Portland Cement NESHAP Compliance Requirements for Hg and
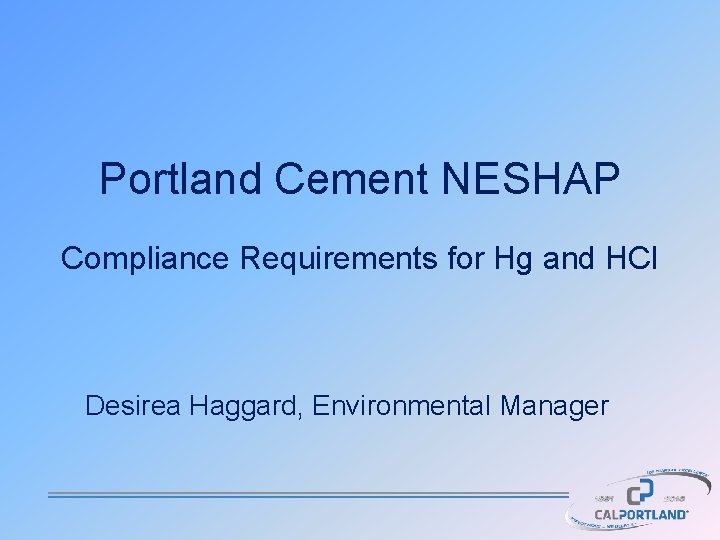
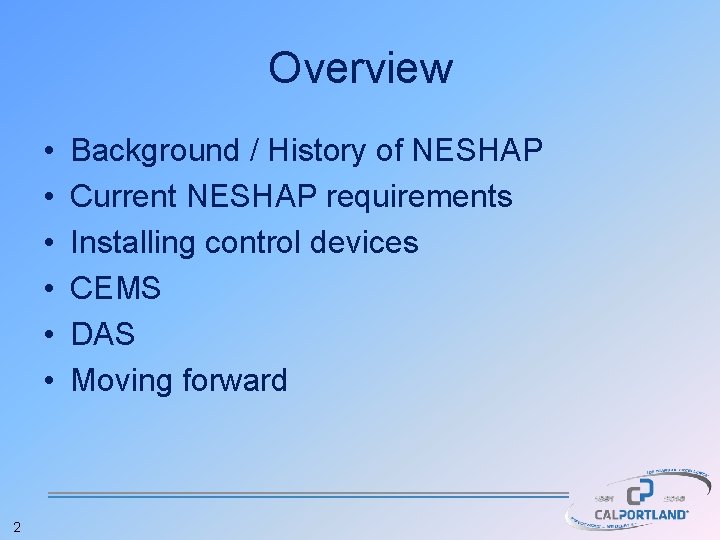
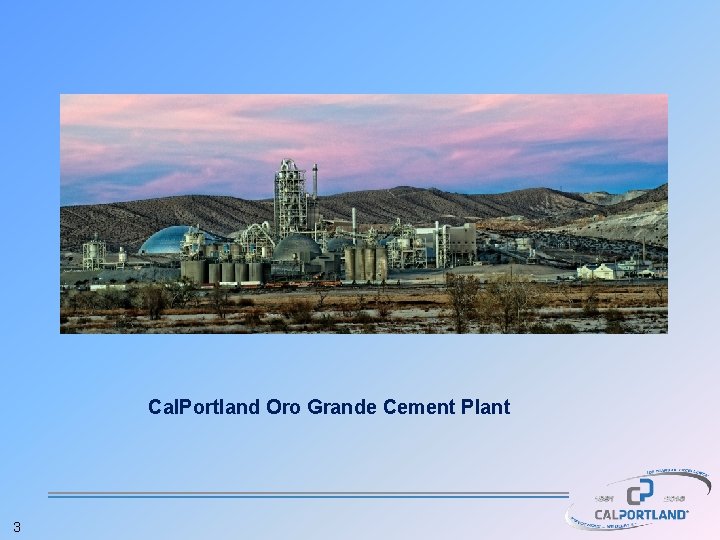
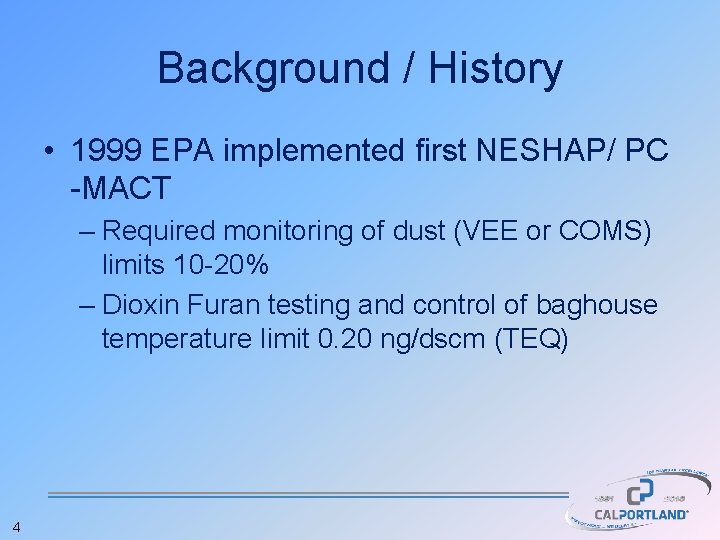
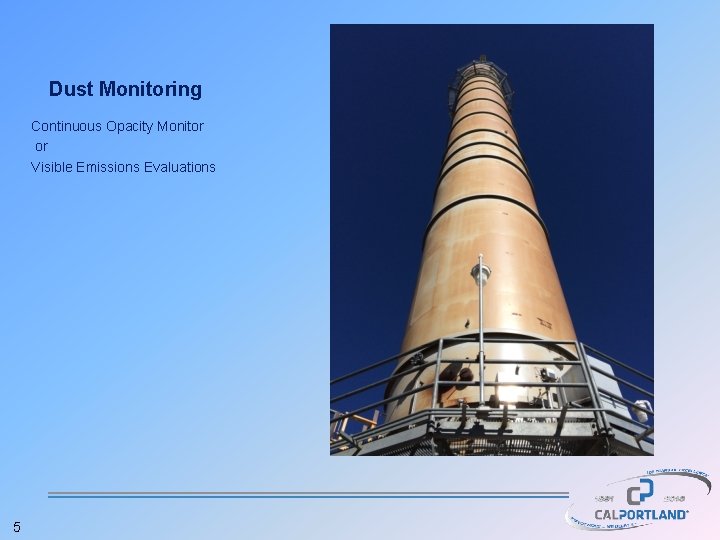
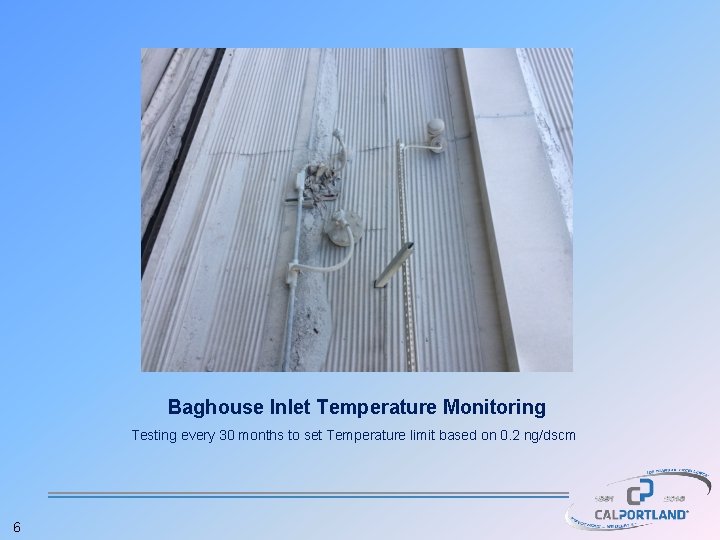
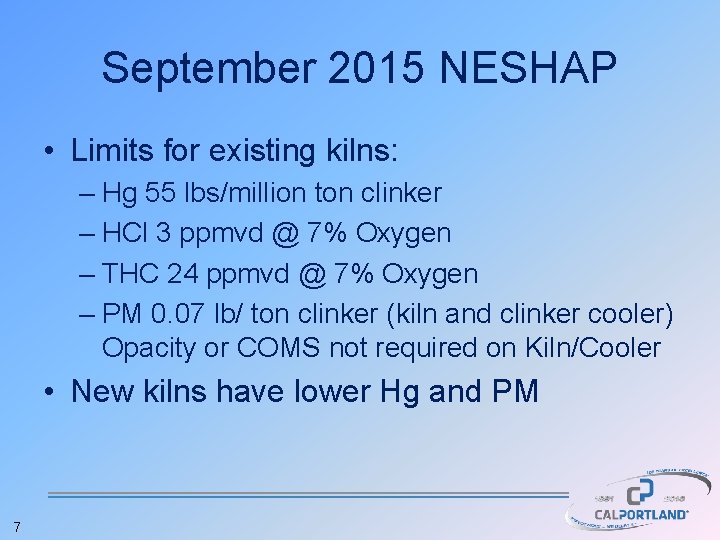
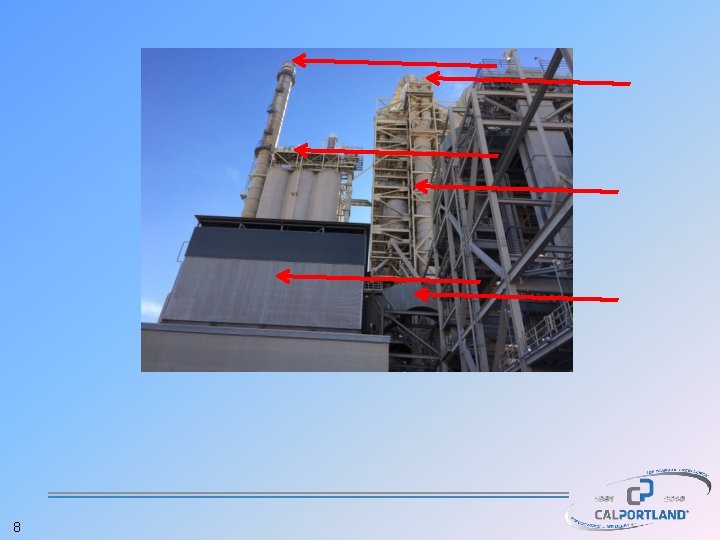
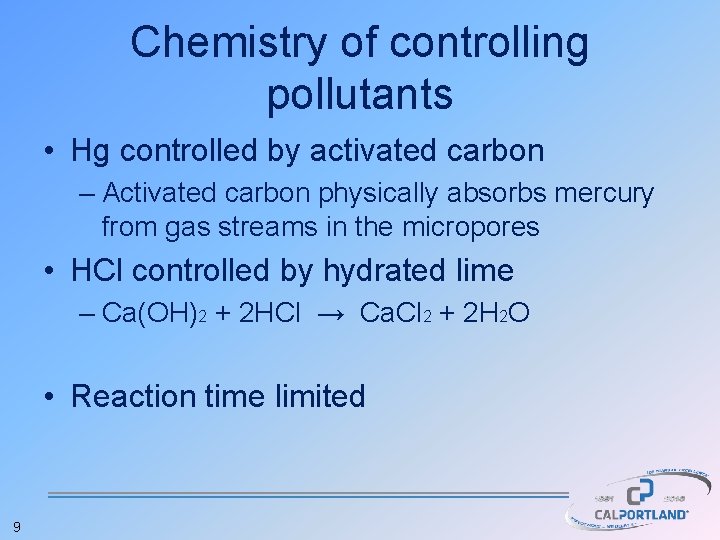

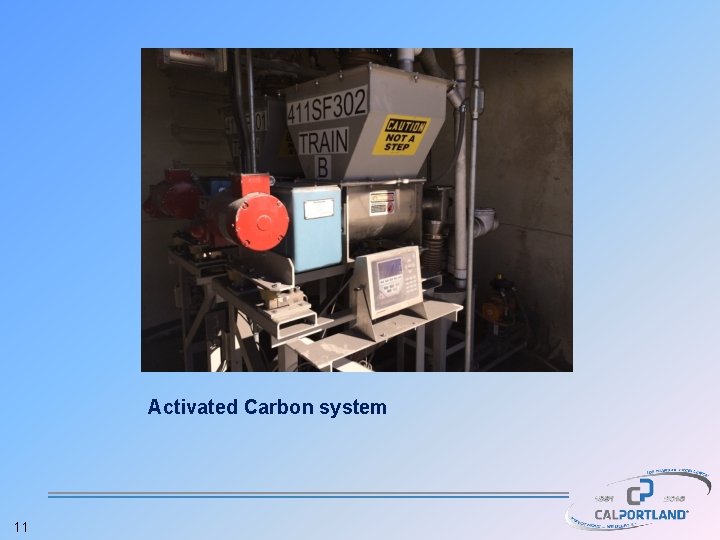
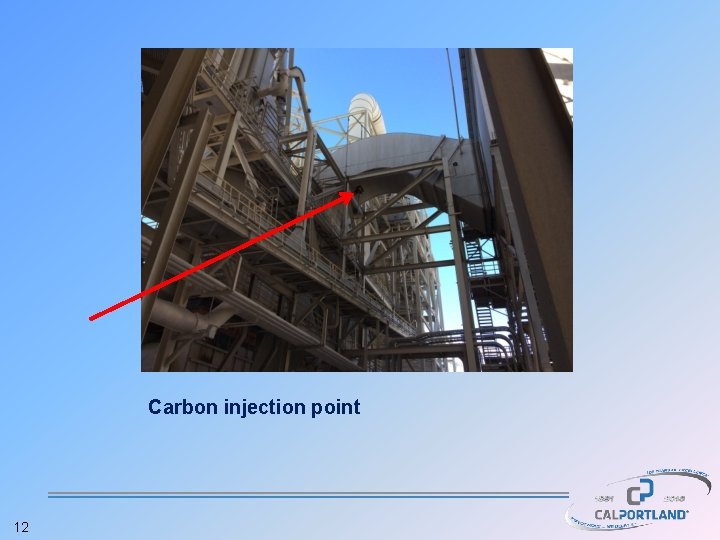
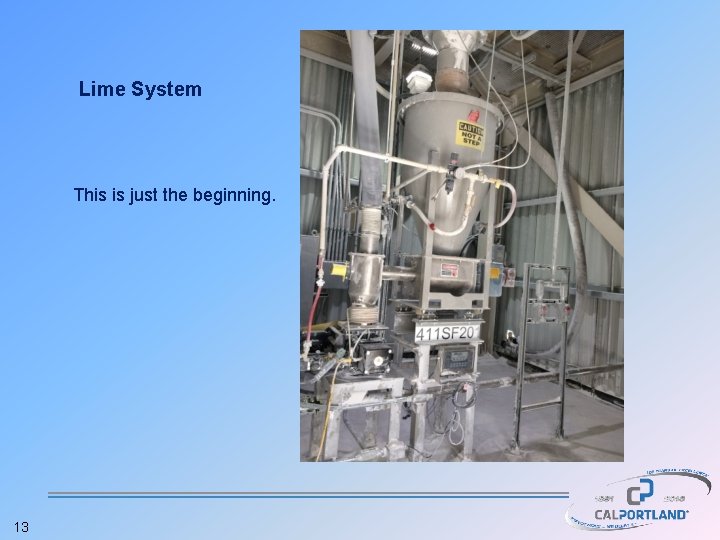
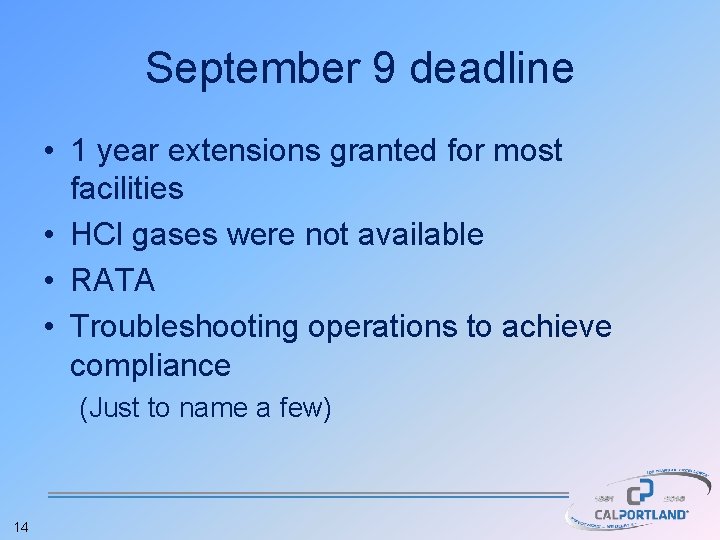
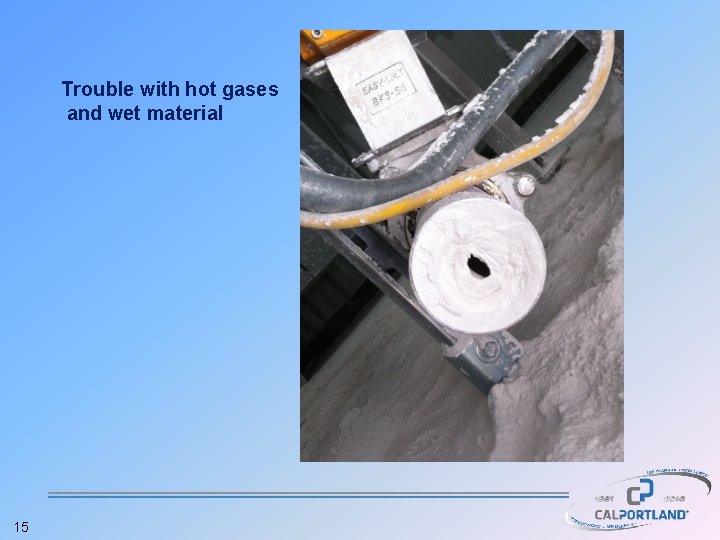
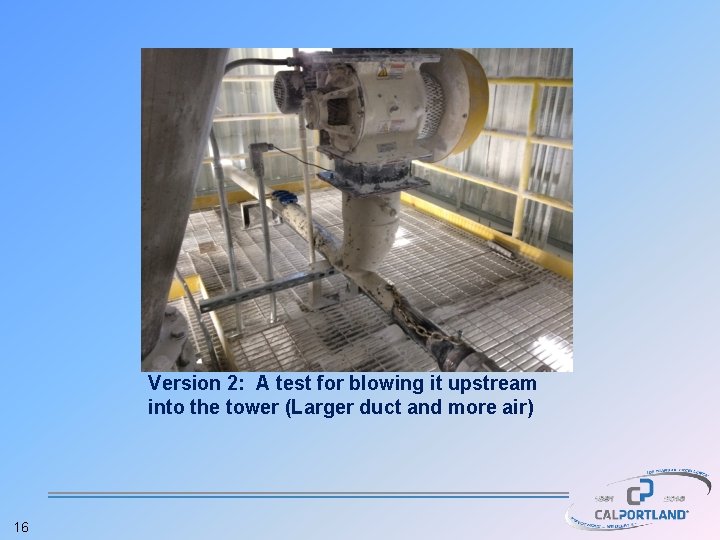
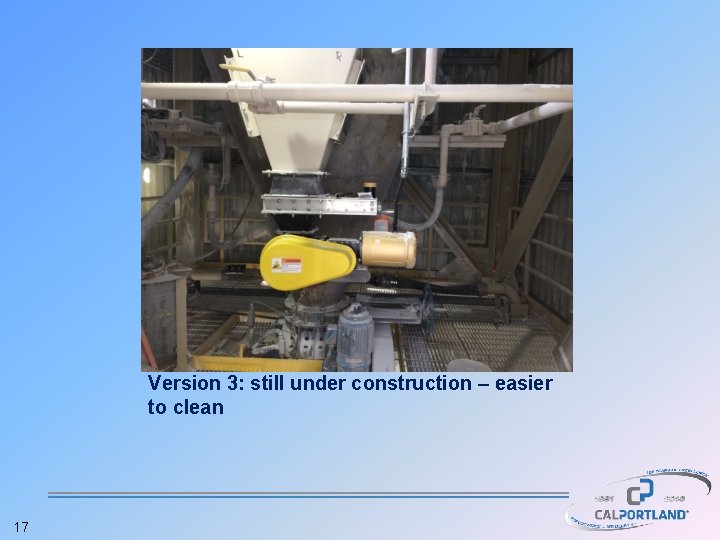
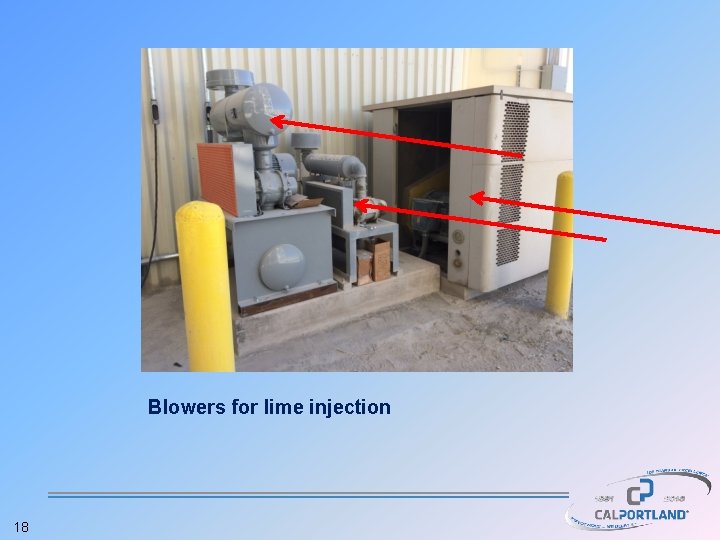
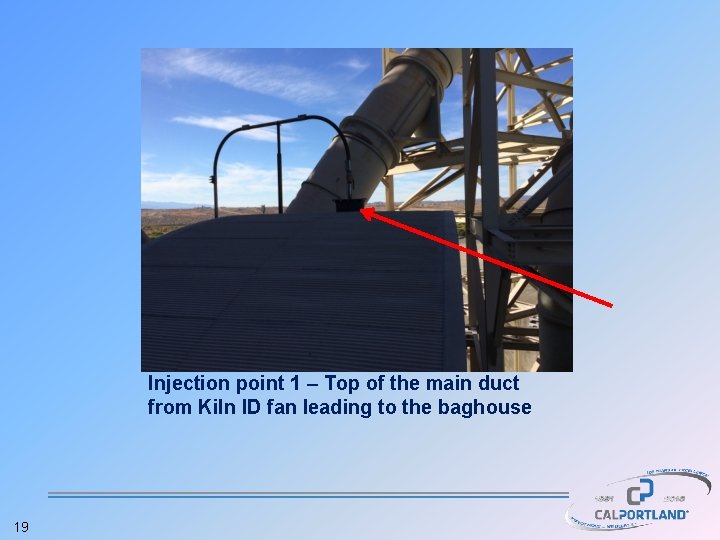
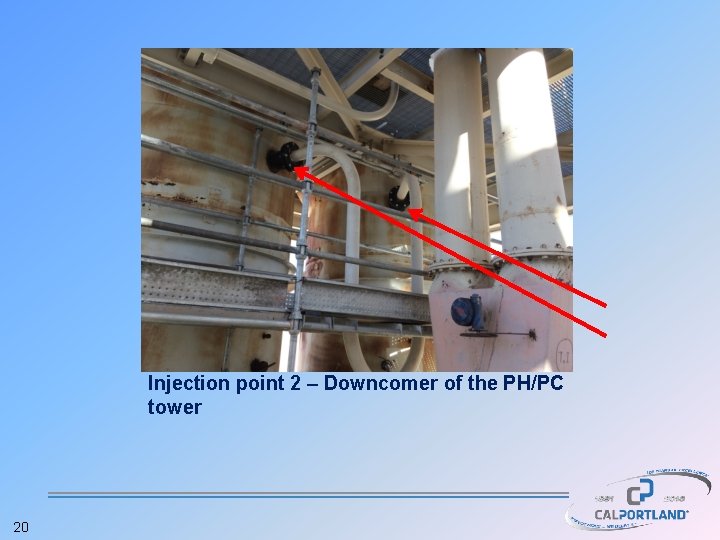
