THEMIS MISSION PREENVIRONMENTAL REVIEW SYSTEMS OVERVIEW Ellen Taylor
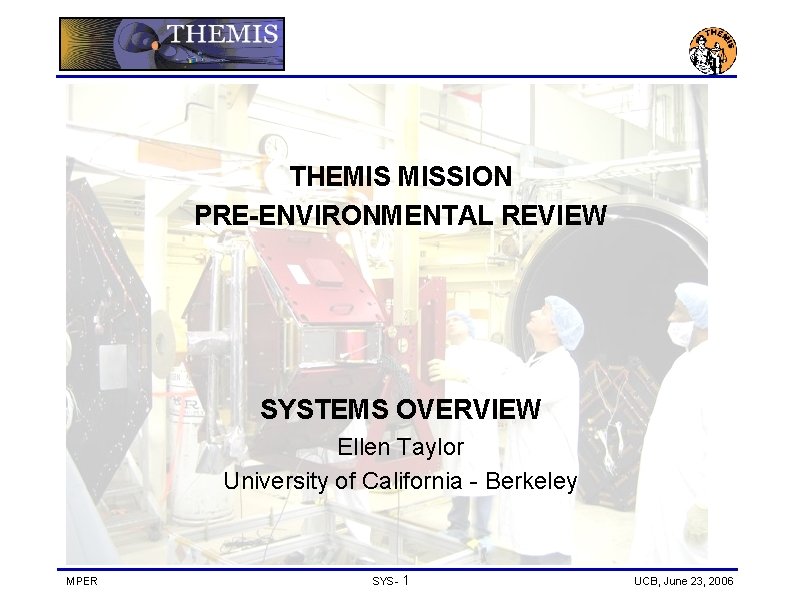
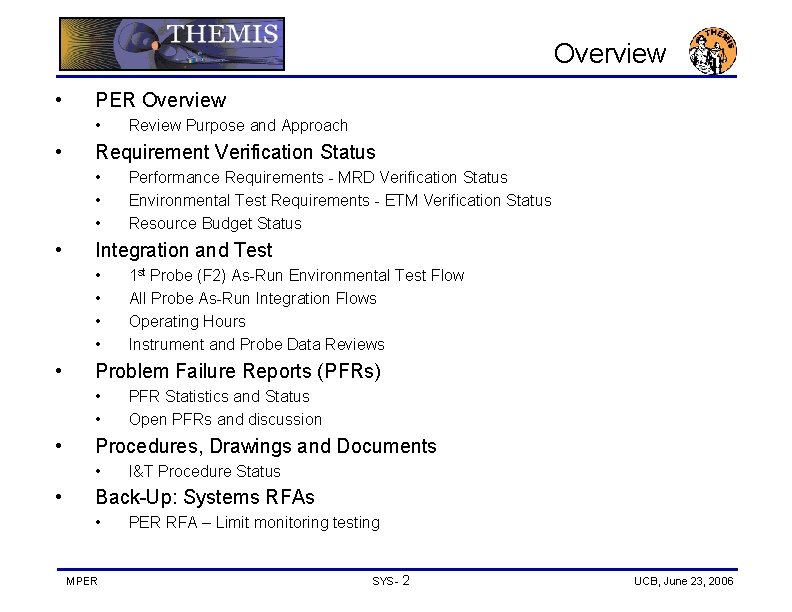
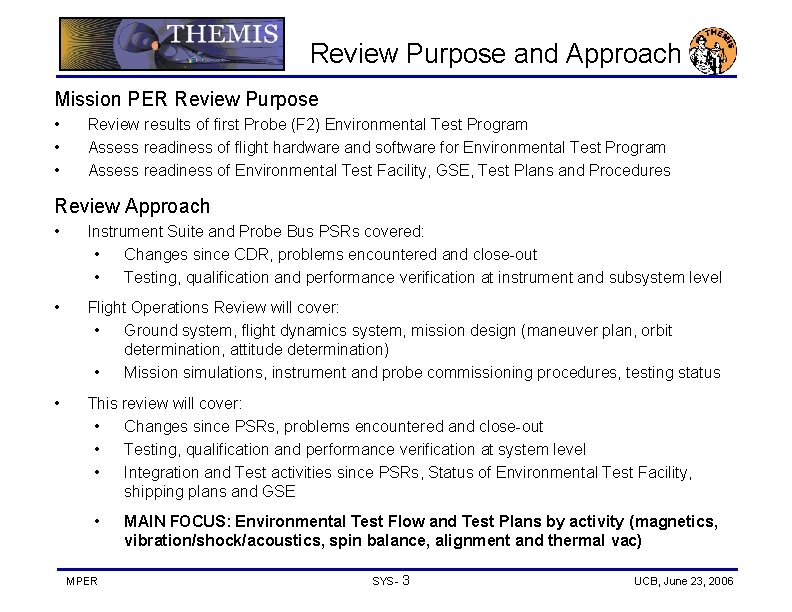
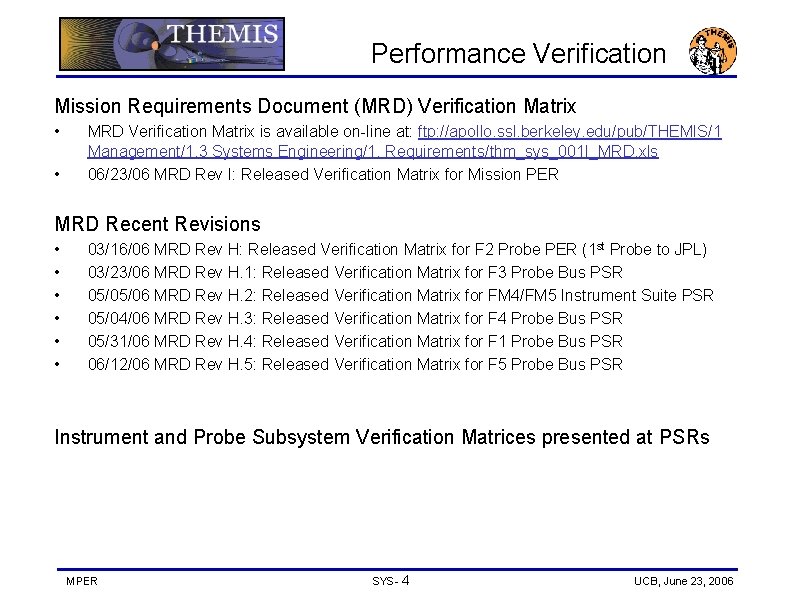
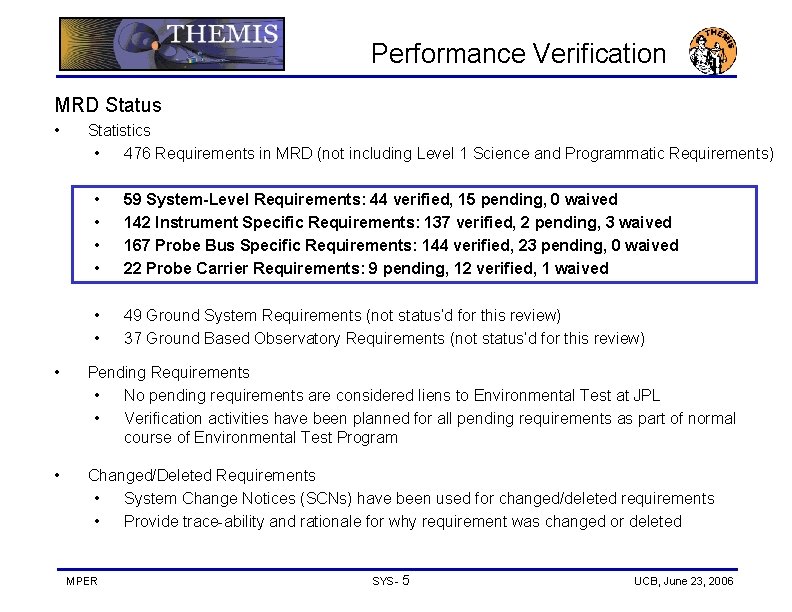
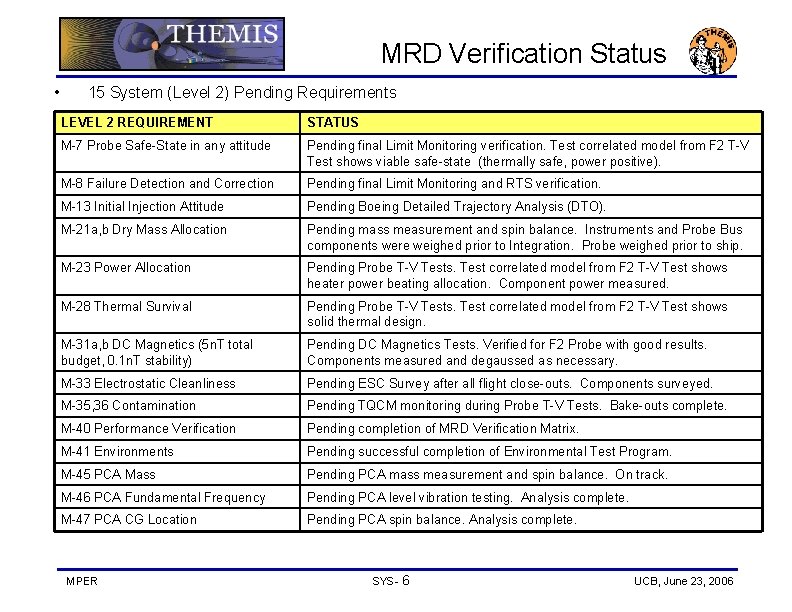
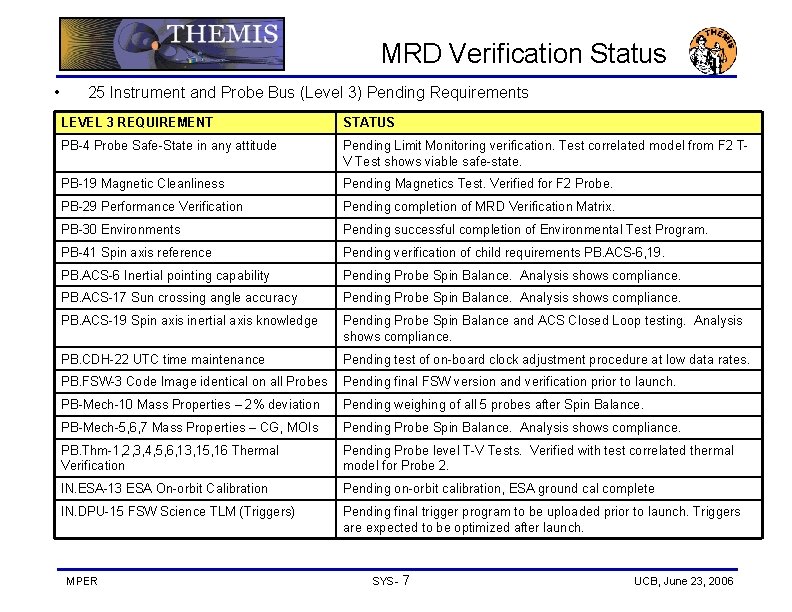
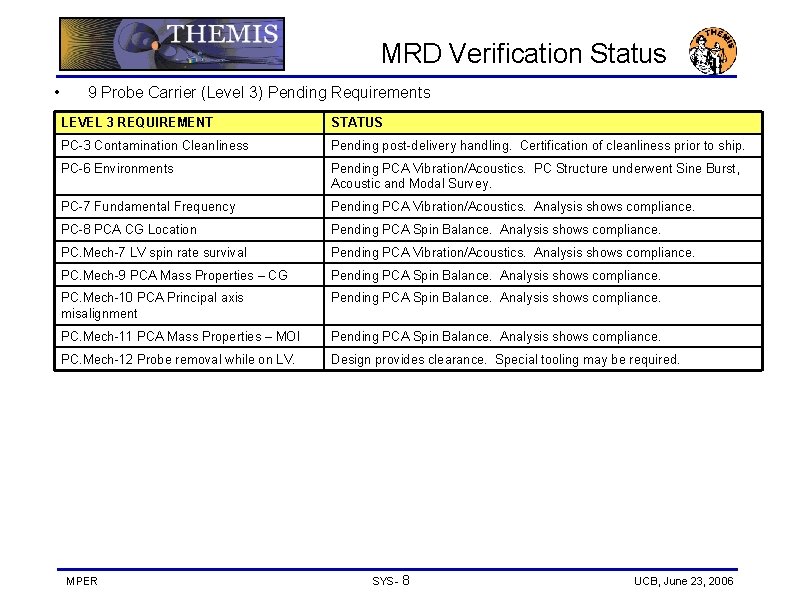
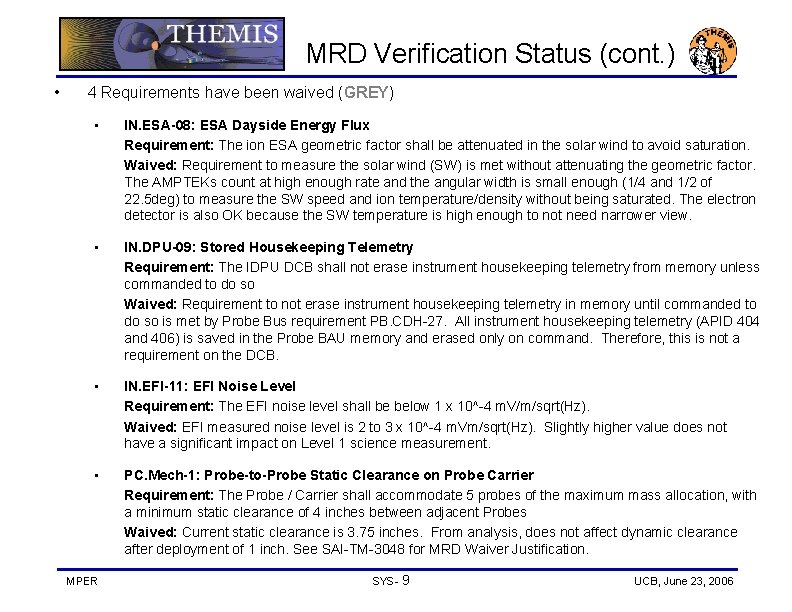
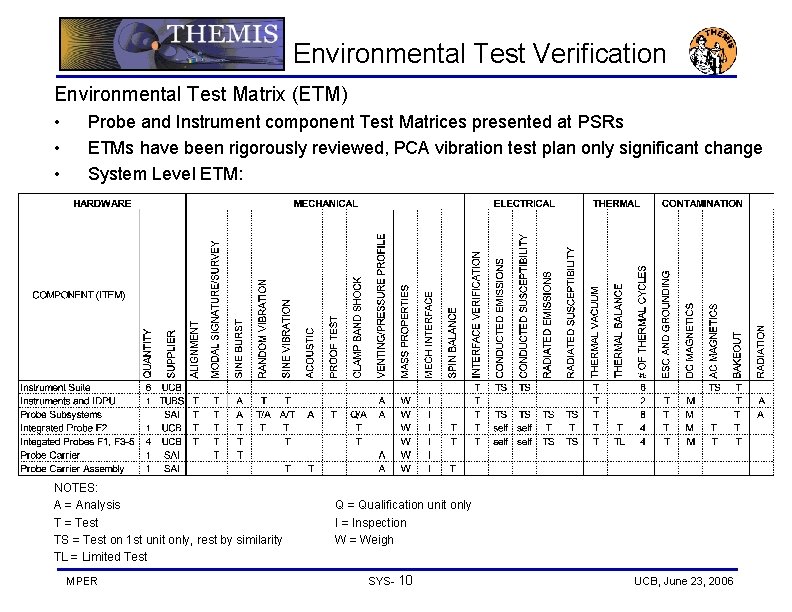
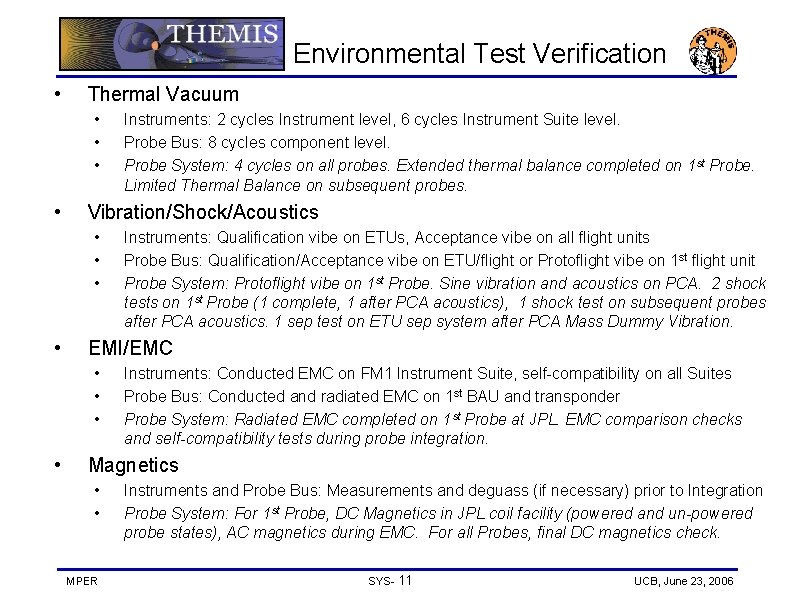
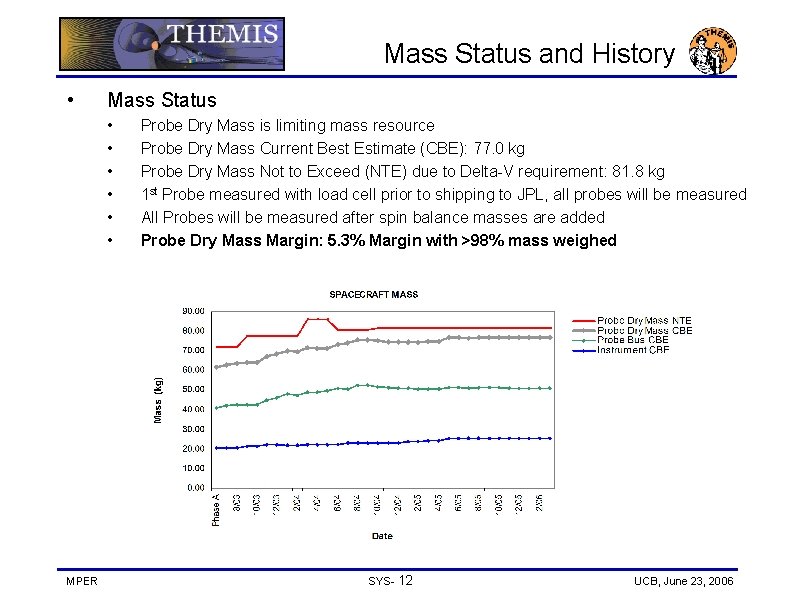
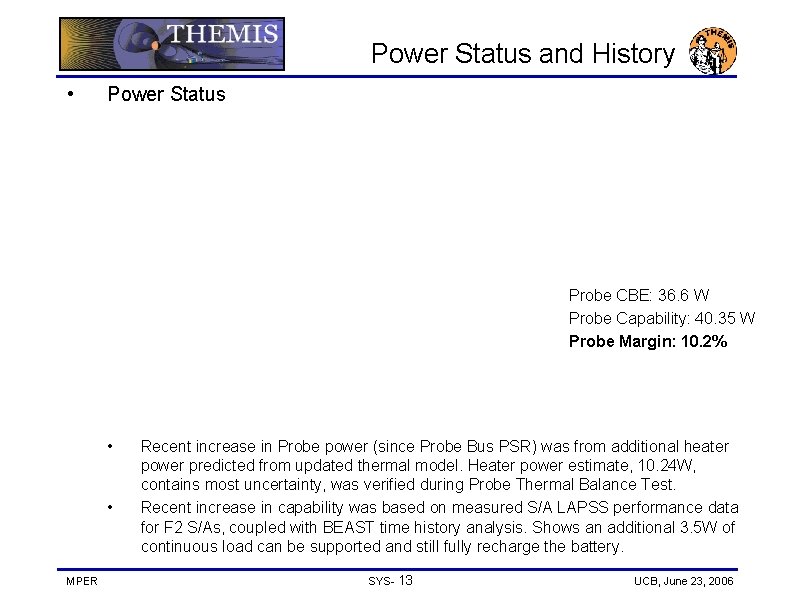
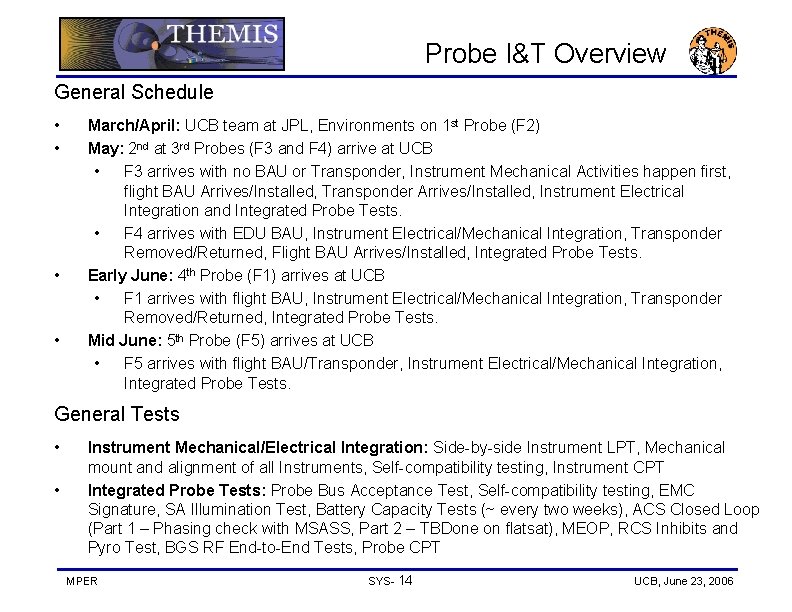
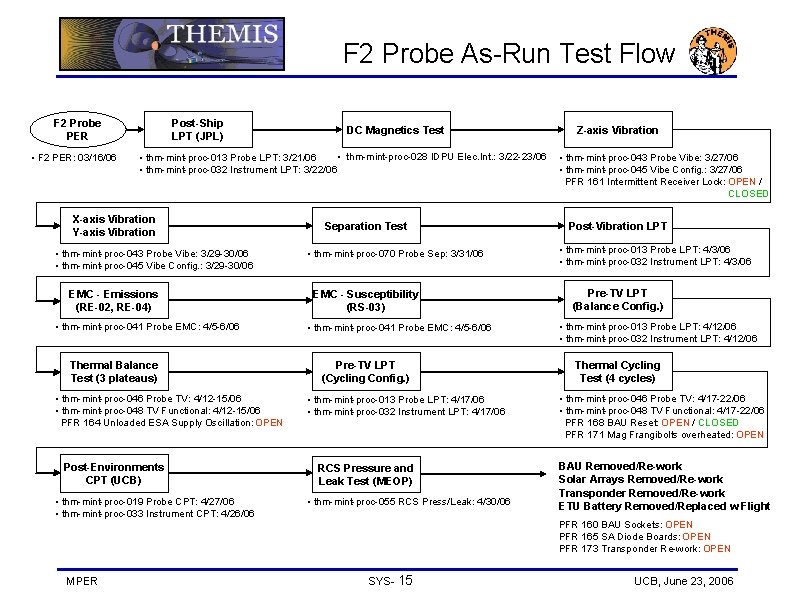
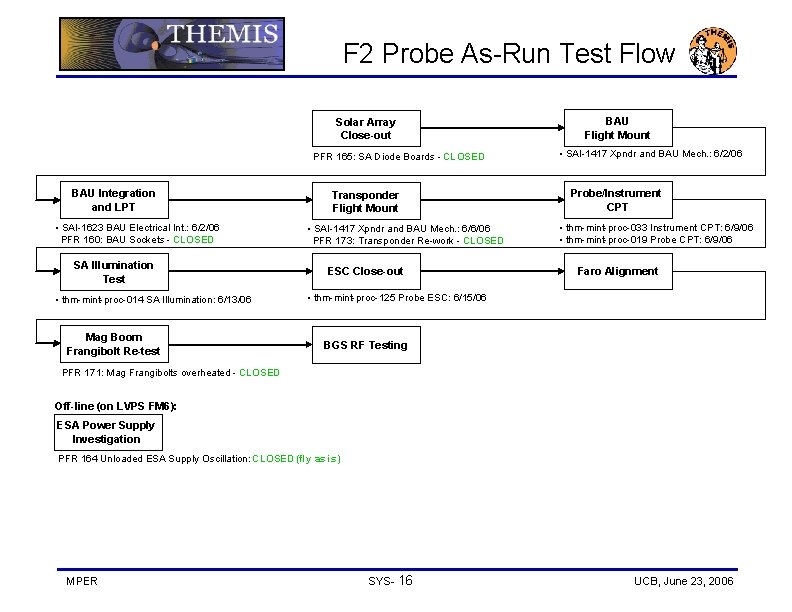
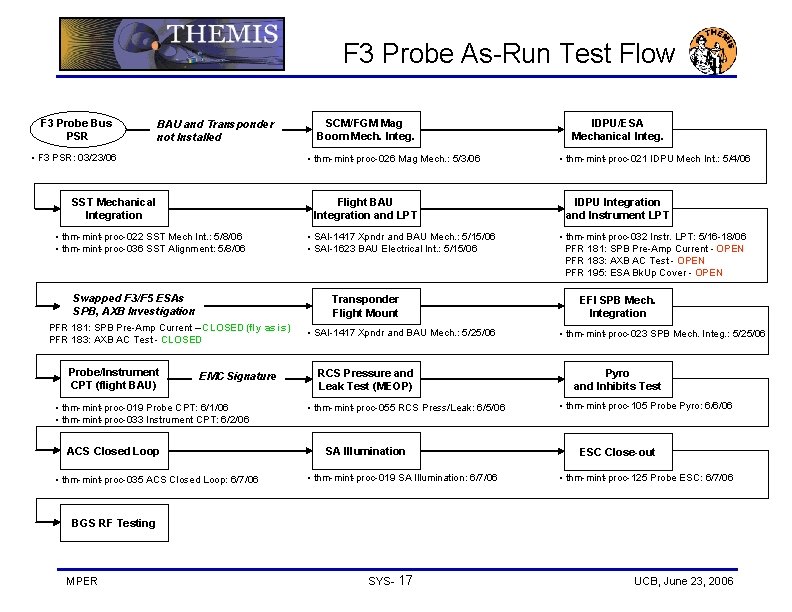
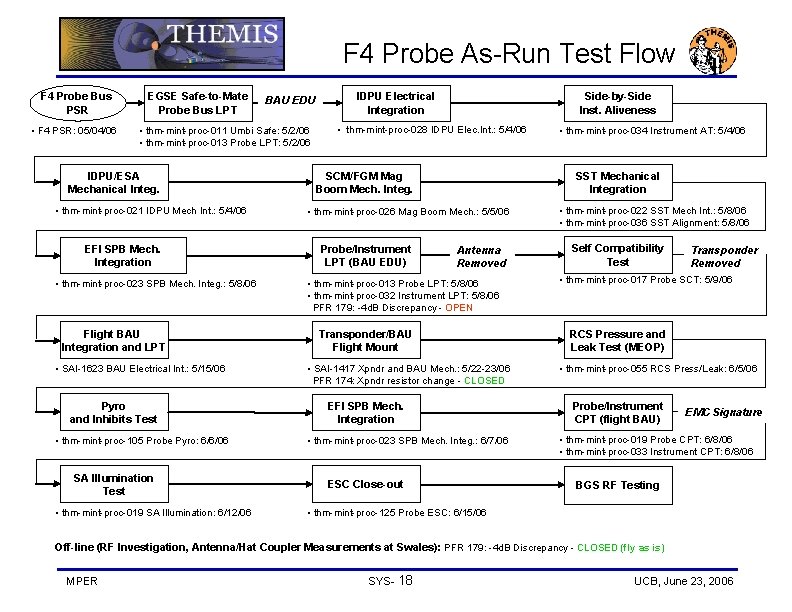
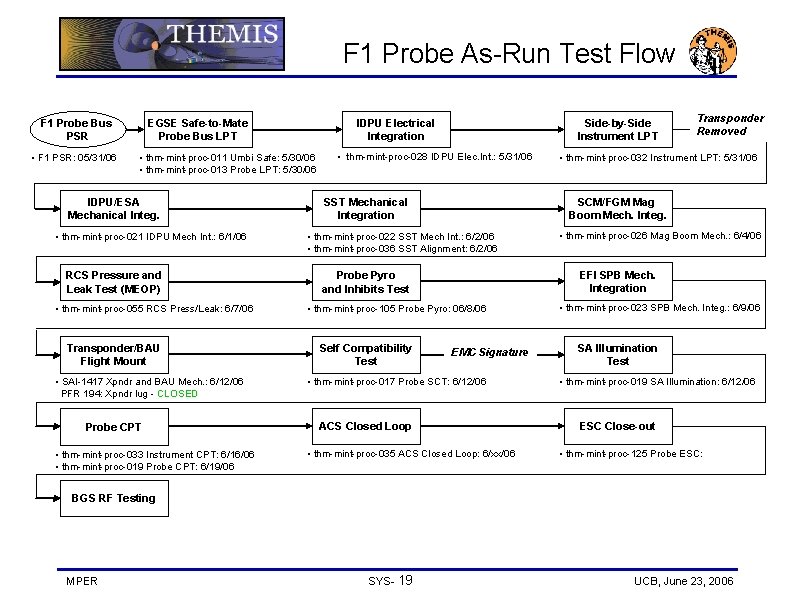
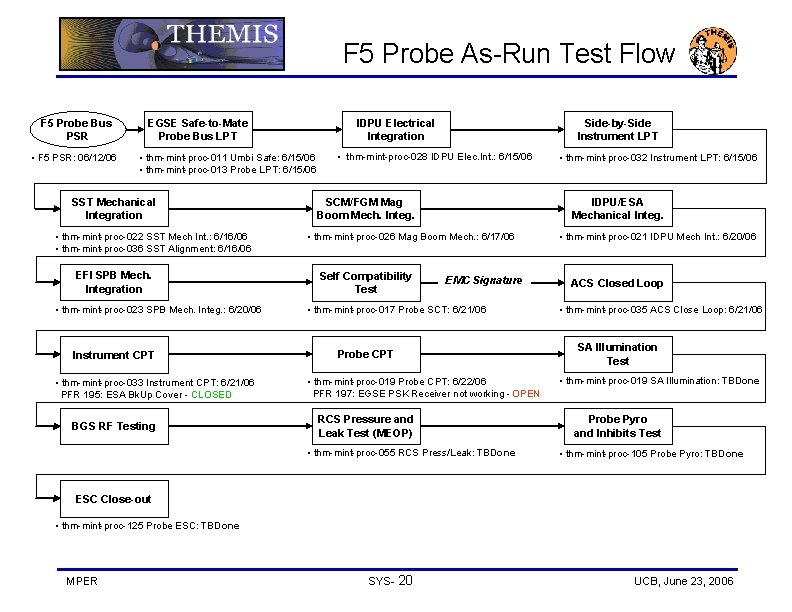
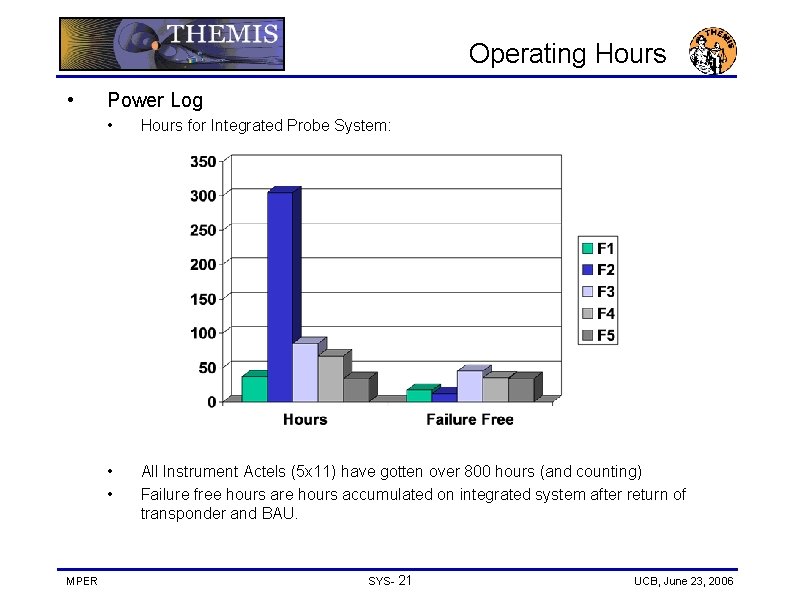
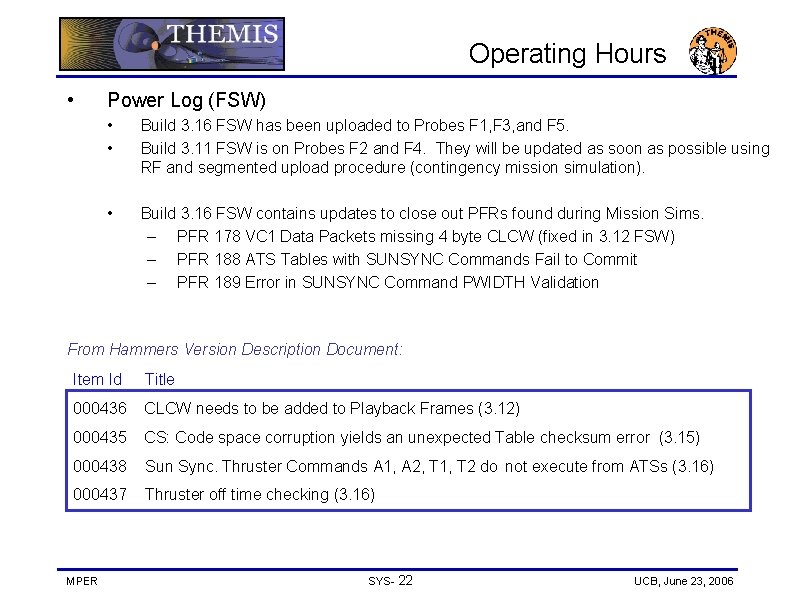
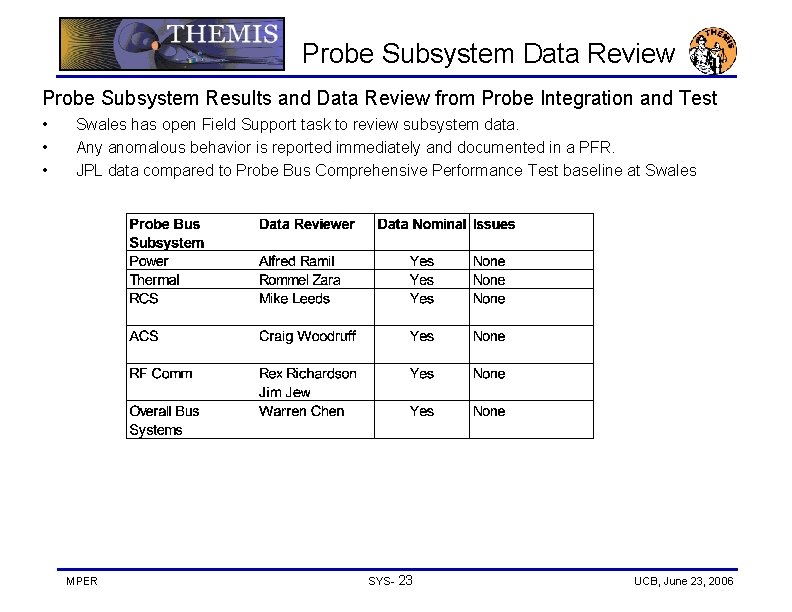
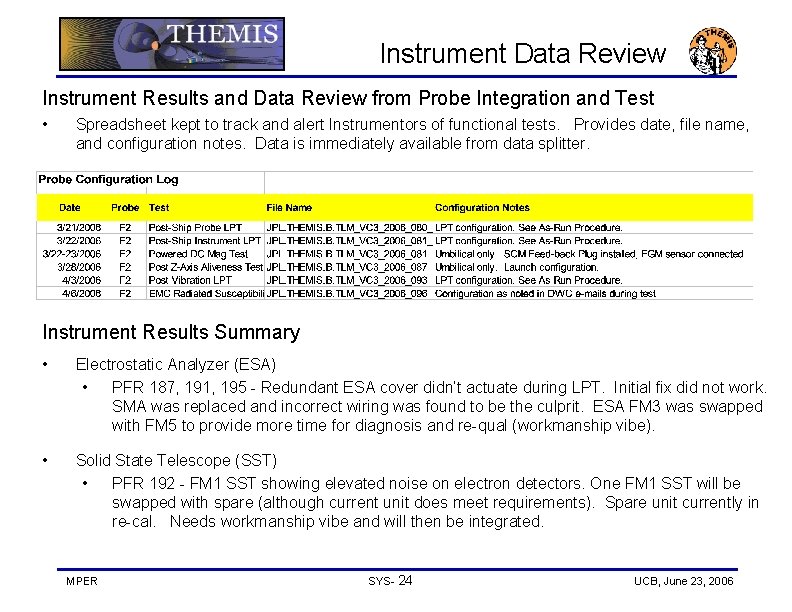
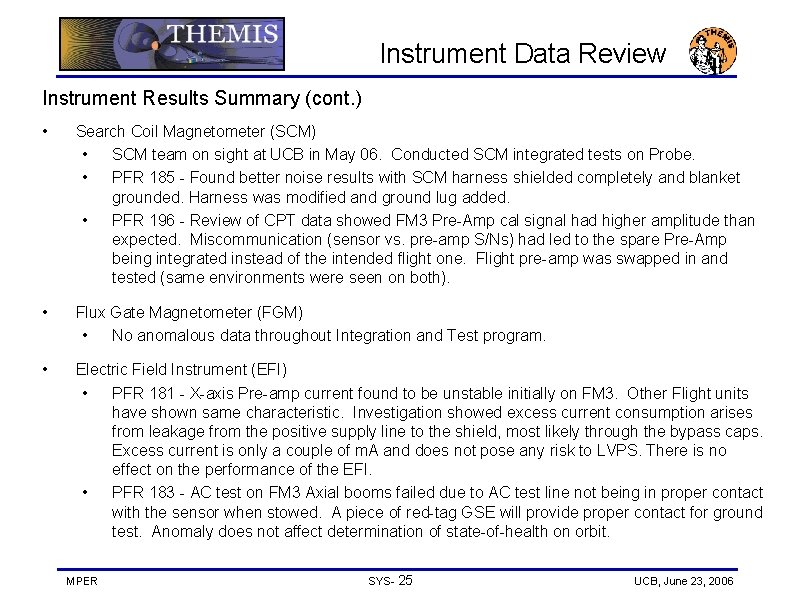
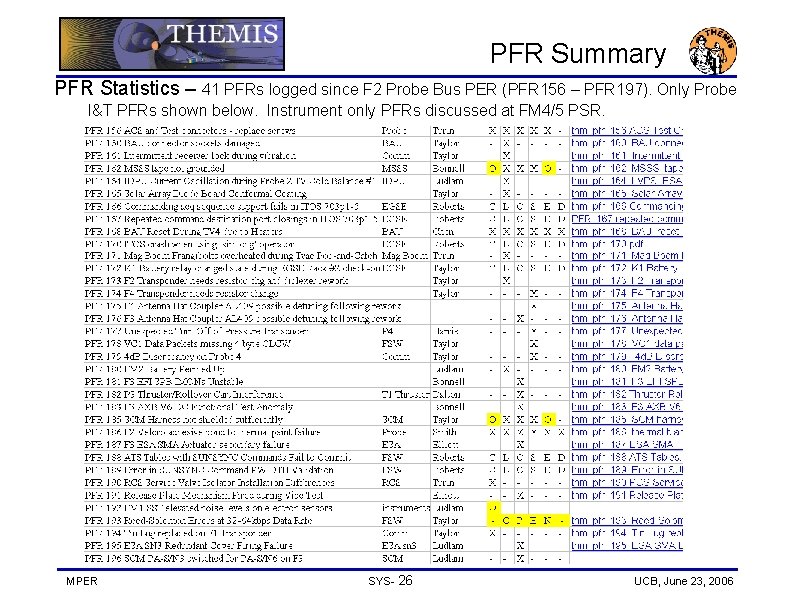
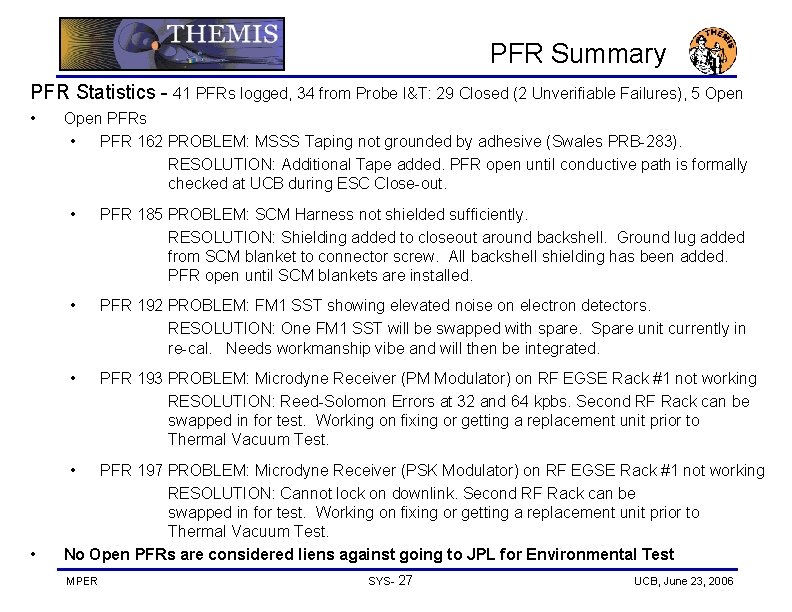
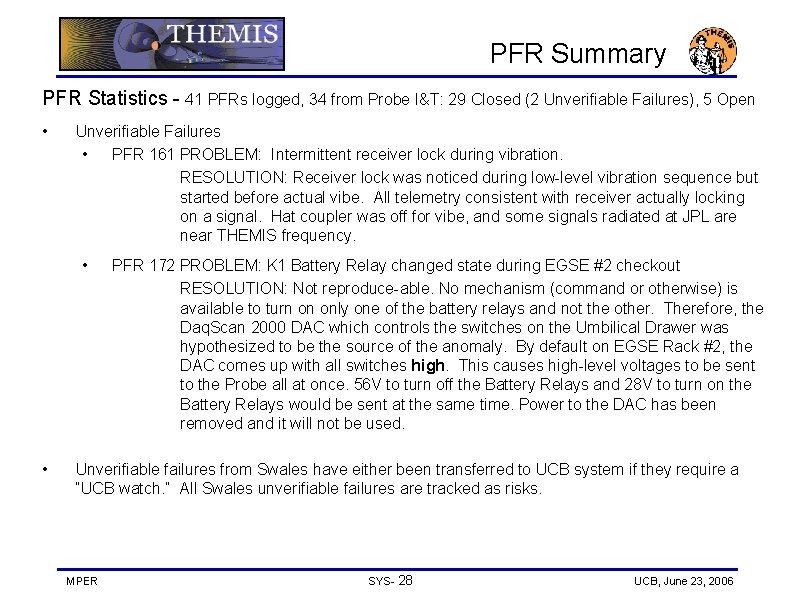
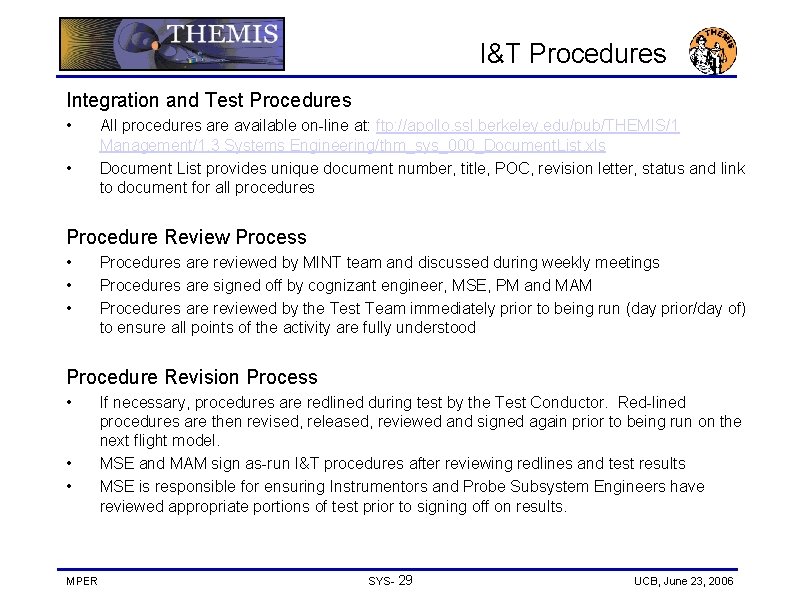
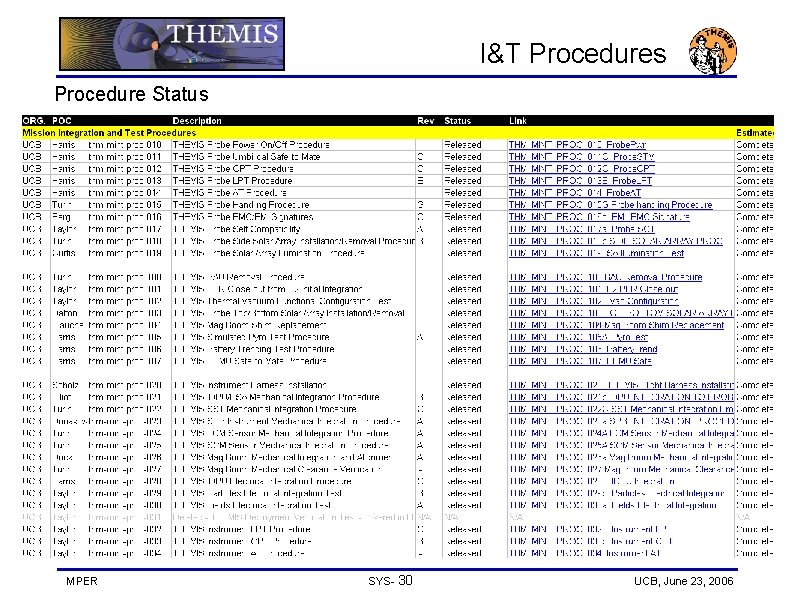
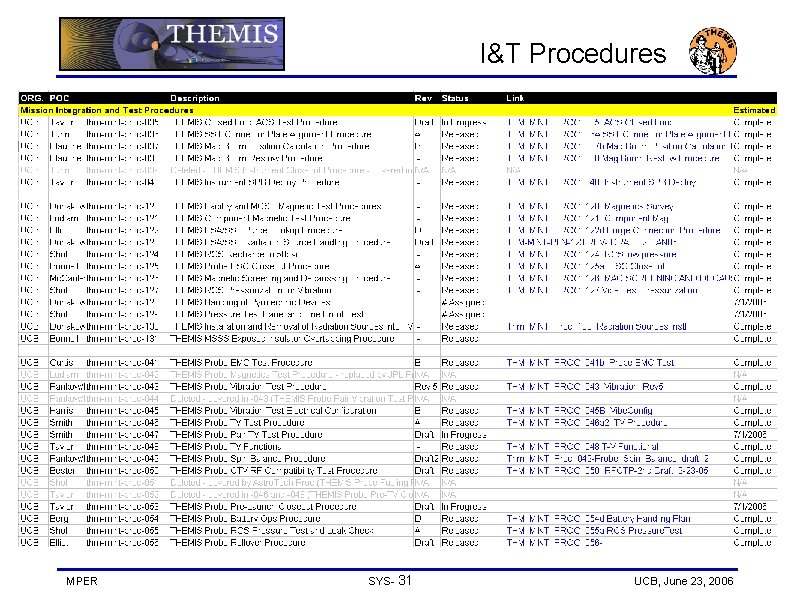
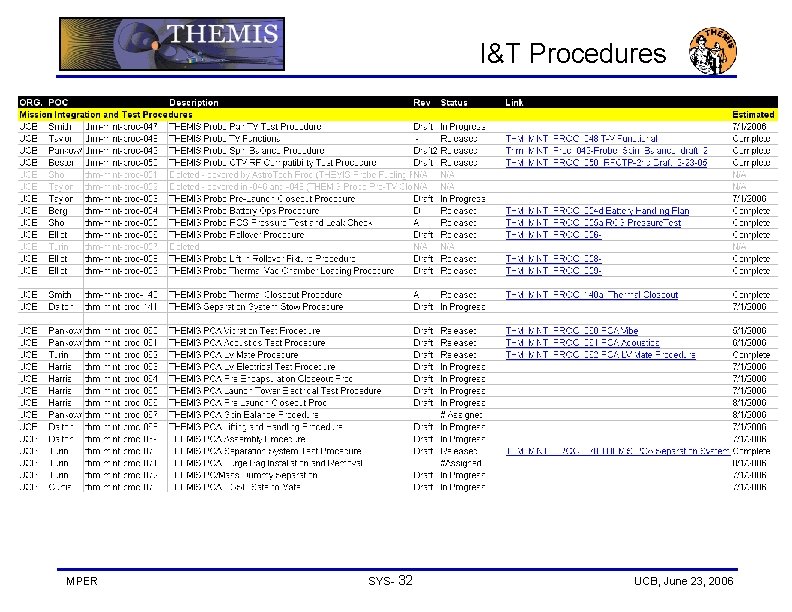
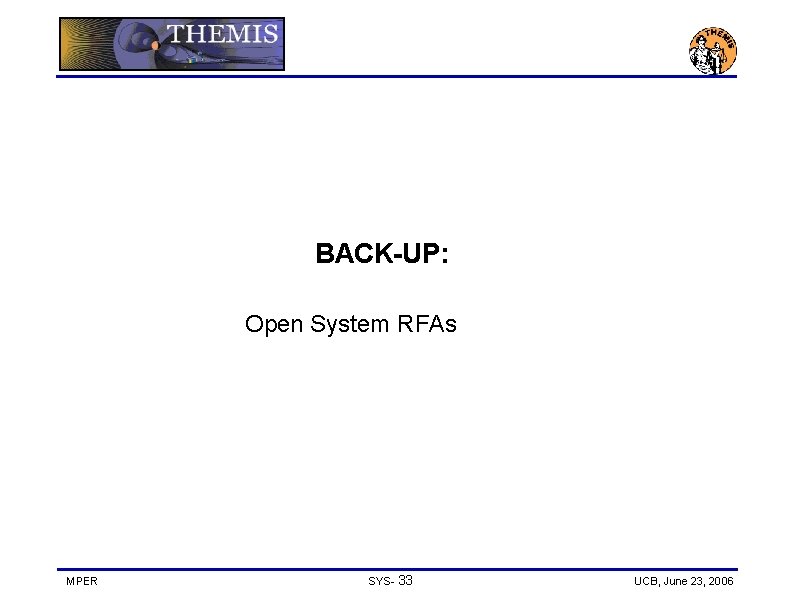
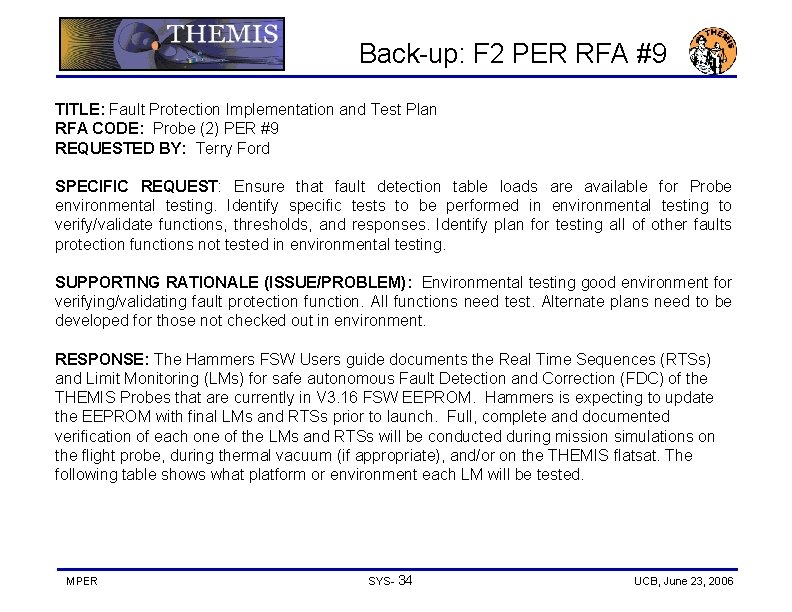
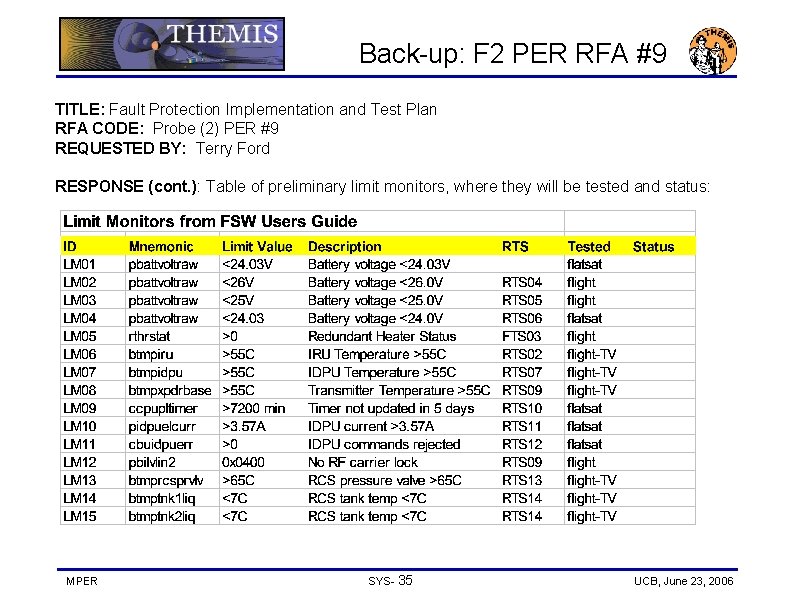
- Slides: 35
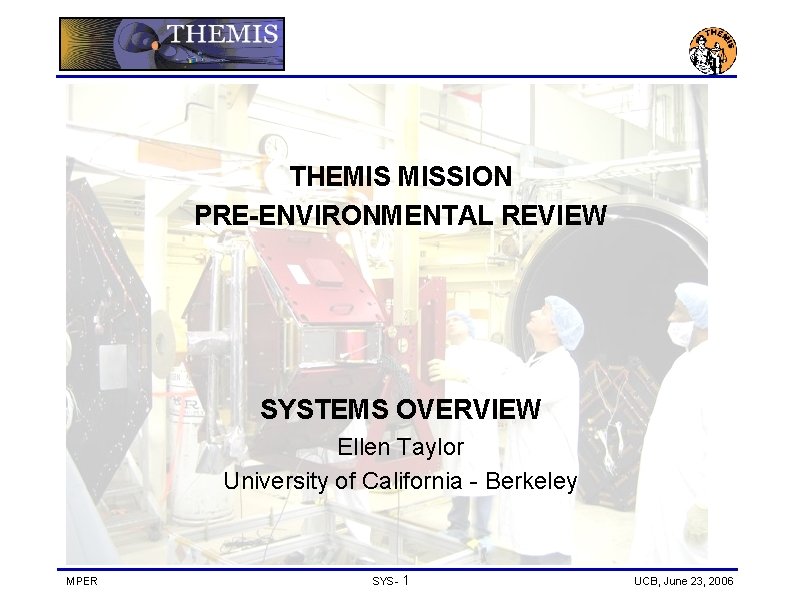
THEMIS MISSION PRE-ENVIRONMENTAL REVIEW SYSTEMS OVERVIEW Ellen Taylor University of California - Berkeley MPER SYS- 1 UCB, June 23, 2006
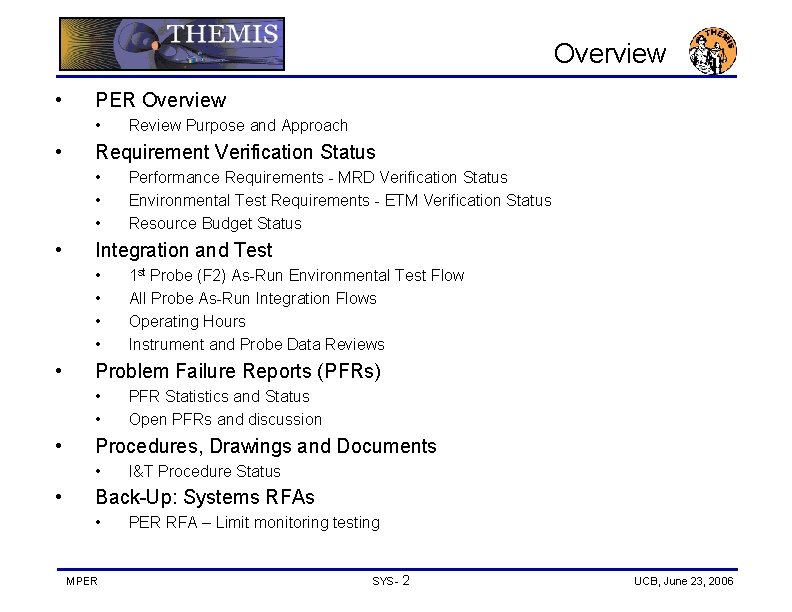
Overview • PER Overview • • Requirement Verification Status • • PFR Statistics and Status Open PFRs and discussion Procedures, Drawings and Documents • • 1 st Probe (F 2) As-Run Environmental Test Flow All Probe As-Run Integration Flows Operating Hours Instrument and Probe Data Reviews Problem Failure Reports (PFRs) • • • Performance Requirements - MRD Verification Status Environmental Test Requirements - ETM Verification Status Resource Budget Status Integration and Test • • • Review Purpose and Approach I&T Procedure Status Back-Up: Systems RFAs • MPER RFA – Limit monitoring testing SYS- 2 UCB, June 23, 2006
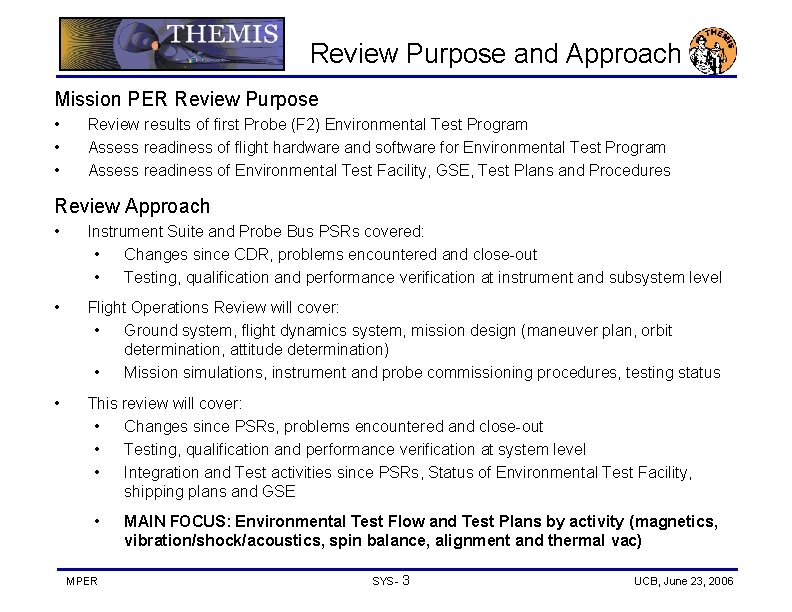
Review Purpose and Approach Mission PER Review Purpose • • • Review results of first Probe (F 2) Environmental Test Program Assess readiness of flight hardware and software for Environmental Test Program Assess readiness of Environmental Test Facility, GSE, Test Plans and Procedures Review Approach • Instrument Suite and Probe Bus PSRs covered: • Changes since CDR, problems encountered and close-out • Testing, qualification and performance verification at instrument and subsystem level • Flight Operations Review will cover: • Ground system, flight dynamics system, mission design (maneuver plan, orbit determination, attitude determination) • Mission simulations, instrument and probe commissioning procedures, testing status • This review will cover: • Changes since PSRs, problems encountered and close-out • Testing, qualification and performance verification at system level • Integration and Test activities since PSRs, Status of Environmental Test Facility, shipping plans and GSE • MPER MAIN FOCUS: Environmental Test Flow and Test Plans by activity (magnetics, vibration/shock/acoustics, spin balance, alignment and thermal vac) SYS- 3 UCB, June 23, 2006
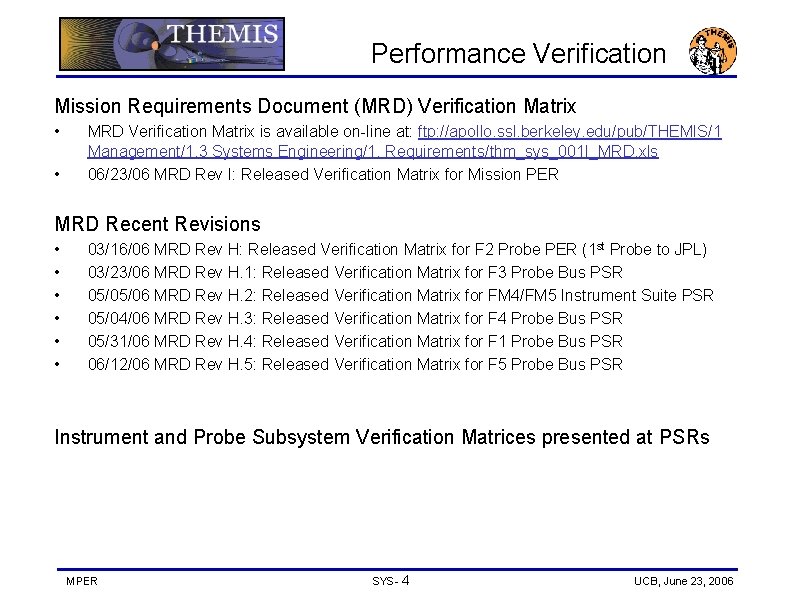
Performance Verification Mission Requirements Document (MRD) Verification Matrix • • MRD Verification Matrix is available on-line at: ftp: //apollo. ssl. berkeley. edu/pub/THEMIS/1 Management/1. 3 Systems Engineering/1. Requirements/thm_sys_001 I_MRD. xls 06/23/06 MRD Rev I: Released Verification Matrix for Mission PER MRD Recent Revisions • • • 03/16/06 MRD Rev H: Released Verification Matrix for F 2 Probe PER (1 st Probe to JPL) 03/23/06 MRD Rev H. 1: Released Verification Matrix for F 3 Probe Bus PSR 05/05/06 MRD Rev H. 2: Released Verification Matrix for FM 4/FM 5 Instrument Suite PSR 05/04/06 MRD Rev H. 3: Released Verification Matrix for F 4 Probe Bus PSR 05/31/06 MRD Rev H. 4: Released Verification Matrix for F 1 Probe Bus PSR 06/12/06 MRD Rev H. 5: Released Verification Matrix for F 5 Probe Bus PSR Instrument and Probe Subsystem Verification Matrices presented at PSRs MPER SYS- 4 UCB, June 23, 2006
