Ecole nationale dingnieurs de Monastir Dpartement de Gnie
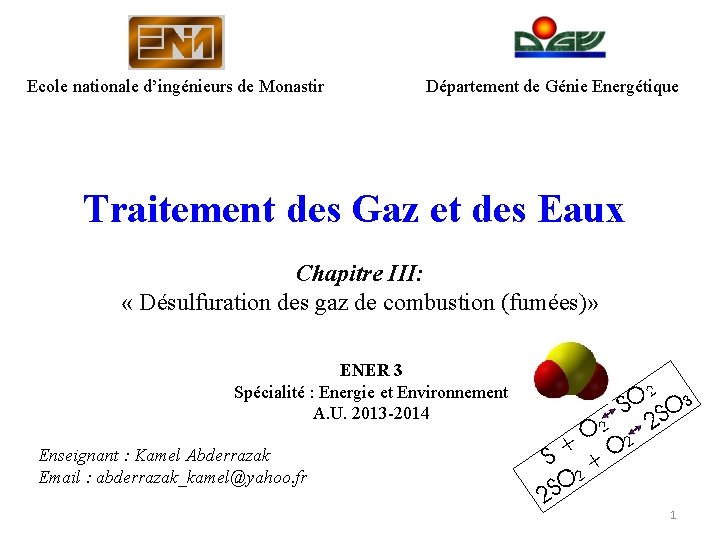
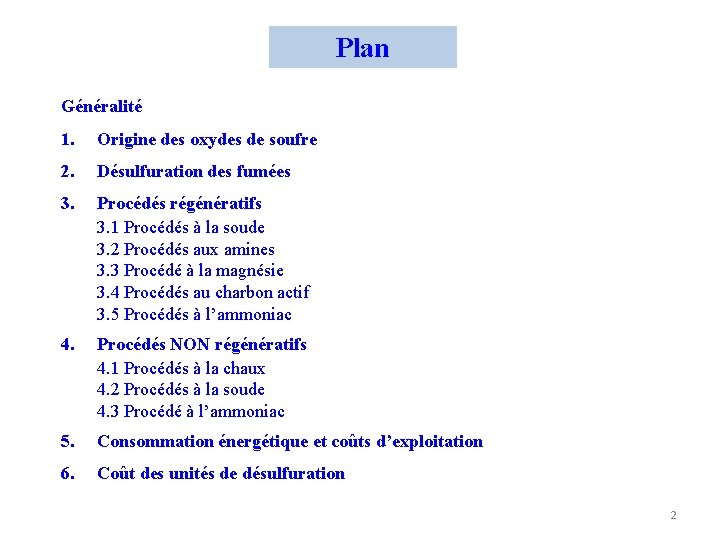
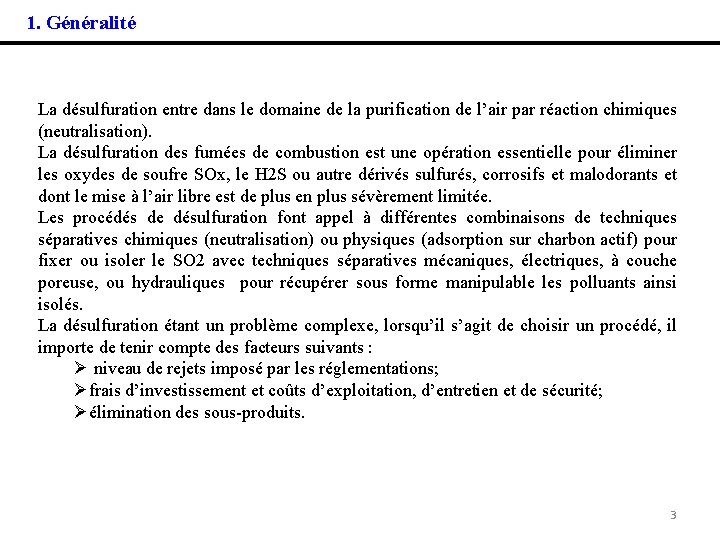
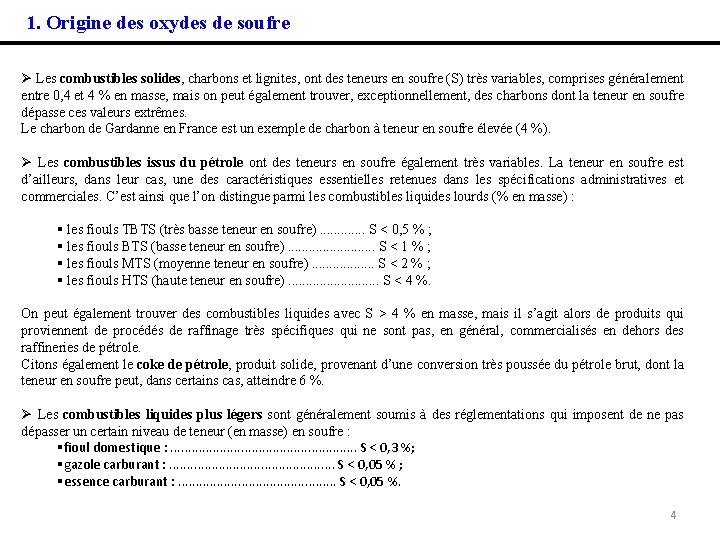
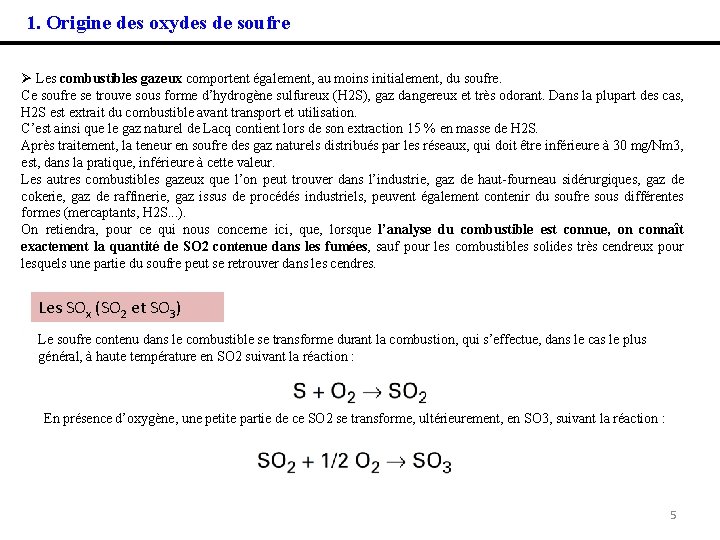
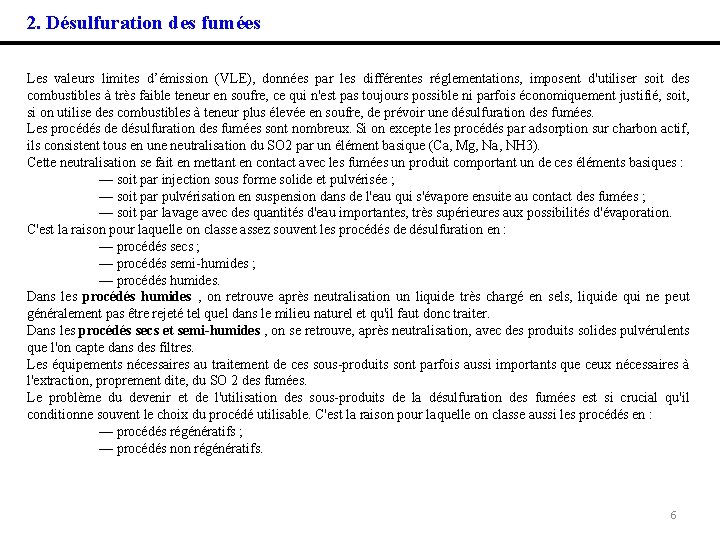
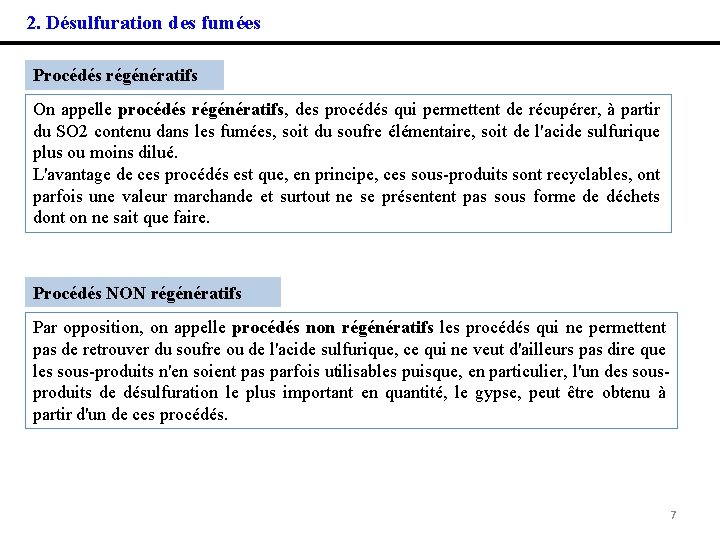
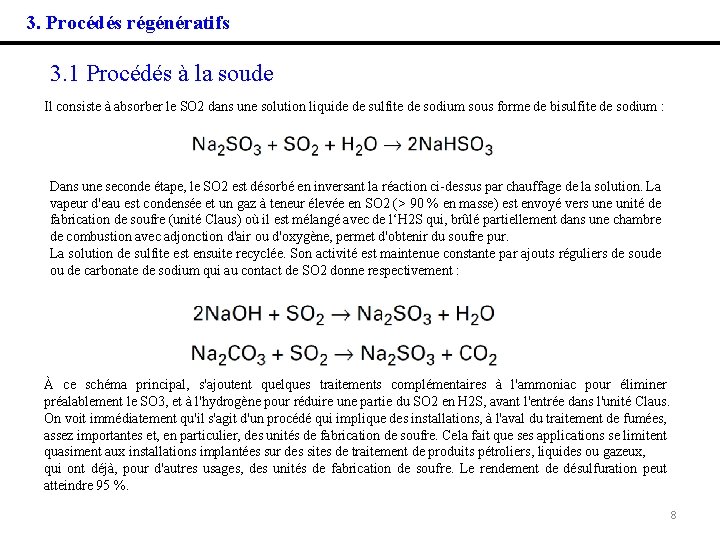
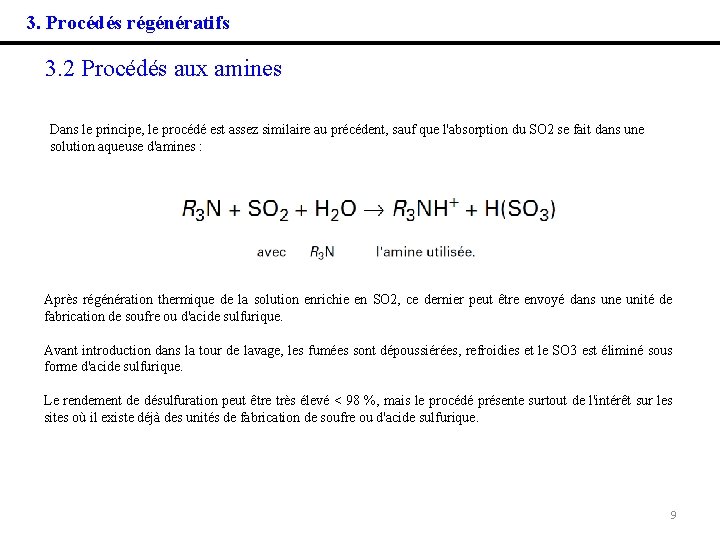
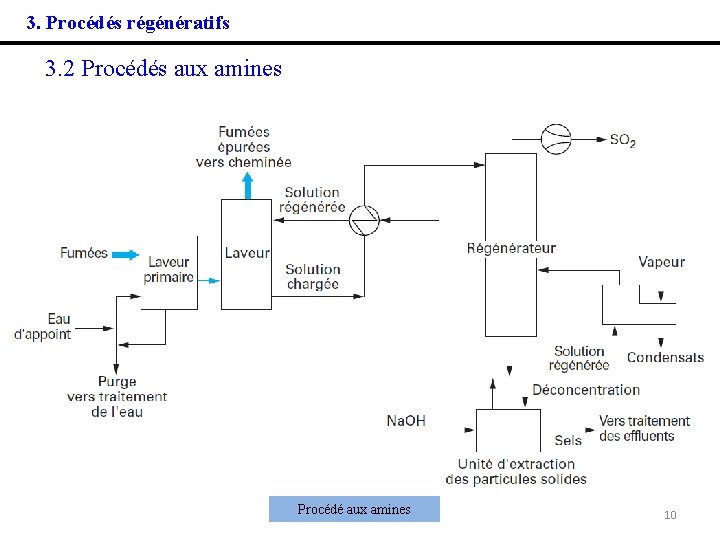
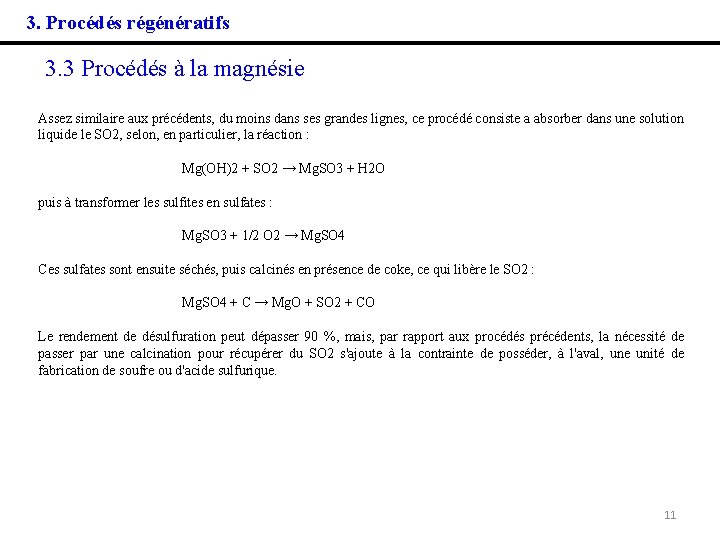
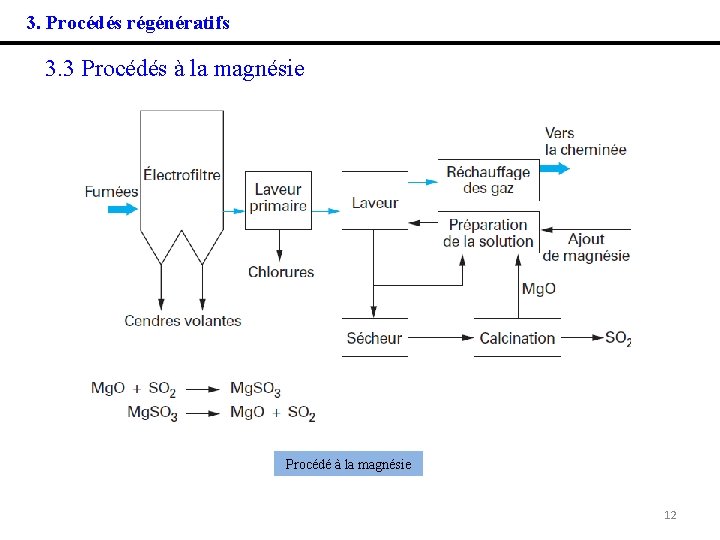
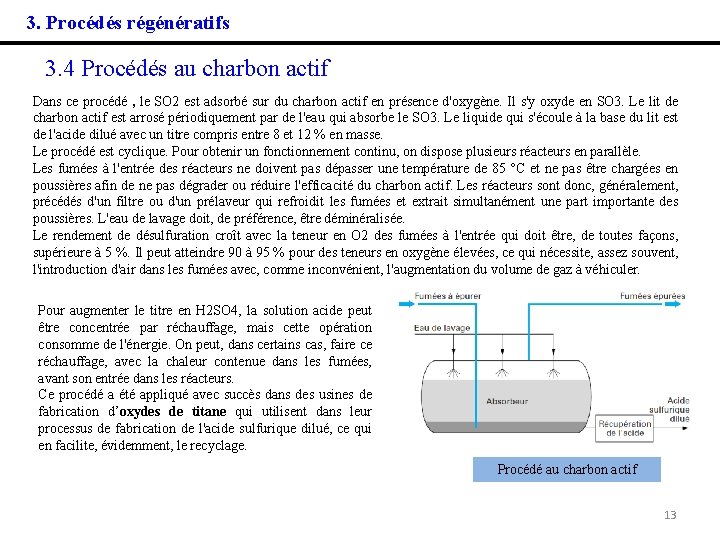
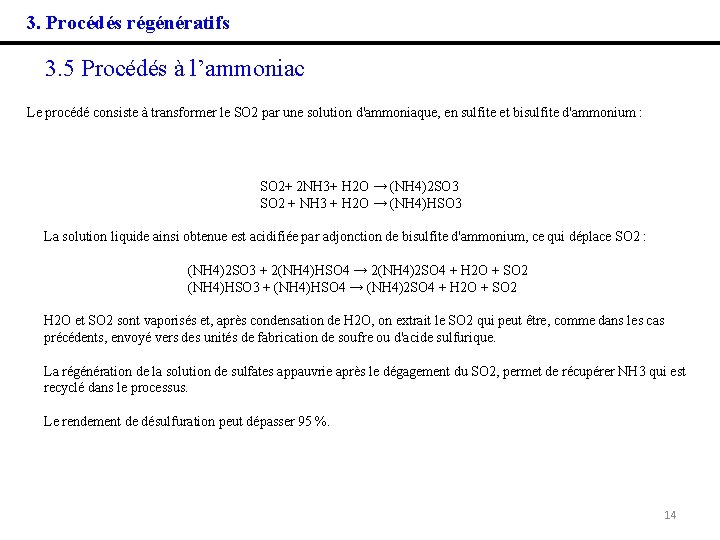
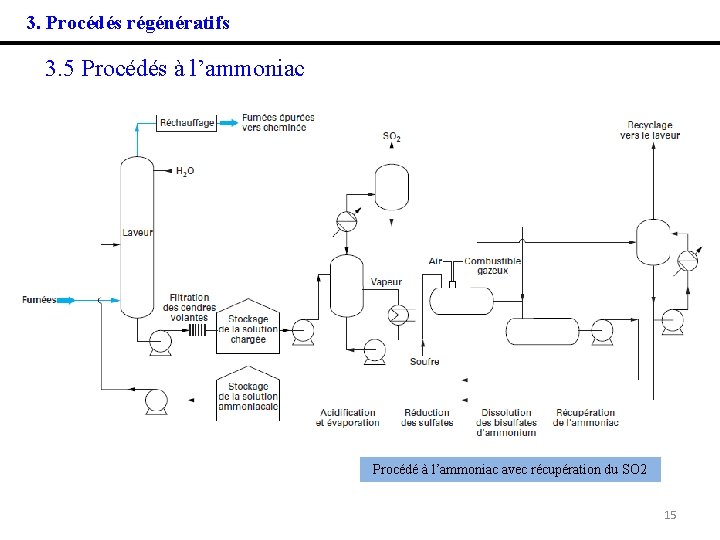
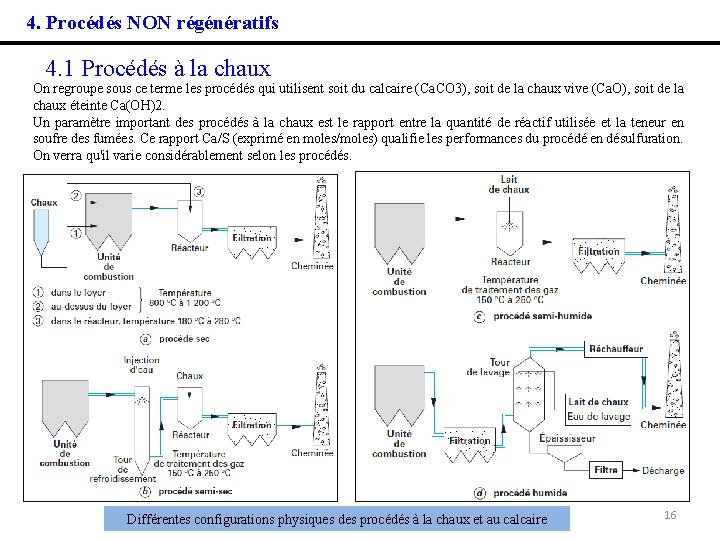
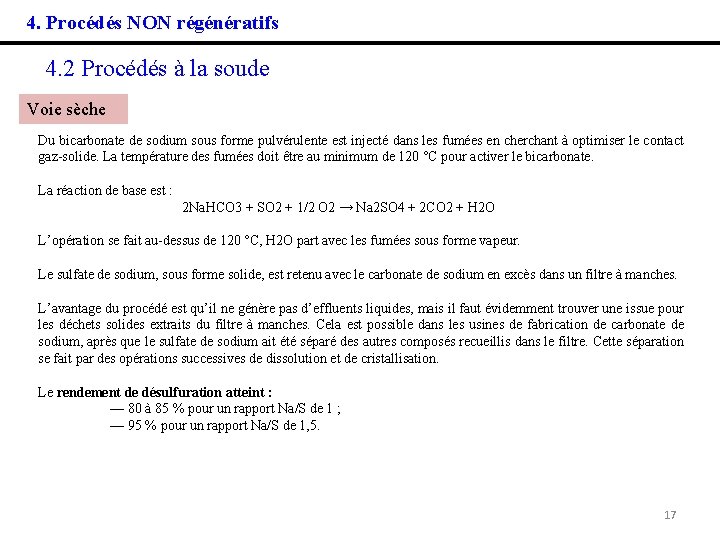
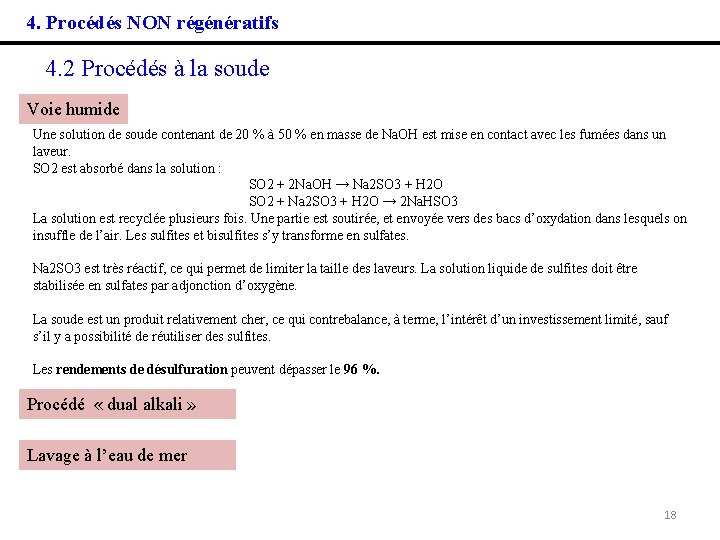
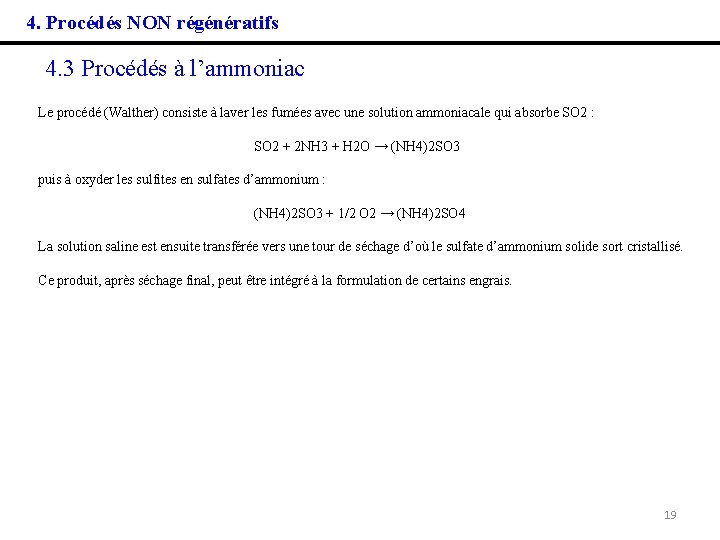
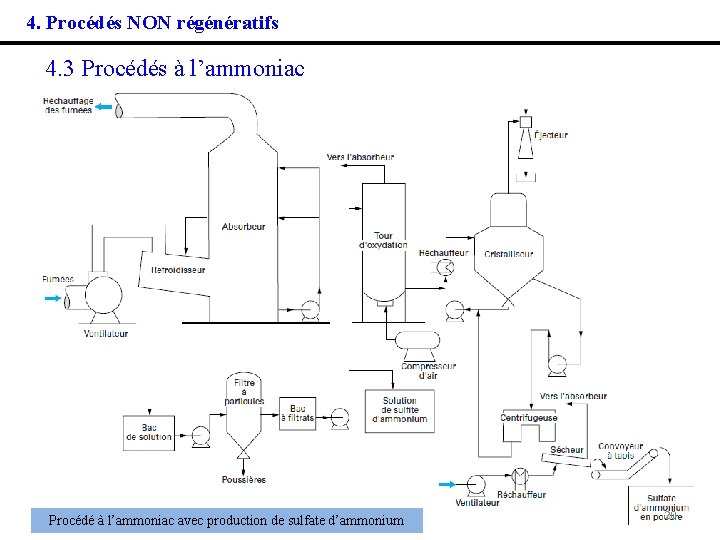
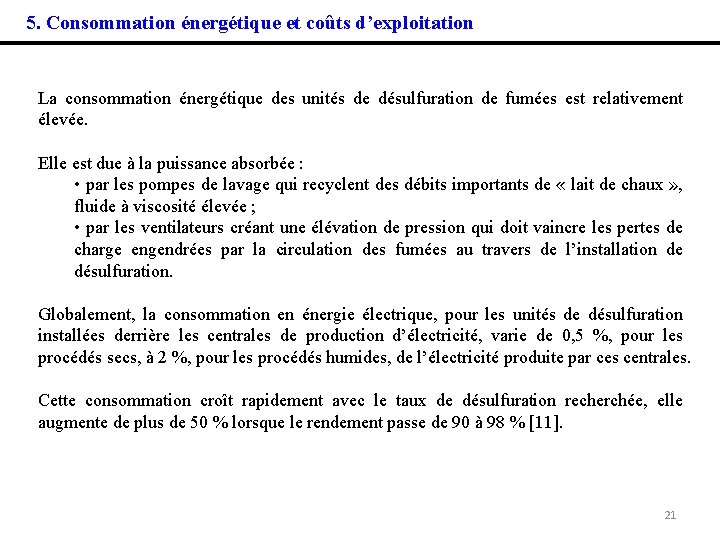
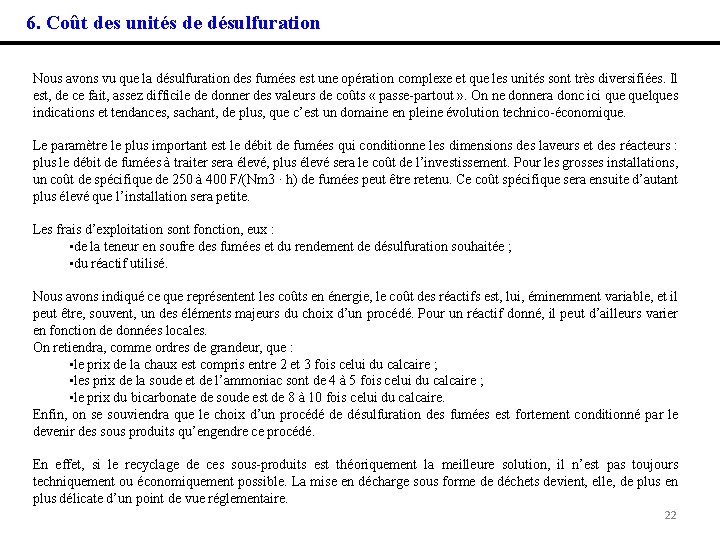
- Slides: 22
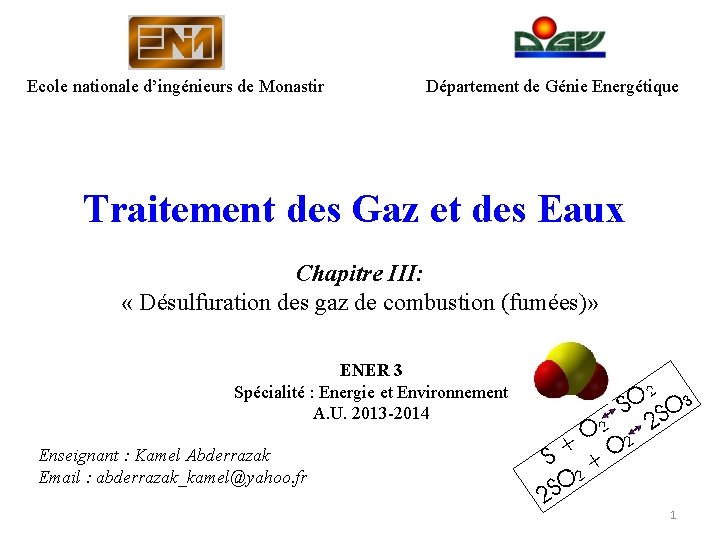
Ecole nationale d’ingénieurs de Monastir Département de Génie Energétique Traitement des Gaz et des Eaux Chapitre III: « Désulfuration des gaz de combustion (fumées)» ENER 3 Spécialité : Energie et Environnement A. U. 2013 -2014 Enseignant : Kamel Abderrazak Email : abderrazak_kamel@yahoo. fr 1
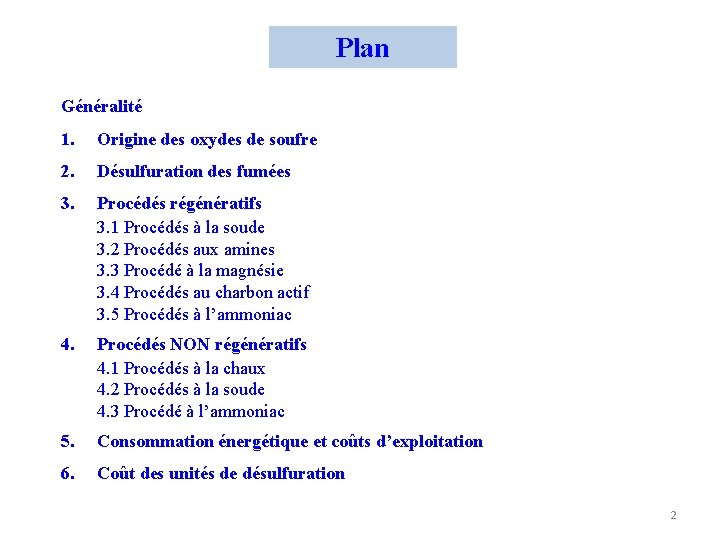
Plan Généralité 1. Origine des oxydes de soufre 2. Désulfuration des fumées 3. Procédés régénératifs 3. 1 Procédés à la soude 3. 2 Procédés aux amines 3. 3 Procédé à la magnésie 3. 4 Procédés au charbon actif 3. 5 Procédés à l’ammoniac 4. Procédés NON régénératifs 4. 1 Procédés à la chaux 4. 2 Procédés à la soude 4. 3 Procédé à l’ammoniac 5. Consommation énergétique et coûts d’exploitation 6. Coût des unités de désulfuration 2
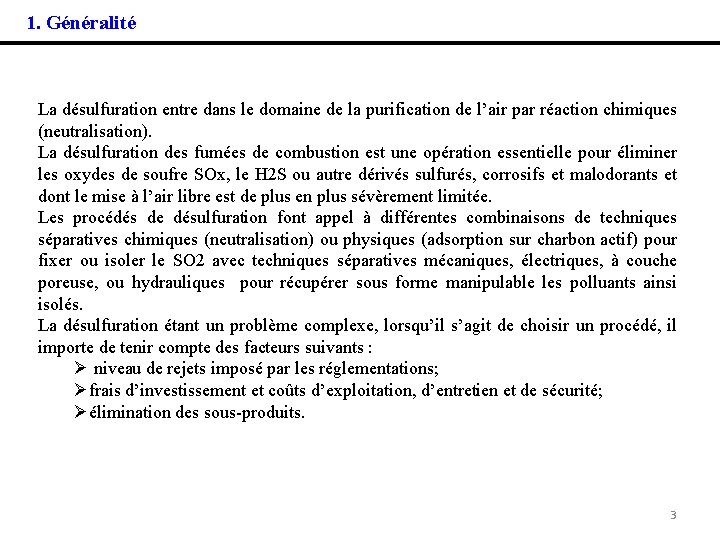
1. Généralité La désulfuration entre dans le domaine de la purification de l’air par réaction chimiques (neutralisation). La désulfuration des fumées de combustion est une opération essentielle pour éliminer les oxydes de soufre SOx, le H 2 S ou autre dérivés sulfurés, corrosifs et malodorants et dont le mise à l’air libre est de plus en plus sévèrement limitée. Les procédés de désulfuration font appel à différentes combinaisons de techniques séparatives chimiques (neutralisation) ou physiques (adsorption sur charbon actif) pour fixer ou isoler le SO 2 avec techniques séparatives mécaniques, électriques, à couche poreuse, ou hydrauliques pour récupérer sous forme manipulable les polluants ainsi isolés. La désulfuration étant un problème complexe, lorsqu’il s’agit de choisir un procédé, il importe de tenir compte des facteurs suivants : Ø niveau de rejets imposé par les réglementations; Øfrais d’investissement et coûts d’exploitation, d’entretien et de sécurité; Øélimination des sous-produits. 3
