Six Sigma Statistical View Dedy Sugiarto 1 What
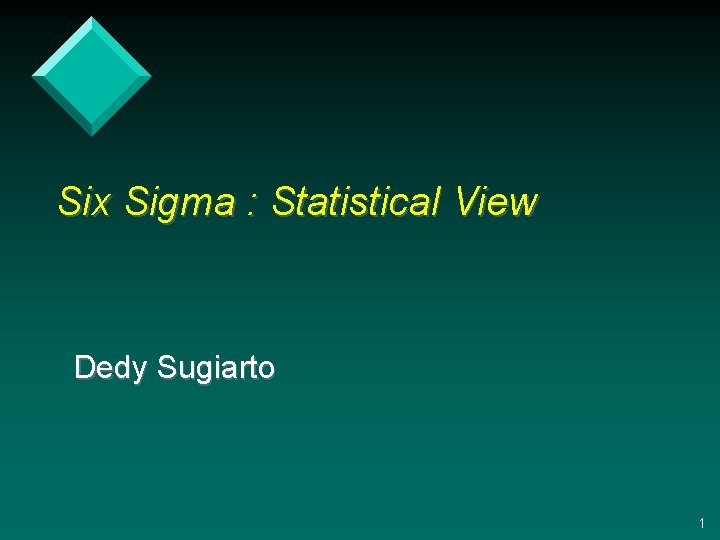

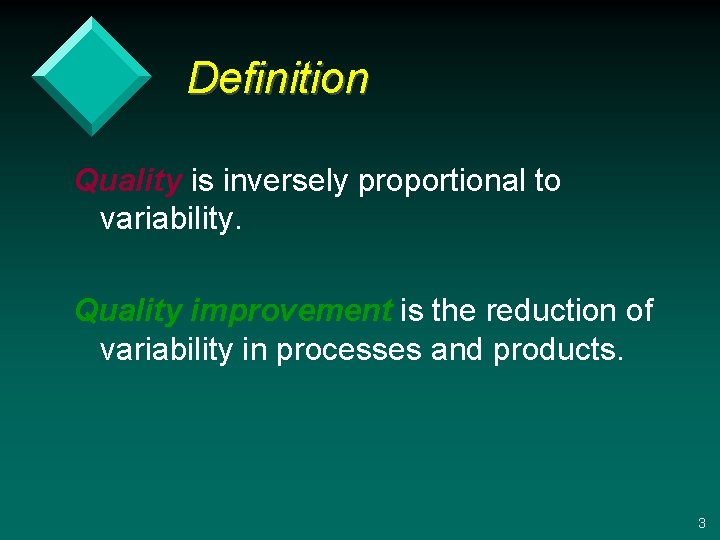
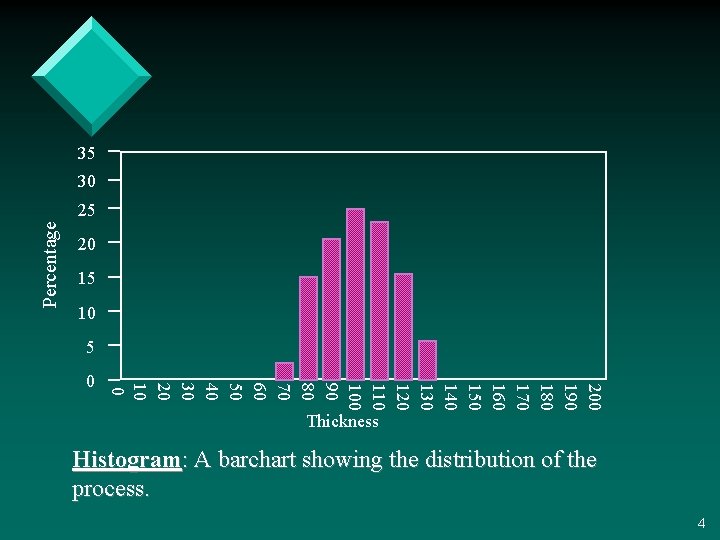
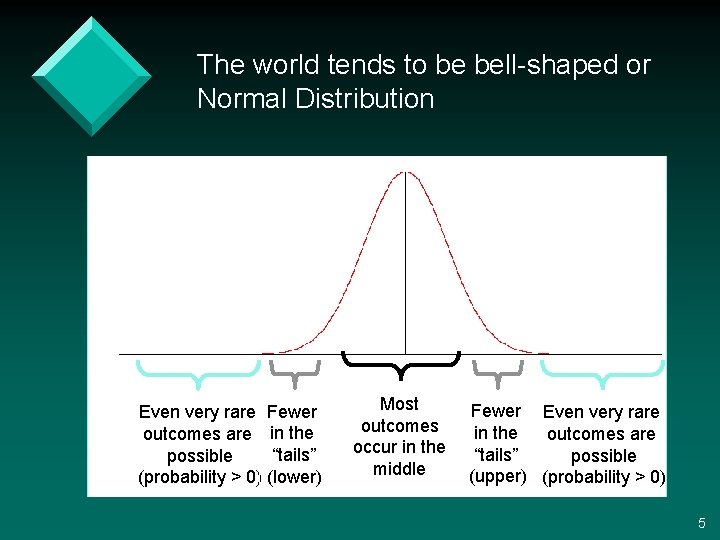
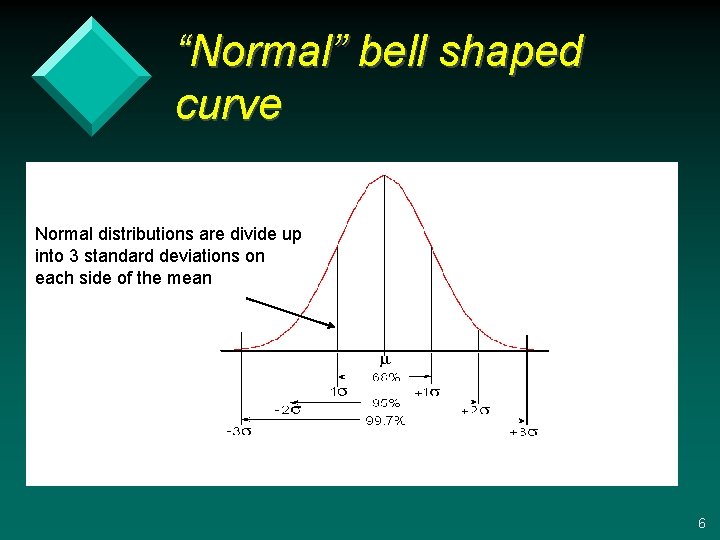
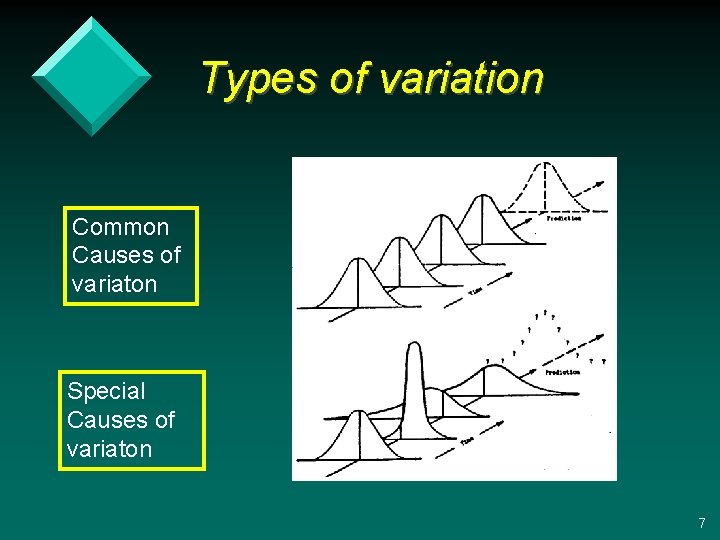
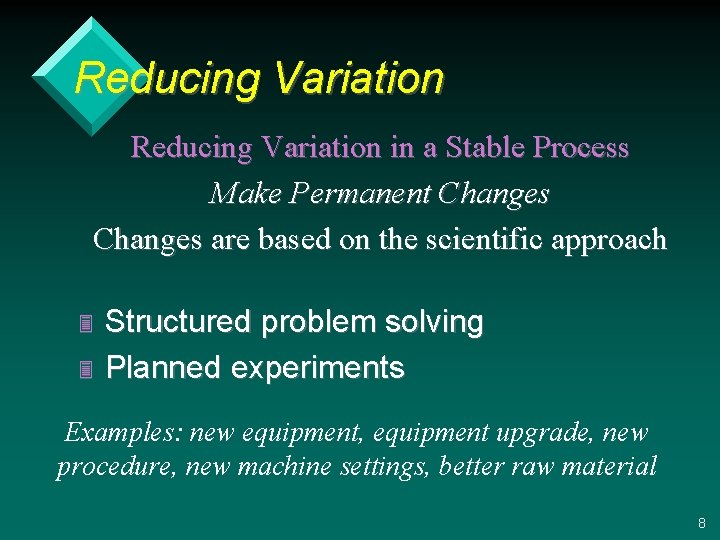
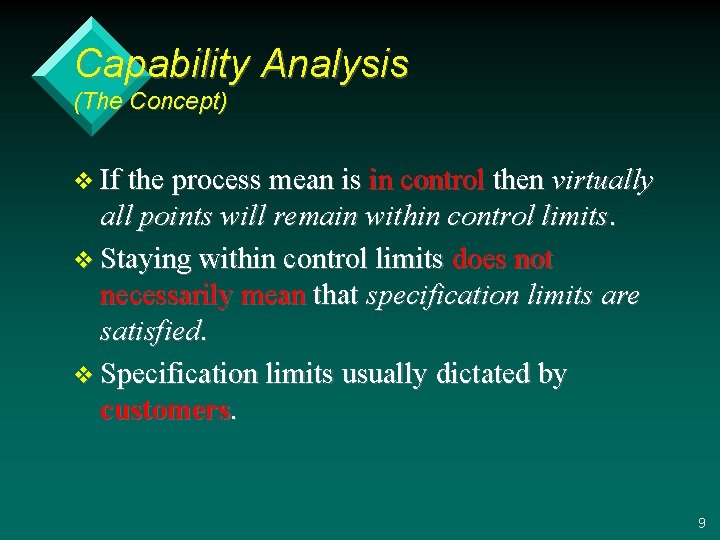
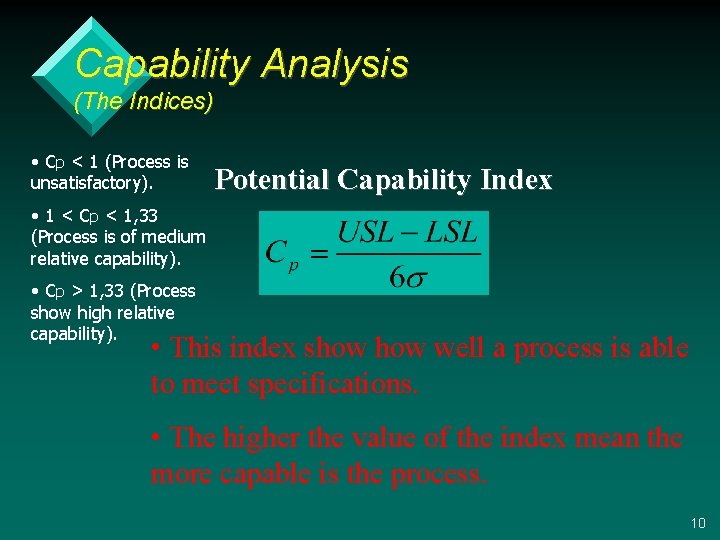