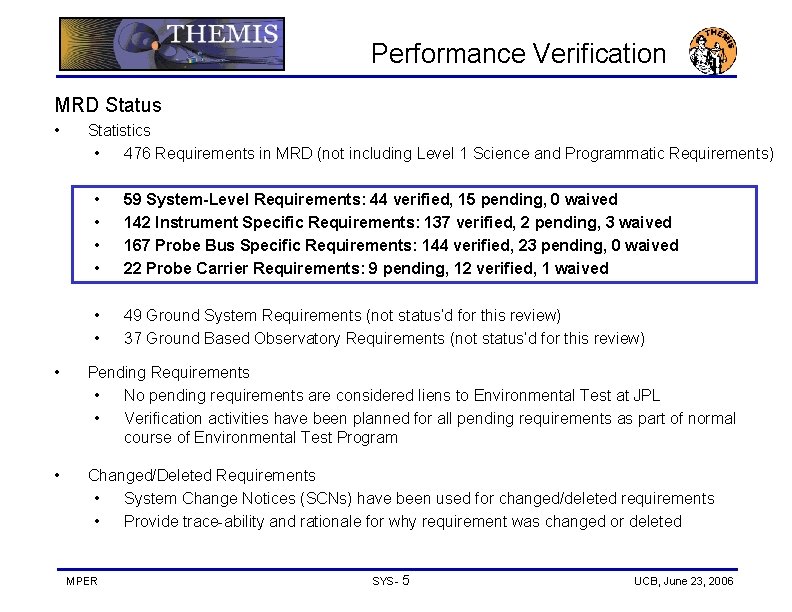
Performance Verification MRD Status • Statistics • 476 Requirements in MRD (not including Level 1 Science and Programmatic Requirements) • • 59 System-Level Requirements: 44 verified, 15 pending, 0 waived 142 Instrument Specific Requirements: 137 verified, 2 pending, 3 waived 167 Probe Bus Specific Requirements: 144 verified, 23 pending, 0 waived 22 Probe Carrier Requirements: 9 pending, 12 verified, 1 waived • • 49 Ground System Requirements (not status’d for this review) 37 Ground Based Observatory Requirements (not status’d for this review) • Pending Requirements • No pending requirements are considered liens to Environmental Test at JPL • Verification activities have been planned for all pending requirements as part of normal course of Environmental Test Program • Changed/Deleted Requirements • System Change Notices (SCNs) have been used for changed/deleted requirements • Provide trace-ability and rationale for why requirement was changed or deleted MPER SYS- 5 UCB, June 23, 2006
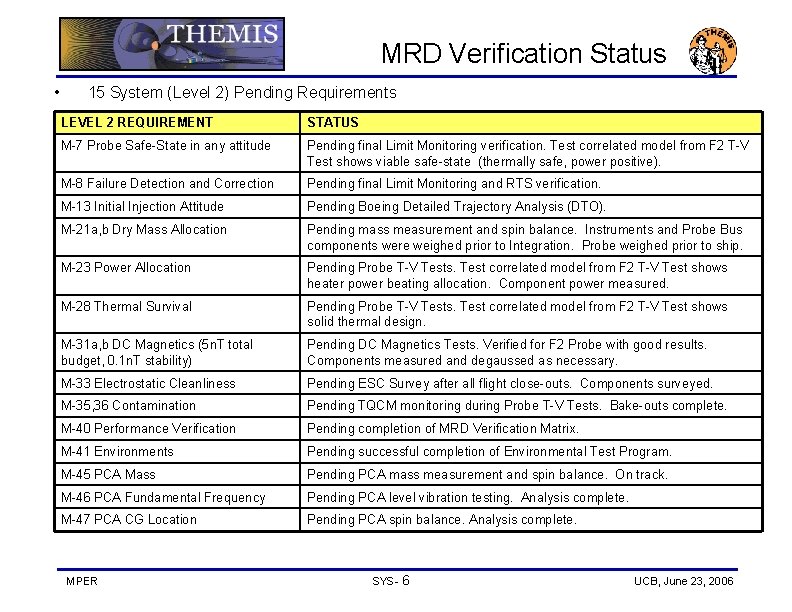
MRD Verification Status • 15 System (Level 2) Pending Requirements LEVEL 2 REQUIREMENT STATUS M-7 Probe Safe-State in any attitude Pending final Limit Monitoring verification. Test correlated model from F 2 T-V Test shows viable safe-state (thermally safe, power positive). M-8 Failure Detection and Correction Pending final Limit Monitoring and RTS verification. M-13 Initial Injection Attitude Pending Boeing Detailed Trajectory Analysis (DTO). M-21 a, b Dry Mass Allocation Pending mass measurement and spin balance. Instruments and Probe Bus components were weighed prior to Integration. Probe weighed prior to ship. M-23 Power Allocation Pending Probe T-V Tests. Test correlated model from F 2 T-V Test shows heater power beating allocation. Component power measured. M-28 Thermal Survival Pending Probe T-V Tests. Test correlated model from F 2 T-V Test shows solid thermal design. M-31 a, b DC Magnetics (5 n. T total budget, 0. 1 n. T stability) Pending DC Magnetics Tests. Verified for F 2 Probe with good results. Components measured and degaussed as necessary. M-33 Electrostatic Cleanliness Pending ESC Survey after all flight close-outs. Components surveyed. M-35, 36 Contamination Pending TQCM monitoring during Probe T-V Tests. Bake-outs complete. M-40 Performance Verification Pending completion of MRD Verification Matrix. M-41 Environments Pending successful completion of Environmental Test Program. M-45 PCA Mass Pending PCA mass measurement and spin balance. On track. M-46 PCA Fundamental Frequency Pending PCA level vibration testing. Analysis complete. M-47 PCA CG Location Pending PCA spin balance. Analysis complete. MPER SYS- 6 UCB, June 23, 2006
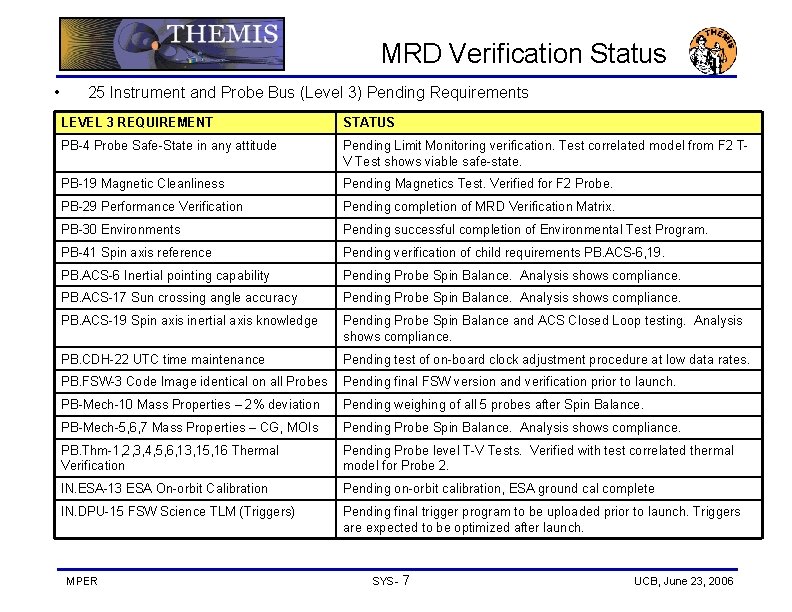
MRD Verification Status • 25 Instrument and Probe Bus (Level 3) Pending Requirements LEVEL 3 REQUIREMENT STATUS PB-4 Probe Safe-State in any attitude Pending Limit Monitoring verification. Test correlated model from F 2 TV Test shows viable safe-state. PB-19 Magnetic Cleanliness Pending Magnetics Test. Verified for F 2 Probe. PB-29 Performance Verification Pending completion of MRD Verification Matrix. PB-30 Environments Pending successful completion of Environmental Test Program. PB-41 Spin axis reference Pending verification of child requirements PB. ACS-6, 19. PB. ACS-6 Inertial pointing capability Pending Probe Spin Balance. Analysis shows compliance. PB. ACS-17 Sun crossing angle accuracy Pending Probe Spin Balance. Analysis shows compliance. PB. ACS-19 Spin axis inertial axis knowledge Pending Probe Spin Balance and ACS Closed Loop testing. Analysis shows compliance. PB. CDH-22 UTC time maintenance Pending test of on-board clock adjustment procedure at low data rates. PB. FSW-3 Code Image identical on all Probes Pending final FSW version and verification prior to launch. PB-Mech-10 Mass Properties – 2% deviation Pending weighing of all 5 probes after Spin Balance. PB-Mech-5, 6, 7 Mass Properties – CG, MOIs Pending Probe Spin Balance. Analysis shows compliance. PB. Thm-1, 2, 3, 4, 5, 6, 13, 15, 16 Thermal Verification Pending Probe level T-V Tests. Verified with test correlated thermal model for Probe 2. IN. ESA-13 ESA On-orbit Calibration Pending on-orbit calibration, ESA ground cal complete IN. DPU-15 FSW Science TLM (Triggers) Pending final trigger program to be uploaded prior to launch. Triggers are expected to be optimized after launch. MPER SYS- 7 UCB, June 23, 2006
