Accident Investigation Todd Mc Carley Loss Control Representative
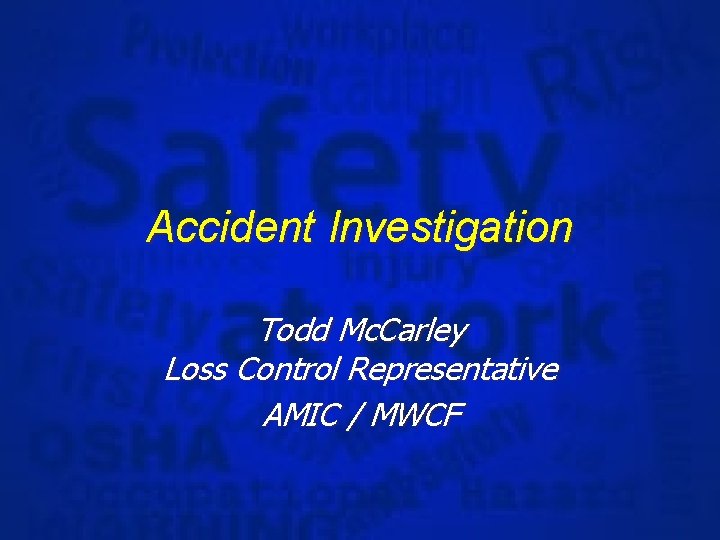
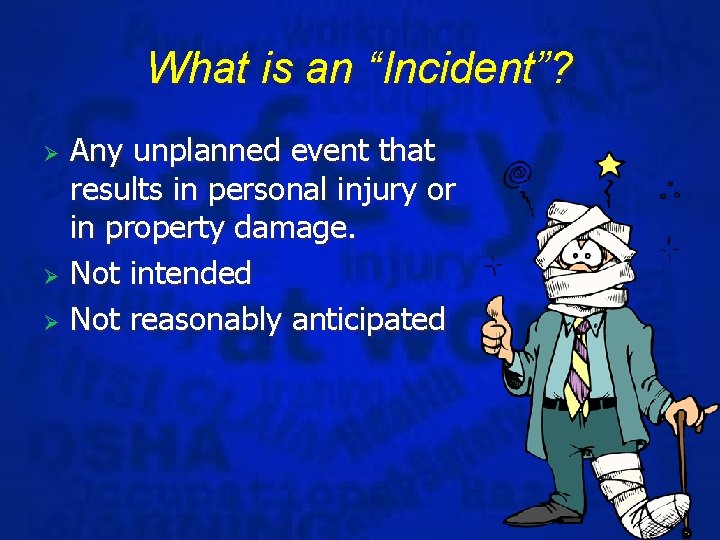
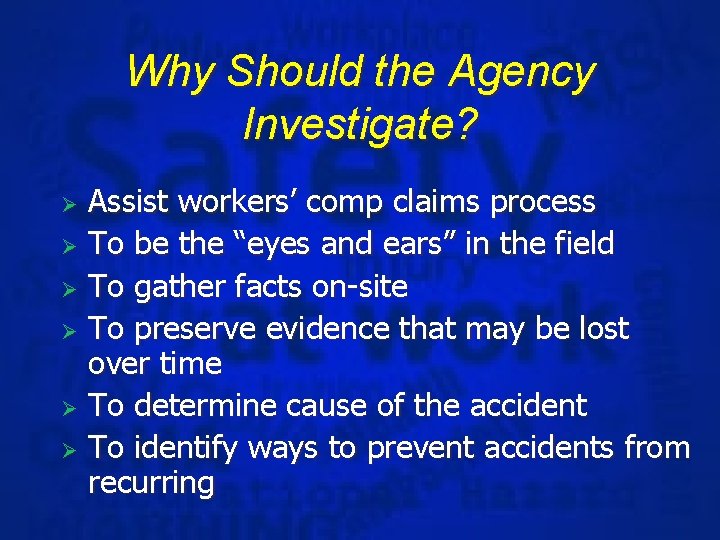
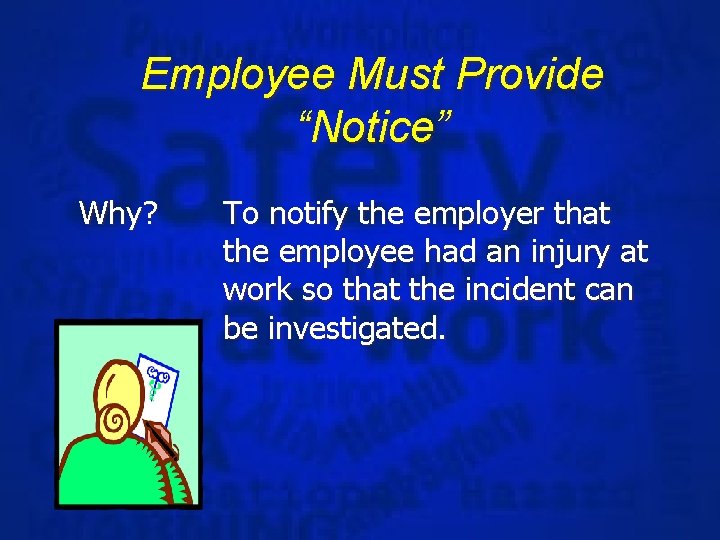
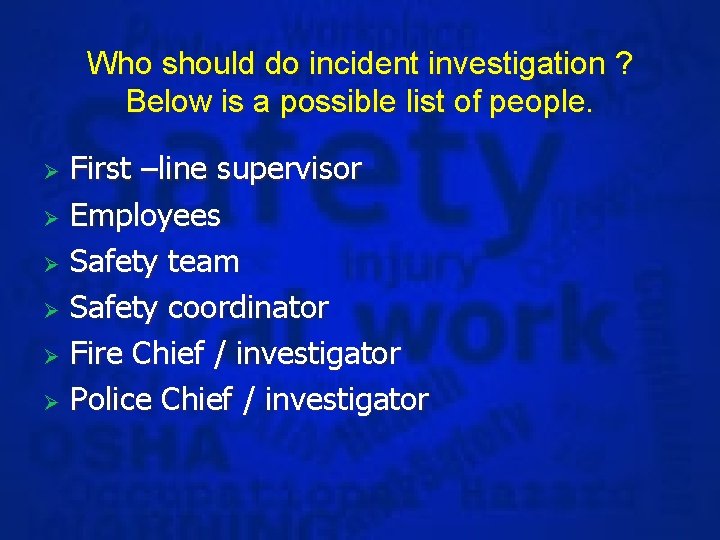
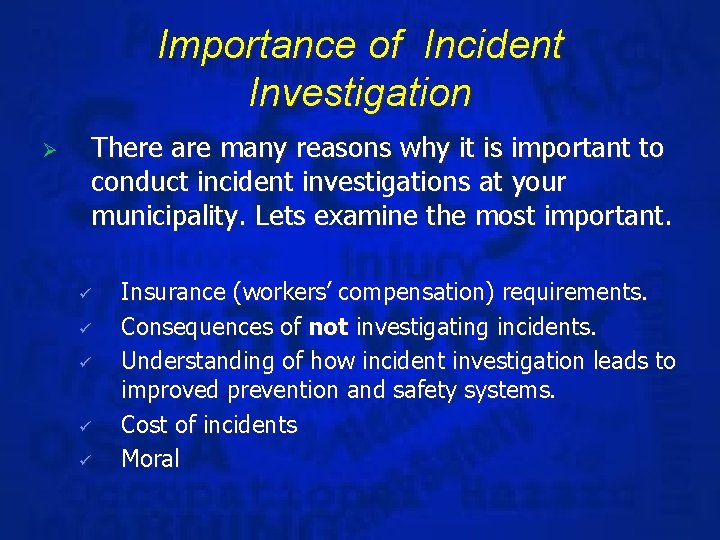
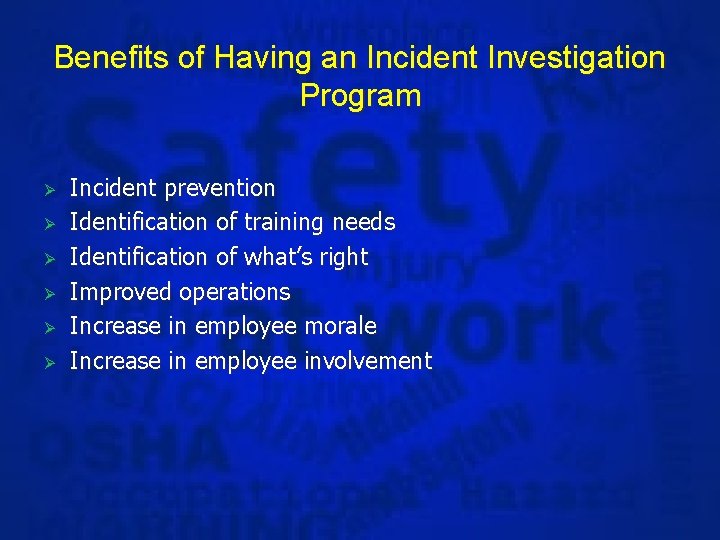
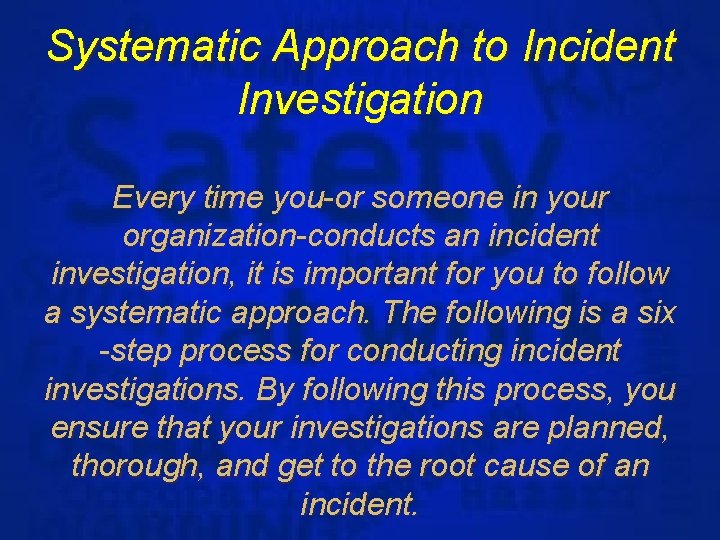
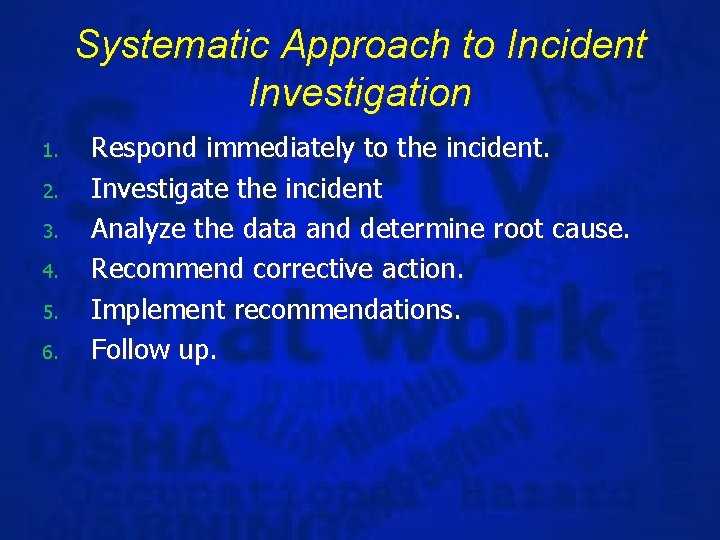
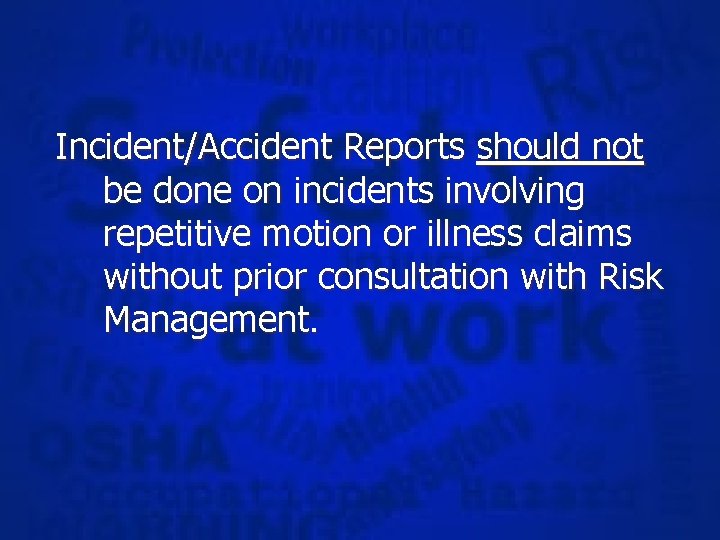
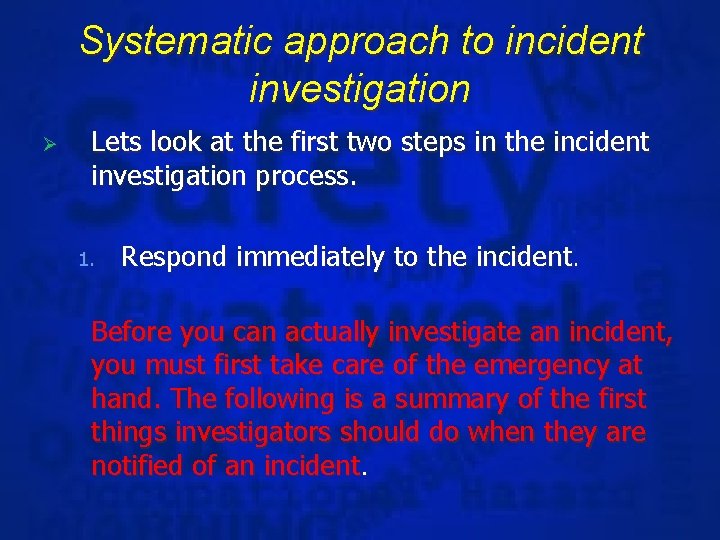
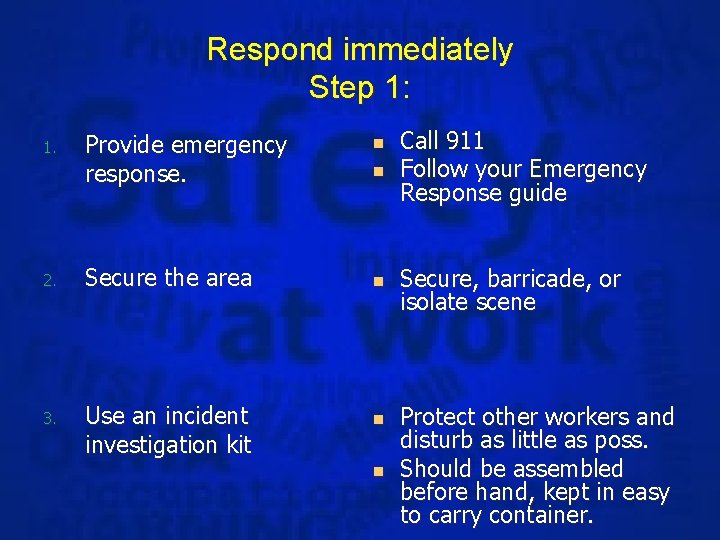
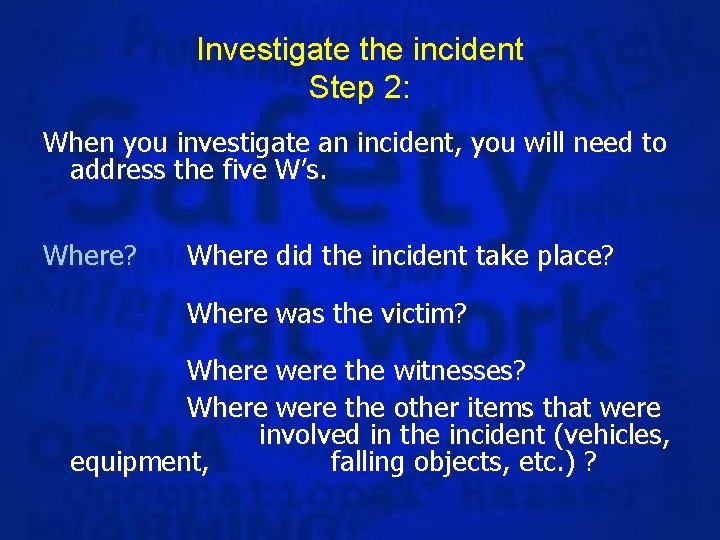
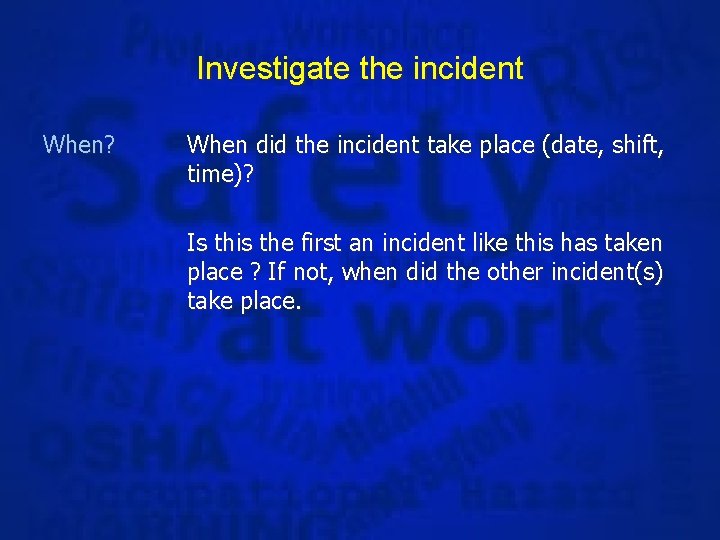

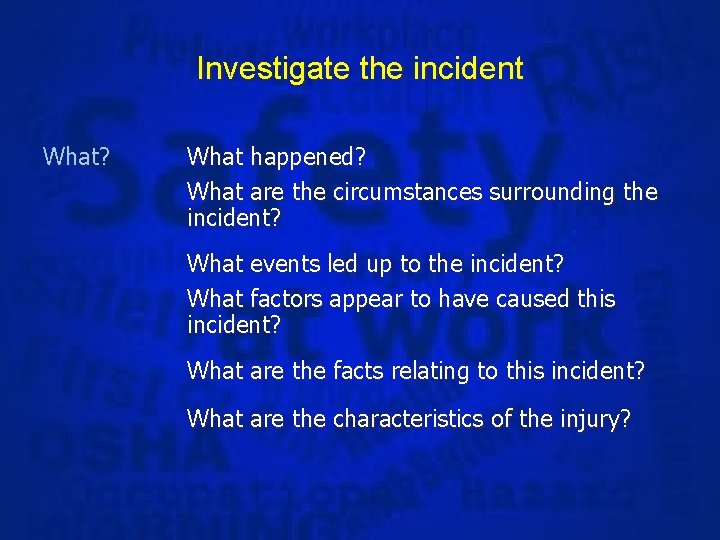
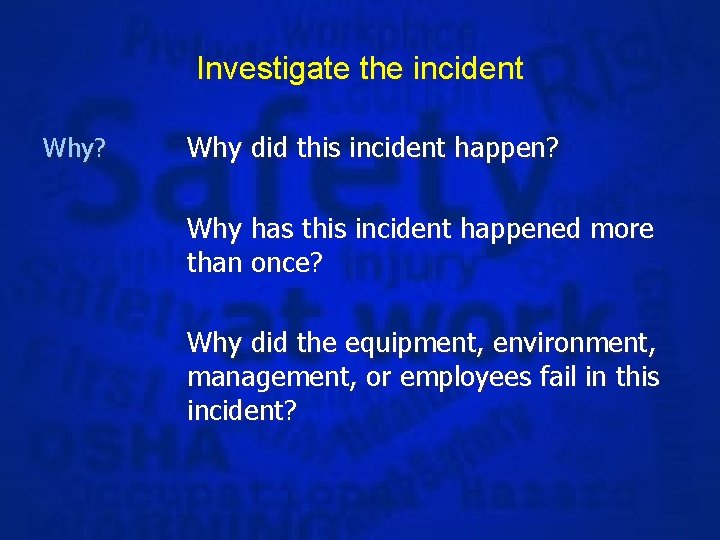
