Detector RD Work at Princeton Changguo Lu Princeton
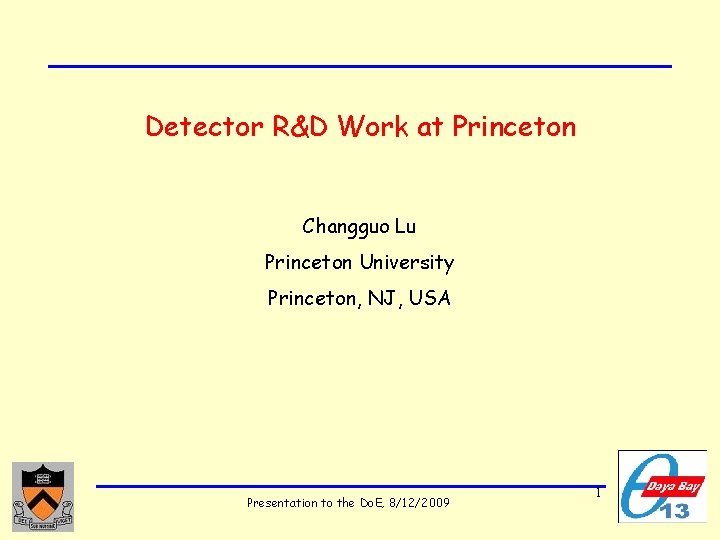
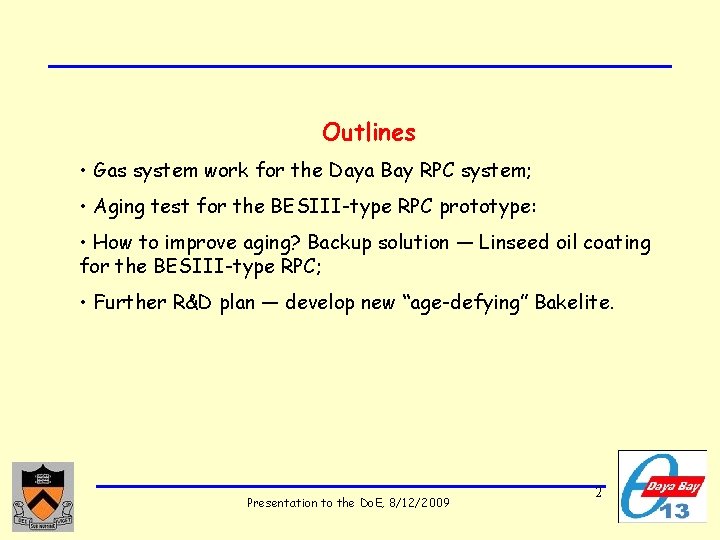
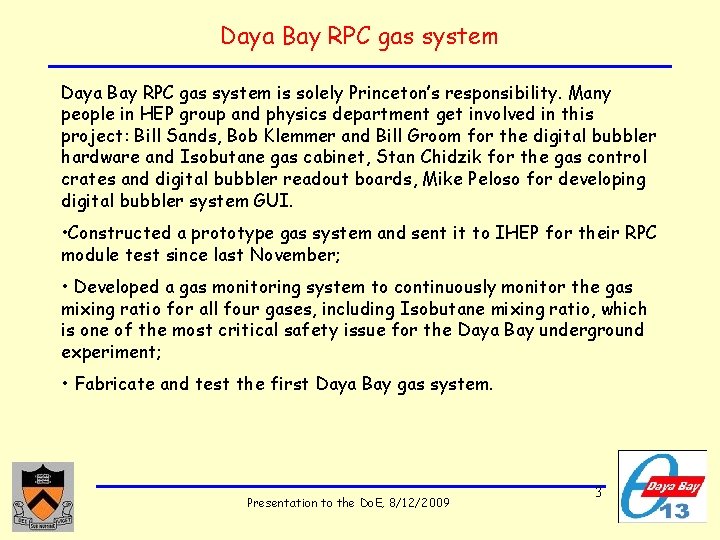
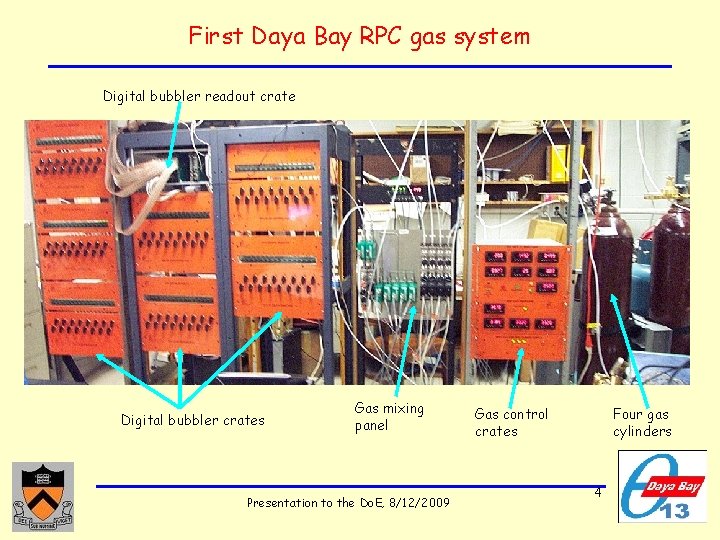
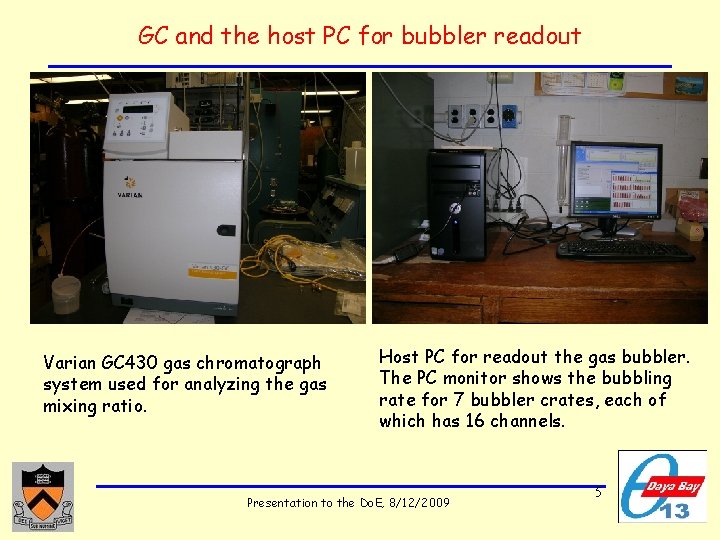

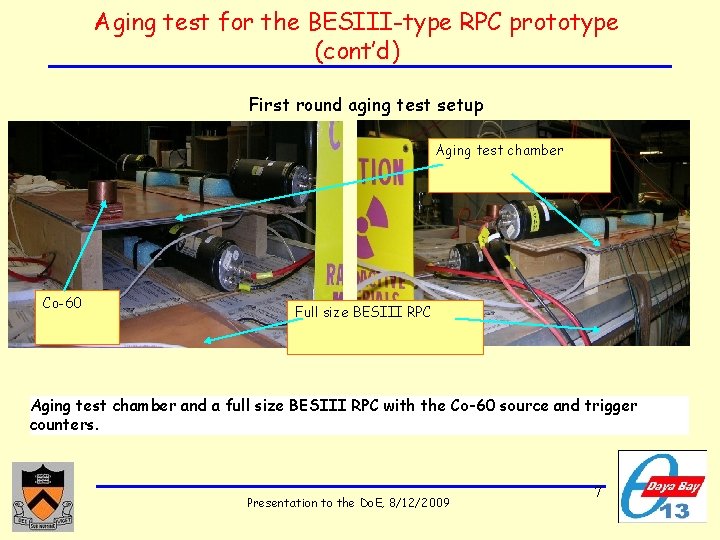
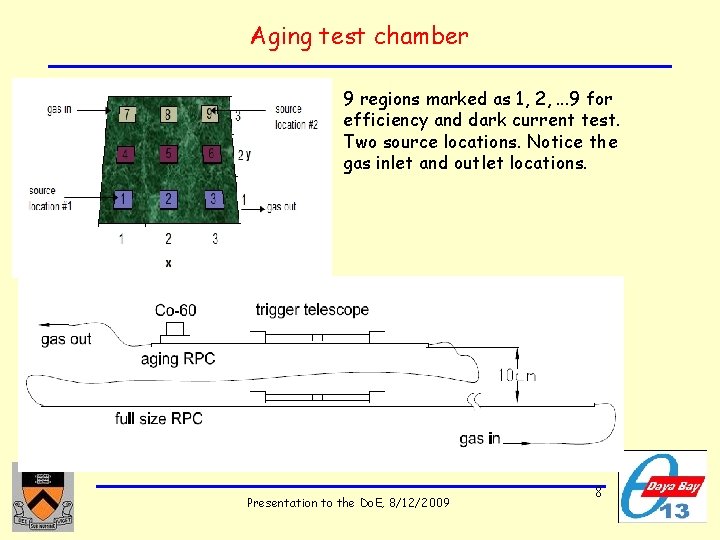
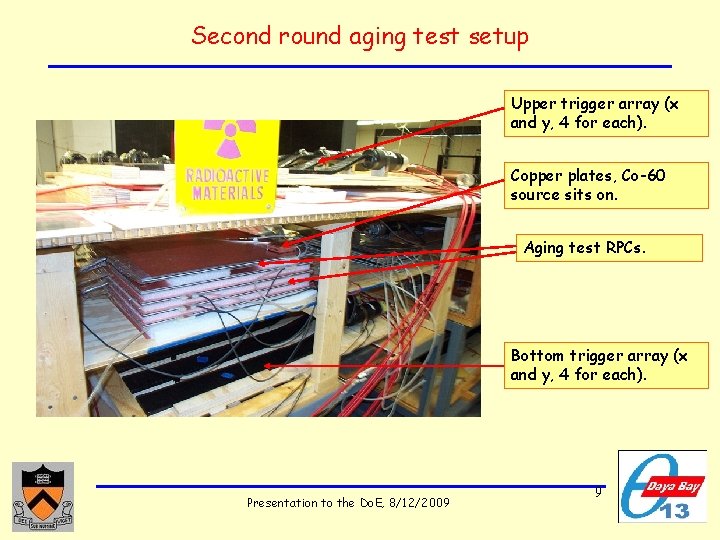
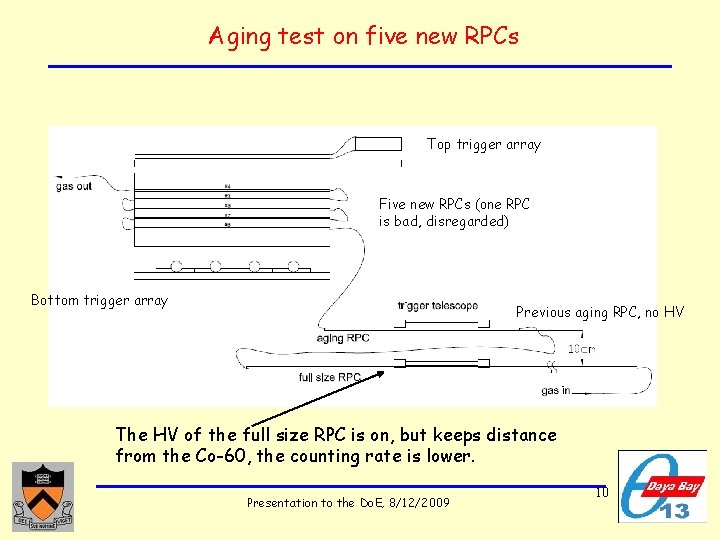
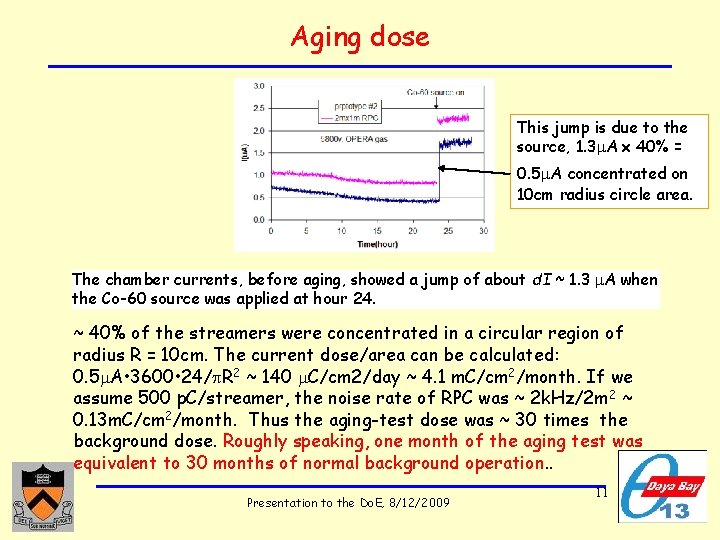
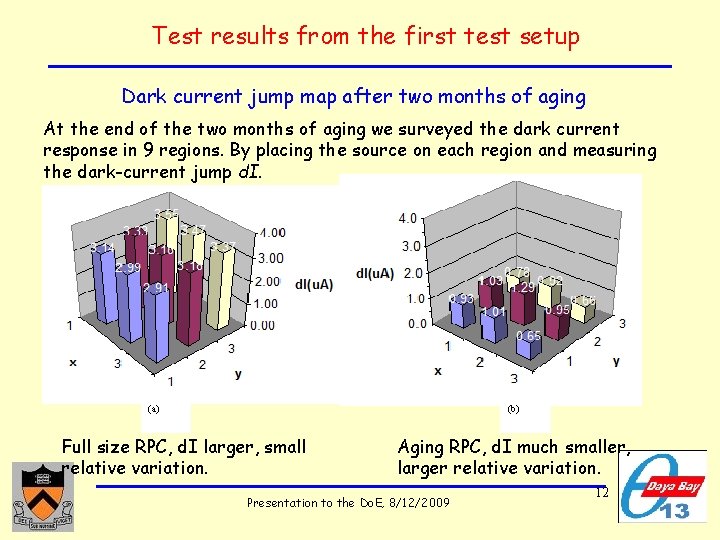
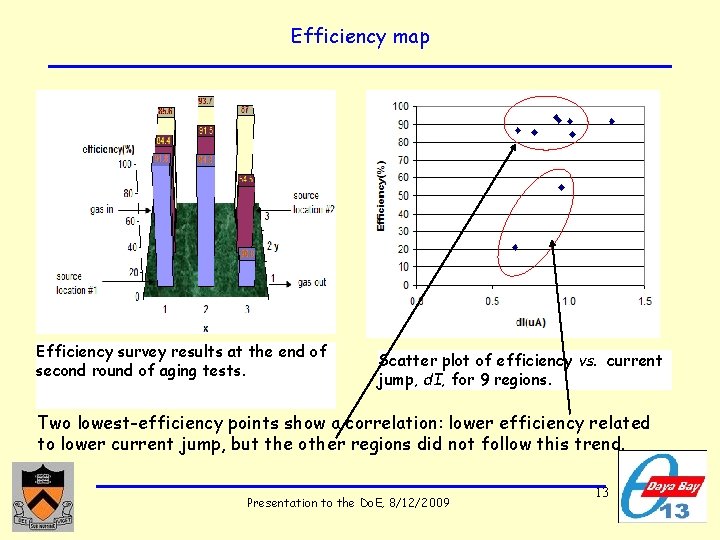
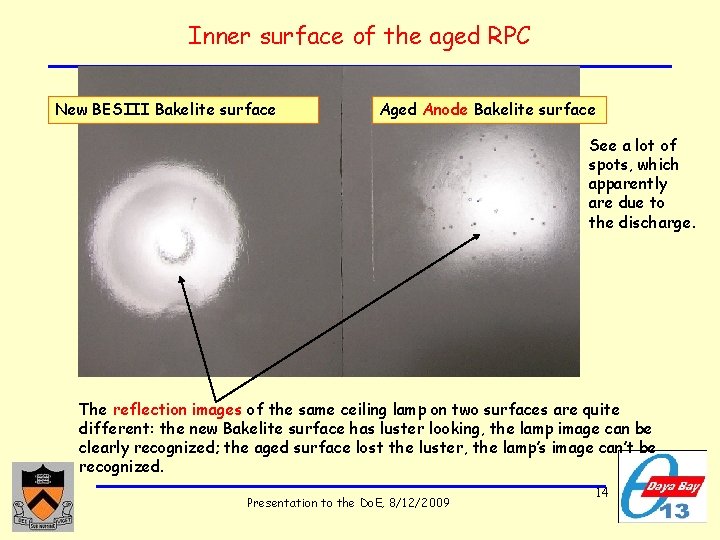
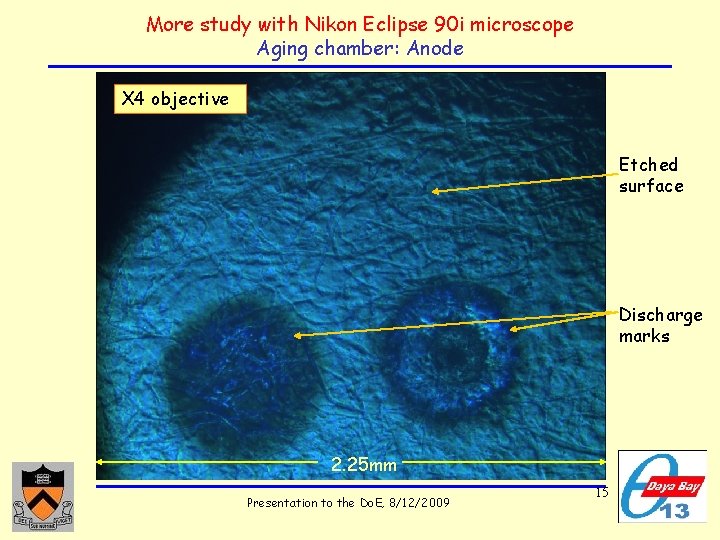
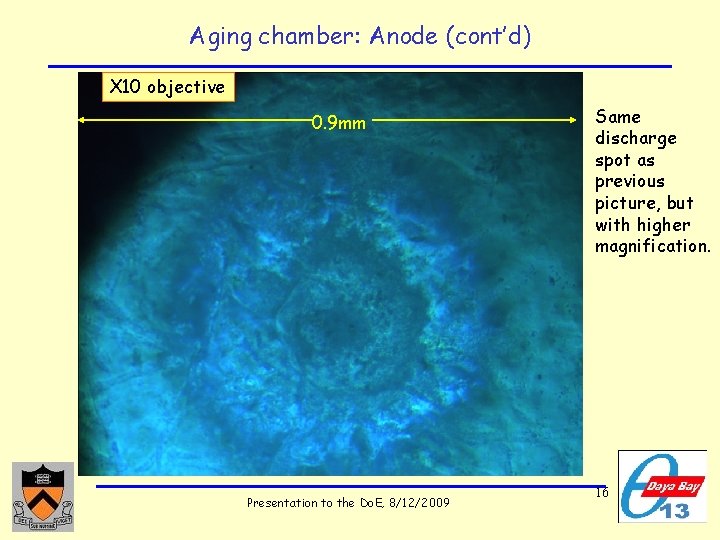
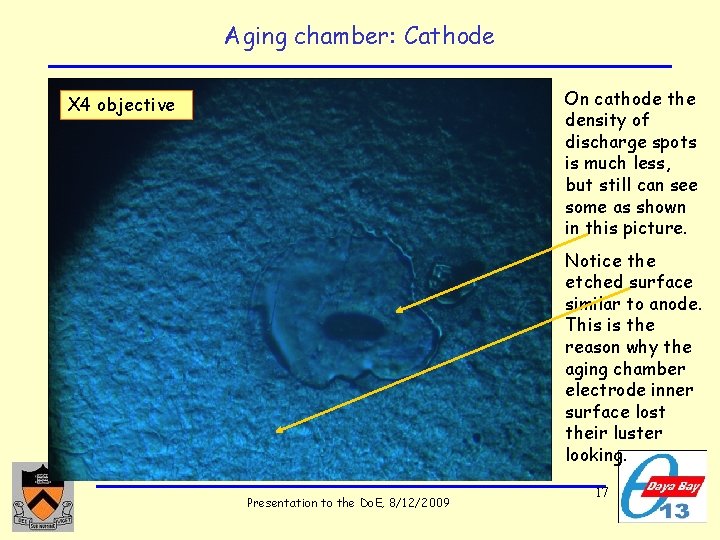

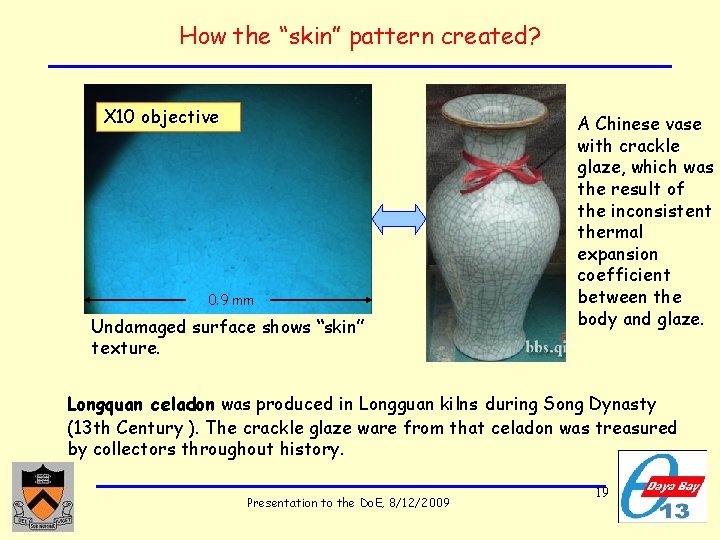
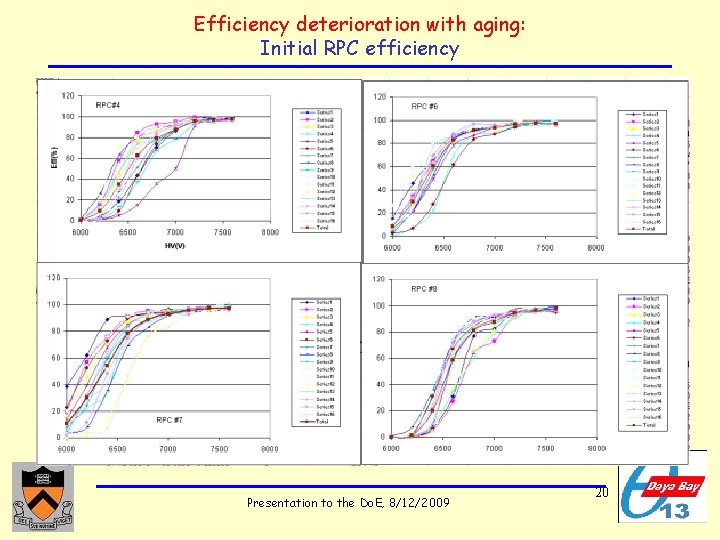
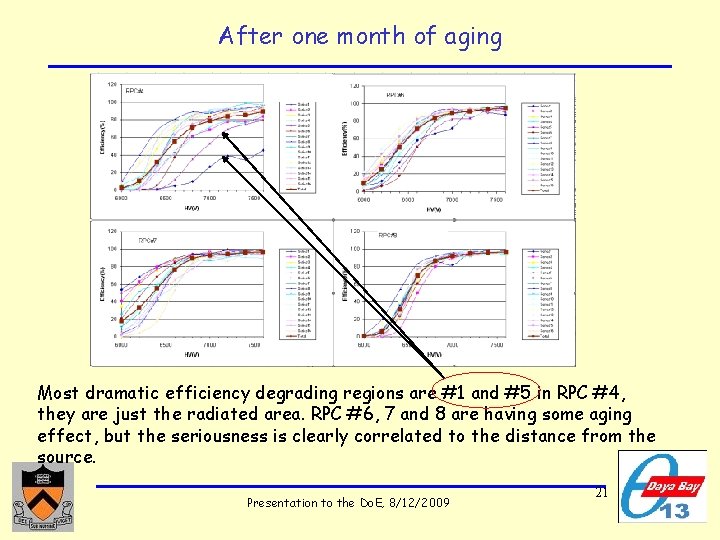
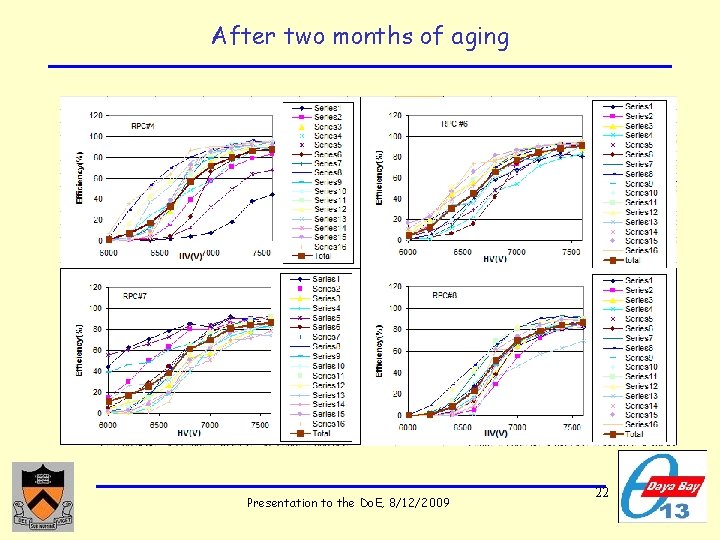
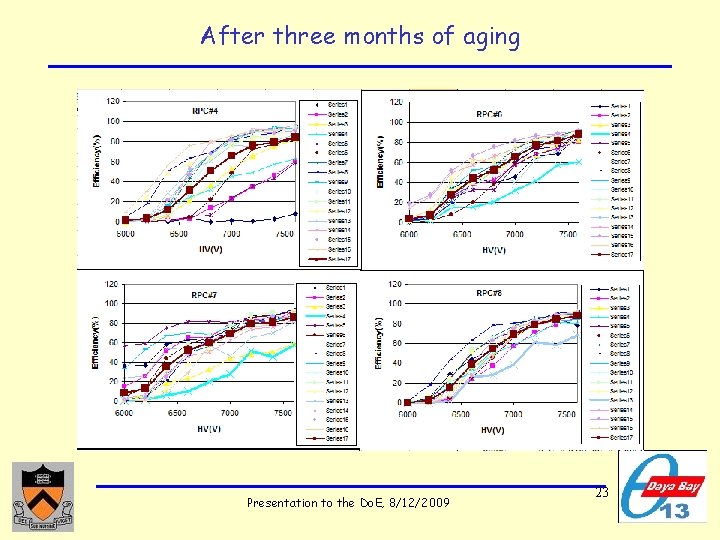
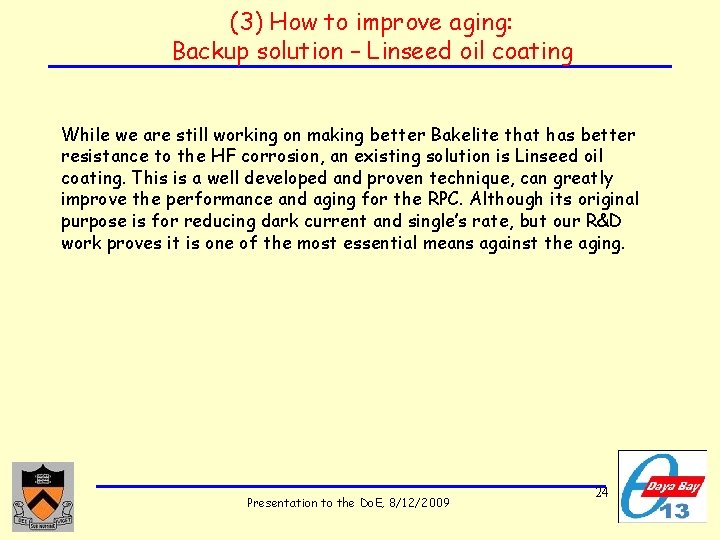
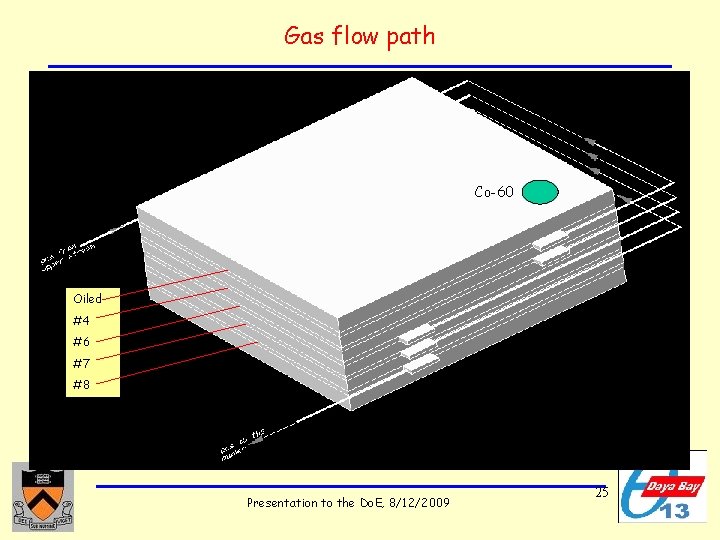
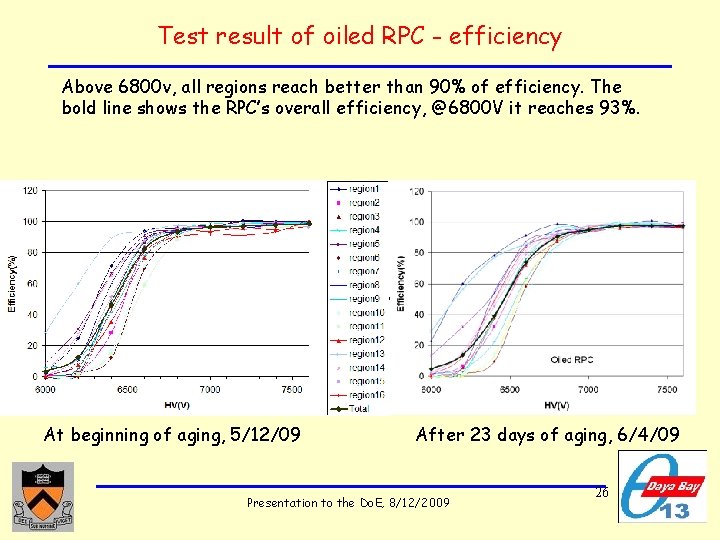
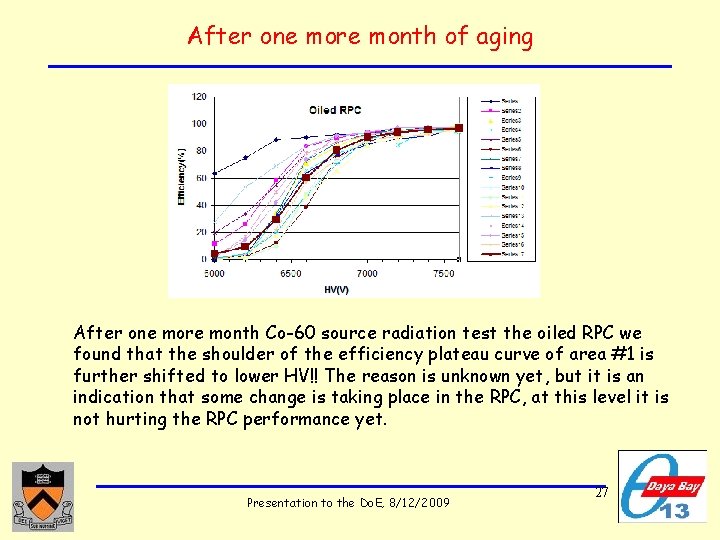
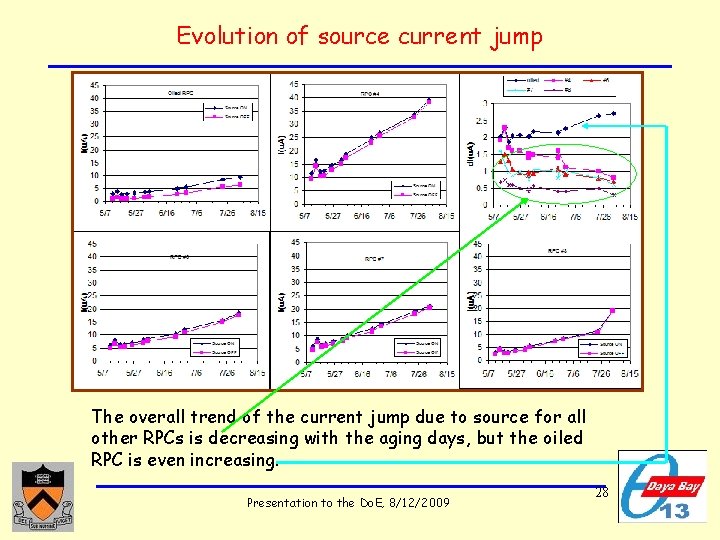
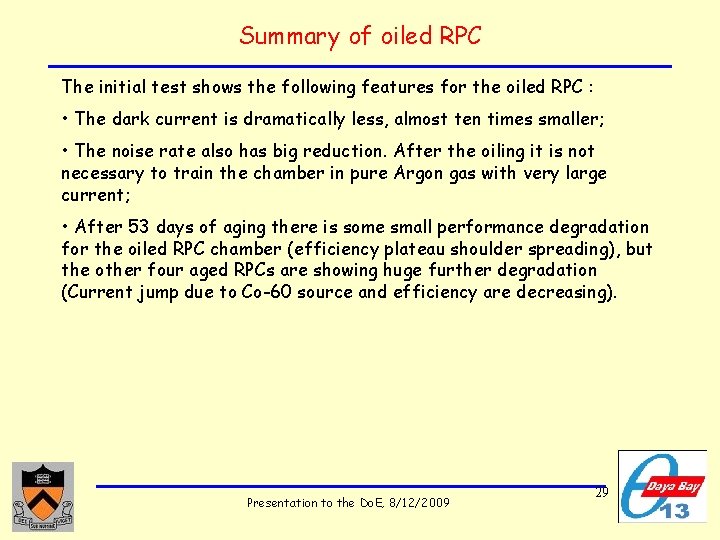
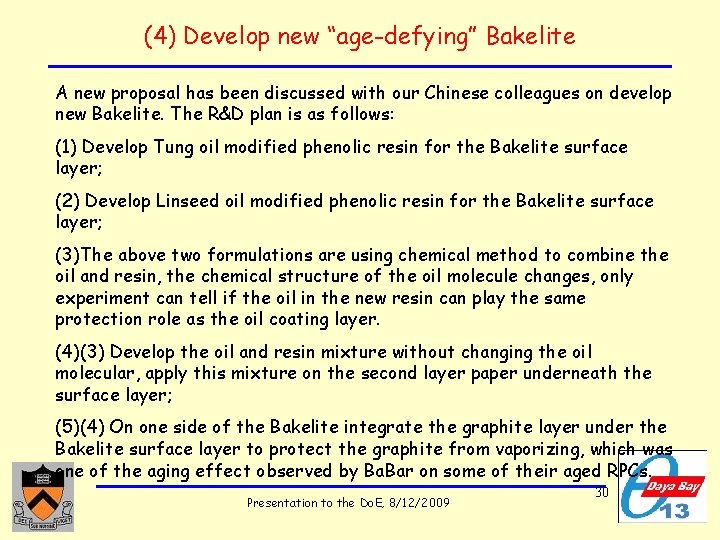
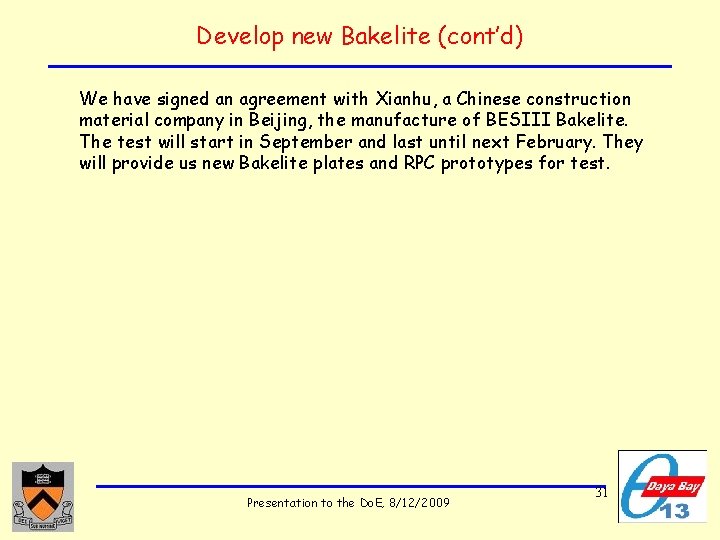
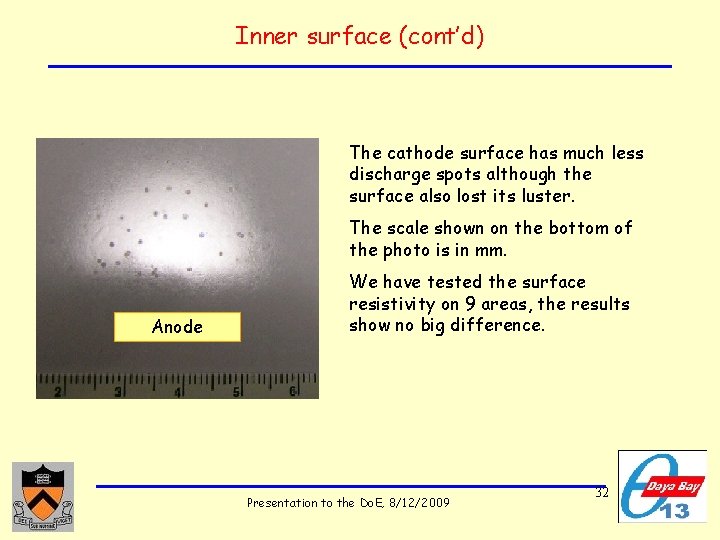
- Slides: 32
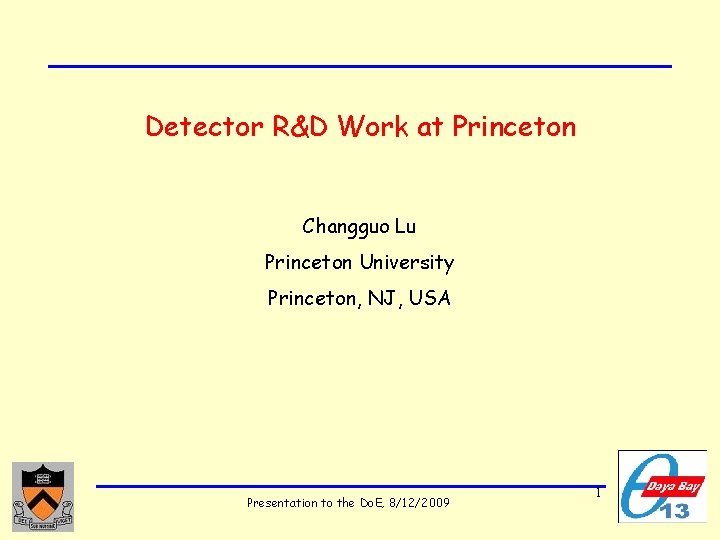
Detector R&D Work at Princeton Changguo Lu Princeton University Princeton, NJ, USA Presentation to the Do. E, 8/12/2009 1
