Process Analysis Chapter 4 To Accompany Krajewski Ritzman
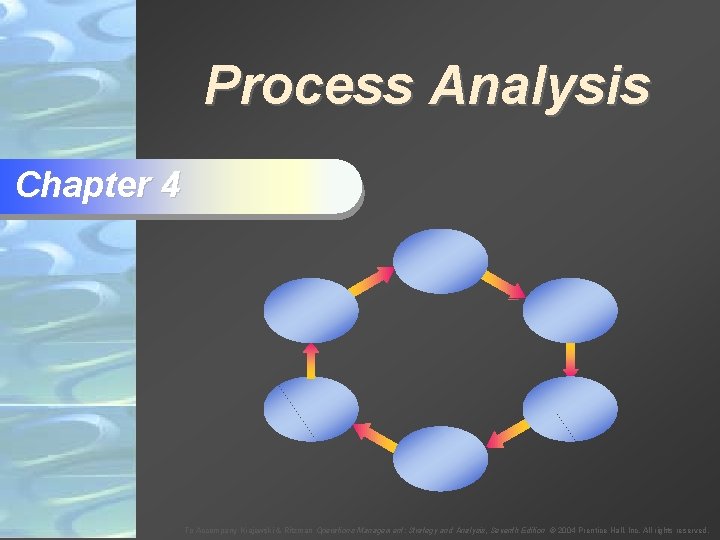
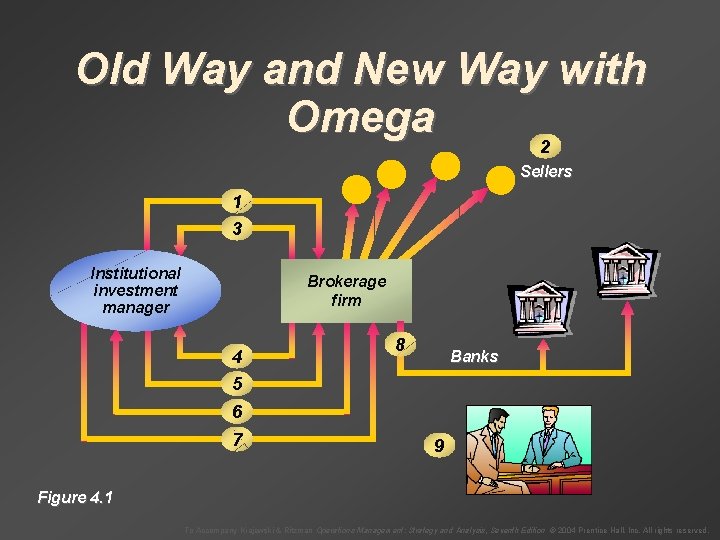
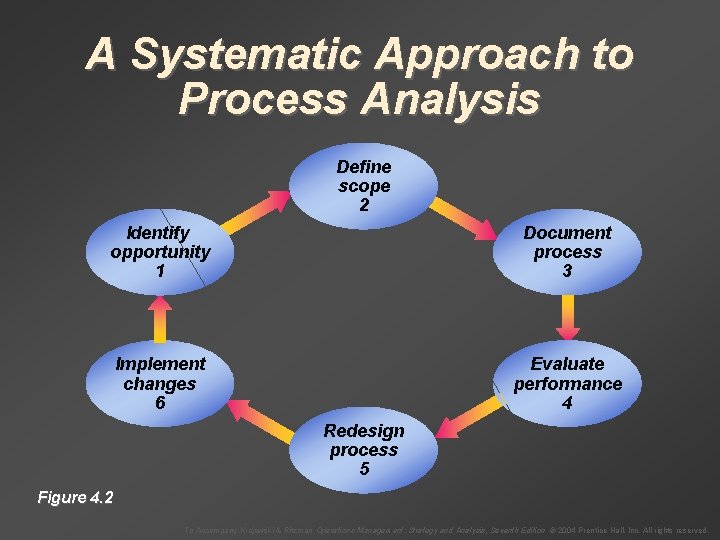
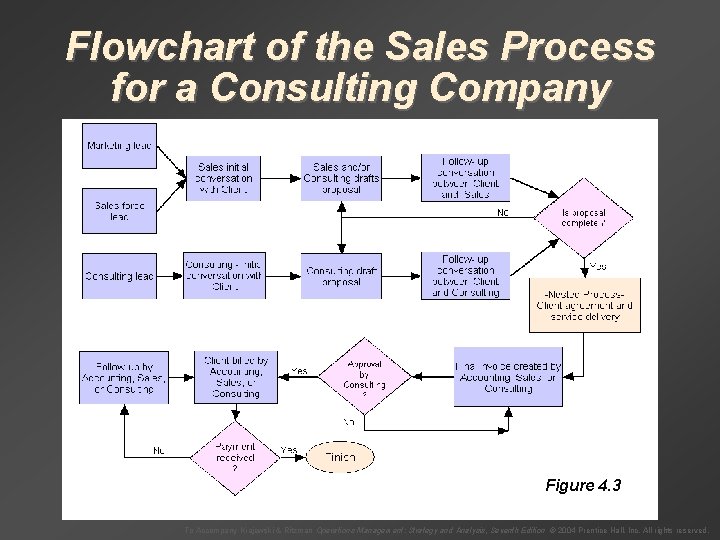
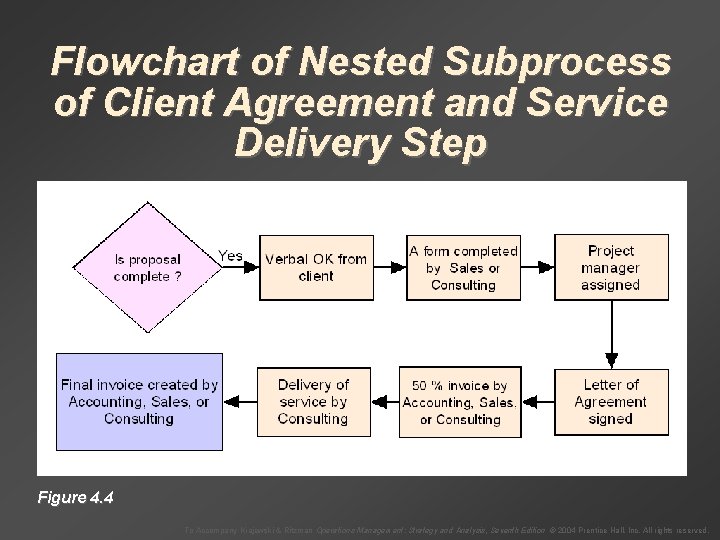
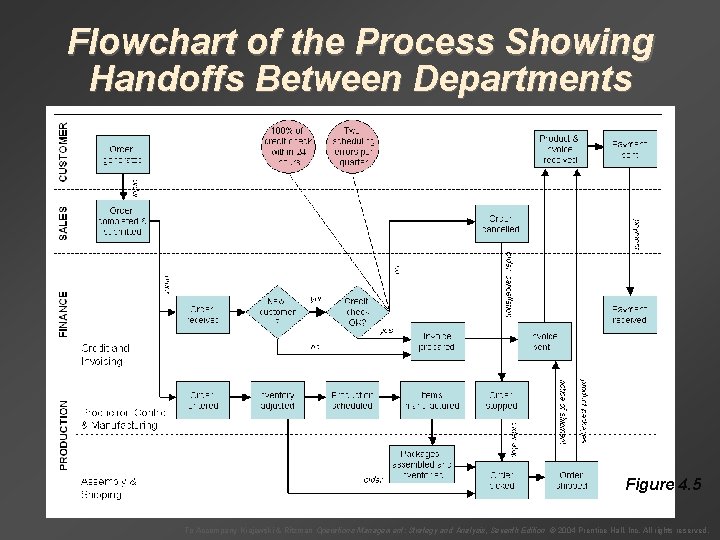
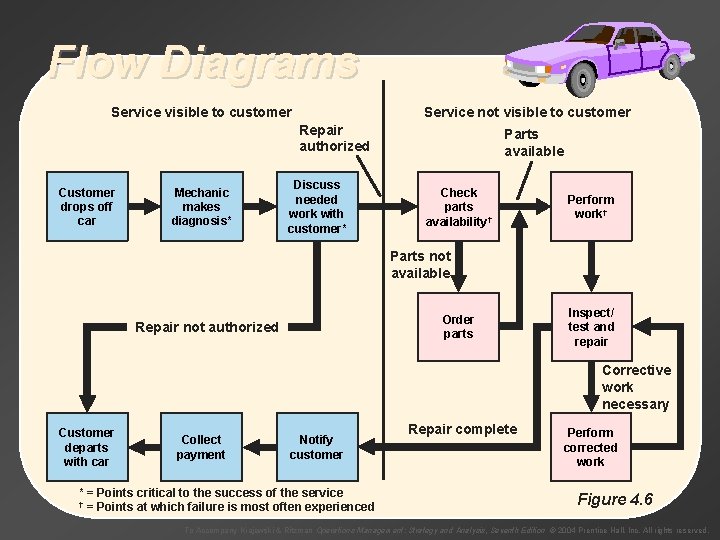

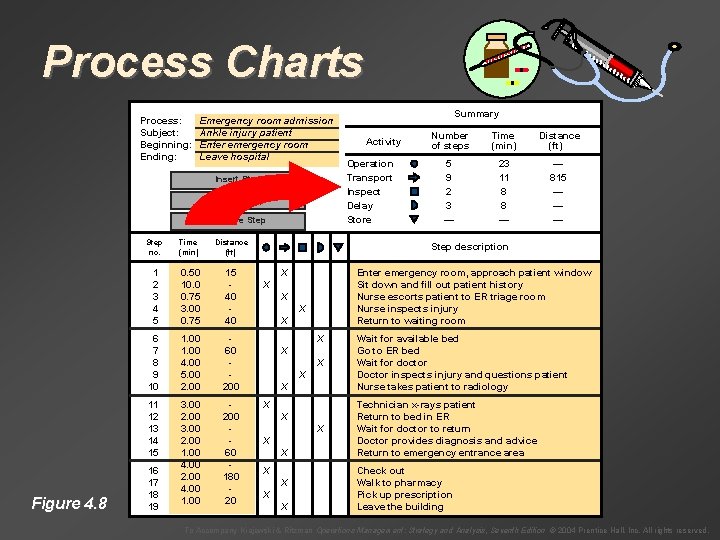
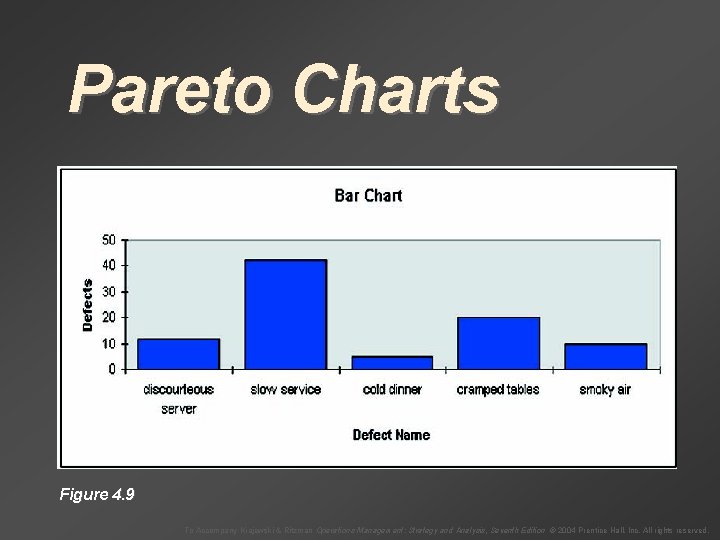
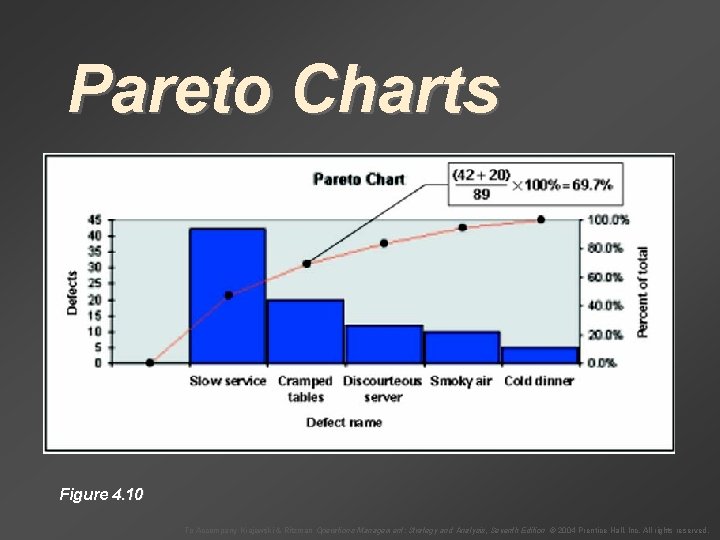
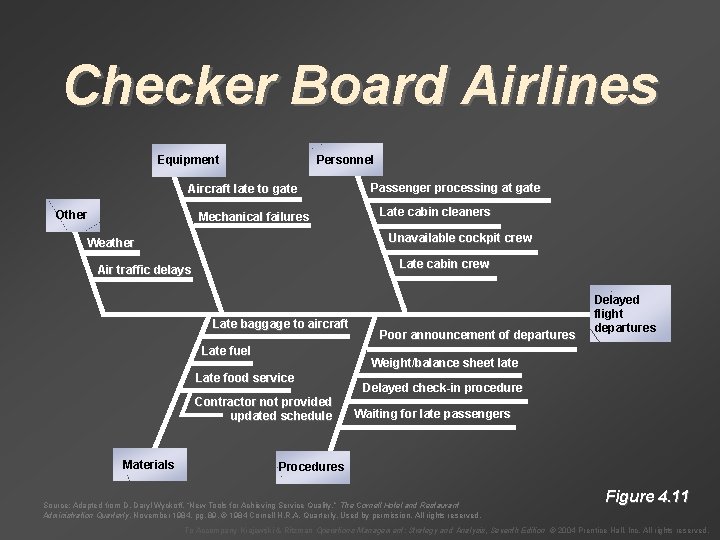
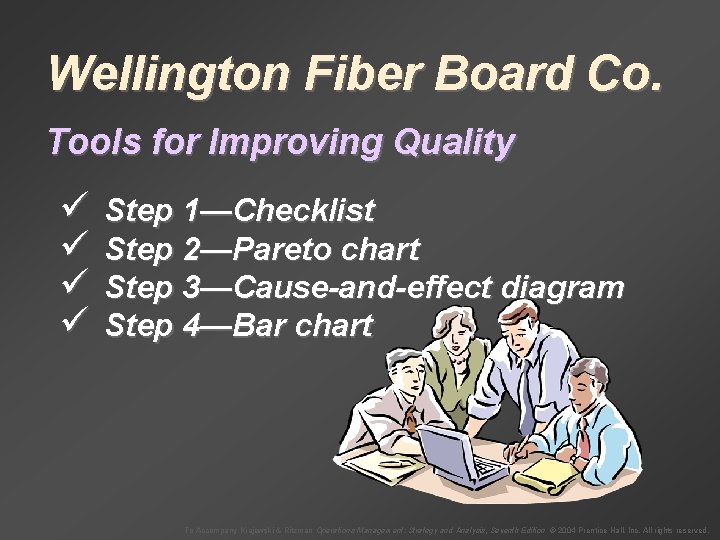
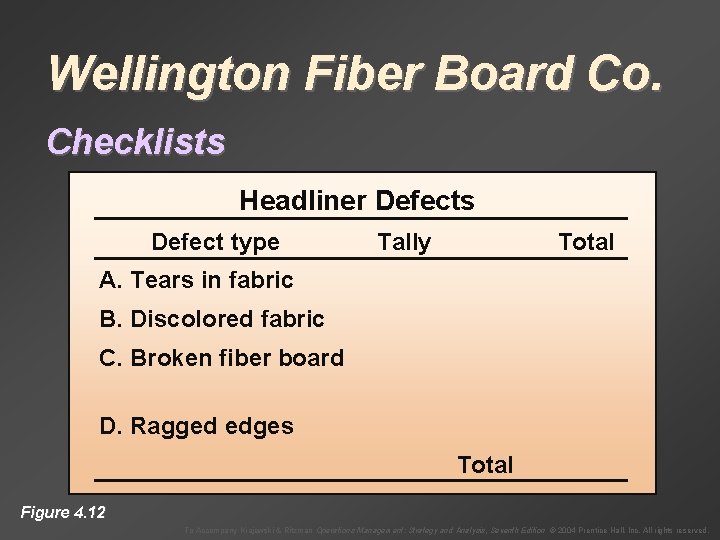
