ADDITIVE MANUFACTURING ENABLING ADVANCED MANUFACTURING NAE Convocation of
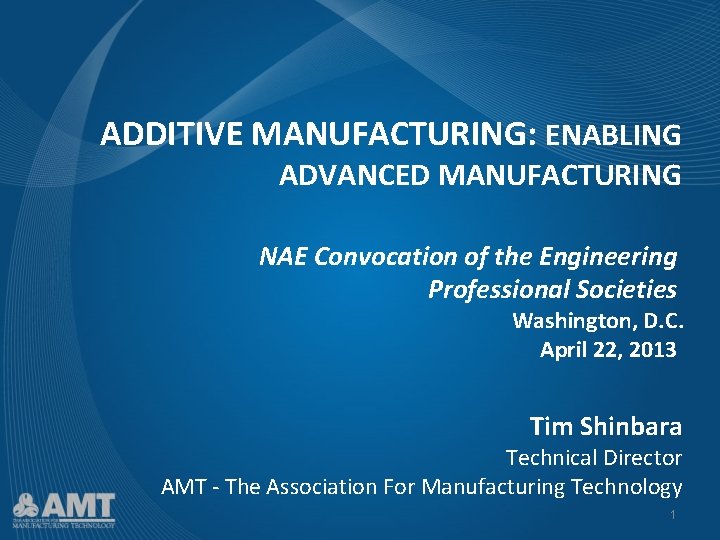
ADDITIVE MANUFACTURING: ENABLING ADVANCED MANUFACTURING NAE Convocation of the Engineering Professional Societies Washington, D. C. April 22, 2013 Tim Shinbara Technical Director AMT - The Association For Manufacturing Technology 1
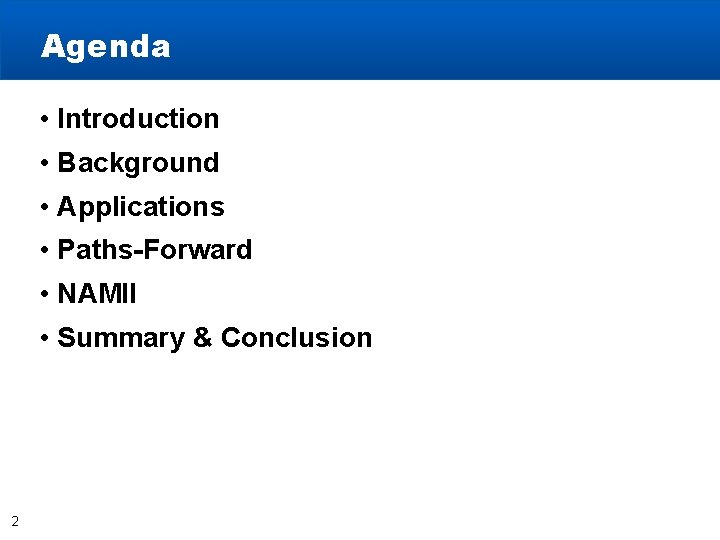
Agenda • Introduction • Background • Applications • Paths-Forward • NAMII • Summary & Conclusion 2
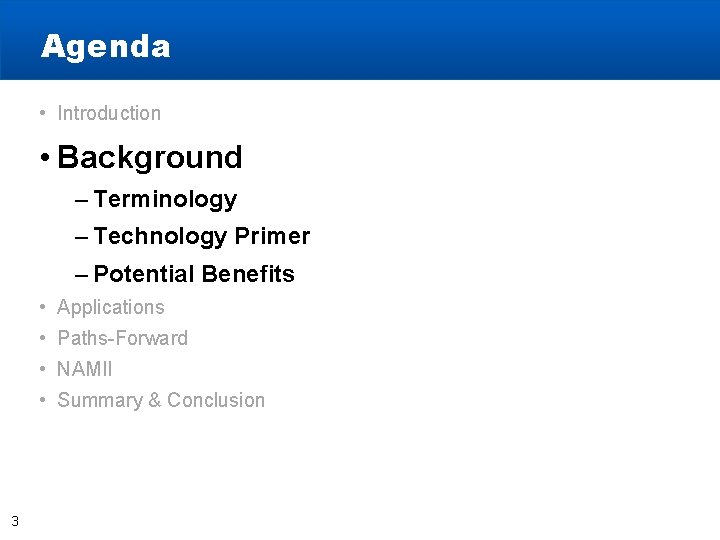
Agenda • Introduction • Background – Terminology – Technology Primer – Potential Benefits • Applications • Paths-Forward • NAMII • Summary & Conclusion 3
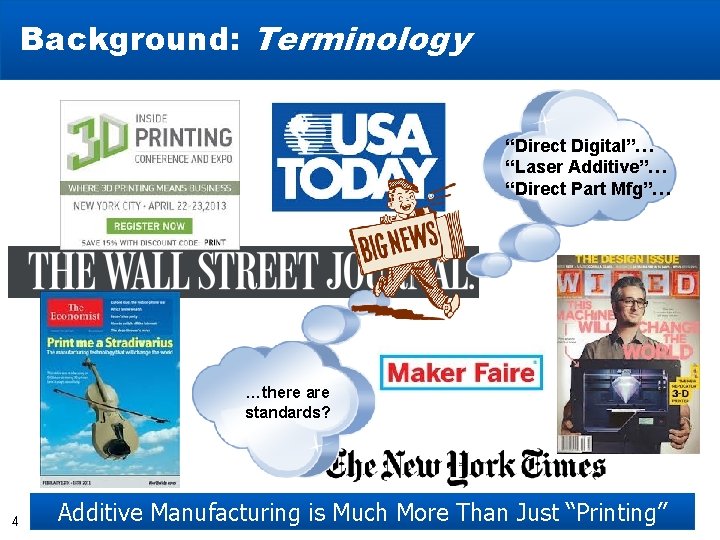
Background: Terminology “Direct Digital”… “Laser Additive”… “Direct Part Mfg”… …there are standards? 4 Additive Manufacturing is Much More Than Just “Printing”
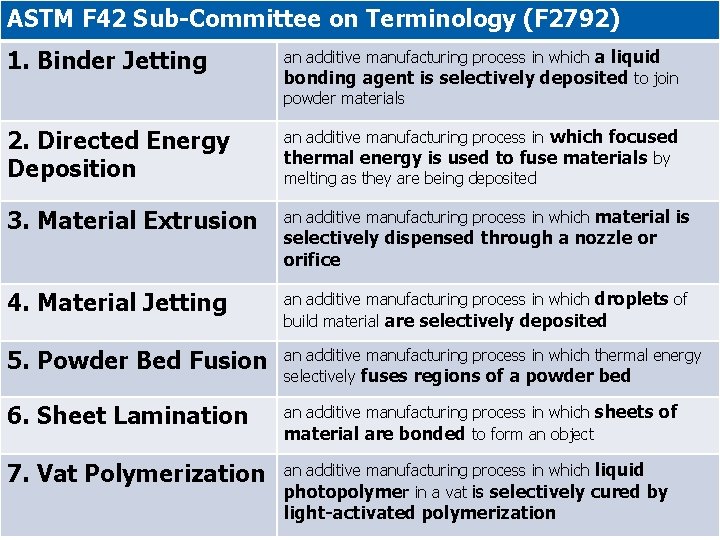
