Direct Production of Titanium Powder from Titanium Ore
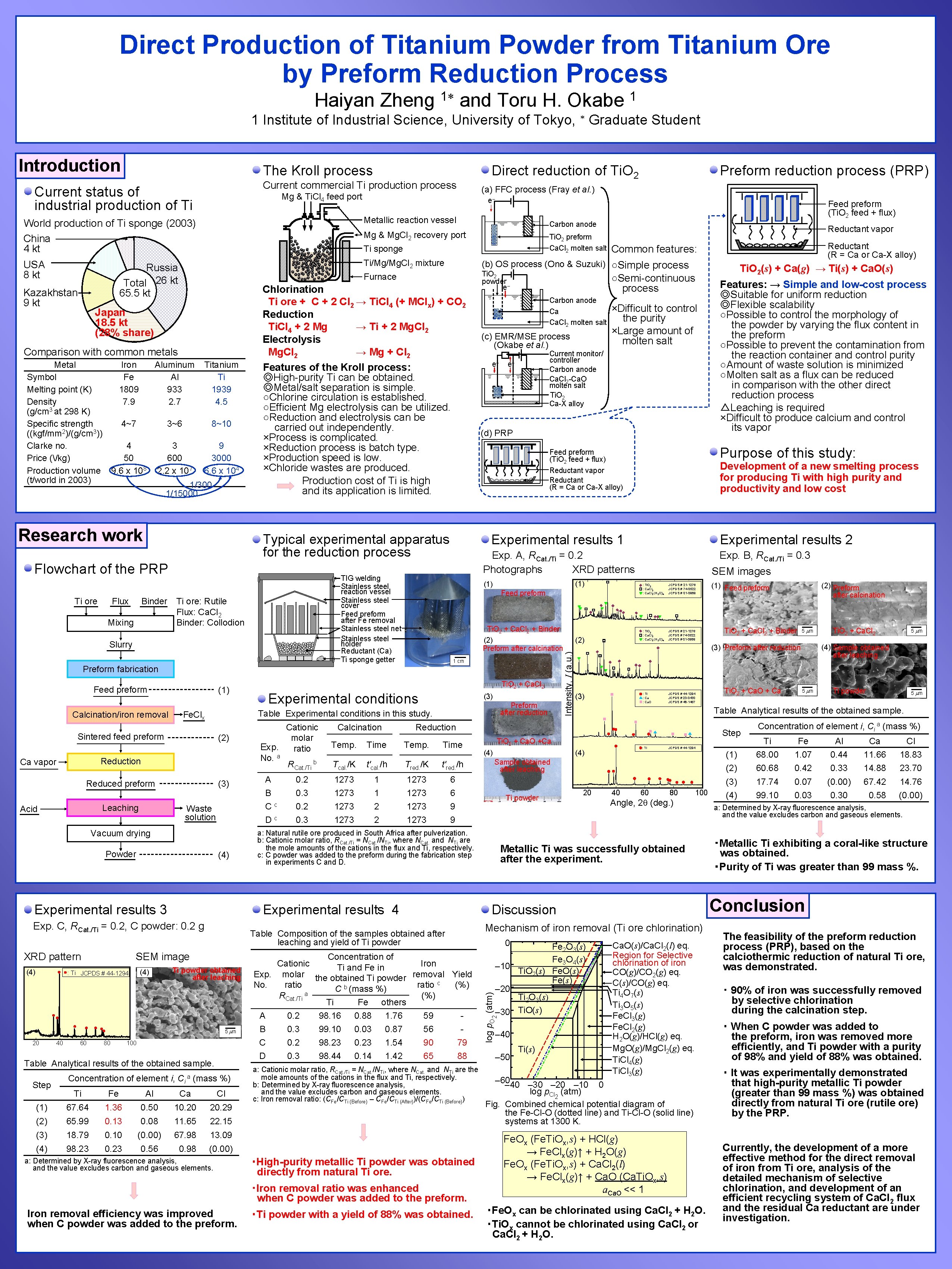
- Slides: 1
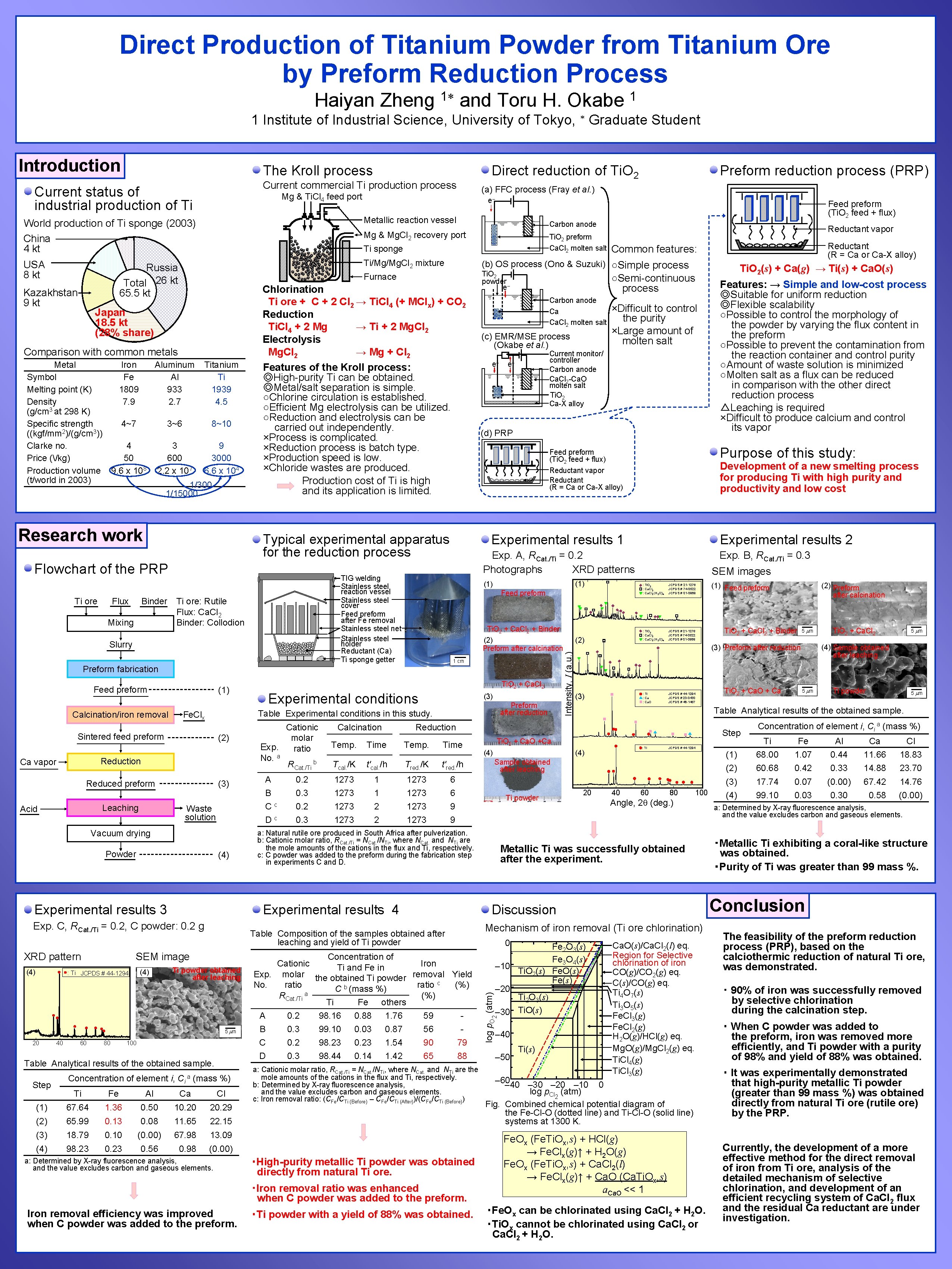
Direct Production of Titanium Powder from Titanium Ore by Preform Reduction Process Haiyan Zheng 1 and Toru H. Okabe 1 1 Institute of Industrial Science, University of Tokyo, Graduate Student The Kroll process Current commercial Ti production process Current status of industrial production of Ti e– Metallic reaction vessel USA 8 kt Ti/Mg/Mg. Cl 2 mixture Metal Iron Aluminum Titanium Symbol Fe Al Ti Melting point (K) 1809 933 1939 Density 7. 9 2. 7 4. 5 (g/cm 3 at 298 K) Specific strength 4~7 3~6 8~10 ((kgf/mm 2)/(g/cm 3)) Clarke no. 4 3 9 Price (/kg) 50 600 3000 Production volume 9. 6 x 108 2. 2 x 107 6. 6 x 104 (t/world in 2003) 1/300 1/15000 Research work Chlorination Ti ore + C + 2 Cl 2 → Ti. Cl 4 (+ MClx) + CO 2 Reduction Ti. Cl 4 + 2 Mg → Ti + 2 Mg. Cl 2 Electrolysis Mg. Cl 2 → Mg + Cl 2 Features of the Kroll process: ◎High-purity Ti can be obtained. ◎Metal/salt separation is simple. ○Chlorine circulation is established. ○Efficient Mg electrolysis can be utilized. ○Reduction and electrolysis can be carried out independently. ×Process is complicated. ×Reduction process is batch type. ×Production speed is low. ×Chloride wastes are produced. Production cost of Ti is high and its application is limited. Typical experimental apparatus for the reduction process Flowchart of the PRP Binder Mixing Ti. O 2 preform Ca. Cl 2 molten salt TIG welding Stainless steel reaction vessel Stainless steel cover Feed preform after Fe removal Stainless steel net Stainless steel holder Reductant (Ca) Ti sponge getter Ti ore: Rutile Flux: Ca. Cl 2 Binder: Collodion Slurry Ti. O 2 powder e– Carbon anode Ca Ca. Cl 2 molten salt (c) EMR/MSE process (Okabe et al. ) e– e– Sintered feed preform (2) Reduction Ca vapor (3) Reduced preform Leaching Acid Waste solution Vacuum drying Powder (4) Experimental results 3 (1) Feed preform Ti. O 2 + Ca. Cl 2 + Binder (2) Preform after calcination 1 cm (4) Ti powder obtained after leaching 5 m 20 40 60 80 100 Table Analytical results of the obtained sample. Step Preform after reduction 0. 