UMass Student Launch Team Preliminary Design Review Presentation
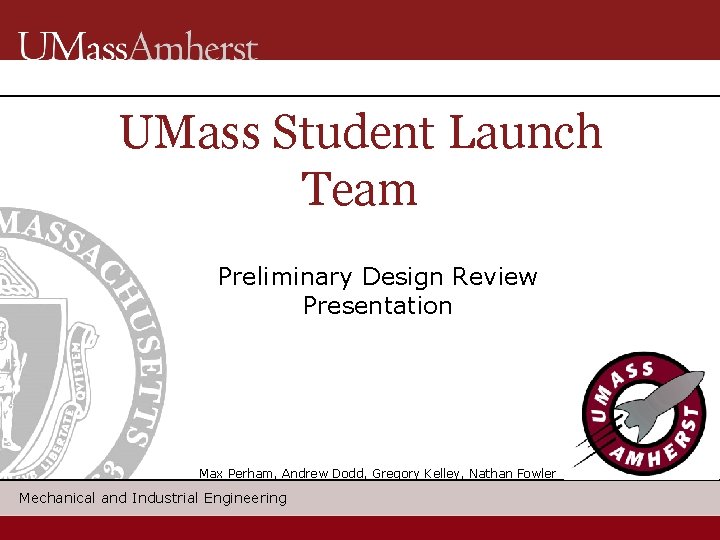
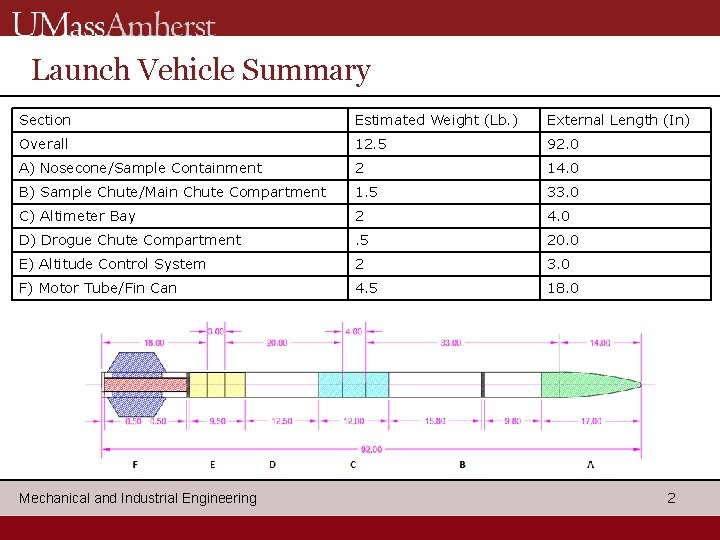
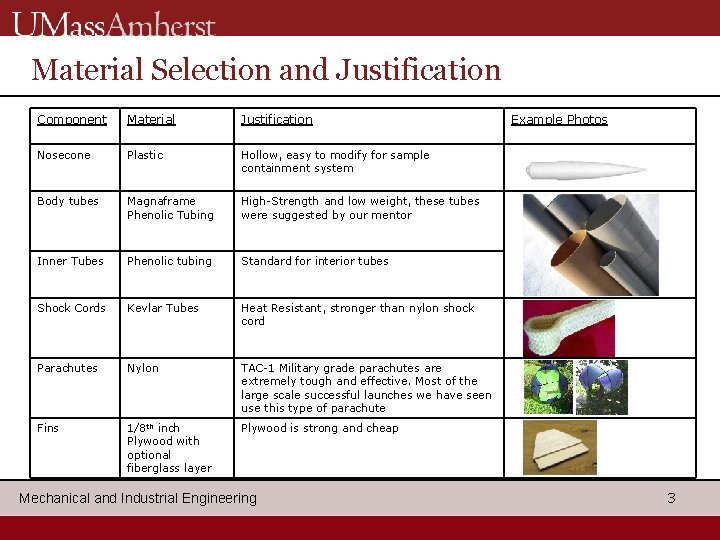
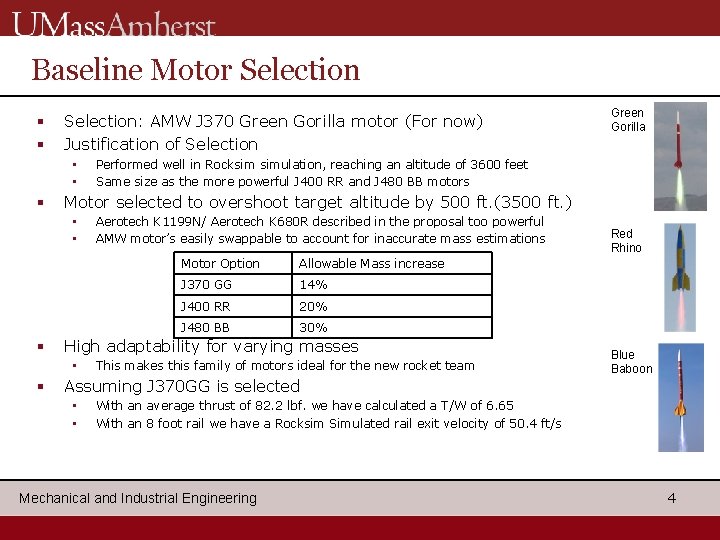
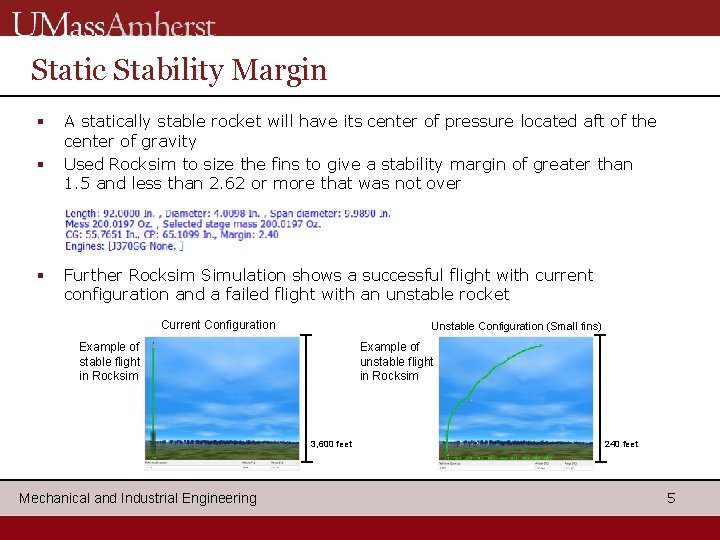
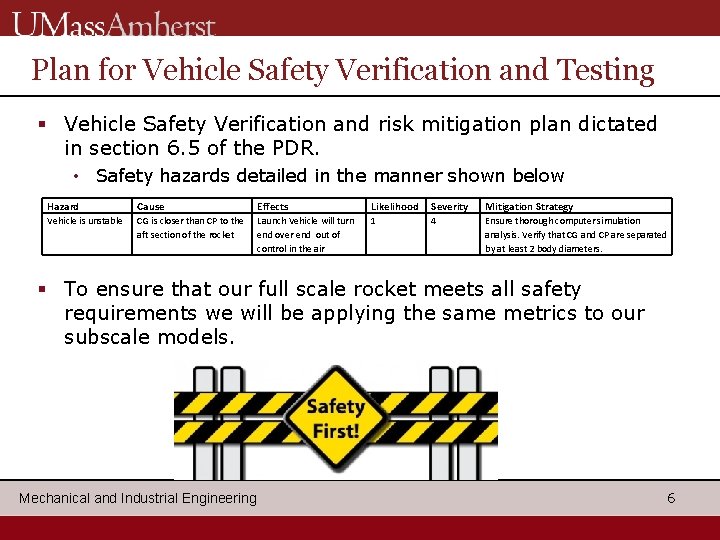
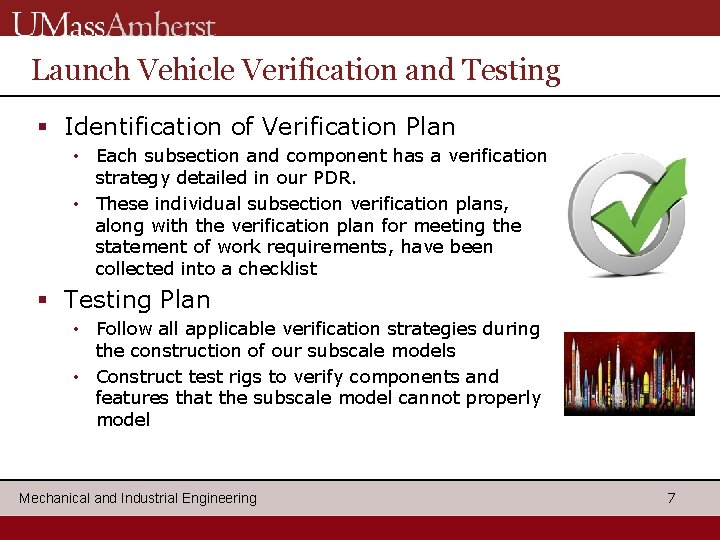
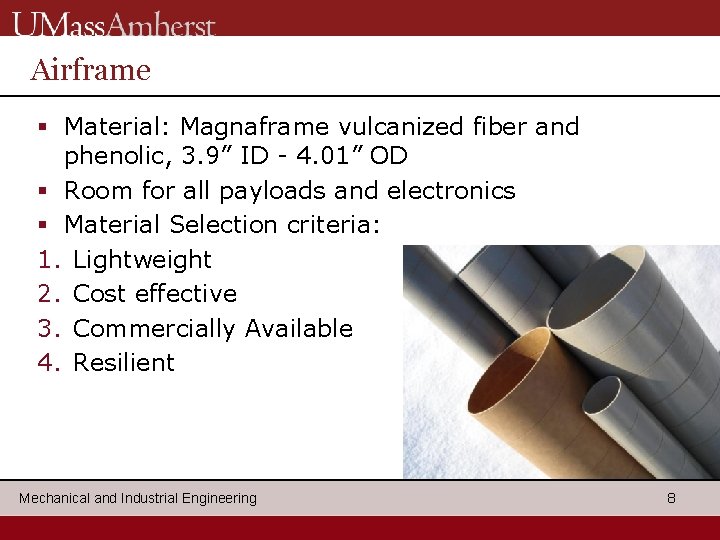
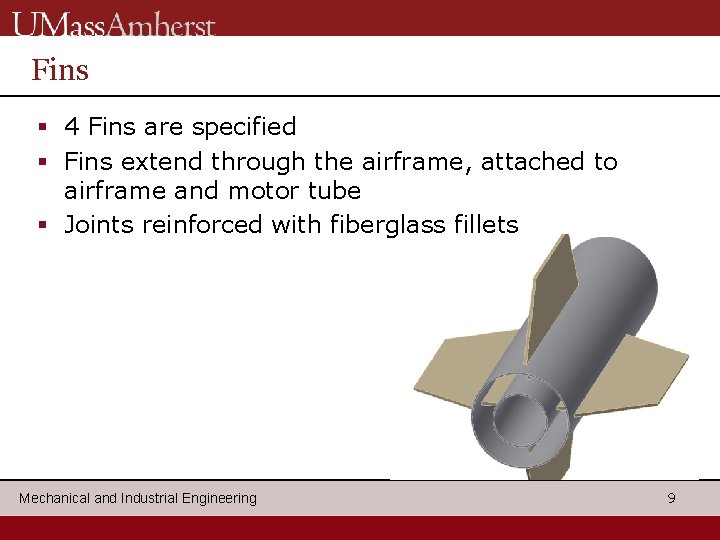
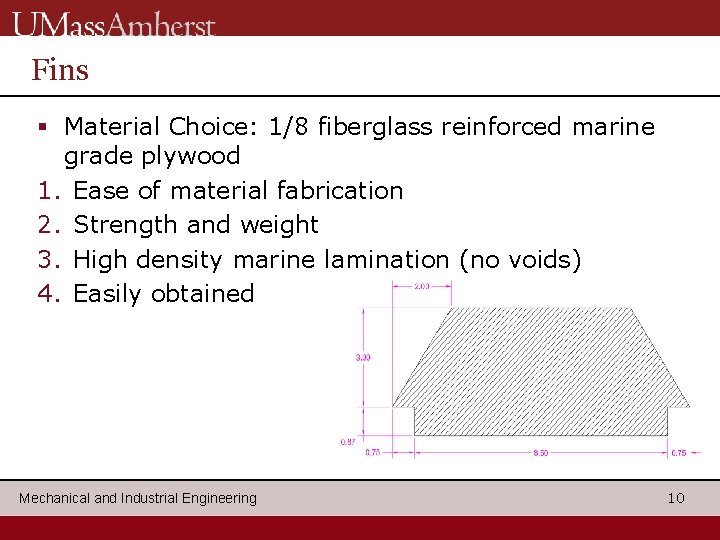
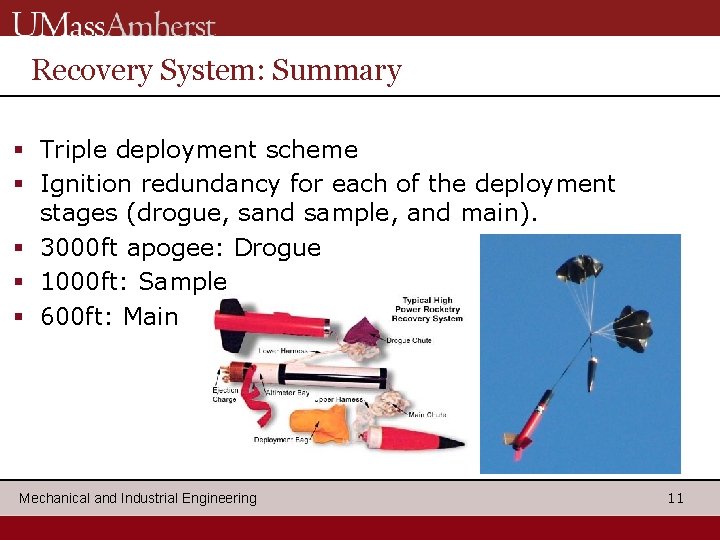
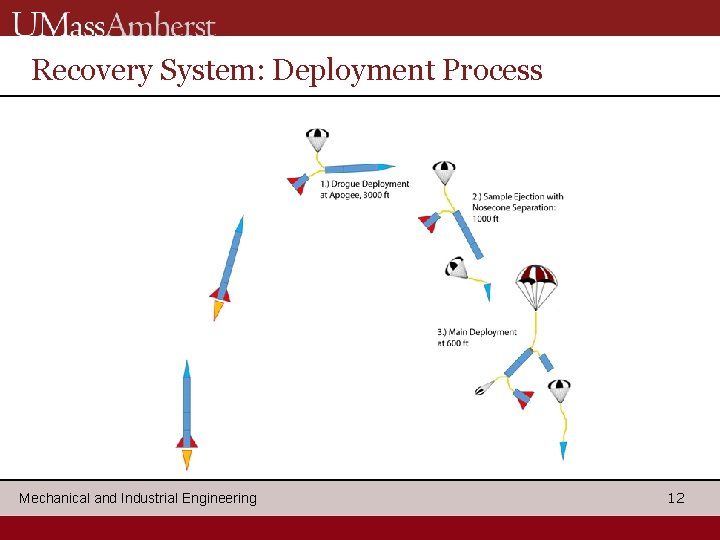
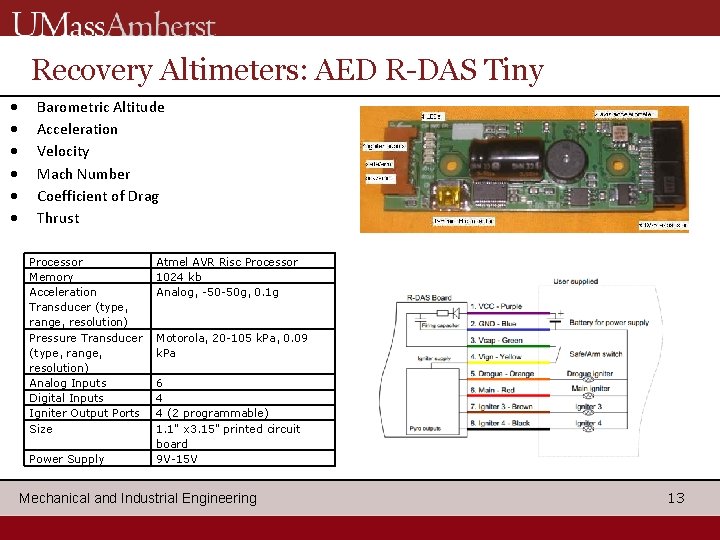
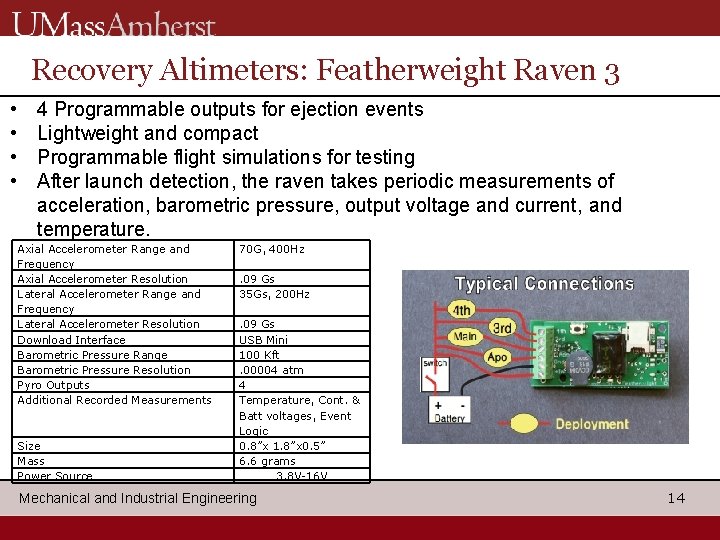
![Recovery System: Parachute Sizing and Specification Parachute Purpose Type Material Diameter [in] Mass [oz] Recovery System: Parachute Sizing and Specification Parachute Purpose Type Material Diameter [in] Mass [oz]](https://slidetodoc.com/presentation_image/a7f0188abd0a1b112f75f88c7848ce60/image-15.jpg)
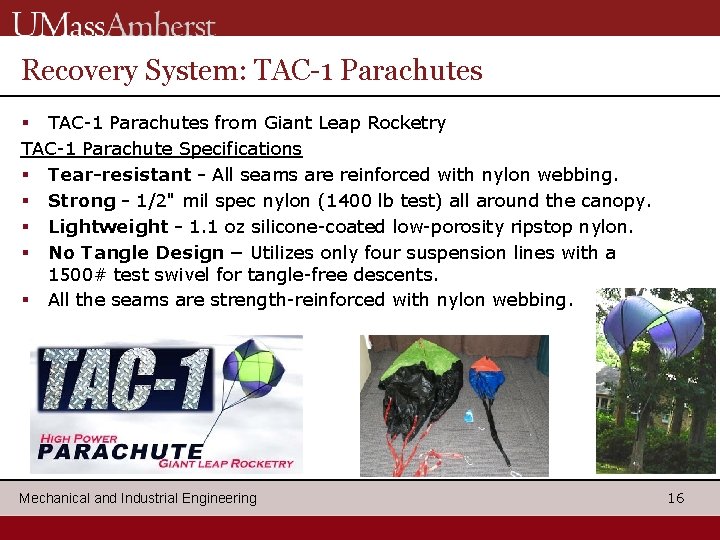
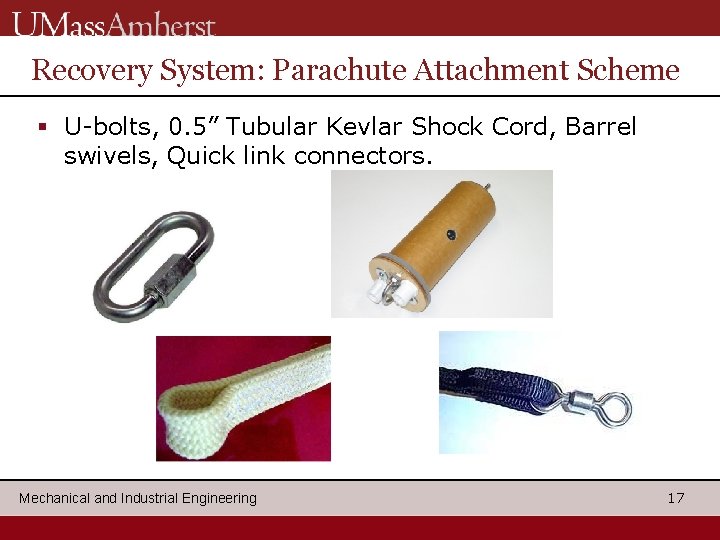
![Recovery System: Ejection Charges Section Charge Size [g] Drogue Bay 1. 16 Force Produced Recovery System: Ejection Charges Section Charge Size [g] Drogue Bay 1. 16 Force Produced](https://slidetodoc.com/presentation_image/a7f0188abd0a1b112f75f88c7848ce60/image-18.jpg)
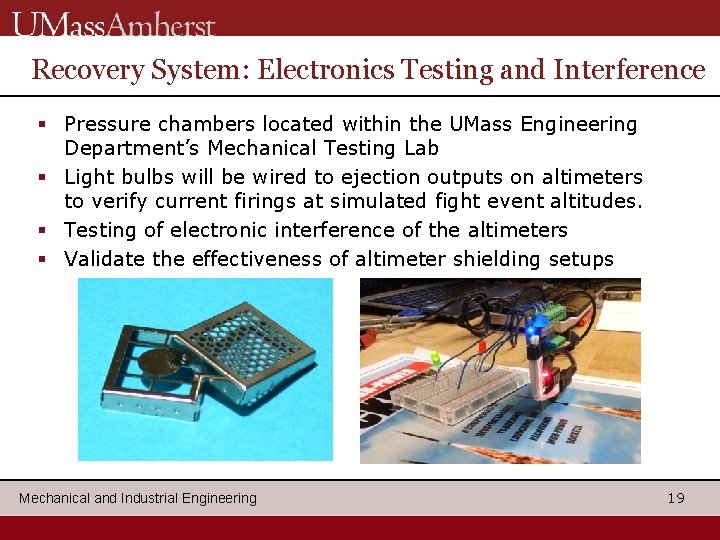
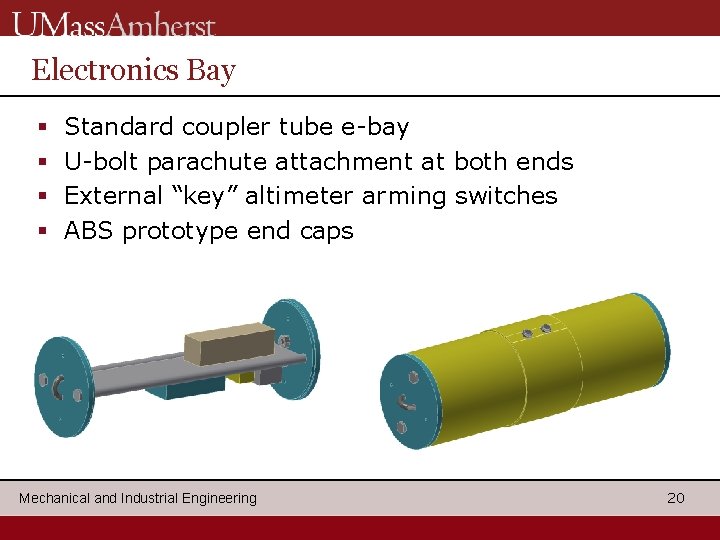
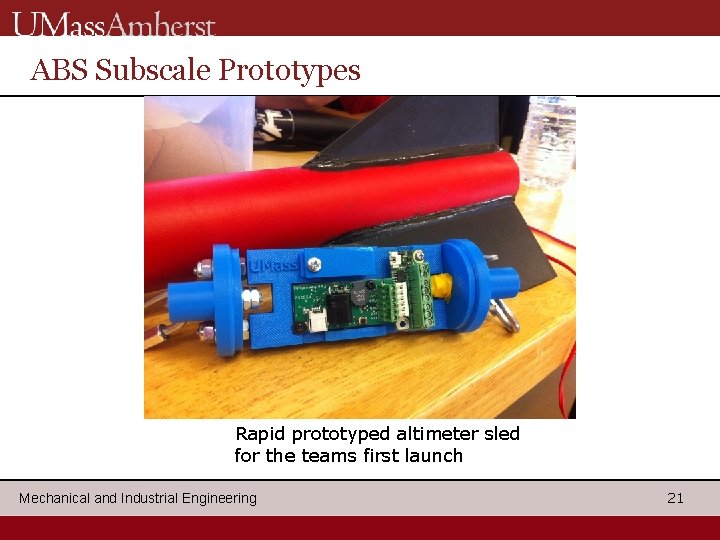
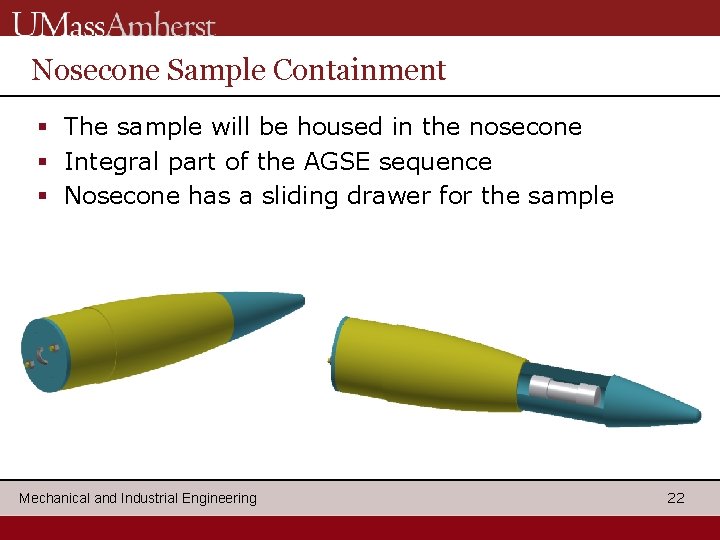
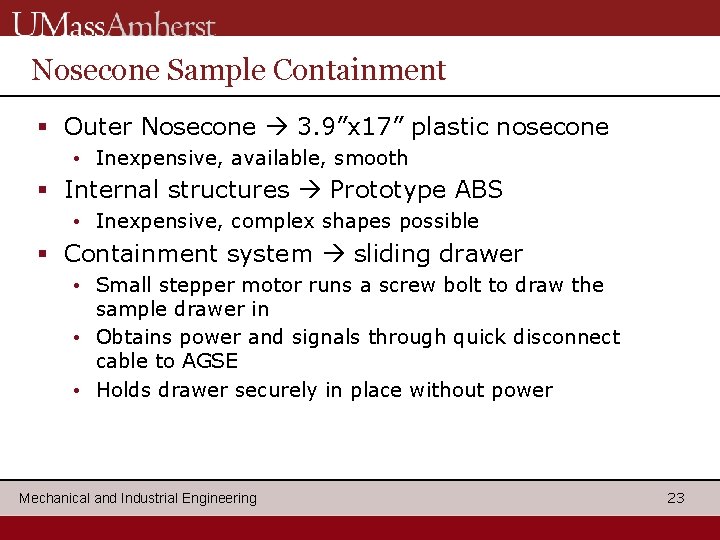
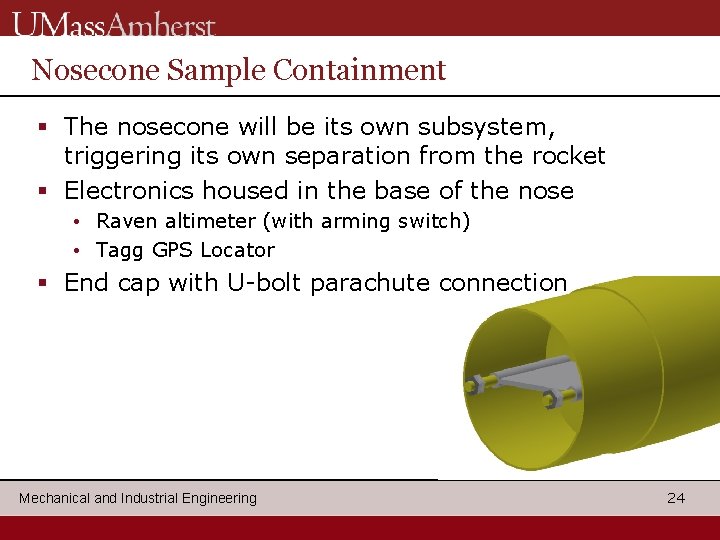
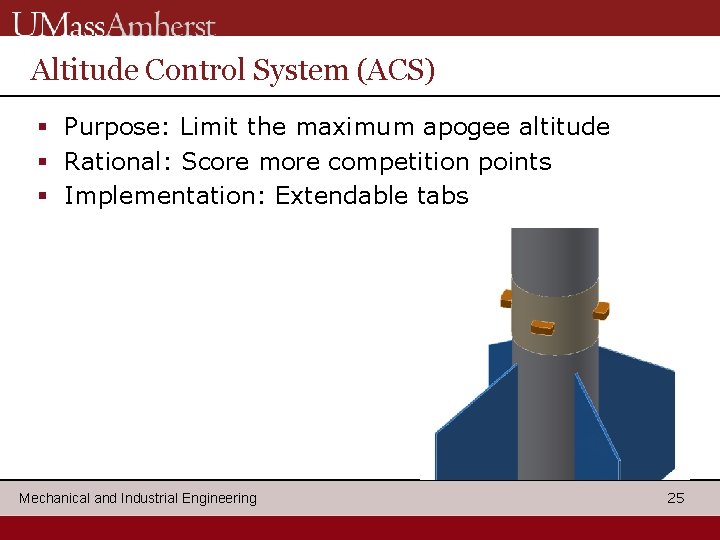

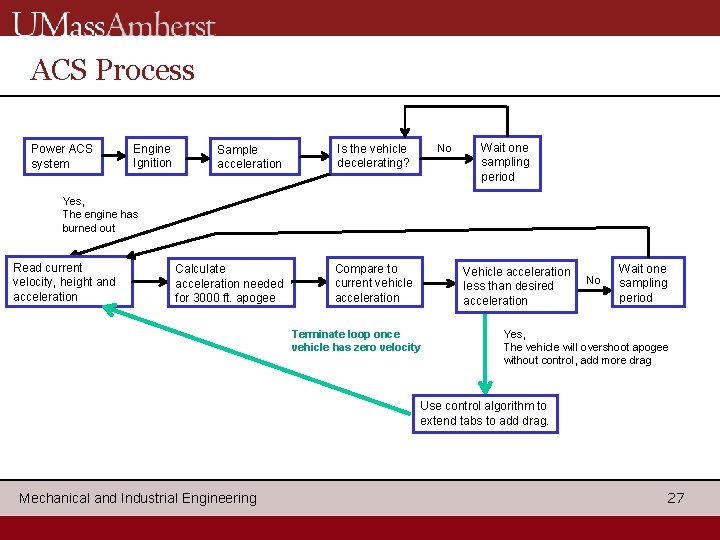
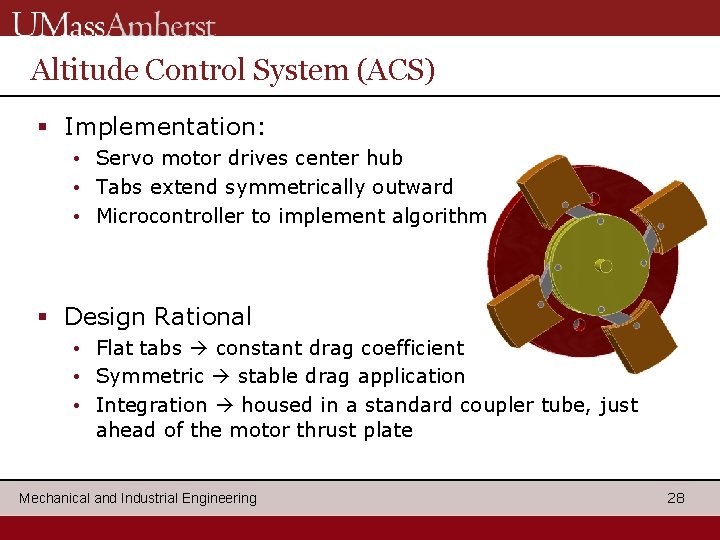
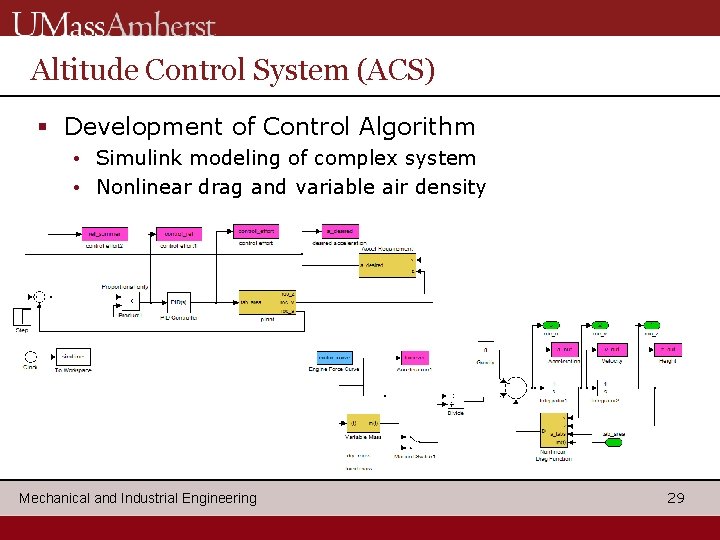
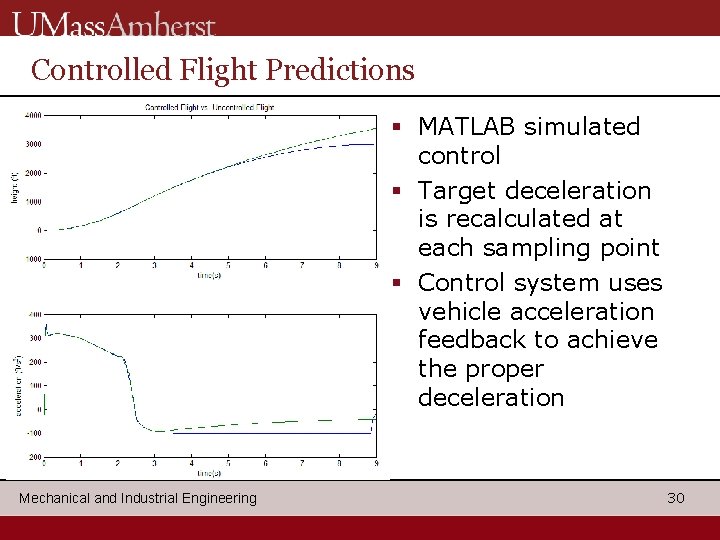
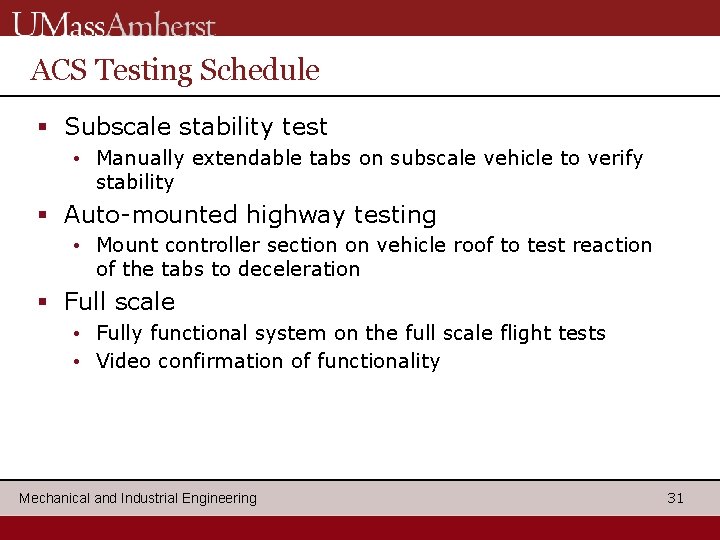
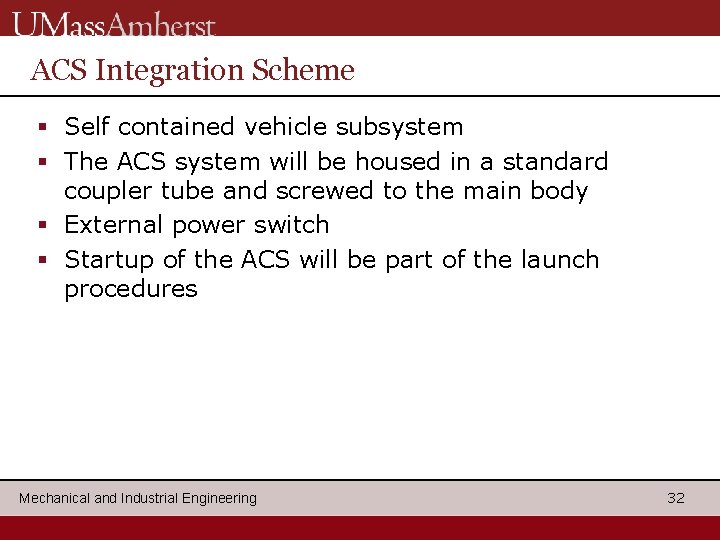
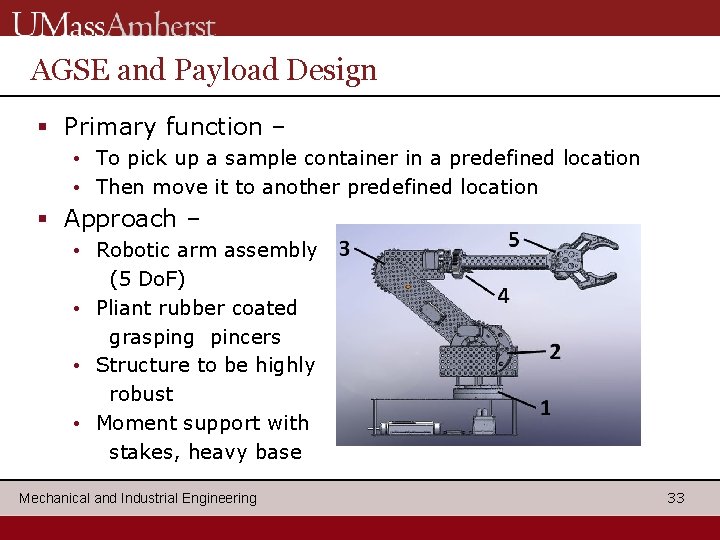
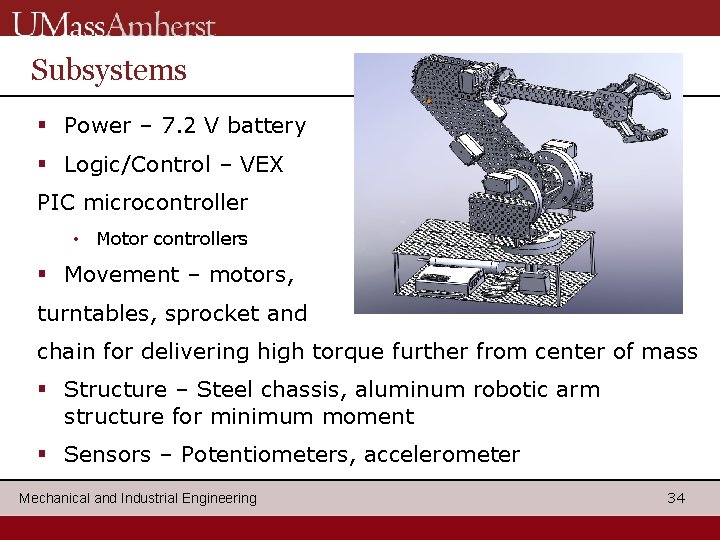
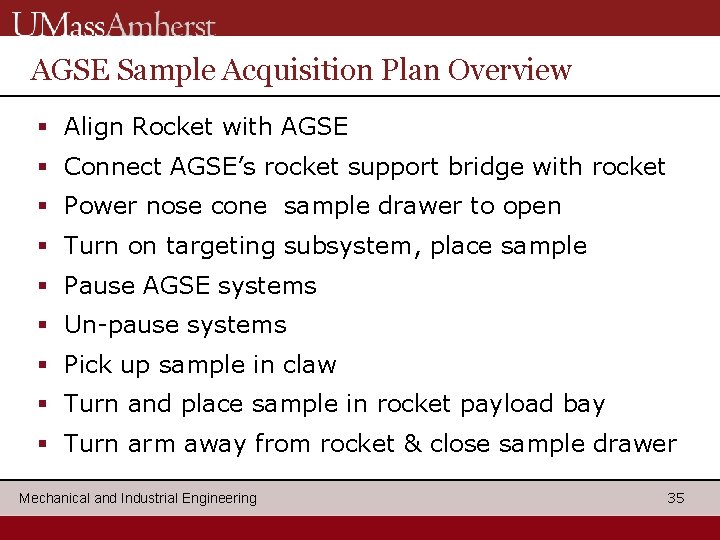
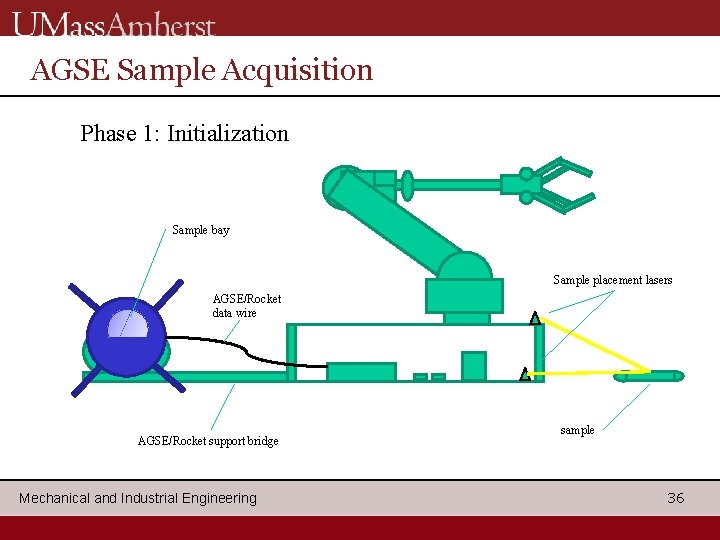
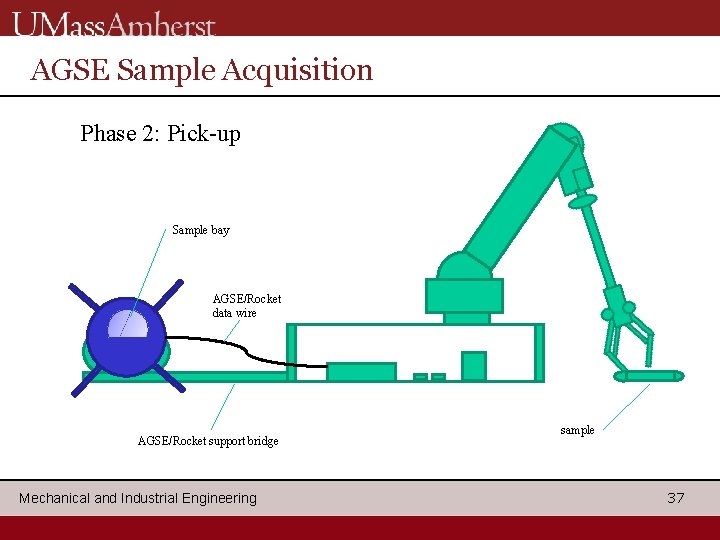
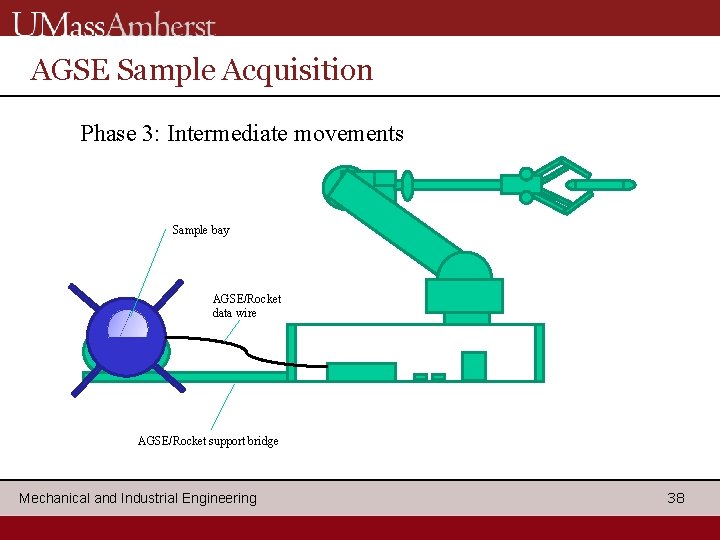
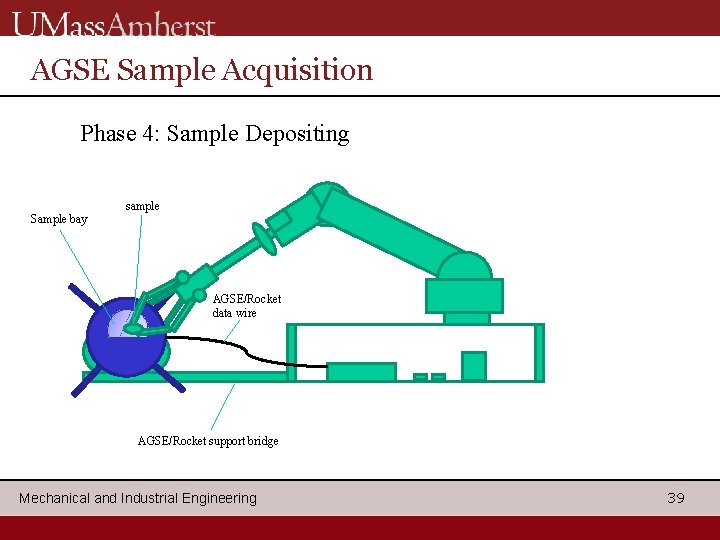
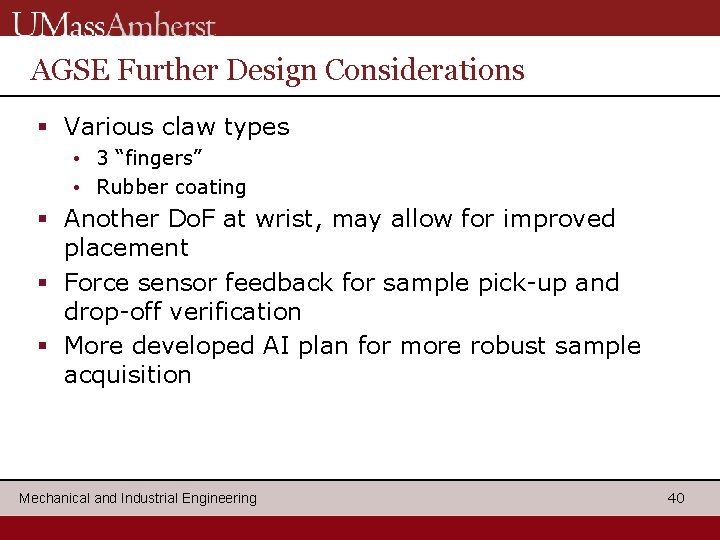
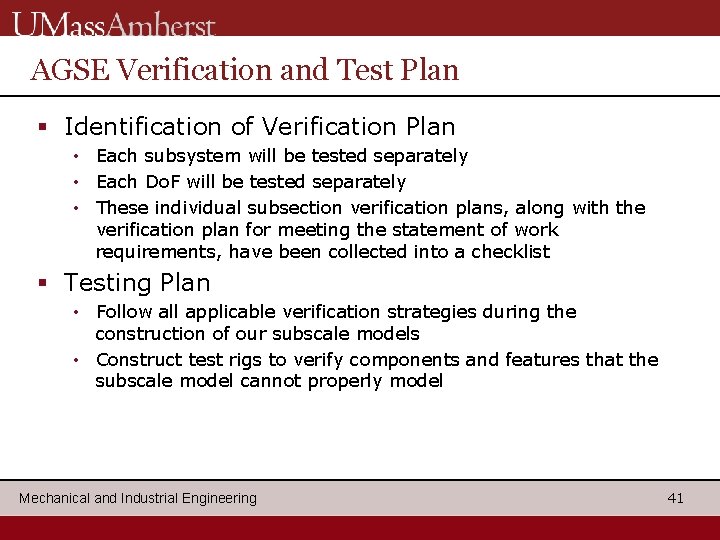
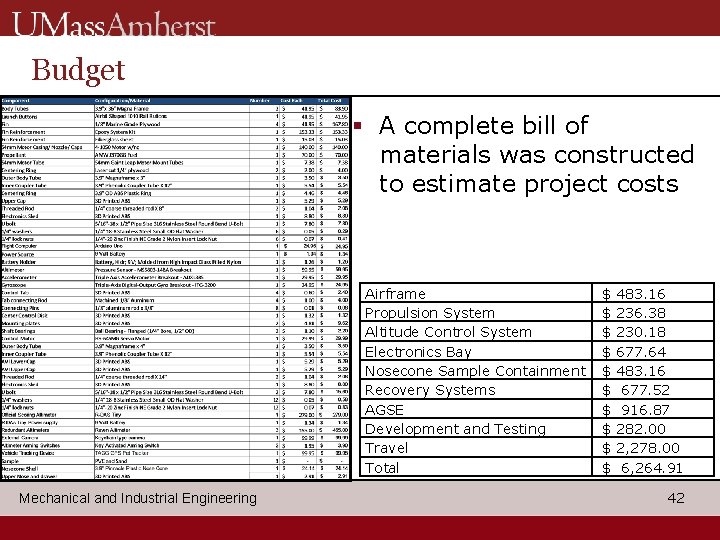
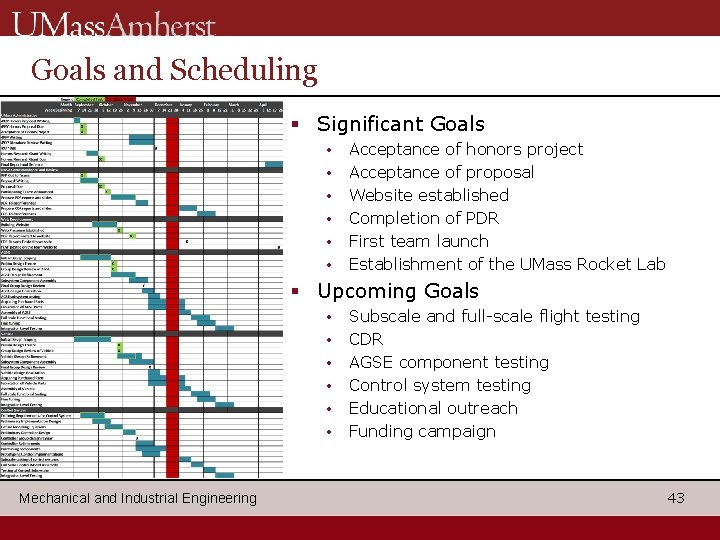
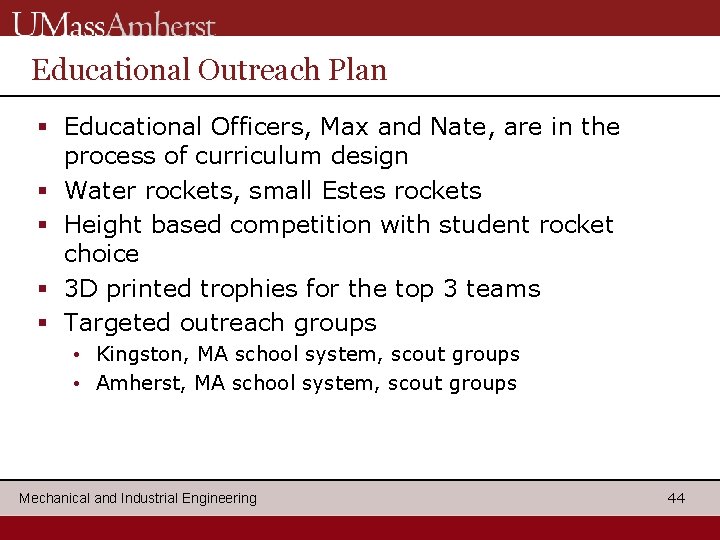
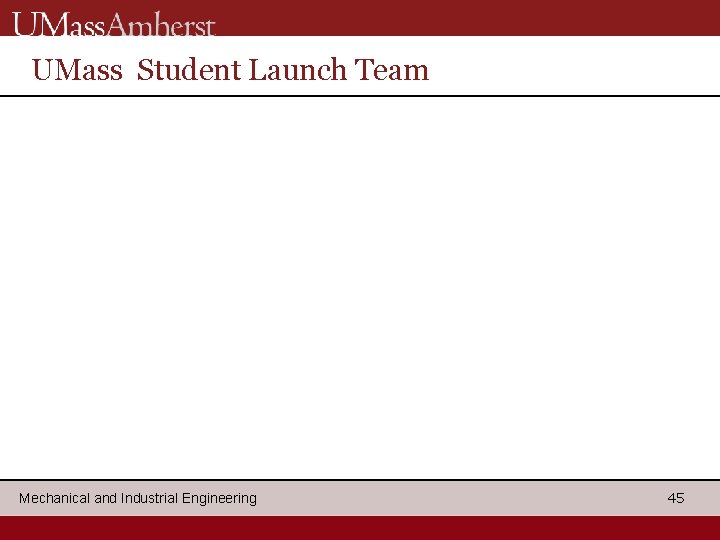
- Slides: 45
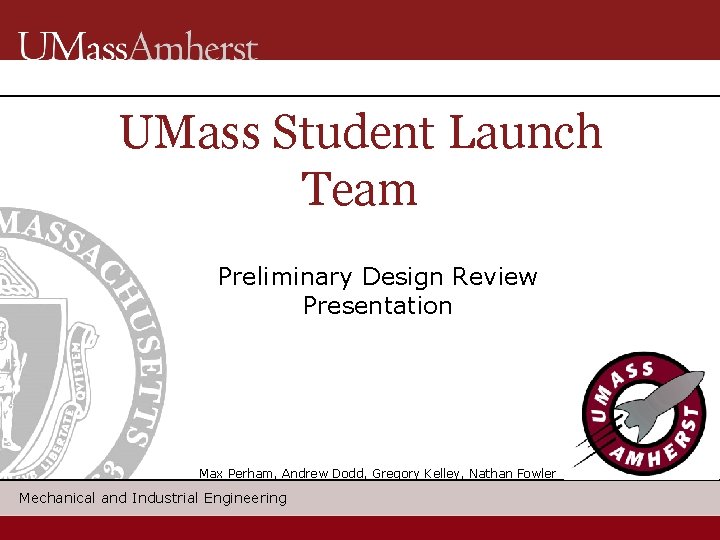
UMass Student Launch Team Preliminary Design Review Presentation Max Perham, Andrew Dodd, Gregory Kelley, Nathan Fowler Mechanical and Industrial Engineering
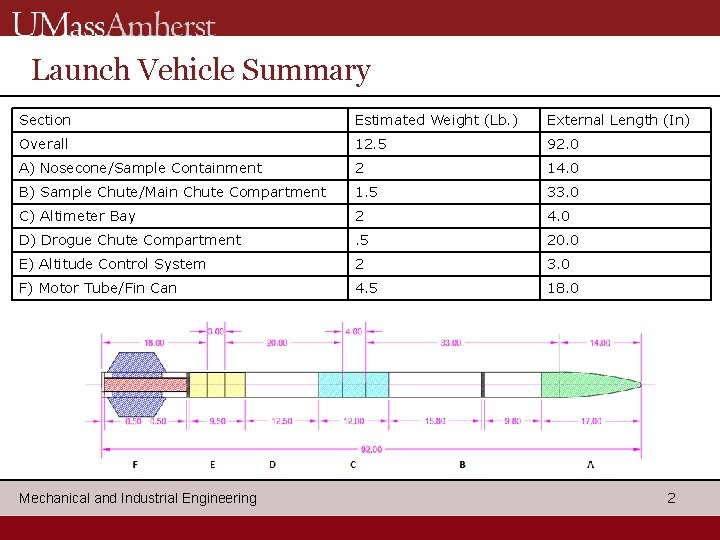
