Modular DCDC System Design Done Right Nathan Yang
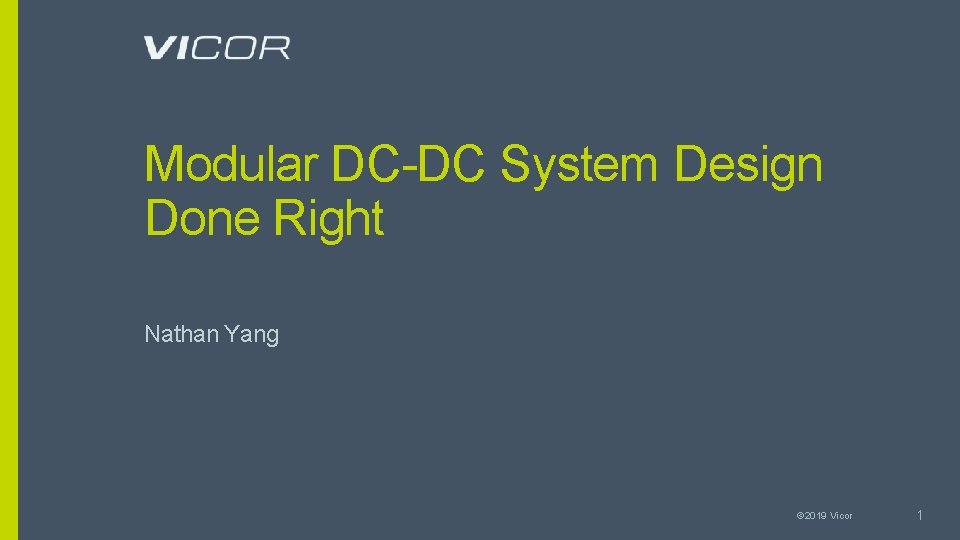
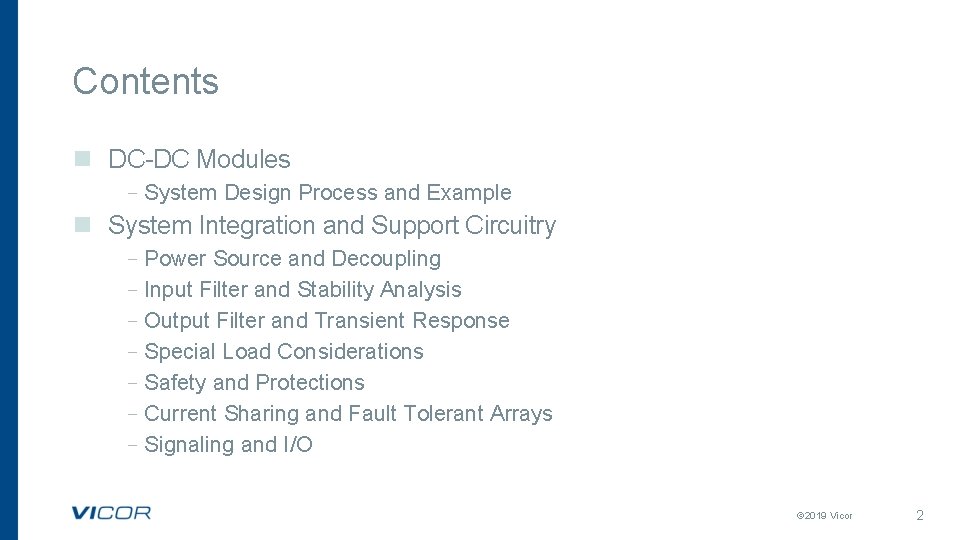
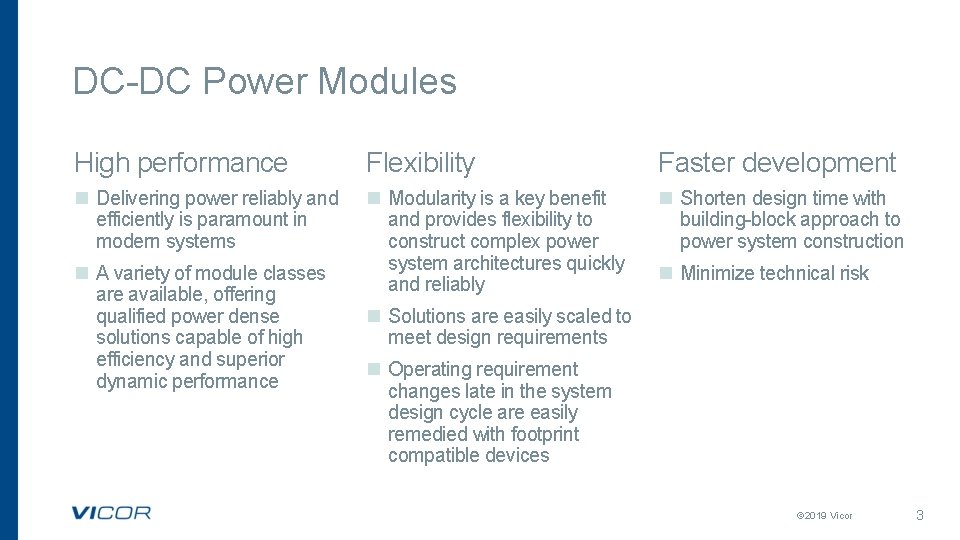
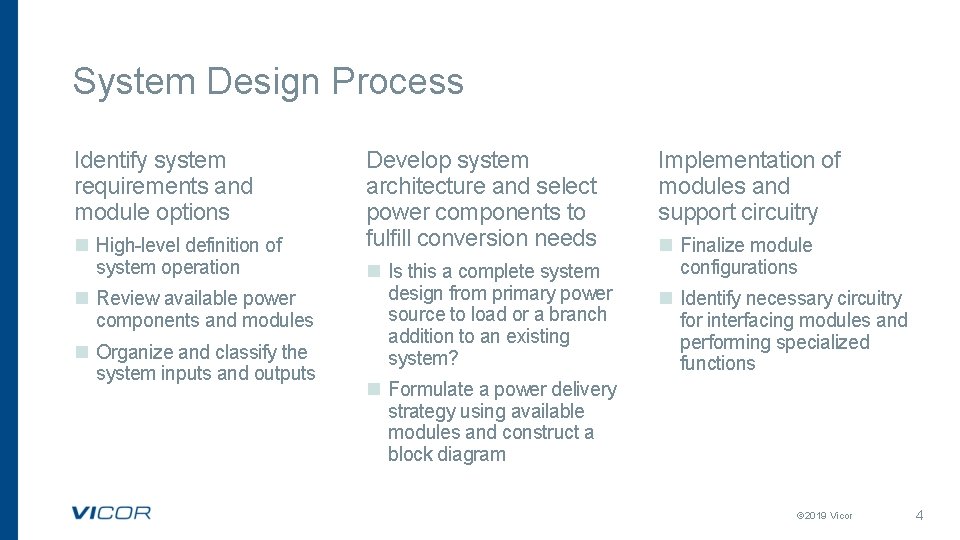
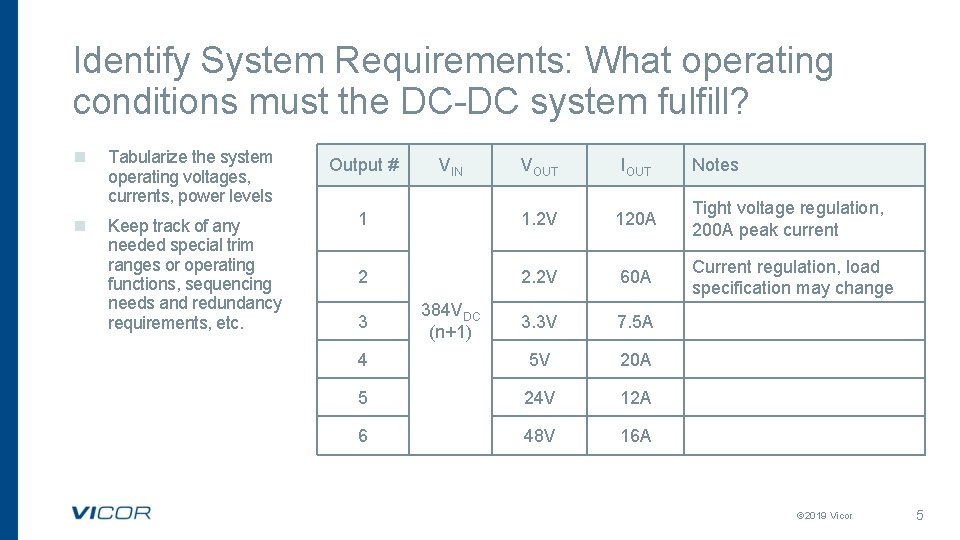
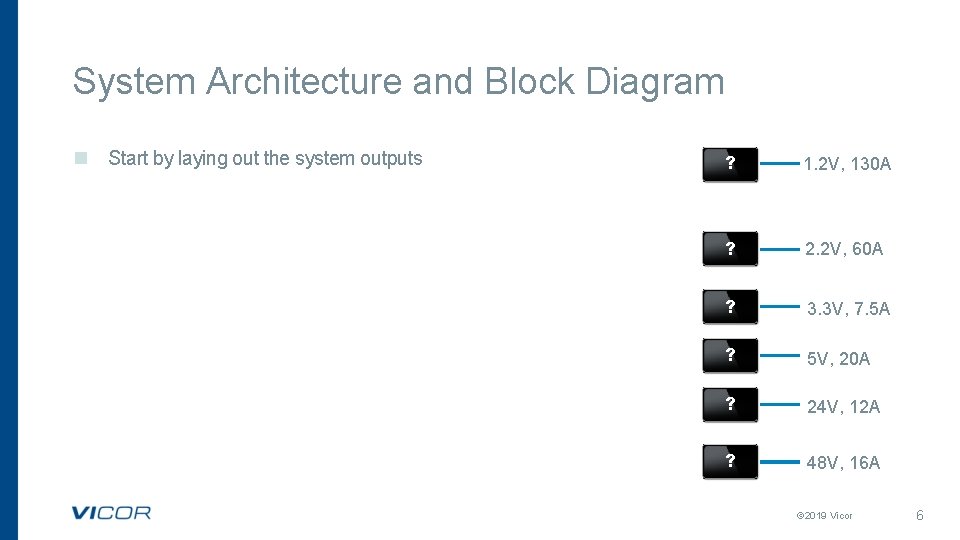
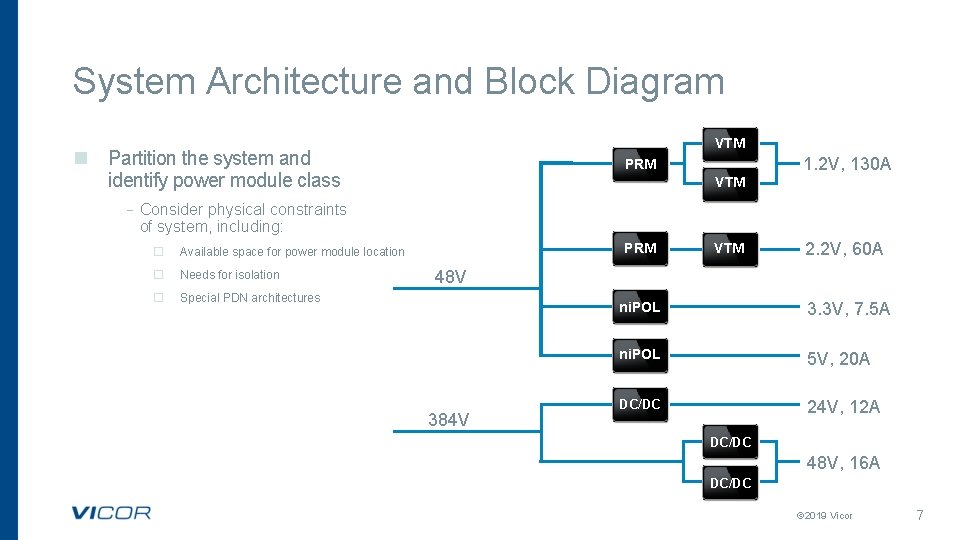
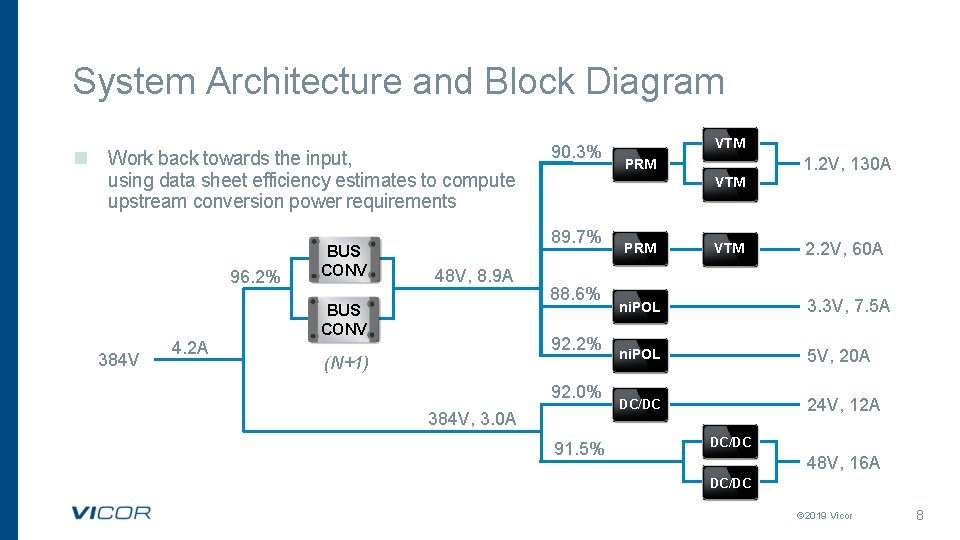
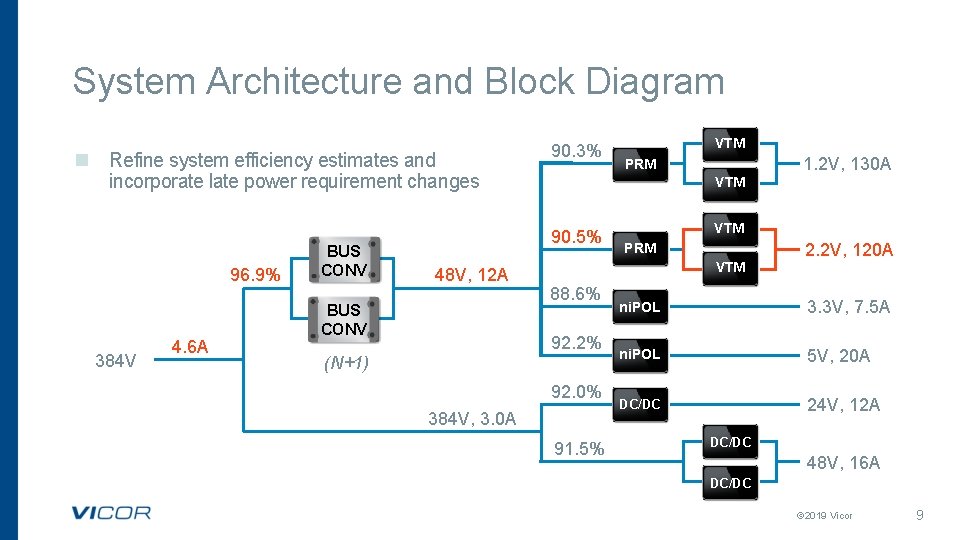
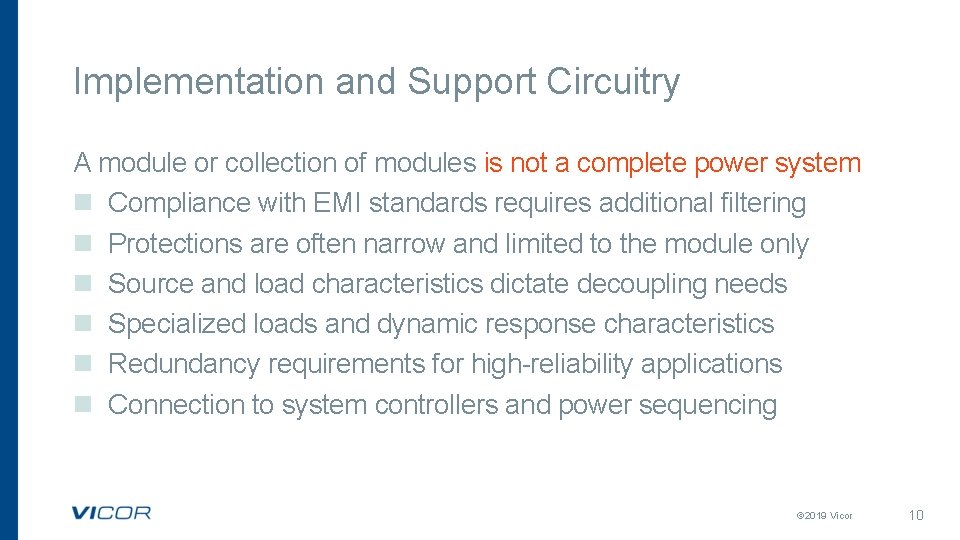
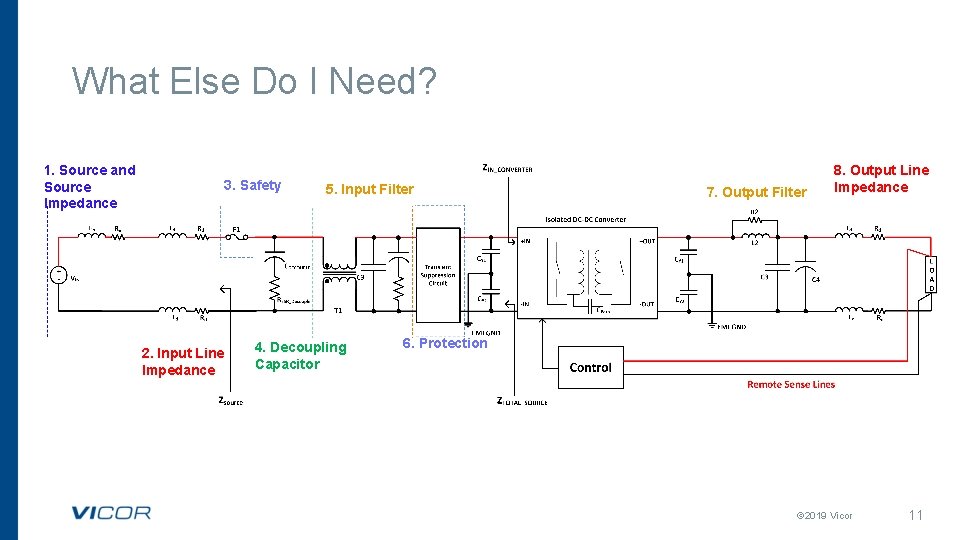
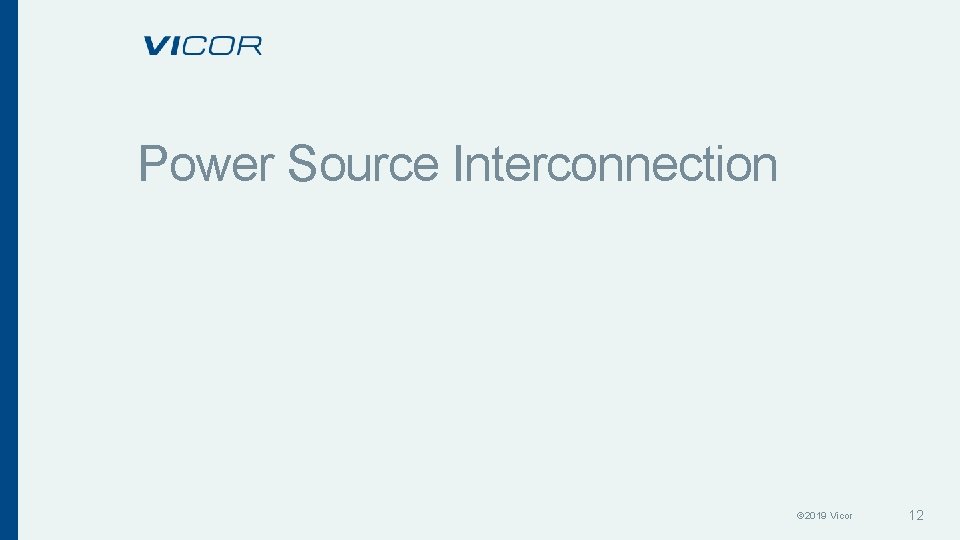
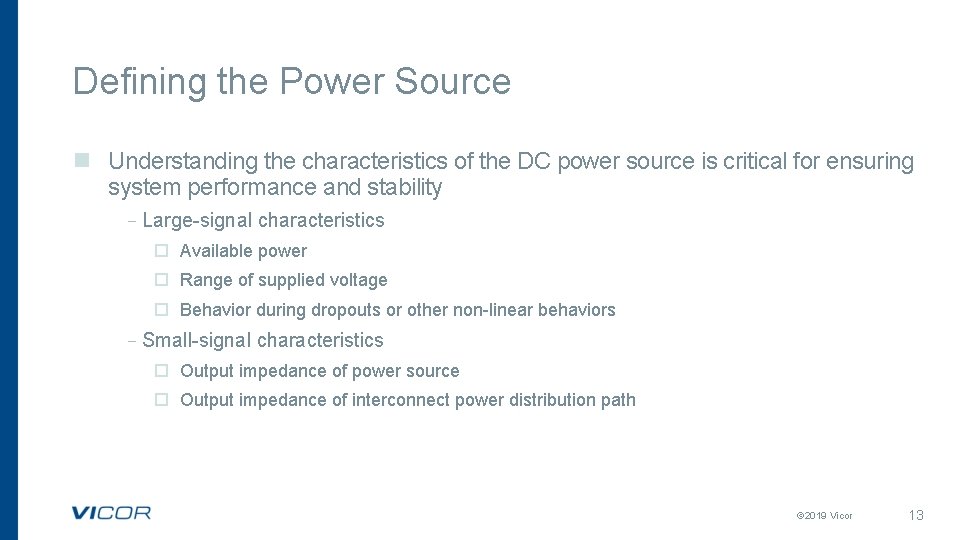
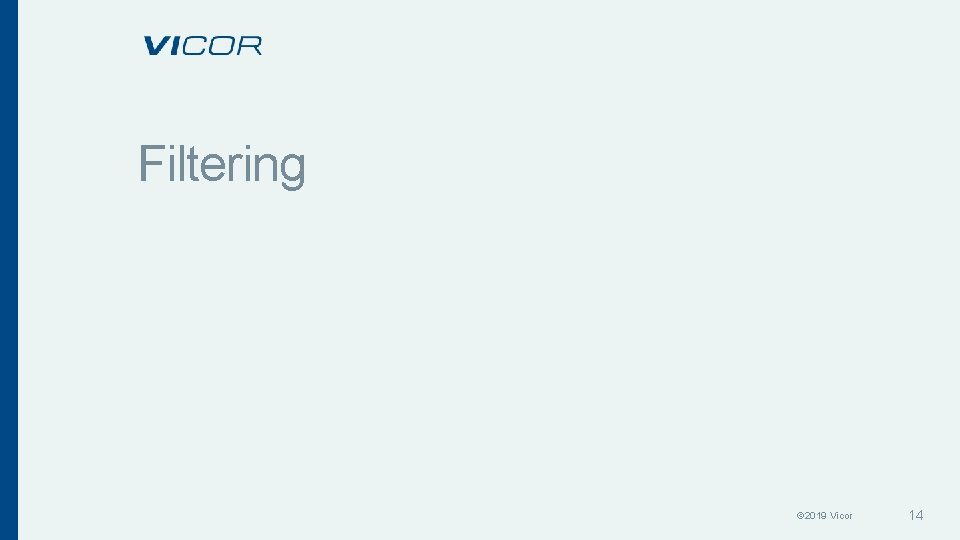
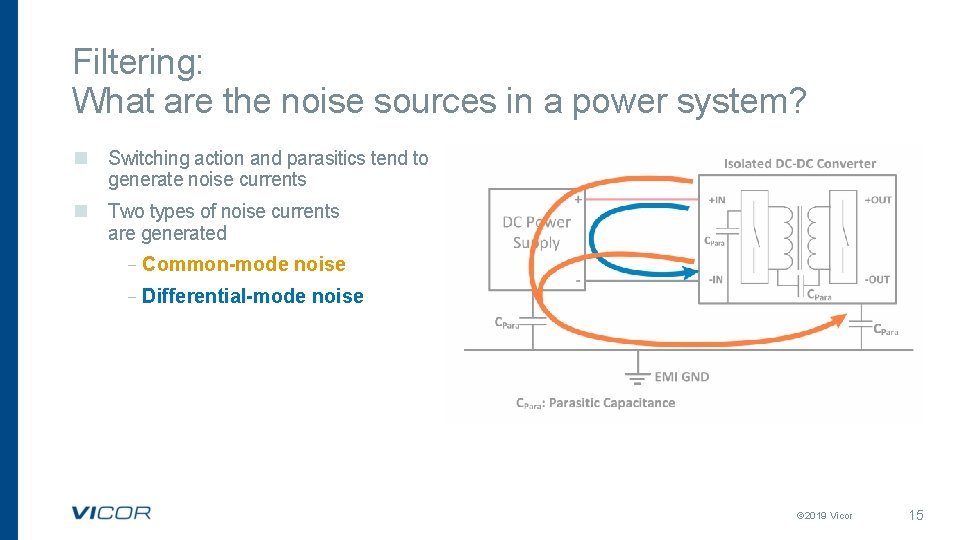
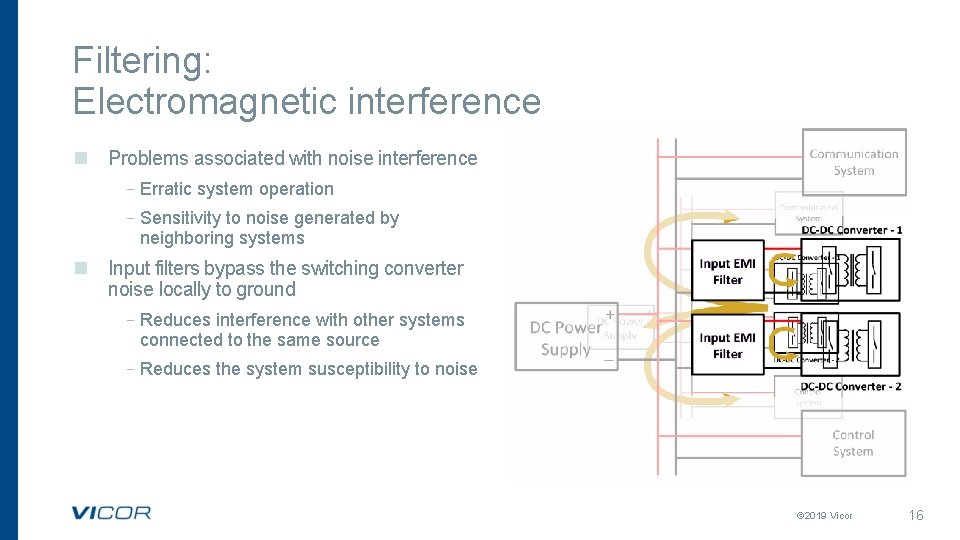
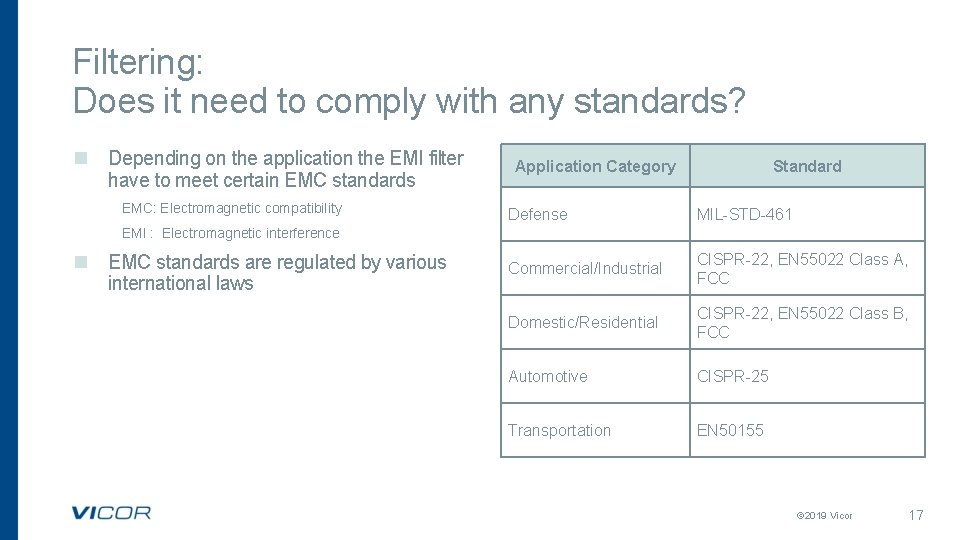
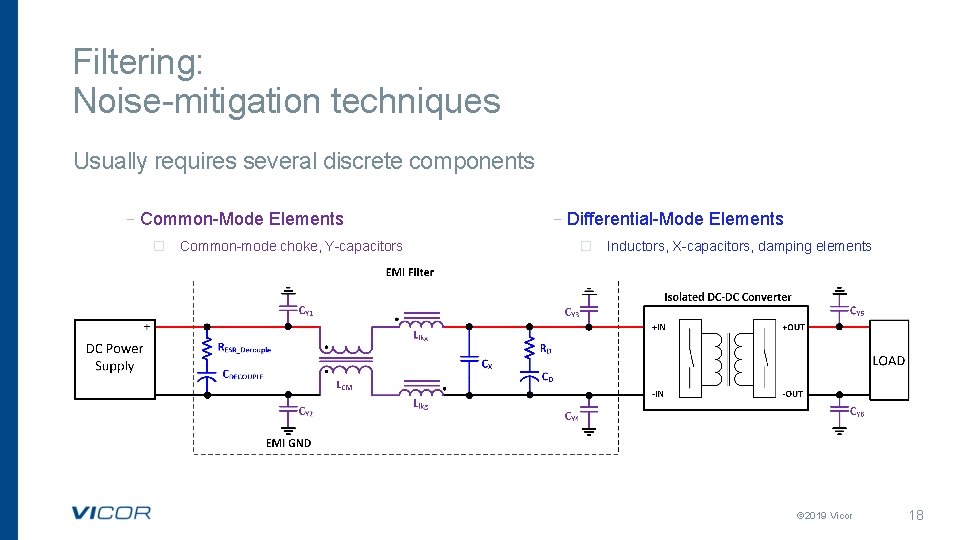
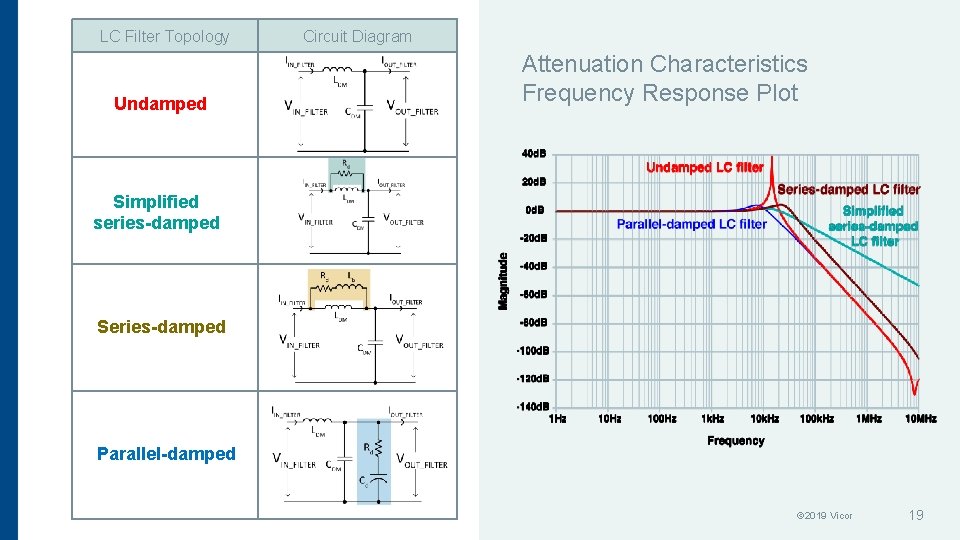
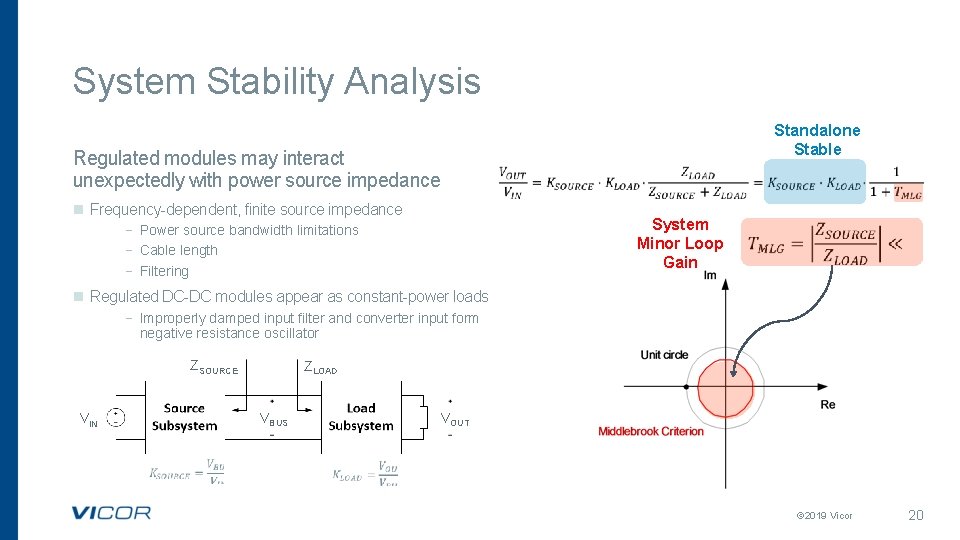
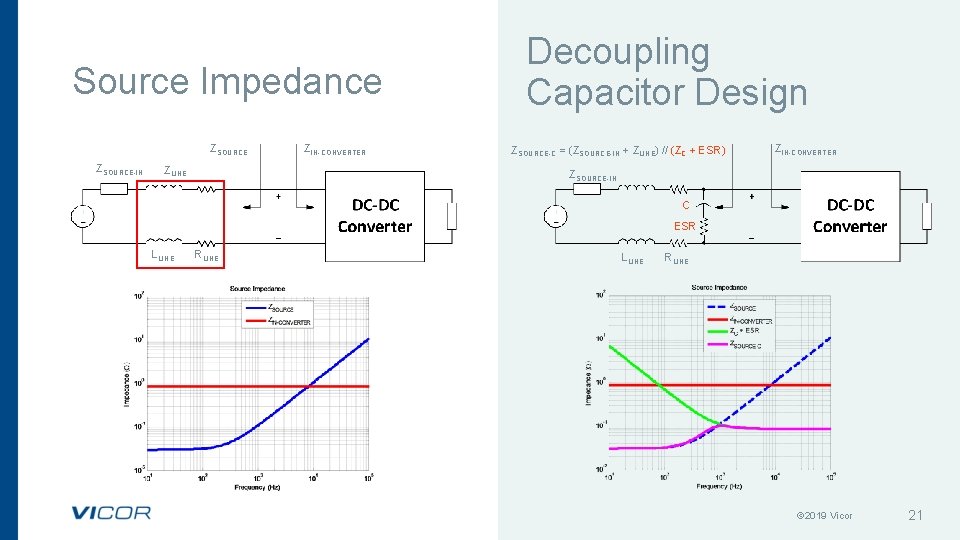
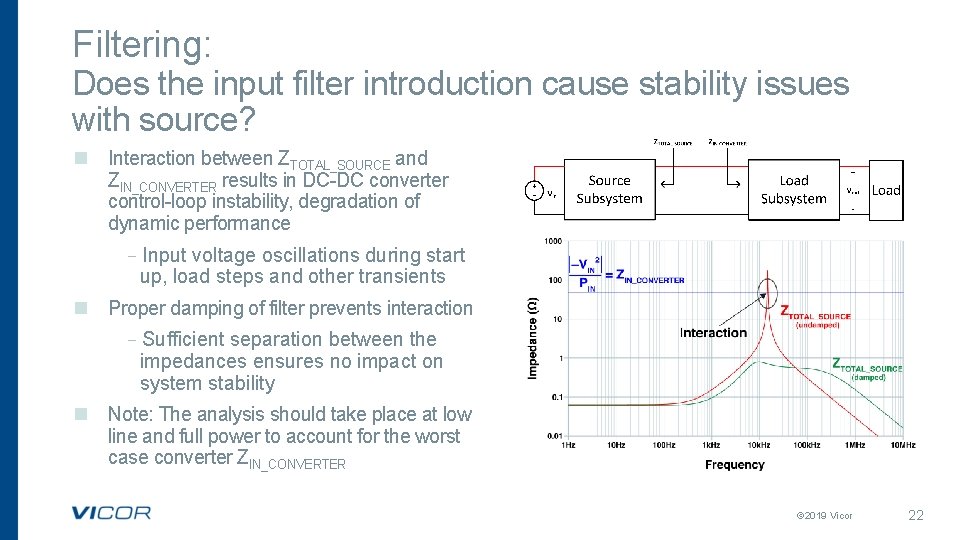
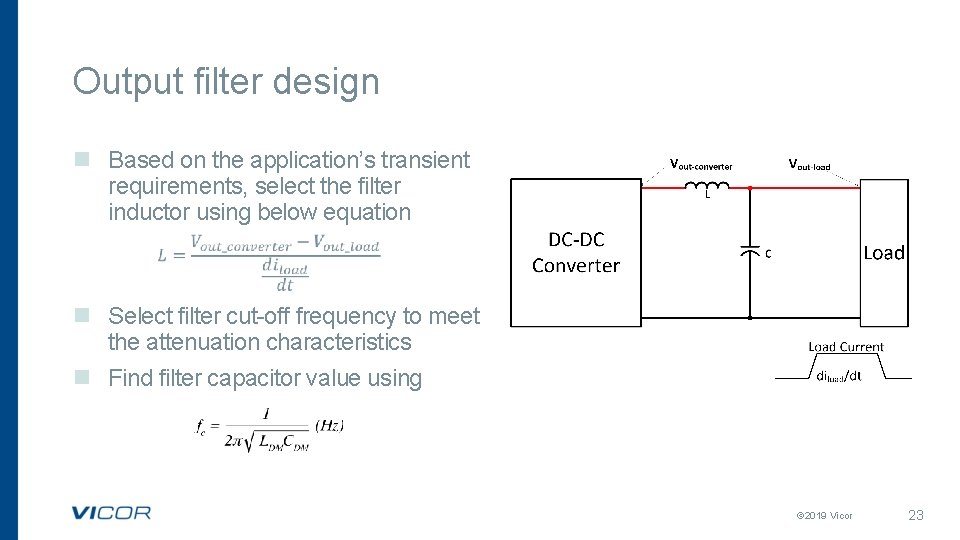
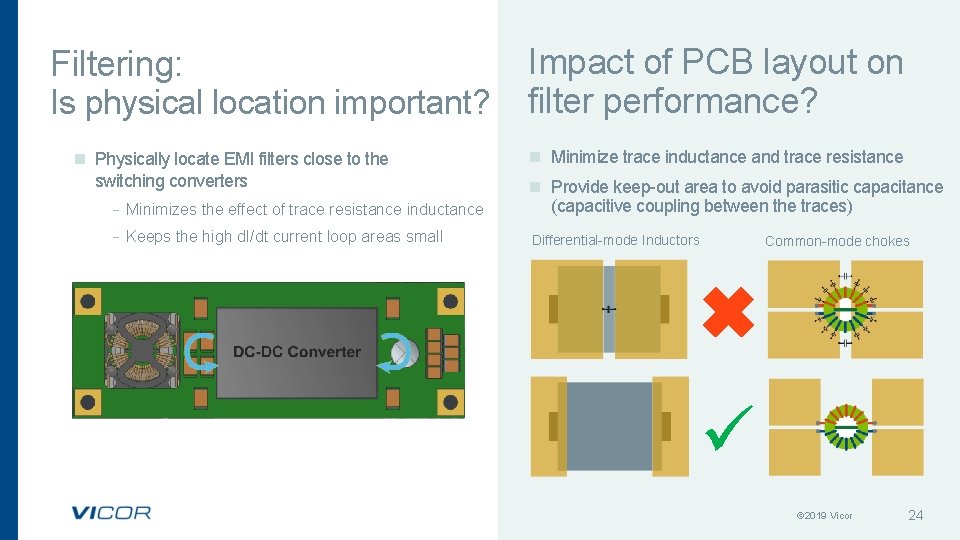
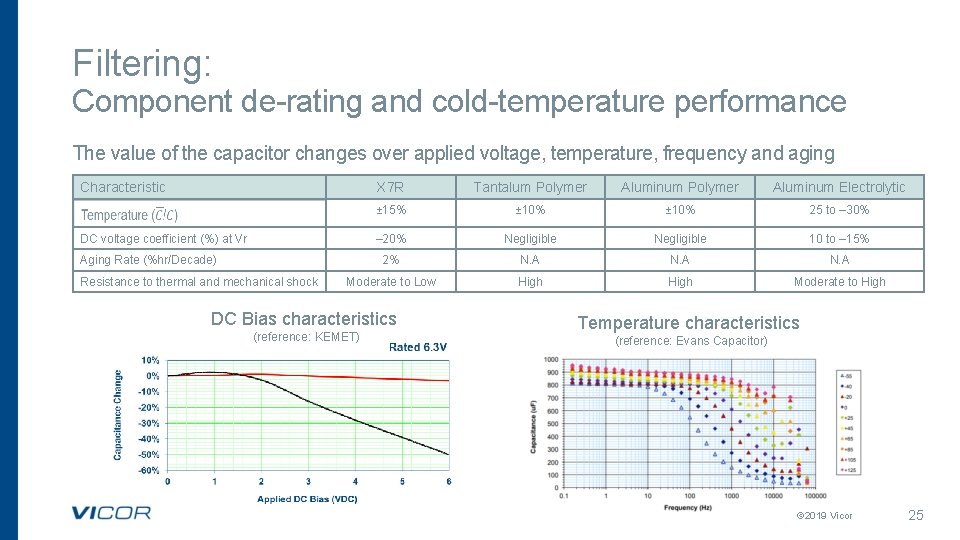
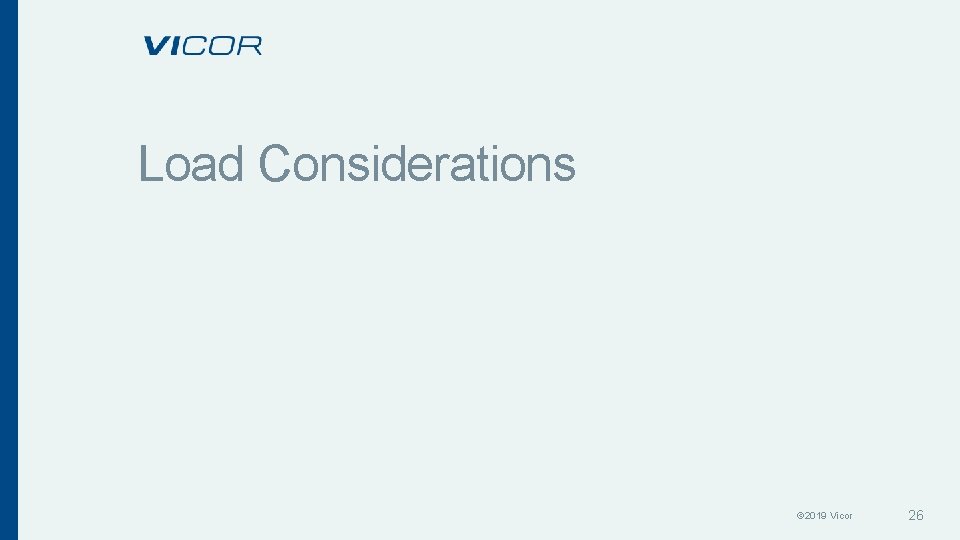
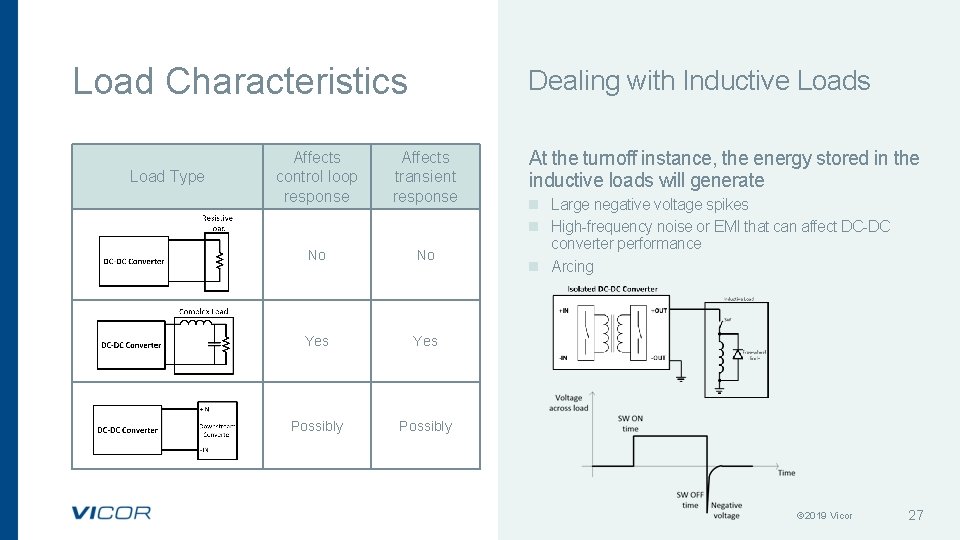
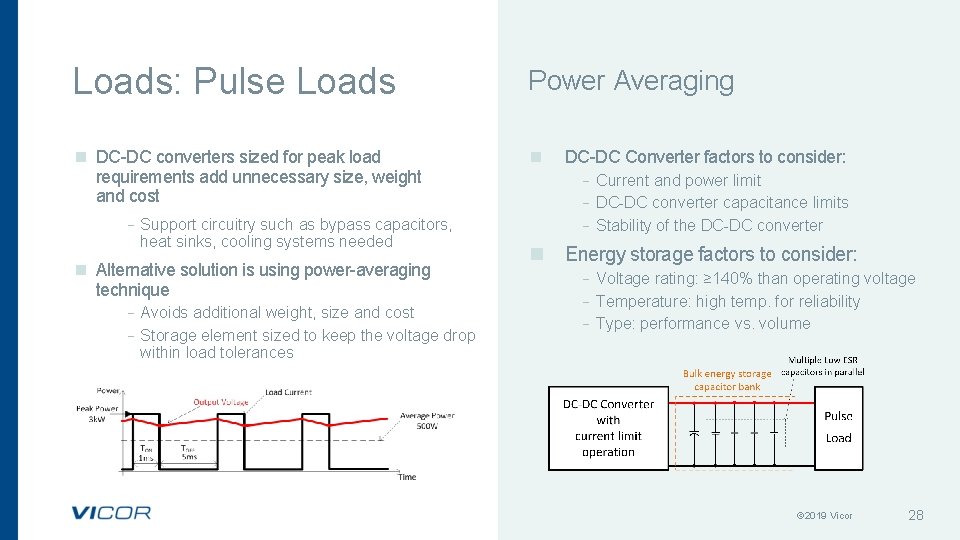
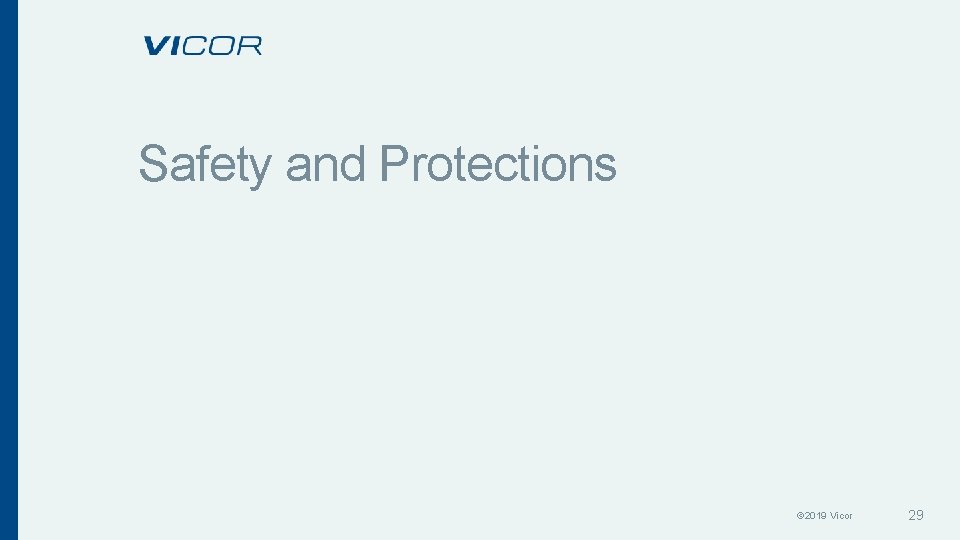
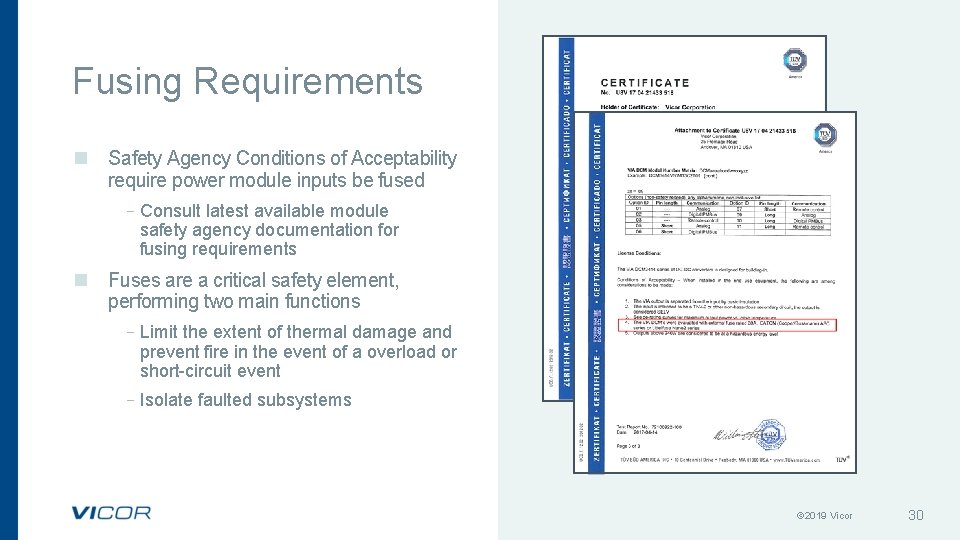
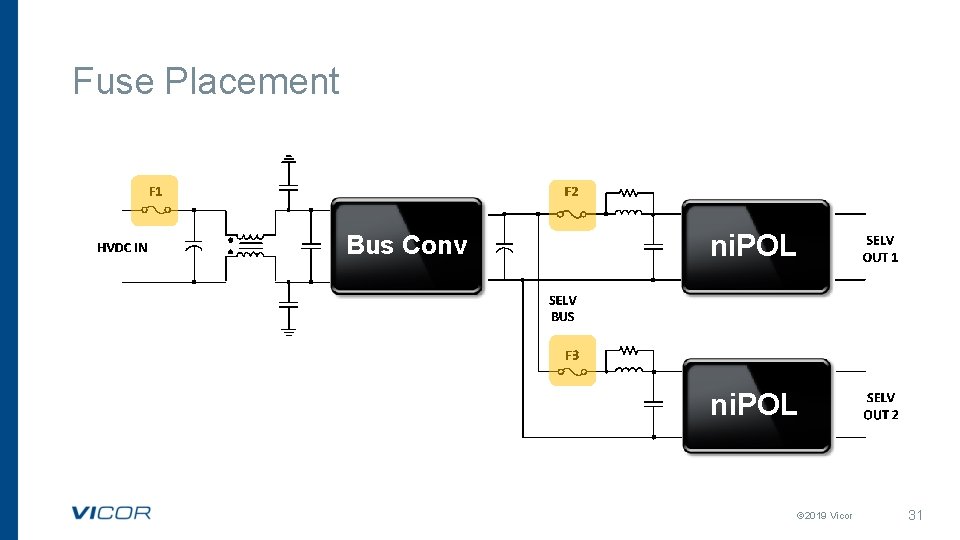
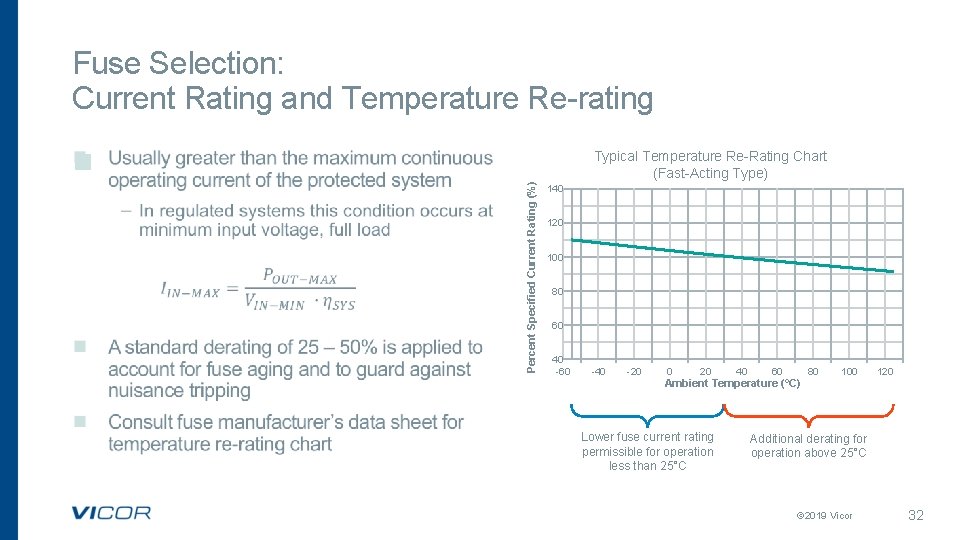
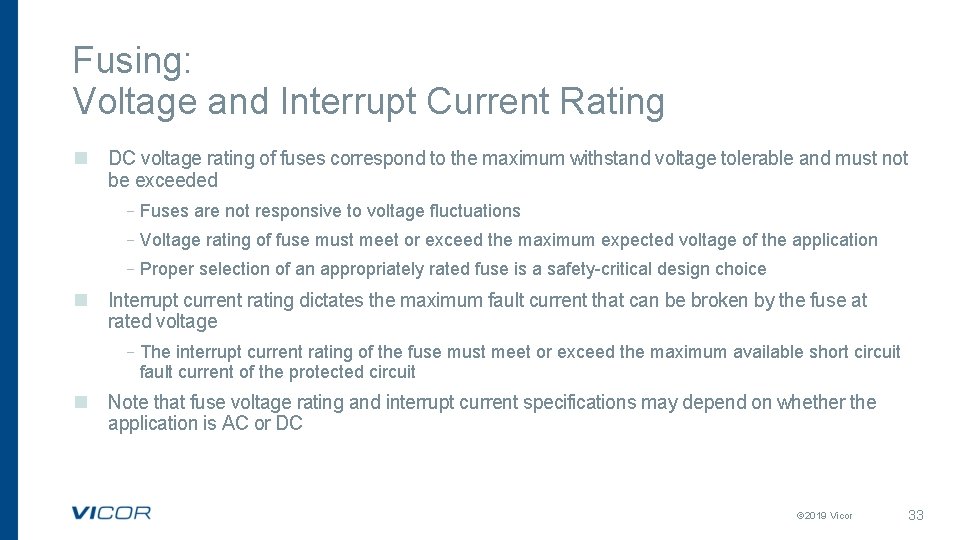
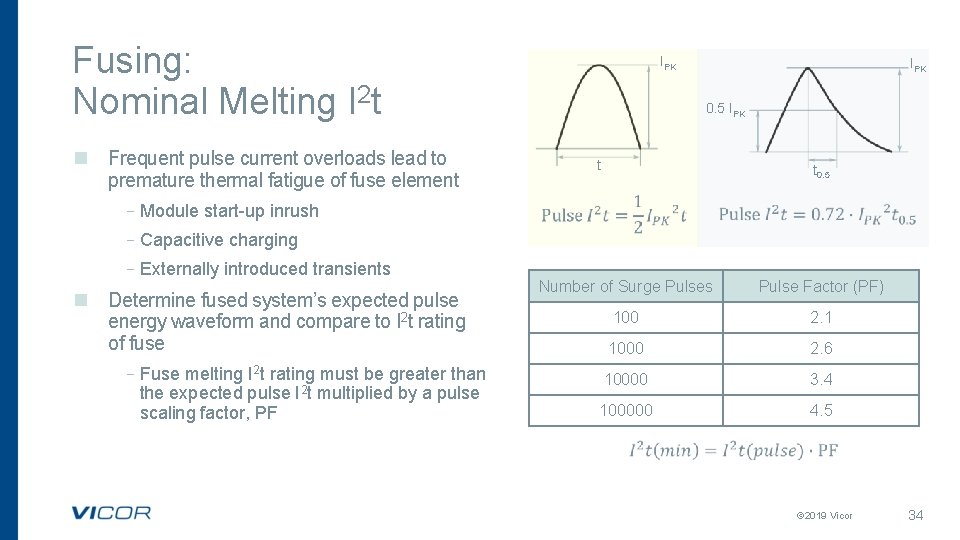
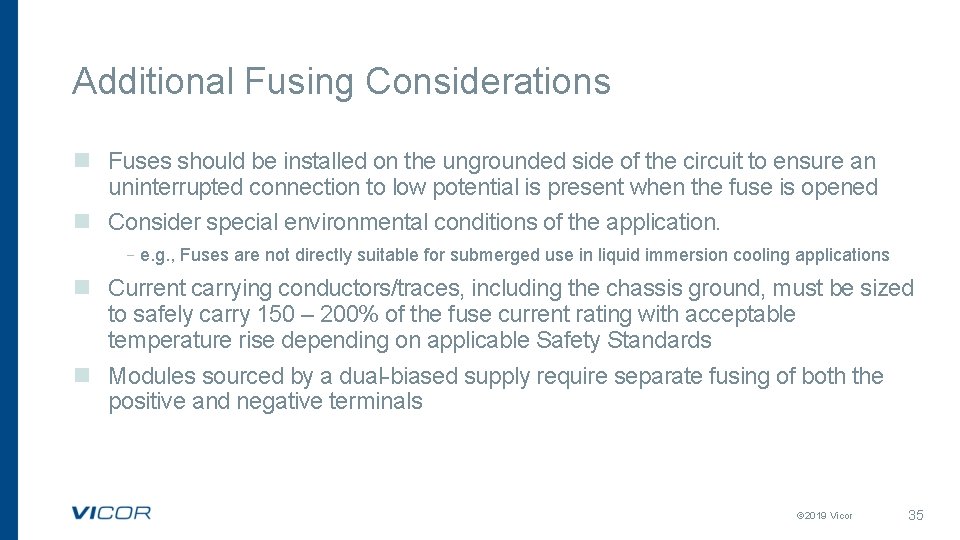
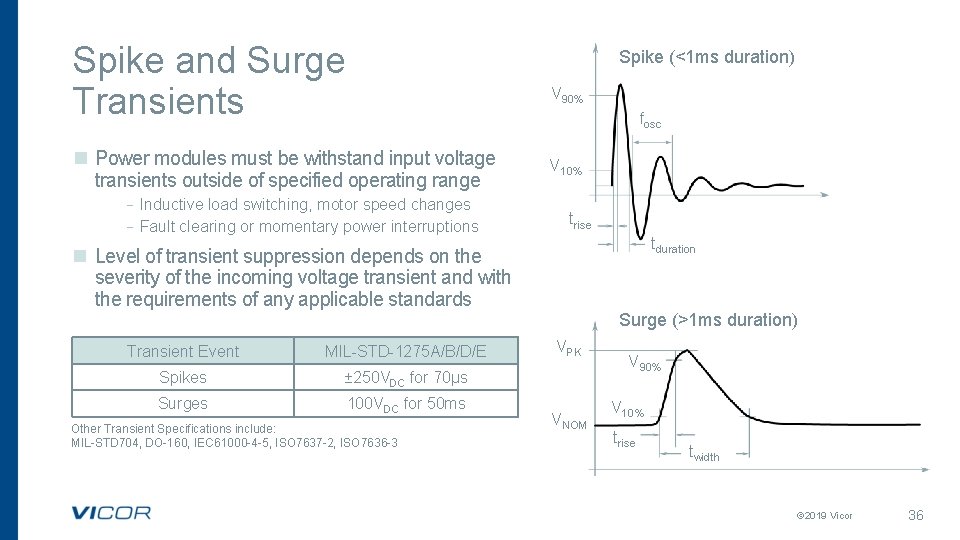
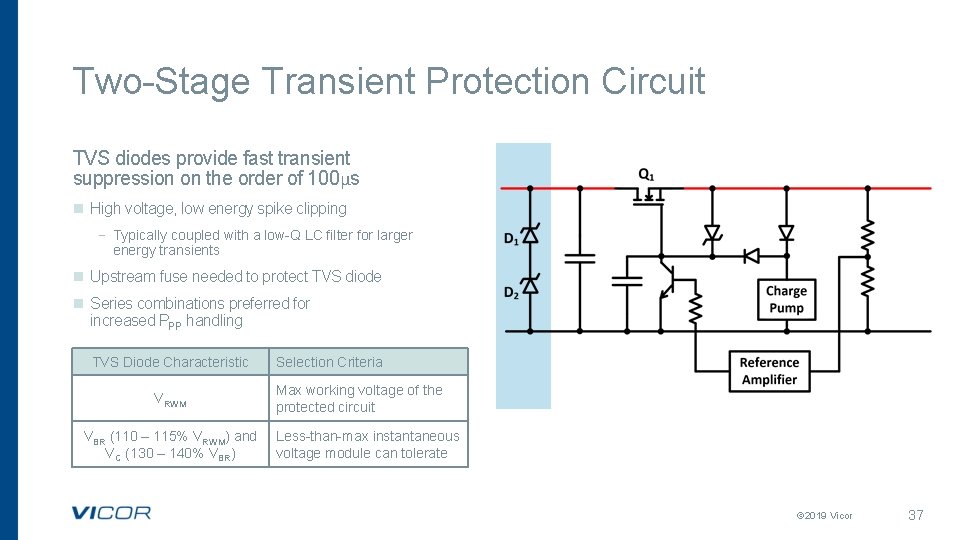
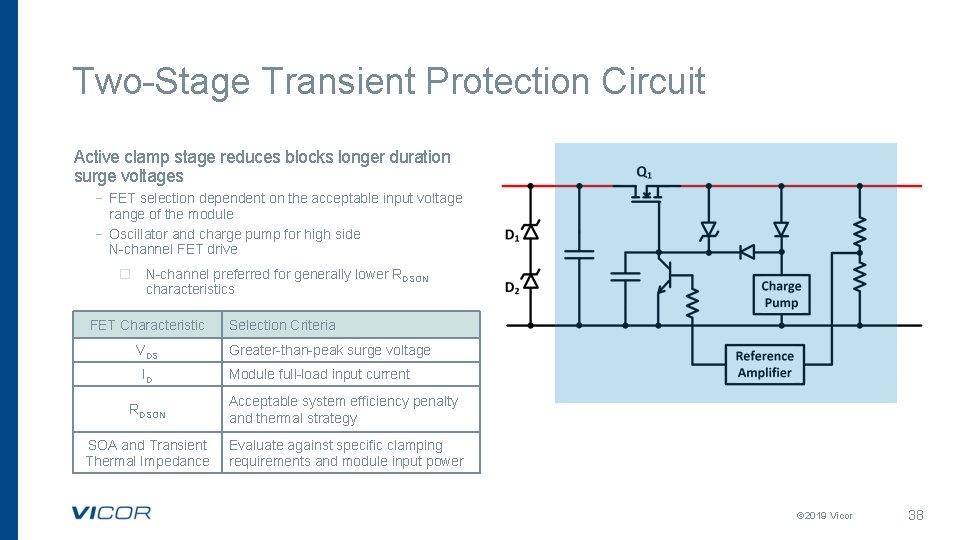
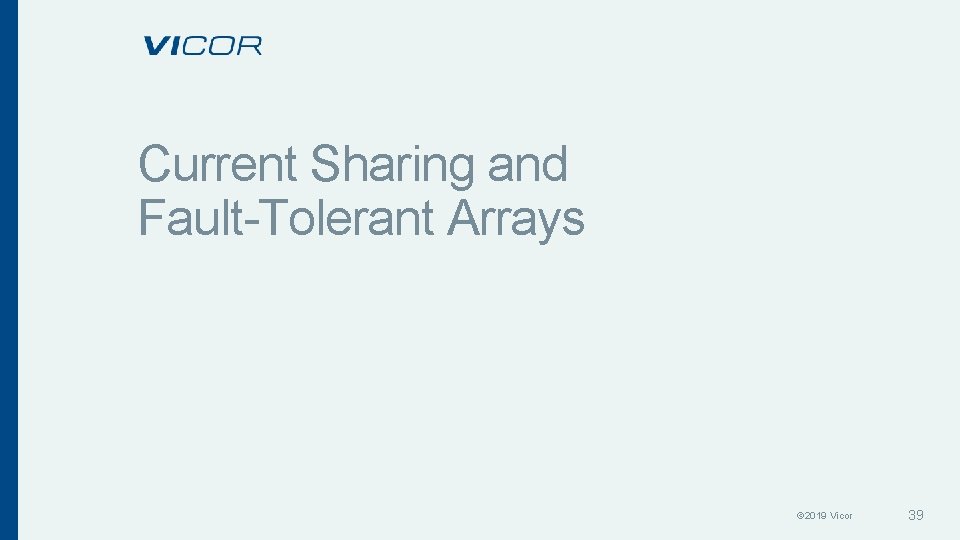
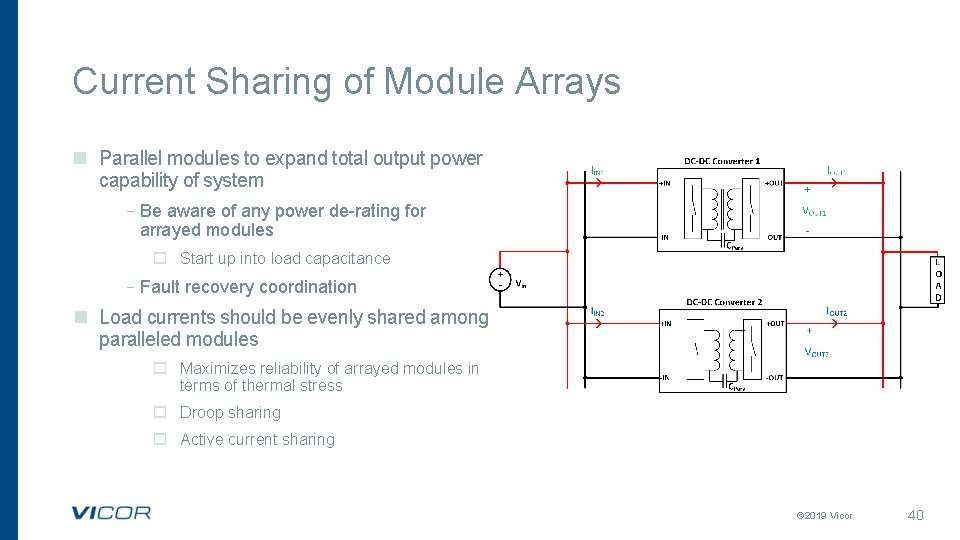
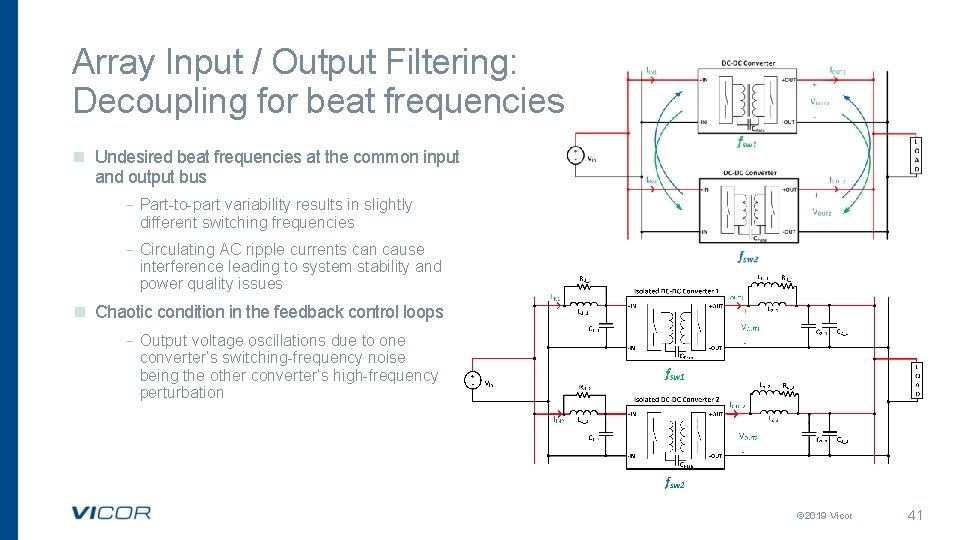
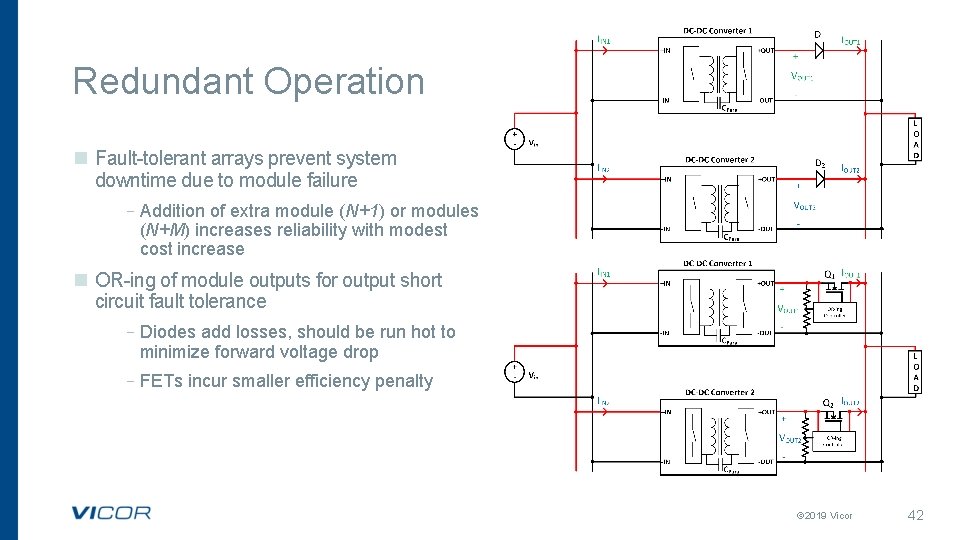
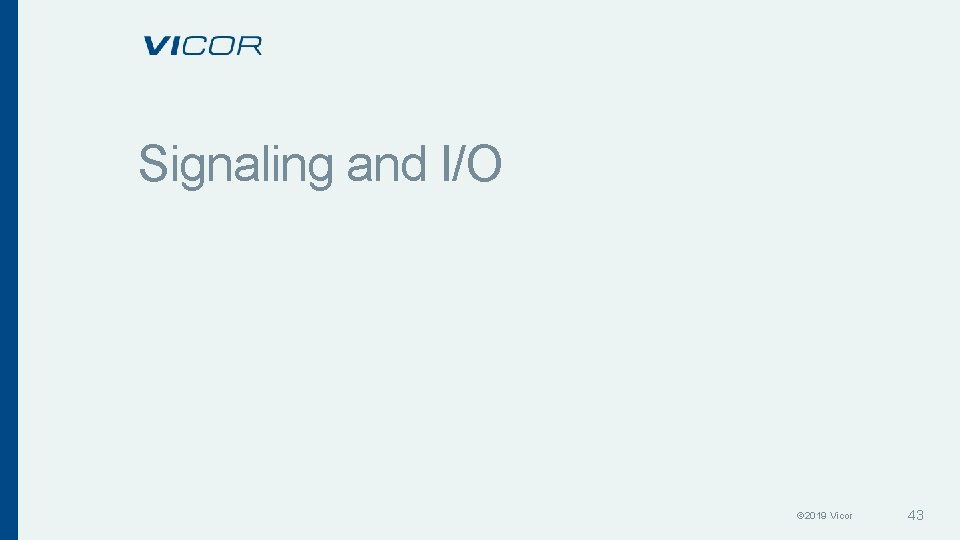
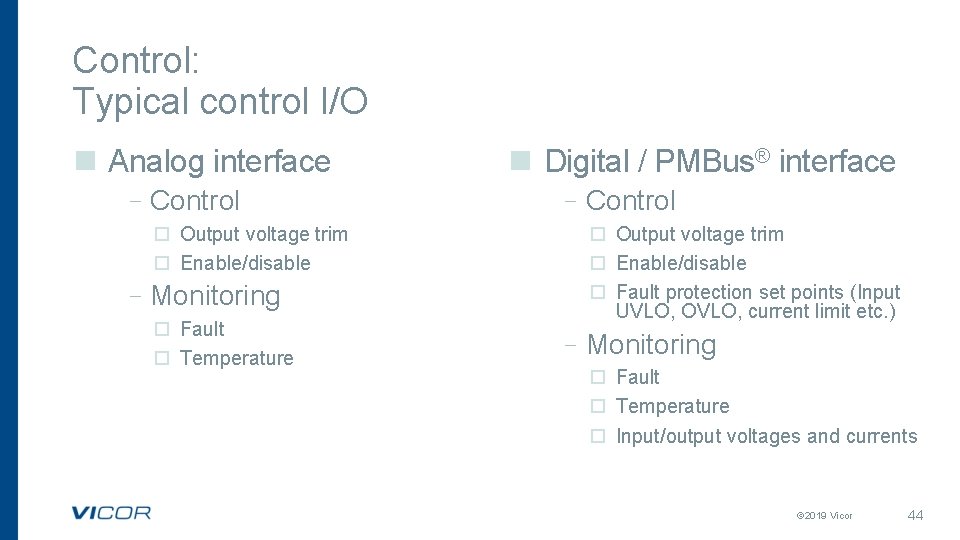
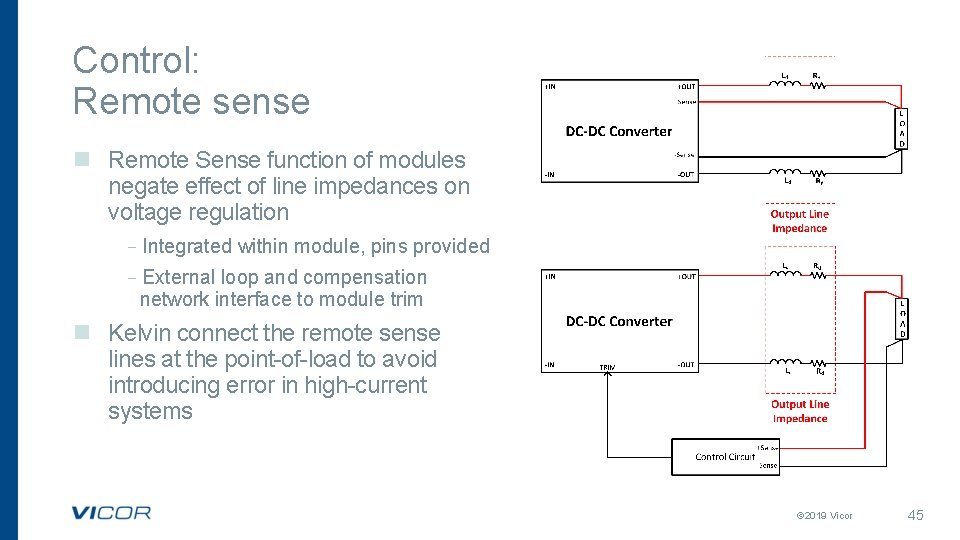
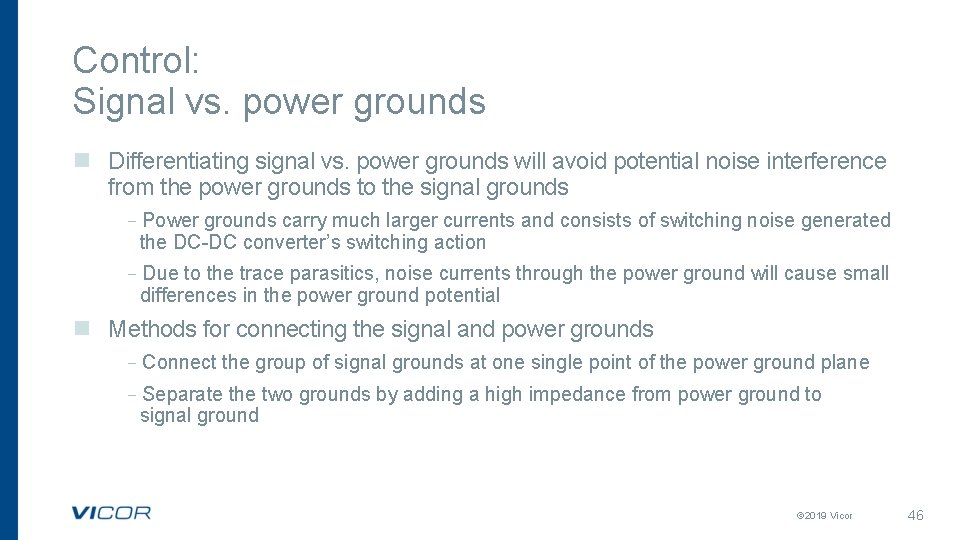
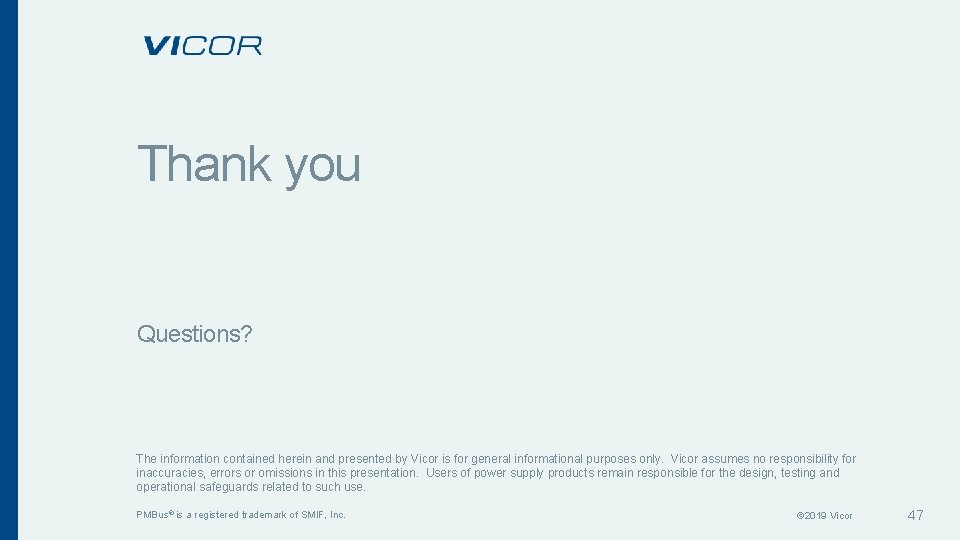
- Slides: 47
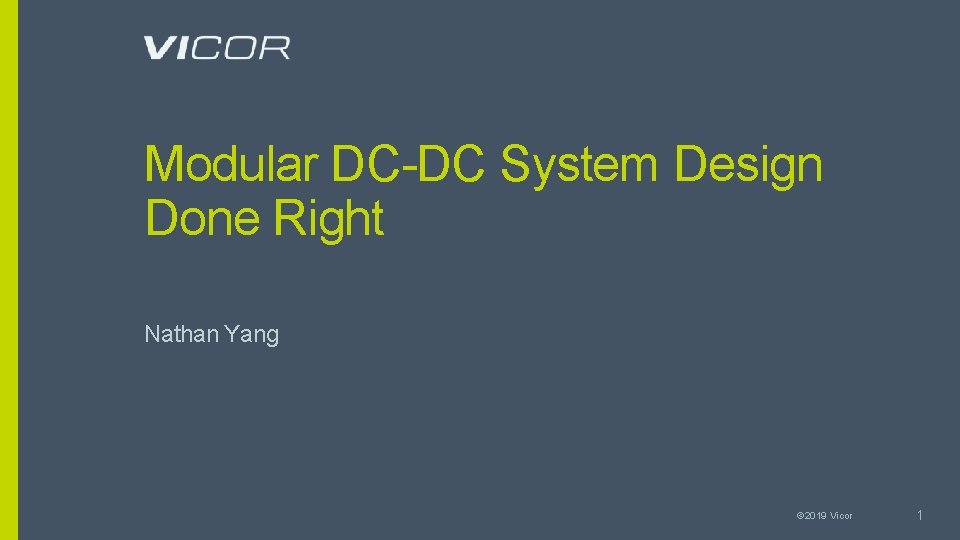
Modular DC-DC System Design Done Right Nathan Yang © 2019 Vicor 1
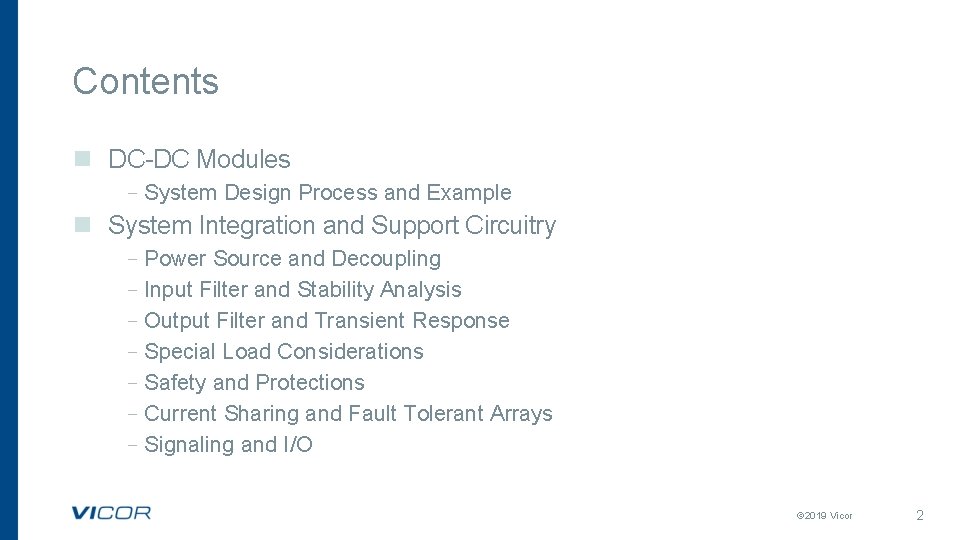
Contents n DC-DC Modules –System Design Process and Example n System Integration and Support Circuitry –Power Source and Decoupling –Input Filter and Stability Analysis –Output Filter and Transient Response –Special Load Considerations –Safety and Protections –Current Sharing and Fault Tolerant Arrays –Signaling and I/O © 2019 Vicor 2
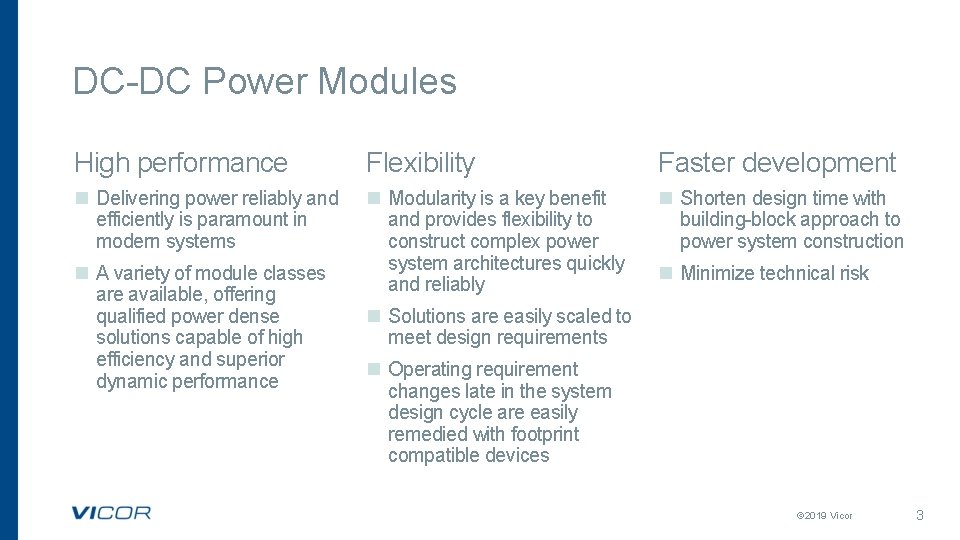
