P 08452 Reciprocating Compressor Install Revamp and Interface
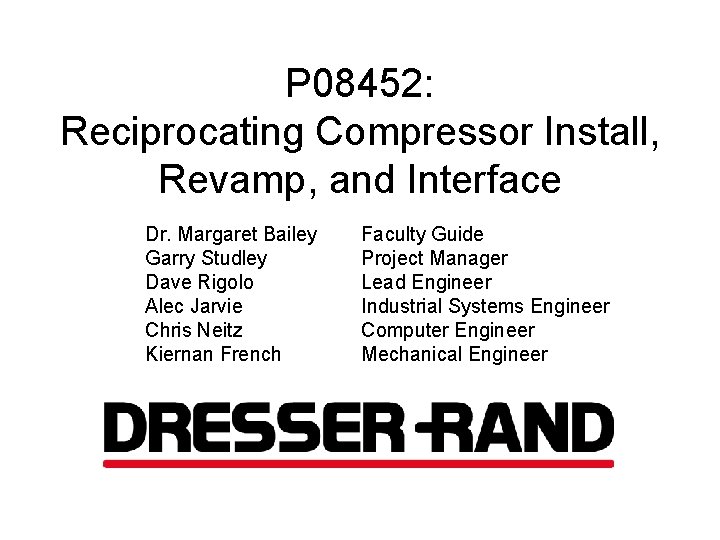
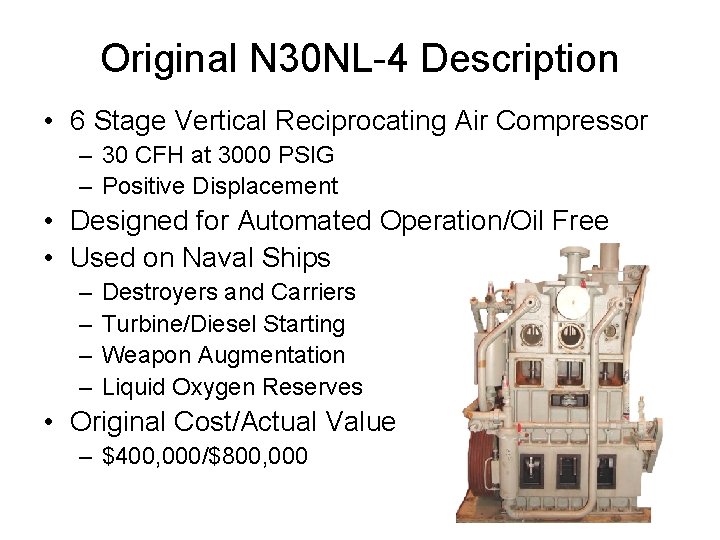
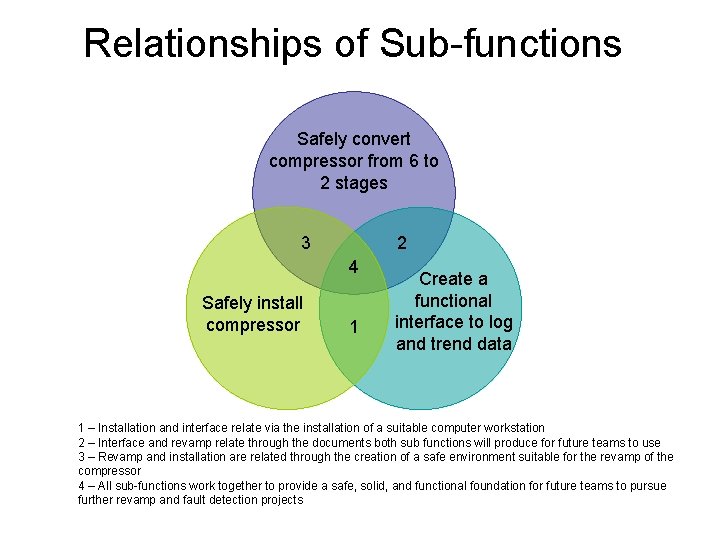
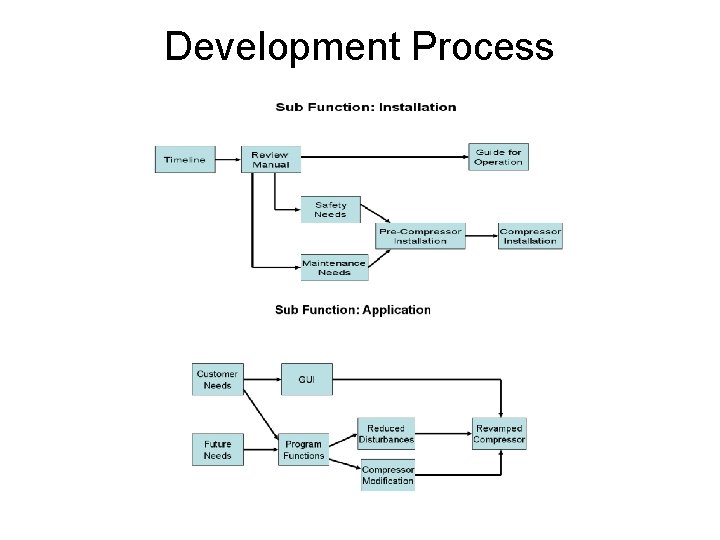
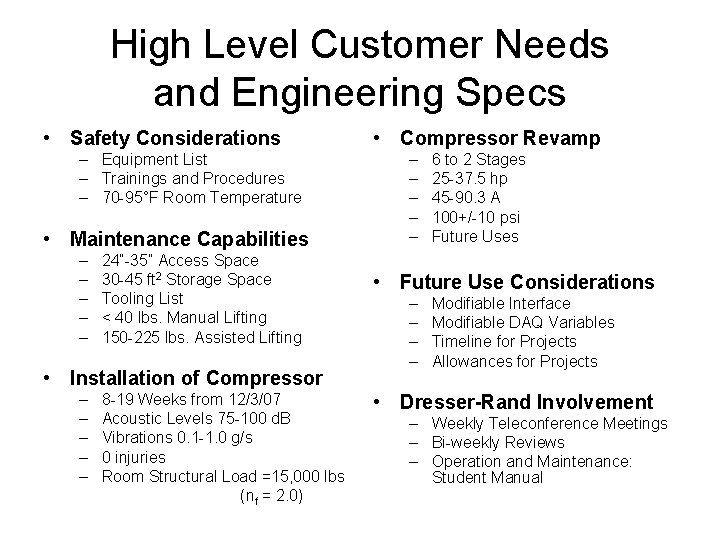
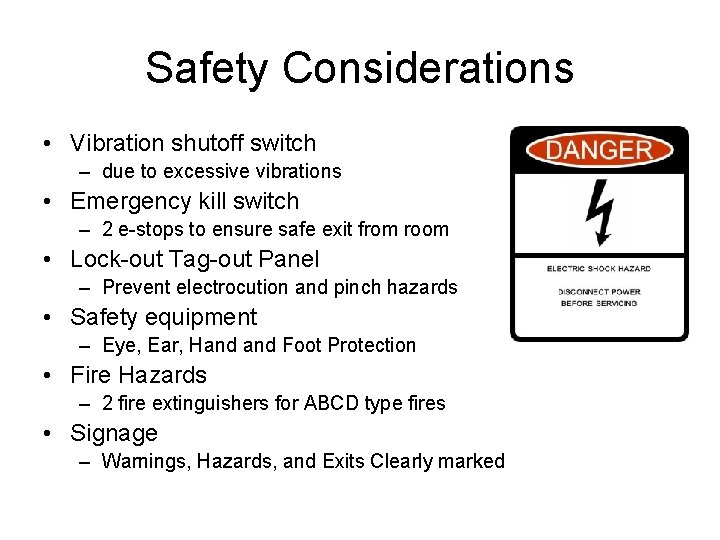
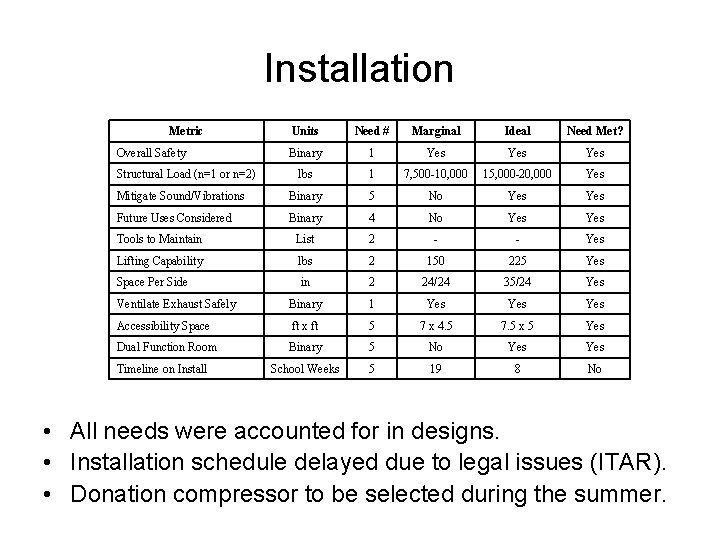
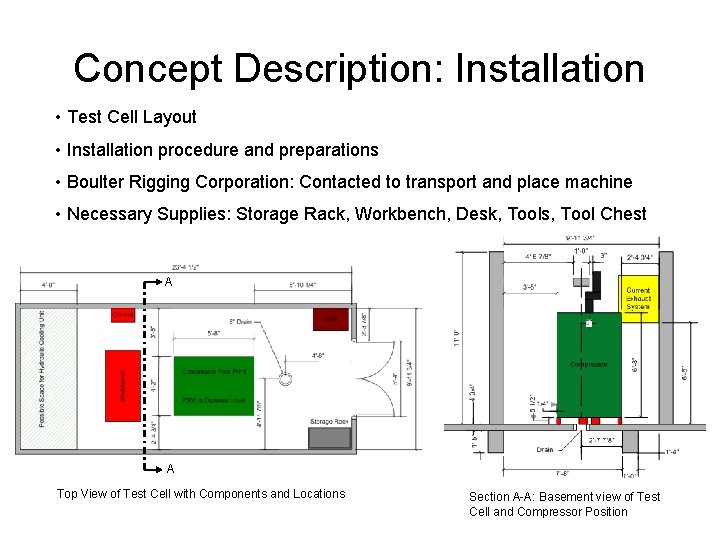
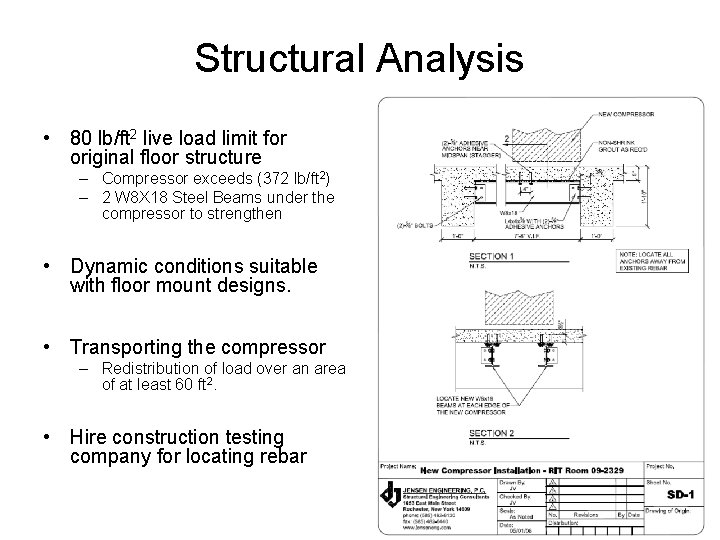
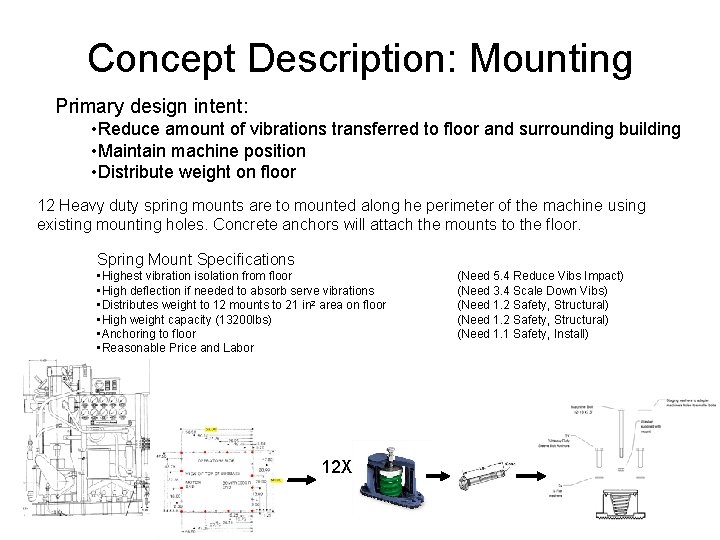
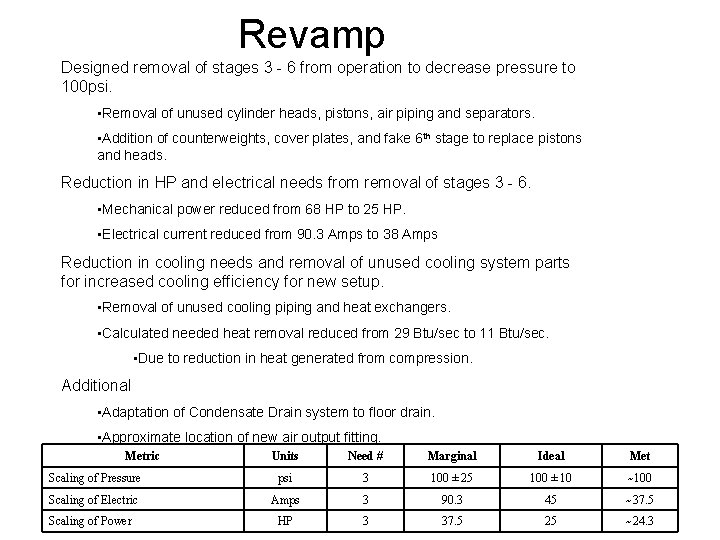
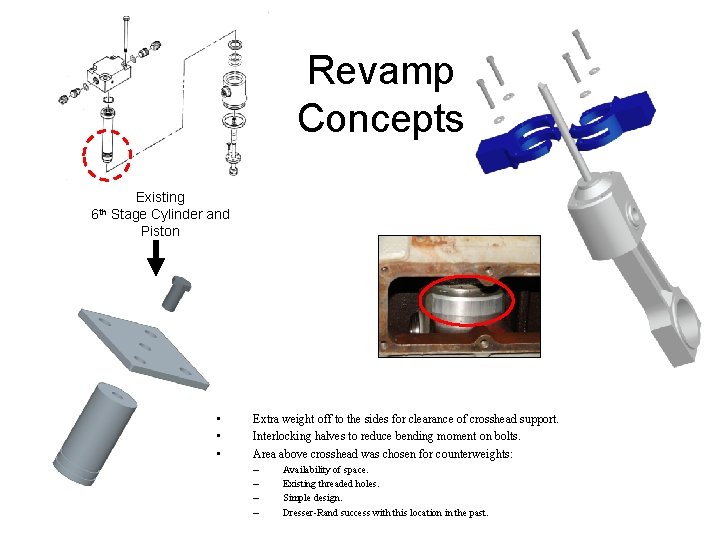
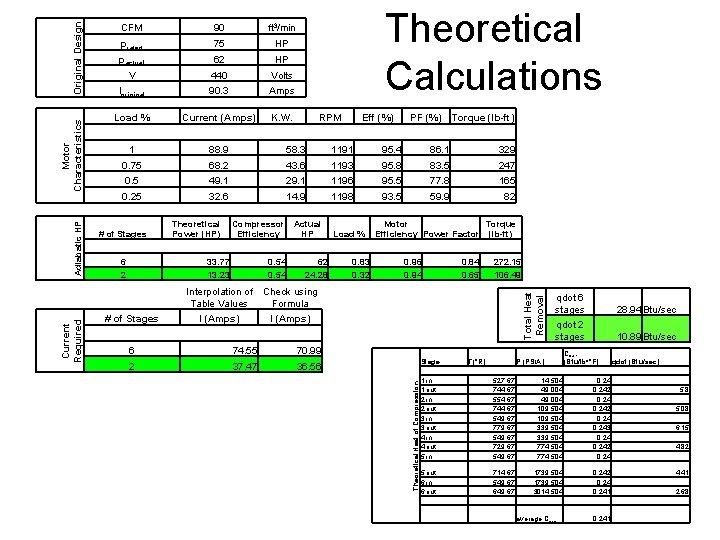
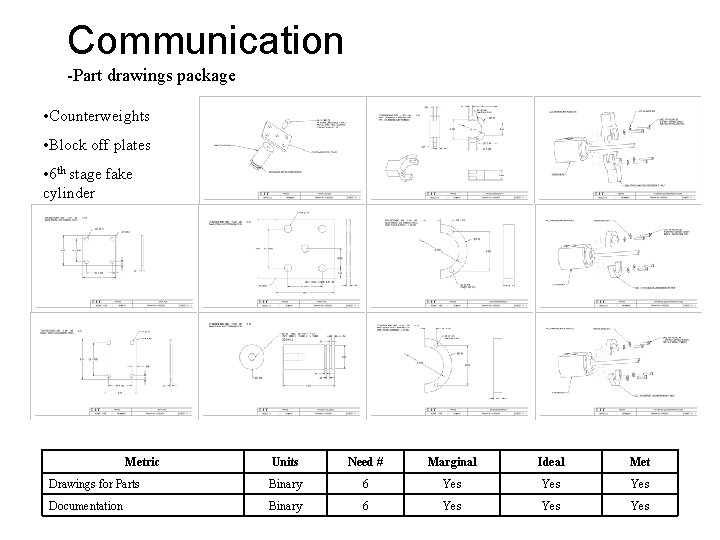
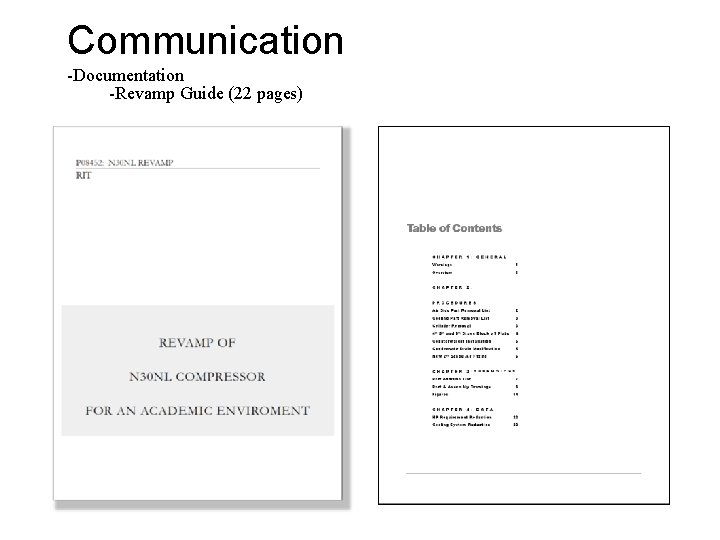
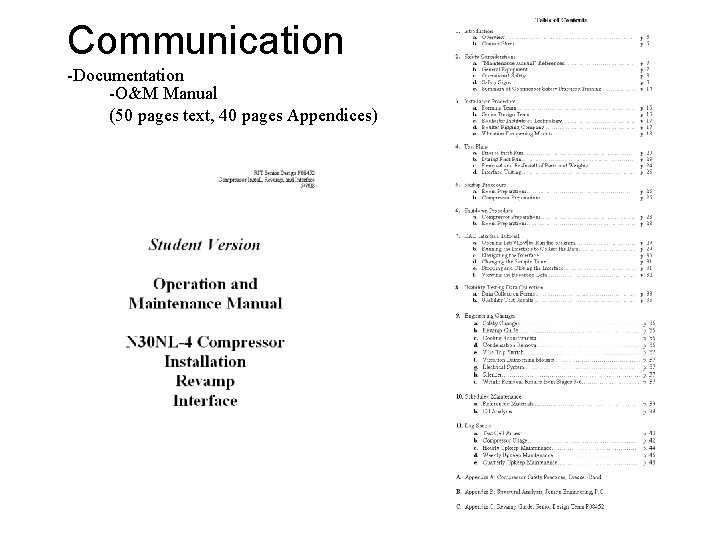
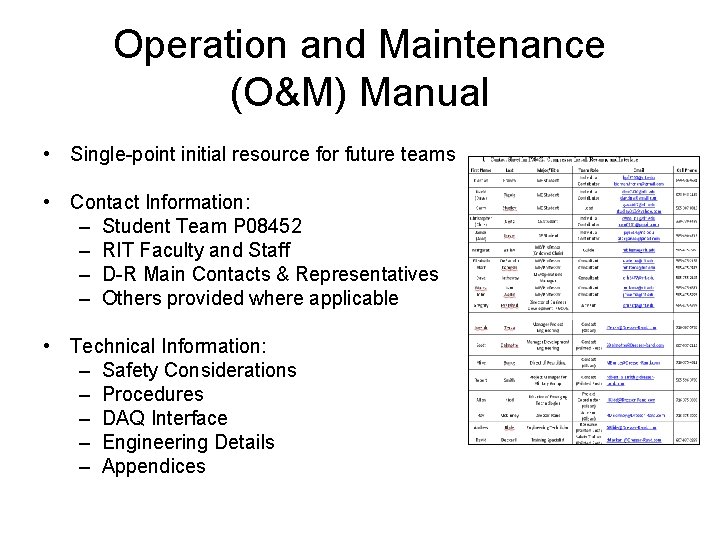
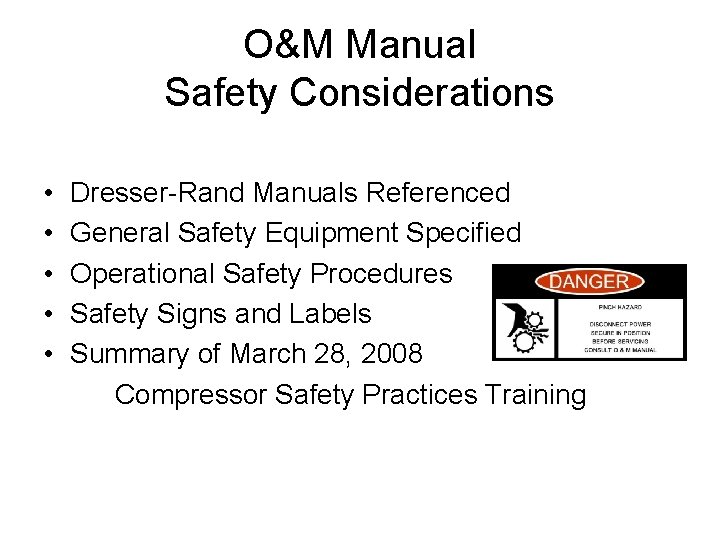
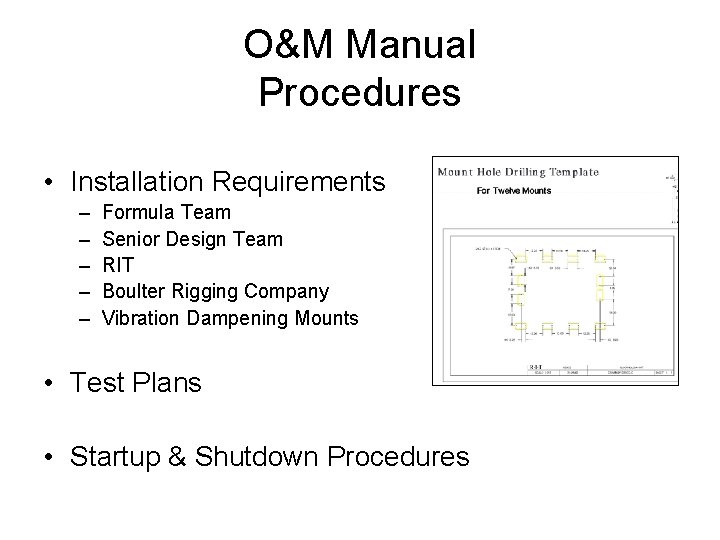
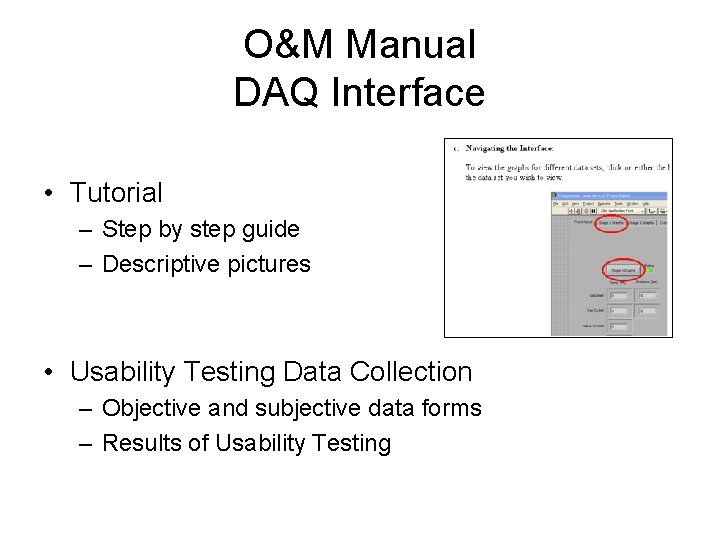
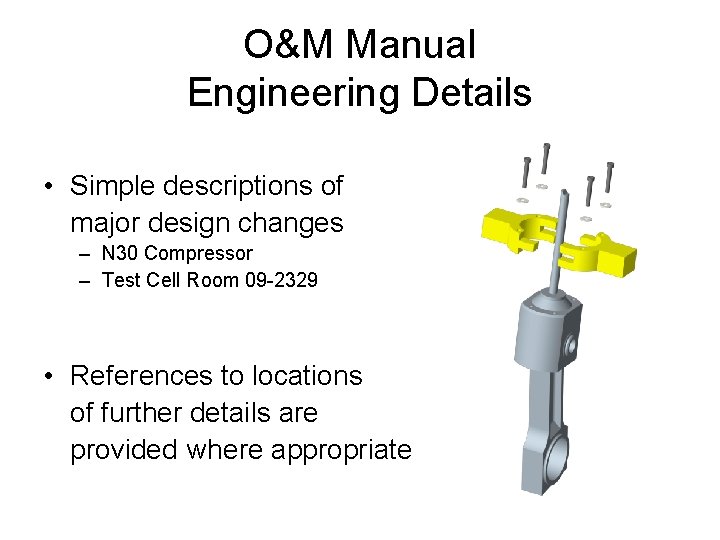
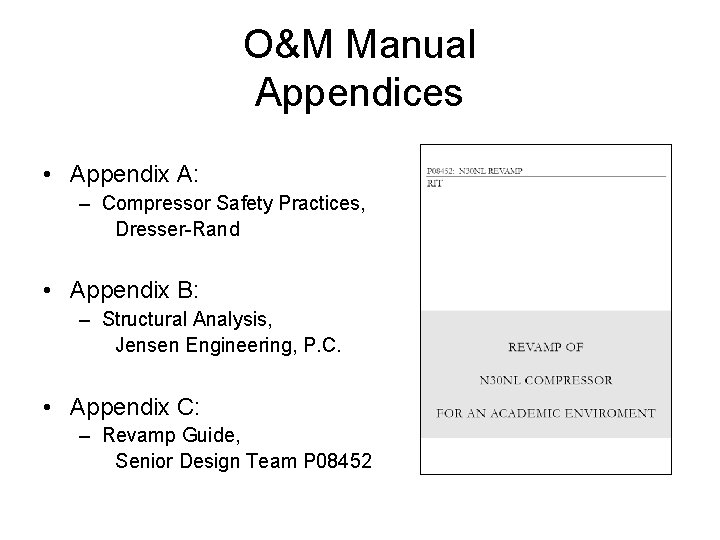
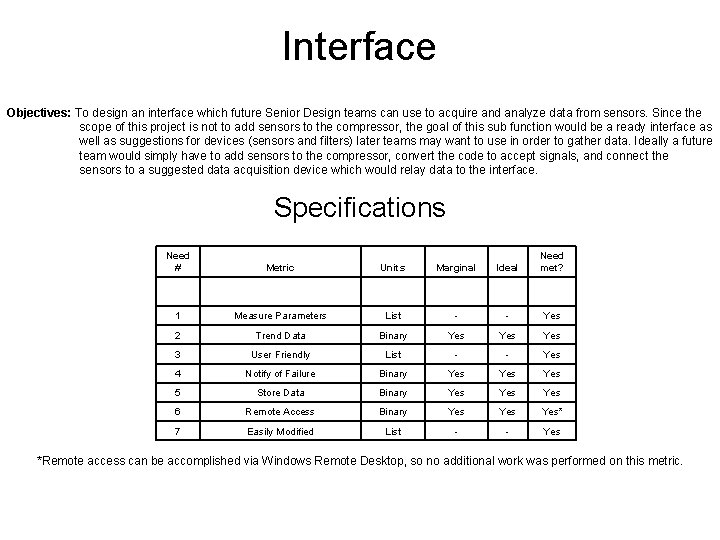
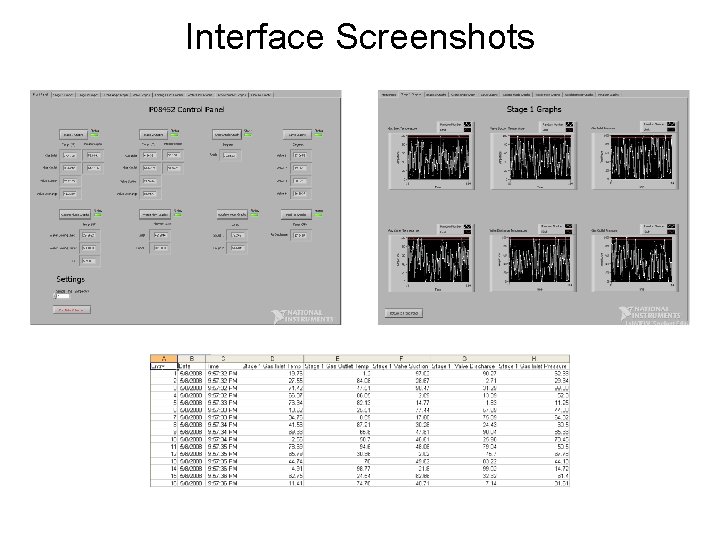
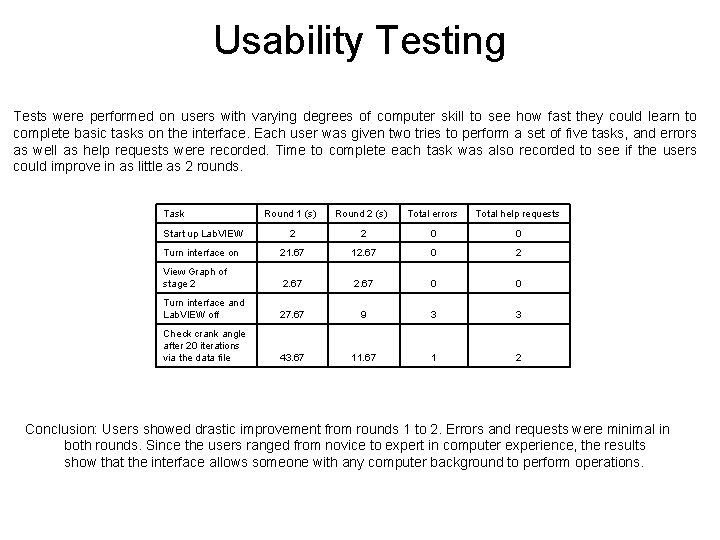
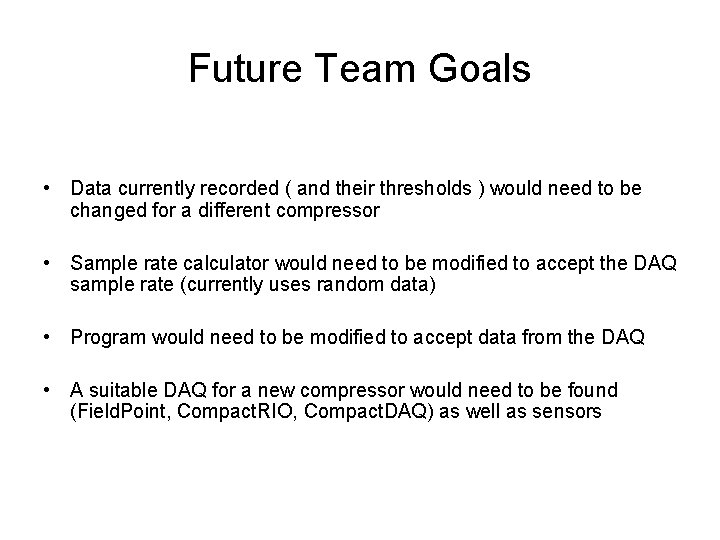
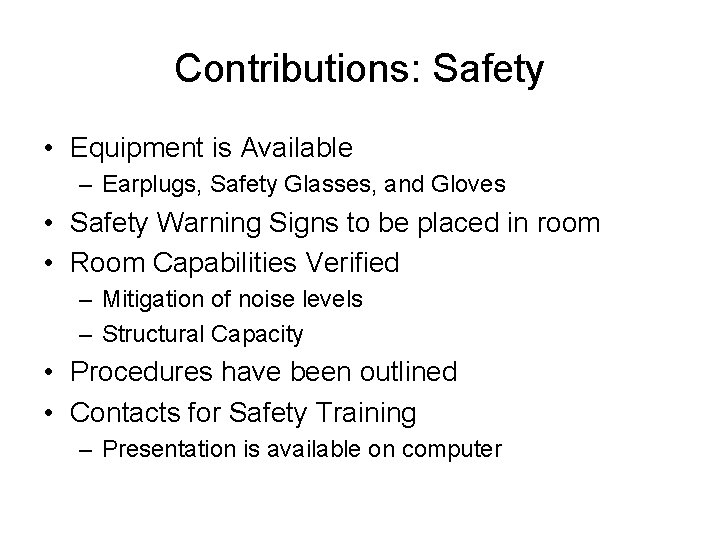
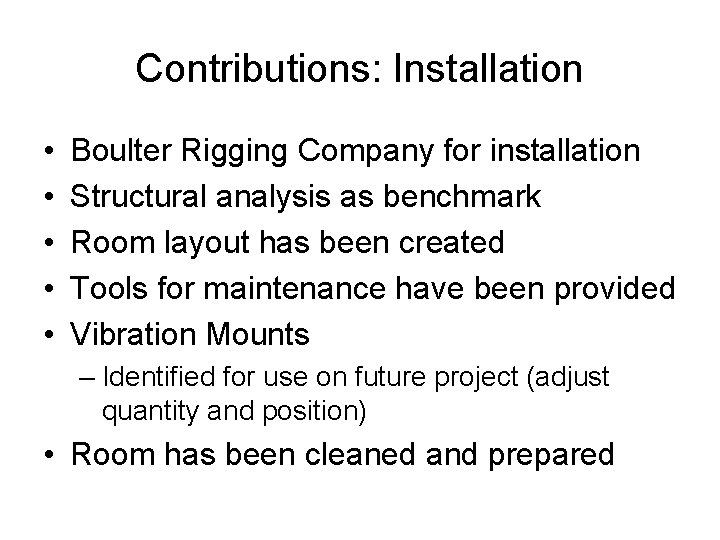
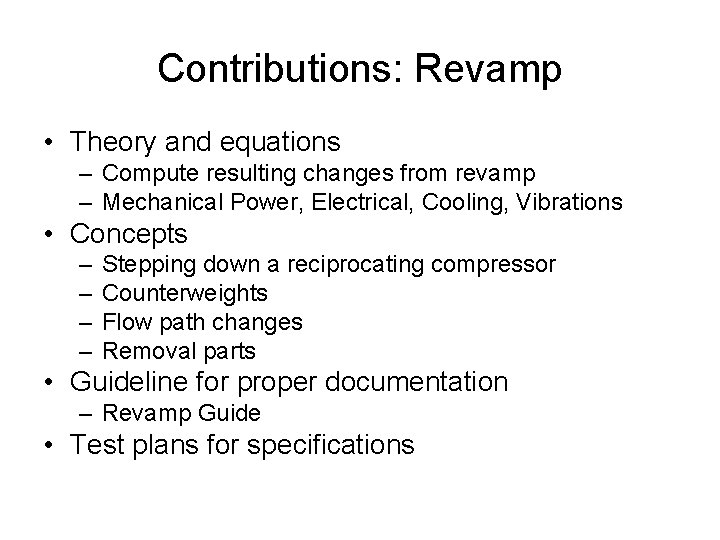
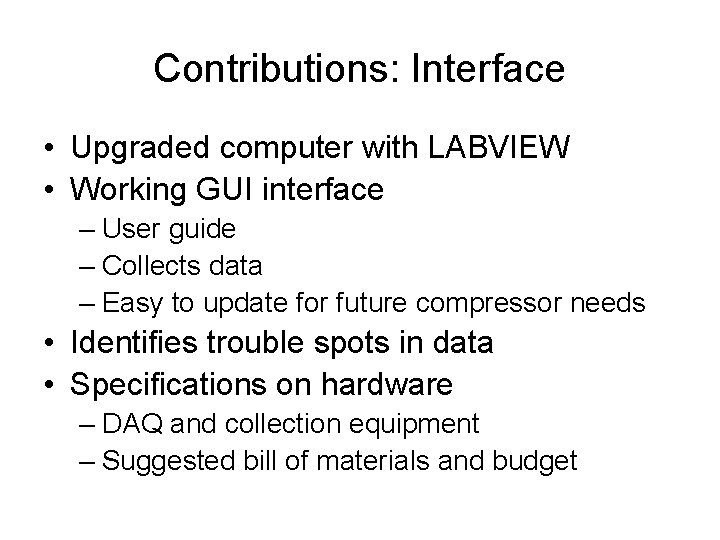
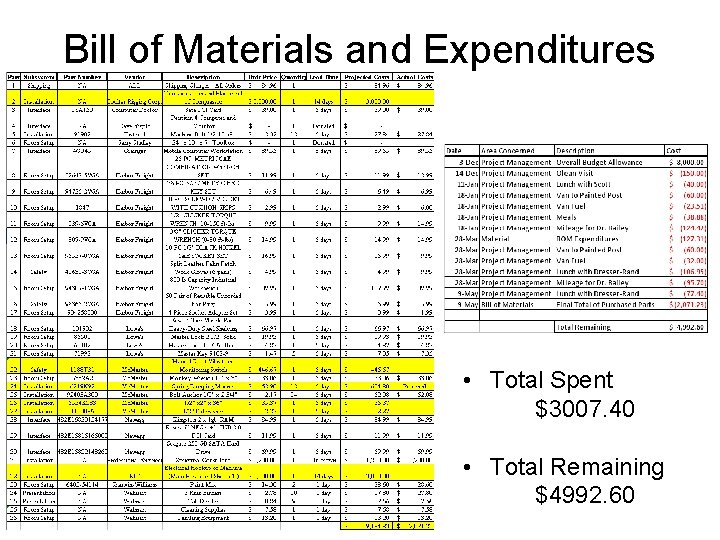
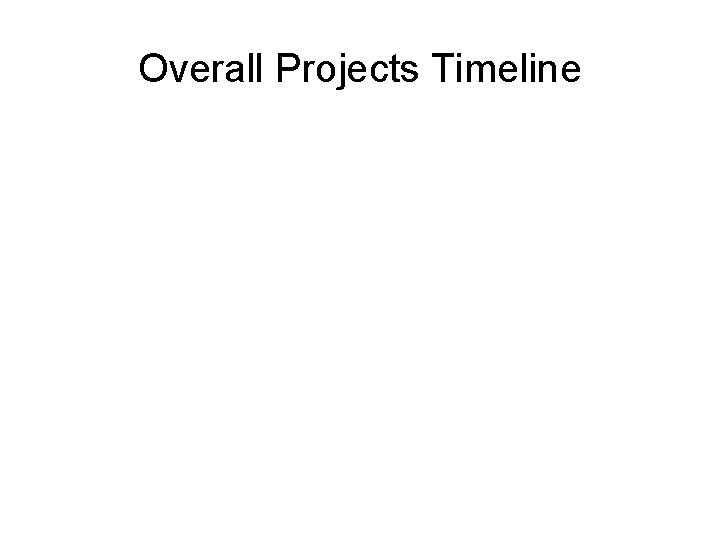
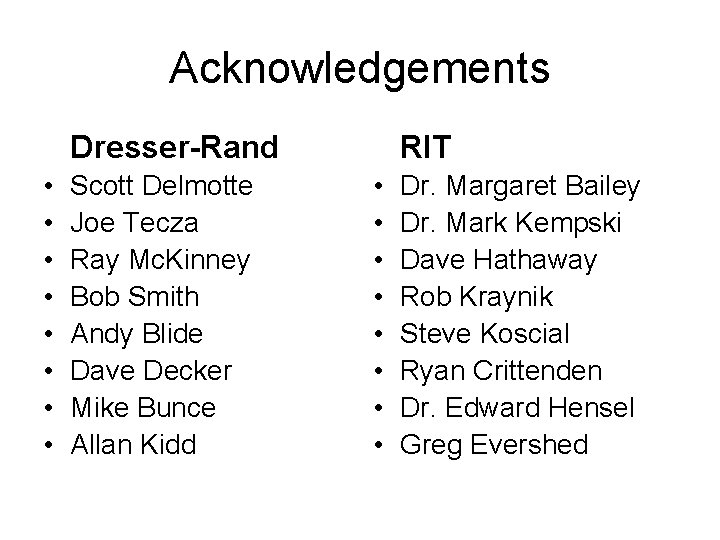
- Slides: 33
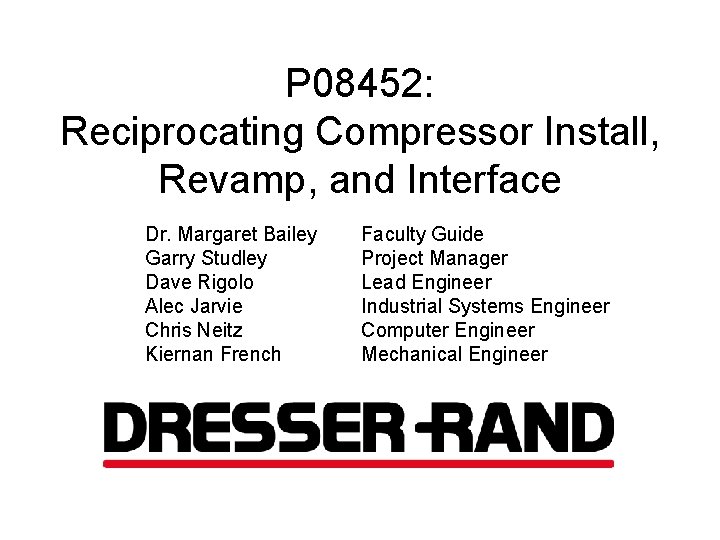
