Simulation of Swelling Radiation Damage in Targets Sujit
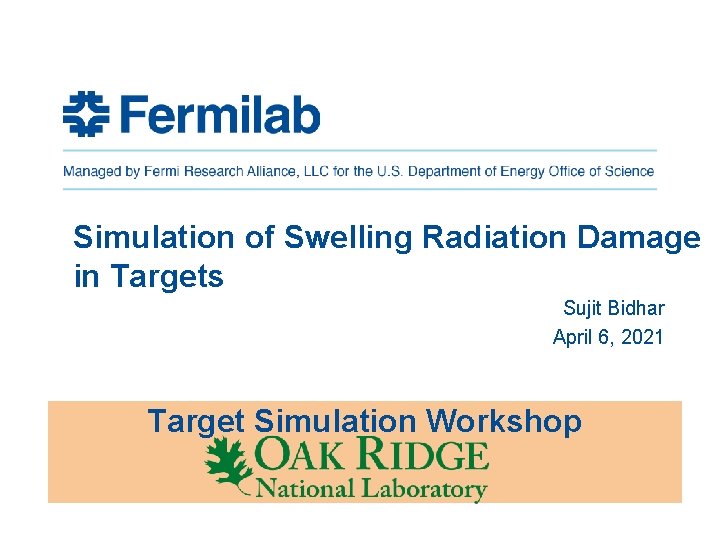
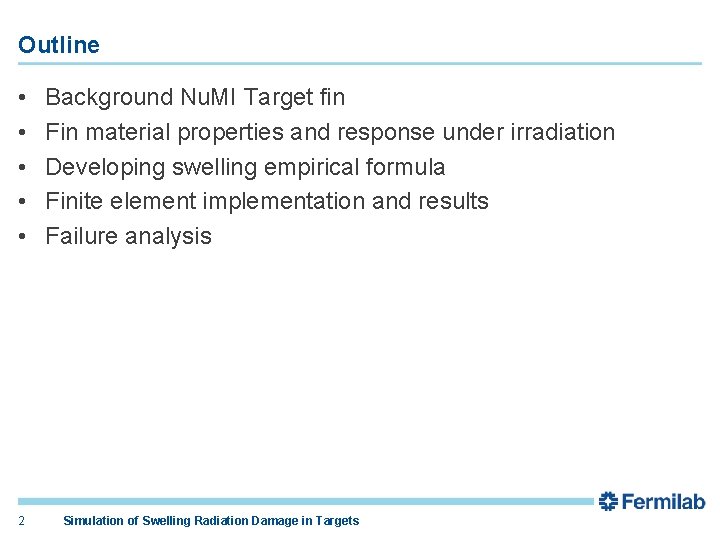

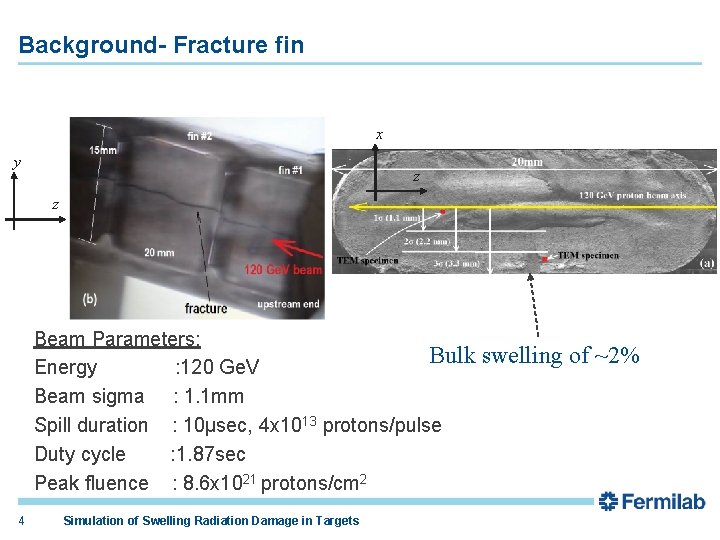
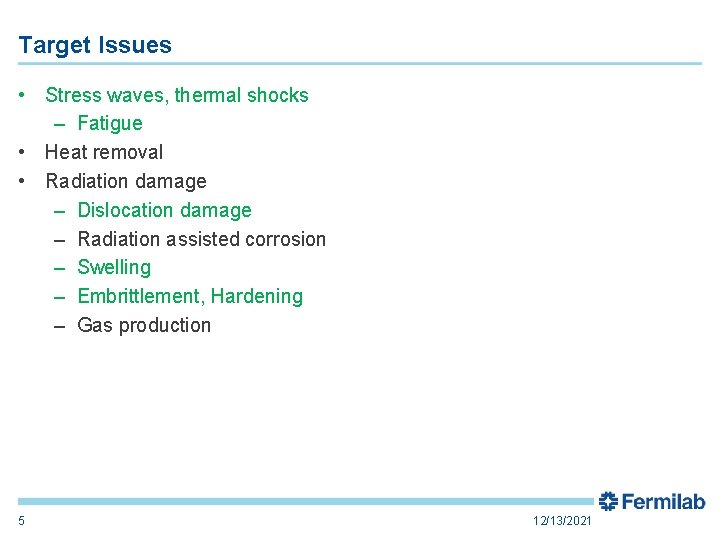
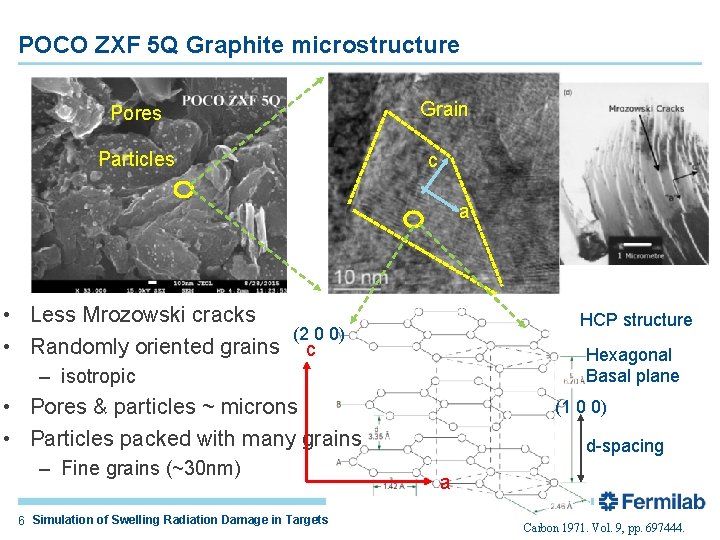
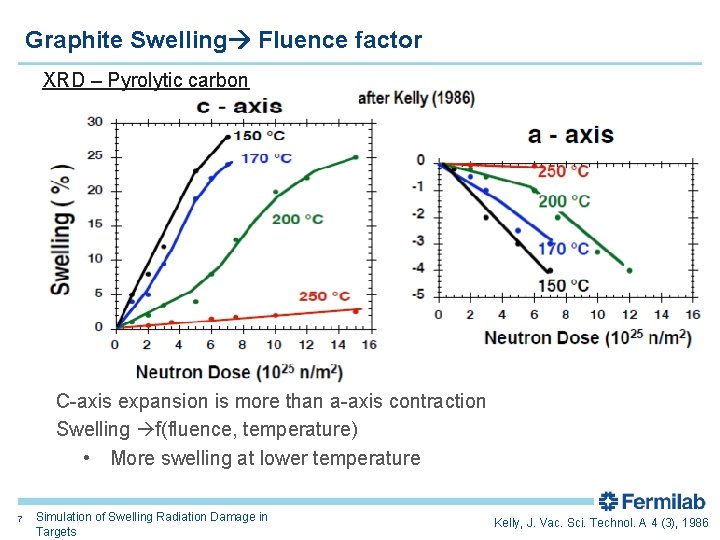
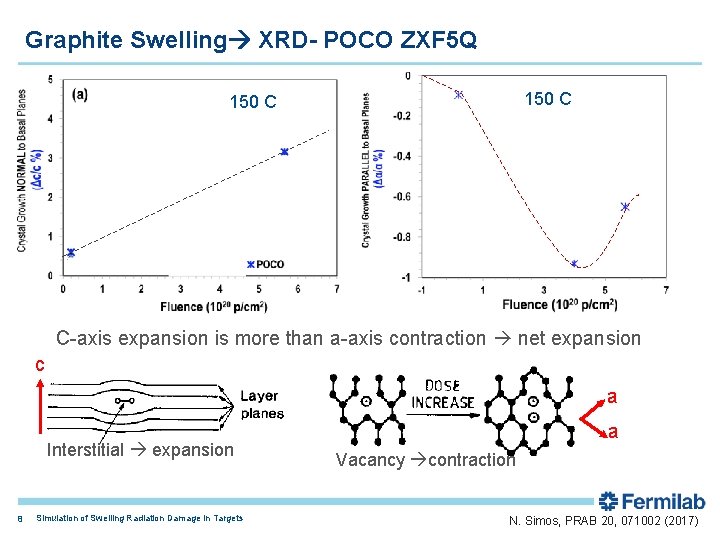
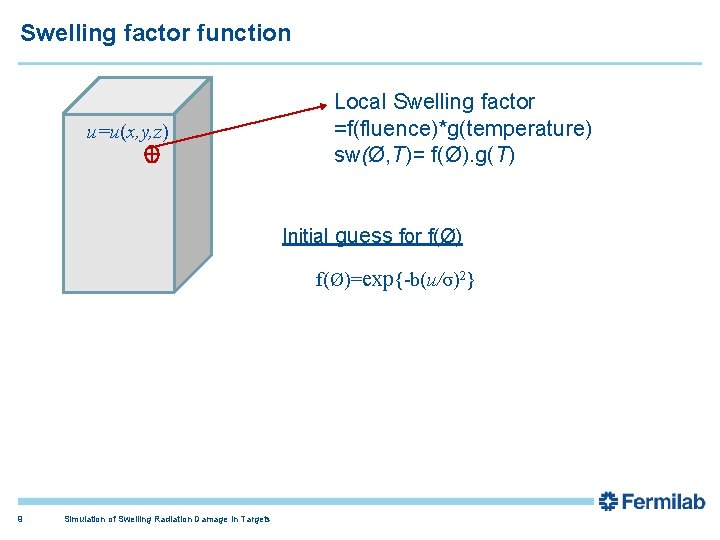
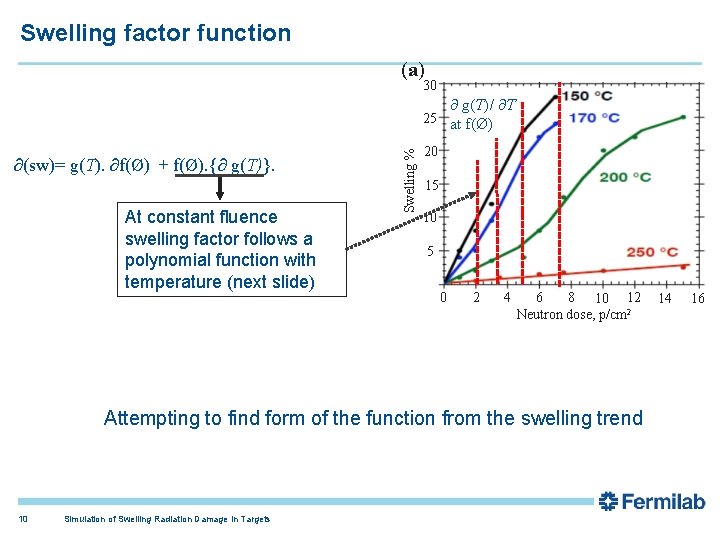
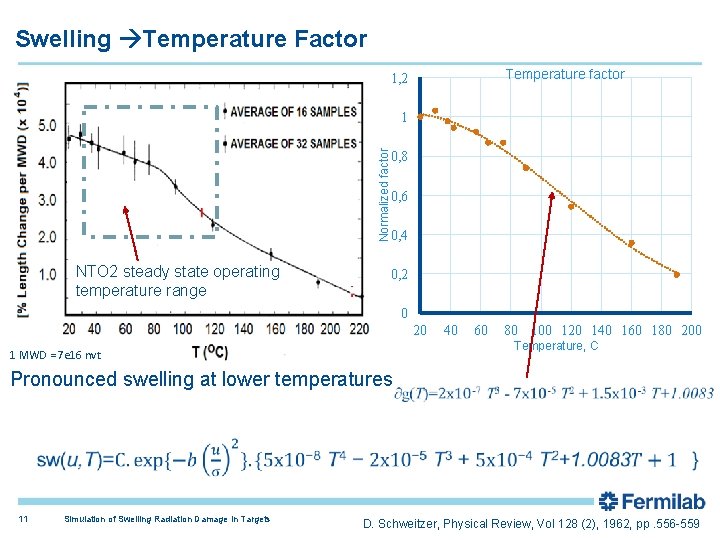
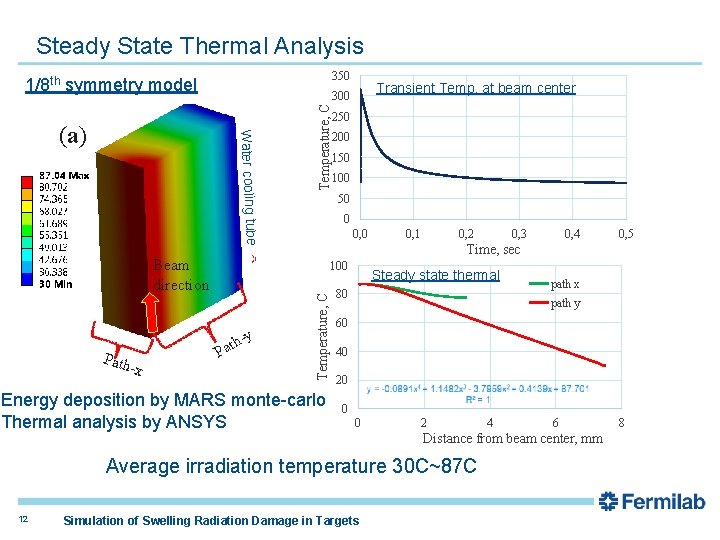
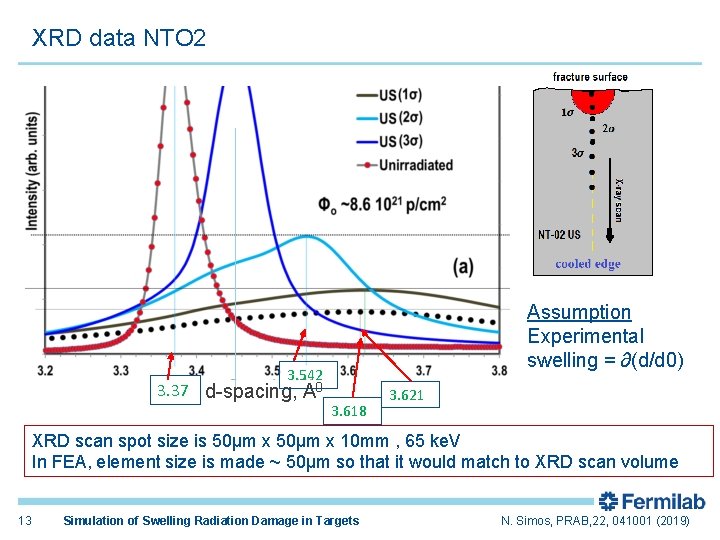
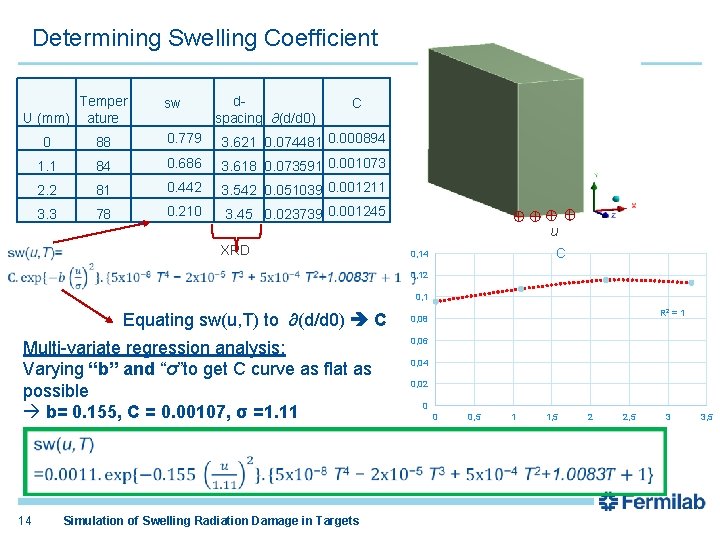
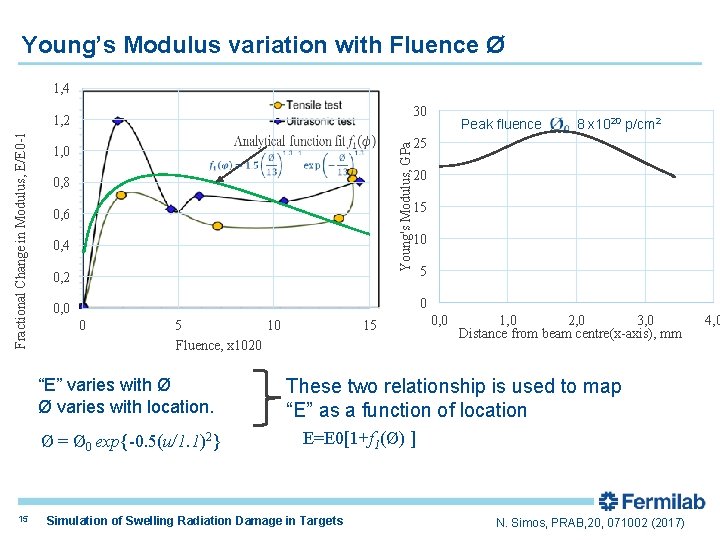
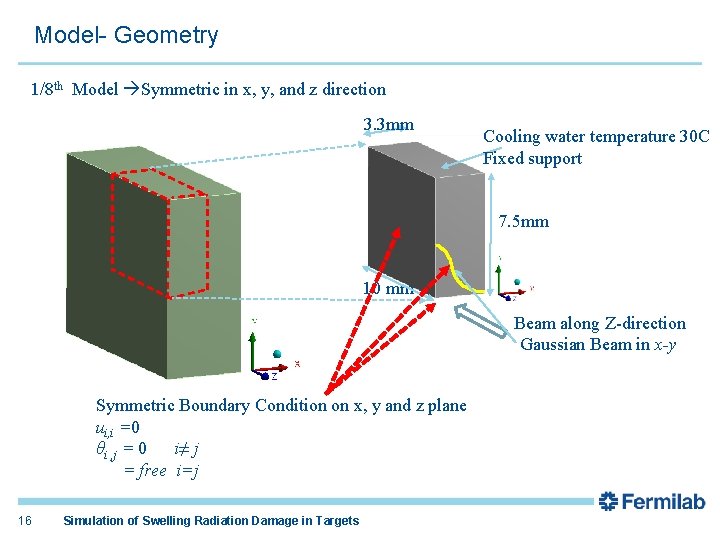