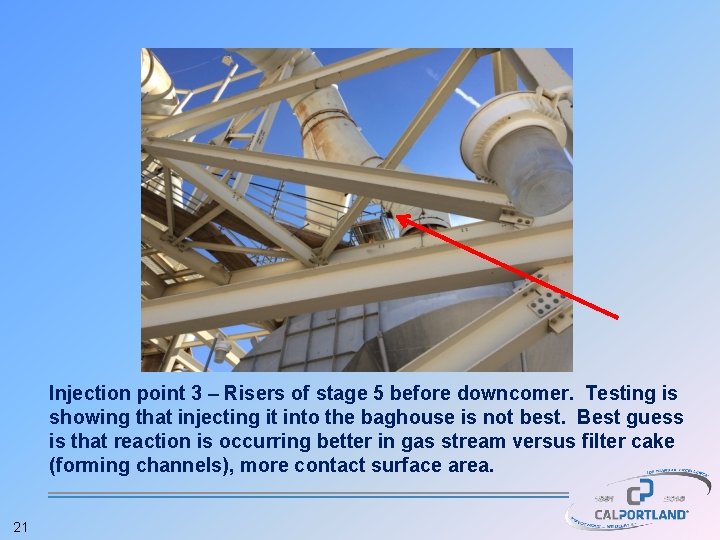
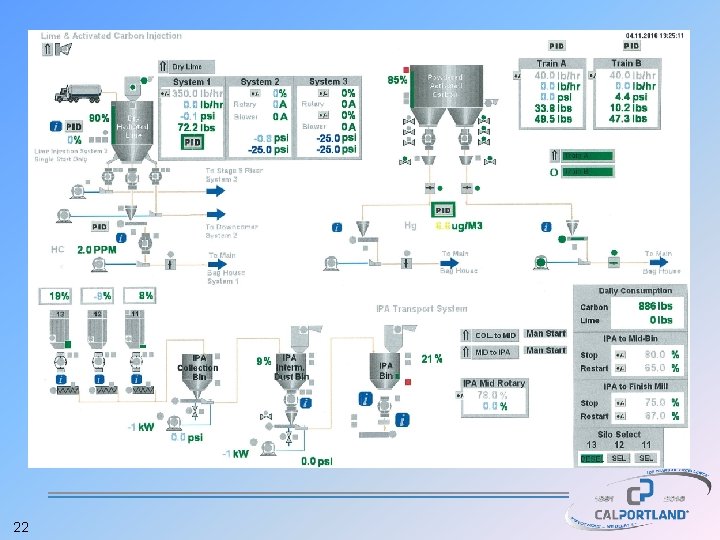
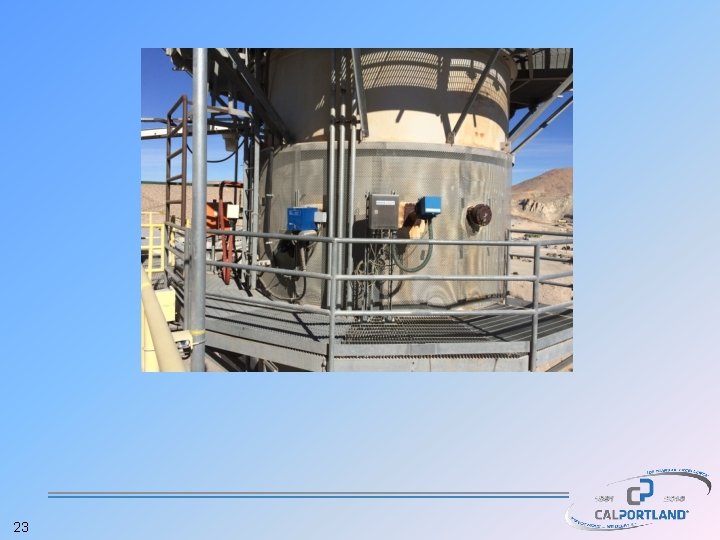
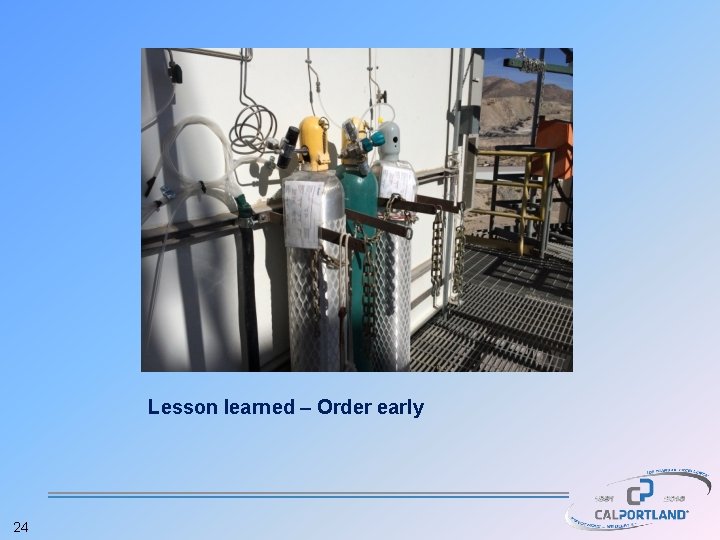
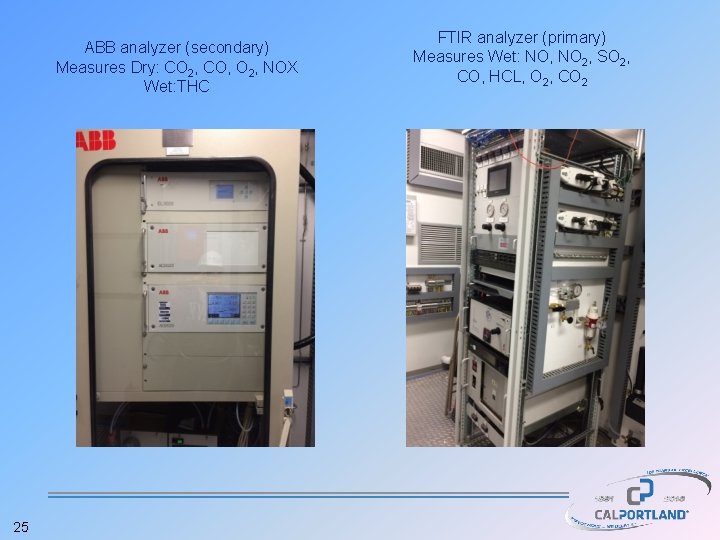
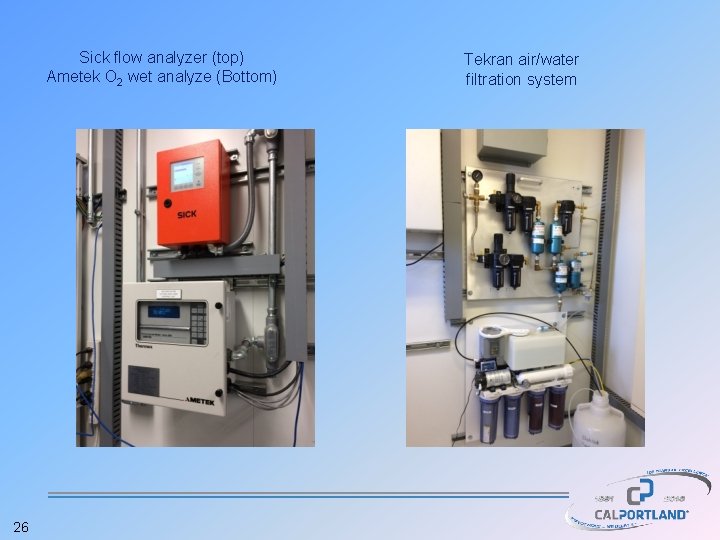
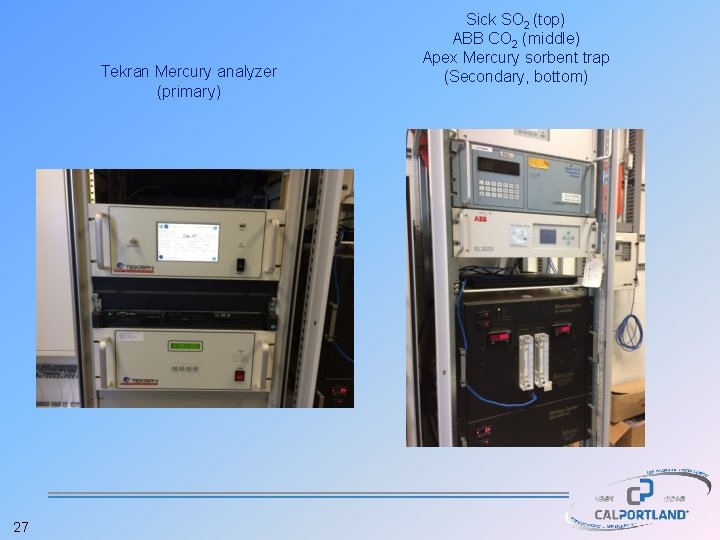
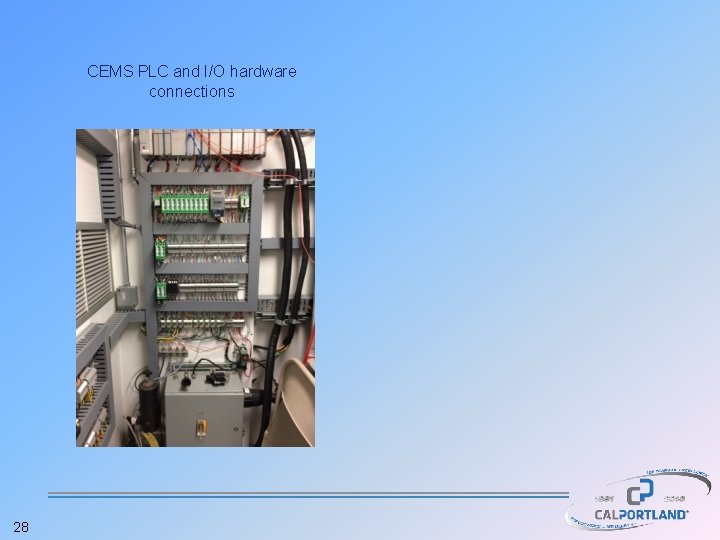
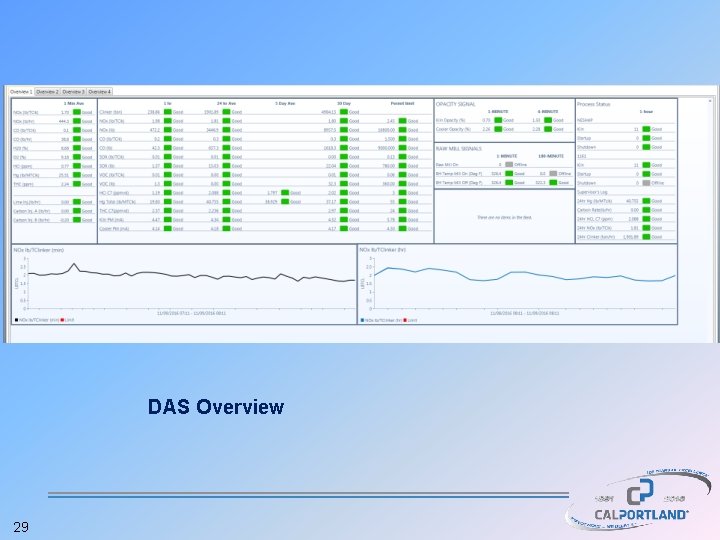
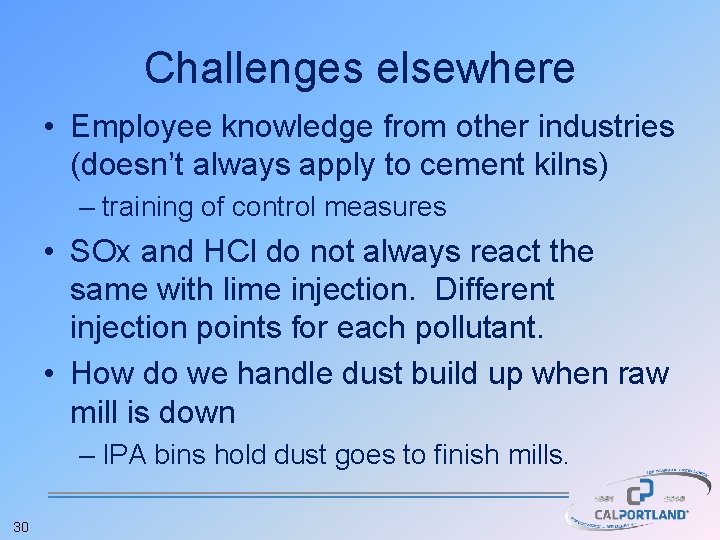
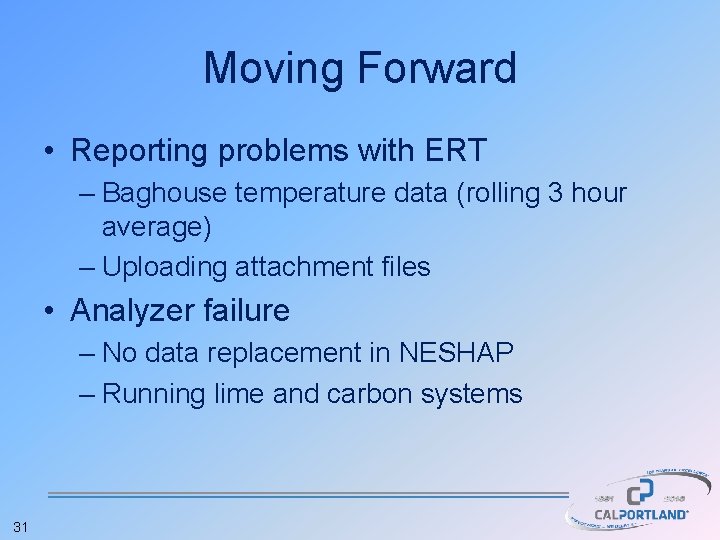
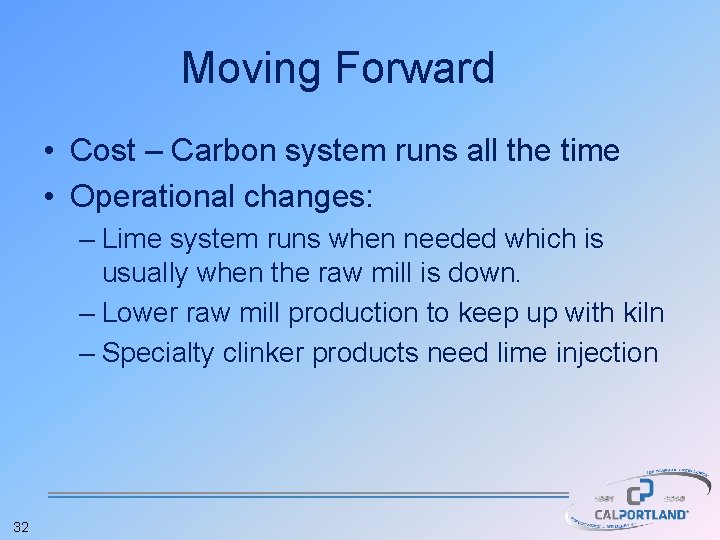
- Slides: 32
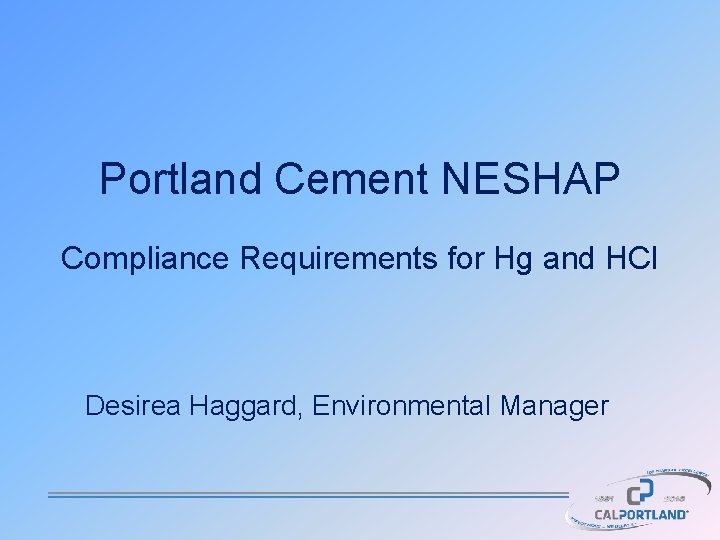
Portland Cement NESHAP Compliance Requirements for Hg and HCl Desirea Haggard, Environmental Manager
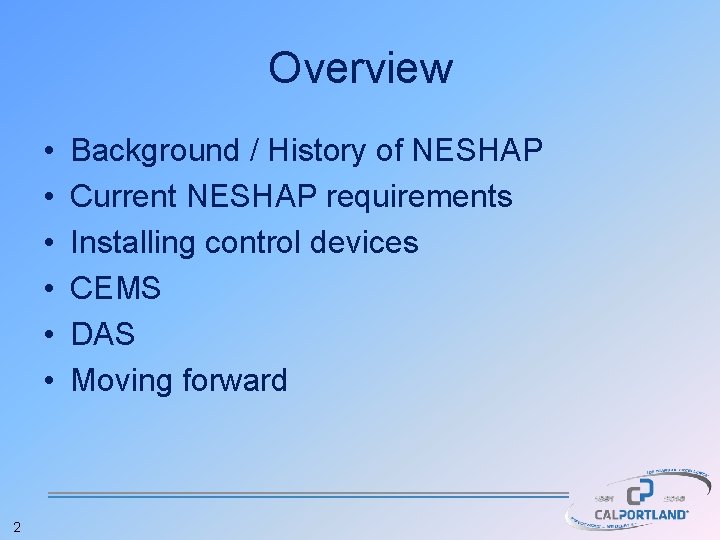
Overview • • • 2 Background / History of NESHAP Current NESHAP requirements Installing control devices CEMS DAS Moving forward
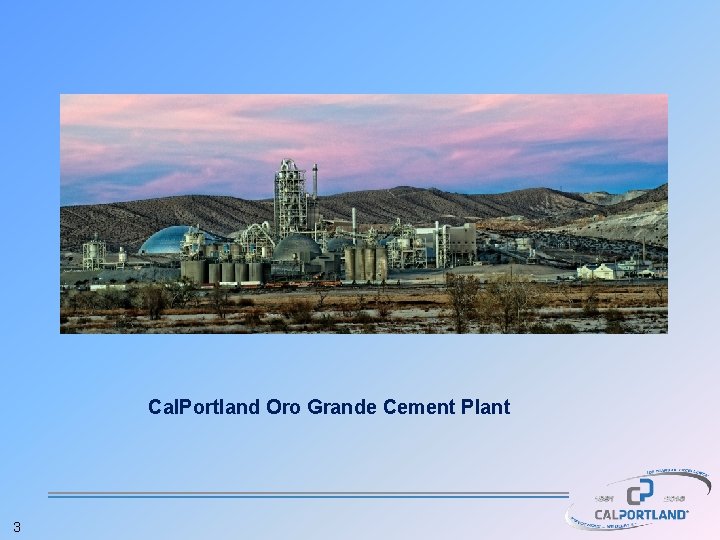