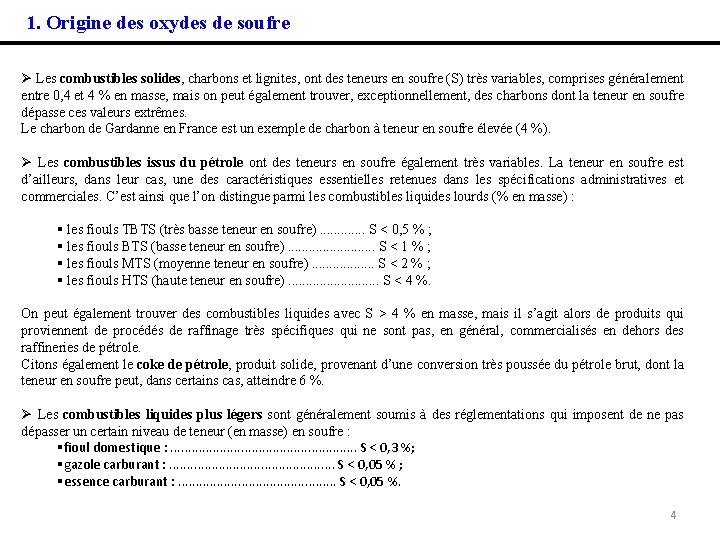
1. Origine des oxydes de soufre Ø Les combustibles solides, charbons et lignites, ont des teneurs en soufre (S) très variables, comprises généralement entre 0, 4 et 4 % en masse, mais on peut également trouver, exceptionnellement, des charbons dont la teneur en soufre dépasse ces valeurs extrêmes. Le charbon de Gardanne en France est un exemple de charbon à teneur en soufre élevée (4 %). Ø Les combustibles issus du pétrole ont des teneurs en soufre également très variables. La teneur en soufre est d’ailleurs, dans leur cas, une des caractéristiques essentielles retenues dans les spécifications administratives et commerciales. C’est ainsi que l’on distingue parmi les combustibles liquides lourds (% en masse) : § les fiouls TBTS (très basse teneur en soufre). . . S < 0, 5 % ; § les fiouls BTS (basse teneur en soufre). . . S < 1 % ; § les fiouls MTS (moyenne teneur en soufre). . . . S < 2 % ; § les fiouls HTS (haute teneur en soufre). . . S < 4 %. On peut également trouver des combustibles liquides avec S > 4 % en masse, mais il s’agit alors de produits qui proviennent de procédés de raffinage très spécifiques qui ne sont pas, en général, commercialisés en dehors des raffineries de pétrole. Citons également le coke de pétrole, produit solide, provenant d’une conversion très poussée du pétrole brut, dont la teneur en soufre peut, dans certains cas, atteindre 6 %. Ø Les combustibles liquides plus légers sont généralement soumis à des réglementations qui imposent de ne pas dépasser un certain niveau de teneur (en masse) en soufre : §fioul domestique : . . . S < 0, 3 %; §gazole carburant : . . . S < 0, 05 % ; §essence carburant : . . . S < 0, 05 %. 4
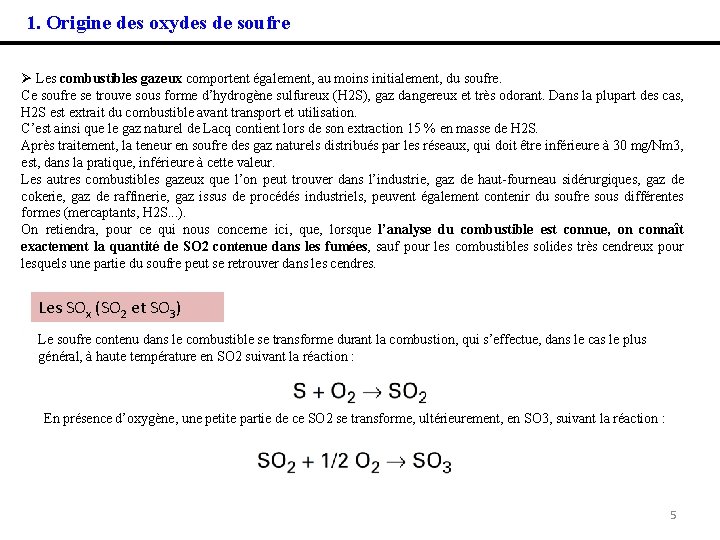
1. Origine des oxydes de soufre Ø Les combustibles gazeux comportent également, au moins initialement, du soufre. Ce soufre se trouve sous forme d’hydrogène sulfureux (H 2 S), gaz dangereux et très odorant. Dans la plupart des cas, H 2 S est extrait du combustible avant transport et utilisation. C’est ainsi que le gaz naturel de Lacq contient lors de son extraction 15 % en masse de H 2 S. Après traitement, la teneur en soufre des gaz naturels distribués par les réseaux, qui doit être inférieure à 30 mg/Nm 3, est, dans la pratique, inférieure à cette valeur. Les autres combustibles gazeux que l’on peut trouver dans l’industrie, gaz de haut-fourneau sidérurgiques, gaz de cokerie, gaz de raffinerie, gaz issus de procédés industriels, peuvent également contenir du soufre sous différentes formes (mercaptants, H 2 S. . . ). On retiendra, pour ce qui nous concerne