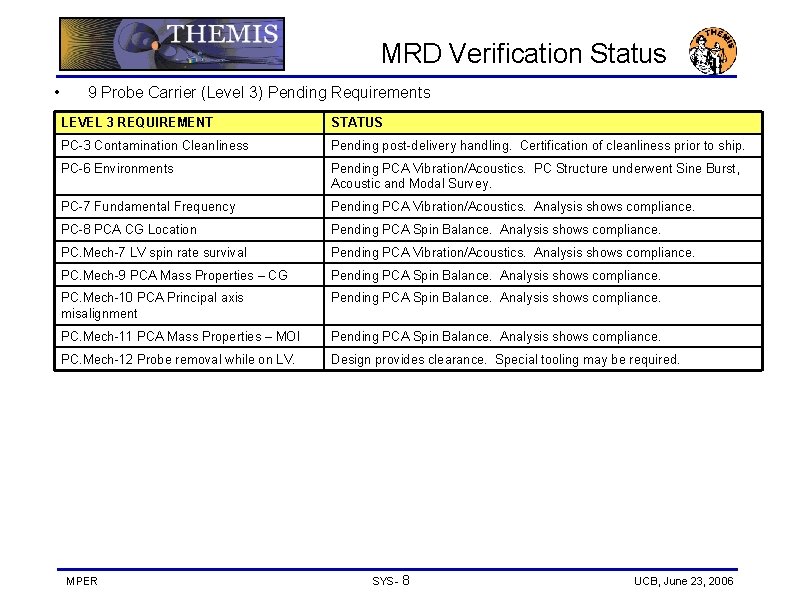
MRD Verification Status • 9 Probe Carrier (Level 3) Pending Requirements LEVEL 3 REQUIREMENT STATUS PC-3 Contamination Cleanliness Pending post-delivery handling. Certification of cleanliness prior to ship. PC-6 Environments Pending PCA Vibration/Acoustics. PC Structure underwent Sine Burst, Acoustic and Modal Survey. PC-7 Fundamental Frequency Pending PCA Vibration/Acoustics. Analysis shows compliance. PC-8 PCA CG Location Pending PCA Spin Balance. Analysis shows compliance. PC. Mech-7 LV spin rate survival Pending PCA Vibration/Acoustics. Analysis shows compliance. PC. Mech-9 PCA Mass Properties – CG Pending PCA Spin Balance. Analysis shows compliance. PC. Mech-10 PCA Principal axis misalignment Pending PCA Spin Balance. Analysis shows compliance. PC. Mech-11 PCA Mass Properties – MOI Pending PCA Spin Balance. Analysis shows compliance. PC. Mech-12 Probe removal while on LV. Design provides clearance. Special tooling may be required. MPER SYS- 8 UCB, June 23, 2006
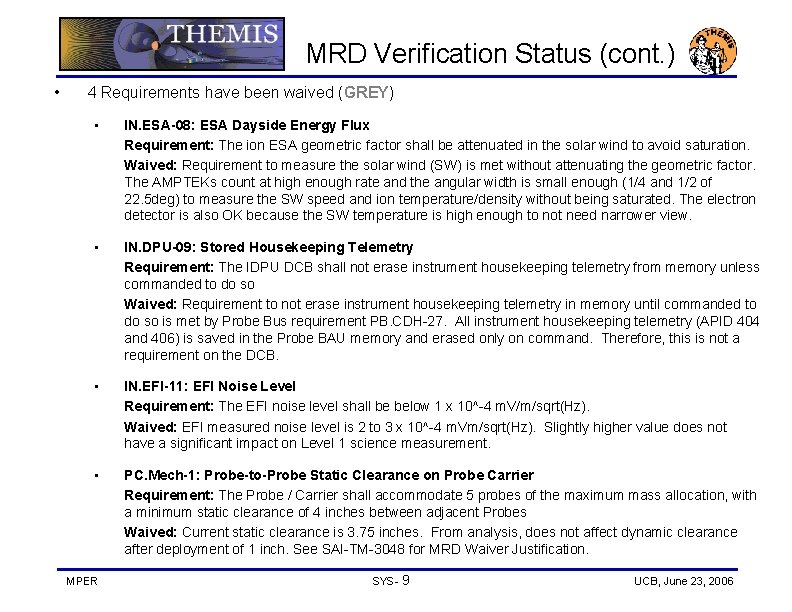
MRD Verification Status (cont. ) • 4 Requirements have been waived (GREY) • IN. ESA-08: ESA Dayside Energy Flux Requirement: The ion ESA geometric factor shall be attenuated in the solar wind to avoid saturation. Waived: Requirement to measure the solar wind (SW) is met without attenuating the geometric factor. The AMPTEKs count at high enough rate and the angular width is small enough (1/4 and 1/2 of 22. 5 deg) to measure the SW speed and ion temperature/density without being saturated. The electron detector is also OK because the SW temperature is high enough to not need narrower view. • IN. DPU-09: Stored Housekeeping Telemetry Requirement: The IDPU DCB shall not erase instrument housekeeping telemetry from memory unless commanded to do so Waived: Requirement to not erase instrument housekeeping telemetry in memory until commanded to do so is met by Probe Bus requirement PB. CDH-27. All instrument housekeeping telemetry (APID 404 and 406) is saved in the Probe BAU memory and erased only on command. Therefore, this is not a requirement on the DCB. • IN. EFI-11: EFI Noise Level Requirement: The EFI noise level shall be below 1 x 10^-4 m. V/m/sqrt(Hz). Waived: EFI measured noise level is 2 to 3 x 10^-4 m. Vm/sqrt(Hz). Slightly higher value does not have a significant impact on Level 1 science measurement. • PC. Mech-1: Probe-to-Probe Static Clearance on Probe Carrier Requirement: The Probe / Carrier shall accommodate 5 probes of the maximum mass allocation, with a minimum static clearance of 4 inches between adjacent Probes Waived: Current static clearance is 3. 75 inches. From analysis, does not affect dynamic clearance after deployment of 1 inch. See SAI-TM-3048 for MRD Waiver Justification. MPER SYS- 9 UCB, June 23, 2006
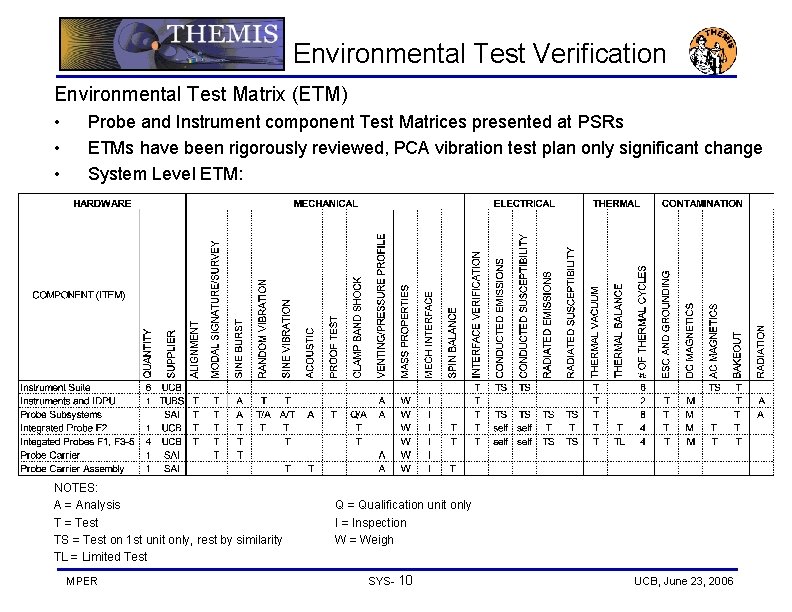
Environmental Test Verification Environmental Test Matrix (ETM) • • • Probe and Instrument component Test Matrices presented at PSRs ETMs have been rigorously reviewed, PCA vibration test plan only significant change System Level ETM: NOTES: A = Analysis T = Test TS = Test on 1 st unit only, rest by similarity TL = Limited Test MPER Q = Qualification unit only I = Inspection W = Weigh SYS- 10 UCB, June 23, 2006
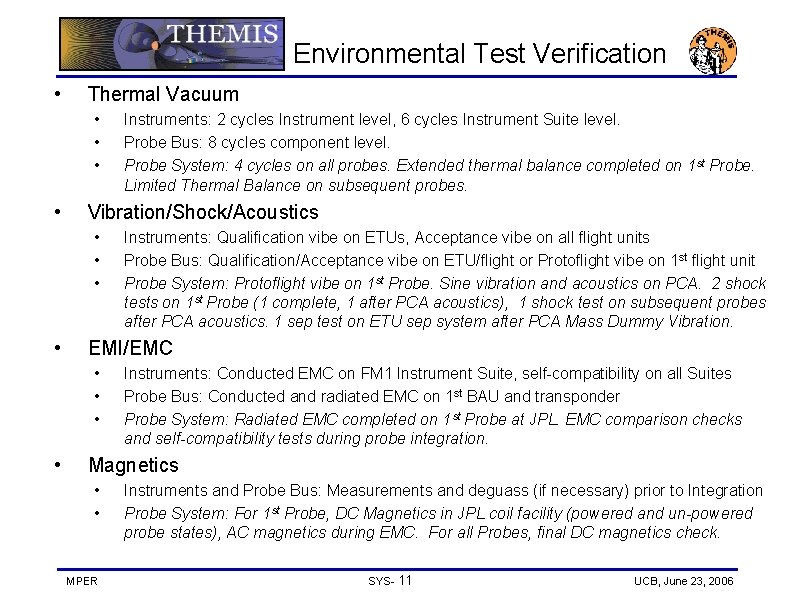
Environmental Test Verification • Thermal Vacuum • • Vibration/Shock/Acoustics • • Instruments: Qualification vibe on ETUs, Acceptance vibe on all flight units Probe Bus: Qualification/Acceptance vibe on ETU/flight or Protoflight vibe on 1 st flight unit Probe System: Protoflight vibe on 1 st Probe. Sine vibration and acoustics on PCA. 2 shock tests on 1 st Probe (1 complete, 1 after PCA acoustics), 1 shock test on subsequent probes after PCA acoustics. 1 sep test on ETU sep system after PCA Mass Dummy Vibration. EMI/EMC • • Instruments: 2 cycles Instrument level, 6 cycles Instrument Suite level. Probe Bus: 8 cycles component level. Probe System: 4 cycles on all probes. Extended thermal balance completed on 1 st Probe. Limited Thermal Balance on subsequent probes. Instruments: Conducted EMC on FM 1 Instrument Suite, self-compatibility on all Suites Probe Bus: Conducted and radiated EMC on 1 st BAU and transponder Probe System: Radiated EMC completed on 1 st Probe at JPL. EMC comparison checks and self-compatibility tests during probe integration. Magnetics • • MPER Instruments and Probe Bus: Measurements and deguass (if necessary) prior to Integration Probe System: For 1 st Probe, DC Magnetics in JPL coil facility (powered and un-powered probe states), AC magnetics during EMC. For all Probes, final DC magnetics check. SYS- 11 UCB, June 23, 2006
