Additive Manufacturing Traditional fabrication Additive manufacturing What Why
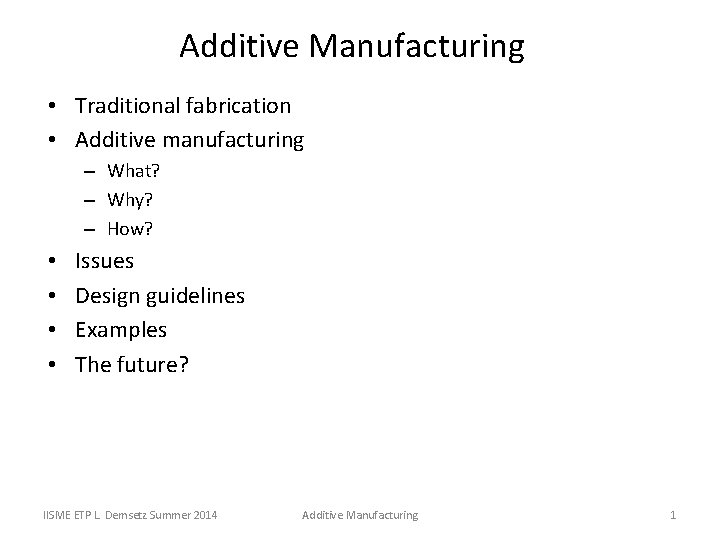
Additive Manufacturing • Traditional fabrication • Additive manufacturing – What? – Why? – How? • • Issues Design guidelines Examples The future? IISME ETP L. Demsetz Summer 2014 Additive Manufacturing 1

Traditional fabrication Remove material (subtractive manufacturing) Image Sources: upper left http: //www. haas. co. uk/case_studies/fender-guitars. html lower left http: //www. rockbats. com/company_manufacturing. html center http: //www. pbase. com/image/91845516 upper right http: //www. pdf-inc. com/cnc-machines. php lower right http: //www. productionmachining. com/articles/precision-lathe-operations-on-a-cnc-mill IISME ETP L. Demsetz Summer 2014 Additive Manufacturing 2
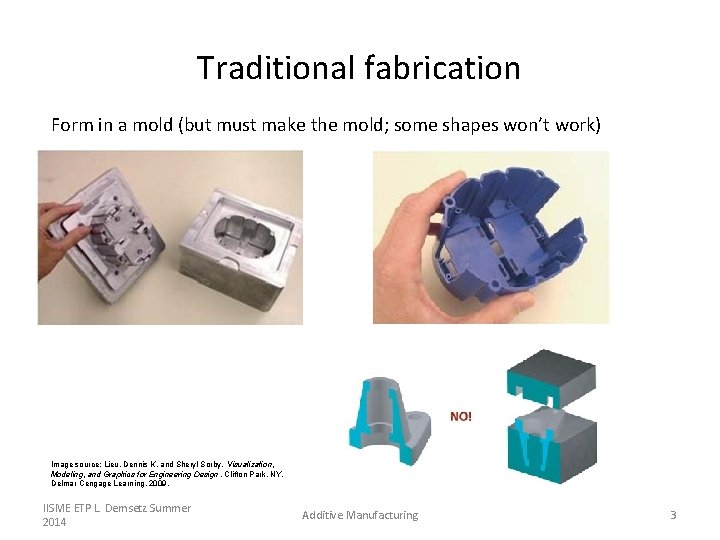
Traditional fabrication Form in a mold (but must make the mold; some shapes won’t work) Image source: Lieu, Dennis K, and Sheryl Sorby. Visualization, Modeling, and Graphics for Engineering Design. Clifton Park, NY. Delmar Cengage Learning, 2009. IISME ETP L. Demsetz Summer 2014 Additive Manufacturing 3
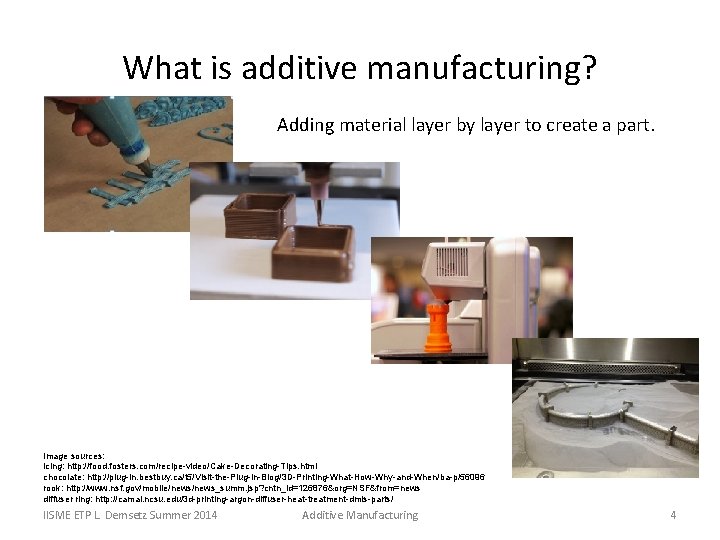