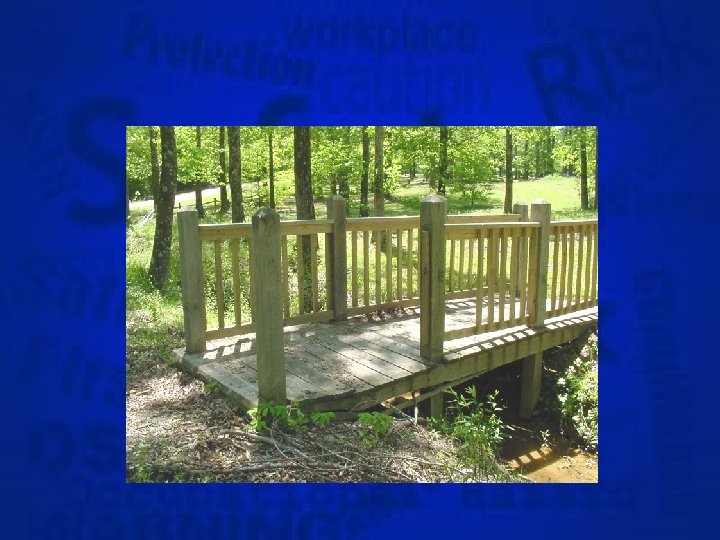
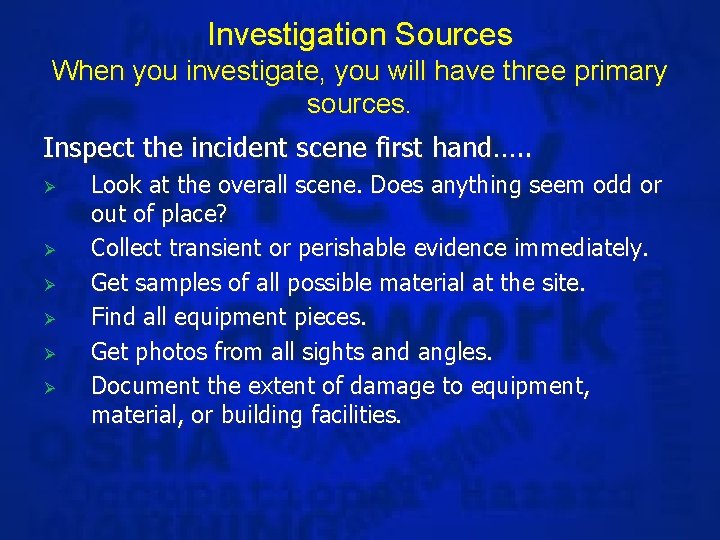
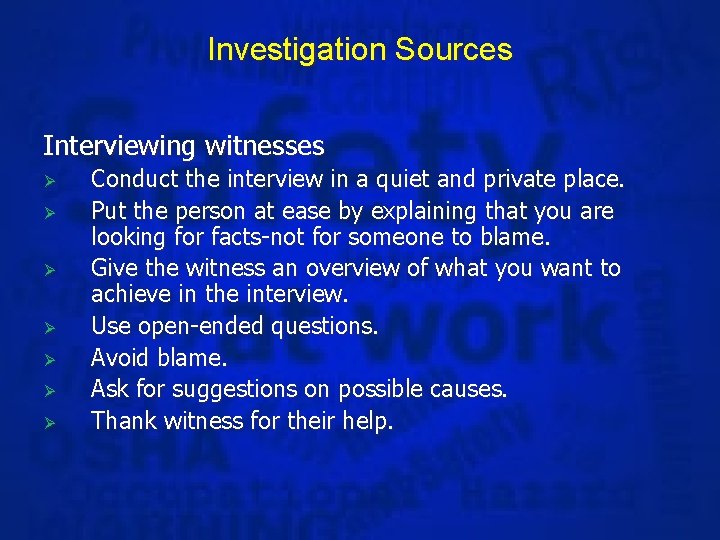
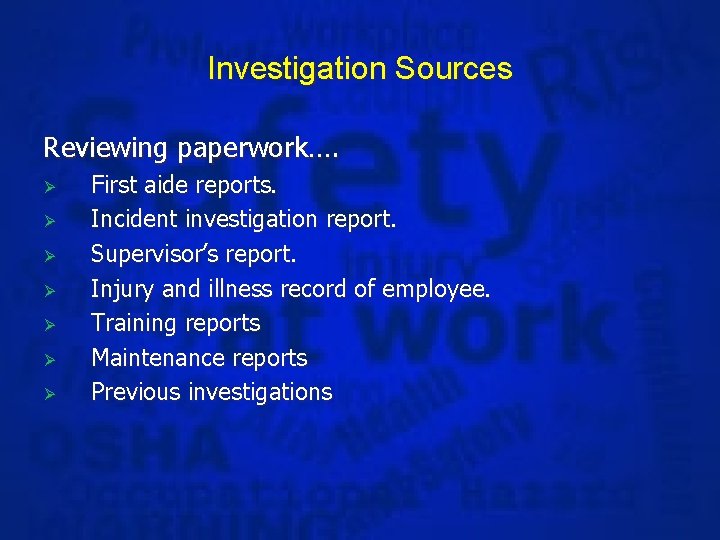
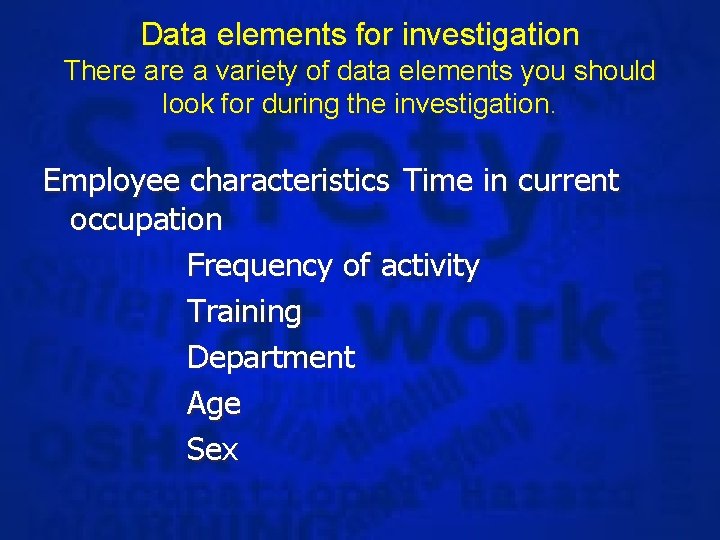
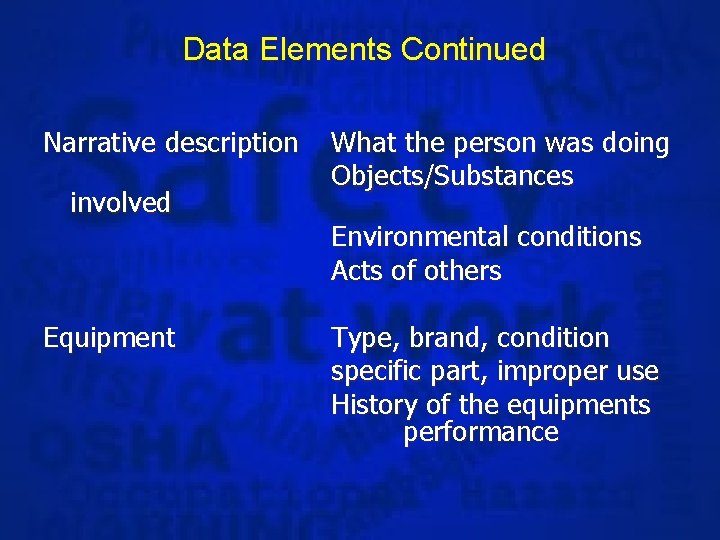
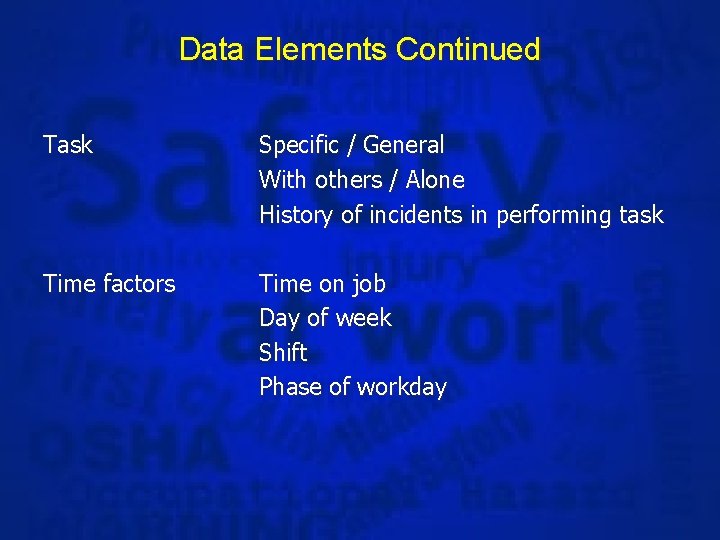
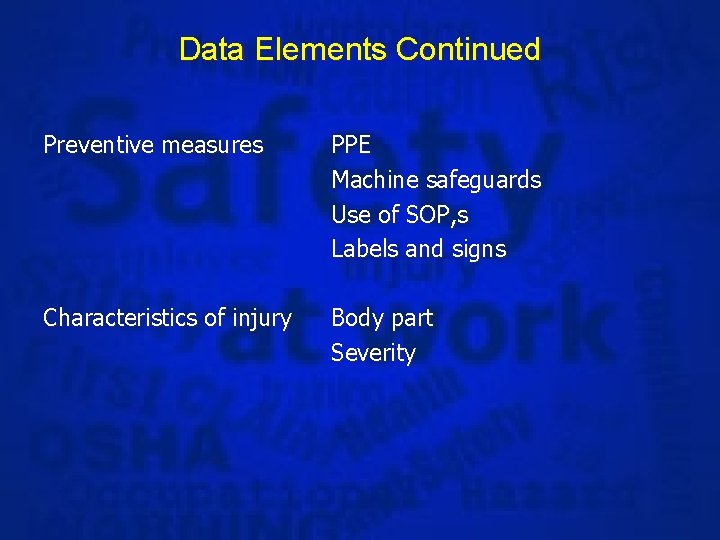
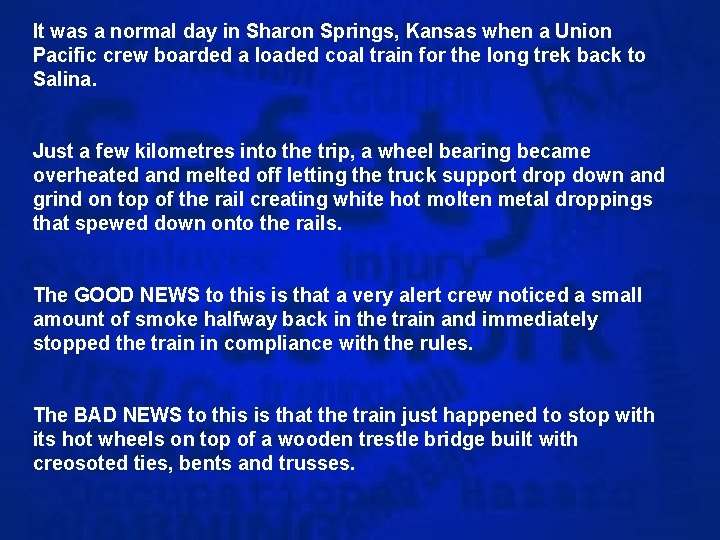
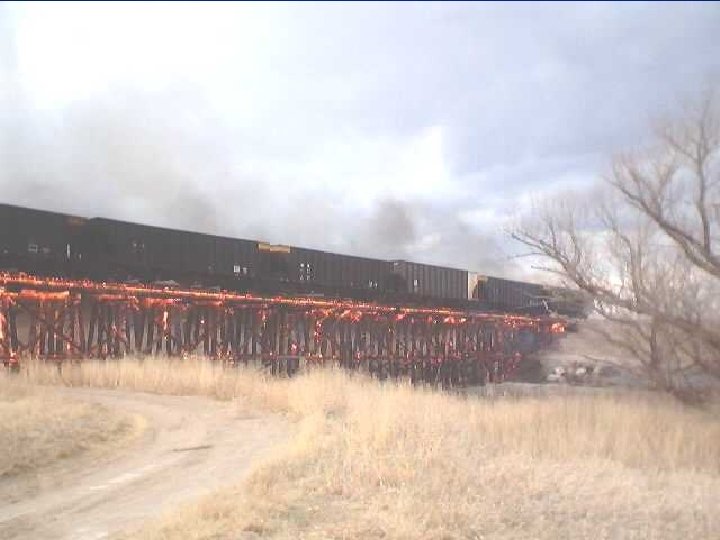
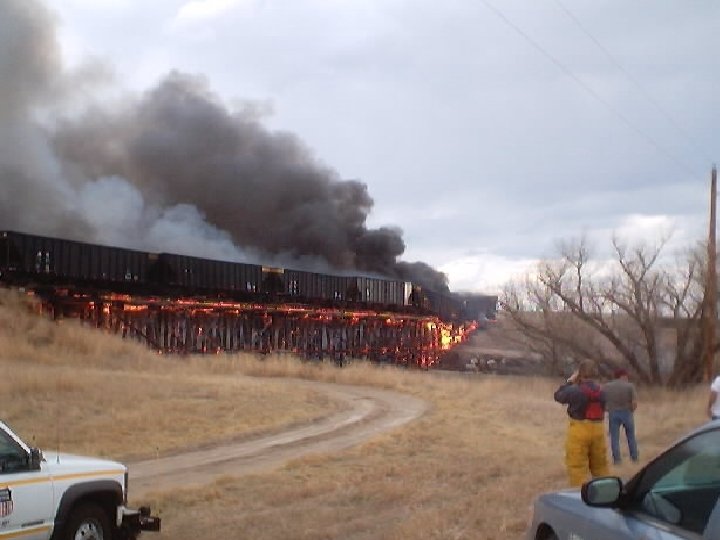
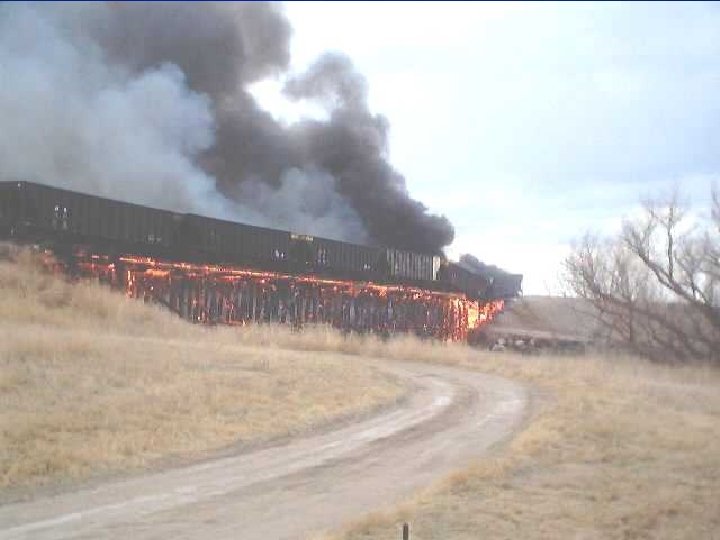
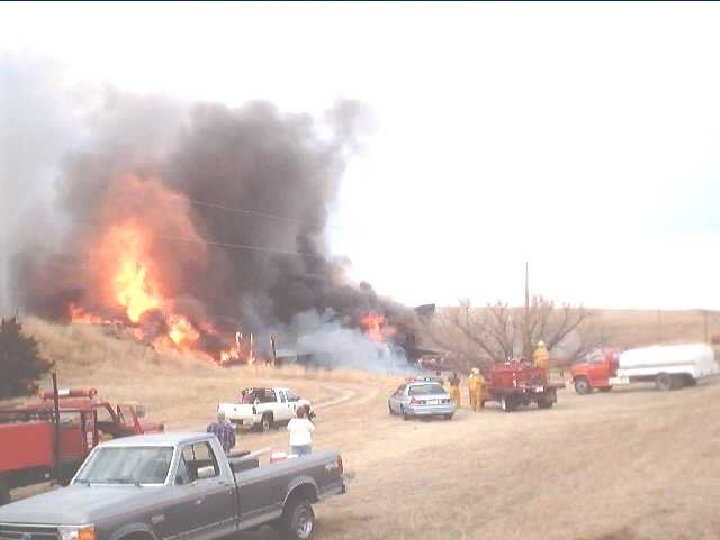
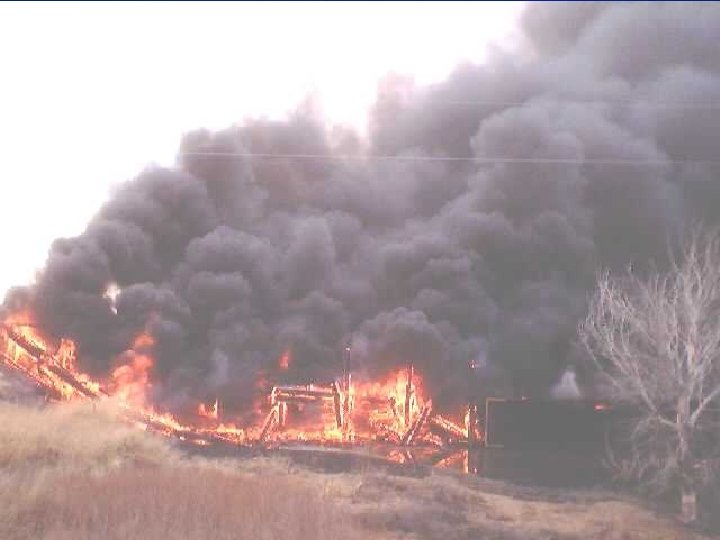
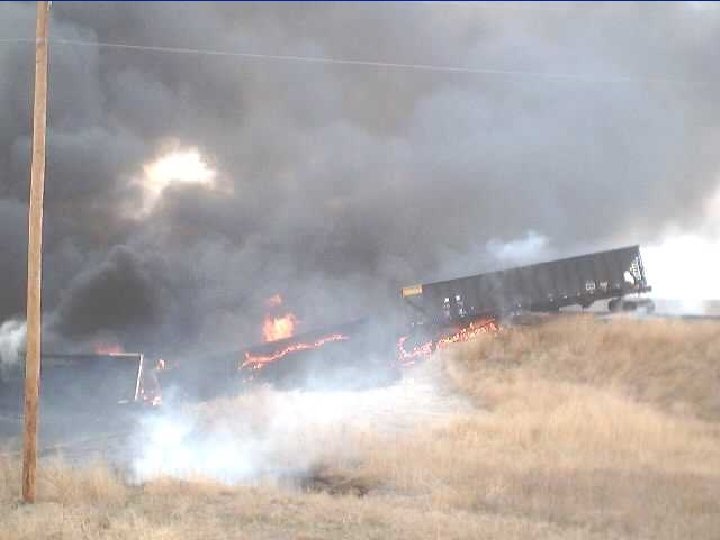
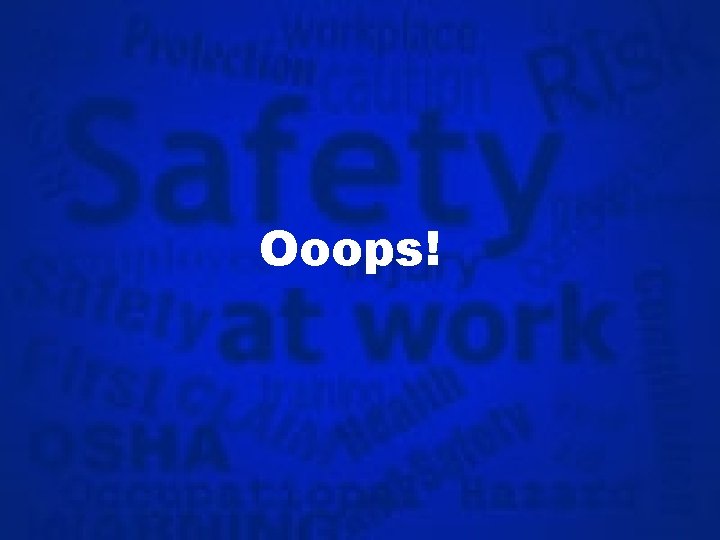
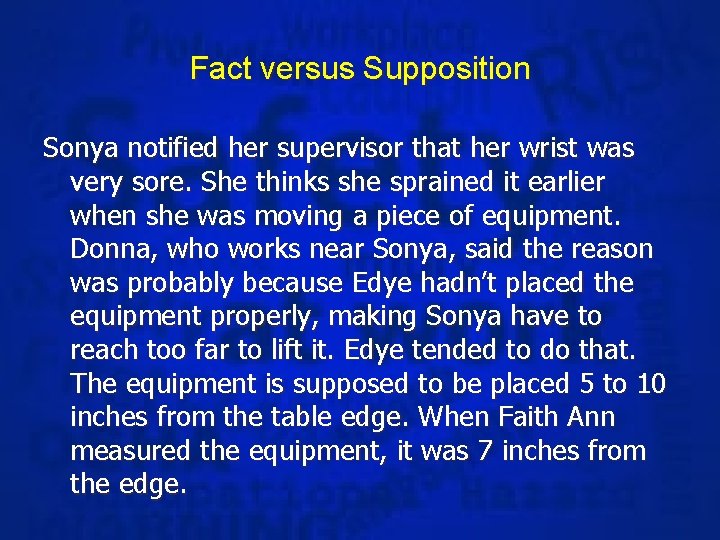
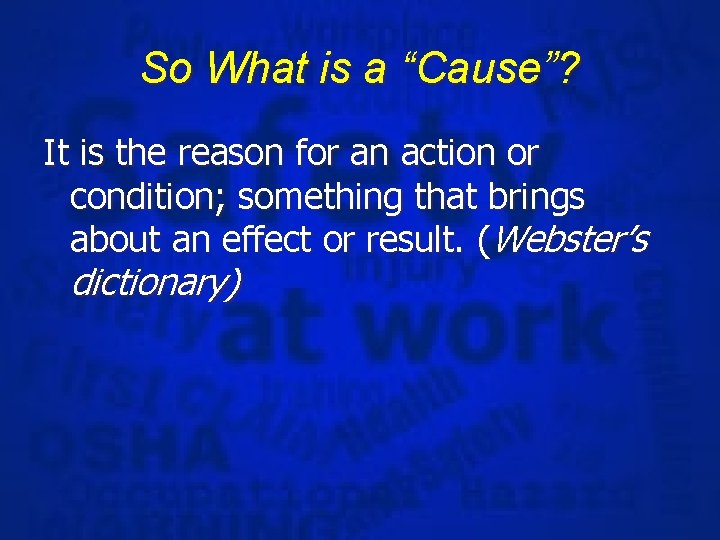