ici, que, lorsque l’analyse du combustible est connue, on connaît exactement la quantité de SO 2 contenue dans les fumées, sauf pour les combustibles solides très cendreux pour lesquels une partie du soufre peut se retrouver dans les cendres. Les SOx (SO 2 et SO 3) Le soufre contenu dans le combustible se transforme durant la combustion, qui s’effectue, dans le cas le plus général, à haute température en SO 2 suivant la réaction : En présence d’oxygène, une petite partie de ce SO 2 se transforme, ultérieurement, en SO 3, suivant la réaction : 5
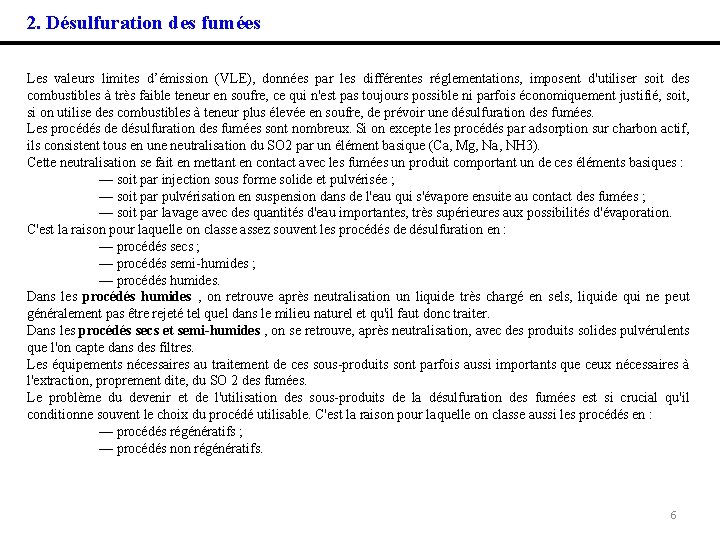
2. Désulfuration des fumées Les valeurs limites d’émission (VLE), données par les différentes réglementations, imposent d'utiliser soit des combustibles à très faible teneur en soufre, ce qui n'est pas toujours possible ni parfois économiquement justifié, soit, si on utilise des combustibles à teneur plus élevée en soufre, de prévoir une désulfuration des fumées. Les procédés de désulfuration des fumées sont nombreux. Si on excepte les procédés par adsorption sur charbon actif, ils consistent tous en une neutralisation du SO 2 par un élément basique (Ca, Mg, Na, NH 3). Cette neutralisation se fait en mettant en contact avec les fumées un produit comportant un de ces éléments basiques : — soit par injection sous forme solide et pulvérisée ; — soit par pulvérisation en suspension dans de l'eau qui s'évapore ensuite au contact des fumées ; — soit par lavage avec des quantités d'eau importantes, très supérieures aux possibilités d'évaporation. C'est la raison pour laquelle on classez souvent les procédés de désulfuration en : — procédés secs ; — procédés semi-humides ; — procédés humides. Dans les procédés humides , on retrouve après neutralisation un liquide très chargé en sels, liquide qui ne peut généralement pas être rejeté tel quel dans le milieu naturel et qu'il faut donc traiter. Dans les procédés secs et semi-humides , on se retrouve, après neutralisation, avec des produits solides pulvérulents que l'on capte dans des filtres. Les équipements nécessaires au traitement de ces sous-produits sont parfois aussi importants que ceux nécessaires à l'extraction, proprement dite, du SO 2 des fumées. Le problème du devenir et de l'utilisation des sous-produits de la désulfuration des fumées est si crucial qu'il conditionne souvent le choix du procédé utilisable. C'est la raison pour laquelle on classe aussi les procédés en : — procédés régénératifs ; — procédés non régénératifs. 6
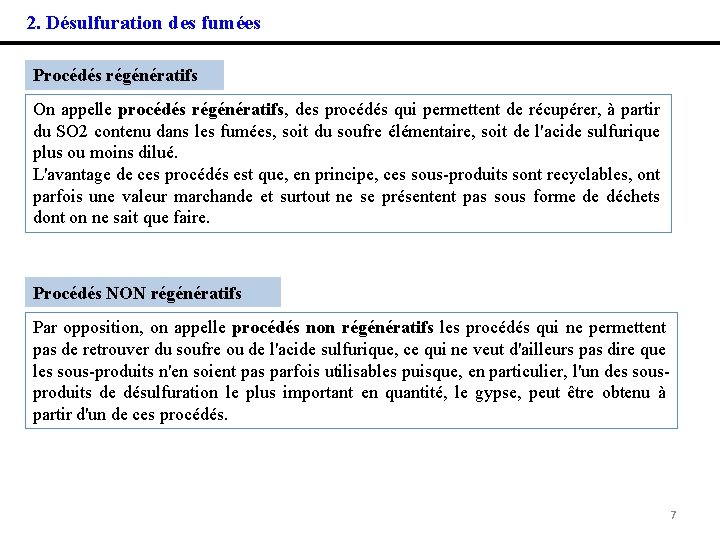
