Computational Analysis of Metal Foams for EMI Shielding
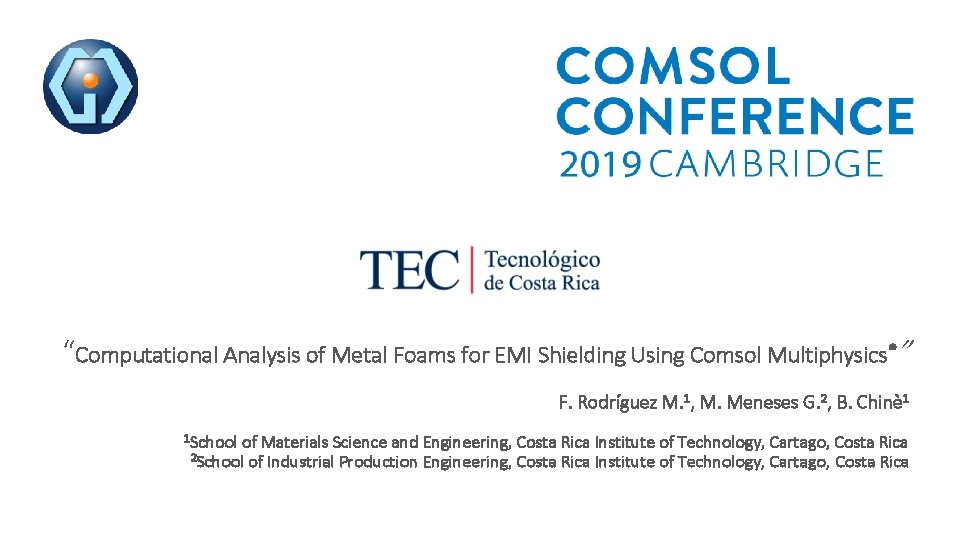
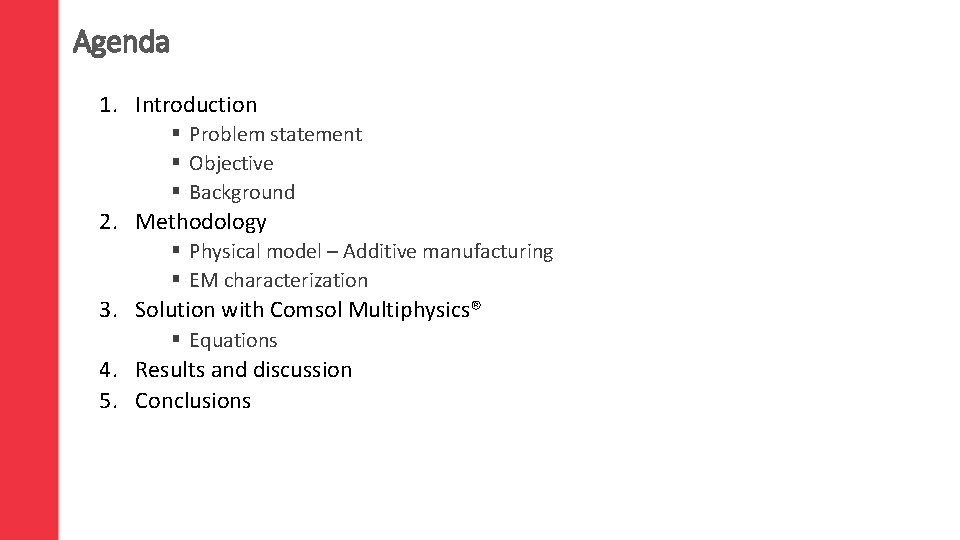
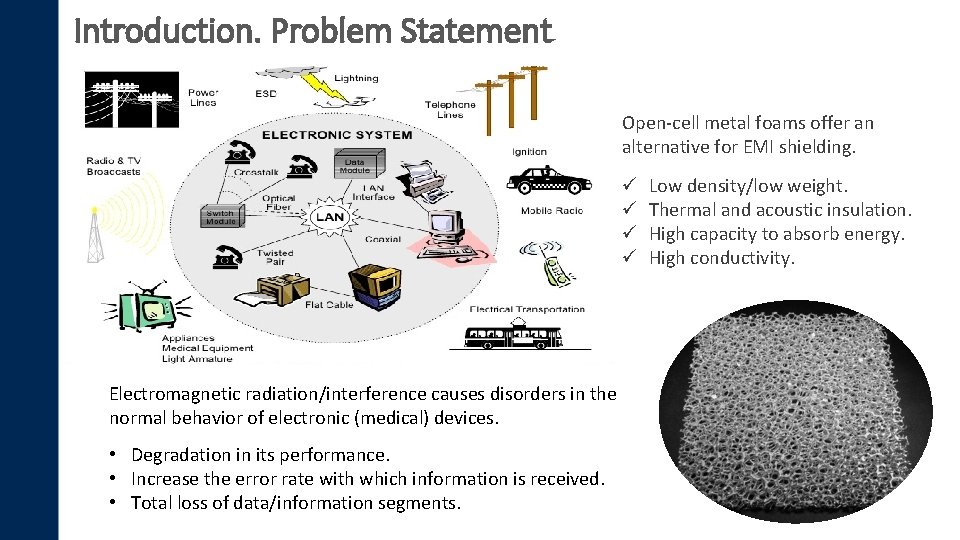
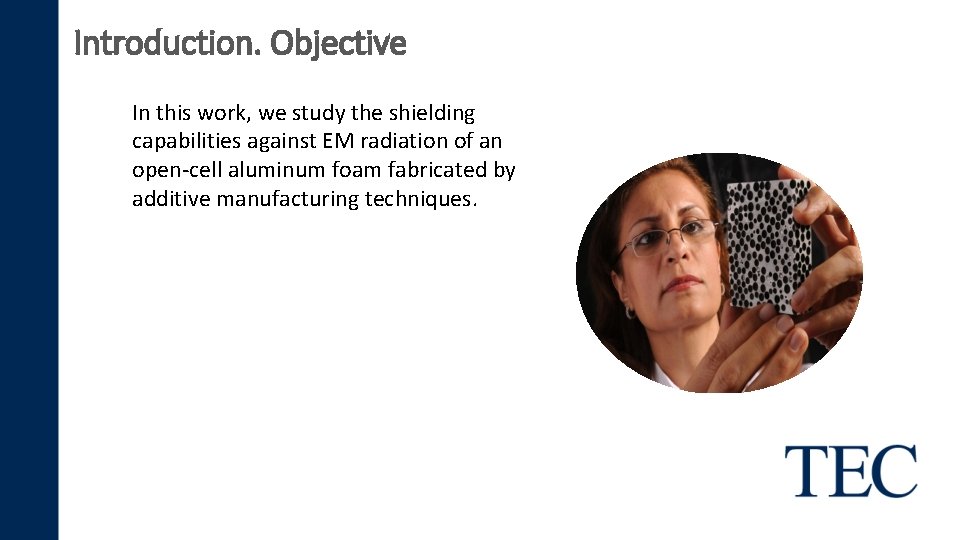
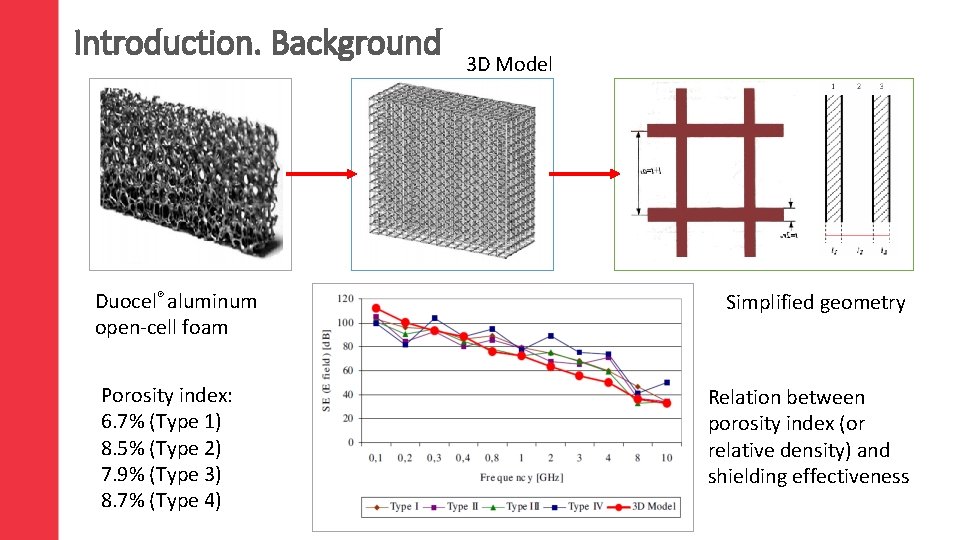
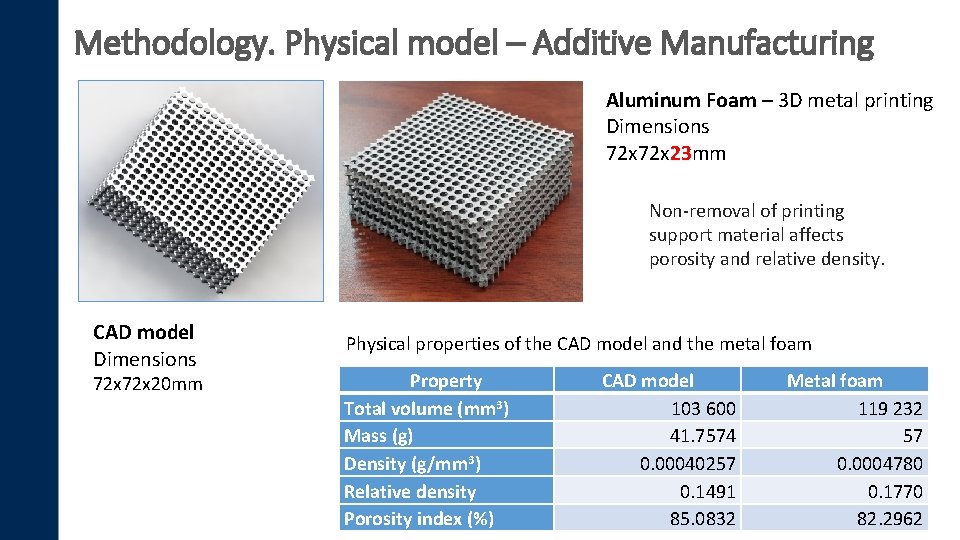
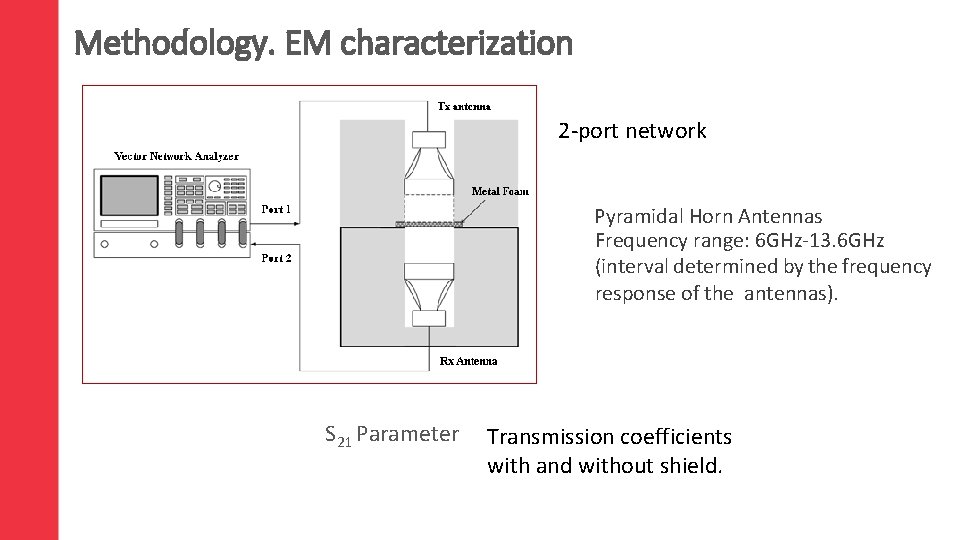
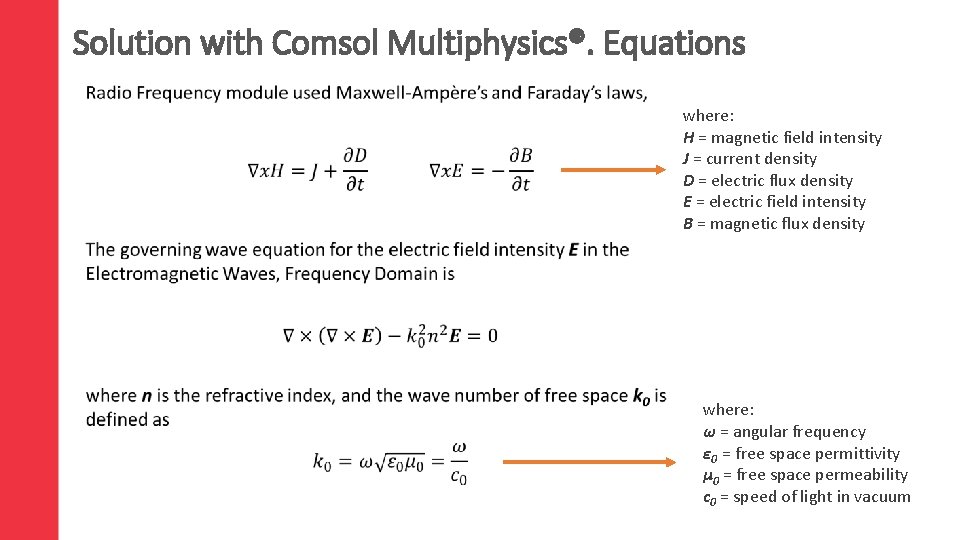
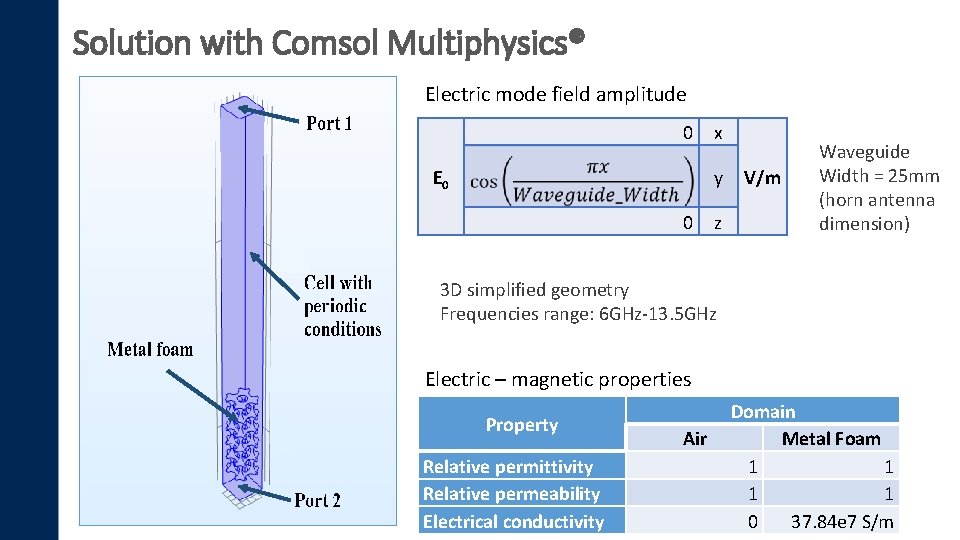