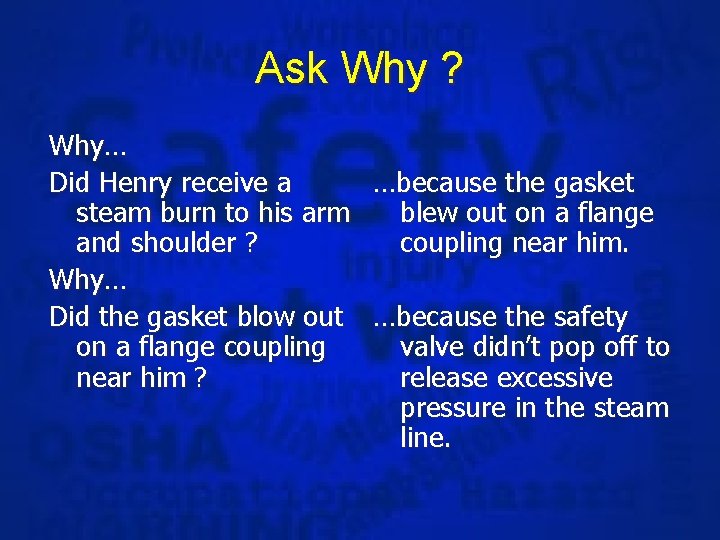
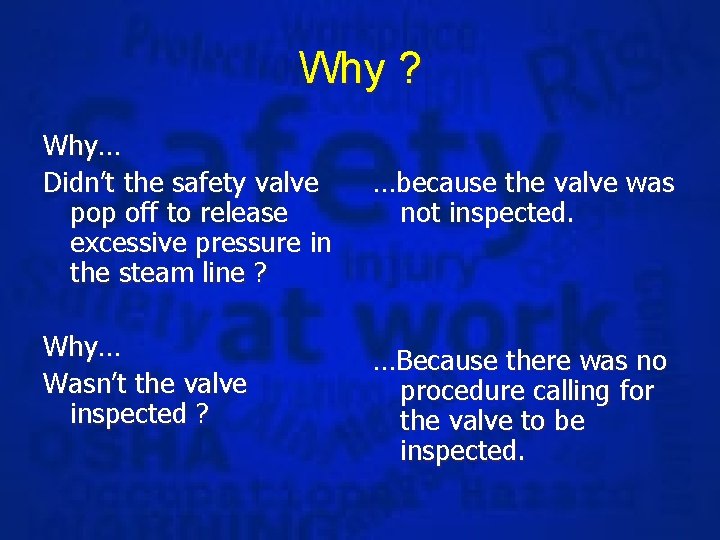
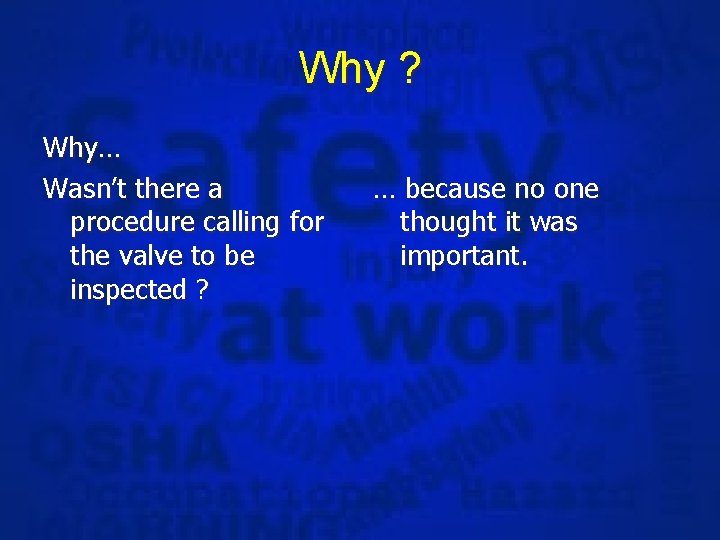
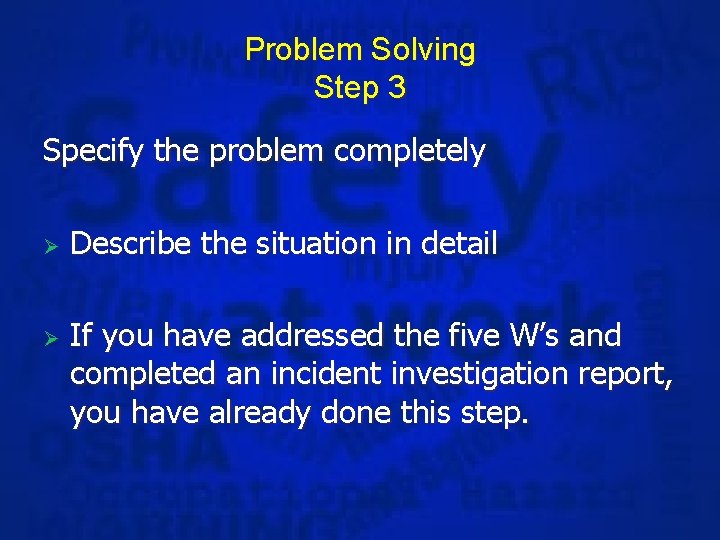
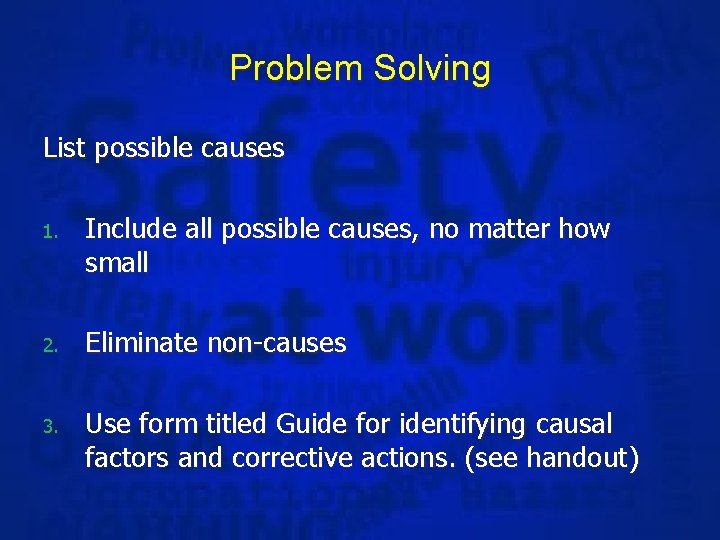
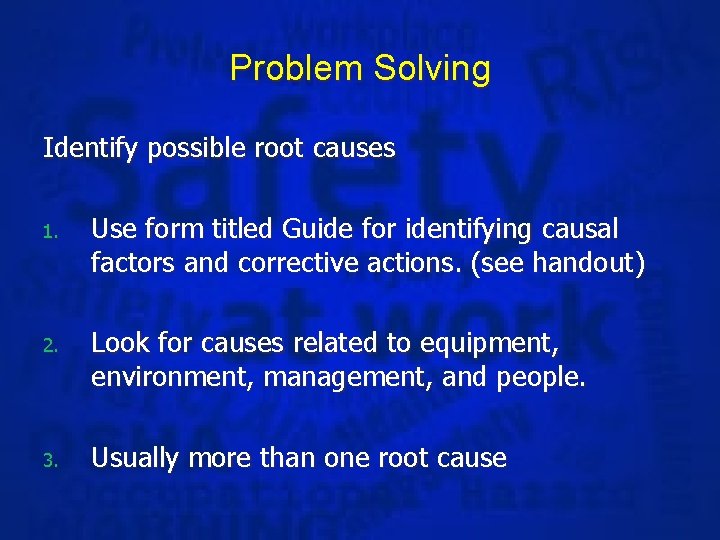
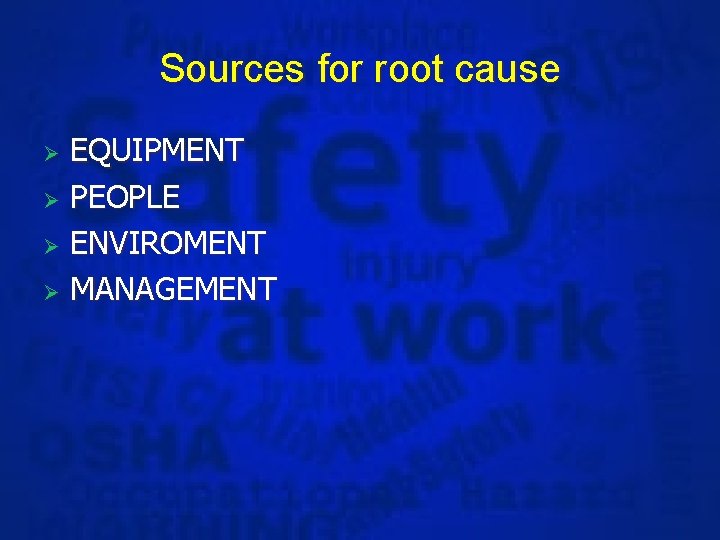
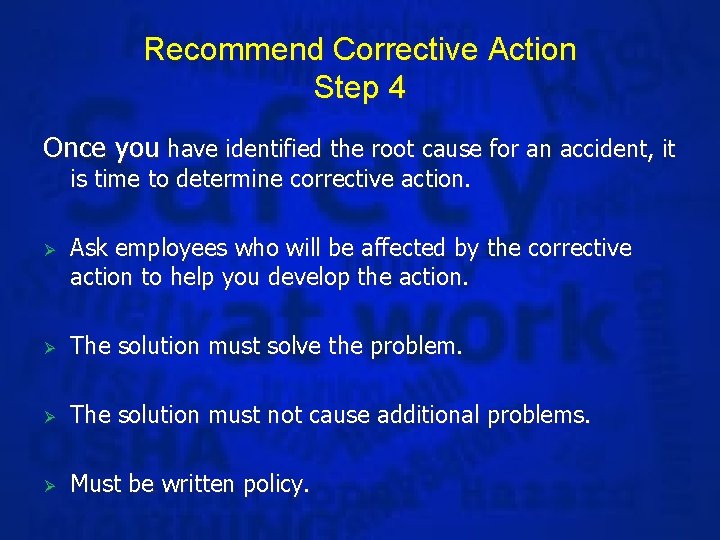
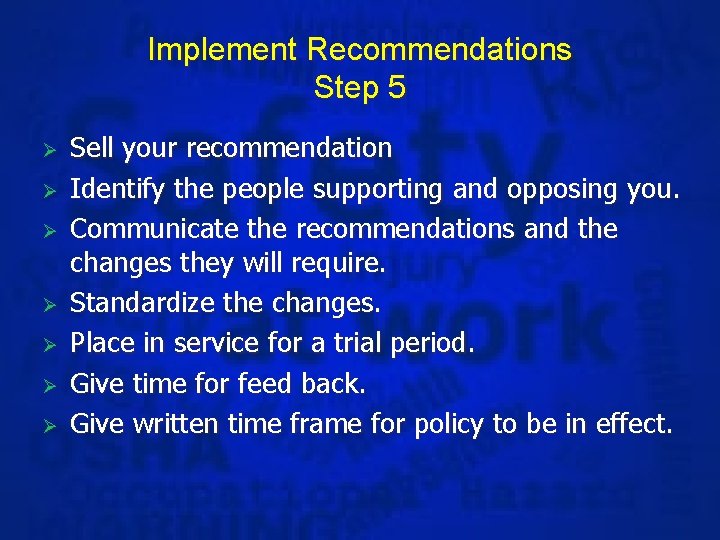
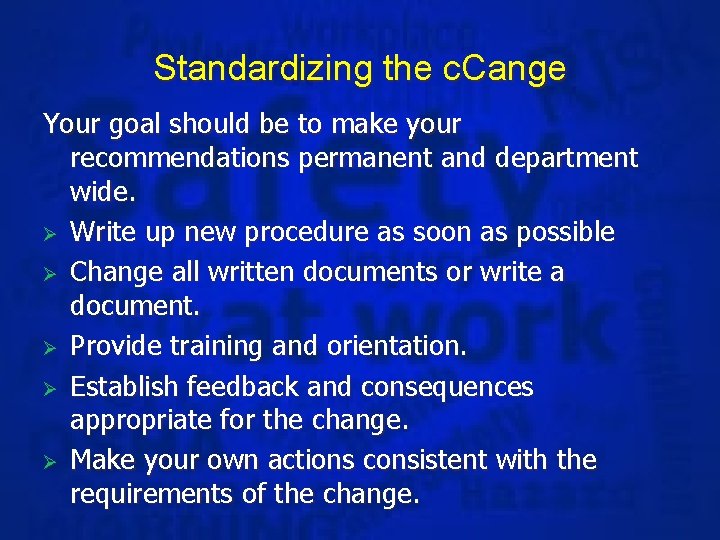
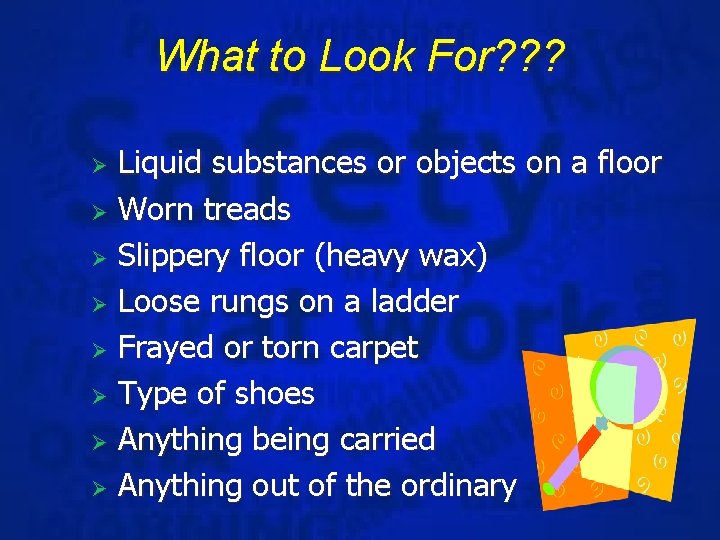
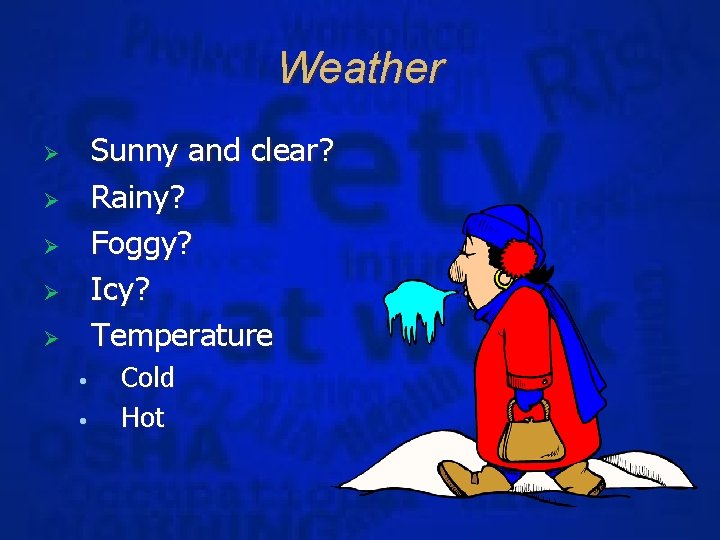
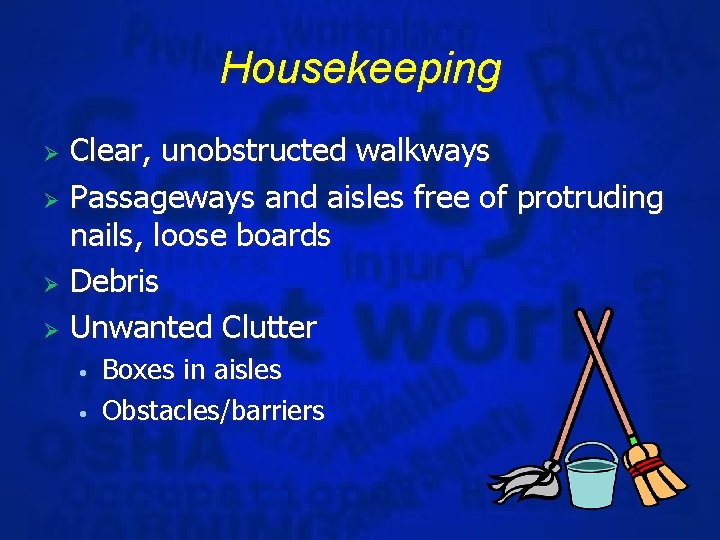
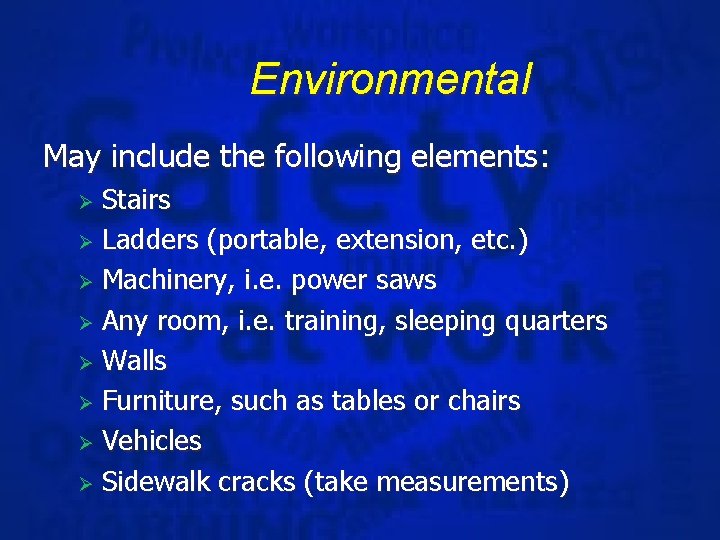
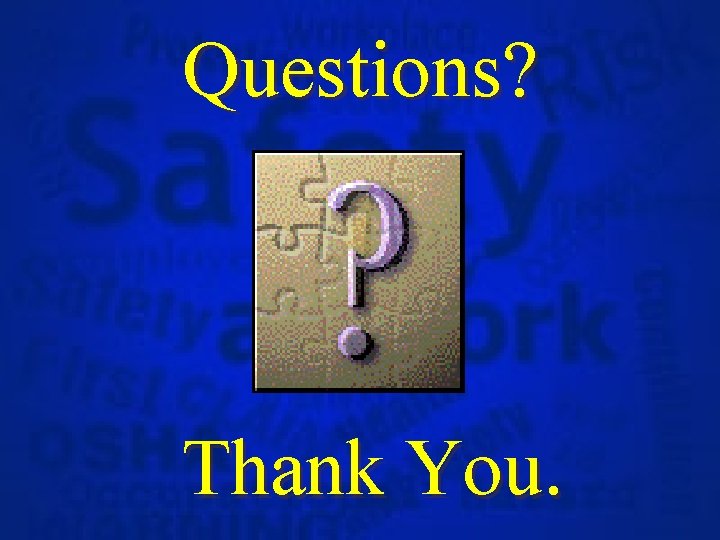
- Slides: 50
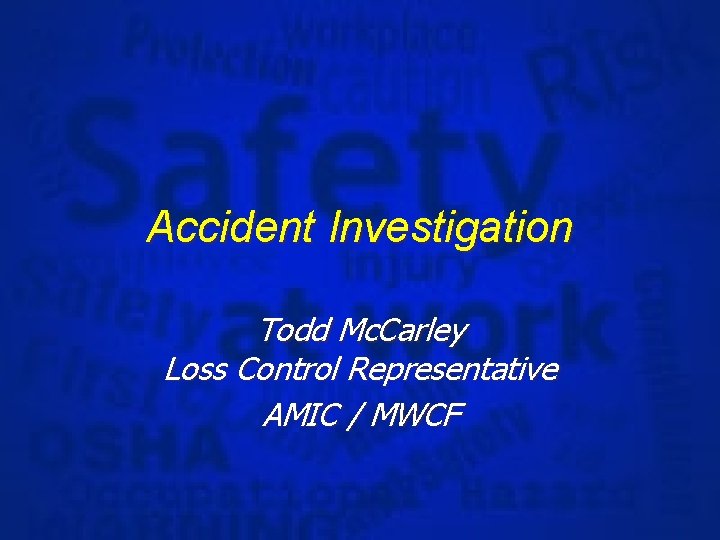
Accident Investigation Todd Mc. Carley Loss Control Representative AMIC / MWCF