Cal. Portland Oro Grande Cement Plant 3
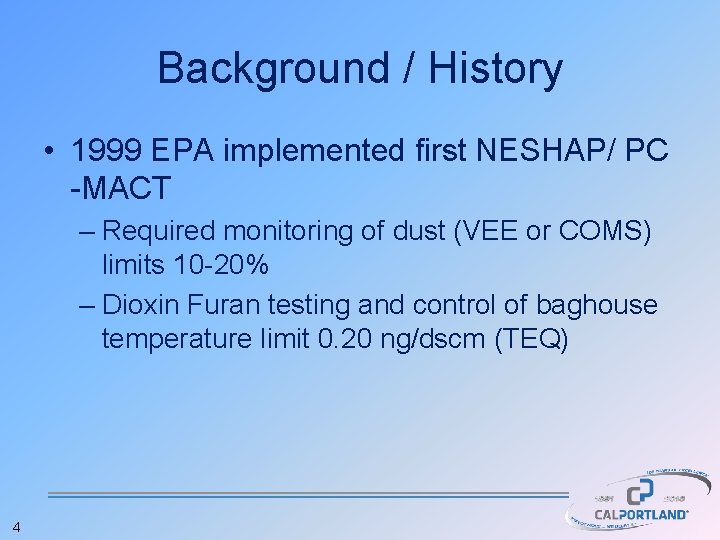
Background / History • 1999 EPA implemented first NESHAP/ PC -MACT – Required monitoring of dust (VEE or COMS) limits 10 -20% – Dioxin Furan testing and control of baghouse temperature limit 0. 20 ng/dscm (TEQ) 4
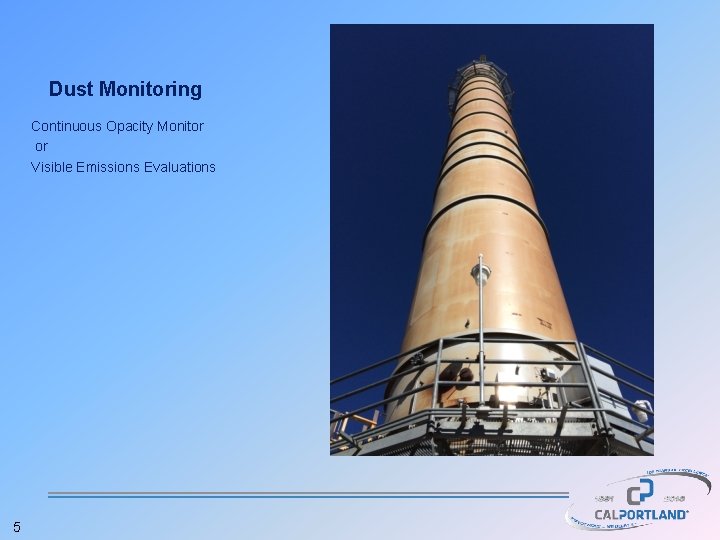
Dust Monitoring Continuous Opacity Monitor or Visible Emissions Evaluations 5
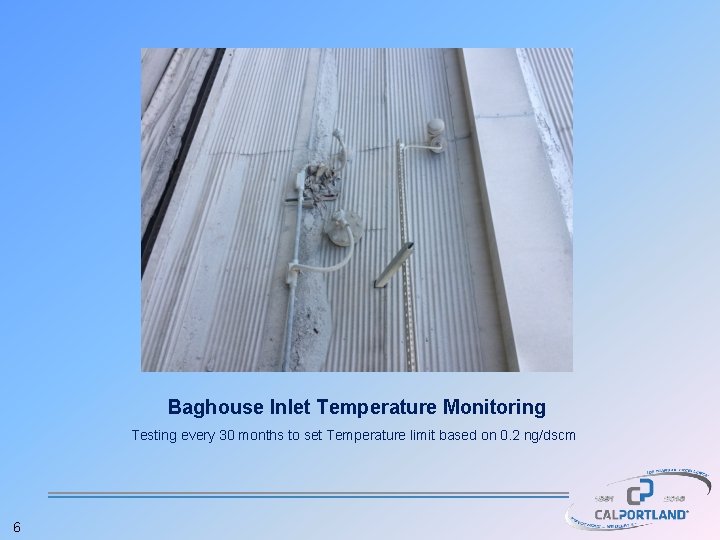
Baghouse Inlet Temperature Monitoring Testing every 30 months to set Temperature limit based on 0. 2 ng/dscm 6
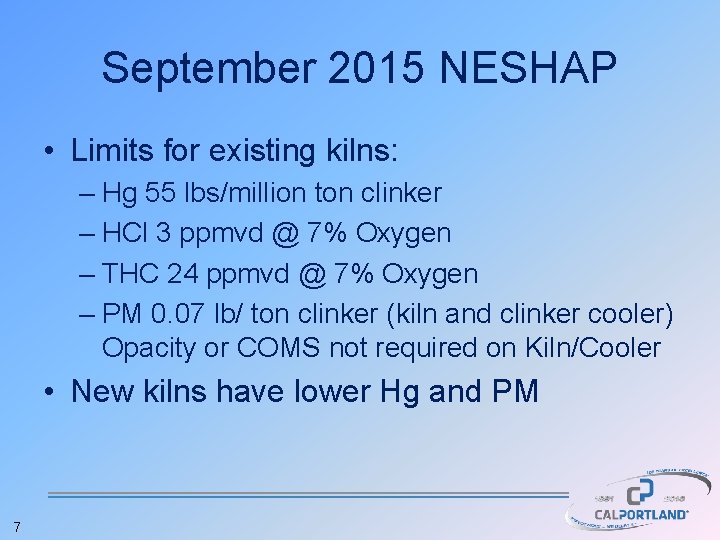
September 2015 NESHAP • Limits for existing kilns: – Hg 55 lbs/million ton clinker – HCl 3 ppmvd @ 7% Oxygen – THC 24 ppmvd @ 7% Oxygen – PM 0. 07 lb/ ton clinker (kiln and clinker cooler) Opacity or COMS not required on Kiln/Cooler • New kilns have lower Hg and PM 7
