EET 273 Electronic Control Systems Week 5 Signaling
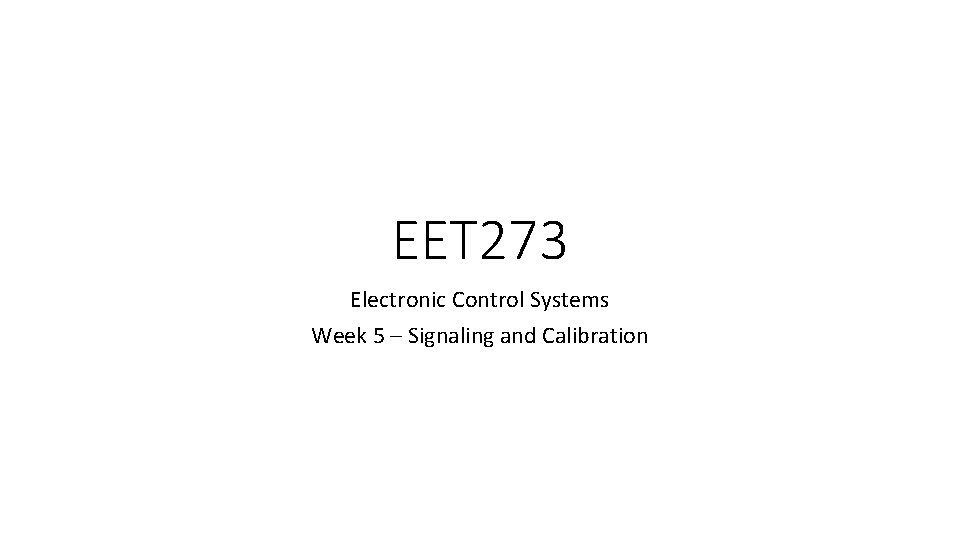
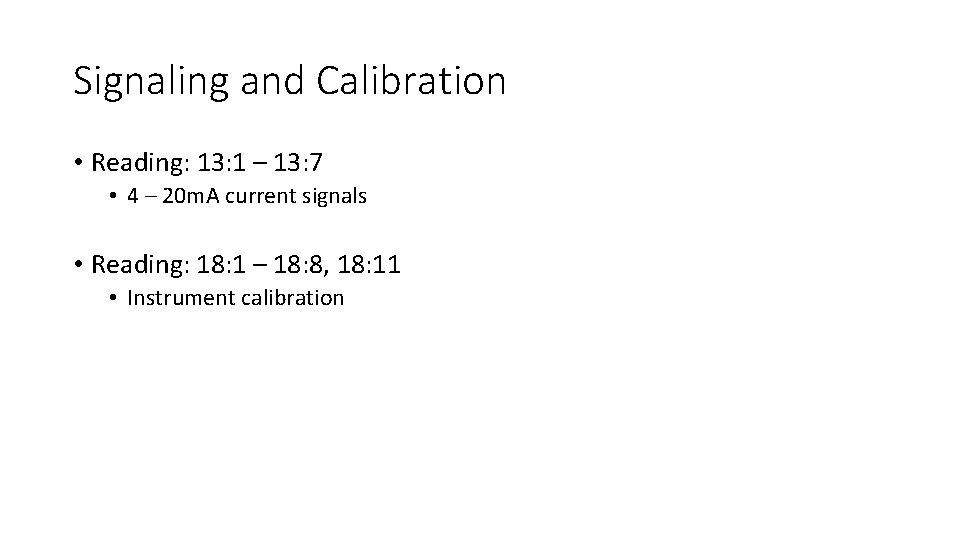
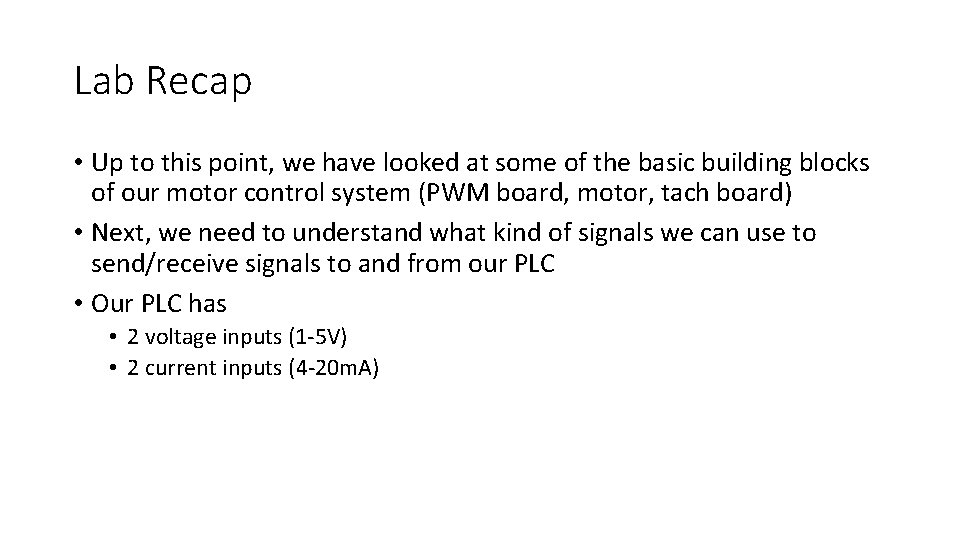
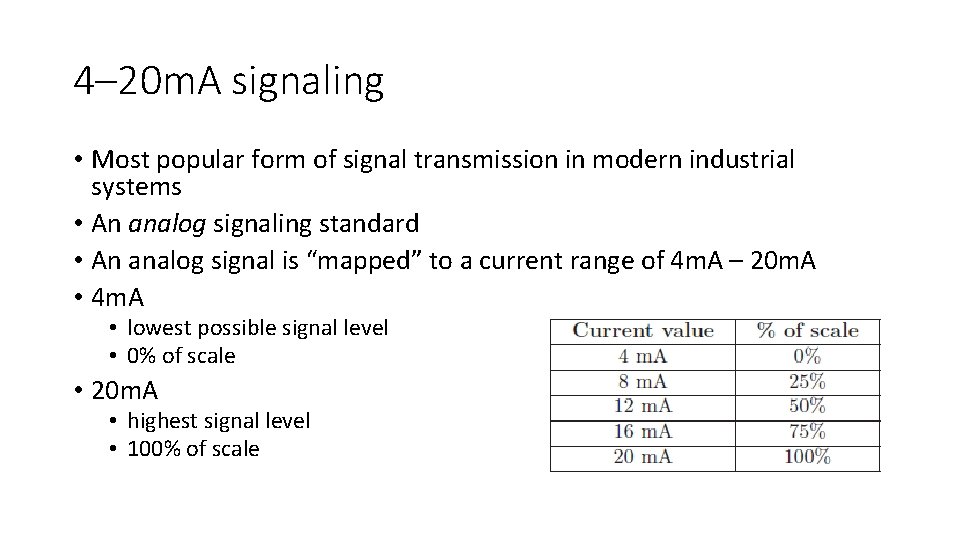
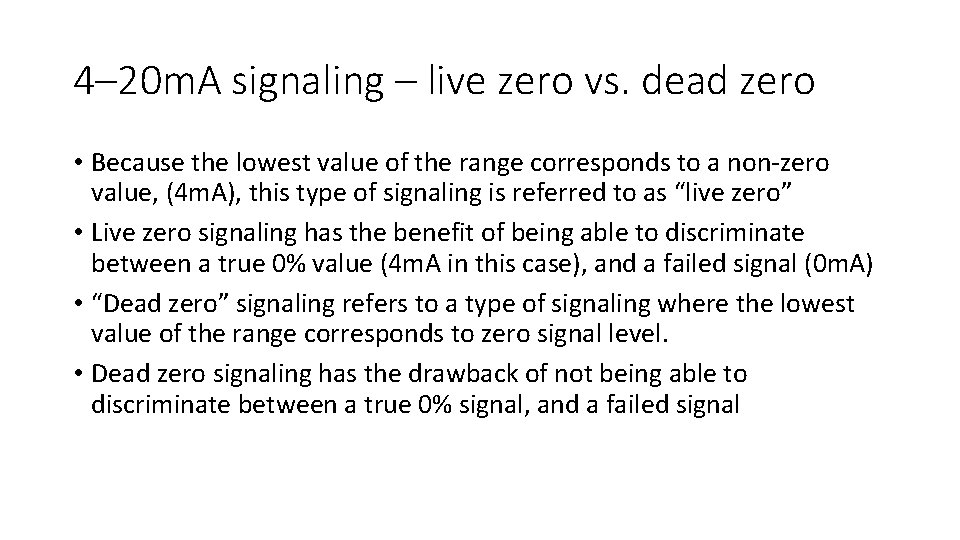
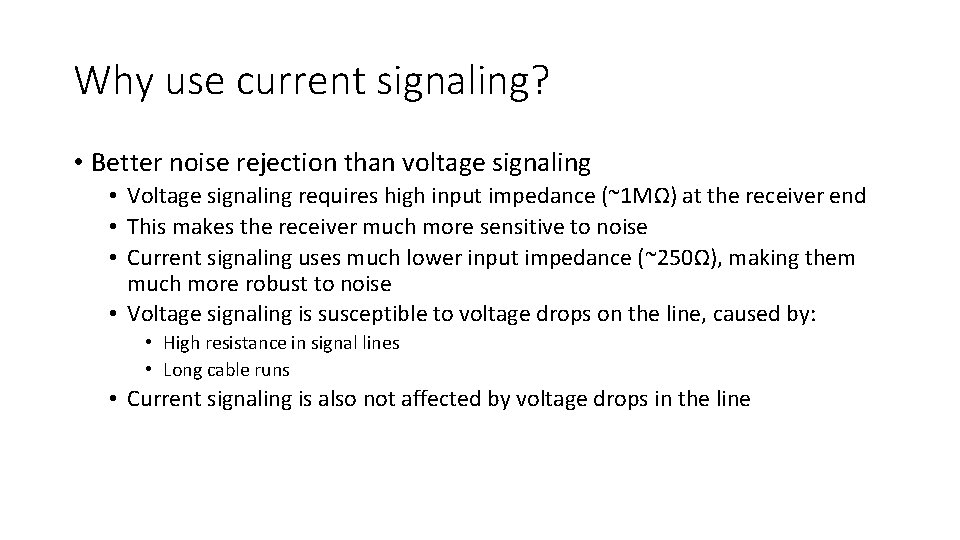
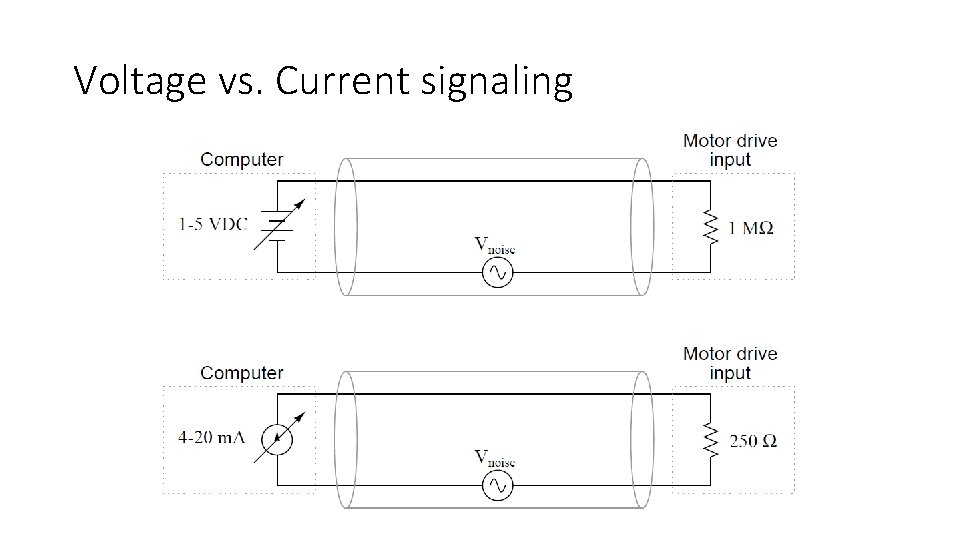
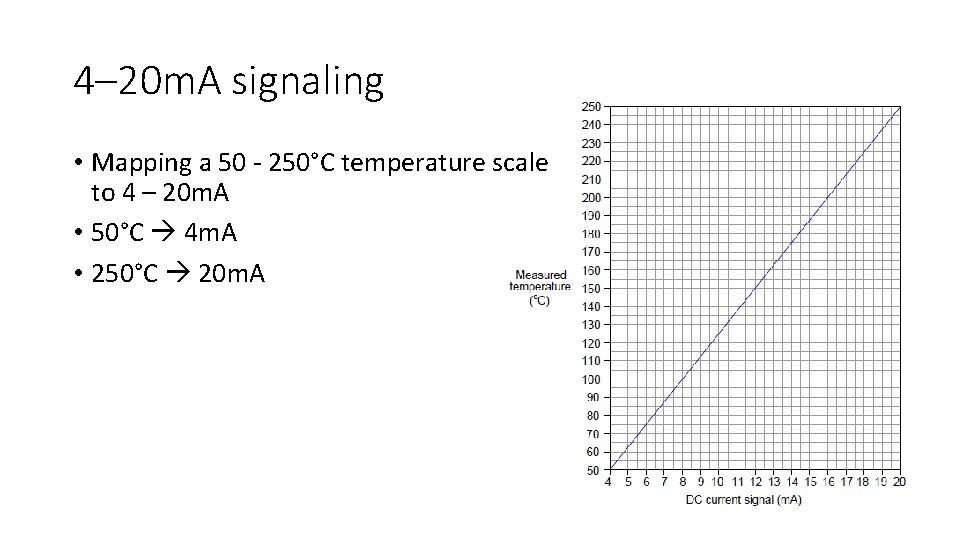
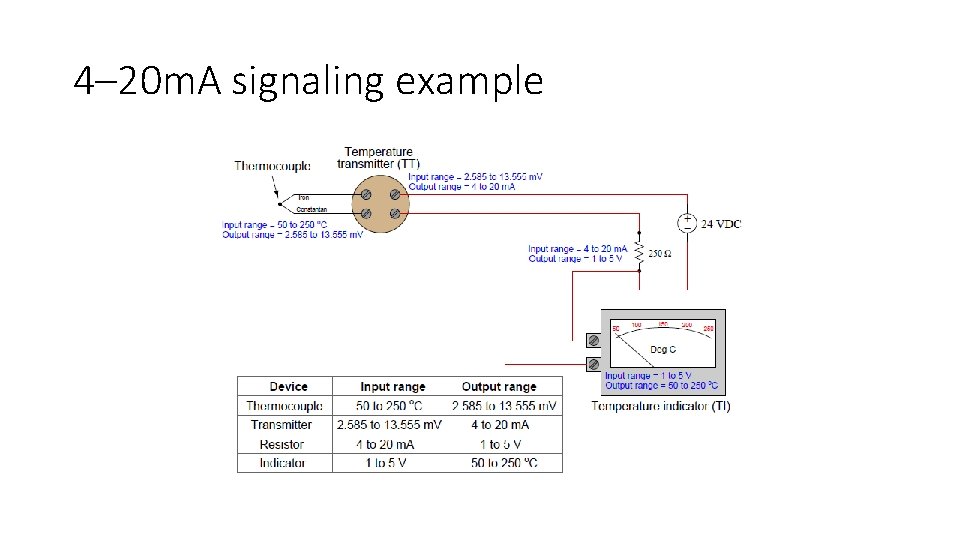
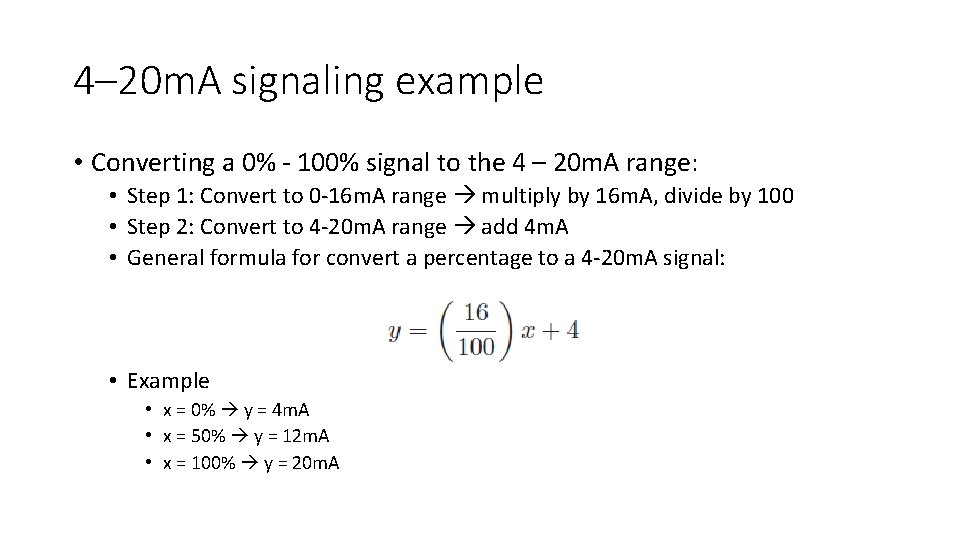
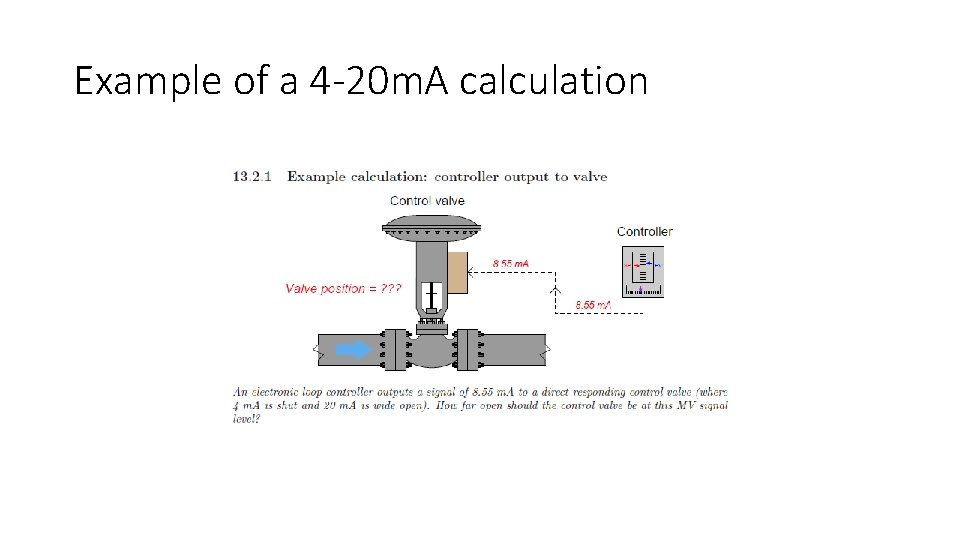
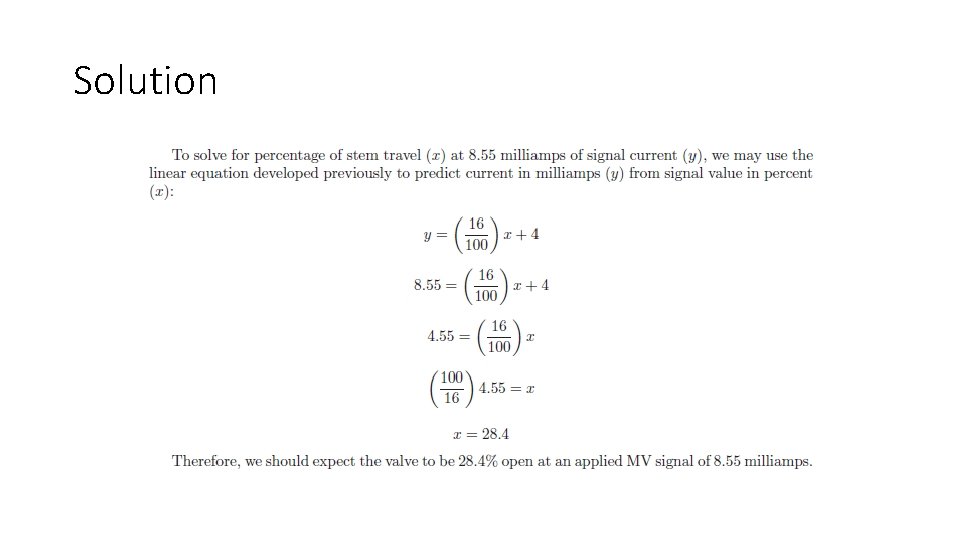
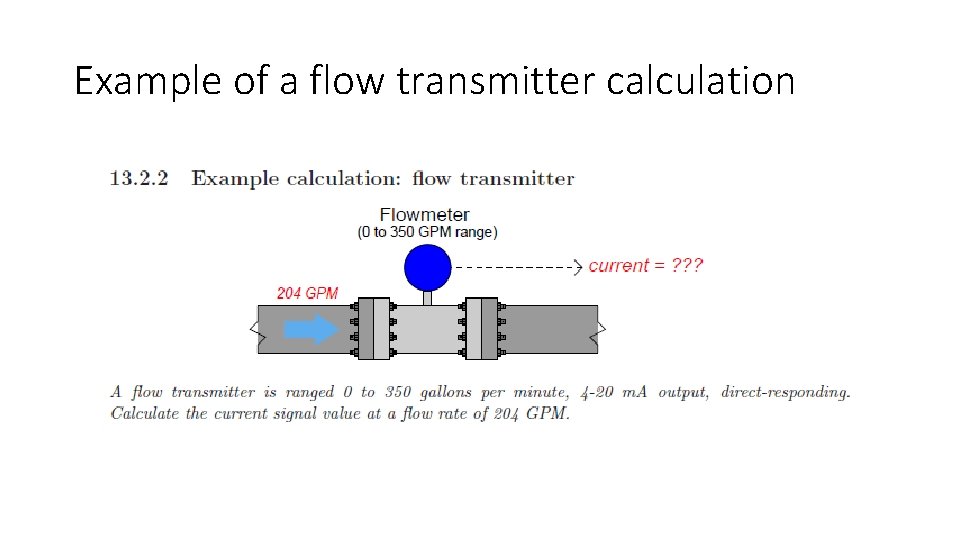
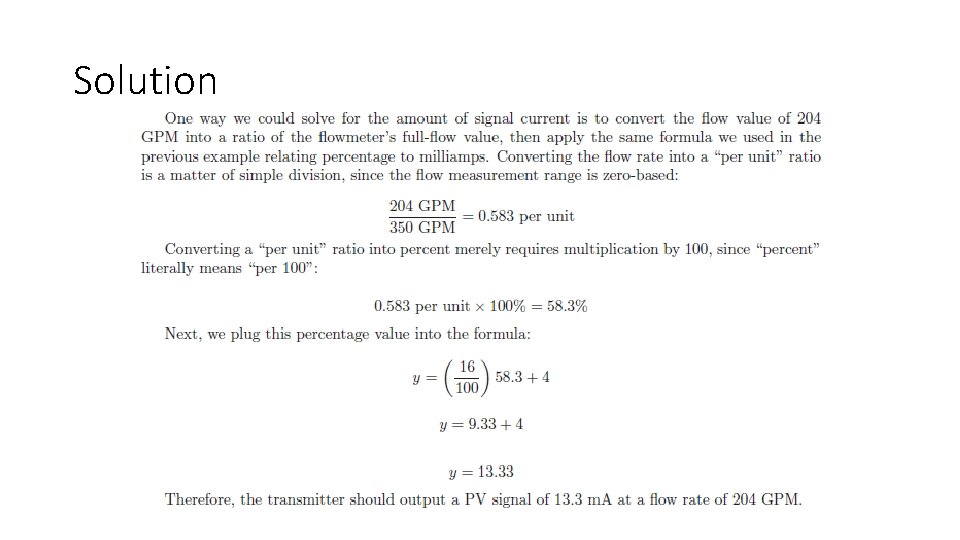
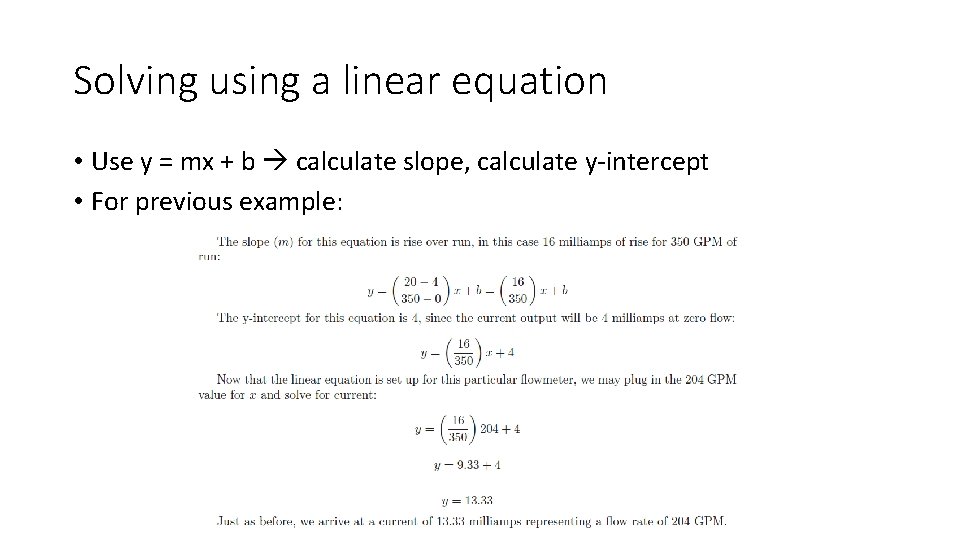
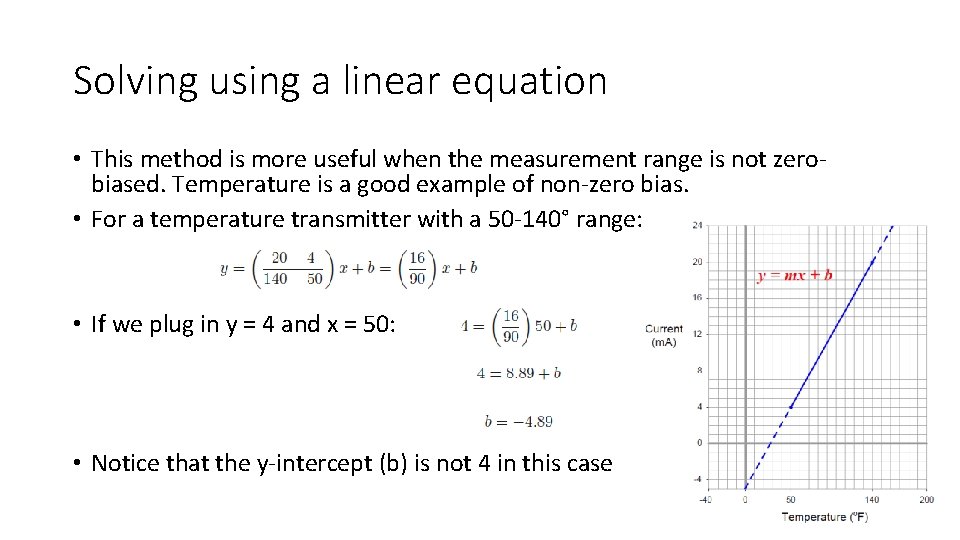
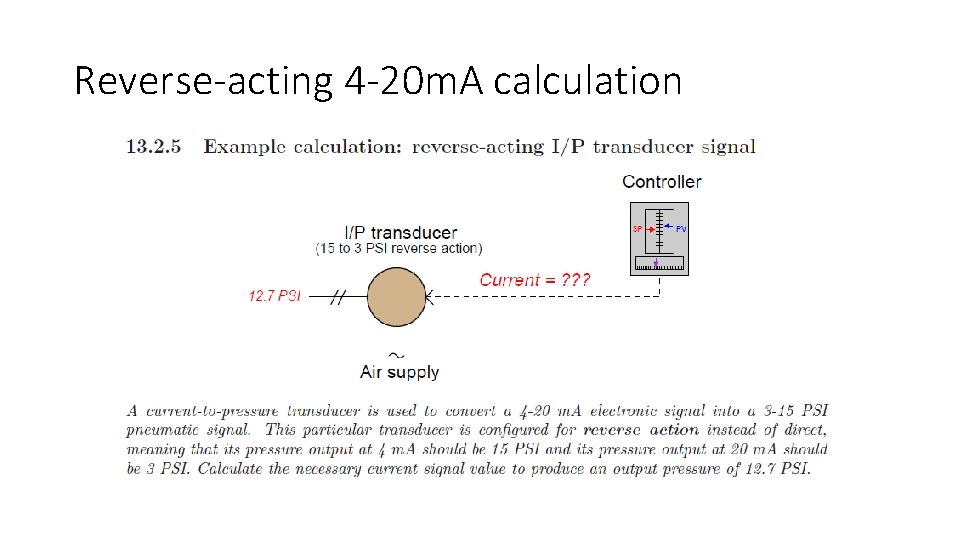
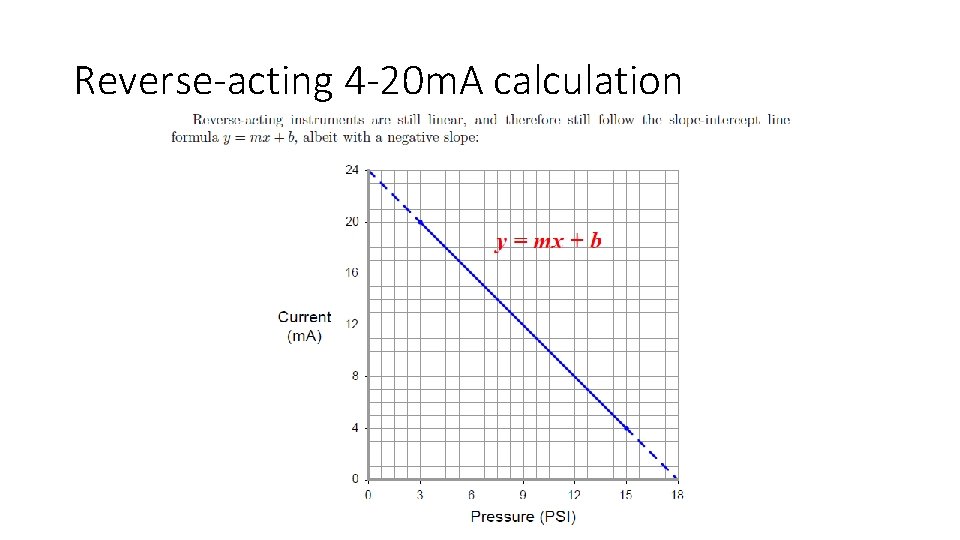
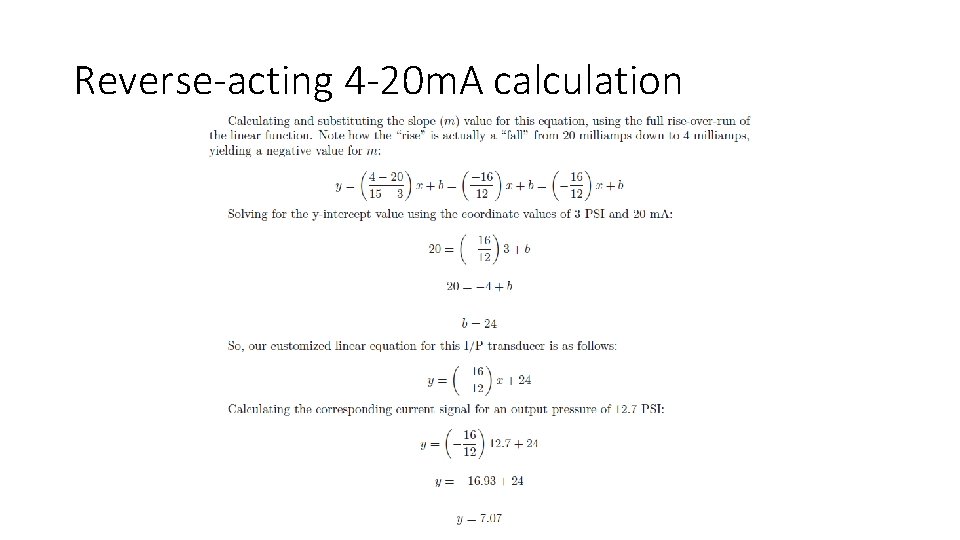
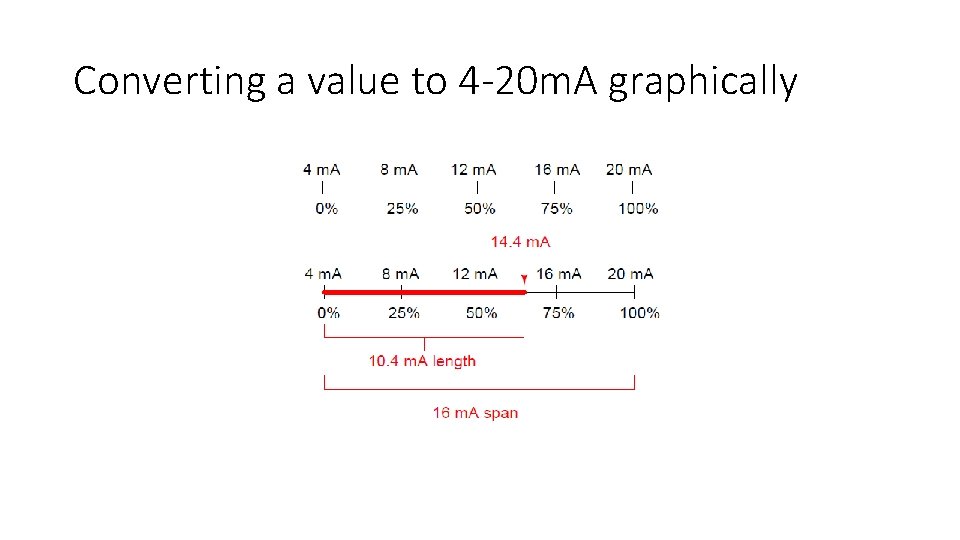
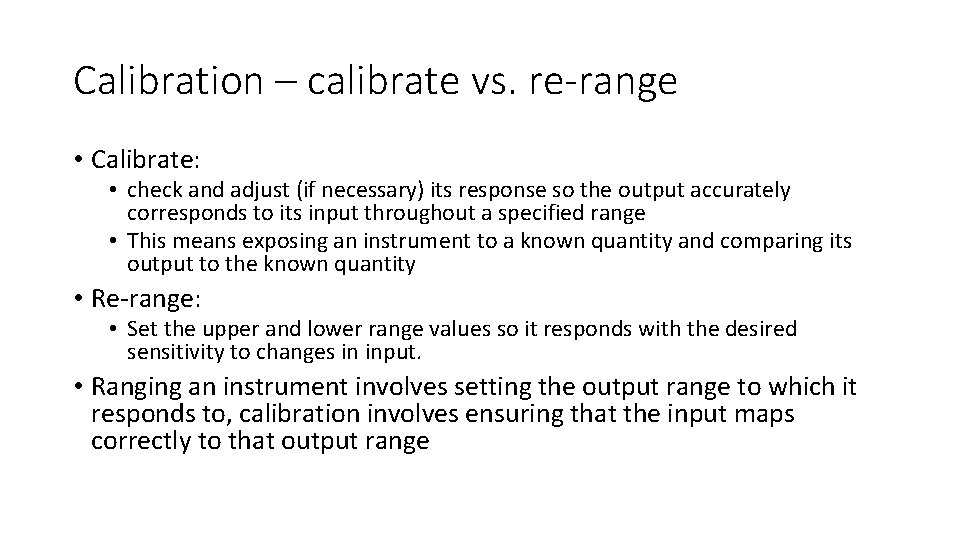
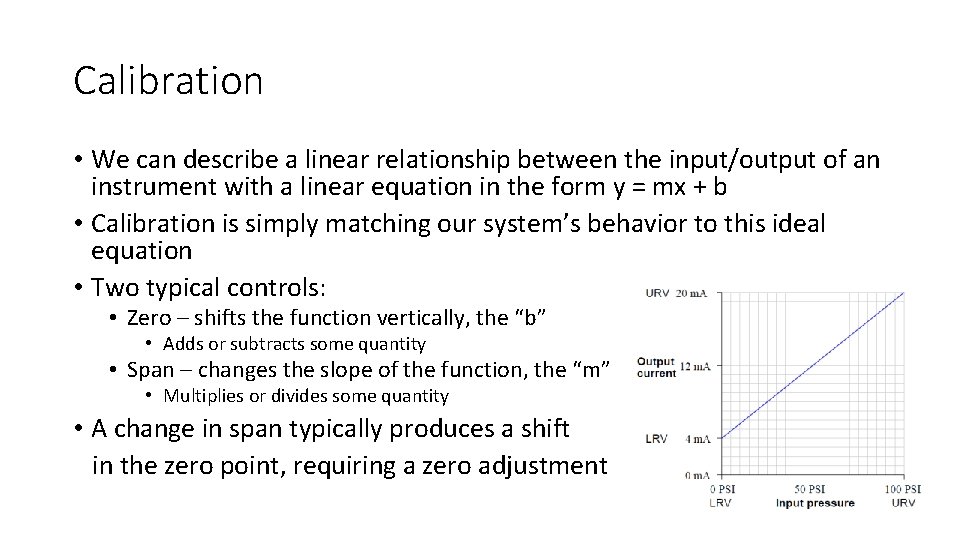

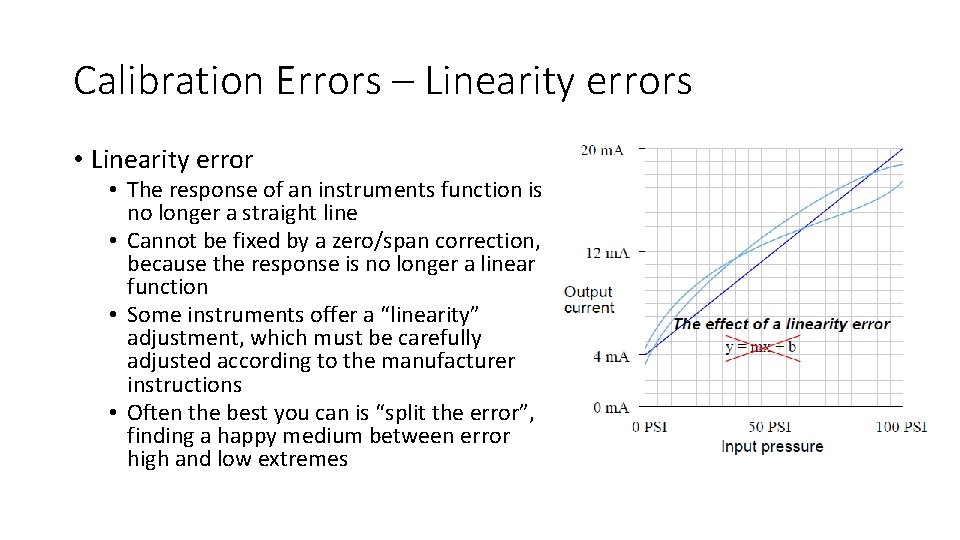
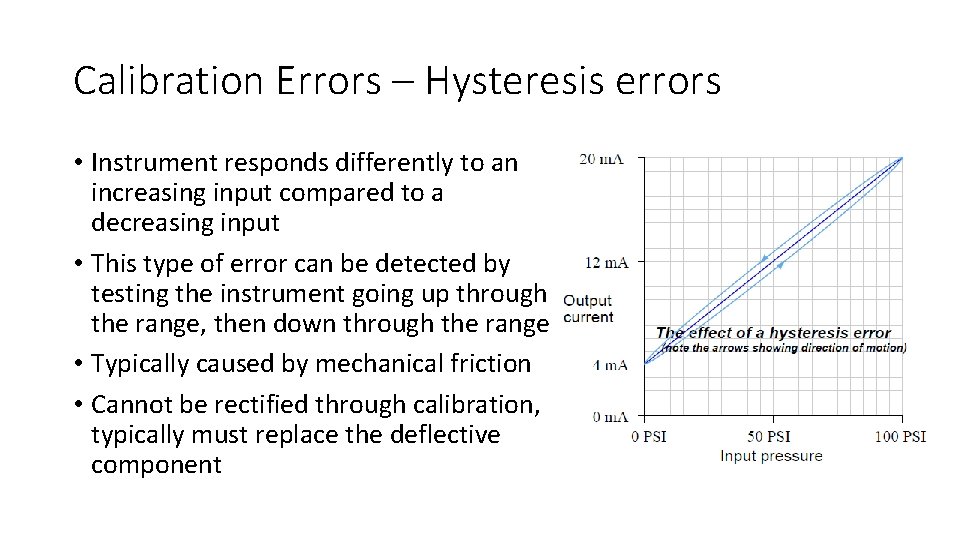
