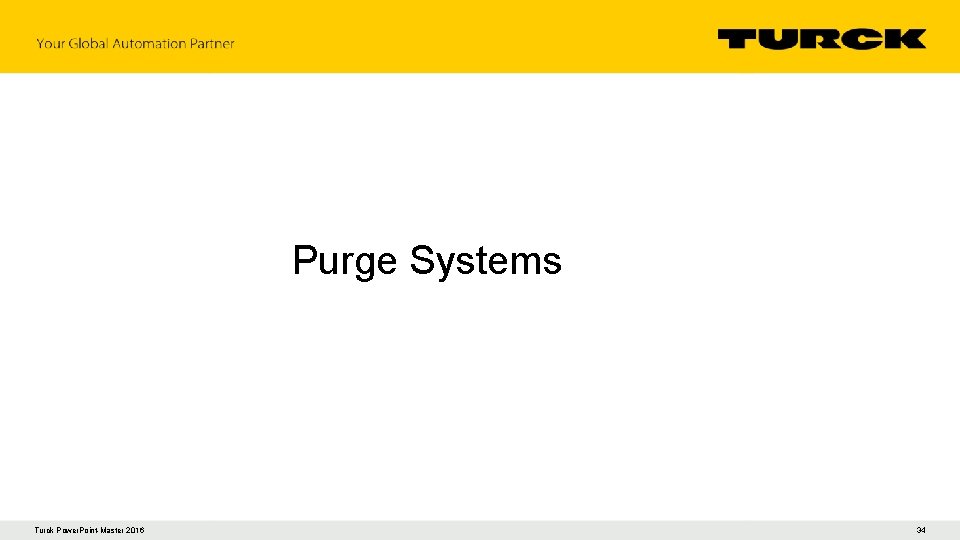
Purge Systems Turck Power. Point-Master 2016 34
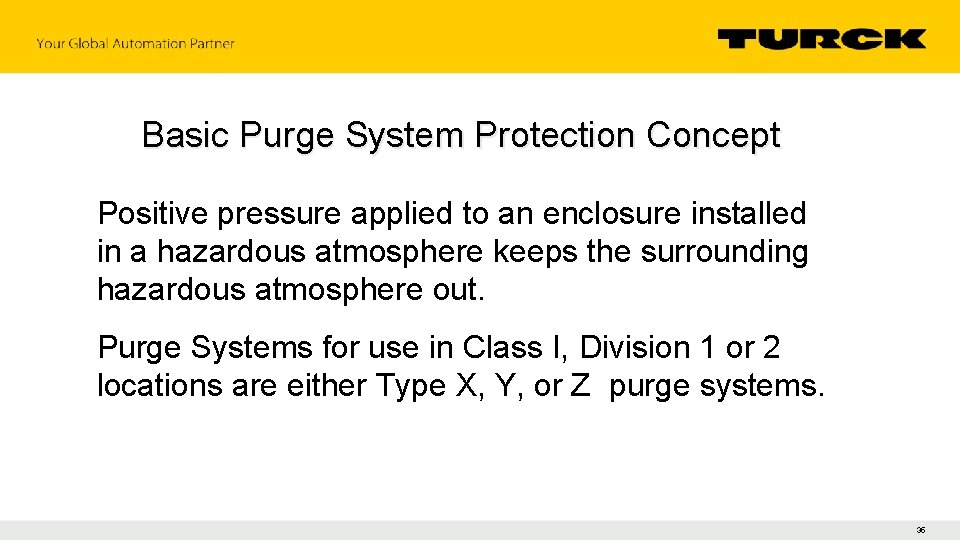
Basic Purge System Protection Concept Positive pressure applied to an enclosure installed in a hazardous atmosphere keeps the surrounding hazardous atmosphere out. Purge Systems for use in Class I, Division 1 or 2 locations are either Type X, Y, or Z purge systems. 35
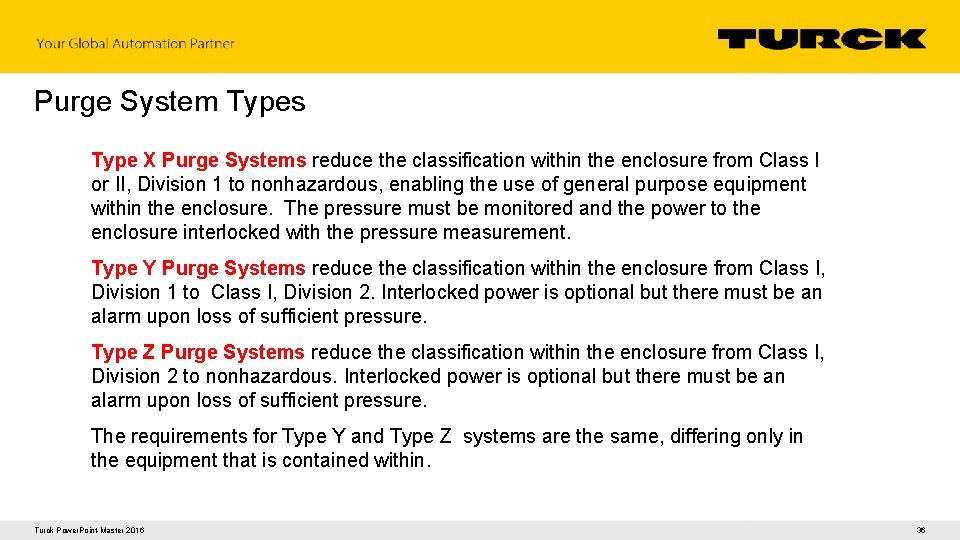
Purge System Types Type X Purge Systems reduce the classification within the enclosure from Class I or II, Division 1 to nonhazardous, enabling the use of general purpose equipment within the enclosure. The pressure must be monitored and the power to the enclosure interlocked with the pressure measurement. Type Y Purge Systems reduce the classification within the enclosure from Class I, Division 1 to Class I, Division 2. Interlocked power is optional but there must be an alarm upon loss of sufficient pressure. Type Z Purge Systems reduce the classification within the enclosure from Class I, Division 2 to nonhazardous. Interlocked power is optional but there must be an alarm upon loss of sufficient pressure. The requirements for Type Y and Type Z systems are the same, differing only in the equipment that is contained within. Turck Power. Point-Master 2016 36