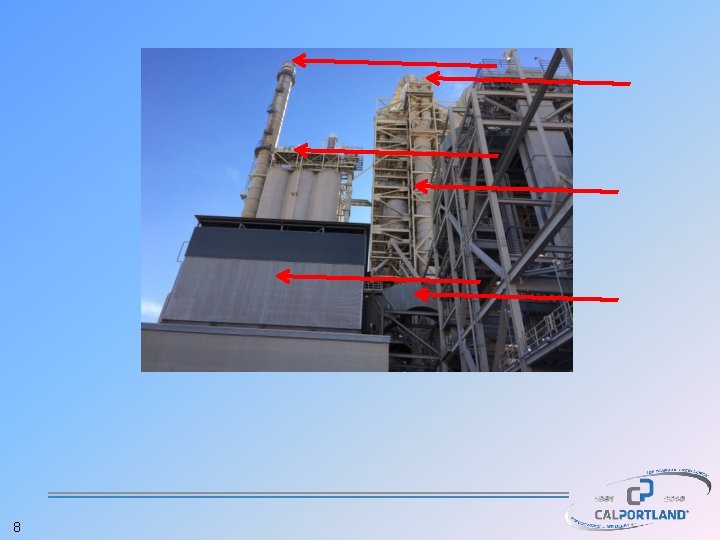
8
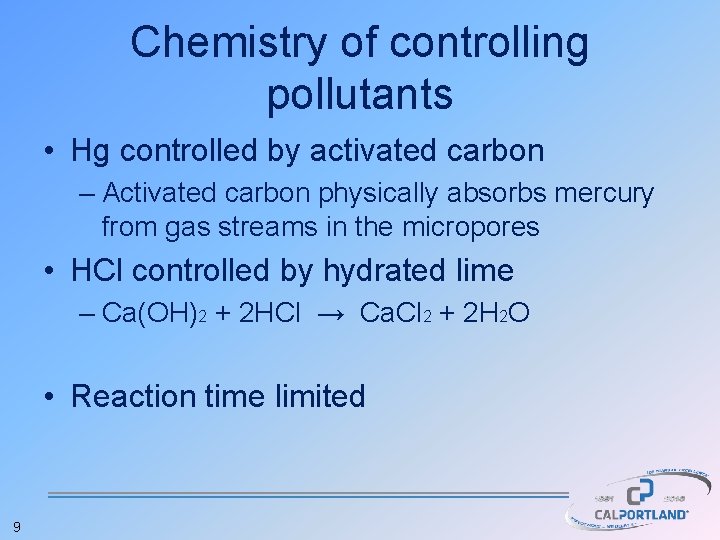
Chemistry of controlling pollutants • Hg controlled by activated carbon – Activated carbon physically absorbs mercury from gas streams in the micropores • HCl controlled by hydrated lime – Ca(OH)2 + 2 HCl → Ca. Cl 2 + 2 H 2 O • Reaction time limited 9

New equipment installed for compliance 10
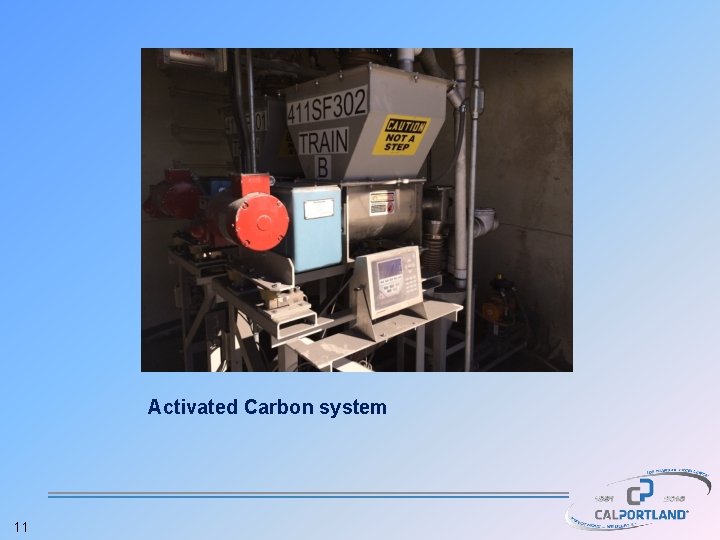
Activated Carbon system 11
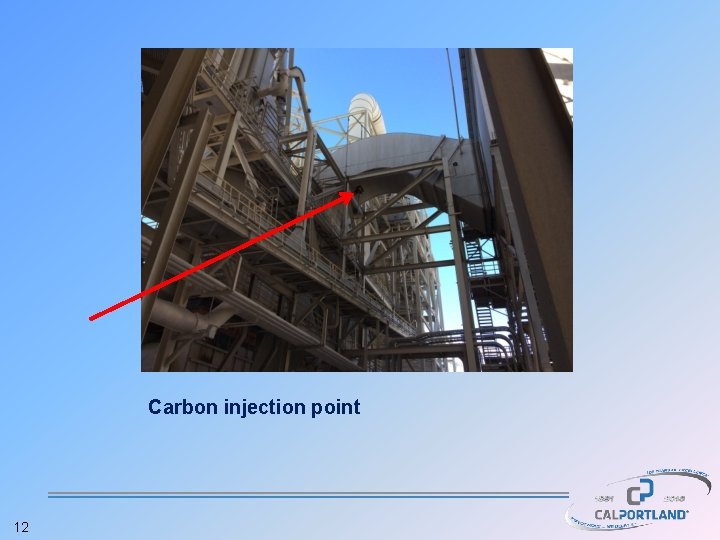
Carbon injection point 12
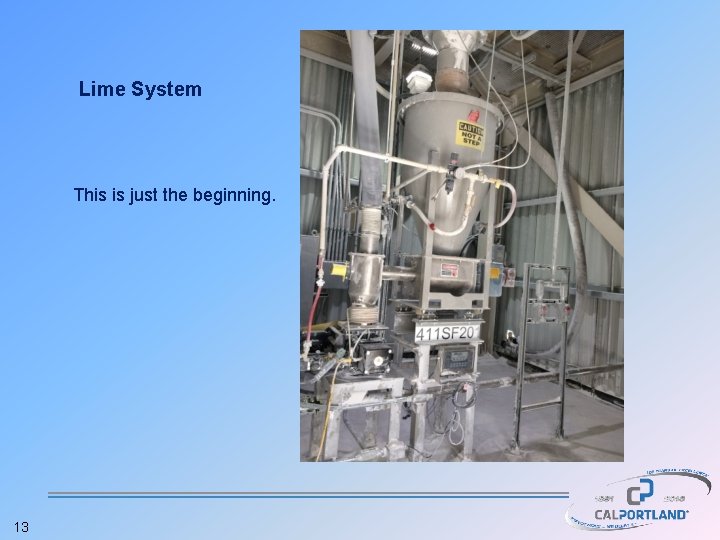
Lime System This is just the beginning. 13
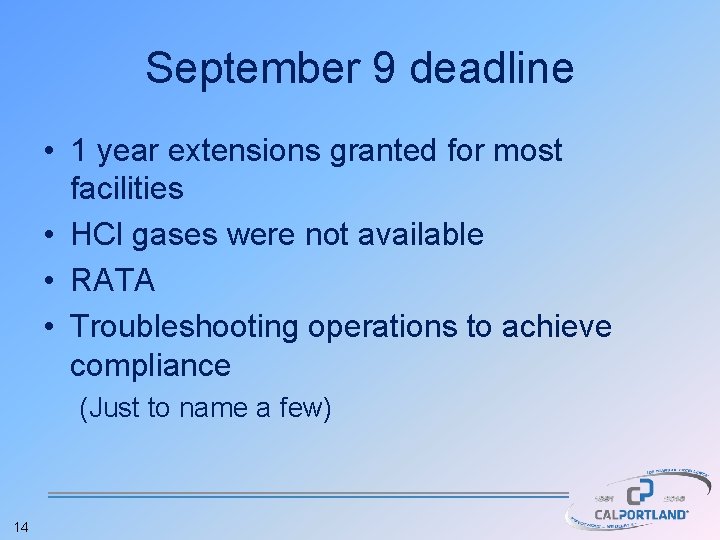
September 9 deadline • 1 year extensions granted for most facilities • HCl gases were not available • RATA • Troubleshooting operations to achieve compliance (Just to name a few) 14
