CHAPTER 7 PORTLAND CEMENT CONCRETE 7 1 Portland
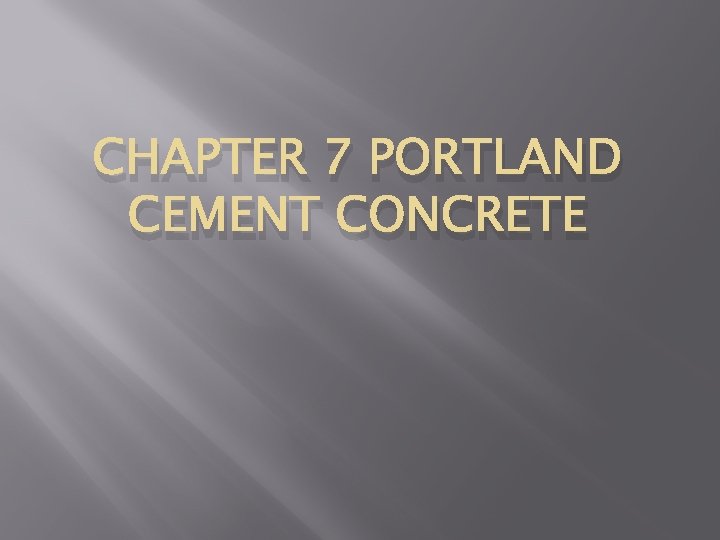
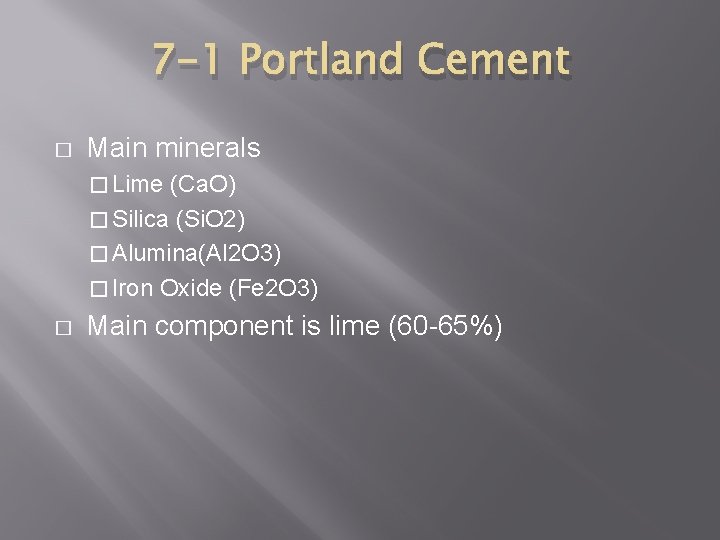
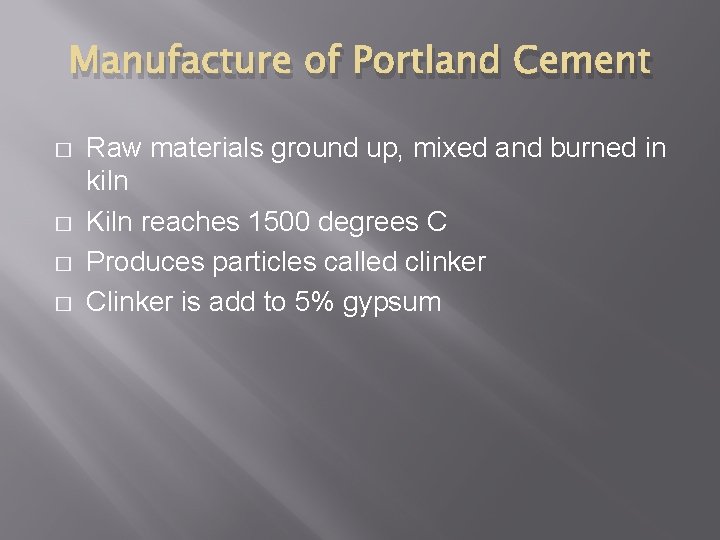
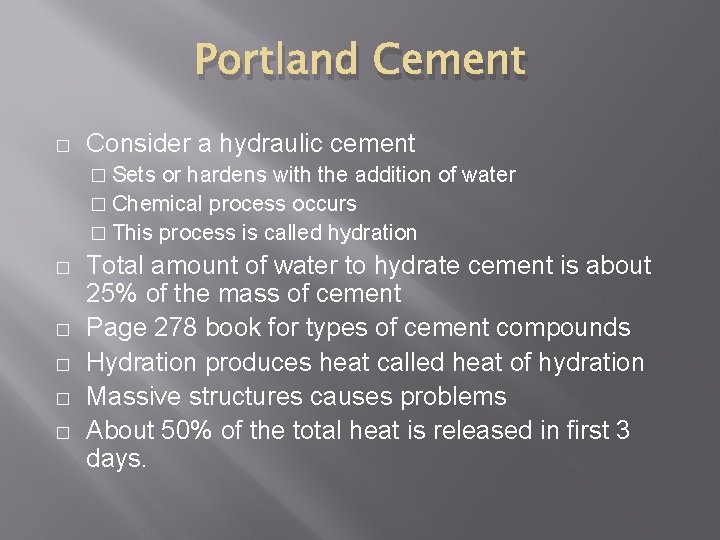
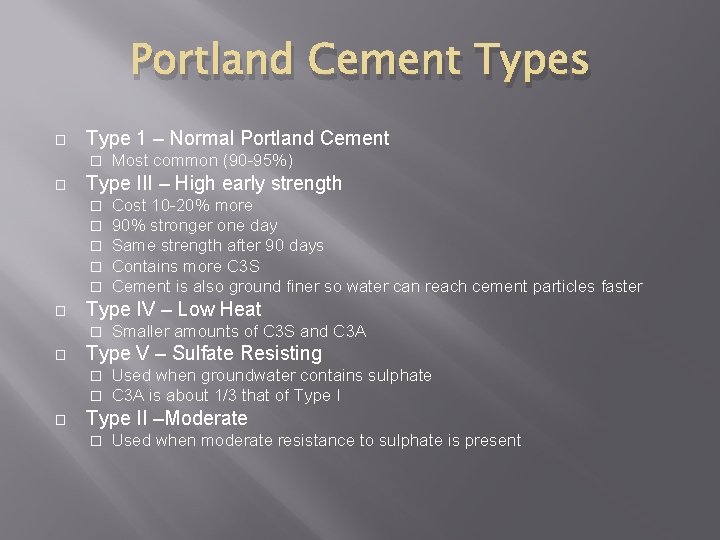
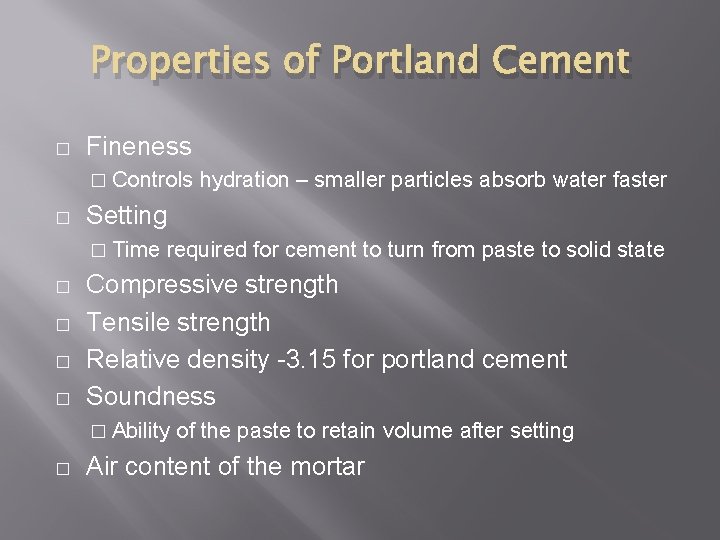
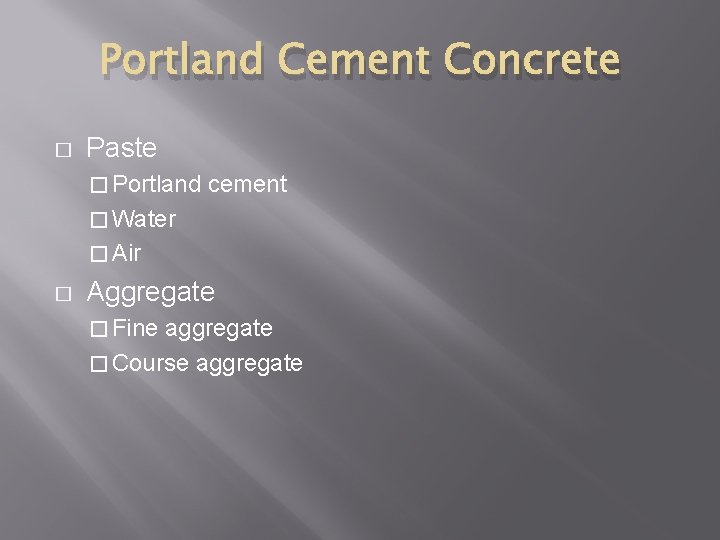
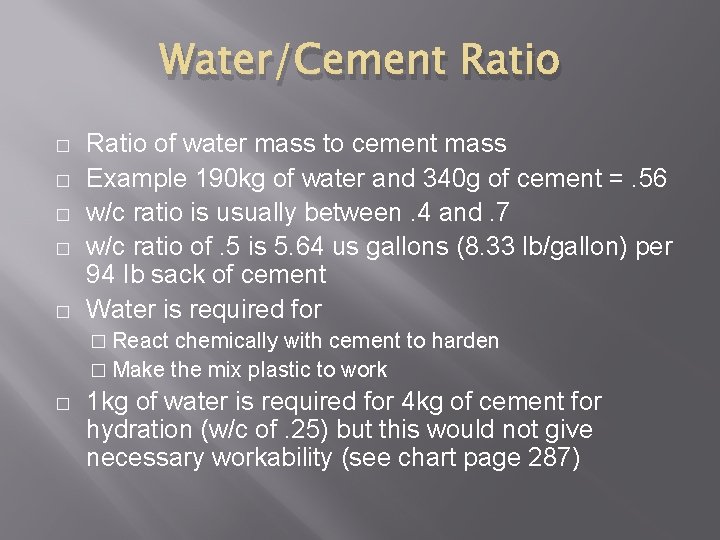
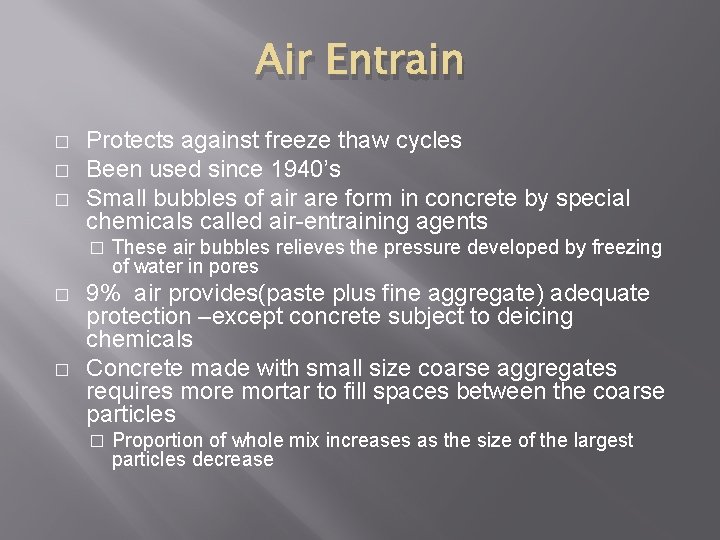
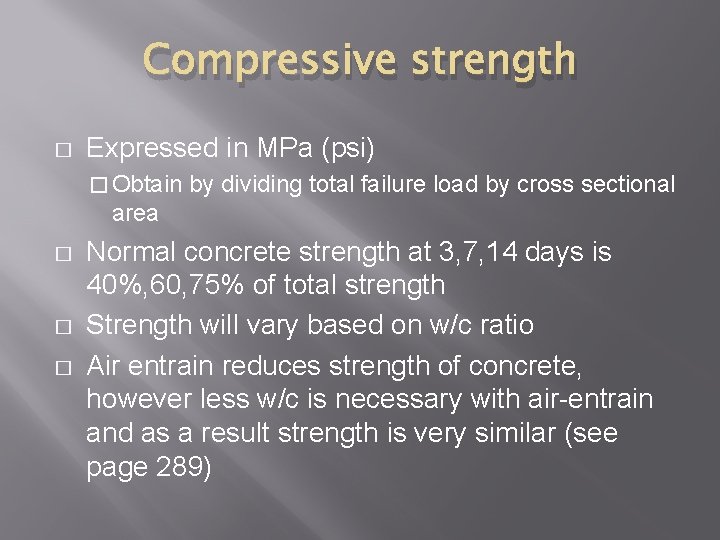
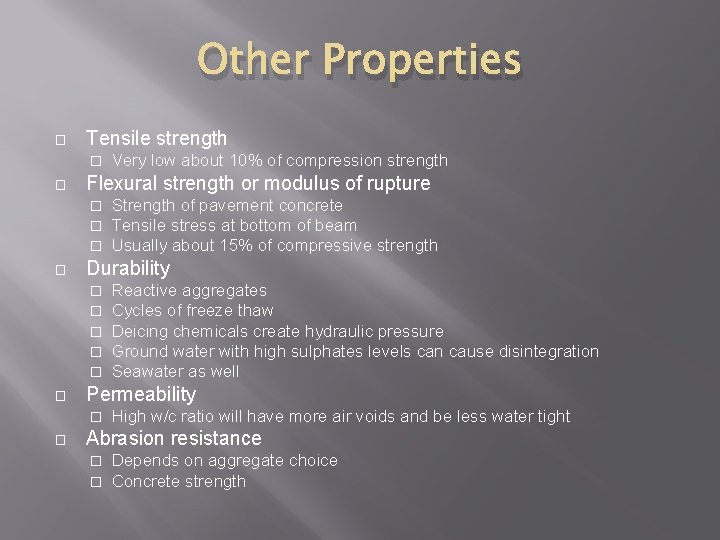
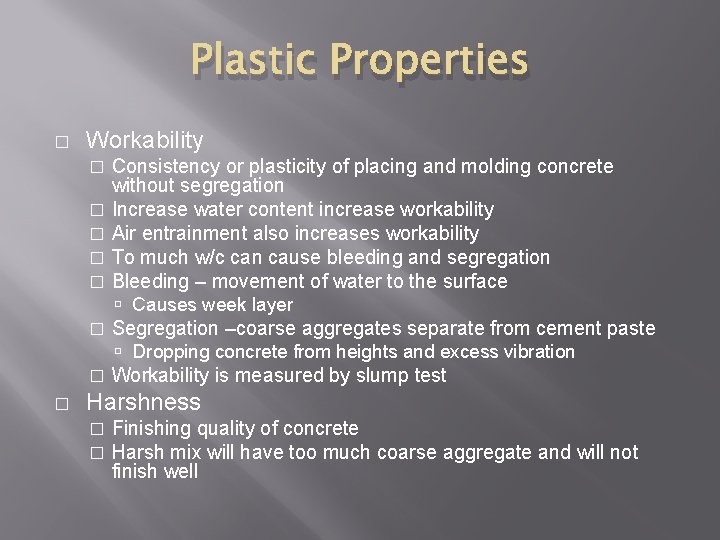
