Tech 147 Unit 5 Green Manufacturing Project Planning
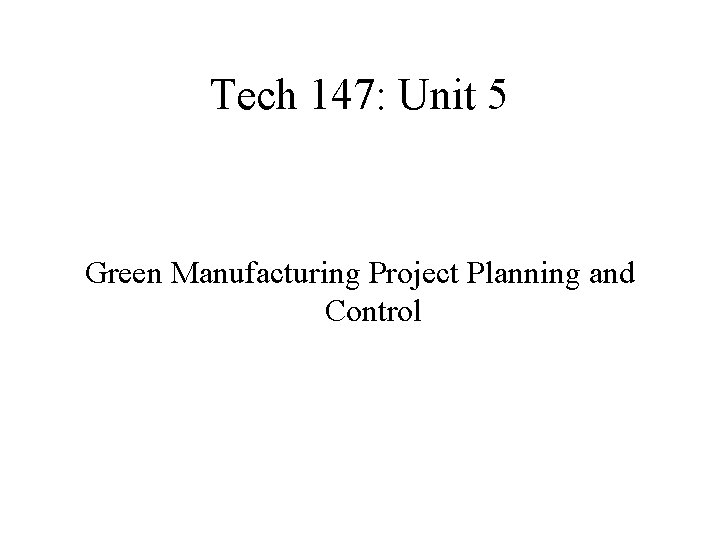
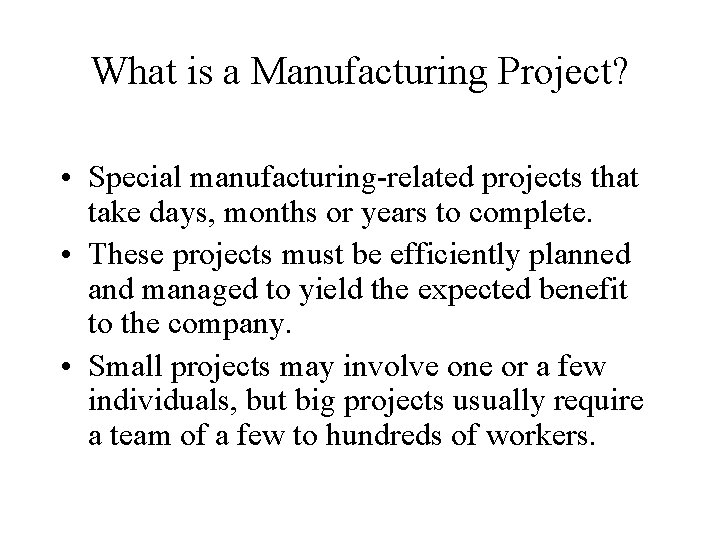
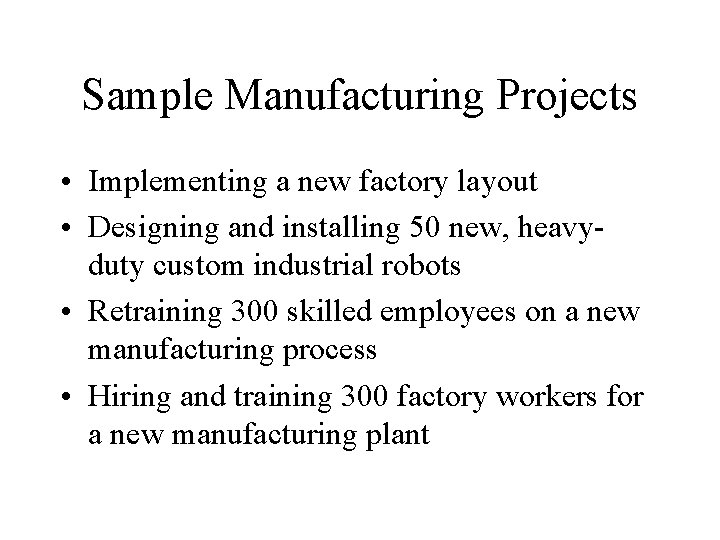
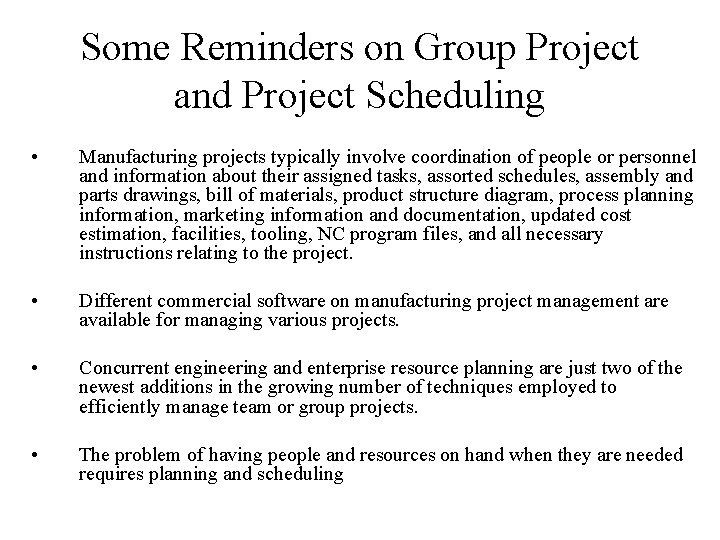
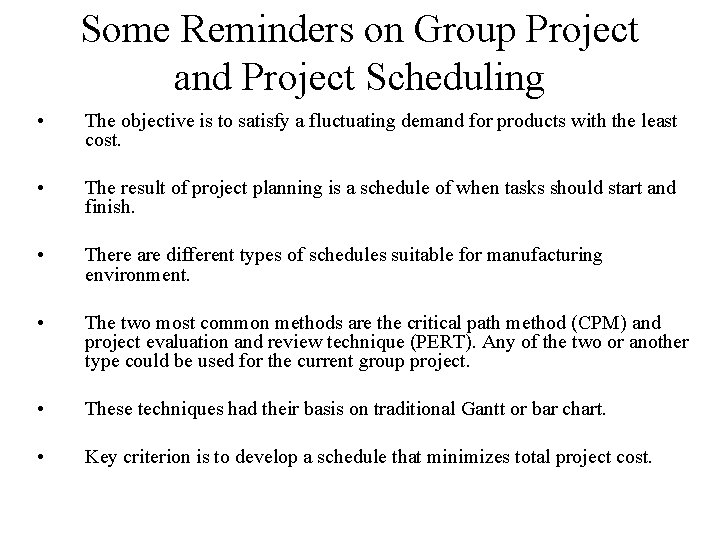
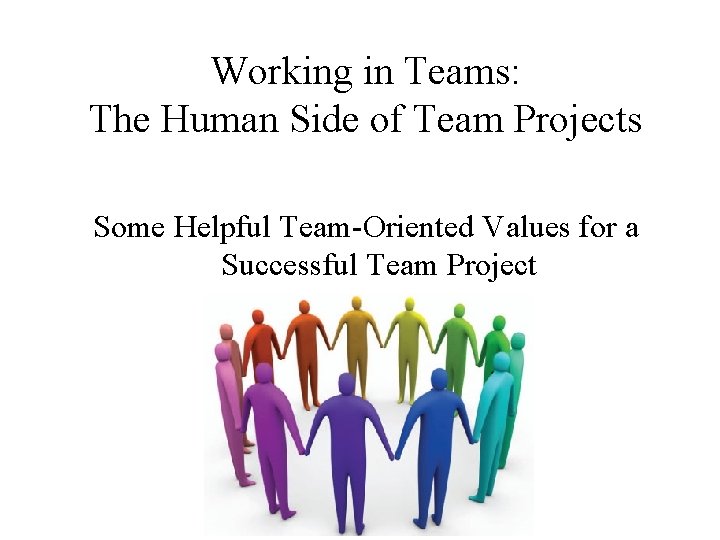
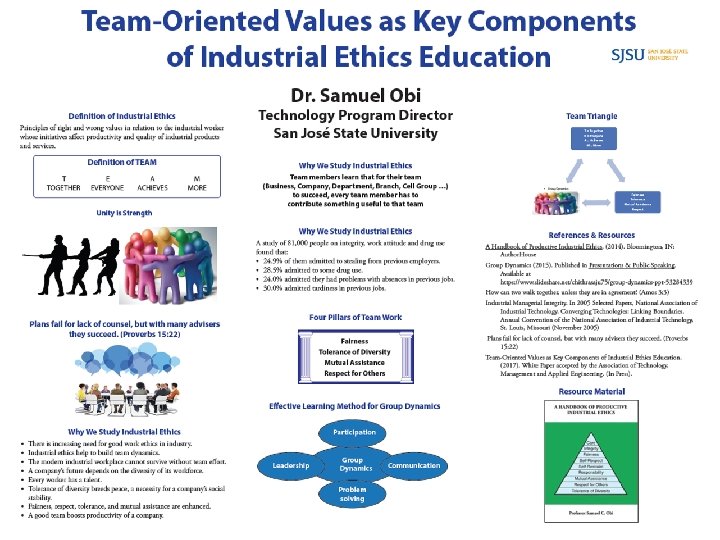
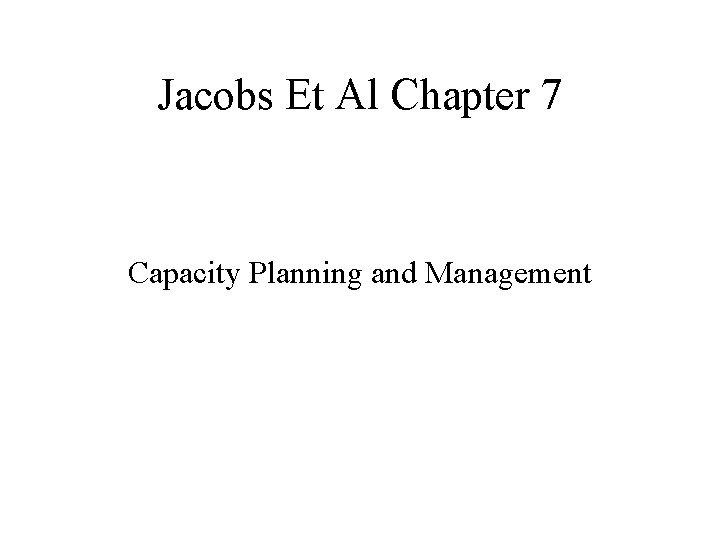
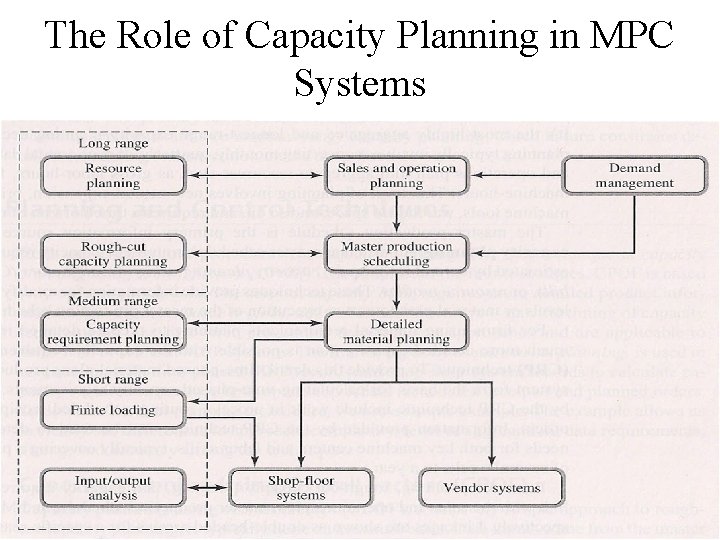
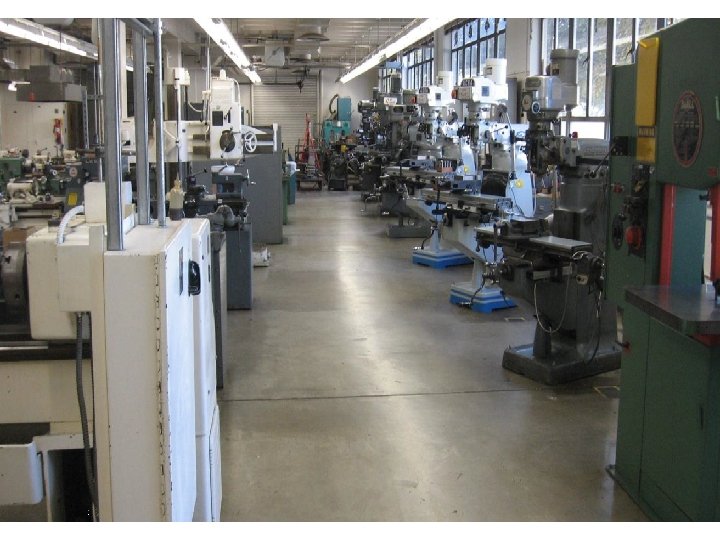
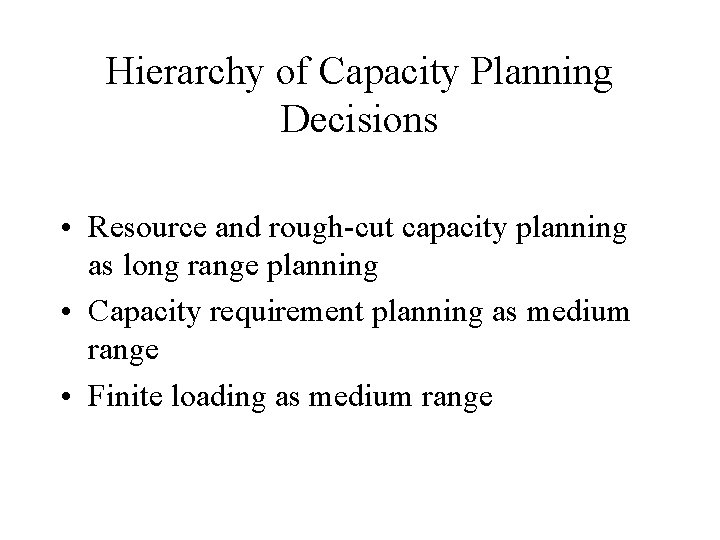
