Review for Exam 2 z Pratt Whitney is
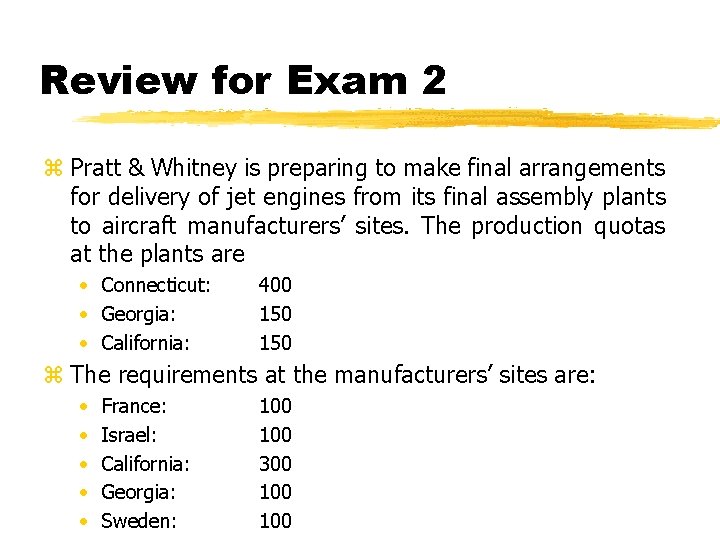
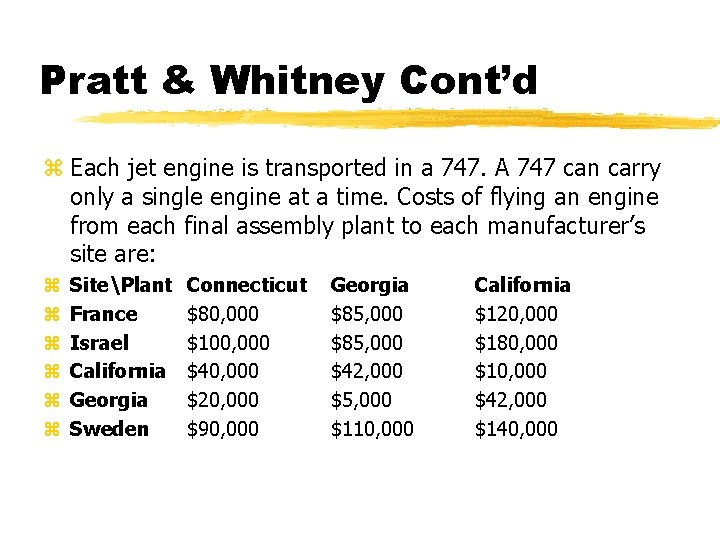
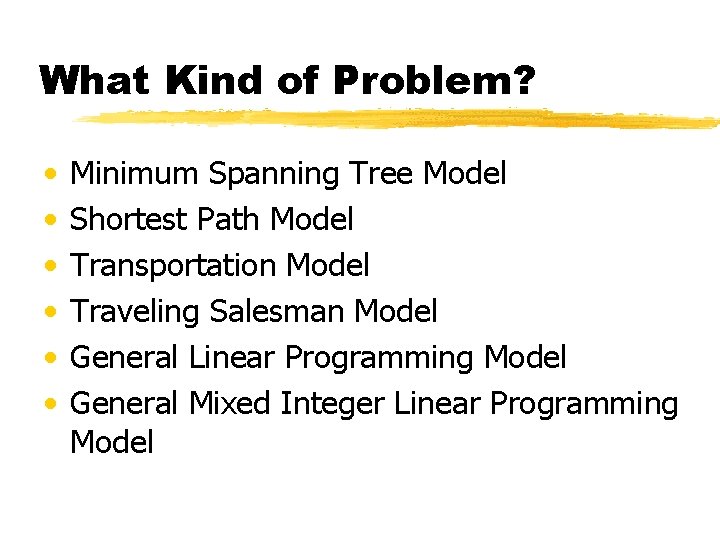
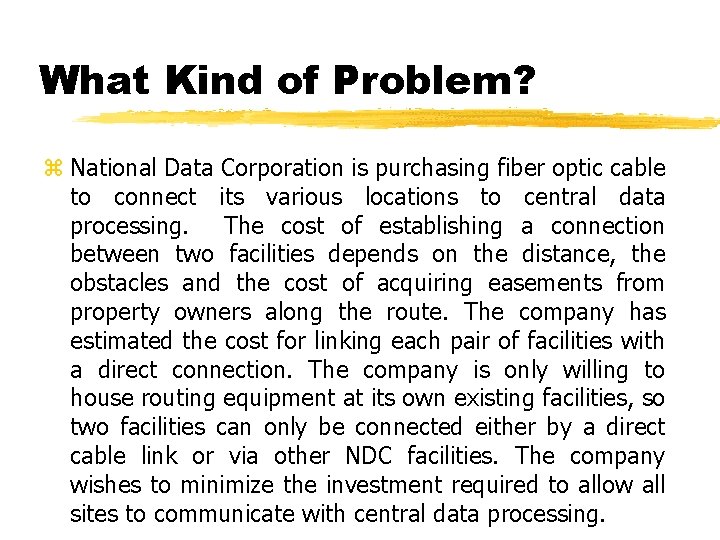
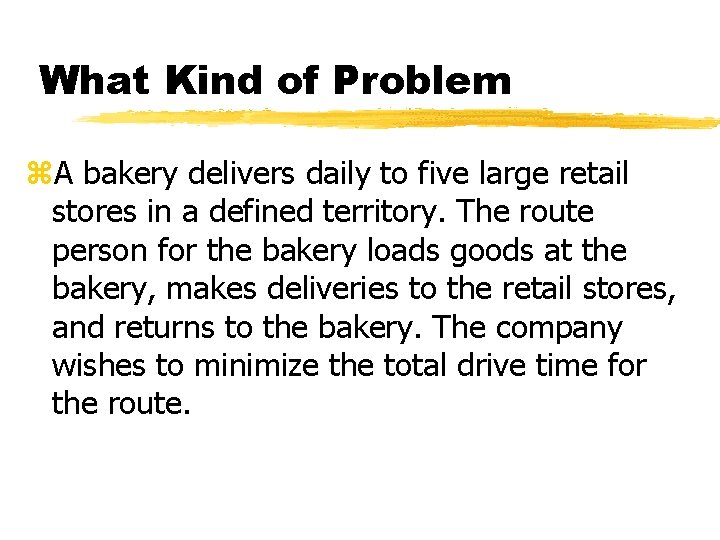
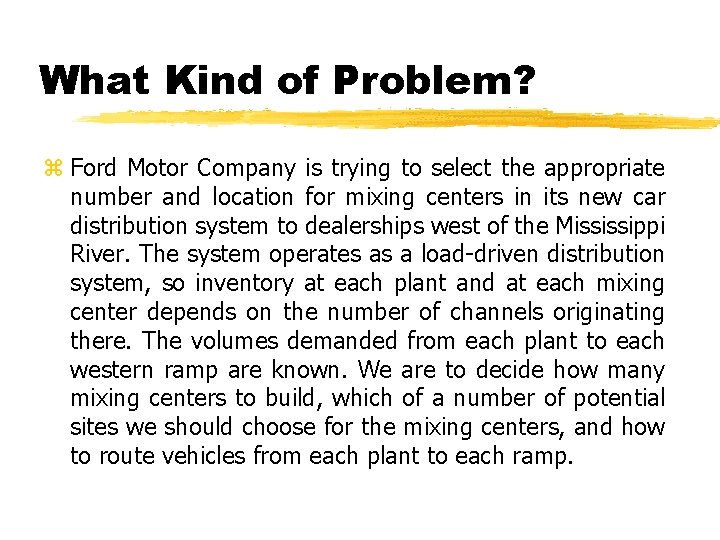

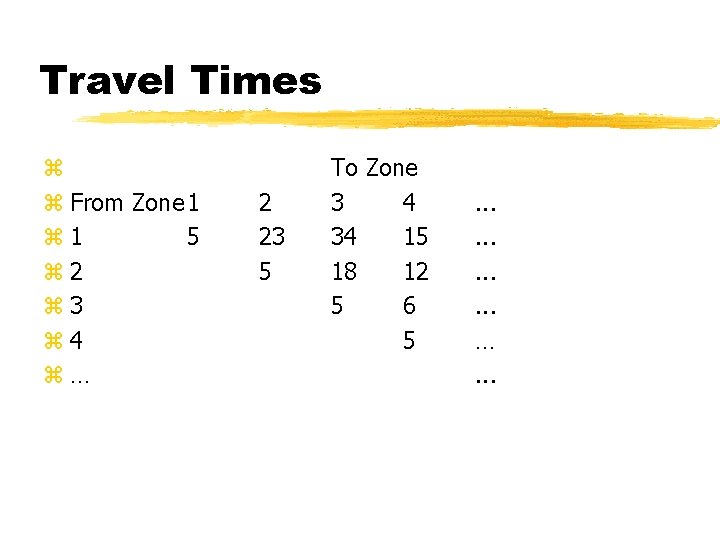
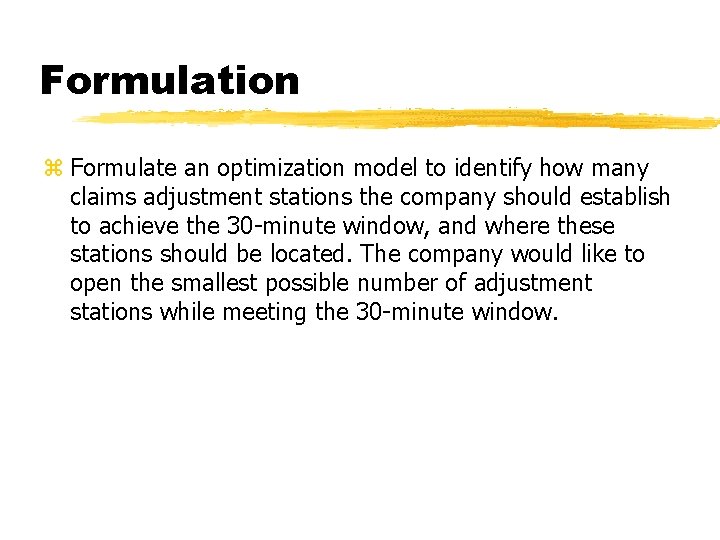
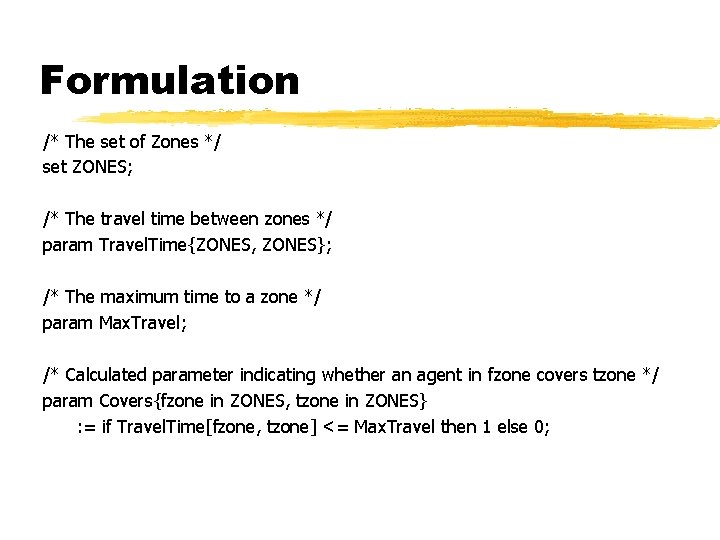
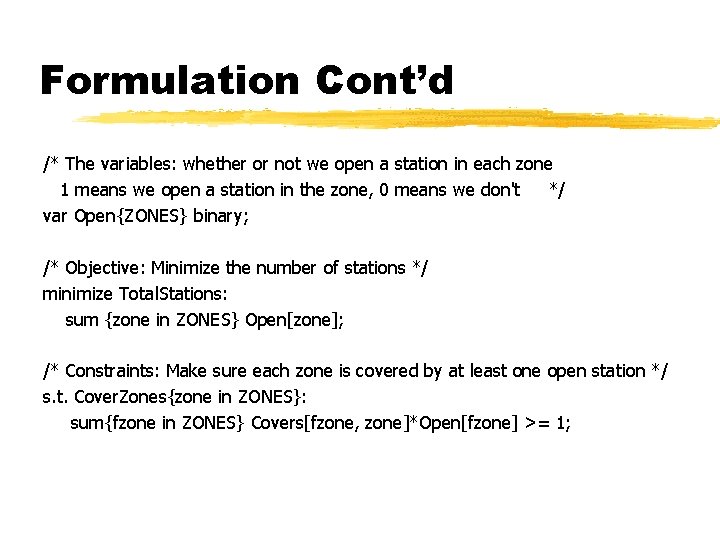
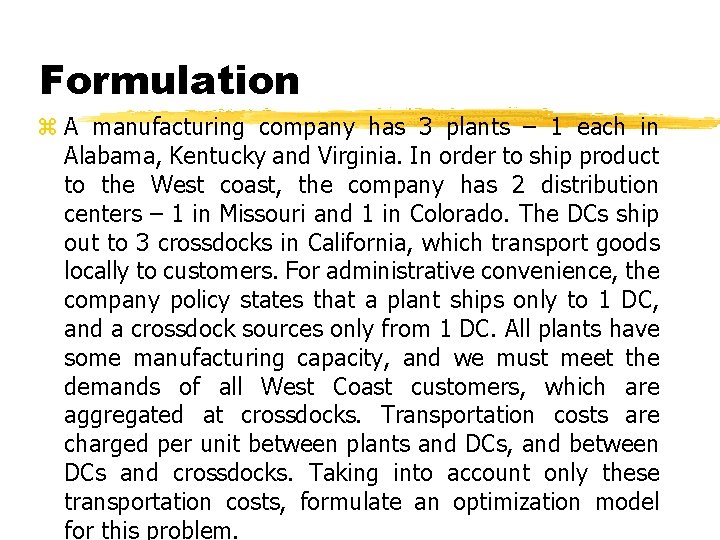
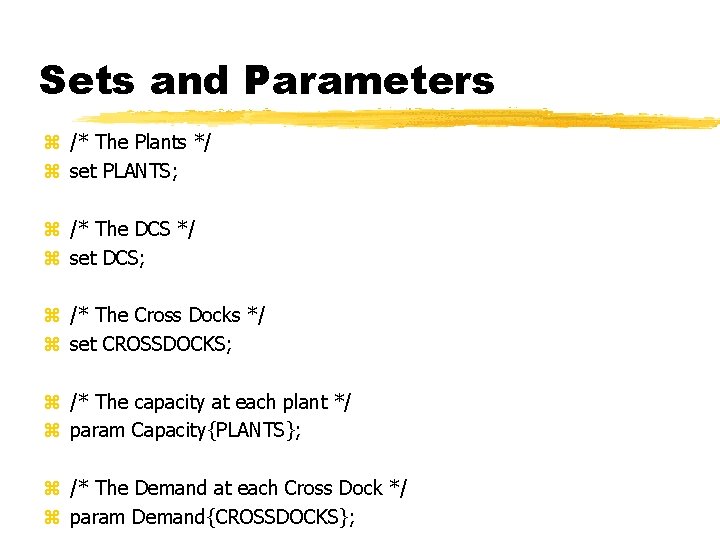
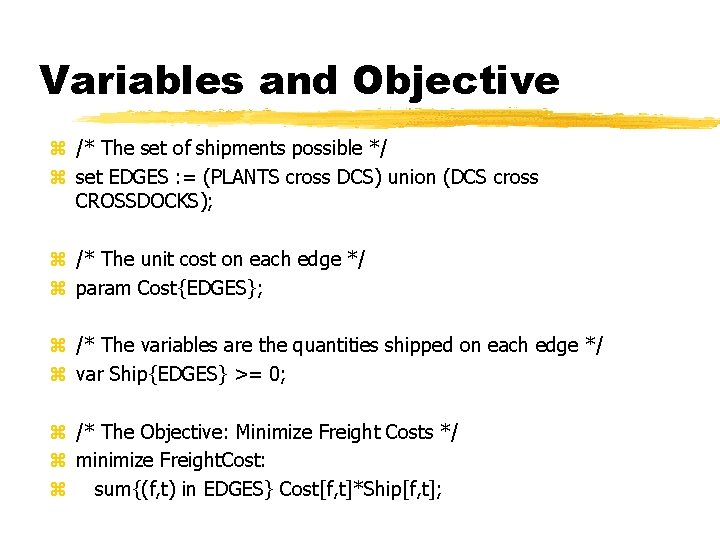
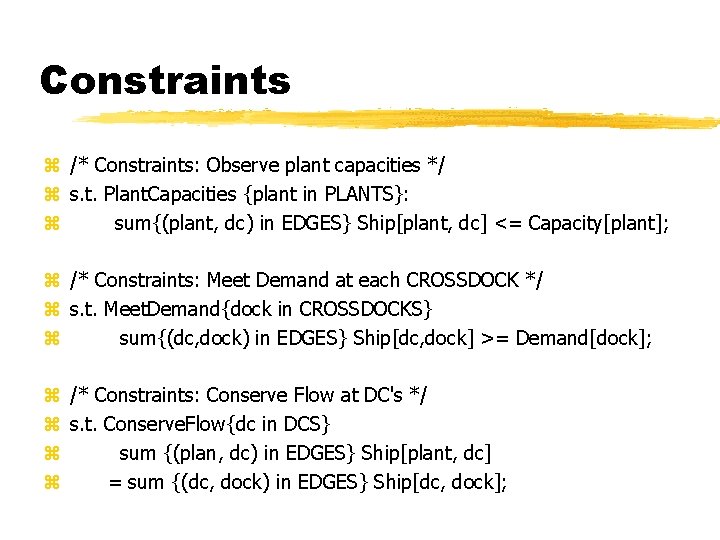
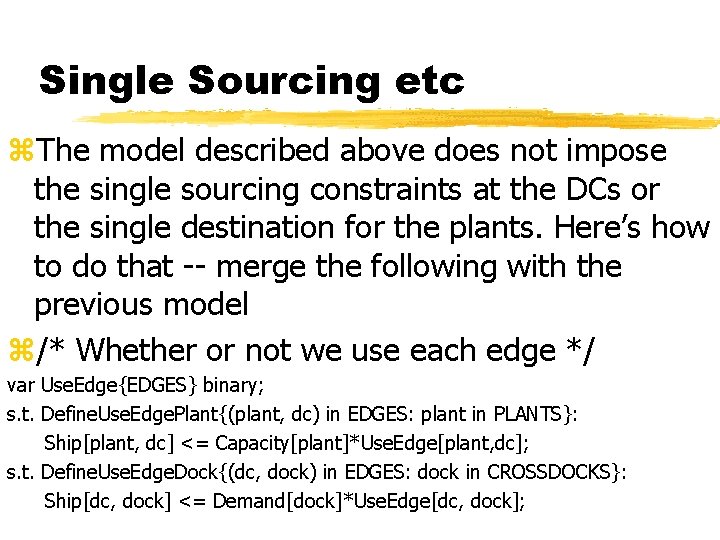
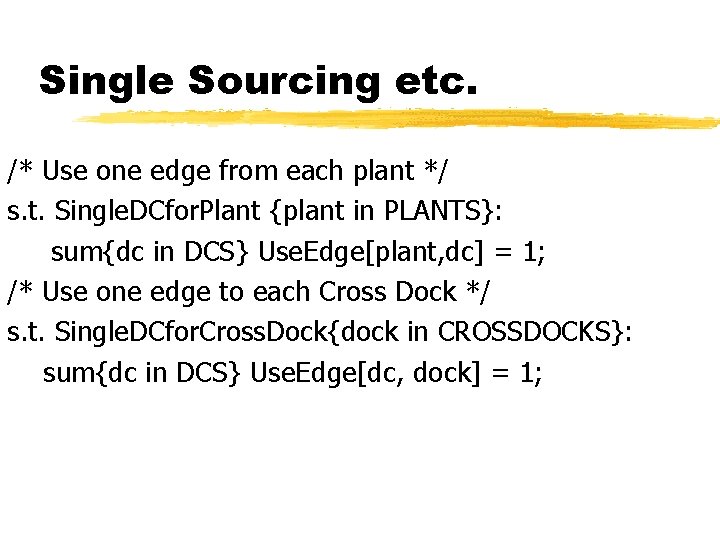
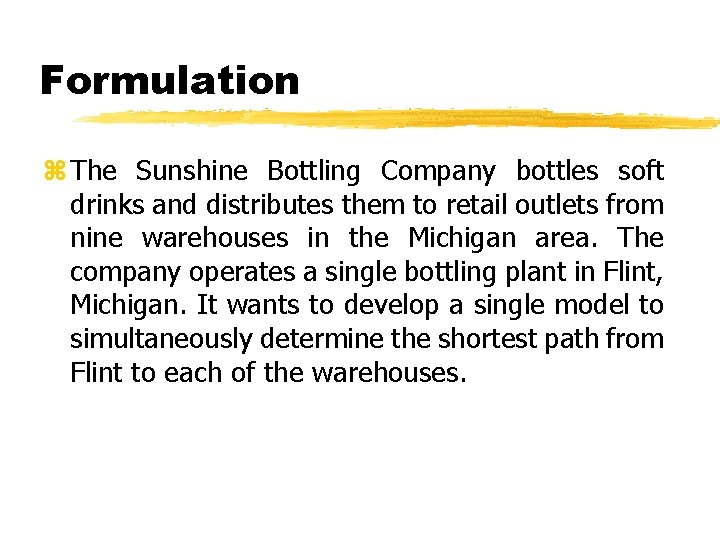
