Fundamental Concept ENT 485 FEA Dr Rakhmad Arief
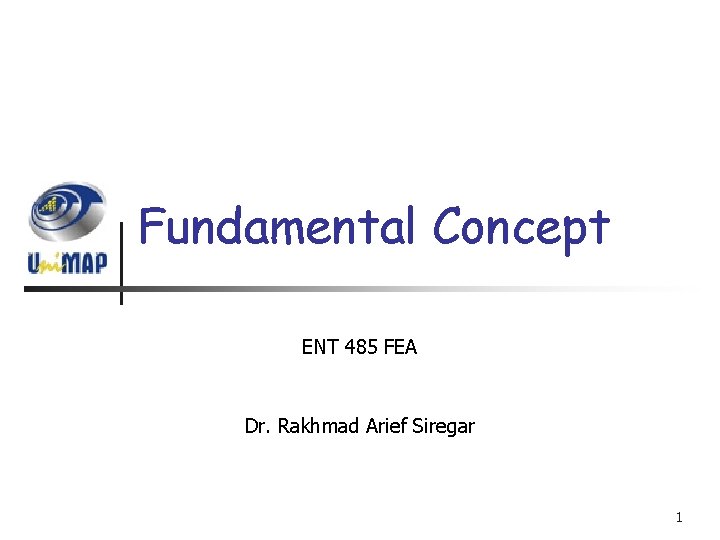
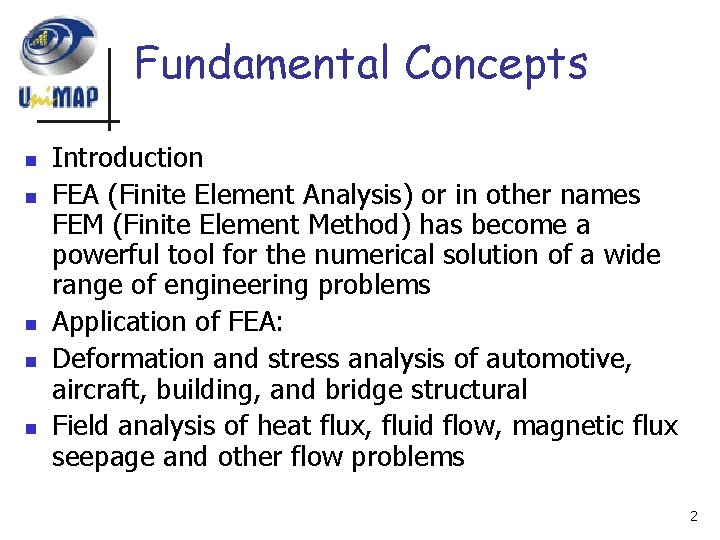
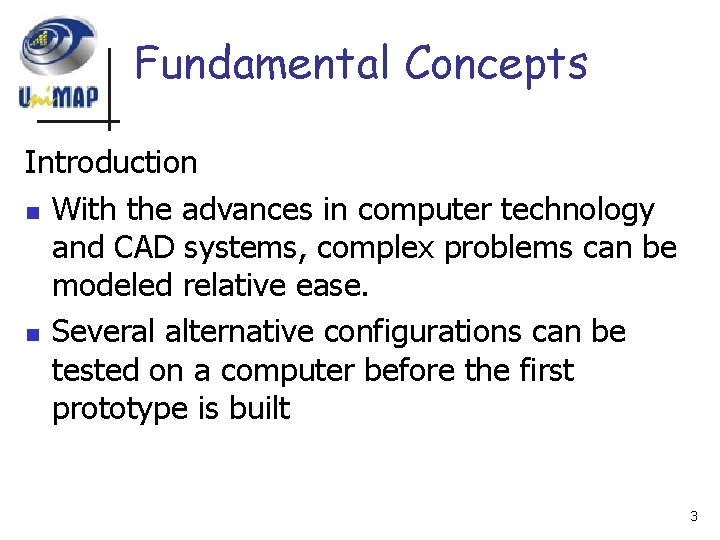
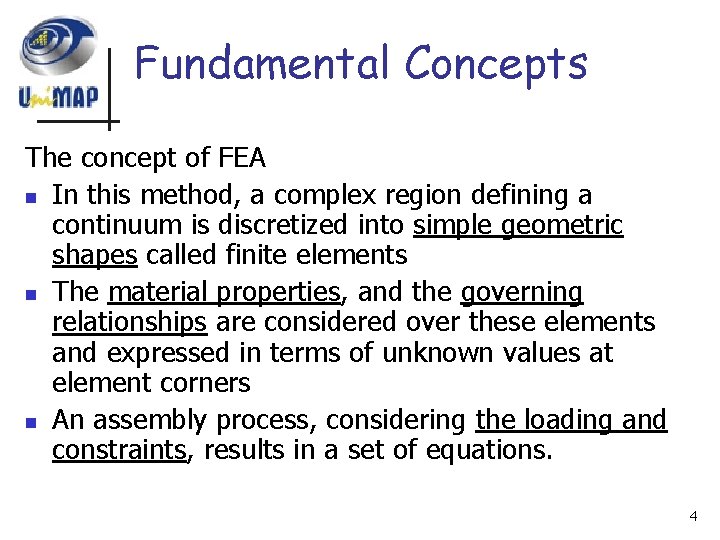
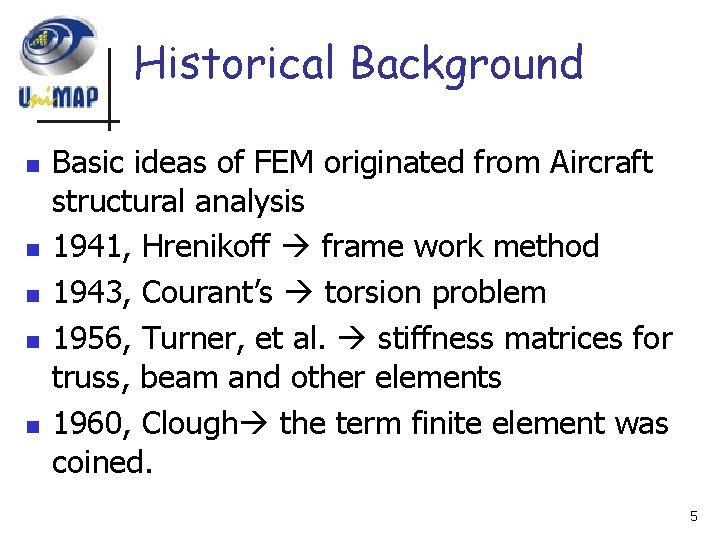
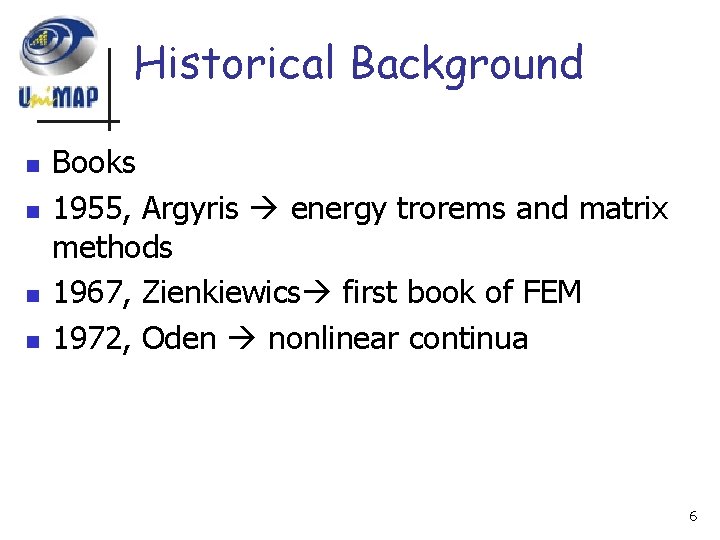
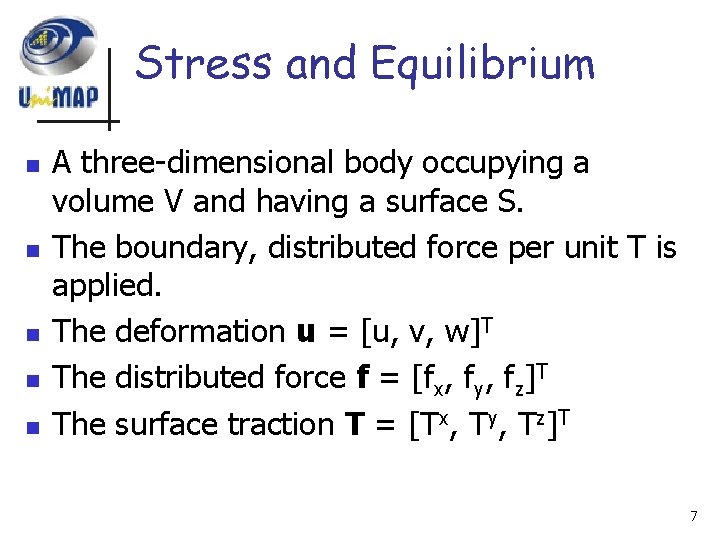
![Stress and Equilibrium n The load Pi = [Px, Py, Pz]T The six independent Stress and Equilibrium n The load Pi = [Px, Py, Pz]T The six independent](https://slidetodoc.com/presentation_image_h/11a15f23d2b47c044a86d6252c33cab9/image-8.jpg)
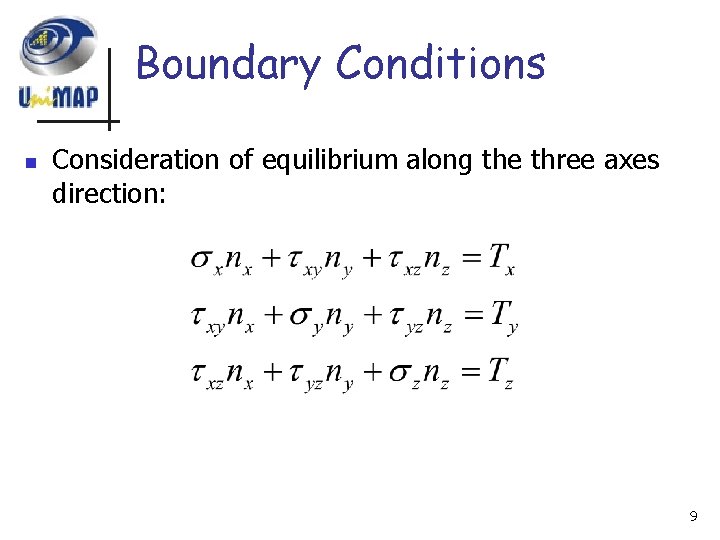
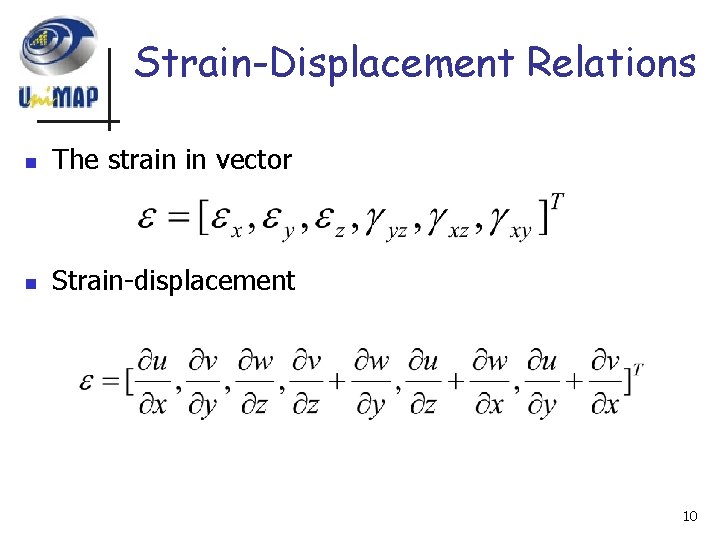
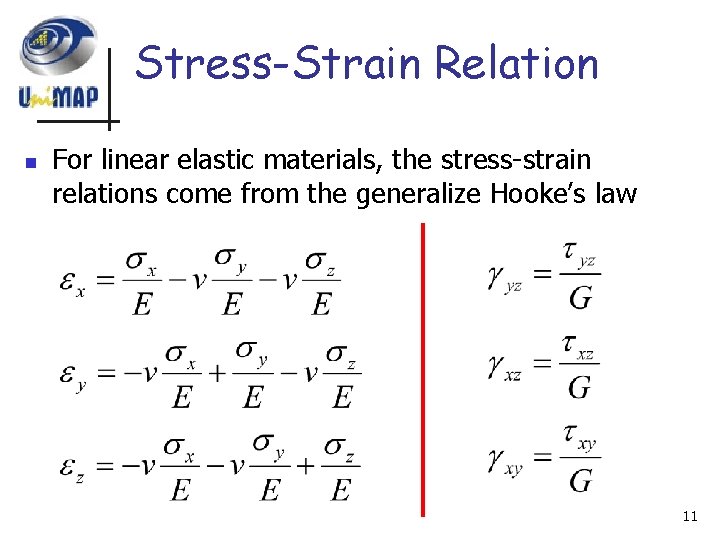
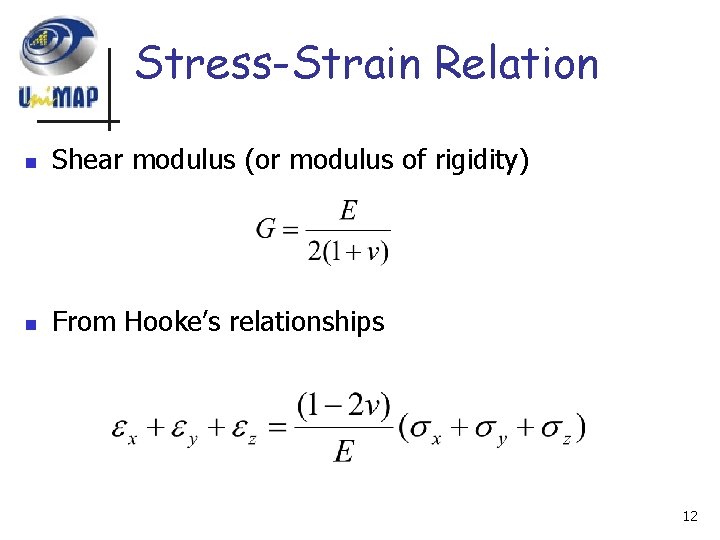
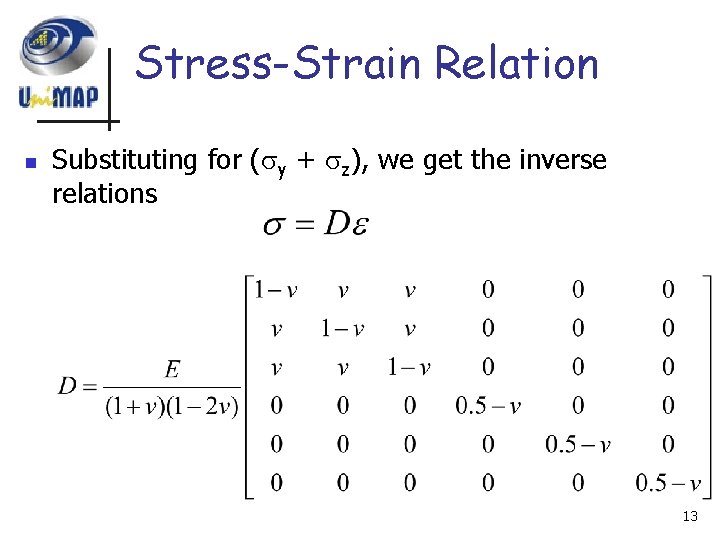
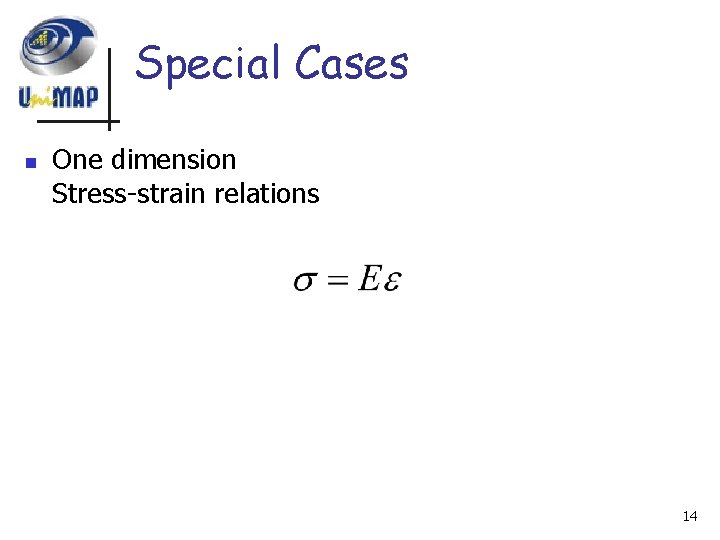
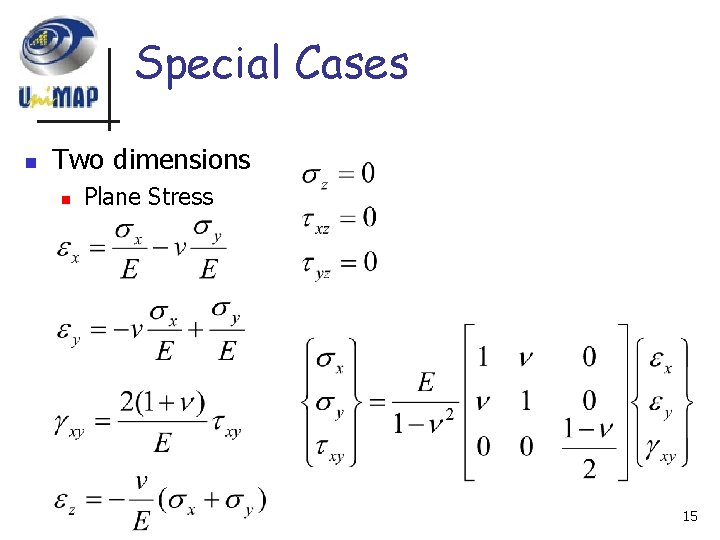
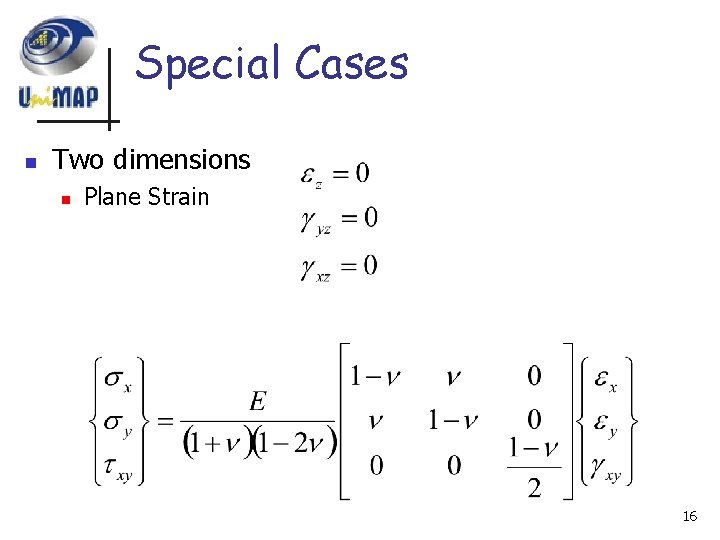
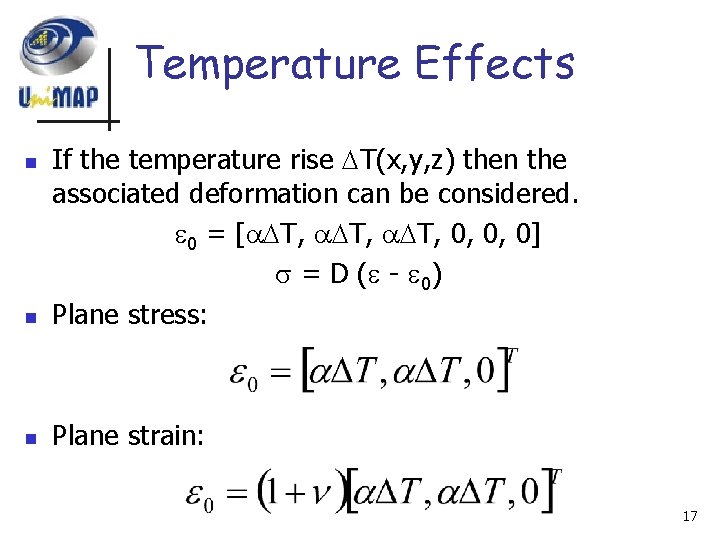
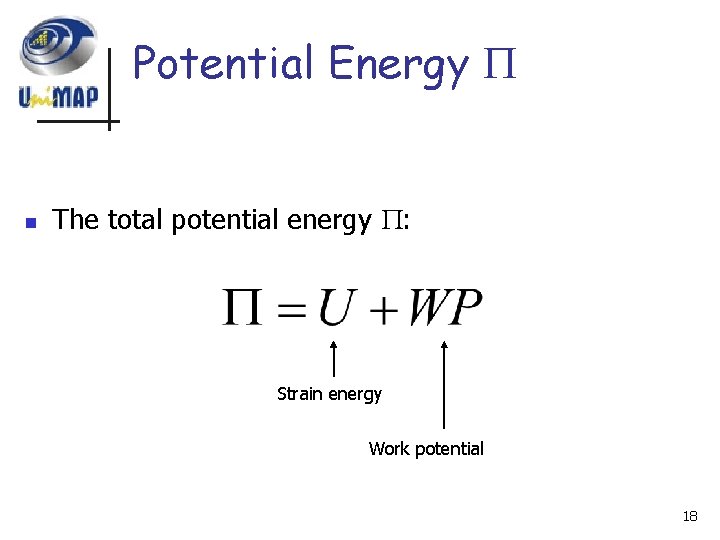

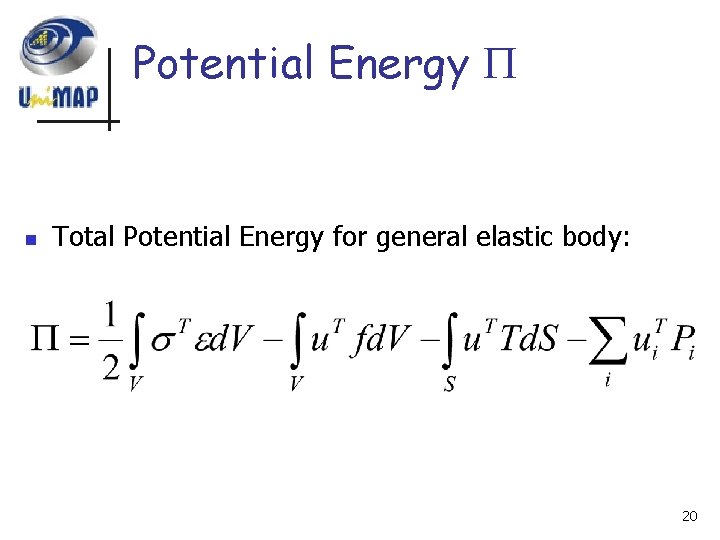
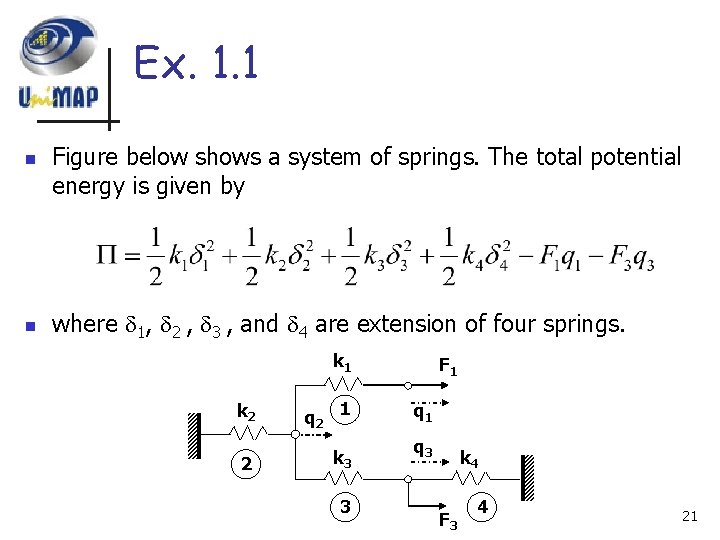
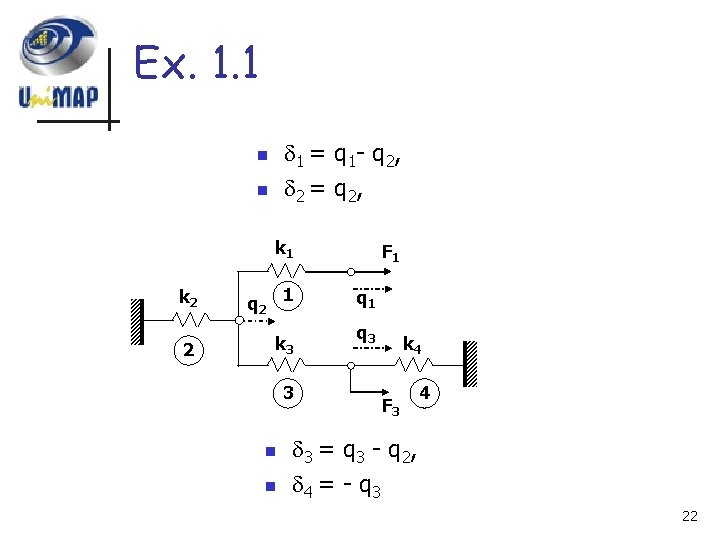
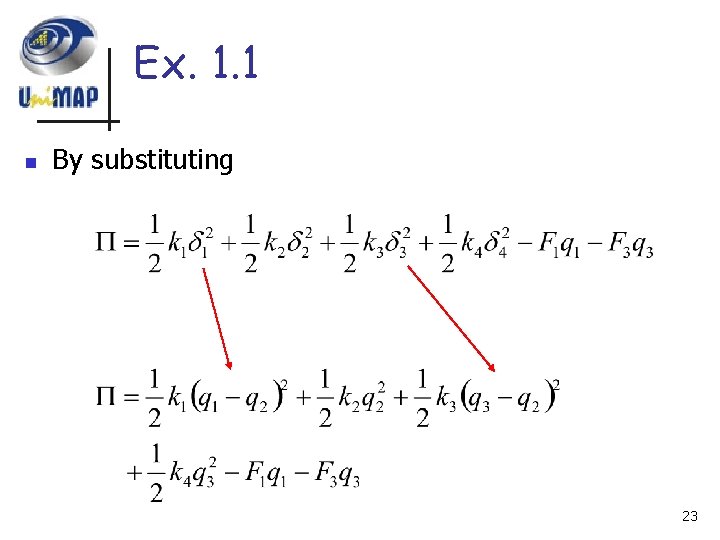
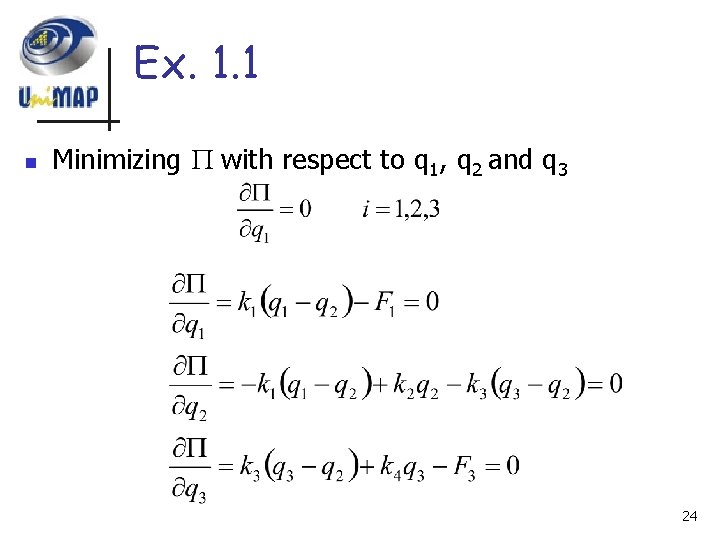