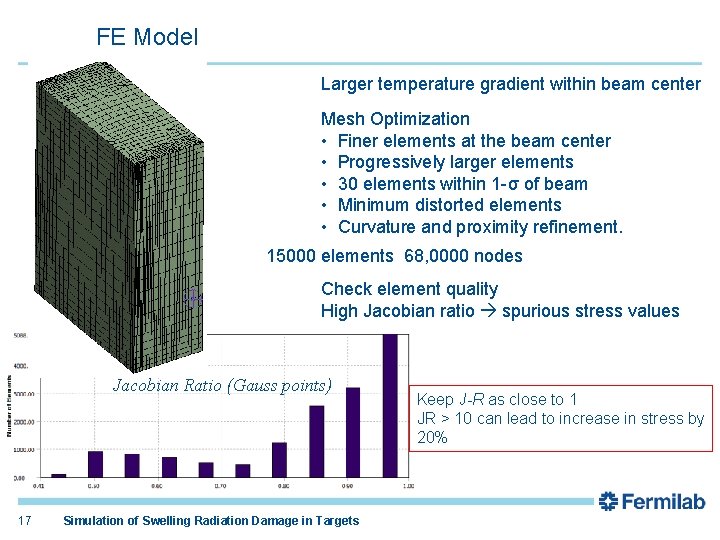
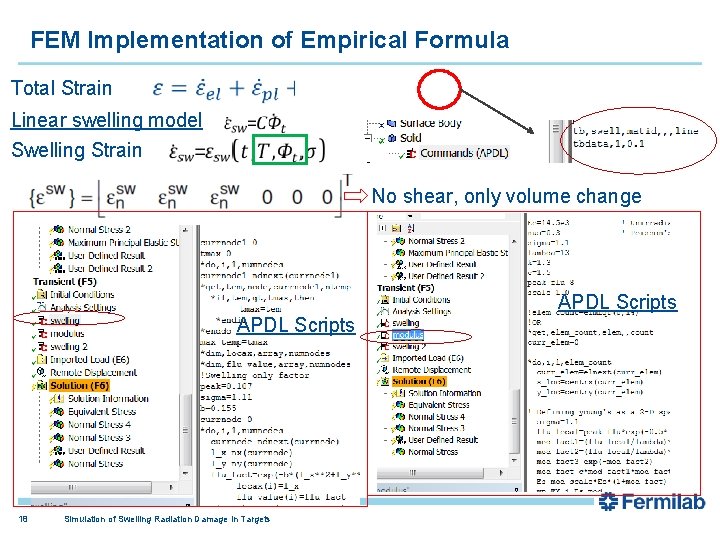
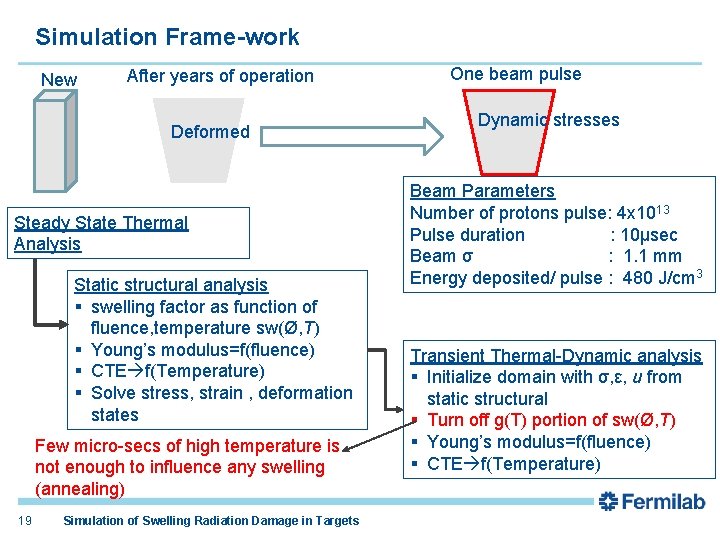
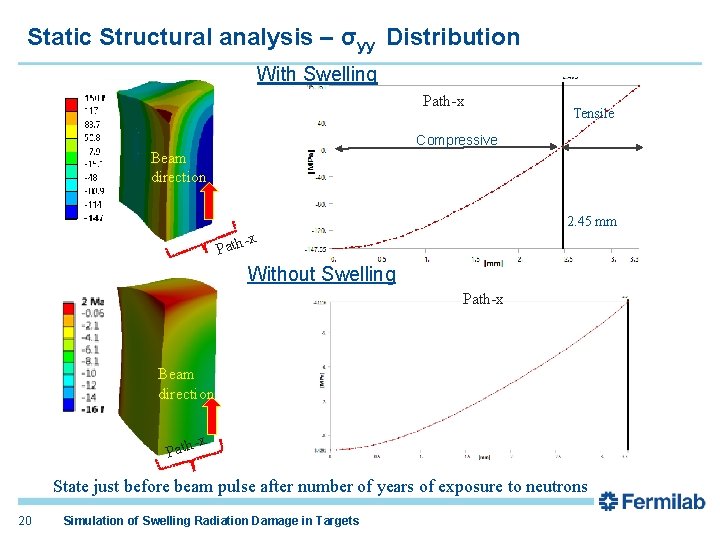
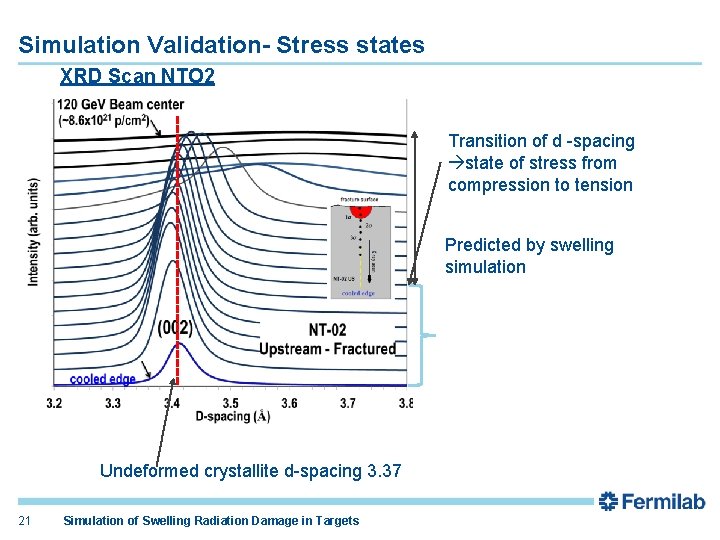
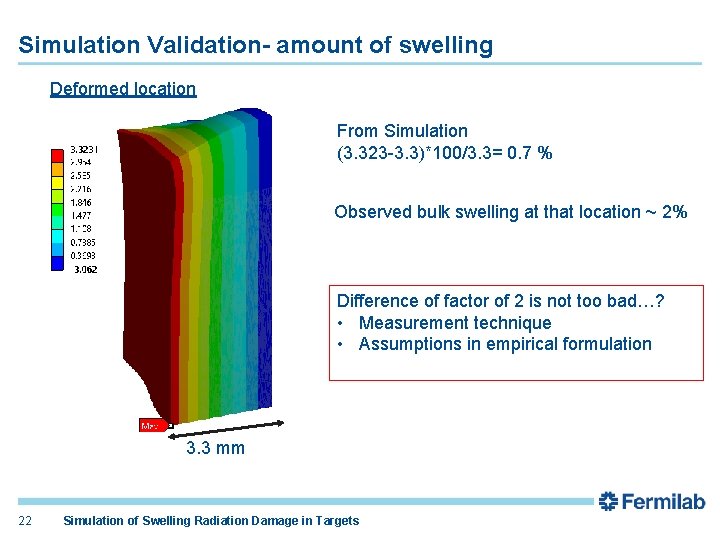
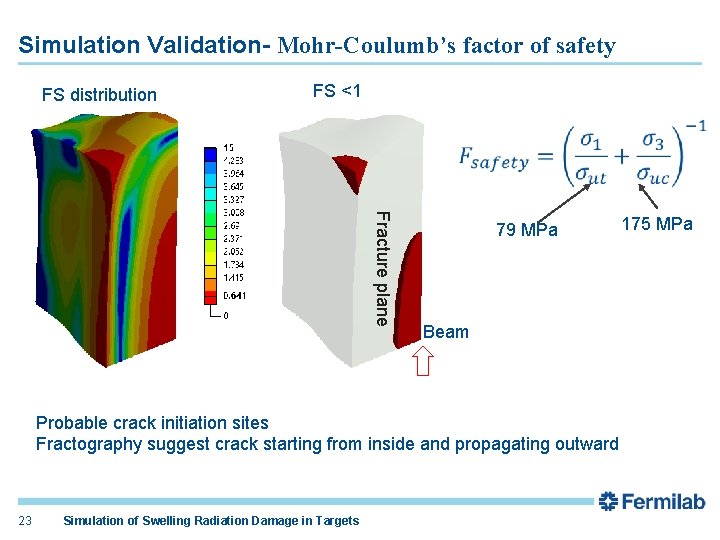
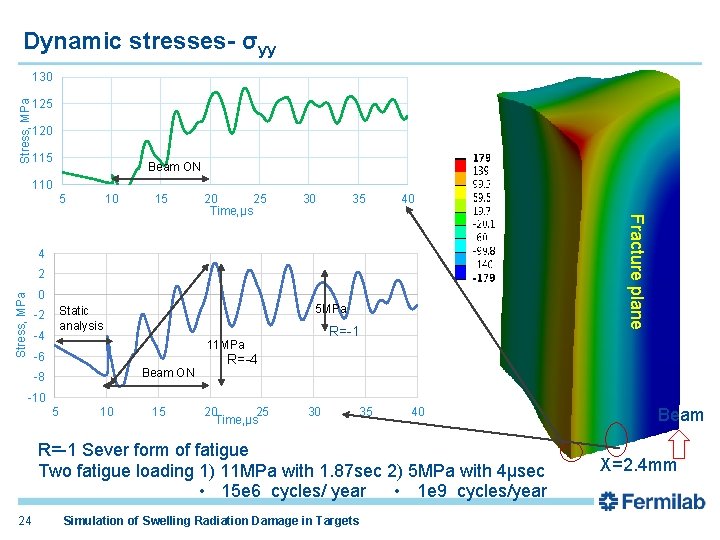
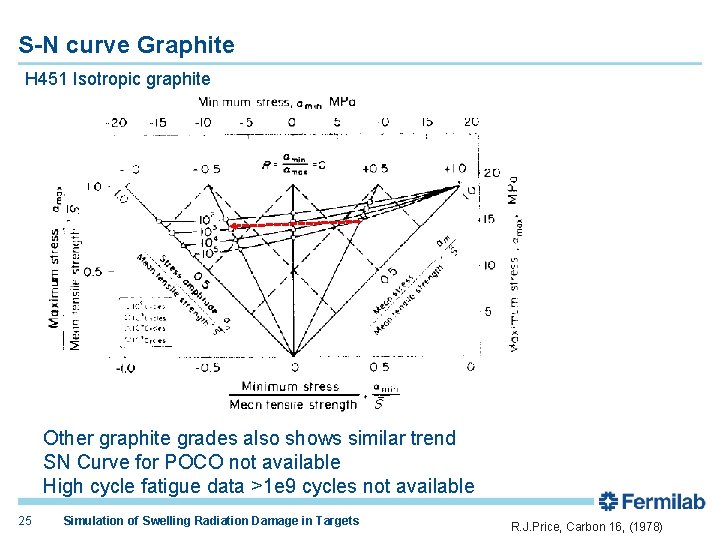
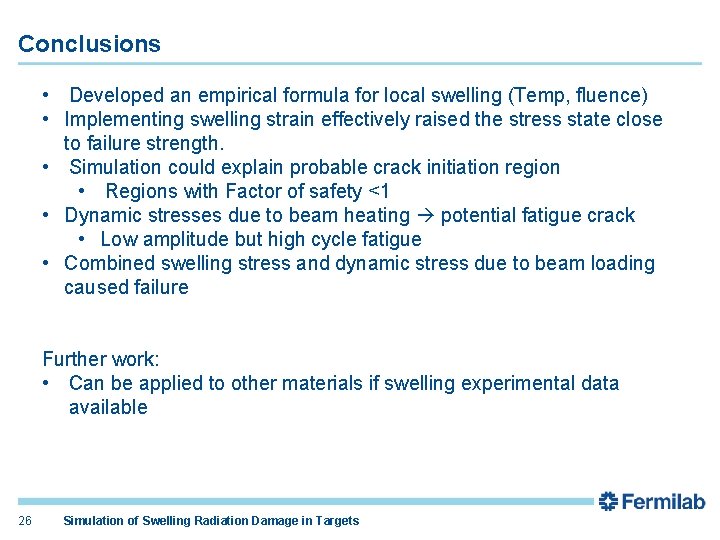
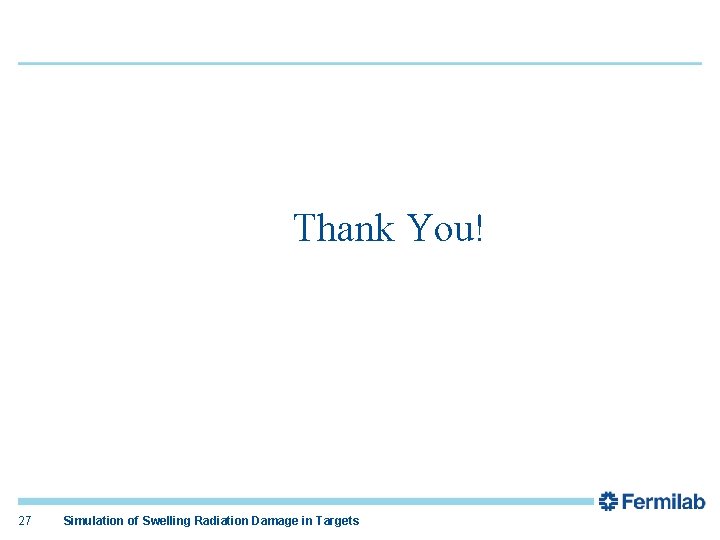
- Slides: 27
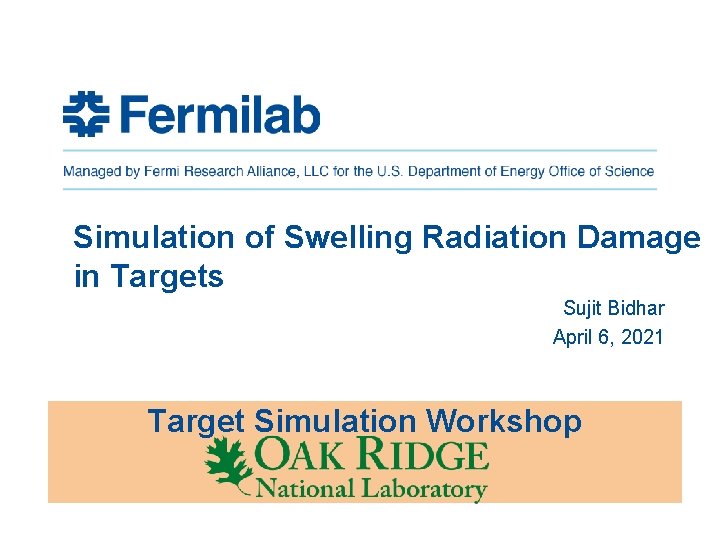
Simulation of Swelling Radiation Damage in Targets Sujit Bidhar April 6, 2021 Target Simulation Workshop
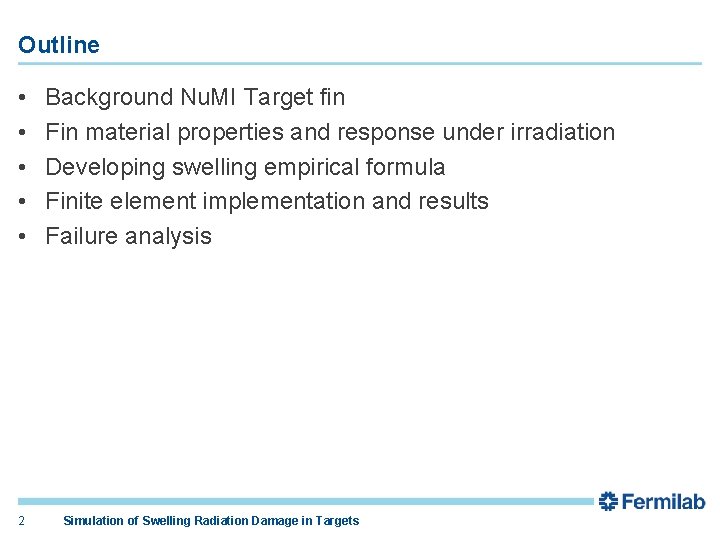
