CHAPTER 10 Mechanical Properties Dislocations and Plastic Deformation
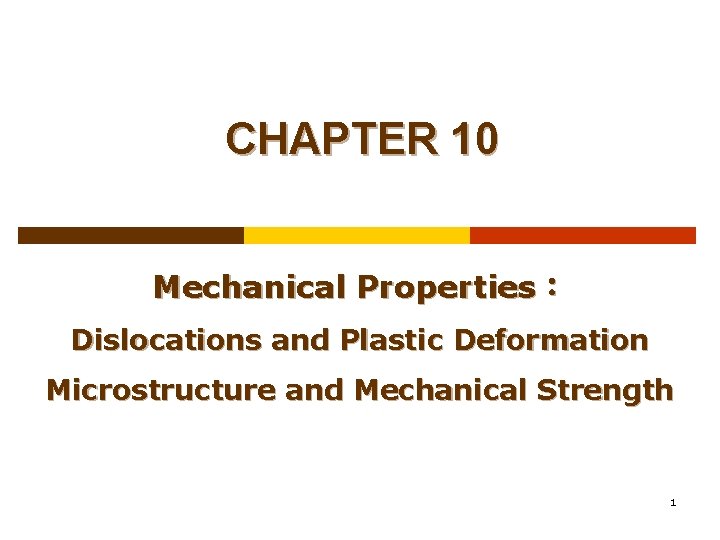
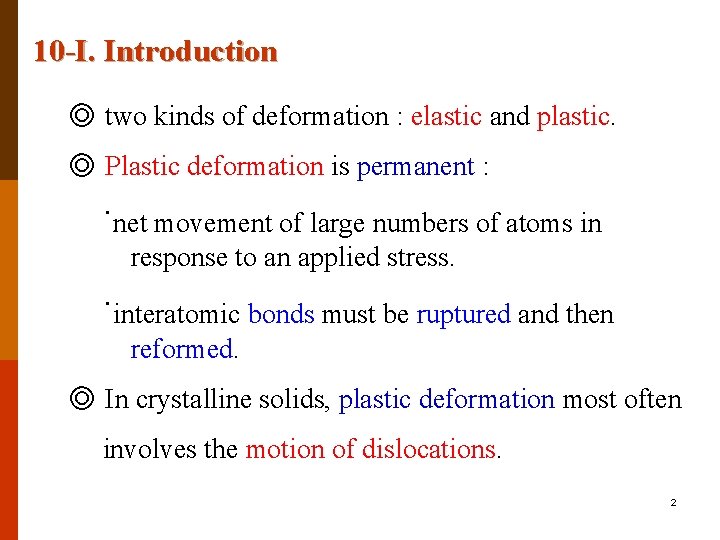
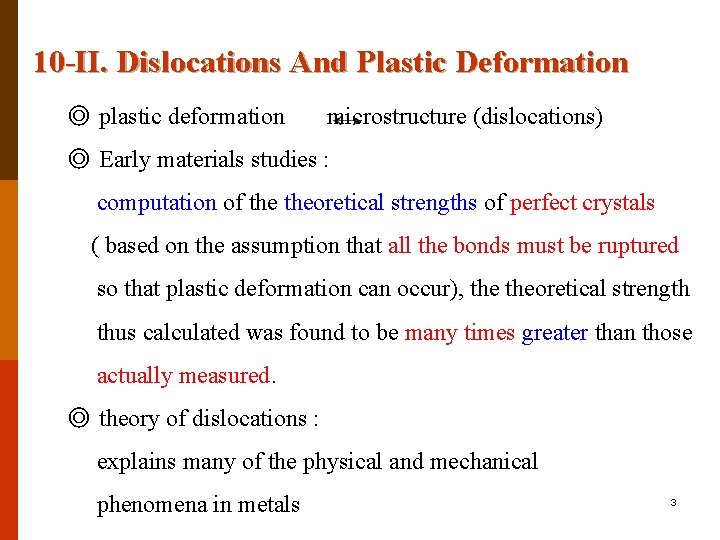
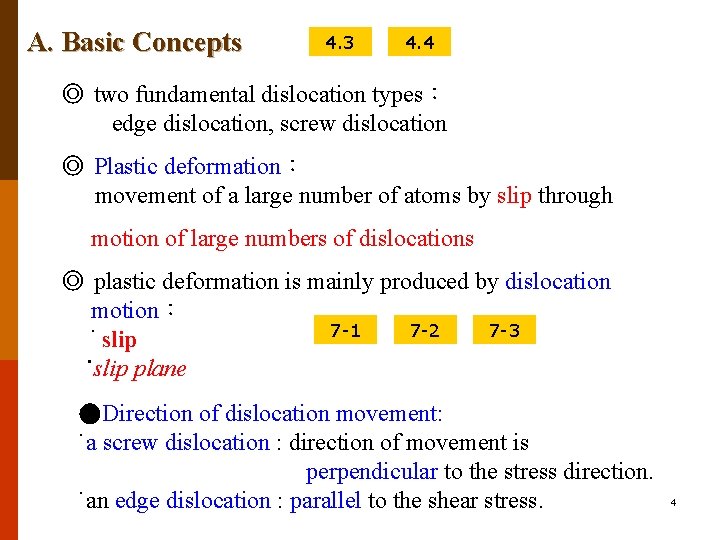

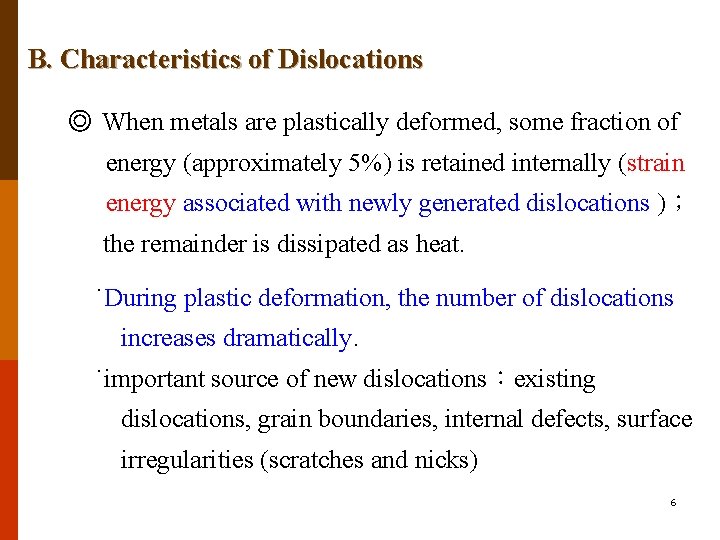
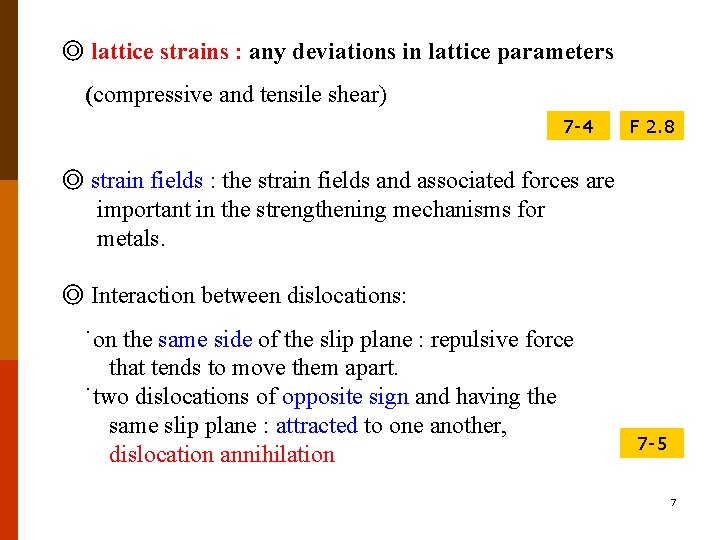
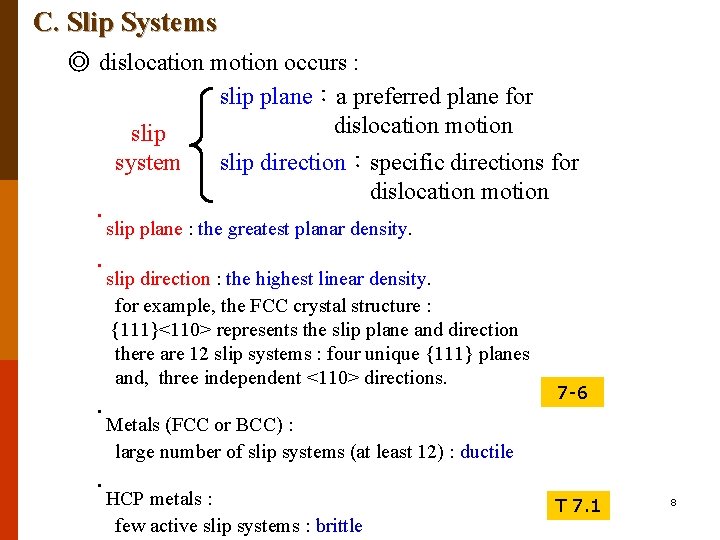
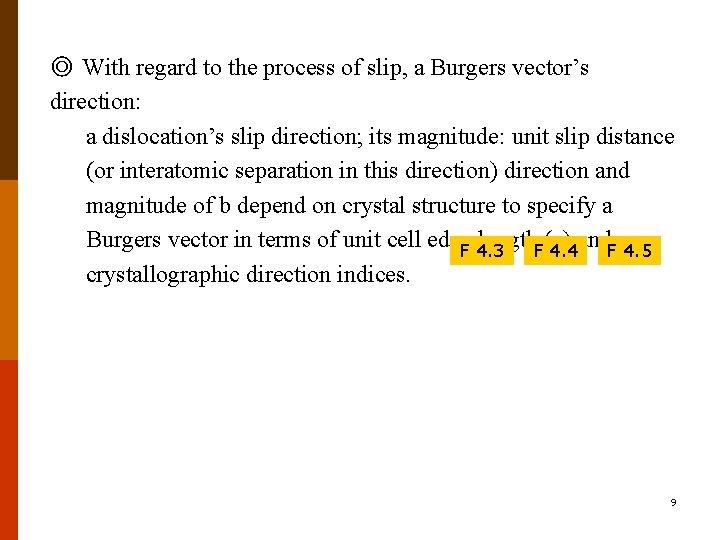
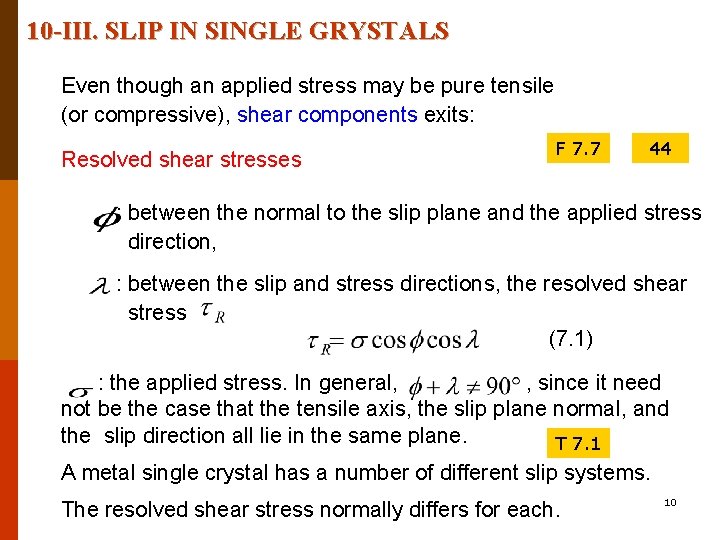
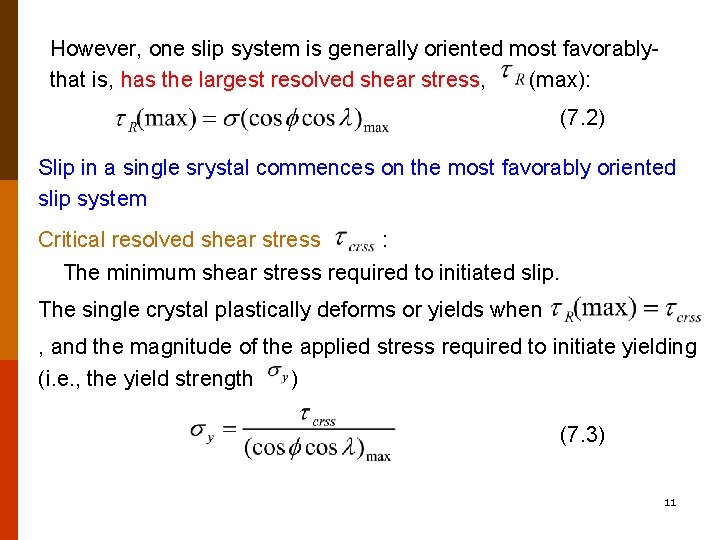
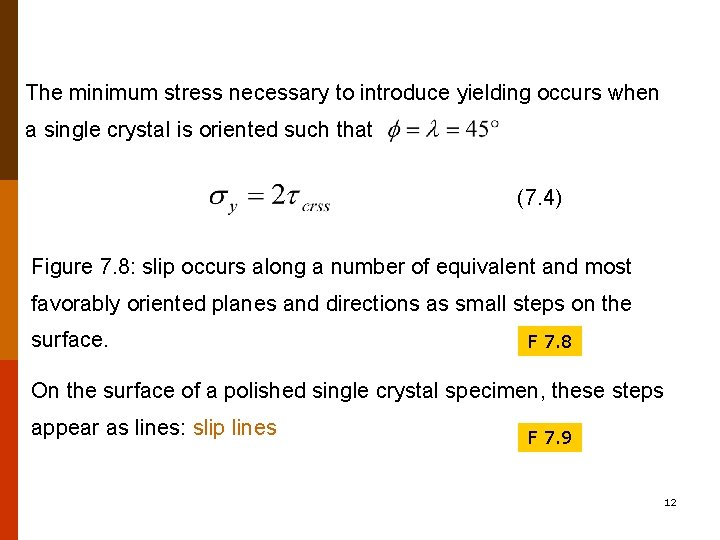
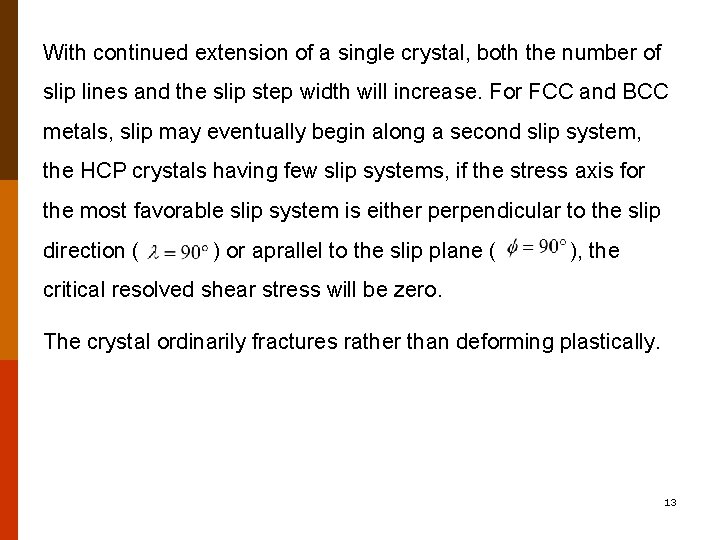
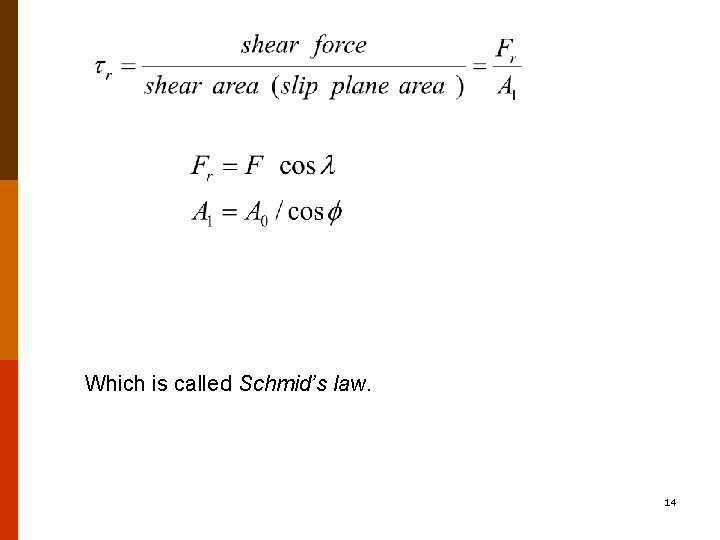
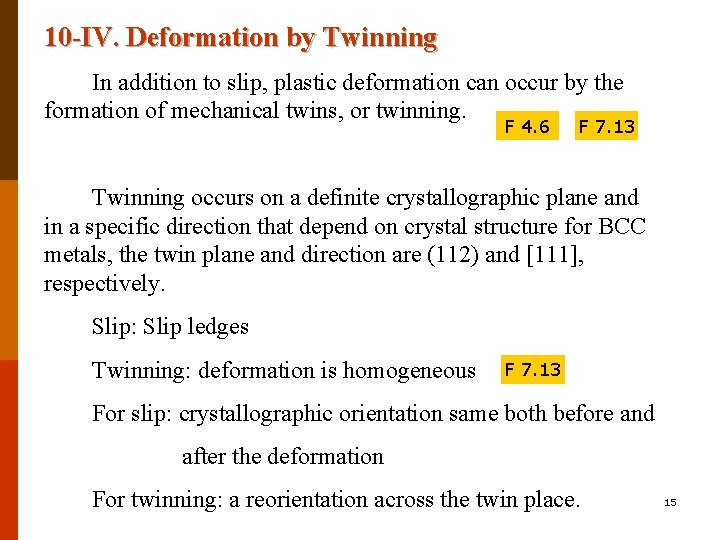
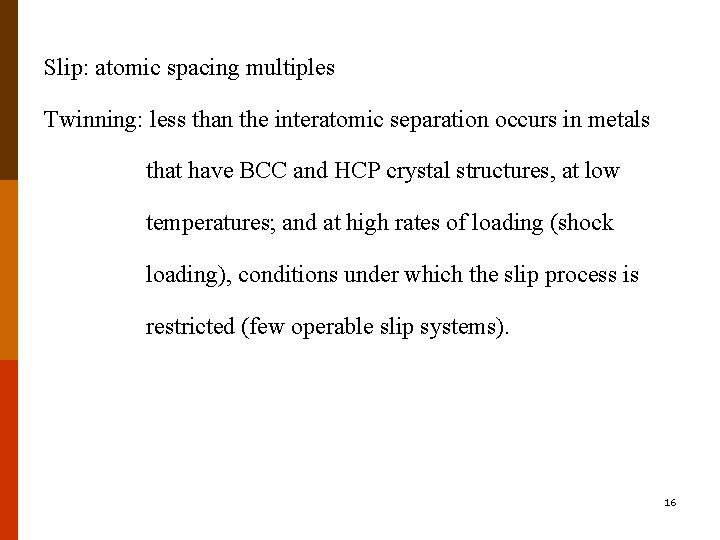
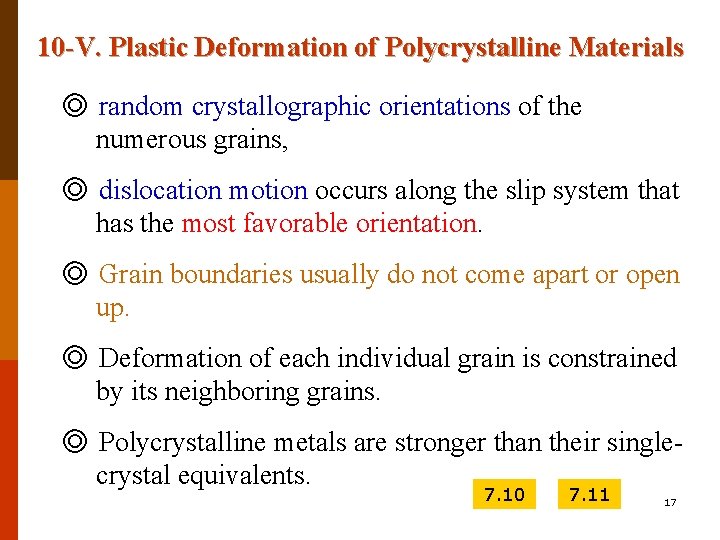
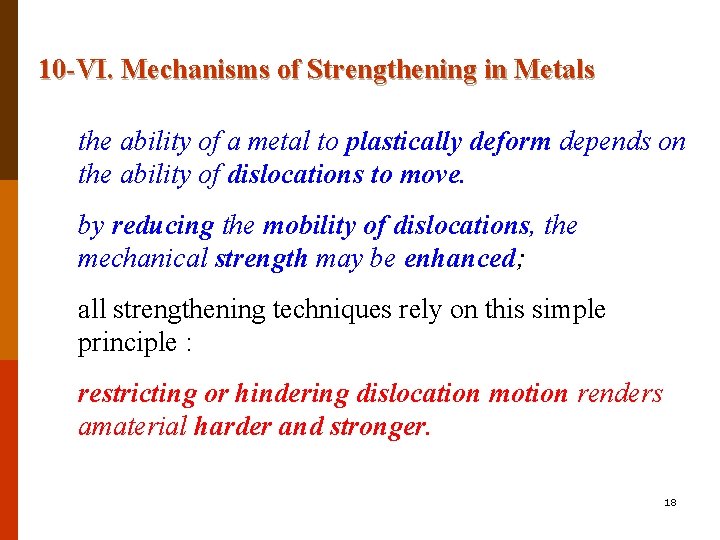
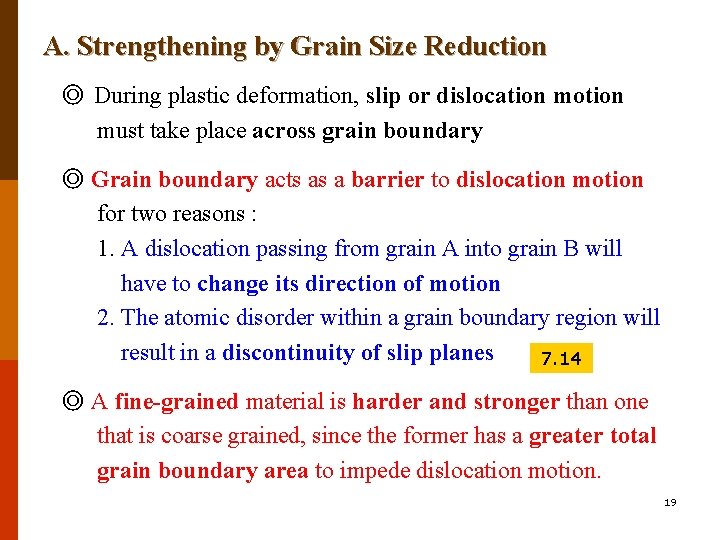
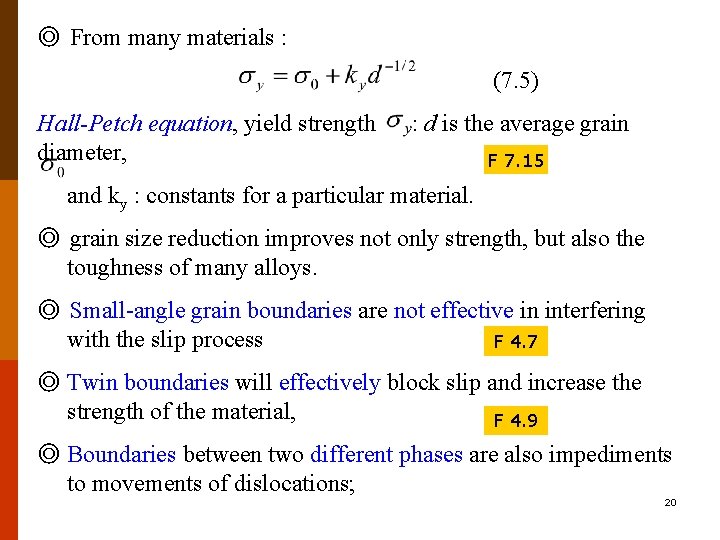
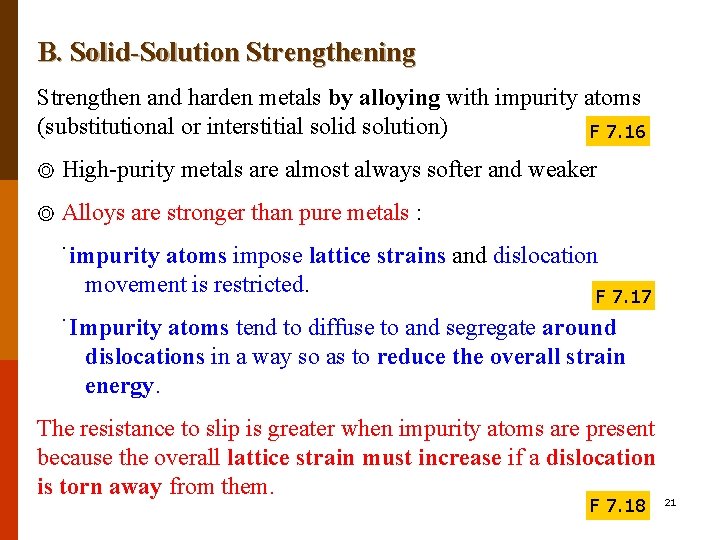

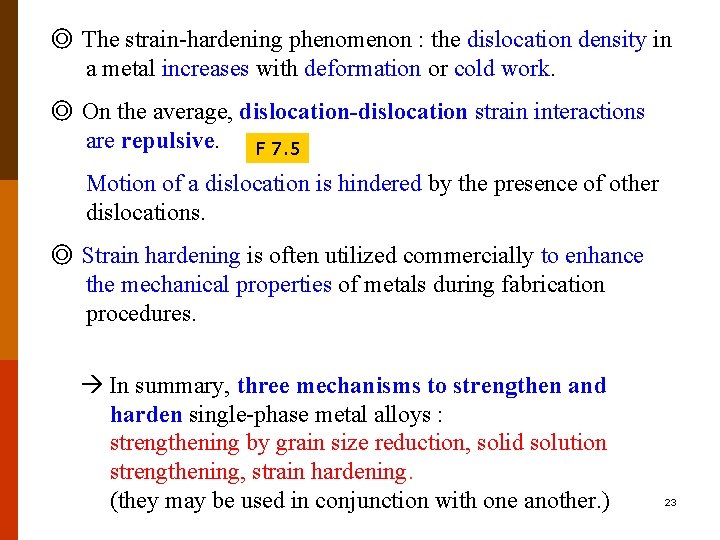
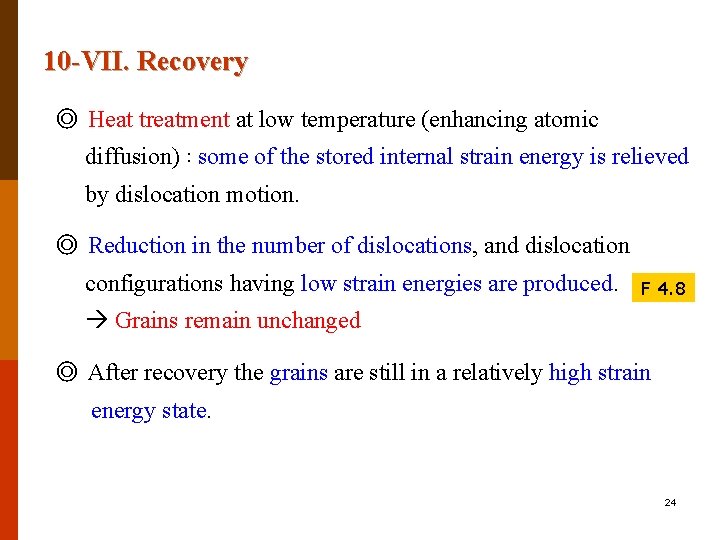
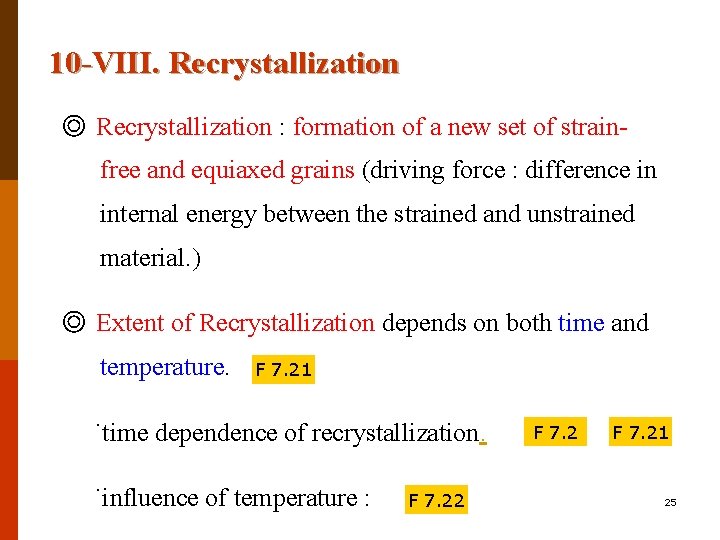
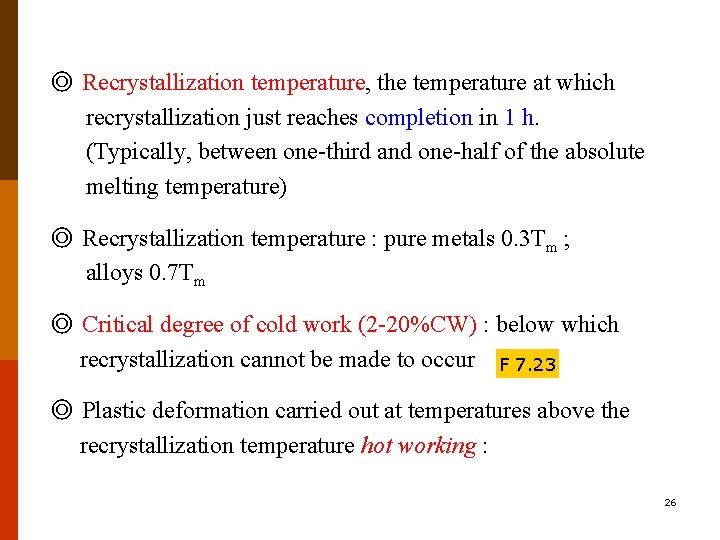
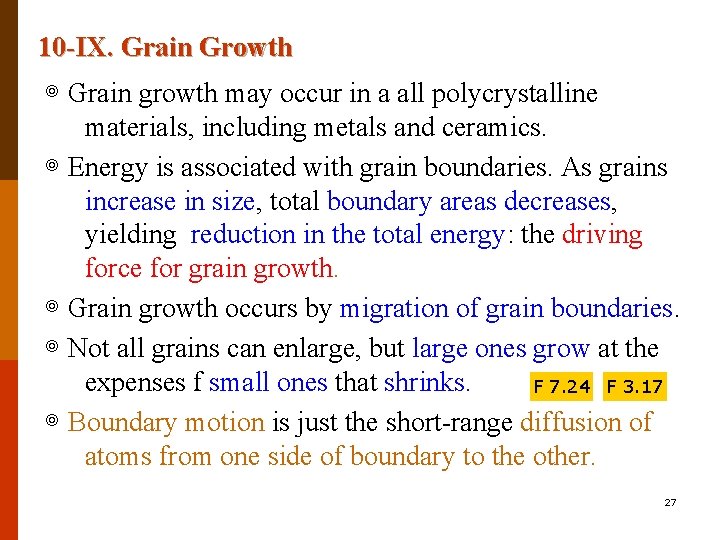
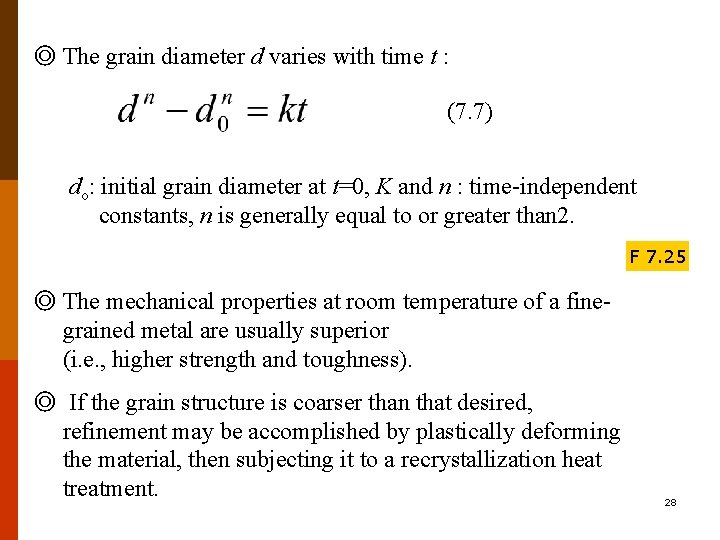
- Slides: 28
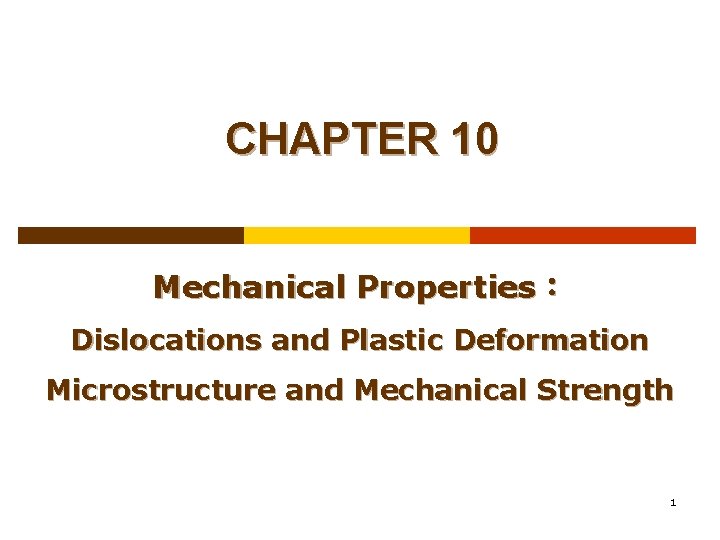
CHAPTER 10 Mechanical Properties: Dislocations and Plastic Deformation Microstructure and Mechanical Strength 1
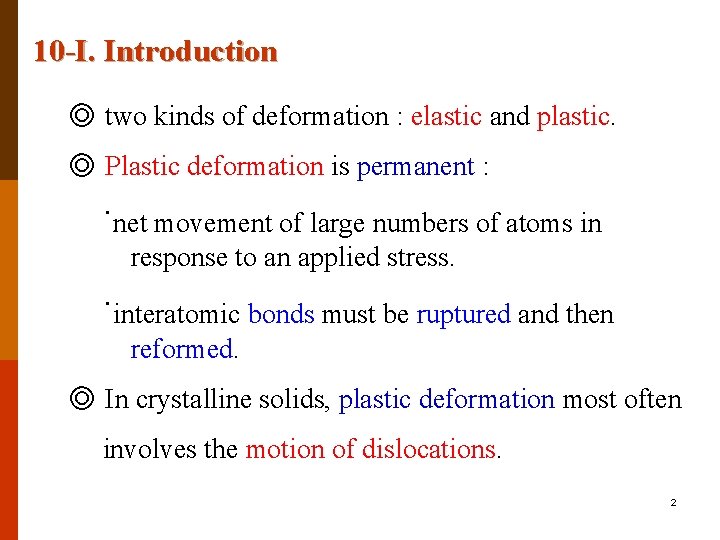
10 -I. Introduction ◎ two kinds of deformation : elastic and plastic. ◎ Plastic deformation is permanent : ˙net movement of large numbers of atoms in response to an applied stress. ˙interatomic bonds must be ruptured and then reformed. ◎ In crystalline solids, plastic deformation most often involves the motion of dislocations. 2
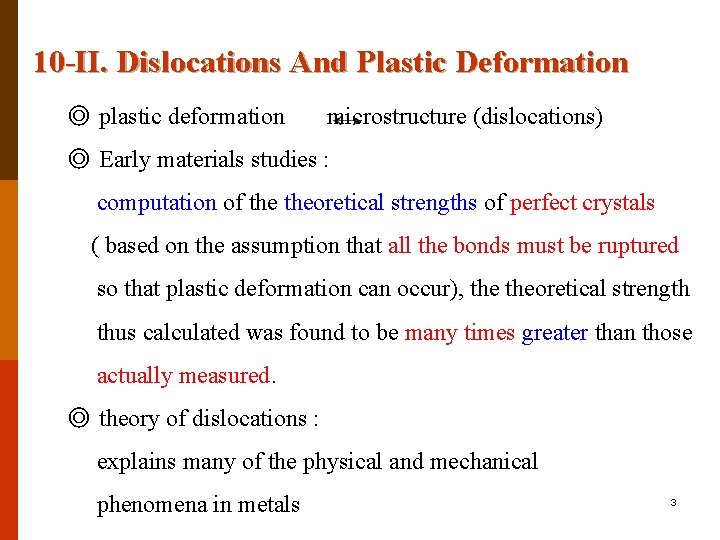
