Wireless Laptop Charger Onur Cam Enrique Ramirez Jason
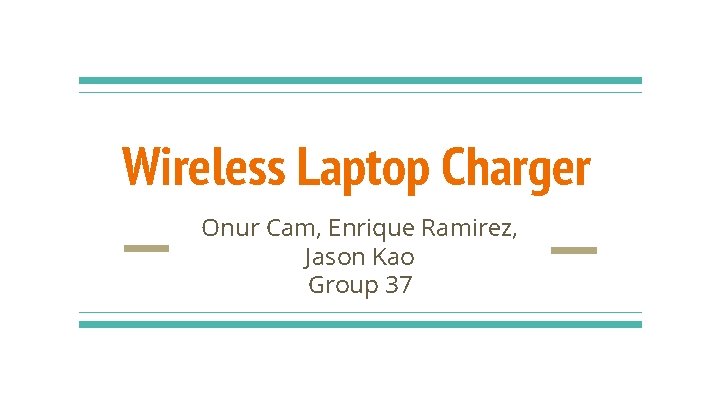
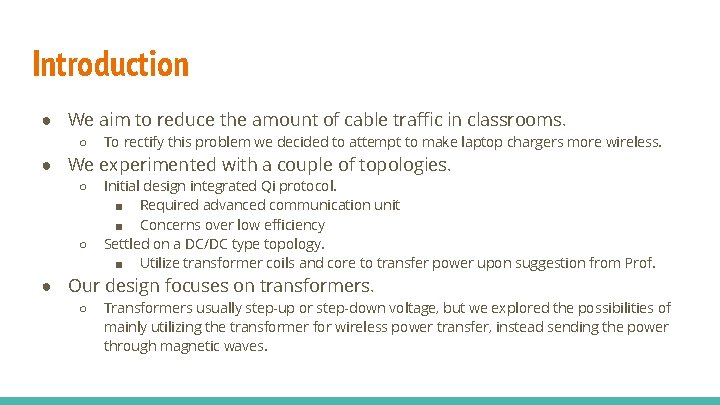
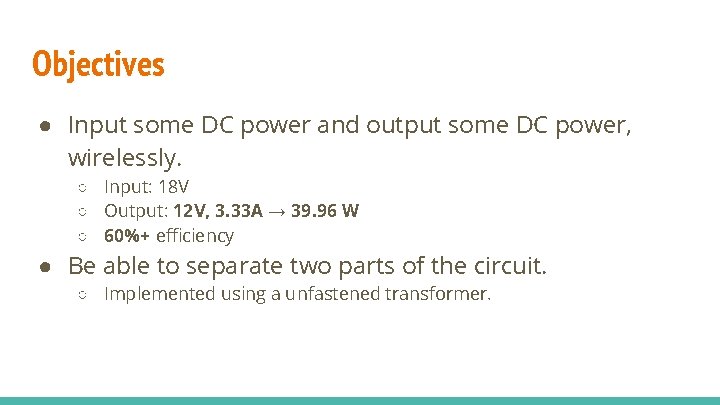
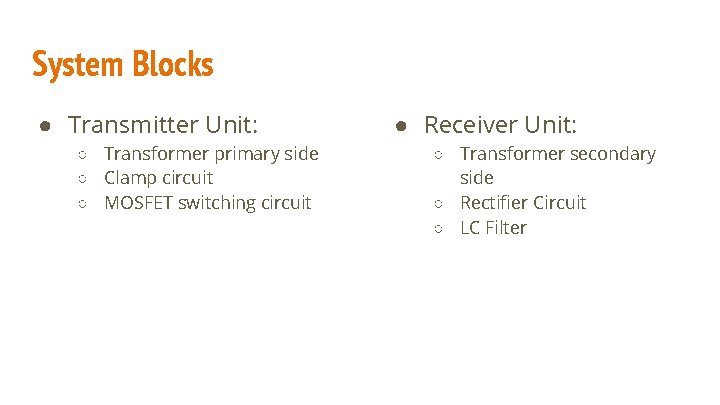
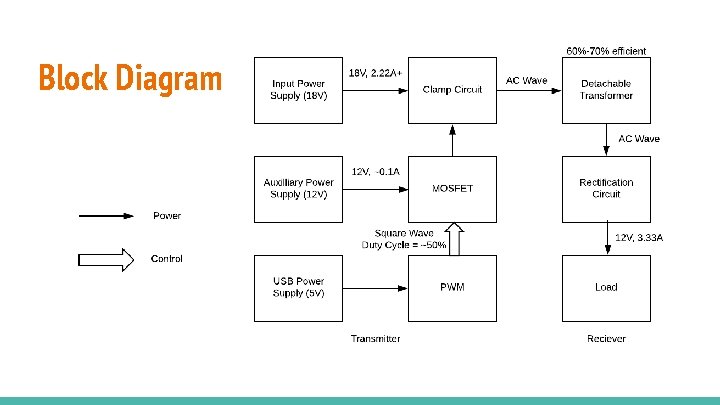
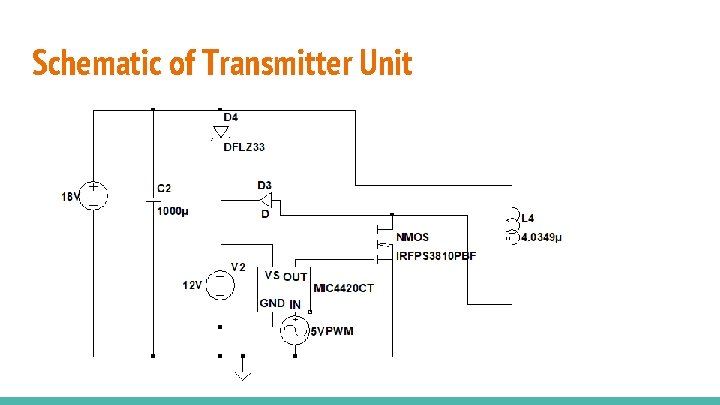
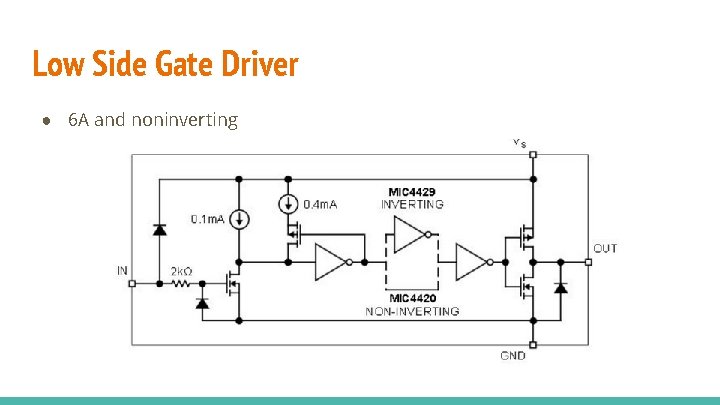
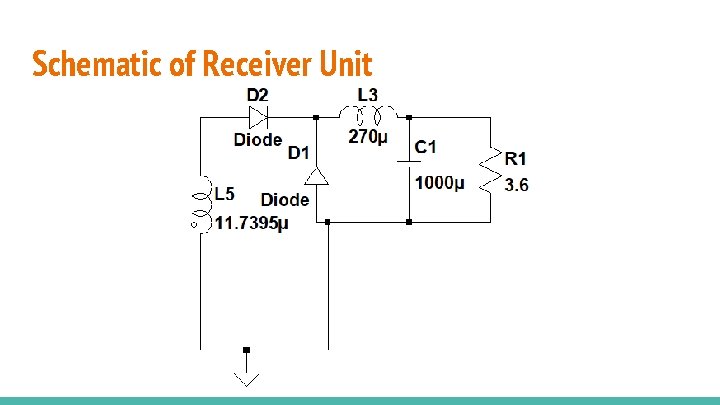
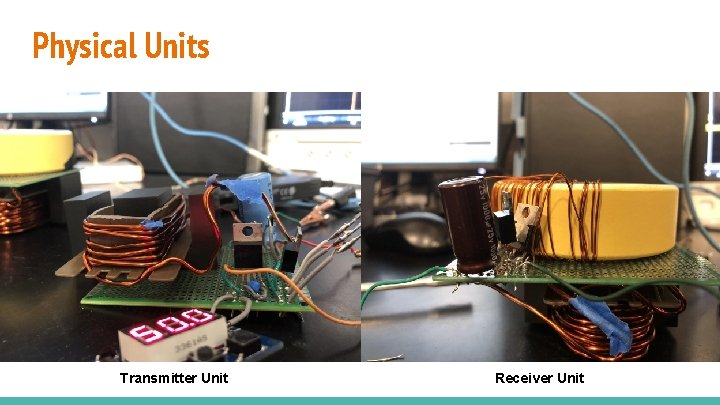
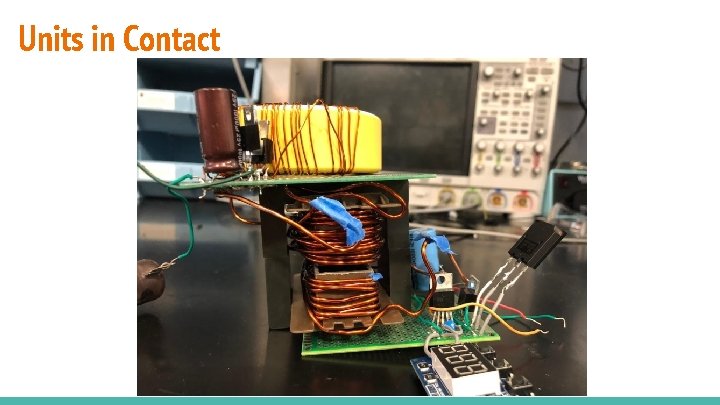
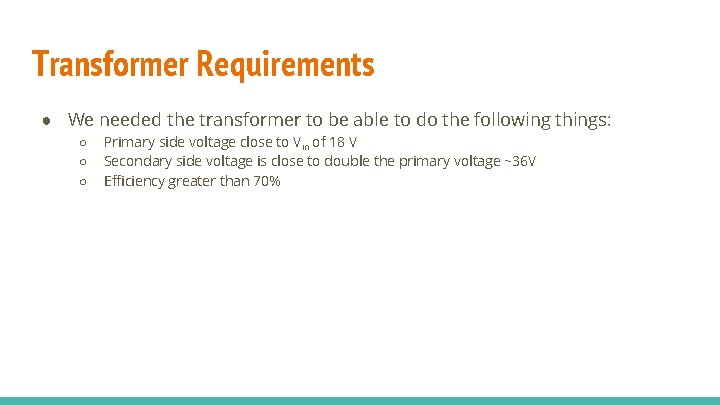
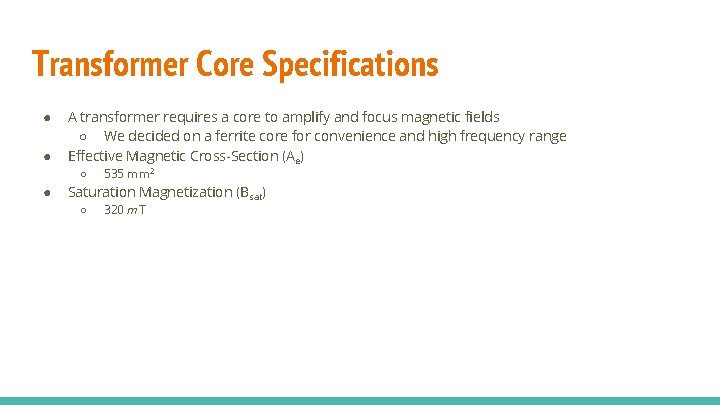
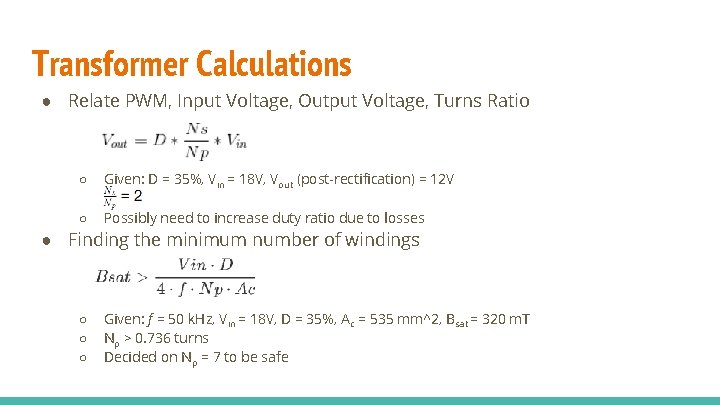
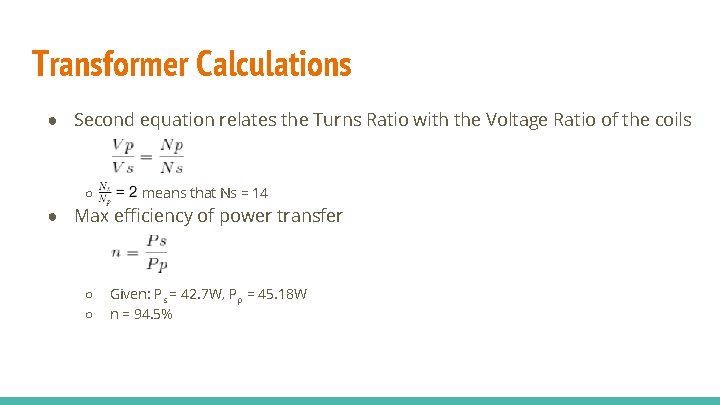