P 08452: Reciprocating Compressor Install, Revamp, and Interface Dr. Margaret Bailey Garry Studley Dave Rigolo Alec Jarvie Chris Neitz Kiernan French Faculty Guide Project Manager Lead Engineer Industrial Systems Engineer Computer Engineer Mechanical Engineer
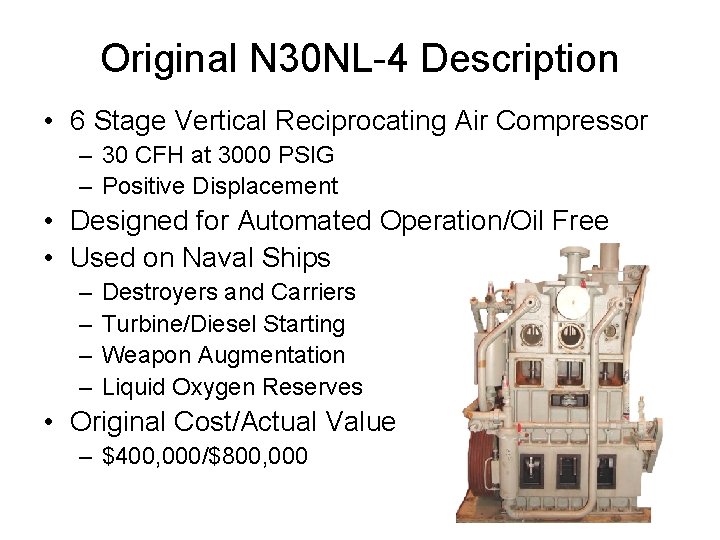
Original N 30 NL-4 Description • 6 Stage Vertical Reciprocating Air Compressor – 30 CFH at 3000 PSIG – Positive Displacement • Designed for Automated Operation/Oil Free • Used on Naval Ships – – Destroyers and Carriers Turbine/Diesel Starting Weapon Augmentation Liquid Oxygen Reserves • Original Cost/Actual Value – $400, 000/$800, 000
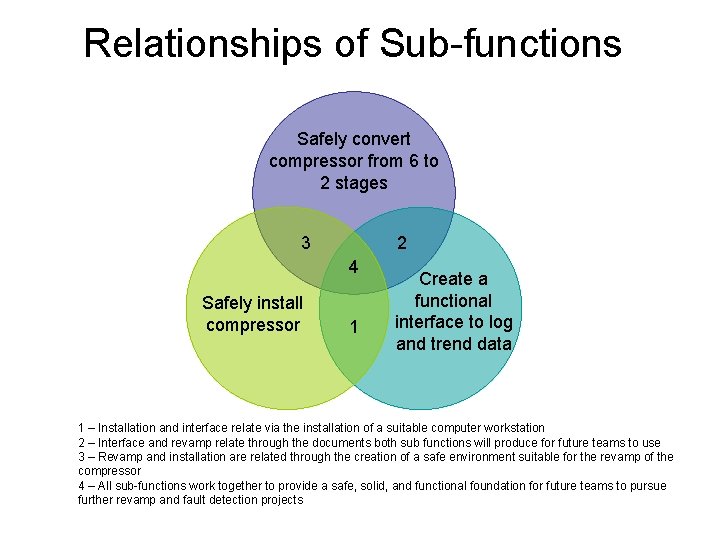
Relationships of Sub-functions Safely convert compressor from 6 to 2 stages 3 2 4 Safely install compressor 1 Create a functional interface to log and trend data 1 – Installation and interface relate via the installation of a suitable computer workstation 2 – Interface and revamp relate through the documents both sub functions will produce for future teams to use 3 – Revamp and installation are related through the creation of a safe environment suitable for the revamp of the compressor 4 – All sub-functions work together to provide a safe, solid, and functional foundation for future teams to pursue further revamp and fault detection projects
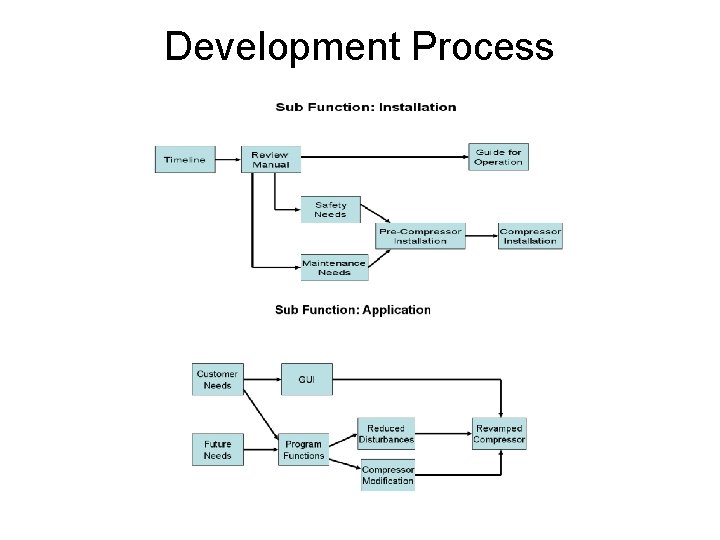
Development Process
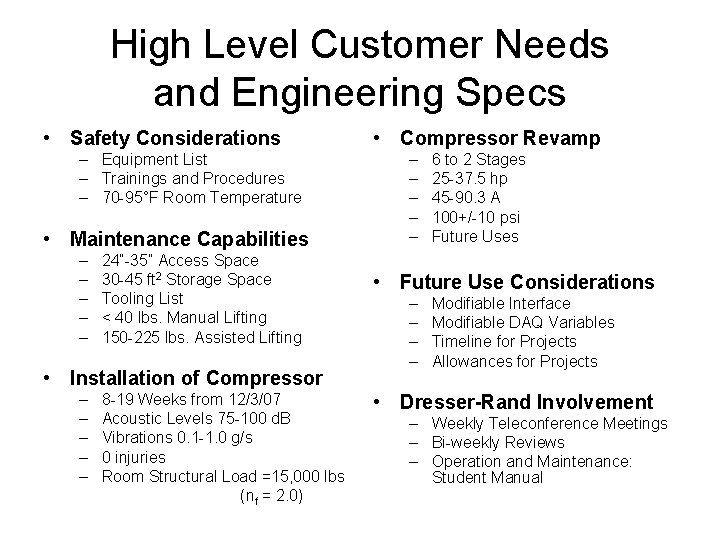
High Level Customer Needs and Engineering Specs • Safety Considerations – Equipment List – Trainings and Procedures – 70 -95°F Room Temperature • Maintenance Capabilities – – – 24”-35” Access Space 30 -45 ft 2 Storage Space Tooling List < 40 lbs. Manual Lifting 150 -225 lbs. Assisted Lifting • Installation of Compressor – – – 8 -19 Weeks from 12/3/07 Acoustic Levels 75 -100 d. B Vibrations 0. 