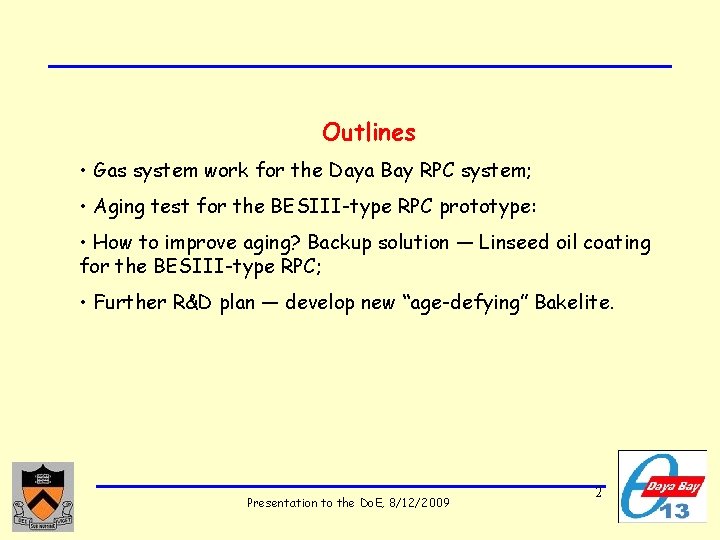
Outlines • Gas system work for the Daya Bay RPC system; • Aging test for the BESIII-type RPC prototype: • How to improve aging? Backup solution — Linseed oil coating for the BESIII-type RPC; • Further R&D plan — develop new “age-defying” Bakelite. Presentation to the Do. E, 8/12/2009 2
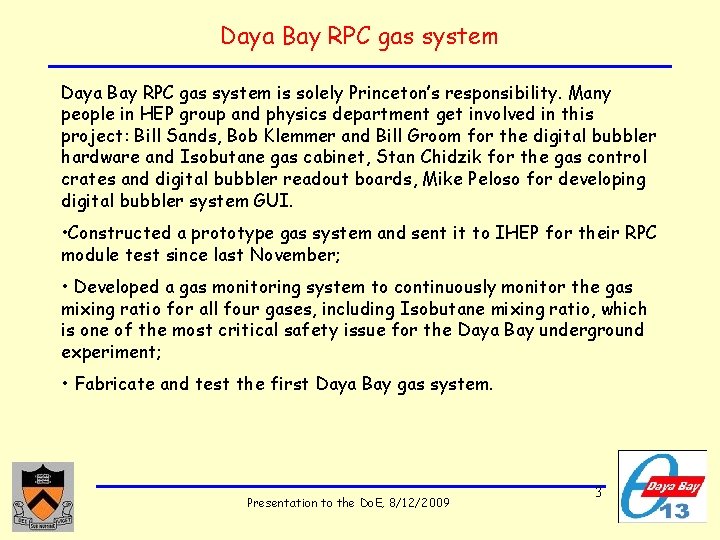
Daya Bay RPC gas system is solely Princeton’s responsibility. Many people in HEP group and physics department get involved in this project: Bill Sands, Bob Klemmer and Bill Groom for the digital bubbler hardware and Isobutane gas cabinet, Stan Chidzik for the gas control crates and digital bubbler readout boards, Mike Peloso for developing digital bubbler system GUI. • Constructed a prototype gas system and sent it to IHEP for their RPC module test since last November; • Developed a gas monitoring system to continuously monitor the gas mixing ratio for all four gases, including Isobutane mixing ratio, which is one of the most critical safety issue for the Daya Bay underground experiment; • Fabricate and test the first Daya Bay gas system. Presentation to the Do. E, 8/12/2009 3
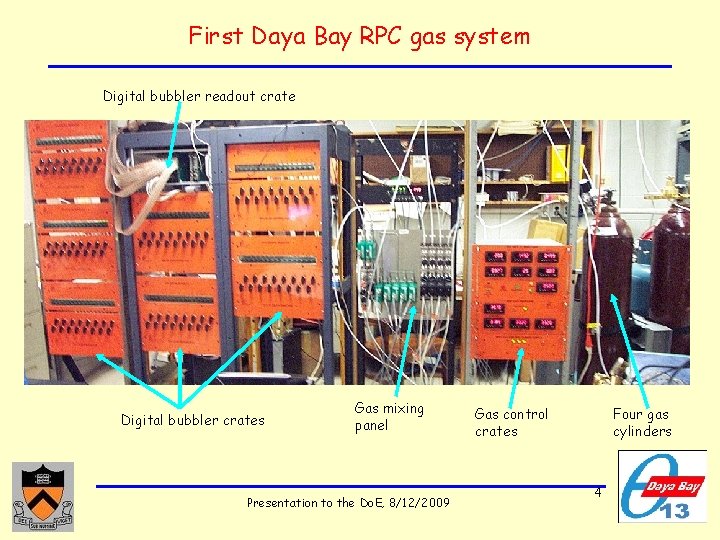
First Daya Bay RPC gas system Digital bubbler readout crate Digital bubbler crates Gas mixing panel Presentation to the Do. E, 8/12/2009 Gas control crates Four gas cylinders 4
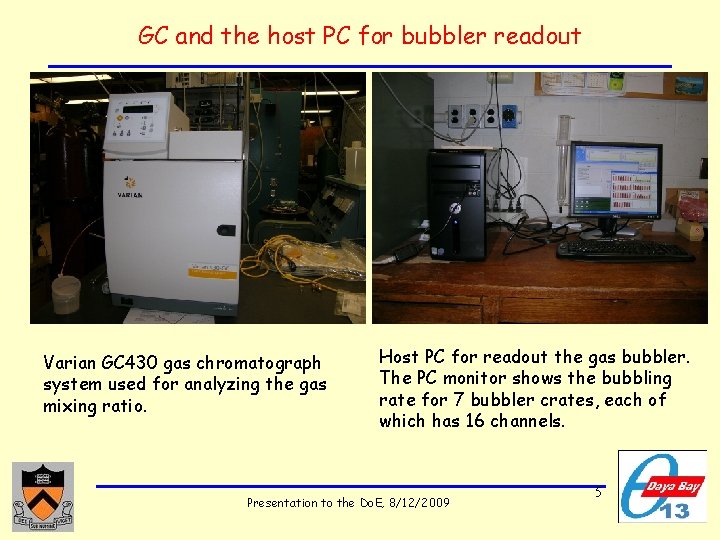
