Jet Propulsion Oil Fuel and Ignition Systems Lecture
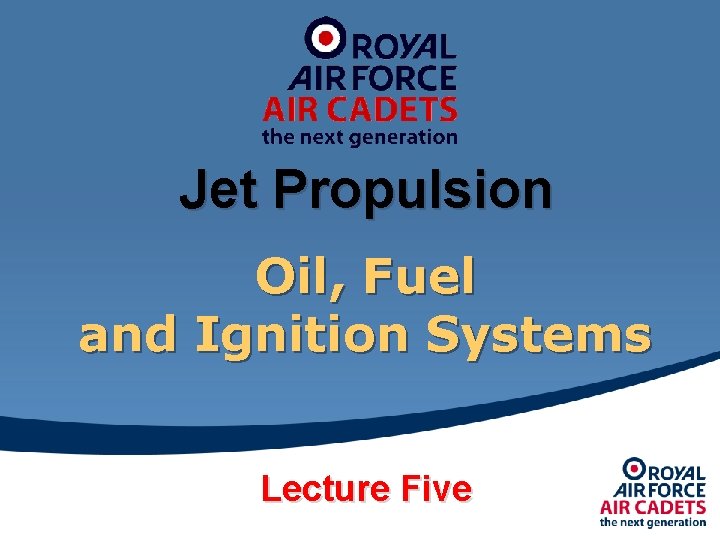
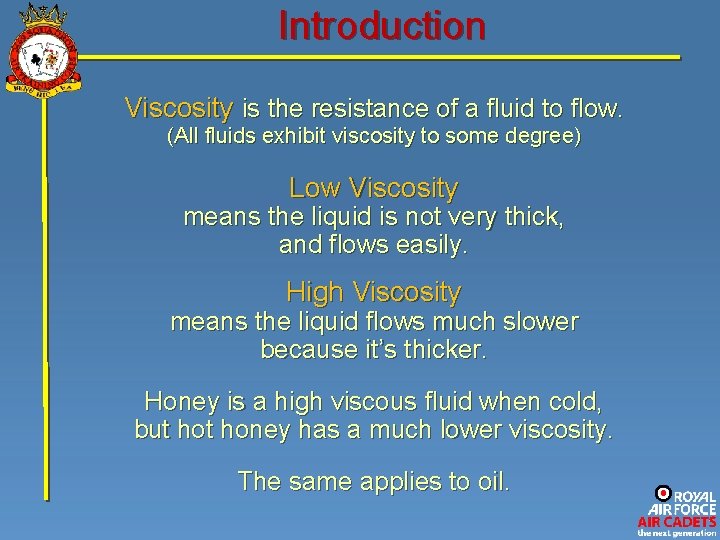
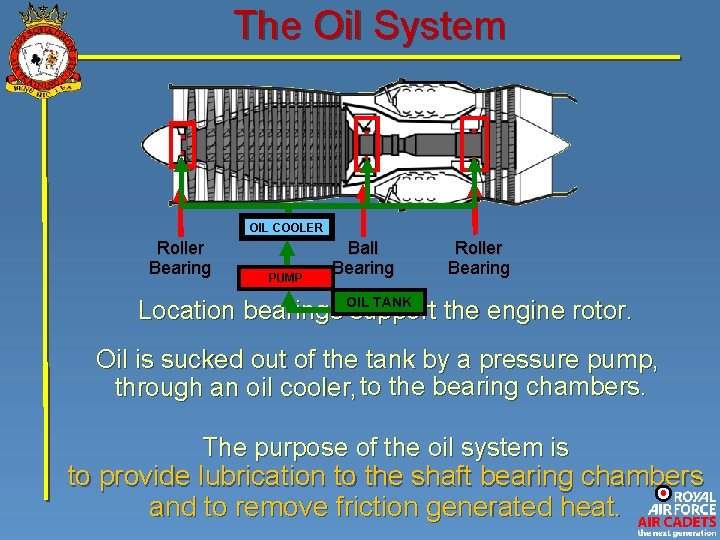
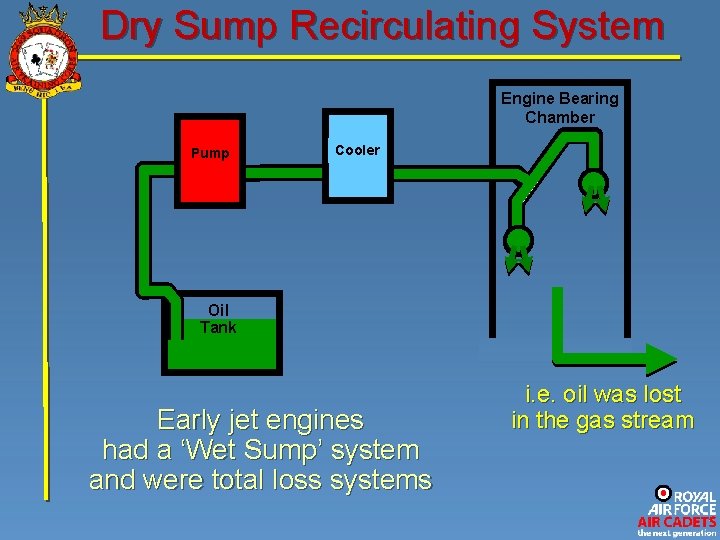
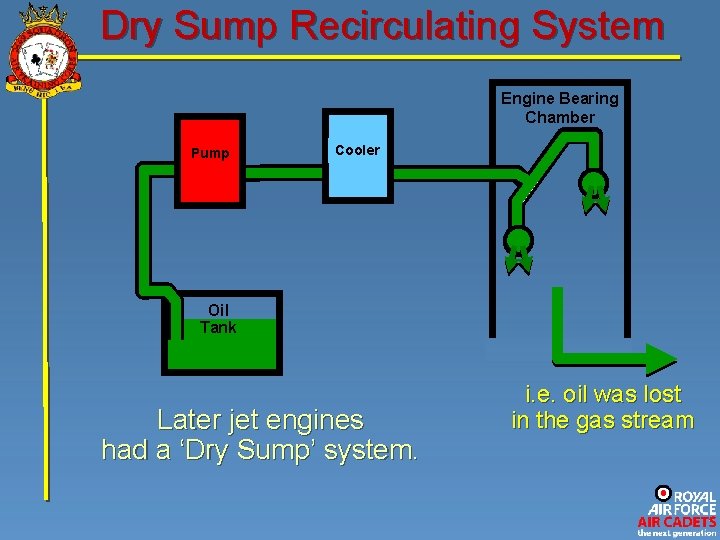
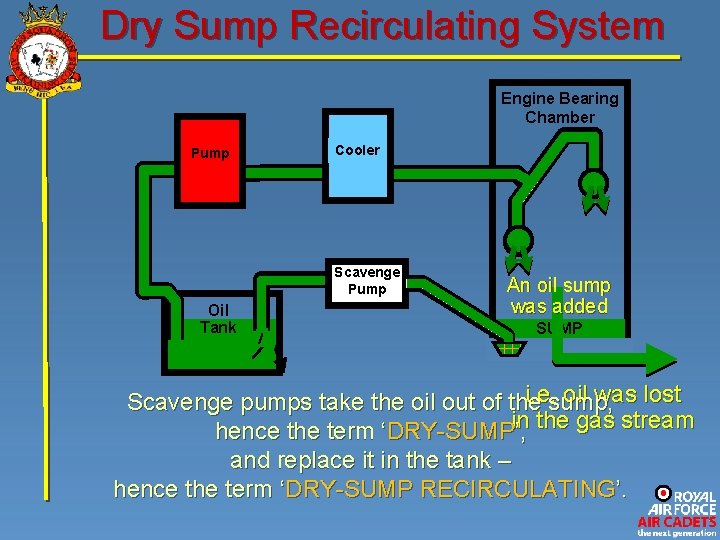
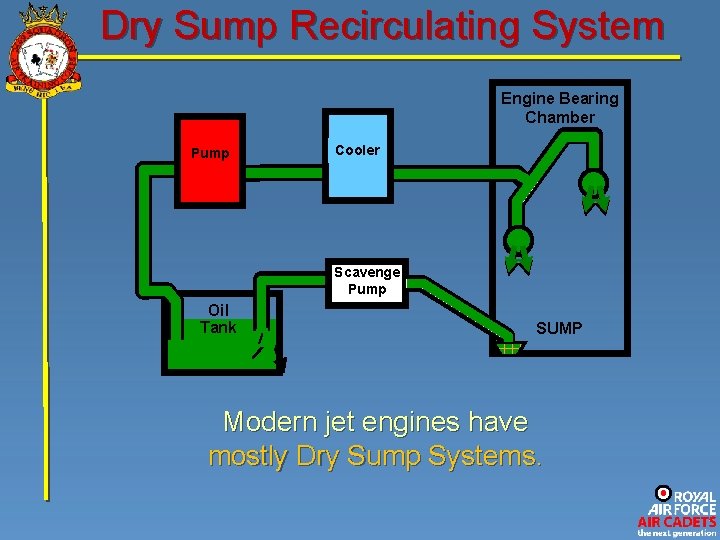
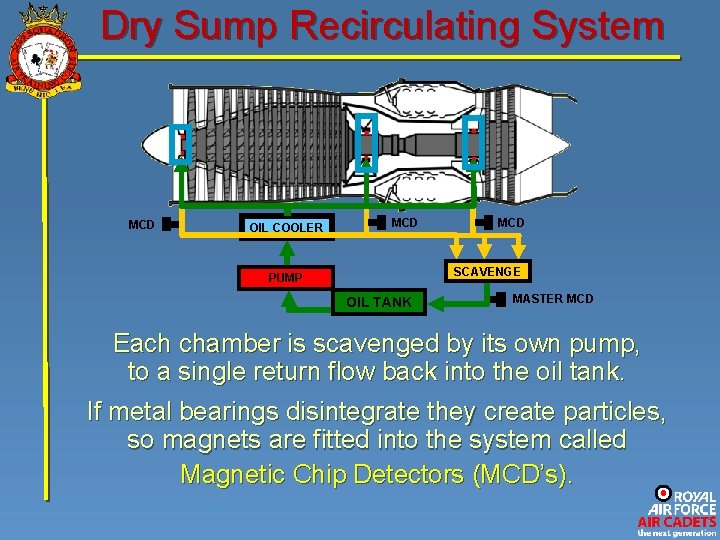
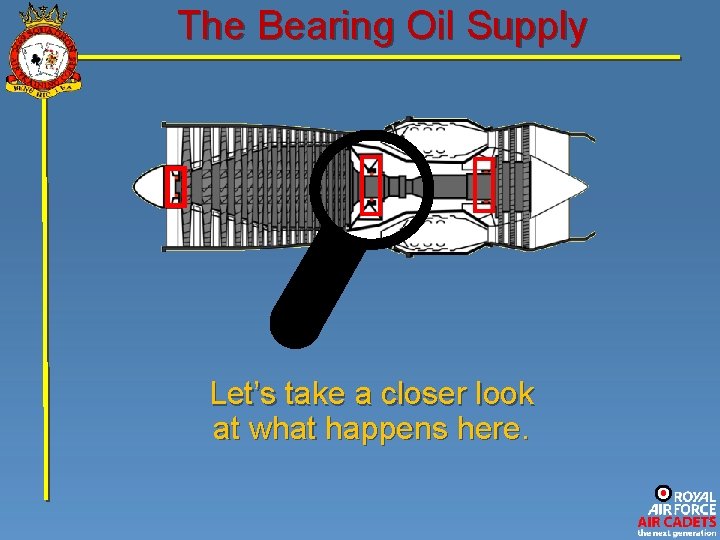
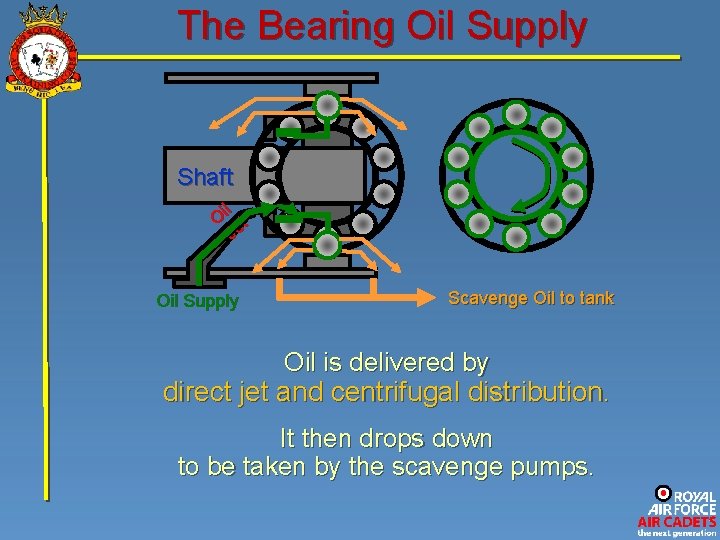
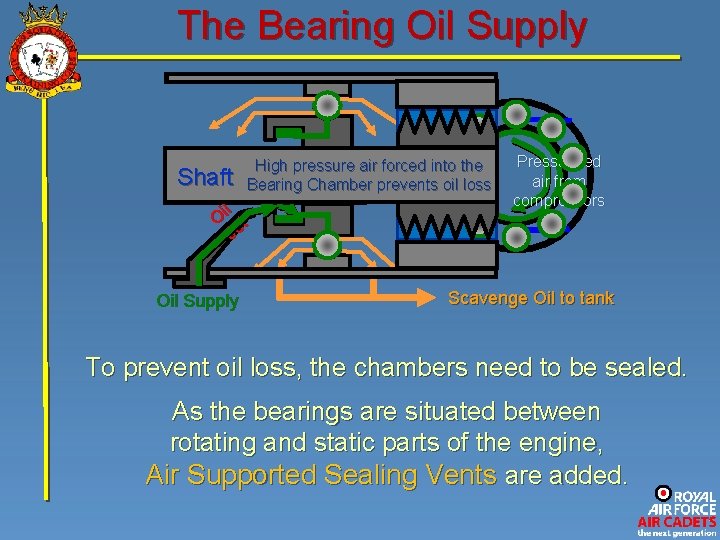
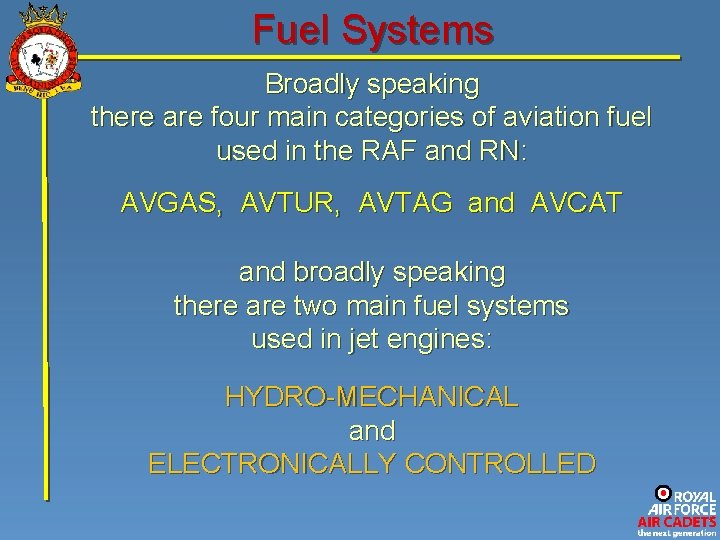
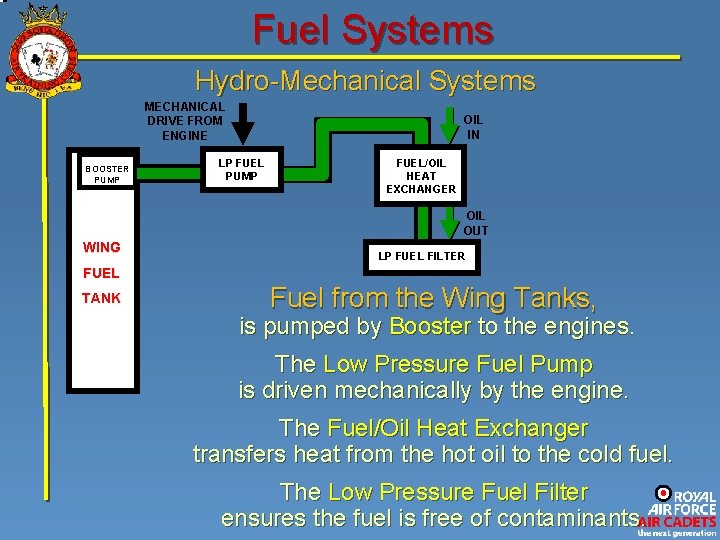
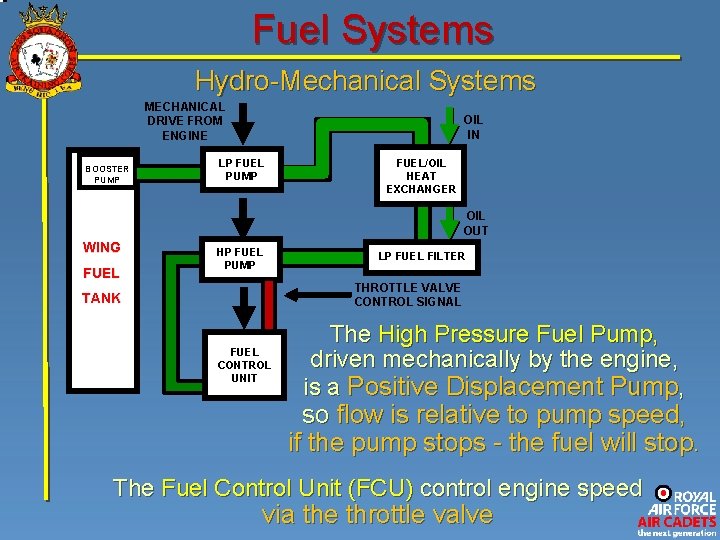
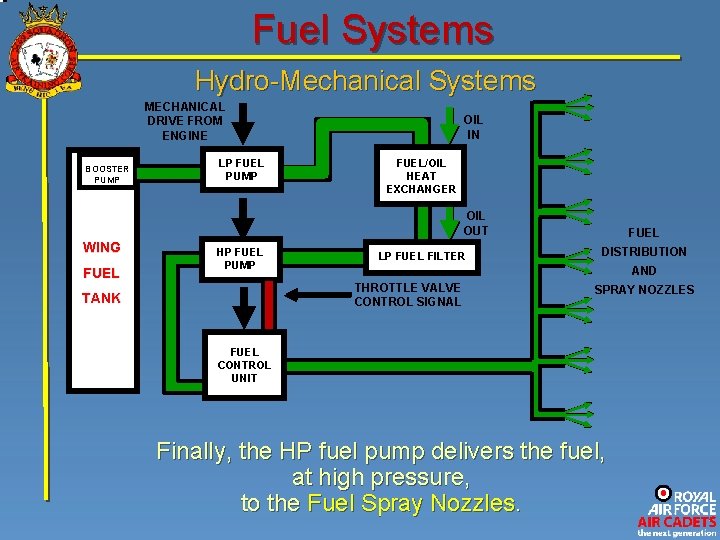
