Largent est le nerf de la guerre Filomeno
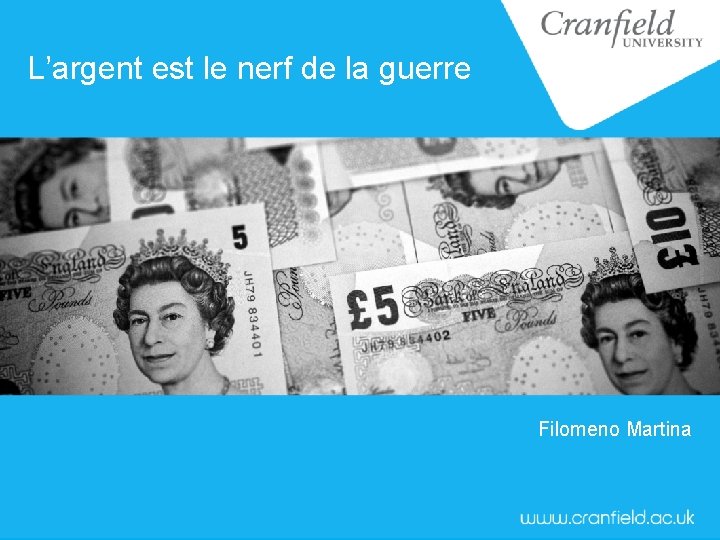
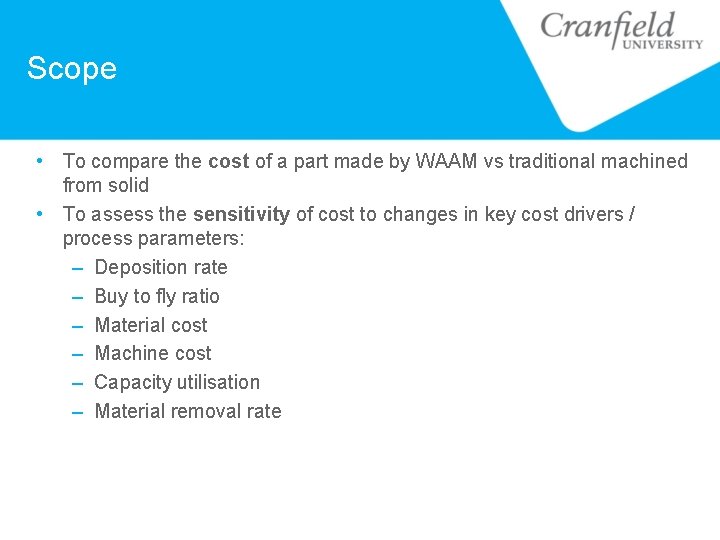
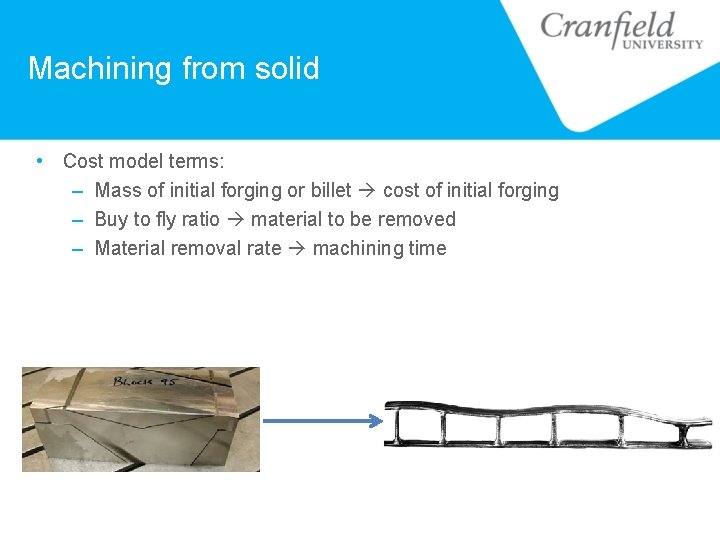
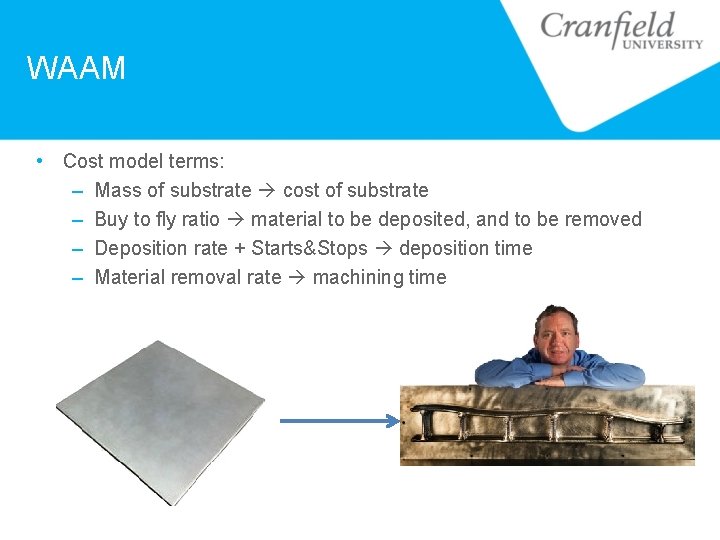
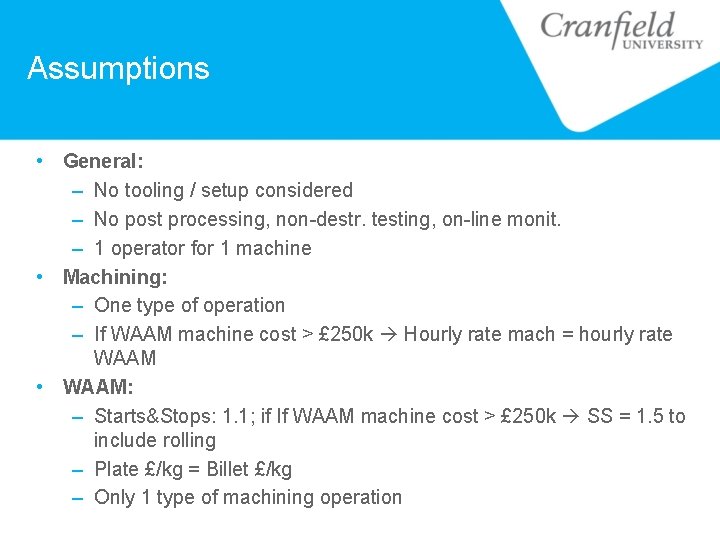
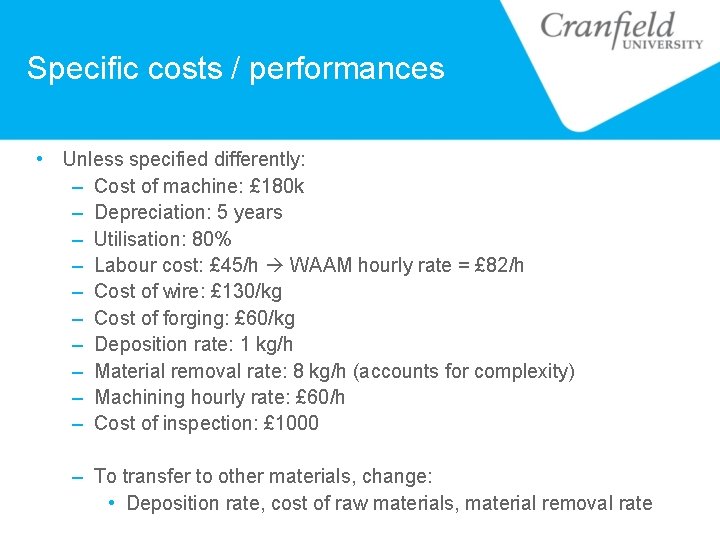
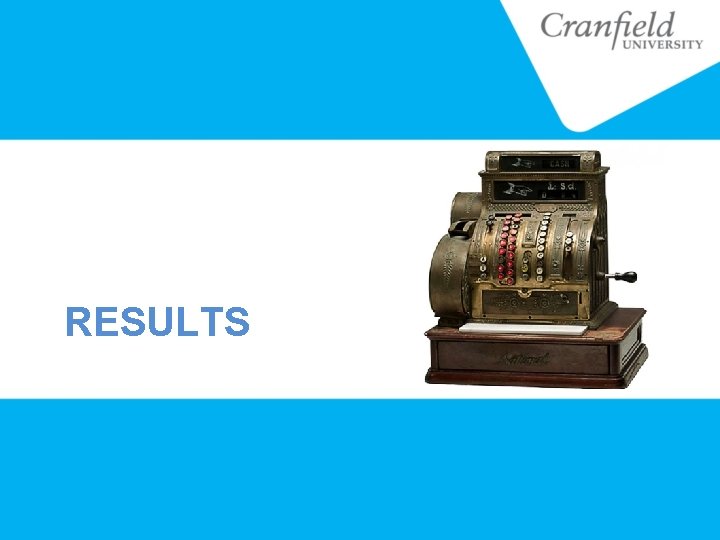

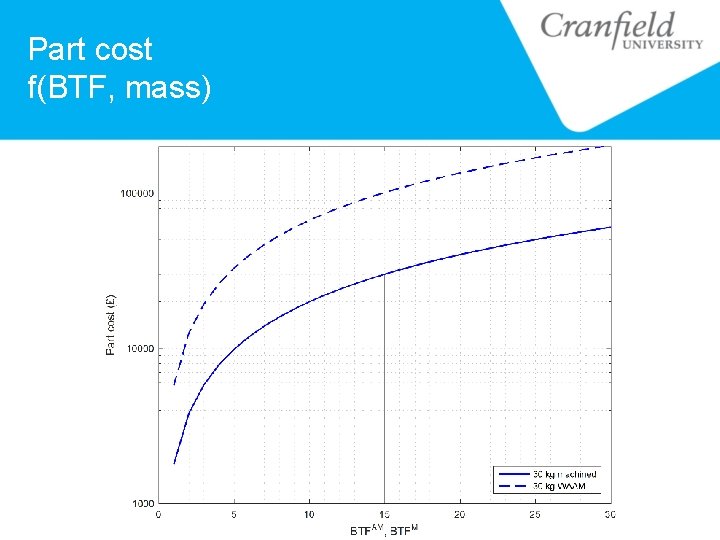
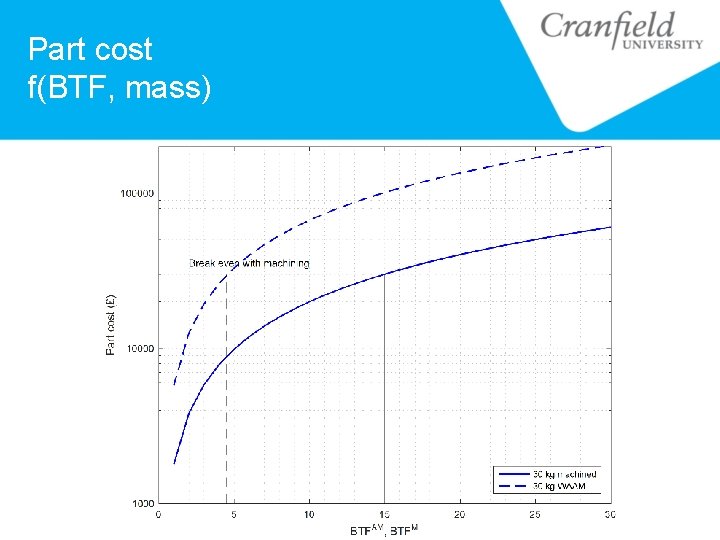

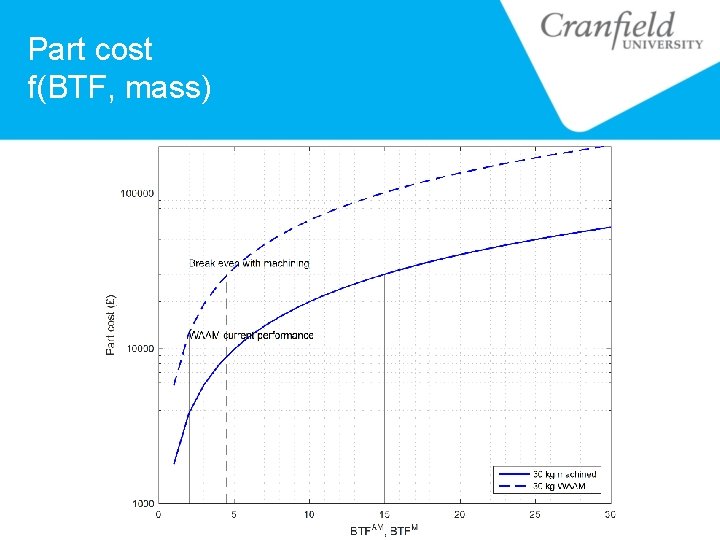
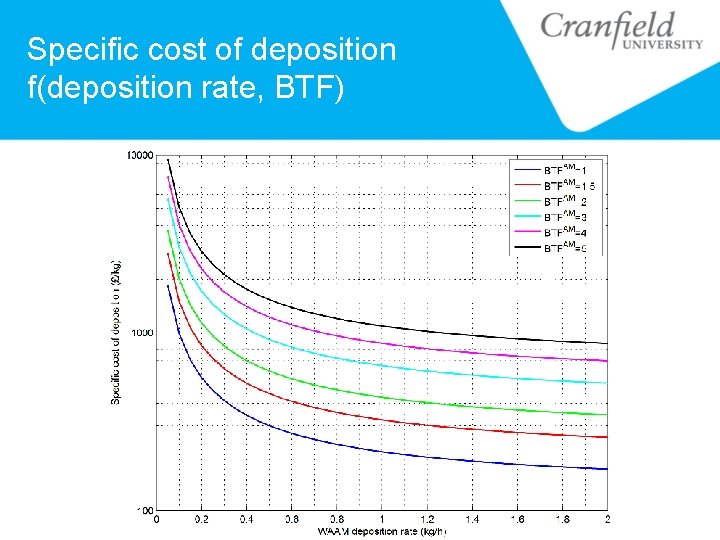
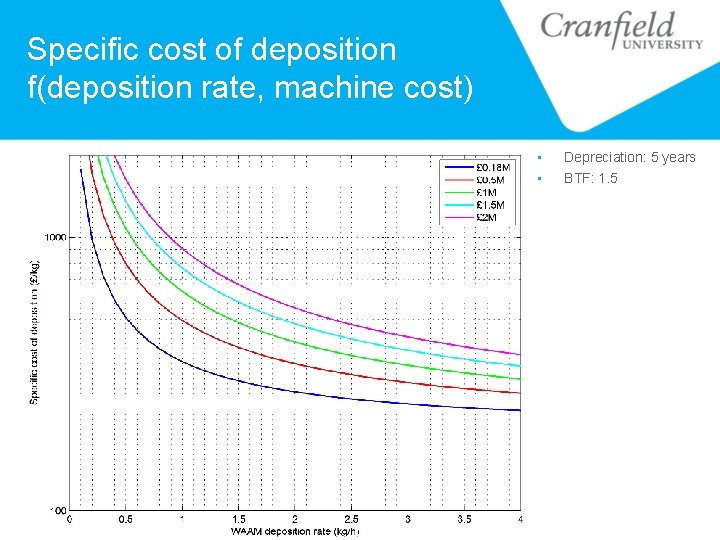
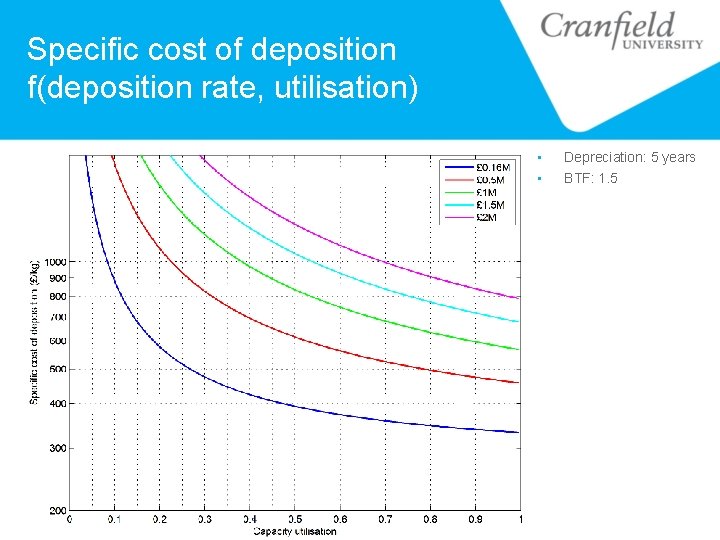
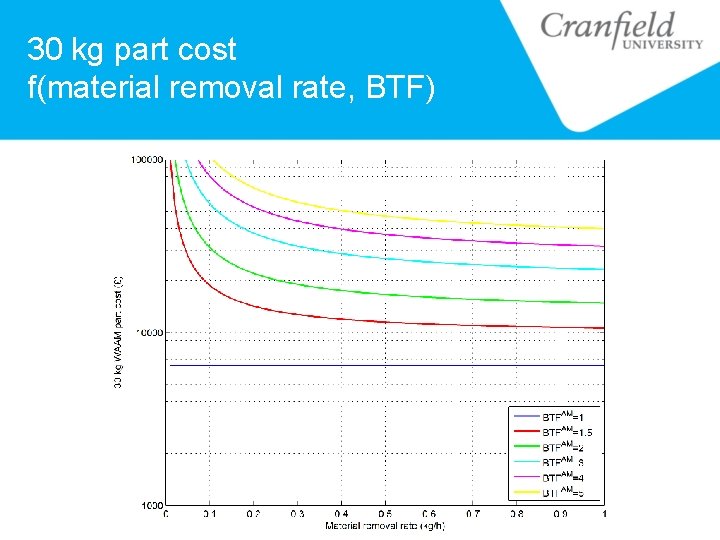
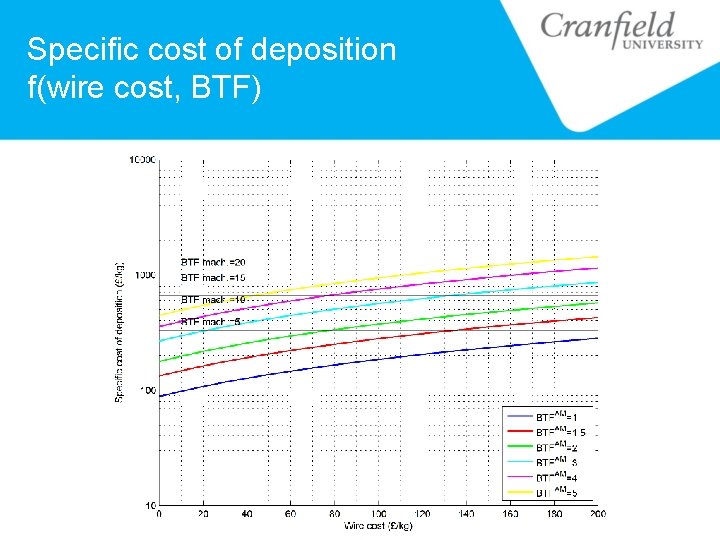
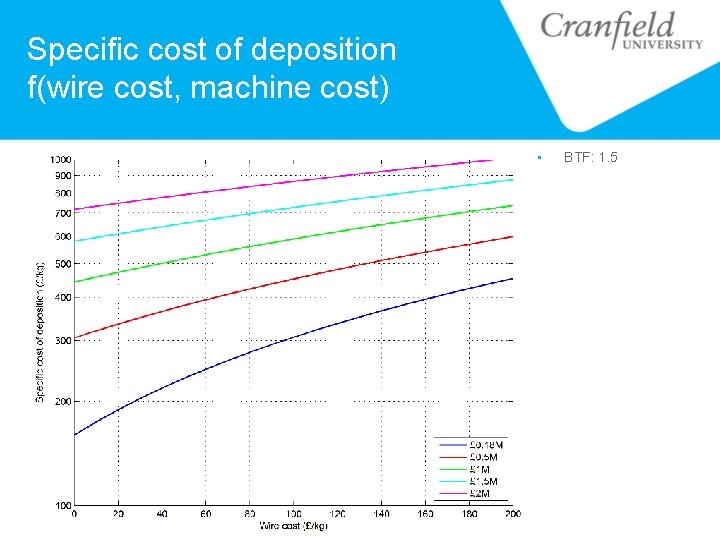
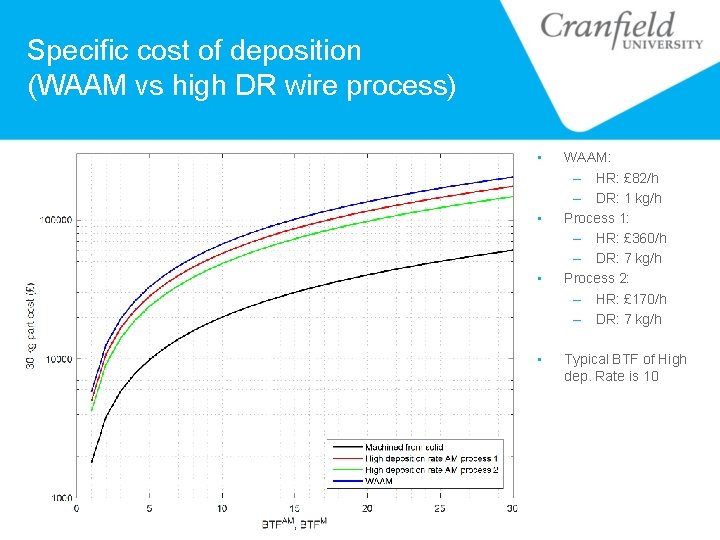
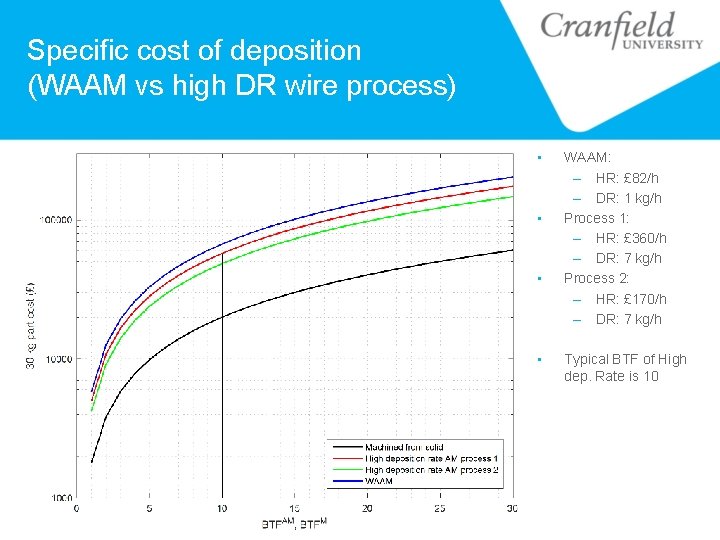
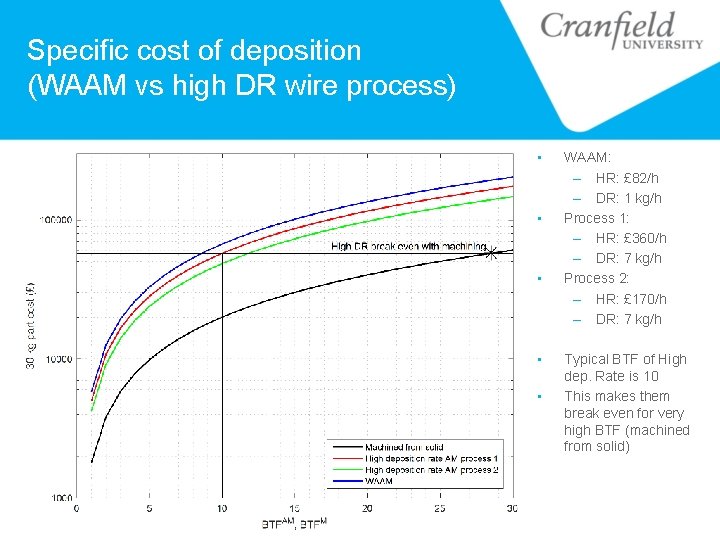
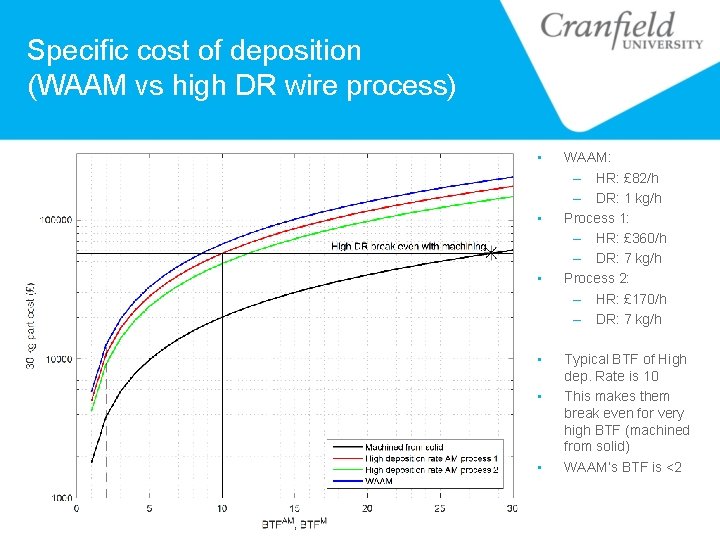
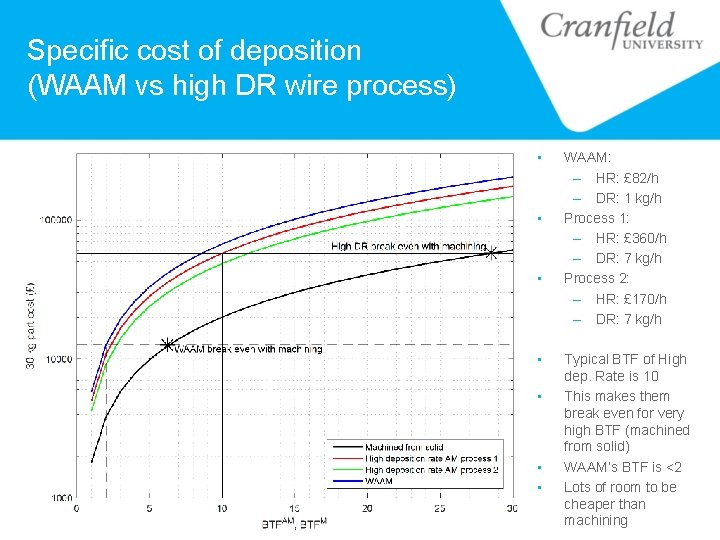
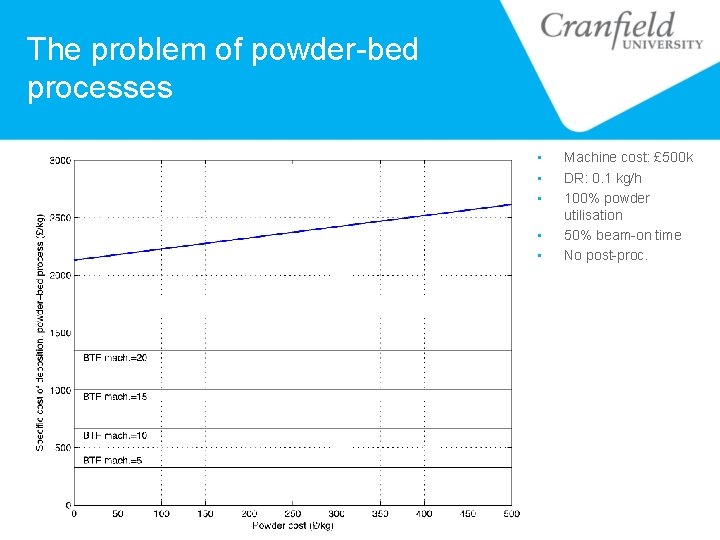
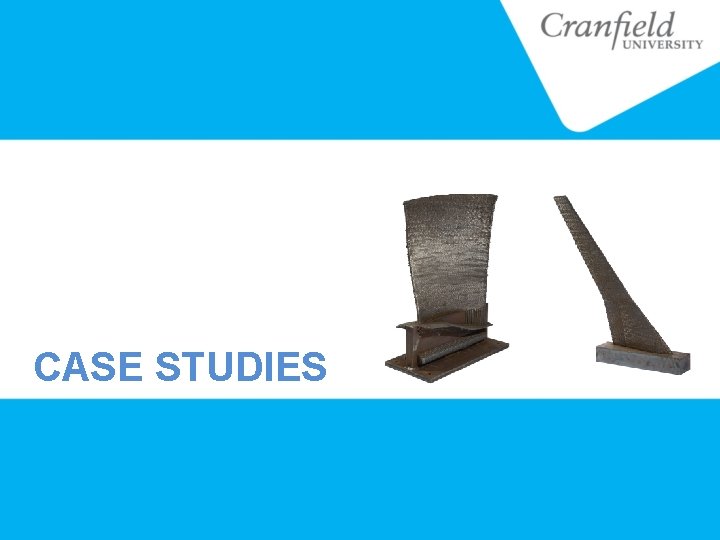
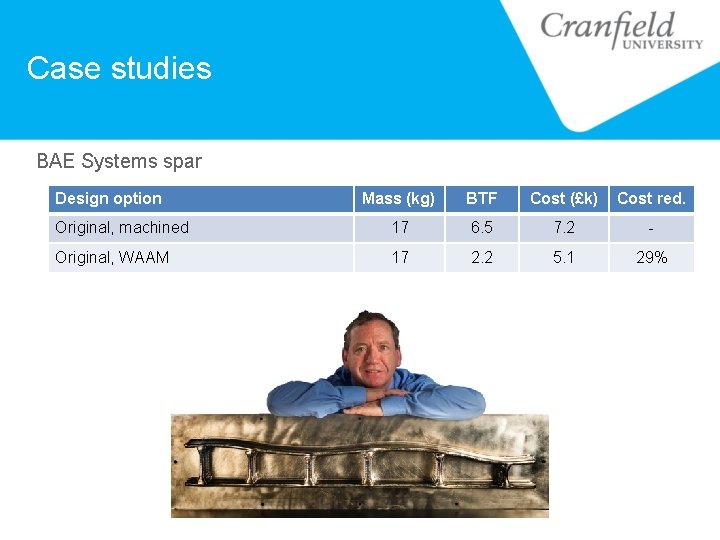
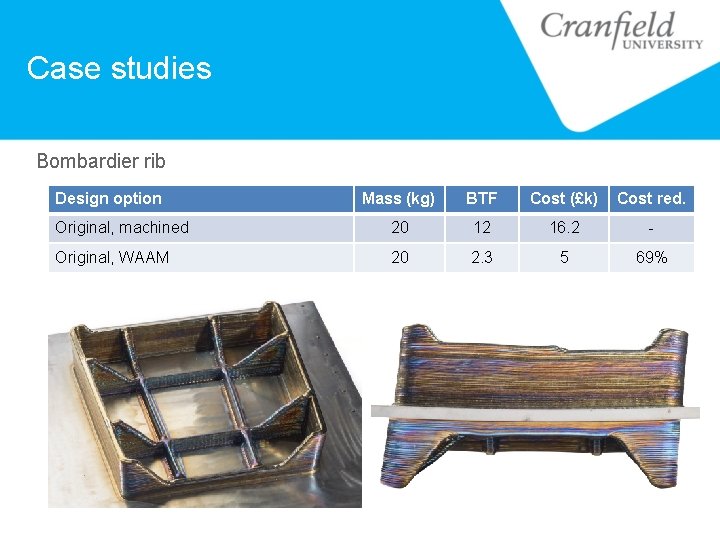
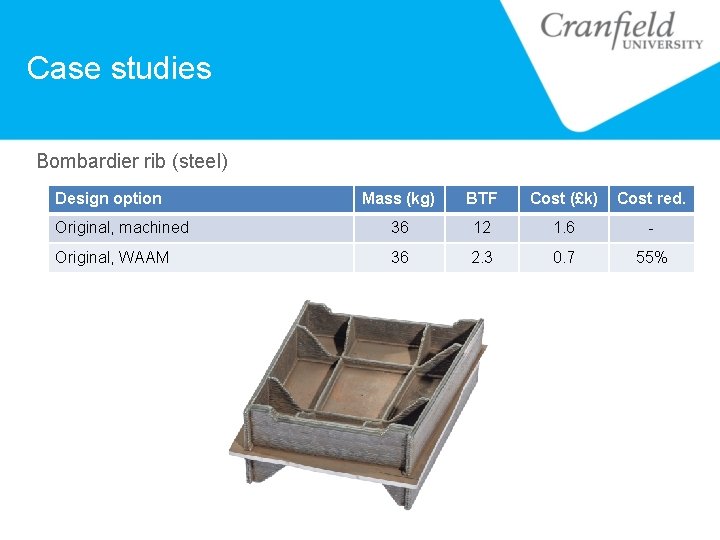
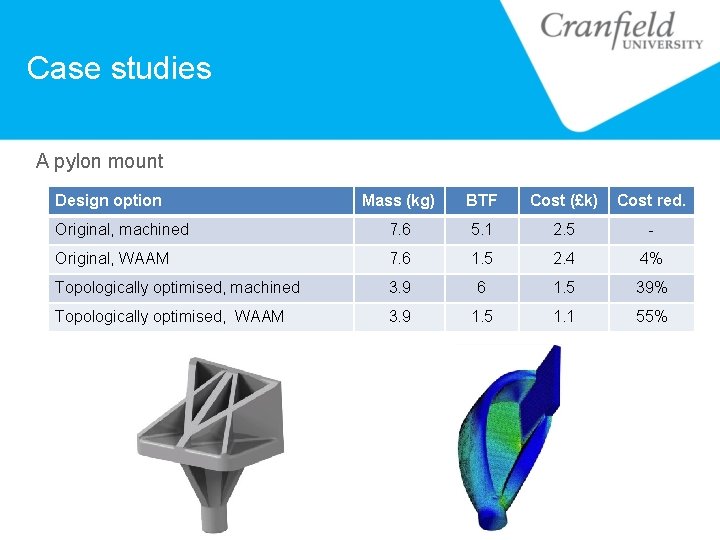
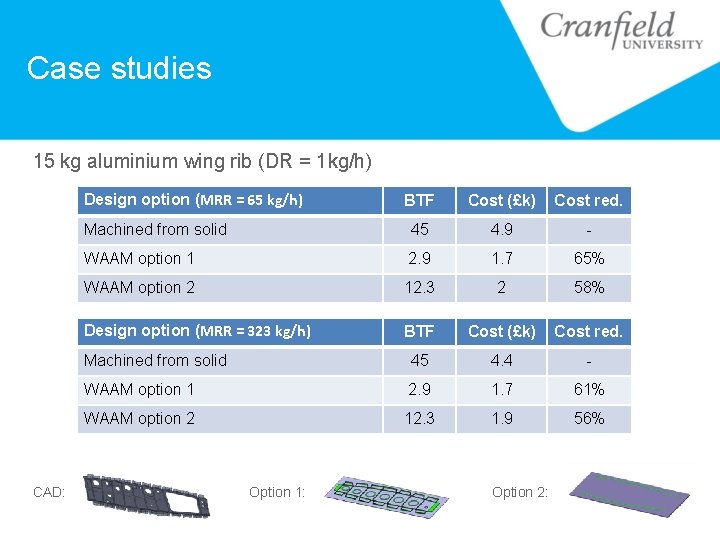
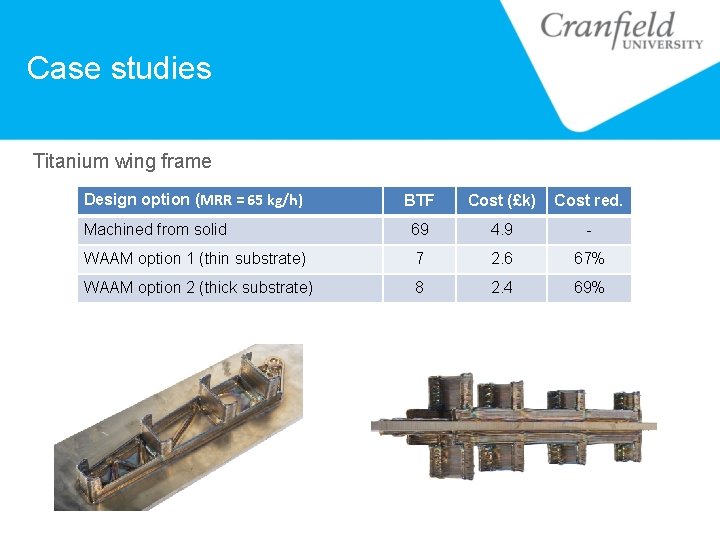