ASTM F 42 Sub-Committee on Terminology (F 2792) 1. Binder Jetting an additive manufacturing process in which a liquid bonding agent is selectively deposited to join powder materials 2. Directed Energy Deposition an additive manufacturing process in which focused thermal energy is used to fuse materials by melting as they are being deposited 3. Material Extrusion an additive manufacturing process in which material is 4. Material Jetting an additive manufacturing process in which droplets of build material are selectively deposited 5. Powder Bed Fusion an additive manufacturing process in which thermal energy selectively fuses regions of a powder bed 6. Sheet Lamination an additive manufacturing process in which sheets of material are bonded to form an object 7. Vat Polymerization an additive manufacturing process in which liquid photopolymer in a vat is selectively cured by 5 selectively dispensed through a nozzle or orifice light-activated polymerization
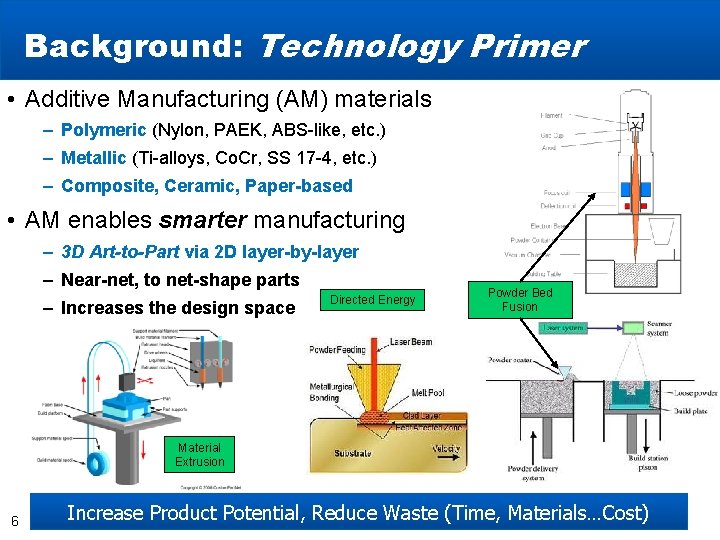
Background: Technology Primer • Additive Manufacturing (AM) materials – Polymeric (Nylon, PAEK, ABS-like, etc. ) – Metallic (Ti-alloys, Co. Cr, SS 17 -4, etc. ) – Composite, Ceramic, Paper-based • AM enables smarter manufacturing – 3 D Art-to-Part via 2 D layer-by-layer – Near-net, to net-shape parts – Increases the design space Directed Energy Powder Bed Fusion Material Extrusion 6 Increase Product Potential, Reduce Waste (Time, Materials…Cost)
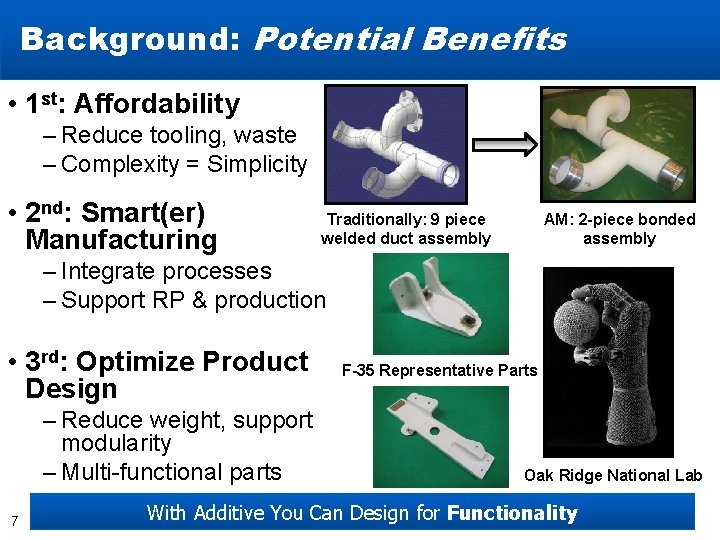
Background: Potential Benefits • 1 st: Affordability – Reduce tooling, waste – Complexity = Simplicity • 2 nd: Smart(er) Manufacturing Traditionally: 9 piece welded duct assembly AM: 2 -piece bonded assembly – Integrate processes – Support RP & production • 3 rd: Optimize Product Design – Reduce weight, support modularity – Multi-functional parts 7 F-35 Representative Parts Oak Ridge National Lab With Additive You Can Design for Functionality
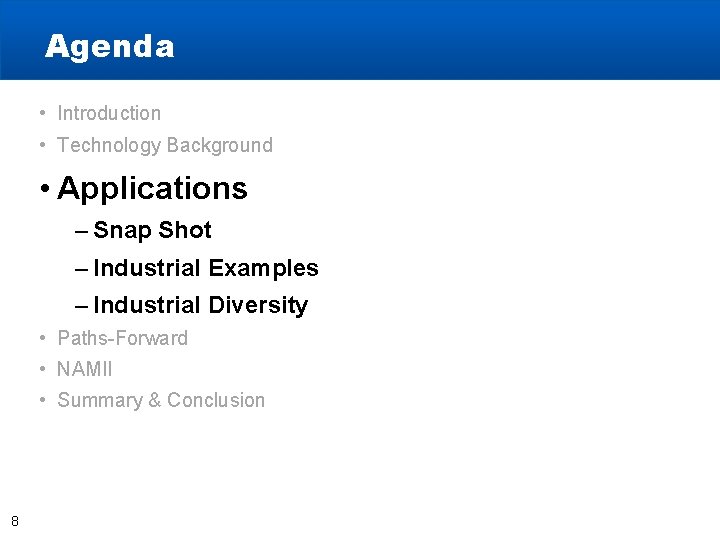
Agenda • Introduction • Technology Background • Applications – Snap Shot – Industrial Examples – Industrial Diversity • Paths-Forward • NAMII • Summary & Conclusion 8
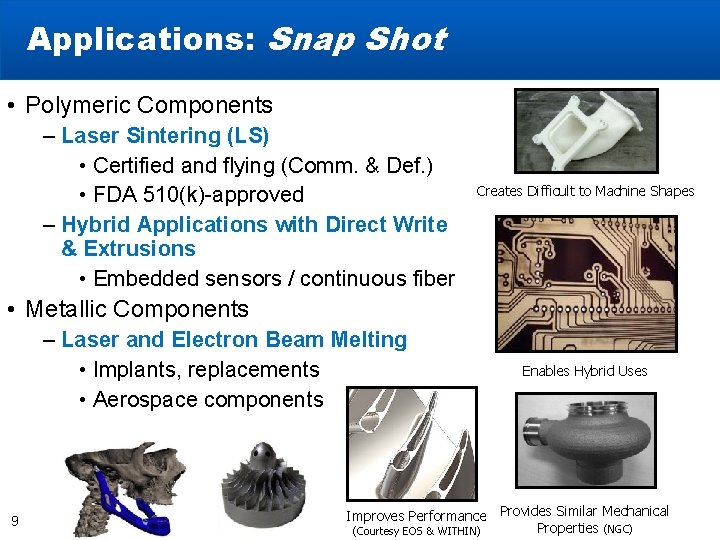
