Engineering Alloys 307 Lecture 9 Titanium II Ti
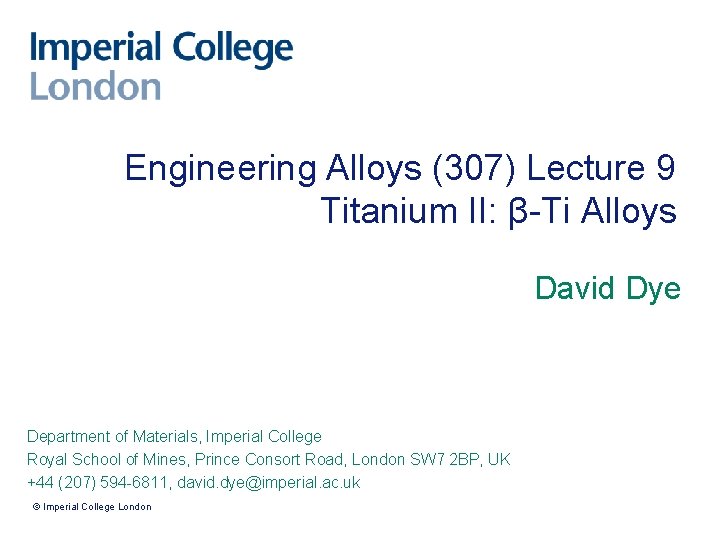
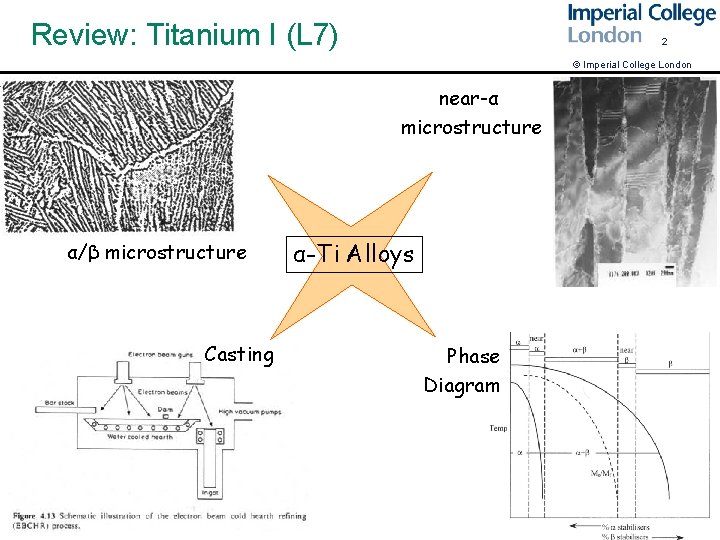
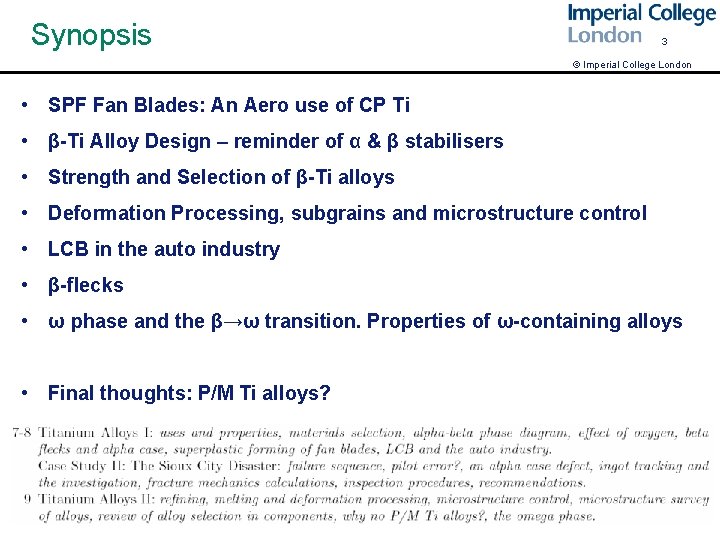
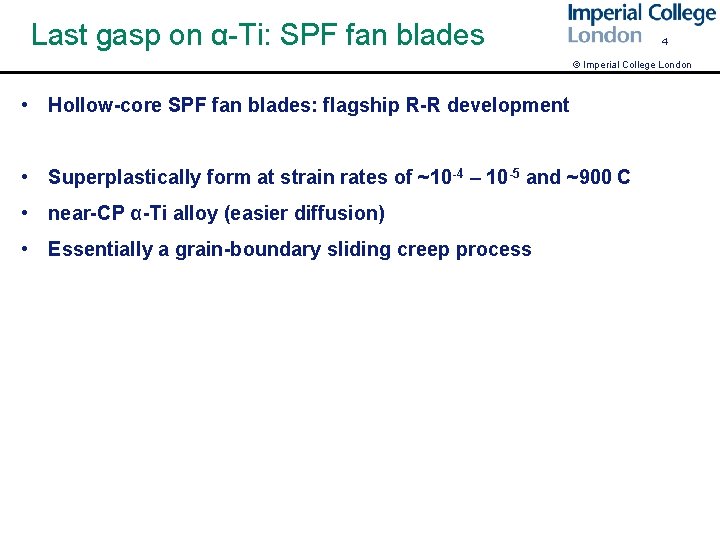
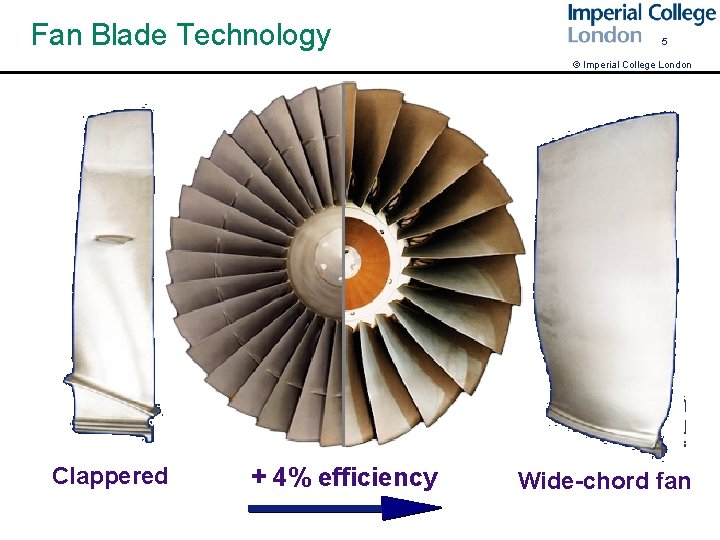
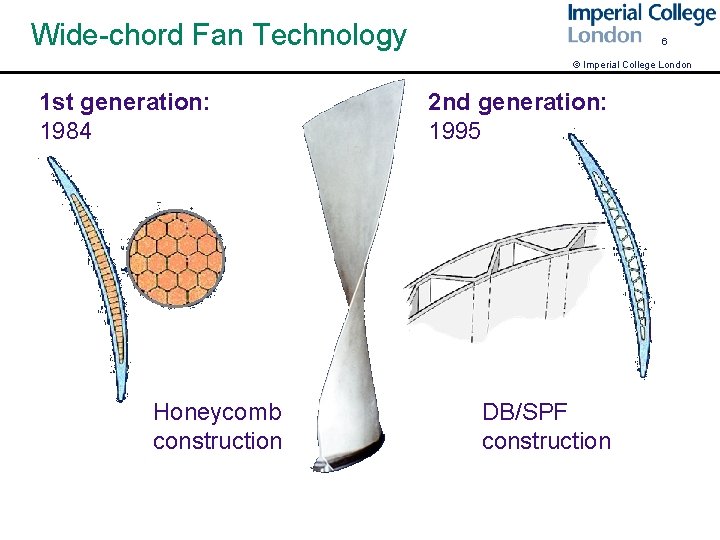
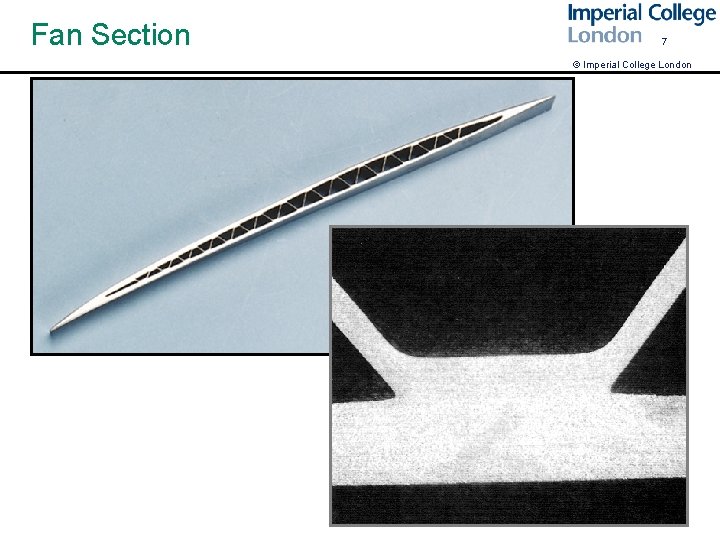
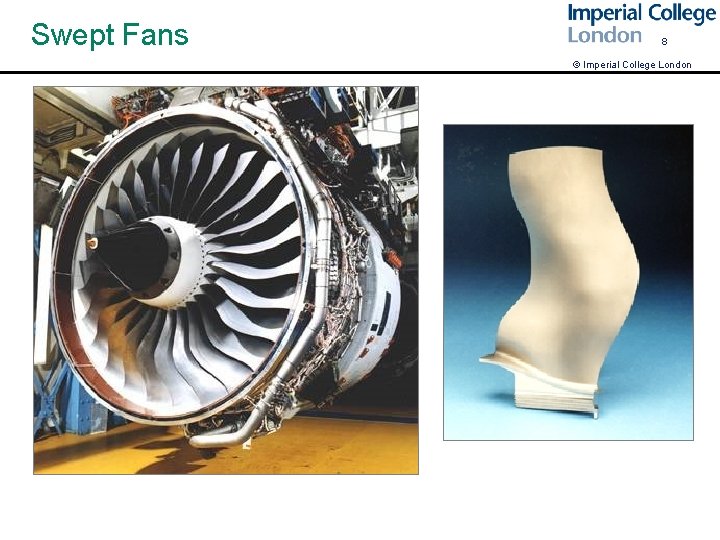
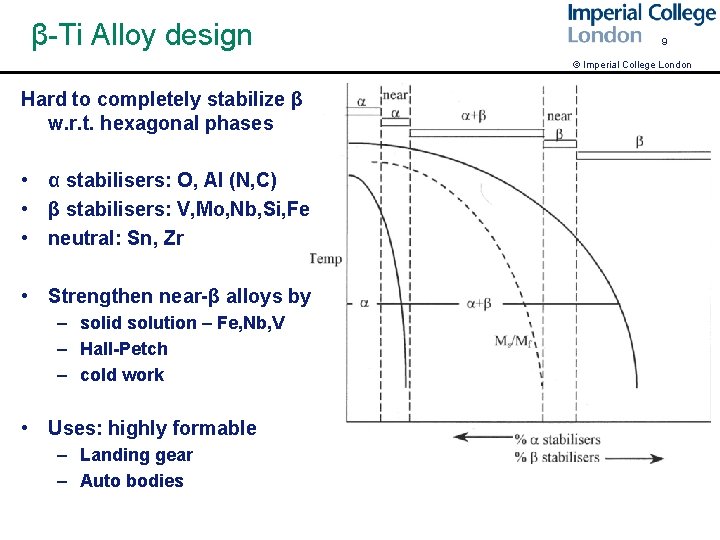
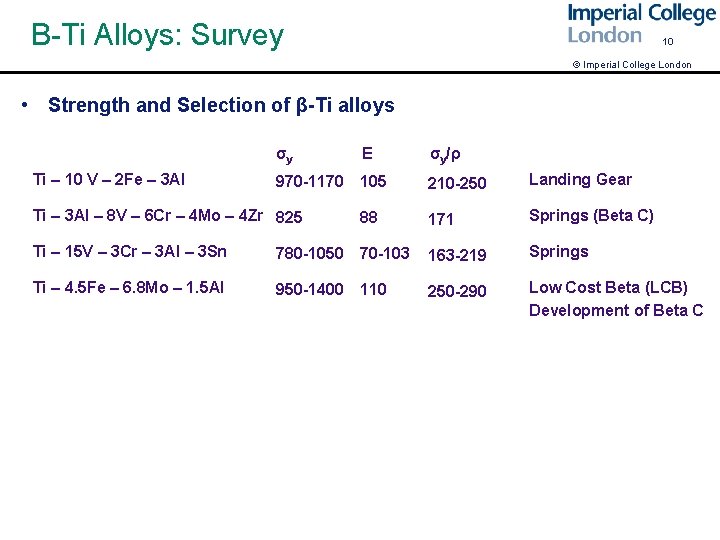