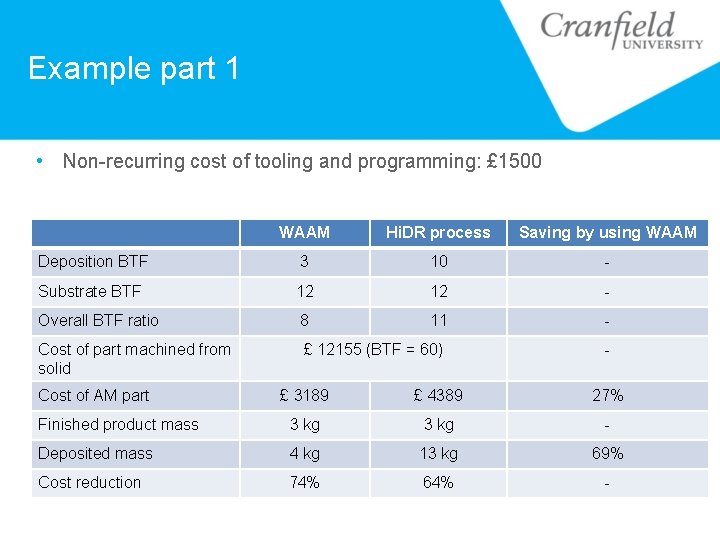
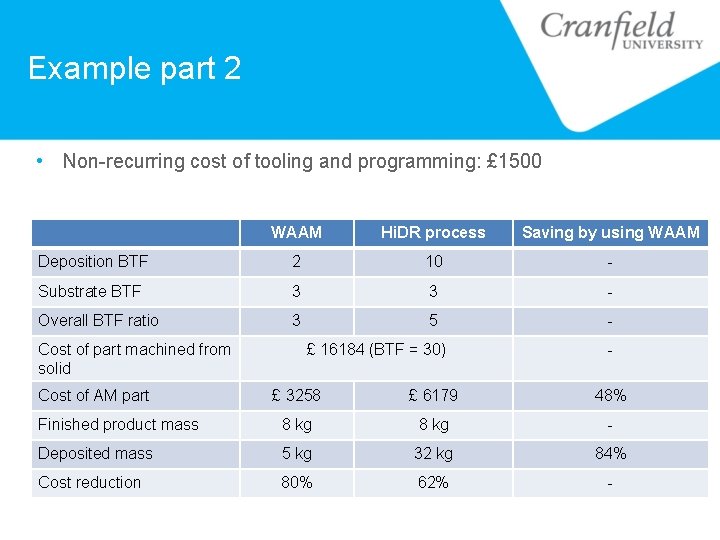
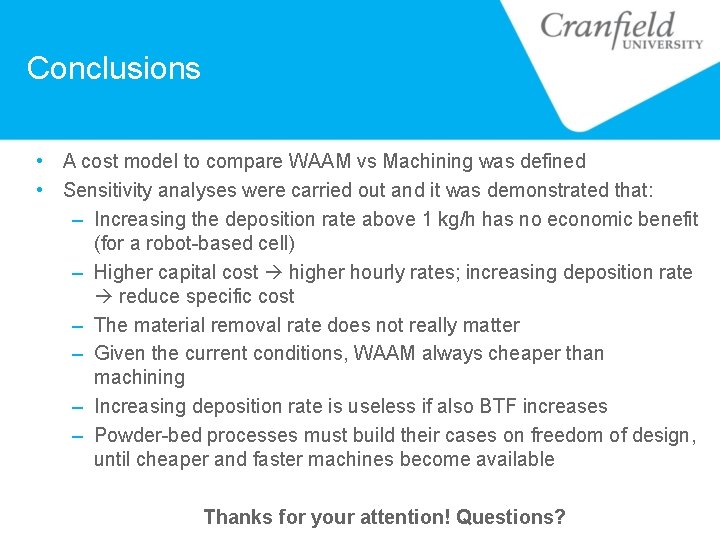
- Slides: 34
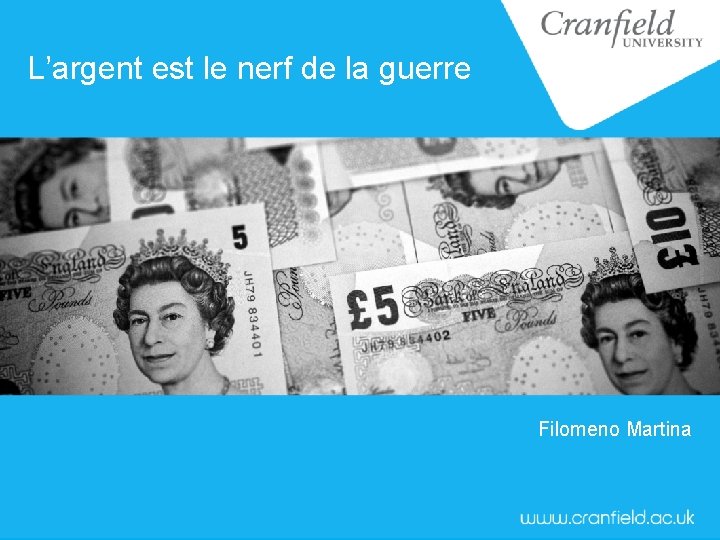
L’argent est le nerf de la guerre Filomeno Martina
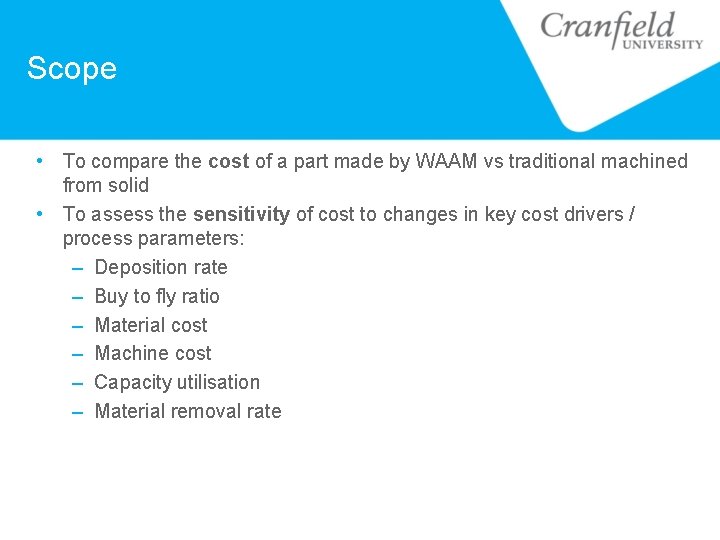
Scope • To compare the cost of a part made by WAAM vs traditional machined from solid • To assess the sensitivity of cost to changes in key cost drivers / process parameters: – Deposition rate – Buy to fly ratio – Material cost – Machine cost – Capacity utilisation – Material removal rate
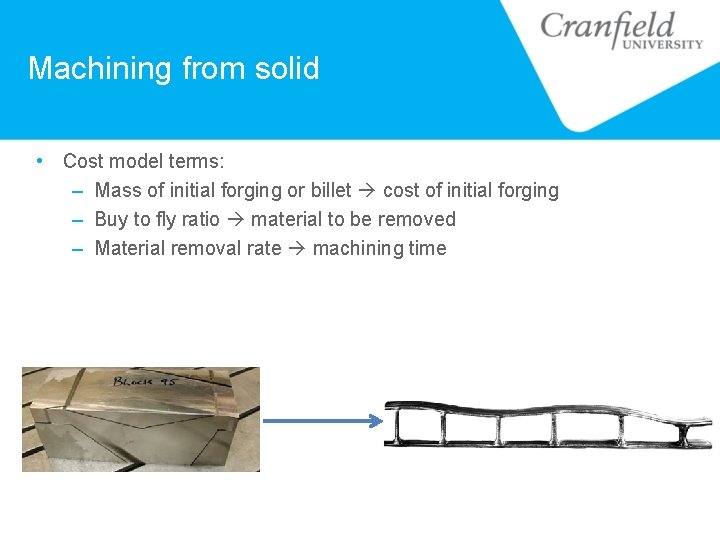
Machining from solid • Cost model terms: – Mass of initial forging or billet cost of initial forging – Buy to fly ratio material to be removed – Material removal rate machining time
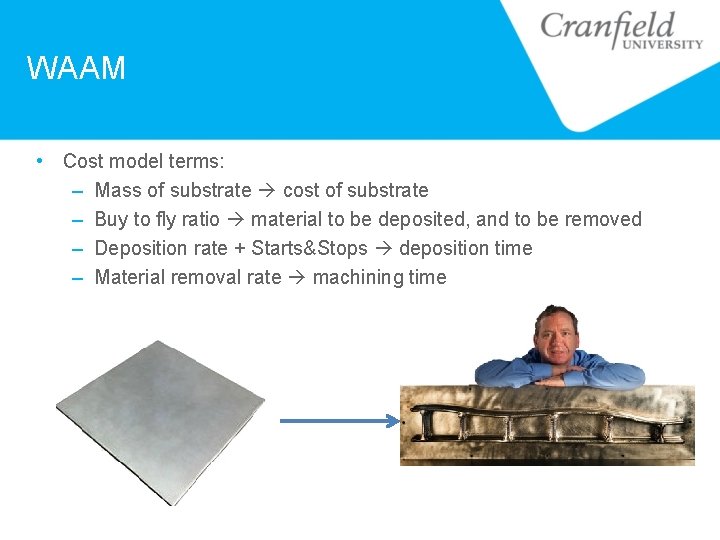
WAAM • Cost model terms: – Mass of substrate cost of substrate – Buy to fly ratio material to be deposited, and to be removed – Deposition rate + Starts&Stops deposition time – Material removal rate machining time
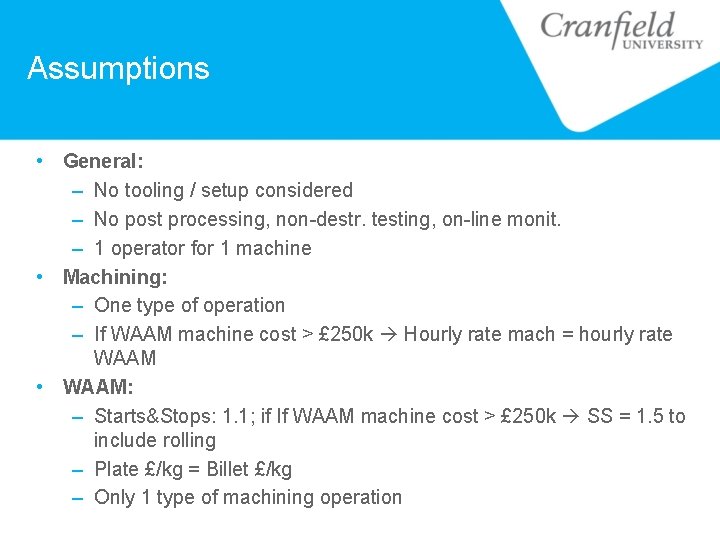
