CEMENT Cement Composition manufacture Tests on cement Varieties
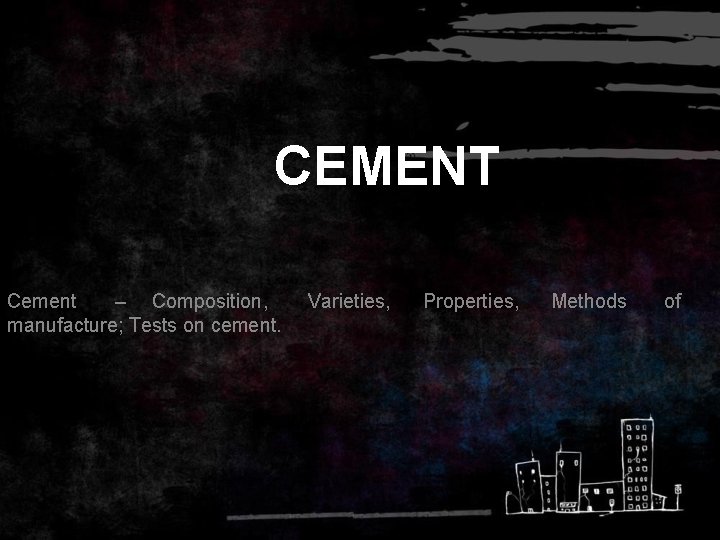
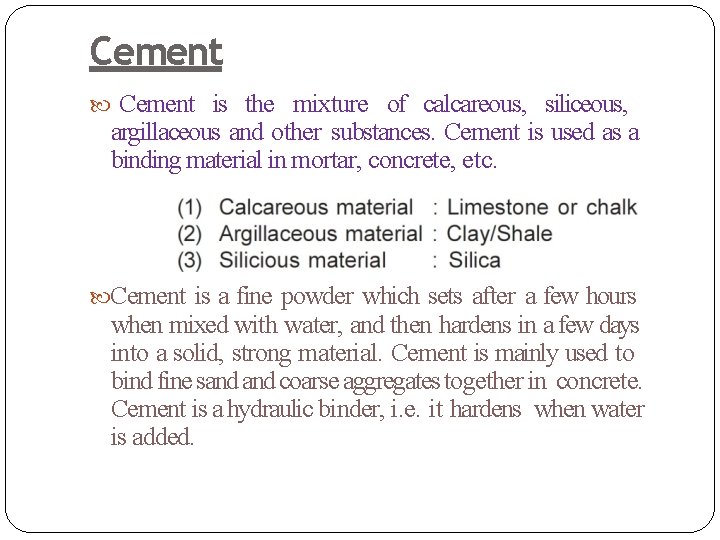
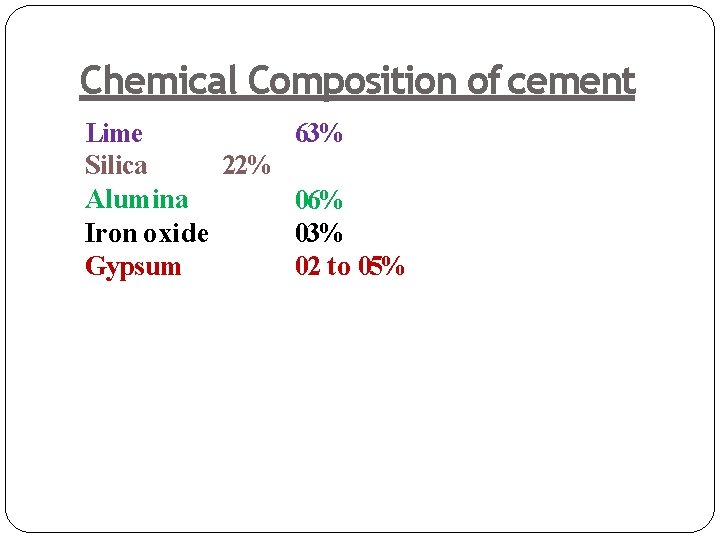
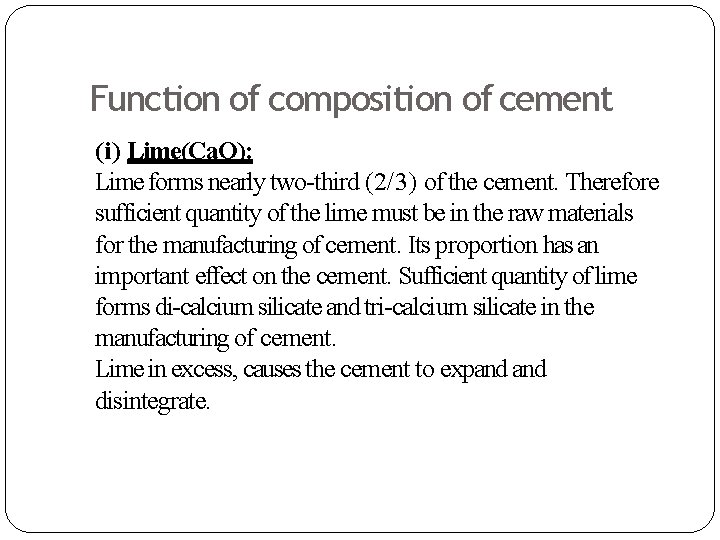
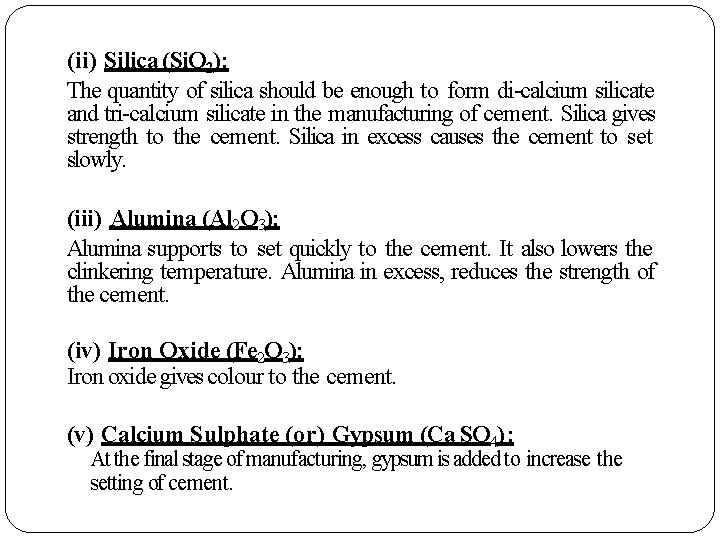
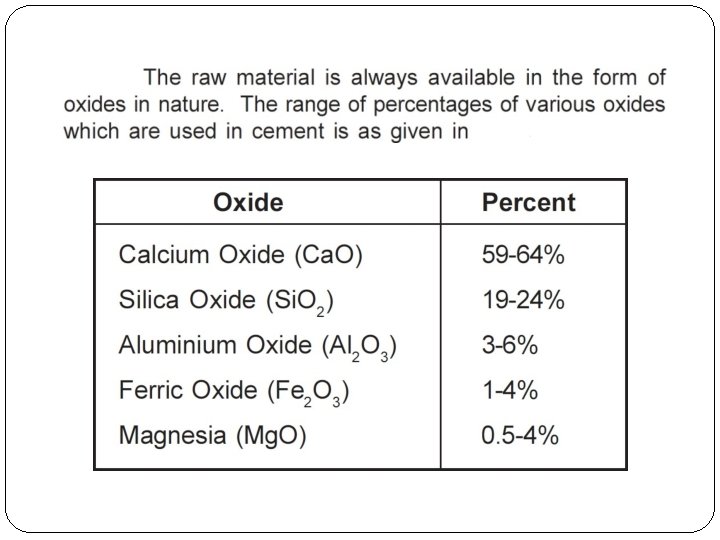
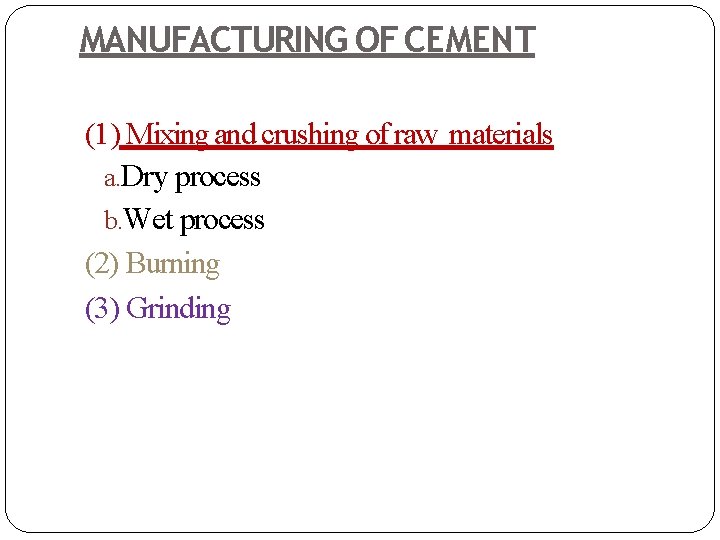
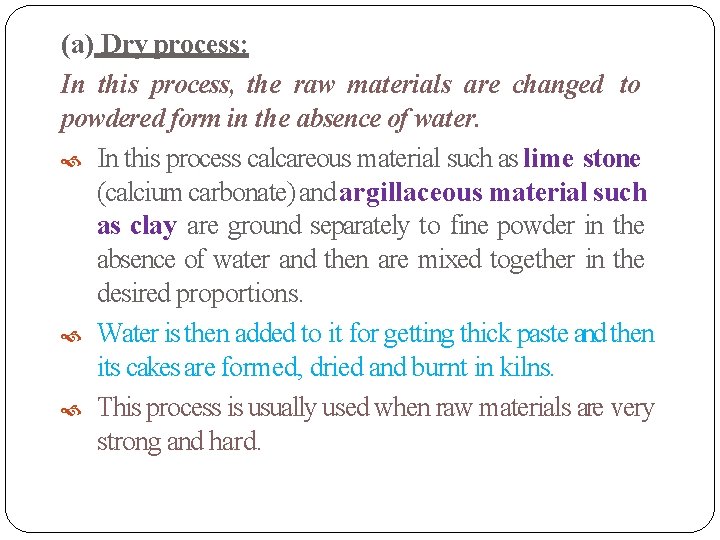
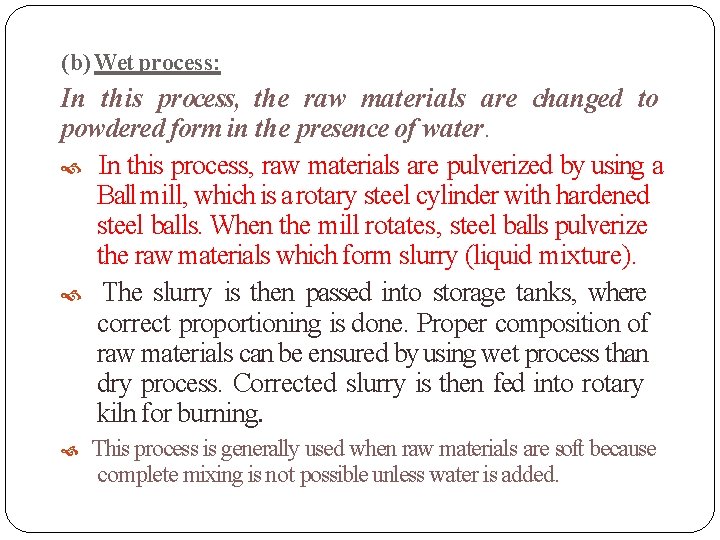
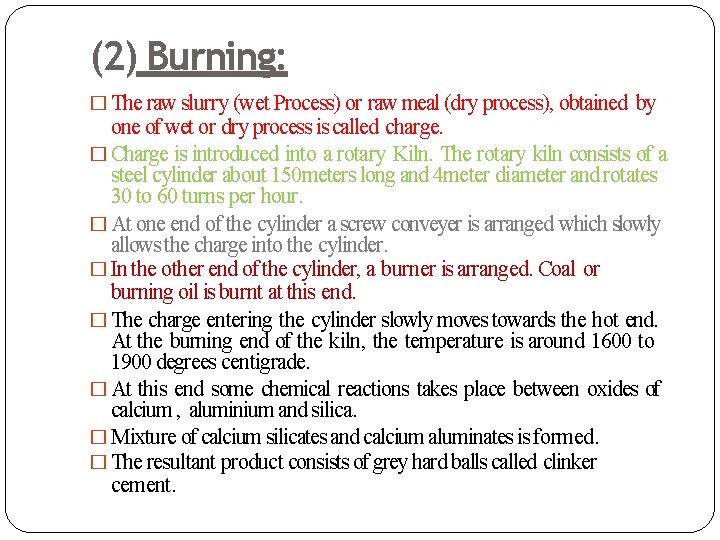
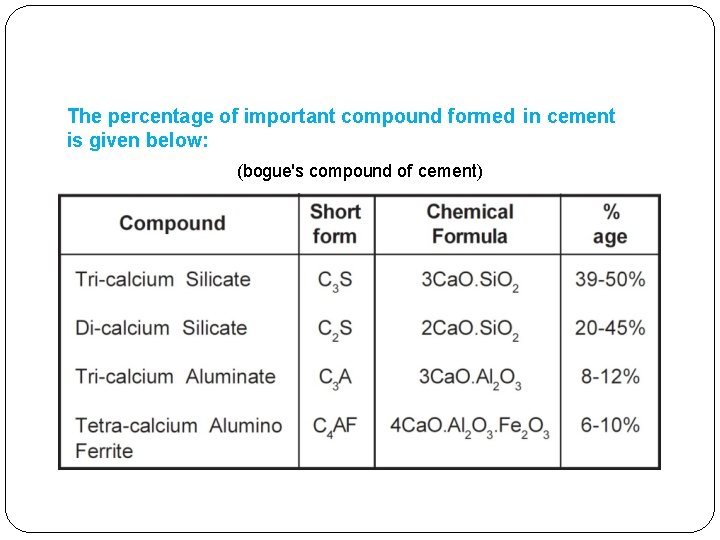
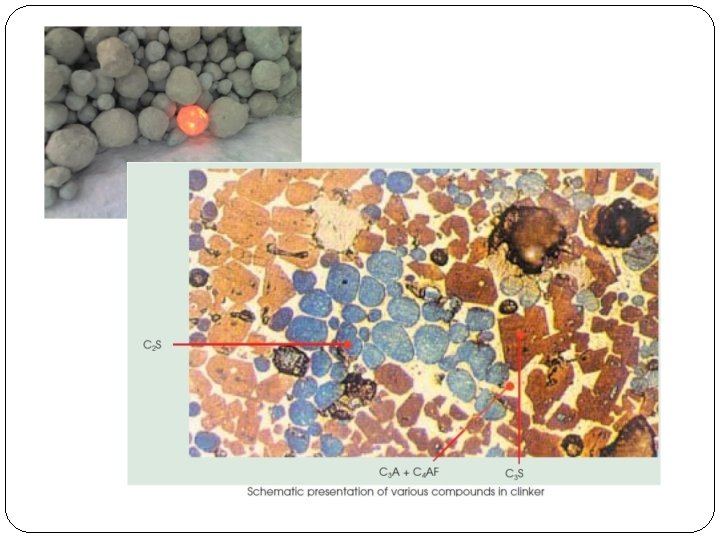
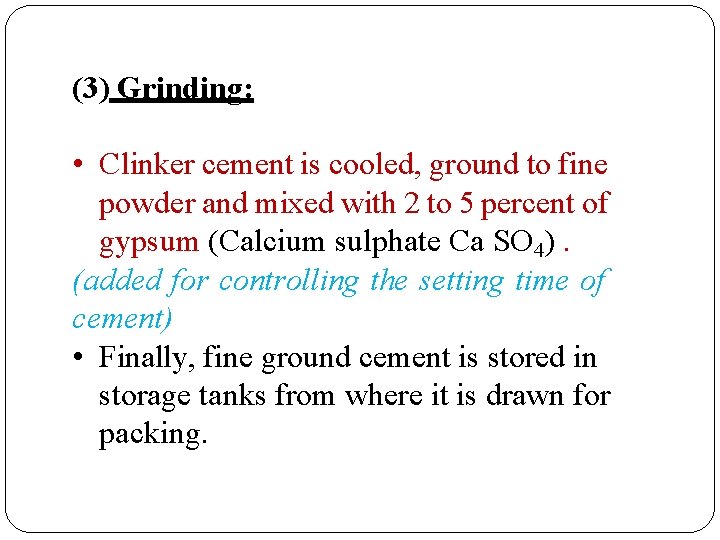
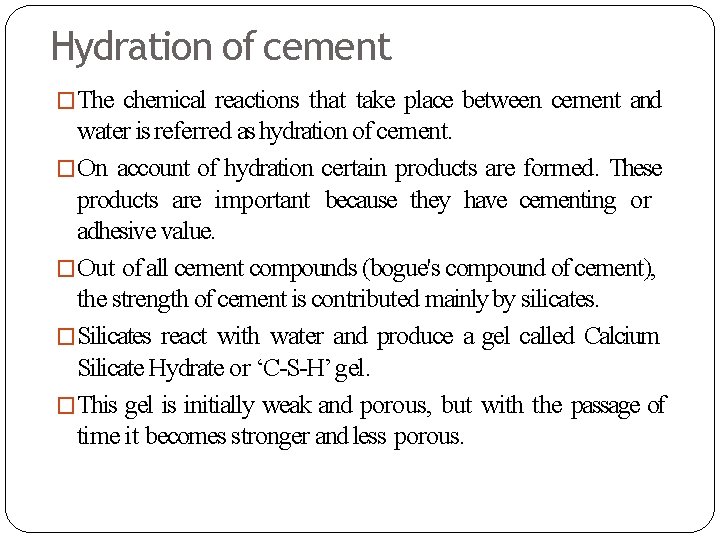