Launch Vehicle Summary Section Estimated Weight (Lb. ) External Length (In) Overall 12. 5 92. 0 A) Nosecone/Sample Containment 2 14. 0 B) Sample Chute/Main Chute Compartment 1. 5 33. 0 C) Altimeter Bay 2 4. 0 D) Drogue Chute Compartment . 5 20. 0 E) Altitude Control System 2 3. 0 F) Motor Tube/Fin Can 4. 5 18. 0 Mechanical and Industrial Engineering 2
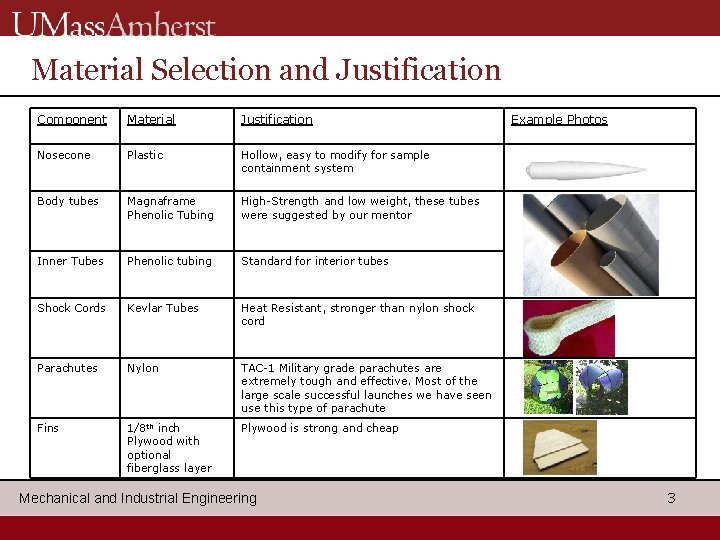
Material Selection and Justification Component Material Justification Nosecone Plastic Hollow, easy to modify for sample containment system Body tubes Magnaframe Phenolic Tubing High-Strength and low weight, these tubes were suggested by our mentor Inner Tubes Phenolic tubing Standard for interior tubes Shock Cords Kevlar Tubes Heat Resistant, stronger than nylon shock cord Parachutes Nylon TAC-1 Military grade parachutes are extremely tough and effective. Most of the large scale successful launches we have seen use this type of parachute Fins 1/8 th inch Plywood with optional fiberglass layer Plywood is strong and cheap Mechanical and Industrial Engineering Example Photos 3
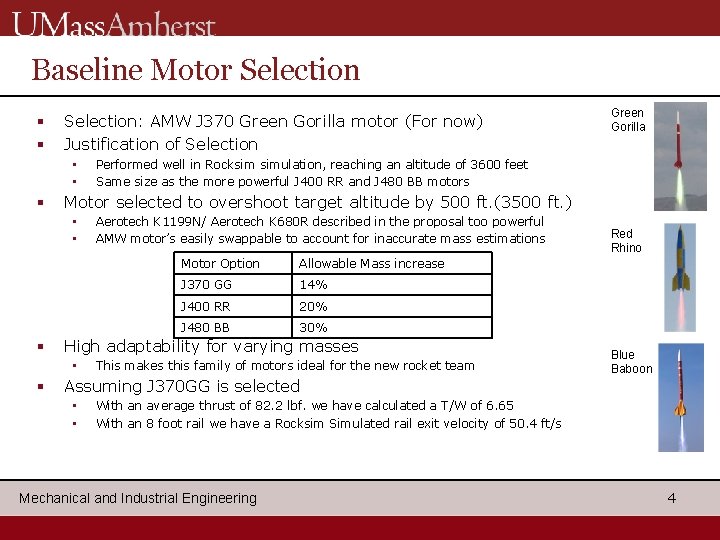
Baseline Motor Selection § § Selection: AMW J 370 Green Gorilla motor (For now) Justification of Selection • • § Aerotech K 1199 N/ Aerotech K 680 R described in the proposal too powerful AMW motor’s easily swappable to account for inaccurate mass estimations Motor Option Allowable Mass increase J 370 GG 14% J 400 RR 20% J 480 BB 30% High adaptability for varying masses • § Performed well in Rocksim simulation, reaching an altitude of 3600 feet Same size as the more powerful J 400 RR and J 480 BB motors Motor selected to overshoot target altitude by 500 ft. (3500 ft. ) • • § Green Gorilla This makes this family of motors ideal for the new rocket team Red Rhino Blue Baboon Assuming J 370 GG is selected • • With an average thrust of 82. 2 lbf. we have calculated a T/W of 6. 65 With an 8 foot rail we have a Rocksim Simulated rail exit velocity of 50. 4 ft/s Mechanical and Industrial Engineering 4
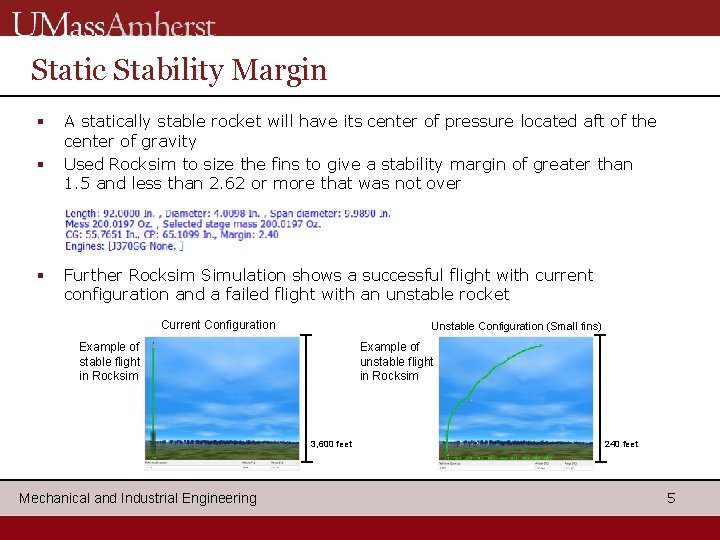
Static Stability Margin § § § A statically stable rocket will have its center of pressure located aft of the center of gravity Used Rocksim to size the fins to give a stability margin of greater than 1. 5 and less than 2. 62 or more that was not over Further Rocksim Simulation shows a successful flight with current configuration and a failed flight with an unstable rocket Current Configuration Unstable Configuration (Small fins) Example of stable flight in Rocksim Example of unstable flight in Rocksim 3, 600 feet Mechanical and Industrial Engineering 240 feet 5
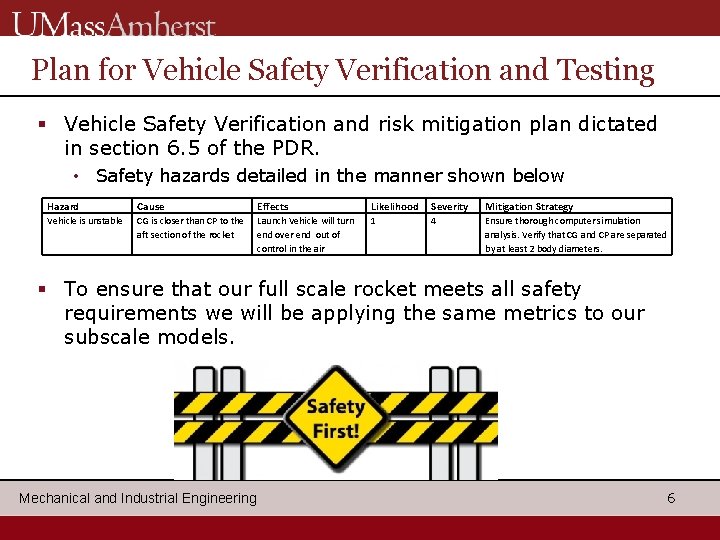