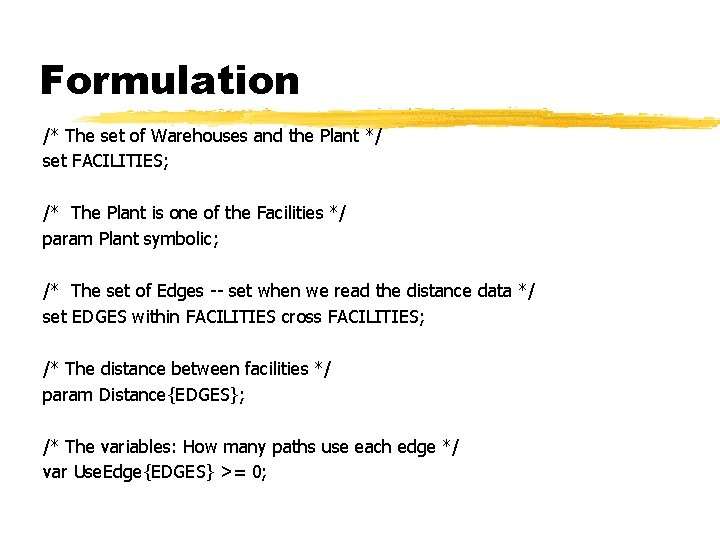
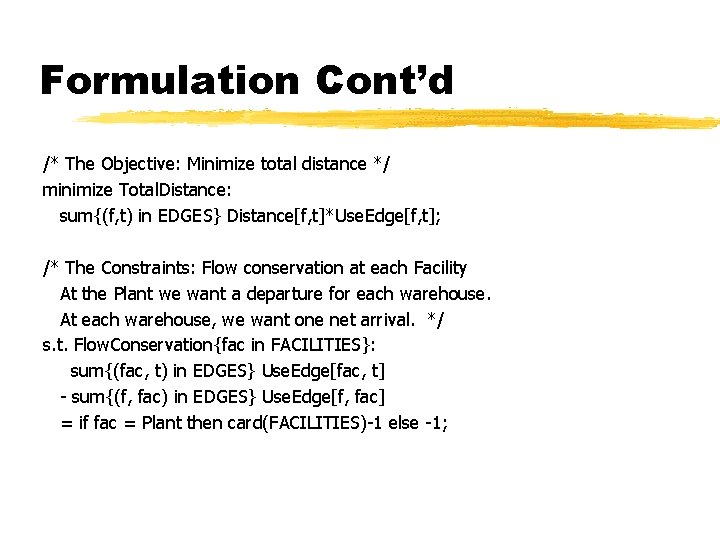
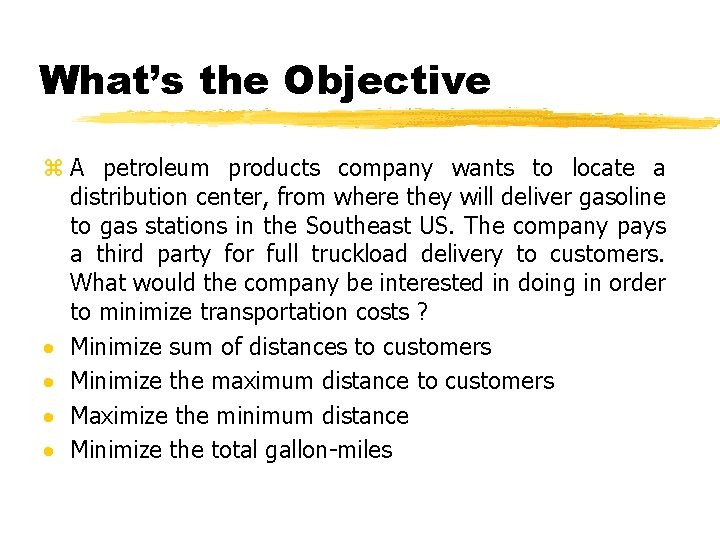
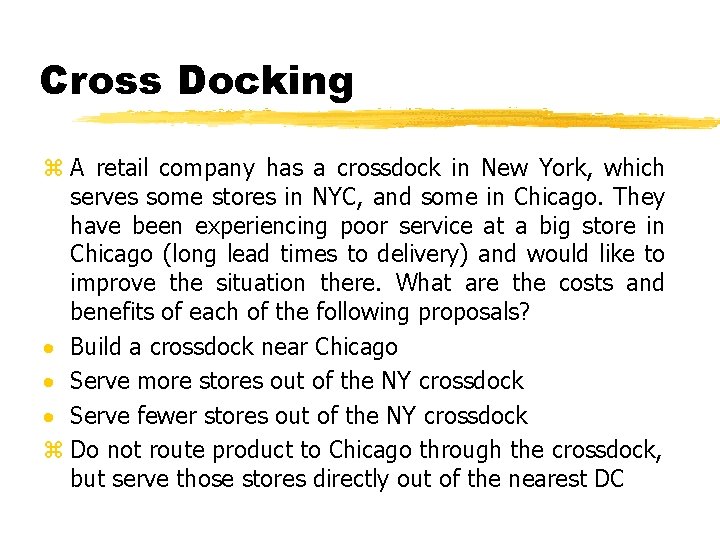
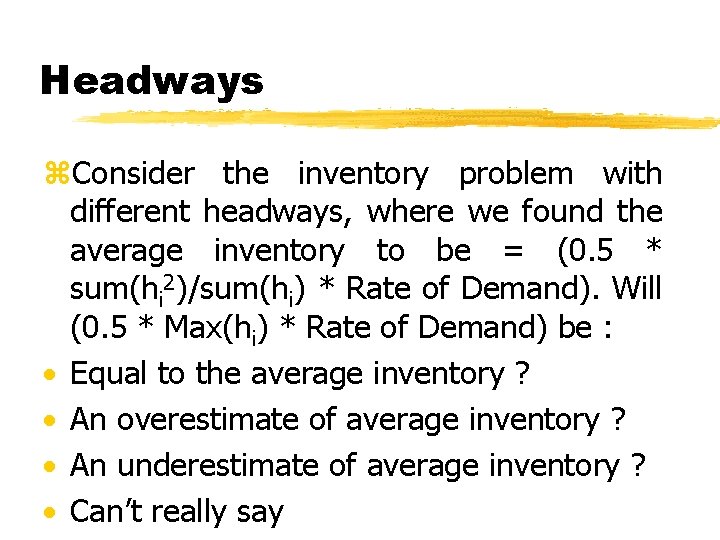
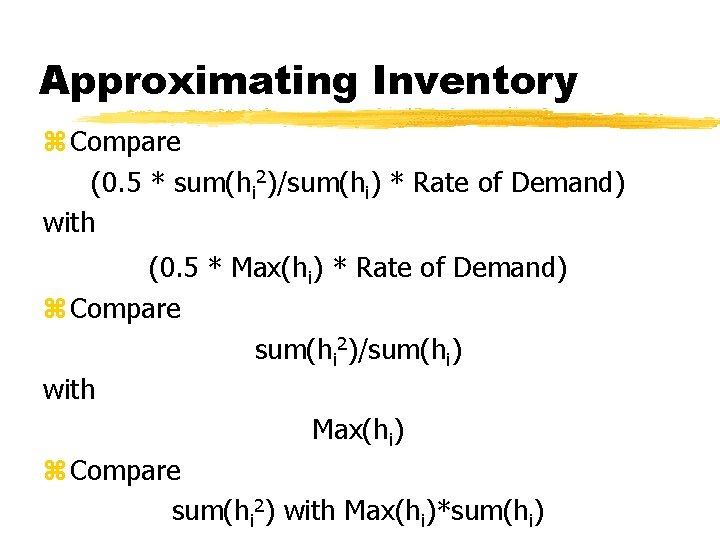
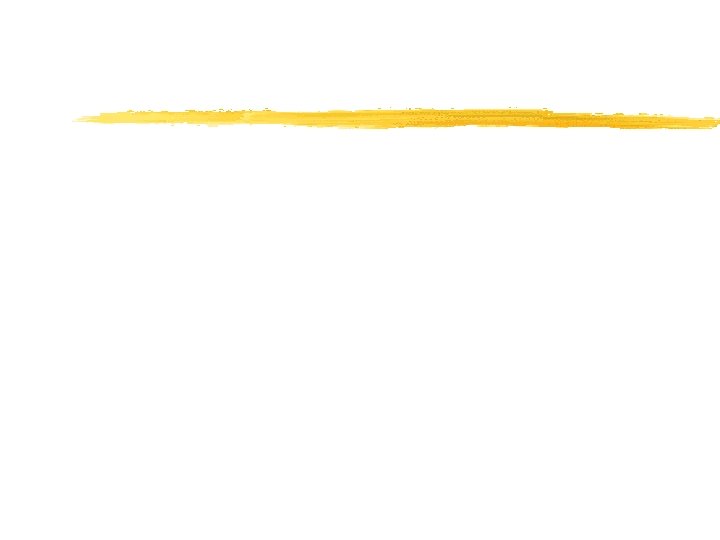
- Slides: 25
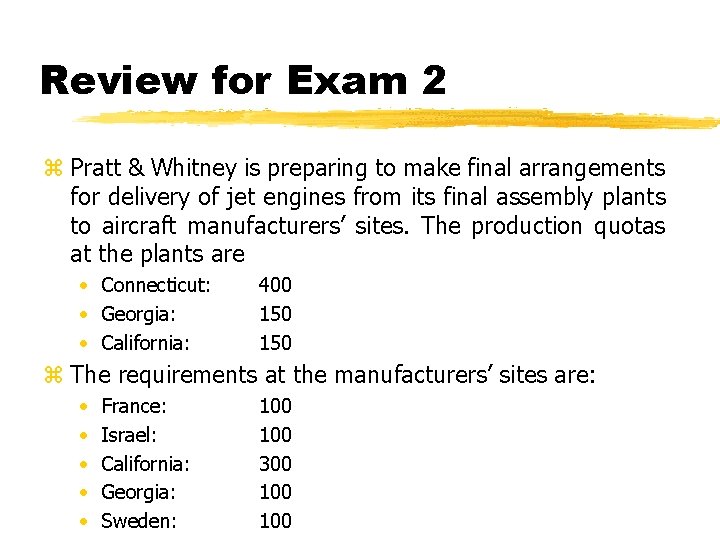
Review for Exam 2 z Pratt & Whitney is preparing to make final arrangements for delivery of jet engines from its final assembly plants to aircraft manufacturers’ sites. The production quotas at the plants are · Connecticut: · Georgia: · California: 400 150 z The requirements at the manufacturers’ sites are: · · · France: Israel: California: Georgia: Sweden: 100 300 100