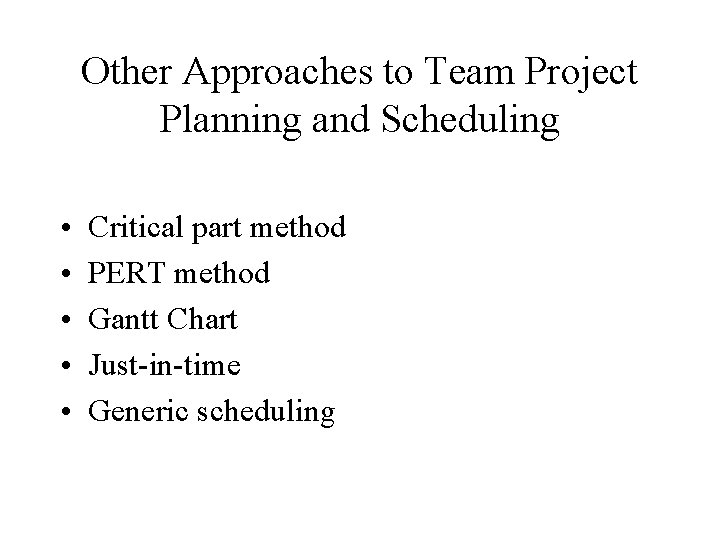
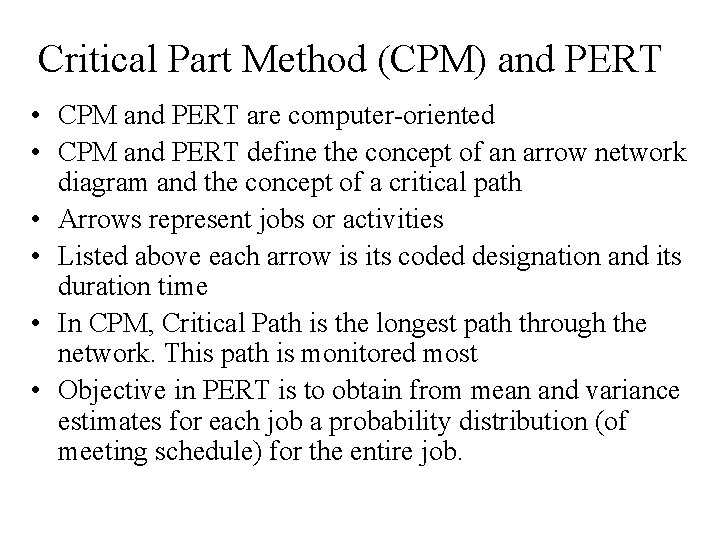
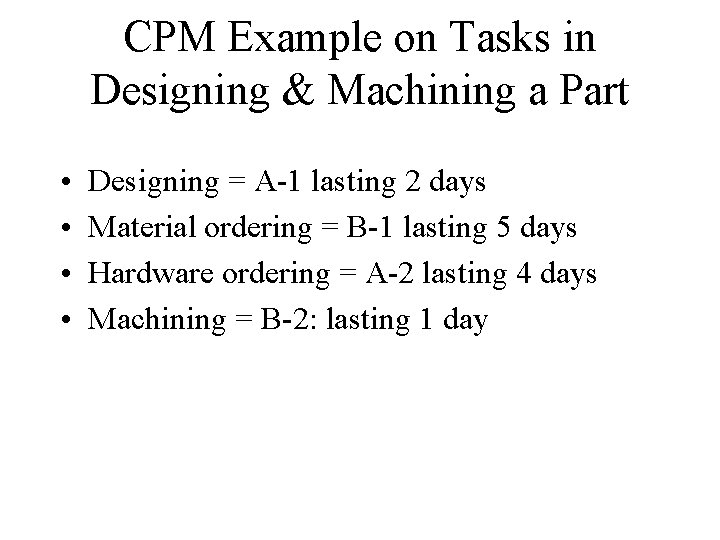
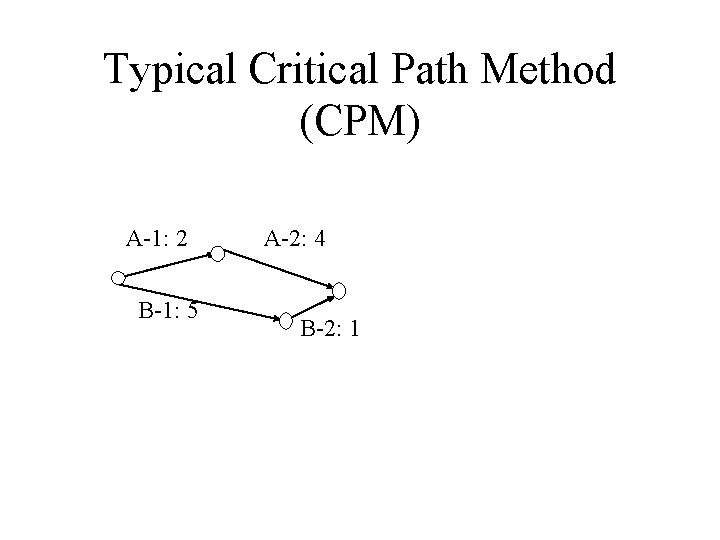
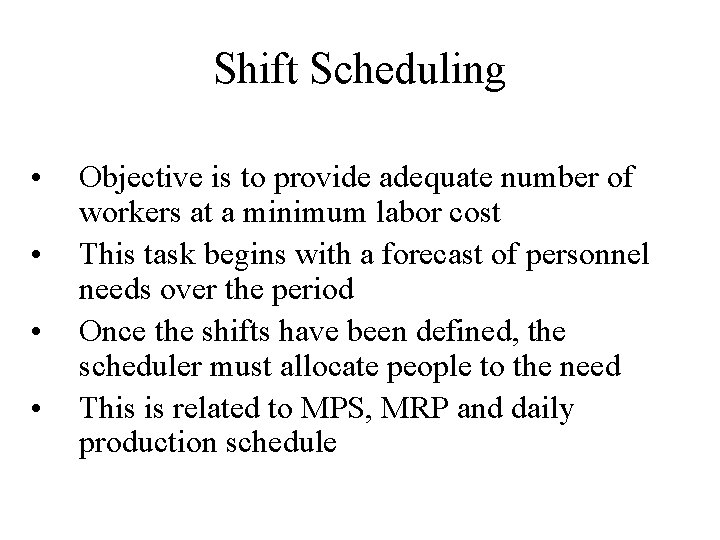
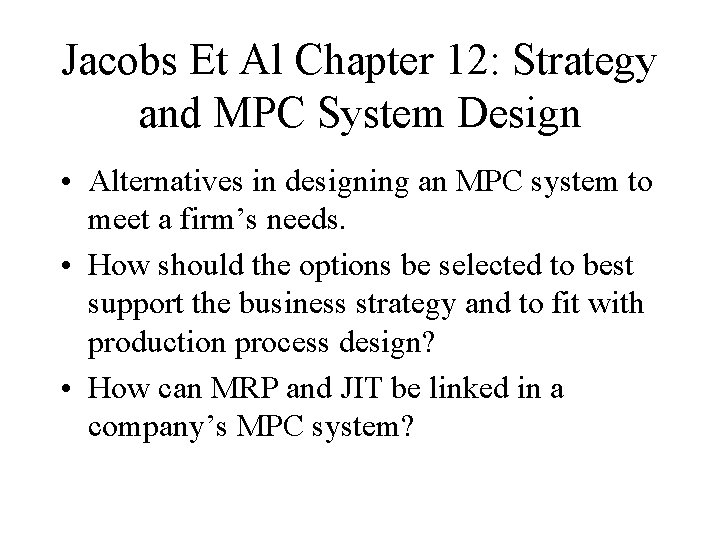
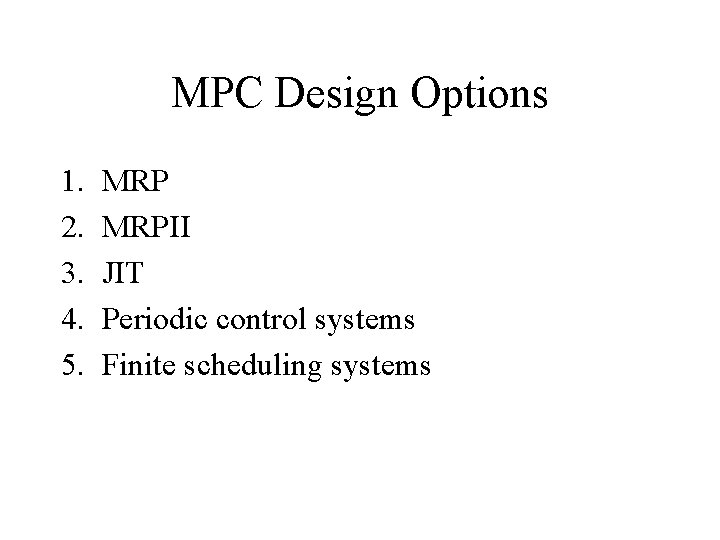
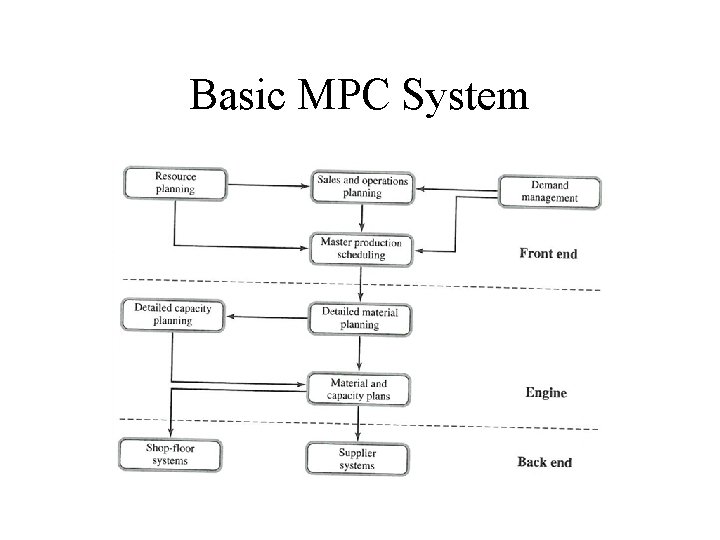
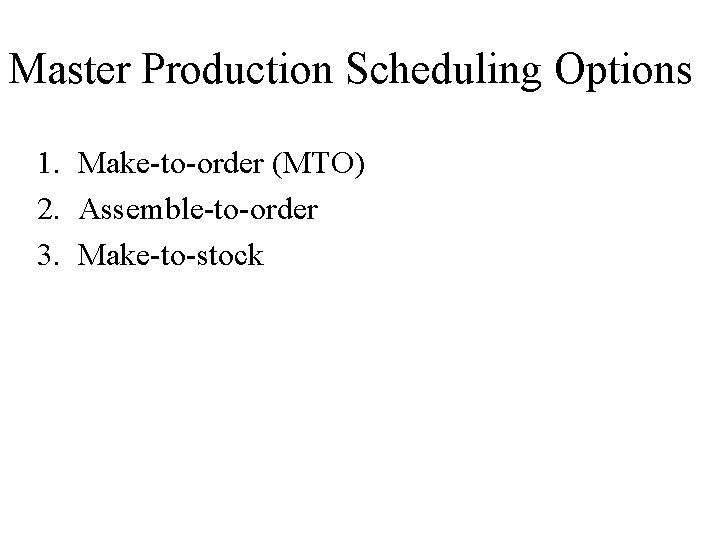
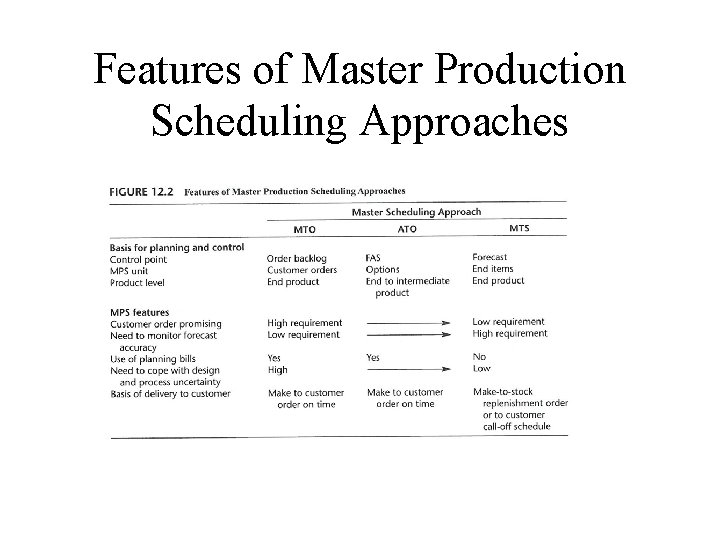
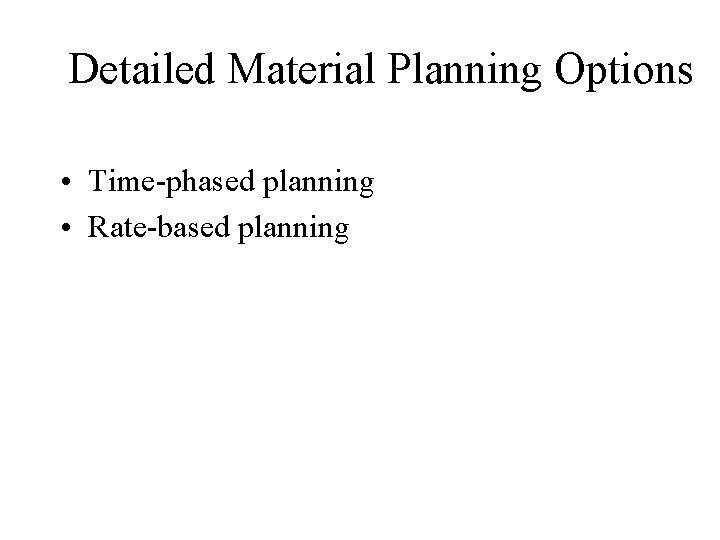
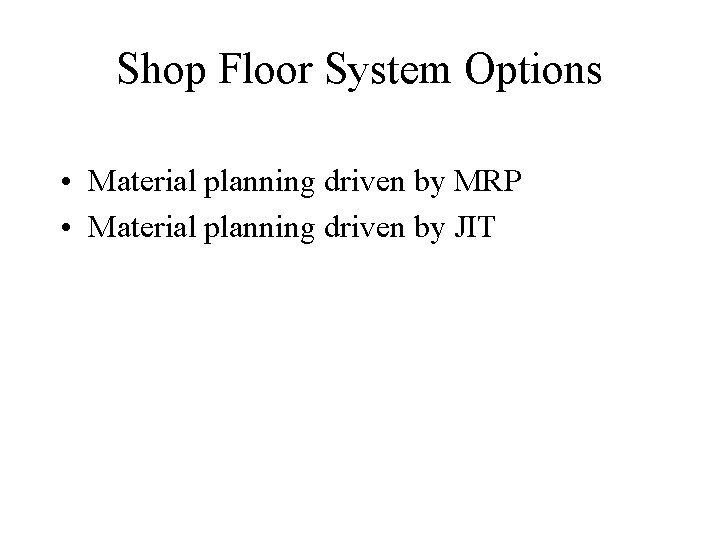
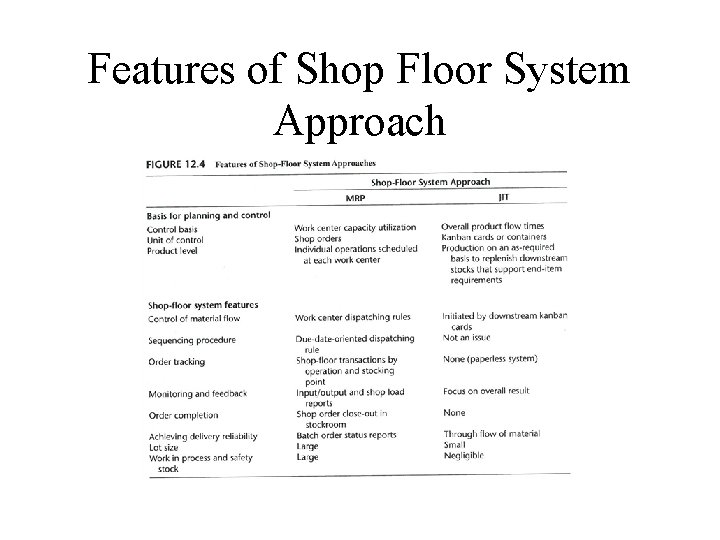
