Cryomodule Pressure Systems Operation and Emergency Venting Joshua
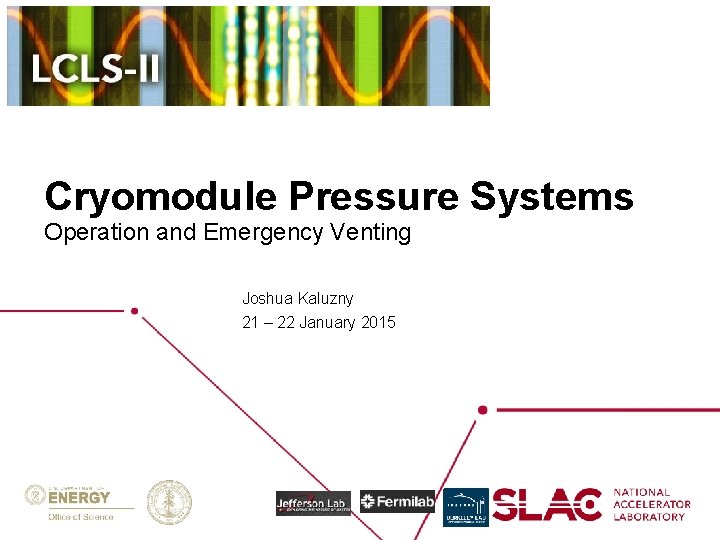
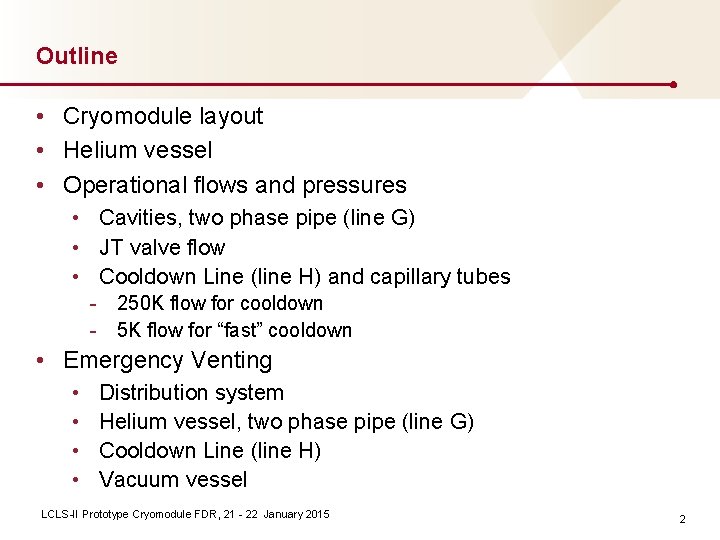
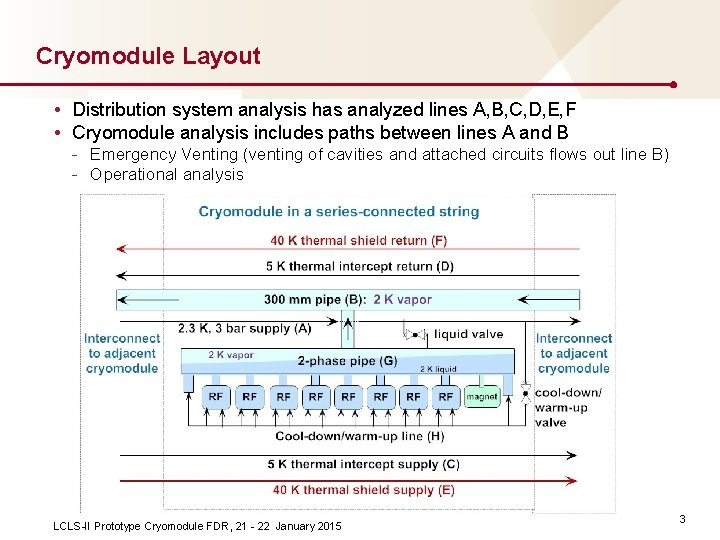
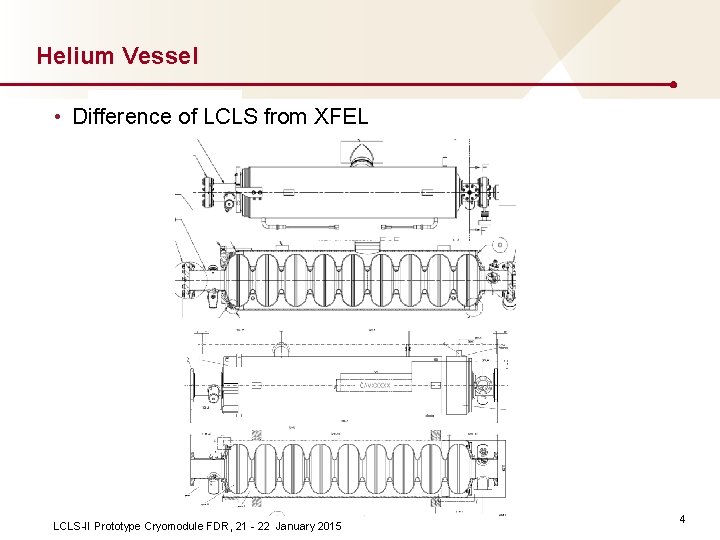
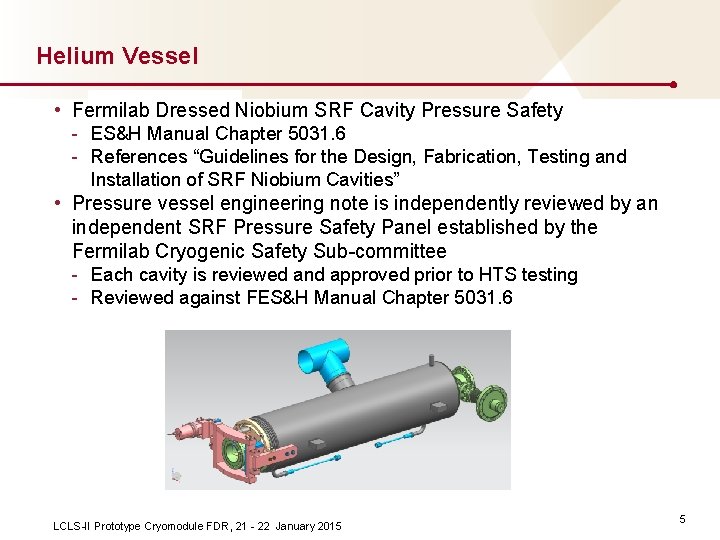
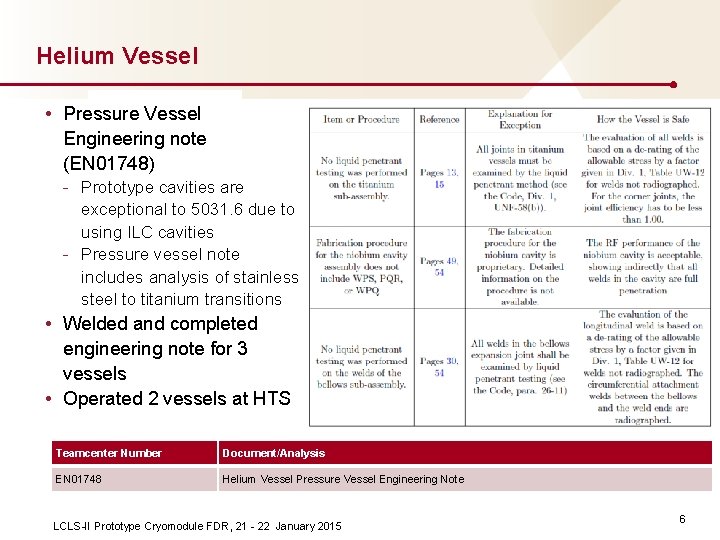
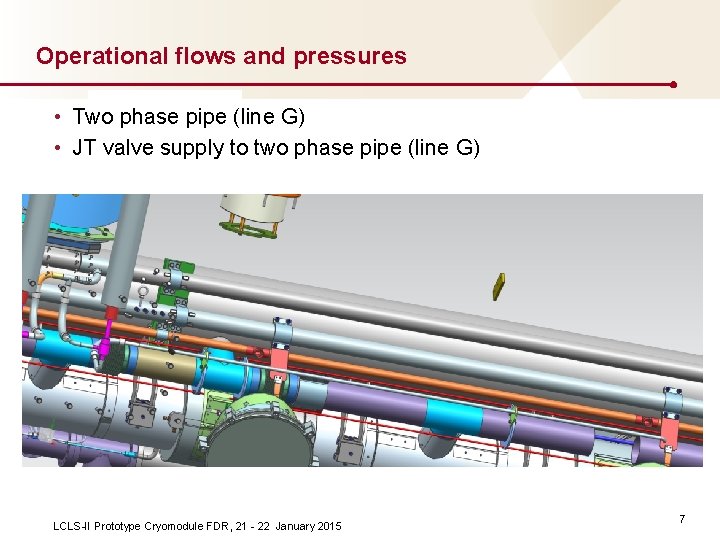
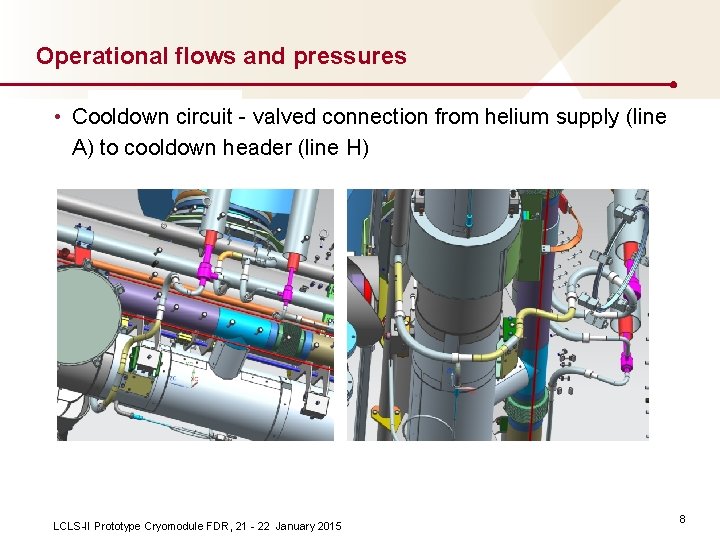
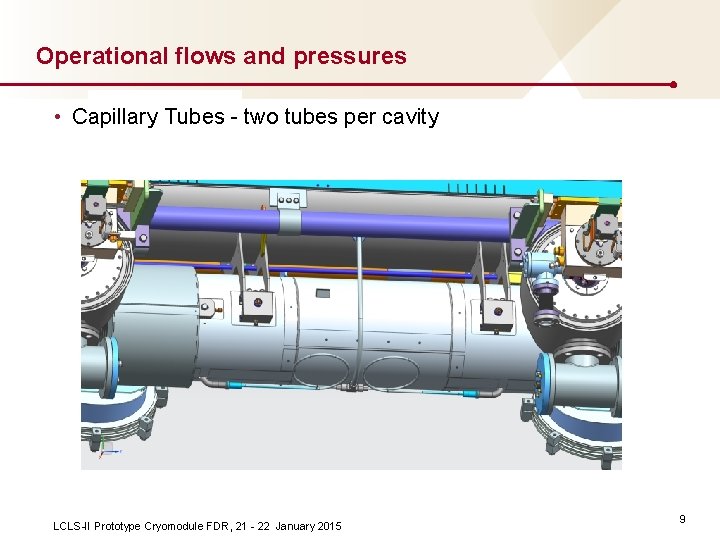
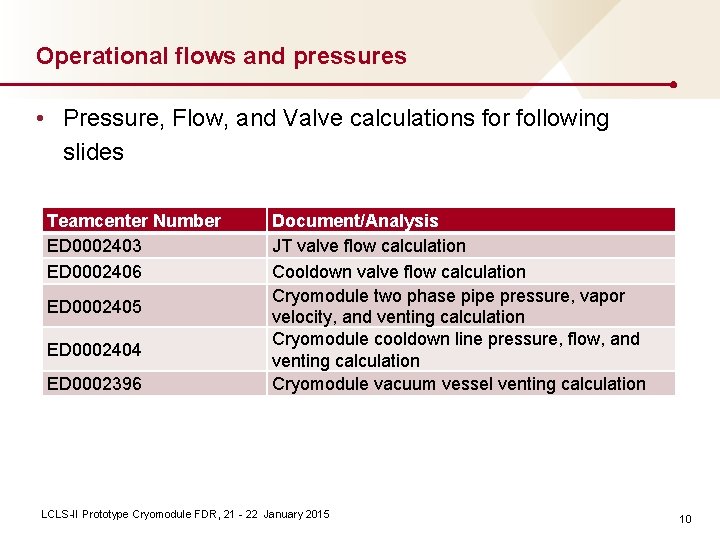
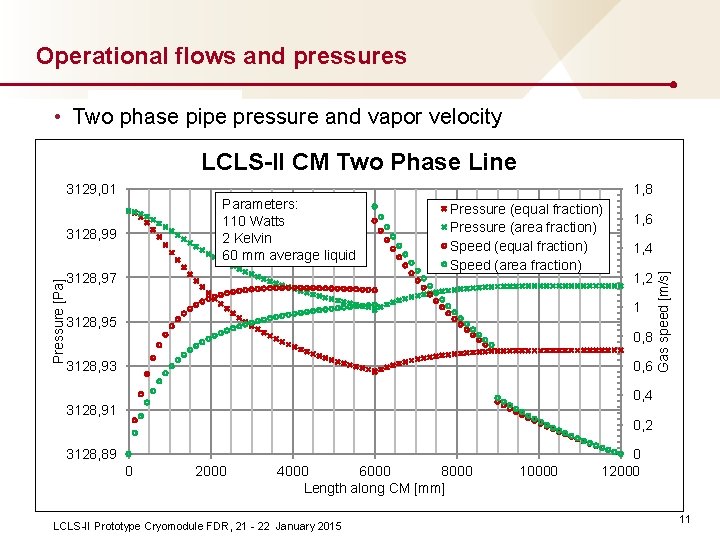
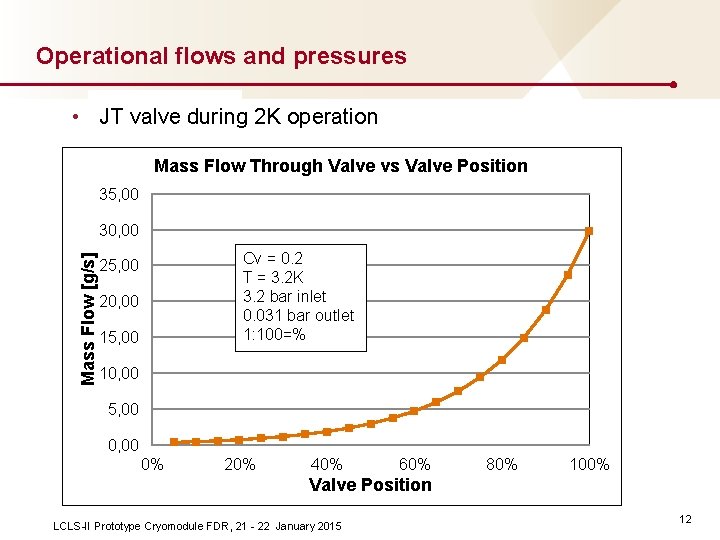
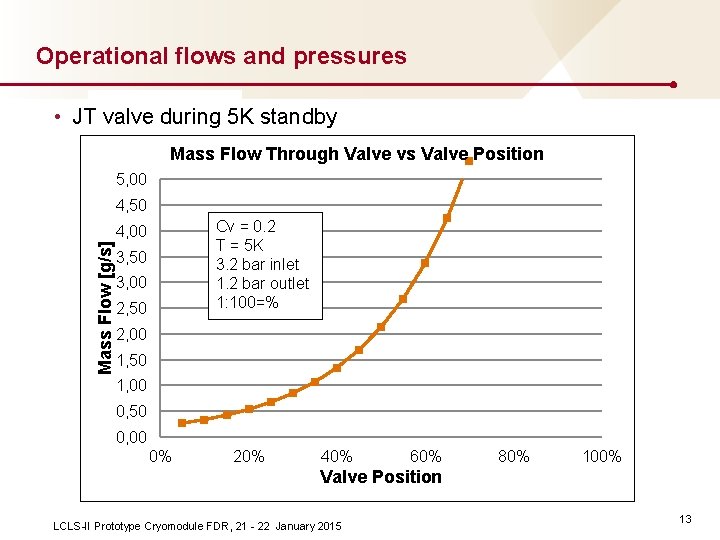
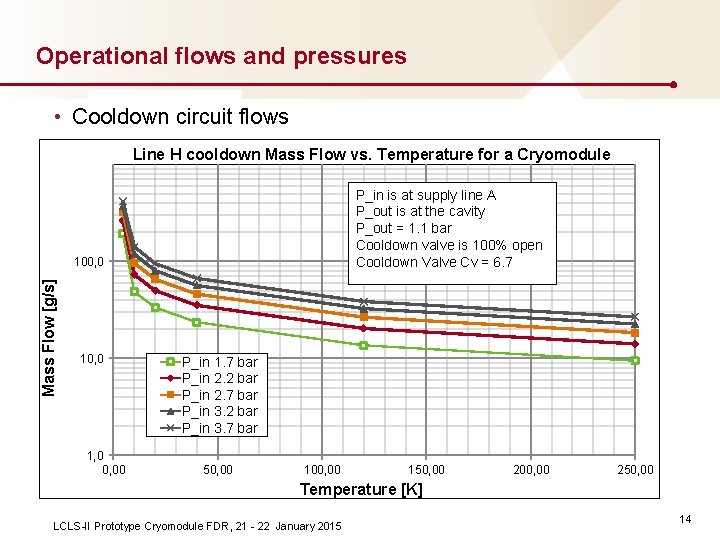
![Emergency Venting Pressure Drop to Relief [%] • Relief analysis has been done in Emergency Venting Pressure Drop to Relief [%] • Relief analysis has been done in](https://slidetodoc.com/presentation_image_h2/0e21e8b94653430fc443274121c60a78/image-15.jpg)
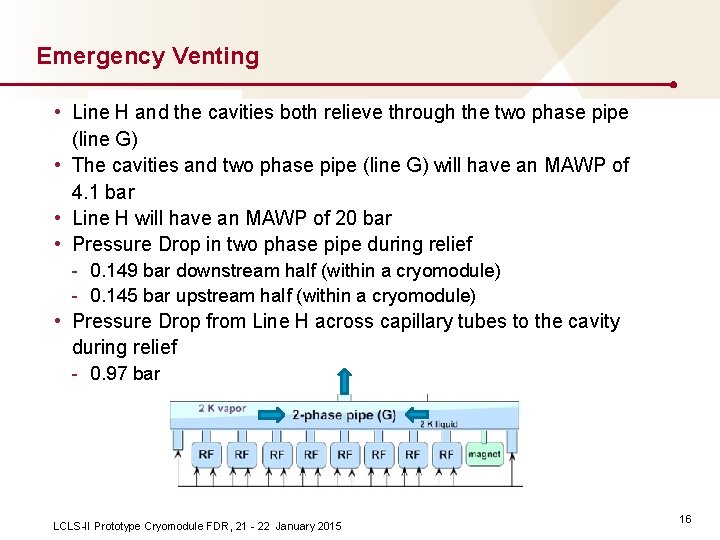
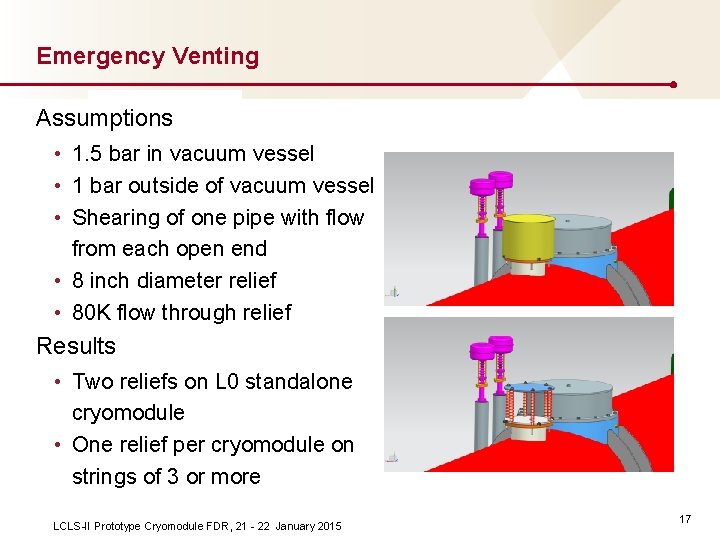
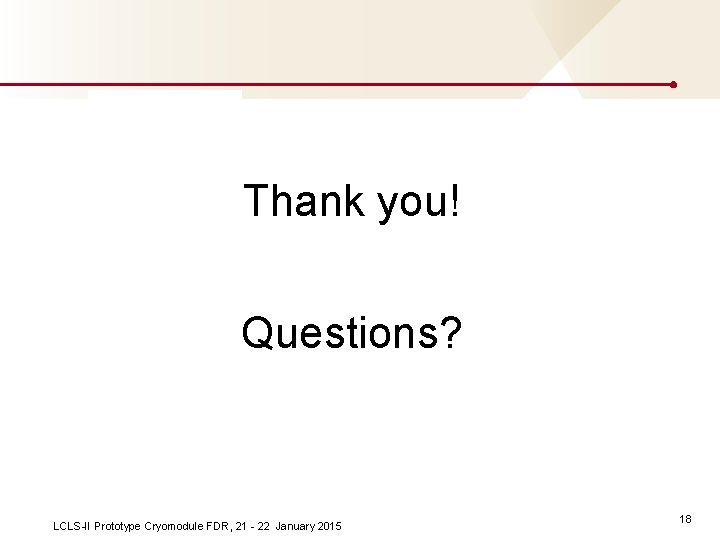
- Slides: 18
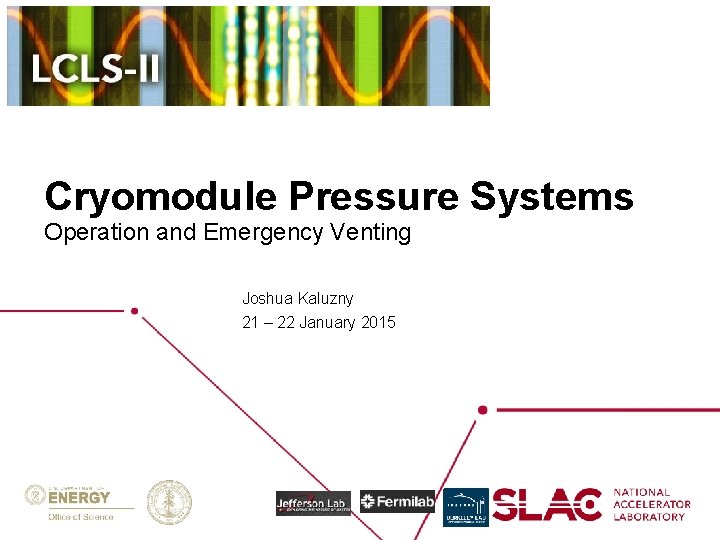
