Failure Modes and Effects Analysis Michigan Lean Consortium
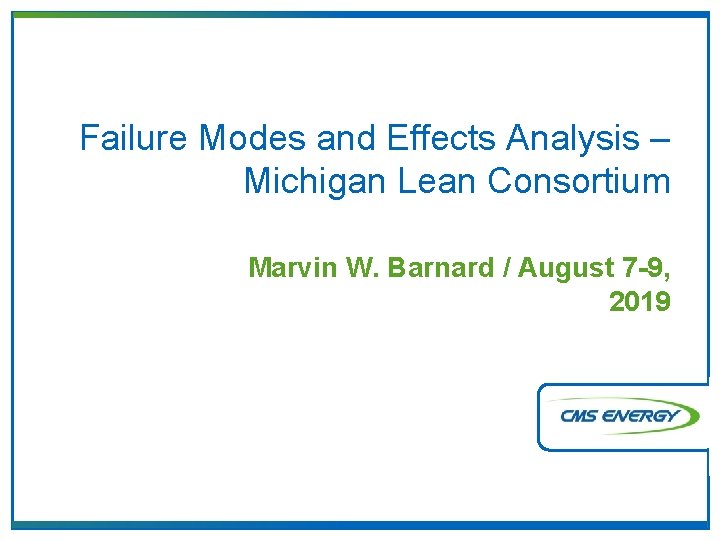
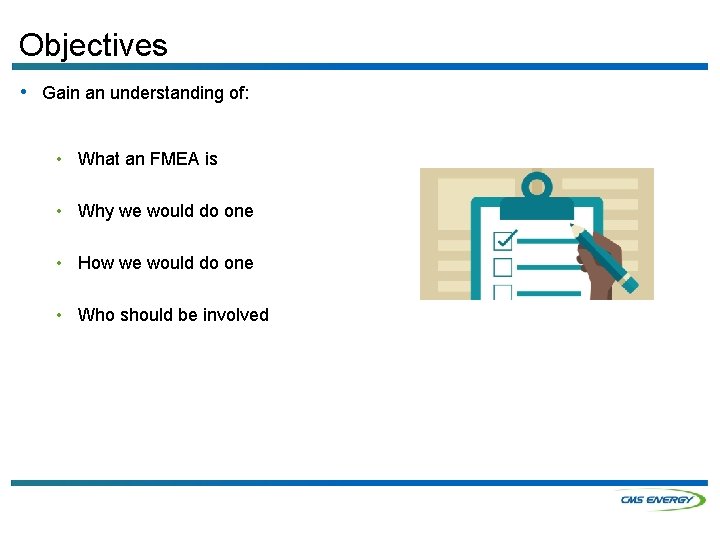
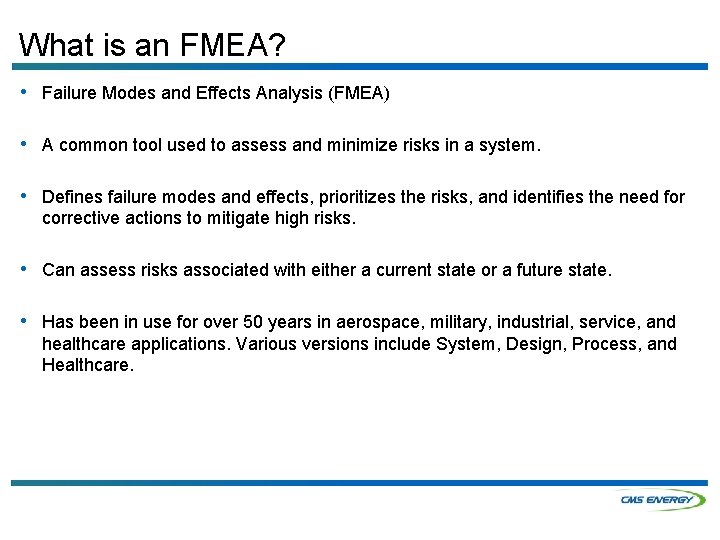
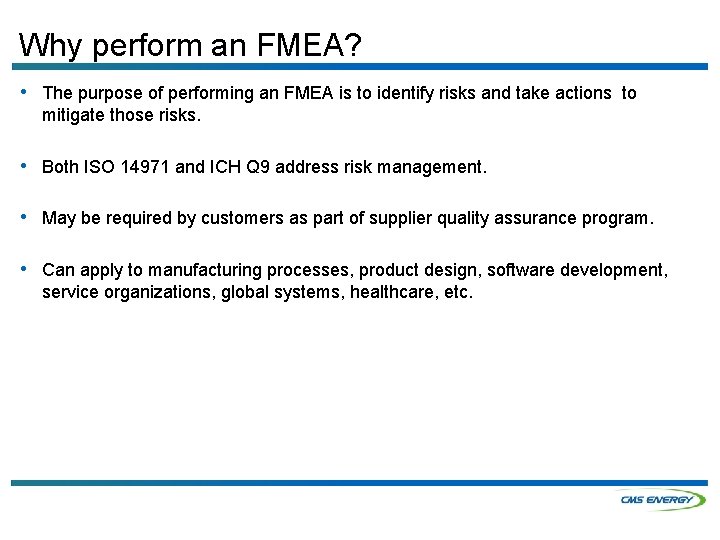
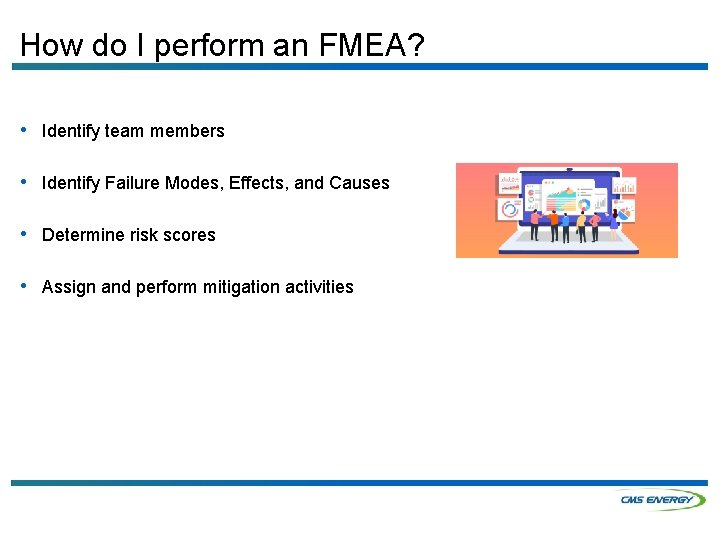
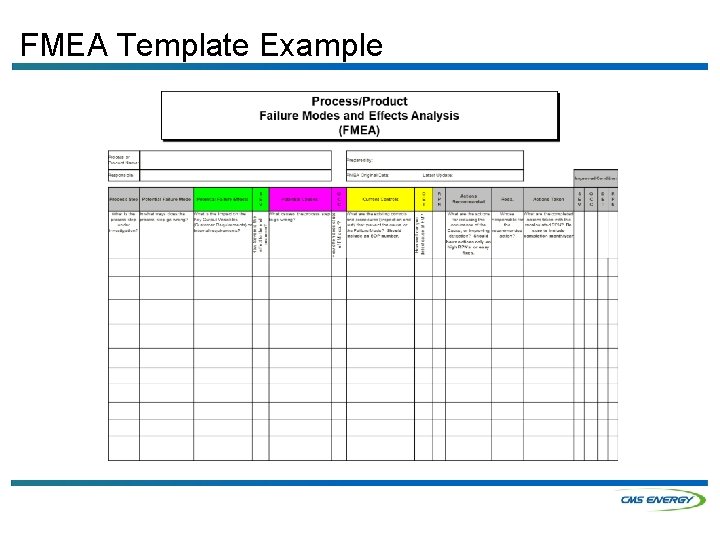
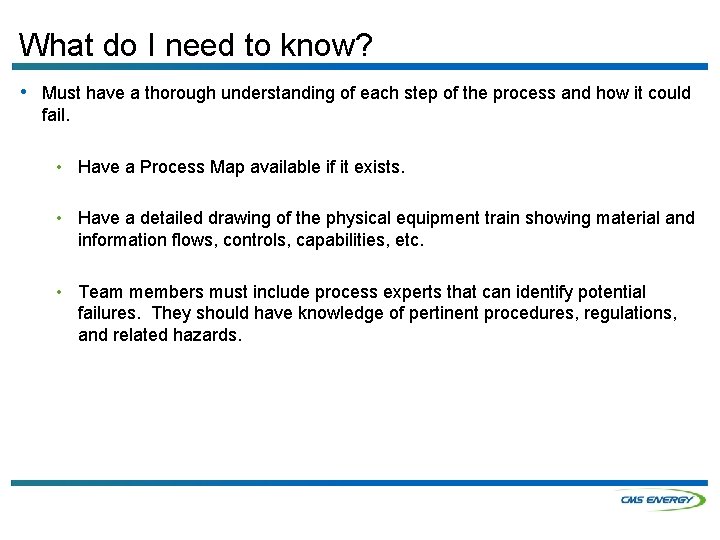
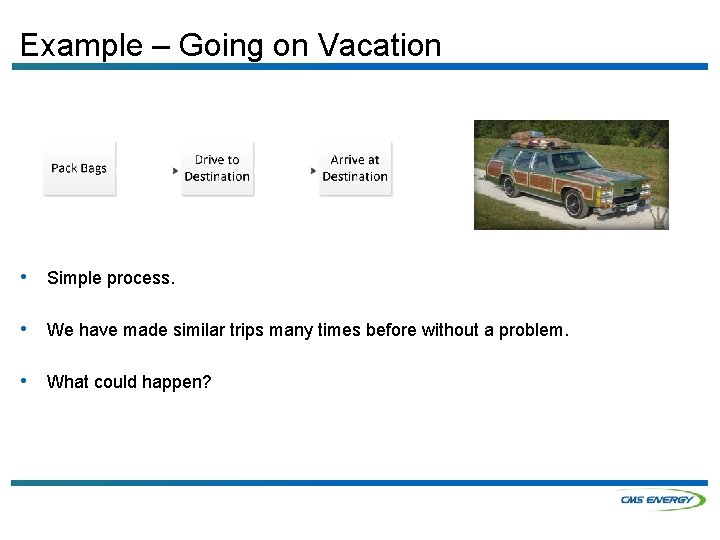
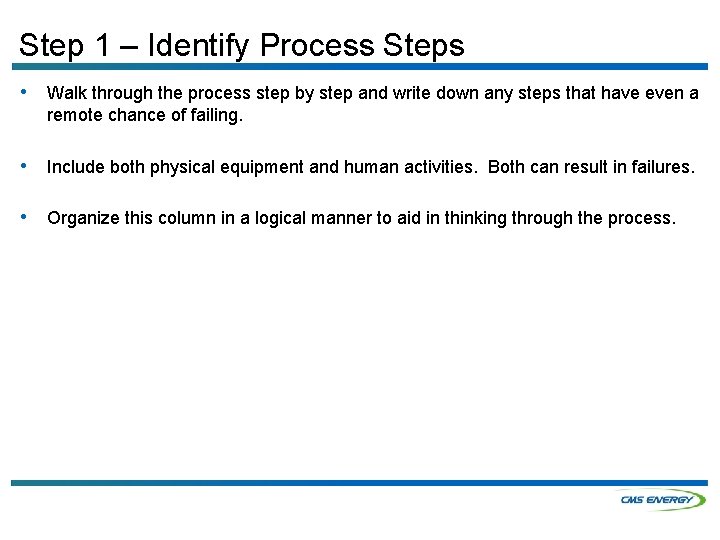
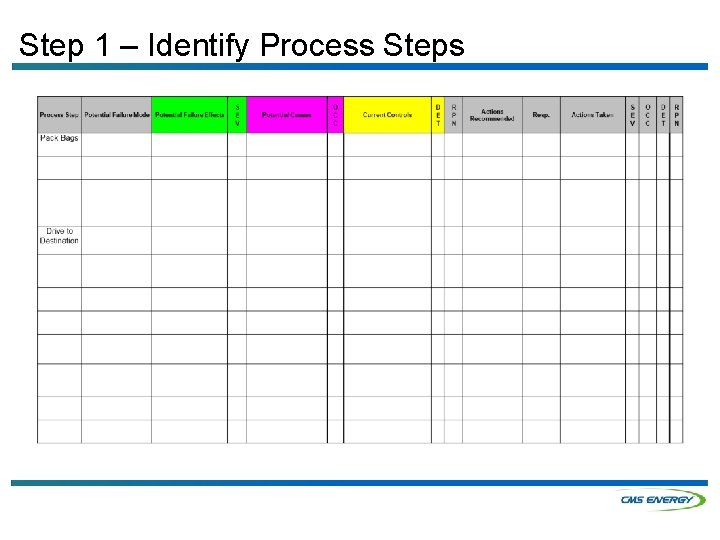
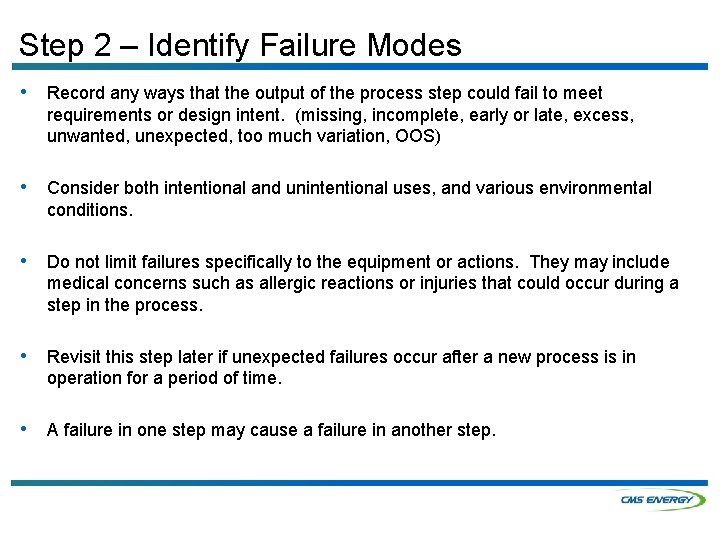
