Use of Raney Nickel in Infiltration at Anode
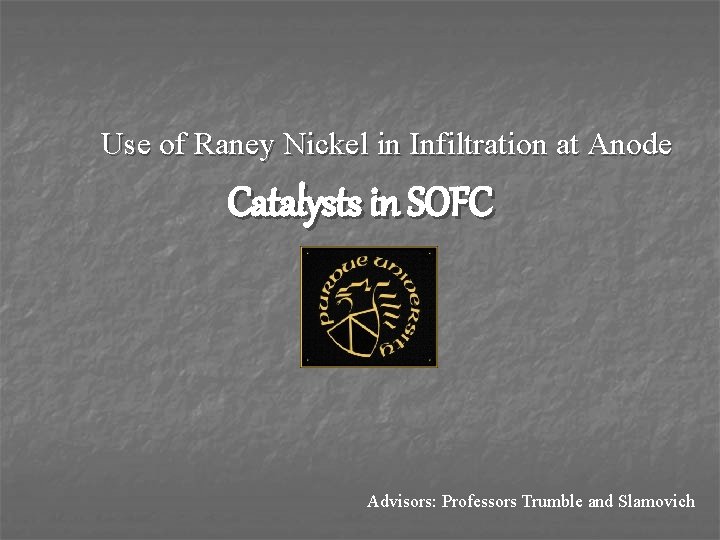
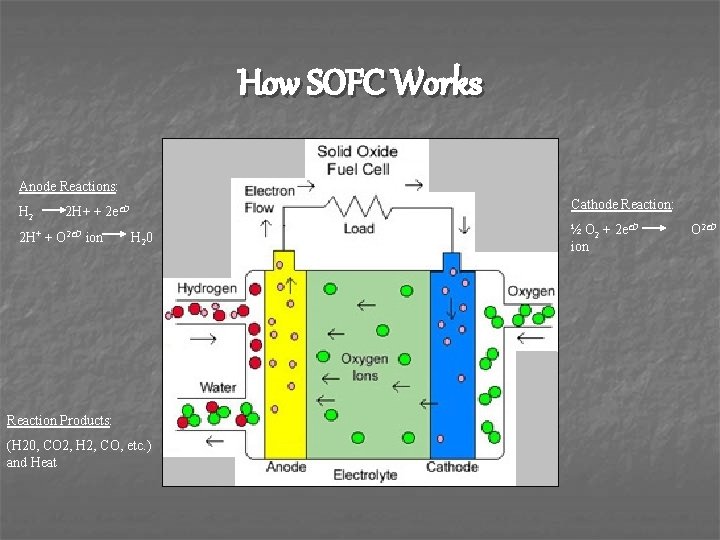
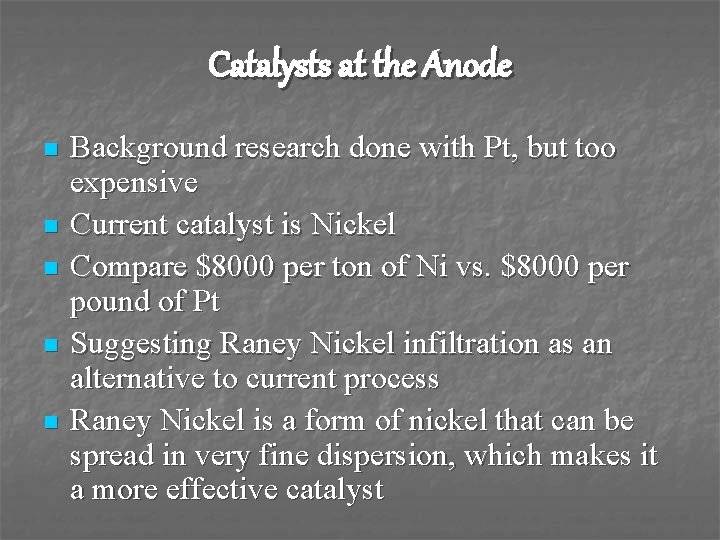
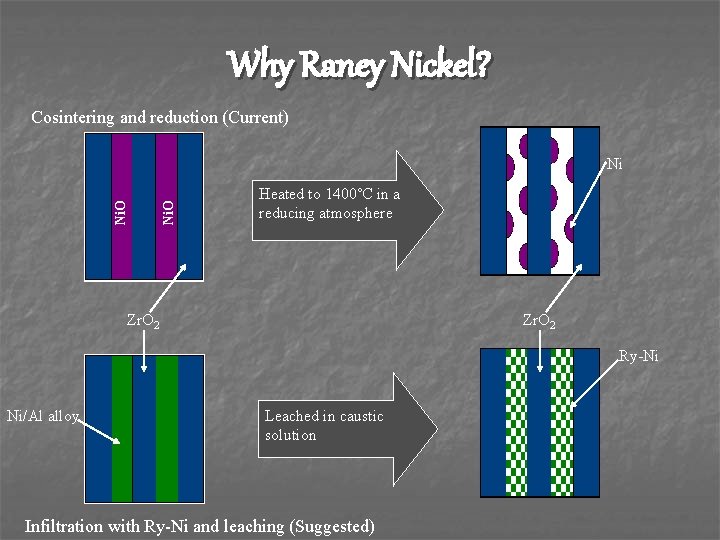
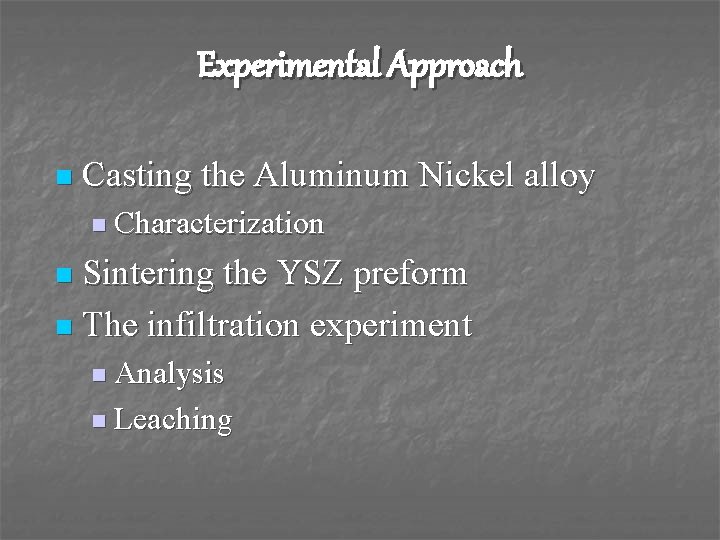
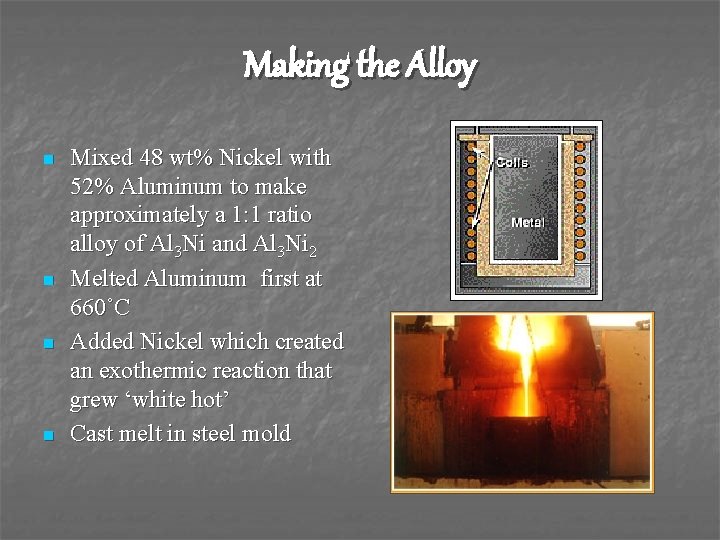
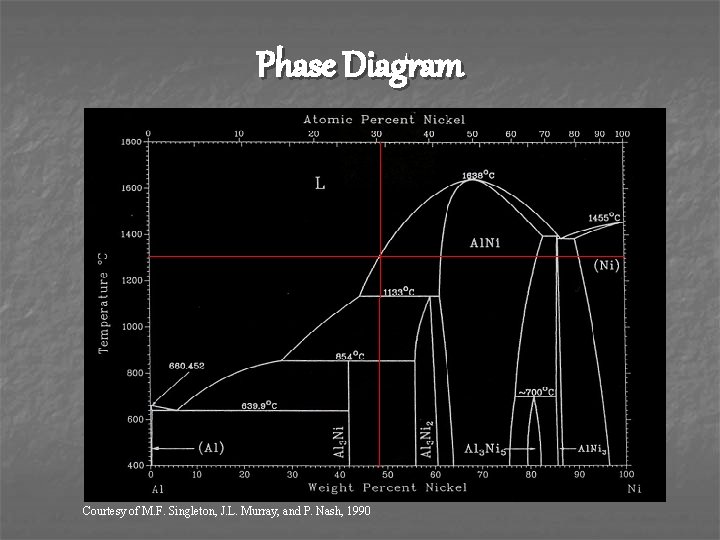
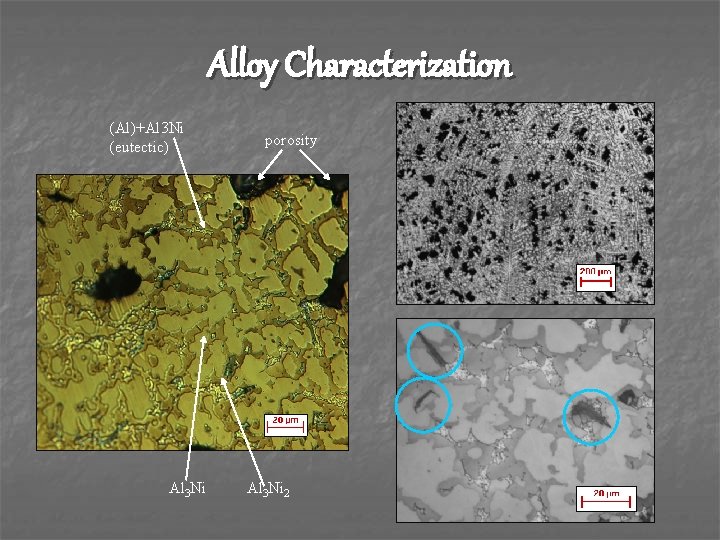
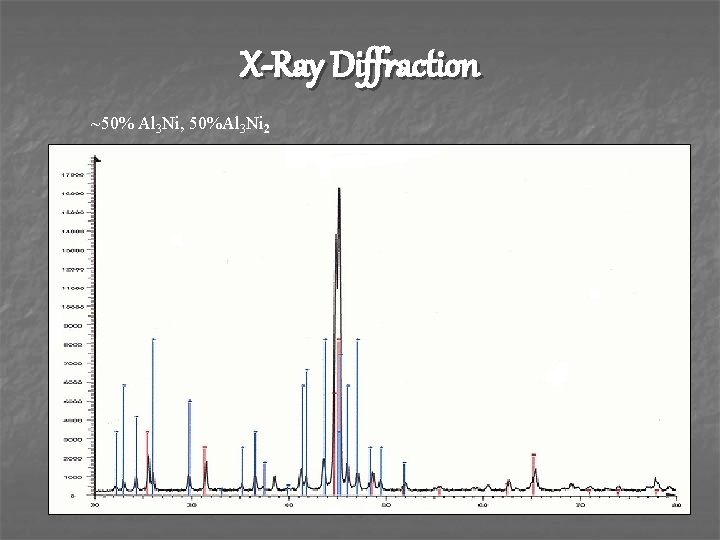
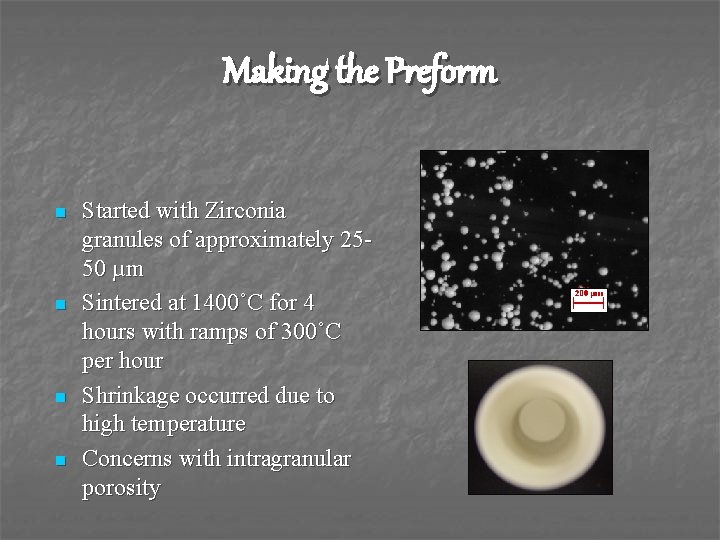
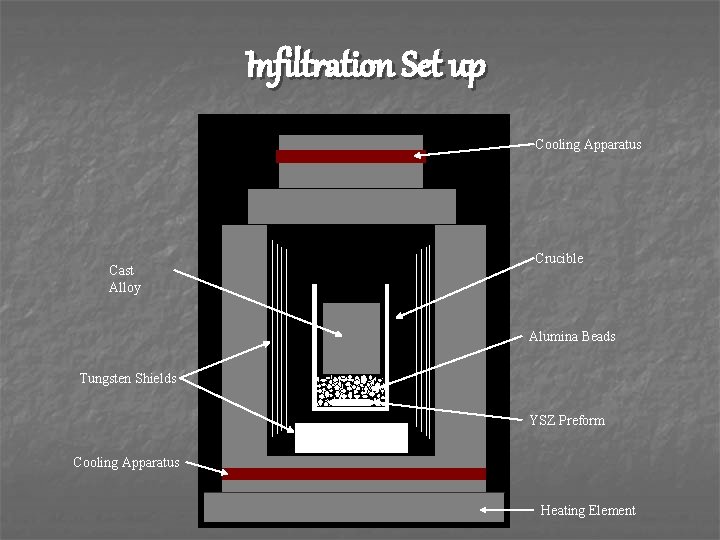
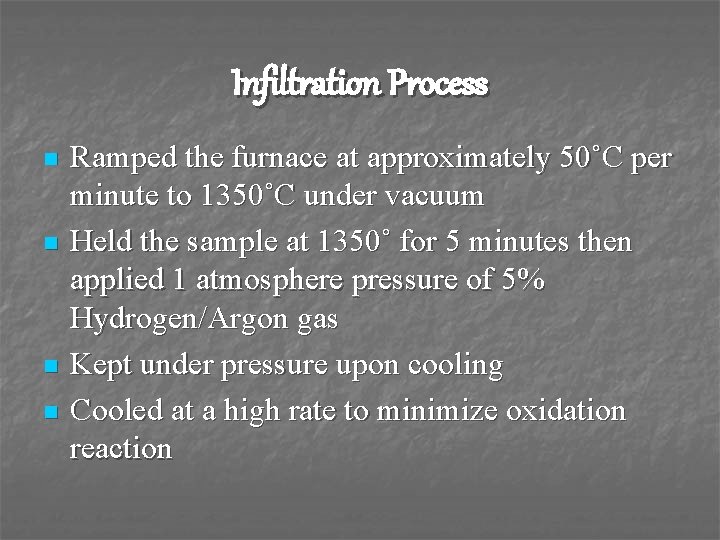

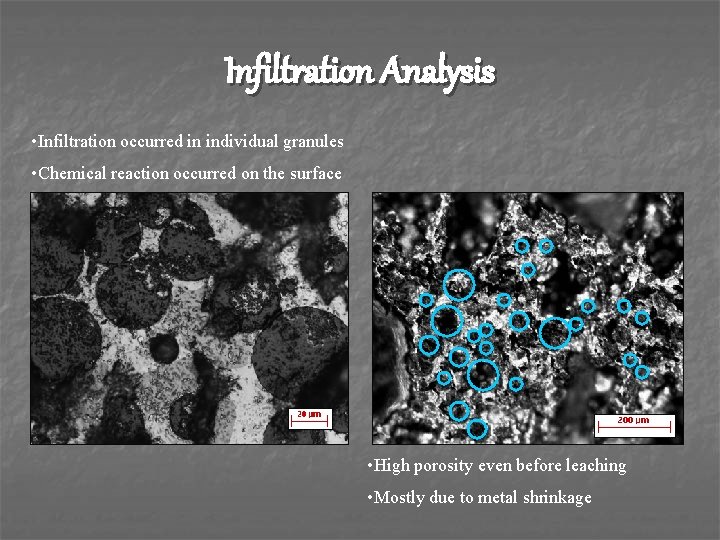
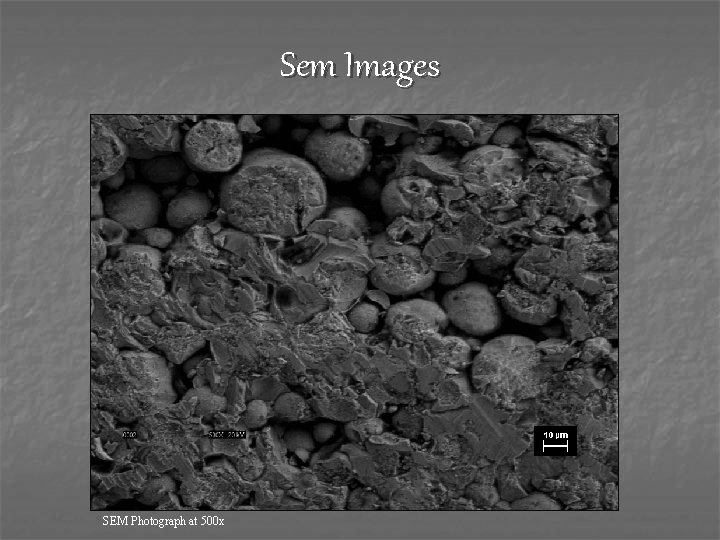
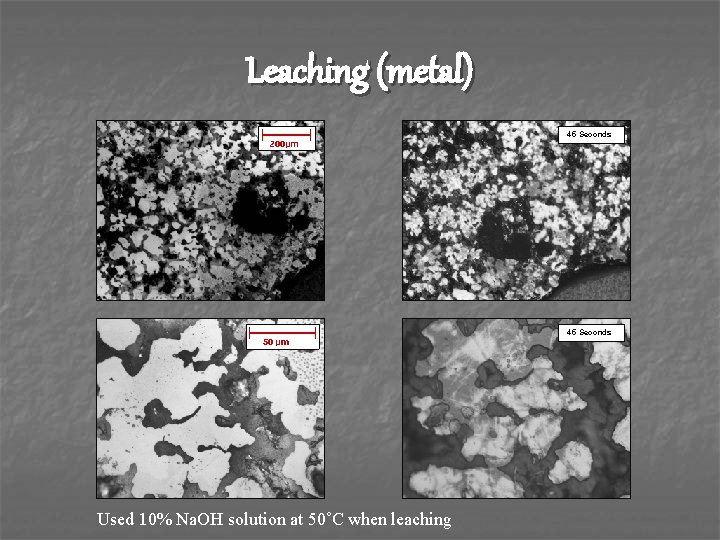
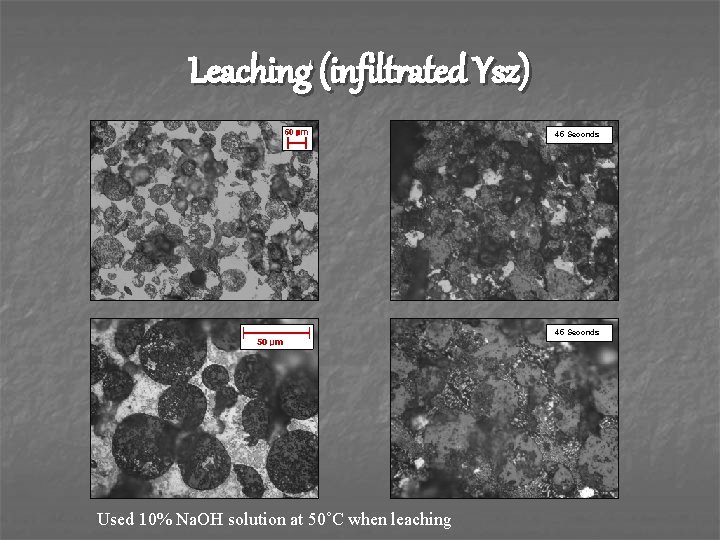
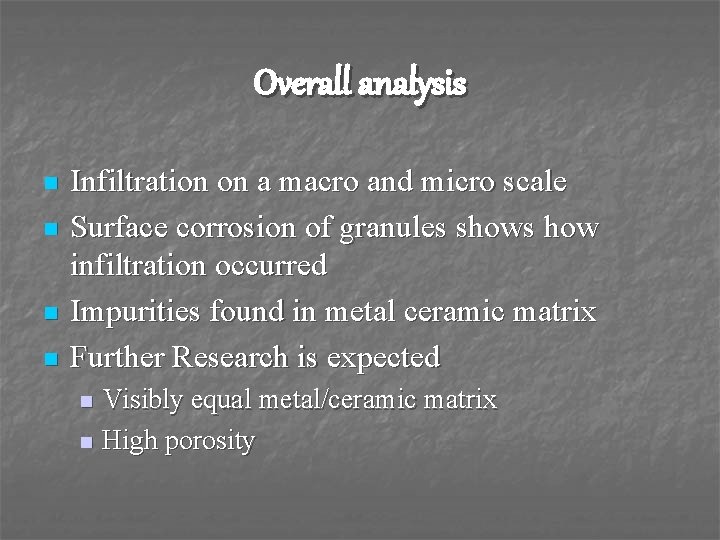