2 0. 3 Temp. Time Tcal. /K t'cal. /h Tred. /K t'red. /h 1273 1 1 2 2 1273 6 6 9 9 Concentration of element i, Ci a (mass %) Ti Fe Al Ca Cl (1) 67. 64 1. 36 0. 50 10. 20 20. 29 (2) 65. 99 0. 13 0. 08 11. 65 22. 15 (3) 18. 79 0. 10 (0. 00) 67. 98 13. 09 (4) 98. 23 0. 56 0. 98 (0. 00) a: Determined by X-ray fluorescence analysis, and the value excludes carbon and gaseous elements. 98. 16 99. 10 98. 23 98. 44 0. 88 0. 03 0. 23 0. 14 JCPDS # 21 -1276 JCPDS # 74 -0522 JCPDS # 01 -0989 : Ti. O 2 : Ca. Cl 2 (H 2 O)4 JCPDS # 21 -1276 JCPDS # 74 -0522 JCPDS # 01 -0989 (3) JCPDS # 44 -1294 JCPDS # 23 -0430 JCPDS # 48 -1467 1. 76 0. 87 1. 54 1. 42 59 56 90 65 : Ti JCPDS # 44 -1294 20 40 60 80 100 Angle, 2 (deg. ) Metallic Ti was successfully obtained after the experiment. a: Cationic molar ratio, RCat. /Ti = NCat. /NTi, where NCat. and NTi are the mole amounts of the cations in the flux and Ti, respectively. b: Determined by X-ray fluorescence analysis, and the value excludes carbon and gaseous elements. c: Iron removal ratio: (CFe/CTi (Before) – CFe/CTi (After))/(CFe/CTi (Before)) ・High-purity metallic Ti powder was obtained directly from natural Ti ore. ・Ti powder with a yield of 88% was obtained. Fe 2 O 3(s) Fe 3 O 4(s) – 10 Ti. O 2(s) Fe. O(s) Fe(s) – 20 Ti 2 O 3(s) – 30 Ti. O(s) – 40 – 50 Ti(s) 5 m Ti. O 2 + Ca. O + Ca Ti. O 2 + Ca. Cl 2 5 m (4) Sample obtained after leaching 5 m Ti powder 5 m Concentration of element i, Ci a (mass %) Ti Fe Al Ca Cl (1) 68. 00 1. 07 0. 44 11. 66 18. 83 (2) 60. 68 0. 42 0. 33 14. 88 23. 70 (3) 17. 74 0. 07 (0. 00) 67. 42 14. 76 (4) 99. 10 0. 03 0. 30 0. 58 (0. 00) a: Determined by X-ray fluorescence analysis, and the value excludes carbon and gaseous elements. ・Metallic Ti exhibiting a coral-like structure was obtained. ・Purity of Ti was greater than 99 mass %. Conclusion Mechanism of iron removal (Ti ore chlorination) 79 88 (2) Preform after calcination Ti. O 2 + Ca. Cl 2 + Binder Step Sample obtained after leaching 0 (1) Feed preform Table Analytical results of