University of Dayton Industrial Assessment Center Kelly Kissock
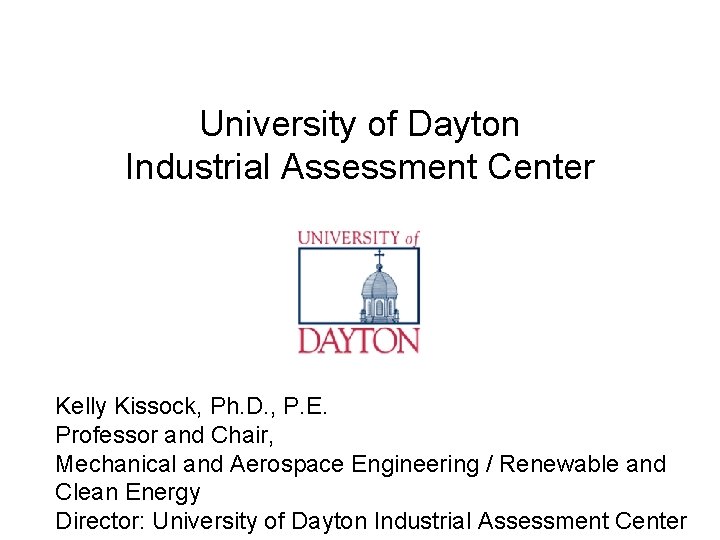
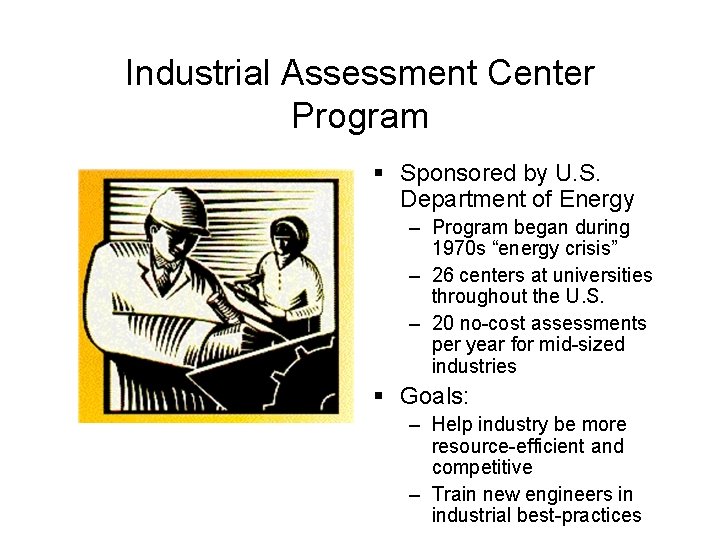
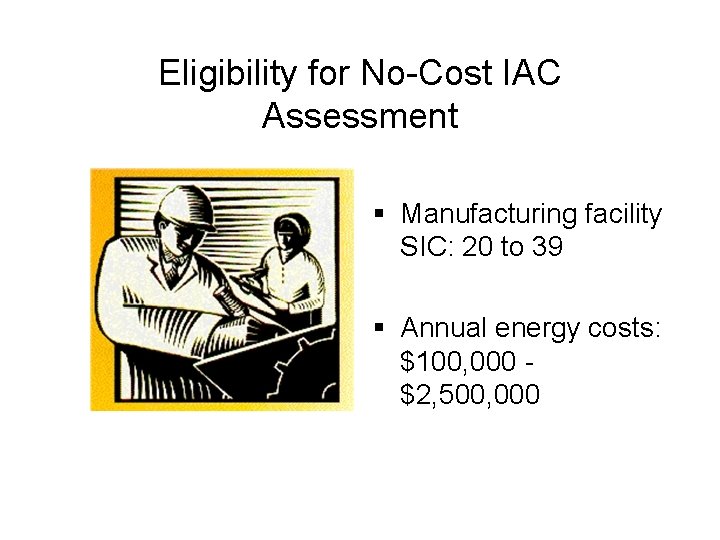
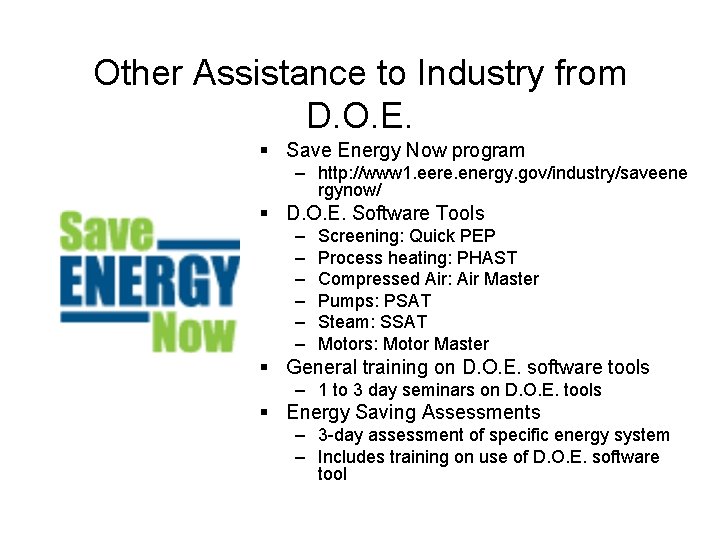
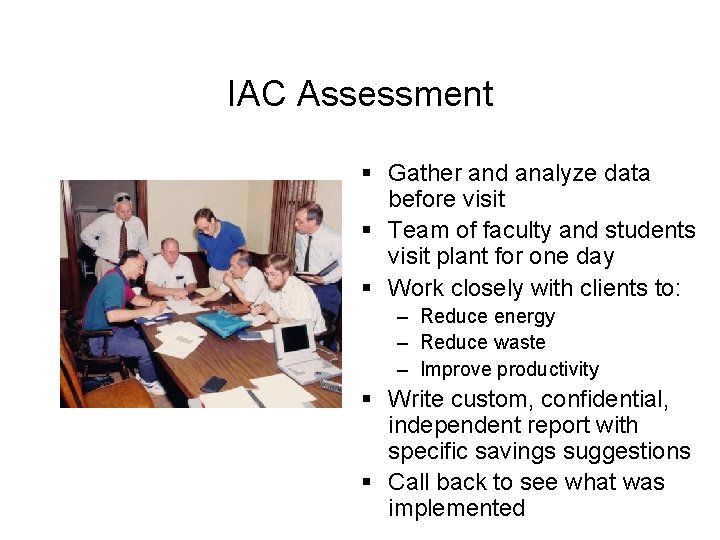

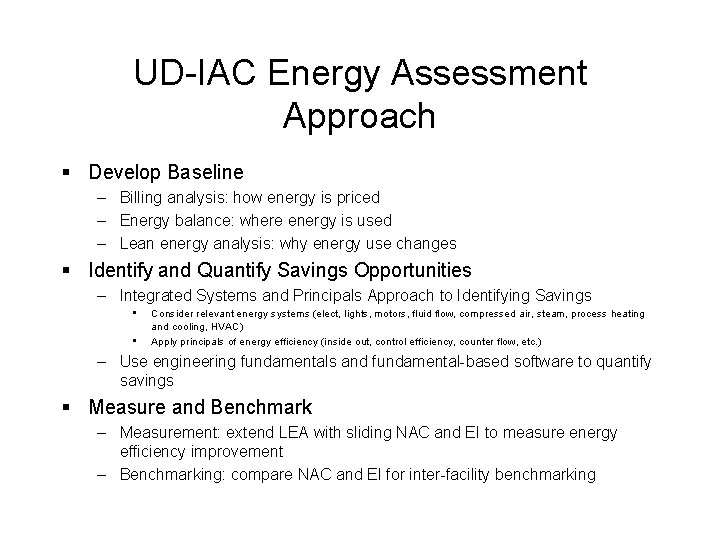
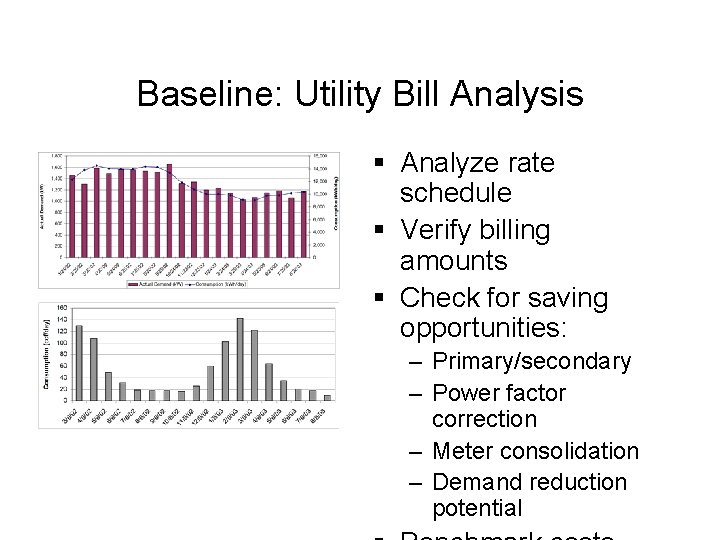
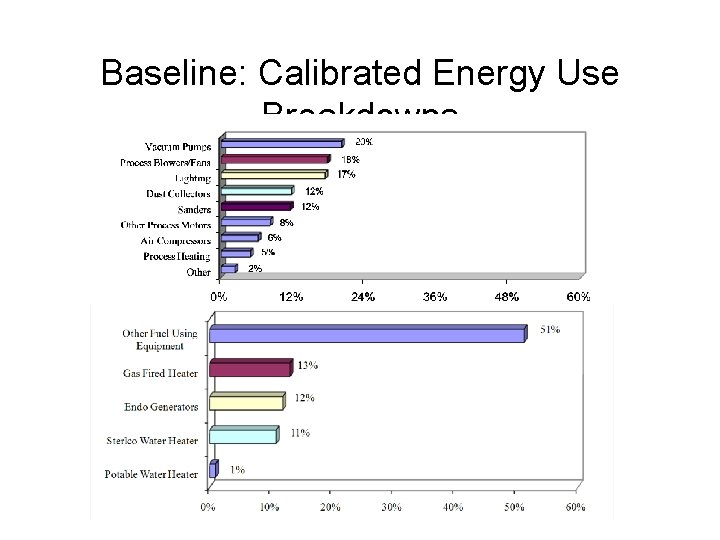
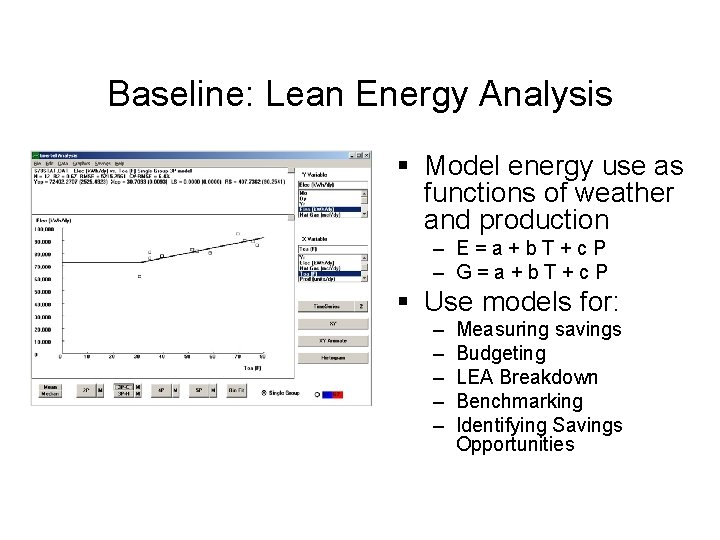
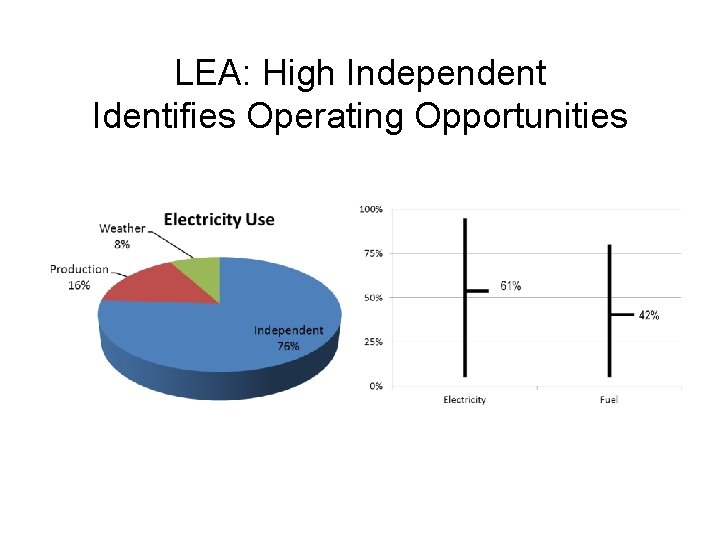
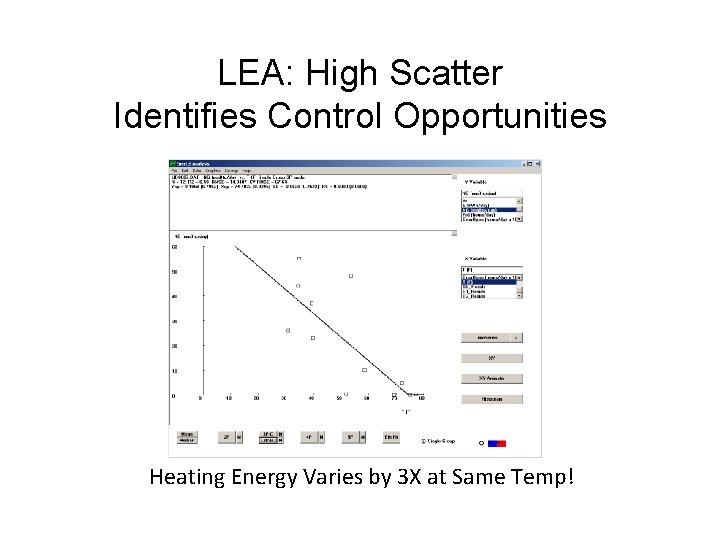
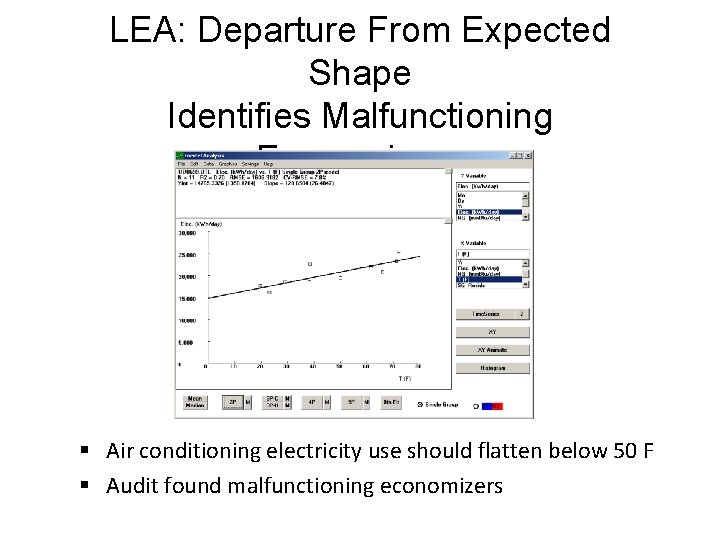
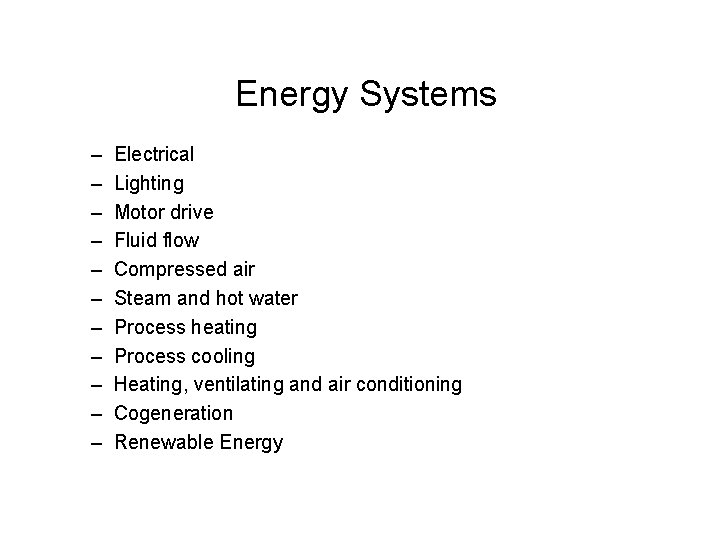
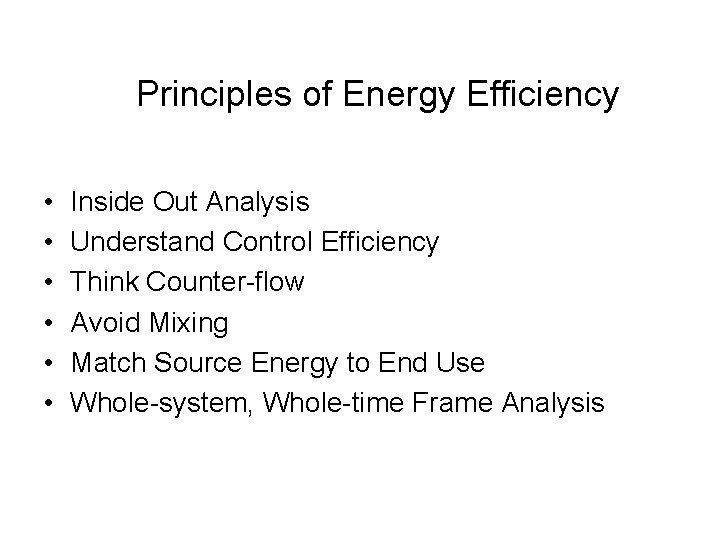
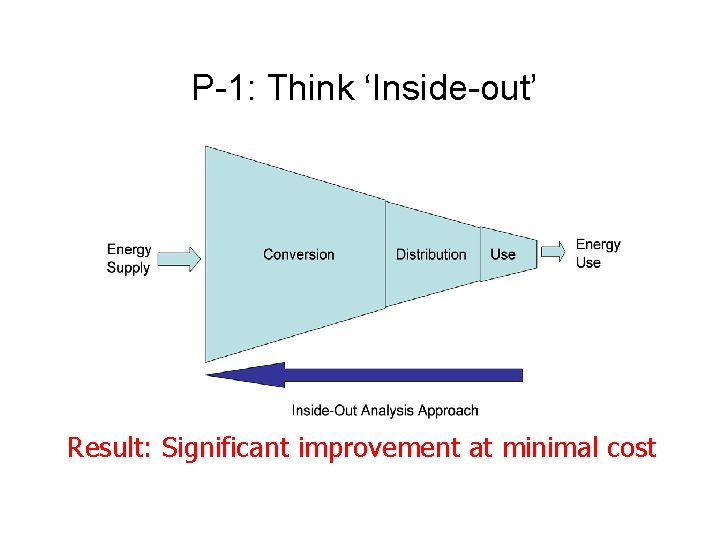
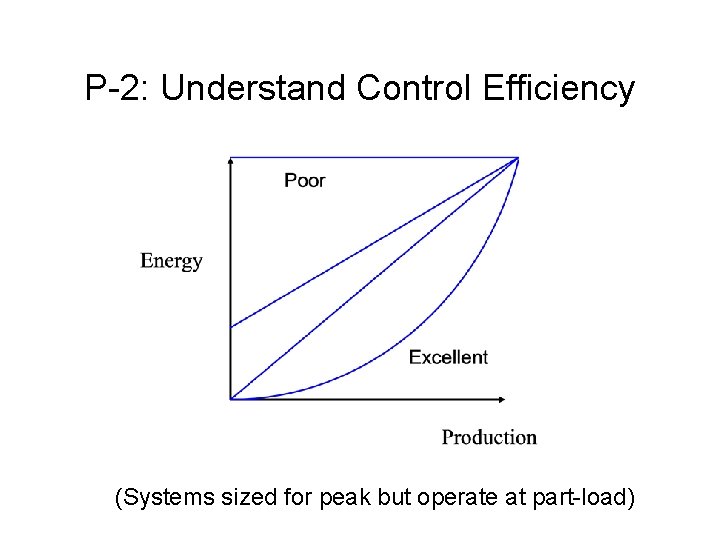
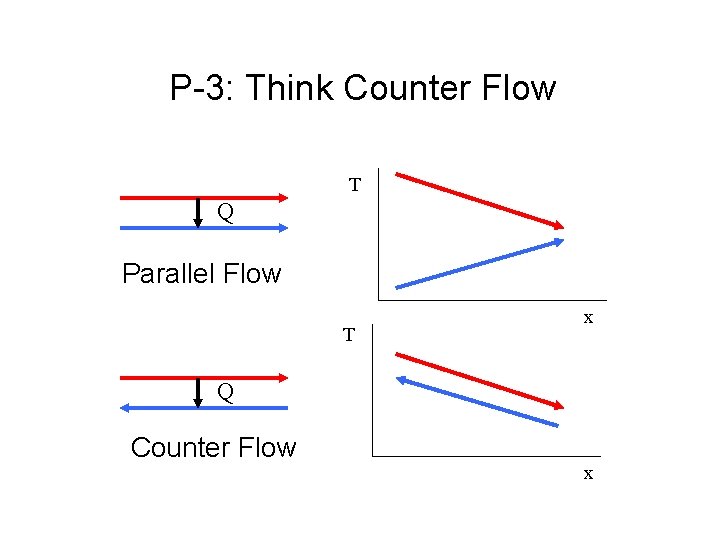
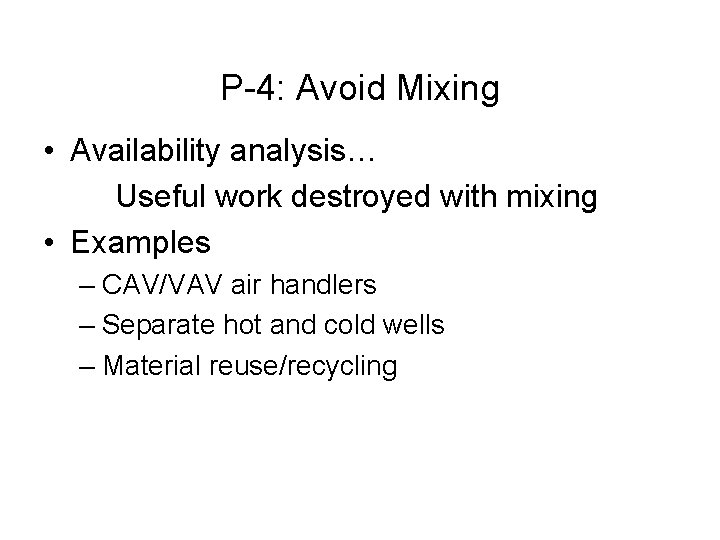
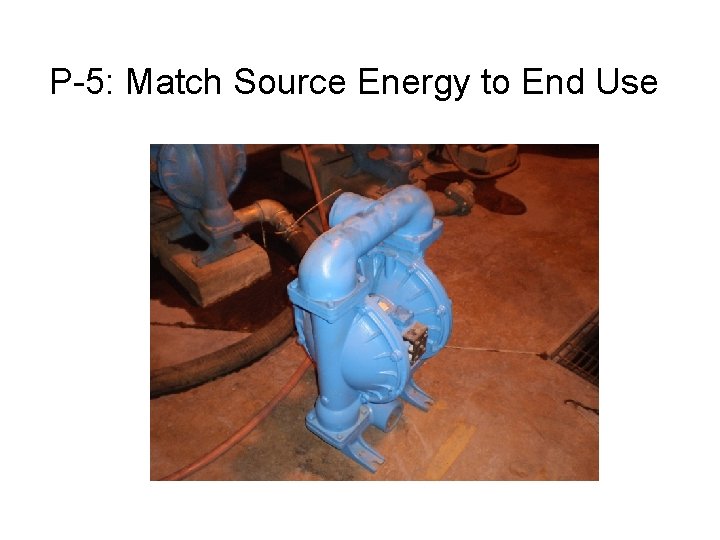
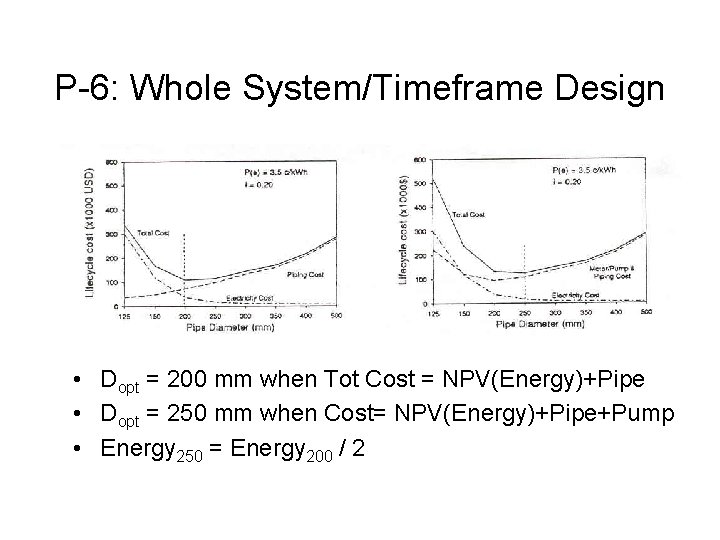
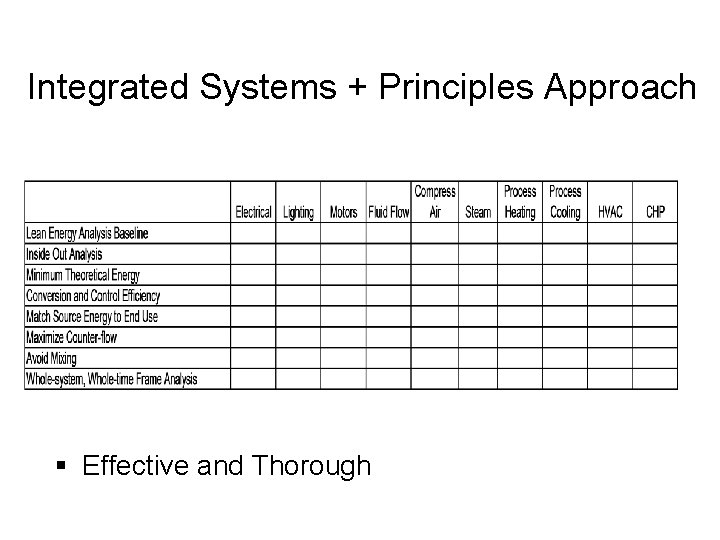
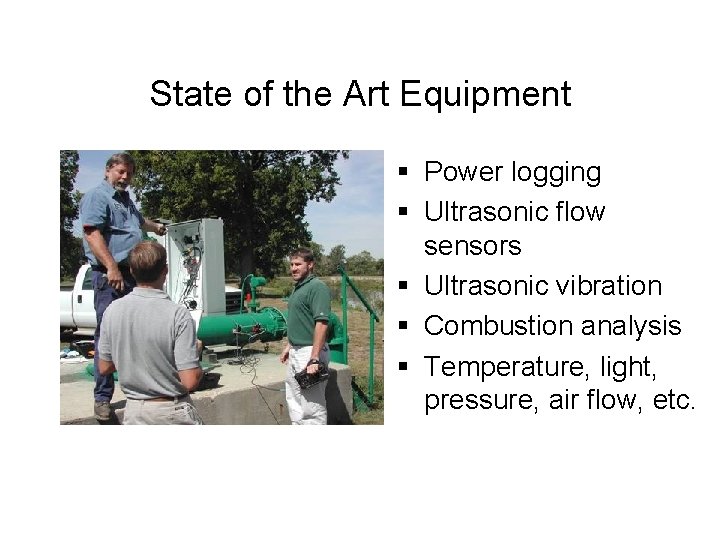
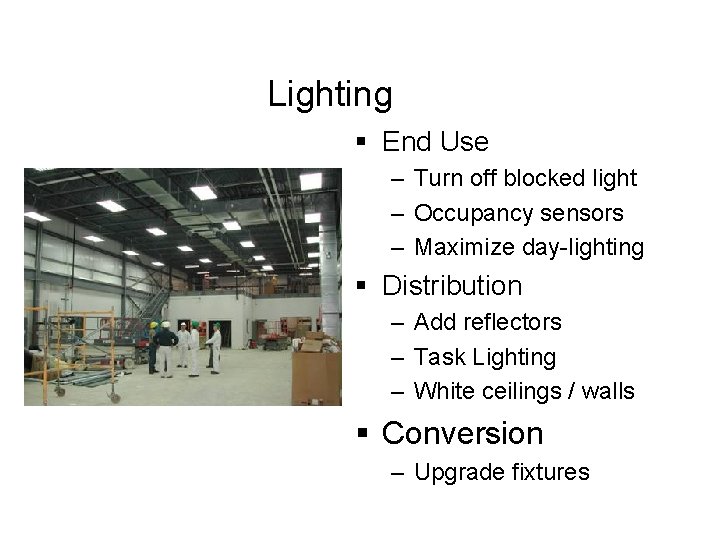
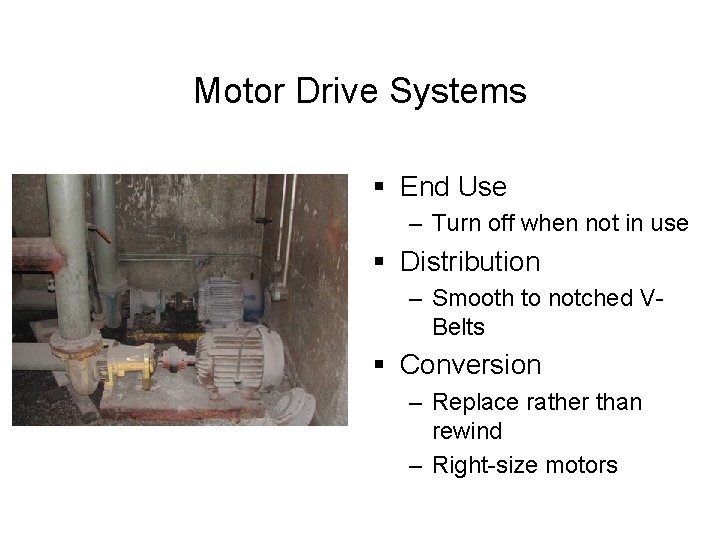