DC-DC Power Modules High performance Flexibility Faster development n Delivering power reliably and efficiently is paramount in modern systems n Modularity is a key benefit and provides flexibility to construct complex power system architectures quickly and reliably n Shorten design time with building-block approach to power system construction n A variety of module classes are available, offering qualified power dense solutions capable of high efficiency and superior dynamic performance n Minimize technical risk n Solutions are easily scaled to meet design requirements n Operating requirement changes late in the system design cycle are easily remedied with footprint compatible devices © 2019 Vicor 3
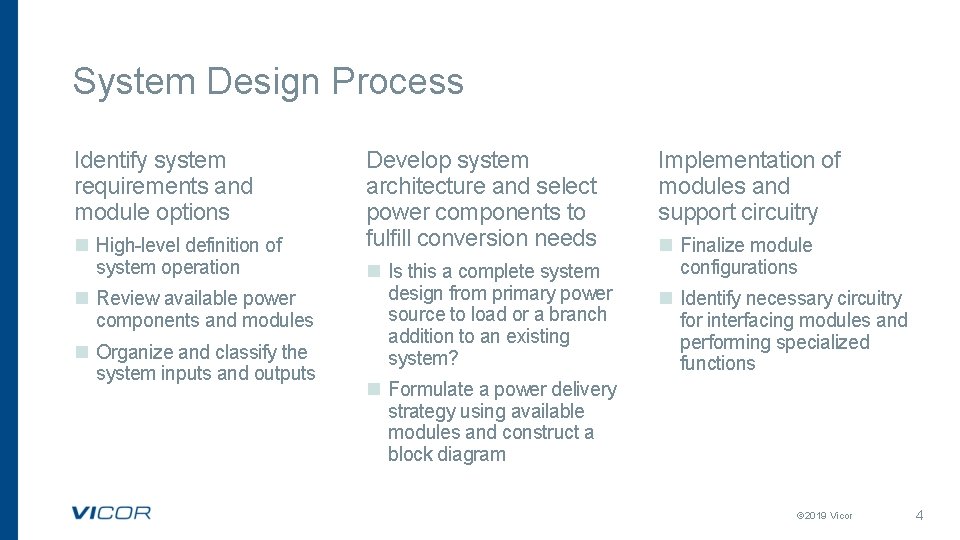
System Design Process Identify system requirements and module options n High-level definition of system operation n Review available power components and modules n Organize and classify the system inputs and outputs Develop system architecture and select power components to fulfill conversion needs n Is this a complete system design from primary power source to load or a branch addition to an existing system? Implementation of modules and support circuitry n Finalize module configurations n Identify necessary circuitry for interfacing modules and performing specialized functions n Formulate a power delivery strategy using available modules and construct a block diagram © 2019 Vicor 4
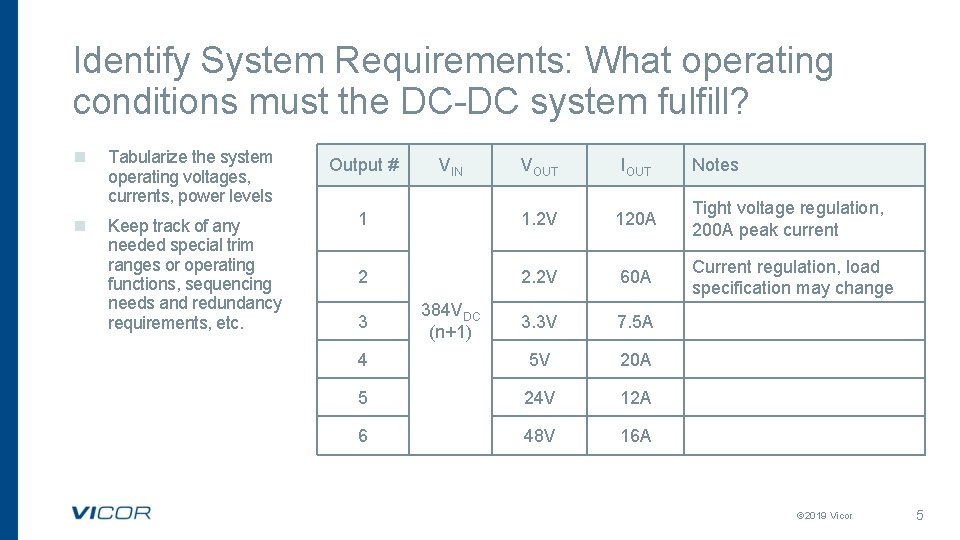
Identify System Requirements: What operating conditions must the DC-DC system fulfill? n n Tabularize the system operating voltages, currents, power levels Output # Keep track of any needed special trim ranges or operating functions, sequencing needs and redundancy requirements, etc. VOUT IOUT 1 1. 2 V 120 A Tight voltage regulation, 200 A peak current 2 2. 2 V 60 A Current regulation, load specification may change 3. 3 V 7. 5 A 4 5 V 20 A 5 24 V 12 A 6 48 V 16 A 3 VIN 384 VDC (n+1) Notes © 2019 Vicor 5
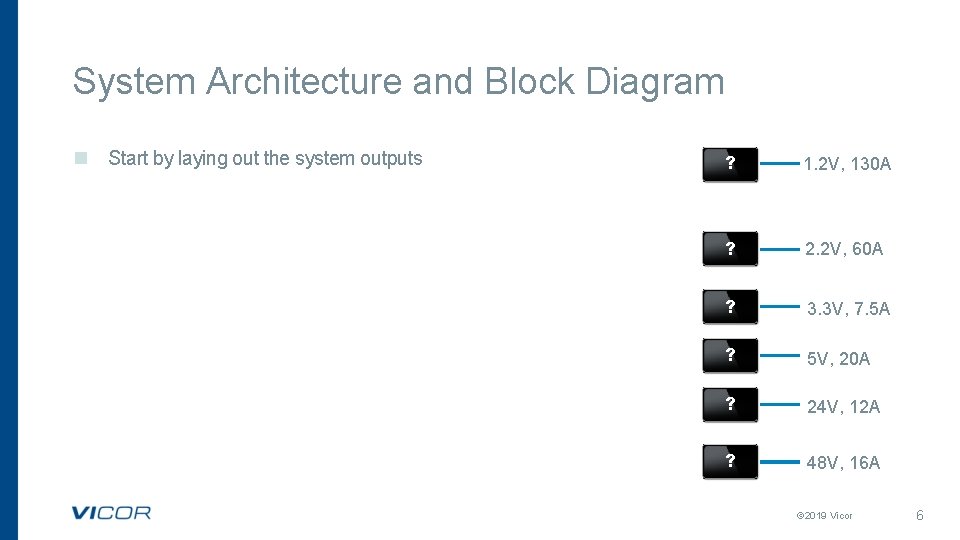
System Architecture and Block Diagram n Start by laying out the system outputs ? 1. 2 V, 130 A ? 2. 2 V, 60 A ? 3. 3 V, 7. 5 A ? 5 V, 20 A ? 24 V, 12 A ? 48 V, 16 A © 2019 Vicor 6
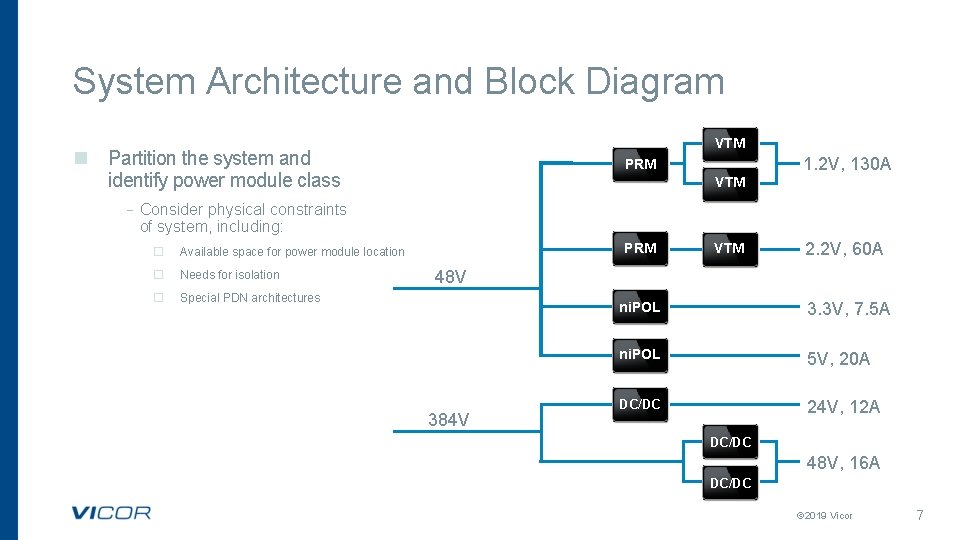
System Architecture and Block Diagram VTM n Partition the system and identify power module class 1. 2 V, 130 A PRM VTM – Consider physical constraints of system, including: Available space for power module location Needs for isolation Special PDN architectures PRM VTM 2. 2 V, 60 A 48 V 384 V ni. POL 3. 3 V, 7. 5 A ni. POL 5 V, 20 A DC/DC 24 V, 12 A DC/DC 48 V, 16 A DC/DC © 2019 Vicor 7
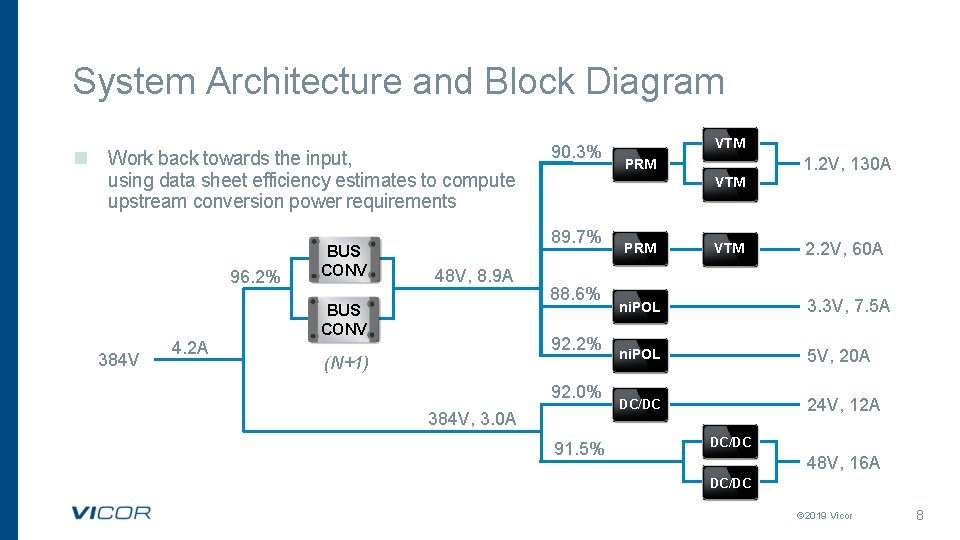
System Architecture and Block Diagram n Work back towards the input, using data sheet efficiency estimates to compute upstream conversion power requirements 96. 2% 384 V 4. 2 A BUS CONV 90. 3% BUS CONV 88. 6% 92. 2% (N+1) 1. 2 V, 130 A PRM VTM 89. 7% 48 V, 8. 9 A VTM 92. 0% 384 V, 3. 0 A 91. 5% PRM VTM 2. 2 V, 60 A ni. POL 3. 3 V, 7. 5 A ni. POL 5 V, 20 A DC/DC 24 V, 12 A DC/DC 48 V, 16 A DC/DC © 2019 Vicor 8
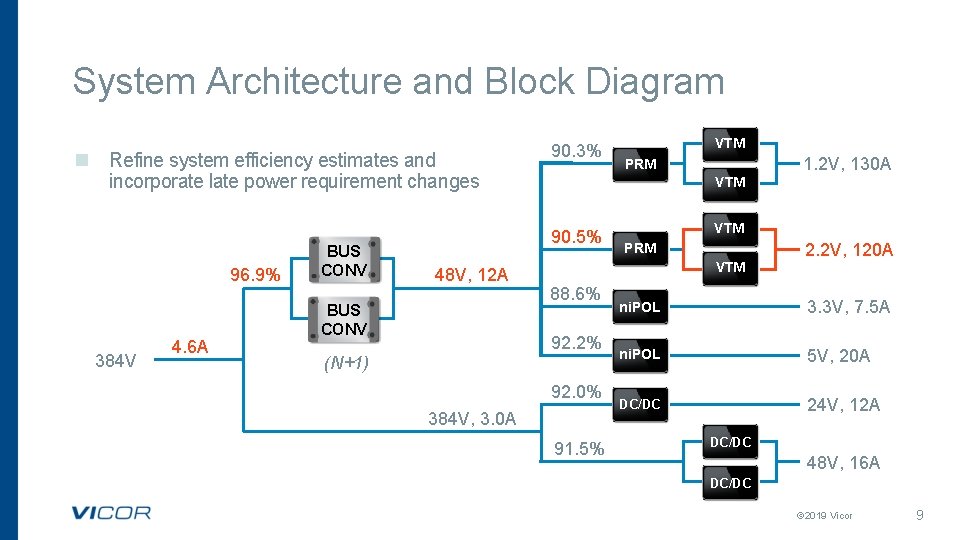