1 -1. 0 g/s 0 injuries Room Structural Load =15, 000 lbs (nf = 2. 0) • Compressor Revamp – – – 6 to 2 Stages 25 -37. 5 hp 45 -90. 3 A 100+/-10 psi Future Uses • Future Use Considerations – – Modifiable Interface Modifiable DAQ Variables Timeline for Projects Allowances for Projects • Dresser-Rand Involvement – Weekly Teleconference Meetings – Bi-weekly Reviews – Operation and Maintenance: Student Manual
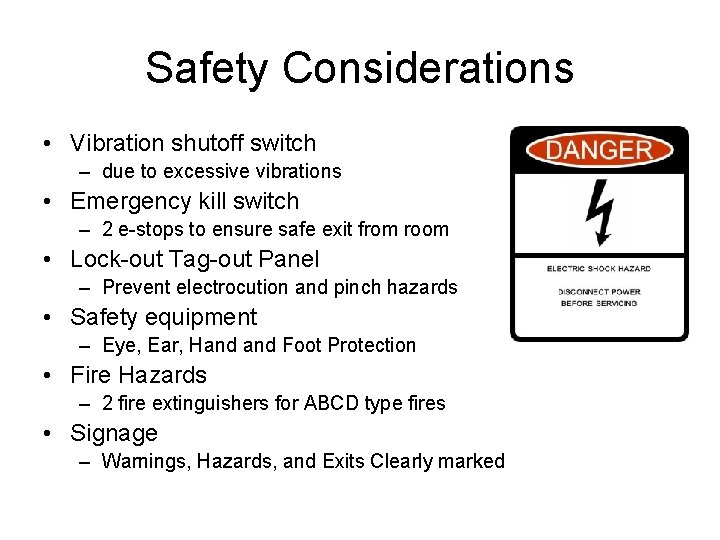
Safety Considerations • Vibration shutoff switch – due to excessive vibrations • Emergency kill switch – 2 e-stops to ensure safe exit from room • Lock-out Tag-out Panel – Prevent electrocution and pinch hazards • Safety equipment – Eye, Ear, Hand Foot Protection • Fire Hazards – 2 fire extinguishers for ABCD type fires • Signage – Warnings, Hazards, and Exits Clearly marked
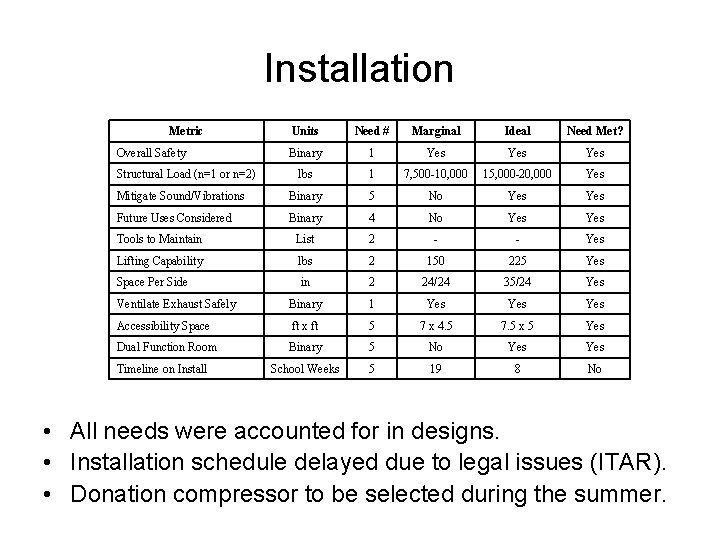
Installation Metric Units Need # Marginal Ideal Need Met? Binary 1 Yes Yes lbs 1 7, 500 -10, 000 15, 000 -20, 000 Yes Mitigate Sound/Vibrations Binary 5 No Yes Future Uses Considered Binary 4 No Yes Tools to Maintain List 2 - - Yes Lifting Capability lbs 2 150 225 Yes Space Per Side in 2 24/24 35/24 Yes Ventilate Exhaust Safely Binary 1 Yes Yes Accessibility Space ft x ft 5 7 x 4. 5 7. 5 x 5 Yes Dual Function Room Binary 5 No Yes School Weeks 5 19 8 No Overall Safety Structural Load (n=1 or n=2) Timeline on Install • All needs were accounted for in designs. • Installation schedule delayed due to legal issues (ITAR). • Donation compressor to be selected during the summer.