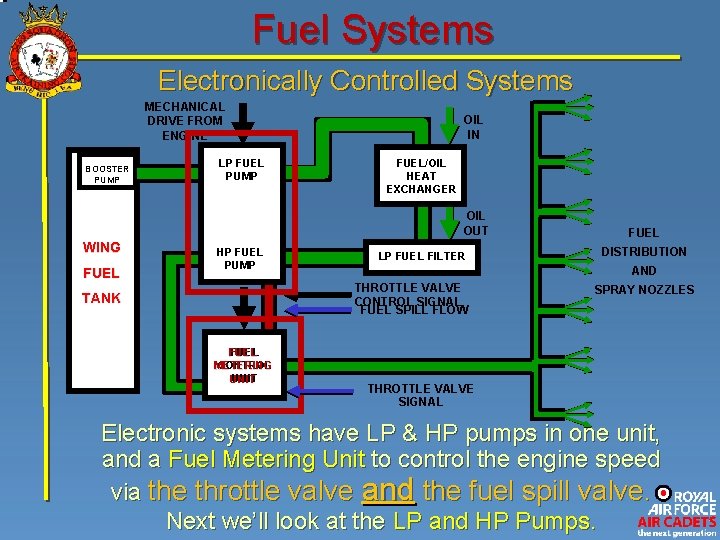
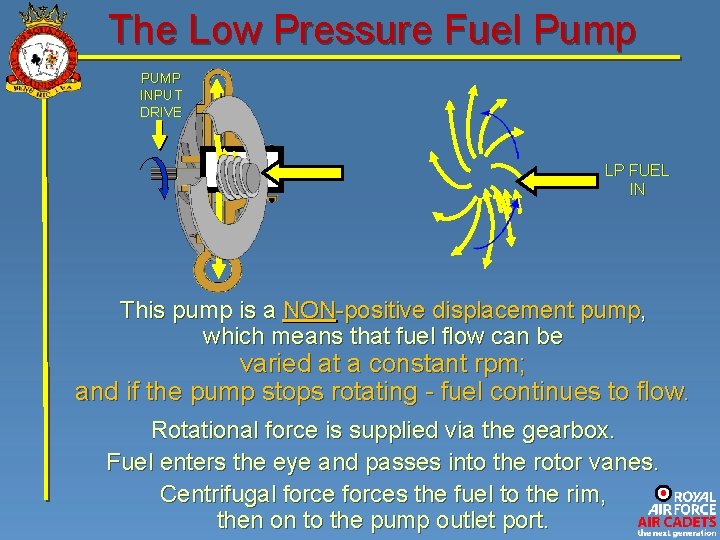
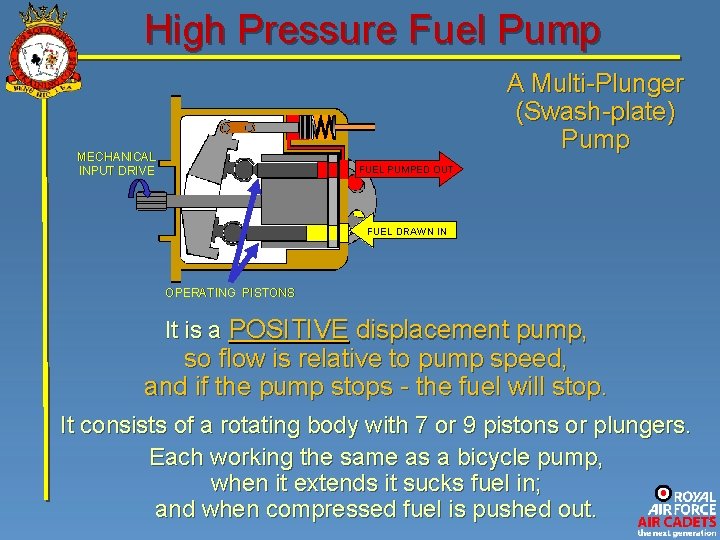
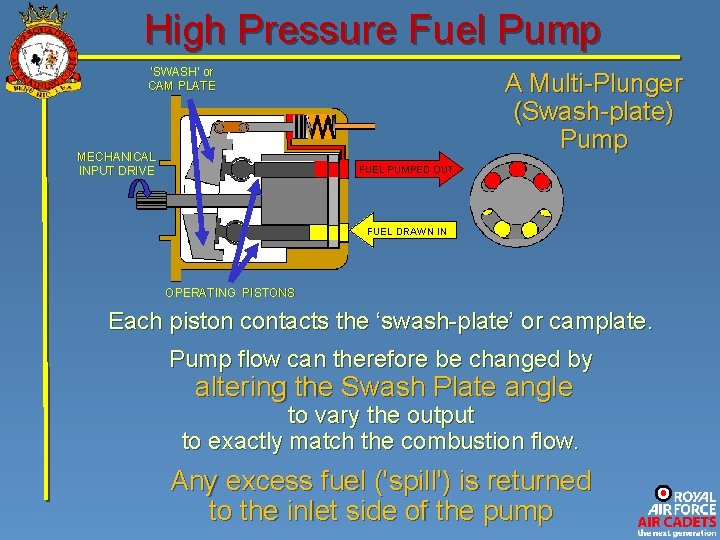
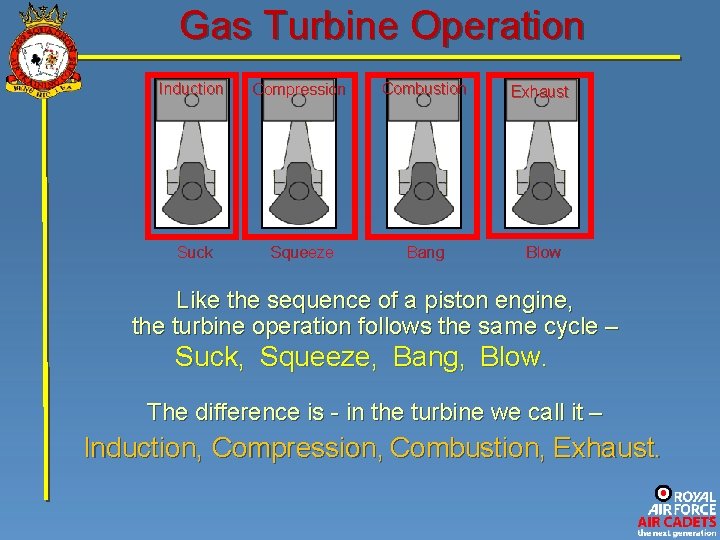
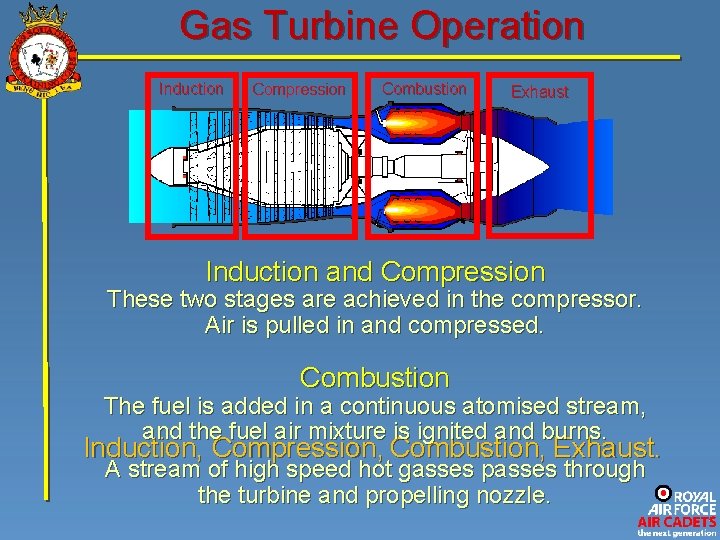
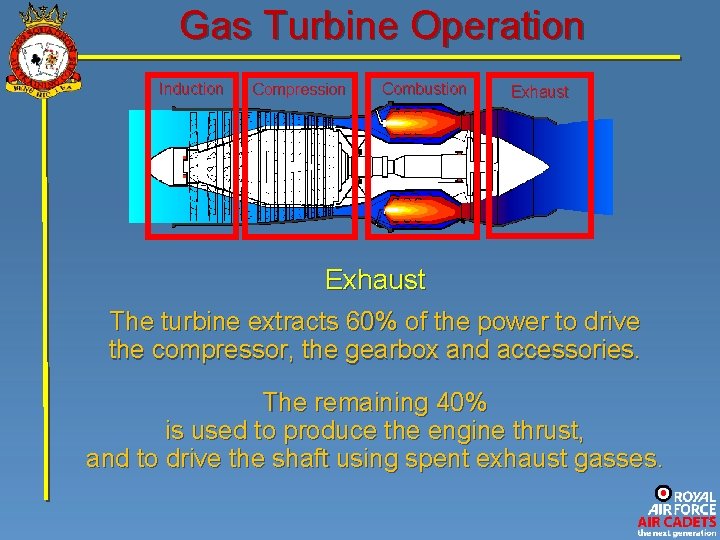
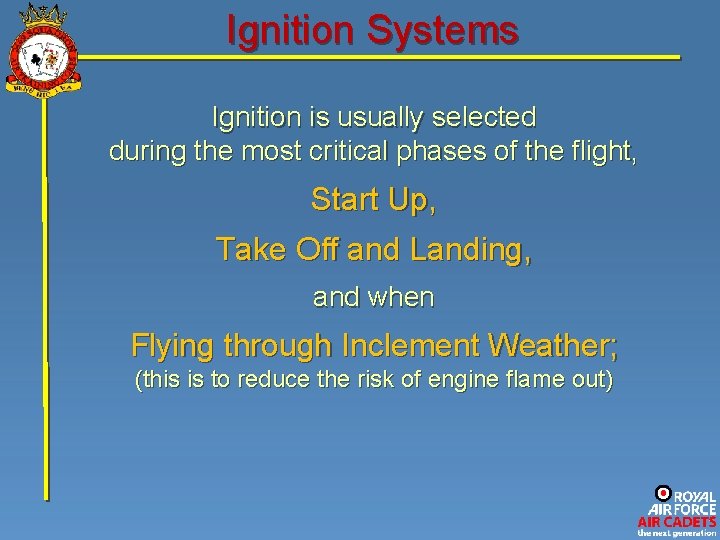
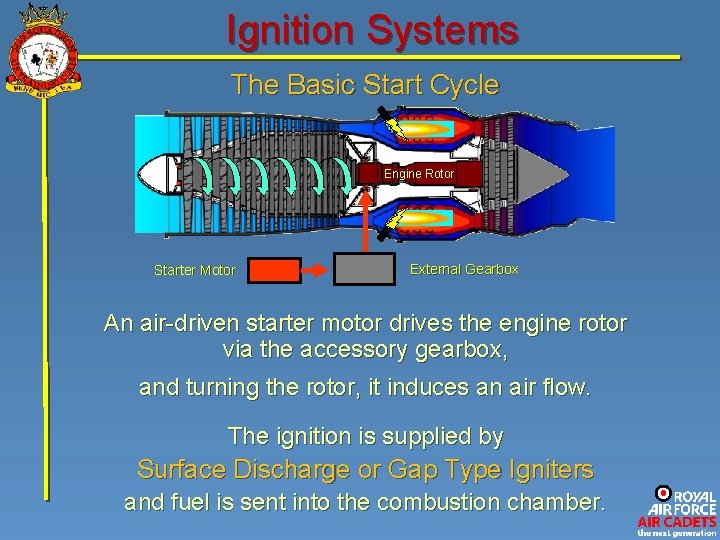
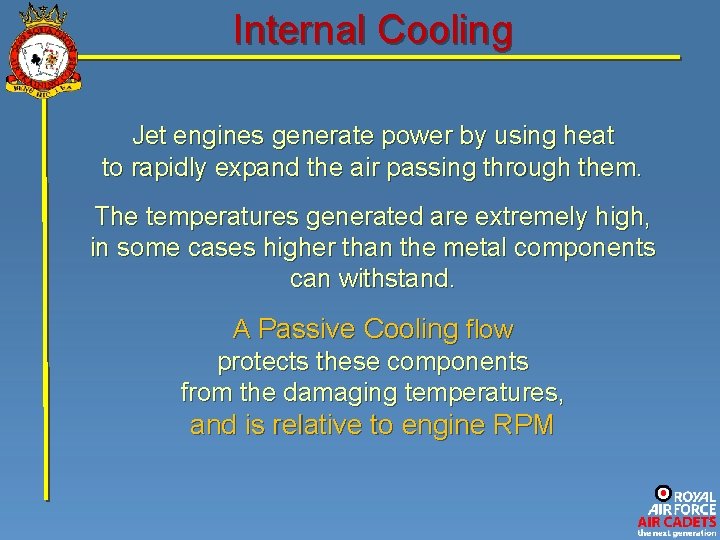
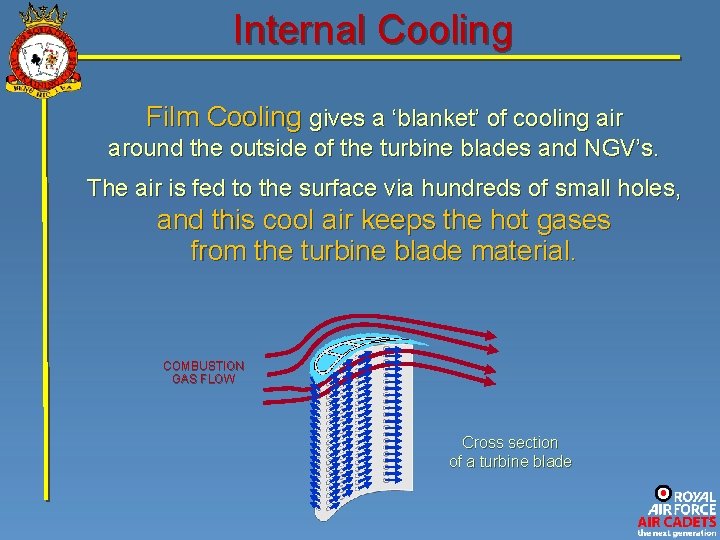
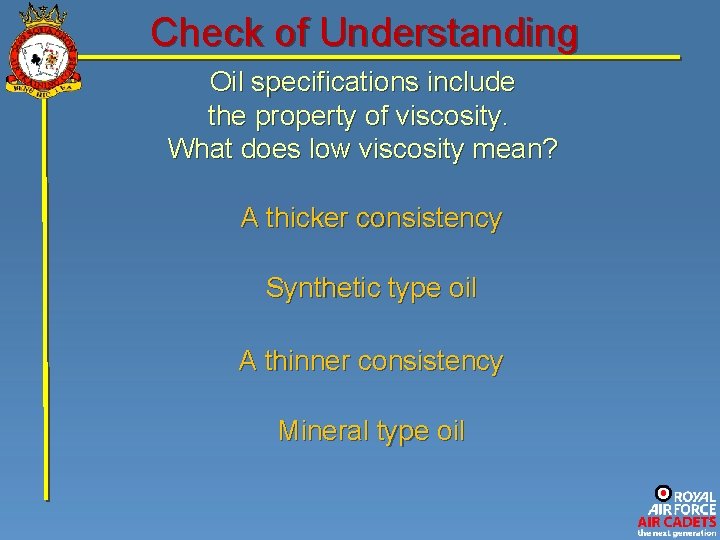
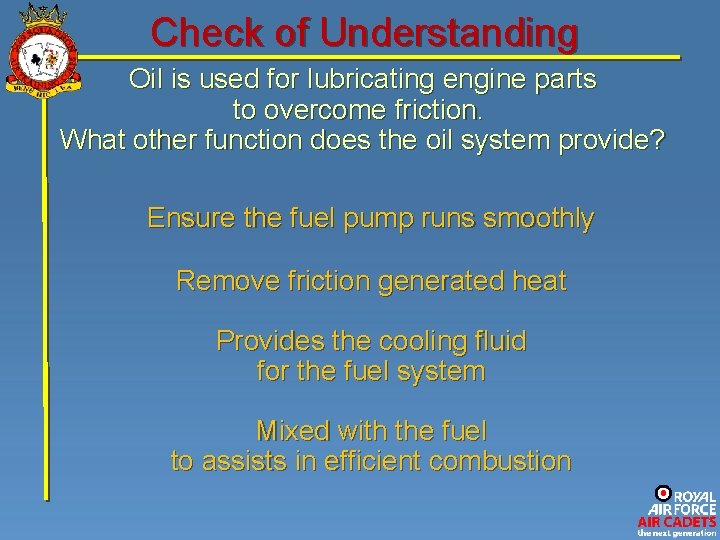
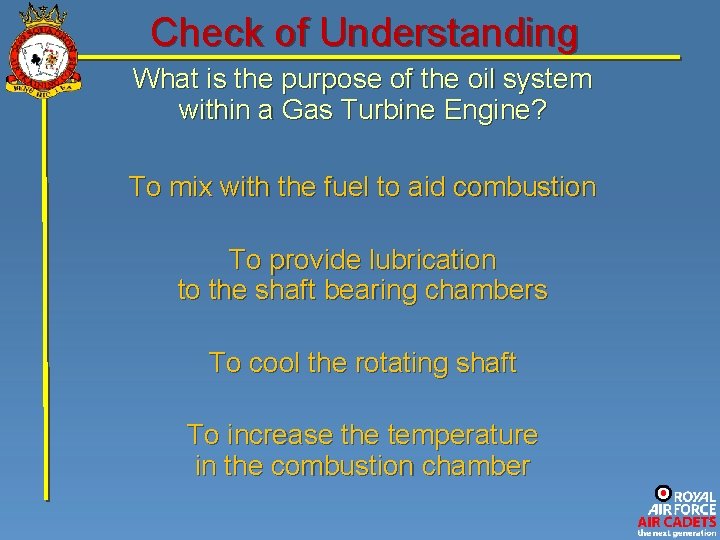
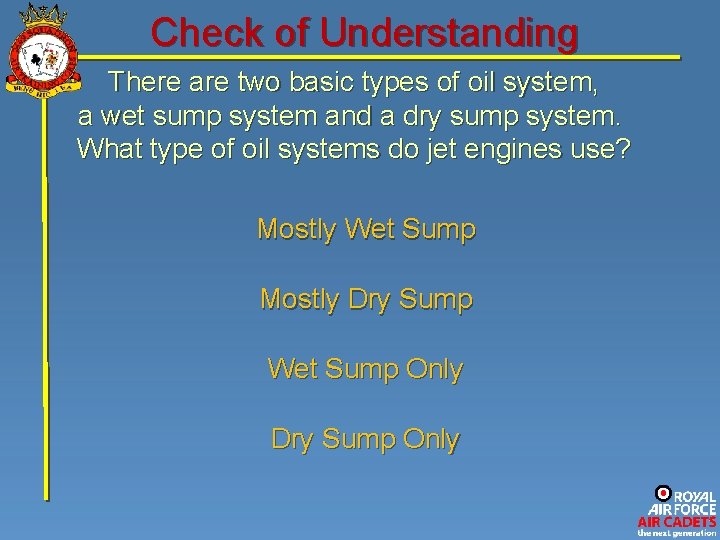
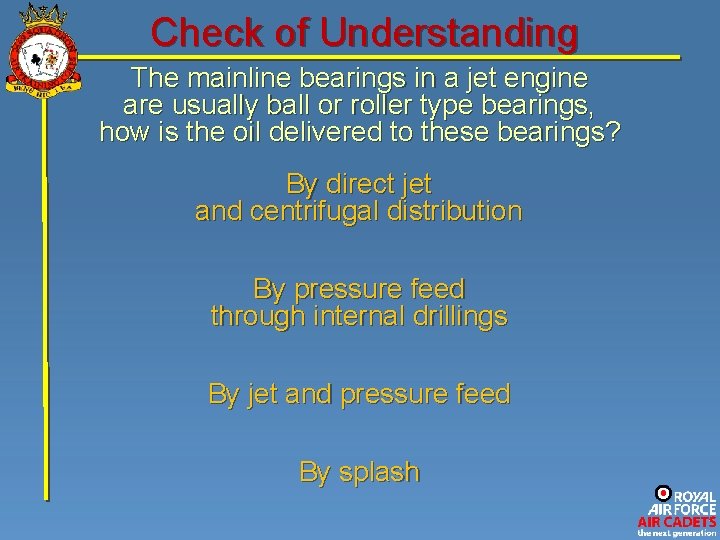
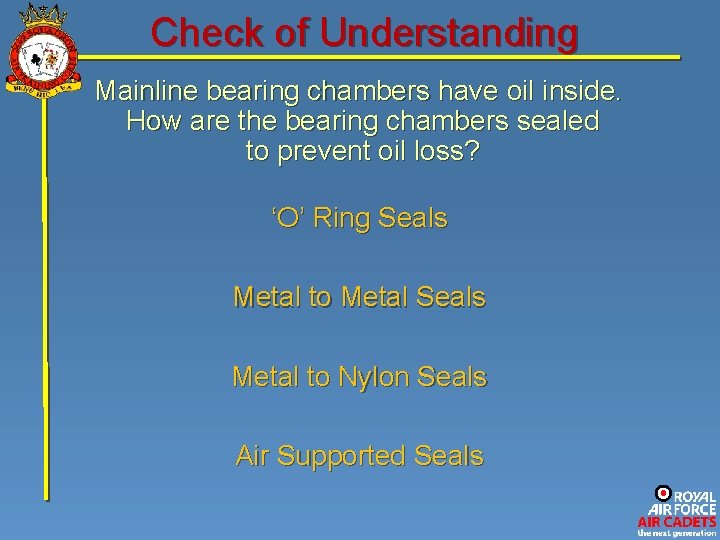
