Storage Ring Vacuum Systems H Hseuh Vacuum Group
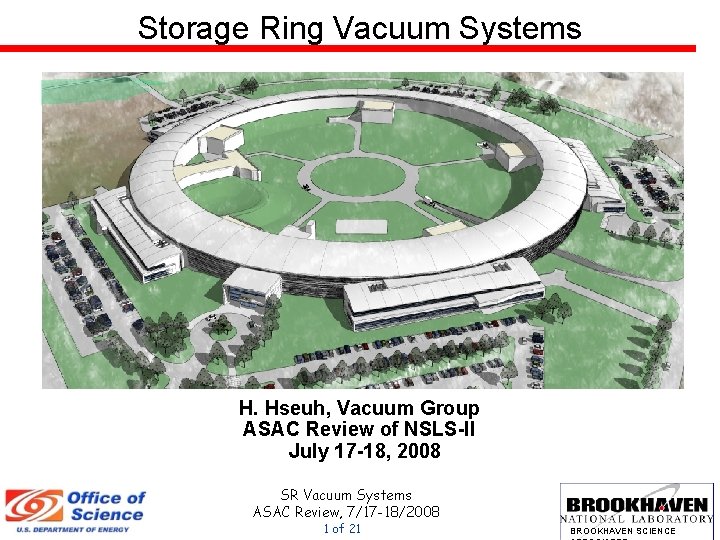
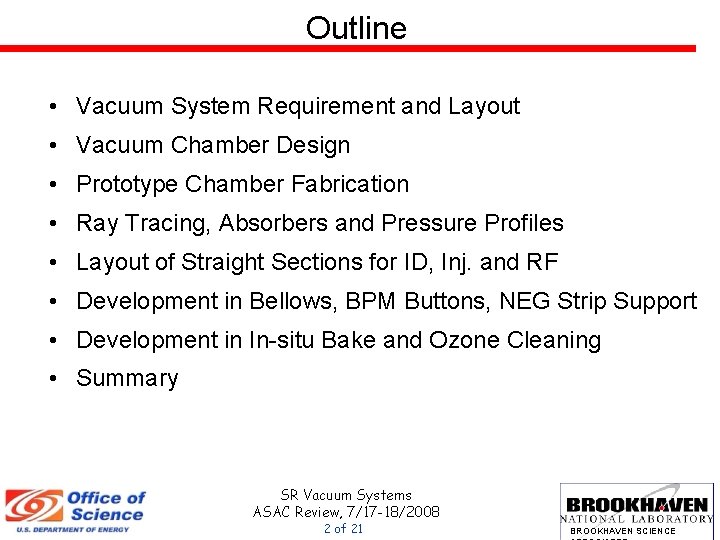
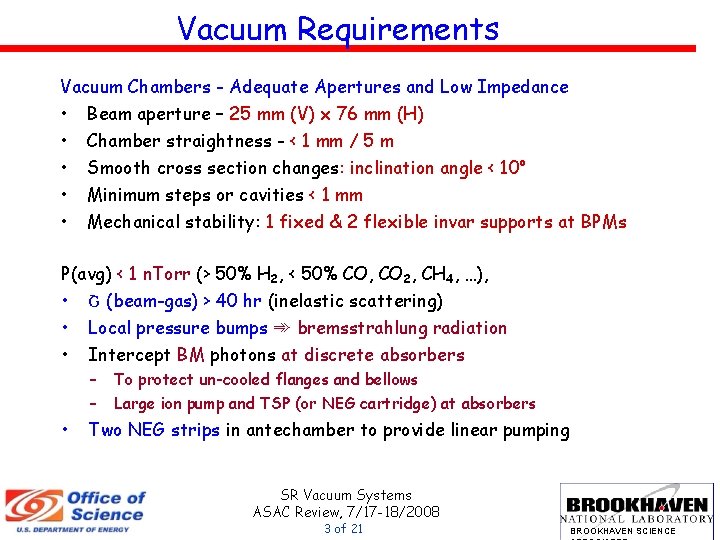
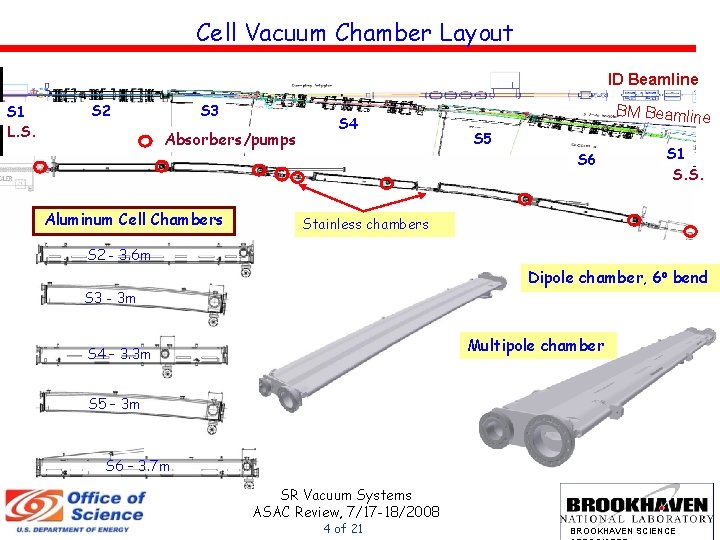

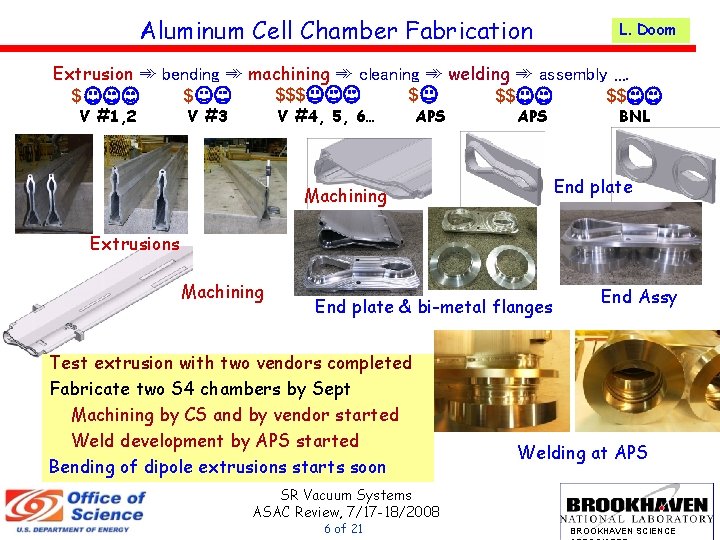
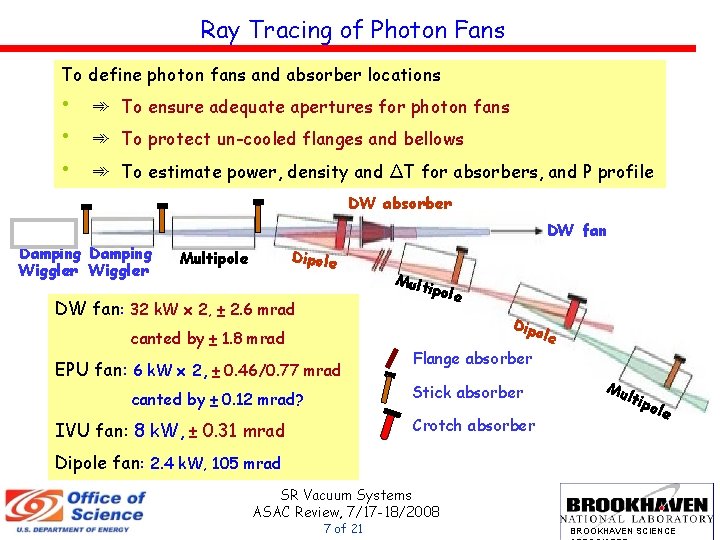
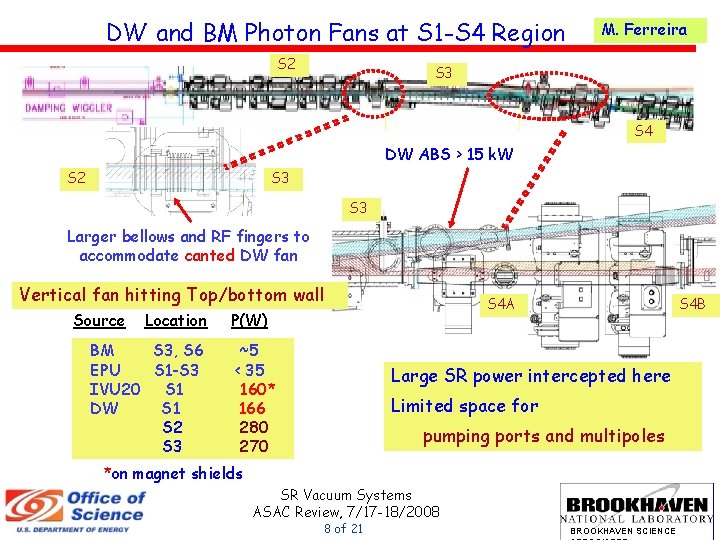
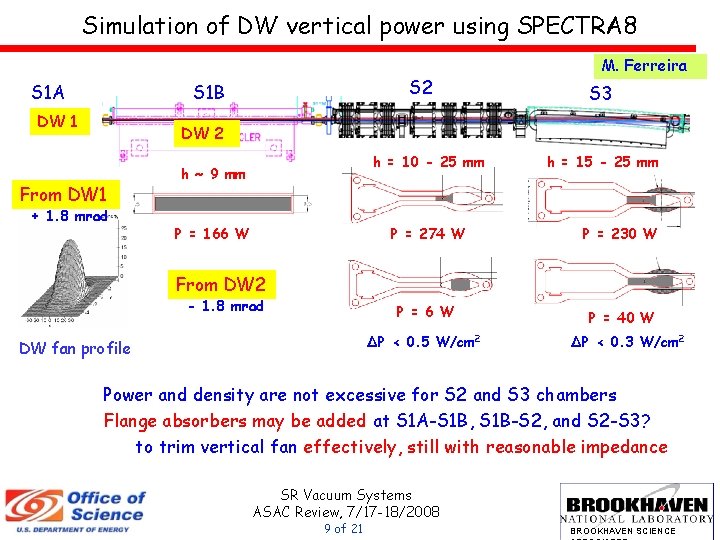
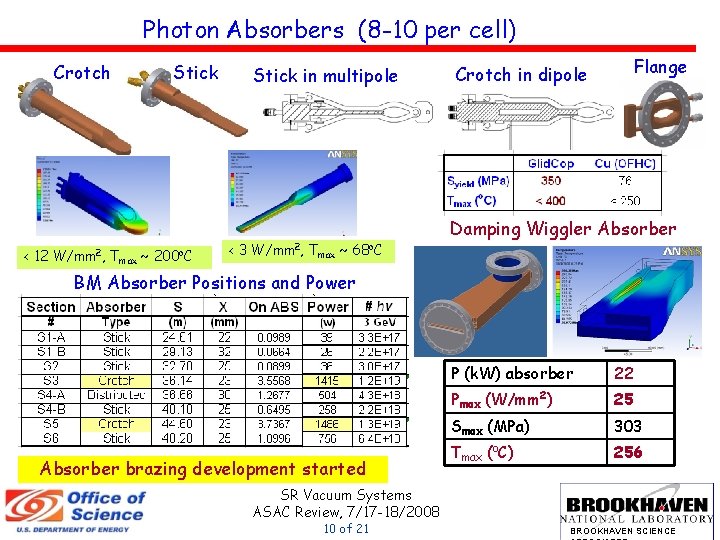
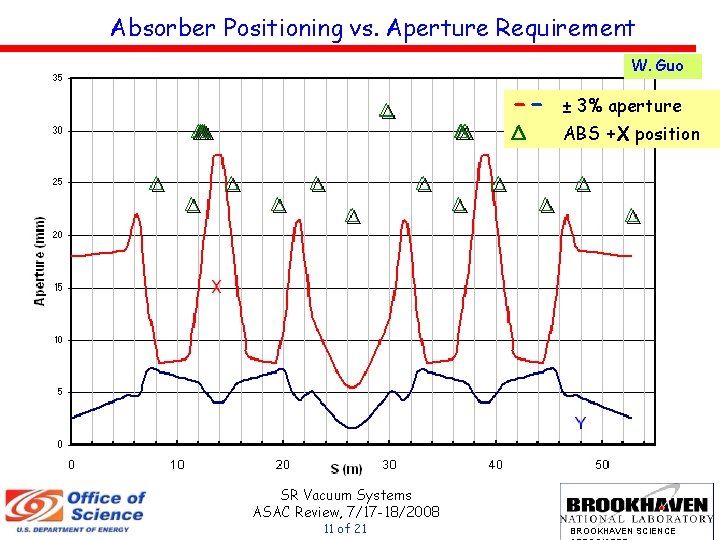
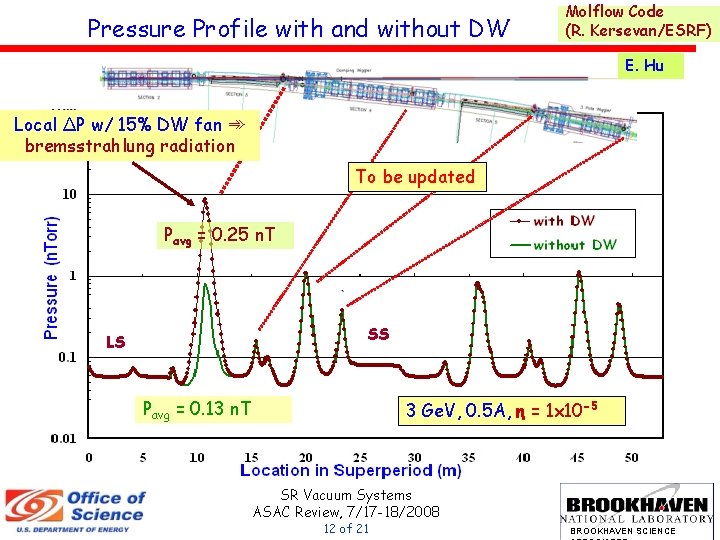
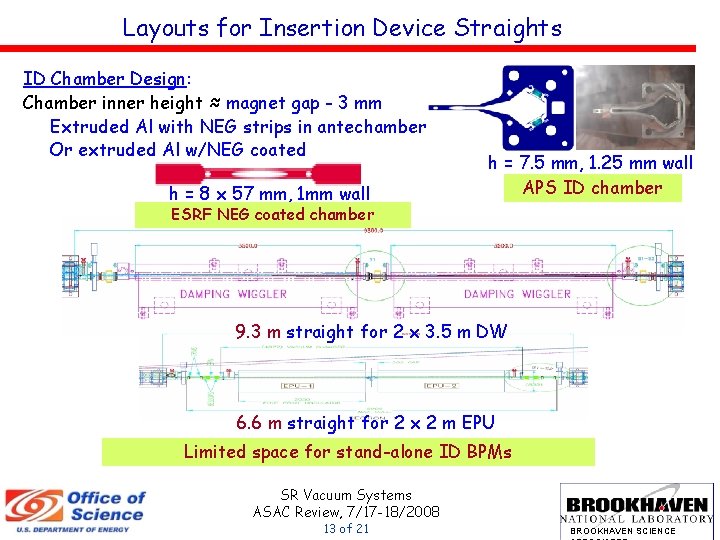
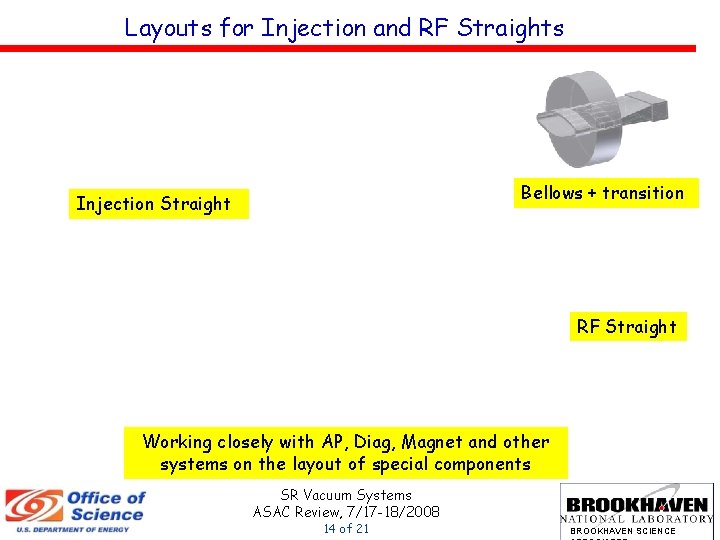
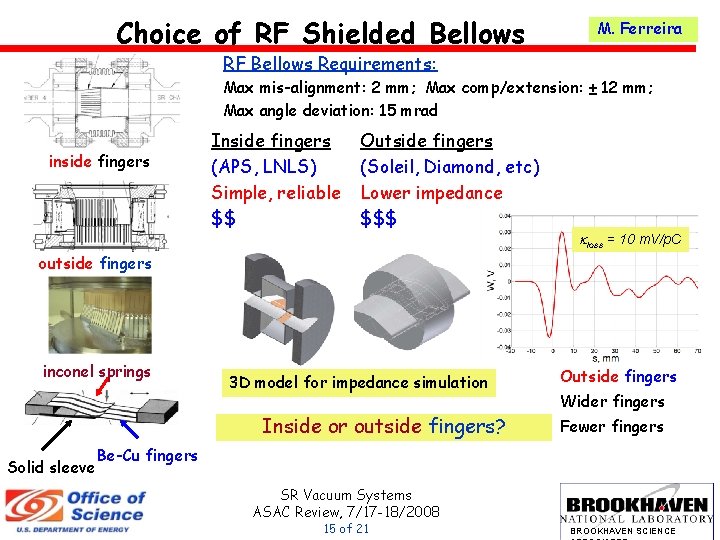
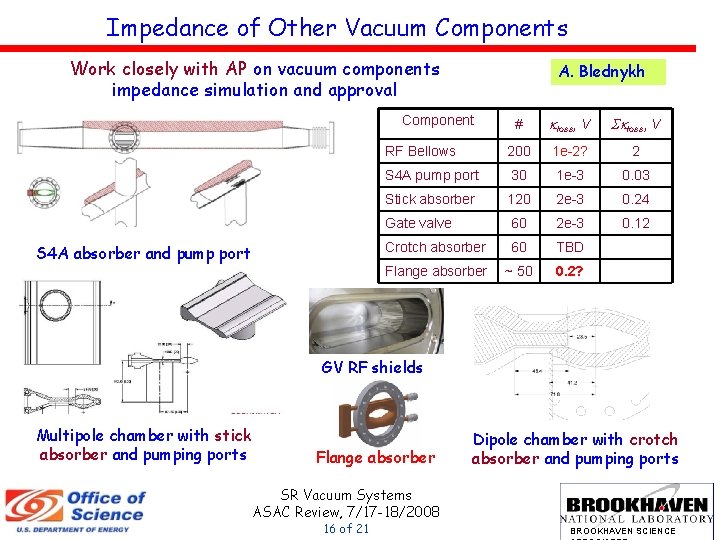
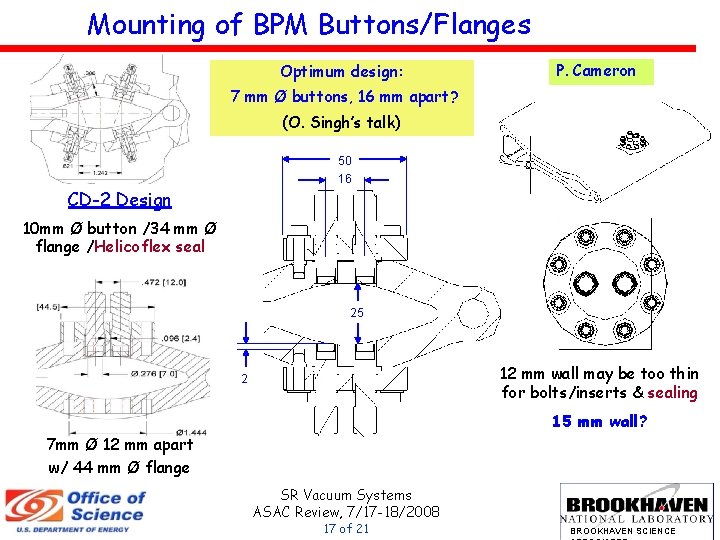
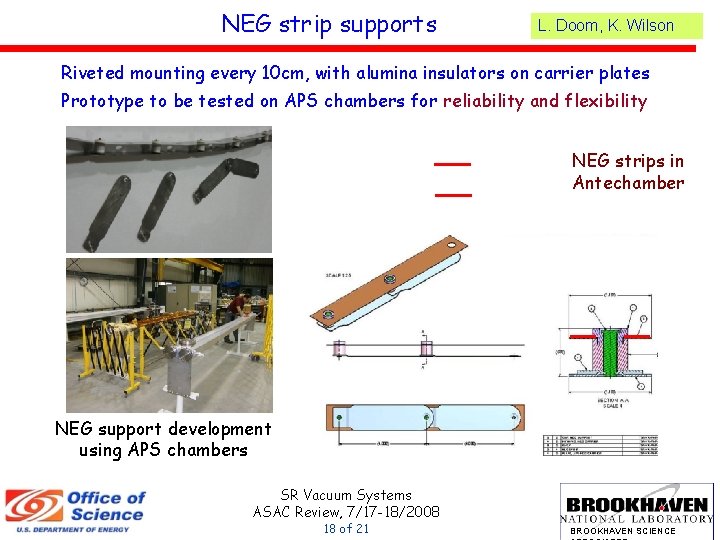
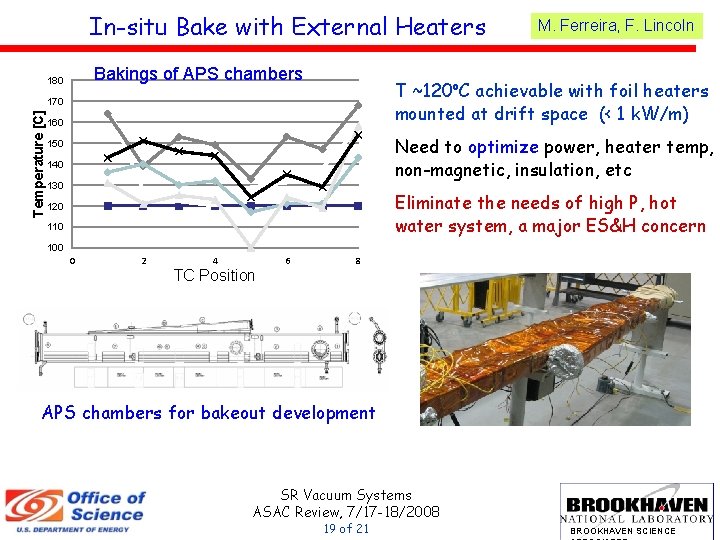
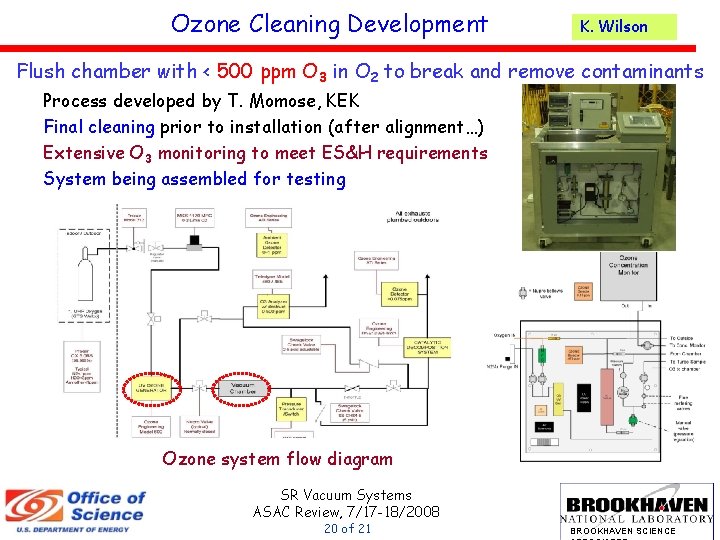
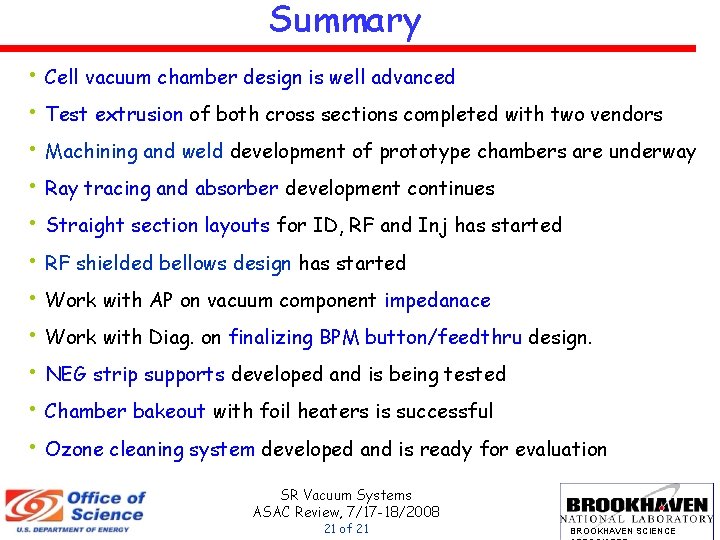
- Slides: 21
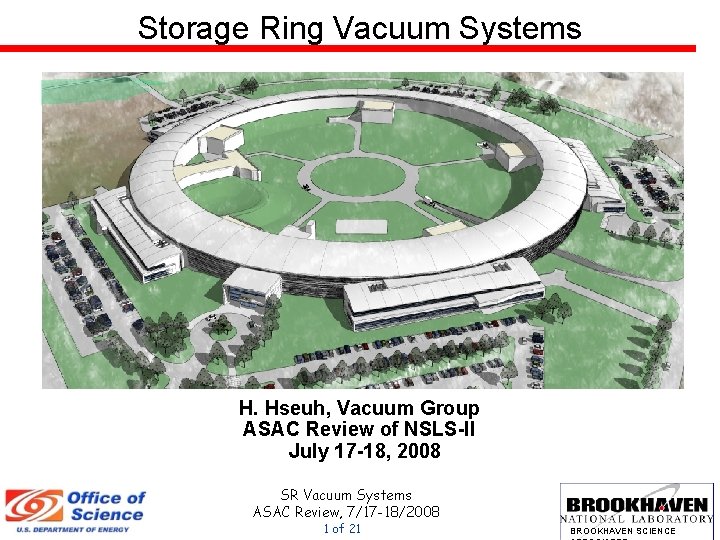
Storage Ring Vacuum Systems H. Hseuh, Vacuum Group ASAC Review of NSLS-II July 17 -18, 2008 SR Vacuum Systems ASAC Review, 7/17 -18/2008 1 of 21 BROOKHAVEN SCIENCE
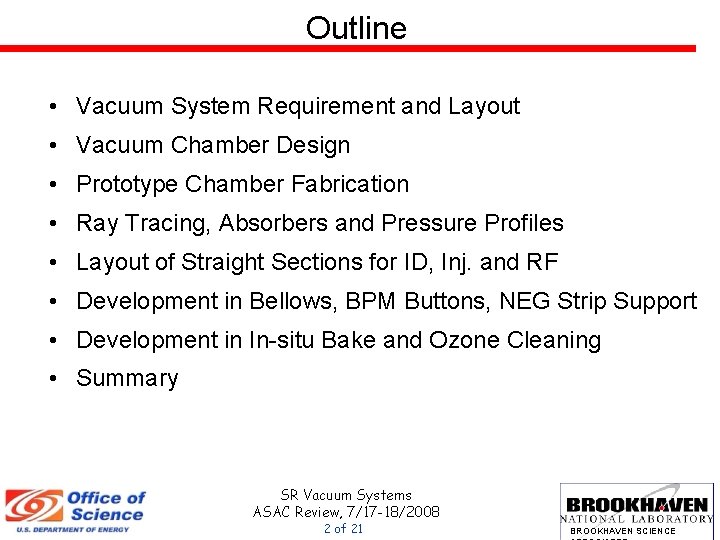
Outline • Vacuum System Requirement and Layout • Vacuum Chamber Design • Prototype Chamber Fabrication • Ray Tracing, Absorbers and Pressure Profiles • Layout of Straight Sections for ID, Inj. and RF • Development in Bellows, BPM Buttons, NEG Strip Support • Development in In-situ Bake and Ozone Cleaning • Summary SR Vacuum Systems ASAC Review, 7/17 -18/2008 2 of 21 BROOKHAVEN SCIENCE