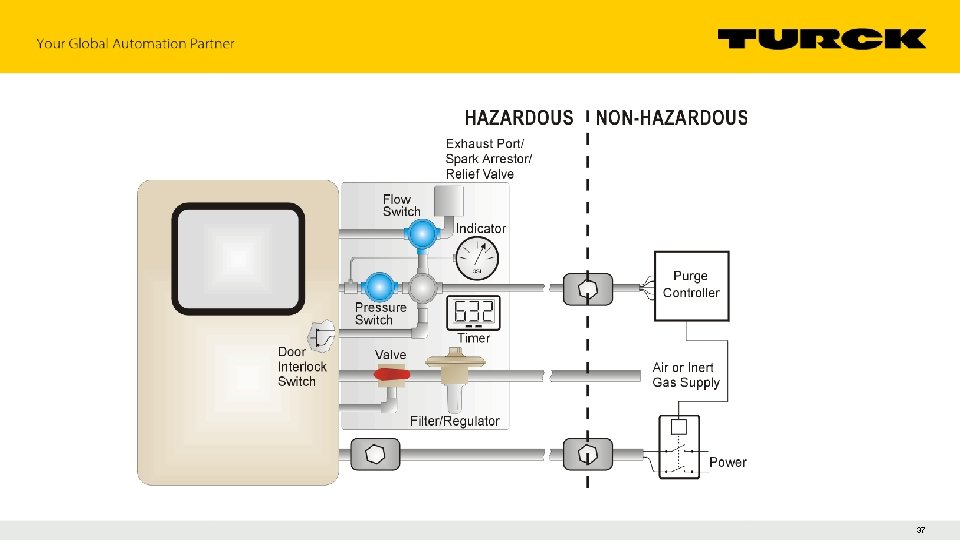
37
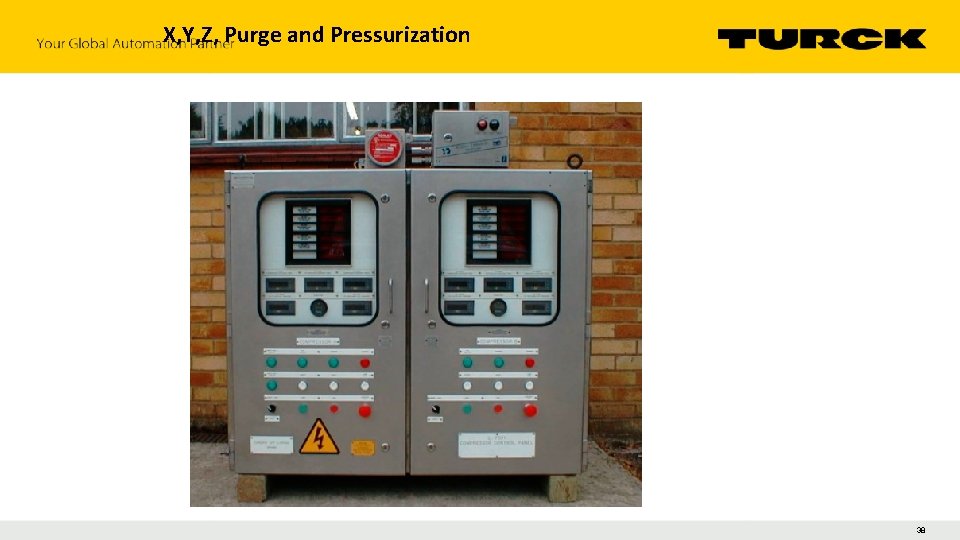
X, Y, Z, Purge and Pressurization 38
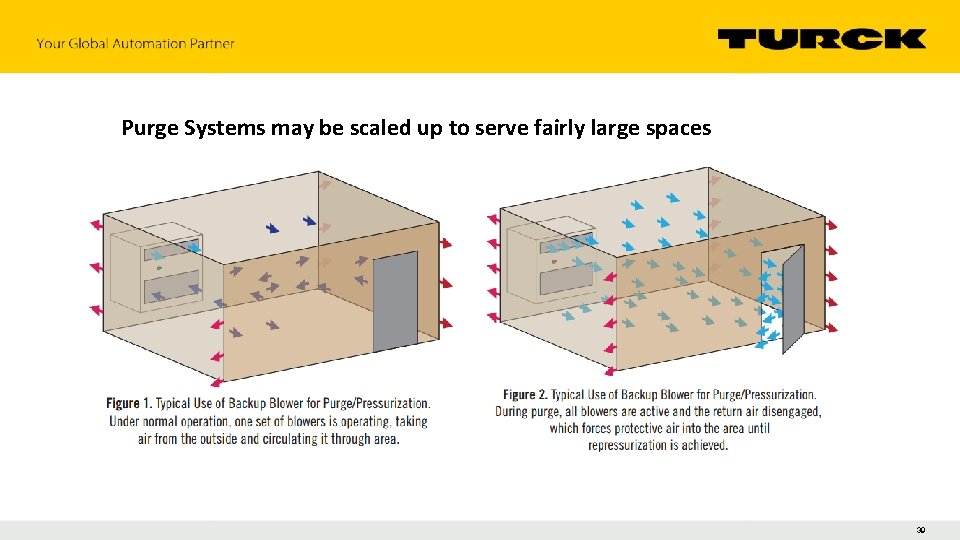
Purge Systems may be scaled up to serve fairly large spaces 39
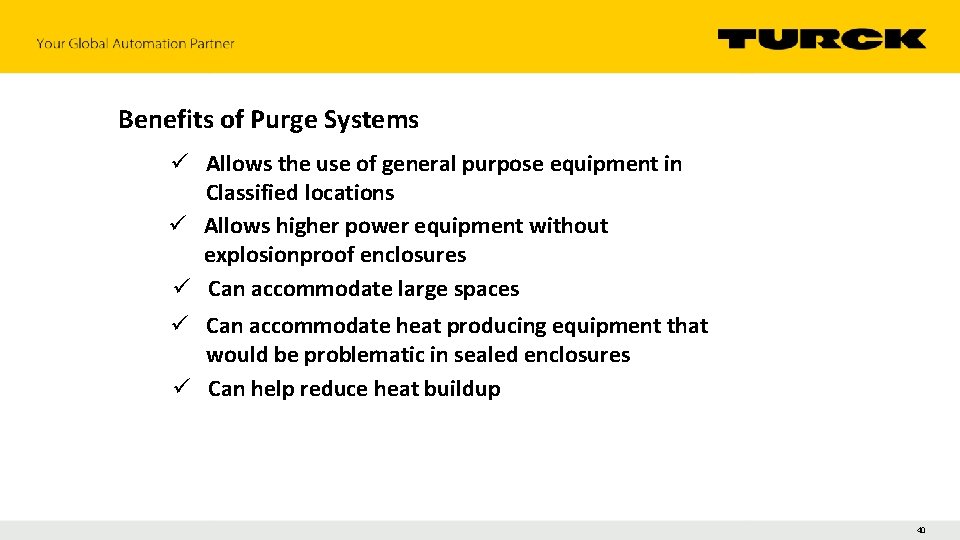
Benefits of Purge Systems ü Allows the use of general purpose equipment in Classified locations ü Allows higher power equipment without explosionproof enclosures ü Can accommodate large spaces ü Can accommodate heat producing equipment that would be problematic in sealed enclosures ü Can help reduce heat buildup 40
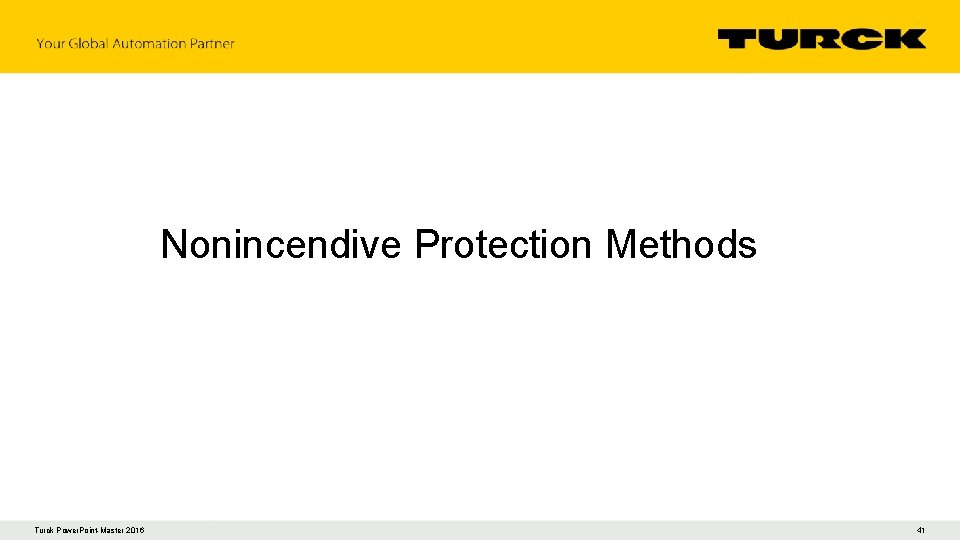
Nonincendive Protection Methods Turck Power. Point-Master 2016 41
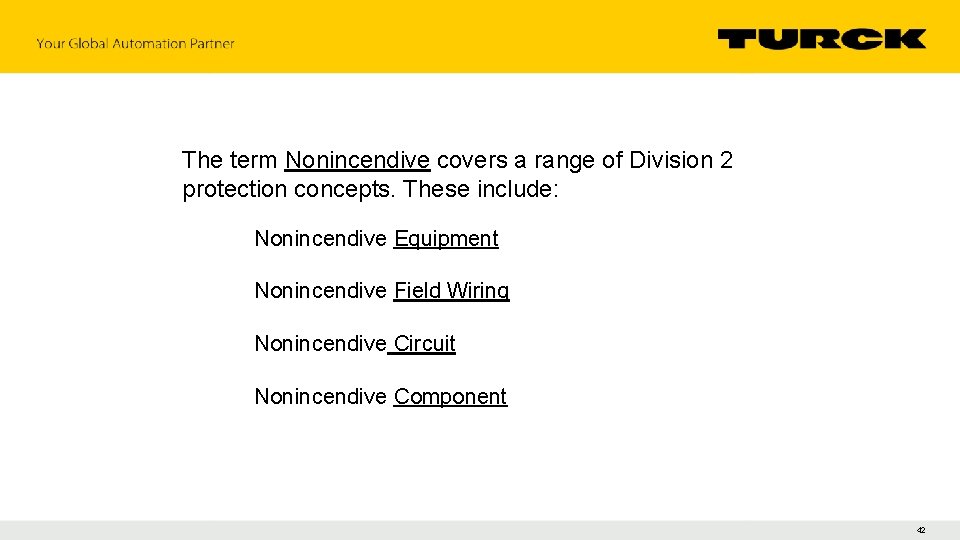
The term Nonincendive covers a range of Division 2 protection concepts. These include: Nonincendive Equipment Nonincendive Field Wiring Nonincendive Circuit Nonincendive Component 42
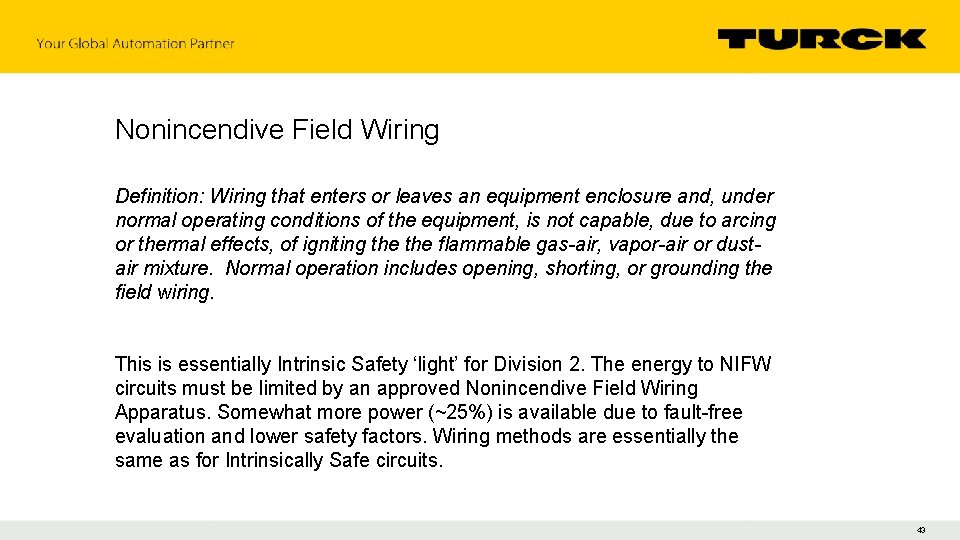