System Architecture and Block Diagram n Refine system efficiency estimates and incorporate late power requirement changes 96. 9% 384 V 4. 6 A BUS CONV 90. 3% BUS CONV VTM PRM VTM 88. 6% 92. 2% (N+1) 1. 2 V, 130 A PRM VTM 90. 5% 48 V, 12 A VTM 92. 0% 384 V, 3. 0 A 91. 5% 2. 2 V, 120 A ni. POL 3. 3 V, 7. 5 A ni. POL 5 V, 20 A DC/DC 24 V, 12 A DC/DC 48 V, 16 A DC/DC © 2019 Vicor 9
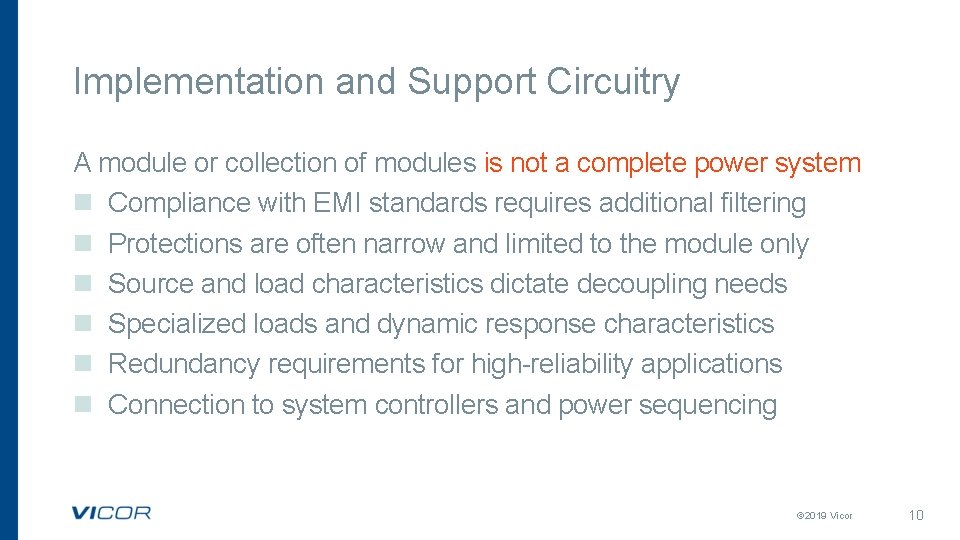
Implementation and Support Circuitry A module or collection of modules is not a complete power system n Compliance with EMI standards requires additional filtering n Protections are often narrow and limited to the module only n Source and load characteristics dictate decoupling needs n Specialized loads and dynamic response characteristics n Redundancy requirements for high-reliability applications n Connection to system controllers and power sequencing © 2019 Vicor 10
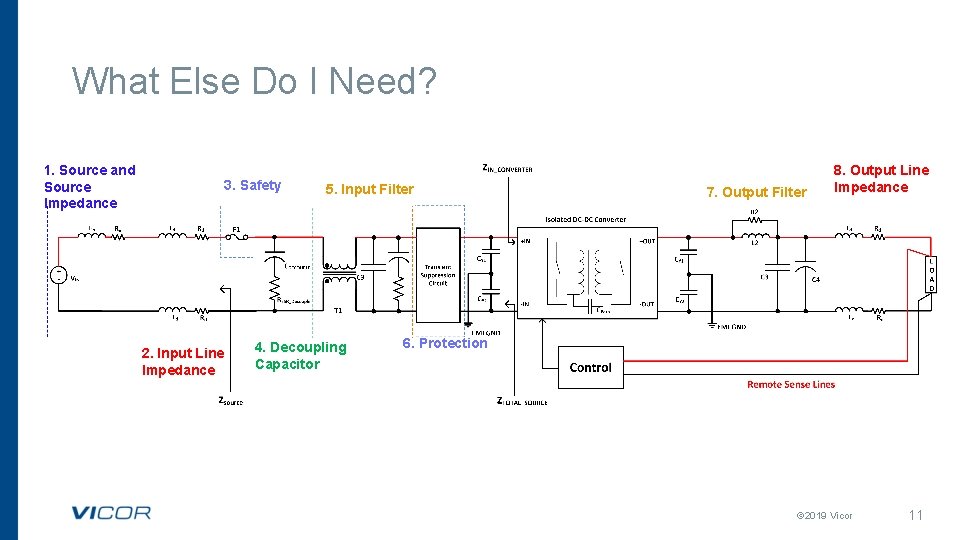
What Else Do I Need? 1. Source and Source Impedance 3. Safety 2. Input Line Impedance 5. Input Filter 4. Decoupling Capacitor 7. Output Filter 8. Output Line Impedance 6. Protection © 2019 Vicor 11
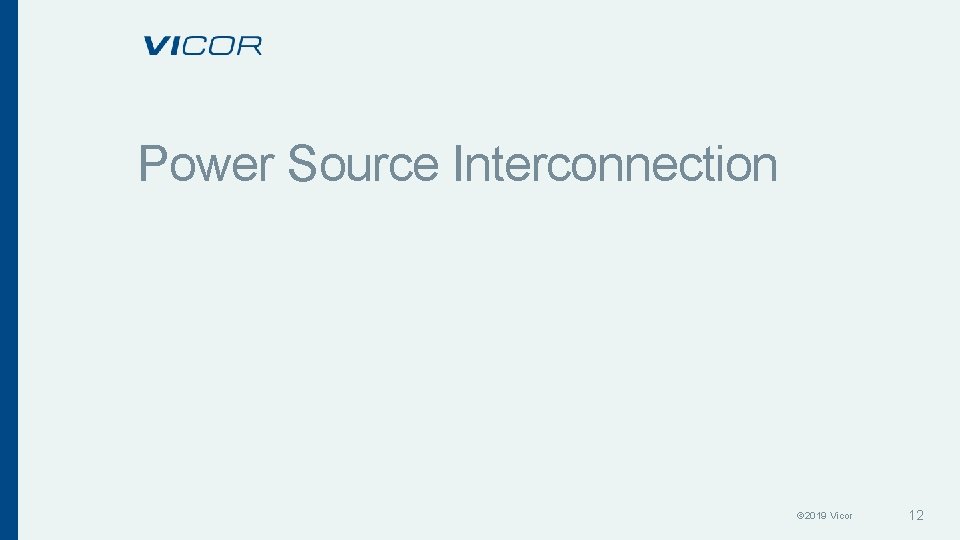
Power Source Interconnection © 2019 Vicor 12
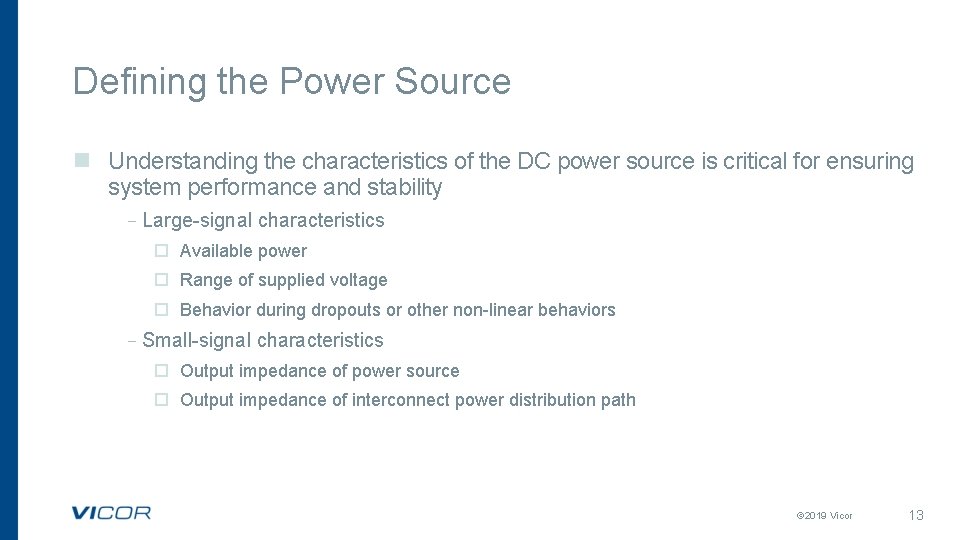
Defining the Power Source n Understanding the characteristics of the DC power source is critical for ensuring system performance and stability –Large-signal characteristics Available power Range of supplied voltage Behavior during dropouts or other non-linear behaviors –Small-signal characteristics Output impedance of power source Output impedance of interconnect power distribution path © 2019 Vicor 13
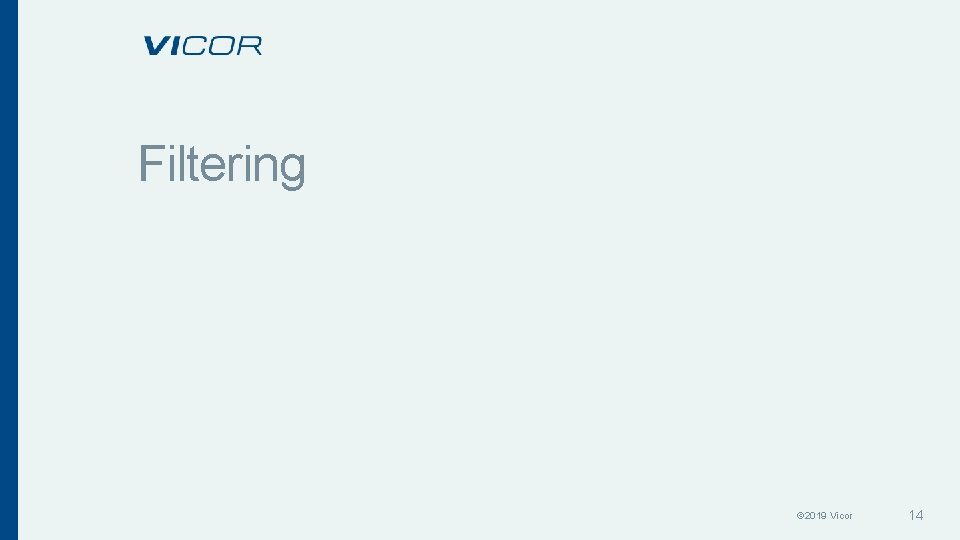
Filtering © 2019 Vicor 14
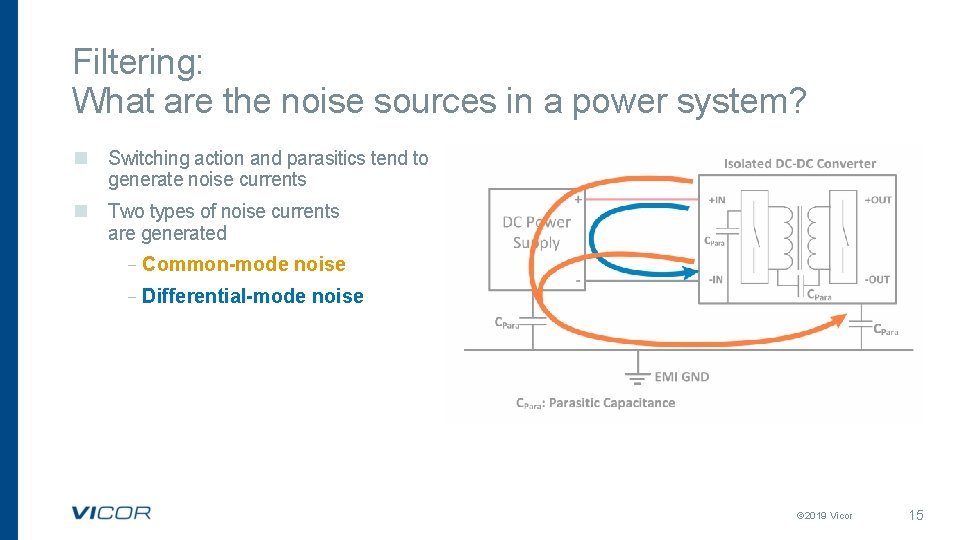
Filtering: What are the noise sources in a power system? n Switching action and parasitics tend to generate noise currents n Two types of noise currents are generated –Common-mode noise –Differential-mode noise © 2019 Vicor 15
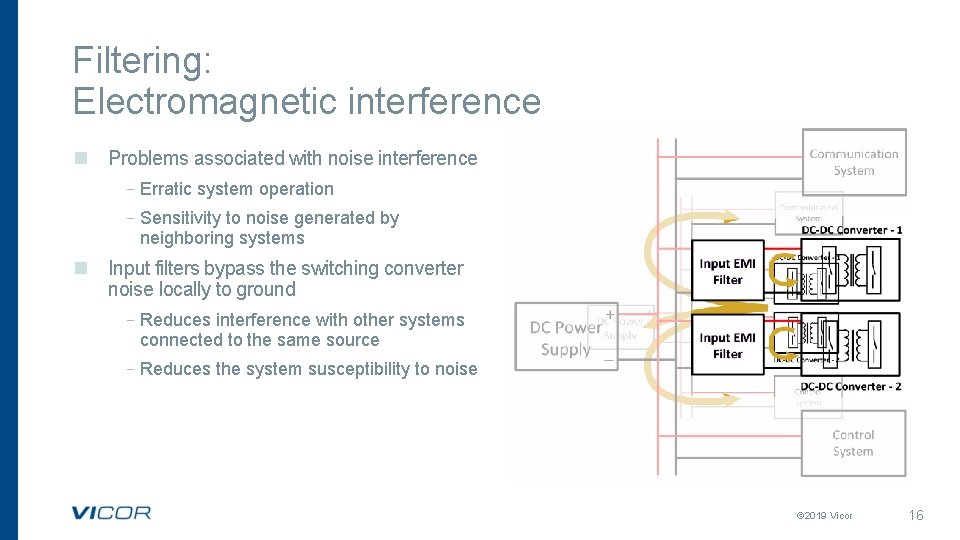
Filtering: Electromagnetic interference n Problems associated with noise interference –Erratic system operation –Sensitivity to noise generated by neighboring systems n Input filters bypass the switching converter noise locally to ground –Reduces interference with other systems connected to the same source –Reduces the system susceptibility to noise © 2019 Vicor 16
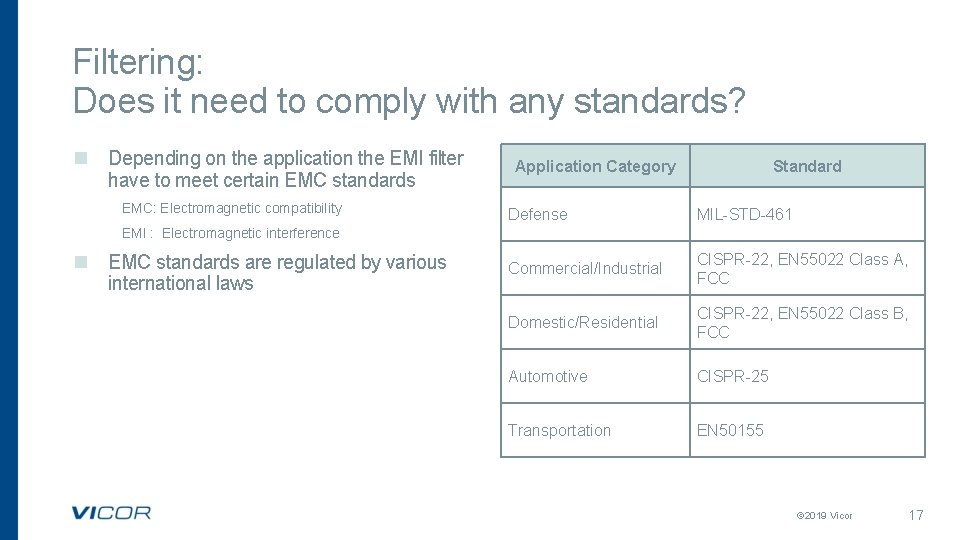
Filtering: Does it need to comply with any standards? n Depending on the application the EMI filter have to meet certain EMC standards EMC: Electromagnetic compatibility Application Category Standard Defense MIL-STD-461 Commercial/Industrial CISPR-22, EN 55022 Class A, FCC Domestic/Residential CISPR-22, EN 55022 Class B, FCC Automotive CISPR-25 Transportation EN 50155 EMI : Electromagnetic interference n EMC standards are regulated by various international laws © 2019 Vicor 17