Applications: Snap Shot • Polymeric Components – Laser Sintering (LS) • Certified and flying (Comm. & Def. ) • FDA 510(k)-approved – Hybrid Applications with Direct Write & Extrusions • Embedded sensors / continuous fiber Creates Difficult to Machine Shapes • Metallic Components – Laser and Electron Beam Melting • Implants, replacements • Aerospace components 9 Enables Hybrid Uses Improves Performance Provides Similar Mechanical Properties (NGC) (Courtesy EOS & WITHIN)
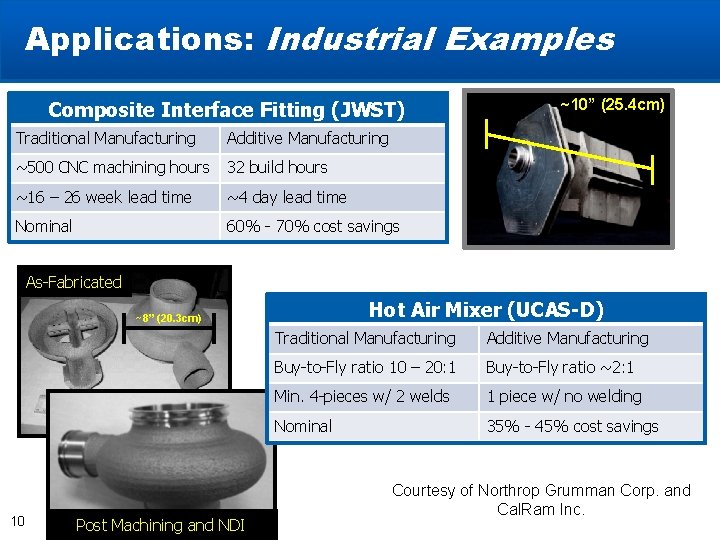
Applications: Industrial Examples Composite Interface Fitting (JWST) Traditional Manufacturing Additive Manufacturing ~500 CNC machining hours 32 build hours ~16 – 26 week lead time ~4 day lead time Nominal 60% - 70% cost savings ~10” (25. 4 cm) As-Fabricated Hot Air Mixer (UCAS-D) ~8” (20. 3 cm) 10 Post Machining and NDI Traditional Manufacturing Additive Manufacturing Buy-to-Fly ratio 10 – 20: 1 Buy-to-Fly ratio ~2: 1 Min. 4 -pieces w/ 2 welds 1 piece w/ no welding Nominal 35% - 45% cost savings Courtesy of Northrop Grumman Corp. and Cal. Ram Inc.