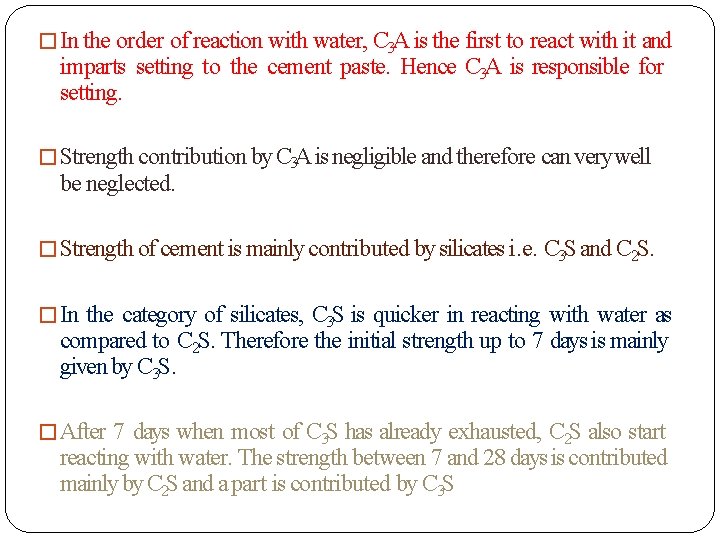
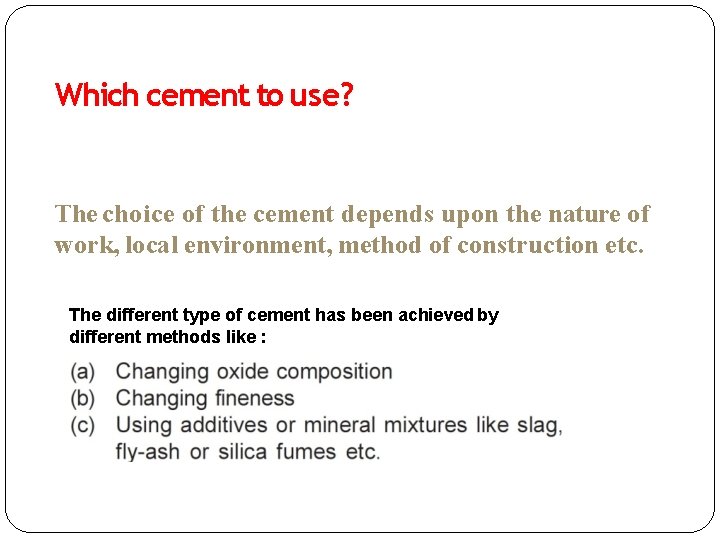
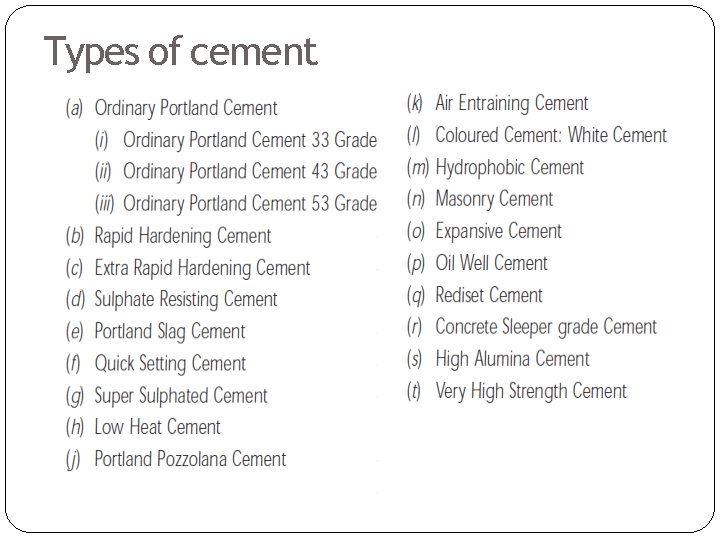
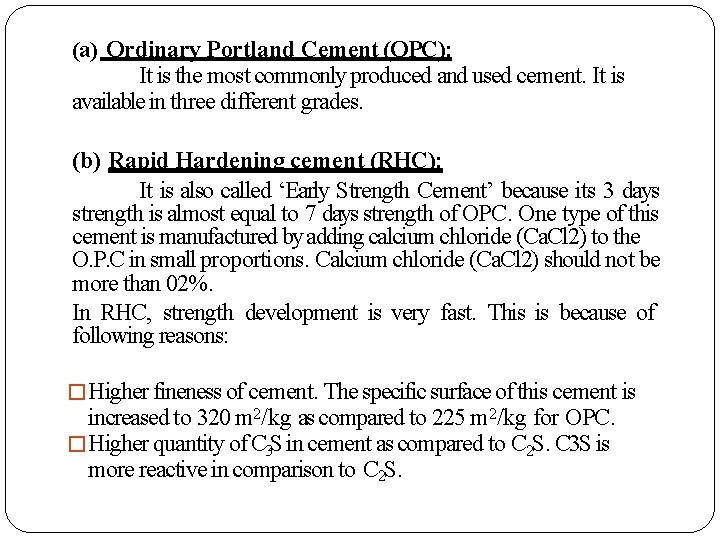
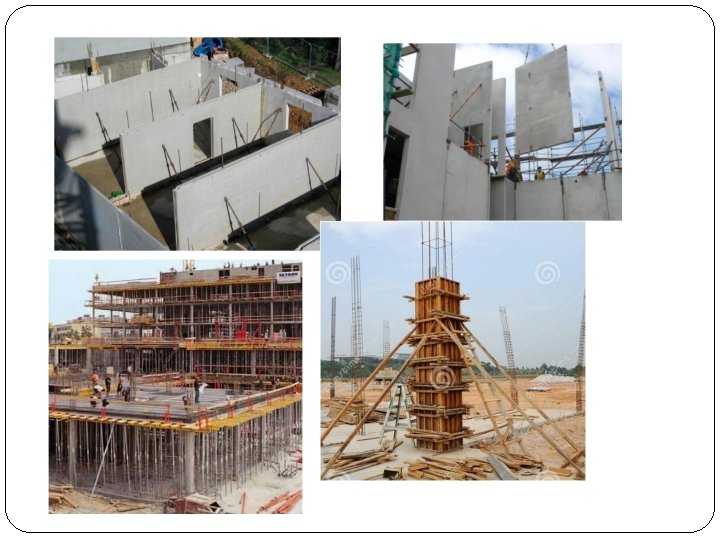
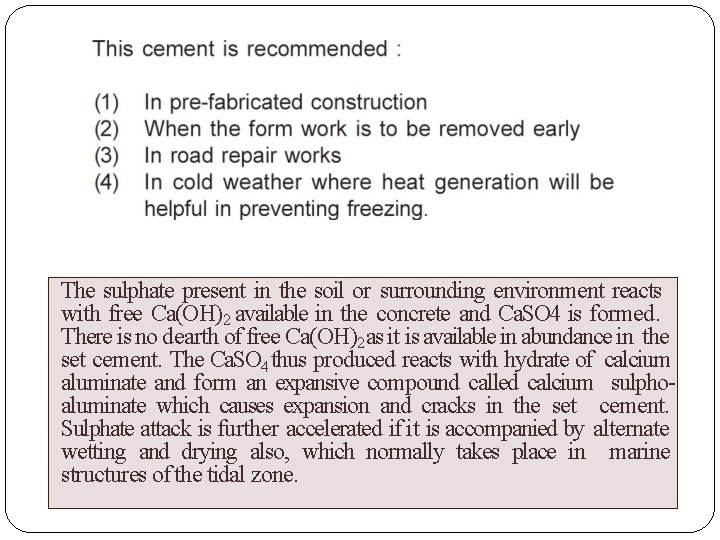
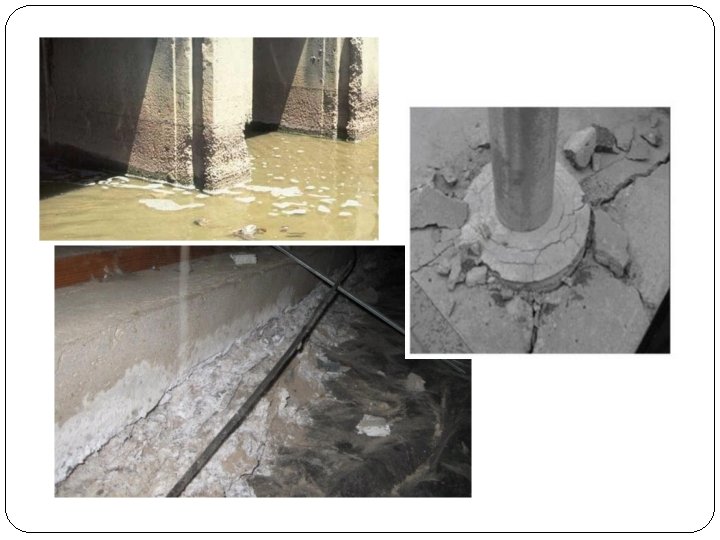
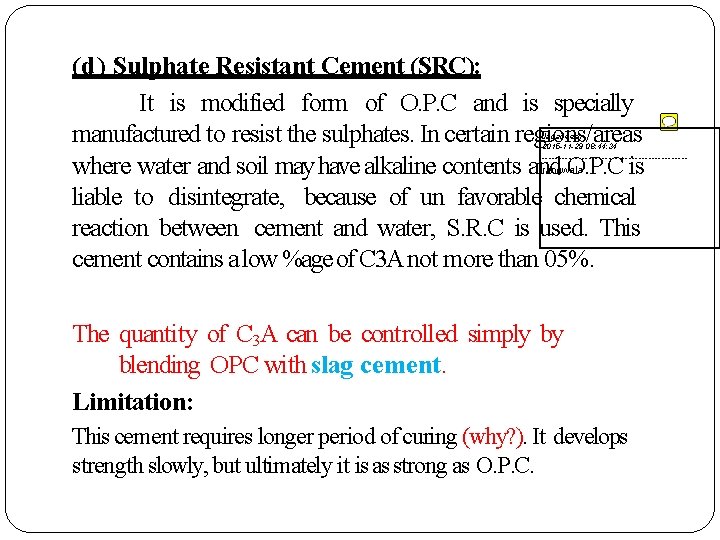
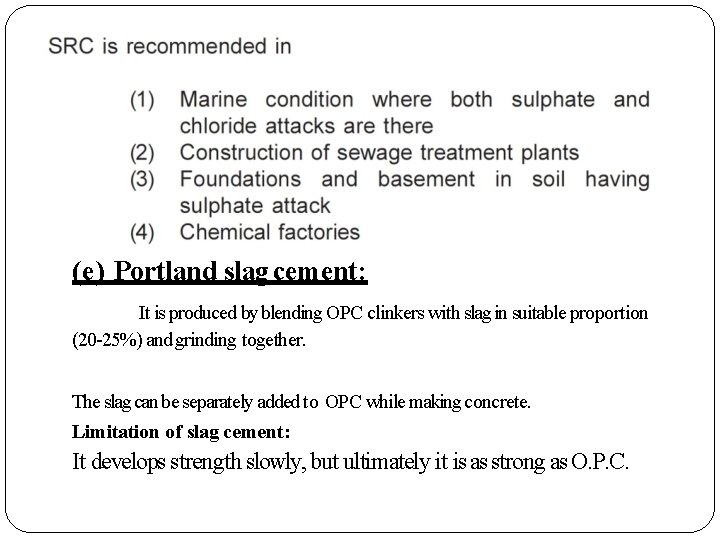
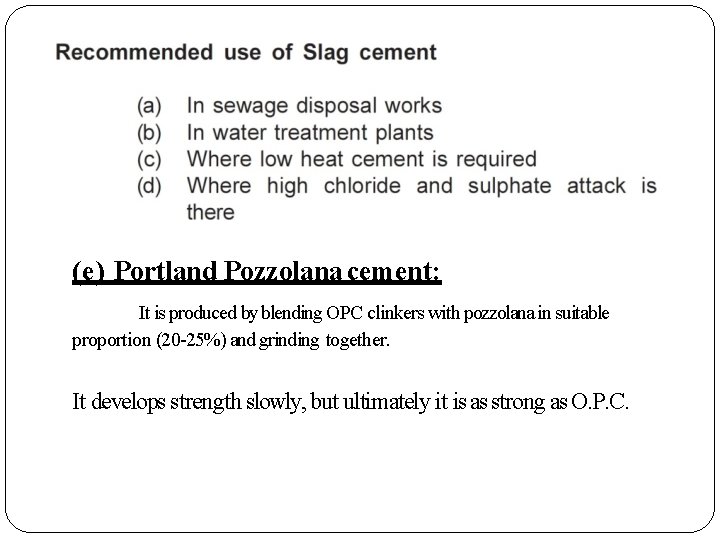
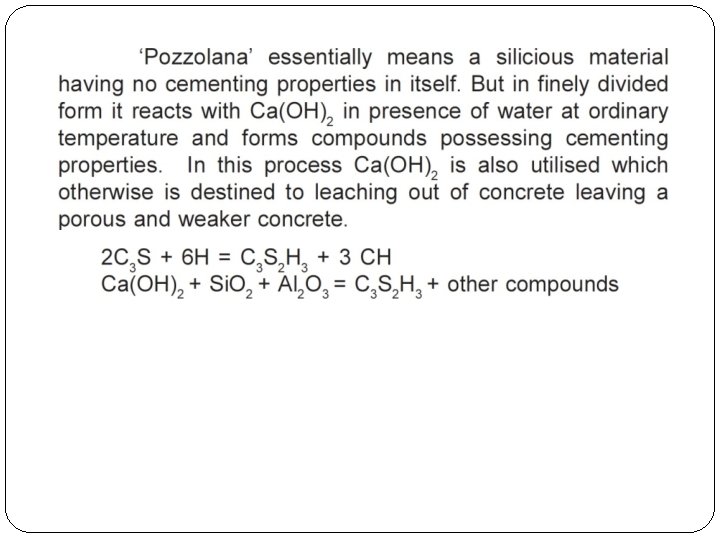
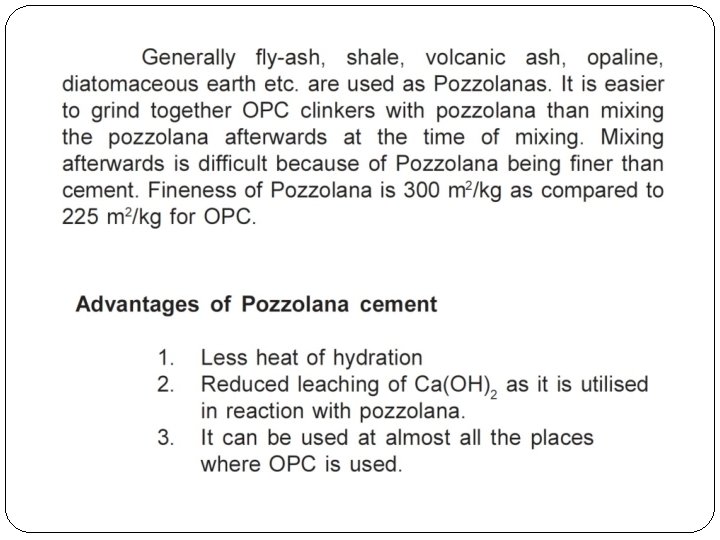
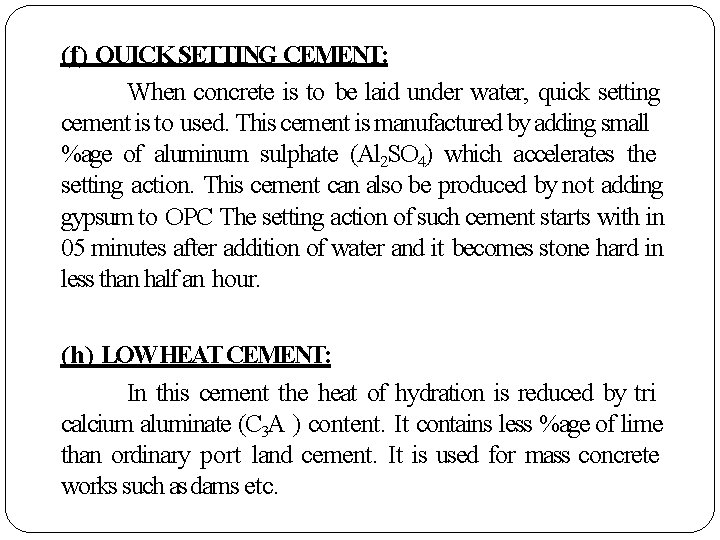
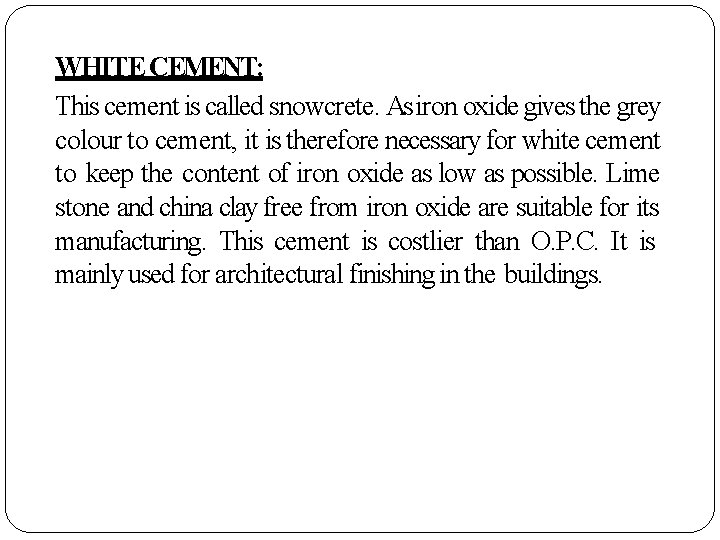
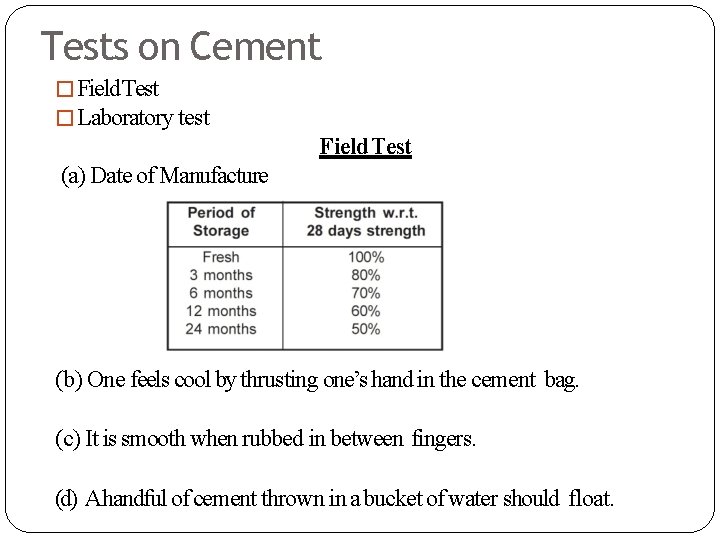