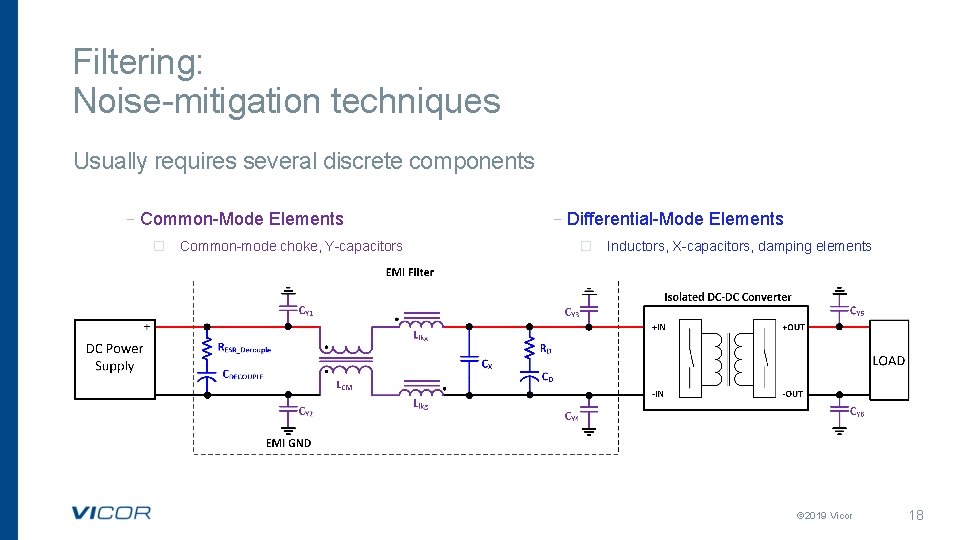
Filtering: Noise-mitigation techniques Usually requires several discrete components –Common-Mode Elements Common-mode choke, Y-capacitors –Differential-Mode Elements Inductors, X-capacitors, damping elements © 2019 Vicor 18
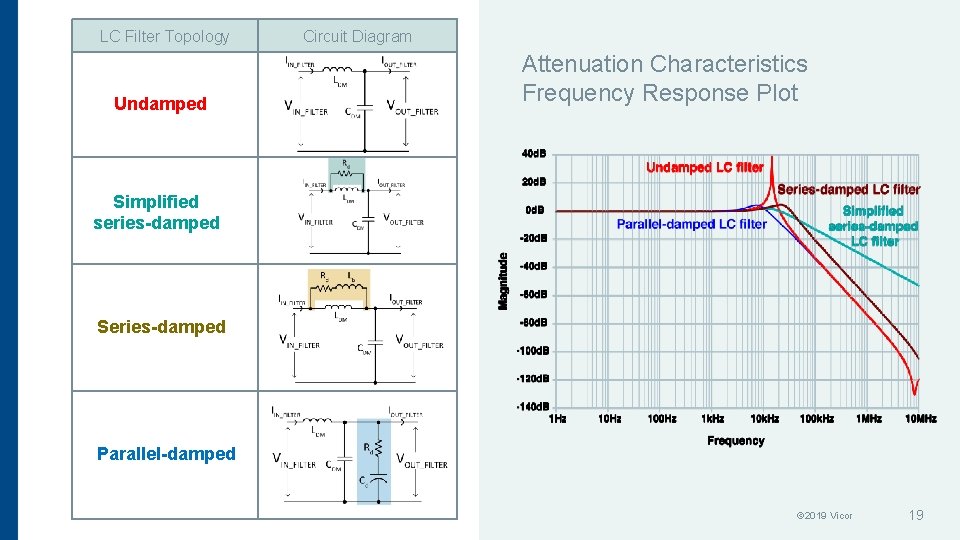
LC Filter Topology Undamped Circuit Diagram Attenuation Characteristics Frequency Response Plot Simplified series-damped Series-damped Parallel-damped © 2019 Vicor 19
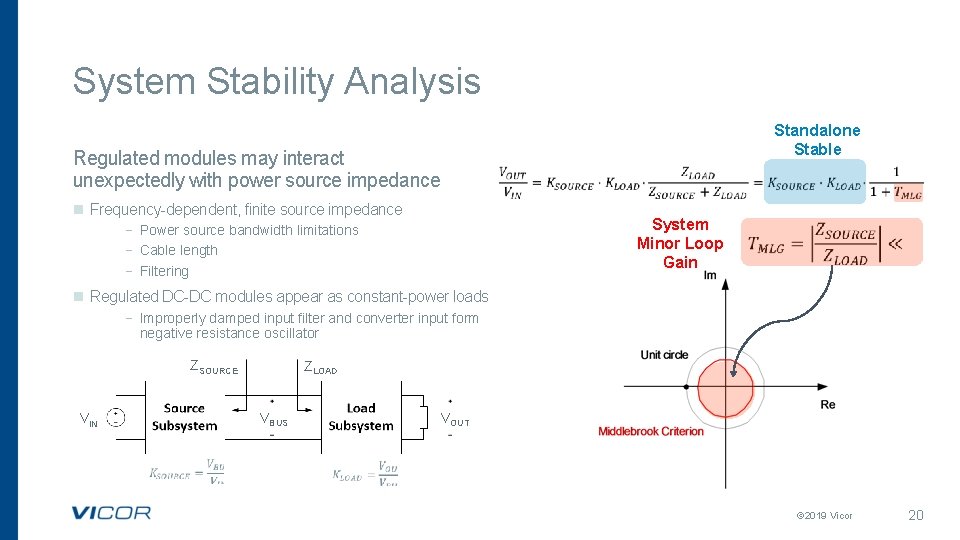
System Stability Analysis Regulated modules may interact unexpectedly with power source impedance Standalone Stable n Frequency-dependent, finite source impedance System Minor Loop Gain – Power source bandwidth limitations – Cable length – Filtering n Regulated DC-DC modules appear as constant-power loads – Improperly damped input filter and converter input form negative resistance oscillator ZSOURCE ZLOAD VOUT VBUS VIN © 2019 Vicor 20
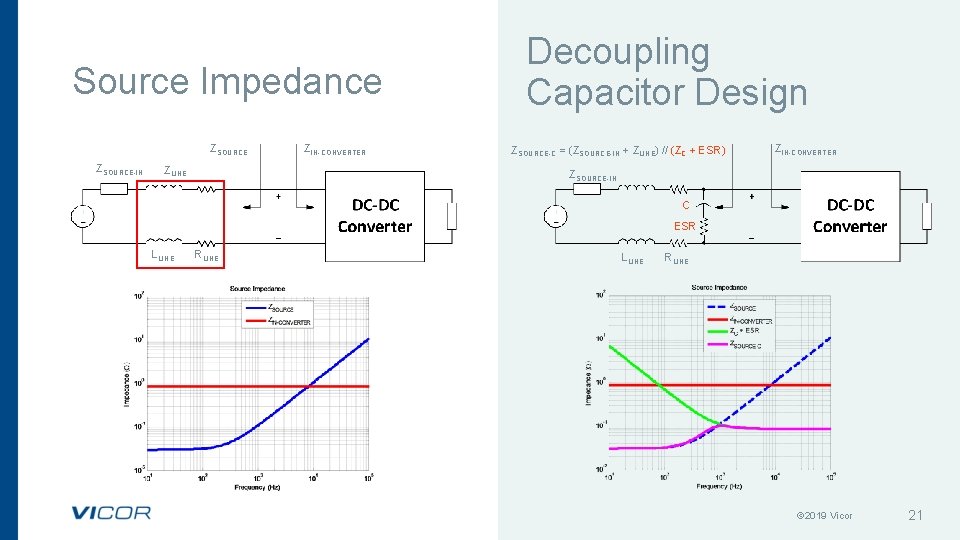
Source Impedance ZSOURCE-IN ZLINE ZIN-CONVERTER Decoupling Capacitor Design ZSOURCE-C = (ZSOURCE-IN + ZLINE) // (ZC + ESR) ZIN-CONVERTER ZSOURCE-IN C ESR LLINE RLINE © 2019 Vicor 21
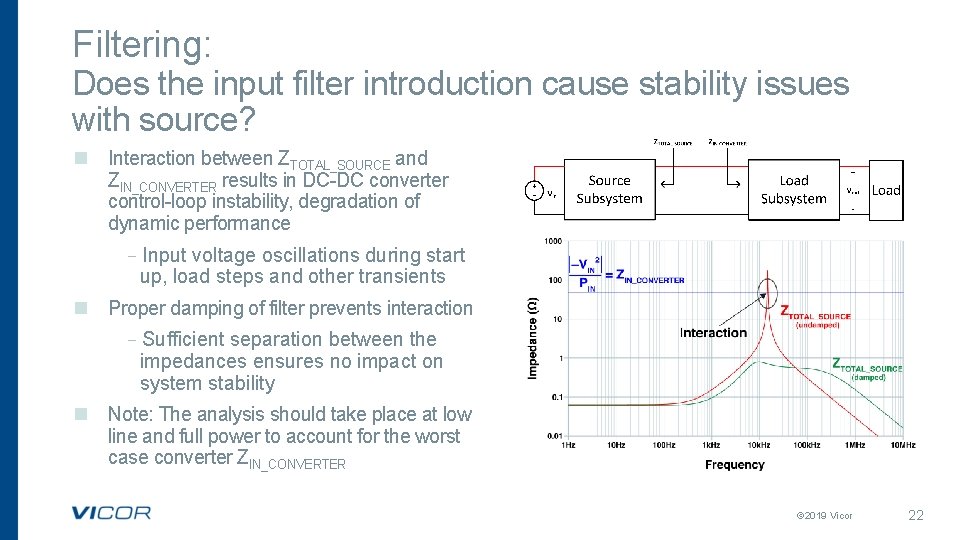
Filtering: Does the input filter introduction cause stability issues with source? n Interaction between ZTOTAL_SOURCE and ZIN_CONVERTER results in DC-DC converter control-loop instability, degradation of dynamic performance –Input voltage oscillations during start up, load steps and other transients n Proper damping of filter prevents interaction –Sufficient separation between the impedances ensures no impact on system stability n Note: The analysis should take place at low line and full power to account for the worst case converter ZIN_CONVERTER © 2019 Vicor 22
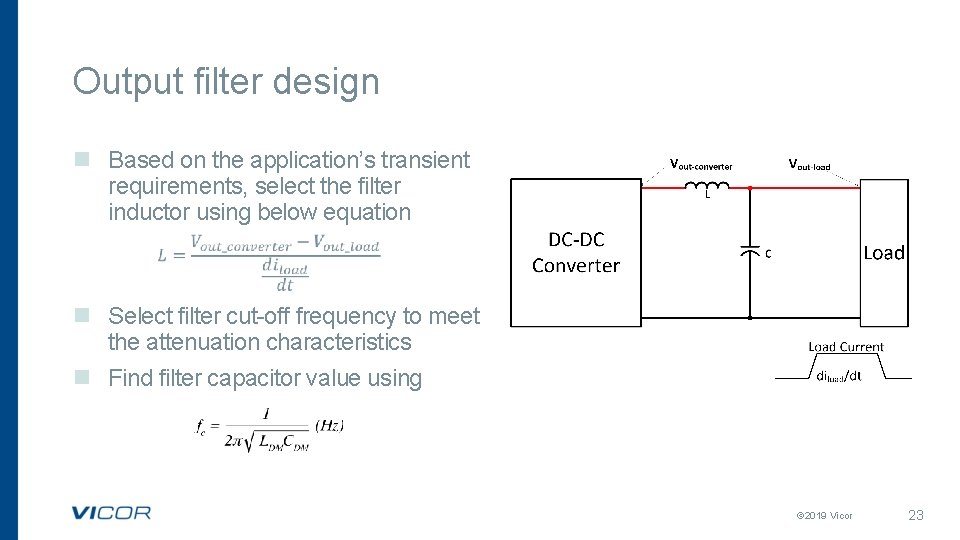
Output filter design n Based on the application’s transient requirements, select the filter inductor using below equation n Select filter cut-off frequency to meet the attenuation characteristics n Find filter capacitor value using © 2019 Vicor 23
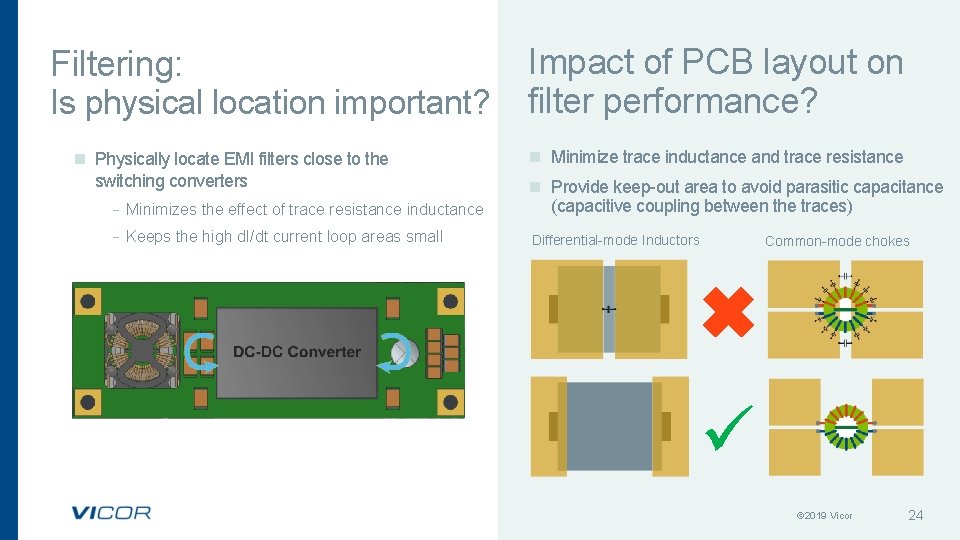
Filtering: Is physical location important? n Physically locate EMI filters close to the switching converters Impact of PCB layout on filter performance? n Minimize trace inductance and trace resistance – Minimizes the effect of trace resistance inductance n Provide keep-out area to avoid parasitic capacitance (capacitive coupling between the traces) – Keeps the high d. I/dt current loop areas small Differential-mode Inductors Common-mode chokes ü © 2019 Vicor 24
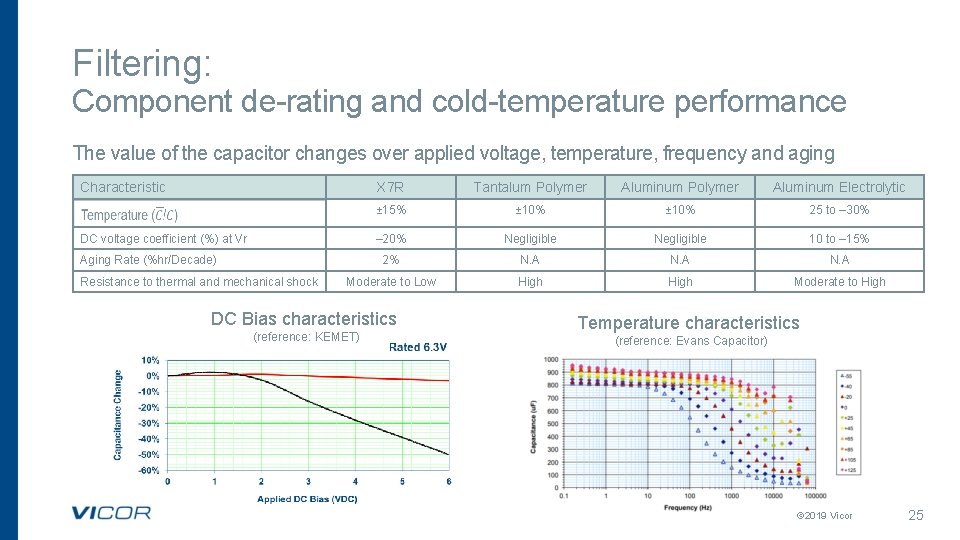