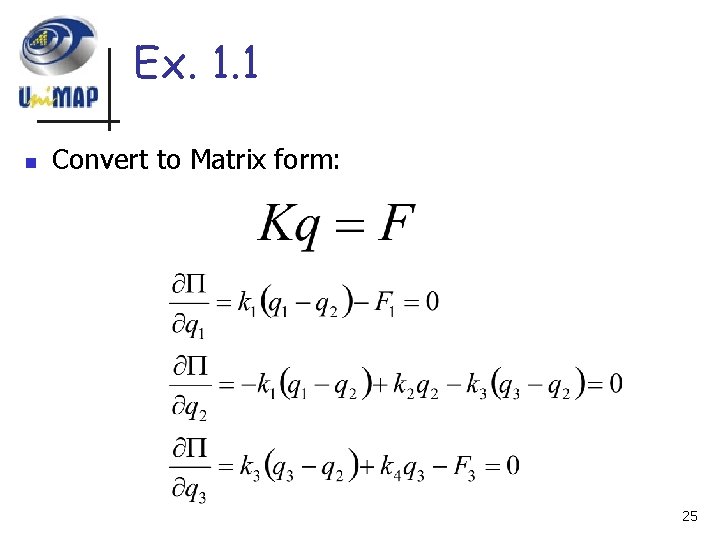
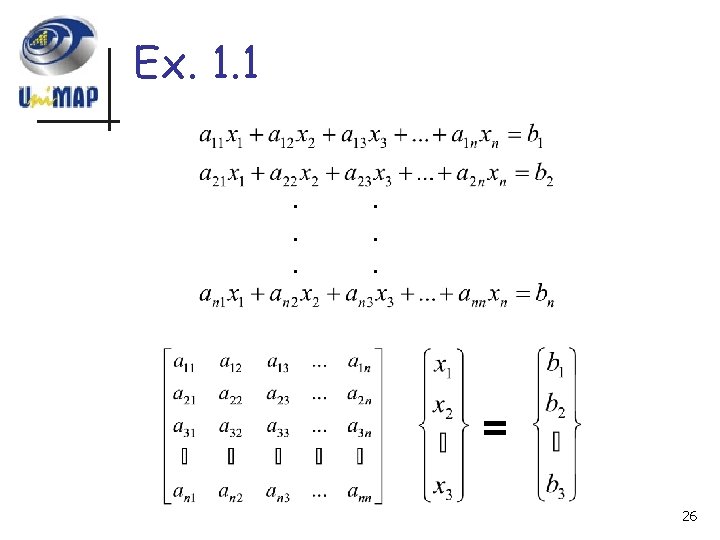
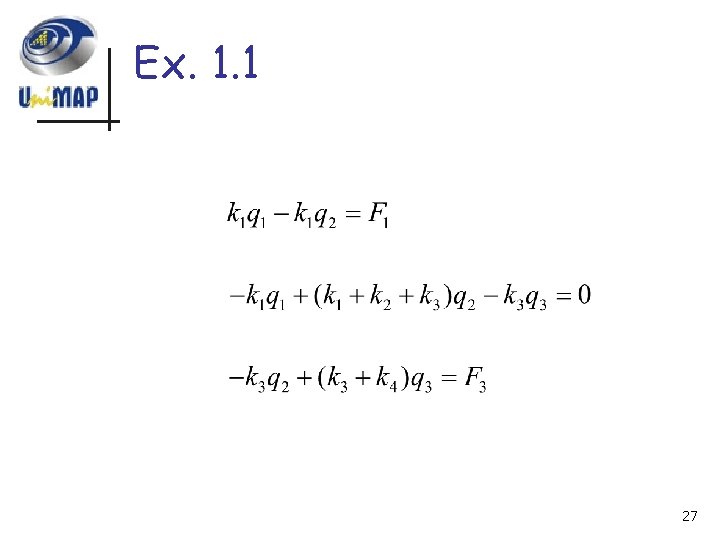
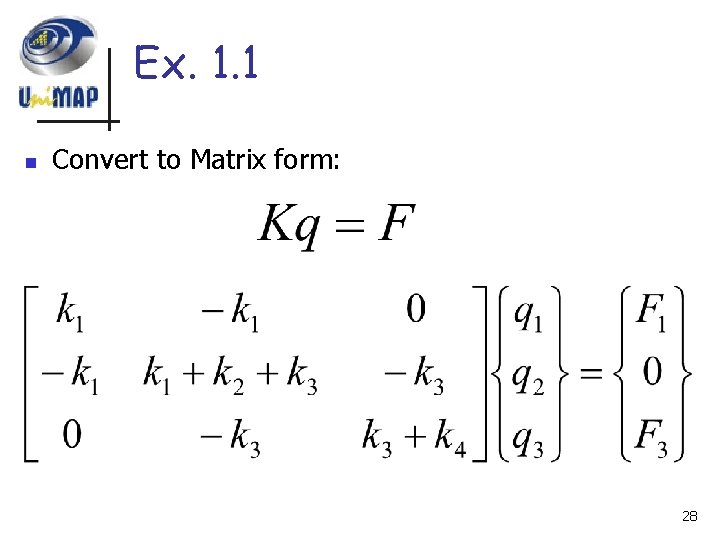
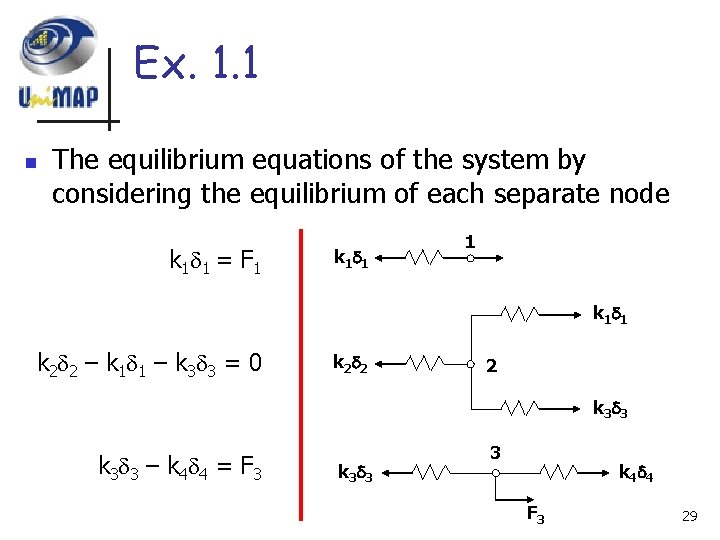
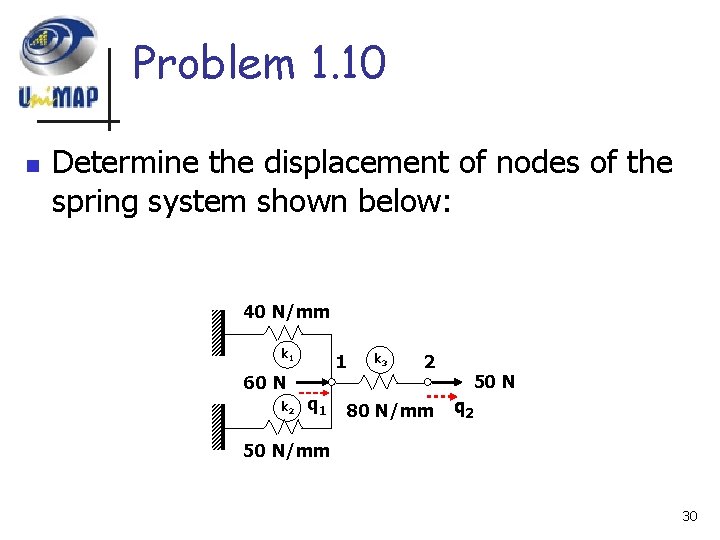
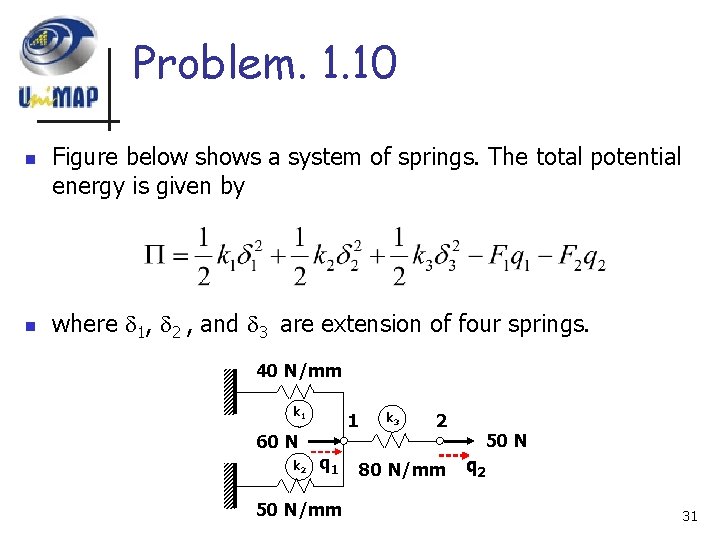
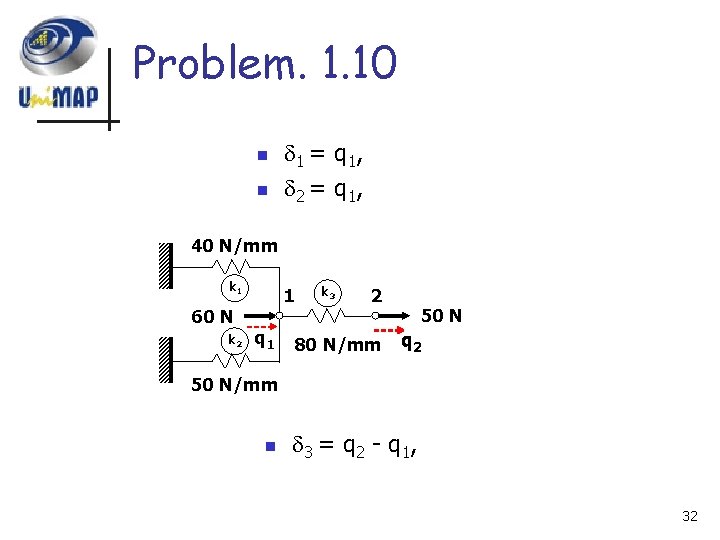
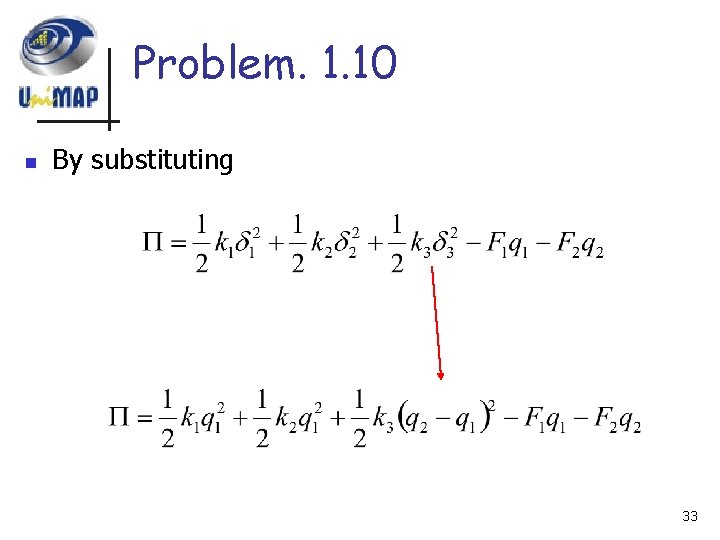
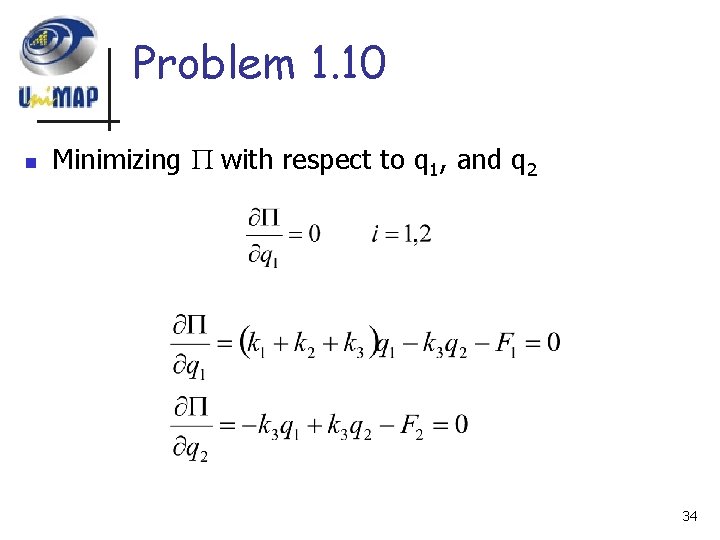

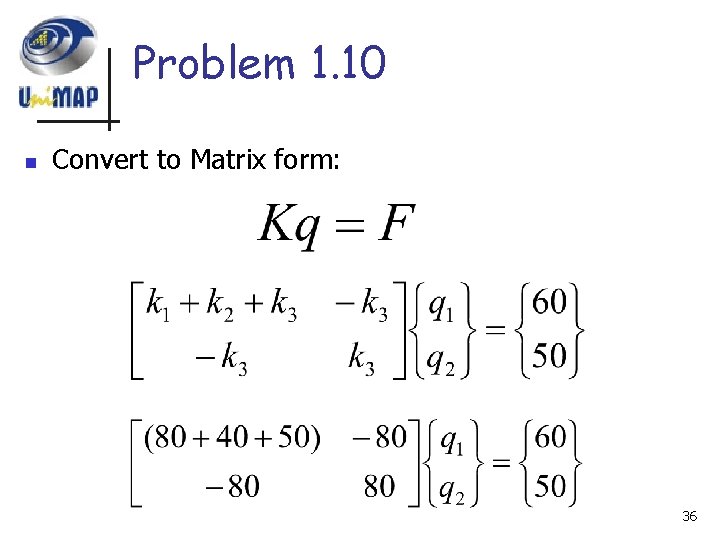
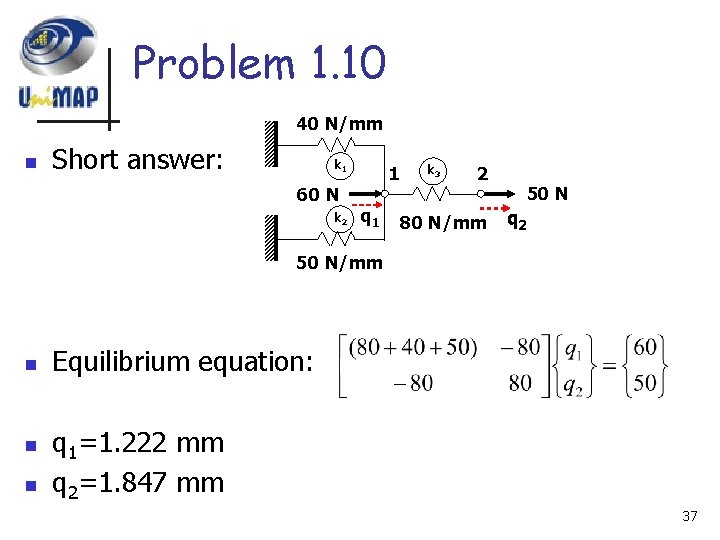
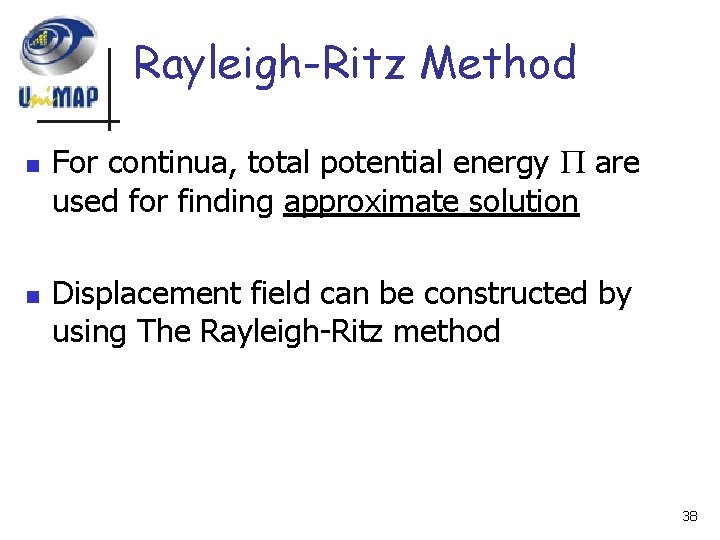
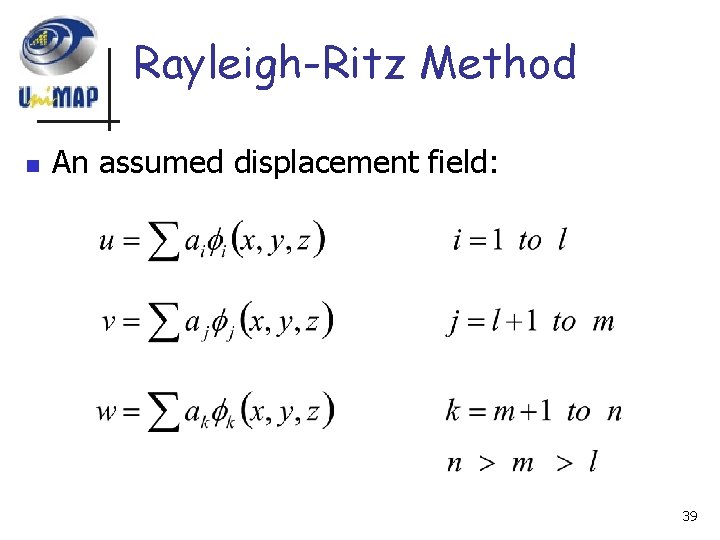
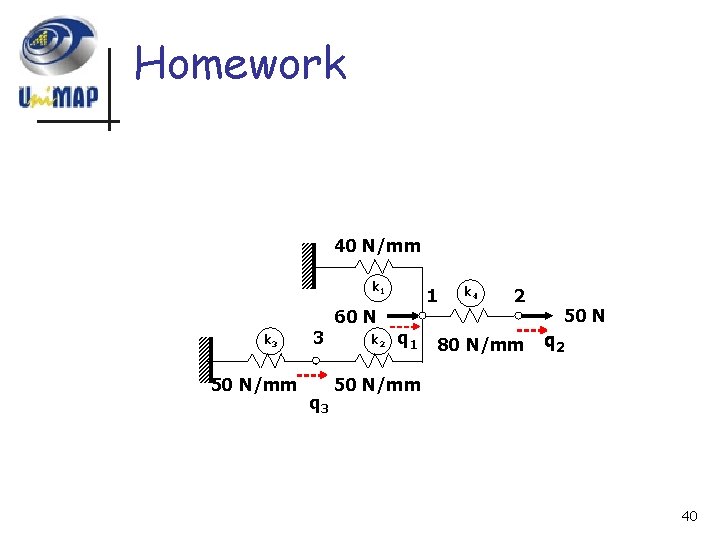
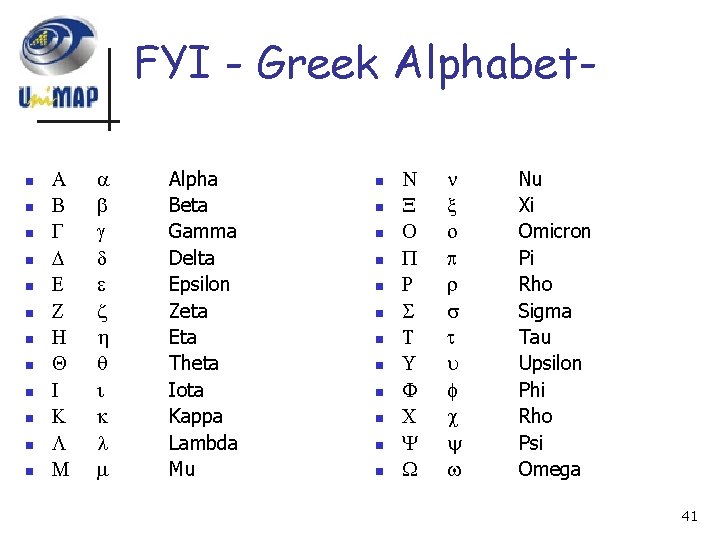
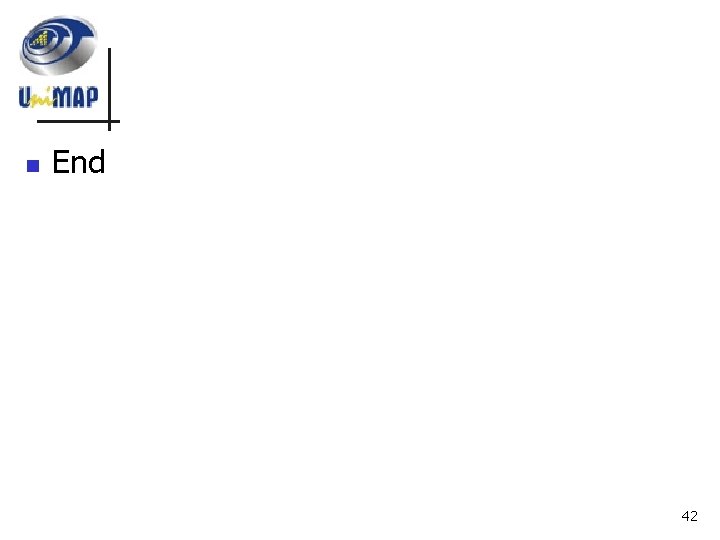
- Slides: 42
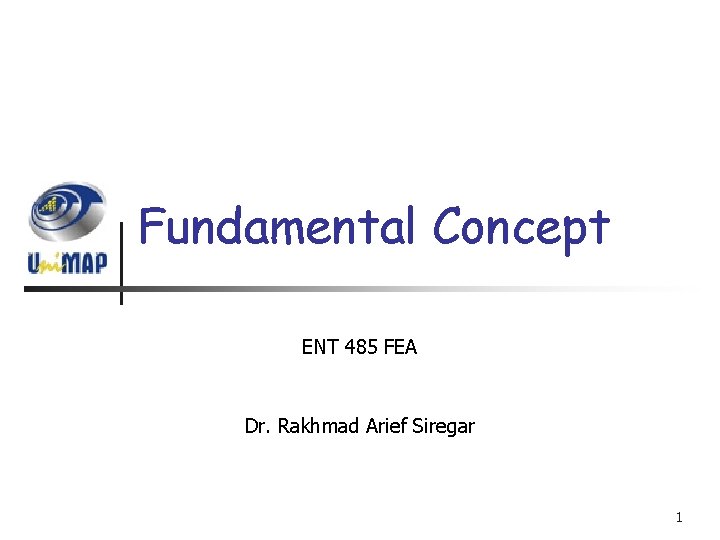
Fundamental Concept ENT 485 FEA Dr. Rakhmad Arief Siregar 1
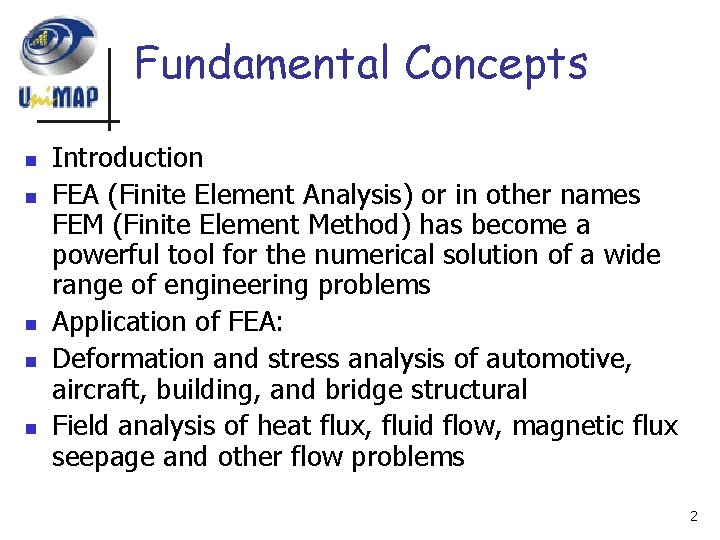
Fundamental Concepts n n n Introduction FEA (Finite Element Analysis) or in other names FEM (Finite Element Method) has become a powerful tool for the numerical solution of a wide range of engineering problems Application of FEA: Deformation and stress analysis of automotive, aircraft, building, and bridge structural Field analysis of heat flux, fluid flow, magnetic flux seepage and other flow problems 2