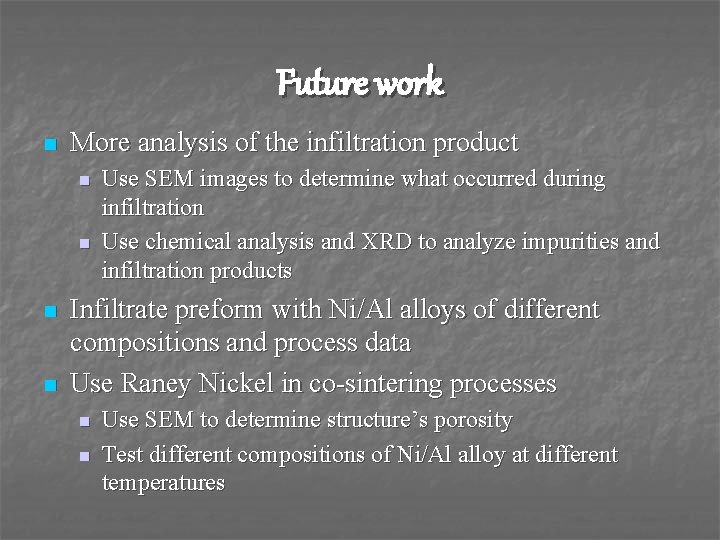
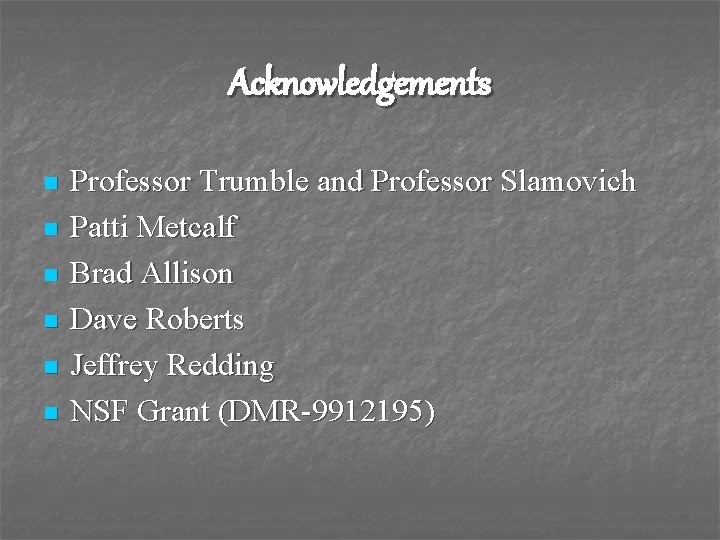
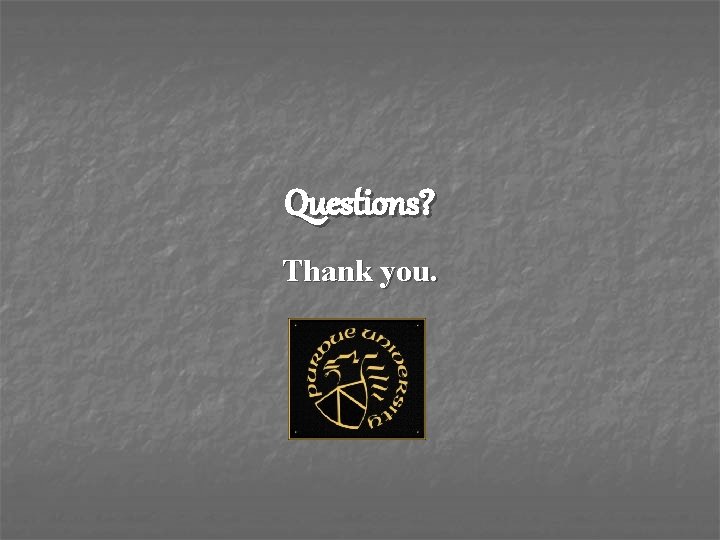
- Slides: 21
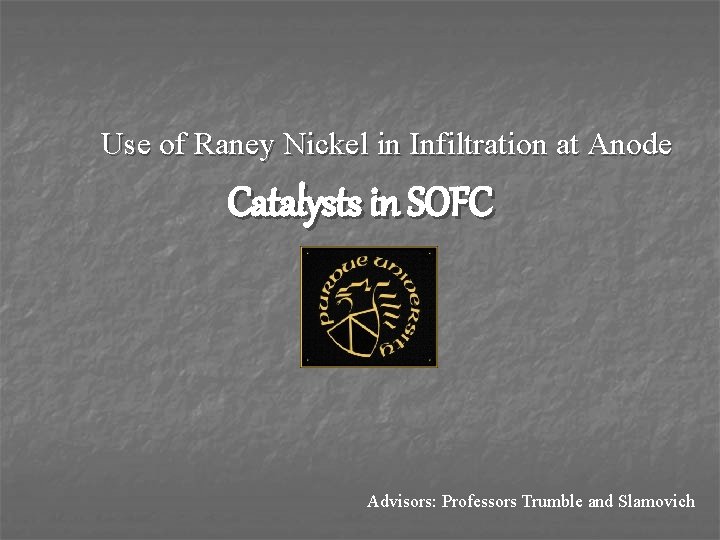
Use of Raney Nickel in Infiltration at Anode Catalysts in SOFC Advisors: Professors Trumble and Slamovich
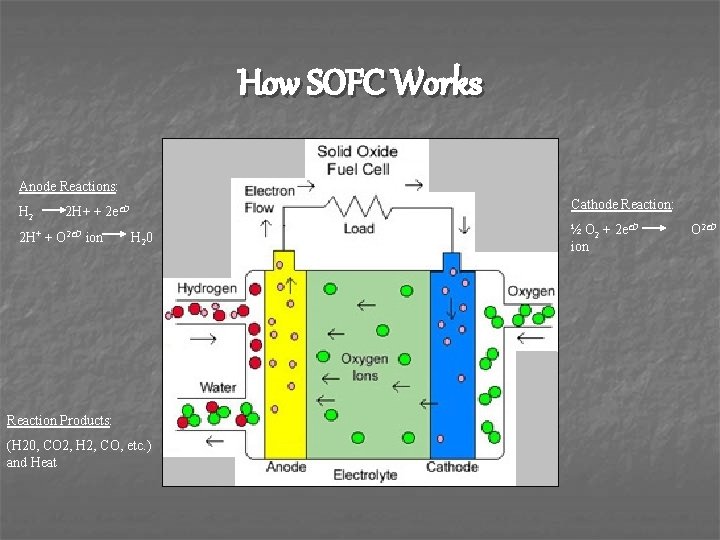
How SOFC Works Anode Reactions: H 2 Cathode Reaction: 2 H+ + 2 e- 2 H+ + O 2 - ion H 20 Reaction Products: (H 20, CO 2, H 2, CO, etc. ) and Heat ½ O 2 + 2 eion O 2 -
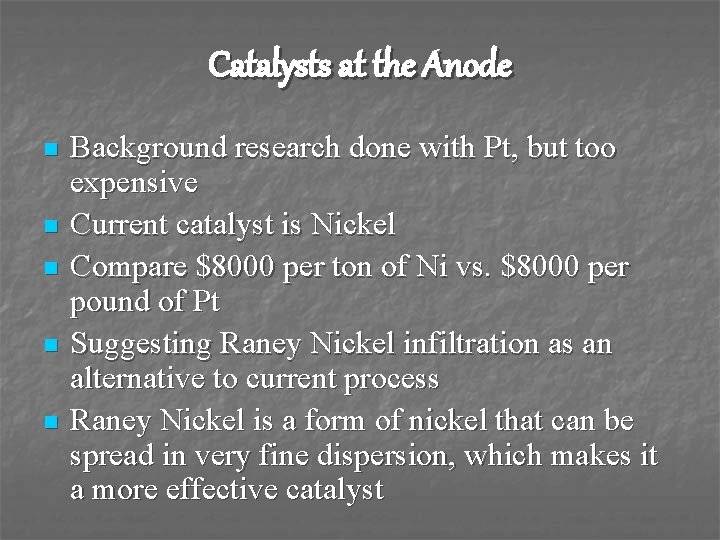
Catalysts at the Anode n n n Background research done with Pt, but too expensive Current catalyst is Nickel Compare $8000 per ton of Ni vs. $8000 per pound of Pt Suggesting