Assumptions • General: – No tooling / setup considered – No post processing, non-destr. testing, on-line monit. – 1 operator for 1 machine • Machining: – One type of operation – If WAAM machine cost > £ 250 k Hourly rate mach = hourly rate WAAM • WAAM: – Starts&Stops: 1. 1; if If WAAM machine cost > £ 250 k SS = 1. 5 to include rolling – Plate £/kg = Billet £/kg – Only 1 type of machining operation
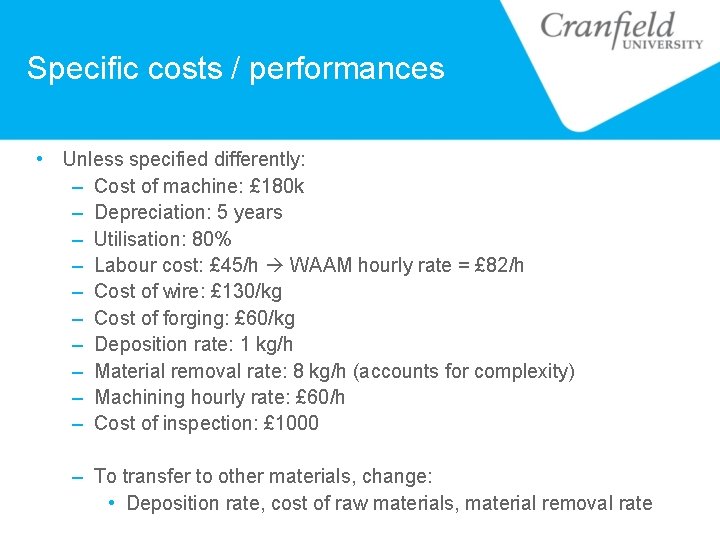
Specific costs / performances • Unless specified differently: – Cost of machine: £ 180 k – Depreciation: 5 years – Utilisation: 80% – Labour cost: £ 45/h WAAM hourly rate = £ 82/h – Cost of wire: £ 130/kg – Cost of forging: £ 60/kg – Deposition rate: 1 kg/h – Material removal rate: 8 kg/h (accounts for complexity) – Machining hourly rate: £ 60/h – Cost of inspection: £ 1000 – To transfer to other materials, change: • Deposition rate, cost of raw materials, material removal rate
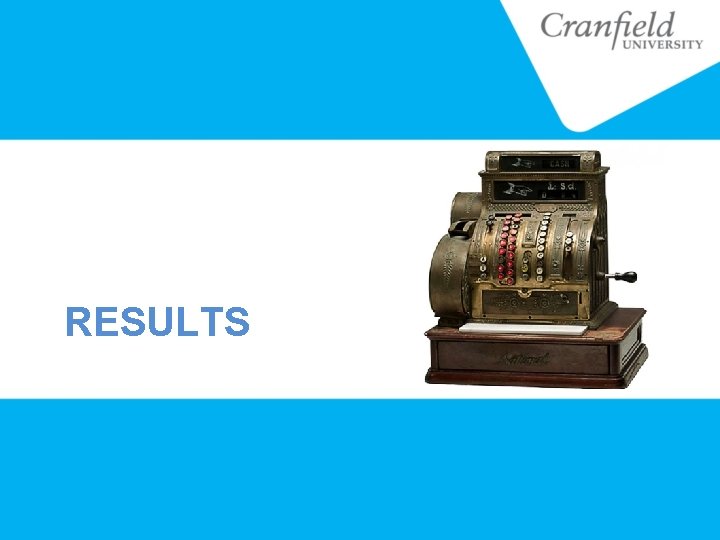
RESULTS

Part cost f(BTF, mass)
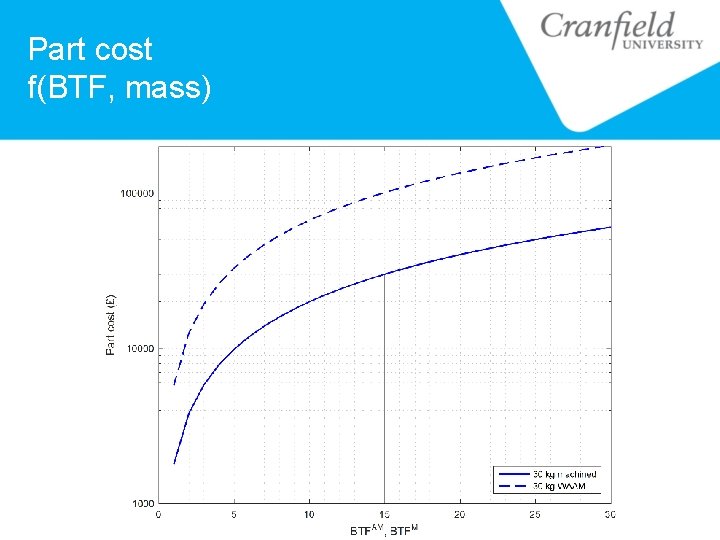
Part cost f(BTF, mass)
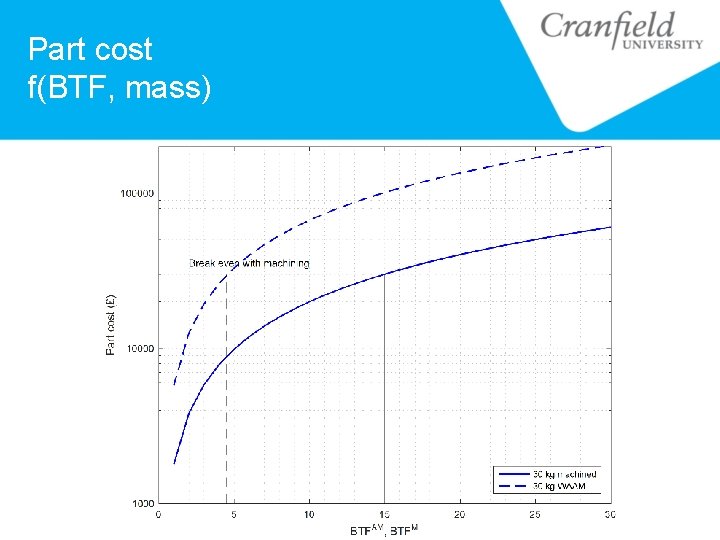
Part cost f(BTF, mass)

Part cost f(BTF, mass)
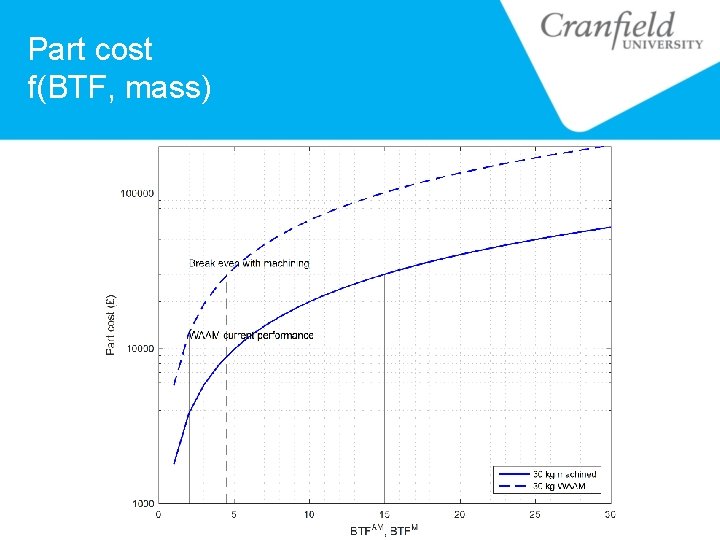
Part cost f(BTF, mass)
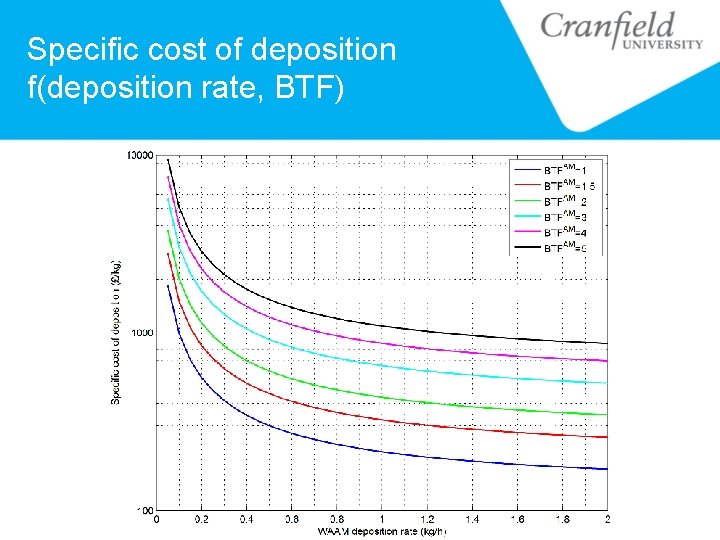
Specific cost of deposition f(deposition rate, BTF)
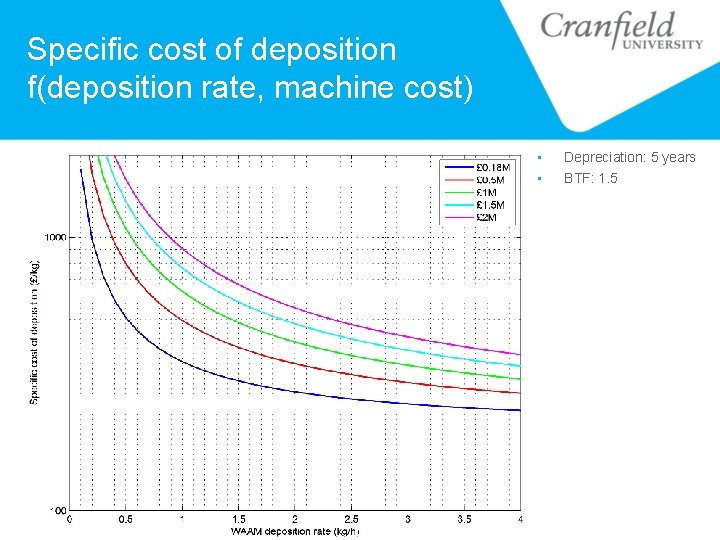