Nonincendive Field Wiring Definition: Wiring that enters or leaves an equipment enclosure and, under normal operating conditions of the equipment, is not capable, due to arcing or thermal effects, of igniting the flammable gas-air, vapor-air or dustair mixture. Normal operation includes opening, shorting, or grounding the field wiring. This is essentially Intrinsic Safety ‘light’ for Division 2. The energy to NIFW circuits must be limited by an approved Nonincendive Field Wiring Apparatus. Somewhat more power (~25%) is available due to fault-free evaluation and lower safety factors. Wiring methods are essentially the same as for Intrinsically Safe circuits. 43
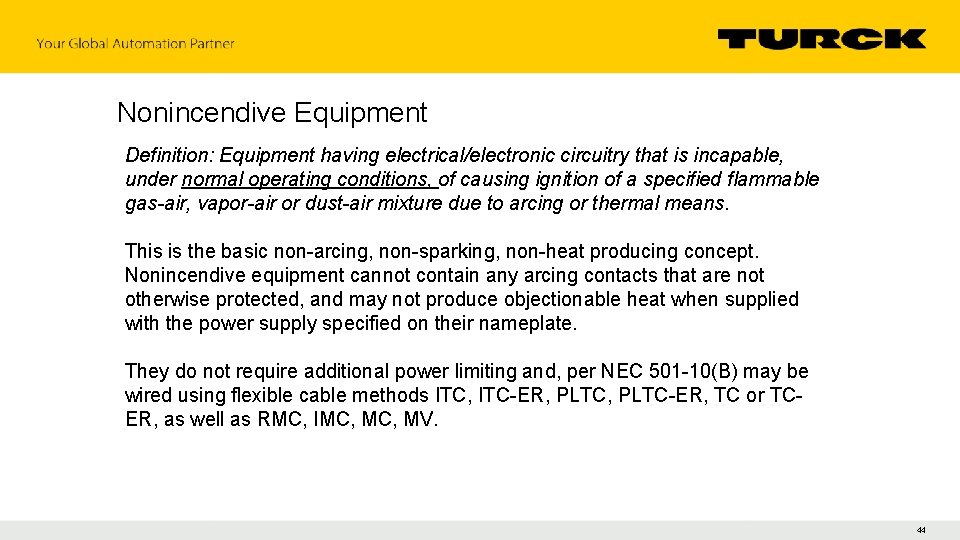
Nonincendive Equipment Definition: Equipment having electrical/electronic circuitry that is incapable, under normal operating conditions, of causing ignition of a specified flammable gas-air, vapor-air or dust-air mixture due to arcing or thermal means. This is the basic non-arcing, non-sparking, non-heat producing concept. Nonincendive equipment cannot contain any arcing contacts that are not otherwise protected, and may not produce objectionable heat when supplied with the power supply specified on their nameplate. They do not require additional power limiting and, per NEC 501 -10(B) may be wired using flexible cable methods ITC, ITC-ER, PLTC-ER, TC or TCER, as well as RMC, IMC, MV. 44
