Development of Industrially Relevant Characterizations of Metal Additive
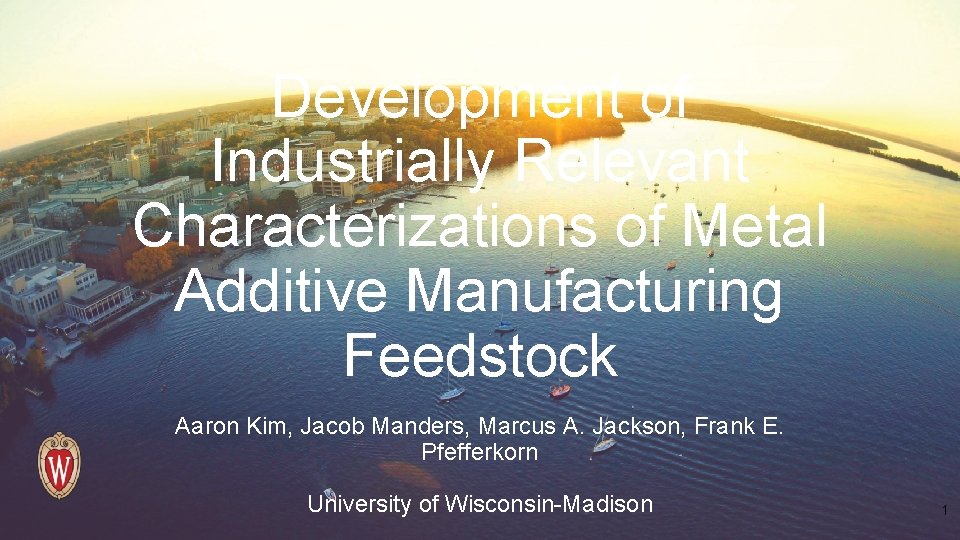
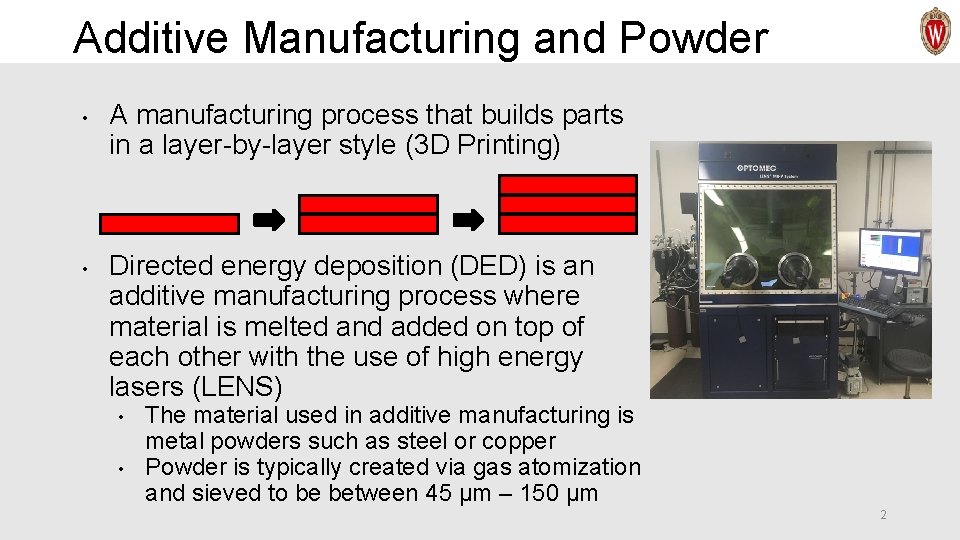
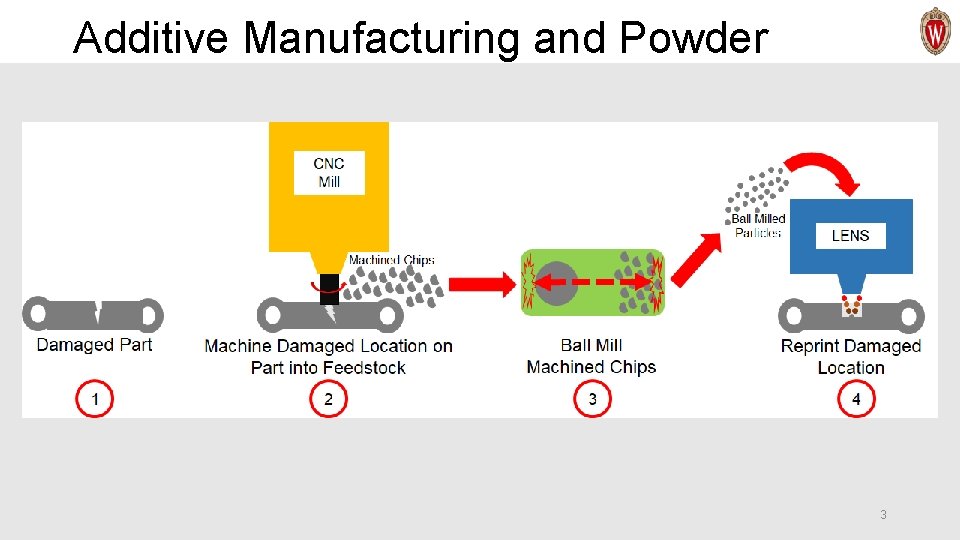
![Particle Shape and Size • R. Hogg et. al. [1] - Pennsylvania State University Particle Shape and Size • R. Hogg et. al. [1] - Pennsylvania State University](https://slidetodoc.com/presentation_image_h2/9318f4361ed895fa6fd1a6f46bc851ff/image-4.jpg)
![Analysis of Irregular Shaped Particles • Rosen et. al. [2] - Northwestern University • Analysis of Irregular Shaped Particles • Rosen et. al. [2] - Northwestern University •](https://slidetodoc.com/presentation_image_h2/9318f4361ed895fa6fd1a6f46bc851ff/image-5.jpg)
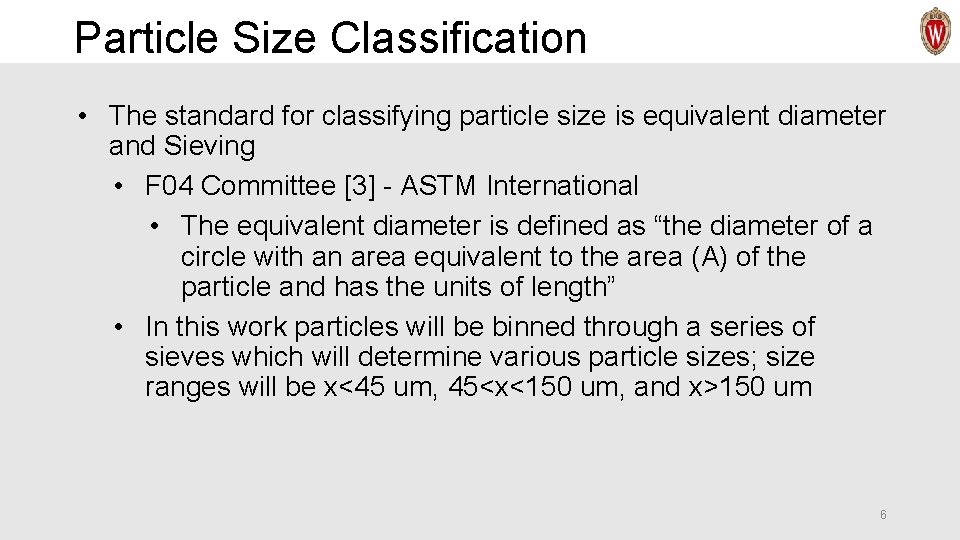
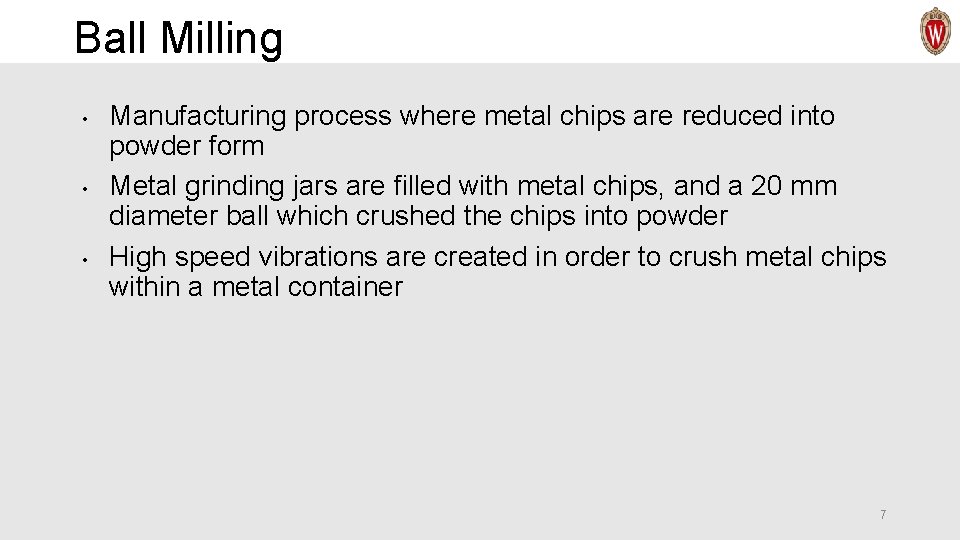
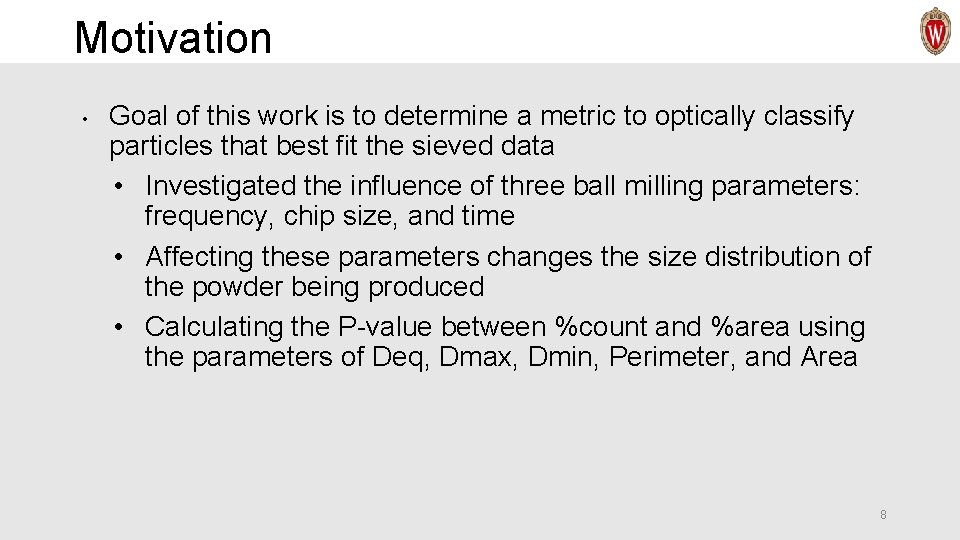
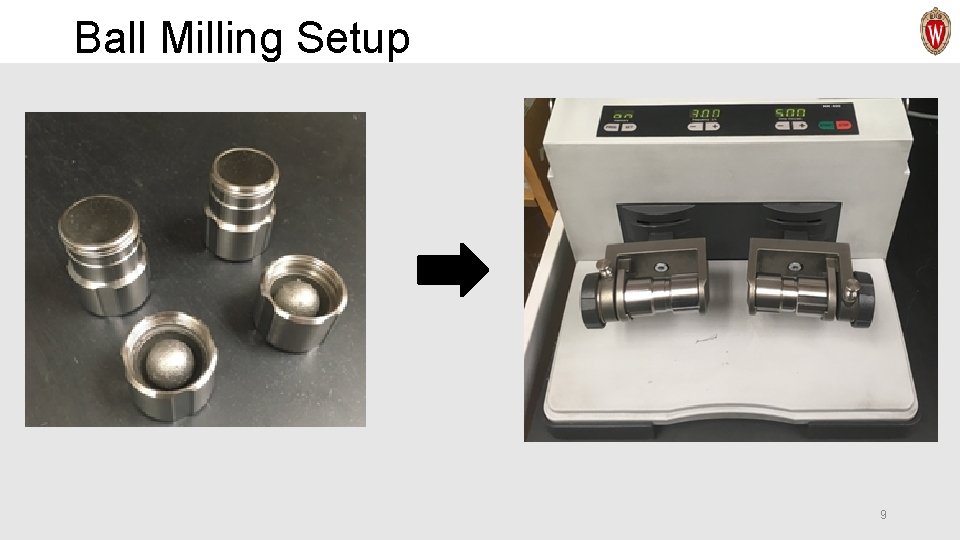
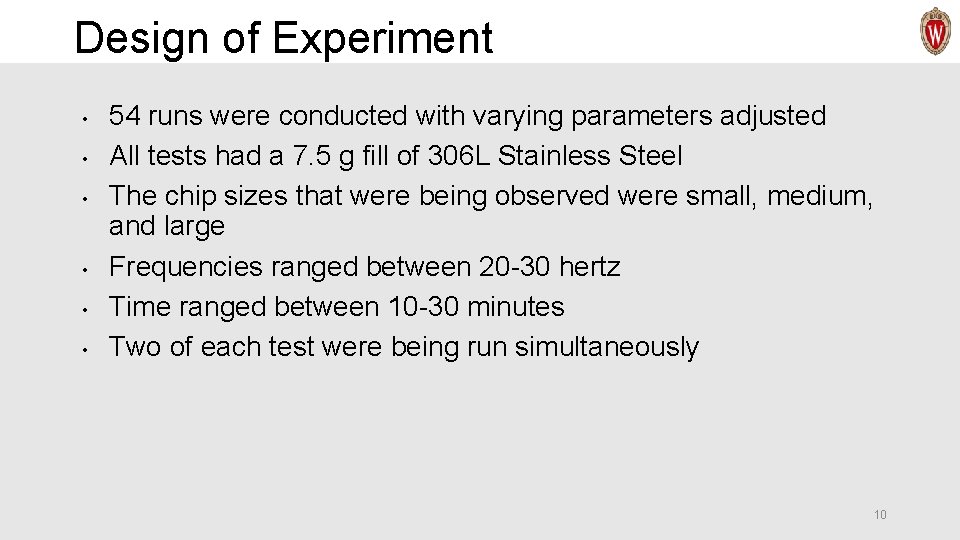
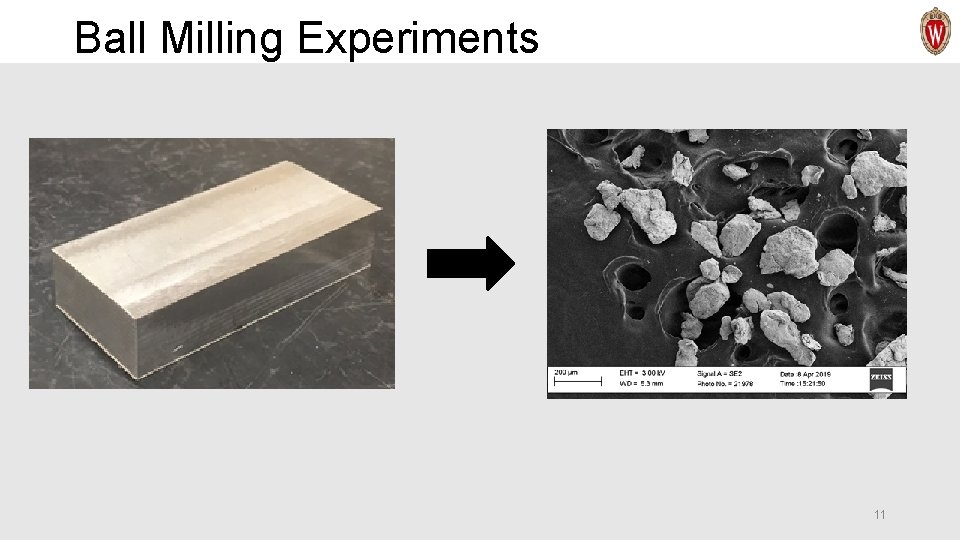
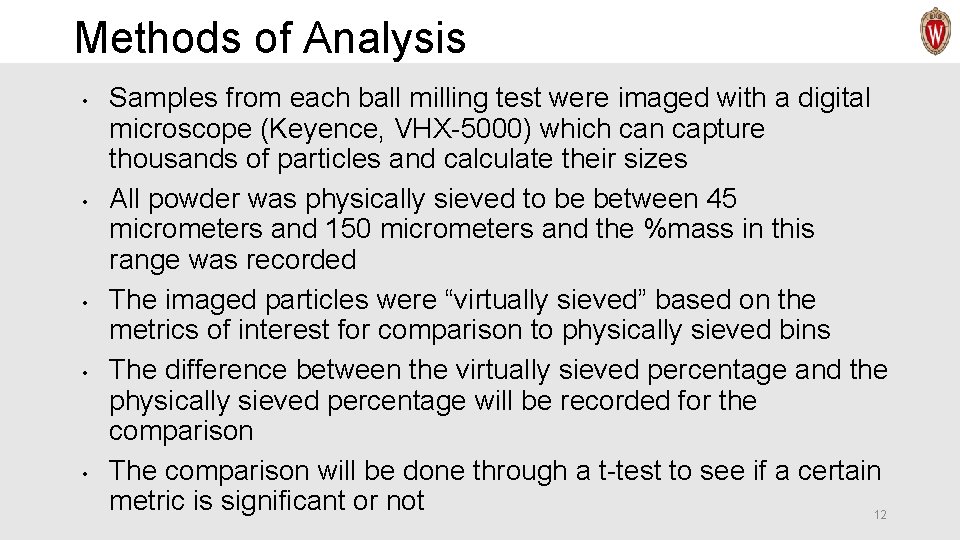
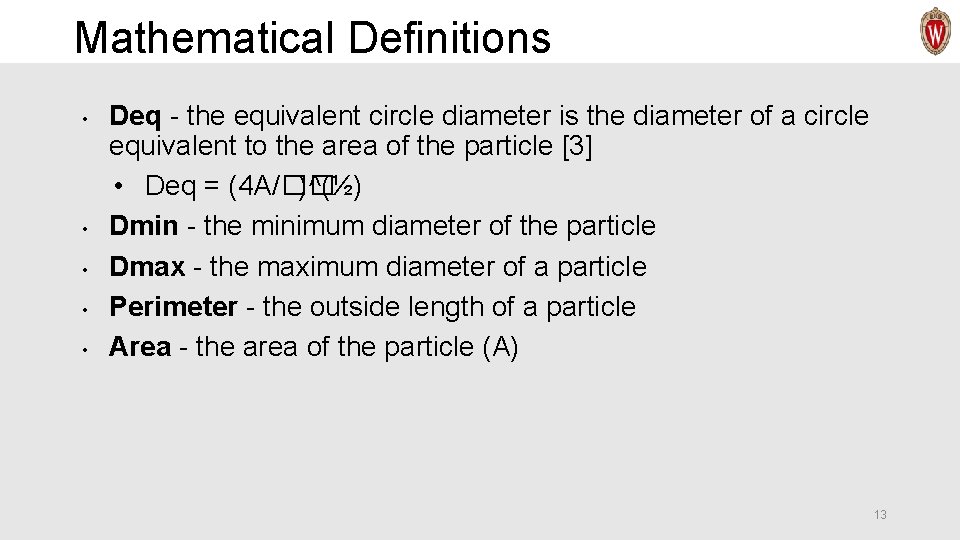
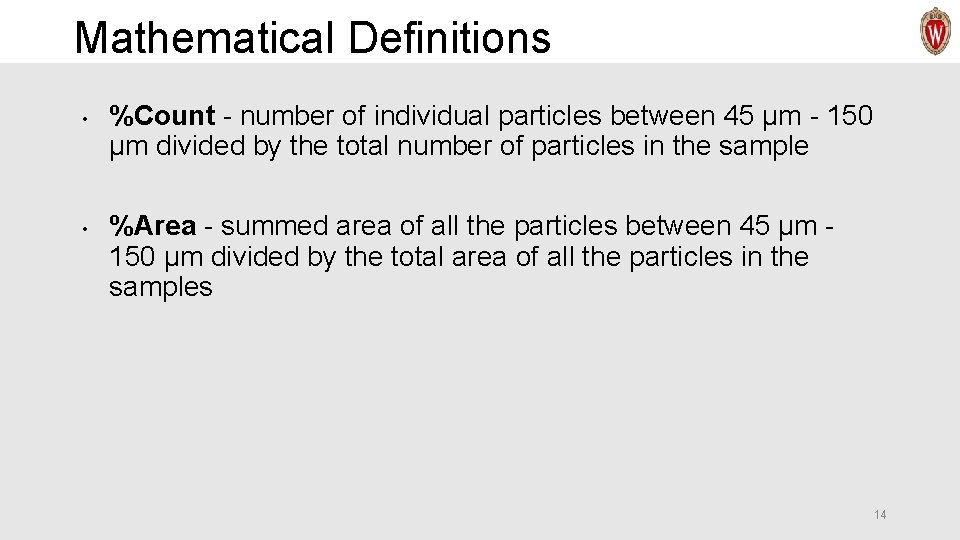
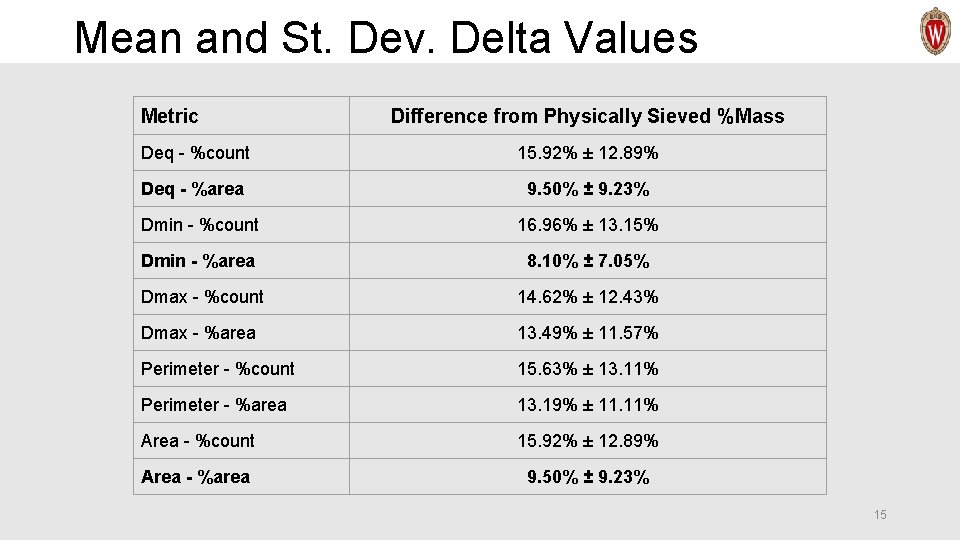
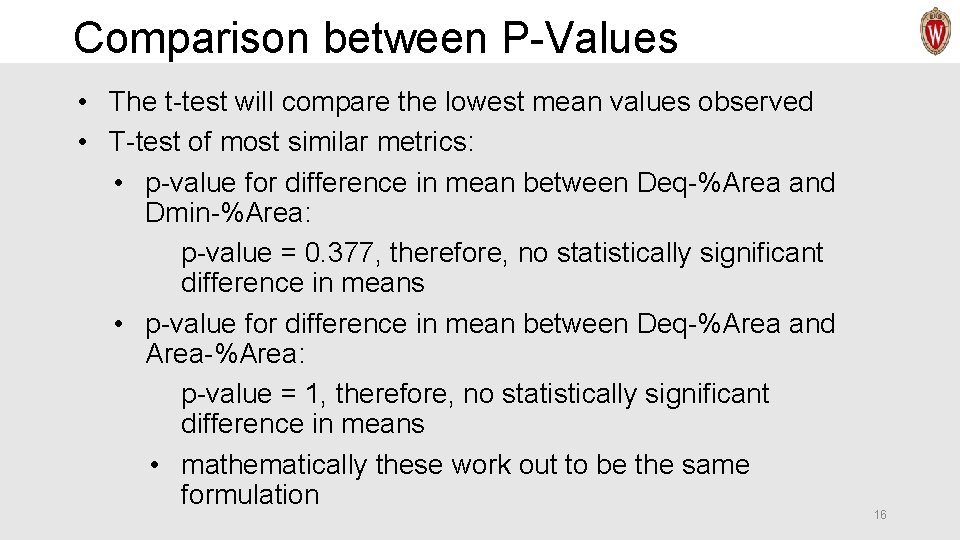
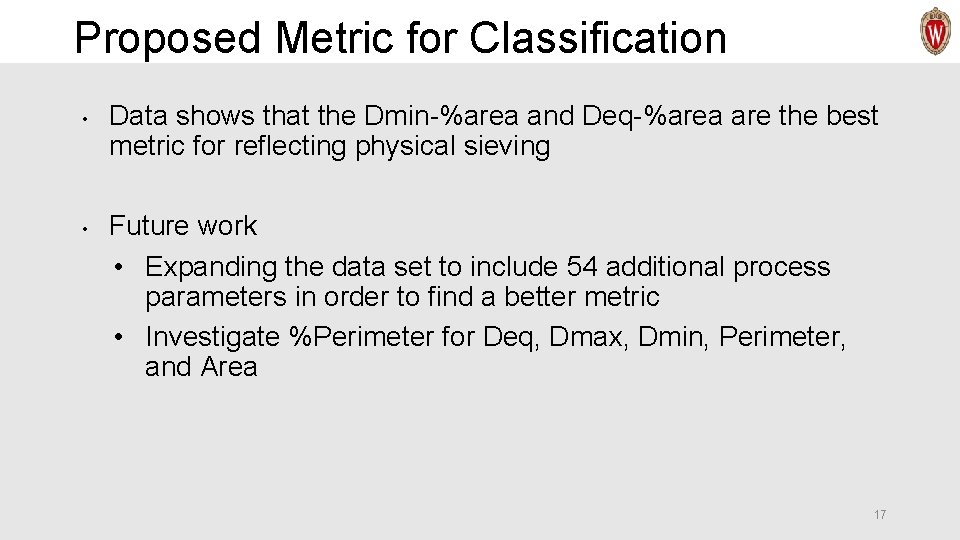