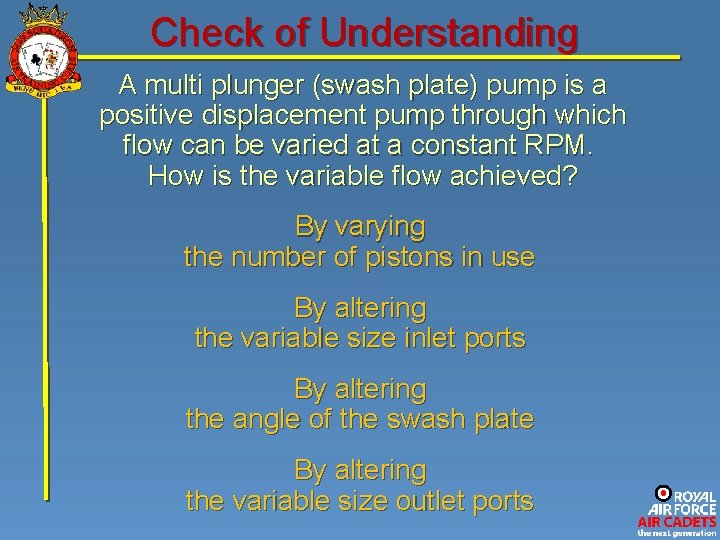
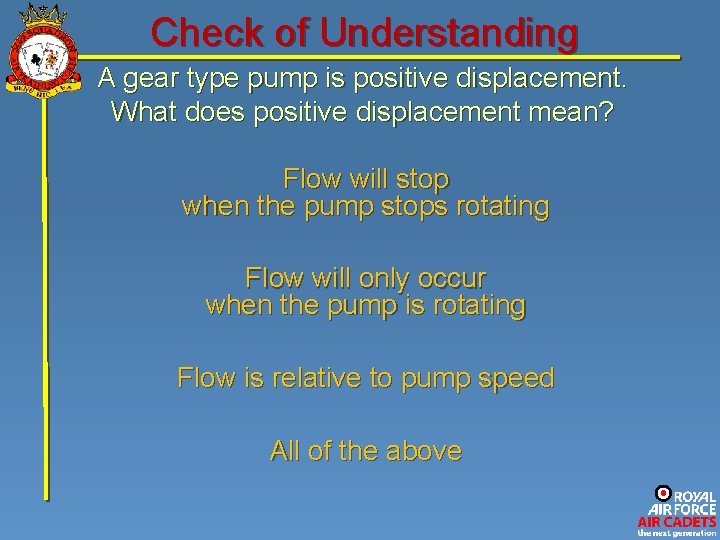
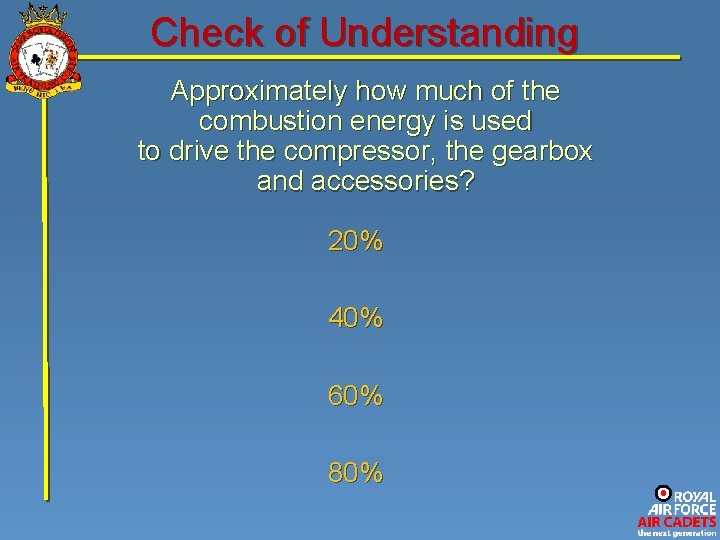
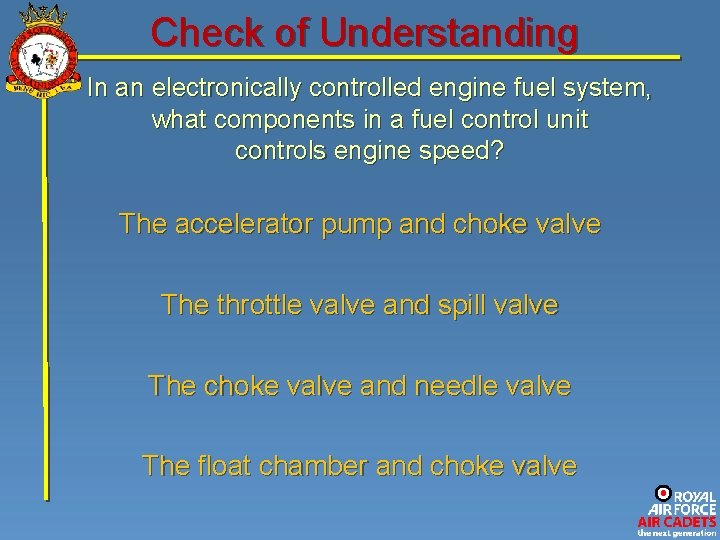
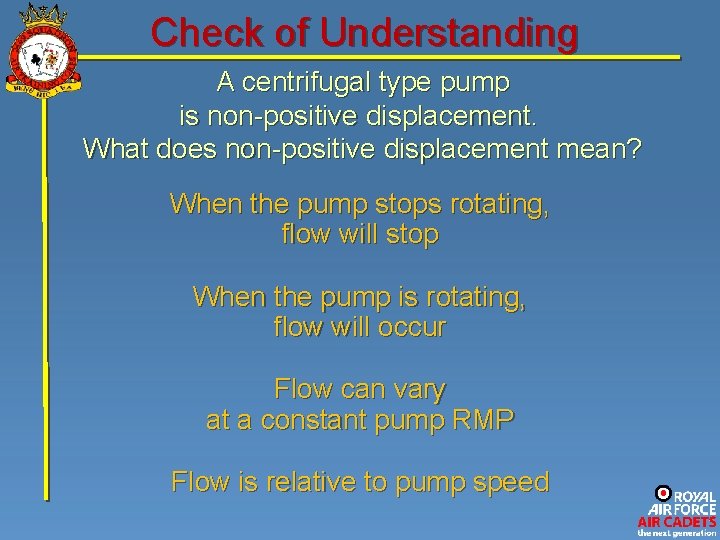
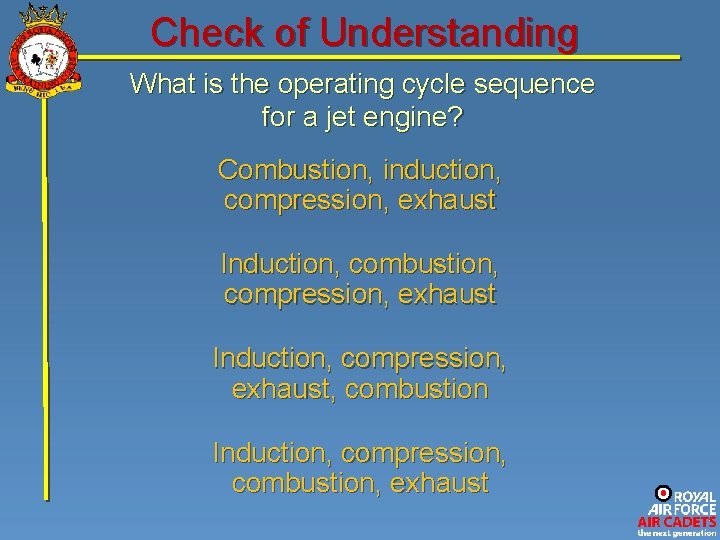
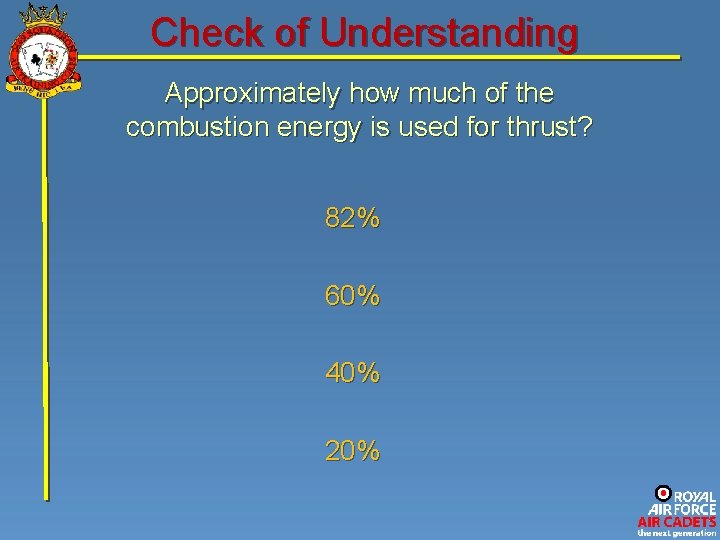
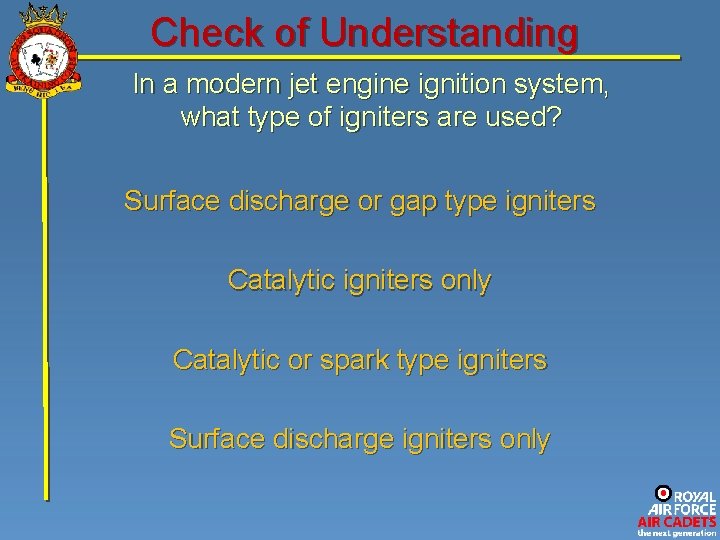
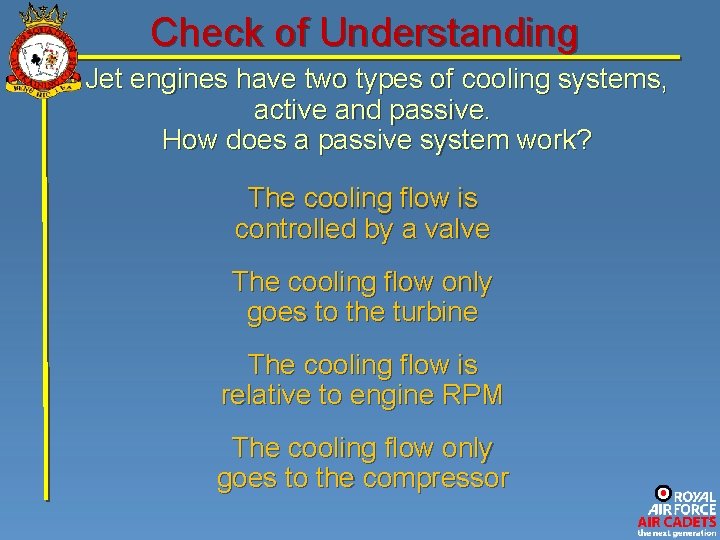
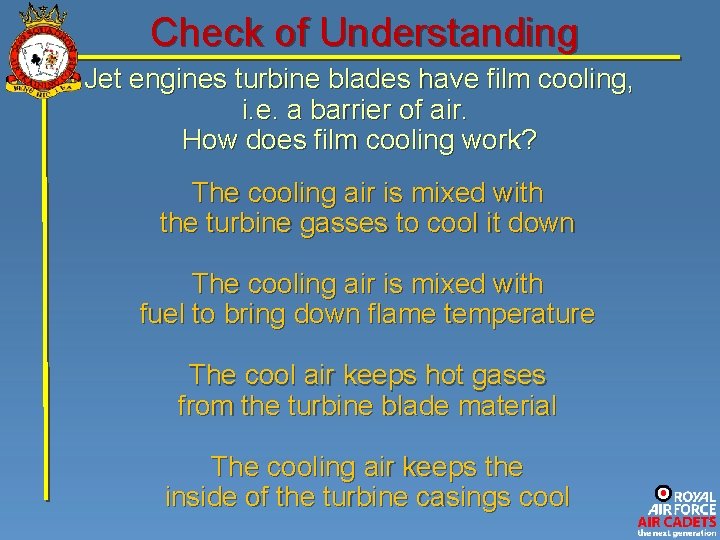
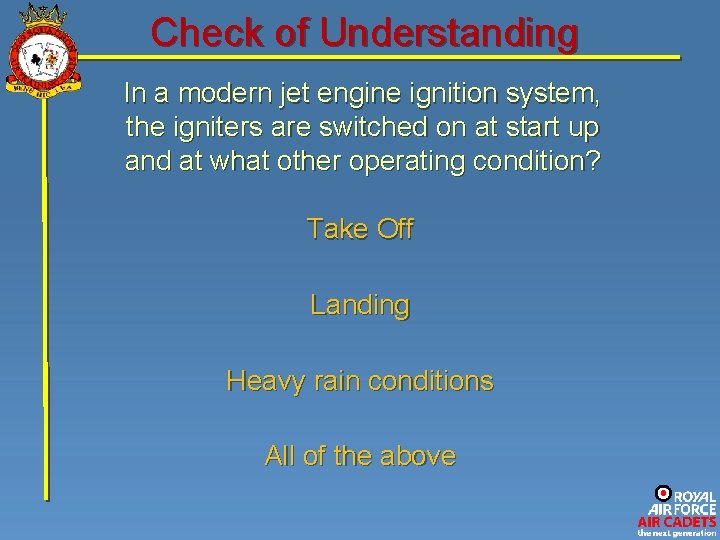
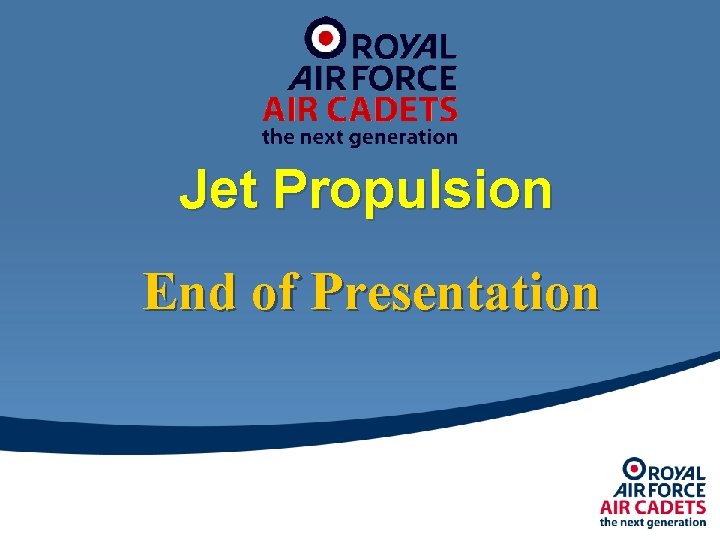
- Slides: 44
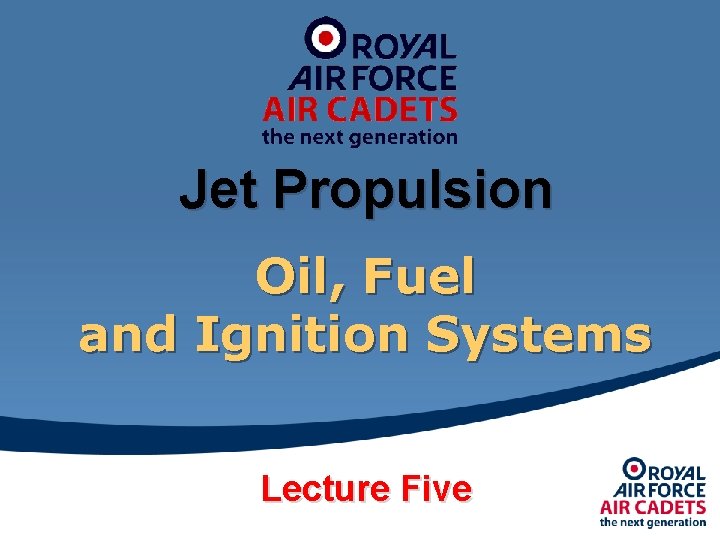
Jet Propulsion Oil, Fuel and Ignition Systems Lecture Five
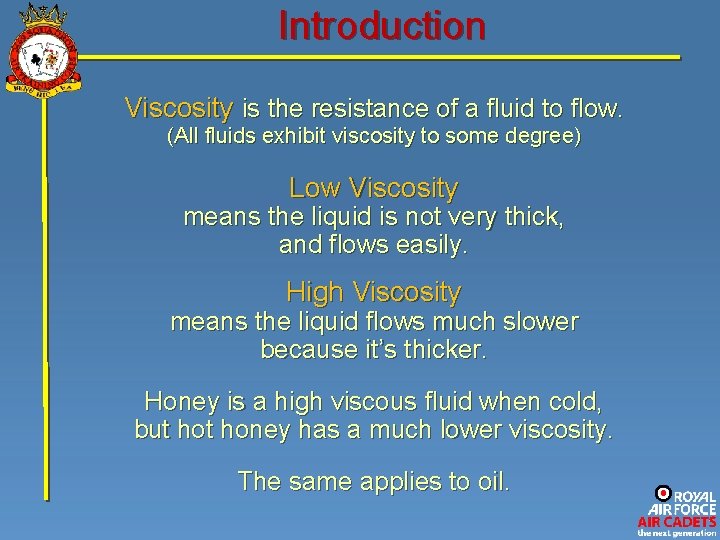