10 -II. Dislocations And Plastic Deformation ◎ plastic deformation microstructure (dislocations) ◎ Early materials studies : computation of theoretical strengths of perfect crystals ( based on the assumption that all the bonds must be ruptured so that plastic deformation can occur), theoretical strength thus calculated was found to be many times greater than those actually measured. ◎ theory of dislocations : explains many of the physical and mechanical phenomena in metals 3
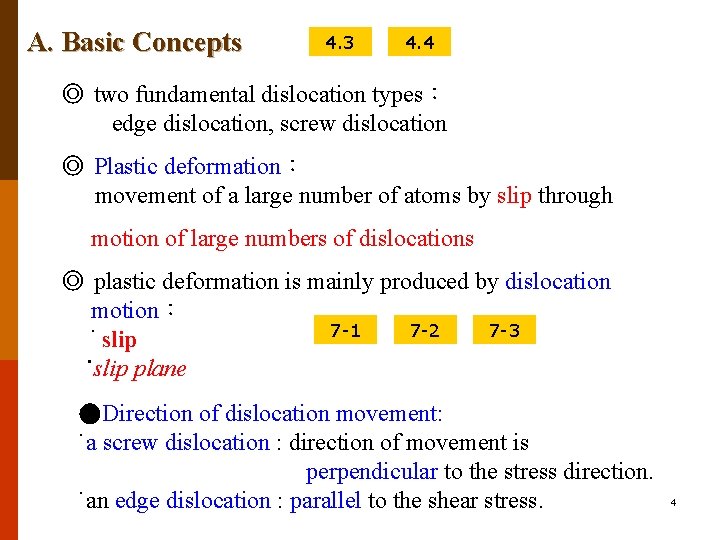
A. Basic Concepts 4. 3 4. 4 ◎ two fundamental dislocation types: edge dislocation, screw dislocation ◎ Plastic deformation: movement of a large number of atoms by slip through motion of large numbers of dislocations ◎ plastic deformation is mainly produced by dislocation motion: 7 -1 7 -2 7 -3 ˙slip plane ●Direction of dislocation movement: ˙a screw dislocation : direction of movement is perpendicular to the stress direction. ˙an edge dislocation : parallel to the shear stress. 4

◎ dislocation density F 0604 ˙total dislocation length per unit volume or number of dislocations that intersect a unit area. ˙for carefully solidified metal crystals : 103 mm-2 ˙for heavily deformed metals : 109 to 1010 mm-2 ˙ceramic materials : 102 and 104 mm-2; ˙silicon single crystals used in integrated circuits : 0. 1 and 1 mm-2. 5
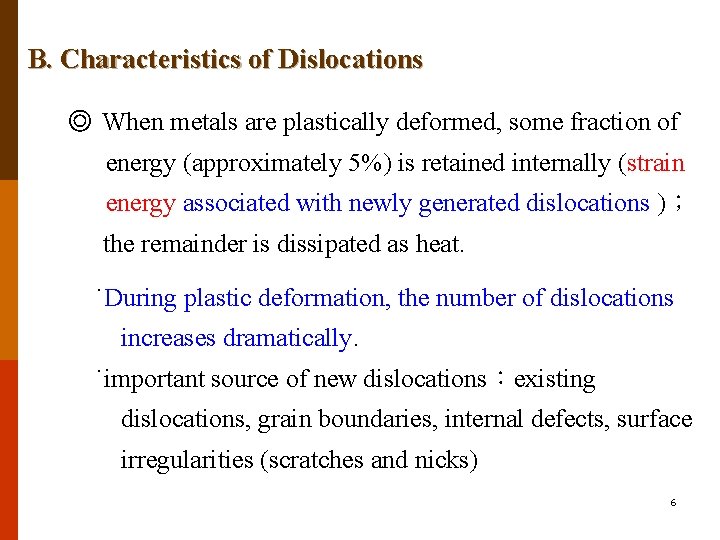
B. Characteristics of Dislocations ◎ When metals are plastically deformed, some fraction of energy (approximately 5%) is retained internally (strain energy associated with newly generated dislocations ); the remainder is dissipated as heat. ˙During plastic deformation, the number of dislocations increases dramatically. ˙important source of new dislocations:existing dislocations, grain boundaries, internal defects, surface irregularities (scratches and nicks) 6
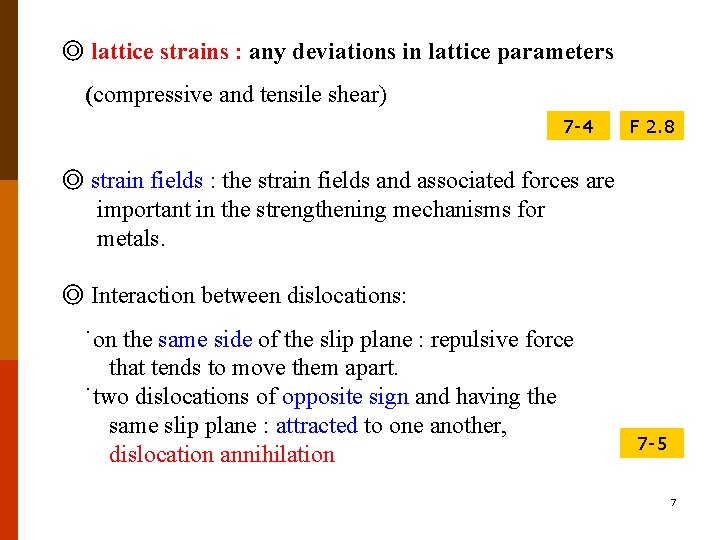
◎ lattice strains : any deviations in lattice parameters (compressive and tensile shear) 7 -4 F 2. 8 ◎ strain fields : the strain fields and associated forces are important in the strengthening mechanisms for metals. ◎ Interaction between dislocations: ˙on the same side of the slip plane : repulsive force that tends to move them apart. ˙two dislocations of opposite sign and having the same slip plane : attracted to one another, dislocation annihilation 7 -5 7
