chapter Drive Shafts and Joints 65 chapter 65
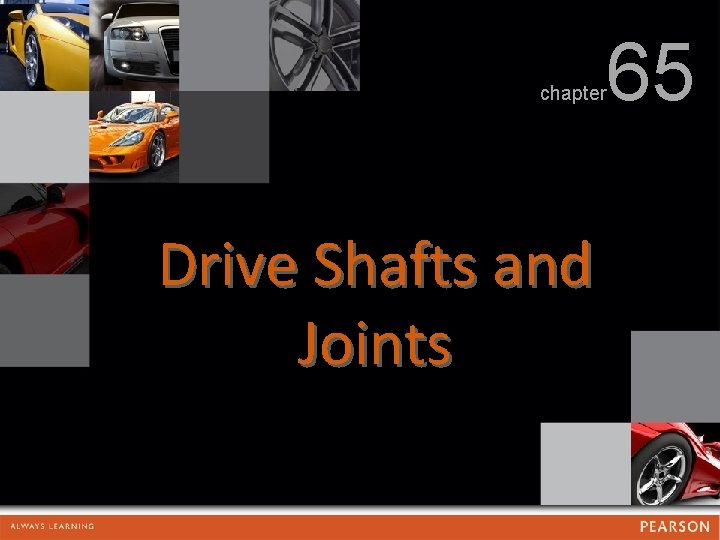
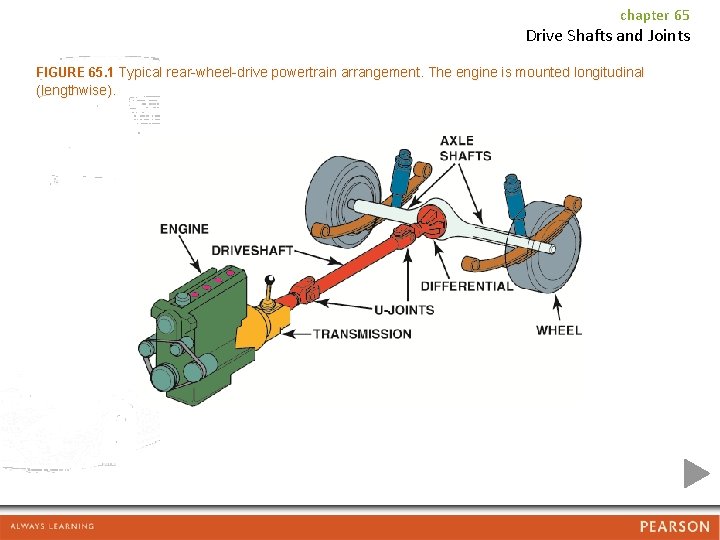
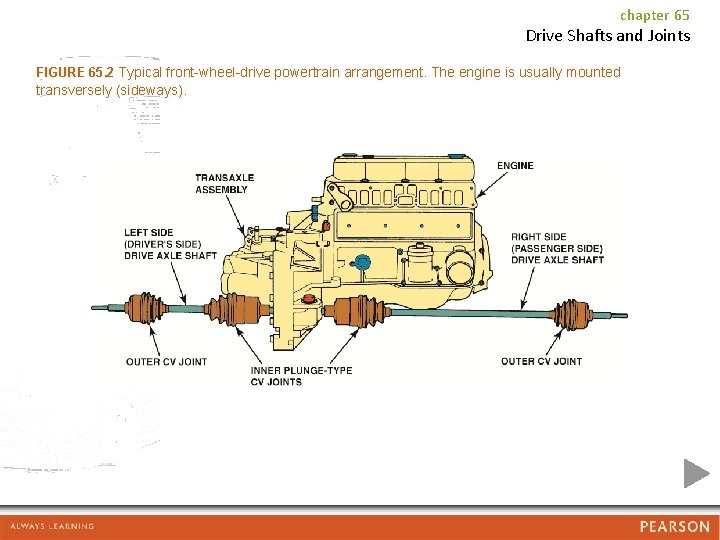
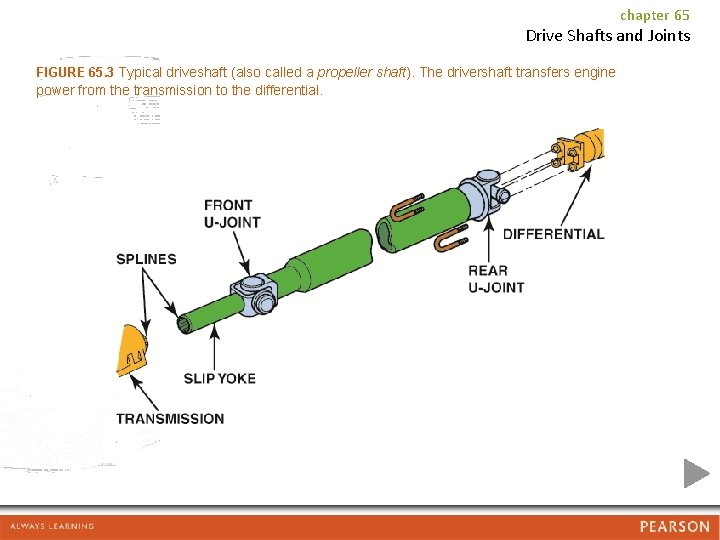
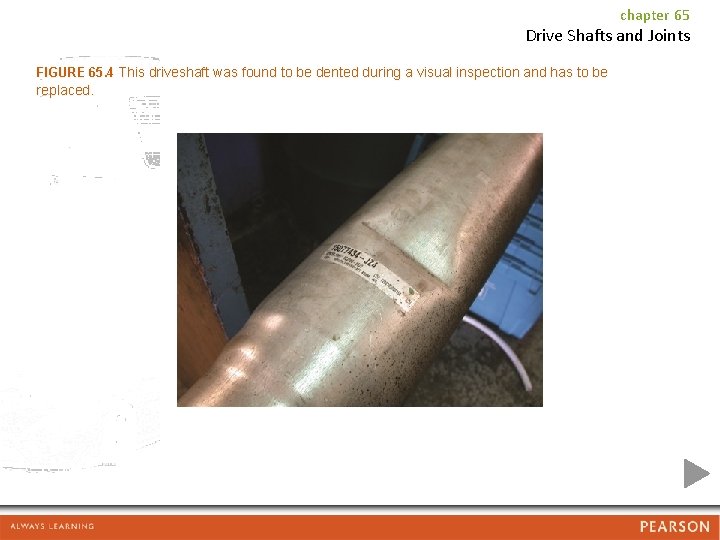
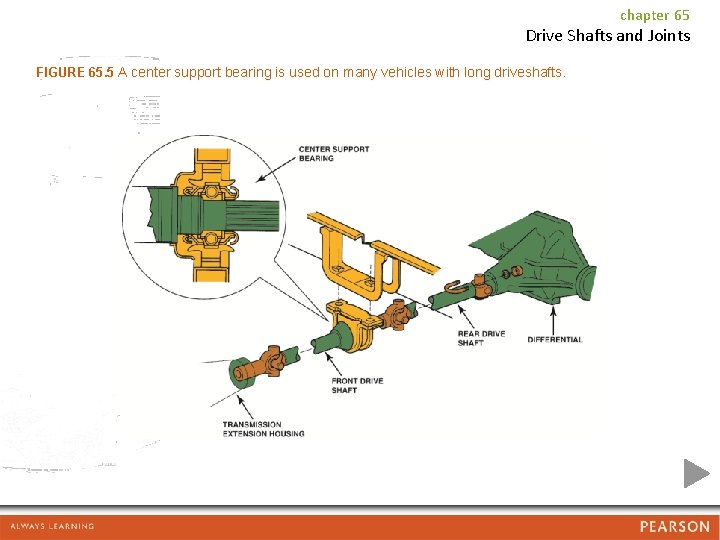
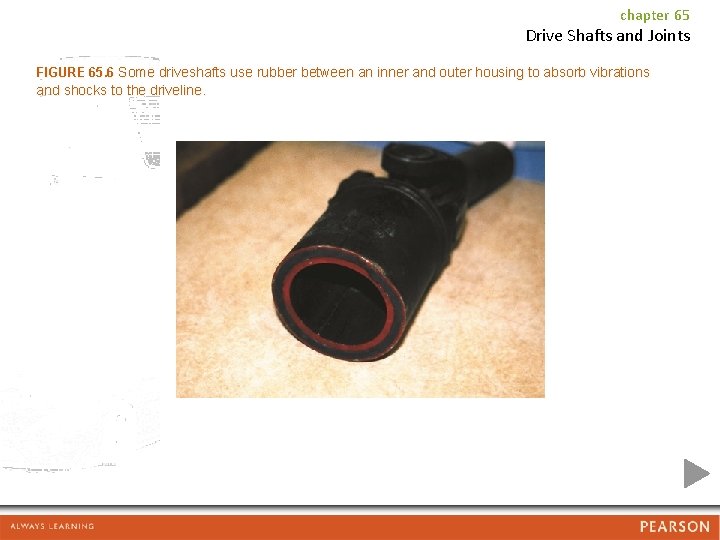
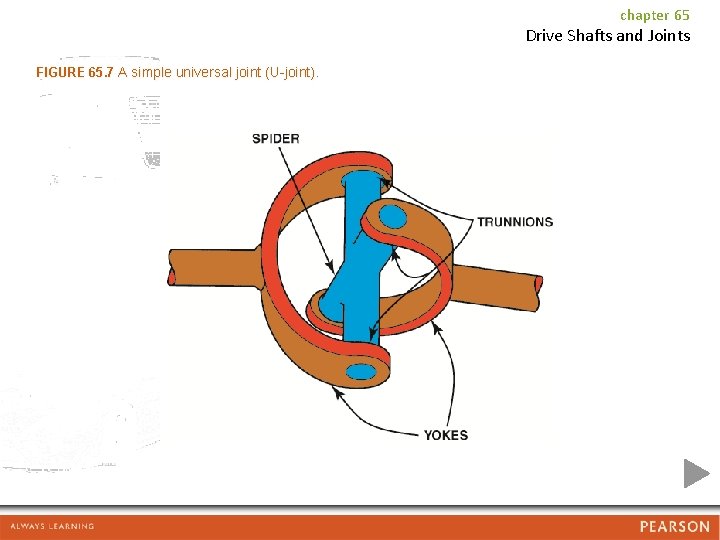
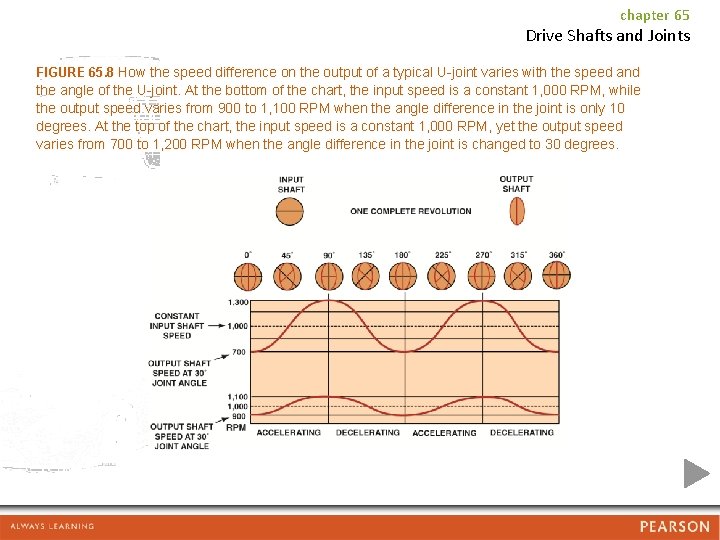
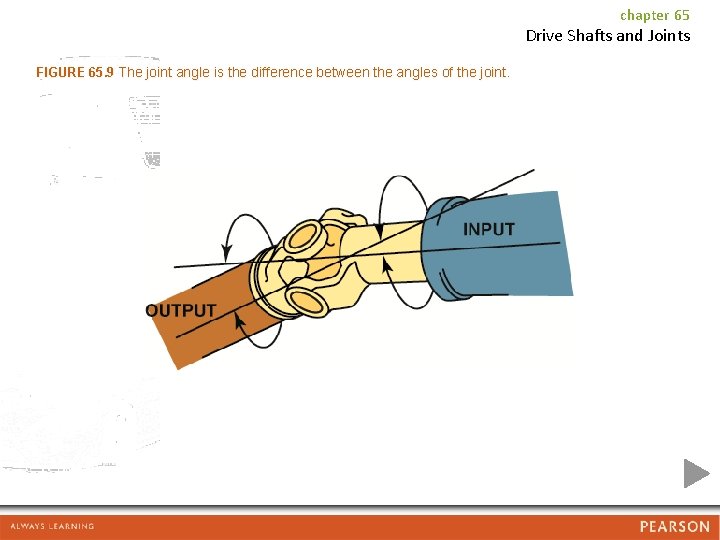
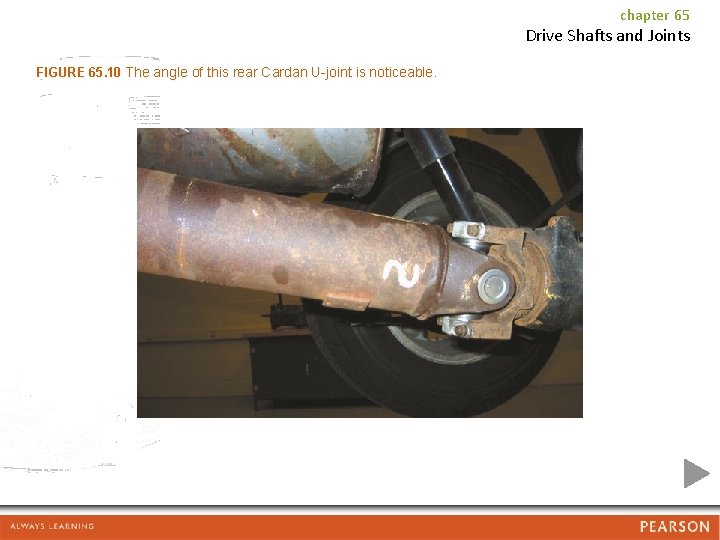
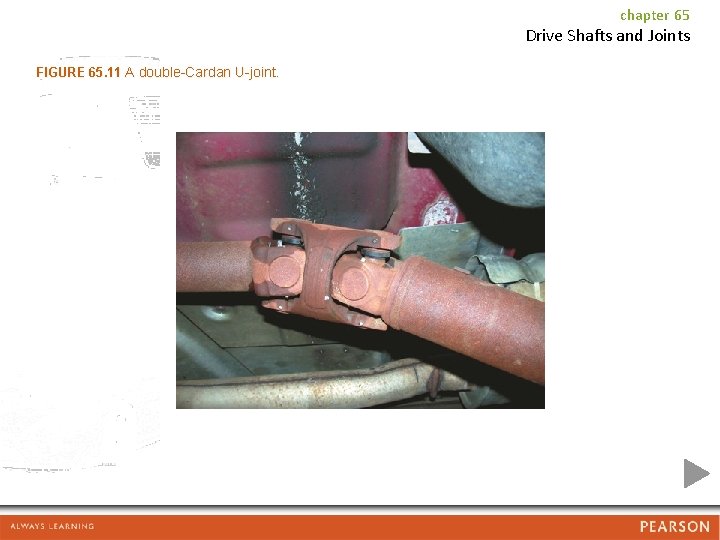
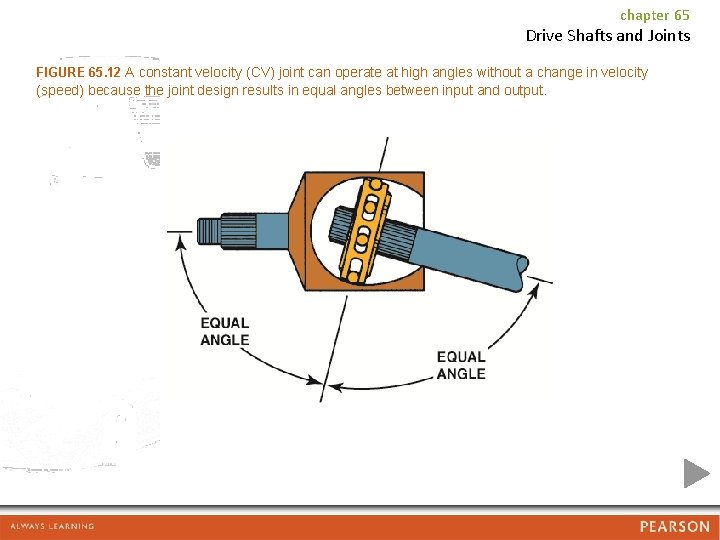