GC and the host PC for bubbler readout Varian GC 430 gas chromatograph system used for analyzing the gas mixing ratio. Host PC for readout the gas bubbler. The PC monitor shows the bubbling rate for 7 bubbler crates, each of which has 16 channels. Presentation to the Do. E, 8/12/2009 5

(2) Aging test for the BESIII-type RPC prototype Aging of Resitive Plate Chambers (RPCs) was a serious problem in the Ba. Bar experiment. This led to a large amount of effort by LHC detector groups to improve the aging and stability of these detectors. BESIII’s development of higher quality Bakelite that does not require linseed-oil treatment is very welcome progress in the field. However, the stability against aging of RPCs produced with this type of Bakelite has not been established. This technology has been used for BESIII muon system and Daya Bay neutrino experiment. The Si. D and ILD groups of ILC are considering RPC as one of the active detector candidate for their hadron calorimetry and muon system. BESIII-type of RPC is very attractive to them. Therefore the detailed aging study for this detector is quite urgent matter. Princeton has gained substantial experience with the aging properties of Bakelite RPCs since the early stage of the Ba. Bar RPC. We understand how important this aging property will be. It is our duty to answer this question and get involved in the R&D for the further improvement of the BESIII-type Bakelite. Presentation to the Do. E, 8/12/2009 6