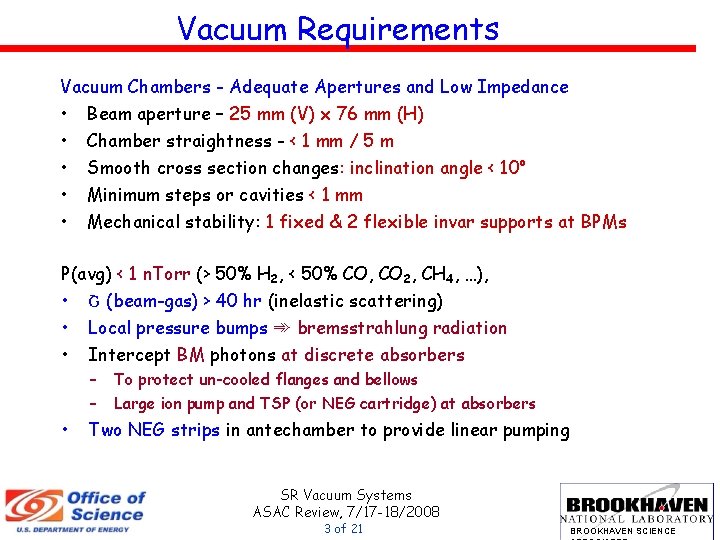
Vacuum Requirements Vacuum Chambers - Adequate Apertures and Low Impedance • • • Beam aperture – 25 mm (V) x 76 mm (H) Chamber straightness - < 1 mm / 5 m Smooth cross section changes: inclination angle < 10 o Minimum steps or cavities < 1 mm Mechanical stability: 1 fixed & 2 flexible invar supports at BPMs P(avg) < 1 n. Torr (> 50% H 2, < 50% CO, CO 2, CH 4, …), • • • Շ (beam-gas) > 40 hr (inelastic scattering) Local pressure bumps ➾ bremsstrahlung radiation Intercept BM photons at discrete absorbers – – • To protect un-cooled flanges and bellows Large ion pump and TSP (or NEG cartridge) at absorbers Two NEG strips in antechamber to provide linear pumping SR Vacuum Systems ASAC Review, 7/17 -18/2008 3 of 21 BROOKHAVEN SCIENCE
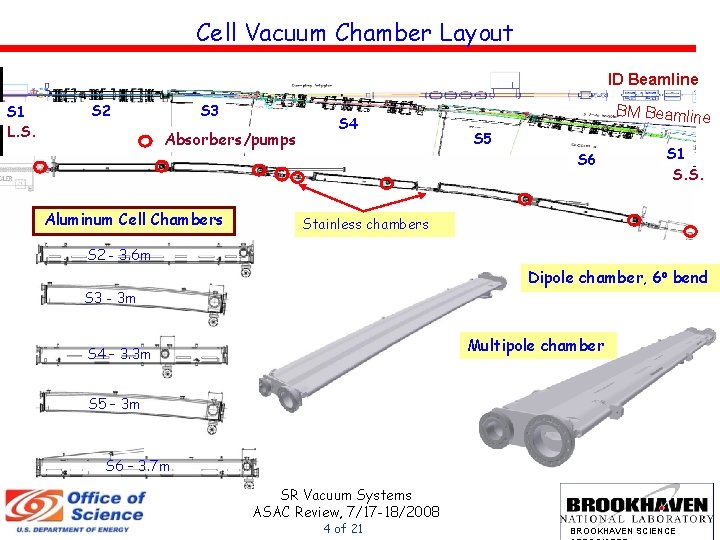
Cell Vacuum Chamber Layout ID Beamline S 1 L. S. S 2 S 3 Absorbers/pumps S 4 BM Beamline S 5 S 6 Aluminum Cell Chambers S 1 S. S. Stainless chambers S 2 - 3. 6 m Dipole chamber, 6 o bend S 3 - 3 m Multipole chamber S 4 – 3. 3 m S 5 – 3 m S 6 – 3. 7 m SR Vacuum Systems ASAC Review, 7/17 -18/2008 4 of 21 BROOKHAVEN SCIENCE

Cell Chamber Cross Sections and Analysis Multipole Chamber Dipole Chamber Extruded cross section 3 mm wall Bended and machined At Quadrupole Maxi. δ = 0. 3 mm x 2 Max. S = 42 MPa Machined at pole locations Maxi. δ = 0. 27 mm x 2 Max. S = 64 MPa At Sextupole 3. 1 mm wall Syield (A 6063 T 5) = 145 MPa Sstress (A 6063 T 5) = 186 MPa SR Vacuum Systems ASAC Review, 7/17 -18/2008 5 of 21 BROOKHAVEN SCIENCE