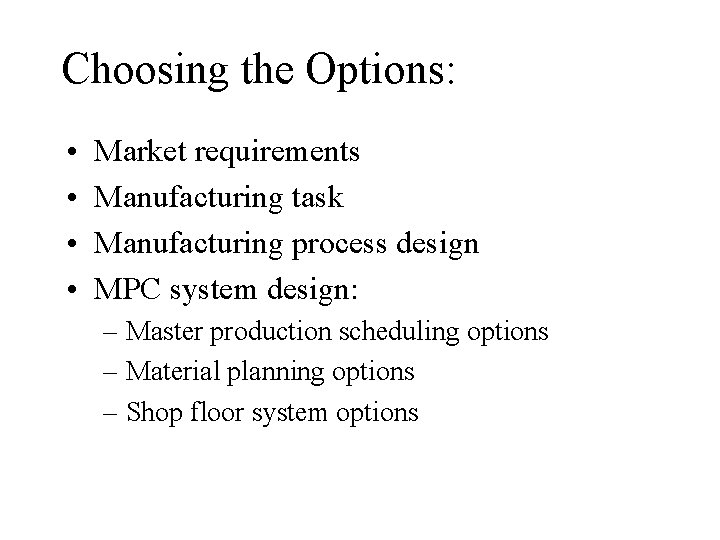
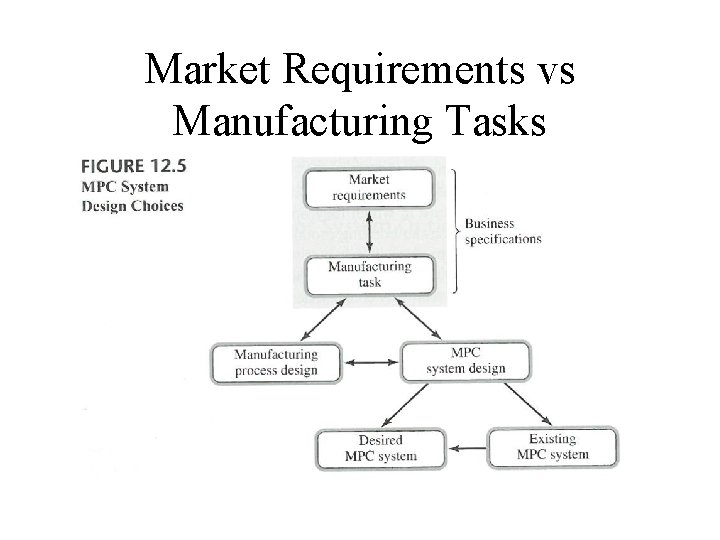
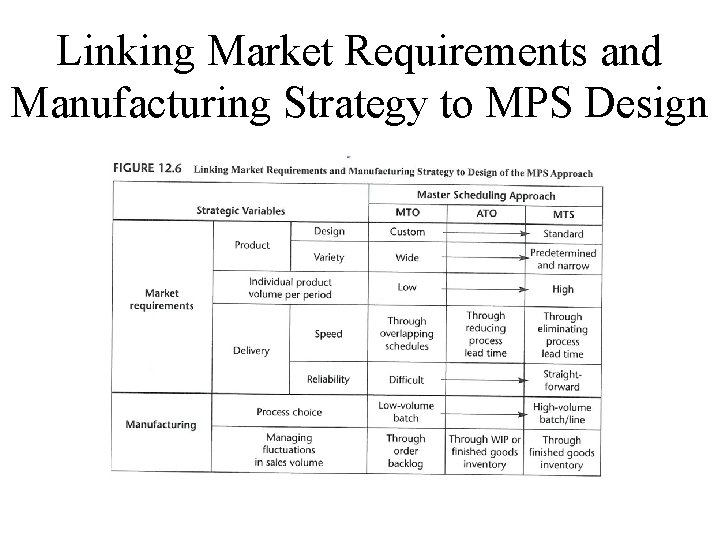
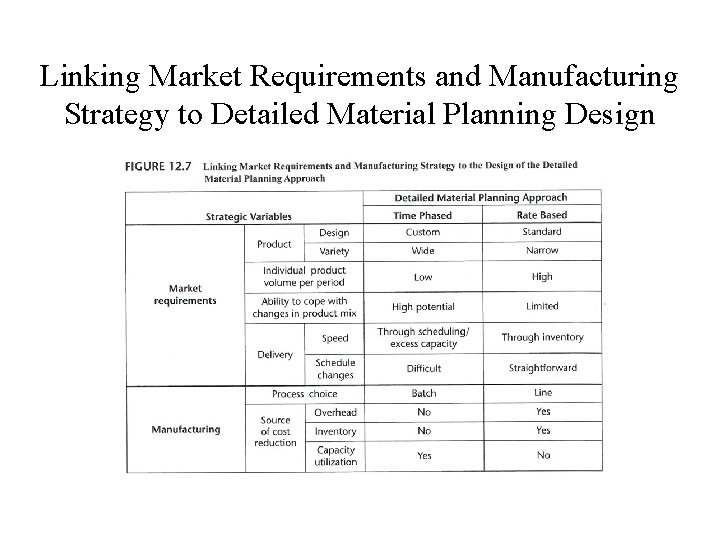
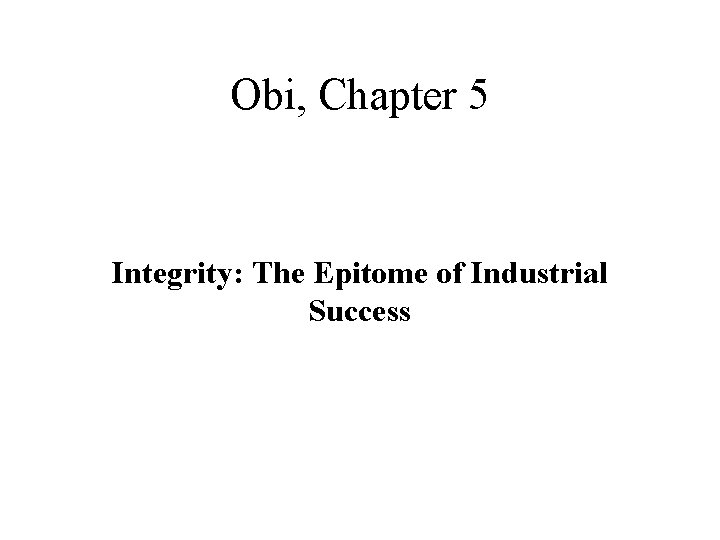
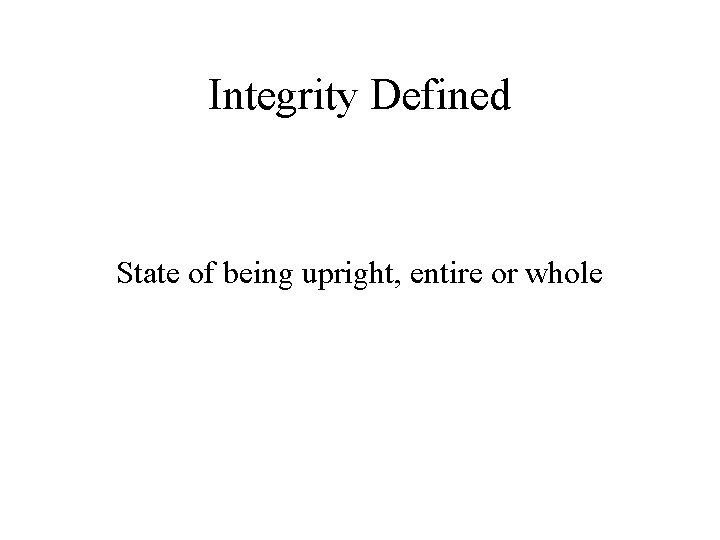
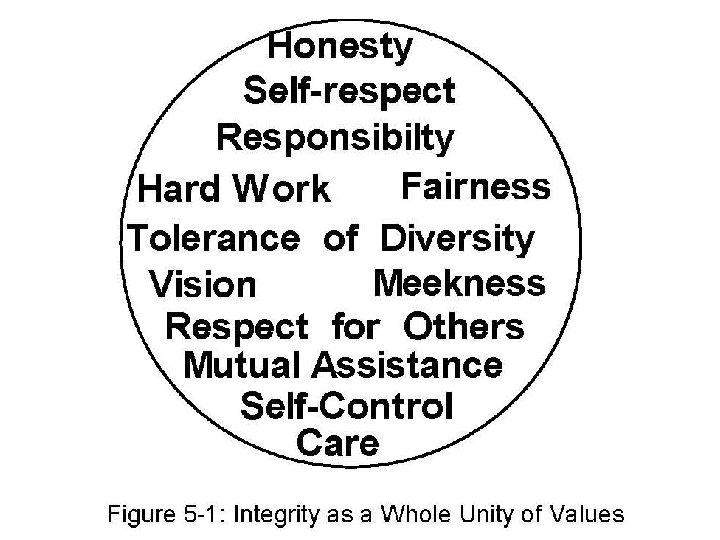
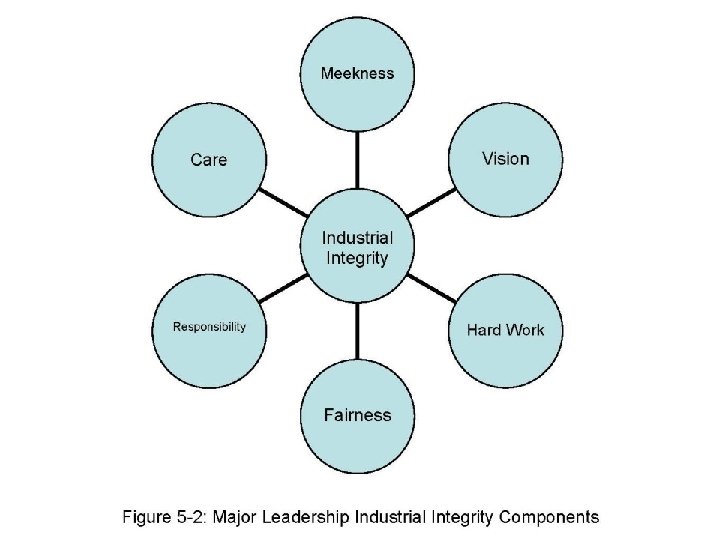
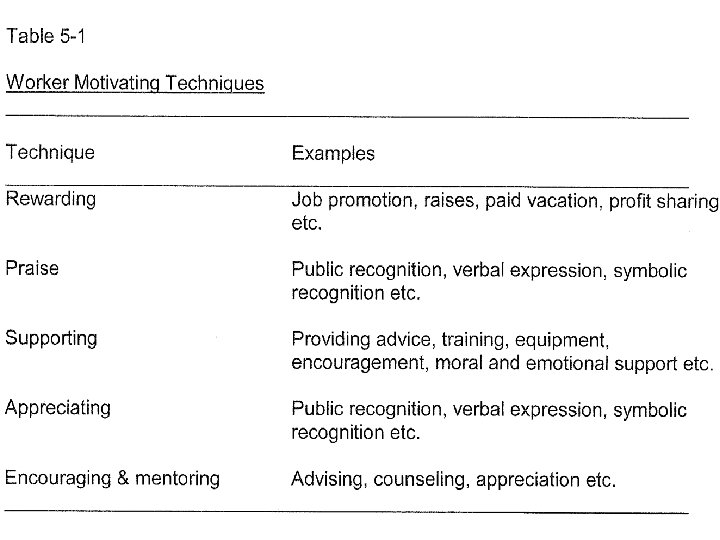
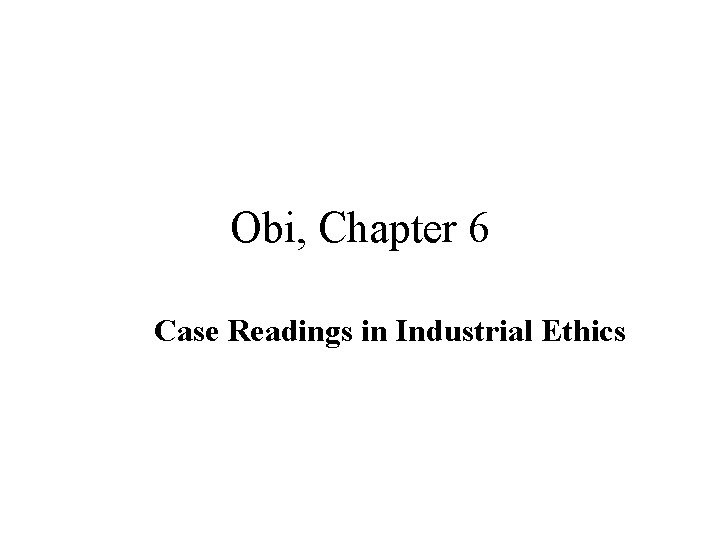
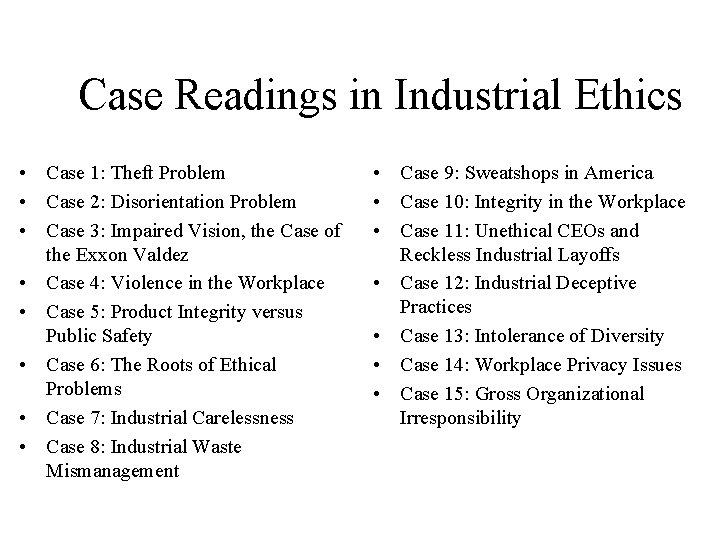
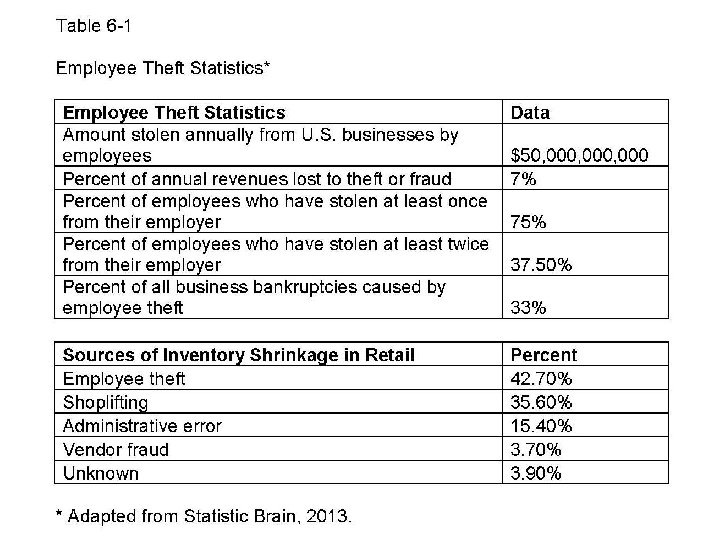