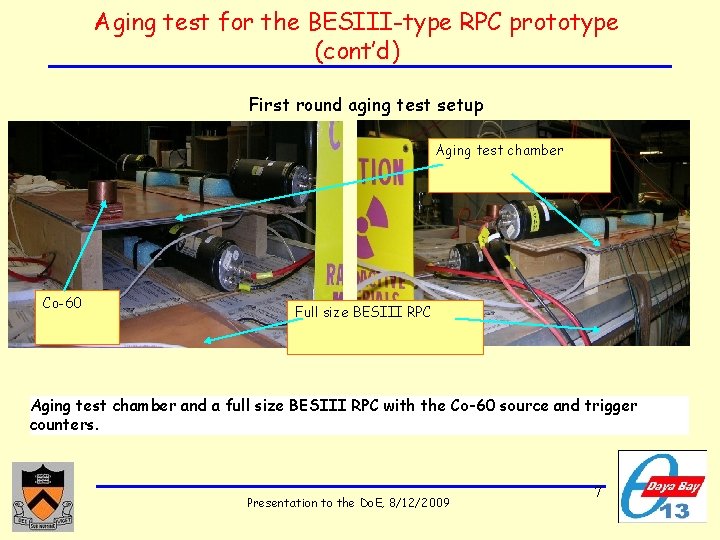
Aging test for the BESIII-type RPC prototype (cont’d) First round aging test setup Aging test chamber Co-60 Full size BESIII RPC Aging test chamber and a full size BESIII RPC with the Co-60 source and trigger counters. Presentation to the Do. E, 8/12/2009 7
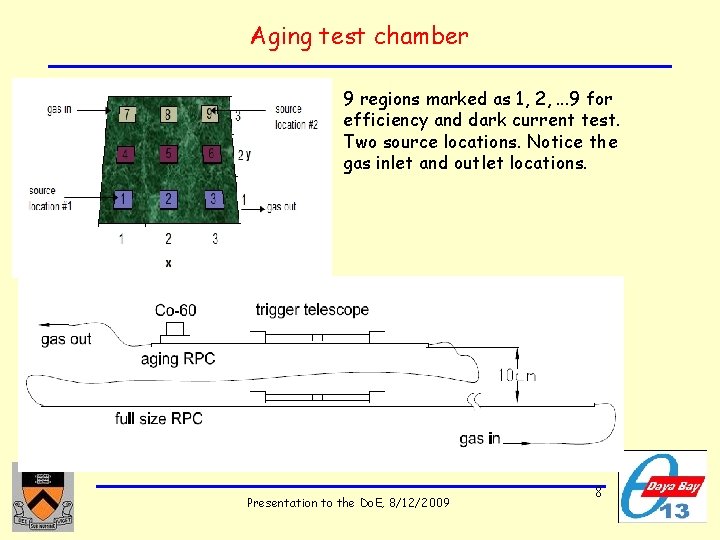
Aging test chamber 9 regions marked as 1, 2, . . . 9 for efficiency and dark current test. Two source locations. Notice the gas inlet and outlet locations. Presentation to the Do. E, 8/12/2009 8
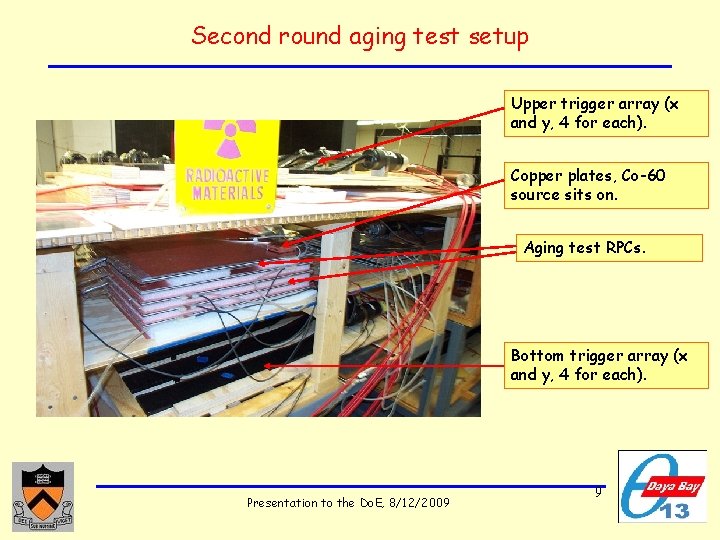
Second round aging test setup Upper trigger array (x and y, 4 for each). Copper plates, Co-60 source sits on. Aging test RPCs. Bottom trigger array (x and y, 4 for each). Presentation to the Do. E, 8/12/2009 9
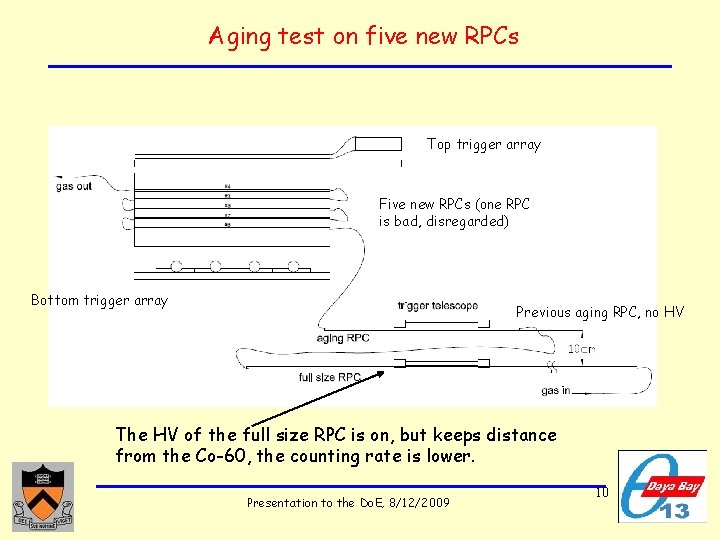
Aging test on five new RPCs Top trigger array Five new RPCs (one RPC is bad, disregarded) Bottom trigger array Previous aging RPC, no HV The HV of the full size RPC is on, but keeps distance from the Co-60, the counting rate is lower. Presentation to the Do. E, 8/12/2009 10
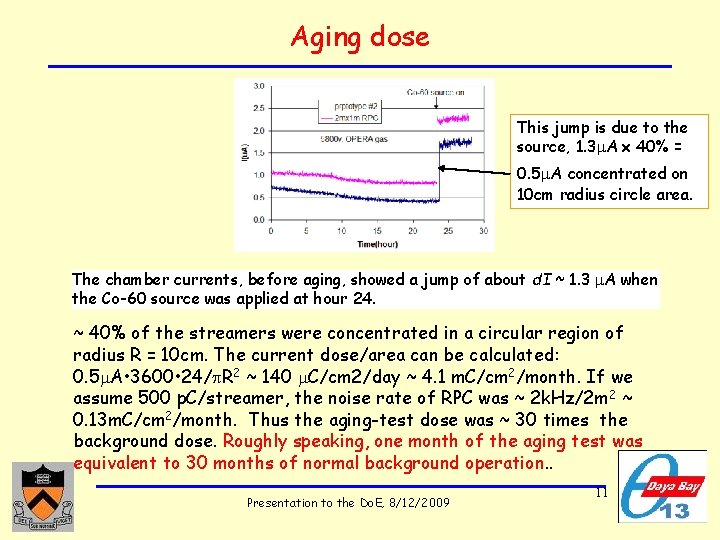
Aging dose This jump is due to the source, 1. 3 A x 40% = 0. 5 A concentrated on 10 cm radius circle area. The chamber currents, before aging, showed a jump of about d. I ~ 1. 3 A when the Co-60 source was applied at hour 24. ~ 40% of the streamers were concentrated in a circular region of radius R = 10 cm. The current dose/area can be calculated: 0. 