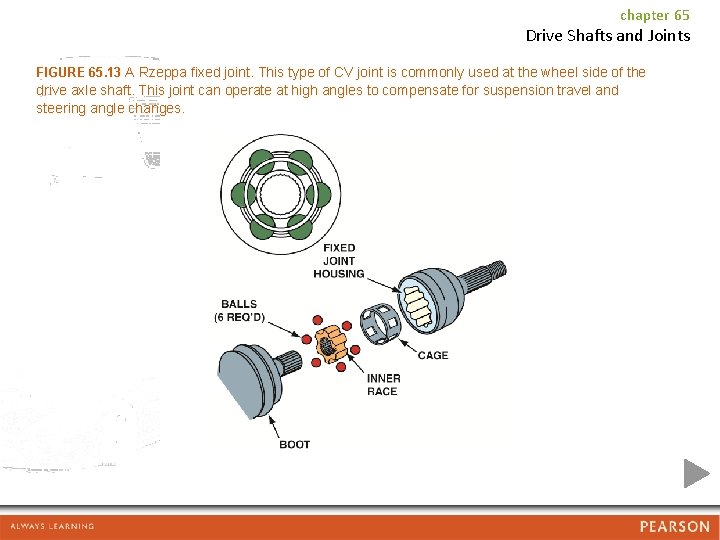
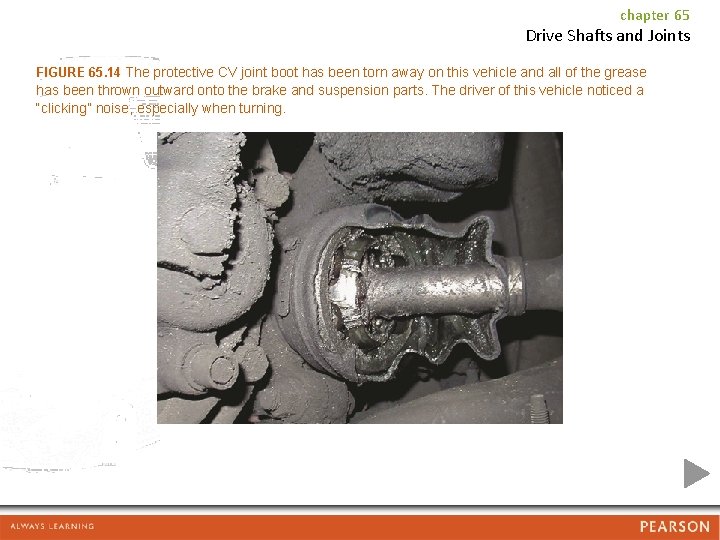
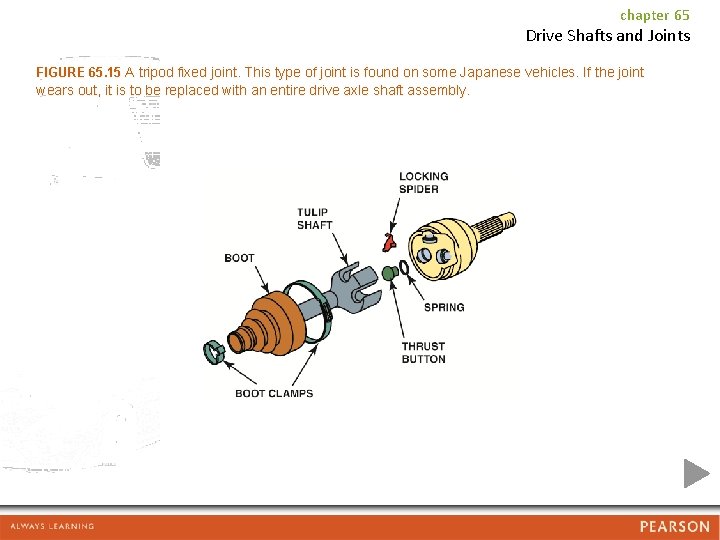
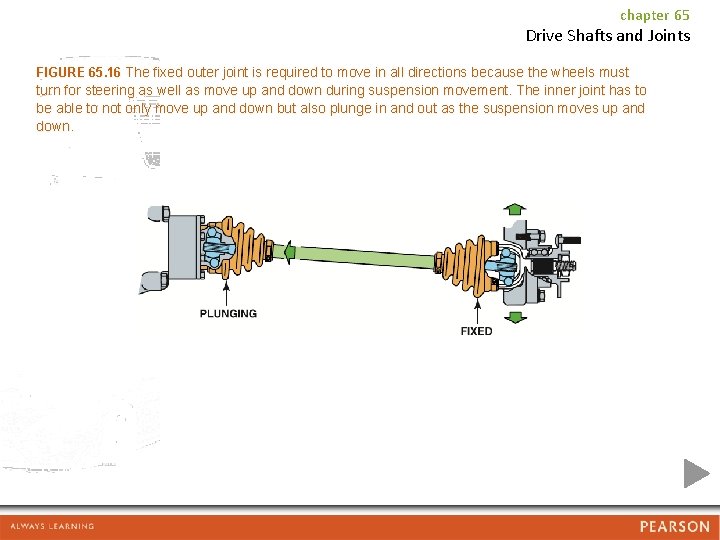
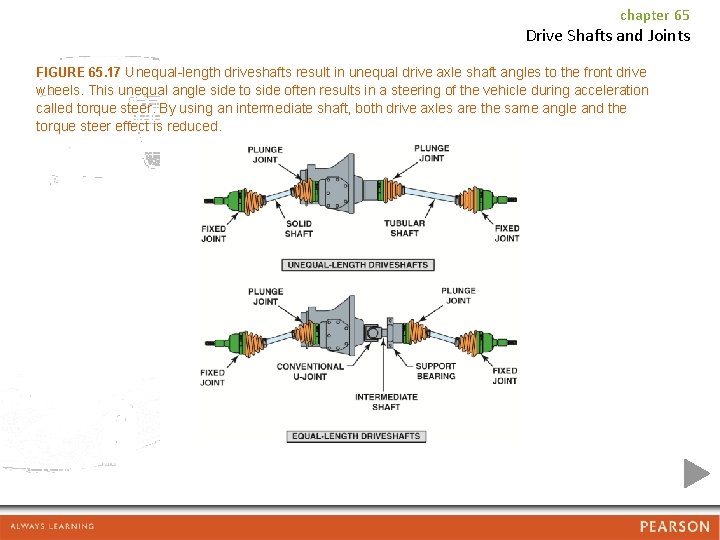
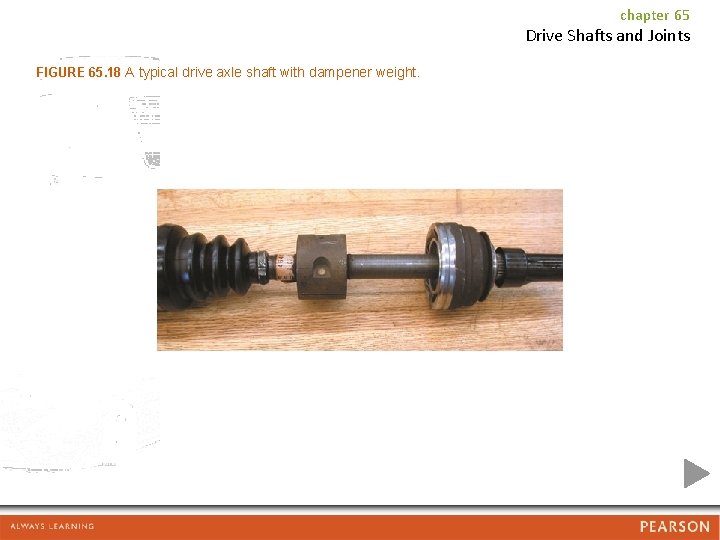
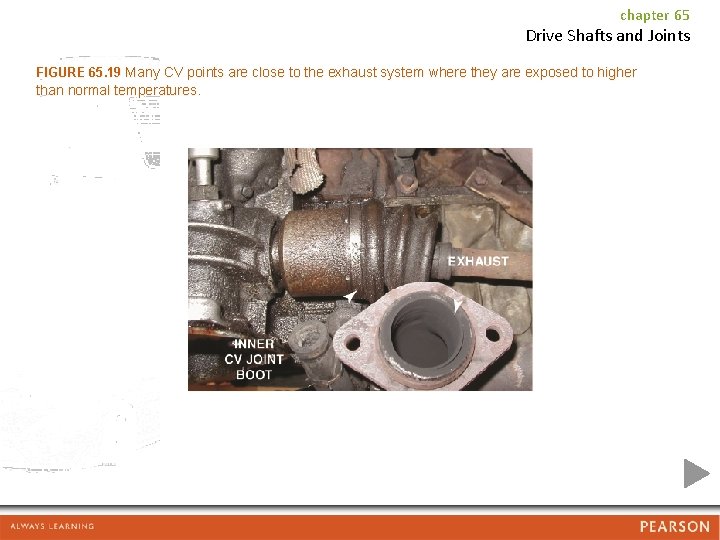
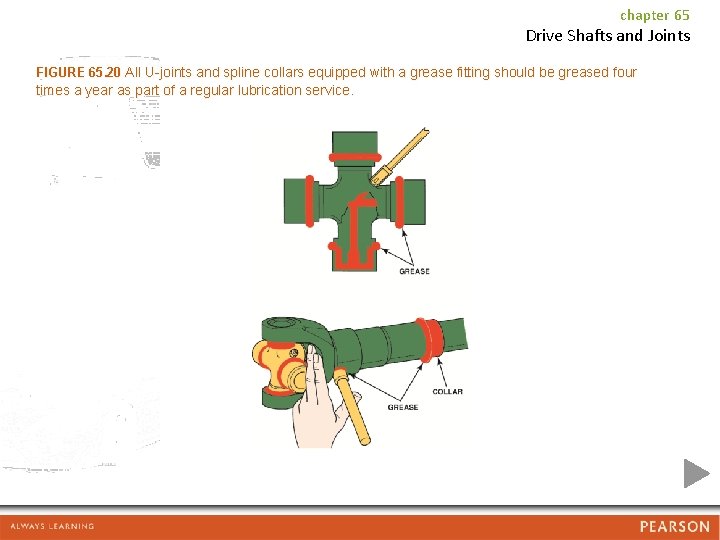
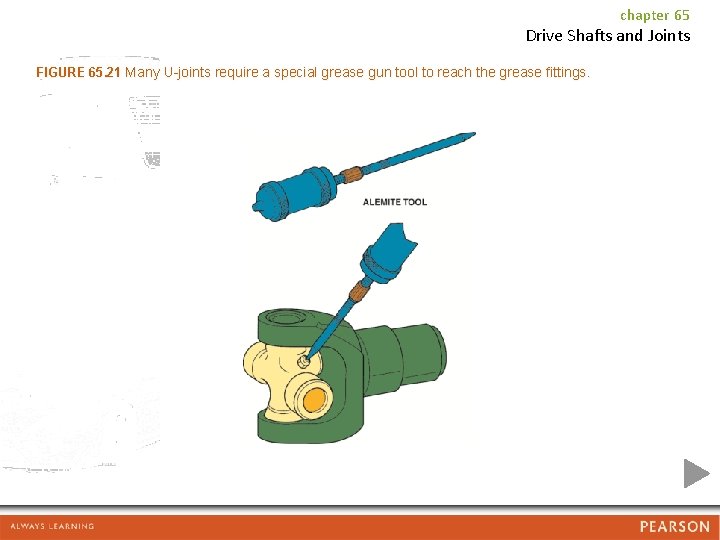
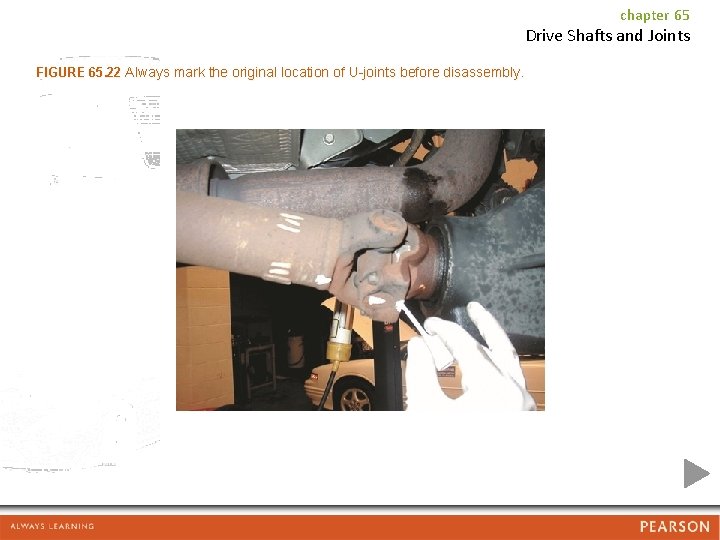
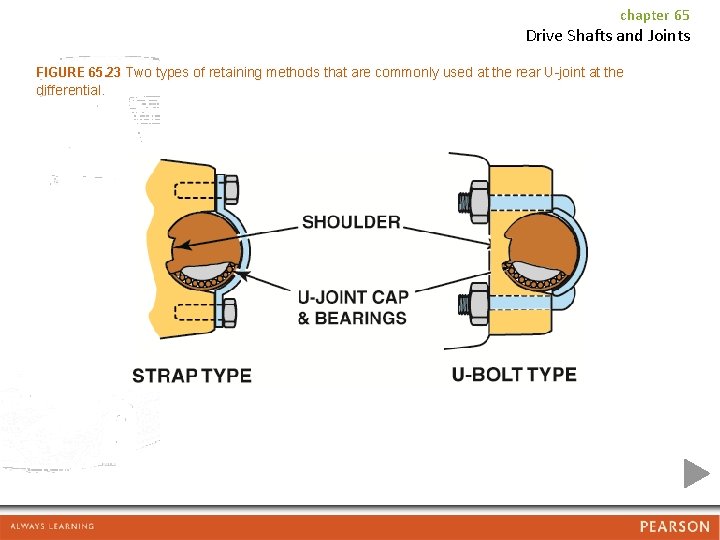
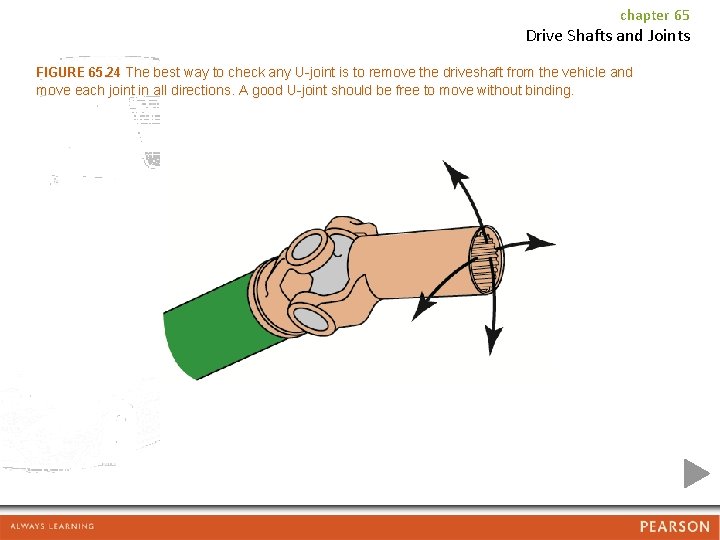
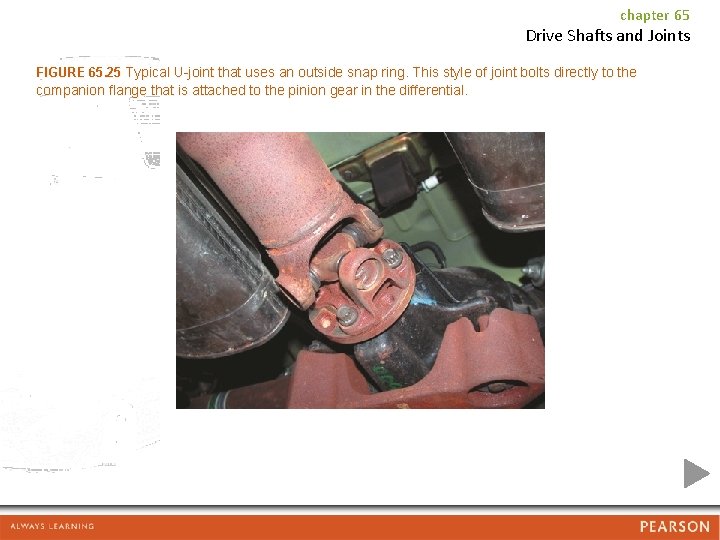
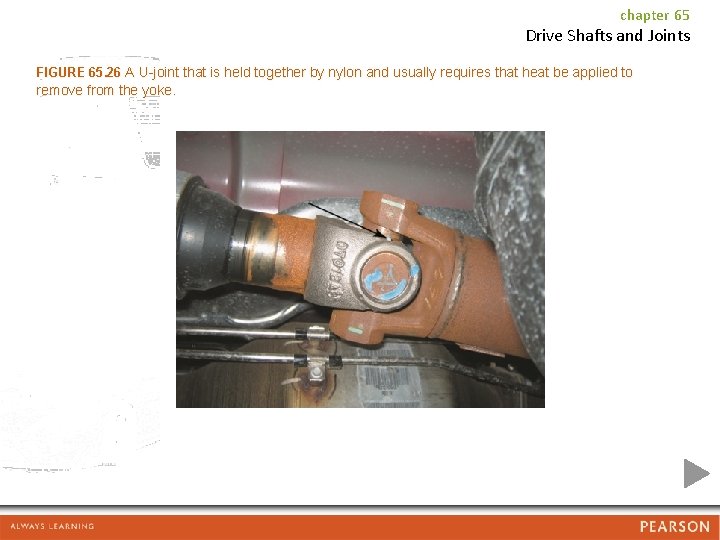

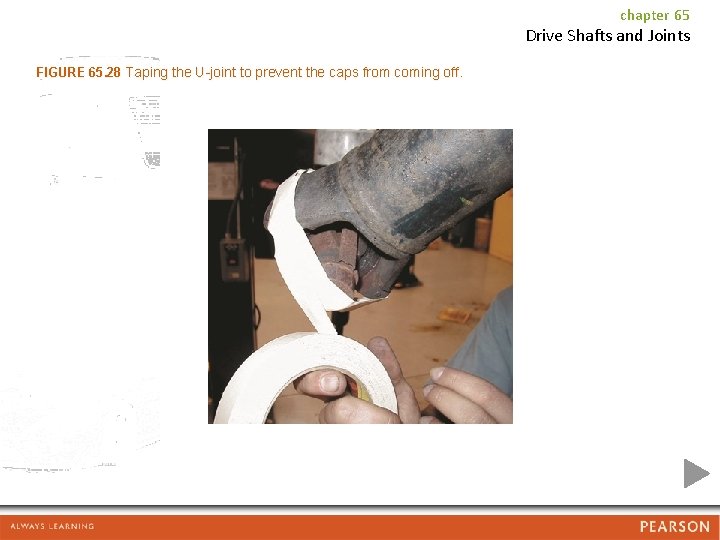