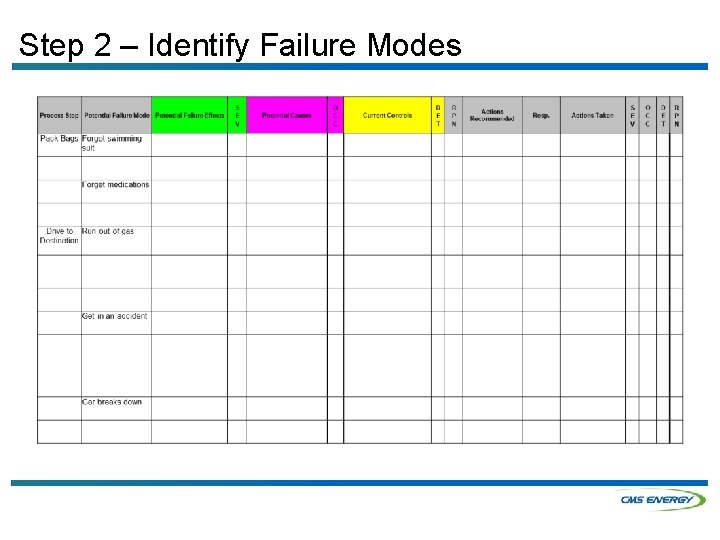
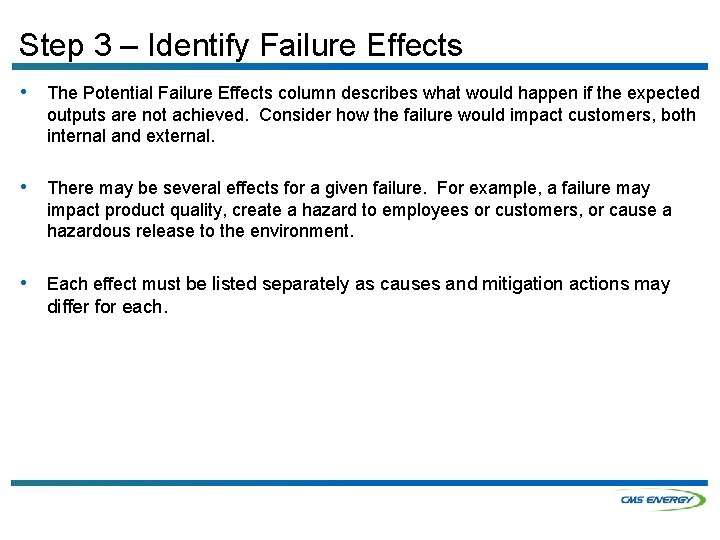
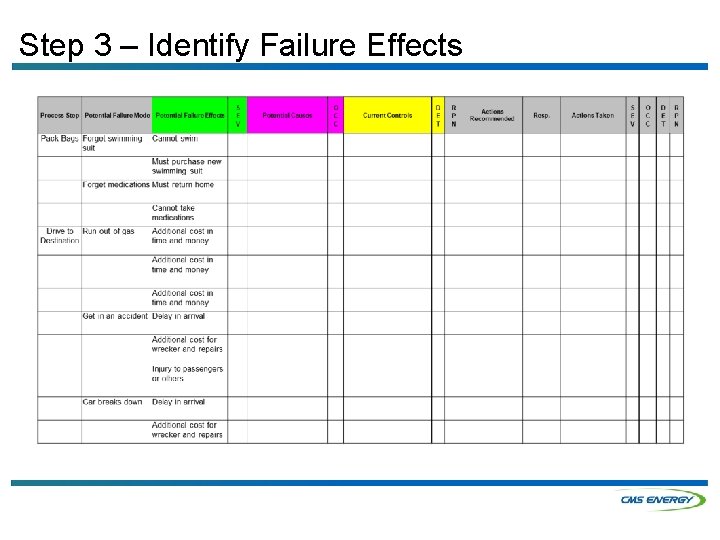
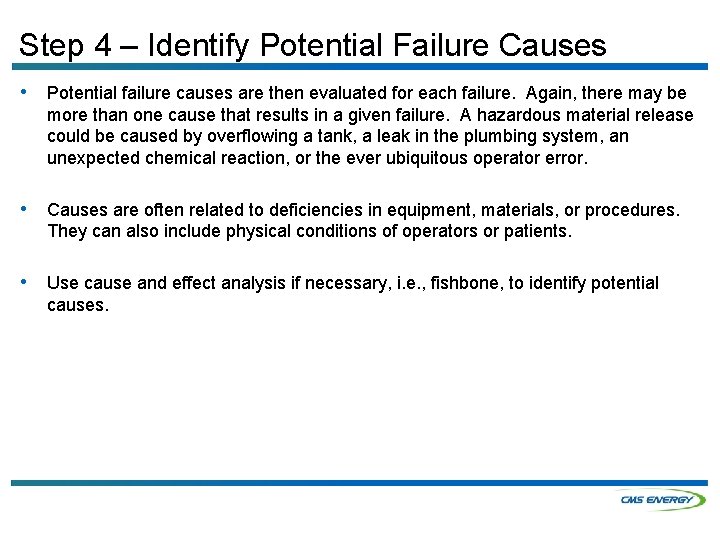
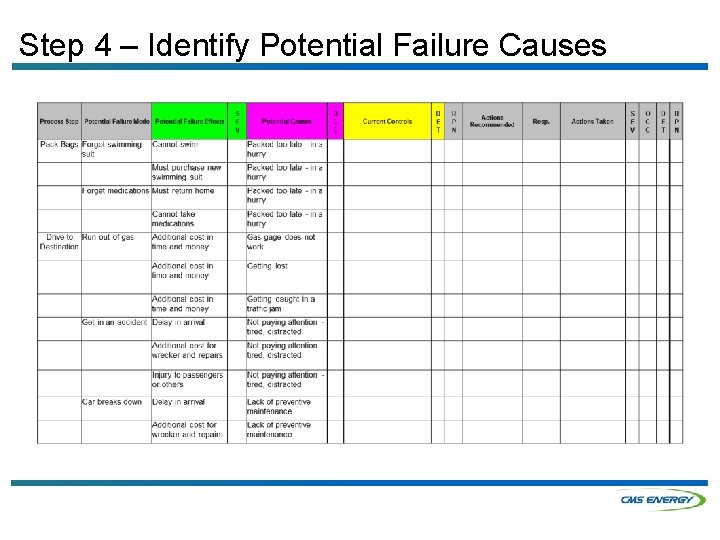
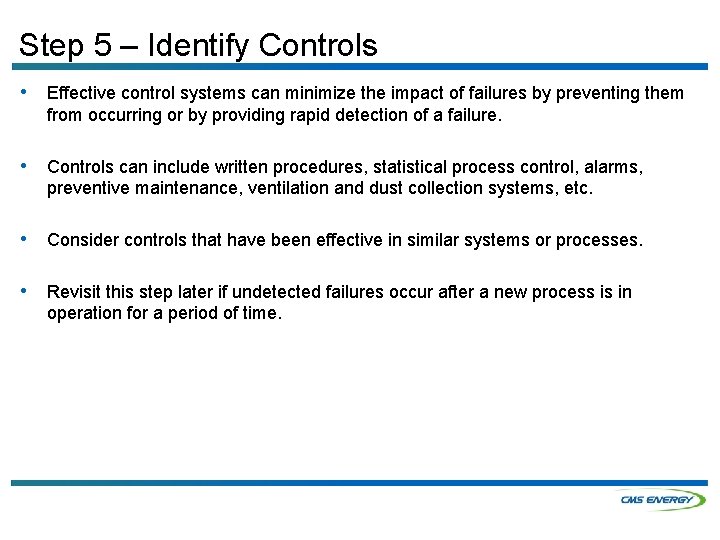
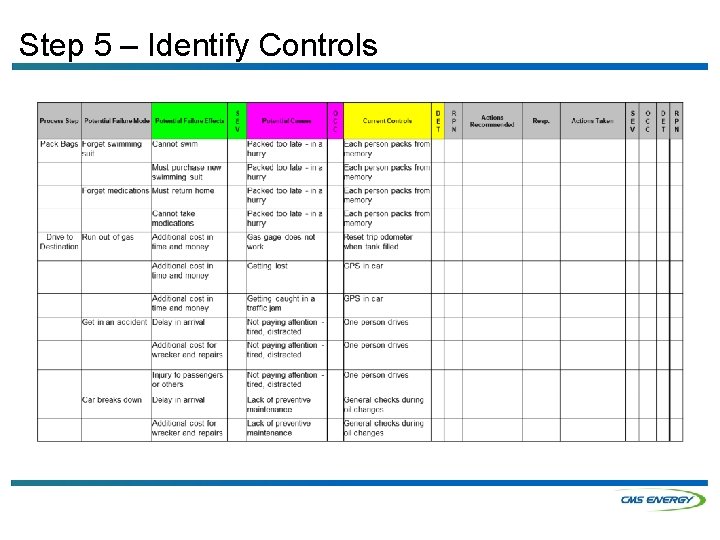
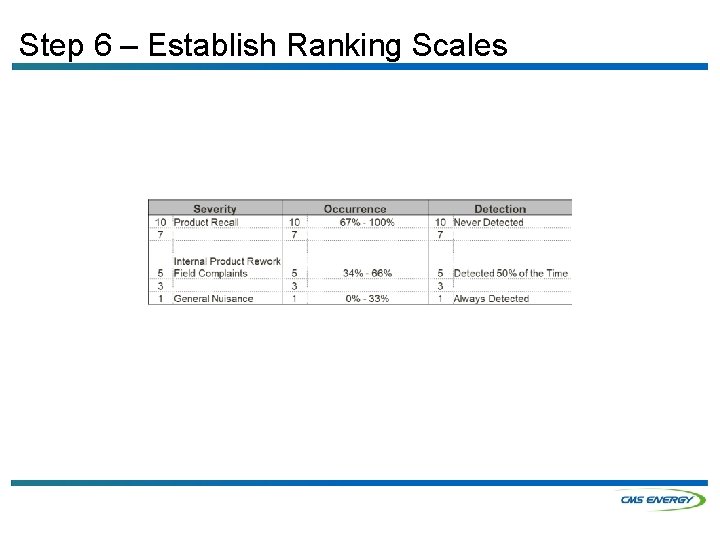
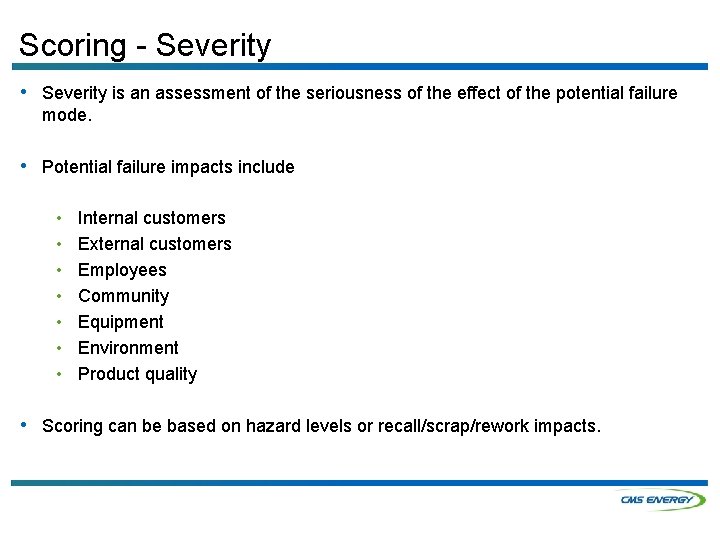
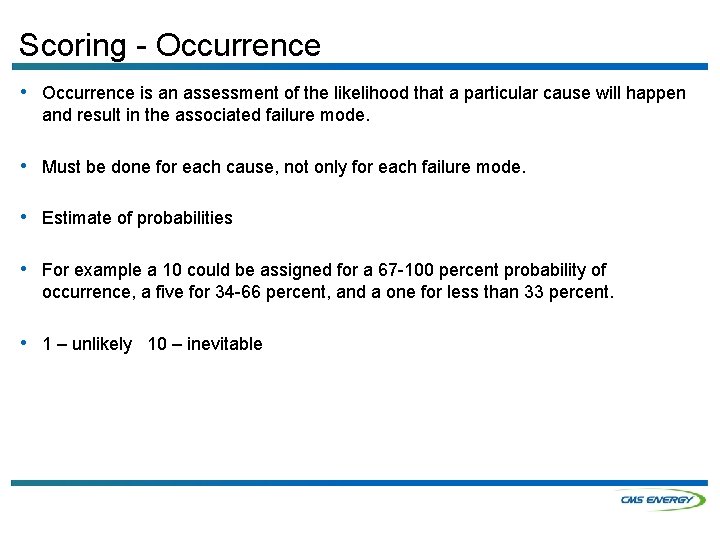
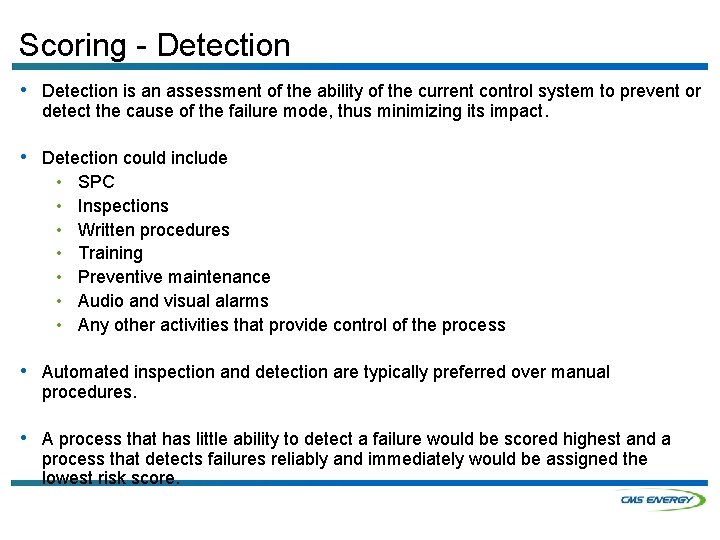
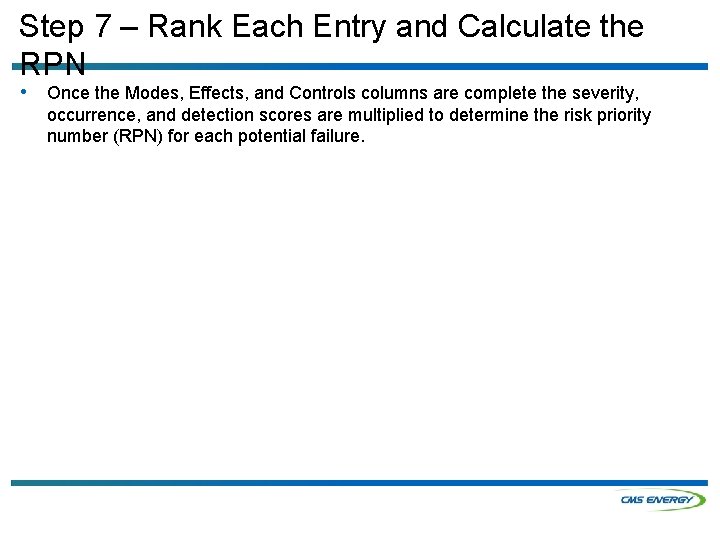
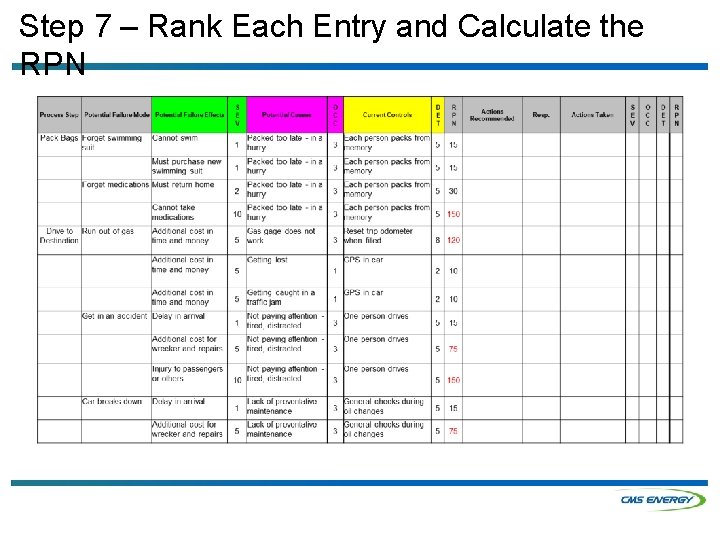
