Section III Sputtering 1998 Angus Rockett 1998 Angus
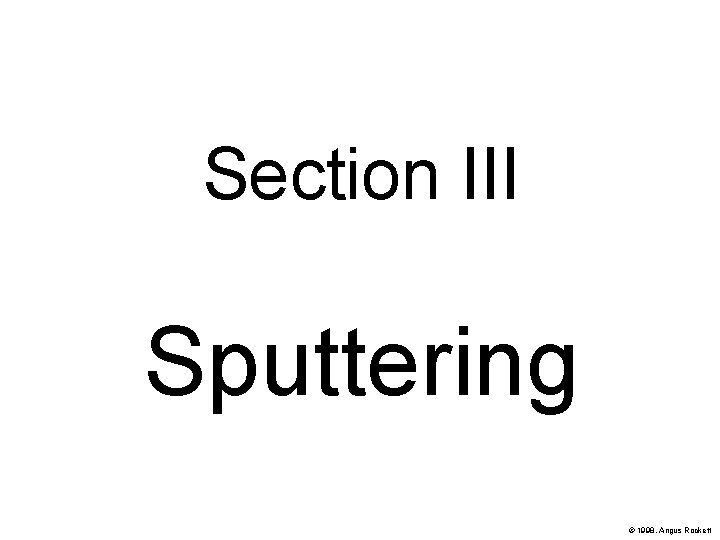
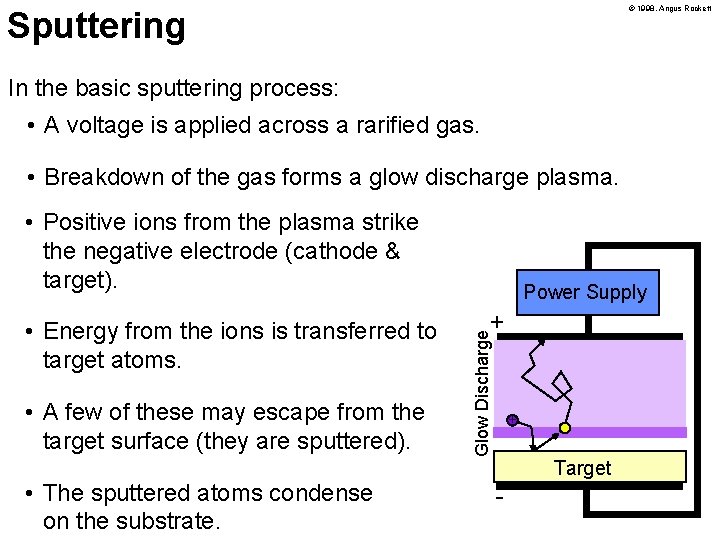

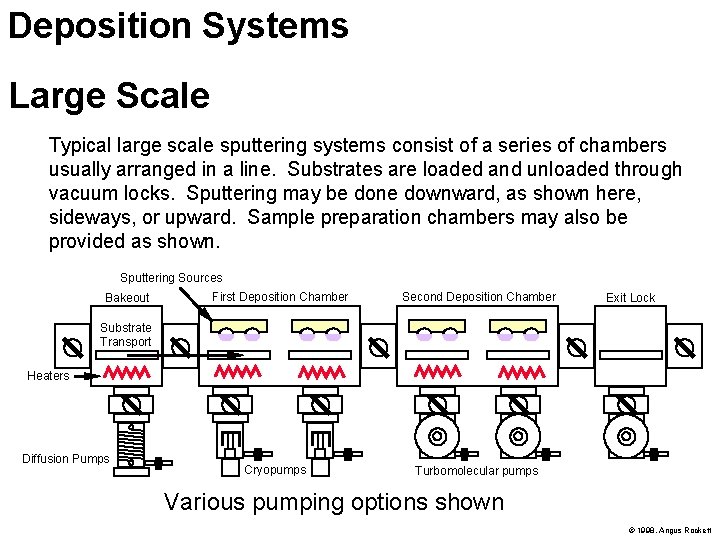
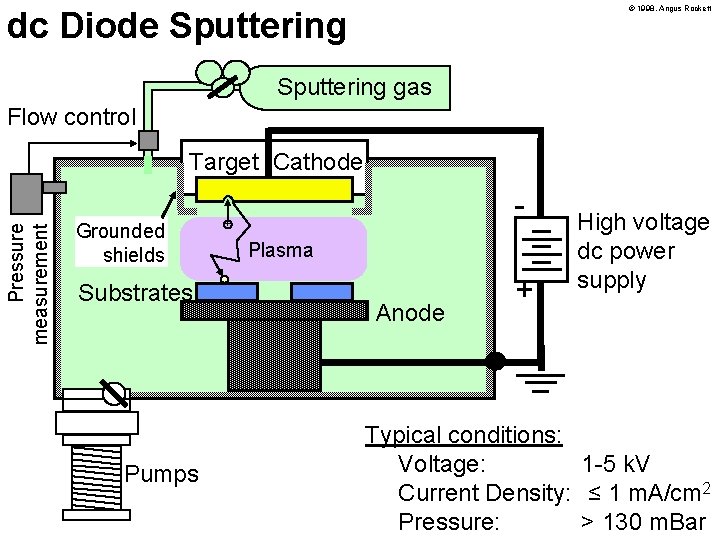
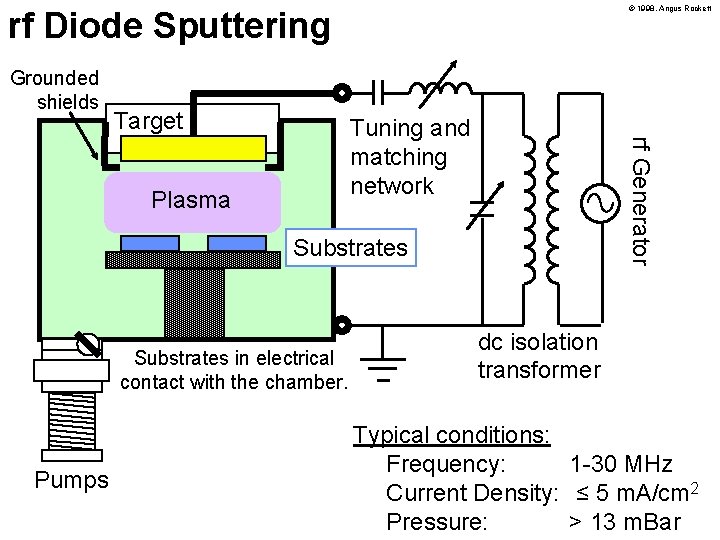
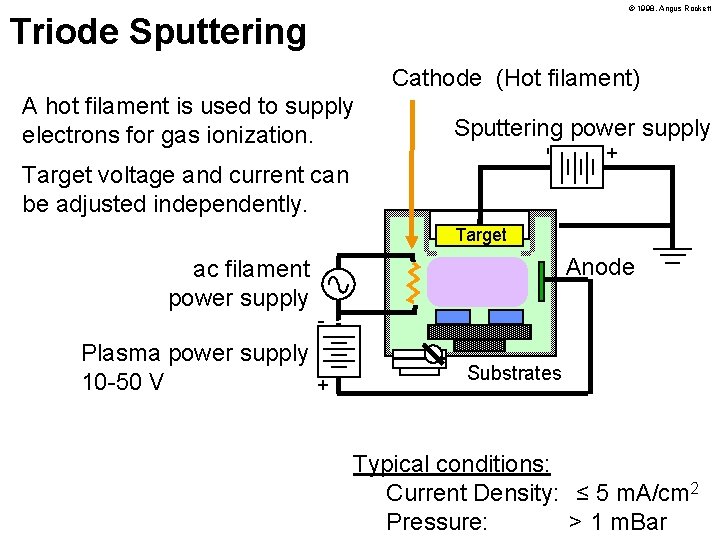
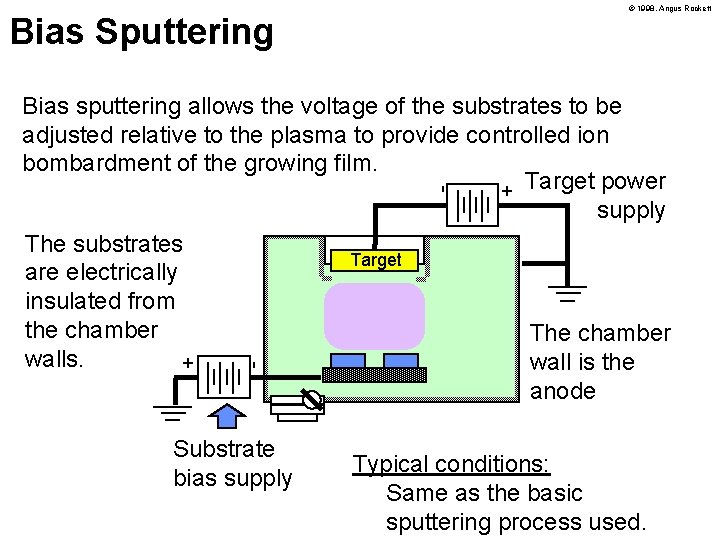
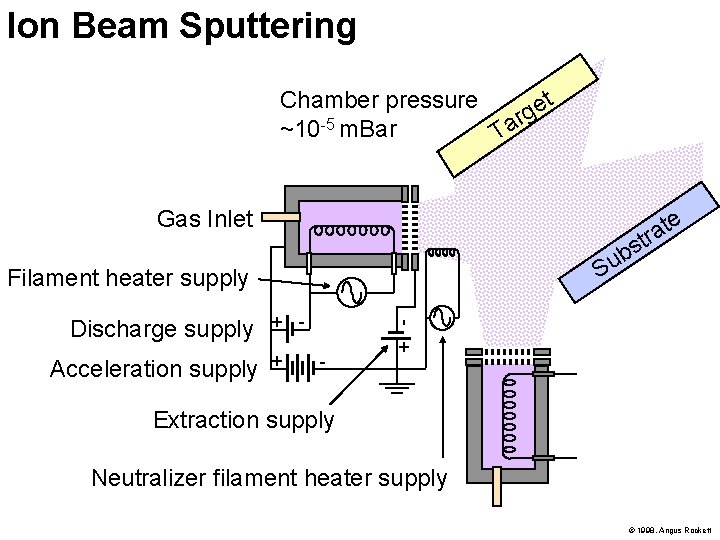
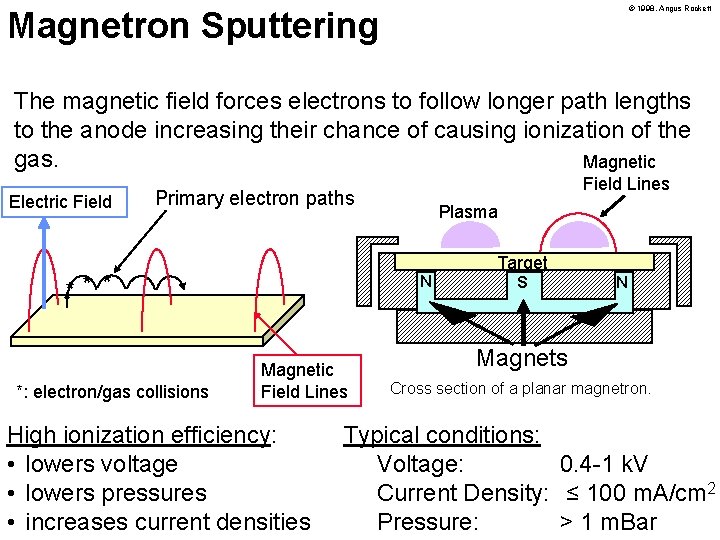
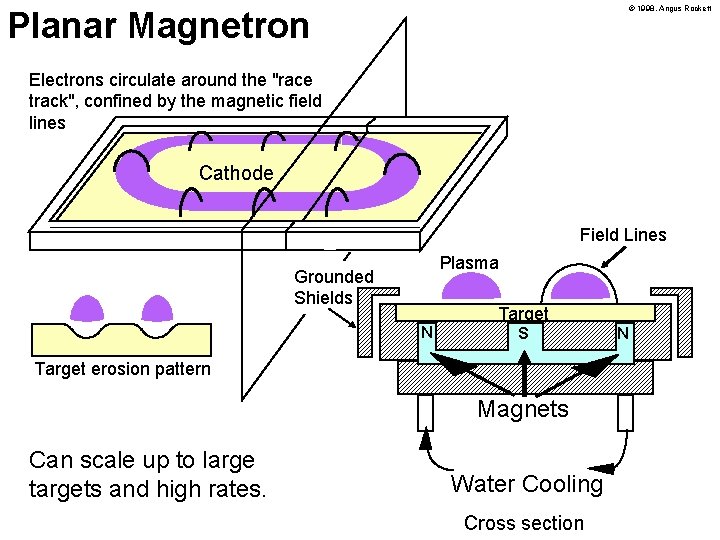
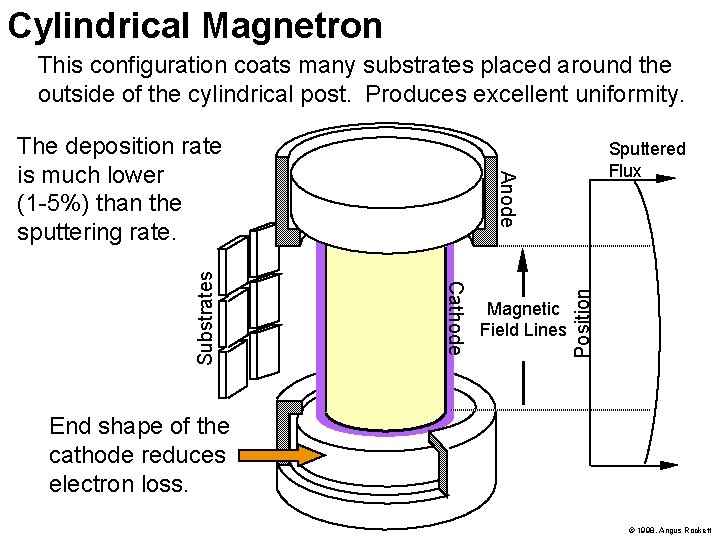
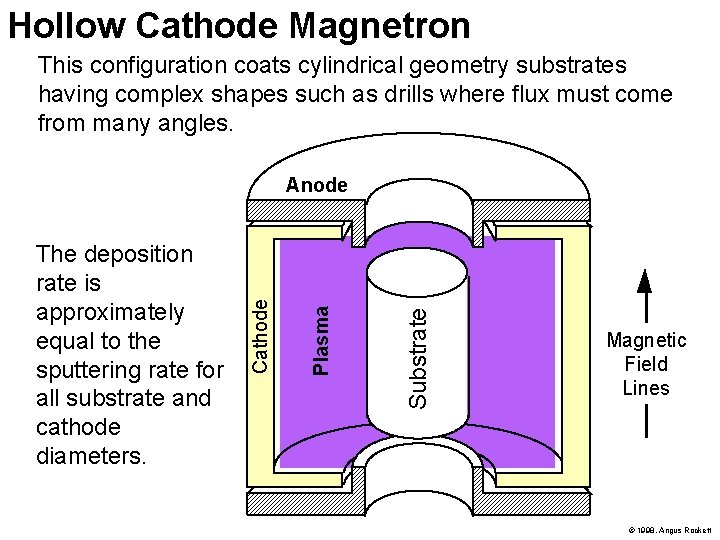
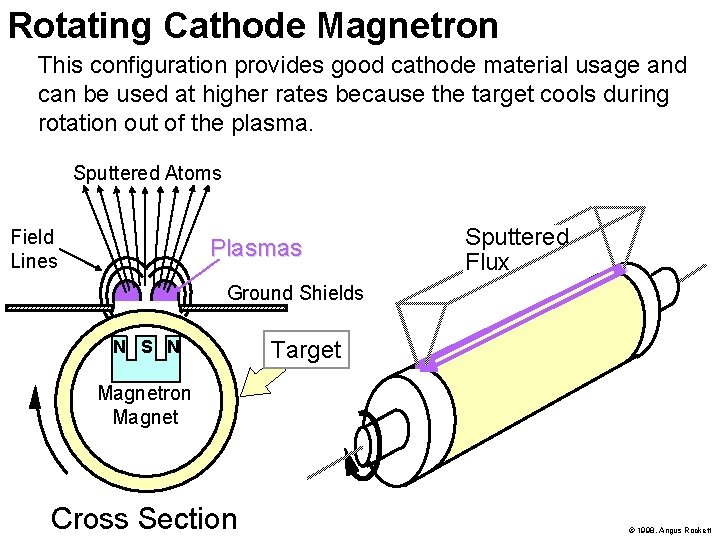
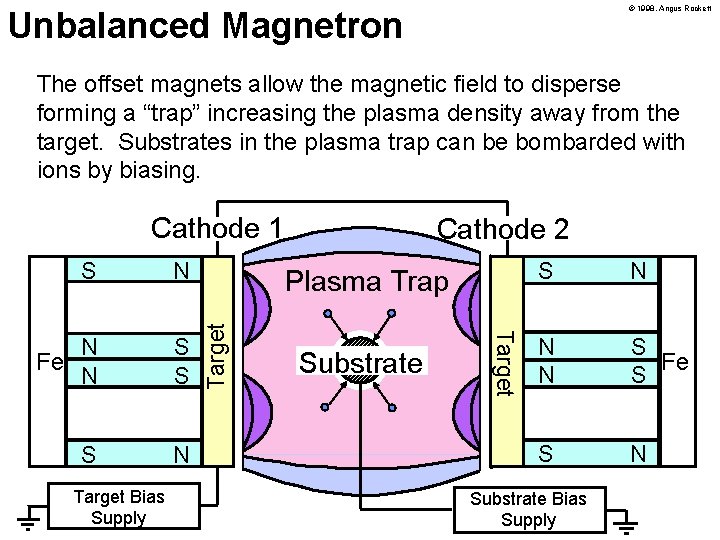
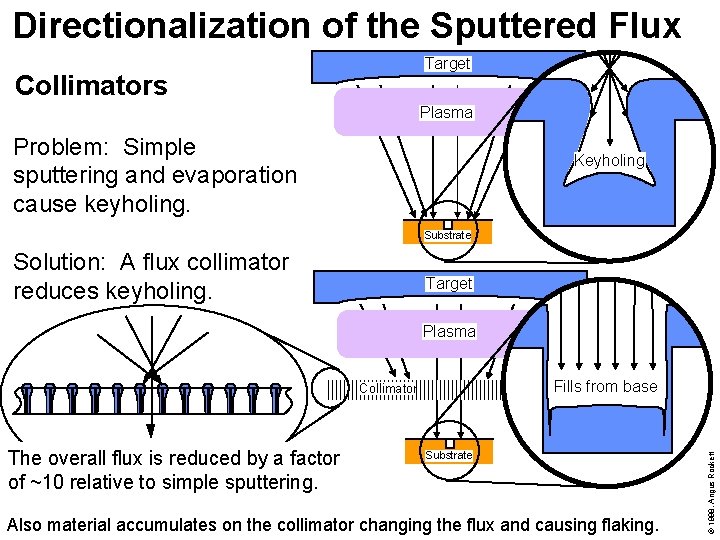
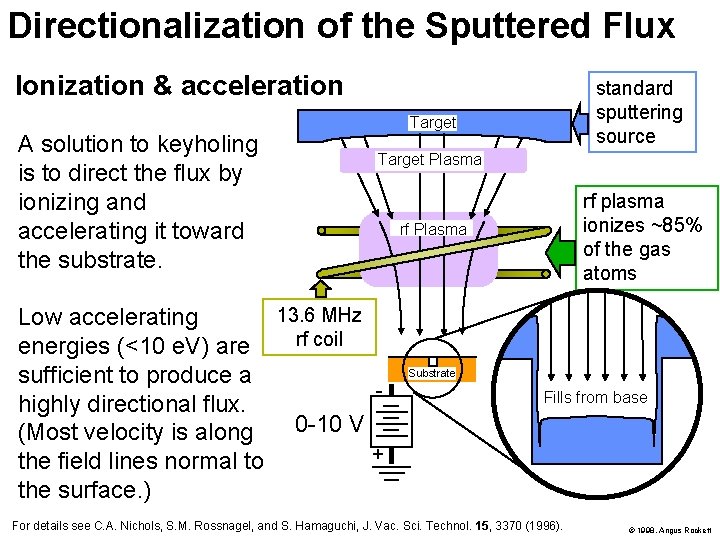
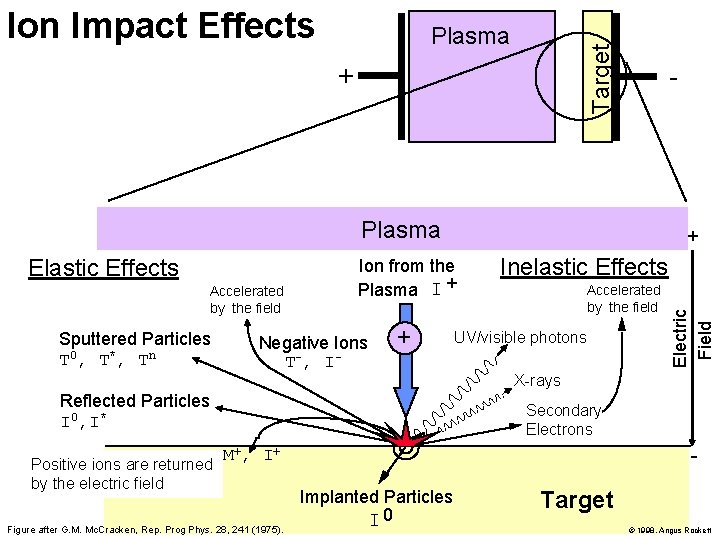
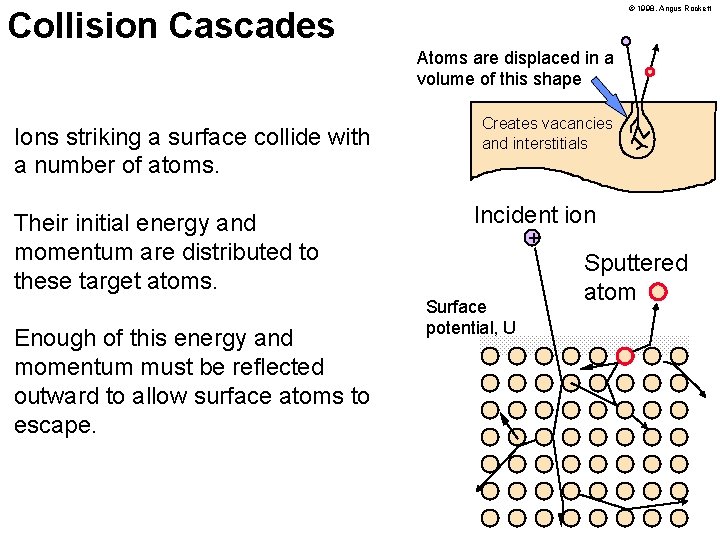
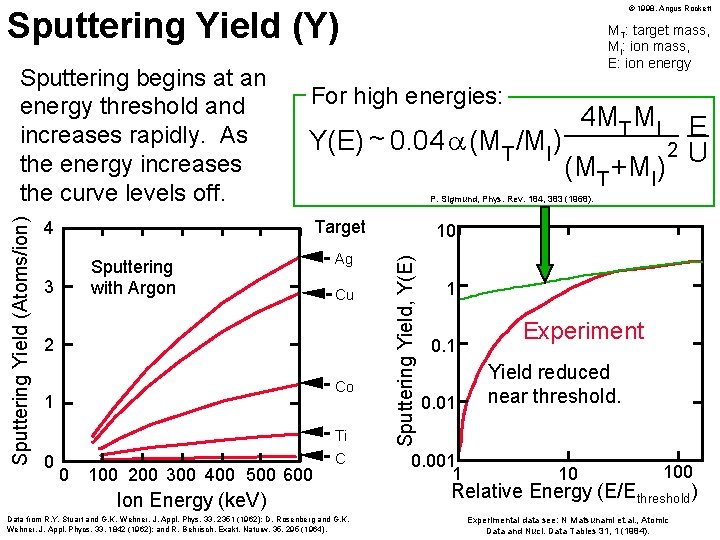

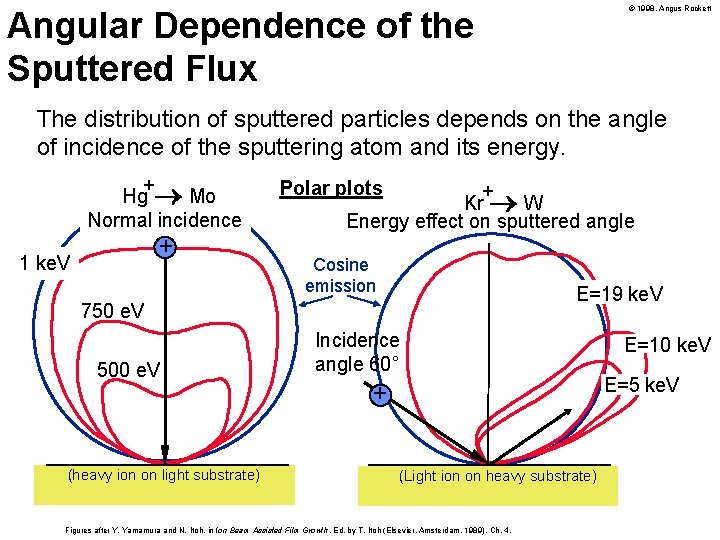
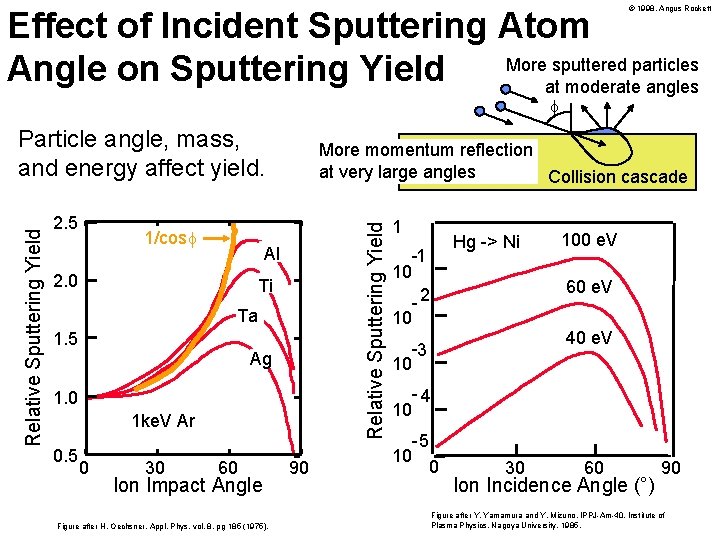
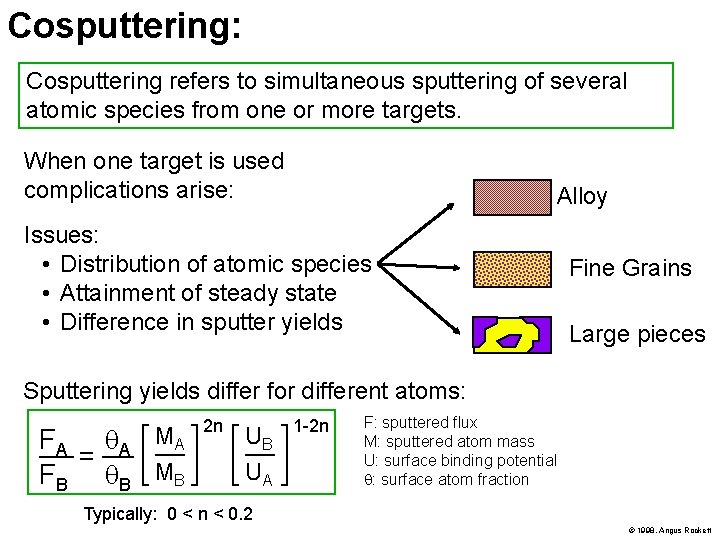
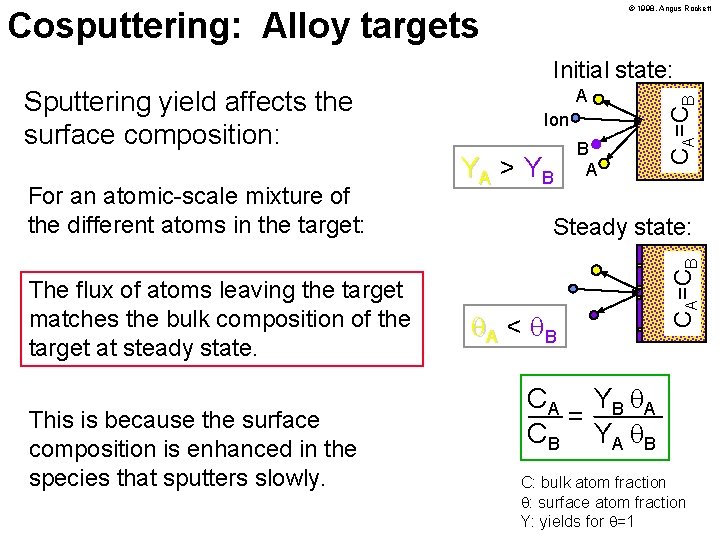
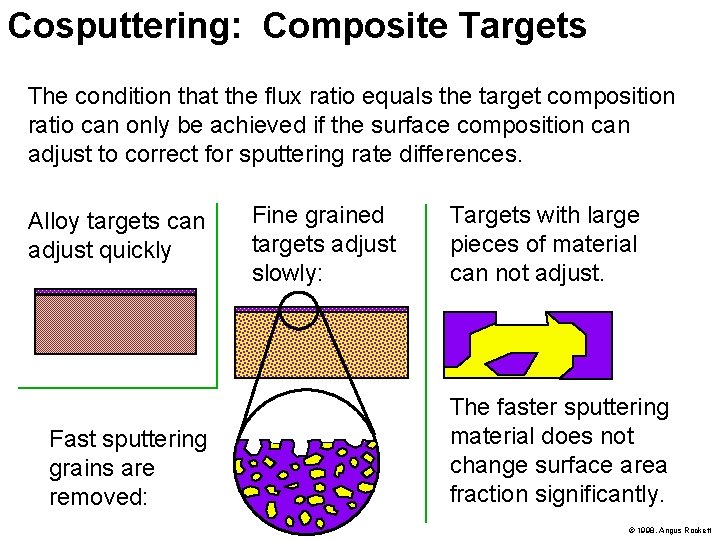
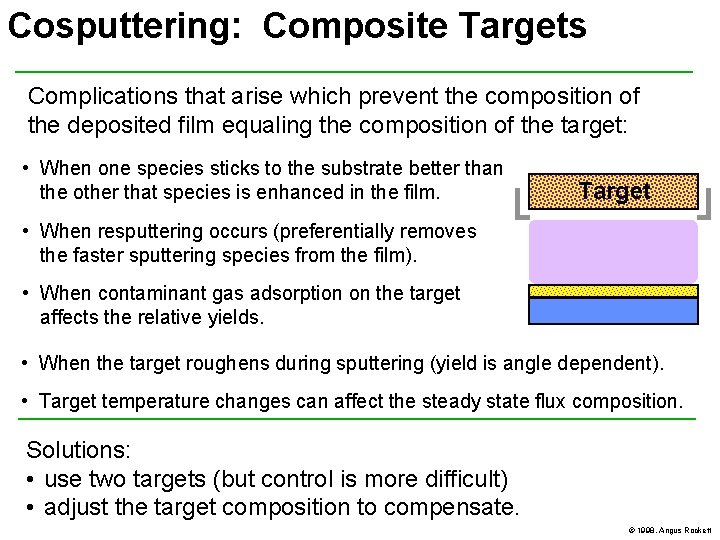
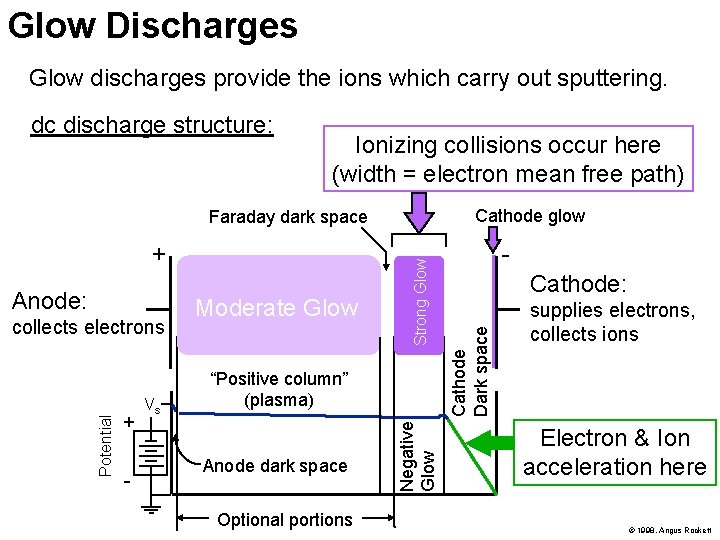
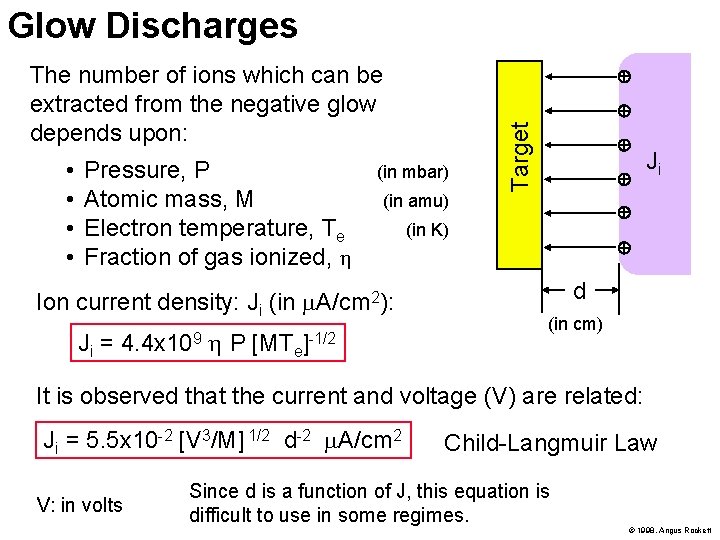
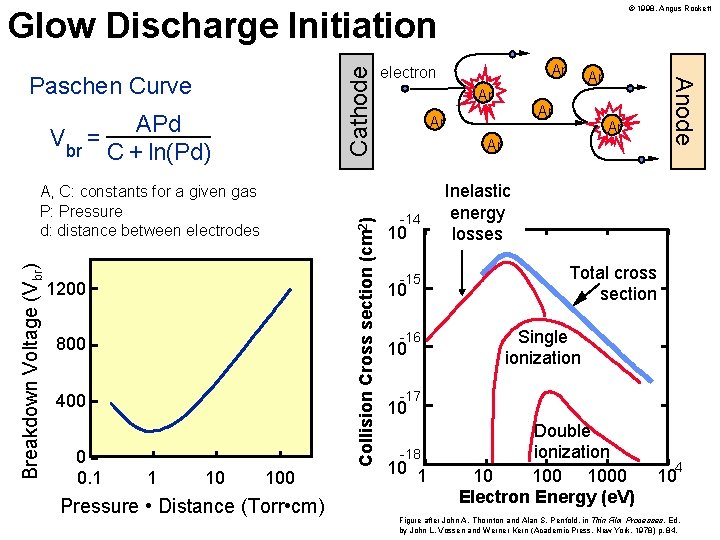
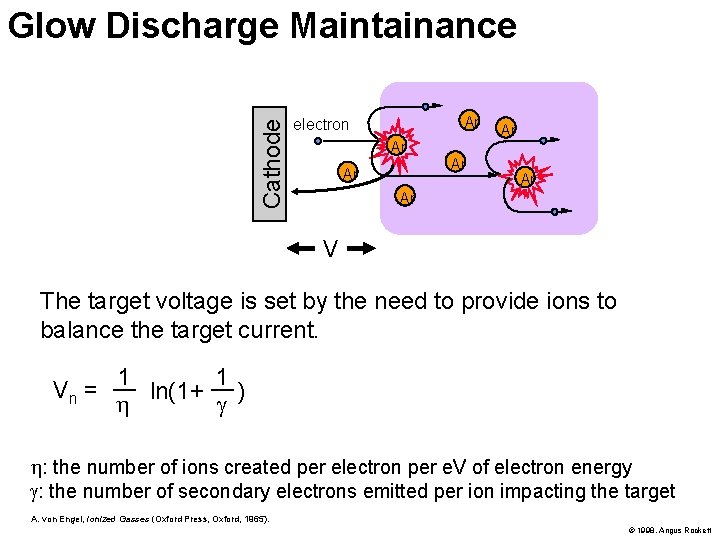