What is additive manufacturing? Adding material layer by layer to create a part. Image sources: icing: http: //food. fosters. com/recipe-video/Cake-Decorating-Tips. html chocolate: http: //plug-in. bestbuy. ca/t 5/Visit-the-Plug-in-Blog/3 D-Printing-What-How-Why-and-When/ba-p/56096 rook: http: //www. nsf. gov/mobile/news_summ. jsp? cntn_id=126876&org=NSF&from=news diffuser ring: http: //camal. ncsu. edu/3 d-printing-argon-diffuser-heat-treatment-dmls-parts/ IISME ETP L. Demsetz Summer 2014 Additive Manufacturing 4
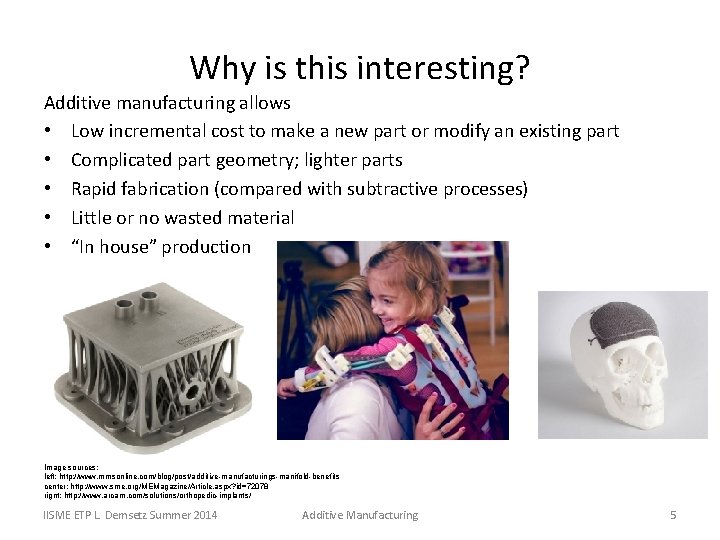
Why is this interesting? Additive manufacturing allows • Low incremental cost to make a new part or modify an existing part • Complicated part geometry; lighter parts • Rapid fabrication (compared with subtractive processes) • Little or no wasted material • “In house” production Image sources: left: http: //www. mmsonline. com/blog/post/additive-manufacturings-manifold-benefits center: http: //www. sme. org/MEMagazine/Article. aspx? id=72078 rignt: http: //www. arcam. com/solutions/orthopedic-implants/ IISME ETP L. Demsetz Summer 2014 Additive Manufacturing 5
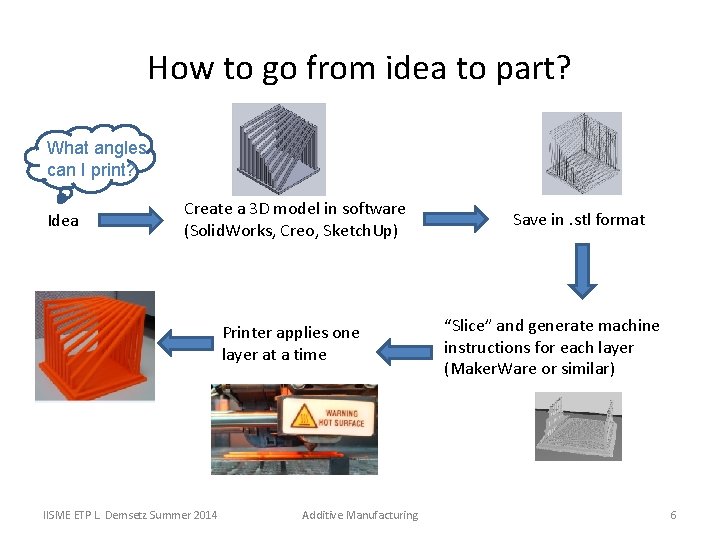