Raney Nickel infiltration as an alternative to current process Raney Nickel is a form of nickel that can be spread in very fine dispersion, which makes it a more effective catalyst
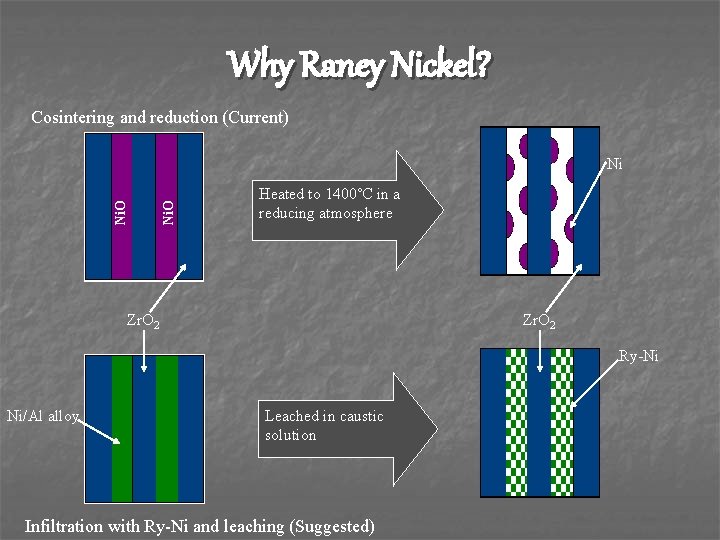
Why Raney Nickel? Cosintering and reduction (Current) Ni. O Ni Heated to 1400˚C in a reducing atmosphere Zr. O 2 Ry-Ni Ni/Al alloy Leached in caustic solution Infiltration with Ry-Ni and leaching (Suggested)
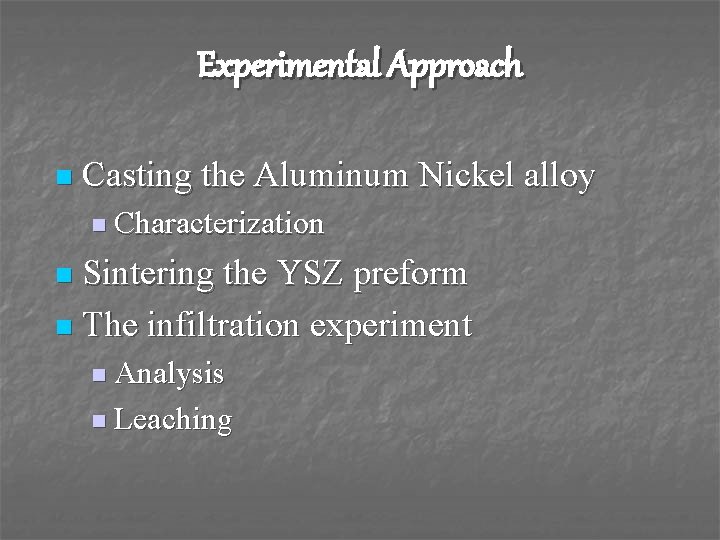
Experimental Approach n Casting the Aluminum Nickel alloy n Characterization Sintering the YSZ preform n The infiltration experiment n n Analysis n Leaching
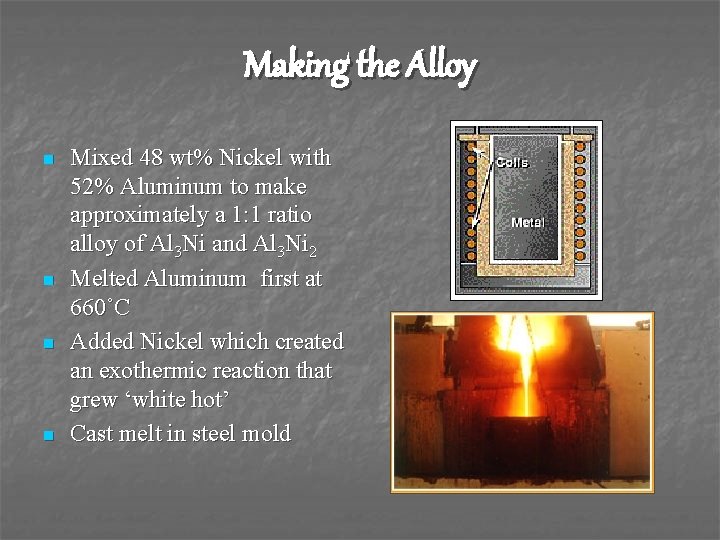