Cryomodule Pressure Systems Operation and Emergency Venting Joshua Kaluzny 21 – 22 January 2015
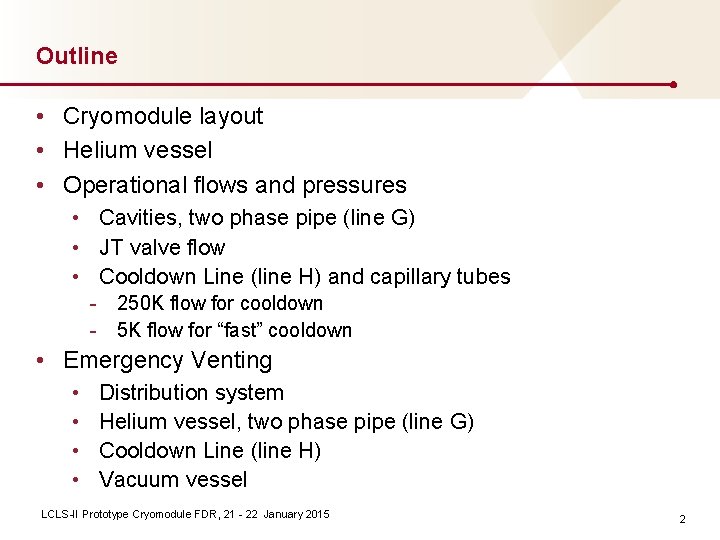
Outline • Cryomodule layout • Helium vessel • Operational flows and pressures • Cavities, two phase pipe (line G) • JT valve flow • Cooldown Line (line H) and capillary tubes - 250 K flow for cooldown - 5 K flow for “fast” cooldown • Emergency Venting • • Distribution system Helium vessel, two phase pipe (line G) Cooldown Line (line H) Vacuum vessel LCLS-II Prototype Cryomodule FDR, 21 - 22 January 2015 2
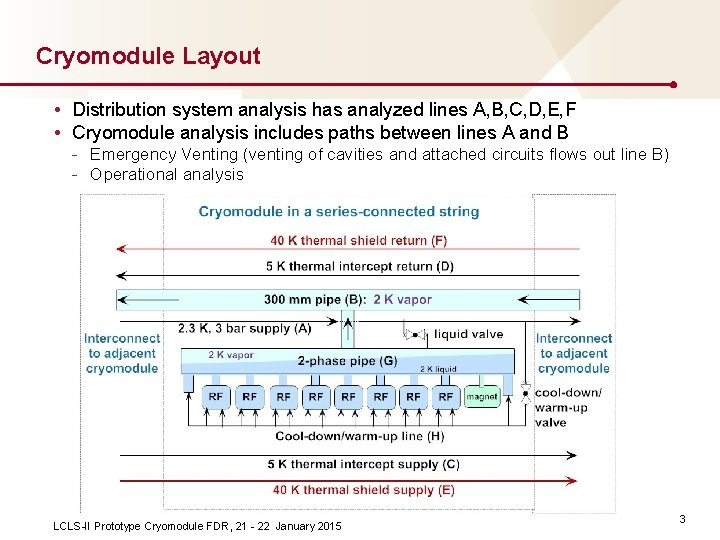
Cryomodule Layout • Distribution system analysis has analyzed lines A, B, C, D, E, F • Cryomodule analysis includes paths between lines A and B - Emergency Venting (venting of cavities and attached circuits flows out line B) - Operational analysis LCLS-II Prototype Cryomodule FDR, 21 - 22 January 2015 3
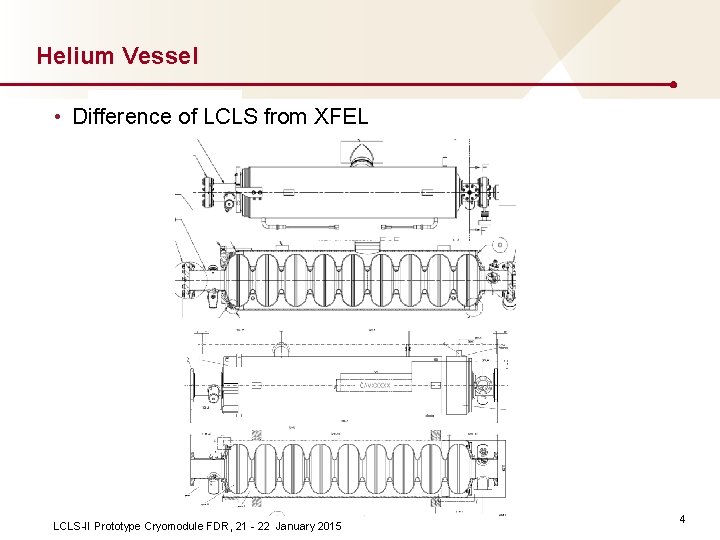
Helium Vessel • Difference of LCLS from XFEL LCLS-II Prototype Cryomodule FDR, 21 - 22 January 2015 4
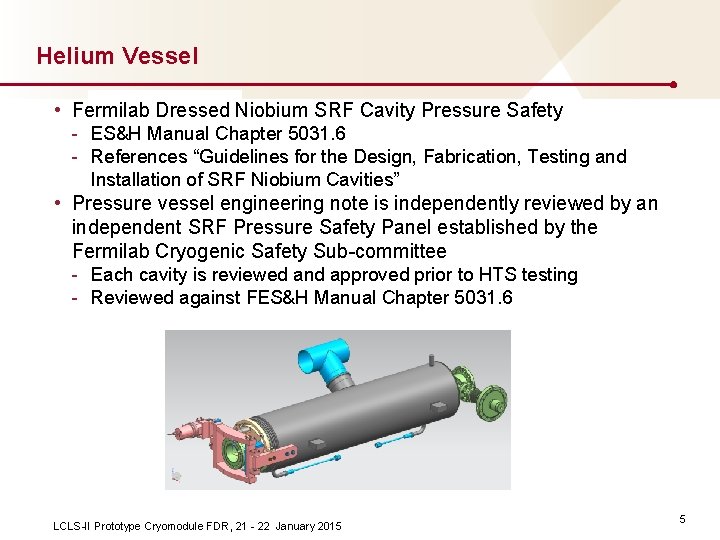