Plan for Vehicle Safety Verification and Testing § Vehicle Safety Verification and risk mitigation plan dictated in section 6. 5 of the PDR. • Safety hazards detailed in the manner shown below Hazard Cause Effects Likelihood Severity Mitigation Strategy Vehicle is unstable CG is closer than CP to the aft section of the rocket Launch Vehicle will turn end over end out of control in the air 1 4 Ensure thorough computer simulation analysis. Verify that CG and CP are separated by at least 2 body diameters. § To ensure that our full scale rocket meets all safety requirements we will be applying the same metrics to our subscale models. Mechanical and Industrial Engineering 6
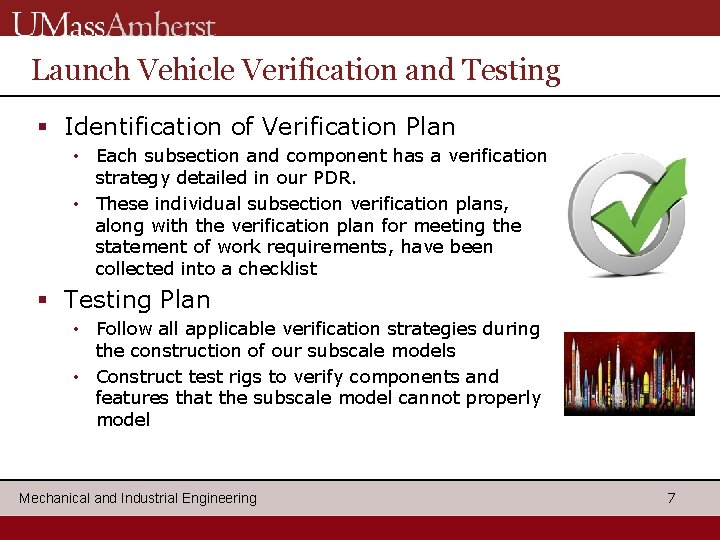
Launch Vehicle Verification and Testing § Identification of Verification Plan • Each subsection and component has a verification strategy detailed in our PDR. • These individual subsection verification plans, along with the verification plan for meeting the statement of work requirements, have been collected into a checklist § Testing Plan • Follow all applicable verification strategies during the construction of our subscale models • Construct test rigs to verify components and features that the subscale model cannot properly model Mechanical and Industrial Engineering 7
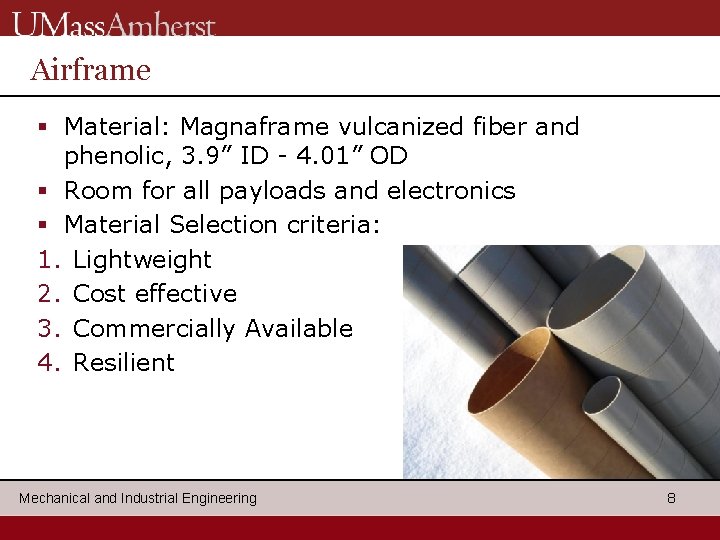
Airframe § Material: Magnaframe vulcanized fiber and phenolic, 3. 9” ID - 4. 01” OD § Room for all payloads and electronics § Material Selection criteria: 1. Lightweight 2. Cost effective 3. Commercially Available 4. Resilient Mechanical and Industrial Engineering 8
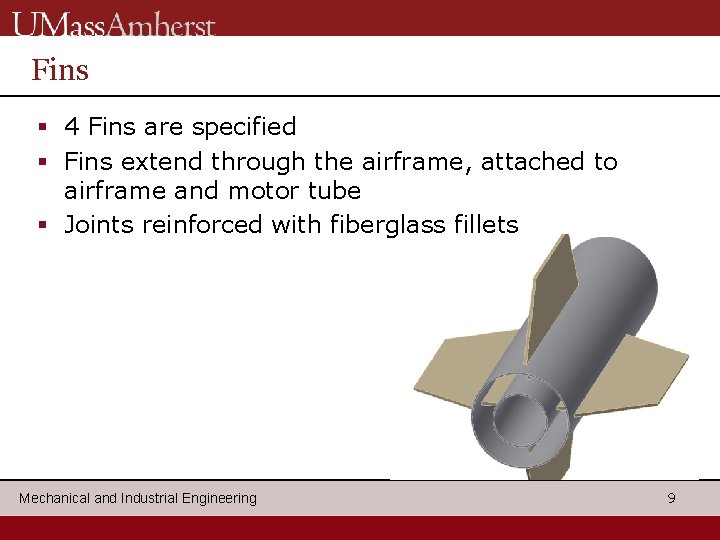
Fins § 4 Fins are specified § Fins extend through the airframe, attached to airframe and motor tube § Joints reinforced with fiberglass fillets Mechanical and Industrial Engineering 9
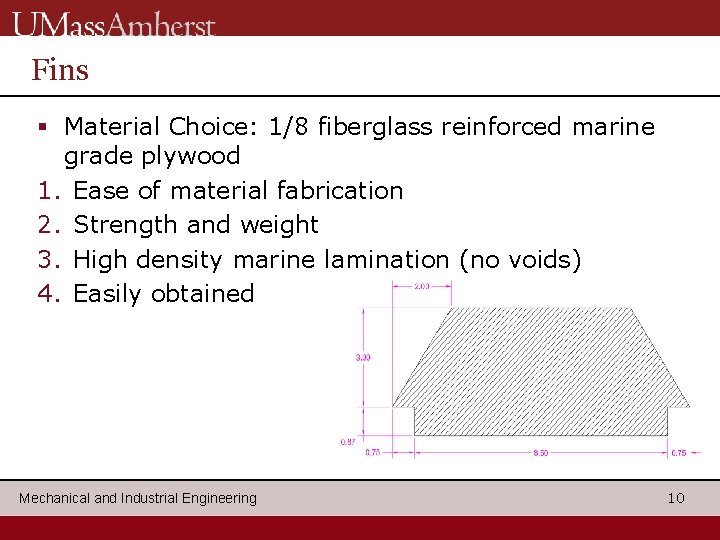
Fins § Material Choice: 1/8 fiberglass reinforced marine grade plywood 1. Ease of material fabrication 2. Strength and weight 3. High density marine lamination (no voids) 4. Easily obtained Mechanical and Industrial Engineering 10
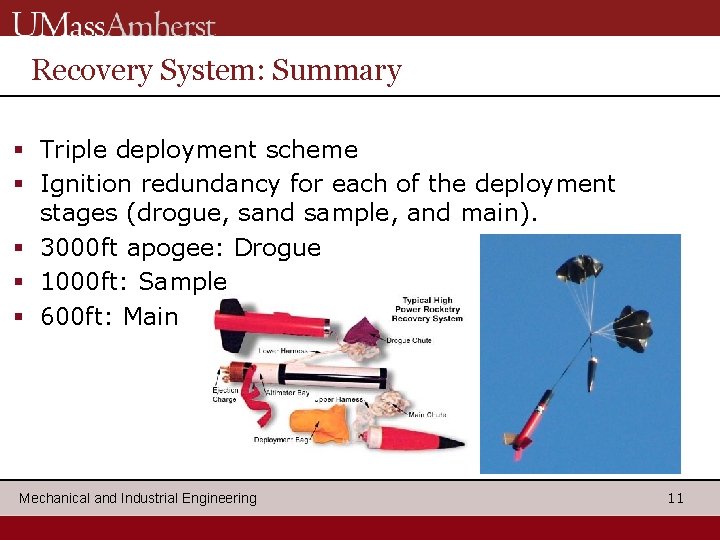
Recovery System: Summary § Triple deployment scheme § Ignition redundancy for each of the deployment stages (drogue, sand sample, and main). § 3000 ft apogee: Drogue § 1000 ft: Sample § 600 ft: Main Mechanical and Industrial Engineering 11
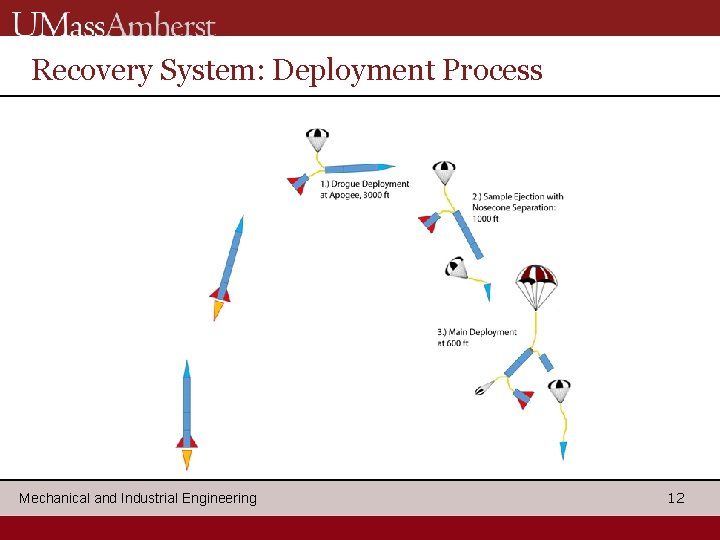
Recovery System: Deployment Process Mechanical and Industrial Engineering 12
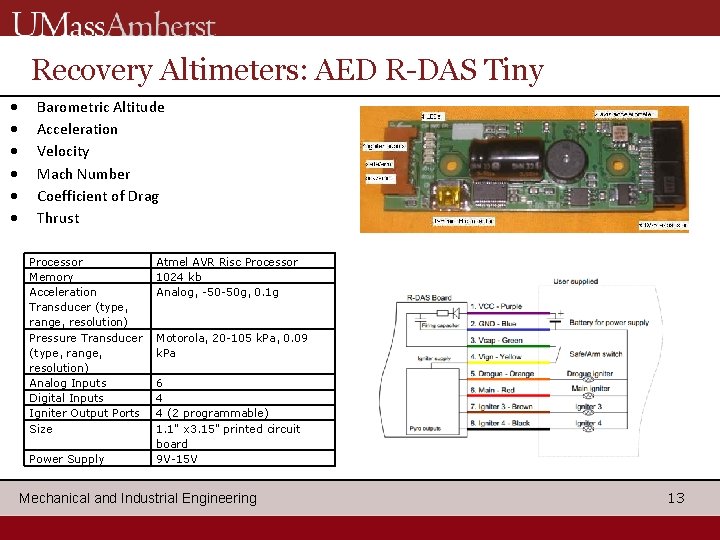