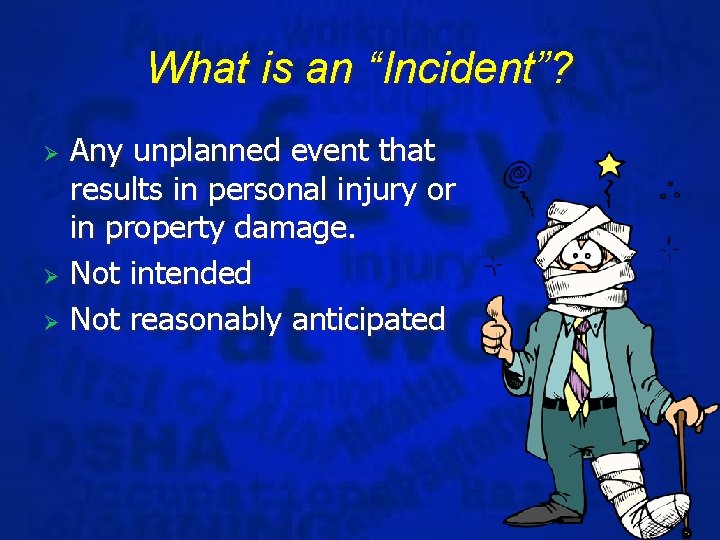
What is an “Incident”? Any unplanned event that results in personal injury or in property damage. Ø Not intended Ø Not reasonably anticipated Ø
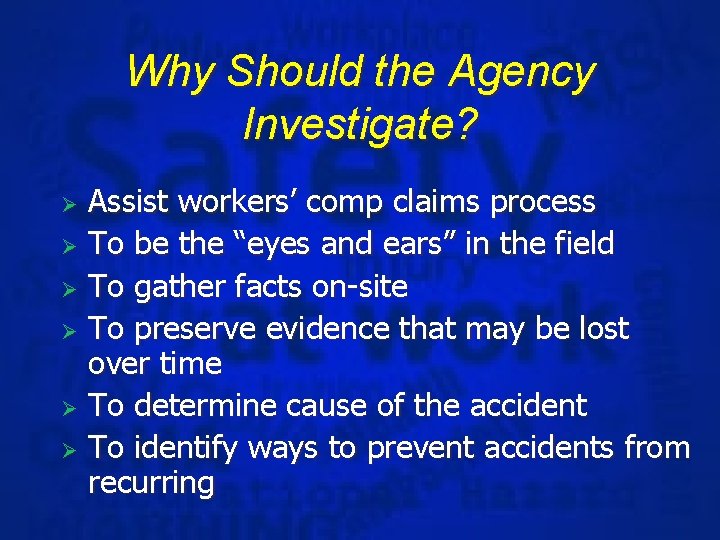
Why Should the Agency Investigate? Assist workers’ comp claims process Ø To be the “eyes and ears” in the field Ø To gather facts on-site Ø To preserve evidence that may be lost over time Ø To determine cause of the accident Ø To identify ways to prevent accidents from recurring Ø
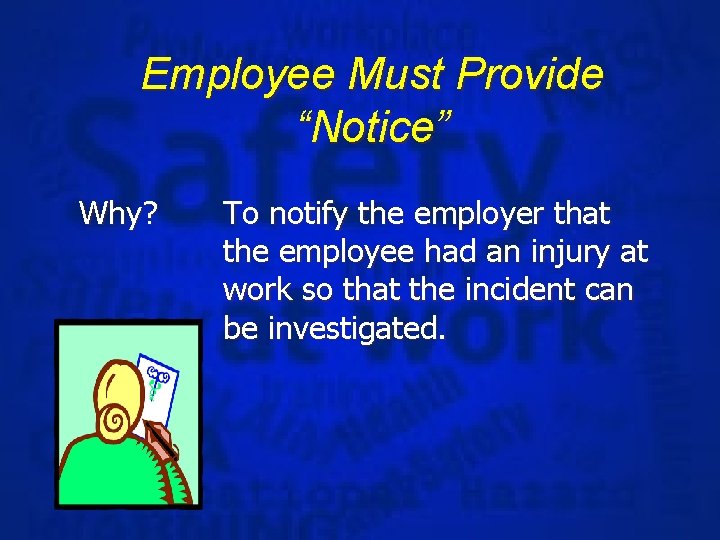
Employee Must Provide “Notice” Why? To notify the employer that the employee had an injury at work so that the incident can be investigated.