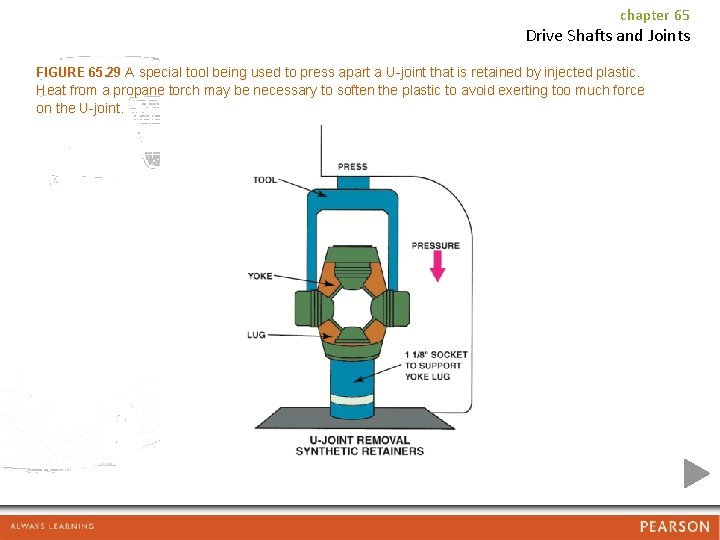
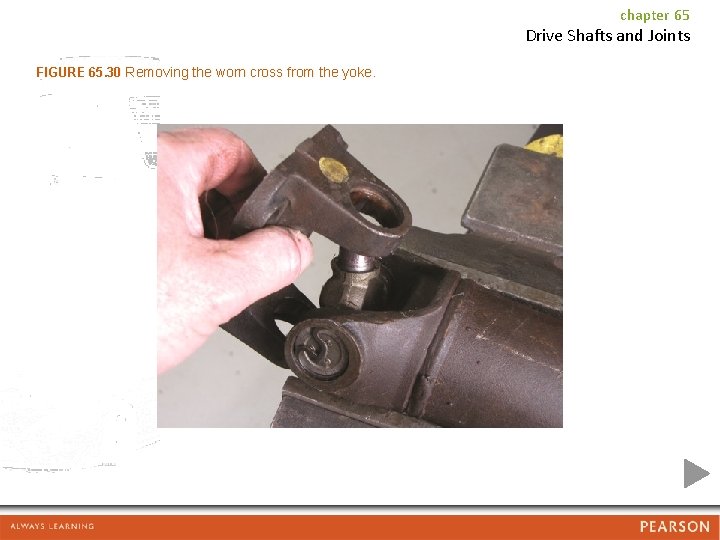
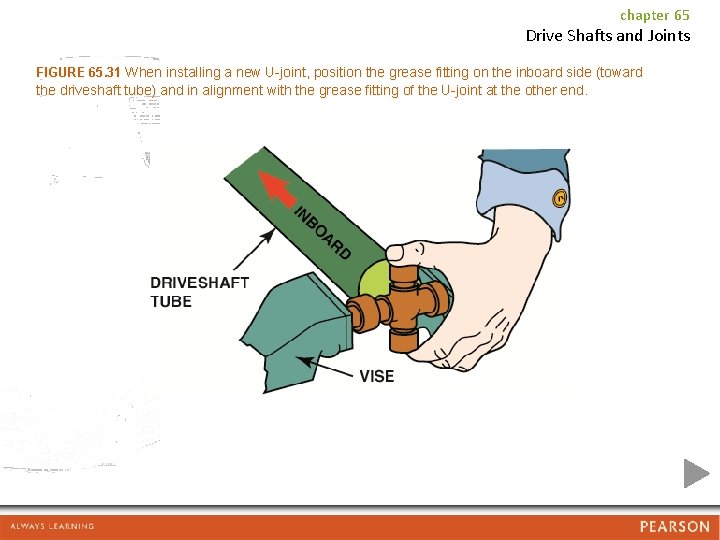
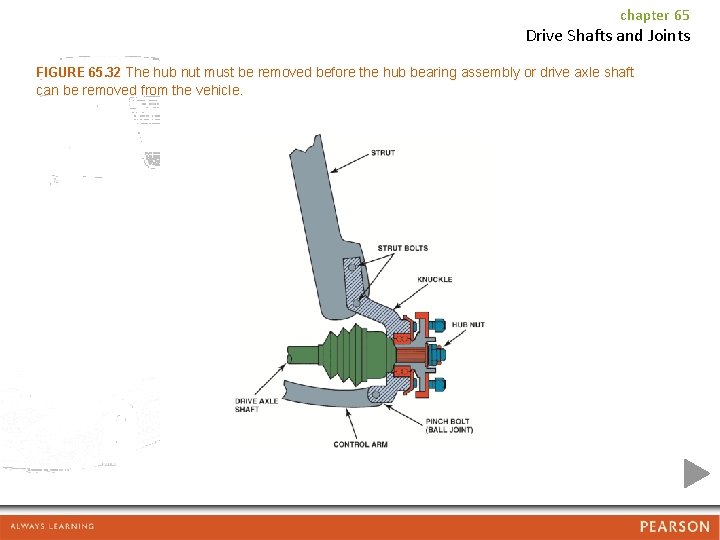
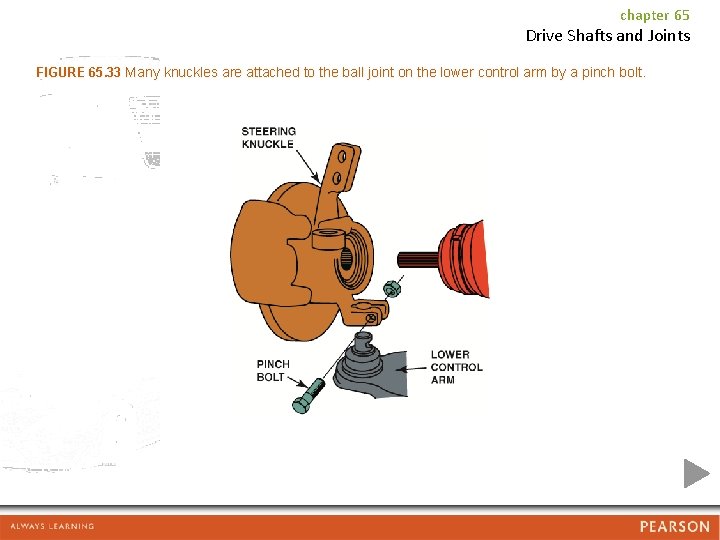
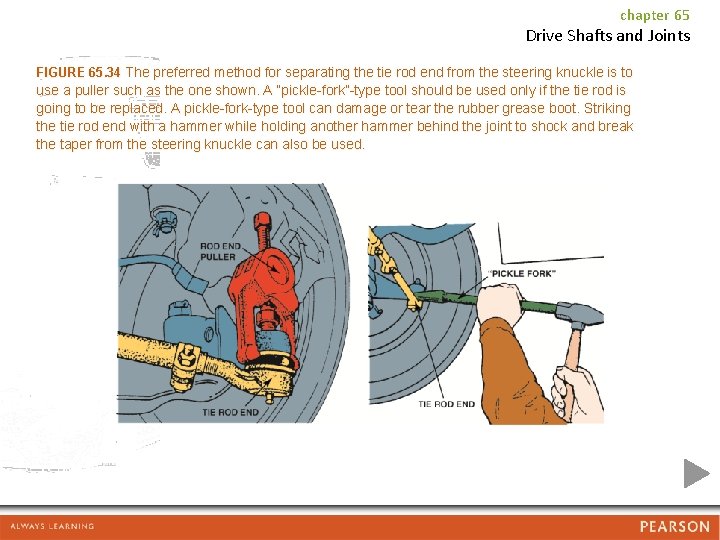
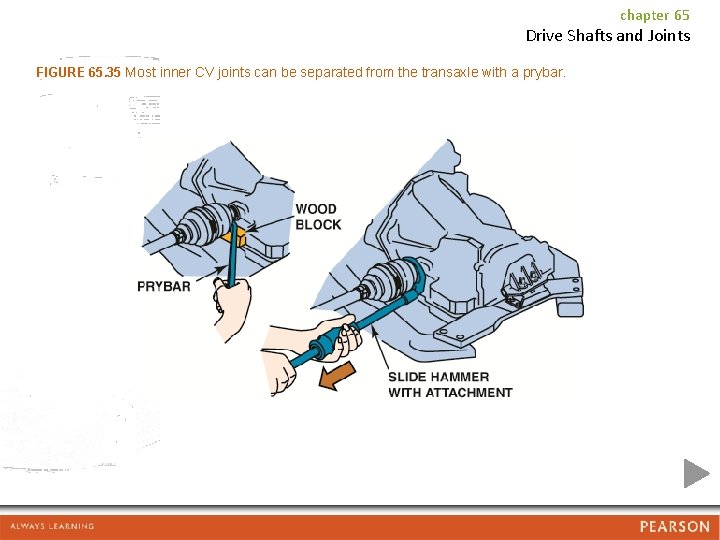
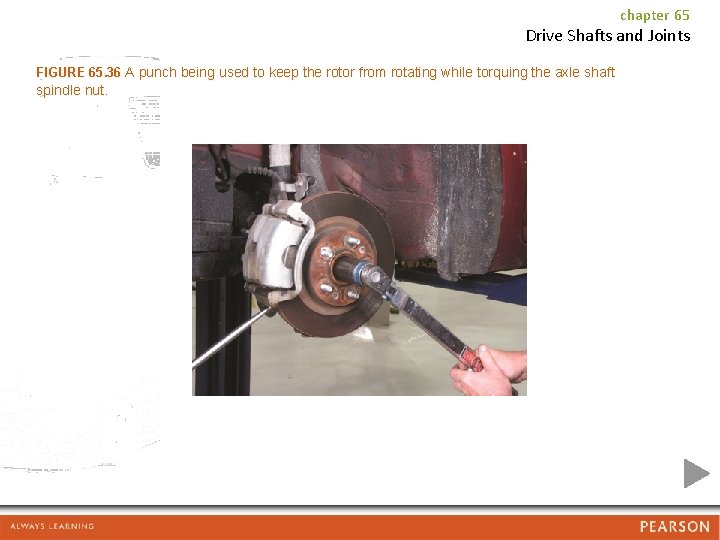
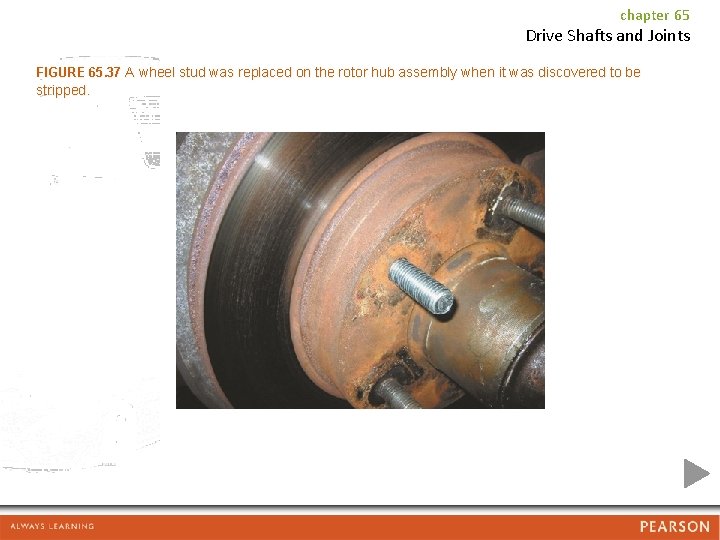
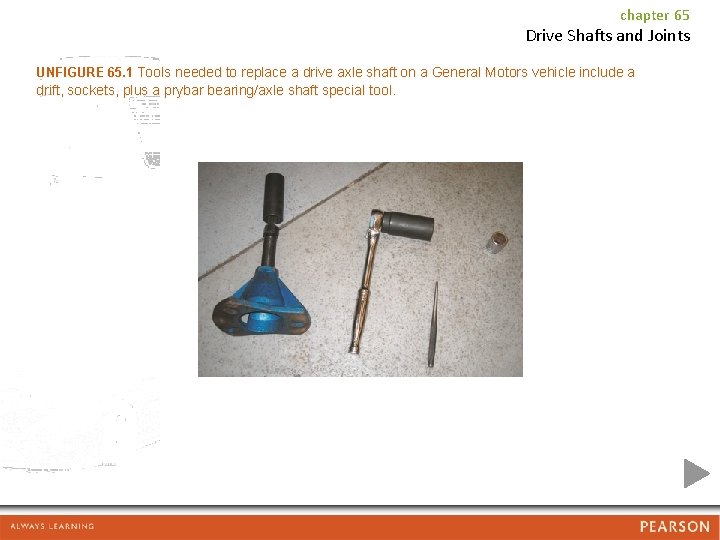
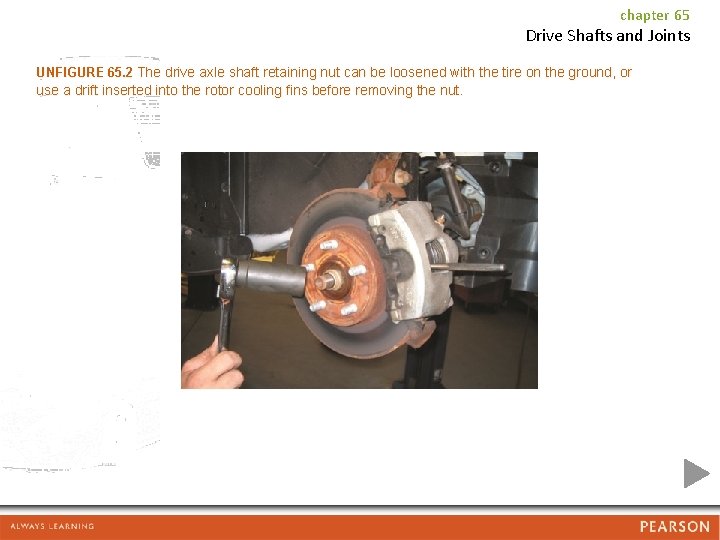
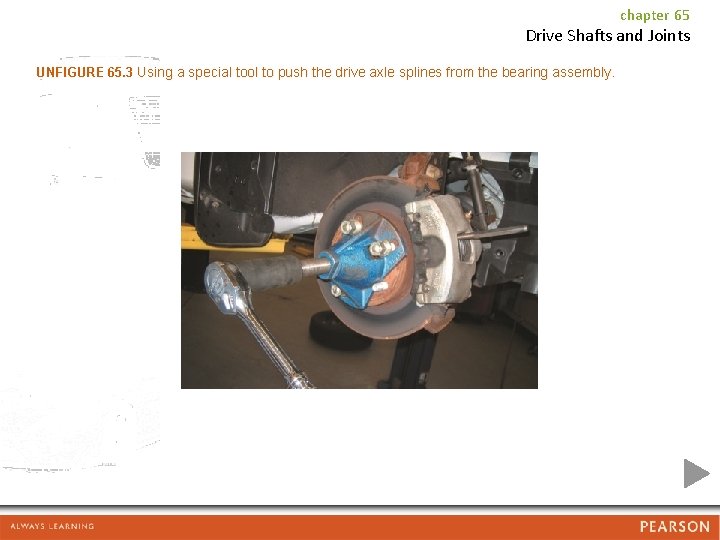
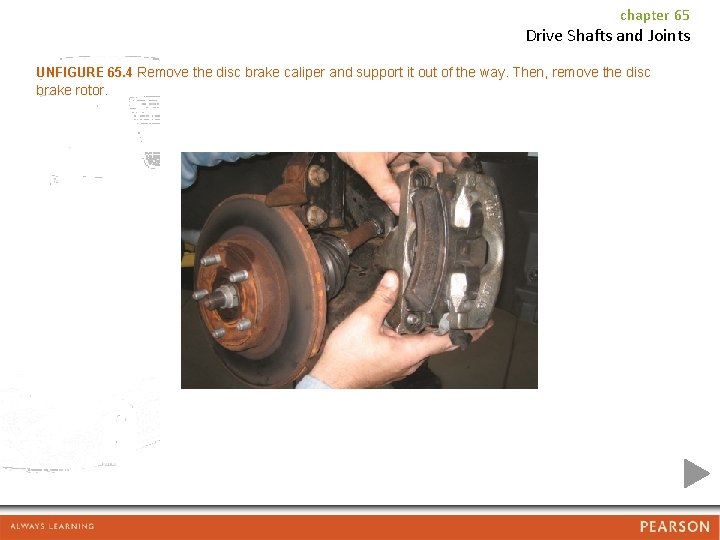
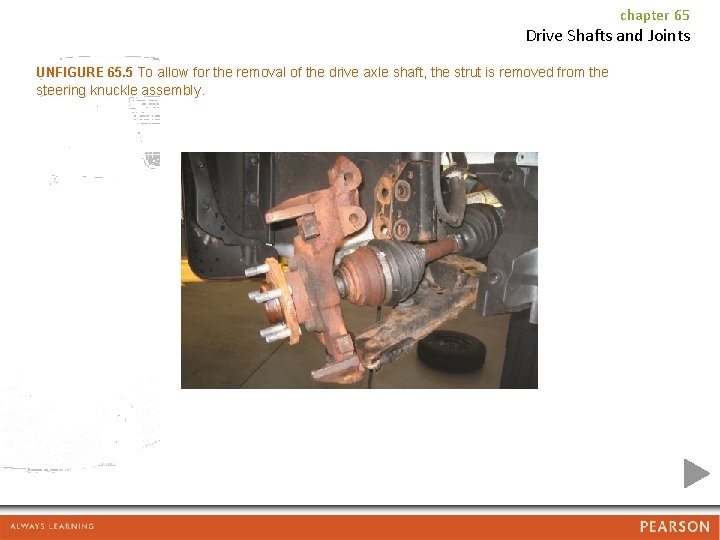