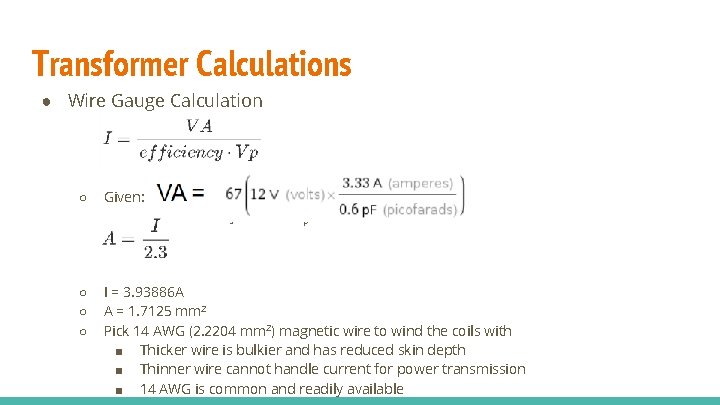
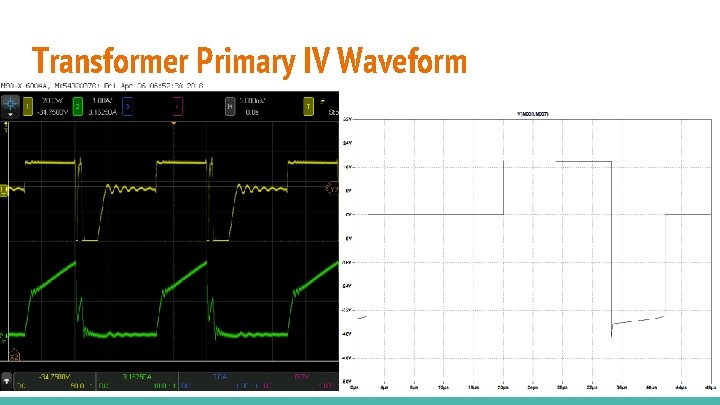
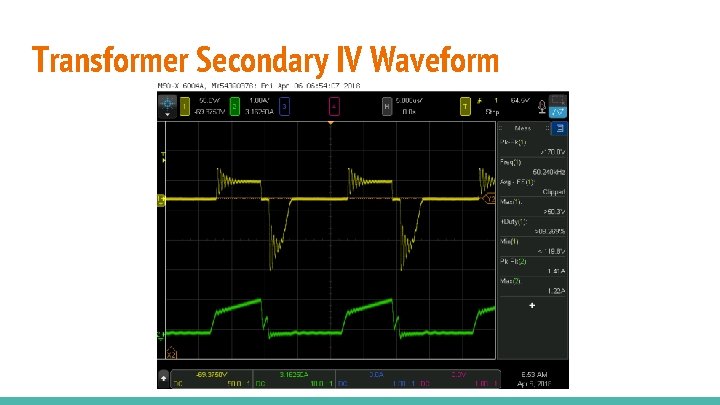
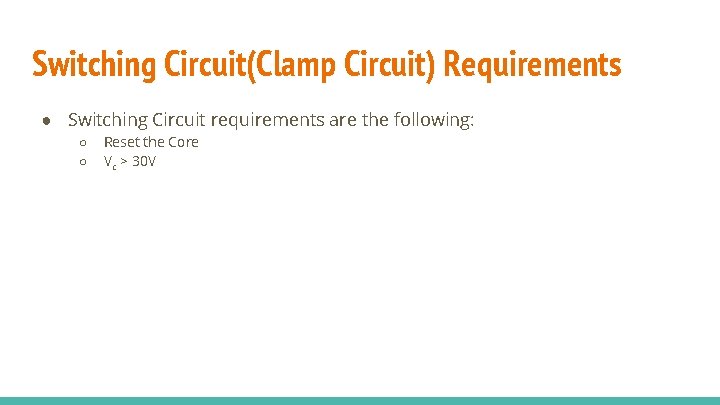
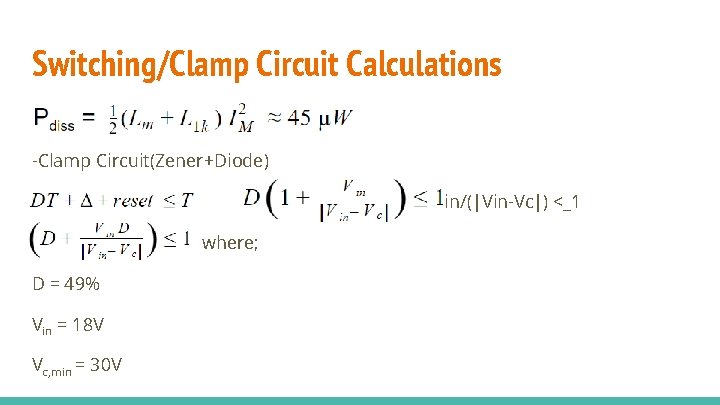
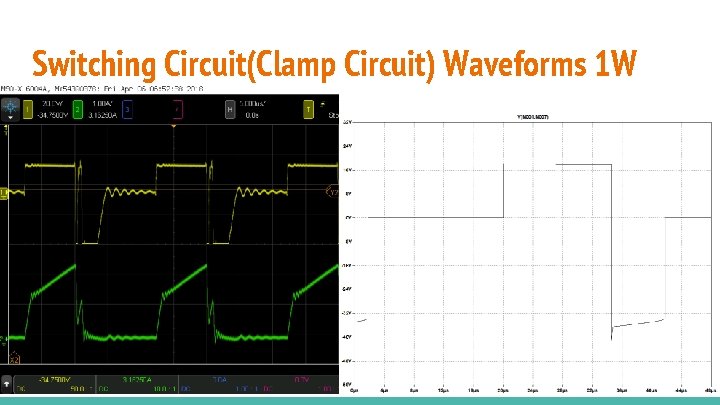
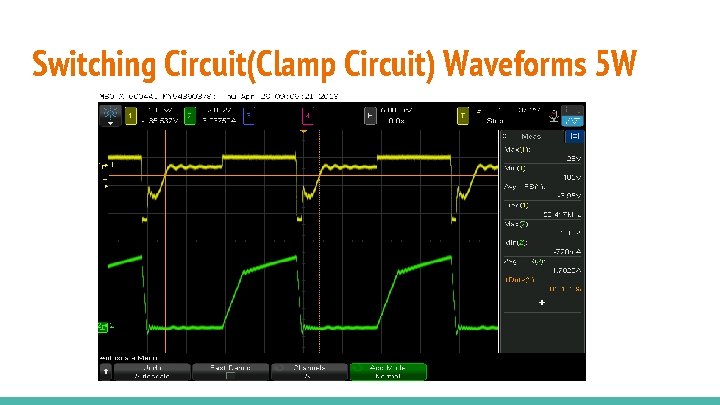
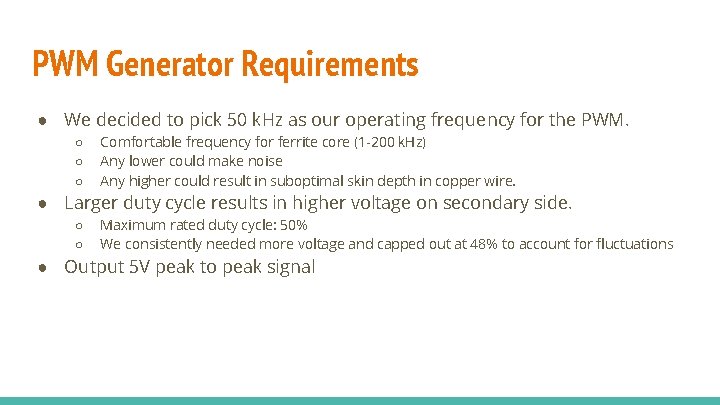
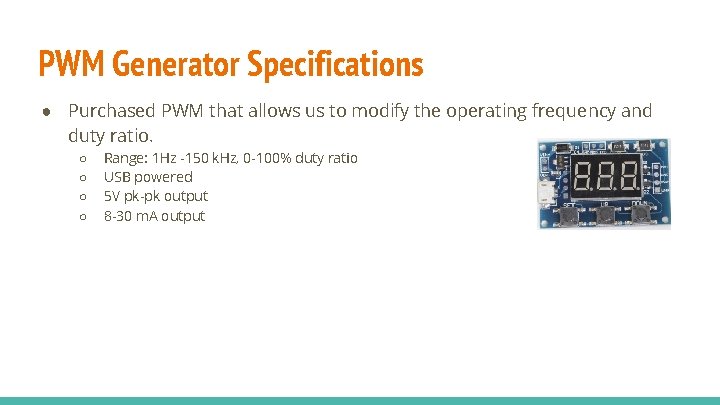
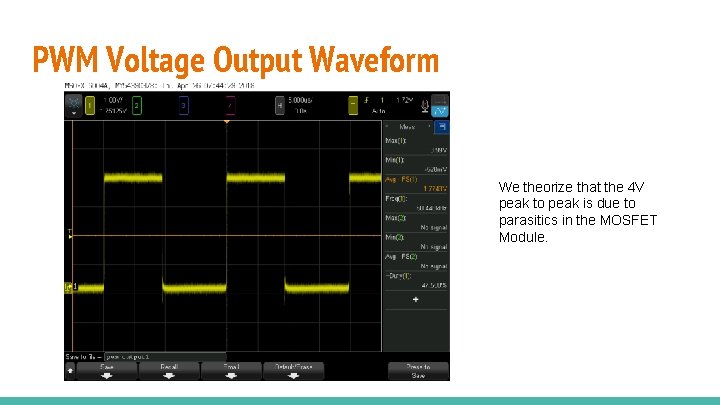
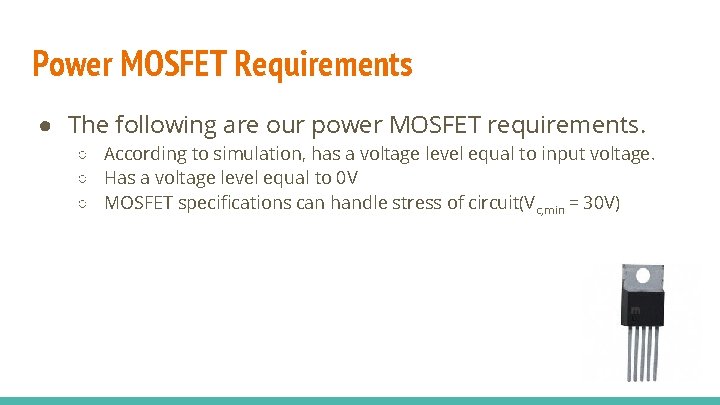
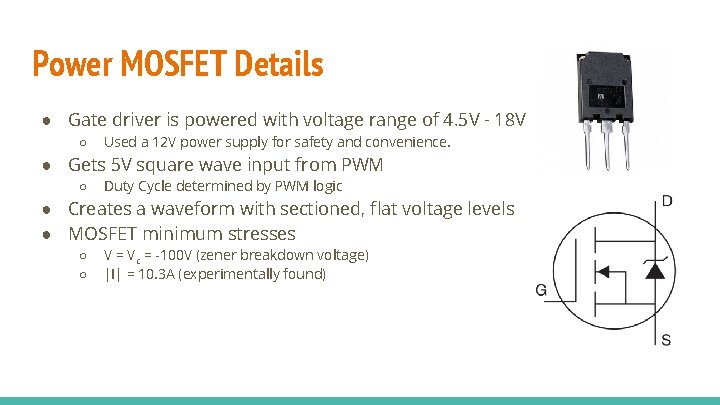
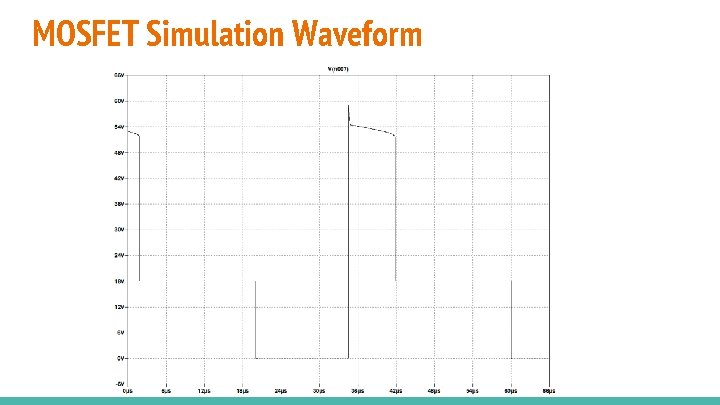
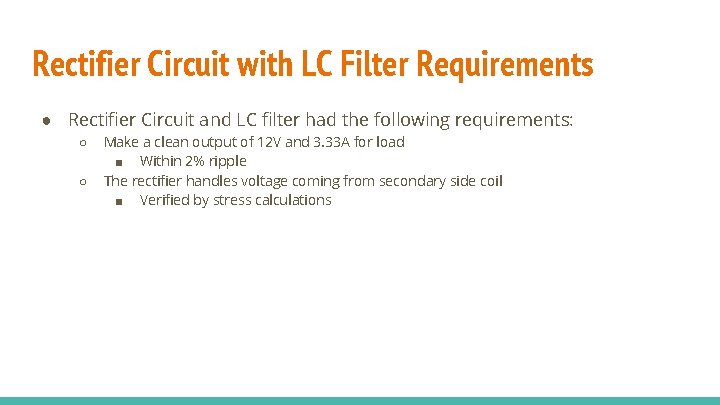
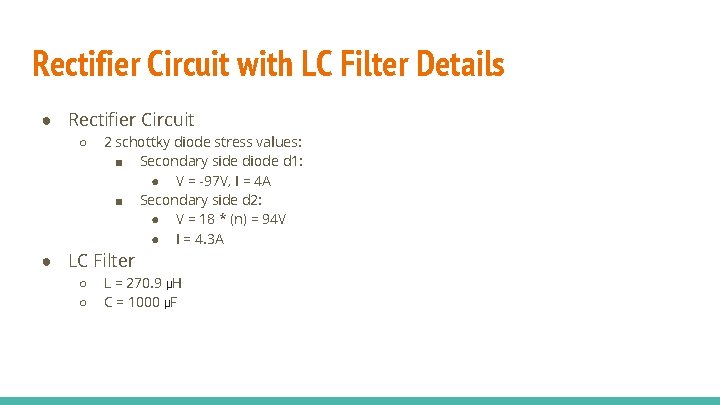
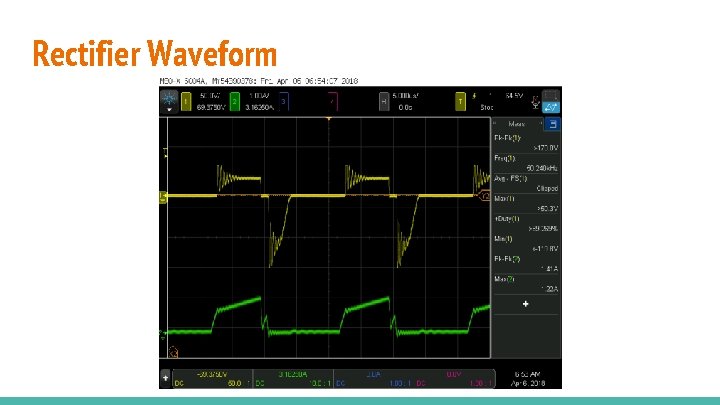