How to go from idea to part? What angles can I print? Idea Create a 3 D model in software (Solid. Works, Creo, Sketch. Up) Printer applies one layer at a time IISME ETP L. Demsetz Summer 2014 Additive Manufacturing Save in. stl format “Slice” and generate machine instructions for each layer (Maker. Ware or similar) 6
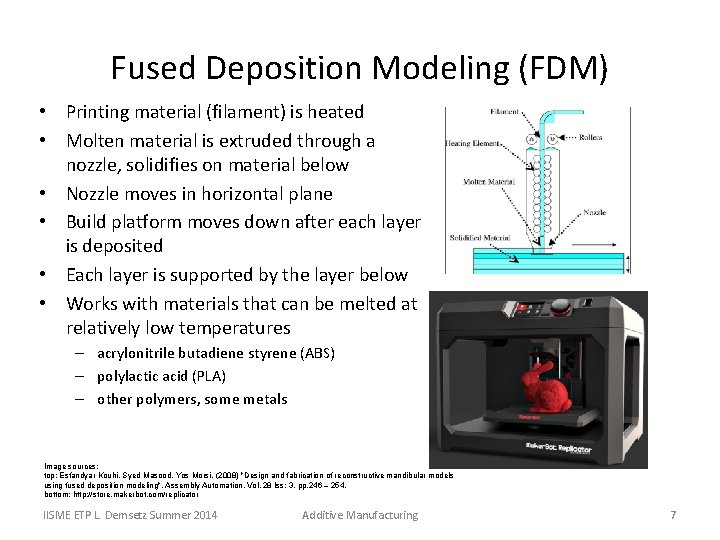
Fused Deposition Modeling (FDM) • Printing material (filament) is heated • Molten material is extruded through a nozzle, solidifies on material below • Nozzle moves in horizontal plane • Build platform moves down after each layer is deposited • Each layer is supported by the layer below • Works with materials that can be melted at relatively low temperatures – acrylonitrile butadiene styrene (ABS) – polylactic acid (PLA) – other polymers, some metals Image sources: top: Esfandyar Kouhi, Syed Masood, Yos Morsi, (2008) "Design and fabrication of reconstructive mandibular models using fused deposition modeling", Assembly Automation, Vol. 28 Iss: 3, pp. 246 – 254. bottom: http: //store. makerbot. com/replicator IISME ETP L. Demsetz Summer 2014 Additive Manufacturing 7
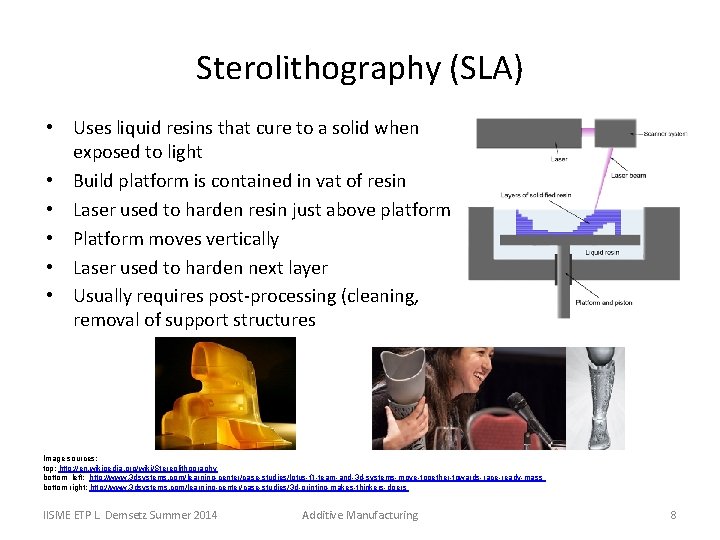