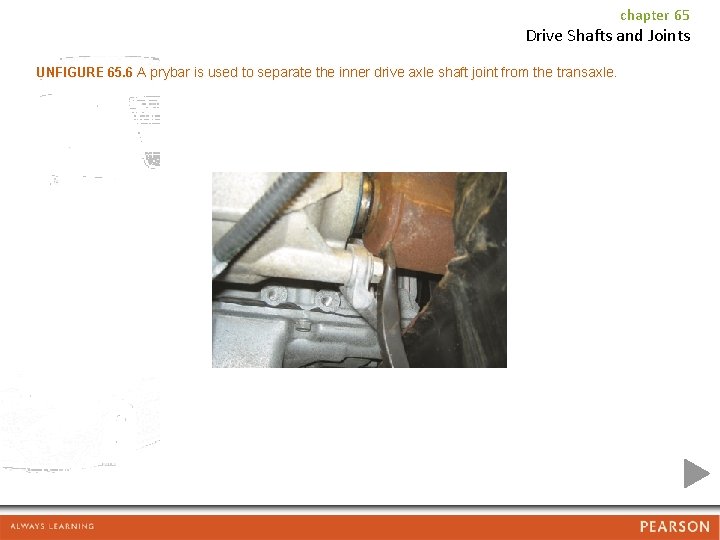

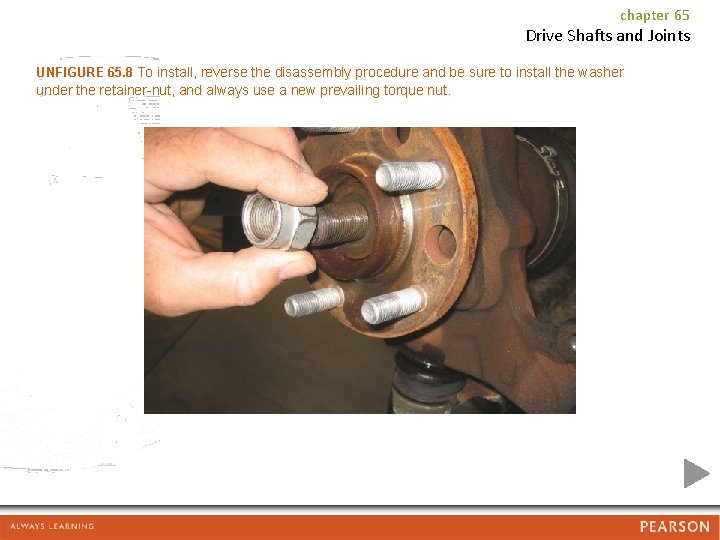
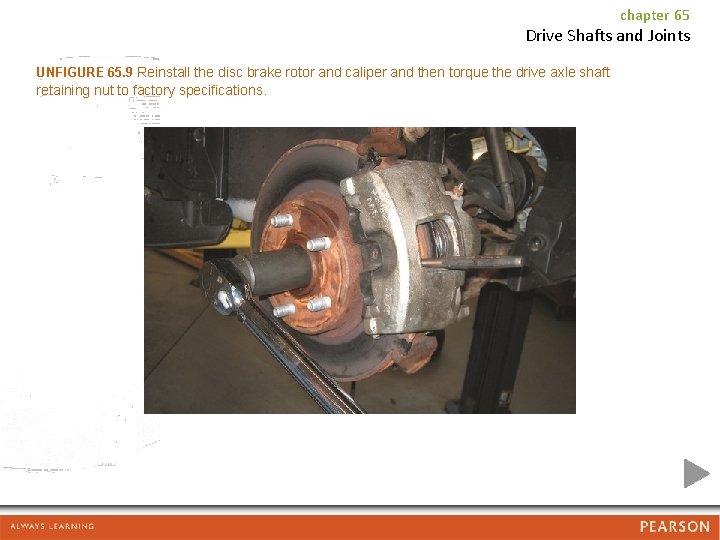
- Slides: 47
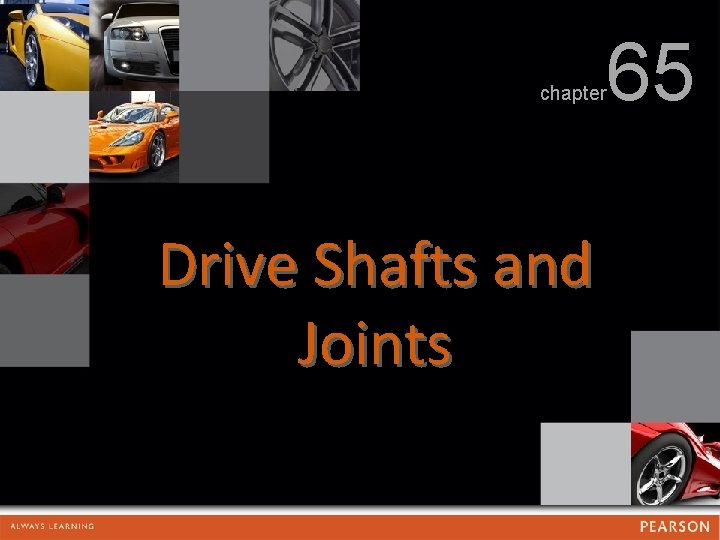
chapter Drive Shafts and Joints 65
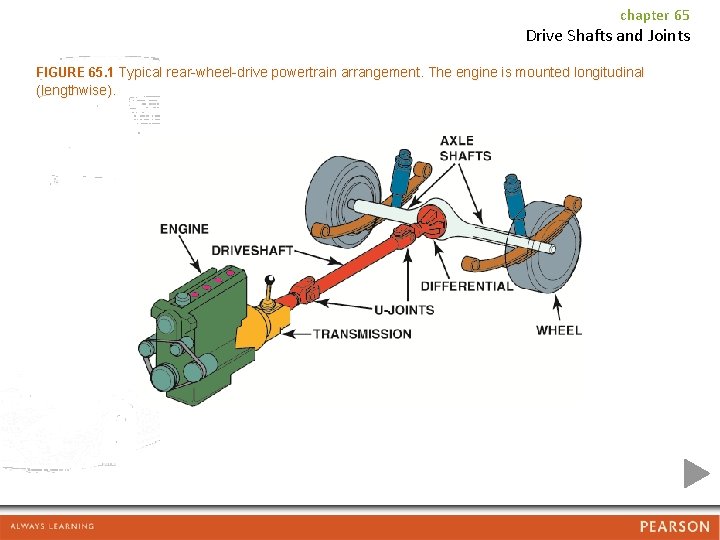
chapter 65 Drive Shafts and Joints FIGURE 65. 1 Typical rear-wheel-drive powertrain arrangement. The engine is mounted longitudinal (lengthwise).
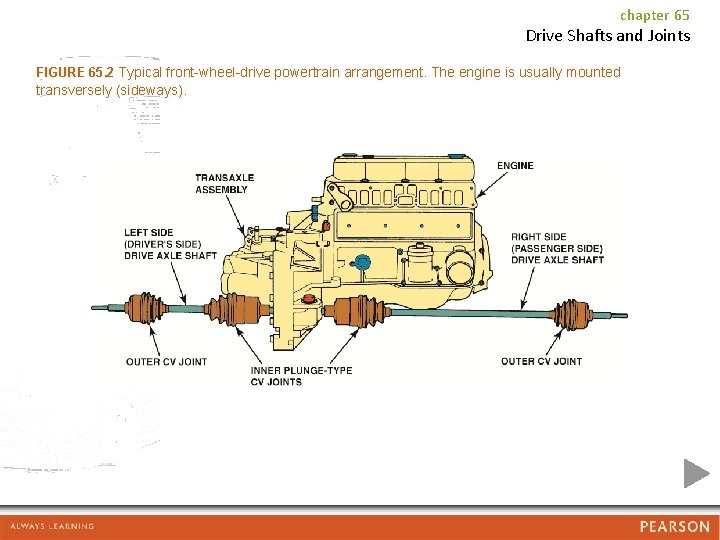
chapter 65 Drive Shafts and Joints FIGURE 65. 2 Typical front-wheel-drive powertrain arrangement. The engine is usually mounted transversely (sideways).