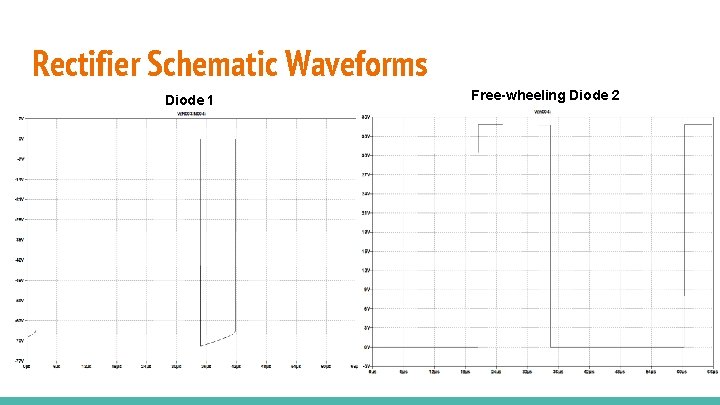
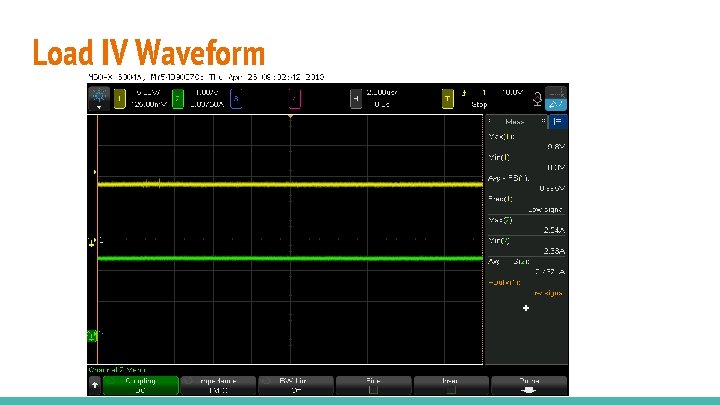
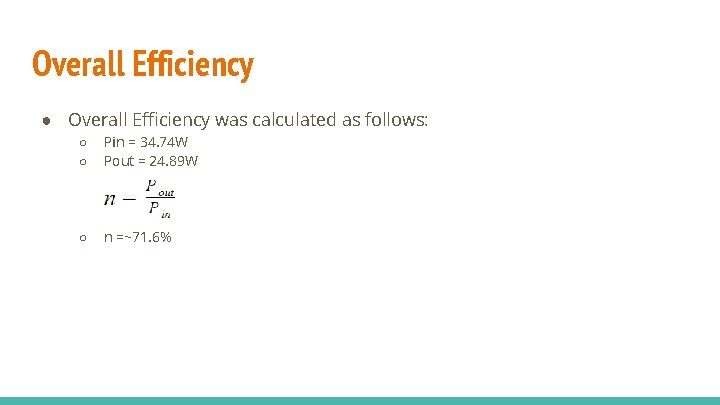
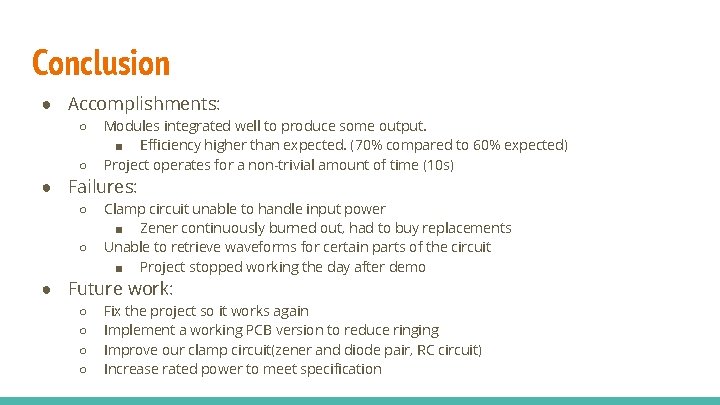
- Slides: 34
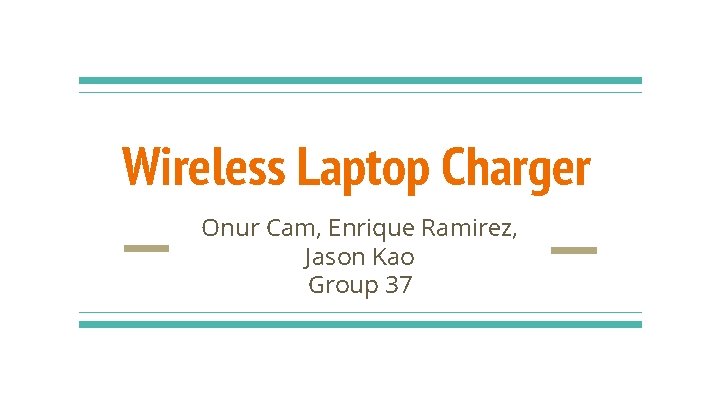
Wireless Laptop Charger Onur Cam, Enrique Ramirez, Jason Kao Group 37
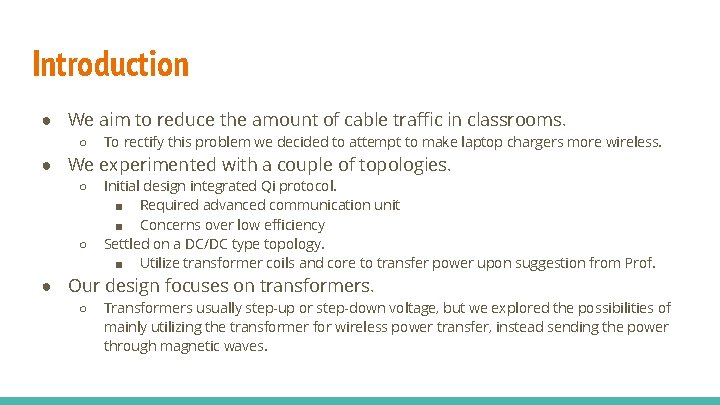
Introduction ● We aim to reduce the amount of cable traffic in classrooms. ○ To rectify this problem we decided to attempt to make laptop chargers more wireless. ● We experimented with a couple of topologies. ○ ○ Initial design integrated Qi protocol. ■ Required advanced communication unit ■ Concerns over low