Introduction Viscosity is the resistance of a fluid to flow. (All fluids exhibit viscosity to some degree) Low Viscosity means the liquid is not very thick, and flows easily. High Viscosity means the liquid flows much slower because it’s thicker. Honey is a high viscous fluid when cold, but honey has a much lower viscosity. The same applies to oil.
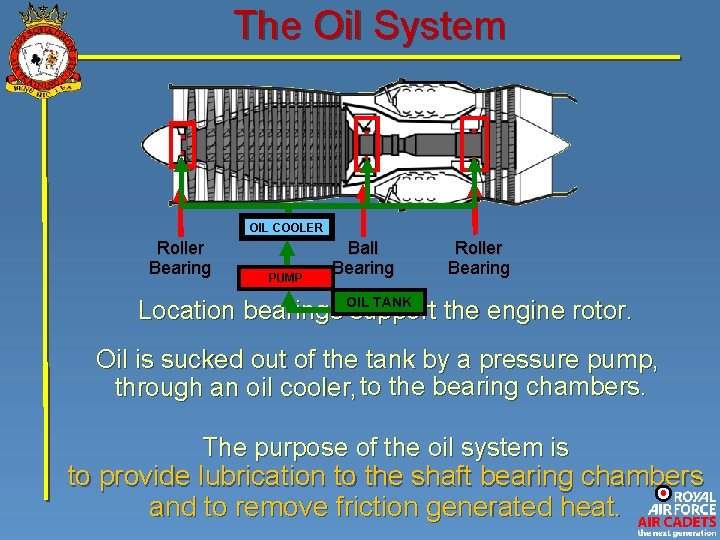
The Oil System OIL COOLER Roller Bearing PUMP Ball Bearing Roller Bearing OIL TANK Location bearings support the engine rotor. Oil is sucked out of the tank by a pressure pump, through an oil cooler, to the bearing chambers. The purpose of the oil system is to provide lubrication to the shaft bearing chambers and to remove friction generated heat.