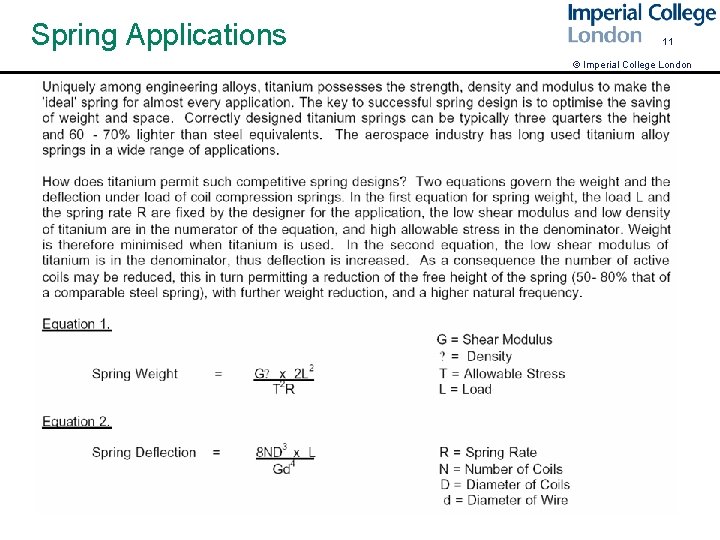
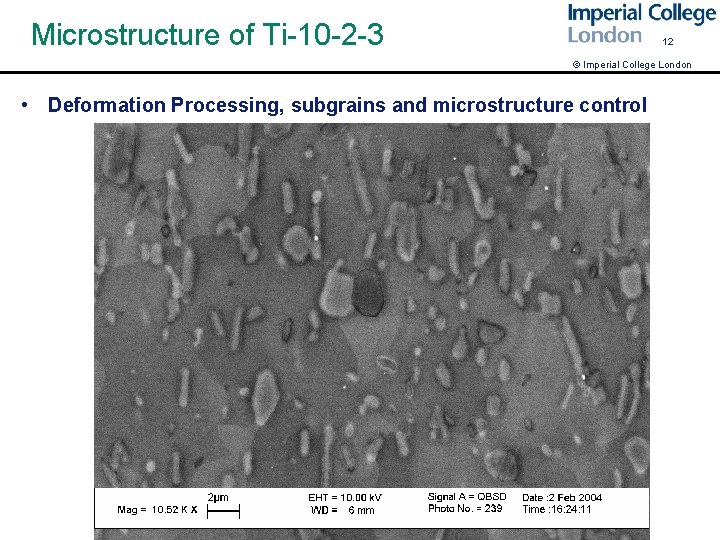
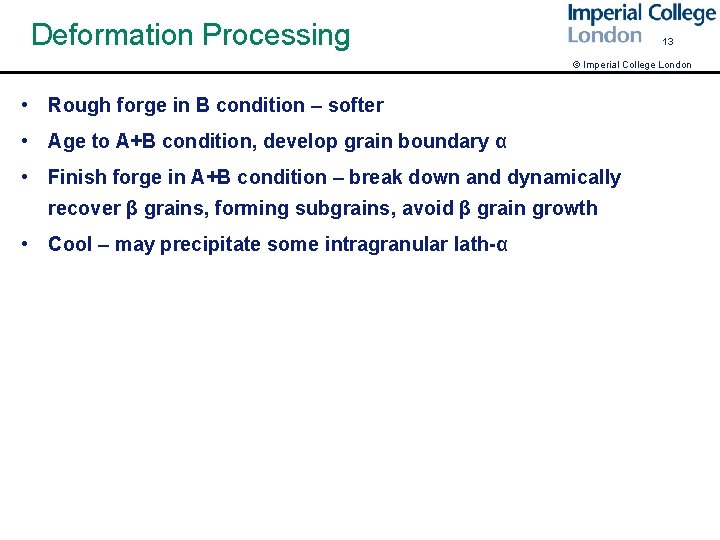
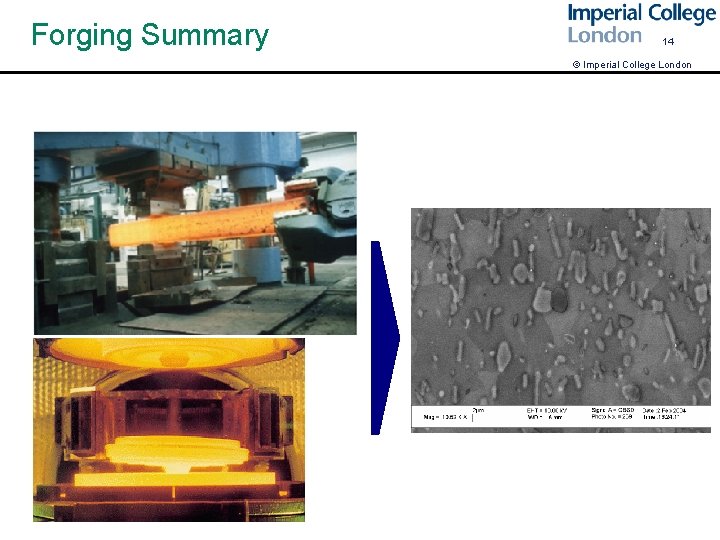
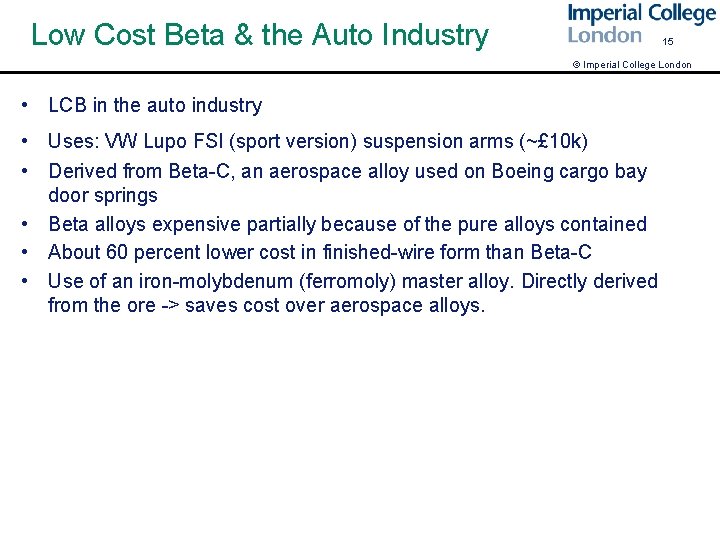
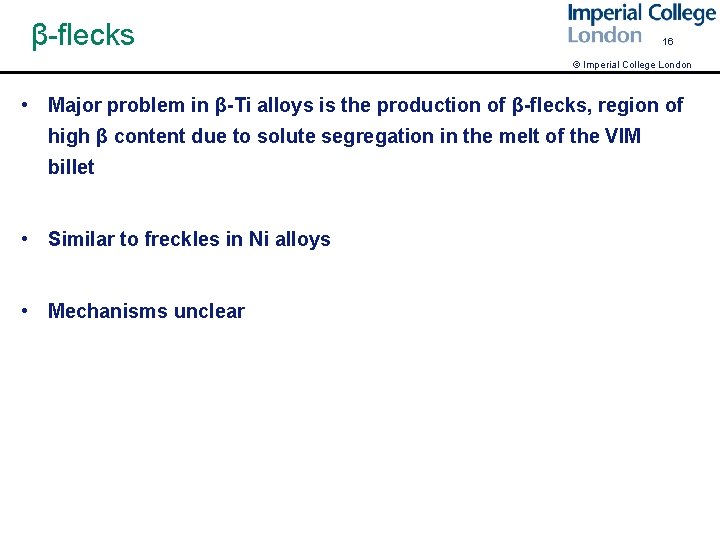
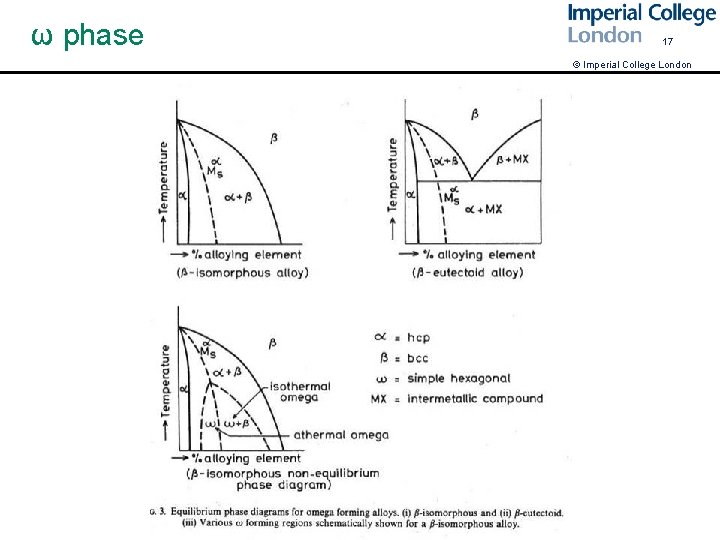
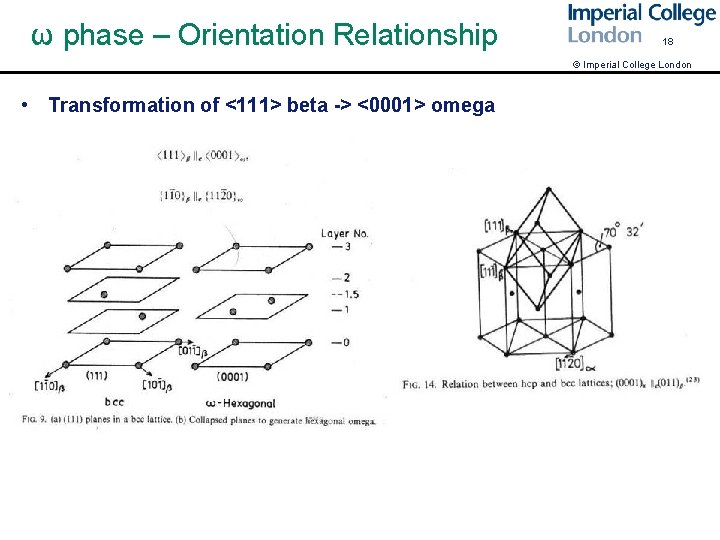
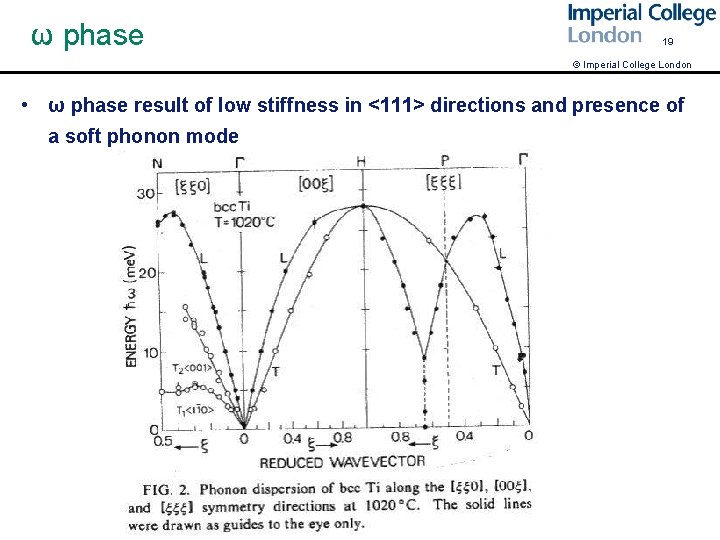
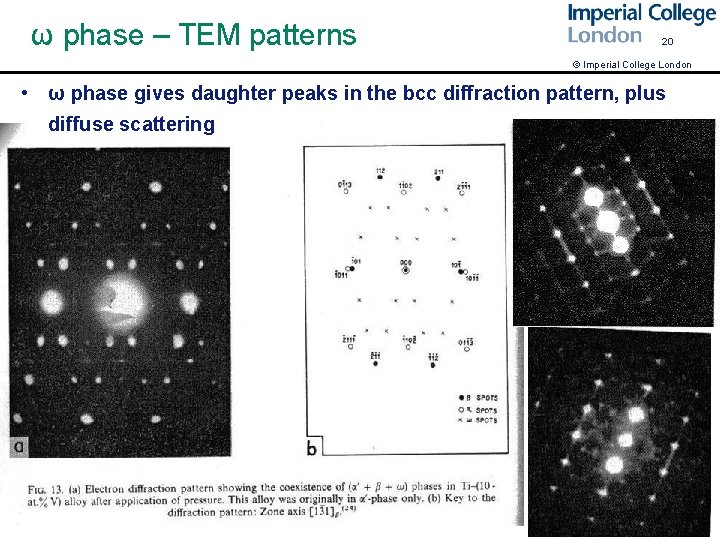
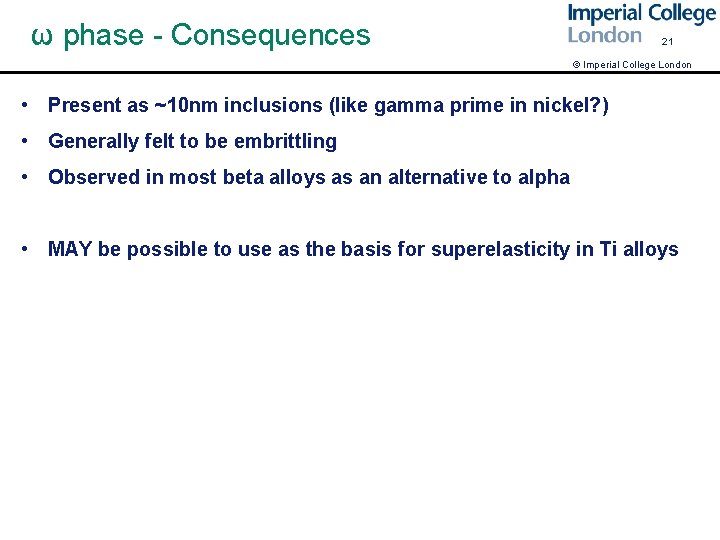
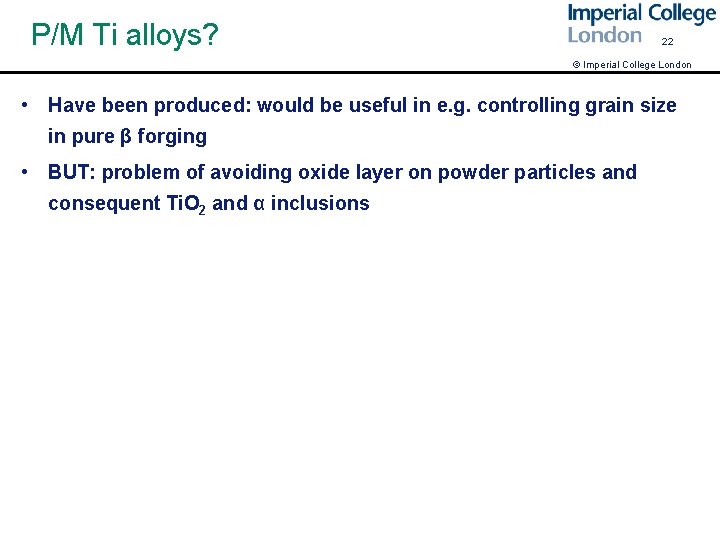