![References [1] Hogg, R. , Turek, M. L. and Kaya, E. (2004)'The Role of References [1] Hogg, R. , Turek, M. L. and Kaya, E. (2004)'The Role of](https://slidetodoc.com/presentation_image_h2/9318f4361ed895fa6fd1a6f46bc851ff/image-18.jpg)
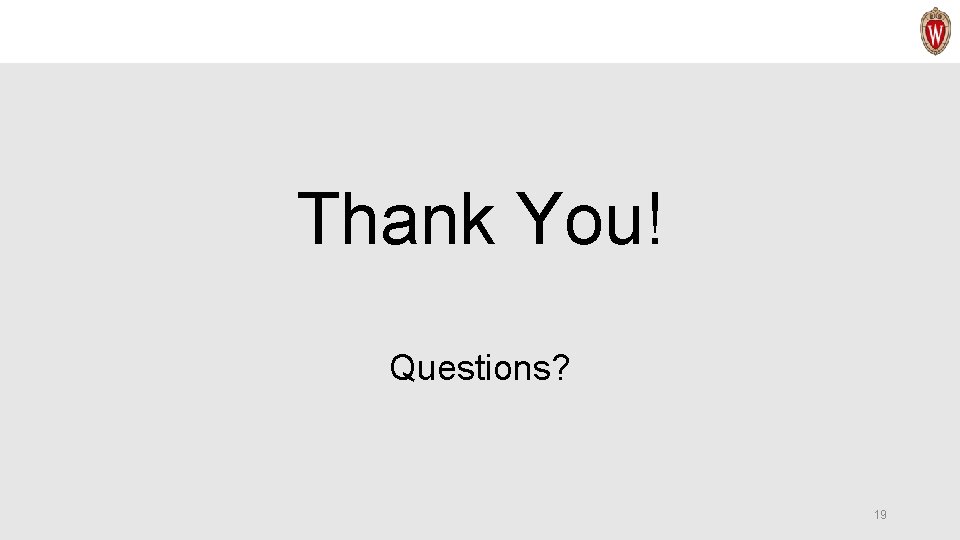
- Slides: 19
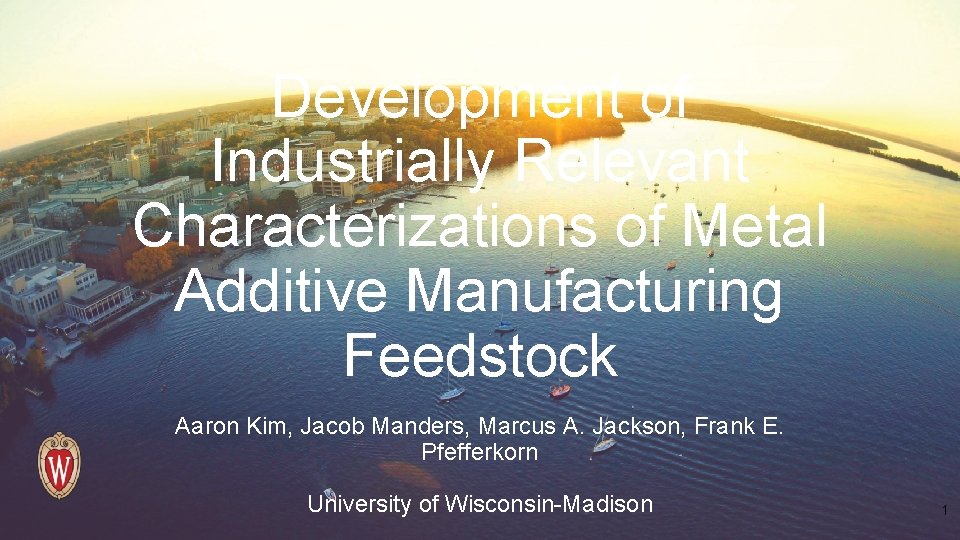
Development of Industrially Relevant Characterizations of Metal Additive Manufacturing Feedstock Aaron Kim, Jacob Manders, Marcus A. Jackson, Frank E. Pfefferkorn University of Wisconsin-Madison 1
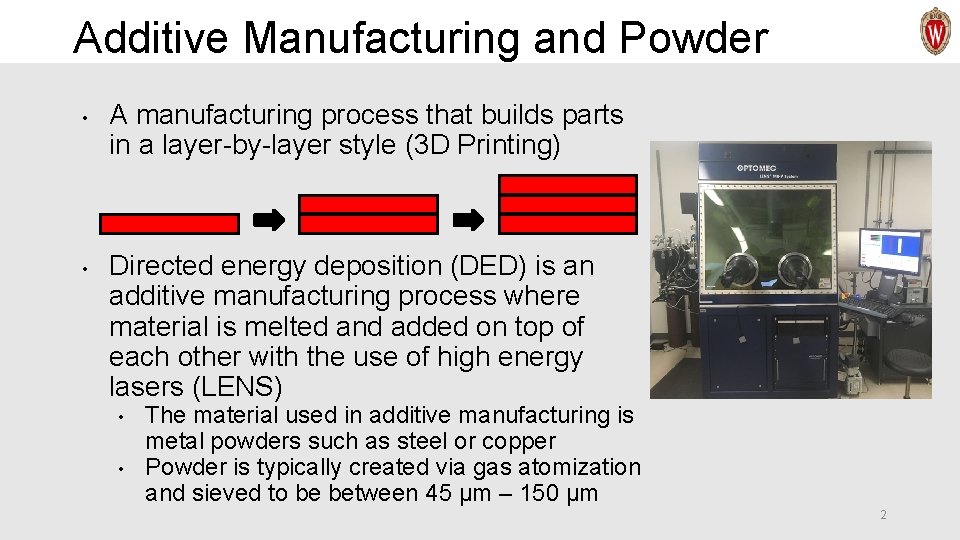
Additive Manufacturing and Powder • • A manufacturing process that builds parts in a layer-by-layer style (3 D Printing) Directed energy deposition (DED) is an additive manufacturing process where material is melted and added on top of each other with the use of high energy lasers (LENS) • • The material used in additive manufacturing is metal powders such as steel or copper Powder is typically created via gas atomization and sieved to be between 45 µm – 150 µm 2
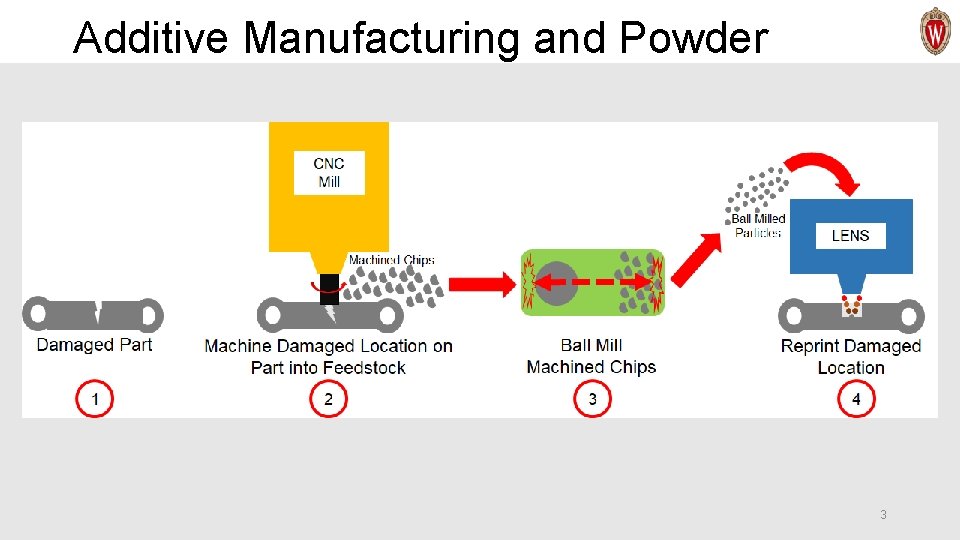
Additive Manufacturing and Powder 3
![Particle Shape and Size R Hogg et al 1 Pennsylvania State University Particle Shape and Size • R. Hogg et. al. [1] - Pennsylvania State University](https://slidetodoc.com/presentation_image_h2/9318f4361ed895fa6fd1a6f46bc851ff/image-4.jpg)
