CCM Power Factor Correction Inductor Design with Powder
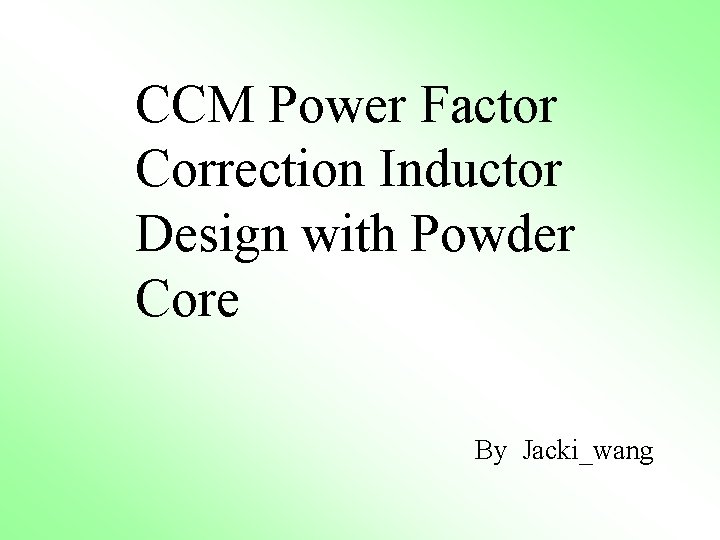
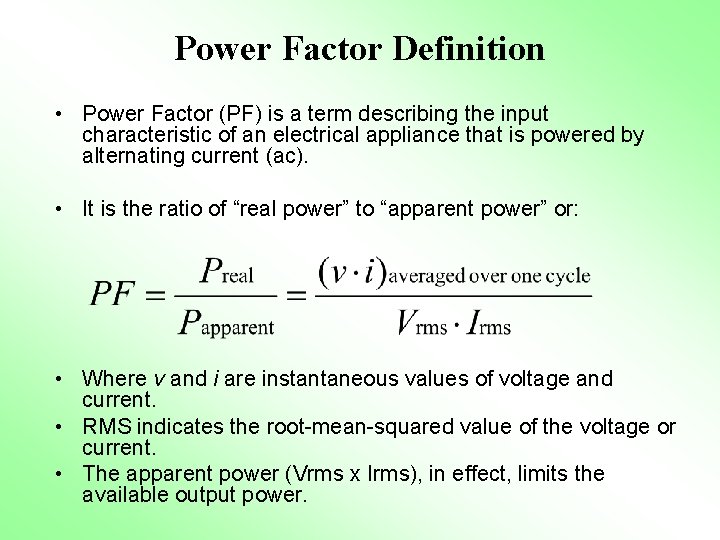
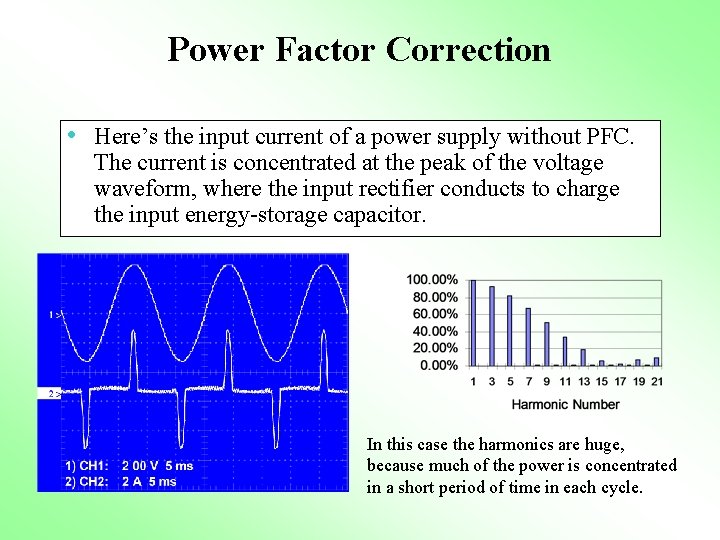
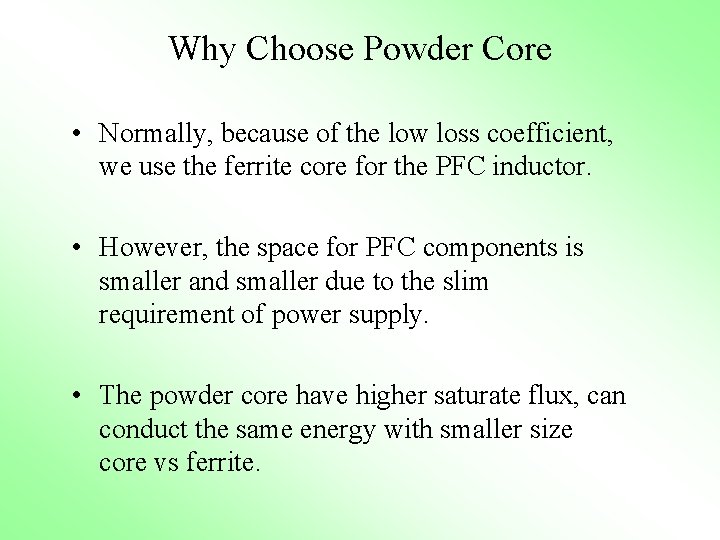
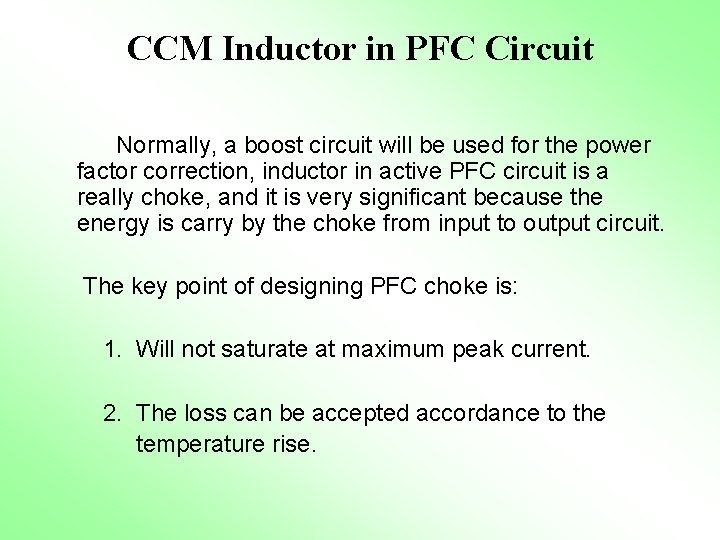
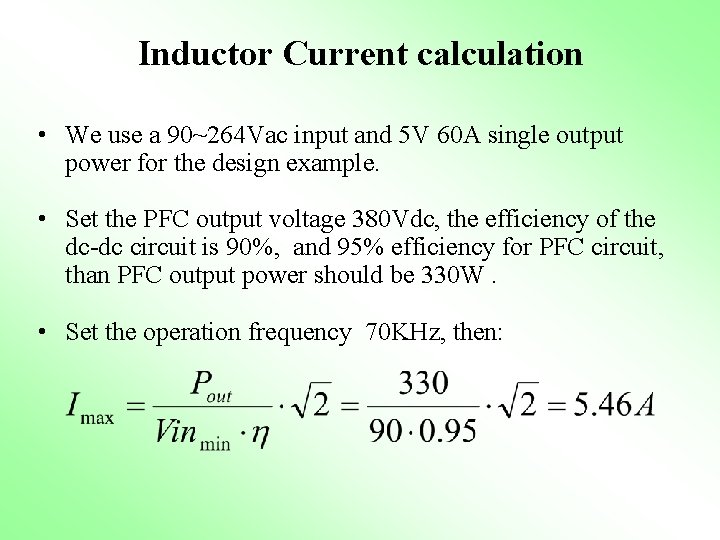
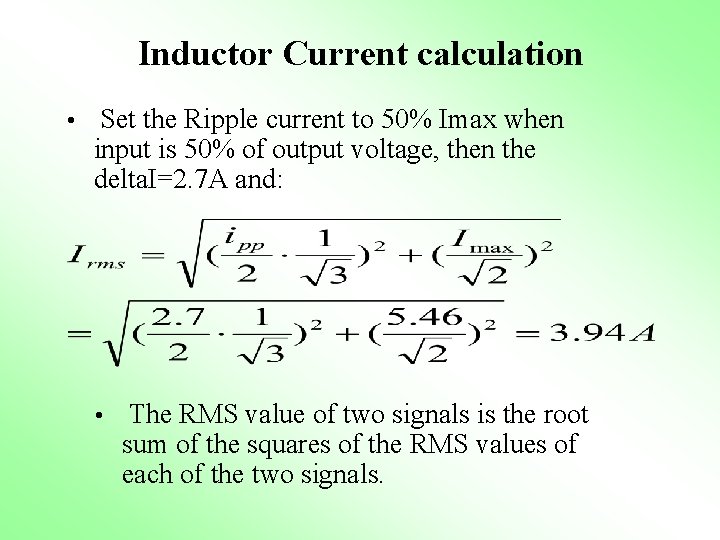
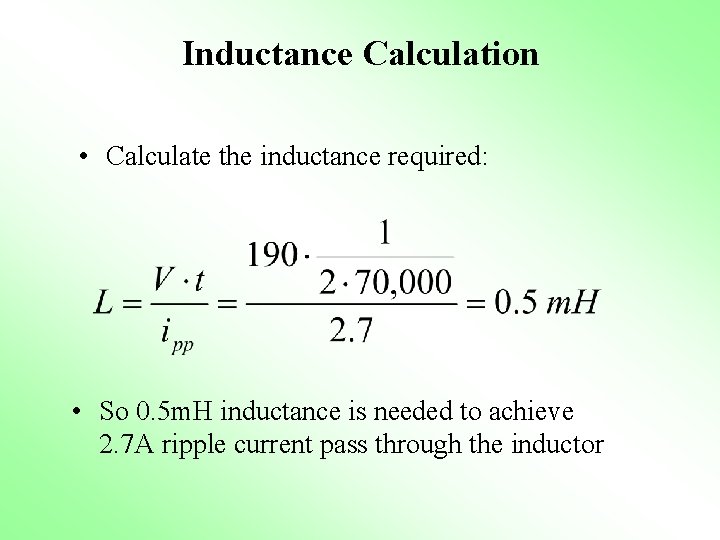