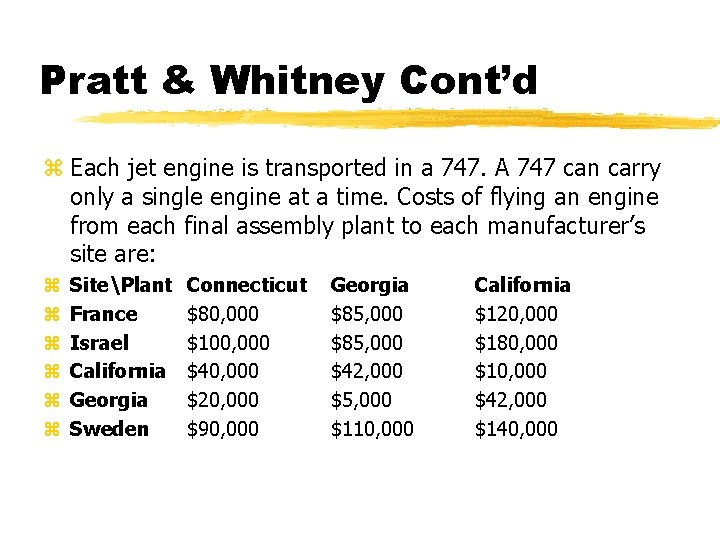
Pratt & Whitney Cont’d z Each jet engine is transported in a 747. A 747 can carry only a single engine at a time. Costs of flying an engine from each final assembly plant to each manufacturer’s site are: z z z SitePlant France Israel California Georgia Sweden Connecticut $80, 000 $100, 000 $40, 000 $20, 000 $90, 000 Georgia $85, 000 $42, 000 $5, 000 $110, 000 California $120, 000 $180, 000 $10, 000 $42, 000 $140, 000
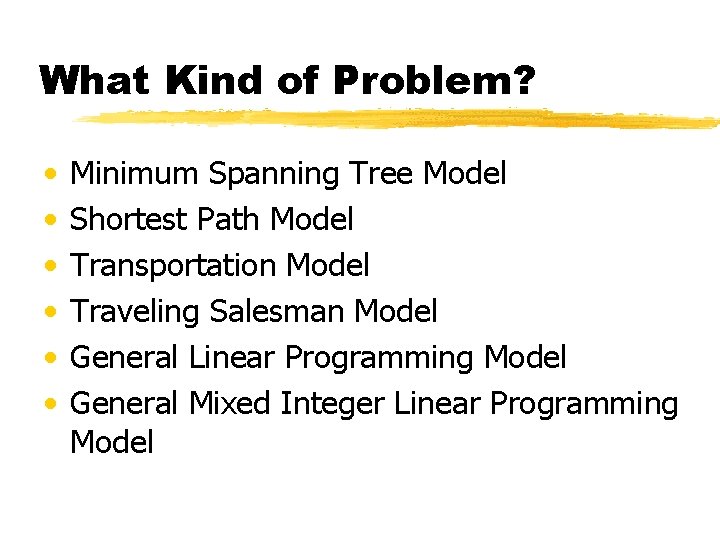
What Kind of Problem? • • • Minimum Spanning Tree Model Shortest Path Model Transportation Model Traveling Salesman Model General Linear Programming Model General Mixed Integer Linear Programming Model
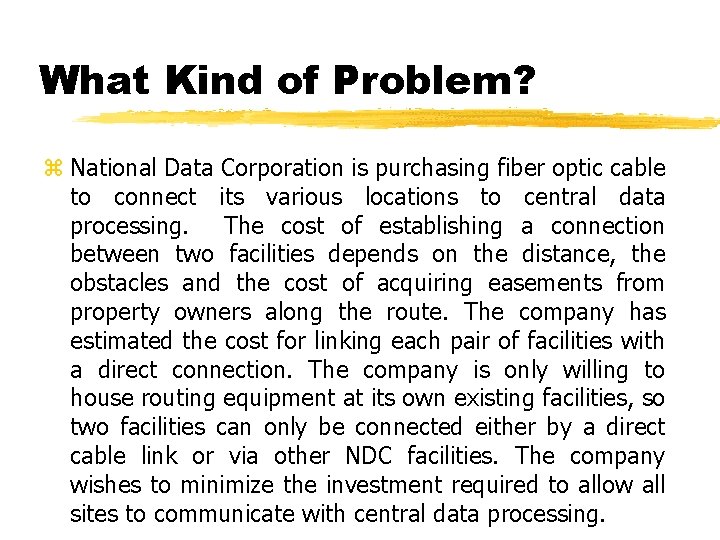
What Kind of Problem? z National Data Corporation is purchasing fiber optic cable to connect its various locations to central data processing. The cost of establishing a connection between two facilities depends on the distance, the obstacles and the cost of acquiring easements from property owners along the route. The company has estimated the cost for linking each pair of facilities with a direct connection. The company is only willing to house routing equipment at its own existing facilities, so two facilities can only be connected either by a direct cable link or via other NDC facilities. The company wishes to minimize the investment required to allow all sites to communicate with central data processing.