Helium Vessel • Fermilab Dressed Niobium SRF Cavity Pressure Safety - ES&H Manual Chapter 5031. 6 - References “Guidelines for the Design, Fabrication, Testing and Installation of SRF Niobium Cavities” • Pressure vessel engineering note is independently reviewed by an independent SRF Pressure Safety Panel established by the Fermilab Cryogenic Safety Sub-committee - Each cavity is reviewed and approved prior to HTS testing - Reviewed against FES&H Manual Chapter 5031. 6 LCLS-II Prototype Cryomodule FDR, 21 - 22 January 2015 5
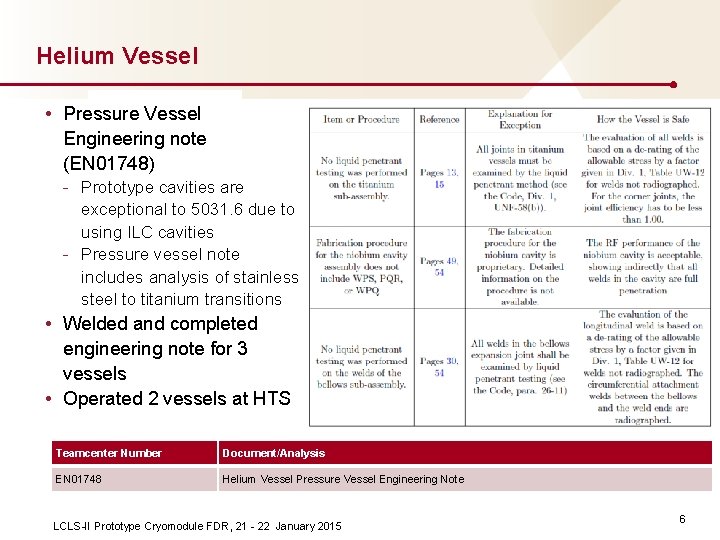
Helium Vessel • Pressure Vessel Engineering note (EN 01748) - Prototype cavities are exceptional to 5031. 6 due to using ILC cavities - Pressure vessel note includes analysis of stainless steel to titanium transitions • Welded and completed engineering note for 3 vessels • Operated 2 vessels at HTS Teamcenter Number Document/Analysis EN 01748 Helium Vessel Pressure Vessel Engineering Note LCLS-II Prototype Cryomodule FDR, 21 - 22 January 2015 6
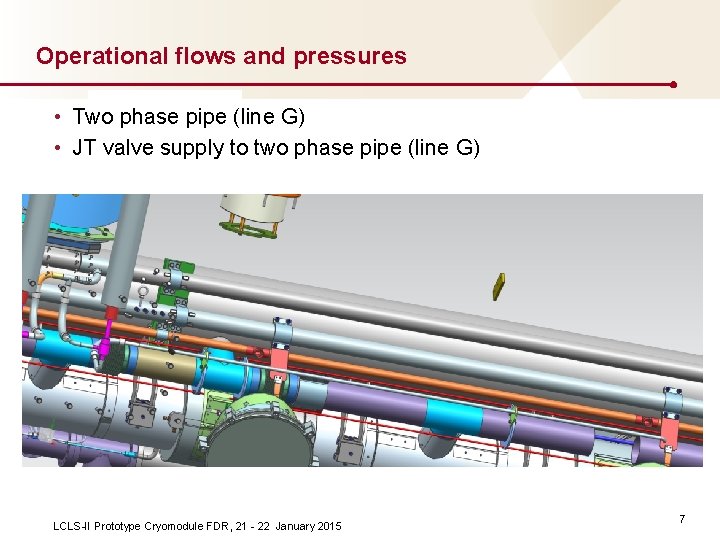