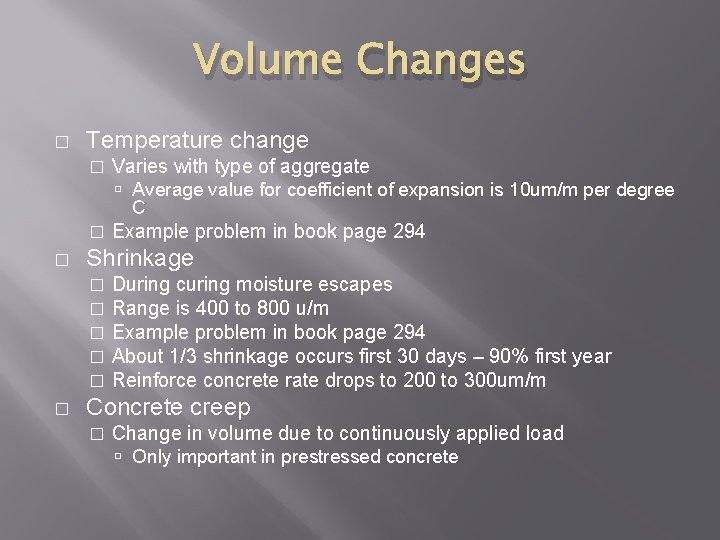
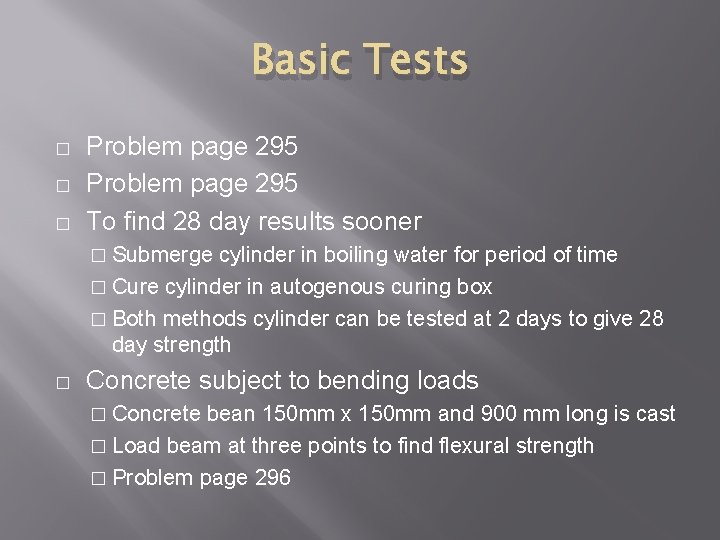
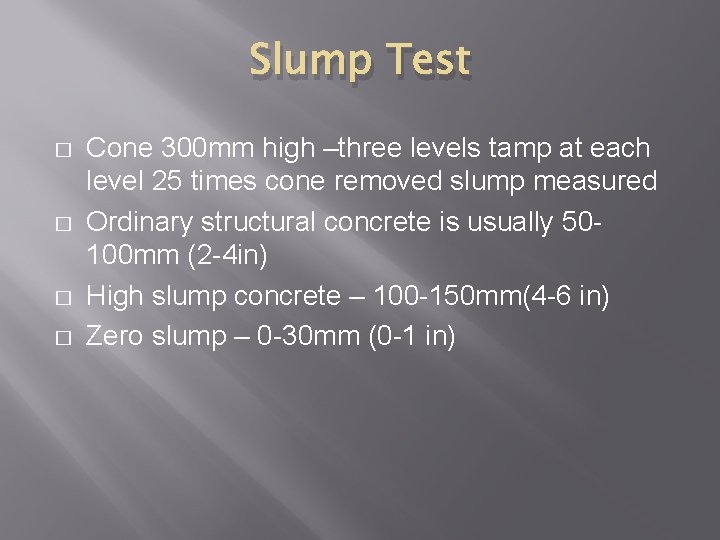
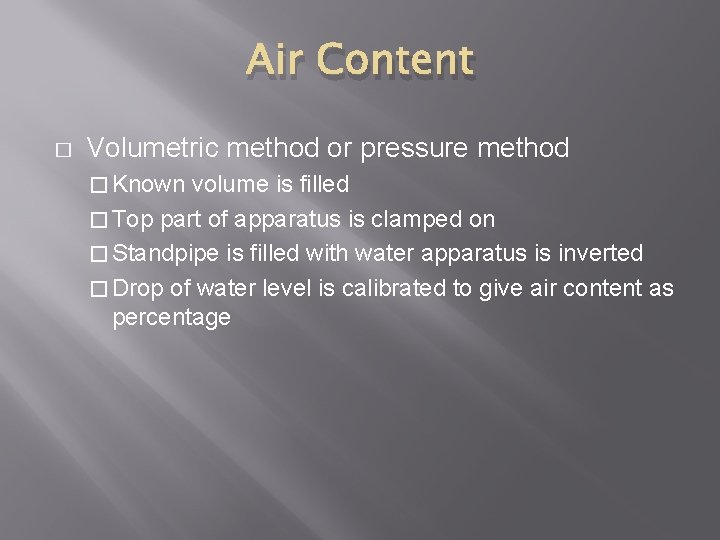

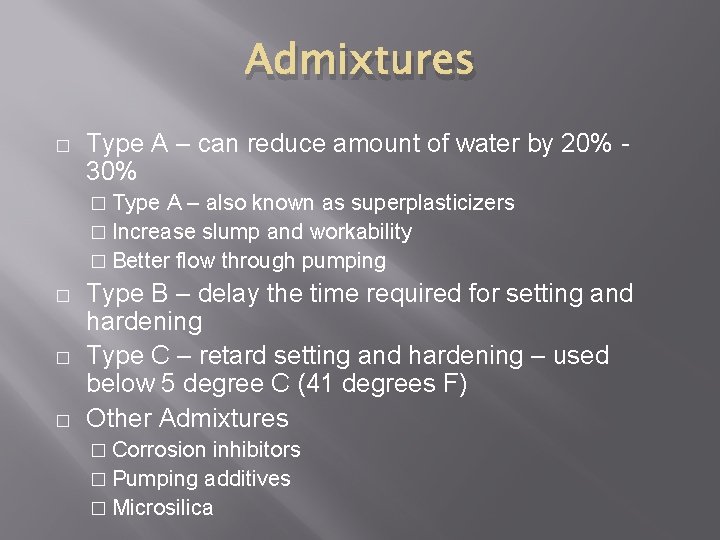
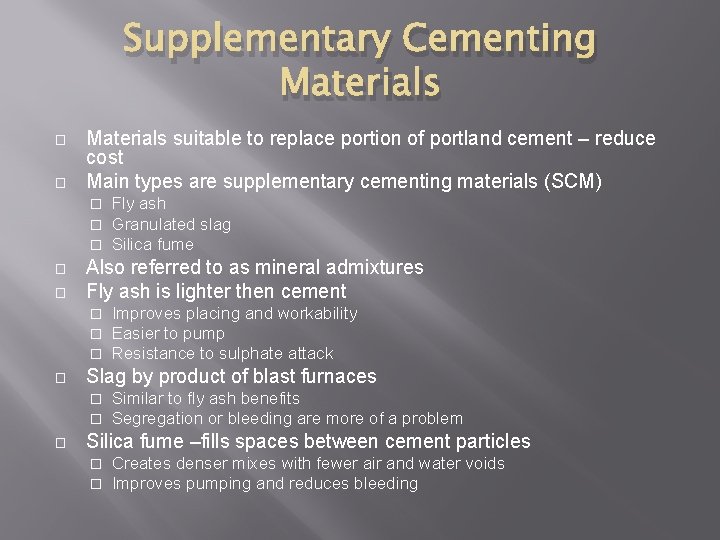
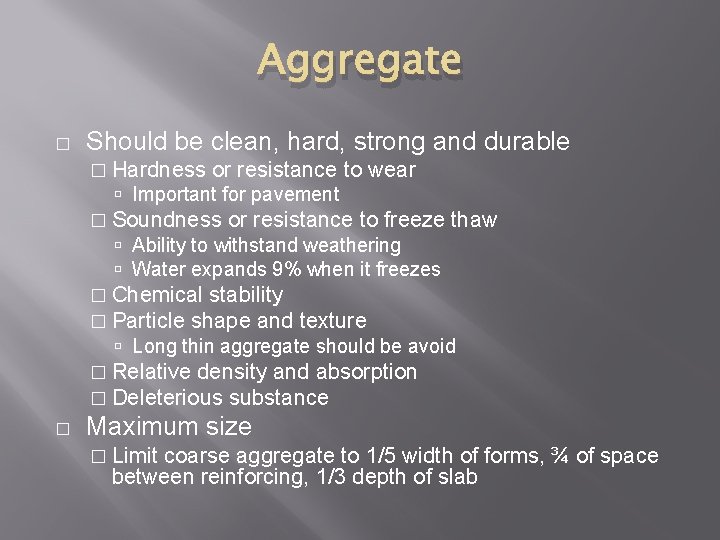
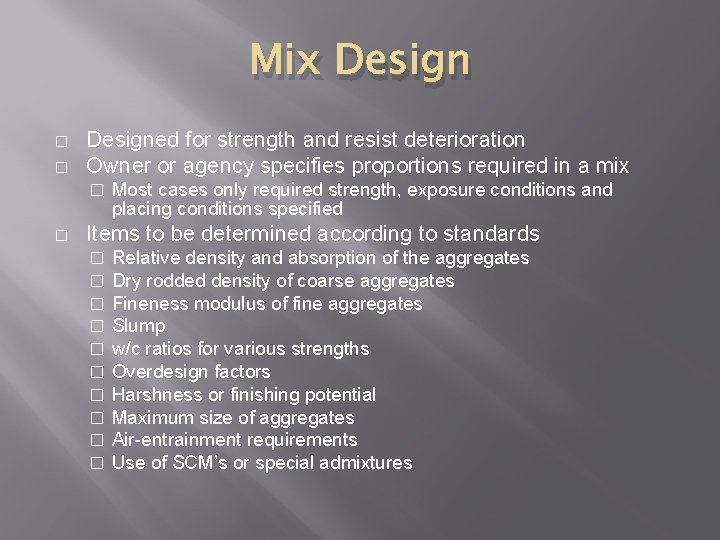
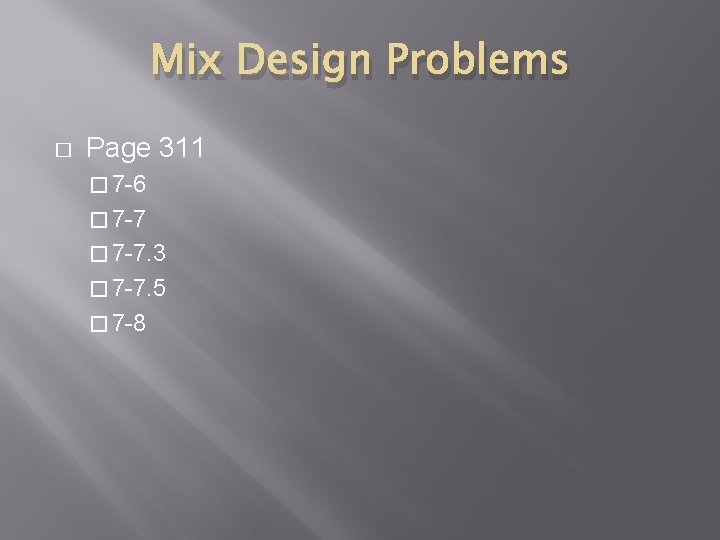
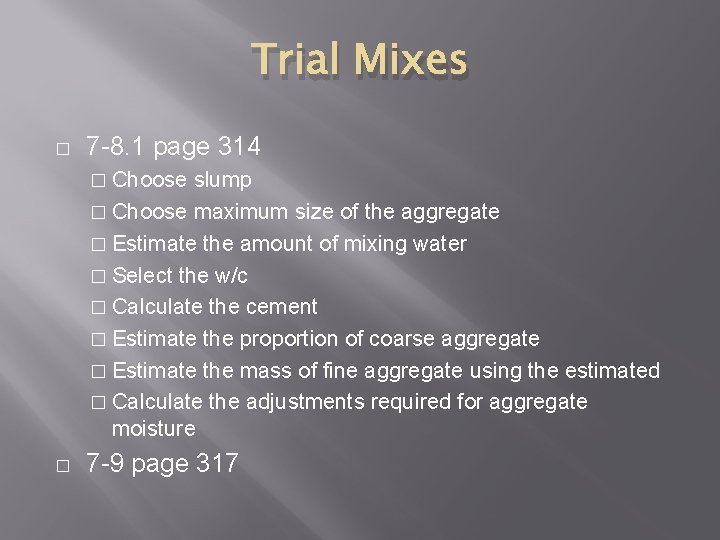
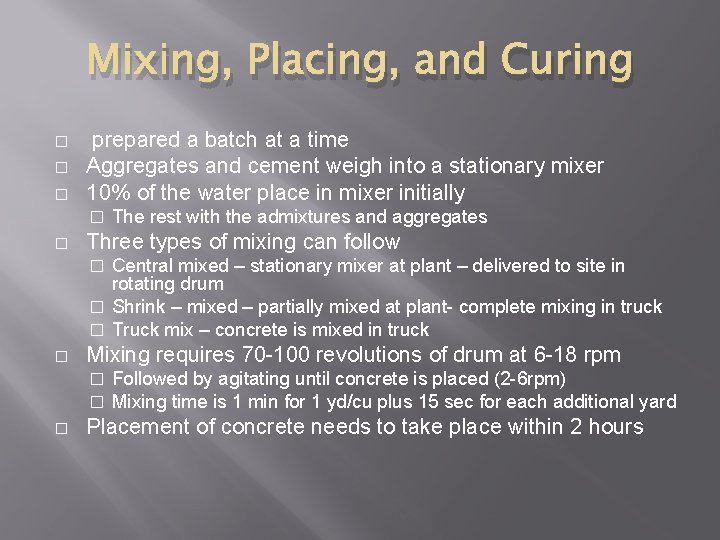
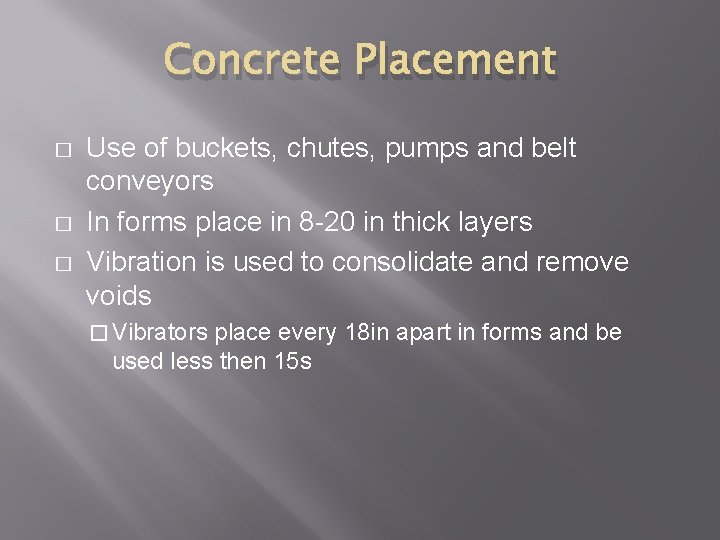
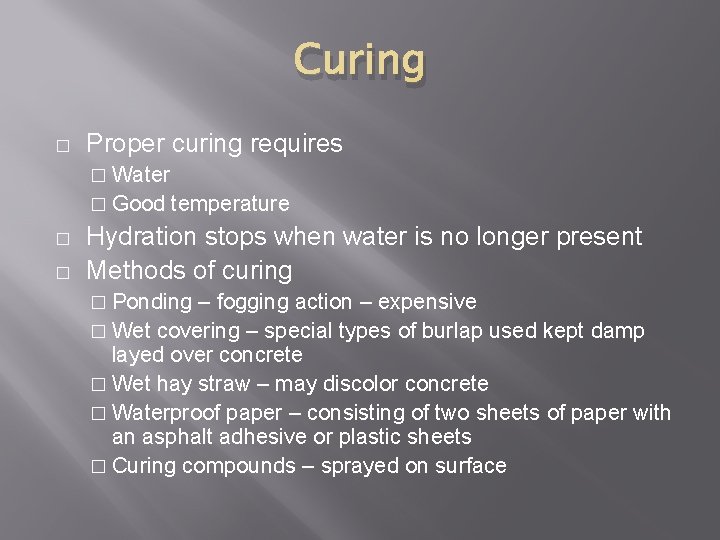
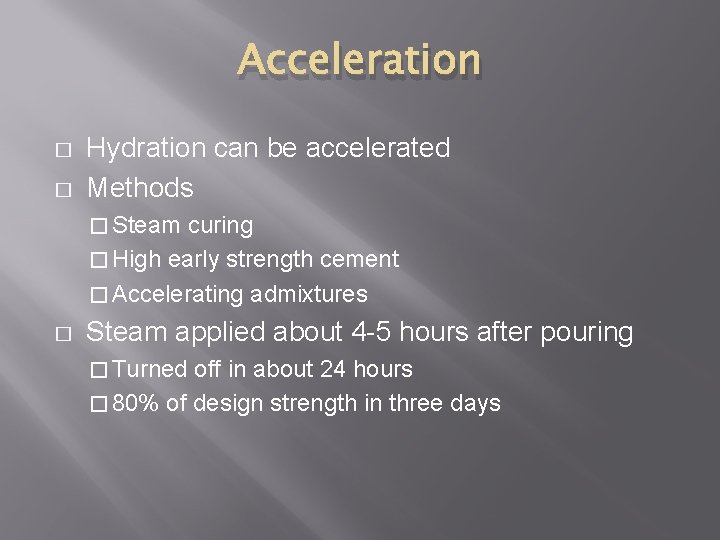