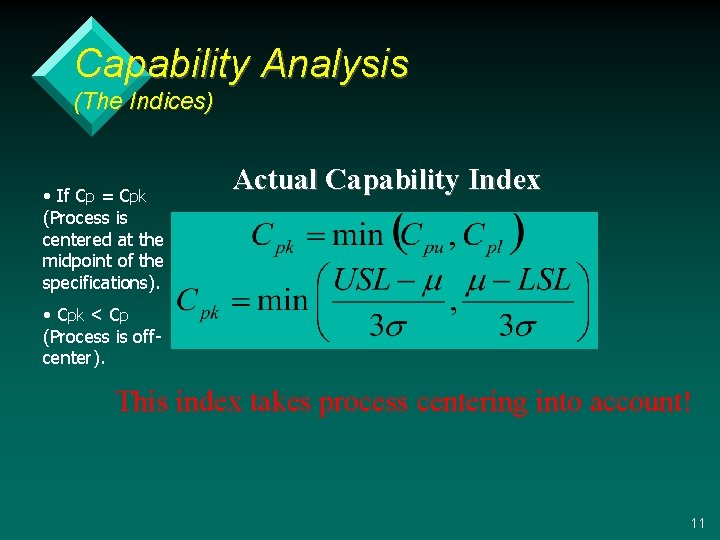
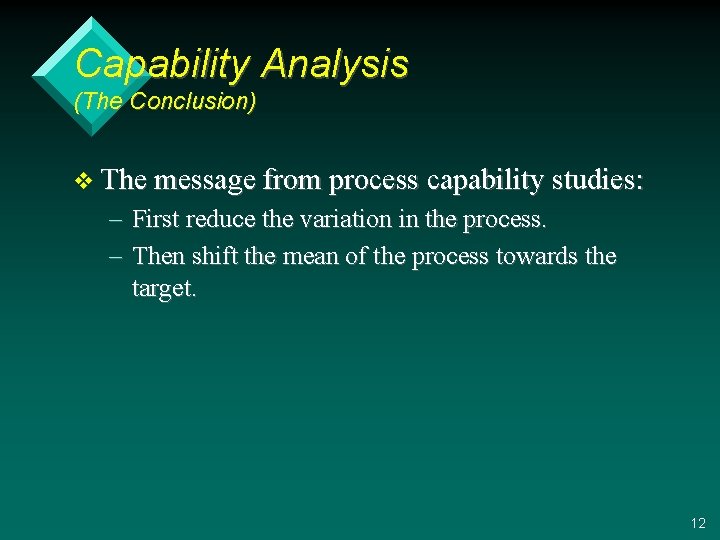
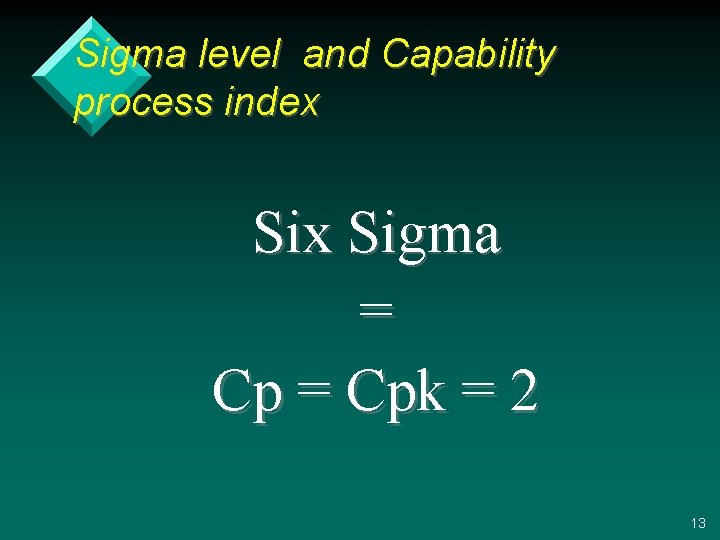
- Slides: 13
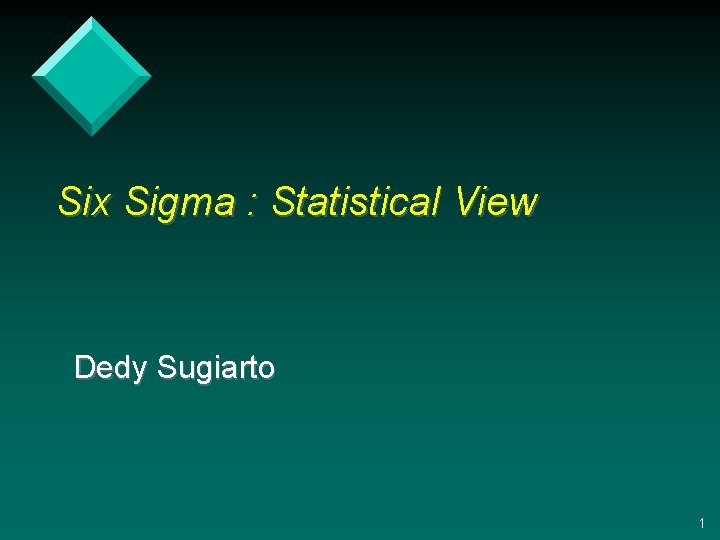
Six Sigma : Statistical View Dedy Sugiarto 1

What is Variation? Less Variation = Higher Quality 2
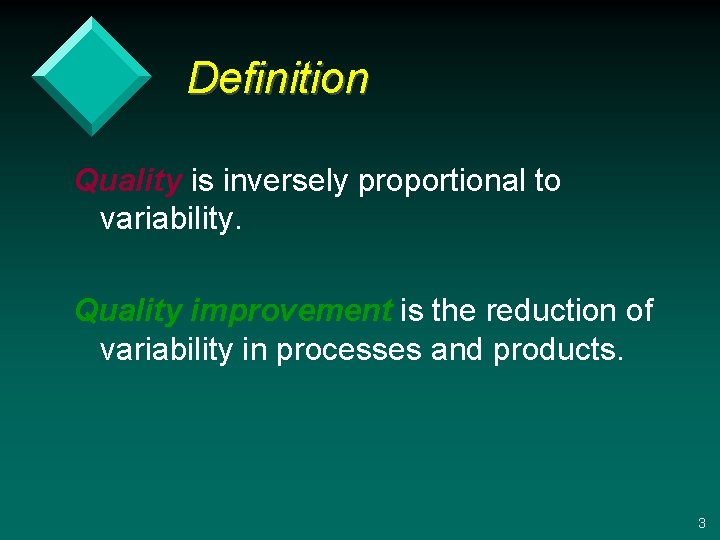
Definition Quality is inversely proportional to variability. Quality improvement is the reduction of variability in processes and products. 3