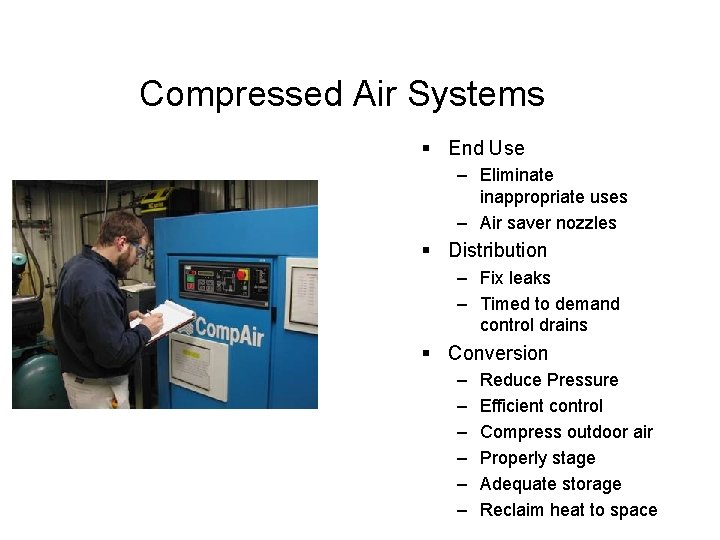
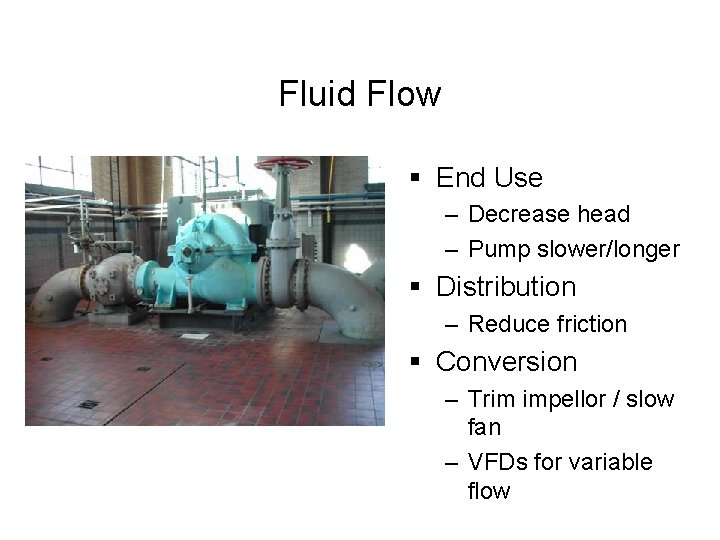
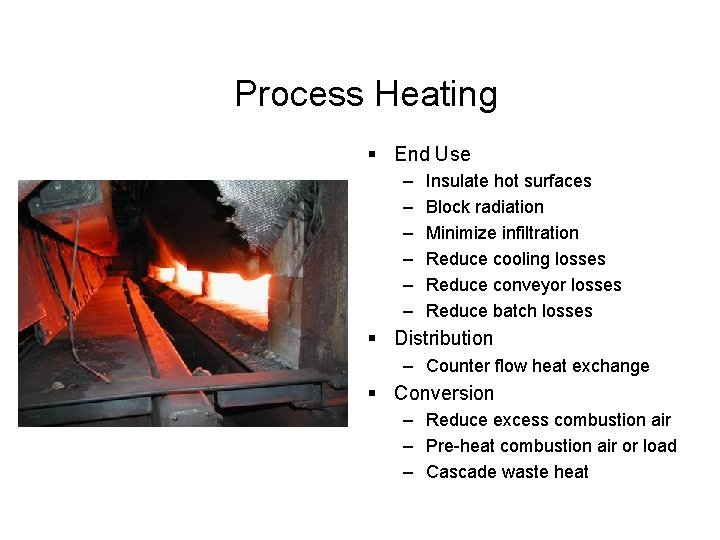
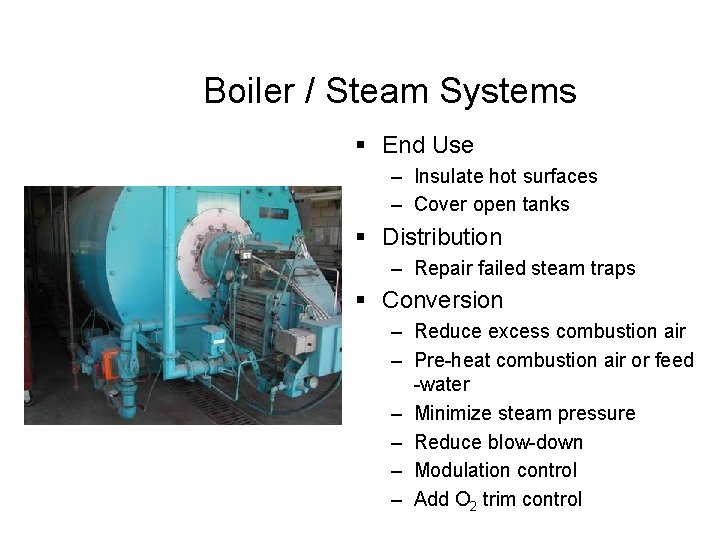
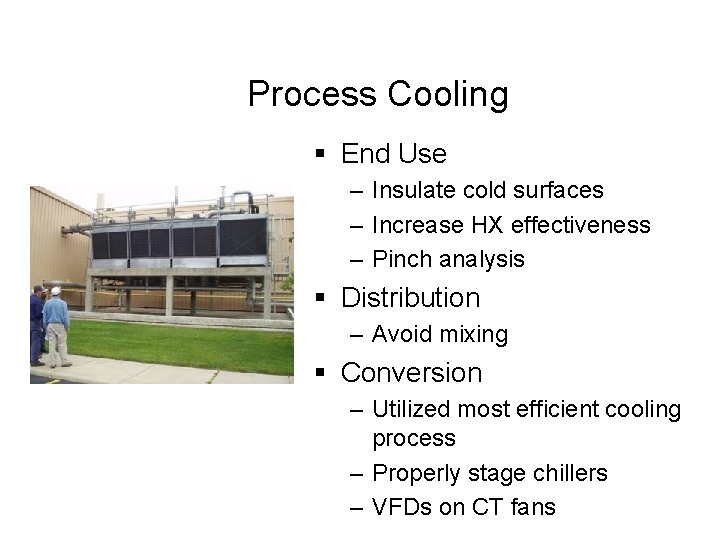
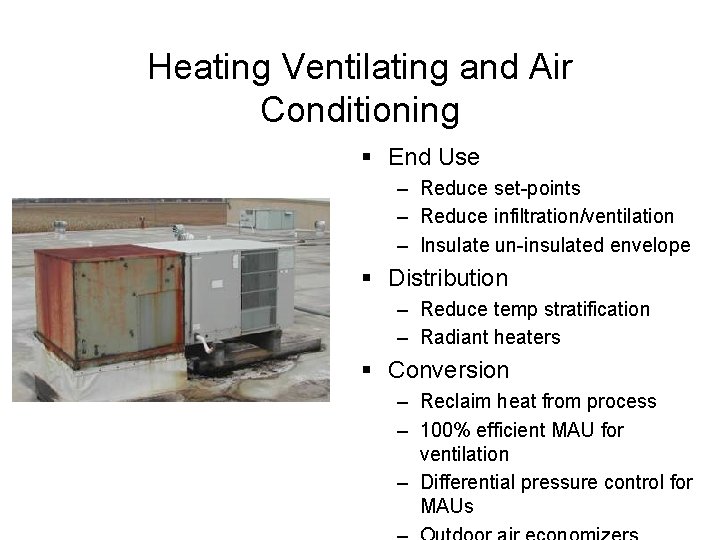
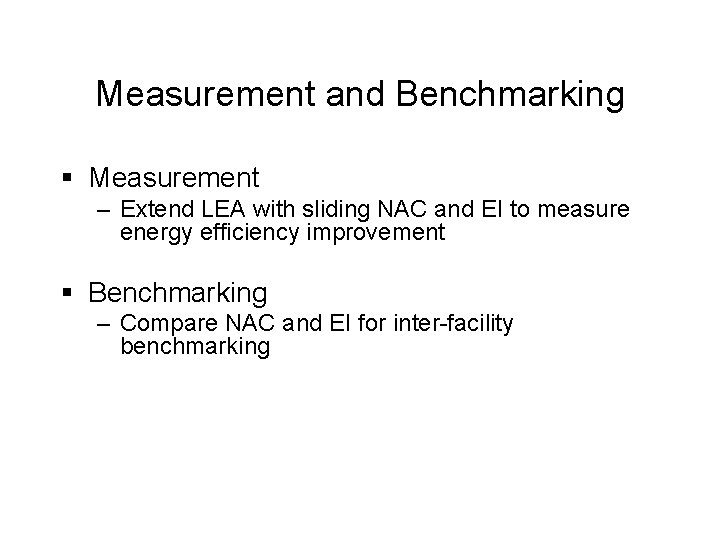
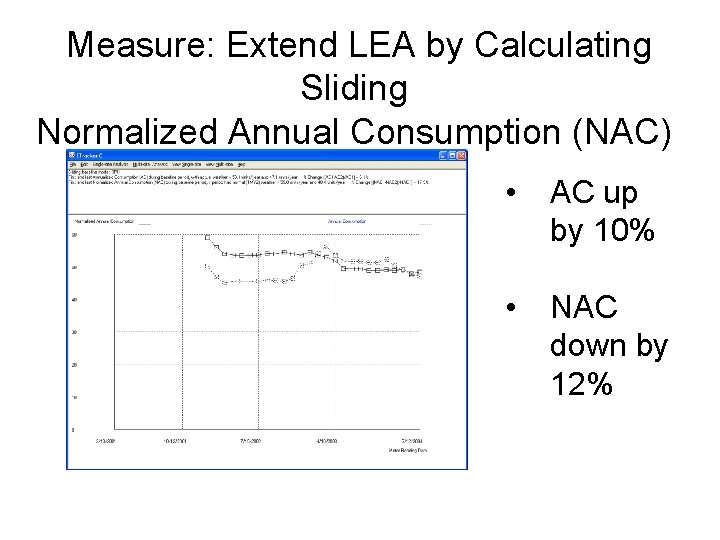
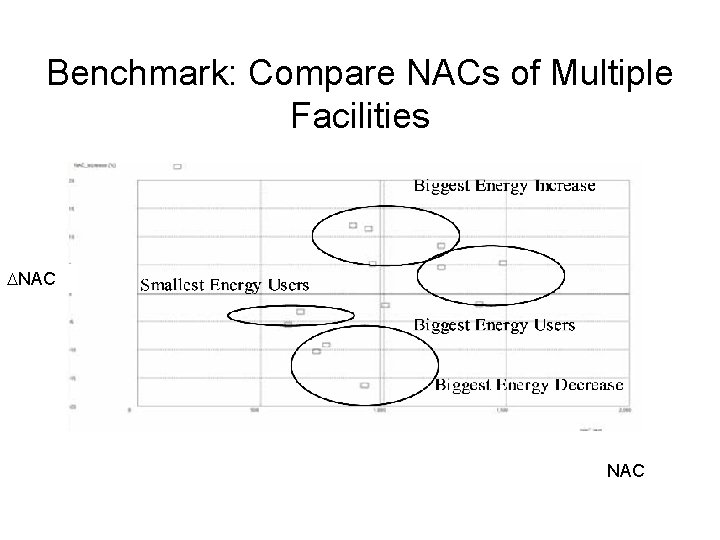
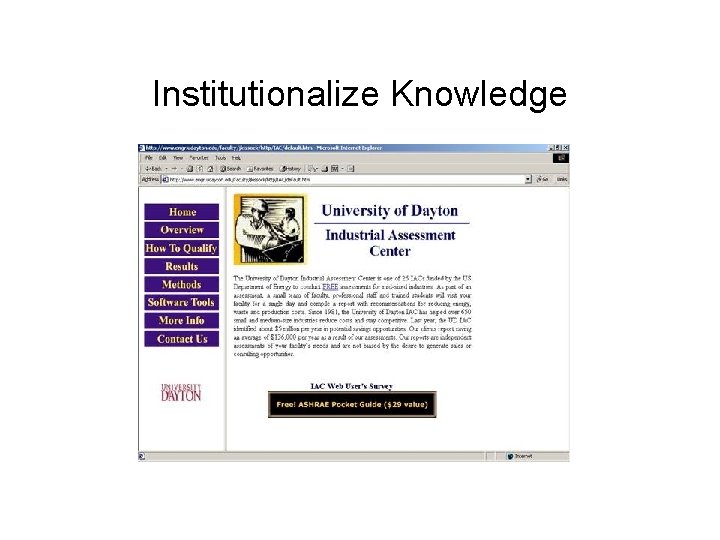
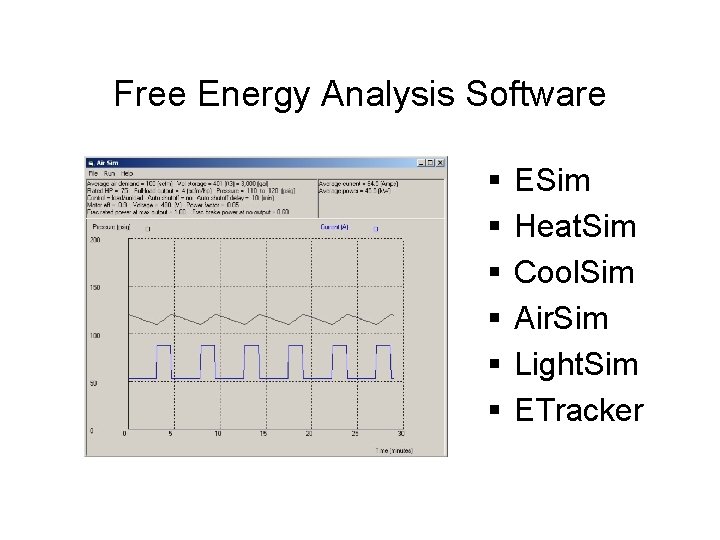
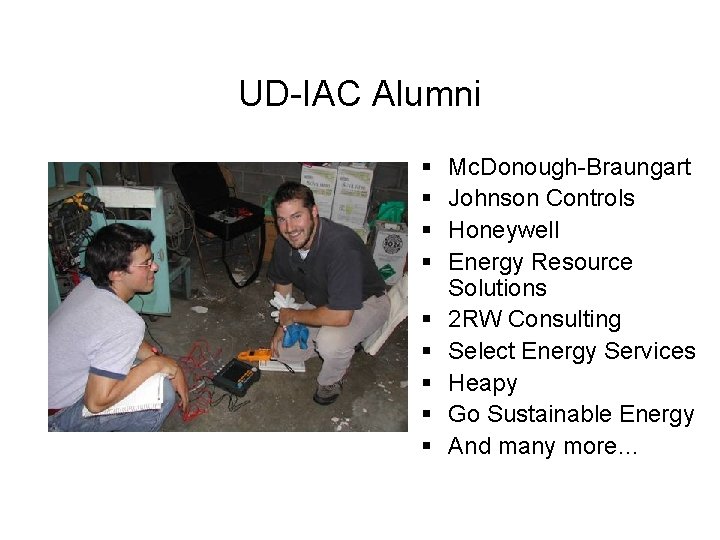
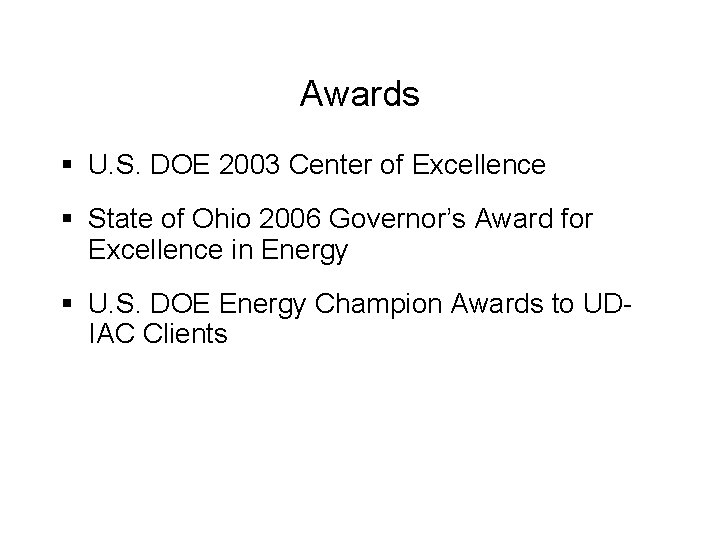
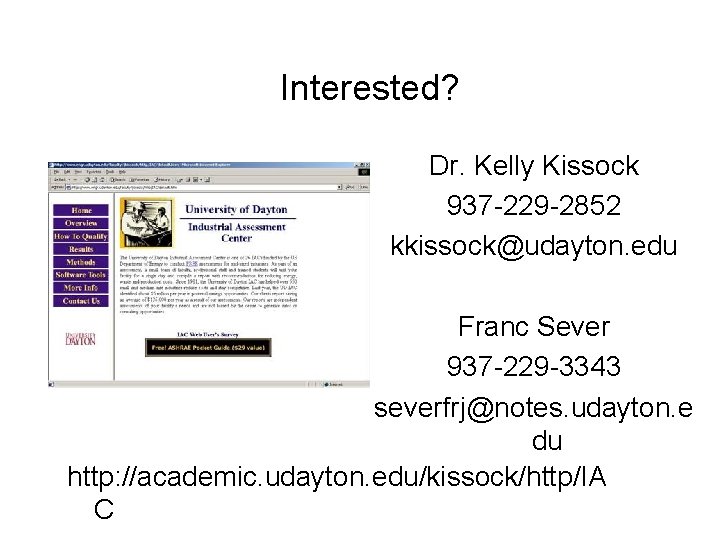
- Slides: 39
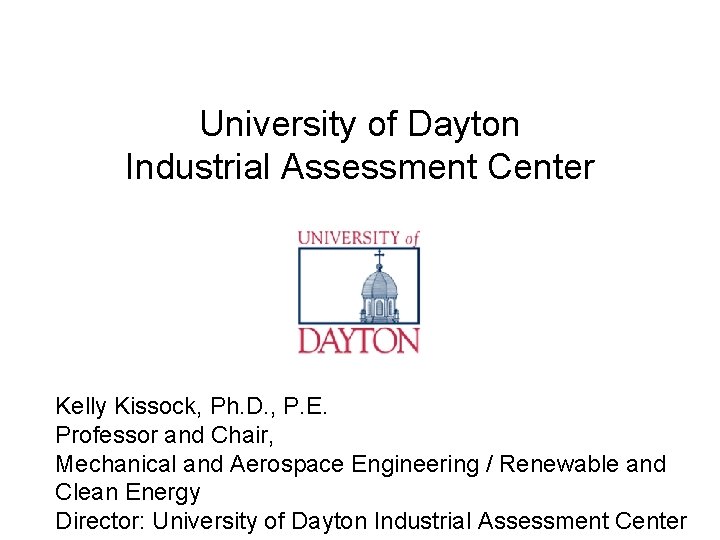
University of Dayton Industrial Assessment Center Kelly Kissock, Ph. D. , P. E. Professor and Chair, Mechanical and Aerospace Engineering / Renewable and Clean Energy Director: University of Dayton Industrial Assessment Center
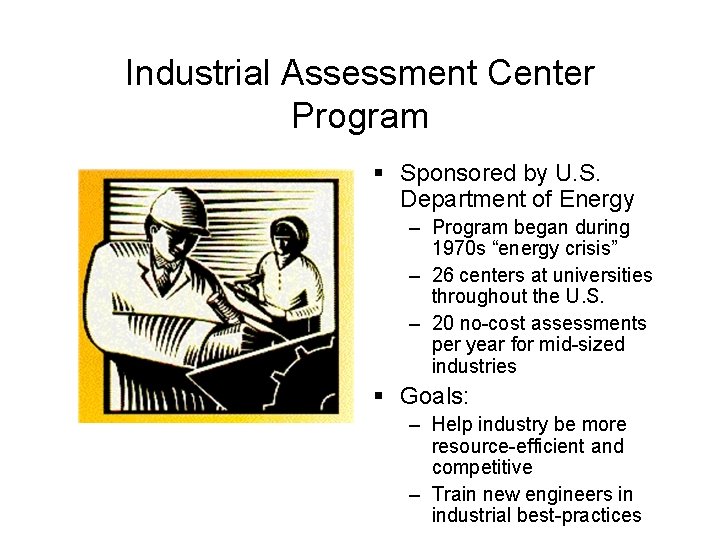