5 A • 3600 • 24/ R 2 ~ 140 C/cm 2/day ~ 4. 1 m. C/cm 2/month. If we assume 500 p. C/streamer, the noise rate of RPC was ~ 2 k. Hz/2 m 2 ~ 0. 13 m. C/cm 2/month. Thus the aging-test dose was ~ 30 times the background dose. Roughly speaking, one month of the aging test was equivalent to 30 months of normal background operation. . Presentation to the Do. E, 8/12/2009 11
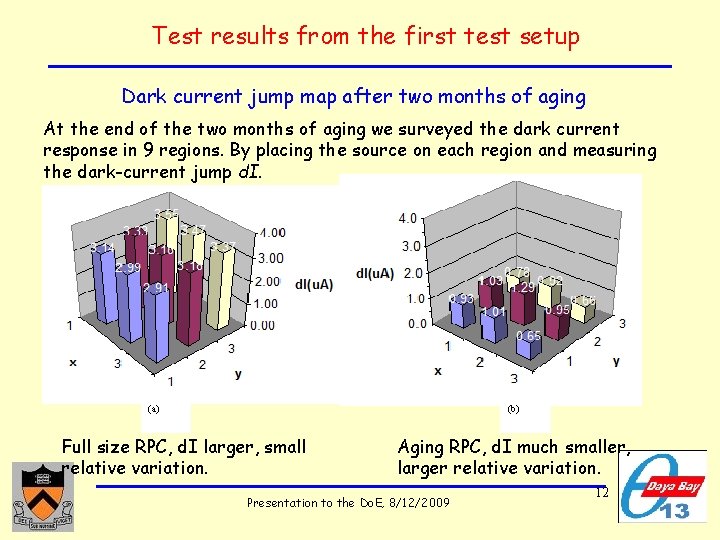
Test results from the first test setup Dark current jump map after two months of aging At the end of the two months of aging we surveyed the dark current response in 9 regions. By placing the source on each region and measuring the dark-current jump d. I. (a) (b) Full size RPC, d. I larger, small relative variation. Aging RPC, d. I much smaller, larger relative variation. Presentation to the Do. E, 8/12/2009 12
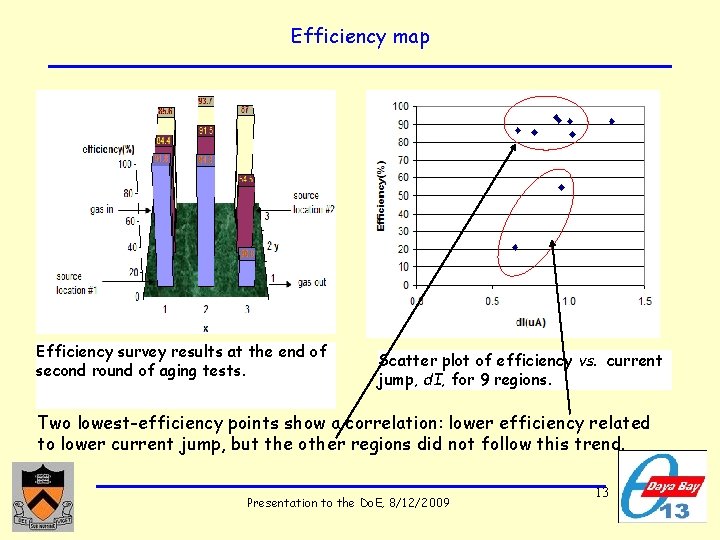
Efficiency map Efficiency survey results at the end of second round of aging tests. Scatter plot of efficiency vs. current jump, d. I, for 9 regions. Two lowest-efficiency points show a correlation: lower efficiency related to lower current jump, but the other regions did not follow this trend. Presentation to the Do. E, 8/12/2009 13
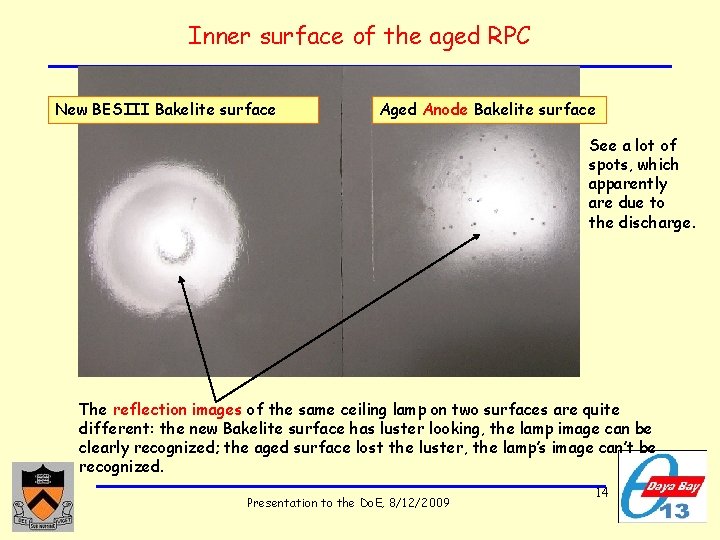