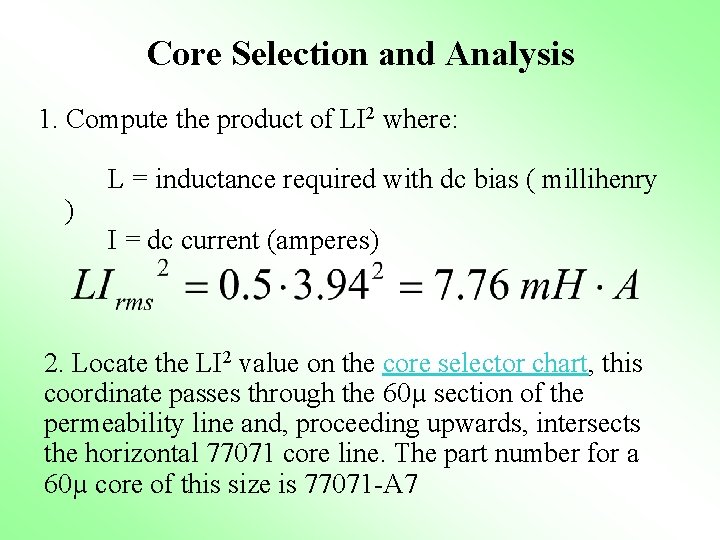
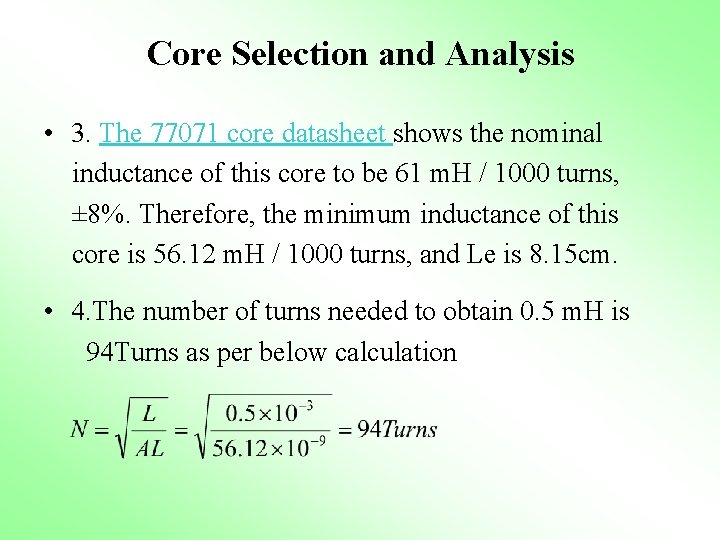
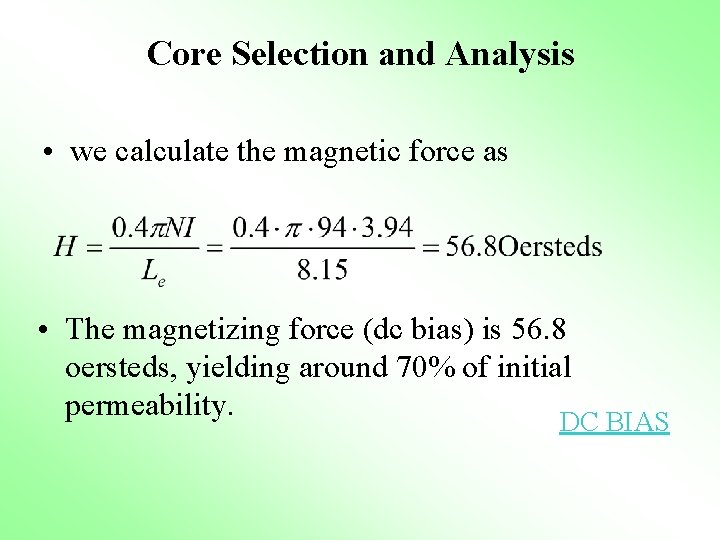
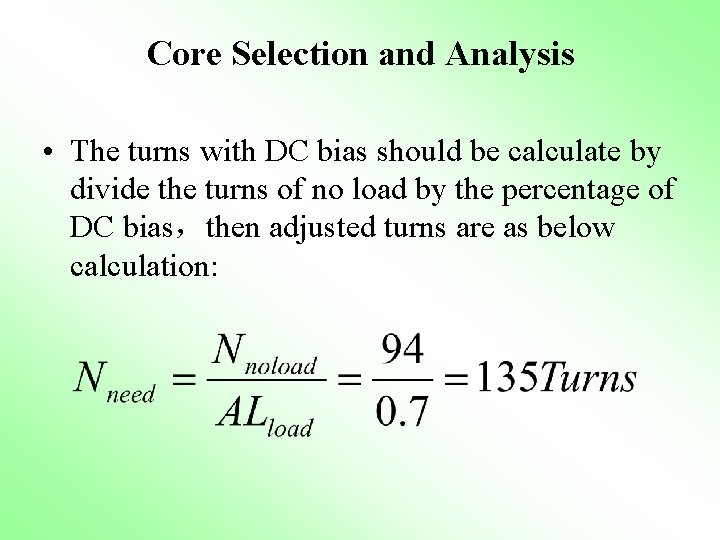
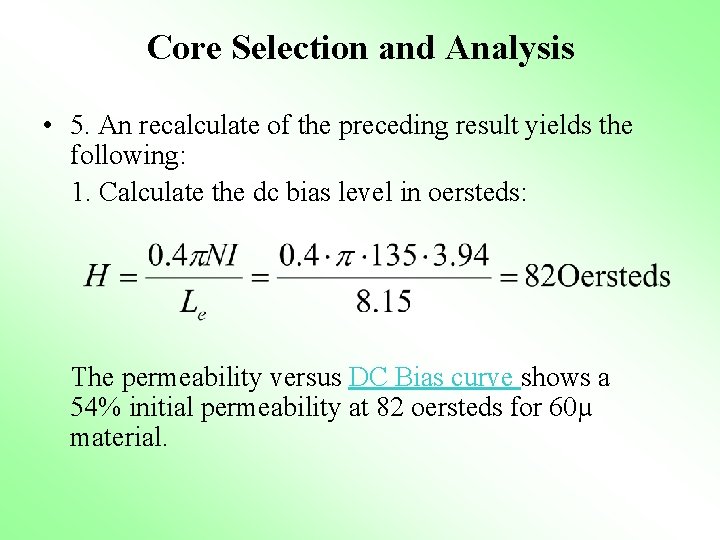
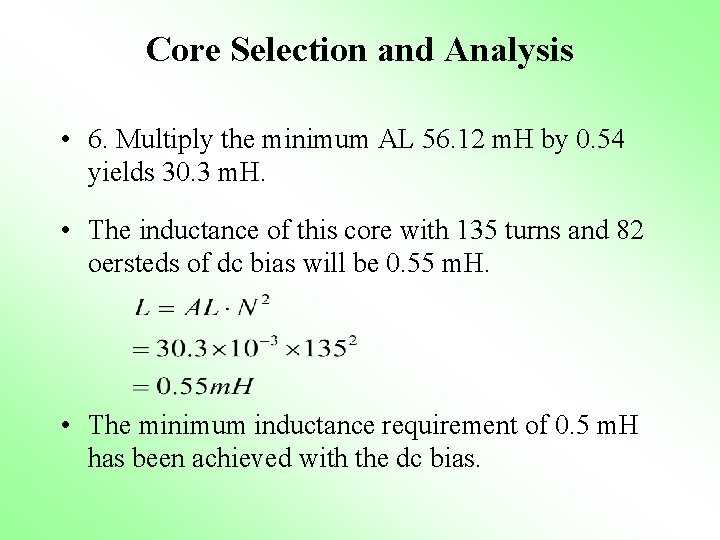
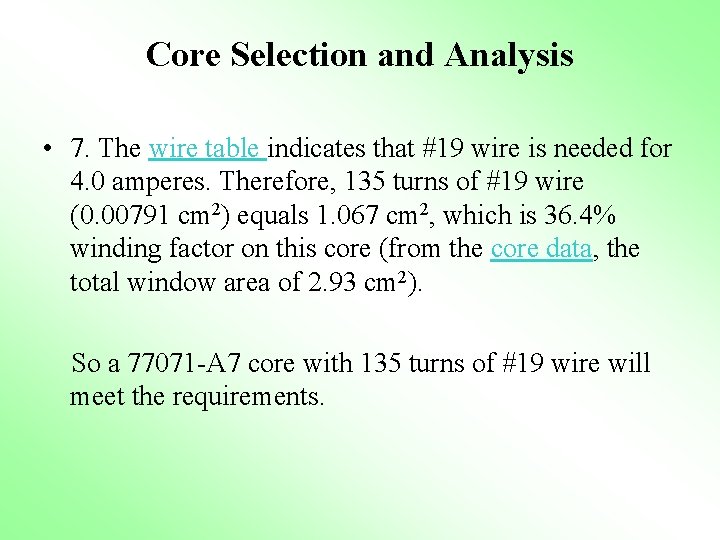
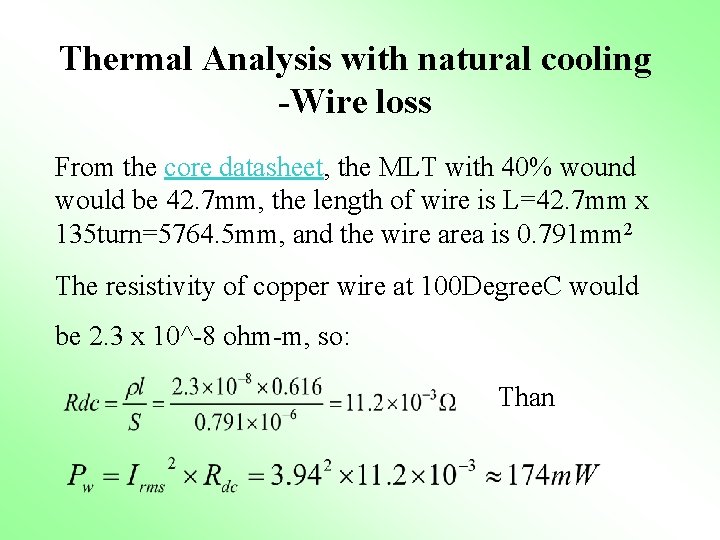
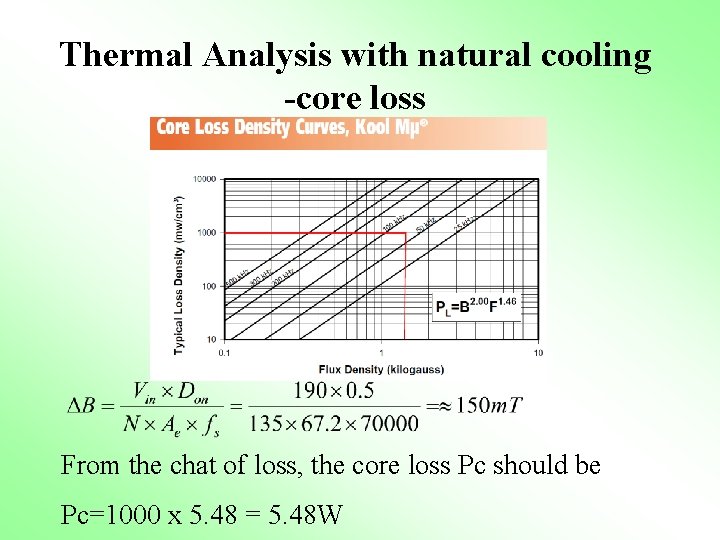
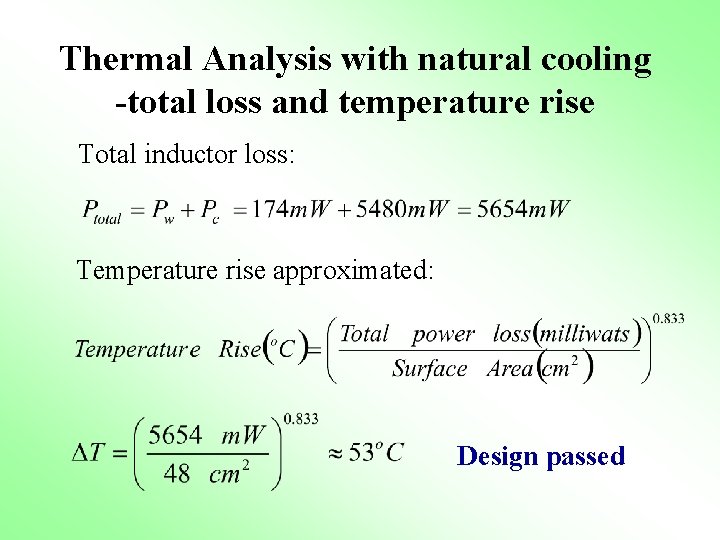