Sterolithography (SLA) • Uses liquid resins that cure to a solid when exposed to light • Build platform is contained in vat of resin • Laser used to harden resin just above platform • Platform moves vertically • Laser used to harden next layer • Usually requires post-processing (cleaning, removal of support structures Image sources: top: http: //en. wikipedia. org/wiki/Stereolithography bottom left: http: //www. 3 dsystems. com/learning-center/case-studies/lotus-f 1 -team-and-3 d-systems-move-together-towards-race-ready-mass bottom right: http: //www. 3 dsystems. com/learning-center/case-studies/3 d-printing-makes-thinkers-doers IISME ETP L. Demsetz Summer 2014 Additive Manufacturing 8
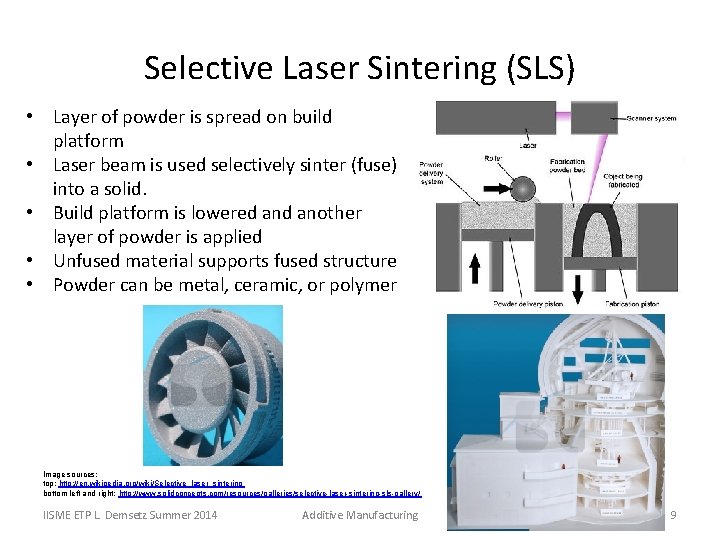
Selective Laser Sintering (SLS) • Layer of powder is spread on build platform • Laser beam is used selectively sinter (fuse) into a solid. • Build platform is lowered another layer of powder is applied • Unfused material supports fused structure • Powder can be metal, ceramic, or polymer Image sources: top: http: //en. wikipedia. org/wiki/Selective_laser_sintering bottom left and right: http: //www. solidconcepts. com/resources/galleries/selective-laser-sintering-sls-gallery/ IISME ETP L. Demsetz Summer 2014 Additive Manufacturing 9
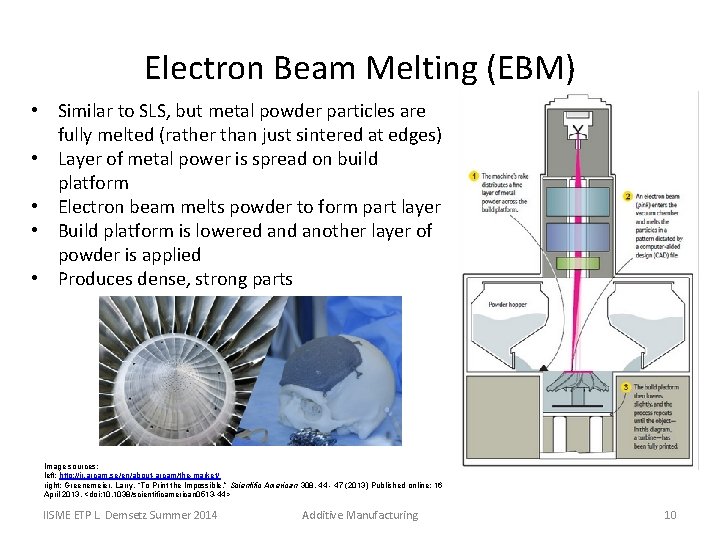