Making the Alloy n n Mixed 48 wt% Nickel with 52% Aluminum to make approximately a 1: 1 ratio alloy of Al 3 Ni and Al 3 Ni 2 Melted Aluminum first at 660˚C Added Nickel which created an exothermic reaction that grew ‘white hot’ Cast melt in steel mold
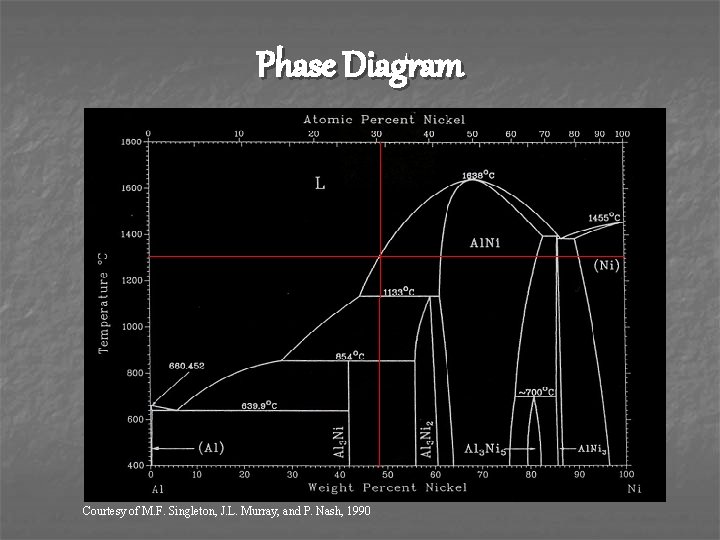
Phase Diagram Courtesy of M. F. Singleton, J. L. Murray, and P. Nash, 1990
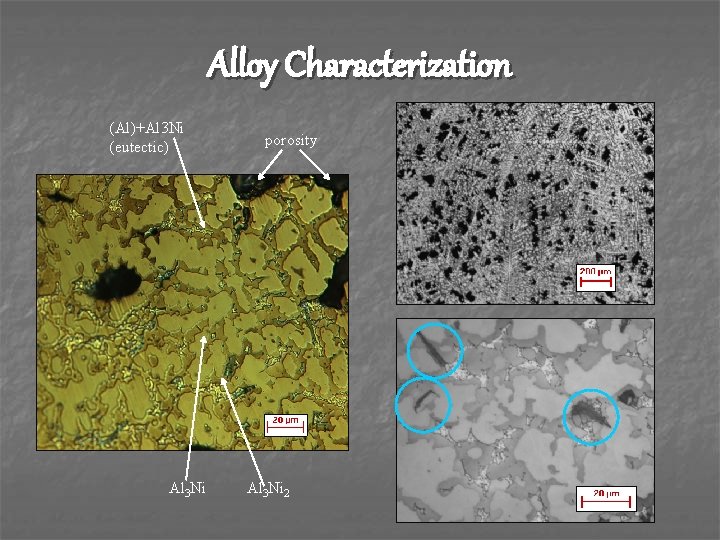
Alloy Characterization (Al)+Al 3 Ni (eutectic) Al 3 Ni porosity Al 3 Ni 2
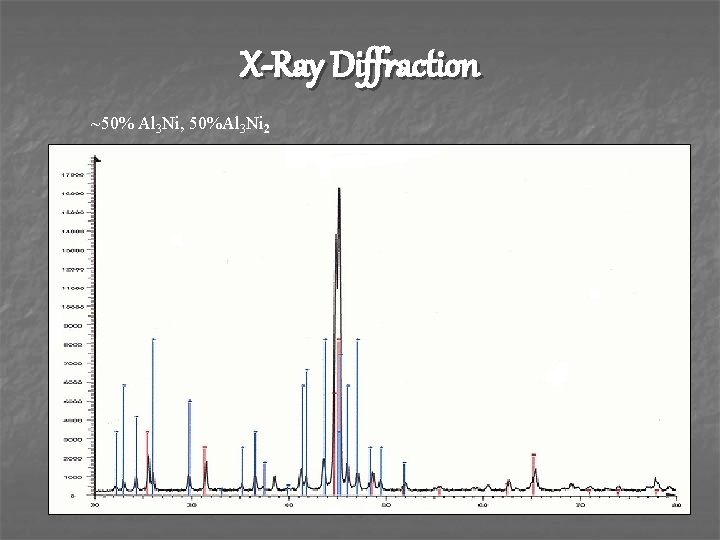
X-Ray Diffraction ~50% Al 3 Ni, 50%Al 3 Ni 2
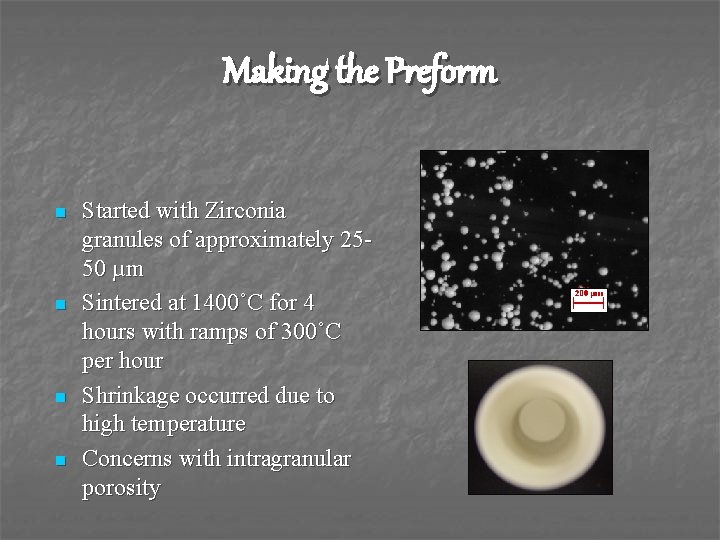
Making the Preform n n Started with Zirconia granules of approximately 2550 µm Sintered at 1400˚C for 4 hours with ramps of 300˚C per hour Shrinkage occurred due to high temperature Concerns with intragranular porosity 200 µm