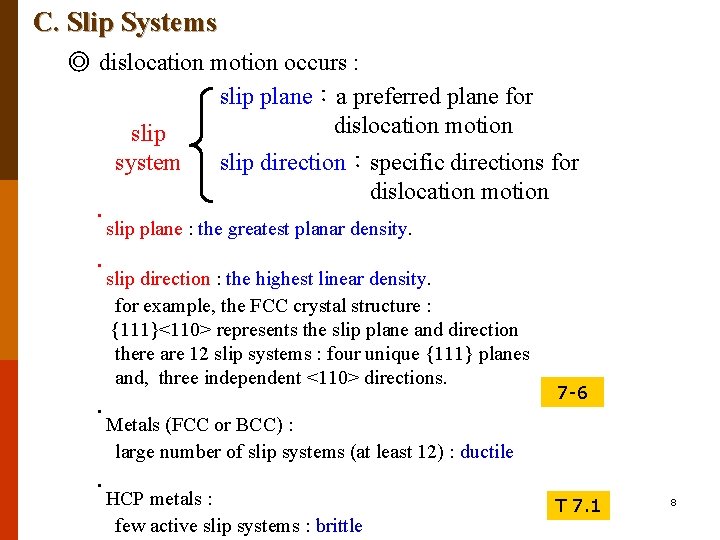
C. Slip Systems ◎ dislocation motion occurs : slip plane:a preferred plane for dislocation motion slip system slip direction:specific directions for dislocation motion ˙slip plane : the greatest planar density. ˙slip direction : the highest linear density. for example, the FCC crystal structure : {111}<110> represents the slip plane and direction there are 12 slip systems : four unique {111} planes and, three independent <110> directions. ˙Metals (FCC or BCC) : 7 -6 large number of slip systems (at least 12) : ductile ˙HCP metals : few active slip systems : brittle T 7. 1 8
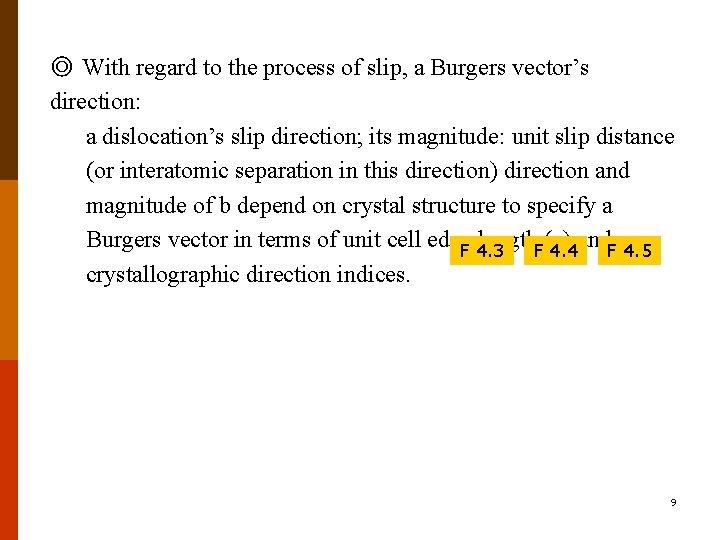
◎ With regard to the process of slip, a Burgers vector’s direction: a dislocation’s slip direction; its magnitude: unit slip distance (or interatomic separation in this direction) direction and magnitude of b depend on crystal structure to specify a Burgers vector in terms of unit cell edge length. F (a) and. F 4. 5 F 4. 3 4. 4 crystallographic direction indices. 9
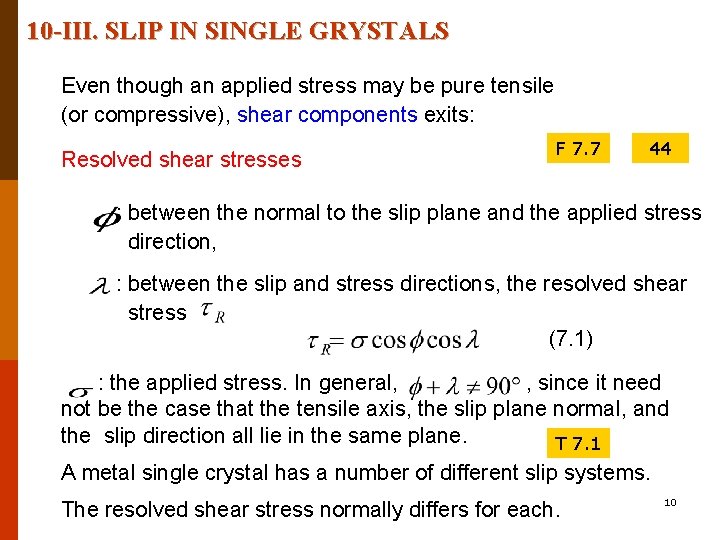
10 -III. SLIP IN SINGLE GRYSTALS Even though an applied stress may be pure tensile (or compressive), shear components exits: Resolved shear stresses F 7. 7 44 : between the normal to the slip plane and the applied stress direction, : between the slip and stress directions, the resolved shear stress (7. 1) : the applied stress. In general, , since it need not be the case that the tensile axis, the slip plane normal, and the slip direction all lie in the same plane. T 7. 1 A metal single crystal has a number of different slip systems. The resolved shear stress normally differs for each. 10
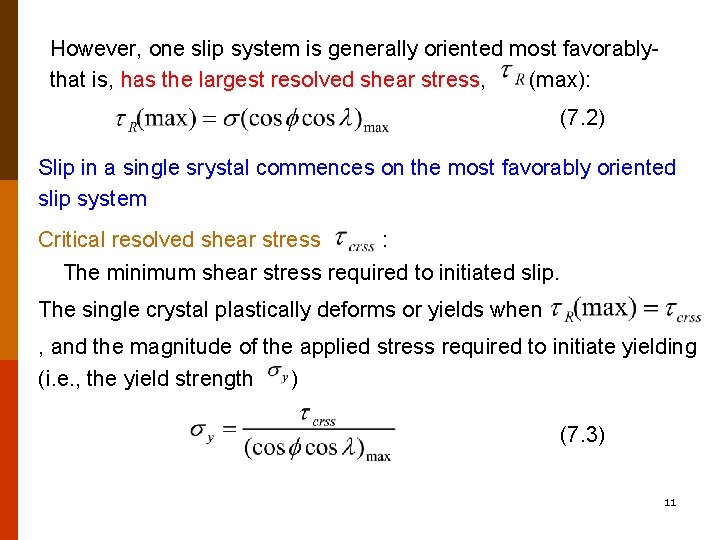