Particle Shape and Size • R. Hogg et. al. [1] - Pennsylvania State University • A relationship between a particle’s shape and size is determined through analysis with lights • Comminution from different actions can create random particle shapes • A particle’s shape can be determined through elongation with various measurements • Glass beads were crushed in order to evaluate size distributions through light scattering • There is a commonality between the measured amount of particles through light scattering versus actual yields found in sieving • Comminution creates a broad range for particles of the same size 4
![Analysis of Irregular Shaped Particles Rosen et al 2 Northwestern University Analysis of Irregular Shaped Particles • Rosen et. al. [2] - Northwestern University •](https://slidetodoc.com/presentation_image_h2/9318f4361ed895fa6fd1a6f46bc851ff/image-5.jpg)
Analysis of Irregular Shaped Particles • Rosen et. al. [2] - Northwestern University • The Coulter Counter device suspends irregular particles in a conducting liquid and moves materials through a small orifice • Different mesh sizes allowed different particle shapes to pass through • The spherical size of a particle may exceed the average opening of a sieve which will alter results • Different crystalline structures of materials will create irregular particles that makes analysis more difficult 5
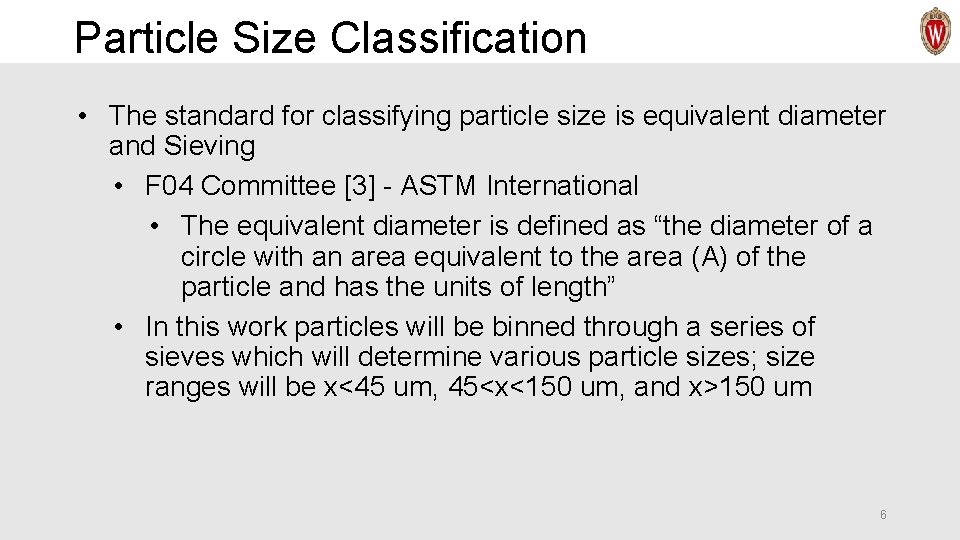
Particle Size Classification • The standard for classifying particle size is equivalent diameter and Sieving • F 04 Committee [3] - ASTM International • The equivalent diameter is defined as “the diameter of a circle with an area equivalent to the area (A) of the particle and has the units of length” • In this work particles will be binned through a series of sieves which will determine various particle sizes; size ranges will be x<45 um, 45<x<150 um, and x>150 um 6
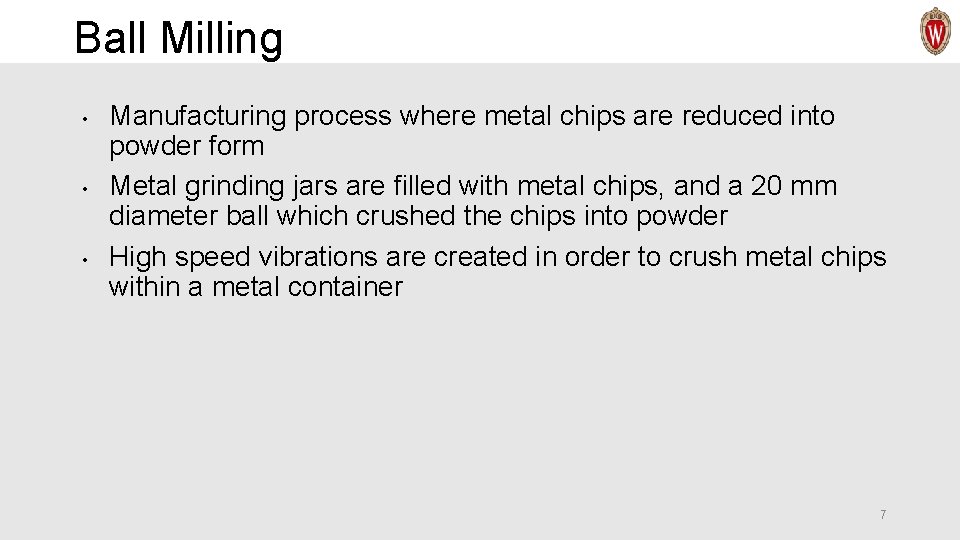
Ball Milling • • • Manufacturing process where metal chips are reduced into powder form Metal grinding jars are filled with metal chips, and a 20 mm diameter ball which crushed the chips into powder High speed vibrations are created in order to crush metal chips within a metal container 7
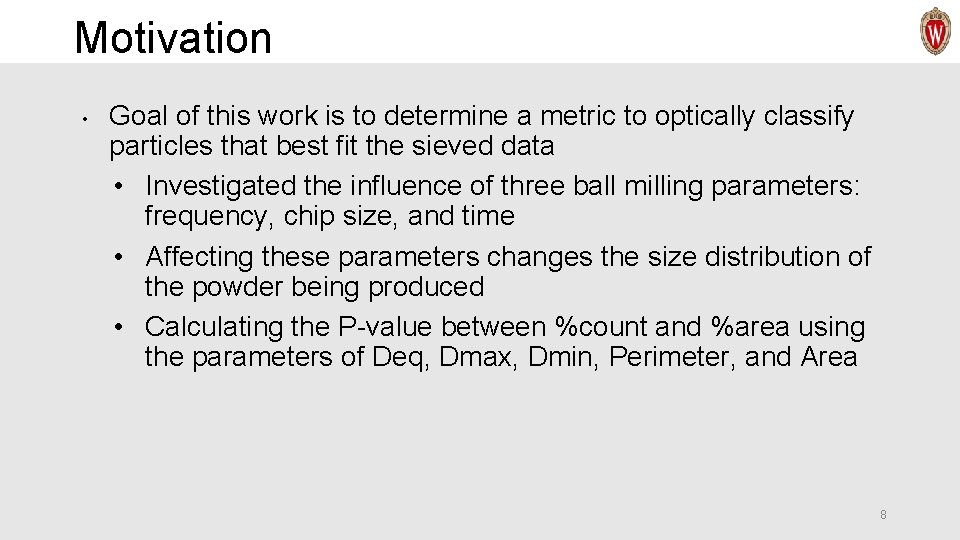