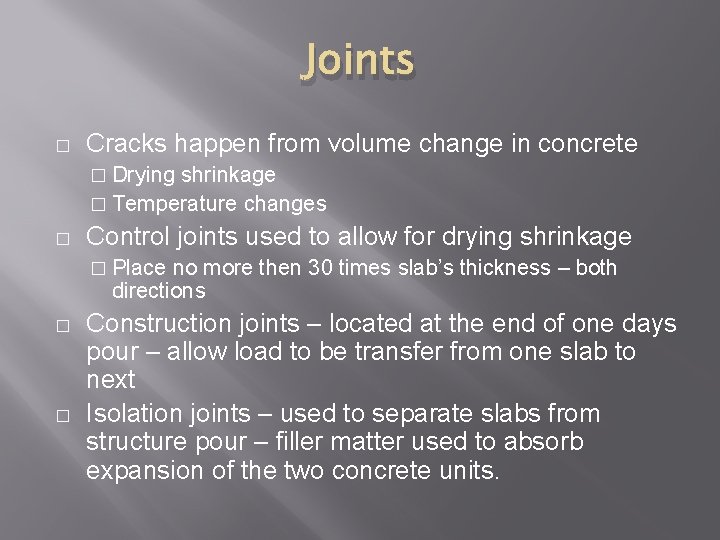
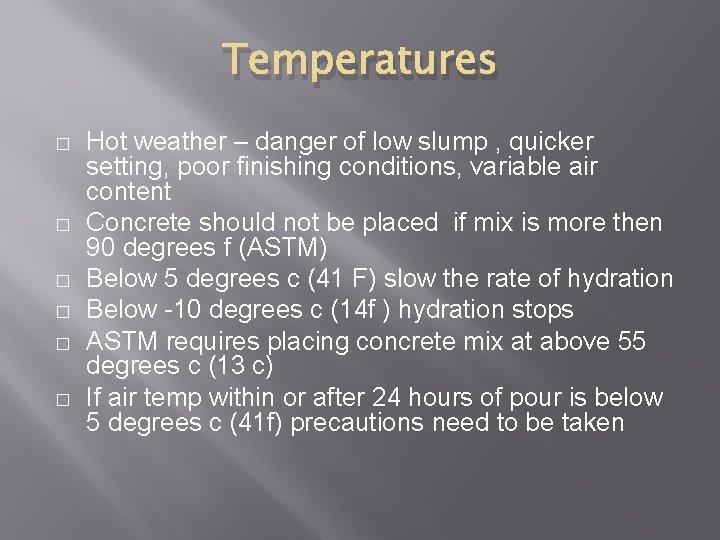
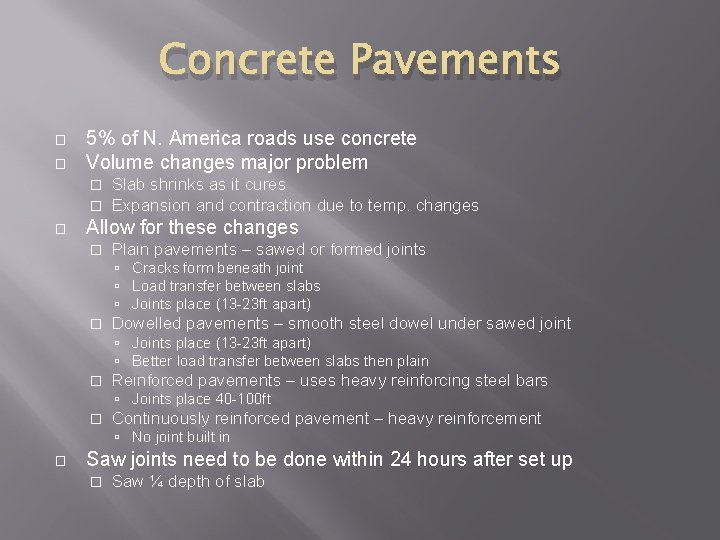
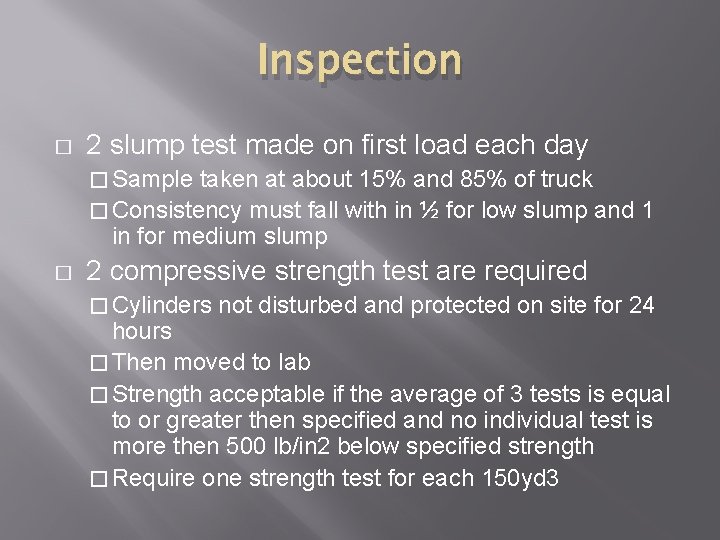
- Slides: 31
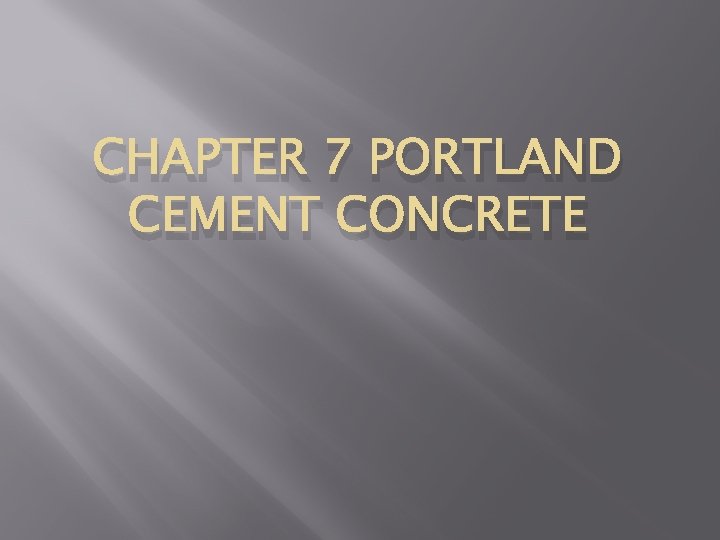
CHAPTER 7 PORTLAND CEMENT CONCRETE
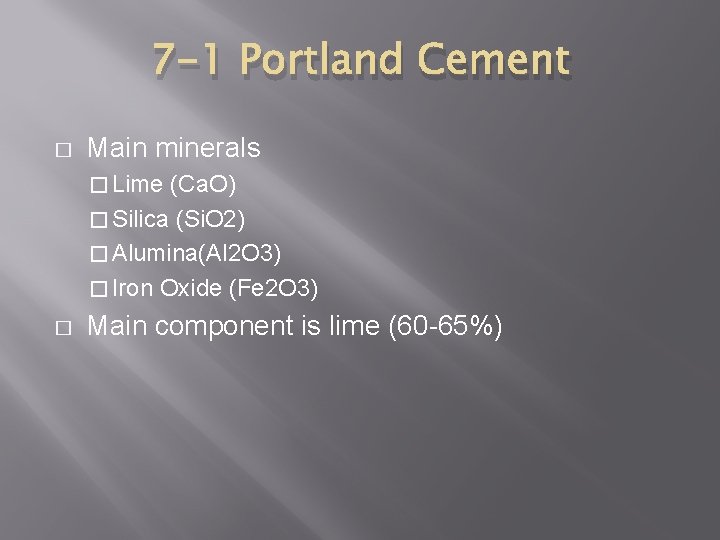
7 -1 Portland Cement � Main minerals � Lime (Ca. O) � Silica (Si. O 2) � Alumina(Al 2 O 3) � Iron Oxide (Fe 2 O 3) � Main component is lime (60 -65%)
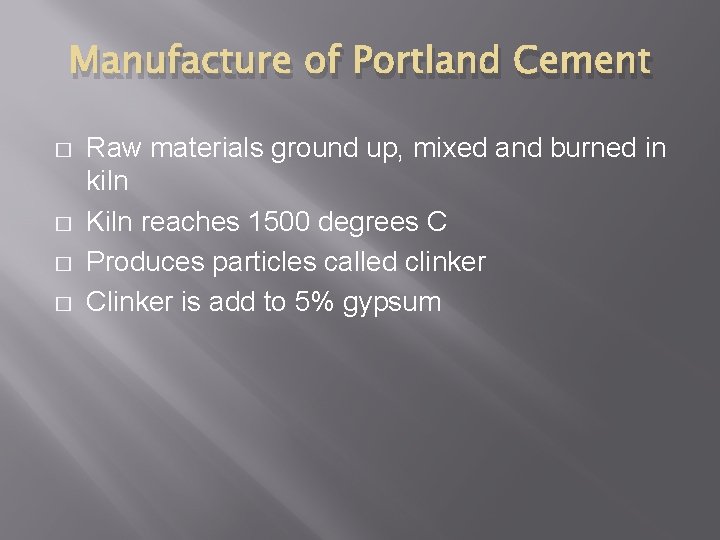