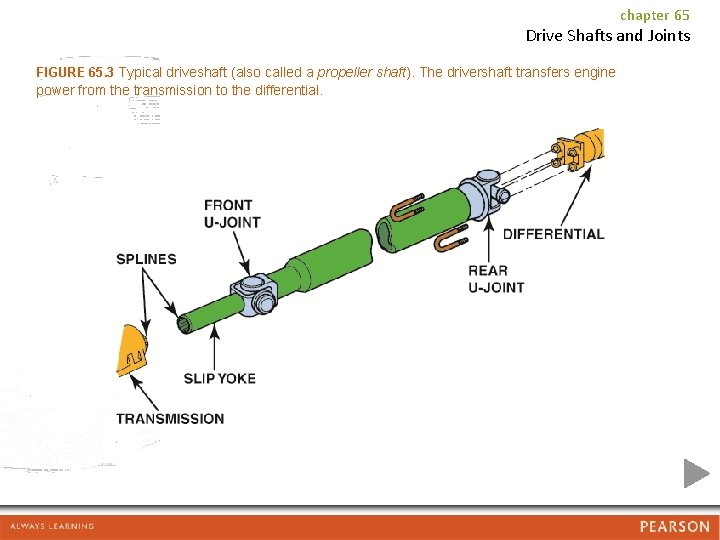
chapter 65 Drive Shafts and Joints FIGURE 65. 3 Typical driveshaft (also called a propeller shaft). The drivershaft transfers engine power from the transmission to the differential.
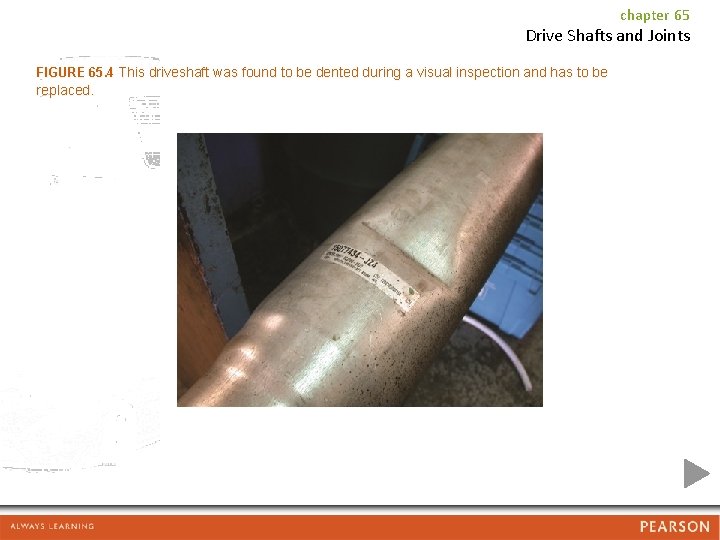
chapter 65 Drive Shafts and Joints FIGURE 65. 4 This driveshaft was found to be dented during a visual inspection and has to be replaced.
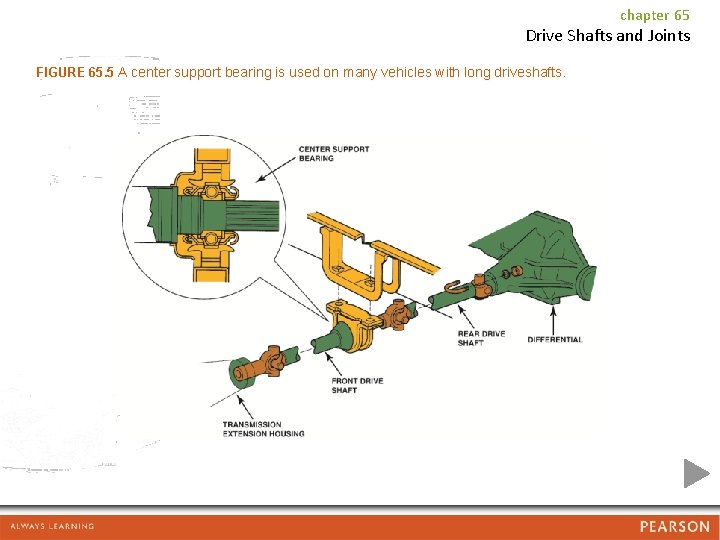
chapter 65 Drive Shafts and Joints FIGURE 65. 5 A center support bearing is used on many vehicles with long driveshafts.
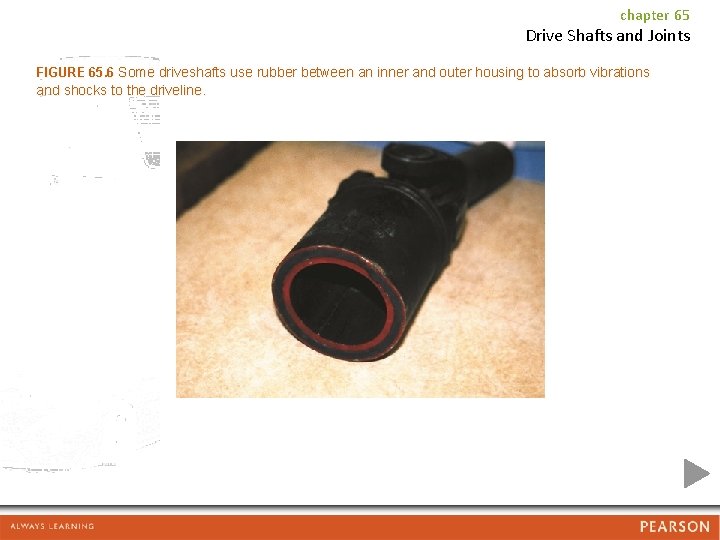
chapter 65 Drive Shafts and Joints FIGURE 65. 6 Some driveshafts use rubber between an inner and outer housing to absorb vibrations and shocks to the driveline.
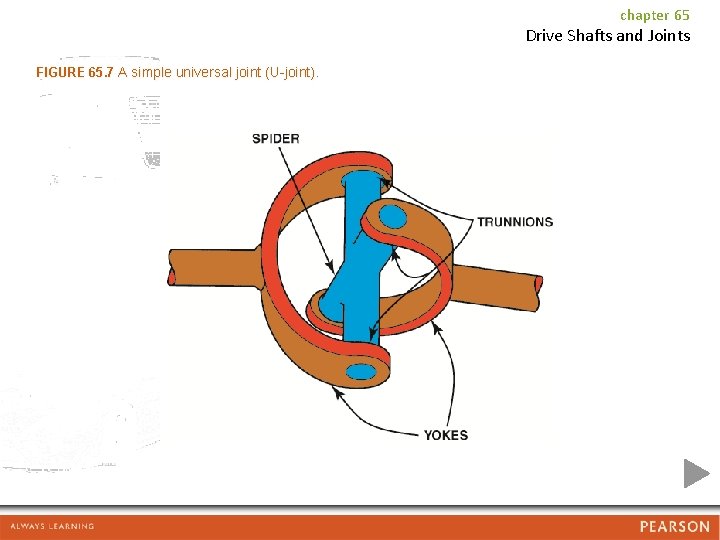
chapter 65 Drive Shafts and Joints FIGURE 65. 7 A simple universal joint (U-joint).
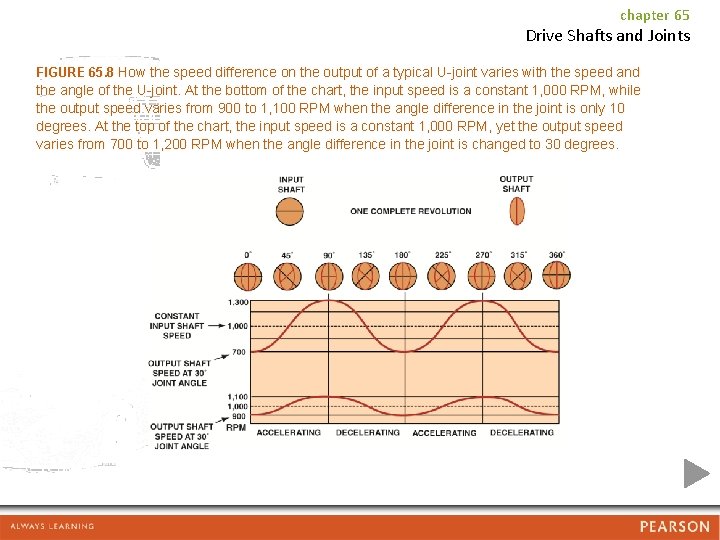
chapter 65 Drive Shafts and Joints FIGURE 65. 8 How the speed difference on the output of a typical U-joint varies with the speed and the angle of the U-joint. At the bottom of the chart, the input speed is a constant 1, 000 RPM, while the output speed varies from 900 to 1, 100 RPM when the angle difference in the joint is only 10 degrees. At the top of the chart, the input speed is a constant 1, 000 RPM, yet the output speed varies from 700 to 1, 200 RPM when the angle difference in the joint is changed to 30 degrees.
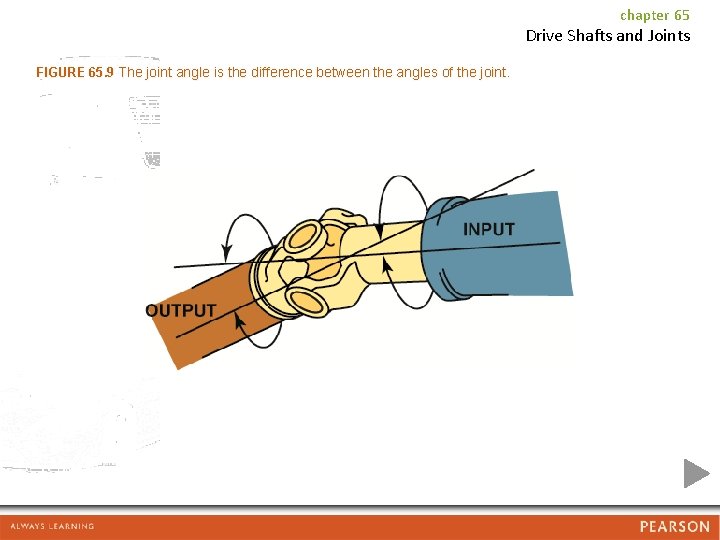
chapter 65 Drive Shafts and Joints FIGURE 65. 9 The joint angle is the difference between the angles of the joint.
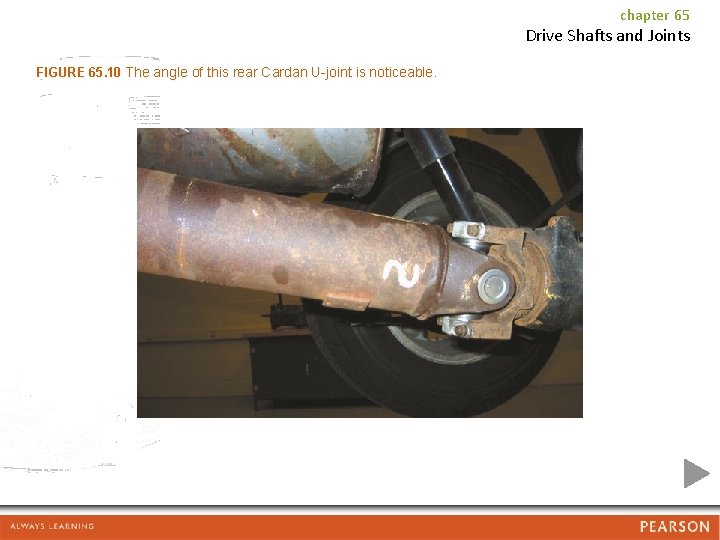
chapter 65 Drive Shafts and Joints FIGURE 65. 10 The angle of this rear Cardan U-joint is noticeable.
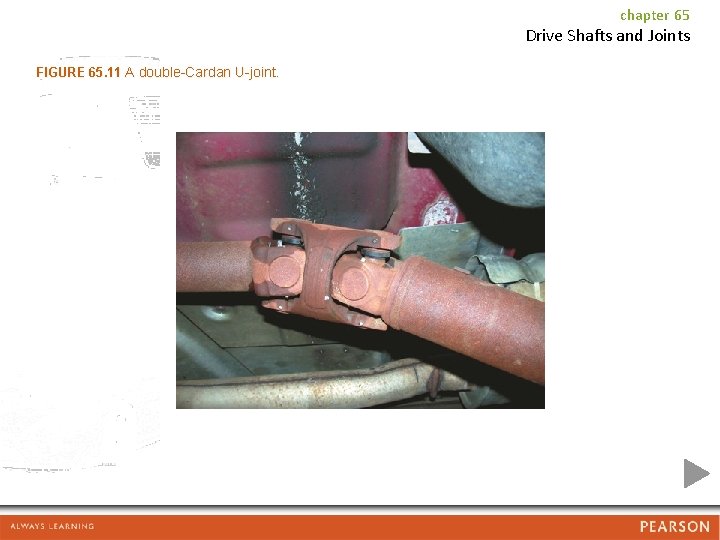
chapter 65 Drive Shafts and Joints FIGURE 65. 11 A double-Cardan U-joint.
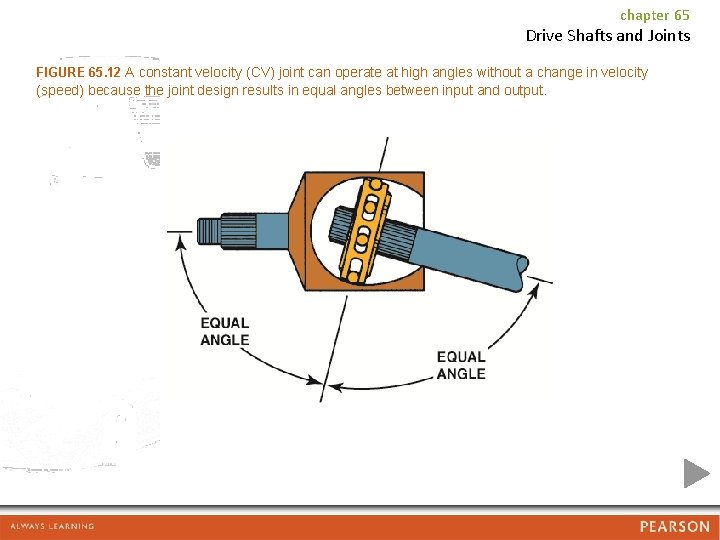
chapter 65 Drive Shafts and Joints FIGURE 65. 12 A constant velocity (CV) joint can operate at high angles without a change in velocity (speed) because the joint design results in equal angles between input and output.
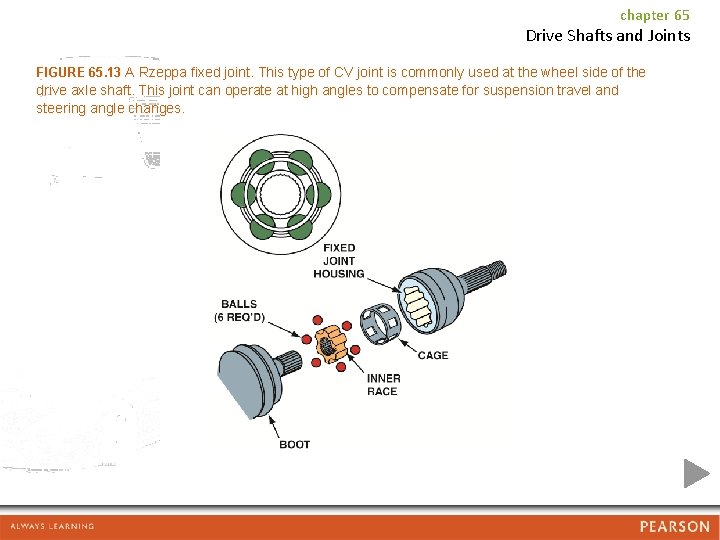
chapter 65 Drive Shafts and Joints FIGURE 65. 13 A Rzeppa fixed joint. This type of CV joint is commonly used at the wheel side of the drive axle shaft. This joint can operate at high angles to compensate for suspension travel and steering angle changes.