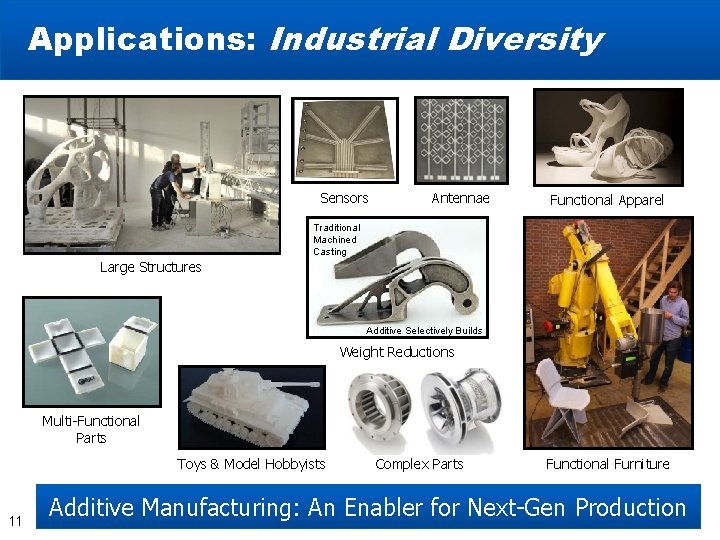
Applications: Industrial Diversity Sensors Antennae Functional Apparel Traditional Machined Casting Large Structures Additive Selectively Builds Weight Reductions Multi-Functional Parts Toys & Model Hobbyists 11 Complex Parts Functional Furniture Additive Manufacturing: An Enabler for Next-Gen Production
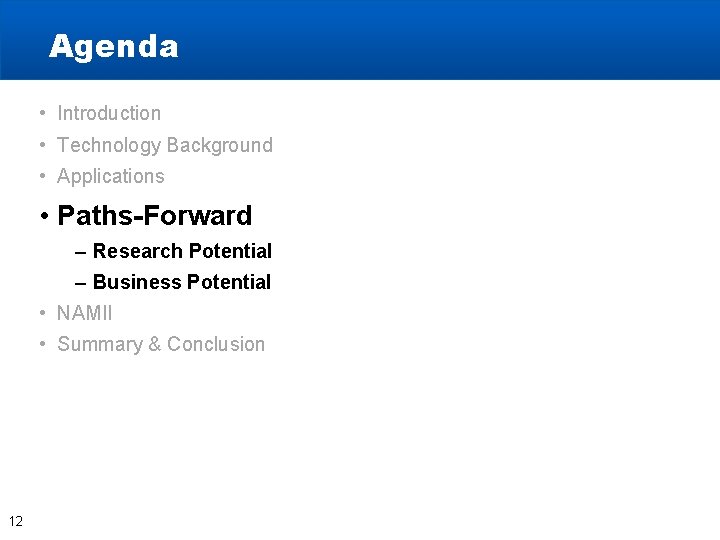
Agenda • Introduction • Technology Background • Applications • Paths-Forward – Research Potential – Business Potential • NAMII • Summary & Conclusion 12
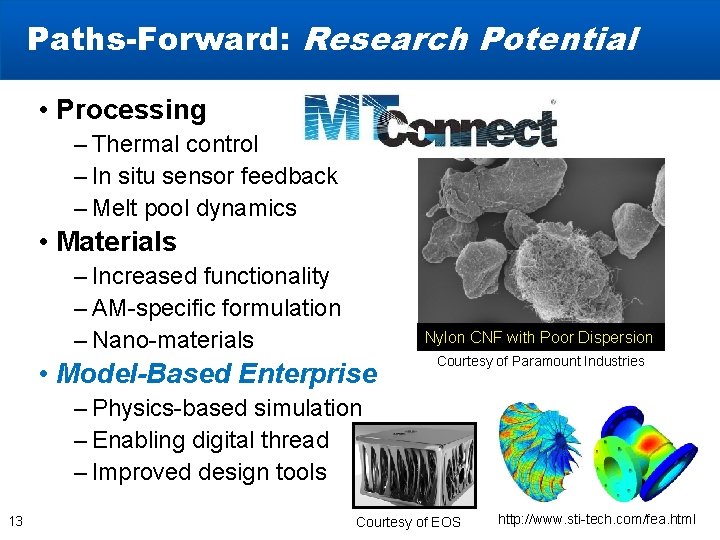
Paths-Forward: Research Potential • Processing – Thermal control – In situ sensor feedback – Melt pool dynamics • Materials – Increased functionality – AM-specific formulation – Nano-materials Nylon CNF with Poor Dispersion • Model-Based Enterprise Courtesy of Paramount Industries – Physics-based simulation – Enabling digital thread – Improved design tools 13 Courtesy of EOS http: //www. sti-tech. com/fea. html