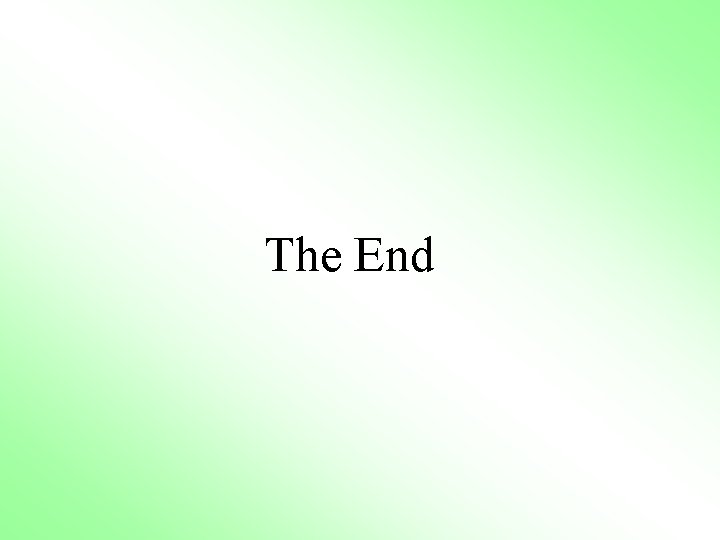
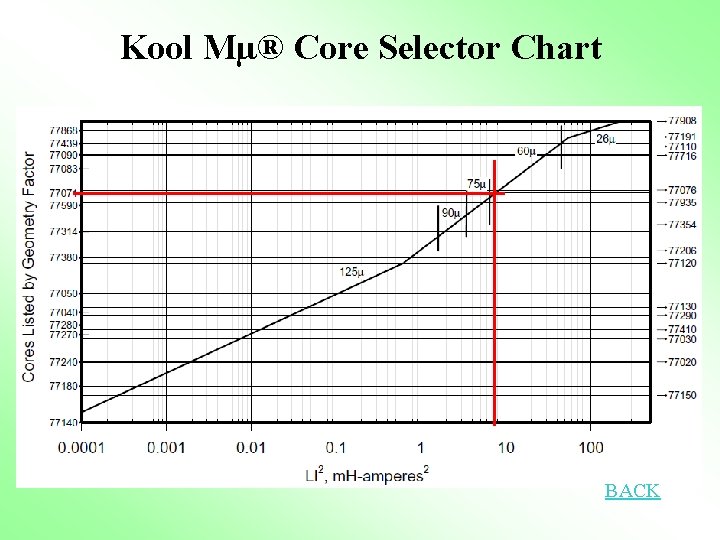
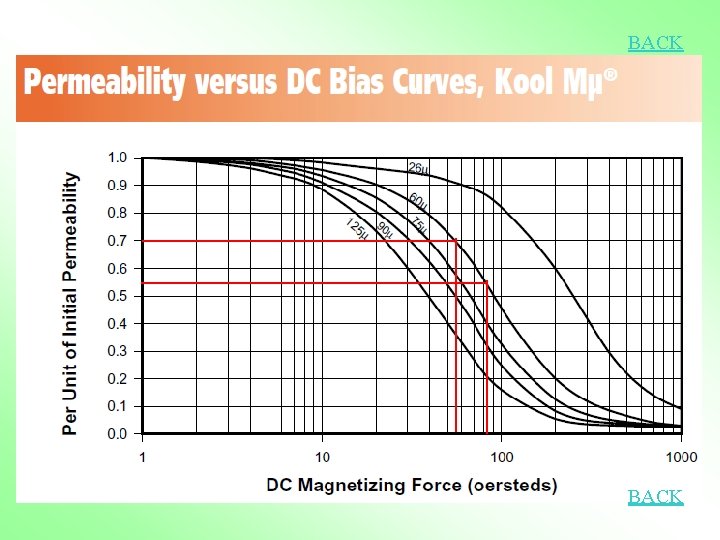
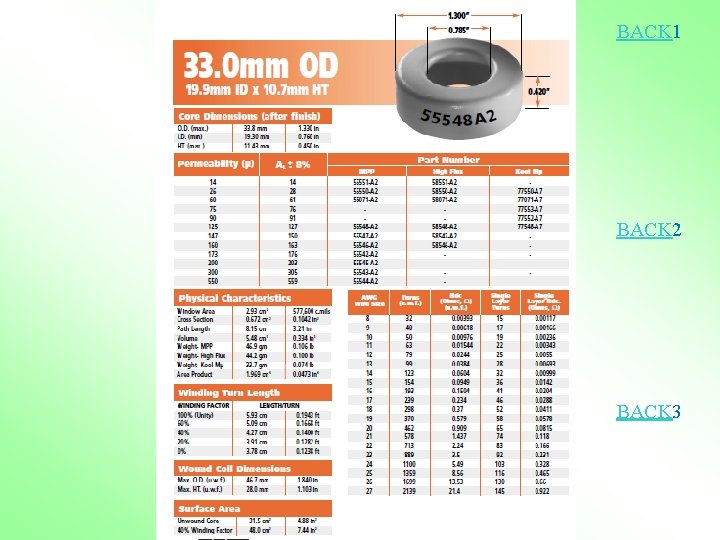
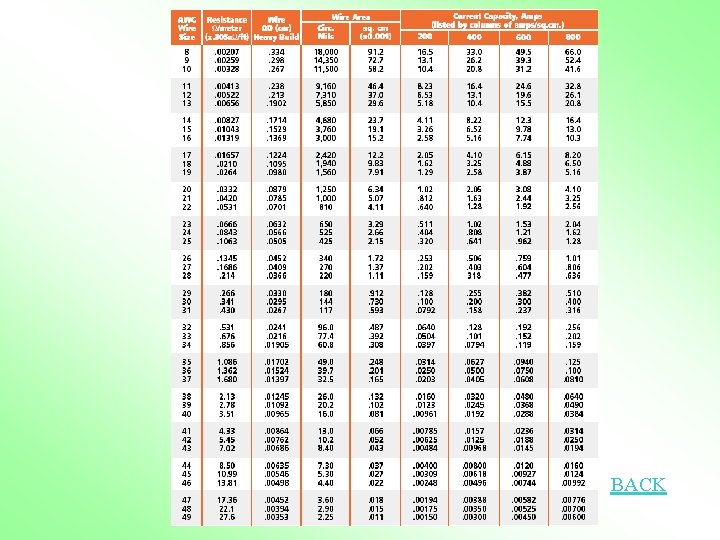
- Slides: 23
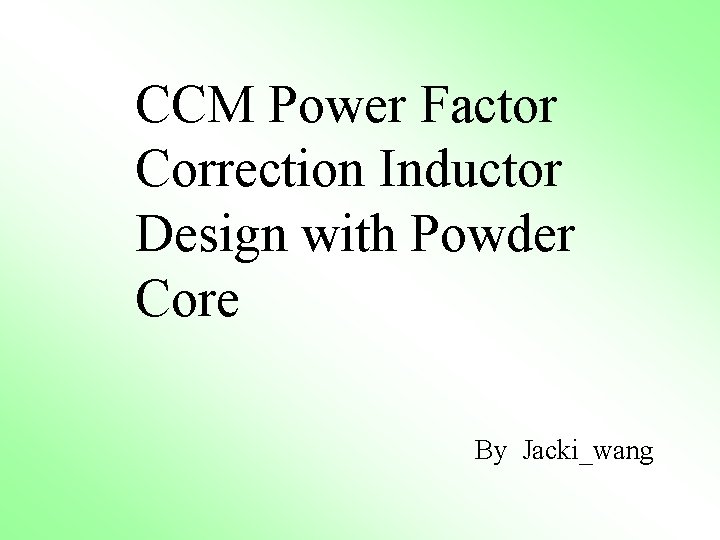
CCM Power Factor Correction Inductor Design with Powder Core By Jacki_wang
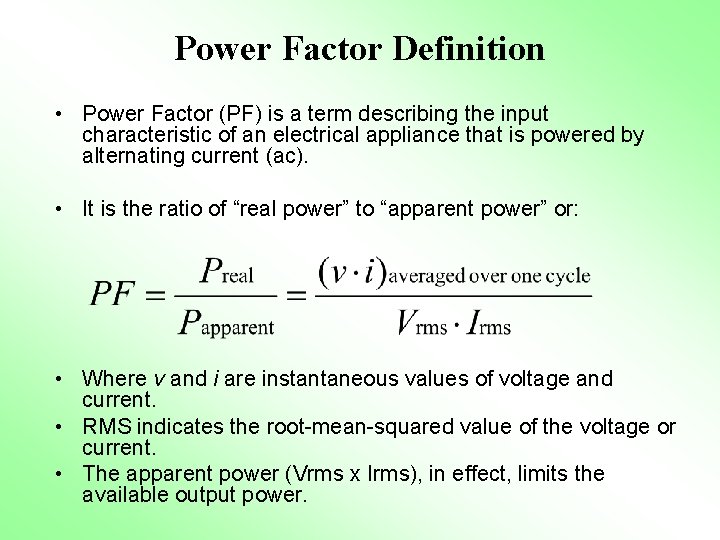
Power Factor Definition • Power Factor (PF) is a term describing the input characteristic of an electrical appliance that is powered by alternating current (ac). • It is the ratio of “real power” to “apparent power” or: • Where v and i are instantaneous values of voltage and current. • RMS indicates the root-mean-squared value of the voltage or current. • The apparent power (Vrms x Irms), in effect, limits the available output power.