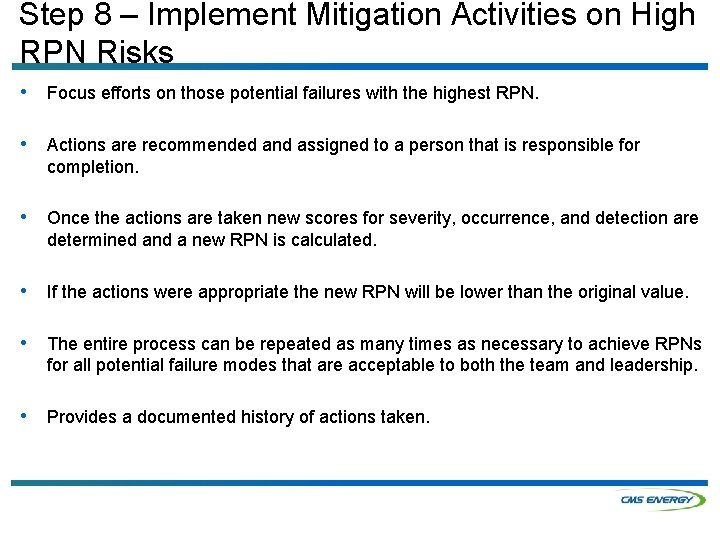
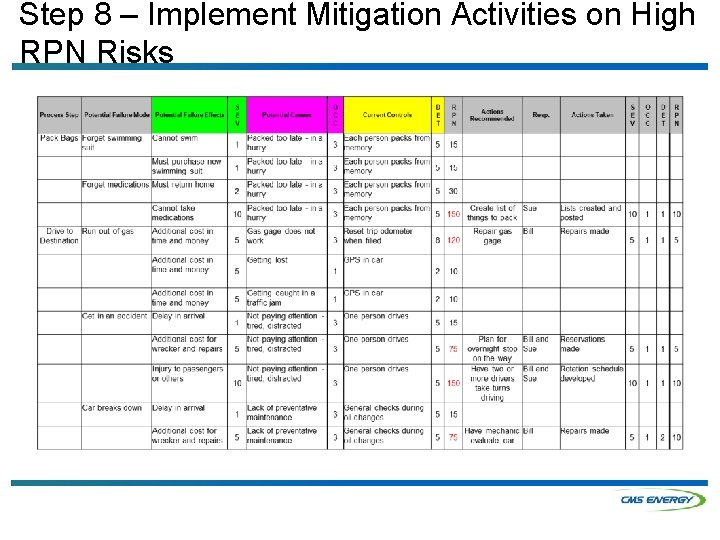
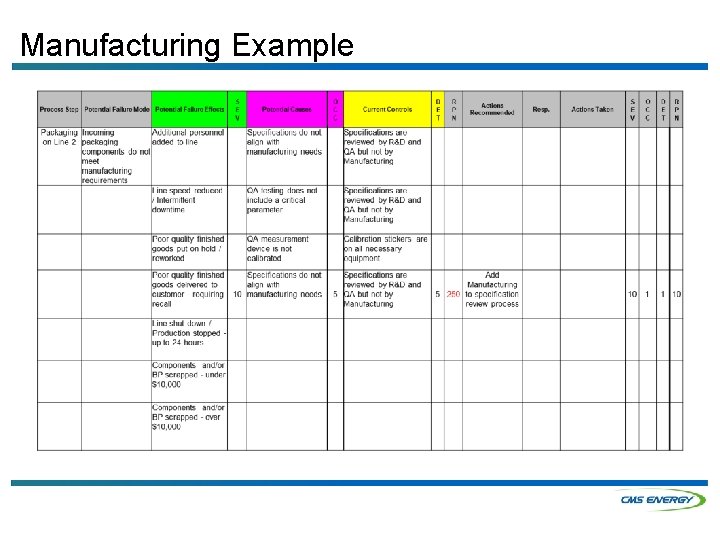
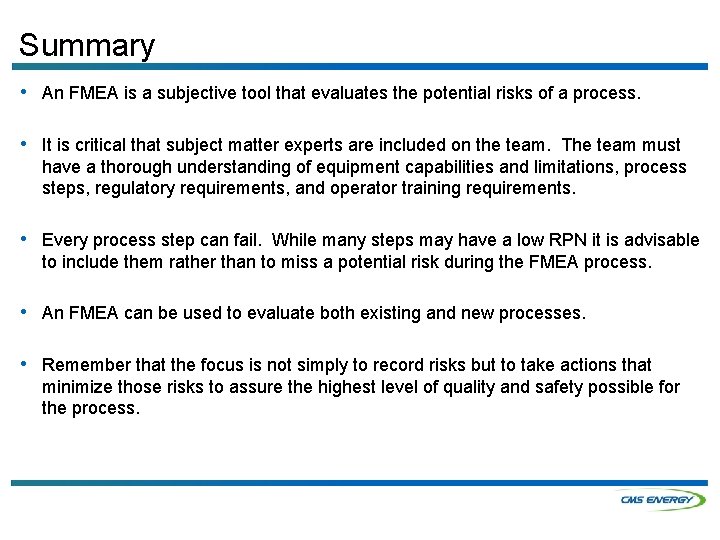
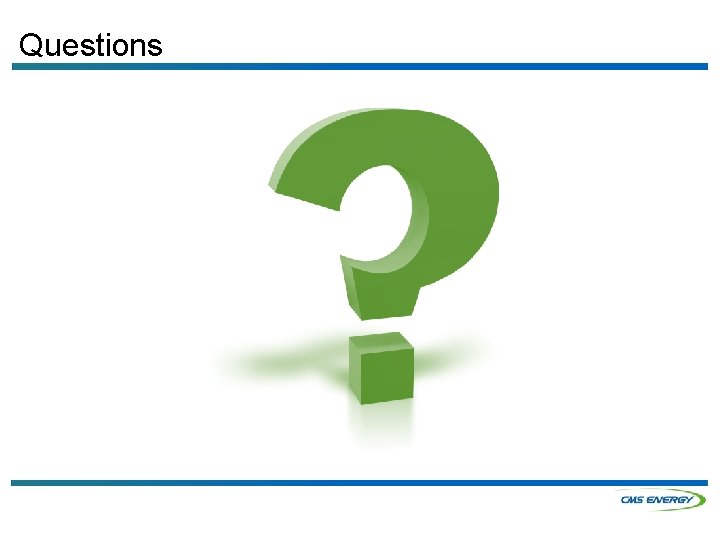
- Slides: 29
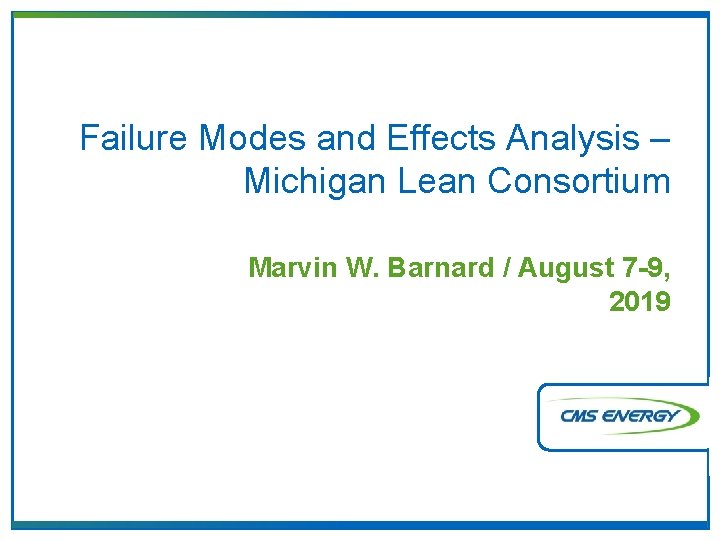
Failure Modes and Effects Analysis – Michigan Lean Consortium Marvin W. Barnard / August 7 -9, 2019
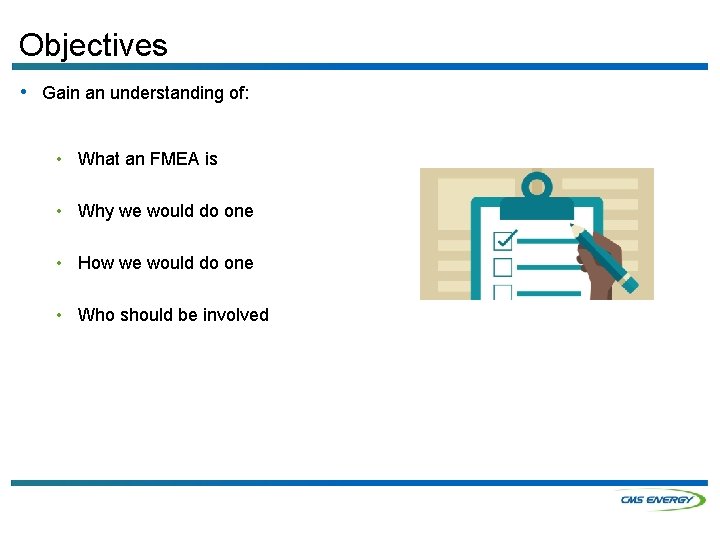
Objectives • Gain an understanding of: • What an FMEA is • Why we would do one • How we would do one • Who should be involved