Specific cost of deposition f(deposition rate, machine cost) • • Depreciation: 5 years BTF: 1. 5
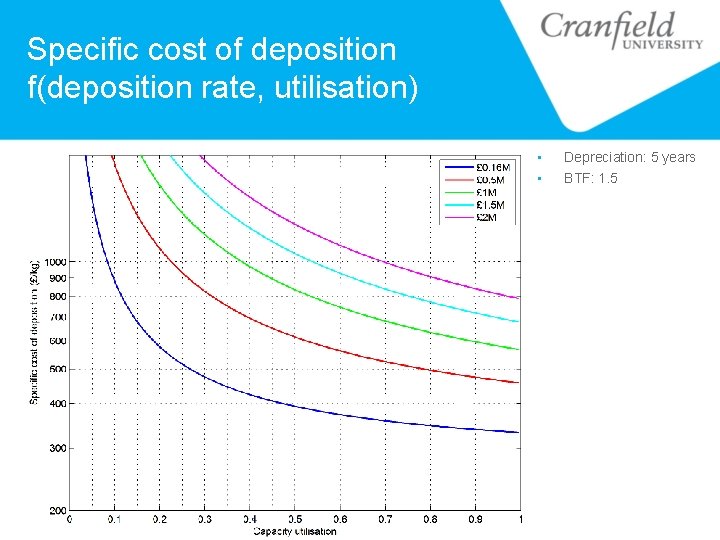
Specific cost of deposition f(deposition rate, utilisation) • • Depreciation: 5 years BTF: 1. 5
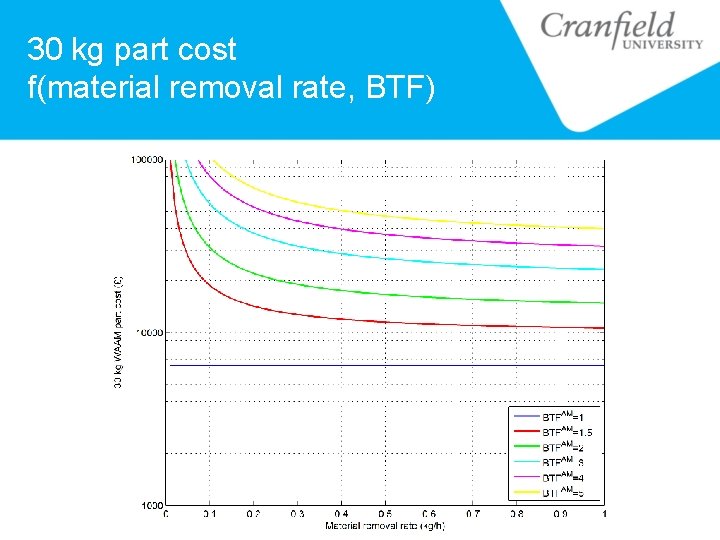
30 kg part cost f(material removal rate, BTF)
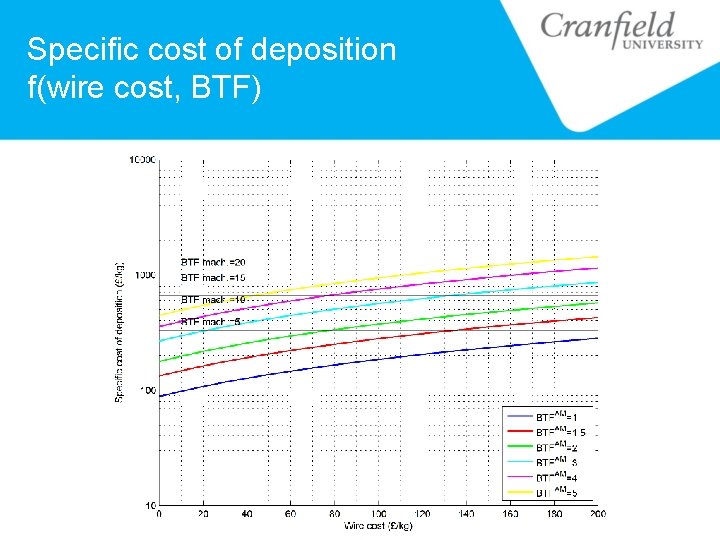
Specific cost of deposition f(wire cost, BTF)
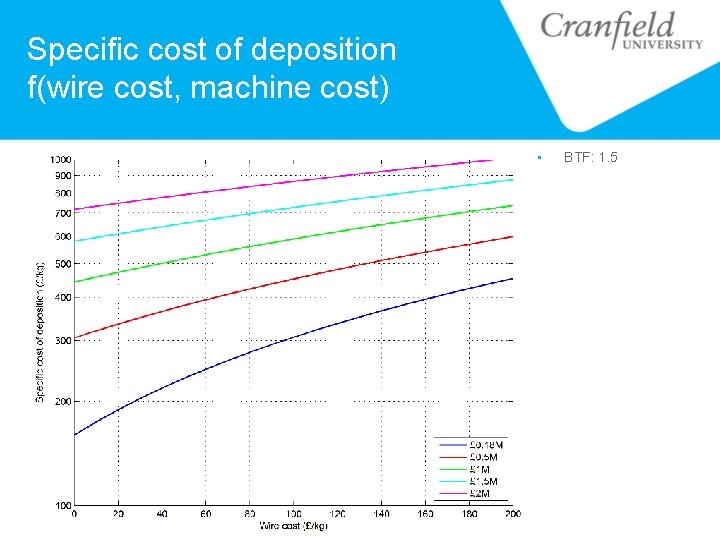
Specific cost of deposition f(wire cost, machine cost) • BTF: 1. 5
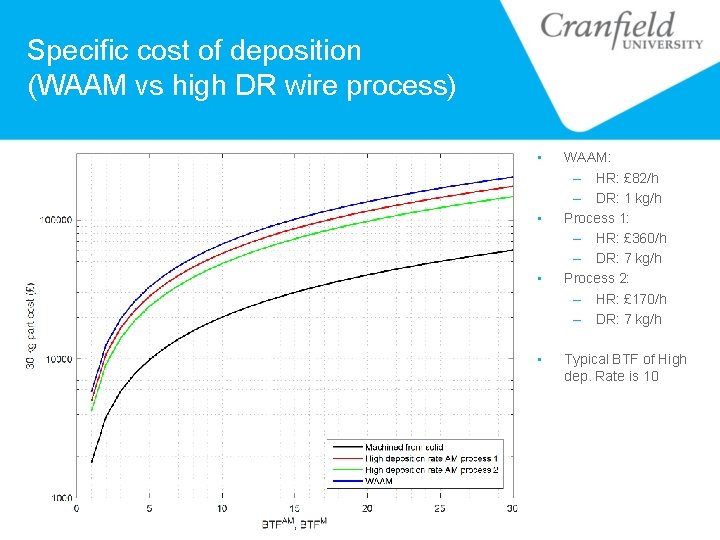
Specific cost of deposition (WAAM vs high DR wire process) • • WAAM: – HR: £ 82/h – DR: 1 kg/h Process 1: – HR: £ 360/h – DR: 7 kg/h Process 2: – HR: £ 170/h – DR: 7 kg/h Typical BTF of High dep. Rate is 10
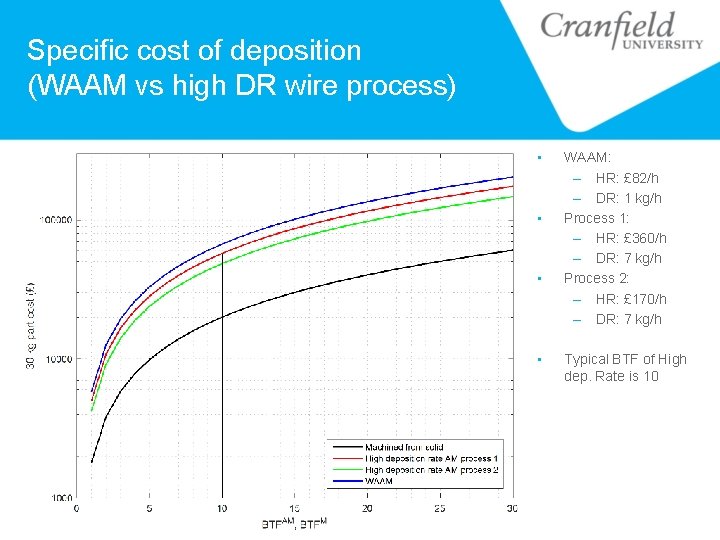
Specific cost of deposition (WAAM vs high DR wire process) • • WAAM: – HR: £ 82/h – DR: 1 kg/h Process 1: – HR: £ 360/h – DR: 7 kg/h Process 2: – HR: £ 170/h – DR: 7 kg/h Typical BTF of High dep. Rate is 10
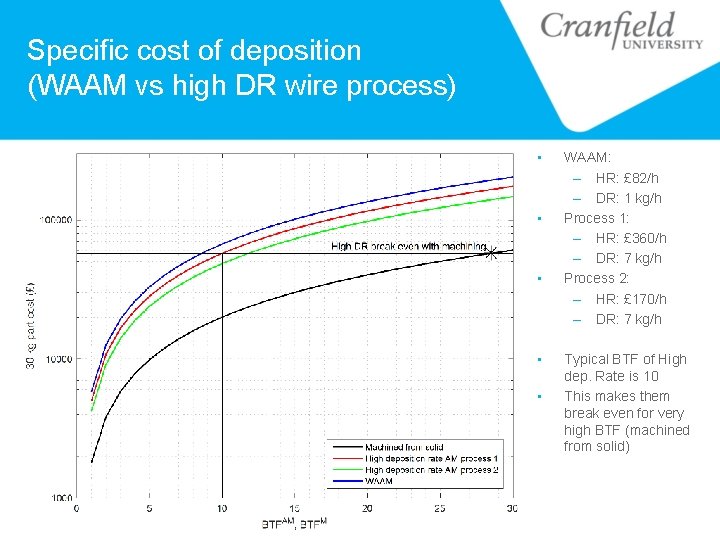
Specific cost of deposition (WAAM vs high DR wire process) • • • WAAM: – HR: £ 82/h – DR: 1 kg/h Process 1: – HR: £ 360/h – DR: 7 kg/h Process 2: – HR: £ 170/h – DR: 7 kg/h Typical BTF of High dep. Rate is 10 This makes them break even for very high BTF (machined from solid)