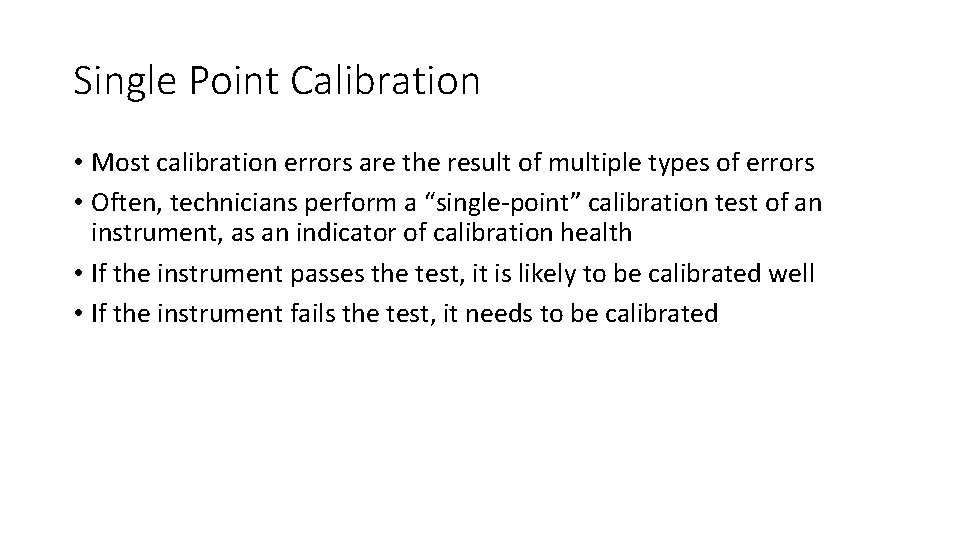
- Slides: 26
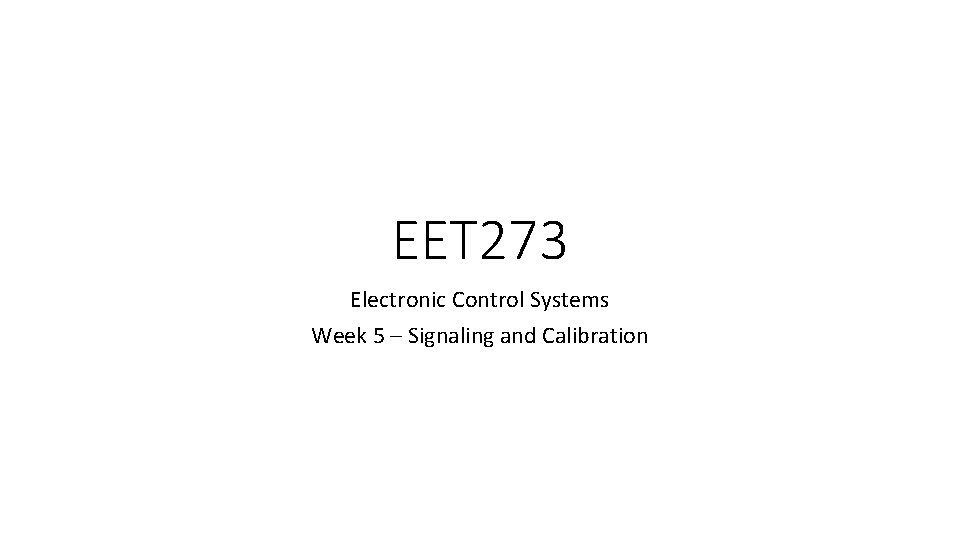
EET 273 Electronic Control Systems Week 5 – Signaling and Calibration
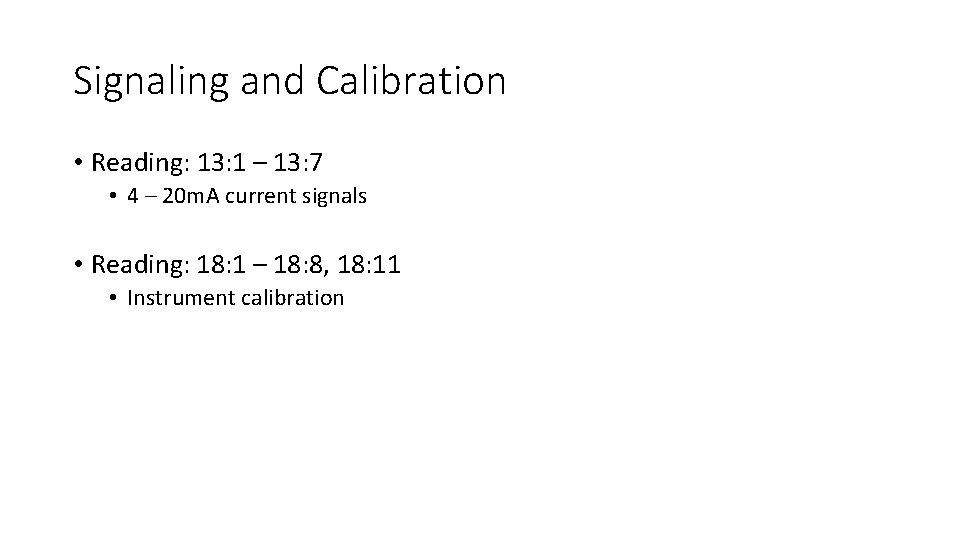
Signaling and Calibration • Reading: 13: 1 – 13: 7 • 4 – 20 m. A current signals • Reading: 18: 1 – 18: 8, 18: 11 • Instrument calibration
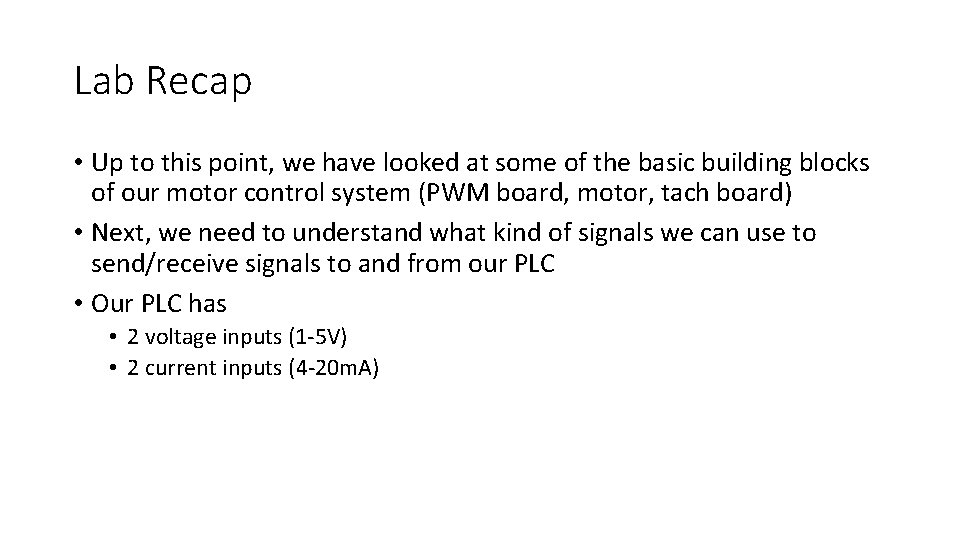
Lab Recap • Up to this point, we have looked at some of the basic building blocks of our motor control system (PWM board, motor, tach board) • Next, we need to understand what kind of signals we can use to send/receive signals to and from our PLC • Our PLC has • 2 voltage inputs (1 -5 V) • 2 current inputs (4 -20 m. A)
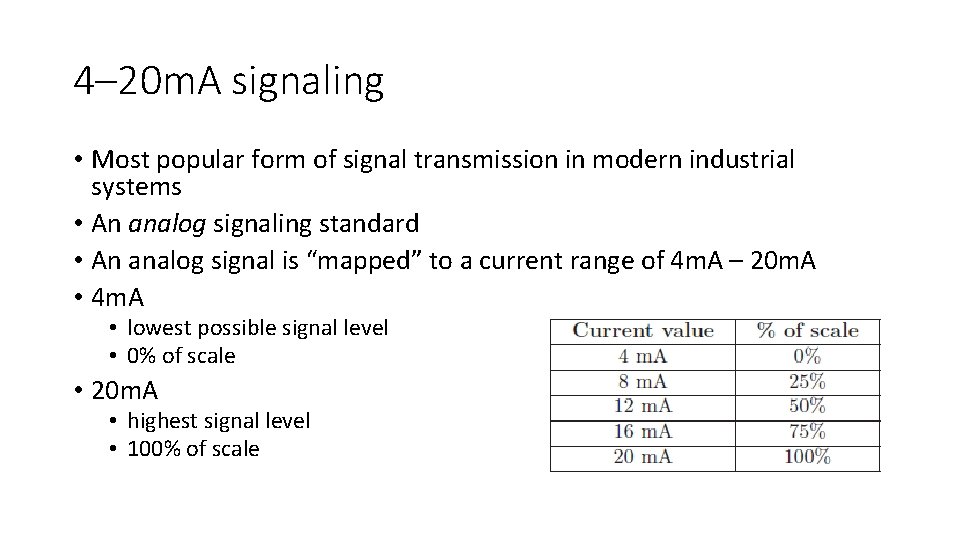
4– 20 m. A signaling • Most popular form of signal transmission in modern industrial systems • An analog signaling standard • An analog signal is “mapped” to a current range of 4 m. A – 20 m. A • 4 m. A • lowest possible signal level • 0% of scale • 20 m. A • highest signal level • 100% of scale