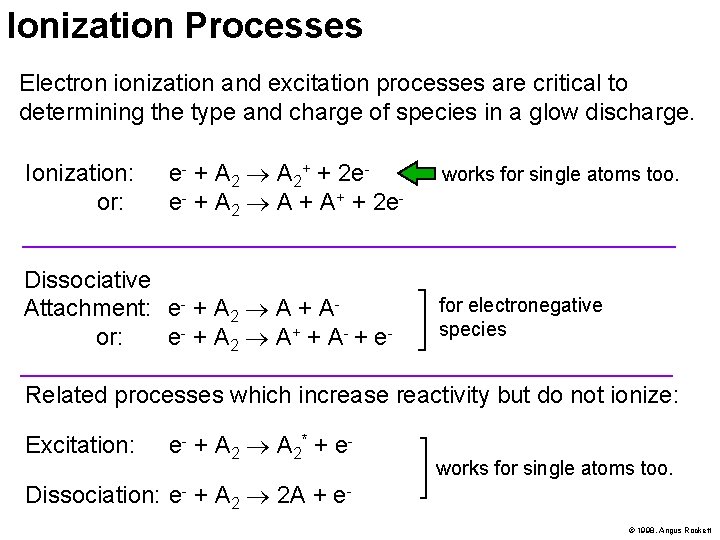
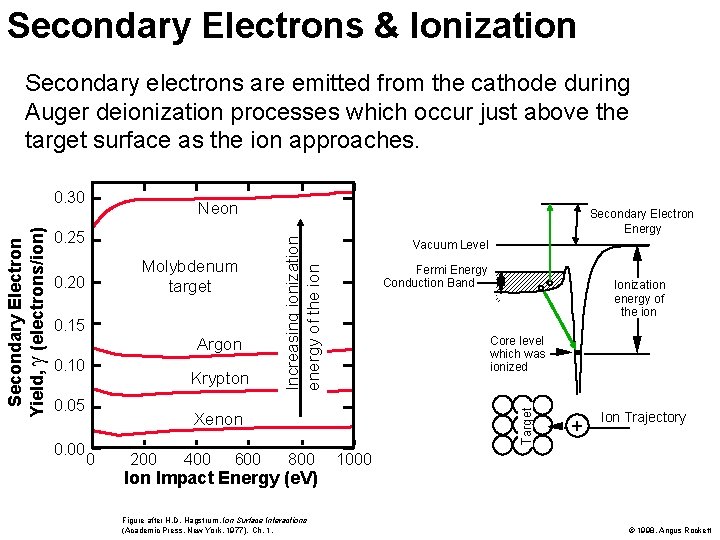
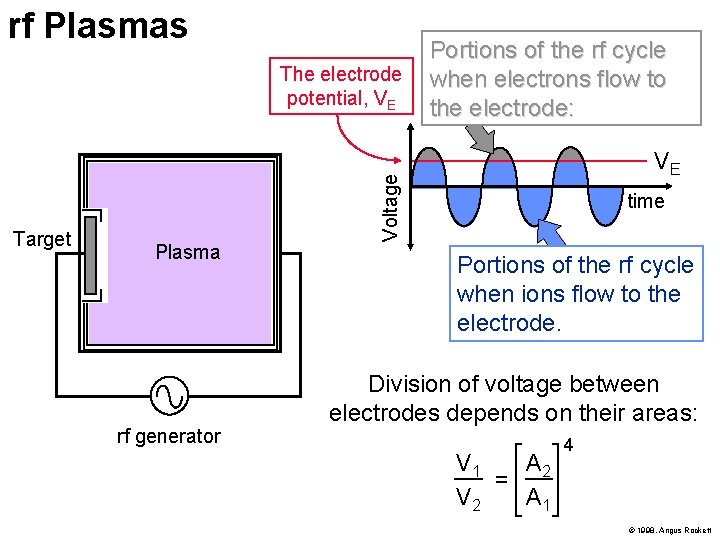
![rf Plasmas Ion Flux: k. Te 1/2 Ji= Ni Mi [ ] Plasma Electron rf Plasmas Ion Flux: k. Te 1/2 Ji= Ni Mi [ ] Plasma Electron](https://slidetodoc.com/presentation_image_h2/6fd6c1d0a023ff623534032537a4101d/image-35.jpg)
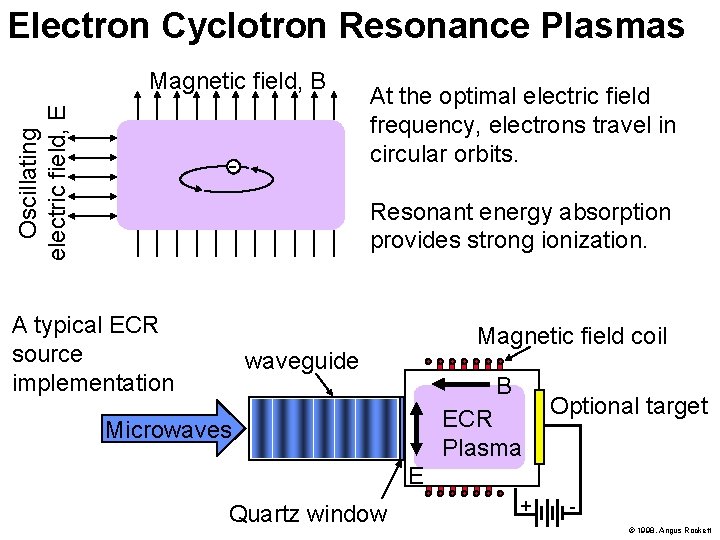
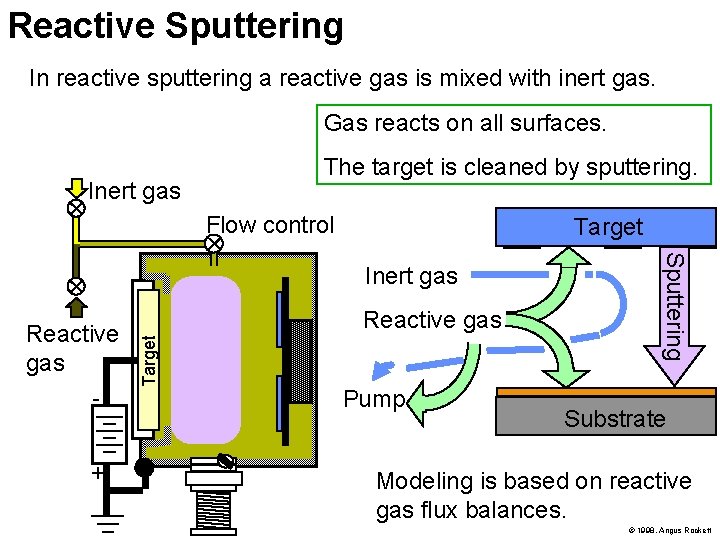
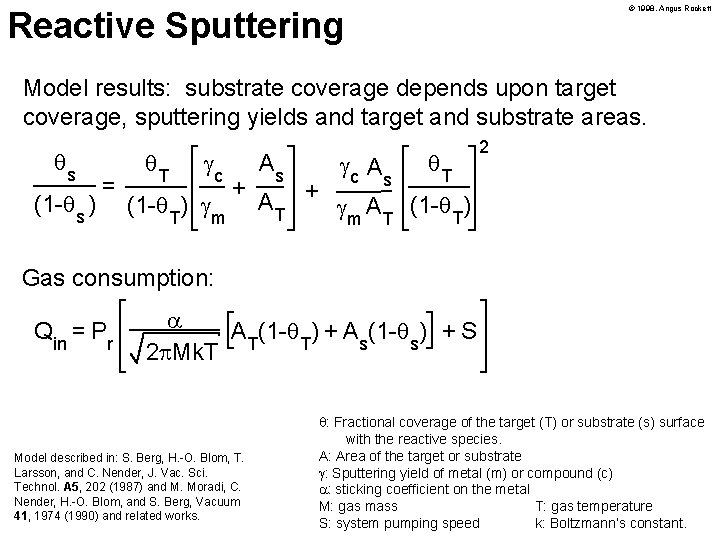
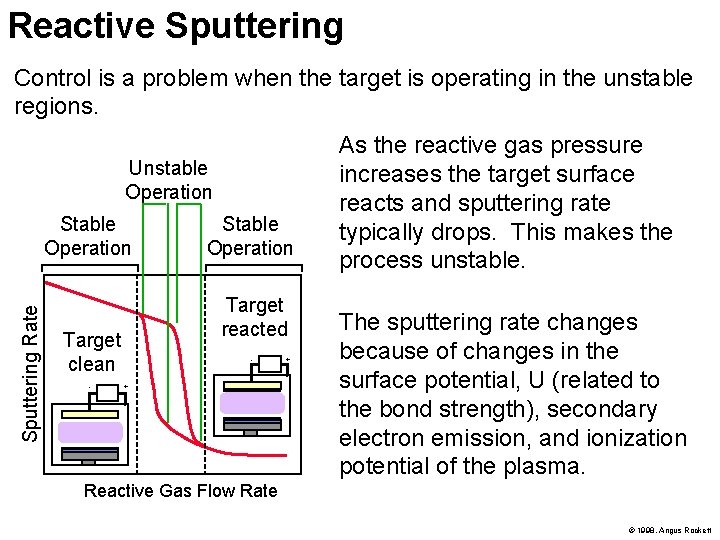
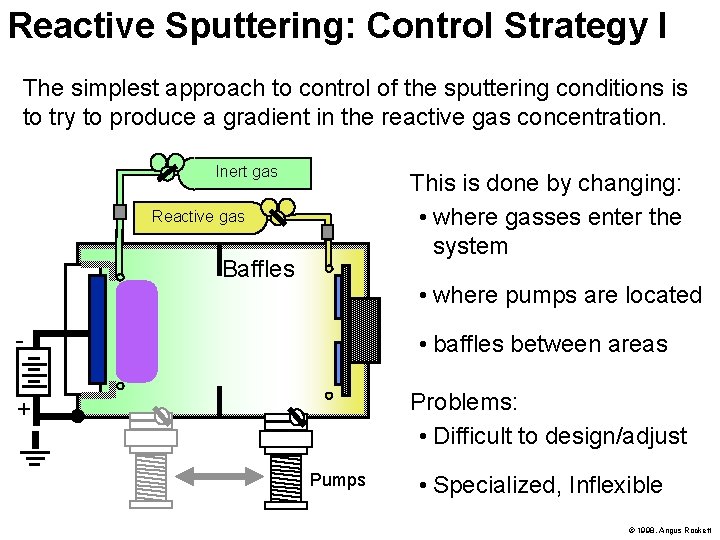
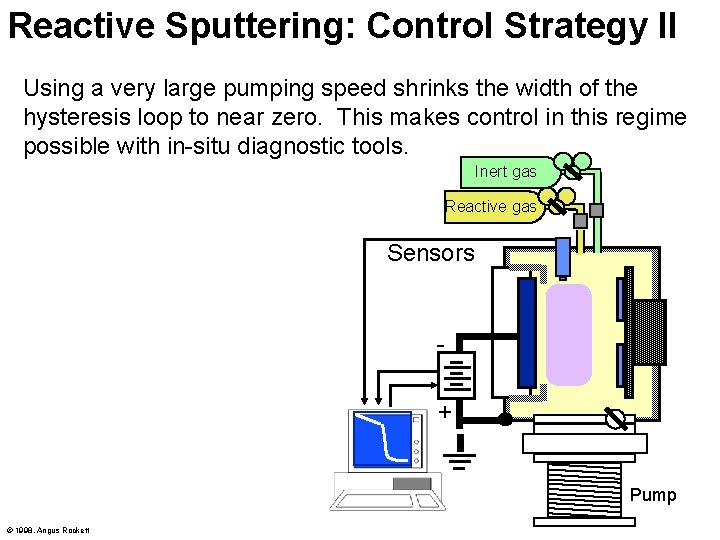
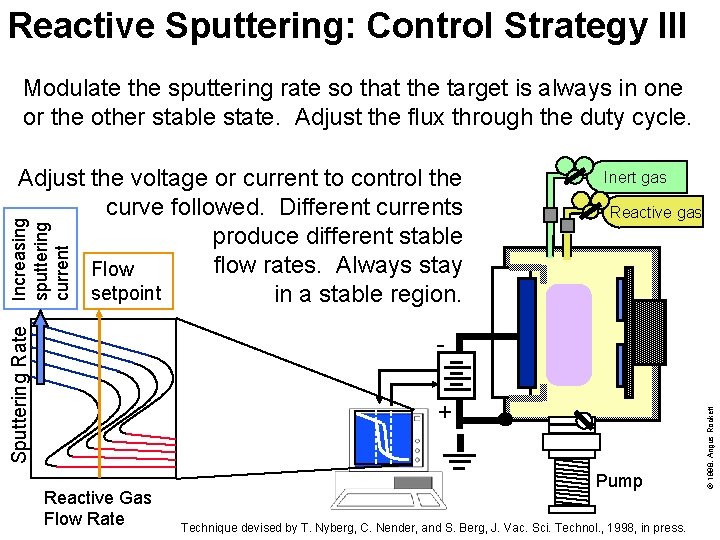
- Slides: 42
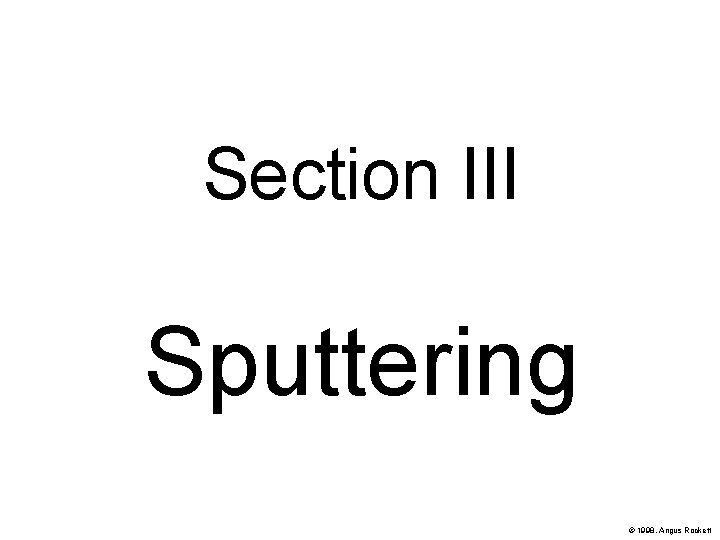
Section III Sputtering © 1998, Angus Rockett
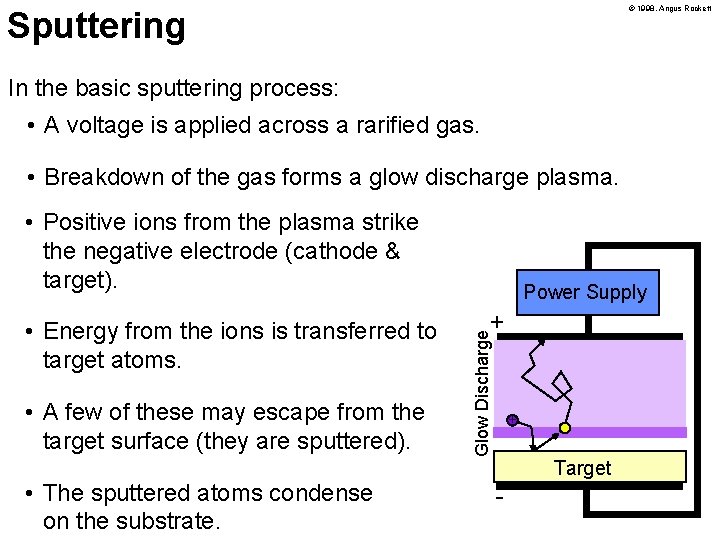
© 1998, Angus Rockett Sputtering In the basic sputtering process: • A voltage is applied across a rarified gas. • Breakdown of the gas forms a glow discharge plasma. • Positive ions from the plasma strike the negative electrode (cathode & target). • A few of these may escape from the target surface (they are sputtered). • The sputtered atoms condense on the substrate. + Glow Discharge • Energy from the ions is transferred to target atoms. Power Supply + Target -