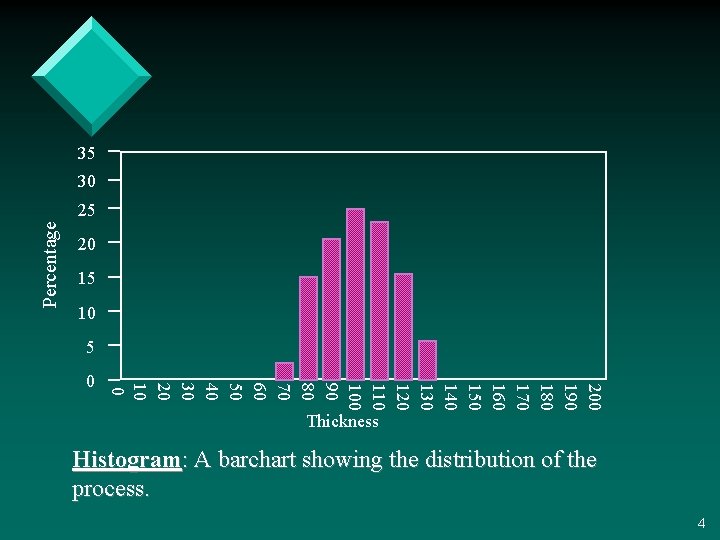
35 30 Percentage 25 20 15 10 5 200 190 180 170 160 150 140 130 120 110 100 90 80 70 60 50 40 30 20 10 0 0 Thickness Histogram: A barchart showing the distribution of the process. 4
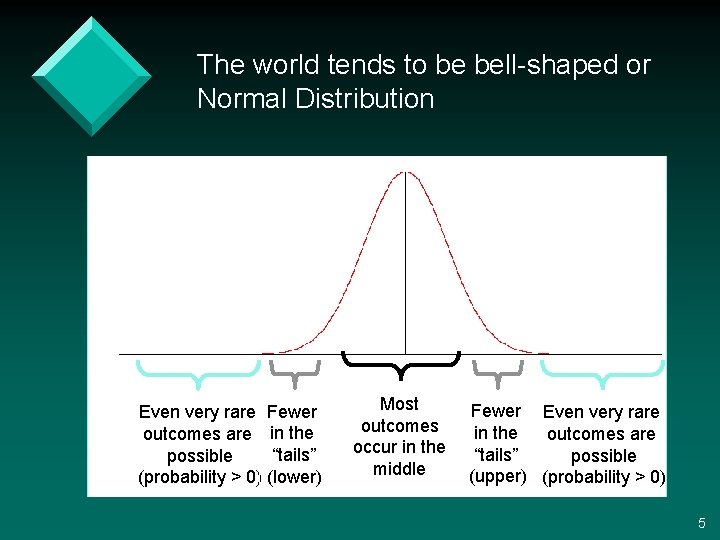
The world tends to be bell-shaped or Normal Distribution Even very rare Fewer outcomes are