Filtering: Component de-rating and cold-temperature performance The value of the capacitor changes over applied voltage, temperature, frequency and aging Characteristic X 7 R Tantalum Polymer Aluminum Electrolytic ± 15% ± 10% 25 to – 30% – 20% Negligible 10 to – 15% 2% N. A Moderate to Low High Moderate to High DC voltage coefficient (%) at Vr Aging Rate (%hr/Decade) Resistance to thermal and mechanical shock DC Bias characteristics (reference: KEMET) Temperature characteristics (reference: Evans Capacitor) © 2019 Vicor 25
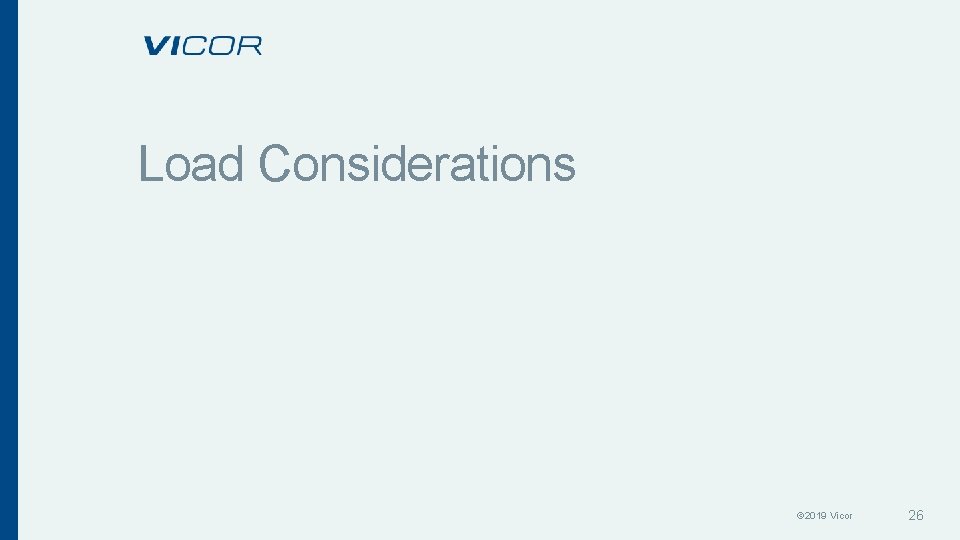
Load Considerations © 2019 Vicor 26
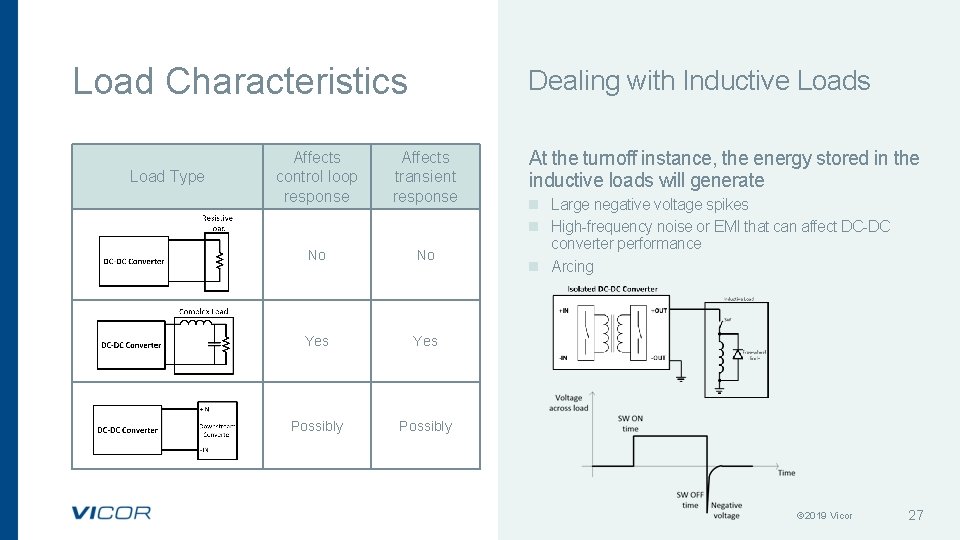
Load Characteristics Load Type Dealing with Inductive Loads Affects control loop response Affects transient response No No Yes Possibly At the turnoff instance, the energy stored in the inductive loads will generate n Large negative voltage spikes n High-frequency noise or EMI that can affect DC-DC converter performance n Arcing © 2019 Vicor 27
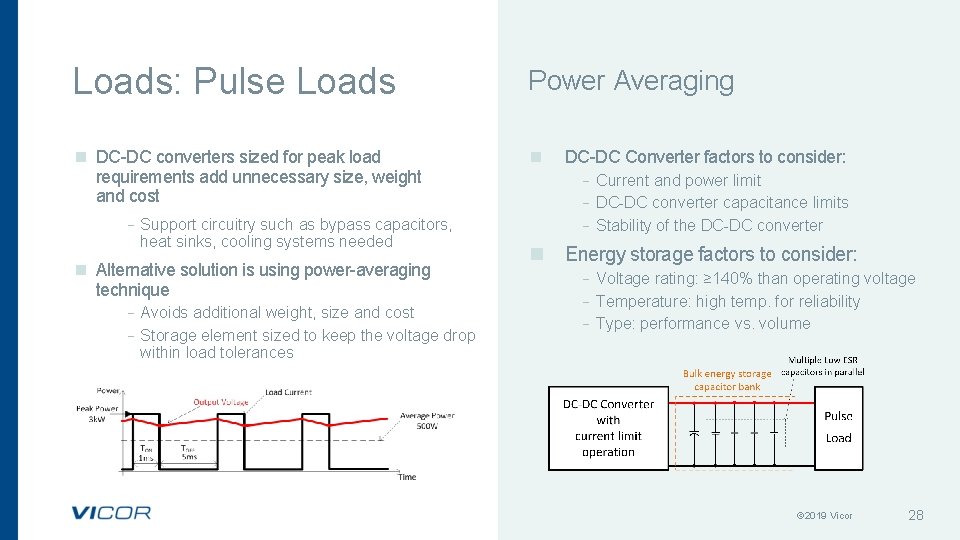
Loads: Pulse Loads Power Averaging n DC-DC converters sized for peak load requirements add unnecessary size, weight and cost n – Support circuitry such as bypass capacitors, heat sinks, cooling systems needed n Alternative solution is using power-averaging technique – Avoids additional weight, size and cost – Storage element sized to keep the voltage drop within load tolerances DC-DC Converter factors to consider: – Current and power limit – DC-DC converter capacitance limits – Stability of the DC-DC converter n Energy storage factors to consider: – Voltage rating: ≥ 140% than operating voltage – Temperature: high temp. for reliability – Type: performance vs. volume © 2019 Vicor 28
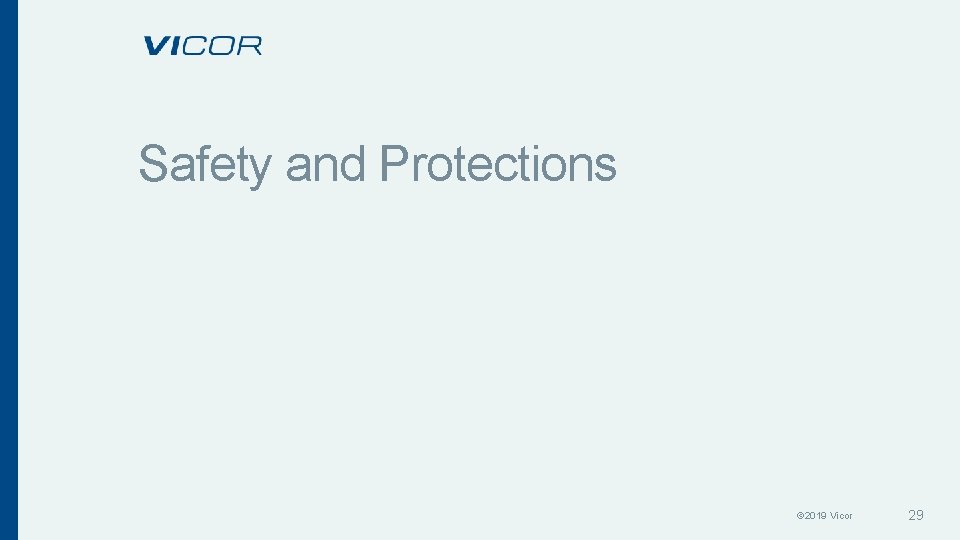
Safety and Protections © 2019 Vicor 29
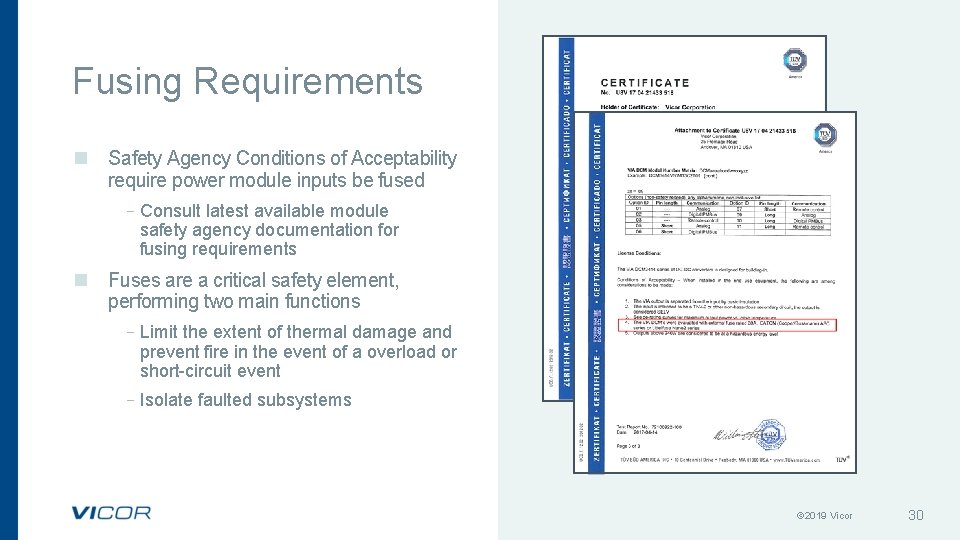
Fusing Requirements n Safety Agency Conditions of Acceptability require power module inputs be fused –Consult latest available module safety agency documentation for fusing requirements n Fuses are a critical safety element, performing two main functions –Limit the extent of thermal damage and prevent fire in the event of a overload or short-circuit event –Isolate faulted subsystems © 2019 Vicor 30
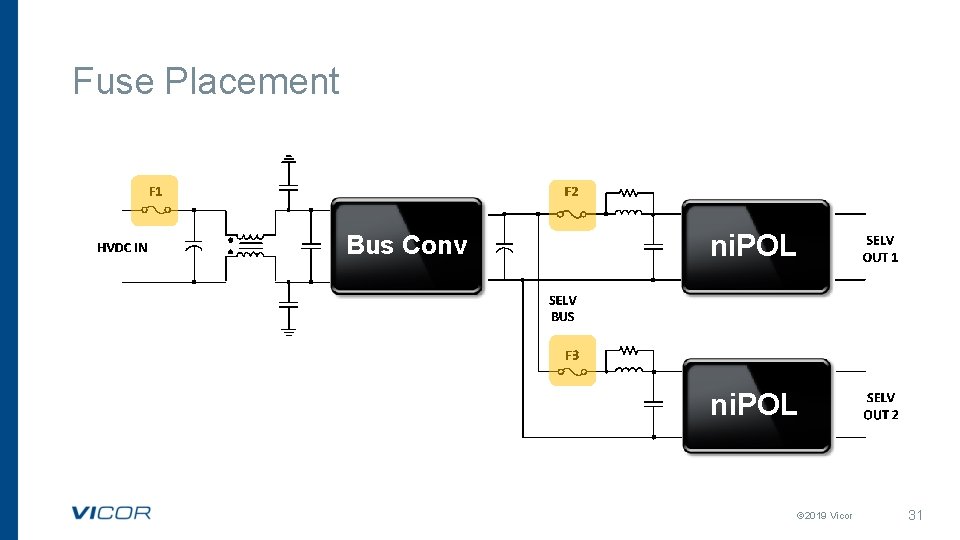
Fuse Placement Bus Conv ni. POL © 2019 Vicor 31
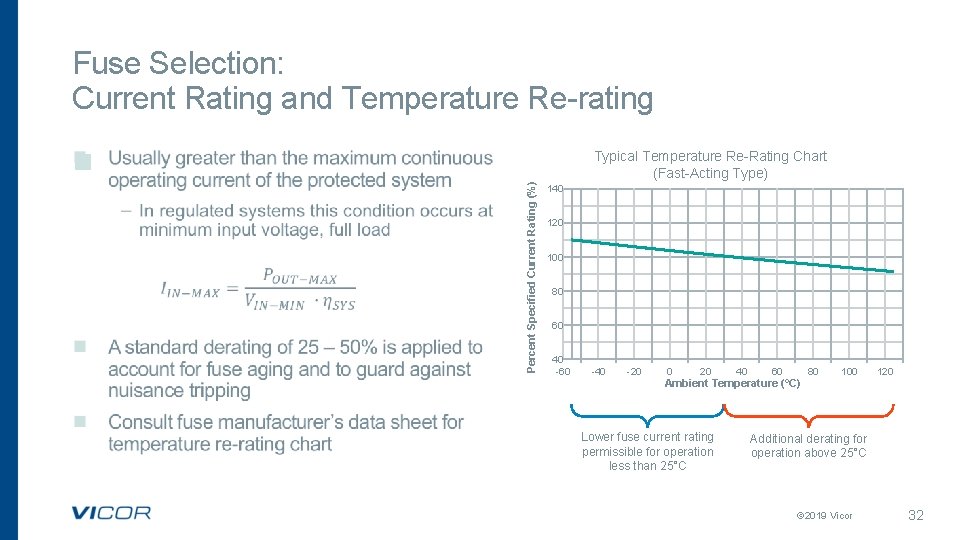
Fuse Selection: Current Rating and Temperature Re-rating n Percent Specified Current Rating (%) Typical Temperature Re-Rating Chart (Fast-Acting Type) 140 120 100 80 60 40 -60 -40 -20 0 20 40 60 80 100 120 Ambient Temperature (°C) Lower fuse current rating permissible for operation less than 25°C Additional derating for operation above 25°C © 2019 Vicor 32
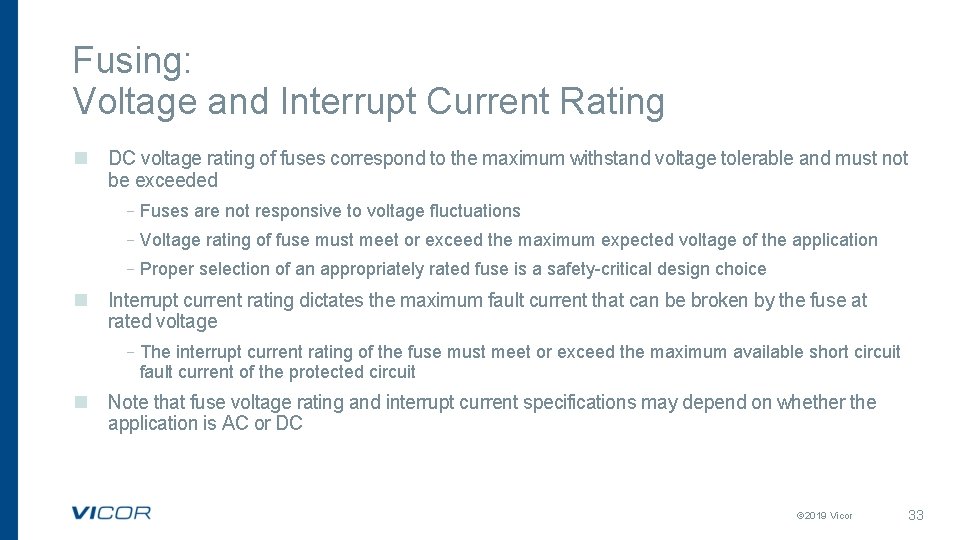