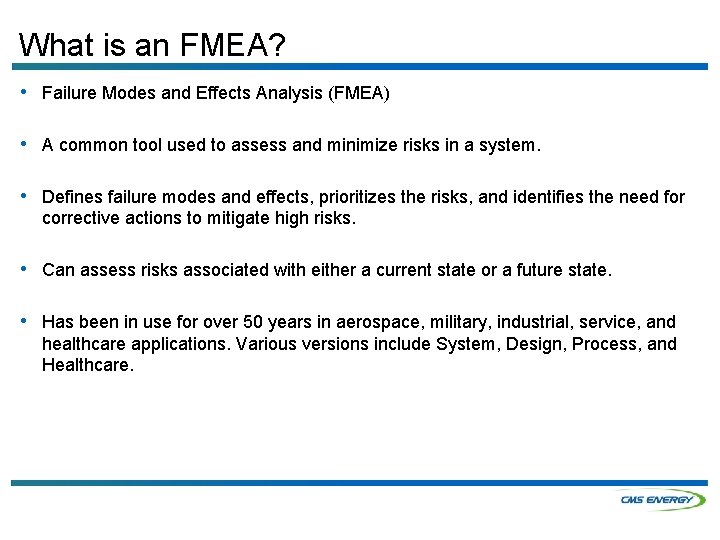
What is an FMEA? • Failure Modes and Effects Analysis (FMEA) • A common tool used to assess and minimize risks in a system. • Defines failure modes and effects, prioritizes the risks, and identifies the need for corrective actions to mitigate high risks. • Can assess risks associated with either a current state or a future state. • Has been in use for over 50 years in aerospace, military, industrial, service, and healthcare applications. Various versions include System, Design, Process, and Healthcare.