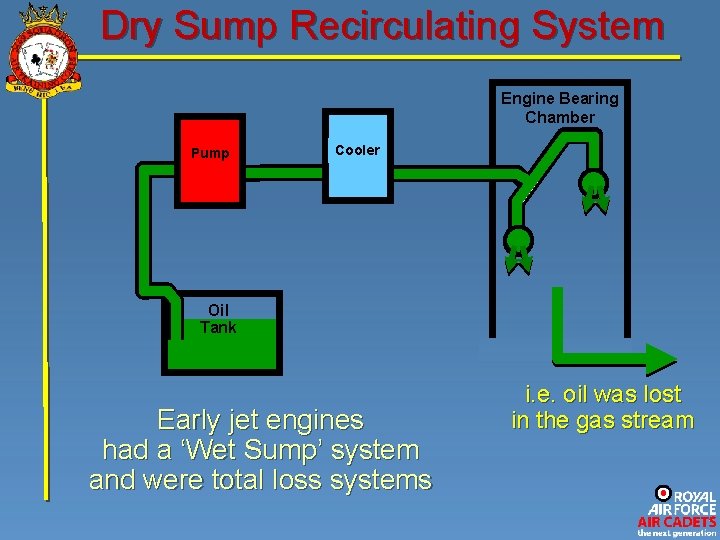
Dry Sump Recirculating System Engine Bearing Chamber Pump Cooler Oil Tank Early jet engines had a ‘Wet Sump’ system and were total loss systems i. e. oil was lost in the gas stream
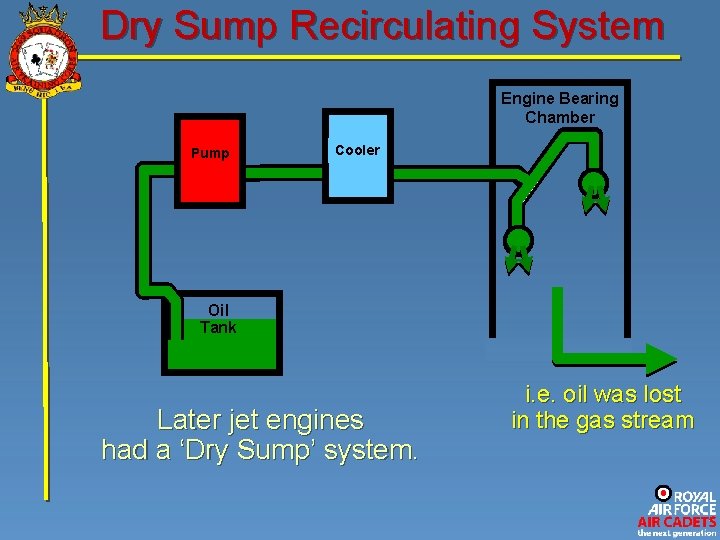
Dry Sump Recirculating System Engine Bearing Chamber Pump Cooler Oil Tank Later jet engines had a ‘Dry Sump’ system. i. e. oil was lost in the gas stream
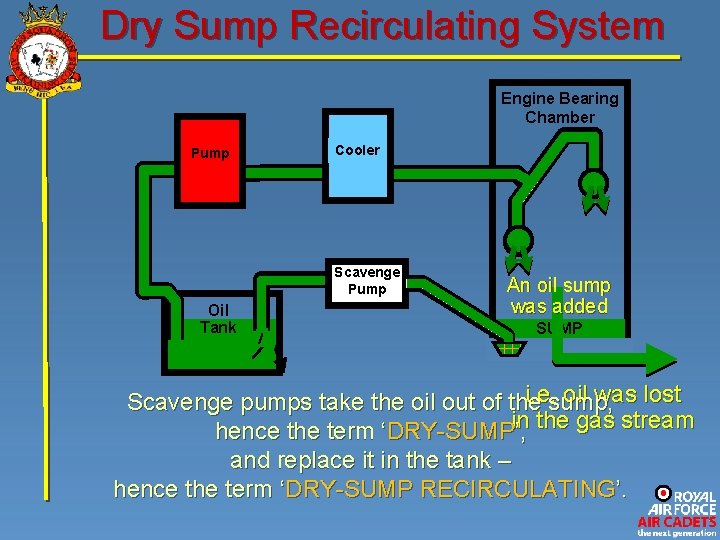
Dry Sump Recirculating System Engine Bearing Chamber Pump Cooler Scavenge Pump Oil Tank An oil sump was added SUMP i. e. oil was lost Scavenge pumps take the oil out of the sump, hence the term ‘DRY-SUMPin ’, the gas stream and replace it in the tank – hence the term ‘DRY-SUMP RECIRCULATING’.
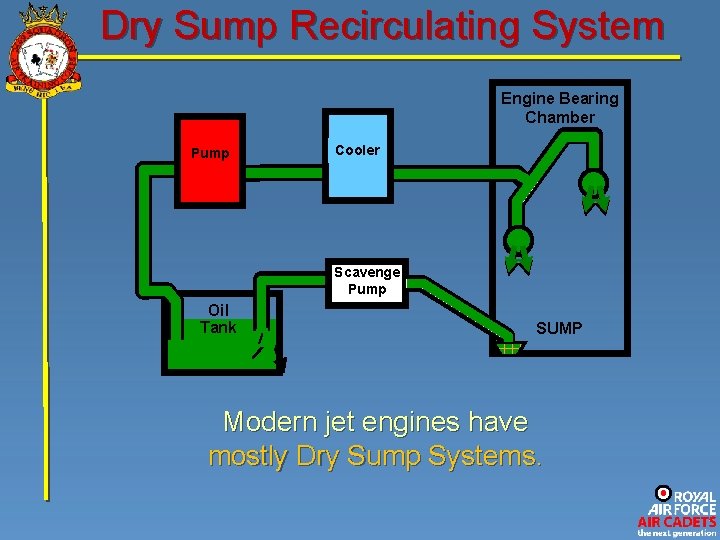
Dry Sump Recirculating System Engine Bearing Chamber Pump Cooler Scavenge Pump Oil Tank SUMP Modern jet engines have mostly Dry Sump Systems.
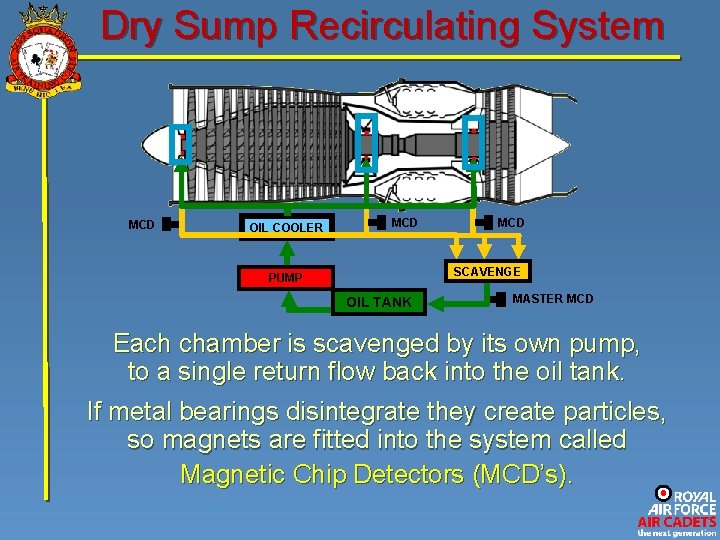
Dry Sump Recirculating System MCD OIL COOLER MCD SCAVENGE PUMP OIL TANK MASTER MCD Each chamber is scavenged by its own pump, to a single return flow back into the oil tank. If metal bearings disintegrate they create particles, so magnets are fitted into the system called Magnetic Chip Detectors (MCD’s).
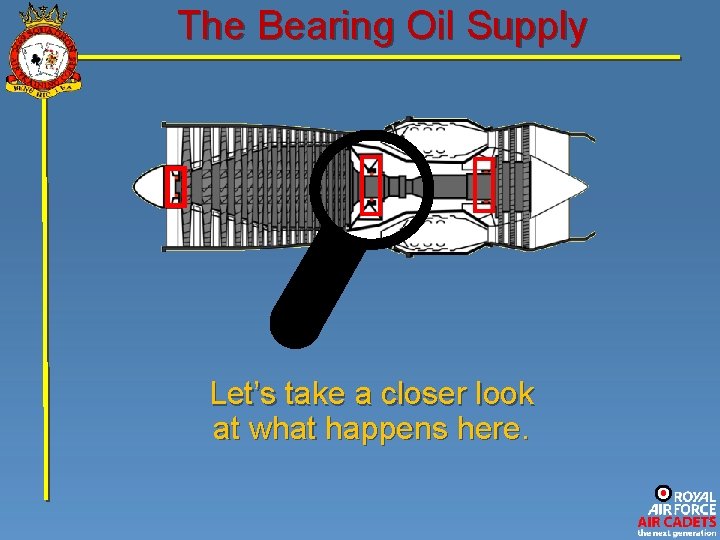
The Bearing Oil Supply Let’s take a closer look at what happens here.
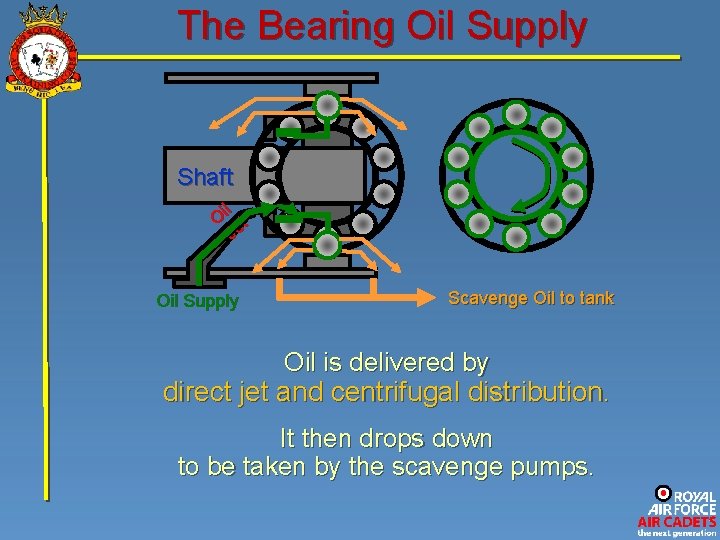
The Bearing Oil Supply Shaft il O t e J Oil Supply Scavenge Oil to tank Oil is delivered by direct jet and centrifugal distribution. It then drops down to be taken by the scavenge pumps.
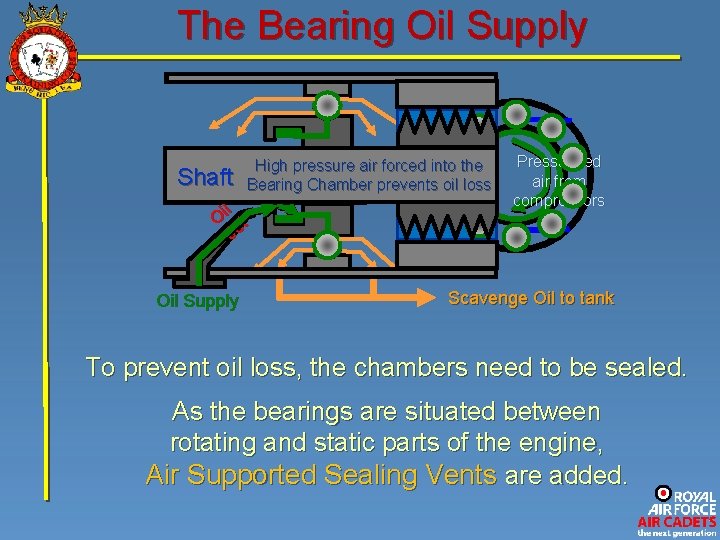
The Bearing Oil Supply Shaft High pressure air forced into the Bearing Chamber prevents oil loss il O t e J Oil Supply Pressurised air from compressors Scavenge Oil to tank To prevent oil loss, the chambers need to be sealed. As the bearings are situated between rotating and static parts of the engine, Air Supported Sealing Vents are added.
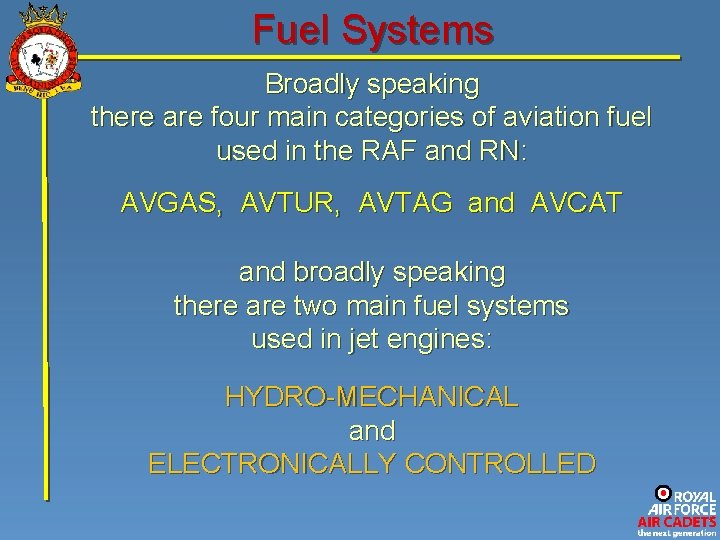
Fuel Systems Broadly speaking there are four main categories of aviation fuel used in the RAF and RN: AVGAS, AVTUR, AVTAG and AVCAT and broadly speaking there are two main fuel systems used in jet engines: HYDRO-MECHANICAL and ELECTRONICALLY CONTROLLED
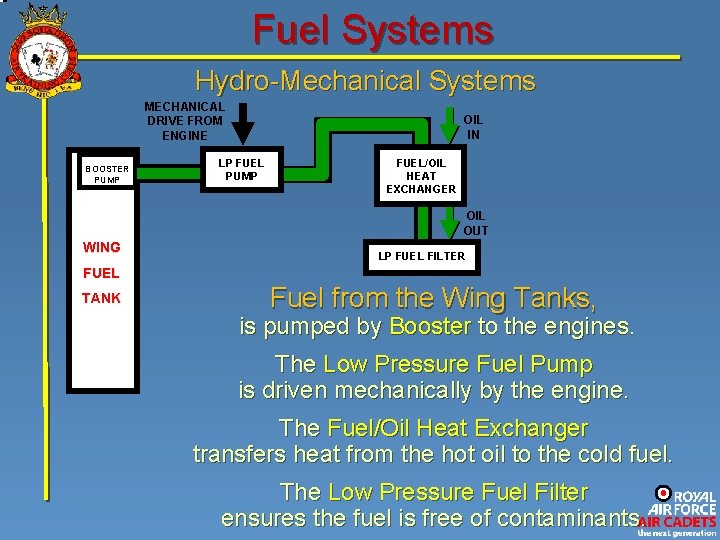
Fuel Systems Hydro-Mechanical Systems MECHANICAL DRIVE FROM ENGINE BOOSTER PUMP OIL IN LP FUEL PUMP FUEL/OIL HEAT EXCHANGER OIL OUT WING LP FUEL FILTER FUEL TANK Fuel from the Wing Tanks, is pumped by Booster to the engines. The Low Pressure Fuel Pump is driven mechanically by the engine. The Fuel/Oil Heat Exchanger transfers heat from the hot oil to the cold fuel. The Low Pressure Fuel Filter ensures the fuel is free of contaminants.
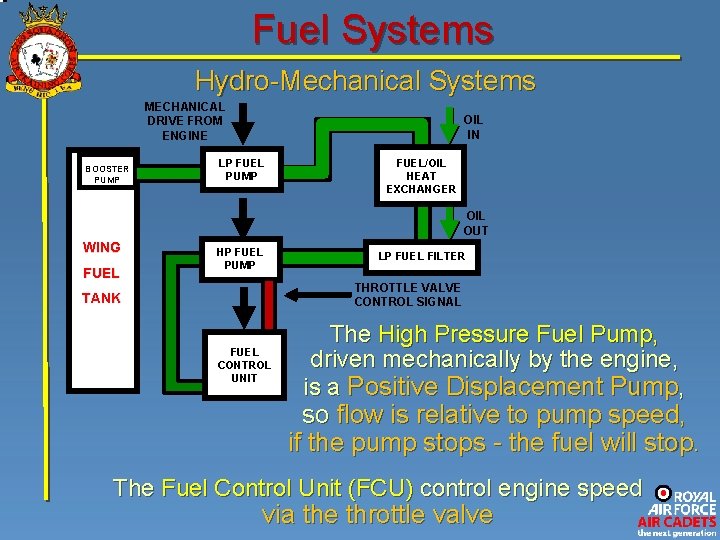
Fuel Systems Hydro-Mechanical Systems MECHANICAL DRIVE FROM ENGINE BOOSTER PUMP OIL IN LP FUEL PUMP FUEL/OIL HEAT EXCHANGER OIL OUT WING FUEL HP FUEL PUMP LP FUEL FILTER THROTTLE VALVE CONTROL SIGNAL TANK FUEL CONTROL UNIT The High Pressure Fuel Pump, driven mechanically by the engine, is a Positive Displacement Pump, so flow is relative to pump speed, if the pump stops - the fuel will stop. The Fuel Control Unit (FCU) control engine speed via the throttle valve
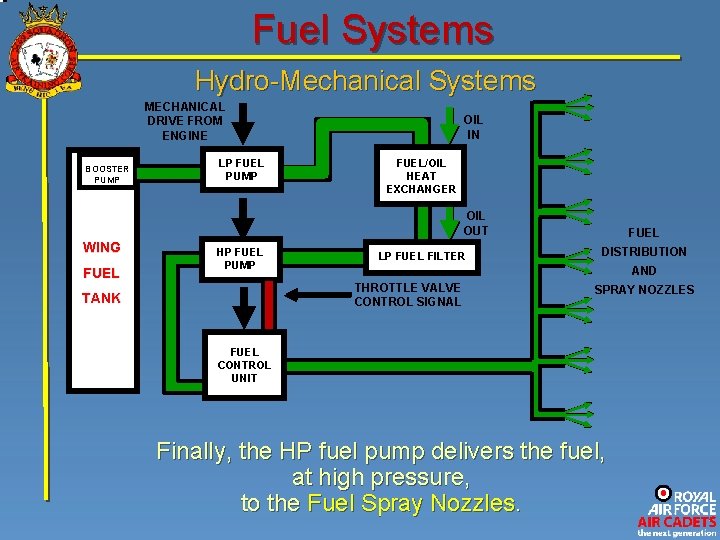
Fuel Systems Hydro-Mechanical Systems MECHANICAL DRIVE FROM ENGINE BOOSTER PUMP LP FUEL PUMP OIL IN FUEL/OIL HEAT EXCHANGER OIL OUT WING FUEL HP FUEL PUMP LP FUEL FILTER DISTRIBUTION AND THROTTLE VALVE CONTROL SIGNAL TANK FUEL SPRAY NOZZLES FUEL CONTROL UNIT Finally, the HP fuel pump delivers the fuel, at high pressure, to the Fuel Spray Nozzles.