However, one slip system is generally oriented most favorablythat is, has the largest resolved shear stress, (max): (7. 2) Slip in a single srystal commences on the most favorably oriented slip system Critical resolved shear stress : The minimum shear stress required to initiated slip. The single crystal plastically deforms or yields when , and the magnitude of the applied stress required to initiate yielding (i. e. , the yield strength ) (7. 3) 11
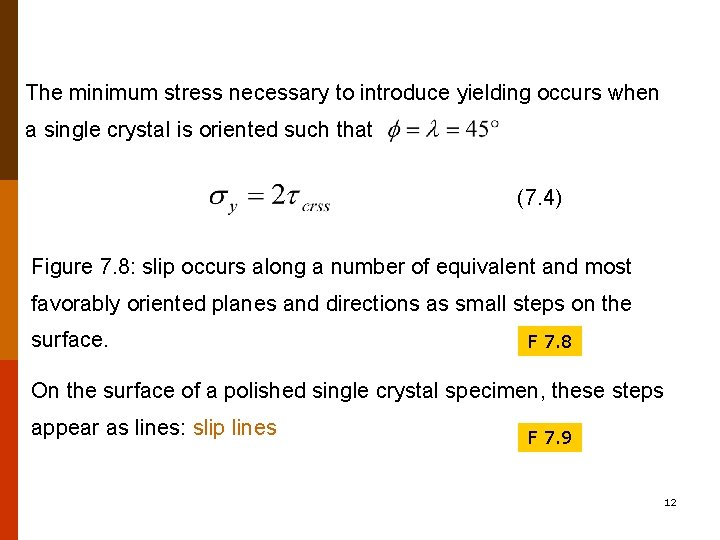
The minimum stress necessary to introduce yielding occurs when a single crystal is oriented such that (7. 4) Figure 7. 8: slip occurs along a number of equivalent and most favorably oriented planes and directions as small steps on the surface. F 7. 8 On the surface of a polished single crystal specimen, these steps appear as lines: slip lines F 7. 9 12
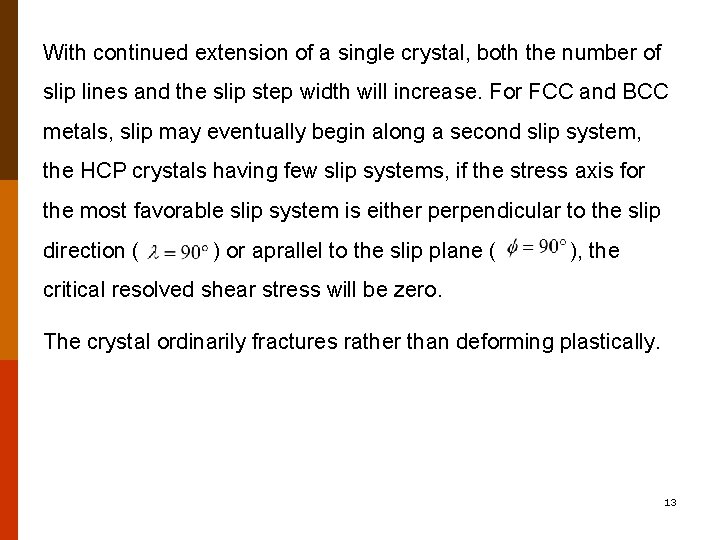
With continued extension of a single crystal, both the number of slip lines and the slip step width will increase. For FCC and BCC metals, slip may eventually begin along a second slip system, the HCP crystals having few slip systems, if the stress axis for the most favorable slip system is either perpendicular to the slip direction ( ) or aprallel to the slip plane ( ), the critical resolved shear stress will be zero. The crystal ordinarily fractures rather than deforming plastically. 13
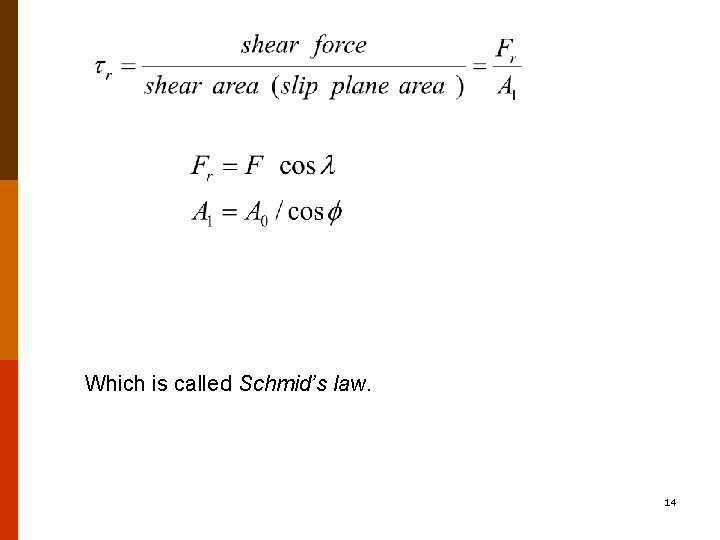
Which is called Schmid’s law. 14
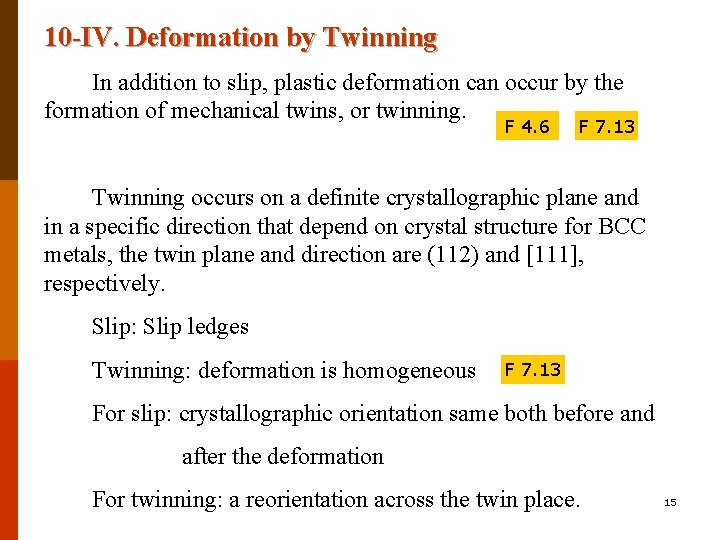
10 -IV. Deformation by Twinning In addition to slip, plastic deformation can occur by the formation of mechanical twins, or twinning. F 4. 6 F 7. 13 Twinning occurs on a definite crystallographic plane and in a specific direction that depend on crystal structure for BCC metals, the twin plane and direction are (112) and [111], respectively. Slip: Slip ledges Twinning: deformation is homogeneous F 7. 13 For slip: crystallographic orientation same both before and after the deformation For twinning: a reorientation across the twin place. 15