Apparatus Options Power Supply dc vs. rf power supply diode vs. triode connection Target Design cylindrical planar hollow cathode rotating cathode single vs. multitarget Substrate Options floating, biased, grounded Glow Discharge + + Target - Plasma Enhancement magnetron microwave / rf Working Gas Chemistry inert gas reactive gas © 1998, Angus Rockett
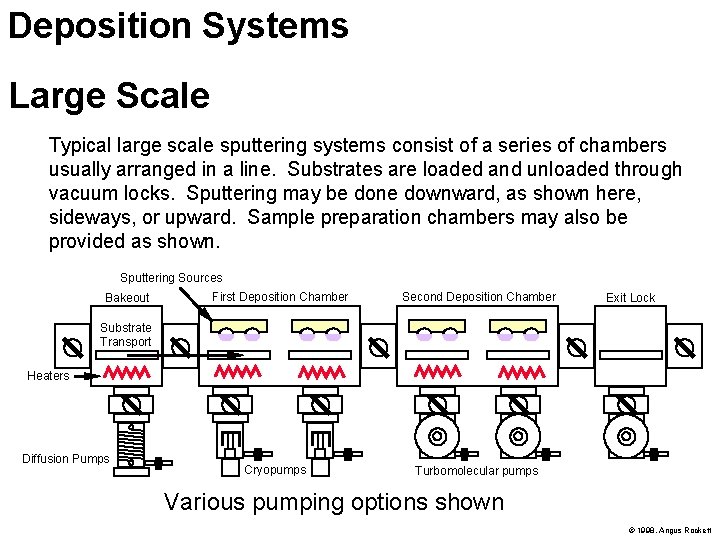
Deposition Systems Large Scale Typical large scale sputtering systems consist of a series of chambers usually arranged in a line. Substrates are loaded and unloaded through vacuum locks. Sputtering may be done downward, as shown here, sideways, or upward. Sample preparation chambers may also be provided as shown. Sputtering Sources Bakeout First Deposition Chamber Second Deposition Chamber Exit Lock Substrate Transport Heaters Diffusion Pumps Cryopumps Turbomolecular pumps Various pumping options shown © 1998, Angus Rockett
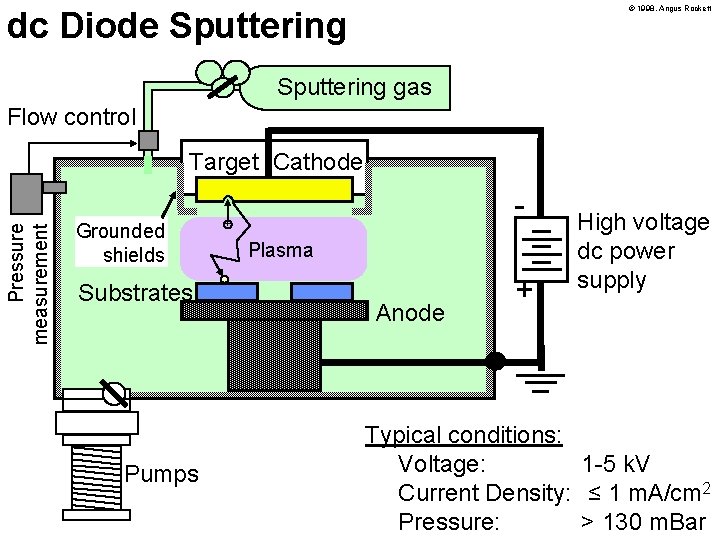
© 1998, Angus Rockett dc Diode Sputtering gas Flow control Pressure measurement Target Cathode Grounded shields Substrates Pumps - + Plasma Anode + High voltage dc power supply Typical conditions: Voltage: 1 -5 k. V Current Density: ≤ 1 m. A/cm 2 Pressure: > 130 m. Bar