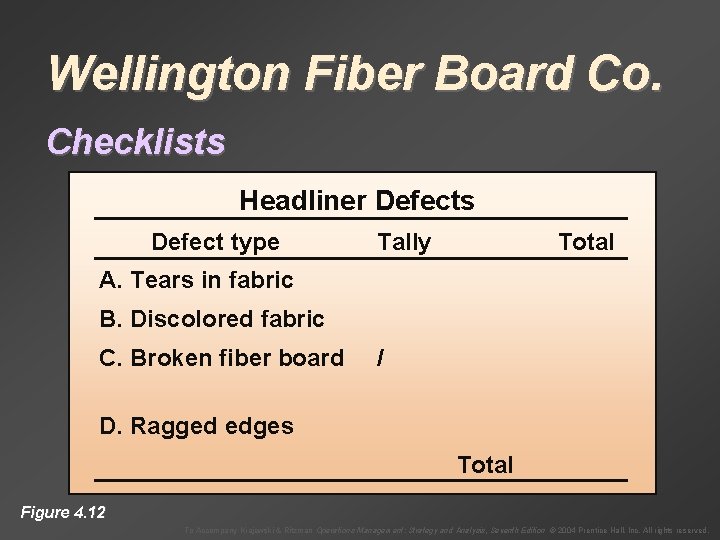
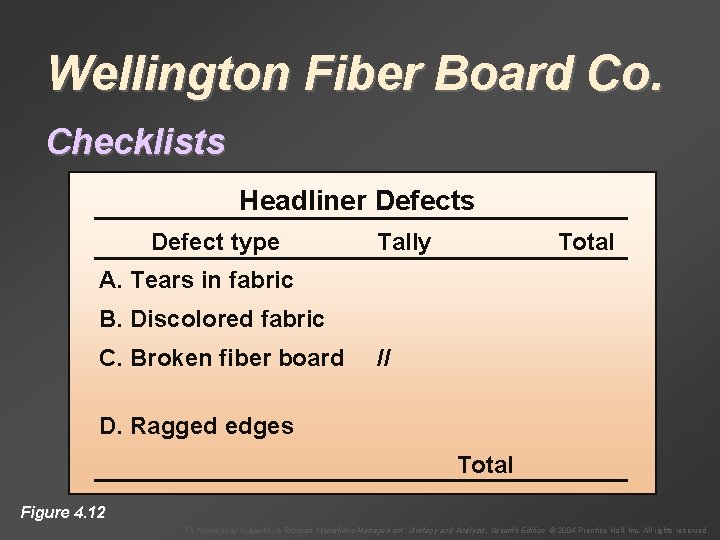
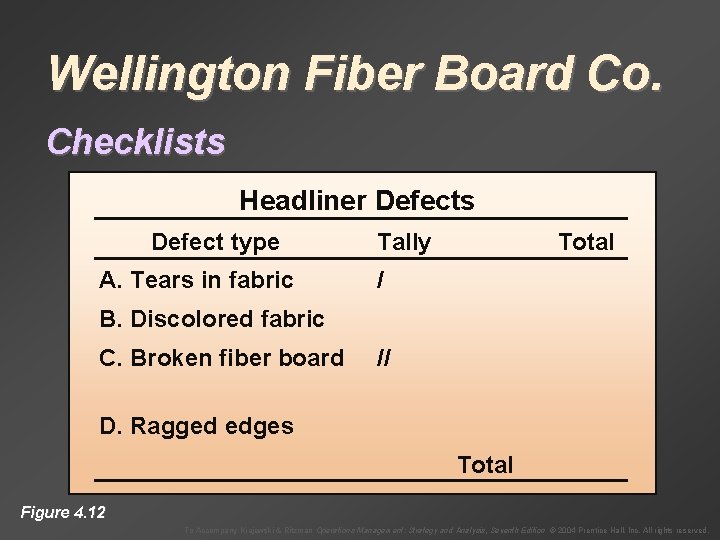
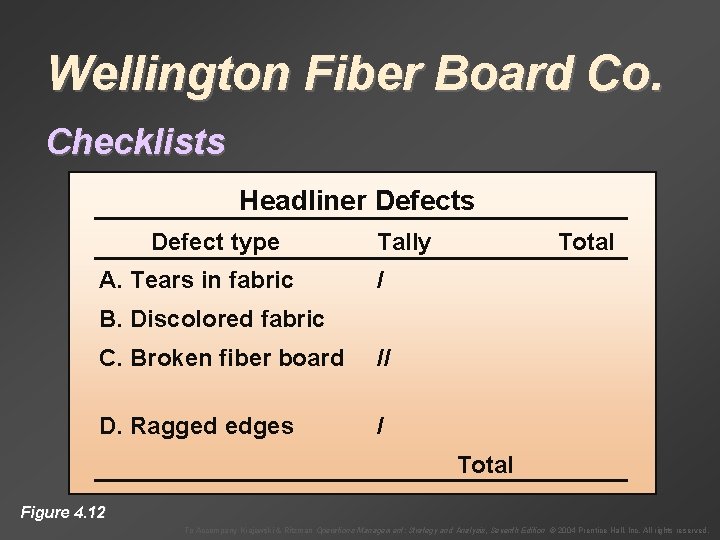
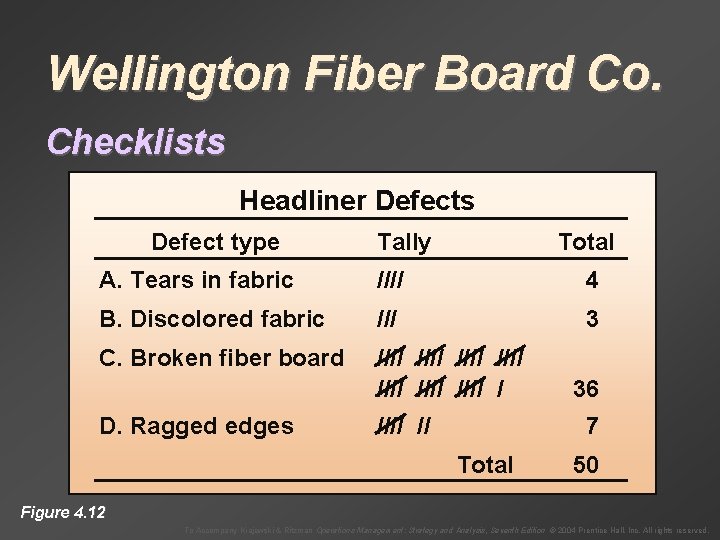
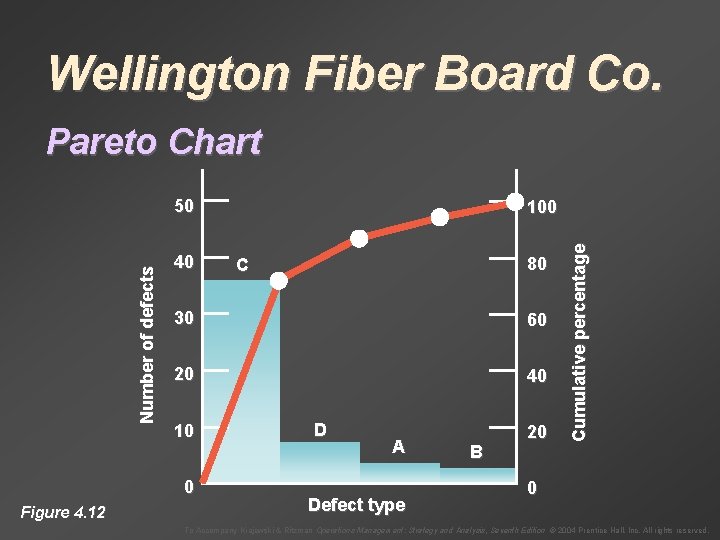
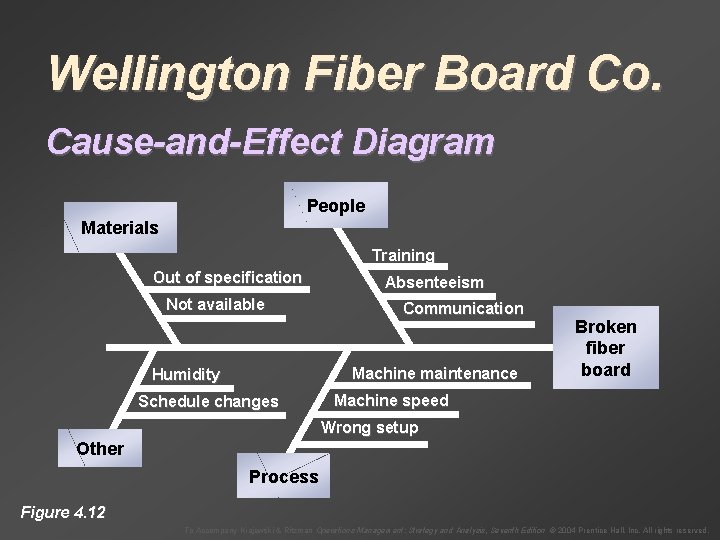
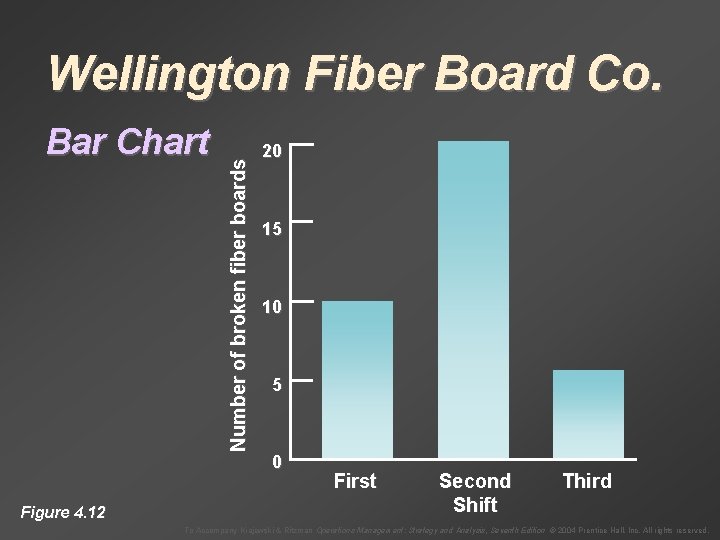
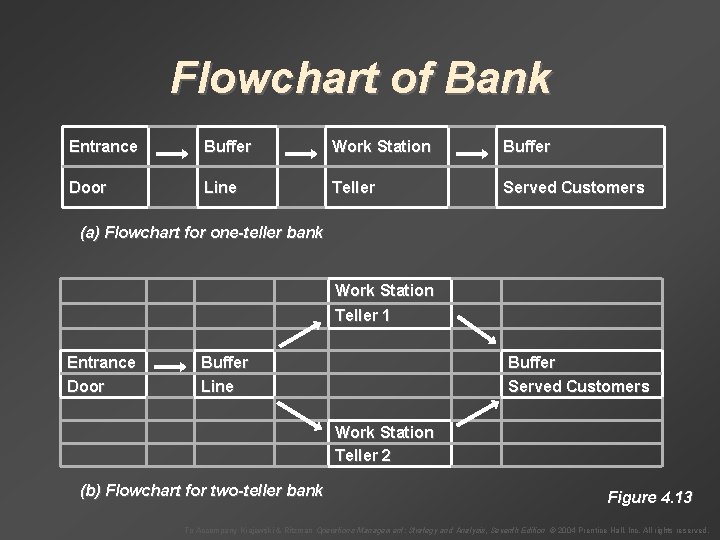
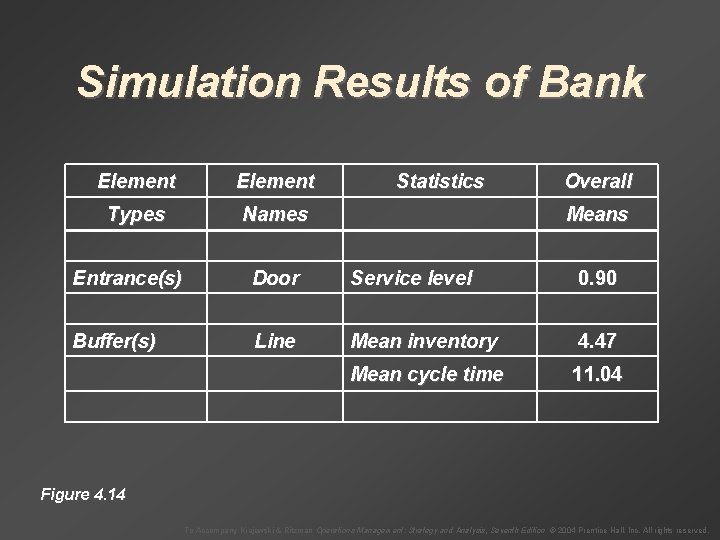
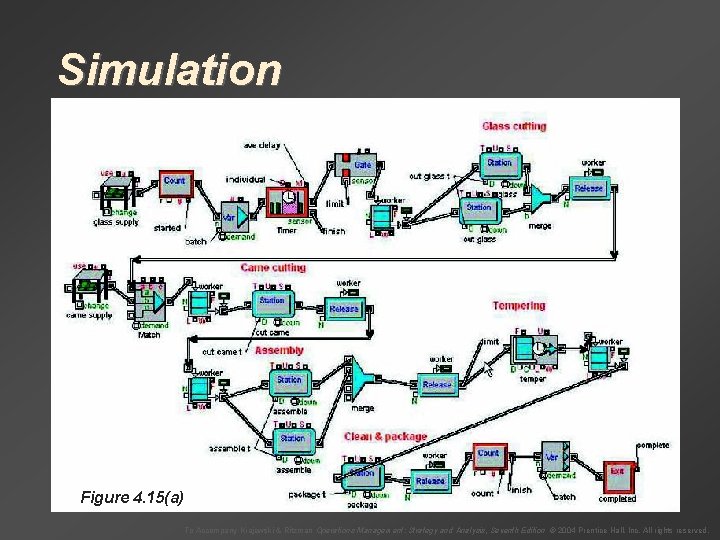
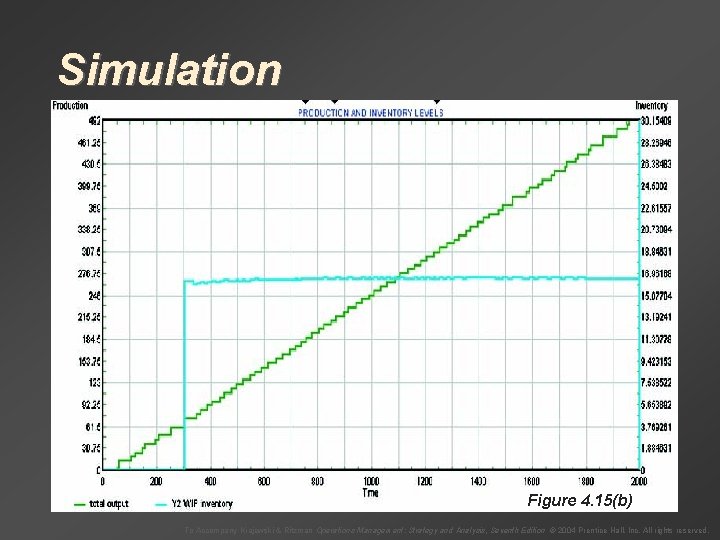
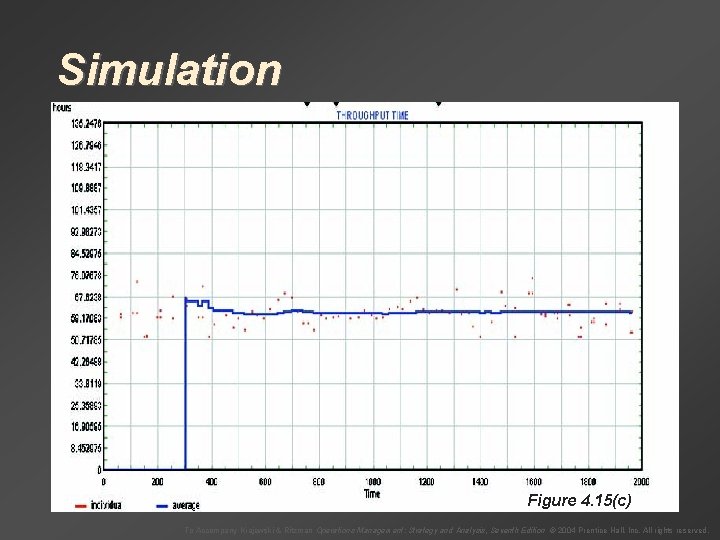
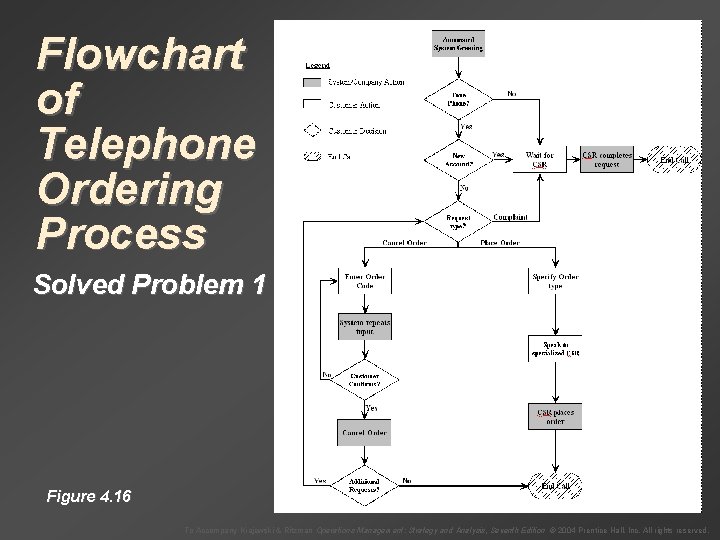
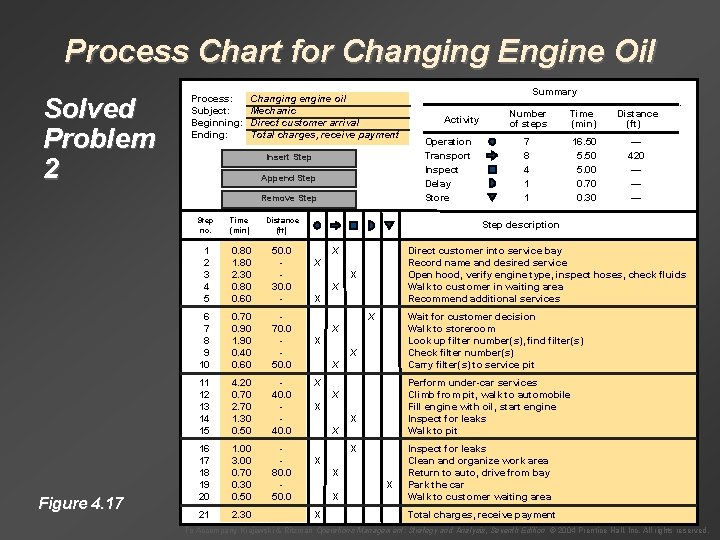