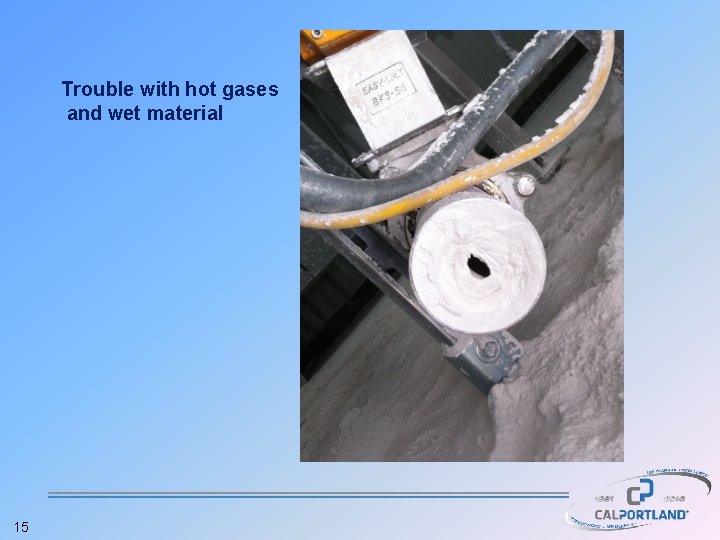
Trouble with hot gases and wet material 15
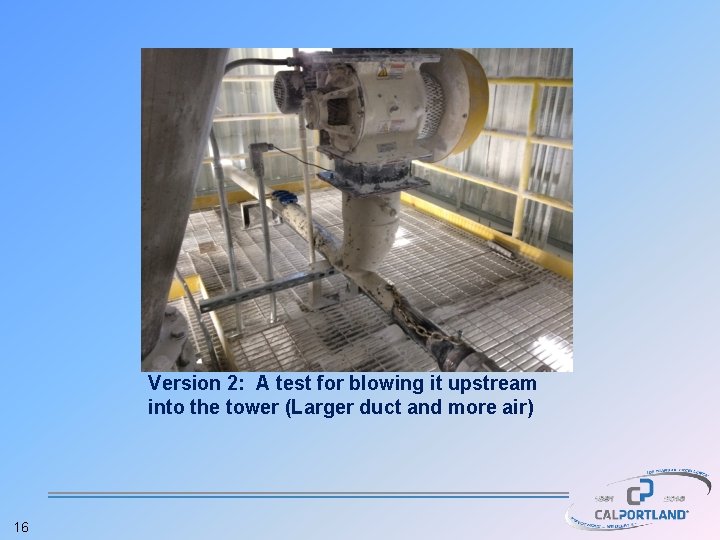
Version 2: A test for blowing it upstream into the tower (Larger duct and more air) 16
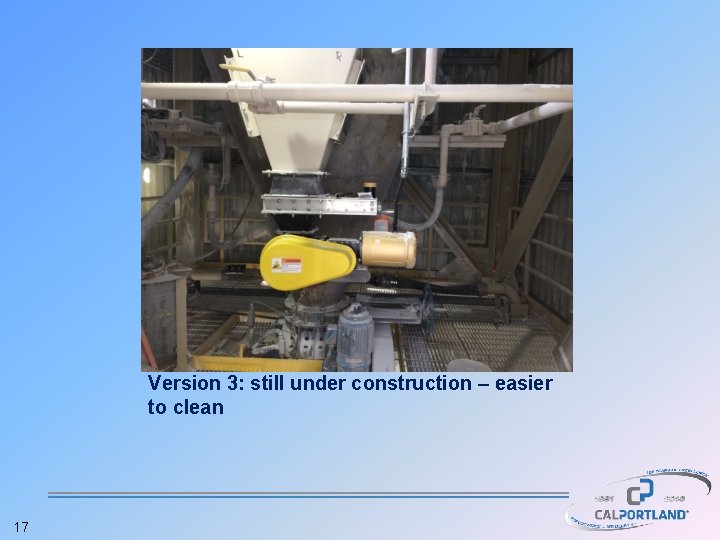
Version 3: still under construction – easier to clean 17
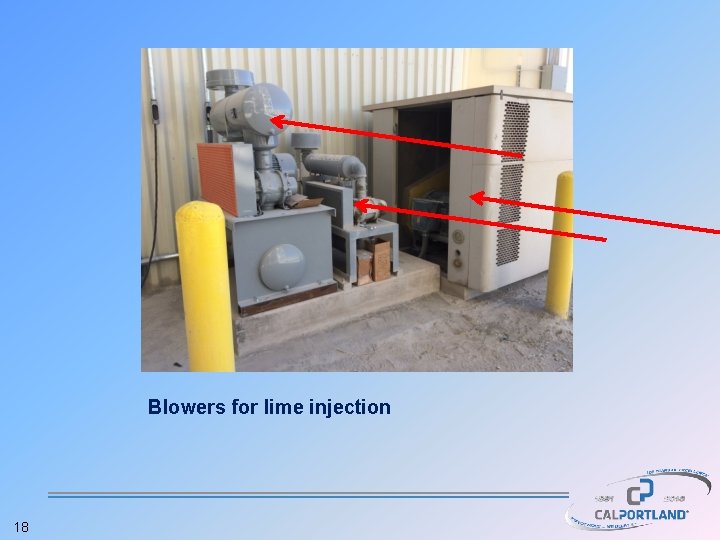
Blowers for lime injection 18
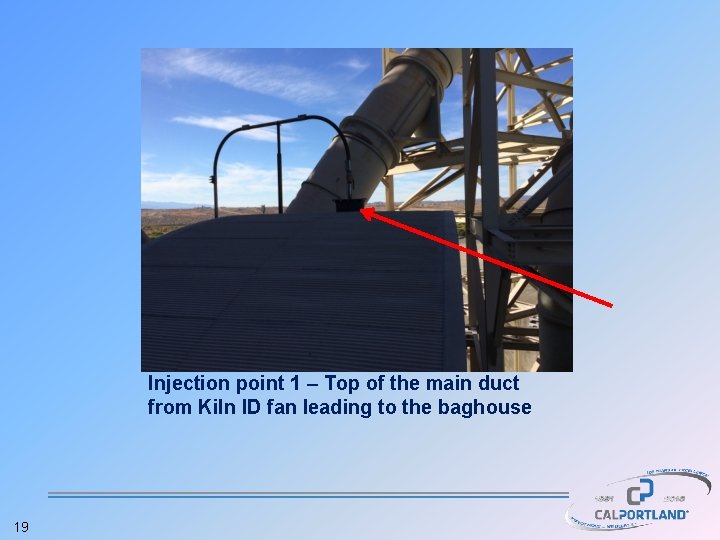
Injection point 1 – Top of the main duct from Kiln ID fan leading to the baghouse 19
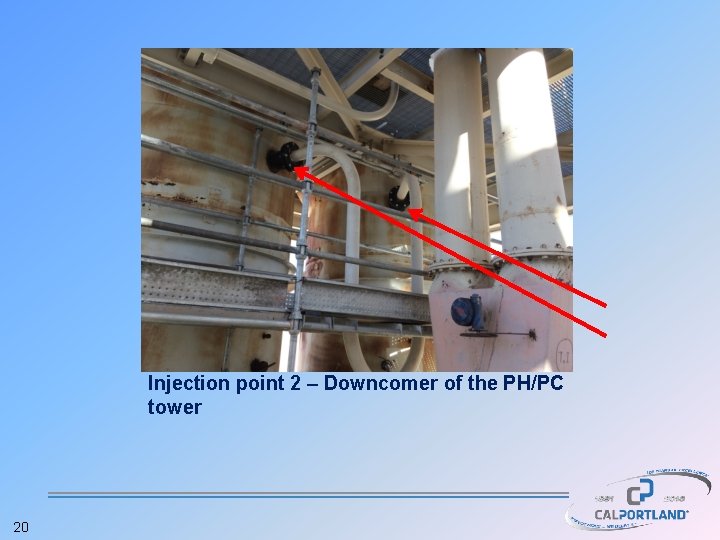
Injection point 2 – Downcomer of the PH/PC tower 20
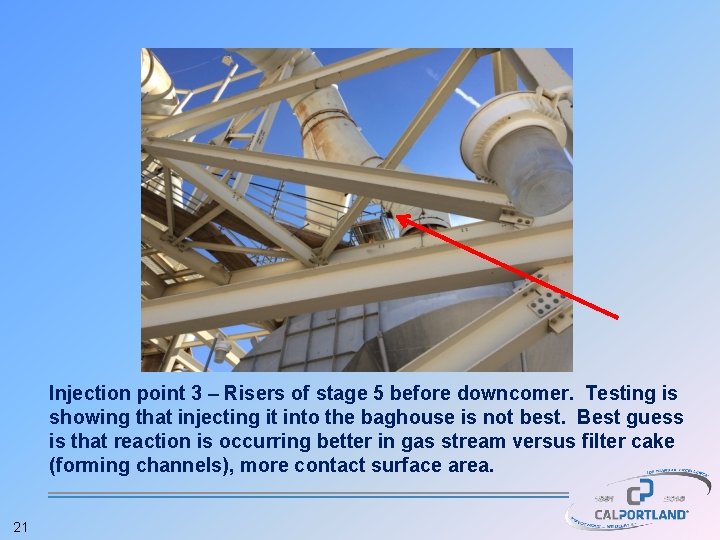
Injection point 3 – Risers of stage 5 before downcomer. Testing is showing that injecting it into the baghouse is not best. Best guess is that reaction is occurring better in gas stream versus filter cake (forming channels), more contact surface area. 21