Inner surface of the aged RPC New BESIII Bakelite surface Aged Anode Bakelite surface See a lot of spots, which apparently are due to the discharge. The reflection images of the same ceiling lamp on two surfaces are quite different: the new Bakelite surface has luster looking, the lamp image can be clearly recognized; the aged surface lost the luster, the lamp’s image can’t be recognized. Presentation to the Do. E, 8/12/2009 14
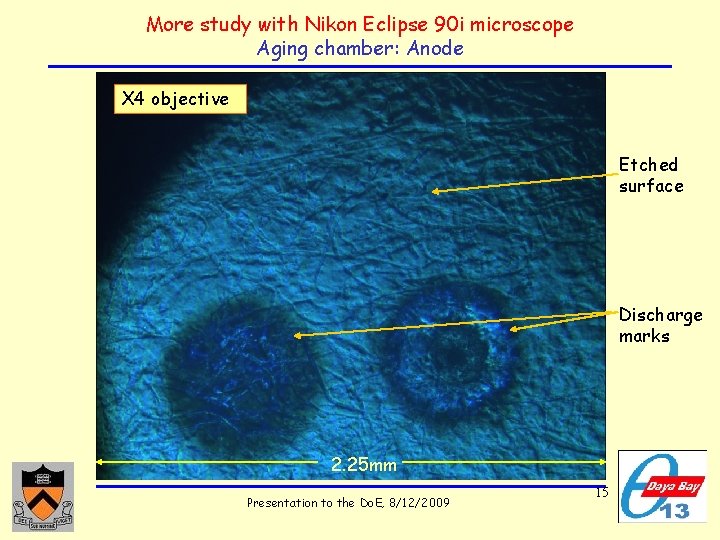
More study with Nikon Eclipse 90 i microscope Aging chamber: Anode X 4 objective Etched surface Discharge marks 2. 25 mm Presentation to the Do. E, 8/12/2009 15
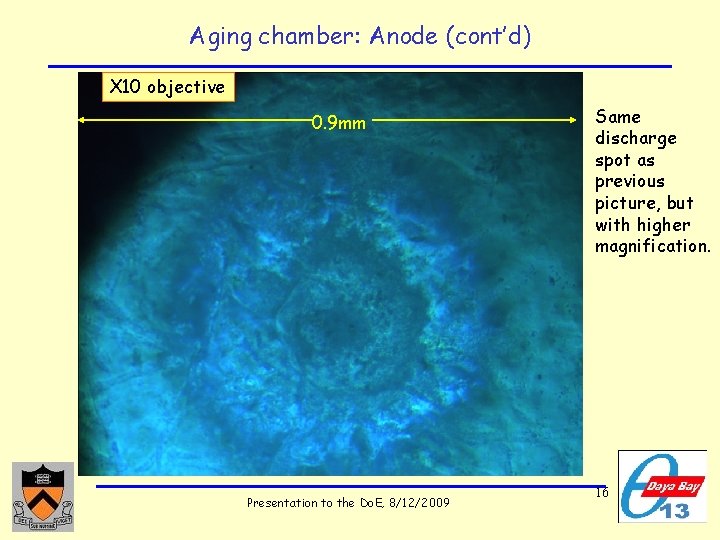
Aging chamber: Anode (cont’d) X 10 objective 0. 9 mm Presentation to the Do. E, 8/12/2009 Same discharge spot as previous picture, but with higher magnification. 16
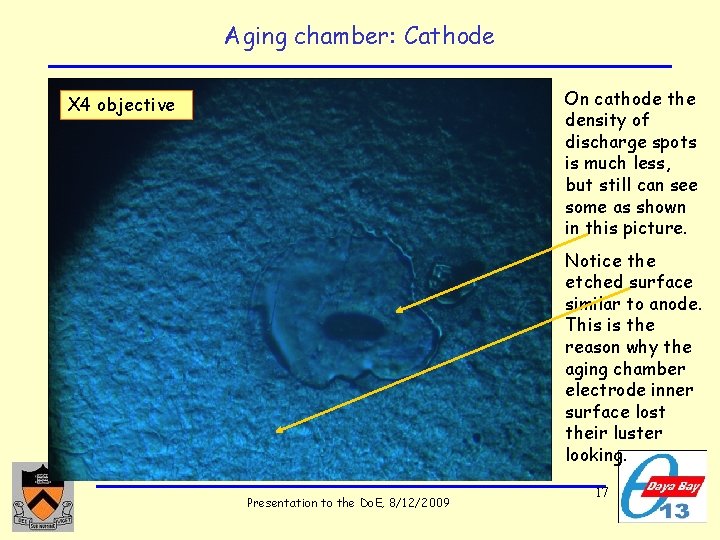
Aging chamber: Cathode On cathode the density of discharge spots is much less, but still can see some as shown in this picture. X 4 objective Notice the etched surface similar to anode. This is the reason why the aging chamber electrode inner surface lost their luster looking. Presentation to the Do. E, 8/12/2009 17

Comparison of BESIII and Italian Bakelite surface X 4 objective BESIII Bakelite sample. Besides the “skin-like” texture there is no serious scratch, looks much better than CMS sample, but we see “wrinkle”, which is quite unique. X 4 objective CMS RPC Bakelite sample. Compare to BESIII Bakelite sample, much worse surface quality can be seen. There is no similar “skin” structure, which may be related to different material and production procedure.