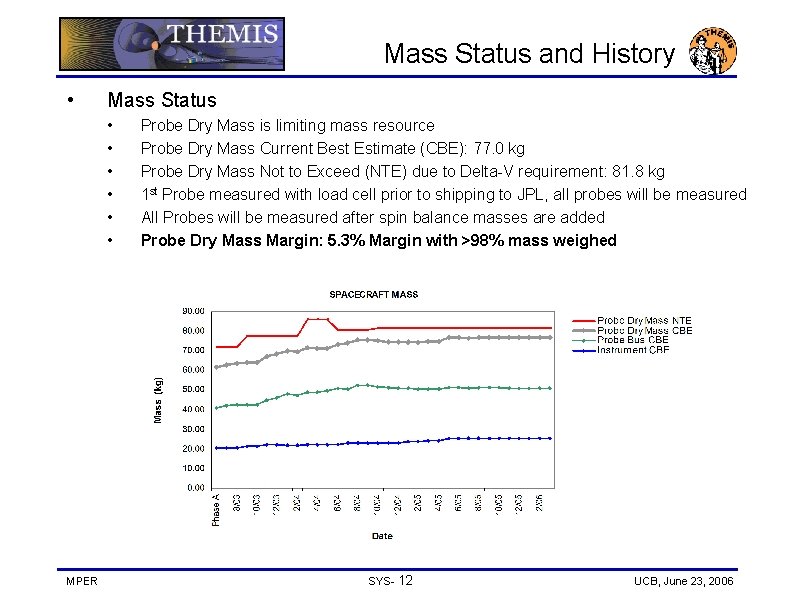
Mass Status and History • Mass Status • • • MPER Probe Dry Mass is limiting mass resource Probe Dry Mass Current Best Estimate (CBE): 77. 0 kg Probe Dry Mass Not to Exceed (NTE) due to Delta-V requirement: 81. 8 kg 1 st Probe measured with load cell prior to shipping to JPL, all probes will be measured All Probes will be measured after spin balance masses are added Probe Dry Mass Margin: 5. 3% Margin with >98% mass weighed SYS- 12 UCB, June 23, 2006
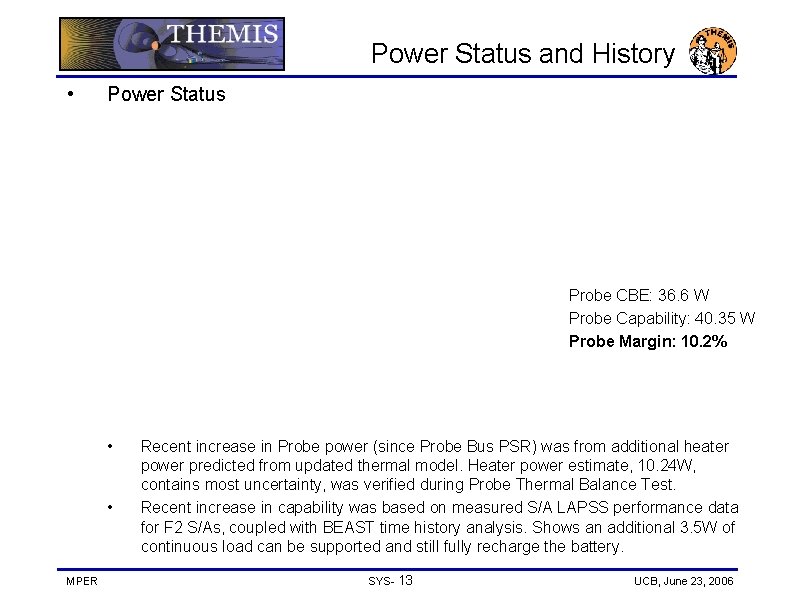
Power Status and History • Power Status Probe CBE: 36. 6 W Probe Capability: 40. 35 W Probe Margin: 10. 2% • • MPER Recent increase in Probe power (since Probe Bus PSR) was from additional heater power predicted from updated thermal model. Heater power estimate, 10. 24 W, contains most uncertainty, was verified during Probe Thermal Balance Test. Recent increase in capability was based on measured S/A LAPSS performance data for F 2 S/As, coupled with BEAST time history analysis. Shows an additional 3. 5 W of continuous load can be supported and still fully recharge the battery. SYS- 13 UCB, June 23, 2006
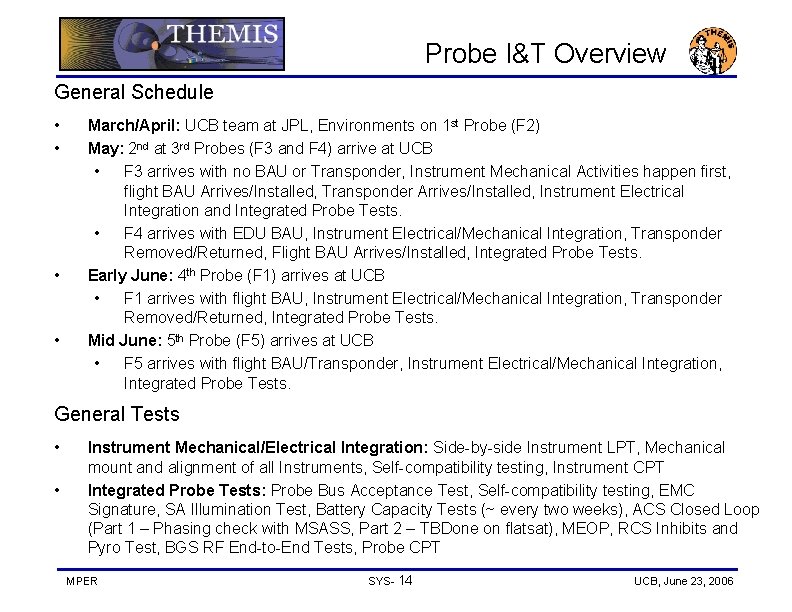
Probe I&T Overview General Schedule • • March/April: UCB team at JPL, Environments on 1 st Probe (F 2) May: 2 nd at 3 rd Probes (F 3 and F 4) arrive at UCB • F 3 arrives with no BAU or Transponder, Instrument Mechanical Activities happen first, flight BAU Arrives/Installed, Transponder Arrives/Installed, Instrument Electrical Integration and Integrated Probe Tests. • F 4 arrives with EDU BAU, Instrument Electrical/Mechanical Integration, Transponder Removed/Returned, Flight BAU Arrives/Installed, Integrated Probe Tests. Early June: 4 th Probe (F 1) arrives at UCB • F 1 arrives with flight BAU, Instrument Electrical/Mechanical Integration, Transponder Removed/Returned, Integrated Probe Tests. Mid June: 5 th Probe (F 5) arrives at UCB • F 5 arrives with flight BAU/Transponder, Instrument Electrical/Mechanical Integration, Integrated Probe Tests. General Tests • • Instrument Mechanical/Electrical Integration: Side-by-side Instrument LPT, Mechanical mount and alignment of all Instruments, Self-compatibility testing, Instrument CPT Integrated Probe Tests: Probe Bus Acceptance Test, Self-compatibility testing, EMC Signature, SA Illumination Test, Battery Capacity Tests (~ every two weeks), ACS Closed Loop (Part 1 – Phasing check with MSASS, Part 2 – TBDone on flatsat), MEOP, RCS Inhibits and Pyro Test, BGS RF End-to-End Tests, Probe CPT MPER SYS- 14 UCB, June 23, 2006
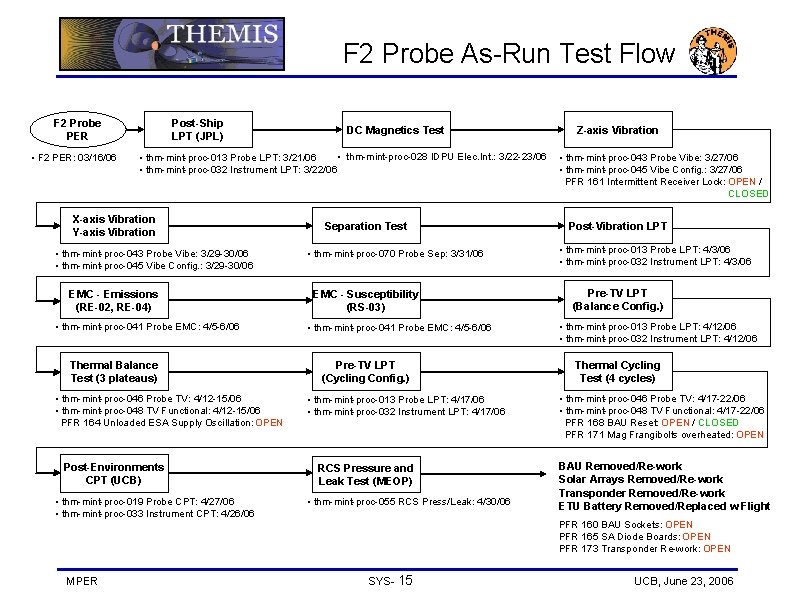
F 2 Probe As-Run Test Flow Post-Ship LPT (JPL) F 2 Probe PER • F 2 PER: 03/16/06 • thm-mint-proc-028 IDPU Elec. Int. : 3/22 -23/06 • thm-mint-proc-013 Probe LPT: 3/21/06 • thm-mint-proc-032 Instrument LPT: 3/22/06 X-axis Vibration Y-axis Vibration • thm-mint-proc-043 Probe Vibe: 3/29 -30/06 • thm-mint-proc-045 Vibe Config. : 3/29 -30/06 EMC - Emissions (RE-02, RE-04) • thm-mint-proc-041 Probe EMC: 4/5 -6/06 Thermal Balance Test (3 plateaus) • thm-mint-proc-046 Probe TV: 4/12 -15/06 • thm-mint-proc-048 TV Functional: 4/12 -15/06 PFR 164 Unloaded ESA Supply Oscillation: OPEN Post-Environments CPT (UCB) • thm-mint-proc-019 Probe CPT: 4/27/06 • thm-mint-proc-033 Instrument CPT: 4/26/06 MPER DC Magnetics Test Separation Test • thm-mint-proc-070 Probe Sep: 3/31/06 EMC - Susceptibility (RS-03) • thm-mint-proc-041 Probe EMC: 4/5 -6/06 Pre-TV LPT (Cycling Config. ) • thm-mint-proc-013 Probe LPT: 4/17/06 • thm-mint-proc-032 Instrument LPT: 4/17/06 RCS Pressure and Leak Test (MEOP) • thm-mint-proc-055 RCS Press/Leak: 4/30/06 Z-axis Vibration • thm-mint-proc-043 Probe Vibe: 3/27/06 • thm-mint-proc-045 Vibe Config. : 3/27/06 PFR 161 Intermittent Receiver Lock: OPEN / CLOSED Post-Vibration LPT • thm-mint-proc-013 Probe LPT: 4/3/06 • thm-mint-proc-032 Instrument LPT: 4/3/06 Pre-TV LPT (Balance Config. ) • thm-mint-proc-013 Probe LPT: 4/12/06 • thm-mint-proc-032 Instrument LPT: 4/12/06 Thermal Cycling Test (4 cycles) • thm-mint-proc-046 Probe TV: 4/17 -22/06 • thm-mint-proc-048 TV Functional: 4/17 -22/06 PFR 168 BAU Reset: OPEN / CLOSED PFR 171 Mag Frangibolts overheated: OPEN BAU Removed/Re-work Solar Arrays Removed/Re-work Transponder Removed/Re-work ETU Battery Removed/Replaced w Flight PFR 160 BAU Sockets: OPEN PFR 165 SA Diode Boards: OPEN PFR 173 Transponder Re-work: OPEN SYS- 15 UCB, June 23, 2006