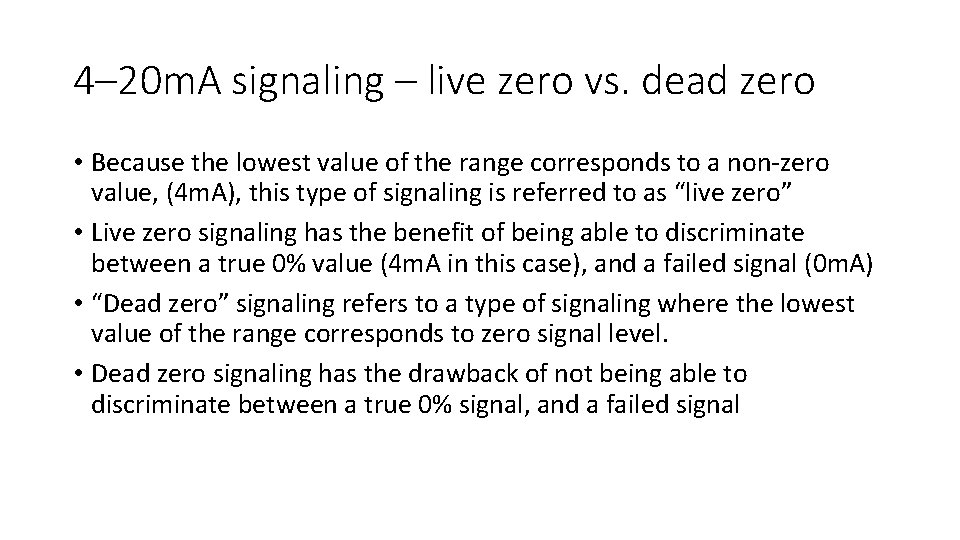
4– 20 m. A signaling – live zero vs. dead zero • Because the lowest value of the range corresponds to a non-zero value, (4 m. A), this type of signaling is referred to as “live zero” • Live zero signaling has the benefit of being able to discriminate between a true 0% value (4 m. A in this case), and a failed signal (0 m. A) • “Dead zero” signaling refers to a type of signaling where the lowest value of the range corresponds to zero signal level. • Dead zero signaling has the drawback of not being able to discriminate between a true 0% signal, and a failed signal
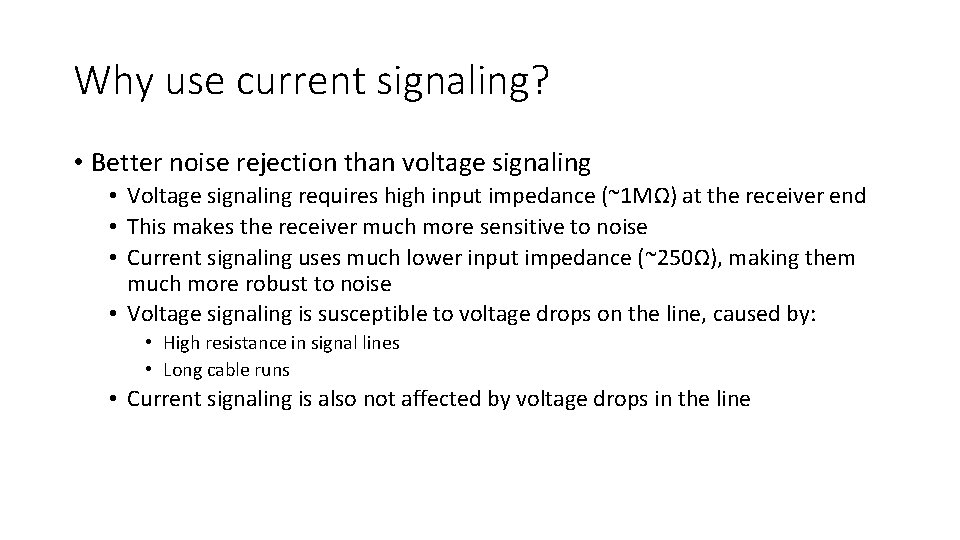
Why use current signaling? • Better noise rejection than voltage signaling • Voltage signaling requires high input impedance (~1 MΩ) at the receiver end • This makes the receiver much more sensitive to noise • Current signaling uses much lower input impedance (~250Ω), making them much more robust to noise • Voltage signaling is