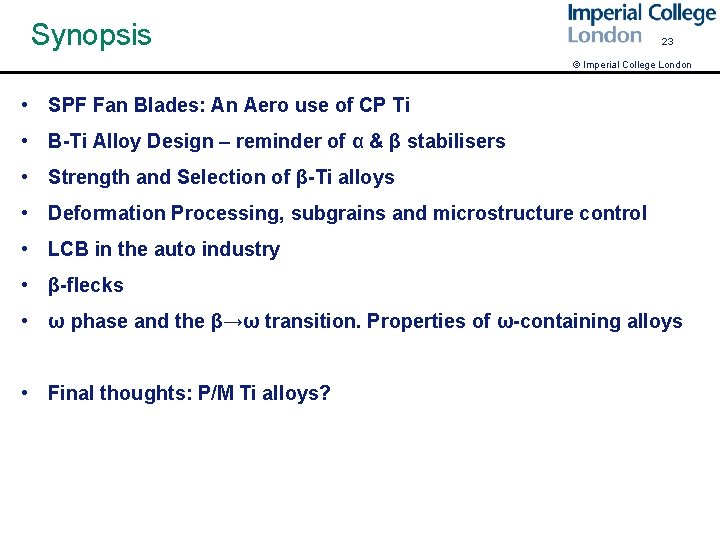
- Slides: 23
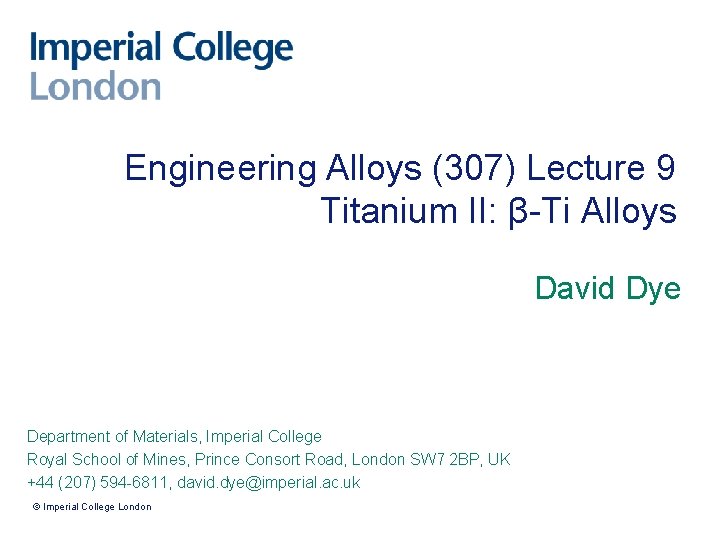
Engineering Alloys (307) Lecture 9 Titanium II: β-Ti Alloys David Dye Department of Materials, Imperial College Royal School of Mines, Prince Consort Road, London SW 7 2 BP, UK +44 (207) 594 -6811, david. dye@imperial. ac. uk © Imperial College London
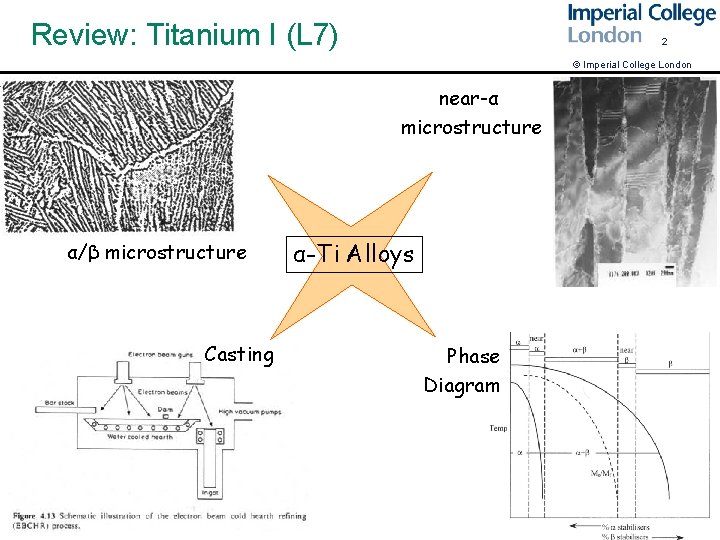
Review: Titanium I (L 7) 2 © Imperial College London near-α microstructure α/β microstructure Casting α-Ti Alloys Phase Diagram