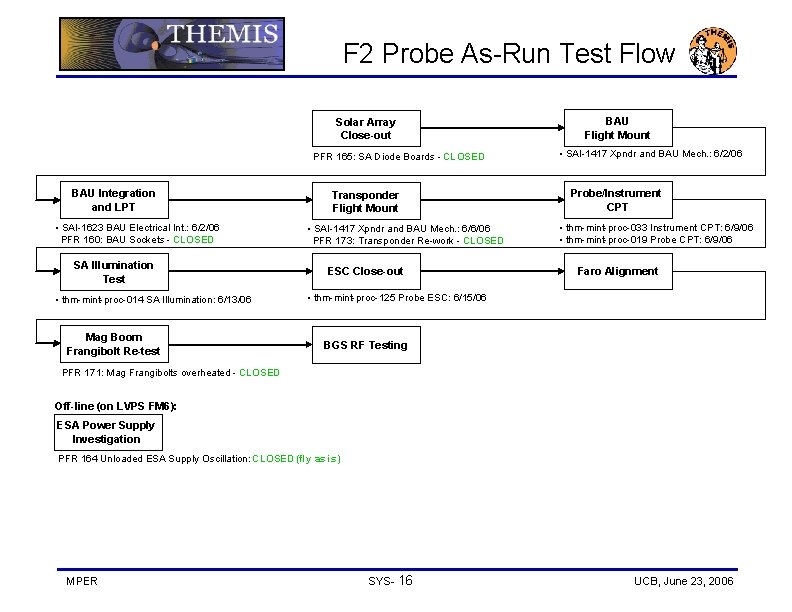
F 2 Probe As-Run Test Flow Solar Array Close-out PFR 165: SA Diode Boards - CLOSED BAU Integration and LPT • SAI-1623 BAU Electrical Int. : 6/2/06 PFR 160: BAU Sockets - CLOSED SA Illumination Test • thm-mint-proc-014 SA Illumination: 6/13/06 Mag Boom Frangibolt Re-test Transponder Flight Mount • SAI-1417 Xpndr and BAU Mech. : 6/6/06 PFR 173: Transponder Re-work - CLOSED ESC Close-out BAU Flight Mount • SAI-1417 Xpndr and BAU Mech. : 6/2/06 Probe/Instrument CPT • thm-mint-proc-033 Instrument CPT: 6/9/06 • thm-mint-proc-019 Probe CPT: 6/9/06 Faro Alignment • thm-mint-proc-125 Probe ESC: 6/15/06 BGS RF Testing PFR 171: Mag Frangibolts overheated - CLOSED Off-line (on LVPS FM 6): ESA Power Supply Investigation PFR 164 Unloaded ESA Supply Oscillation: CLOSED (fly as is) MPER SYS- 16 UCB, June 23, 2006
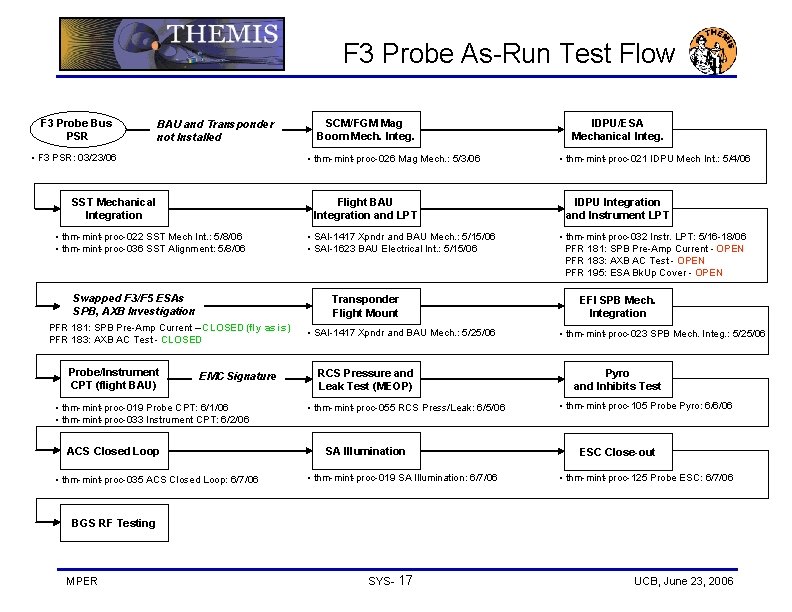
F 3 Probe As-Run Test Flow F 3 Probe Bus PSR BAU and Transponder not Installed • F 3 PSR: 03/23/06 • thm-mint-proc-026 Mag Mech. : 5/3/06 SST Mechanical Integration Flight BAU Integration and LPT • thm-mint-proc-022 SST Mech Int. : 5/8/06 • thm-mint-proc-036 SST Alignment: 5/8/06 Swapped F 3/F 5 ESAs SPB, AXB Investigation • SAI-1417 Xpndr and BAU Mech. : 5/15/06 • SAI-1623 BAU Electrical Int. : 5/15/06 Transponder Flight Mount PFR 181: SPB Pre-Amp Current – CLOSED (fly as is) PFR 183: AXB AC Test - CLOSED Probe/Instrument CPT (flight BAU) SCM/FGM Mag Boom Mech. Integ. EMC Signature • thm-mint-proc-019 Probe CPT: 6/1/06 • thm-mint-proc-033 Instrument CPT: 6/2/06 ACS Closed Loop • thm-mint-proc-035 ACS Closed Loop: 6/7/06 • SAI-1417 Xpndr and BAU Mech. : 5/25/06 RCS Pressure and Leak Test (MEOP) • thm-mint-proc-055 RCS Press/Leak: 6/5/06 SA Illumination • thm-mint-proc-019 SA Illumination: 6/7/06 IDPU/ESA Mechanical Integ. • thm-mint-proc-021 IDPU Mech Int. : 5/4/06 IDPU Integration and Instrument LPT • thm-mint-proc-032 Instr. LPT: 5/16 -18/06 PFR 181: SPB Pre-Amp Current - OPEN PFR 183: AXB AC Test - OPEN PFR 195: ESA Bk. Up Cover - OPEN EFI SPB Mech. Integration • thm-mint-proc-023 SPB Mech. Integ. : 5/25/06 Pyro and Inhibits Test • thm-mint-proc-105 Probe Pyro: 6/6/06 ESC Close-out • thm-mint-proc-125 Probe ESC: 6/7/06 BGS RF Testing MPER SYS- 17 UCB, June 23, 2006
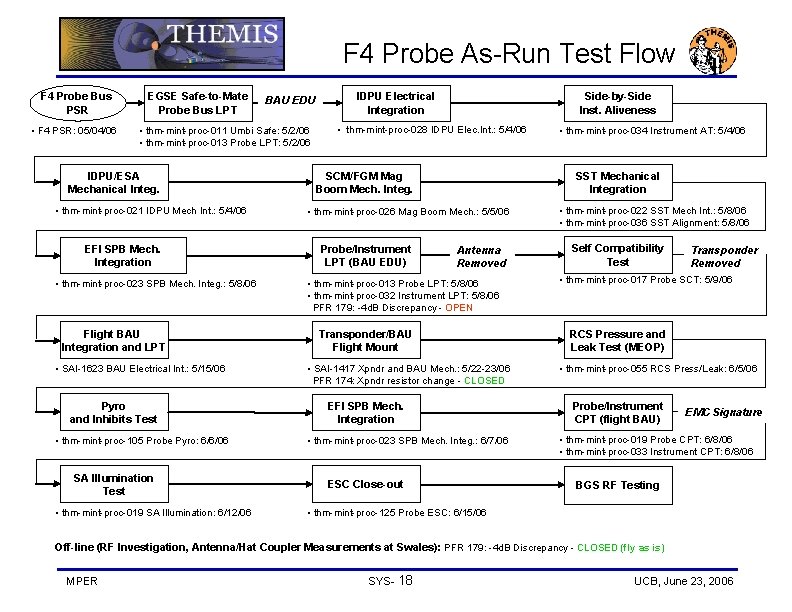
F 4 Probe As-Run Test Flow F 4 Probe Bus PSR • F 4 PSR: 05/04/06 EGSE Safe-to-Mate Probe Bus LPT BAU EDU • thm-mint-proc-011 Umbi Safe: 5/2/06 • thm-mint-proc-013 Probe LPT: 5/2/06 IDPU/ESA Mechanical Integ. • thm-mint-proc-021 IDPU Mech Int. : 5/4/06 EFI SPB Mech. Integration • thm-mint-proc-023 SPB Mech. Integ. : 5/8/06 Flight BAU Integration and LPT • SAI-1623 BAU Electrical Int. : 5/15/06 Pyro and Inhibits Test • thm-mint-proc-105 Probe Pyro: 6/6/06 SA Illumination Test • thm-mint-proc-019 SA Illumination: 6/12/06 IDPU Electrical Integration Side-by-Side Inst. Aliveness • thm-mint-proc-028 IDPU Elec. Int. : 5/4/06 SCM/FGM Mag Boom Mech. Integ. SST Mechanical Integration • thm-mint-proc-026 Mag Boom Mech. : 5/5/06 Probe/Instrument LPT (BAU EDU) • thm-mint-proc-034 Instrument AT: 5/4/06 Antenna Removed • thm-mint-proc-013 Probe LPT: 5/8/06 • thm-mint-proc-032 Instrument LPT: 5/8/06 PFR 179: -4 d. B Discrepancy - OPEN Transponder/BAU Flight Mount • SAI-1417 Xpndr and BAU Mech. : 5/22 -23/06 PFR 174: Xpndr resistor change - CLOSED EFI SPB Mech. Integration • thm-mint-proc-023 SPB Mech. Integ. : 6/7/06 ESC Close-out • thm-mint-proc-022 SST Mech Int. : 5/8/06 • thm-mint-proc-036 SST Alignment: 5/8/06 Self Compatibility Test Transponder Removed • thm-mint-proc-017 Probe SCT: 5/9/06 RCS Pressure and Leak Test (MEOP) • thm-mint-proc-055 RCS Press/Leak: 6/5/06 Probe/Instrument CPT (flight BAU) EMC Signature • thm-mint-proc-019 Probe CPT: 6/8/06 • thm-mint-proc-033 Instrument CPT: 6/8/06 BGS RF Testing • thm-mint-proc-125 Probe ESC: 6/15/06 Off-line (RF Investigation, Antenna/Hat Coupler Measurements at Swales): PFR 179: -4 d. B Discrepancy - CLOSED (fly as is) MPER SYS- 18 UCB, June 23, 2006
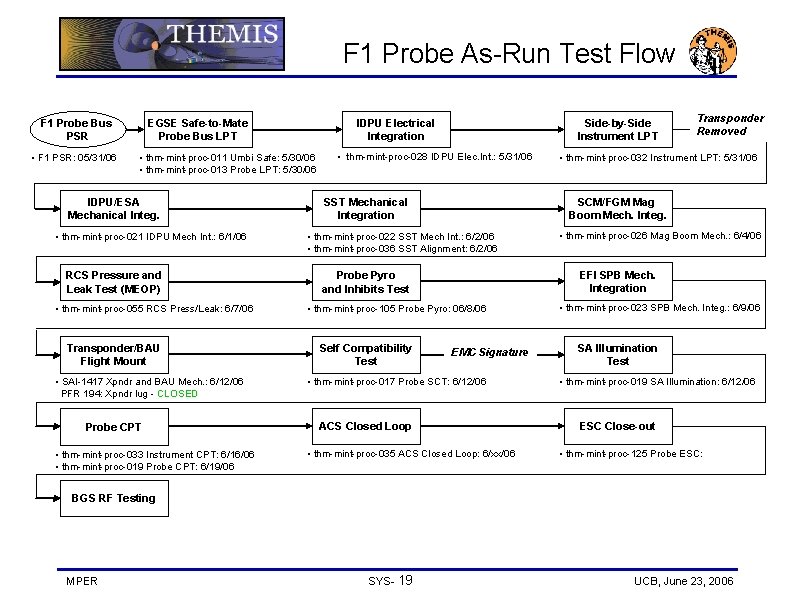