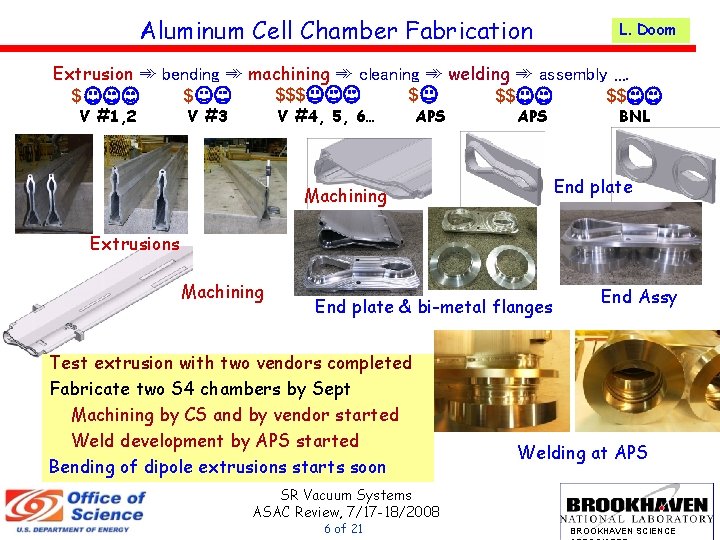
Aluminum Cell Chamber Fabrication L. Doom Extrusion ➾ bending ➾ machining ➾ cleaning ➾ welding ➾ assembly …. $$$ $$ V #1, 2 V #3 V #4, 5, 6… APS BNL End plate Machining Extrusions Machining End plate & bi-metal flanges Test extrusion with two vendors completed Fabricate two S 4 chambers by Sept Machining by CS and by vendor started Weld development by APS started Bending of dipole extrusions starts soon End Assy Welding at APS SR Vacuum Systems ASAC Review, 7/17 -18/2008 6 of 21 BROOKHAVEN SCIENCE
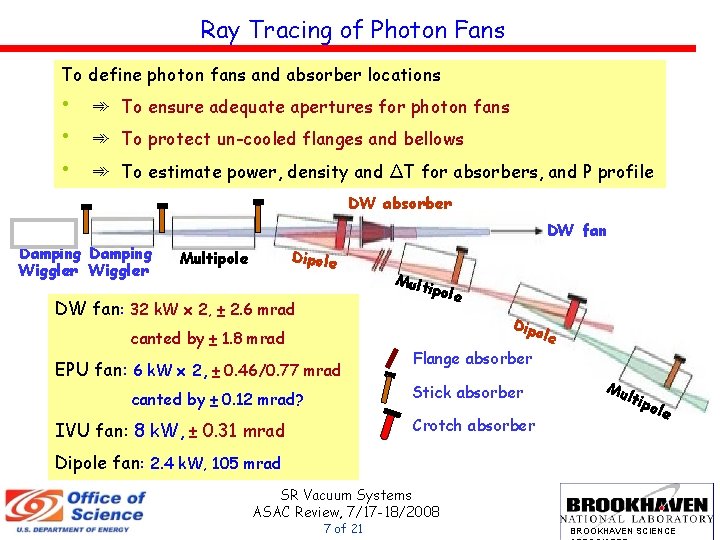
Ray Tracing of Photon Fans To define photon fans and absorber locations • • • ➾ To ensure adequate apertures for photon fans ➾ To protect un-cooled flanges and bellows ➾ To estimate power, density and ΔT for absorbers, and P profile DW absorber DW fan Damping Wiggler Dipole Mult ipole DW fan: 32 k. W x 2, ± 2. 6 mrad Dip ole canted by ± 1. 8 mrad EPU fan: 6 k. W x 2, ± 0. 46/0. 77 mrad canted by ± 0. 12 mrad? Flange absorber Stick absorber Crotch absorber IVU fan: 8 k. W, ± 0. 31 mrad Mu ltip ole Dipole fan: 2. 4 k. W, 105 mrad SR Vacuum Systems ASAC Review, 7/17 -18/2008 7 of 21 BROOKHAVEN SCIENCE
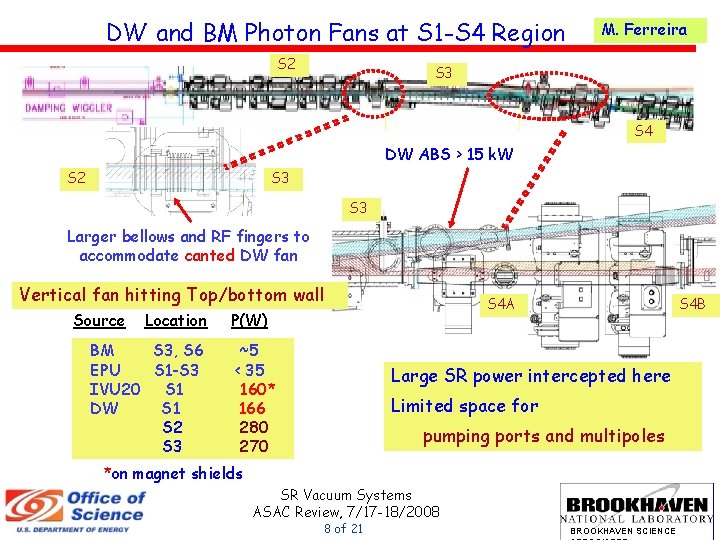