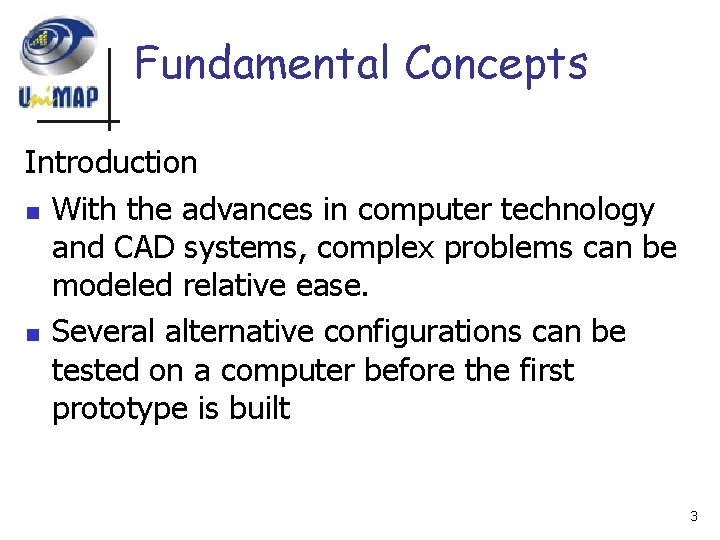
Fundamental Concepts Introduction n With the advances in computer technology and CAD systems, complex problems can be modeled relative ease. n Several alternative configurations can be tested on a computer before the first prototype is built 3
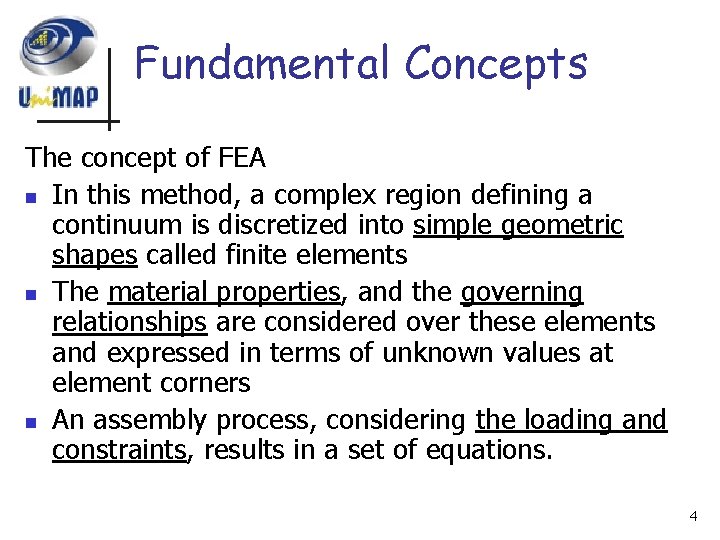
Fundamental Concepts The concept of FEA n In this method, a complex region defining a continuum is discretized into simple geometric shapes called finite elements n The material properties, and the governing relationships are considered over these elements and expressed in terms of unknown values at element corners n An assembly process, considering the loading and constraints, results in a set of equations. 4
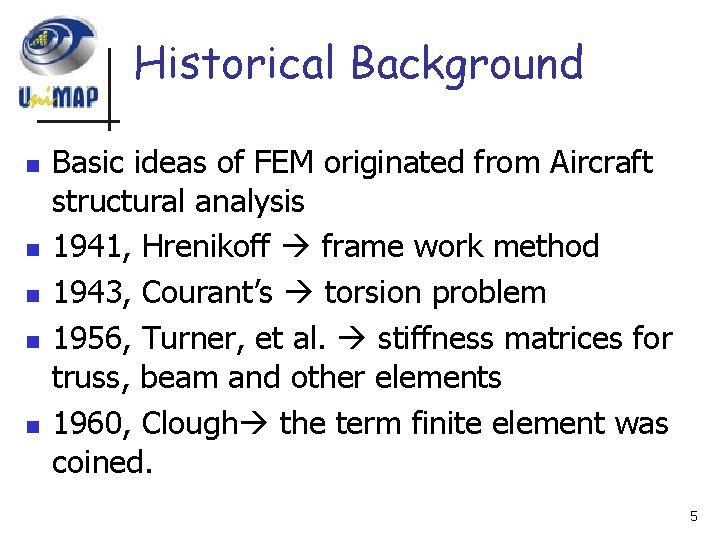
Historical Background n n n Basic ideas of FEM originated from Aircraft structural analysis 1941, Hrenikoff frame work method 1943, Courant’s torsion problem 1956, Turner, et al. stiffness matrices for truss, beam and other elements 1960, Clough the term finite element was coined. 5
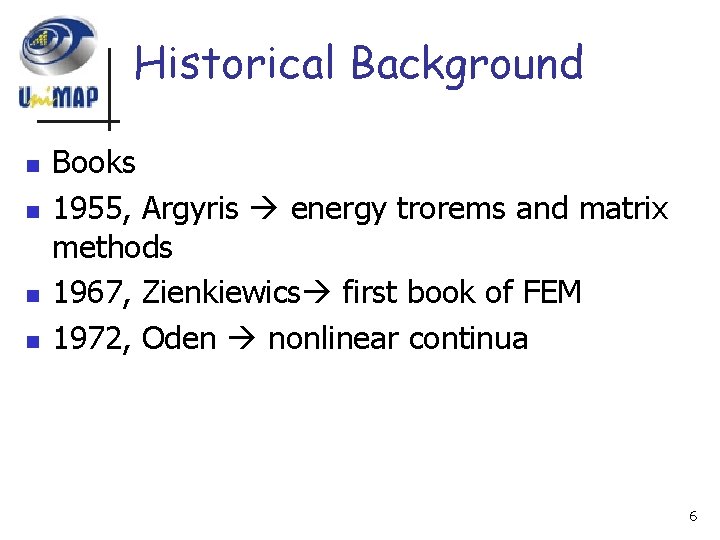