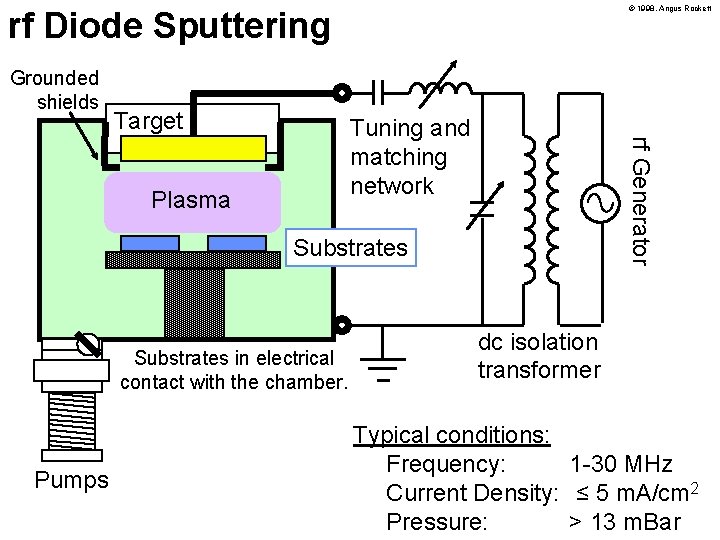
© 1998, Angus Rockett rf Diode Sputtering Grounded shields Target Plasma rf Generator Tuning and matching network Substrates in electrical contact with the chamber. Pumps dc isolation transformer Typical conditions: Frequency: 1 -30 MHz Current Density: ≤ 5 m. A/cm 2 Pressure: > 13 m. Bar
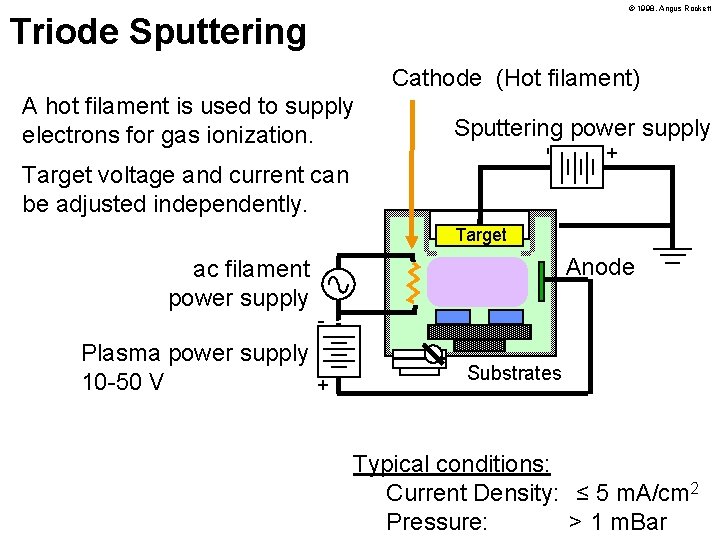
© 1998, Angus Rockett Triode Sputtering Cathode (Hot filament) + Sputtering power supply - A hot filament is used to supply electrons for gas ionization. Target voltage and current can be adjusted independently. Target ac filament power supply Anode - Plasma power supply 10 -50 V + Substrates Typical conditions: Current Density: ≤ 5 m. A/cm 2 Pressure: > 1 m. Bar
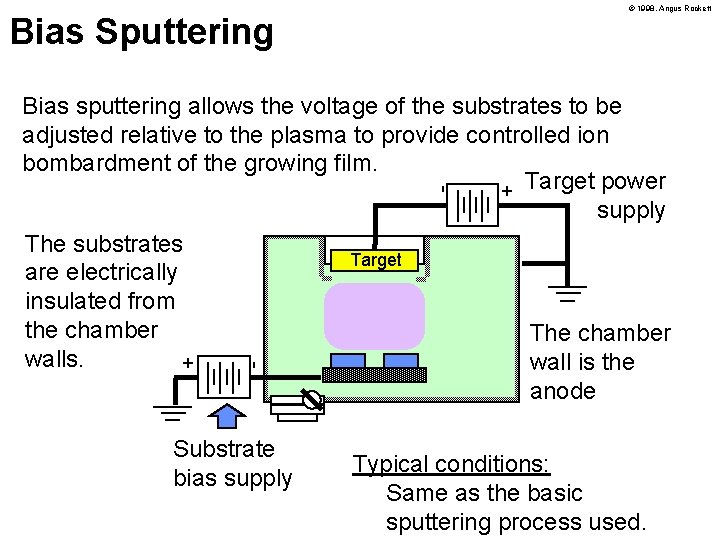
© 1998, Angus Rockett Bias Sputtering + - Bias sputtering allows the voltage of the substrates to be adjusted relative to the plasma to provide controlled ion bombardment of the growing film. Target power supply The substrates Target are electrically insulated from the chamber The chamber walls. wall is the anode - + Substrate bias supply Typical conditions: Same as the basic sputtering process used.