Motivation • Goal of this work is to determine a metric to optically classify particles that best fit the sieved data • Investigated the influence of three ball milling parameters: frequency, chip size, and time • Affecting these parameters changes the size distribution of the powder being produced • Calculating the P-value between %count and %area using the parameters of Deq, Dmax, Dmin, Perimeter, and Area 8
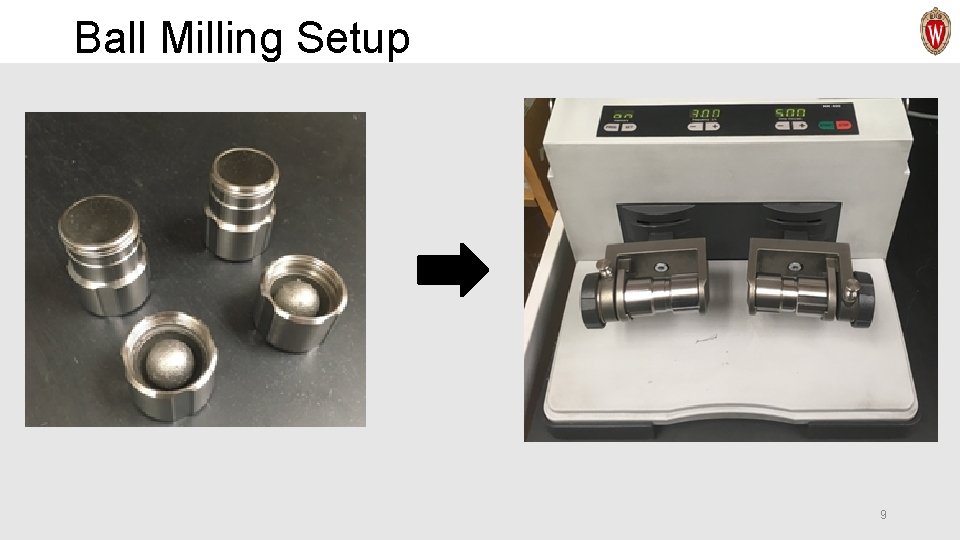
Ball Milling Setup 9
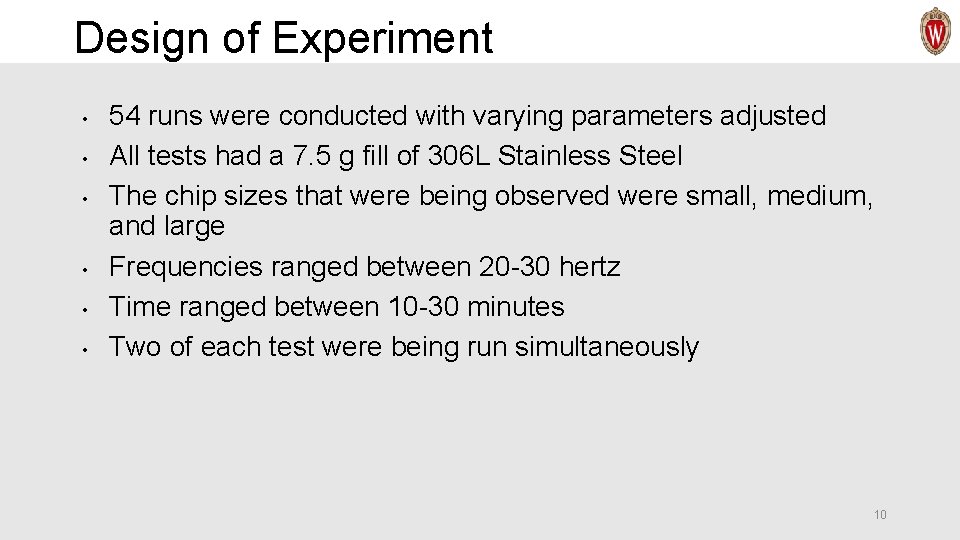
Design of Experiment • • • 54 runs were conducted with varying parameters adjusted All tests had a 7. 5 g fill of 306 L Stainless Steel The chip sizes that were being observed were small, medium, and large Frequencies ranged between 20 -30 hertz Time ranged between 10 -30 minutes Two of each test were being run simultaneously 10
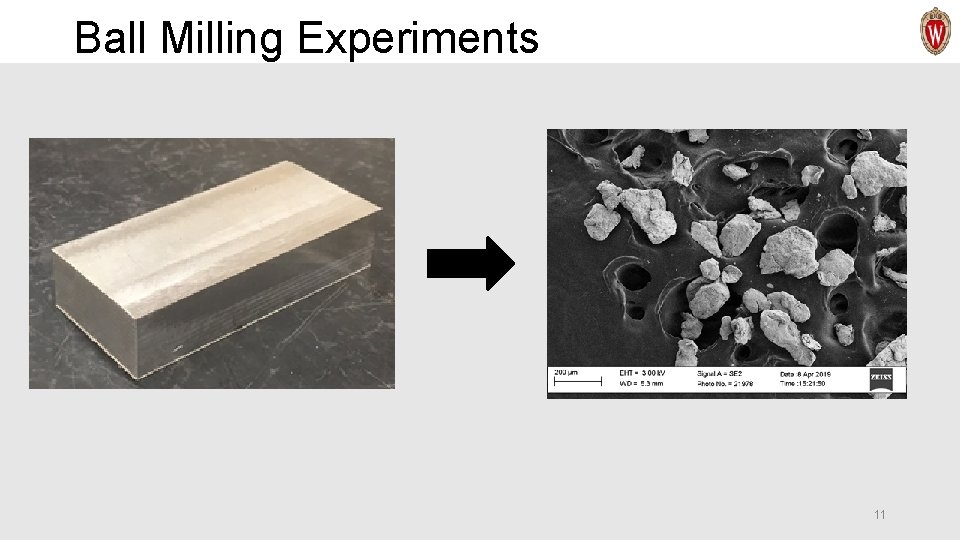
Ball Milling Experiments 11
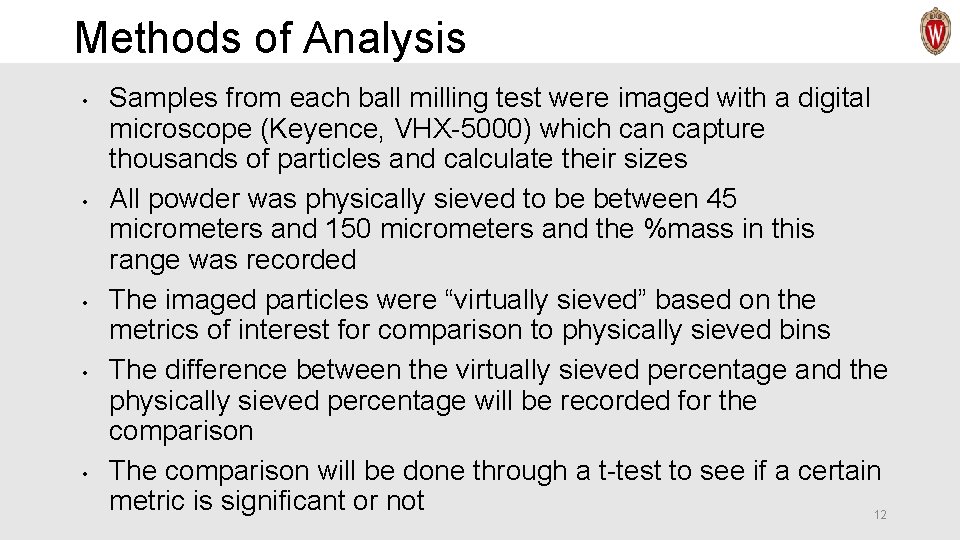
Methods of Analysis • • • Samples from each ball milling test were imaged with a digital microscope (Keyence, VHX-5000) which can capture thousands of particles and calculate their sizes All powder was physically sieved to be between 45 micrometers and 150 micrometers and the %mass in this range was recorded The imaged particles were “virtually sieved” based on the metrics of interest for comparison to physically sieved bins The difference