Operational flows and pressures • Two phase pipe (line G) • JT valve supply to two phase pipe (line G) LCLS-II Prototype Cryomodule FDR, 21 - 22 January 2015 7
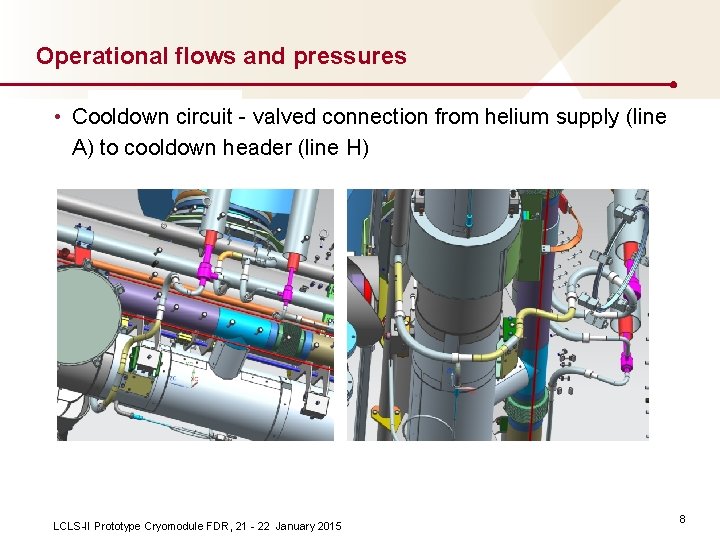
Operational flows and pressures • Cooldown circuit - valved connection from helium supply (line A) to cooldown header (line H) LCLS-II Prototype Cryomodule FDR, 21 - 22 January 2015 8
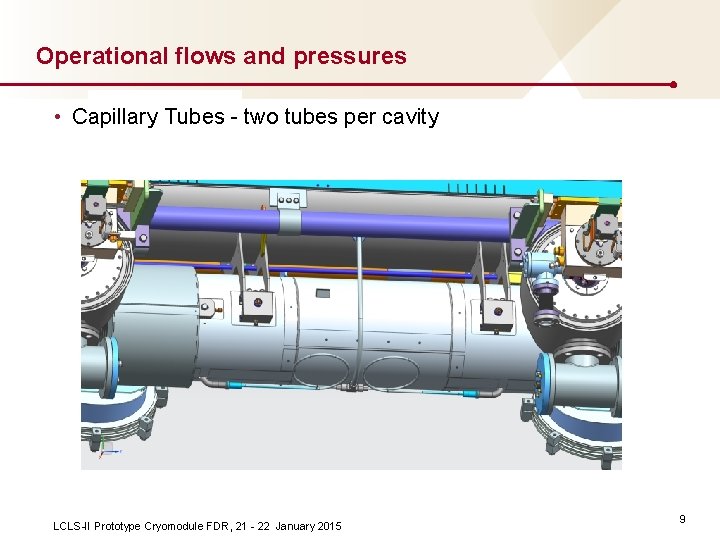
Operational flows and pressures • Capillary Tubes - two tubes per cavity LCLS-II Prototype Cryomodule FDR, 21 - 22 January 2015 9
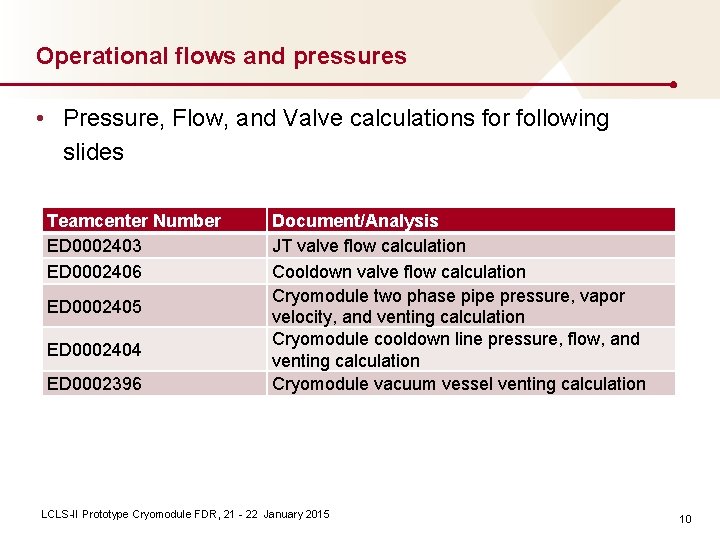
Operational flows and pressures • Pressure, Flow, and Valve calculations for following slides Teamcenter Number ED 0002403 ED 0002406 ED 0002405 ED 0002404 ED 0002396 Document/Analysis JT valve flow calculation Cooldown valve flow calculation Cryomodule two phase pipe pressure, vapor velocity, and venting calculation Cryomodule cooldown line pressure, flow, and venting calculation Cryomodule vacuum vessel venting calculation LCLS-II Prototype Cryomodule FDR, 21 - 22 January 2015 10