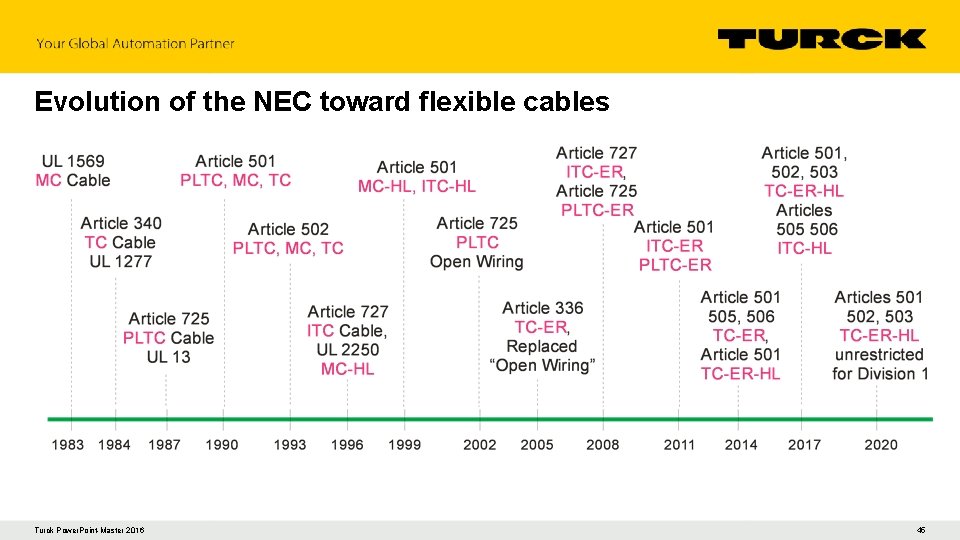
Evolution of the NEC toward flexible cables Turck Power. Point-Master 2016 45
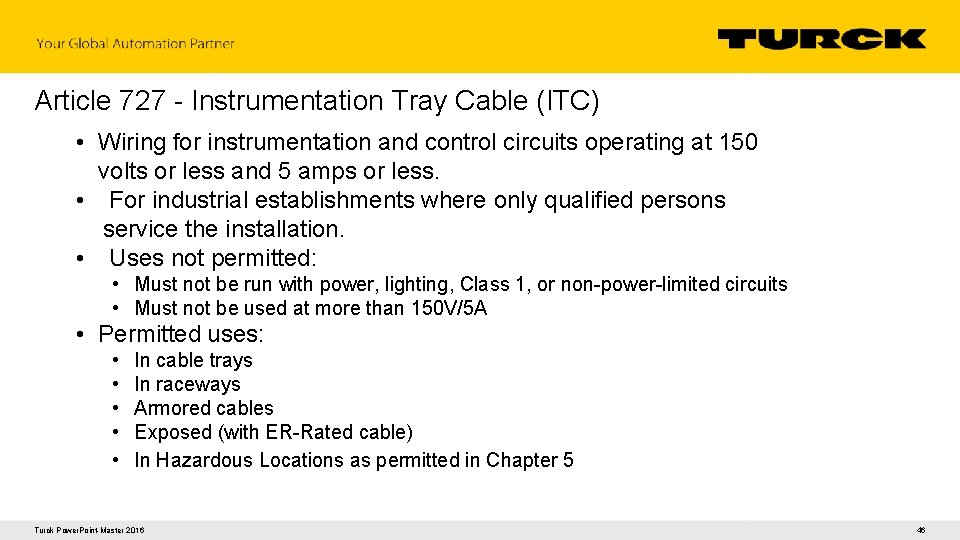
Article 727 - Instrumentation Tray Cable (ITC) • Wiring for instrumentation and control circuits operating at 150 volts or less and 5 amps or less. • For industrial establishments where only qualified persons service the installation. • Uses not permitted: • Must not be run with power, lighting, Class 1, or non-power-limited circuits • Must not be used at more than 150 V/5 A • Permitted uses: • • • In cable trays In raceways Armored cables Exposed (with ER-Rated cable) In Hazardous Locations as permitted in Chapter 5 Turck Power. Point-Master 2016 46
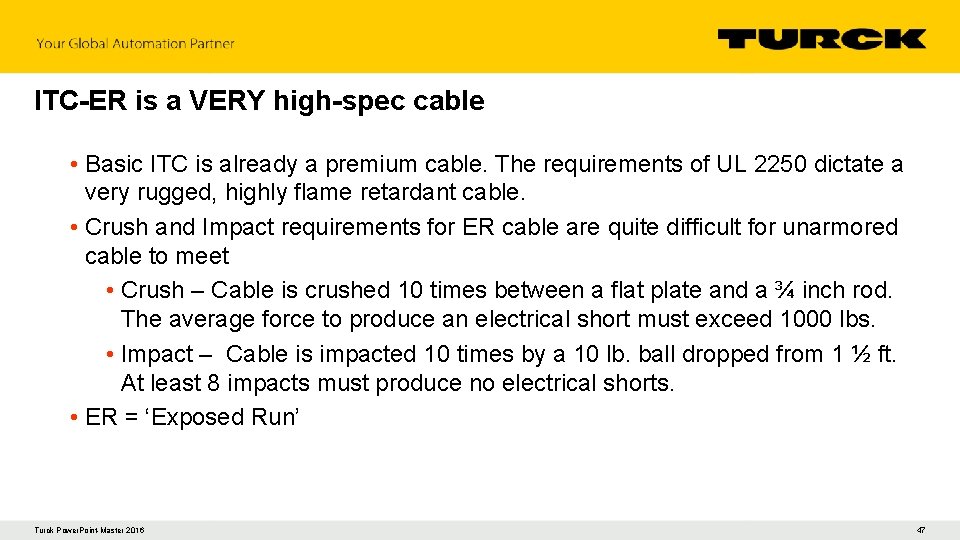
ITC-ER is a VERY high-spec cable • Basic ITC is already a premium cable. The requirements of UL 2250 dictate a very rugged, highly flame retardant cable. • Crush and Impact requirements for ER cable are quite difficult for unarmored cable to meet • Crush – Cable is crushed 10 times between a flat plate and a ¾ inch rod. The average force to produce an electrical short must exceed 1000 lbs. • Impact – Cable is impacted 10 times by a 10 lb. ball dropped from 1 ½ ft. At least 8 impacts must produce no electrical shorts. • ER = ‘Exposed Run’ Turck Power. Point-Master 2016 47