- Slides: 36
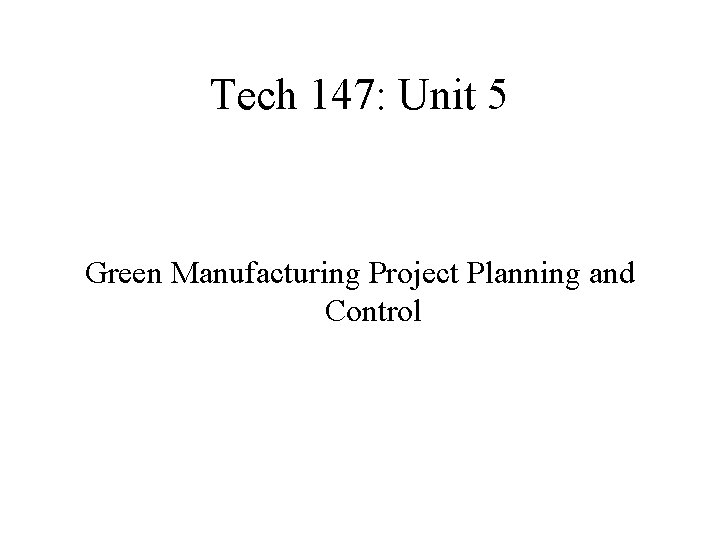
Tech 147: Unit 5 Green Manufacturing Project Planning and Control
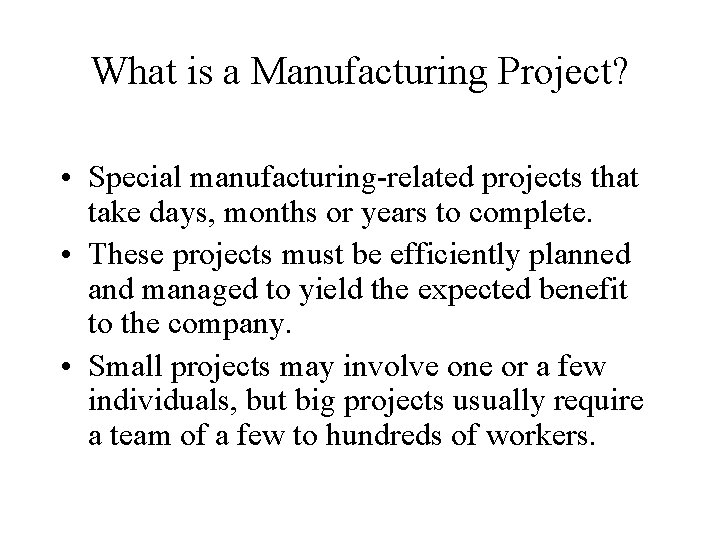
What is a Manufacturing Project? • Special manufacturing-related projects that take days, months or years to complete. • These projects must be efficiently planned and managed to yield the expected benefit to the company. • Small projects may involve one or a few individuals, but big projects usually require a team of a few to hundreds of workers.