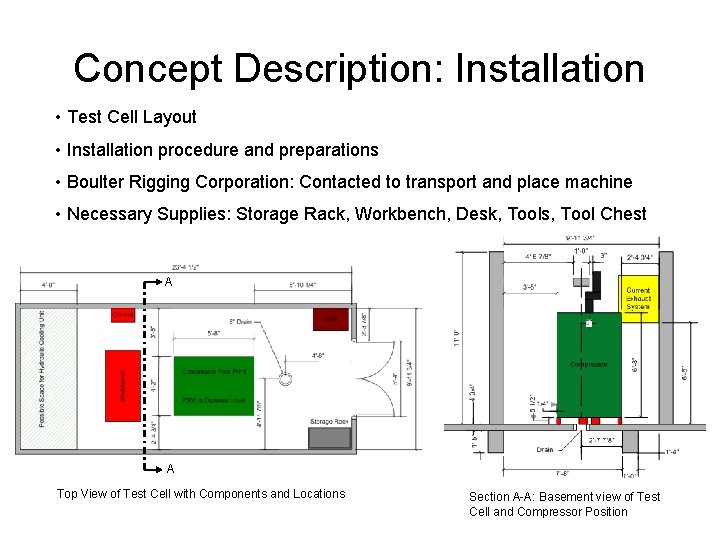
Concept Description: Installation • Test Cell Layout • Installation procedure and preparations • Boulter Rigging Corporation: Contacted to transport and place machine • Necessary Supplies: Storage Rack, Workbench, Desk, Tools, Tool Chest A A Top View of Test Cell with Components and Locations Section A-A: Basement view of Test Cell and Compressor Position
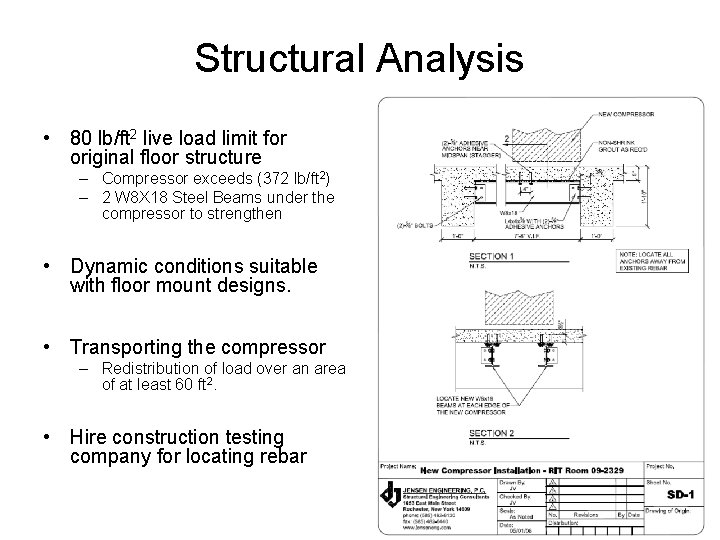
Structural Analysis • 80 lb/ft 2 live load limit for original floor structure – Compressor exceeds (372 lb/ft 2) – 2 W 8 X 18 Steel Beams under the compressor to strengthen • Dynamic conditions suitable with floor mount designs. • Transporting the compressor – Redistribution of load over an area of at least 60 ft 2. • Hire construction testing company for locating rebar
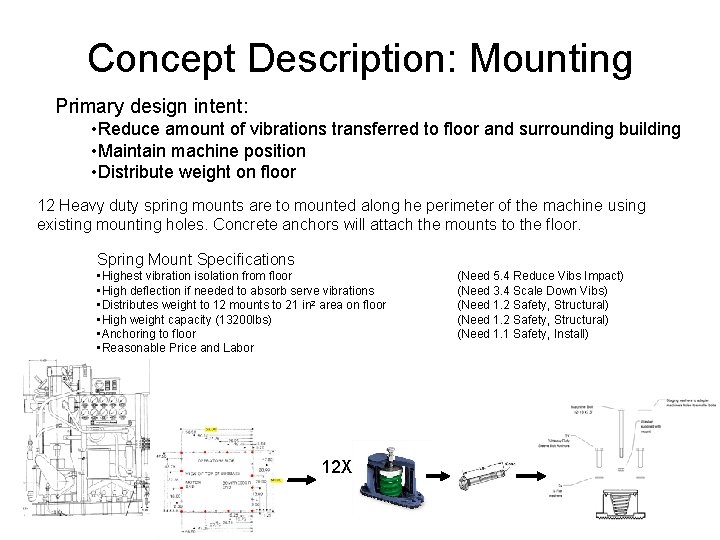
Concept Description: Mounting Primary design intent: • Reduce amount of vibrations transferred to floor and surrounding building • Maintain machine position • Distribute weight on floor 12 Heavy duty spring mounts are to mounted along he perimeter of the machine using existing mounting holes. Concrete anchors will attach the mounts to the floor. Spring Mount Specifications • Highest vibration isolation from floor • High deflection if needed to absorb serve vibrations • Distributes weight to 12 mounts to 21 in 2 area on floor • High weight capacity (13200 lbs) • Anchoring to floor • Reasonable Price and Labor 12 X (Need 5. 4 Reduce Vibs Impact) (Need 3. 4 Scale Down Vibs) (Need 1. 2 Safety, Structural) (Need 1. 1 Safety, Install)