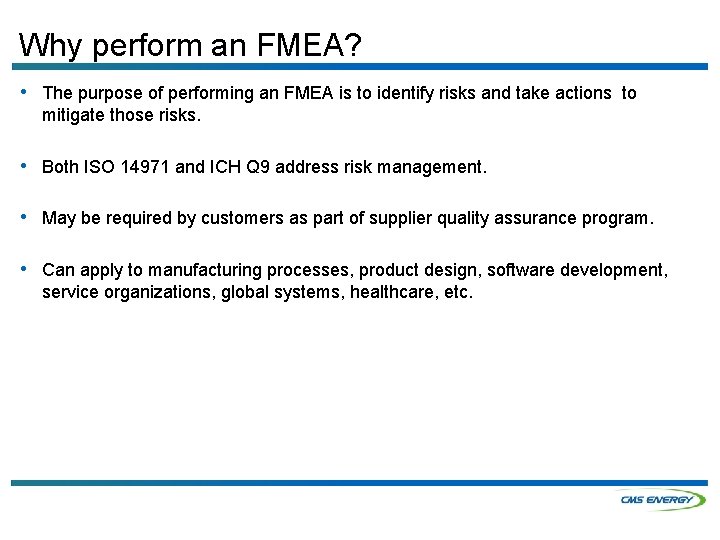
Why perform an FMEA? • The purpose of performing an FMEA is to identify risks and take actions to mitigate those risks. • Both ISO 14971 and ICH Q 9 address risk management. • May be required by customers as part of supplier quality assurance program. • Can apply to manufacturing processes, product design, software development, service organizations, global systems, healthcare, etc.
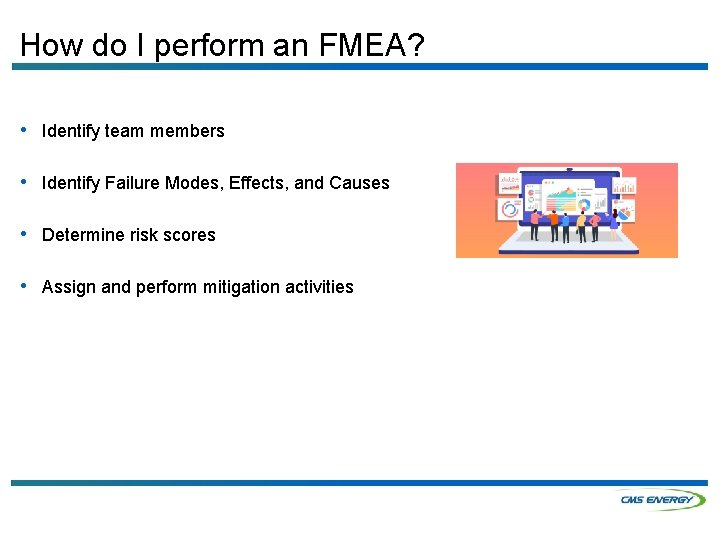
How do I perform an FMEA? • Identify team members • Identify Failure Modes, Effects, and Causes • Determine risk scores • Assign and perform mitigation activities
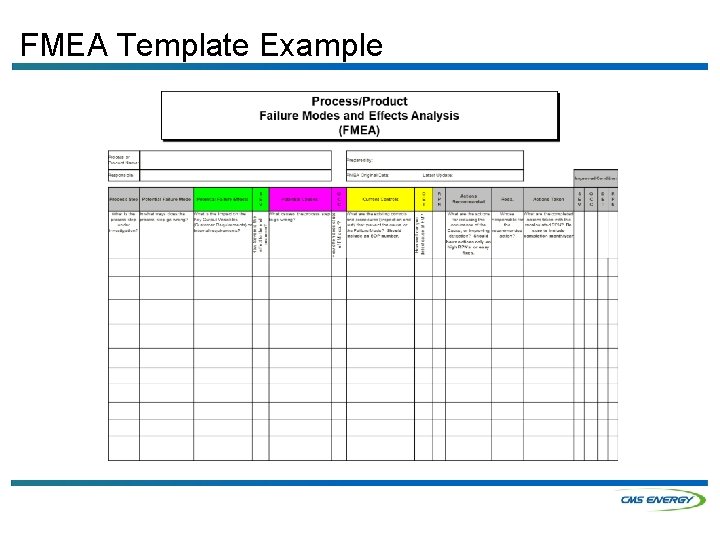
FMEA Template Example
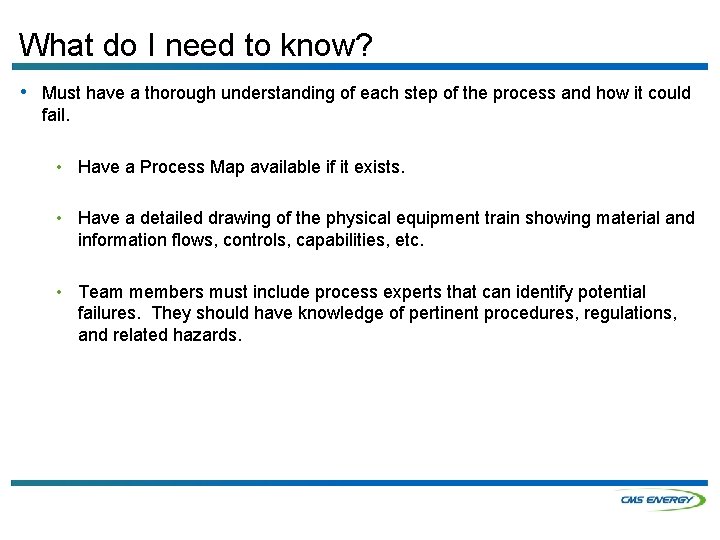
What do I need to know? • Must have a thorough understanding of each step of the process and how it could fail. • Have a Process Map available if it exists. • Have a detailed drawing of the physical equipment train showing material and information flows, controls, capabilities, etc. • Team members must include process experts that can identify potential failures. They should have knowledge of pertinent procedures, regulations, and related hazards.
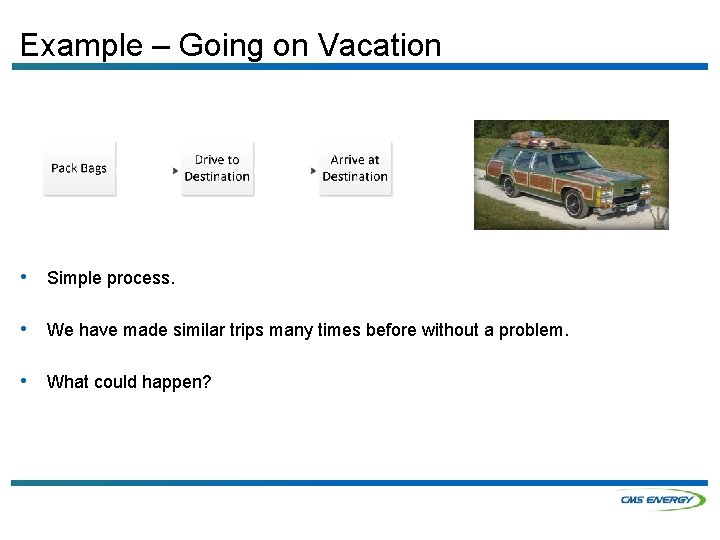
Example – Going on Vacation • Simple process. • We have made similar trips many times before without a problem. • What could happen?
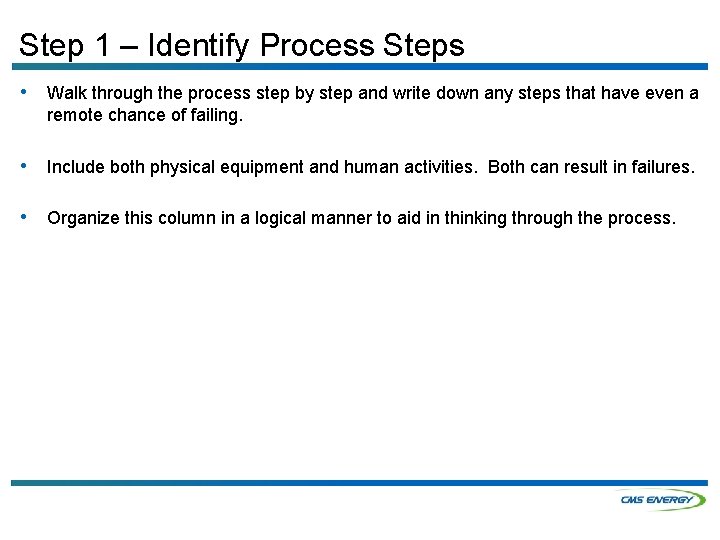
Step 1 – Identify Process Steps • Walk through the process step by step and write down any steps that have even a remote chance of failing. • Include both physical equipment and human activities. Both can result in failures. • Organize this column in a logical manner to aid in thinking through the process.