Electron Beam Melting (EBM) • Similar to SLS, but metal powder particles are fully melted (rather than just sintered at edges) • Layer of metal power is spread on build platform • Electron beam melts powder to form part layer • Build platform is lowered another layer of powder is applied • Produces dense, strong parts Image sources: left: http: //ir. arcam. se/en/about-arcam/the-market/ right: Greenemeier, Larry. “To Print the Impossible. ” Scientific American 308, 44 - 47 (2013) Published online: 16 April 2013. <doi: 10. 1038/scientificamerican 0513 -44> IISME ETP L. Demsetz Summer 2014 Additive Manufacturing 10
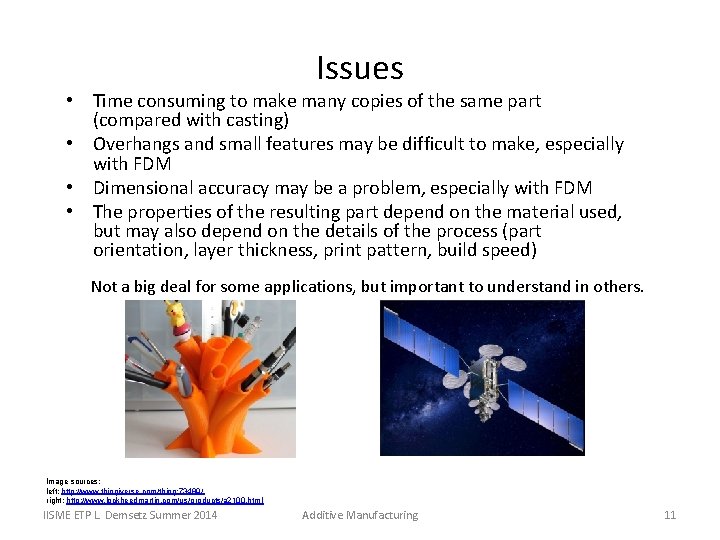
Issues • Time consuming to make many copies of the same part (compared with casting) • Overhangs and small features may be difficult to make, especially with FDM • Dimensional accuracy may be a problem, especially with FDM • The properties of the resulting part depend on the material used, but may also depend on the details of the process (part orientation, layer thickness, print pattern, build speed) Not a big deal for some applications, but important to understand in others. Image sources: left: http: //www. thingiverse. com/thing: 73489/ right: http: //www. lockheedmartin. com/us/products/a 2100. html IISME ETP L. Demsetz Summer 2014 Additive Manufacturing 11