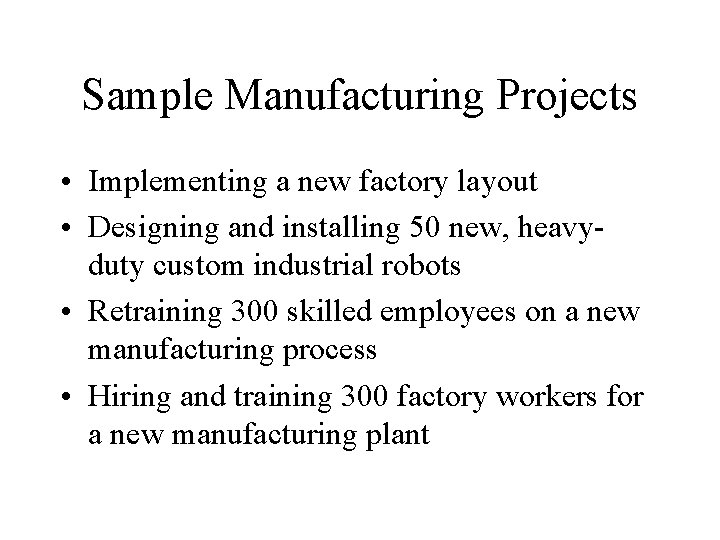
Sample Manufacturing Projects • Implementing a new factory layout • Designing and installing 50 new, heavyduty custom industrial robots • Retraining 300 skilled employees on a new manufacturing process • Hiring and training 300 factory workers for a new manufacturing plant
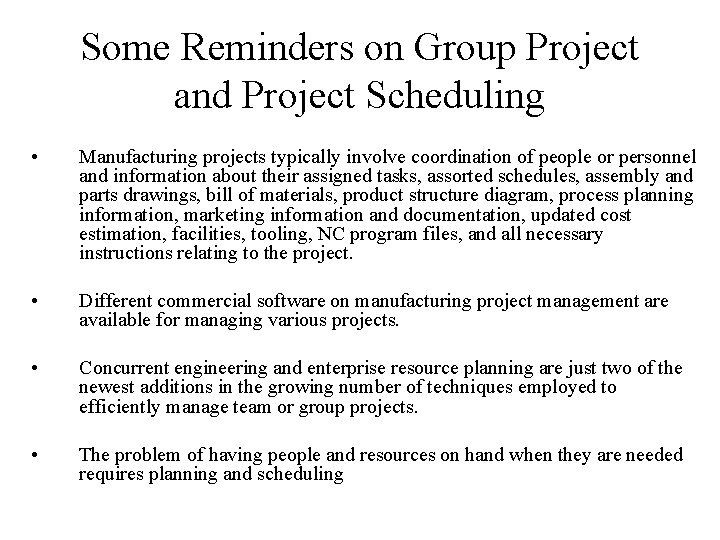
Some Reminders on Group Project and Project Scheduling • Manufacturing projects typically involve coordination of people or personnel and information about their assigned tasks, assorted schedules, assembly and parts drawings, bill of materials, product structure diagram, process planning information, marketing information and documentation, updated cost estimation, facilities, tooling, NC program files, and all necessary instructions relating to the project. • Different commercial software on manufacturing project management are available for managing various projects. • Concurrent engineering and enterprise resource planning are just two of the newest additions in the growing number of techniques employed to efficiently manage team or group projects. • The problem of having people and resources on hand when they are needed requires planning and scheduling
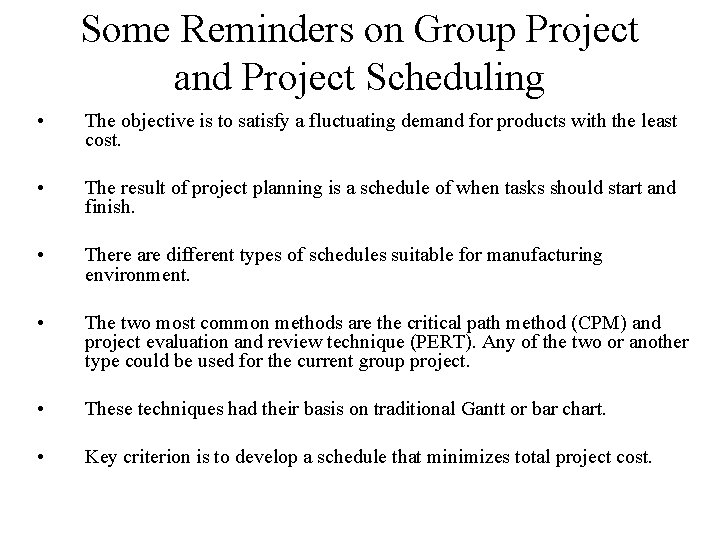
Some Reminders on Group Project and Project Scheduling • The objective is to satisfy a fluctuating demand for products with the least cost. • The result of project planning is a schedule of when tasks should start and finish. • There are different types of schedules suitable for manufacturing environment. • The two most common methods are the critical path method (CPM) and project evaluation and review technique (PERT). Any of the two or another type could be used for the current group project. • These techniques had their basis on traditional Gantt or bar chart. • Key criterion is to develop a schedule that minimizes total project cost.
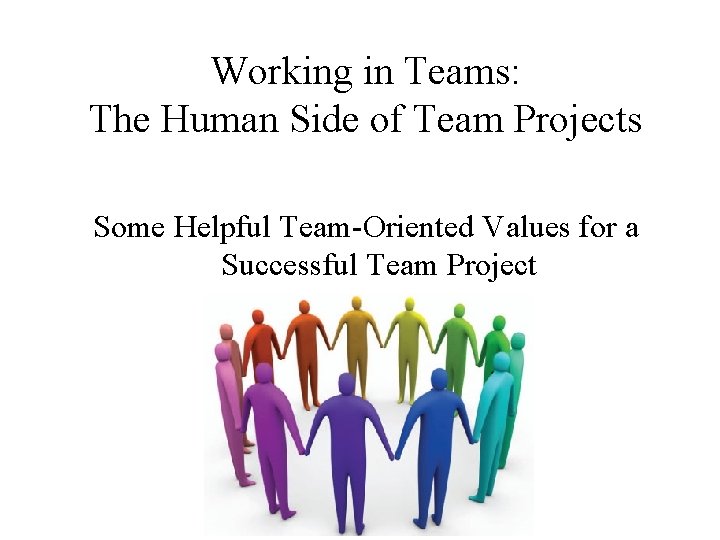
Working in Teams: The Human Side of Team Projects Some Helpful Team-Oriented Values for a Successful Team Project
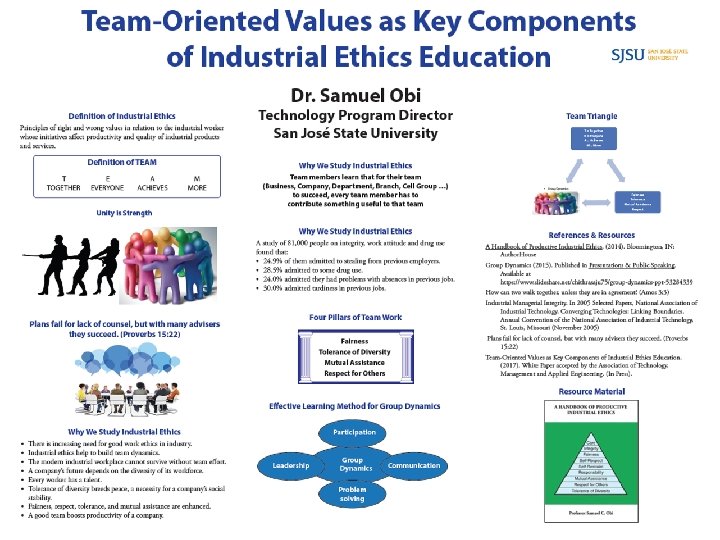
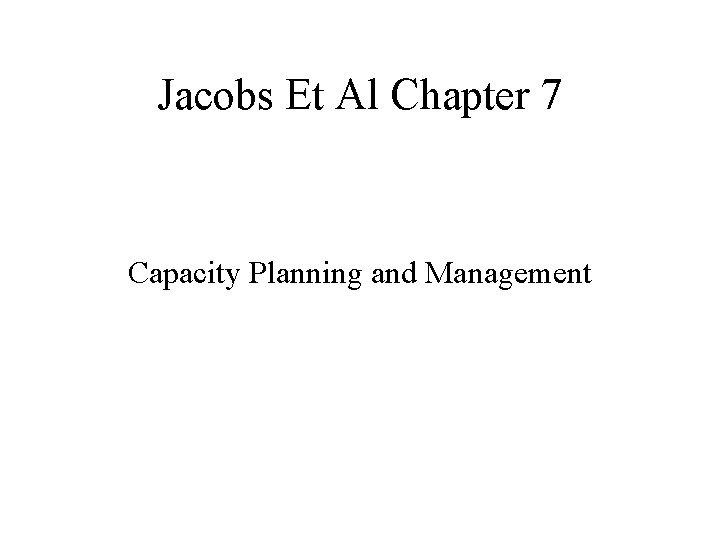