susceptible to voltage drops on the line, caused by: • High resistance in signal lines • Long cable runs • Current signaling is also not affected by voltage drops in the line
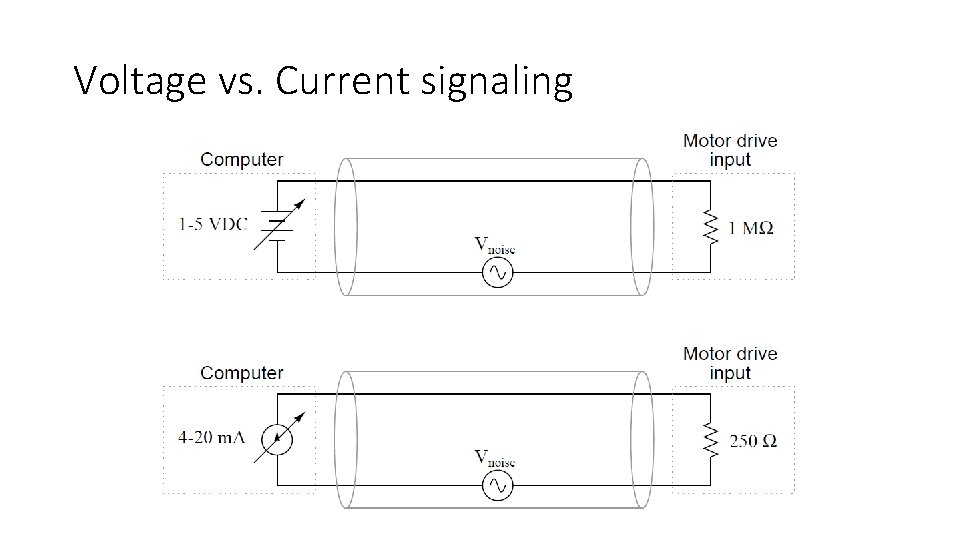
Voltage vs. Current signaling
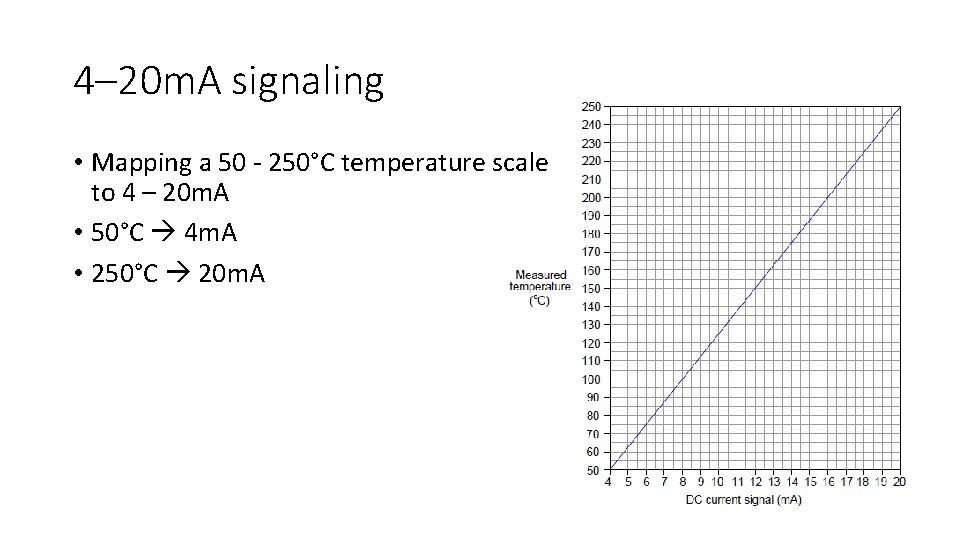
4– 20 m. A signaling • Mapping a 50 - 250°C temperature scale to 4 – 20 m. A • 50°C 4 m. A • 250°C 20 m. A
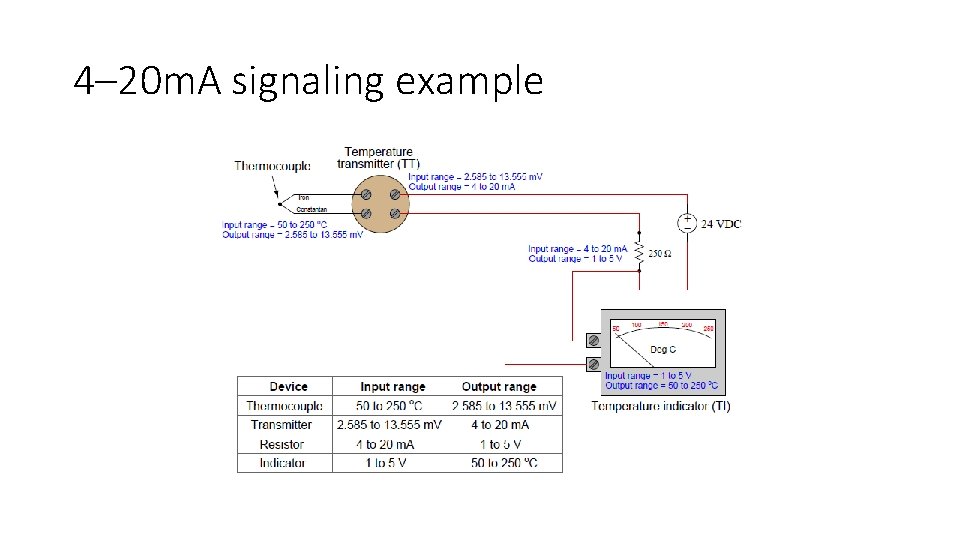
4– 20 m. A signaling example
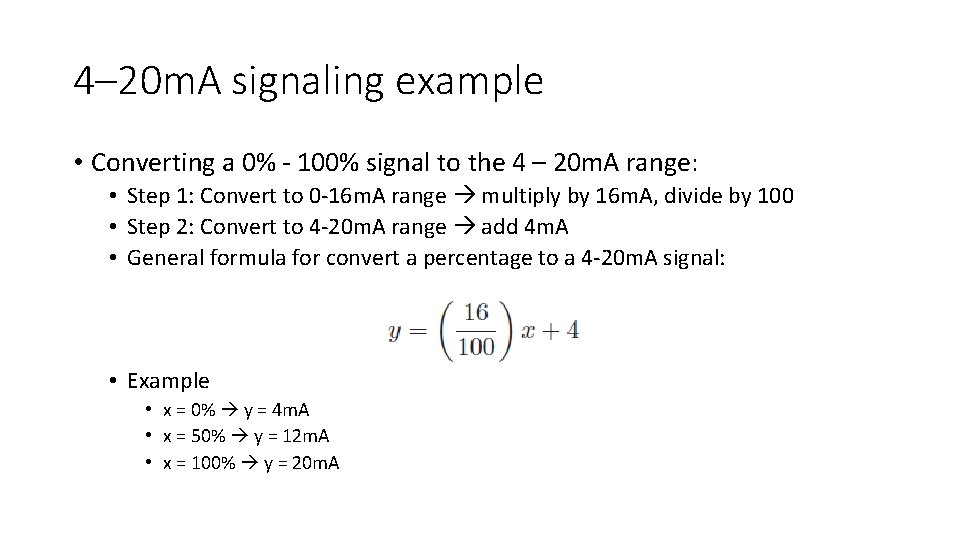
4– 20 m. A signaling example • Converting a 0% - 100% signal to the 4 – 20 m. A range: • Step 1: Convert to 0 -16 m. A range multiply by 16 m. A, divide by 100 • Step 2: Convert to 4 -20 m. A range add 4 m. A • General formula for convert a percentage to a 4 -20 m. A signal: • Example • x = 0% y = 4 m. A • x = 50% y = 12 m. A • x = 100% y = 20 m. A
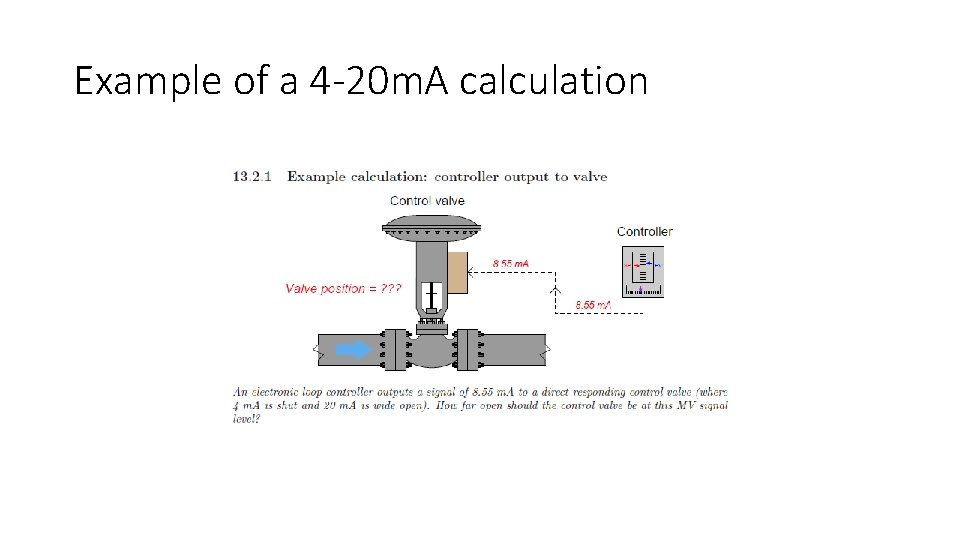
Example of a 4 -20 m. A calculation
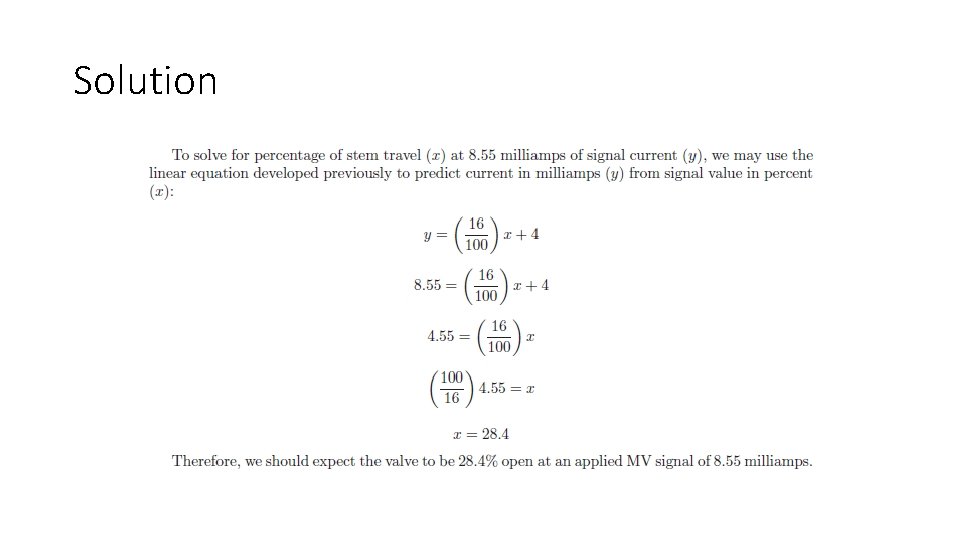
Solution
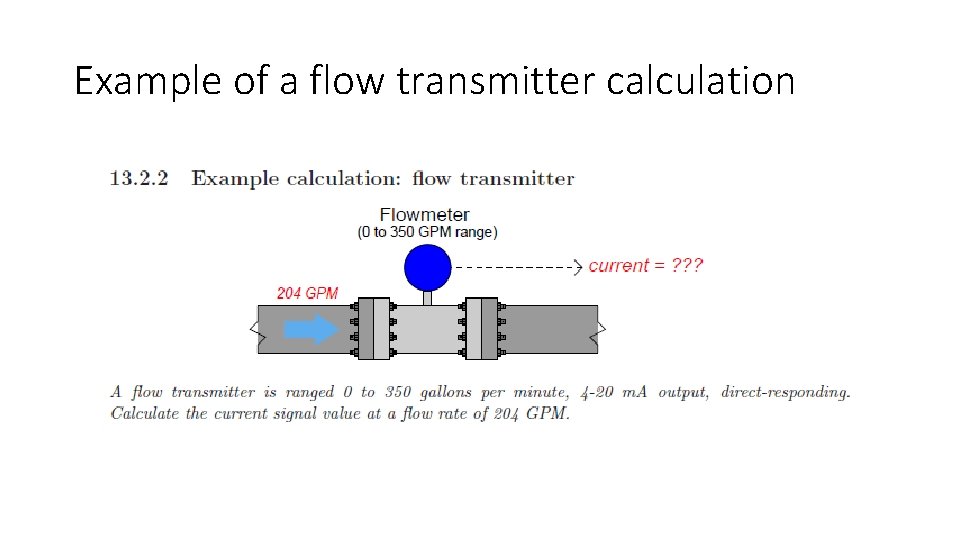