Outline • • • 2 Background Nu. MI Target fin Fin material properties and response under irradiation Developing swelling empirical formula Finite element implementation and results Failure analysis Simulation of Swelling Radiation Damage in Targets

Background- Nu. MI Target Fin 95 cm Segmented Fins- 47 pieces Material : POCO ZXF 5 Q graphite Isotropic 3 Simulation of Swelling Radiation Damage in Targets Individual target fin 20 mm x 15 mm x 6. 6 mm
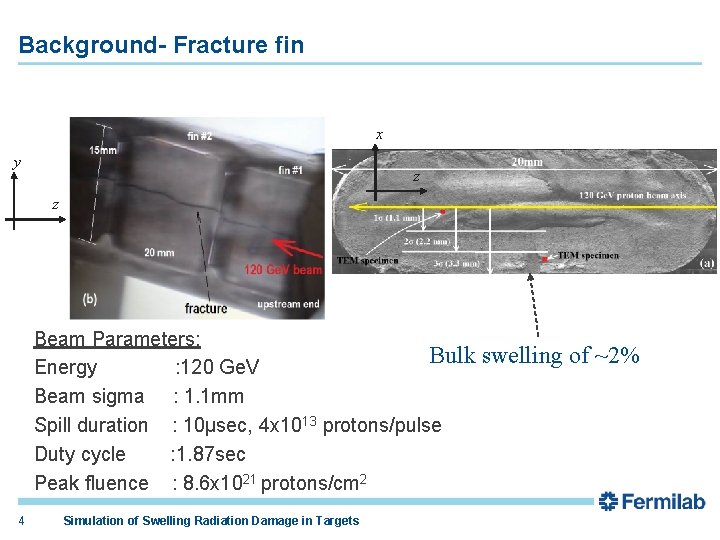
Background- Fracture fin x y z z Beam Parameters: Bulk Energy : 120 Ge. V Beam sigma : 1. 1 mm Spill duration : 10µsec, 4 x 1013 protons/pulse Duty cycle : 1. 87 sec Peak fluence : 8. 6 x 1021 protons/cm 2 4 Simulation of Swelling Radiation Damage in Targets swelling of ~2%