efficiency Settled on a DC/DC type topology. ■ Utilize transformer coils and core to transfer power upon suggestion from Prof. ● Our design focuses on transformers. ○ Transformers usually step-up or step-down voltage, but we explored the possibilities of mainly utilizing the transformer for wireless power transfer, instead sending the power through magnetic waves.
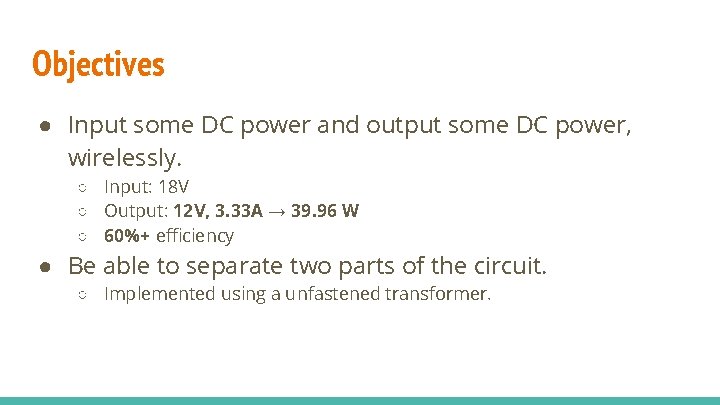
Objectives ● Input some DC power and output some DC power, wirelessly. ○ Input: 18 V ○ Output: 12 V, 3. 33 A → 39. 96 W ○ 60%+ efficiency ● Be able to separate two parts of the circuit. ○ Implemented using a unfastened transformer.