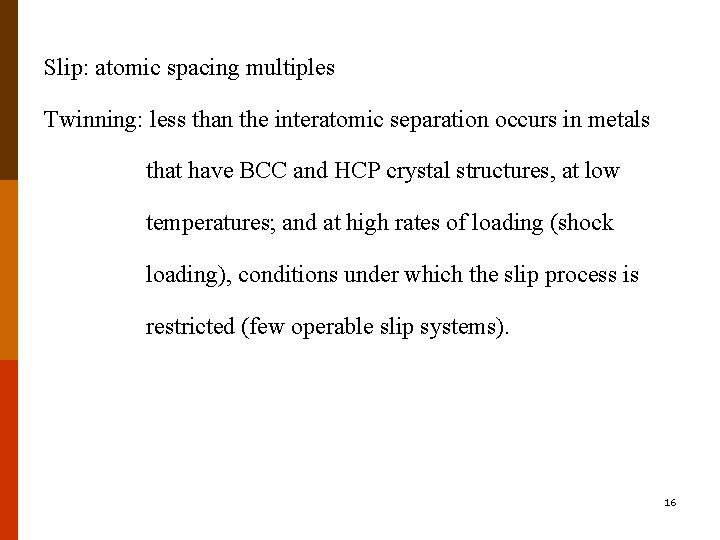
Slip: atomic spacing multiples Twinning: less than the interatomic separation occurs in metals that have BCC and HCP crystal structures, at low temperatures; and at high rates of loading (shock loading), conditions under which the slip process is restricted (few operable slip systems). 16
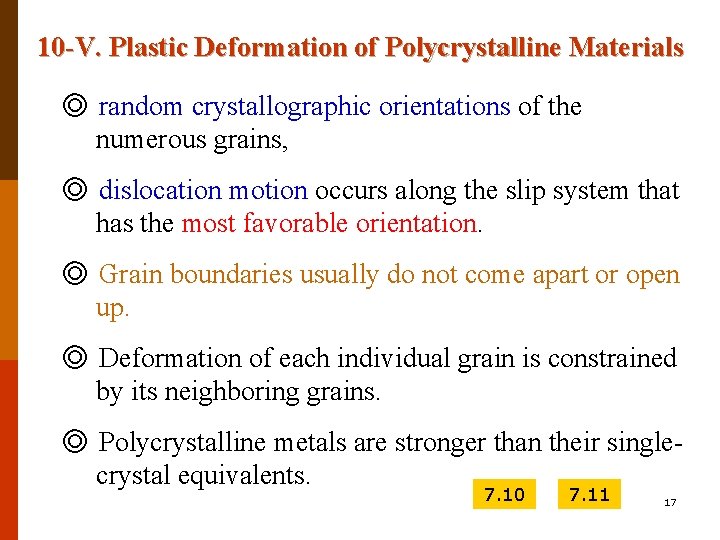
10 -V. Plastic Deformation of Polycrystalline Materials ◎ random crystallographic orientations of the numerous grains, ◎ dislocation motion occurs along the slip system that has the most favorable orientation. ◎ Grain boundaries usually do not come apart or open up. ◎ Deformation of each individual grain is constrained by its neighboring grains. ◎ Polycrystalline metals are stronger than their singlecrystal equivalents. 7. 10 7. 11 17
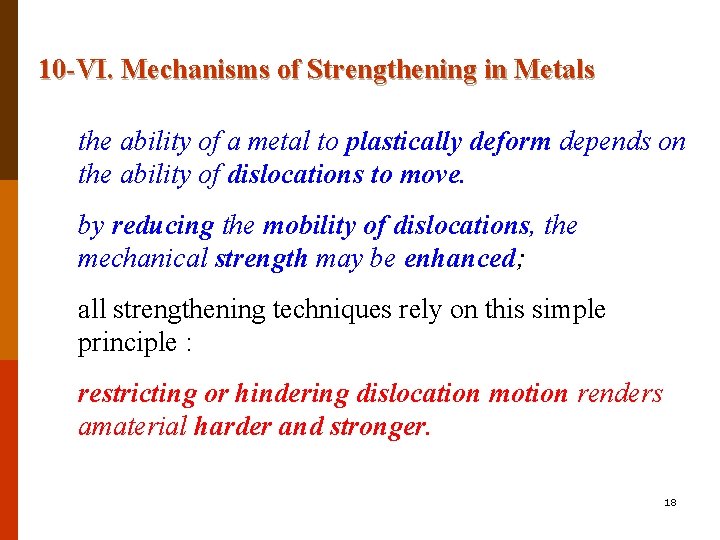
10 -VI. Mechanisms of Strengthening in Metals the ability of a metal to plastically deform depends on the ability of dislocations to move. by reducing the mobility of dislocations, the mechanical strength may be enhanced; all strengthening techniques rely on this simple principle : restricting or hindering dislocation motion renders amaterial harder and stronger. 18
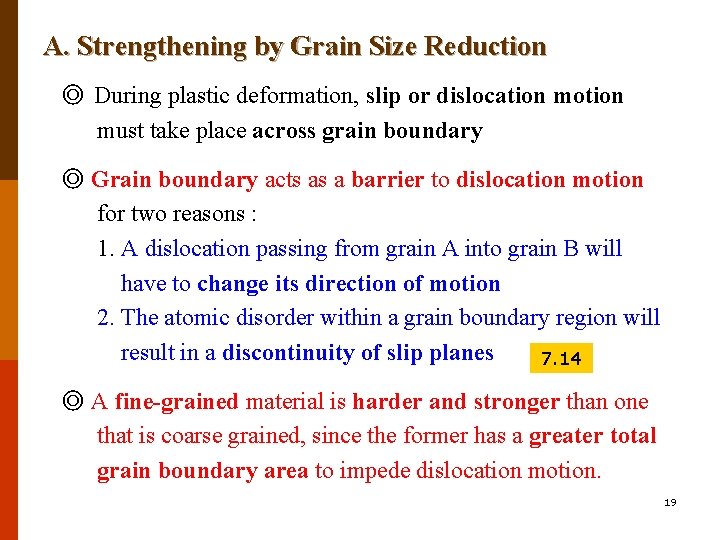
A. Strengthening by Grain Size Reduction ◎ During plastic deformation, slip or dislocation motion must take place across grain boundary ◎ Grain boundary acts as a barrier to dislocation motion for two reasons : 1. A dislocation passing from grain A into grain B will have to change its direction of motion 2. The atomic disorder within a grain boundary region will result in a discontinuity of slip planes 7. 14 ◎ A fine-grained material is harder and stronger than one that is coarse grained, since the former has a greater total grain boundary area to impede dislocation motion. 19