Recovery Altimeters: AED R-DAS Tiny Barometric Altitude Acceleration Velocity Mach Number Coefficient of Drag Thrust Processor Memory Acceleration Transducer (type, range, resolution) Pressure Transducer (type, range, resolution) Analog Inputs Digital Inputs Igniter Output Ports Size Power Supply Atmel AVR Risc Processor 1024 kb Analog, -50 -50 g, 0. 1 g Motorola, 20 -105 k. Pa, 0. 09 k. Pa 6 4 4 (2 programmable) 1. 1" x 3. 15" printed circuit board 9 V-15 V Mechanical and Industrial Engineering 13
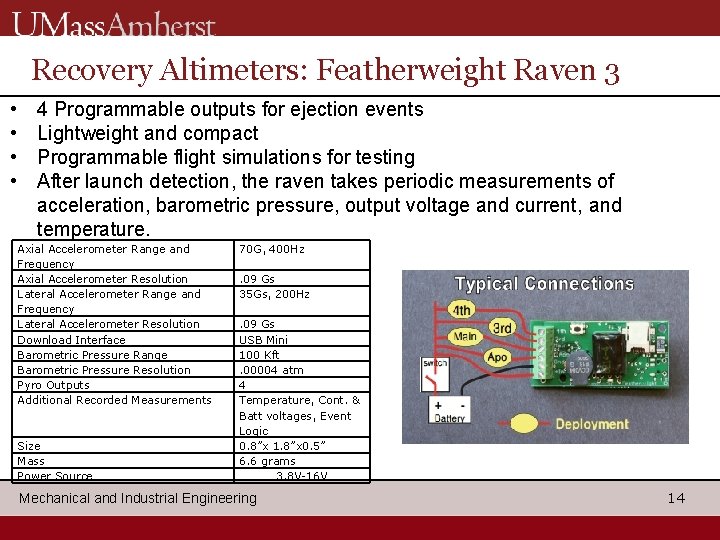
Recovery Altimeters: Featherweight Raven 3 • • 4 Programmable outputs for ejection events Lightweight and compact Programmable flight simulations for testing After launch detection, the raven takes periodic measurements of acceleration, barometric pressure, output voltage and current, and temperature. Axial Accelerometer Range and Frequency Axial Accelerometer Resolution Lateral Accelerometer Range and Frequency Lateral Accelerometer Resolution Download Interface Barometric Pressure Range Barometric Pressure Resolution Pyro Outputs Additional Recorded Measurements Size Mass Power Source 70 G, 400 Hz. 09 Gs 35 Gs, 200 Hz. 09 Gs USB Mini 100 Kft. 00004 atm 4 Temperature, Cont. & Batt voltages, Event Logic 0. 8”x 1. 8”x 0. 5” 6. 6 grams 3. 8 V-16 V Mechanical and Industrial Engineering 14
![Recovery System Parachute Sizing and Specification Parachute Purpose Type Material Diameter in Mass oz Recovery System: Parachute Sizing and Specification Parachute Purpose Type Material Diameter [in] Mass [oz]](https://slidetodoc.com/presentation_image/a7f0188abd0a1b112f75f88c7848ce60/image-15.jpg)
Recovery System: Parachute Sizing and Specification Parachute Purpose Type Material Diameter [in] Mass [oz] Descent Rate Impact Energy [ft/s] [ft-lbf] Impact Margin Drogue (full launch vehicle) TAC-1 36 Mil Spec Nylon (1400 lb test) 36 8. 1 33. 97 N/A (no impact under drogue) N/A Main (separated launch vehicle) TAC-1 72 Mil Spec Nylon (1400 lb test) 72 18. 0 16. 37 31. 942 58. 11% Sample (nosecone) TAC-1 24 Mil Spec Nylon (1400 lb test) 24 5. 4 23. 57 28. 814 61. 58% Mechanical and Industrial Engineering 15
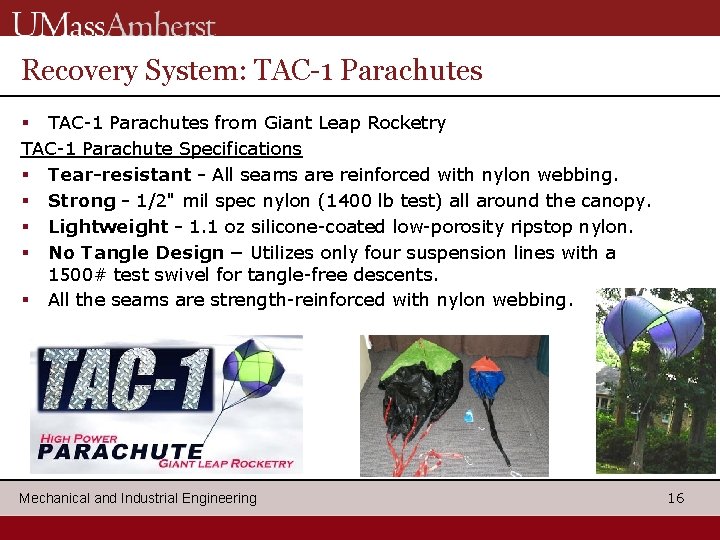
Recovery System: TAC-1 Parachutes § TAC-1 Parachutes from Giant Leap Rocketry TAC-1 Parachute Specifications § Tear-resistant - All seams are reinforced with nylon webbing. § Strong - 1/2" mil spec nylon (1400 lb test) all around the canopy. § Lightweight - 1. 1 oz silicone-coated low-porosity ripstop nylon. § No Tangle Design – Utilizes only four suspension lines with a 1500# test swivel for tangle-free descents. § All the seams are strength-reinforced with nylon webbing. Mechanical and Industrial Engineering 16
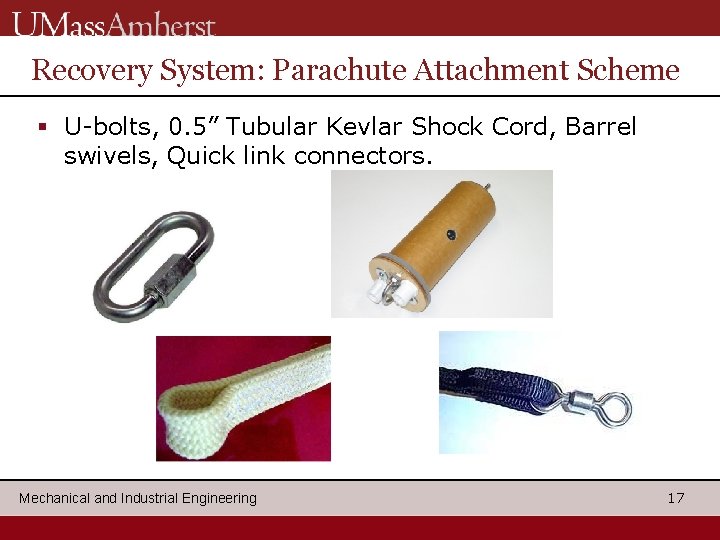
Recovery System: Parachute Attachment Scheme § U-bolts, 0. 5” Tubular Kevlar Shock Cord, Barrel swivels, Quick link connectors. Mechanical and Industrial Engineering 17