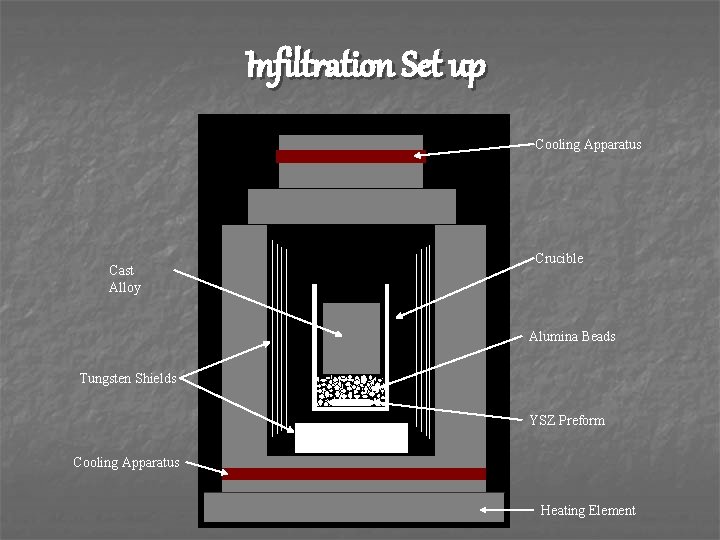
Infiltration Set up Cooling Apparatus Cast Alloy Crucible Alumina Beads Tungsten Shields YSZ Preform Cooling Apparatus Heating Element
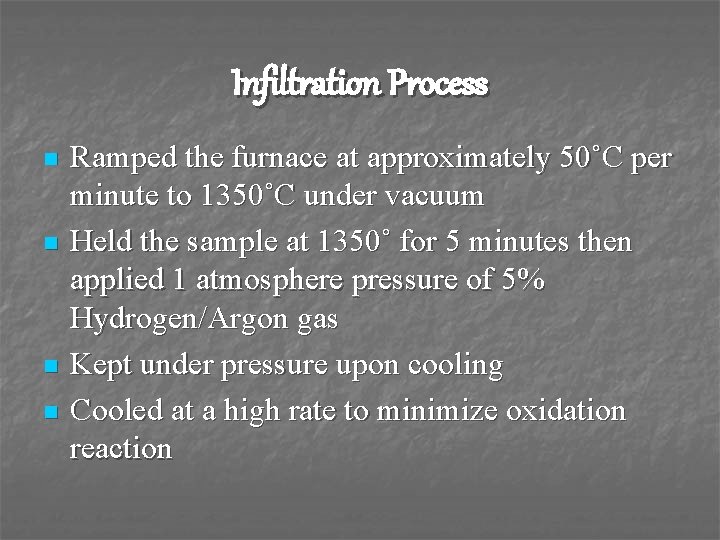
Infiltration Process n n Ramped the furnace at approximately 50˚C per minute to 1350˚C under vacuum Held the sample at 1350˚ for 5 minutes then applied 1 atmosphere pressure of 5% Hydrogen/Argon gas Kept under pressure upon cooling Cooled at a high rate to minimize oxidation reaction

Infiltration Results n n It worked!! It did not infiltrate the YSZ disk fully Redox reaction prevention appears to have worked well Unanalyzed metallic impurities more plentiful in infiltrated disk Crucible Melted Ni/Al alloy Alumina Beads Infiltrated Zirconia