the obtained sample. Discussion ・Iron removal ratio was enhanced when C powder was added to the preform. Iron removal efficiency was improved when C powder was added to the preform. : Ti. O 2 : Ca. Cl 2 (H 2 O)4 : Ti : Ca. O (4) Ti powder Concentration of Cationic Iron Ti and Fe in Exp. molar the obtained Ti powder removal Yield c No. ratio (%) b C (mass %) RCat. /Ti a (%) Ti Fe others 0. 2 0. 3 SEM images (3) Preform after reduction Ti. O 2 + Ca. O +Ca a: Natural rutile ore produced in South Africa after pulverization. b: Cationic molar ratio, RCat. /Ti = NCat. /NTi, where NCat. and NTi are the mole amounts of the cations in the flux and Ti, respectively. c: C powder was added to the preform during the fabrication step in experiments C and D. A B C D (2) Exp. B, RCat. /Ti = 0. 3 Reduction Table Composition of the samples obtained after leaching and yield of Ti powder SEM image : Ti JCPDS # 44 -1294 (3) Experimental results 4 Exp. C, RCat. /Ti = 0. 2, C powder: 0. 2 g XRD pattern A B Cc Dc Calcination Experimental results 2 Exp. A, RCat. /Ti = 0. 2 Photographs XRD patterns Experimental conditions Cationic molar Exp. ratio No. a RCat. /Ti b Development of a new smelting process for producing Ti with high purity and productivity and low cost Experimental results 1 (1) Features: → Simple and low-cost process ◎Suitable for uniform reduction ◎Flexible scalability ○Possible to control the morphology of the powder by varying the flux content in the preform ○Possible to prevent the contamination from the reaction container and control purity ○Amount of waste solution is minimized ○Molten salt as a flux can be reduced in comparison with the other direct reduction process △Leaching is required ×Difficult to produce calcium and control its vapor Purpose of this study: Feed preform (Ti. O 2 feed + flux) Reductant vapor Reductant (R = Ca or Ca-X alloy) Table Experimental conditions in this study. Fe. Clx ×Difficult to control the purity ×Large amount of molten salt (d) PRP log p. O 2 (atm) Calcination/iron removal Ti. O 2(s) + Ca(g) → Ti(s) + Ca. O(s) Current monitor/ controller