Historical Background n n Books 1955, Argyris energy trorems and matrix methods 1967, Zienkiewics first book of FEM 1972, Oden nonlinear continua 6
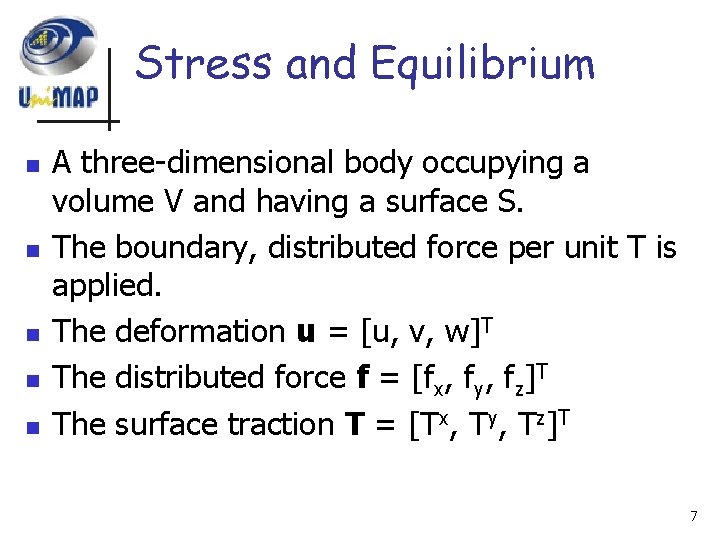
Stress and Equilibrium n n n A three-dimensional body occupying a volume V and having a surface S. The boundary, distributed force per unit T is applied. The deformation u = [u, v, w]T The distributed force f = [fx, fy, fz]T The surface traction T = [Tx, Ty, Tz]T 7
![Stress and Equilibrium n The load Pi Px Py PzT The six independent Stress and Equilibrium n The load Pi = [Px, Py, Pz]T The six independent](https://slidetodoc.com/presentation_image_h/11a15f23d2b47c044a86d6252c33cab9/image-8.jpg)
Stress and Equilibrium n The load Pi = [Px, Py, Pz]T The six independent components are: n The equilibrium equations n 8
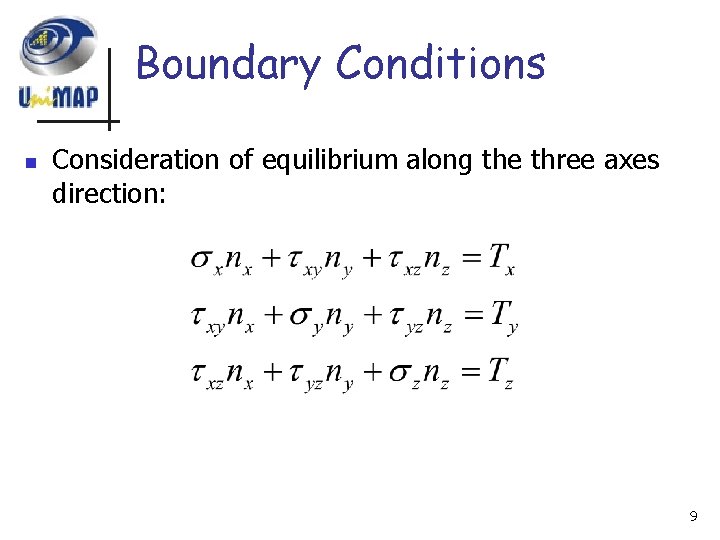
Boundary Conditions n Consideration of equilibrium along the three axes direction: 9
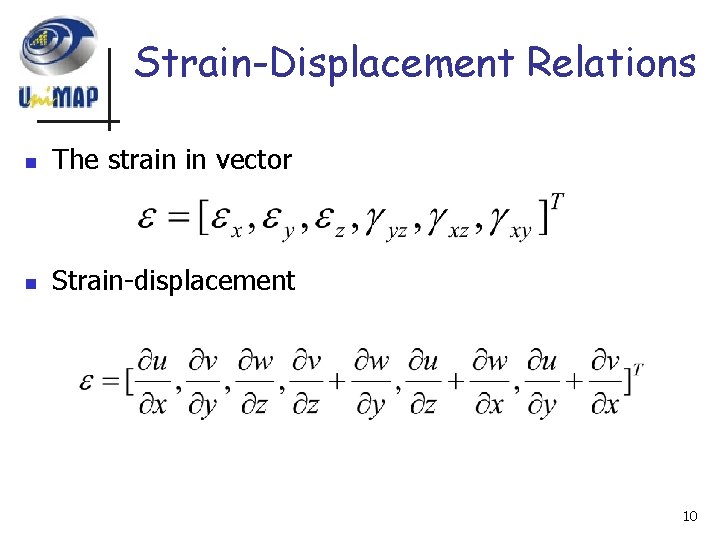
Strain-Displacement Relations n The strain in vector n Strain-displacement 10
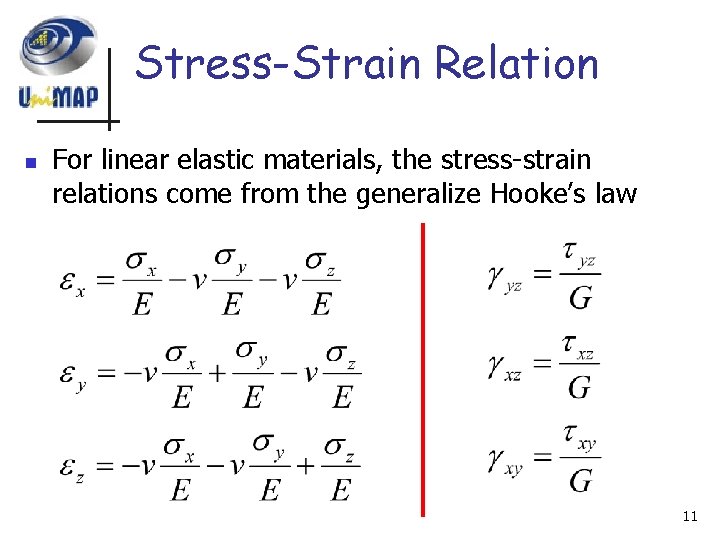
Stress-Strain Relation n For linear elastic materials, the stress-strain relations come from the generalize Hooke’s law 11
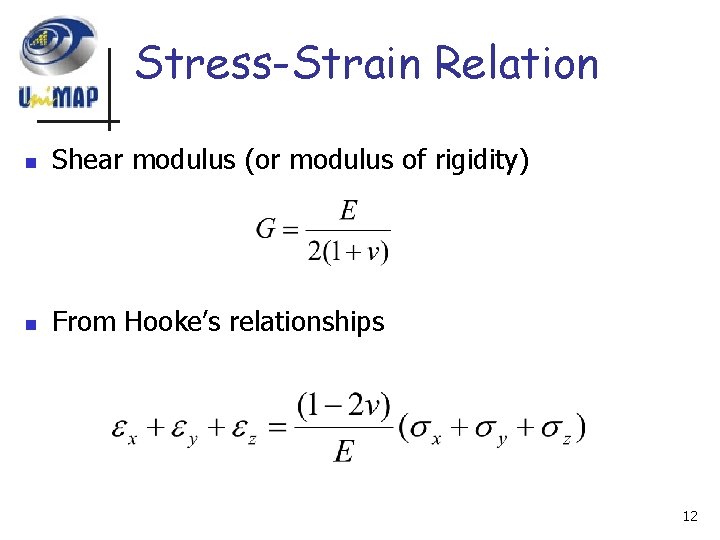