Example of a flow transmitter calculation
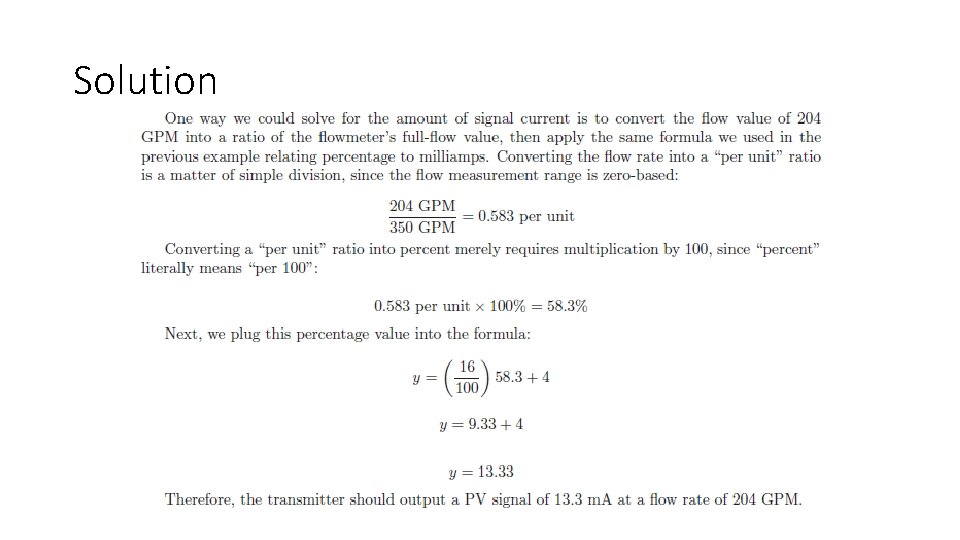
Solution
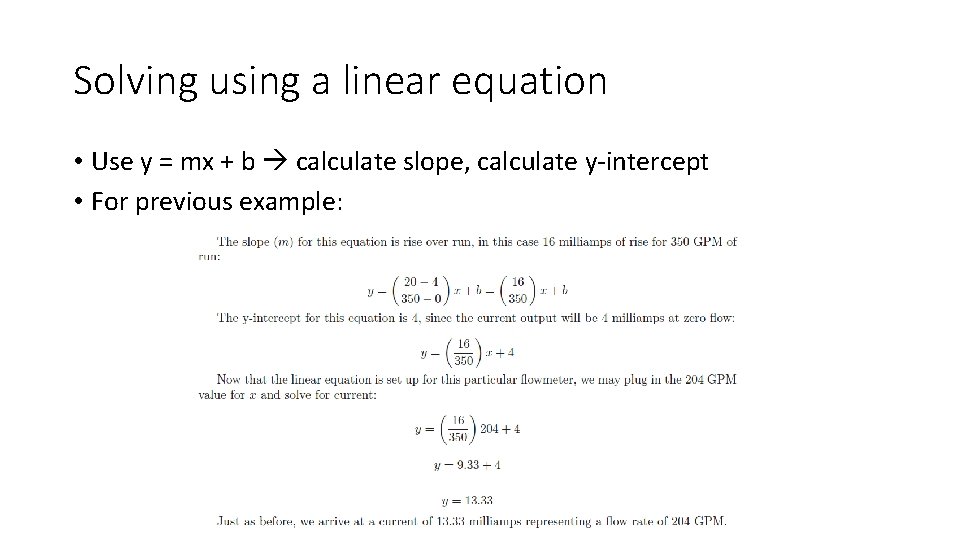
Solving using a linear equation • Use y = mx + b calculate slope, calculate y-intercept • For previous example:
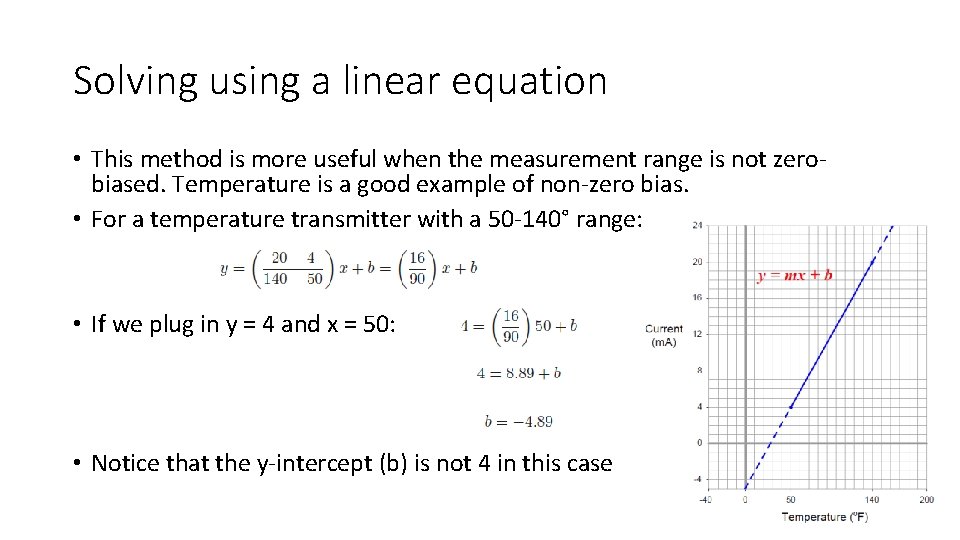
Solving using a linear equation • This method is more useful when the measurement range is not zerobiased. Temperature is a good example of non-zero bias. • For a temperature transmitter with a 50 -140° range: • If we plug in y = 4 and x = 50: • Notice that the y-intercept (b) is not 4 in this case
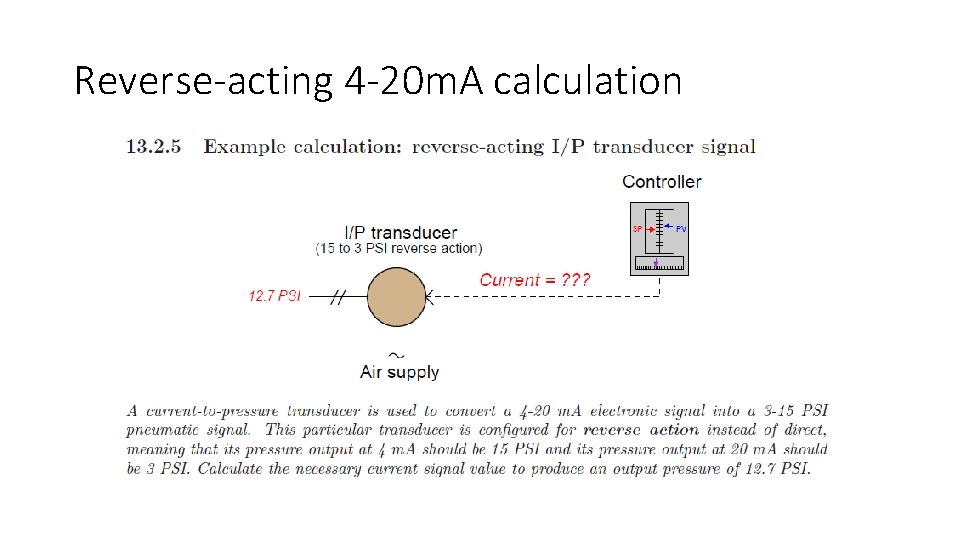
Reverse-acting 4 -20 m. A calculation
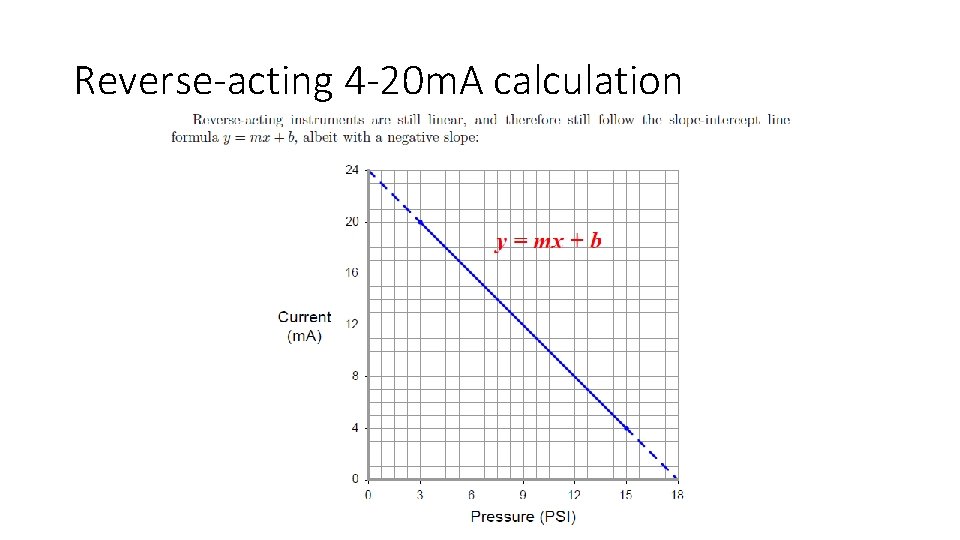
Reverse-acting 4 -20 m. A calculation
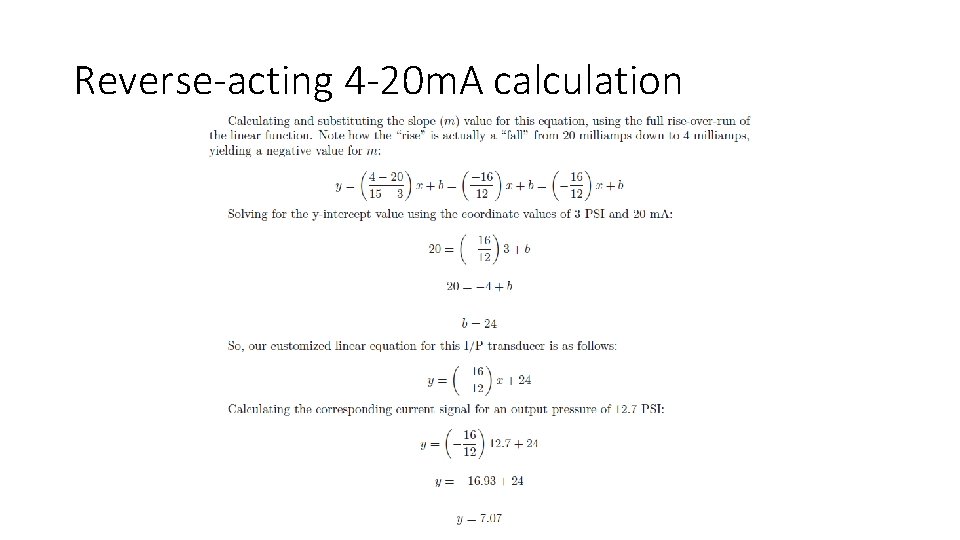
Reverse-acting 4 -20 m. A calculation
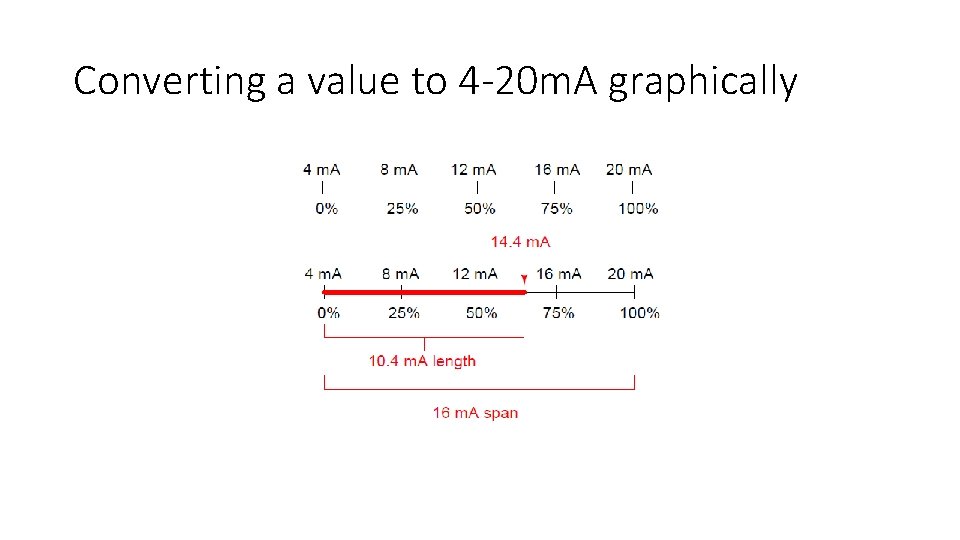
Converting a value to 4 -20 m. A graphically
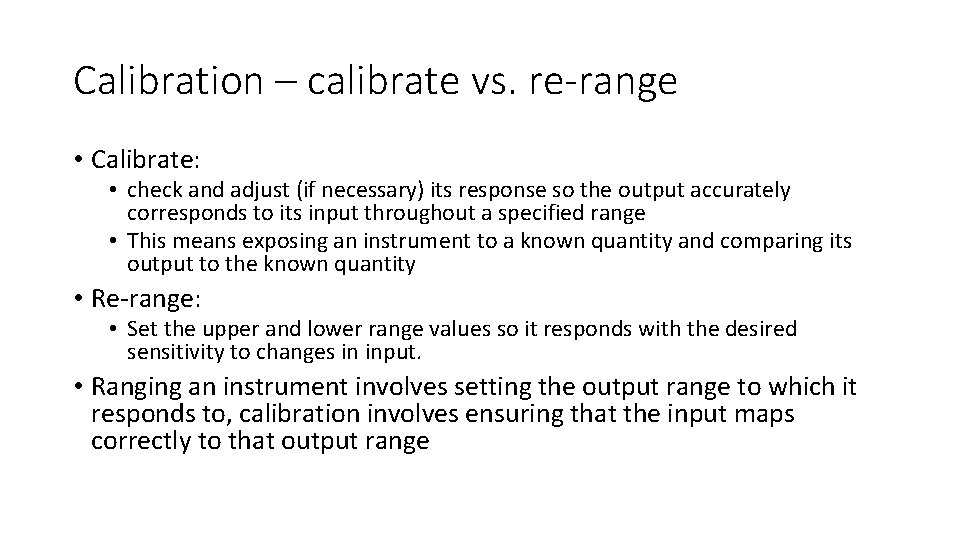