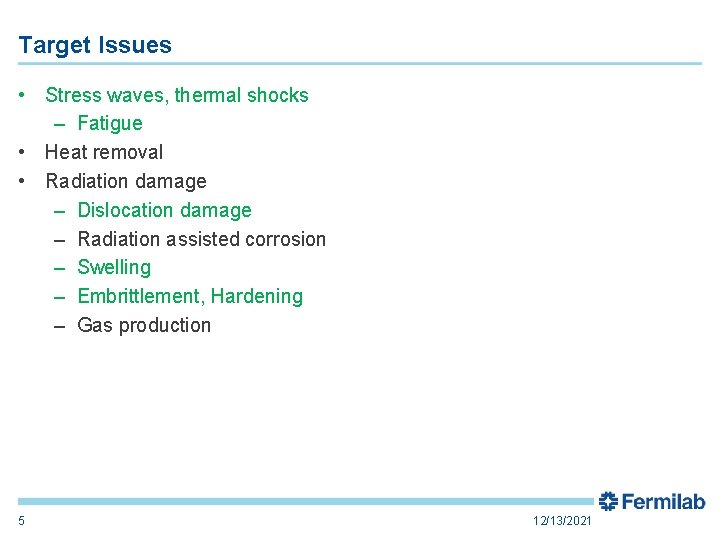
Target Issues • Stress waves, thermal shocks – Fatigue • Heat removal • Radiation damage – Dislocation damage – Radiation assisted corrosion – Swelling – Embrittlement, Hardening – Gas production 5 12/13/2021
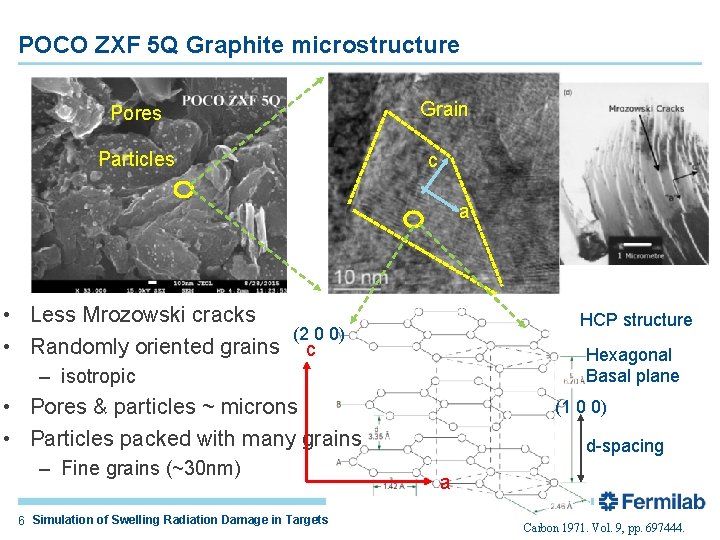
POCO ZXF 5 Q Graphite microstructure Grain Pores Particles c a • Less Mrozowski cracks • Randomly oriented grains HCP structure (2 0 0) c Hexagonal Basal plane – isotropic • Pores & particles ~ microns • Particles packed with many grains – Fine grains (~30 nm) 6 Simulation of Swelling Radiation Damage in Targets (1 0 0) d-spacing a Carbon 1971. Vol. 9, pp. 697444.