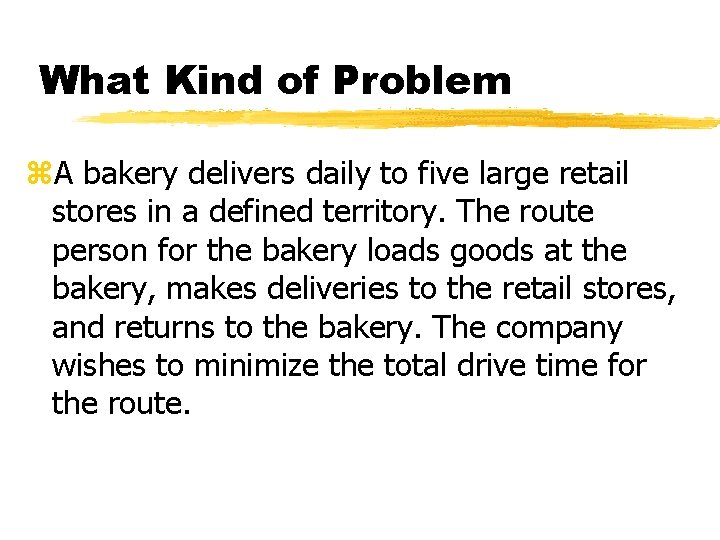
What Kind of Problem z. A bakery delivers daily to five large retail stores in a defined territory. The route person for the bakery loads goods at the bakery, makes deliveries to the retail stores, and returns to the bakery. The company wishes to minimize the total drive time for the route.
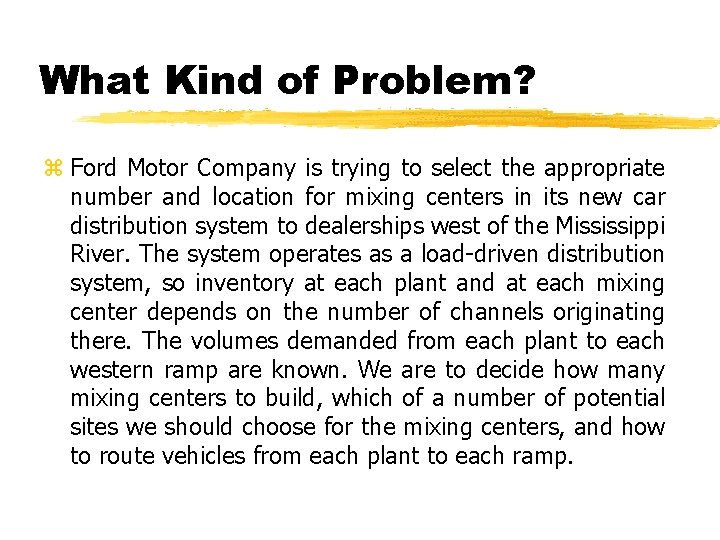
What Kind of Problem? z Ford Motor Company is trying to select the appropriate number and location for mixing centers in its new car distribution system to dealerships west of the Mississippi River. The system operates as a load-driven distribution system, so inventory at each plant and at each mixing center depends on the number of channels originating there. The volumes demanded from each plant to each western ramp are known. We are to decide how many mixing centers to build, which of a number of potential sites we should choose for the mixing centers, and how to route vehicles from each plant to each ramp.

Globe Casualty z The Globe Casualty Company positions claims adjusters around a metropolitan area to respond quickly to insurance claims resulting from auto accident, fires, crimes and other emergencies that may occur. It is a competitive feature of the company’s business to be able to be on-site within 30 minutes of a call. The company divides the city into 10 zones from which calls originate and in which adjusters may be stationed. The response times in minutes between the 10 zones are:
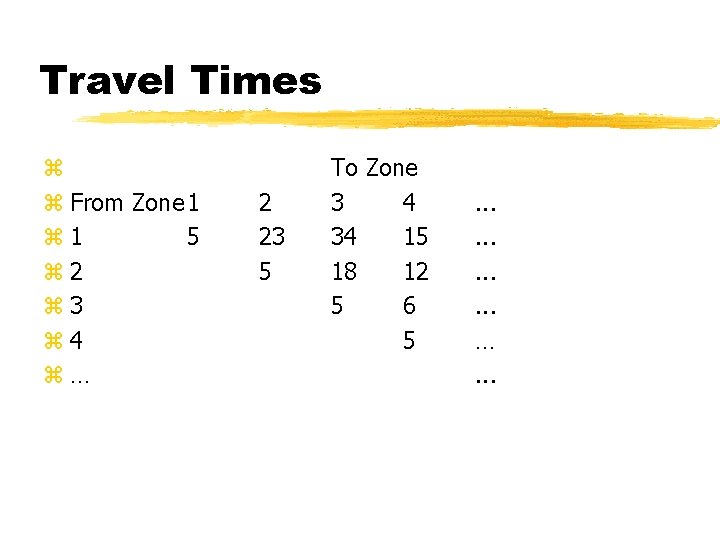
Travel Times z z From Zone 1 z 1 5 z 2 z 3 z 4 z… 2 23 5 To Zone 3 4 34 15 18 12 5 6 5 . . . …. . .
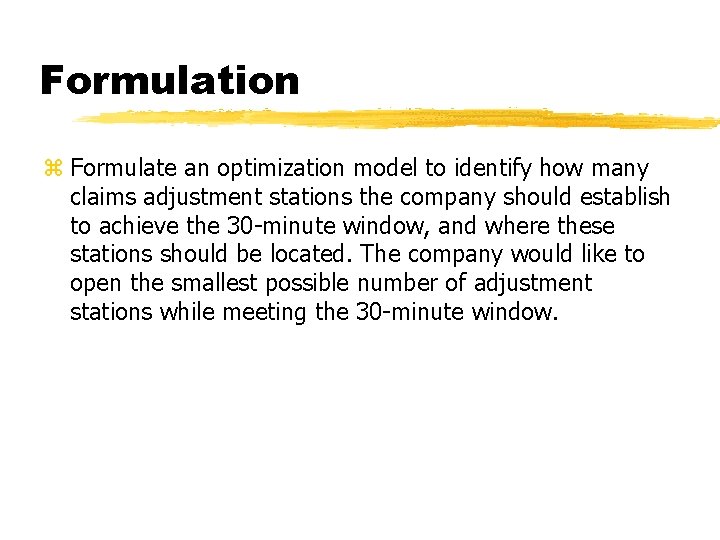
Formulation z Formulate an optimization model to identify how many claims adjustment stations the company should establish to achieve the 30 -minute window, and where these stations should be located. The company would like to open the smallest possible number of adjustment stations while meeting the 30 -minute window.