Stress-Strain Relation n Shear modulus (or modulus of rigidity) n From Hooke’s relationships 12
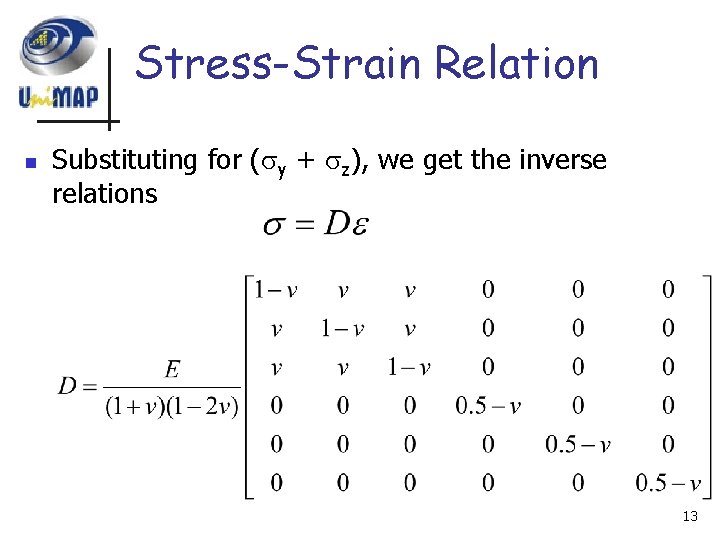
Stress-Strain Relation n Substituting for ( y + z), we get the inverse relations 13
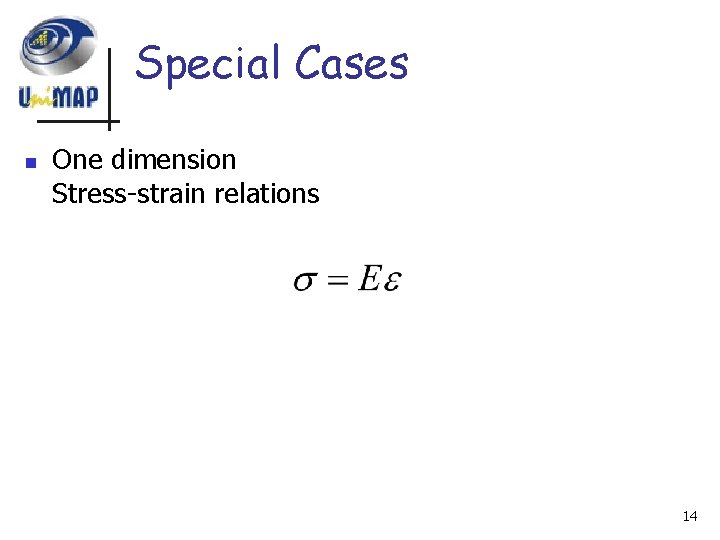
Special Cases n One dimension Stress-strain relations 14
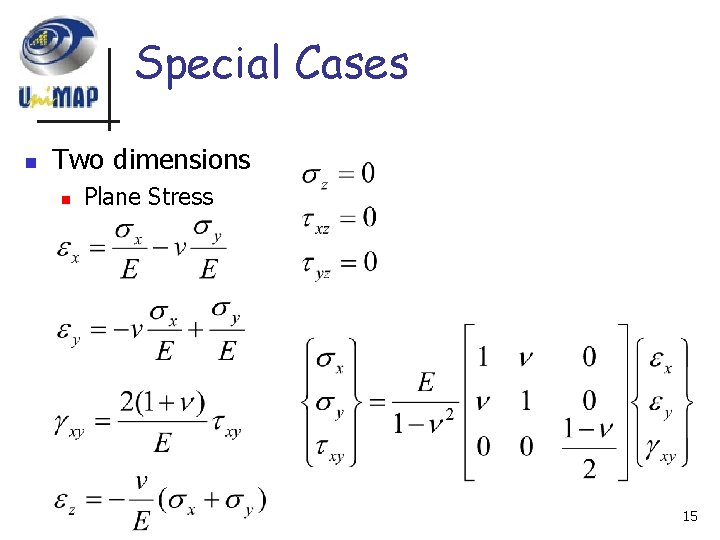
Special Cases n Two dimensions n Plane Stress 15
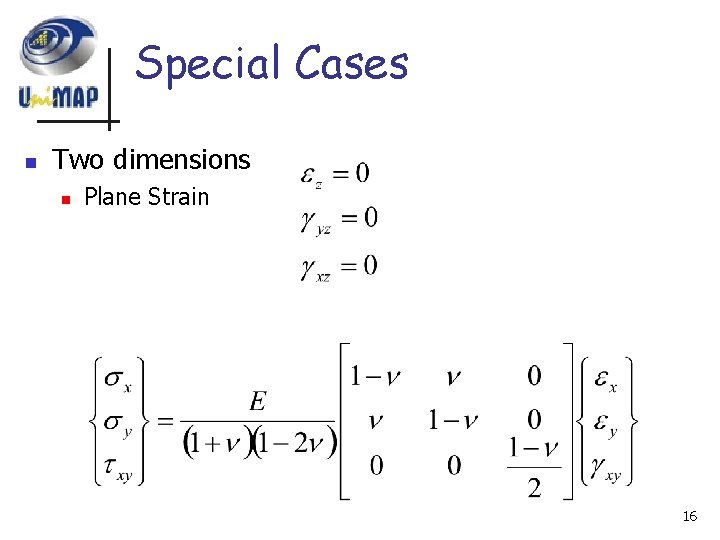
Special Cases n Two dimensions n Plane Strain 16
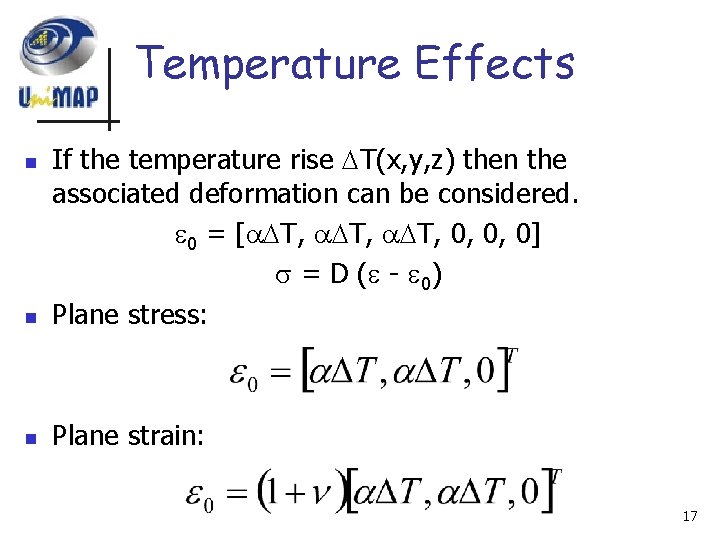
Temperature Effects n If the temperature rise T(x, y, z) then the associated deformation can be considered. 0 = [ T, T, 0, 0, 0] = D ( - 0) Plane stress: n Plane strain: n 17
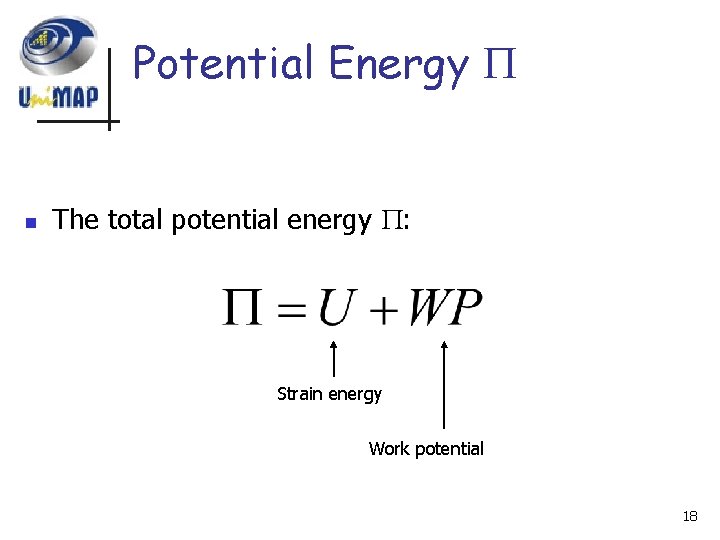
Potential Energy n The total potential energy : Strain energy Work potential 18

Potential Energy n Total strain energy (U): n The work potential (WP): 19
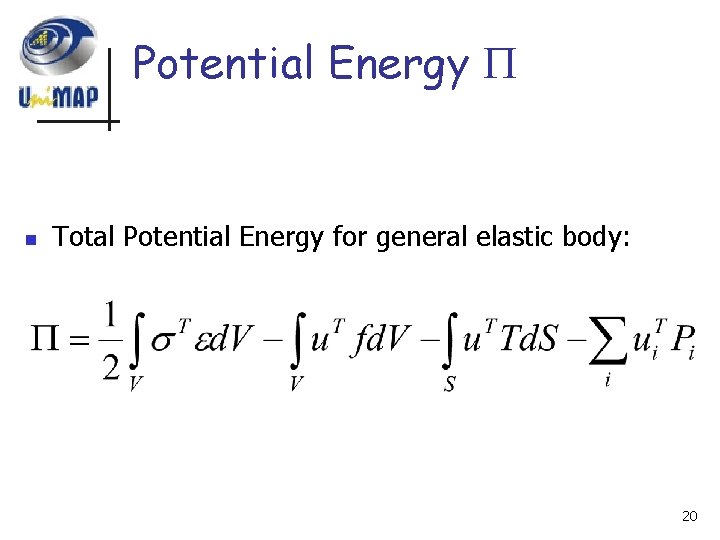
Potential Energy n Total Potential Energy for general elastic body: 20
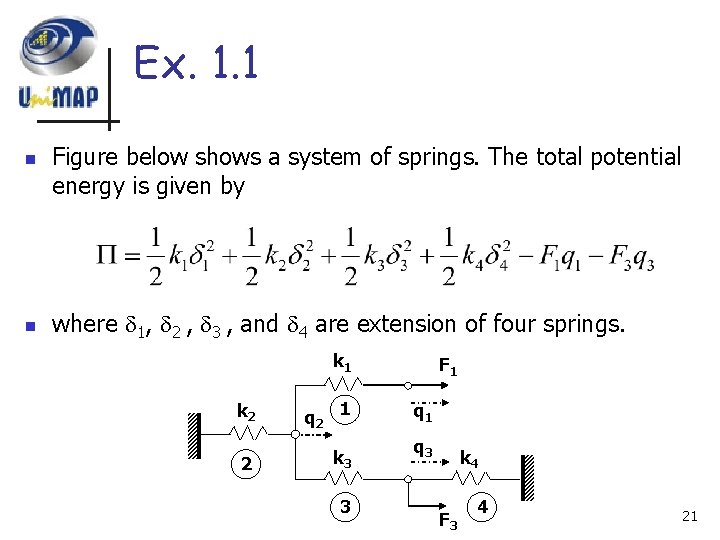
Ex. 1. 1 n n Figure below shows a system of springs. The total potential energy is given by where 1, 2 , 3 , and 4 are extension of four springs. k 1 k 2 q 2 1 2 k 3 3 F 1 q 3 k 4 F 3 4 21