Manufacture of Portland Cement � � Raw materials ground up, mixed and burned in kiln Kiln reaches 1500 degrees C Produces particles called clinker Clinker is add to 5% gypsum
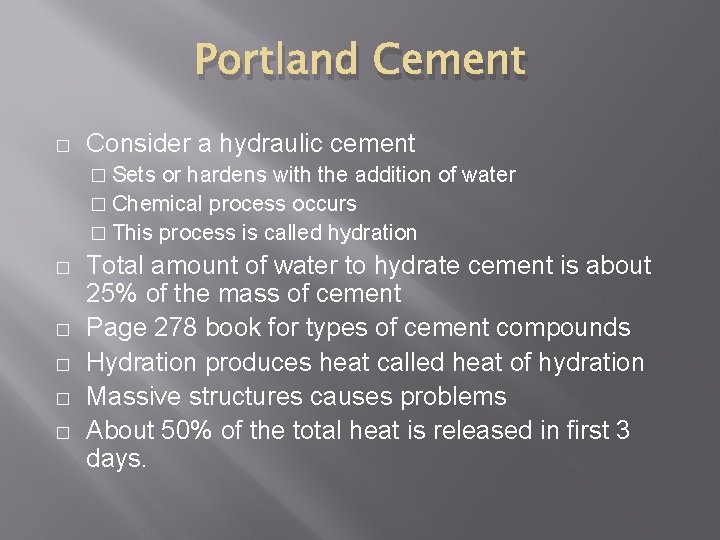
Portland Cement � Consider a hydraulic cement � Sets or hardens with the addition of water � Chemical process occurs � This process is called hydration � � � Total amount of water to hydrate cement is about 25% of the mass of cement Page 278 book for types of cement compounds Hydration produces heat called heat of hydration Massive structures causes problems About 50% of the total heat is released in first 3 days.