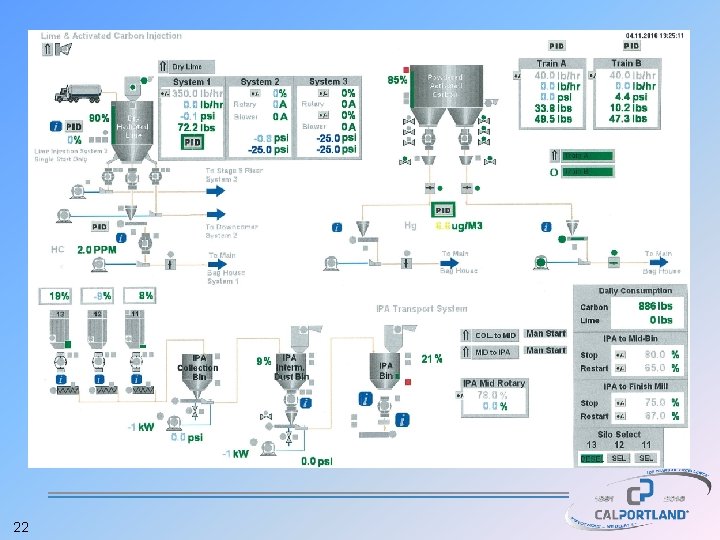
22
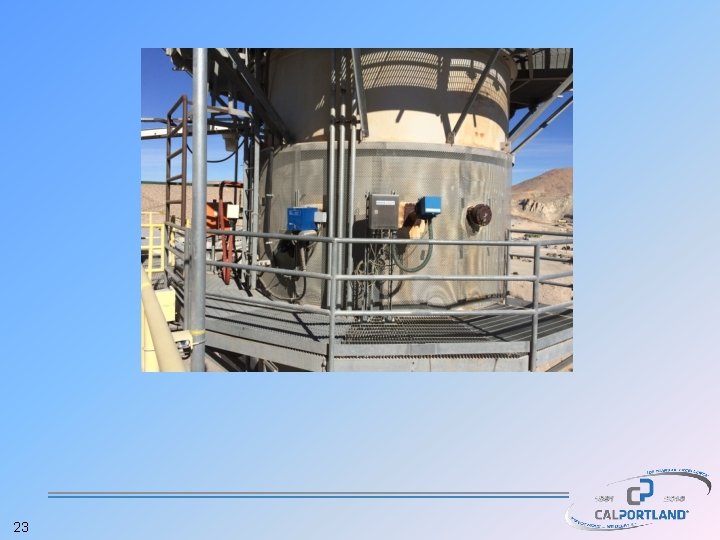
23
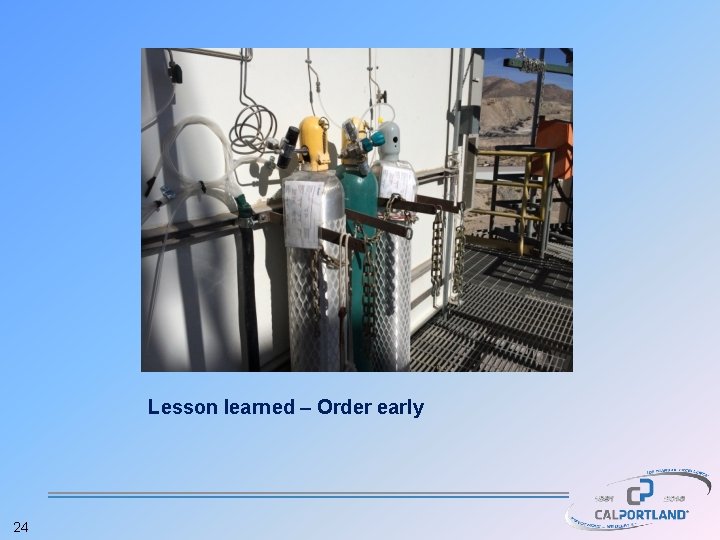
Lesson learned – Order early 24
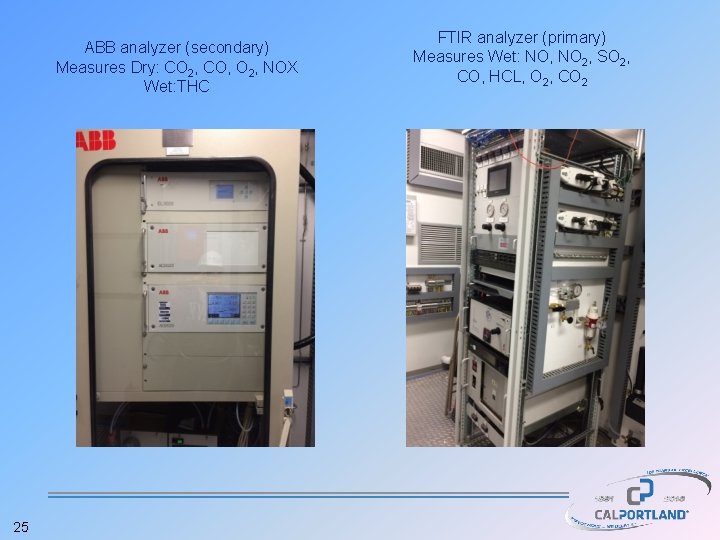
ABB analyzer (secondary) Measures Dry: CO 2, CO, O 2, NOX Wet: THC 25 FTIR analyzer (primary) Measures Wet: NO, NO 2, SO 2, CO, HCL, O 2, CO 2
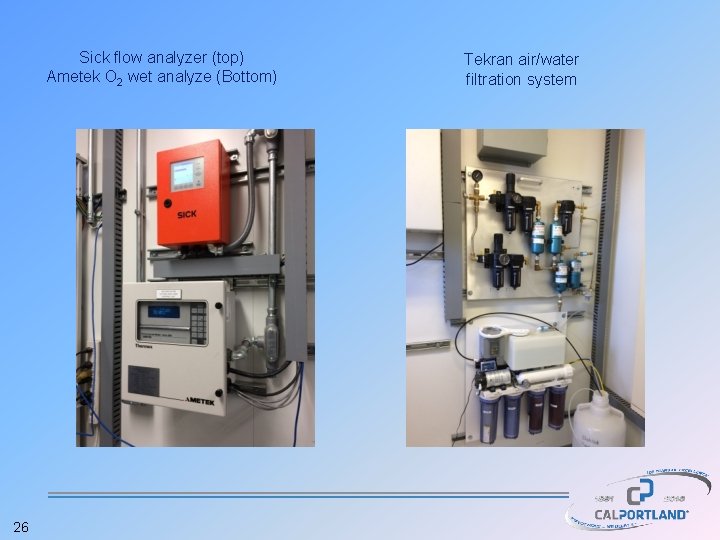
Sick flow analyzer (top) Ametek O 2 wet analyze (Bottom) 26 Tekran air/water filtration system
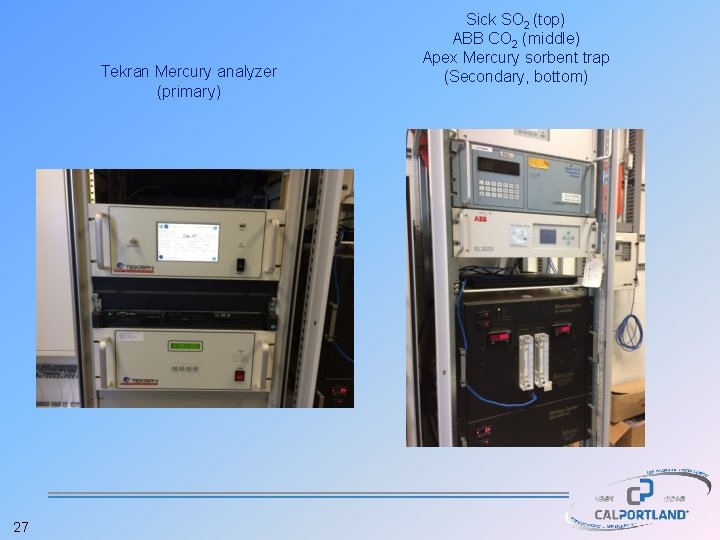
Tekran Mercury analyzer (primary) 27 Sick SO 2 (top) ABB CO 2 (middle) Apex Mercury sorbent trap (Secondary, bottom)
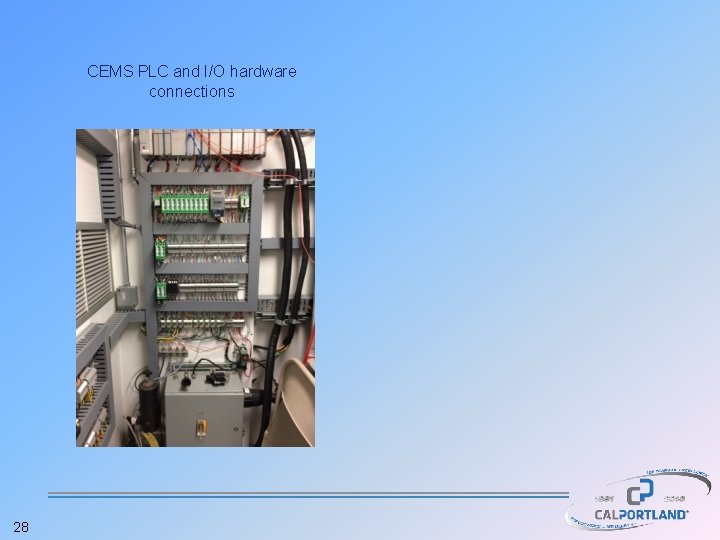
CEMS PLC and I/O hardware connections 28
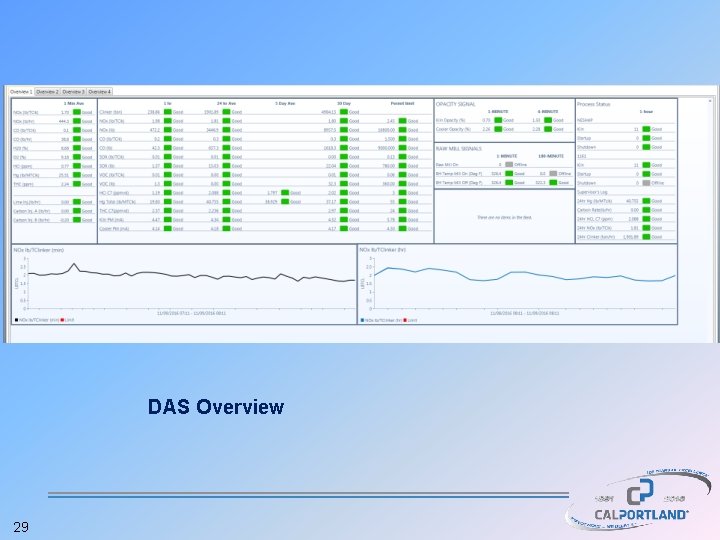
DAS Overview 29
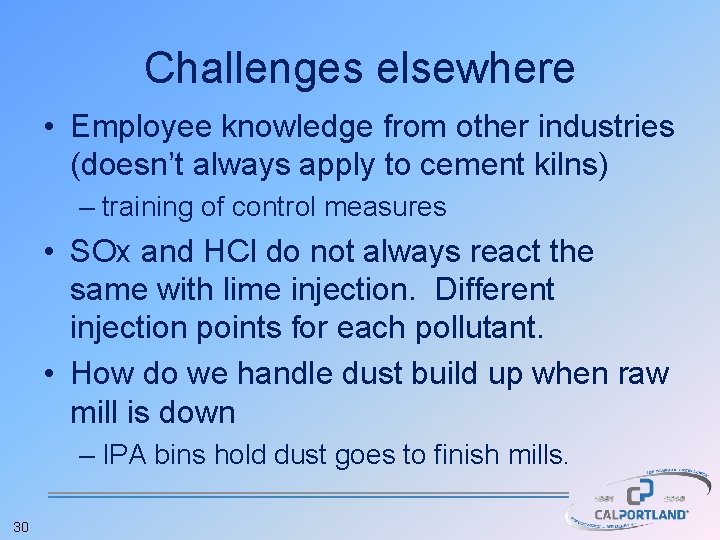