DW and BM Photon Fans at S 1 -S 4 Region S 2 M. Ferreira S 3 S 4 DW ABS > 15 k. W S 2 S 3 Larger bellows and RF fingers to accommodate canted DW fan Vertical fan hitting Top/bottom wall Source Location BM S 3, S 6 EPU S 1 -S 3 IVU 20 S 1 DW S 1 S 2 S 3 S 4 A P(W) ~5 < 35 160* 166 280 270 S 4 B Large SR power intercepted here Limited space for pumping ports and multipoles *on magnet shields SR Vacuum Systems ASAC Review, 7/17 -18/2008 8 of 21 BROOKHAVEN SCIENCE
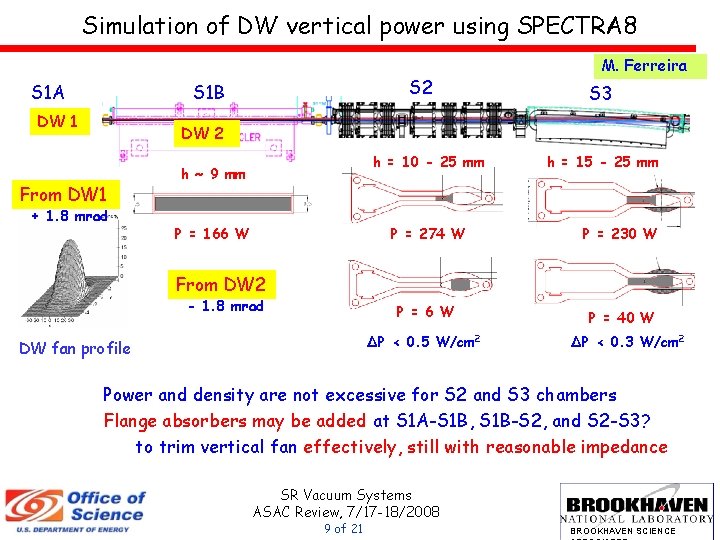
Simulation of DW vertical power using SPECTRA 8 S 1 A S 2 S 1 B DW 1 M. Ferreira S 3 DW 2 From DW 1 + 1. 8 mrad h = 10 - 25 mm h ~ 9 mm P = 166 W h = 15 - 25 mm P = 274 W P = 230 W P = 6 W P = 40 W From DW 2 - 1. 8 mrad ΔP < 0. 5 W/cm 2 DW fan profile ΔP < 0. 3 W/cm 2 Power and density are not excessive for S 2 and S 3 chambers Flange absorbers may be added at S 1 A-S 1 B, S 1 B-S 2, and S 2 -S 3? to trim vertical fan effectively, still with reasonable impedance SR Vacuum Systems ASAC Review, 7/17 -18/2008 9 of 21 BROOKHAVEN SCIENCE
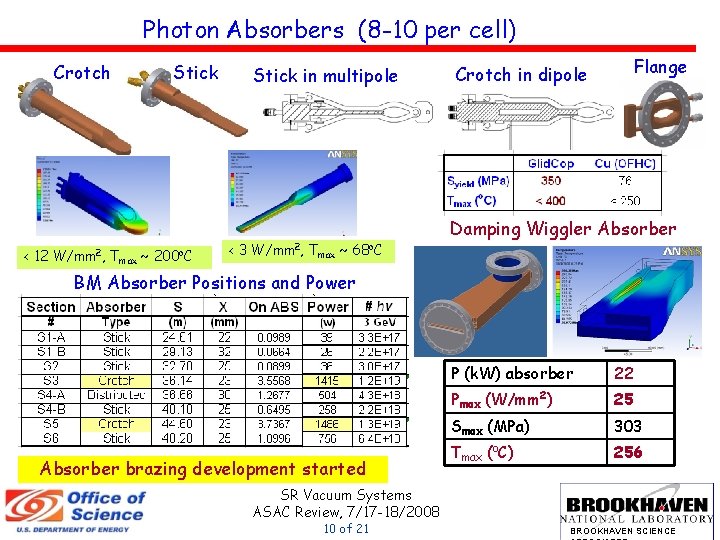
Photon Absorbers (8 -10 per cell) Crotch Stick < 12 W/mm 2, Tmax ~ 200 o. C Stick in multipole < 3 W/mm 2, Tmax ~ 68 o. C Flange Crotch in dipole Damping Wiggler Absorber BM Absorber Positions and Power Absorber brazing development started P (k. W) absorber 22 Pmax (W/mm 2) 25 Smax (MPa) 303 Tmax (o. C) 256 SR Vacuum Systems ASAC Review, 7/17 -18/2008 10 of 21 BROOKHAVEN SCIENCE