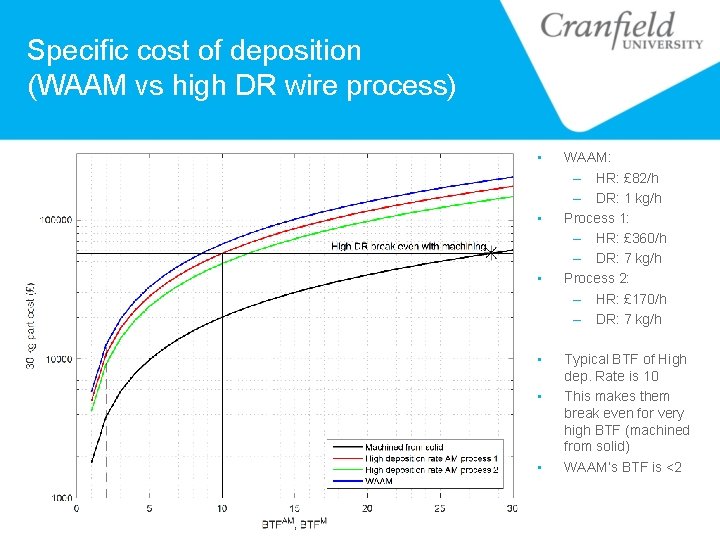
Specific cost of deposition (WAAM vs high DR wire process) • • • WAAM: – HR: £ 82/h – DR: 1 kg/h Process 1: – HR: £ 360/h – DR: 7 kg/h Process 2: – HR: £ 170/h – DR: 7 kg/h Typical BTF of High dep. Rate is 10 This makes them break even for very high BTF (machined from solid) WAAM’s BTF is <2
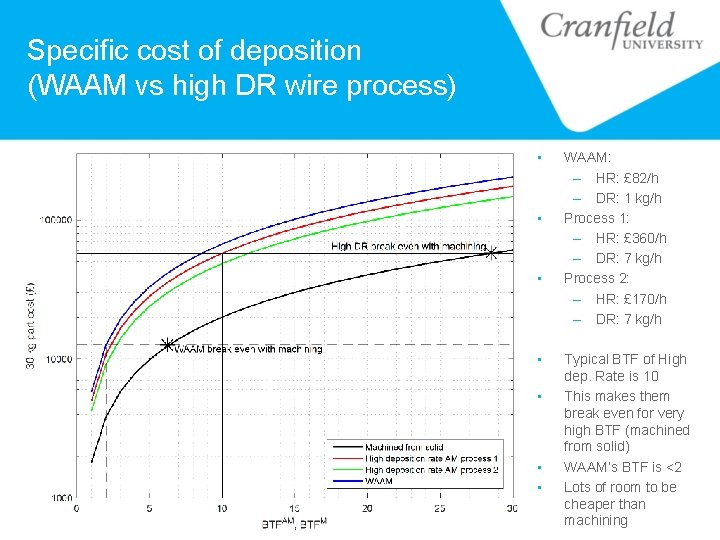
Specific cost of deposition (WAAM vs high DR wire process) • • WAAM: – HR: £ 82/h – DR: 1 kg/h Process 1: – HR: £ 360/h – DR: 7 kg/h Process 2: – HR: £ 170/h – DR: 7 kg/h Typical BTF of High dep. Rate is 10 This makes them break even for very high BTF (machined from solid) WAAM’s BTF is <2 Lots of room to be cheaper than machining
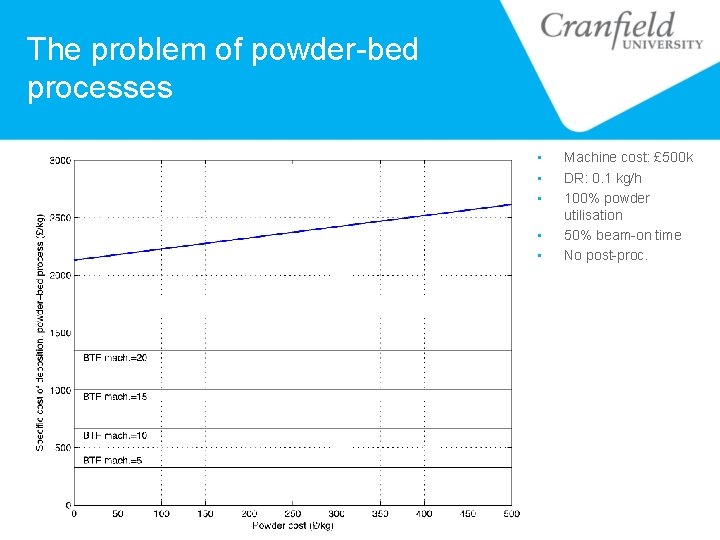
The problem of powder-bed processes • • • Machine cost: £ 500 k DR: 0. 1 kg/h 100% powder utilisation 50% beam-on time No post-proc.
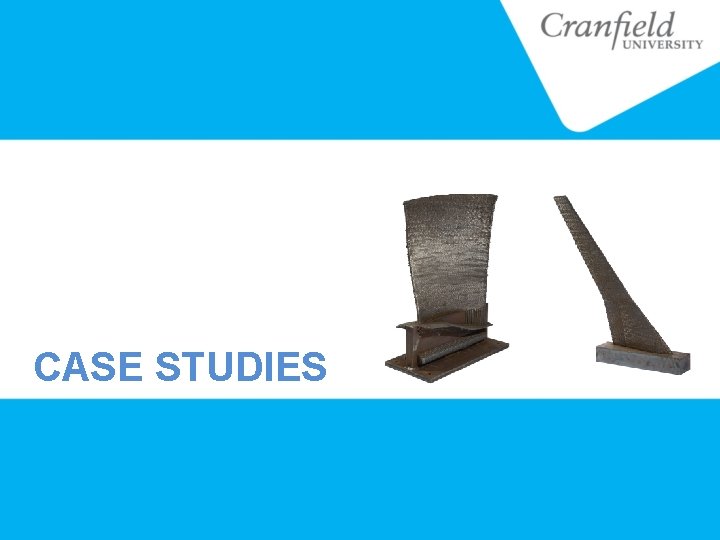
CASE STUDIES
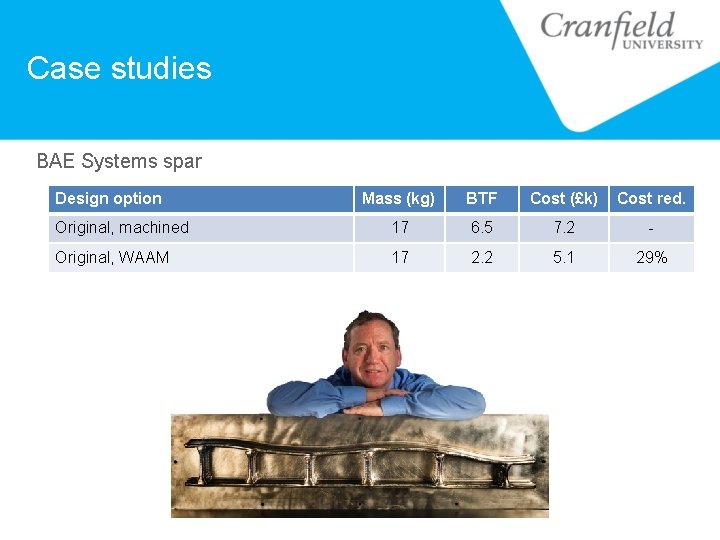
Case studies BAE Systems spar Design option Mass (kg) BTF Cost (£k) Cost red. Original, machined 17 6. 5 7. 2 - Original, WAAM 17 2. 2 5. 1 29%
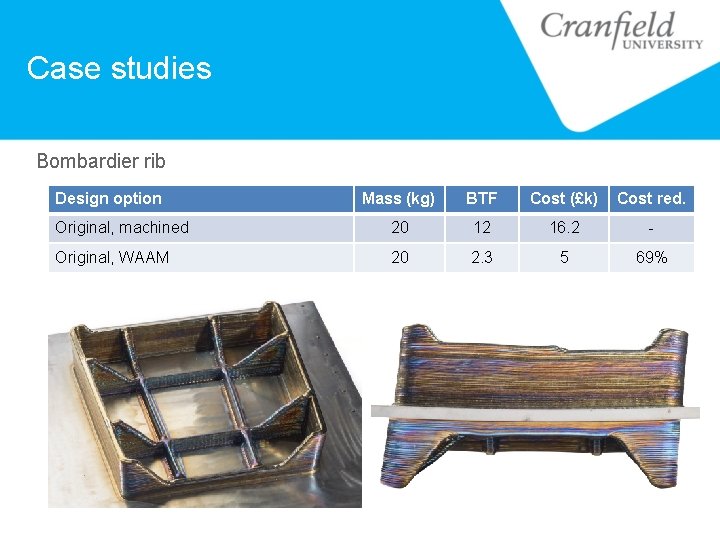