![Recovery System Ejection Charges Section Charge Size g Drogue Bay 1 16 Force Produced Recovery System: Ejection Charges Section Charge Size [g] Drogue Bay 1. 16 Force Produced](https://slidetodoc.com/presentation_image/a7f0188abd0a1b112f75f88c7848ce60/image-18.jpg)
Recovery System: Ejection Charges Section Charge Size [g] Drogue Bay 1. 16 Force Produced [lbf] 179. 19 Sample Bay 0. 91 179. 19 Main Bay 1. 46 179. 19 Mechanical and Industrial Engineering Shear Pin Specs (3) 4 -40 Nylon screws 18
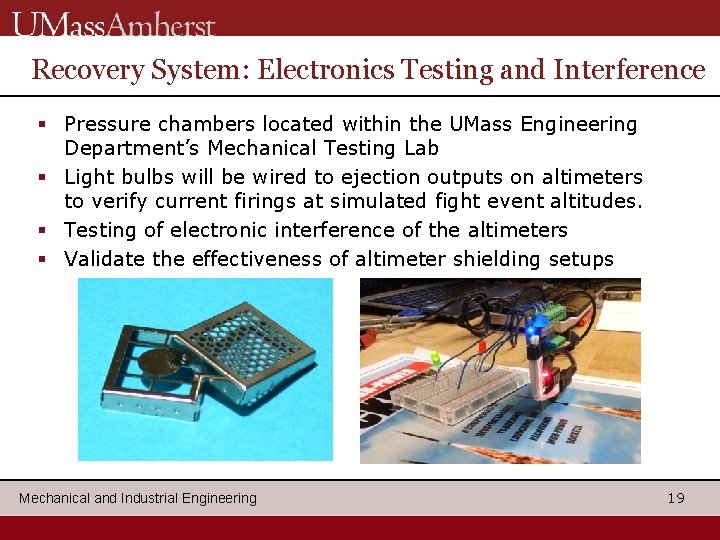
Recovery System: Electronics Testing and Interference § Pressure chambers located within the UMass Engineering Department’s Mechanical Testing Lab § Light bulbs will be wired to ejection outputs on altimeters to verify current firings at simulated fight event altitudes. § Testing of electronic interference of the altimeters § Validate the effectiveness of altimeter shielding setups Mechanical and Industrial Engineering 19
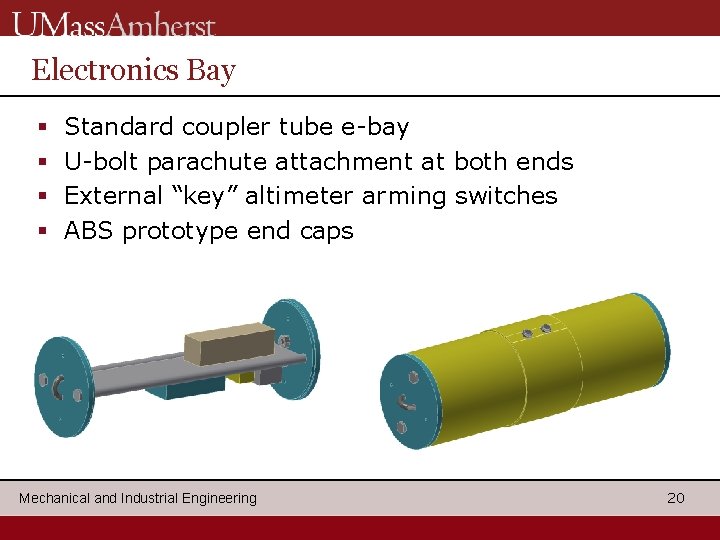
Electronics Bay § § Standard coupler tube e-bay U-bolt parachute attachment at both ends External “key” altimeter arming switches ABS prototype end caps Mechanical and Industrial Engineering 20
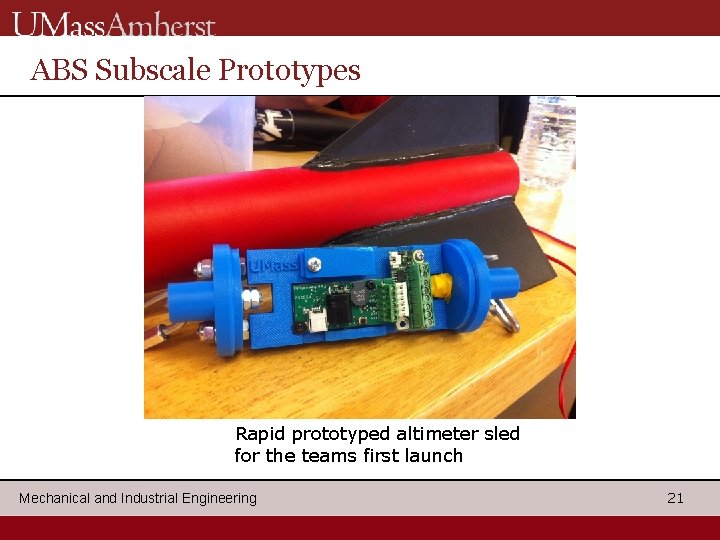
ABS Subscale Prototypes Rapid prototyped altimeter sled for the teams first launch Mechanical and Industrial Engineering 21
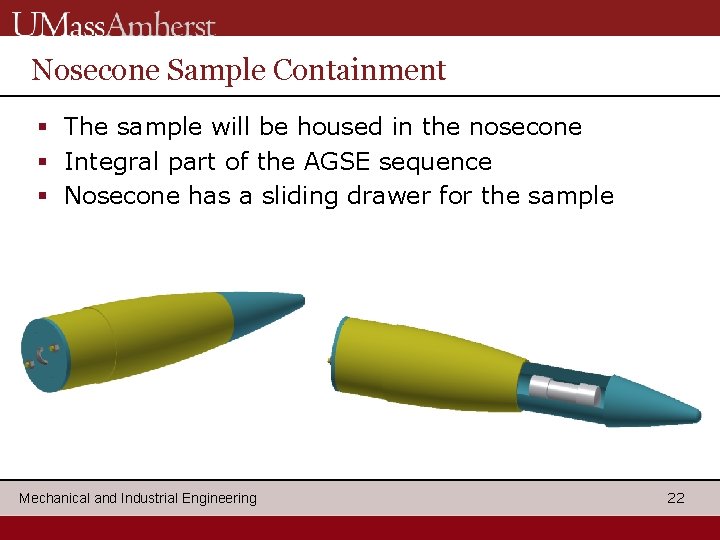
Nosecone Sample Containment § The sample will be housed in the nosecone § Integral part of the AGSE sequence § Nosecone has a sliding drawer for the sample Mechanical and Industrial Engineering 22
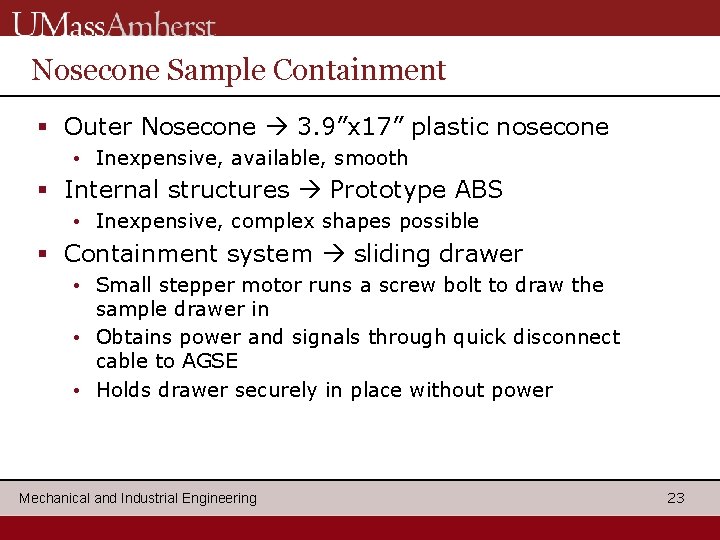
Nosecone Sample Containment § Outer Nosecone 3. 9”x 17” plastic nosecone • Inexpensive, available, smooth § Internal structures Prototype ABS • Inexpensive, complex shapes possible § Containment system sliding drawer • Small stepper motor runs a screw bolt to draw the sample drawer in • Obtains power and signals through quick disconnect cable to AGSE • Holds drawer securely in place without power Mechanical and Industrial Engineering 23
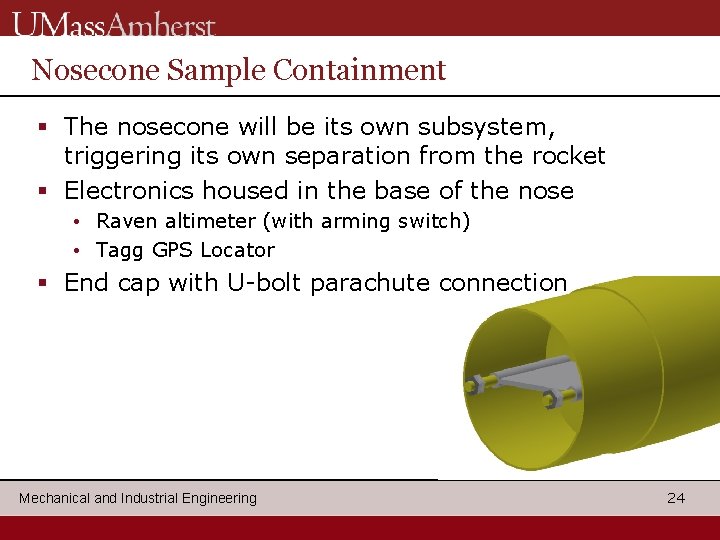
Nosecone Sample Containment § The nosecone will be its own subsystem, triggering its own separation from the rocket § Electronics housed in the base of the nose • Raven altimeter (with arming switch) • Tagg GPS Locator § End cap with U-bolt parachute connection Mechanical and Industrial Engineering 24
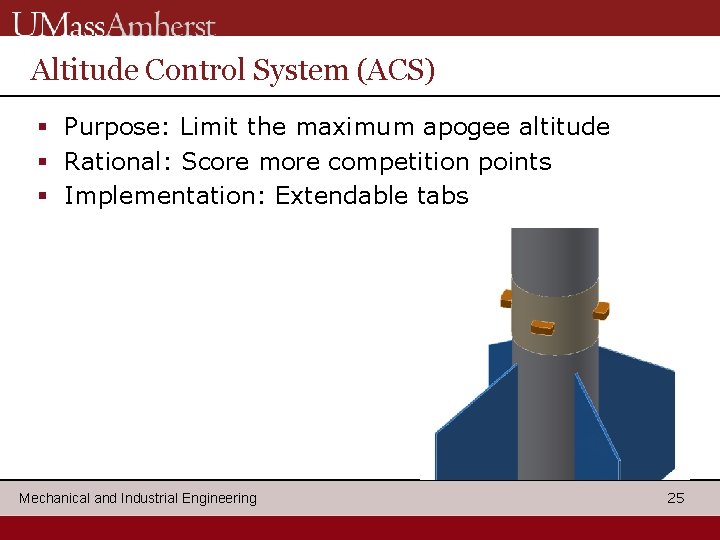
Altitude Control System (ACS) § Purpose: Limit the maximum apogee altitude § Rational: Score more competition points § Implementation: Extendable tabs Mechanical and Industrial Engineering 25