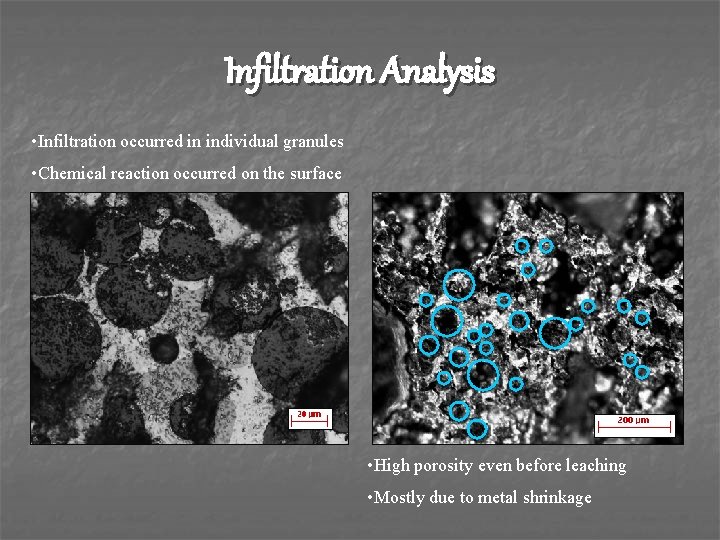
Infiltration Analysis • Infiltration occurred in individual granules • Chemical reaction occurred on the surface • High porosity even before leaching • Mostly due to metal shrinkage
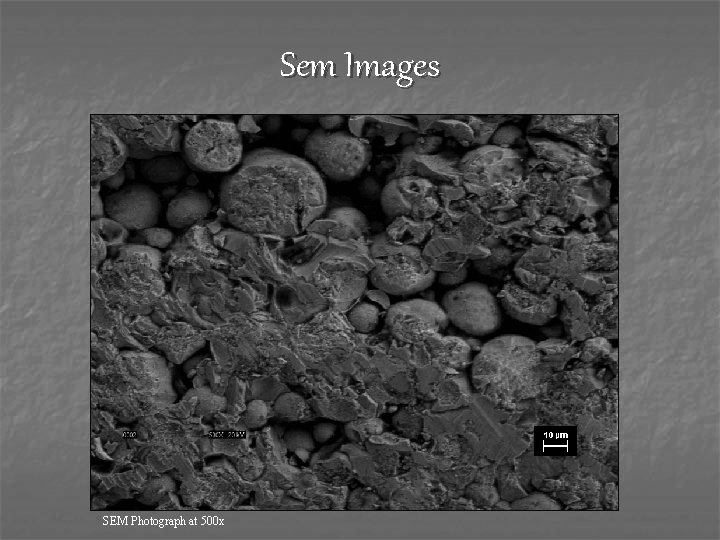
Sem Images SEM Photograph at 500 x
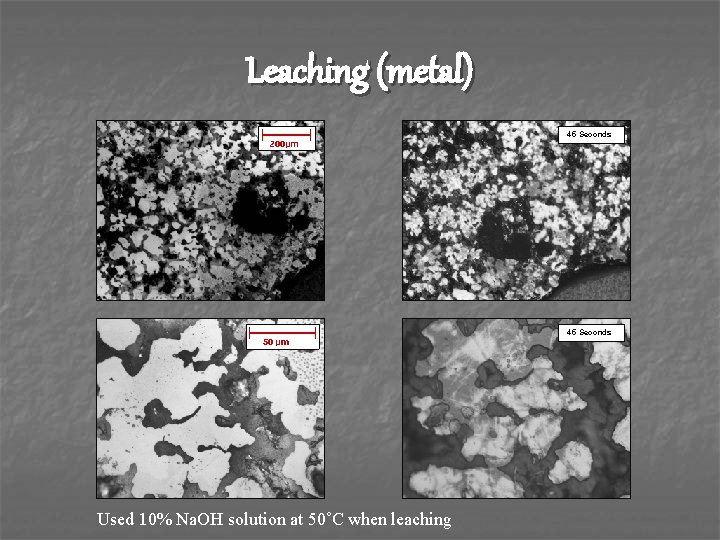
Leaching (metal) 255 Seconds 45 Seconds Used 10% Na. OH solution at 50˚C when leaching
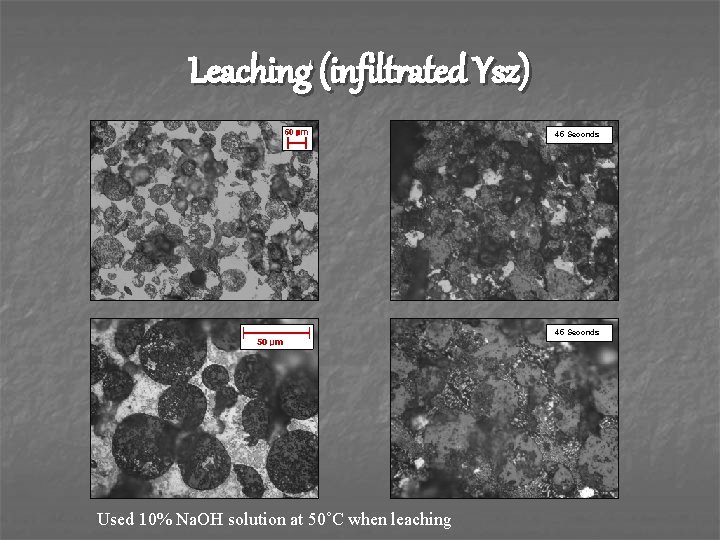
Leaching (infiltrated Ysz) 255 Seconds 45 Seconds Used 10% Na. OH solution at 50˚C when leaching
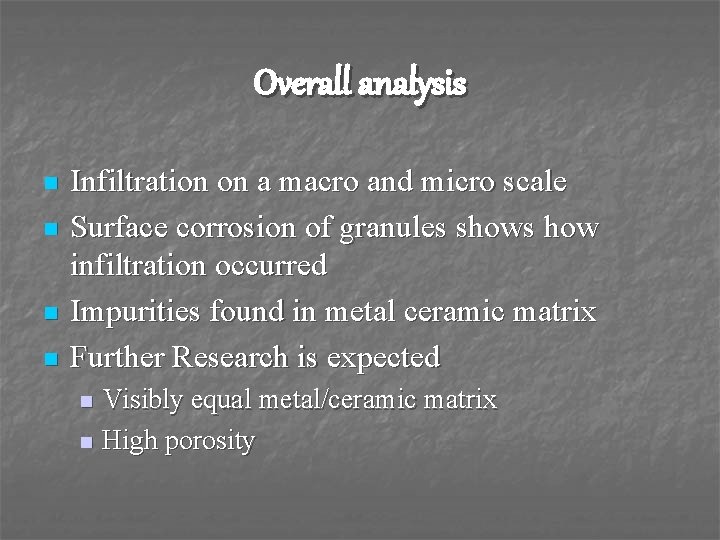