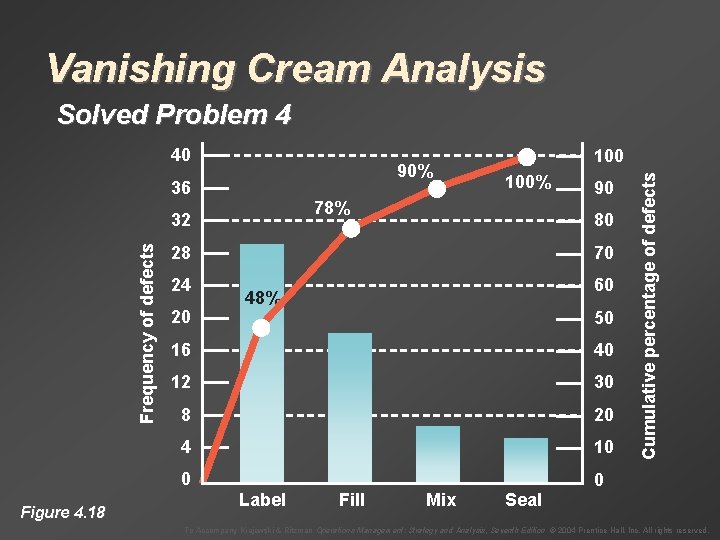
- Slides: 30
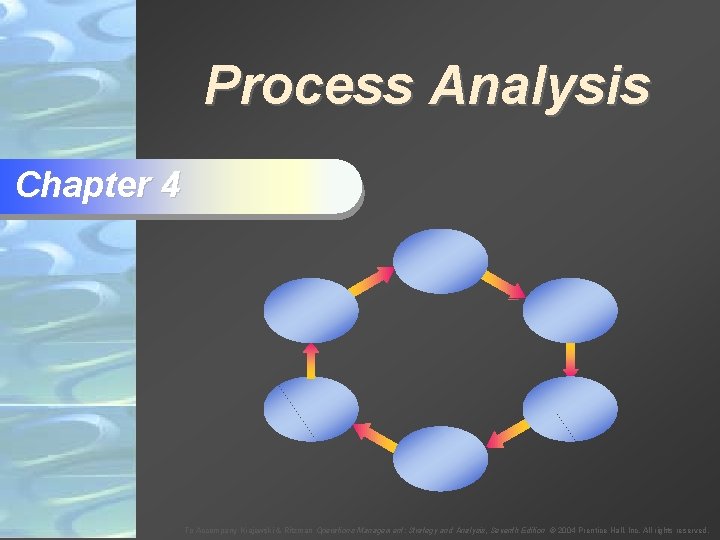
Process Analysis Chapter 4 To Accompany Krajewski & Ritzman Operations Management: Strategy and Analysis, Seventh Edition © 2004 Prentice Hall, Inc. All rights reserved.
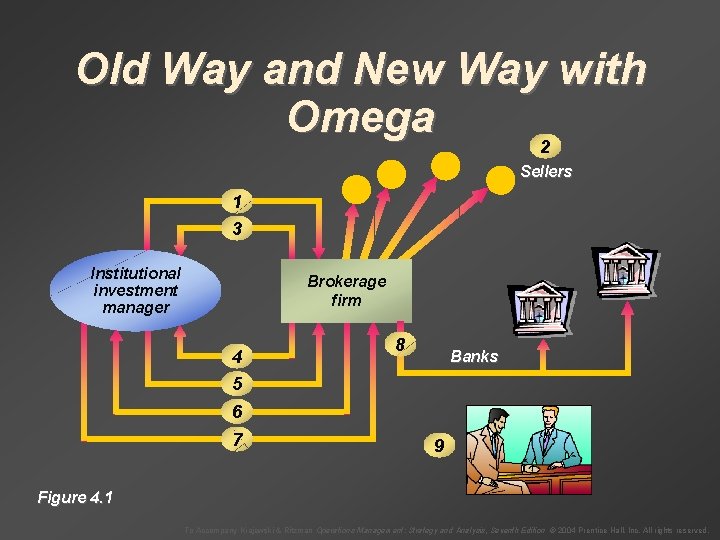
Old Way and New Way with Omega 2 Sellers 1 3 Institutional investment manager Brokerage firm 4 8 Banks 5 6 7 9 Figure 4. 1 To Accompany Krajewski & Ritzman Operations Management: Strategy and Analysis, Seventh Edition © 2004 Prentice Hall, Inc. All rights reserved.