Altitude Control System (ACS) § The control tabs will extend beyond the airframe after engine burnout § Sensors will calculate apogee based on current vehicle state, enact control effort to add drag to the vehicle as necessary Mechanical and Industrial Engineering 26
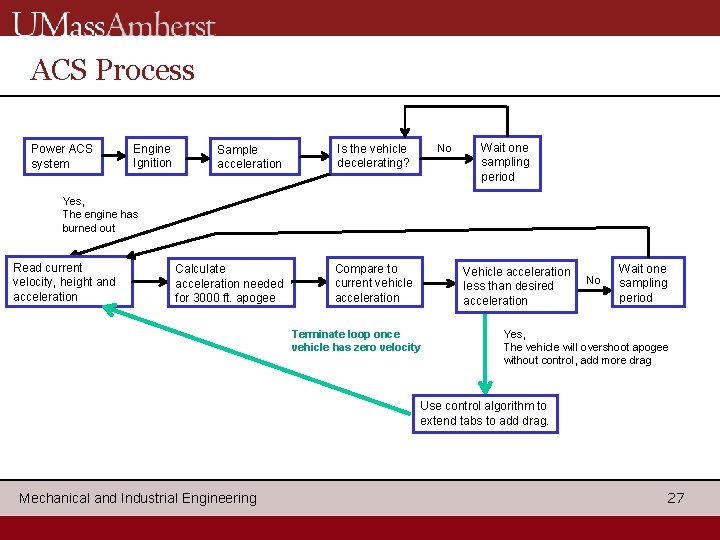
ACS Process Power ACS system Engine Ignition Sample acceleration Is the vehicle decelerating? Calculate acceleration needed for 3000 ft. apogee Compare to current vehicle acceleration No Wait one sampling period Yes, The engine has burned out Read current velocity, height and acceleration Vehicle acceleration less than desired acceleration Terminate loop once vehicle has zero velocity No Wait one sampling period Yes, The vehicle will overshoot apogee without control, add more drag Use control algorithm to extend tabs to add drag. Mechanical and Industrial Engineering 27
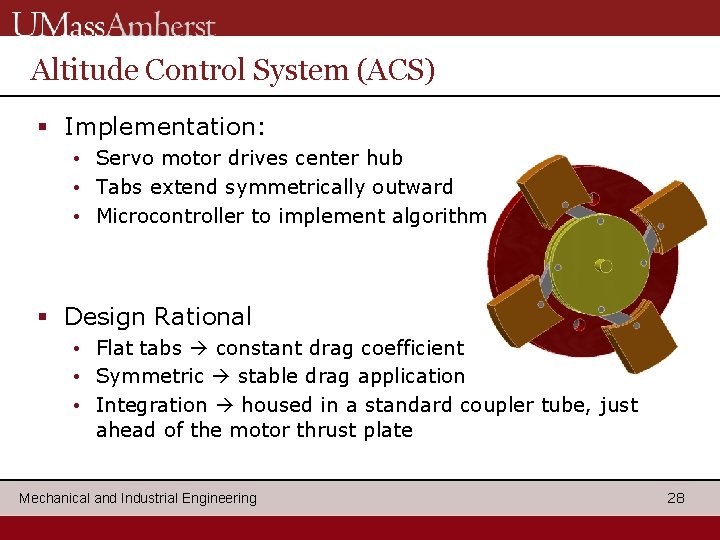
Altitude Control System (ACS) § Implementation: • Servo motor drives center hub • Tabs extend symmetrically outward • Microcontroller to implement algorithm § Design Rational • Flat tabs constant drag coefficient • Symmetric stable drag application • Integration housed in a standard coupler tube, just ahead of the motor thrust plate Mechanical and Industrial Engineering 28
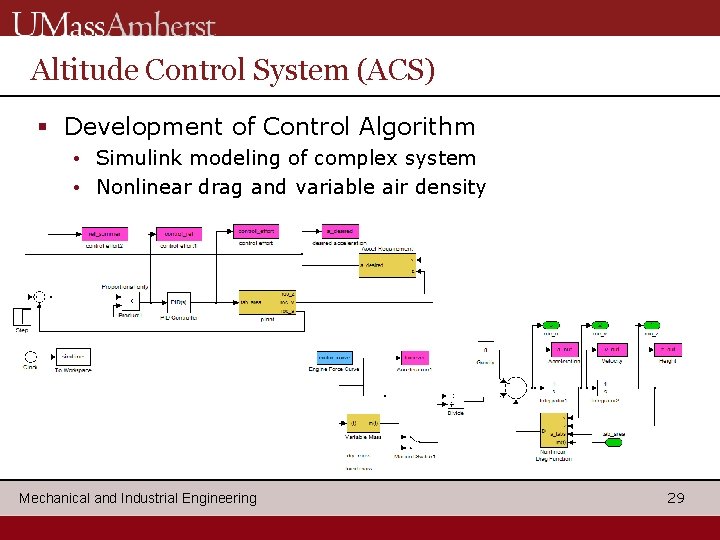
Altitude Control System (ACS) § Development of Control Algorithm • Simulink modeling of complex system • Nonlinear drag and variable air density Mechanical and Industrial Engineering 29
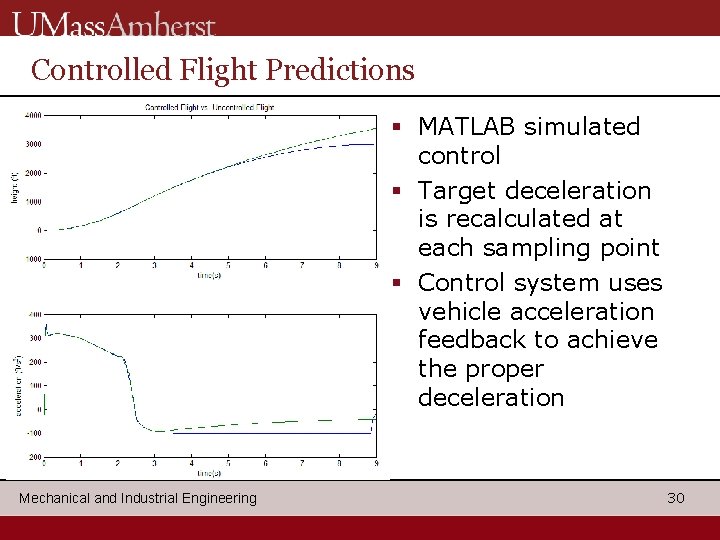
Controlled Flight Predictions § MATLAB simulated control § Target deceleration is recalculated at each sampling point § Control system uses vehicle acceleration feedback to achieve the proper deceleration Mechanical and Industrial Engineering 30
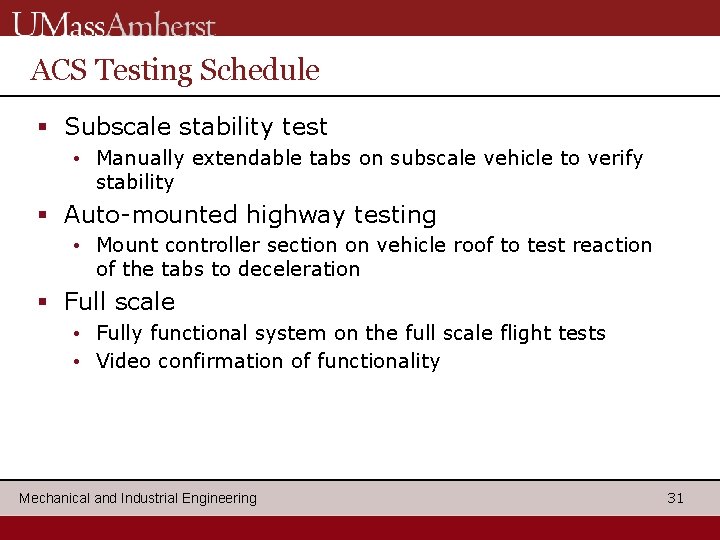
ACS Testing Schedule § Subscale stability test • Manually extendable tabs on subscale vehicle to verify stability § Auto-mounted highway testing • Mount controller section on vehicle roof to test reaction of the tabs to deceleration § Full scale • Fully functional system on the full scale flight tests • Video confirmation of functionality Mechanical and Industrial Engineering 31
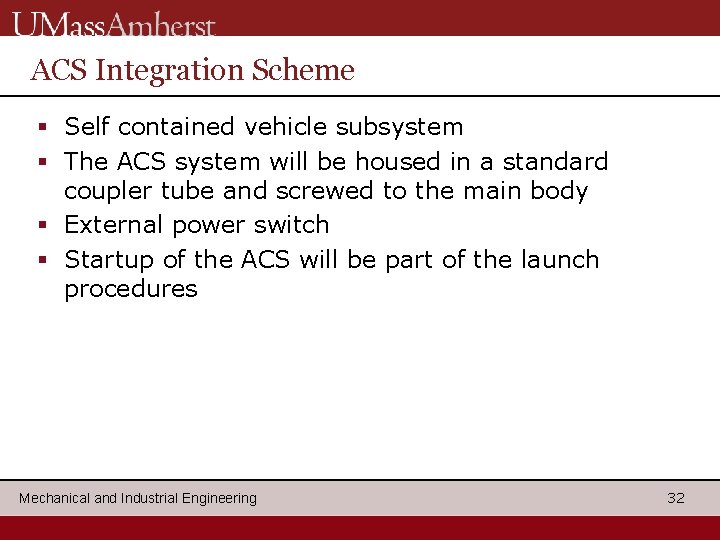
ACS Integration Scheme § Self contained vehicle subsystem § The ACS system will be housed in a standard coupler tube and screwed to the main body § External power switch § Startup of the ACS will be part of the launch procedures Mechanical and Industrial Engineering 32
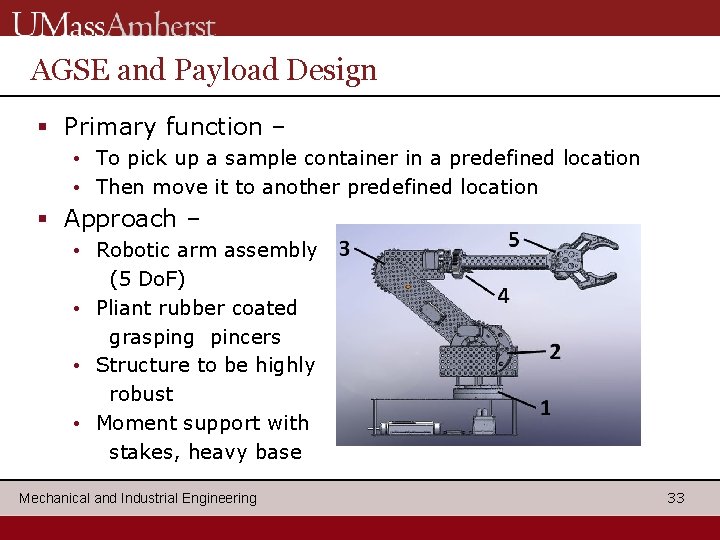