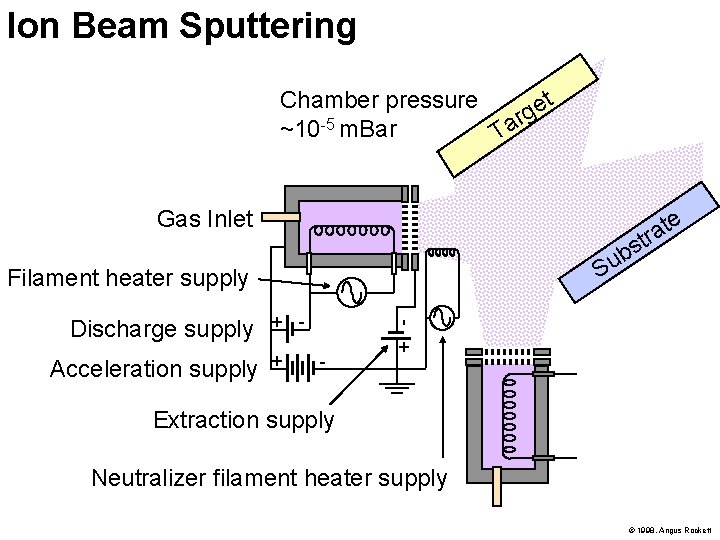
Ion Beam Sputtering t Chamber pressure e g r -5 a ~10 m. Bar T Gas Inlet e t a tr s b u S Discharge supply Acceleration supply + + - Filament heater supply Extraction supply Neutralizer filament heater supply © 1998, Angus Rockett
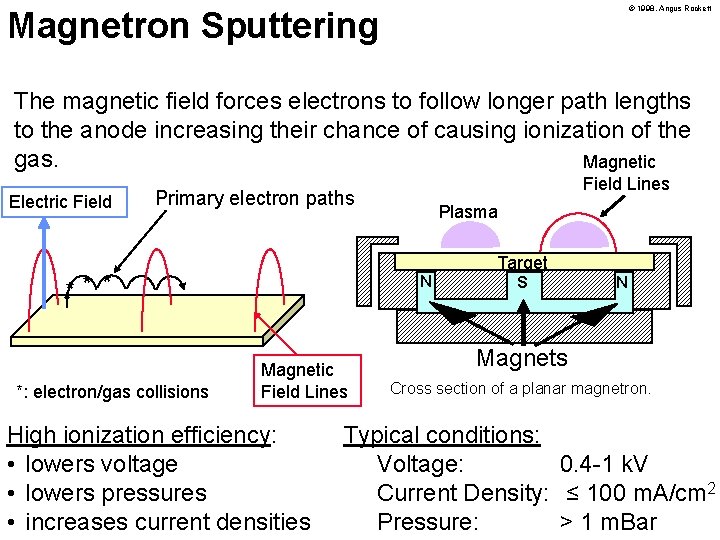
© 1998, Angus Rockett Magnetron Sputtering The magnetic field forces electrons to follow longer path lengths to the anode increasing their chance of causing ionization of the gas. Magnetic Electric Field Lines Primary electron paths Target * * *: electron/gas collisions Plasma N Magnetic Field Lines High ionization efficiency: • lowers voltage • lowers pressures • increases current densities S N Magnets Cross section of a planar magnetron. Typical conditions: Voltage: 0. 4 -1 k. V Current Density: ≤ 100 m. A/cm 2 Pressure: > 1 m. Bar
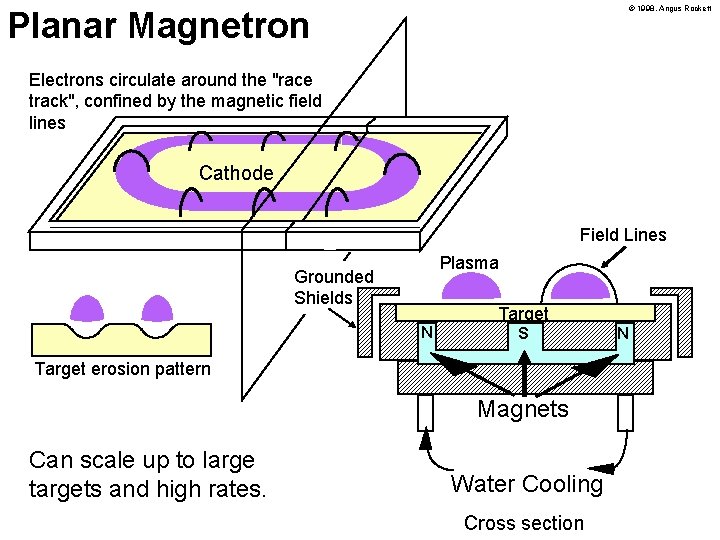
© 1998, Angus Rockett Planar Magnetron Electrons circulate around the "race track", confined by the magnetic field lines Cathode Field Lines Plasma Grounded Shields Target N S Target erosion pattern Magnets Can scale up to large targets and high rates. Water Cooling Cross section N
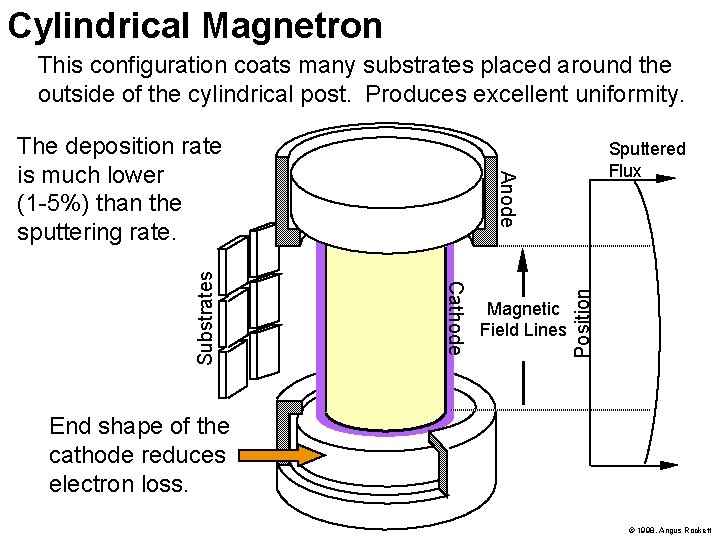
Cylindrical Magnetron This configuration coats many substrates placed around the outside of the cylindrical post. Produces excellent uniformity. Magnetic Field Lines Position Cathode Substrates Sputtered Flux Anode The deposition rate is much lower (1 -5%) than the sputtering rate. End shape of the cathode reduces electron loss. © 1998, Angus Rockett
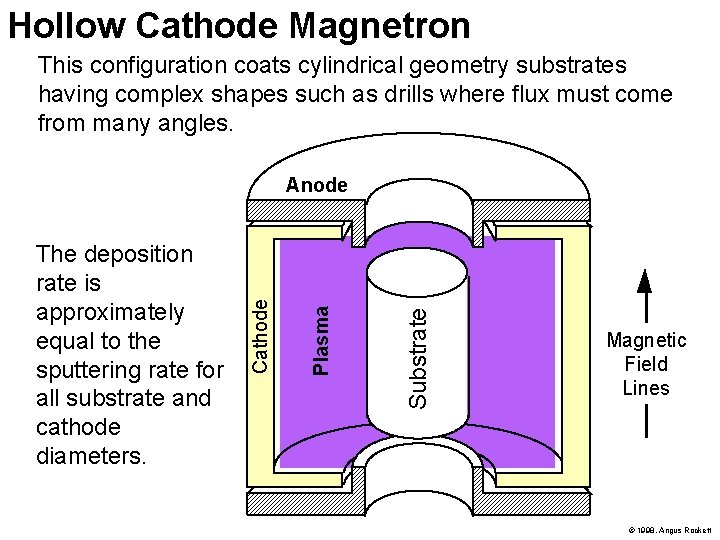
Hollow Cathode Magnetron This configuration coats cylindrical geometry substrates having complex shapes such as drills where flux must come from many angles. Substrate Plasma The deposition rate is approximately equal to the sputtering rate for all substrate and cathode diameters. Cathode Anode Magnetic Field Lines © 1998, Angus Rockett
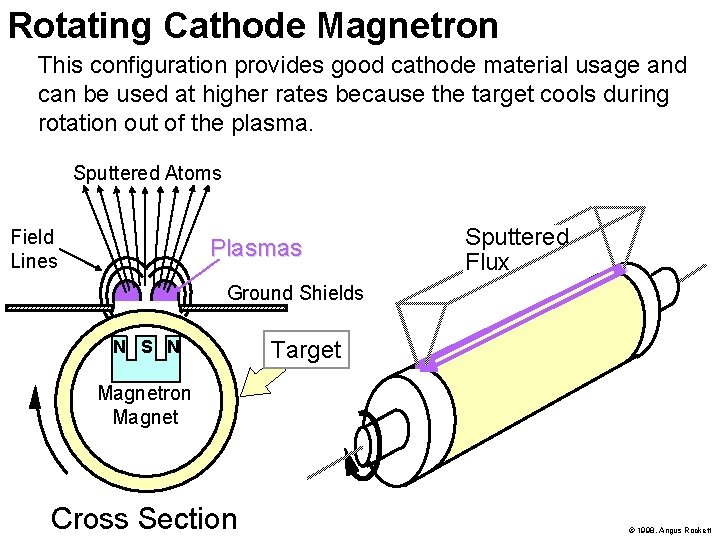
Rotating Cathode Magnetron This configuration provides good cathode material usage and can be used at higher rates because the target cools during rotation out of the plasma. Sputtered Atoms Field Lines Plasmas Sputtered Flux Ground Shields N S N Target Magnetron Magnet Cross Section © 1998, Angus Rockett
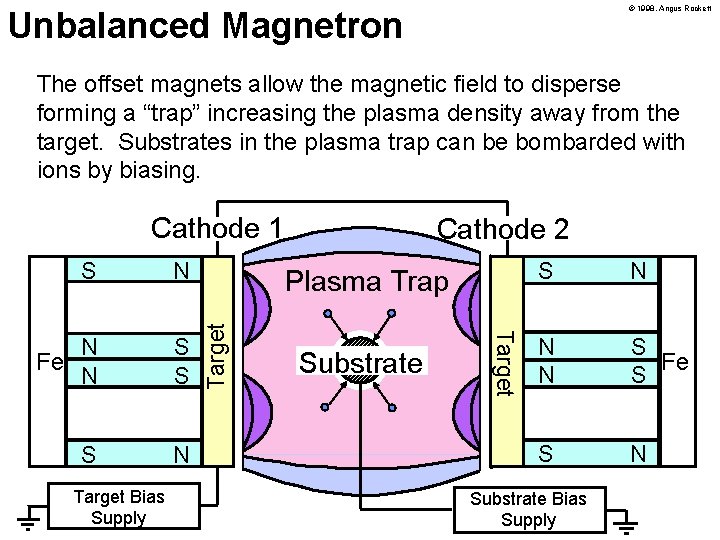
© 1998, Angus Rockett Unbalanced Magnetron The offset magnets allow the magnetic field to disperse forming a “trap” increasing the plasma density away from the target. Substrates in the plasma trap can be bombarded with ions by biasing. Cathode 1 N Fe N S S S N Target Bias Supply Plasma Trap Target N Substrate Target S Cathode 2 S N N N S Fe S S N Substrate Bias Supply
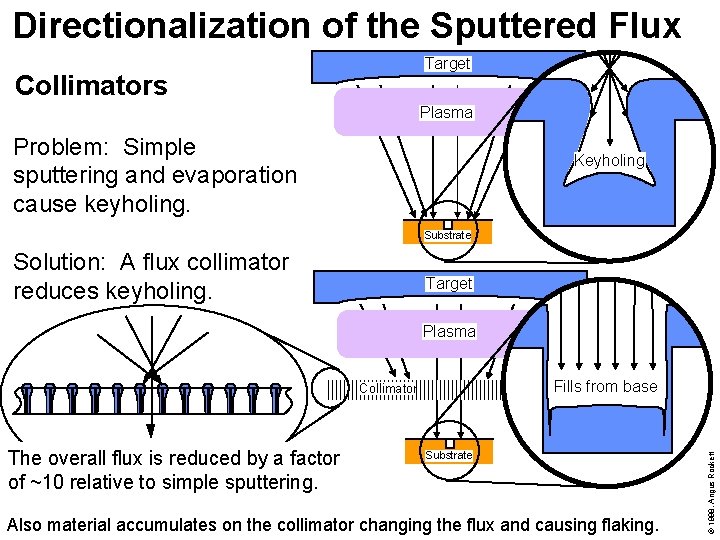
Directionalization of the Sputtered Flux Target Collimators Plasma Problem: Simple sputtering and evaporation cause keyholing. Keyholing Substrate Solution: A flux collimator reduces keyholing. Target Plasma The overall flux is reduced by a factor of ~10 relative to simple sputtering. Substrate Also material accumulates on the collimator changing the flux and causing flaking. © 1998, Angus Rockett Fills from base Collimator
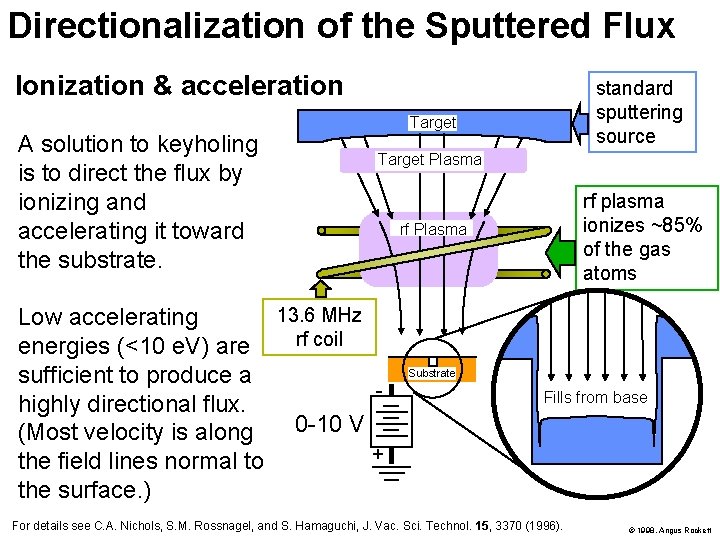
Directionalization of the Sputtered Flux Ionization & acceleration A solution to keyholing is to direct the flux by ionizing and accelerating it toward the substrate. standard sputtering source Target Plasma 13. 6 MHz Low accelerating rf coil energies (<10 e. V) are sufficient to produce a highly directional flux. 0 -10 V (Most velocity is along + the field lines normal to the surface. ) rf plasma ionizes ~85% of the gas atoms rf Plasma Substrate Fills from base For details see C. A. Nichols, S. M. Rossnagel, and S. Hamaguchi, J. Vac. Sci. Technol. 15, 3370 (1996). © 1998, Angus Rockett