Calibration – calibrate vs. re-range • Calibrate: • check and adjust (if necessary) its response so the output accurately corresponds to its input throughout a specified range • This means exposing an instrument to a known quantity and comparing its output to the known quantity • Re-range: • Set the upper and lower range values so it responds with the desired sensitivity to changes in input. • Ranging an instrument involves setting the output range to which it responds to, calibration involves ensuring that the input maps correctly to that output range
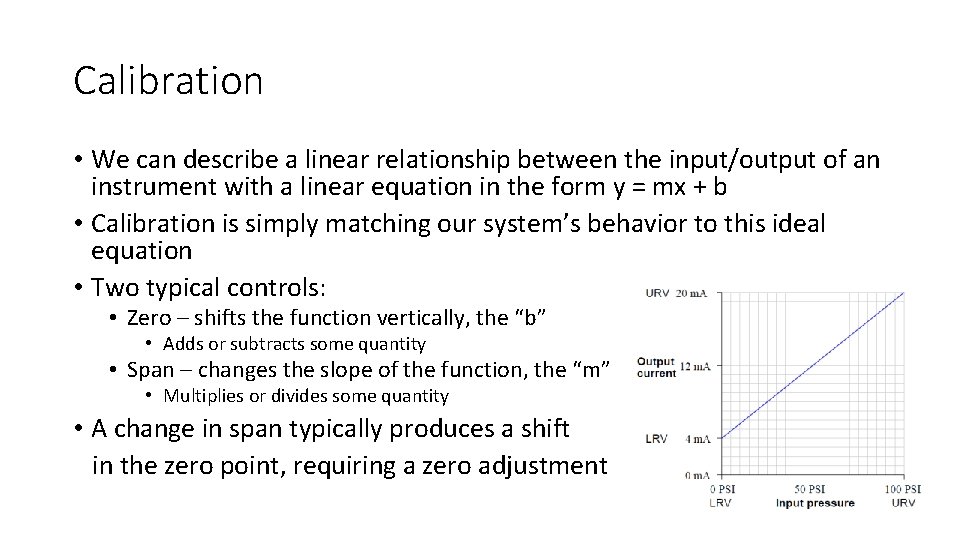
Calibration • We can describe a linear relationship between the input/output of an instrument with a linear equation in the form y = mx + b • Calibration is simply matching our system’s behavior to this ideal equation • Two typical controls: • Zero – shifts the function vertically, the “b” • Adds or subtracts some quantity • Span – changes the slope of the function, the “m” • Multiplies or divides some quantity • A change in span typically produces a shift in the zero point, requiring a zero adjustment