in the “tails” possible (probability > 0) (lower) Most outcomes occur in the middle Fewer Even very rare in the outcomes are “tails” possible (upper) (probability > 0) 5
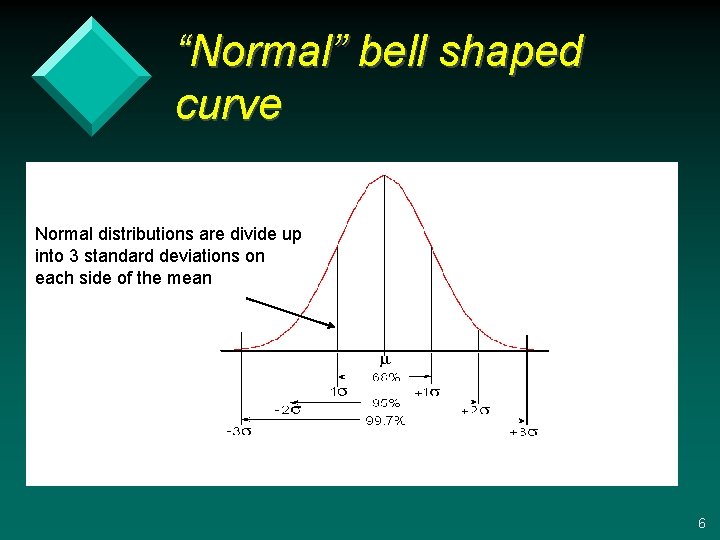
“Normal” bell shaped curve Normal distributions are divide up into 3 standard deviations on each side of the mean 6
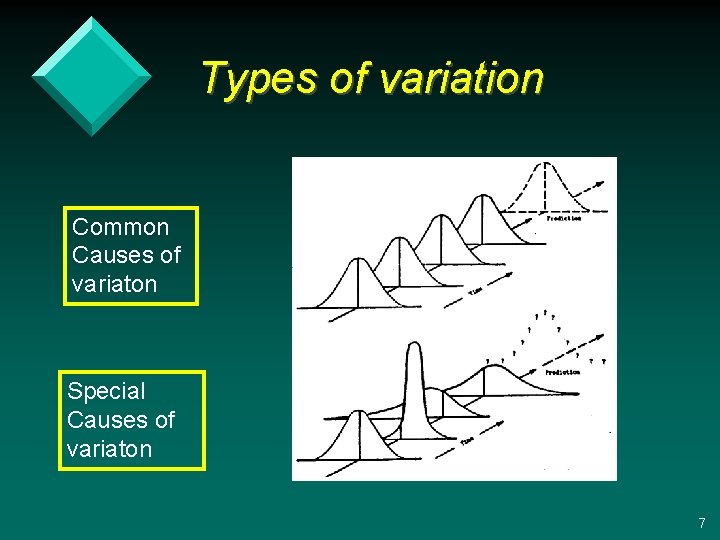
Types of variation Common Causes of variaton Special Causes of variaton 7