Industrial Assessment Center Program § Sponsored by U. S. Department of Energy – Program began during 1970 s “energy crisis” – 26 centers at universities throughout the U. S. – 20 no-cost assessments per year for mid-sized industries § Goals: – Help industry be more resource-efficient and competitive – Train new engineers in industrial best-practices
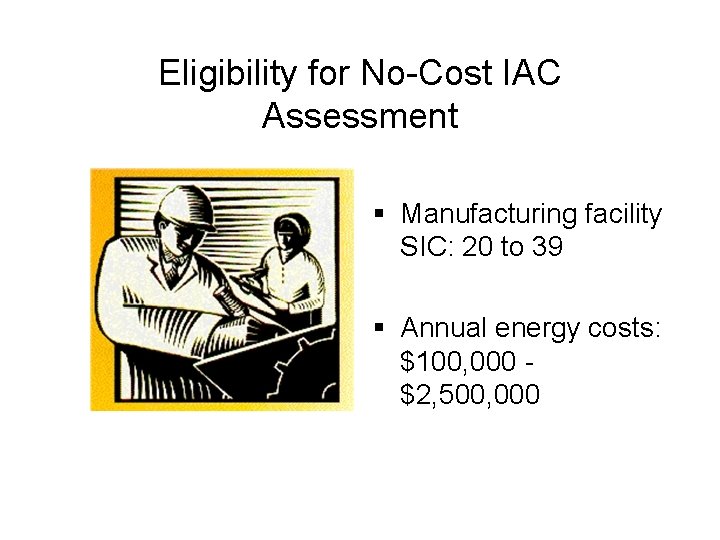
Eligibility for No-Cost IAC Assessment § Manufacturing facility SIC: 20 to 39 § Annual energy costs: $100, 000 $2, 500, 000
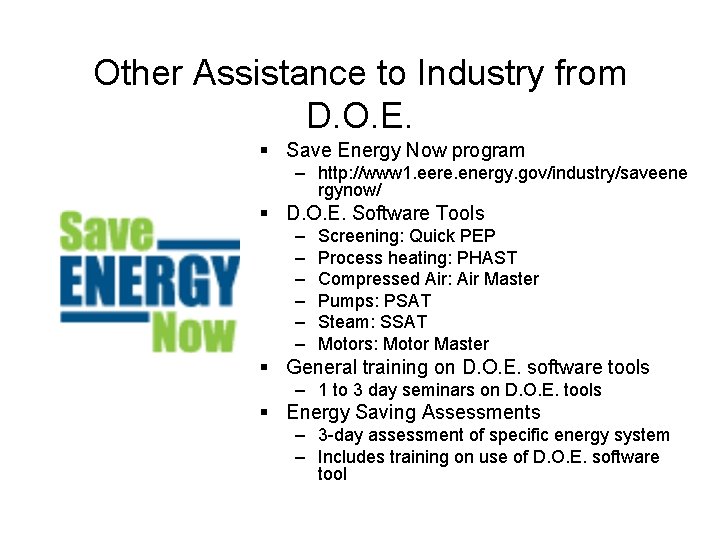
Other Assistance to Industry from D. O. E. § Save Energy Now program – http: //www 1. eere. energy. gov/industry/saveene rgynow/ § D. O. E. Software Tools – – – Screening: Quick PEP Process heating: PHAST Compressed Air: Air Master Pumps: PSAT Steam: SSAT Motors: Motor Master § General training on D. O. E. software tools – 1 to 3 day seminars on D. O. E. tools § Energy Saving Assessments – 3 -day assessment of specific energy system – Includes training on use of D. O. E. software tool
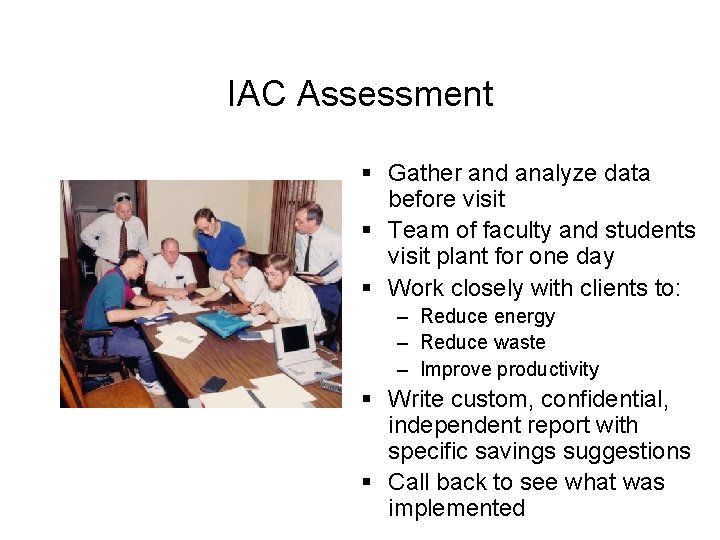