Overall analysis n n Infiltration on a macro and micro scale Surface corrosion of granules shows how infiltration occurred Impurities found in metal ceramic matrix Further Research is expected Visibly equal metal/ceramic matrix n High porosity n
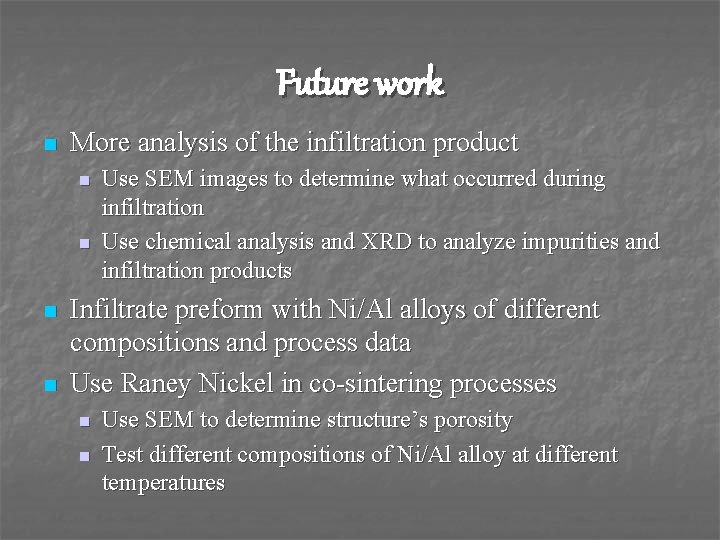
Future work n More analysis of the infiltration product n n Use SEM images to determine what occurred during infiltration Use chemical analysis and XRD to analyze impurities and infiltration products Infiltrate preform with Ni/Al alloys of different compositions and process data Use Raney Nickel in co-sintering processes n n Use SEM to determine structure’s porosity Test different compositions of Ni/Al alloy at different temperatures
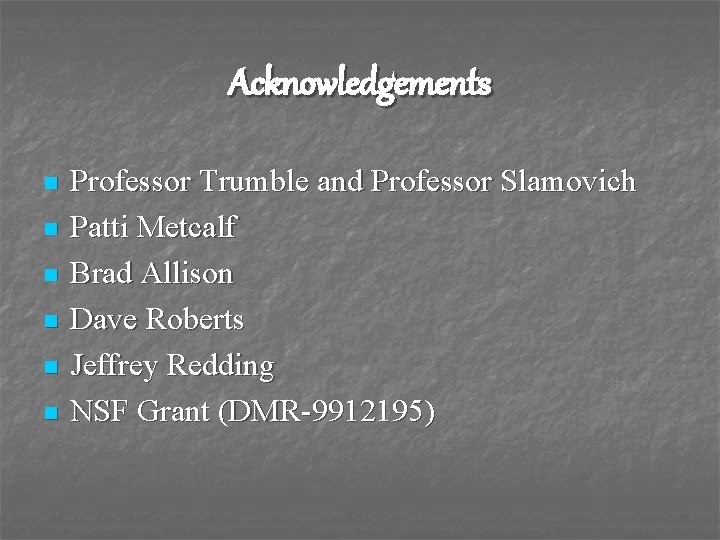