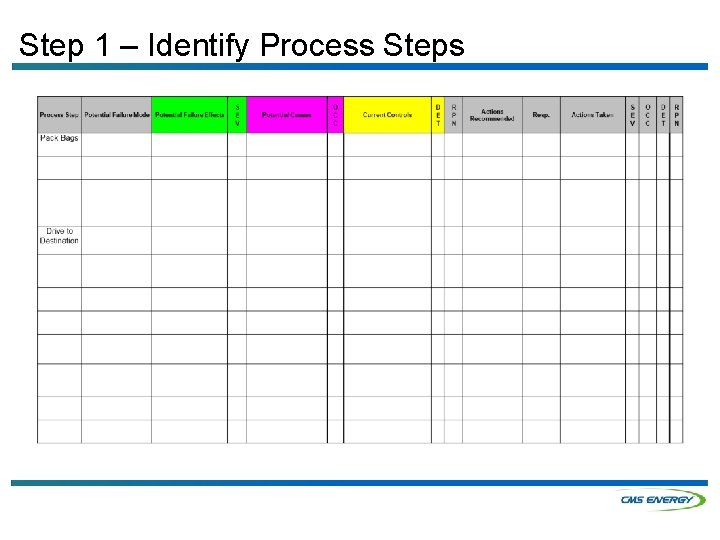
Step 1 – Identify Process Steps
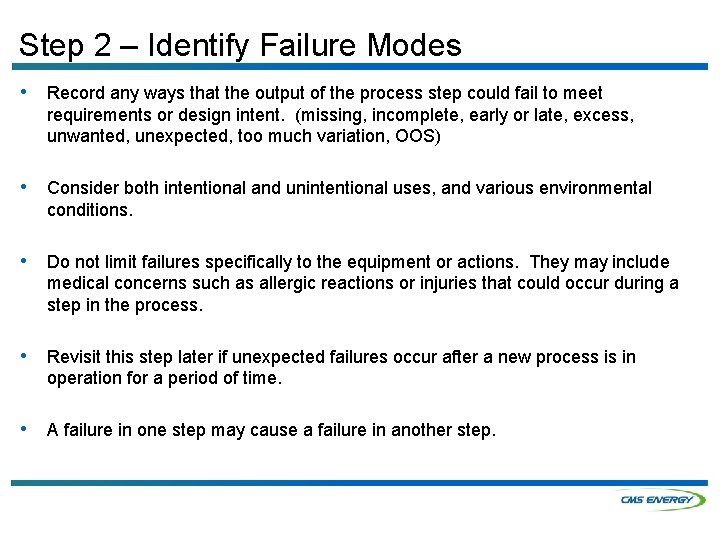
Step 2 – Identify Failure Modes • Record any ways that the output of the process step could fail to meet requirements or design intent. (missing, incomplete, early or late, excess, unwanted, unexpected, too much variation, OOS) • Consider both intentional and unintentional uses, and various environmental conditions. • Do not limit failures specifically to the equipment or actions. They may include medical concerns such as allergic reactions or injuries that could occur during a step in the process. • Revisit this step later if unexpected failures occur after a new process is in operation for a period of time. • A failure in one step may cause a failure in another step.
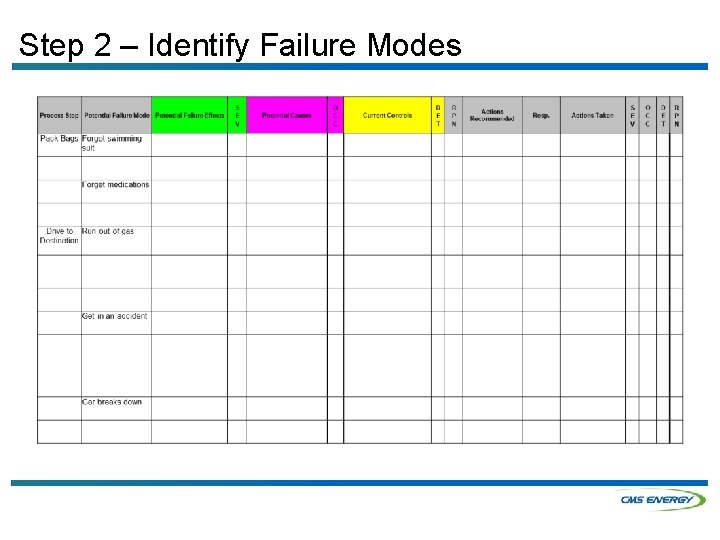
Step 2 – Identify Failure Modes
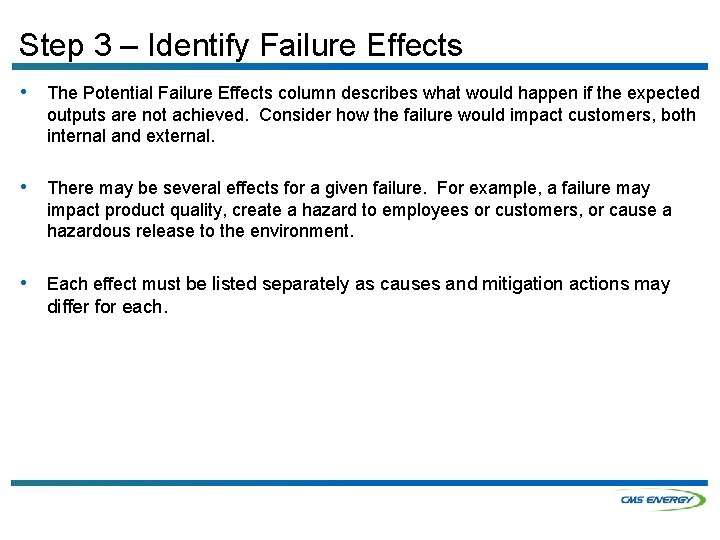
Step 3 – Identify Failure Effects • The Potential Failure Effects column describes what would happen if the expected outputs are not achieved. Consider how the failure would impact customers, both internal and external. • There may be several effects for a given failure. For example, a failure may impact product quality, create a hazard to employees or customers, or cause a hazardous release to the environment. • Each effect must be listed separately as causes and mitigation actions may differ for each.
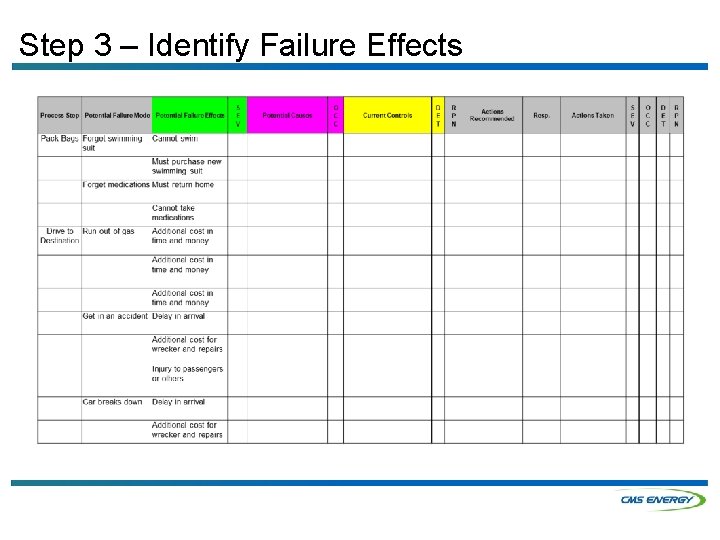
Step 3 – Identify Failure Effects
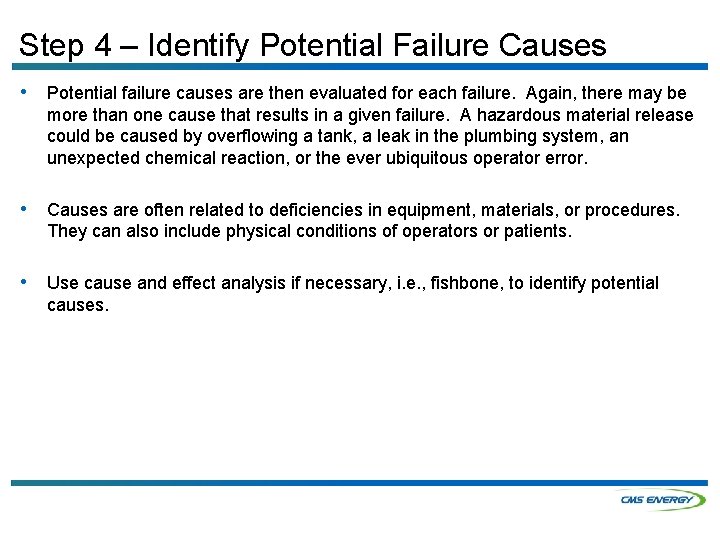
Step 4 – Identify Potential Failure Causes • Potential failure causes are then evaluated for each failure. Again, there may be more than one cause that results in a given failure. A hazardous material release could be caused by overflowing a tank, a leak in the plumbing system, an unexpected chemical reaction, or the ever ubiquitous operator error. • Causes are often related to deficiencies in equipment, materials, or procedures. They can also include physical conditions of operators or patients. • Use cause and effect analysis if necessary, i. e. , fishbone, to identify potential causes.