IAC Assessment § Gather and analyze data before visit § Team of faculty and students visit plant for one day § Work closely with clients to: – Reduce energy – Reduce waste – Improve productivity § Write custom, confidential, independent report with specific savings suggestions § Call back to see what was implemented

UD Industrial Assessment Center § Performed over 800 assessments since 1981 § Check implementation results after one year – Half of recommendations implemented < 2 year
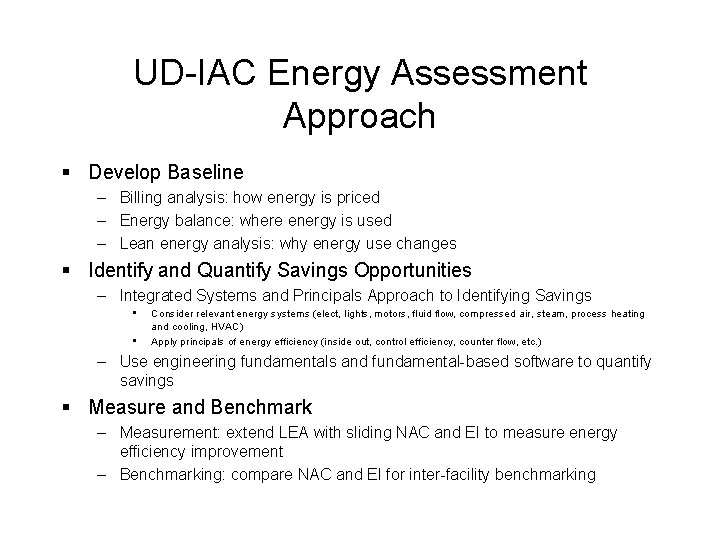
UD-IAC Energy Assessment Approach § Develop Baseline – Billing analysis: how energy is priced – Energy balance: where energy is used – Lean energy analysis: why energy use changes § Identify and Quantify Savings Opportunities – Integrated Systems and Principals Approach to Identifying Savings • • Consider relevant energy systems (elect, lights, motors, fluid flow, compressed air, steam, process heating and cooling, HVAC) Apply principals of energy efficiency (inside out, control efficiency, counter flow, etc. ) – Use engineering fundamentals and fundamental-based software to quantify