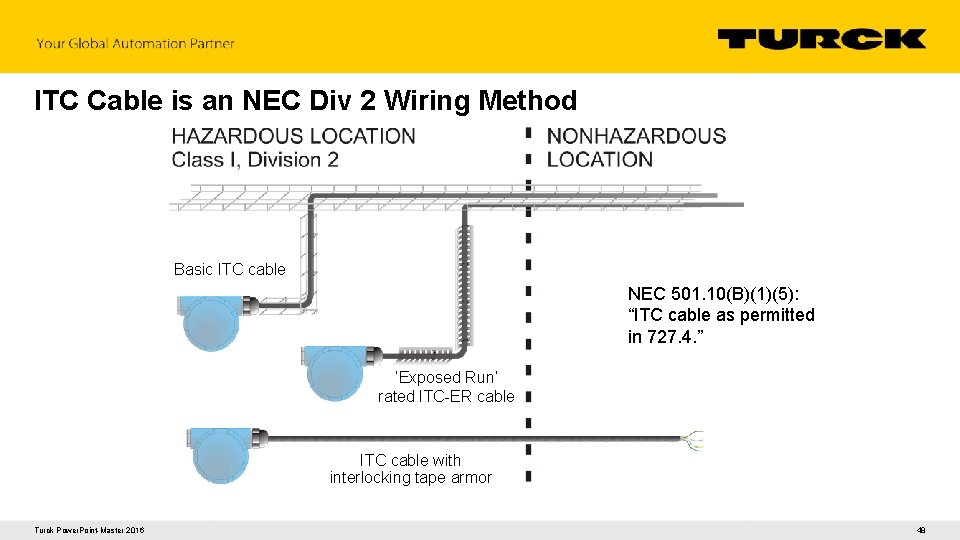
ITC Cable is an NEC Div 2 Wiring Method Basic ITC cable NEC 501. 10(B)(1)(5): “ITC cable as permitted in 727. 4. ” ‘Exposed Run’ rated ITC-ER cable ITC cable with interlocking tape armor Turck Power. Point-Master 2016 48
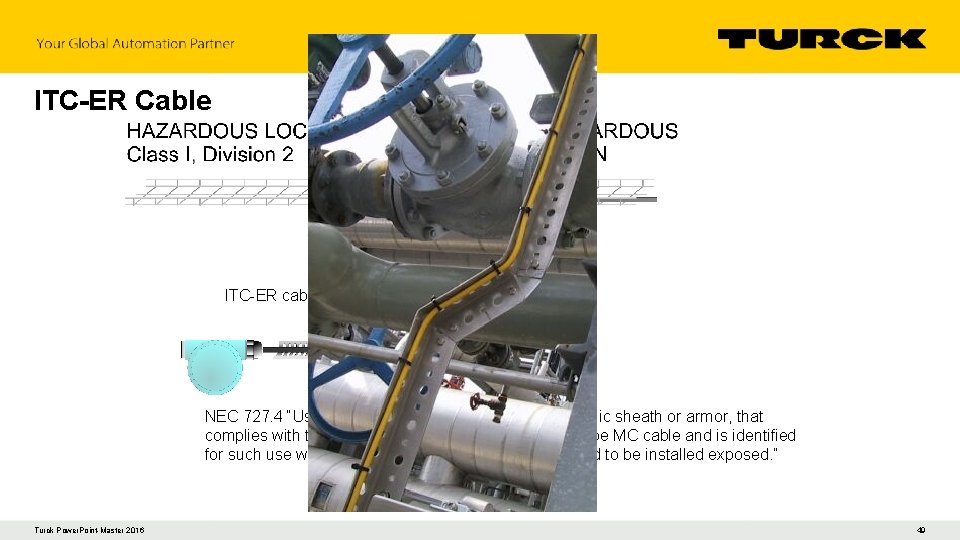
ITC-ER Cable ITC-ER cable NEC 727. 4 “Uses Permitted” (5) “Cable, without a metalic sheath or armor, that complies with the crush and impact requirements of Type MC cable and is identified for such use with the marking ITC-ER shall be permitted to be installed exposed. ” Turck Power. Point-Master 2016 49
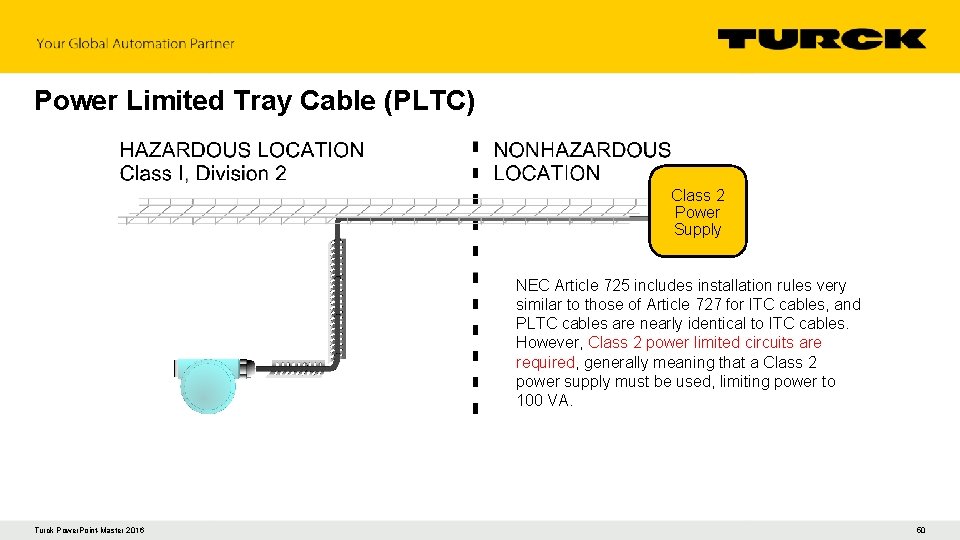
Power Limited Tray Cable (PLTC) Class 2 Power Supply NEC Article 725 includes installation rules very similar to those of Article 727 for ITC cables, and PLTC cables are nearly identical to ITC cables. However, Class 2 power limited circuits are required, generally meaning that a Class 2 power supply must be used, limiting power to 100 VA. Turck Power. Point-Master 2016 50