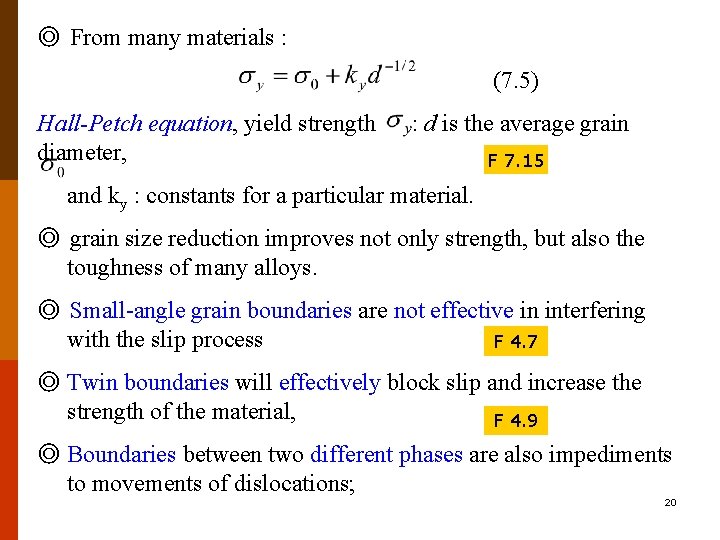
◎ From many materials : (7. 5) Hall-Petch equation, yield strength diameter, : d is the average grain F 7. 15 and ky : constants for a particular material. ◎ grain size reduction improves not only strength, but also the toughness of many alloys. ◎ Small-angle grain boundaries are not effective in interfering with the slip process F 4. 7 ◎ Twin boundaries will effectively block slip and increase the strength of the material, F 4. 9 ◎ Boundaries between two different phases are also impediments to movements of dislocations; 20
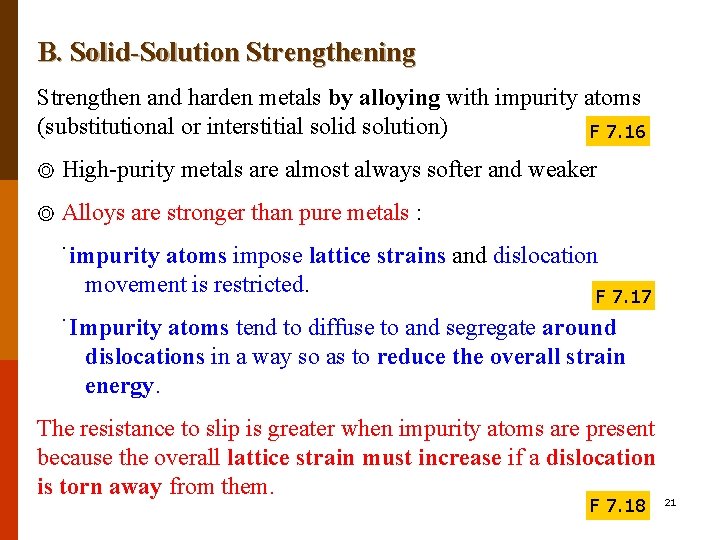
B. Solid-Solution Strengthening Strengthen and harden metals by alloying with impurity atoms (substitutional or interstitial solid solution) F 7. 16 ◎ High-purity metals are almost always softer and weaker ◎ Alloys are stronger than pure metals : ˙impurity atoms impose lattice strains and dislocation movement is restricted. F 7. 17 ˙Impurity atoms tend to diffuse to and segregate around dislocations in a way so as to reduce the overall strain energy. The resistance to slip is greater when impurity atoms are present because the overall lattice strain must increase if a dislocation is torn away from them. F 7. 18 21

C. Strain Hardening ◎ A ductile metal becomes harder and stronger as it is plastically deformed. (also called work hardening or cold working. ) ◎ It is sometimes convenient to express the degree of plastic deformation as percent cold work (%CW) rather than as strain. (7. 6) A 0 : original area of the cross section Ad : the area after deformation. ◎ Strain hardening can be demonstrated in a stress-strain diagram : F 7. 19 F 7. 20 22
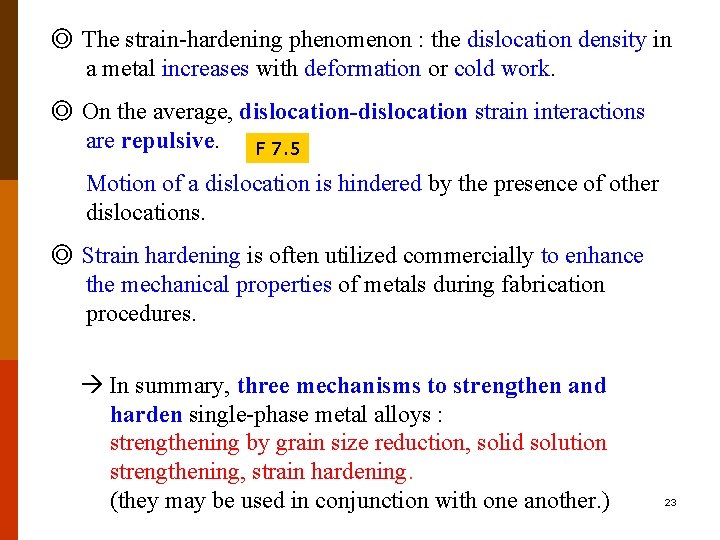