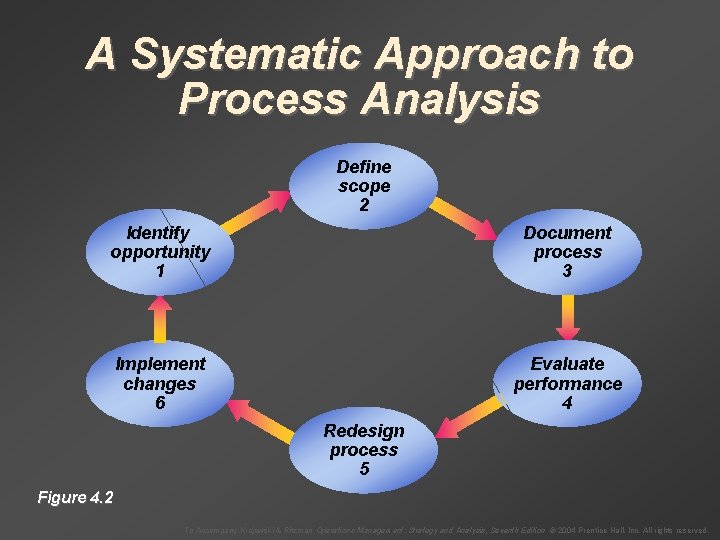
A Systematic Approach to Process Analysis Define scope 2 Identify opportunity 1 Document process 3 Implement changes 6 Evaluate performance 4 Redesign process 5 Figure 4. 2 To Accompany Krajewski & Ritzman Operations Management: Strategy and Analysis, Seventh Edition © 2004 Prentice Hall, Inc. All rights reserved.
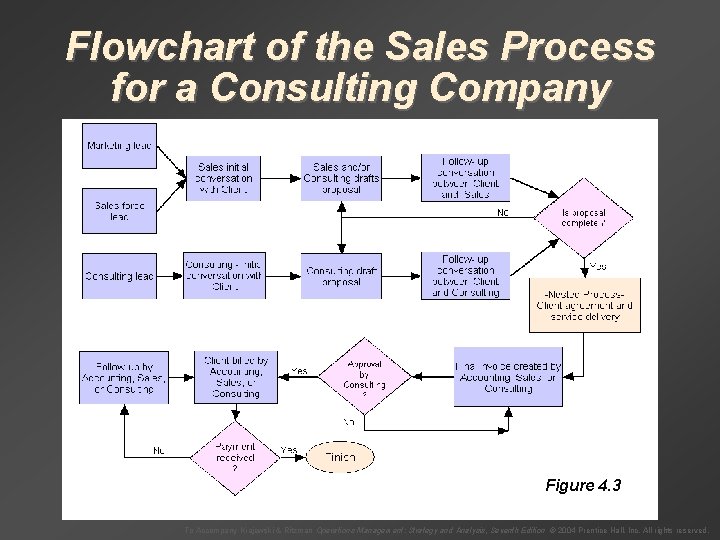
Flowchart of the Sales Process for a Consulting Company Figure 4. 3 To Accompany Krajewski & Ritzman Operations Management: Strategy and Analysis, Seventh Edition © 2004 Prentice Hall, Inc. All rights reserved.