Acknowledgements n n n Professor Trumble and Professor Slamovich Patti Metcalf Brad Allison Dave Roberts Jeffrey Redding NSF Grant (DMR-9912195)
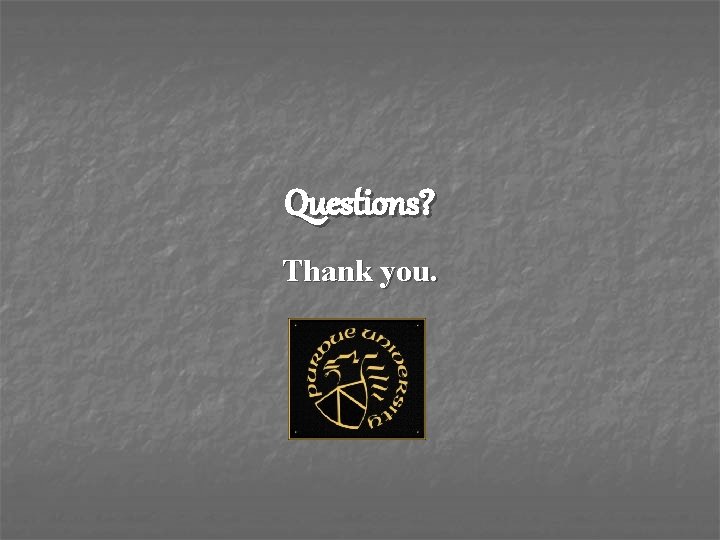
Questions? Thank you.
Nickel cadmium cell primary secondary
Steve raney
Kevin raney
Ni symbol
Nickel ion charge
How to memorise the reactivity series
Nickel 111 carbonate
Operation nickel grass
A quoi sert le nickel
Thifty nickel
High pressure acid leaching nickel
Nickel element family
Bio-nickl
Gpa
Orbital diagram for nickel
Nickel institute
Cathy has a nickel a dime
Orbital notation for nickel
A quoi sert le nickel
In mond's process nickel is made to react with
James nickel morris
Nickel affinity chromatography