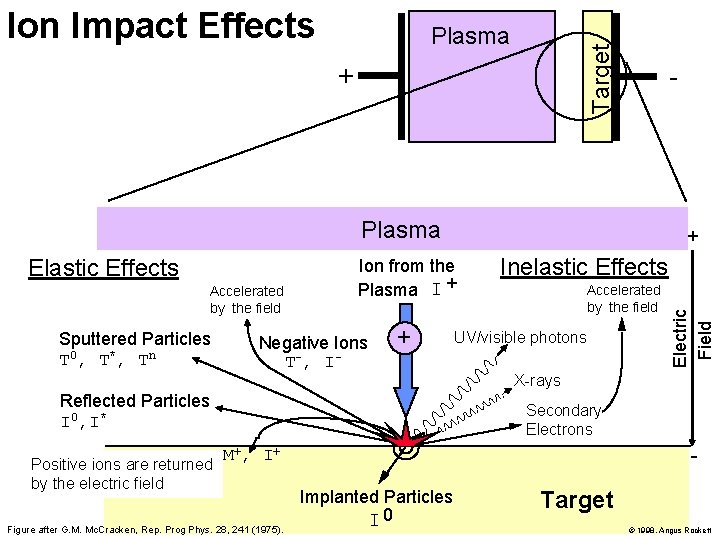
Target Plasma + - Plasma Elastic Effects Accelerated by the field Sputtered Particles T 0, T*, Tn Ion from the Plasma I + Negative Ions T-, I- + Reflected Particles I 0, I* Positive ions are returned by the electric field + Inelastic Effects Accelerated by the field UV/visible photons Electric Field Ion Impact Effects X-rays Secondary Electrons - M+, I+ Figure after G. M. Mc. Cracken, Rep. Prog Phys. 28, 241 (1975). Implanted Particles I 0 Target © 1998, Angus Rockett
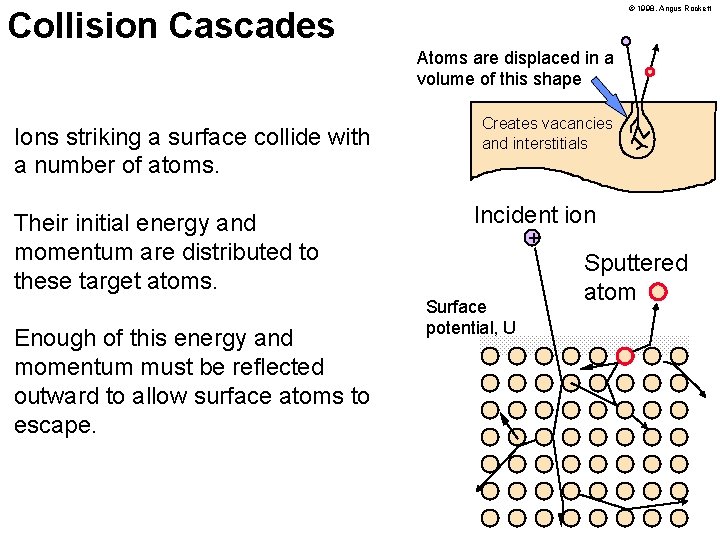
© 1998, Angus Rockett Collision Cascades Atoms are displaced in a volume of this shape Ions striking a surface collide with a number of atoms. Their initial energy and momentum are distributed to these target atoms. Enough of this energy and momentum must be reflected outward to allow surface atoms to escape. Creates vacancies and interstitials Incident ion + Surface potential, U Sputtered atom
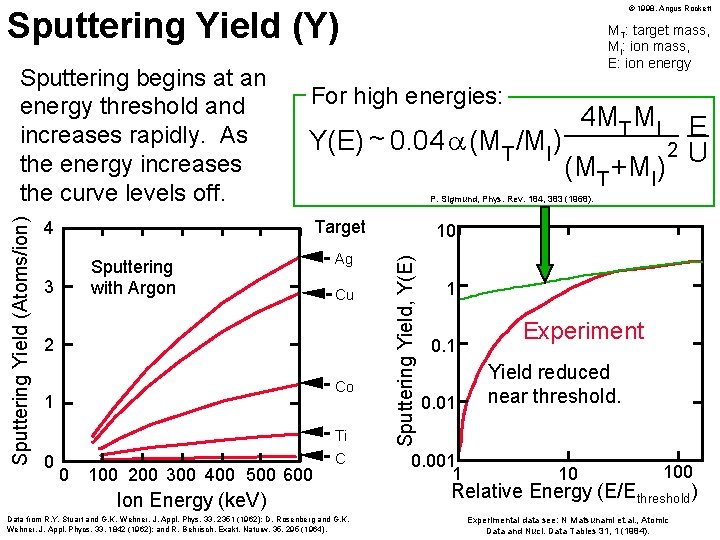
© 1998, Angus Rockett Sputtering Yield (Y) For high energies: 4 MT MI E Y(E) ~ 0. 04 (MT /MI ) 2 U (MT +MI ) P. Sigmund, Phys. Rev. 184, 383 (1968). Target 4 Sputtering with Argon 3 Ag Cu 2 Co 1 Ti 0 0 100 200 300 400 500 600 C Ion Energy (ke. V) Data from R. Y. Stuart and G. K. Wehner, J. Appl. Phys. 33, 2351 (1962); D. Rosenberg and G. K. Wehner, J. Appl. Phycs. 33, 1842 (1962); and R. Behrisch, Exakt. Naturw. 35, 295 (1964). 10 Sputtering Yield, Y(E) Sputtering Yield (Atoms/ion) Sputtering begins at an energy threshold and increases rapidly. As the energy increases the curve levels off. MT: target mass, MI: ion mass, E: ion energy 1 0. 01 0. 001 1 Experiment Yield reduced near threshold. 10 100 Relative Energy (E/Ethreshold) Experimental data see: N Matsunami et. al. , Atomic Data and Nucl. Data Tables 31, 1 (1984).

© 1998, Angus Rockett Sputtering Threshold (ETh) Sputtering begins at an energy threshold that depends on the efficiency of momentum transfer to the target. This depends on the mass match. It also depends on the binding energy of atoms in the target. Empirically the threshold energy Eth/U is: 0. 57 MT MI 0. 21 + 4. 8 + 0. 26 MI MT Y. Yamamura and Y. Mizuo, J. Nucl. Mater. 128, 9, 559 (1984). To correct the yield formula for threshold, multiply Y(E) by: (1 -f 2/3)(1 -1/f)2 J. Bohdansky, Nucl. Instr. Meth. B 2, 151 (1984). f= Eth E Threshold Energy/U 1000 10 1 0. 1 1 10 100 Colliding Atom-totarget Mass Ratio MT/MI Figure after Y. Yamamura and N. Itoh, in Ion Beam Assisted Film Growth, Ed. by T. Itoh (Elsevier, Amsterdam, 1989), Ch. 4.
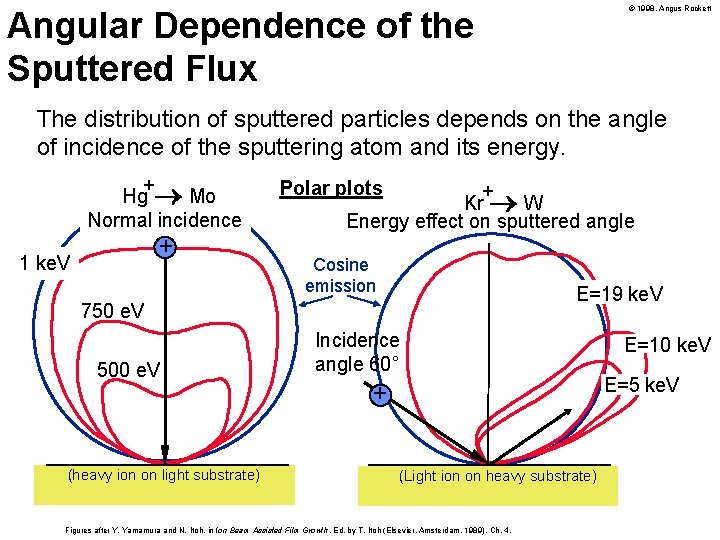
© 1998, Angus Rockett Angular Dependence of the Sputtered Flux The distribution of sputtered particles depends on the angle of incidence of the sputtering atom and its energy. + Hg Mo Normal incidence + 1 ke. V Polar plots + Kr W Energy effect on sputtered angle Cosine emission E=19 ke. V 750 e. V 500 e. V (heavy ion on light substrate) Incidence angle 60° + (Light ion on heavy substrate) Figures after Y. Yamamura and N. Itoh, in Ion Beam Assisted Film Growth, Ed. by T. Itoh (Elsevier, Amsterdam, 1989), Ch. 4. E=10 ke. V E=5 ke. V
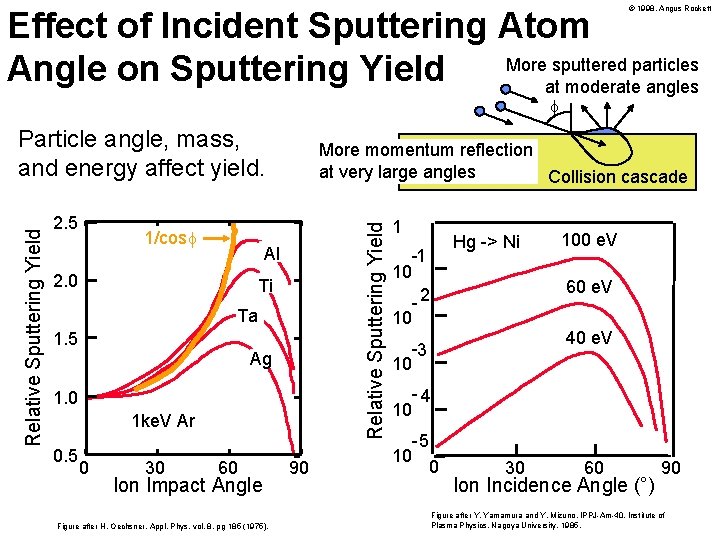
© 1998, Angus Rockett Effect of Incident Sputtering Atom More sputtered particles Angle on Sputtering Yield at moderate angles 2. 5 1/cos More momentum reflection at very large angles Collision cascade Relative Sputtering Yield Particle angle, mass, and energy affect yield. Al 2. 0 Ti Ta 1. 5 Ag 1. 0 1 ke. V Ar 0. 5 0 30 60 Ion Impact Angle Figure after H. Oechsner, Appl. Phys. vol. 8, pg 185 (1975). 90 1 Hg -> Ni -1 10 -2 10 100 e. V 60 e. V 40 e. V -3 10 -4 10 -5 10 0 30 60 Ion Incidence Angle (°) 90 Figure after Y. Yamamura and Y. Mizuno, IPPJ-Am-40, Institute of Plasma Physics, Nagoya University, 1985.