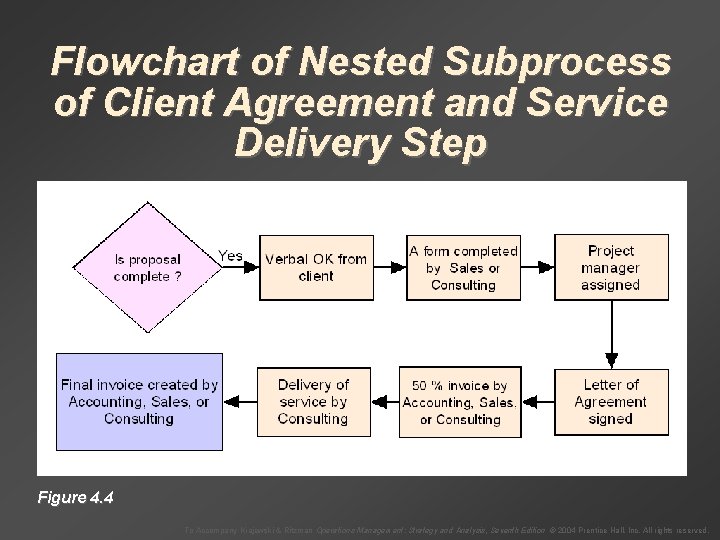
Flowchart of Nested Subprocess of Client Agreement and Service Delivery Step Figure 4. 4 To Accompany Krajewski & Ritzman Operations Management: Strategy and Analysis, Seventh Edition © 2004 Prentice Hall, Inc. All rights reserved.
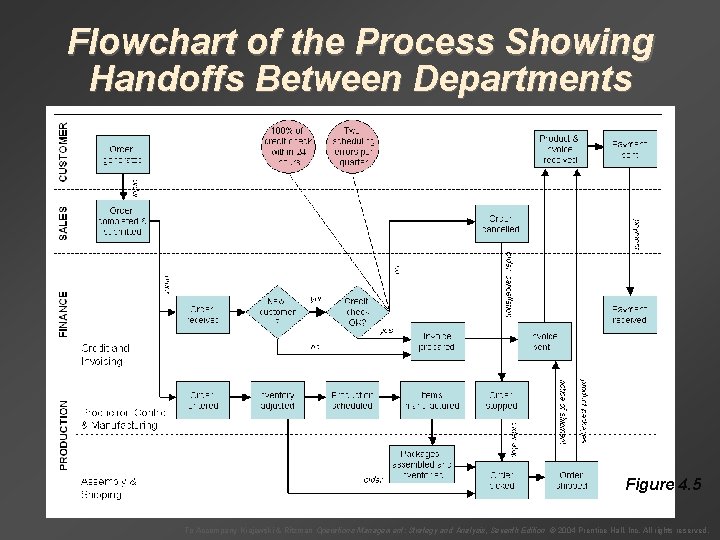
Flowchart of the Process Showing Handoffs Between Departments Figure 4. 5 To Accompany Krajewski & Ritzman Operations Management: Strategy and Analysis, Seventh Edition © 2004 Prentice Hall, Inc. All rights reserved.
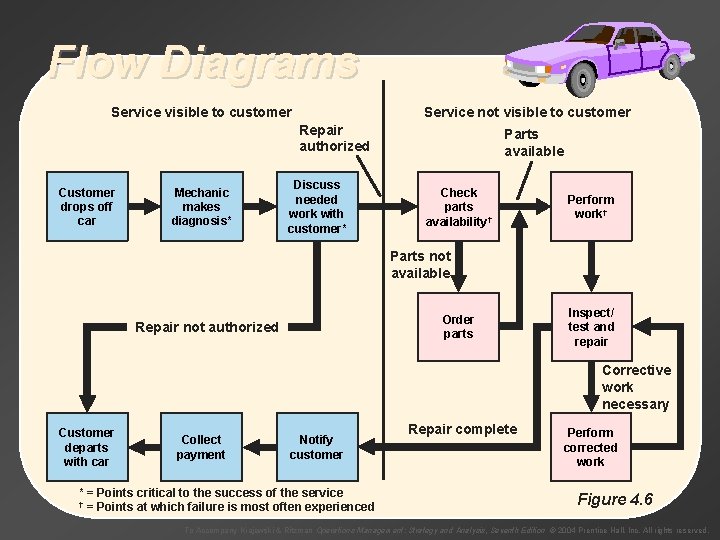
Flow Diagrams Service visible to customer Service not visible to customer Repair authorized Customer drops off car Mechanic makes diagnosis* Discuss needed work with customer* Parts available Check parts availability† Perform work† Parts not available Order parts Repair not authorized Inspect/ test and repair Corrective work necessary Customer departs with car Collect payment Notify customer * = Points critical to the success of the service † = Points at which failure is most often experienced Repair complete Perform corrected work Figure 4. 6 To Accompany Krajewski & Ritzman Operations Management: Strategy and Analysis, Seventh Edition © 2004 Prentice Hall, Inc. All rights reserved.

Service Blueprint of Consulting Company’s Inventory Appraisal Process Figure 4. 7 To Accompany Krajewski & Ritzman Operations Management: Strategy and Analysis, Seventh Edition © 2004 Prentice Hall, Inc. All rights reserved.
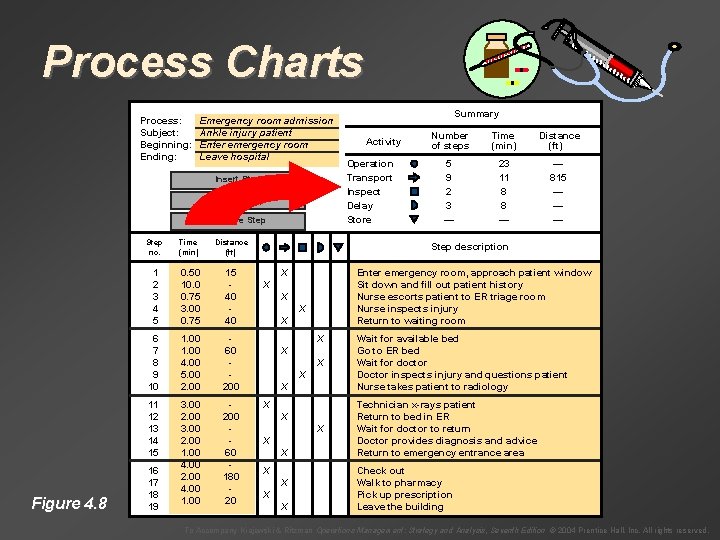
Process Charts Process: Subject: Beginning: Ending: Emergency room admission Ankle injury patient Enter emergency room Leave hospital Insert Step Append Step Remove Step Figure 4. 8 Step no. Time (min) Distance (ft) 1 2 3 4 5 0. 50 10. 0 0. 75 3. 00 0. 75 15 40 40 6 7 8 9 10 1. 00 4. 00 5. 00 2. 00 60 200 11 12 13 14 15 3. 00 2. 00 1. 00 4. 00 2. 00 4. 00 1. 00 200 60 180 20 16 17 18 19 Summary Activity Operation Transport Inspect Delay Store Number of steps Time (min) Distance (ft) 5 9 2 3 — 23 11 8 8 — — 815 — — — Step description X Enter emergency room, approach patient window Sit down and fill out patient history Nurse escorts patient to ER triage room Nurse inspects injury Return to waiting room X X X Wait for available bed Go to ER bed Wait for doctor Doctor inspects injury and questions patient Nurse takes patient to radiology X Technician x-rays patient Return to bed in ER Wait for doctor to return Doctor provides diagnosis and advice Return to emergency entrance area X X X Check out Walk to pharmacy Pick up prescription Leave the building To Accompany Krajewski & Ritzman Operations Management: Strategy and Analysis, Seventh Edition © 2004 Prentice Hall, Inc. All rights reserved.
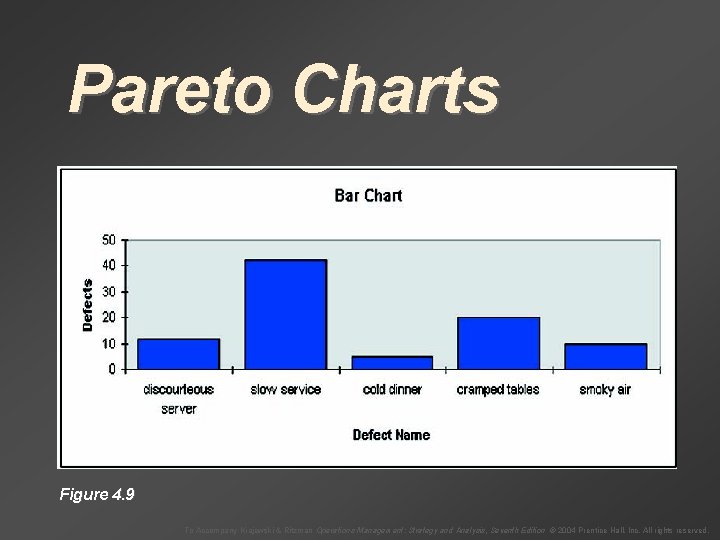
Pareto Charts Figure 4. 9 To Accompany Krajewski & Ritzman Operations Management: Strategy and Analysis, Seventh Edition © 2004 Prentice Hall, Inc. All rights reserved.
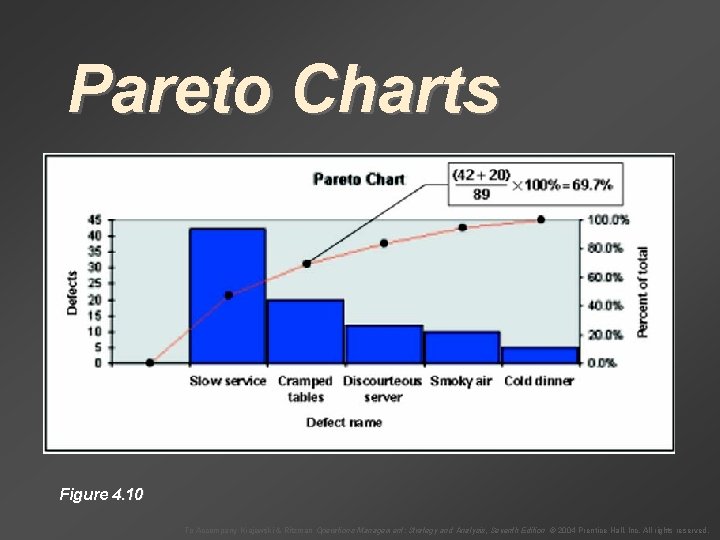
Pareto Charts Figure 4. 10 To Accompany Krajewski & Ritzman Operations Management: Strategy and Analysis, Seventh Edition © 2004 Prentice Hall, Inc. All rights reserved.