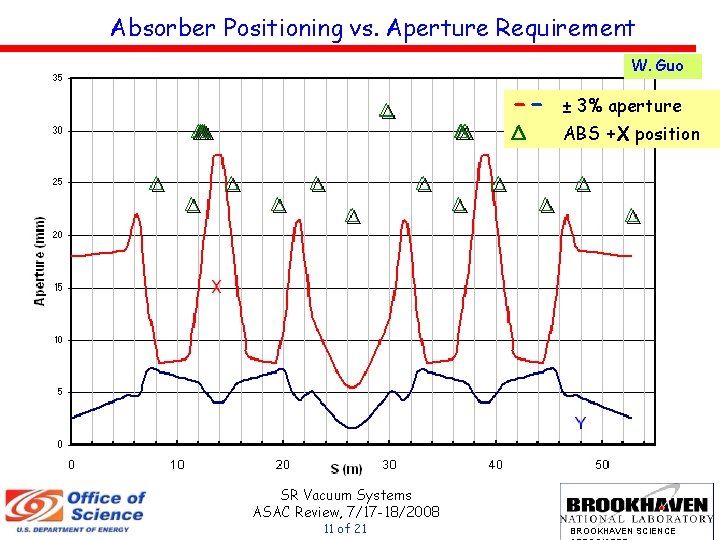
Absorber Positioning vs. Aperture Requirement W. Guo -Δ ± 3% aperture ABS +X position SR Vacuum Systems ASAC Review, 7/17 -18/2008 11 of 21 BROOKHAVEN SCIENCE
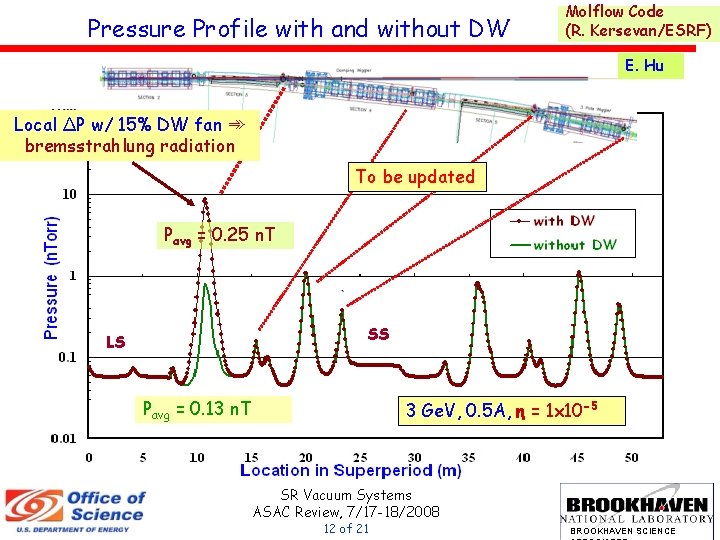
Pressure Profile with and without DW Molflow Code (R. Kersevan/ESRF) E. Hu Local ΔP w/ 15% DW fan ➾ bremsstrahlung radiation To be updated Pavg = 0. 25 n. T SS LS Pavg = 0. 13 n. T 3 Ge. V, 0. 5 A, η = 1 x 10 -5 SR Vacuum Systems ASAC Review, 7/17 -18/2008 12 of 21 BROOKHAVEN SCIENCE
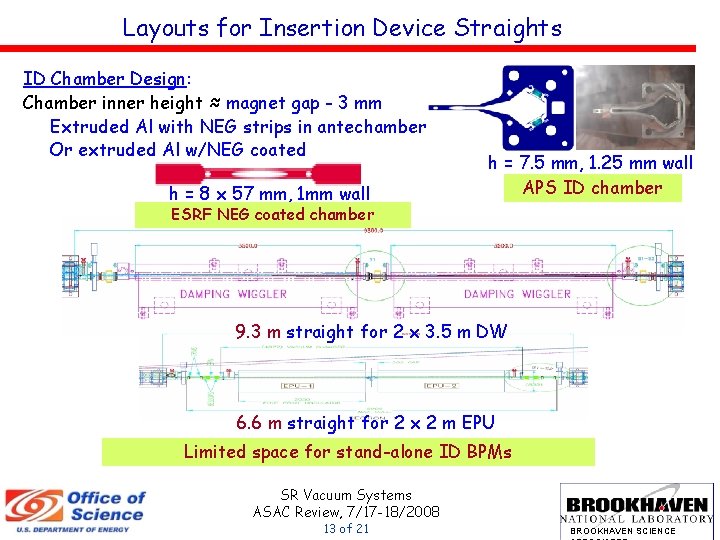
Layouts for Insertion Device Straights ID Chamber Design: Chamber inner height ≈ magnet gap - 3 mm Extruded Al with NEG strips in antechamber Or extruded Al w/NEG coated h = 8 x 57 mm, 1 mm wall h = 7. 5 mm, 1. 25 mm wall APS ID chamber ESRF NEG coated chamber 9. 3 m straight for 2 x 3. 5 m DW 6. 6 m straight for 2 x 2 m EPU Limited space for stand-alone ID BPMs SR Vacuum Systems ASAC Review, 7/17 -18/2008 13 of 21 BROOKHAVEN SCIENCE
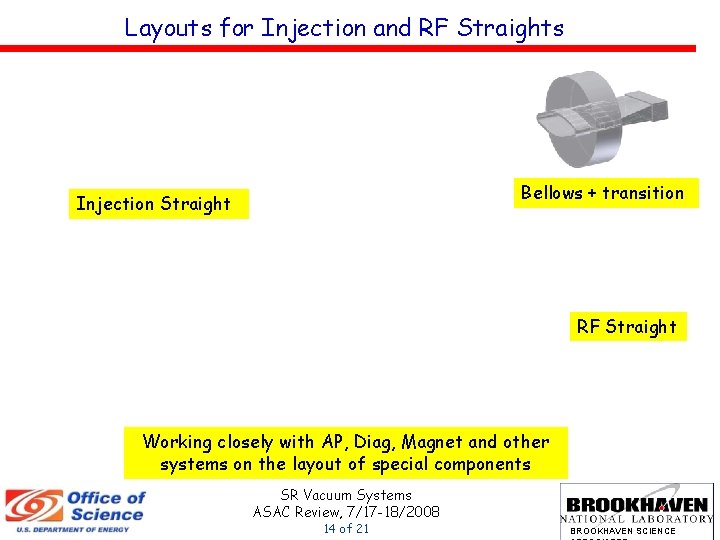
Layouts for Injection and RF Straights Bellows + transition Injection Straight RF Straight Working closely with AP, Diag, Magnet and other systems on the layout of special components SR Vacuum Systems ASAC Review, 7/17 -18/2008 14 of 21 BROOKHAVEN SCIENCE
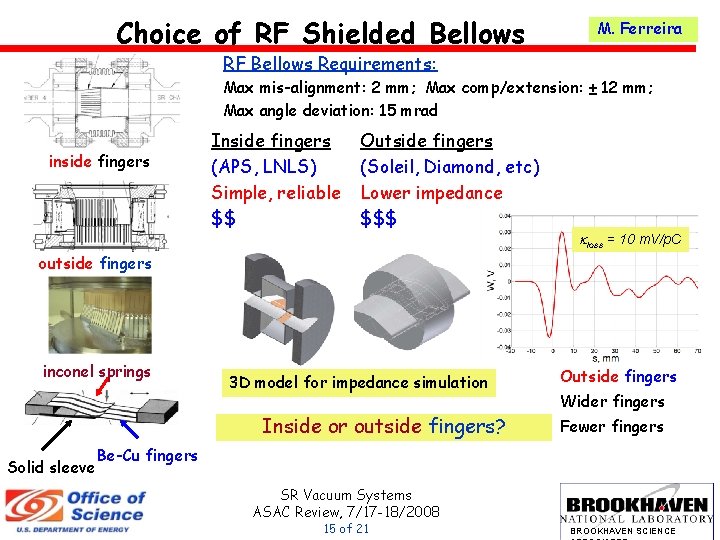