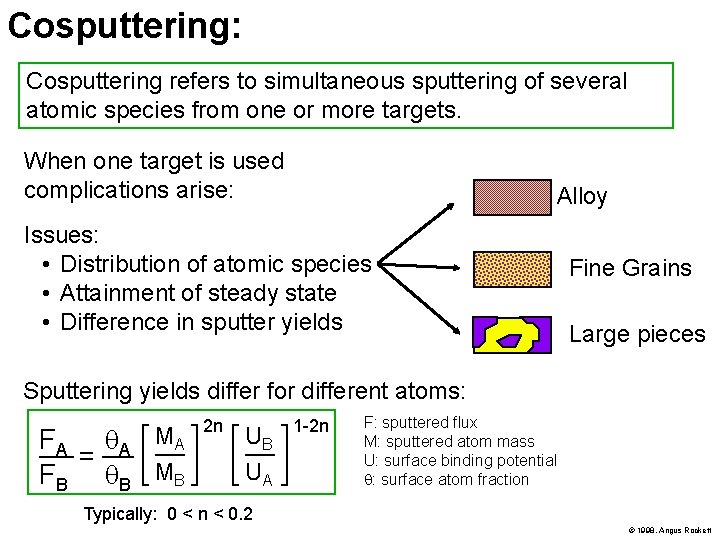
Cosputtering: Cosputtering refers to simultaneous sputtering of several atomic species from one or more targets. When one target is used complications arise: Alloy Issues: • Distribution of atomic species • Attainment of steady state • Difference in sputter yields Fine Grains Large pieces Sputtering yields differ for different atoms: F A A MA = F B B MB 2 n UB UA 1 -2 n F: sputtered flux M: sputtered atom mass U: surface binding potential : surface atom fraction Typically: 0 < n < 0. 2 © 1998, Angus Rockett
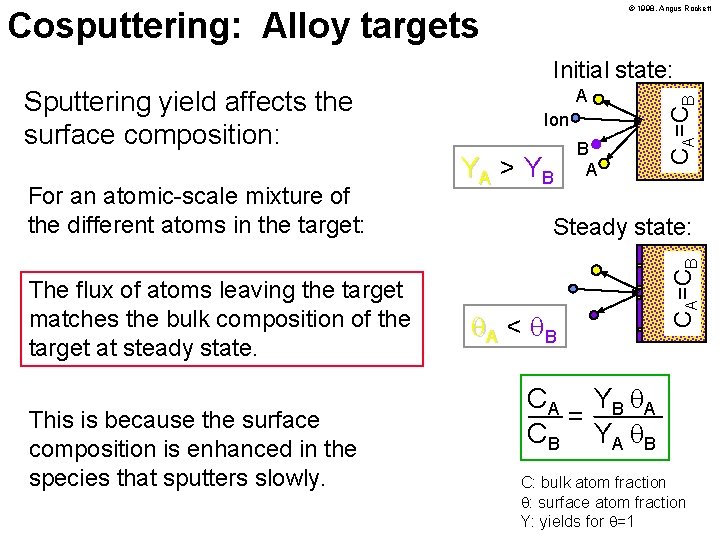
© 1998, Angus Rockett Cosputtering: Alloy targets For an atomic-scale mixture of the different atoms in the target: The flux of atoms leaving the target matches the bulk composition of the target at steady state. This is because the surface composition is enhanced in the species that sputters slowly. A Ion YA > YB B A Steady state: A < B CA=CB Sputtering yield affects the surface composition: CA=CB Initial state: CA Y B A = CB Y A B C: bulk atom fraction : surface atom fraction Y: yields for =1
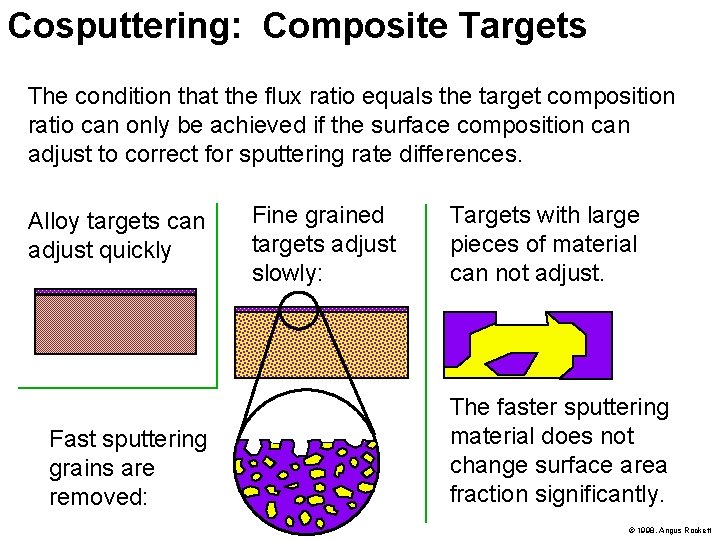
Cosputtering: Composite Targets The condition that the flux ratio equals the target composition ratio can only be achieved if the surface composition can adjust to correct for sputtering rate differences. Alloy targets can adjust quickly Fast sputtering grains are removed: Fine grained targets adjust slowly: Targets with large pieces of material can not adjust. The faster sputtering material does not change surface area fraction significantly. © 1998, Angus Rockett
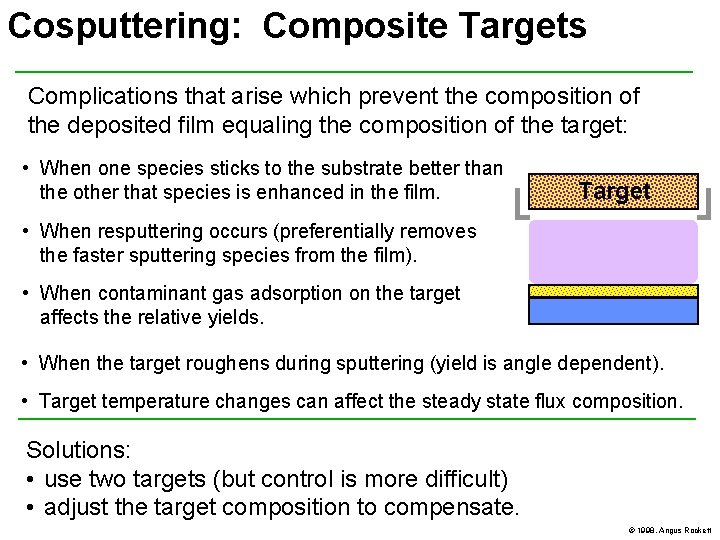
Cosputtering: Composite Targets Complications that arise which prevent the composition of the deposited film equaling the composition of the target: • When one species sticks to the substrate better than the other that species is enhanced in the film. Target • When resputtering occurs (preferentially removes the faster sputtering species from the film). • When contaminant gas adsorption on the target affects the relative yields. • When the target roughens during sputtering (yield is angle dependent). • Target temperature changes can affect the steady state flux composition. Solutions: • use two targets (but control is more difficult) • adjust the target composition to compensate. © 1998, Angus Rockett
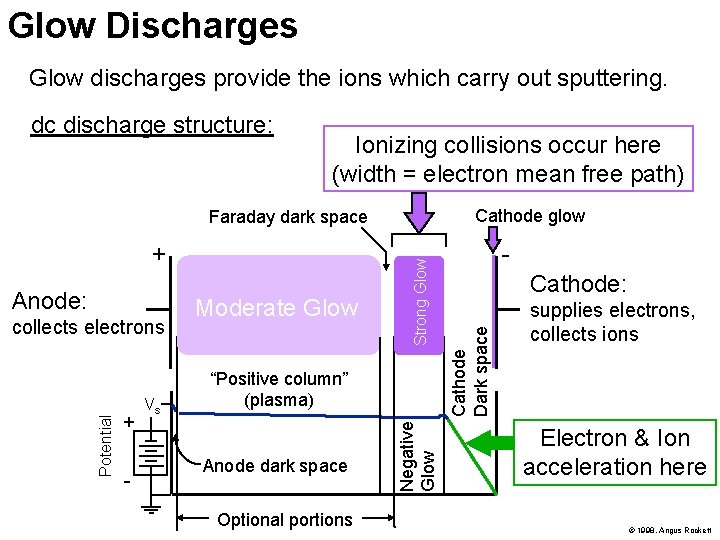
Glow Discharges Glow discharges provide the ions which carry out sputtering. Ionizing collisions occur here (width = electron mean free path) Cathode glow + Potential collects electrons + - Vs Moderate Glow “Positive column” (plasma) Anode dark space Optional portions Negative Glow Anode: Strong Glow Faraday dark space Cathode: Cathode Dark space dc discharge structure: supplies electrons, collects ions Electron & Ion acceleration here © 1998, Angus Rockett
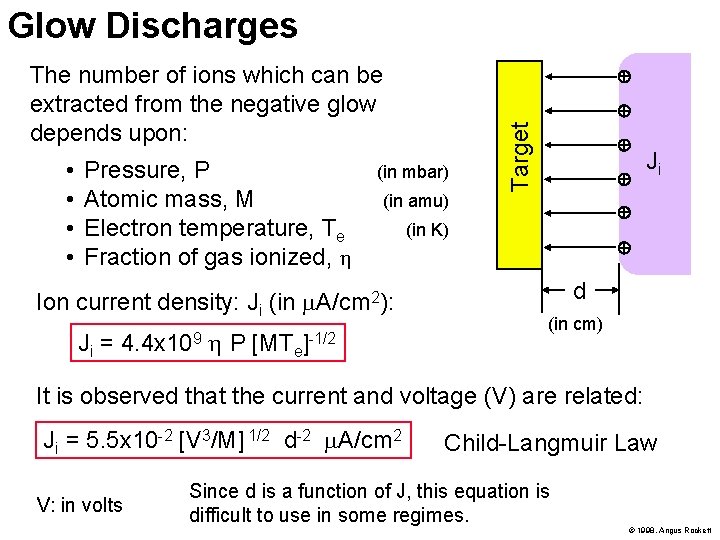
Glow Discharges The number of ions which can be extracted from the negative glow depends upon: Pressure, P Atomic mass, M Electron temperature, Te Fraction of gas ionized, (in mbar) (in amu) Ion current density: Ji (in A/cm 2): Ji = 4. 4 x 109 P [MTe + ]-1/2 Target • • + + + Ji + (in K) + d (in cm) It is observed that the current and voltage (V) are related: Ji = 5. 5 x 10 -2 [V 3/M] 1/2 d-2 A/cm 2 V: in volts Child-Langmuir Law Since d is a function of J, this equation is difficult to use in some regimes. © 1998, Angus Rockett
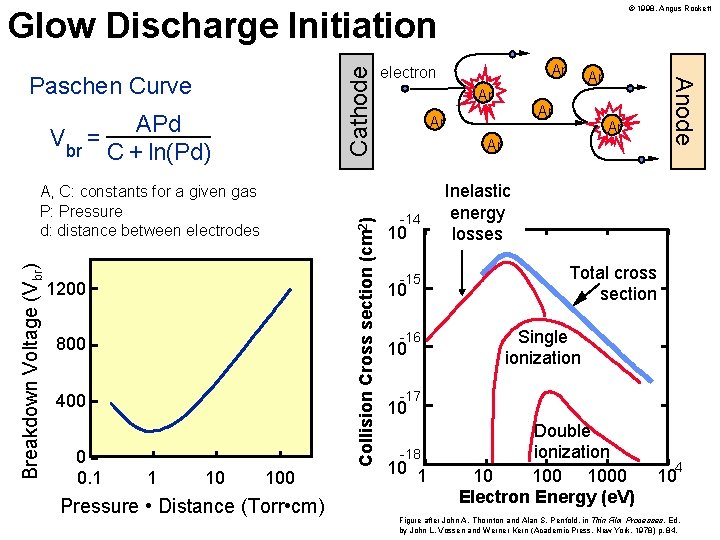
© 1998, Angus Rockett Paschen Curve Vbr = APd C + ln(Pd) Collision Cross section (cm 2) Breakdown Voltage (Vbr) A, C: constants for a given gas P: Pressure d: distance between electrodes 1200 800 400 0 0. 1 1 10 100 Pressure • Distance (Torr • cm) Ar electron Ar Ar Anode Cathode Glow Discharge Initiation Ar Ar -14 10 -15 10 -16 10 Inelastic energy losses Total cross section Single ionization -17 10 -18 10 1 Double ionization 10 1000 Electron Energy (e. V) 4 10 Figure after John A. Thornton and Alan S. Penfold, in Thin Film Processes, Ed. by John L. Vossen and Werner Kern (Academic Press, New York, 1978) p. 84.
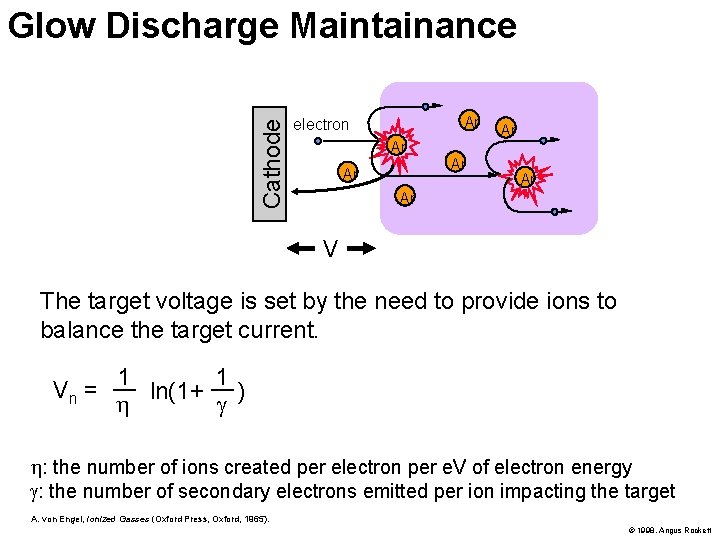
Cathode Glow Discharge Maintainance Ar electron Ar Ar Ar V The target voltage is set by the need to provide ions to balance the target current. Vn = 1 1 ln(1+ ) : the number of ions created per electron per e. V of electron energy : the number of secondary electrons emitted per ion impacting the target A. von Engel, Ionized Gasses (Oxford Press, Oxford, 1965). © 1998, Angus Rockett
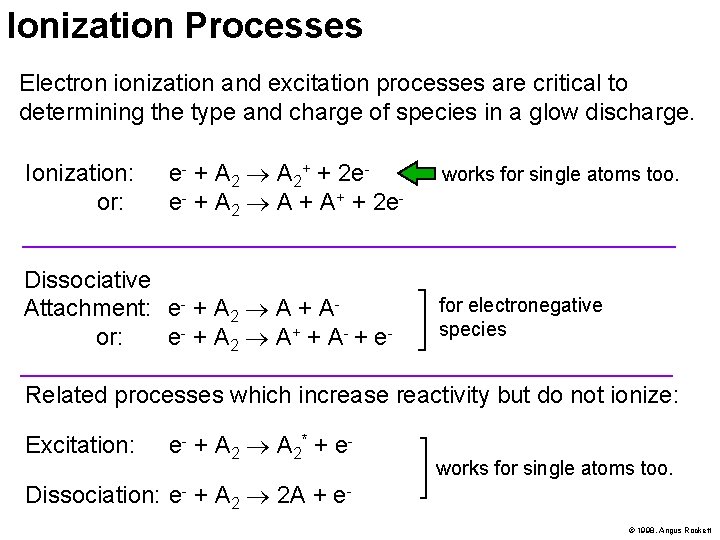
Ionization Processes Electron ionization and excitation processes are critical to determining the type and charge of species in a glow discharge. Ionization: or: e- + A 2+ + 2 ee- + A 2 A + A+ + 2 e- Dissociative Attachment: e- + A 2 A + Aor: e- + A 2 A + + A - + e - works for single atoms too. for electronegative species Related processes which increase reactivity but do not ionize: Excitation: e - + A 2* + e - Dissociation: e- + A 2 2 A + e- works for single atoms too. © 1998, Angus Rockett
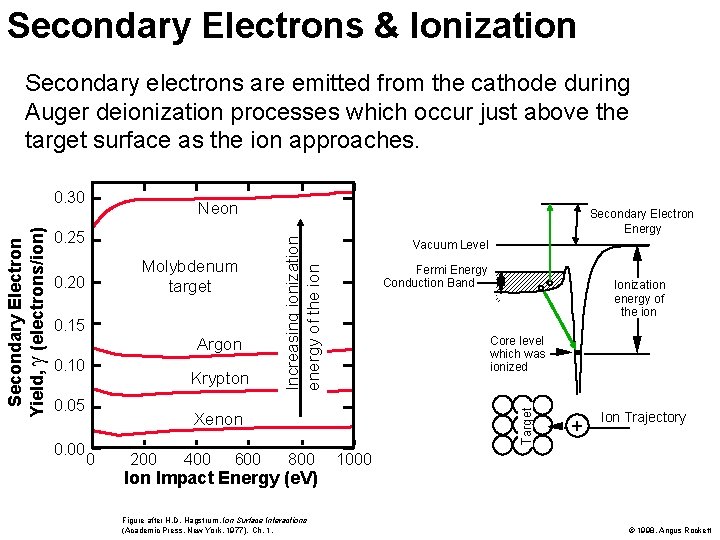
Secondary Electrons & Ionization Secondary electrons are emitted from the cathode during Auger deionization processes which occur just above the target surface as the ion approaches. Neon Molybdenum target 0. 20 0. 15 Argon 0. 10 Krypton 0. 05 0. 00 Vacuum Level Fermi Energy Conduction Band Core level which was ionized Xenon 0 200 400 600 Ionization energy of the ion Target 0. 25 Secondary Electron Energy Increasing ionization energy of the ion Secondary Electron Yield, (electrons/ion) 0. 30 800 Ion Impact Energy (e. V) Figure after H. D. Hagstrum, Ion Surface Interactions (Academic Press, New York, 1977), Ch. 1. + Ion Trajectory 1000 © 1998, Angus Rockett