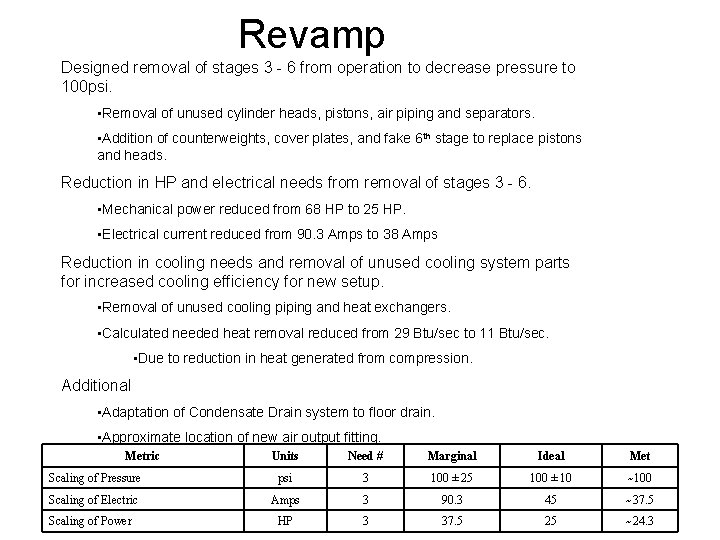
Revamp Designed removal of stages 3 - 6 from operation to decrease pressure to 100 psi. • Removal of unused cylinder heads, pistons, air piping and separators. • Addition of counterweights, cover plates, and fake 6 th stage to replace pistons and heads. Reduction in HP and electrical needs from removal of stages 3 - 6. • Mechanical power reduced from 68 HP to 25 HP. • Electrical current reduced from 90. 3 Amps to 38 Amps Reduction in cooling needs and removal of unused cooling system parts for increased cooling efficiency for new setup. • Removal of unused cooling piping and heat exchangers. • Calculated needed heat removal reduced from 29 Btu/sec to 11 Btu/sec. • Due to reduction in heat generated from compression. Additional • Adaptation of Condensate Drain system to floor drain. • Approximate location of new air output fitting. Metric Units Need # Marginal Ideal Met Scaling of Pressure psi 3 100 ± 25 100 ± 10 ~100 Scaling of Electric Amps 3 90. 3 45 ~37. 5 Scaling of Power HP 3 37. 5 25 ~24. 3
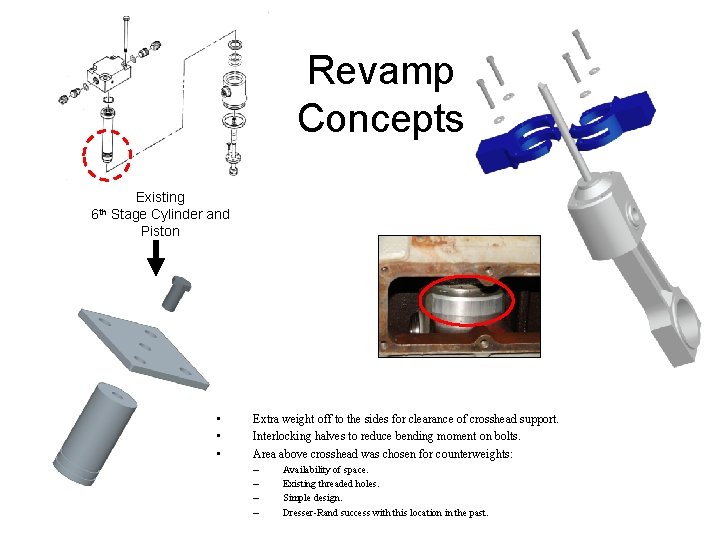
Revamp Concepts 6 th Existing Stage Cylinder and Piston • • • Extra weight off to the sides for clearance of crosshead support. Interlocking halves to reduce bending moment on bolts. Area above crosshead was chosen for counterweights: – – Availability of space. Existing threaded holes. Simple design. Dresser-Rand success with this location in the past.