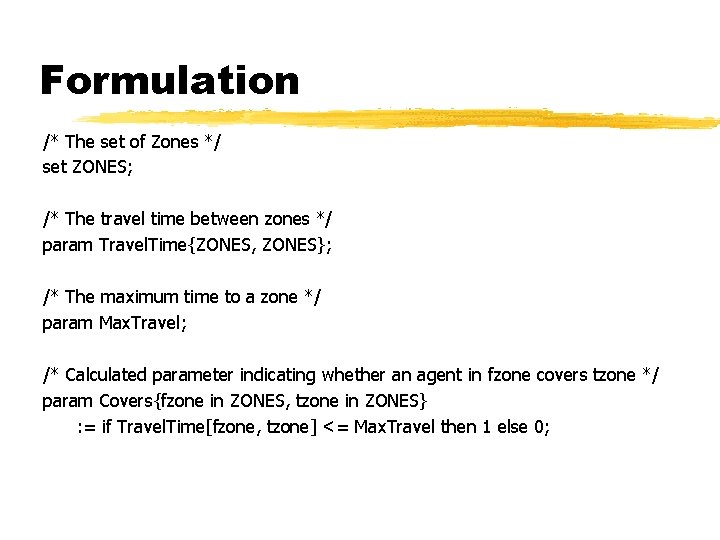
Formulation /* The set of Zones */ set ZONES; /* The travel time between zones */ param Travel. Time{ZONES, ZONES}; /* The maximum time to a zone */ param Max. Travel; /* Calculated parameter indicating whether an agent in fzone covers tzone */ param Covers{fzone in ZONES, tzone in ZONES} : = if Travel. Time[fzone, tzone] <= Max. Travel then 1 else 0;
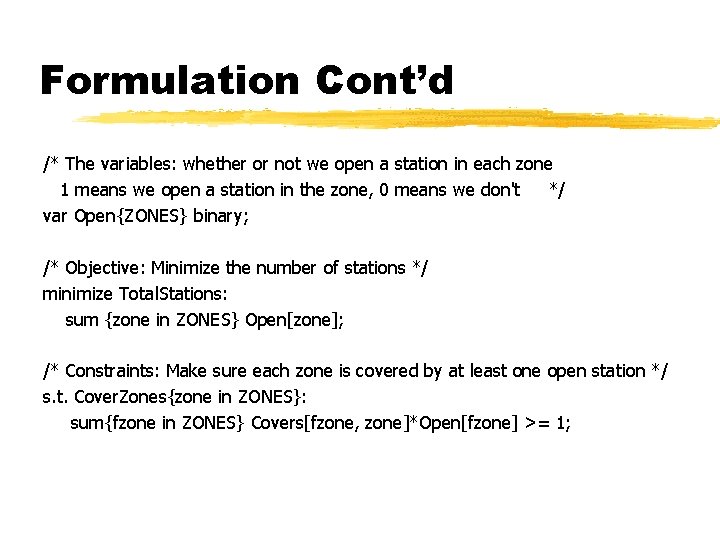
Formulation Cont’d /* The variables: whether or not we open a station in each zone 1 means we open a station in the zone, 0 means we don't */ var Open{ZONES} binary; /* Objective: Minimize the number of stations */ minimize Total. Stations: sum {zone in ZONES} Open[zone]; /* Constraints: Make sure each zone is covered by at least one open station */ s. t. Cover. Zones{zone in ZONES}: sum{fzone in ZONES} Covers[fzone, zone]*Open[fzone] >= 1;
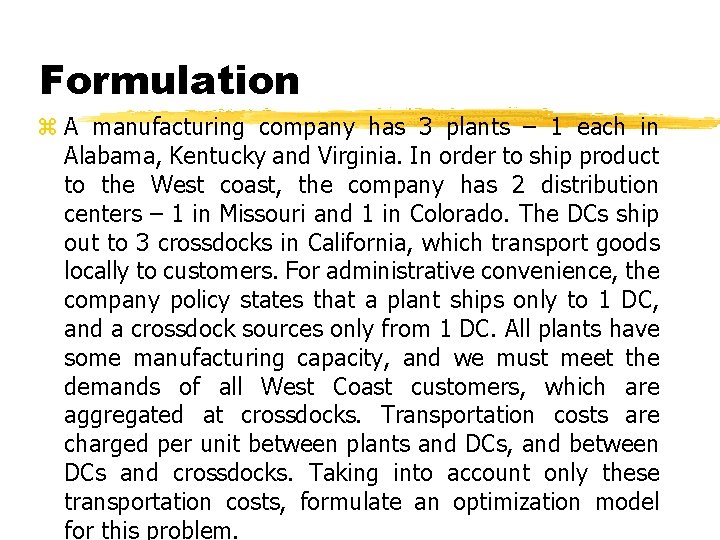
Formulation z A manufacturing company has 3 plants – 1 each in Alabama, Kentucky and Virginia. In order to ship product to the West coast, the company has 2 distribution centers – 1 in Missouri and 1 in Colorado. The DCs ship out to 3 crossdocks in California, which transport goods locally to customers. For administrative convenience, the company policy states that a plant ships only to 1 DC, and a crossdock sources only from 1 DC. All plants have some manufacturing capacity, and we must meet the demands of all West Coast customers, which are aggregated at crossdocks. Transportation costs are charged per unit between plants and DCs, and between DCs and crossdocks. Taking into account only these transportation costs, formulate an optimization model for this problem.
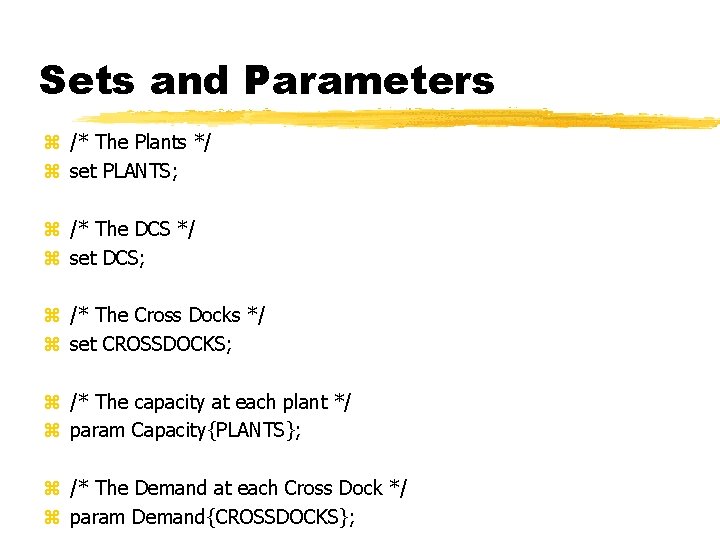
Sets and Parameters z /* The Plants */ z set PLANTS; z /* The DCS */ z set DCS; z /* The Cross Docks */ z set CROSSDOCKS; z /* The capacity at each plant */ z param Capacity{PLANTS}; z /* The Demand at each Cross Dock */ z param Demand{CROSSDOCKS};
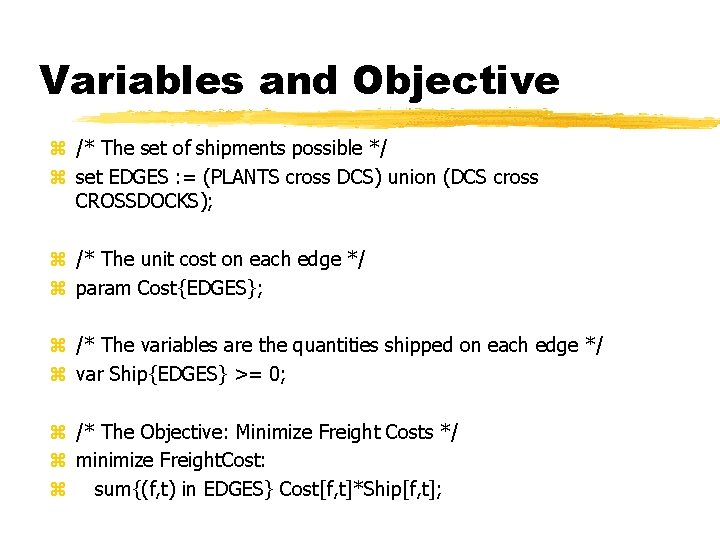
Variables and Objective z /* The set of shipments possible */ z set EDGES : = (PLANTS cross DCS) union (DCS cross CROSSDOCKS); z /* The unit cost on each edge */ z param Cost{EDGES}; z /* The variables are the quantities shipped on each edge */ z var Ship{EDGES} >= 0; z /* The Objective: Minimize Freight Costs */ z minimize Freight. Cost: z sum{(f, t) in EDGES} Cost[f, t]*Ship[f, t];
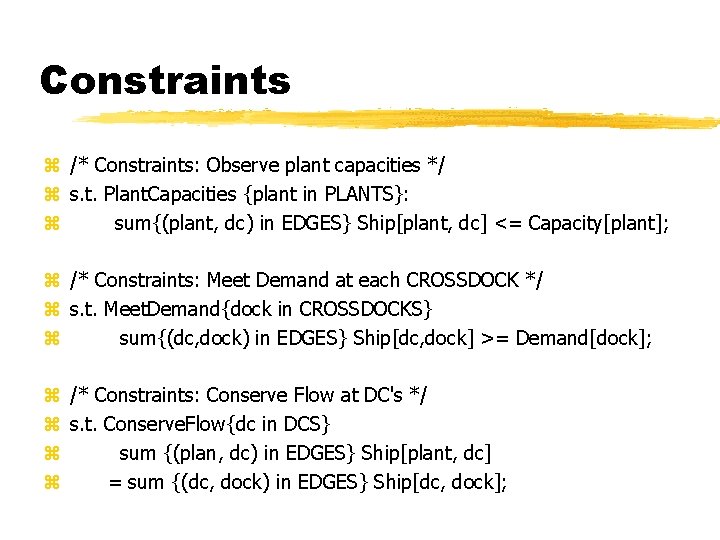