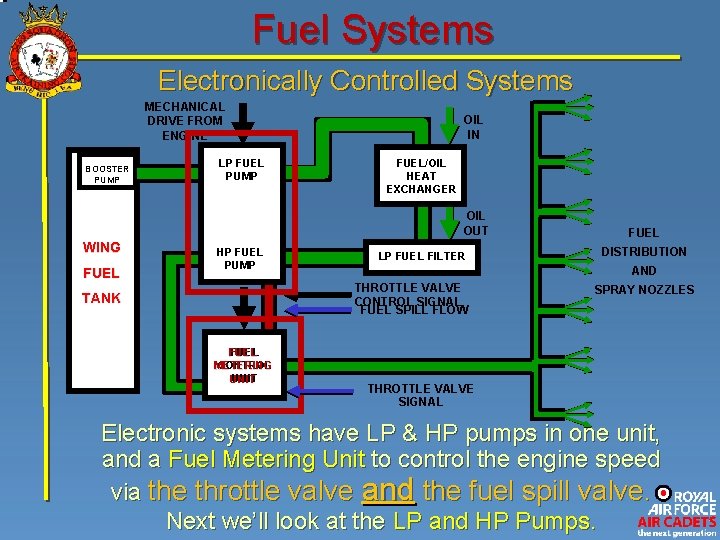
Fuel Systems Electronically Controlled Systems MECHANICAL DRIVE FROM ENGINE BOOSTER PUMP LP FUEL PUMP OIL IN FUEL/OIL HEAT EXCHANGER OIL OUT WING FUEL HP FUEL PUMP LP FUEL FILTER FUEL CONTROL METERING UNIT DISTRIBUTION AND THROTTLE VALVE CONTROL SIGNAL FUEL SPILL FLOW TANK FUEL SPRAY NOZZLES THROTTLE VALVE SIGNAL Electronic systems have LP & HP pumps in one unit, and a Fuel Metering Unit to control the engine speed via the throttle valve and the fuel spill valve. Next we’ll look at the LP and HP Pumps.
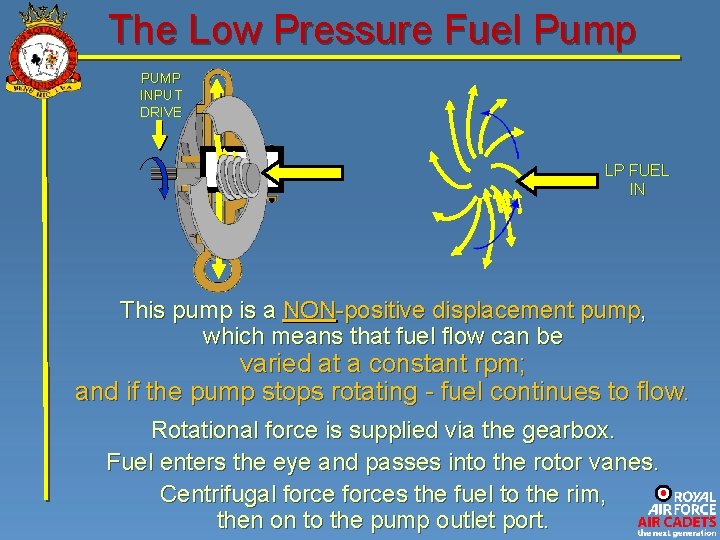
The Low Pressure Fuel Pump PUMP INPUT DRIVE LP FUEL PUMP LP FUEL IN This pump is a NON-positive displacement pump, which means that fuel flow can be varied at a constant rpm; and if the pump stops rotating - fuel continues to flow. Rotational force is supplied via the gearbox. Fuel enters the eye and passes into the rotor vanes. Centrifugal forces the fuel to the rim, then on to the pump outlet port.
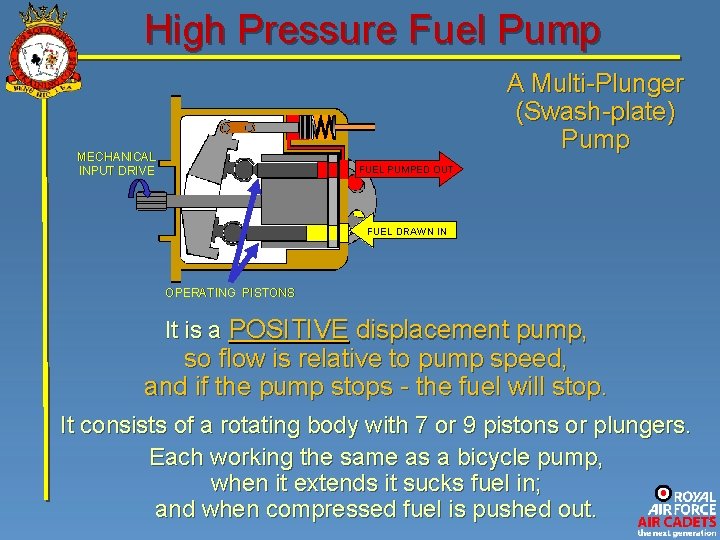
High Pressure Fuel Pump A Multi-Plunger (Swash-plate) Pump MECHANICAL INPUT DRIVE FUEL PUMPED OUT FUEL DRAWN IN OPERATING PISTONS It is a POSITIVE displacement pump, so flow is relative to pump speed, and if the pump stops - the fuel will stop. It consists of a rotating body with 7 or 9 pistons or plungers. Each working the same as a bicycle pump, when it extends it sucks fuel in; and when compressed fuel is pushed out.
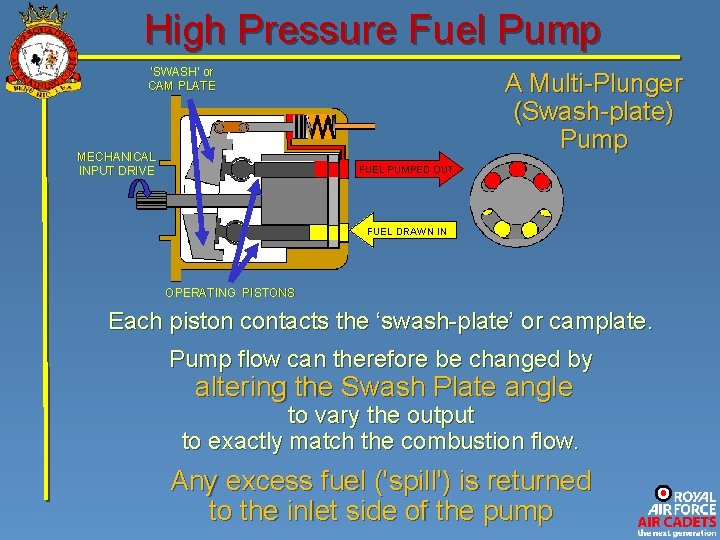
High Pressure Fuel Pump ‘SWASH’ or CAM PLATE MECHANICAL INPUT DRIVE A Multi-Plunger (Swash-plate) Pump FUEL PUMPED OUT FUEL DRAWN IN OPERATING PISTONS Each piston contacts the ‘swash-plate’ or camplate. Pump flow can therefore be changed by altering the Swash Plate angle to vary the output to exactly match the combustion flow. Any excess fuel ('spill') is returned to the inlet side of the pump
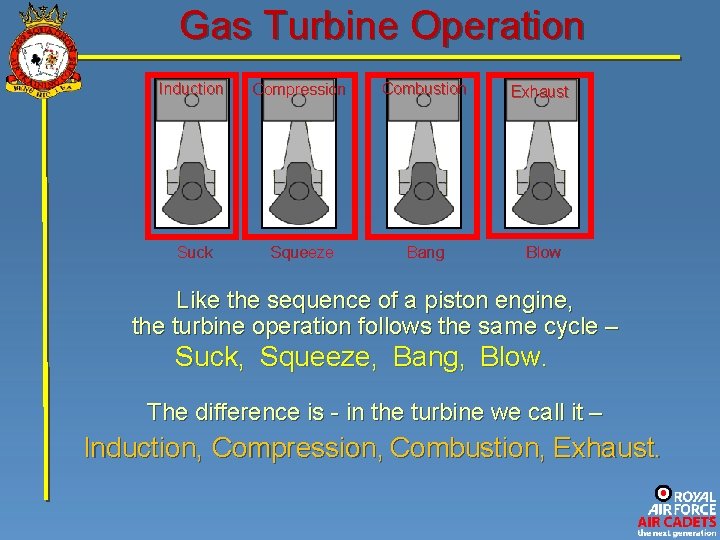
Gas Turbine Operation Induction Compression Combustion Exhaust Suck Squeeze Bang Blow Like the sequence of a piston engine, the turbine operation follows the same cycle – Suck, Squeeze, Bang, Blow. The difference is - in the turbine we call it – Induction, Compression, Combustion, Exhaust.
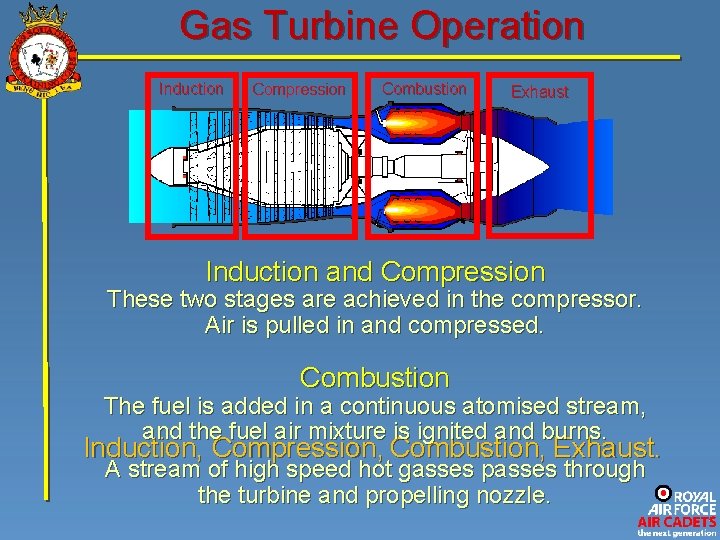
Gas Turbine Operation Induction Compression Combustion Exhaust Induction and Compression These two stages are achieved in the compressor. Air is pulled in and compressed. Combustion The fuel is added in a continuous atomised stream, and the fuel air mixture is ignited and burns. Induction, Compression, Combustion, Exhaust. A stream of high speed hot gasses passes through the turbine and propelling nozzle.
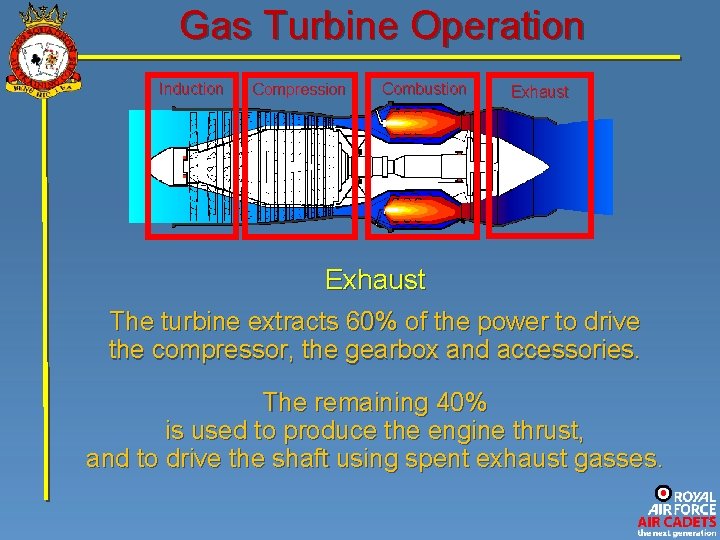
Gas Turbine Operation Induction Compression Combustion Exhaust The turbine extracts 60% of the power to drive the compressor, the gearbox and accessories. The remaining 40% is used to produce the engine thrust, and to drive the shaft using spent exhaust gasses.
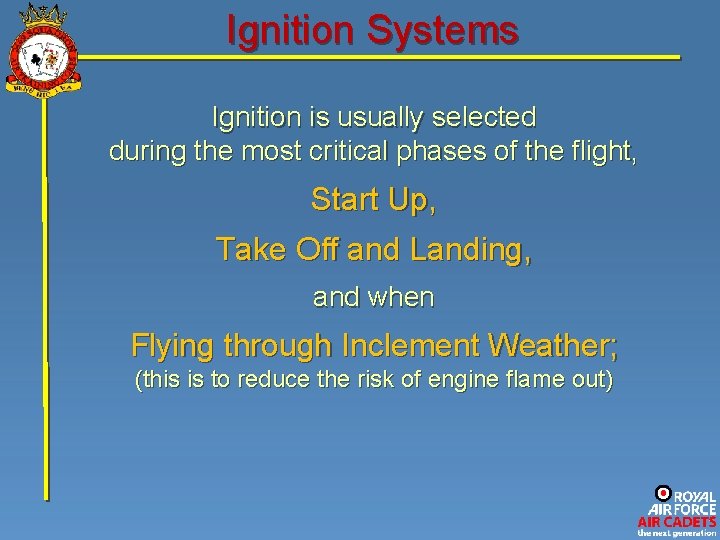
Ignition Systems Ignition is usually selected during the most critical phases of the flight, Start Up, Take Off and Landing, and when Flying through Inclement Weather; (this is to reduce the risk of engine flame out)
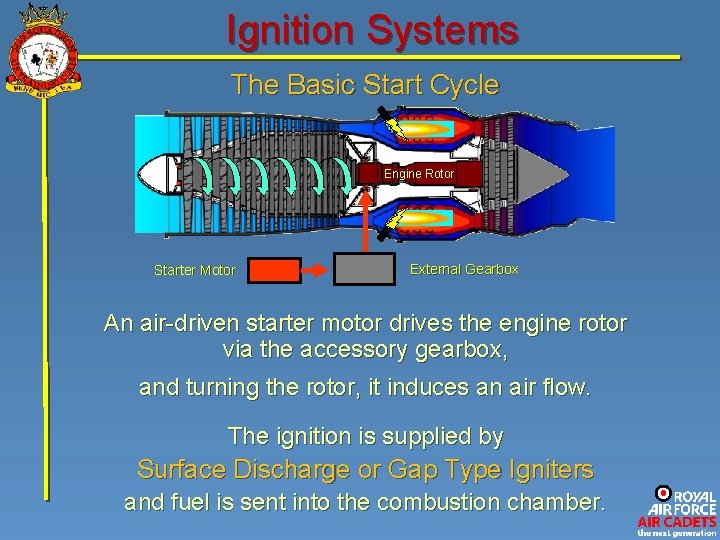
Ignition Systems The Basic Start Cycle Engine Rotor Starter Motor External Gearbox An air-driven starter motor drives the engine rotor via the accessory gearbox, and turning the rotor, it induces an air flow. The ignition is supplied by Surface Discharge or Gap Type Igniters and fuel is sent into the combustion chamber.