Calibration Errors Zero shift Span shift
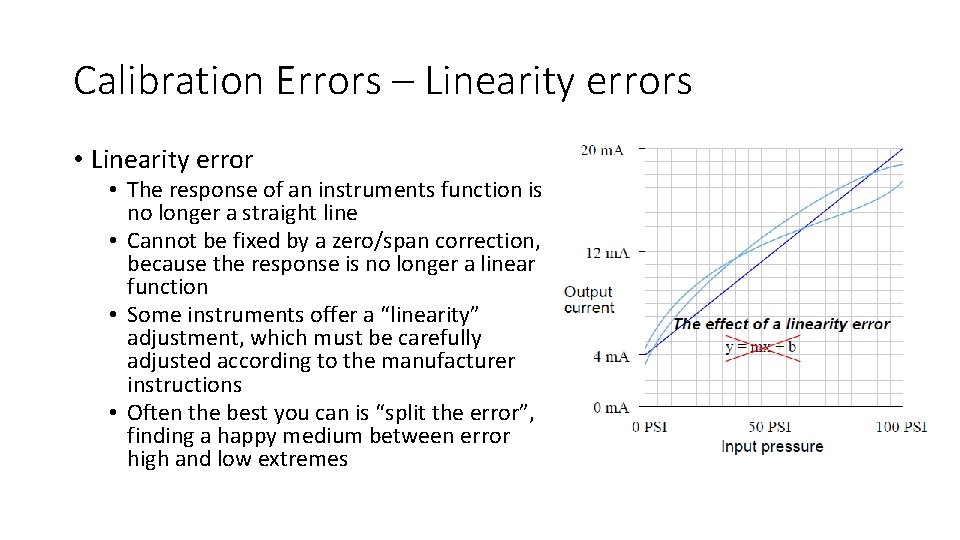
Calibration Errors – Linearity errors • Linearity error • The response of an instruments function is no longer a straight line • Cannot be fixed by a zero/span correction, because the response is no longer a linear function • Some instruments offer a “linearity” adjustment, which must be carefully adjusted according to the manufacturer instructions • Often the best you can is “split the error”, finding a happy medium between error high and low extremes
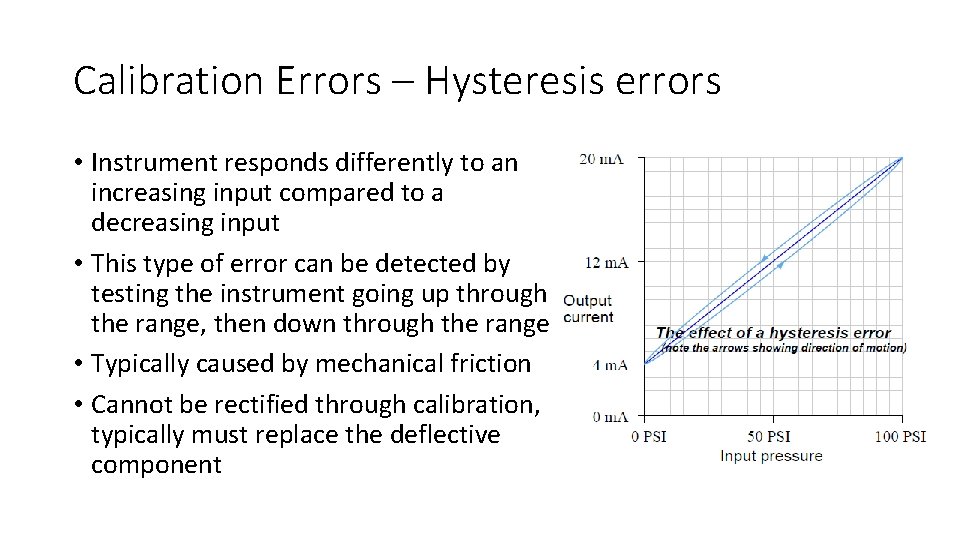
Calibration Errors – Hysteresis errors • Instrument responds differently to an increasing input compared to a decreasing input • This type of error can be detected by testing the instrument going up through the range, then down through the range • Typically caused by mechanical friction • Cannot be rectified through calibration, typically must replace the deflective component
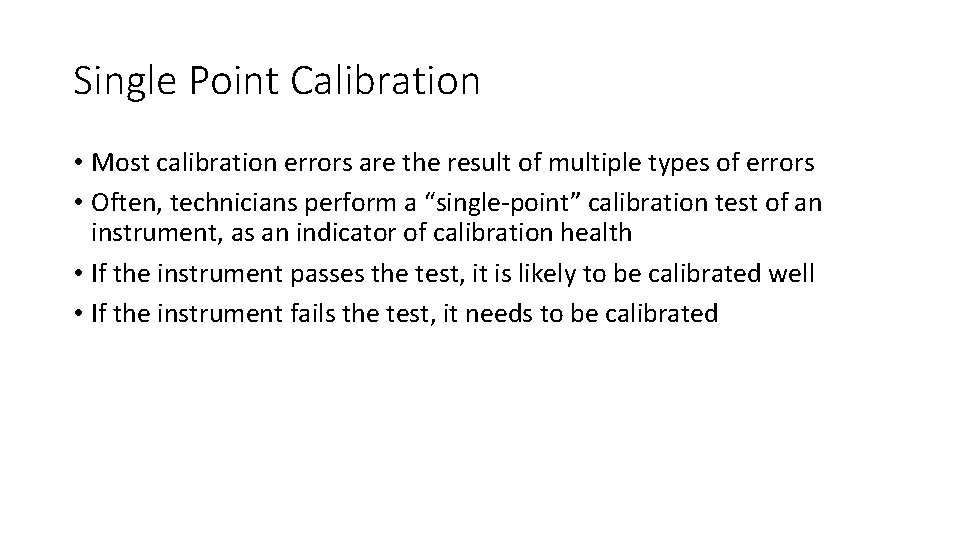
Single Point Calibration • Most calibration errors are the result of multiple types of errors • Often, technicians perform a “single-point” calibration test of an instrument, as an indicator of calibration health • If the instrument passes the test, it is likely to be calibrated well • If the instrument fails the test, it needs to be calibrated
Week by week plans for documenting children's development
Scrip exchange
Electronic field production
What is a signal phrase
Discourse analysis and vocabulary
Discourse analysis and vocabulary
Ground guide signals
Cell communication types
3 types of cell signaling
3 stages of cell communication
3 stages of cell communication
Ligand signaling molecule
Signaling system 7
Autocrine and juxtacrine signaling
Juxtacrine communication
Chemical signaling
Exocrine cell signaling
Paracrine signaling
Chemical signaling
Chemical signaling
Mature industry
Friendship warmth touch
Chapter 48 neurons synapses and signaling
Cell signaling
Cell signaling overview
Pdi cell signaling
Scp 3710