between the virtually sieved percentage and the physically sieved percentage will be recorded for the comparison The comparison will be done through a t-test to see if a certain metric is significant or not 12
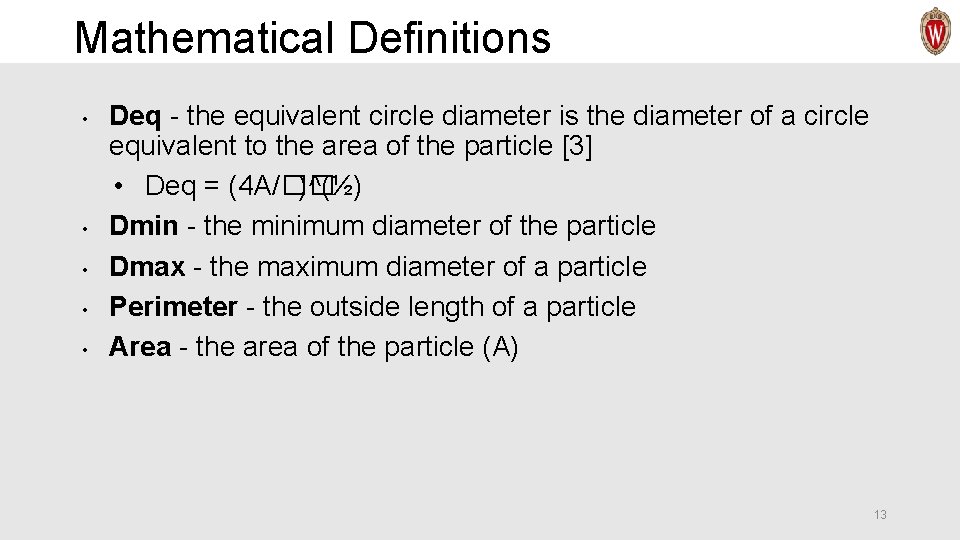
Mathematical Definitions • • • Deq - the equivalent circle diameter is the diameter of a circle equivalent to the area of the particle [3] • Deq = (4 A/�� )^(½) Dmin - the minimum diameter of the particle Dmax - the maximum diameter of a particle Perimeter - the outside length of a particle Area - the area of the particle (A) 13
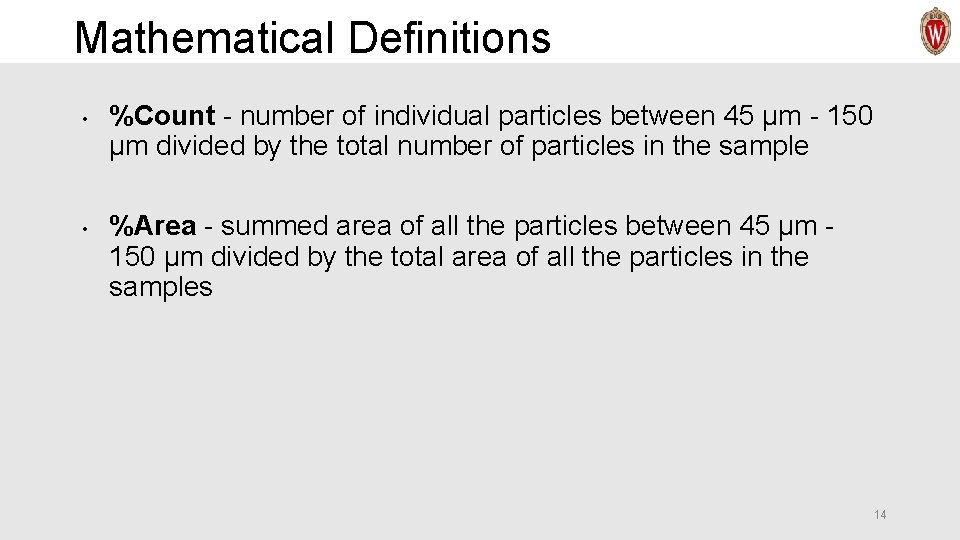
Mathematical Definitions • • %Count - number of individual particles between 45 µm - 150 µm divided by the total number of particles in the sample %Area - summed area of all the particles between 45 µm 150 µm divided by the total area of all the particles in the samples 14
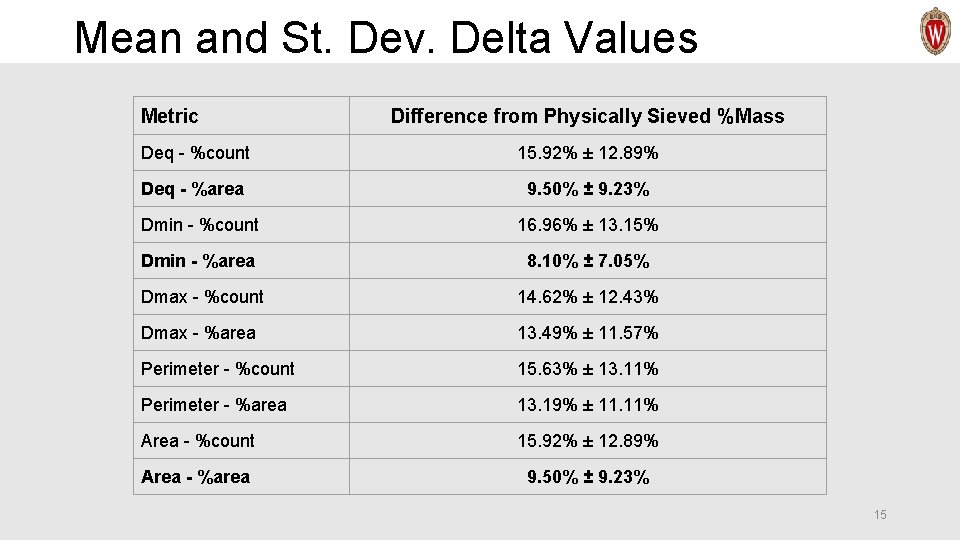
Mean and St. Dev. Delta Values Metric Difference from Physically Sieved %Mass Deq - %count 15. 92% ± 12. 89% Deq - %area 9. 50% ± 9. 23% Dmin - %count 16. 96% ± 13. 15% Dmin - %area 8. 10% ± 7. 05% Dmax - %count 14. 62% ± 12. 43% Dmax - %area 13. 49% ± 11. 57% Perimeter - %count 15. 63% ± 13. 11% Perimeter - %area 13. 19% ± 11. 11% Area - %count 15. 92% ± 12. 89% Area - %area 9. 50% ± 9. 23% 15