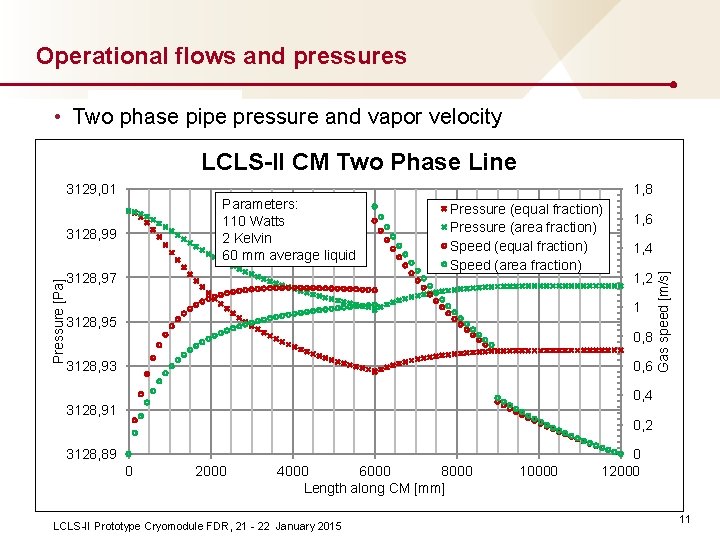
Operational flows and pressures • Two phase pipe pressure and vapor velocity LCLS-II CM Two Phase Line Parameters: 110 Watts 2 Kelvin 60 mm average liquid Pressure [Pa] 3128, 99 3128, 97 1, 8 Pressure (equal fraction) Pressure (area fraction) Speed (equal fraction) Speed (area fraction) 1, 6 1, 4 1, 2 1 3128, 95 0, 8 3128, 93 0, 6 Gas speed [m/s] 3129, 01 0, 4 3128, 91 0, 2 3128, 89 0 2000 4000 6000 8000 Length along CM [mm] LCLS-II Prototype Cryomodule FDR, 21 - 22 January 2015 10000 0 12000 11
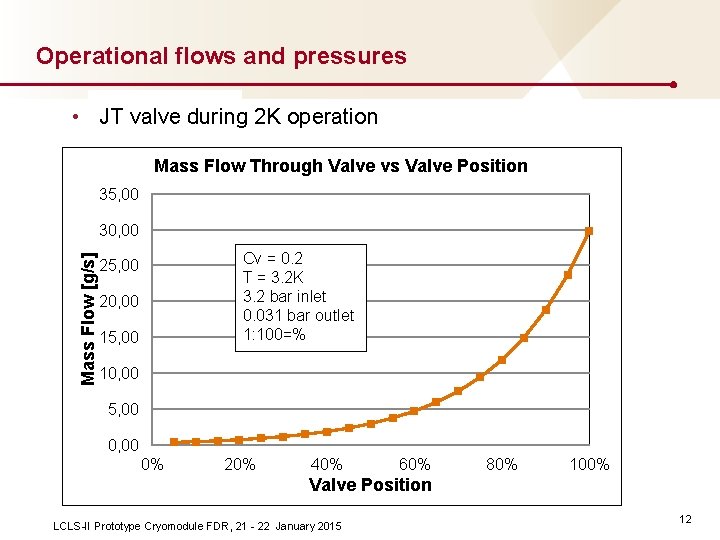
Operational flows and pressures • JT valve during 2 K operation Mass Flow Through Valve vs Valve Position 35, 00 Mass Flow [g/s] 30, 00 Cv = 0. 2 T = 3. 2 K 3. 2 bar inlet 0. 031 bar outlet 1: 100=% 25, 00 20, 00 15, 00 10, 00 5, 00 0% 20% 40% 60% 80% 100% Valve Position LCLS-II Prototype Cryomodule FDR, 21 - 22 January 2015 12
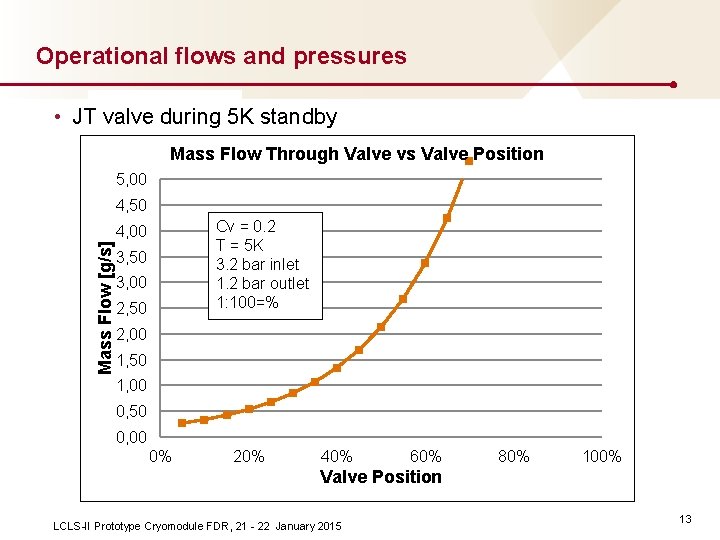