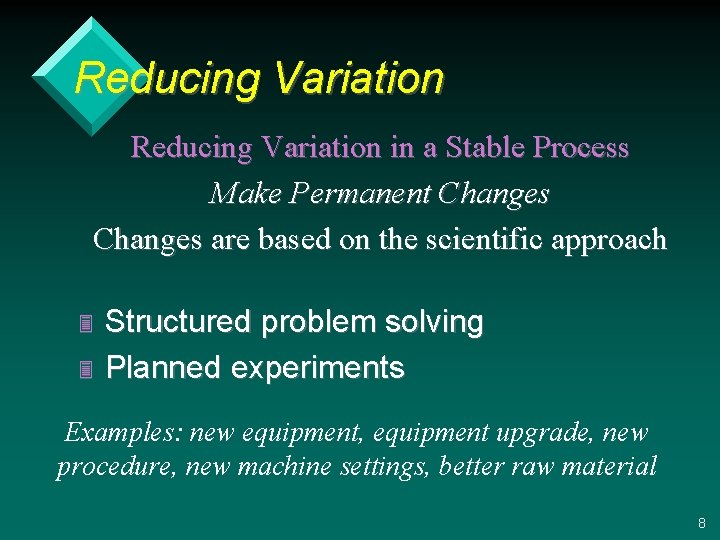
Reducing Variation in a Stable Process Make Permanent Changes are based on the scientific approach Structured problem solving 3 Planned experiments 3 Examples: new equipment, equipment upgrade, new procedure, new machine settings, better raw material 8
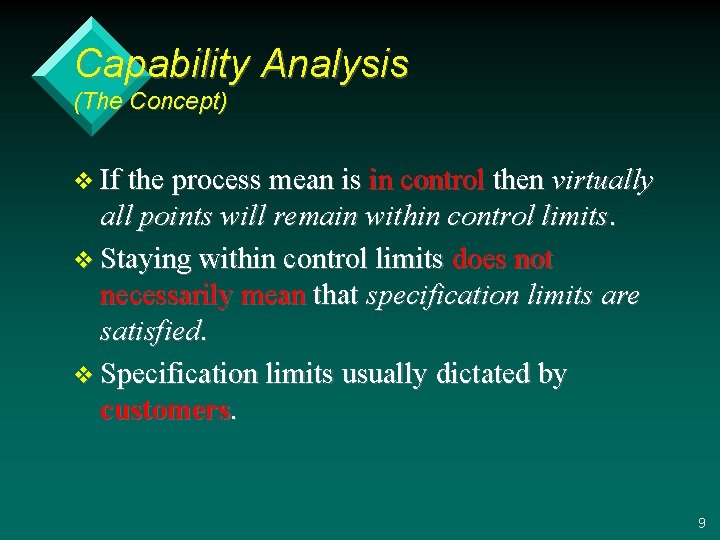