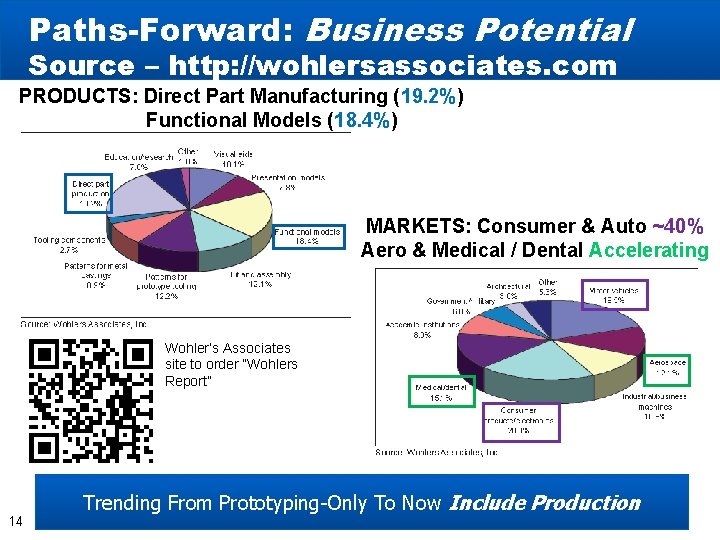
Paths-Forward: Business Potential Source – http: //wohlersassociates. com PRODUCTS: Direct Part Manufacturing (19. 2%) Functional Models (18. 4%) MARKETS: Consumer & Auto ~40% Aero & Medical / Dental Accelerating Wohler’s Associates site to order “Wohlers Report” Trending From Prototyping-Only To Now Include Production 14
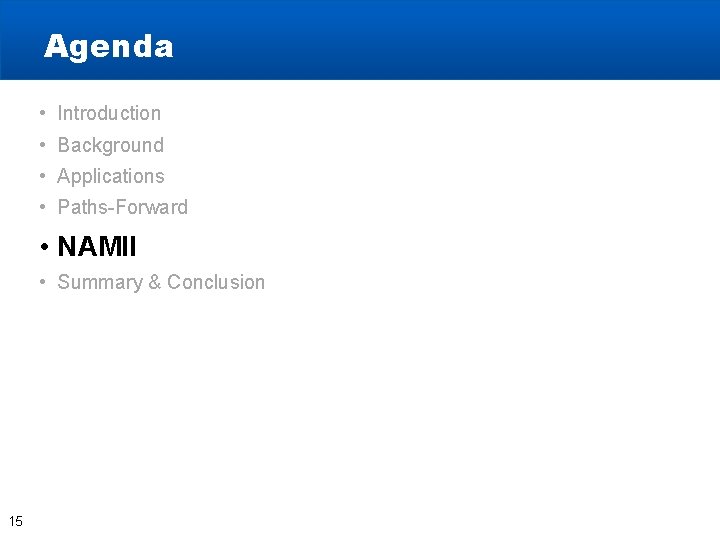
Agenda • Introduction • Background • Applications • Paths-Forward • NAMII • Summary & Conclusion 15
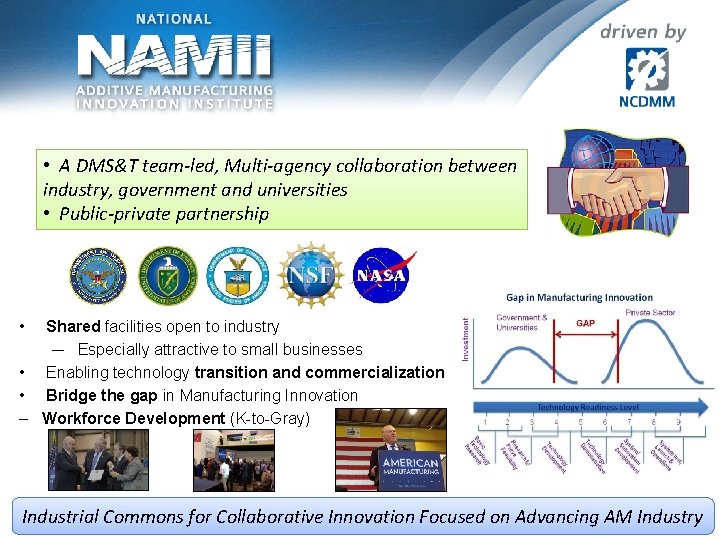
• A DMS&T team-led, Multi-agency collaboration between industry, government and universities • Public-private partnership • Shared facilities open to industry ― Especially attractive to small businesses • Enabling technology transition and commercialization • Bridge the gap in Manufacturing Innovation – Workforce Development (K-to-Gray) Industrial Commons for Collaborative Innovation Focused on Advancing AM Industry