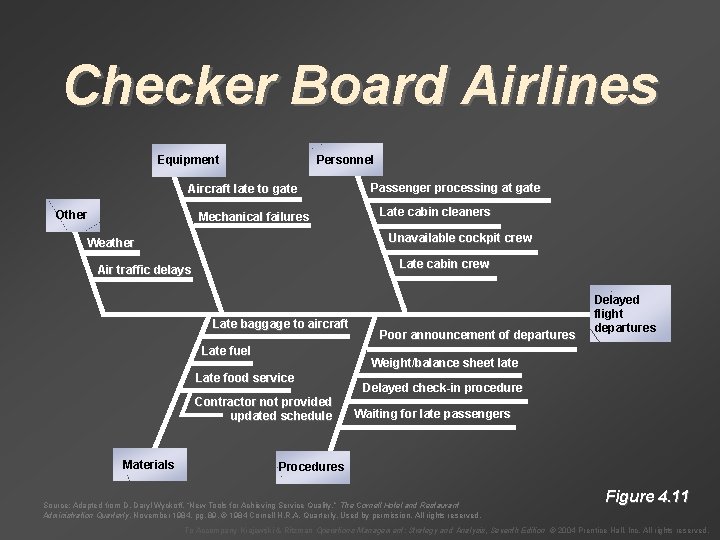
Checker Board Airlines Personnel Equipment Aircraft late to gate Other Mechanical failures Late cabin cleaners Unavailable cockpit crew Weather Late cabin crew Air traffic delays Late baggage to aircraft Late fuel Poor announcement of departures Delayed flight departures Weight/balance sheet late Late food service Contractor not provided updated schedule Materials Passenger processing at gate Delayed check-in procedure Waiting for late passengers Procedures Source: Adapted from D. Daryl Wyckoff, “New Tools for Achieving Service Quality. ” The Cornell Hotel and Restaurant Administration Quarterly, November 1984, pg. 89. © 1984 Cornell H. R. A. Quarterly. Used by permission. All rights reserved. Figure 4. 11 To Accompany Krajewski & Ritzman Operations Management: Strategy and Analysis, Seventh Edition © 2004 Prentice Hall, Inc. All rights reserved.
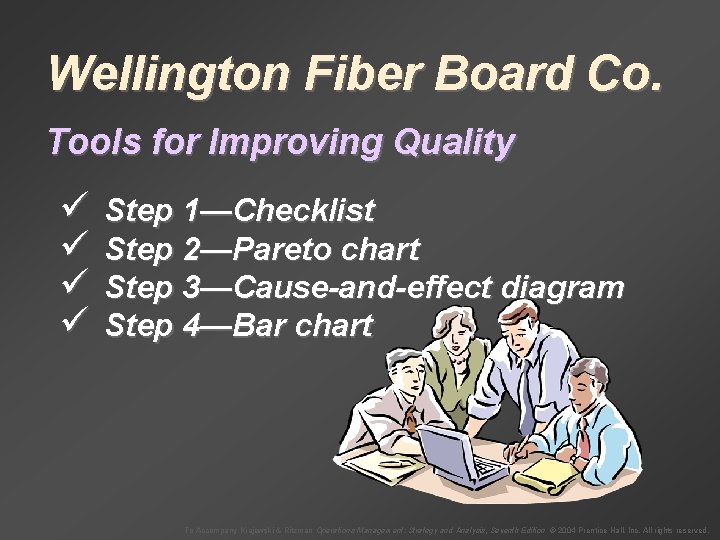
Wellington Fiber Board Co. Tools for Improving Quality ü ü Step 1—Checklist Step 2—Pareto chart Step 3—Cause-and-effect diagram Step 4—Bar chart To Accompany Krajewski & Ritzman Operations Management: Strategy and Analysis, Seventh Edition © 2004 Prentice Hall, Inc. All rights reserved.
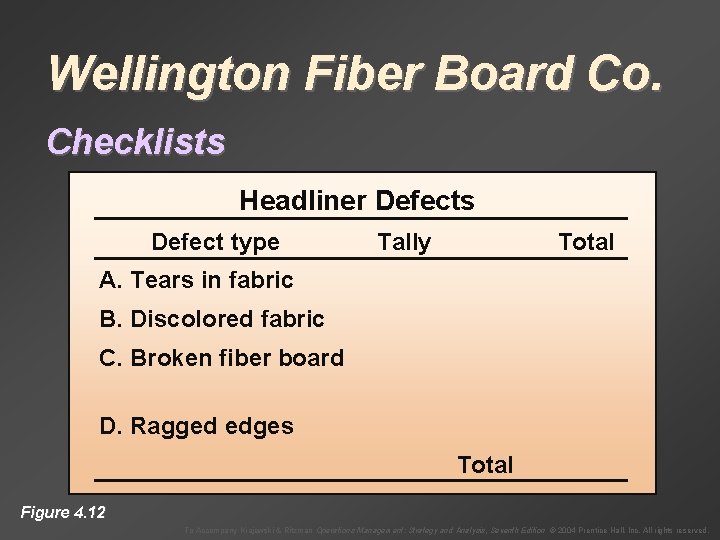
Wellington Fiber Board Co. Checklists Headliner Defects Defect type Tally Total A. Tears in fabric B. Discolored fabric C. Broken fiber board D. Ragged edges Total Figure 4. 12 To Accompany Krajewski & Ritzman Operations Management: Strategy and Analysis, Seventh Edition © 2004 Prentice Hall, Inc. All rights reserved.
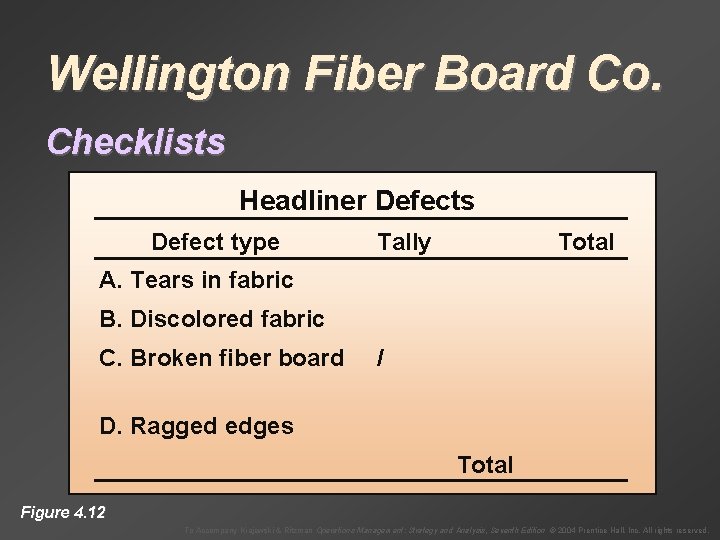
Wellington Fiber Board Co. Checklists Headliner Defects Defect type Tally Total A. Tears in fabric B. Discolored fabric C. Broken fiber board / D. Ragged edges Total Figure 4. 12 To Accompany Krajewski & Ritzman Operations Management: Strategy and Analysis, Seventh Edition © 2004 Prentice Hall, Inc. All rights reserved.
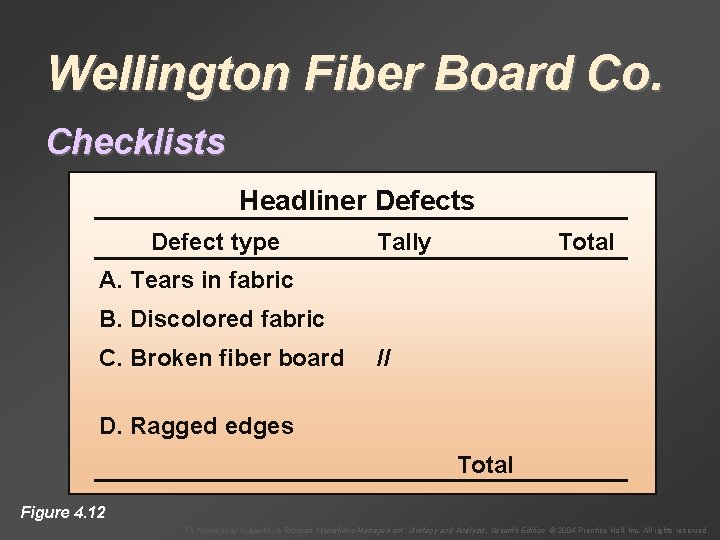
Wellington Fiber Board Co. Checklists Headliner Defects Defect type Tally Total A. Tears in fabric B. Discolored fabric C. Broken fiber board // D. Ragged edges Total Figure 4. 12 To Accompany Krajewski & Ritzman Operations Management: Strategy and Analysis, Seventh Edition © 2004 Prentice Hall, Inc. All rights reserved.
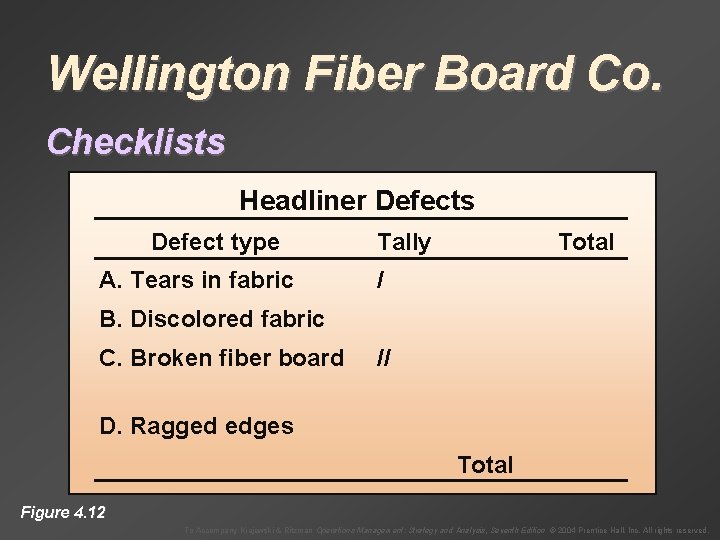
Wellington Fiber Board Co. Checklists Headliner Defects Defect type A. Tears in fabric Tally Total / B. Discolored fabric C. Broken fiber board // D. Ragged edges Total Figure 4. 12 To Accompany Krajewski & Ritzman Operations Management: Strategy and Analysis, Seventh Edition © 2004 Prentice Hall, Inc. All rights reserved.
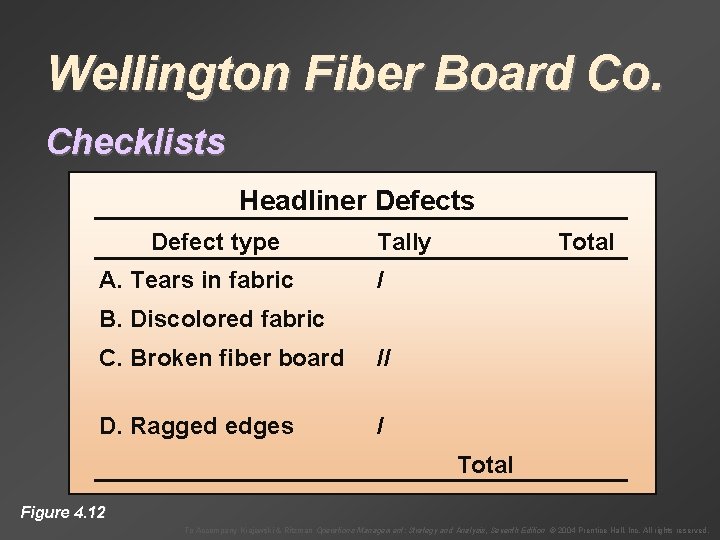
Wellington Fiber Board Co. Checklists Headliner Defects Defect type A. Tears in fabric Tally Total / B. Discolored fabric C. Broken fiber board // D. Ragged edges / Total Figure 4. 12 To Accompany Krajewski & Ritzman Operations Management: Strategy and Analysis, Seventh Edition © 2004 Prentice Hall, Inc. All rights reserved.