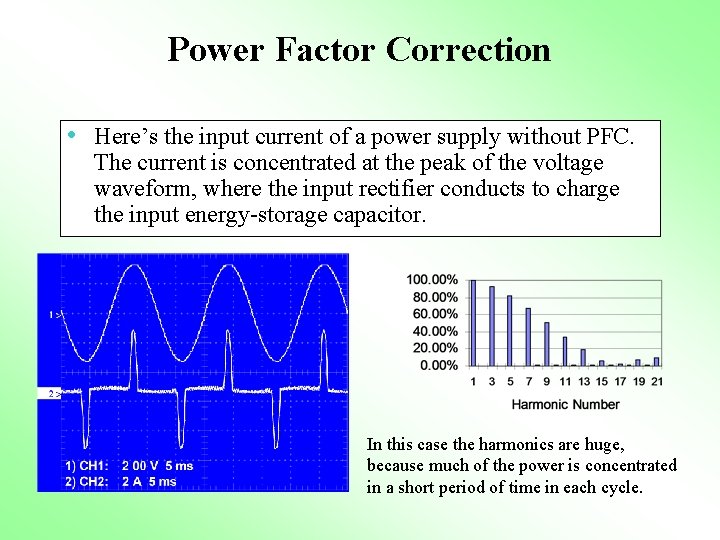
Power Factor Correction • Here’s the input current of a power supply without PFC. The current is concentrated at the peak of the voltage waveform, where the input rectifier conducts to charge the input energy-storage capacitor. In this case the harmonics are huge, because much of the power is concentrated in a short period of time in each cycle.
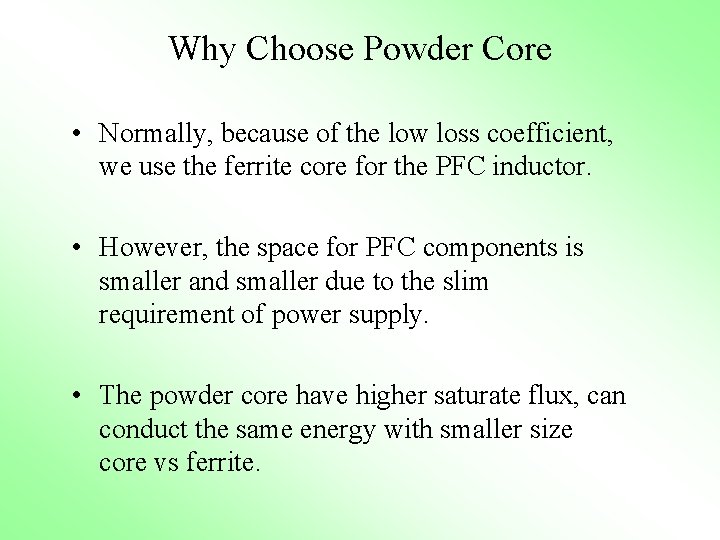
Why Choose Powder Core • Normally, because of the low loss coefficient, we use the ferrite core for the PFC inductor. • However, the space for PFC components is smaller and smaller due to the slim requirement of power supply. • The powder core have higher saturate flux, can conduct the same energy with smaller size core vs ferrite.
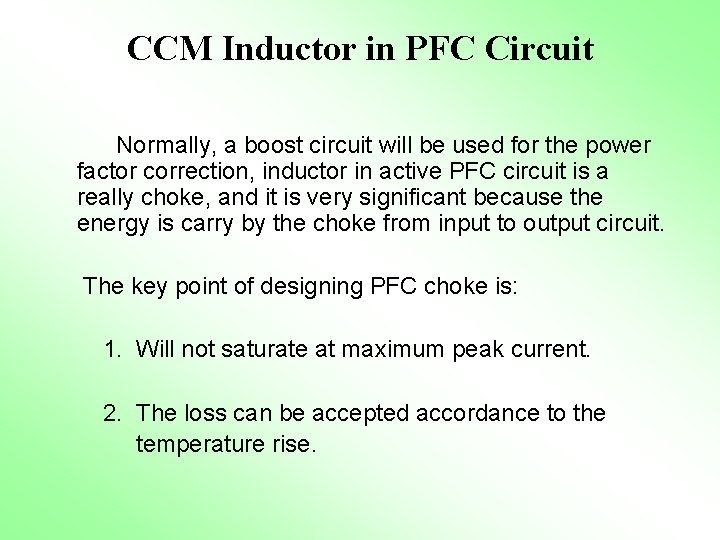
CCM Inductor in PFC Circuit Normally, a boost circuit will be used for the power factor correction, inductor in active PFC circuit is a really choke, and it is very significant because the energy is carry by the choke from input to output circuit. The key point of designing PFC choke is: 1. Will not saturate at maximum peak current. 2. The loss can be accepted accordance to the temperature rise.
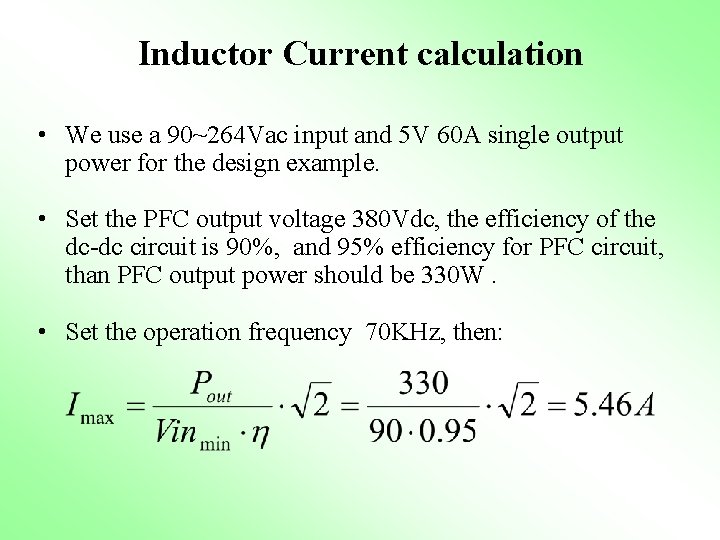
Inductor Current calculation • We use a 90~264 Vac input and 5 V 60 A single output power for the design example. • Set the PFC output voltage 380 Vdc, the efficiency of the dc-dc circuit is 90%, and 95% efficiency for PFC circuit, than PFC output power should be 330 W. • Set the operation frequency 70 KHz, then:
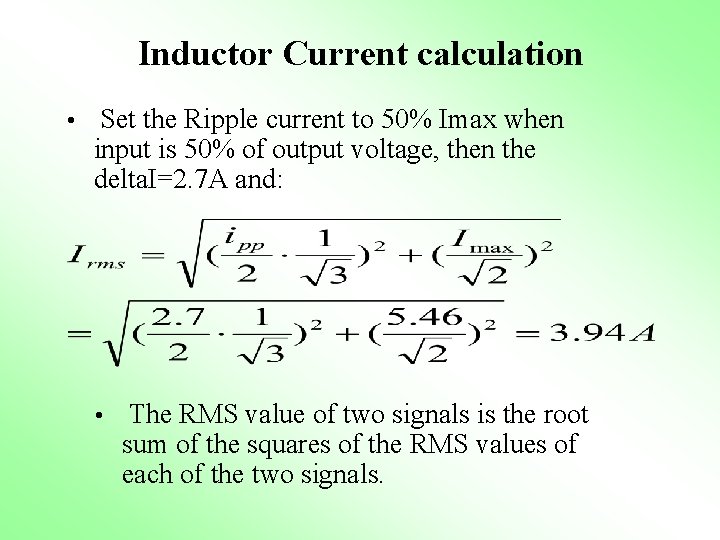
Inductor Current calculation • Set the Ripple current to 50% Imax when input is 50% of output voltage, then the delta. I=2. 7 A and: • The RMS value of two signals is the root sum of the squares of the RMS values of each of the two signals.