2. Désulfuration des fumées Procédés régénératifs On appelle procédés régénératifs, des procédés qui permettent de récupérer, à partir du SO 2 contenu dans les fumées, soit du soufre élémentaire, soit de l'acide sulfurique plus ou moins dilué. L'avantage de ces procédés est que, en principe, ces sous-produits sont recyclables, ont parfois une valeur marchande et surtout ne se présentent pas sous forme de déchets dont on ne sait que faire. Procédés NON régénératifs Par opposition, on appelle procédés non régénératifs les procédés qui ne permettent pas de retrouver du soufre ou de l'acide sulfurique, ce qui ne veut d'ailleurs pas dire que les sous-produits n'en soient pas parfois utilisables puisque, en particulier, l'un des sousproduits de désulfuration le plus important en quantité, le gypse, peut être obtenu à partir d'un de ces procédés. 7
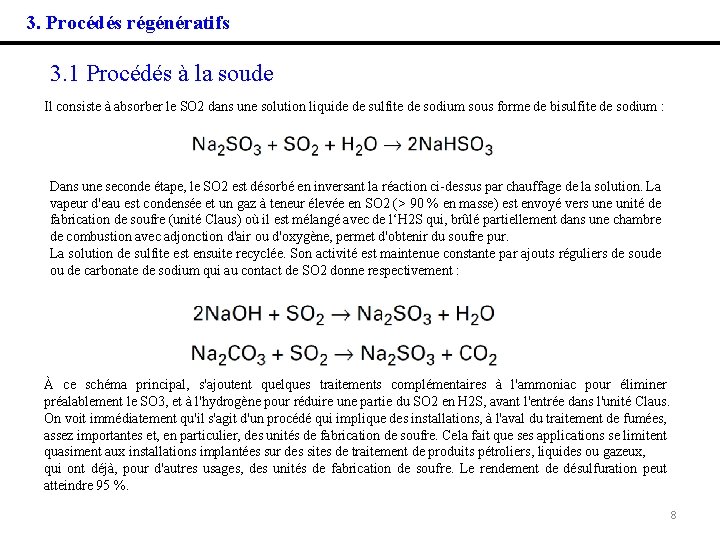
3. Procédés régénératifs 3. 1 Procédés à la soude Il consiste à absorber le SO 2 dans une solution liquide de sulfite de sodium sous forme de bisulfite de sodium : Dans une seconde étape, le SO 2 est désorbé en inversant la réaction ci-dessus par chauffage de la solution. La vapeur d'eau est condensée et un gaz à teneur élevée en SO 2 (> 90 % en masse) est envoyé vers une unité de fabrication de soufre (unité Claus) où il est mélangé avec de l‘H 2 S qui, brûlé partiellement dans une chambre de combustion avec adjonction d'air ou d'oxygène, permet d'obtenir du soufre pur. La solution de sulfite est ensuite recyclée. Son activité est maintenue constante par ajouts réguliers de soude ou de carbonate de sodium qui au contact de SO 2 donne respectivement : À ce schéma principal, s'ajoutent quelques traitements complémentaires à l'ammoniac pour éliminer préalablement le SO 3, et à l'hydrogène pour réduire une partie du SO 2 en H 2 S, avant l'entrée dans l'unité Claus. On voit immédiatement qu'il s'agit d'un procédé qui implique des installations, à l'aval du traitement de fumées, assez importantes et, en particulier, des unités de fabrication de soufre. Cela fait que ses applications se limitent quasiment aux installations implantées sur des sites de traitement de produits pétroliers, liquides ou gazeux, qui ont déjà, pour d'autres usages, des unités de fabrication de soufre. Le rendement de désulfuration peut atteindre 95 %. 8
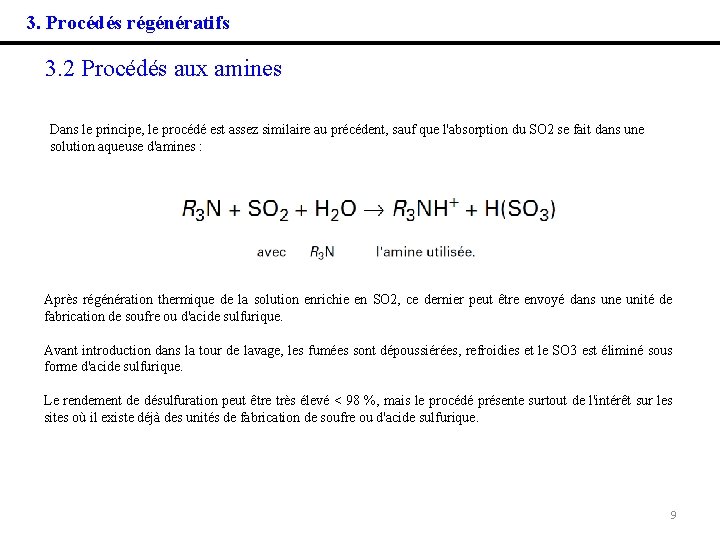
3. Procédés régénératifs 3. 2 Procédés aux amines Dans le principe, le procédé est assez similaire au précédent, sauf que l'absorption du SO 2 se fait dans une solution aqueuse d'amines : Après régénération thermique de la solution enrichie en SO 2, ce dernier peut être envoyé dans une unité de fabrication de soufre ou d'acide sulfurique. Avant introduction dans la tour de lavage, les fumées sont dépoussiérées, refroidies et le SO 3 est éliminé sous forme d'acide sulfurique. Le rendement de désulfuration peut être très élevé < 98 %, mais le procédé présente surtout de l'intérêt sur les sites où il existe déjà des unités de fabrication de soufre ou d'acide sulfurique. 9