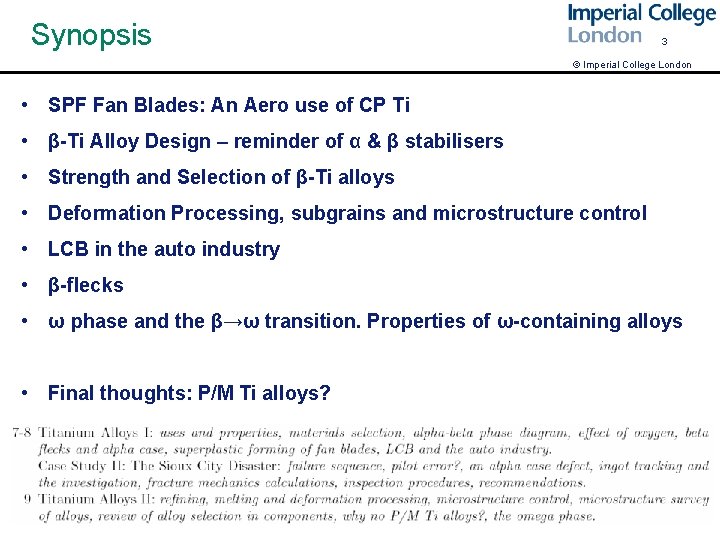
Synopsis 3 © Imperial College London • SPF Fan Blades: An Aero use of CP Ti • β-Ti Alloy Design – reminder of α & β stabilisers • Strength and Selection of β-Ti alloys • Deformation Processing, subgrains and microstructure control • LCB in the auto industry • β-flecks • ω phase and the β→ω transition. Properties of ω-containing alloys • Final thoughts: P/M Ti alloys?