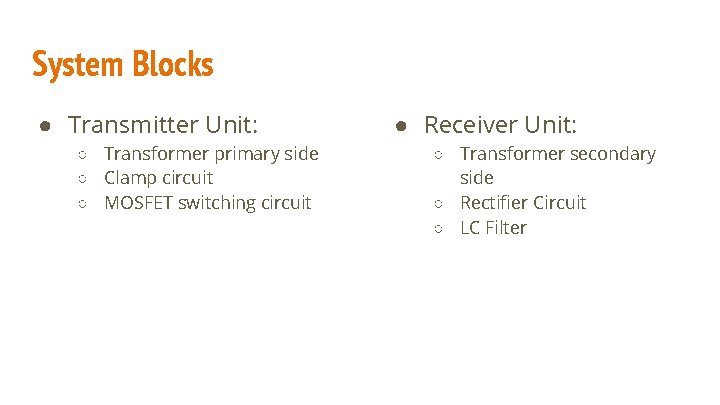
System Blocks ● Transmitter Unit: ○ Transformer primary side ○ Clamp circuit ○ MOSFET switching circuit ● Receiver Unit: ○ Transformer secondary side ○ Rectifier Circuit ○ LC Filter
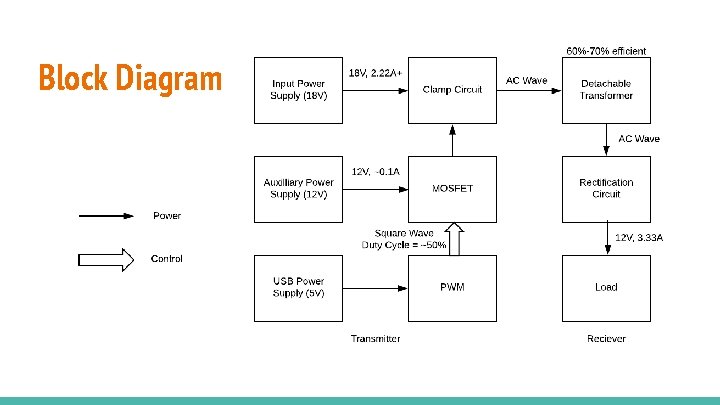
Block Diagram
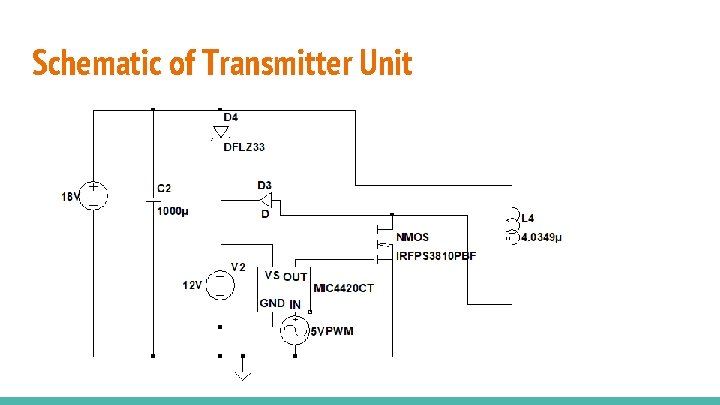
Schematic of Transmitter Unit
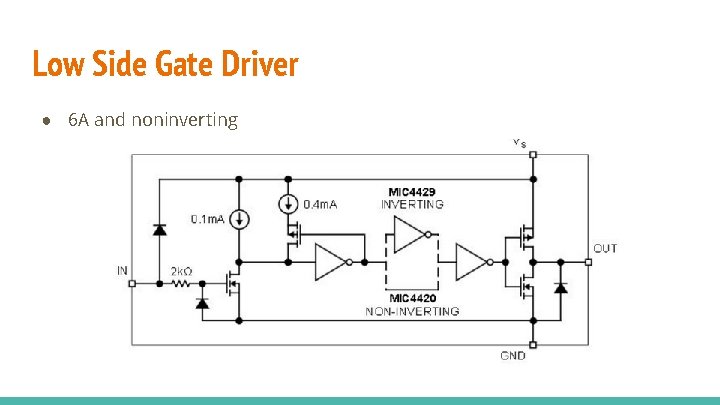
Low Side Gate Driver ● 6 A and noninverting
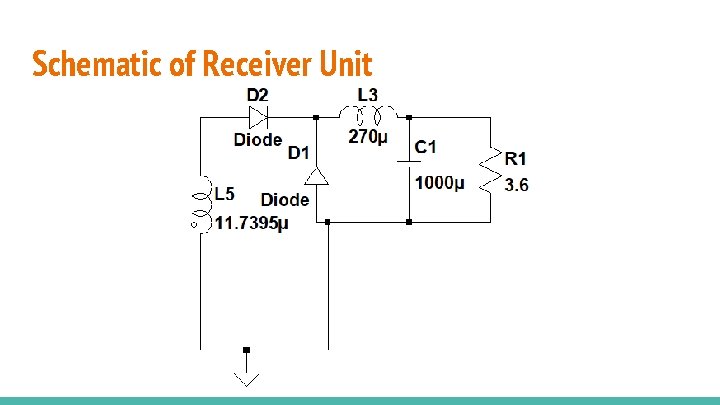
Schematic of Receiver Unit
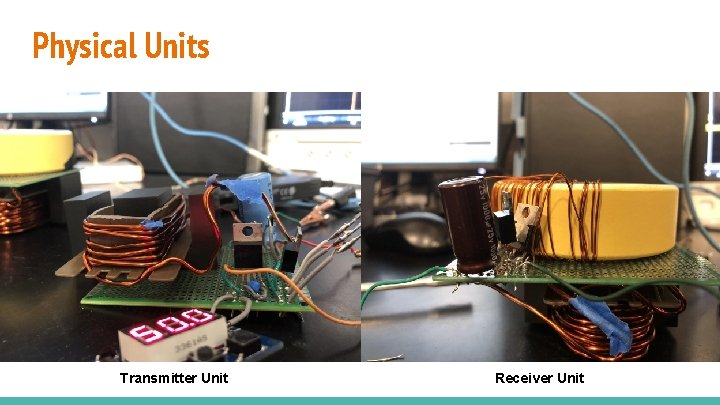
Physical Units Transmitter Unit Receiver Unit
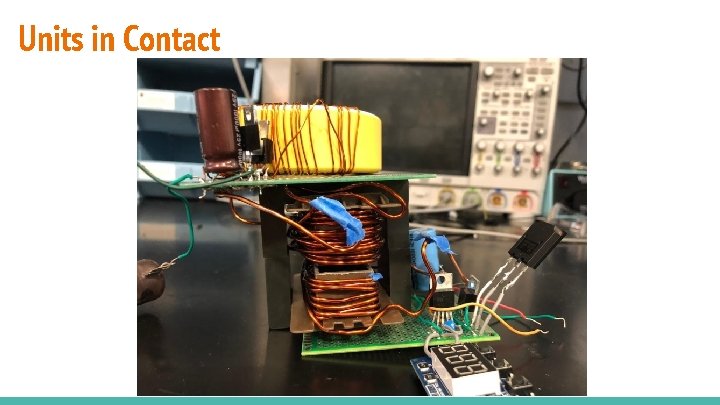
Units in Contact
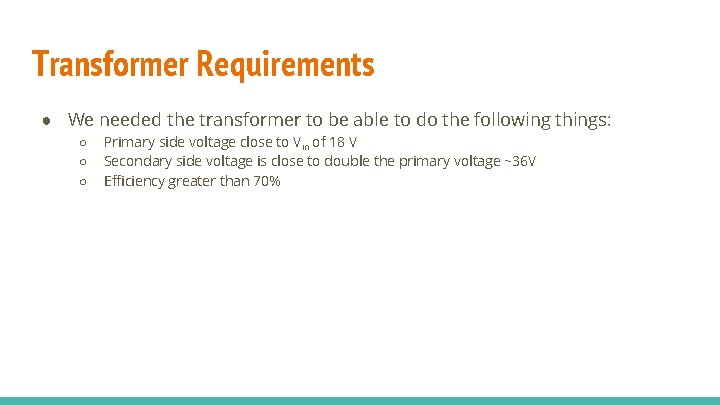
Transformer Requirements ● We needed the transformer to be able to do the following things: ○ ○ ○ Primary side voltage close to Vin of 18 V Secondary side voltage is close to double the primary voltage ~36 V Efficiency greater than 70%
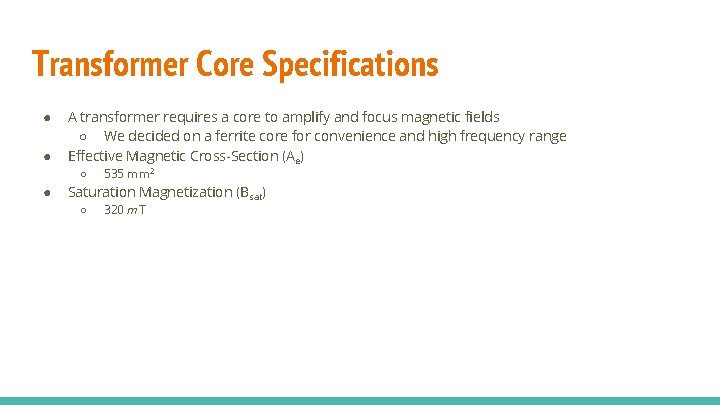
Transformer Core Specifications ● ● A transformer requires a core to amplify and focus magnetic fields ○ We decided on a ferrite core for convenience and high frequency range Effective Magnetic Cross-Section (Ae) ○ ● 535 mm 2 Saturation Magnetization (Bsat) ○ 320 m. T
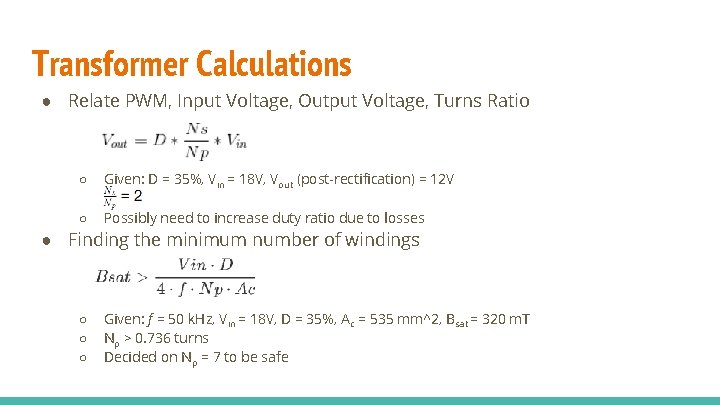
Transformer Calculations ● Relate PWM, Input Voltage, Output Voltage, Turns Ratio ○ Given: D = 35%, Vin = 18 V, Vout (post-rectification) = 12 V ○ Possibly need to increase duty ratio due to losses ● Finding the minimum number of windings ○ ○ ○ Given: f = 50 k. Hz, Vin = 18 V, D = 35%, Ac = 535 mm^2, Bsat = 320 m. T Np > 0. 736 turns Decided on Np = 7 to be safe
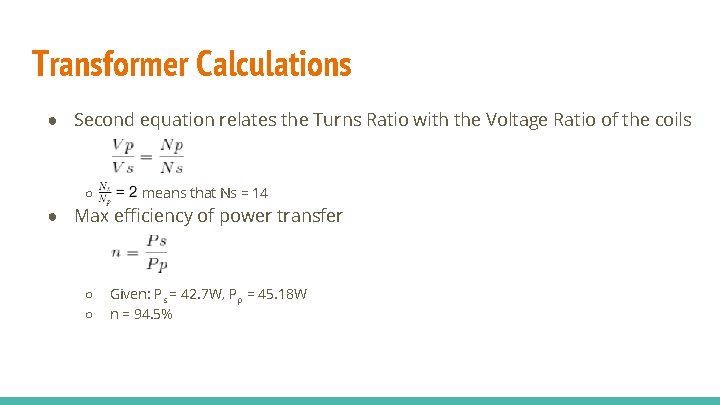
Transformer Calculations ● Second equation relates the Turns Ratio with the Voltage Ratio of the coils ○ means that Ns = 14 ● Max efficiency of power transfer ○ ○ Given: Ps = 42. 7 W, Pp = 45. 18 W n = 94. 5%