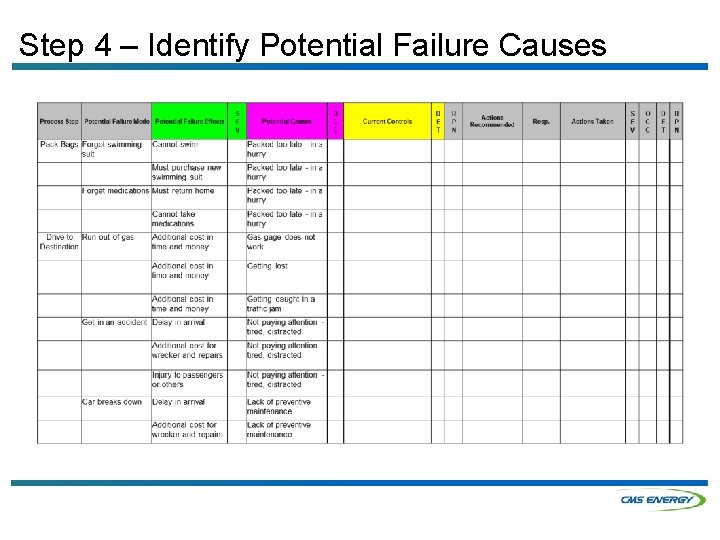
Step 4 – Identify Potential Failure Causes
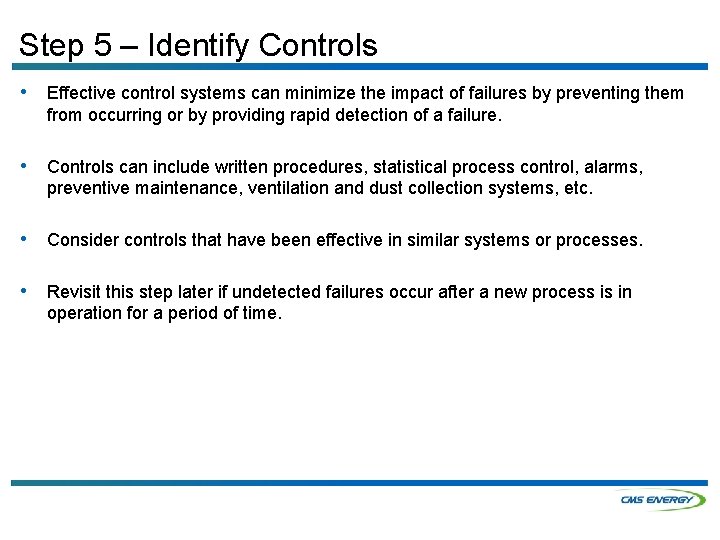
Step 5 – Identify Controls • Effective control systems can minimize the impact of failures by preventing them from occurring or by providing rapid detection of a failure. • Controls can include written procedures, statistical process control, alarms, preventive maintenance, ventilation and dust collection systems, etc. • Consider controls that have been effective in similar systems or processes. • Revisit this step later if undetected failures occur after a new process is in operation for a period of time.
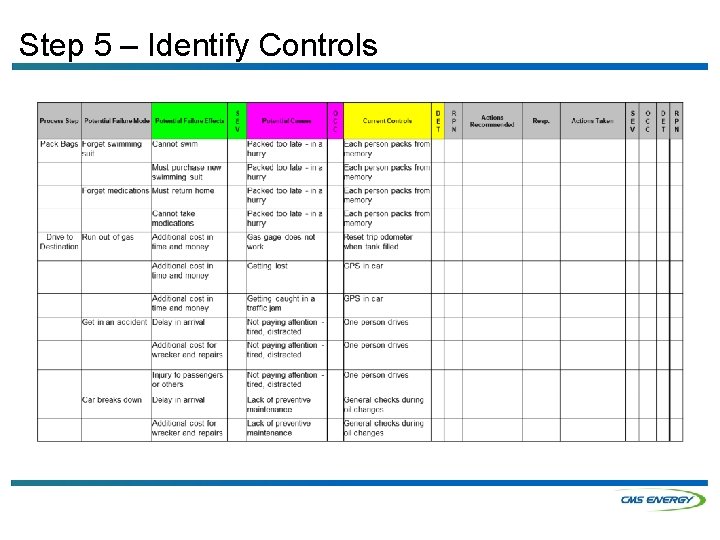
Step 5 – Identify Controls
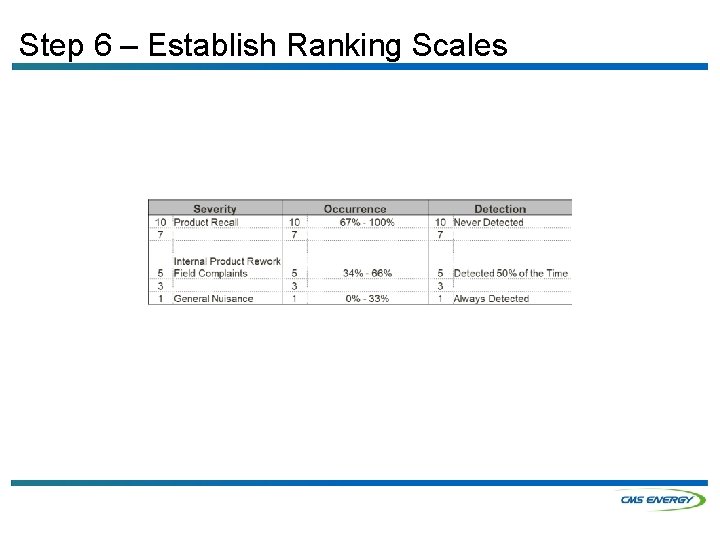
Step 6 – Establish Ranking Scales
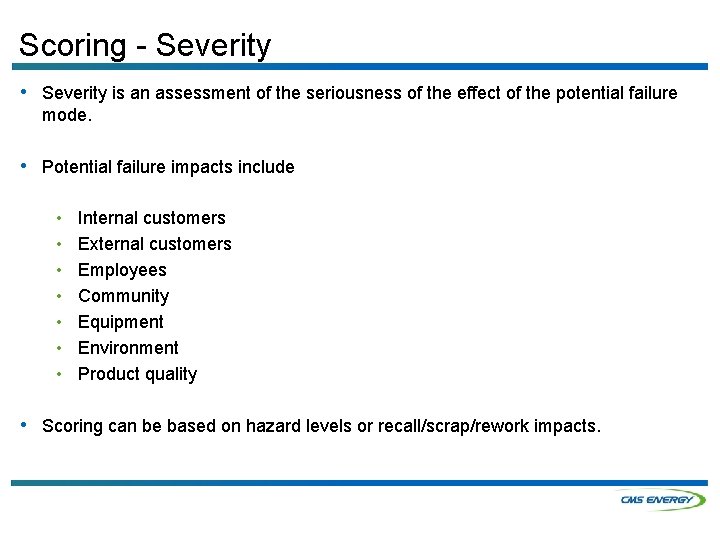
Scoring - Severity • Severity is an assessment of the seriousness of the effect of the potential failure mode. • Potential failure impacts include • • Internal customers External customers Employees Community Equipment Environment Product quality • Scoring can be based on hazard levels or recall/scrap/rework impacts.
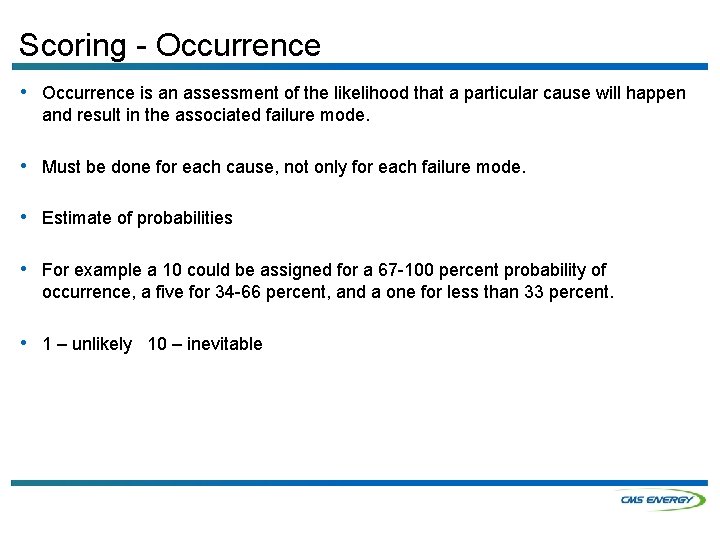
Scoring - Occurrence • Occurrence is an assessment of the likelihood that a particular cause will happen and result in the associated failure mode. • Must be done for each cause, not only for each failure mode. • Estimate of probabilities • For example a 10 could be assigned for a 67 -100 percent probability of occurrence, a five for 34 -66 percent, and a one for less than 33 percent. • 1 – unlikely 10 – inevitable
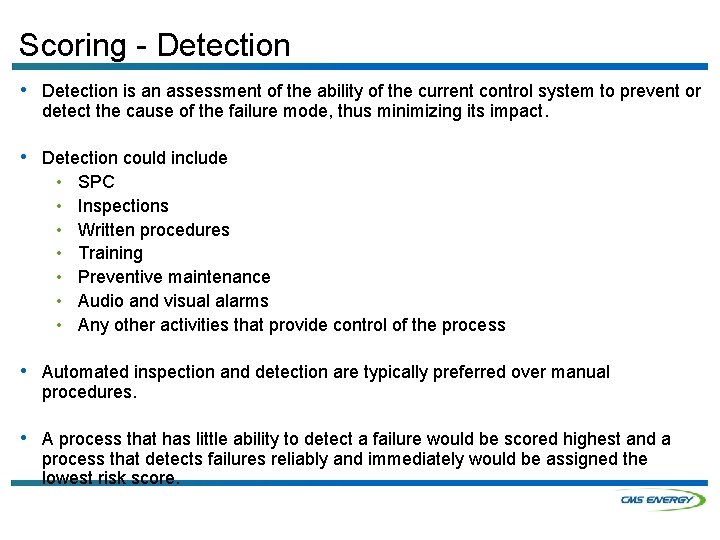
Scoring - Detection • Detection is an assessment of the ability of the current control system to prevent or detect the cause of the failure mode, thus minimizing its impact. • Detection could include • • SPC Inspections Written procedures Training Preventive maintenance Audio and visual alarms Any other activities that provide control of the process • Automated inspection and detection are typically preferred over manual procedures. • A process that has little ability to detect a failure would be scored highest and a process that detects failures reliably and immediately would be assigned the lowest risk score.
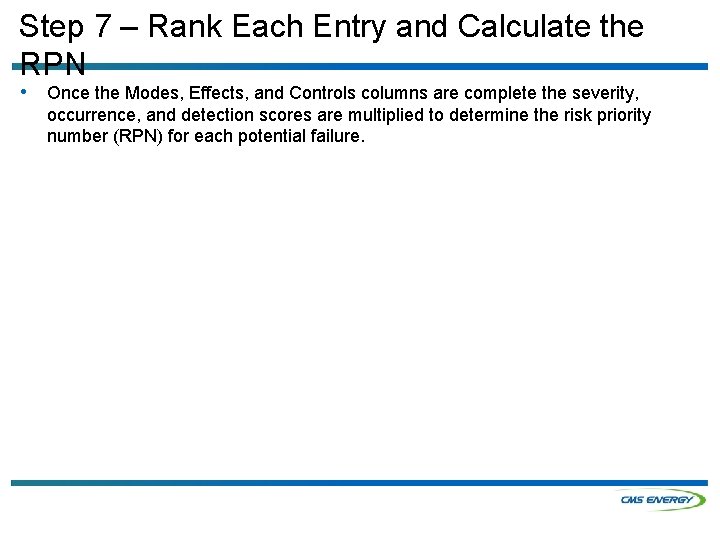
Step 7 – Rank Each Entry and Calculate the RPN • Once the Modes, Effects, and Controls columns are complete the severity, occurrence, and detection scores are multiplied to determine the risk priority number (RPN) for each potential failure.