F 1 Probe As-Run Test Flow EGSE Safe-to-Mate Probe Bus LPT F 1 Probe Bus PSR • F 1 PSR: 05/31/06 IDPU Electrical Integration • thm-mint-proc-011 Umbi Safe: 5/30/06 • thm-mint-proc-013 Probe LPT: 5/30/06 IDPU/ESA Mechanical Integ. • thm-mint-proc-021 IDPU Mech Int. : 6/1/06 RCS Pressure and Leak Test (MEOP) • thm-mint-proc-055 RCS Press/Leak: 6/7/06 Transponder/BAU Flight Mount • SAI-1417 Xpndr and BAU Mech. : 6/12/06 PFR 194: Xpndr lug - CLOSED Probe CPT • thm-mint-proc-033 Instrument CPT: 6/16/06 • thm-mint-proc-019 Probe CPT: 6/19/06 Side-by-Side Instrument LPT • thm-mint-proc-028 IDPU Elec. Int. : 5/31/06 SST Mechanical Integration • thm-mint-proc-032 Instrument LPT: 5/31/06 SCM/FGM Mag Boom Mech. Integ. • thm-mint-proc-022 SST Mech Int. : 6/2/06 • thm-mint-proc-036 SST Alignment: 6/2/06 • thm-mint-proc-026 Mag Boom Mech. : 6/4/06 EFI SPB Mech. Integration Probe Pyro and Inhibits Test • thm-mint-proc-105 Probe Pyro: 06/8/06 Self Compatibility Test Transponder Removed EMC Signature • thm-mint-proc-017 Probe SCT: 6/12/06 ACS Closed Loop • thm-mint-proc-035 ACS Closed Loop: 6/xx/06 • thm-mint-proc-023 SPB Mech. Integ. : 6/9/06 SA Illumination Test • thm-mint-proc-019 SA Illumination: 6/12/06 ESC Close-out • thm-mint-proc-125 Probe ESC: BGS RF Testing MPER SYS- 19 UCB, June 23, 2006
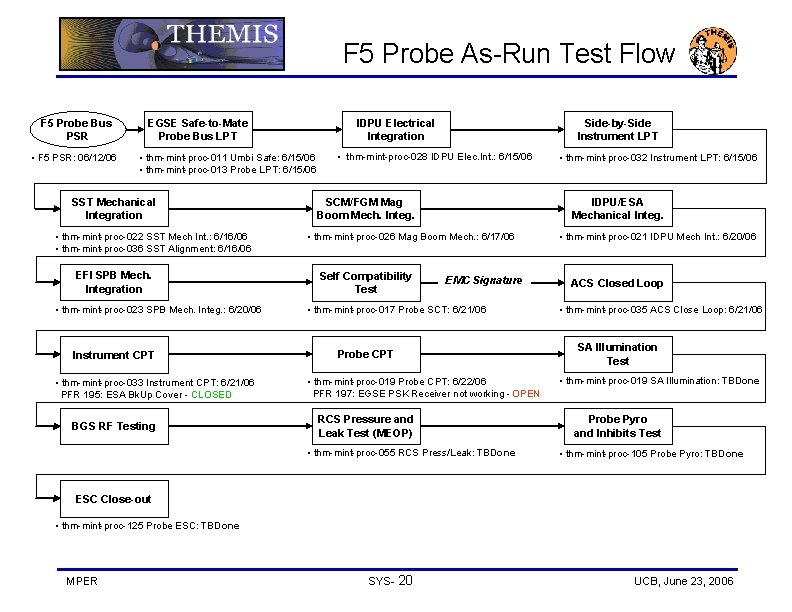
F 5 Probe As-Run Test Flow F 5 Probe Bus PSR • F 5 PSR: 06/12/06 EGSE Safe-to-Mate Probe Bus LPT IDPU Electrical Integration • thm-mint-proc-011 Umbi Safe: 6/15/06 • thm-mint-proc-013 Probe LPT: 6/15/06 SST Mechanical Integration • thm-mint-proc-022 SST Mech Int. : 6/16/06 • thm-mint-proc-036 SST Alignment: 6/16/06 EFI SPB Mech. Integration • thm-mint-proc-023 SPB Mech. Integ. : 6/20/06 Instrument CPT • thm-mint-proc-033 Instrument CPT: 6/21/06 PFR 195: ESA Bk. Up Cover - CLOSED BGS RF Testing Side-by-Side Instrument LPT • thm-mint-proc-028 IDPU Elec. Int. : 6/15/06 SCM/FGM Mag Boom Mech. Integ. IDPU/ESA Mechanical Integ. • thm-mint-proc-026 Mag Boom Mech. : 6/17/06 Self Compatibility Test • thm-mint-proc-032 Instrument LPT: 6/15/06 EMC Signature • thm-mint-proc-017 Probe SCT: 6/21/06 Probe CPT • thm-mint-proc-019 Probe CPT: 6/22/06 PFR 197: EGSE PSK Receiver not working - OPEN RCS Pressure and Leak Test (MEOP) • thm-mint-proc-055 RCS Press/Leak: TBDone • thm-mint-proc-021 IDPU Mech Int. : 6/20/06 ACS Closed Loop • thm-mint-proc-035 ACS Close Loop: 6/21/06 SA Illumination Test • thm-mint-proc-019 SA Illumination: TBDone Probe Pyro and Inhibits Test • thm-mint-proc-105 Probe Pyro: TBDone ESC Close-out • thm-mint-proc-125 Probe ESC: TBDone MPER SYS- 20 UCB, June 23, 2006
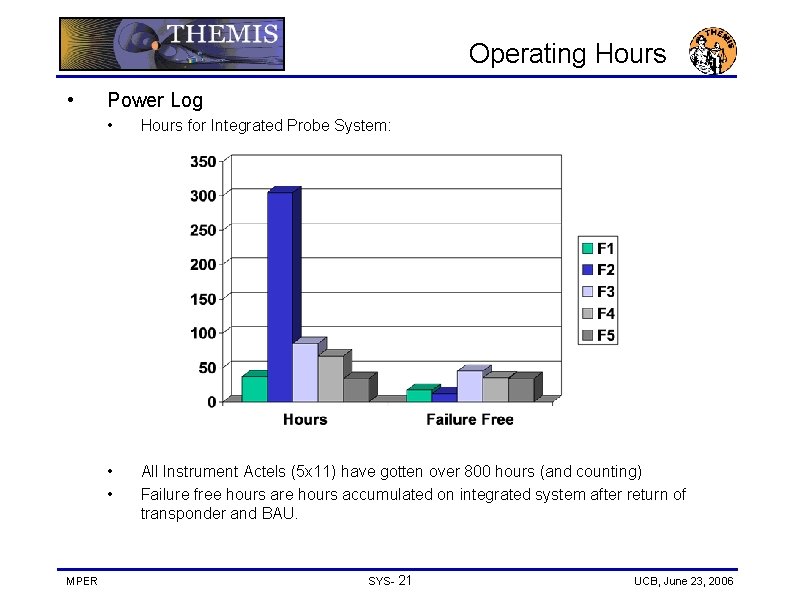
Operating Hours • MPER Power Log • Hours for Integrated Probe System: • • All Instrument Actels (5 x 11) have gotten over 800 hours (and counting) Failure free hours are hours accumulated on integrated system after return of transponder and BAU. SYS- 21 UCB, June 23, 2006
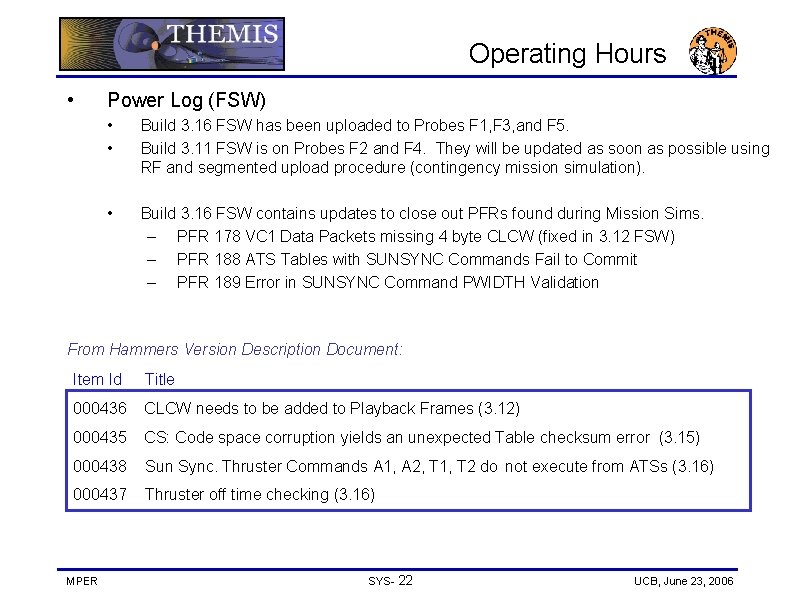
Operating Hours • Power Log (FSW) • • Build 3. 16 FSW has been uploaded to Probes F 1, F 3, and F 5. Build 3. 11 FSW is on Probes F 2 and F 4. They will be updated as soon as possible using RF and segmented upload procedure (contingency mission simulation). • Build 3. 16 FSW contains updates to close out PFRs found during Mission Sims. – PFR 178 VC 1 Data Packets missing 4 byte CLCW (fixed in 3. 12 FSW) – PFR 188 ATS Tables with SUNSYNC Commands Fail to Commit – PFR 189 Error in SUNSYNC Command PWIDTH Validation From Hammers Version Description Document: Item Id Title 000436 CLCW needs to be added to Playback Frames (3. 12) 000435 CS: Code space corruption yields an unexpected Table checksum error (3. 15) 000438 Sun Sync. Thruster Commands A 1, A 2, T 1, T 2 do not execute from ATSs (3. 16) 000437 Thruster off time checking (3. 16) MPER SYS- 22 UCB, June 23, 2006
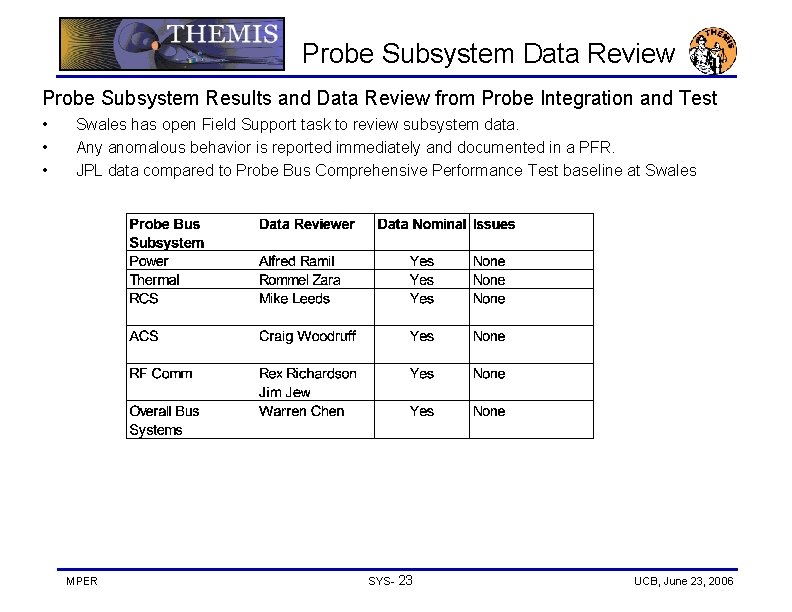
Probe Subsystem Data Review Probe Subsystem Results and Data Review from Probe Integration and Test • • • Swales has open Field Support task to review subsystem data. Any anomalous behavior is reported immediately and documented in a PFR. JPL data compared to Probe Bus Comprehensive Performance Test baseline at Swales MPER SYS- 23 UCB, June 23, 2006
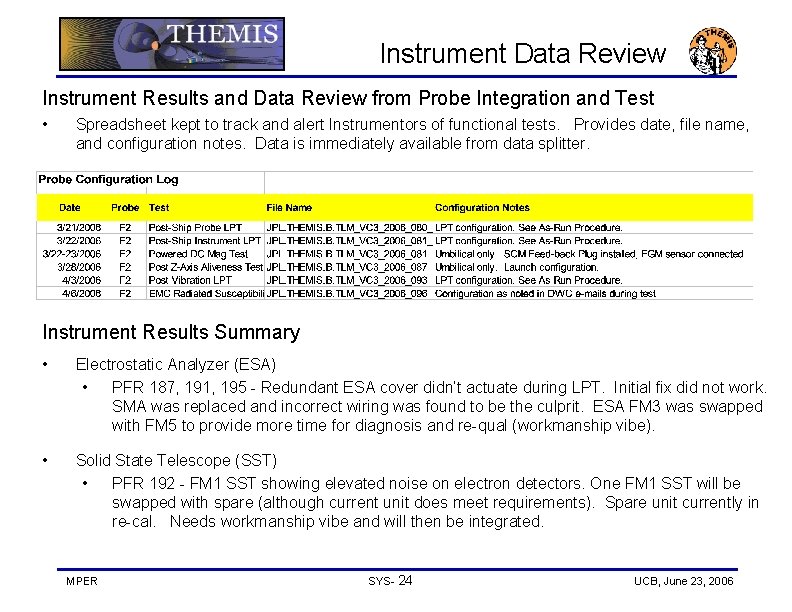