Jacobs Et Al Chapter 7 Capacity Planning and Management
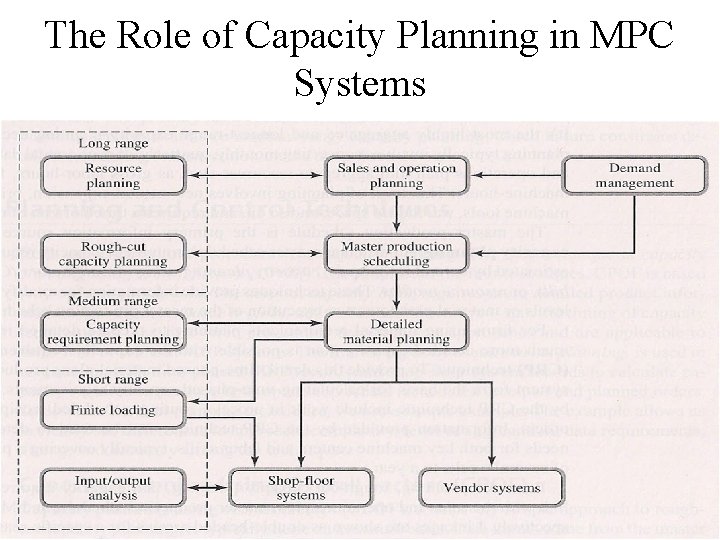
The Role of Capacity Planning in MPC Systems
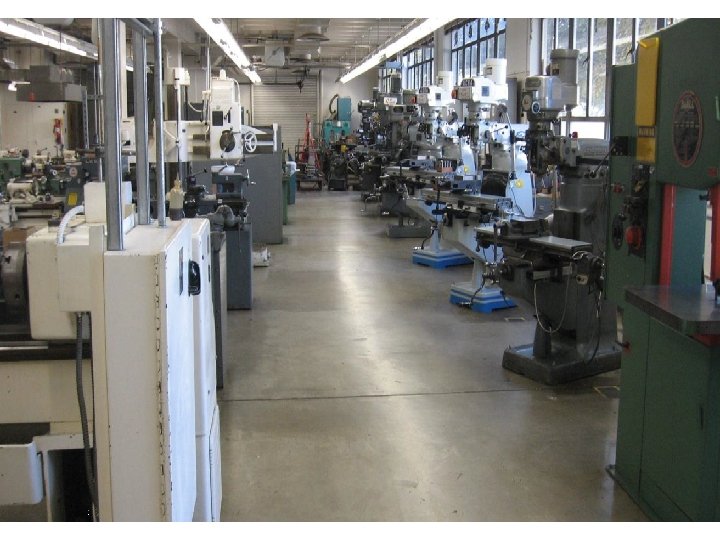
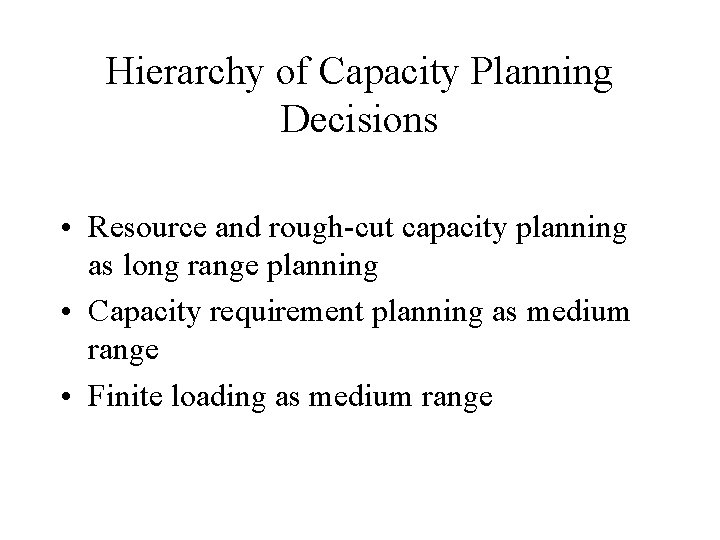
Hierarchy of Capacity Planning Decisions • Resource and rough-cut capacity planning as long range planning • Capacity requirement planning as medium range • Finite loading as medium range
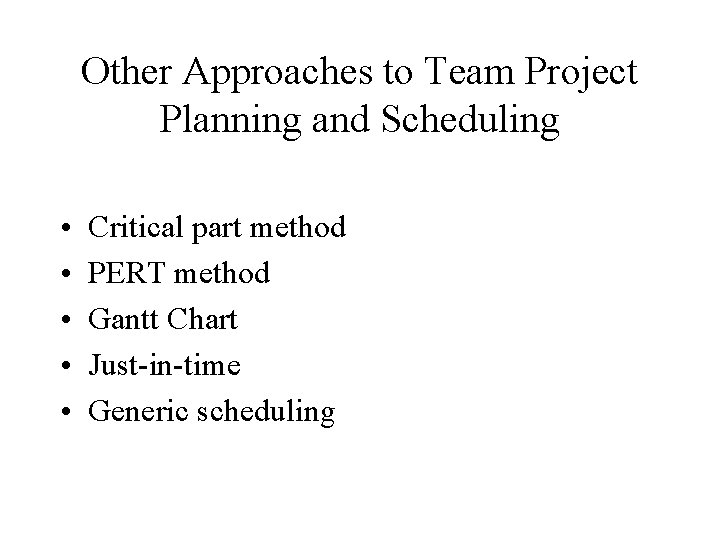
Other Approaches to Team Project Planning and Scheduling • • • Critical part method PERT method Gantt Chart Just-in-time Generic scheduling
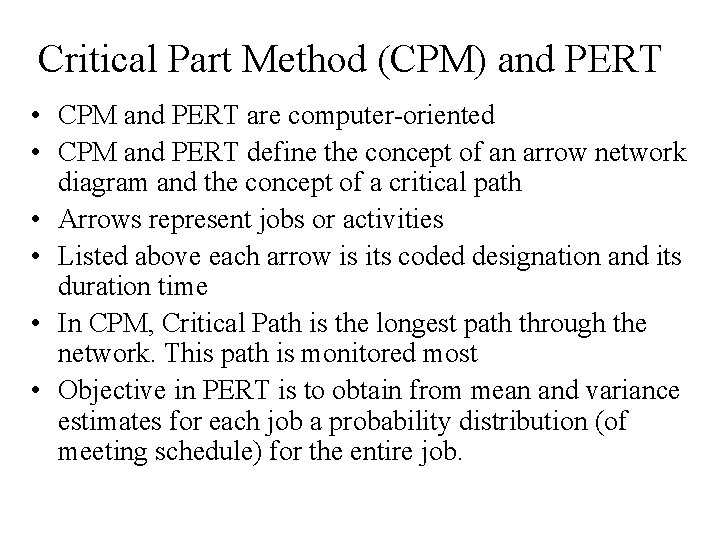
Critical Part Method (CPM) and PERT • CPM and PERT are computer-oriented • CPM and PERT define the concept of an arrow network diagram and the concept of a critical path • Arrows represent jobs or activities • Listed above each arrow is its coded designation and its duration time • In CPM, Critical Path is the longest path through the network. This path is monitored most • Objective in PERT is to obtain from mean and variance estimates for each job a probability distribution (of meeting schedule) for the entire job.
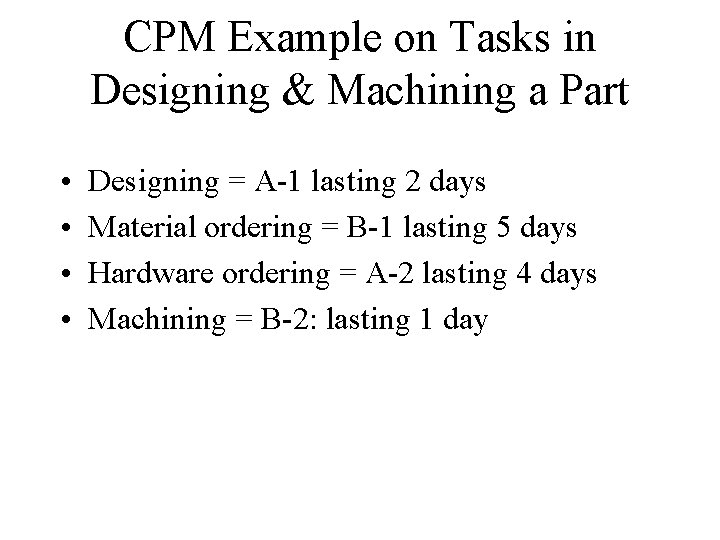
CPM Example on Tasks in Designing & Machining a Part • • Designing = A-1 lasting 2 days Material ordering = B-1 lasting 5 days Hardware ordering = A-2 lasting 4 days Machining = B-2: lasting 1 day
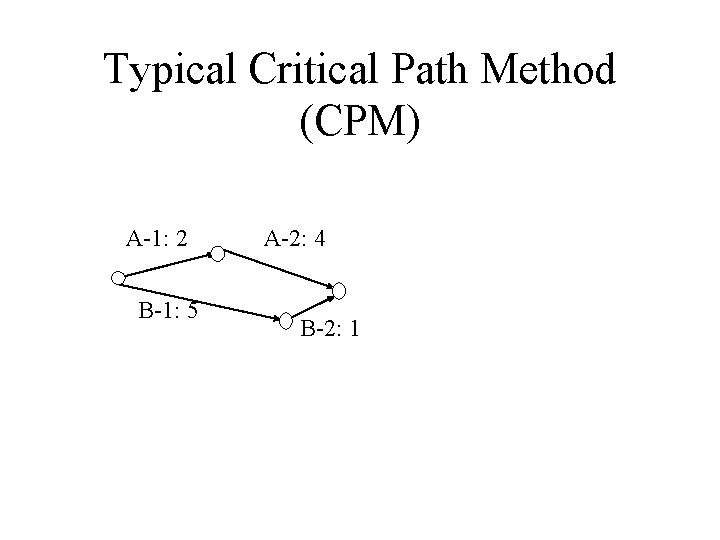
Typical Critical Path Method (CPM) A-1: 2 B-1: 5 A-2: 4 B-2: 1
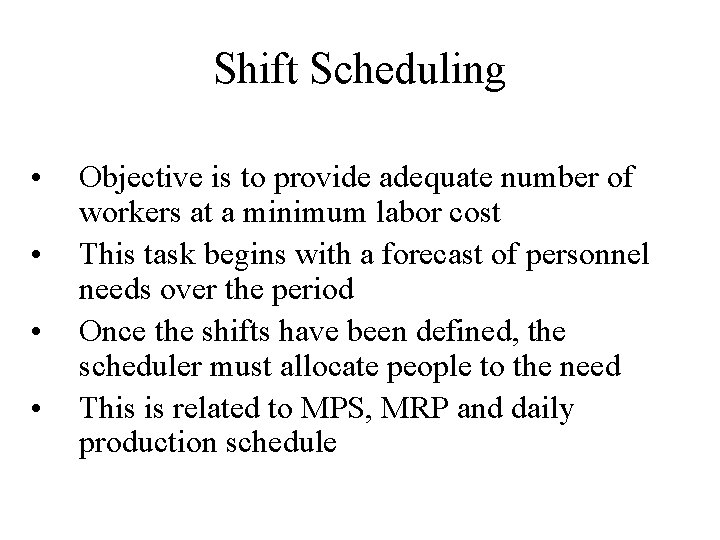
Shift Scheduling • • Objective is to provide adequate number of workers at a minimum labor cost This task begins with a forecast of personnel needs over the period Once the shifts have been defined, the scheduler must allocate people to the need This is related to MPS, MRP and daily production schedule
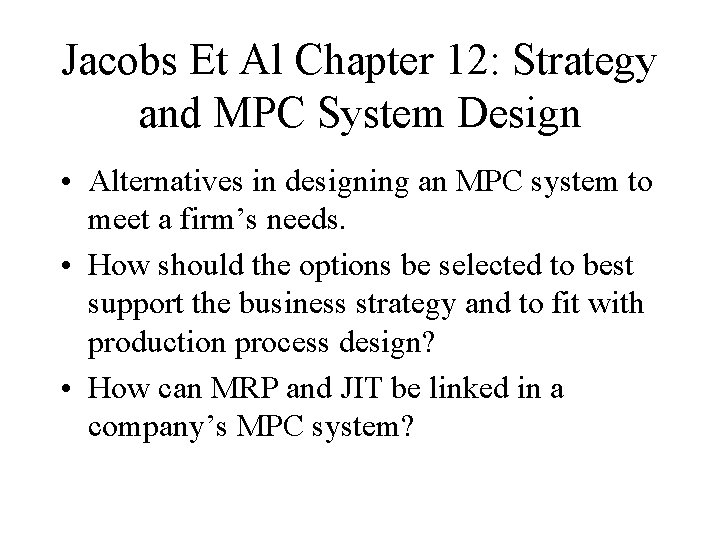
Jacobs Et Al Chapter 12: Strategy and MPC System Design • Alternatives in designing an MPC system to meet a firm’s needs. • How should the options be selected to best support the business strategy and to fit with production process design? • How can MRP and JIT be linked in a company’s MPC system?