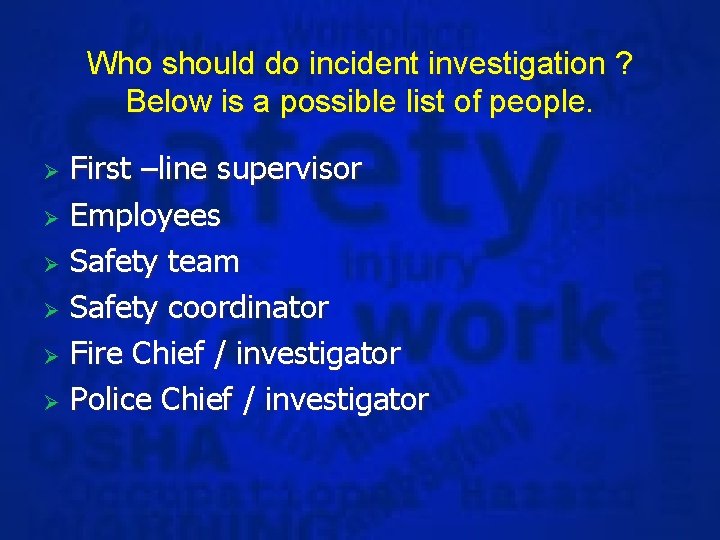
Who should do incident investigation ? Below is a possible list of people. First –line supervisor Ø Employees Ø Safety team Ø Safety coordinator Ø Fire Chief / investigator Ø Police Chief / investigator Ø
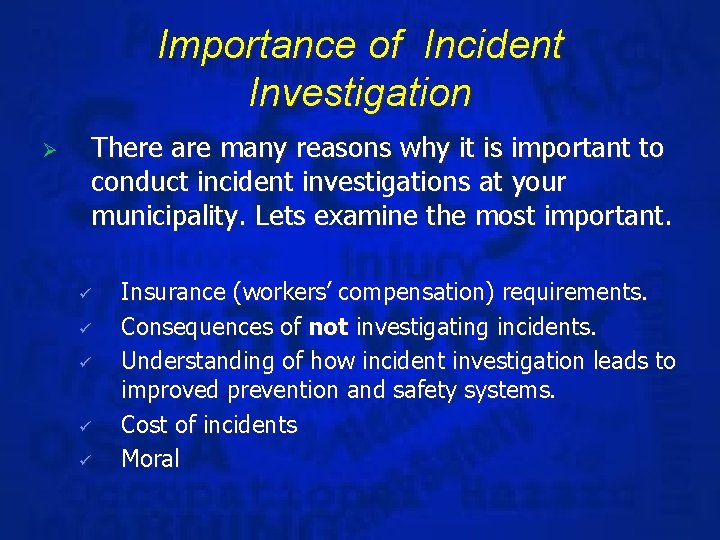
Importance of Incident Investigation Ø There are many reasons why it is important to conduct incident investigations at your municipality. Lets examine the most important. ü ü ü Insurance (workers’ compensation) requirements. Consequences of not investigating incidents. Understanding of how incident investigation leads to improved prevention and safety systems. Cost of incidents Moral
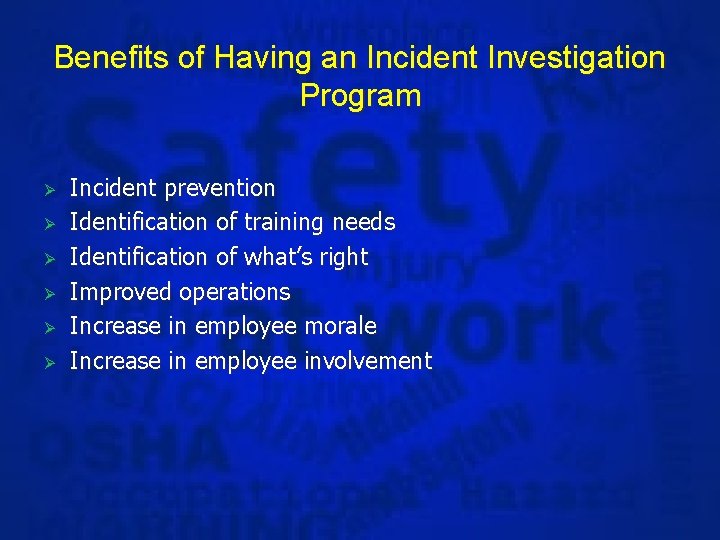
Benefits of Having an Incident Investigation Program Ø Ø Ø Incident prevention Identification of training needs Identification of what’s right Improved operations Increase in employee morale Increase in employee involvement
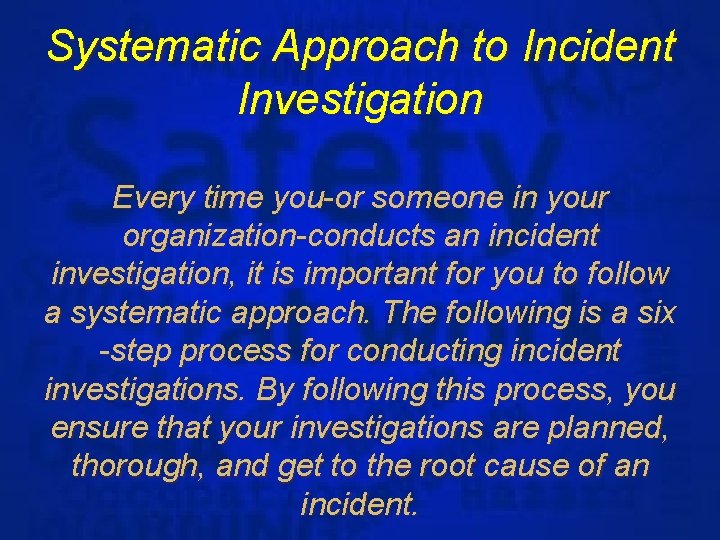
Systematic Approach to Incident Investigation Every time you-or someone in your organization-conducts an incident investigation, it is important for you to follow a systematic approach. The following is a six -step process for conducting incident investigations. By following this process, you ensure that your investigations are planned, thorough, and get to the root cause of an incident.
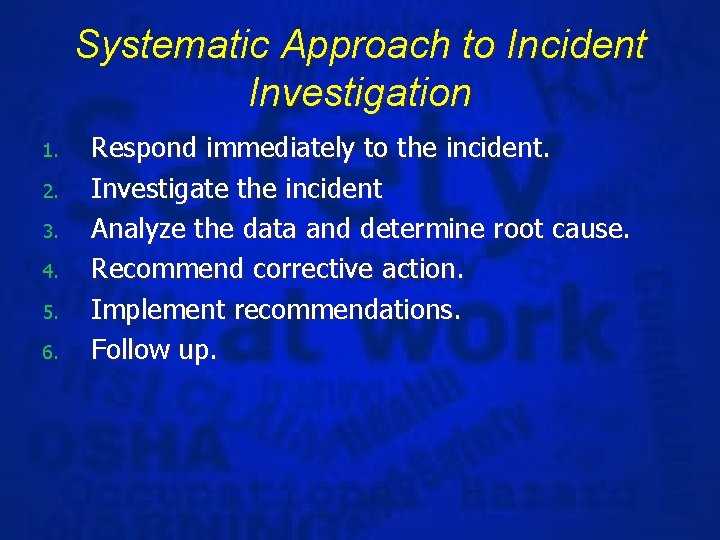
Systematic Approach to Incident Investigation 1. 2. 3. 4. 5. 6. Respond immediately to the incident. Investigate the incident Analyze the data and determine root cause. Recommend corrective action. Implement recommendations. Follow up.
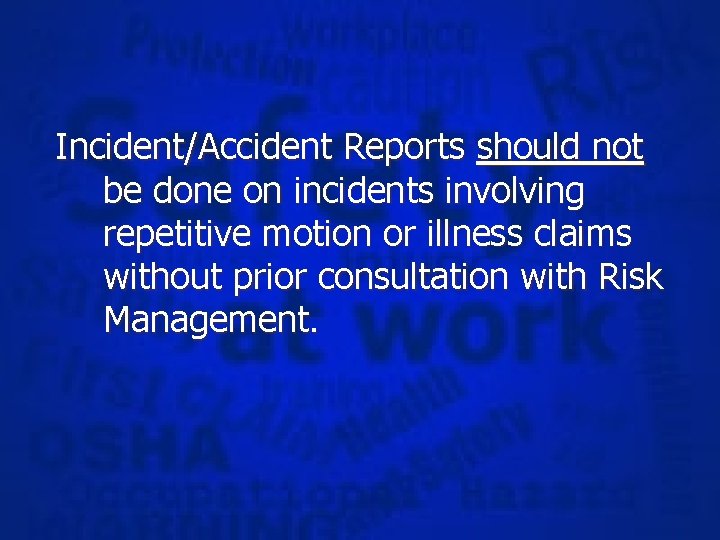
Incident/Accident Reports should not be done on incidents involving repetitive motion or illness claims without prior consultation with Risk Management.
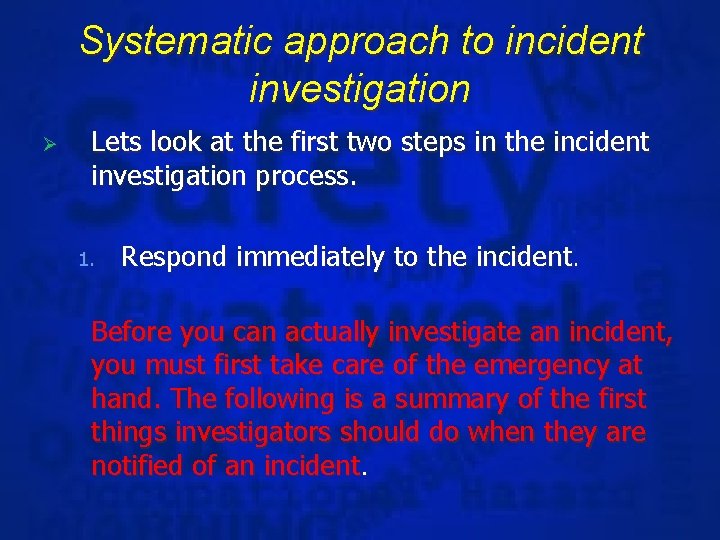
Systematic approach to incident investigation Ø Lets look at the first two steps in the incident investigation process. 1. Respond immediately to the incident. Before you can actually investigate an incident, you must first take care of the emergency at hand. The following is a summary of the first things investigators should do when they are notified of an incident.
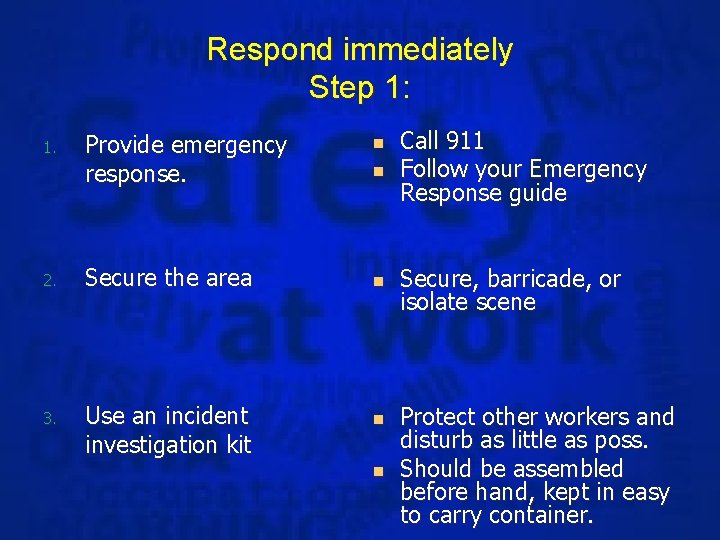
Respond immediately Step 1: 1. Provide emergency response. 2. Secure the area 3. Use an incident investigation kit n Call 911 Follow your Emergency Response guide n Secure, barricade, or isolate scene n n n Protect other workers and disturb as little as poss. Should be assembled before hand, kept in easy to carry container.
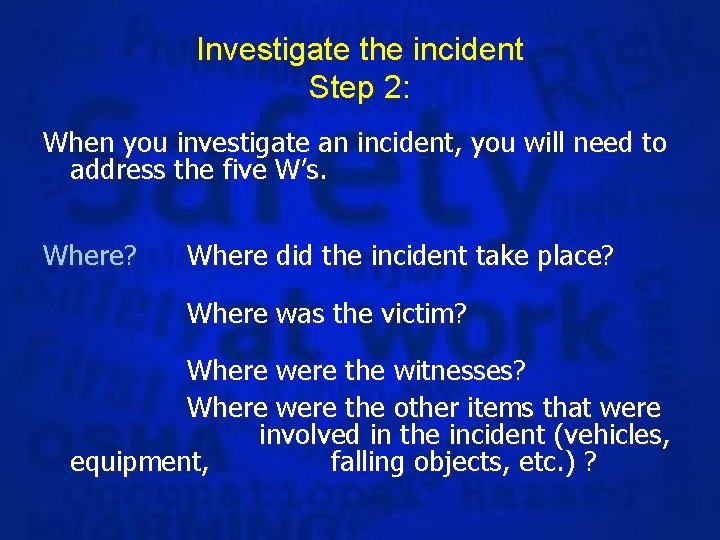
Investigate the incident Step 2: When you investigate an incident, you will need to address the five W’s. Where? Where did the incident take place? Where was the victim? Where were the witnesses? Where were the other items that were involved in the incident (vehicles, equipment, falling objects, etc. ) ?
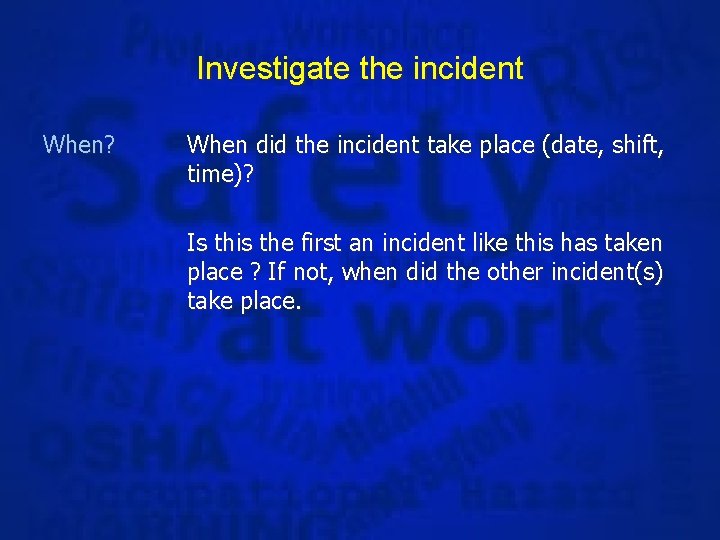
Investigate the incident When? When did the incident take place (date, shift, time)? Is this the first an incident like this has taken place ? If not, when did the other incident(s) take place.

Investigate the incident Who ? Who was involved in the incident? Who was injured? Who was at the scene prior to the incident? Who were the eyewitnesses? Who heard the incident? Who came upon the scene after the incident? Who might have useful information about the incident?
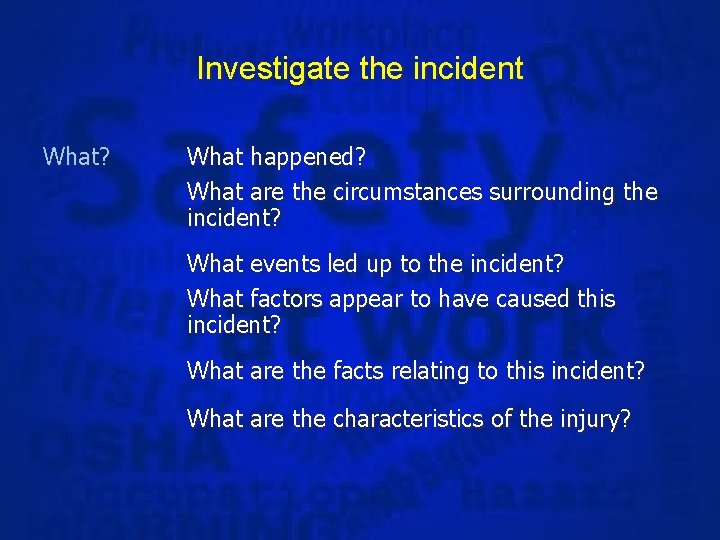
Investigate the incident What? What happened? What are the circumstances surrounding the incident? What events led up to the incident? What factors appear to have caused this incident? What are the facts relating to this incident? What are the characteristics of the injury?