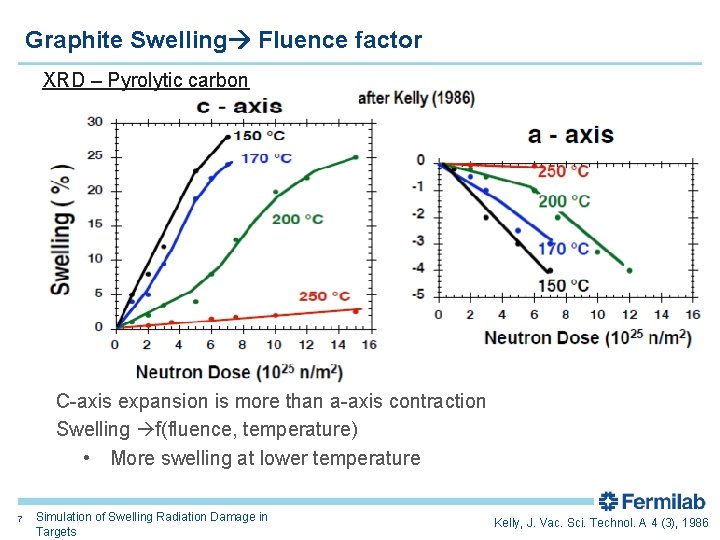
Graphite Swelling Fluence factor XRD – Pyrolytic carbon C-axis expansion is more than a-axis contraction Swelling f(fluence, temperature) • More swelling at lower temperature 7 Simulation of Swelling Radiation Damage in Targets Kelly, J. Vac. Sci. Technol. A 4 (3), 1986
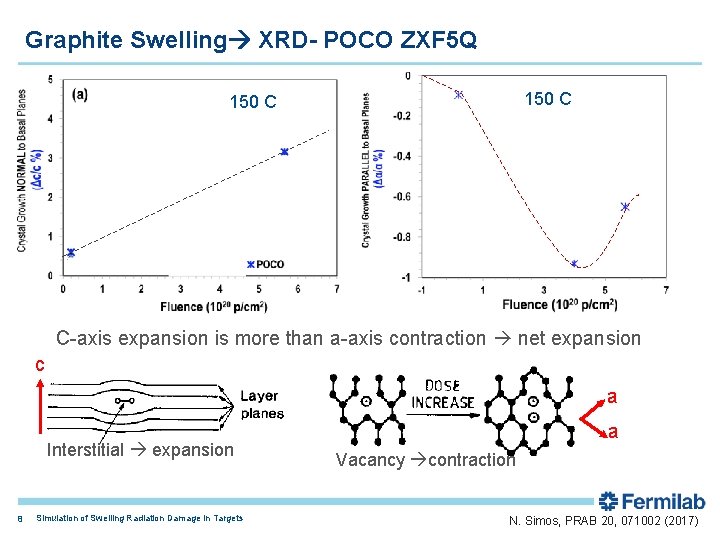
Graphite Swelling XRD- POCO ZXF 5 Q 150 C C-axis expansion is more than a-axis contraction net expansion c a Interstitial expansion 8 Simulation of Swelling Radiation Damage in Targets a Vacancy contraction N. Simos, PRAB 20, 071002 (2017)
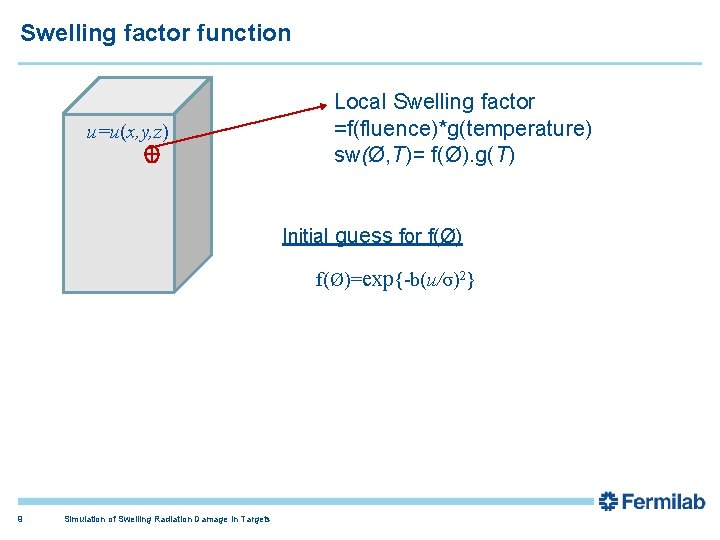
Swelling factor function u=u(x, y, z) Local Swelling factor =f(fluence)*g(temperature) sw(Ø, T)= f(Ø). g(T) Initial guess for f(Ø)=exp{-b(u/σ)2} 9 Simulation of Swelling Radiation Damage in Targets
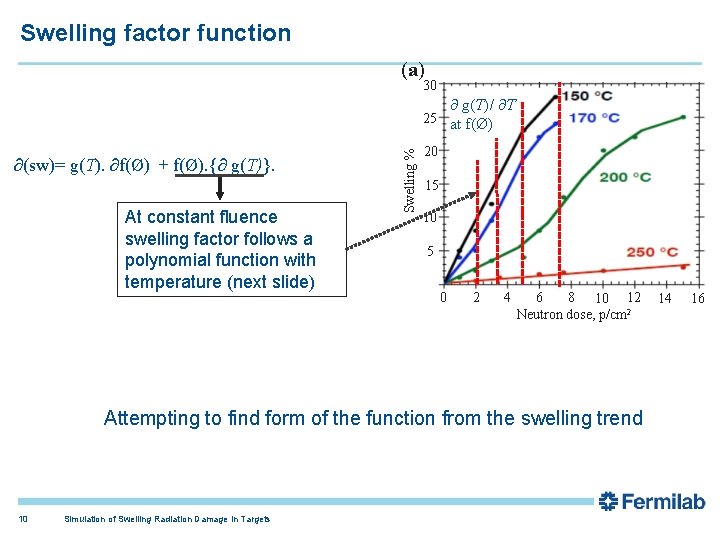
Swelling factor function (a) 30 ∂ g(T)/ ∂T ∂(sw)= g(T). ∂f(Ø) + f(Ø). {∂ g(T)}. At constant fluence swelling factor follows a polynomial function with temperature (next slide) Swelling % 25 at f(Ø) 20 15 10 5 0 2 4 6 8 10 12 Neutron dose, p/cm 2 Attempting to find form of the function from the swelling trend 10 Simulation of Swelling Radiation Damage in Targets 14 16
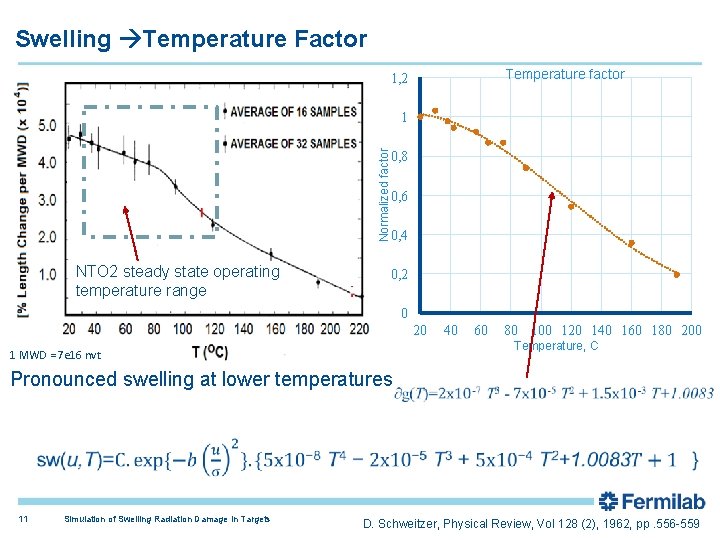
Swelling Temperature Factor Temperature factor 1, 2 Normalized factor 1 NTO 2 steady state operating temperature range 0, 8 0, 6 0, 4 0, 2 0 20 40 60 80 100 120 140 160 180 200 Temperature, C 1 MWD = 7 e 16 nvt Pronounced swelling at lower temperatures 11 Simulation of Swelling Radiation Damage in Targets D. Schweitzer, Physical Review, Vol 128 (2), 1962, pp. 556 -559
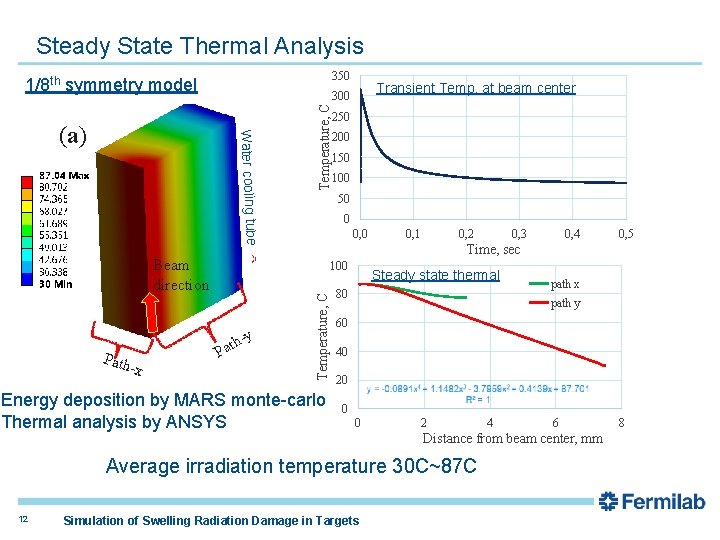
Steady State Thermal Analysis 350 1/8 th symmetry model Temperature, C Water cooling tube (a) 200 150 100 0 0, 0 Temperature, C th Pa 0, 1 0, 2 Energy deposition by MARS monte-carlo Thermal analysis by ANSYS Steady state thermal 80 0, 4 0, 5 path x path y 60 40 20 0 0 2 Simulation of Swelling Radiation Damage in Targets 4 6 Distance from beam center, mm Average irradiation temperature 30 C~87 C 12 0, 3 Time, sec 100 -y -x 250 50 Beam direction Path Transient Temp. at beam center 300 8
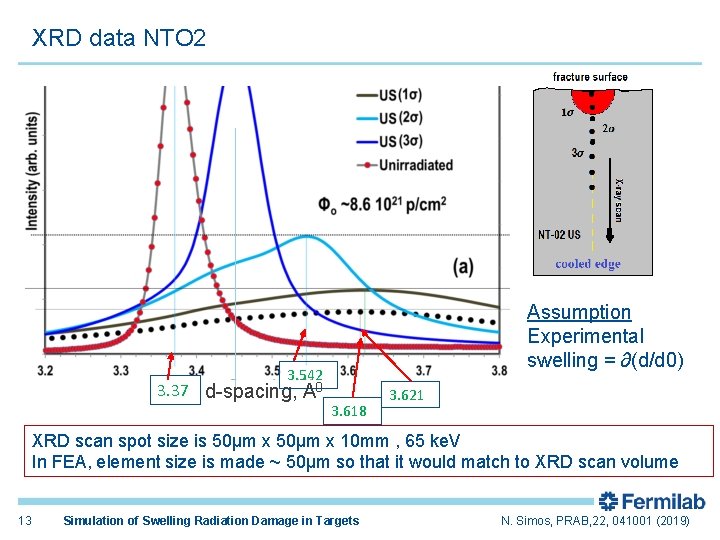