Operational flows and pressures • JT valve during 5 K standby Mass Flow Through Valve vs Valve Position 5, 00 4, 50 Cv = 0. 2 T = 5 K 3. 2 bar inlet 1. 2 bar outlet 1: 100=% Mass Flow [g/s] 4, 00 3, 50 3, 00 2, 50 2, 00 1, 50 1, 00 0, 50 0, 00 0% 20% 40% 60% 80% 100% Valve Position LCLS-II Prototype Cryomodule FDR, 21 - 22 January 2015 13
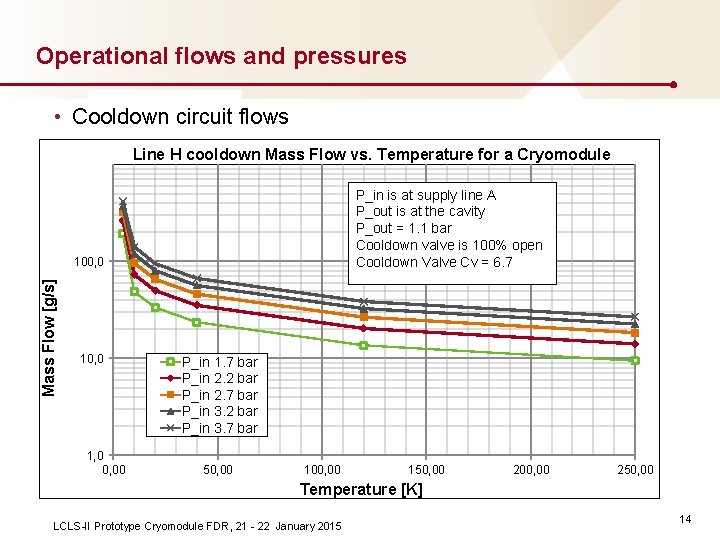
Operational flows and pressures • Cooldown circuit flows Line H cooldown Mass Flow vs. Temperature for a Cryomodule P_in is at supply line A P_out is at the cavity P_out = 1. 1 bar Cooldown valve is 100% open Cooldown Valve Cv = 6. 7 Mass Flow [g/s] 100, 0 1, 0 0, 00 P_in 1. 7 bar P_in 2. 2 bar P_in 2. 7 bar P_in 3. 2 bar P_in 3. 7 bar 50, 00 100, 00 150, 00 200, 00 250, 00 Temperature [K] LCLS-II Prototype Cryomodule FDR, 21 - 22 January 2015 14
![Emergency Venting Pressure Drop to Relief Relief analysis has been done in Emergency Venting Pressure Drop to Relief [%] • Relief analysis has been done in](https://slidetodoc.com/presentation_image_h2/0e21e8b94653430fc443274121c60a78/image-15.jpg)