Fusing: Voltage and Interrupt Current Rating n DC voltage rating of fuses correspond to the maximum withstand voltage tolerable and must not be exceeded –Fuses are not responsive to voltage fluctuations –Voltage rating of fuse must meet or exceed the maximum expected voltage of the application –Proper selection of an appropriately rated fuse is a safety-critical design choice n Interrupt current rating dictates the maximum fault current that can be broken by the fuse at rated voltage –The interrupt current rating of the fuse must meet or exceed the maximum available short circuit fault current of the protected circuit n Note that fuse voltage rating and interrupt current specifications may depend on whether the application is AC or DC © 2019 Vicor 33
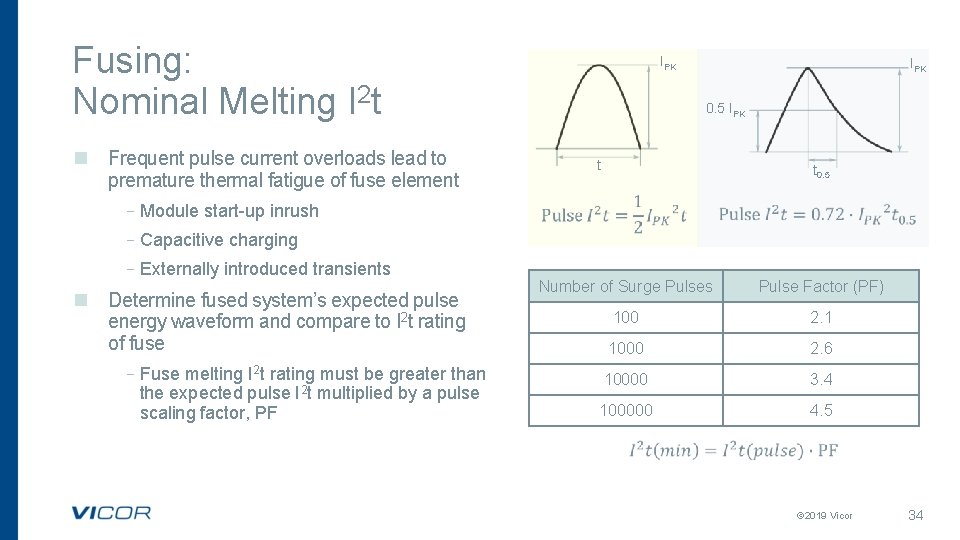
Fusing: Nominal Melting I 2 t IPK 0. 5 IPK n Frequent pulse current overloads lead to premature thermal fatigue of fuse element –Module start-up inrush IPK t t 0. 5 –Capacitive charging –Externally introduced transients n Determine fused system’s expected pulse energy waveform and compare to I 2 t rating of fuse –Fuse melting I 2 t rating must be greater than the expected pulse I 2 t multiplied by a pulse scaling factor, PF Number of Surge Pulses Pulse Factor (PF) 100 2. 1 1000 2. 6 10000 3. 4 100000 4. 5 © 2019 Vicor 34
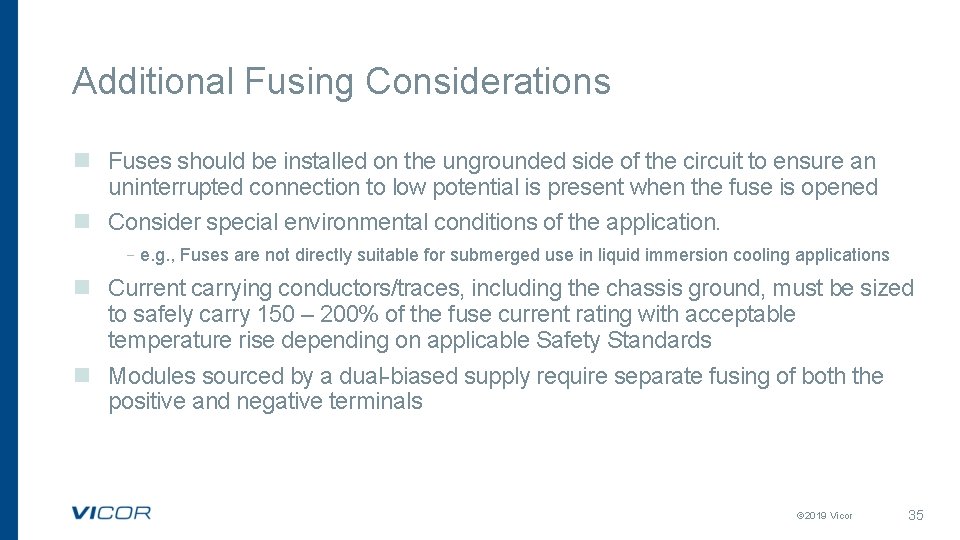
Additional Fusing Considerations n Fuses should be installed on the ungrounded side of the circuit to ensure an uninterrupted connection to low potential is present when the fuse is opened n Consider special environmental conditions of the application. –e. g. , Fuses are not directly suitable for submerged use in liquid immersion cooling applications n Current carrying conductors/traces, including the chassis ground, must be sized to safely carry 150 – 200% of the fuse current rating with acceptable temperature rise depending on applicable Safety Standards n Modules sourced by a dual-biased supply require separate fusing of both the positive and negative terminals © 2019 Vicor 35
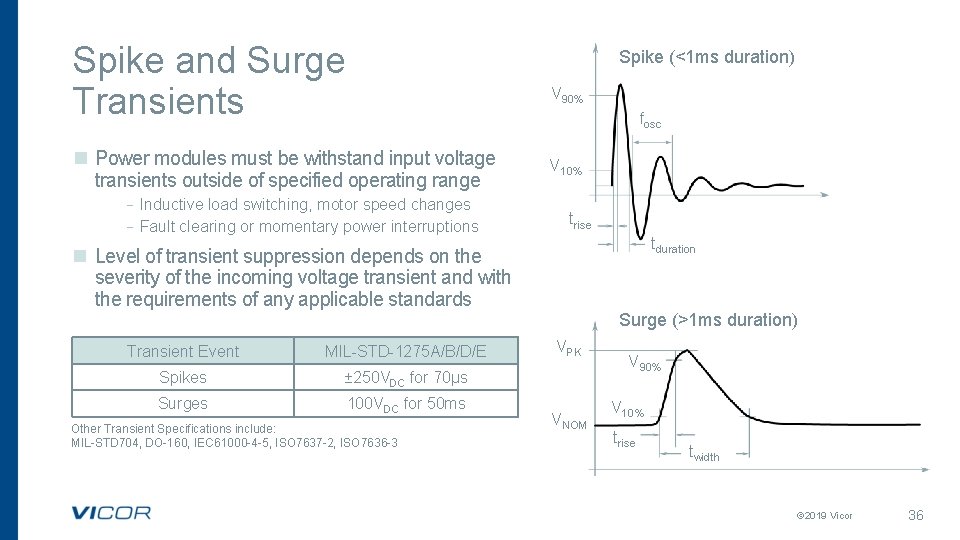
Spike and Surge Transients n Power modules must be withstand input voltage transients outside of specified operating range – Inductive load switching, motor speed changes – Fault clearing or momentary power interruptions Spike (<1 ms duration) V 90% fosc V 10% trise tduration n Level of transient suppression depends on the severity of the incoming voltage transient and with the requirements of any applicable standards Transient Event MIL-STD-1275 A/B/D/E Spikes ± 250 VDC for 70μs Surges 100 VDC for 50 ms Other Transient Specifications include: MIL-STD 704, DO-160, IEC 61000 -4 -5, ISO 7637 -2, ISO 7636 -3 Surge (>1 ms duration) VPK VNOM V 90% V 10% trise twidth © 2019 Vicor 36
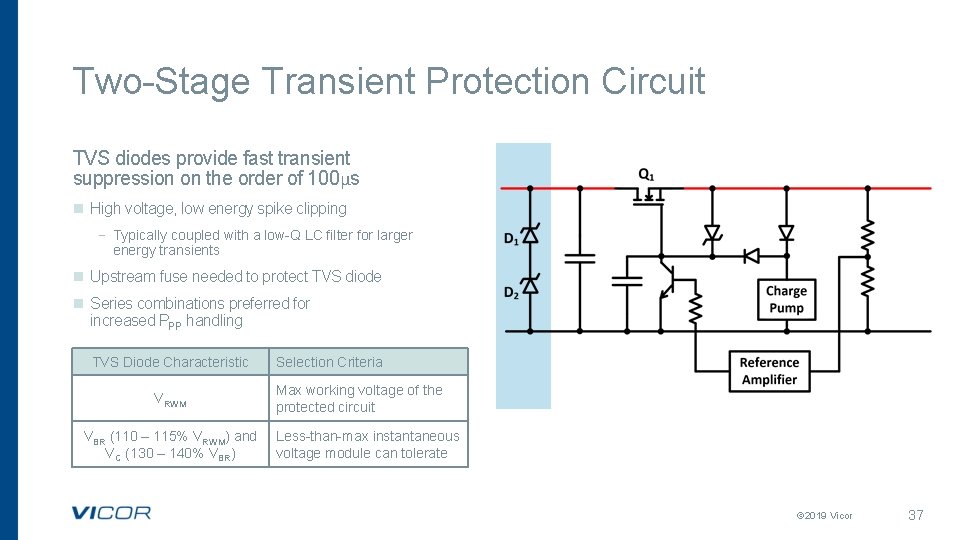