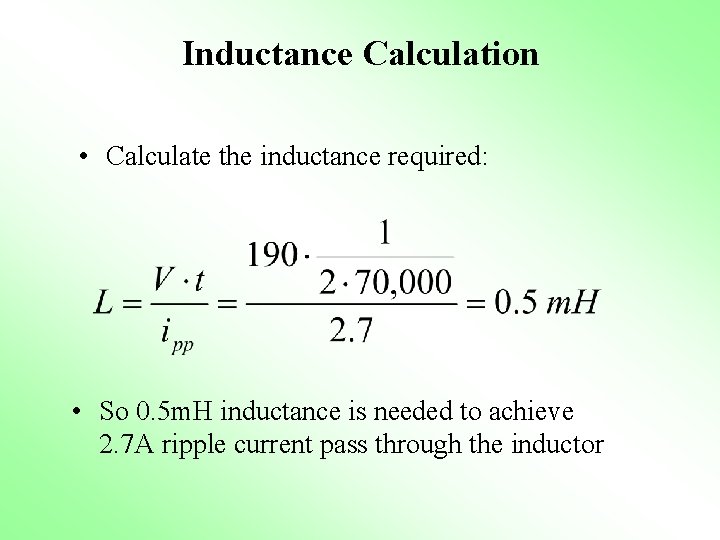
Inductance Calculation • Calculate the inductance required: • So 0. 5 m. H inductance is needed to achieve 2. 7 A ripple current pass through the inductor
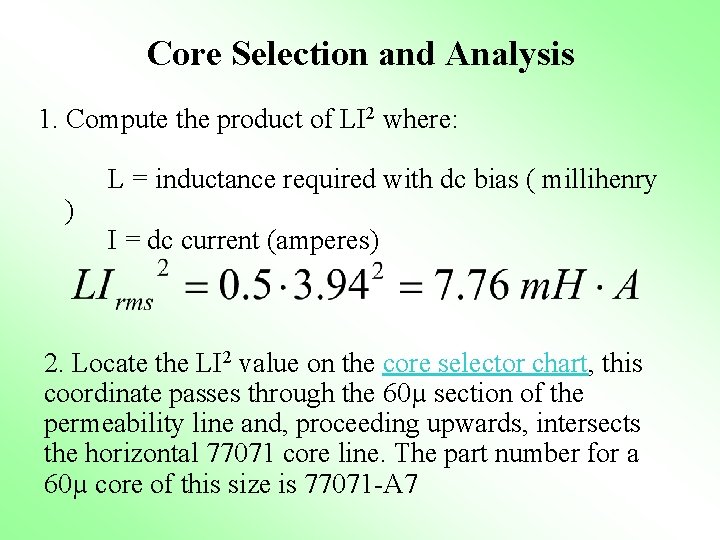
Core Selection and Analysis 1. Compute the product of LI 2 where: ) L = inductance required with dc bias ( millihenry I = dc current (amperes) 2. Locate the LI 2 value on the core selector chart, this coordinate passes through the 60µ section of the permeability line and, proceeding upwards, intersects the horizontal 77071 core line. The part number for a 60µ core of this size is 77071 -A 7
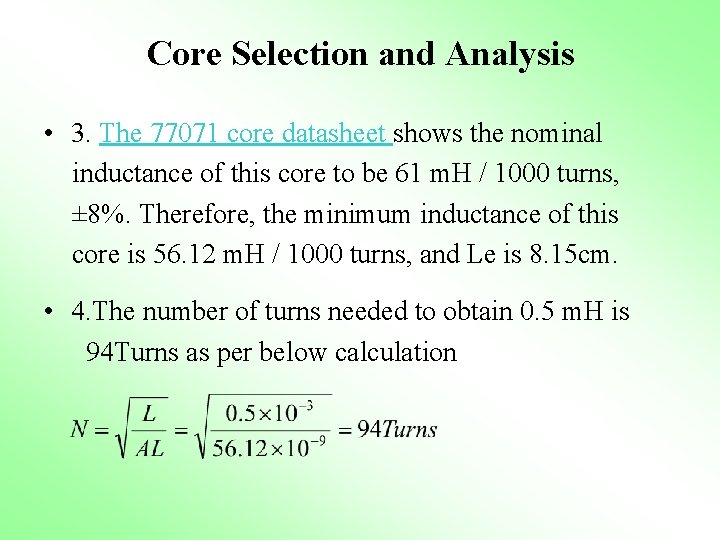
Core Selection and Analysis • 3. The 77071 core datasheet shows the nominal inductance of this core to be 61 m. H / 1000 turns, ± 8%. Therefore, the minimum inductance of this core is 56. 12 m. H / 1000 turns, and Le is 8. 15 cm. • 4. The number of turns needed to obtain 0. 5 m. H is 94 Turns as per below calculation
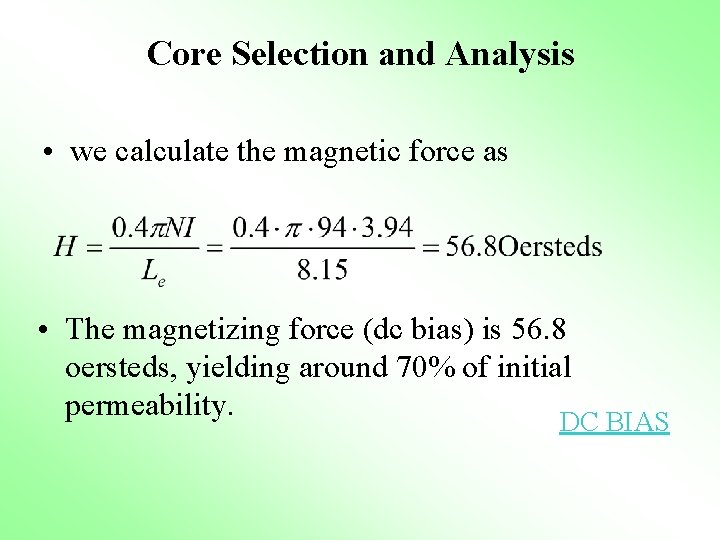
Core Selection and Analysis • we calculate the magnetic force as • The magnetizing force (dc bias) is 56. 8 oersteds, yielding around 70% of initial permeability. DC BIAS
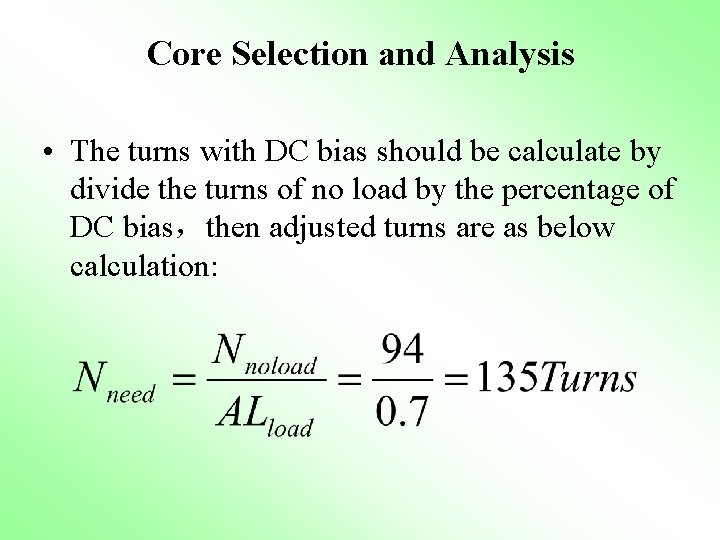
Core Selection and Analysis • The turns with DC bias should be calculate by divide the turns of no load by the percentage of DC bias,then adjusted turns are as below calculation:
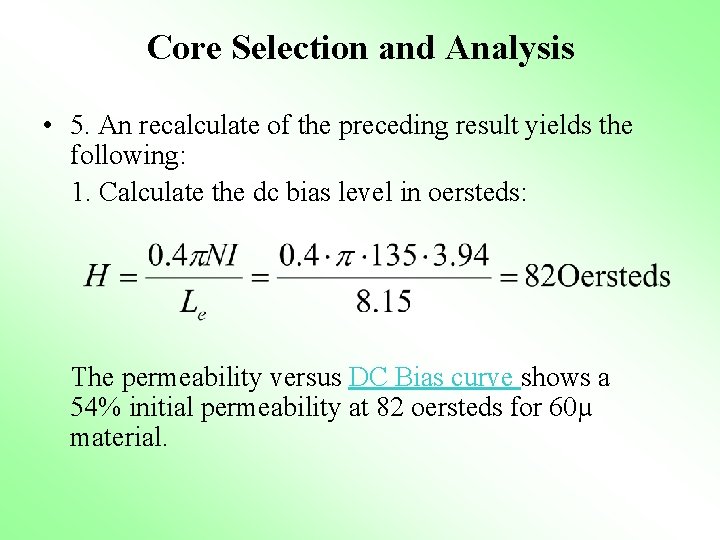
Core Selection and Analysis • 5. An recalculate of the preceding result yields the following: 1. Calculate the dc bias level in oersteds: The permeability versus DC Bias curve shows a 54% initial permeability at 82 oersteds for 60µ material.