Carbon anode Ca. Cl 2 -Ca. O molten salt Ti. O 2 Ca-X alloy Ti. O 2 + Ca. Cl 2 (1) Reductant (R = Ca or Ca-X alloy) Common features: ○Semi-continuous process Preform fabrication Feed preform Reductant vapor (b) OS process (Ono & Suzuki) ○Simple process Furnace Comparison with common metals Flux Carbon anode Ti sponge Japan 18. 5 kt (28% share) Ti ore Feed preform (Ti. O 2 feed + flux) Mg & Mg. Cl 2 recovery port Russia Total 26 kt 65. 5 kt Preform reduction process (PRP) (a) FFC process (Fray et al. ) Mg & Ti. Cl 4 feed port World production of Ti sponge (2003) China 4 kt Kazakhstan 9 kt Direct reduction of Ti. O 2 Intensity, I (a. u. ) Introduction Ca. O(s)/Ca. Cl 2(l) eq. Region for Selective chlorination of iron CO(g)/CO 2(g) eq. C(s)/CO(g) eq. Ti 4 O 7(s) Ti 3 O 5(s) Fe. Cl 3(g) Fe. Cl 2(g) H 2 O(g)/HCl(g) eq. Mg. O(g)/Mg. Cl 2(g) eq. Ti. Cl 4(g) Ti. Cl 3(g) – 60 – 40 – 30 – 20 – 10 0 log p. Cl 2 (atm) Fig. Combined chemical potential diagram of the Fe-Cl-O (dotted line) and Ti-Cl-O (solid line) systems at 1300 K. Fe. Ox (Fe. Ti. Ox, s) + HCl(g) → Fe. Clx(g)↑ + H 2 O(g) Fe. Ox (Fe. Ti. Ox, s) + Ca. Cl 2(l) → Fe. Clx(g)↑ + Ca. O (Ca. Ti. Ox, s) a. Ca. O << 1 ・Fe. Ox can be chlorinated using Ca. Cl 2 + H 2 O. ・Ti. Ox cannot be chlorinated using Ca. Cl 2 or Ca. Cl 2 + H 2 O. The feasibility of the preform reduction process (PRP), based on the calciothermic reduction of natural Ti ore, was demonstrated. ・ 90% of iron was successfully removed by selective chlorination during the calcination step. ・ When C powder was added to the preform, iron was removed more efficiently, and Ti powder with a purity of 98% and yield of 88% was obtained. ・ It was experimentally demonstrated that high-purity metallic Ti powder (greater than 99 mass %) was obtained directly from natural Ti ore (rutile ore) by the PRP. Currently, the development of a more effective method for the direct removal of iron from Ti ore, analysis of the detailed mechanism of selective chlorination, and development of an efficient recycling system of Ca. Cl 2 flux and the residual Ca reductant are under investigation.