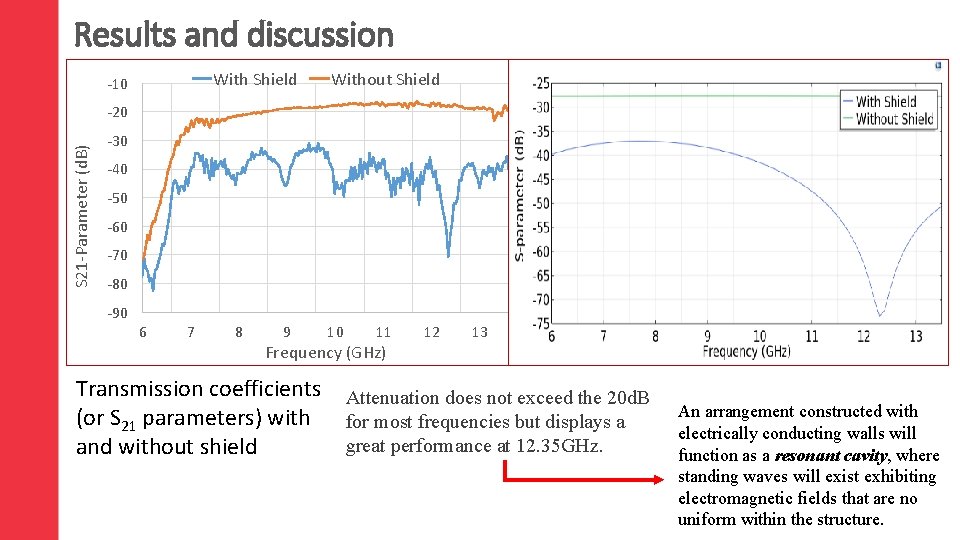
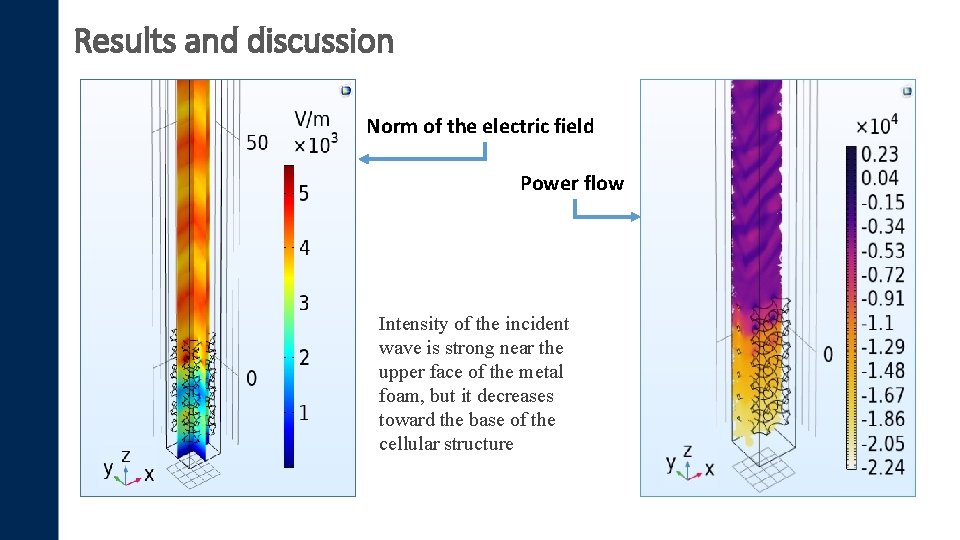
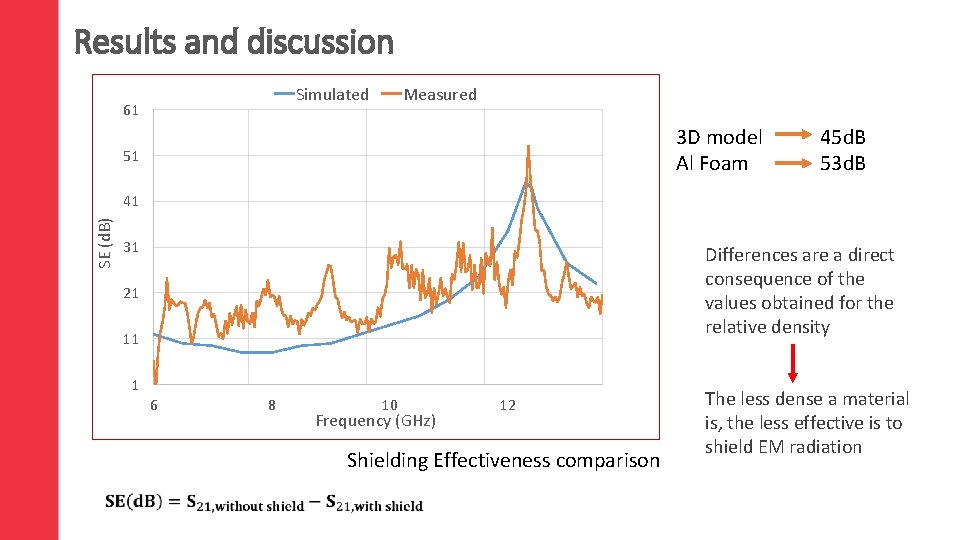
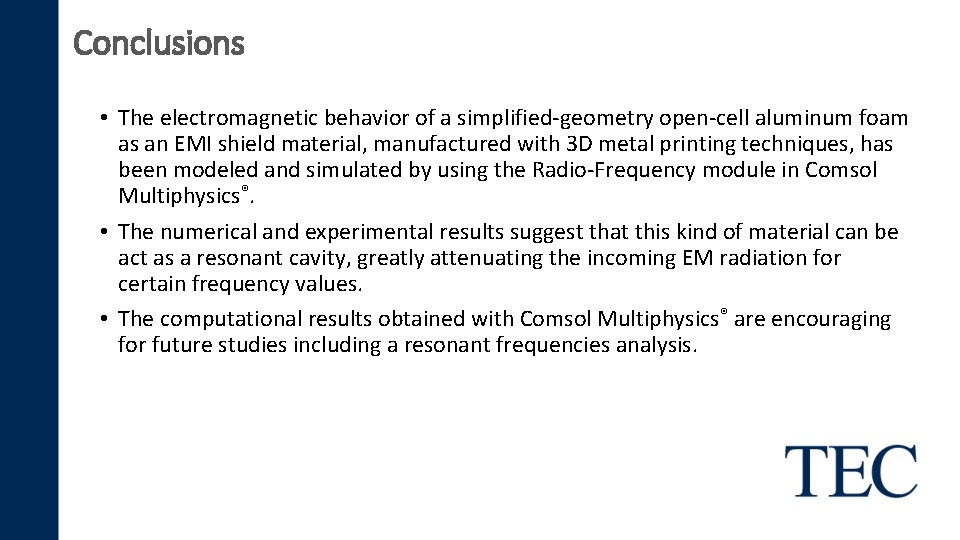
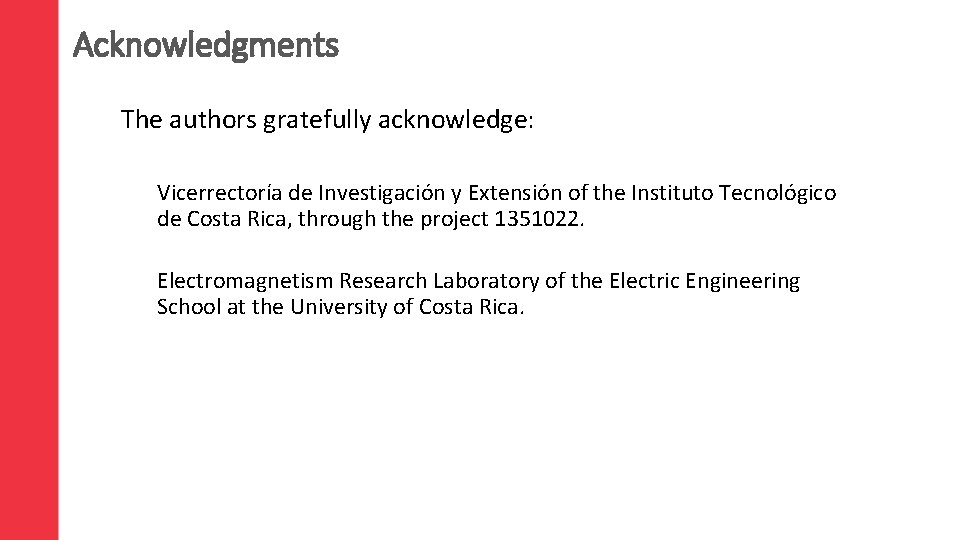
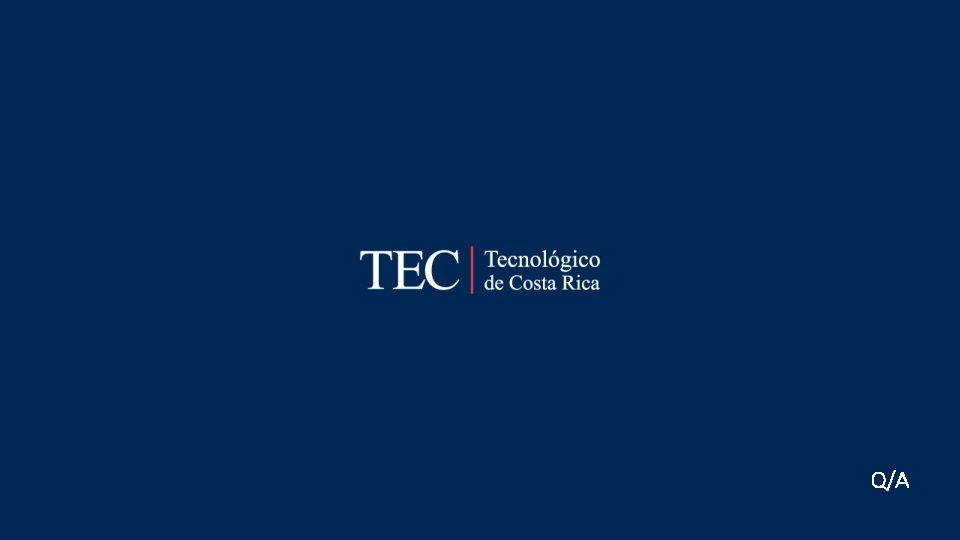
- Slides: 15
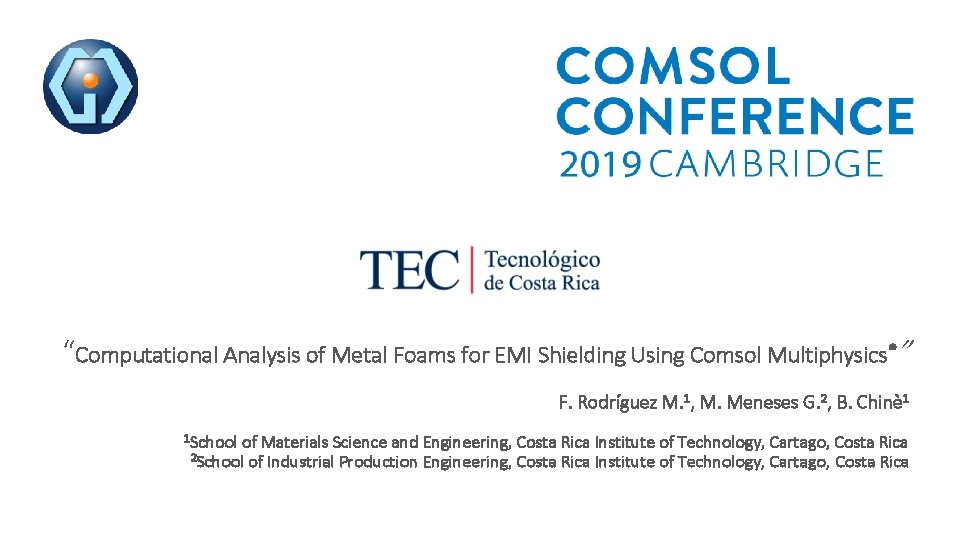
“Computational Analysis of Metal Foams for EMI Shielding Using Comsol Multiphysics®” F. Rodríguez