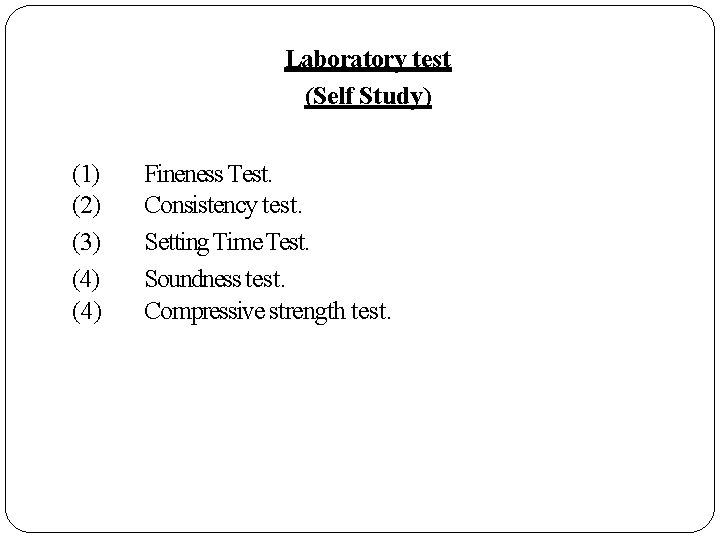
- Slides: 30
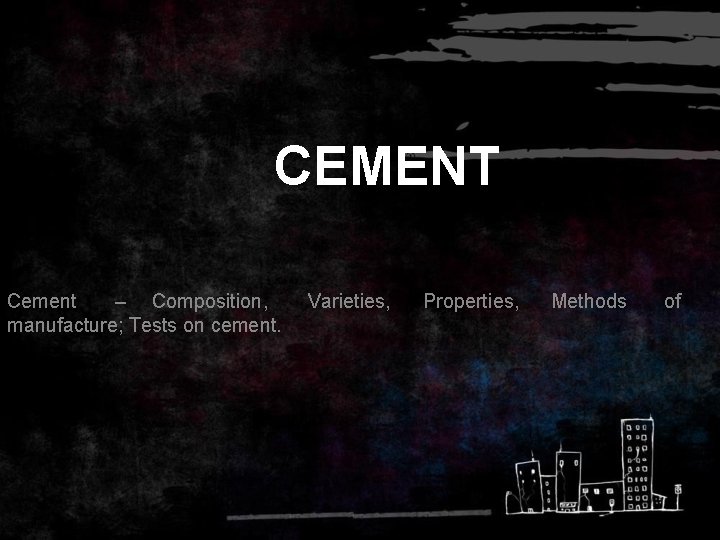
CEMENT Cement – Composition, manufacture; Tests on cement. Varieties, Properties, Methods of
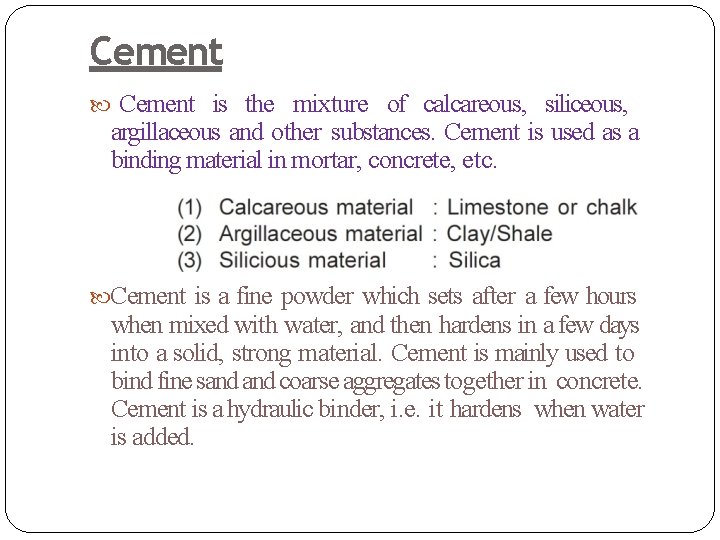
Cement is the mixture of calcareous, siliceous, argillaceous and other substances. Cement is used as a binding material in mortar, concrete, etc. Cement is a fine powder which sets after a few hours when mixed with water, and then hardens in a few days into a solid, strong material. Cement is mainly used to bind fine sand coarse aggregates together in concrete. Cement is a hydraulic binder, i. e. it hardens when water is added.