savings § Measure and Benchmark – Measurement: extend LEA with sliding NAC and EI to measure energy efficiency improvement – Benchmarking: compare NAC and EI for inter-facility benchmarking
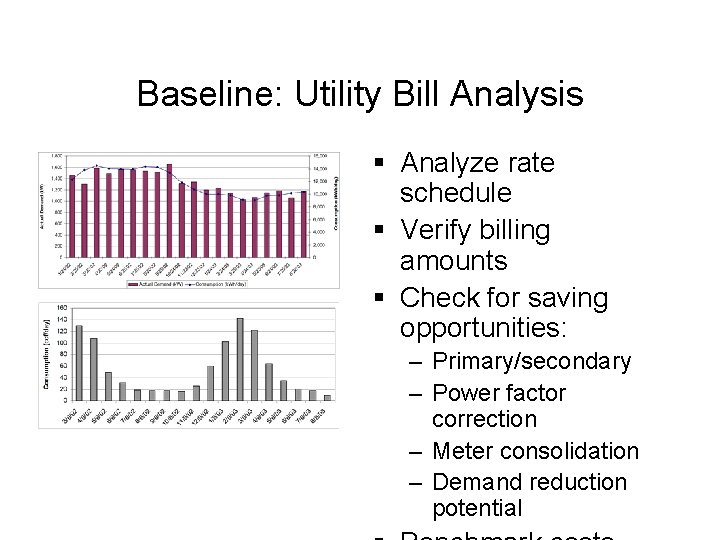
Baseline: Utility Bill Analysis § Analyze rate schedule § Verify billing amounts § Check for saving opportunities: – Primary/secondary – Power factor correction – Meter consolidation – Demand reduction potential
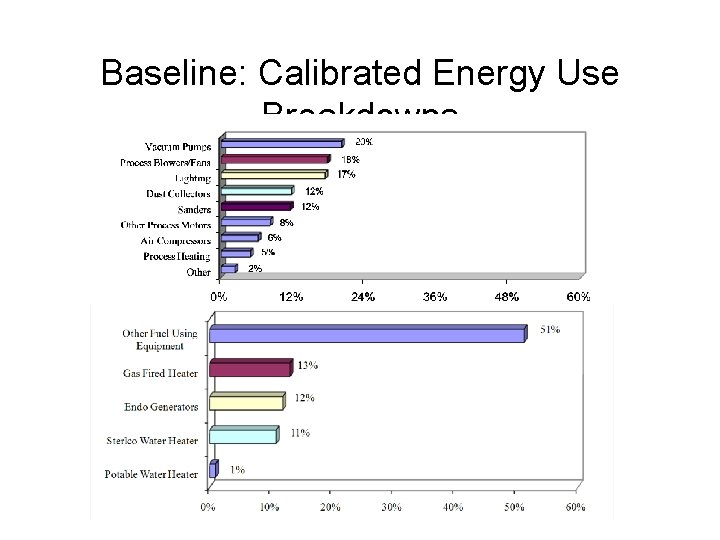
Baseline: Calibrated Energy Use Breakdowns
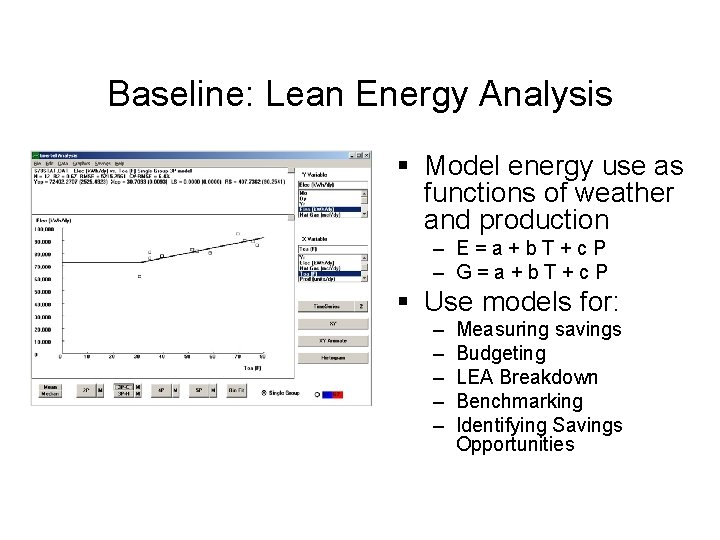
Baseline: Lean Energy Analysis § Model energy use as functions of weather and production – E=a+b. T+c. P – G=a+b. T+c. P § Use models for: – – – Measuring savings Budgeting LEA Breakdown Benchmarking Identifying Savings Opportunities
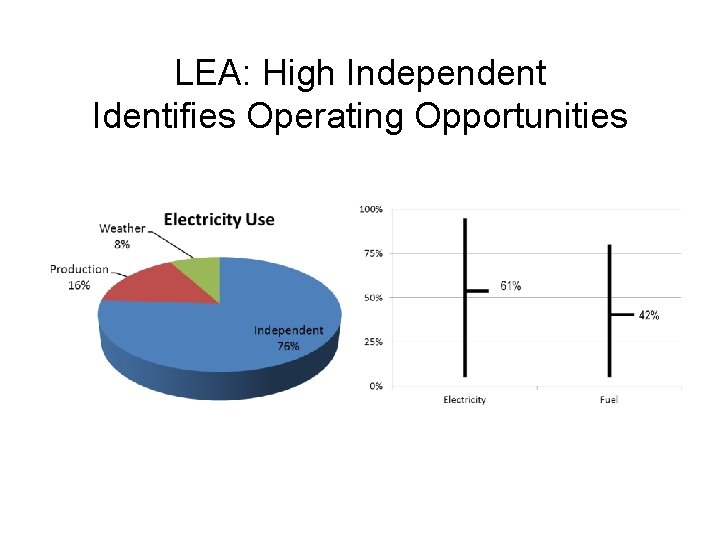
LEA: High Independent Identifies Operating Opportunities
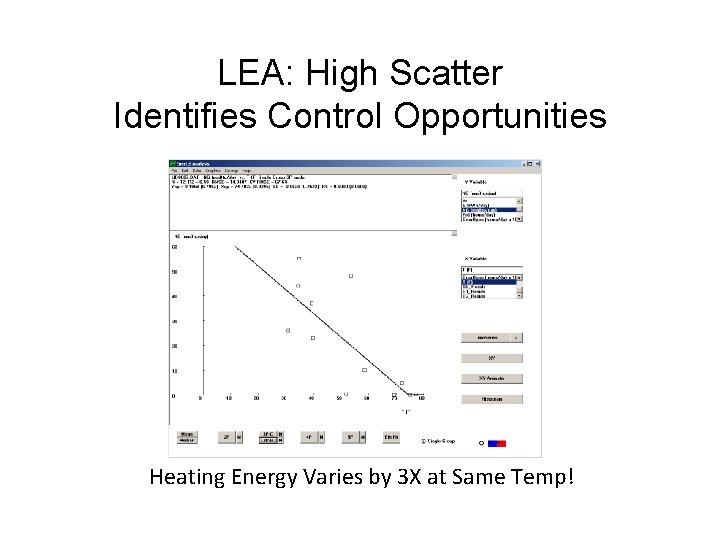
LEA: High Scatter Identifies Control Opportunities Heating Energy Varies by 3 X at Same Temp!