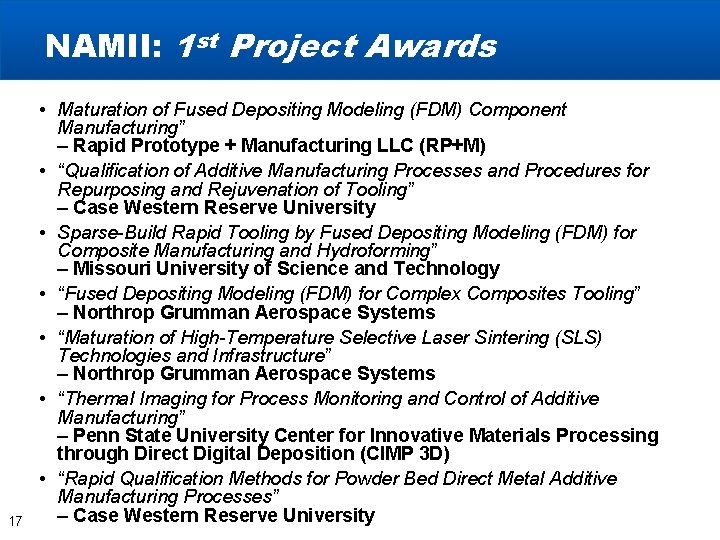
NAMII: 1 st Project Awards 17 • Maturation of Fused Depositing Modeling (FDM) Component Manufacturing” – Rapid Prototype + Manufacturing LLC (RP+M) • “Qualification of Additive Manufacturing Processes and Procedures for Repurposing and Rejuvenation of Tooling” – Case Western Reserve University • Sparse-Build Rapid Tooling by Fused Depositing Modeling (FDM) for Composite Manufacturing and Hydroforming” – Missouri University of Science and Technology • “Fused Depositing Modeling (FDM) for Complex Composites Tooling” – Northrop Grumman Aerospace Systems • “Maturation of High-Temperature Selective Laser Sintering (SLS) Technologies and Infrastructure” – Northrop Grumman Aerospace Systems • “Thermal Imaging for Process Monitoring and Control of Additive Manufacturing” – Penn State