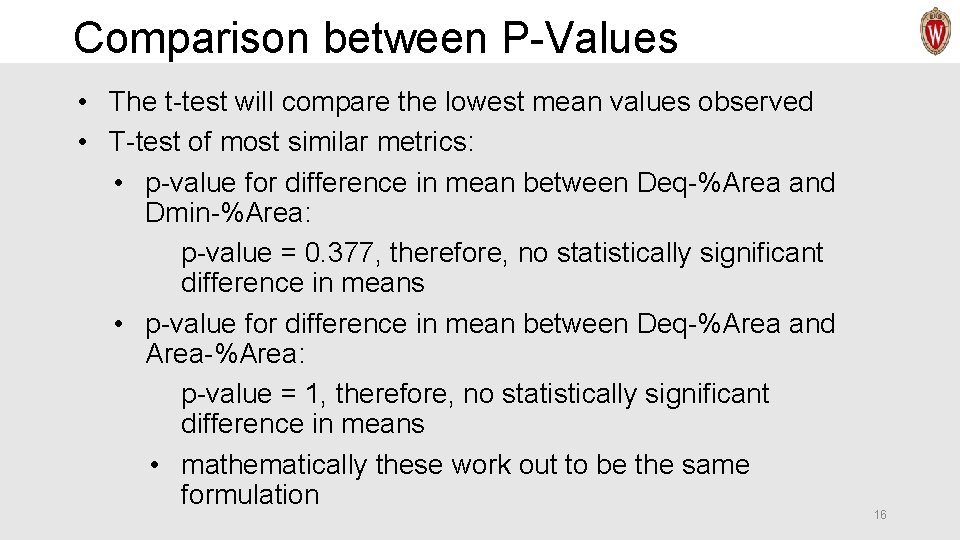
Comparison between P-Values • The t-test will compare the lowest mean values observed • T-test of most similar metrics: • p-value for difference in mean between Deq-%Area and Dmin-%Area: p-value = 0. 377, therefore, no statistically significant difference in means • p-value for difference in mean between Deq-%Area and Area-%Area: p-value = 1, therefore, no statistically significant difference in means • mathematically these work out to be the same formulation 16
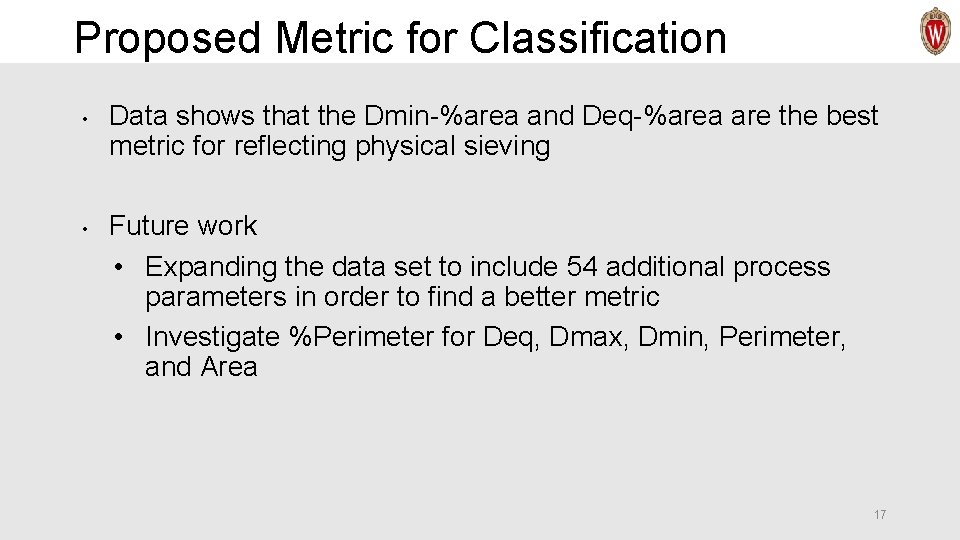
Proposed Metric for Classification • • Data shows that the Dmin-%area and Deq-%area are the best metric for reflecting physical sieving Future work • Expanding the data set to include 54 additional process parameters in order to find a better metric • Investigate %Perimeter for Deq, Dmax, Dmin, Perimeter, and Area 17
![References 1 Hogg R Turek M L and Kaya E 2004The Role of References [1] Hogg, R. , Turek, M. L. and Kaya, E. (2004)'The Role of](https://slidetodoc.com/presentation_image_h2/9318f4361ed895fa6fd1a6f46bc851ff/image-18.jpg)