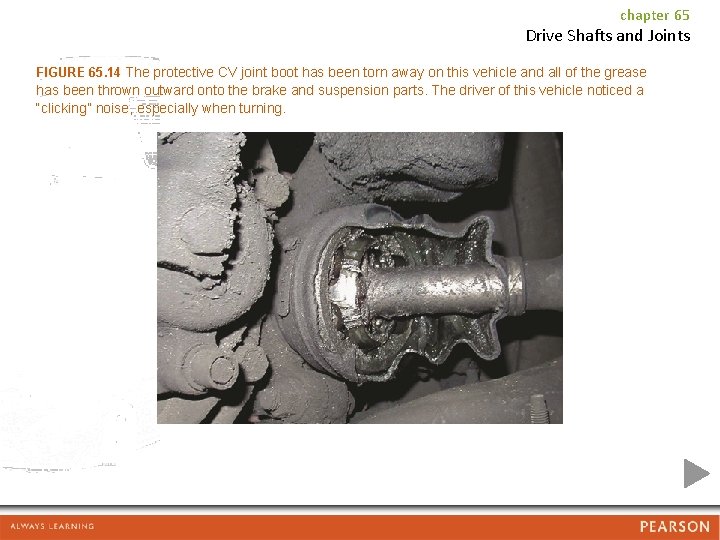
chapter 65 Drive Shafts and Joints FIGURE 65. 14 The protective CV joint boot has been torn away on this vehicle and all of the grease has been thrown outward onto the brake and suspension parts. The driver of this vehicle noticed a “clicking” noise, especially when turning.
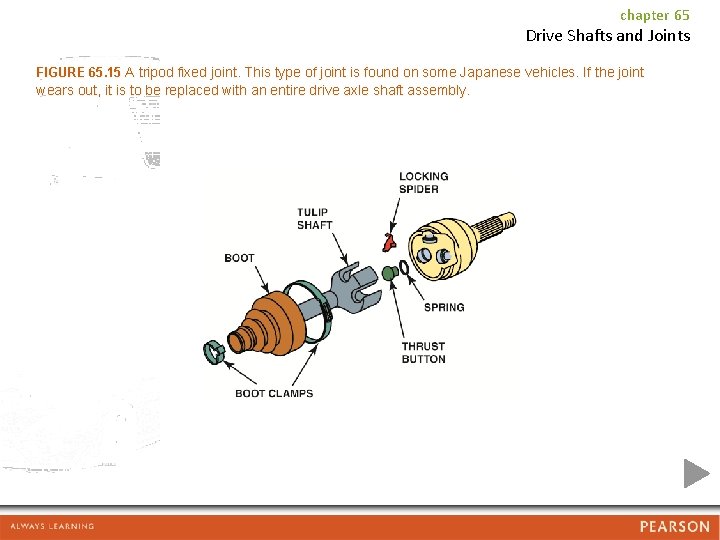
chapter 65 Drive Shafts and Joints FIGURE 65. 15 A tripod fixed joint. This type of joint is found on some Japanese vehicles. If the joint wears out, it is to be replaced with an entire drive axle shaft assembly.
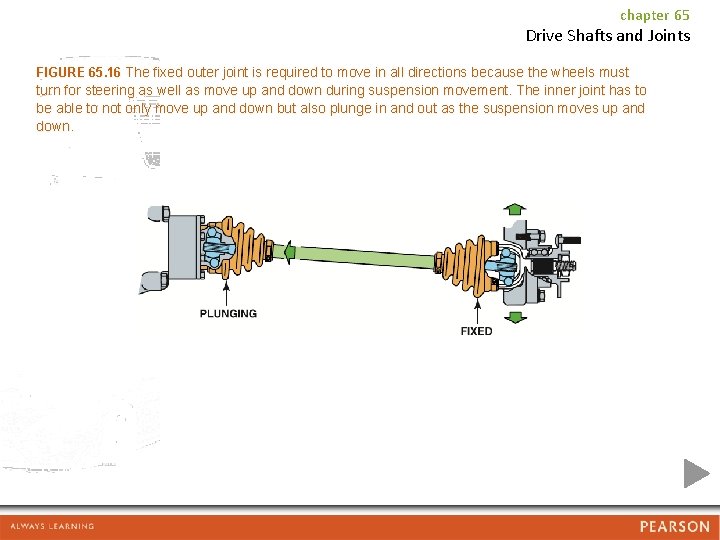
chapter 65 Drive Shafts and Joints FIGURE 65. 16 The fixed outer joint is required to move in all directions because the wheels must turn for steering as well as move up and down during suspension movement. The inner joint has to be able to not only move up and down but also plunge in and out as the suspension moves up and down.
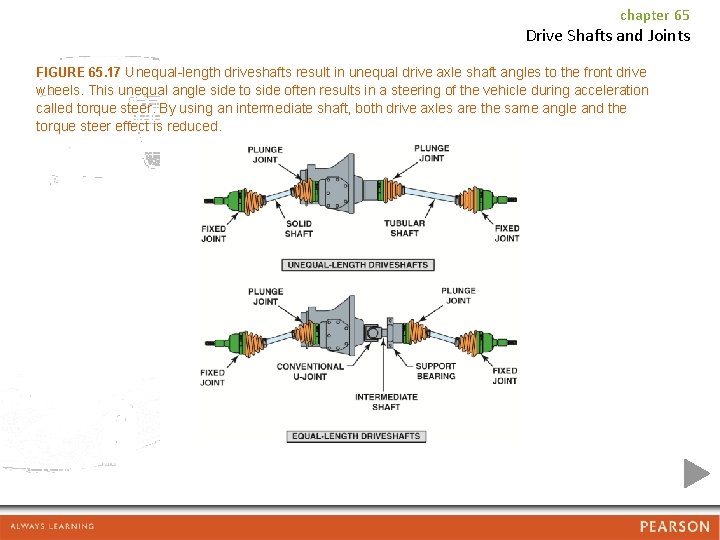
chapter 65 Drive Shafts and Joints FIGURE 65. 17 Unequal-length driveshafts result in unequal drive axle shaft angles to the front drive wheels. This unequal angle side to side often results in a steering of the vehicle during acceleration called torque steer. By using an intermediate shaft, both drive axles are the same angle and the torque steer effect is reduced.
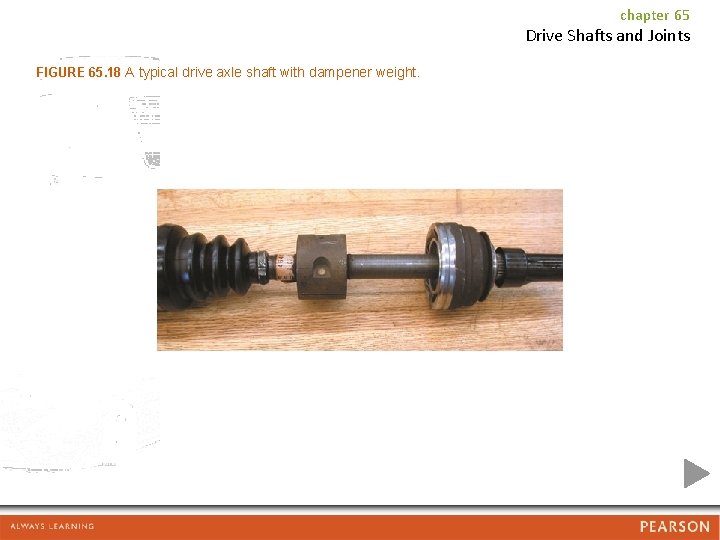
chapter 65 Drive Shafts and Joints FIGURE 65. 18 A typical drive axle shaft with dampener weight.
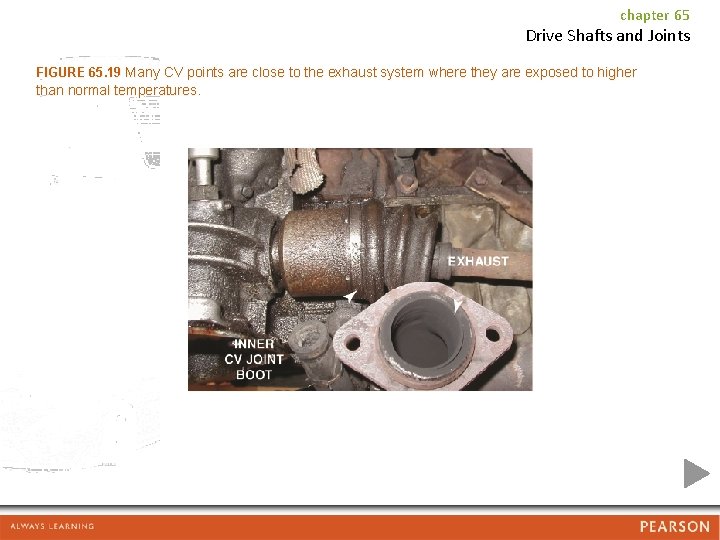
chapter 65 Drive Shafts and Joints FIGURE 65. 19 Many CV points are close to the exhaust system where they are exposed to higher than normal temperatures.
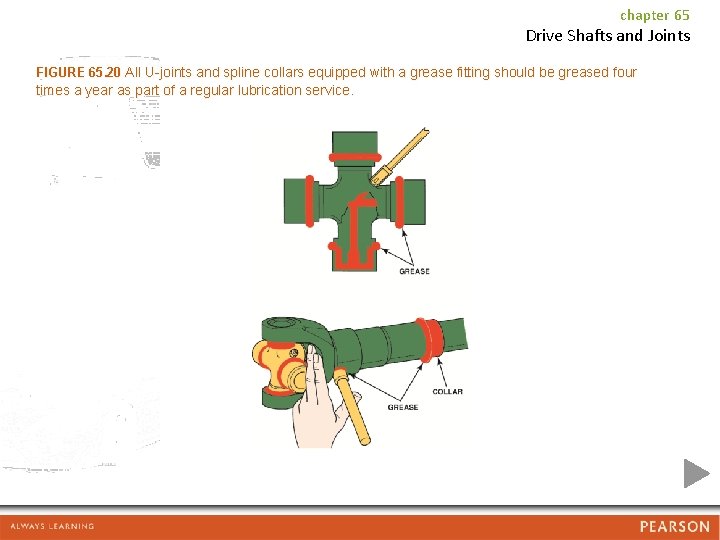
chapter 65 Drive Shafts and Joints FIGURE 65. 20 All U-joints and spline collars equipped with a grease fitting should be greased four times a year as part of a regular lubrication service.
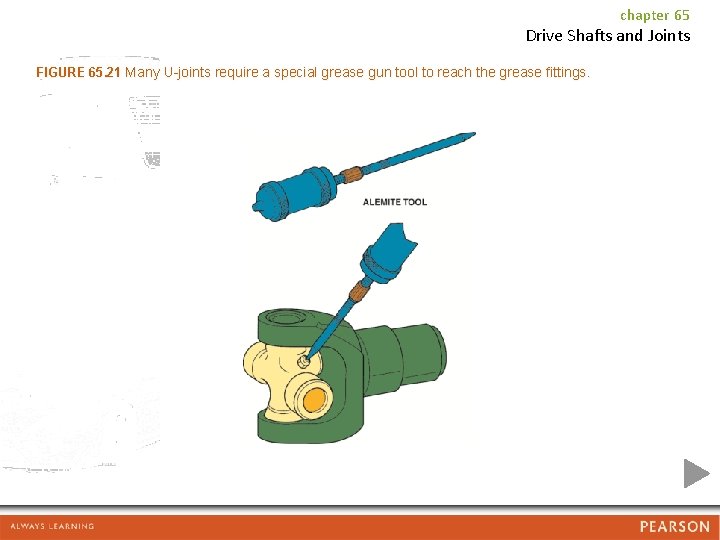
chapter 65 Drive Shafts and Joints FIGURE 65. 21 Many U-joints require a special grease gun tool to reach the grease fittings.
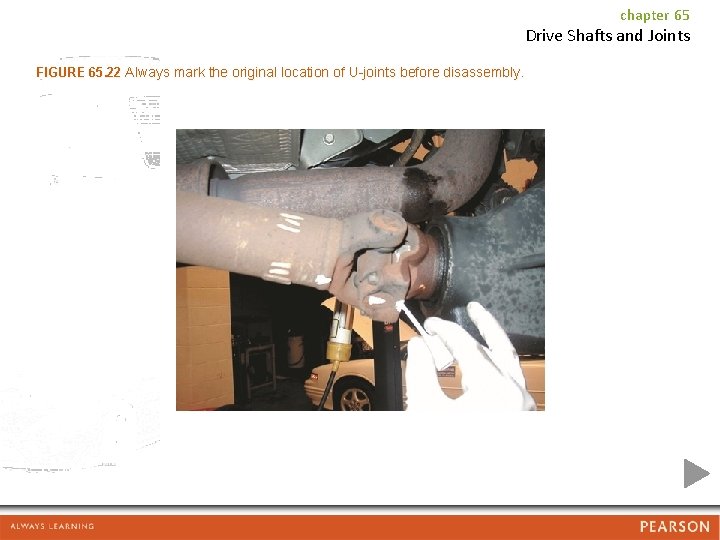
chapter 65 Drive Shafts and Joints FIGURE 65. 22 Always mark the original location of U-joints before disassembly.
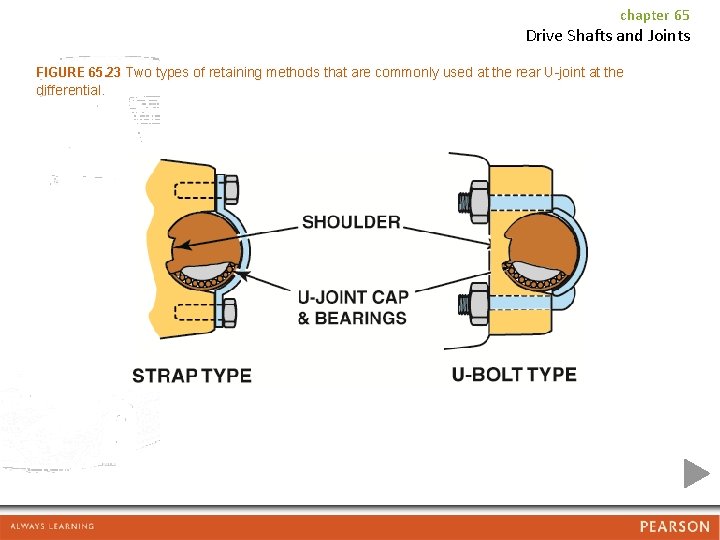
chapter 65 Drive Shafts and Joints FIGURE 65. 23 Two types of retaining methods that are commonly used at the rear U-joint at the differential.
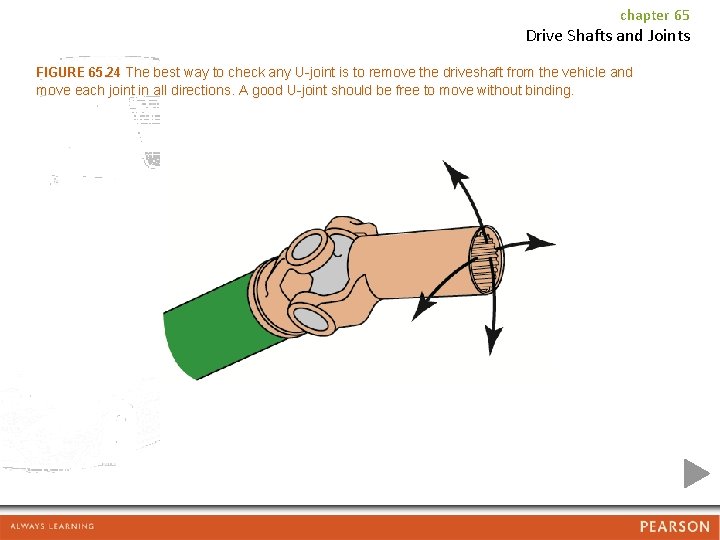
chapter 65 Drive Shafts and Joints FIGURE 65. 24 The best way to check any U-joint is to remove the driveshaft from the vehicle and move each joint in all directions. A good U-joint should be free to move without binding.