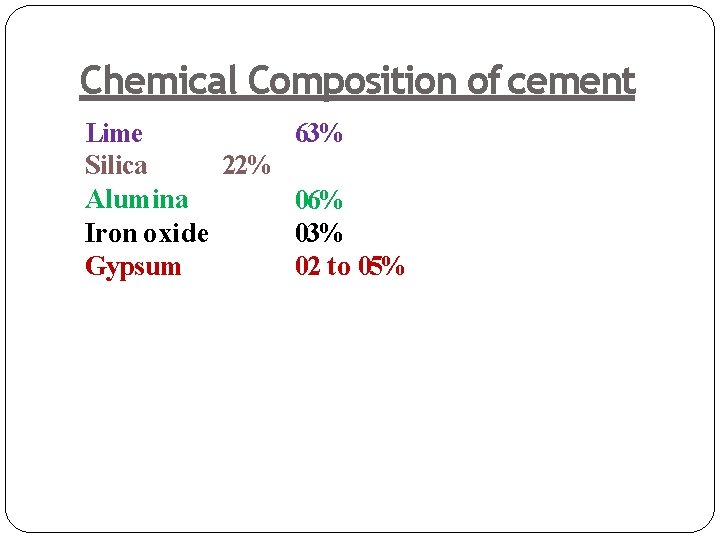
Chemical Composition of cement Lime 63% 22% Silica Alumina 06% Iron oxide 03% Gypsum 02 to 05%
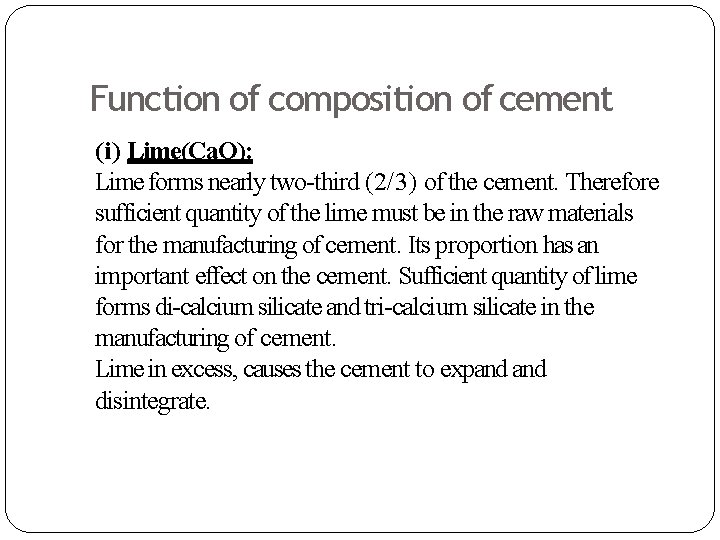
Function of composition of cement (i) Lime(Ca. O): Lime forms nearly two-third (2/3) of the cement. Therefore sufficient quantity of the lime must be in the raw materials for the manufacturing of cement. Its proportion has an important effect on the cement. Sufficient quantity of lime forms di-calcium silicate and tri-calcium silicate in the manufacturing of cement. Lime in excess, causes the cement to expand disintegrate.