Constraints z /* Constraints: Observe plant capacities */ z s. t. Plant. Capacities {plant in PLANTS}: z sum{(plant, dc) in EDGES} Ship[plant, dc] <= Capacity[plant]; z /* Constraints: Meet Demand at each CROSSDOCK */ z s. t. Meet. Demand{dock in CROSSDOCKS} z sum{(dc, dock) in EDGES} Ship[dc, dock] >= Demand[dock]; z /* Constraints: Conserve Flow at DC's */ z s. t. Conserve. Flow{dc in DCS} z sum {(plan, dc) in EDGES} Ship[plant, dc] z = sum {(dc, dock) in EDGES} Ship[dc, dock];
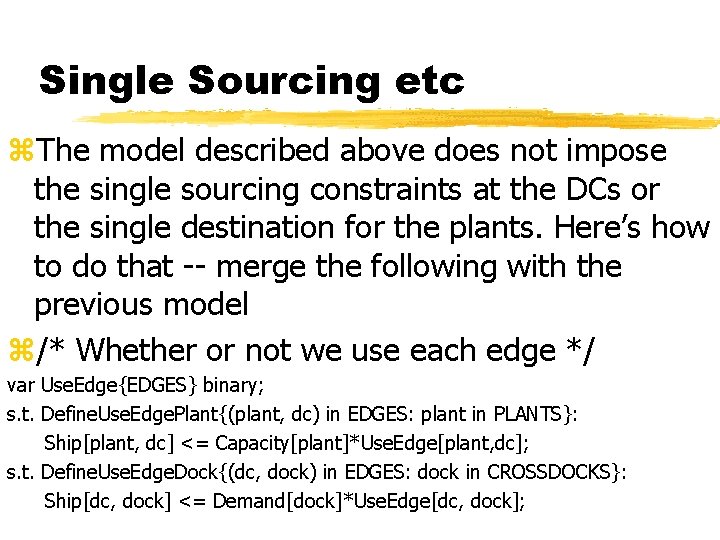
Single Sourcing etc z. The model described above does not impose the single sourcing constraints at the DCs or the single destination for the plants. Here’s how to do that -- merge the following with the previous model z/* Whether or not we use each edge */ var Use. Edge{EDGES} binary; s. t. Define. Use. Edge. Plant{(plant, dc) in EDGES: plant in PLANTS}: Ship[plant, dc] <= Capacity[plant]*Use. Edge[plant, dc]; s. t. Define. Use. Edge. Dock{(dc, dock) in EDGES: dock in CROSSDOCKS}: Ship[dc, dock] <= Demand[dock]*Use. Edge[dc, dock];
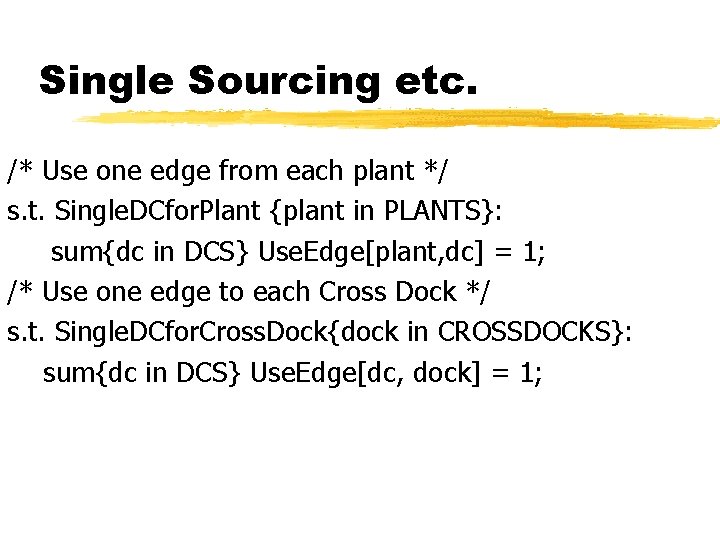
Single Sourcing etc. /* Use one edge from each plant */ s. t. Single. DCfor. Plant {plant in PLANTS}: sum{dc in DCS} Use. Edge[plant, dc] = 1; /* Use one edge to each Cross Dock */ s. t. Single. DCfor. Cross. Dock{dock in CROSSDOCKS}: sum{dc in DCS} Use. Edge[dc, dock] = 1;
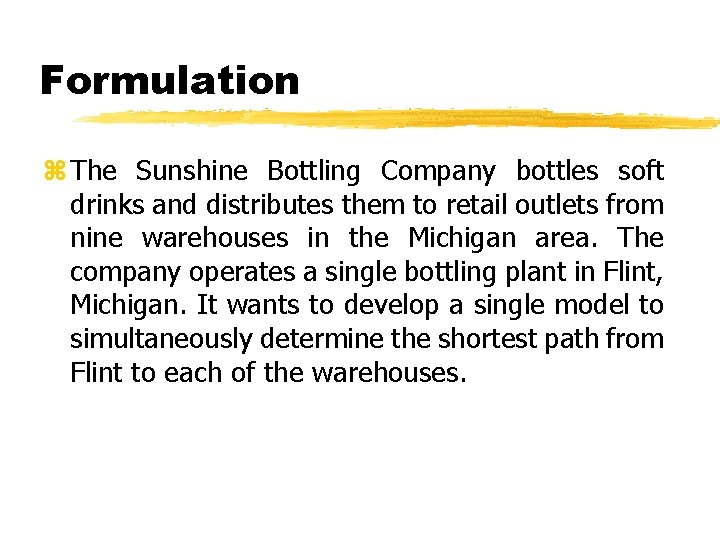
Formulation z The Sunshine Bottling Company bottles soft drinks and distributes them to retail outlets from nine warehouses in the Michigan area. The company operates a single bottling plant in Flint, Michigan. It wants to develop a single model to simultaneously determine the shortest path from Flint to each of the warehouses.
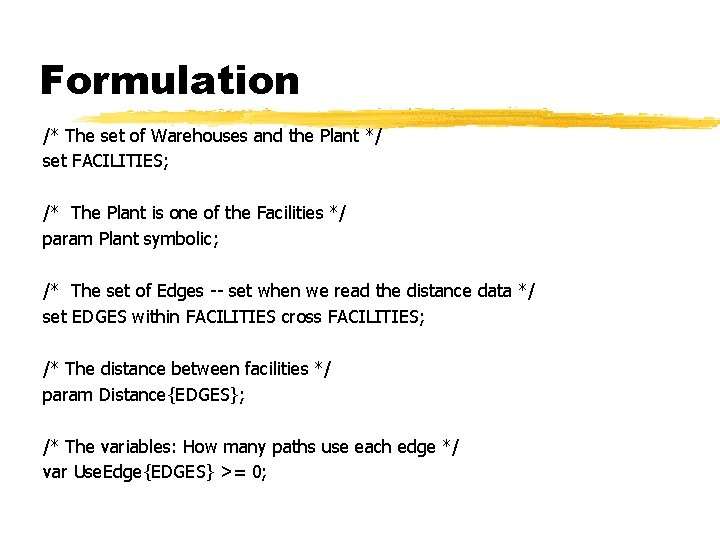
Formulation /* The set of Warehouses and the Plant */ set FACILITIES; /* The Plant is one of the Facilities */ param Plant symbolic; /* The set of Edges -- set when we read the distance data */ set EDGES within FACILITIES cross FACILITIES; /* The distance between facilities */ param Distance{EDGES}; /* The variables: How many paths use each edge */ var Use. Edge{EDGES} >= 0;
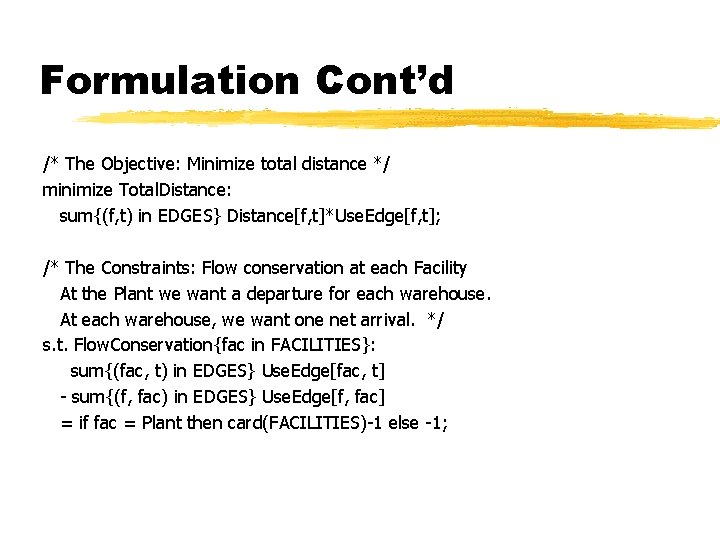
Formulation Cont’d /* The Objective: Minimize total distance */ minimize Total. Distance: sum{(f, t) in EDGES} Distance[f, t]*Use. Edge[f, t]; /* The Constraints: Flow conservation at each Facility At the Plant we want a departure for each warehouse. At each warehouse, we want one net arrival. */ s. t. Flow. Conservation{fac in FACILITIES}: sum{(fac, t) in EDGES} Use. Edge[fac, t] - sum{(f, fac) in EDGES} Use. Edge[f, fac] = if fac = Plant then card(FACILITIES)-1 else -1;