M. 1, M. Meneses G. 2, B. Chinè 1 1 School of Materials Science and Engineering, Costa Rica Institute of Technology, Cartago, Costa Rica 2 School of Industrial Production Engineering, Costa Rica Institute of Technology, Cartago, Costa Rica
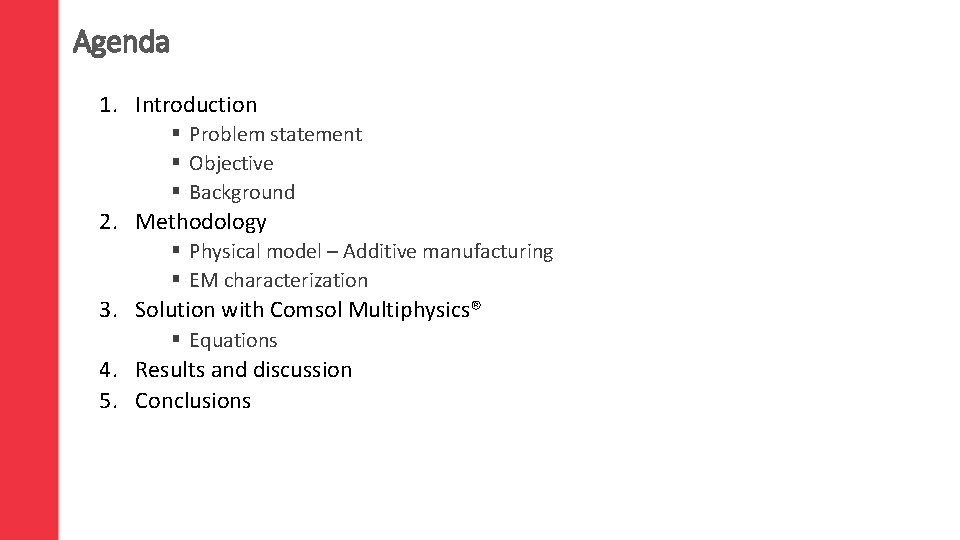
Agenda 1. Introduction § Problem statement § Objective § Background 2. Methodology § Physical model – Additive manufacturing § EM