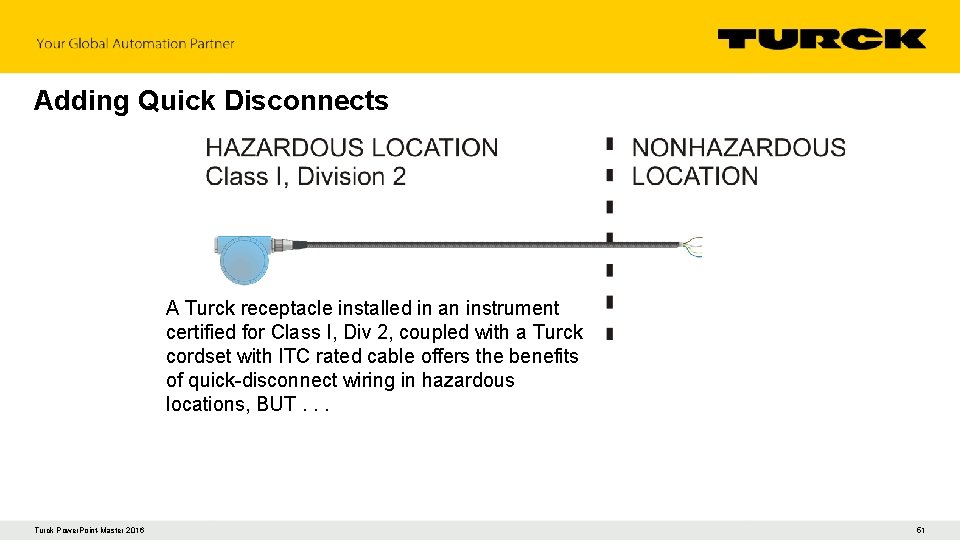
Adding Quick Disconnects A Turck receptacle installed in an instrument certified for Class I, Div 2, coupled with a Turck cordset with ITC rated cable offers the benefits of quick-disconnect wiring in hazardous locations, BUT. . . Turck Power. Point-Master 2016 51
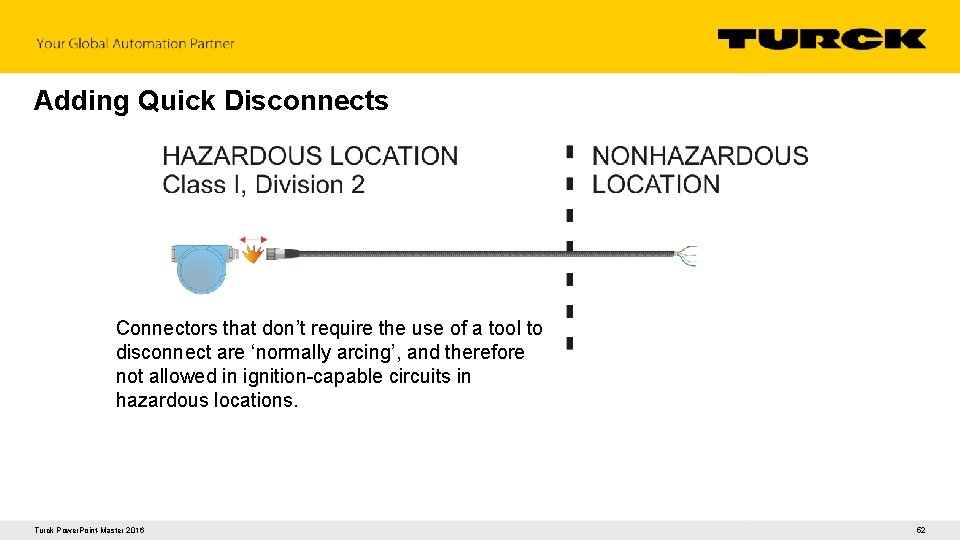
Adding Quick Disconnects Connectors that don’t require the use of a tool to disconnect are ‘normally arcing’, and therefore not allowed in ignition-capable circuits in hazardous locations. Turck Power. Point-Master 2016 52
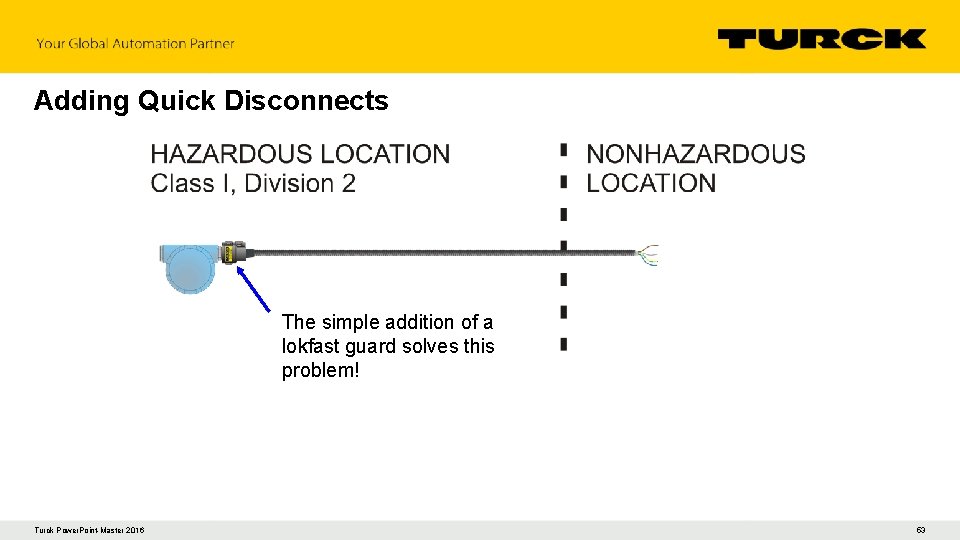
Adding Quick Disconnects The simple addition of a lokfast guard solves this problem! Turck Power. Point-Master 2016 53
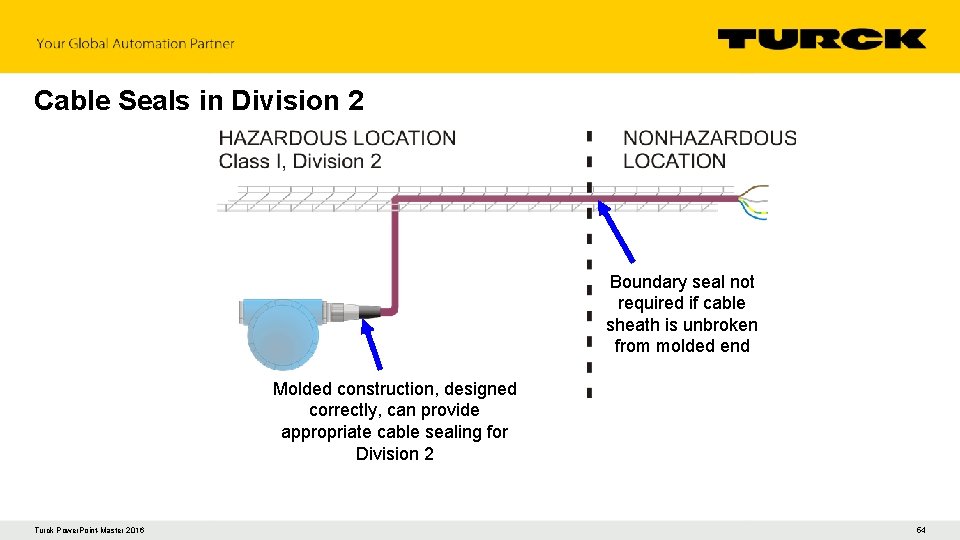
Cable Seals in Division 2 Boundary seal not required if cable sheath is unbroken from molded end Molded construction, designed correctly, can provide appropriate cable sealing for Division 2 Turck Power. Point-Master 2016 54
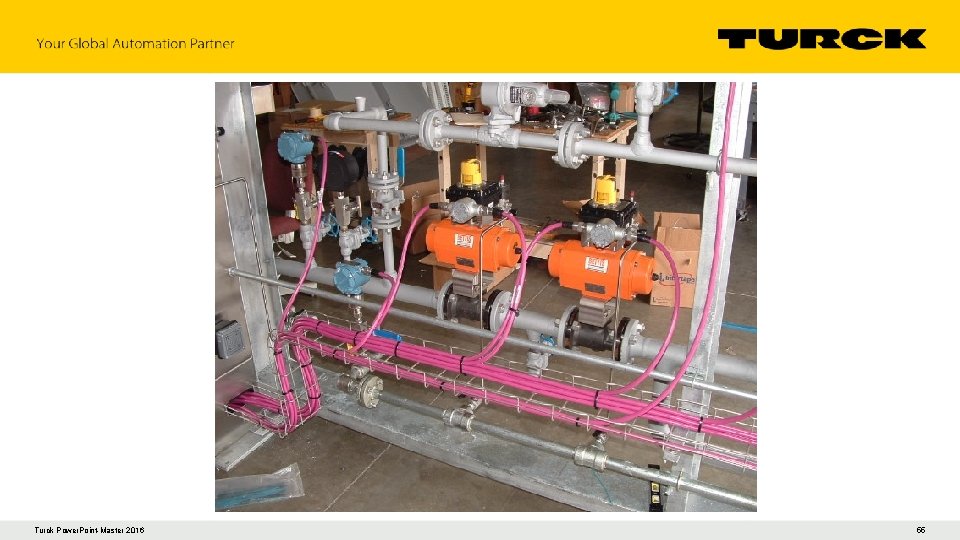
Turck Power. Point-Master 2016 55

(www. turck. com/fmcd) Turck Power. Point-Master 2016
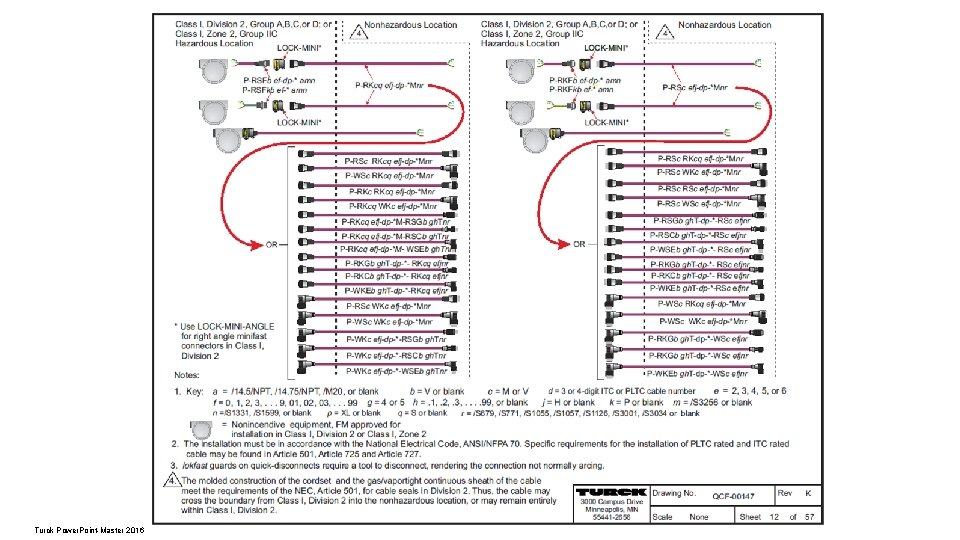
Turck Power. Point-Master 2016
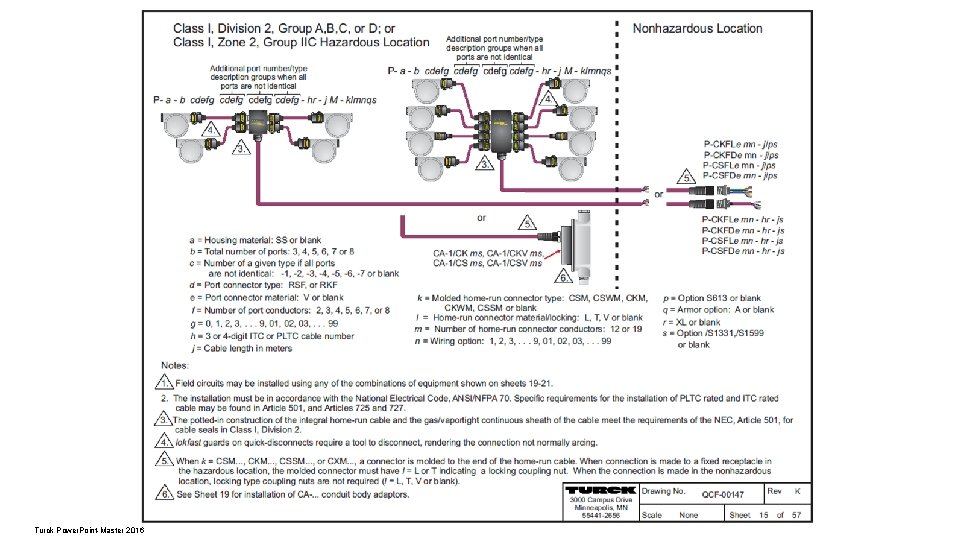