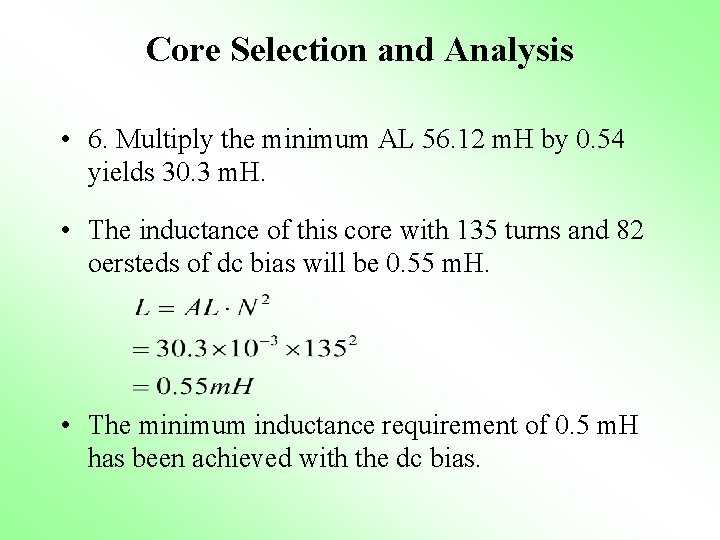
Core Selection and Analysis • 6. Multiply the minimum AL 56. 12 m. H by 0. 54 yields 30. 3 m. H. • The inductance of this core with 135 turns and 82 oersteds of dc bias will be 0. 55 m. H. • The minimum inductance requirement of 0. 5 m. H has been achieved with the dc bias.
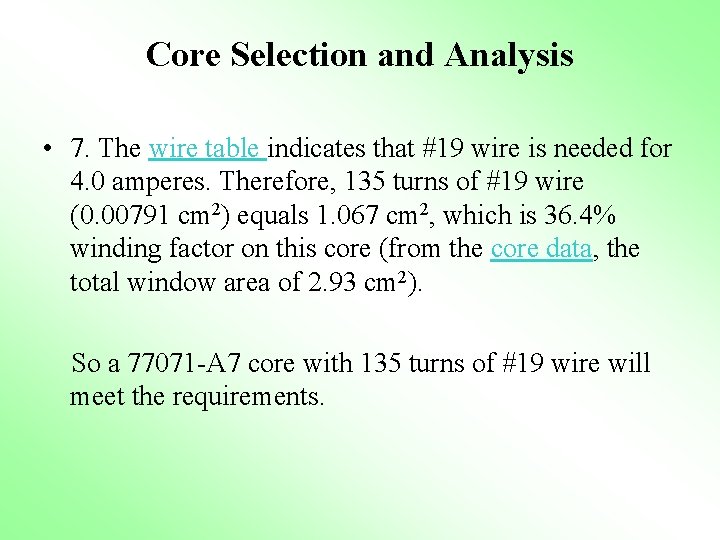
Core Selection and Analysis • 7. The wire table indicates that #19 wire is needed for 4. 0 amperes. Therefore, 135 turns of #19 wire (0. 00791 cm 2) equals 1. 067 cm 2, which is 36. 4% winding factor on this core (from the core data, the total window area of 2. 93 cm 2). So a 77071 -A 7 core with 135 turns of #19 wire will meet the requirements.
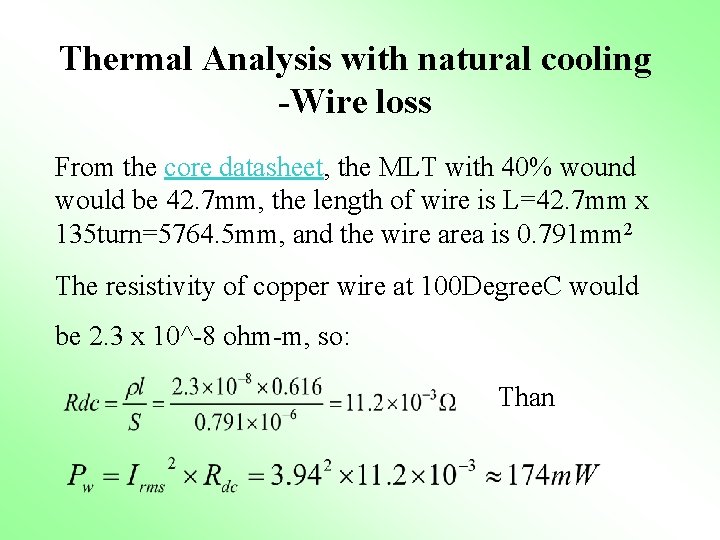
Thermal Analysis with natural cooling -Wire loss From the core datasheet, the MLT with 40% wound would be 42. 7 mm, the length of wire is L=42. 7 mm x 135 turn=5764. 5 mm, and the wire area is 0. 791 mm 2 The resistivity of copper wire at 100 Degree. C would be 2. 3 x 10^-8 ohm-m, so: Than
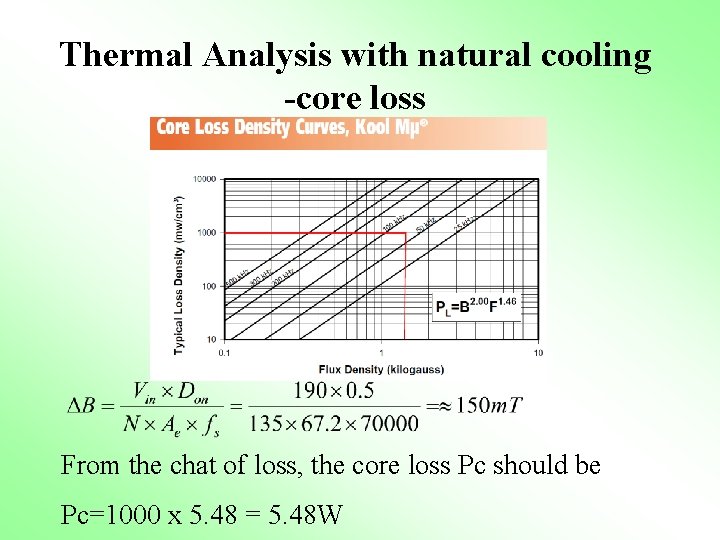
Thermal Analysis with natural cooling -core loss From the chat of loss, the core loss Pc should be Pc=1000 x 5. 48 = 5. 48 W