characterization 3. Solution with Comsol Multiphysics® § Equations 4. Results and discussion 5. Conclusions
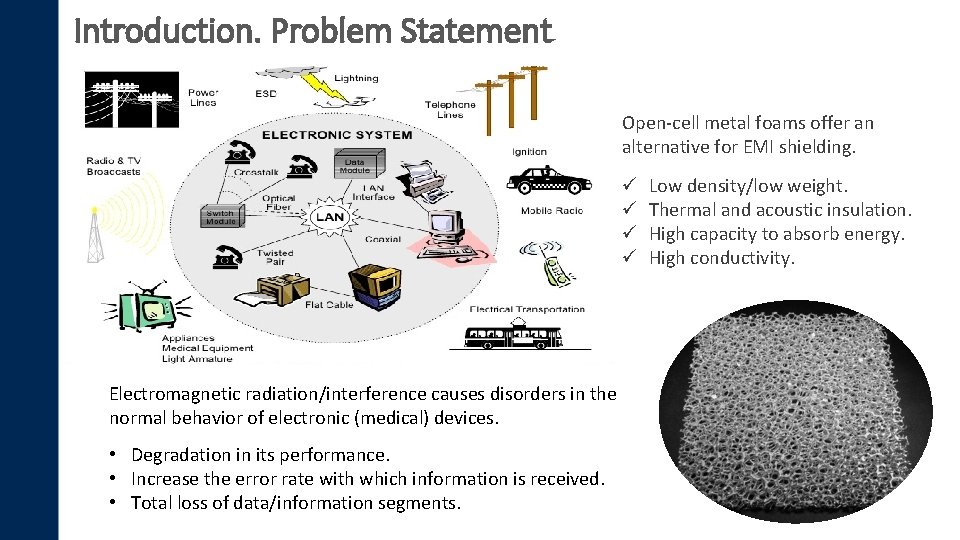
Introduction. Problem Statement Open-cell metal foams offer an alternative for EMI shielding. ü ü Electromagnetic radiation/interference causes disorders in the normal behavior of electronic (medical) devices. • Degradation in its performance. • Increase the