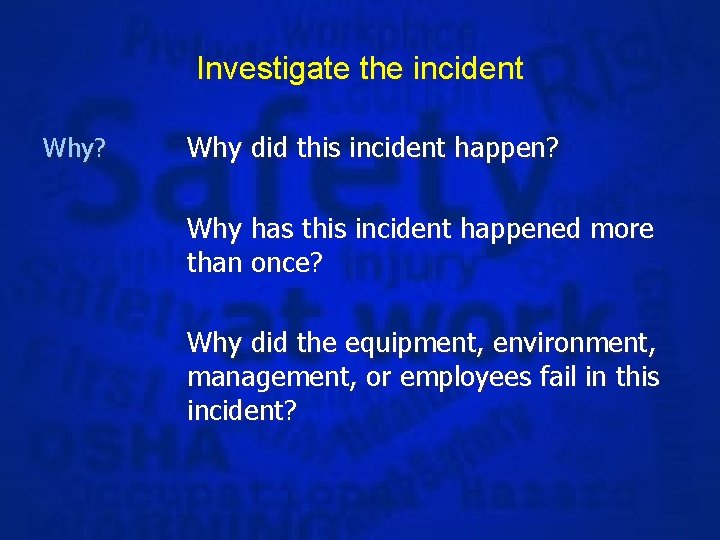
Investigate the incident Why? Why did this incident happen? Why has this incident happened more than once? Why did the equipment, environment, management, or employees fail in this incident?
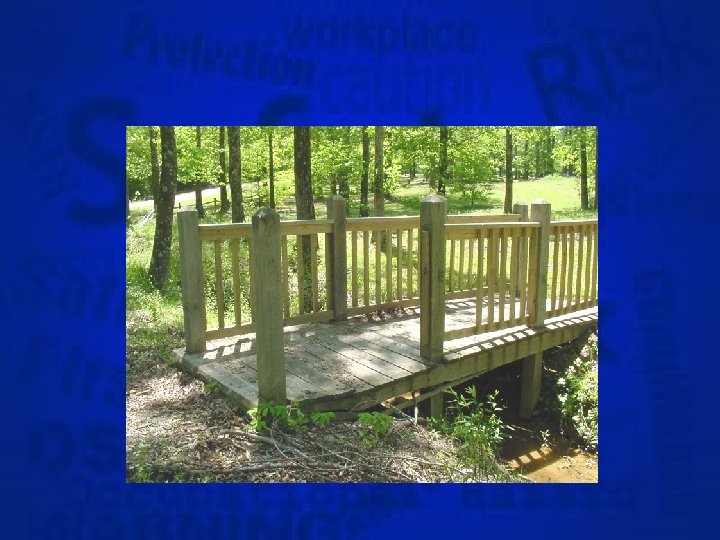
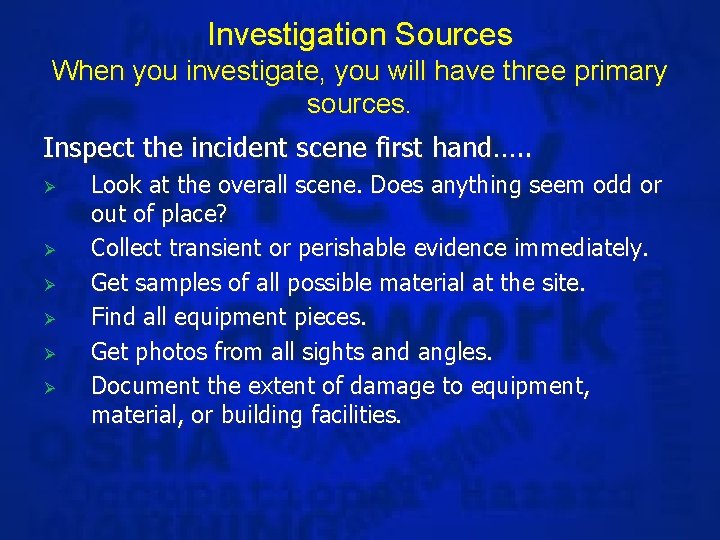
Investigation Sources When you investigate, you will have three primary sources. Inspect the incident scene first hand…. . Ø Ø Ø Look at the overall scene. Does anything seem odd or out of place? Collect transient or perishable evidence immediately. Get samples of all possible material at the site. Find all equipment pieces. Get photos from all sights and angles. Document the extent of damage to equipment, material, or building facilities.
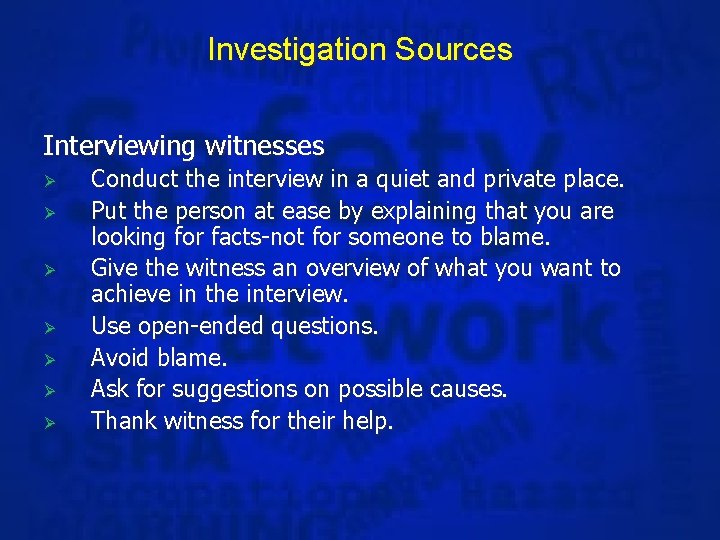
Investigation Sources Interviewing witnesses Ø Ø Ø Ø Conduct the interview in a quiet and private place. Put the person at ease by explaining that you are looking for facts-not for someone to blame. Give the witness an overview of what you want to achieve in the interview. Use open-ended questions. Avoid blame. Ask for suggestions on possible causes. Thank witness for their help.
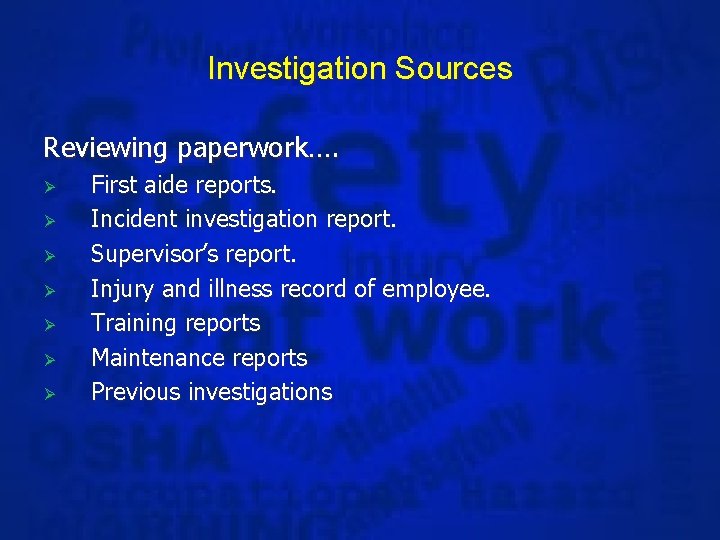
Investigation Sources Reviewing paperwork…. Ø Ø Ø Ø First aide reports. Incident investigation report. Supervisor’s report. Injury and illness record of employee. Training reports Maintenance reports Previous investigations
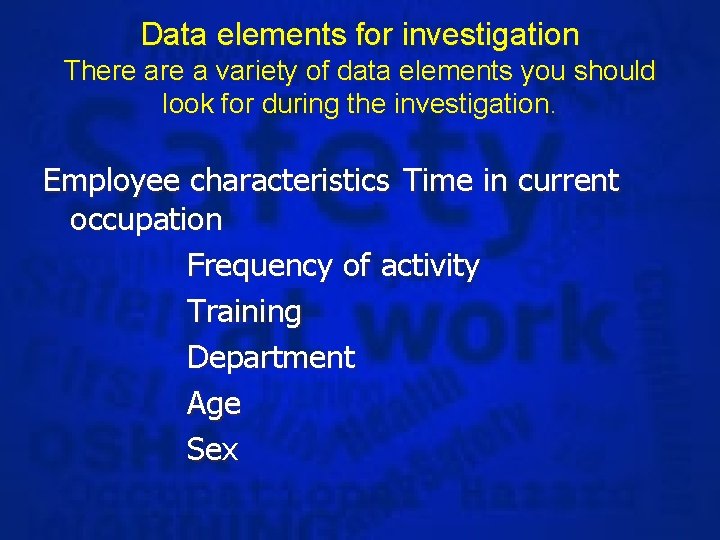
Data elements for investigation There a variety of data elements you should look for during the investigation. Employee characteristics Time in current occupation Frequency of activity Training Department Age Sex
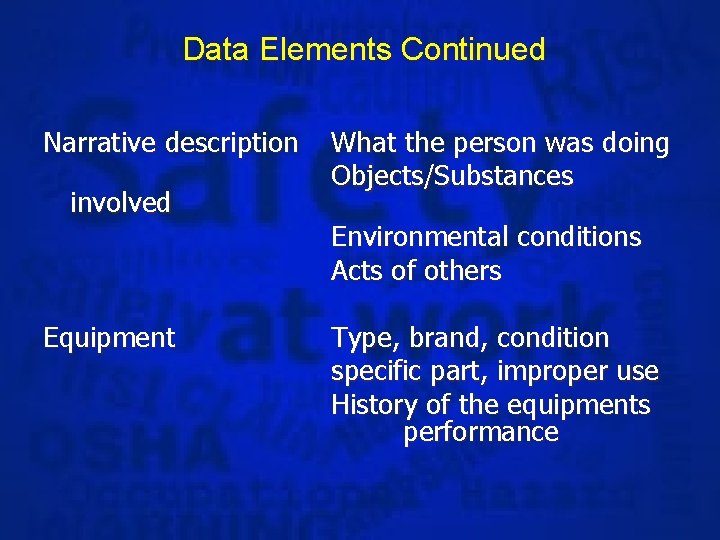
Data Elements Continued Narrative description involved Equipment What the person was doing Objects/Substances Environmental conditions Acts of others Type, brand, condition specific part, improper use History of the equipments performance
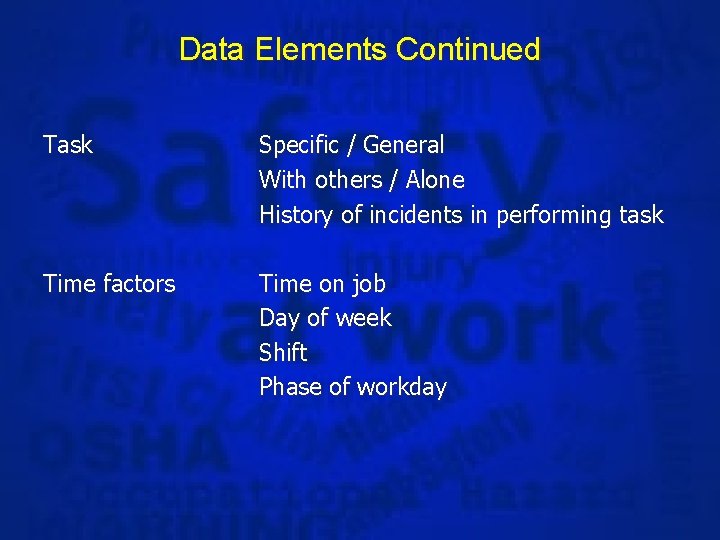
Data Elements Continued Task Specific / General With others / Alone History of incidents in performing task Time factors Time on job Day of week Shift Phase of workday
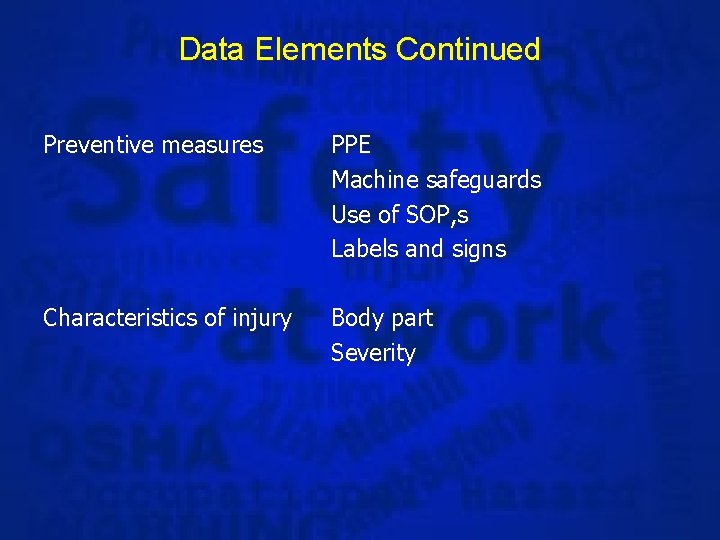
Data Elements Continued Preventive measures PPE Machine safeguards Use of SOP, s Labels and signs Characteristics of injury Body part Severity
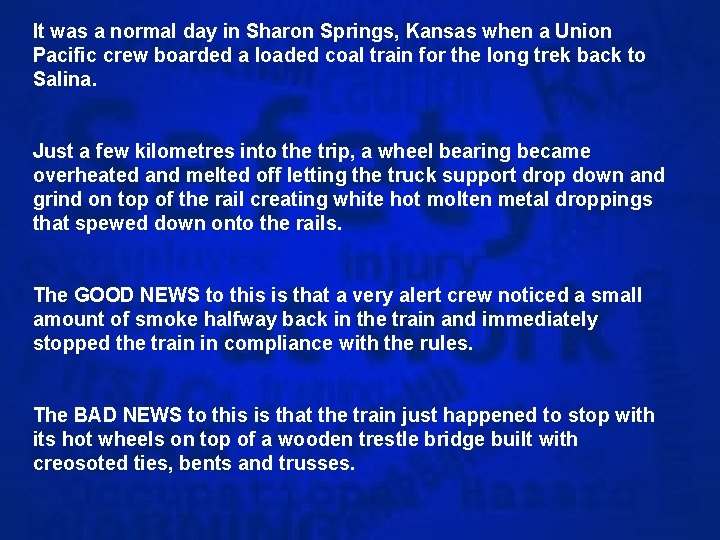
It was a normal day in Sharon Springs, Kansas when a Union Pacific crew boarded a loaded coal train for the long trek back to Salina. Just a few kilometres into the trip, a wheel bearing became overheated and melted off letting the truck support drop down and grind on top of the rail creating white hot molten metal droppings that spewed down onto the rails. The GOOD NEWS to this is that a very alert crew noticed a small amount of smoke halfway back in the train and immediately stopped the train in compliance with the rules. The BAD NEWS to this is that the train just happened to stop with its hot wheels on top of a wooden trestle bridge built with creosoted ties, bents and trusses.