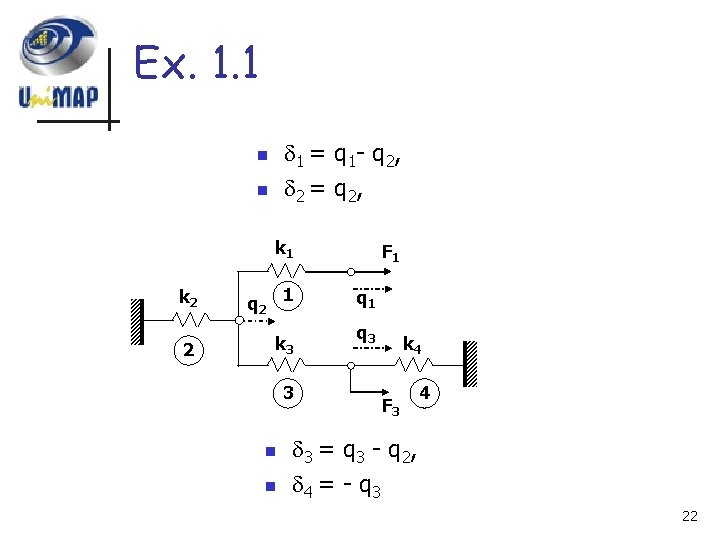
Ex. 1. 1 1 = q 1 - q 2 , 2 = q 2 , n n k 1 k 2 q 2 1 2 k 3 3 n n F 1 q 3 k 4 F 3 4 3 = q 3 - q 2 , 4 = - q 3 22
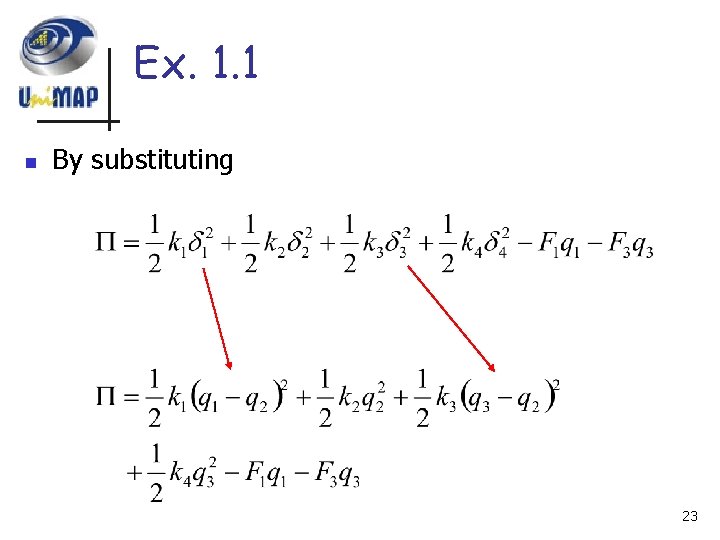
Ex. 1. 1 n By substituting 23
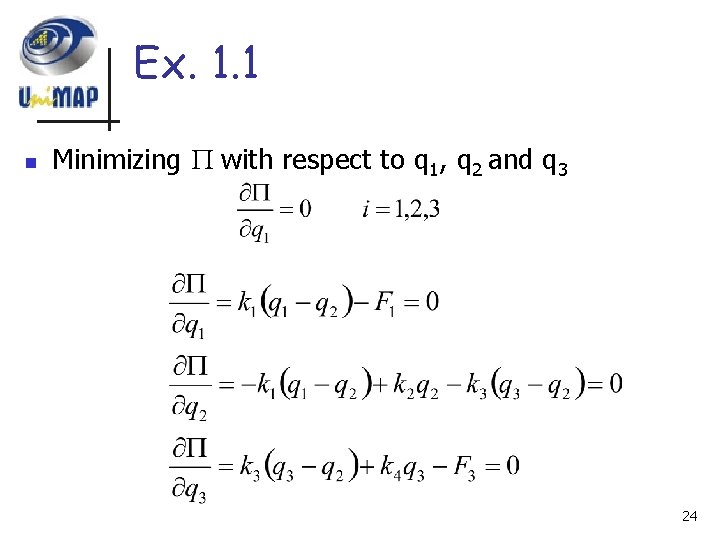
Ex. 1. 1 n Minimizing with respect to q 1, q 2 and q 3 24
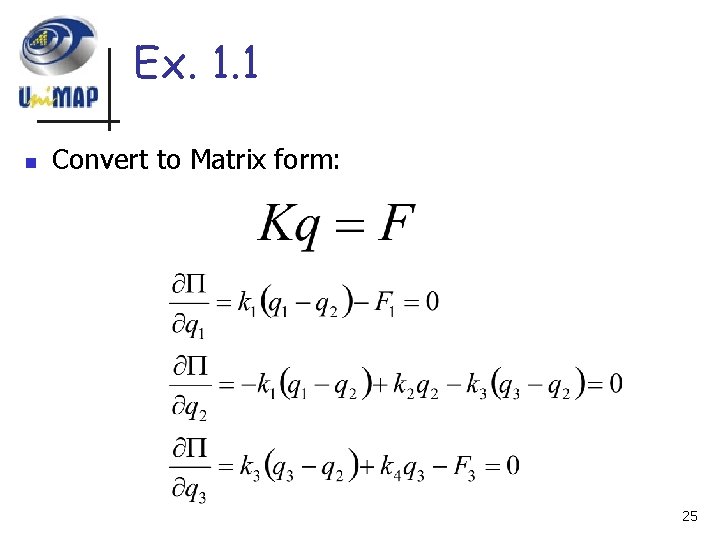
Ex. 1. 1 n Convert to Matrix form: 25
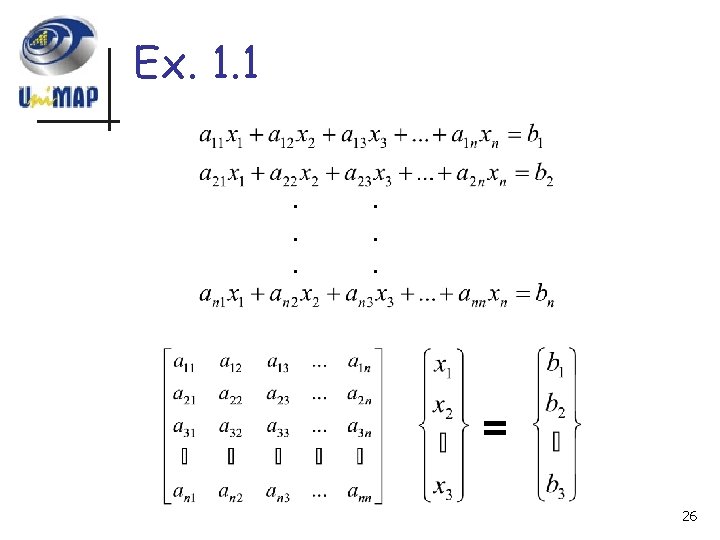
Ex. 1. 1. . . = 26
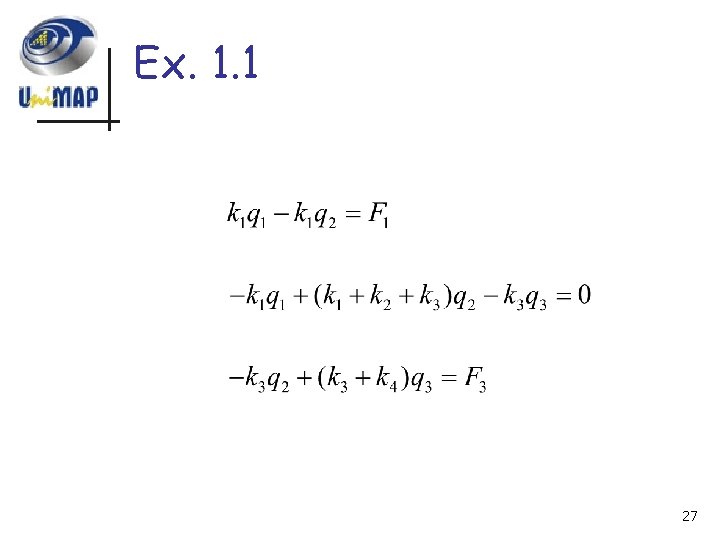
Ex. 1. 1 27
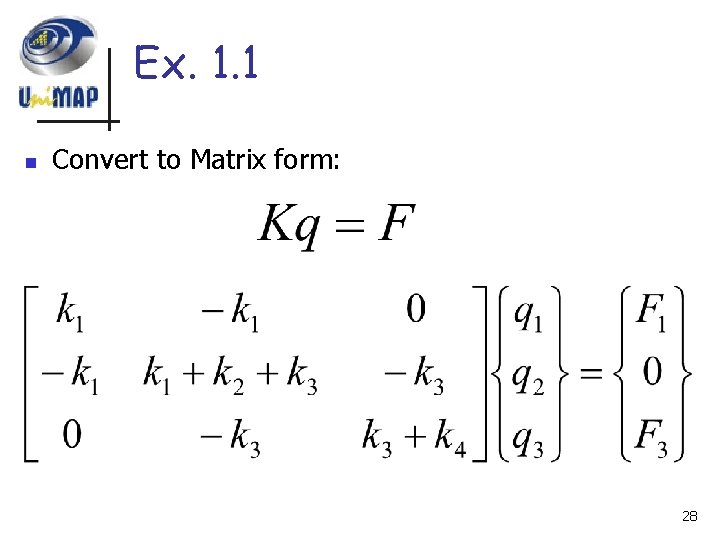
Ex. 1. 1 n Convert to Matrix form: 28
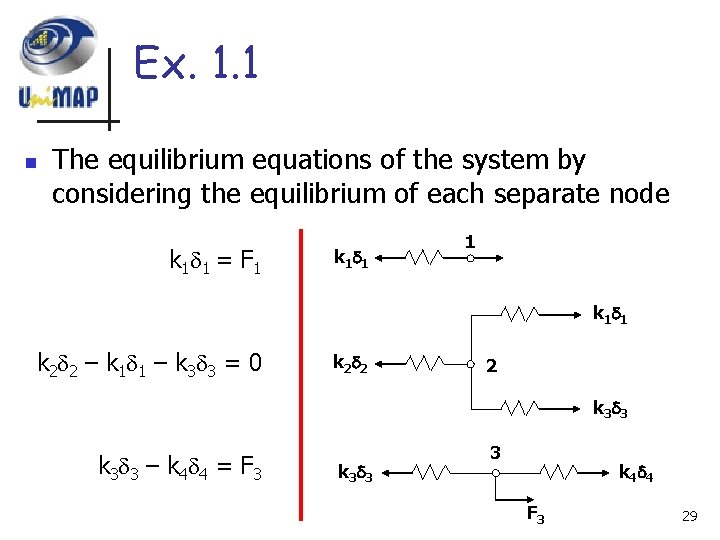
Ex. 1. 1 n The equilibrium equations of the system by considering the equilibrium of each separate node k 1 1 = F 1 k 1 1 k 2 2 – k 1 1 – k 3 3 = 0 k 2 2 2 k 3 3 k 3 3 – k 4 4 = F 3 k 3 3 3 k 4 4 F 3 29
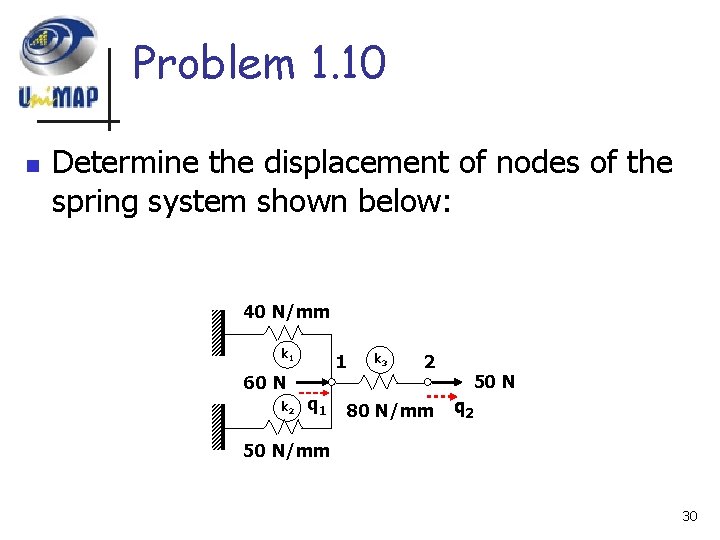
Problem 1. 10 n Determine the displacement of nodes of the spring system shown below: 40 N/mm k 1 60 N k 2 1 q 1 k 3 2 80 N/mm 50 N q 2 50 N/mm 30
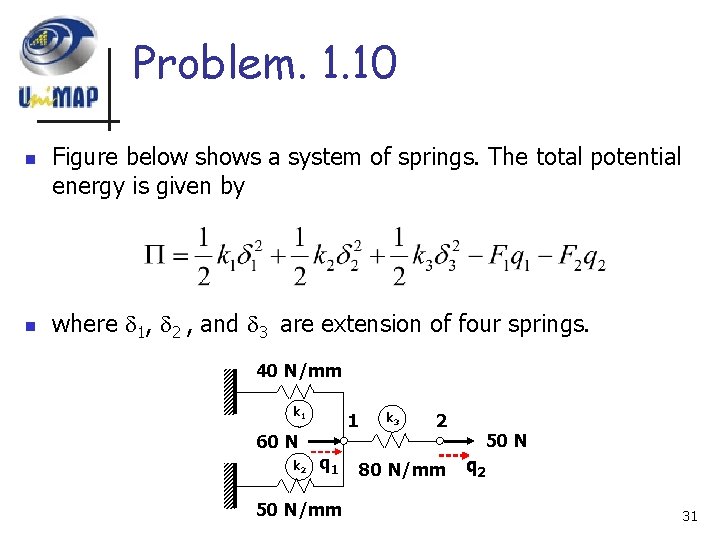