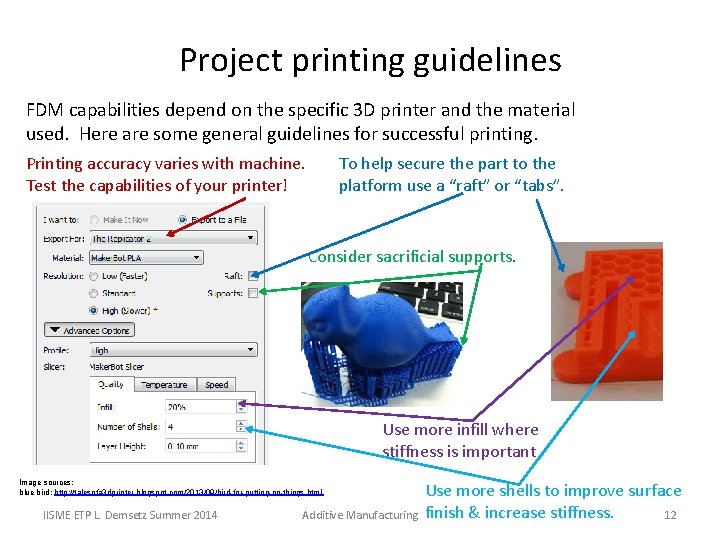
Project printing guidelines FDM capabilities depend on the specific 3 D printer and the material used. Here are some general guidelines for successful printing. Printing accuracy varies with machine. Test the capabilities of your printer! To help secure the part to the platform use a “raft” or “tabs”. Consider sacrificial supports. Use more infill where stiffness is important Image sources: blue bird: http: //talesofa 3 dprinter. blogspot. com/2013/09/bird-for-putting-on-things. html IISME ETP L. Demsetz Summer 2014 Additive Manufacturing Use more shells to improve surface finish & increase stiffness. 12
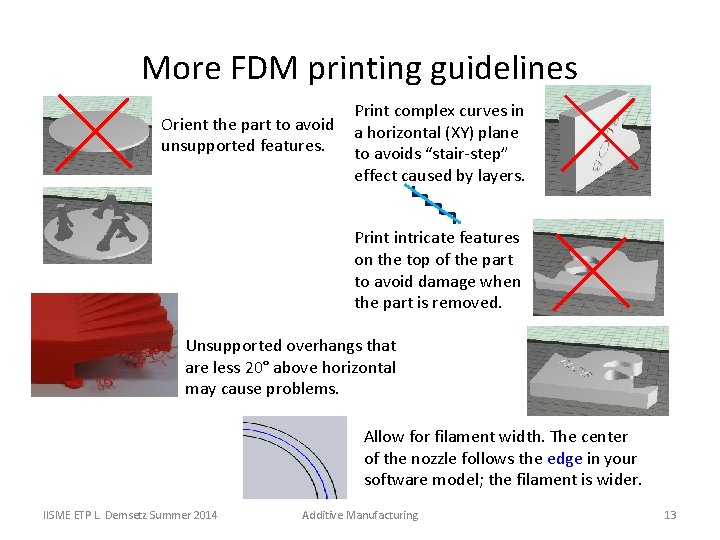
More FDM printing guidelines Orient the part to avoid unsupported features. Print complex curves in a horizontal (XY) plane to avoids “stair-step” effect caused by layers. Print intricate features on the top of the part to avoid damage when the part is removed. Unsupported overhangs that are less 20° above horizontal may cause problems. Allow for filament width. The center of the nozzle follows the edge in your software model; the filament is wider. IISME ETP L. Demsetz Summer 2014 Additive Manufacturing 13