Instrument Data Review Instrument Results and Data Review from Probe Integration and Test • Spreadsheet kept to track and alert Instrumentors of functional tests. Provides date, file name, and configuration notes. Data is immediately available from data splitter. Instrument Results Summary • Electrostatic Analyzer (ESA) • PFR 187, 191, 195 - Redundant ESA cover didn’t actuate during LPT. Initial fix did not work. SMA was replaced and incorrect wiring was found to be the culprit. ESA FM 3 was swapped with FM 5 to provide more time for diagnosis and re-qual (workmanship vibe). • Solid State Telescope (SST) • PFR 192 - FM 1 SST showing elevated noise on electron detectors. One FM 1 SST will be swapped with spare (although current unit does meet requirements). Spare unit currently in re-cal. Needs workmanship vibe and will then be integrated. MPER SYS- 24 UCB, June 23, 2006
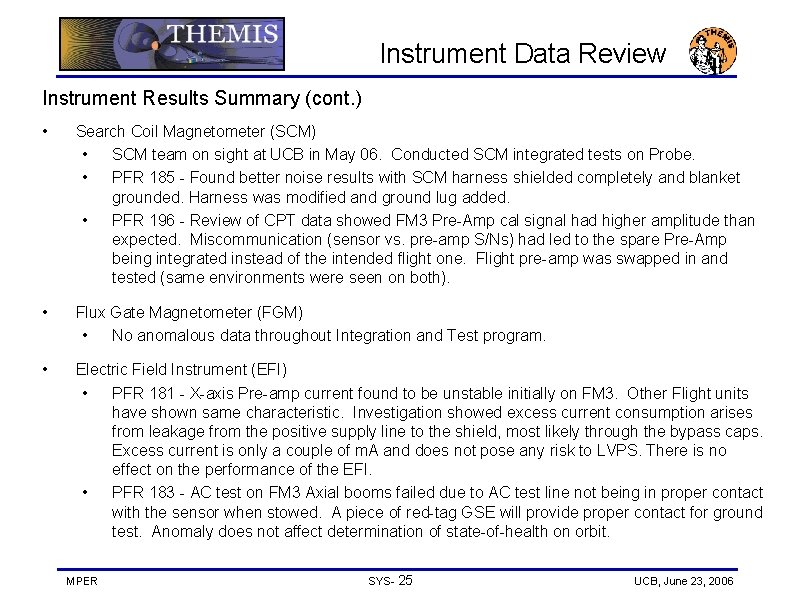
Instrument Data Review Instrument Results Summary (cont. ) • Search Coil Magnetometer (SCM) • SCM team on sight at UCB in May 06. Conducted SCM integrated tests on Probe. • PFR 185 - Found better noise results with SCM harness shielded completely and blanket grounded. Harness was modified and ground lug added. • PFR 196 - Review of CPT data showed FM 3 Pre-Amp cal signal had higher amplitude than expected. Miscommunication (sensor vs. pre-amp S/Ns) had led to the spare Pre-Amp being integrated instead of the intended flight one. Flight pre-amp was swapped in and tested (same environments were seen on both). • Flux Gate Magnetometer (FGM) • No anomalous data throughout Integration and Test program. • Electric Field Instrument (EFI) • PFR 181 - X-axis Pre-amp current found to be unstable initially on FM 3. Other Flight units have shown same characteristic. Investigation showed excess current consumption arises from leakage from the positive supply line to the shield, most likely through the bypass caps. Excess current is only a couple of m. A and does not pose any risk to LVPS. There is no effect on the performance of the EFI. • PFR 183 - AC test on FM 3 Axial booms failed due to AC test line not being in proper contact with the sensor when stowed. A piece of red-tag GSE will provide proper contact for ground test. Anomaly does not affect determination of state-of-health on orbit. MPER SYS- 25 UCB, June 23, 2006
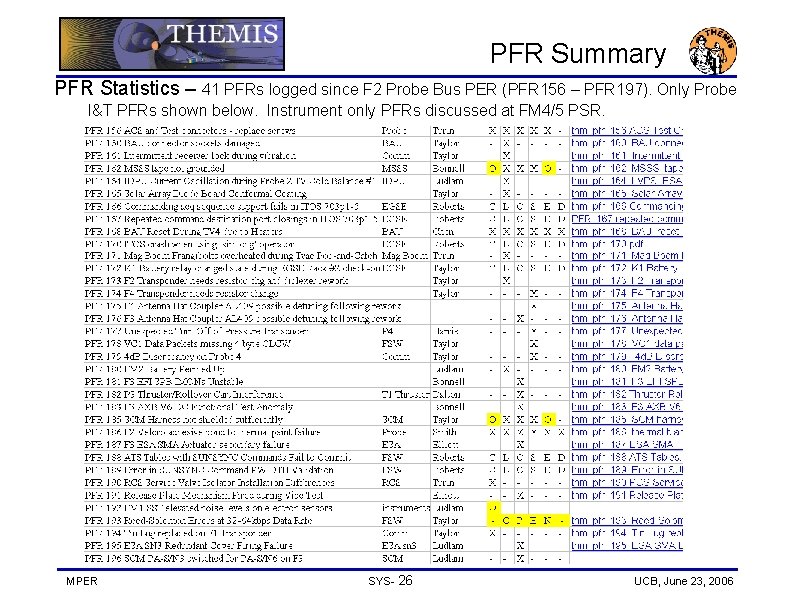
PFR Summary PFR Statistics – 41 PFRs logged since F 2 Probe Bus PER (PFR 156 – PFR 197). Only Probe I&T PFRs shown below. Instrument only PFRs discussed at FM 4/5 PSR. MPER SYS- 26 UCB, June 23, 2006
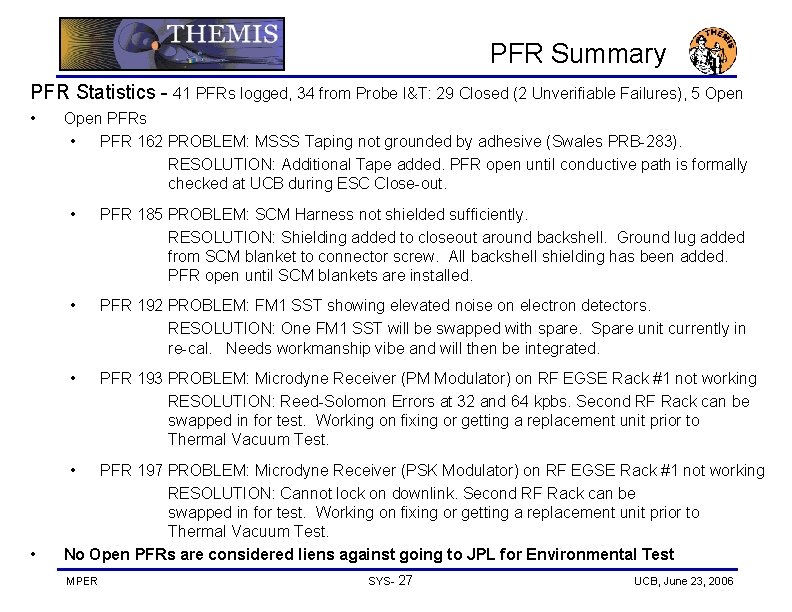
PFR Summary PFR Statistics - 41 PFRs logged, 34 from Probe I&T: 29 Closed (2 Unverifiable Failures), 5 Open • Open PFRs • PFR 162 PROBLEM: MSSS Taping not grounded by adhesive (Swales PRB-283). RESOLUTION: Additional Tape added. PFR open until conductive path is formally checked at UCB during ESC Close-out. • PFR 185 PROBLEM: SCM Harness not shielded sufficiently. RESOLUTION: Shielding added to closeout around backshell. Ground lug added from SCM blanket to connector screw. All backshell shielding has been added. PFR open until SCM blankets are installed. • PFR 192 PROBLEM: FM 1 SST showing elevated noise on electron detectors. RESOLUTION: One FM 1 SST will be swapped with spare. Spare unit currently in re-cal. Needs workmanship vibe and will then be integrated. • PFR 193 PROBLEM: Microdyne Receiver (PM Modulator) on RF EGSE Rack #1 not working RESOLUTION: Reed-Solomon Errors at 32 and 64 kpbs. Second RF Rack can be swapped in for test. Working on fixing or getting a replacement unit prior to Thermal Vacuum Test. • • PFR 197 PROBLEM: Microdyne Receiver (PSK Modulator) on RF EGSE Rack #1 not working RESOLUTION: Cannot lock on downlink. Second RF Rack can be swapped in for test. Working on fixing or getting a replacement unit prior to Thermal Vacuum Test. No Open PFRs are considered liens against going to JPL for Environmental Test MPER SYS- 27 UCB, June 23, 2006
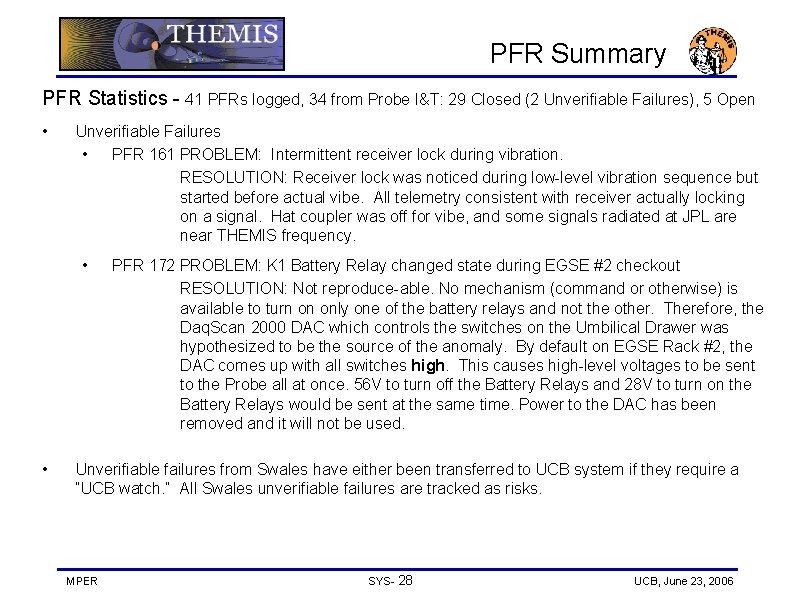
PFR Summary PFR Statistics - 41 PFRs logged, 34 from Probe I&T: 29 Closed (2 Unverifiable Failures), 5 Open • Unverifiable Failures • PFR 161 PROBLEM: Intermittent receiver lock during vibration. RESOLUTION: Receiver lock was noticed during low-level vibration sequence but started before actual vibe. All telemetry consistent with receiver actually locking on a signal. Hat coupler was off for vibe, and some signals radiated at JPL are near THEMIS frequency. • • PFR 172 PROBLEM: K 1 Battery Relay changed state during EGSE #2 checkout RESOLUTION: Not reproduce-able. No mechanism (command or otherwise) is available to turn on only one of the battery relays and not the other. Therefore, the Daq. Scan 2000 DAC which controls the switches on the Umbilical Drawer was hypothesized to be the source of the anomaly. By default on EGSE Rack #2, the DAC comes up with all switches high. This causes high-level voltages to be sent to the Probe all at once. 56 V to turn off the Battery Relays and 28 V to turn on the Battery Relays would be sent at the same time. Power to the DAC has been removed and it will not be used. Unverifiable failures from Swales have either been transferred to UCB system if they require a “UCB watch. ” All Swales unverifiable failures are tracked as risks. MPER SYS- 28 UCB, June 23, 2006