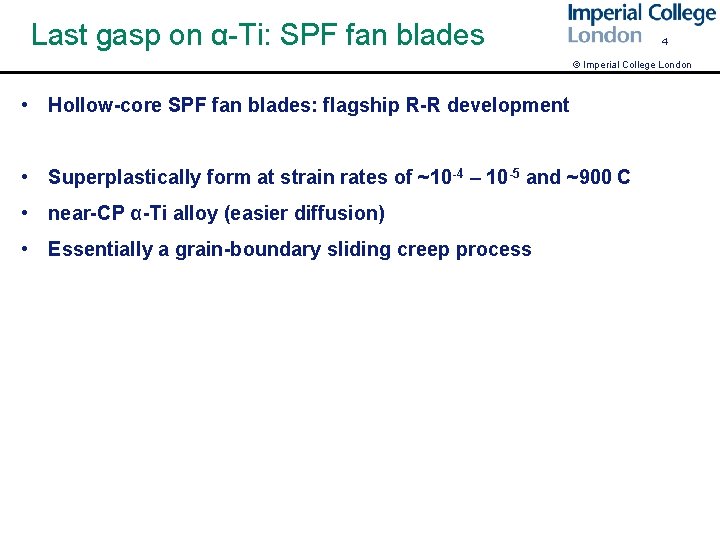
Last gasp on α-Ti: SPF fan blades 4 © Imperial College London • Hollow-core SPF fan blades: flagship R-R development • Superplastically form at strain rates of ~10 -4 – 10 -5 and ~900 C • near-CP α-Ti alloy (easier diffusion) • Essentially a grain-boundary sliding creep process
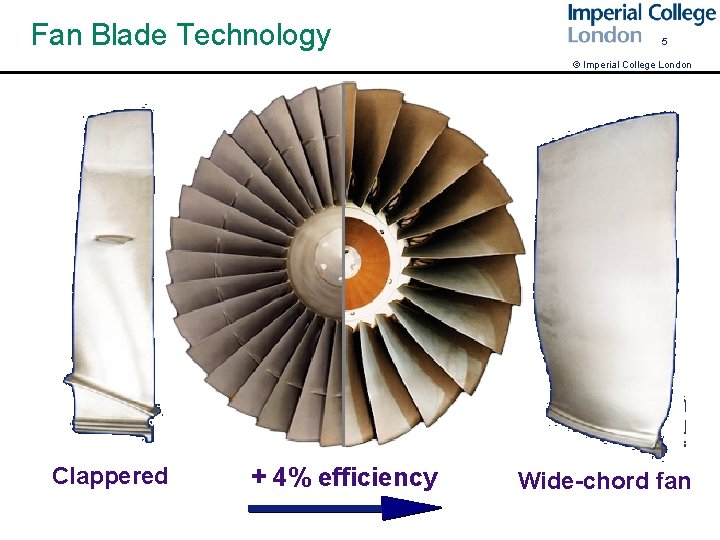
Fan Blade Technology 5 © Imperial College London Clappered + 4% efficiency Wide-chord fan
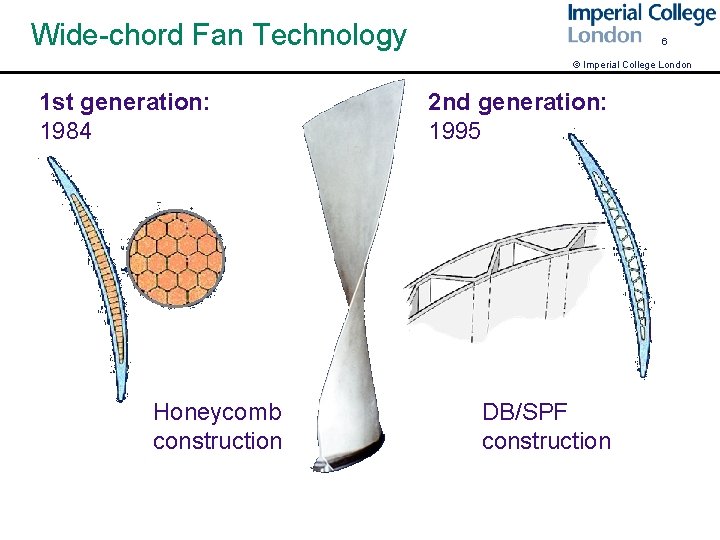
Wide-chord Fan Technology 6 © Imperial College London 1 st generation: 1984 Honeycomb construction 2 nd generation: 1995 DB/SPF construction
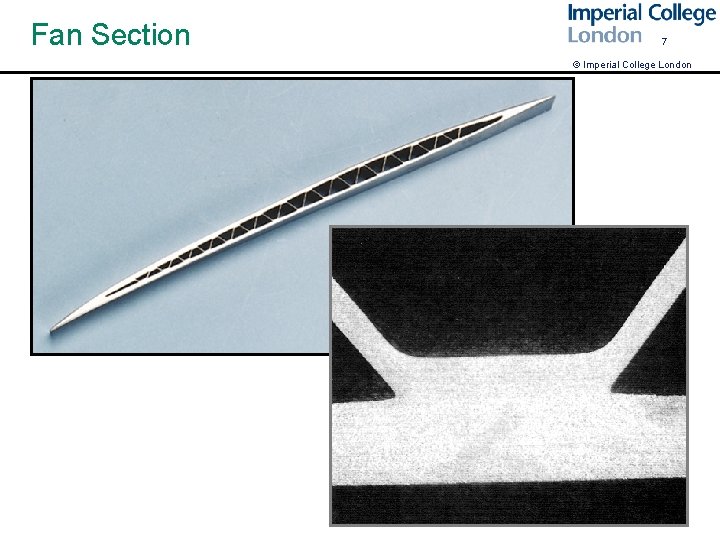
Fan Section 7 © Imperial College London
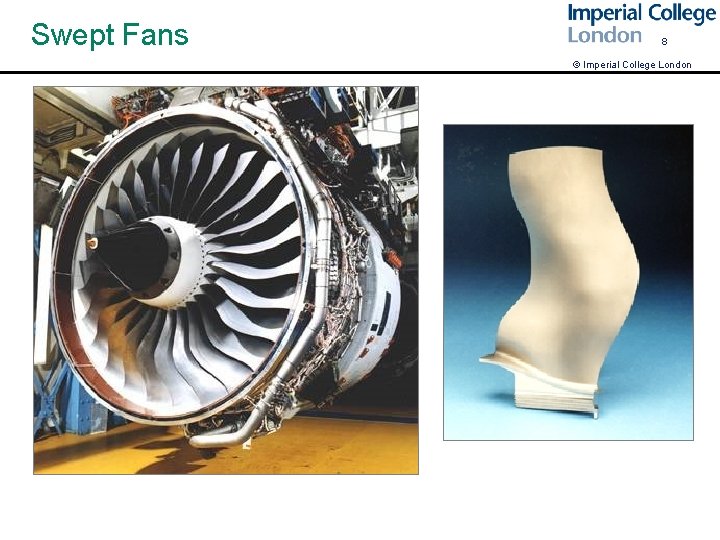
Swept Fans 8 © Imperial College London
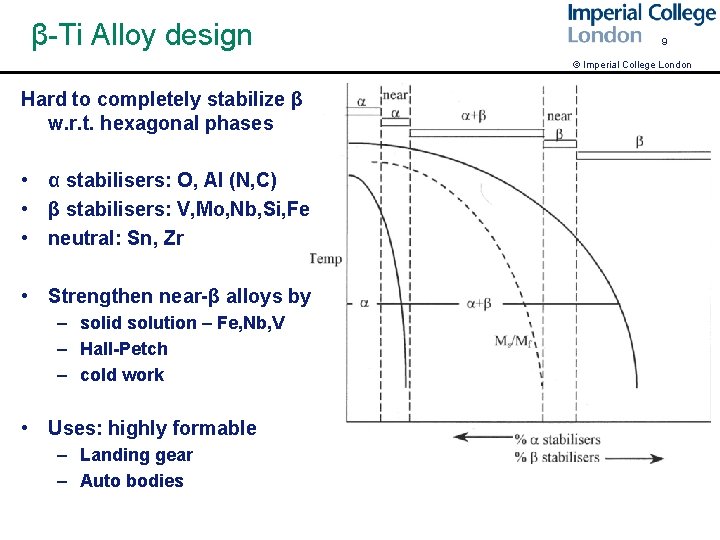
β-Ti Alloy design 9 © Imperial College London Hard to completely stabilize β w. r. t. hexagonal phases • α stabilisers: O, Al (N, C) • β stabilisers: V, Mo, Nb, Si, Fe • neutral: Sn, Zr • Strengthen near-β alloys by – solid solution – Fe, Nb, V – Hall-Petch – cold work • Uses: highly formable – Landing gear – Auto bodies
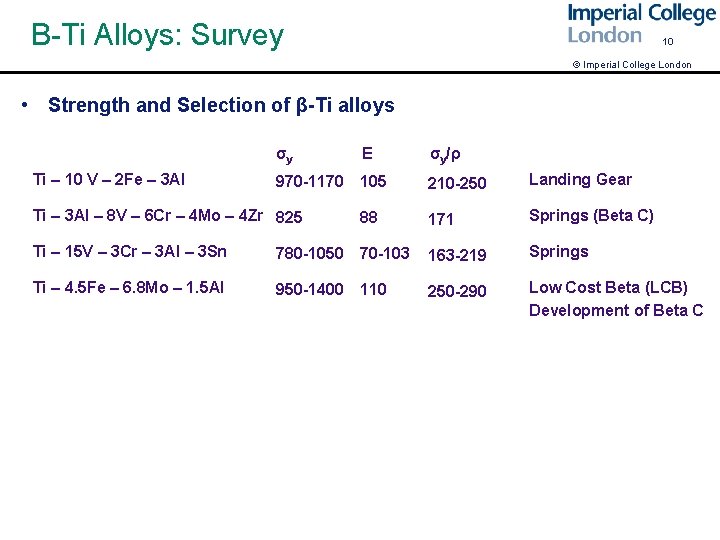