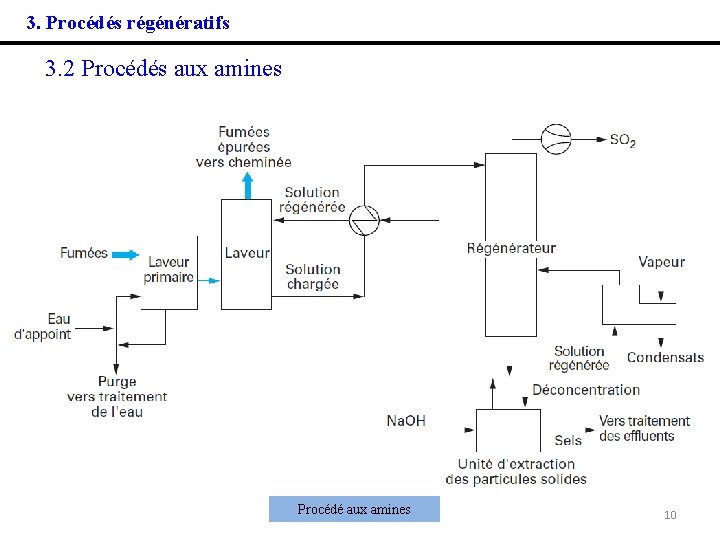
3. Procédés régénératifs 3. 2 Procédés aux amines Procédé aux amines 10
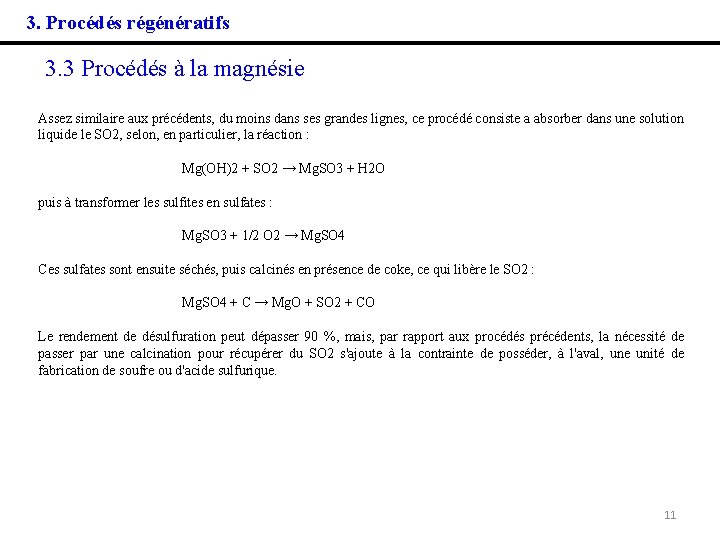
3. Procédés régénératifs 3. 3 Procédés à la magnésie Assez similaire aux précédents, du moins dans ses grandes lignes, ce procédé consiste a absorber dans une solution liquide le SO 2, selon, en particulier, la réaction : Mg(OH)2 + SO 2 → Mg. SO 3 + H 2 O puis à transformer les sulfites en sulfates : Mg. SO 3 + 1/2 O 2 → Mg. SO 4 Ces sulfates sont ensuite séchés, puis calcinés en présence de coke, ce qui libère le SO 2 : Mg. SO 4 + C → Mg. O + SO 2 + CO Le rendement de désulfuration peut dépasser 90 %, mais, par rapport aux procédés précédents, la nécessité de passer par une calcination pour récupérer du SO 2 s'ajoute à la contrainte de posséder, à l'aval, une unité de fabrication de soufre ou d'acide sulfurique. 11
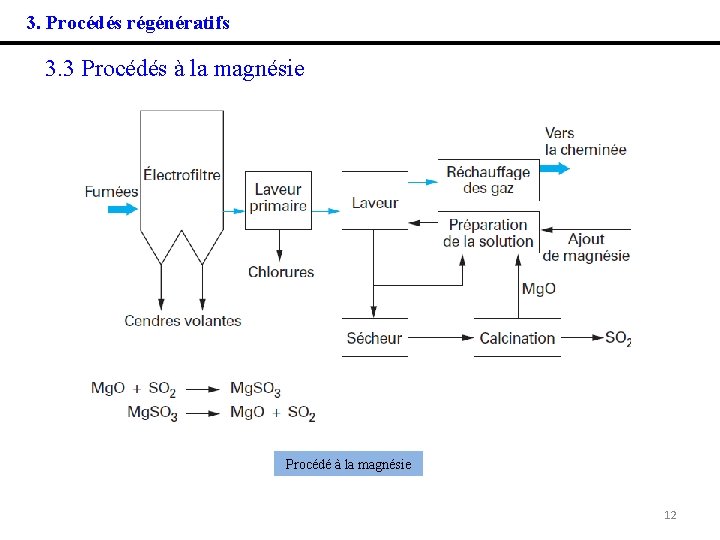
3. Procédés régénératifs 3. 3 Procédés à la magnésie Procédé à la magnésie 12
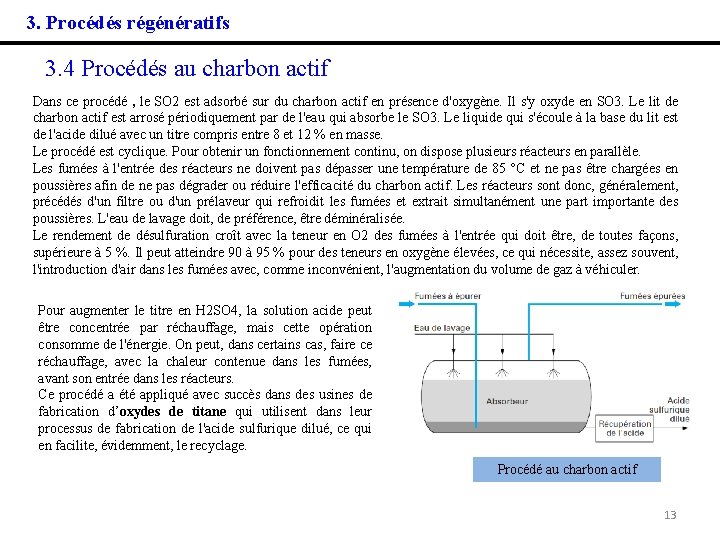
3. Procédés régénératifs 3. 4 Procédés au charbon actif Dans ce procédé , le SO 2 est adsorbé sur du charbon actif en présence d'oxygène. Il s'y oxyde en SO 3. Le lit de charbon actif est arrosé périodiquement par de l'eau qui absorbe le SO 3. Le liquide qui s'écoule à la base du lit est de l'acide dilué avec un titre compris entre 8 et 12 % en masse. Le procédé est cyclique. Pour obtenir un fonctionnement continu, on dispose plusieurs réacteurs en parallèle. Les fumées à l'entrée des réacteurs ne doivent pas dépasser une température de 85 °C et ne pas être chargées en poussières afin de ne pas dégrader ou réduire l'efficacité du charbon actif. Les réacteurs sont donc, généralement, précédés d'un filtre ou d'un prélaveur qui refroidit les fumées et extrait simultanément une part importante des poussières. L'eau de lavage doit, de préférence, être déminéralisée. Le rendement de désulfuration croît avec la teneur en O 2 des fumées à l'entrée qui doit être, de toutes façons, supérieure à 5 %. Il peut atteindre 90 à 95 % pour des teneurs en oxygène élevées, ce qui nécessite, assez souvent, l'introduction d'air dans les fumées avec, comme inconvénient, l'augmentation du volume de gaz à véhiculer. Pour augmenter le titre en H 2 SO 4, la solution acide peut être concentrée par réchauffage, mais cette opération consomme de l'énergie. On peut, dans certains cas, faire ce réchauffage, avec la chaleur contenue dans les fumées, avant son entrée dans les réacteurs. Ce procédé a été appliqué avec succès dans des usines de fabrication d’oxydes de titane qui utilisent dans leur processus de fabrication de l'acide sulfurique dilué, ce qui en facilite, évidemment, le recyclage. Procédé au charbon actif 13