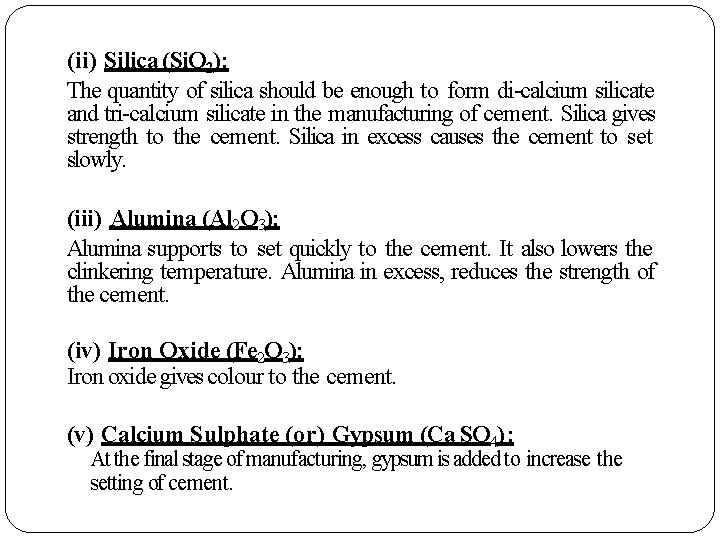
(ii) Silica (Si. O 2): The quantity of silica should be enough to form di-calcium silicate and tri-calcium silicate in the manufacturing of cement. Silica gives strength to the cement. Silica in excess causes the cement to set slowly. (iii) Alumina (Al 2 O 3): Alumina supports to set quickly to the cement. It also lowers the clinkering temperature. Alumina in excess, reduces the strength of the cement. (iv) Iron Oxide (Fe 2 O 3): Iron oxide gives colour to the cement. (v) Calcium Sulphate (or) Gypsum (Ca SO 4) : At the final stage of manufacturing, gypsum is added to increase the setting of cement.
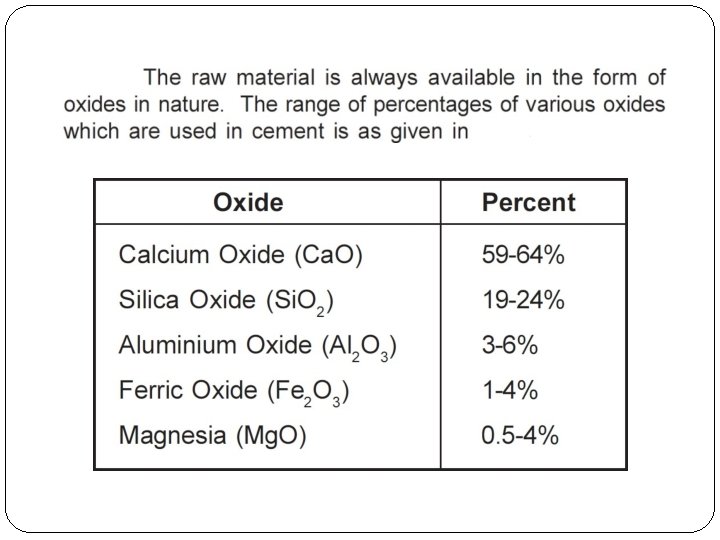
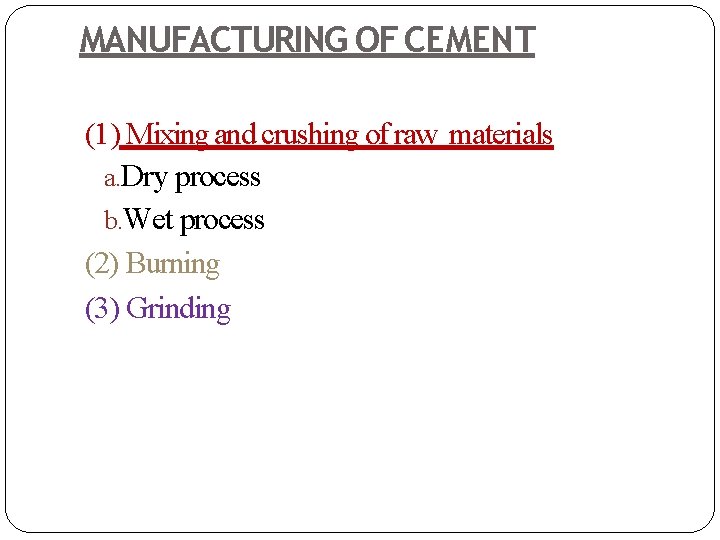
MANUFACTURING OF CEMENT (1) Mixing and crushing of raw materials a. Dry process b. Wet process (2) Burning (3) Grinding
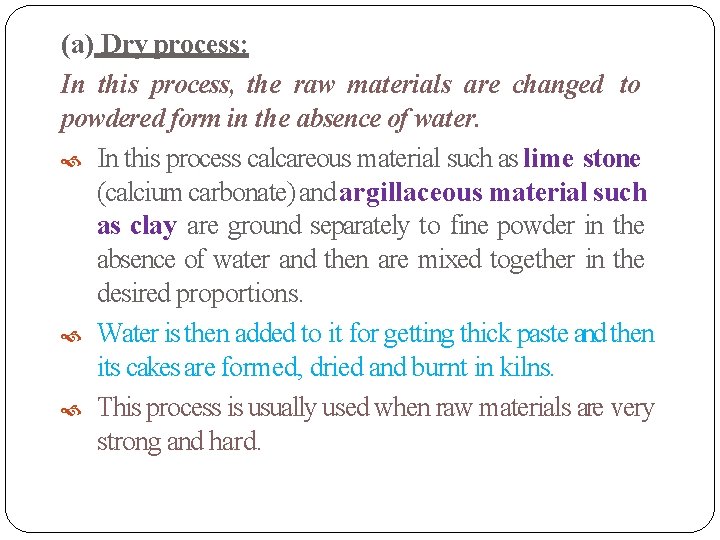
(a) Dry process: In this process, the raw materials are changed to powdered form in the absence of water. In this process calcareous material such as lime stone (calcium carbonate) and argillaceous material such as clay are ground separately to fine powder in the absence of water and then are mixed together in the desired proportions. Water is then added to it for getting thick paste and then its cakes are formed, dried and burnt in kilns. This process is usually used when raw materials are very strong and hard.
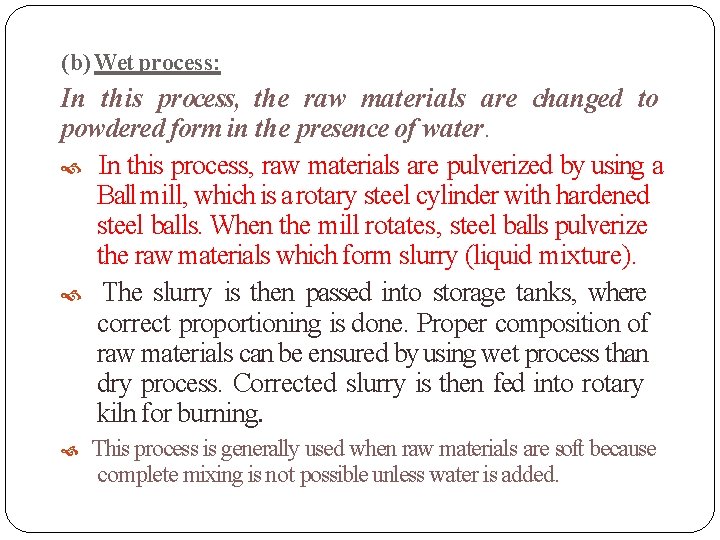
(b) Wet process: In this process, the raw materials are changed to powdered form in the presence of water. In this process, raw materials are pulverized by using a Ball mill, which is a rotary steel cylinder with hardened steel balls. When the mill rotates, steel balls pulverize the raw materials which form slurry (liquid mixture). The slurry is then passed into storage tanks, where correct proportioning is done. Proper composition of raw materials can be ensured by using wet process than dry process. Corrected slurry is then fed into rotary kiln for burning. This process is generally used when raw materials are soft because complete mixing is not possible unless water is added.
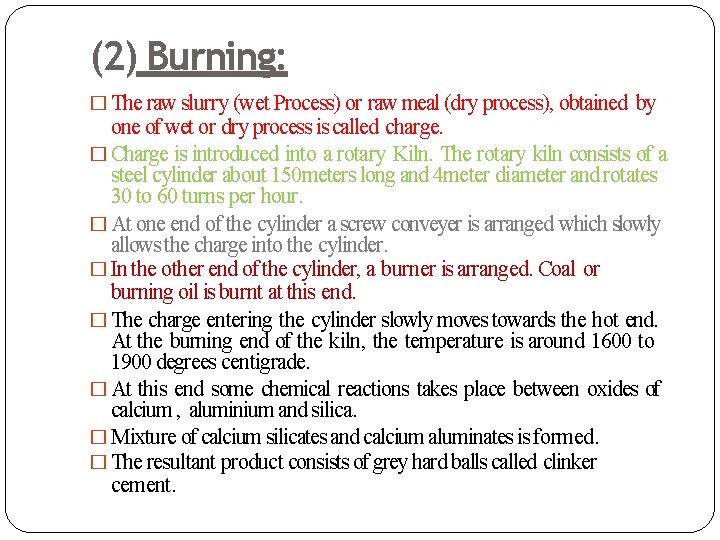
(2) Burning: � The raw slurry (wet Process) or raw meal (dry process), obtained by one of wet or dry process is called charge. � Charge is introduced into a rotary Kiln. The rotary kiln consists of a steel cylinder about 150 meters long and 4 meter diameter and rotates 30 to 60 turns per hour. � At one end of the cylinder a screw conveyer is arranged which slowly allows the charge into the cylinder. � In the other end of the cylinder, a burner is arranged. Coal or burning oil is burnt at this end. � The charge entering the cylinder slowly moves towards the hot end. At the burning end of the kiln, the temperature is around 1600 to 1900 degrees centigrade. � At this end some chemical reactions takes place between oxides of calcium , aluminium and silica. � Mixture of calcium silicates and calcium aluminates is formed. � The resultant product consists of grey hard balls called clinker cement.