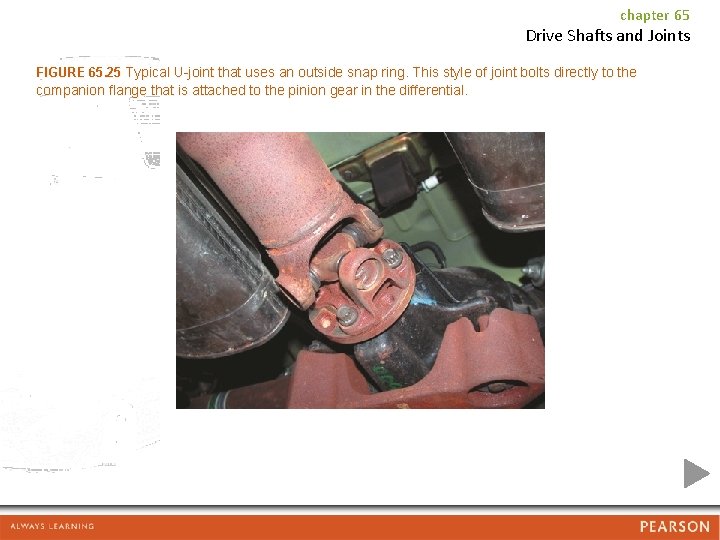
chapter 65 Drive Shafts and Joints FIGURE 65. 25 Typical U-joint that uses an outside snap ring. This style of joint bolts directly to the companion flange that is attached to the pinion gear in the differential.
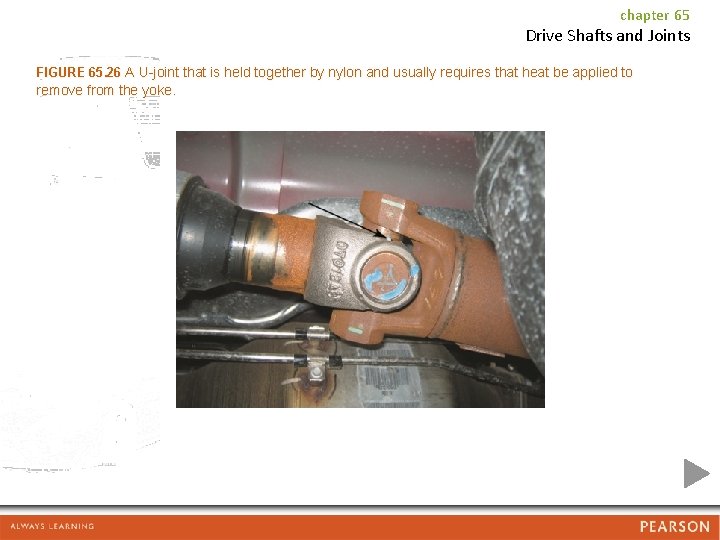
chapter 65 Drive Shafts and Joints FIGURE 65. 26 A U-joint that is held together by nylon and usually requires that heat be applied to remove from the yoke.

chapter 65 Drive Shafts and Joints FIGURE 65. 27 Use a vise and two sockets to replace a U-joint. One socket fits over the bearing cup and the other fits on the bearing to press-fit the cups from the crosspiece.
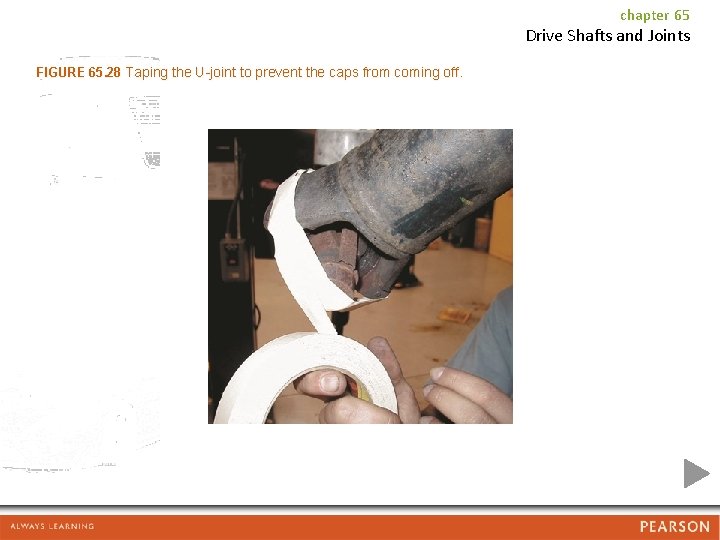
chapter 65 Drive Shafts and Joints FIGURE 65. 28 Taping the U-joint to prevent the caps from coming off.
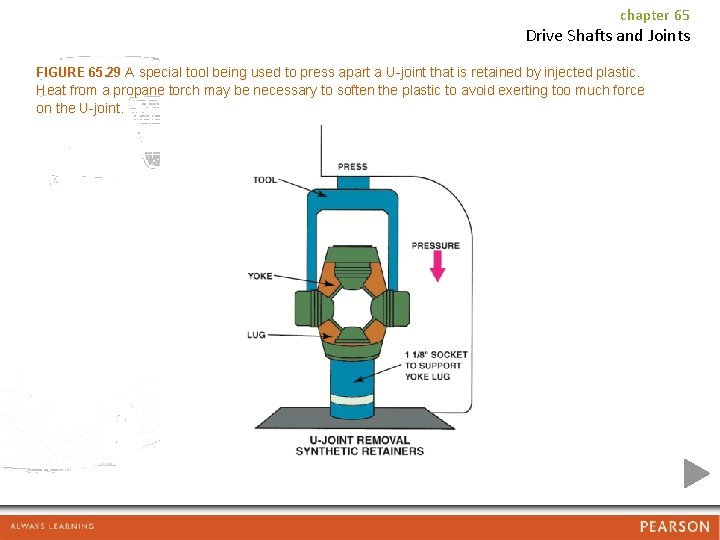
chapter 65 Drive Shafts and Joints FIGURE 65. 29 A special tool being used to press apart a U-joint that is retained by injected plastic. Heat from a propane torch may be necessary to soften the plastic to avoid exerting too much force on the U-joint.
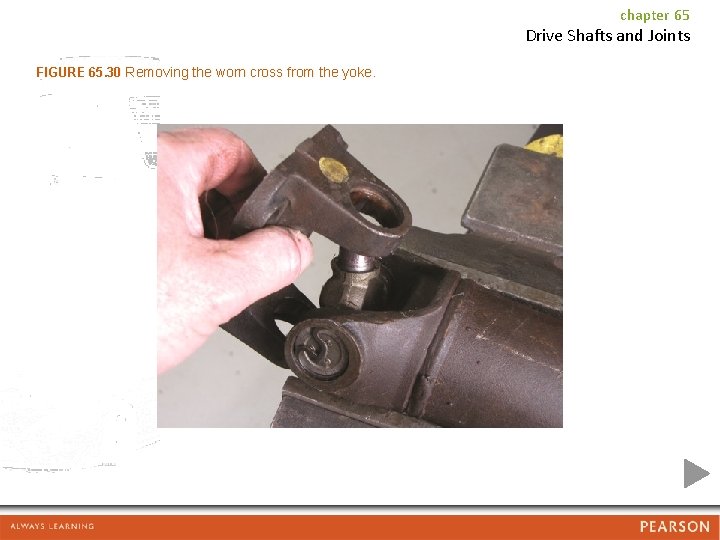
chapter 65 Drive Shafts and Joints FIGURE 65. 30 Removing the worn cross from the yoke.
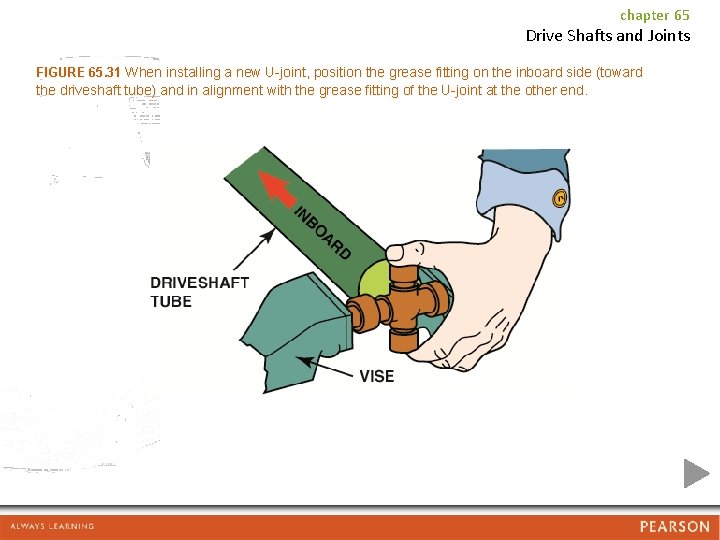
chapter 65 Drive Shafts and Joints FIGURE 65. 31 When installing a new U-joint, position the grease fitting on the inboard side (toward the driveshaft tube) and in alignment with the grease fitting of the U-joint at the other end.
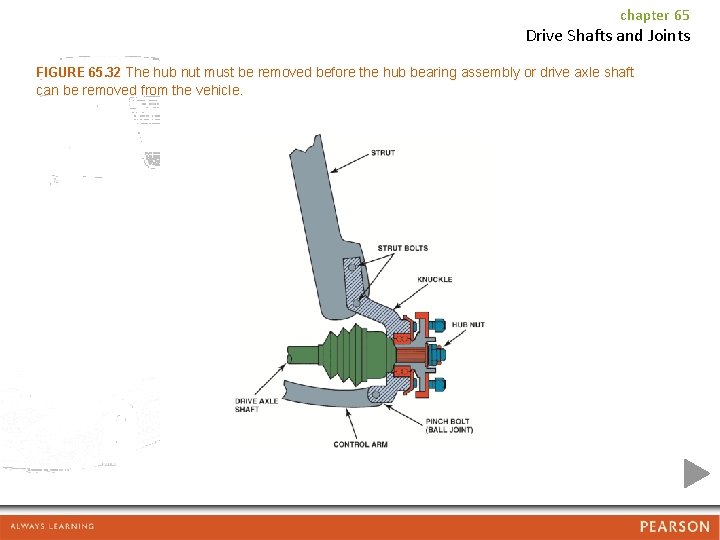
chapter 65 Drive Shafts and Joints FIGURE 65. 32 The hub nut must be removed before the hub bearing assembly or drive axle shaft can be removed from the vehicle.
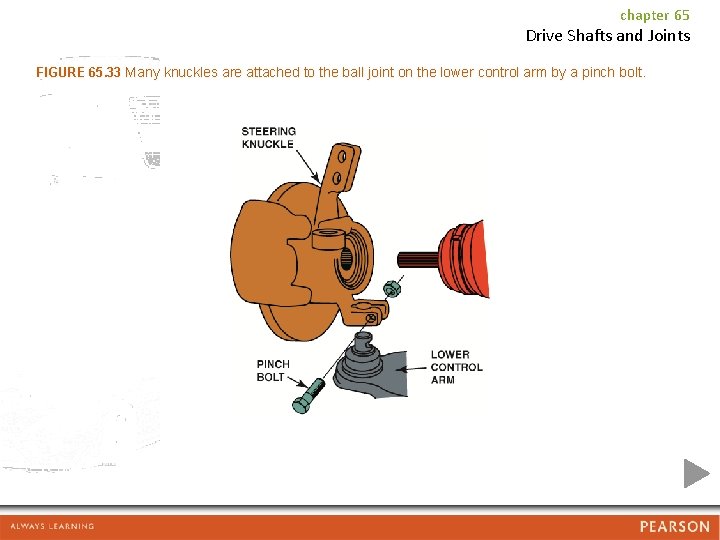
chapter 65 Drive Shafts and Joints FIGURE 65. 33 Many knuckles are attached to the ball joint on the lower control arm by a pinch bolt.
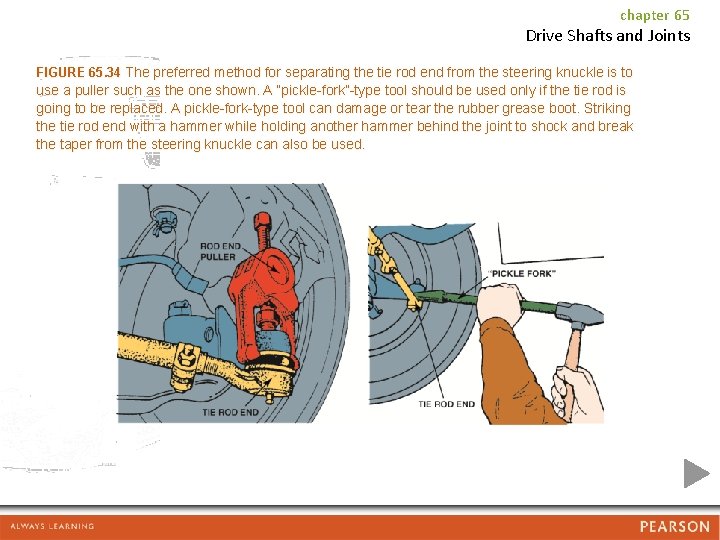
chapter 65 Drive Shafts and Joints FIGURE 65. 34 The preferred method for separating the tie rod end from the steering knuckle is to use a puller such as the one shown. A “pickle-fork”-type tool should be used only if the tie rod is going to be replaced. A pickle-fork-type tool can damage or tear the rubber grease boot. Striking the tie rod end with a hammer while holding another hammer behind the joint to shock and break the taper from the steering knuckle can also be used.
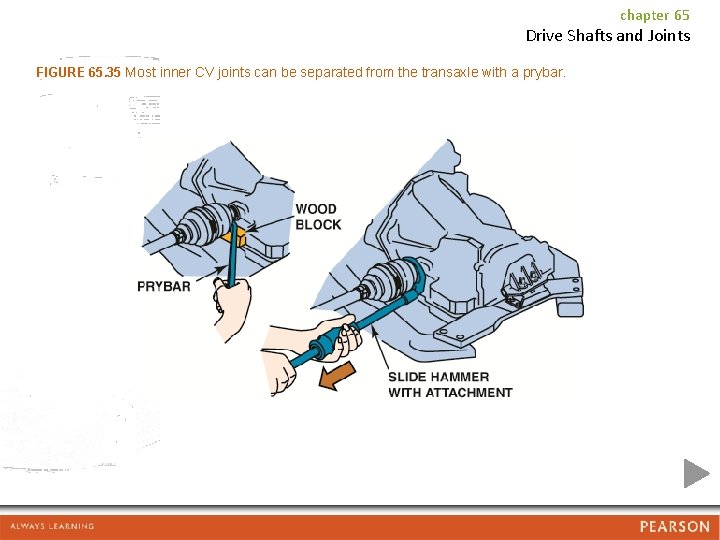
chapter 65 Drive Shafts and Joints FIGURE 65. 35 Most inner CV joints can be separated from the transaxle with a prybar.