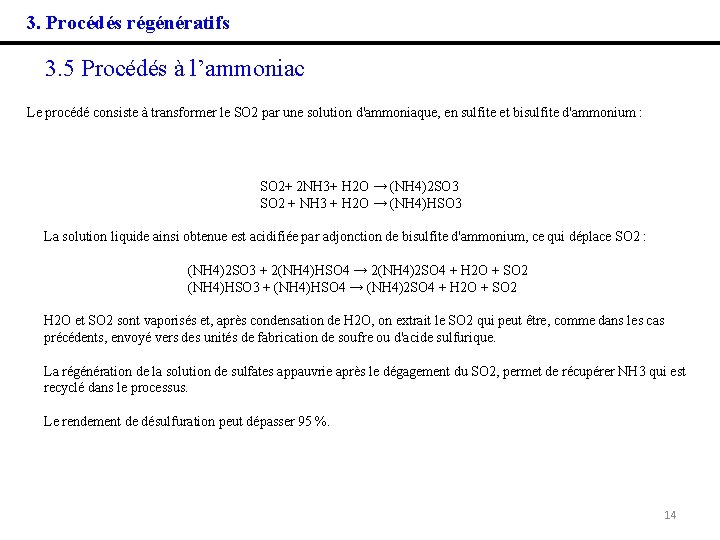
3. Procédés régénératifs 3. 5 Procédés à l’ammoniac Le procédé consiste à transformer le SO 2 par une solution d'ammoniaque, en sulfite et bisulfite d'ammonium : SO 2+ 2 NH 3+ H 2 O → (NH 4)2 SO 3 SO 2 + NH 3 + H 2 O → (NH 4)HSO 3 La solution liquide ainsi obtenue est acidifiée par adjonction de bisulfite d'ammonium, ce qui déplace SO 2 : (NH 4)2 SO 3 + 2(NH 4)HSO 4 → 2(NH 4)2 SO 4 + H 2 O + SO 2 (NH 4)HSO 3 + (NH 4)HSO 4 → (NH 4)2 SO 4 + H 2 O + SO 2 H 2 O et SO 2 sont vaporisés et, après condensation de H 2 O, on extrait le SO 2 qui peut être, comme dans les cas précédents, envoyé vers des unités de fabrication de soufre ou d'acide sulfurique. La régénération de la solution de sulfates appauvrie après le dégagement du SO 2, permet de récupérer NH 3 qui est recyclé dans le processus. Le rendement de désulfuration peut dépasser 95 %. 14
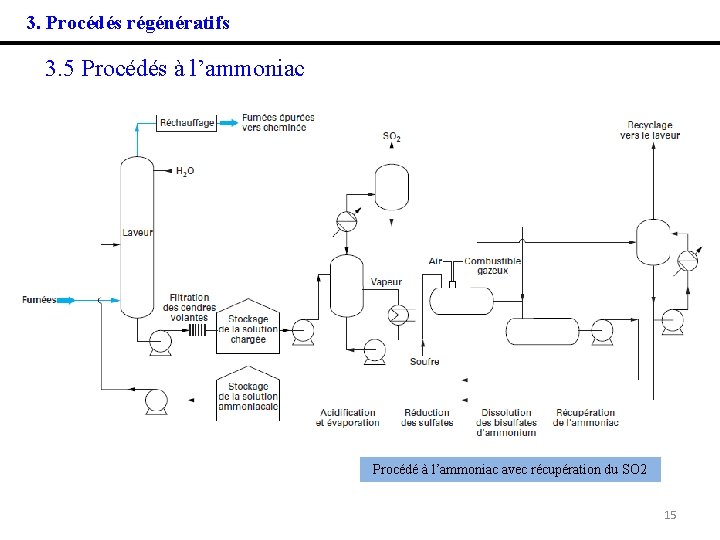
3. Procédés régénératifs 3. 5 Procédés à l’ammoniac Procédé à l’ammoniac avec récupération du SO 2 15
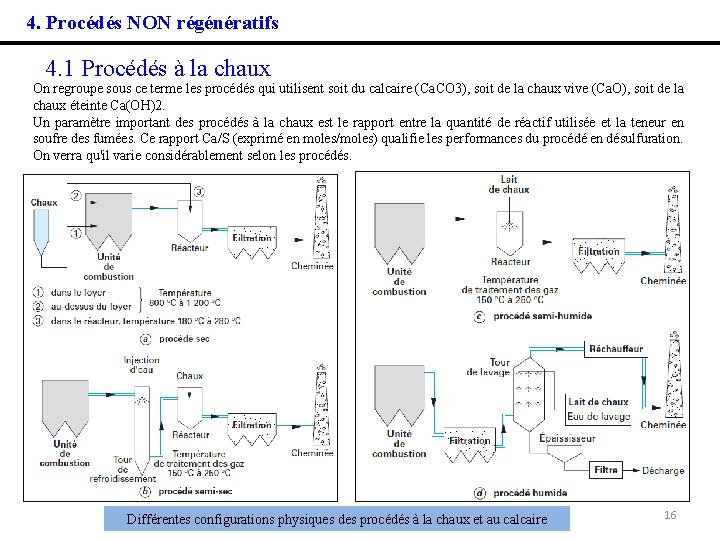
4. Procédés NON régénératifs 4. 1 Procédés à la chaux On regroupe sous ce terme les procédés qui utilisent soit du calcaire (Ca. CO 3), soit de la chaux vive (Ca. O), soit de la chaux éteinte Ca(OH)2. Un paramètre important des procédés à la chaux est le rapport entre la quantité de réactif utilisée et la teneur en soufre des fumées. Ce rapport Ca/S (exprimé en moles/moles) qualifie les performances du procédé en désulfuration. On verra qu'il varie considérablement selon les procédés. Différentes configurations physiques des procédés à la chaux et au calcaire 16
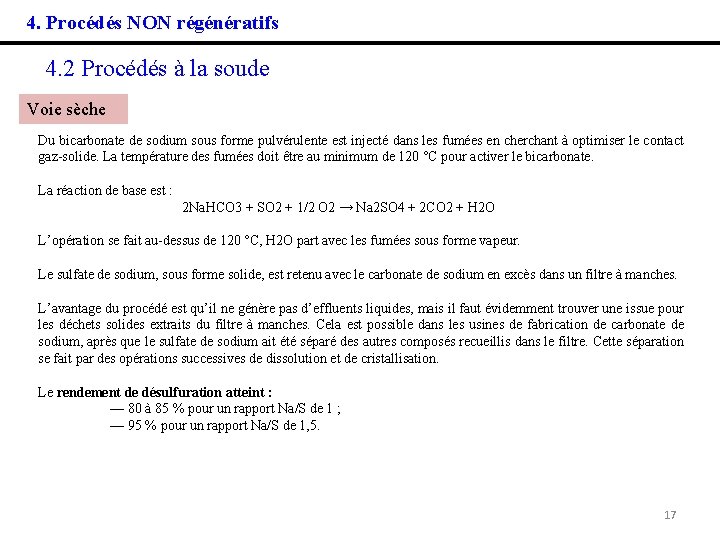
4. Procédés NON régénératifs 4. 2 Procédés à la soude Voie sèche Du bicarbonate de sodium sous forme pulvérulente est injecté dans les fumées en cherchant à optimiser le contact gaz-solide. La température des fumées doit être au minimum de 120 °C pour activer le bicarbonate. La réaction de base est : 2 Na. HCO 3 + SO 2 + 1/2 O 2 → Na 2 SO 4 + 2 CO 2 + H 2 O L’opération se fait au-dessus de 120 °C, H 2 O part avec les fumées sous forme vapeur. Le sulfate de sodium, sous forme solide, est retenu avec le carbonate de sodium en excès dans un filtre à manches. L’avantage du procédé est qu’il ne génère pas d’effluents liquides, mais il faut évidemment trouver une issue pour les déchets solides extraits du filtre à manches. Cela est possible dans les usines de fabrication de carbonate de sodium, après que le sulfate de sodium ait été séparé des autres composés recueillis dans le filtre. Cette séparation se fait par des opérations successives de dissolution et de cristallisation. Le rendement de désulfuration atteint : — 80 à 85 % pour un rapport Na/S de 1 ; — 95 % pour un rapport Na/S de 1, 5. 17