Capability Analysis (The Concept) v If the process mean is in control then virtually all points will remain within control limits. v Staying within control limits does not necessarily mean that specification limits are satisfied. v Specification limits usually dictated by customers. 9
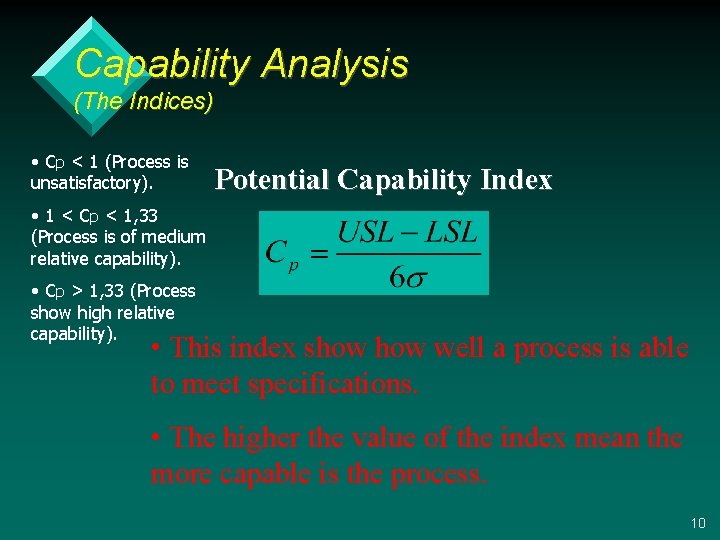
Capability Analysis (The Indices) • Cp < 1 (Process is unsatisfactory). Potential Capability Index • 1 < Cp < 1, 33 (Process