error rate with which information is received. • Total loss of data/information segments. Low density/low weight. Thermal and acoustic insulation. High capacity to absorb energy. High conductivity.
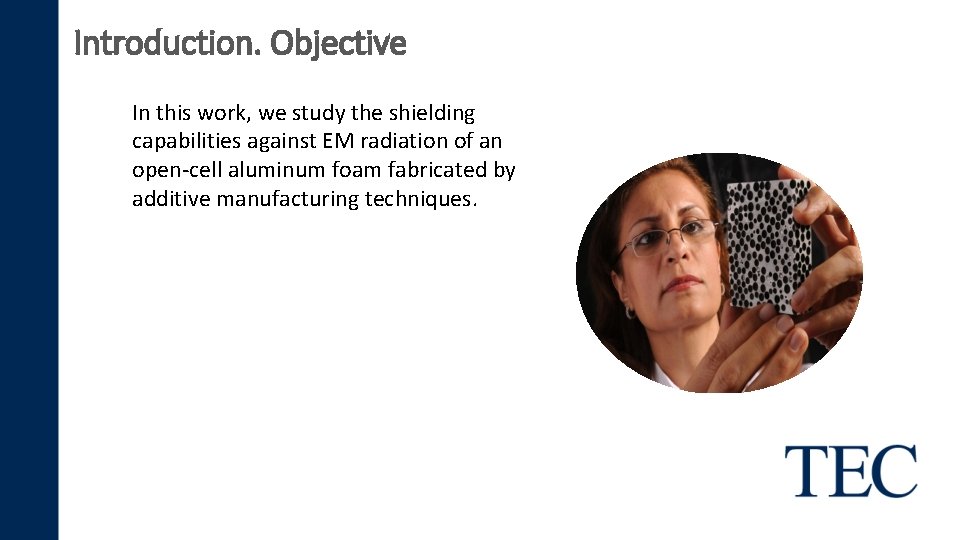
Introduction. Objective In this work, we study the shielding capabilities against EM radiation of an open-cell aluminum foam fabricated by additive manufacturing techniques.