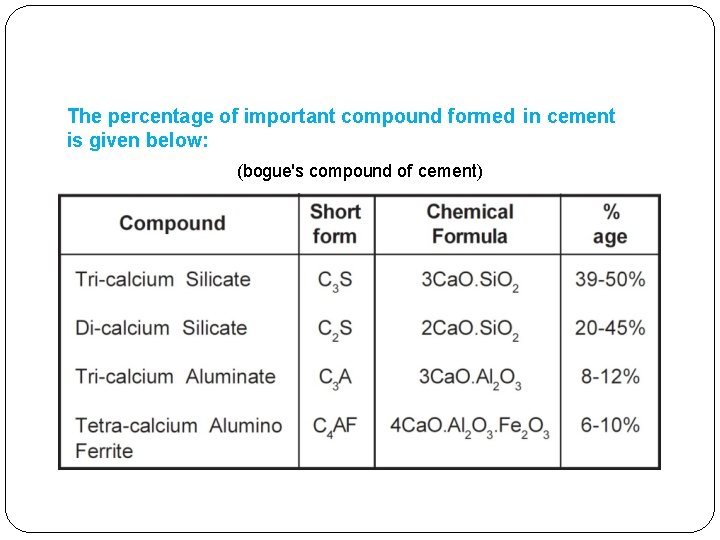
The percentage of important compound formed in cement is given below: (bogue's compound of cement)
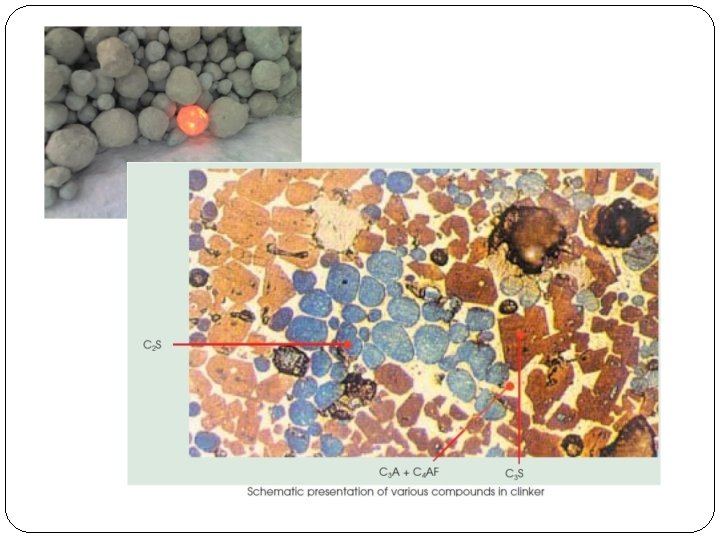
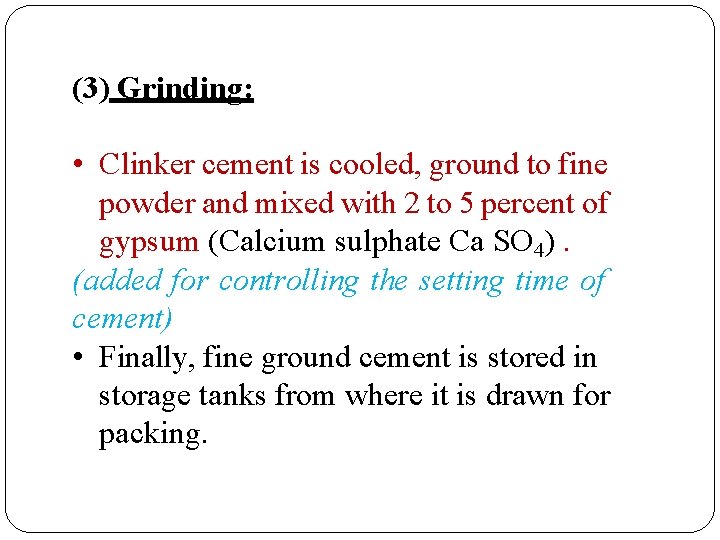
(3) Grinding: • Clinker cement is cooled, ground to fine powder and mixed with 2 to 5 percent of gypsum (Calcium sulphate Ca SO 4). (added for controlling the setting time of cement) • Finally, fine ground cement is stored in storage tanks from where it is drawn for packing.
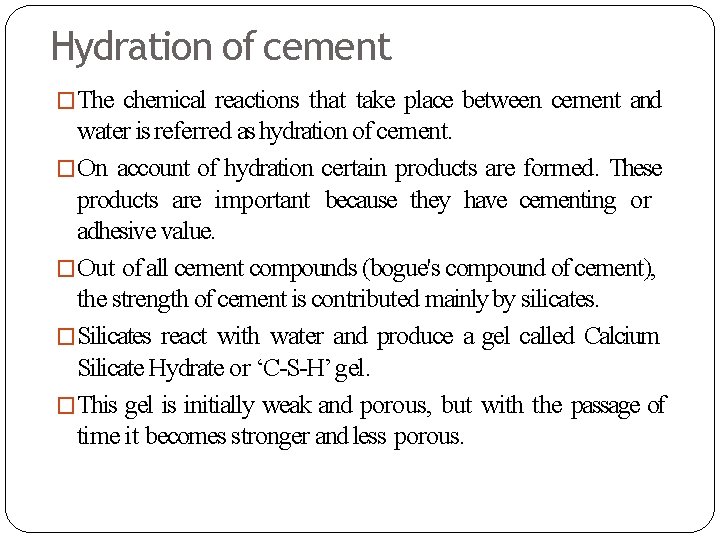
Hydration of cement �The chemical reactions that take place between cement and water is referred as hydration of cement. �On account of hydration certain products are formed. These products are important because they have cementing or adhesive value. �Out of all cement compounds (bogue's compound of cement), the strength of cement is contributed mainly by silicates. �Silicates react with water and produce a gel called Calcium Silicate Hydrate or ‘C-S-H’ gel. �This gel is initially weak and porous, but with the passage of time it becomes stronger and less porous.
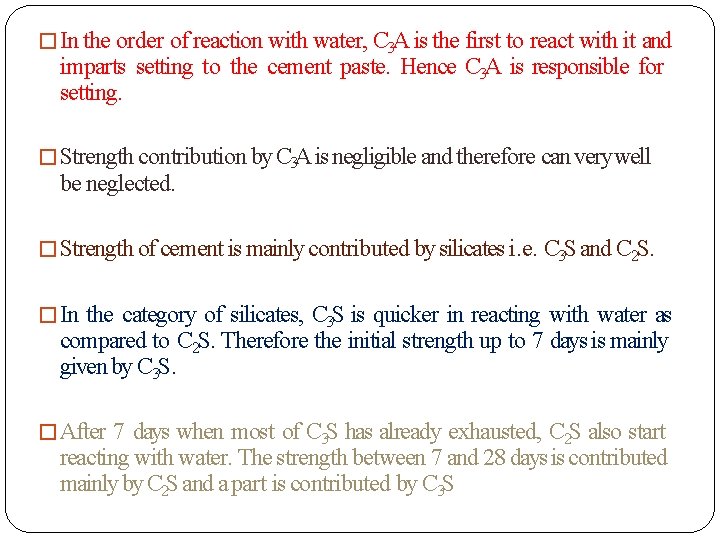
� In the order of reaction with water, C 3 A is the first to react with it and imparts setting to the cement paste. Hence C 3 A is responsible for setting. � Strength contribution by C 3 A is negligible and therefore can very well be neglected. � Strength of cement is mainly contributed by silicates i. e. C 3 S and C 2 S. � In the category of silicates, C 3 S is quicker in reacting with water as compared to C 2 S. Therefore the initial strength up to 7 days is mainly given by C 3 S. � After 7 days when most of C 3 S has already exhausted, C 2 S also start reacting with water. The strength between 7 and 28 days is contributed mainly by C 2 S and a part is contributed by C 3 S
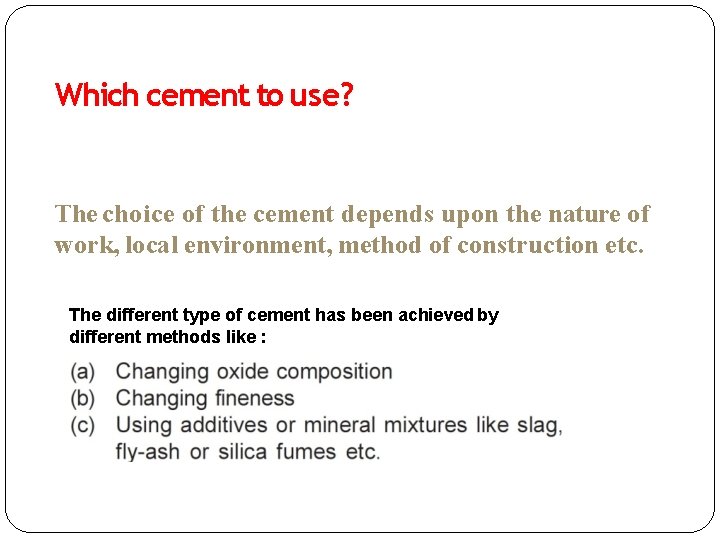
Which cement to use? The choice of the cement depends upon the nature of work, local environment, method of construction etc. The different type of cement has been achieved by different methods like :
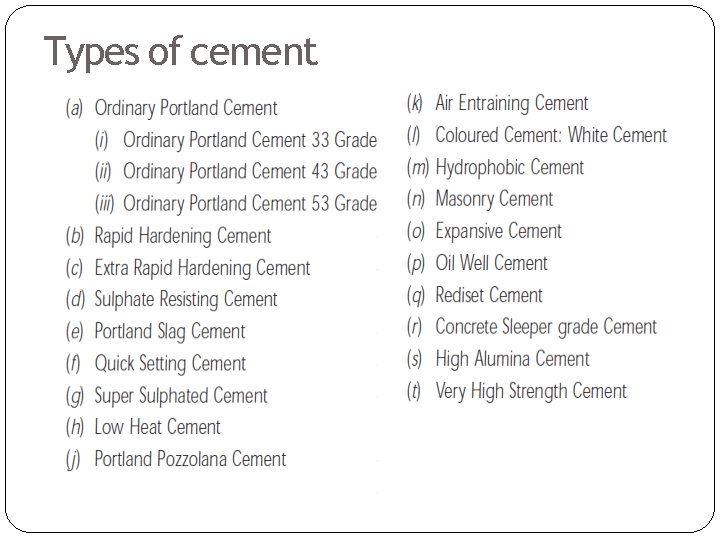
Types of cement
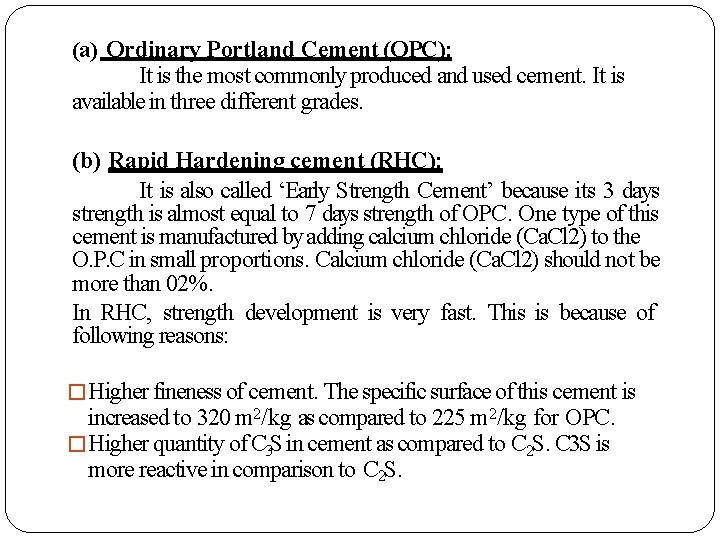
(a) Ordinary Portland Cement (OPC): It is the most commonly produced and used cement. It is available in three different grades. (b) Rapid Hardening cement (RHC): It is also called ‘Early Strength Cement’ because its 3 days strength is almost equal to 7 days strength of OPC. One type of this cement is manufactured by adding calcium chloride (Ca. Cl 2) to the O. P. C in small proportions. Calcium chloride (Ca. Cl 2) should not be more than 02%. In RHC, strength development is very fast. This is because of following reasons: �Higher fineness of cement. The specific surface of this cement is increased to 320 m 2/kg as compared to 225 m 2/kg for OPC. �Higher quantity of C 3 S in cement as compared to C 2 S. C 3 S is more reactive in comparison to C 2 S.