Case studies Bombardier rib Design option Mass (kg) BTF Cost (£k) Cost red. Original, machined 20 12 16. 2 - Original, WAAM 20 2. 3 5 69%
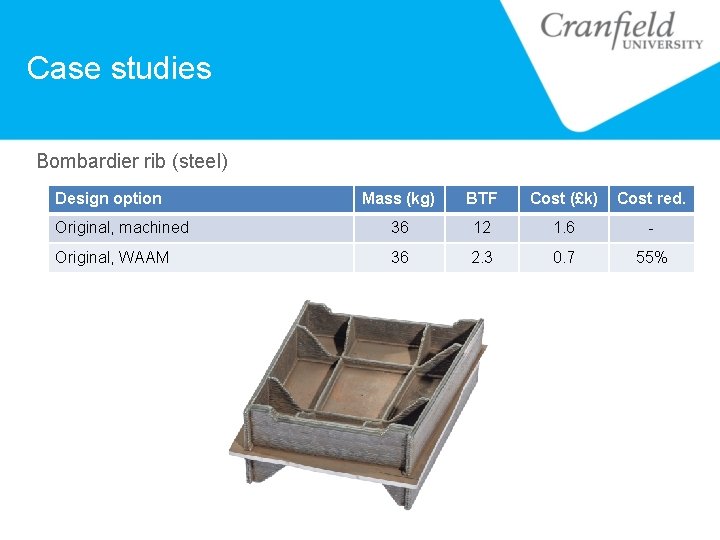
Case studies Bombardier rib (steel) Design option Mass (kg) BTF Cost (£k) Cost red. Original, machined 36 12 1. 6 - Original, WAAM 36 2. 3 0. 7 55%
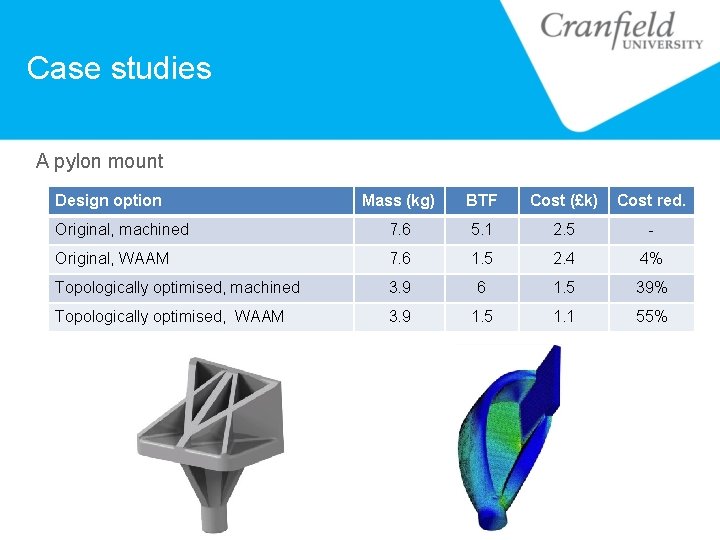
Case studies A pylon mount Design option Mass (kg) BTF Cost (£k) Cost red. Original, machined 7. 6 5. 1 2. 5 - Original, WAAM 7. 6 1. 5 2. 4 4% Topologically optimised, machined 3. 9 6 1. 5 39% Topologically optimised, WAAM 3. 9 1. 5 1. 1 55%
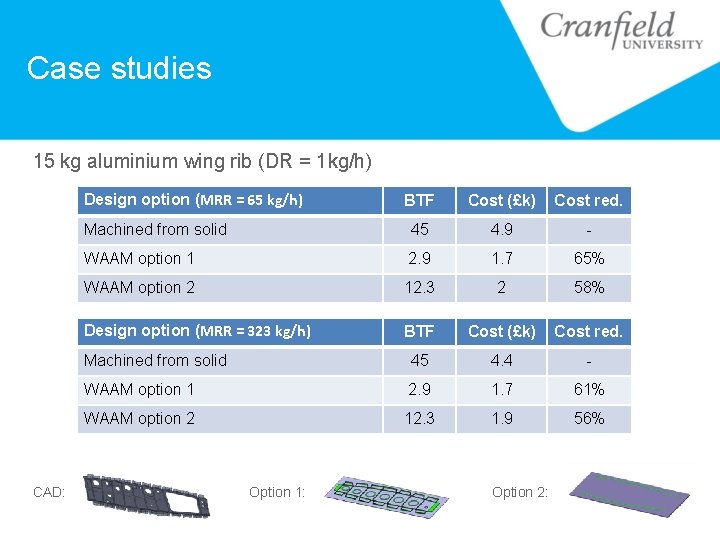
Case studies 15 kg aluminium wing rib (DR = 1 kg/h) Design option (MRR = 65 kg/h) CAD: BTF Cost (£k) Cost red. Machined from solid 45 4. 9 - WAAM option 1 2. 9 1. 7 65% WAAM option 2 12. 3 2 58% Design option (MRR = 323 kg/h) BTF Cost (£k) Cost red. Machined from solid 45 4. 4 - WAAM option 1 2. 9 1. 7 61% WAAM option 2 12. 3 1. 9 56% Option 1: Option 2:
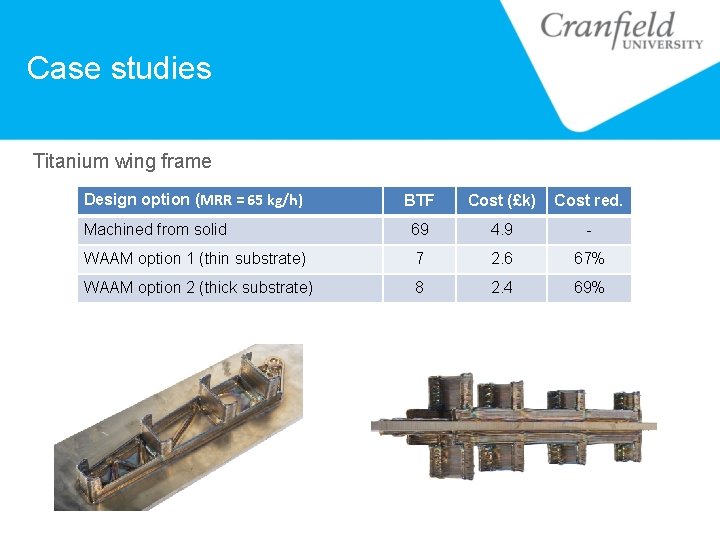
Case studies Titanium wing frame Design option (MRR = 65 kg/h) BTF Cost (£k) Cost red. Machined from solid 69 4. 9 - WAAM option 1 (thin substrate) 7 2. 6 67% WAAM option 2 (thick substrate) 8 2. 4 69%