Two-Stage Transient Protection Circuit TVS diodes provide fast transient suppression on the order of 100μs n High voltage, low energy spike clipping – Typically coupled with a low-Q LC filter for larger energy transients n Upstream fuse needed to protect TVS diode n Series combinations preferred for increased PPP handling TVS Diode Characteristic VRWM VBR (110 – 115% VRWM) and VC (130 – 140% VBR) Selection Criteria Max working voltage of the protected circuit Less-than-max instantaneous voltage module can tolerate © 2019 Vicor 37
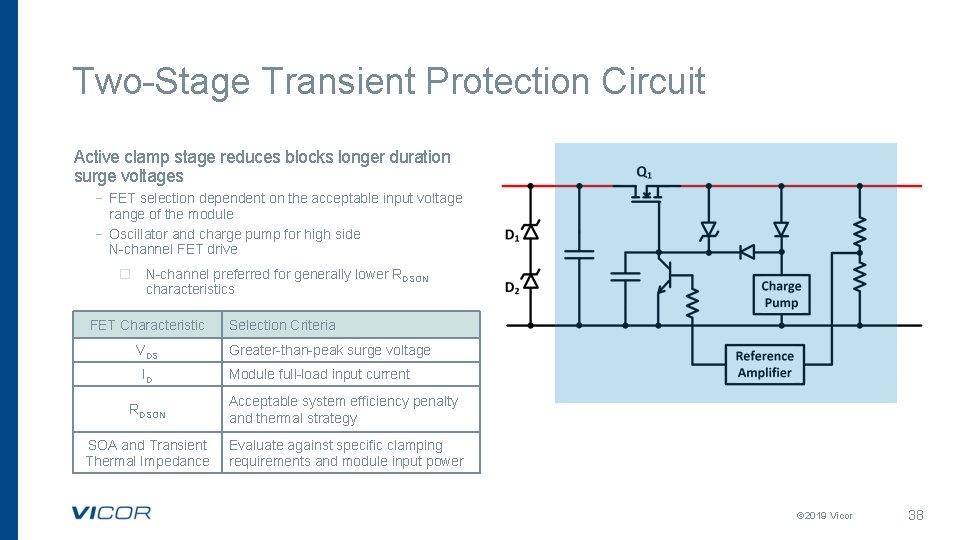
Two-Stage Transient Protection Circuit Active clamp stage reduces blocks longer duration surge voltages – FET selection dependent on the acceptable input voltage range of the module – Oscillator and charge pump for high side N-channel FET drive N-channel preferred for generally lower RDSON characteristics FET Characteristic VDS ID Selection Criteria Greater-than-peak surge voltage Module full-load input current RDSON Acceptable system efficiency penalty and thermal strategy SOA and Transient Thermal Impedance Evaluate against specific clamping requirements and module input power © 2019 Vicor 38
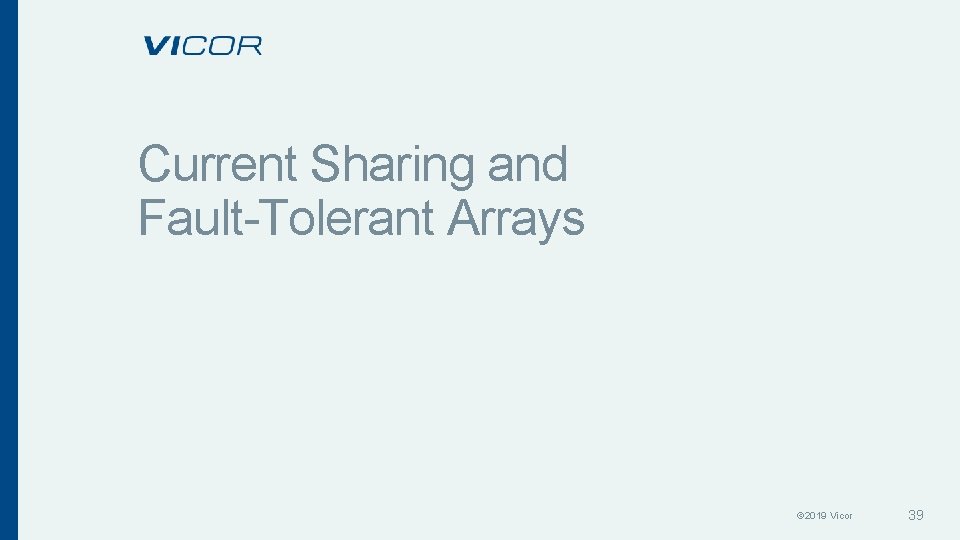
Current Sharing and Fault-Tolerant Arrays © 2019 Vicor 39
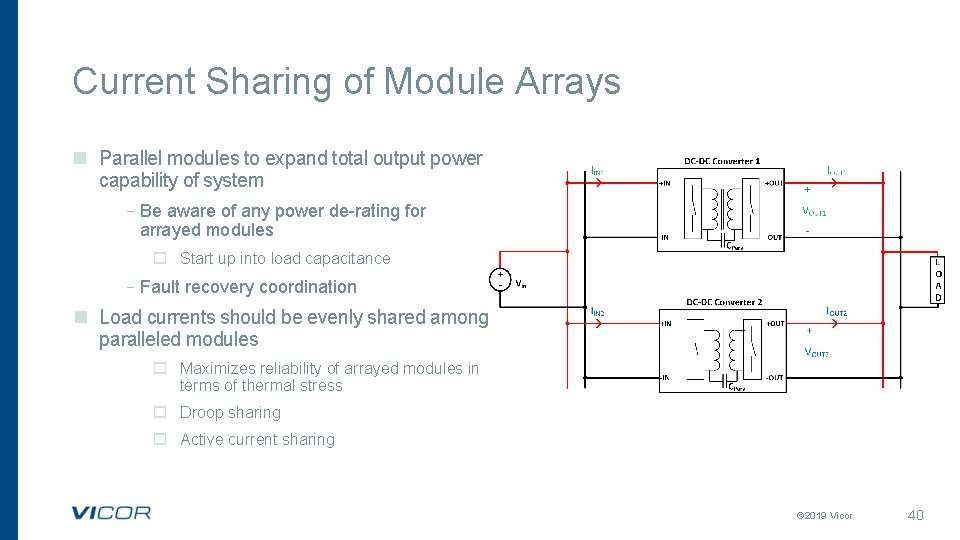
Current Sharing of Module Arrays n Parallel modules to expand total output power capability of system –Be aware of any power de-rating for arrayed modules Start up into load capacitance –Fault recovery coordination n Load currents should be evenly shared among paralleled modules Maximizes reliability of arrayed modules in terms of thermal stress Droop sharing Active current sharing © 2019 Vicor 40
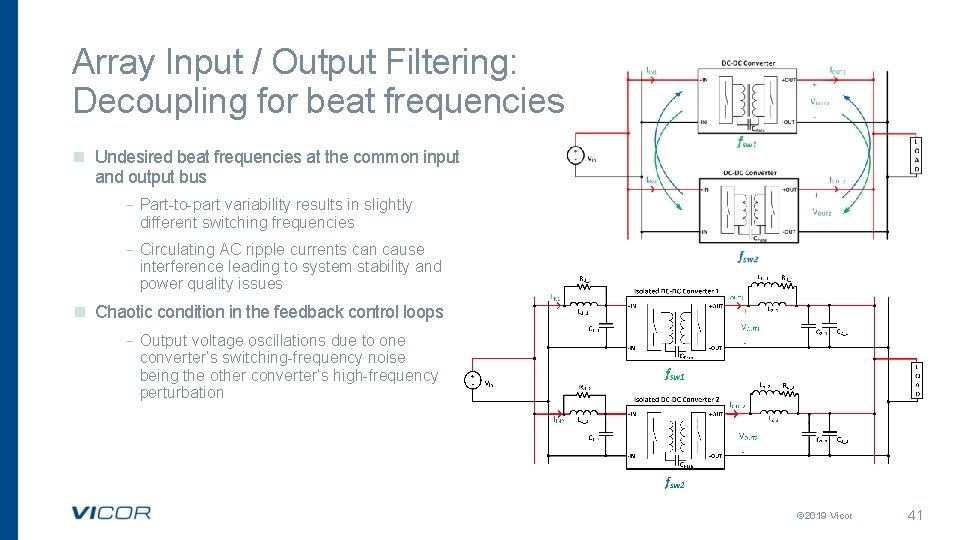
Array Input / Output Filtering: Decoupling for beat frequencies n Undesired beat frequencies at the common input and output bus – Part-to-part variability results in slightly different switching frequencies – Circulating AC ripple currents can cause interference leading to system stability and power quality issues n Chaotic condition in the feedback control loops – Output voltage oscillations due to one converter’s switching-frequency noise being the other converter’s high-frequency perturbation © 2019 Vicor 41
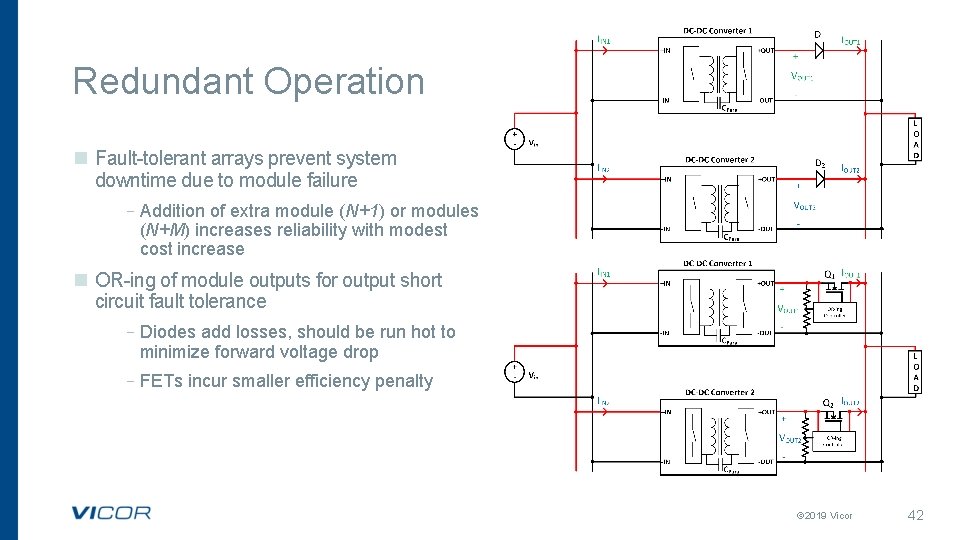
Redundant Operation n Fault-tolerant arrays prevent system downtime due to module failure –Addition of extra module (N+1) or modules (N+M) increases reliability with modest cost increase n OR-ing of module outputs for output short circuit fault tolerance –Diodes add losses, should be run hot to minimize forward voltage drop –FETs incur smaller efficiency penalty © 2019 Vicor 42
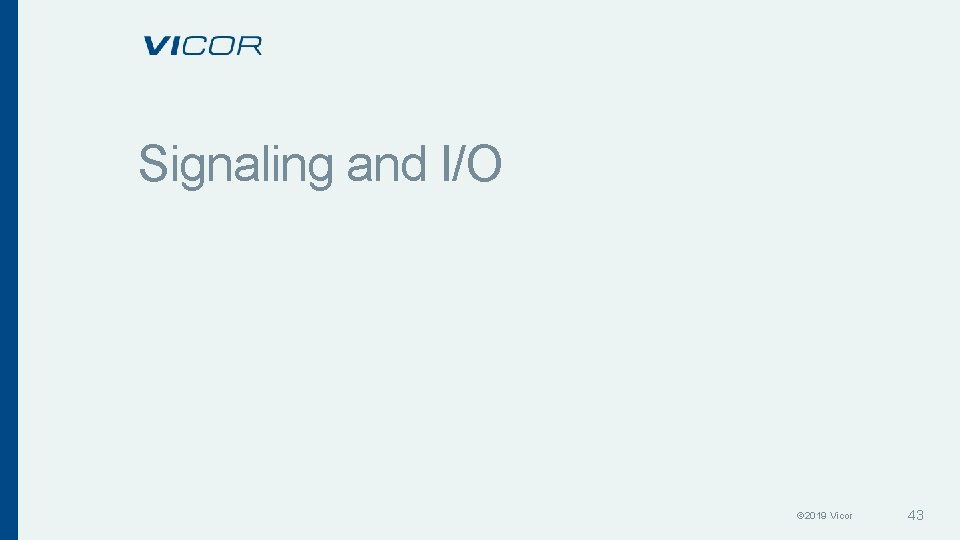
Signaling and I/O © 2019 Vicor 43
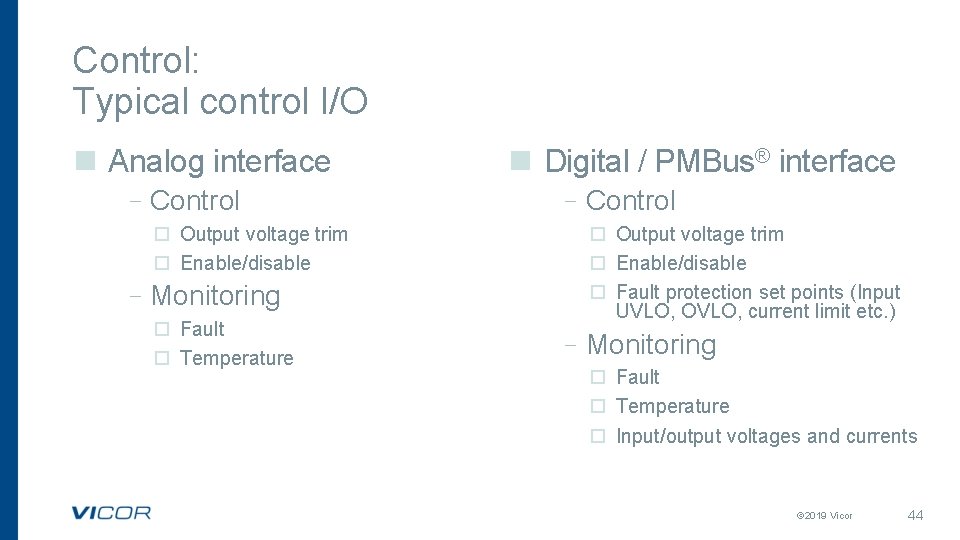
Control: Typical control I/O n Analog interface –Control Output voltage trim Enable/disable –Monitoring Fault Temperature n Digital / PMBus® interface –Control Output voltage trim Enable/disable Fault protection set points (Input UVLO, OVLO, current limit etc. ) –Monitoring Fault Temperature Input/output voltages and currents © 2019 Vicor 44