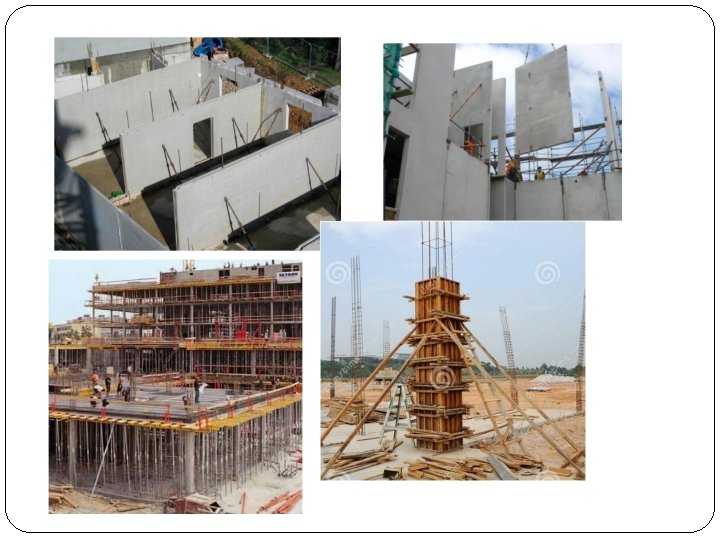
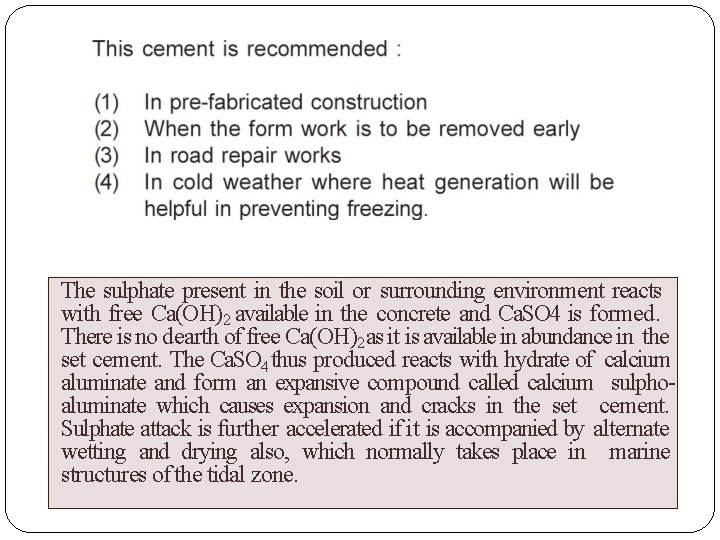
The sulphate present in the soil or surrounding environment reacts with free Ca(OH)2 available in the concrete and Ca. SO 4 is formed. There is no dearth of free Ca(OH)2 as it is available in abundance in the set cement. The Ca. SO 4 thus produced reacts with hydrate of calcium aluminate and form an expansive compound called calcium sulphoaluminate which causes expansion and cracks in the set cement. Sulphate attack is further accelerated if it is accompanied by alternate wetting and drying also, which normally takes place in marine structures of the tidal zone.
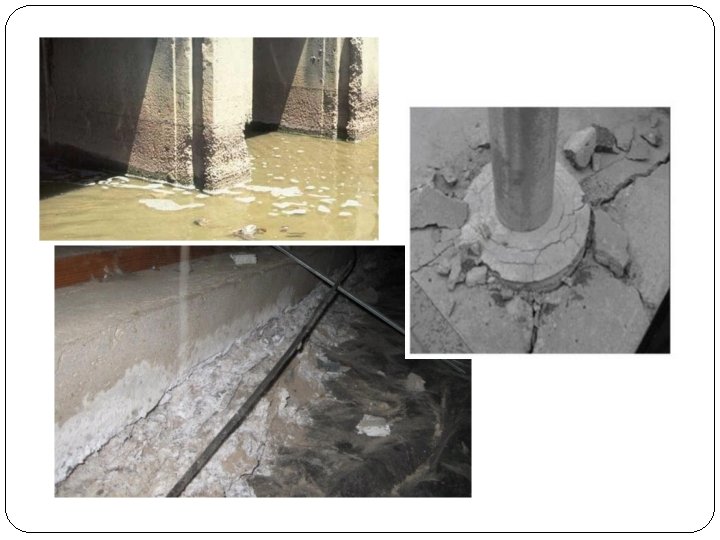
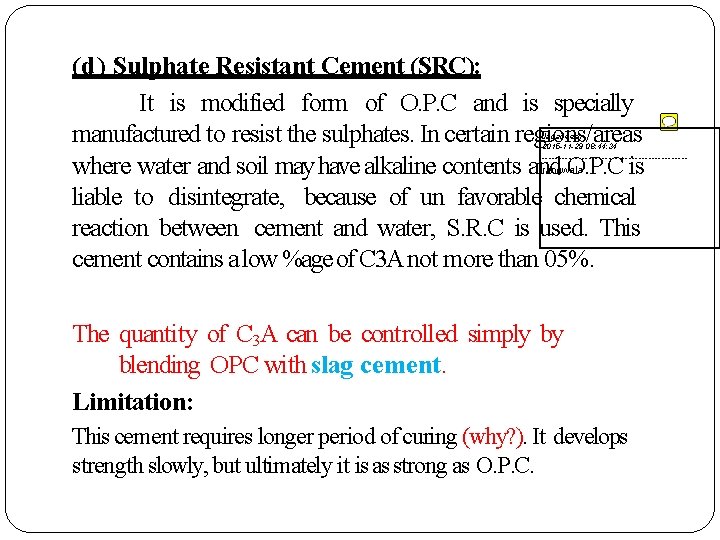
(d) Sulphate Resistant Cement (SRC): It is modified form of O. P. C and is specially manufactured to resist the sulphates. In certain regions/areas where water and soil may have alkaline contents and O. P. C is liable to disintegrate, because of un favorable chemical reaction between cement and water, S. R. C is used. This cement contains a low %age of C 3 A not more than 05%. Jagadeesh 2015 -11 -29 08: 44: 34 ----------------------rangwala The quantity of C 3 A can be controlled simply by blending OPC with slag cement. Limitation: This cement requires longer period of curing (why? ). It develops strength slowly, but ultimately it is as strong as O. P. C.
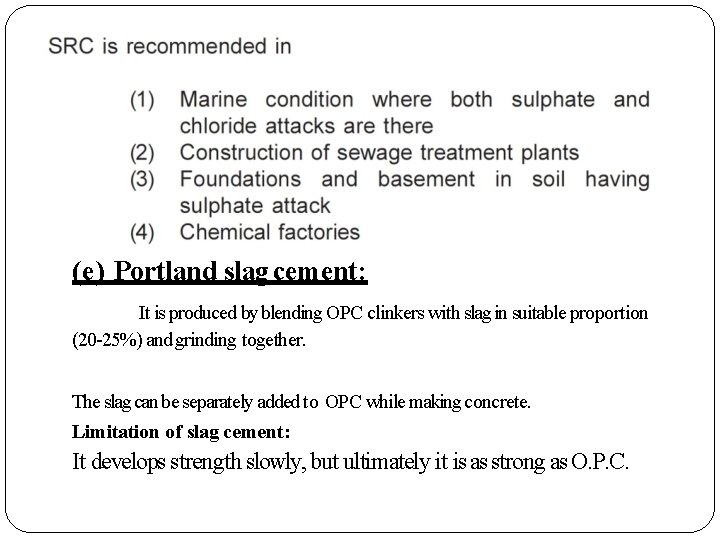
(e) Portland slag cement: It is produced by blending OPC clinkers with slag in suitable proportion (20 -25%) and grinding together. The slag can be separately added to OPC while making concrete. Limitation of slag cement: It develops strength slowly, but ultimately it is as strong as O. P. C.