References [1] Hogg, R. , Turek, M. L. and Kaya, E. (2004)'The Role of Particle Shape in Size Analysis and the Evaluation of Comminution Processes', Particulate Science and Technology, 22: 4, 355 — 366 [2] Rosen, H. N. , and H. M. Hulburt. “Size Analysis of Irregularly Shaped Particles in Sieving. Comparison with the Coulter Counter. ” Industrial & Engineering Chemistry Fundamentals, vol. 9, no. 4, 1970, pp. 658– 661. , doi: 10. 1021/i 160036 a 023. [3] F 04 Committee, “Practice for Characterization of Particles, ” ASTM International. 18
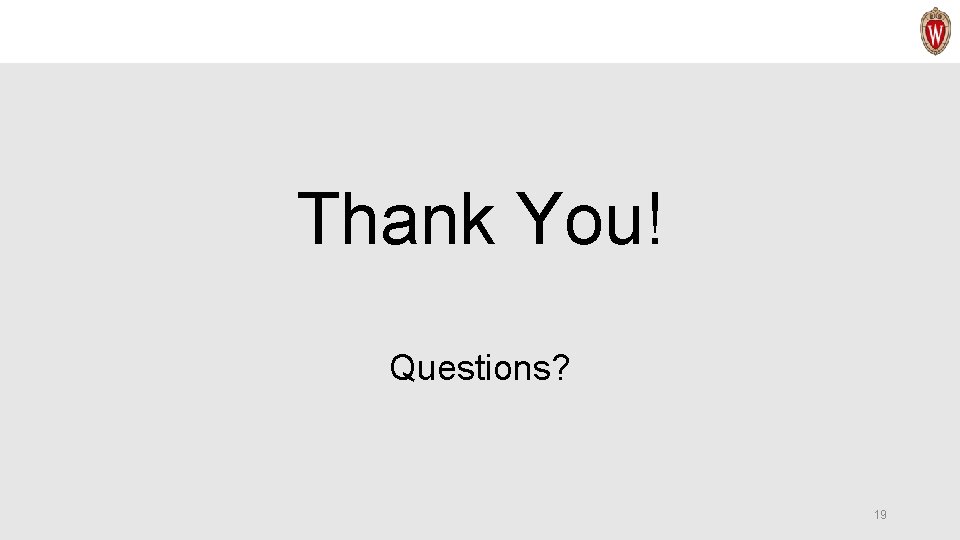
Thank You! Questions? 19
An industrially important element contains 26
An industrially important element contains 26
Characterization direct vs indirect
Indirect and direct characterization
Indirect characterization thoughts examples
Teaching direct and indirect characterization
Define invertible matrix
Venn diagram of conduction, convection and radiation
Metals vs nonmetals vs metalloids
Difference between metal oxides and non metal oxides
Melting point of diamond
Hot nwell
Non metals uses
Properties of semimetals
Metals react with nonmetals to form ionic compounds by
P
Metal and non metal definition
Clasificación de los metales y no metales
Metalloids
Existen tres isotopos naturales del potasio 39k 40k y 41k