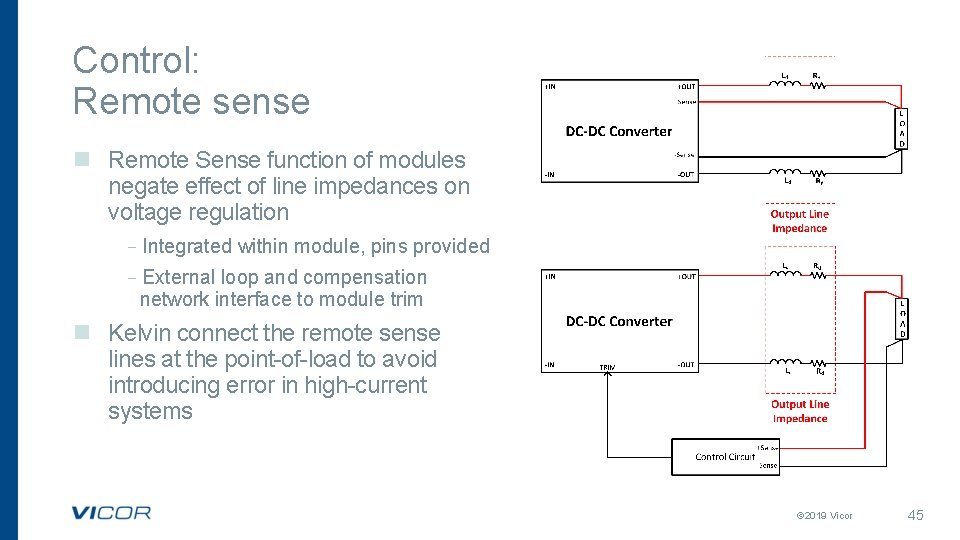
Control: Remote sense n Remote Sense function of modules negate effect of line impedances on voltage regulation –Integrated within module, pins provided –External loop and compensation network interface to module trim n Kelvin connect the remote sense lines at the point-of-load to avoid introducing error in high-current systems © 2019 Vicor 45
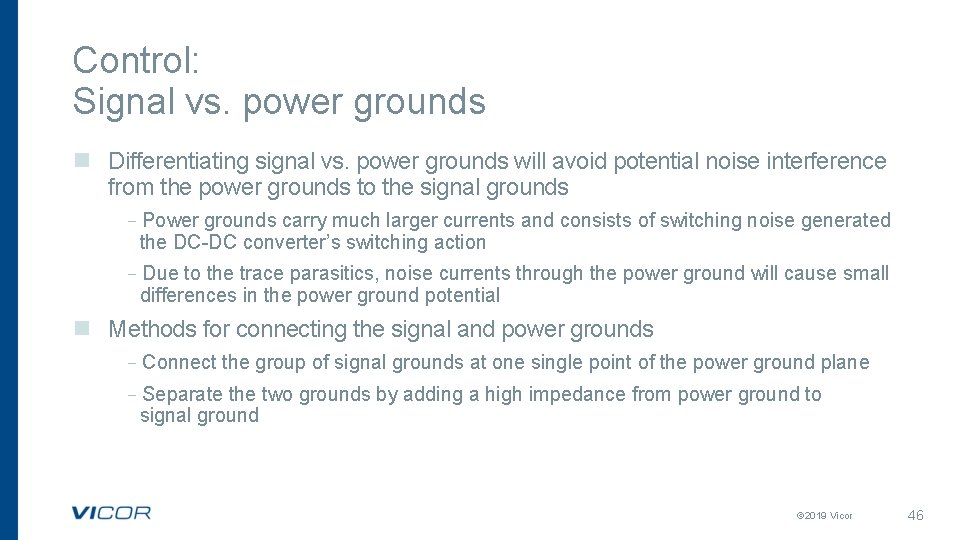
Control: Signal vs. power grounds n Differentiating signal vs. power grounds will avoid potential noise interference from the power grounds to the signal grounds –Power grounds carry much larger currents and consists of switching noise generated the DC-DC converter’s switching action –Due to the trace parasitics, noise currents through the power ground will cause small differences in the power ground potential n Methods for connecting the signal and power grounds –Connect the group of signal grounds at one single point of the power ground plane –Separate the two grounds by adding a high impedance from power ground to signal ground © 2019 Vicor 46
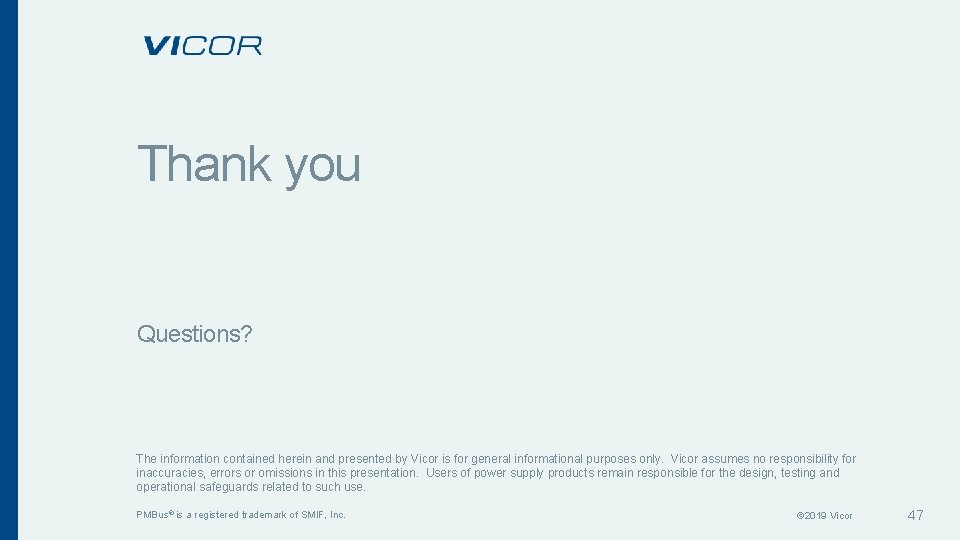
Thank you Questions? The information contained herein and presented by Vicor is for general informational purposes only. Vicor assumes no responsibility for inaccuracies, errors or omissions in this presentation. Users of power supply products remain responsible for the design, testing and operational safeguards related to such use. PMBus® is a registered trademark of SMIF, Inc. © 2019 Vicor 47
Dcdc detroit
Right product right place right time right price
Family time
Design done right
The right man on the right place at the right time
Unit 42 passive 1 (is done / was done)
Size reduction
Sen bir koyun olsan bende bir kuzu sözleri
Redos and retakes done right
Monday done right meaning
Modular design programming
Integral vs modular design
Delayed differentiation and modular design
Modular design yearbook
Objectives of modular software design
Service design generally differs from product design
Modular plant design
Supplementary design
Modular servo system
And a modular collimation system
Standard modular fixturing system
Go left left right right
You put your right foot in you put your right foot out
Left left right right go go go
Nathan dickinson
Nathan barrios
Nathan seiberg
Nathan brunelle
Nathan burk
Marybeth tinning husband
Nathan dalrymple
Nathan liskov
Nathan rinne
Nathan dalrymple
Nathan seiberg
Nathan ackerman family therapy
Minnieamy
Nathan weiss graduate college
Glenn nathan
Nathan boylan
Nathan younge
Nathan zohner
Miss emma page
Nathan gamble poker
Nathan alba
Nathan elvery
Mutualism in the rainforest
Industrial revolution powerpoint