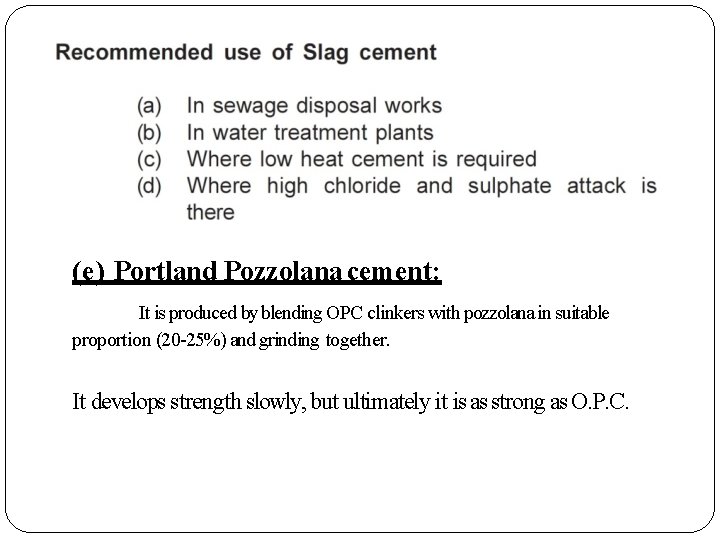
(e) Portland Pozzolana cement: It is produced by blending OPC clinkers with pozzolana in suitable proportion (20 -25%) and grinding together. It develops strength slowly, but ultimately it is as strong as O. P. C.
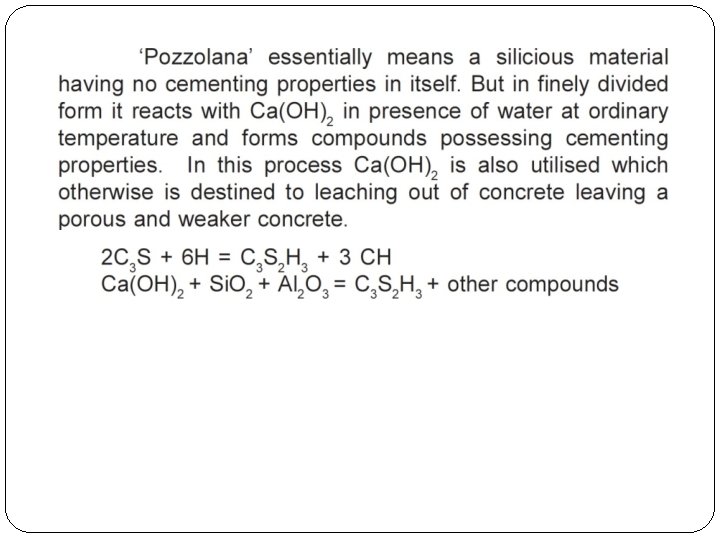
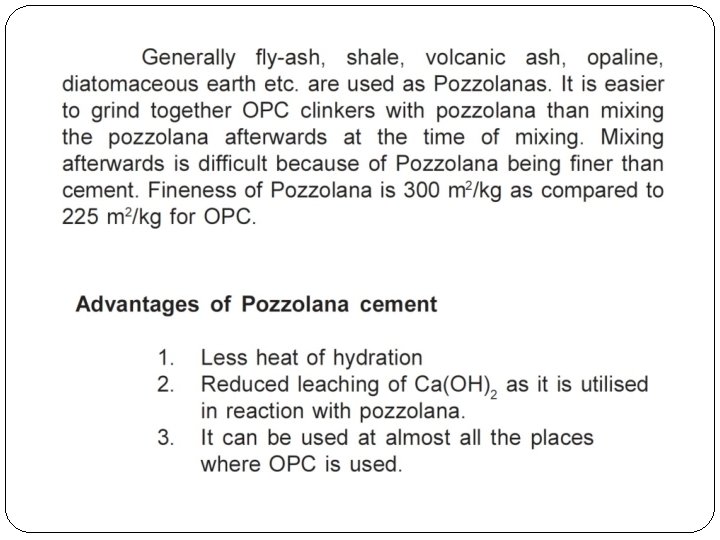
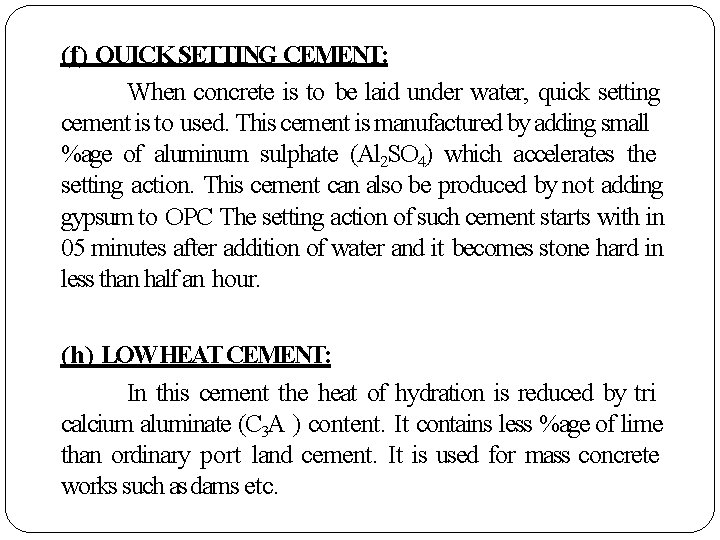
(f) QUICK SETTING CEMENT: When concrete is to be laid under water, quick setting cement is to used. This cement is manufactured by adding small %age of aluminum sulphate (Al 2 SO 4) which accelerates the setting action. This cement can also be produced by not adding gypsum to OPC The setting action of such cement starts with in 05 minutes after addition of water and it becomes stone hard in less than half an hour. (h) LOWHEAT CEMENT: In this cement the heat of hydration is reduced by tri calcium aluminate (C 3 A ) content. It contains less %age of lime than ordinary port land cement. It is used for mass concrete works such as dams etc.
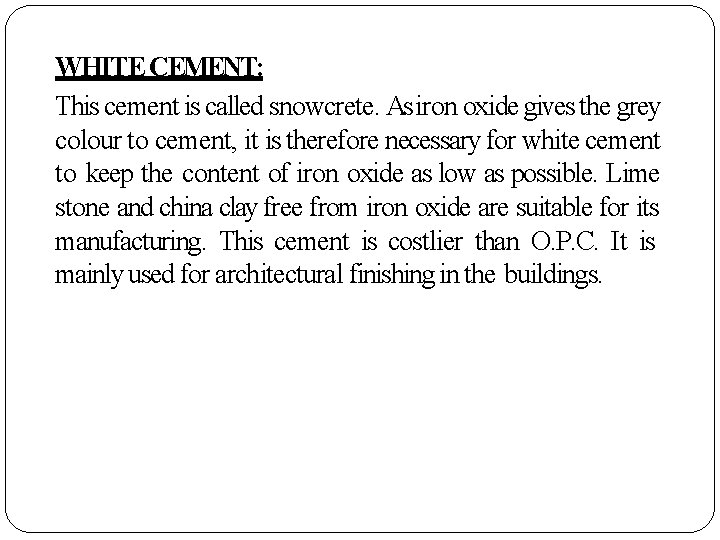
WHITE CEMENT: This cement is called snowcrete. As iron oxide gives the grey colour to cement, it is therefore necessary for white cement to keep the content of iron oxide as low as possible. Lime stone and china clay free from iron oxide are suitable for its manufacturing. This cement is costlier than O. P. C. It is mainly used for architectural finishing in the buildings.
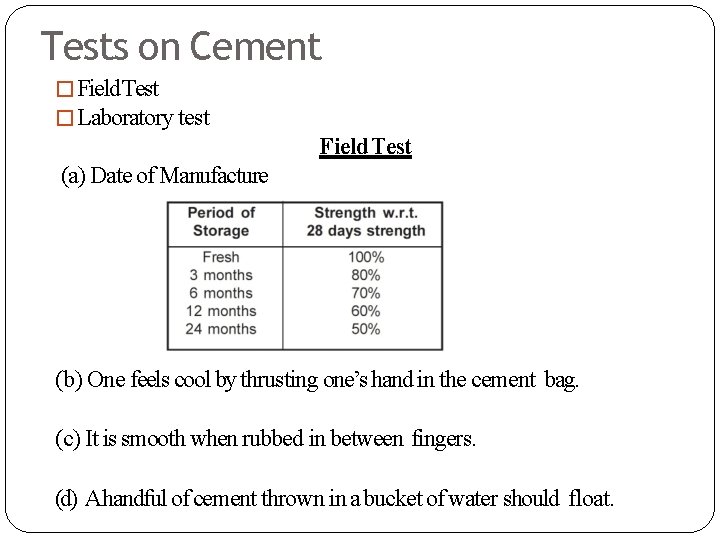
Tests on Cement � Field Test � Laboratory test Field Test (a) Date of Manufacture (b) One feels cool by thrusting one’s hand in the cement bag. (c) It is smooth when rubbed in between fingers. (d) Ahandful of cement thrown in a bucket of water should float.
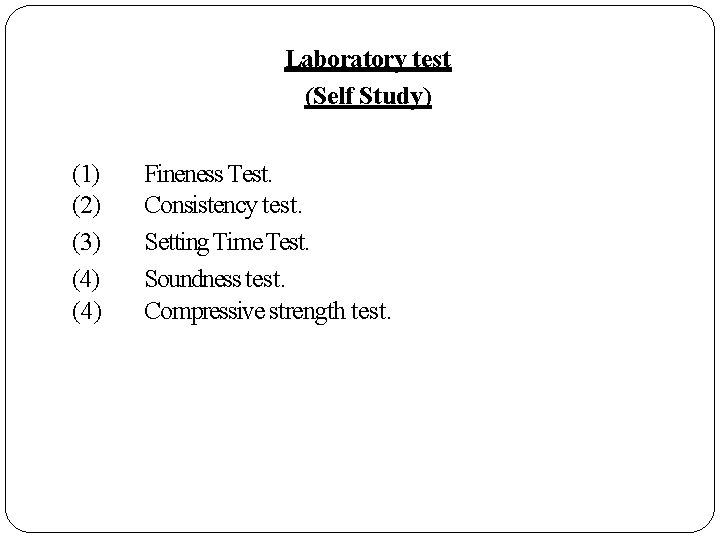
Laboratory test (Self Study) (1) (2) (3) (4) Fineness Test. Consistency test. Setting Time Test. Soundness test. Compressive strength test.
Manufacture of portland cement
Manufacture of cement
Ace different iq tests still make
Zinc phosphate cement setting reaction
Type 9 gic indications
Extra rapid hardening cement setting time
Otto hoffman by product oven
Payback chapter 23
Manufacture vs production
A manufacturing firm has discontinued production
Terylene properties
Earl beaver
A firm is planning to manufacture a new product
Clark forklift year identification
The rapid manufacture of large numbers of identical objects
Cambridge technicals level 3 engineering
Components manufacture
Higher design and manufacture
Krishijivan
Foundry machinery manufacture exporters
Iihr china aster varieties
Varieties of culture
Varieties of drama
Bell's seven criteria for language
Chapter 8 varieties of american nationalism
Which organism
Linum usitatissimum l.
Social variety of language
A merchant mixes three varieties of rice
Linguistic varieties and multilingual nations
Territorial varieties of english pronunciation