AGSE and Payload Design § Primary function – • To pick up a sample container in a predefined location • Then move it to another predefined location § Approach – • Robotic arm assembly (5 Do. F) • Pliant rubber coated grasping pincers • Structure to be highly robust • Moment support with stakes, heavy base Mechanical and Industrial Engineering 33
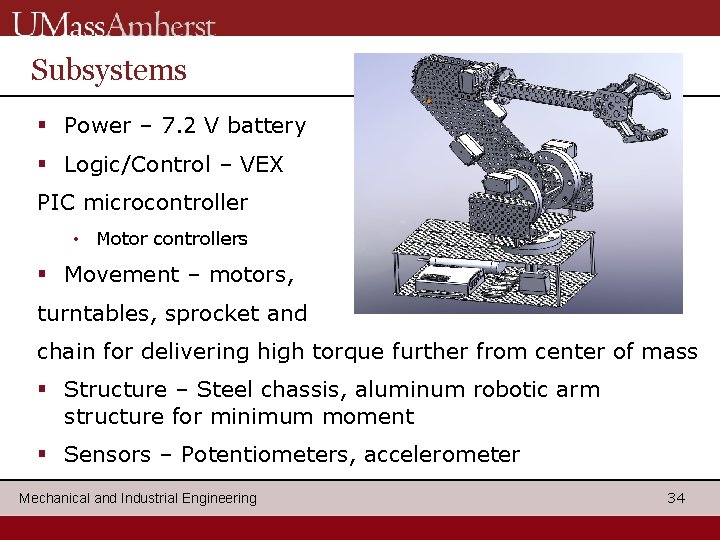
Subsystems § Power – 7. 2 V battery § Logic/Control – VEX PIC microcontroller • Motor controllers § Movement – motors, turntables, sprocket and chain for delivering high torque further from center of mass § Structure – Steel chassis, aluminum robotic arm structure for minimum moment § Sensors – Potentiometers, accelerometer Mechanical and Industrial Engineering 34
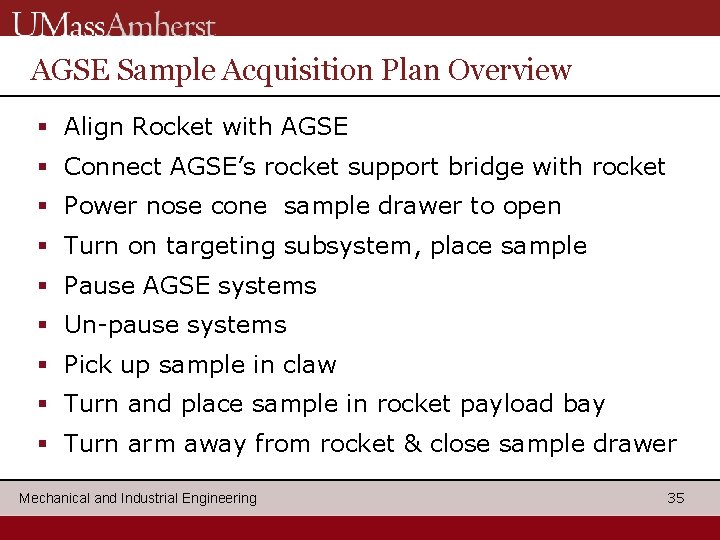
AGSE Sample Acquisition Plan Overview § Align Rocket with AGSE § Connect AGSE’s rocket support bridge with rocket § Power nose cone sample drawer to open § Turn on targeting subsystem, place sample § Pause AGSE systems § Un-pause systems § Pick up sample in claw § Turn and place sample in rocket payload bay § Turn arm away from rocket & close sample drawer Mechanical and Industrial Engineering 35
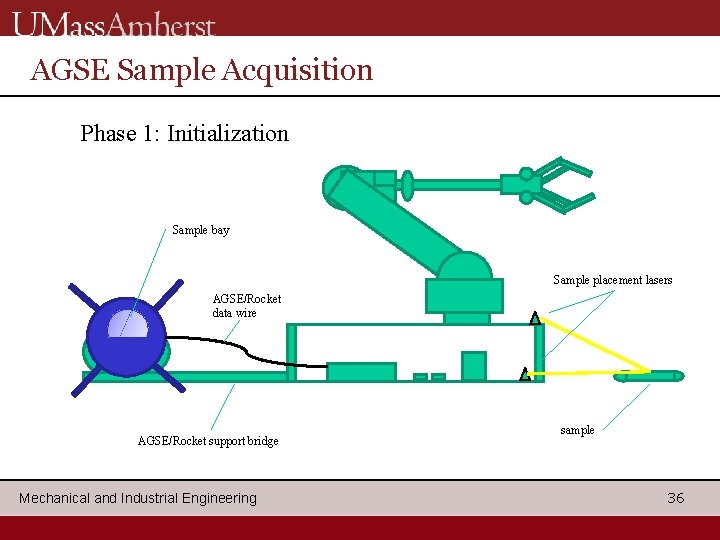
AGSE Sample Acquisition Phase 1: Initialization Sample bay Sample placement lasers AGSE/Rocket data wire AGSE/Rocket support bridge Mechanical and Industrial Engineering sample 36
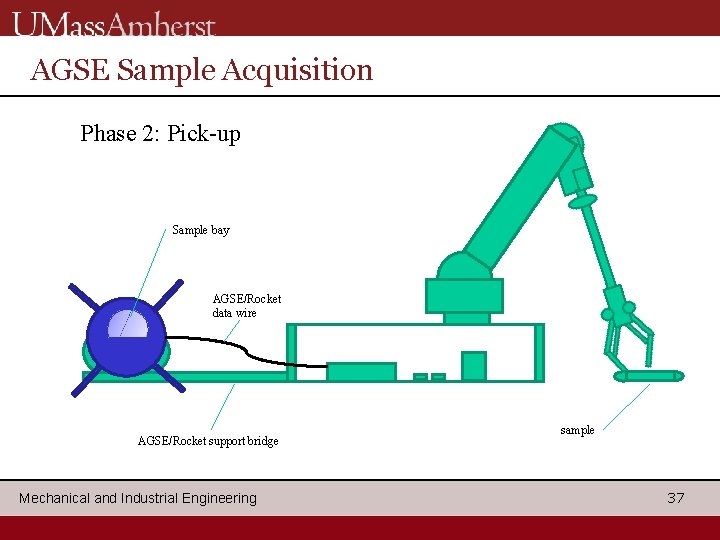
AGSE Sample Acquisition Phase 2: Pick-up Sample bay AGSE/Rocket data wire AGSE/Rocket support bridge Mechanical and Industrial Engineering sample 37
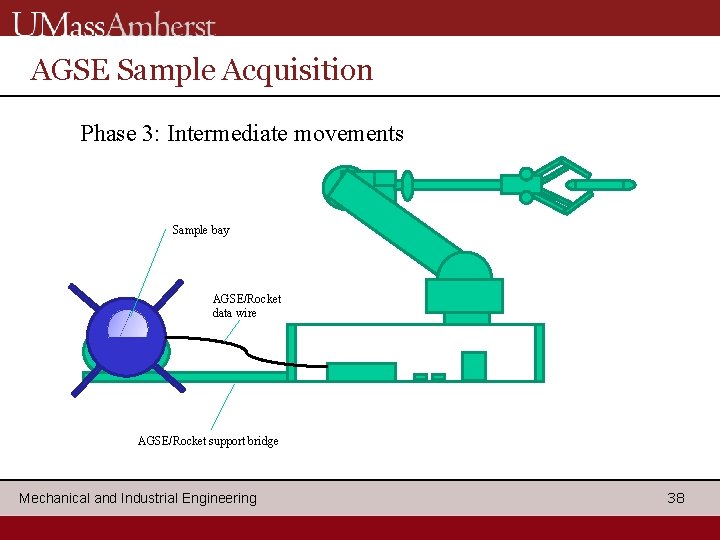
AGSE Sample Acquisition Phase 3: Intermediate movements Sample bay AGSE/Rocket data wire AGSE/Rocket support bridge Mechanical and Industrial Engineering 38
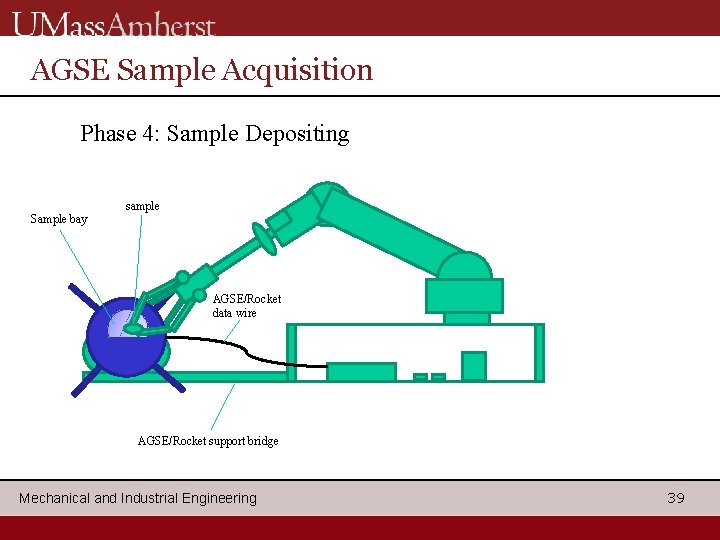
AGSE Sample Acquisition Phase 4: Sample Depositing Sample bay sample AGSE/Rocket data wire AGSE/Rocket support bridge Mechanical and Industrial Engineering 39
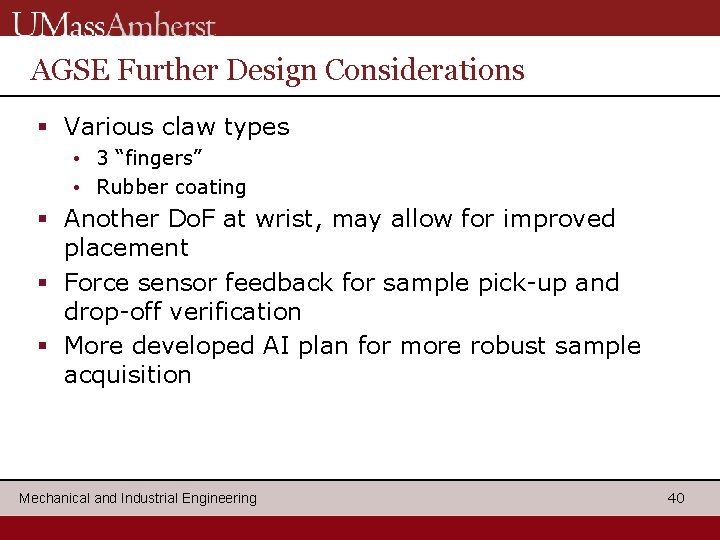
AGSE Further Design Considerations § Various claw types • 3 “fingers” • Rubber coating § Another Do. F at wrist, may allow for improved placement § Force sensor feedback for sample pick-up and drop-off verification § More developed AI plan for more robust sample acquisition Mechanical and Industrial Engineering 40
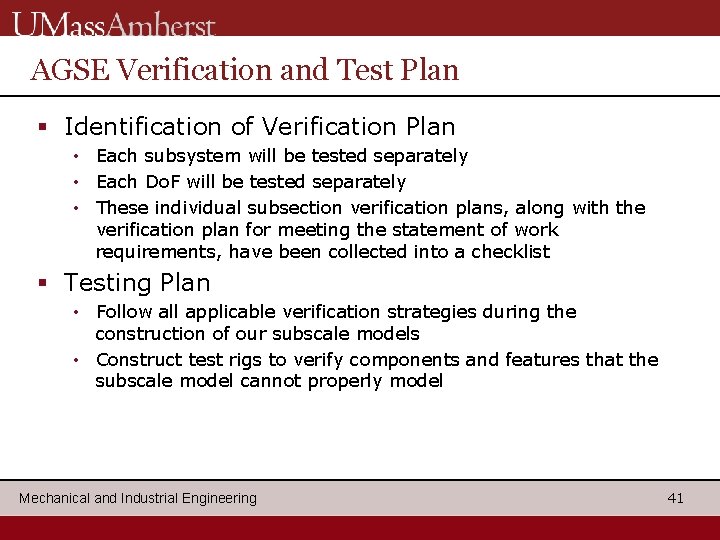
AGSE Verification and Test Plan § Identification of Verification Plan • Each subsystem will be tested separately • Each Do. F will be tested separately • These individual subsection verification plans, along with the verification plan for meeting the statement of work requirements, have been collected into a checklist § Testing Plan • Follow all applicable verification strategies during the construction of our subscale models • Construct test rigs to verify components and features that the subscale model cannot properly model Mechanical and Industrial Engineering 41