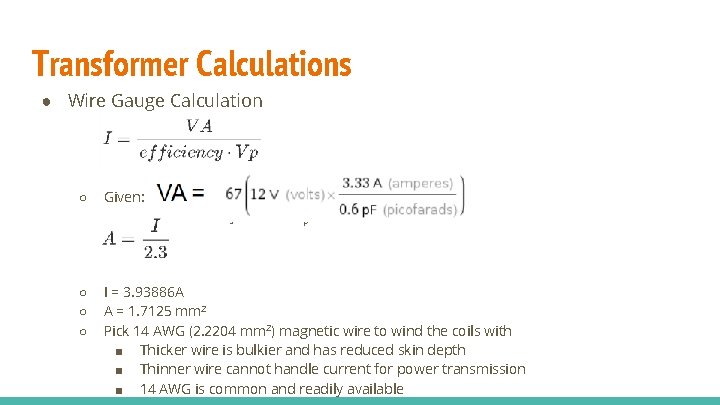
Transformer Calculations ● Wire Gauge Calculation ○ Given: VA = 67 (12 V * 3. 33 A / 0. 6 PF), efficiency = 0. 945, Vp = 18 V ○ ○ ○ I = 3. 93886 A A = 1. 7125 mm 2 Pick 14 AWG (2. 2204 mm 2) magnetic wire to wind the coils with ■ Thicker wire is bulkier and has reduced skin depth ■ Thinner wire cannot handle current for power transmission ■ 14 AWG is common and readily available
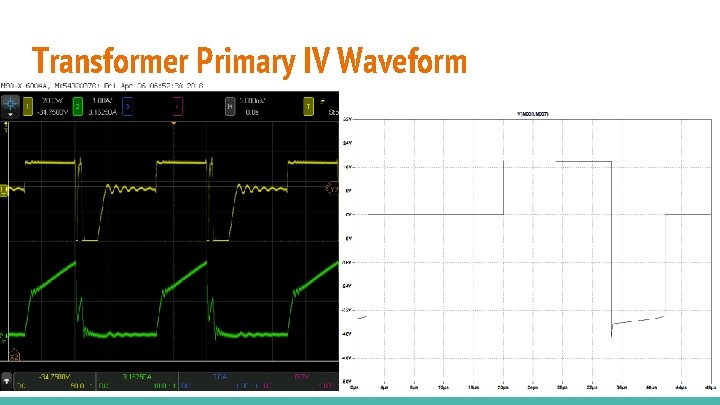
Transformer Primary IV Waveform
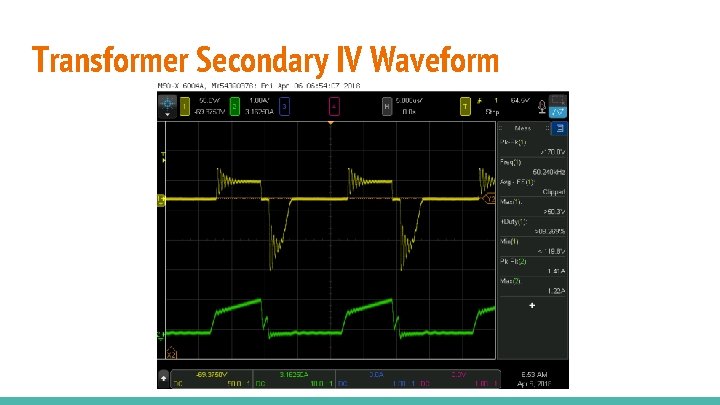
Transformer Secondary IV Waveform
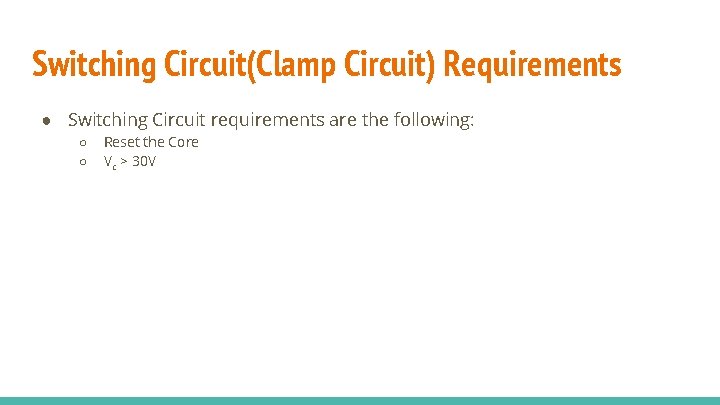
Switching Circuit(Clamp Circuit) Requirements ● Switching Circuit requirements are the following: ○ ○ Reset the Core Vc > 30 V
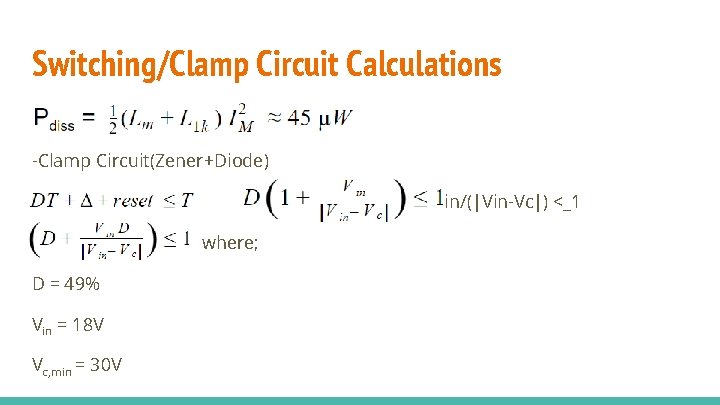
Switching/Clamp Circuit Calculations Pdiss= 1/2 (Lm+L 1 k (Im)^2 =~ 45 u. W -Clamp Circuit(Zener+Diode) DT+Deltareset <_ T D+Vin/|Vin-Vc|<_1 where; D = 49% Vin = 18 V Vc, min = 30 V so P(1+(Vin/(|Vin-Vc|) <_1
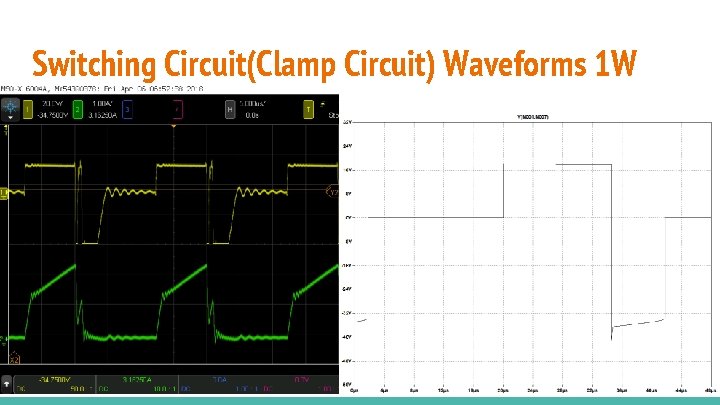
Switching Circuit(Clamp Circuit) Waveforms 1 W
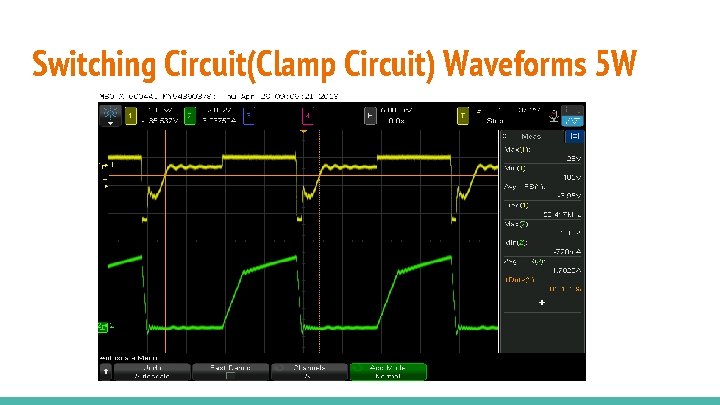
Switching Circuit(Clamp Circuit) Waveforms 5 W
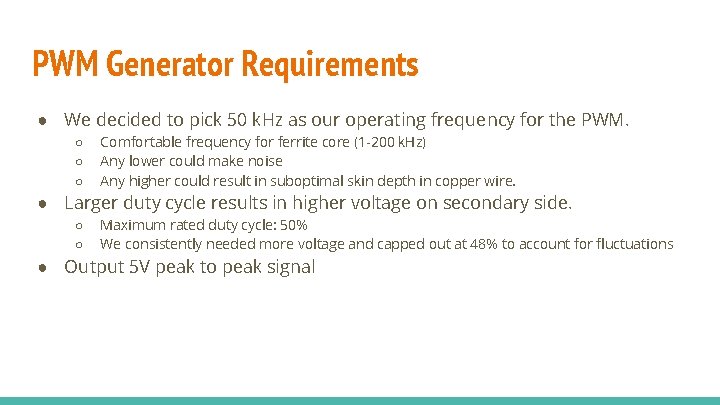
PWM Generator Requirements ● We decided to pick 50 k. Hz as our operating frequency for the PWM. ○ ○ ○ Comfortable frequency for ferrite core (1 -200 k. Hz) Any lower could make noise Any higher could result in suboptimal skin depth in copper wire. ● Larger duty cycle results in higher voltage on secondary side. ○ ○ Maximum rated duty cycle: 50% We consistently needed more voltage and capped out at 48% to account for fluctuations ● Output 5 V peak to peak signal
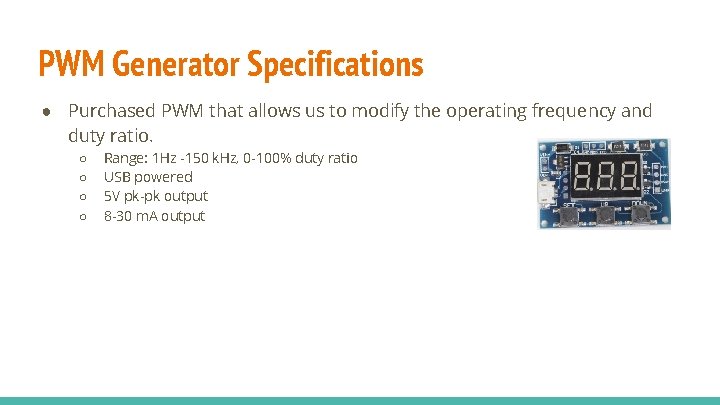