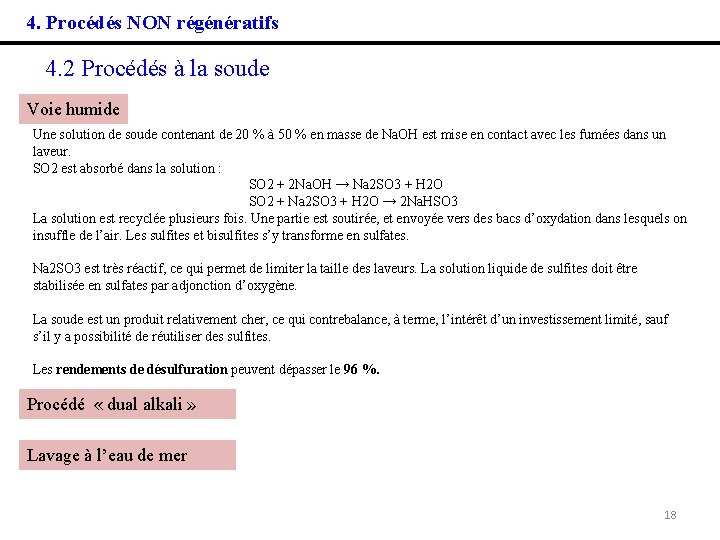
4. Procédés NON régénératifs 4. 2 Procédés à la soude Voie humide Une solution de soude contenant de 20 % à 50 % en masse de Na. OH est mise en contact avec les fumées dans un laveur. SO 2 est absorbé dans la solution : SO 2 + 2 Na. OH → Na 2 SO 3 + H 2 O SO 2 + Na 2 SO 3 + H 2 O → 2 Na. HSO 3 La solution est recyclée plusieurs fois. Une partie est soutirée, et envoyée vers des bacs d’oxydation dans lesquels on insuffle de l’air. Les sulfites et bisulfites s’y transforme en sulfates. Na 2 SO 3 est très réactif, ce qui permet de limiter la taille des laveurs. La solution liquide de sulfites doit être stabilisée en sulfates par adjonction d’oxygène. La soude est un produit relativement cher, ce qui contrebalance, à terme, l’intérêt d’un investissement limité, sauf s’il y a possibilité de réutiliser des sulfites. Les rendements de désulfuration peuvent dépasser le 96 %. Procédé « dual alkali » Lavage à l’eau de mer 18
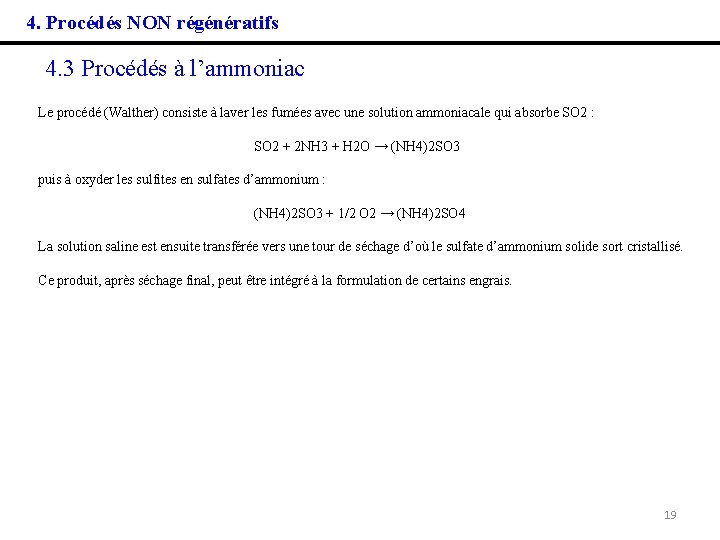
4. Procédés NON régénératifs 4. 3 Procédés à l’ammoniac Le procédé (Walther) consiste à laver les fumées avec une solution ammoniacale qui absorbe SO 2 : SO 2 + 2 NH 3 + H 2 O → (NH 4)2 SO 3 puis à oxyder les sulfites en sulfates d’ammonium : (NH 4)2 SO 3 + 1/2 O 2 → (NH 4)2 SO 4 La solution saline est ensuite transférée vers une tour de séchage d’où le sulfate d’ammonium solide sort cristallisé. Ce produit, après séchage final, peut être intégré à la formulation de certains engrais. 19
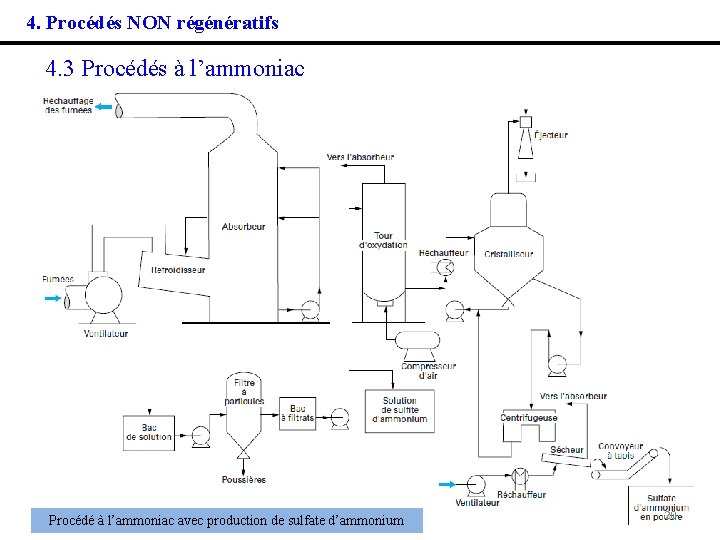
4. Procédés NON régénératifs 4. 3 Procédés à l’ammoniac Procédé à l’ammoniac avec production de sulfate d’ammonium 20
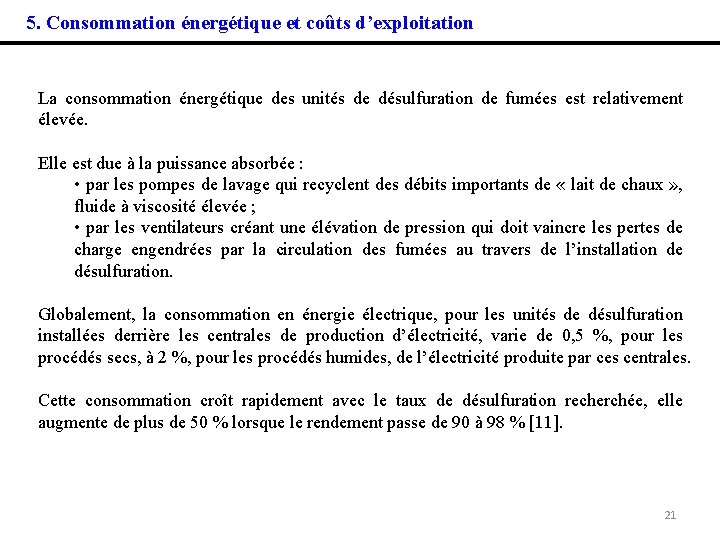
5. Consommation énergétique et coûts d’exploitation La consommation énergétique des unités de désulfuration de fumées est relativement élevée. Elle est due à la puissance absorbée : • par les pompes de lavage qui recyclent des débits importants de « lait de chaux » , fluide à viscosité élevée ; • par les ventilateurs créant une élévation de pression qui doit vaincre les pertes de charge engendrées par la circulation des fumées au travers de l’installation de désulfuration. Globalement, la consommation en énergie électrique, pour les unités de désulfuration installées derrière les centrales de production d’électricité, varie de 0, 5 %, pour les procédés secs, à 2 %, pour les procédés humides, de l’électricité produite par ces centrales. Cette consommation croît rapidement avec le taux de désulfuration recherchée, elle augmente de plus de 50 % lorsque le rendement passe de 90 à 98 % [11]. 21