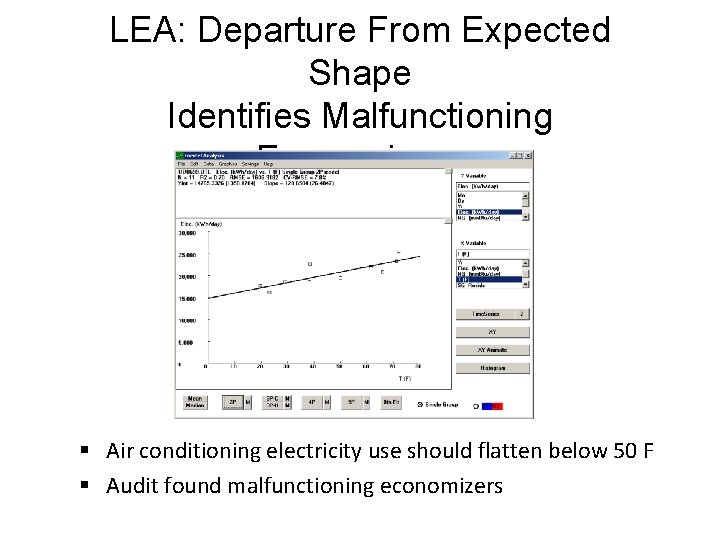
LEA: Departure From Expected Shape Identifies Malfunctioning Economizers § Air conditioning electricity use should flatten below 50 F § Audit found malfunctioning economizers
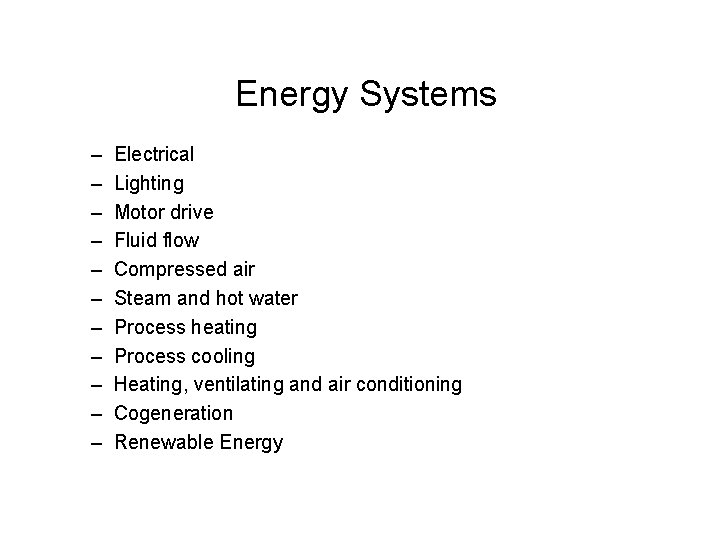
Energy Systems – – – Electrical Lighting Motor drive Fluid flow Compressed air Steam and hot water Process heating Process cooling Heating, ventilating and air conditioning Cogeneration Renewable Energy
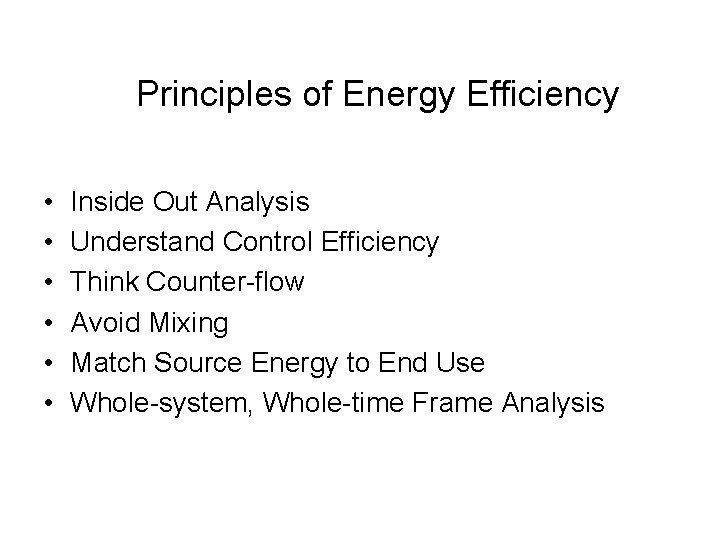
Principles of Energy Efficiency • • • Inside Out Analysis Understand Control Efficiency Think Counter-flow Avoid Mixing Match Source Energy to End Use Whole-system, Whole-time Frame Analysis
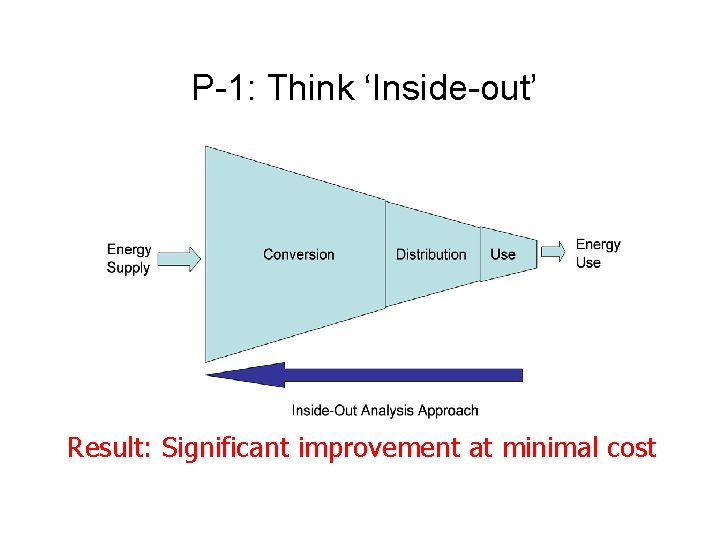
P-1: Think ‘Inside-out’ Result: Significant improvement at minimal cost
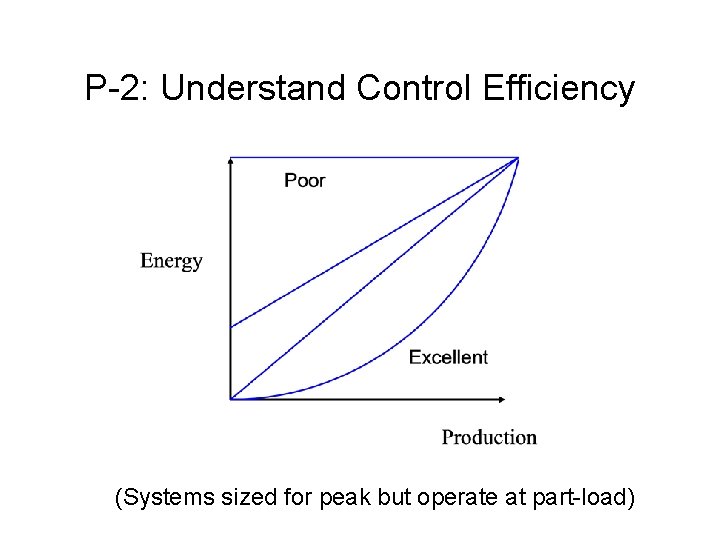
P-2: Understand Control Efficiency (Systems sized for peak but operate at part-load)
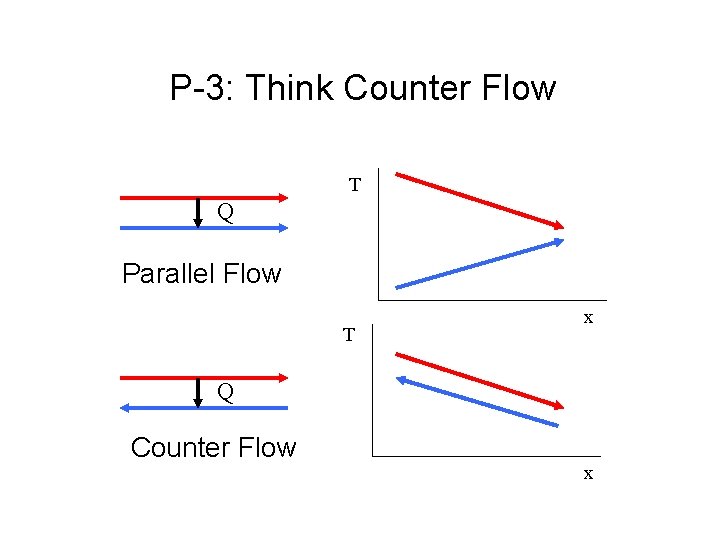
P-3: Think Counter Flow T Q Parallel Flow T x Q Counter Flow x
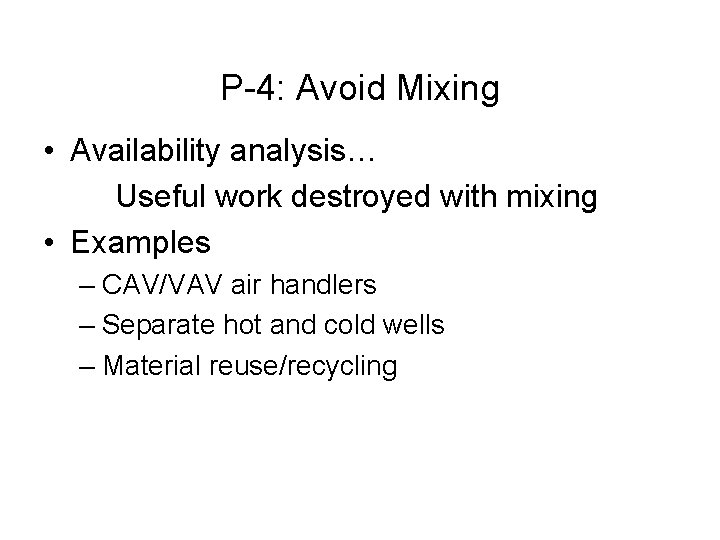
P-4: Avoid Mixing • Availability analysis… Useful work destroyed with mixing • Examples – CAV/VAV air handlers – Separate hot and cold wells – Material reuse/recycling
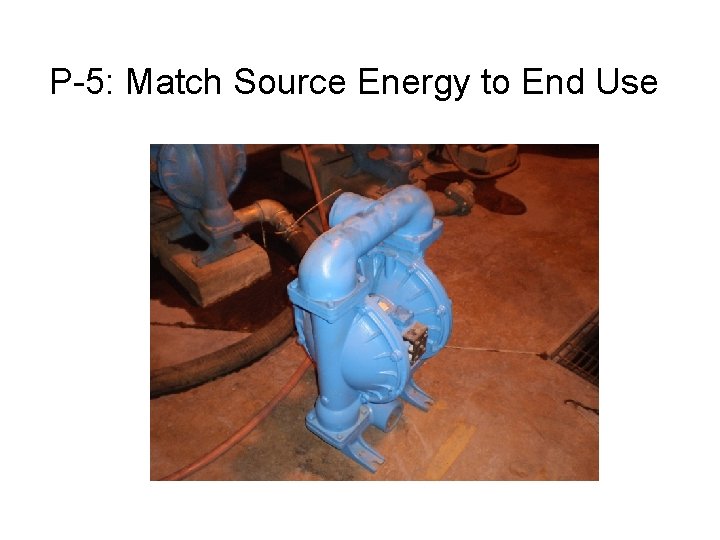
P-5: Match Source Energy to End Use
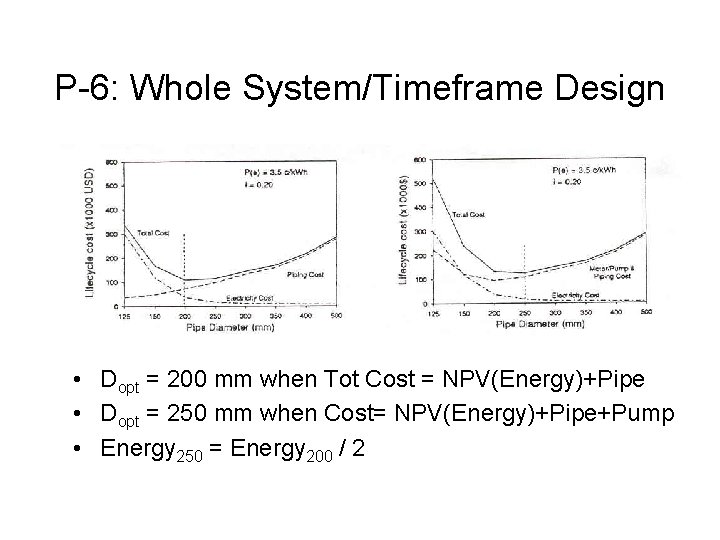
P-6: Whole System/Timeframe Design • Dopt = 200 mm when Tot Cost = NPV(Energy)+Pipe • Dopt = 250 mm when Cost= NPV(Energy)+Pipe+Pump • Energy 250 = Energy 200 / 2
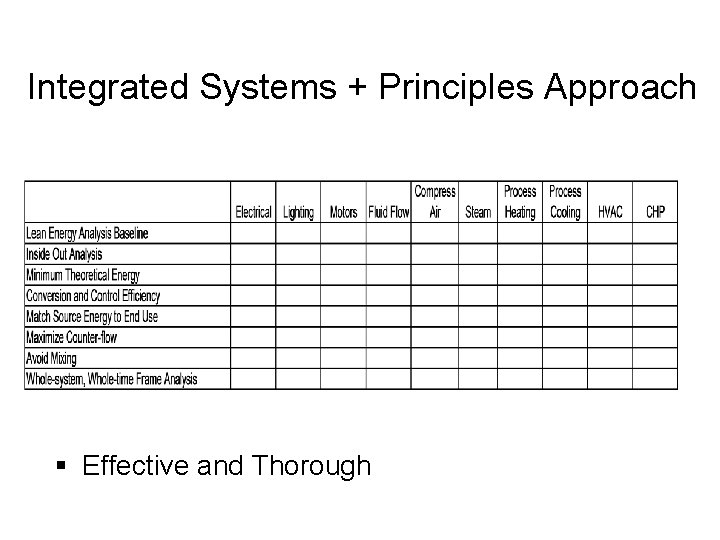
Integrated Systems + Principles Approach § Effective and Thorough
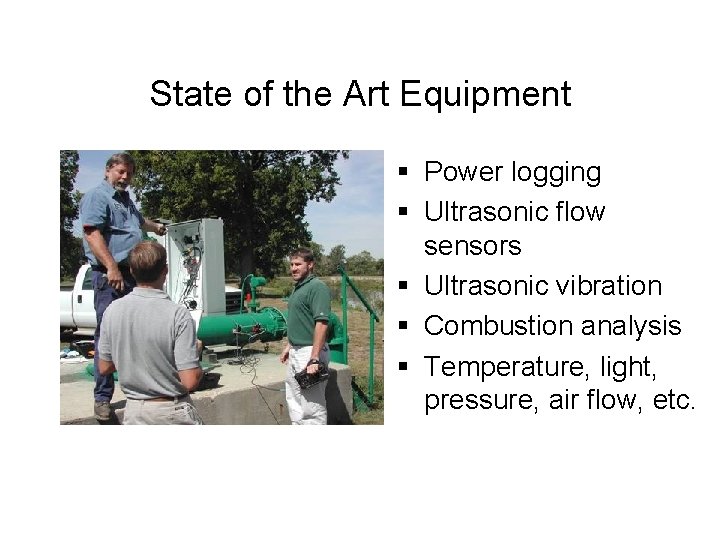
State of the Art Equipment § Power logging § Ultrasonic flow sensors § Ultrasonic vibration § Combustion analysis § Temperature, light, pressure, air flow, etc.