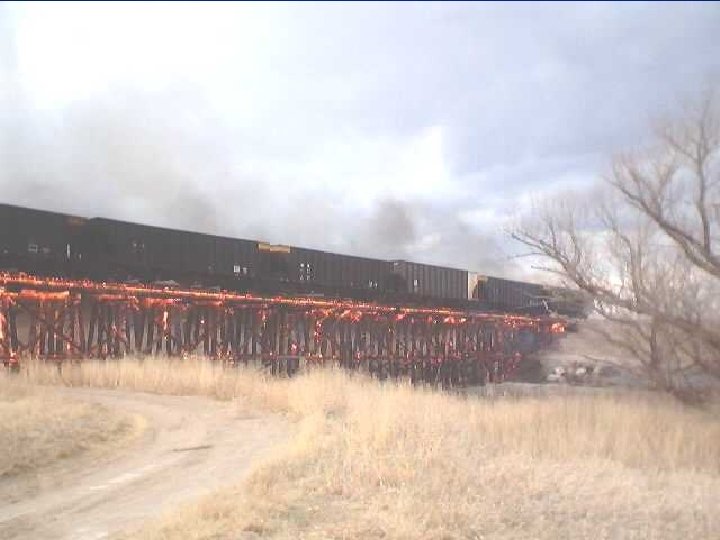
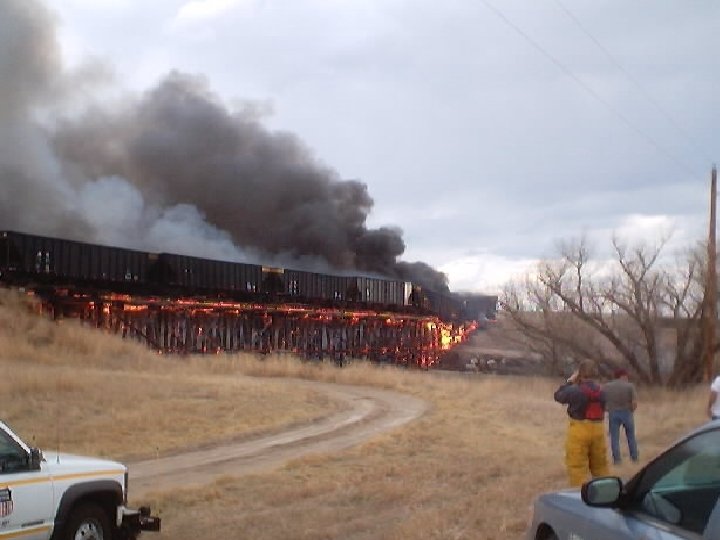
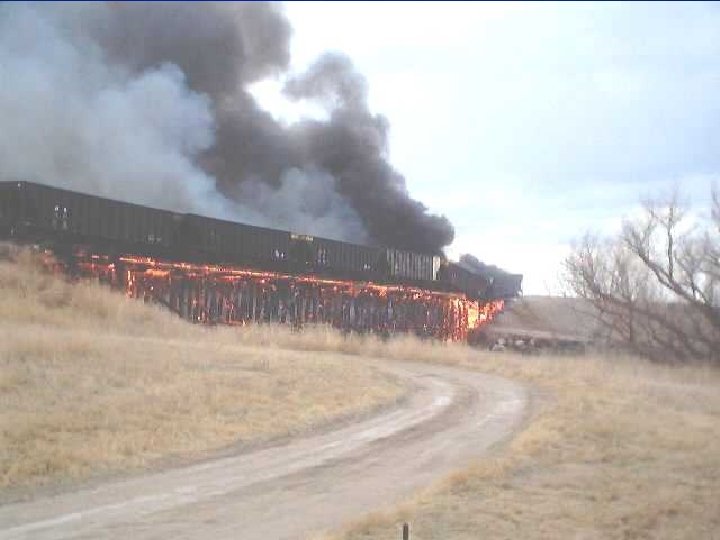
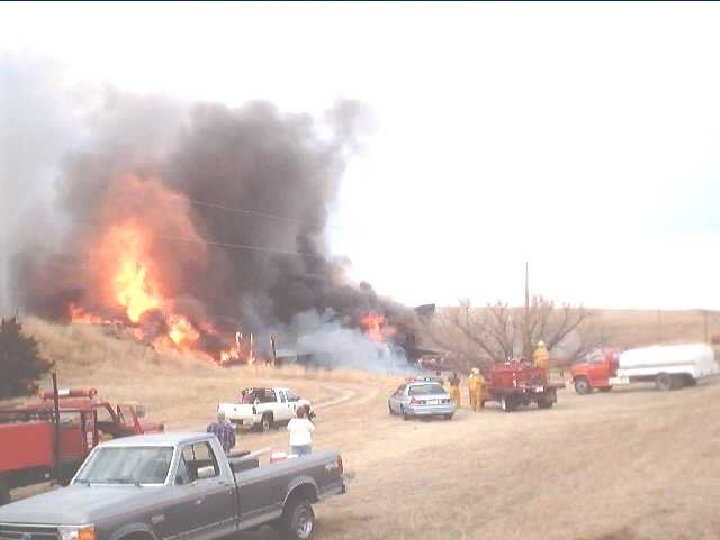
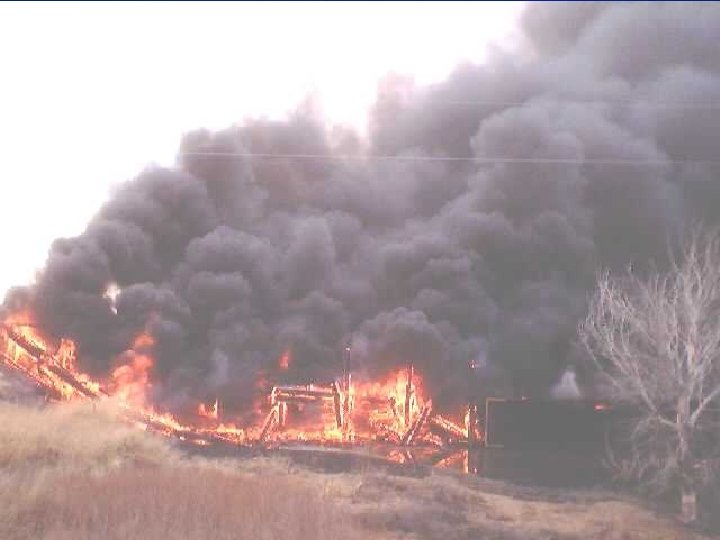
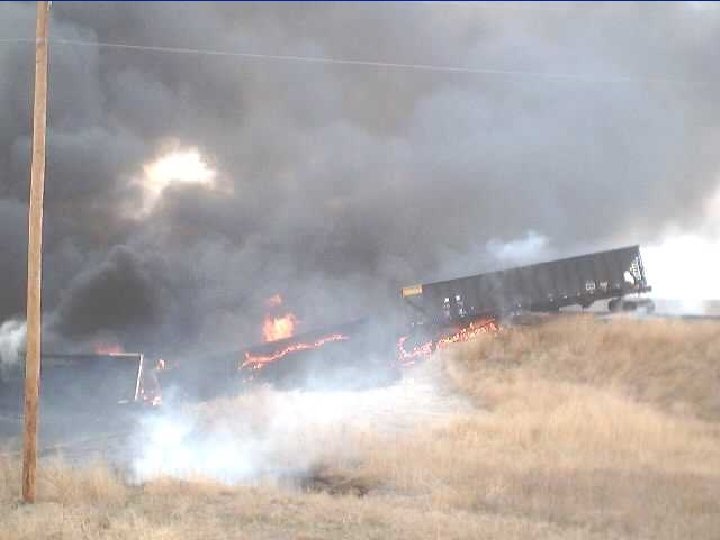
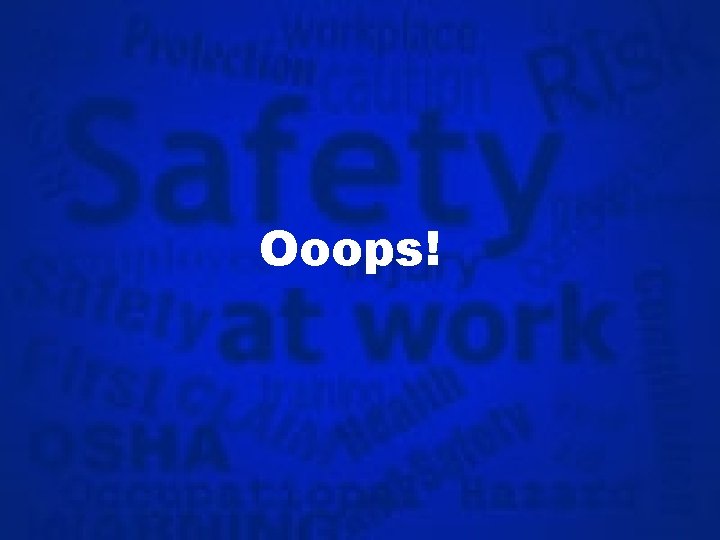
Ooops!
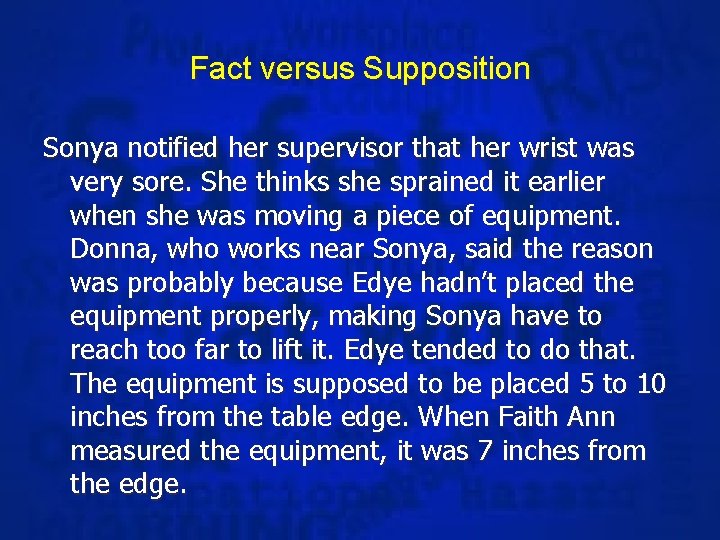
Fact versus Supposition Sonya notified her supervisor that her wrist was very sore. She thinks she sprained it earlier when she was moving a piece of equipment. Donna, who works near Sonya, said the reason was probably because Edye hadn’t placed the equipment properly, making Sonya have to reach too far to lift it. Edye tended to do that. The equipment is supposed to be placed 5 to 10 inches from the table edge. When Faith Ann measured the equipment, it was 7 inches from the edge.
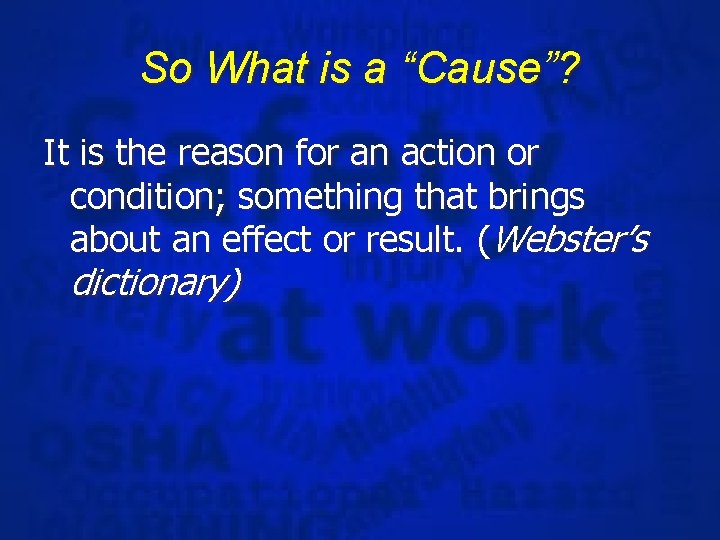
So What is a “Cause”? It is the reason for an action or condition; something that brings about an effect or result. (Webster’s dictionary)
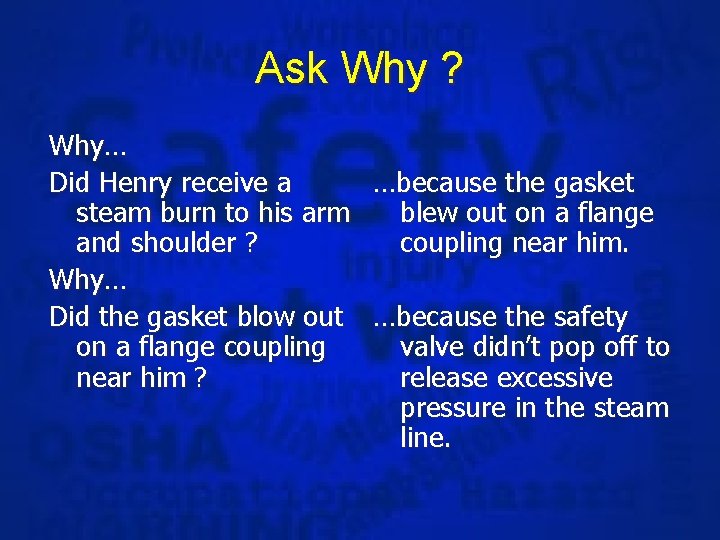
Ask Why ? Why… Did Henry receive a …because the gasket steam burn to his arm blew out on a flange and shoulder ? coupling near him. Why… Did the gasket blow out …because the safety on a flange coupling valve didn’t pop off to near him ? release excessive pressure in the steam line.
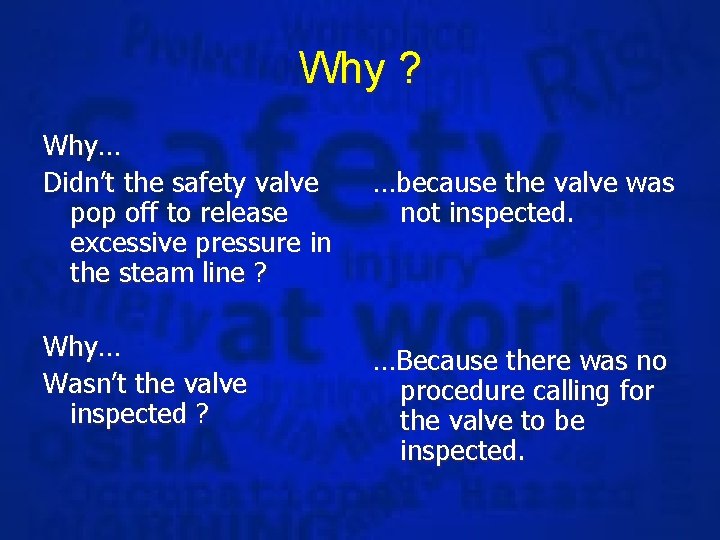
Why ? Why… Didn’t the safety valve pop off to release excessive pressure in the steam line ? Why… Wasn’t the valve inspected ? …because the valve was not inspected. …Because there was no procedure calling for the valve to be inspected.
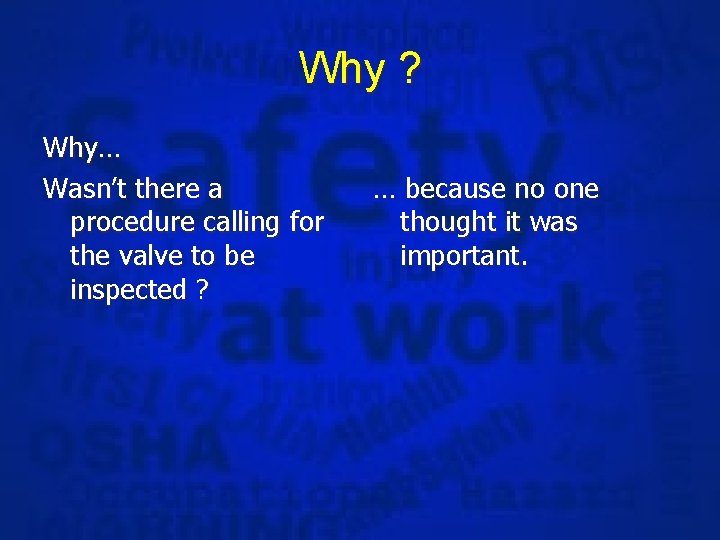
Why ? Why… Wasn’t there a procedure calling for the valve to be inspected ? … because no one thought it was important.
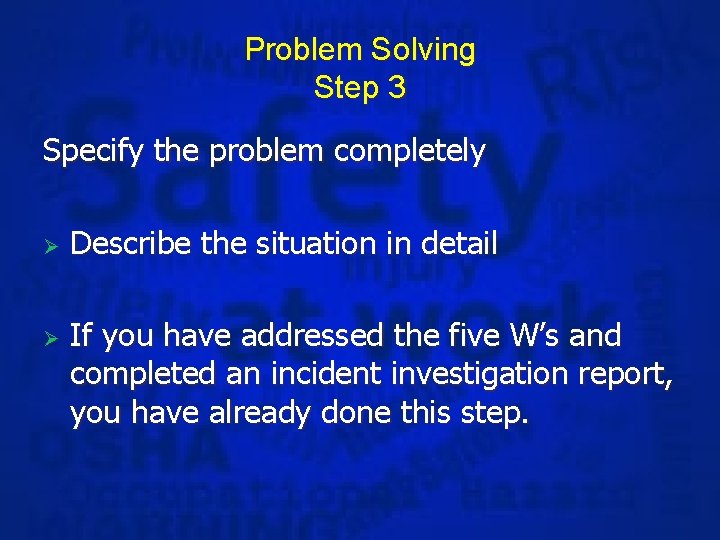
Problem Solving Step 3 Specify the problem completely Ø Ø Describe the situation in detail If you have addressed the five W’s and completed an incident investigation report, you have already done this step.