University Center for Innovative Materials Processing through Direct Digital Deposition (CIMP 3 D) • “Rapid Qualification Methods for Powder Bed Direct Metal Additive Manufacturing Processes” – Case Western Reserve University
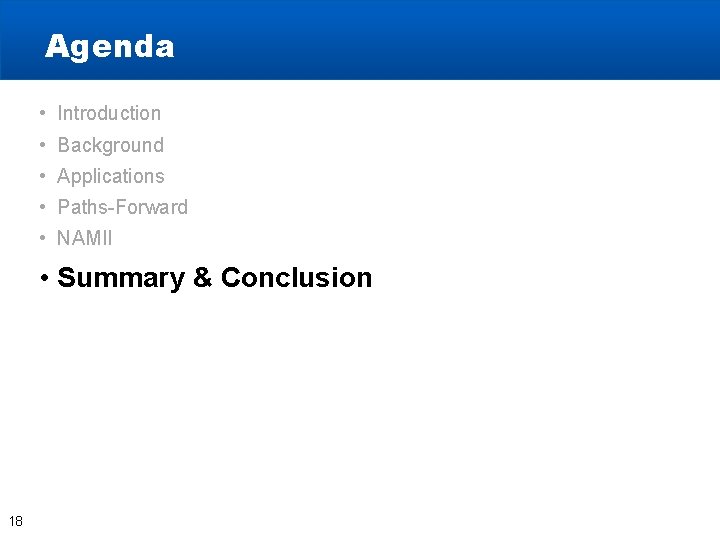
Agenda • Introduction • Background • Applications • Paths-Forward • NAMII • Summary & Conclusion 18
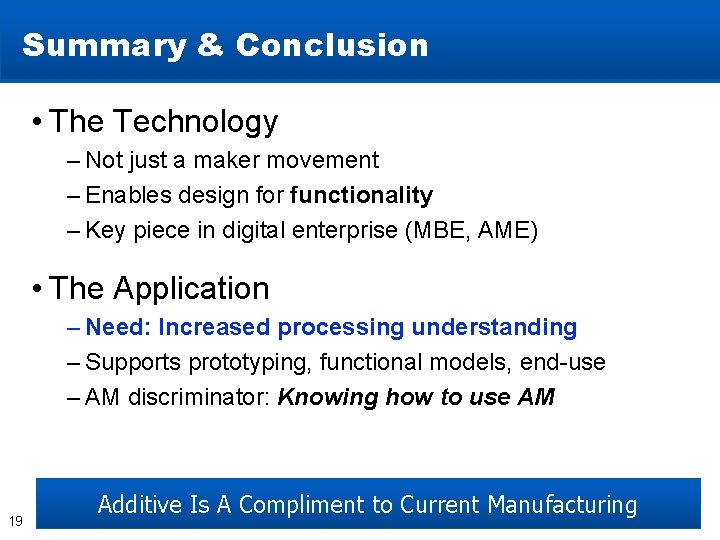
Summary & Conclusion • The Technology – Not just a maker movement – Enables design for functionality – Key piece in digital enterprise (MBE, AME) • The Application – Need: Increased processing understanding – Supports prototyping, functional models, end-use – AM discriminator: Knowing how to use AM 19 Additive Is A Compliment to Current Manufacturing
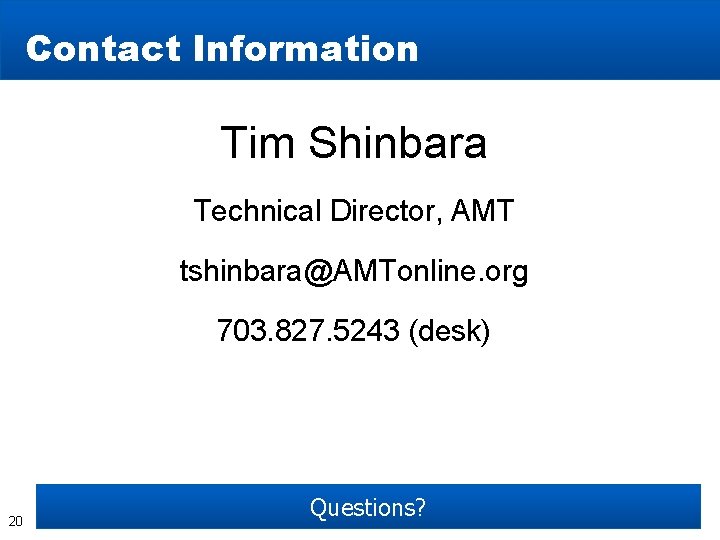
Contact Information Tim Shinbara Technical Director, AMT tshinbara@AMTonline. org 703. 827. 5243 (desk) 20 Questions?
- Slides: 20