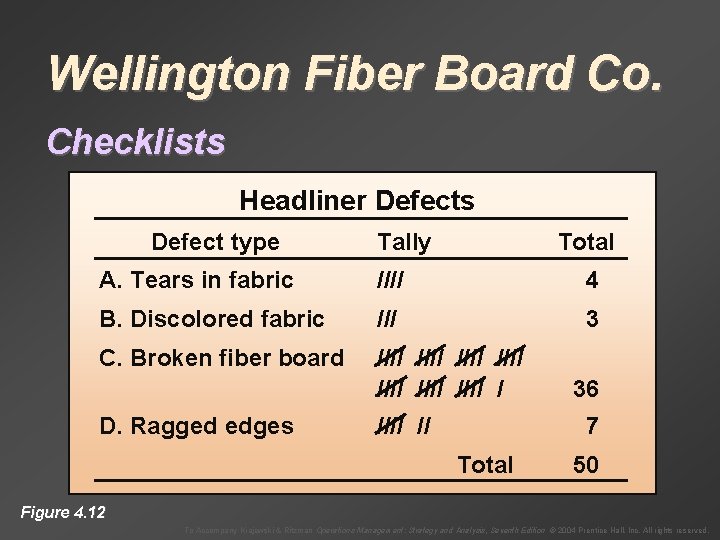
Wellington Fiber Board Co. Checklists Headliner Defects Defect type Tally Total A. Tears in fabric //// 4 B. Discolored fabric /// 3 C. Broken fiber board //// //// / D. Ragged edges //// // 36 7 Total 50 Figure 4. 12 To Accompany Krajewski & Ritzman Operations Management: Strategy and Analysis, Seventh Edition © 2004 Prentice Hall, Inc. All rights reserved.
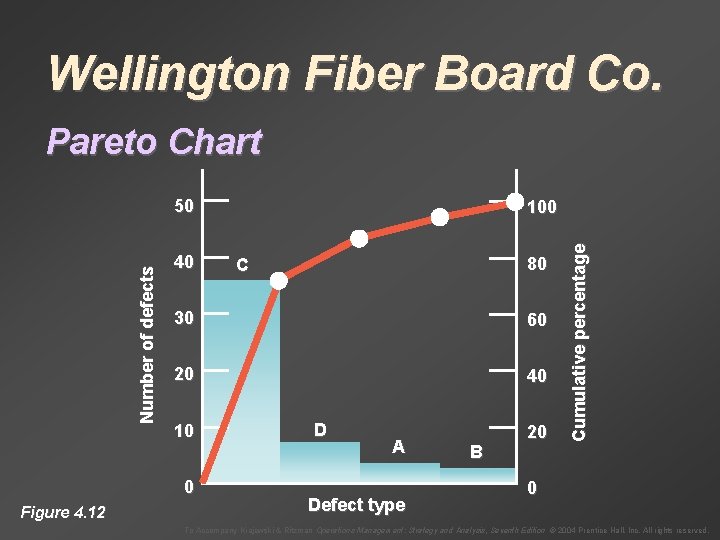
Wellington Fiber Board Co. Pareto Chart 40 80 C 30 60 20 40 10 0 Figure 4. 12 100 D A Defect type B 20 Cumulative percentage Number of defects 50 0 To Accompany Krajewski & Ritzman Operations Management: Strategy and Analysis, Seventh Edition © 2004 Prentice Hall, Inc. All rights reserved.
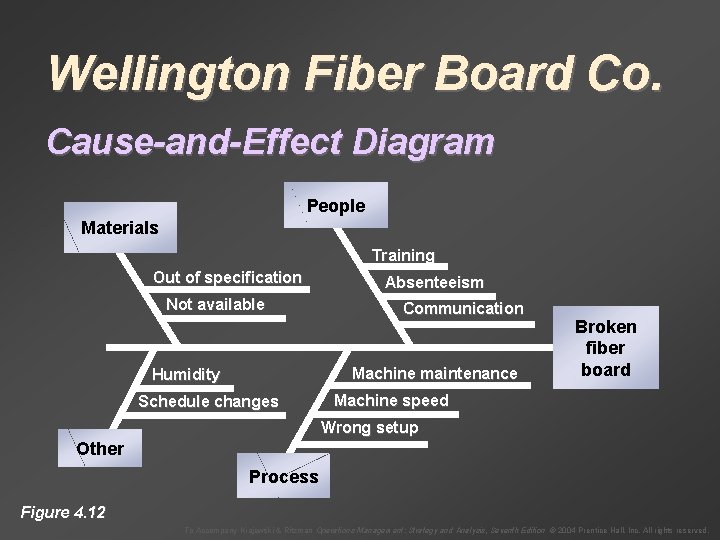
Wellington Fiber Board Co. Cause-and-Effect Diagram People Materials Training Out of specification Not available Absenteeism Communication Machine maintenance Humidity Schedule changes Broken fiber board Machine speed Wrong setup Other Process Figure 4. 12 To Accompany Krajewski & Ritzman Operations Management: Strategy and Analysis, Seventh Edition © 2004 Prentice Hall, Inc. All rights reserved.
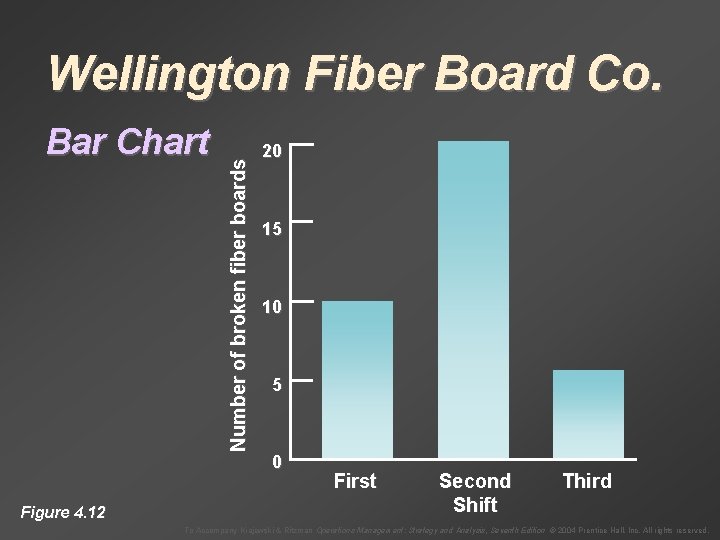
Bar Chart Number of broken fiber boards Wellington Fiber Board Co. 20 15 10 5 0 Figure 4. 12 First Second Shift Third To Accompany Krajewski & Ritzman Operations Management: Strategy and Analysis, Seventh Edition © 2004 Prentice Hall, Inc. All rights reserved.
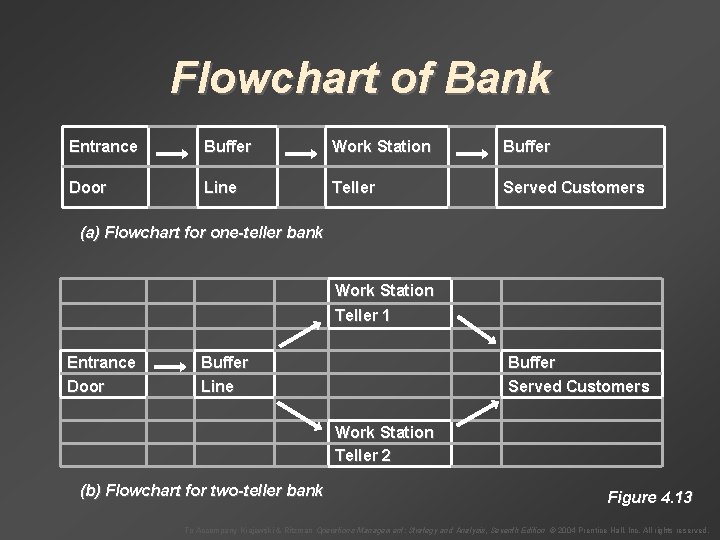
Flowchart of Bank Entrance Buffer Work Station Buffer Door Line Teller Served Customers (a) Flowchart for one-teller bank Work Station Teller 1 Entrance Door Buffer Line Buffer Served Customers Work Station Teller 2 (b) Flowchart for two-teller bank Figure 4. 13 To Accompany Krajewski & Ritzman Operations Management: Strategy and Analysis, Seventh Edition © 2004 Prentice Hall, Inc. All rights reserved.
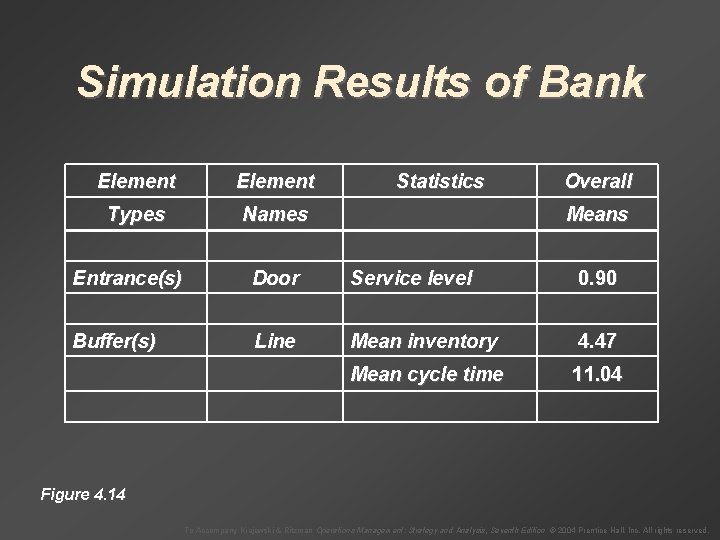
Simulation Results of Bank Element Types Names Statistics Overall Means Entrance(s) Door Service level 0. 90 Buffer(s) Line Mean inventory 4. 47 Mean cycle time 11. 04 Figure 4. 14 To Accompany Krajewski & Ritzman Operations Management: Strategy and Analysis, Seventh Edition © 2004 Prentice Hall, Inc. All rights reserved.