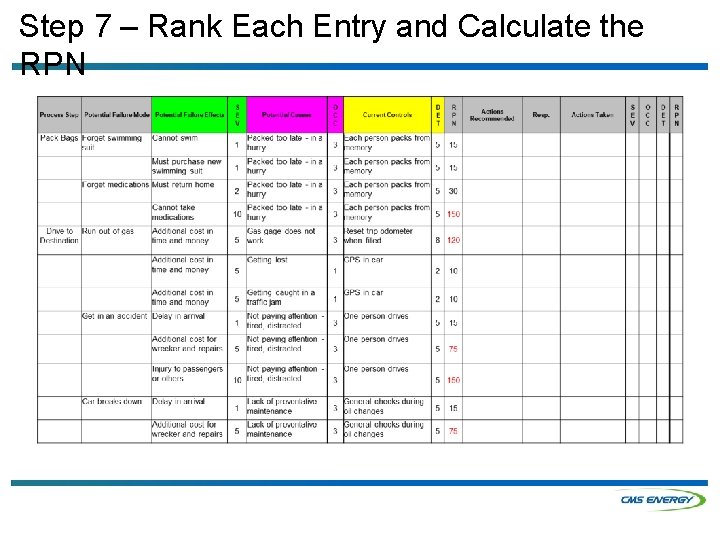
Step 7 – Rank Each Entry and Calculate the RPN
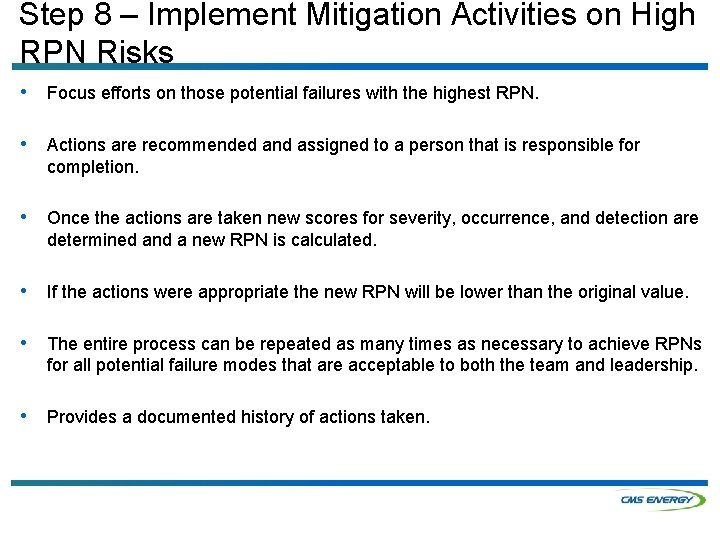
Step 8 – Implement Mitigation Activities on High RPN Risks • Focus efforts on those potential failures with the highest RPN. • Actions are recommended and assigned to a person that is responsible for completion. • Once the actions are taken new scores for severity, occurrence, and detection are determined and a new RPN is calculated. • If the actions were appropriate the new RPN will be lower than the original value. • The entire process can be repeated as many times as necessary to achieve RPNs for all potential failure modes that are acceptable to both the team and leadership. • Provides a documented history of actions taken.
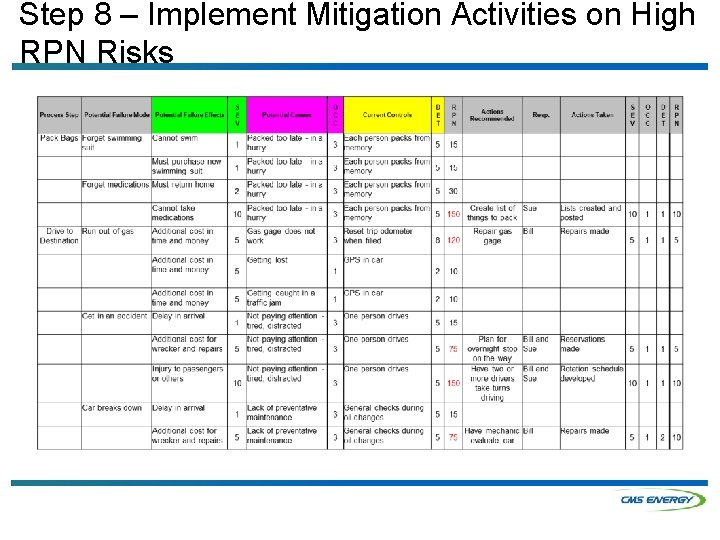
Step 8 – Implement Mitigation Activities on High RPN Risks
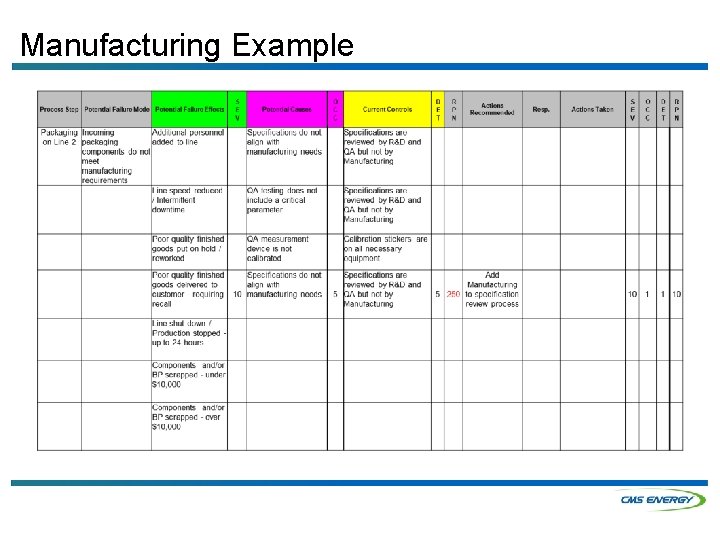
Manufacturing Example
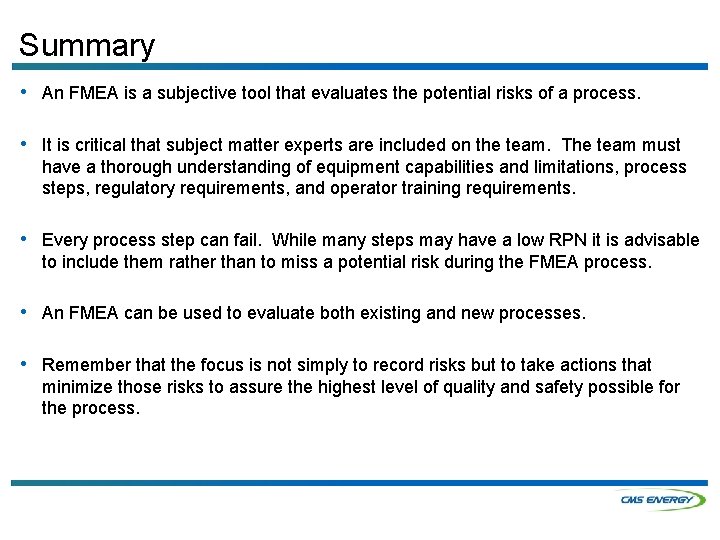
Summary • An FMEA is a subjective tool that evaluates the potential risks of a process. • It is critical that subject matter experts are included on the team. The team must have a thorough understanding of equipment capabilities and limitations, process steps, regulatory requirements, and operator training requirements. • Every process step can fail. While many steps may have a low RPN it is advisable to include them rather than to miss a potential risk during the FMEA process. • An FMEA can be used to evaluate both existing and new processes. • Remember that the focus is not simply to record risks but to take actions that minimize those risks to assure the highest level of quality and safety possible for the process.
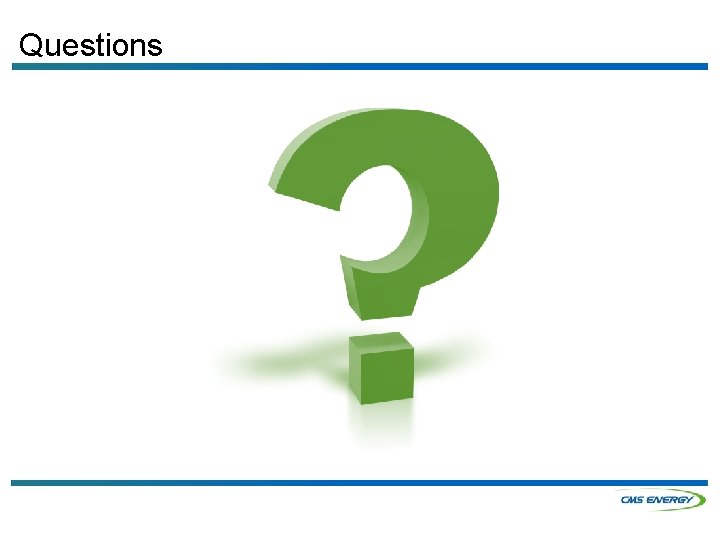
Questions
Michigan lean consortium
Standard work pig template
Michigan lean consortium
Michigan assessment consortium
Capture beat
Failure to sense pacemaker
Ductile fracture
Dc dc converter failure modes
Bond failure
Connector theory
Justin kiswardy
Centrifugal pump failure modes
Fmea rpn 기준표
Failure mode and effect analysis
Failure point analysis
Photo emission microscopy failure analysis
Kukum analyse
Ndt failure analysis
Define rhetorical mode
Summary lean startup
Lean bi analysis
Gcche
Failure of supporting utilities and structural collapse
Forrester classification heart failure
Advantages and challenges of multigrade teaching
Ddmin
Factors of project success and failure
People in service marketing
Vetsulin dosage chart for dogs
Diabetes and heart failure