PWM Generator Specifications ● Purchased PWM that allows us to modify the operating frequency and duty ratio. ○ ○ Range: 1 Hz -150 k. Hz, 0 -100% duty ratio USB powered 5 V pk-pk output 8 -30 m. A output
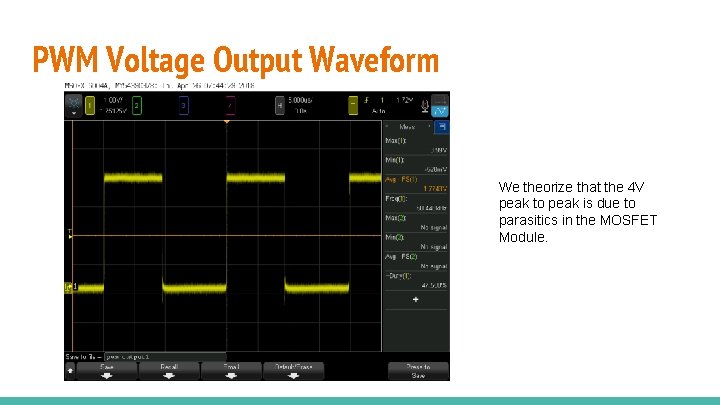
PWM Voltage Output Waveform We theorize that the 4 V peak to peak is due to parasitics in the MOSFET Module.
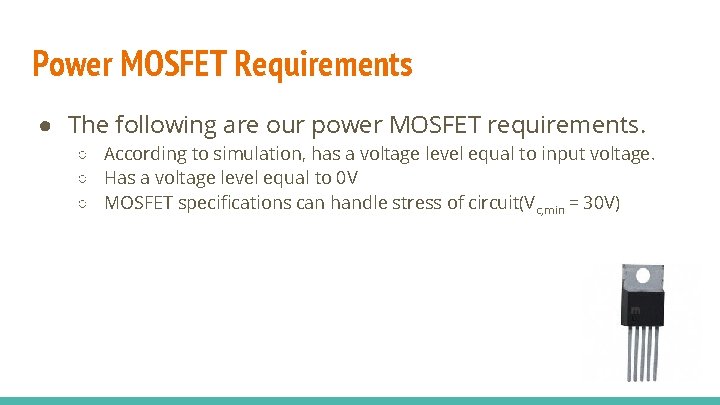
Power MOSFET Requirements ● The following are our power MOSFET requirements. ○ According to simulation, has a voltage level equal to input voltage. ○ Has a voltage level equal to 0 V ○ MOSFET specifications can handle stress of circuit(Vc, min = 30 V)
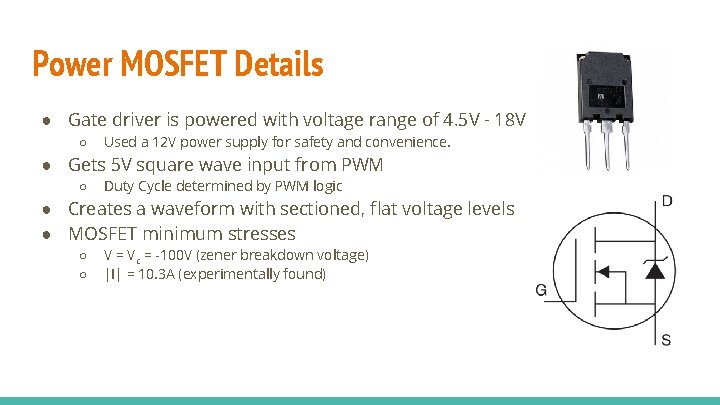
Power MOSFET Details ● Gate driver is powered with voltage range of 4. 5 V - 18 V ○ Used a 12 V power supply for safety and convenience. ● Gets 5 V square wave input from PWM ○ Duty Cycle determined by PWM logic ● Creates a waveform with sectioned, flat voltage levels ● MOSFET minimum stresses ○ ○ V = Vc = -100 V (zener breakdown voltage) |I| = 10. 3 A (experimentally found)
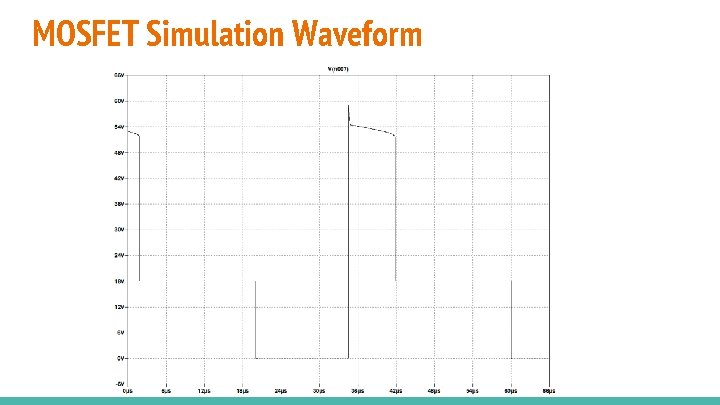
MOSFET Simulation Waveform
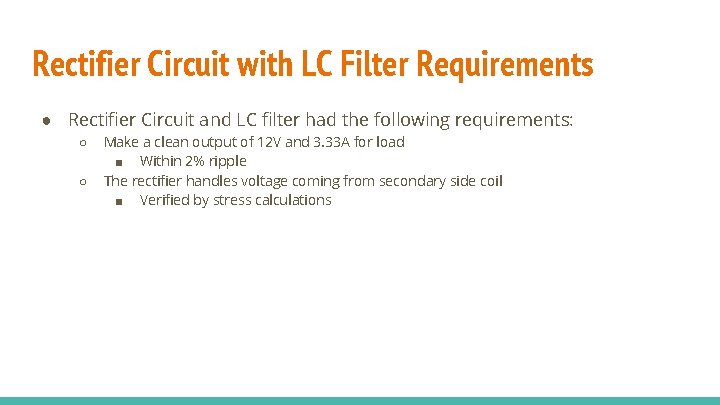
Rectifier Circuit with LC Filter Requirements ● Rectifier Circuit and LC filter had the following requirements: ○ ○ Make a clean output of 12 V and 3. 33 A for load ■ Within 2% ripple The rectifier handles voltage coming from secondary side coil ■ Verified by stress calculations
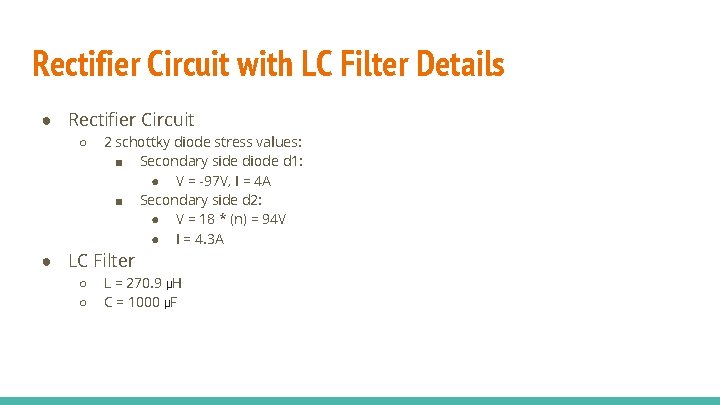
Rectifier Circuit with LC Filter Details ● Rectifier Circuit ○ 2 schottky diode stress values: ■ Secondary side diode d 1: ● V = -97 V, I = 4 A ■ Secondary side d 2: ● V = 18 * (n) = 94 V ● I = 4. 3 A ● LC Filter ○ ○ L = 270. 9 µH C = 1000 µF
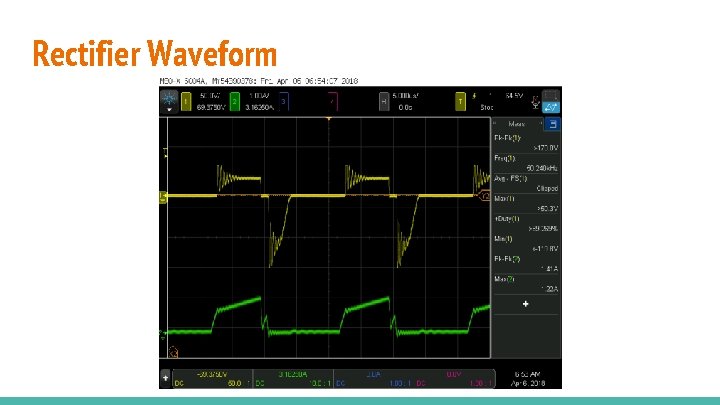
Rectifier Waveform
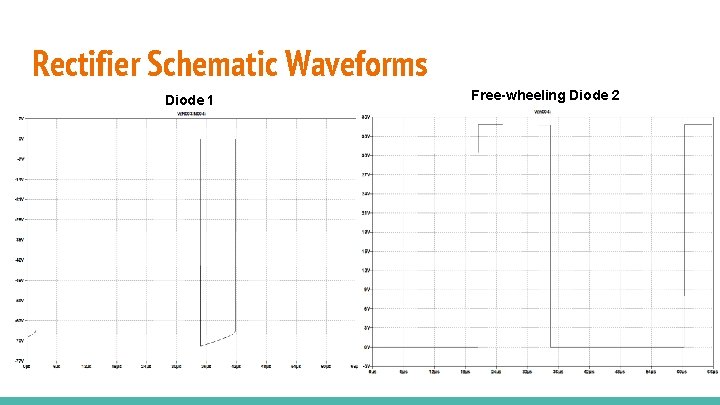