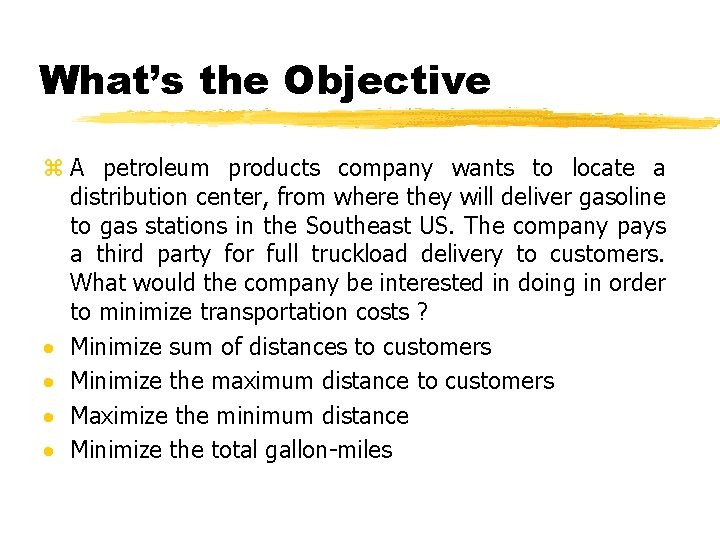
What’s the Objective z A petroleum products company wants to locate a distribution center, from where they will deliver gasoline to gas stations in the Southeast US. The company pays a third party for full truckload delivery to customers. What would the company be interested in doing in order to minimize transportation costs ? · Minimize sum of distances to customers · Minimize the maximum distance to customers · Maximize the minimum distance · Minimize the total gallon-miles
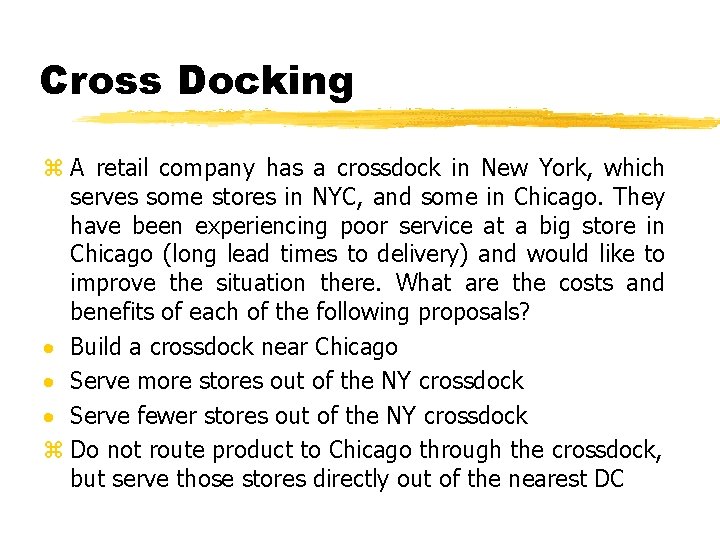
Cross Docking z A retail company has a crossdock in New York, which serves some stores in NYC, and some in Chicago. They have been experiencing poor service at a big store in Chicago (long lead times to delivery) and would like to improve the situation there. What are the costs and benefits of each of the following proposals? · Build a crossdock near Chicago · Serve more stores out of the NY crossdock · Serve fewer stores out of the NY crossdock z Do not route product to Chicago through the crossdock, but serve those stores directly out of the nearest DC
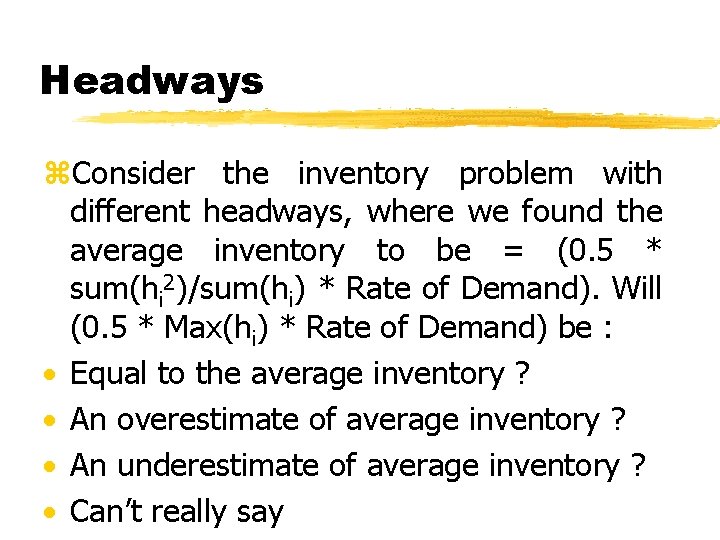
Headways z. Consider the inventory problem with different headways, where we found the average inventory to be = (0. 5 * sum(hi 2)/sum(hi) * Rate of Demand). Will (0. 5 * Max(hi) * Rate of Demand) be : · Equal to the average inventory ? · An overestimate of average inventory ? · An underestimate of average inventory ? · Can’t really say
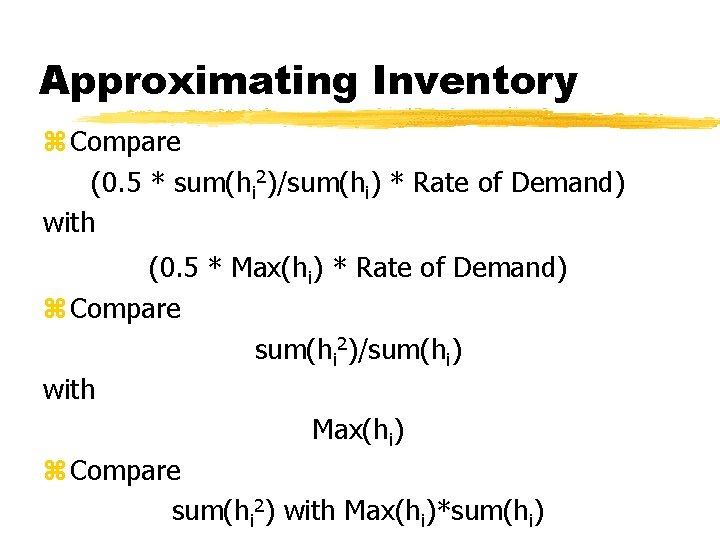
Approximating Inventory z Compare (0. 5 * sum(hi 2)/sum(hi) * Rate of Demand) with (0. 5 * Max(hi) * Rate of Demand) z Compare sum(hi 2)/sum(hi) with Max(hi) z Compare sum(hi 2) with Max(hi)*sum(hi)
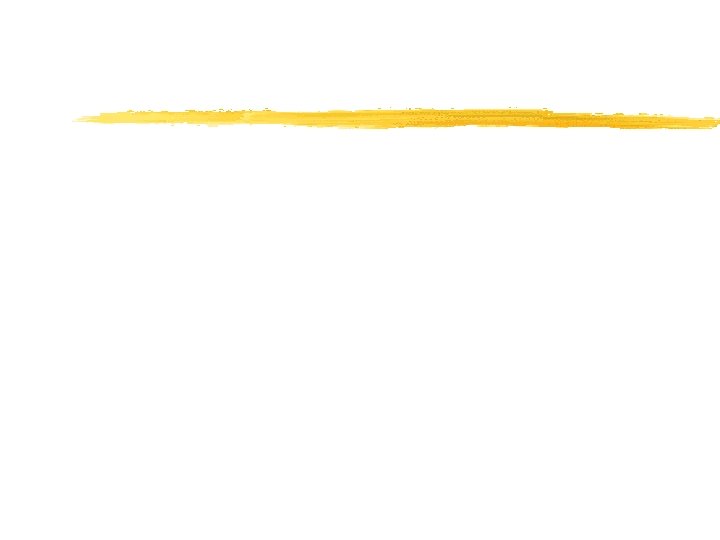
Pratt & whitney customer training center
Durable tooling
Pratt & whitney
Pratt and whitney new hampshire
Uncontrollable spending ap gov
Signo homans y pratt
Knuth morris pratt algorithm time complexity
Jack the
Section 7 partnership act 1961
Francesca pratt
Steel roof details
Jon rowney camden
Sinal da bandeira e sinal de homans
Font matching
Pratt hypothesis formula
Hamilton pratt
Kmp automat
Trendelenburg procedure
Vene sentinelle di pratt
Jembatan tipe pratt
Ezra thayer
Pratt test dvt
Inverted champagne bottle sign in dvt
Viga pratt vs warren
Maniobra de homans
Thrombose bilder