Turck Power. Point-Master 2016
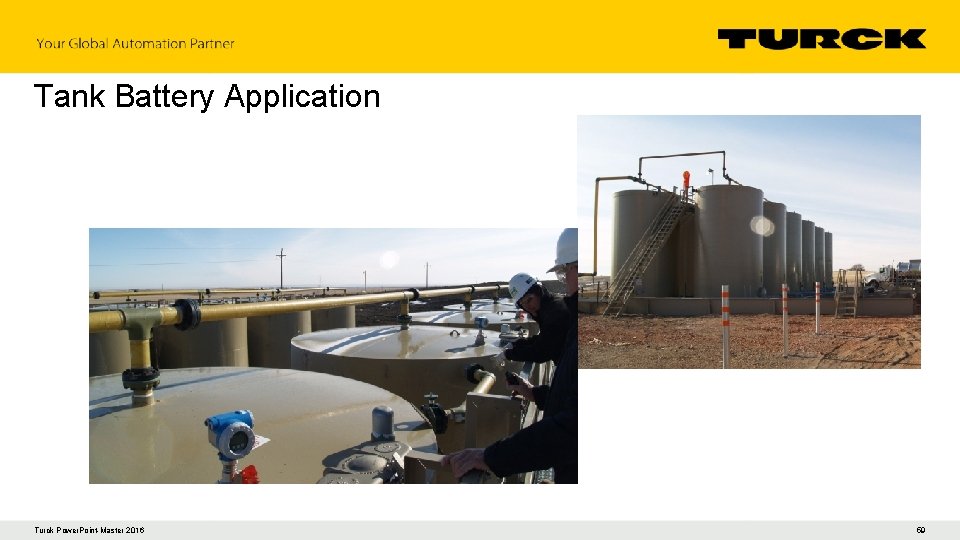
Tank Battery Application Turck Power. Point-Master 2016 59
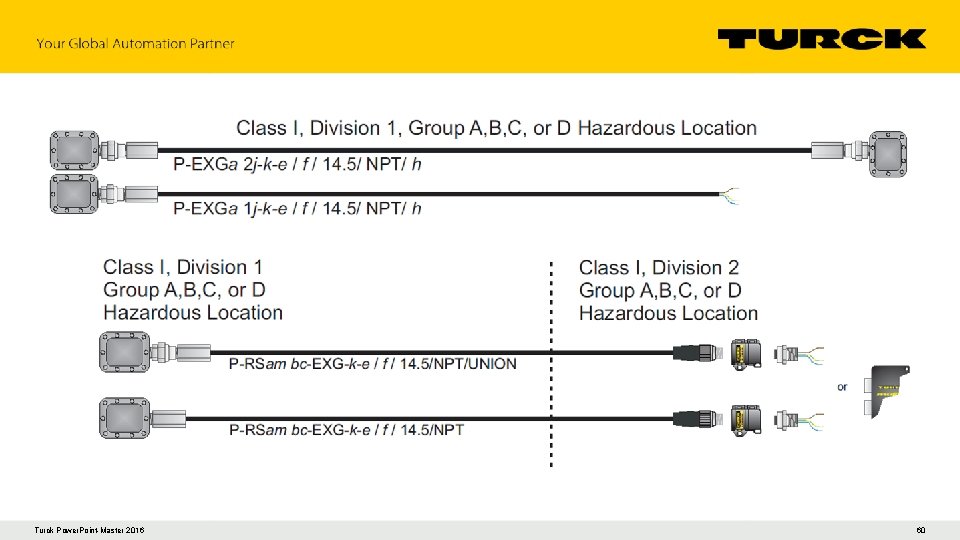
Turck Power. Point-Master 2016 60
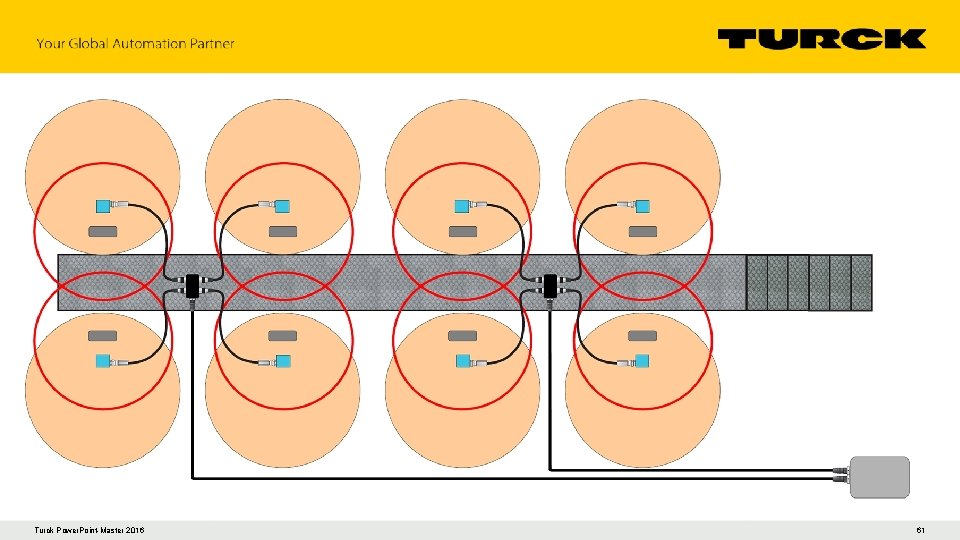
Turck Power. Point-Master 2016 61
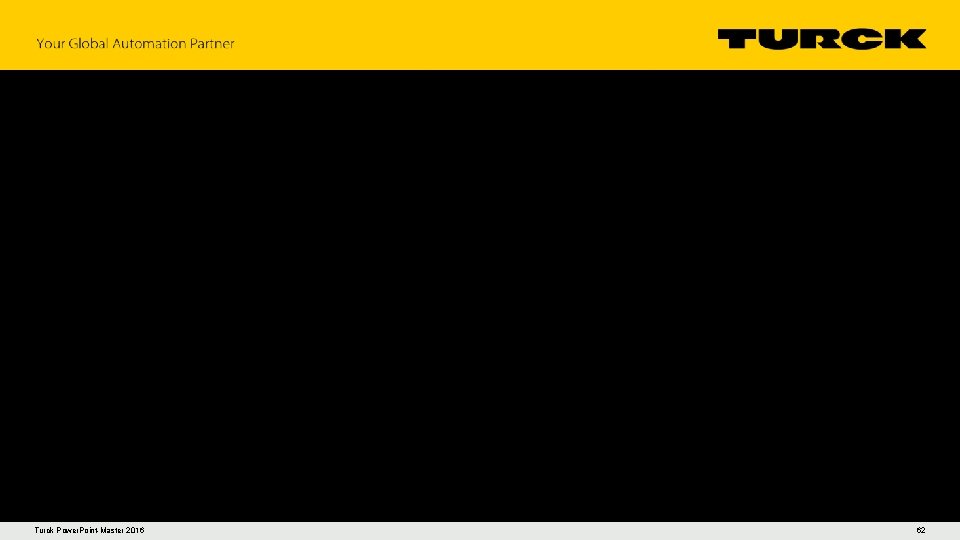
Turck Power. Point-Master 2016 62
Wiring
Methods of wiring flowers
Protected objects and methods of protection
A positioning device system is a fall arrest system
Solid and hazardous waste
Pipeline and hazardous materials administration
Direct wax pattern technique
A cross country skier moves from location a to location b
Location planning and analysis summary
When is jekyll and hyde set
Themes about hate
How is power presented in ozymandias and london
Ozymandias and my last duchess comparison
Example of text structure cause and effect
Section 3 hazardous waste answers
Aviation hazardous attitudes
Hospital waste management introduction
Hazmat table
Hazardous materials table
Us military marking system for hazardous materials
Pa-psfa-hazardous materials awareness
Avhf
Aviation hazardous attitudes
Workplace hazardous materials information system (whmis)
Isachmm
Transverse motion machine
Hazardous waste apes
Hazardous waste examples
Stanislaus county hazardous waste
Nj crtk environmental hazardous substances
Low pressure hazardous vacuum switch
Hazardous materials transportation act of 1975
Hazardous area training darwin
Hazardous symbols
Hazardous materials managing the incident
Keeping food safe chapter 1
Hazardous drug api
On july 18 2001 a train carrying hazardous chemicals
Waste management references
Hazardous materials reference books
Hazardous area response teams
Hazardous movement asl
Hazardous weather testbed
Tagout
Keller hazardous waste disposal
Hazardous materials incident report
Hazardous materials business plan
What are the 3 things required on a workplace label
Rcra hazardous waste refresher
Hazardous materials managing the incident
29 cfr 1910 hazardous materials
Les fonctions techniques et les solutions techniques
Example of kicker in newspaper
Presenter's name
Identify a key term used in both passages.
Title of presenter
Jerome bruner cognitive theory
Hyde as a frightening outsider
Talisman presented
Topics presented in chapters
Kamikaze and prelude comparison
Technological design loop
How is marley's ghost presented in stave 1