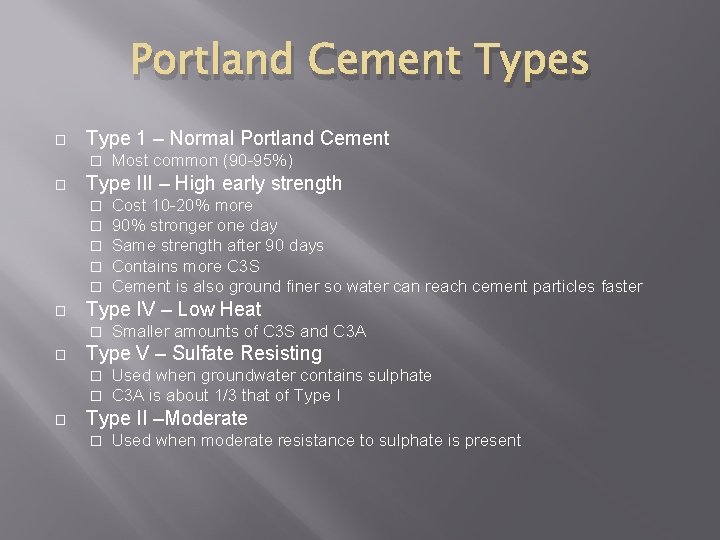
Portland Cement Types � Type 1 – Normal Portland Cement � � Type III – High early strength � � � Smaller amounts of C 3 S and C 3 A Type V – Sulfate Resisting � � � Cost 10 -20% more 90% stronger one day Same strength after 90 days Contains more C 3 S Cement is also ground finer so water can reach cement particles faster Type IV – Low Heat � � Most common (90 -95%) Used when groundwater contains sulphate C 3 A is about 1/3 that of Type II –Moderate � Used when moderate resistance to sulphate is present
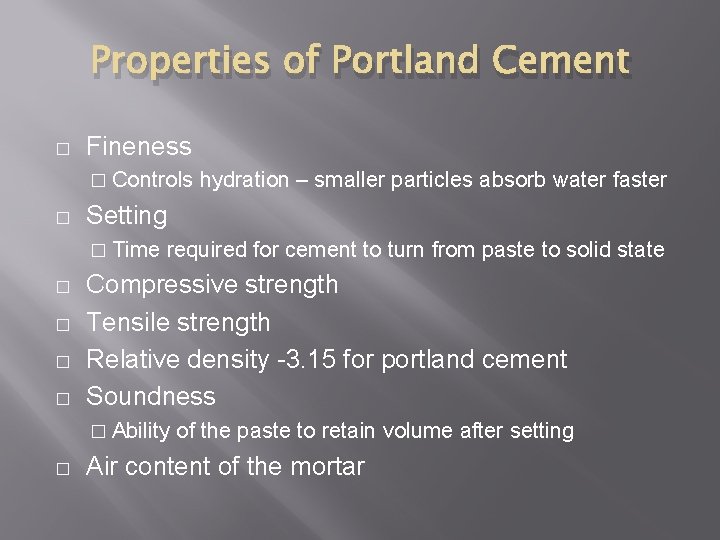
Properties of Portland Cement � Fineness � Controls � Setting � Time � � required for cement to turn from paste to solid state Compressive strength Tensile strength Relative density -3. 15 for portland cement Soundness � Ability � hydration – smaller particles absorb water faster of the paste to retain volume after setting Air content of the mortar
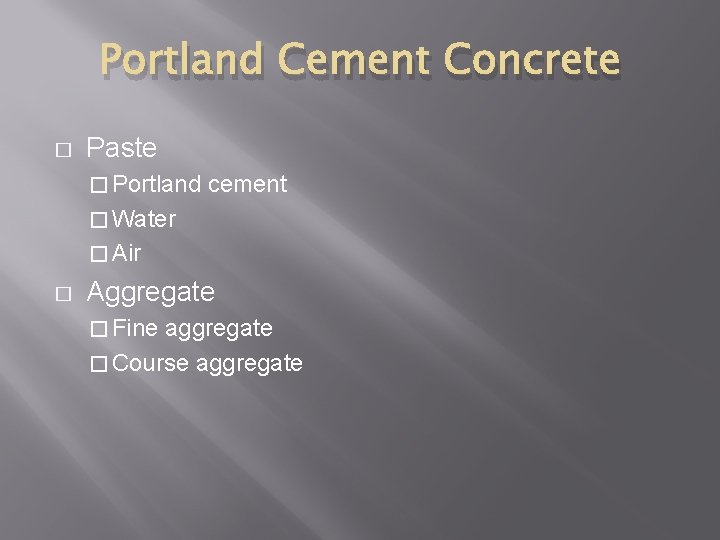
Portland Cement Concrete � Paste � Portland cement � Water � Air � Aggregate � Fine aggregate � Course aggregate
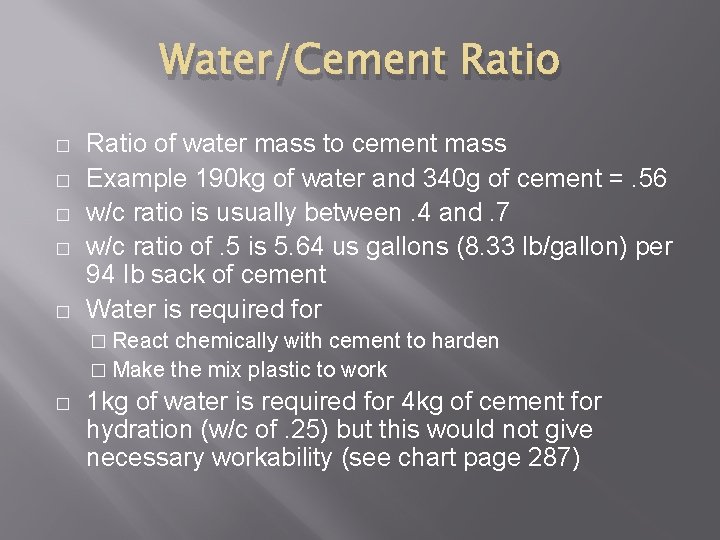
Water/Cement Ratio � � � Ratio of water mass to cement mass Example 190 kg of water and 340 g of cement =. 56 w/c ratio is usually between. 4 and. 7 w/c ratio of. 5 is 5. 64 us gallons (8. 33 lb/gallon) per 94 Ib sack of cement Water is required for � React chemically with cement to harden � Make the mix plastic to work � 1 kg of water is required for 4 kg of cement for hydration (w/c of. 25) but this would not give necessary workability (see chart page 287)
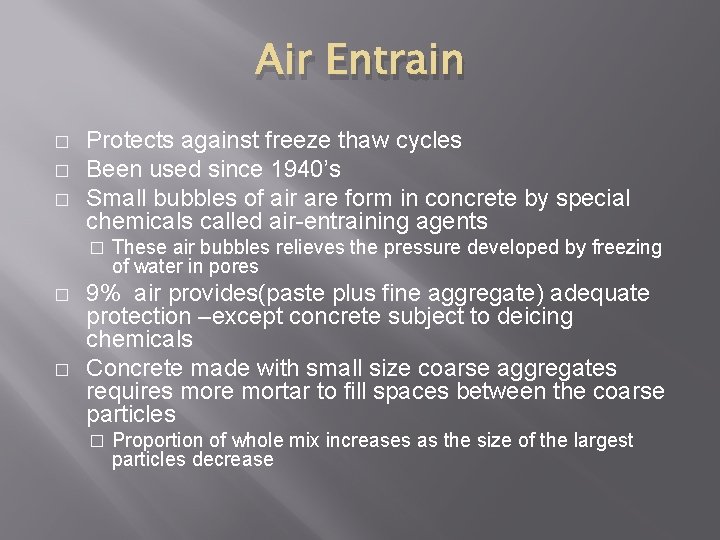
Air Entrain � � � Protects against freeze thaw cycles Been used since 1940’s Small bubbles of air are form in concrete by special chemicals called air-entraining agents � � � These air bubbles relieves the pressure developed by freezing of water in pores 9% air provides(paste plus fine aggregate) adequate protection –except concrete subject to deicing chemicals Concrete made with small size coarse aggregates requires more mortar to fill spaces between the coarse particles � Proportion of whole mix increases as the size of the largest particles decrease
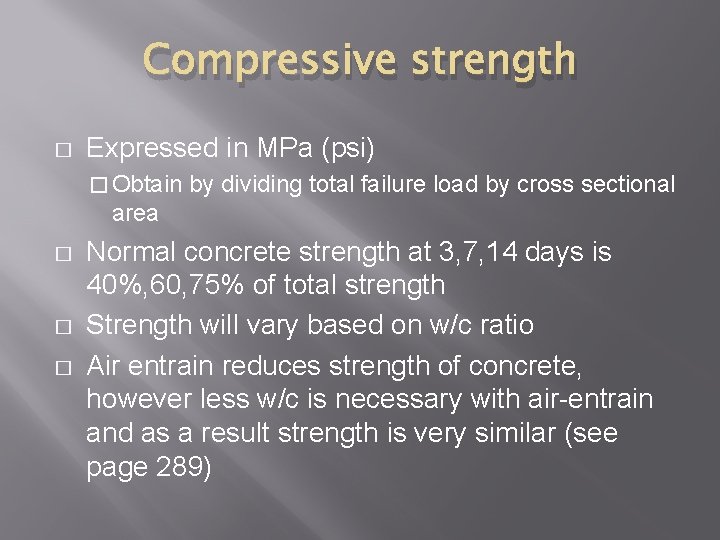
Compressive strength � Expressed in MPa (psi) � Obtain by dividing total failure load by cross sectional area � � � Normal concrete strength at 3, 7, 14 days is 40%, 60, 75% of total strength Strength will vary based on w/c ratio Air entrain reduces strength of concrete, however less w/c is necessary with air-entrain and as a result strength is very similar (see page 289)
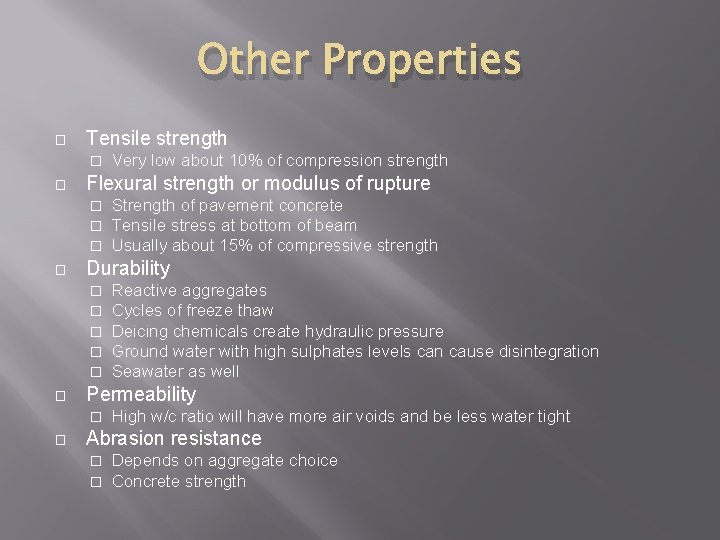
Other Properties � Tensile strength � � Flexural strength or modulus of rupture � � Reactive aggregates Cycles of freeze thaw Deicing chemicals create hydraulic pressure Ground water with high sulphates levels can cause disintegration Seawater as well Permeability � � Strength of pavement concrete Tensile stress at bottom of beam Usually about 15% of compressive strength Durability � � � Very low about 10% of compression strength High w/c ratio will have more air voids and be less water tight Abrasion resistance � � Depends on aggregate choice Concrete strength
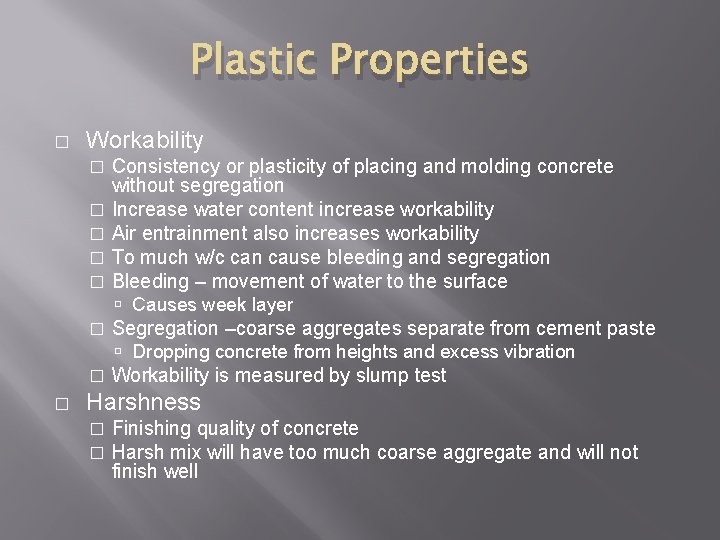