◎ The strain-hardening phenomenon : the dislocation density in a metal increases with deformation or cold work. ◎ On the average, dislocation-dislocation strain interactions are repulsive. F 7. 5 Motion of a dislocation is hindered by the presence of other dislocations. ◎ Strain hardening is often utilized commercially to enhance the mechanical properties of metals during fabrication procedures. In summary, three mechanisms to strengthen and harden single-phase metal alloys : strengthening by grain size reduction, solid solution strengthening, strain hardening. (they may be used in conjunction with one another. ) 23
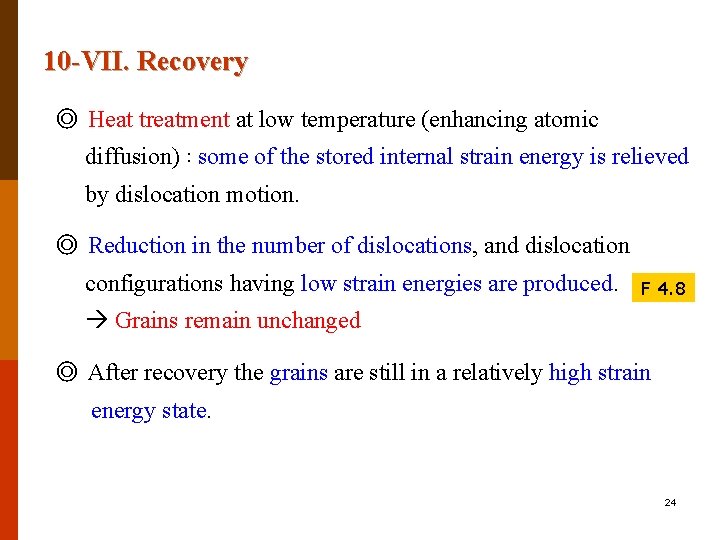
10 -VII. Recovery ◎ Heat treatment at low temperature (enhancing atomic diffusion):some of the stored internal strain energy is relieved by dislocation motion. ◎ Reduction in the number of dislocations, and dislocation configurations having low strain energies are produced. F 4. 8 Grains remain unchanged ◎ After recovery the grains are still in a relatively high strain energy state. 24
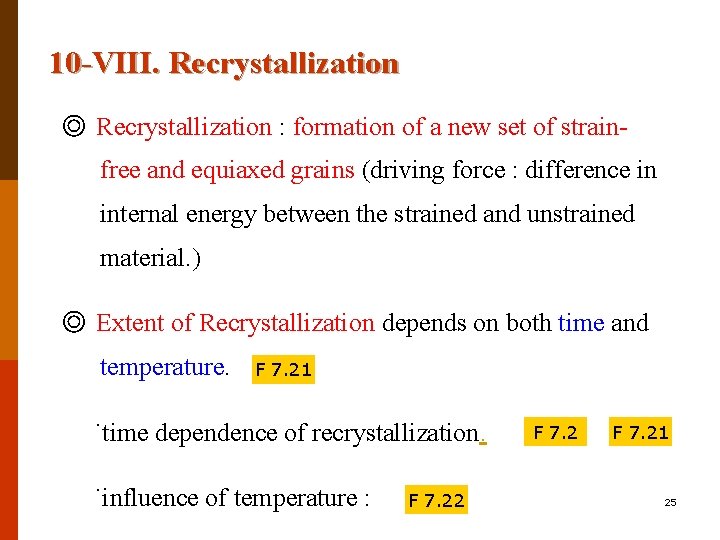
10 -VIII. Recrystallization ◎ Recrystallization : formation of a new set of strainfree and equiaxed grains (driving force : difference in internal energy between the strained and unstrained material. ) ◎ Extent of Recrystallization depends on both time and temperature. F 7. 21 ˙time dependence of recrystallization. ˙influence of temperature : F 7. 22 F 7. 21 25
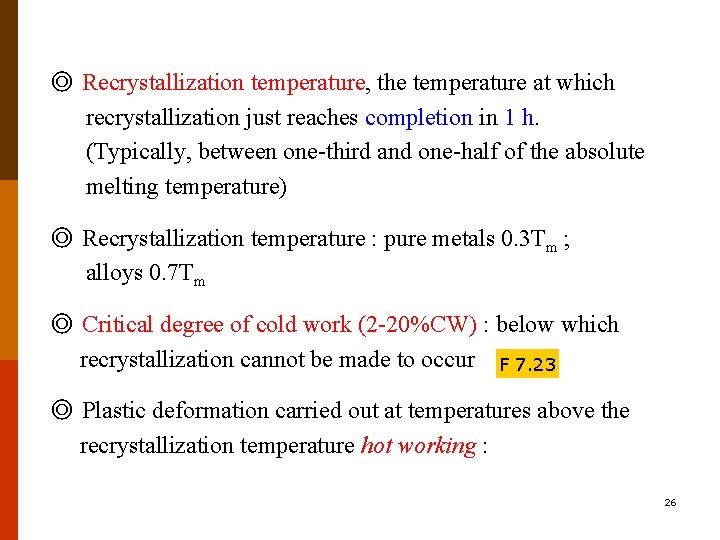
◎ Recrystallization temperature, the temperature at which recrystallization just reaches completion in 1 h. (Typically, between one-third and one-half of the absolute melting temperature) ◎ Recrystallization temperature : pure metals 0. 3 Tm ; alloys 0. 7 Tm ◎ Critical degree of cold work (2 -20%CW) : below which recrystallization cannot be made to occur F 7. 23 ◎ Plastic deformation carried out at temperatures above the recrystallization temperature hot working : 26
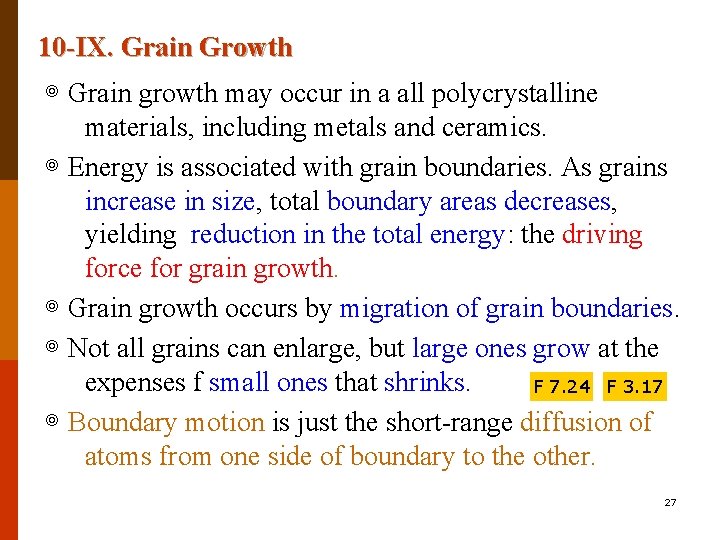