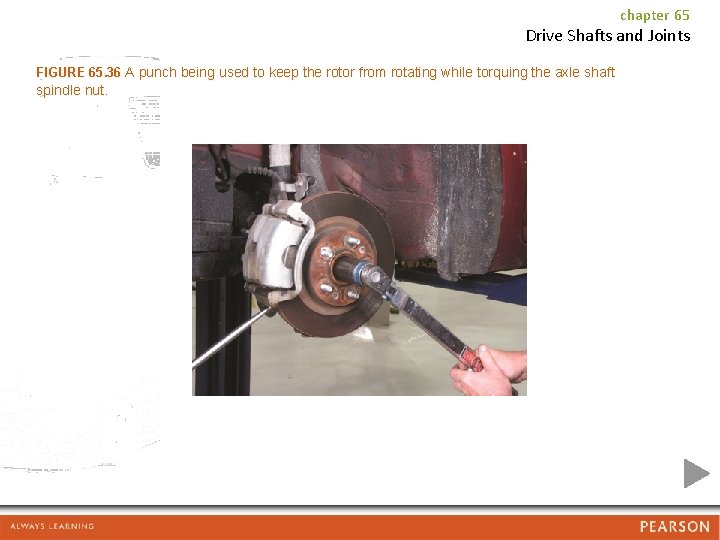
chapter 65 Drive Shafts and Joints FIGURE 65. 36 A punch being used to keep the rotor from rotating while torquing the axle shaft spindle nut.
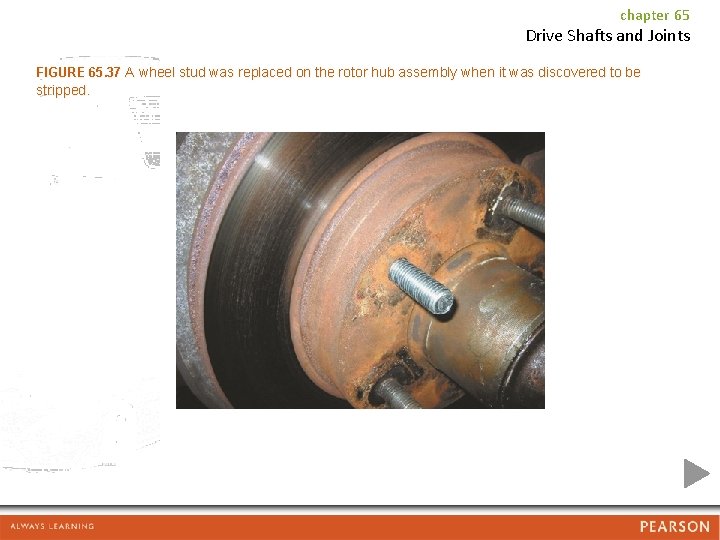
chapter 65 Drive Shafts and Joints FIGURE 65. 37 A wheel stud was replaced on the rotor hub assembly when it was discovered to be stripped.
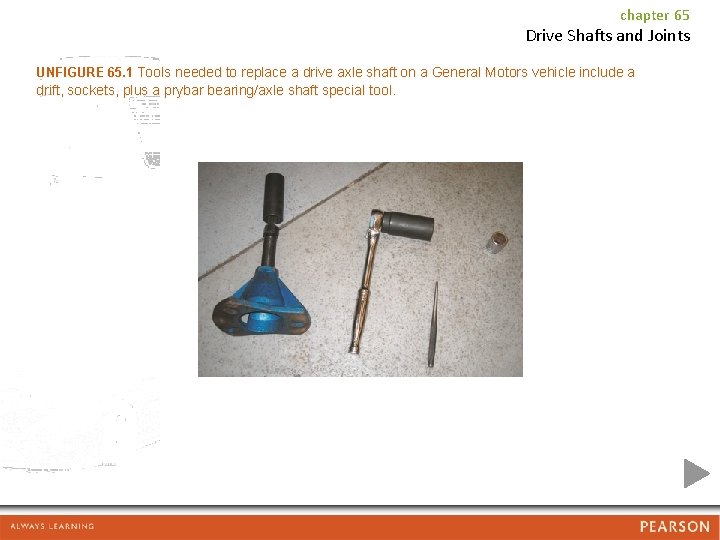
chapter 65 Drive Shafts and Joints UNFIGURE 65. 1 Tools needed to replace a drive axle shaft on a General Motors vehicle include a drift, sockets, plus a prybar bearing/axle shaft special tool.
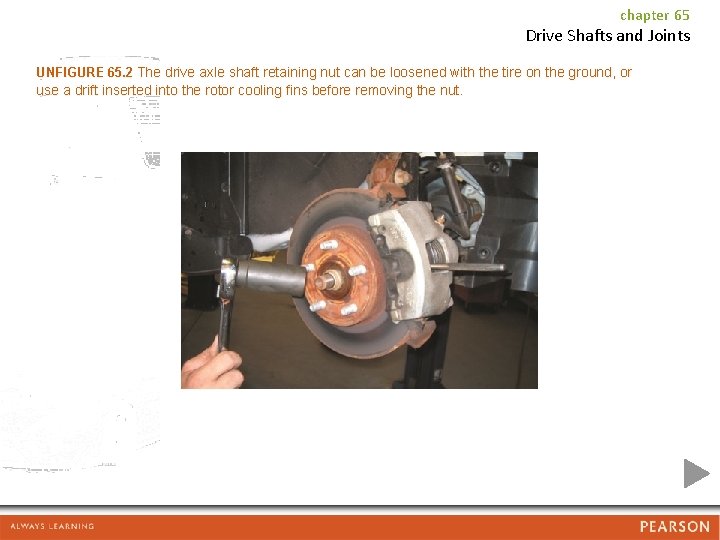
chapter 65 Drive Shafts and Joints UNFIGURE 65. 2 The drive axle shaft retaining nut can be loosened with the tire on the ground, or use a drift inserted into the rotor cooling fins before removing the nut.
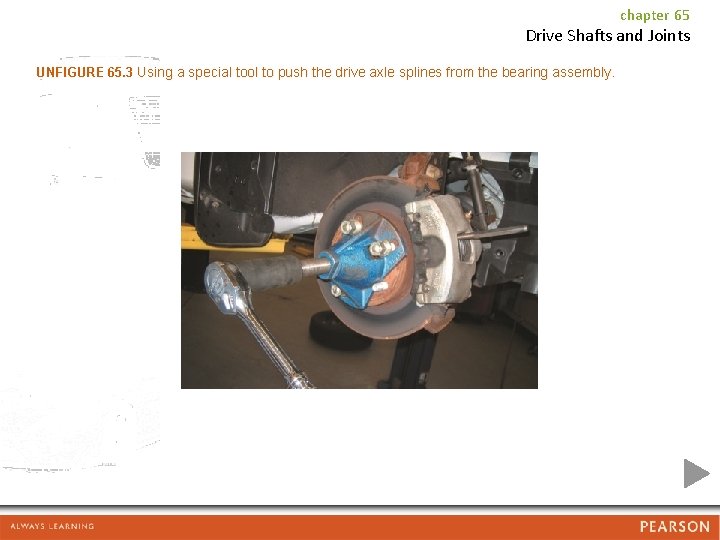
chapter 65 Drive Shafts and Joints UNFIGURE 65. 3 Using a special tool to push the drive axle splines from the bearing assembly.
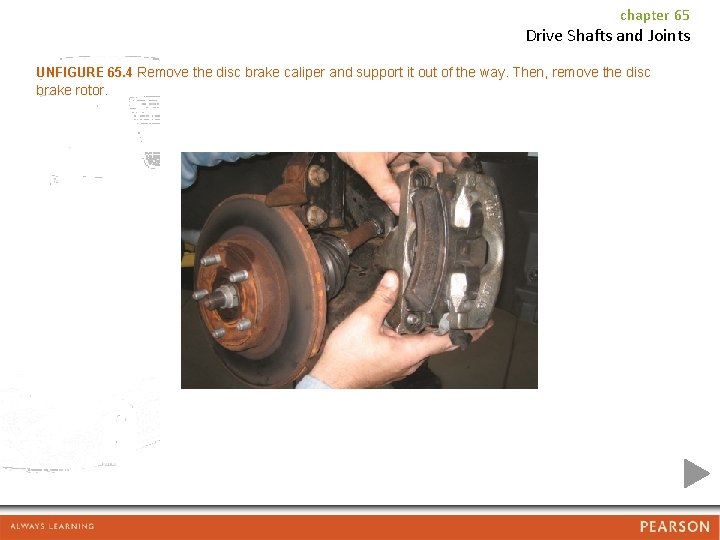
chapter 65 Drive Shafts and Joints UNFIGURE 65. 4 Remove the disc brake caliper and support it out of the way. Then, remove the disc brake rotor.
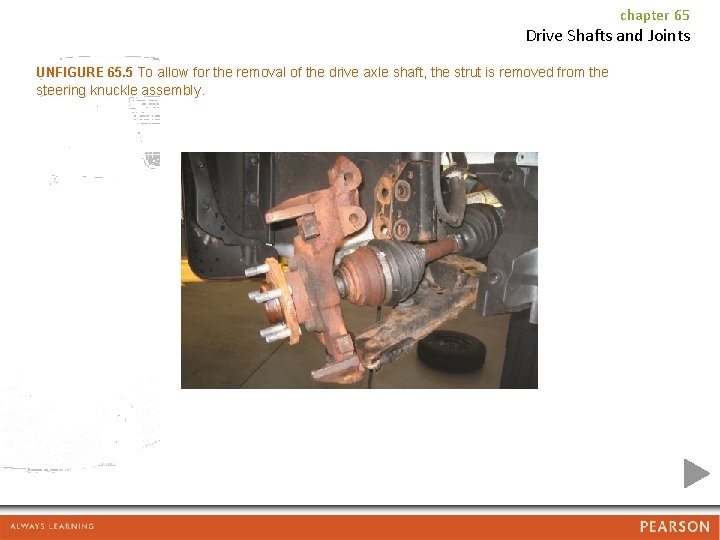
chapter 65 Drive Shafts and Joints UNFIGURE 65. 5 To allow for the removal of the drive axle shaft, the strut is removed from the steering knuckle assembly.
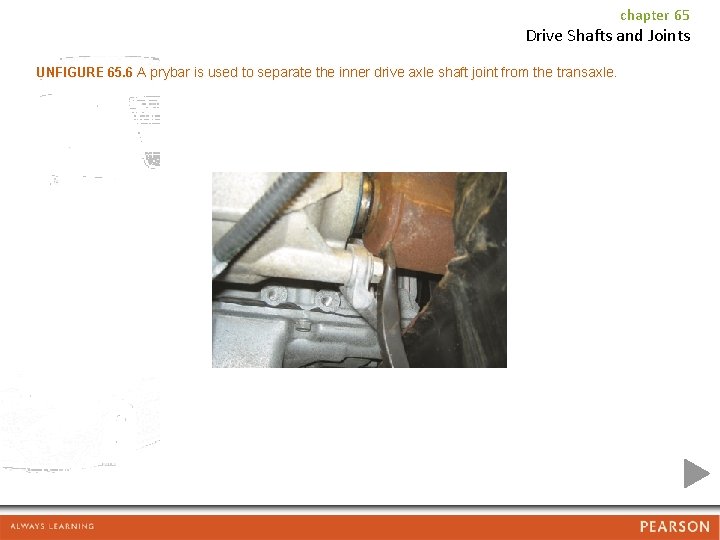
chapter 65 Drive Shafts and Joints UNFIGURE 65. 6 A prybar is used to separate the inner drive axle shaft joint from the transaxle.

chapter 65 Drive Shafts and Joints UNFIGURE 65. 7 After the inner joint splines have been released from the transaxle, carefully remove the drive axle shaft assembly from the vehicle.
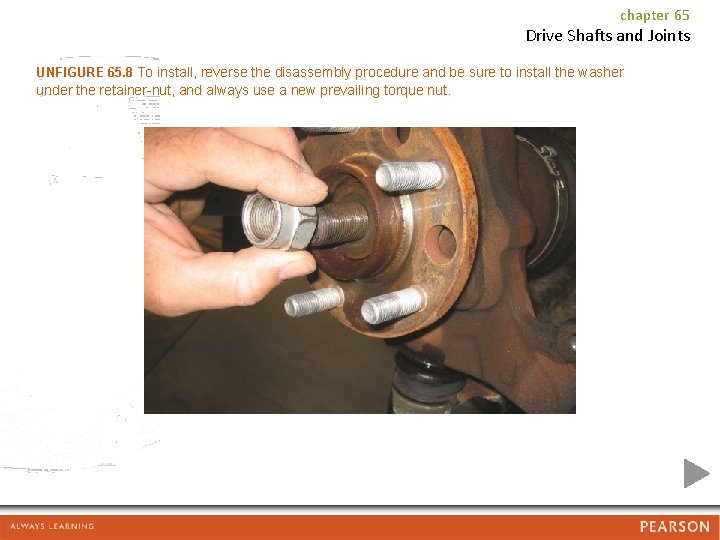
chapter 65 Drive Shafts and Joints UNFIGURE 65. 8 To install, reverse the disassembly procedure and be sure to install the washer under the retainer-nut, and always use a new prevailing torque nut.
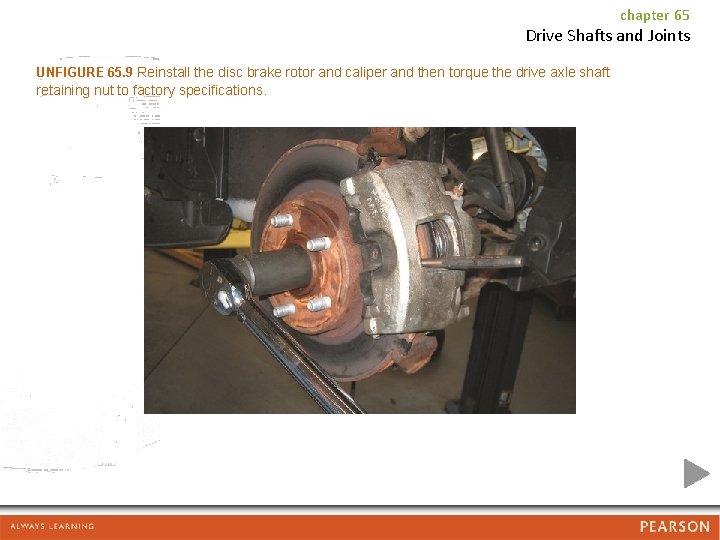
chapter 65 Drive Shafts and Joints UNFIGURE 65. 9 Reinstall the disc brake rotor and caliper and then torque the drive axle shaft retaining nut to factory specifications.
Googlehttps://drive.google.com/drive/my-drive
Https://slidetodoc.com
Rit google drive
Elastic curve of a beam
Globed like a full sail strung
Cross belt drive
Difference between chain drive and belt drive
Shafts are designed on the basis of
Drawing section views
Technical drawing cut view
Coaxial shafts
To connect two intersecting shafts we use
Torsion equation
Https drive google com file d 1zphjwy1qqf1g
Http drive google com
Comait
Chapter 7 wood joints
Intermittent weld
Link and joint
Folds faults and joints
Seaming sheet metal
Figure 6-4 the skeleton axial and appendicular divisions
Seam joints
Temporary wood joints
3g welding position
Difference between
Why fiber joints and couplers are necessary?
Why is carcase meat prepared into cuts joints and mince
Homeostatic imbalances of bones and joints
Wood joining methods
Types of construction joints
Diarthrotic joints
Tectonic joints
Tectonic joints
Transverse tarsal joints
Synformal anticline
Different types of welded connections
Spinal canal
Gomphoses
Syndesmosis and synchondrosis
Knee joint figure
What are gliding movements
Articulation joint definition
Elbow diagram
Types of joints in concrete pavement
Dissecting chicken leg
Joints geology
Interlocking cement concrete pavement