Plastic Properties � Workability Consistency or plasticity of placing and molding concrete without segregation � Increase water content increase workability � Air entrainment also increases workability � To much w/c can cause bleeding and segregation � Bleeding – movement of water to the surface � Causes week layer � Segregation –coarse aggregates separate from cement paste Dropping concrete from heights and excess vibration � � Workability is measured by slump test Harshness � � Finishing quality of concrete Harsh mix will have too much coarse aggregate and will not finish well
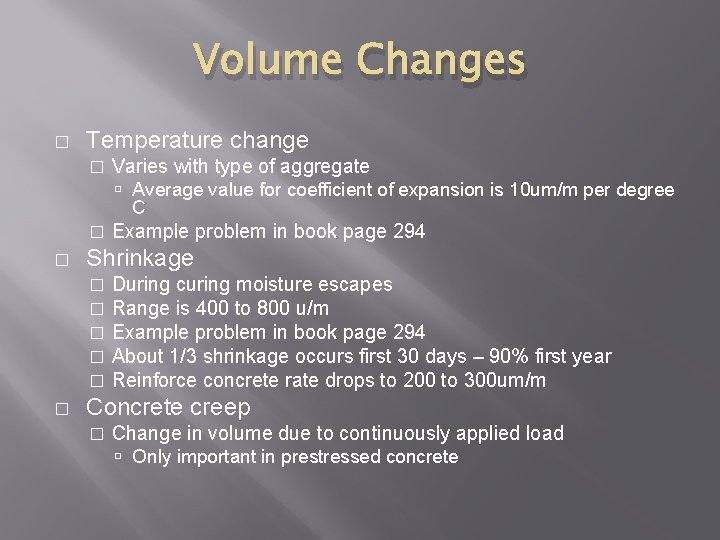
Volume Changes � Temperature change � Varies with type of aggregate Average value for coefficient of expansion is 10 um/m per degree C � � Shrinkage � � � Example problem in book page 294 During curing moisture escapes Range is 400 to 800 u/m Example problem in book page 294 About 1/3 shrinkage occurs first 30 days – 90% first year Reinforce concrete rate drops to 200 to 300 um/m Concrete creep � Change in volume due to continuously applied load Only important in prestressed concrete
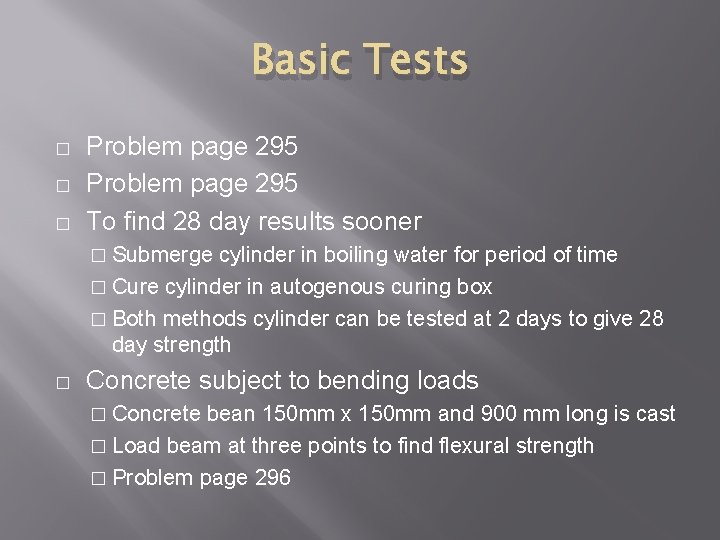
Basic Tests � � � Problem page 295 To find 28 day results sooner � Submerge cylinder in boiling water for period of time � Cure cylinder in autogenous curing box � Both methods cylinder can be tested at 2 days to give 28 day strength � Concrete subject to bending loads � Concrete bean 150 mm x 150 mm and 900 mm long is cast � Load beam at three points to find flexural strength � Problem page 296
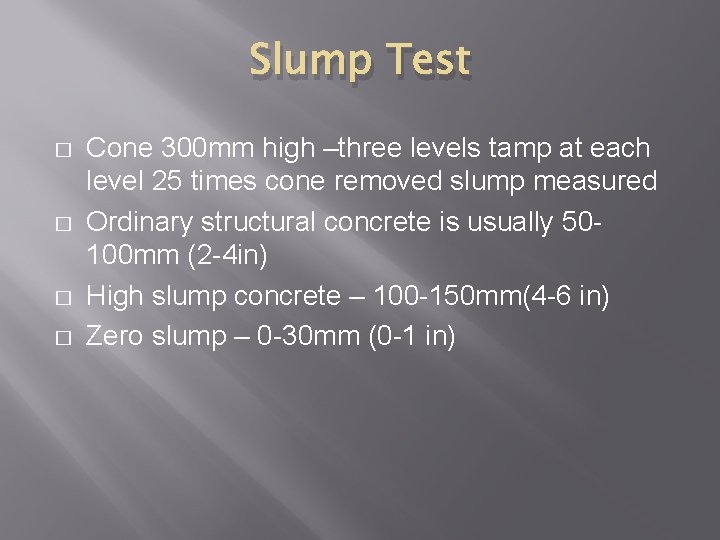
Slump Test � � Cone 300 mm high –three levels tamp at each level 25 times cone removed slump measured Ordinary structural concrete is usually 50100 mm (2 -4 in) High slump concrete – 100 -150 mm(4 -6 in) Zero slump – 0 -30 mm (0 -1 in)
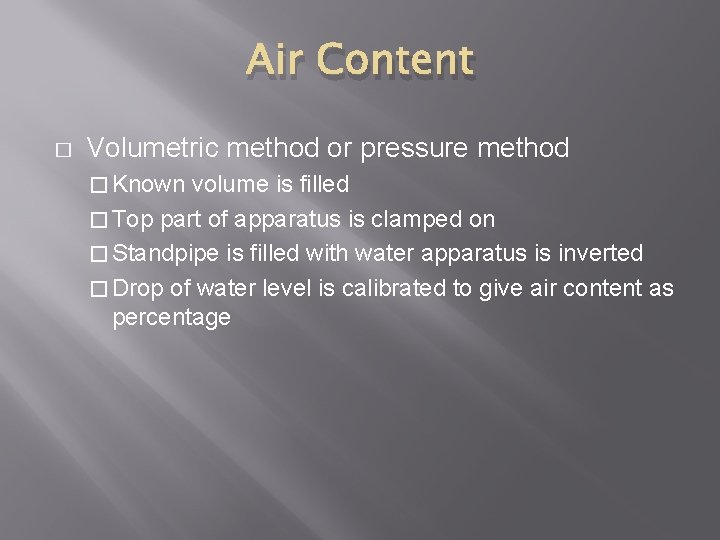
Air Content � Volumetric method or pressure method � Known volume is filled � Top part of apparatus is clamped on � Standpipe is filled with water apparatus is inverted � Drop of water level is calibrated to give air content as percentage

Admixtures � � 80% concrete produced in North America has chemical additives Used since 1900’s Small quantities up to 1% to 2% of mass of cement ASTM Standard � Type A-water reducing � Type B- retarding � Type C –accelerating � Type D – water reducing and retarding � Type E –water reducing and accelerating � Type F – high range water reducing (HRWR) � Type G- high range water reducing and retarding
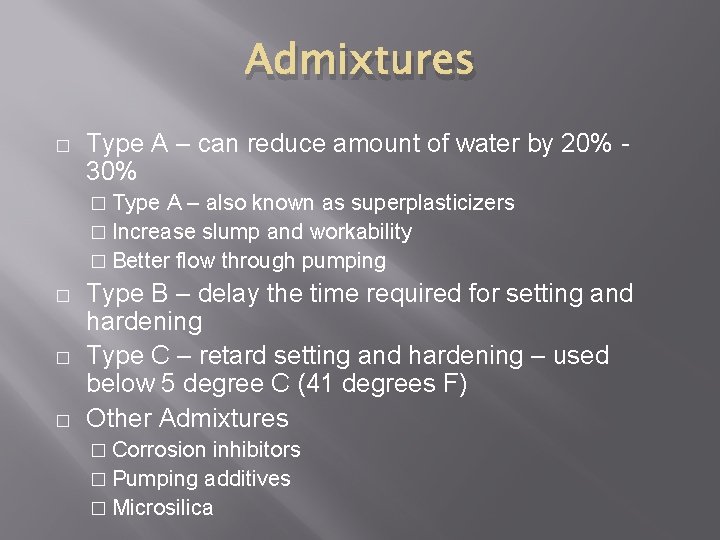
Admixtures � Type A – can reduce amount of water by 20% 30% � Type A – also known as superplasticizers � Increase slump and workability � Better flow through pumping � � � Type B – delay the time required for setting and hardening Type C – retard setting and hardening – used below 5 degree C (41 degrees F) Other Admixtures � Corrosion inhibitors � Pumping additives � Microsilica
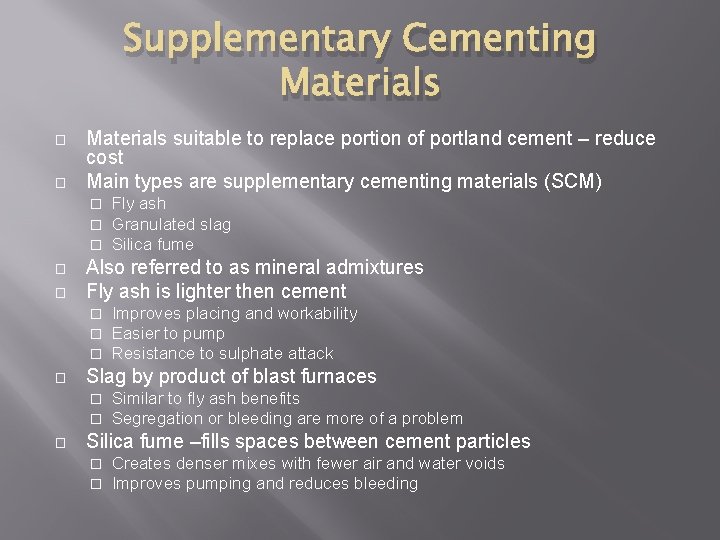
Supplementary Cementing Materials � � Materials suitable to replace portion of portland cement – reduce cost Main types are supplementary cementing materials (SCM) � � � Also referred to as mineral admixtures Fly ash is lighter then cement � � Improves placing and workability Easier to pump Resistance to sulphate attack Slag by product of blast furnaces � � � Fly ash Granulated slag Silica fume Similar to fly ash benefits Segregation or bleeding are more of a problem Silica fume –fills spaces between cement particles � � Creates denser mixes with fewer air and water voids Improves pumping and reduces bleeding