XRD data NTO 2 Assumption Experimental swelling = ∂(d/d 0) 3. 542 3. 37 d-spacing, A 0 3. 618 3. 621 XRD scan spot size is 50µm x 10 mm , 65 ke. V In FEA, element size is made ~ 50µm so that it would match to XRD scan volume 13 Simulation of Swelling Radiation Damage in Targets N. Simos, PRAB, 22, 041001 (2019)
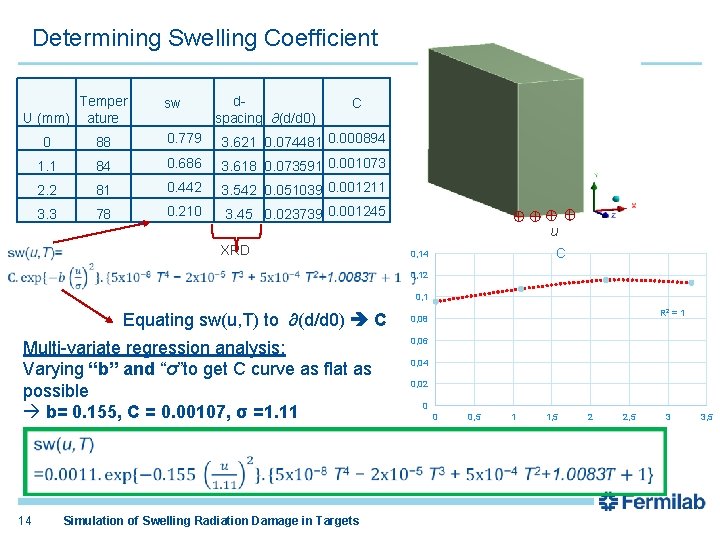
Determining Swelling Coefficient Temper U (mm) ature sw 0 88 0. 779 1. 1 84 0. 686 2. 2 81 0. 442 3. 3 78 0. 210 dspacing ∂(d/d 0) C 3. 621 0. 074481 0. 000894 3. 618 0. 073591 0. 001073 3. 542 0. 051039 0. 001211 3. 45 0. 023739 0. 001245 Equating sw(u, T) to ∂(d/d 0) C
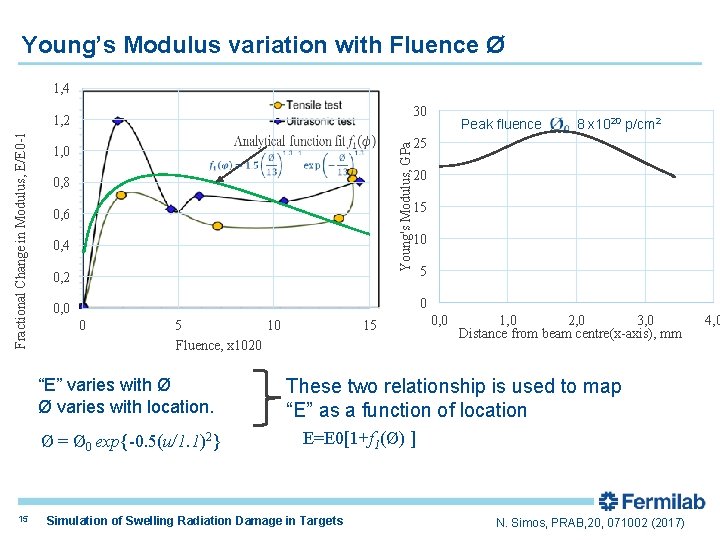
Young’s Modulus variation with Fluence Ø 1, 4 30 Young's Modulus, GPa Fractional Change in Modulus, E/E 0 -1 1, 2 1, 0 0, 8 0, 6 0, 4 0, 2 8 x 1020 p/cm 2 25 20 15 10 5 0 0, 0 0 5 10 Fluence, x 1020 “E” varies with Ø Ø varies with location. Ø = Ø 0 exp{-0. 5(u/1. 1)2} 15 Peak fluence 15 0, 0 1, 0 2, 0 3, 0 Distance from beam centre(x-axis), mm These two relationship is used to map “E” as a function of location E=E 0[1+f 1(Ø) ] Simulation of Swelling Radiation Damage in Targets N. Simos, PRAB, 20, 071002 (2017) 4, 0
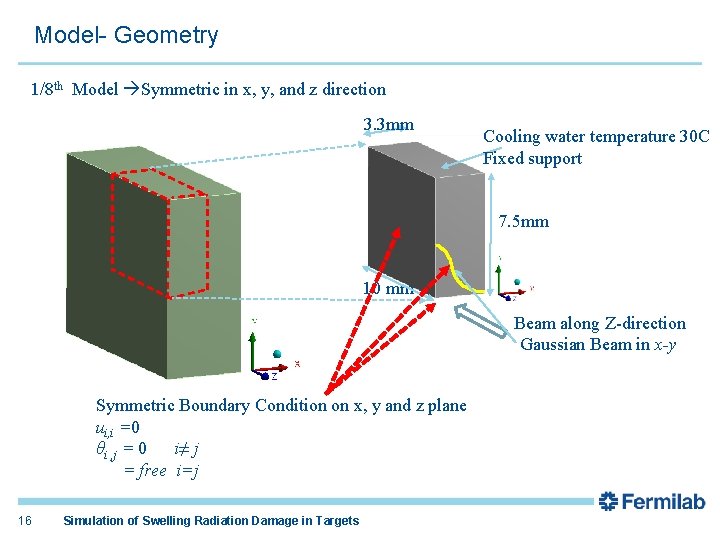
Model- Geometry 1/8 th Model Symmetric in x, y, and z direction 3. 3 mm Cooling water temperature 30 C Fixed support 7. 5 mm 10 mm Beam along Z-direction Gaussian Beam in x-y Symmetric Boundary Condition on x, y and z plane ui, i =0 θi , j = 0 i≠ j = free i=j 16 Simulation of Swelling Radiation Damage in Targets
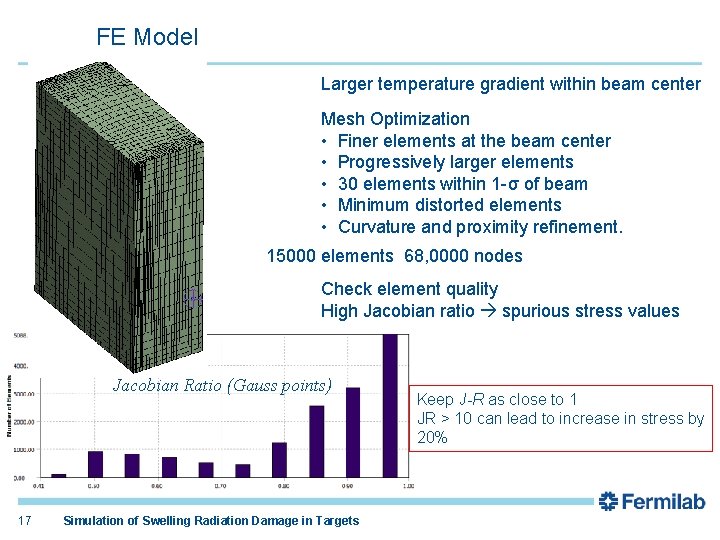
FE Model Larger temperature gradient within beam center Mesh Optimization • Finer elements at the beam center • Progressively larger elements • 30 elements within 1 -σ of beam • Minimum distorted elements • Curvature and proximity refinement. 15000 elements 68, 0000 nodes Check element quality High Jacobian ratio spurious stress values Jacobian Ratio (Gauss points) 17 Simulation of Swelling Radiation Damage in Targets Keep J-R as close to 1 JR > 10 can lead to increase in stress by 20%
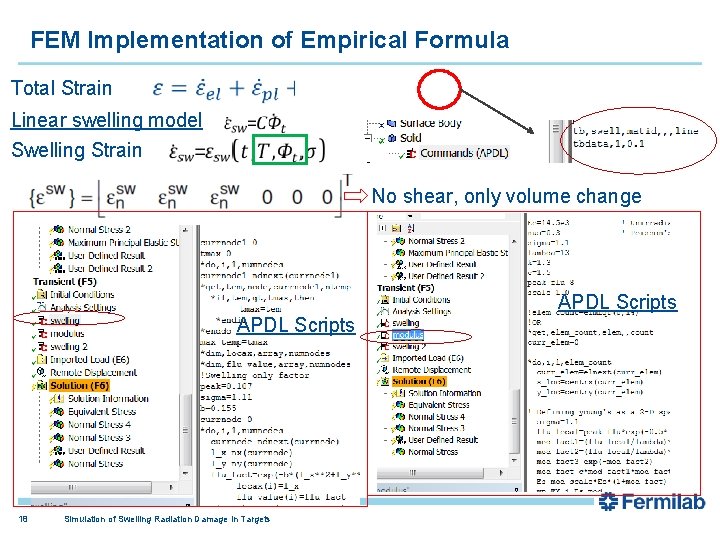