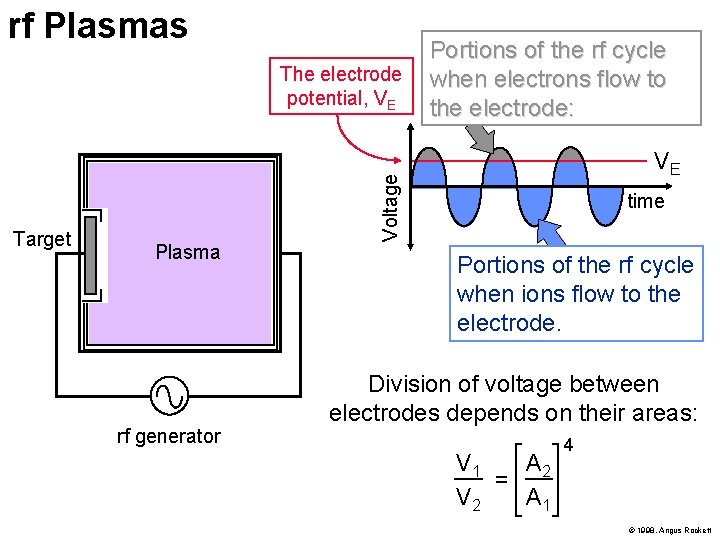
rf Plasmas Target Plasma rf generator VE Voltage The electrode potential, VE Portions of the rf cycle when electrons flow to the electrode: time Portions of the rf cycle when ions flow to the electrode. Division of voltage between electrodes depends on their areas: V 1 A 2 = V 2 A 1 4 © 1998, Angus Rockett
![rf Plasmas Ion Flux k Te 12 Ji Ni Mi Plasma Electron rf Plasmas Ion Flux: k. Te 1/2 Ji= Ni Mi [ ] Plasma Electron](https://slidetodoc.com/presentation_image_h2/6fd6c1d0a023ff623534032537a4101d/image-35.jpg)
rf Plasmas Ion Flux: k. Te 1/2 Ji= Ni Mi [ ] Plasma Electron Flux: plasma N 8 k. Te e Je = 4 me ( ) Electron flux Ion flux Electrode Potential k. Te Mi VE = log 2 e 2 me Chamber wall or target Vp: plasma potential e: electron charge k: Boltzmann’s constant Ni: Ion density Te: electron temperature me: electron mass Mi: ion mass Ne: electron density Jiwall = Jewall : a constant © 1998, Angus Rockett
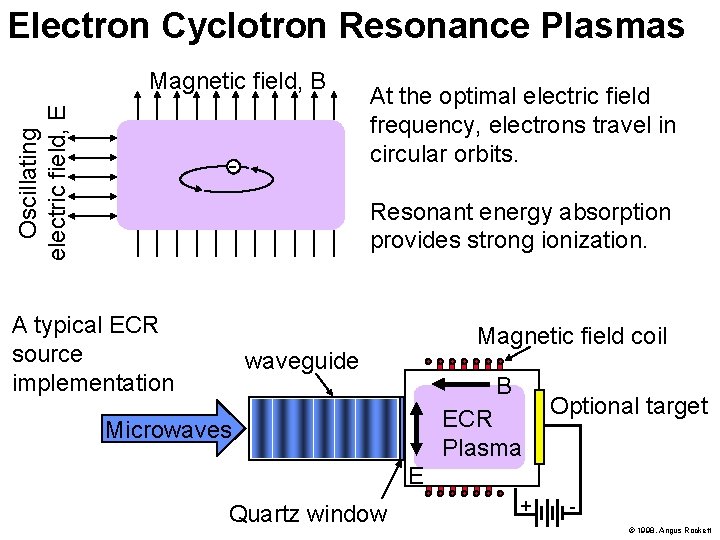
Electron Cyclotron Resonance Plasmas Oscillating electric field, E Magnetic field, B - At the optimal electric field frequency, electrons travel in circular orbits. Resonant energy absorption provides strong ionization. A typical ECR source implementation Magnetic field coil waveguide B ECR Plasma Microwaves Optional target E Quartz window + © 1998, Angus Rockett
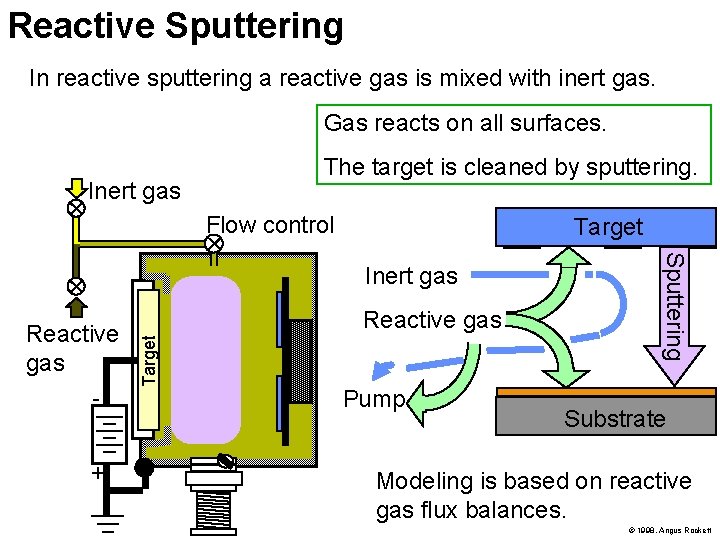
Reactive Sputtering In reactive sputtering a reactive gas is mixed with inert gas. Gas reacts on all surfaces. Inert gas The target is cleaned by sputtering. Flow control Target + Target Reactive gas - Reactive gas Pump Sputtering Inert gas Substrate Modeling is based on reactive gas flux balances. © 1998, Angus Rockett
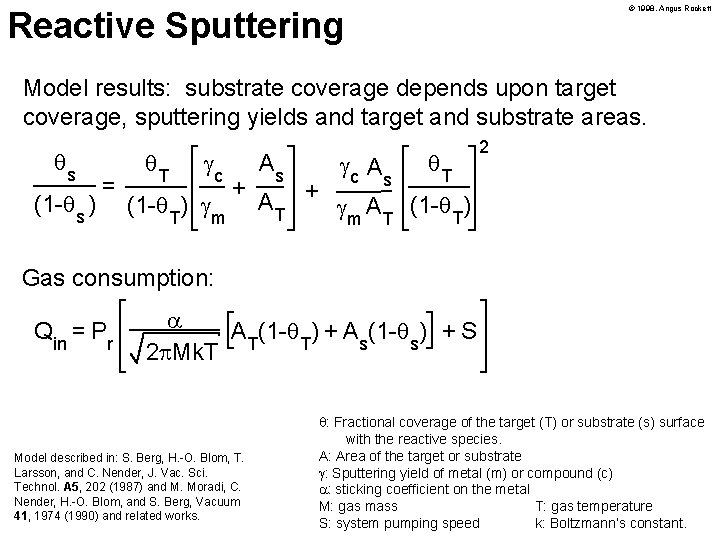
© 1998, Angus Rockett Reactive Sputtering Model results: substrate coverage depends upon target coverage, sputtering yields and target and substrate areas. s (1 - s ) = T c (1 - T) m + As c A s T 2 AT + A (1 - ) T m T Gas consumption: Qin = Pr AT(1 - T) + As(1 - s) + S 2 Mk. T Model described in: S. Berg, H. -O. Blom, T. Larsson, and C. Nender, J. Vac. Sci. Technol. A 5, 202 (1987) and M. Moradi, C. Nender, H. -O. Blom, and S. Berg, Vacuum 41, 1974 (1990) and related works. : Fractional coverage of the target (T) or substrate (s) surface with the reactive species. A: Area of the target or substrate : Sputtering yield of metal (m) or compound (c) : sticking coefficient on the metal M: gas mass T: gas temperature S: system pumping speed k: Boltzmann’s constant.
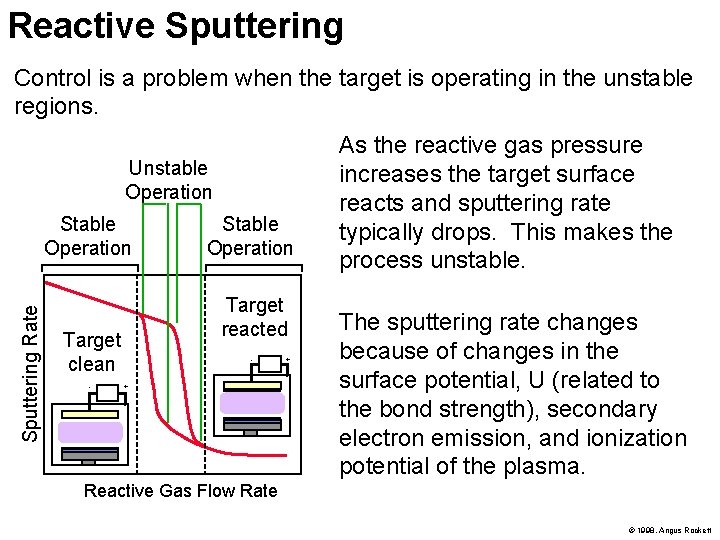
Reactive Sputtering Control is a problem when the target is operating in the unstable regions. Unstable Operation Sputtering Rate Stable Operation Target reacted Target clean - Stable Operation + + As the reactive gas pressure increases the target surface reacts and sputtering rate typically drops. This makes the process unstable. The sputtering rate changes because of changes in the surface potential, U (related to the bond strength), secondary electron emission, and ionization potential of the plasma. Reactive Gas Flow Rate © 1998, Angus Rockett
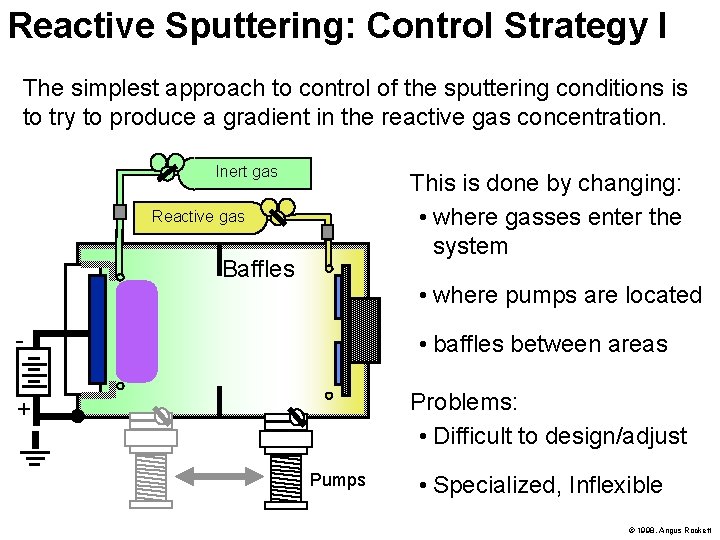
Reactive Sputtering: Control Strategy I The simplest approach to control of the sputtering conditions is to try to produce a gradient in the reactive gas concentration. Inert gas This is done by changing: • where gasses enter the system Reactive gas Baffles • where pumps are located - • baffles between areas + Problems: • Difficult to design/adjust Pumps • Specialized, Inflexible © 1998, Angus Rockett
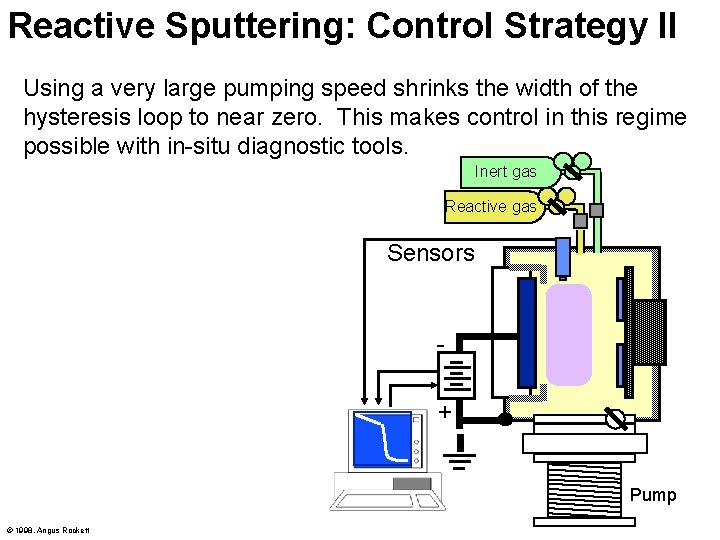
Reactive Sputtering: Control Strategy II Using a very large pumping speed shrinks the width of the hysteresis loop to near zero. This makes control in this regime possible with in-situ diagnostic tools. Inert gas Reactive gas Sensors + Pump © 1998, Angus Rockett
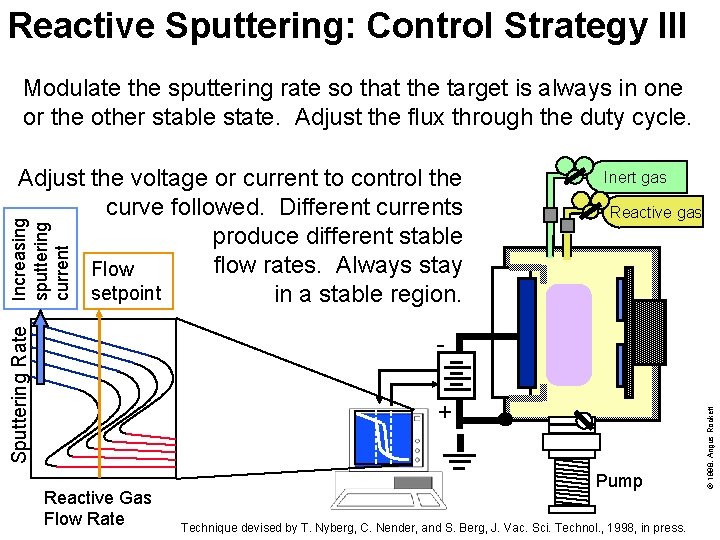
Reactive Sputtering: Control Strategy III Modulate the sputtering rate so that the target is always in one or the other stable state. Adjust the flux through the duty cycle. Sputtering Rate Increasing sputtering current Adjust the voltage or current to control the curve followed. Different currents produce different stable flow rates. Always stay Flow setpoint in a stable region. Inert gas Reactive gas + Reactive Gas Flow Rate Pump Technique devised by T. Nyberg, C. Nender, and S. Berg, J. Vac. Sci. Technol. , 1998, in press. © 1998, Angus Rockett -
Dc sputtering
Sputtering yield
Advantages and disadvantages of dc sputtering
Thin
Selenio blanco de sputtering
Magnetron sputtering
Hamlet act iii scene ii
Who is the thane of glamis in macbeth
Domino angus
Escala de marmoleo wagyu
American angus assn
Angus foulis
Dominos angus
Red angus advantages
Macbeth character collage
Sports injuries angus, on
Angus vincent rvi
Angus lund
Tovne pasmine goveda
1998 sosyal bilgiler öğretim programı
Sabah water resources enactment 1998
Cutler friedmann and mccoy (1998)
Nation vs state
Bruscia 1998
Müge gördürür
Kdd cup 1998 solution
Portaria svs/ms 27/1998
Ieee 829 standard
Jenny jones killer
Wba&as salary
Kalender jawa 1998
Numération romaine
Ktn kallo haven 1998
Video game 1998
Corkery v carpenter 1951
National education policy 1998 to 2010
Dpa 1998
Rys 9 1998
Loler 1998
Lei nº 9.605 de 12 de fevereiro de 1998
Ribozymy
Elicitação de requisitos
Torp y sage 1998