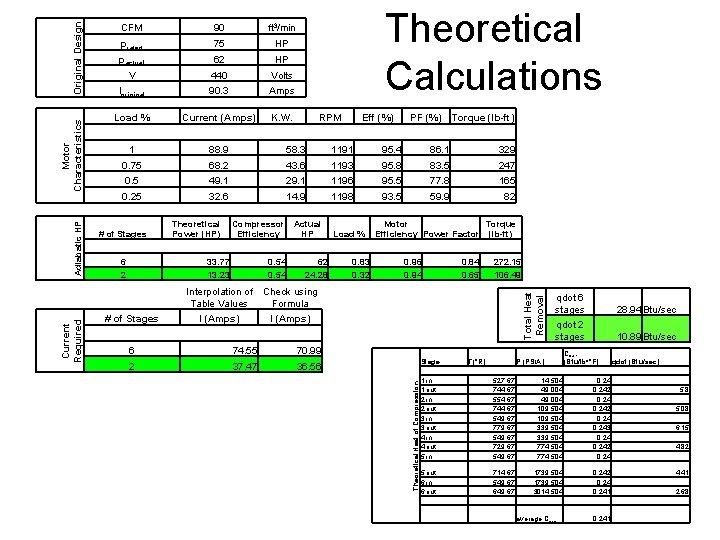
90 ft 3/min prated 75 HP pactual 62 HP V 440 Volts Ioriginal 90. 3 Amps Load % Current (Amps) K. W. 1 88. 9 58. 3 1191 95. 4 86. 1 329 0. 75 68. 2 43. 6 1193 95. 8 83. 5 247 0. 5 49. 1 29. 1 1196 95. 5 77. 8 165 0. 25 32. 6 14. 9 1198 93. 5 59. 9 82 # of Stages Theoretical Power (HP) RPM Compressor Actual Efficiency HP Eff (%) Load % PF (%) Torque (lb-ft) Motor Torque Efficiency Power Factor (lb-ft) 33. 77 0. 54 62 0. 83 0. 96 0. 84 272. 15 2 13. 23 0. 54 24. 28 0. 32 0. 94 0. 65 106. 49 # of Stages 6 2 Interpolation of Table Values Check using Formula I (Amps) 74. 55 37. 47 Total Heat Removal 6 qdot 6 stages qdot 2 stages 70. 99 Stage 36. 56 Theoretical Heat of Compression Original Design Motor Characteristics Adiabatic HP Current Required Theoretical Calculations CFM T(°R) P (PSIA) 28. 94 Btu/sec 10. 89 Btu/sec Cpair (Btu/lb*°F) 1 in 1 out 2 in 2 out 3 in 3 out 4 in 4 out 5 in 527. 67 744. 67 554. 67 744. 67 549. 67 779. 67 549. 67 729. 67 549. 67 14. 504 49. 004 109. 504 339. 504 774. 504 0. 242 0. 243 0. 242 0. 24 5 out 6 in 6 out 714. 67 549. 67 649. 67 1739. 504 3014. 504 0. 242 0. 241 average Cpair 0. 241 qdot (Btu/sec) 5. 8 5. 08 6. 15 4. 82 4. 41 2. 68
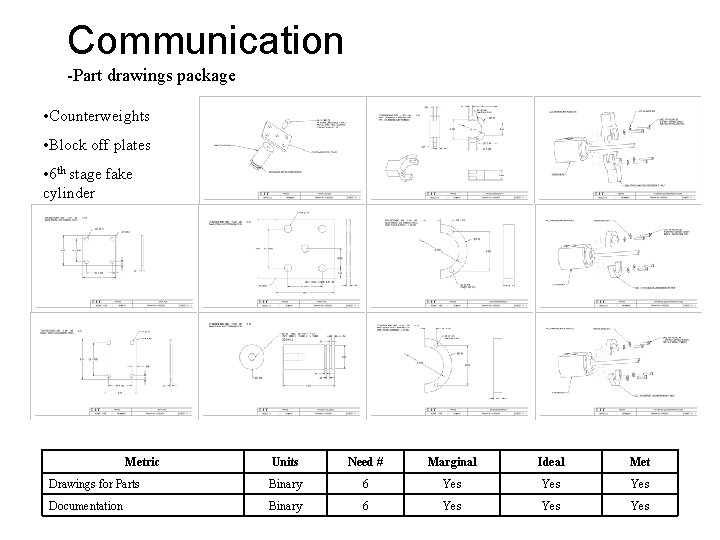
Communication -Part drawings package • Counterweights • Block off plates • 6 th stage fake cylinder Metric Units Need # Marginal Ideal Met Drawings for Parts Binary 6 Yes Yes Documentation Binary 6 Yes Yes
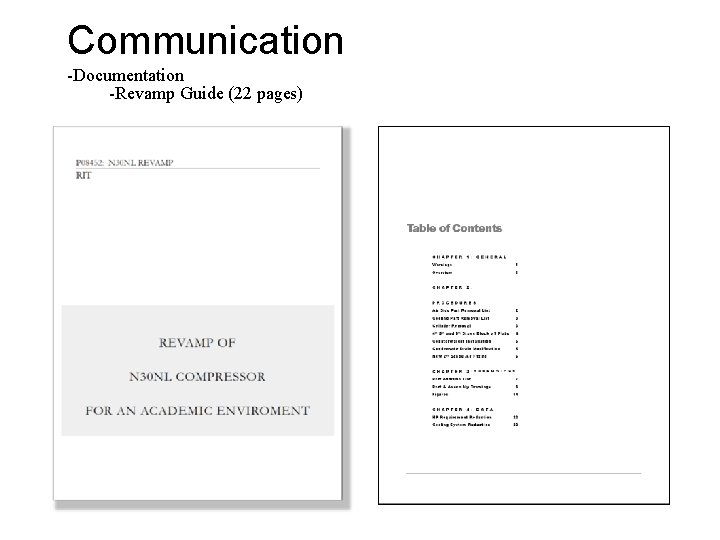
Communication -Documentation -Revamp Guide (22 pages)
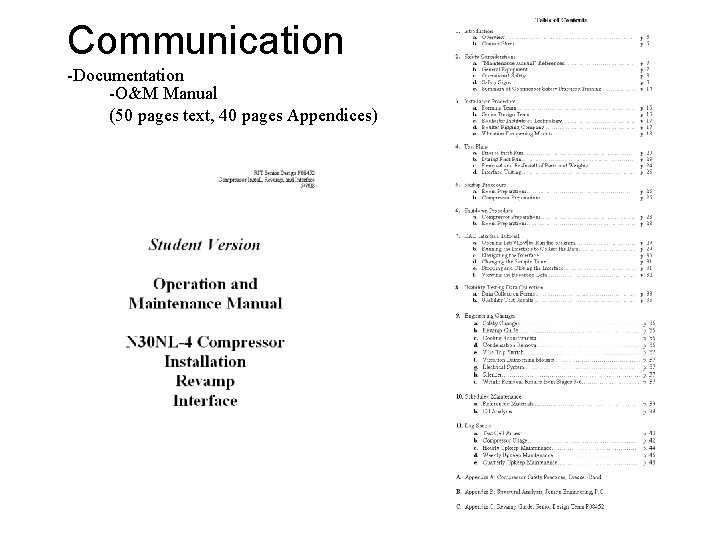
Communication -Documentation -O&M Manual (50 pages text, 40 pages Appendices)
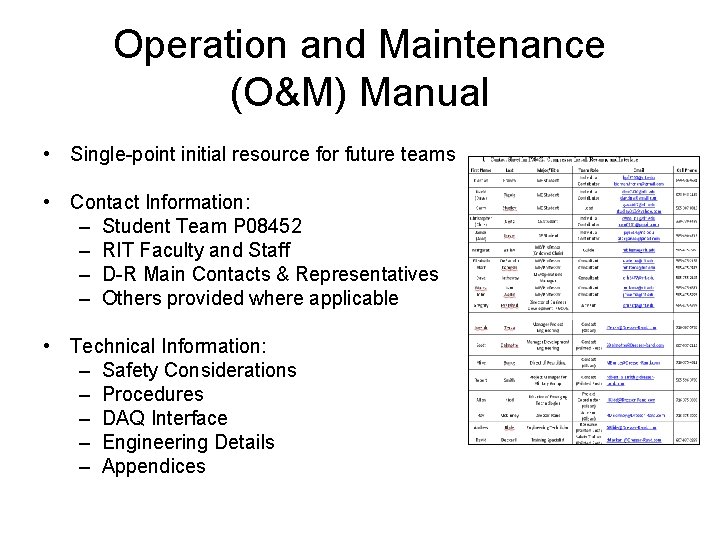
Operation and Maintenance (O&M) Manual • Single-point initial resource for future teams • Contact Information: – Student Team P 08452 – RIT Faculty and Staff – D-R Main Contacts & Representatives – Others provided where applicable • Technical Information: – Safety Considerations – Procedures – DAQ Interface – Engineering Details – Appendices
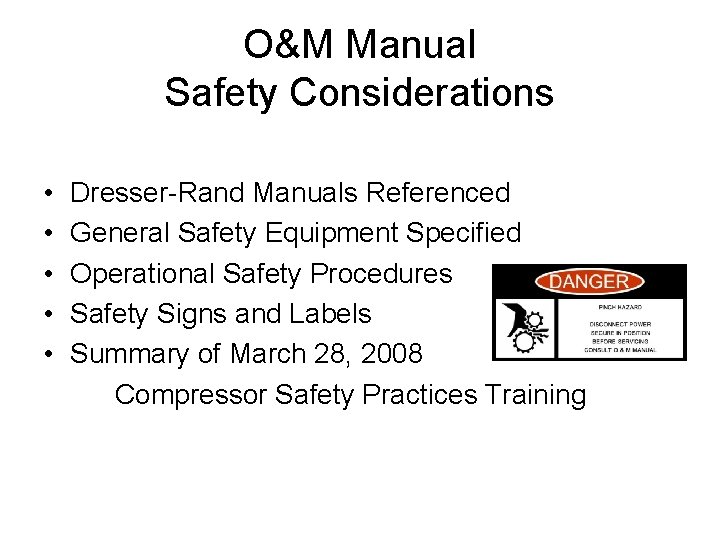
O&M Manual Safety Considerations • • • Dresser-Rand Manuals Referenced General Safety Equipment Specified Operational Safety Procedures Safety Signs and Labels Summary of March 28, 2008 Compressor Safety Practices Training
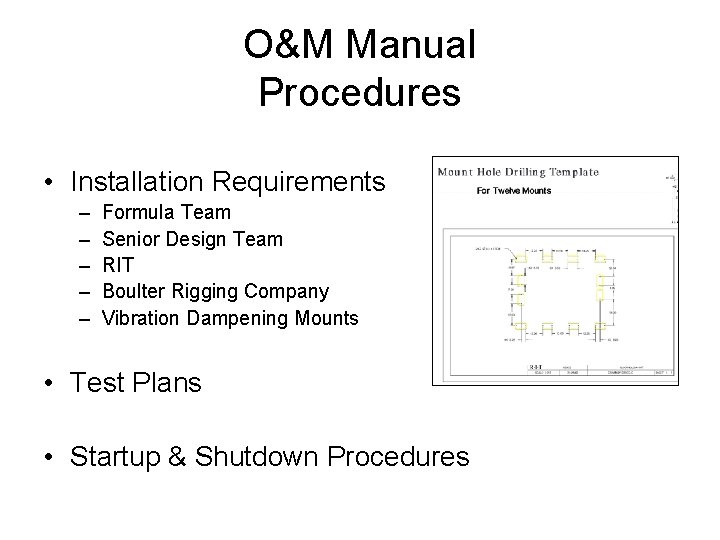
O&M Manual Procedures • Installation Requirements – – – Formula Team Senior Design Team RIT Boulter Rigging Company Vibration Dampening Mounts • Test Plans • Startup & Shutdown Procedures
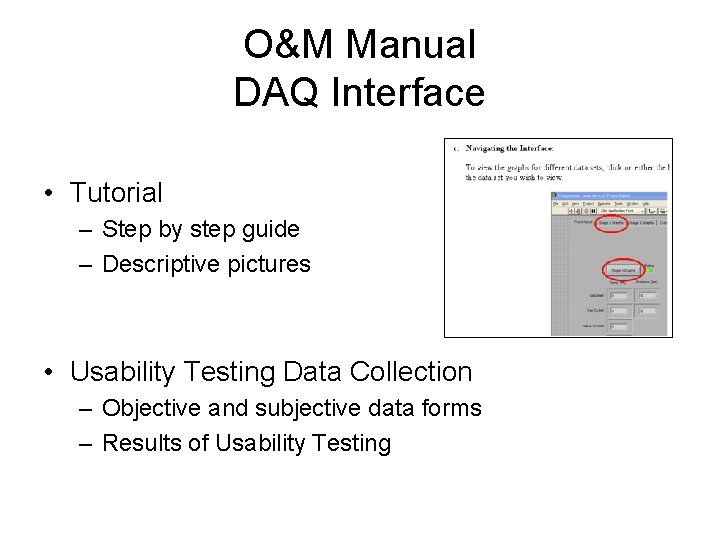