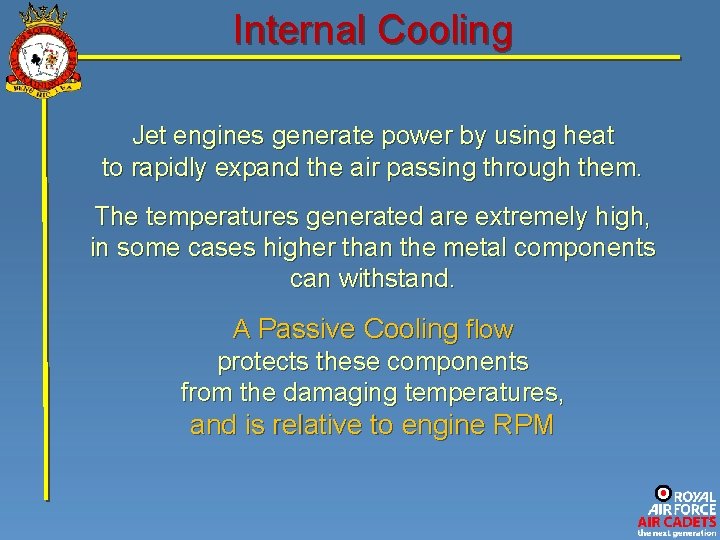
Internal Cooling Jet engines generate power by using heat to rapidly expand the air passing through them. The temperatures generated are extremely high, in some cases higher than the metal components can withstand. A Passive Cooling flow protects these components from the damaging temperatures, and is relative to engine RPM
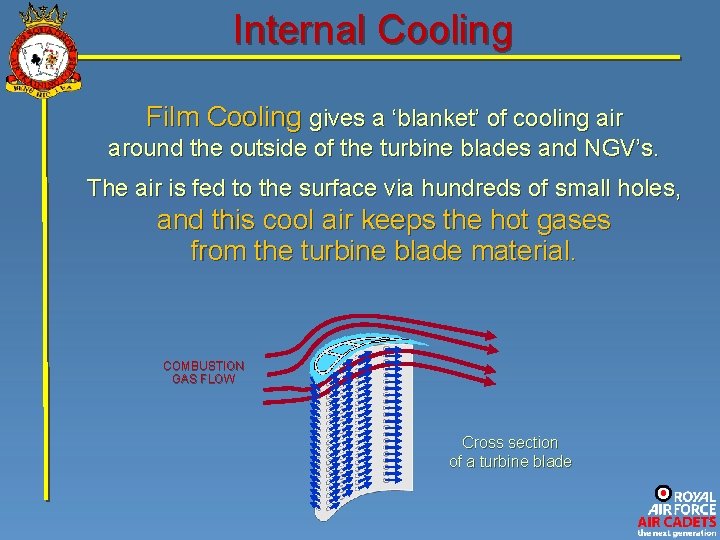
Internal Cooling Film Cooling gives a ‘blanket’ of cooling air around the outside of the turbine blades and NGV’s. The air is fed to the surface via hundreds of small holes, and this cool air keeps the hot gases from the turbine blade material. COMBUSTION GAS FLOW Cross section of a turbine blade
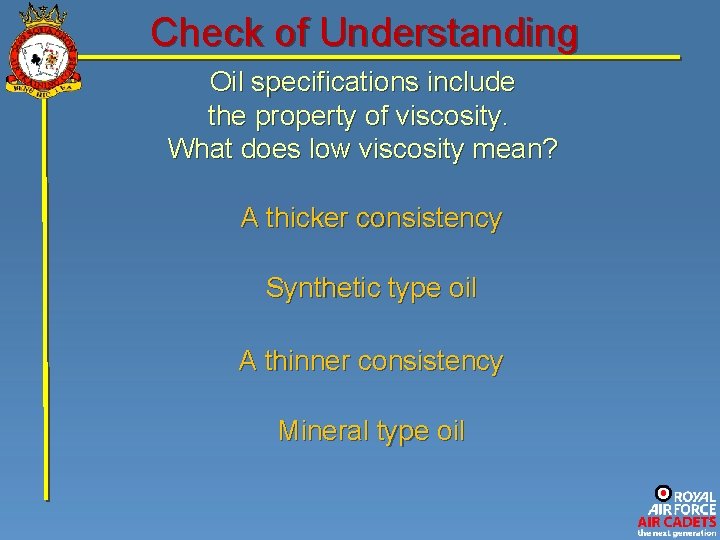
Check of Understanding Oil specifications include the property of viscosity. What does low viscosity mean? A thicker consistency Synthetic type oil A thinner consistency Mineral type oil
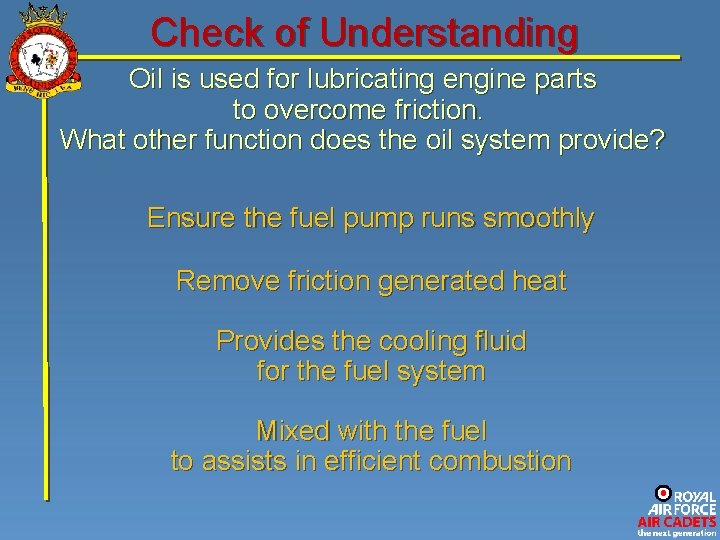
Check of Understanding Oil is used for lubricating engine parts to overcome friction. What other function does the oil system provide? Ensure the fuel pump runs smoothly Remove friction generated heat Provides the cooling fluid for the fuel system Mixed with the fuel to assists in efficient combustion
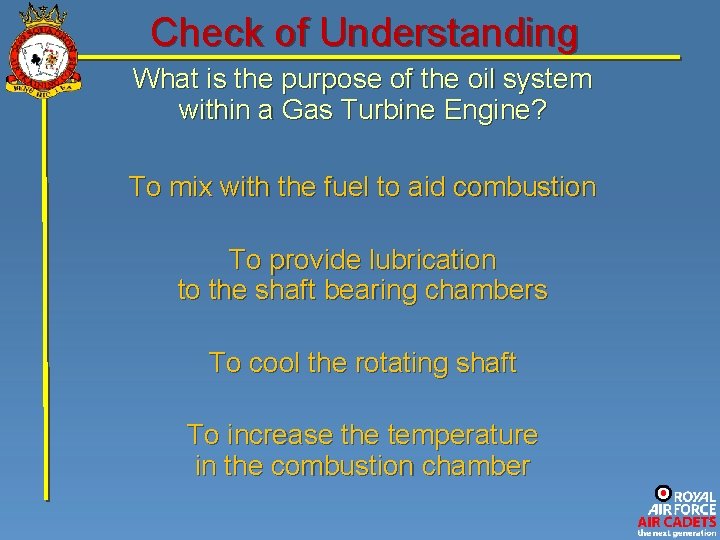
Check of Understanding What is the purpose of the oil system within a Gas Turbine Engine? To mix with the fuel to aid combustion To provide lubrication to the shaft bearing chambers To cool the rotating shaft To increase the temperature in the combustion chamber
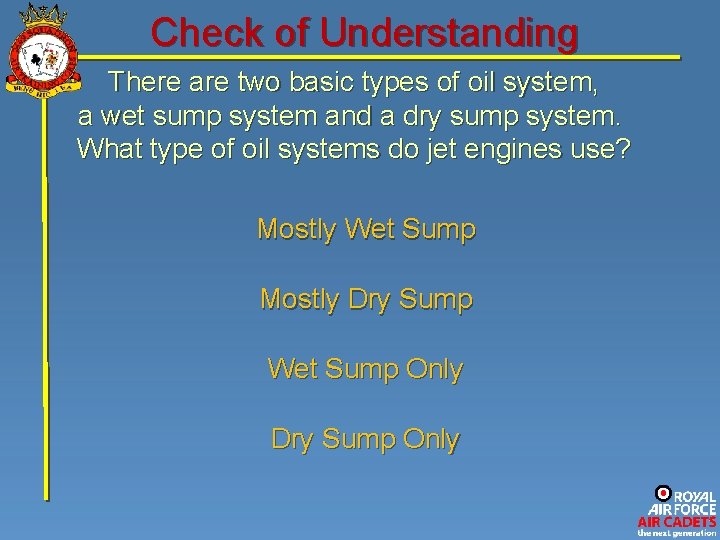
Check of Understanding There are two basic types of oil system, a wet sump system and a dry sump system. What type of oil systems do jet engines use? Mostly Wet Sump Mostly Dry Sump Wet Sump Only Dry Sump Only
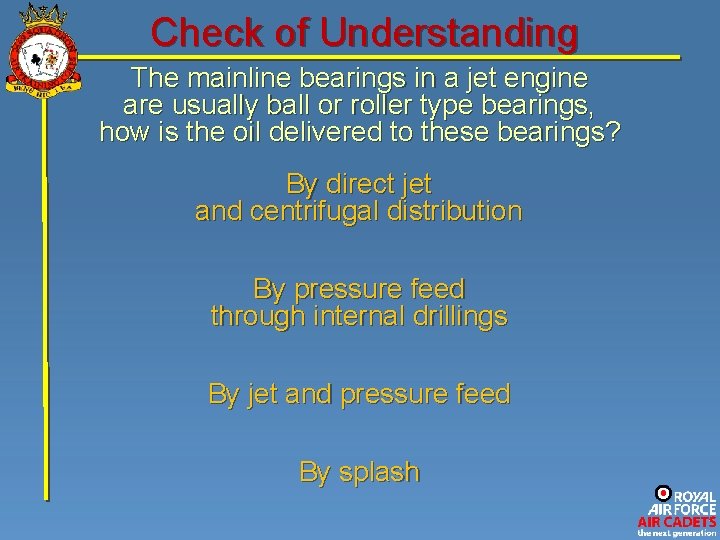
Check of Understanding The mainline bearings in a jet engine are usually ball or roller type bearings, how is the oil delivered to these bearings? By direct jet and centrifugal distribution By pressure feed through internal drillings By jet and pressure feed By splash
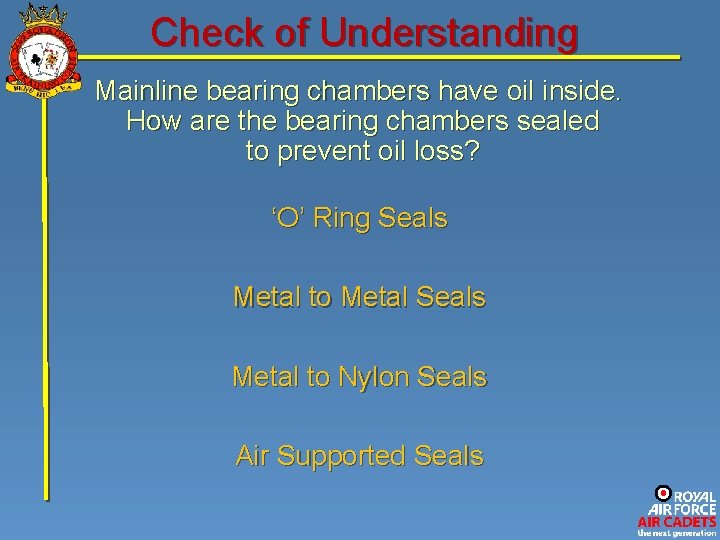
Check of Understanding Mainline bearing chambers have oil inside. How are the bearing chambers sealed to prevent oil loss? ‘O’ Ring Seals Metal to Metal Seals Metal to Nylon Seals Air Supported Seals
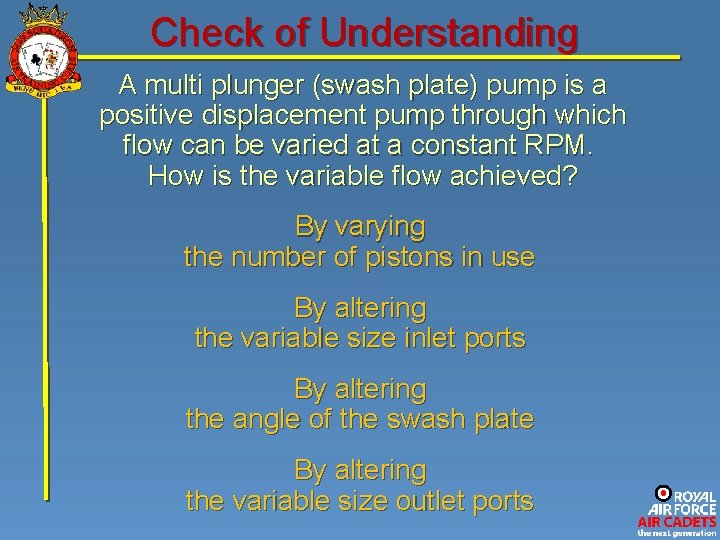
Check of Understanding A multi plunger (swash plate) pump is a positive displacement pump through which flow can be varied at a constant RPM. How is the variable flow achieved? By varying the number of pistons in use By altering the variable size inlet ports By altering the angle of the swash plate By altering the variable size outlet ports
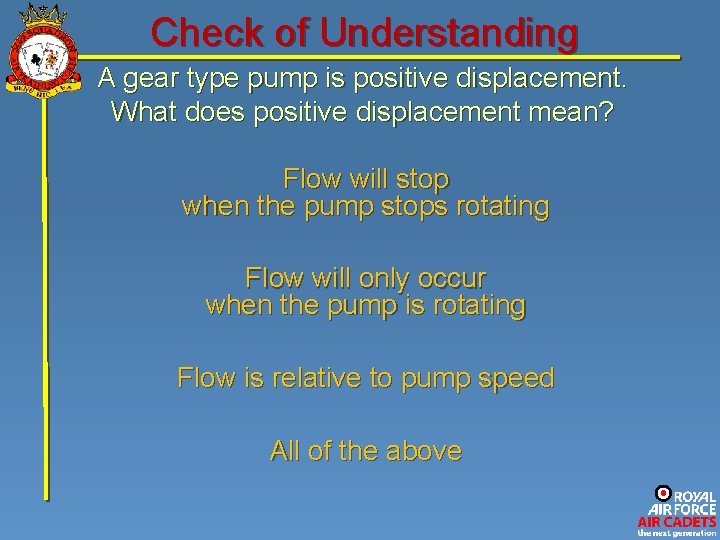
Check of Understanding A gear type pump is positive displacement. What does positive displacement mean? Flow will stop when the pump stops rotating Flow will only occur when the pump is rotating Flow is relative to pump speed All of the above
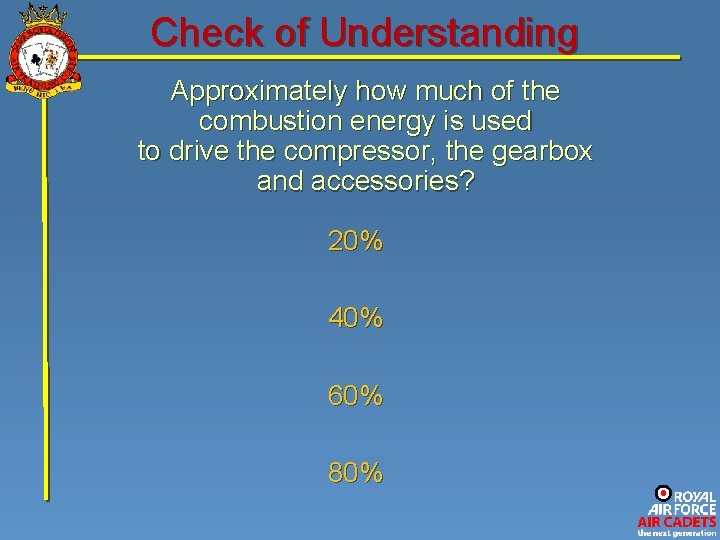
Check of Understanding Approximately how much of the combustion energy is used to drive the compressor, the gearbox and accessories? 20% 40% 60% 80%
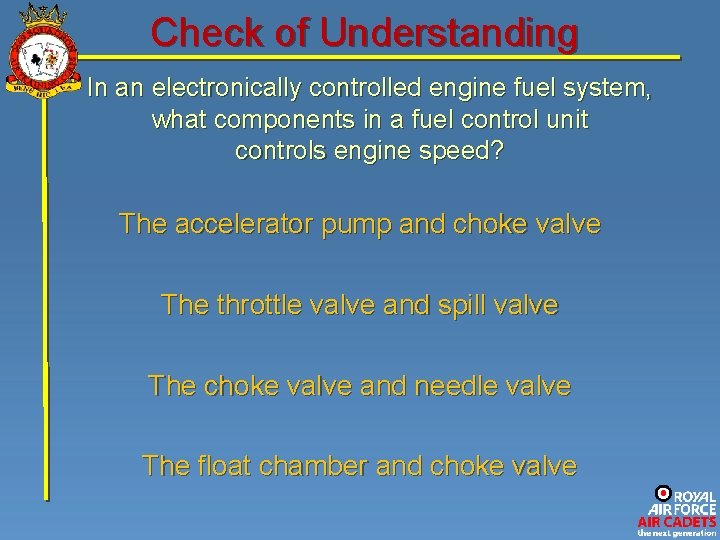
Check of Understanding In an electronically controlled engine fuel system, what components in a fuel control unit controls engine speed? The accelerator pump and choke valve The throttle valve and spill valve The choke valve and needle valve The float chamber and choke valve