Problem. 1. 10 n n Figure below shows a system of springs. The total potential energy is given by where 1, 2 , and 3 are extension of four springs. 40 N/mm k 1 60 N k 2 1 q 1 50 N/mm k 3 2 80 N/mm 50 N q 2 31
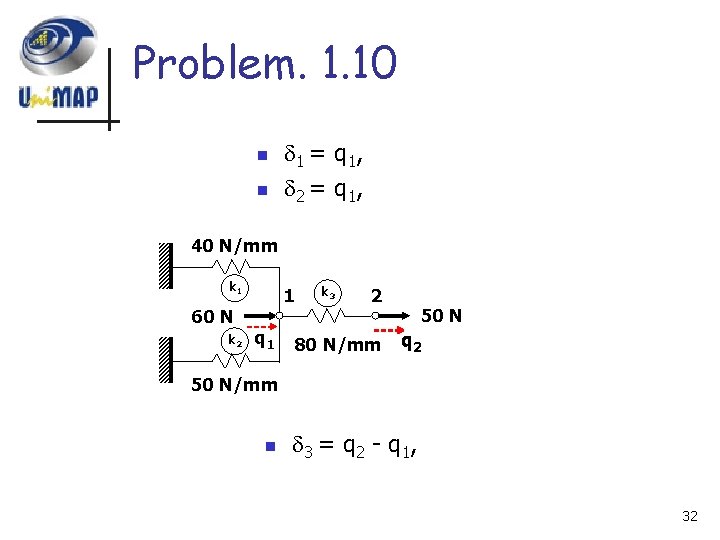
Problem. 1. 10 n n 1 = q 1 , 2 = q 1 , 40 N/mm k 1 60 N k 2 1 q 1 k 3 2 80 N/mm 50 N q 2 50 N/mm n 3 = q 2 - q 1 , 32
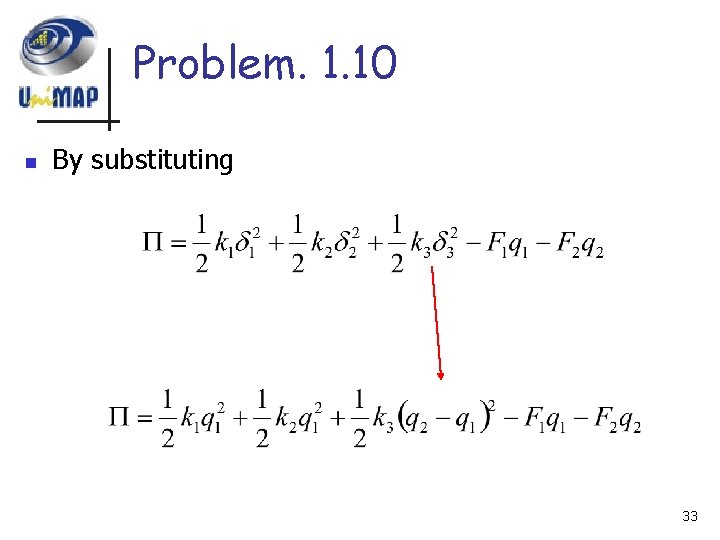
Problem. 1. 10 n By substituting 33
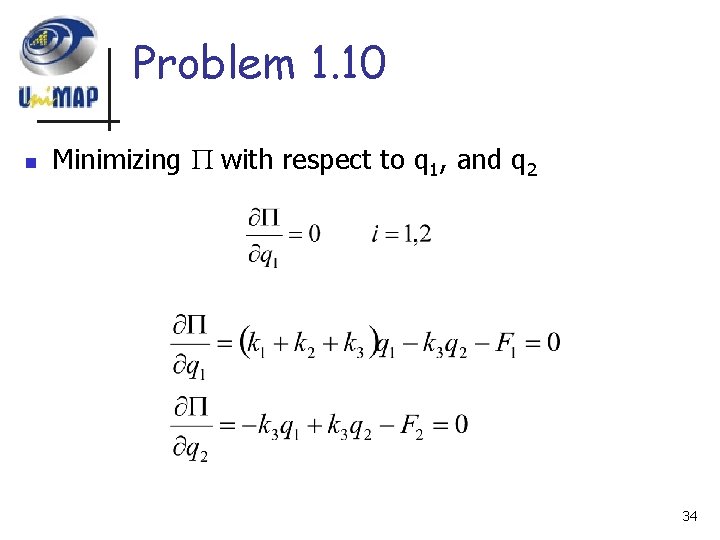
Problem 1. 10 n Minimizing with respect to q 1, and q 2 34

Problem 1. 10 35
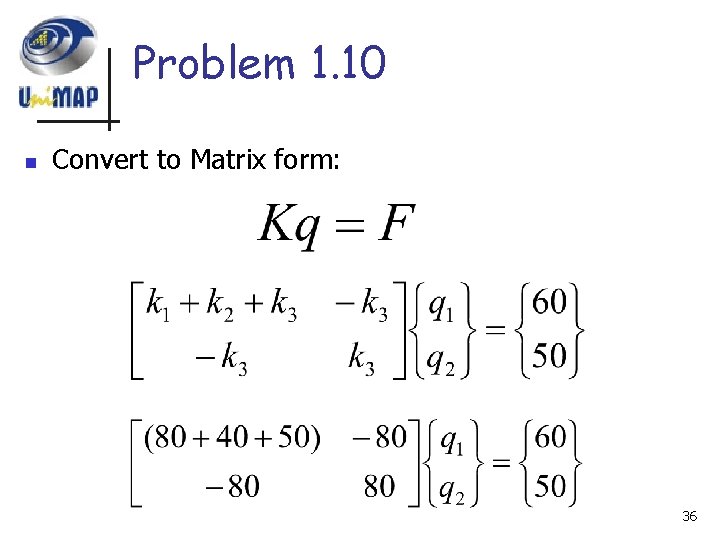
Problem 1. 10 n Convert to Matrix form: 36
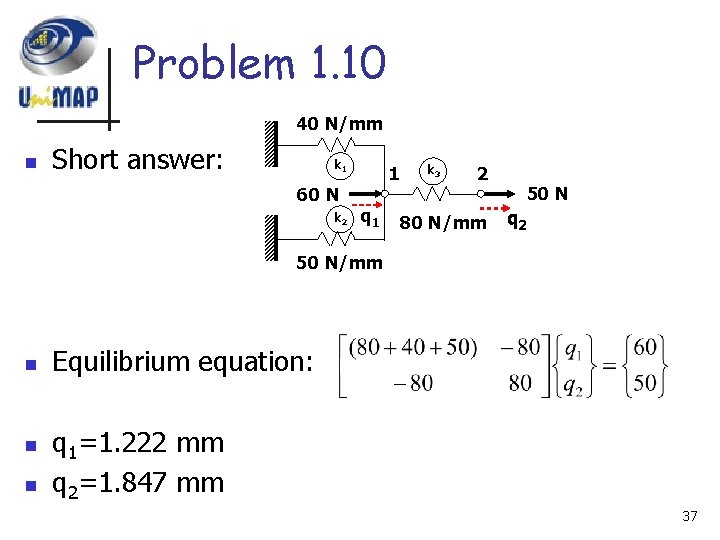
Problem 1. 10 40 N/mm n Short answer: k 1 60 N k 2 1 q 1 k 3 2 80 N/mm 50 N q 2 50 N/mm n n n Equilibrium equation: q 1=1. 222 mm q 2=1. 847 mm 37
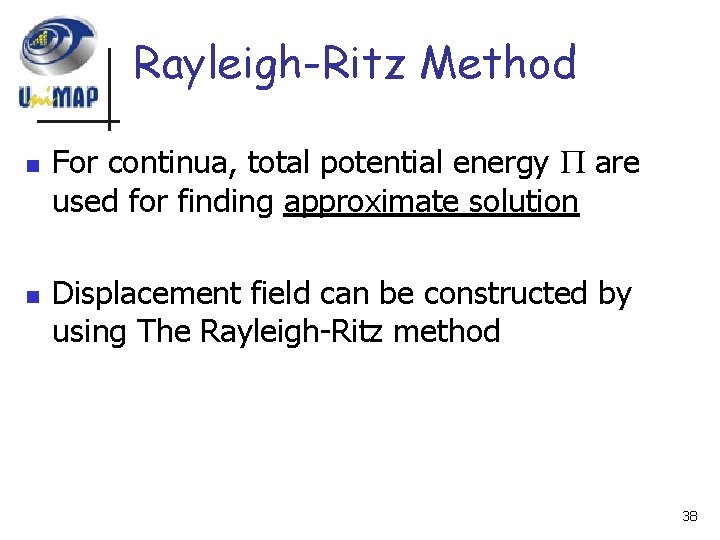
Rayleigh-Ritz Method n n For continua, total potential energy are used for finding approximate solution Displacement field can be constructed by using The Rayleigh-Ritz method 38
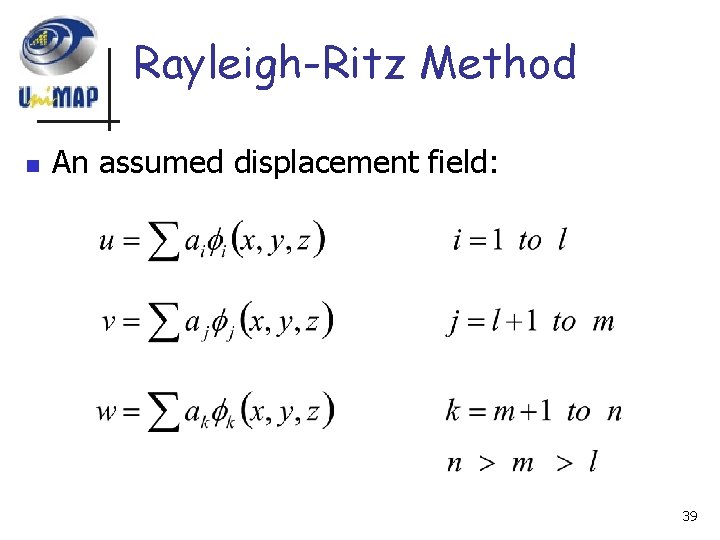
Rayleigh-Ritz Method n An assumed displacement field: 39
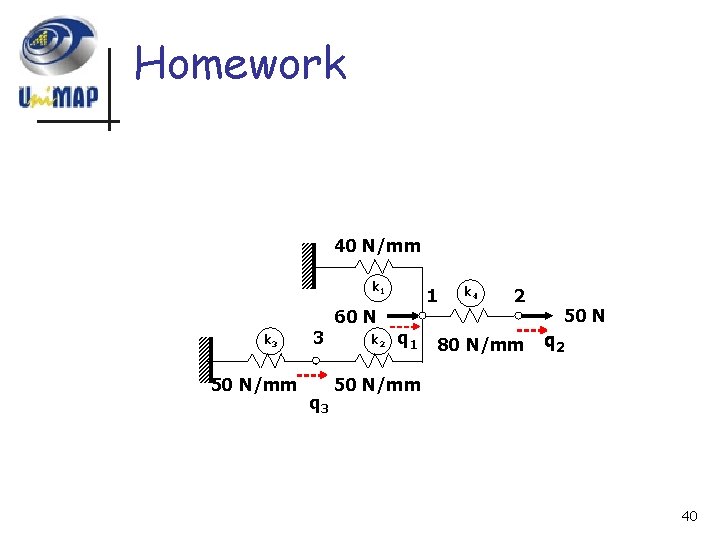
Homework 40 N/mm k 1 k 3 50 N/mm 3 q 3 60 N k 2 1 q 1 k 4 2 80 N/mm 50 N q 2 50 N/mm 40
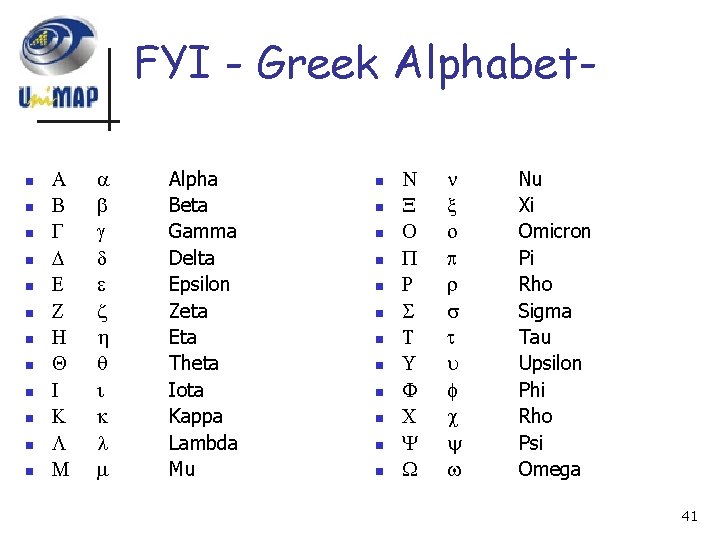