Challenges elsewhere • Employee knowledge from other industries (doesn’t always apply to cement kilns) – training of control measures • SOx and HCl do not always react the same with lime injection. Different injection points for each pollutant. • How do we handle dust build up when raw mill is down – IPA bins hold dust goes to finish mills. 30
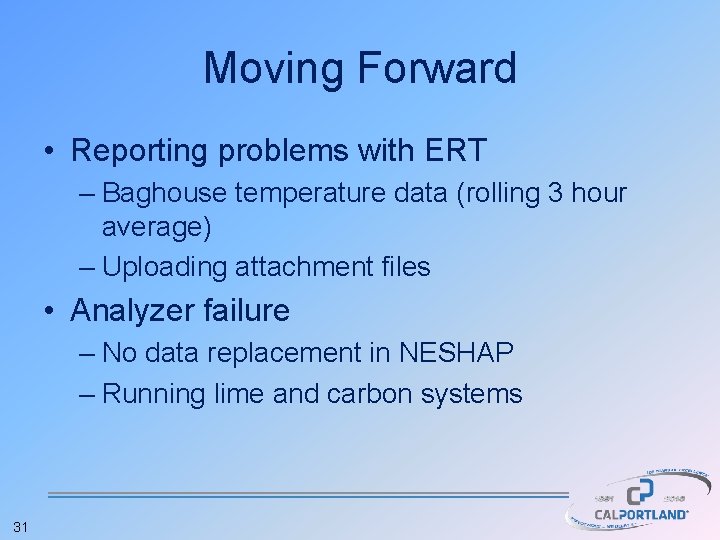
Moving Forward • Reporting problems with ERT – Baghouse temperature data (rolling 3 hour average) – Uploading attachment files • Analyzer failure – No data replacement in NESHAP – Running lime and carbon systems 31
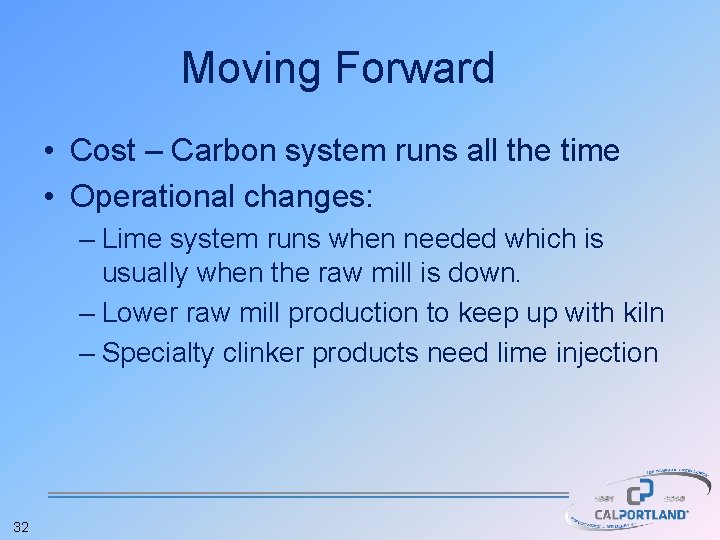
Moving Forward • Cost – Carbon system runs all the time • Operational changes: – Lime system runs when needed which is usually when the raw mill is down. – Lower raw mill production to keep up with kiln – Specialty clinker products need lime injection 32
Manufacture of portland cement
Portland cement definition
Praxis portland cement
Berry compliance requirements
Ppaca compliance program requirements
Tar and cement verdelle smith
Melamine formaldehyde advantages and disadvantages
Portland state university undergraduate tuition and fees
Cement alicia's manufacturers
Rcc reinforced cement concrete
Liquid solvent cement
Shargh white cement
Suspension grouting
Glass ionomer cement types
Mortar mix water ratio
Squeeze cementing
Vicatt
Non hydraulic cement
1:2:3 concrete
Absolute volume of concrete formula
Zinc phosphate cement setting reaction
Wolfs law
Zinc phosphate cement setting reaction
Dalmacija cement
Gic types
Tobermonite gel
Vertical example
Extra rapid hardening cement setting time
Bargarh cement works
Semen sbc
Komprimálható
Reco cement
Klas cement