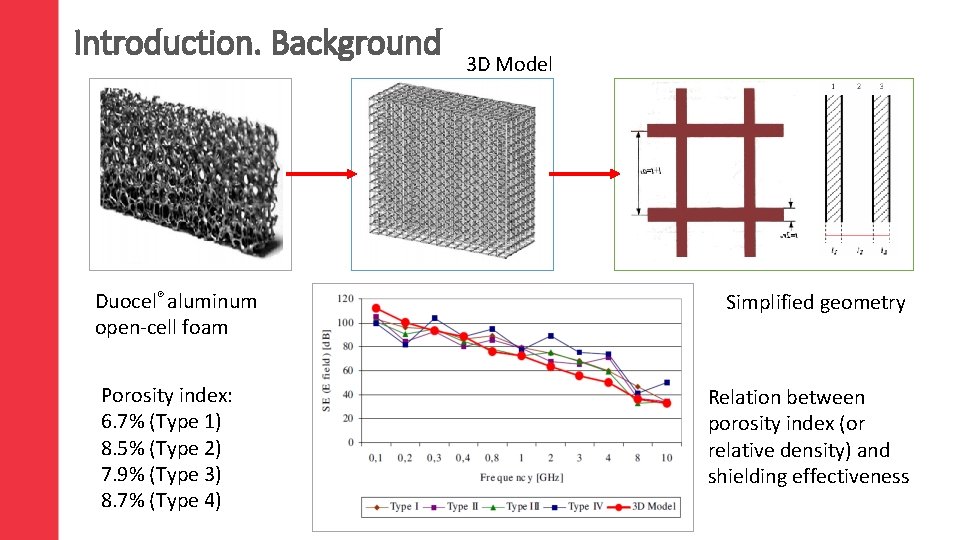
Introduction. Background Duocel® aluminum open-cell foam Porosity index: 6. 7% (Type 1) 8. 5% (Type 2) 7. 9% (Type 3) 8. 7% (Type 4) 3 D Model Simplified geometry Relation between porosity index (or relative density) and shielding effectiveness
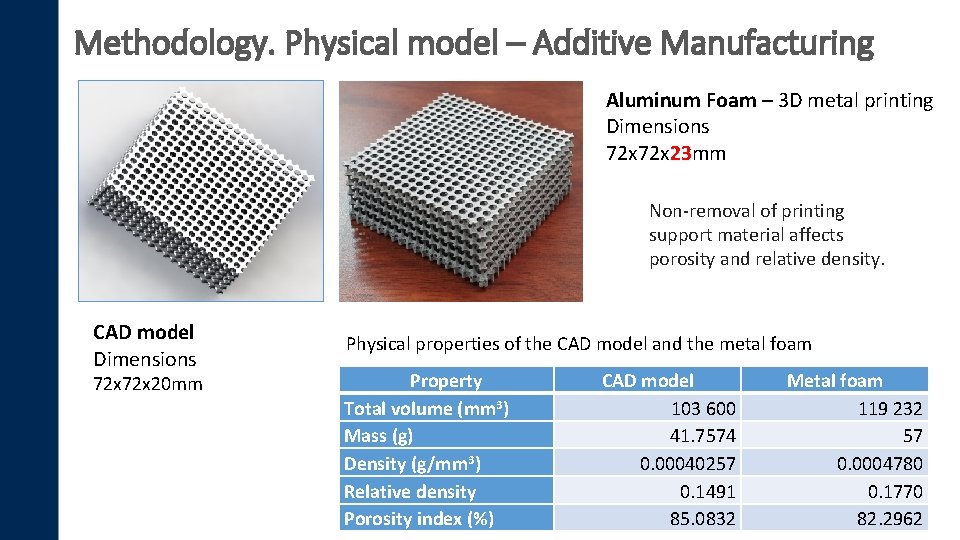
Methodology. Physical model – Additive Manufacturing Aluminum Foam – 3 D metal printing Dimensions 72 x 23 mm Non-removal of printing support material affects porosity and relative density. CAD model Dimensions 72 x 20 mm Physical properties of the CAD model and the metal foam Property Total volume (mm 3) Mass (g) Density (g/mm 3) Relative density Porosity index (%) CAD model 103 600 41. 7574 0. 00040257 0. 1491 85. 0832 Metal foam 119 232 57 0. 0004780 0. 1770 82. 2962
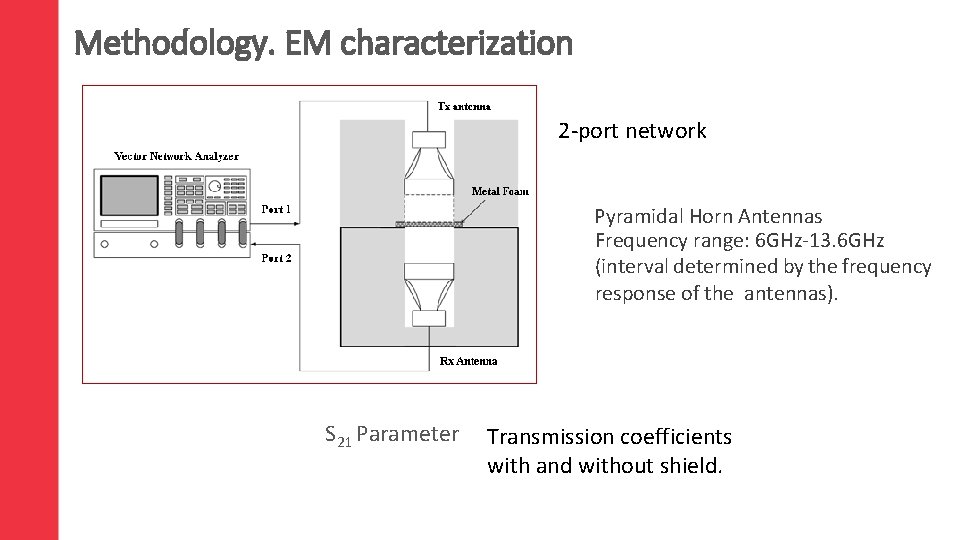
Methodology. EM characterization 2 -port network Pyramidal Horn Antennas Frequency range: 6 GHz-13. 6 GHz (interval determined by the frequency response of the antennas). S 21 Parameter Transmission coefficients with and without shield.
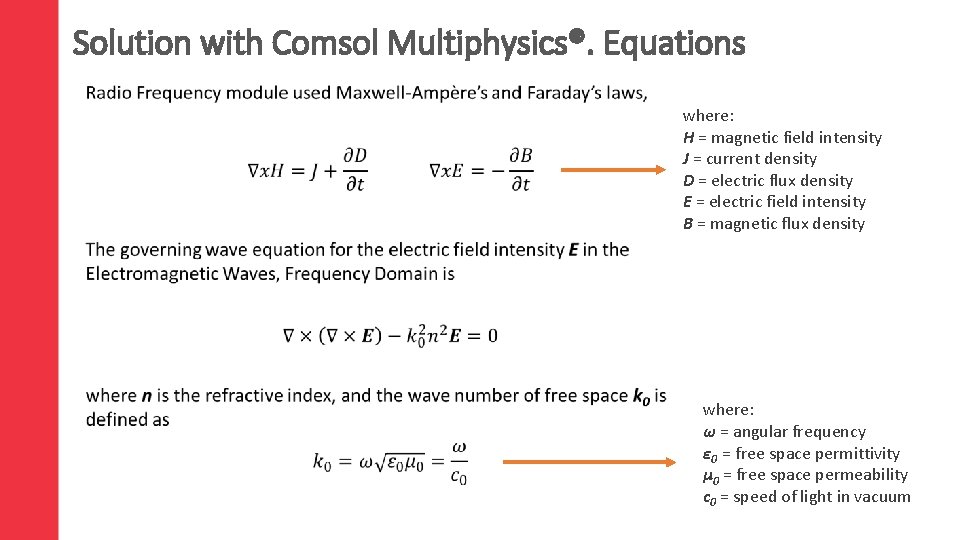
Solution with Comsol Multiphysics®. Equations • where: H = magnetic field intensity J = current density D = electric flux density E = electric field intensity B = magnetic flux density where: ω = angular frequency ε 0 = free space permittivity µ 0 = free space permeability c 0 = speed of light in vacuum
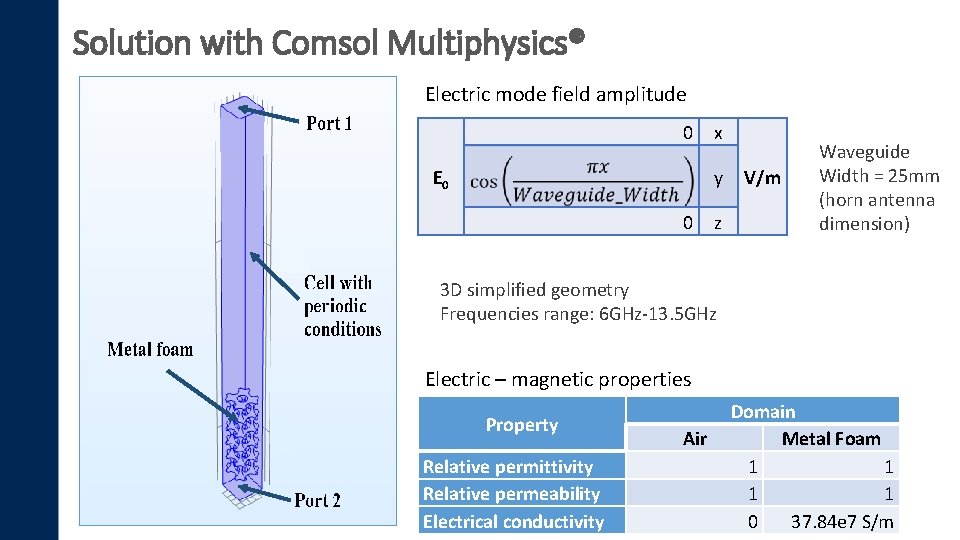