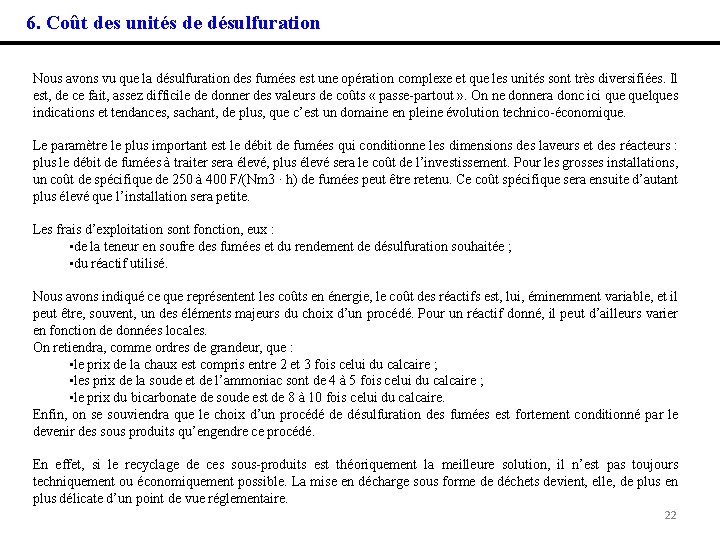
6. Coût des unités de désulfuration Nous avons vu que la désulfuration des fumées est une opération complexe et que les unités sont très diversifiées. Il est, de ce fait, assez difficile de donner des valeurs de coûts « passe-partout » . On ne donnera donc ici quelques indications et tendances, sachant, de plus, que c’est un domaine en pleine évolution technico-économique. Le paramètre le plus important est le débit de fumées qui conditionne les dimensions des laveurs et des réacteurs : plus le débit de fumées à traiter sera élevé, plus élevé sera le coût de l’investissement. Pour les grosses installations, un coût de spécifique de 250 à 400 F/(Nm 3 · h) de fumées peut être retenu. Ce coût spécifique sera ensuite d’autant plus élevé que l’installation sera petite. Les frais d’exploitation sont fonction, eux : • de la teneur en soufre des fumées et du rendement de désulfuration souhaitée ; • du réactif utilisé. Nous avons indiqué ce que représentent les coûts en énergie, le coût des réactifs est, lui, éminemment variable, et il peut être, souvent, un des éléments majeurs du choix d’un procédé. Pour un réactif donné, il peut d’ailleurs varier en fonction de données locales. On retiendra, comme ordres de grandeur, que : • le prix de la chaux est compris entre 2 et 3 fois celui du calcaire ; • les prix de la soude et de l’ammoniac sont de 4 à 5 fois celui du calcaire ; • le prix du bicarbonate de soude est de 8 à 10 fois celui du calcaire. Enfin, on se souviendra que le choix d’un procédé de désulfuration des fumées est fortement conditionné par le devenir des sous produits qu’engendre ce procédé. En effet, si le recyclage de ces sous-produits est théoriquement la meilleure solution, il n’est pas toujours techniquement ou économiquement possible. La mise en décharge sous forme de déchets devient, elle, de plus en plus délicate d’un point de vue réglementaire. 22
Ensb constantine
Ensb constantine
Ensb constantine
Ecole biotechnologie
Faculté de medecine dentaire de monastir
Faculté de pharmacie monastir
Biotechnologie monastir
Economielokaal
Royaume du maroc ministère de l'éducation nationale
Ministère de l'éducation nationale
Allemagne devise nationale
Chambre nationale des commissaires aux comptes
La devise de l'allemagne
Det nationale kvalitetsprogram
Royaume du maroc ministère de l'éducation nationale
Charte nationale
Ramsese education nationale
Punctaj evaluare nationala clasa 2
Royaume du maroc ministère de l'éducation nationale
Testogprever
Smepta
Aanbesteden voor contractmanagers
Hiérarchie éducation nationale