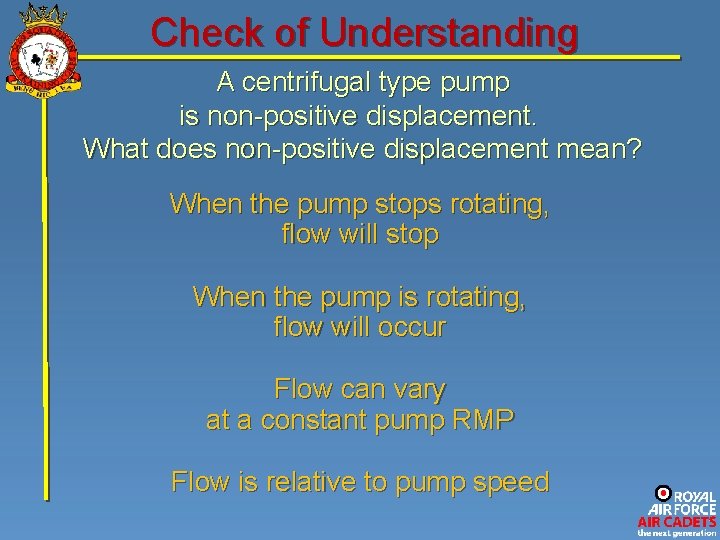
Check of Understanding A centrifugal type pump is non-positive displacement. What does non-positive displacement mean? When the pump stops rotating, flow will stop When the pump is rotating, flow will occur Flow can vary at a constant pump RMP Flow is relative to pump speed
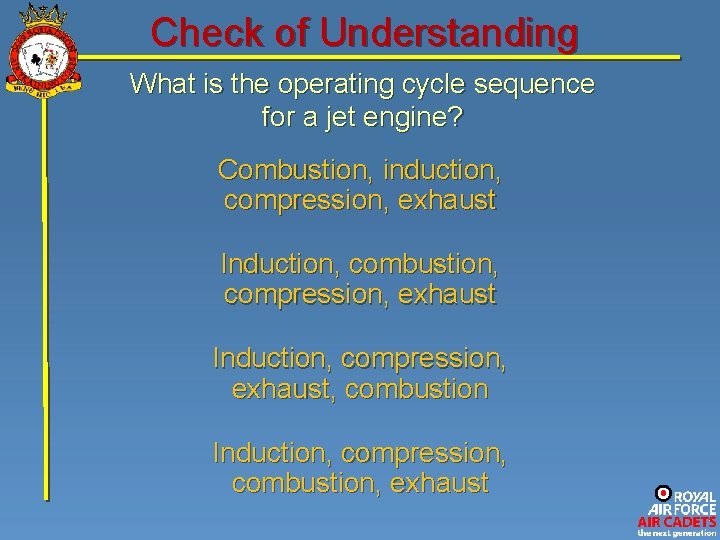
Check of Understanding What is the operating cycle sequence for a jet engine? Combustion, induction, compression, exhaust Induction, combustion, compression, exhaust Induction, compression, exhaust, combustion Induction, compression, combustion, exhaust
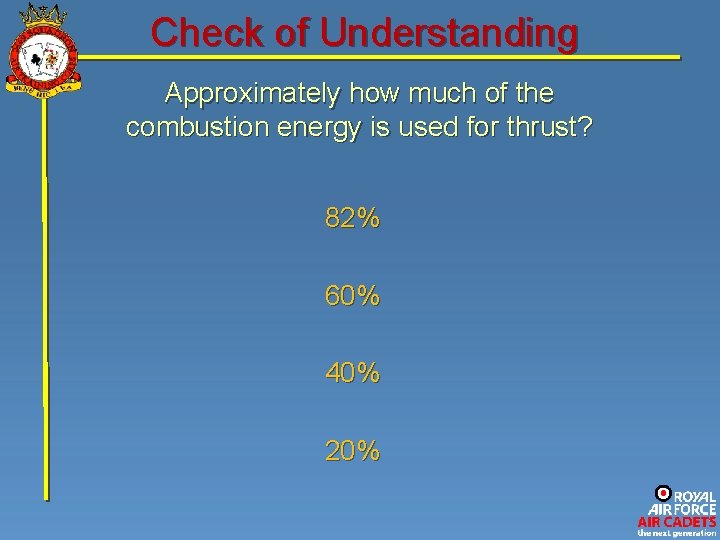
Check of Understanding Approximately how much of the combustion energy is used for thrust? 82% 60% 40% 20%
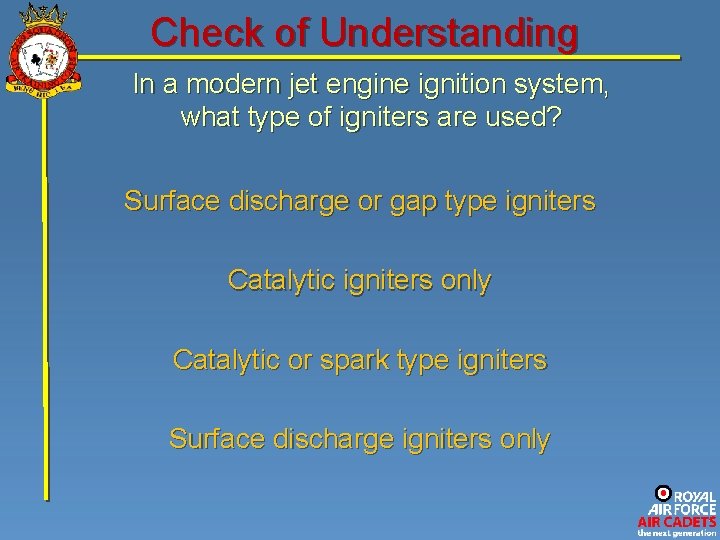
Check of Understanding In a modern jet engine ignition system, what type of igniters are used? Surface discharge or gap type igniters Catalytic igniters only Catalytic or spark type igniters Surface discharge igniters only
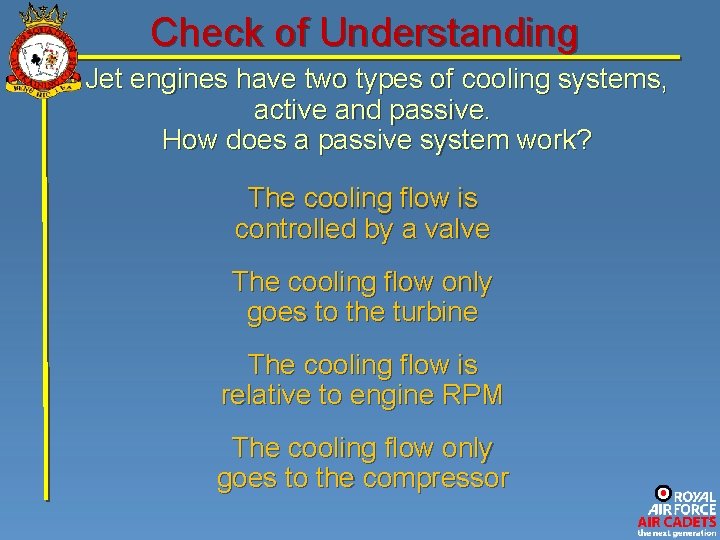
Check of Understanding Jet engines have two types of cooling systems, active and passive. How does a passive system work? The cooling flow is controlled by a valve The cooling flow only goes to the turbine The cooling flow is relative to engine RPM The cooling flow only goes to the compressor
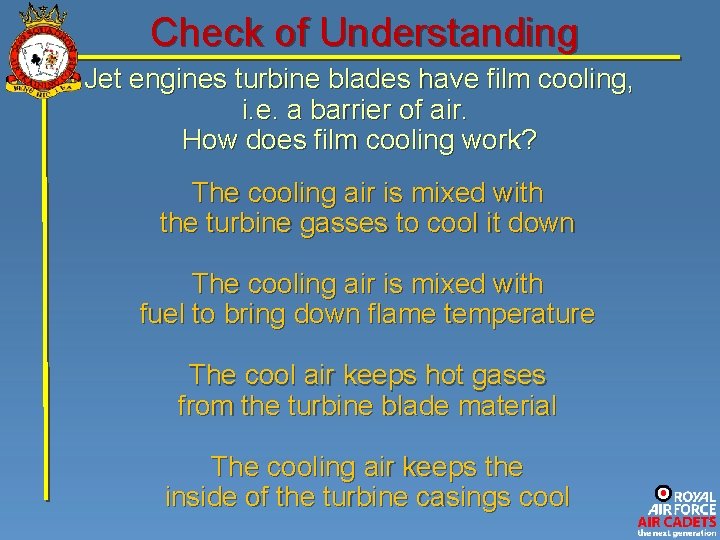
Check of Understanding Jet engines turbine blades have film cooling, i. e. a barrier of air. How does film cooling work? The cooling air is mixed with the turbine gasses to cool it down The cooling air is mixed with fuel to bring down flame temperature The cool air keeps hot gases from the turbine blade material The cooling air keeps the inside of the turbine casings cool
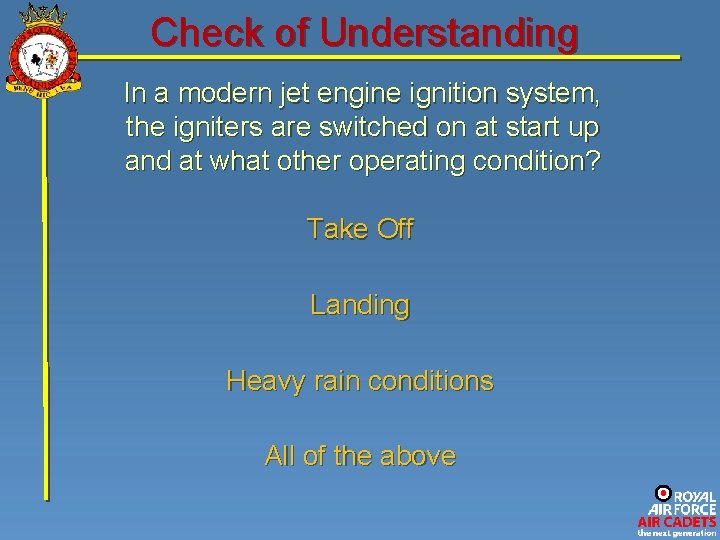
Check of Understanding In a modern jet engine ignition system, the igniters are switched on at start up and at what other operating condition? Take Off Landing Heavy rain conditions All of the above
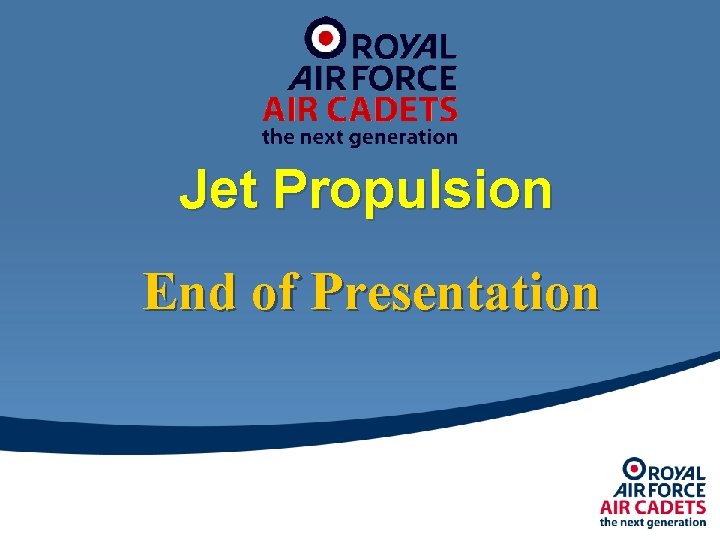
Jet Propulsion End of Presentation
Yelvington jet aviation jet fuel
10 year old sarah stands on a skateboard
L-3 combat propulsion systems
Pharmaceutical application of emulsion
Chapter 10 ignition systems
Chapter 10 ignition systems
Distributor ignition systems can be triggered by a
01:640:244 lecture notes - lecture 15: plat, idah, farad
Inertial propulsion
Propulsión en el sistema digestivo
Propulsion et diduction
Jet engine diffuser
Turbojet vs turbofan
Sea transport solutions stern landing vessel
Magnetic space propulsion
Nuclear propulsion officer
Spacex starting salary
Siva de scalzo
Nuclear propulsion
Andrew ketsdever
Nuclear thermal propulsion
Petro vend k800
"fuel management systems"
Dampeners are used on some fuel rails to
Experimental study of hydrogen release and ignition from
Operating systems lecture notes
Articulators
Lecture sound systems
Initially all rocks on earth were
Ignition coil windings
Small engine ignition system
Smart start breathalyzer hack
Ignition interlock device reviews
An ignition coil operates using the principle of
Missouri ignition interlock
Ignition interlock device definition
Ignition extinction curve
Cdi vs idi ignition
Ignition interlock coffee cup
Sepasoft ignition
Fungsi dari centrifugal governor advancer adalah
Honeywell 8610u
Define ignition system
Ignition temperature
Minimum ignition current