Β-Ti Alloys: Survey 10 © Imperial College London • Strength and Selection of β-Ti alloys σy E σy/ρ 970 -1170 105 210 -250 Landing Gear Ti – 3 Al – 8 V – 6 Cr – 4 Mo – 4 Zr 825 88 171 Springs (Beta C) Ti – 15 V – 3 Cr – 3 Al – 3 Sn 780 -1050 70 -103 163 -219 Springs Ti – 4. 5 Fe – 6. 8 Mo – 1. 5 Al 950 -1400 110 250 -290 Low Cost Beta (LCB) Development of Beta C Ti – 10 V – 2 Fe – 3 Al
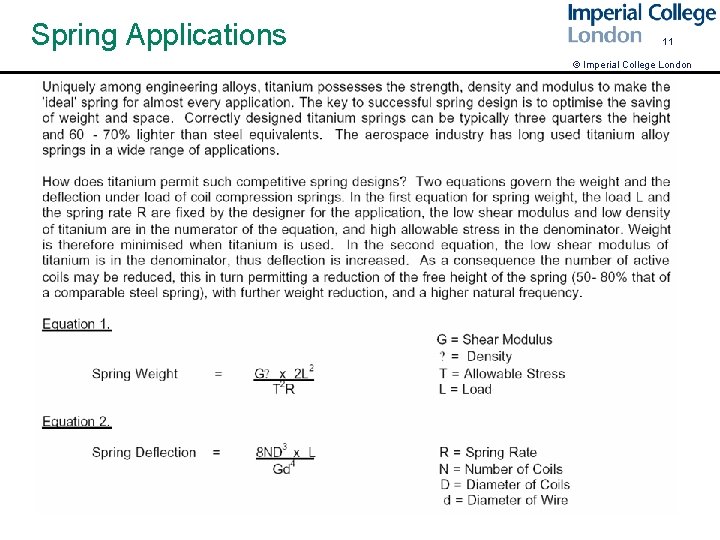
Spring Applications 11 © Imperial College London
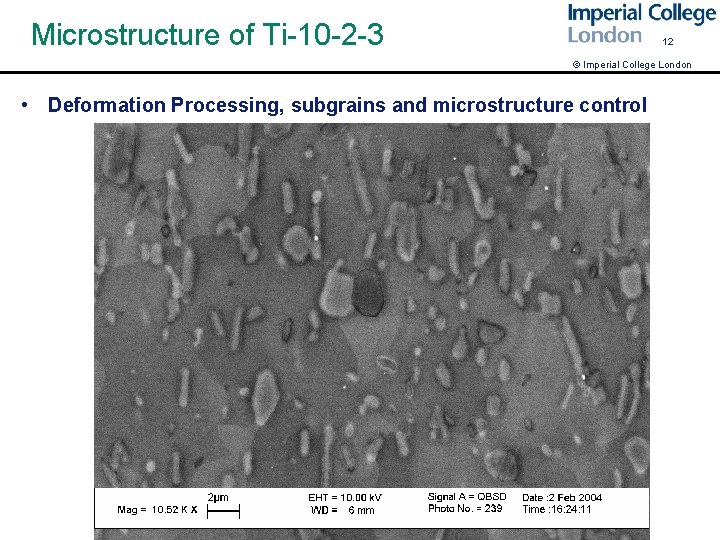
Microstructure of Ti-10 -2 -3 12 © Imperial College London • Deformation Processing, subgrains and microstructure control
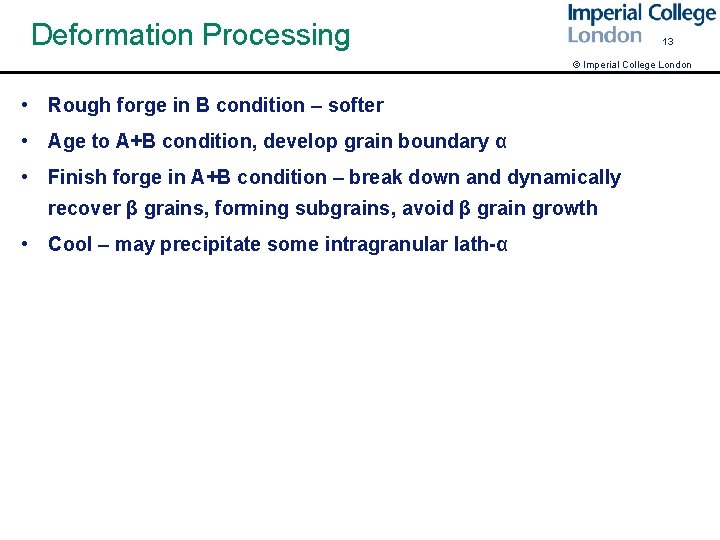
Deformation Processing 13 © Imperial College London • Rough forge in B condition – softer • Age to A+B condition, develop grain boundary α • Finish forge in A+B condition – break down and dynamically recover β grains, forming subgrains, avoid β grain growth • Cool – may precipitate some intragranular lath-α
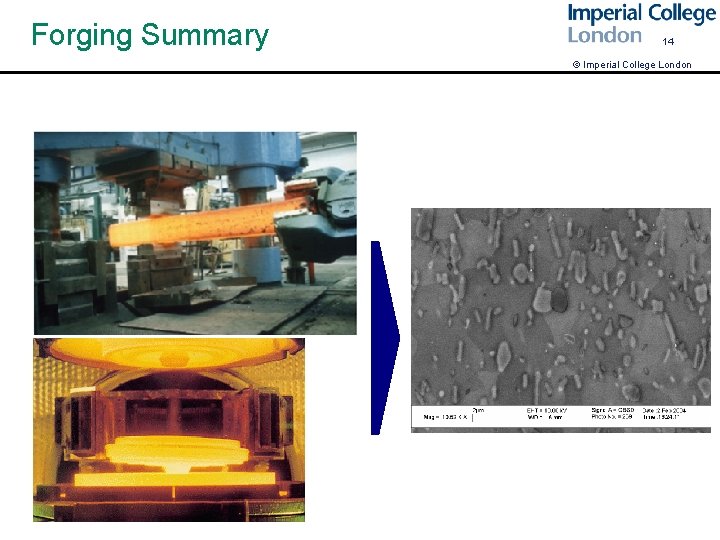
Forging Summary 14 © Imperial College London
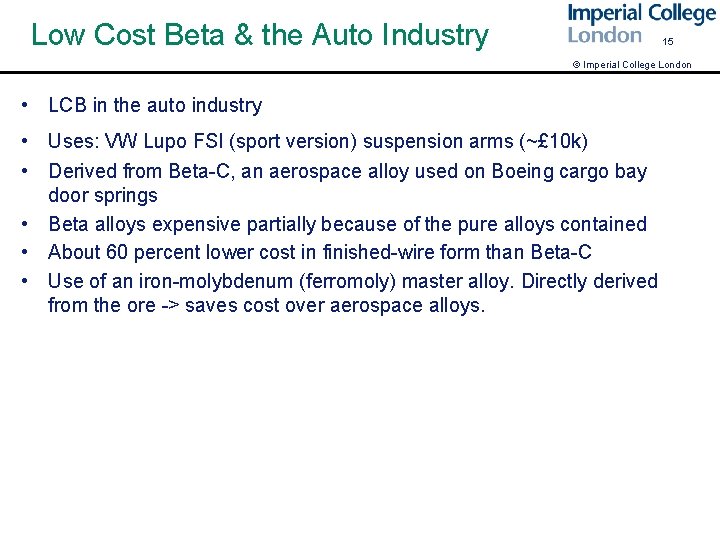
Low Cost Beta & the Auto Industry 15 © Imperial College London • LCB in the auto industry • Uses: VW Lupo FSI (sport version) suspension arms (~£ 10 k) • Derived from Beta-C, an aerospace alloy used on Boeing cargo bay