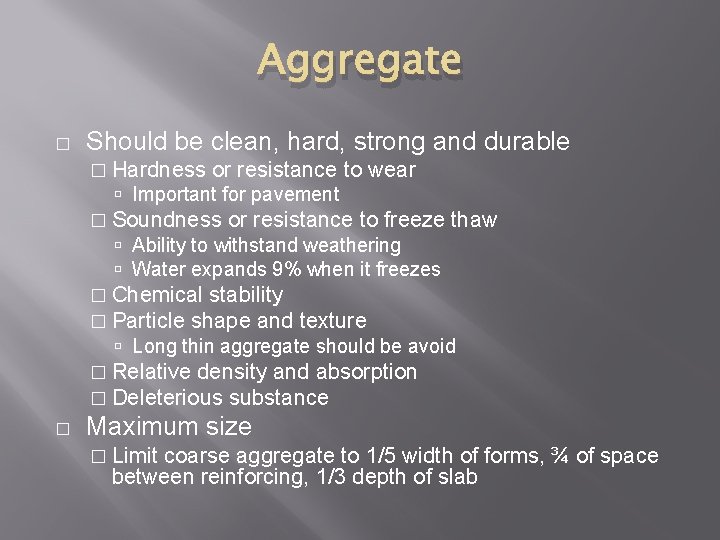
Aggregate � Should be clean, hard, strong and durable � Hardness or resistance to wear Important for pavement � Soundness or resistance to freeze thaw Ability to withstand weathering Water expands 9% when it freezes � Chemical stability � Particle shape and texture Long thin aggregate should be avoid � Relative density and absorption � Deleterious substance � Maximum size � Limit coarse aggregate to 1/5 width of forms, ¾ of space between reinforcing, 1/3 depth of slab
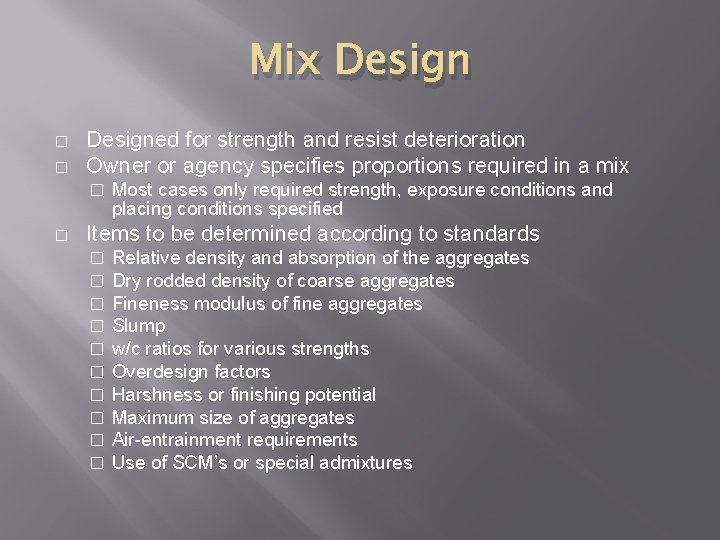
Mix Design � � Designed for strength and resist deterioration Owner or agency specifies proportions required in a mix � � Most cases only required strength, exposure conditions and placing conditions specified Items to be determined according to standards � � � � � Relative density and absorption of the aggregates Dry rodded density of coarse aggregates Fineness modulus of fine aggregates Slump w/c ratios for various strengths Overdesign factors Harshness or finishing potential Maximum size of aggregates Air-entrainment requirements Use of SCM’s or special admixtures
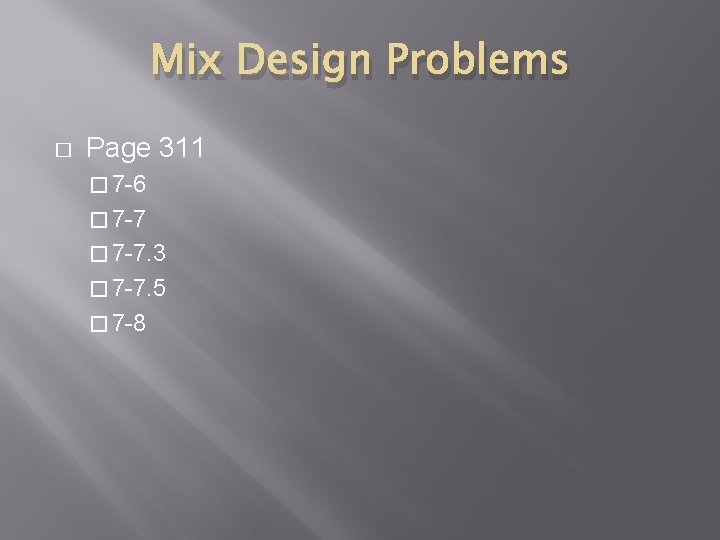
Mix Design Problems � Page 311 � 7 -6 � 7 -7. 3 � 7 -7. 5 � 7 -8
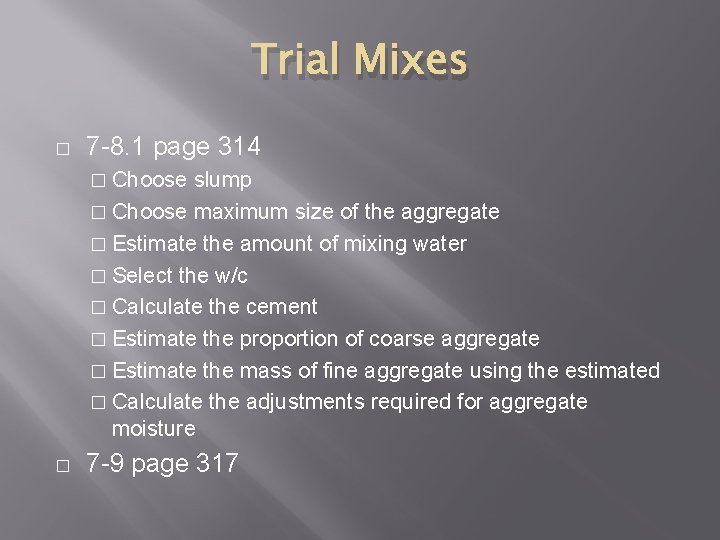
Trial Mixes � 7 -8. 1 page 314 � Choose slump � Choose maximum size of the aggregate � Estimate the amount of mixing water � Select the w/c � Calculate the cement � Estimate the proportion of coarse aggregate � Estimate the mass of fine aggregate using the estimated � Calculate the adjustments required for aggregate moisture � 7 -9 page 317
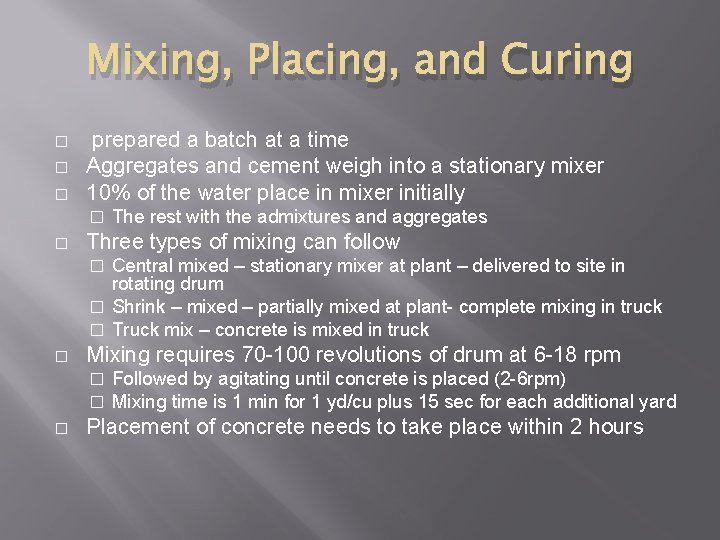
Mixing, Placing, and Curing � � � prepared a batch at a time Aggregates and cement weigh into a stationary mixer 10% of the water place in mixer initially � � The rest with the admixtures and aggregates Three types of mixing can follow Central mixed – stationary mixer at plant – delivered to site in rotating drum � Shrink – mixed – partially mixed at plant- complete mixing in truck � Truck mix – concrete is mixed in truck � � Mixing requires 70 -100 revolutions of drum at 6 -18 rpm � � � Followed by agitating until concrete is placed (2 -6 rpm) Mixing time is 1 min for 1 yd/cu plus 15 sec for each additional yard Placement of concrete needs to take place within 2 hours
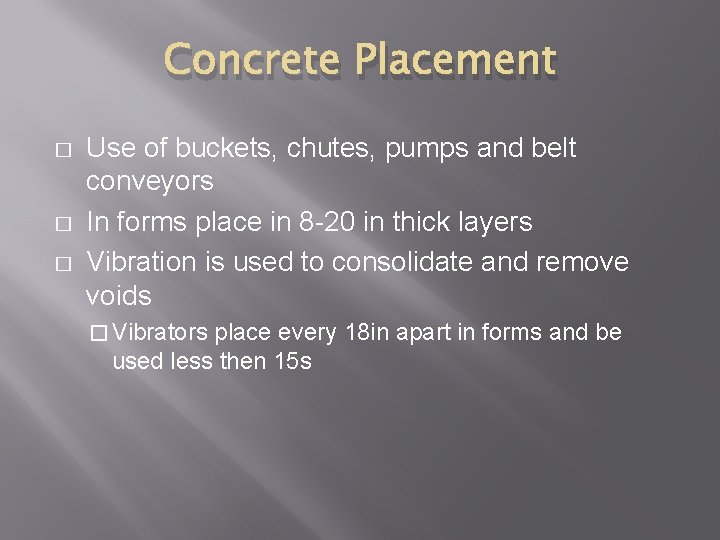
Concrete Placement � � � Use of buckets, chutes, pumps and belt conveyors In forms place in 8 -20 in thick layers Vibration is used to consolidate and remove voids � Vibrators place every 18 in apart in forms and be used less then 15 s
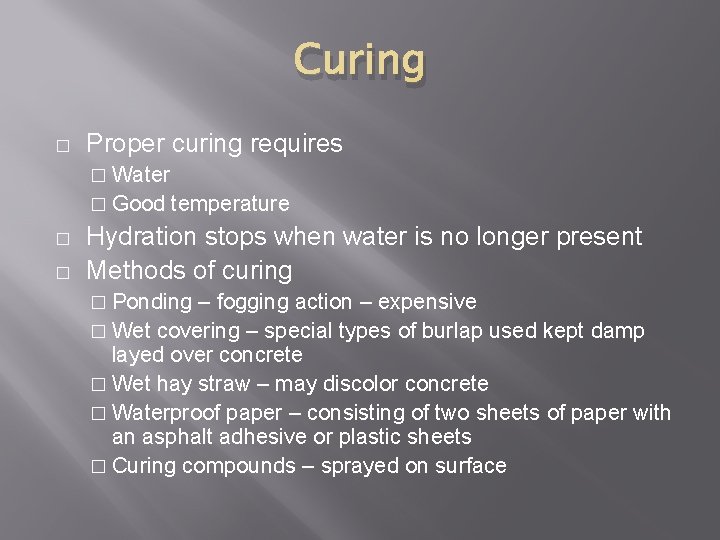
Curing � Proper curing requires � Water � Good � � temperature Hydration stops when water is no longer present Methods of curing � Ponding – fogging action – expensive � Wet covering – special types of burlap used kept damp layed over concrete � Wet hay straw – may discolor concrete � Waterproof paper – consisting of two sheets of paper with an asphalt adhesive or plastic sheets � Curing compounds – sprayed on surface