Emergency Venting Pressure Drop to Relief [%] • Relief analysis has been done in collaboration with the Cryogenic Distribution System • All helium circuit relief paths are through the Cryogenic Distribution System • Cavity and cooldown (line H) reliefs flow out the helium gas return pipe (line B) 10% 9% 8% 7% 6% 5% 4% 3% 2% 1% 0% Line B Pressure Drop at 4 bar - Loss of insulating vacuum P up P down (450) (400) (350) (300) (250) (200) (150) (100) (50) - 50 100 150 200 250 300 350 400 Linac Beam Line Distance [m] Andrew Dalesandro, CDS Tunnel Components Engineering Analysis, CDS PDR, December 16, 2014 LCLS-II Prototype Cryomodule FDR, 21 - 22 January 2015 15
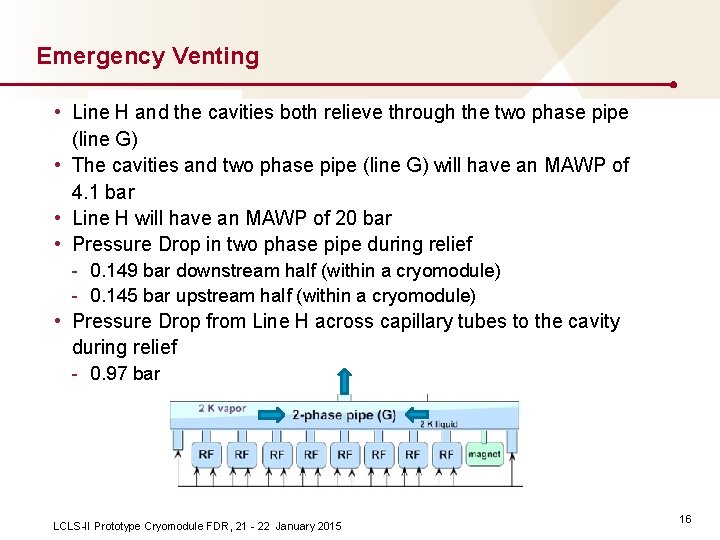
Emergency Venting • Line H and the cavities both relieve through the two phase pipe (line G) • The cavities and two phase pipe (line G) will have an MAWP of 4. 1 bar • Line H will have an MAWP of 20 bar • Pressure Drop in two phase pipe during relief - 0. 149 bar downstream half (within a cryomodule) - 0. 145 bar upstream half (within a cryomodule) • Pressure Drop from Line H across capillary tubes to the cavity during relief - 0. 97 bar LCLS-II Prototype Cryomodule FDR, 21 - 22 January 2015 16