door springs • Beta alloys expensive partially because of the pure alloys contained • About 60 percent lower cost in finished-wire form than Beta-C • Use of an iron-molybdenum (ferromoly) master alloy. Directly derived from the ore -> saves cost over aerospace alloys.
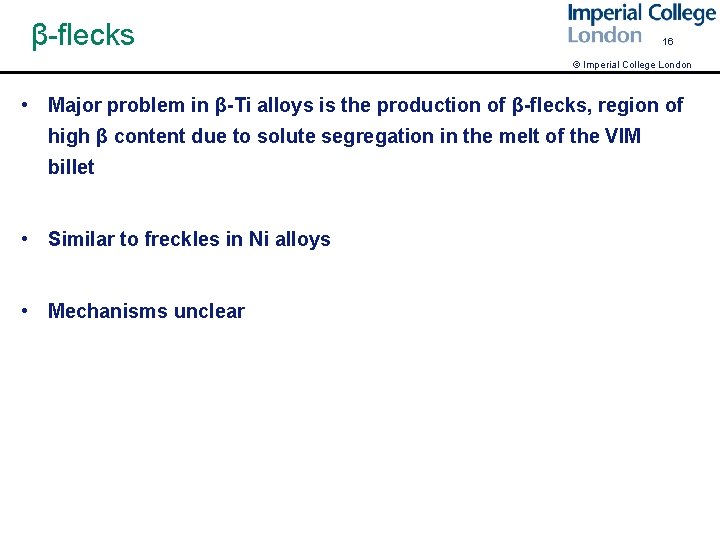
β-flecks 16 © Imperial College London • Major problem in β-Ti alloys is the production of β-flecks, region of high β content due to solute segregation in the melt of the VIM billet • Similar to freckles in Ni alloys • Mechanisms unclear
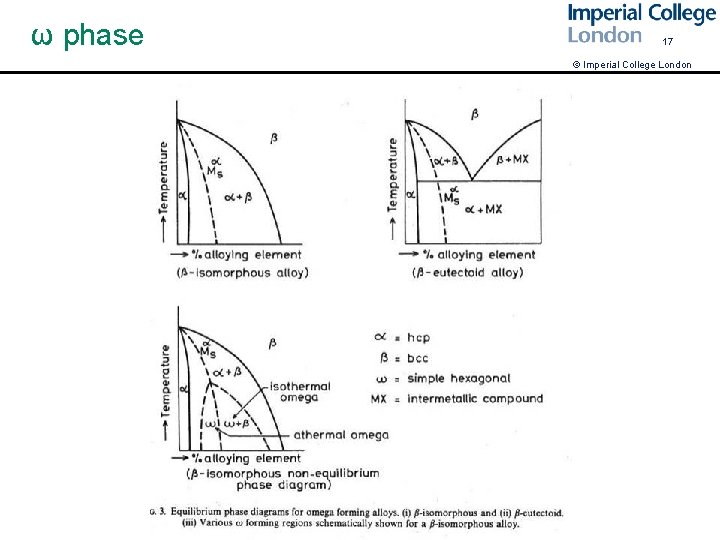
ω phase 17 © Imperial College London
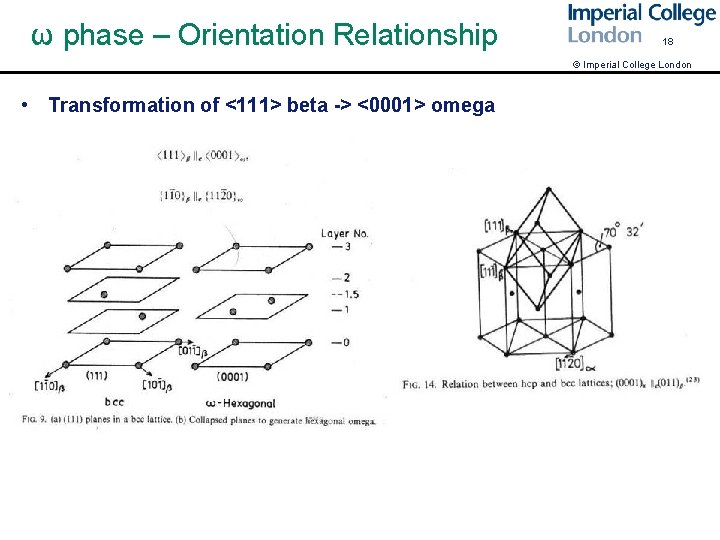
ω phase – Orientation Relationship 18 © Imperial College London • Transformation of <111> beta -> <0001> omega
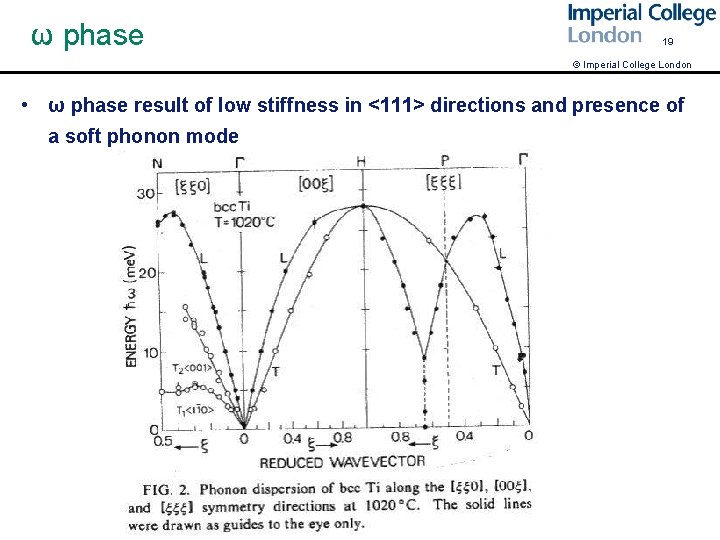
ω phase 19 © Imperial College London • ω phase result of low stiffness in <111> directions and presence of a soft phonon mode
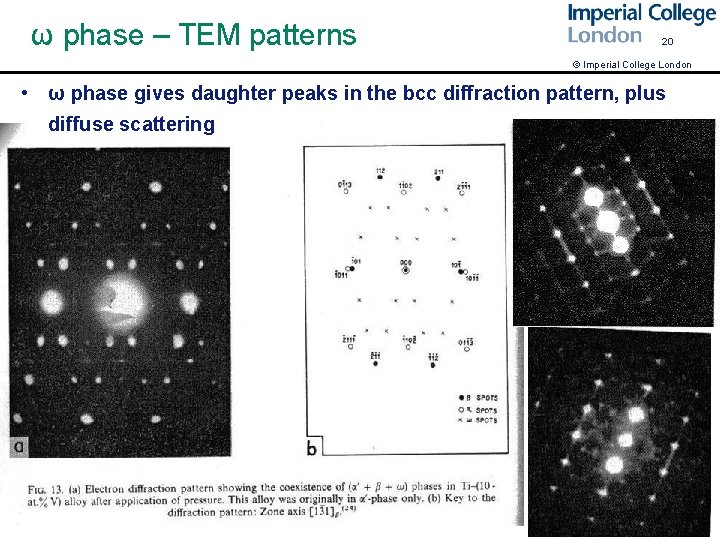
ω phase – TEM patterns 20 © Imperial College London • ω phase gives daughter peaks in the bcc diffraction pattern, plus diffuse scattering
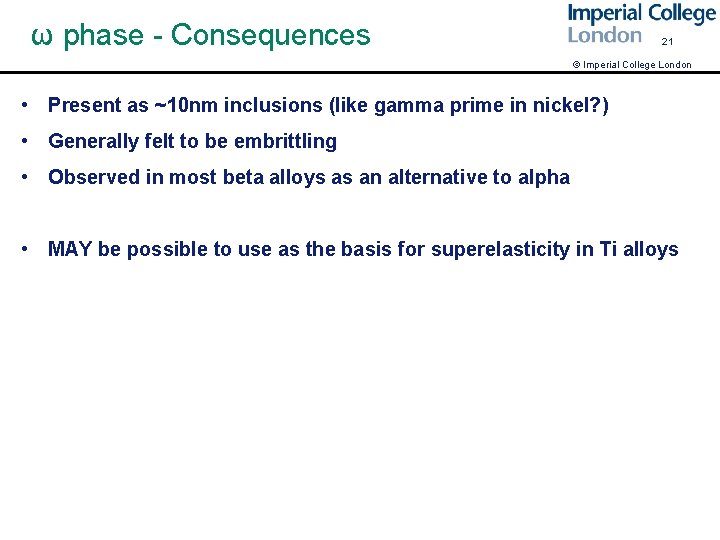