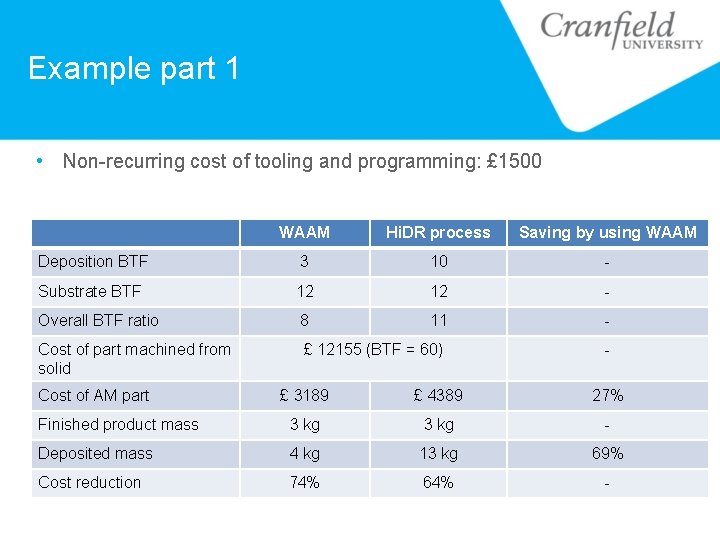
Example part 1 • Non-recurring cost of tooling and programming: £ 1500 WAAM Hi. DR process Saving by using WAAM Deposition BTF 3 10 - Substrate BTF 12 12 - Overall BTF ratio 8 11 - Cost of part machined from solid £ 12155 (BTF = 60) - Cost of AM part £ 3189 £ 4389 27% Finished product mass 3 kg - Deposited mass 4 kg 13 kg 69% Cost reduction 74% 64% -
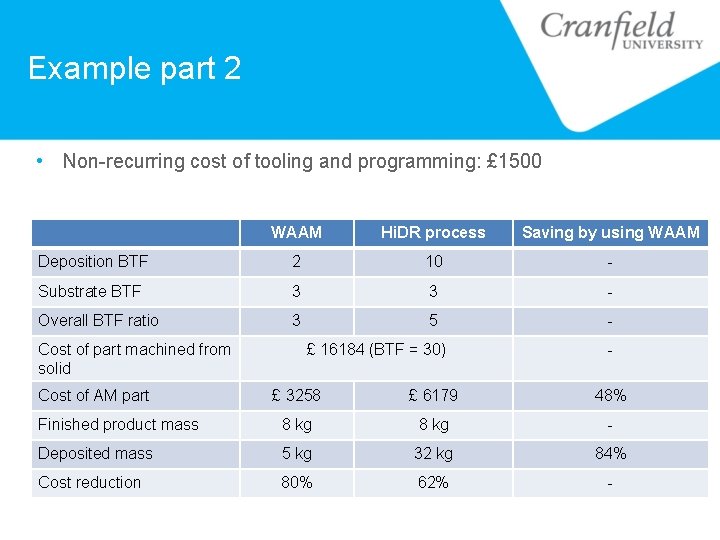
Example part 2 • Non-recurring cost of tooling and programming: £ 1500 WAAM Hi. DR process Saving by using WAAM Deposition BTF 2 10 - Substrate BTF 3 3 - Overall BTF ratio 3 5 - Cost of part machined from solid Cost of AM part £ 16184 (BTF = 30) - £ 3258 £ 6179 48% Finished product mass 8 kg - Deposited mass 5 kg 32 kg 84% Cost reduction 80% 62% -
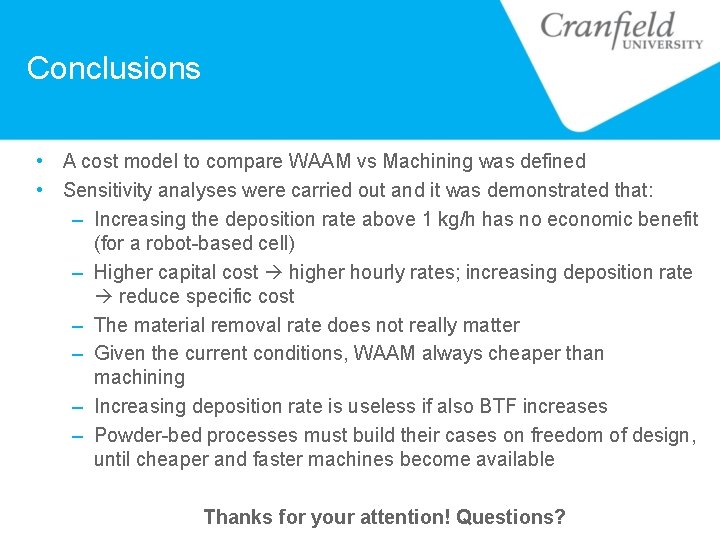
Conclusions • A cost model to compare WAAM vs Machining was defined • Sensitivity analyses were carried out and it was demonstrated that: – Increasing the deposition rate above 1 kg/h has no economic benefit (for a robot-based cell) – Higher capital cost higher hourly rates; increasing deposition rate reduce specific cost – The material removal rate does not really matter – Given the current conditions, WAAM always