Rectifier Schematic Waveforms Diode 1 Free-wheeling Diode 2
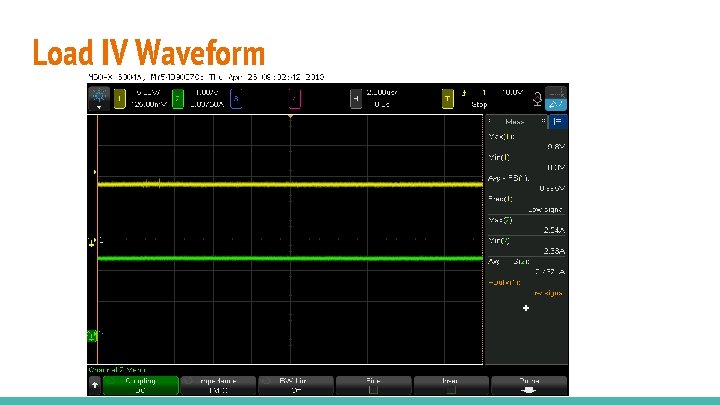
Load IV Waveform
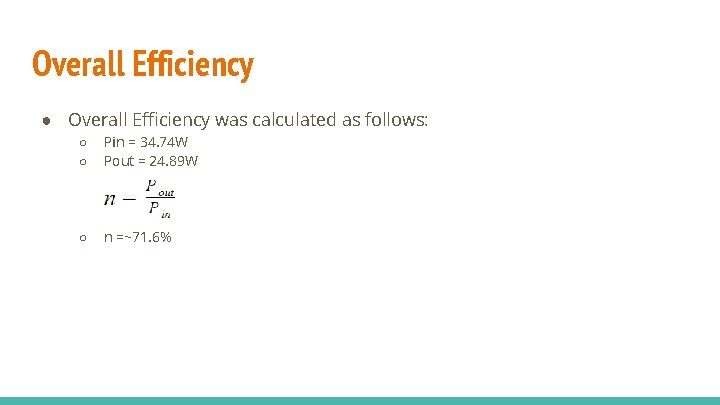
Overall Efficiency ● Overall Efficiency was calculated as follows: ○ ○ Pin = 34. 74 W Pout = 24. 89 W ○ n =~71. 6%
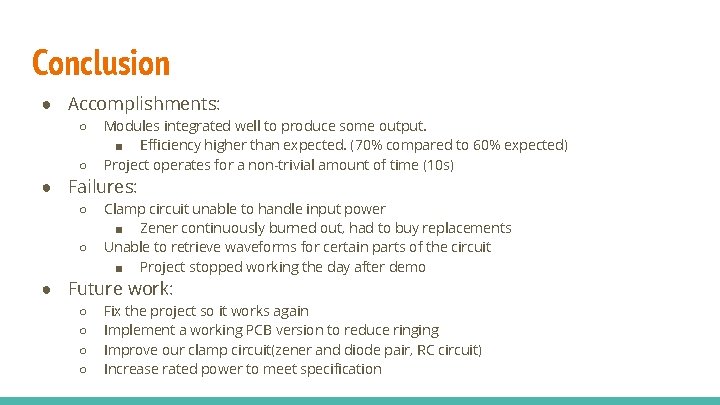
Conclusion ● Accomplishments: ○ ○ Modules integrated well to produce some output. ■ Efficiency higher than expected. (70% compared to 60% expected) Project operates for a non-trivial amount of time (10 s) ● Failures: ○ ○ Clamp circuit unable to handle input power ■ Zener continuously burned out, had to buy replacements Unable to retrieve waveforms for certain parts of the circuit ■ Project stopped working the day after demo ● Future work: ○ ○ Fix the project so it works again Implement a working PCB version to reduce ringing Improve our clamp circuit(zener and diode pair, RC circuit) Increase rated power to meet specification
Wireless charger cvs
Chat med webcam
Cam cam cc
Requested home axis switch is active
Cam and follower examples
Telecommunications the internet and wireless technology
Tıbbi atık ambleminin bulunması zorun olan alanlar
Onur kayiran
Computer architecture onur mutlu
Onur mutlu computer architecture
Computer architecture
Ahmet nezih erverdi
Rahmi onur
Dr hasan onur yavuz
Dr onur polat
Onur alakas
740
Korgün koyunpınar
Prof. onur mutlu
Energizer 1 hour charger
Keepower
Brigade system culinary definition
Pcb design for charger
Freedom combi inverter charger
Battery battery north bay
Charger characteristics of life
Motorola apx8000xe
Cern
Tesla charging stations in montana
Eric battery charger
Block diagram of solar mobile charger
Decathlon solar charger
Pg&e ev fleet
Efficiency of half wave rectifier
Wholesale solar panel is made up of