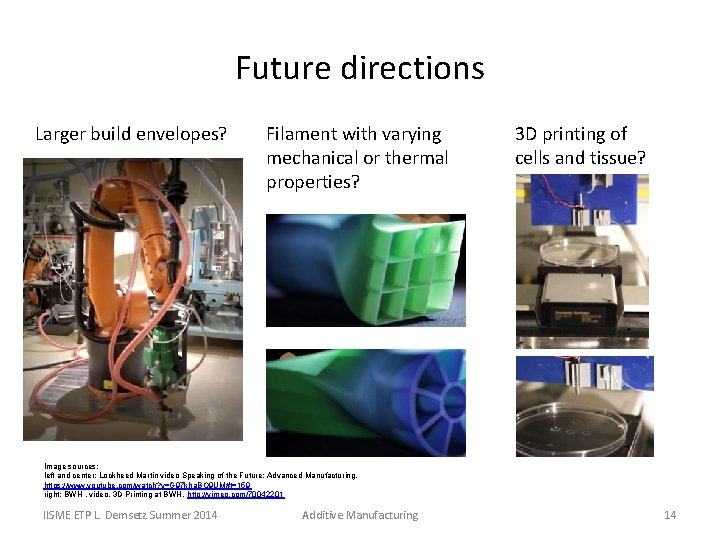
Future directions Larger build envelopes? Filament with varying mechanical or thermal properties? 3 D printing of cells and tissue? Image sources: left and center: Lockheed Martin video Speaking of the Future: Advanced Manufacturing, https: //www. youtube. com/watch? v=G 97 kha. BO 9 UM#t=159 right: BWH , video, 3 D Printing at BWH, http: //vimeo. com/70042201 IISME ETP L. Demsetz Summer 2014 Additive Manufacturing 14
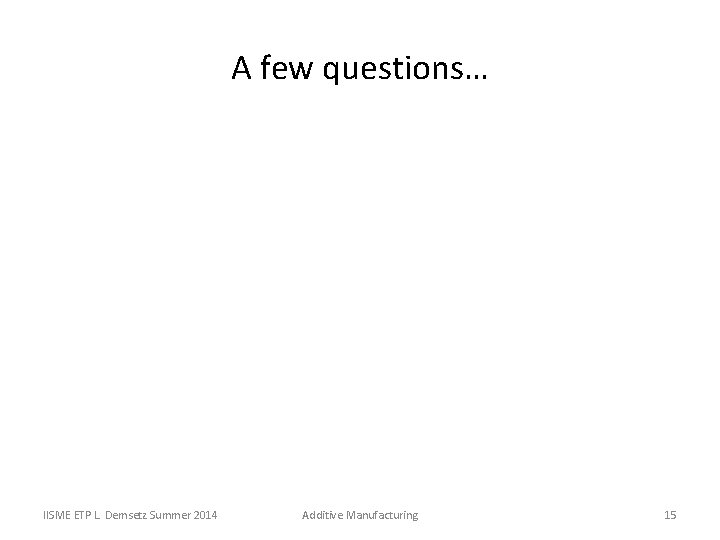
A few questions… IISME ETP L. Demsetz Summer 2014 Additive Manufacturing 15
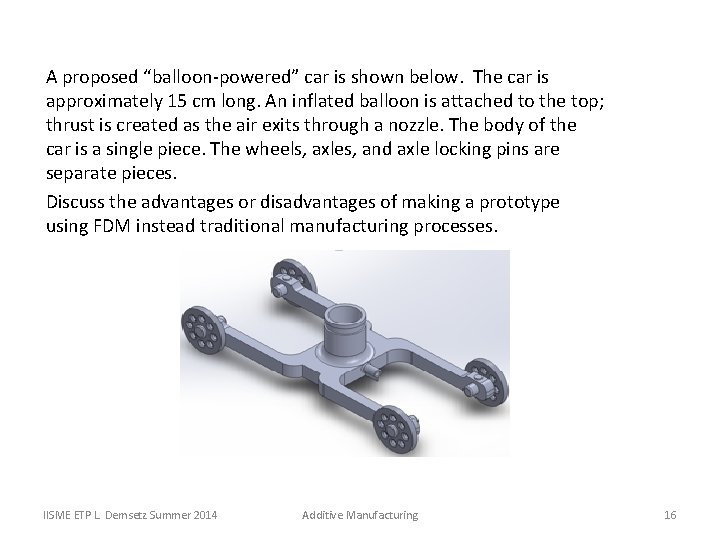
A proposed “balloon-powered” car is shown below. The car is approximately 15 cm long. An inflated balloon is attached to the top; thrust is created as the air exits through a nozzle. The body of the car is a single piece. The wheels, axles, and axle locking pins are separate pieces. Discuss the advantages or disadvantages of making a prototype using FDM instead traditional manufacturing processes. IISME ETP L. Demsetz Summer 2014 Additive Manufacturing 16