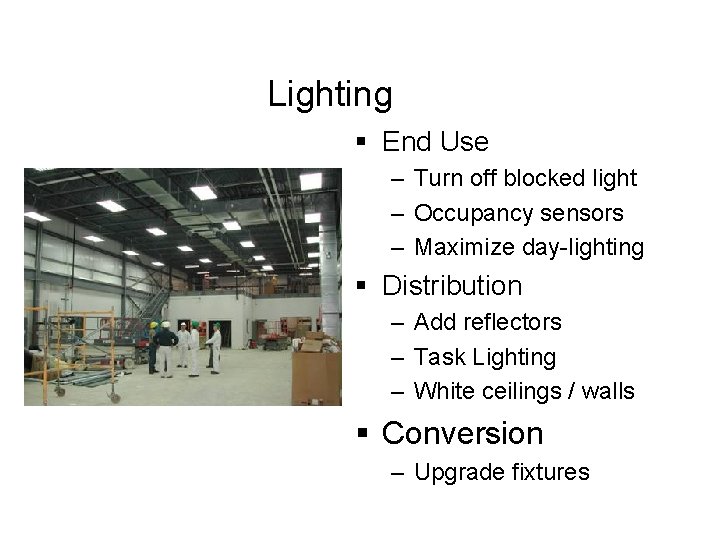
Lighting § End Use – Turn off blocked light – Occupancy sensors – Maximize day-lighting § Distribution – Add reflectors – Task Lighting – White ceilings / walls § Conversion – Upgrade fixtures
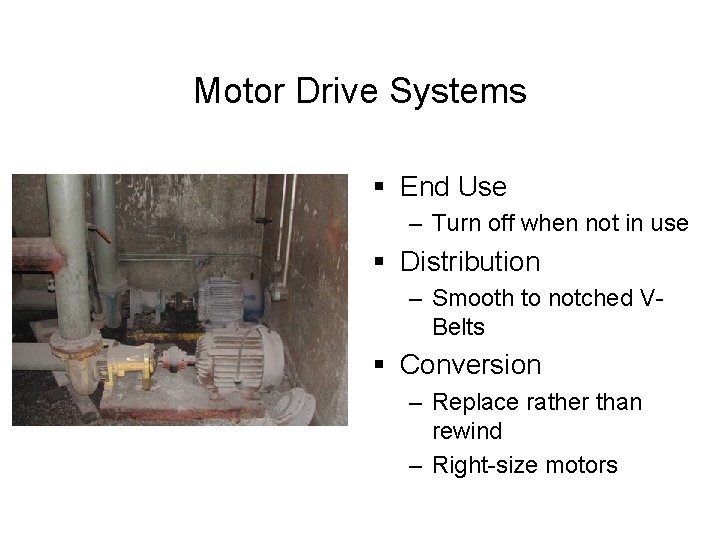
Motor Drive Systems § End Use – Turn off when not in use § Distribution – Smooth to notched VBelts § Conversion – Replace rather than rewind – Right-size motors
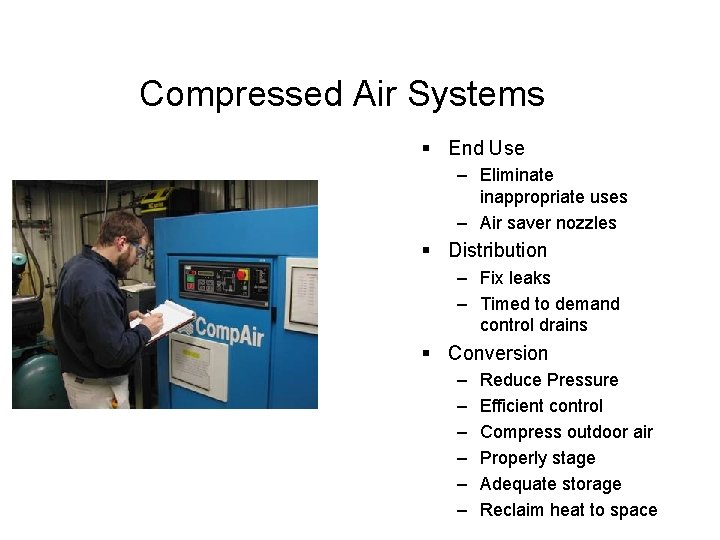
Compressed Air Systems § End Use – Eliminate inappropriate uses – Air saver nozzles § Distribution – Fix leaks – Timed to demand control drains § Conversion – – – Reduce Pressure Efficient control Compress outdoor air Properly stage Adequate storage Reclaim heat to space
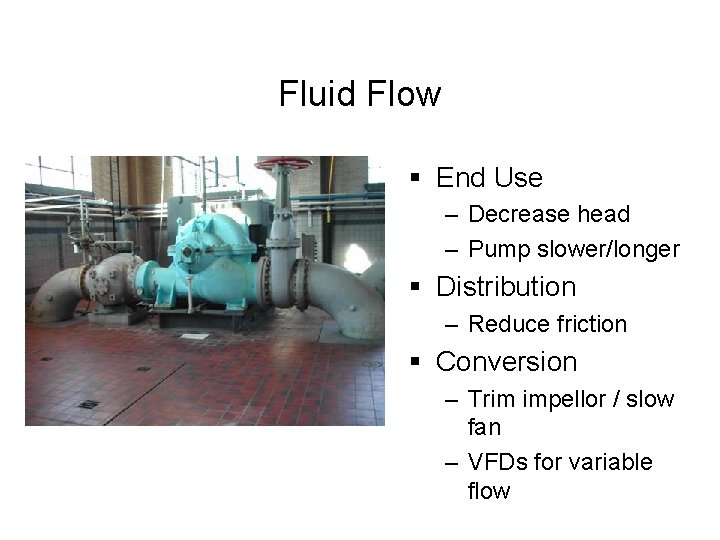
Fluid Flow § End Use – Decrease head – Pump slower/longer § Distribution – Reduce friction § Conversion – Trim impellor / slow fan – VFDs for variable flow
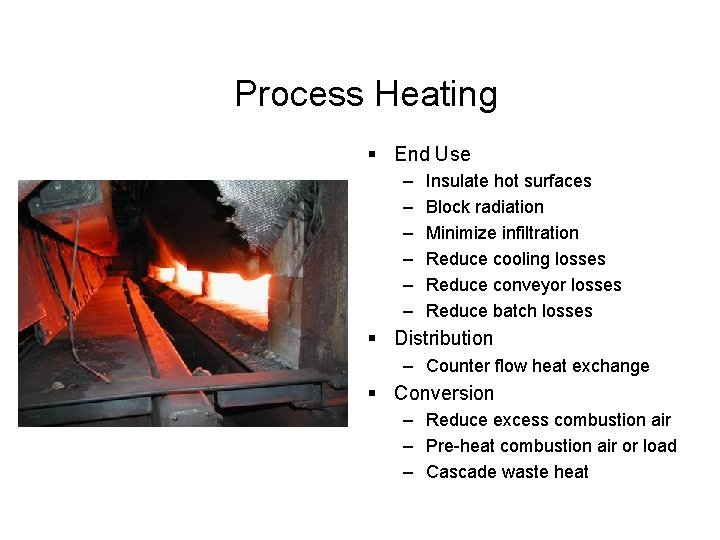
Process Heating § End Use – – – Insulate hot surfaces Block radiation Minimize infiltration Reduce cooling losses Reduce conveyor losses Reduce batch losses § Distribution – Counter flow heat exchange § Conversion – Reduce excess combustion air – Pre-heat combustion air or load – Cascade waste heat
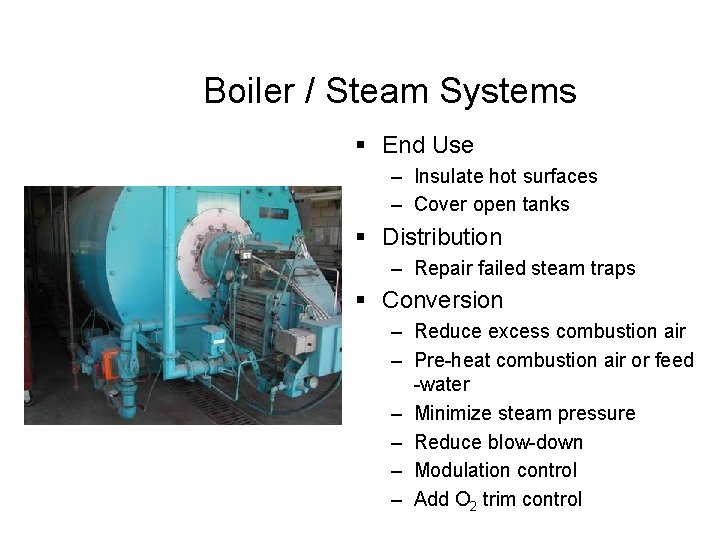
Boiler / Steam Systems § End Use – Insulate hot surfaces – Cover open tanks § Distribution – Repair failed steam traps § Conversion – Reduce excess combustion air – Pre-heat combustion air or feed -water – Minimize steam pressure – Reduce blow-down – Modulation control – Add O 2 trim control
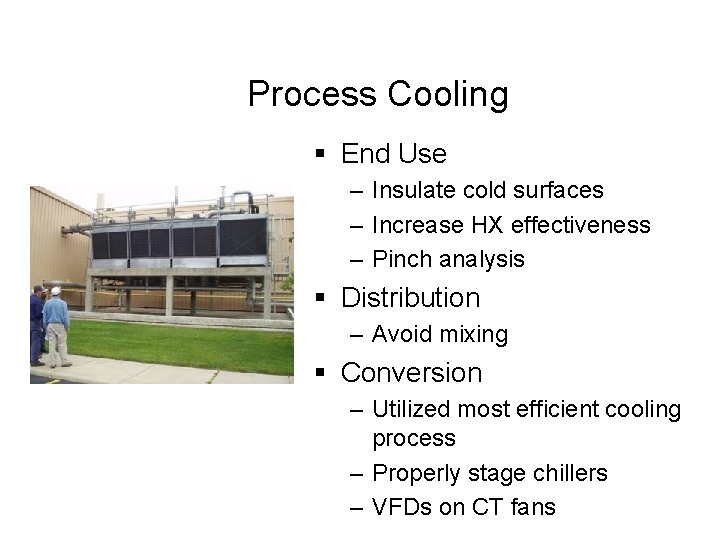
Process Cooling § End Use – Insulate cold surfaces – Increase HX effectiveness – Pinch analysis § Distribution – Avoid mixing § Conversion – Utilized most efficient cooling process – Properly stage chillers – VFDs on CT fans
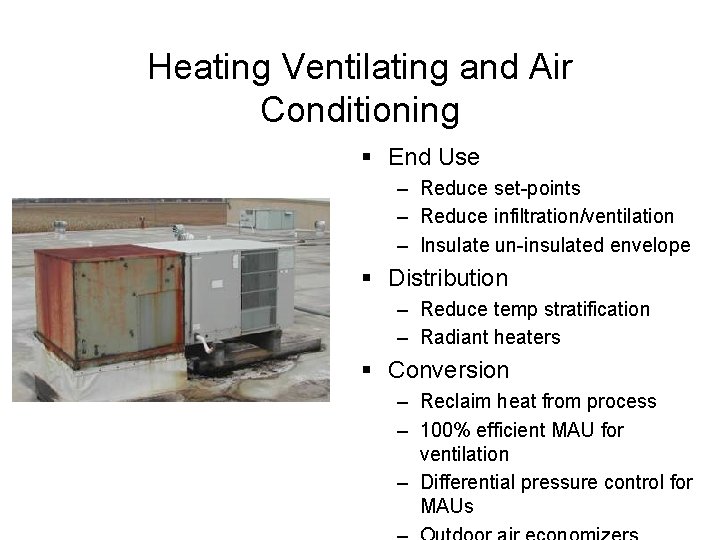
Heating Ventilating and Air Conditioning § End Use – Reduce set-points – Reduce infiltration/ventilation – Insulate un-insulated envelope § Distribution – Reduce temp stratification – Radiant heaters § Conversion – Reclaim heat from process – 100% efficient MAU for ventilation – Differential pressure control for MAUs
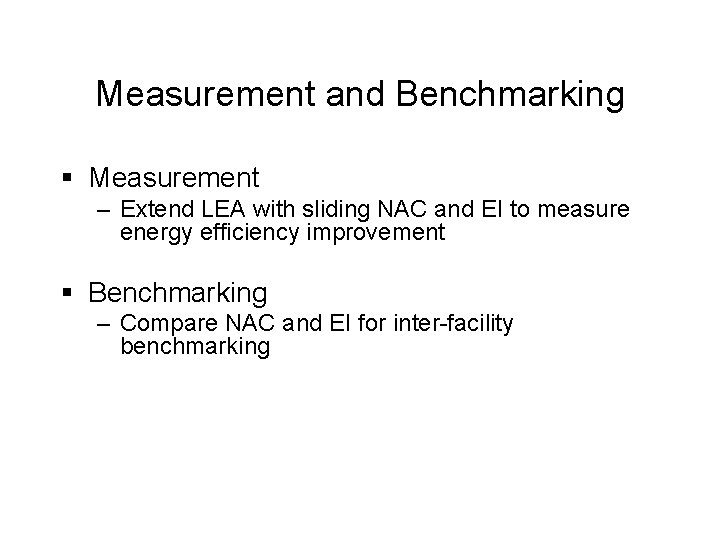
Measurement and Benchmarking § Measurement – Extend LEA with sliding NAC and EI to measure energy efficiency improvement § Benchmarking – Compare NAC and EI for inter-facility benchmarking