FEM Implementation of Empirical Formula Total Strain Linear swelling model Swelling Strain No shear, only volume change APDL Scripts 18 Simulation of Swelling Radiation Damage in Targets
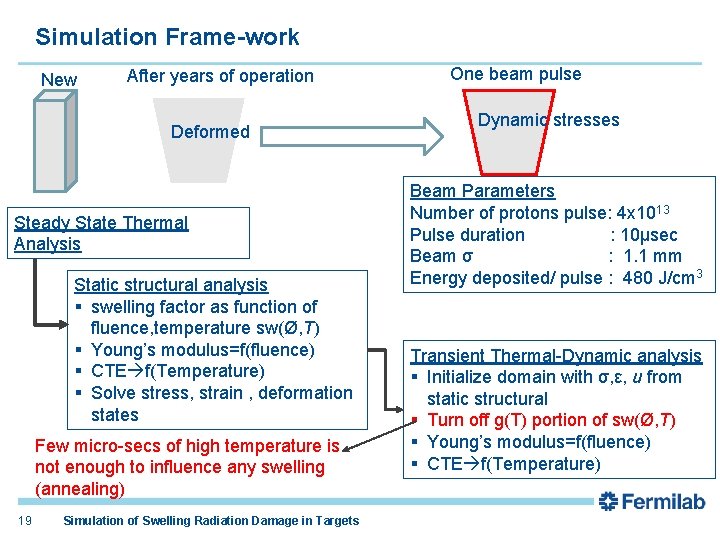
Simulation Frame-work New After years of operation Deformed Steady State Thermal Analysis Static structural analysis § swelling factor as function of fluence, temperature sw(Ø, T) § Young’s modulus=f(fluence) § CTE f(Temperature) § Solve stress, strain , deformation states Few micro-secs of high temperature is not enough to influence any swelling (annealing) 19 Simulation of Swelling Radiation Damage in Targets One beam pulse Dynamic stresses Beam Parameters Number of protons pulse: 4 x 1013 Pulse duration : 10µsec Beam σ : 1. 1 mm Energy deposited/ pulse : 480 J/cm 3 Transient Thermal-Dynamic analysis § Initialize domain with σ, ε, u from static structural § Turn off g(T) portion of sw(Ø, T) § Young’s modulus=f(fluence) § CTE f(Temperature)
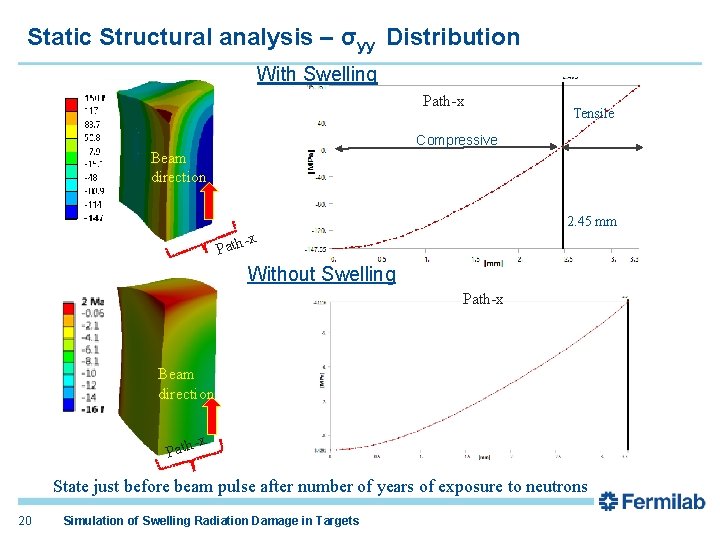
Static Structural analysis – σyy Distribution With Swelling Path-x Tensile Compressive Beam direction 2. 45 mm x Path Without Swelling Path-x Beam direction x Path State just before beam pulse after number of years of exposure to neutrons 20 Simulation of Swelling Radiation Damage in Targets
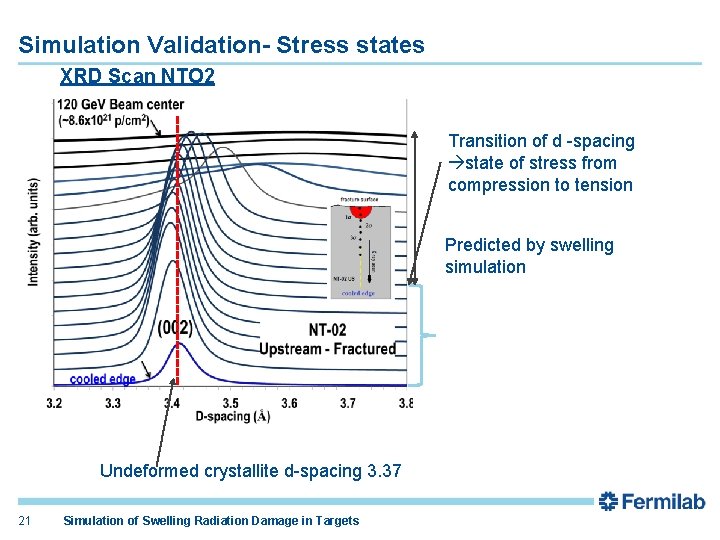
Simulation Validation- Stress states XRD Scan NTO 2 Transition of d -spacing state of stress from compression to tension Predicted by swelling simulation Undeformed crystallite d-spacing 3. 37 21 Simulation of Swelling Radiation Damage in Targets
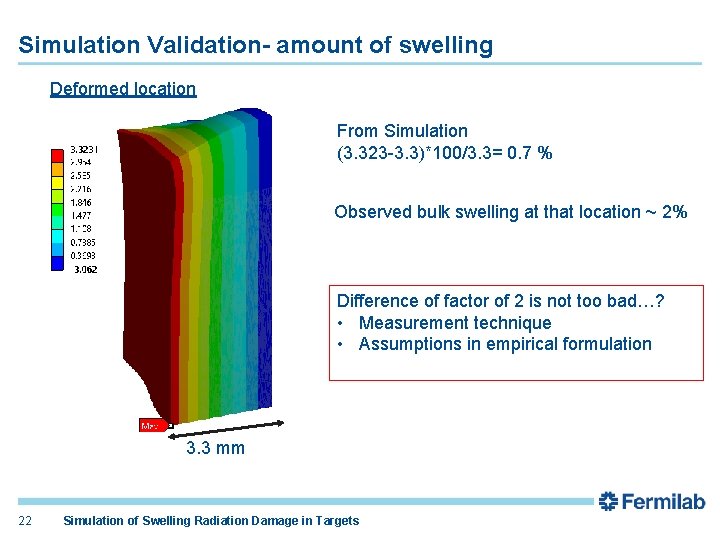
Simulation Validation- amount of swelling Deformed location From Simulation (3. 323 -3. 3)*100/3. 3= 0. 7 % Observed bulk swelling at that location ~ 2% Difference of factor of 2 is not too bad…? • Measurement technique • Assumptions in empirical formulation 3. 3 mm 22 Simulation of Swelling Radiation Damage in Targets
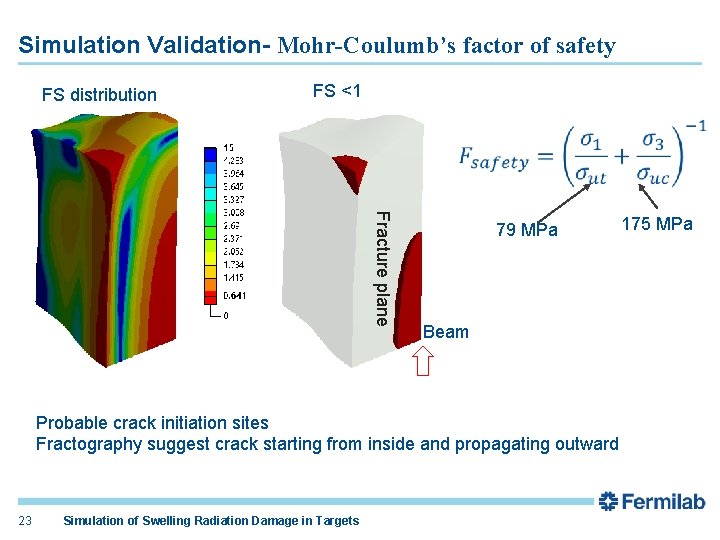
Simulation Validation- Mohr-Coulumb’s factor of safety FS distribution FS <1 Fracture plane 79 MPa Beam Probable crack initiation sites Fractography suggest crack starting from inside and propagating outward 23 Simulation of Swelling Radiation Damage in Targets 175 MPa
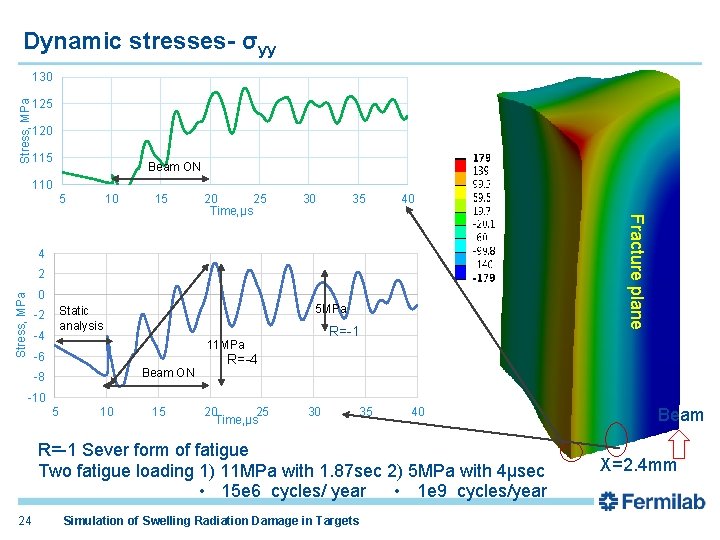