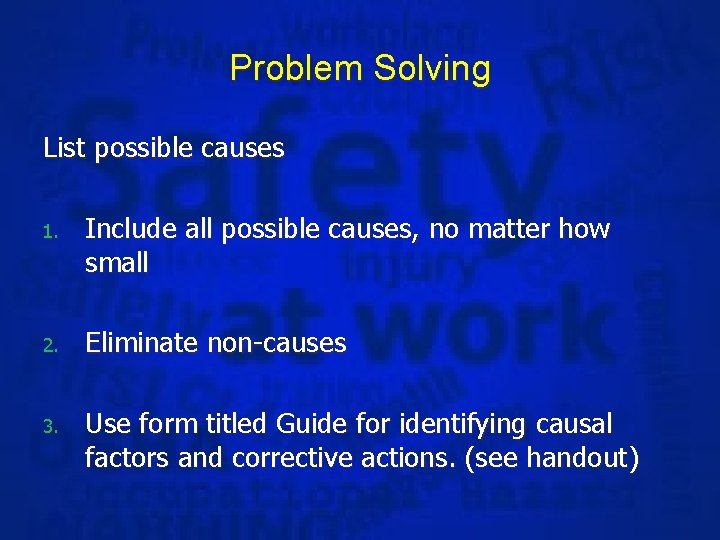
Problem Solving List possible causes 1. Include all possible causes, no matter how small 2. Eliminate non-causes 3. Use form titled Guide for identifying causal factors and corrective actions. (see handout)
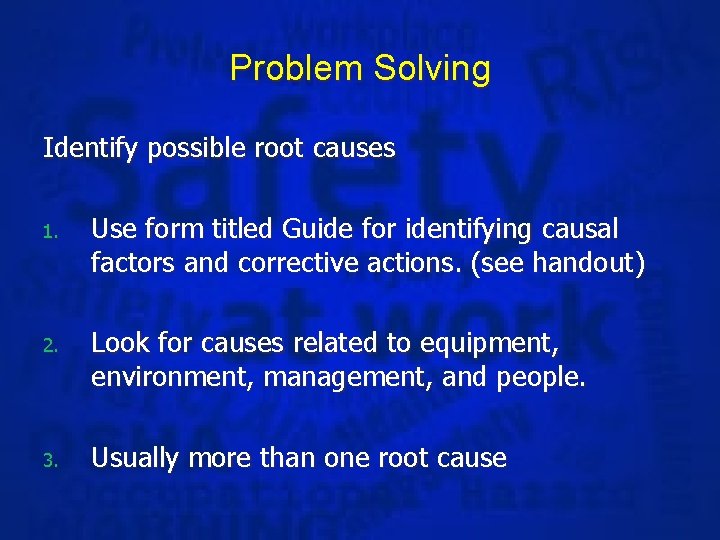
Problem Solving Identify possible root causes 1. Use form titled Guide for identifying causal factors and corrective actions. (see handout) 2. Look for causes related to equipment, environment, management, and people. 3. Usually more than one root cause
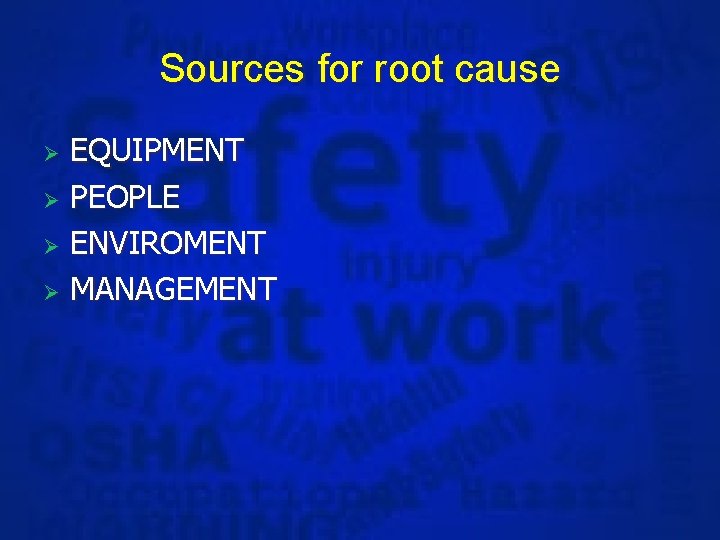
Sources for root cause EQUIPMENT Ø PEOPLE Ø ENVIROMENT Ø MANAGEMENT Ø
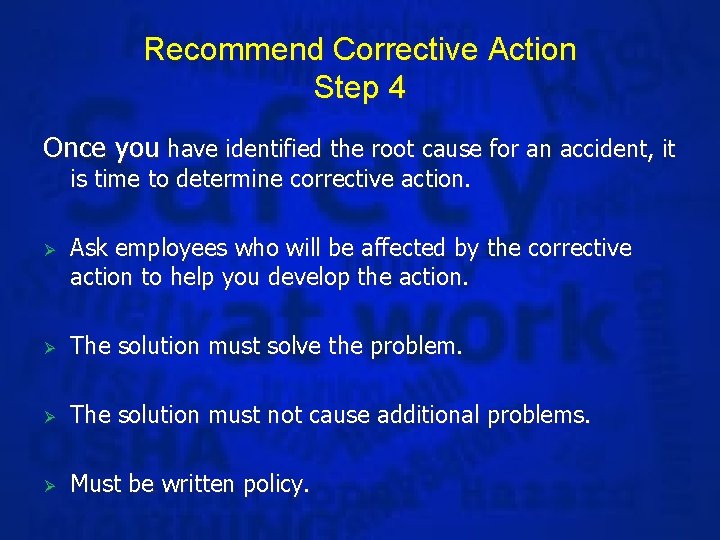
Recommend Corrective Action Step 4 Once you have identified the root cause for an accident, it is time to determine corrective action. Ø Ask employees who will be affected by the corrective action to help you develop the action. Ø The solution must solve the problem. Ø The solution must not cause additional problems. Ø Must be written policy.
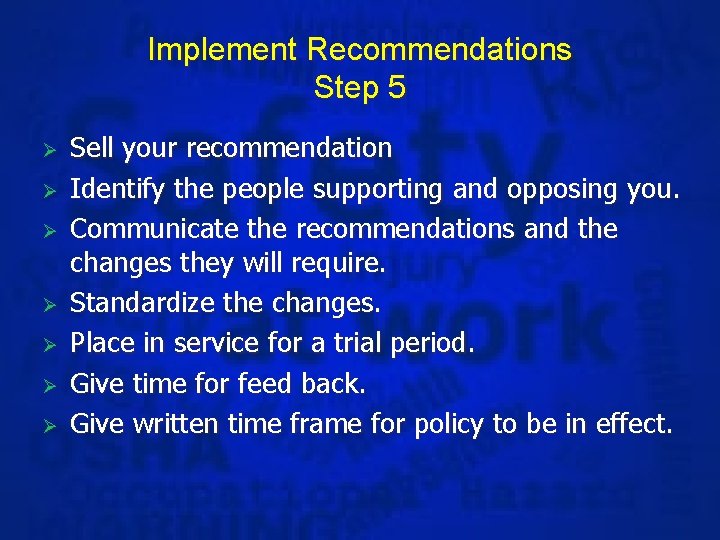
Implement Recommendations Step 5 Ø Ø Ø Ø Sell your recommendation Identify the people supporting and opposing you. Communicate the recommendations and the changes they will require. Standardize the changes. Place in service for a trial period. Give time for feed back. Give written time frame for policy to be in effect.
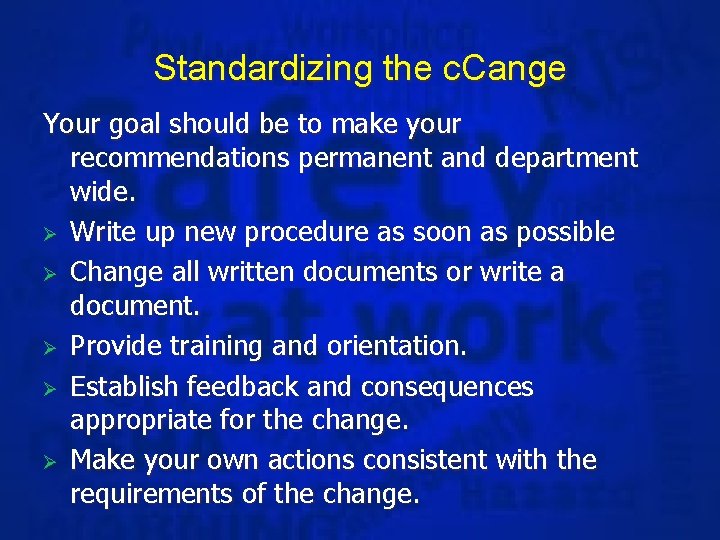
Standardizing the c. Cange Your goal should be to make your recommendations permanent and department wide. Ø Write up new procedure as soon as possible Ø Change all written documents or write a document. Ø Provide training and orientation. Ø Establish feedback and consequences appropriate for the change. Ø Make your own actions consistent with the requirements of the change.
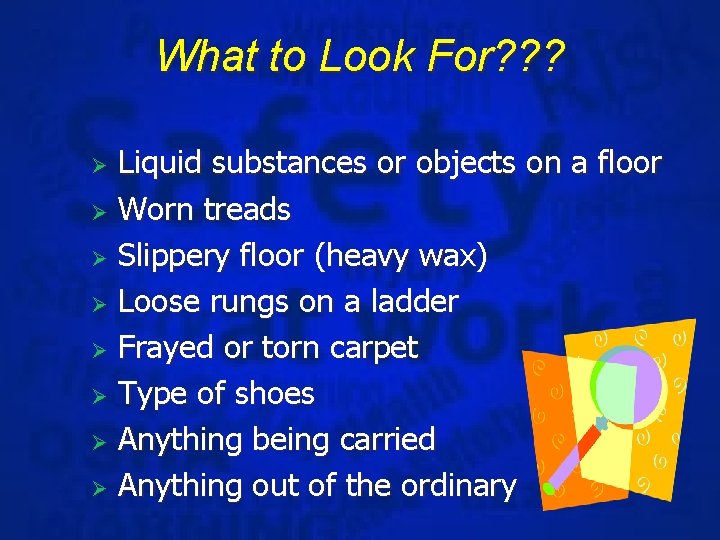
What to Look For? ? ? Liquid substances or objects on a floor Ø Worn treads Ø Slippery floor (heavy wax) Ø Loose rungs on a ladder Ø Frayed or torn carpet Ø Type of shoes Ø Anything being carried Ø Anything out of the ordinary Ø
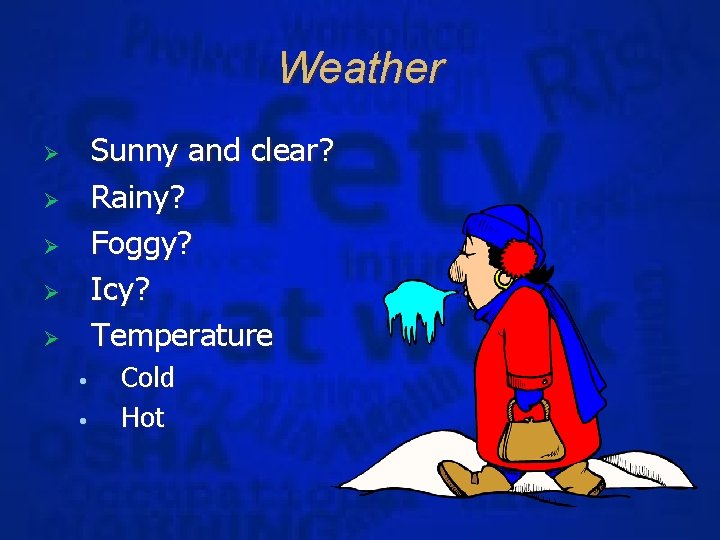
Weather Sunny and clear? Rainy? Foggy? Icy? Temperature Ø Ø Ø • • Cold Hot
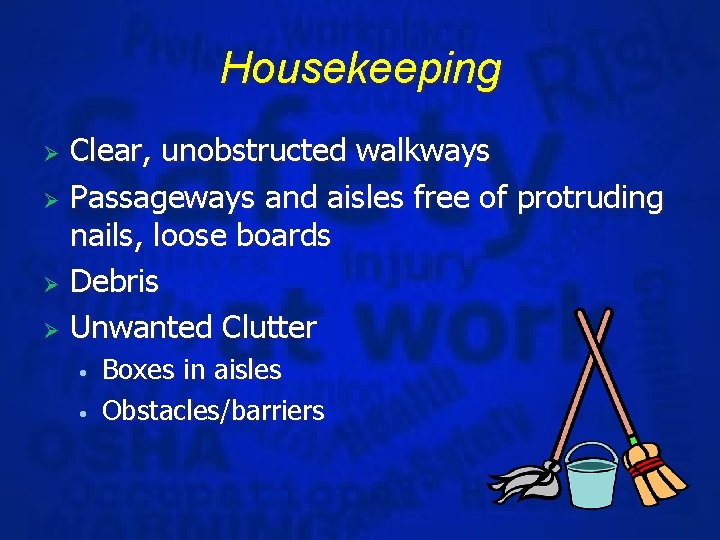
Housekeeping Clear, unobstructed walkways Ø Passageways and aisles free of protruding nails, loose boards Ø Debris Ø Unwanted Clutter Ø • • Boxes in aisles Obstacles/barriers
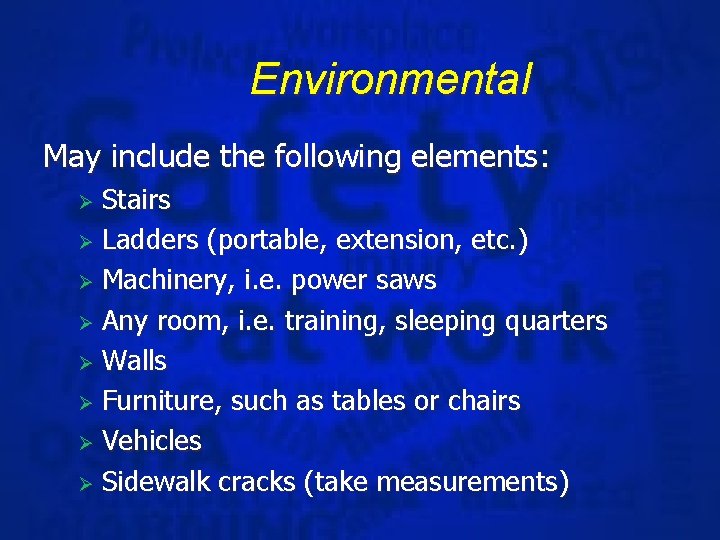
Environmental May include the following elements: Stairs Ø Ladders (portable, extension, etc. ) Ø Machinery, i. e. power saws Ø Any room, i. e. training, sleeping quarters Ø Walls Ø Furniture, such as tables or chairs Ø Vehicles Ø Sidewalk cracks (take measurements) Ø
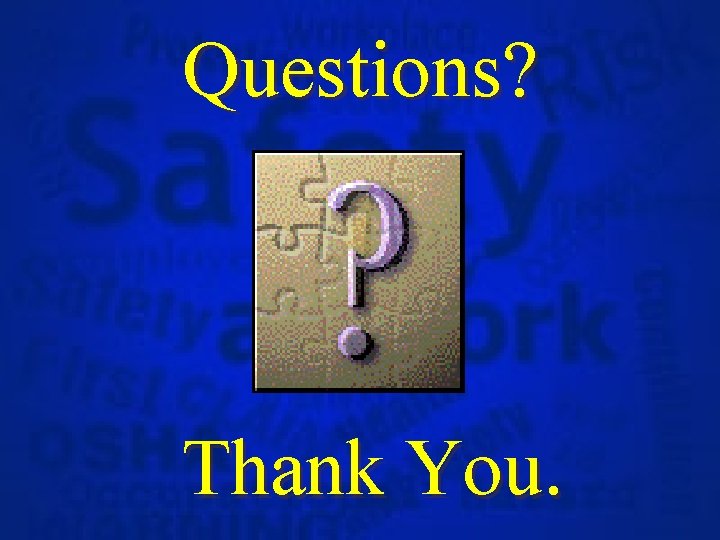
Questions? Thank You.
Brad henning
Carley matthews
5-9 accident investigation data answers
Accident investigation data analysis
385+40
The method of unit costing is adopted by
Todd franzen
The wave novel
Todd parker byu
Todd conklin quotes
Ajh photography
Dr todd baron
Paced decision model
Does print pushing work
Todd tannenbaum
Pipe network
Fda oimt
Todd ullah
Todd jackson hockey canada
Richard watson todd
Amanda todd foto
Joachimson v swiss bank corporation
Mappa di todd
Decomposition
Condor_prio
Emilie todd helm
Todd is trying to quit cheating
Dr todd borus
Petra todd
Sweeney todd storyline
Colin todd fire
Todd c. mowry
Adaptive lanning
Todd bacastow
Dr todd fox
Todd sosna
David todd lee
Todd humes
Programming language
Dr todd stoner
Alan todd psni
Tableau buffer
Connor durrell
Todd j. martinez
Todd kopelman
Vikram shakkottai
Richard watson todd
Todd huffman oxford
Todd richardson hud
Todd wernet
Todd humphreys