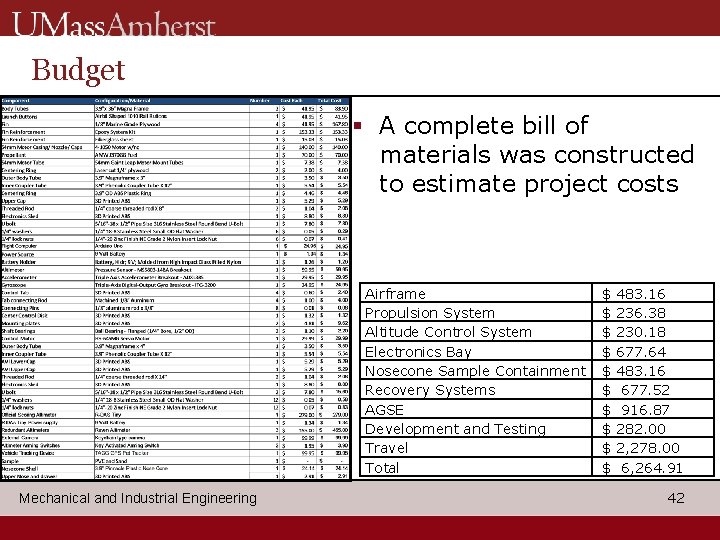
Budget § A complete bill of materials was constructed to estimate project costs Airframe Propulsion System Altitude Control System Electronics Bay Nosecone Sample Containment Recovery Systems AGSE Development and Testing Travel Total Mechanical and Industrial Engineering $ 483. 16 $ 236. 38 $ 230. 18 $ 677. 64 $ 483. 16 $ 677. 52 $ 916. 87 $ 282. 00 $ 2, 278. 00 $ 6, 264. 91 42
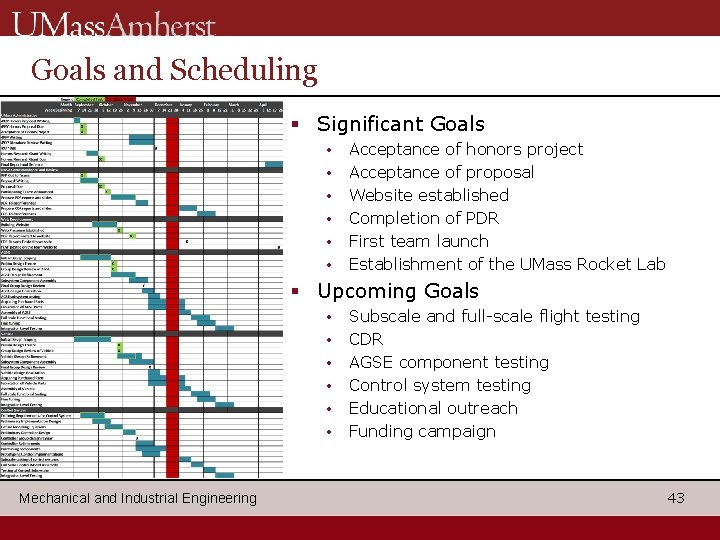
Goals and Scheduling § Significant Goals • • • Acceptance of honors project Acceptance of proposal Website established Completion of PDR First team launch Establishment of the UMass Rocket Lab § Upcoming Goals • • • Mechanical and Industrial Engineering Subscale and full-scale flight testing CDR AGSE component testing Control system testing Educational outreach Funding campaign 43
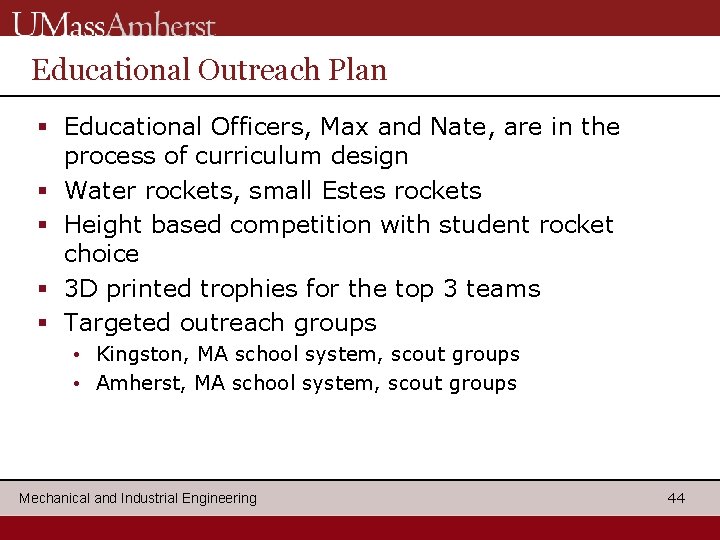
Educational Outreach Plan § Educational Officers, Max and Nate, are in the process of curriculum design § Water rockets, small Estes rockets § Height based competition with student rocket choice § 3 D printed trophies for the top 3 teams § Targeted outreach groups • Kingston, MA school system, scout groups • Amherst, MA school system, scout groups Mechanical and Industrial Engineering 44
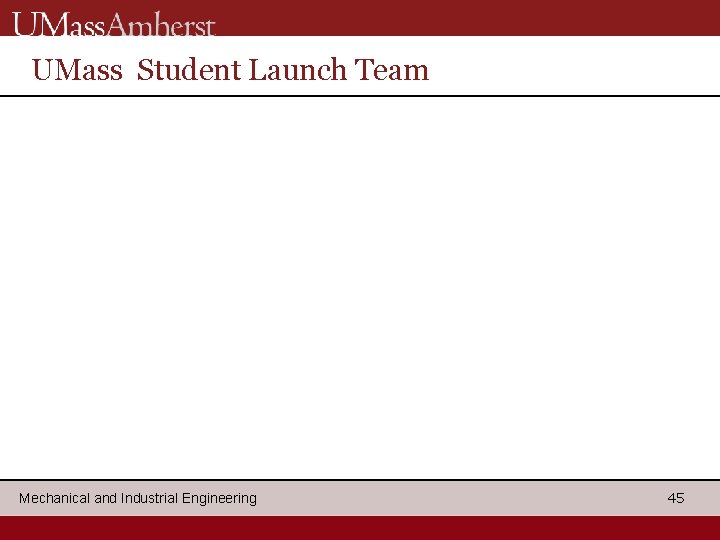
UMass Student Launch Team Mechanical and Industrial Engineering 45
Preliminary design review example
Pdr preliminary design review
Preliminary design review example
Ardu recovery center
Product launch presentation
Post launch review
Launch readiness review
Launch readiness review
Umass rocket team
Preliminary review definition
Design review presentation
Bureaucratic bypass syndrome
Team spirit becomes team infatuation
The white team cheers for the blue team, just like
Narrow product launch windows
Jeff walker plf
Nphce launch date
Let down in the deep
Yammer contest ideas
Launch comms
Optimal driver launch angle and spin rate chart
Wbs for product launch
Narrow product launch windows
Elastic launch glider
Launch housing vacancies
Jwst timeline
Launch simulink
James nasa says space launch its
What is a fighter brand
Syngenta new product launch
Sample introduction for project
That was due today
First nations launch
Launch out into the deep
Launch yourself
Ublt
Horizontal motion
Stm brighton launch
Pltw launch modules
Some month with no attached launch
Genesis point ddo
How to launch an sto
Preliminary budget
Preliminary treatment adalah
Preliminary survey
Preliminary reference earth model