Dynamic stresses- σyy Stress, MPa 130 125 120 115 Beam ON 110 5 10 15 30 35 40 Fracture plane 20 25 Time, µs 4 2 Stress, MPa 0 5 MPa Static analysis -2 -4 R=-1 11 MPa -6 Beam ON -8 R=-4 -10 5 10 15 20 25 Time, µs 30 35 40 R=-1 Sever form of fatigue Two fatigue loading 1) 11 MPa with 1. 87 sec 2) 5 MPa with 4µsec • 15 e 6 cycles/ year • 1 e 9 cycles/year 24 Simulation of Swelling Radiation Damage in Targets Beam X=2. 4 mm
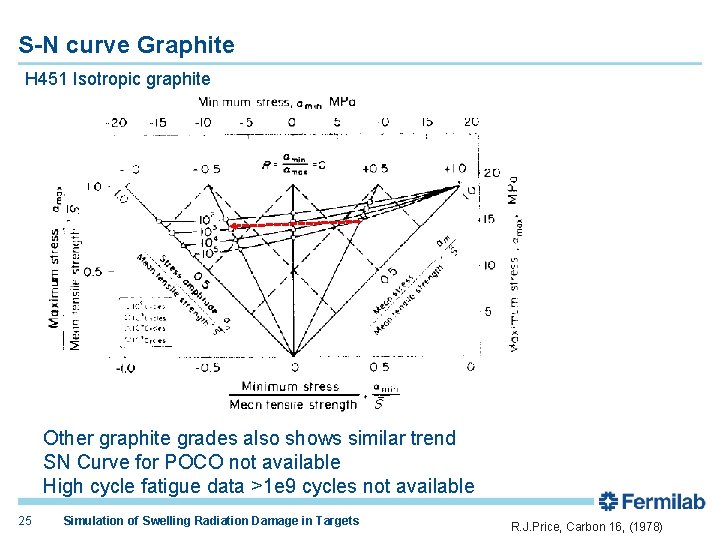
S-N curve Graphite H 451 Isotropic graphite Other graphite grades also shows similar trend SN Curve for POCO not available High cycle fatigue data >1 e 9 cycles not available 25 Simulation of Swelling Radiation Damage in Targets R. J. Price, Carbon 16, (1978)
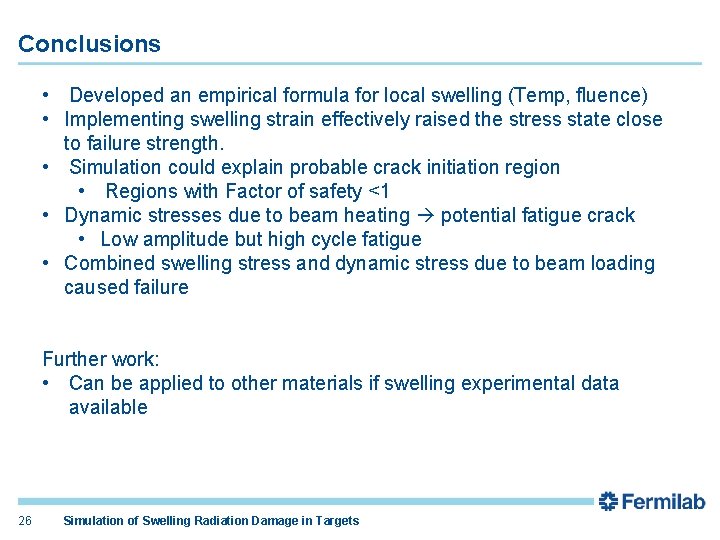
Conclusions • Developed an empirical formula for local swelling (Temp, fluence) • Implementing swelling strain effectively raised the stress state close to failure strength. • Simulation could explain probable crack initiation region • Regions with Factor of safety <1 • Dynamic stresses due to beam heating potential fatigue crack • Low amplitude but high cycle fatigue • Combined swelling stress and dynamic stress due to beam loading caused failure Further work: • Can be applied to other materials if swelling experimental data available 26 Simulation of Swelling Radiation Damage in Targets
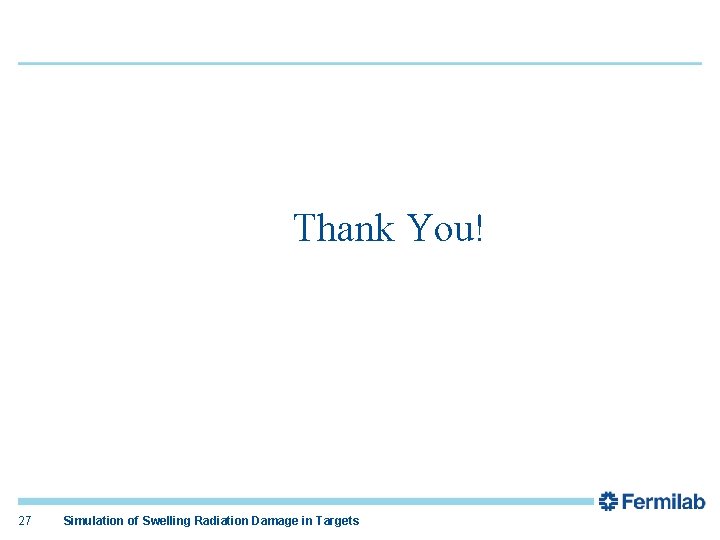
Thank You! 27 Simulation of Swelling Radiation Damage in Targets
Subhyoid bursitis
Subhyoid bursitis ppt
Mitochondrial swelling
Scalp swelling differential diagnosis
Fomiversin
Swelling
Periarticular soft tissue swelling
Incision for parotid abscess
Iv therapy complications
Preseptal cellulitis
Branchial cyst aspiration
Deep ring occlusion test
Ulcer examination mnemonic
Cross fluctuation test in psoas abscess
Two truths are told as happy prologues to the swelling act
Councilman bodies
Iv site complications
Disease of external nose
On training targets for supervised speech separation
Target network
Finished sketch
Identifying market segments and targets chapter 9
Racial etiquette region
Europe 2020 targets
Early childhood education barbados
Learning targets
Segment invasion plan
Knowledge targets