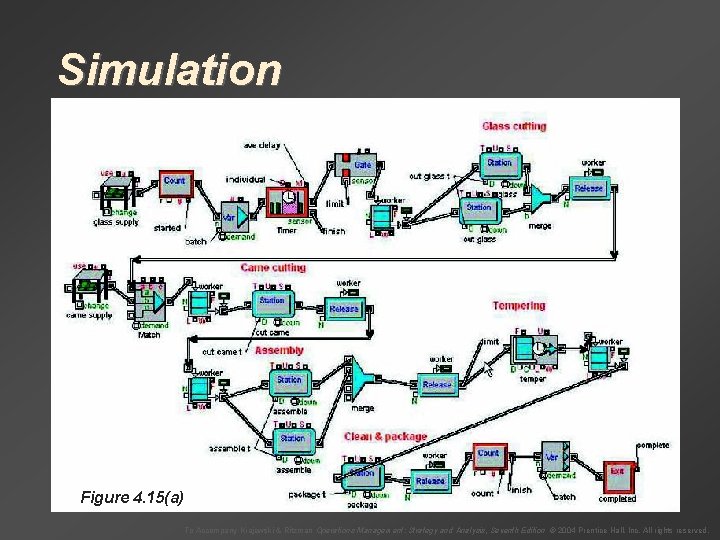
Simulation Figure 4. 15(a) To Accompany Krajewski & Ritzman Operations Management: Strategy and Analysis, Seventh Edition © 2004 Prentice Hall, Inc. All rights reserved.
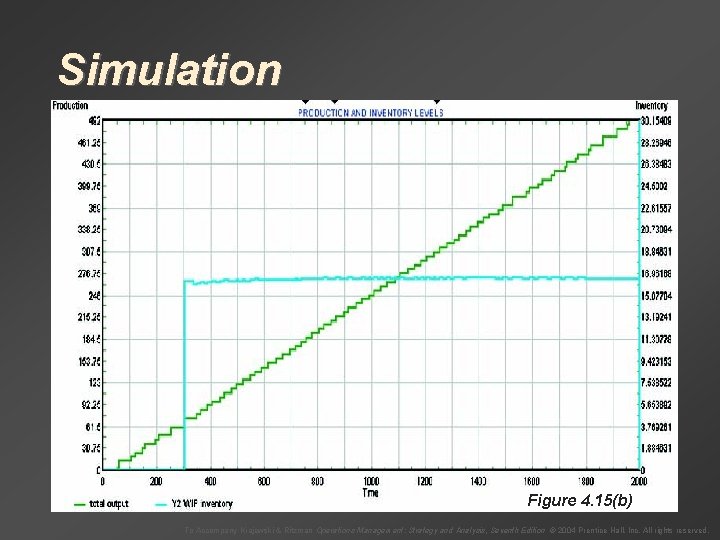
Simulation Figure 4. 15(b) To Accompany Krajewski & Ritzman Operations Management: Strategy and Analysis, Seventh Edition © 2004 Prentice Hall, Inc. All rights reserved.
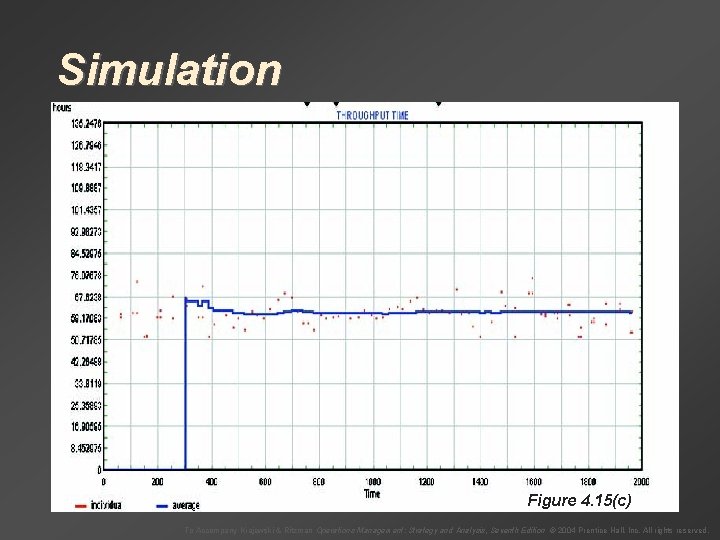
Simulation Figure 4. 15(c) To Accompany Krajewski & Ritzman Operations Management: Strategy and Analysis, Seventh Edition © 2004 Prentice Hall, Inc. All rights reserved.
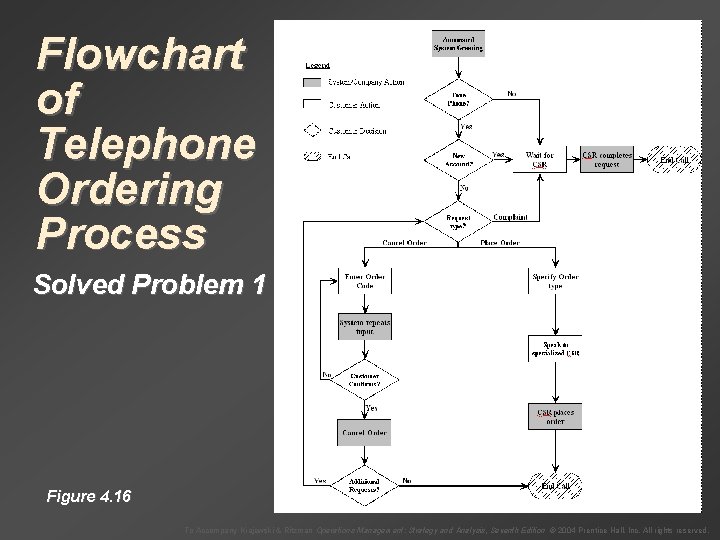
Flowchart of Telephone Ordering Process Solved Problem 1 Figure 4. 16 To Accompany Krajewski & Ritzman Operations Management: Strategy and Analysis, Seventh Edition © 2004 Prentice Hall, Inc. All rights reserved.
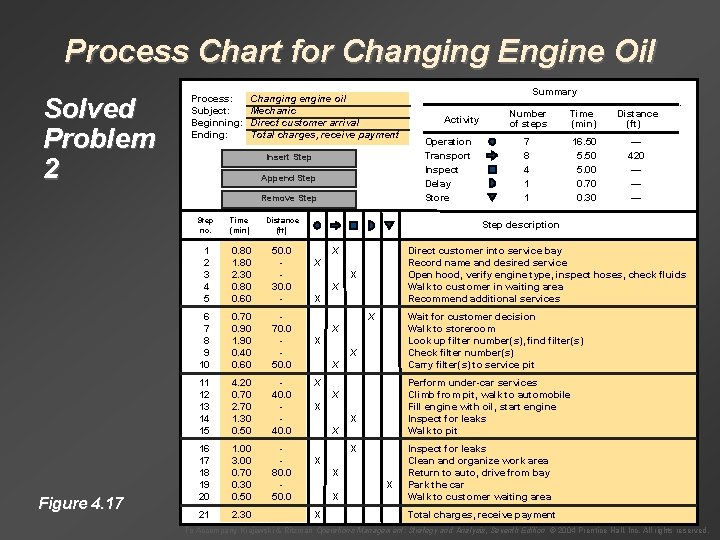
Process Chart for Changing Engine Oil Solved Problem 2 Process: Subject: Beginning: Ending: Changing engine oil Mechanic Direct customer arrival Total charges, receive payment Insert Step Append Step Remove Step Figure 4. 17 Step no. Time (min) Distance (ft) 1 2 3 4 5 0. 80 1. 80 2. 30 0. 80 0. 60 50. 0 30. 0 - 6 7 8 9 10 0. 70 0. 90 1. 90 0. 40 0. 60 70. 0 50. 0 11 12 13 14 15 4. 20 0. 70 2. 70 1. 30 0. 50 40. 0 16 17 18 19 20 1. 00 3. 00 0. 70 0. 30 0. 50 80. 0 50. 0 21 2. 30 Summary Activity Operation Transport Inspect Delay Store Number of steps Time (min) Distance (ft) 7 8 4 1 1 16. 50 5. 00 0. 70 0. 30 — 420 — — — Step description X Direct customer into service bay Record name and desired service Open hood, verify engine type, inspect hoses, check fluids Walk to customer in waiting area Recommend additional services X X X Wait for customer decision Walk to storeroom Look up filter number(s), find filter(s) Check filter number(s) Carry filter(s) to service pit X X X Perform under-car services Climb from pit, walk to automobile Fill engine with oil, start engine Inspect for leaks Walk to pit X X X X X Inspect for leaks Clean and organize work area Return to auto, drive from bay Park the car Walk to customer waiting area Total charges, receive payment To Accompany Krajewski & Ritzman Operations Management: Strategy and Analysis, Seventh Edition © 2004 Prentice Hall, Inc. All rights reserved.
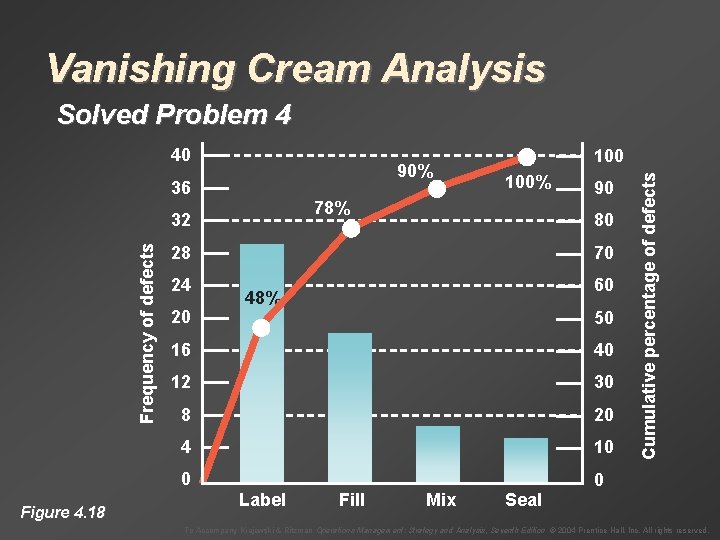
Vanishing Cream Analysis Solved Problem 4 90% 36 Frequency of defects 100% 78% 32 Figure 4. 18 100 90 80 28 70 24 60 20 48% 50 16 40 12 30 8 20 4 10 0 0 Label Fill Mix Cumulative percentage of defects 40 Seal To Accompany Krajewski & Ritzman Operations Management: Strategy and Analysis, Seventh Edition © 2004 Prentice Hall, Inc. All rights reserved.
Slide to doc.com
Accompany chapter 1
Prof. mirosław krajewski
Prof wojciech krajewski
Andy krajewski
Hebrews 6:9-12 sermon
Dorsal arch veins
Inkjet printers are considered legacy technology
Chapter 4 job analysis and the talent management process
Coronoid process and coracoid process
Procedural due process vs substantive due process
Business process levels
Ergodicity
What is process to process delivery
Condylar and coronoid process
Stable process has to be a capable process
Process-to-process delivery
Process street vs sweet process
Process street vs sweet process
Business process analysis
Gap analysis of incident management process
The business analysis process model
Sap solution manager process management
Policy process analysis
Process mapping for root cause analysis
Process analysis toolkit
Phonological process analysis
Example of narrative
Example of definition in patterns of development
Job analysis information hierarchy
Cigital's architectural risk analysis process