Choice of RF Shielded Bellows M. Ferreira RF Bellows Requirements: Max mis-alignment: 2 mm; Max comp/extension: ± 12 mm; Max angle deviation: 15 mrad inside fingers Inside fingers (APS, LNLS) Simple, reliable $$ Outside fingers (Soleil, Diamond, etc) Lower impedance $$$ loss = 10 m. V/p. C outside fingers inconel springs 3 D model for impedance simulation Inside or outside fingers? Solid sleeve Outside fingers Wider fingers Fewer fingers Be-Cu fingers SR Vacuum Systems ASAC Review, 7/17 -18/2008 15 of 21 BROOKHAVEN SCIENCE
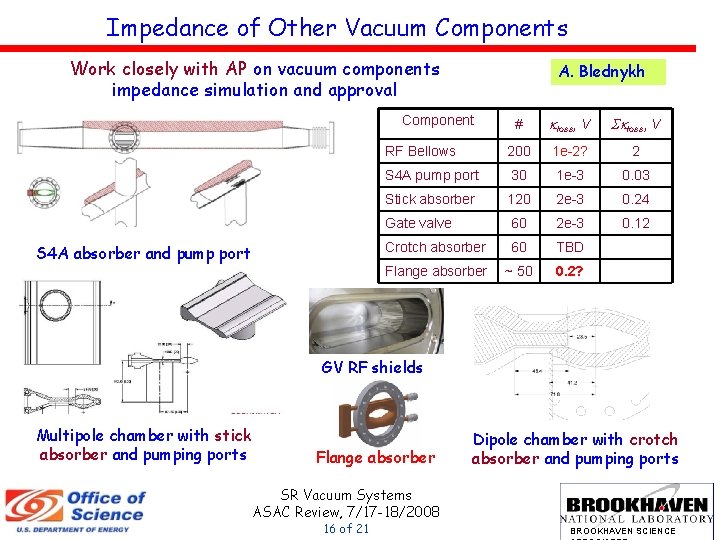
Impedance of Other Vacuum Components Work closely with AP on vacuum components impedance simulation and approval A. Blednykh Component S 4 A chamber with absorber and shielded pumping ports S 4 A absorber and pump port # loss, V RF Bellows 200 1 e-2? 2 S 4 A pump port 30 1 e-3 0. 03 Stick absorber 120 2 e-3 0. 24 Gate valve 60 2 e-3 0. 12 Crotch absorber 60 TBD Flange absorber ~ 50 0. 2? GV RF shields Multipole chamber with stick absorber and pumping ports Flange absorber Dipole chamber with crotch absorber and pumping ports SR Vacuum Systems ASAC Review, 7/17 -18/2008 16 of 21 BROOKHAVEN SCIENCE
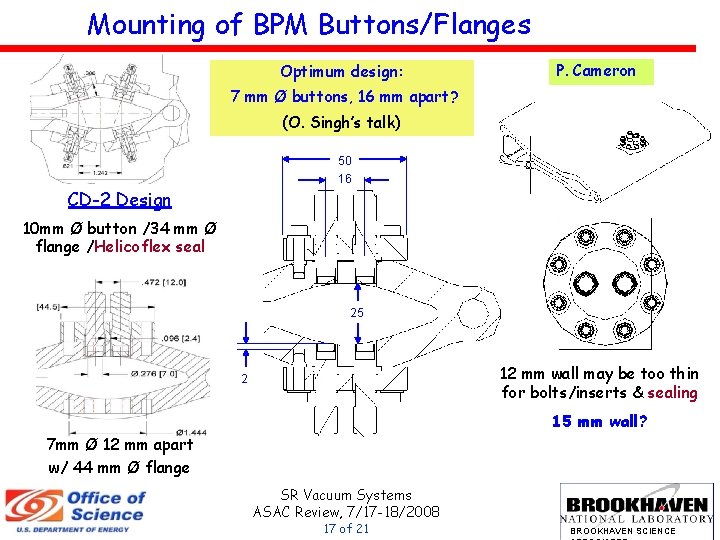
Mounting of BPM Buttons/Flanges Optimum design: P. Cameron 7 mm Ø buttons, 16 mm apart? (O. Singh’s talk) 50 16 CD-2 Design 10 mm Ø button /34 mm Ø flange /Helicoflex seal 25 2 7 mm Ø 12 mm apart w/ 44 mm Ø flange Rectangular flange? Sealing reliability? 12 mm wall may be too thin for bolts/inserts & sealing 15 mm wall? SR Vacuum Systems ASAC Review, 7/17 -18/2008 17 of 21 BROOKHAVEN SCIENCE