cheaper than machining – Increasing deposition rate is useless if also BTF increases – Powder-bed processes must build their cases on freedom of design, until cheaper and faster machines become available Thanks for your attention! Questions?
Faire la guerre faire la paix hggsp
La barricade otto dix
Dalle guerre persiane alla guerra del peloponneso
Types de guerres
Otase
Ti-jacques la guerre des tuques
Guerre civili romane scuola primaria
La guerre de sept ans
Le guerre sannitiche
Poème de prévert sur la guerre
Conclusion sur la guerre froide
Caricature berlin guerre froide
Guerre persiane hub scuola
Triptyque la guerre
Guerre del '700 schema
Guerre del 700
Guerre dalgerie
Guerre des gaules
Plan marshall affiche
Qui veut la paix prépare la guerre sun tzu
Le guerre del 700
Héroïne dans la guerre de 100 ans (100 years war).
Candide ou l optimisme
Guerre religiose
Guerre persiane schema
Cosa sono le guerre di successione
Seconde guerre mondiale
Desert storm map
Architettura tra le due guerre
Je suis il est tu es
Alleluia le christ est vivant
Group nominal exemple
Seul le silence est grand tout le reste n'est que faiblesse
Il est douteux que le metteur en scène où est l’acteur.
Mon pays ce n'est pas un pays c'est l'hiver