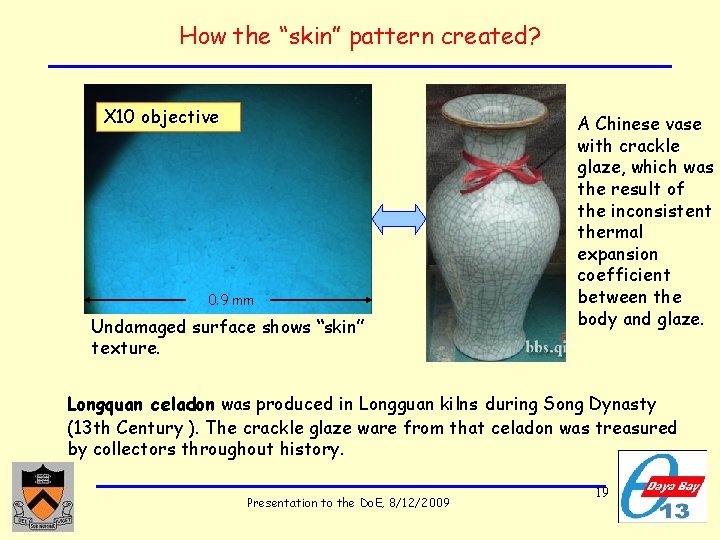
How the “skin” pattern created? X 10 objective 0. 9 mm Undamaged surface shows “skin” texture. A Chinese vase with crackle glaze, which was the result of the inconsistent thermal expansion coefficient between the body and glaze. Longquan celadon was produced in Longguan kilns during Song Dynasty (13 th Century ). The crackle glaze ware from that celadon was treasured by collectors throughout history. Presentation to the Do. E, 8/12/2009 19
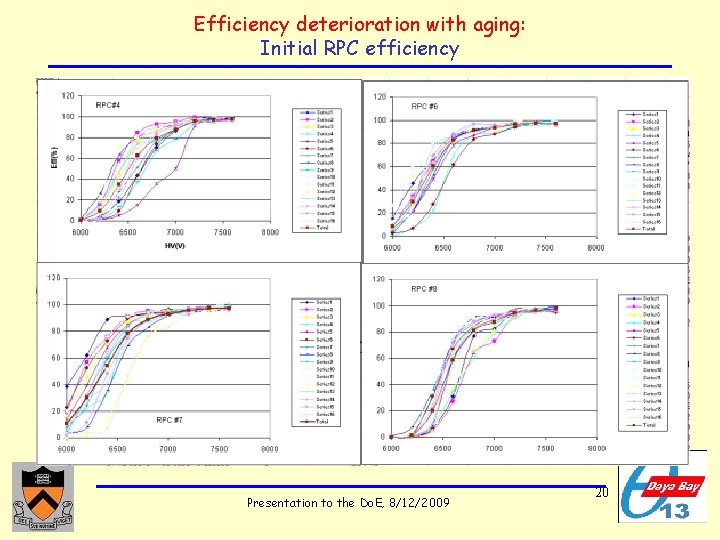
Efficiency deterioration with aging: Initial RPC efficiency Presentation to the Do. E, 8/12/2009 20
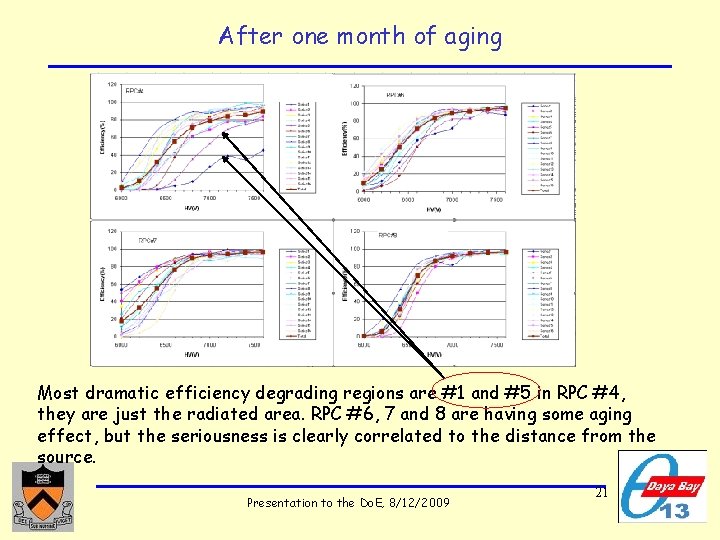
After one month of aging Most dramatic efficiency degrading regions are #1 and #5 in RPC #4, they are just the radiated area. RPC #6, 7 and 8 are having some aging effect, but the seriousness is clearly correlated to the distance from the source. Presentation to the Do. E, 8/12/2009 21
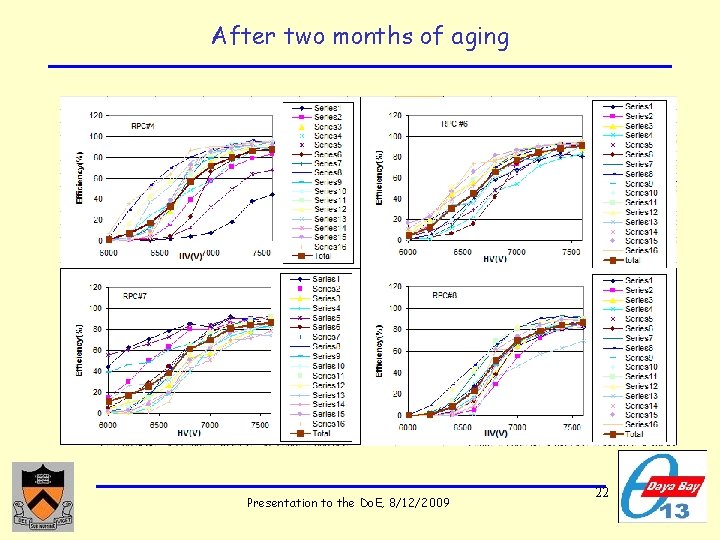
After two months of aging Presentation to the Do. E, 8/12/2009 22
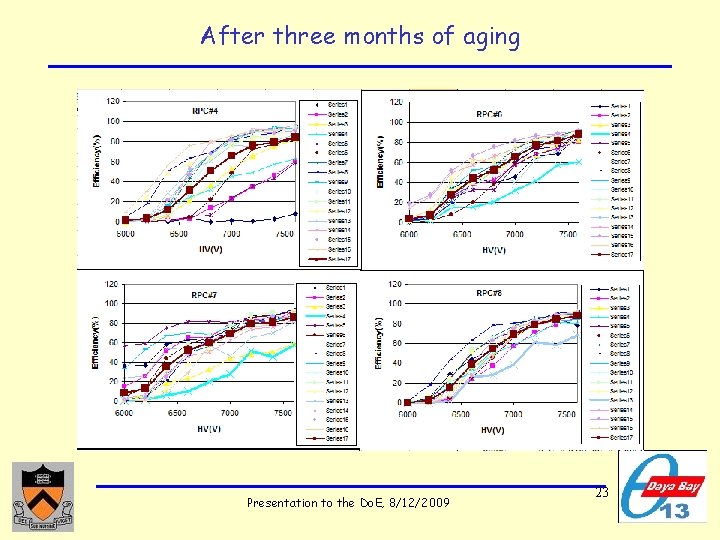
After three months of aging Presentation to the Do. E, 8/12/2009 23
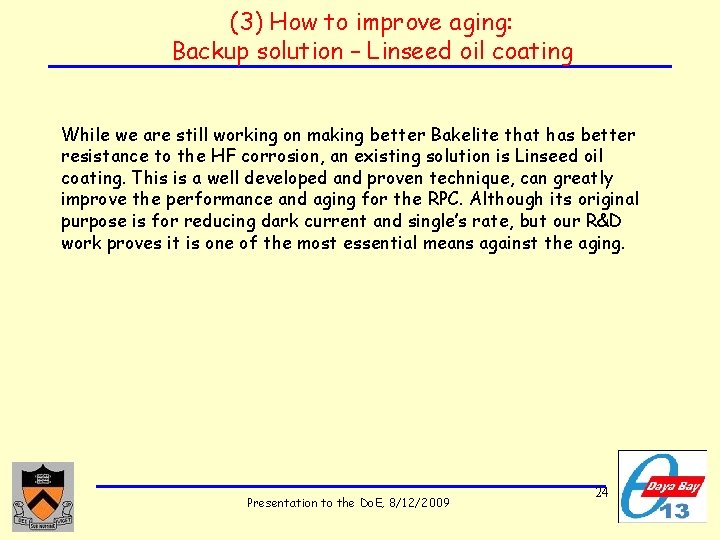
(3) How to improve aging: Backup solution – Linseed oil coating While we are still working on making better Bakelite that has better resistance to the HF corrosion, an existing solution is Linseed oil coating. This is a well developed and proven technique, can greatly improve the performance and aging for the RPC. Although its original purpose is for reducing dark current and single’s rate, but our R&D work proves it is one of the most essential means against the aging. Presentation to the Do. E, 8/12/2009 24
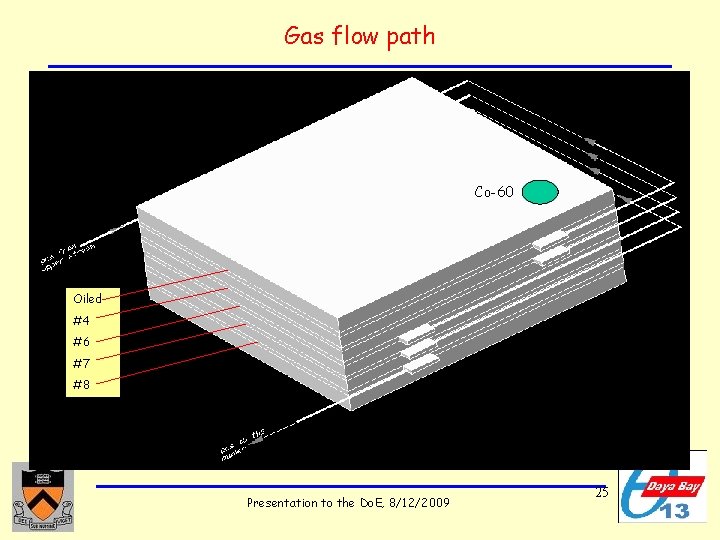
Gas flow path Co-60 Oiled #4 #6 #7 #8 Presentation to the Do. E, 8/12/2009 25
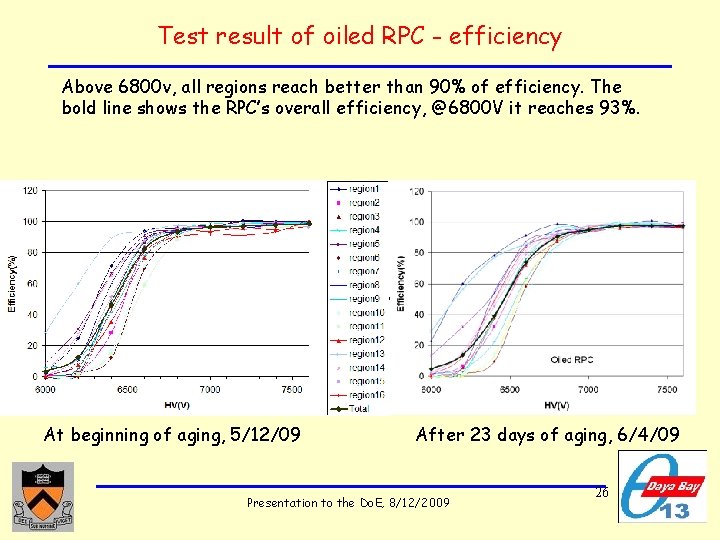
Test result of oiled RPC - efficiency Above 6800 v, all regions reach better than 90% of efficiency. The bold line shows the RPC’s overall efficiency, @6800 V it reaches 93%. At beginning of aging, 5/12/09 After 23 days of aging, 6/4/09 Presentation to the Do. E, 8/12/2009 26
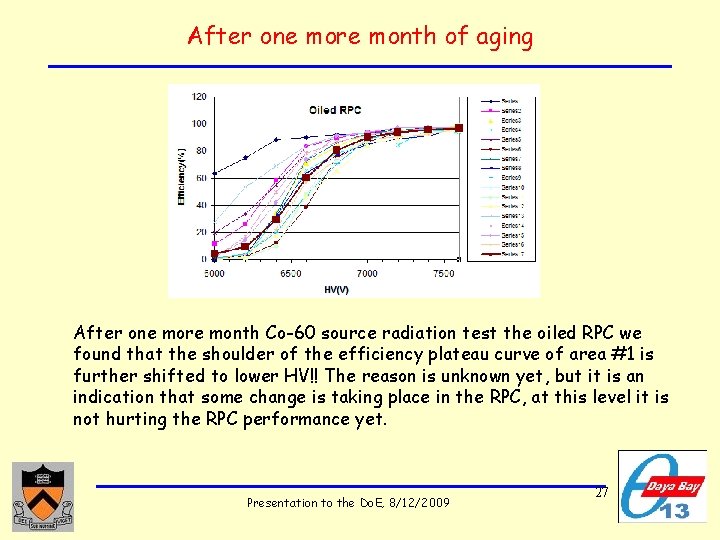
After one more month of aging After one more month Co-60 source radiation test the oiled RPC we found that the shoulder of the efficiency plateau curve of area #1 is further shifted to lower HV!! The reason is unknown yet, but it is an indication that some change is taking place in the RPC, at this level it is not hurting the RPC performance yet. Presentation to the Do. E, 8/12/2009 27
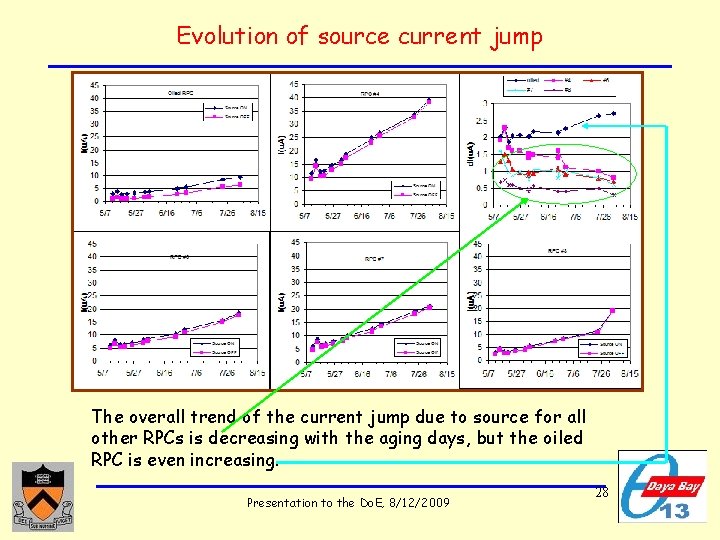
Evolution of source current jump The overall trend of the current jump due to source for all other RPCs is decreasing with the aging days, but the oiled RPC is even increasing. Presentation to the Do. E, 8/12/2009 28
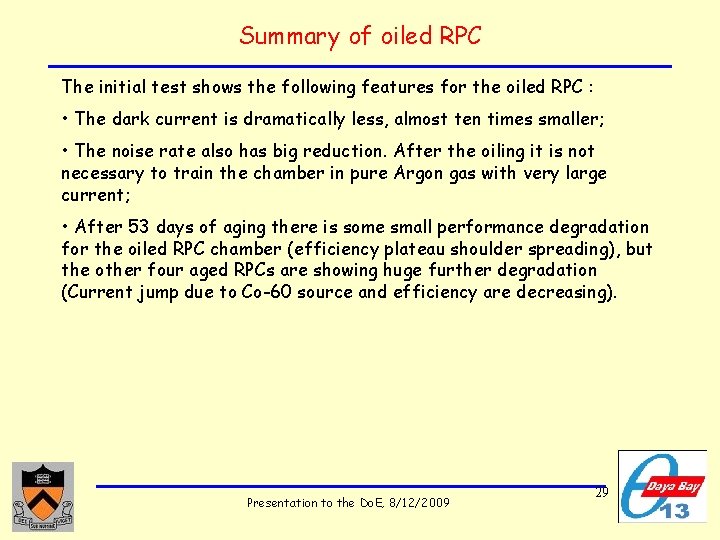