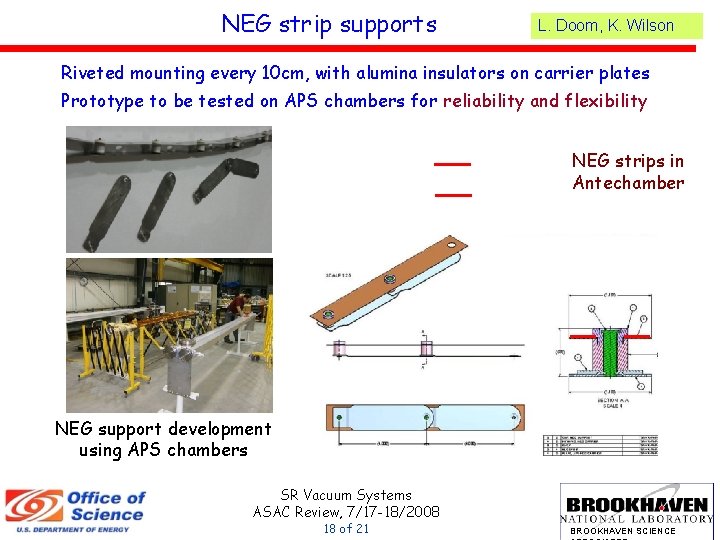
NEG strip supports L. Doom, K. Wilson Riveted mounting every 10 cm, with alumina insulators on carrier plates Prototype to be tested on APS chambers for reliability and flexibility NEG strips in Antechamber NEG support development using APS chambers SR Vacuum Systems ASAC Review, 7/17 -18/2008 18 of 21 BROOKHAVEN SCIENCE
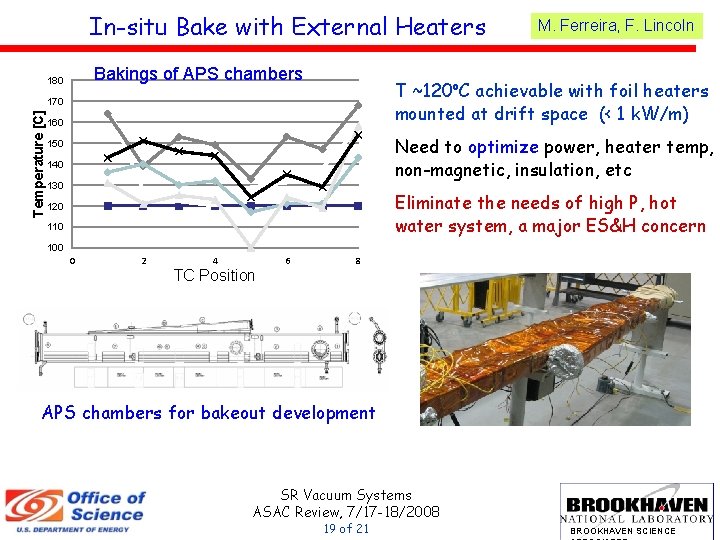
In-situ Bake with External Heaters Bakings of APS chambers 180 T ~120 o. C achievable with foil heaters mounted at drift space (< 1 k. W/m) 170 Temperature [C] M. Ferreira, F. Lincoln 160 Need to optimize power, heater temp, non-magnetic, insulation, etc 150 140 130 Eliminate the needs of high P, hot water system, a major ES&H concern 120 110 100 0 2 4 6 8 TC Position APS chambers for bakeout development SR Vacuum Systems ASAC Review, 7/17 -18/2008 19 of 21 BROOKHAVEN SCIENCE
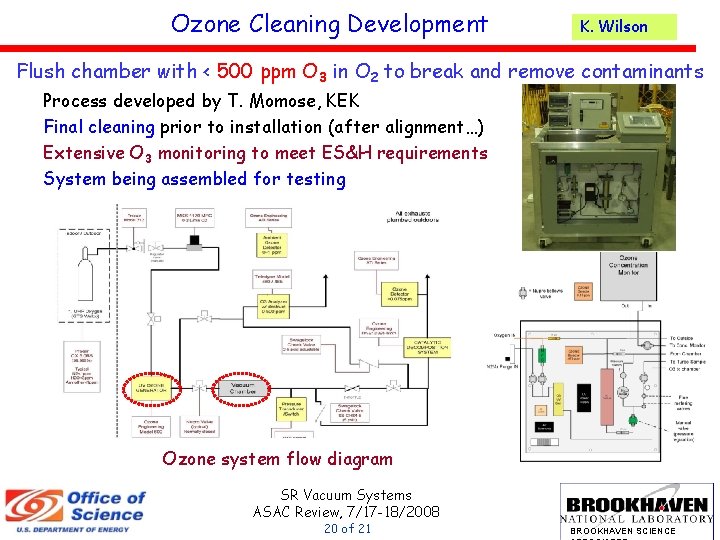
Ozone Cleaning Development K. Wilson Flush chamber with < 500 ppm O 3 in O 2 to break and remove contaminants Process developed by T. Momose, KEK Final cleaning prior to installation (after alignment…) Extensive O 3 monitoring to meet ES&H requirements System being assembled for testing Ozone system flow diagram SR Vacuum Systems ASAC Review, 7/17 -18/2008 20 of 21 BROOKHAVEN SCIENCE
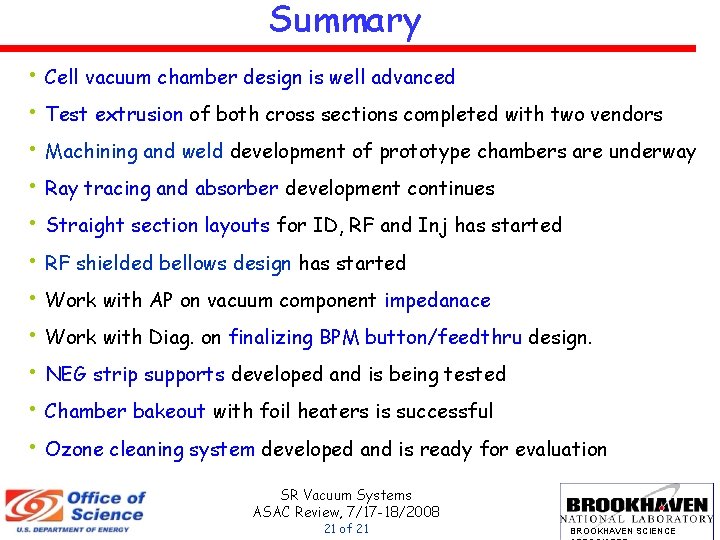