O&M Manual DAQ Interface • Tutorial – Step by step guide – Descriptive pictures • Usability Testing Data Collection – Objective and subjective data forms – Results of Usability Testing
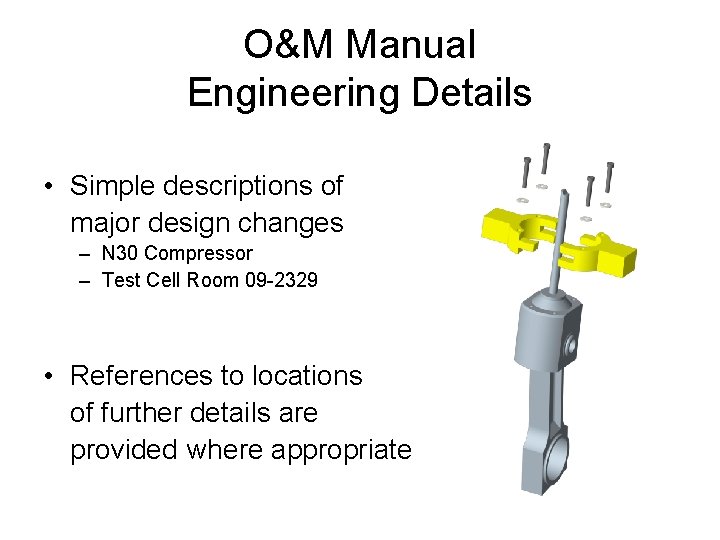
O&M Manual Engineering Details • Simple descriptions of major design changes – N 30 Compressor – Test Cell Room 09 -2329 • References to locations of further details are provided where appropriate
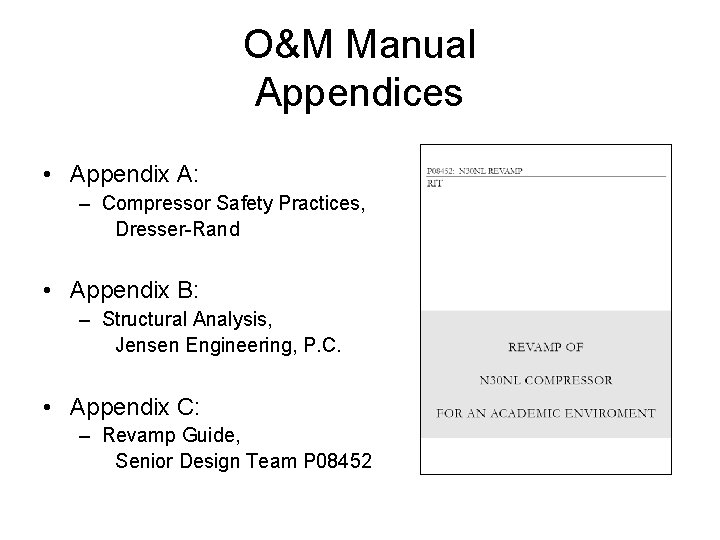
O&M Manual Appendices • Appendix A: – Compressor Safety Practices, Dresser-Rand • Appendix B: – Structural Analysis, Jensen Engineering, P. C. • Appendix C: – Revamp Guide, Senior Design Team P 08452
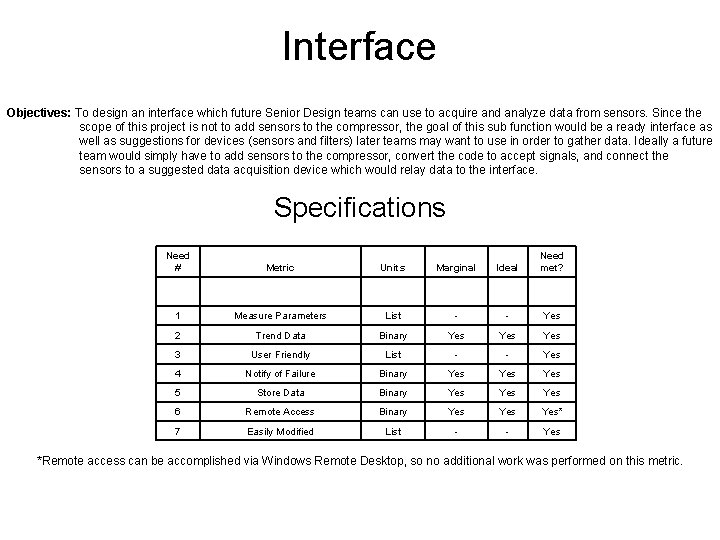
Interface Objectives: To design an interface which future Senior Design teams can use to acquire and analyze data from sensors. Since the scope of this project is not to add sensors to the compressor, the goal of this sub function would be a ready interface as well as suggestions for devices (sensors and filters) later teams may want to use in order to gather data. Ideally a future team would simply have to add sensors to the compressor, convert the code to accept signals, and connect the sensors to a suggested data acquisition device which would relay data to the interface. Specifications Need # Metric Units Marginal Ideal Need met? 1 Measure Parameters List - - Yes 2 Trend Data Binary Yes Yes 3 User Friendly List - - Yes 4 Notify of Failure Binary Yes Yes 5 Store Data Binary Yes Yes 6 Remote Access Binary Yes Yes* 7 Easily Modified List - - Yes *Remote access can be accomplished via Windows Remote Desktop, so no additional work was performed on this metric.
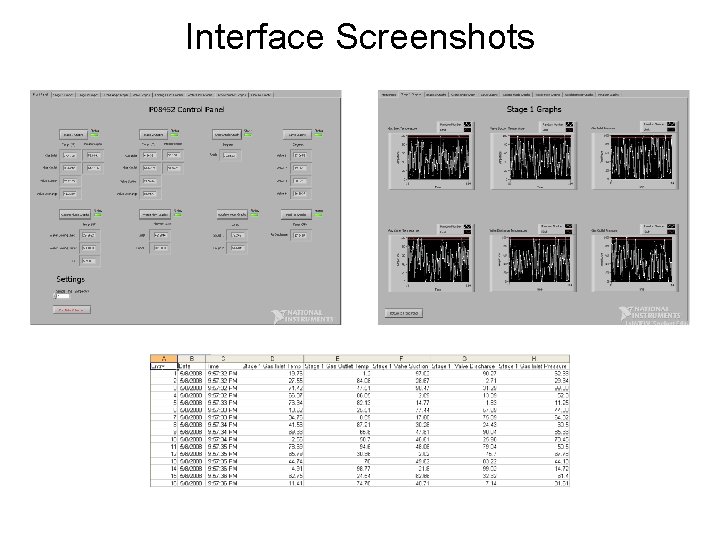
Interface Screenshots
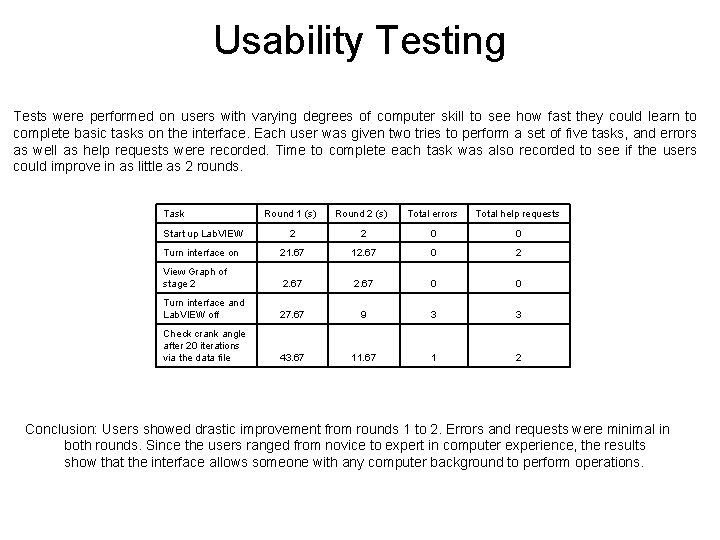
Usability Testing Tests were performed on users with varying degrees of computer skill to see how fast they could learn to complete basic tasks on the interface. Each user was given two tries to perform a set of five tasks, and errors as well as help requests were recorded. Time to complete each task was also recorded to see if the users could improve in as little as 2 rounds. Task Round 1 (s) Round 2 (s) Total errors Total help requests Start up Lab. VIEW 2 2 0 0 Turn interface on 21. 67 12. 67 0 2 View Graph of stage 2 2. 67 0 0 Turn interface and Lab. VIEW off 27. 67 9 3 3 Check crank angle after 20 iterations via the data file 43. 67 11. 67 1 2 Conclusion: Users showed drastic improvement from rounds 1 to 2. Errors and requests were minimal in both rounds. Since the users ranged from novice to expert in computer experience, the results show that the interface allows someone with any computer background to perform operations.