ω phase - Consequences 21 © Imperial College London • Present as ~10 nm inclusions (like gamma prime in nickel? ) • Generally felt to be embrittling • Observed in most beta alloys as an alternative to alpha • MAY be possible to use as the basis for superelasticity in Ti alloys
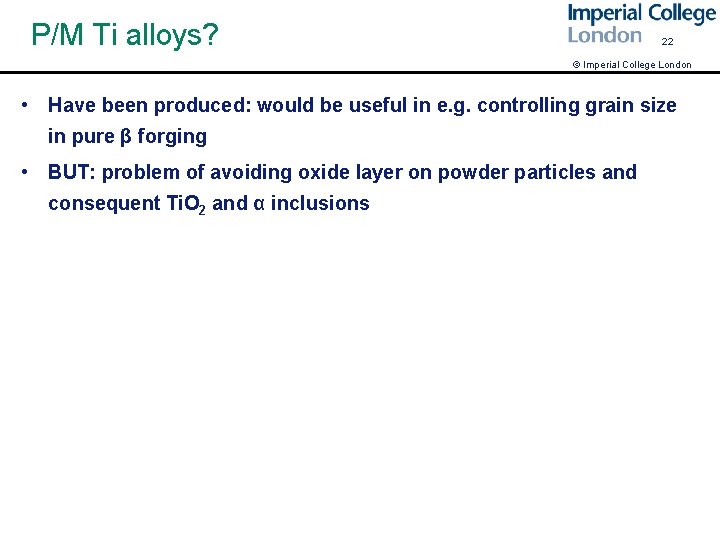
P/M Ti alloys? 22 © Imperial College London • Have been produced: would be useful in e. g. controlling grain size in pure β forging • BUT: problem of avoiding oxide layer on powder particles and consequent Ti. O 2 and α inclusions
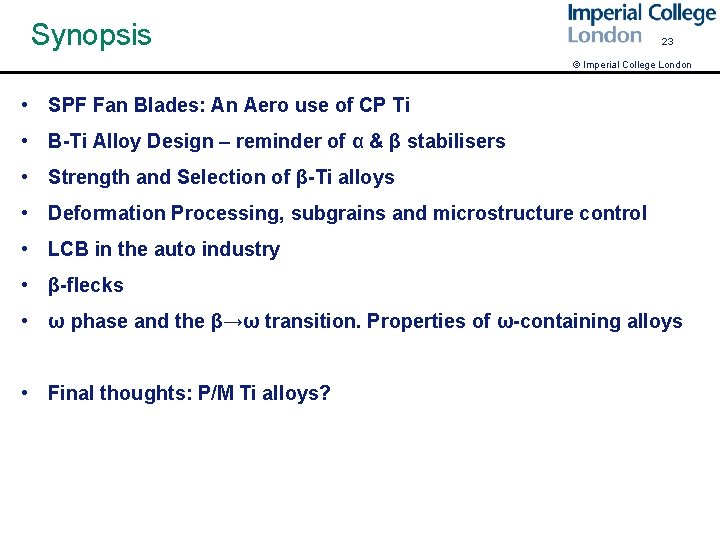
Synopsis 23 © Imperial College London • SPF Fan Blades: An Aero use of CP Ti • Β-Ti Alloy Design – reminder of α & β stabilisers • Strength and Selection of β-Ti alloys • Deformation Processing, subgrains and microstructure control • LCB in the auto industry • β-flecks • ω phase and the β→ω transition. Properties of ω-containing alloys • Final thoughts: P/M Ti alloys?
Titanium alloys
Shape memory alloys lecture notes
01:640:244 lecture notes - lecture 15: plat, idah, farad
Iso tc 307
Cmpt 307
Byk 333
Xm 307
Kaman dayron
P 307 2016
30 tac 307
Smita duorah
Wac 296-307
360-307
Iso/tc 307 blockchain and distributed ledger technologies
Wac 296-307
Ce 307
Szkoła podstawowa nr 307
Mis 307
Cse 307
Cmpt307
Buad 307
Cmpt 733 github
Microfusion cast & alloys
Unicompositional amalgam