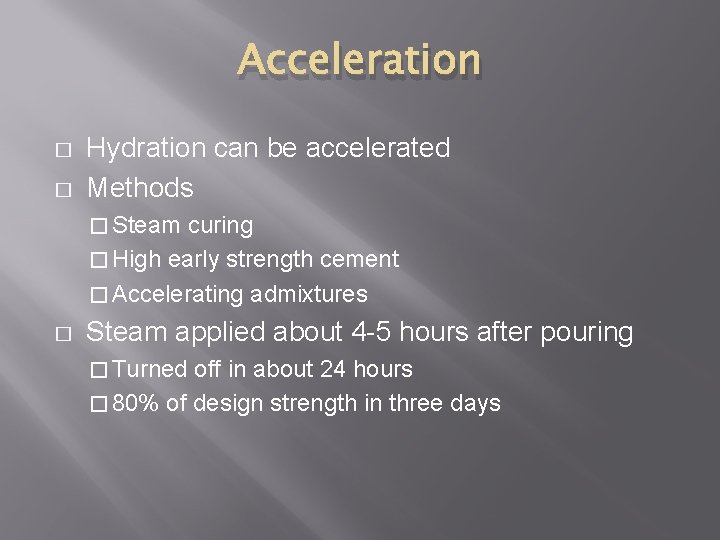
Acceleration � � Hydration can be accelerated Methods � Steam curing � High early strength cement � Accelerating admixtures � Steam applied about 4 -5 hours after pouring � Turned off in about 24 hours � 80% of design strength in three days
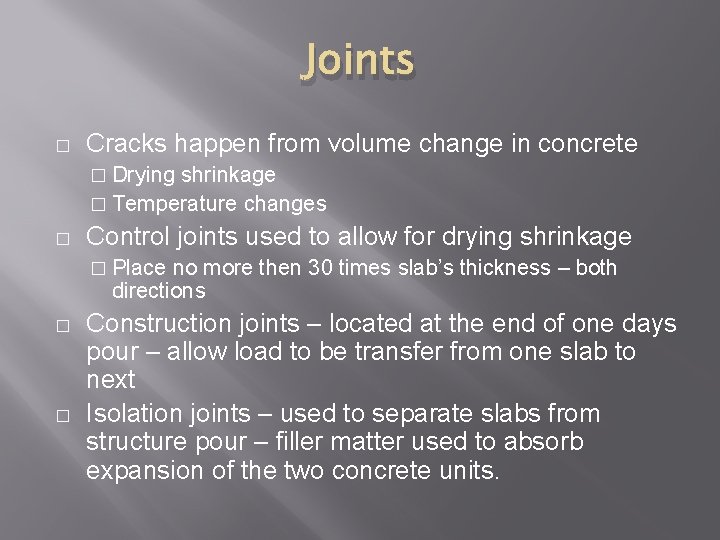
Joints � Cracks happen from volume change in concrete � Drying shrinkage � Temperature changes � Control joints used to allow for drying shrinkage � Place no more then 30 times slab’s thickness – both directions � � Construction joints – located at the end of one days pour – allow load to be transfer from one slab to next Isolation joints – used to separate slabs from structure pour – filler matter used to absorb expansion of the two concrete units.
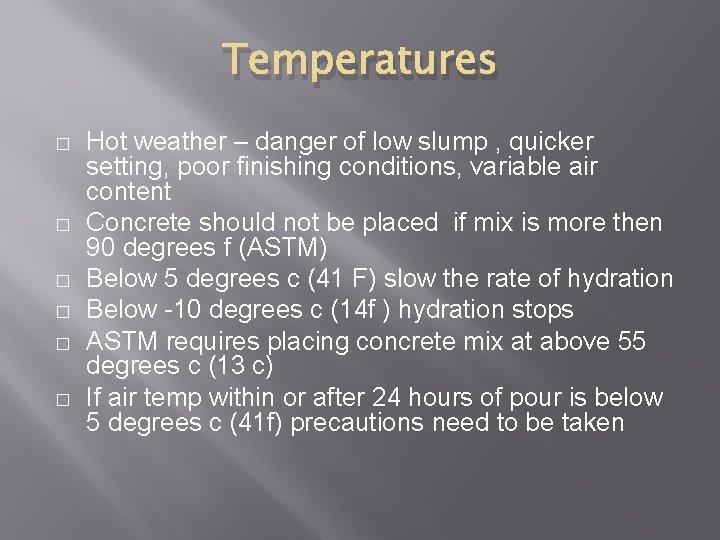
Temperatures � � � Hot weather – danger of low slump , quicker setting, poor finishing conditions, variable air content Concrete should not be placed if mix is more then 90 degrees f (ASTM) Below 5 degrees c (41 F) slow the rate of hydration Below -10 degrees c (14 f ) hydration stops ASTM requires placing concrete mix at above 55 degrees c (13 c) If air temp within or after 24 hours of pour is below 5 degrees c (41 f) precautions need to be taken
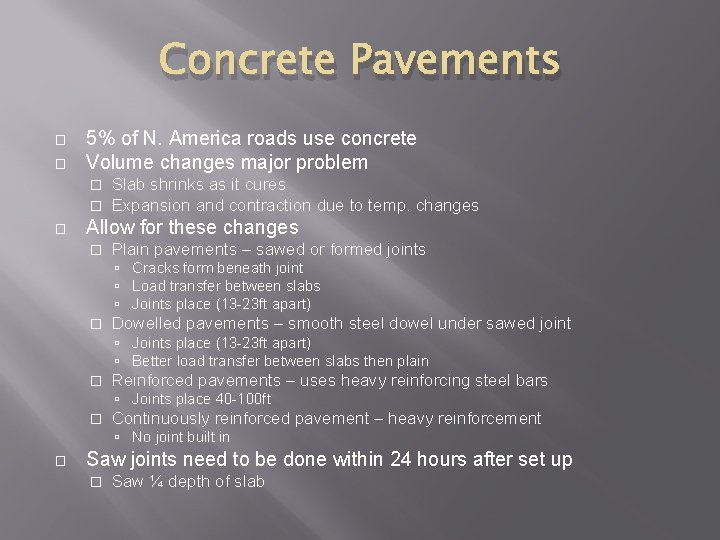
Concrete Pavements � � 5% of N. America roads use concrete Volume changes major problem � � � Slab shrinks as it cures Expansion and contraction due to temp. changes Allow for these changes � Plain pavements – sawed or formed joints Cracks form beneath joint Load transfer between slabs Joints place (13 -23 ft apart) � Dowelled pavements – smooth steel dowel under sawed joint Joints place (13 -23 ft apart) Better load transfer between slabs then plain � Reinforced pavements – uses heavy reinforcing steel bars Joints place 40 -100 ft � Continuously reinforced pavement – heavy reinforcement No joint built in � Saw joints need to be done within 24 hours after set up � Saw ¼ depth of slab
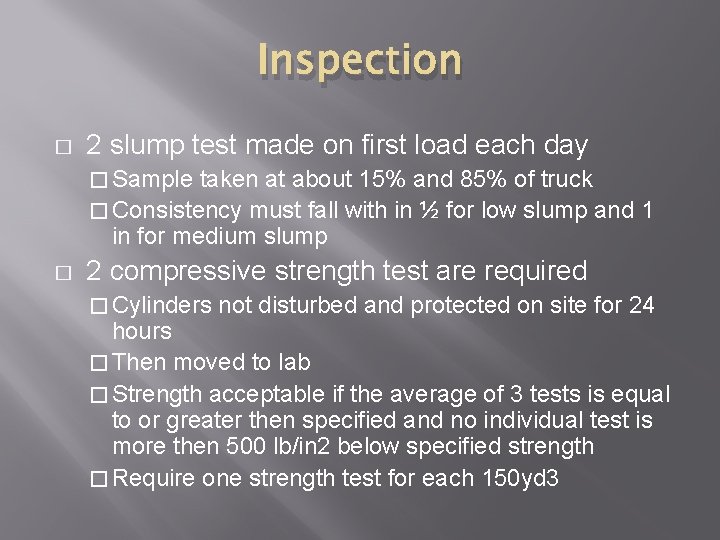
Inspection � 2 slump test made on first load each day � Sample taken at about 15% and 85% of truck � Consistency must fall with in ½ for low slump and 1 in for medium slump � 2 compressive strength test are required � Cylinders not disturbed and protected on site for 24 hours � Then moved to lab � Strength acceptable if the average of 3 tests is equal to or greater then specified and no individual test is more then 500 lb/in 2 below specified strength � Require one strength test for each 150 yd 3
Manufacture of portland cement
Portland cement definition
Metselcement praxis
Rcc reinforced cement concrete
Types of slump in concrete
Dr pavor
Informal inventory
Concrete semi concrete abstract
Cement chapter in civil engineering
Tar and cement verdelle smith
Sillmax
Liquid solvent cement
Shargh white cement
Cement grouting method
Glass ionomer cement indications
Mortar water ratio
Casing repair techniques
Vicatt
Non hydraulic cement
Water absorption formula
Absolute volume of cement
Tensol cement advantages and disadvantages
Setting reaction of zinc phosphate cement
Wolff law
Zinc phosphate cement composition
Dalmacija cement
Composition of gic
Tobermonite gel
Vertical example
Extra rapid hardening cement setting time
Bargarh cement works
Semen sbc