is of medium relative capability). • Cp > 1, 33 (Process show high relative capability). • This index show well a process is able to meet specifications. • The higher the value of the index mean the more capable is the process. 10
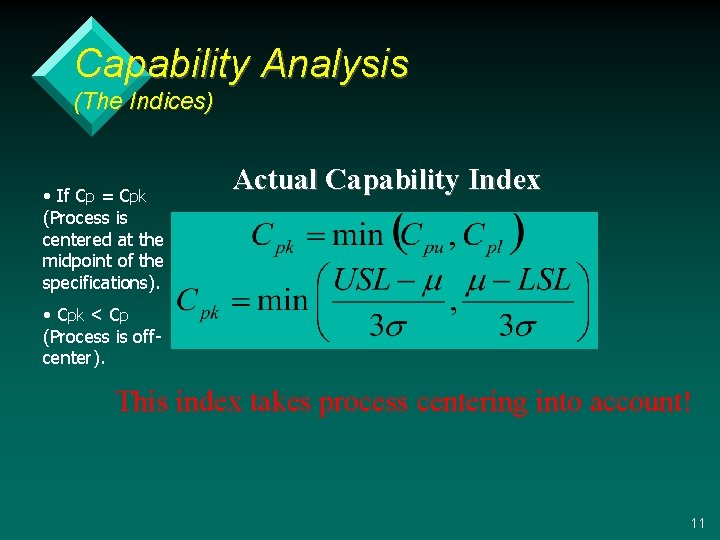
Capability Analysis (The Indices) • If Cp = Cpk (Process is centered at the midpoint of the specifications). Actual Capability Index • Cpk < Cp (Process is offcenter). This index takes process centering into account! 11
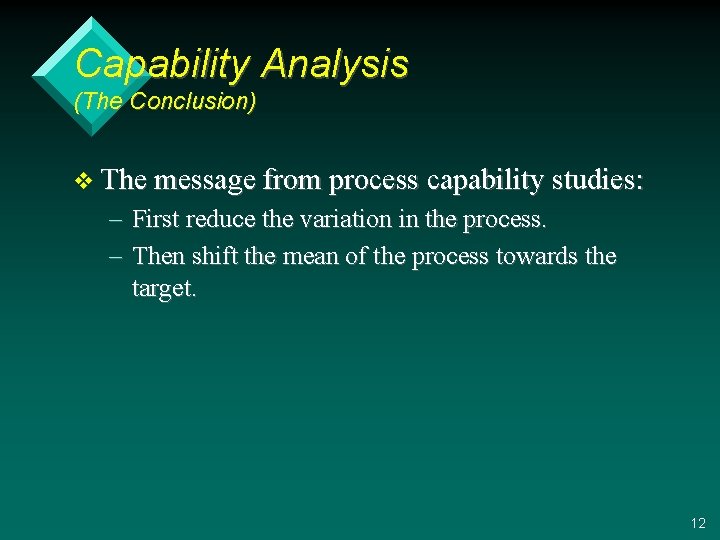
Capability Analysis (The Conclusion) v The message from process capability studies: – First reduce the variation in the process. – Then shift the mean of the process towards the target. 12
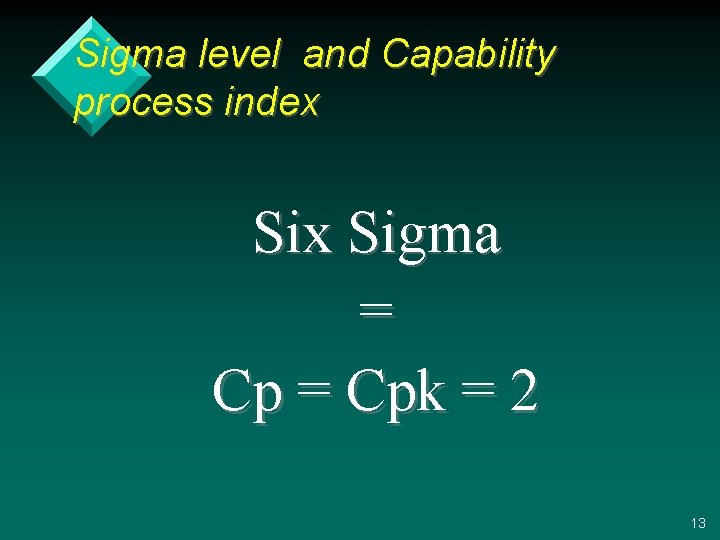
Sigma level and Capability process index Sigma = Cpk = 2 13