Solution with Comsol Multiphysics® Electric mode field amplitude 0 x y E 0 0 z V/m Waveguide Width = 25 mm (horn antenna dimension) 3 D simplified geometry Frequencies range: 6 GHz-13. 5 GHz Electric – magnetic properties Property Relative permittivity Relative permeability Electrical conductivity Air Domain Metal Foam 1 1 0 37. 84 e 7 S/m
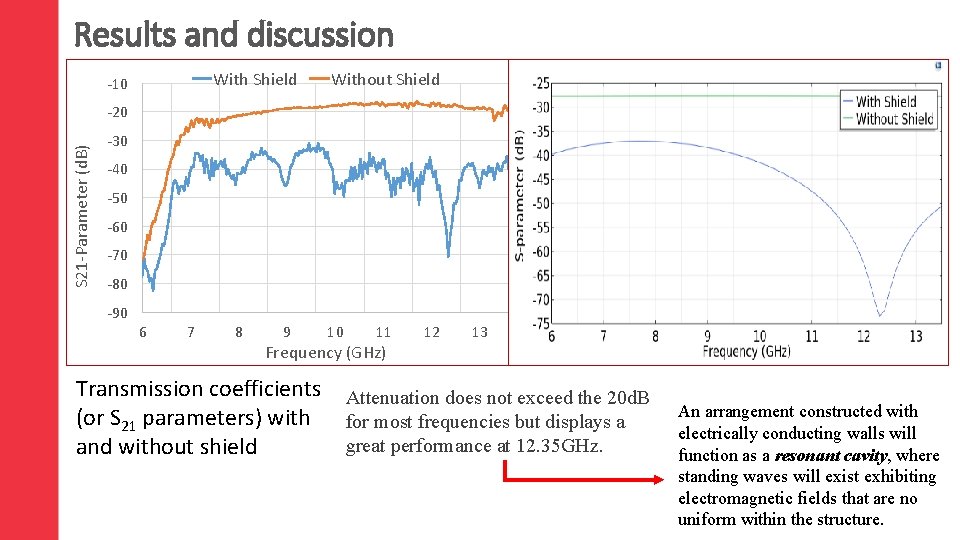
Results and discussion With Shield -10 5 GHz Without Shield S 21 -Parameter (d. B) -20 -30 -40 -50 -60 10 GHz -70 -80 -90 6 7 8 9 10 11 Frequency (GHz) Transmission coefficients (or S 21 parameters) with and without shield 12 13 Attenuation does not exceed the 20 d. B for most frequencies but displays a great performance at 12. 35 GHz. An arrangement constructed with electrically conducting walls will function as a resonant cavity, where standing waves will exist exhibiting electromagnetic fields that are no uniform within the structure.
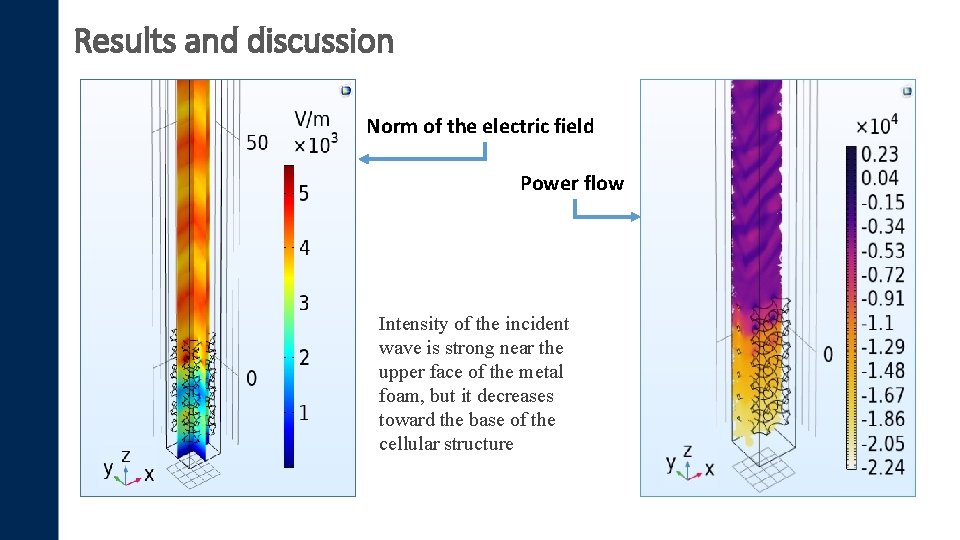
5 GHz Results and discussion Norm of the electric field Power flow Intensity of the incident wave is strong near the upper face of the metal foam, but it decreases toward the base of the cellular structure 12. 3 GHz 13. 5 GHz
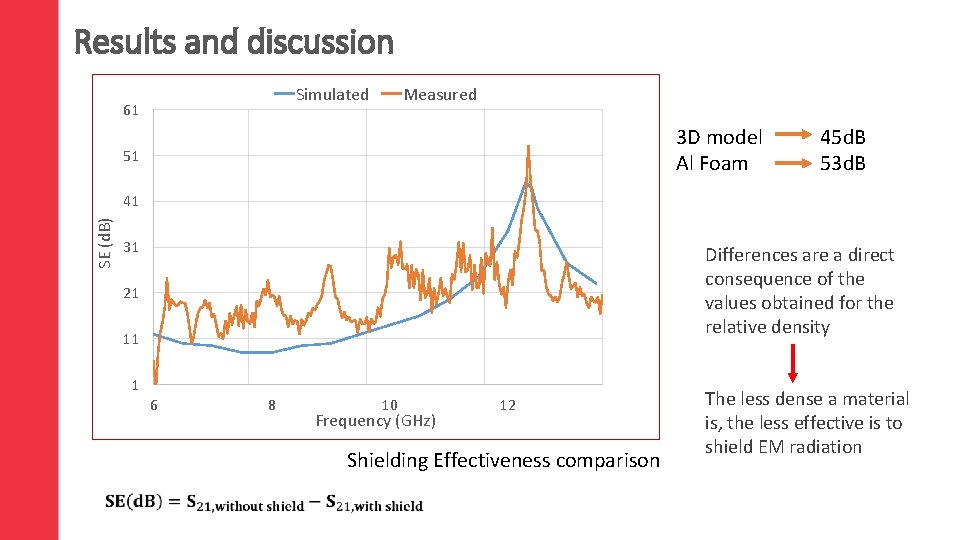
5 GHz Results and discussion Simulated 61 Measured 3 D model Al Foam 51 SE (d. B) 41 45 d. B 53 d. B 11. 7 GHz 31 Differences are a direct consequence of the values obtained for the relative density 21 11 1 6 8 10 Frequency (GHz) 12 13. 5 GHz The less dense a material is, the less effective is to shield EM radiation Shielding Effectiveness comparison