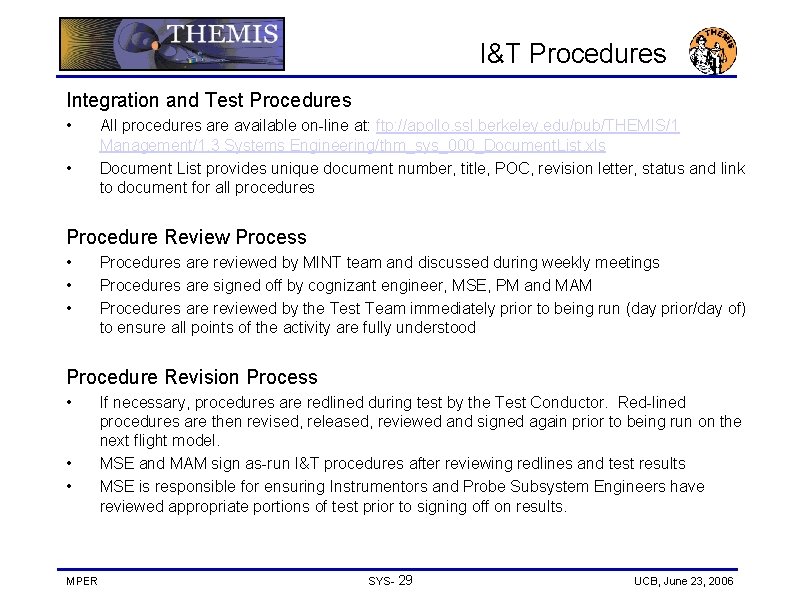
I&T Procedures Integration and Test Procedures • • All procedures are available on-line at: ftp: //apollo. ssl. berkeley. edu/pub/THEMIS/1 Management/1. 3 Systems Engineering/thm_sys_000_Document. List. xls Document List provides unique document number, title, POC, revision letter, status and link to document for all procedures Procedure Review Process • • • Procedures are reviewed by MINT team and discussed during weekly meetings Procedures are signed off by cognizant engineer, MSE, PM and MAM Procedures are reviewed by the Test Team immediately prior to being run (day prior/day of) to ensure all points of the activity are fully understood Procedure Revision Process • • • MPER If necessary, procedures are redlined during test by the Test Conductor. Red-lined procedures are then revised, released, reviewed and signed again prior to being run on the next flight model. MSE and MAM sign as-run I&T procedures after reviewing redlines and test results MSE is responsible for ensuring Instrumentors and Probe Subsystem Engineers have reviewed appropriate portions of test prior to signing off on results. SYS- 29 UCB, June 23, 2006
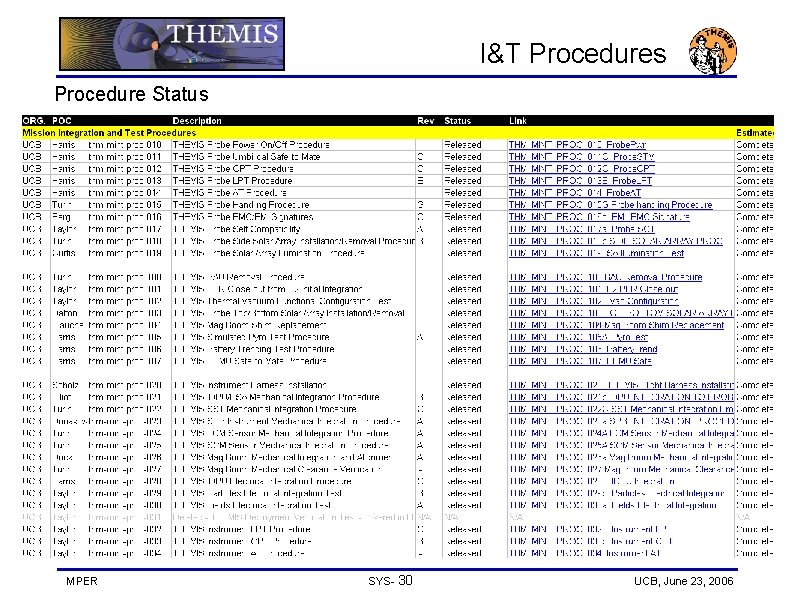
I&T Procedures Procedure Status MPER SYS- 30 UCB, June 23, 2006
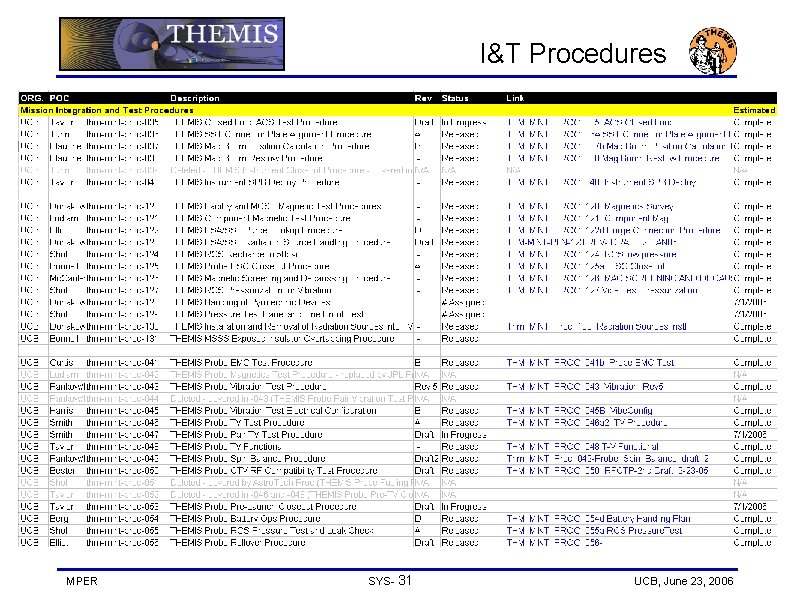
I&T Procedures MPER SYS- 31 UCB, June 23, 2006
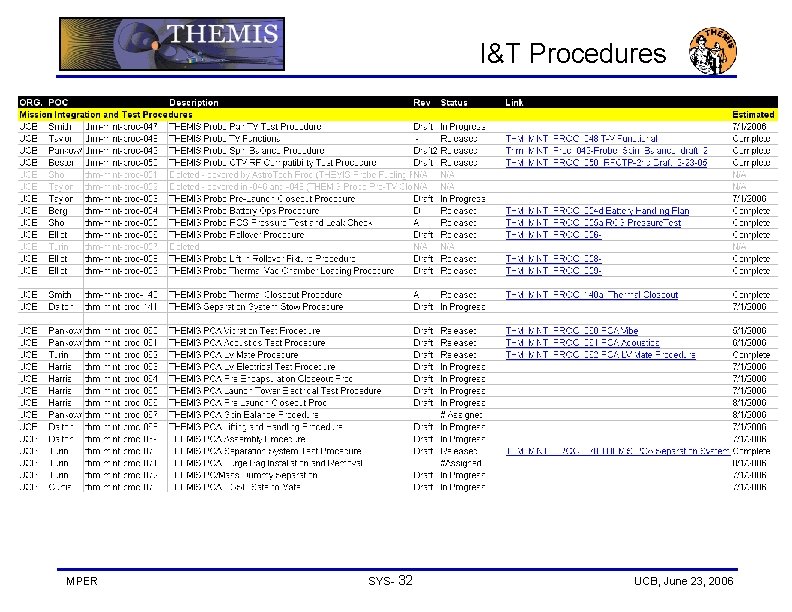
I&T Procedures MPER SYS- 32 UCB, June 23, 2006
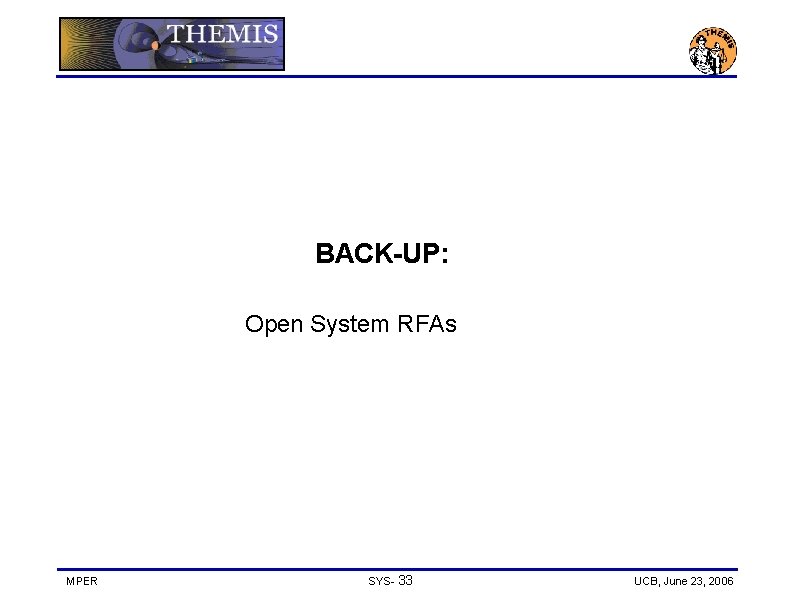
BACK-UP: Open System RFAs MPER SYS- 33 UCB, June 23, 2006
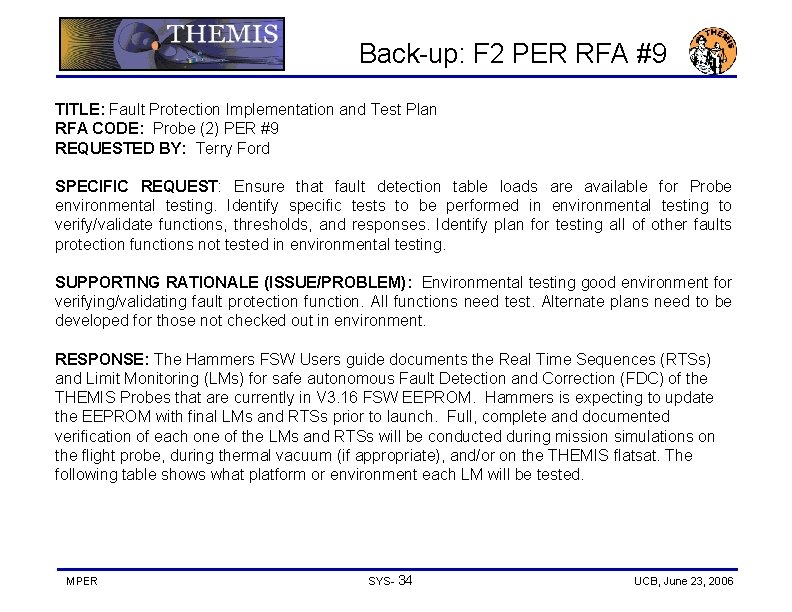
Back-up: F 2 PER RFA #9 TITLE: Fault Protection Implementation and Test Plan RFA CODE: Probe (2) PER #9 REQUESTED BY: Terry Ford SPECIFIC REQUEST: Ensure that fault detection table loads are available for Probe environmental testing. Identify specific tests to be performed in environmental testing to verify/validate functions, thresholds, and responses. Identify plan for testing all of other faults protection functions not tested in environmental testing. SUPPORTING RATIONALE (ISSUE/PROBLEM): Environmental testing good environment for verifying/validating fault protection function. All functions need test. Alternate plans need to be developed for those not checked out in environment. RESPONSE: The Hammers FSW Users guide documents the Real Time Sequences (RTSs) and Limit Monitoring (LMs) for safe autonomous Fault Detection and Correction (FDC) of the THEMIS Probes that are currently in V 3. 16 FSW EEPROM. Hammers is expecting to update the EEPROM with final LMs and RTSs prior to launch. Full, complete and documented verification of each one of the LMs and RTSs will be conducted during mission simulations on the flight probe, during thermal vacuum (if appropriate), and/or on the THEMIS flatsat. The following table shows what platform or environment each LM will be tested. MPER SYS- 34 UCB, June 23, 2006
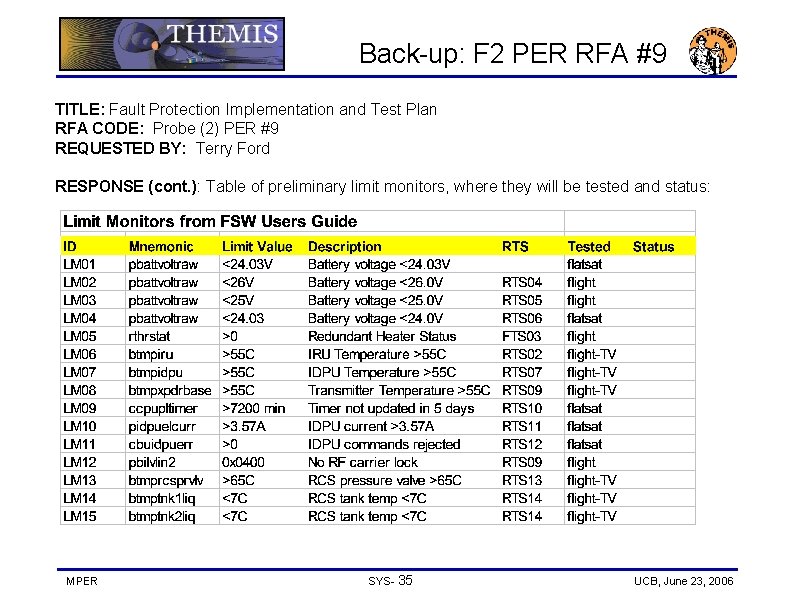
Back-up: F 2 PER RFA #9 TITLE: Fault Protection Implementation and Test Plan RFA CODE: Probe (2) PER #9 REQUESTED BY: Terry Ford RESPONSE (cont. ): Table of preliminary limit monitors, where they will be tested and status: MPER SYS- 35 UCB, June 23, 2006
Preenvironmental
Preenvironmental
Preenvironmental
Cowhorn brace
Themis quiz builder
Themis fm
Themis pi
Themis lenguaje inclusivo
Themis athanassiadou
Themis
Themis dc
Themis plugin
Themis
Themis
Themis
Themis constellation
Artemis
Themis
Themis athanassiadou
Themis competition
Esa themis
Themis software
Distributed systems
Sap ps
Distributed systems overview
Dual mode in os
Operating system overview
Who the father of scientific management
System definition review
Common review mission
Common review mission
Northrop grumman mission systems organization chart
Ellen friar
Quem foi ellen white
Ellen goldring
Why was everyone celebrating in denmark number the stars