10 -IX. Grain Growth ◎ Grain growth may occur in a all polycrystalline materials, including metals and ceramics. ◎ Energy is associated with grain boundaries. As grains increase in size, total boundary areas decreases, yielding reduction in the total energy: the driving force for grain growth. ◎ Grain growth occurs by migration of grain boundaries. ◎ Not all grains can enlarge, but large ones grow at the expenses f small ones that shrinks. F 7. 24 F 3. 17 ◎ Boundary motion is just the short-range diffusion of atoms from one side of boundary to the other. 27
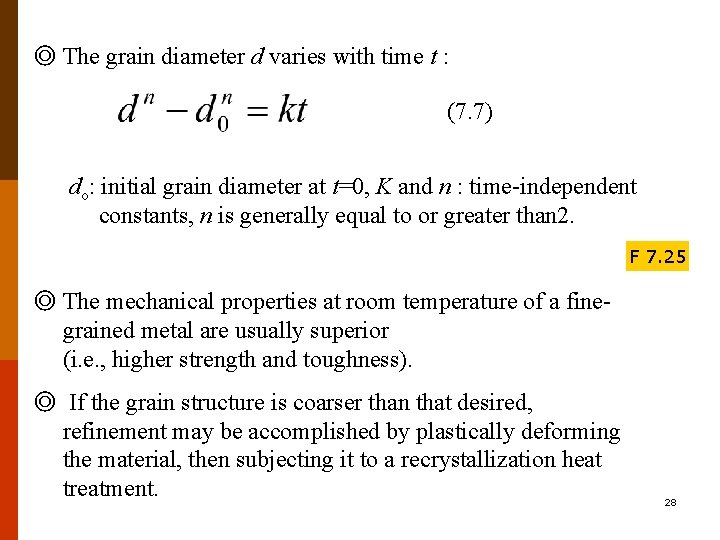
◎ The grain diameter d varies with time t : (7. 7) do: initial grain diameter at t=0, K and n : time-independent constants, n is generally equal to or greater than 2. F 7. 25 ◎ The mechanical properties at room temperature of a finegrained metal are usually superior (i. e. , higher strength and toughness). ◎ If the grain structure is coarser than that desired, refinement may be accomplished by plastically deforming the material, then subjecting it to a recrystallization heat treatment. 28
Elasticdeformation
Dislocations in crystals
Consider two edge dislocations of opposite sign
Plastic region
Elastic and plastic deformation
Deformation plastic
Elastic rebound theory
Properties of plastic
Styrene flammability
Actual mechanical advantage vs ideal mechanical advantage
Extensive examples
Is smell a physical property
Ductility
Mechanical properties of materials
Hardness of nanomaterials
Properties of mechanical waves
Mechanical properties of cardboard
Properties of mechanical waves
Properties of mechanical waves
Mechanical properties of biomaterials
Mechanical properties of metals ppt
Fast and deep deformation approximations
Volcano cutaway
Stress-strain relationship of anisotropic materials are
Deformation and flow of matter
Fundamentals of metal forming
Linear approximations and differentials
Rossby radius of deformation
Torsion sign convention