Summary • Cell vacuum chamber design is well advanced • Test extrusion of both cross sections completed with two vendors • Machining and weld development of prototype chambers are underway • Ray tracing and absorber development continues • Straight section layouts for ID, RF and Inj has started • RF shielded bellows design has started • Work with AP on vacuum component impedanace • Work with Diag. on finalizing BPM button/feedthru design. • NEG strip supports developed and is being tested • Chamber bakeout with foil heaters is successful • Ozone cleaning system developed and is ready for evaluation SR Vacuum Systems ASAC Review, 7/17 -18/2008 21 of 21 BROOKHAVEN SCIENCE
What is the brown ring in the brown ring test
Constriction ring uterus
Inguinal canal anatomy
Inguinal ring
Merrily merrily christmas bells are ringing
Ring christmas bells ring them loud
Inner ring and outer ring
Token ring and resilient packet ring
Secondary storage vs primary storage
Primary storage and secondary storage
Secondary storage provides temporary or volatile storage
Unified storage vs traditional storage
Vacuum systems commissioning
Samer al-kiswany
Storage for ibm power systems
Tactical storage systems
Tactical storage systems
Availability in globally distributed storage systems
Decision support systems and intelligent systems
Engineering elegant systems: theory of systems engineering
Embedded systems vs cyber physical systems
Elegant systems