FYI - Greek Alphabetn n n Alpha Beta Gamma Delta Epsilon Zeta Eta Theta Iota Kappa Lambda Mu n n n Nu Xi Omicron Pi Rho Sigma Tau Upsilon Phi Rho Psi Omega 41
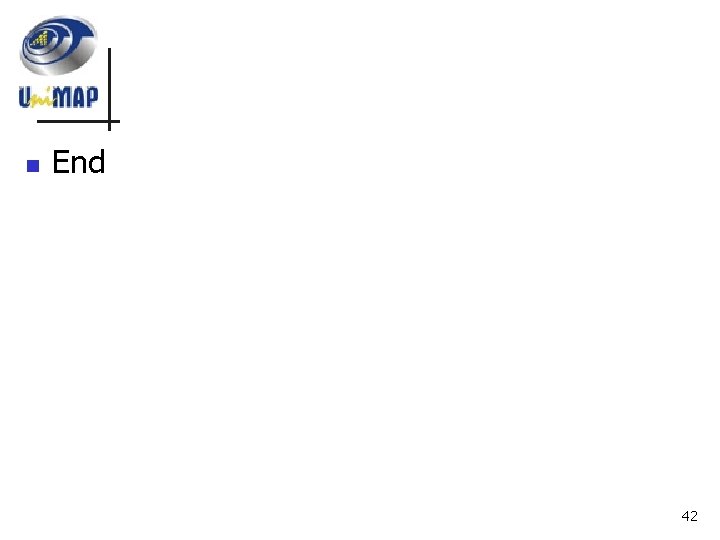
n End 42
Ig5a 485 통신 예제
Ley 26 485
Arief isti pramusinta
Dokter paru paru terdekat
Lokasi infark berdasarkan ekg
Krisis hipertensi
Dr budi arief waskito
Prof. dr. arief s. rachmat
Bakso arief trunojoyo bandung
Arief yuwono
Arief wibowo fkm unair
Difference between fea and fem
What is fea
Fea
Fpix
Fea framework
Internal design review
Ucsd immunology course
Maya fea
La niña negrita y el conejo blanco
Fem applications
Rimas del poema la higuera
Data reference model
Alva myrda
The fundamental concept of economics is
What is the fundamental concept behind premium marketing?
Discounting concept in managerial economics
What is the fundamental concept of the gmdss?
What is the similarities of actual self and ideal self
Contoh selling concept
Dr max klein ent
Fsjes el jadida
Mark draper ent
Ent supelec
163 ent
Swedish ent
Dr abdul hadi ent specialist
Lesson 5: electrical nonmetallic tubing (ent)
Ent collège claude cornac
143 ent
Ent marne mon bureau numérique
Ent uh1
Hennebert sign