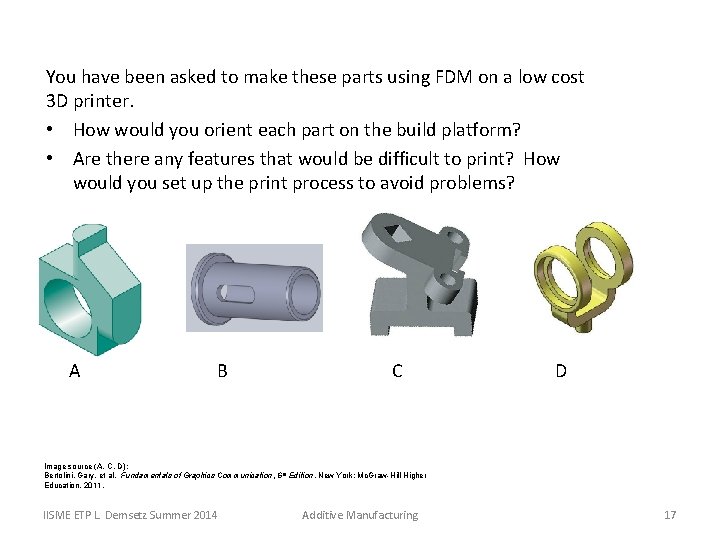
You have been asked to make these parts using FDM on a low cost 3 D printer. • How would you orient each part on the build platform? • Are there any features that would be difficult to print? How would you set up the print process to avoid problems? A B C D Image source (A, C, D): Bertolini, Gary, et al. Fundamentals of Graphics Communication, 6 th Edition. New York: Mc. Graw-Hill Higher Education, 2011. IISME ETP L. Demsetz Summer 2014 Additive Manufacturing 17
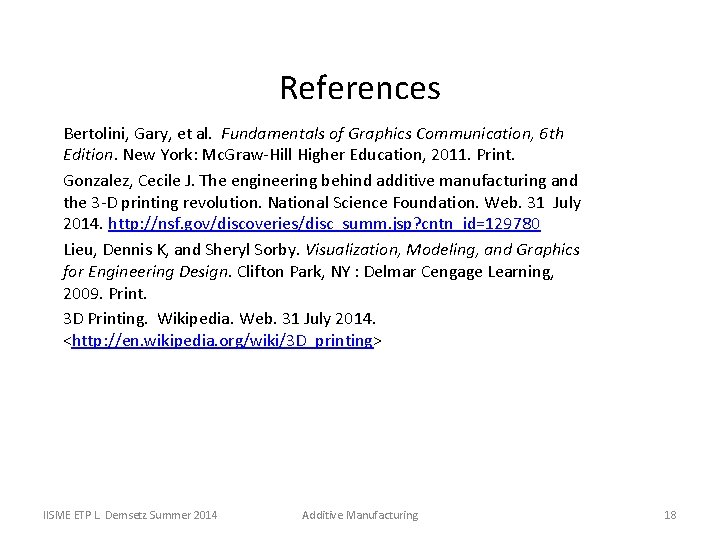
References Bertolini, Gary, et al. Fundamentals of Graphics Communication, 6 th Edition. New York: Mc. Graw-Hill Higher Education, 2011. Print. Gonzalez, Cecile J. The engineering behind additive manufacturing and the 3 -D printing revolution. National Science Foundation. Web. 31 July 2014. http: //nsf. gov/discoveries/disc_summ. jsp? cntn_id=129780 Lieu, Dennis K, and Sheryl Sorby. Visualization, Modeling, and Graphics for Engineering Design. Clifton Park, NY : Delmar Cengage Learning, 2009. Print. 3 D Printing. Wikipedia. Web. 31 July 2014. <http: //en. wikipedia. org/wiki/3 D_printing> IISME ETP L. Demsetz Summer 2014 Additive Manufacturing 18
- Slides: 18