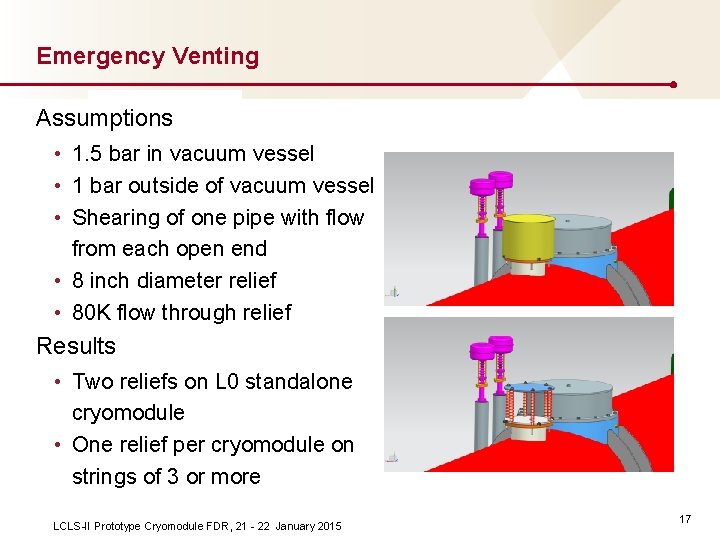
Emergency Venting Assumptions • 1. 5 bar in vacuum vessel • 1 bar outside of vacuum vessel • Shearing of one pipe with flow from each open end • 8 inch diameter relief • 80 K flow through relief Results • Two reliefs on L 0 standalone cryomodule • One relief per cryomodule on strings of 3 or more LCLS-II Prototype Cryomodule FDR, 21 - 22 January 2015 17
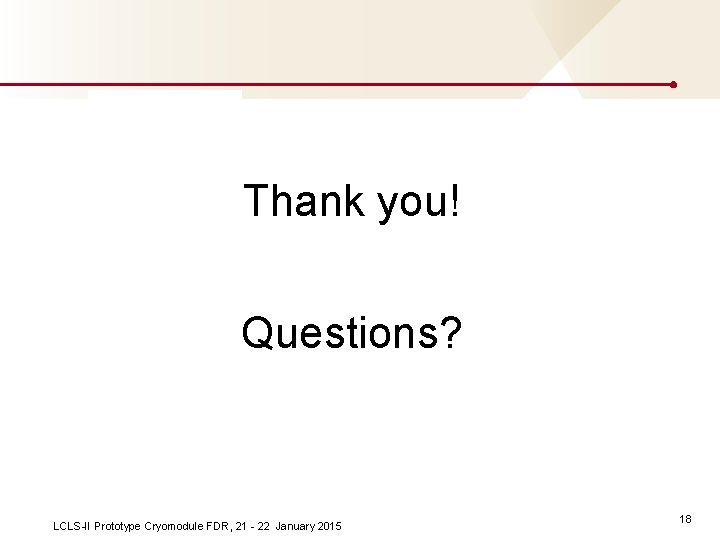
Thank you! Questions? LCLS-II Prototype Cryomodule FDR, 21 - 22 January 2015 18
Vent sexing chicken
Wet venting rules
Thaad energy management steering maneuver
Laboratory contingency plan example
Static pressure and dynamic pressure
Hydrostatic pressure and osmotic pressure
High pressure and low pressure
High pressure and low pressure
Green shield app
Vmo advancement cpt
Pressure support vs pressure control
Pressure mapping for pressure ulcers
Intrapulmonary pressure vs intrapleural pressure
Describing edema
Partial pressure
Tripod position breathing
Metamorphic grade
ütube
Oncotic pressure vs hydrostatic