Summary of oiled RPC The initial test shows the following features for the oiled RPC : • The dark current is dramatically less, almost ten times smaller; • The noise rate also has big reduction. After the oiling it is not necessary to train the chamber in pure Argon gas with very large current; • After 53 days of aging there is some small performance degradation for the oiled RPC chamber (efficiency plateau shoulder spreading), but the other four aged RPCs are showing huge further degradation (Current jump due to Co-60 source and efficiency are decreasing). Presentation to the Do. E, 8/12/2009 29
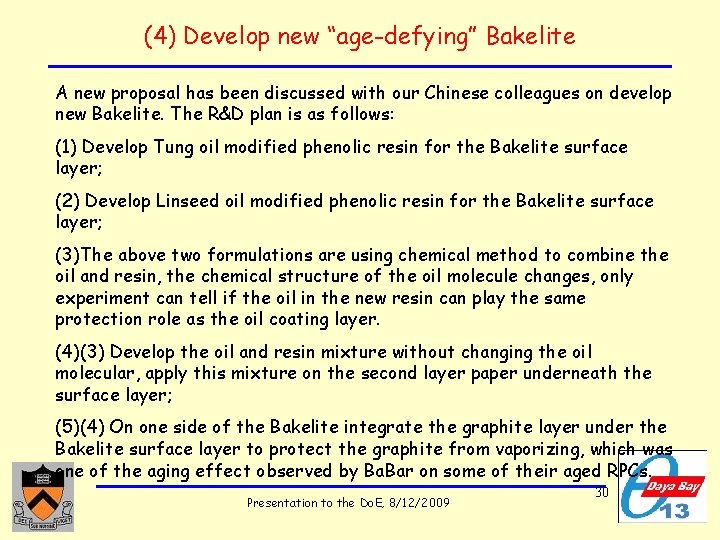
(4) Develop new “age-defying” Bakelite A new proposal has been discussed with our Chinese colleagues on develop new Bakelite. The R&D plan is as follows: (1) Develop Tung oil modified phenolic resin for the Bakelite surface layer; (2) Develop Linseed oil modified phenolic resin for the Bakelite surface layer; (3)The above two formulations are using chemical method to combine the oil and resin, the chemical structure of the oil molecule changes, only experiment can tell if the oil in the new resin can play the same protection role as the oil coating layer. (4)(3) Develop the oil and resin mixture without changing the oil molecular, apply this mixture on the second layer paper underneath the surface layer; (5)(4) On one side of the Bakelite integrate the graphite layer under the Bakelite surface layer to protect the graphite from vaporizing, which was one of the aging effect observed by Ba. Bar on some of their aged RPCs. Presentation to the Do. E, 8/12/2009 30
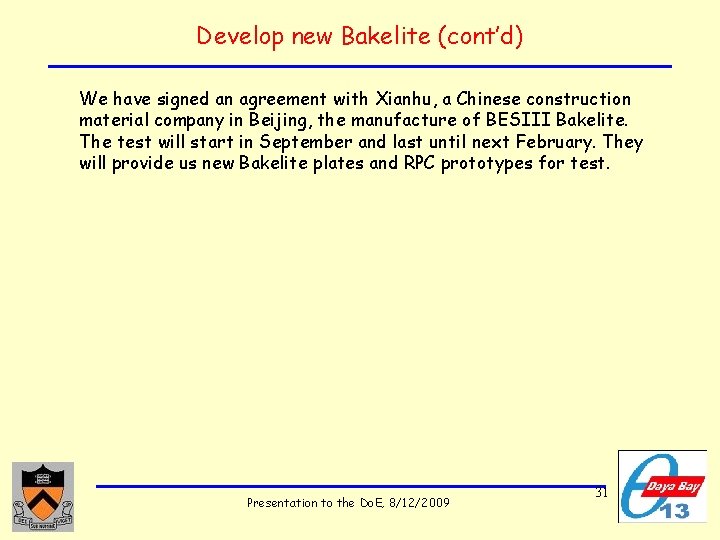
Develop new Bakelite (cont’d) We have signed an agreement with Xianhu, a Chinese construction material company in Beijing, the manufacture of BESIII Bakelite. The test will start in September and last until next February. They will provide us new Bakelite plates and RPC prototypes for test. Presentation to the Do. E, 8/12/2009 31
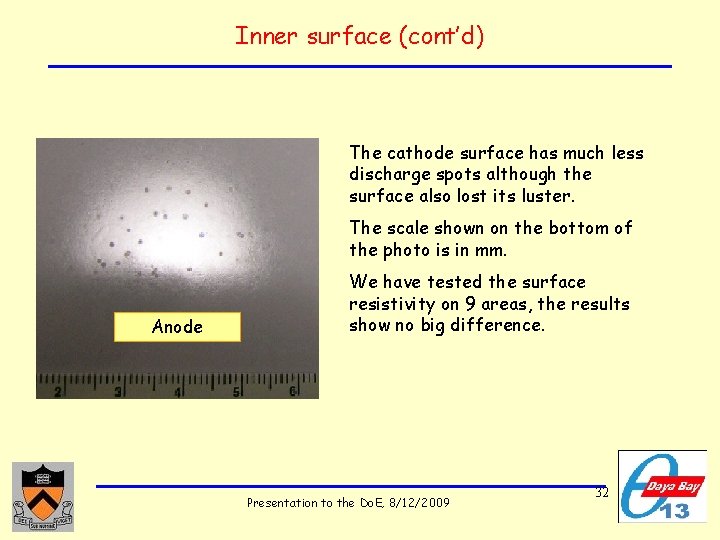
Inner surface (cont’d) The cathode surface has much less discharge spots although the surface also lost its luster. The scale shown on the bottom of the photo is in mm. Anode We have tested the surface resistivity on 9 areas, the results show no big difference. Presentation to the Do. E, 8/12/2009 32
Font detector
Gas chromatography
Javascript plagiarism detector
Cutie pie ionization chamber
Detector
Blood flow detector
Moth smoke summary
Harris corner detector
Colour code detector
Charge coupled device detector
Font detector
What is cohesive devices
Lowe sift
Hogge phase detector
Particle detector
Roforkad
Comb/ex gas detector meaning
Font detector
Chipset detector
"perkin elmer"
Smoke detector repair montgomery county
Edhallpass
Optical fibre system
Ct scan detector
Timepix detector
Hplc detector types
Smoke detector installation kentucky
Detector
Timepix detector
Carbon monixde detector
Microchannel plate detector
Digital detector array
Spaghetti detector