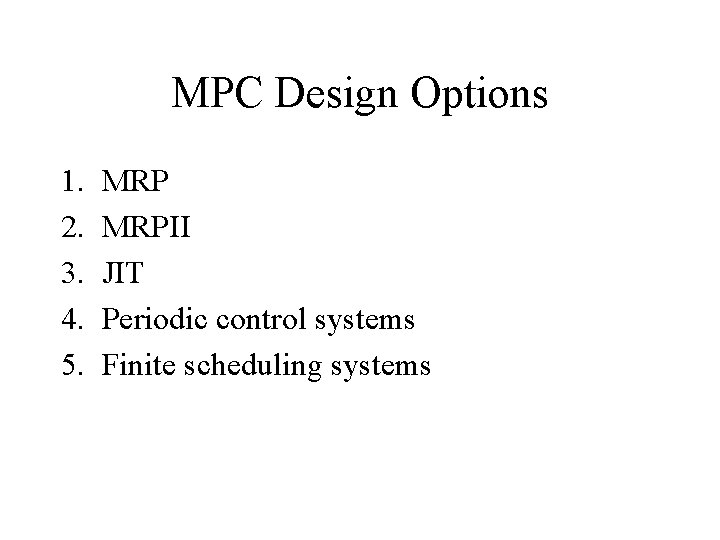
MPC Design Options 1. 2. 3. 4. 5. MRPII JIT Periodic control systems Finite scheduling systems
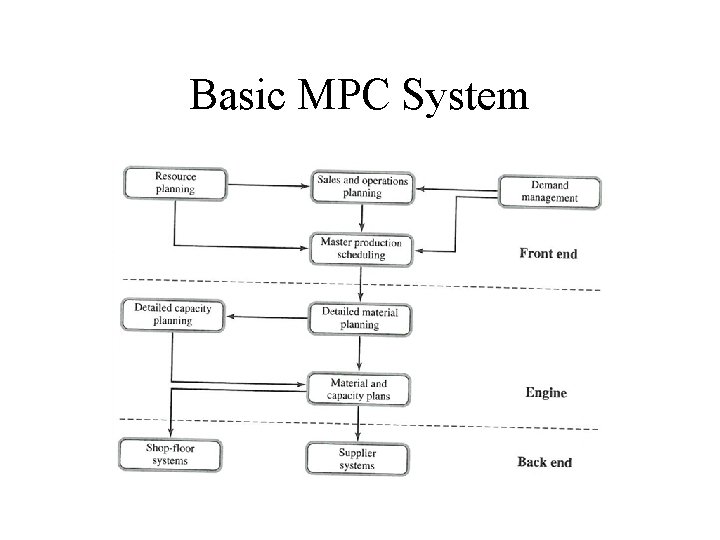
Basic MPC System
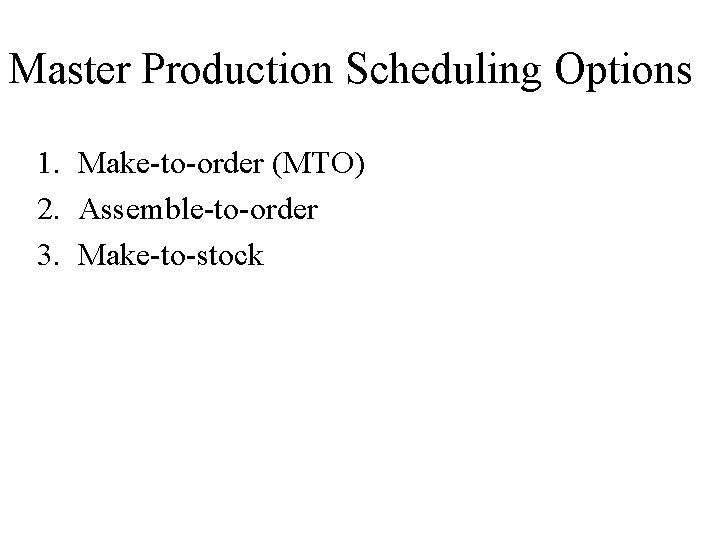
Master Production Scheduling Options 1. Make-to-order (MTO) 2. Assemble-to-order 3. Make-to-stock
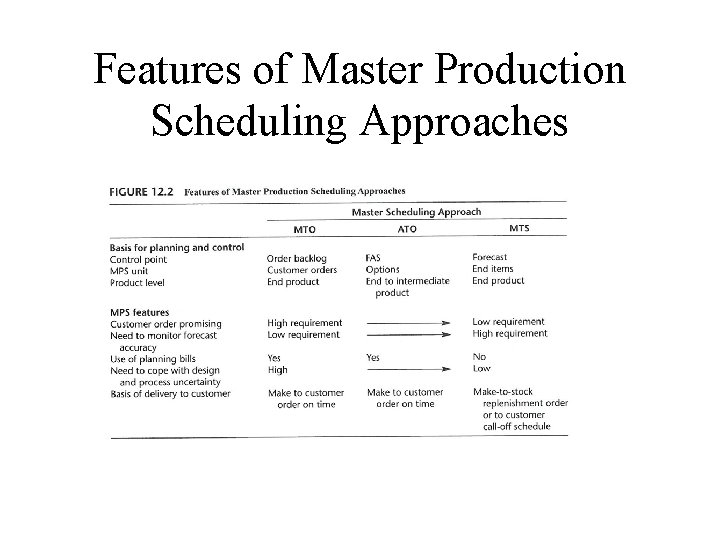
Features of Master Production Scheduling Approaches
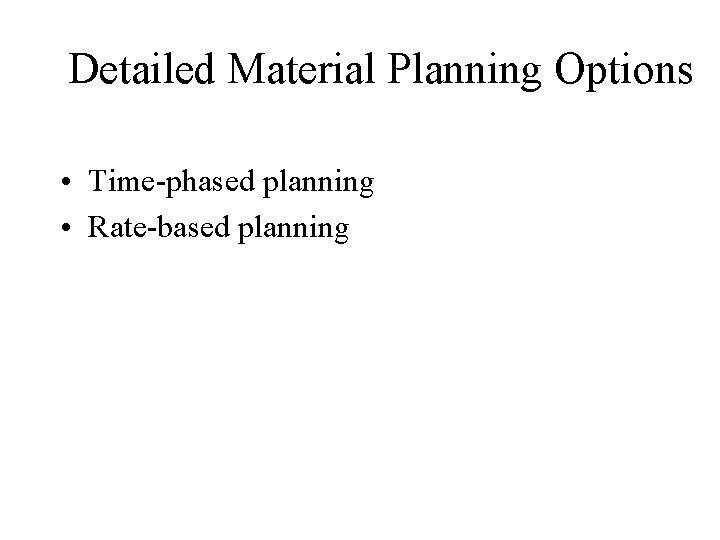
Detailed Material Planning Options • Time-phased planning • Rate-based planning
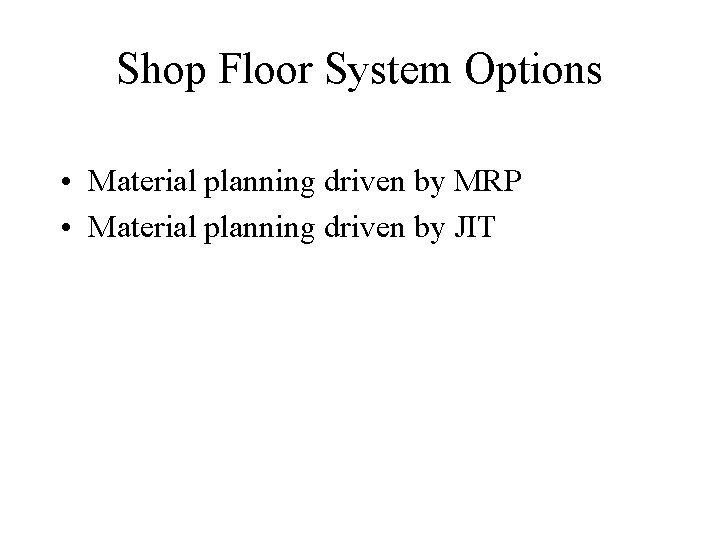
Shop Floor System Options • Material planning driven by MRP • Material planning driven by JIT
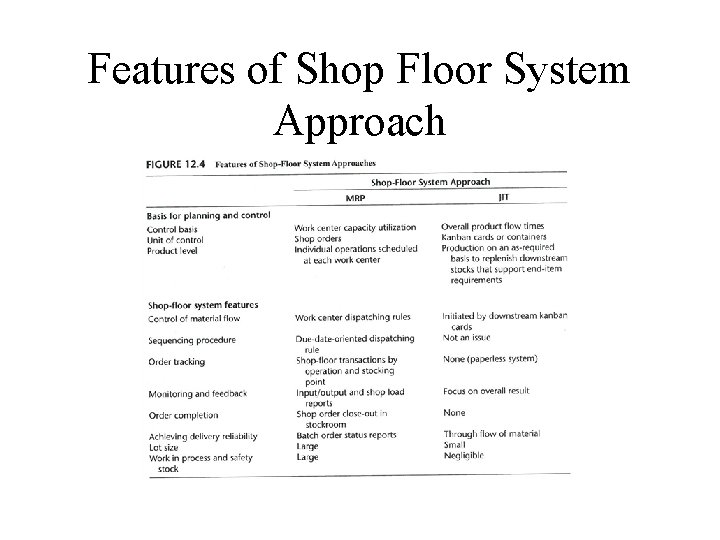
Features of Shop Floor System Approach
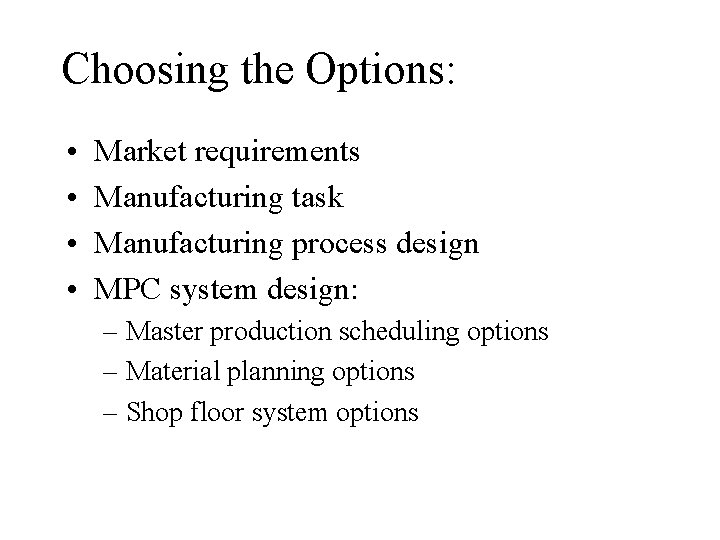
Choosing the Options: • • Market requirements Manufacturing task Manufacturing process design MPC system design: – Master production scheduling options – Material planning options – Shop floor system options
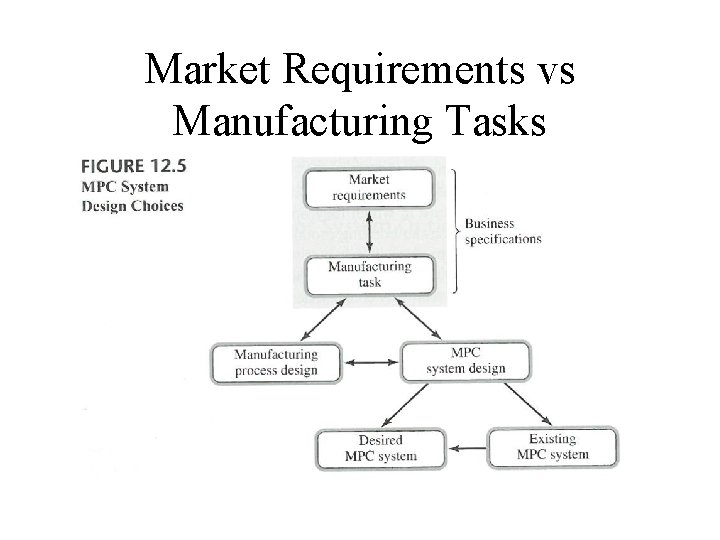
Market Requirements vs Manufacturing Tasks
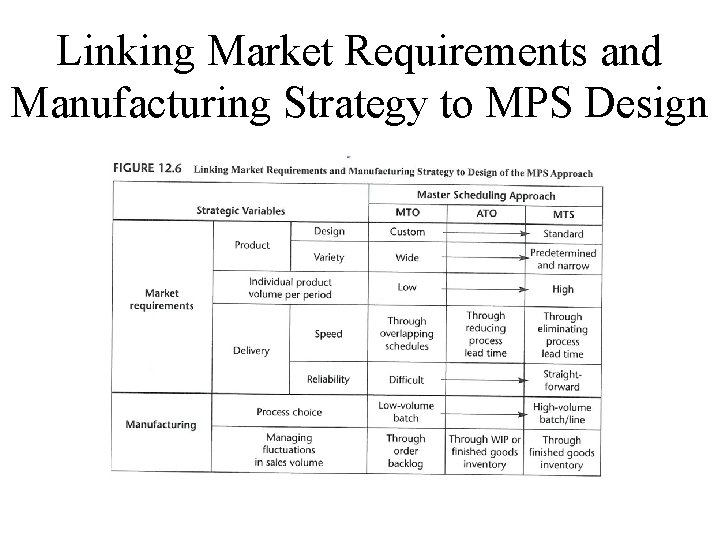
Linking Market Requirements and Manufacturing Strategy to MPS Design
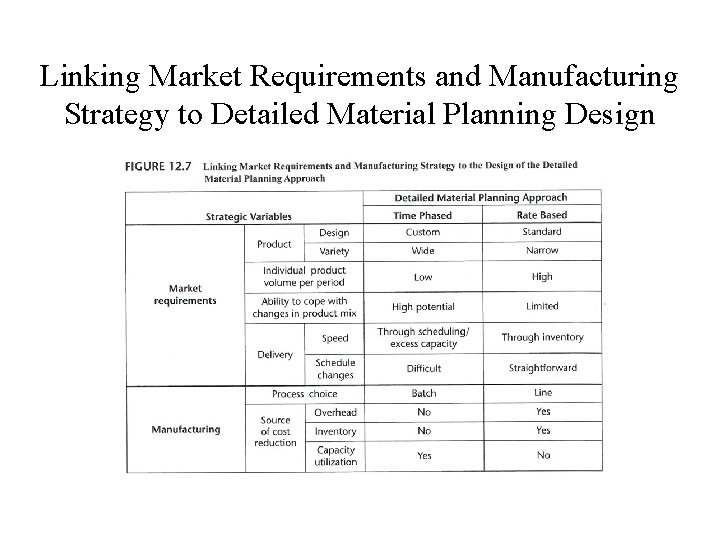
Linking Market Requirements and Manufacturing Strategy to Detailed Material Planning Design
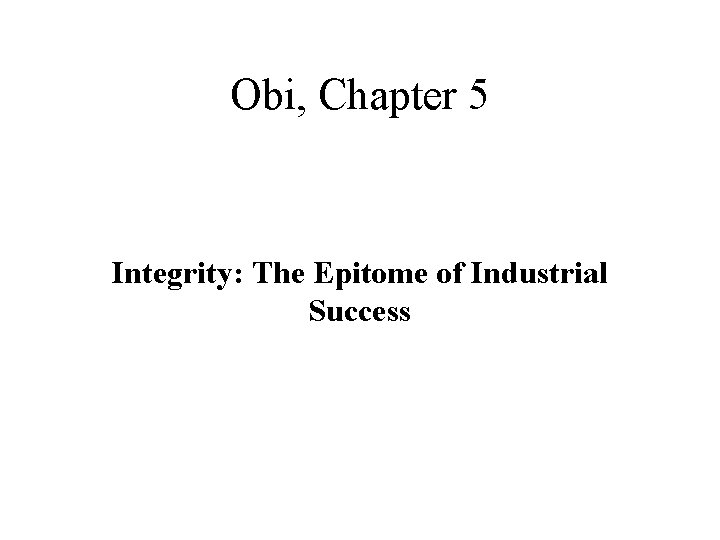
Obi, Chapter 5 Integrity: The Epitome of Industrial Success
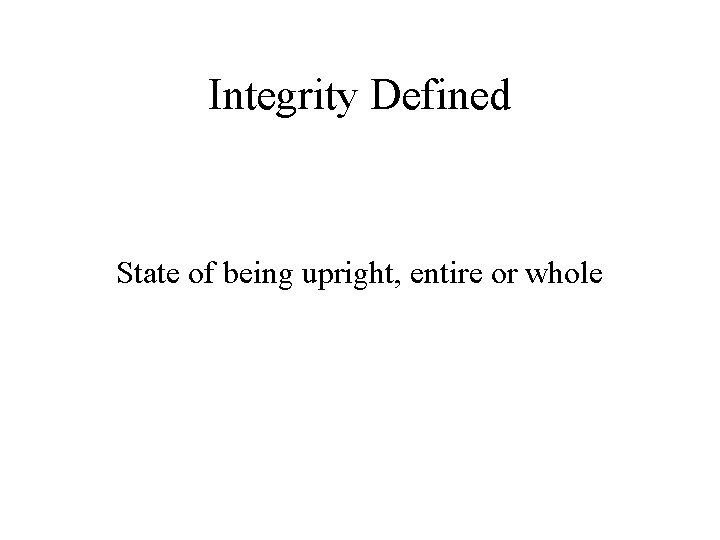
Integrity Defined State of being upright, entire or whole
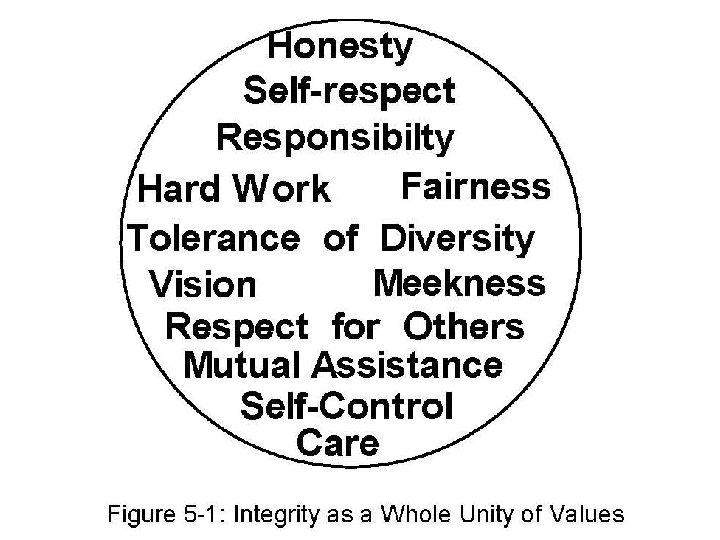
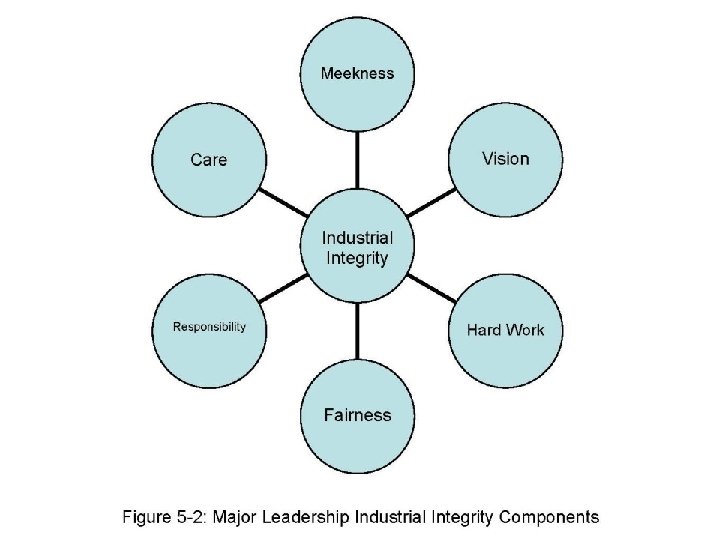