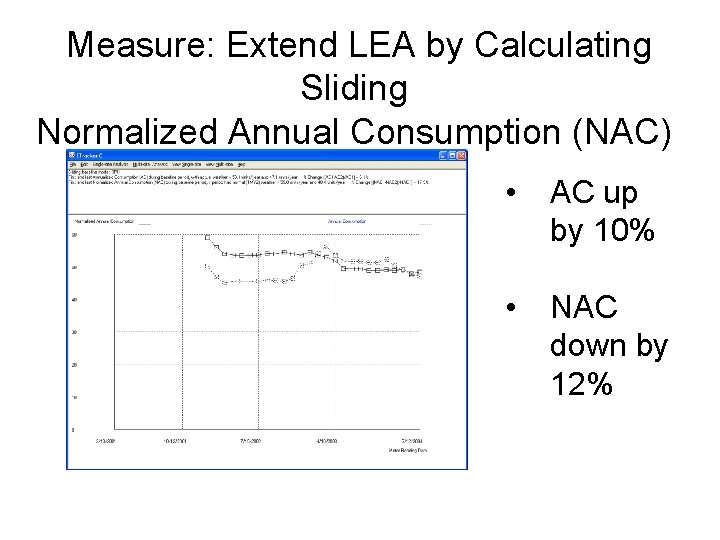
Measure: Extend LEA by Calculating Sliding Normalized Annual Consumption (NAC) • AC up by 10% • NAC down by 12%
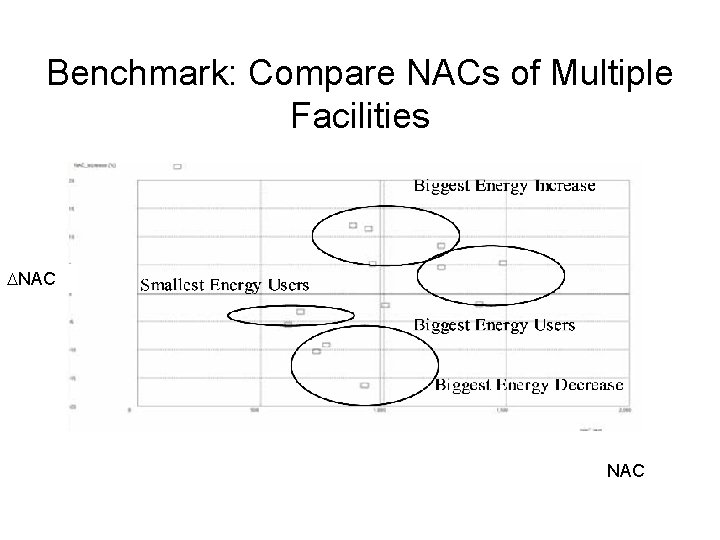
Benchmark: Compare NACs of Multiple Facilities DNAC
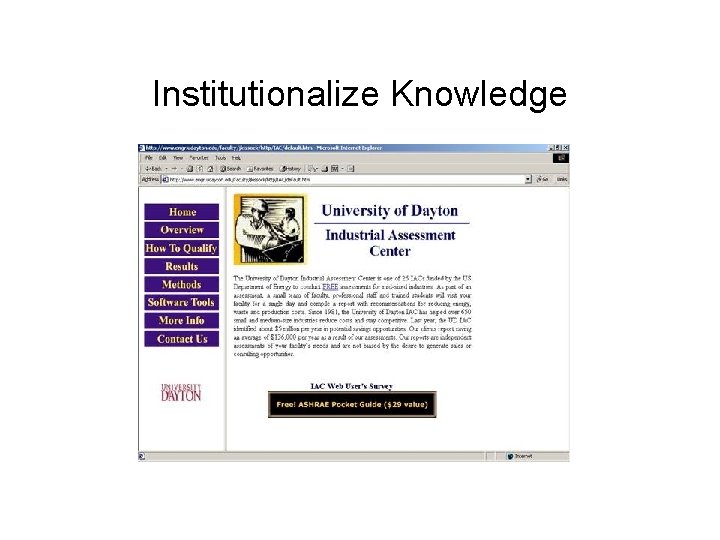
Institutionalize Knowledge
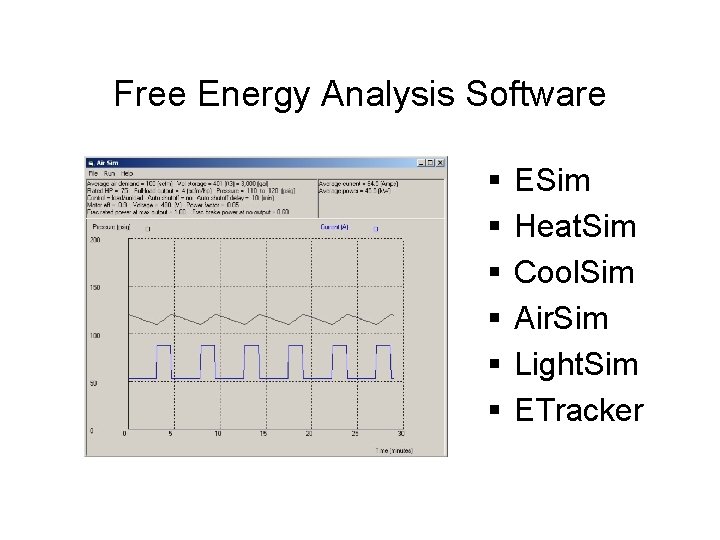
Free Energy Analysis Software § § § ESim Heat. Sim Cool. Sim Air. Sim Light. Sim ETracker
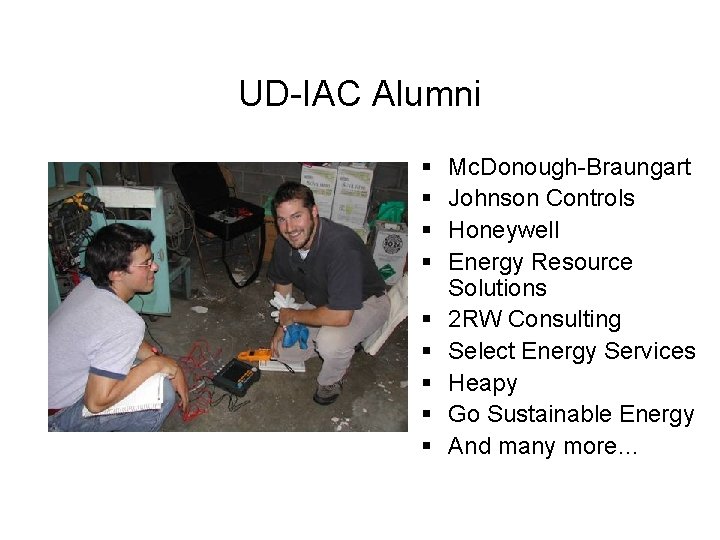
UD-IAC Alumni § § § § § Mc. Donough-Braungart Johnson Controls Honeywell Energy Resource Solutions 2 RW Consulting Select Energy Services Heapy Go Sustainable Energy And many more…
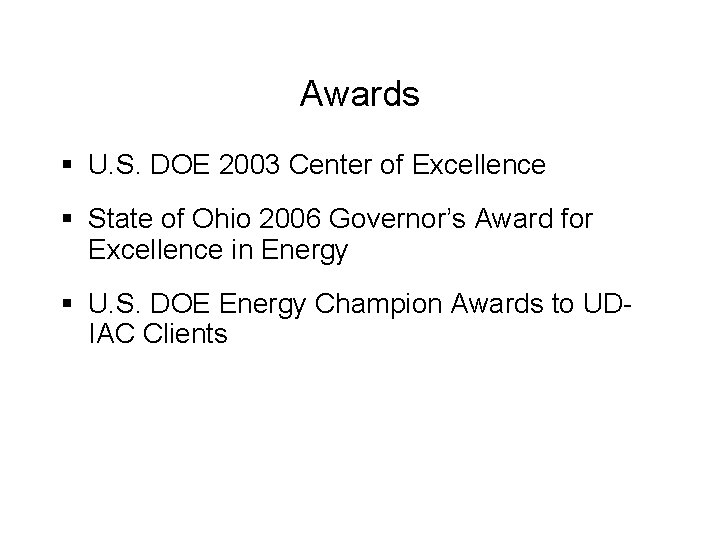
Awards § U. S. DOE 2003 Center of Excellence § State of Ohio 2006 Governor’s Award for Excellence in Energy § U. S. DOE Energy Champion Awards to UDIAC Clients
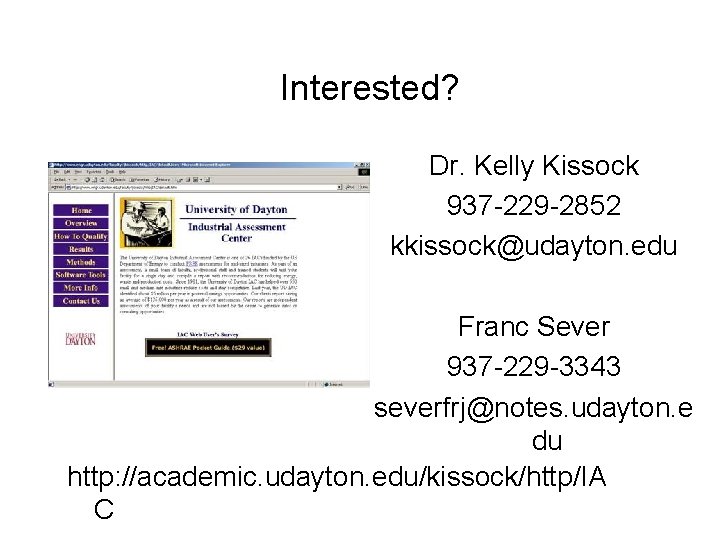
Interested? Dr. Kelly Kissock 937 -229 -2852 kkissock@udayton. edu Franc Sever 937 -229 -3343 severfrj@notes. udayton. e du http: //academic. udayton. edu/kissock/http/IA C
University of dayton powerpoint template
University of dayton premed
Clasroomü
Dayton juniors volleyball
Dayton financial aid
Watsons dayton ohio
Dayton infonet
Lakeside amusement park dayton ohio
Presidents club of dayton
Dayton mn police
7 hawthorne street dayton ohio
Dayton oaks elementary school
Dayton juniors volleyball club
Salt triage colors
Loa dayton
Hygiene risk assessment
Institute of industrial science the university of tokyo
Features of portfolio assessment
Static assessment vs dynamic assessment
Portfolio assessment matches assessment to teaching
National center for credibility assessment
National center for credibility assessment
National center for credibility assessment
National center for credibility assessment
Paperless assessment center
Pengertian assessment center
Nspire hud
Miami-dade county juvenile services department
National center for credibility assessment
Orange county juvenile assessment center
Acqt
Liberty university writing center
Uky disability resource center
University clinical center tuzla
Oakland
American university career center
University of kansas writing center
University clinical center tuzla
Empp university medical center
Slowenien university medical center