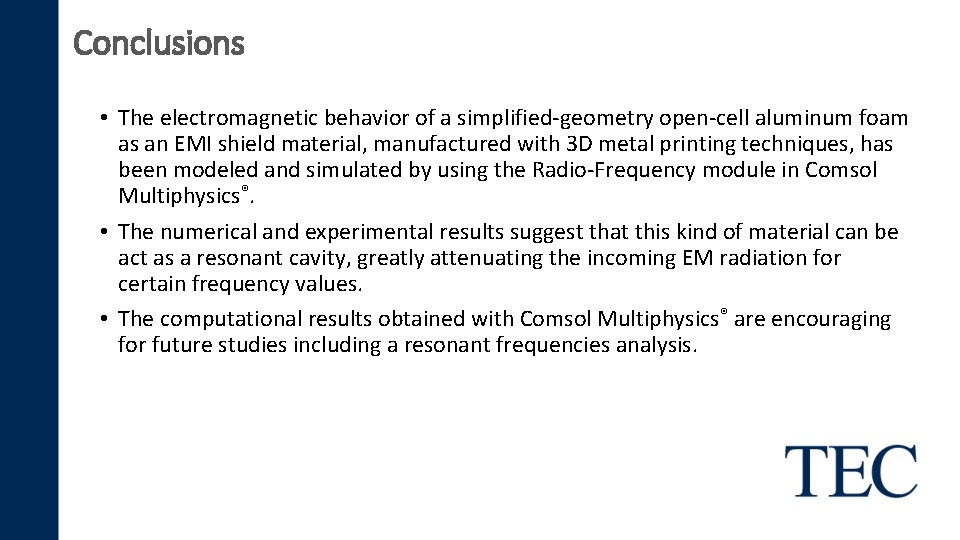
Conclusions • The electromagnetic behavior of a simplified-geometry open-cell aluminum foam as an EMI shield material, manufactured with 3 D metal printing techniques, has been modeled and simulated by using the Radio-Frequency module in Comsol Multiphysics®. • The numerical and experimental results suggest that this kind of material can be act as a resonant cavity, greatly attenuating the incoming EM radiation for certain frequency values. • The computational results obtained with Comsol Multiphysics® are encouraging for future studies including a resonant frequencies analysis.
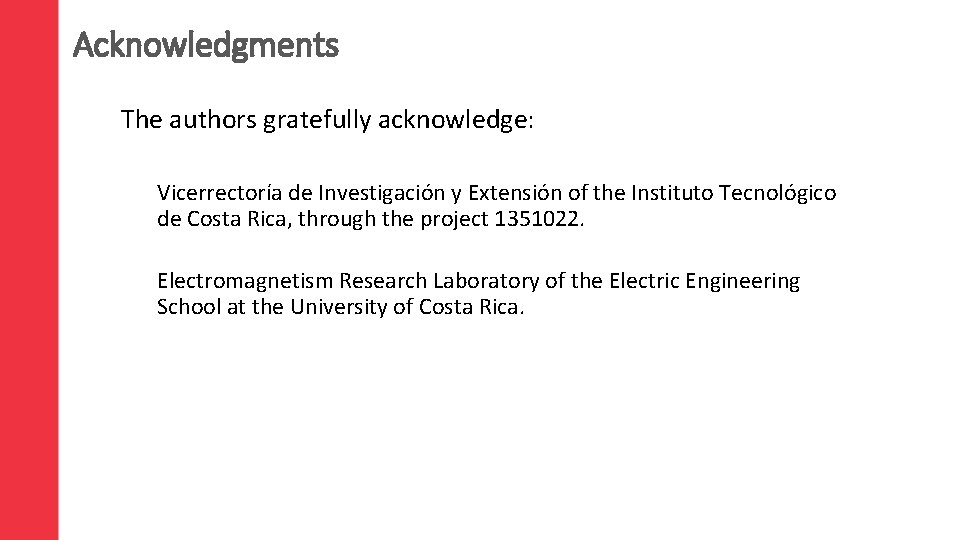
Acknowledgments The authors gratefully acknowledge: Vicerrectoría de Investigación y Extensión of the Instituto Tecnológico de Costa Rica, through the project 1351022. Electromagnetism Research Laboratory of the Electric Engineering School at the University of Costa Rica.
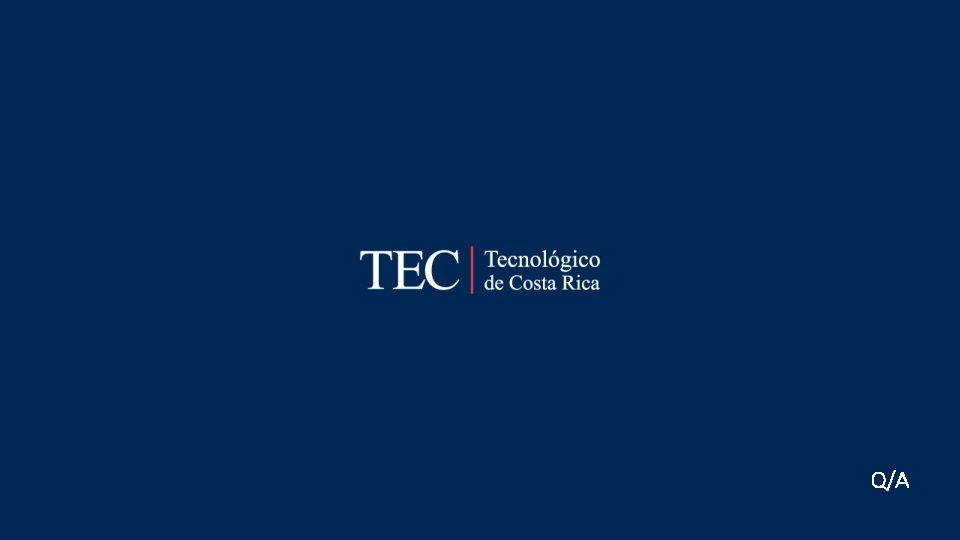
Q/A
What are the downsides of metal foam
This method is based on egg white foams and contain no fat
Thermally conductive foam
Venn diagram gas liquid solid
Metals vs nonmetals vs metalloids
Difference between metal oxides and non metal oxides
Melting point of nonmetals
Nwell
Used of metals
Metal and non metal elements in periodic table
Metals react with nonmetals to form ionic compounds by
Periodo y grupo
Spraggins fitness
Caracteristicas del carbono
Metal and non metal example
Electrones de valencia de francio