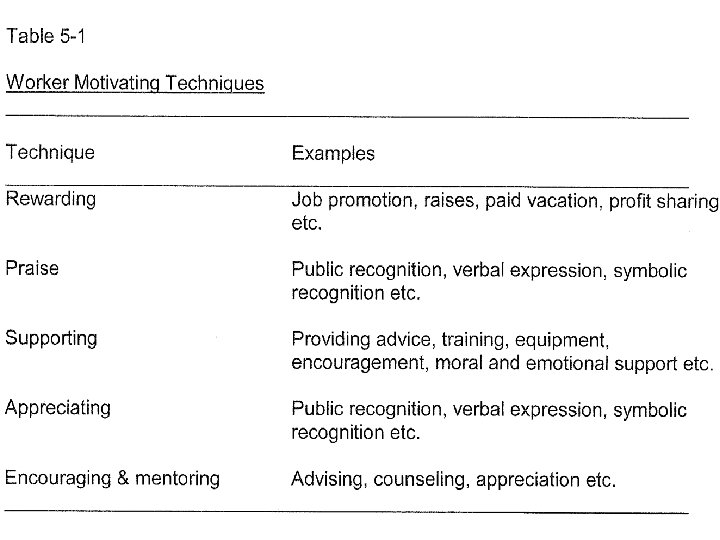
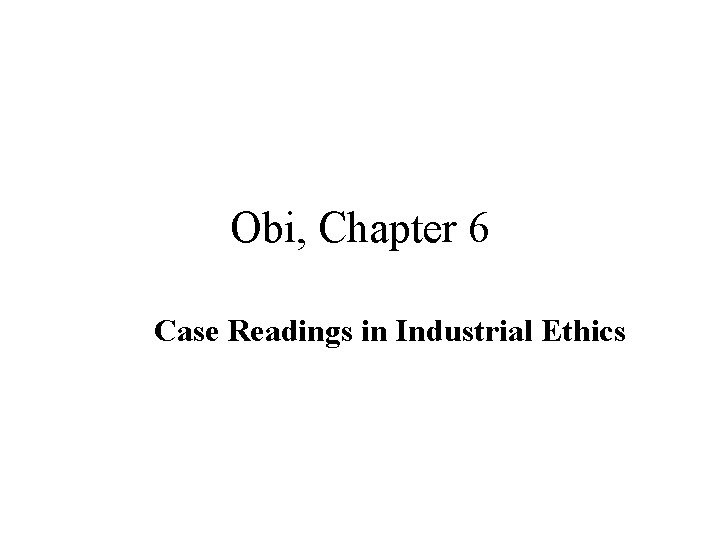
Obi, Chapter 6 Case Readings in Industrial Ethics
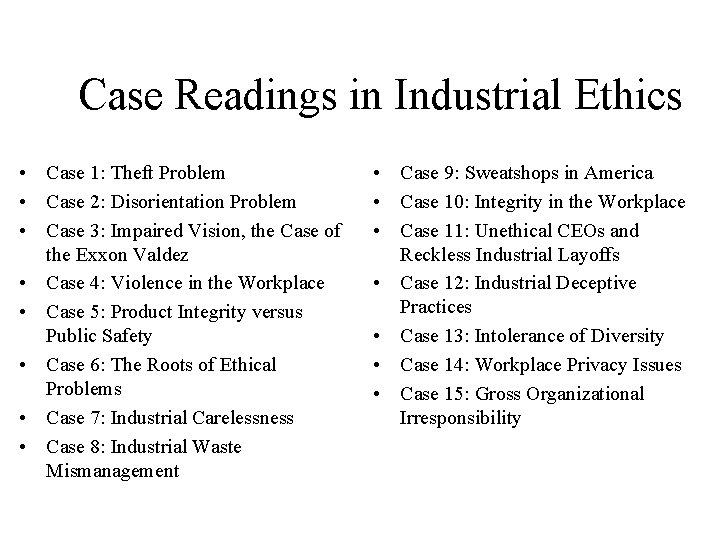
Case Readings in Industrial Ethics • Case 1: Theft Problem • Case 2: Disorientation Problem • Case 3: Impaired Vision, the Case of the Exxon Valdez • Case 4: Violence in the Workplace • Case 5: Product Integrity versus Public Safety • Case 6: The Roots of Ethical Problems • Case 7: Industrial Carelessness • Case 8: Industrial Waste Mismanagement • Case 9: Sweatshops in America • Case 10: Integrity in the Workplace • Case 11: Unethical CEOs and Reckless Industrial Layoffs • Case 12: Industrial Deceptive Practices • Case 13: Intolerance of Diversity • Case 14: Workplace Privacy Issues • Case 15: Gross Organizational Irresponsibility
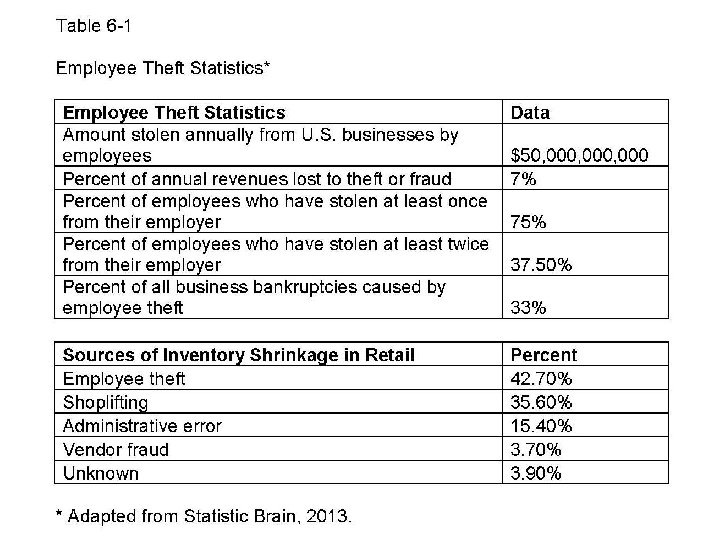
Show me green
Manufacturing cost vs non manufacturing cost
Job costing vs. process costing
Uncontrollable cost example
Manufacturing cost vs non manufacturing cost
Additive manufacturing steps
Manufacturing technician license
Low tech assistive technology definition
Manufacturing planning and control
Georgia tech urban planning masters
Addition radicals examples
147% as a fraction
My love is as a fever
Sat to iq
Pkj 147
Nkb 147
Position 147 kamasutra
Plan de ordenamiento territorial sincelejo
734-147-911
29 cfr 1910
1910 147
Psalm 147 vers 6
Cs 147 stanford
Stanford cs 147
Psalm 147:1 niv
Denoporte
Cs 147
Cs 147
147 kaça bölünür
Words which relate to racism tkam chapter 9-10
Aashto m 147
147 mhz
Elena fox
Sht 147
오라클 프로시저 cursor
Ps 147:3
Stanford cs 147