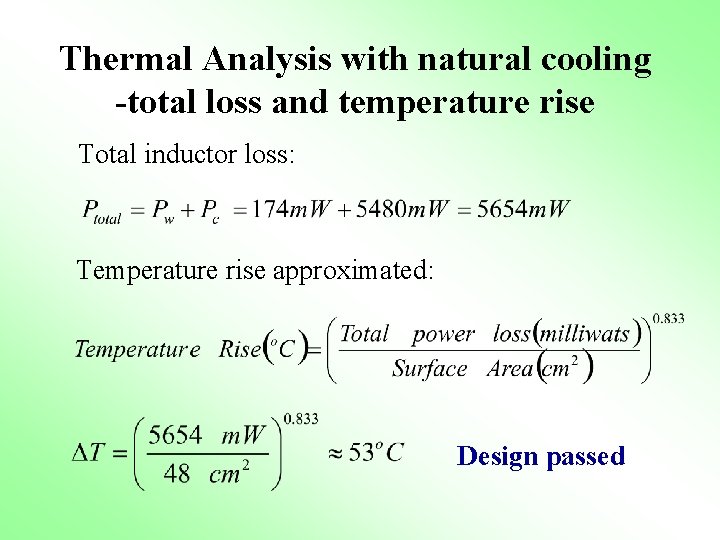
Thermal Analysis with natural cooling -total loss and temperature rise Total inductor loss: Temperature rise approximated: Design passed
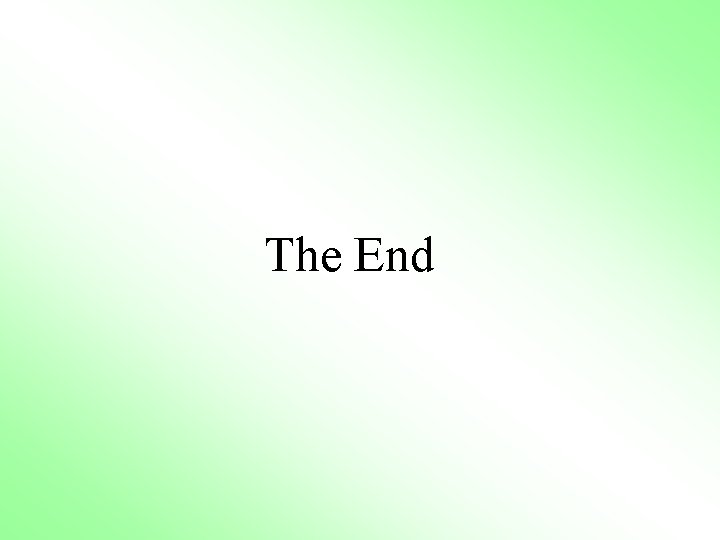
The End
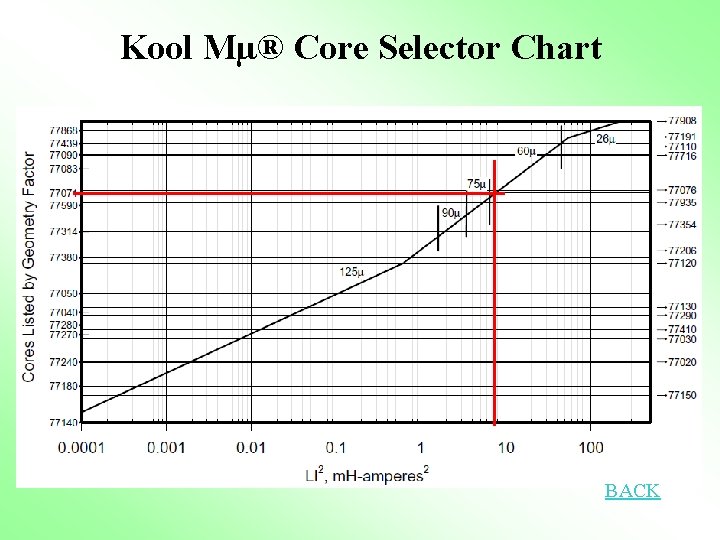
Kool Mµ® Core Selector Chart BACK
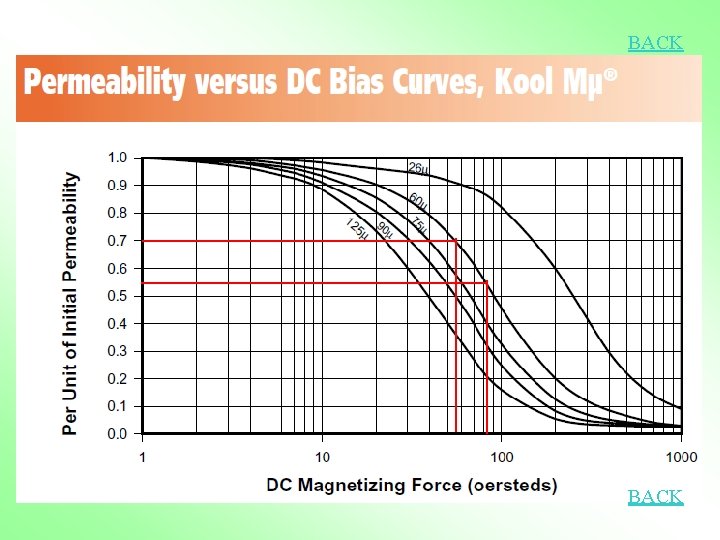
BACK
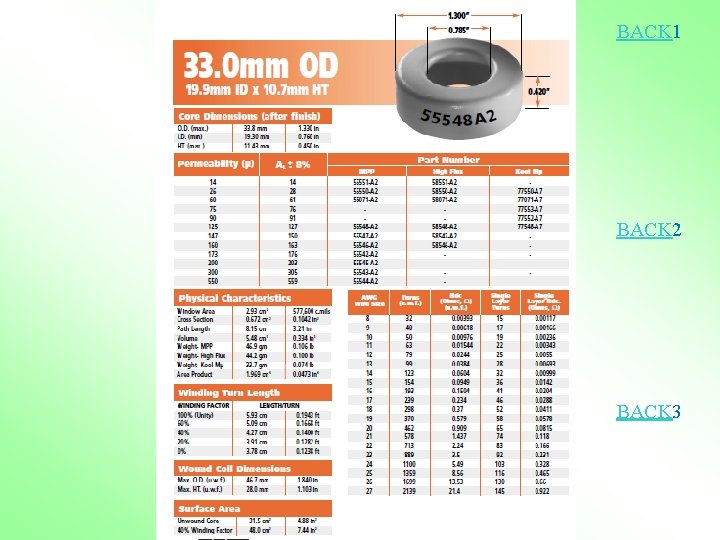
BACK 1 BACK 2 BACK 3
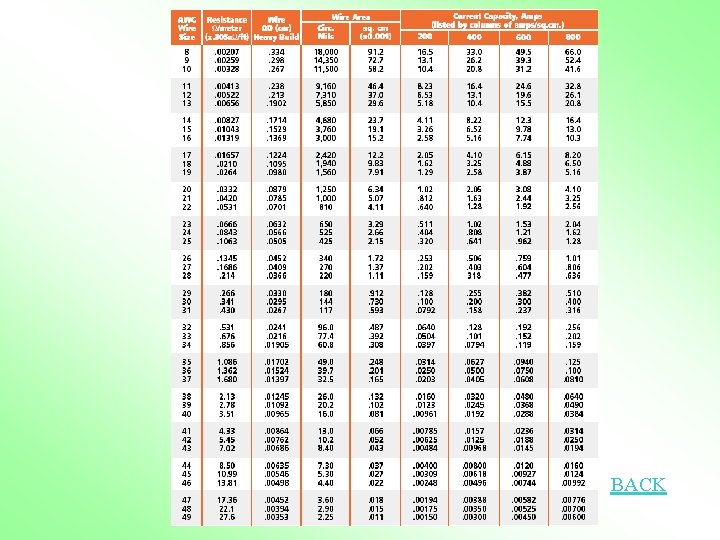
BACK
Power factor correction inductor
Power factor correction design
Lesson 1 power factor
Power factor correction
Low voltage three phase choke coil filter reactor in pfc
Factor hawk
Conjugate prior cheat sheet
Lesson 2 power factor correction
Define divided powders
Disadvantages of powder as a dosage form
Powder characterization in powder metallurgy
Bulk powder and divided powder
Correction factor
Insulin correction dose
Insulin dose per kg
Diabetic diet plan
Ion recombination correction factor
Faktor koreksi kontinuitas
Fluid energy
Jacobian correction factor
Continuity correction factor
Enterprise ccm
Ccm certification construction
Ccm chimie