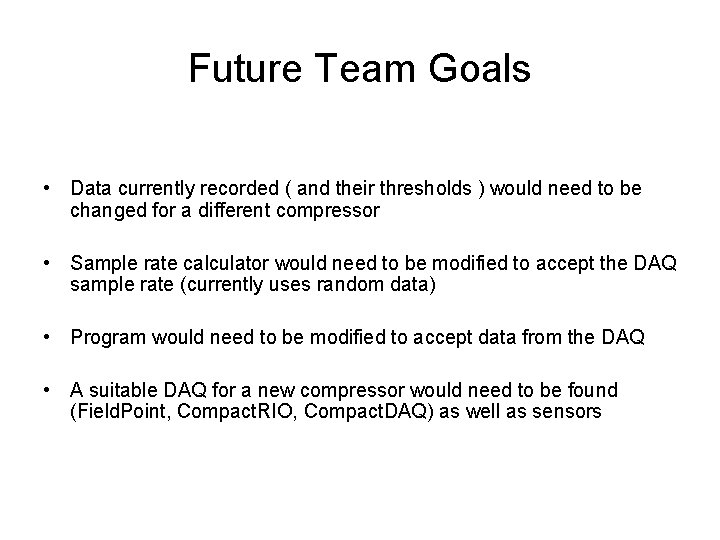
Future Team Goals • Data currently recorded ( and their thresholds ) would need to be changed for a different compressor • Sample rate calculator would need to be modified to accept the DAQ sample rate (currently uses random data) • Program would need to be modified to accept data from the DAQ • A suitable DAQ for a new compressor would need to be found (Field. Point, Compact. RIO, Compact. DAQ) as well as sensors
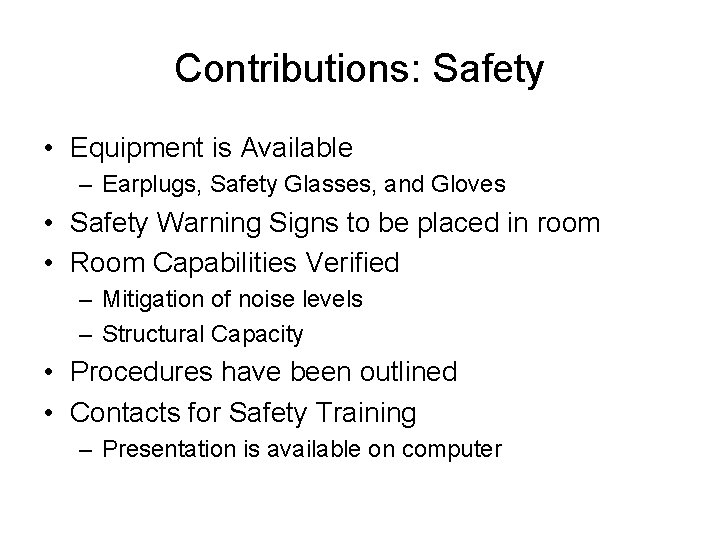
Contributions: Safety • Equipment is Available – Earplugs, Safety Glasses, and Gloves • Safety Warning Signs to be placed in room • Room Capabilities Verified – Mitigation of noise levels – Structural Capacity • Procedures have been outlined • Contacts for Safety Training – Presentation is available on computer
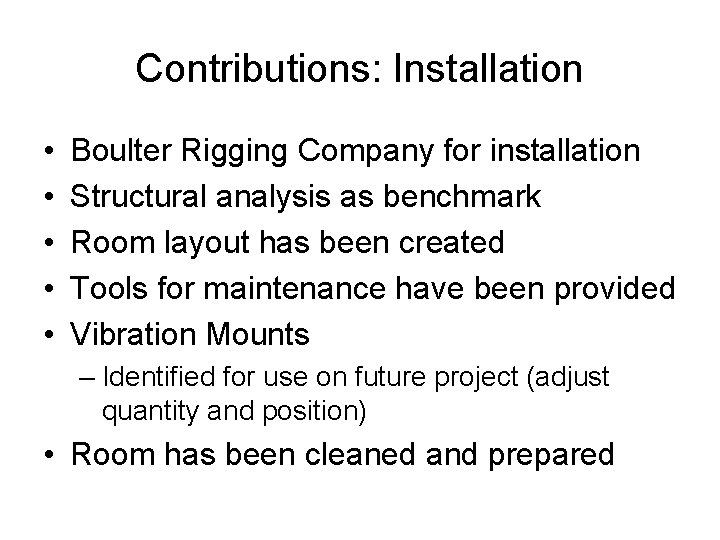
Contributions: Installation • • • Boulter Rigging Company for installation Structural analysis as benchmark Room layout has been created Tools for maintenance have been provided Vibration Mounts – Identified for use on future project (adjust quantity and position) • Room has been cleaned and prepared
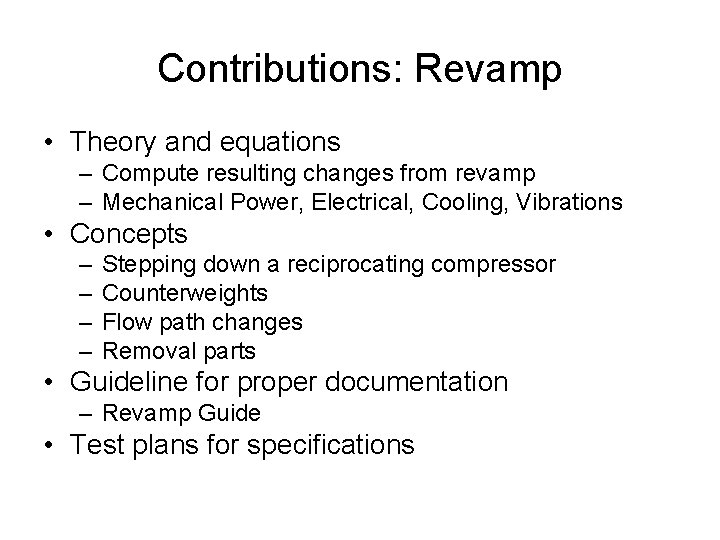
Contributions: Revamp • Theory and equations – Compute resulting changes from revamp – Mechanical Power, Electrical, Cooling, Vibrations • Concepts – – Stepping down a reciprocating compressor Counterweights Flow path changes Removal parts • Guideline for proper documentation – Revamp Guide • Test plans for specifications
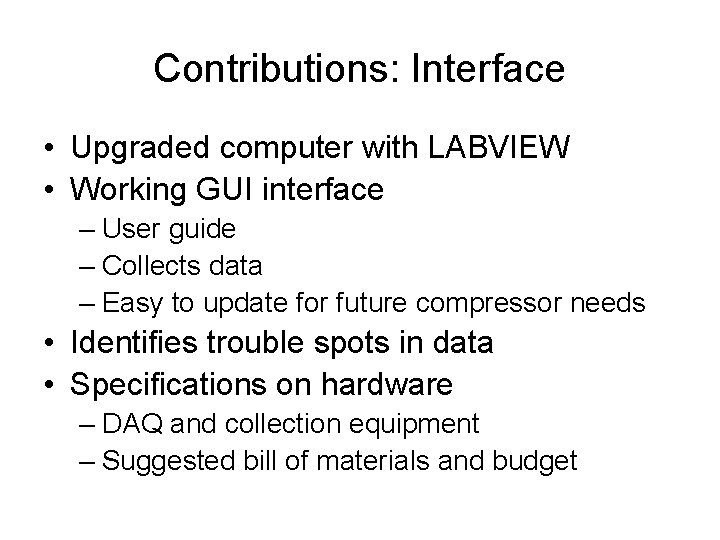
Contributions: Interface • Upgraded computer with LABVIEW • Working GUI interface – User guide – Collects data – Easy to update for future compressor needs • Identifies trouble spots in data • Specifications on hardware – DAQ and collection equipment – Suggested bill of materials and budget
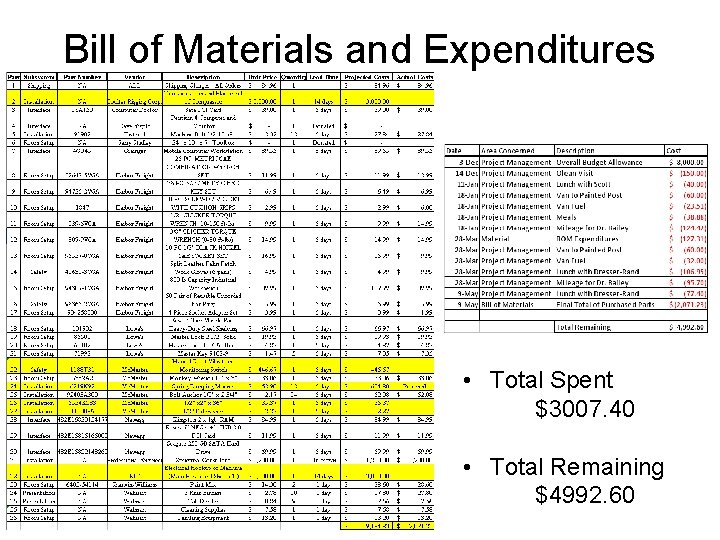
Bill of Materials and Expenditures • Total Spent $3007. 40 • Total Remaining $4992. 60
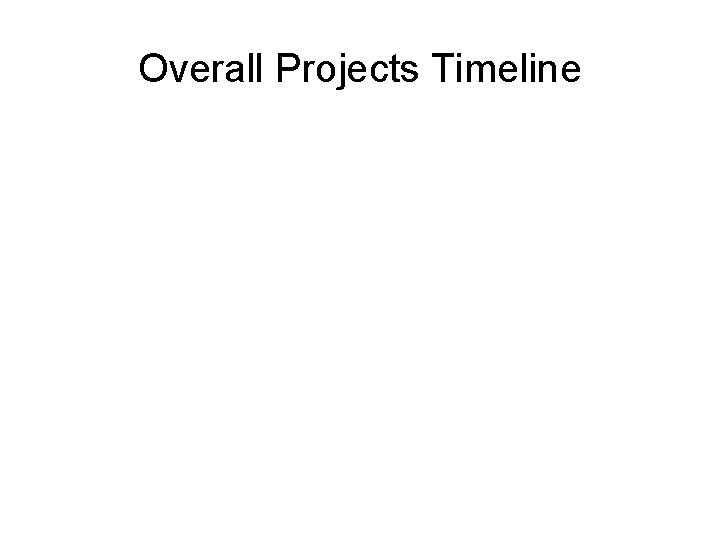
Overall Projects Timeline
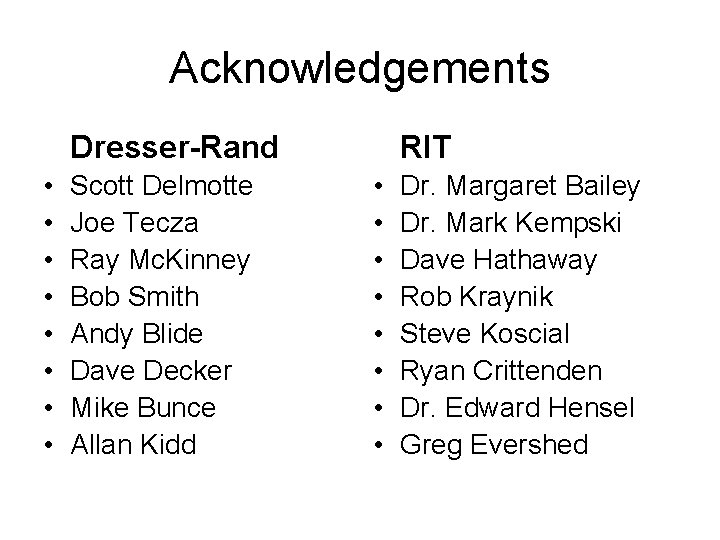
Acknowledgements Dresser-Rand • • Scott Delmotte Joe Tecza Ray Mc. Kinney Bob Smith Andy Blide Dave Decker Mike Bunce Allan Kidd RIT • • Dr. Margaret Bailey Dr. Mark Kempski Dave Hathaway Rob Kraynik Steve Koscial Ryan Crittenden Dr. Edward Hensel Greg Evershed
Single acting reciprocating air compressor
Isothermal efficiency of reciprocating compressor
A reciprocating compressor handles
Interface in interface java
Fluidity in hci
Industrial interfaces
An interface
Bharat pumps and compressors
Orthodromic reciprocating tachycardia
Classification of reciprocating pump
Fail safe hydraulic circuit
Mact zzzz flowchart
Radial engine valve operating mechanism
Generally speaking, the use of carburetor heat tends to
Classification of shaper machine
Reciprocating pump image
Gerak bolak-balik di sekitar kedudukan
Lab 3-5: install and configure dhcp and dns servers
Indoor outdoor communication error
Fixed displacement compressor symbol
How a jet engine works animation
Multipurpose refrigeration systems with a single compressor
York turbomaster compressor
Isentropic efficiency of a compressor
Gas turbine working principle
Compressor stonewall
Asb45r
Ccc compressor anti surge control
Gambar actuator silinder double action adalah
Helirotor compressor
State second law of thermodynamics
Pdr compressor
Air compressor introduction
First law of thermodynamics compressor